
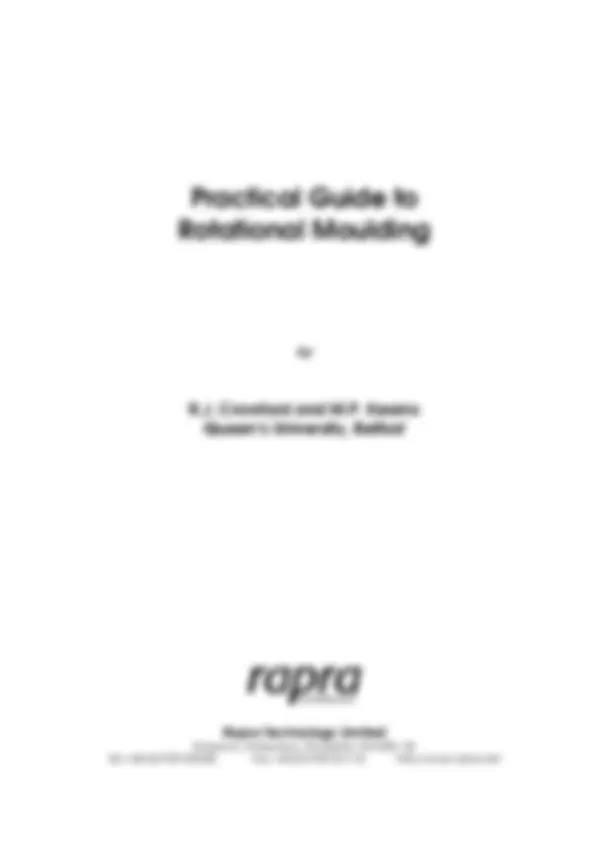
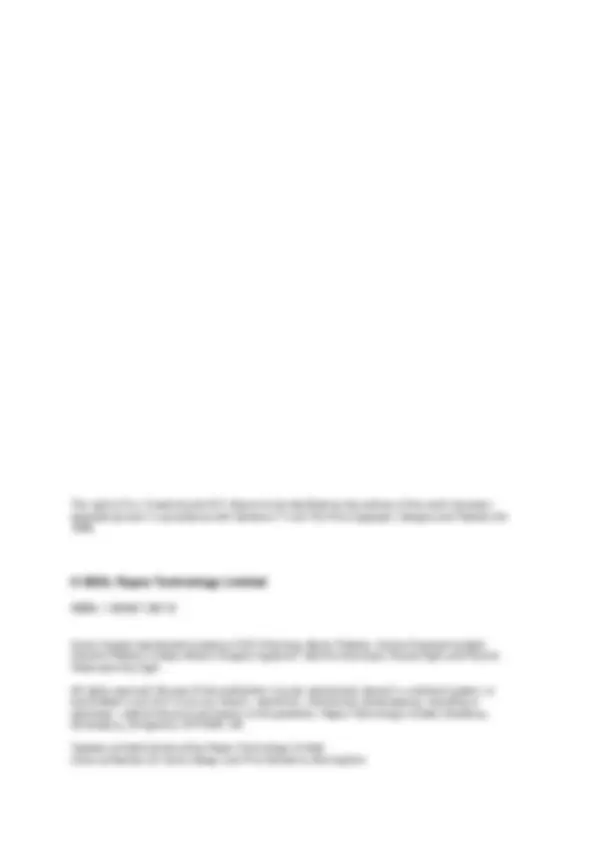
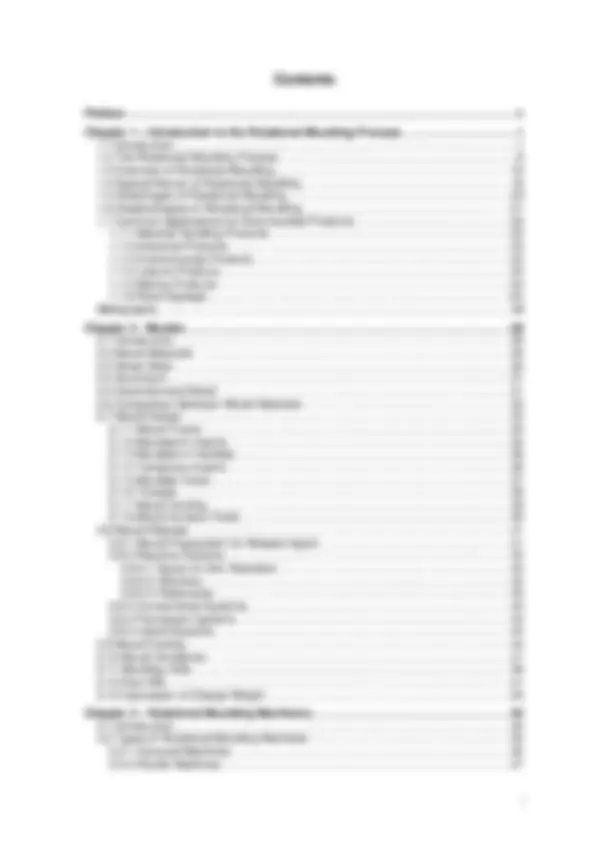
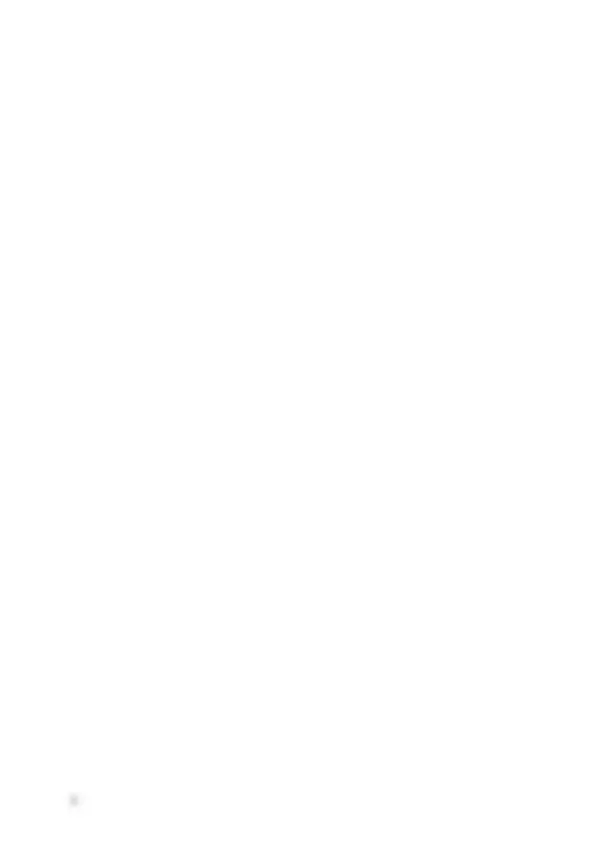
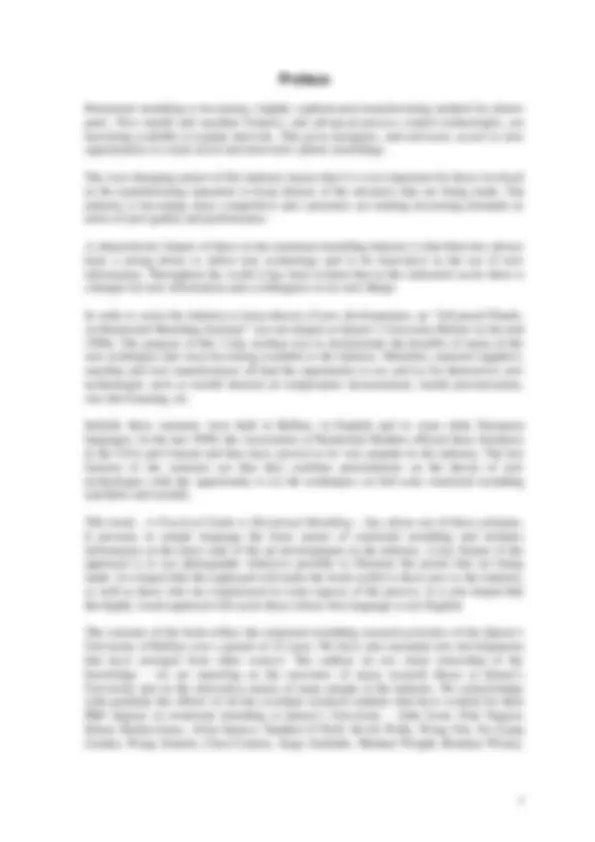

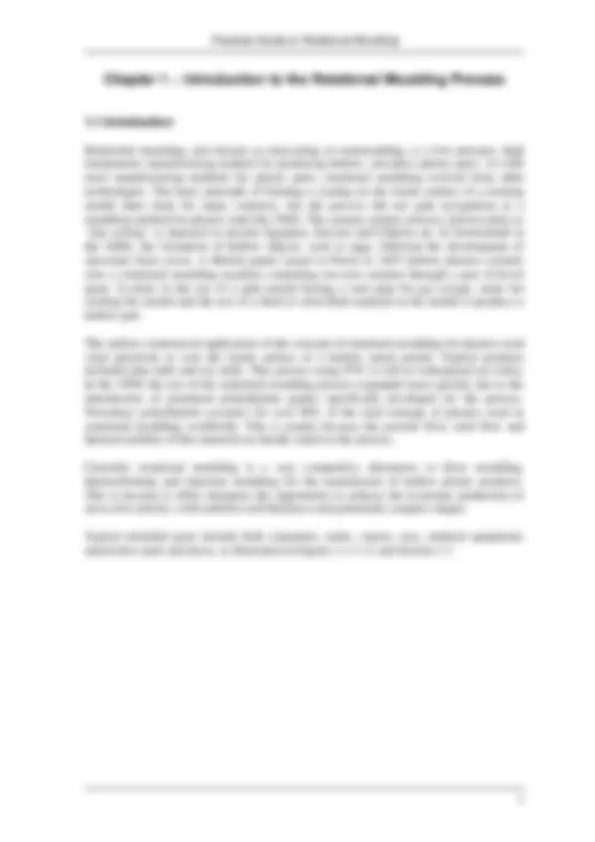
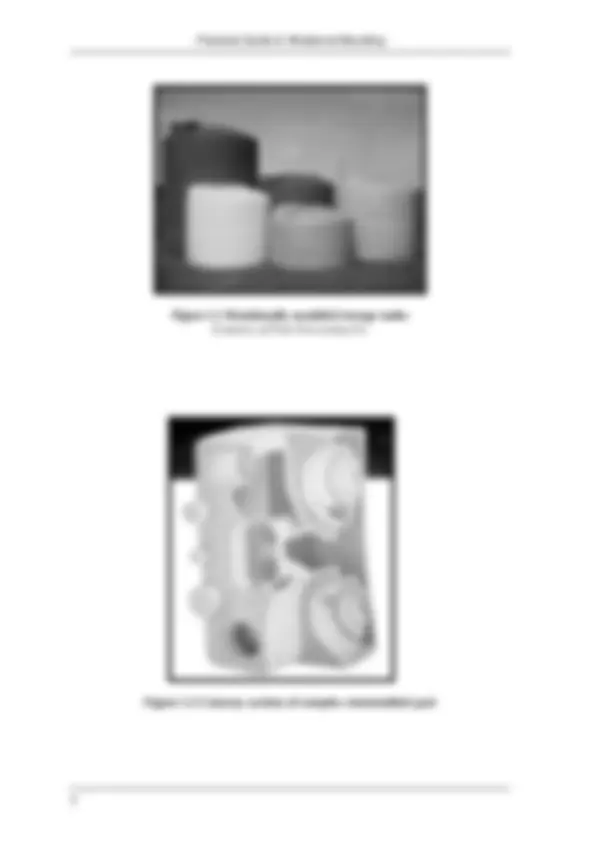
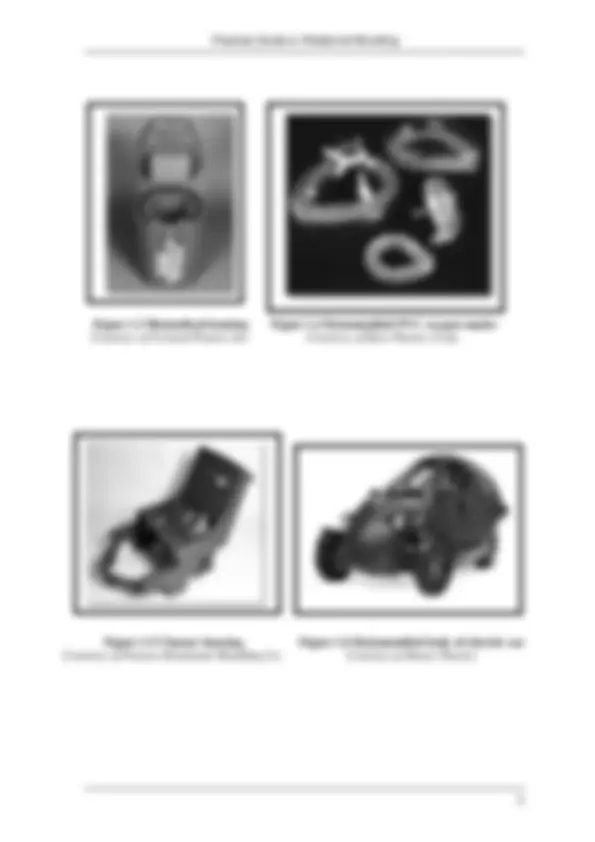
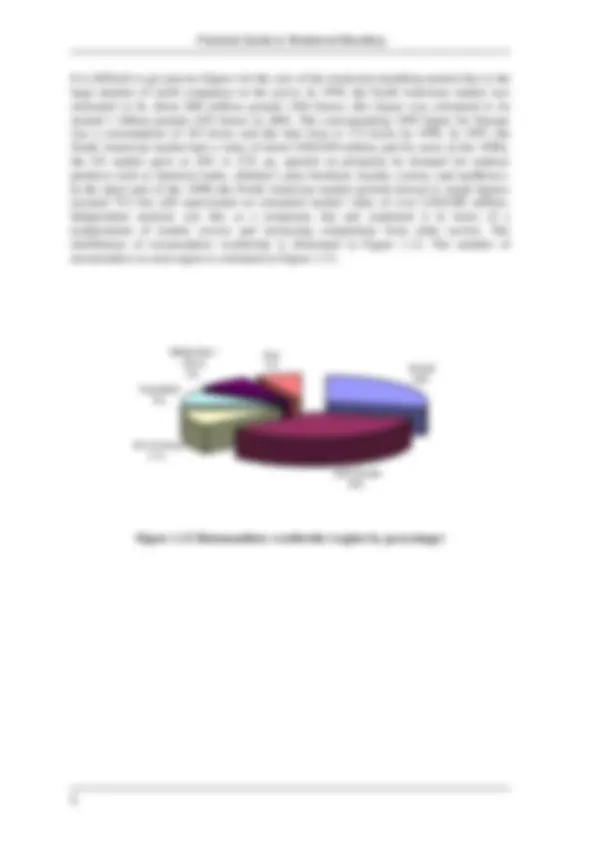
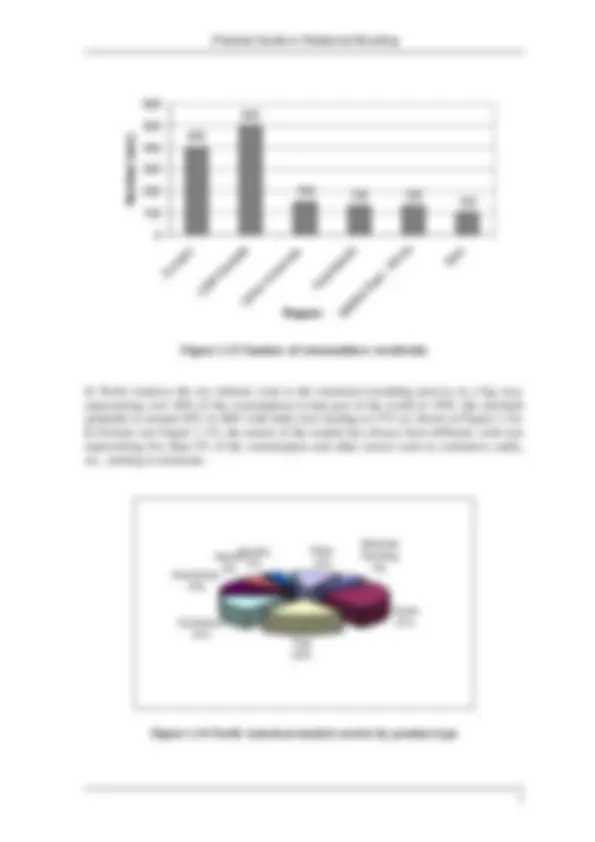
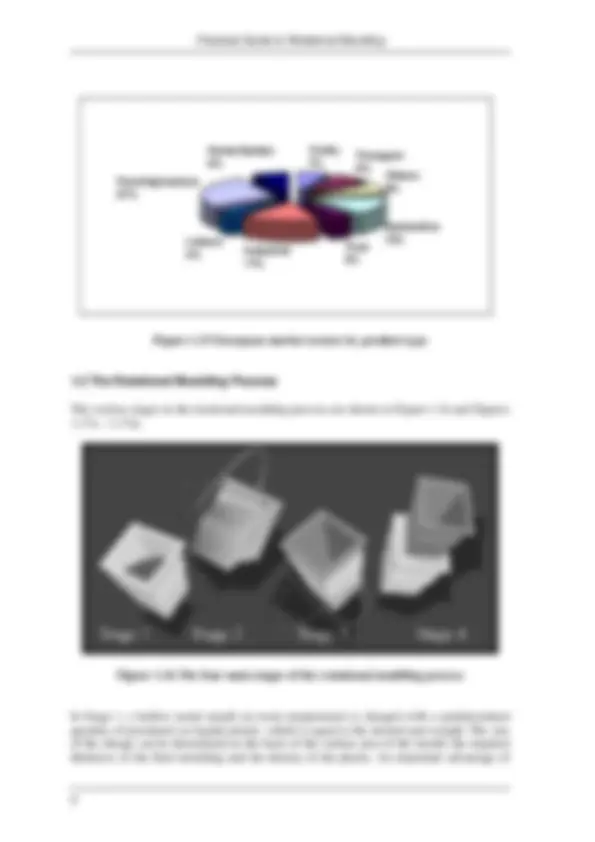
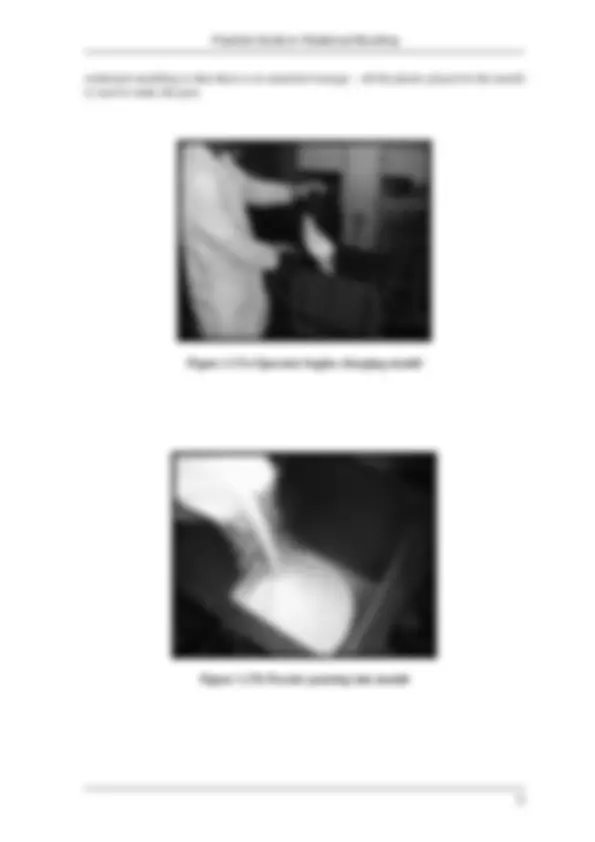
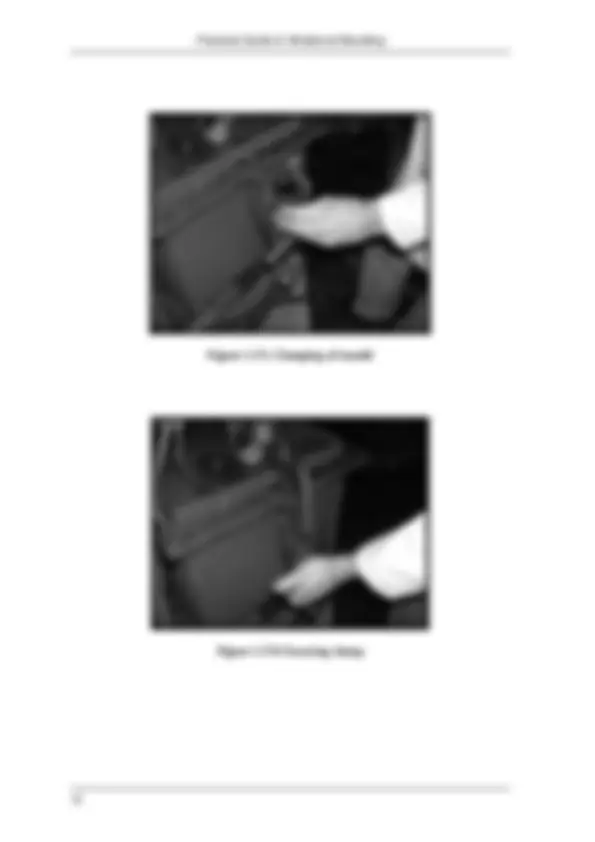
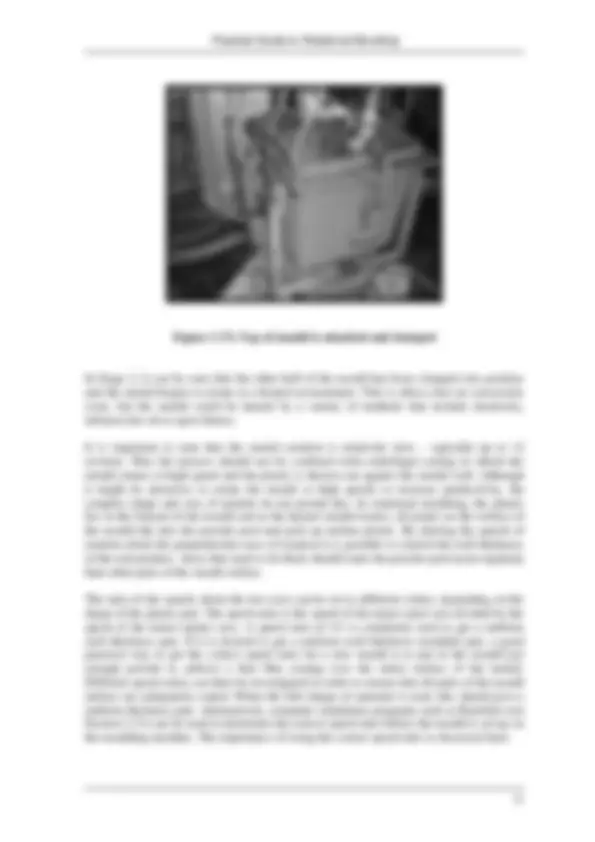
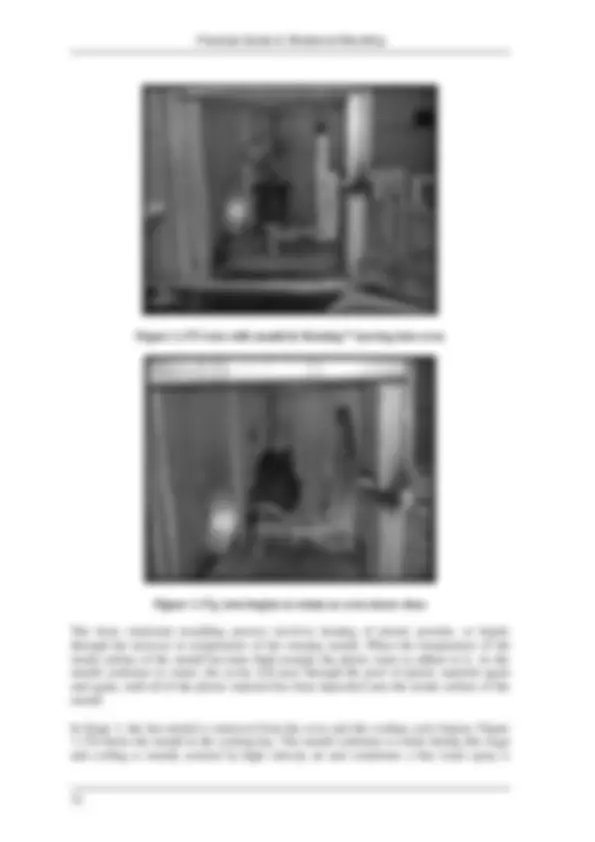
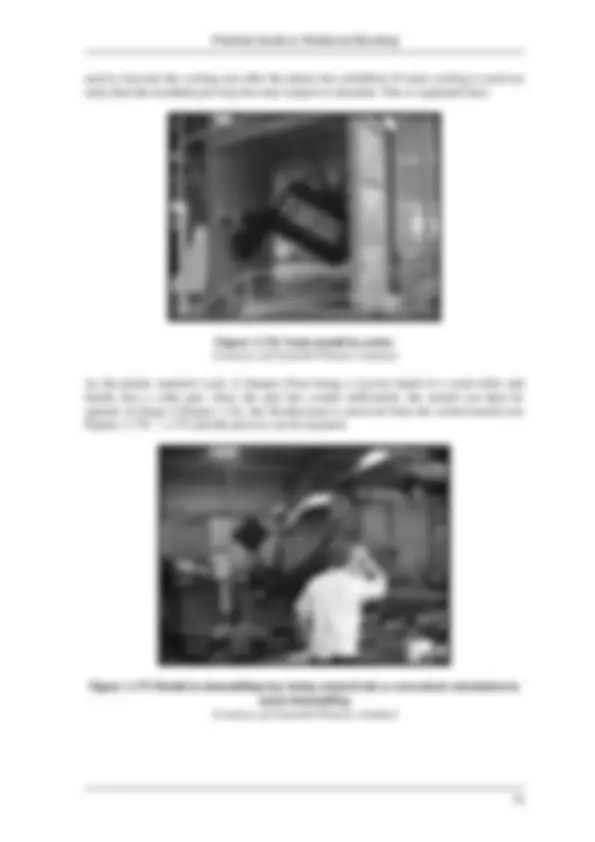
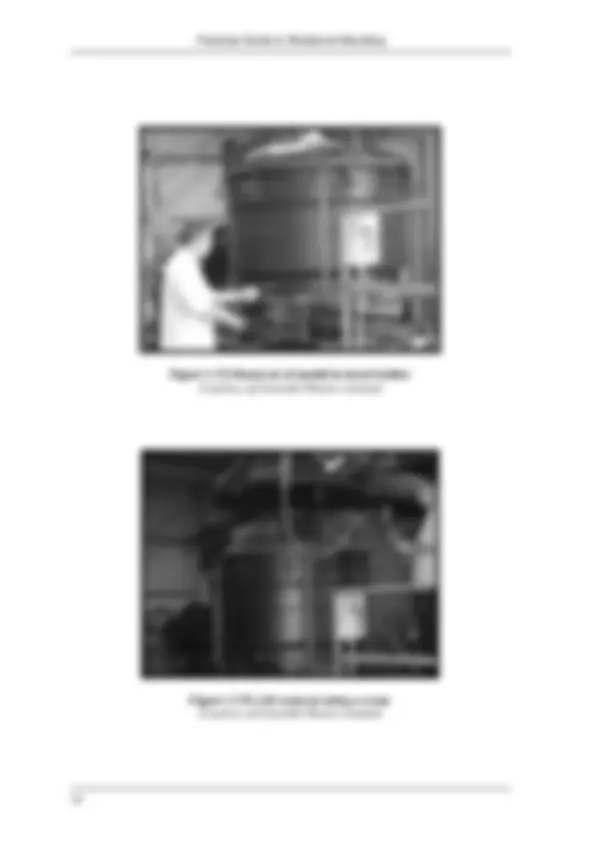
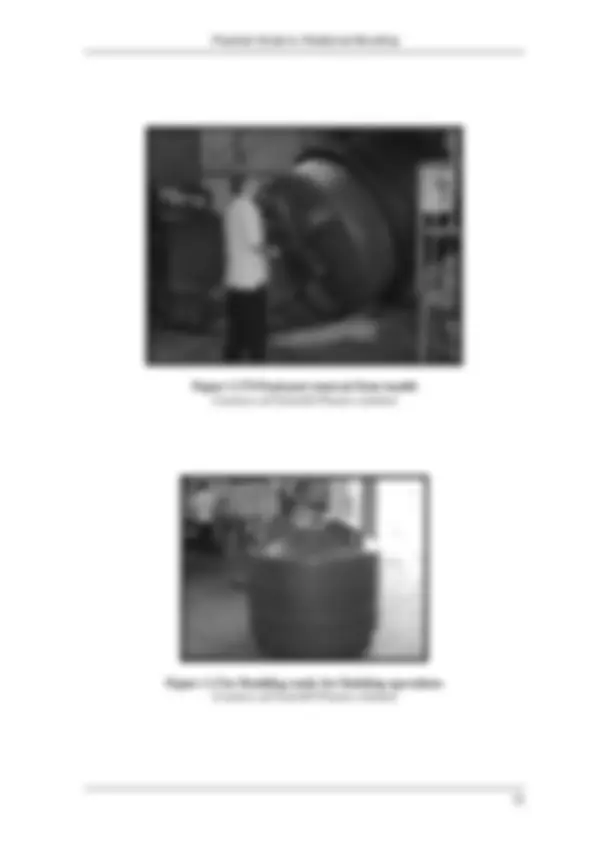
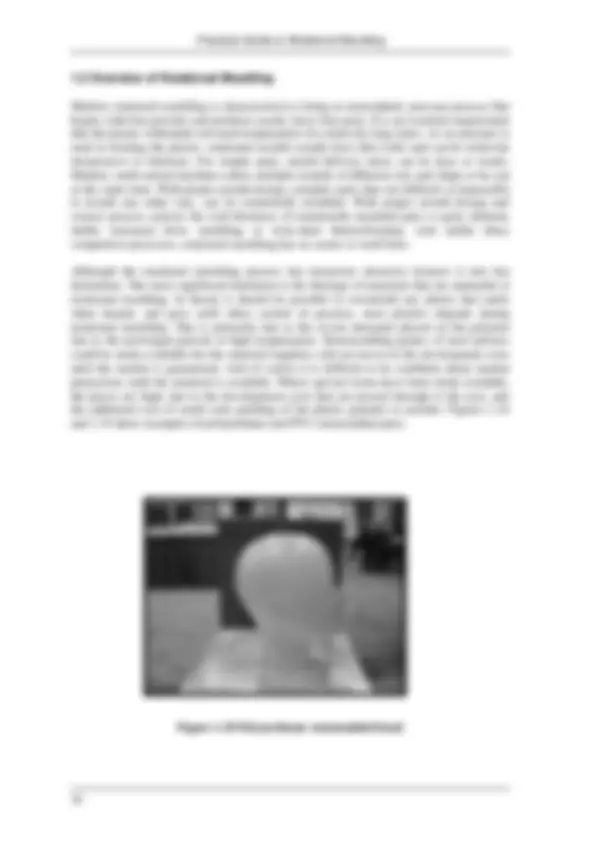
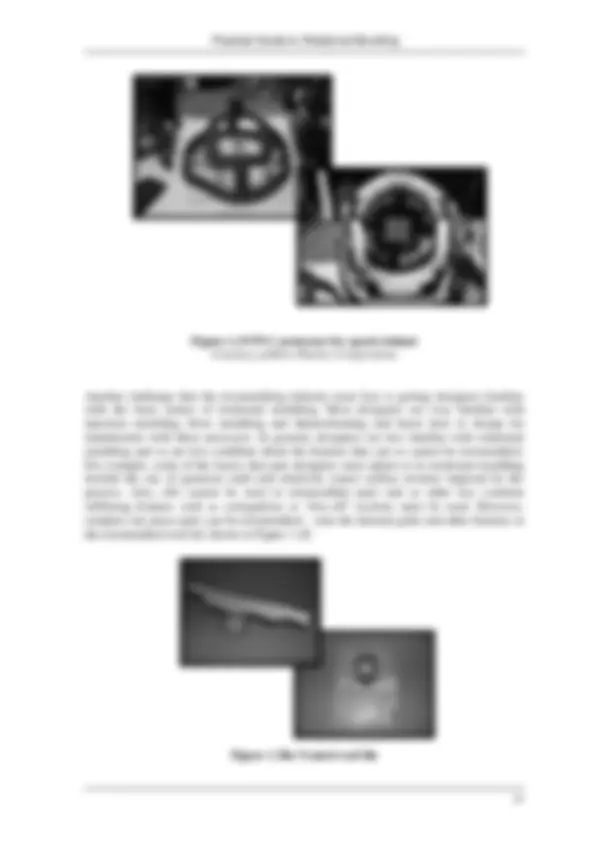
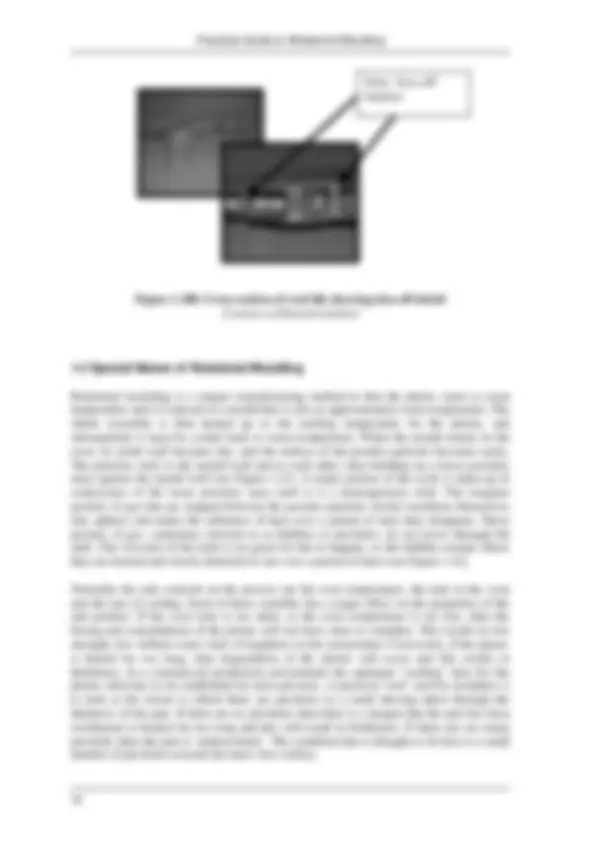
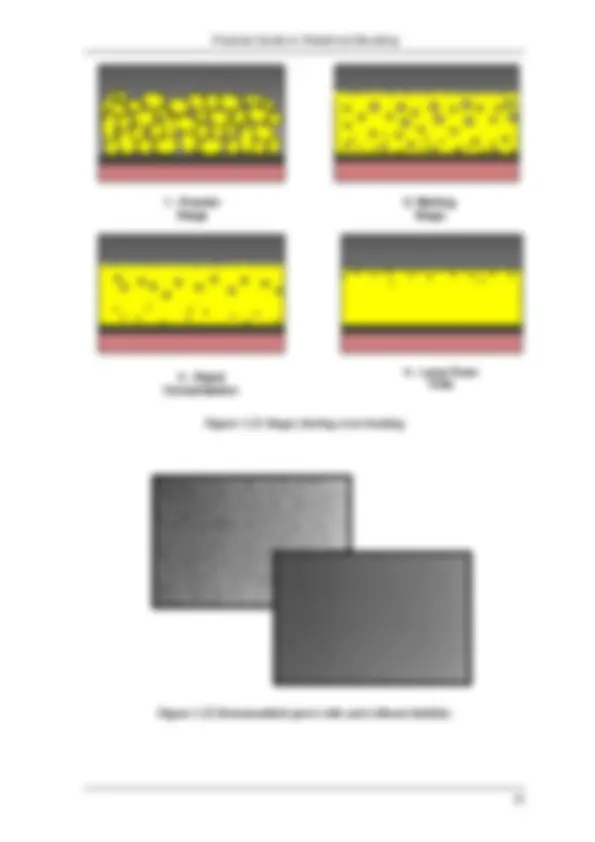
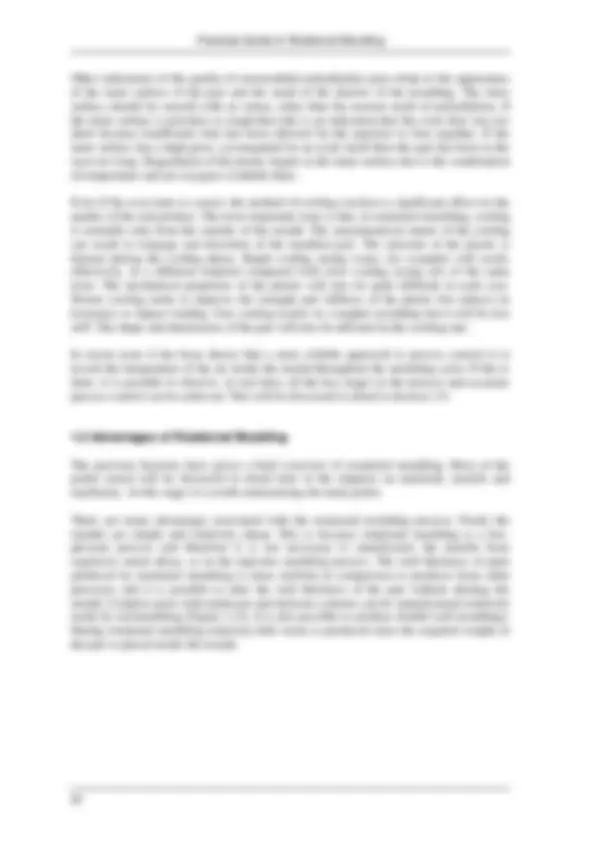
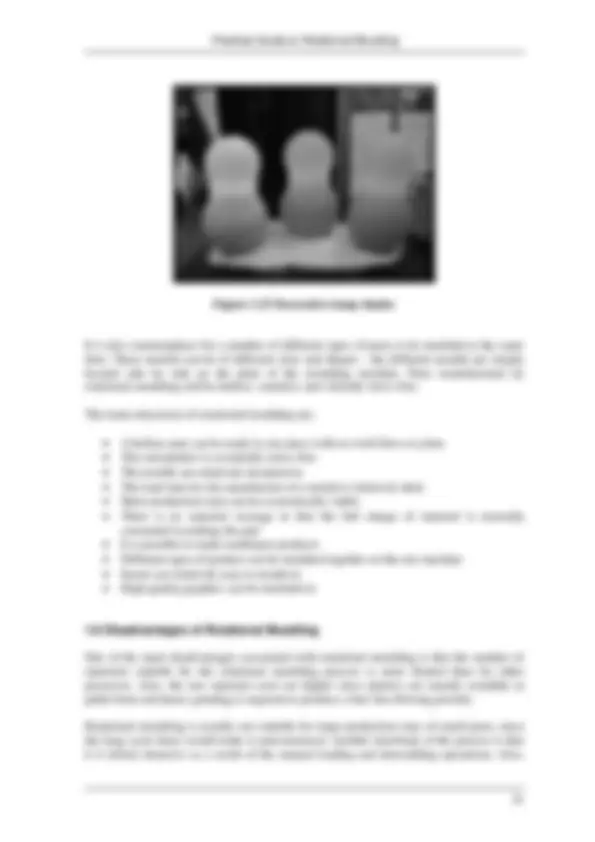
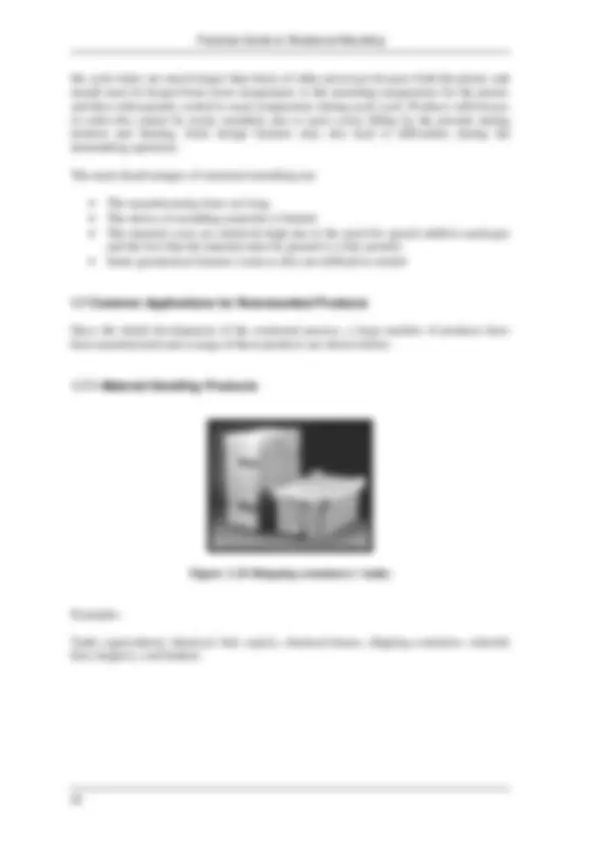
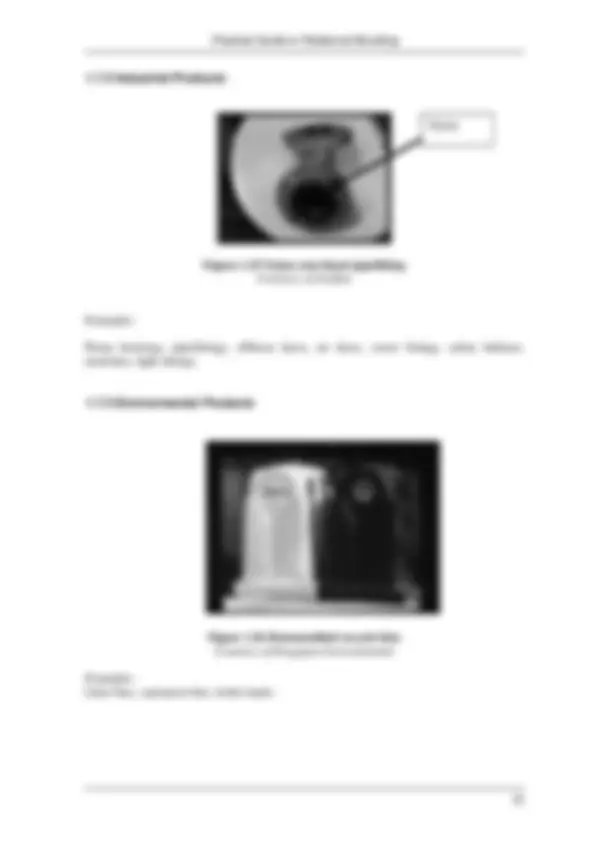
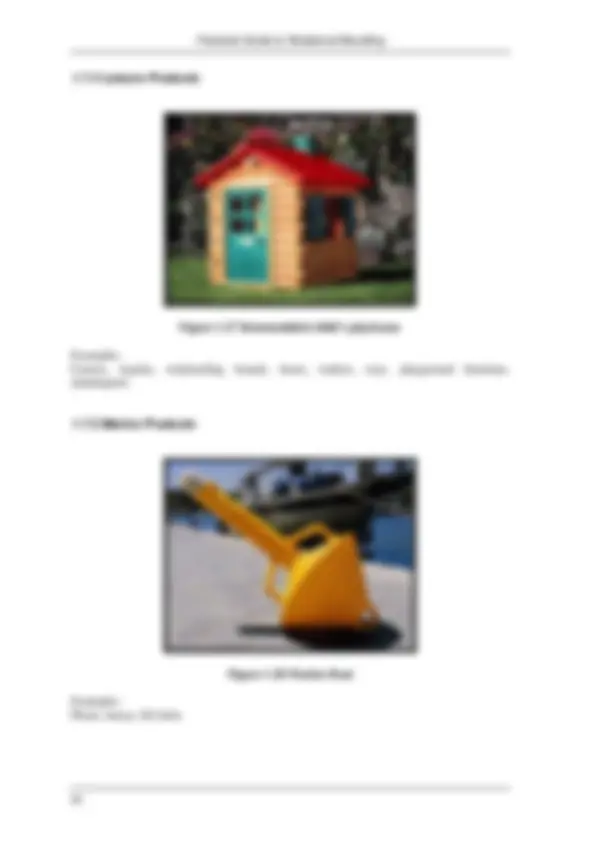
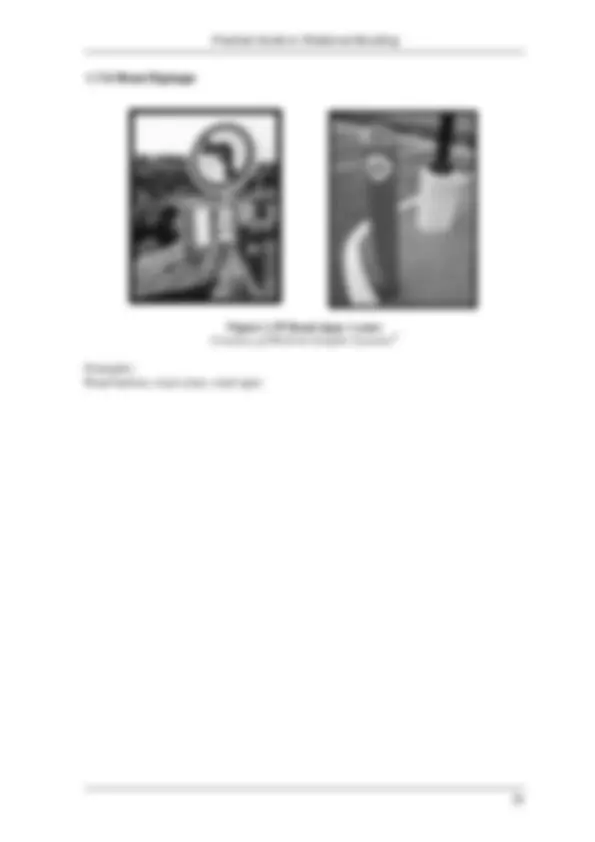
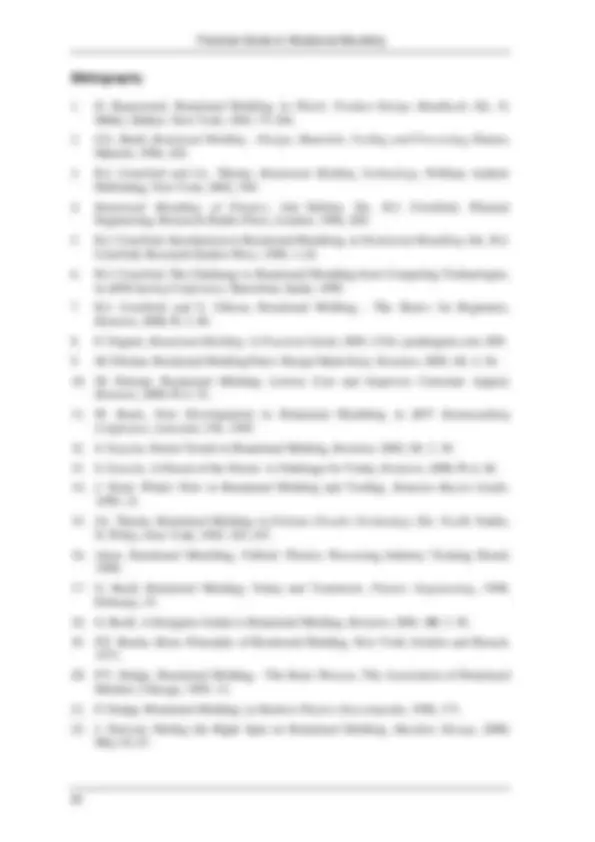
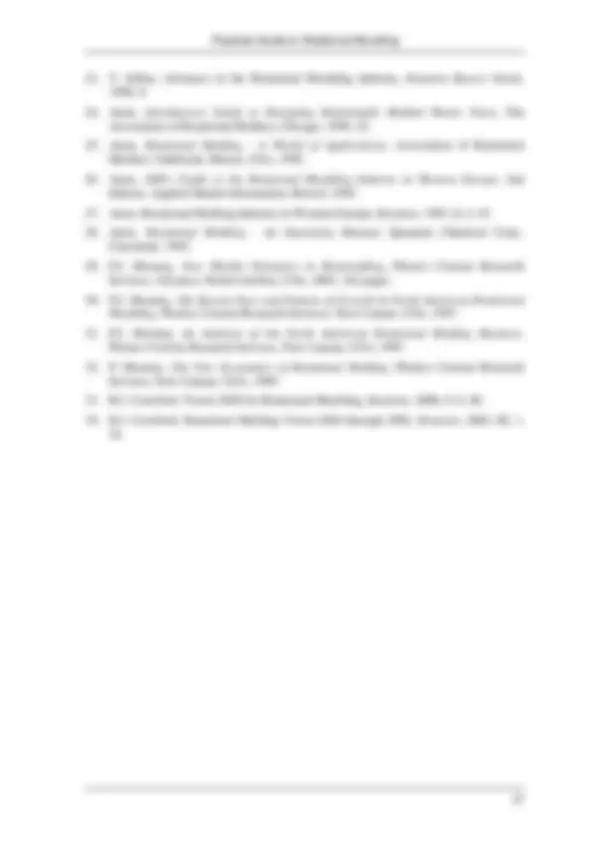
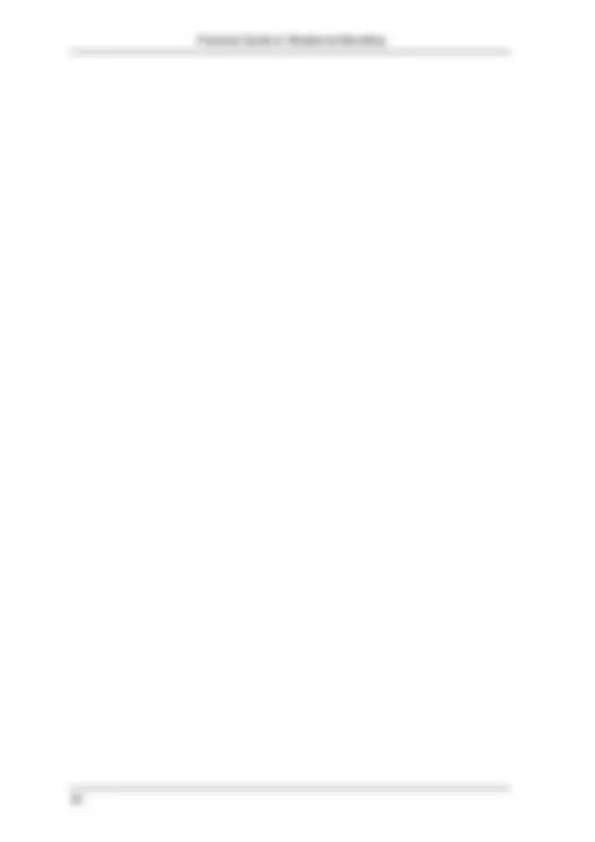
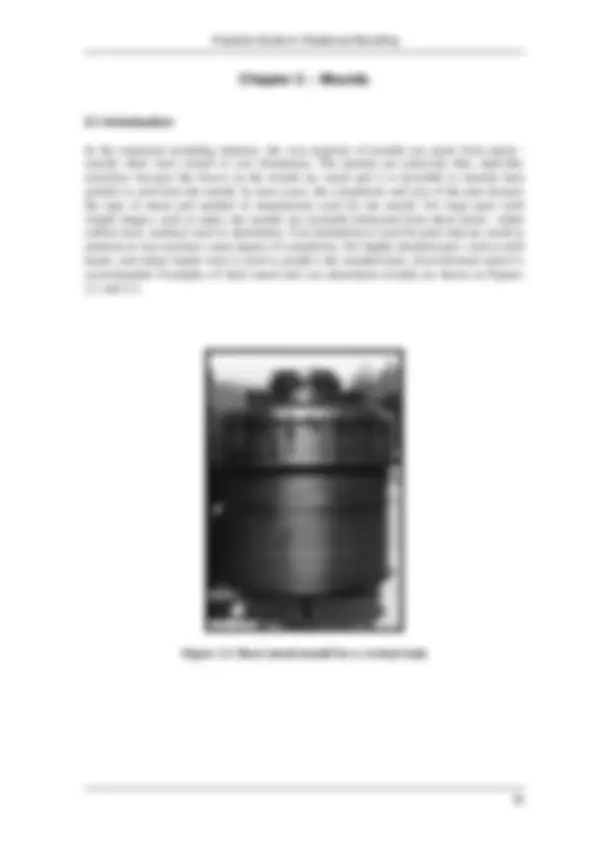
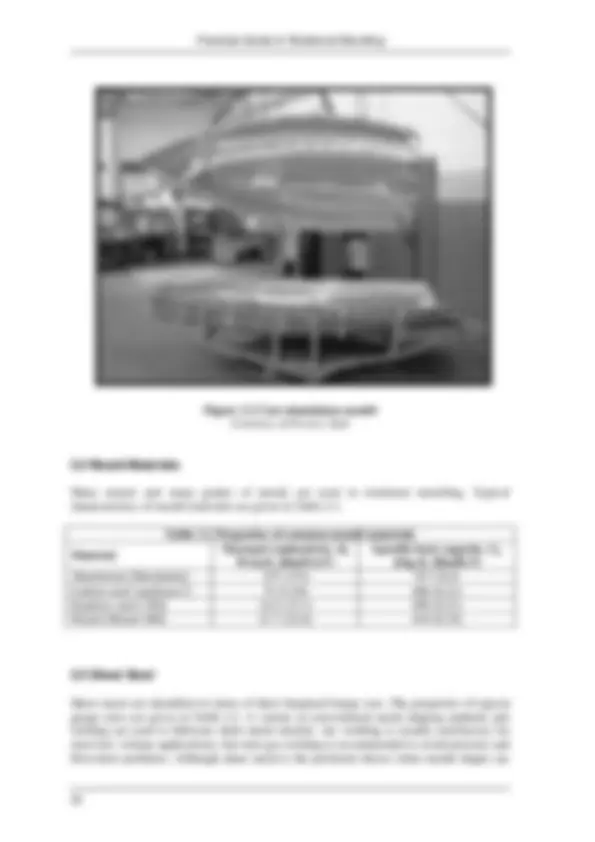
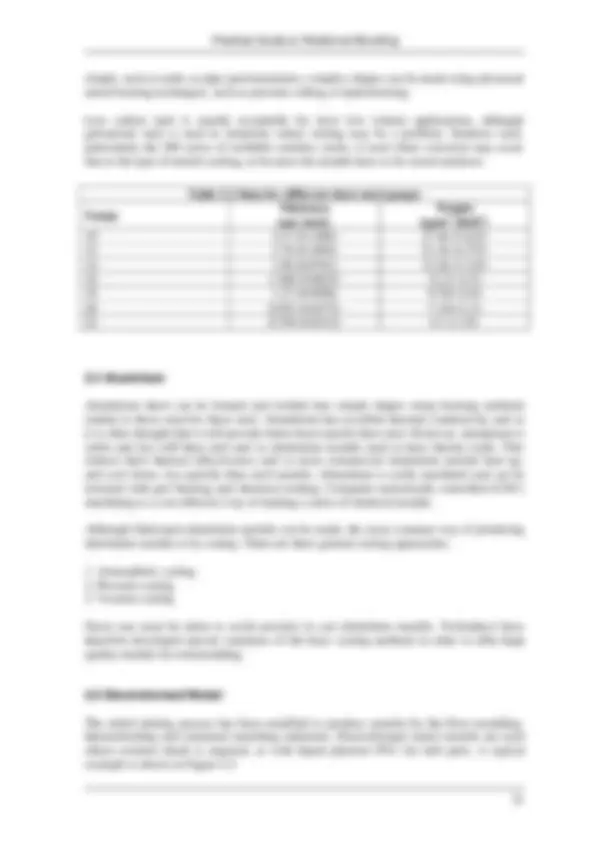
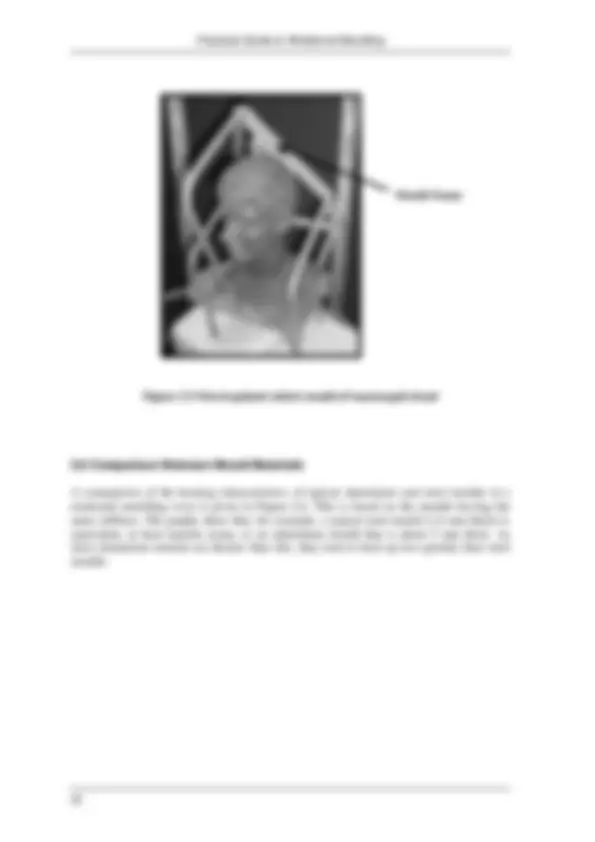
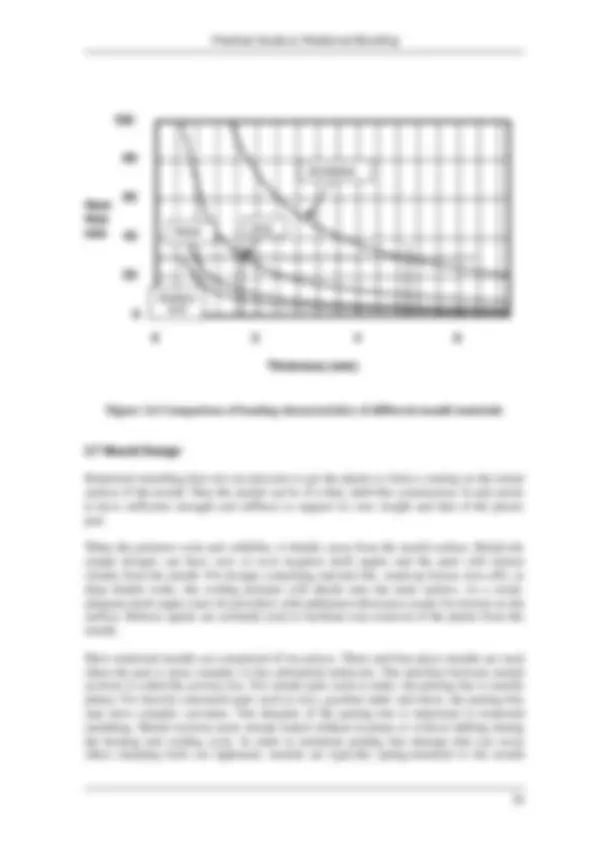
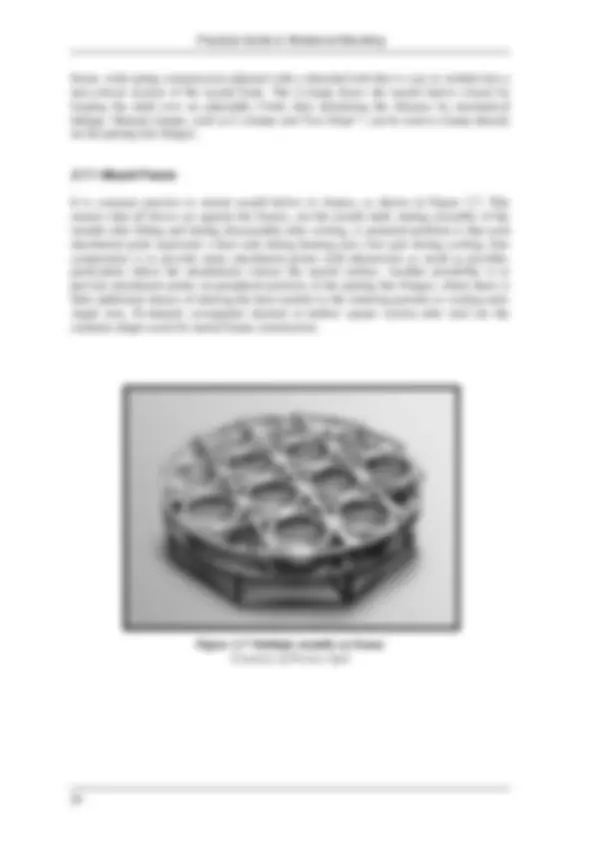
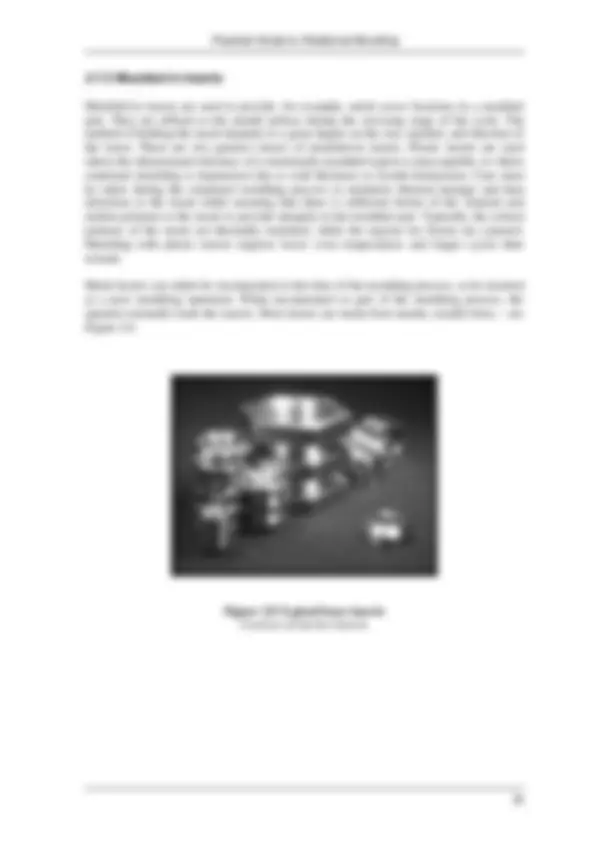
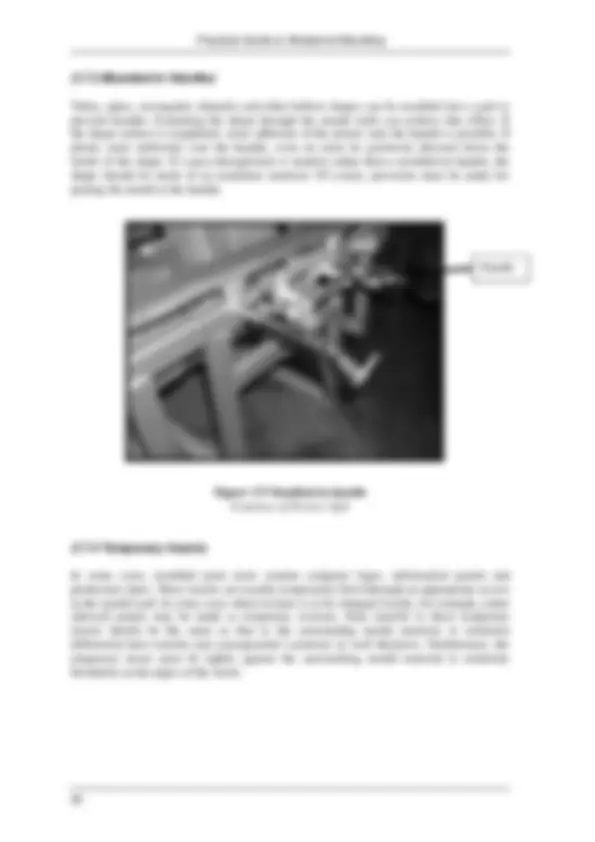
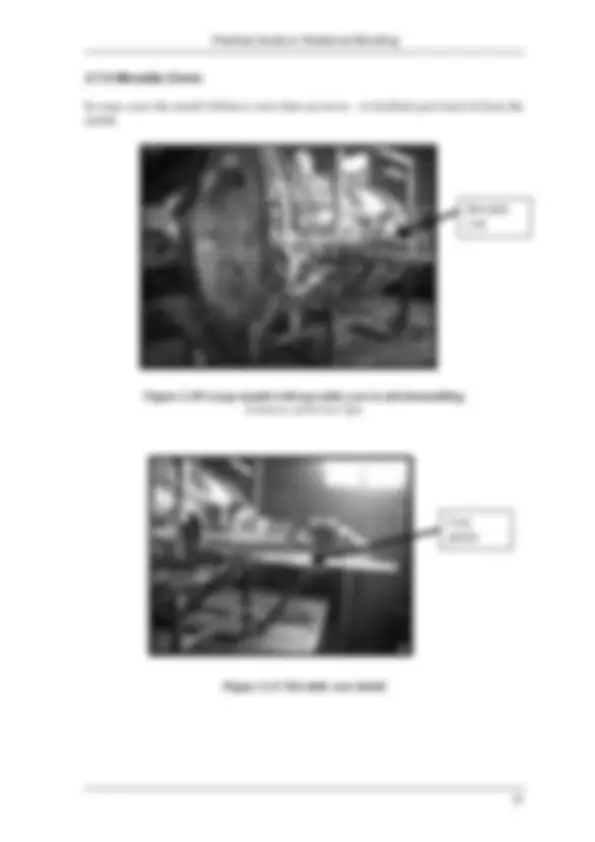
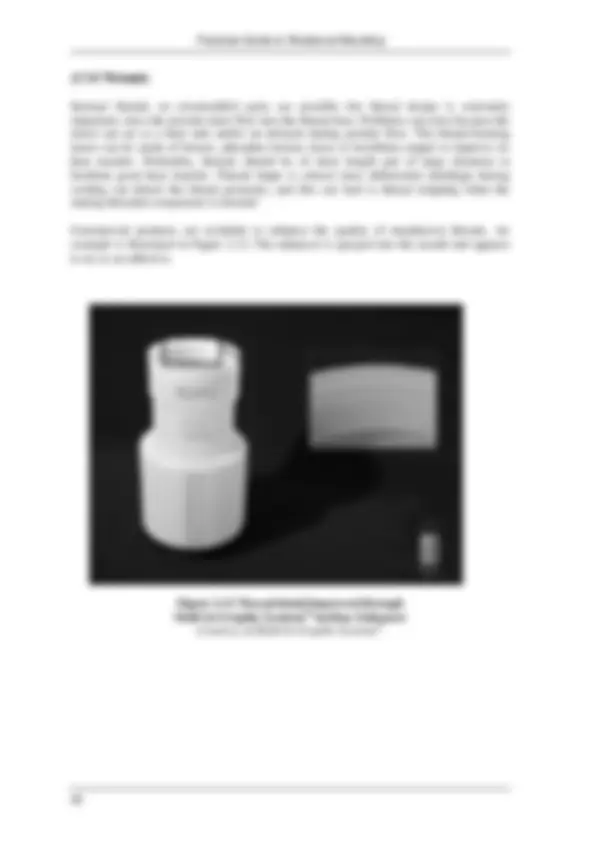
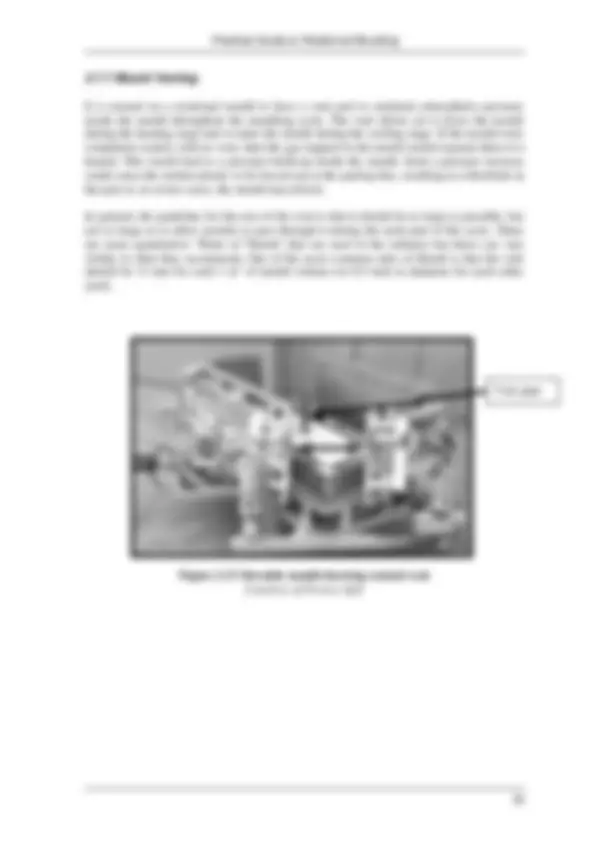
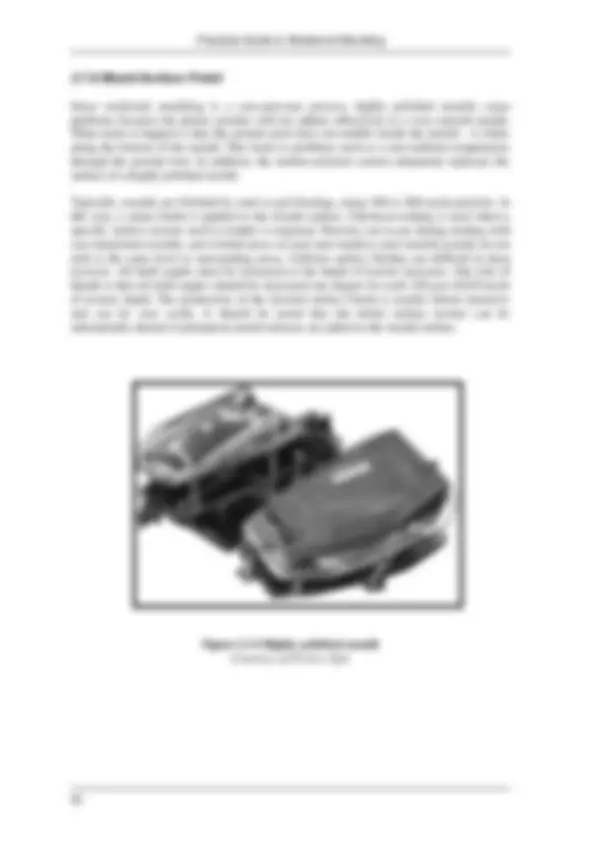
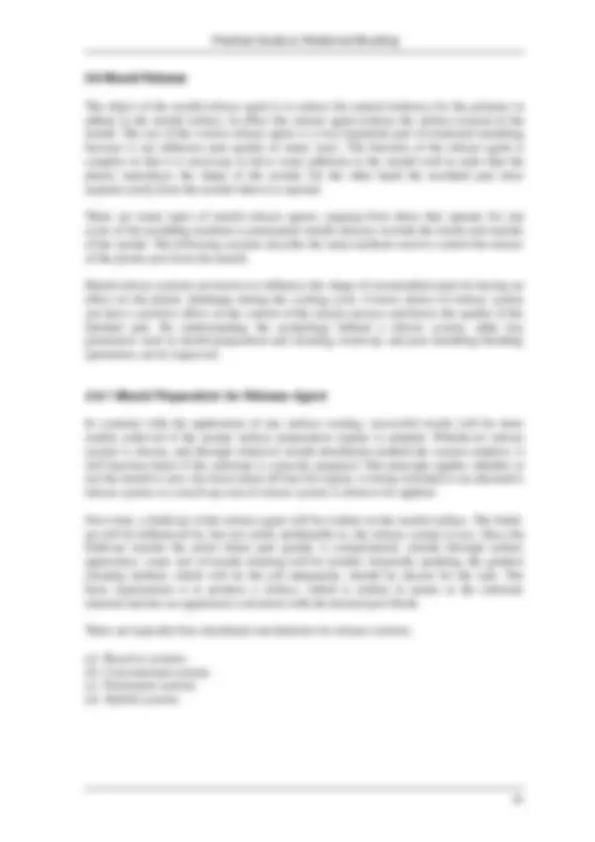
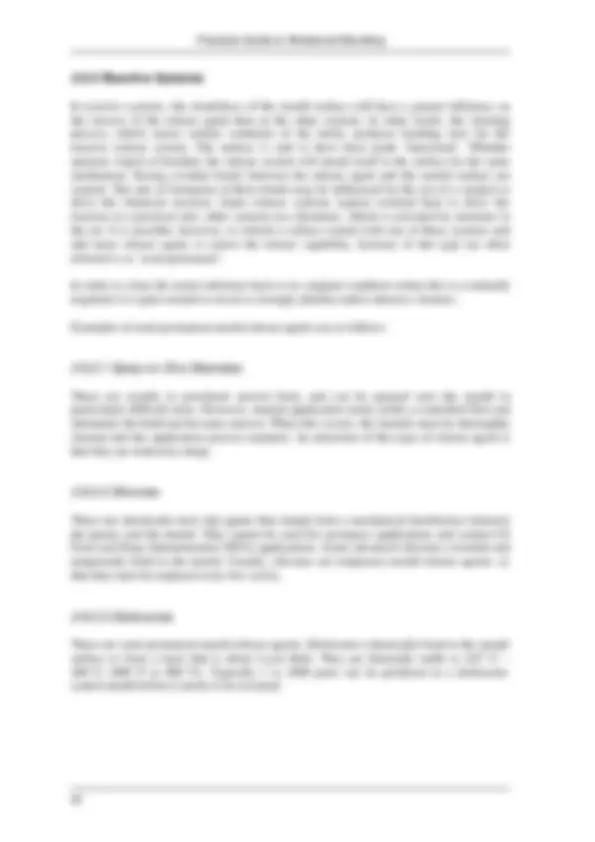

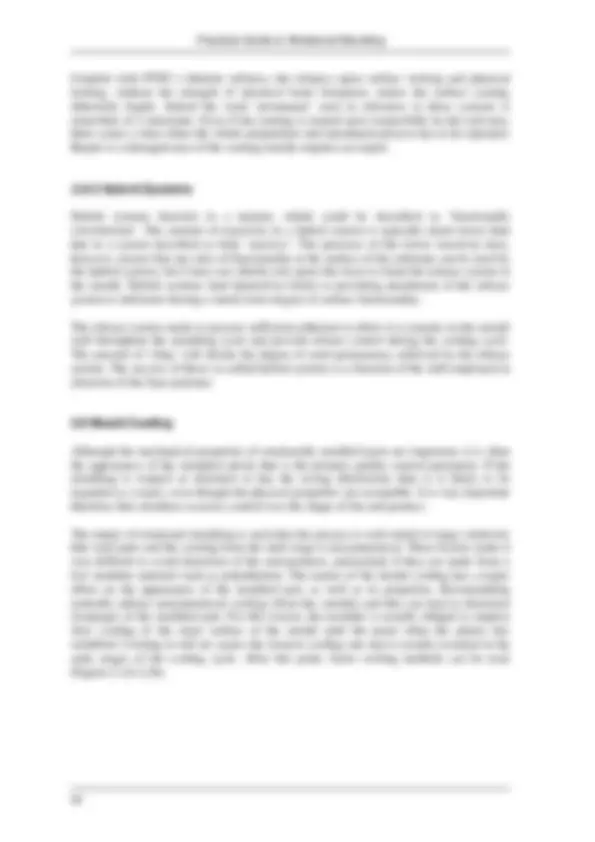
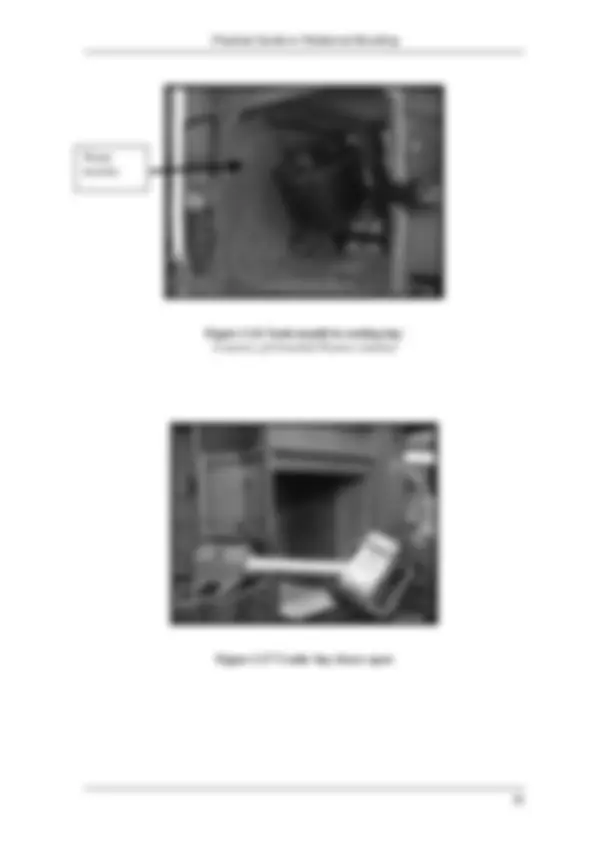
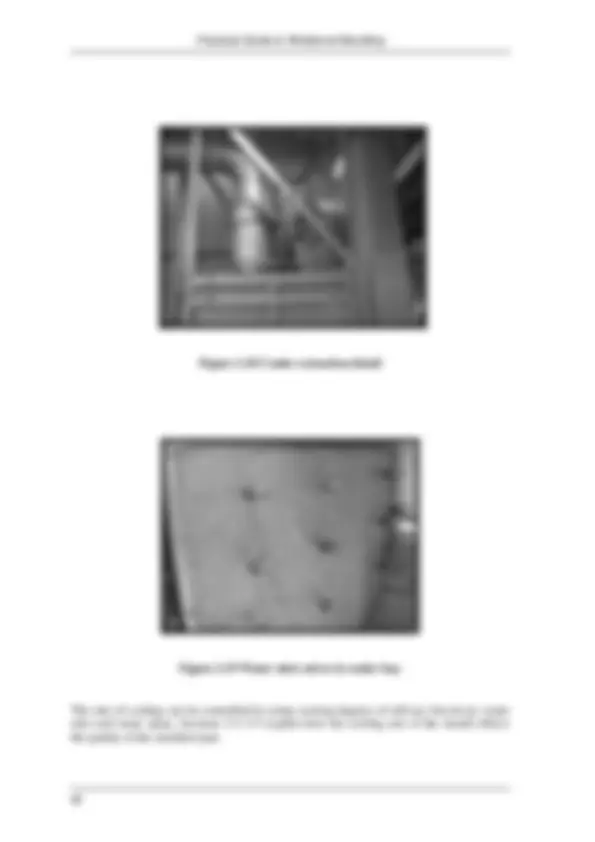
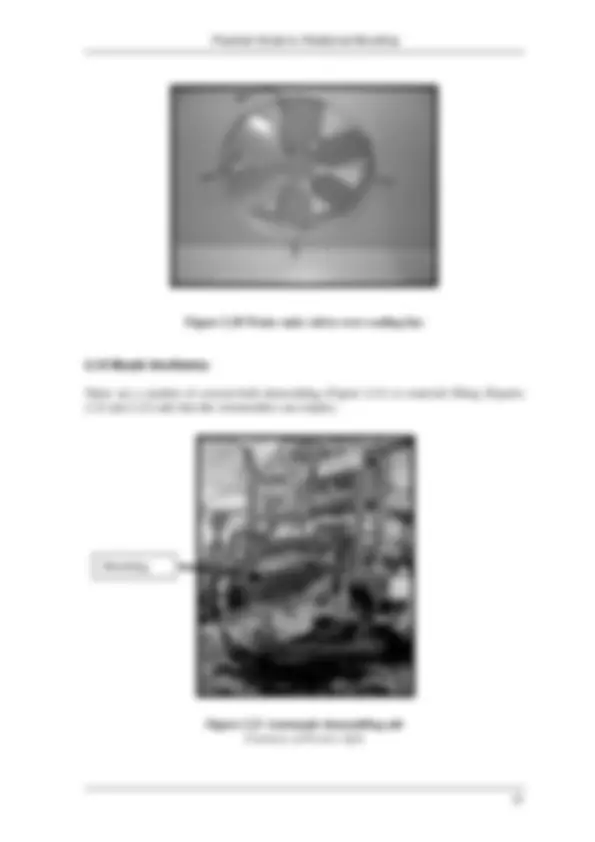
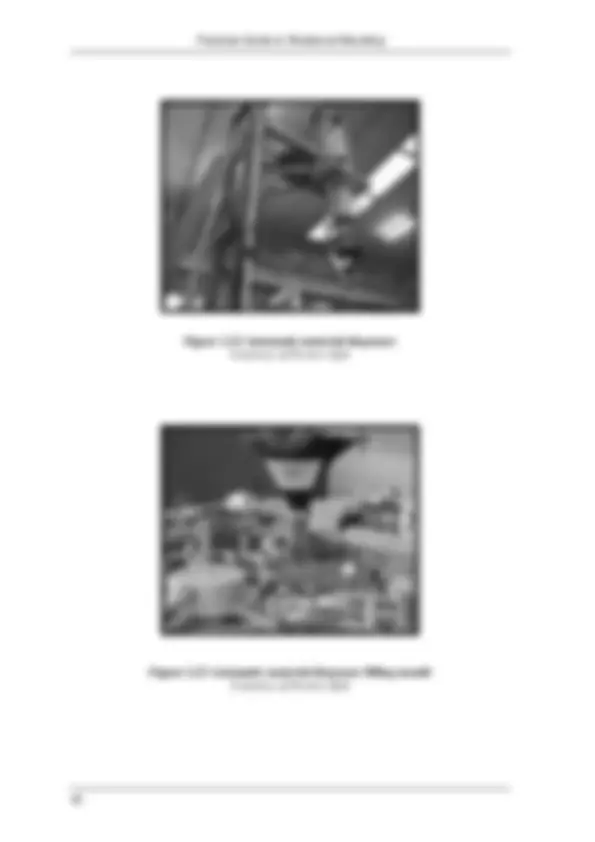
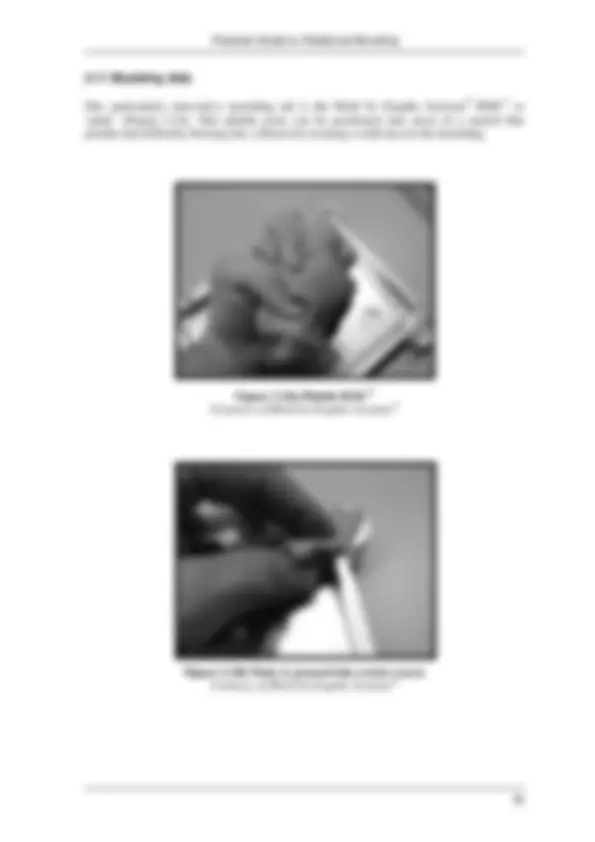
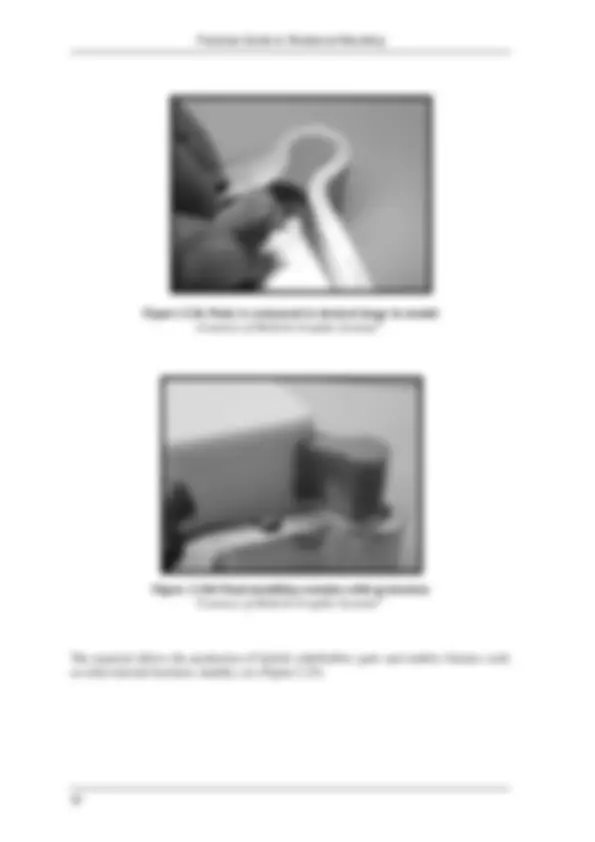
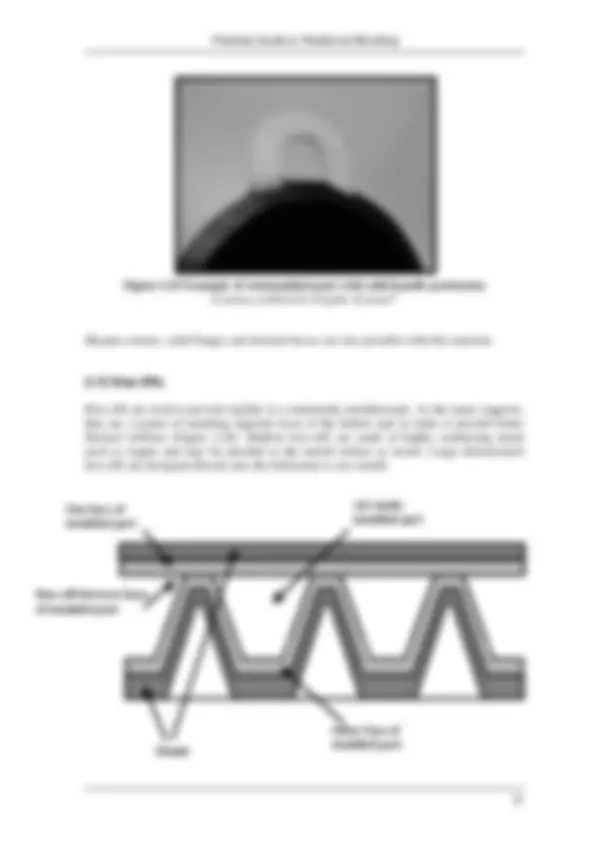
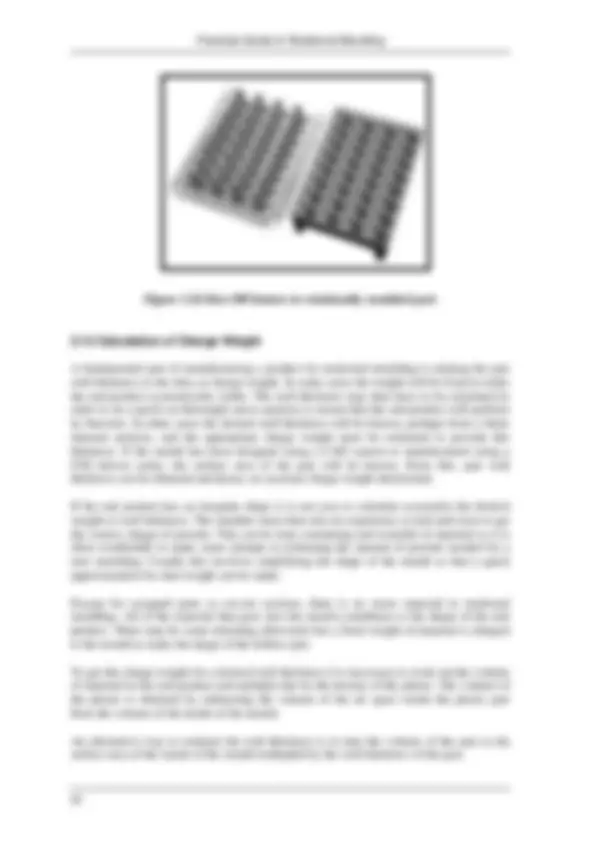
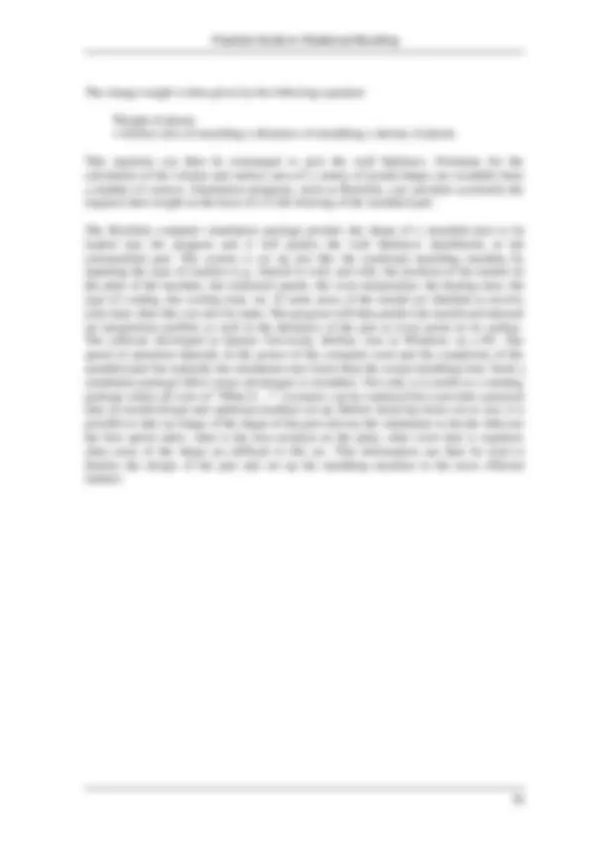
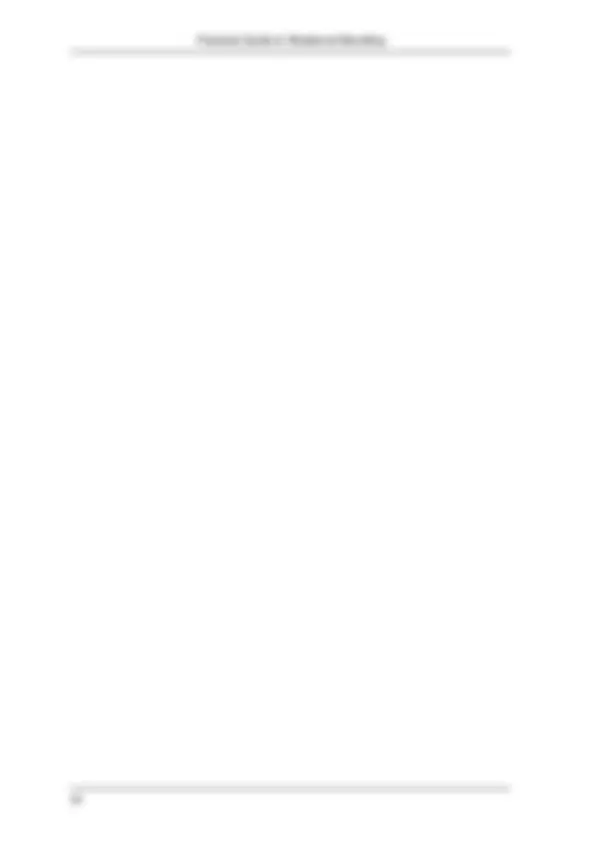
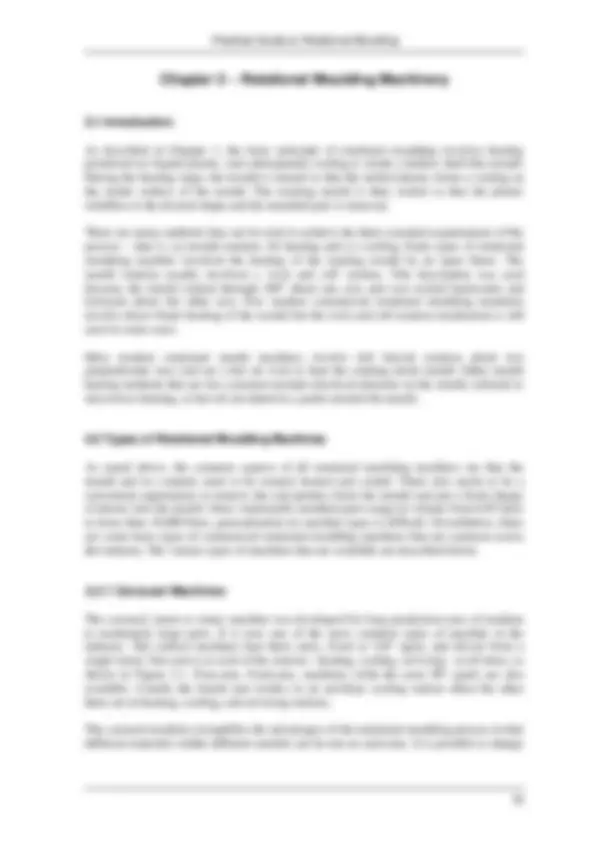
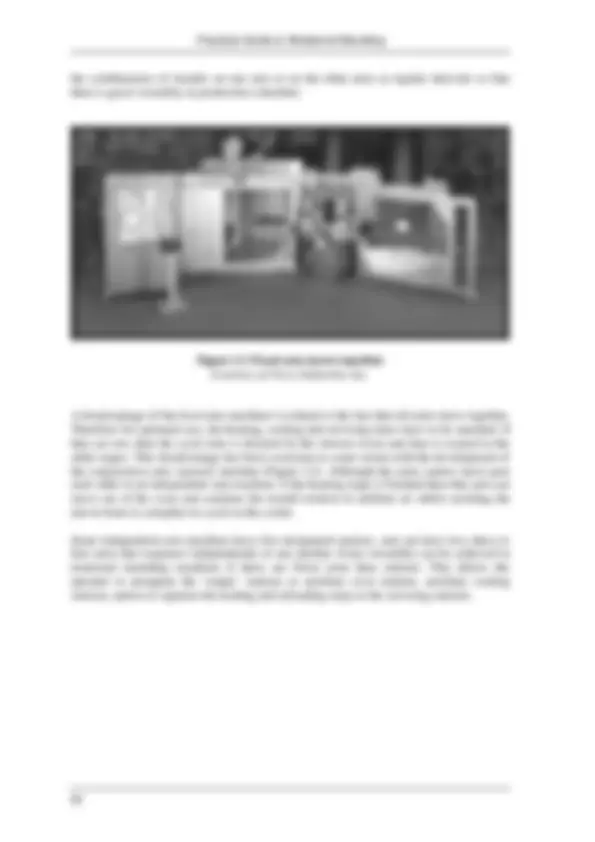
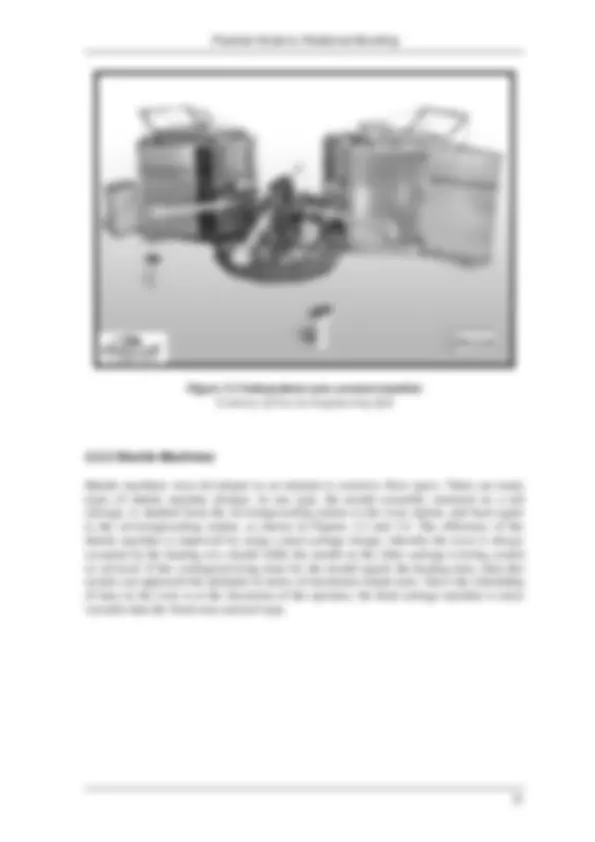
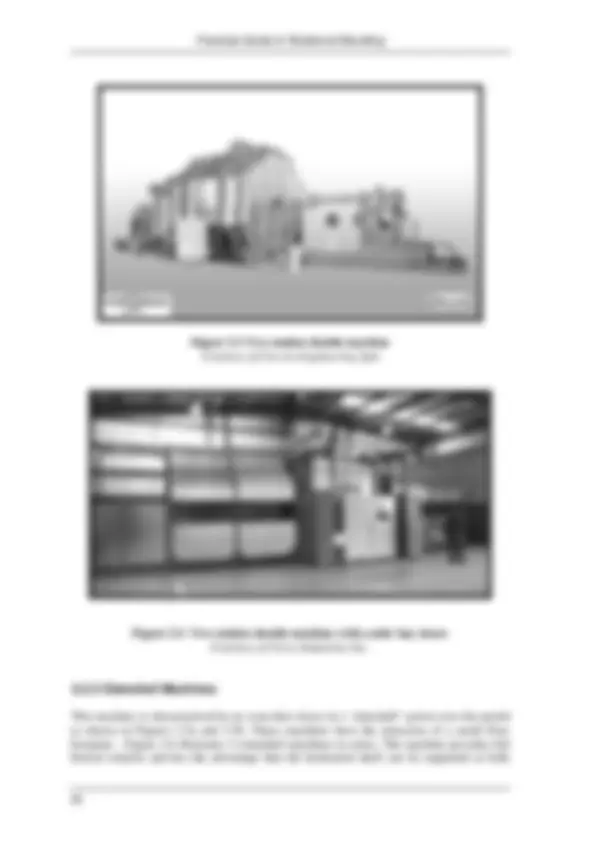
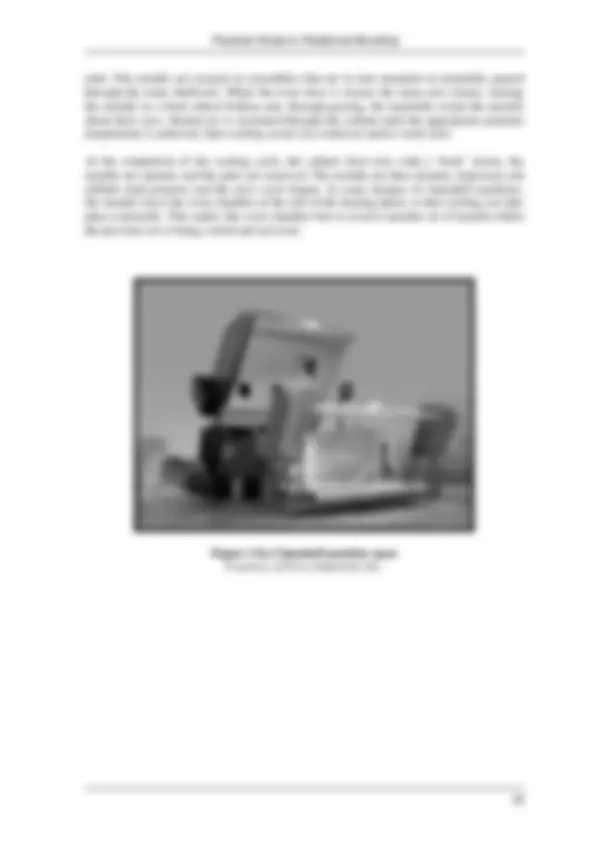
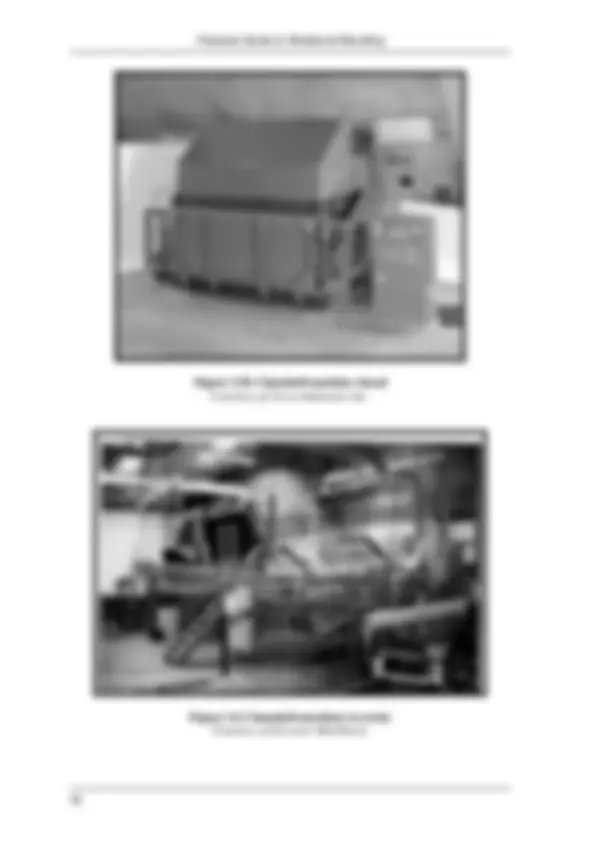
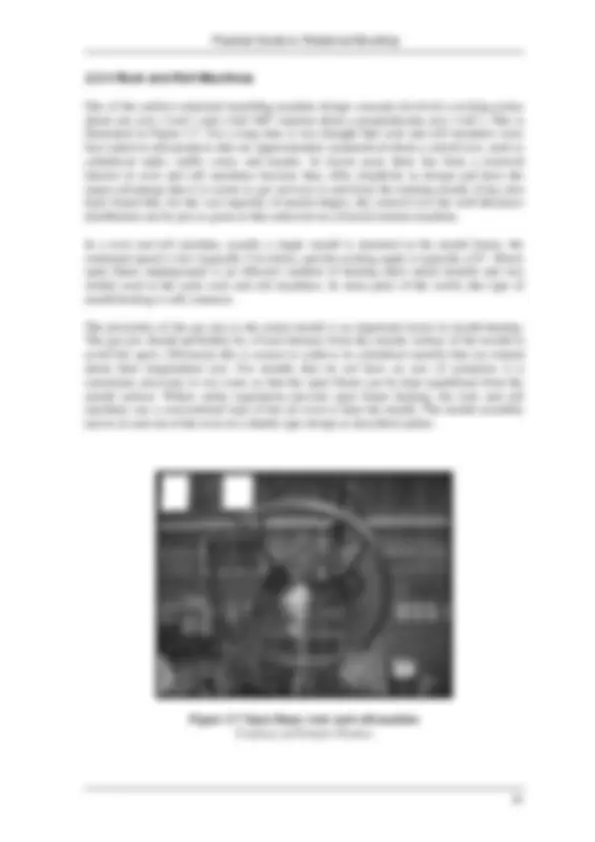
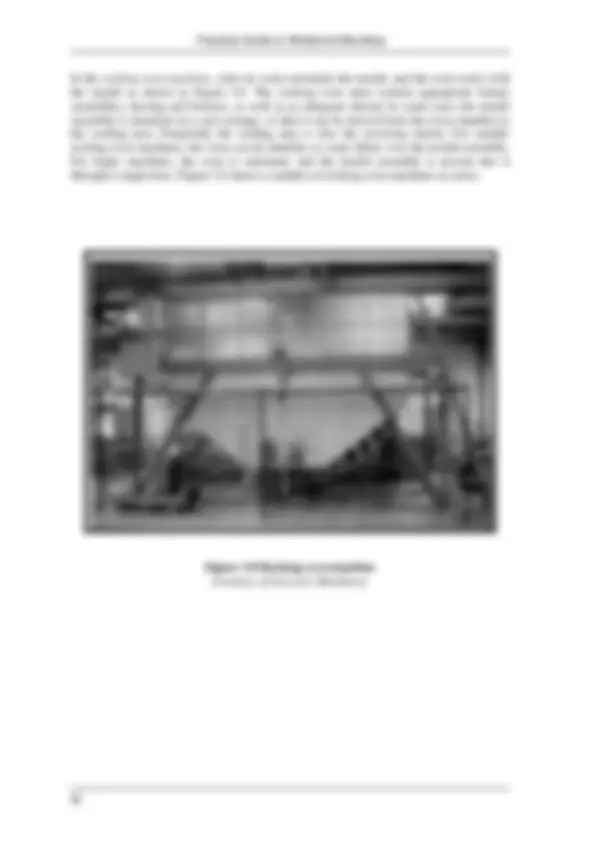
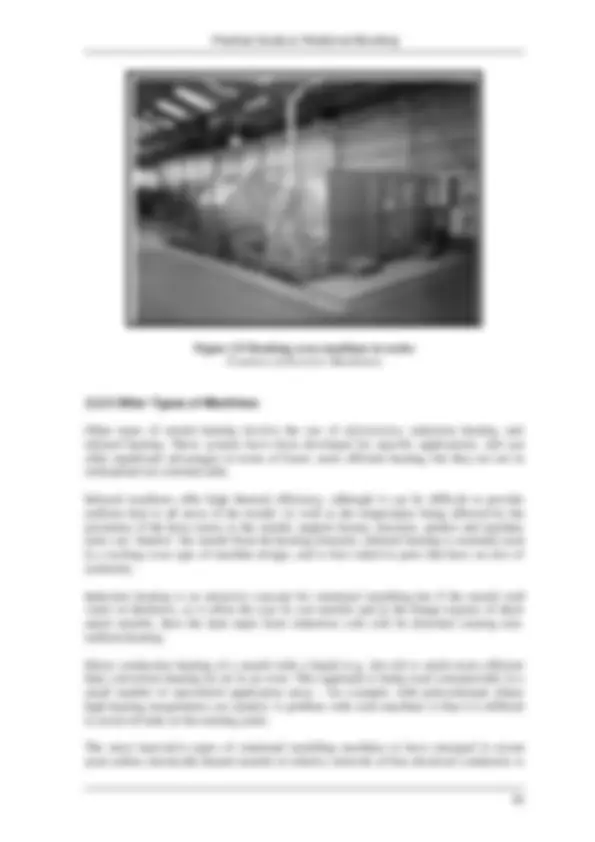
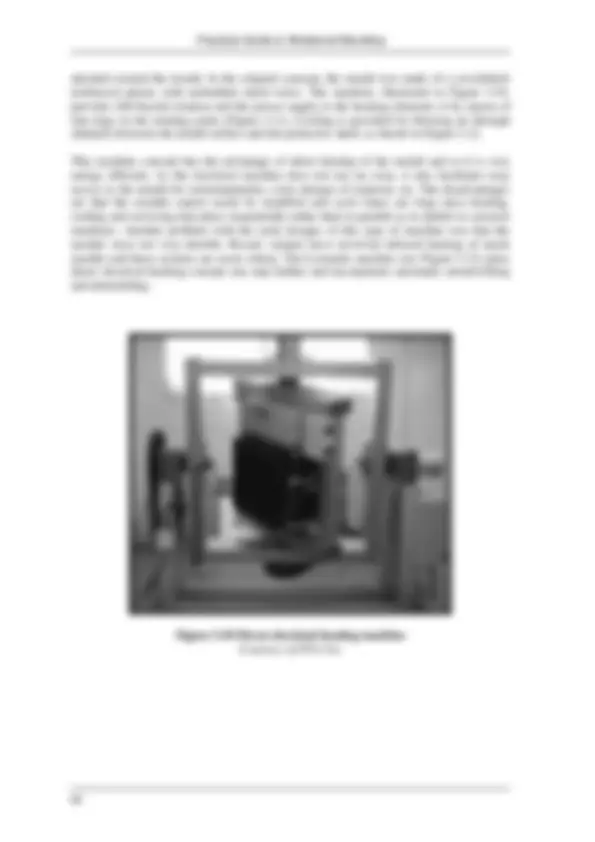
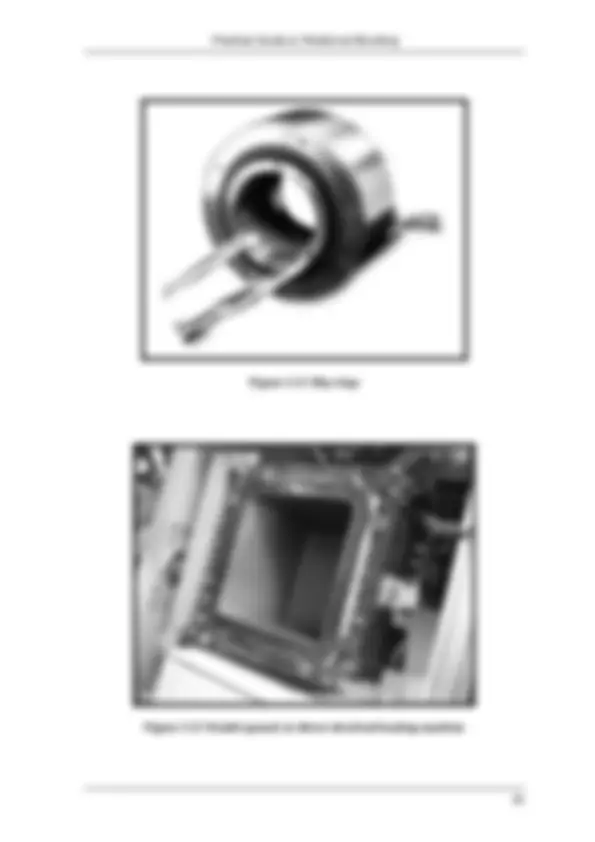
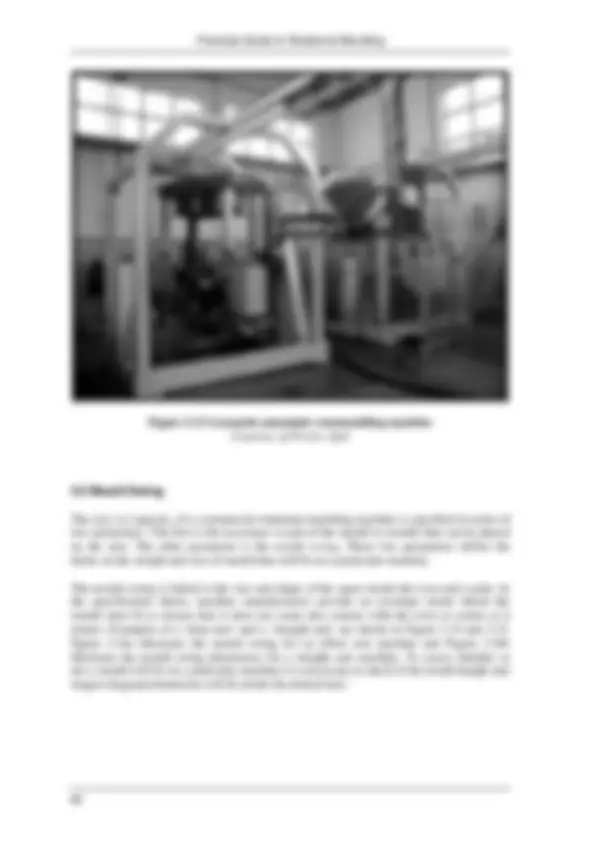
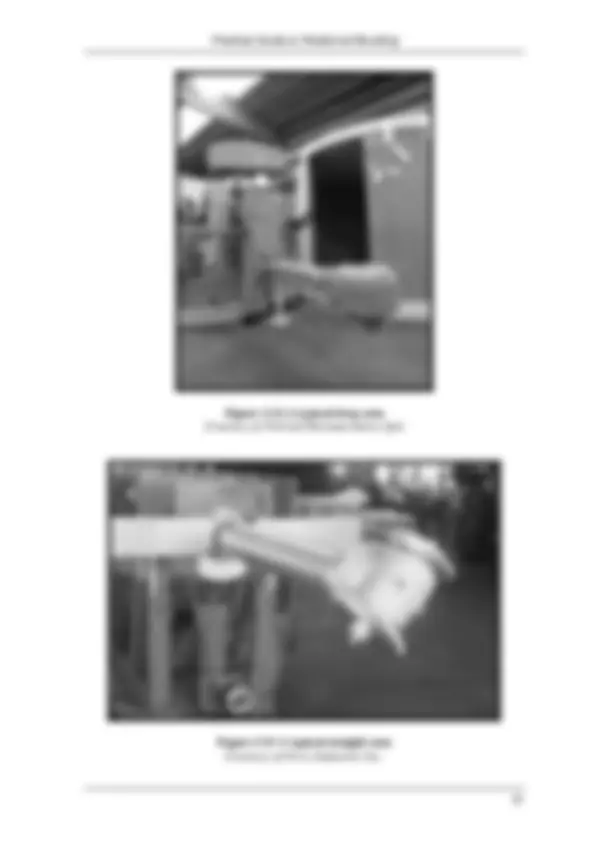
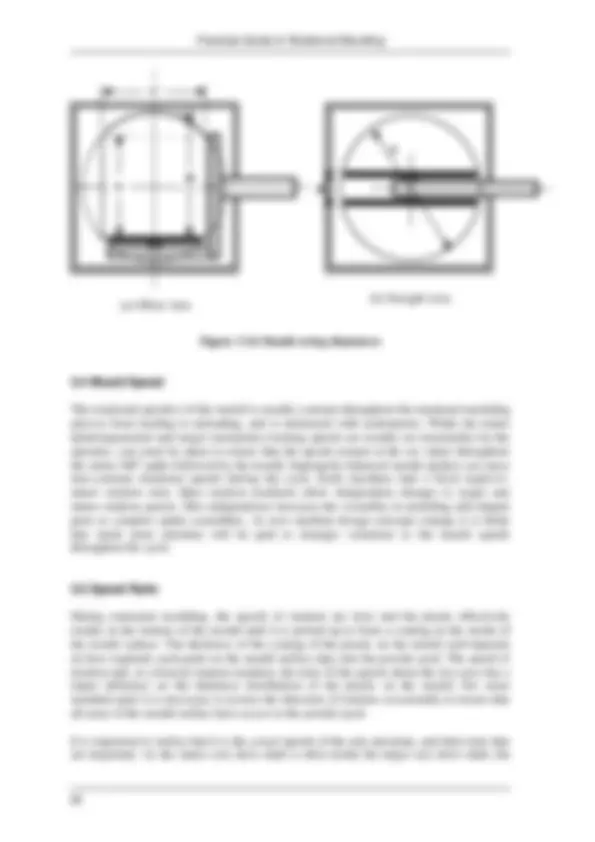
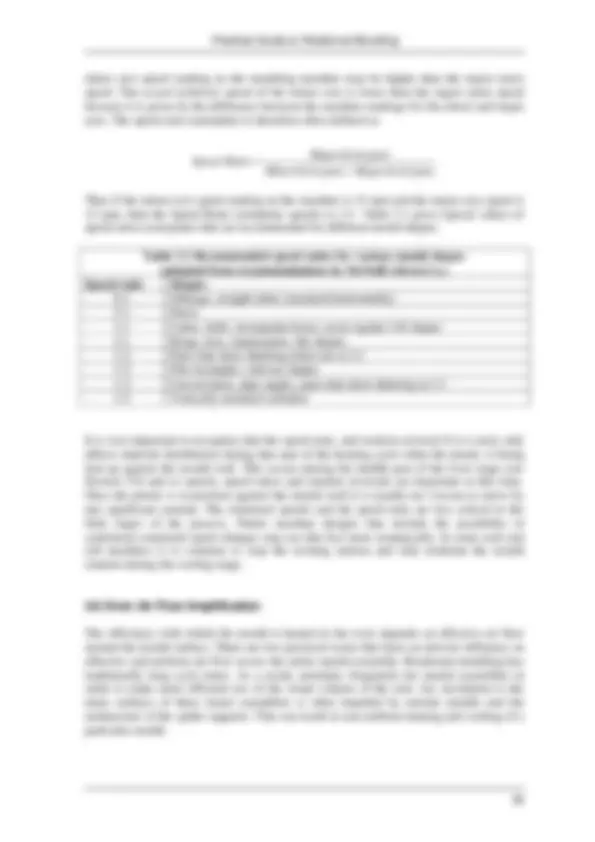
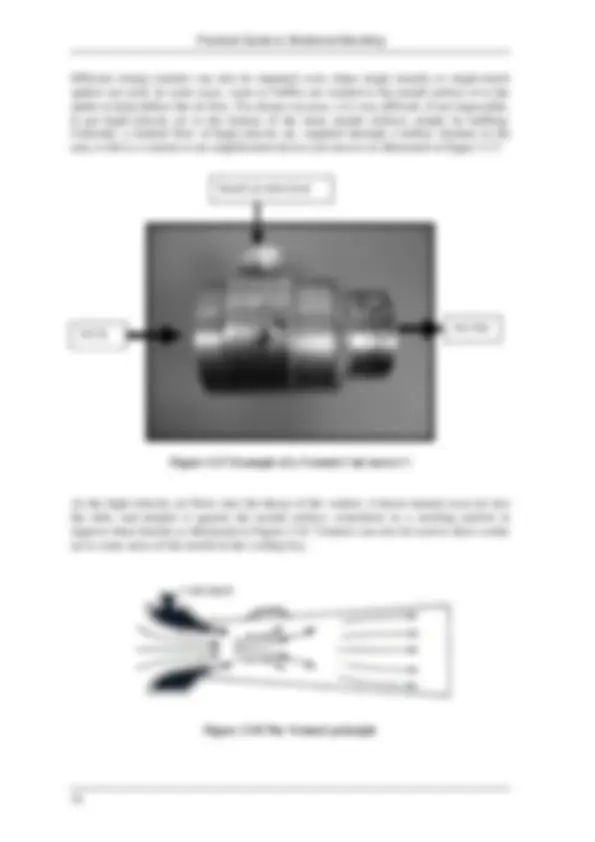
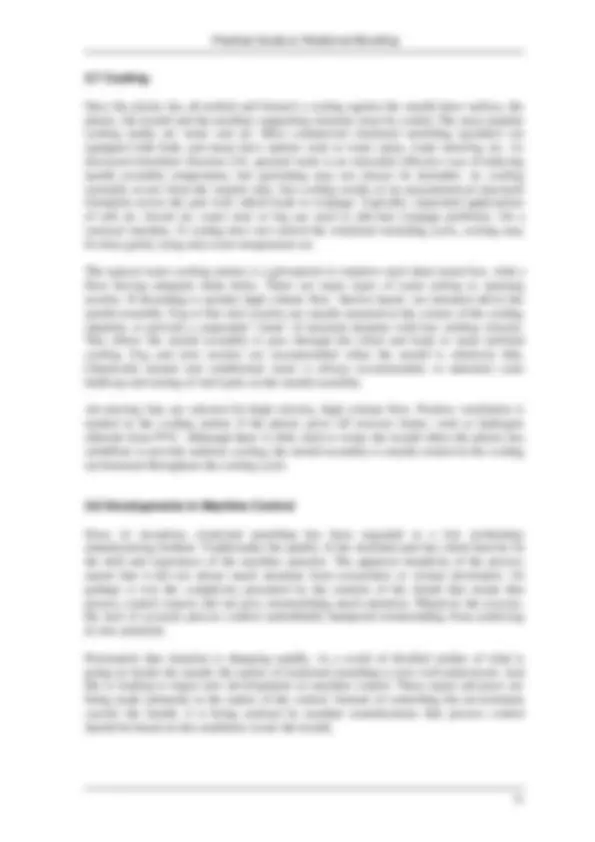
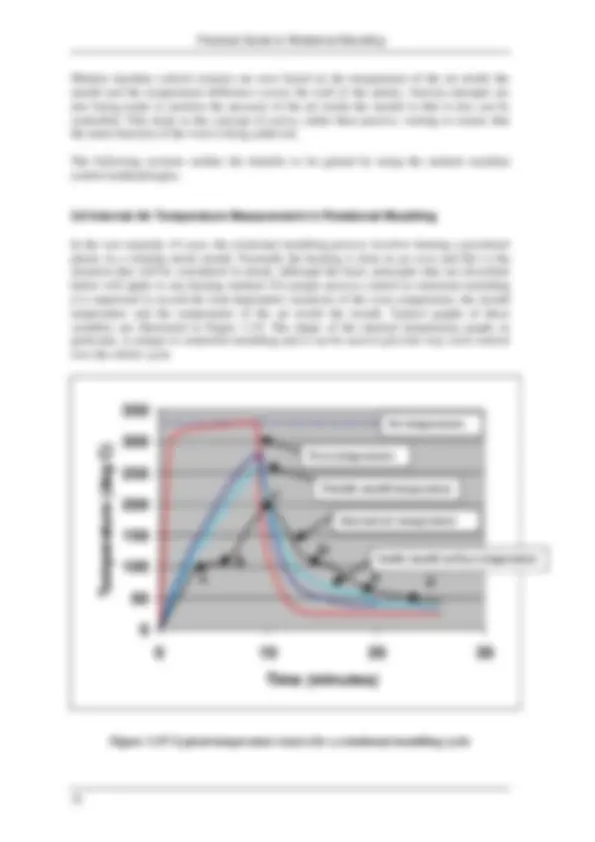
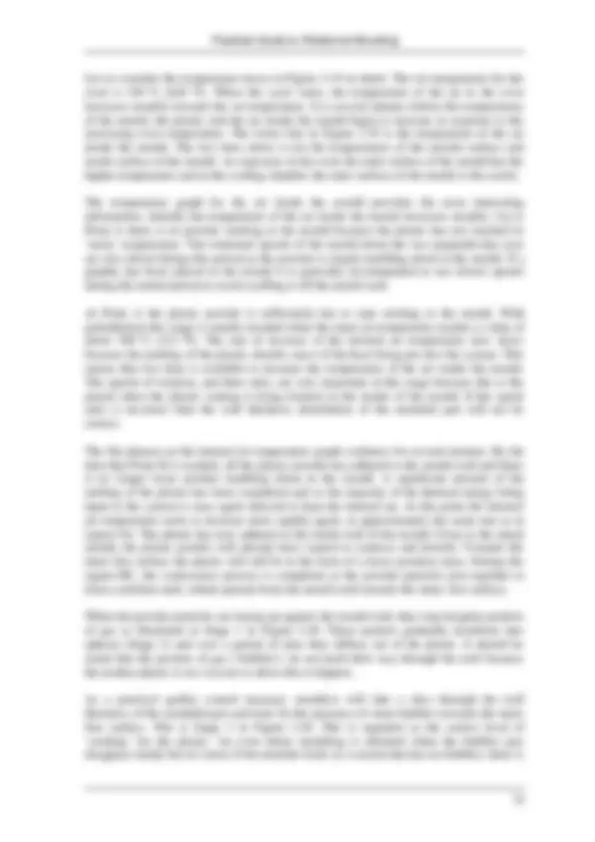
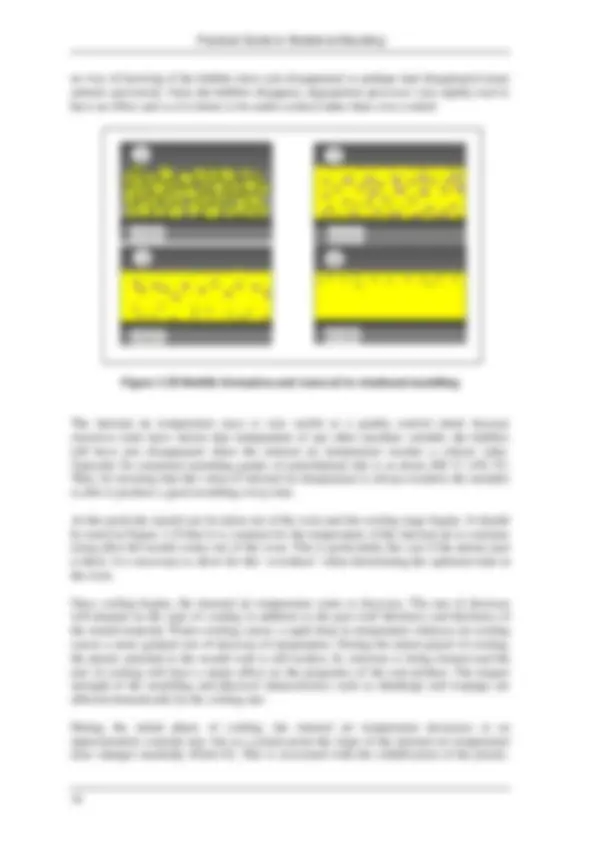

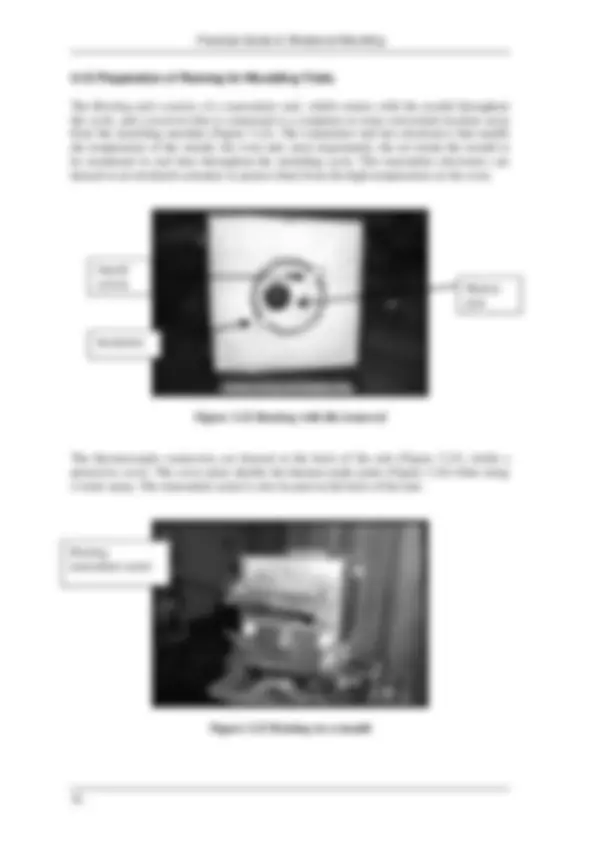
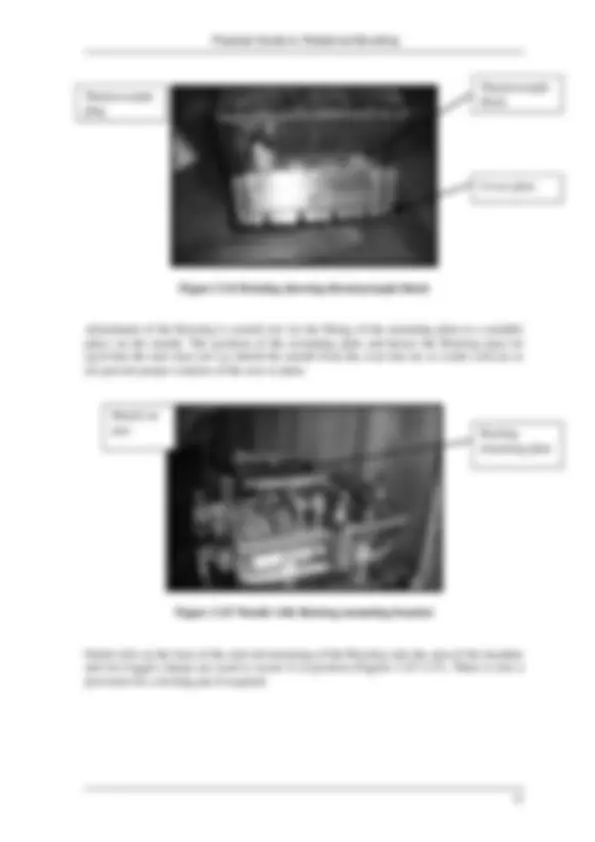
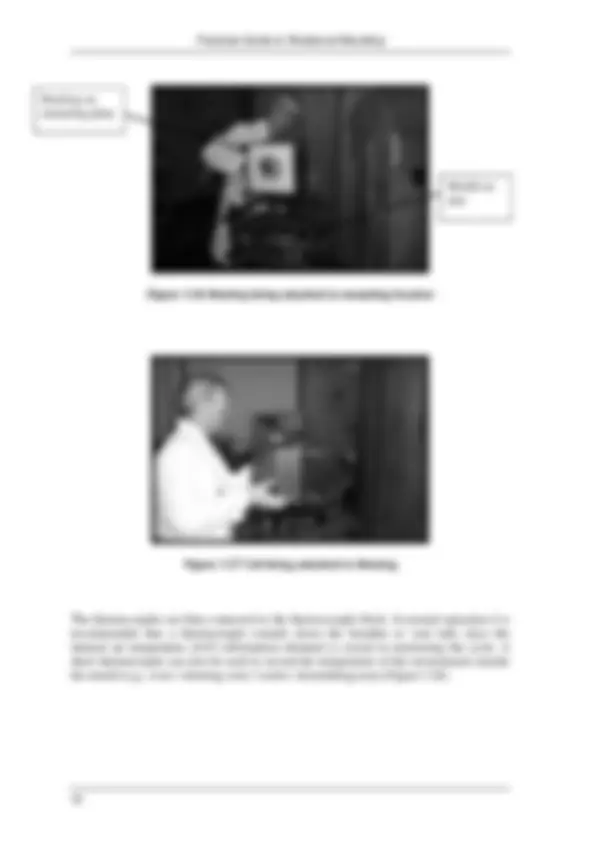
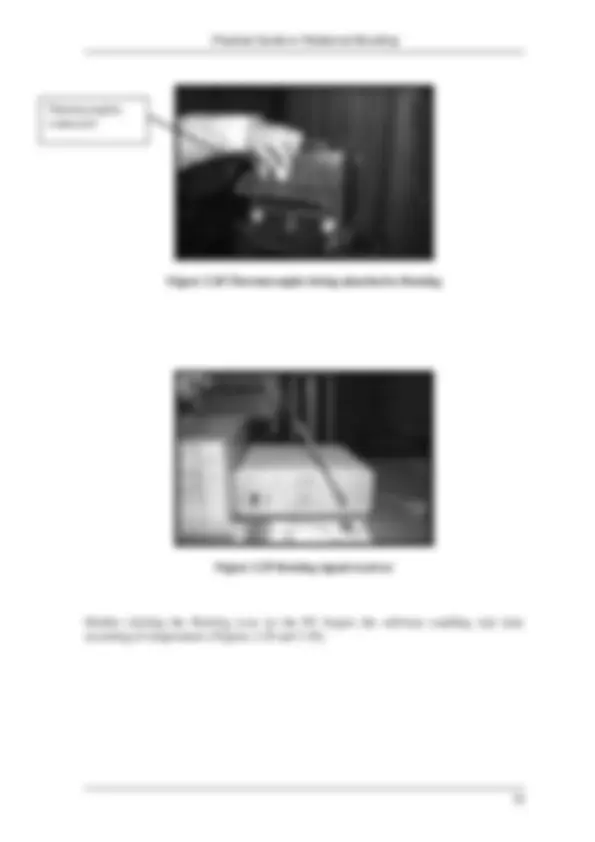
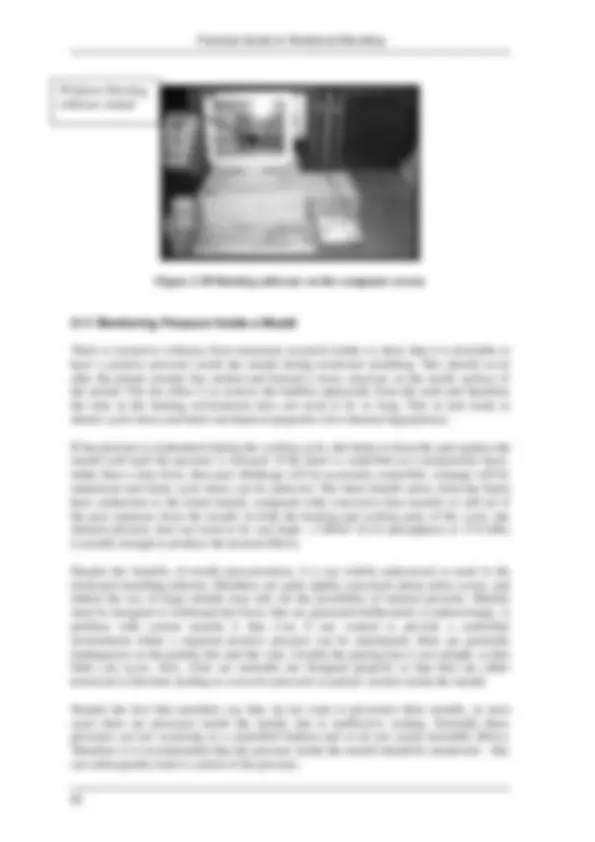
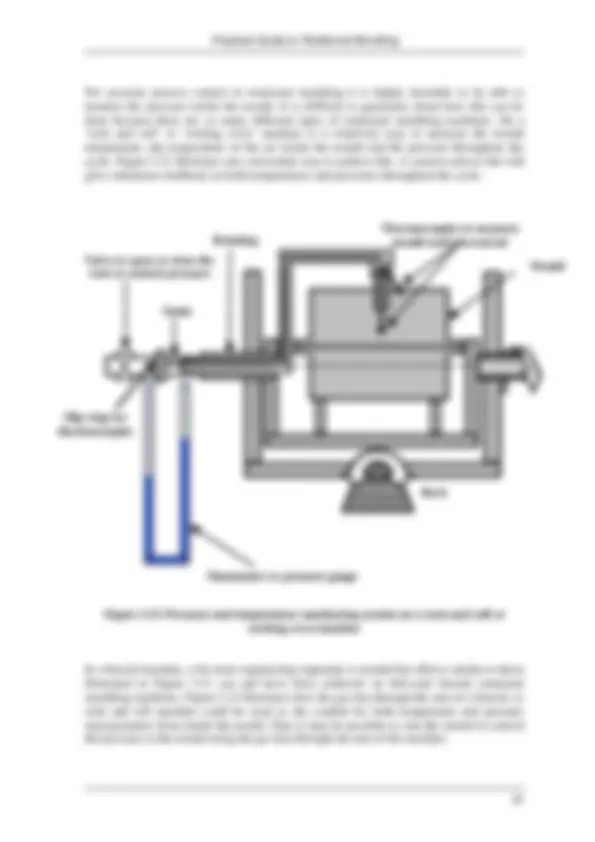
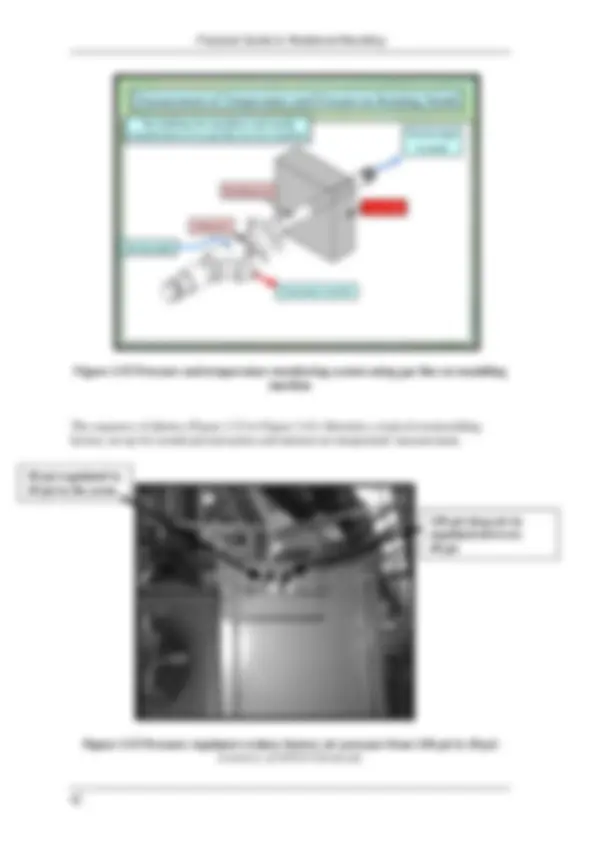
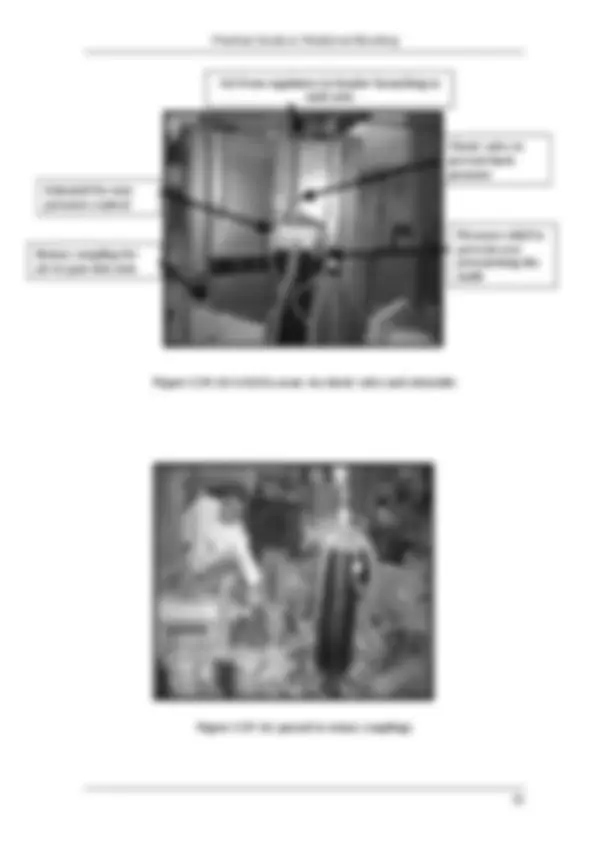
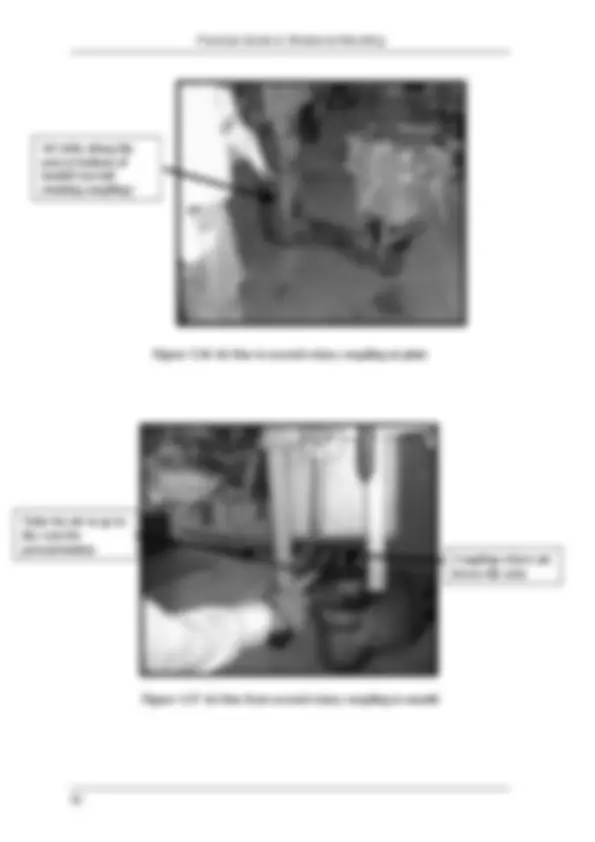
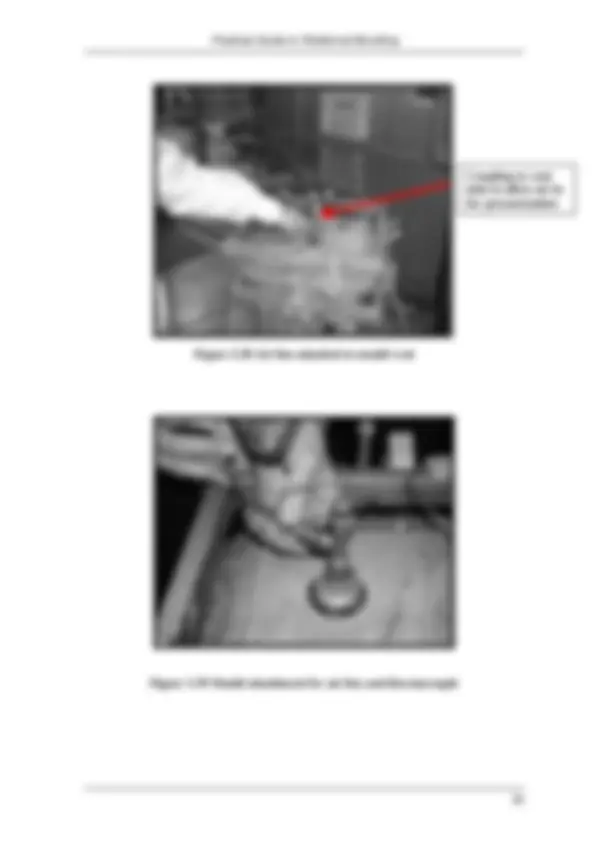
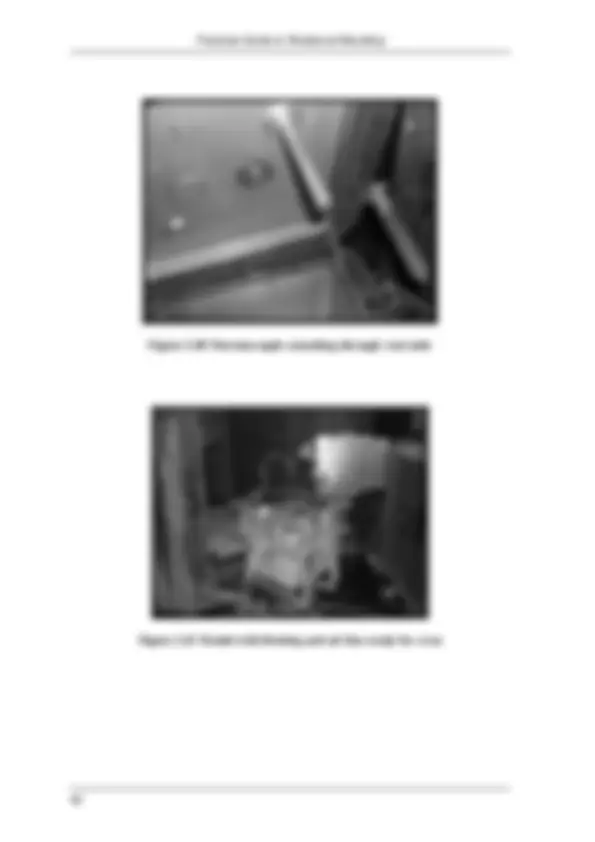
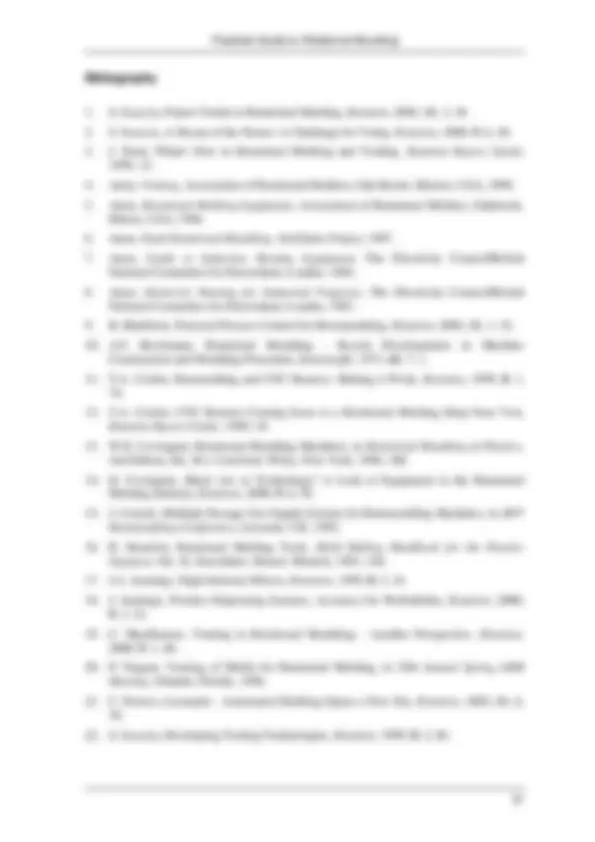
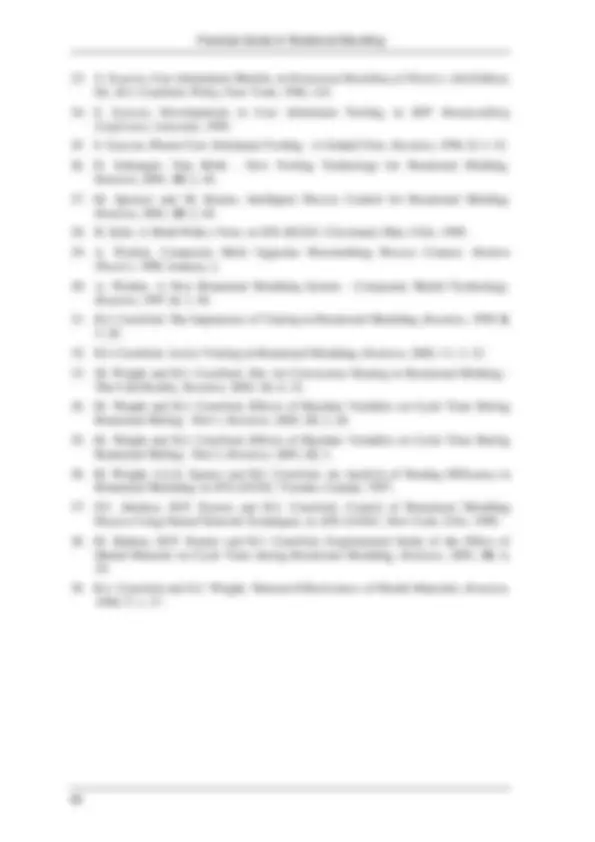
Estude fácil! Tem muito documento disponível na Docsity
Ganhe pontos ajudando outros esrudantes ou compre um plano Premium
Prepare-se para as provas
Estude fácil! Tem muito documento disponível na Docsity
Prepare-se para as provas com trabalhos de outros alunos como você, aqui na Docsity
Os melhores documentos à venda: Trabalhos de alunos formados
Prepare-se com as videoaulas e exercícios resolvidos criados a partir da grade da sua Universidade
Responda perguntas de provas passadas e avalie sua preparação.
Ganhe pontos para baixar
Ganhe pontos ajudando outros esrudantes ou compre um plano Premium
Comunidade
Peça ajuda à comunidade e tire suas dúvidas relacionadas ao estudo
Descubra as melhores universidades em seu país de acordo com os usuários da Docsity
Guias grátis
Baixe gratuitamente nossos guias de estudo, métodos para diminuir a ansiedade, dicas de TCC preparadas pelos professores da Docsity
The 'practical guide to rotational moulding' document provides a comprehensive overview of the rotational moulding process, covering various aspects such as mould design, machinery, materials, and post-moulding decoration. It includes detailed information on the advantages and limitations of rotational moulding compared to other plastic fabrication processes, as well as a wide range of applications and examples of rotomoulded products. Intended to serve as a valuable resource for professionals, students, and anyone interested in understanding the fundamentals and practical applications of this versatile manufacturing technique.
Tipologia: Esquemas
1 / 188
Esta página não é visível na pré-visualização
Não perca as partes importantes!
The right of R.J. Crawford and M.P. Kearns to be identified as the authors of this work has been asserted by them in accordance with Sections 77 and 78 of the Copyright, Designs and Patents Act
© 2003, Rapra Technology Limited
ISBN: 1-85957-387-
Cover images reproduced courtesy of ICO Polymers, Bonar Plastics, Caccia Engineering SpA, Clarehill Plastics Limited, Mold In Graphic Systems®^ , NOVA Chemicals, Persico SpA and Polivinil Rotomachinery SpA.
All rights reserved. No part of this publication may be reproduced, stored in a retrieval system, or transmitted in any form or by any means—electronic, mechanical, photocopying, recording or otherwise—without the prior permission of the publisher, Rapra Technology Limited, Shawbury, Shrewsbury, Shropshire, SY4 4NR, UK.
Typeset, printed and bound by Rapra Technology Limited. Cover printed by LG Davis Design and Print Solutions, Birmingham.
Contents
iv
vi
Raquel Soares, Arnaud Robert, Gareth McDowell, Eunan O’Brien, Julia McDaid, Niamh Corrigan, Louise Pick, Edward Archer and Raji Khouri.
There have also been a very large number of Masters degree students and undergraduates who have contributed through their project work. These have all contributed to our understanding of the rotational moulding process. We are also grateful to Paul Nugent and Alvin Spence in their roles as the Managers of the Rotational Moulding Research Centre, during the period when we were getting established with our research investigations and seminar work.
We would also like to acknowledge the contribution and support from staff and colleagues at the Polymer Processing Research Centre (PPRC), in particular: Centre Director, Prof. Raymond Murphy; Process Engineers, Michael Murphy, Neil Callan, Mark McCourt and Paul Hanna; and Senior Laboratory Technician, John Kissick.
In the preparation of this book we have received very willing support from the following companies:
Association of Rotational Molders Alan Yorke Engineering Anchor Inserts Atofina Chemicals Inc Atlas Plastics Borealis AS Bonar Plastics Ciba Speciality Chemicals Chem-Trend Chroma Corporation Caccia Engineering SpA Clarehill Plastics Limited Dutchland Plastics Corp. Equistar Chemicals Ferry Industries Inc Formed Plastics ICO Polymers Persico SpA Kingspan Maus GmbH Mold In Graphic® Norstar Aluminium Molds Nova Chemicals Rotation Magazine Rototek Limited Poly Processing Company Pioneer Plastics PPA Teo Plastic Consulting Research Services Polivinil Roto Plastics Corporation Reinhart Roto-Machines
vii
Reduction Engineering Sorcerer Rotational Moulding Machinery SAT Solar Plastics STP Equipment Wheeler Boyce
They have given freely of their time to assist us and to provide photographs for inclusion in the book. We thank you for all your help.
Finally we would like to thank Sally Humphreys at Rapra for her help. Sally had the original idea for the book and was very supportive, helpful and patient as we wrote the book and tried to retain some credibility in our day jobs.
Roy Crawford Mark Kearns
June 2003
Practical Guide to Rotational Moulding
1
Chapter 1 – Introduction to the Rotational Moulding Process
1.1 Introduction
Rotational moulding, also known as rotocasting or rotomoulding, is a low pressure, high temperature manufacturing method for producing hollow, one-piece plastic parts. As with most manufacturing methods for plastic parts, rotational moulding evolved from other technologies. The basic principle of forming a coating on the inside surface of a rotating mould dates back for many centuries, but the process did not gain recognition as a moulding method for plastics until the 1940s. The ceramic pottery process, known today as ‘slip casting’, is depicted in ancient Egyptian, Grecian and Chinese art. In Switzerland in the 1600s, the formation of hollow objects, such as eggs, followed the development of chocolate from cocoa. A British patent issued to Peters in 1855 (before plastics existed) cites a rotational moulding machine containing two-axis rotation through a pair of bevel gears. It refers to the use of a split mould having a vent pipe for gas escape, water for cooling the mould and the use of a fluid or semi-fluid material in the mould to produce a hollow part.
The earliest commercial application of the concept of rotational moulding for plastics used vinyl plastisols to coat the inside surface of a hollow metal mould. Typical products included play balls and toy dolls. This process using PVC is still in widespread use today. In the 1950s the use of the rotational moulding process expanded more quickly due to the introduction of powdered polyethylene grades specifically developed for the process. Nowadays polyethylene accounts for over 90% of the total tonnage of plastics used in rotational moulding worldwide. This is mainly because the powder flow, melt flow and thermal stability of this material are ideally suited to the process.
Currently rotational moulding is a very competitive alternative to blow moulding, thermoforming and injection moulding for the manufacture of hollow plastic products. This is because it offers designers the opportunity to achieve the economic production of stress-free articles, with uniform wall thickness and potentially complex shapes.
Typical moulded parts include bulk containers, tanks, canoes, toys, medical equipment, automotive parts and ducts, as illustrated in Figures 1.1-1.11 and Section 1.7.
Practical Guide to Rotational Moulding
2
Figure 1.1 Rotationally moulded storage tanks Courtesy of Poly Processing Co.
Figure 1.2 Cutaway section of complex rotomoulded part
Practical Guide to Rotational Moulding
4
Figure 1.7 Point-of-display items Courtesy of Association of Rotational Molders
Figure 1.8 Protective casing Courtesy of New England Plastics Corp.
Figure 1.9 Decorative items Courtesy of Dutchland Plastics
Figure 1.10 Machine housing Courtesy of Association of Rotational Molders
Practical Guide to Rotational Moulding
5
Figure 1.11 Painted PVC cowboy figurine
A drawback of rotational moulding is that the cycle times are relatively long compared to other plastic fabrication processes. Table 1.1 shows typical processing conditions, tooling costs and production rates associated with blow moulding, thermoforming and rotational moulding. In general, rotomoulding is best suited to applications where the volumes are not large. There are, of course, always exceptions to this generalisation and the versatility of rotational moulding means that nowadays it is being used in most market sectors. Over the past decade, rotational moulding has enjoyed the fastest growth rate of any manufacturing method for plastics, mainly because the economics are attractive to designers and as it is a low pressure process, the moulded parts are essentially stress-free.
Table 1.1 Comparison between blow moulding, thermoforming and rotational moulding Factor Blow moulding Thermoforming Rotational moulding Plastics available limited broad limited Feedstock pellets sheet powder/liquid Mould materials steel/aluminium aluminium steel/aluminium Mould pressure <1 MPa <0.3 MPa <0.1 MPa Mould cost high moderate moderate Wall thickness uniformity
Tends to be non- uniform
Tends to be non- uniform Uniformity possible
Inserts feasible no yes Residual stress moderate high low Part detailing very good good, with pressure adequate In-mould graphics yes possible yes Cycle time fast fast slow Labour intensive no moderate yes
Practical Guide to Rotational Moulding
7
400
500
(^150 130 ) 100
0
100
200
300
400
500
600
Europe USA/Canada Other Americas
Australasia
Middle East / Africa
Asia
Region
Number (est.)
Figure 1.13 Number of rotomoulders worldwide
In North America the toy industry took to the rotational moulding process in a big way, representing over 40% of the consumption in that part of the world in 1995, this declined gradually to around 20% in 2001 with tanks now leading at 27% (as shown in Figure 1.14). In Europe (see Figure 1.15), the nature of the market has always been different, with toys representing less than 5% of the consumption and other sectors such as containers, tanks, etc., tending to dominate.
Tanks 27% Toys 20%
Containers 15%
Automotive 10%
Marine 6%
Kayaks 5%
Other 12%
Materials Handling 5%
Figure 1.14 North American market sectors by product type
Practical Guide to Rotational Moulding
8
Figure 1.15 European market sectors by product type
1.2 The Rotational Moulding Process
The various stages in the rotational moulding process are shown in Figure 1.16 and Figures 1.17a – 1.17m.
Figure 1.16 The four main stages of the rotational moulding process
In Stage 1, a hollow metal mould (at room temperature) is charged with a predetermined quantity of powdered (or liquid) plastic, which is equal to the desired part weight. The size of the charge can be determined on the basis of the surface area of the mould, the required thickness of the final moulding and the density of the plastic. An important advantage of
Traffic 7%
Transport 8% Others 9%
Automotive 15% Toys 5%
Industrial 17%
Leisure 4%
Food/Agriculture 27%
Home/Garden 8%