
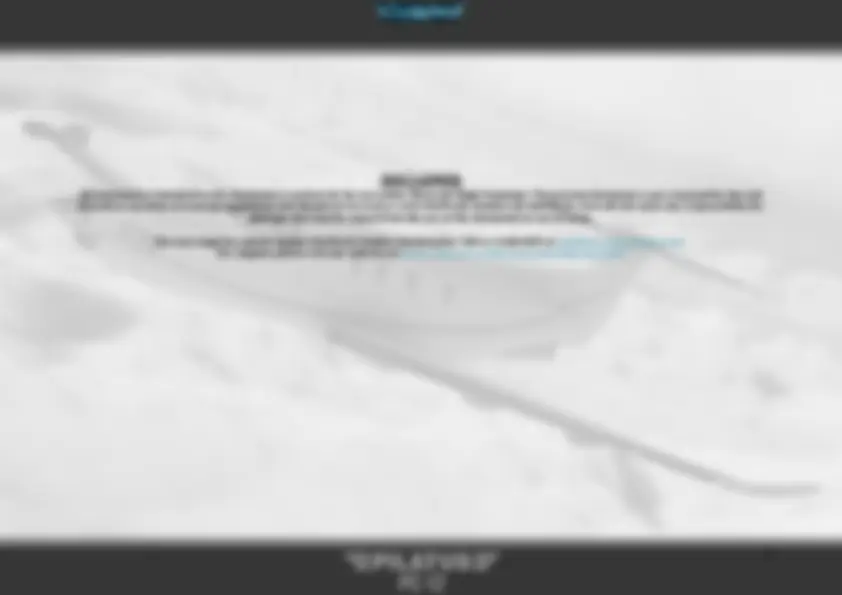
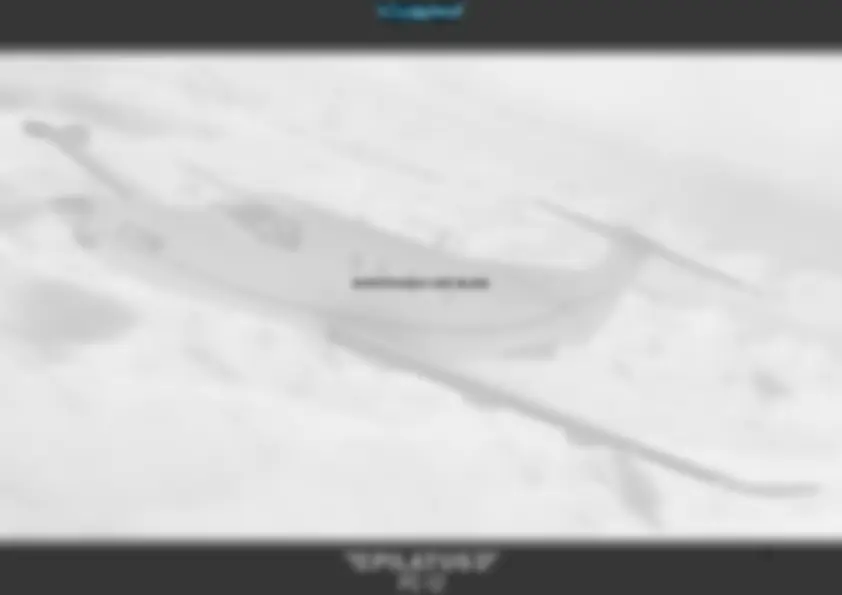
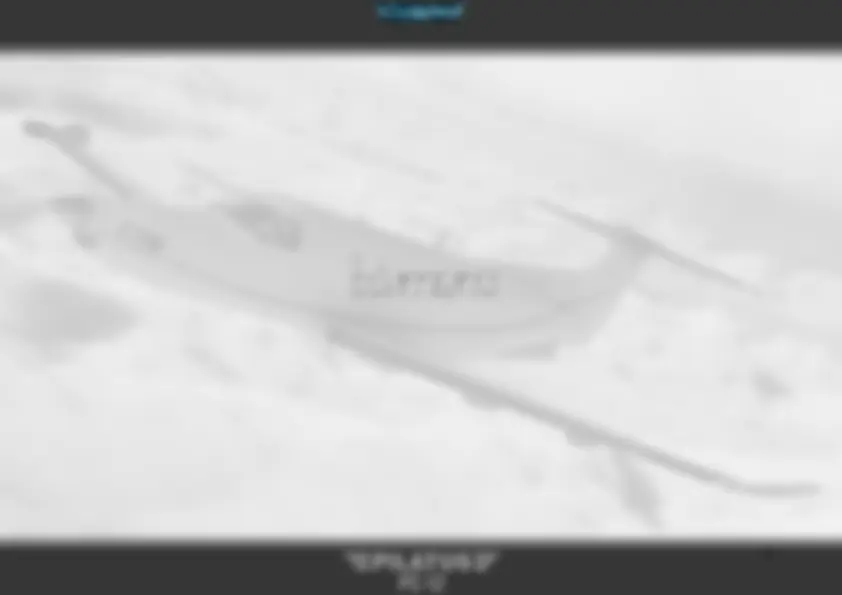
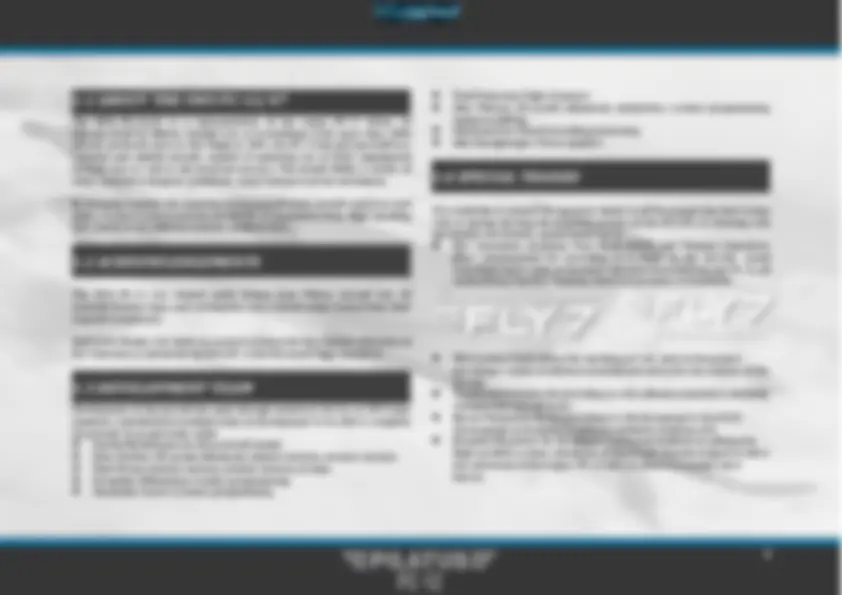
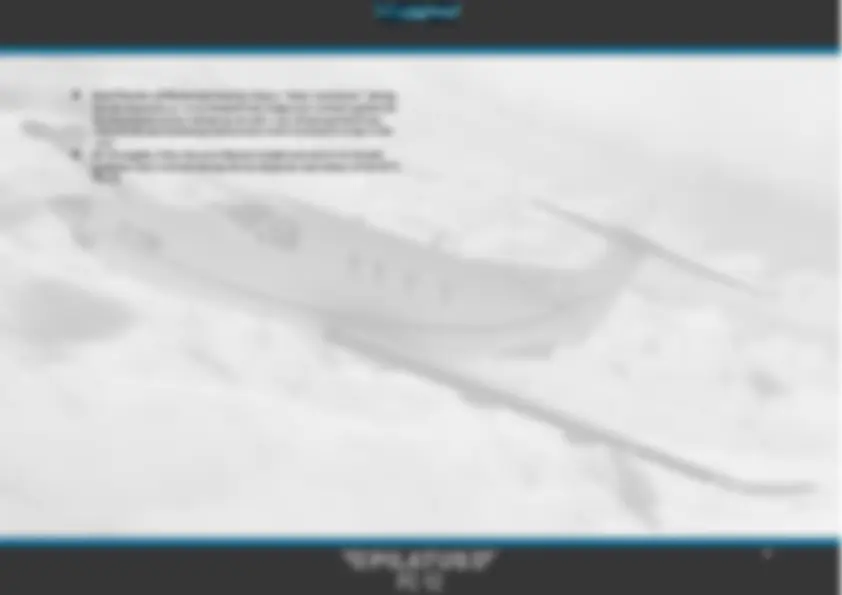
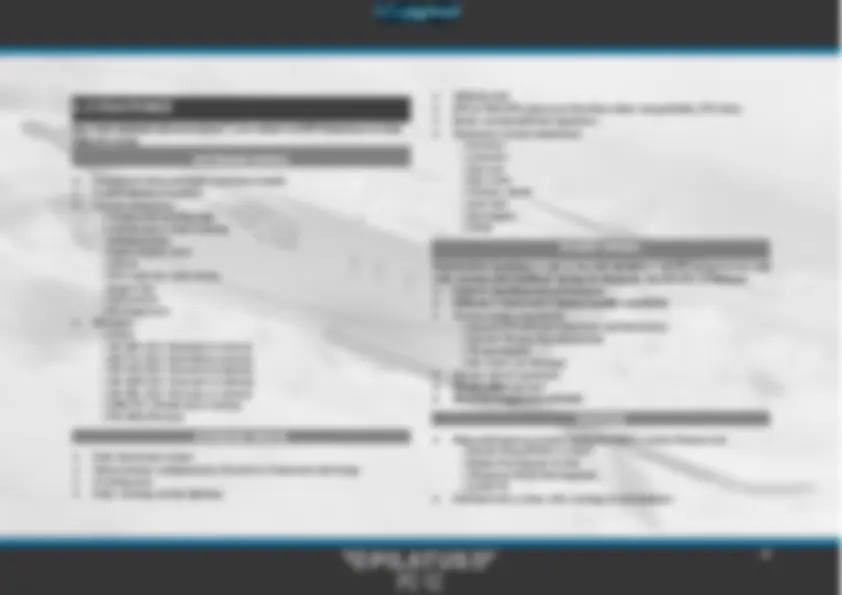
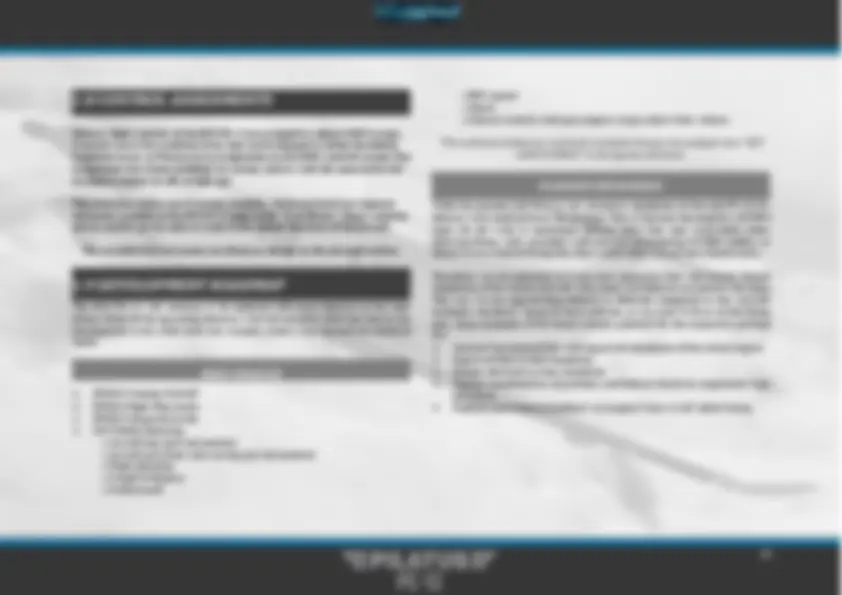
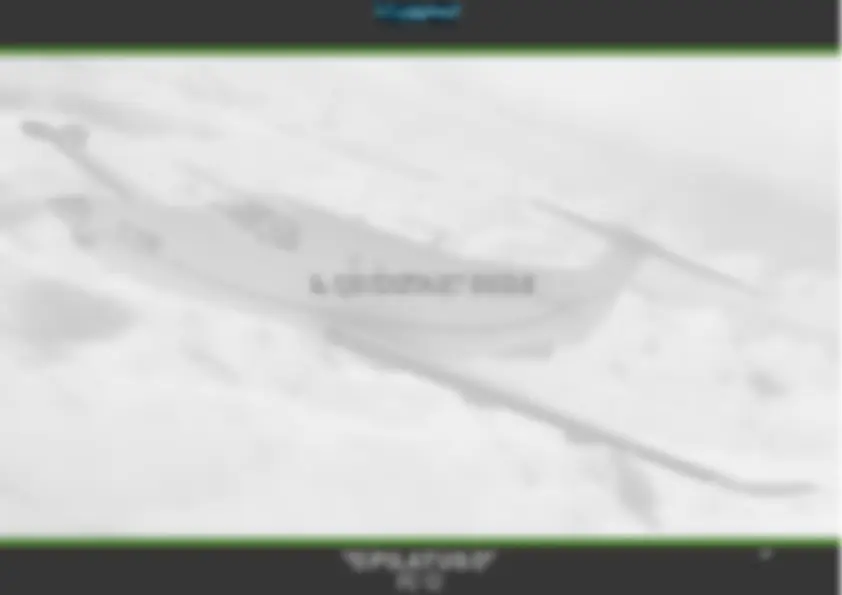
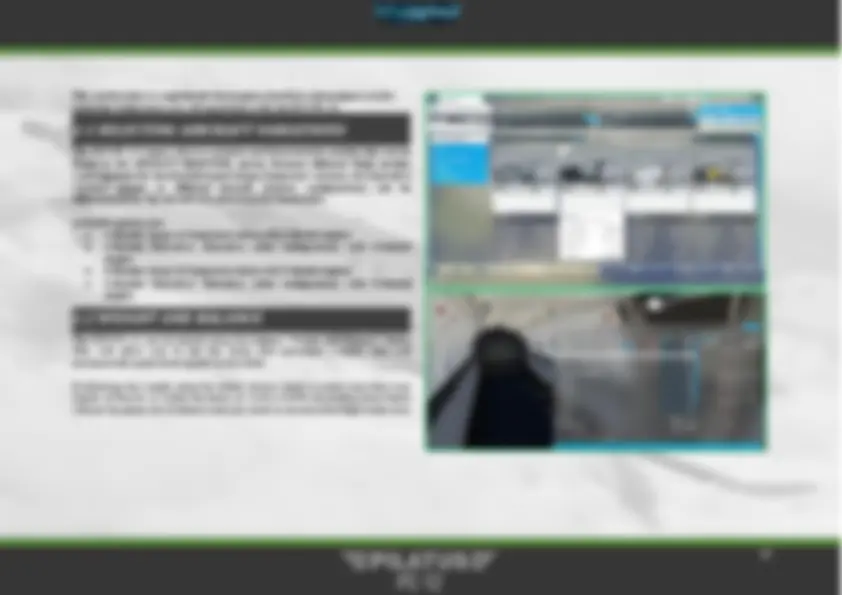
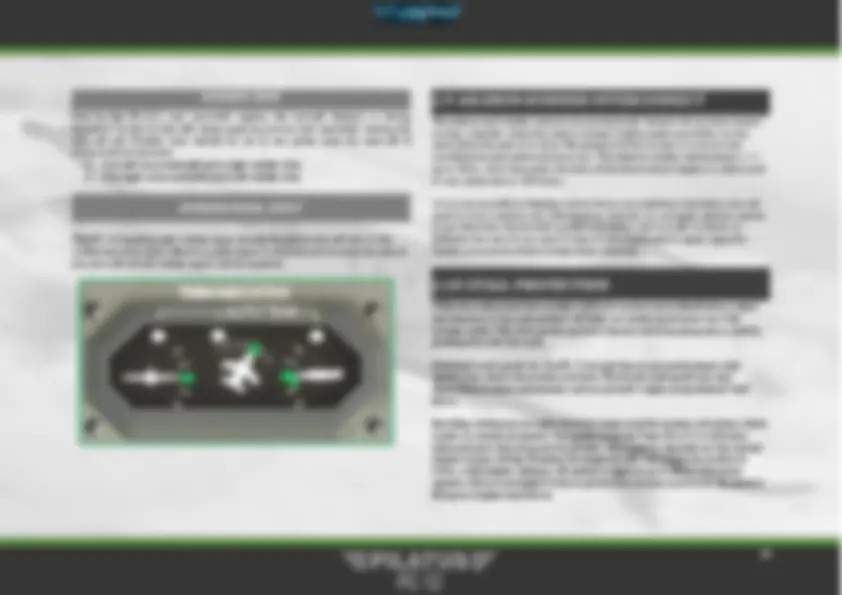
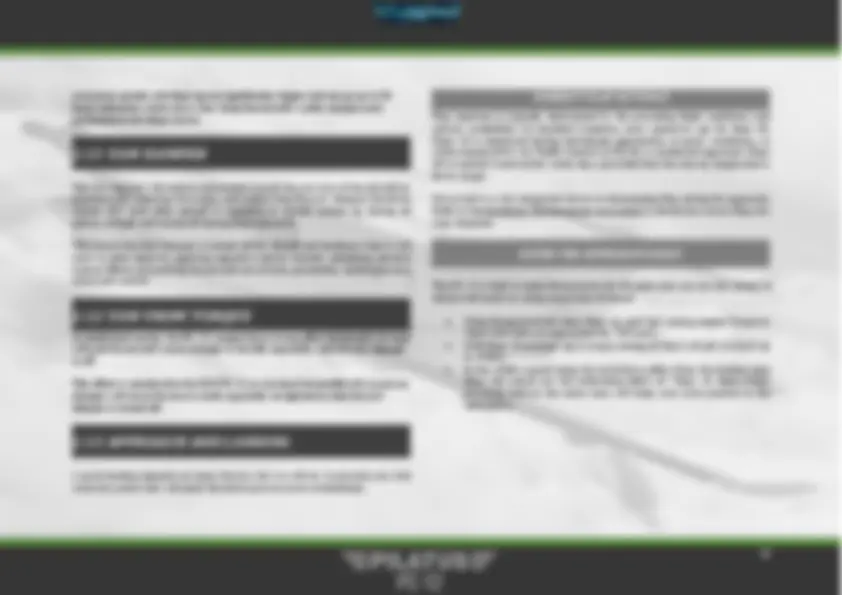
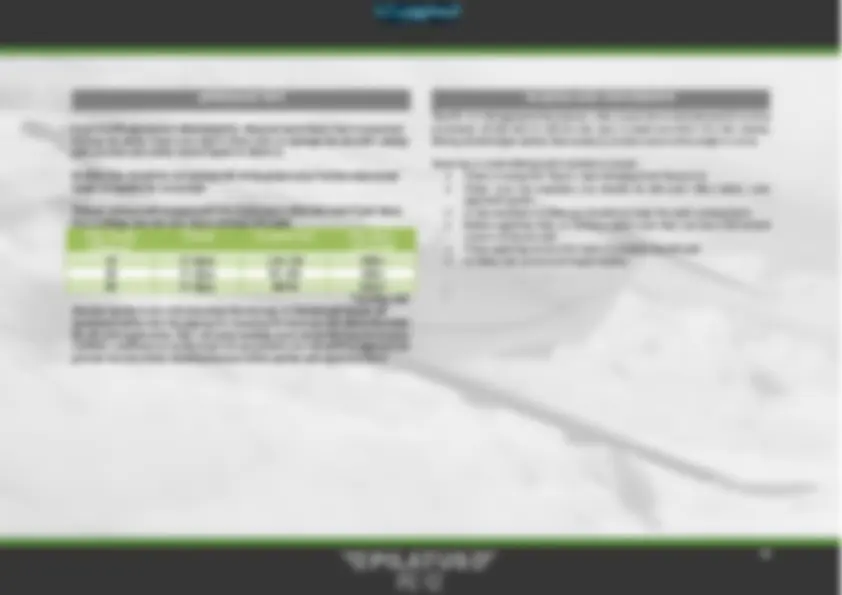
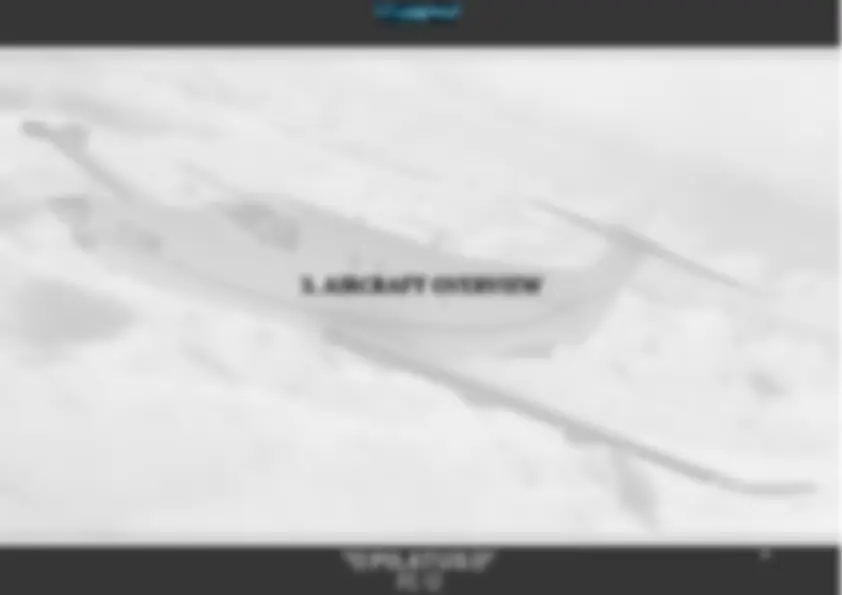
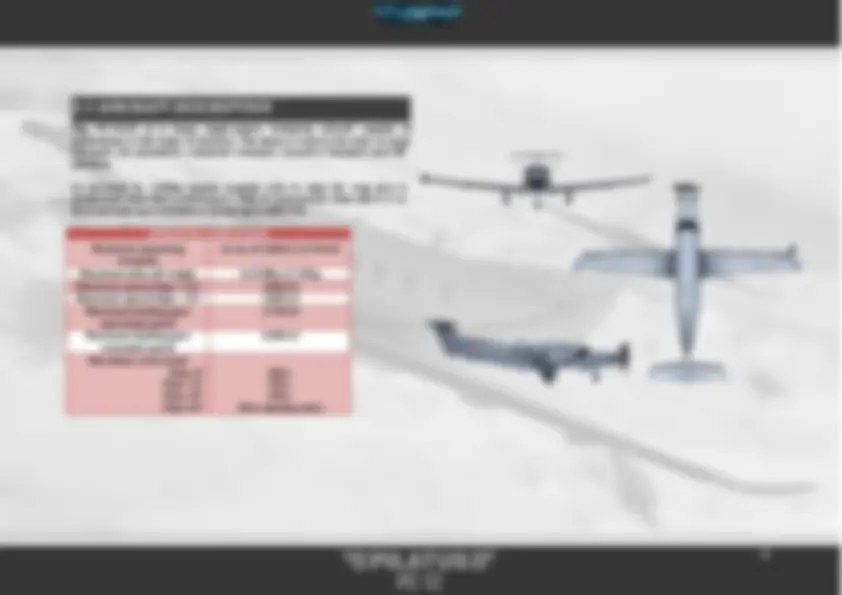
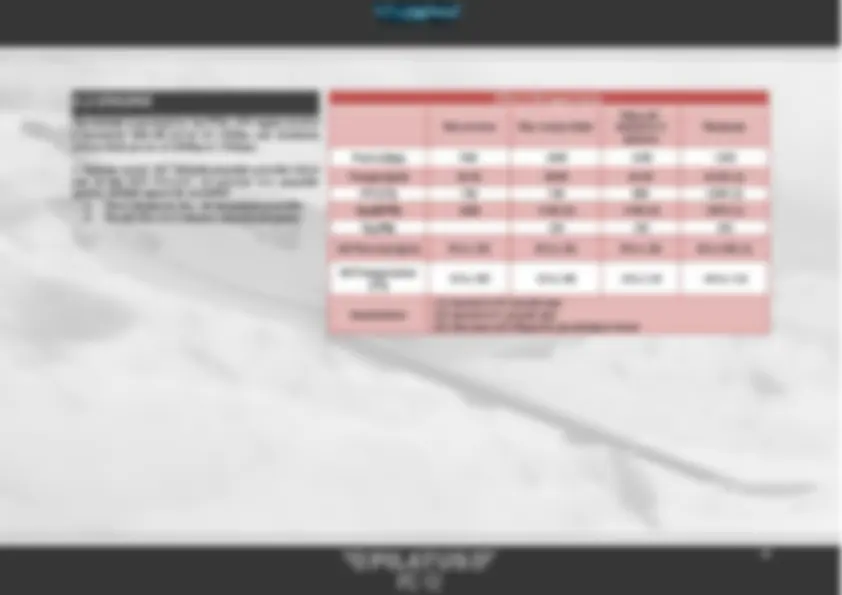
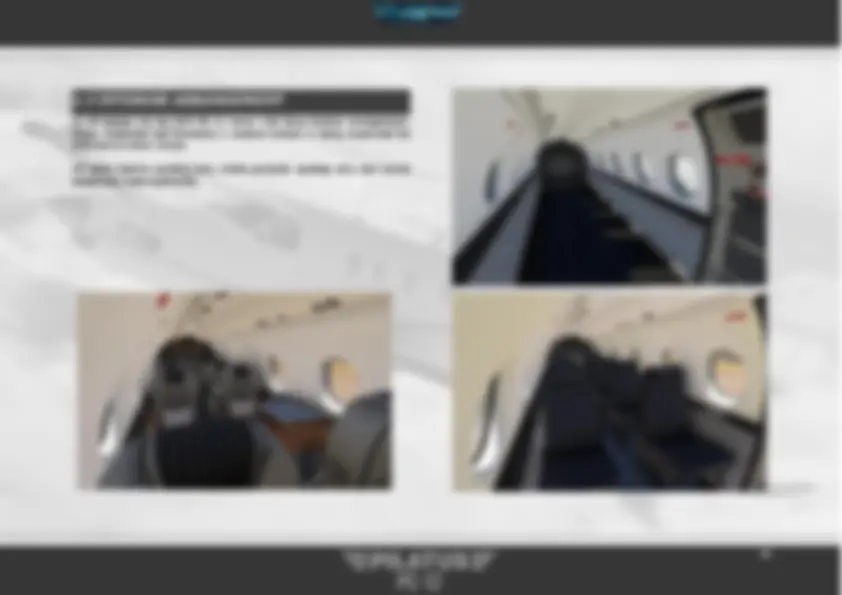
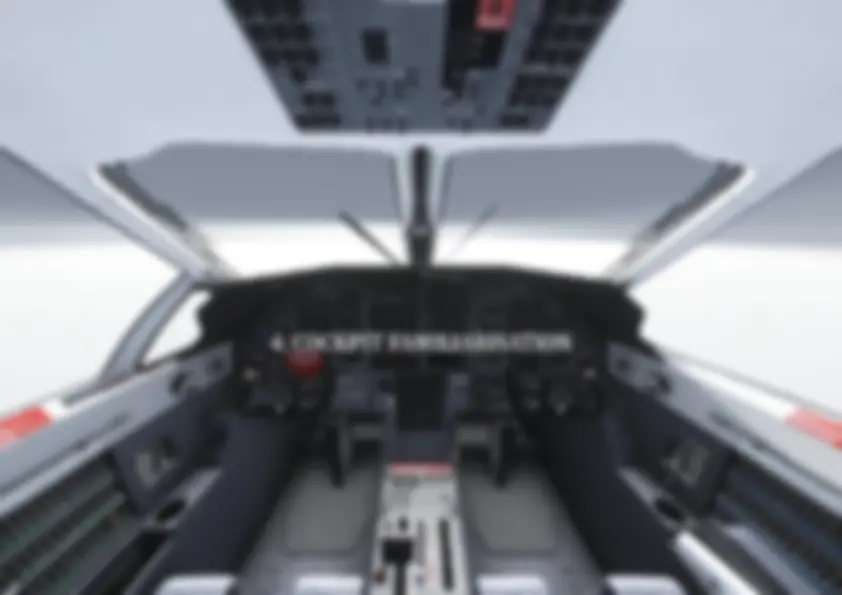
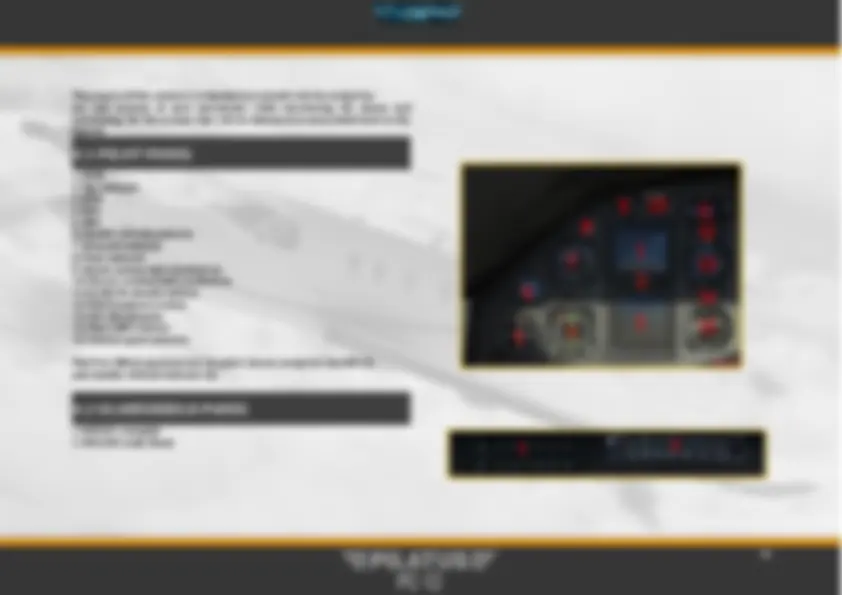
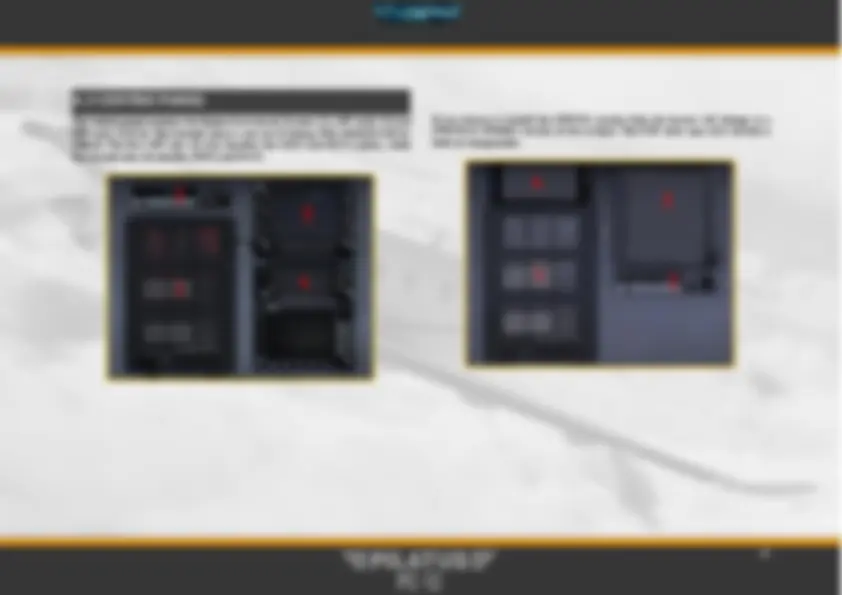
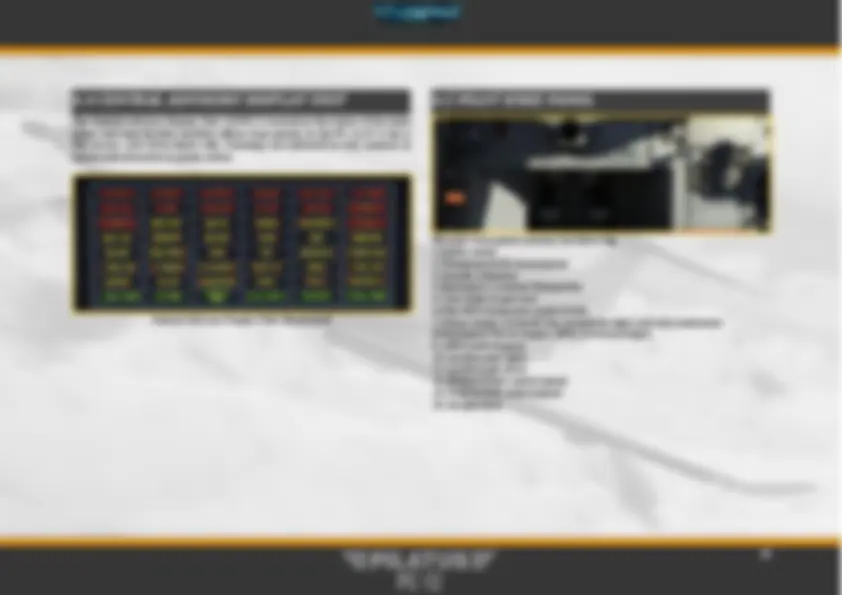
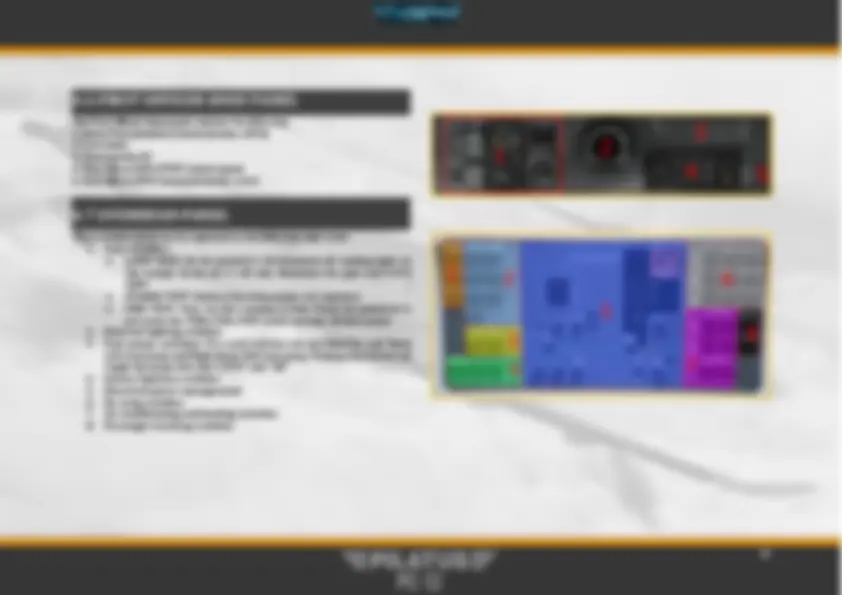
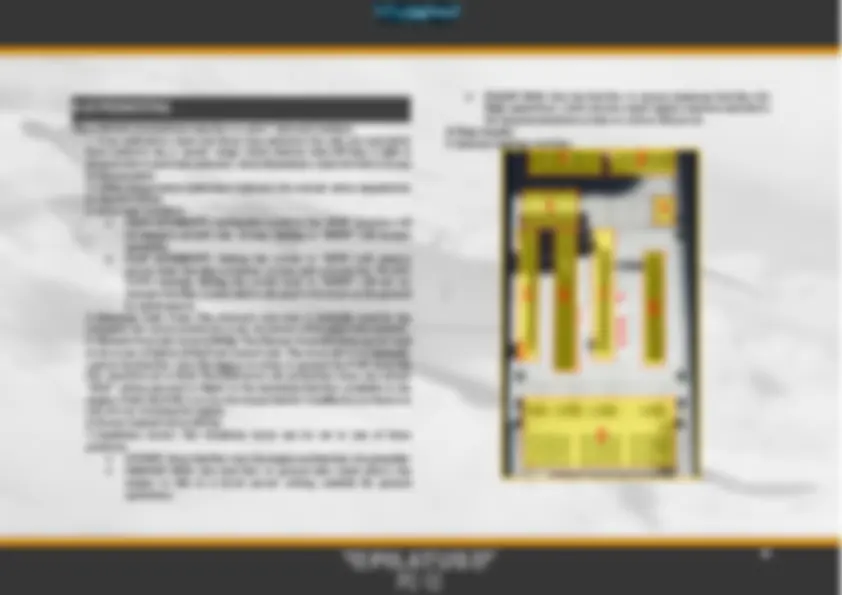
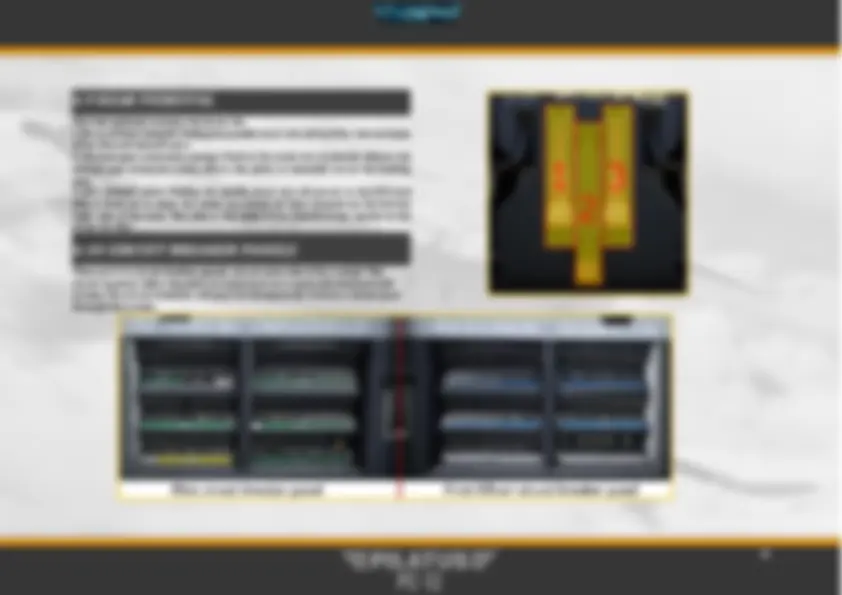
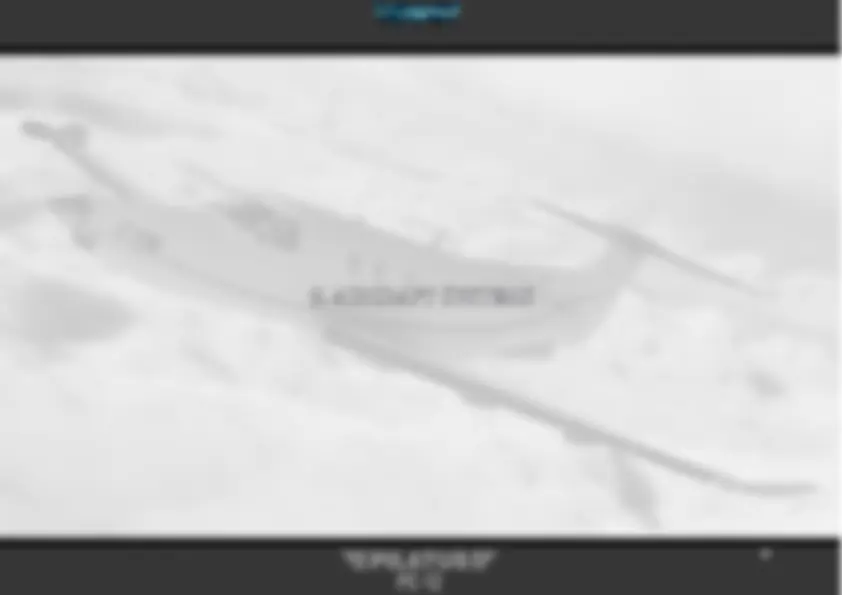
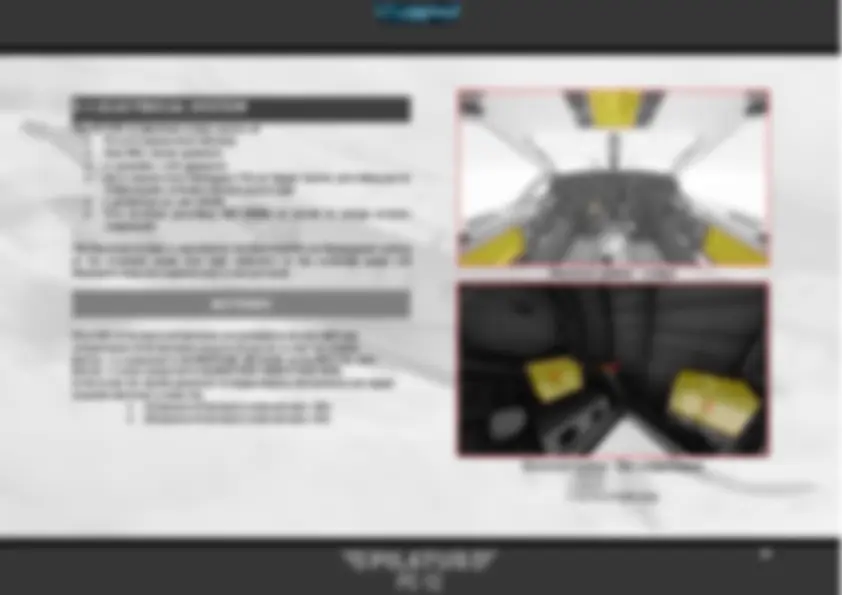
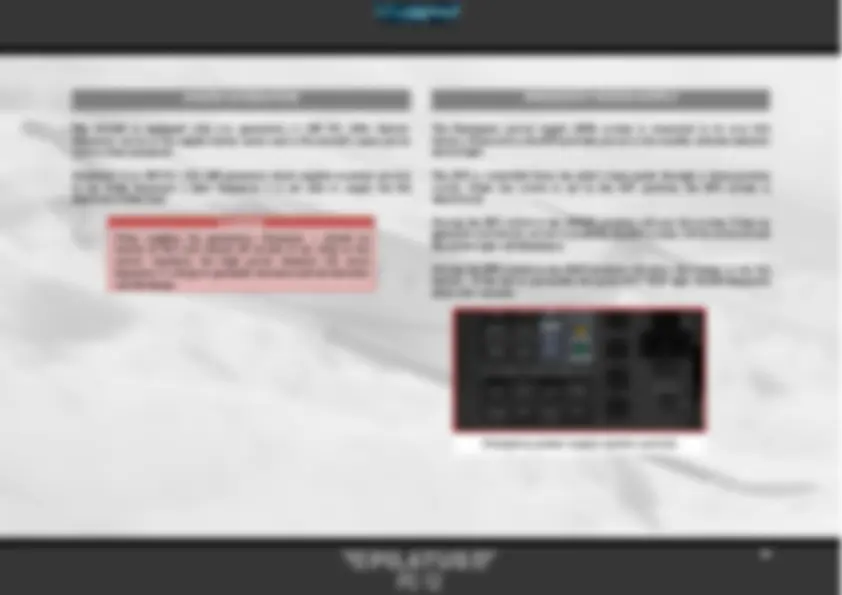
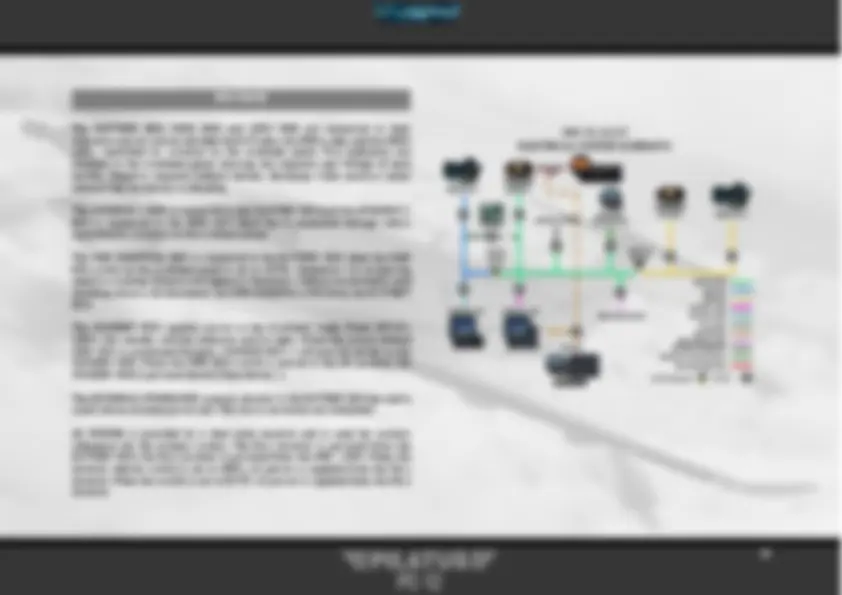
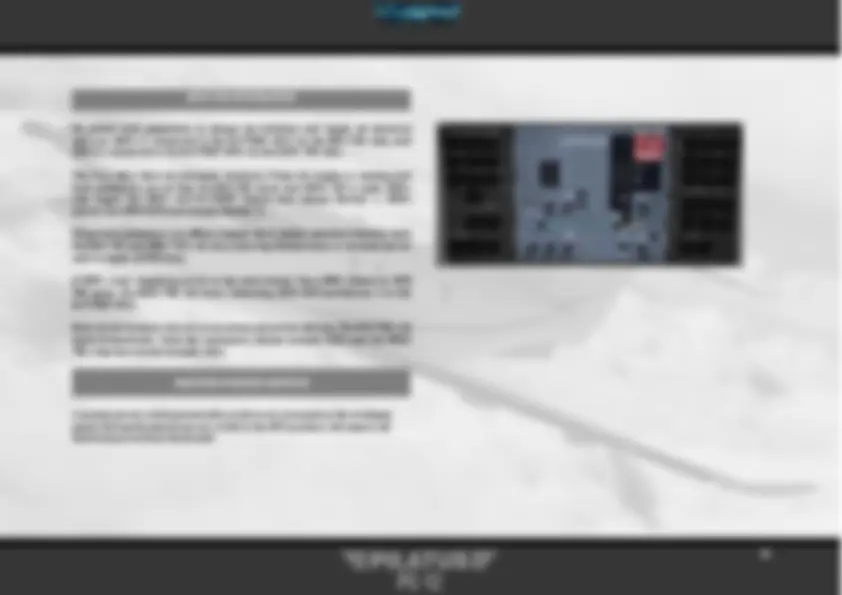
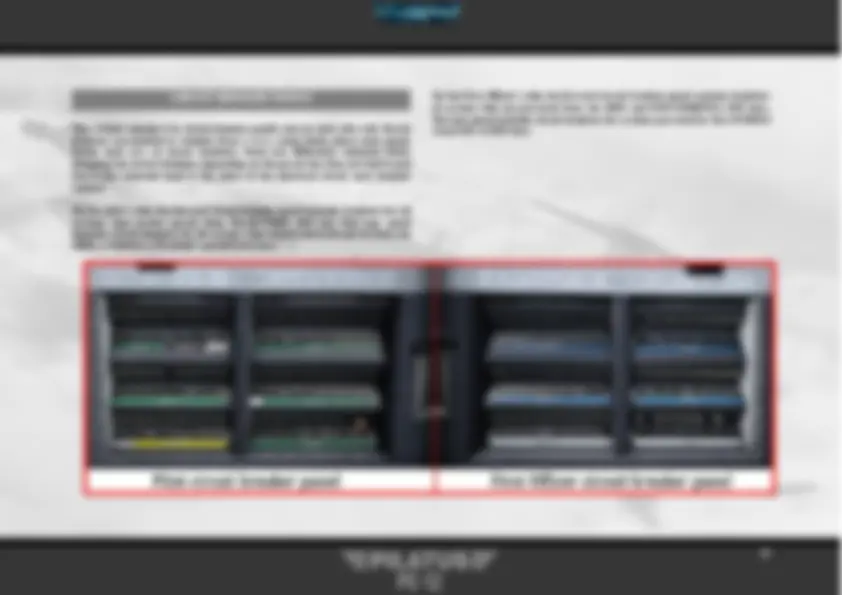
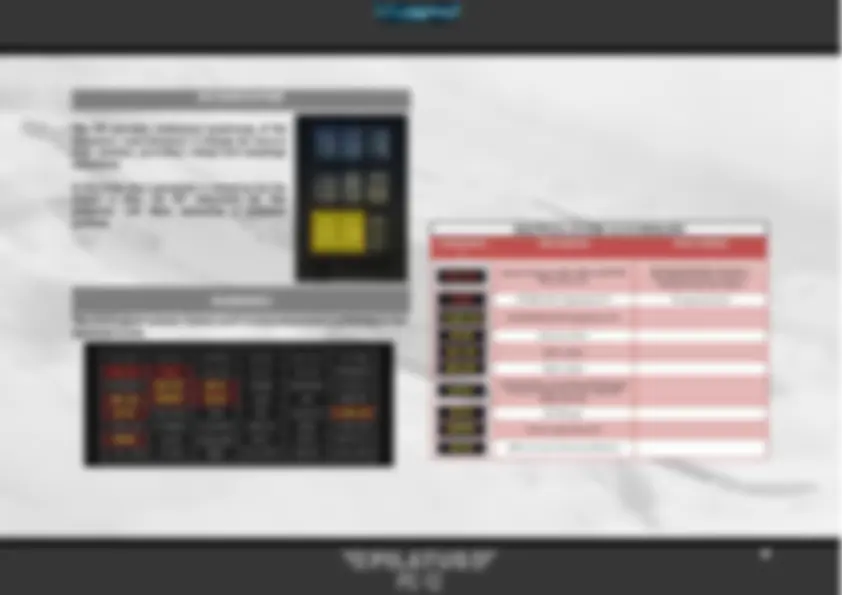
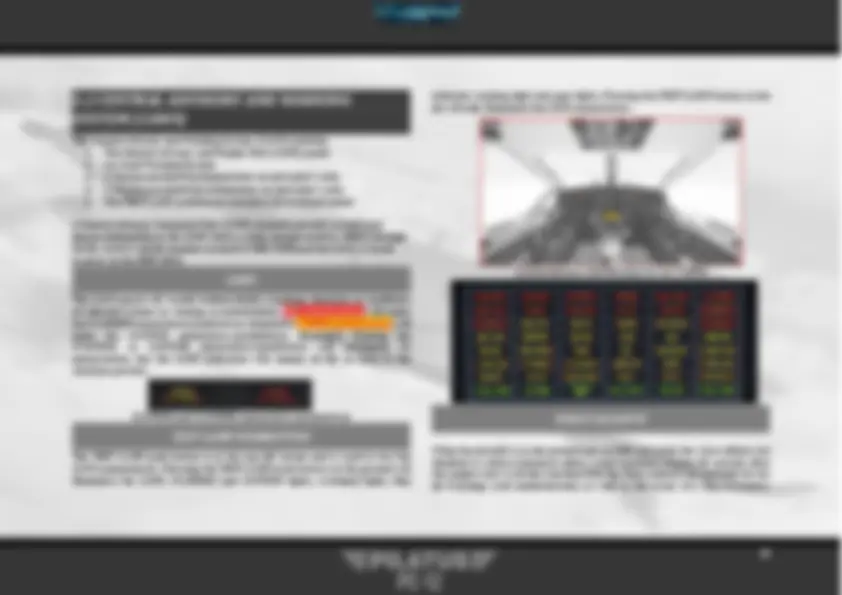
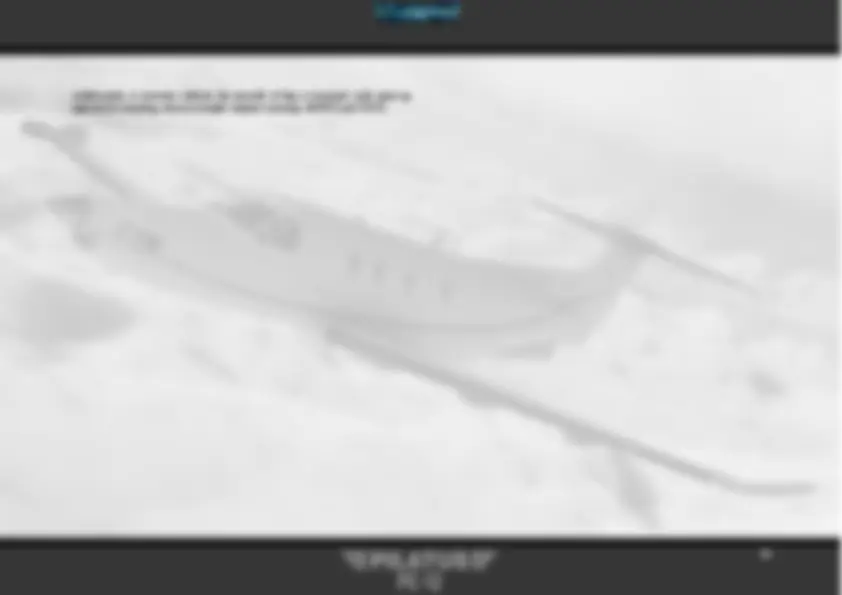
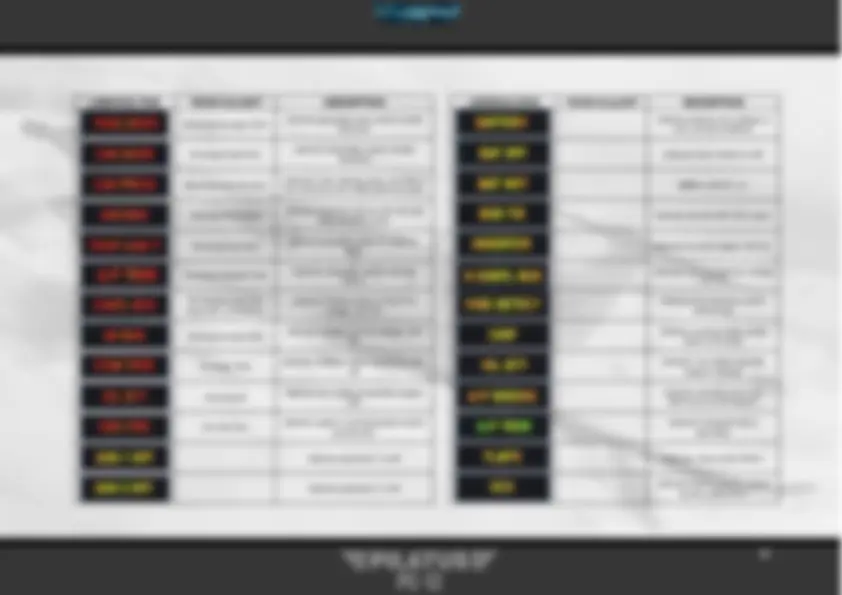
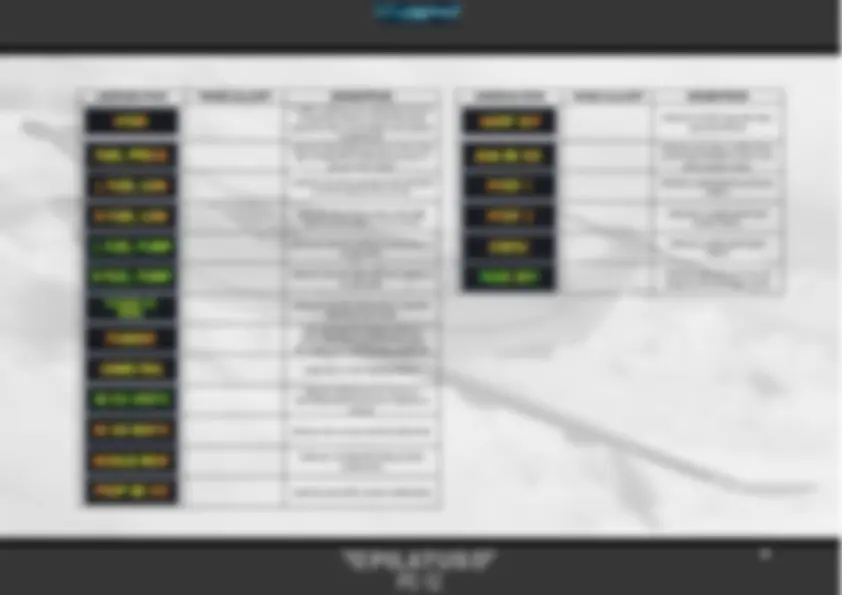
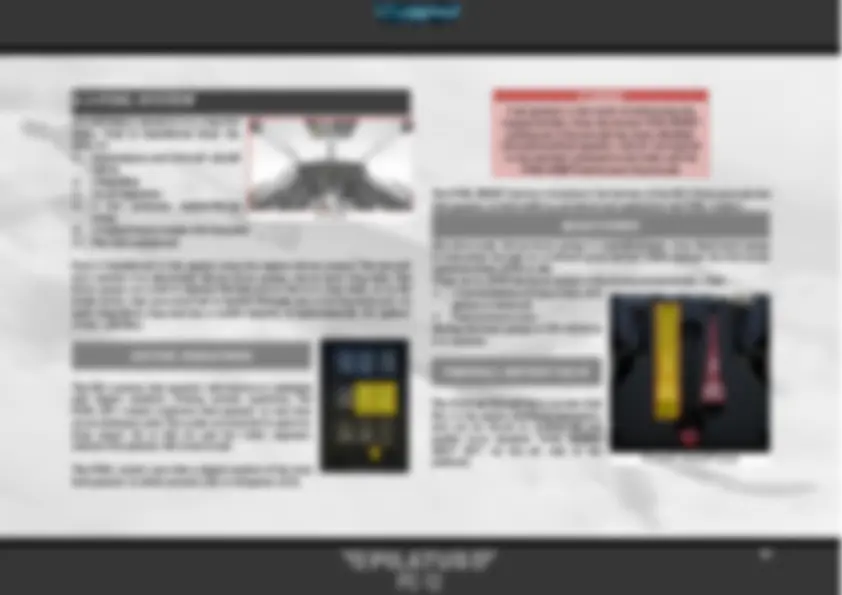
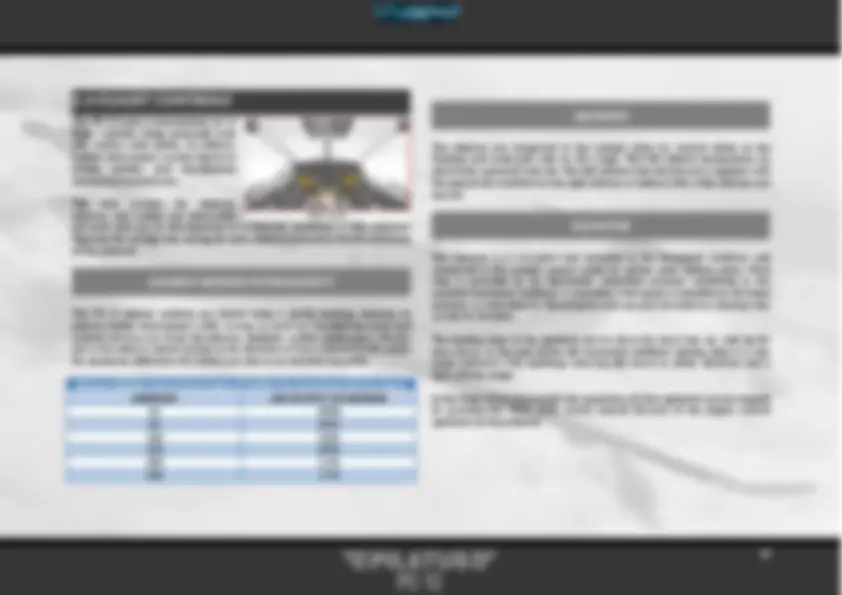
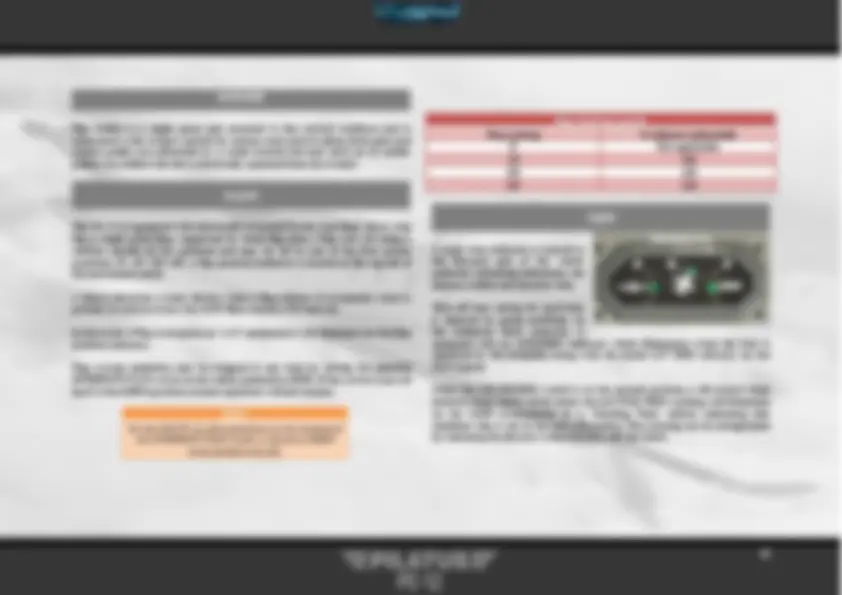
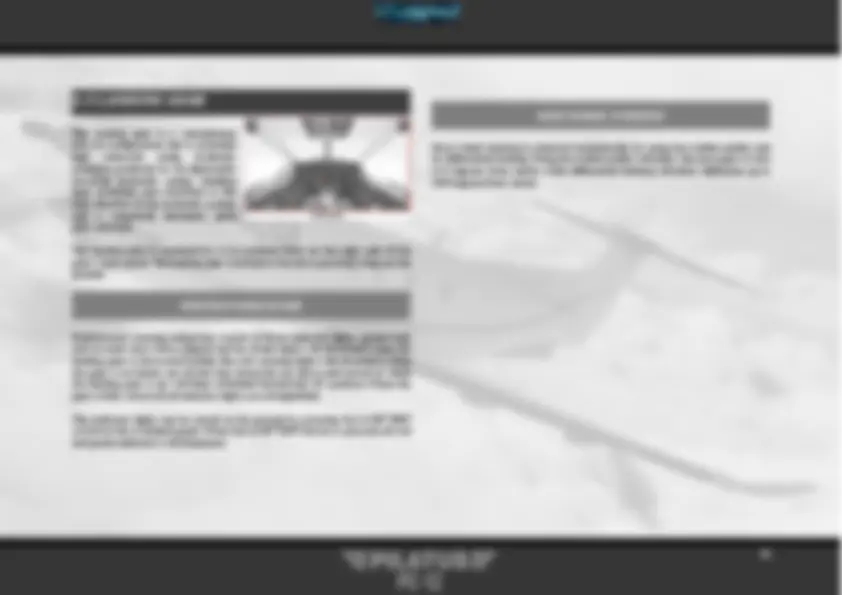
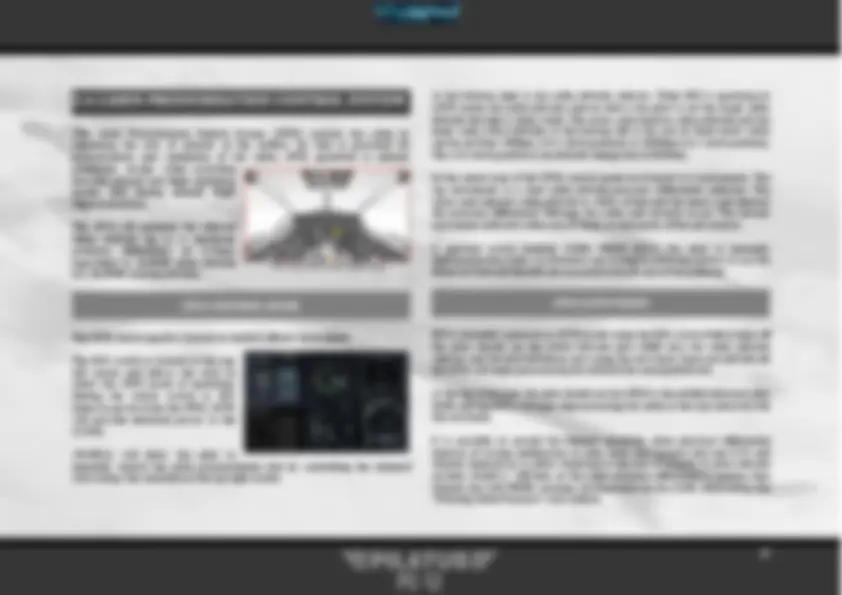
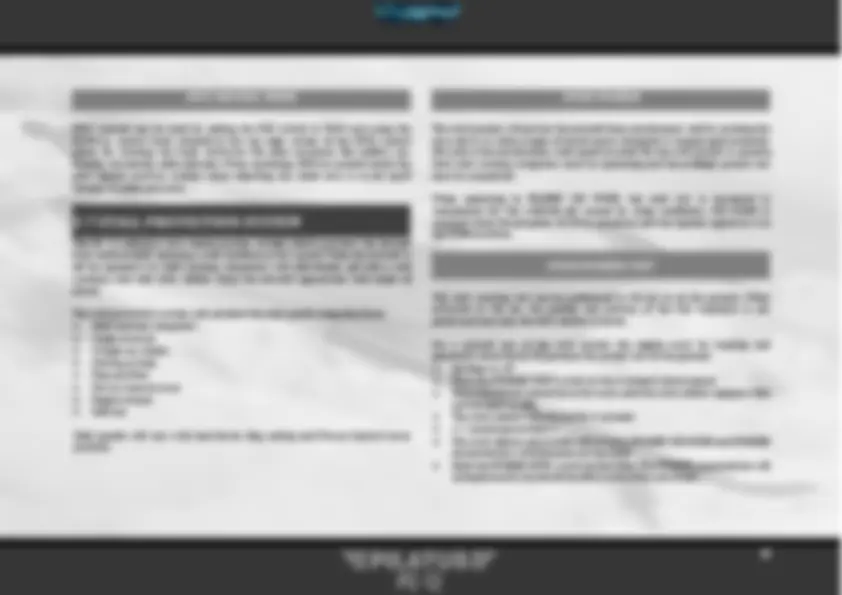
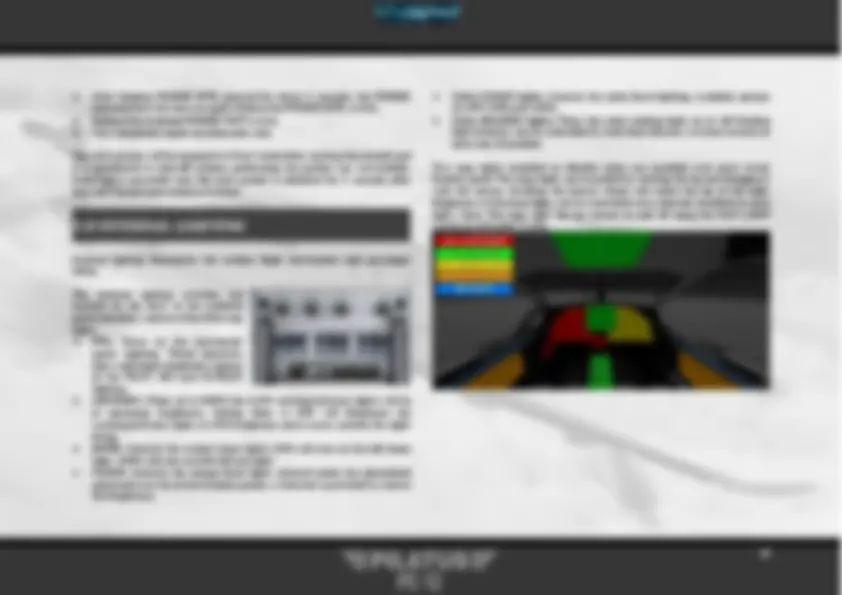
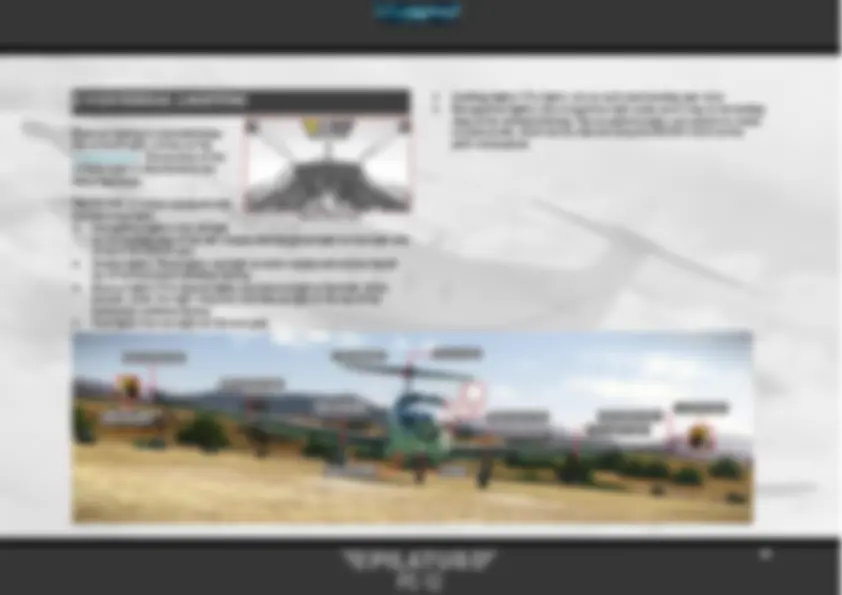
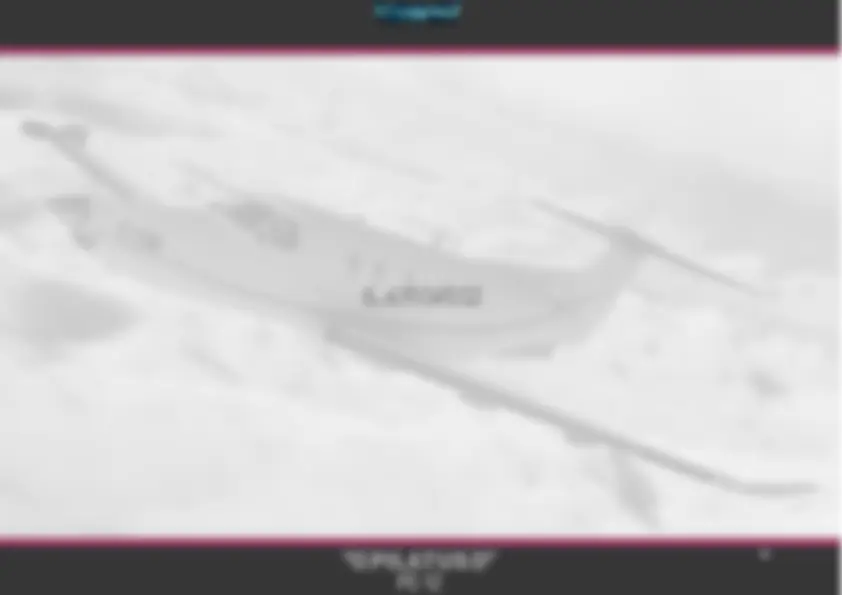
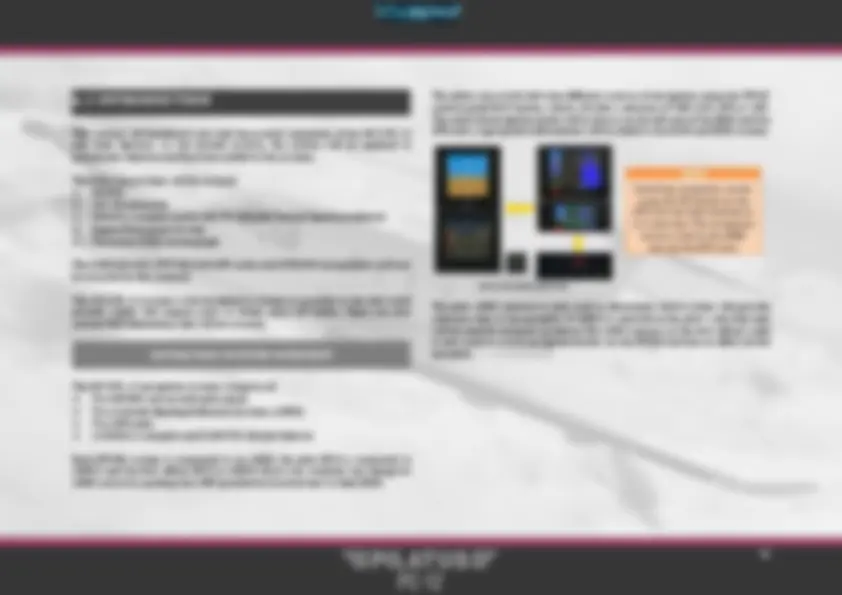
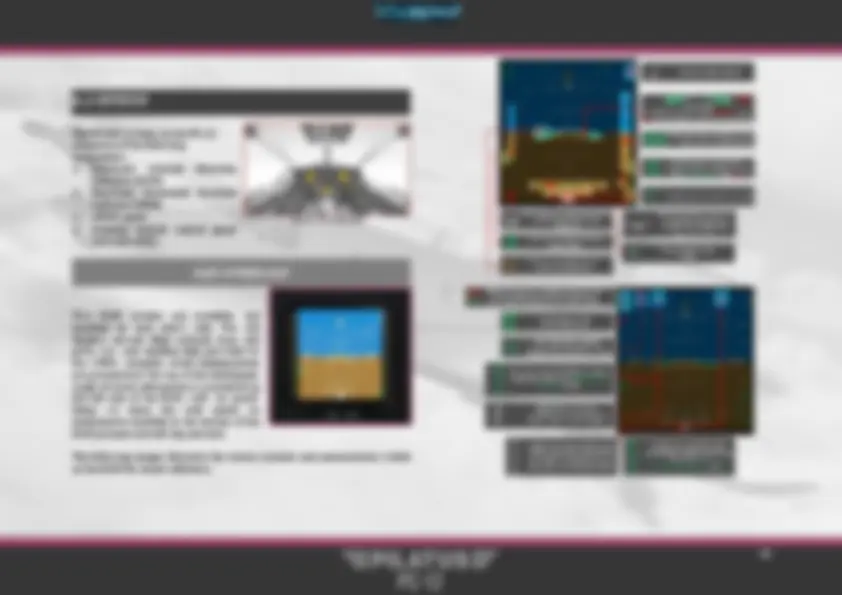
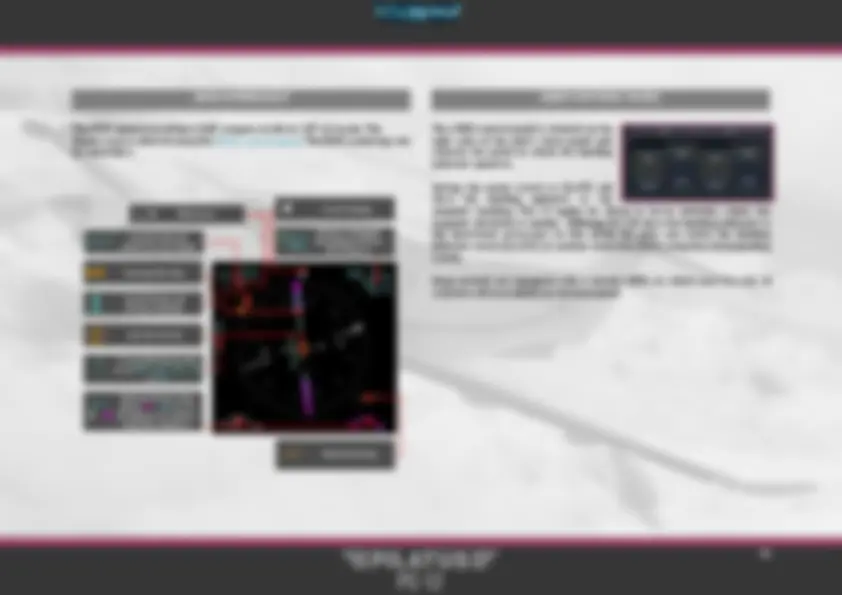
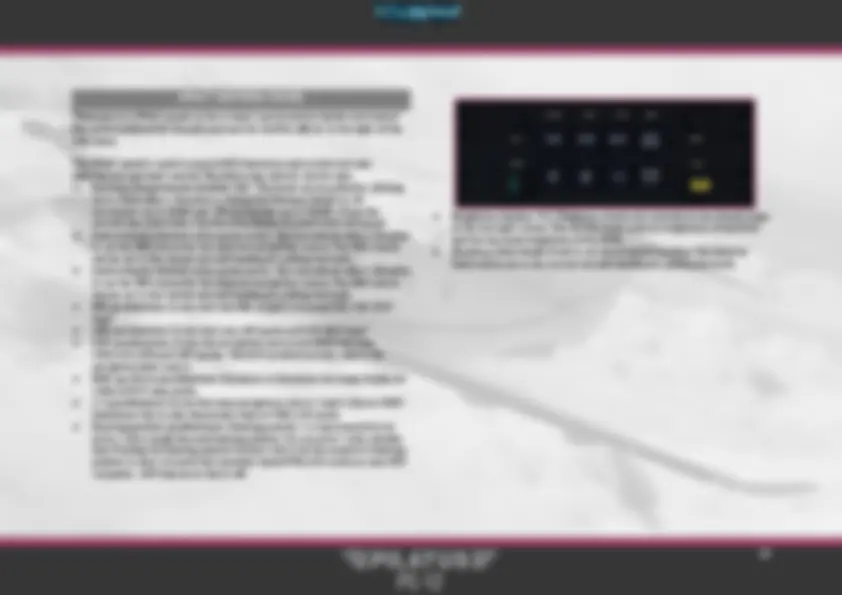
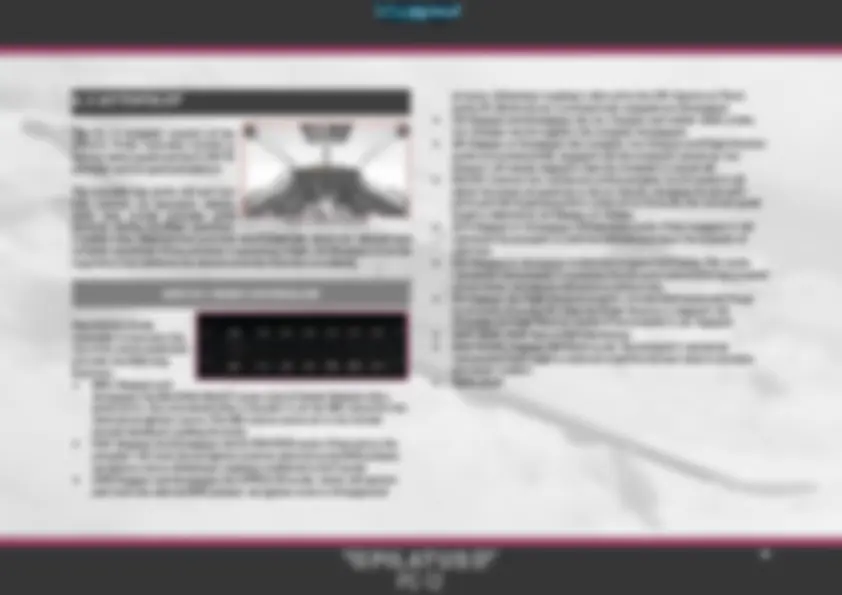
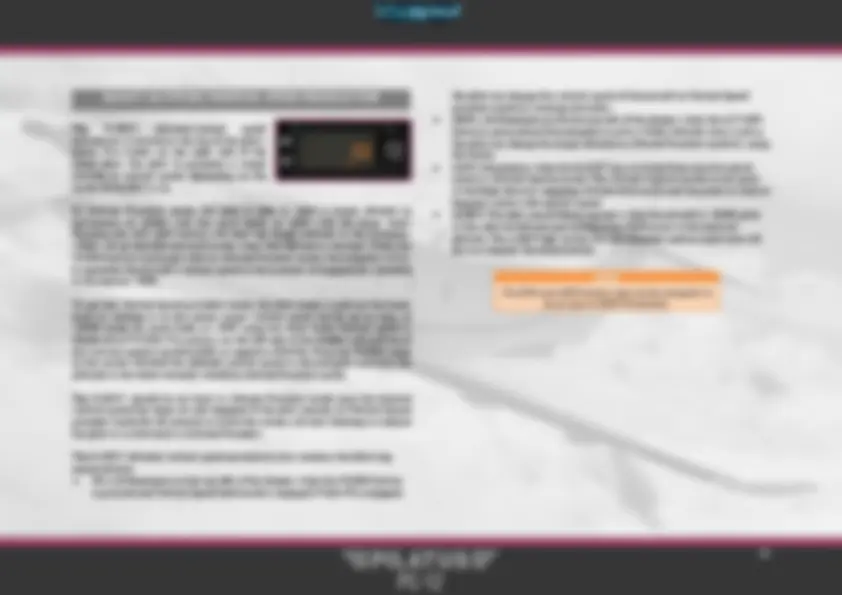
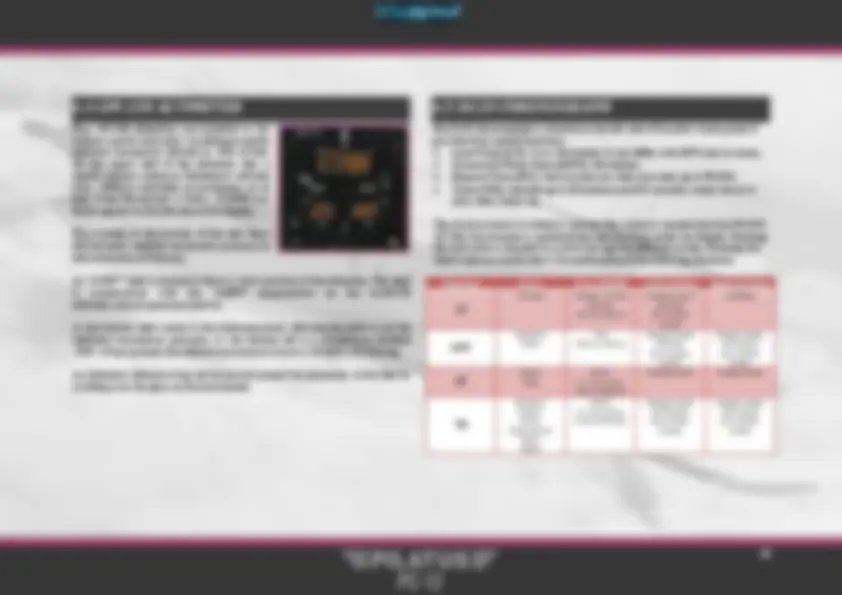
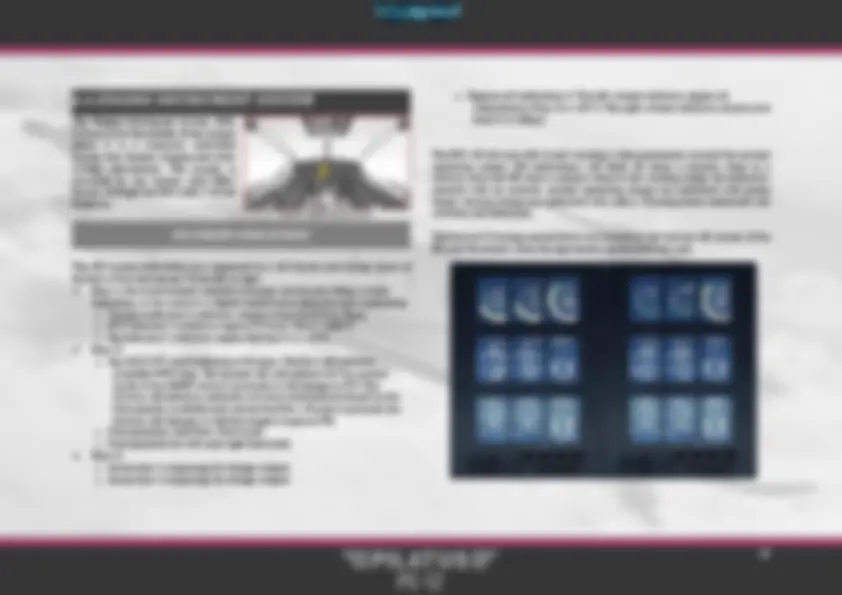
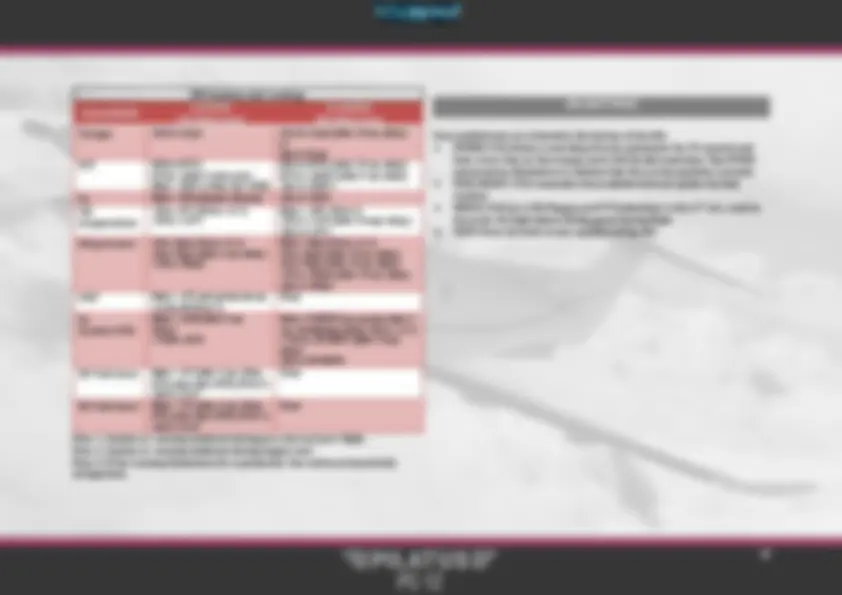
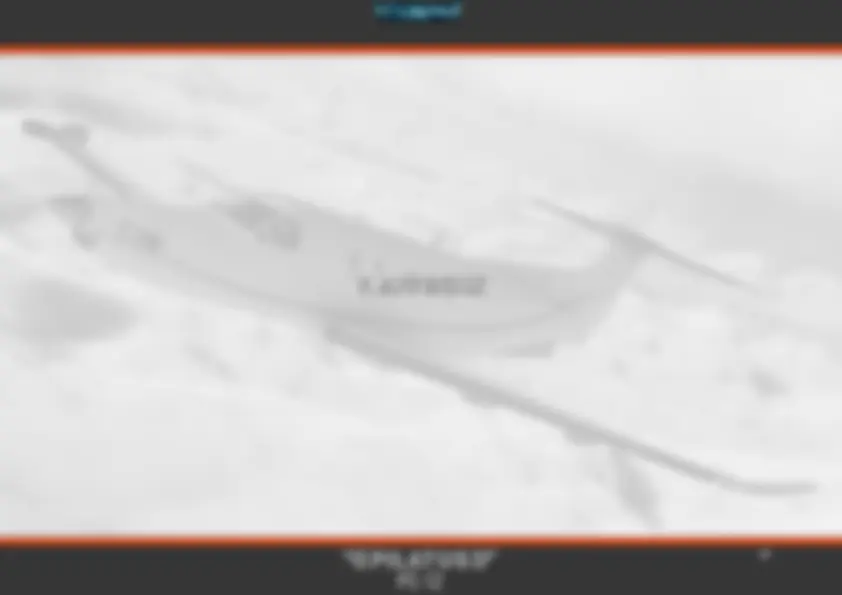
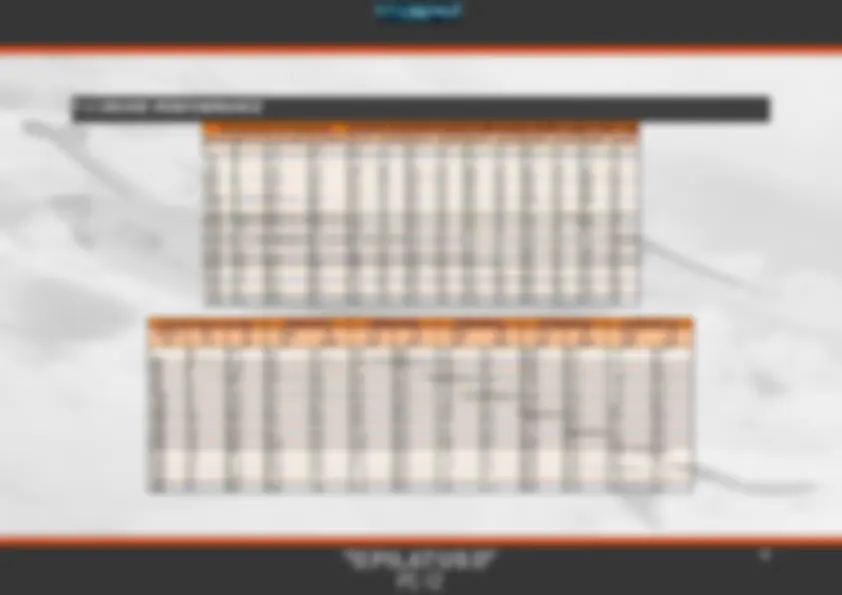
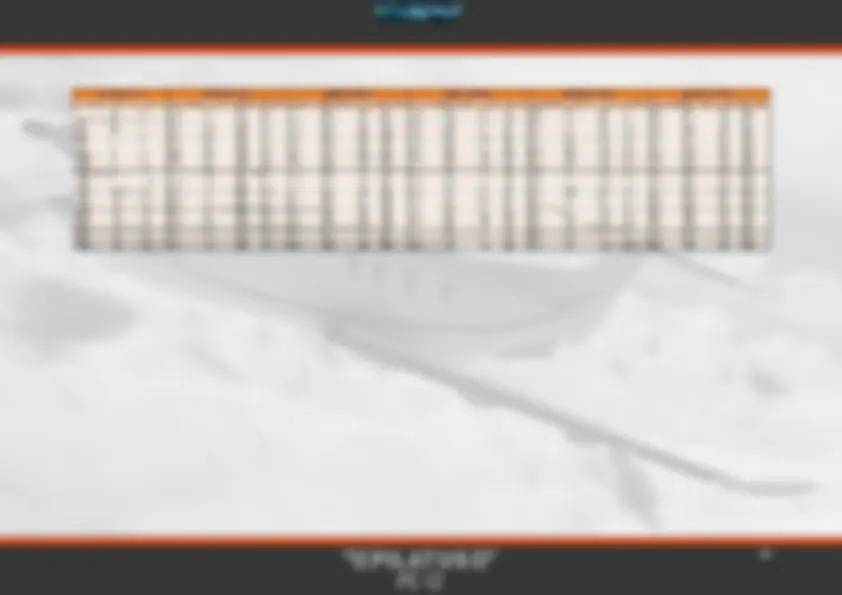
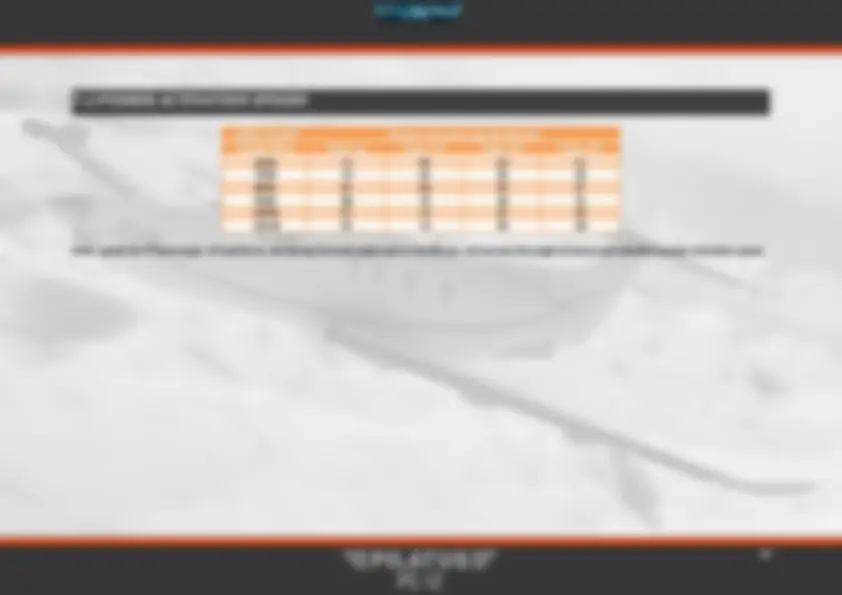
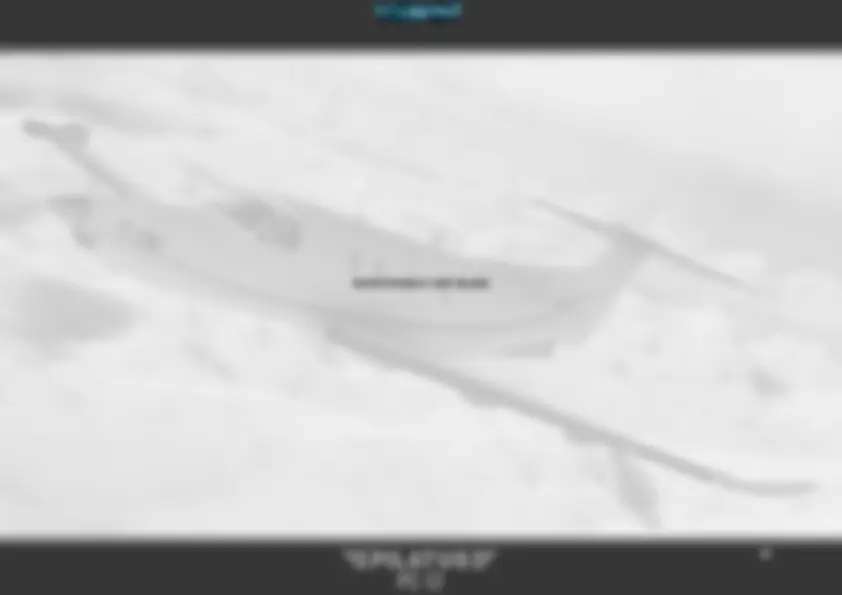
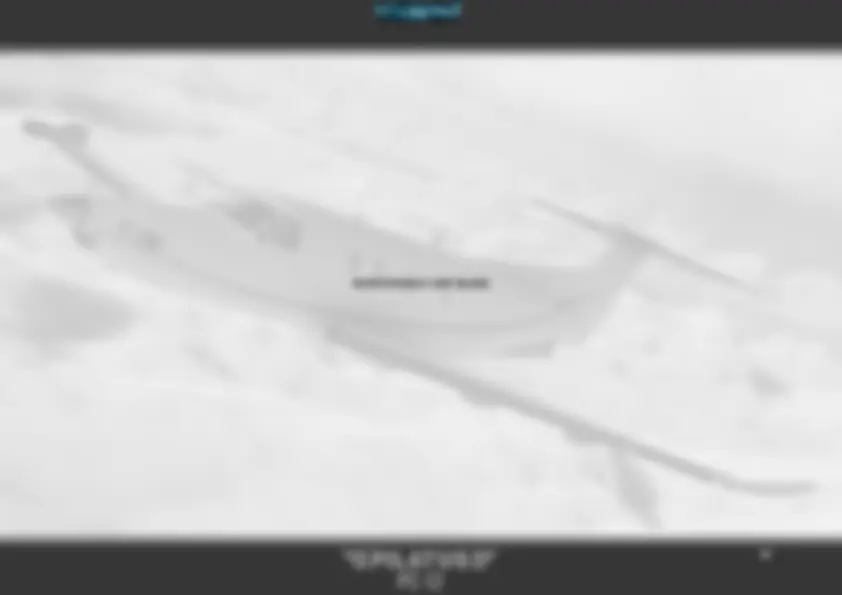
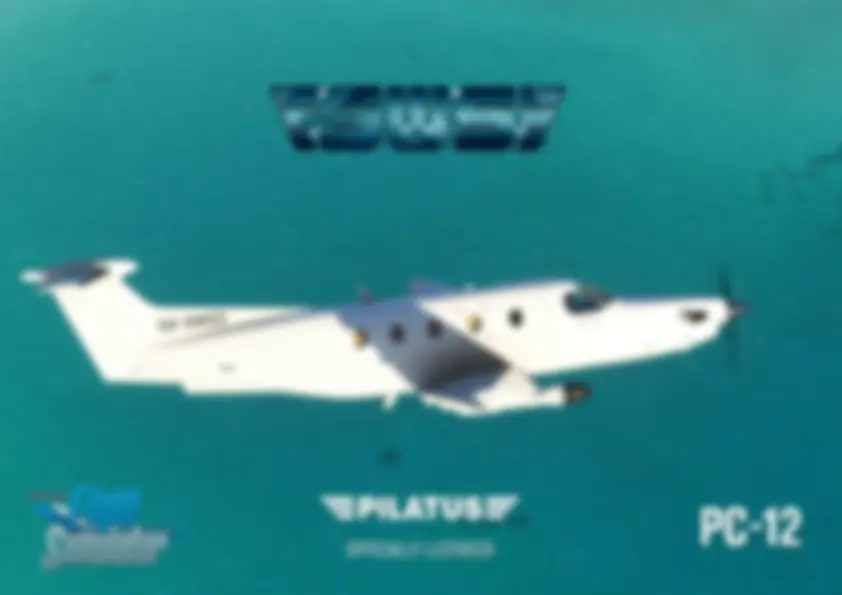
Estude fácil! Tem muito documento disponível na Docsity
Ganhe pontos ajudando outros esrudantes ou compre um plano Premium
Prepare-se para as provas
Estude fácil! Tem muito documento disponível na Docsity
Prepare-se para as provas com trabalhos de outros alunos como você, aqui na Docsity
Os melhores documentos à venda: Trabalhos de alunos formados
Prepare-se com as videoaulas e exercícios resolvidos criados a partir da grade da sua Universidade
Responda perguntas de provas passadas e avalie sua preparação.
Ganhe pontos para baixar
Ganhe pontos ajudando outros esrudantes ou compre um plano Premium
Comunidade
Peça ajuda à comunidade e tire suas dúvidas relacionadas ao estudo
Descubra as melhores universidades em seu país de acordo com os usuários da Docsity
Guias grátis
Baixe gratuitamente nossos guias de estudo, métodos para diminuir a ansiedade, dicas de TCC preparadas pelos professores da Docsity
A comprehensive guide to the sws pc-12 flight simulator, covering its systems, flight dynamics, and operational procedures. It delves into the aircraft's electrical system, engine generators, fuel system, stall protection, navigation systems, and more. The document also includes detailed information on control assignments, flight model, and troubleshooting tips.
Tipologia: Resumos
1 / 67
Esta página não é visível na pré-visualização
Não perca as partes importantes!
The SWS PC-12/47 is a representation of the iconic PC-12 Series 10 manufactured by Pilatus Aircraft Ltd. of Switzerland. With more than 2000 aircraft produced since its first flight in 1991, the PC-12 has proven itself as a versatile and reliable aircraft, capable of operating out of short, unprepared airstrips just as well as out of paved runways. The aicraft fulfills a variety of roles: executive transport, commuter, cargo transport and air ambulance. By bringing together the expertise of the manufacturer, aircraft operators and pilots, we have tried to provide the full PC-12 experience, from flight handling and sounds, to the different interior configuartions.
The SWS PC-12 was created under license from Pilatus Aircraft Ltd. All included liveries, logos and trademarks were created under license from their respective operators. SimWorks Studios Ltd. holds an exclusive license for the creation of liveries of Fly7 Executive Aviation for the SWS PC-12 for Microsoft Flight Simulator.
Development of the aircraft has gone through numerous downs, so SWS team members contributed in multiple areas of development to be able to complete the aircraft. In no particular order: Nawfal Benbennasser: Base aircraft model Elias Strikos: 3D model refinement, interior textures, exterior textures Matt Wynn: interior textures, exterior textures, liveries Evripides Efthymiou: Avionics programming Alexander Losev: Avionics programming Paul Frimston: Flight dynamics Alex Vletsas: 3D model refinement, animations, systems programming, engine modelling SimAcoustics: Sound recording and mixing Akis Karagiorgos: Vector graphics
We would like to extend our sincerest thanks to all the people that had to bear with us during the long development process of the SWS PC-12. Starting with our families and friends, special thanks go to: Fly7 Executive Aviation, Yves Roch (CEO) and Thomas Goncalves (Fly7 Community) for providing us a flight in the aircraft, sound recordings and a week of simulator time and instruction on the PC-12, all undertaken at the Fly7 Training Center in Lausanne, Switzerland. MS Aviation South Africa for reaching out very early in the project, providing a wealth of reference material and advice for the creation of the aircraft. Tradewind Aviation for providing us with reference material to faithfully recreate their aircraft livery. Revue Thommen AG for providing us with the manual to the DC Chronograph and helping us make an authentic rendition of it. Brandon Hostetter f or his diligent testing and feedback in refining the flight model & systems simulation of the aircraft. Brandon helped us delve into intricacies of the Legacy PC-12 that we otherwise couldn’t have known.
Any items marked with an asterisk (*) are subject to MSFS limitations in their respective area.
Accurate riveting and high resolution stencils 4 and 5-bladed propellers Custom animations oTrailing link landing gear oCustom nose wheel steering oStabilator trim oEngine bypass door oChocks oPitot and AoA vane covers oEngine bay oTail interior oDe-icing boots 8 liveries: oWhite oOH-JEM (Fly7 Executive Aviation) oHB-FVA (Fly7 Executive Aviation) oOH-FUK (Fly7 Executive Aviation) oOH-DEN (Fly7 Executive Aviation) oOH-PBL (Fly7 Executive Aviation) oN881TW (Tradewind Aviation) oPH-ONE (Private)
Fully functional cockpit Three interior configurations: Executive, Commuter and Cargo Working exits Fully working custom lighting
PMS & TDS GTN option and Sky4Sim tablet compatiblility (PC-Only) Easily customisable for repainters Numerous custom animations: oLavatory oArmrests oDrawers oSun visors oWindow shade oGust lock oPassengers oCargo
Created after spending a week in the real simulator with PC-12 instructors and with constant pilot feedback during development, the SWS PC-12 features: Realistic handling and performance Different 5-blade and 4-blade propeller simulation Custom engine simulation: oCorrect ITT/altitude behaviour and limitations oCorrect Torque/Ng relationship oTorque limiter oHot starts (no damage) Correct starter operation Torque effect on yaw* Nose-down approach attitude*
High performance avionics using the MSFS Avionics Framework: oBendix/King^ EFIS50^ Avionics oEngine Instrument System oThommen DC20 Chronograph oKAS927B Full Electrical system with working circuit breakers
Custom stall protection system: oStall warning system oStick shaker oStick pusher, including pusher ice & test modes Custom nosewheel steering system with free-castering nosewheel when applying brakes Custom trim system with realistic timings* Custom de-icing system: oRealistic boot operation oIndividual windshield heating Custom air conditioning & heating system: oAdjustable temperatures based on real system limits oFlow and volume based temperature distribution oInsulation & open door effects Custom oxygen system, accounting for number of crew and passengers on board Custom warning system: oFully working CAWS system oNumerous aural warnings for aircraft systems oEGPWS system mode 1, 2, 3 and 5* and TAWS inhibition
High quality sounds recorded from three different aircraft 5-bladed engine sounds 4-bladed engine sounds Full aircraft sounds including starter, ignition, flap actuators, hydraulic pumps, warnings and electrical system components Full interior aircraft soundscape Correct sound insulation properties
All basic flight controls of the SWS PC-12 are assigned to default MSFS events. A special case is the condition lever, that can be mapped to either the default Condition Lever, or Mixture lever assignments in the MSFS controls screen. The assignments have been modified via custom code to work the same and avoid accidental engine cut offs or light ups. The plane also makes use of custom variables, which are listed in a separate document available in the SWS PC12 page under “Free Extras”. These variables can be used by power users to control non-default functions of the aircraft. The variable list and names are likely to change as the aircraft evolves.
The SWS PC-12 will continue to be updated with more features in the near future. Some of the upcoming features were not possible until very late in the development cycle, while until very recently, others were beyond our technical reach.
EFIS50 Weather RADAR* EFIS50 Flight Plan mode EFIS50 Composite mode SWS Tablet featuring: oAircraft logs (per tail number) oAircraft persistent state saving (per tail number) oFlight planning oWeight & Balance oWalkaround* oPDF reader* oCharts oFeature controls: hide passengers/cargo, adjust their volume *The walkaround feature is partially available through the preflight item “EXT LIGHTS CHECK” in the ingame checklists.
While the present add-on is a very extensive simulation of the real PC-12/47, failures were omitted from the package. This is because the majority of MSFS users do not wish to experience failures since they may overwhelm them, cause problems with secondary software (i.e. interrupting VATSIM traffic), or detract from a limited flying time that would otherwise not have distractions.. Therefore, we are planning on a payware expansion that will include deeper simulation of the various aircraft subsystems and failures associated with them. The way we are approaching failures is different compared to the “aircraft mechanic simulator” taken by most add-ons, as we want to focus on the flying part. Some examples of the improvements planned for the expansion package are: Custom Fuel Control Unit with improved simulation of the various inputs Improved fuel system simulation Deeper electrical system simulation Organic manifestation of problems and failures based on component wear and abuse Realistic maintenance feedback -no magical “know-it-all” tablet listing
When the aircraft is cold & dark and the gust lock is installed, a large clickable area will occupy the forward windshield. Clicking this area allows you to install or remove the cockpit sun shade. When the sun shade is installed, the visors will automatically move down to support it. The sunshade can be removed by clicking on the forward windshield area or removing the gust lock from the pilot’s yoke. The visors will not retract automatically when the sun shade is removed. In order to quickly retract the visors you may click at their pivot on the outboard corner of each glareshield window. Sunshade and sun visor clickspots The SWS PC-12 also features a working gust lock. When the plane is started cold & dark, the gust lock will be on the yoke. When starting in any other state, the gust lock can be found on the left cockpit wall, next to the pilot’s seat. When the gust lock is inserted into the yoke’s base, the aircraft controls can no longer be moved. To insert the gust lock: Click on the stowed gust lock on the left cockpit wall. Doing so will put it “in your hand” A new clickspot will become available above the pilot’s yoke and in front of the HSI. Make sure the yoke is centered and insert the gust lock by clicking this area. This will lock all flight controls in a centered position. To remove the gust lock: Click above the pilot’s yoke to remove it from the controls. This will put the gust lock “in your hand’. Find the stow on the left cockpit wall. Click on the stow area to secure the gust lock If you do not stow the gust lock it will remain “in hand”. This allows you to insert it by accident and jam your controls. This was done on purpose to ensure that users will learn how to stow and unstow the gust lock correctly and familiarise themselves with the procedure.
The co-pilot headrest can be used to show or hide the passengers in the executive and commuter variants. The adjument handle at the bottom of the pilot and co-pilot seats can be used to show or hide the respective crew member avatar.
Drawers can be dragged open by clicking on their faceplate and dragging UP to close or DOWN to open them. A left/right operation was not possible due to the perspective being different depending on the camera position.
Exits in all SWS aircraft open and close in a two-step process. The first step is to unlock the exit using the handle. When the engine is unlocked, a clickspot will become available that will allow you to open and close the door. To open the passenger exit, click on the red handle to unlock it. Afterwards, click on the middle of the door to open or close it. To open the cargo door, first click on the handle area, at the center of the door. To open or close it, click on the area under the cargo door window.
The plane was developed to be flown with linear response curves. Setting the curves to anything else will adversely affect the aircraft’s response to control inputs.
The trim indicators can be found on the forward edge of the pedestal. There are three indicators for aileron, rudder and elevator trim. Green markings on the indicators denote the optimum trim for take-off.
Knowing your CG from the previous step is important in setting the take-off trim correctly. The aircraft is trimmed nose-down in order to avoid early rotation of the aircraft on take-off. Takeoff trim range is from the green rectangle down to the green diamond. For CG position greater than 39% MAC trim should be set to the green diamond.
Activation speeds with flaps up are significantly higher and can go up to 93 knots indicated, which shows how large the aircraft’s safety margins and performance envelope can be.
The yaw damper will reduce unintended around the yaw axis of the aircraft by automatically adjusting the pedals and rudder trim.The yaw damper should be turned OFF until after takeoff is complete. It should remain on during all phases of flight and turned off during final approach. The reason the Yaw Damper is turned off for takeoff and landing is that it will react to pilot input by applying opposite control, thereby enhancing adverse control effects and putting the aircraft out-of-trim, potentially resulting in loss of aircraft control.
As mentioned earlier, the PC-12’s engine has a strong effect on aircraft yaw and will pull the aircraft’s nose strongly to the left, especially with the yaw damper is off. This effect is simulated in the SWS PC-12 so you must be mindful of it as power changes will cause the nose to drift, especially on approach when the yaw damper is turned off.
A good landing depends on many factors, but we will try to provide you with some key points that will make the entire process more streamlined.
Flap selection is typically determined by the prevailing flight conditions and runway availability. In standard scenarios, most operators opt for flaps 40. Flaps 15 is employed during instrument approaches, in gusty conditions, or when requested by Air Traffic Control (ATC) for a condensed approach. Flaps 30 is typically reserved for windy days, provided that the runway length allows for its usage. Crosswind is a very important factor in determining flap setting for approach. Refer to the maximum demonstrated crosswinds to decide the correct flaps for your situation.
The PC-12 is built to make flying easier for the pilot and you can stay ahead of the aircraft easily by using some rules of thumb. When flying level and clean (flaps up, gear up), setting engine Torque to 15psi will yield you approximately 150 knots. With flaps 15 and gear up, a torque setting of 20psi will get you back up to 150kts. In the 150kts speed range the nose-down effect from the landing gear drag will cancel out the ballooning effect of Flaps 15 deployment. Lowering both at the same time will keep your nose pointed in the same place.
A successful approach is determined by doing no more than what is necessary to keep the plane where you want it. Know how to manage the aircraft’s energy and use trim and subtle control inputs to direct it. Rudder trim should be set one line left of the green zone. Further adjustment might be needed for crosswind. Torque setting used on approach is 9-12 psi, most often between 9 and 10psi. For a 500fpm descent rate, these settings will yield: Flap setting (Degrees) Torque Airspeed (kts) Max demo. crosswind 15 9-10psi 110-120 25kts 30 9-10psi 95-105 20kts 40 9-10psi 80-90 15kts* *Landing only One last tip has to do with trimming the nose up. As the aircraft bleeds off speed and settles into the approach, trimming the nose up will reduce the need for aft yoke application. This will make landing much easier but beware in poor visibility conditions as in the event of a go-around you will need to aggressively prevent the nose from climbing because of the uptrim and speed increase.
The PC-12 will approach the runway with a nose-down attitude and if you lose awareness of that fact it will be very easy to land nose-first. For this reason, flaring should begin earlier than usual as you have more of an angle to cover. Some tips to make flaring and touchdown easier: When crossing the “fence”, start bringing back the power When over the numbers you should be idle and 10kts below your approach speed At the touchdown point you should just hear the stall warning horn Before applying beta or reverse, make sure that you have full lateral control of the aircraft. When applying reverse be ready to counter the left pull At 50kts exit reverse and apply brakes