
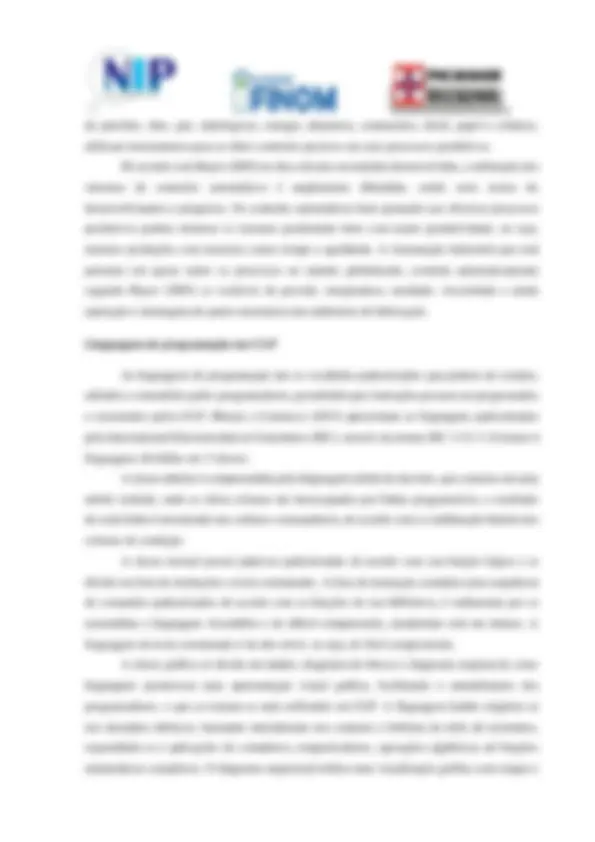
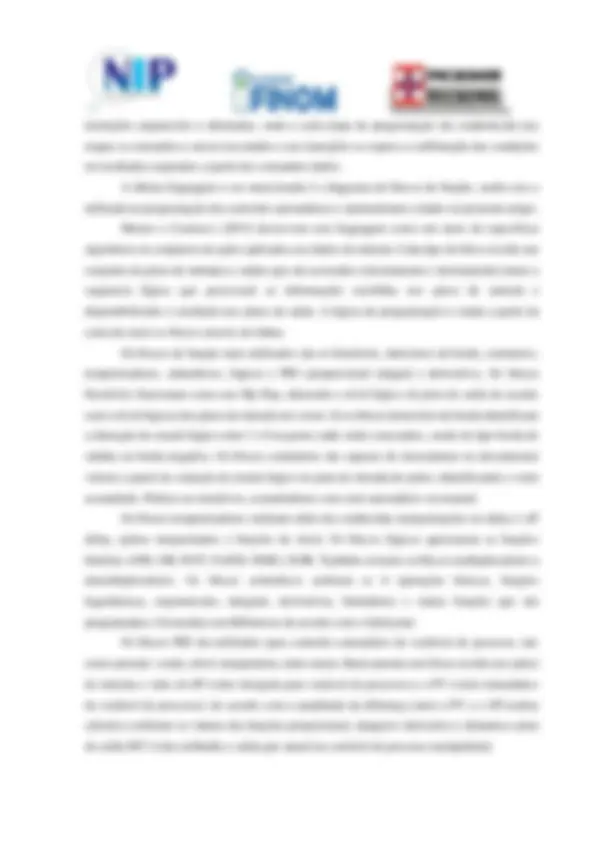
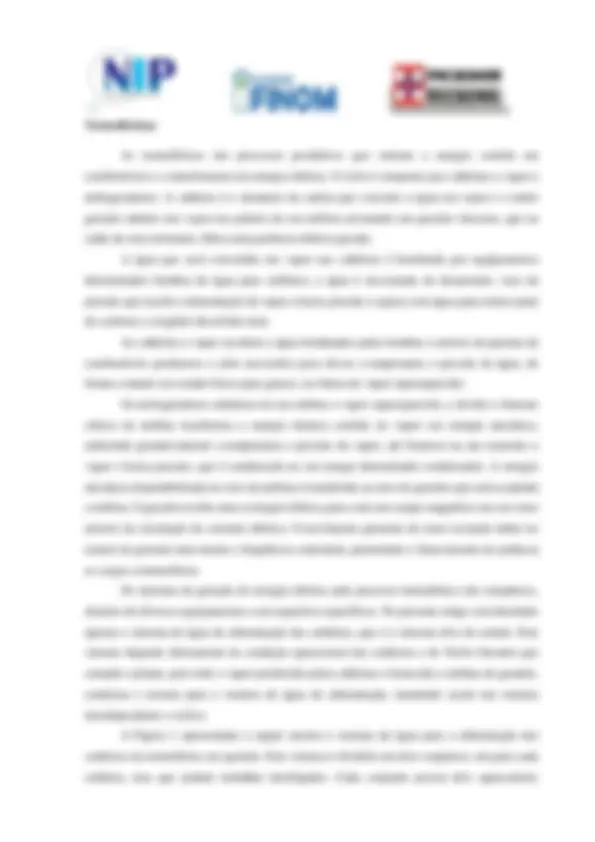
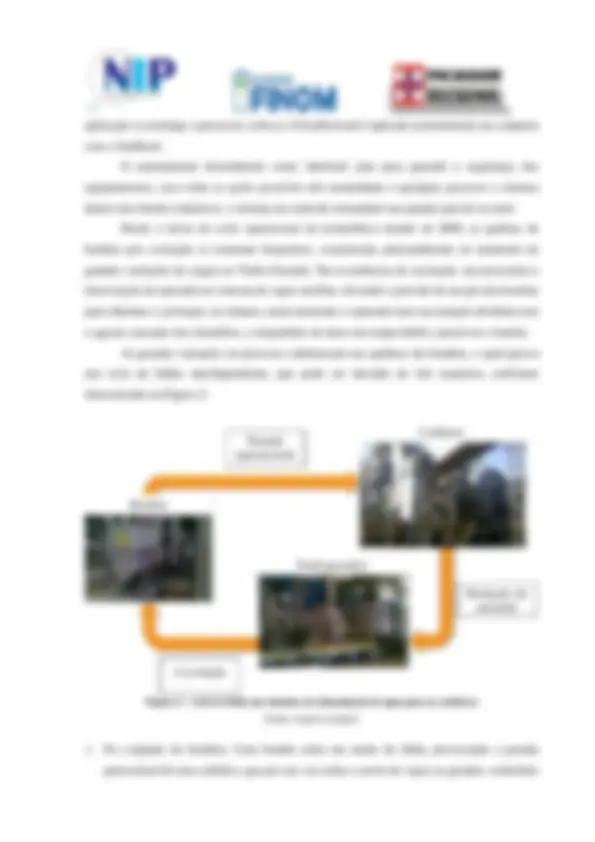
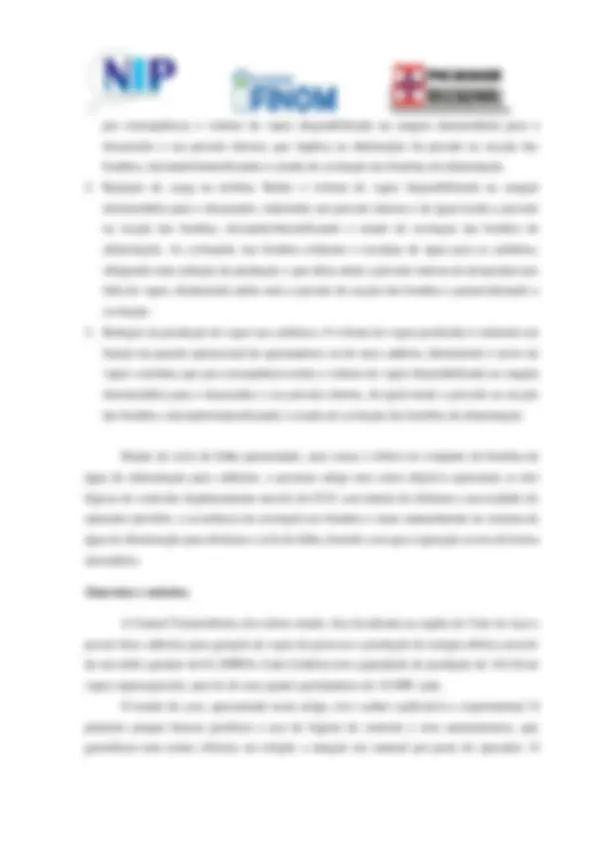
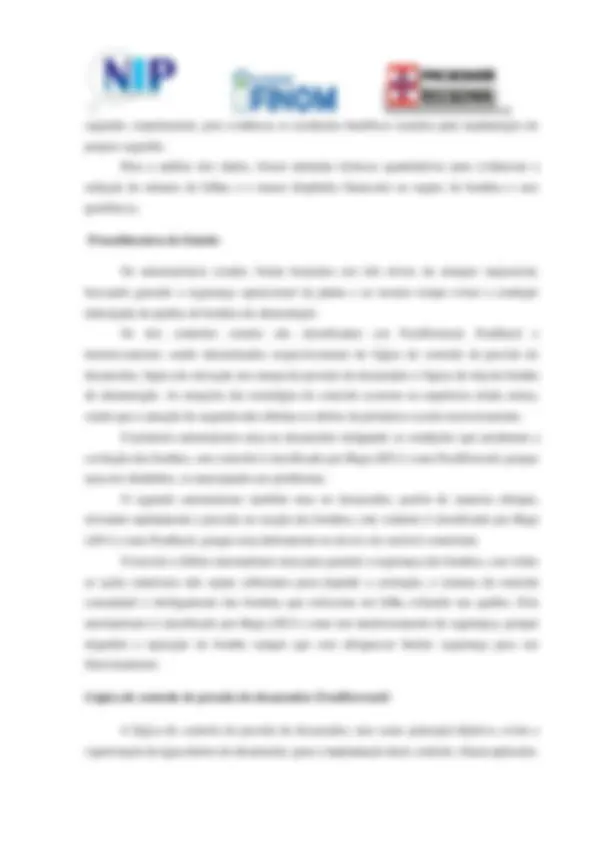
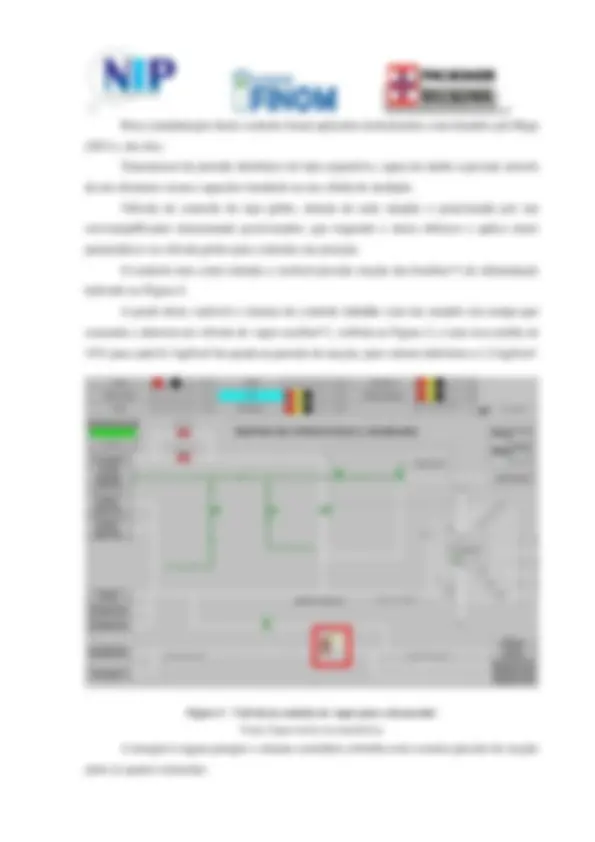
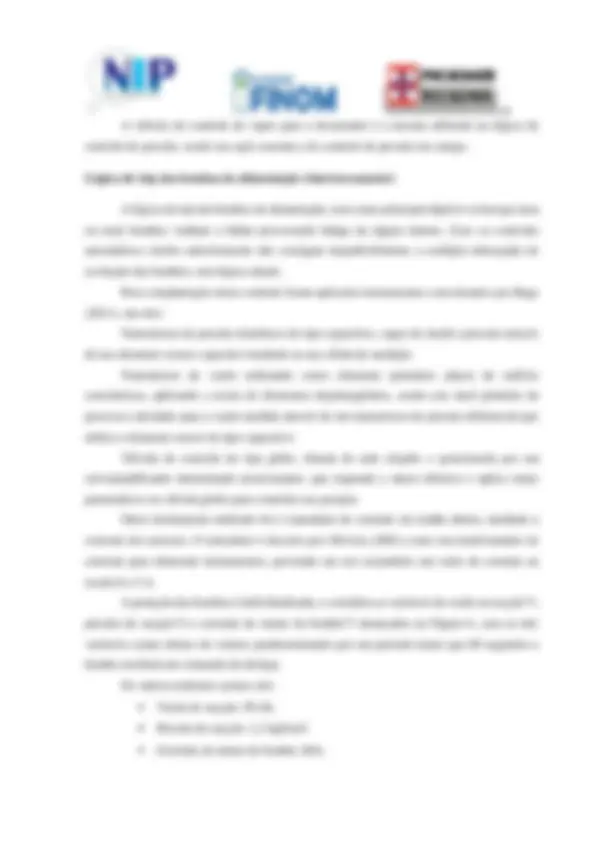
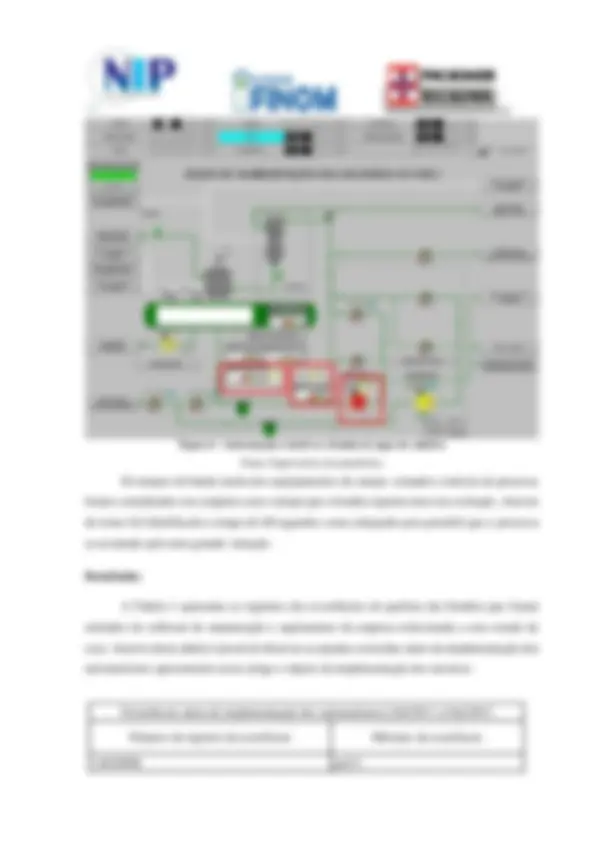
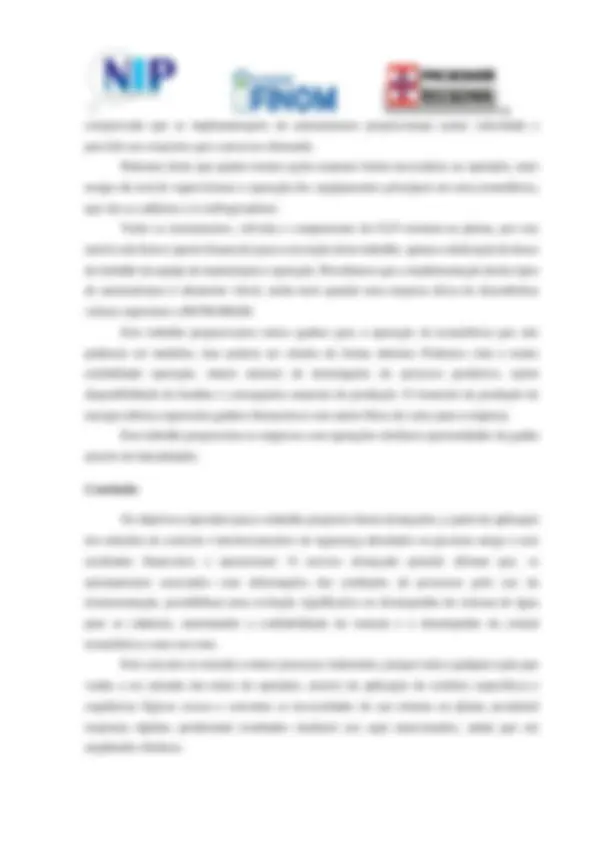
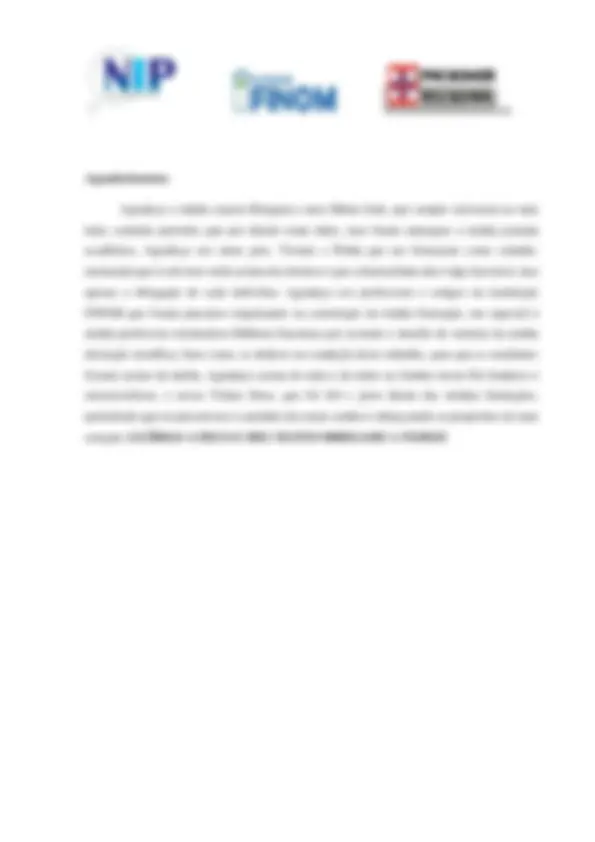
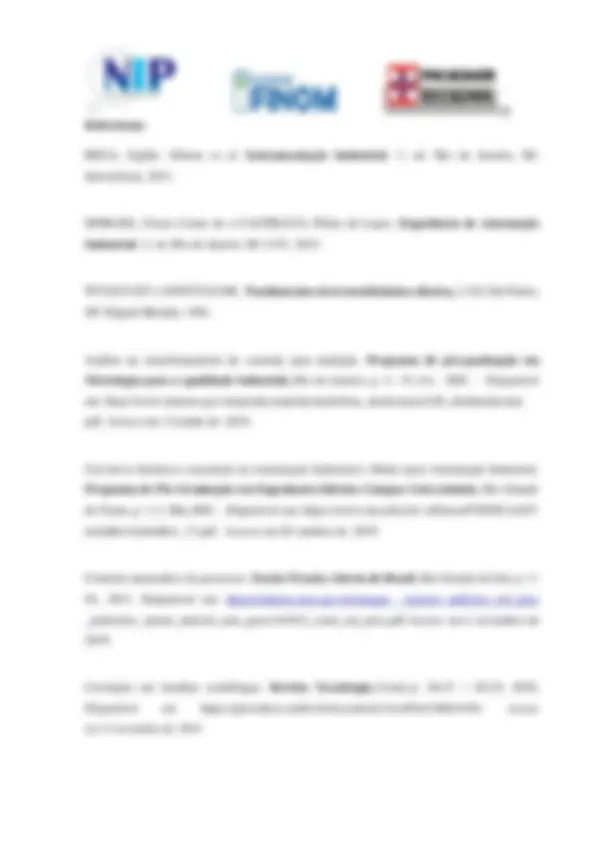
Estude fácil! Tem muito documento disponível na Docsity
Ganhe pontos ajudando outros esrudantes ou compre um plano Premium
Prepare-se para as provas
Estude fácil! Tem muito documento disponível na Docsity
Prepare-se para as provas com trabalhos de outros alunos como você, aqui na Docsity
Os melhores documentos à venda: Trabalhos de alunos formados
Prepare-se com as videoaulas e exercícios resolvidos criados a partir da grade da sua Universidade
Responda perguntas de provas passadas e avalie sua preparação.
Ganhe pontos para baixar
Ganhe pontos ajudando outros esrudantes ou compre um plano Premium
Comunidade
Peça ajuda à comunidade e tire suas dúvidas relacionadas ao estudo
Descubra as melhores universidades em seu país de acordo com os usuários da Docsity
Guias grátis
Baixe gratuitamente nossos guias de estudo, métodos para diminuir a ansiedade, dicas de TCC preparadas pelos professores da Docsity
Uma análise de quebras de bombas de água para caldeiras em uma empresa siderúrgica localizada no vale do aço, minas gerais. As causas encontradas levaram à implementação de lógicas de controle com a utilização de instrumentos de campo, automatizando a operação das bombas, tornando-a mais robusta. O artigo apresenta as lógicas de controle para preservação das bombas de água de caldeiras, com o objetivo de aumentar sua disponibilidade e reduzir as quebras, além de aumentar a produtividade. O documento discute a cavitação como um fenômeno que pode ocorrer em bombas de água para caldeiras, causando excesso de ruído, vibração e danos no rotor da bomba. Três controles criados são classificados em feedforward, feedback e intertravamento, sendo denominados respectivamente de lógica de controle de pressão do desaerador, lógica de elevação em rampa da pressão do desaerador e lógica de trip da bomba de alimentação.
Tipologia: Teses (TCC)
1 / 20
Esta página não é visível na pré-visualização
Não perca as partes importantes!
Engenharia Elétrica Artigo Original REDUÇÃO DE CUSTOS ATRAVÉS DA AUTOMAÇÃO E INSTRUMENTAÇÃO EM UMA TERMELETRICA NO VALE DO AÇO COST REDUCTION THROUGH AUTOMATION AND INSTRUMENTATION IN A THERMAL ELECTRIC IN THE VALE DO AÇO Rolfimam Teixeira Melo^1 , Dhébora Sayonara de Morais Severo^2 (^1) Aluno de Iniciação Cientifica e do curso de Engenharia Elétrica da Faculdade do Noroeste de Minas Finom/Faculdade Tecsoma – Paracatu – MG. (^2) Professor especialista do curso de Engenharia Elétrica e Engenharia Mecatrônica Orientador de Iniciação Científica da Faculdade do Noroeste de Minas – Finom/Faculdade Tecsoma – Paracatu - MG. Resumo Este trabalho é baseado na ocorrência de quebras das bombas de água para caldeiras a vapor de uma empresa do ramo siderúrgico, localizada na região do Vale do Aço, interior de Minas Gerais. O presente artigo apresenta a história dos CLP (Controlador Lógico Programável), descreve suscintamente o processo de uma termelétrica e o seu sistema de bombeamento de água para caldeiras. Foi realizado um estudo de caso para identificar a causa das quebras de bombas de água para caldeiras. Foi identificado a cavitação como causa básica para a quebra das bombas, e a inexistência de automatismo que promove a dependência da atuação manual dos operadores para evitar ou minimizar a cavitação das bombas como a causa raiz. Diante das causas encontradas foram implementadas lógicas de controle com a utilização de instrumentos de campo, que automatizaram a operação das bombas, deixando a operação mais robusta. É extremamente importante a utilização de lógicas de controle automáticos em processos industriais, promovendo maior velocidade e precisão nas ações que precisam ser tomadas em respostas as variações do processo. Assim sendo será apresentado as lógicas de controle para preservação das bombas de água de caldeiras, de forma a aumentar sua disponibilidade e reduzir suas quebras e aumentar a produtividade. Palavras-chave: Automatismos; instrumentação; lógicas de controle. Abstract This work is based on the occurrence of water pump breaks for steam boilers of a company in the steel branch, located in the Steel Valley region, periphery of Minas Gerais. This article presents the history of plc (Programmable Logical Controller), briefly describes the process of a thermoelectric plant and its boiler water pumping system. A case study was conducted to identify the cause of water pump breaks for boilers. Cavitation was identified as a basic cause for bomb breaking, and the lack of automatism that promotes dependence on the manual
performance of operators to avoid or minimize the cavitation of pumps as the root cause. Given the causes found, control logic was implemented with the use of field instruments, which automated the operation of the pumps, leaving the operation more robust. It is extremely important to use automatic control logics in industrial processes, promoting greater speed and accuracy in actions that need to be taken in response the variations of the process. Therefore, the control logics will be presented for the preservation of boiler water pumps, in order to increase their availability, reduce their breaks and increase the productivity. Keywords: Automatism; instrumentation; Control Logic. Contato : rolfimam.teixeira@hotmail.com Introdução Segundo Siqueira (2003) a automação industrial surgiu de forma simplória no século XVIII, quando foram criadas a máquinas a vapor e as primeiras indústrias de manufatura, este período ficou conhecido com a revolução industrial. No século XIV sugiram elementos eletromecânicos chamados relés, que são dotados de contatos elétricos acionados por uma bobina e um núcleo ferromagnético, estes relés impulsionaram a chamada segunda revolução industrial. No século XX as indústrias necessitavam cada vez mais de produtividade e sinergia em seus processos produtivos, foi neste momento que de acordo com Bega (2011) foi concebido pela a General Motors Co. (GM) o primeiro controlador lógico programável (CLP) de nome MOdular DIgital CONtroler (MODICON), datado em 1968. Neste primeiro momento o CLP foi criado para substituir os grandes painéis de relés utilizados nas linhas produtivas da GM, reduzindo o número de falhas devido a robustez do CLP e versatilidade de programação em relação aos painéis de relés, que eram cabeados. Ainda segundo Bega (2011), no início da década de 1970 foram desenvolvidos os microprocessadores que deram ao CLP melhorias de interface, flexibilidade de programação e “inteligência” para realizar cálculos aritméticos. Seguindo o ciclo de evolução no final da mesma década, os CLP receberam melhorias como: aumento de memória; controle sobre variáveis analógicas; como por exemplo servomecanismos, e linhas de comunicação em alta velocidade, permitindo a interface homem máquina IHM. As variáveis analógicas são oriundas da conversão de informações do processo produtivo em sinais padronizados para os CLP e a conversão de comandos do CLP para sinais padronizados aos instrumentos de saída. Segundo Bega (2011), a maioria das industriais da área
transições sequenciais e alternadas, onde a cada etapa de programação são estabelecido nas etapas os comandos a serem executados e nas transições se espera a confirmação das condições ou resultados esperados a partir dos comandos dados. A última linguagem a ser mencionada é a diagrama de blocos de função, sendo esta a utilizada na programação dos controles automáticos e automatismos citados no presente artigo. Moraes e Castrucci (2015) descrevem esta linguagem como um meio de especificar algoritmos ou conjuntos de ações aplicados aos dados de entrada. Cada tipo de bloco recebe um conjunto de pinos de entradas e saídas que são acessados externamente e internamente temos a sequencia lógica que processará as informações recebidas nos pinos de entrada e disponibilizarão o resultado nos pinos de saída. A lógica de programação é criada a partir da conexão entre os blocos através de linhas. Os blocos de função mais utilizados são os biestáveis, detectores de borda, contatores, temporizadores, aritméticos, lógicos e PID (proporcional integral e derivativo). Os blocos biestáveis funcionam como um flip flop, alterando o nível lógico do pino de saída de acordo com o nível lógicos dos pinos de entrada set e reset. Já os blocos detectores de borda identificam a alteração do estado lógico entre 1 e 0 no ponto onde estão conectados, sendo do tipo borda de subida ou borda negativa. Os blocos contadores são capazes de incrementar ou decrementar valores a partir da variação do estado lógico no pino de entrada de pulso, identificando o valor acumulado. Podem ser retentivos, acumuladores com reset automático ou manual. Os blocos temporizadores realizam além das conhecidas temporizações on delay e off delay, pulsos temporizados e funções de clock. Os blocos lógicos apresentam as funções binárias AND, OR, NOT, NAND, NOR e XOR. Também existem os blocos multiplexadores e demultiplexadores. Os blocos aritméticos realizam as 6 operações básicas, funções logarítmicas, exponenciais, integrais, derivativas, limitadores e outras funções que são programadas e fornecidas em bibliotecas de acordo com o fabricante. Os blocos PID são utilizados para controles automático de variáveis de processo, tais como pressão, vazão, nível, temperatura, entre outras. Basicamente este bloco recebe nos pinos de entrada o valor do SP (valor desejado para variável do processo) e a PV (valor instantâneo da variável de processo), de acordo com a amplitude da diferença entre a PV e o SP realiza cálculos conforme os valores das funções proporcional, integral e derivativo e alimenta o pino de saída MV (valor atribuído a saída que atuará na variável de processo manipulada).
Termelétricas As termelétricas são processos produtivos que retiram a energia contida em combustíveis e a transformam em energia elétrica. O ciclo é composto por caldeiras a vapor e turbogeradores. A caldeira é o elemento da cadeia que converte a água em vapor e o turbo gerador admite este vapor nas paletas da sua turbina acionando um gerador síncrono, que na saída de seus terminais, libera uma potência elétrica gerada. A água que será convertida em vapor nas caldeiras é bombeada por equipamentos denominados bombas de água para caldeiras, a água é succionada do desaerador, vaso de pressão que recebe a alimentação de vapor a baixa pressão e aquece esta água para retirar parte do carbono e oxigênio dissolvido nela. As caldeiras a vapor recebem a água bombeadas pelas bombas e através da queima de combustíveis produzem o calor necessário para elevar a temperatura e pressão da água, de forma a mudar seu estado físico para gasoso, na forma de vapor superaquecido. Os turbogeradores admitem em sua turbina o vapor superaquecido, e devido o formato cônico da turbina transforma a energia térmica contida no vapor em energia mecânica, reduzindo gradativamente a temperatura e pressão do vapor, até fornecer na sua exaustão o vapor a baixa pressão, que é condensado no seu tanque denominado condensador. A energia mecânica disponibilizada no eixo da turbina é transferida ao eixo do gerador que está acoplado a turbina. O gerador recebe uma excitação elétrica para criar um campo magnético em seu rotor através da circulação da corrente elétrica. O movimento giratório do rotor excitado induz no estator do gerador uma tensão e frequência controlada, permitindo o fornecimento de potência as cargas consumidoras. Os sistemas de geração de energia elétrica pelo processo termelétrico são complexos, dotados de diversos equipamentos com requisitos específicos. No presente artigo será abordado apenas o sistema de água de alimentação das caldeiras, que é o sistema alvo do estudo. Este sistema depende diretamente da condição operacional das caldeiras e do Turbo Gerador que compõe a planta, pois todo o vapor produzido pelas caldeiras e fornecido a turbina do gerador, condensa e retorna para o sistema de água de alimentação, mantendo assim um sistema interdependente e cíclico. A Figura 1 apresentada a seguir mostra o sistema de água para a alimentação das caldeiras da termelétrica em questão. Este sistema é dividido em dois conjuntos, um para cada caldeira, mas que podem trabalhar interligados. Cada conjunto possui dois aquecedores
deseja manter o fluído em estado líquido, é necessário elevar a pressão ou reduzir a temperatura até que o ponto de tensão de vaporização seja superado. Segundo Monteiro (2011) quando um determinado líquido em bombeamento atinge um valor de pressão abaixo da tensão de vaporização, há a formação de vapor no interior da bomba, podendo produzir bolhas que interrompem o bombeamento devido o fragmento da massa líquida. Caso a bomba continue em operação, estas bolhas serão escoadas para a região de maior pressão do rotor, onde serão comprimidas e submetidas a uma pressão superior a tensão de vaporização, provocando o esmagamento das bolhas e sua destruição, causando aos internos da bomba uma fadiga e perda de material devido aos choques mecânicos. Outro dano na bomba é a ação perfuradora na carcaça e internos da bomba, que são causados pela entrada súbita de água para ocupar o volume deixado pelas bolhas destruídas, esta água flui com muita energia para ocupar os espaços vazios. Controle em malha aberta e malha fechada Os instrumentos interagem com os CLP e o processo produtivo através duas formas básicas, malha aberta e malha fechada. Segundo Bega (2011) a malha aberta é aquela que as informações lidas do processo não são utilizadas para ajustar o processo, mas sim para conhecer a sua dinâmica. A malha fechada utiliza das informações obtidas do processo para manipular uma variável a fim de se obter o valor desejado em uma variável controlada. Os controles de variáveis são descritos por Bega (2011) como, manual típico, Feedback e Feedforward. Bega (2011) ainda fala sobre intertravamentos de segurança. O controle manual típico depende exclusivamente do operador, que recebe informações do processo através de instrumentos ou até mesmo dos seus sentidos in loco no processo, a partir dos dados obtidos ele define como e quando intervir no processo. O controle Feedback, traduzido por realimentação negativa atua diretamente no desvio da variável controlada. Este controle não precisa se alimentado com variáveis que lhe deem conhecimento antecipado de variações do processo, por consequência também não há relação entre os distúrbios e seus efeitos sobre o processo. O controle Feedforward, traduzido como controle por antecipação, atua nos distúrbios que poderão apresentar variações no processo, se antecipando aos problemas. Este controle demanda alto conhecimento do processo e maior dispêndio de tempo e dinheiro, por isso sua
aplicação se restringe a processos críticos. O feedforward é aplicado normalmente em conjunto com o feedback. O automatismo denominado como interlock atua para garantir a segurança dos equipamentos, caso todas as ações possíveis não mantenham o qualquer processo o sistema dentro dos limites toleráveis, o sistema de controle comandará sua parada parcial ou total. Desde o início do ciclo operacional da termelétrica datado de 2009, as quebras de bombas por cavitação se tornaram frequentes, ocasionadas principalmente no momento de grandes variações de cargas no Turbo Gerador. Nas ocorrências de cavitação, era necessário a intervenção do operador no sistema de vapor auxiliar, elevando a pressão de sucção das bombas para eliminar a cavitação, no entanto, neste momento o operador tem sua atenção dividida com o agente causador dos distúrbios, o impedindo de atuar em tempo hábil e preservar a bomba. As grandes variações no processo culminavam nas quebras das bombas, o qual gerava um ciclo de falhas interdependente, que pode ser iniciado de três maneiras, conforme demonstrado na Figura 2: Figura 2 – ciclo de falha nas bombas de alimentação de água para as caldeiras Fonte: Arquivo próprio
segundo, experimental, pois evidência os resultados benéficos trazidos pela implantação do projeto sugerido. Para a análise dos dados, foram adotadas técnicas quantitativas para evidenciar a redução do número de falhas e o menor dispêndio financeiro no reparo de bombas e seus periféricos. Procedimentos do Estudo Os automatismos criados foram baseados em três níveis de atuação sequencial, buscando garantir a segurança operacional da planta e ao mesmo tempo evitar a condição indesejada de quebra de bombas de alimentação. Os três controles criados são classificados em Feedforward, Feedback e intertravamento, sendo denominados respectivamente de lógica de controle de pressão do desaerador, lógica de elevação em rampa da pressão do desaerador e lógica de trip da bomba de alimentação. As atuações das estratégias de controle ocorrem na sequência citada acima, sendo que a atuação da segunda não elimina os efeitos da primeira e assim sucessivamente. O primeiro automatismo atua no desaerador mitigando as condições que produzem a cavitação das bombas, este controle é classificado por Bega (2011) como Feedforward, porque atua nos distúrbios, se antecipando aos problemas. O segundo automatismo também atua no desaerador, porém de maneira abrupta, elevando rapidamente a pressão na sucção das bombas, este controle é classificado por Bega (2011) como Feedback, porque atua diretamente no desvio da variável controlada. O terceiro e último automatismo atua para garantir a segurança das bombas, caso todas as ações anteriores não sejam suficientes para impedir a cavitação, o sistema de controle comandará o desligamento das bombas que estiverem em falha evitando sua quebra. Este automatismo é classificado por Bega (2011) como um intertravamento de segurança, porque impedirá a operação da bomba sempre que esta ultrapassar limites segurança para seu funcionamento. Lógica de controle de pressão do desaerador (Feedforward) A lógica de controle de pressão do desaerador, tem como principal objetivo, evitar a vaporização da água dentro do desaerador, para a implantação deste controle, foram aplicados
instrumentos conceituados por Bega (2011), são eles: Transmissor de pressão eletrônico do tipo capacitivo, capaz de medir a pressão através de um elemento sensor capacitor instalado na sua célula de medição. Sensor de temperatura do tipo PT100, um dos mais comuns sensores para este fim, que utiliza um elemento de platina padronizado que confere ao sensor estabilidade, repetibilidade, precisão e ampla faixa de operação. Válvula de controle do tipo globo, dotada de sede simples e posicionada por um servoamplificador denominado posicionador, que responde a sinais elétricos e aplica sinais pneumáticos na válvula globo para controlar sua posição. O controle tem como entrada as variáveis de processo do próprio desaerador, que são a pressão e temperatura*1 evidenciadas na Figura 3. A partir destas duas variáveis de entrada o sistema de controle trabalha com um modelo baseado no Diagrama de Mollier anteriormente explanado, produzindo como resultado de saída o valor de pressão ideal para o desaerador na condição operacional de momento, o sinal de saída deste modelo é a variável de SetPoint do PID que atua na válvula de controle do vapor auxiliar para manter a pressão do desaerador acima da pressão mínima para que a tensão de vaporização não seja atingida. Figura 3 – Instrumentos do desaerador Fonte: Supervisório da termelétrica
Para a implantação deste controle foram aplicados instrumentos conceituados por Bega (2011), são eles: Transmissor de pressão eletrônico do tipo capacitivo, capaz de medir a pressão através de um elemento sensor capacitor instalado na sua célula de medição. Válvula de controle do tipo globo, dotada de sede simples e posicionada por um servoamplificador denominado posicionador, que responde a sinais elétricos e aplica sinais pneumáticos na válvula globo para controlar sua posição. O controle tem como entrada a variável pressão sucção das bombas1 de alimentação indicado na Figura 4. A partir desta variável o sistema de controle trabalha com um modelo em rampa que comanda a abertura da válvula de vapor auxiliar1, exibida na Figura 5, a uma taxa média de 15% para cada 0,1 kgf/cm² de queda na pressão de sucção, para valores inferiores a 1,2 kgf/cm². Figura 5 – Válvula de controle de vapor para o desaerador Fonte: Supervisório da termelétrica A atuação é segura porque o sistema considera a bomba com a menor pressão de sucção entre as quatro existentes.
A válvula de controle de vapor para o desaerador é a mesma utilizado na lógica de controle de pressão, sendo sua ação somada a do controle de pressão em rampa. Lógica de trip das bombas de alimentação (intertravamento) A lógica de trip das bombas de alimentação, tem como principal objetivo evitar que uma ou mais bombas venham a falhar provocando fadiga de algum interno. Caso os controles automáticos citados anteriormente não consigam impedir/eliminar a condição indesejada de cavitação das bombas, esta lógica atuará. Para a implantação deste controle foram aplicados instrumentos conceituados por Bega (2011), são eles: Transmissor de pressão eletrônico do tipo capacitivo, capaz de medir a pressão através de um elemento sensor capacitor instalado na sua célula de medição. Transmissor de vazão utilizando como elemento primários placas de orifício concêntricas, aplicando a teoria de elementos deprimogênitos, sendo este sinal primário do processo calculado para a vazão medida através de um transmissor de pressão diferencial que utiliza o elemento sensor do tipo capacitivo Válvula de controle do tipo globo, dotada de sede simples e posicionada por um servoamplificador denominado posicionador, que responde a sinais elétricos e aplica sinais pneumáticos na válvula globo para controlar sua posição. Outro instrumento utilizado foi o transdutor de corrente em malha aberta, medindo a corrente dos motores. O transdutor é descrito por Oliveira (2001) como um transformador de corrente para alimentar instrumentos, provendo em seu secundário um valor de corrente na escala 0 a 5 A. A proteção das bombas é individualizada, e considera as variáveis de vazão na sucção1, pressão de sucção2 e corrente do motor da bomba*3 destacados na Figura 6, caso as três variáveis caiam abaixo de valores predeterminados por um período maior que 60 segundos a bomba receberá um comando de desliga. Os valores mínimos aceitos são:
14893926 jul/ 14971847 mar/ 15398440 fev/ 15693608 mai/ 15874115 jul/ 15892759 ago/ 15950778 ago/ 16162905 ago/ 16287094 ago/ 16289816 jan/ 16653275 mai/ 16978075 set/ Ocorrências após implementação dos automatismos (Nov/2013 a Out/2017) Número de registro da ocorrência Mês/ano da ocorrência 17450991 jan/ 17451010 jan/ Tabela 1 – Ocorrência de quebras da bomba. Fonte: Software de gestão da manutenção e suprimentos da termelétrica No período amostrado antes das implementação, que compreende os meses de julho de 2011 a outubro de 2013 (total de 28 meses) ocorreram 13 quebras de bombas. No mês de novembro de 2013 foram concluídos e validados todos os automatismos citados neste documento. No período apurado de novembro de 2013 até fevereiro de 2016 (total de 28 meses) ocorreram apenas 2 quebras, representando uma redução de 650% no número de ocorrência. No período compreendido entre março de 2016 a outubro de 2017 (total de 16 meses) não ocorreu nenhuma quebra de bomba. O Gráfico 1 apresentado a seguir foi extraído da Tabela 1 apresentada, e através dele é possível observar a redução ocorrida na quebra de bombas do período analisado antes e depois da implementação dos automatismos, ou seja, o período que compreende de Julho de 2011 a Outubro de 2017.
13 2 0 Jul/2011 a Out/2013 Nov/2013 a Fev/2016 Mar/2016 a Out/ Gráfico 1 – Ocorrências de falhas por período Fonte: Software de gestão da manutenção e suprimentos da termelétrica Como observado no Gráfico 1 ocorreu uma redução significativa de falhas após a implementação dos automatismos, uma redução de 650%. O ganho financeiro, proporcionado pela redução no desembolso com reparo de bombas pode ser mensurado a partir da inferência sobre a relação entre o número de reparos evitados e o custo médio de reparo de uma bomba. Considerando os dados de custo para reparo em uma bomba, tais como: sobressalentes R$ 26.786,86, mão de obra área R$ 1.254,54 e custos de reparo em oficina R$ 20.610,23, chega- se ao custo total aproximado de 48.651,63 para reparo de uma bomba. A estimativa da economia alcançada fica em torno de R$ 729.774,45. Os valores apresentados foram retirados do software de manutenção e suprimentos da empresa onde foi realizado este trabalho. Discussão Quando se analisou as condições de operação originais do sistema das bombas de água para as caldeiras foram identificadas ineficiências que levavam o sistema ao colapso, evidenciado neste trabalho pelas constantes quebras de bombas. No aprofundamento do estudo das causas das falhas, percebeu-se que todas as alterações nos parâmetros de operação que poderiam evitar a ocorrência, ou mesmo, contornar o problema, dependiam da ação do operador no modo manual. Pelos resultados apresentados acima, fica Redução: 650 %
Agradecimentos Agradeço a minha esposa Morgana e meu filhote João, que sempre estiveram ao meu lado, cedendo períodos que por direito eram deles, mas foram entregues a minha jornada acadêmica. Agradeço aos meus pais, Vicente e Penha que me formaram como cidadão, ensinando que os deveres estão acima dos direitos e que a honestidade não é algo louvável, mas apenas a obrigação de cada indivíduo. Agradeço aos professores e amigos da instituição FINOM que foram parceiros importantes na construção da minha formação, em especial à minha professora orientadora Dhébora Sayonara por assumir o desafio de orientar da minha iniciação científica, bem como, se dedicar na condução deste trabalho, para que os resultados fossem acima da média. Agradeço acima de tudo e de todos ao Senhor nosso Pai bondoso e misericordioso, o nosso Triúno Deus, que foi fiel e justo diante das minhas limitações, permitindo que eu percorresse o caminho dos meus sonhos e abençoando os propósitos do meu coração. GLÓRIAS A DEUS E MEU MUITO OBRIGADO A TODOS!
Referências BEGA, Egídio Alberto et al. Instrumentação Industrial. 3. ed. Rio de Janeiro, RJ: Interciência, 2011. MORAES, Cícero Couto de e CASTRUCCI, Plínio de Lauro. Engenharia de Automação Industrial. 2. ed. Rio de Janeiro, RJ: LTC, 2015. WYLEN GJV e SONNTAG RE. Fundamentos da termodinâmica clássica, 2. Ed. São Paulo, SP: Edgard Blucher, 1981. Análise de transformadores de corrente para medição. Programa de pós-graduação em Metrologia para a qualidade industrial, Rio de Janeiro, p. 4 - 5 3, fev. 2001. Disponível em: http://www.inmetro.gov.br/producaointelectual/obras_intelectuais/228_obraIntelectual. pdf. Acesso em 13 junho de 2019. Um breve histórico conceitual da Automação Industrial e Redes para Automação Industrial. Programa de Pós Graduação em Engenharia Elétrica Campus Universitário, Rio Grande do Norte, p. 1-3, Mai.2003. Disponível em: https://www.dca.ufrn.br/~affonso/FTP/DCA447/ trabalho1/trabalho1_13.pdf. Acesso em 20 outubro de 2019. Controle automático de processos. Escola Técnica Aberta do Brasil, Rio Grande do Sul, p. 1– 92, 2011. Disponível em: http://redeetec.mec.gov.br/images /stories/ pdf/eixo_ctrl_proc _indust/tec_autom_ind/ctrl_auto_proc/161012_contr_aut_proc.pdf.Acesso em 2 novembro de
Cavitação em bombas centrífugas. Revista Tecnologia, Ceará, p. 84.15 – 84.19, 2010. Disponível em https://periodicos.unifor.br/tec/article/viewFile/1406/4184. Acesso em 12 novembro de 2019.