
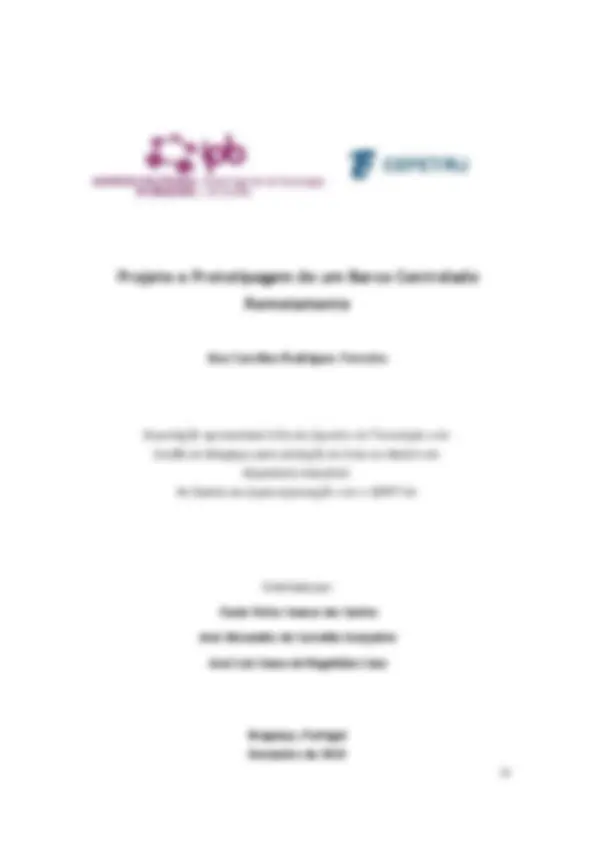
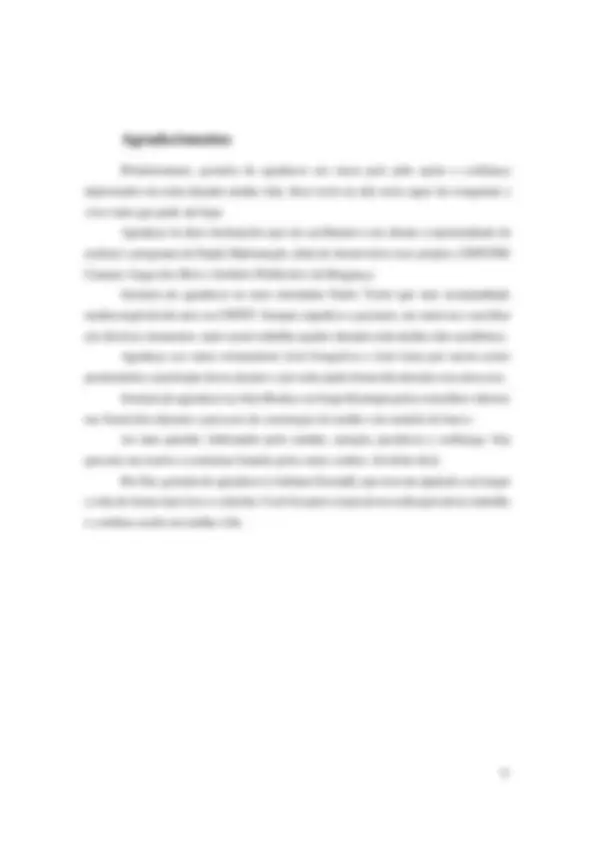
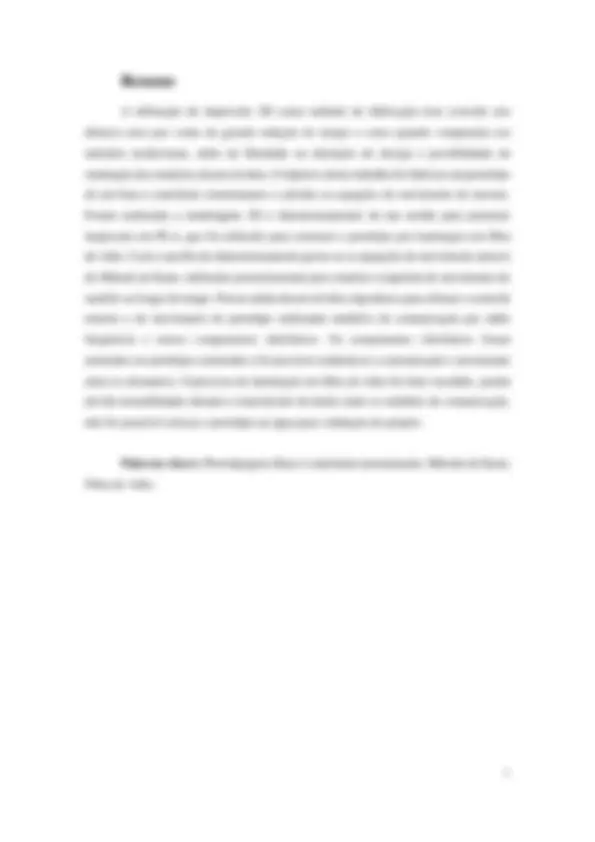
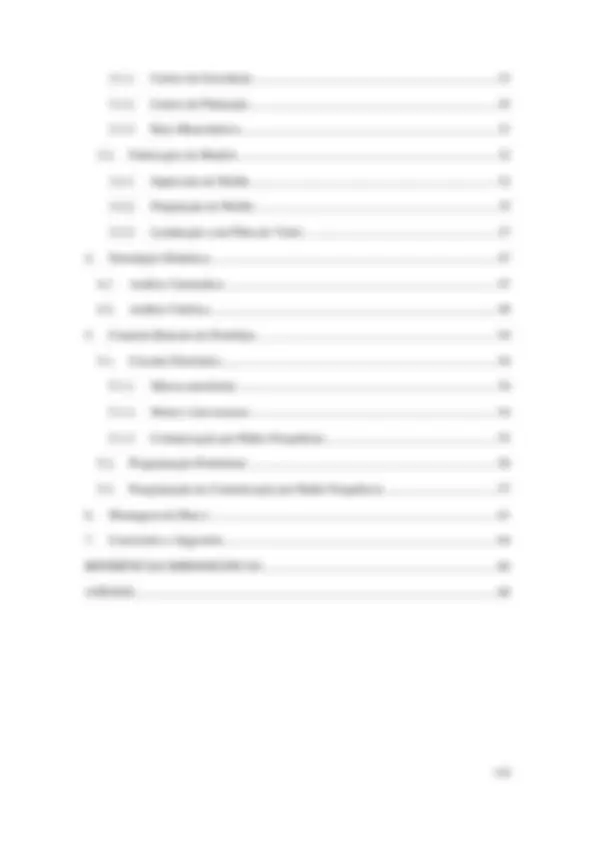
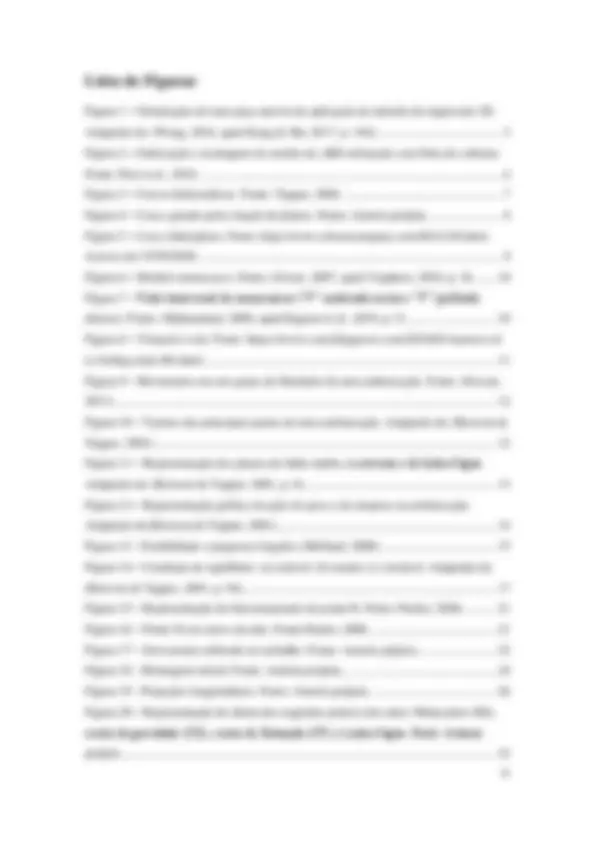
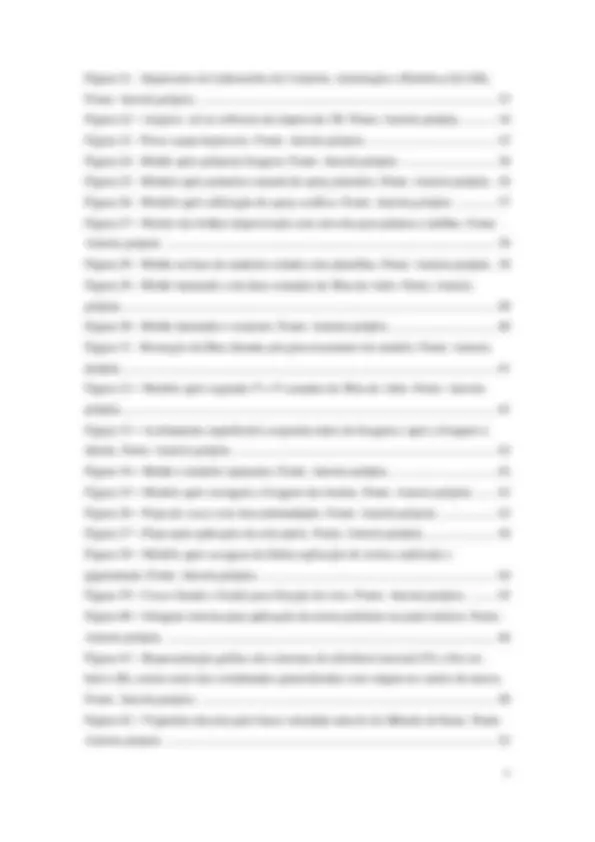
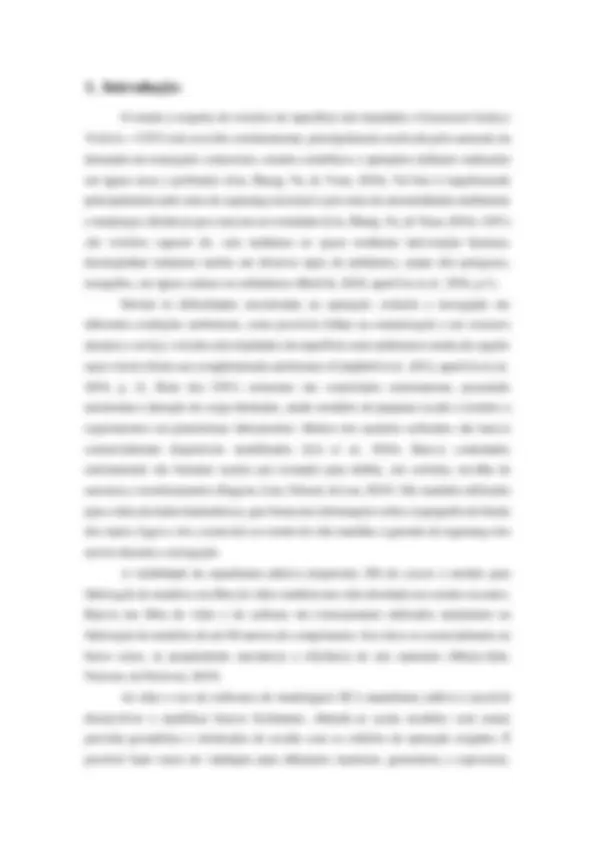
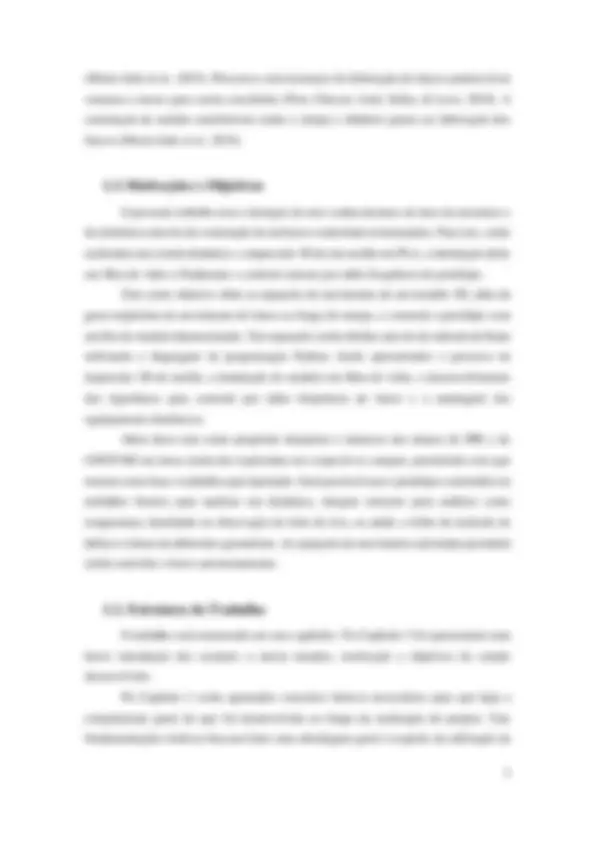
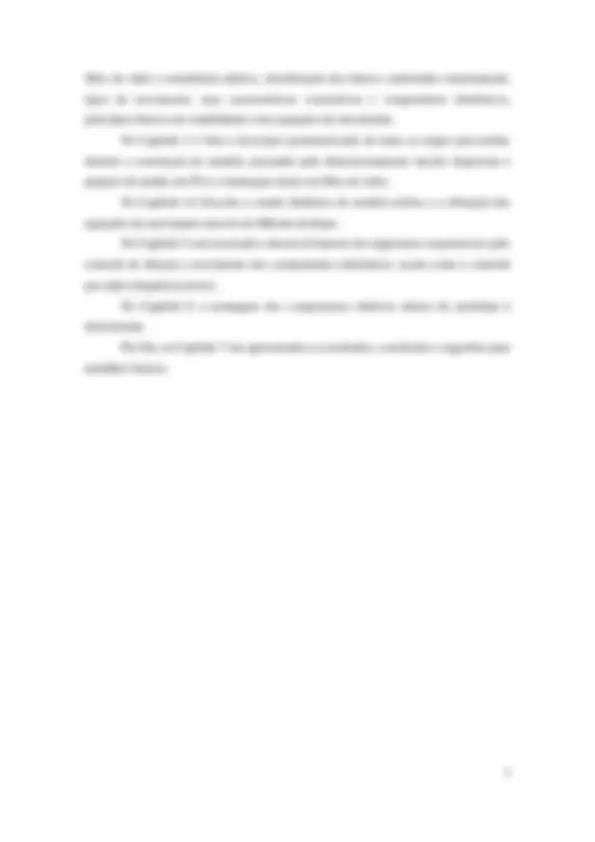
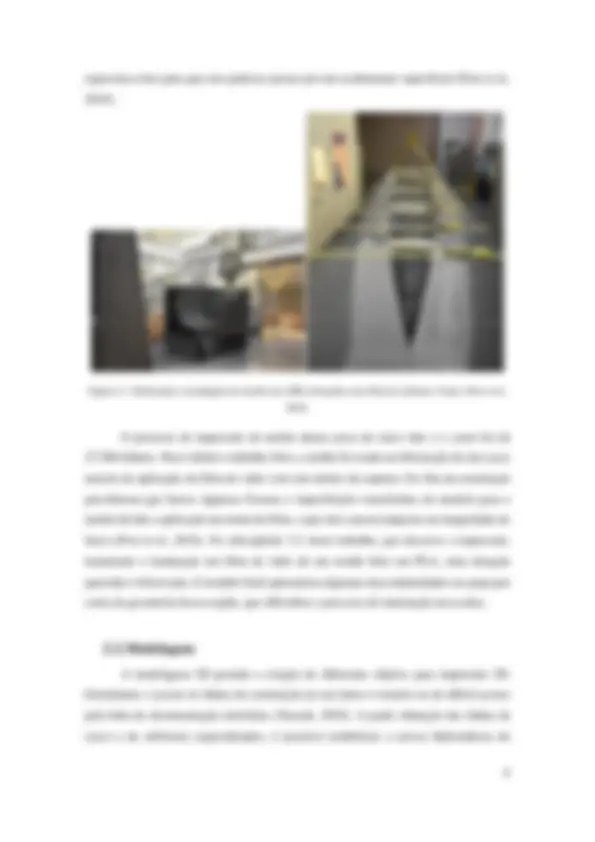
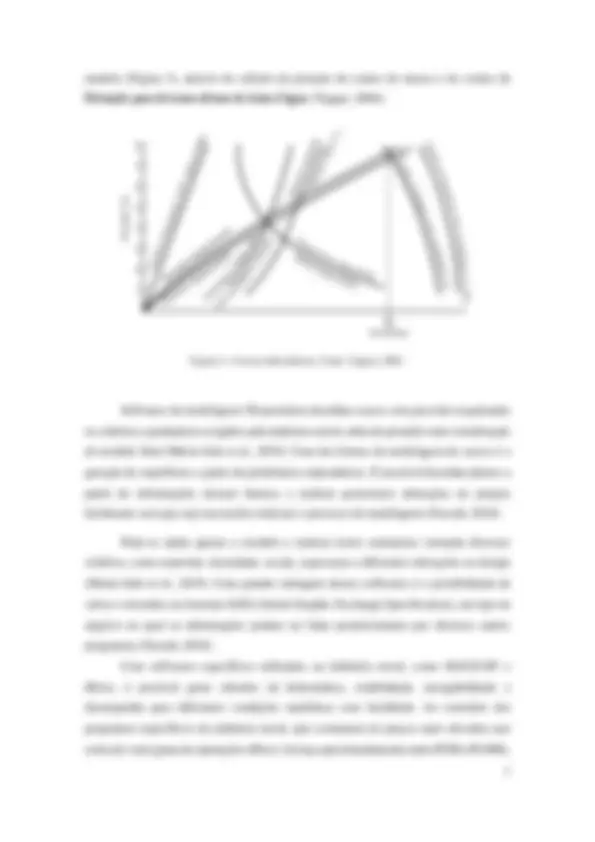
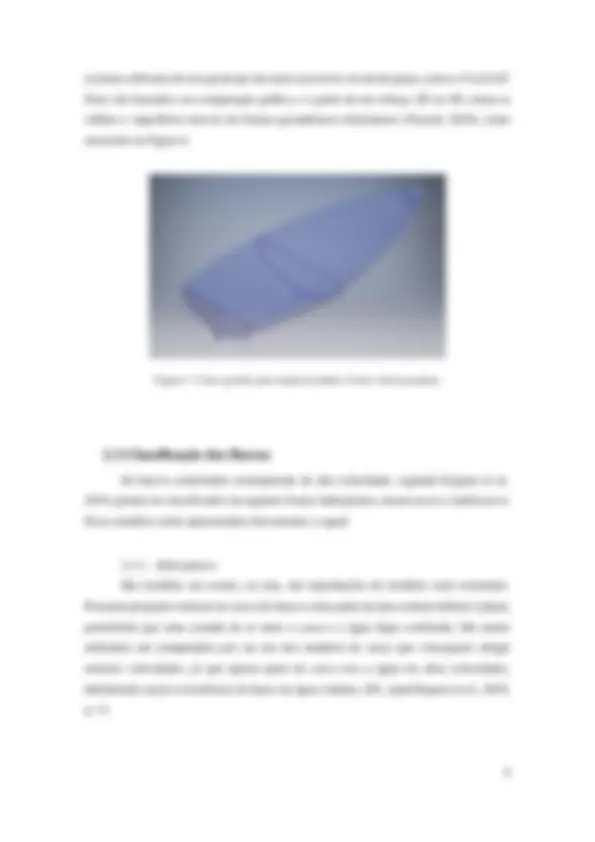
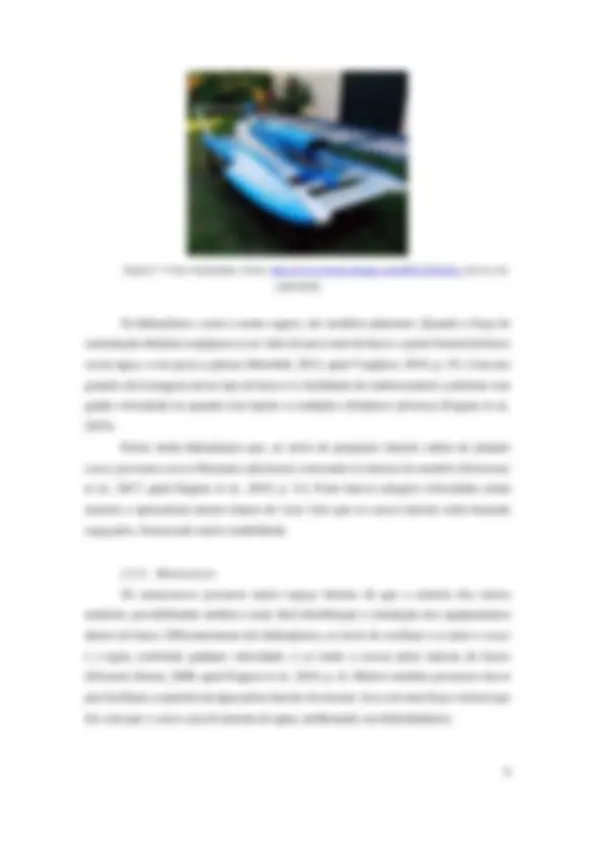
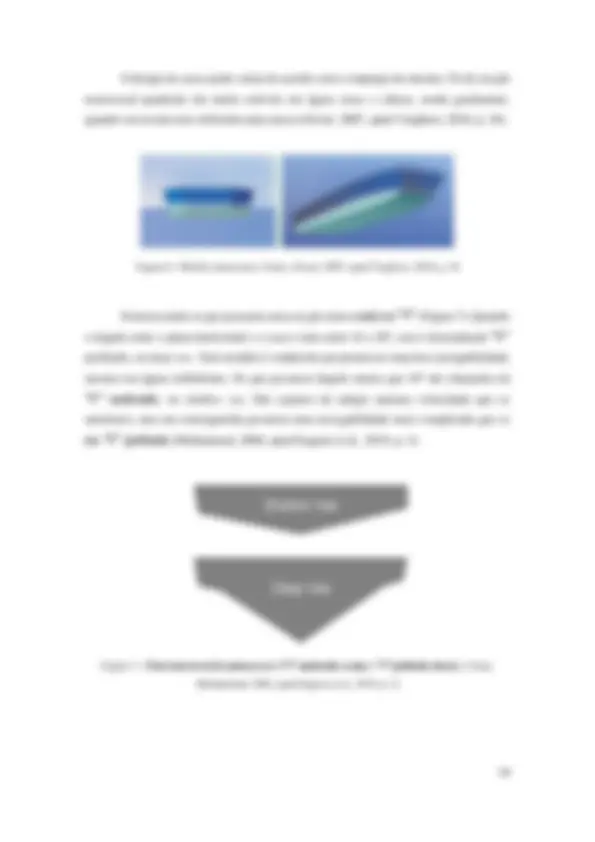
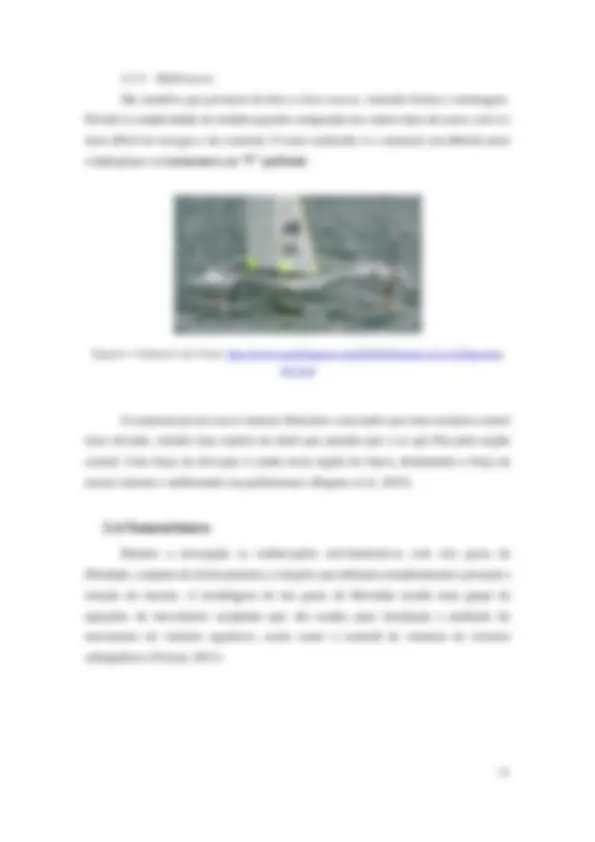
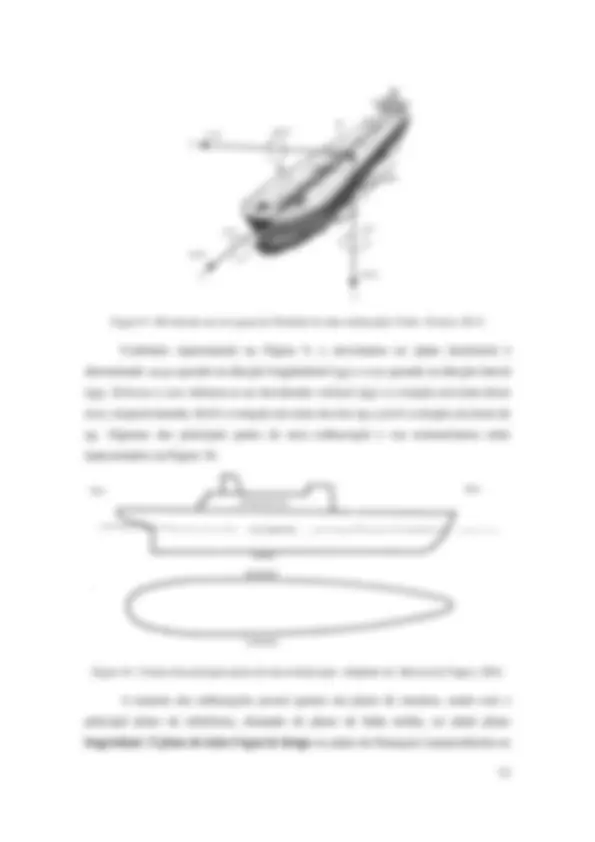
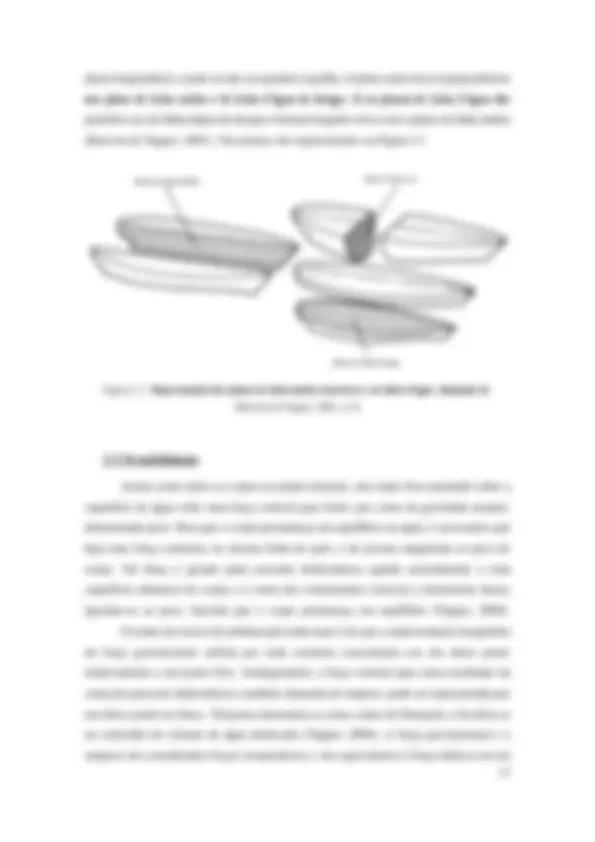
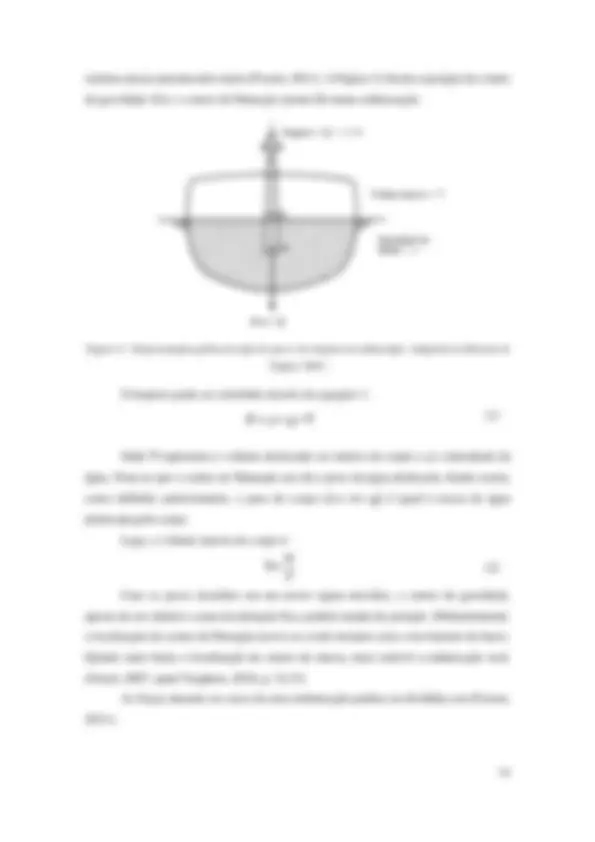
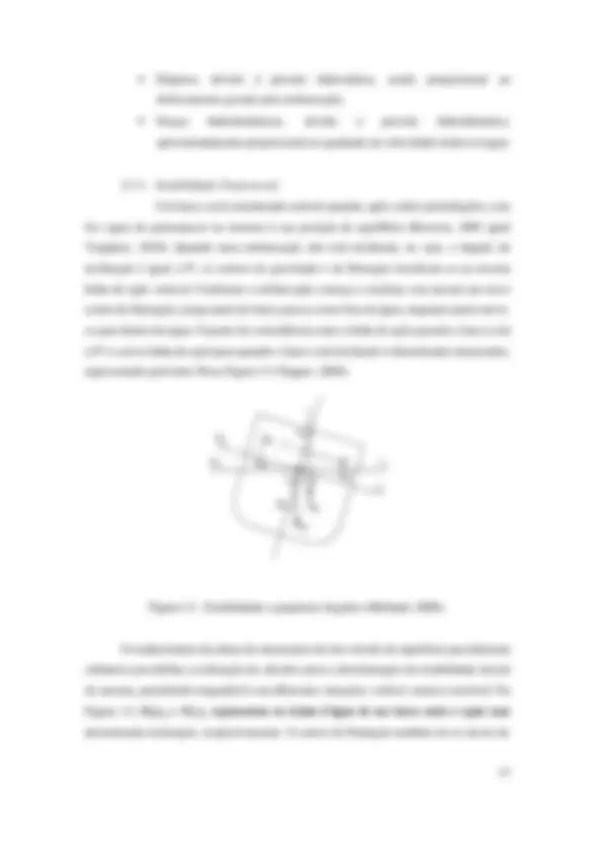
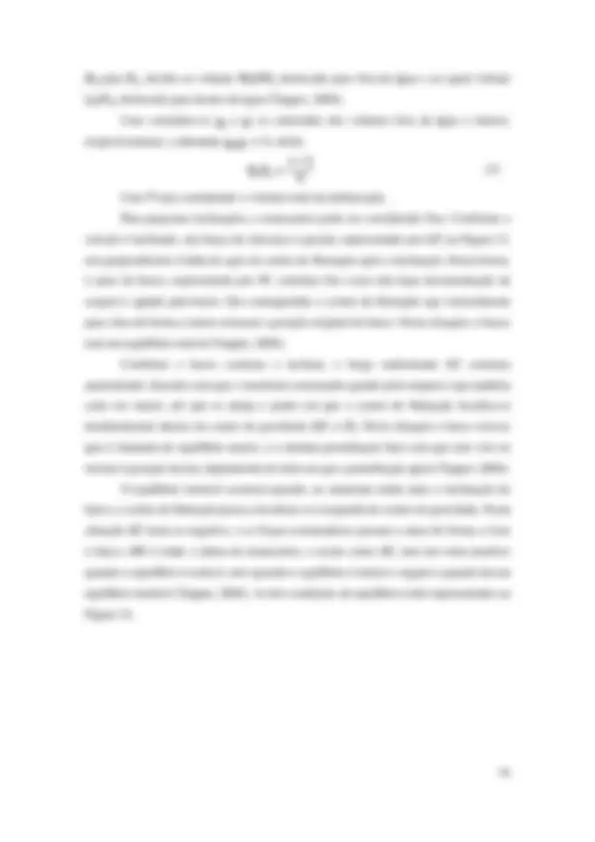
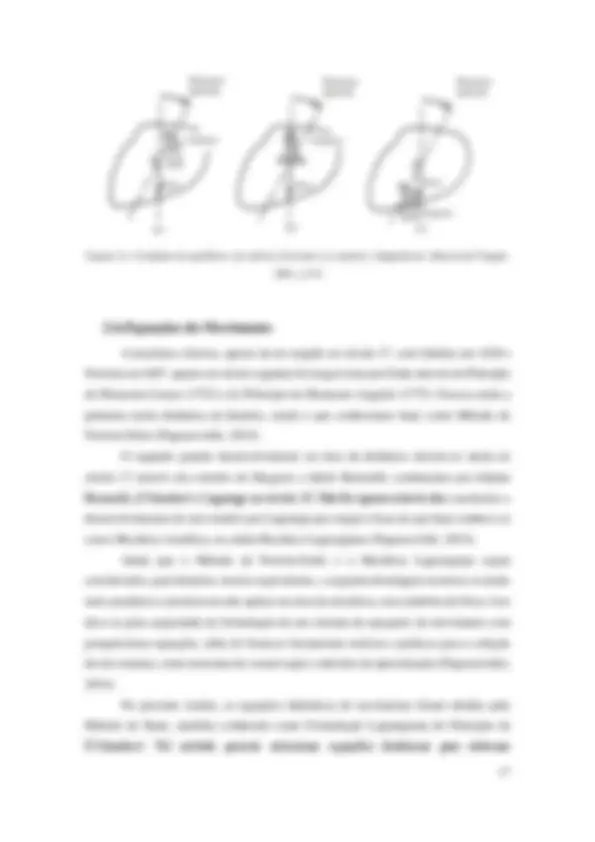
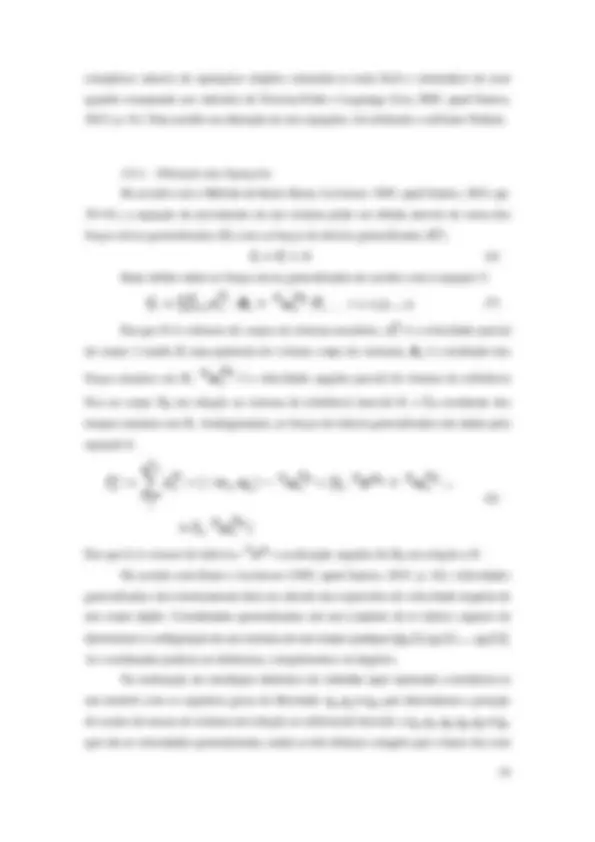
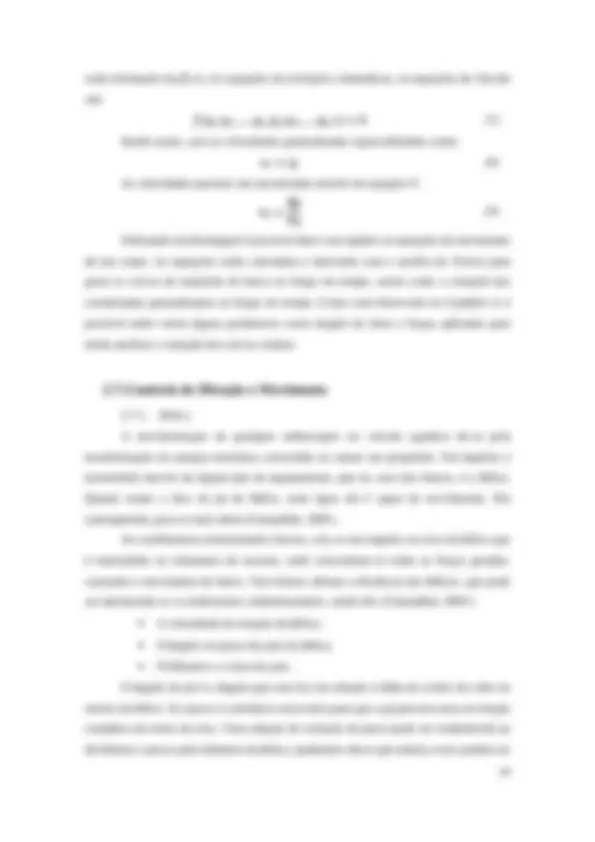
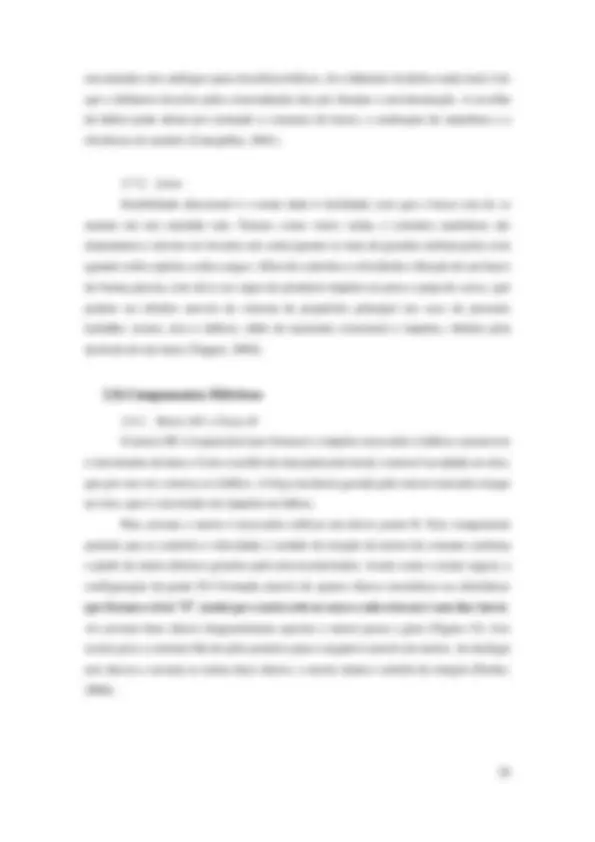
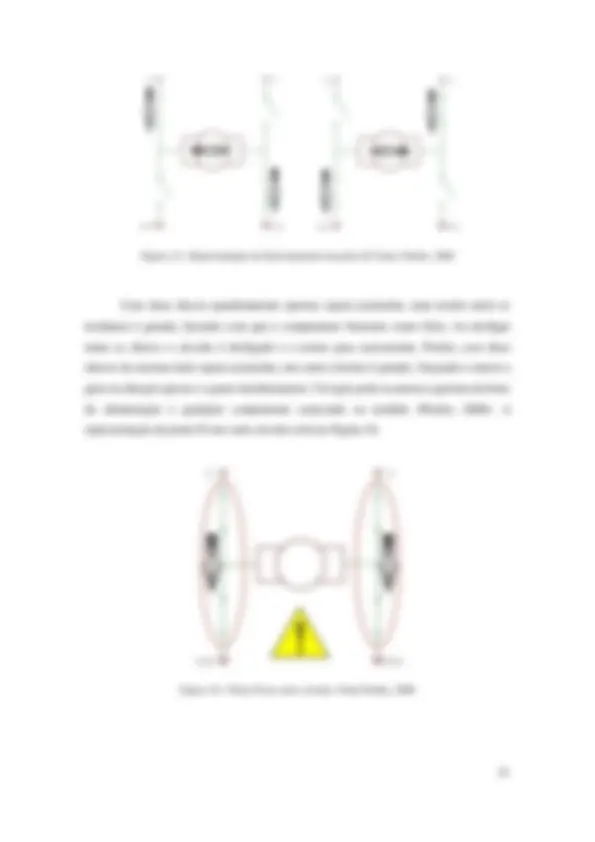
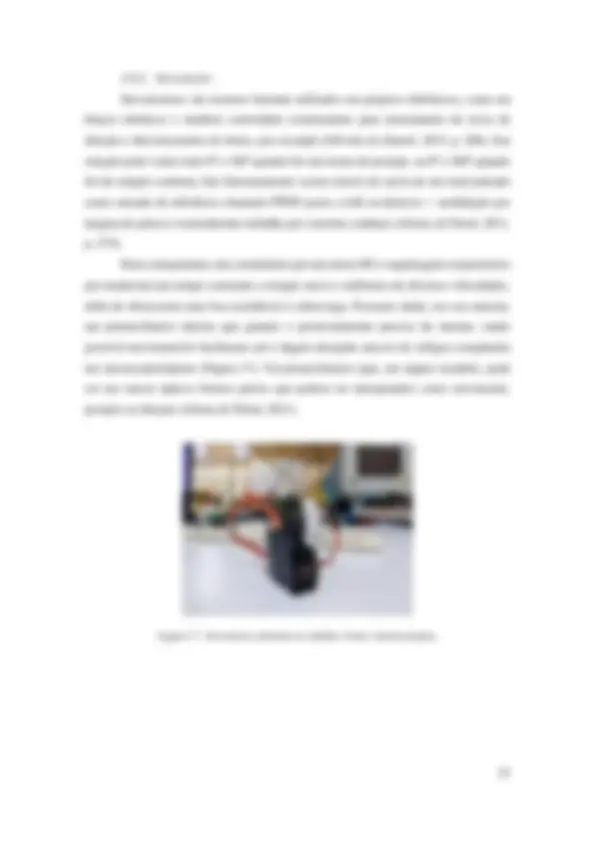
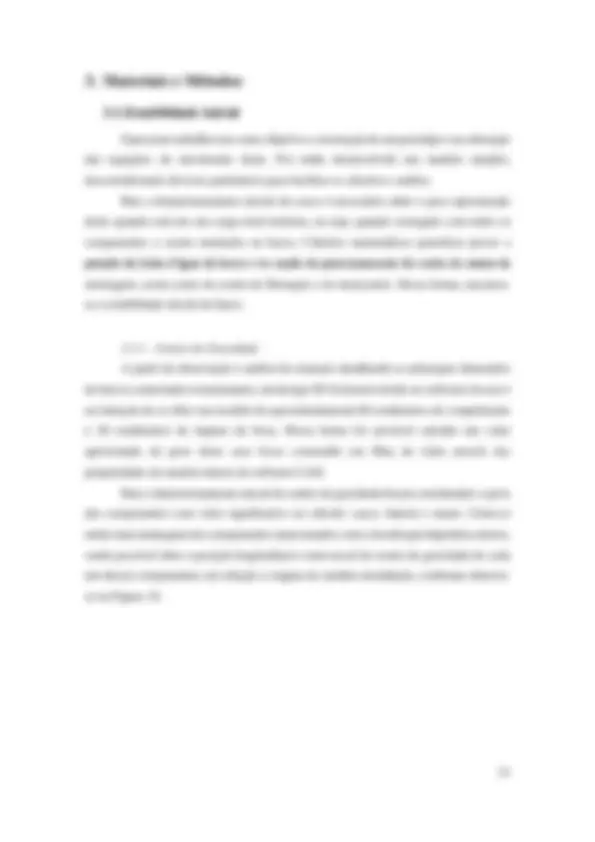
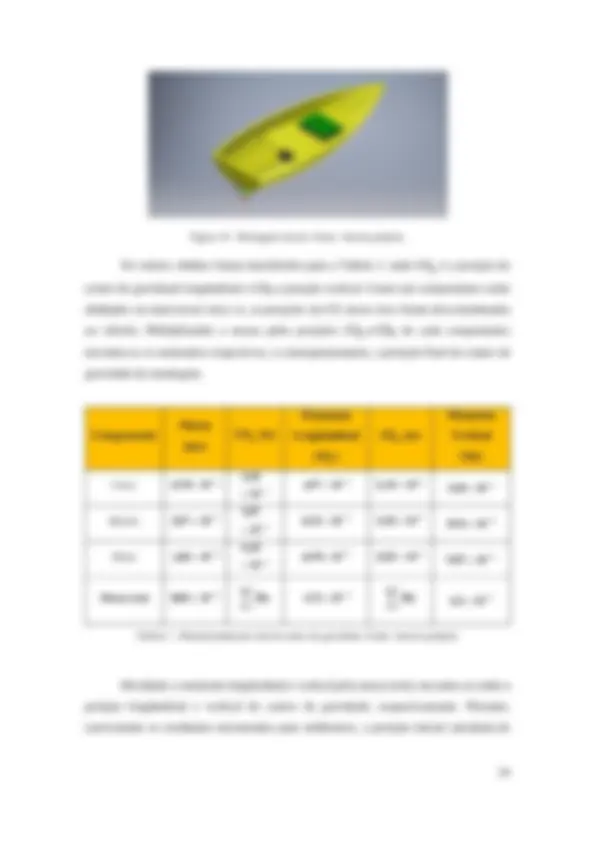

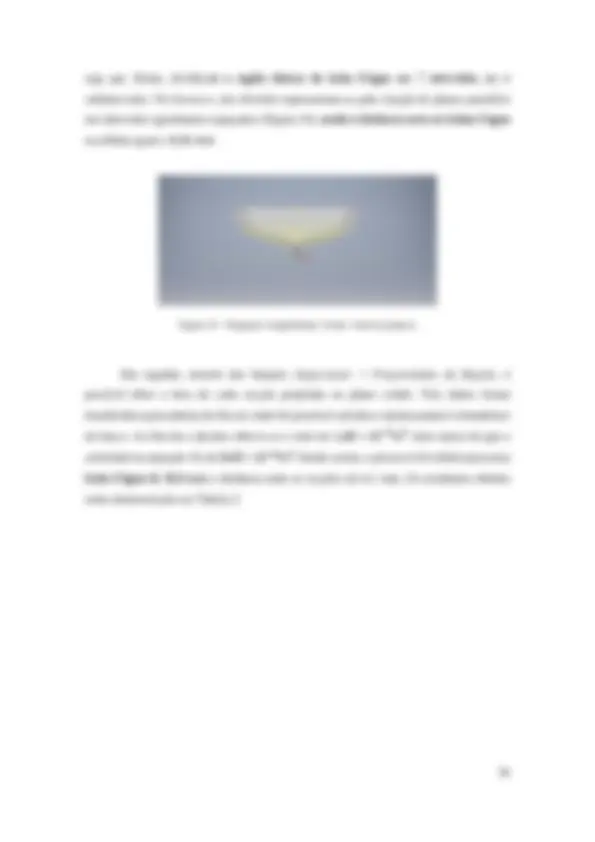

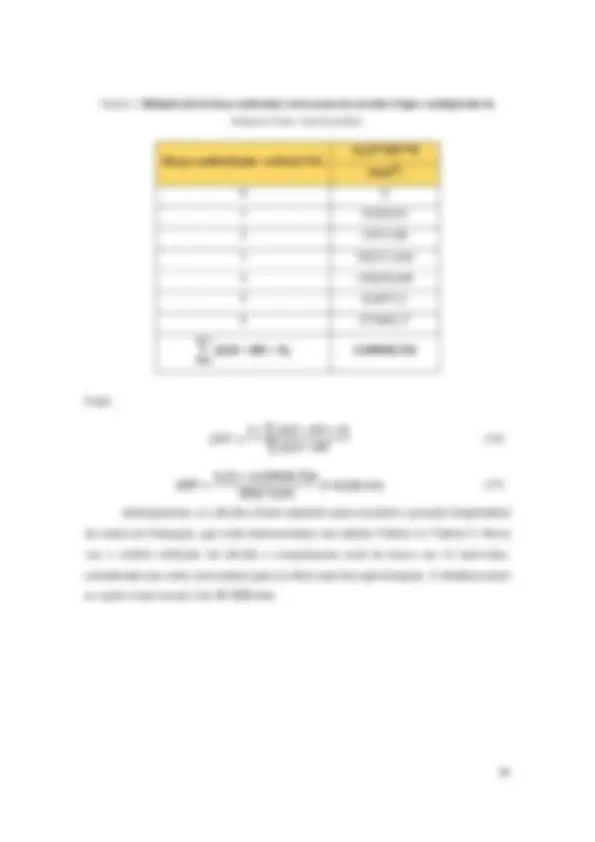
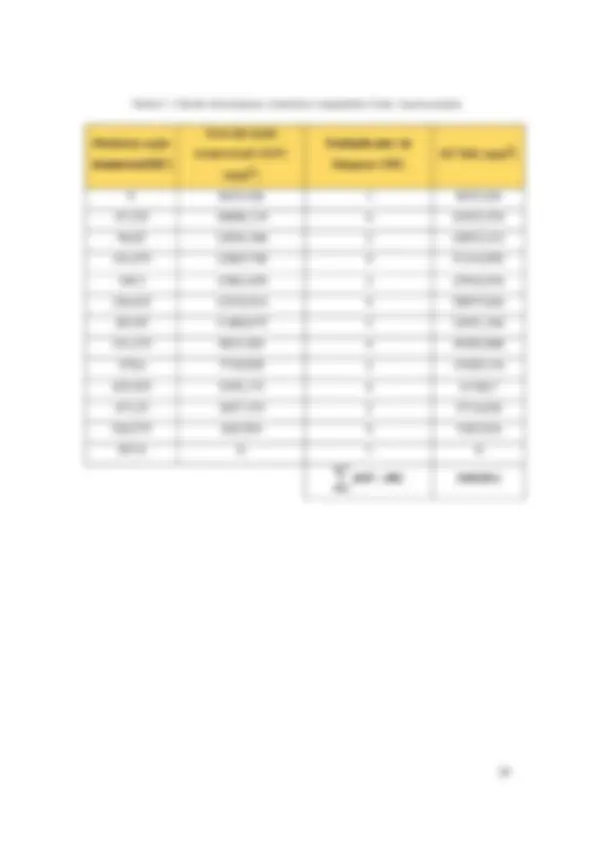
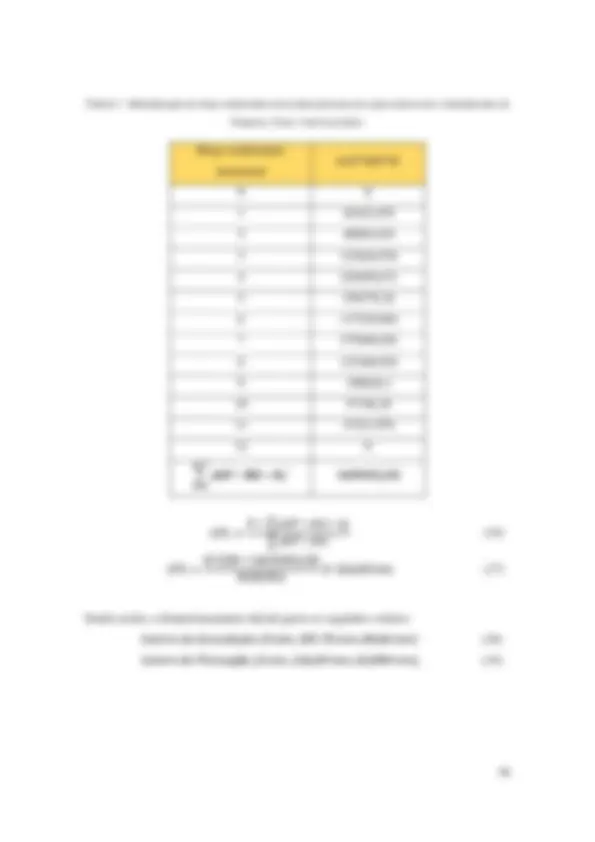
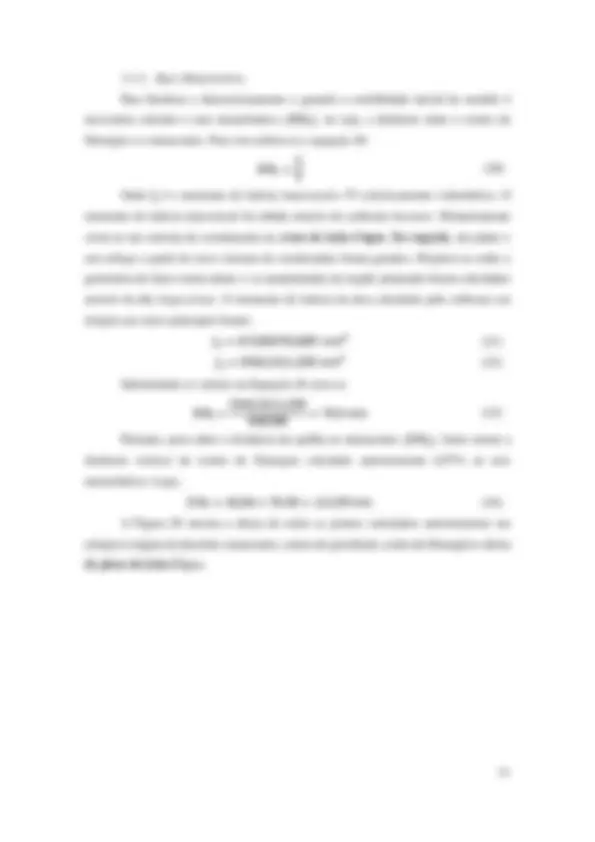
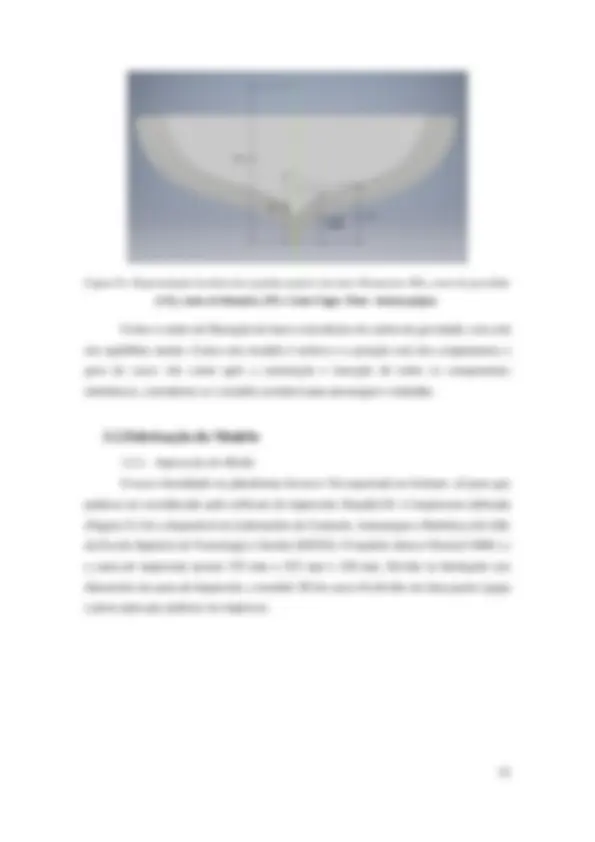
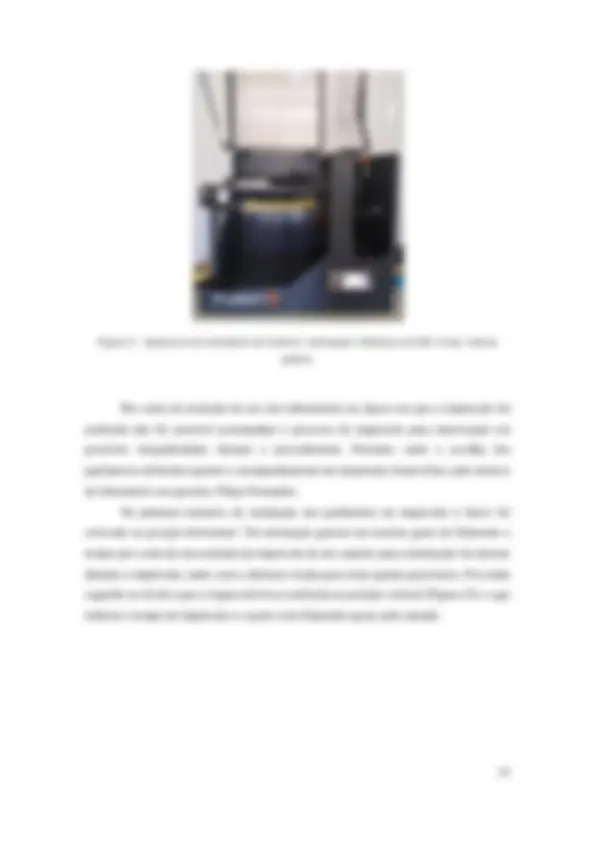
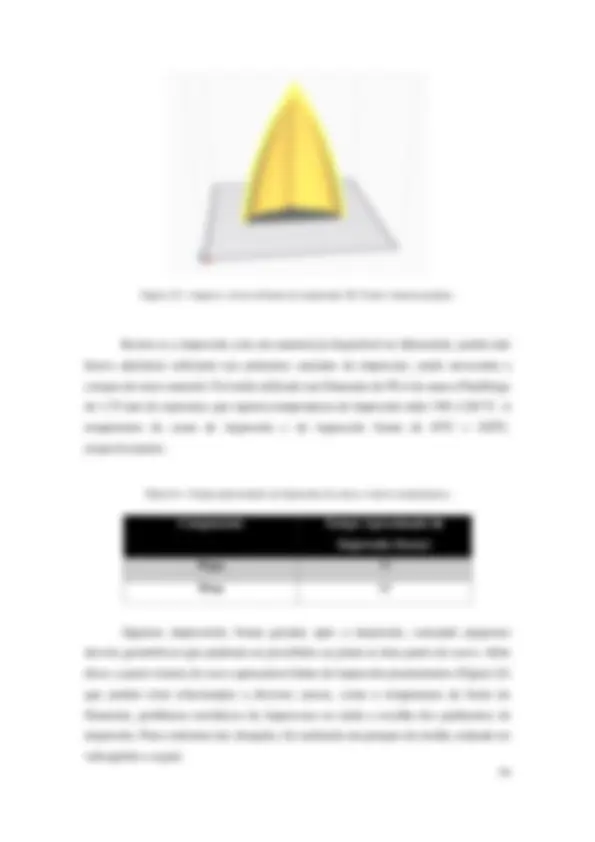
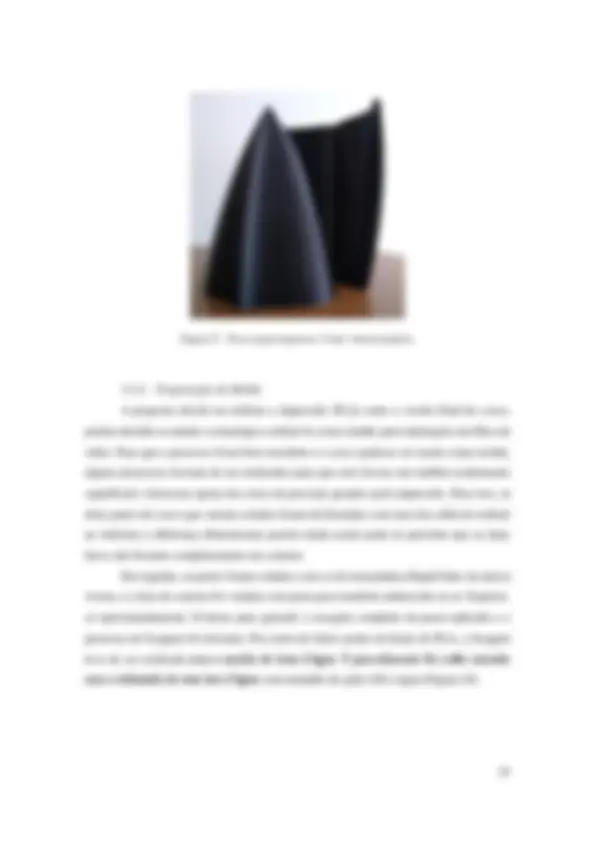
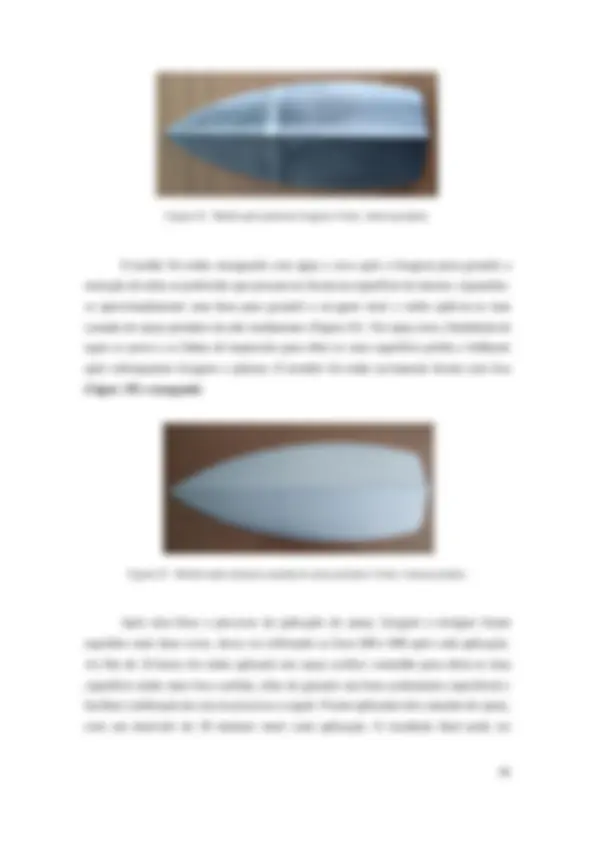
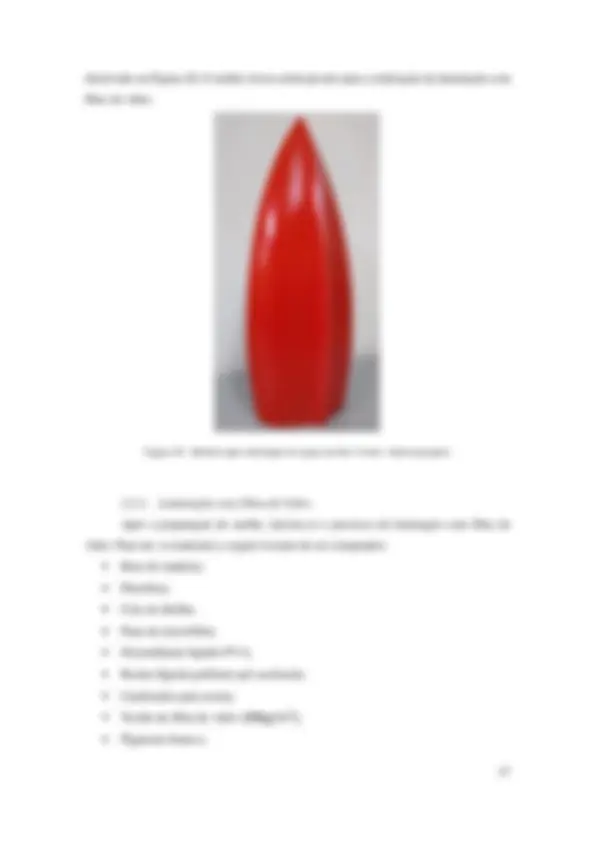
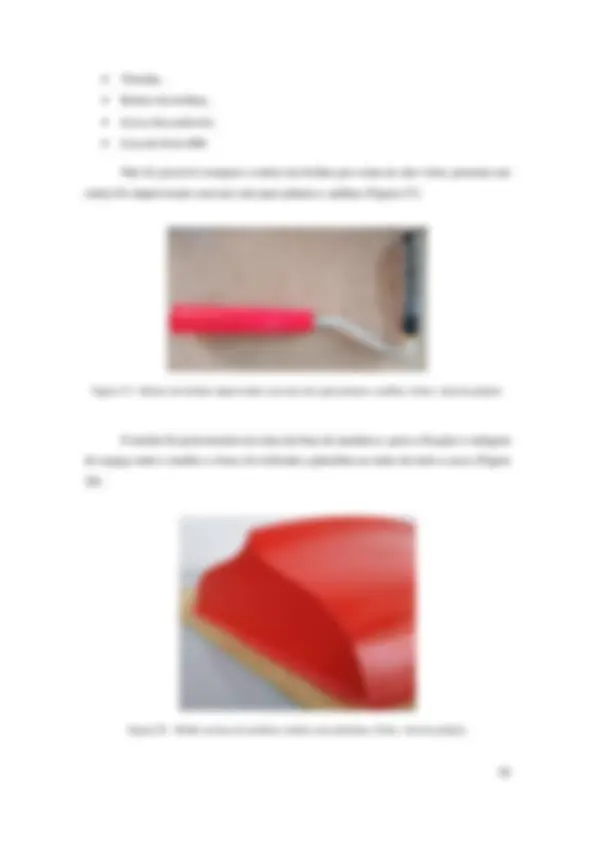
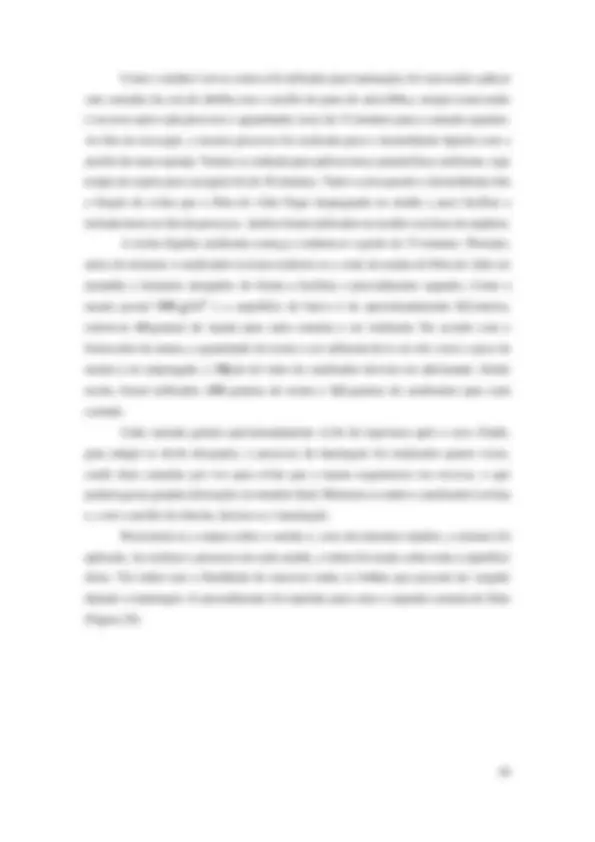
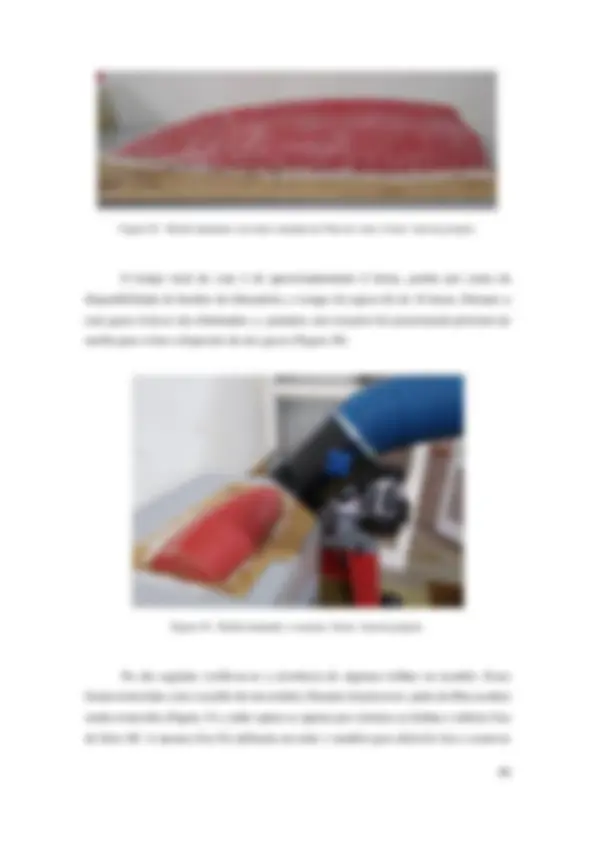
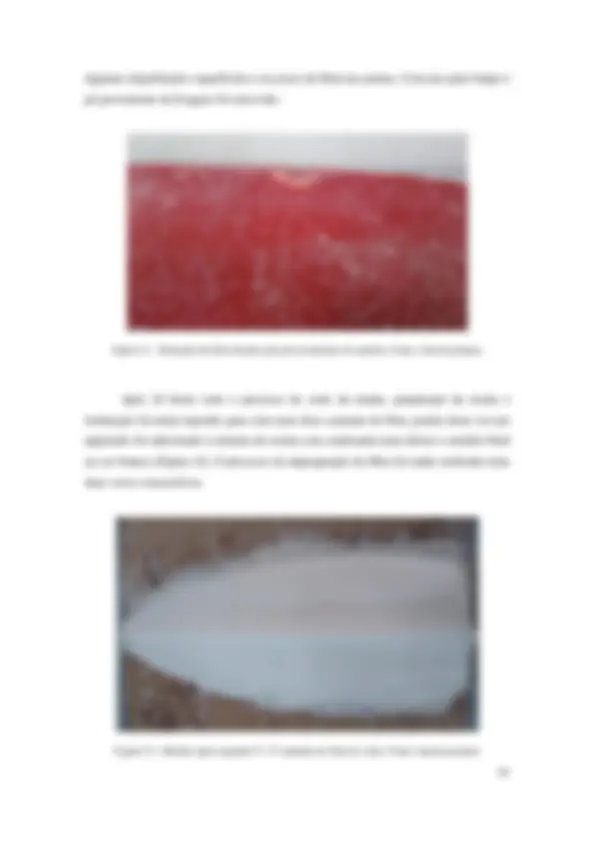
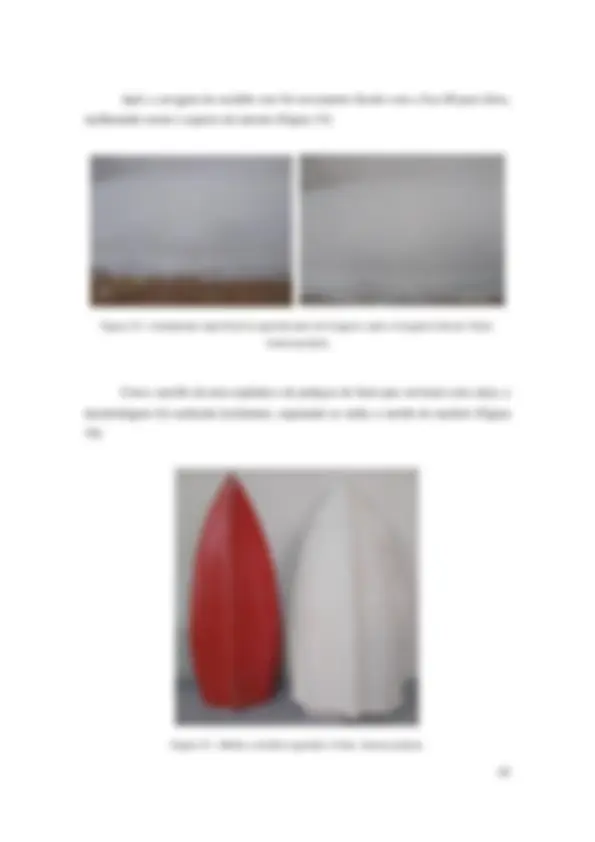
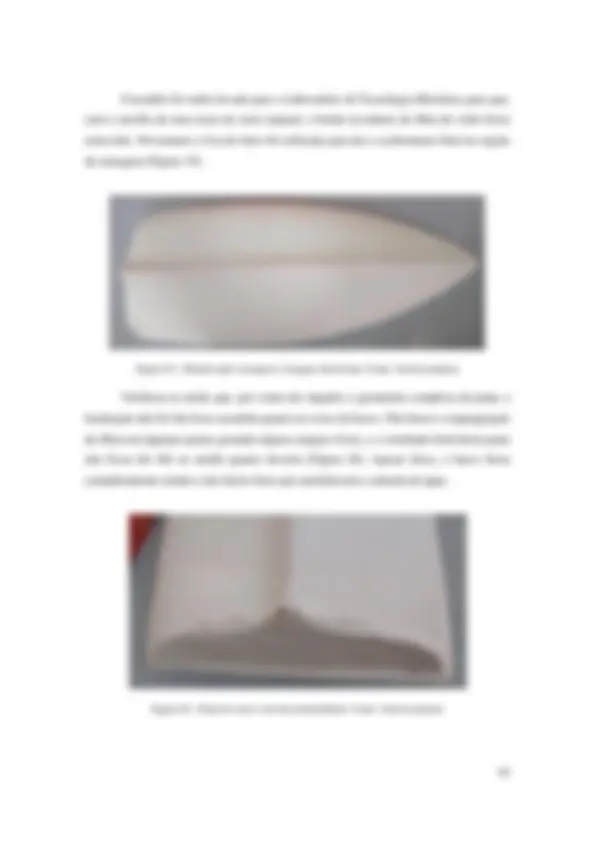
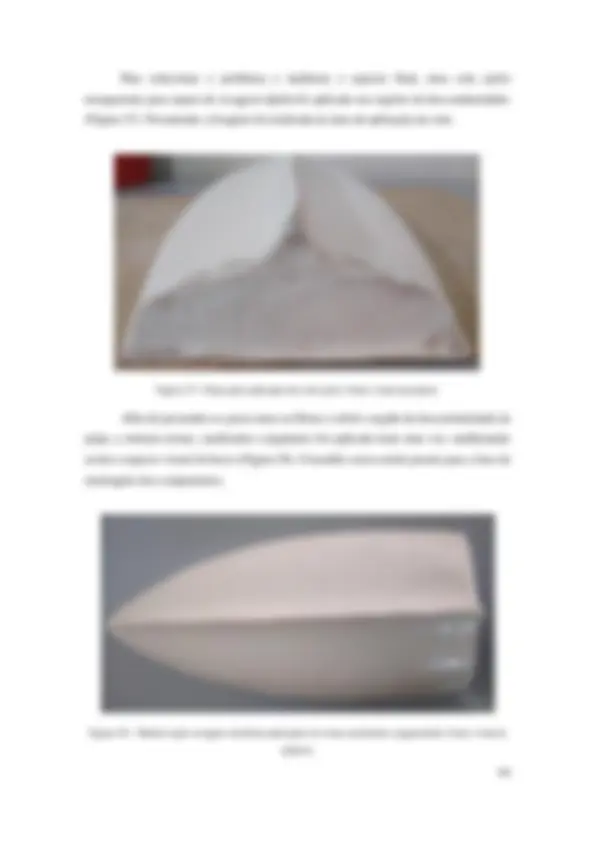
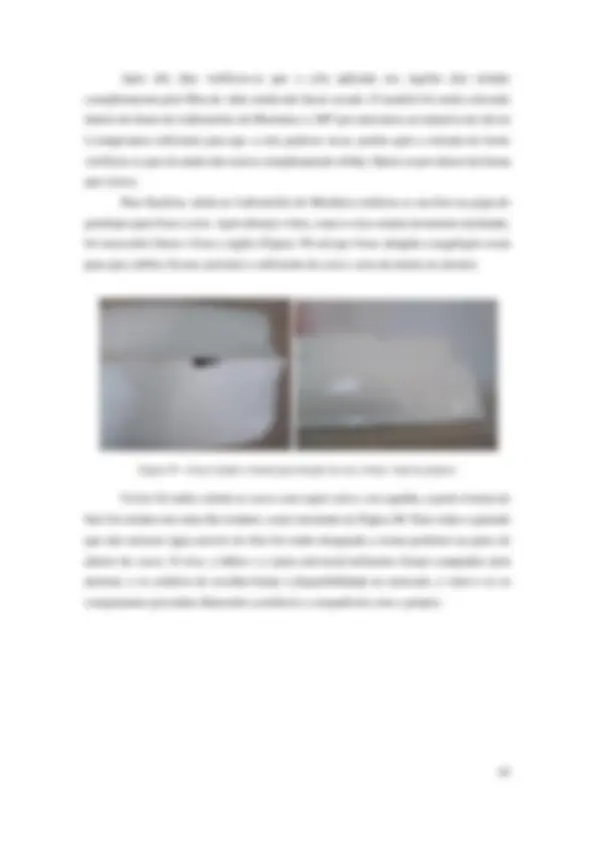
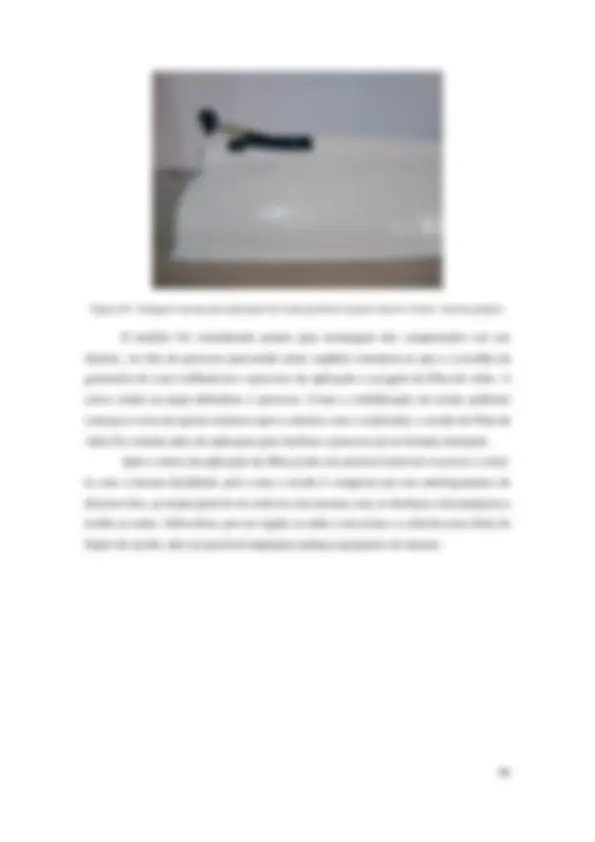
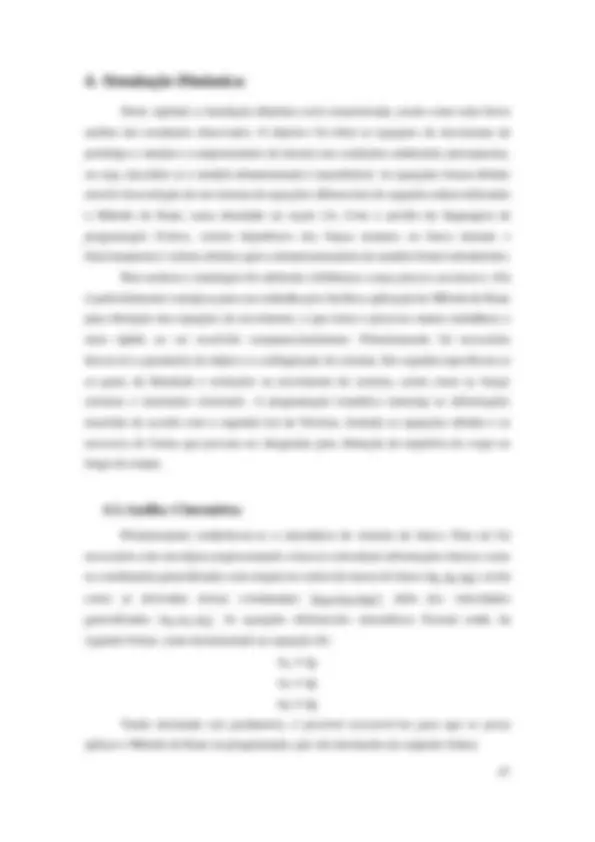
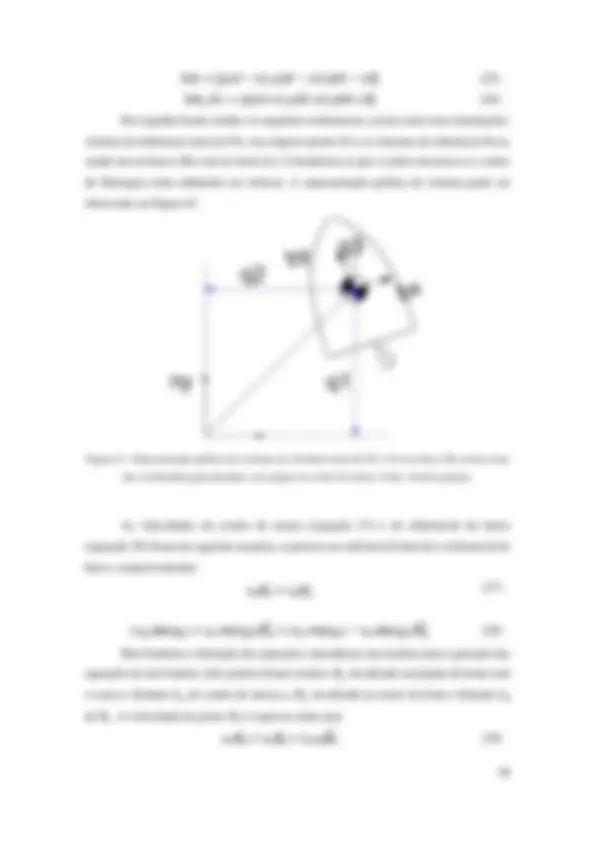
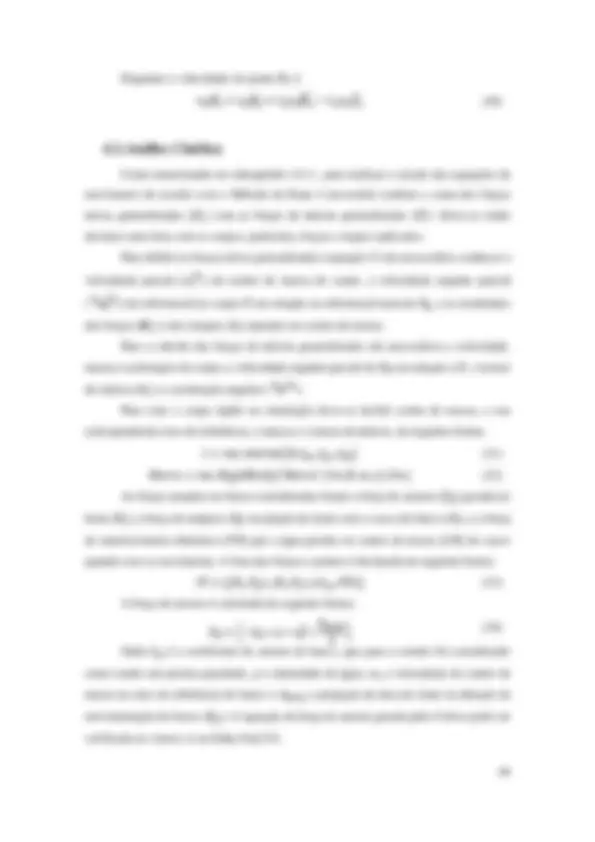
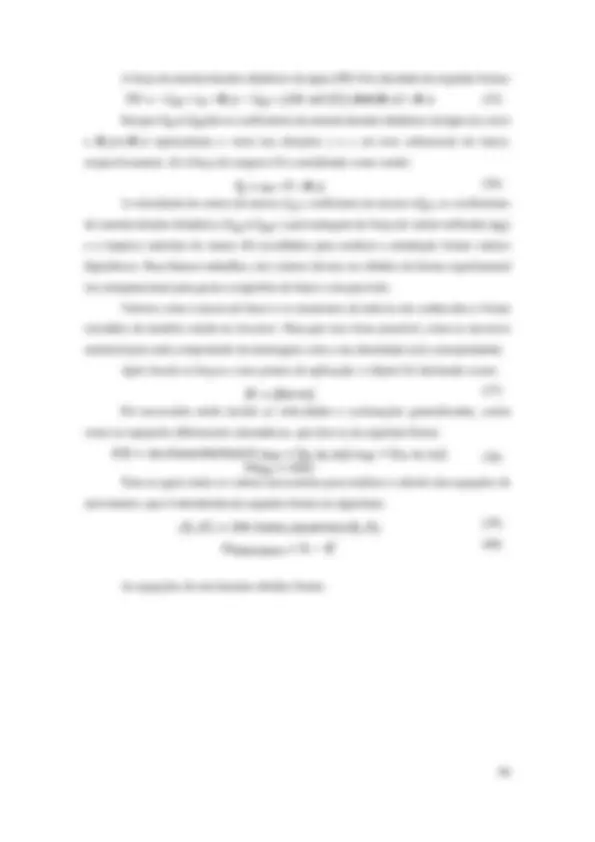
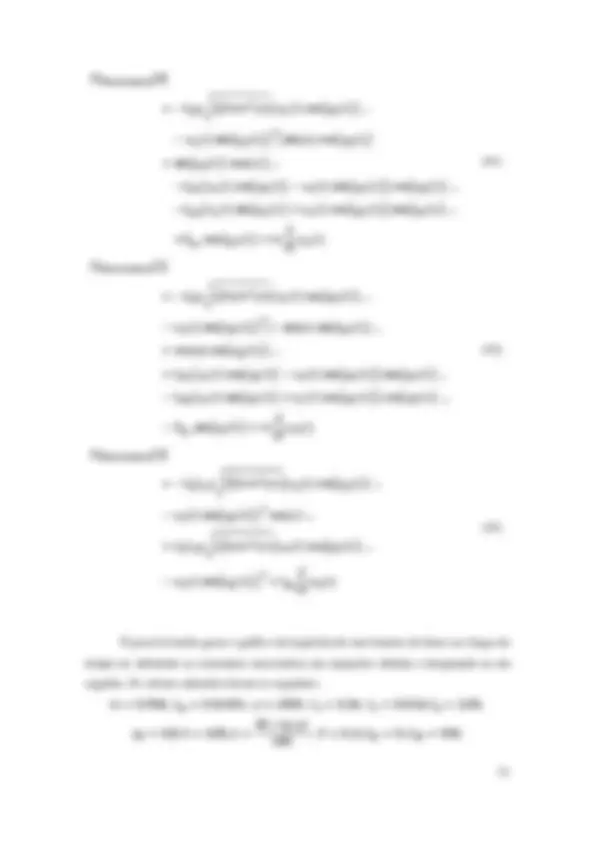
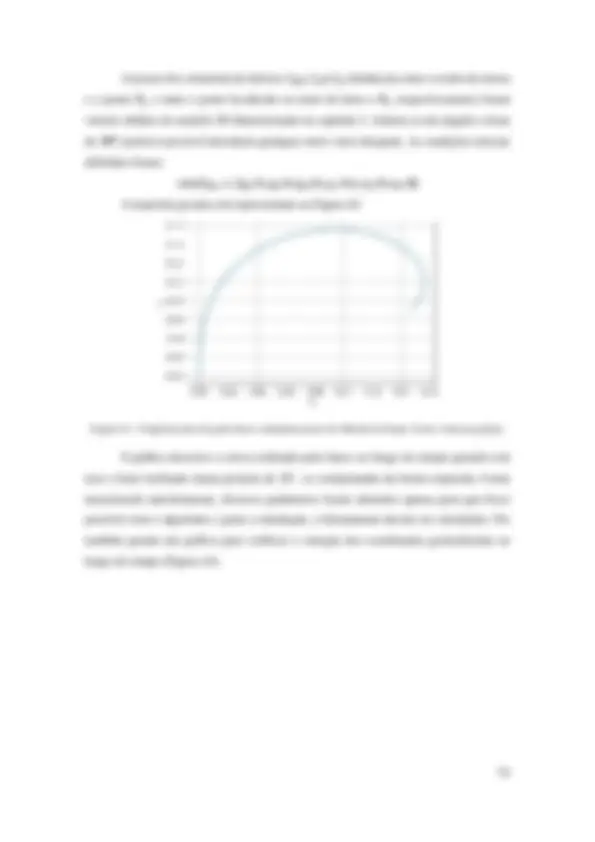
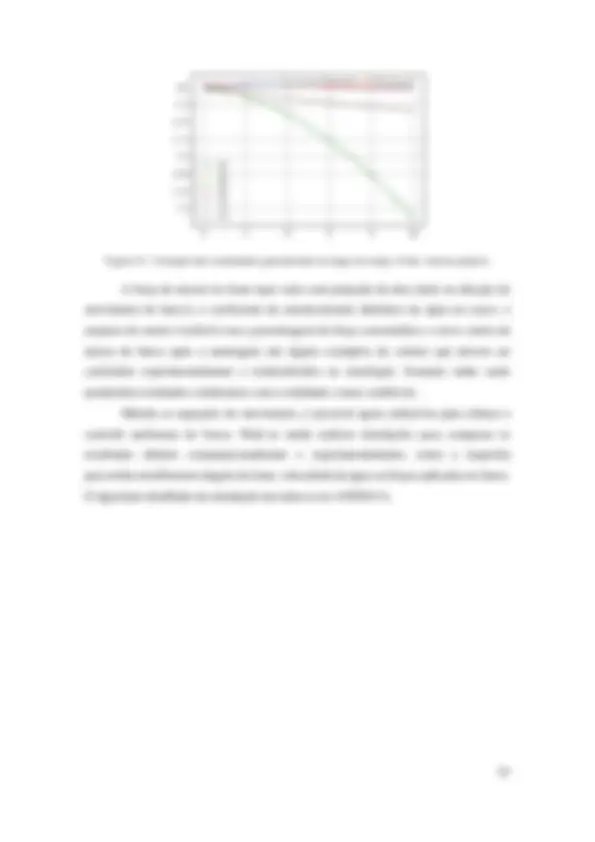
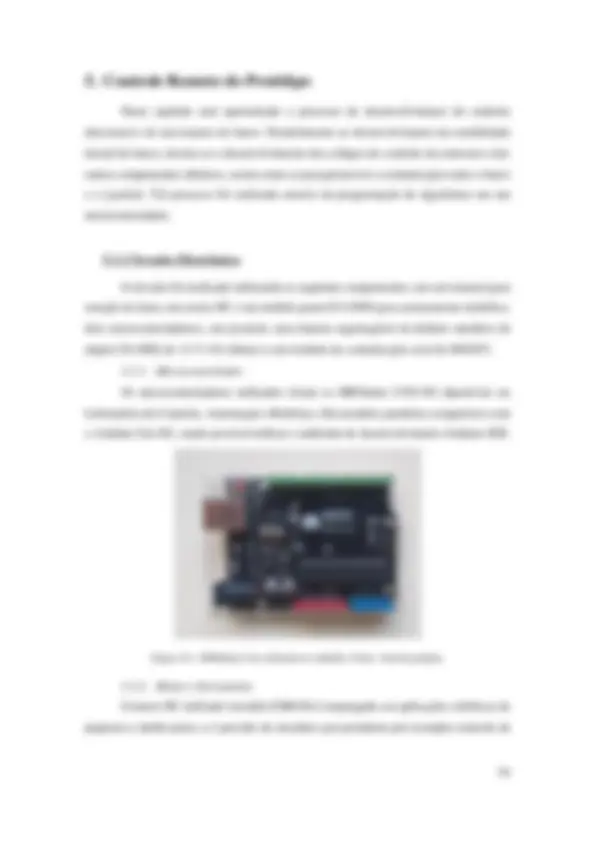
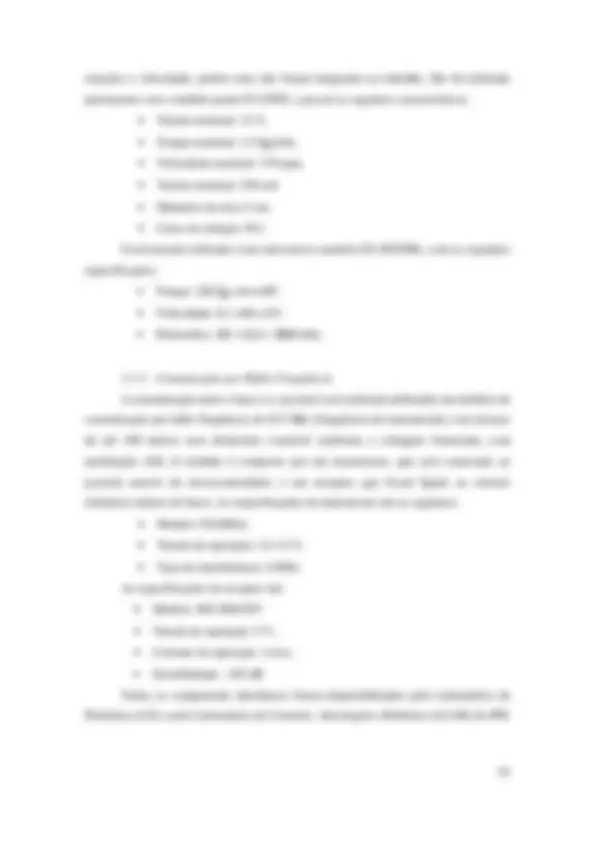
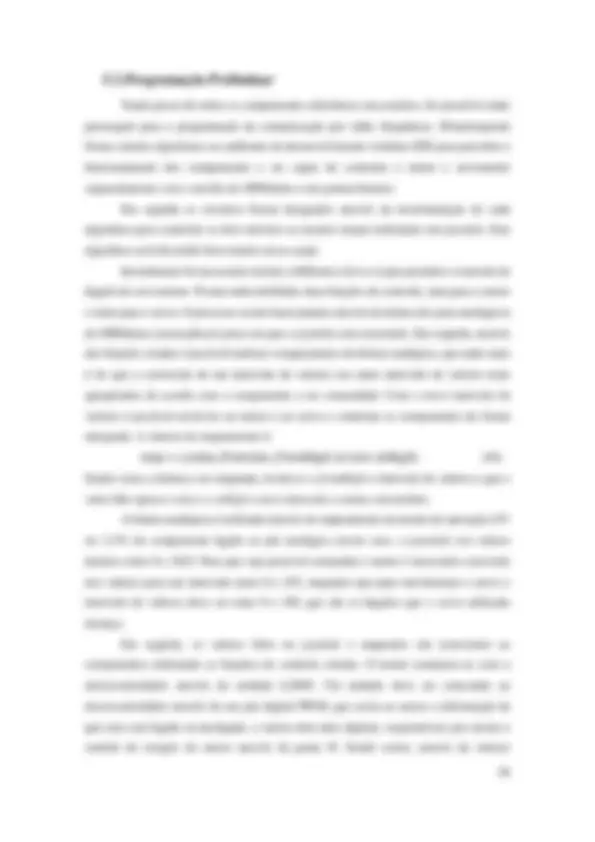
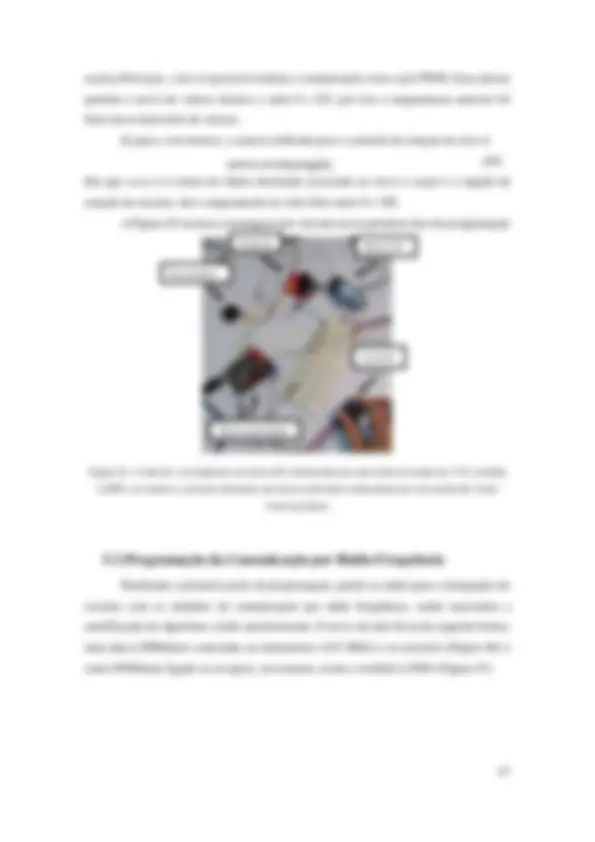
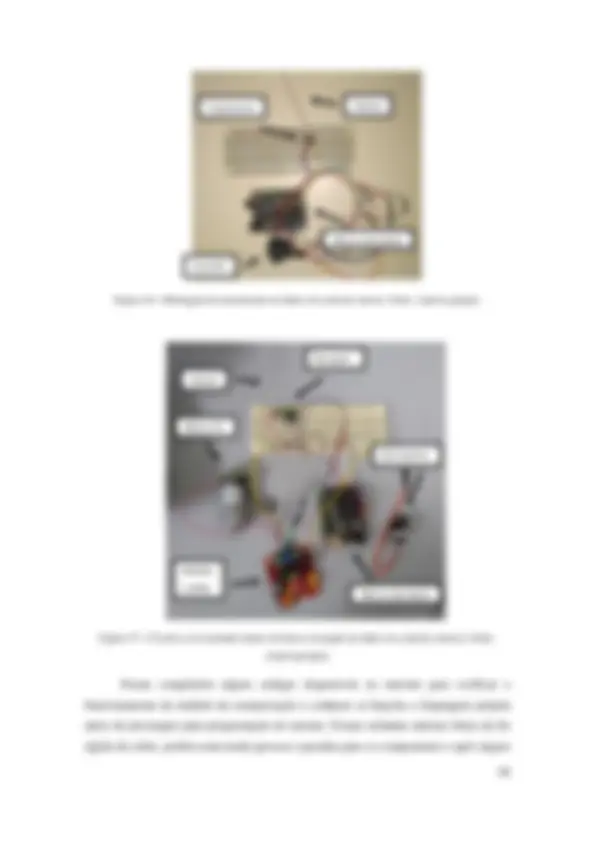
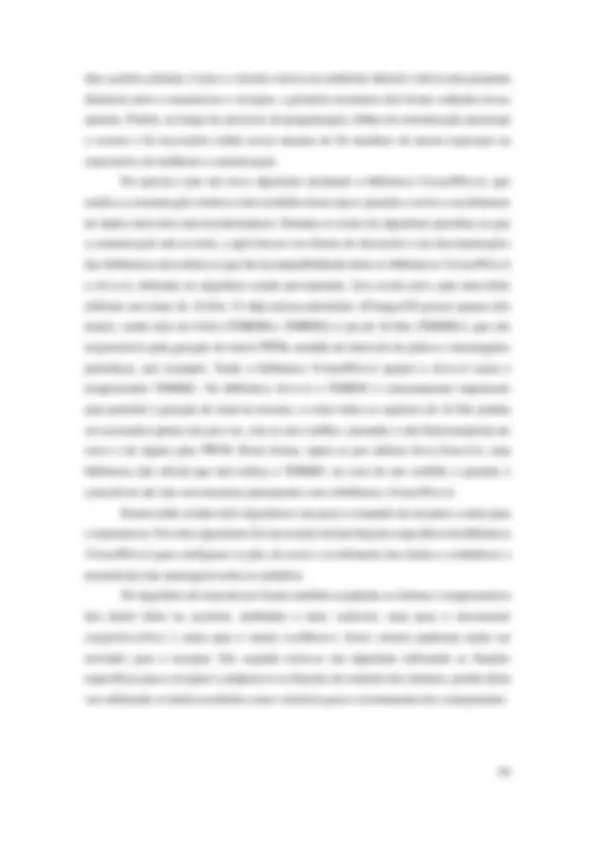

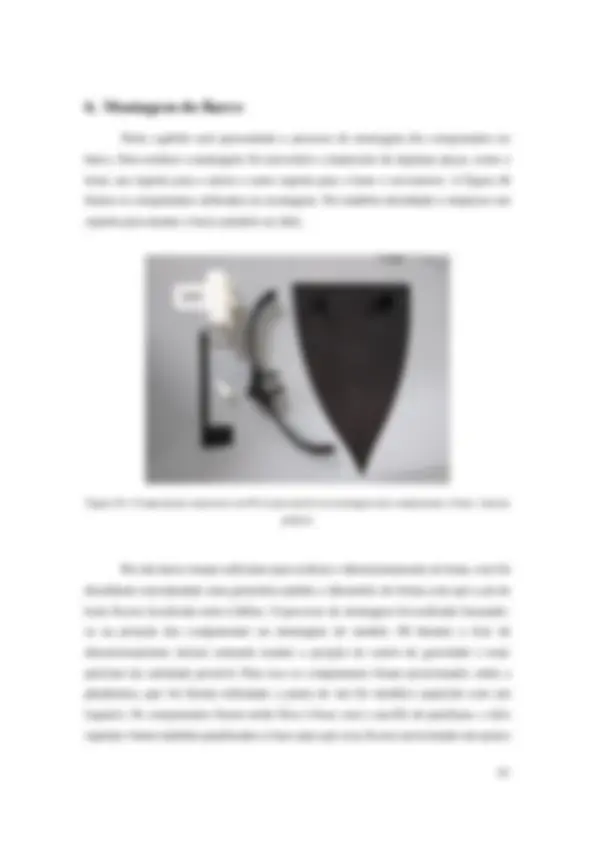
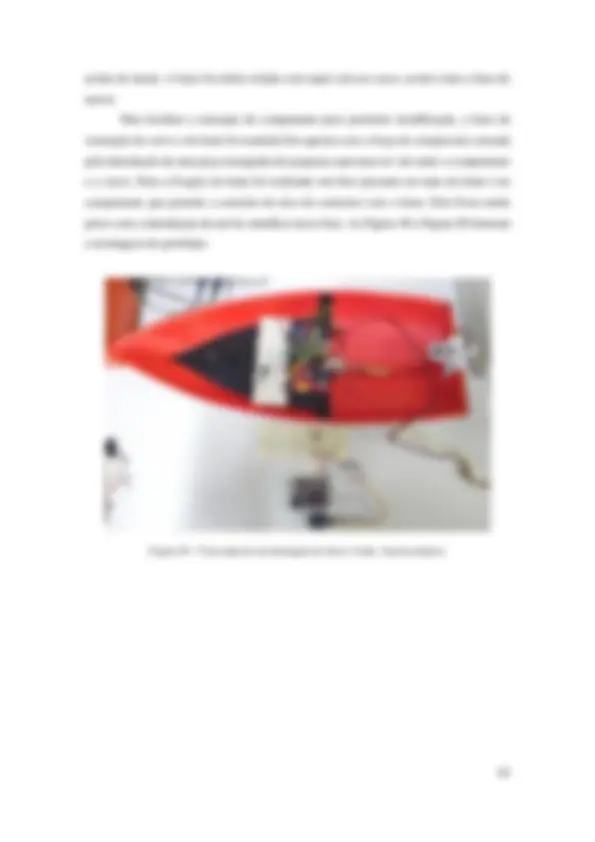
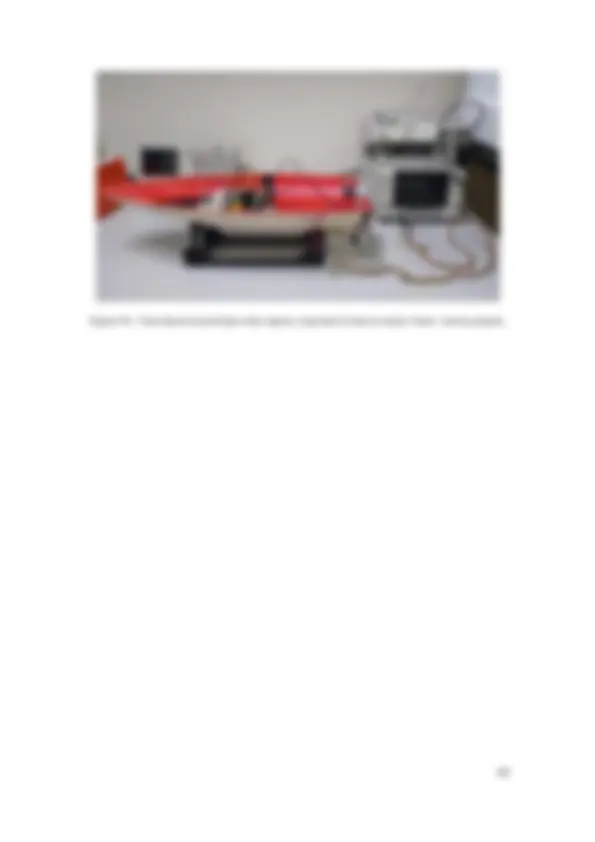
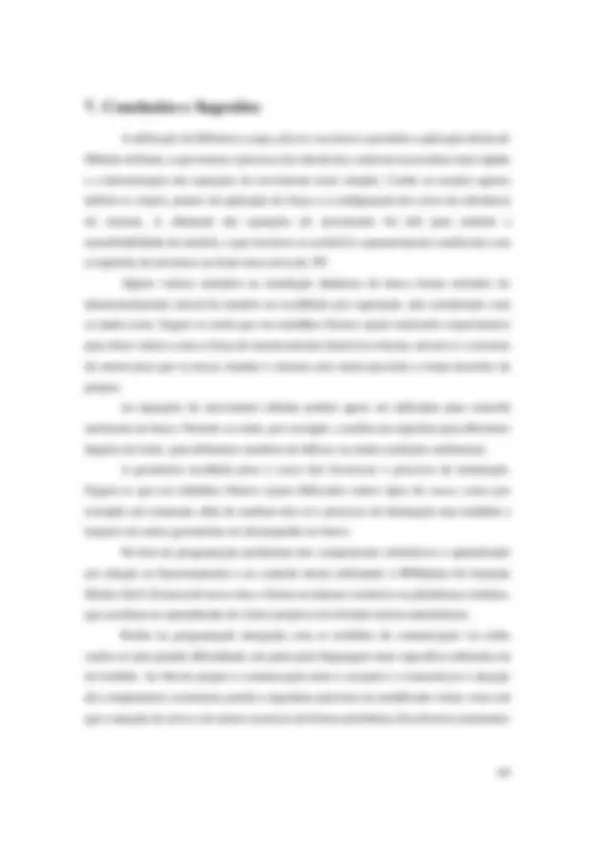
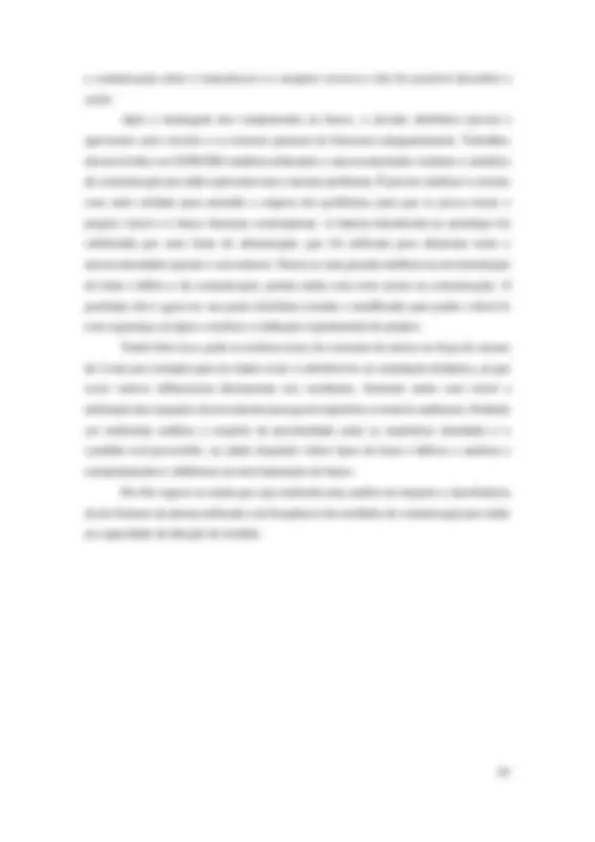
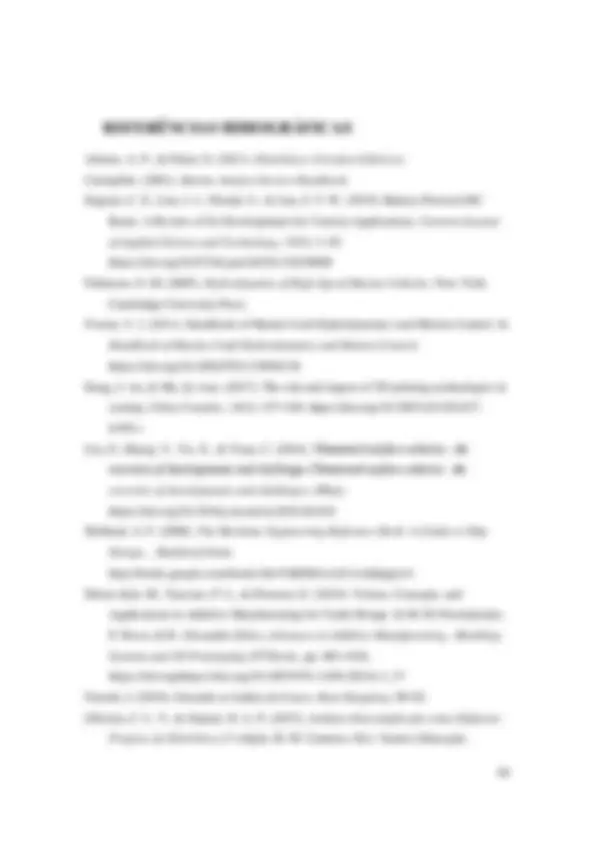
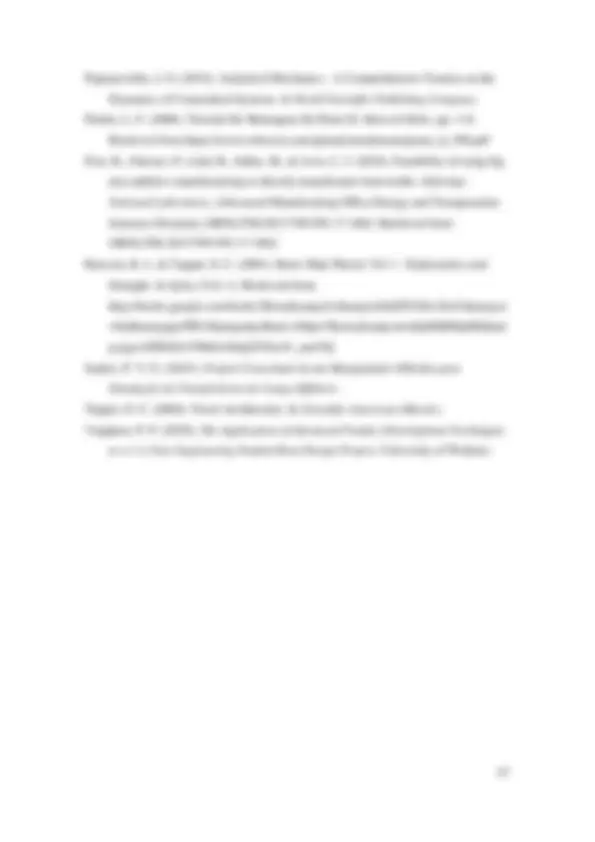
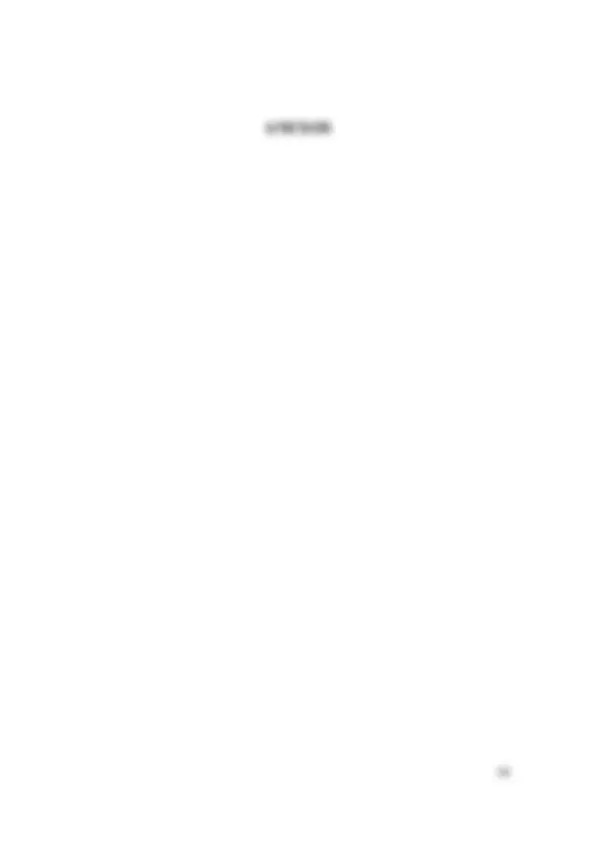

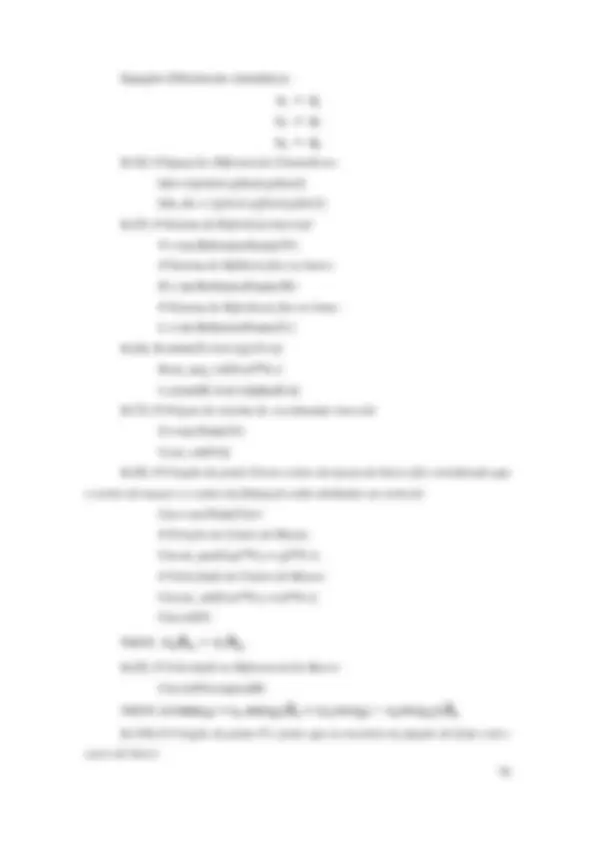
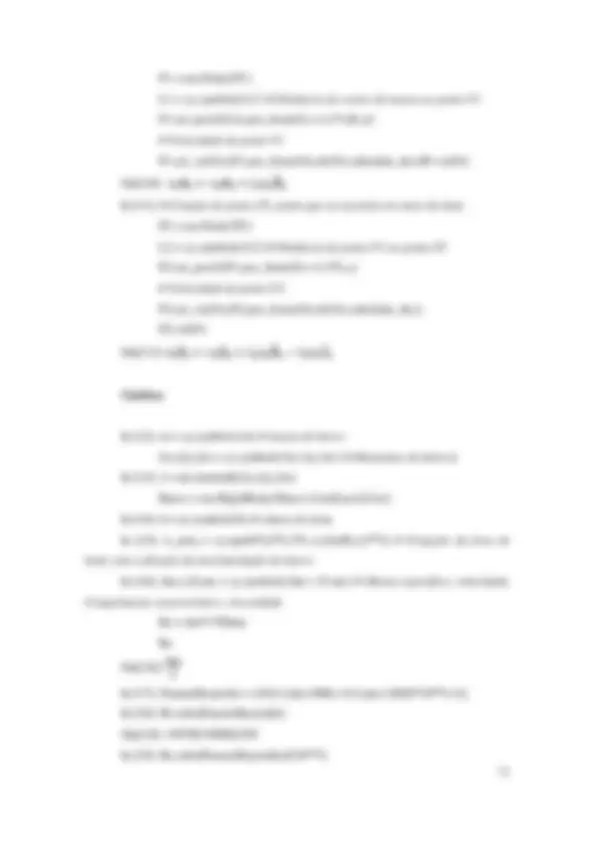
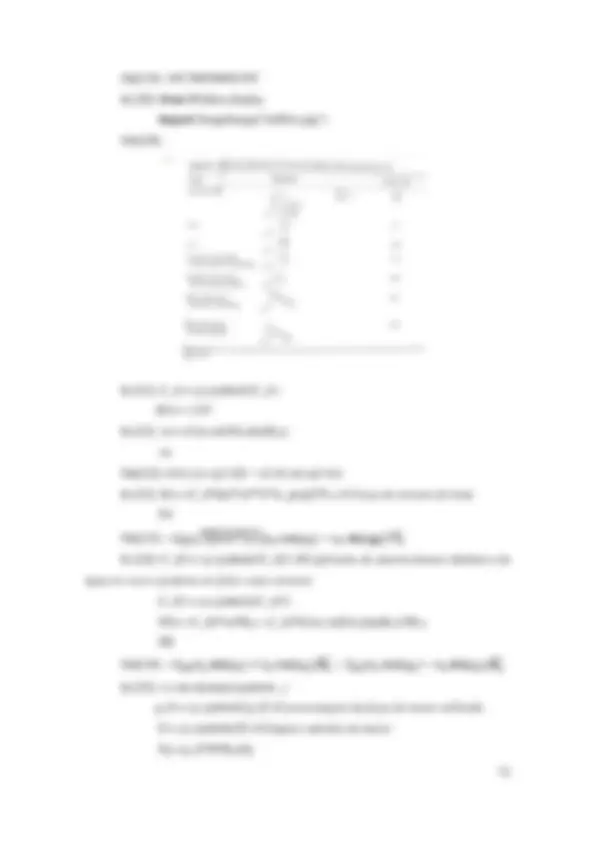
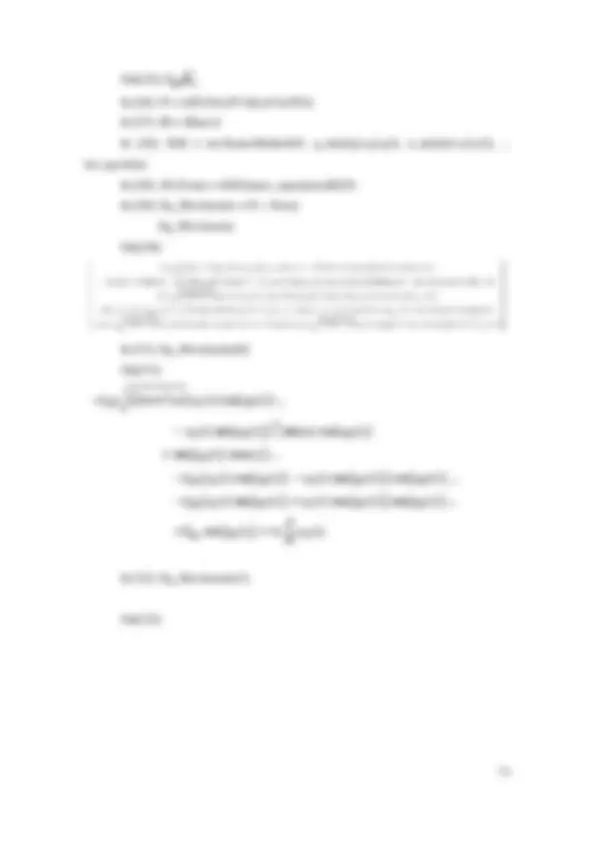
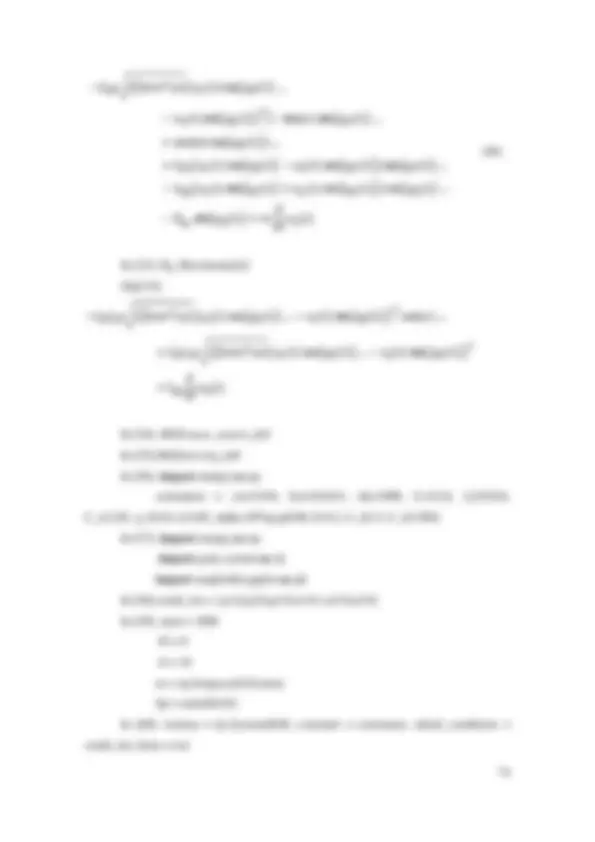
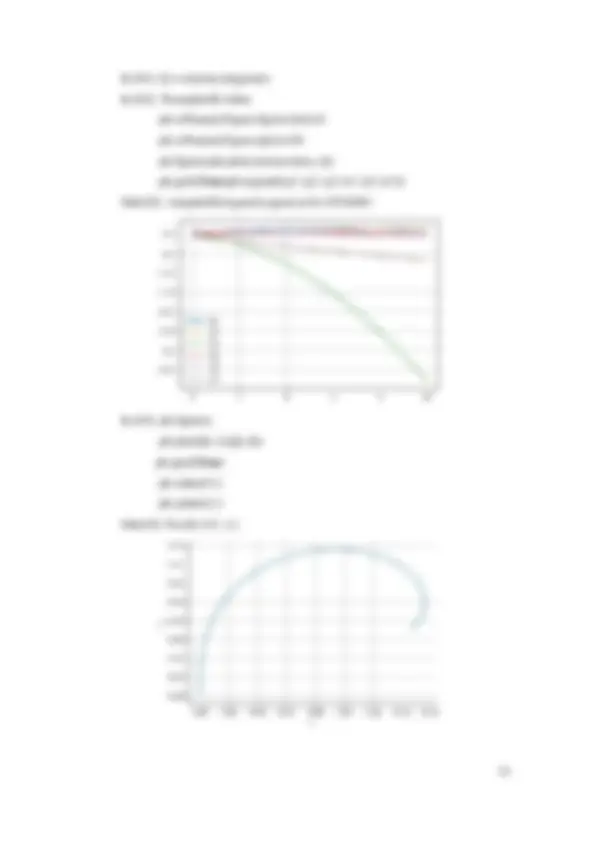
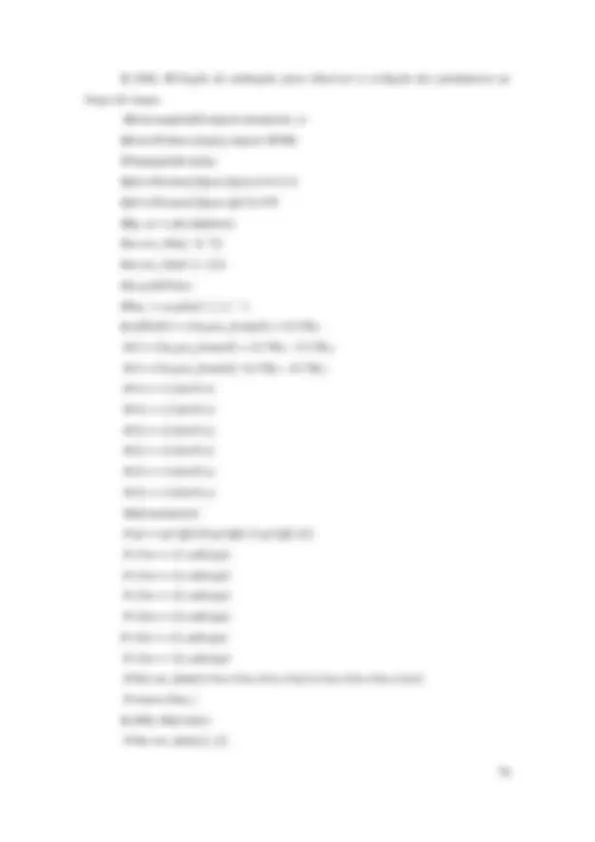
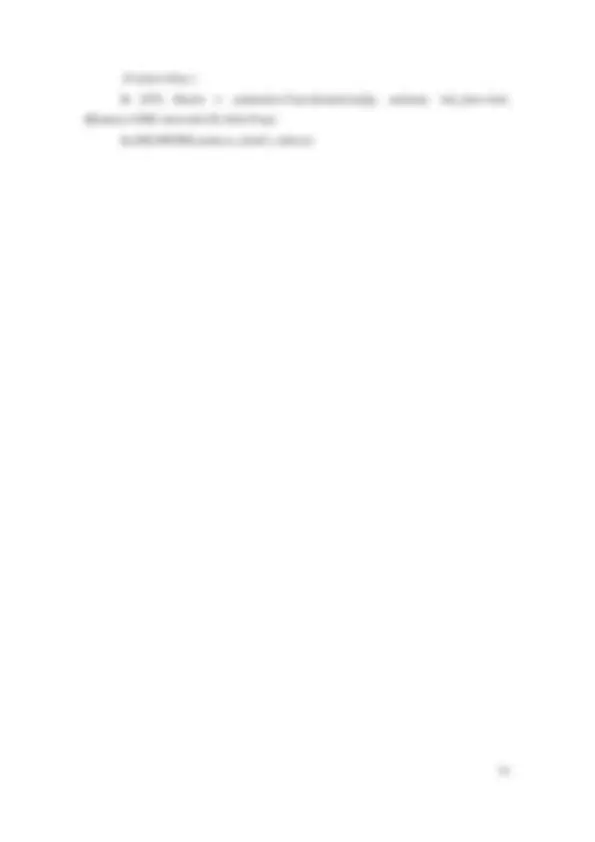
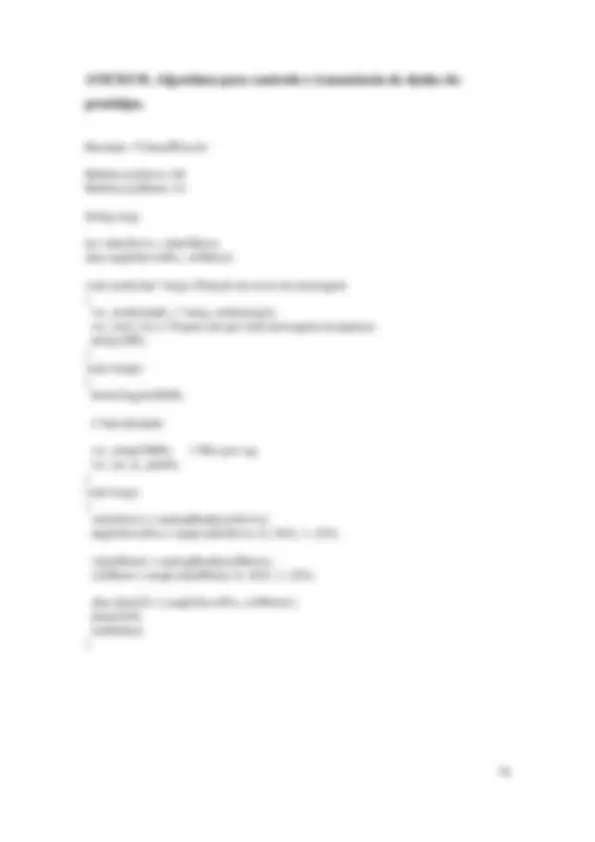
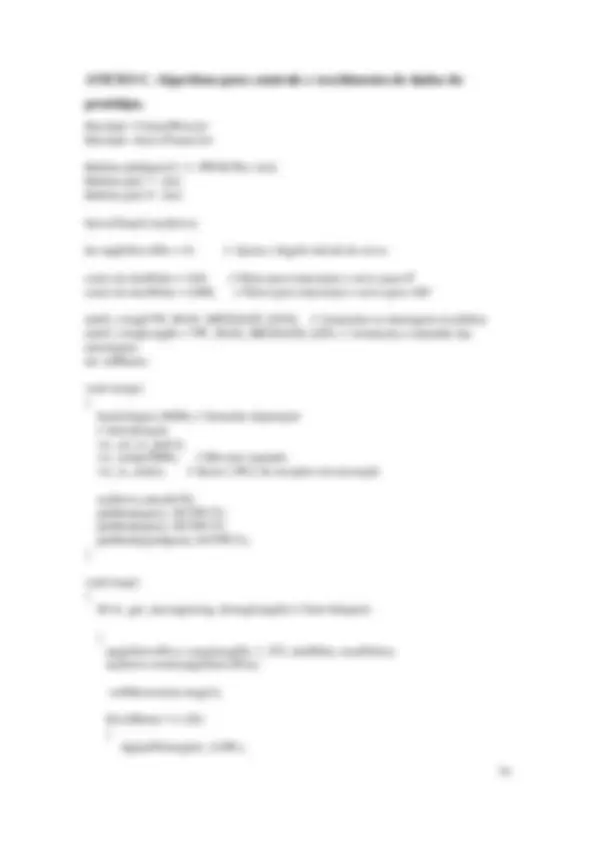
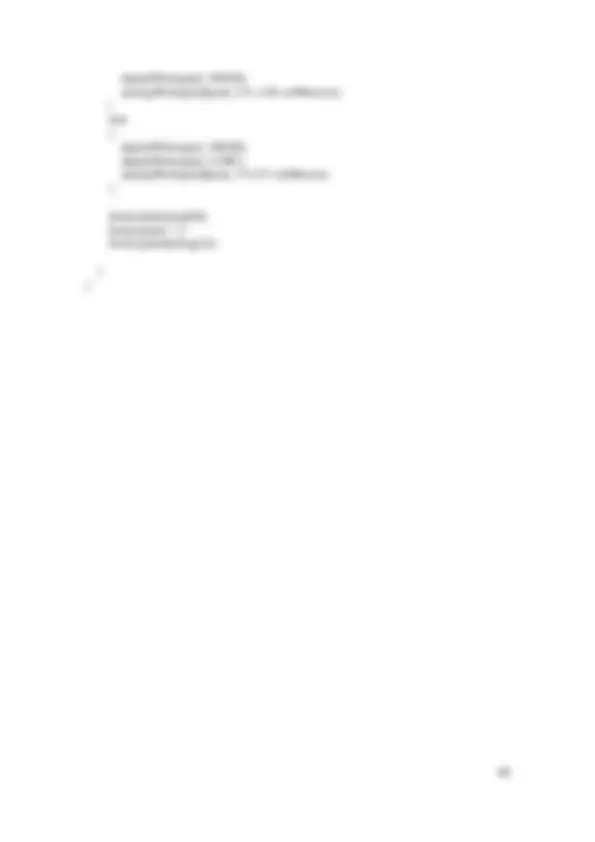
Estude fácil! Tem muito documento disponível na Docsity
Ganhe pontos ajudando outros esrudantes ou compre um plano Premium
Prepare-se para as provas
Estude fácil! Tem muito documento disponível na Docsity
Prepare-se para as provas com trabalhos de outros alunos como você, aqui na Docsity
Os melhores documentos à venda: Trabalhos de alunos formados
Prepare-se com as videoaulas e exercícios resolvidos criados a partir da grade da sua Universidade
Responda perguntas de provas passadas e avalie sua preparação.
Ganhe pontos para baixar
Ganhe pontos ajudando outros esrudantes ou compre um plano Premium
Comunidade
Peça ajuda à comunidade e tire suas dúvidas relacionadas ao estudo
Descubra as melhores universidades em seu país de acordo com os usuários da Docsity
Guias grátis
Baixe gratuitamente nossos guias de estudo, métodos para diminuir a ansiedade, dicas de TCC preparadas pelos professores da Docsity
As fundamentações teóricas para o desenvolvimento de modelos 3d de barcos controlados remotamente usando fibra de vidro e manufatura aditiva. O texto aborda o processo de impressão 3d do molde, a laminação em fibra de vidro, o desenvolvimento de algoritmos para controle por rádio frequência, a montagem de equipamentos eletrônicos e a classificação de diferentes tipos de barcos, suas características construtivas e componentes eletrônicos, princípios básicos de estabilidade e equações de movimento. Conhecimentos aplicados da engenharia naval permitem dimensionar barcos com precisão, mas a construção tradicional apresenta problemas semelhantes àqueles encontrados na construção de madeira. As novas possibilidades trazidas pela soldadura e fibra de vidro para a fabricação de barcos reduziram o tempo de fabricação, mas ainda há desafios a serem superados.
Tipologia: Resumos
1 / 92
Esta página não é visível na pré-visualização
Não perca as partes importantes!
Ana Carolina Rodrigues Ferreira Bragança, Portugal Dezembro de 2020
ii
iv
Primeiramente, gostaria de agradecer aos meus pais pelo apoio e confiança depositados em mim durante minha vida. Sem vocês eu não seria capaz de conquistar e viver tudo que pude até hoje. Agradeço às duas instituições que me acolheram e me deram a oportunidade de realizar o programa de Dupla Diplomação, além de desenvolver esse projeto, CEFET/RJ Campus Angra dos Reis e Instituto Politécnico de Bragança. Gostaria de agradecer ao meu orientador Paulo Victor que tem acompanhado minha trajetória há anos no CEFET. Sempre empático e paciente, me motivou e auxiliou em diversos momentos, tanto neste trabalho quanto durante toda minha vida acadêmica. Agradeço aos meus orientadores José Gonçalves e José Lima por terem aceito prontamente a participar desse projeto e por toda ajuda fornecida durante esse processo. Gostaria de agradecer ao João Rocha e ao Jorge Henrique pelos conselhos valiosos me fornecidos durante o processo de construção do molde e do modelo do barco. Ao meu querido Aleksander pelo carinho, atenção, paciência e confiança. Sua parceria me motiva a continuar lutando pelos meus sonhos. Ich liebe dich. Por fim, gostaria de agradecer à Adriana Gesualdi, que tem me ajudado a enxergar a vida de forma mais leve e colorida. Você foi parte essencial na realização desse trabalho e continua sendo em minha vida.
v
A utilização de impressão 3D como método de fabricação tem crescido nos últimos anos por conta da grande redução de tempo e custo quando comparada aos métodos tradicionais, além da liberdade na alteração do design e possibilidade de simulação dos modelos desenvolvidos. O objetivo deste trabalho foi fabricar um protótipo de um barco controlado remotamente e calcular as equações do movimento do mesmo. Foram realizadas a modelagem 3D e dimensionamento de um molde para posterior impressão em PLA, que foi utilizado para construir o protótipo por laminação em fibra de vidro. Com o auxílio do dimensionamento gerou-se as equações de movimento através do Método de Kane, utilizadas posteriormente para simular a trajetória de movimento do modelo ao longo do tempo. Foram ainda desenvolvidos algoritmos para efetuar o controle remoto e de movimento do protótipo utilizando módulos de comunicação por rádio frequência e outros componentes eletrônicos. Os componentes eletrônicos foram montados no protótipo construído e foi possível estabelecer a comunicação e movimento entre os elementos. O processo de laminação em fibra de vidro foi bem sucedido, porém devido instabilidades durante a transmissão de dados entre os módulos de comunicação, não foi possível colocar o protótipo na água para validação do projeto. Palavras chave: Prototipagem; Barco controlado remotamente; Método de Kane; Fibra de vidro.
Lista de Figuras ............................................................................................................... ix
x Figura 21 - Impressora do Laboratório de Controlo, Automação e Robótica (LCAR). Fonte: Autoria própria. ................................................................................................... 33 Figura 22 – Arquivo .stl no software de impressão 3D. Fonte: Autoria própria. ........... 34 Figura 23 - Proa e popa impressos. Fonte: Autoria própria............................................ 35 Figura 24 - Molde após primeira lixagem. Fonte: Autoria própria. ............................... 36 Figura 25 - Modelo após primeira camada de spray primário. Fonte: Autoria própria.. 36 Figura 26 - Modelo após utilização do spray acrílico. Fonte: Autoria própria. ............. 37 Figura 27 – Rolete tira bolhas improvisado com um rolo para pintura e anilhas. Fonte: Autoria própria. .............................................................................................................. 38 Figura 28 - Molde na base de madeira vedado com plastilina. Fonte: Autoria própria. 38 Figura 29 - Molde laminado com duas camadas de fibra de vidro. Fonte: Autoria própria............................................................................................................................. 40 Figura 30 - Molde laminado e exaustor. Fonte: Autoria própria. ................................... 40 Figura 31 - Remoção da fibra durante pós processamento do modelo. Fonte: Autoria própria............................................................................................................................. 41 Figura 32 – Modelo após segunda 3ª e 4ª camadas de fibra de vidro. Fonte: Autoria própria............................................................................................................................. 41 Figura 33 – Acabamento superficial à esquerda antes da lixagem e após a lixagem à direita. Fonte: Autoria própria. ....................................................................................... 42 Figura 34 – Molde e modelo separados. Fonte: Autoria própria. ................................... 42 Figura 3 5 – Modelo após serragem e lixagem das bordas. Fonte: Autoria própria. ....... 43 Figura 36 – Popa do casco com descontinuidades. Fonte: Autoria própria. .................. 43 Figura 37 – Popa após aplicação da cola epóxi. Fonte: Autoria própria. ....................... 44 Figura 38 – Modelo após secagem da última aplicação de resina catalisada e pigmentada. Fonte: Autoria própria................................................................................ 44 Figura 39 – Casco furado e lixado para fixação do eixo. Fonte: Autoria própria. ......... 45 Figura 40 – Selagem externa para aplicação da resina poliéster na parte interior. Fonte: Autoria própria. .............................................................................................................. 46 Figura 41 – Representação gráfica dos sistemas de referência inercial (N) e fixo no barco (B), assim como das coordenadas generalizadas com origem no centro de massa. Fonte: Autoria própria. ................................................................................................... 48 Figura 42 – Trajetória descrita pelo barco simulada através do Método de Kane. Fonte: Autoria própria. .............................................................................................................. 52
xi Figura 43 – Variação das coordenadas generalizadas ao longo do tempo. Fonte: Autoria própria............................................................................................................................. 53 Figura 44 – DFRduino Uno utilizado no trabalho. Fonte: Autoria própria. ................... 54 Figura 45 – Controle e acionamento do motor DC (alimentado por uma fonte de tensão de 12V), módulo L298N, servomotor e joystick utilizando um microcontrolador (alimentado por um notebook). Fonte Autoria própria................................................... 57 Figura 46 – Montagem da transmissão de dados do controle remoto. Fonte: Autoria própria............................................................................................................................. 58 Figura 47 – Circuito a ser montado dentro do barco (recepção de dados do controle remoto). Fonte: Autoria própria. .................................................................................... 58 Figura 48 – Componentes impressos em PLA para auxílio na montagem dos componentes. Fonte: Autoria própria. ............................................................................ 61 Figura 49 – Vista superior da montagem do barco. Fonte: Autoria própria. .................. 62 Figura 50 – Vista lateral do protótipo sobre suporte conectado à fonte de tensão. Fonte: Autoria própria. .............................................................................................................. 63
O estudo a respeito de veículos de superfície não tripulados ( Unmanned Surface Vehicles – USV) tem crescido continuamente, principalmente motivado pelo aumento da demanda em transações comerciais, estudos científicos e operações militares realizados em águas rasas e profundas (Liu, Zhang, Yu, & Yuan, 2016). Tal fato é impulsionado principalmente pelo setor de segurança nacional e por conta de anormalidades ambientais e mudanças climáticas que carecem ser estudadas (Liu, Zhang, Yu, & Yuan, 2016). USVs são veículos capazes de, sem nenhuma ou quase nenhuma intervenção humana, desempenhar inúmeras tarefas em diversos tipos de ambientes, sejam eles perigosos, tranquilos, em águas calmas ou turbulentas (Breivik, 2010, apud Liu et al., 2016, p.1). Devido às dificuldades encontradas na operação, controle e navegação em diferentes condições ambientais, como possíveis falhas na comunicação e nos sensores durante o serviço, veículos não tripulados de superfície semi-autônomos ainda são opções mais viáveis frente aos completamente autônomos (Campbell et al., 2012, apud Liu et al., 2016, p. 2). Parte dos USVs existentes são controlados remotamente, possuindo autonomia e duração de carga limitadas, sendo modelos de pequena escala e restritos a experimentos em plataformas laboratoriais. Muitos dos modelos utilizados são barcos comercialmente disponíveis modificados (Liu et al., 2016). Barcos controlados remotamente são bastante usados por exemplo para hobby, em corridas, recolha de amostras e monitoramento (Eugene, Lim, Nirmal, & Lau, 2019). São também utilizados para coleta de dados batimétricos, que fornecem informações sobre a topografia do fundo dos mares, lagos e rios, essenciais ao estudo da vida marinha e garantia da segurança dos navios durante a navegação. A viabilidade da manufatura aditiva (impressão 3D) de cascos e moldes para fabricação de modelos em fibra de vidro também tem sido abordada em estudos recentes. Barcos em fibra de vidro e de carbono são extensamente utilizados atualmente na fabricação de modelos de até 40 metros de comprimento. Isso deve-se essencialmente ao baixo custo, às propriedades mecânicas e eficiência de tais materiais (Musio-Sale, Nazzaro, & Peterson, 2019). Ao aliar o uso de softwares de modelagem 3D à manufatura aditiva é possível desenvolver e modificar barcos facilmente, obtendo-se assim modelos com maior precisão geométrica e otimizados de acordo com os critérios de operação exigidos. É possível fazer testes de validação para diferentes materiais, geometrias e espessuras.
(Musio-Sale et al., 2019). Processos convencionais de fabricação de barcos podem levar semanas a meses para serem concluídos (Post, Chesser, Lind, Sallas, & Love, 2018). A construção de moldes reutilizáveis reduz o tempo e dinheiro gastos na fabricação dos barcos (Musio-Sale et al., 2019).
O presente trabalho tem a intenção de unir conhecimentos da área da mecânica e da eletrônica através da construção de um barco controlado remotamente. Para isso, serão realizados um estudo dinâmico, a impressão 3D de um molde em PLA, a laminação deste em fibra de vidro e finalmente o controle remoto por rádio frequência do protótipo. Tem como objetivo obter as equações de movimento de um modelo 3D, afim de gerar trajetórias do movimento do barco ao longo do tempo, e construir o protótipo com auxílio do modelo dimensionado. Tais equações serão obtidas através do método de Kane utilizando a linguagem de programação Python. Serão apresentados o processo de impressão 3D do molde, a laminação do modelo em fibra de vidro, o desenvolvimento dos algoritmos para controle por rádio frequência do barco e a montagem dos equipamento eletrônicos. Além disso tem como propósito despertar o interesse dos alunos do IPB e do CEFET/RJ em áreas ainda não exploradas nos respectivos campus, permitindo com que tomem como base o trabalho aqui reportado. Será possível usar o protótipo construído em trabalhos futuros para analisar sua dinâmica, integrar sensores para análises como temperatura, humidade ou observação do leito de rios, ou ainda o efeito da inclusão de hélices e lemes de diferentes geometrias. As equações de movimento calculadas permitirá ainda controlar o barco autonomamente.
O trabalho está estruturado em sete capítulos. No Capítulo 1 foi apresentado uma breve introdução dos assuntos a serem tratados, motivação e objetivos do estudo desenvolvido. No Capítulo 2 serão apontados conceitos básicos necessários para que haja a compreensão geral do que foi desenvolvido ao longo da realização do projeto. Tais fundamentações teóricas buscam fazer uma abordagem geral a respeito da utilização da
A construção de um barco de navegação eficiente exige conhecimento em campos como estabilidade, hidrostática, dinâmica, resistência e materiais. São necessários diversos dimensionamentos e análises para se obter um modelo que opere e corresponda ao objetivo desejado. Conhecimentos aplicados da engenharia naval permitem dimensionar barcos de forma precisa a partir do estudo de fatores como a influência de determinados designs na velocidade, estabilidade e resistência do barco quando submetido a variadas condições. Busca-se então, a partir de diversas iterações, otimizá- lo de forma a satisfazer as condições iniciais impostas, conforme a performance final desejada. Muitos barcos existentes são feitos a partir de modelos já existentes ou a partir de pequenas alterações dimensionais visando a adequação à necessidade do usuário (Nasseh, 2010). Por milénios os barcos foram contruídos em madeira a partir da junção de diferentes partes para criar um único casco sólido, através da utilização de materiais como cordas, colas e pregos. A maior dificuldade encontrada era como manter as partes em movimento unidas, além da corrosão e degradação dos materiais utilizados. Com a revolução industrial no século XIX, o metal passou a ser utilizado na construção de cascos. Apesar do grande avanço na resistência e durabilidade do material, a construção dos barcos era realizada de forma semelhante aos feitos de madeira, enfrentando problemas parecidos (Musio-Sale et al., 2019). No século XX, com a adoção da soldadura de metais, os barcos puderam então ser construídos sem nenhuma descontinuidade estrutural em suas superfícies. Foi também quando surgiu a aplicação da fibra de vidro em moldes reutilizáveis de madeira na produção de barco de pequena escala, em resposta à grande demanda para produção de baixo custo. Tais tecnologias foram primordiais na solução de problemas da construção naval da época, como fragilidade das montagens, altos custos de produção, isolamento do casco para evitar a entrada de água e a necessidade de manutenção periódica (Musio-Sale et al., 2019). Apesar das novas possiblidades que a soldadura e a fibra de vidro trouxeram para a fabricação de barcos, o tempo de fabricação dos modelos através das técnicas convencionais pode durar de semanas até meses (Post et al., 2018). Como resposta à
necessidade de fabricar moldes mais rapidamente, mais eficientes e com custos relativamente bem menores (Musio-Sale et al., 2019), a utilização da manufatura aditiva tem sido estudada por diversos autores, mostrando-se inclusive como um potencial substituto dos atuais métodos de fabricação, como a fundição (Kang & Ma, 2017). A impressão 3D permite criar protótipos, estruturas interiores, carcaças e moldes em diversos tipos de materiais, como ceras, plásticos, cerâmica e metal (Kang & Ma, 2017). Através dos softwares simulação e modelagem 3D é possível otimizar projetos a partir de simulações computacionais, realizando análises estruturais, mecânicas, dinâmicas, entre outras. Pode-se então averiguar, por exemplo, se o protótipo construído representa o design desejado, ou ainda prever se o molde a ser fabricado será capaz de suportar as solicitações a que estará submetido durante operação. A Figura 1 exemplifica um processo de otimização da fabricação de uma peça pelo método de manufatura aditiva. Como será mostrado no Capítulo 3, um molde de barco de pequenas dimensões foi desenhado e impresso em PLA para laminação em fibra de vidro. Figura 1 – Otimização de uma peça através da aplicação do método de impressão 3D. Adaptado de: (Wang, 2016, apud Kang & Ma, 2017, p. 164). Em 2018 um projeto desenvolvido no Laboratório Nacional de Oak Ridge analisou a viabilidade da construção de moldes para fabricação de barcos através da manufatura aditiva. Um molde foi então modelado, fabricado, usinado e montado (Figura 2 ). O material utilizado foi ABS reforçado com fibra de carbono, e foi fabricado com uma
modelo (Figura 3 ), através do cálculo da posição do centro de massa e do centro de flutuação para diversas alturas de linha d’água (Tupper, 2004). Figura 3 – Curvas hidrostáticas. Fonte: Tupper, 2004. Softwares de modelagem 3D permitem desenhar cascos com precisão respeitando os critérios e parâmetros exigidos pela indústria naval, além de permitir uma visualização do modelo final (Musio-Sale et al., 2019). Uma das formas de modelagem de cascos é a geração de superfícies a partir de polinômios matemáticos. É possível desenhar planos a partir de informações iniciais básicas e realizar posteriores alterações no projeto facilmente sem que seja necessário reiniciar o processo de modelagem (Nasseh, 2010). Pode-se ainda ajustar o modelo e realizar testes estruturais variando diversos critérios, como materiais, densidade, escala, espessuras e diferentes alterações no design (Musio-Sale et al., 2019). Uma grande vantagem desses softwares é a possibilidade de salvar o desenho em formato IGES (Initial Graphic Exchange Specification), um tipo de arquivo no qual as informações podem ser lidas posteriormente por diversos outros programas (Nasseh, 2010). Com softwares específicos utilizados na indústria naval, como MAXSURF e Rhino , é possível gerar cálculos de hidrostática, estabilidade, navegabilidade e desempenho para diferentes condições marítimas com facilidade. Ao contrário dos programas específicos da indústria naval, que costumam ter preços mais elevados por conta da vasta gama de operações ( Rhino : licença aproximadamente entre € 500 e € 1000),
existem softwares de uso geral que são mais acessíveis ou até de graça, como o FreeCAD. Estes são baseados em computação gráfica, e a partir de um esboço 2D ou 3D, criam-se sólidos e superfícies através de formas geométricas elementares (Nasseh, 2010), como mostrado na Figura 4. Figura 4 – Casco gerado pela criação de planos. Fonte: Autoria própria.
Os barcos controlados remotamente de alta velocidade, segundo Eugene et al., 2019 , podem ser classificados da seguinte forma: hidroplanos, monocascos e multicascos. Esses modelos serão apresentados brevemente a seguir. 2.3.1. Hidroplanos São modelos em escala, ou seja, são reproduções de modelos reais existentes. Possuem projeções laterais no casco do barco e uma parte da área central inferior é plana, permitindo que uma camada de ar entre o casco e a água fique confinada. São muito utilizados em competições por ser um dos modelos de casco que conseguem atingir maiores velocidades, já que apenas parte do casco toca a água em altas velocidades, diminuindo assim a resistência do barco na água (Adams, 201, apud Eugene et al., 2019, p. 1).