
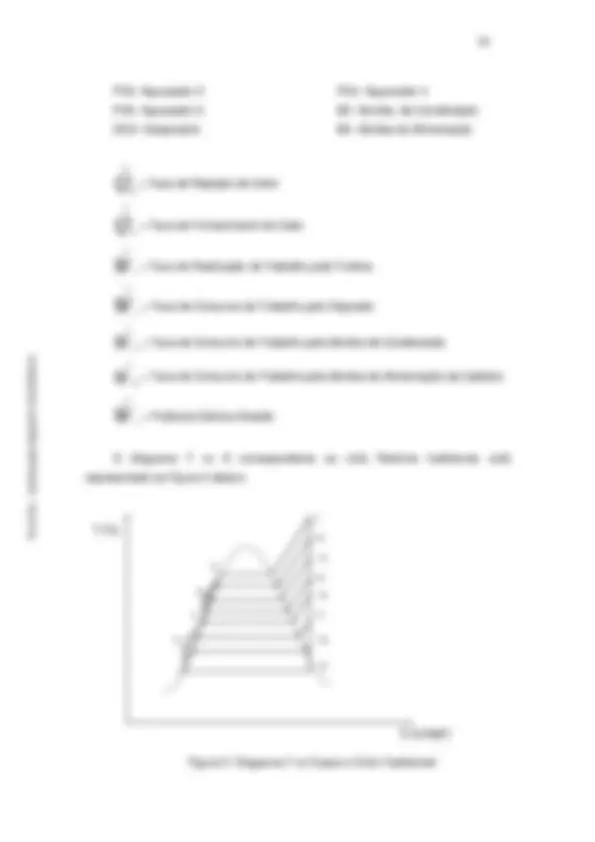
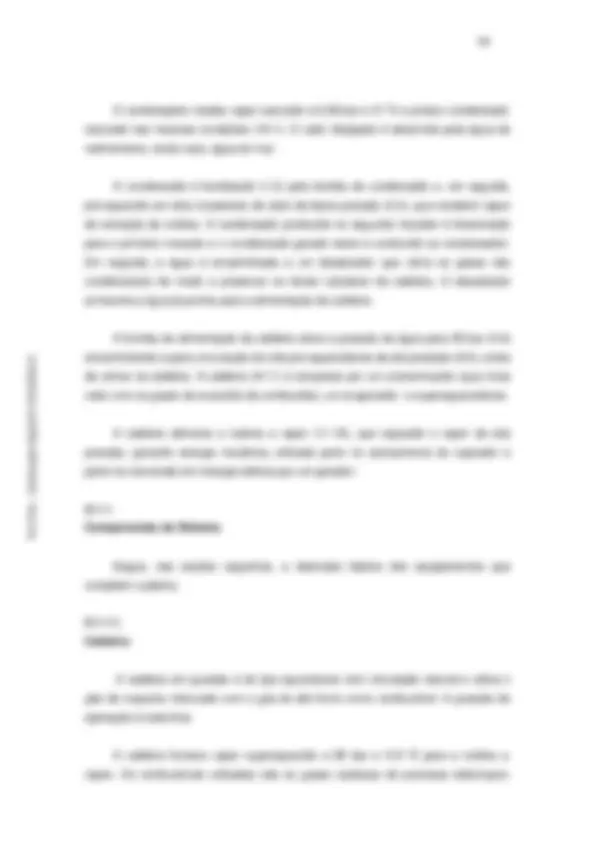
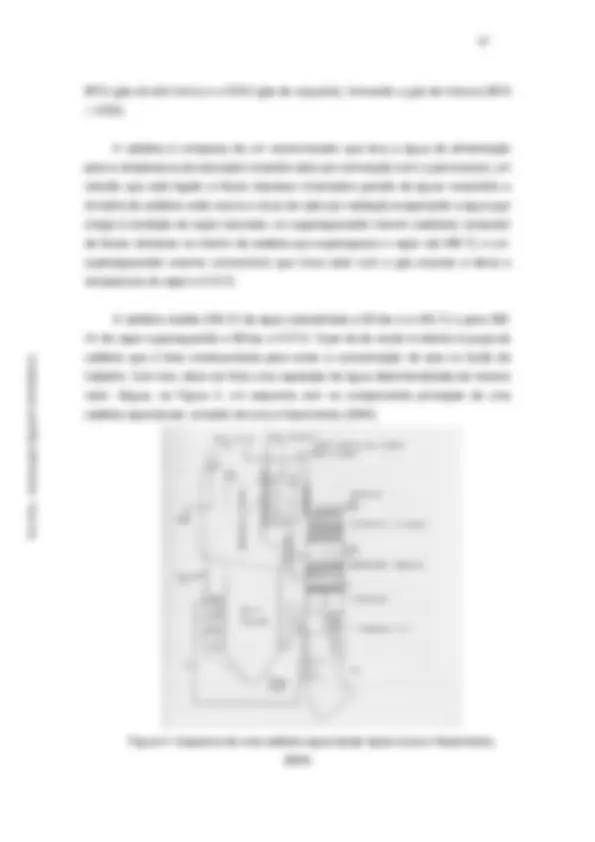
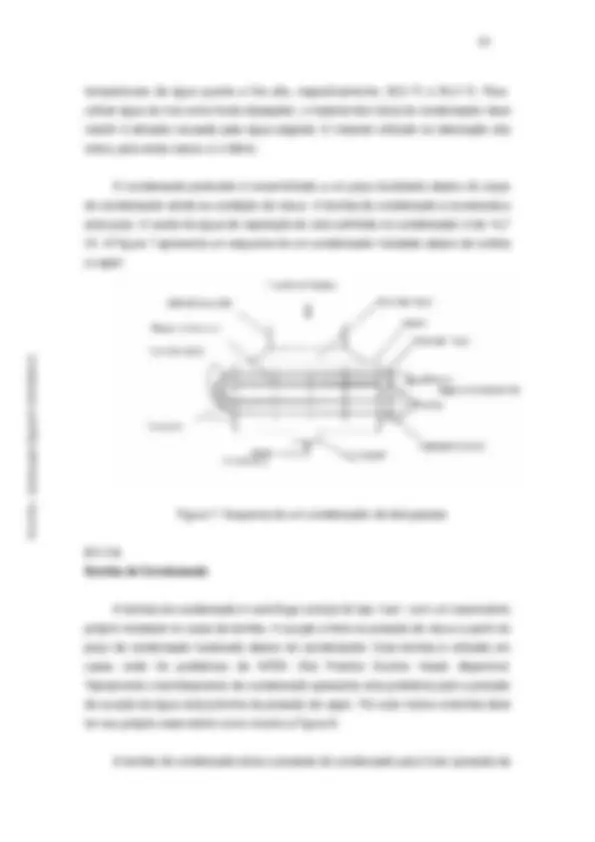
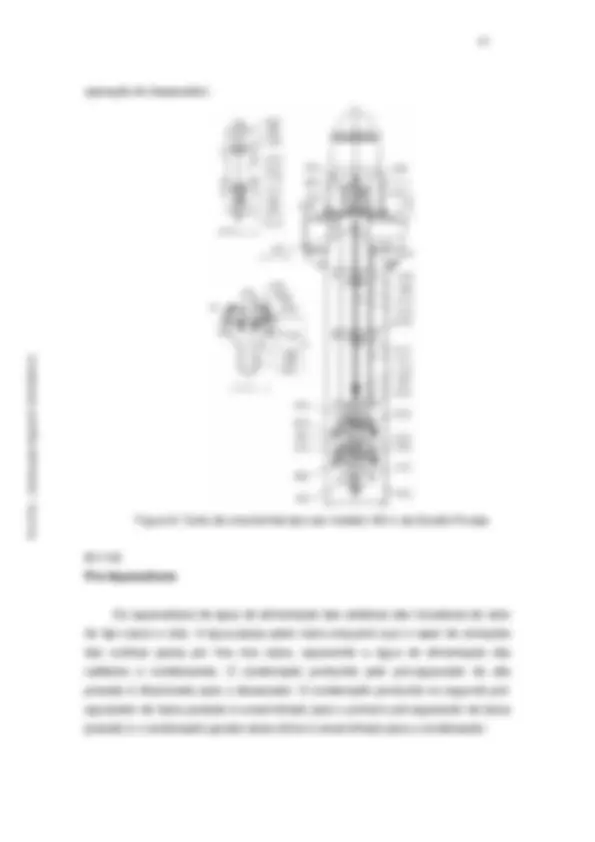
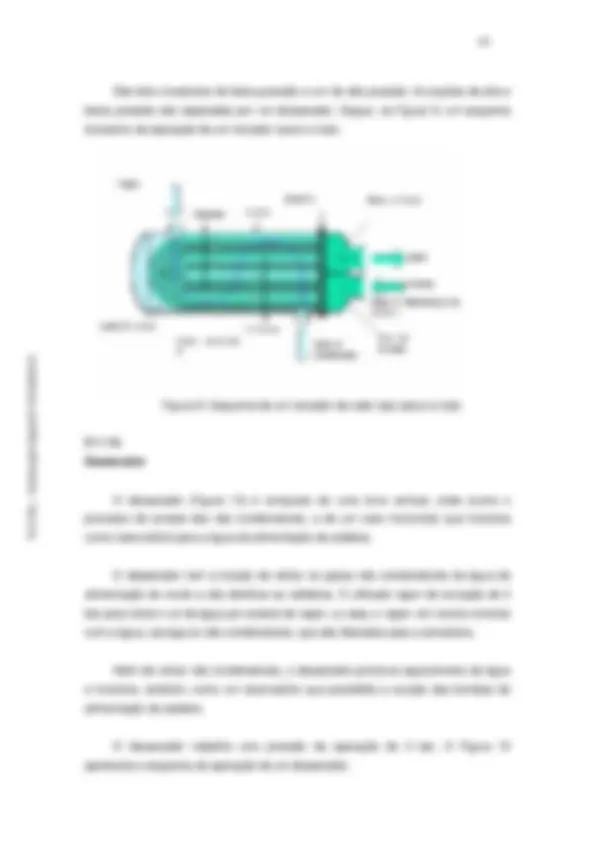

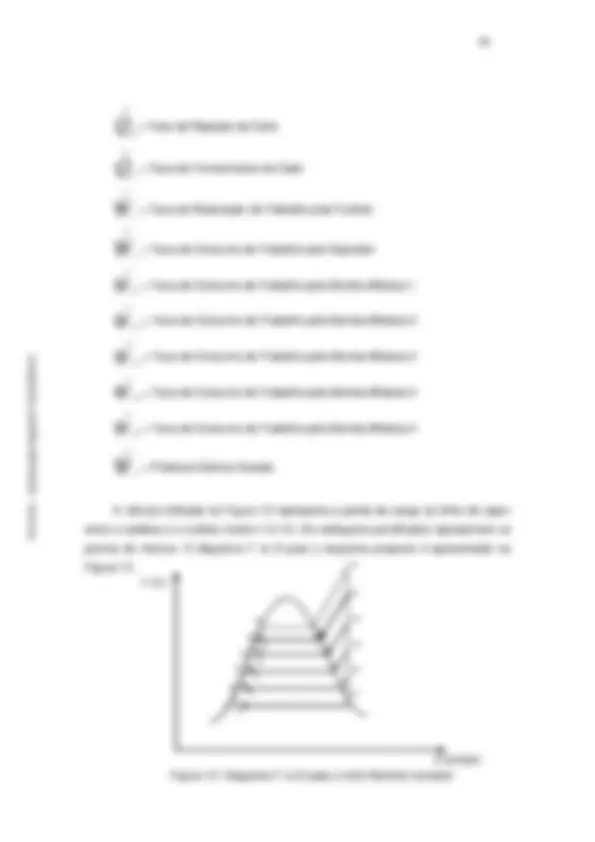
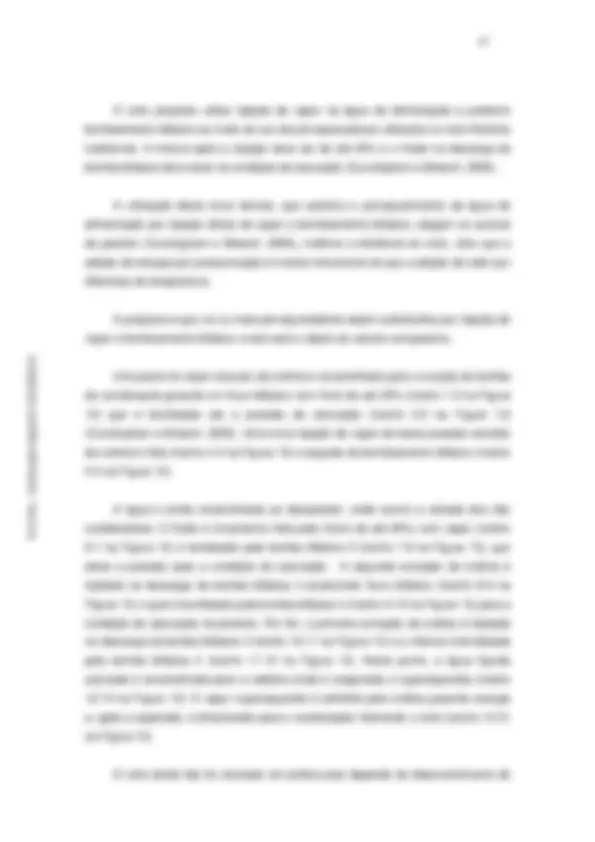
Estude fácil! Tem muito documento disponível na Docsity
Ganhe pontos ajudando outros esrudantes ou compre um plano Premium
Prepare-se para as provas
Estude fácil! Tem muito documento disponível na Docsity
Prepare-se para as provas com trabalhos de outros alunos como você, aqui na Docsity
Os melhores documentos à venda: Trabalhos de alunos formados
Prepare-se com as videoaulas e exercícios resolvidos criados a partir da grade da sua Universidade
Responda perguntas de provas passadas e avalie sua preparação.
Ganhe pontos para baixar
Ganhe pontos ajudando outros esrudantes ou compre um plano Premium
Comunidade
Peça ajuda à comunidade e tire suas dúvidas relacionadas ao estudo
Descubra as melhores universidades em seu país de acordo com os usuários da Docsity
Guias grátis
Baixe gratuitamente nossos guias de estudo, métodos para diminuir a ansiedade, dicas de TCC preparadas pelos professores da Docsity
Um estudo sobre a otimização de um ciclo rankine em uma usina siderúrgica. O ciclo é baseado em uma planta existente de cogeração, com a implementação de um sistema de regeneração por trocadores de calor. O documento detalha o funcionamento do ciclo tradicional e do ciclo inovador proposto, que utiliza injeção de vapor na água de alimentação e bombeamento bifásico, visando melhorar a eficiência do sistema. São abordados os principais componentes do ciclo, como a caldeira, a turbina a vapor, o condensador e as bombas. O texto também discute as vantagens da nova técnica em comparação ao ciclo tradicional. Com uma descrição detalhada do processo e dos equipamentos envolvidos, este documento pode ser útil para estudantes e pesquisadores interessados em sistemas de cogeração e otimização de ciclos termodinâmicos na indústria siderúrgica.
Tipologia: Manuais, Projetos, Pesquisas
1 / 16
Esta página não é visível na pré-visualização
Não perca as partes importantes!
A seguir são descritos em detalhes os dois ciclos objetos de comparação. O ciclo tradicional é baseado em uma planta existente. O ciclo inovador é o resultado do estudo de alternativas realizado no capítulo 4. No capítulo 4 são apresentadas e analisadas diversas configurações e alternativas de aplicação da nova tecnologia.
O estudo é feito para uma planta de cogeração na indústria siderúrgica. O processo siderúrgico tem como resíduos do seu processo os gases provenientes da coqueria, do alto-forno e da aciaria. No presente trabalho os dois primeiros são misturados e utilizados como combustível nas caldeiras de geração de vapor.
O ciclo convencional é composto de uma cadeira de geração de vapor superaquecido, uma turbina a vapor, um condensador, bombas e sistema de regeneração com trocadores de calor casco e tubo. O ciclo aqui estudado é baseado em uma planta existente de cogeração na indústria siderúrgica, porém otimizando o sistema de regeneração por trocadores de calor pelo método demonstrado no item 2- 13 do livro Powerplant Technology (El Wakil, 1984). A Figura 2 apresenta o esquema do ciclo tradicional.
A caldeira recebe líquido próximo da saturação e produz vapor superaquecido a 86 bar alimentando uma turbina a vapor de condensação com 7 extrações e pressão de vapor exausto de 0,06 bar.
A potência mecânica bruta gerada pela turbina a vapor é de 77,3 MW. Descontando-se os consumos das bombas de condensado e de alimentação da caldeira, tem-se a potência mecânica líquida de 76,3 MW. A planta tem como principal função atender à demanda de ar para o alto-forno (6.800 Nm³/min @ 5,2 bar). Isto é feito com um soprador acoplado ao eixo da turbina a vapor consumindo 36 MW. A segunda prioridade é atender à demanda de vapor de processo (10 t/h a 15 bar) para diversas aplicações na planta. A produção adicional de energia é convertida em
energia elétrica através de um gerador acoplado ao eixo da turbina.
Segue, na Figura 2, um esquema simplificado da planta. A válvula indicada representa a perda de carga na linha de vapor entre a caldeira e a turbina.
Figura 2- Esquema do Ciclo Rankine Tradicional
onde: CAL- Caldeira TV- Turbina a Vapor SOP- Soprador CND- Condensador PA1- Aquecedor 1 PA2- Aquecedor 2
2 BC
W (^) bc
CAL
8
10
16
6
PA 3
W (^) s
TV SOP
-^ W^ t W (^) e
11
CND
15 1
12
13
14
18
PA
BA
W (^) ba
5
DES 4
19
PA
7
9
17
QR
PA
PA
20
21
22
23
24
O condensador recebe vapor saturado a 0,06 bar e 37 °C e produz condensado saturado nas mesmas condições (19-1). O calor dissipado é absorvido pela água de resfriamento, neste caso, água do mar.
O condensado é bombeado (1-2) pela bomba de condensado e, em seguida, pré-aquecido em dois trocadores de calor de baixa pressão (2-5), que recebem vapor de extração da turbina. O condensado produzido no segundo trocador é direcionado para o primeiro trocador e o condensado gerado neste é conduzido ao condensador. Em seguida, a água é encaminhada a um desaerador que retira os gases não condensáveis de modo a preservar os feixes tubulares da caldeira. O desaerador armazena a água já pronta para a alimentação da caldeira.
A bomba de alimentação da caldeira eleva a pressão da água para 95 bar (5-6) encaminhando-a para uma seção de três pré-aquecedores de alta pressão (6-9), antes de entrar na caldeira. A caldeira (9-11) é composta por um economizador (que troca calor com os gases de exaustão da combustão), um evaporador e superaquecedores.
A caldeira alimenta a turbina a vapor (11-19), que expande o vapor de alta pressão, gerando energia mecânica utilizada parte no acionamento do soprador e parte na conversão em energia elétrica por um gerador.
2.1.1. Componentes do Sistema
Segue, nas seções seguintes, a descrição básica dos equipamentos que compõem a planta.
2.1.1.1. Caldeira
A caldeira em questão é do tipo aquotubular com circulação natural e utiliza o gás de coqueria misturado com o gás de alto-forno como combustível. A pressão de operação é subcrítica.
A caldeira fornece vapor superaquecido a 86 bar e 510 °C para a turbina a vapor. Os combustíveis utilizados são os gases residuais do processo siderúrgico:
BFG (gás de alto forno) e o COG (gás de coqueria), formando o gás de mistura (BFG
A caldeira é composta de um economizador que leva a água de alimentação para a temperatura de saturação trocando calor por convecção com o gás exausto; um tubulão que está ligado a feixes tubulares (chamados parede de água) revestindo a fornalha da caldeira onde ocorre a troca de calor por radiação evaporando a água que chega à condição de vapor saturado; um superaquecedor interno (radiante) composto de feixes tubulares no interior da caldeira que superaquece o vapor até 480 °C; e um superaquecedor externo (convectivo) que troca calor com o gás exausto e eleva a temperatura do vapor a 510 °C.
A caldeira recebe 309 t/h de água subresfriada a 93 bar a e 255 °C e gera 306 t/h de vapor superaquecido a 86 bar e 510 °C. A per da de vazão é relativa à purga da caldeira que é feita continuamente para evitar a concentração de sais no fluido de trabalho. Com isto, deve ser feita uma reposição de água desmineralizada de mesmo valor. Segue, na Figura 4, um esquema com os componentes principais de uma caldeira aquotubular, extraído de Lora e Nascimento (2004).
Figura 4- Esquema de uma caldeira aquotubular típica (Lora e Nascimento,
Para turbinas de grande porte é utilizada a configuração com dupla exaustão radial e dupla carcaça (uma com os estágios de alta e média pressão e outra com o estágio de baixa pressão) como mostra a Figura 6, abaixo.
Figura 6- Esquema de uma turbina a vapor de grande porte
Para turbinas a vapor de grande porte, é construída uma estrutura de suportação da máquina, de modo a permitir que o condensador seja posicionado abaixo da mesma.
2.1.1.3. Condensador
O condensador é de superfície, posicionado abaixo da turbina a vapor, resfriado a água e com dois passes. A água é circula pelos tubos trocando calor com o vapor vindo da turbina. O calor latente de condensação é transferido para a água de resfriamento, a qual é direcionada para o mar. Bombas captam água fria do mar para o condensador. Este é o chamado ciclo aberto de condensação. Para localidades com pouca disponibilidade de água ou com restrições ambientais, é adotado o circuito fechado de resfriamento com a instalação de uma torre de resfriamento.
A operação do condensador ocorre na pressão manométrica negativa (vácuo) que é mantida por bombas de vácuo ou por ejetores a vapor. Os ejetores utilizam vapor de extração da turbina e têm dupla função; além de manter o vácuo de operação do condensador, retirar parte dos não condensáveis.
O condensador recebe o vapor exausto da turbina (187 t/h) a 0,06 bar e utiliza água do mar para condensar esse vapor e realimentar o ciclo com condensado. A vazão nominal de água do mar para condensação do vapor é de 13.500 t/h e as
temperaturas da água quente e fria são, respectivamente, 32,5 °C e 25,5 °C. Para utilizar água do mar como fluido dissipador, o material dos tubos do condensador deve resistir à abrasão causada pela água salgada. O material utilizado na fabricação dos tubos, para estes casos, é o titânio.
O condensado produzido é encaminhado a um poço localizado abaixo do corpo do condensador ainda na condição de vácuo. A bomba de condensado é conectada a este poço. A vazão de água de reposição do ciclo admitida no condensador é de 14, t/h. A Figura 7 apresenta um esquema de um condensador instalado abaixo da turbina a vapor:
Figura 7- Esquema de um condensador de dois passes
2.1.1.4. Bomba de Condensado
A bomba de condensado é centrífuga vertical do tipo “can”, com um reservatório próprio instalado no corpo da bomba. A sucção é feita na pressão de vácuo a partir do poço de condensado localizado abaixo do condensador. Esta bomba é utilizada em casos onde há problemas de NPSH (Net Positive Suction Head) disponível. Tipicamente o bombeamento de condensado apresenta este problema pois a pressão de sucção da água está próxima da pressão de vapor. Por este motivo a bomba deve ter seu próprio reservatório como mostra a Figura 8.
A bomba de condensado eleva a pressão do condensado para 5 bar (pressão de
São dois trocadores de baixa pressão e um de alta pressão. As seções de alta e baixa pressão são separadas por um desaerador. Segue, na Figura 9, um esquema ilustrativo da operação de um trocador casco e tubo.
Figura 9- Esquema de um trocador de calor tipo casco e tubo
2.1.1.6. Desaerador
O desaerador (Figura 10) é composto de uma torre vertical, onde ocorre o processo de arraste dos não condensáveis, e de um vaso horizontal, que funciona como reservatório para a água de alimentação da caldeira.
O desaerador tem a função de retirar os gases não condensáveis da água de alimentação de modo a não danificar as caldeiras. É utilizado vapor de extração de 5 bar para retirar o ar da água por arraste de vapor, ou seja, o vapor, em contra-corrente com a água, carrega os não condensáveis, que são liberados para a atmosfera.
Além de retirar não condensáveis, o desaerador promove aquecimento da água e funciona, também, como um reservatório que possibilita a sucção das bombas de alimentação da caldeira.
O desaerador trabalha com pressão de operação de 5 bar. A Figura 10 apresenta o esquema de operação de um desaerador.
Figura 10- Esquema de um desaerador
2.1.1.7. Bomba de Alimentação da Caldeira
A bomba de alimentação de caldeira é centrífuga horizontal do tipo barril com multi-estágios e eleva a pressão de 5 bar a da água proveniente do desaerador, para 95 bar de maneira que a pressão na entrada da turbina seja de 86 bar. A Figura 11 apresenta o esquema de operação da bomba:
Figura 11- Esquema em corte de uma bomba horizontal multiestágios
Figura 12- Esquema do ciclo Rankine inovador
Onde: CAL- Caldeira TV- Turbina a Vapor SOP- Soprador CND- Condensador BBF1- Bomba Bifásica 1 BBF2- Bomba Bifásica 2 DES- Desaerador BBF3- Bomba Bifásica 3 BBF4- Bomba Bifásica 4 BBF5- Bomba Bifásica 5 BA- Bomba de Alimentação
CAL
BBF
CND
TV SOP
BBF4 DES^ BBF
BBF
W (^) b 4
BBF
W (^) b 5
22
2
1
(^543)
6 7
8
(^1110)
12
14
15
16
17
18
19
20
21
23
13
9
A válvula indicada na Figura 12 representa a perda de carga na linha de vapor entre a caldeira e a turbina (trecho 13-14). Os retângulos pontilhados representam os pontos de mistura. O diagrama T vs S para o esquema proposto é apresentado na Figura 13.
Figura 13- Diagrama T vs S para o ciclo Rankine inovador
(^1 )
(^3 )
5
10
T (°C)
S (kJ/kgK)
12
14
15
7
(^8 ) 11
16 19 20 21
bombas que suportem os efeitos da cavitação proporcionados pelo fluxo bifásico. É necessário um esforço de pesquisa e desenvolvimento para viabilizar tais equipamentos.
2.2.1. Componentes do Sistema
Os componentes do ciclo inovador são os mesmos descritos no item 2.1. acrescidos das bombas bifásicas e excluídos os pré-aquecedores. Algumas condições operacionais variam, mas estas serão apresentadas na simulação. Portanto, neste item somente será descrito o equipamento adicional, a bomba bifásica.
2.2.1.1. Bombas Bifásicas
Duas bombas bifásicas são utilizadas para aumentar a pressão do fluido bifásico até a pressão de saturação. Na linha de descarga das bombas vapor na mesma pressão de descarga da bomba a montante é injetado de modo a se obter uma mistura com título de até 20%.
Embora bombas bifásicas para esta aplicação ainda não estejam disponíveis comercialmente, os autores da patente (Cunningham e Briesch, 2005) acreditam que o desenvolvimento do projeto e a produção de tais equipamentos sejam possíveis com as tecnologias existentes, já que existem bombas bifásicas para aplicação na indústria petroquímica em operação (de Salis, 1996).
As bombas bifásicas foram modeladas com eficiência isentrópica de 75% baseado na consideração feita pelos inventores do ciclo inovador (Cunningham e Briesch, 2005). Este valor pode ser considerado baixo mas foi adotado pois, como já foi dito, tais equipamentos ainda não foram desenvolvidos e não existem dados de performance disponíveis sobre os mesmos. Sendo assim foi optado por um valor conservativo.
No capítulo 4 é feito um estudo de alternativas de configuração do ciclo inovador. A alternativa de melhor eficiência será selecionada para comparação pela Segunda Lei da Termodinâmica com o ciclo tradicional.