
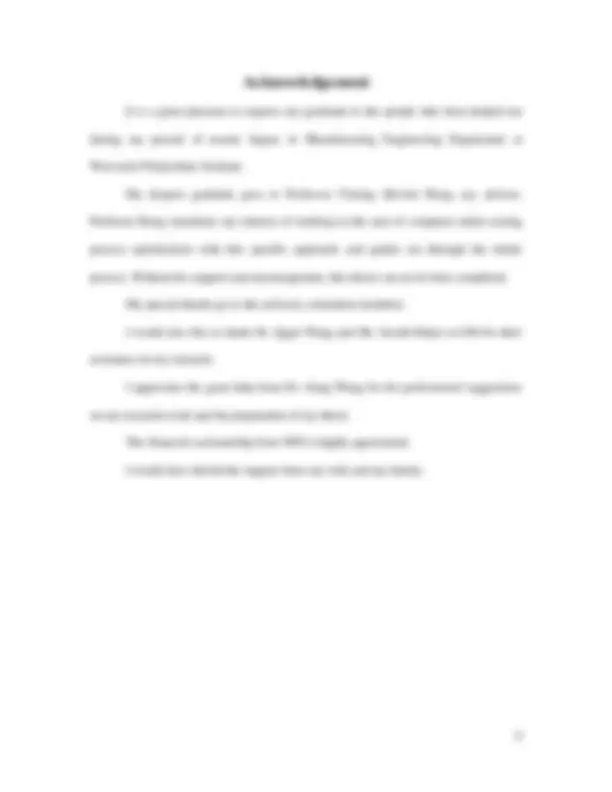
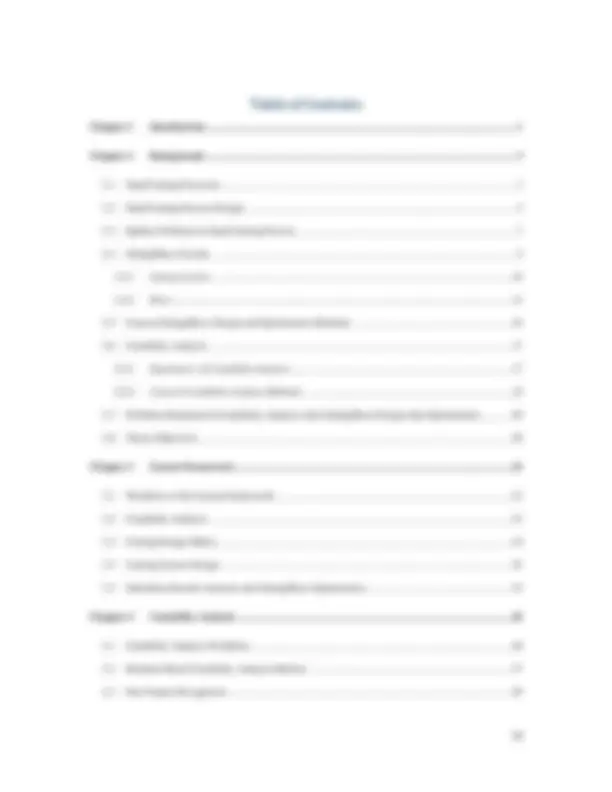
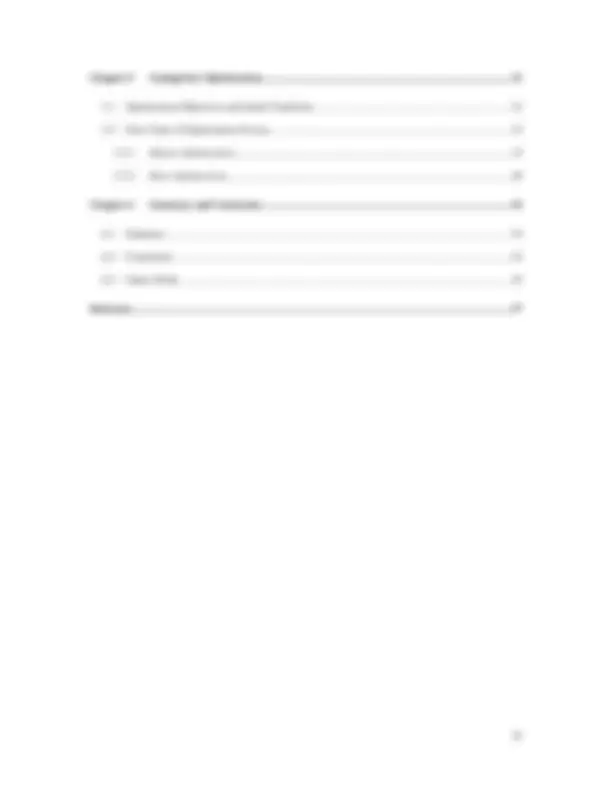
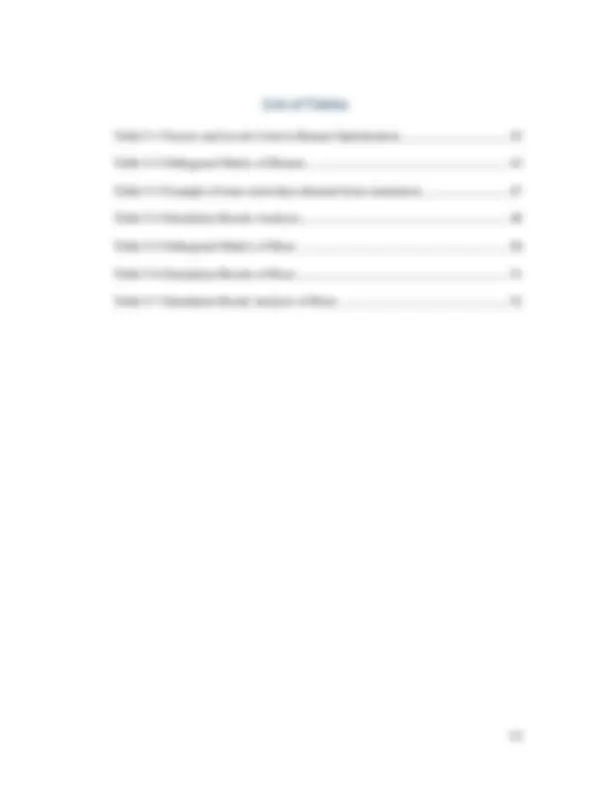
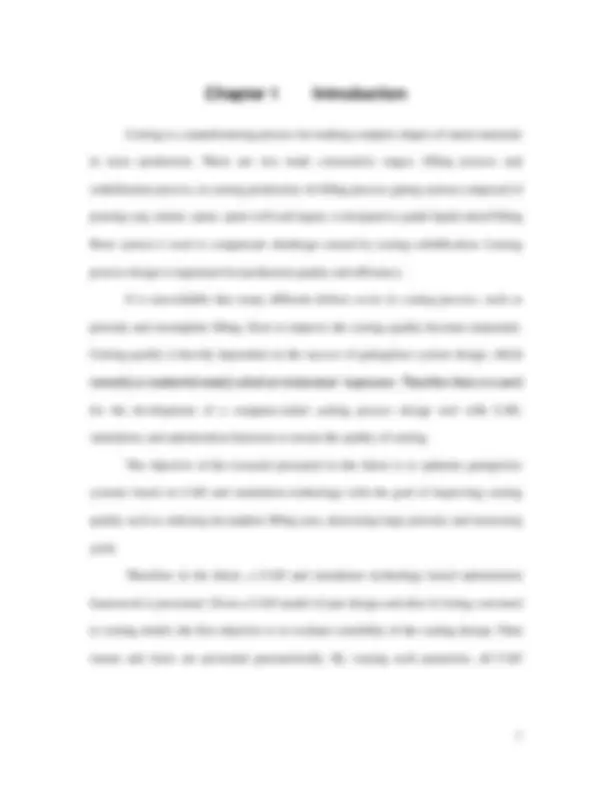
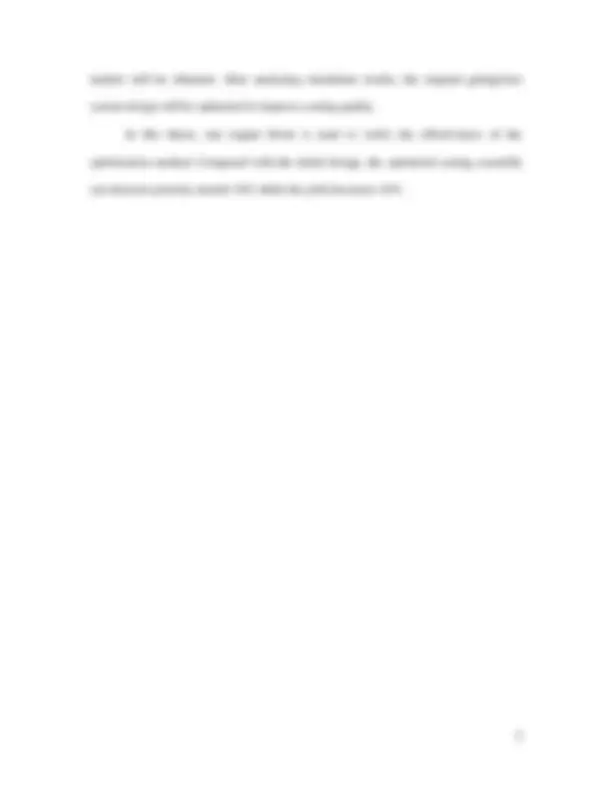
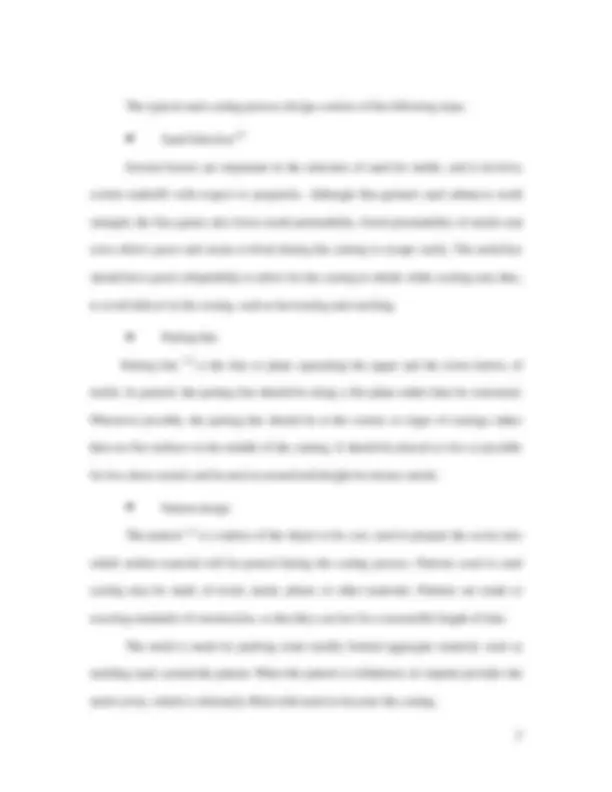
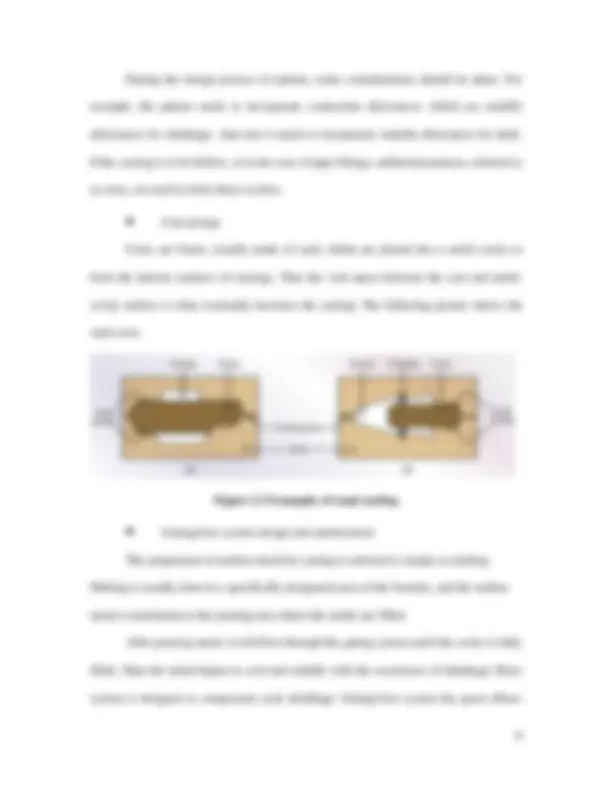
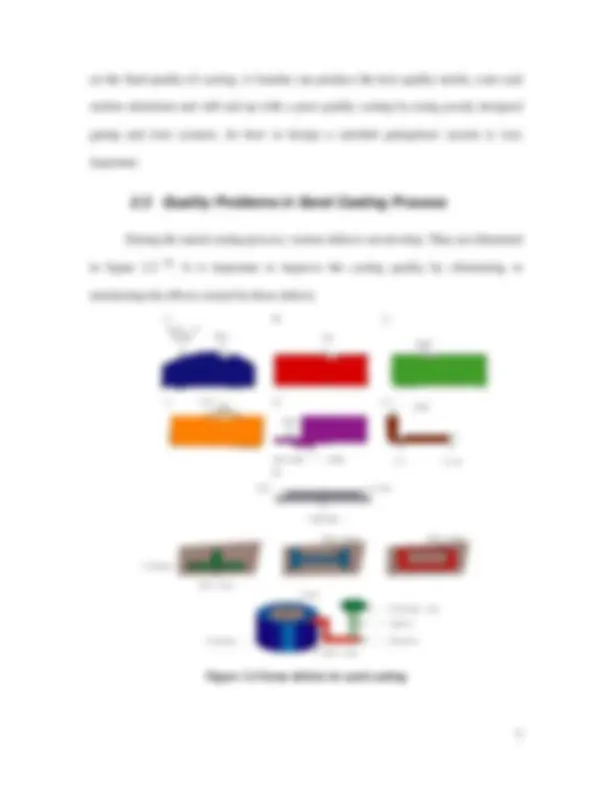
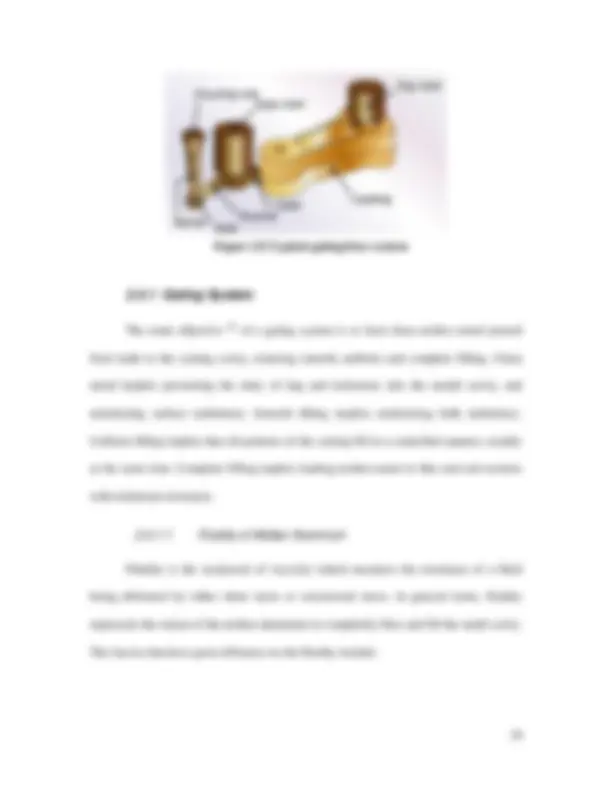
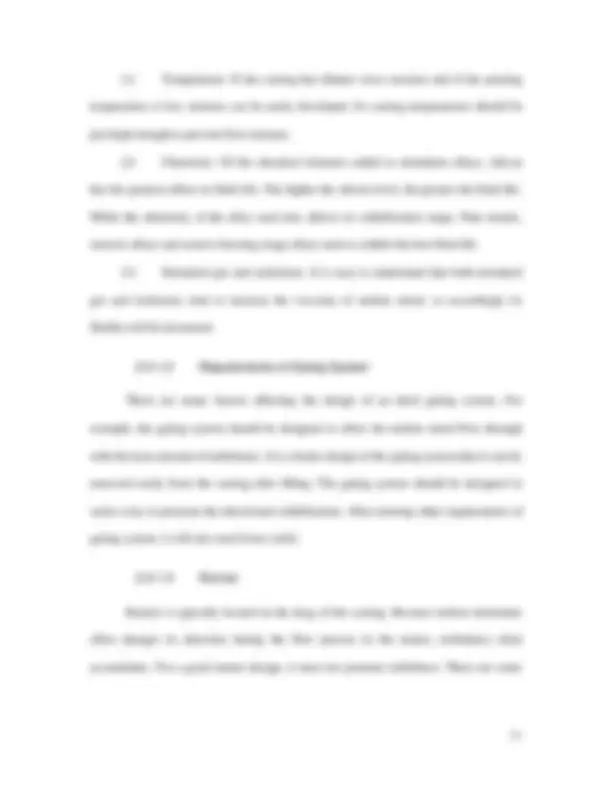
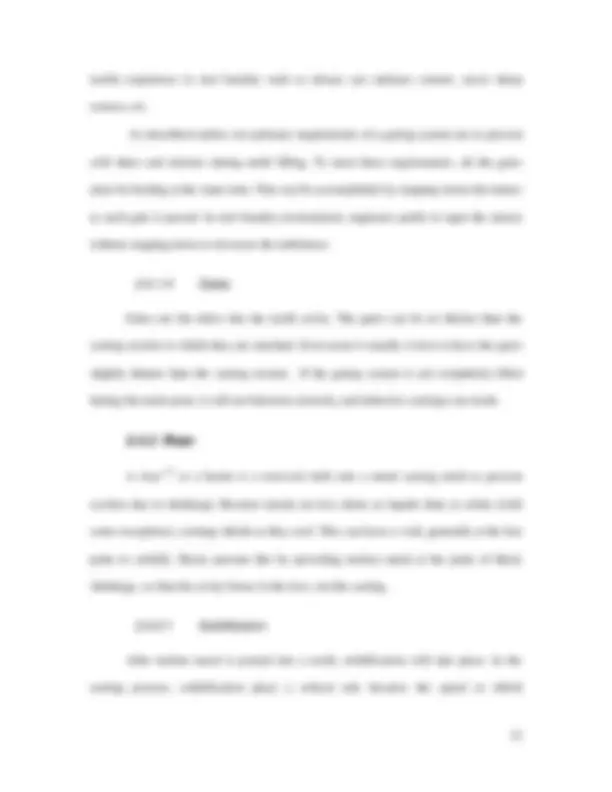
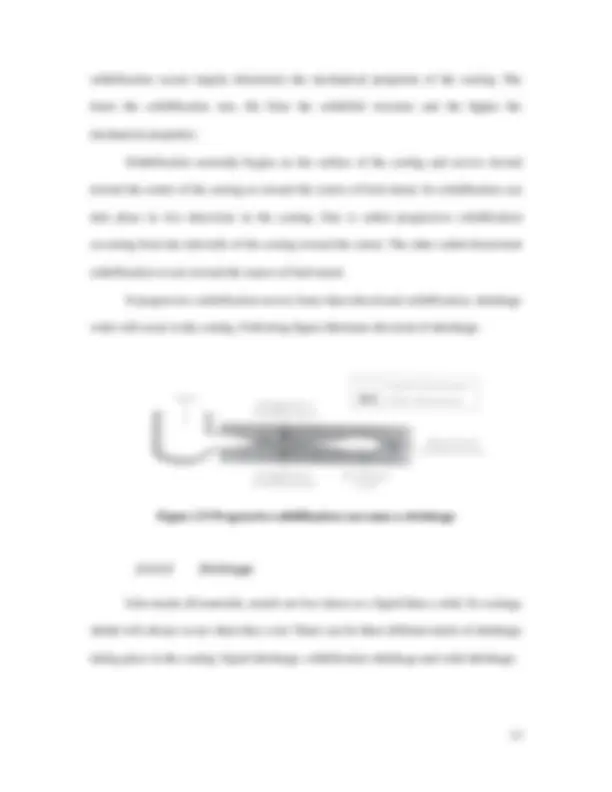


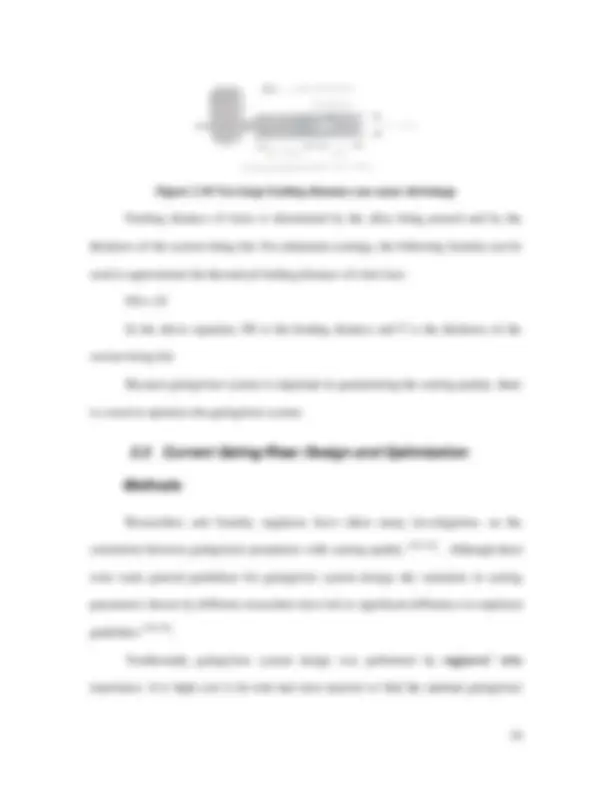
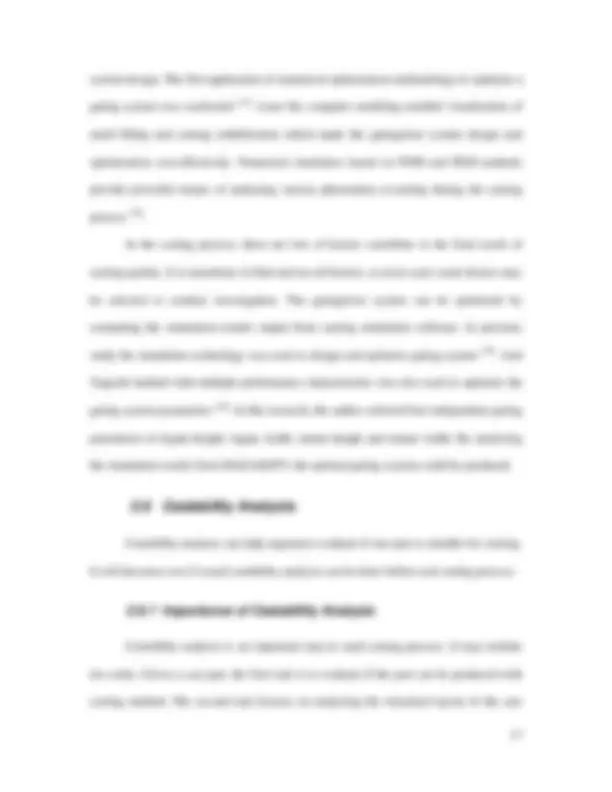
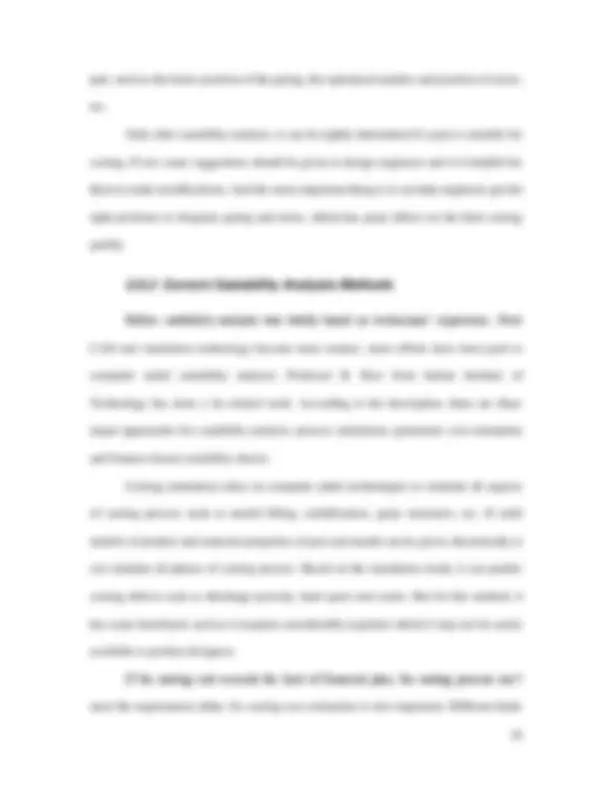
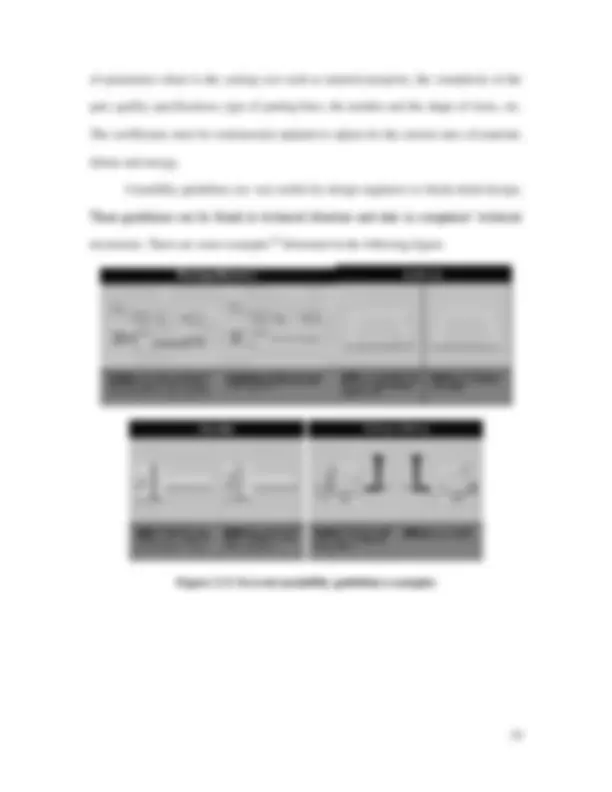
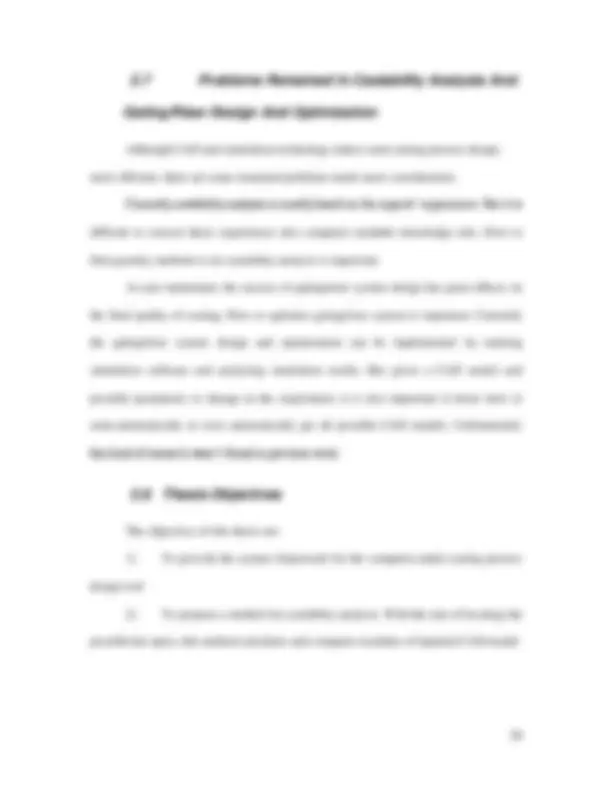
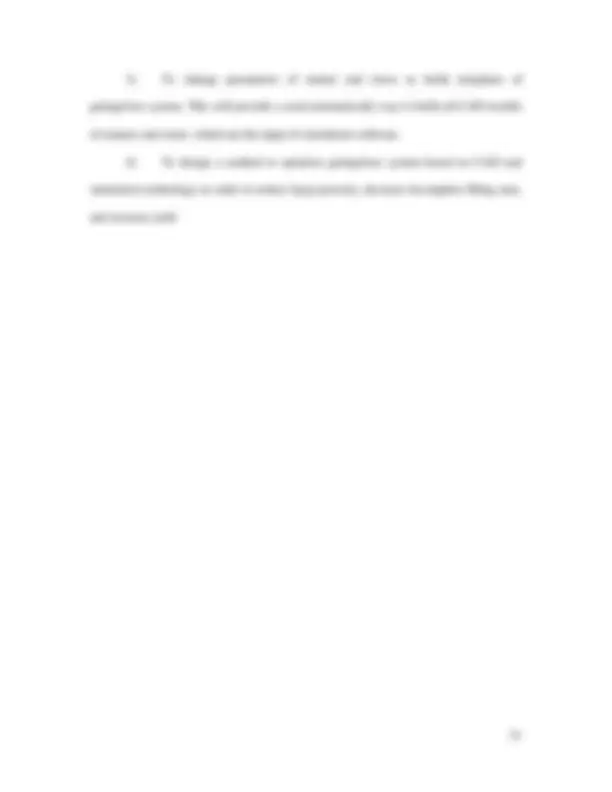
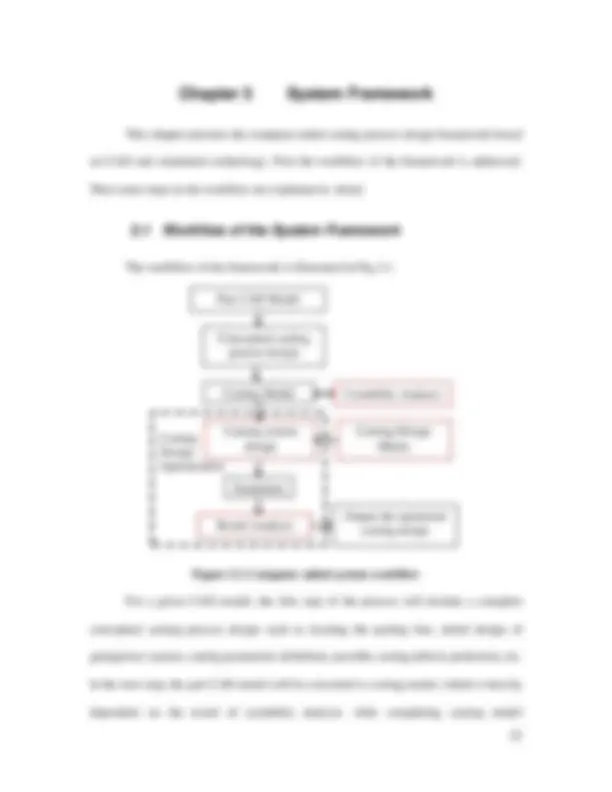
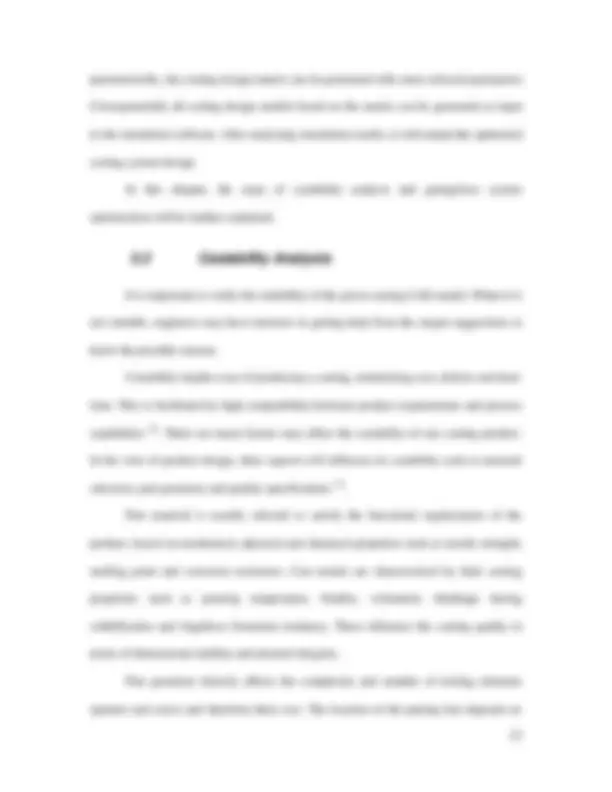
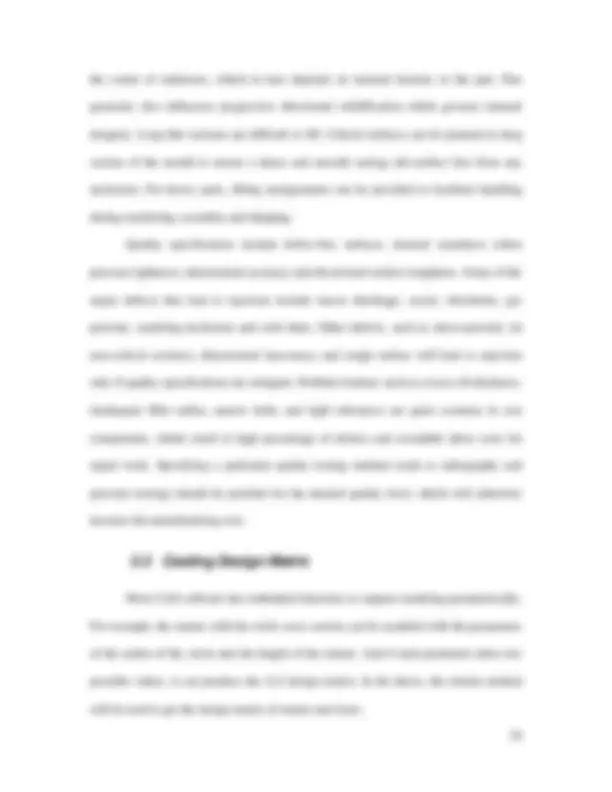
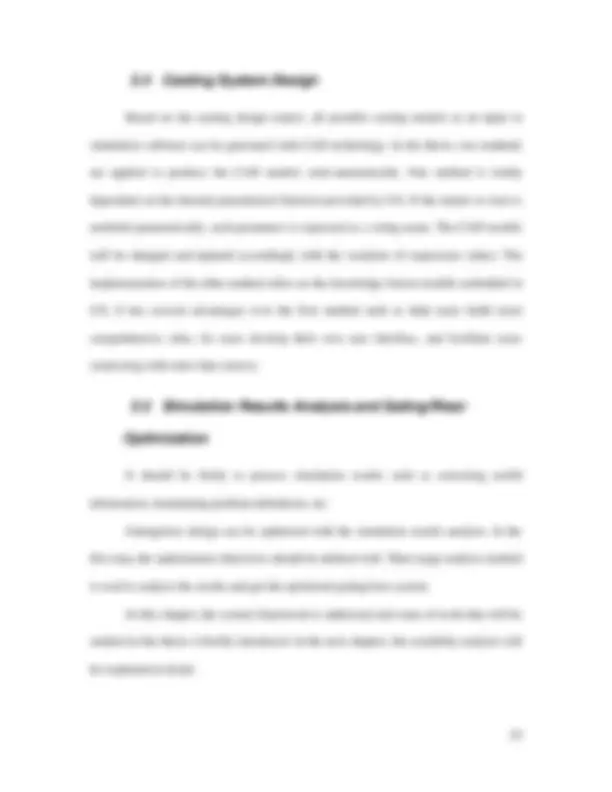

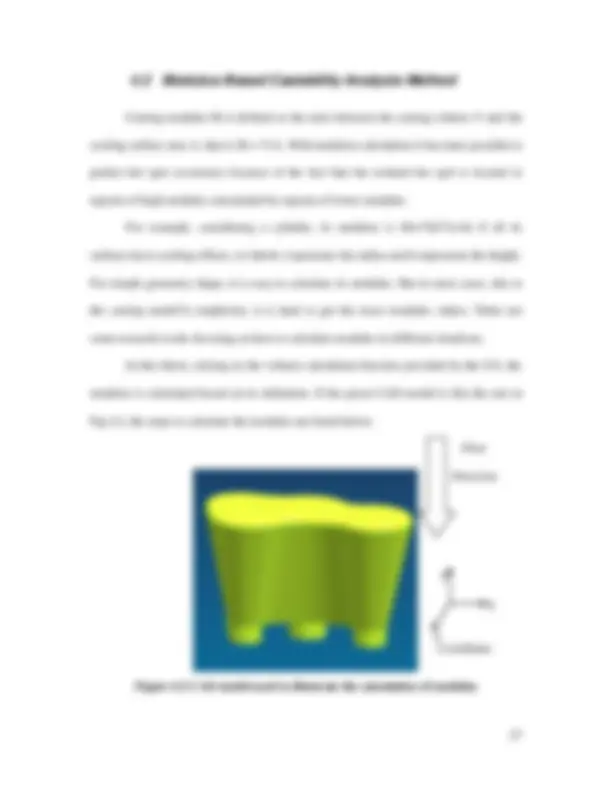
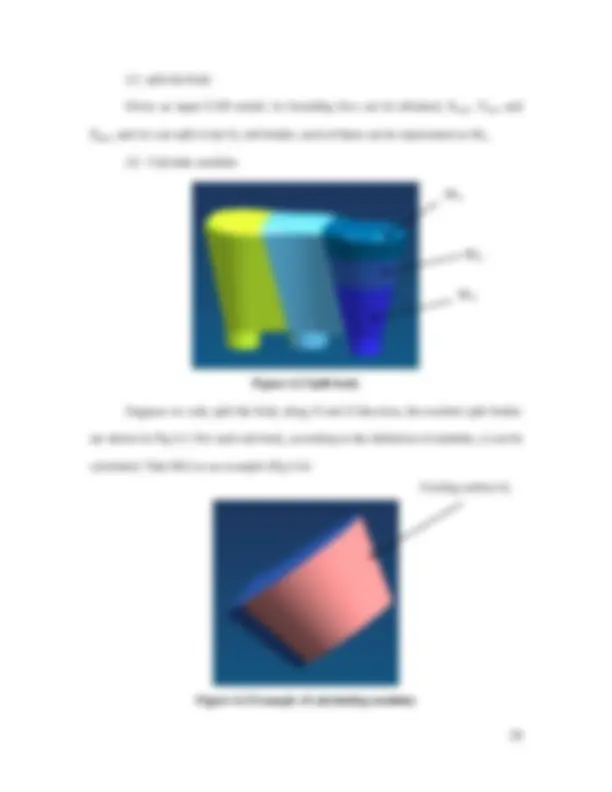
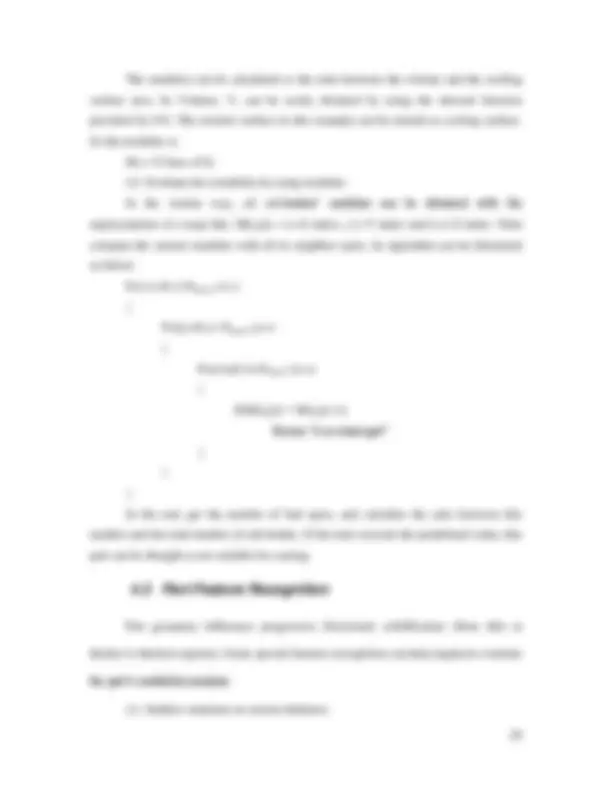
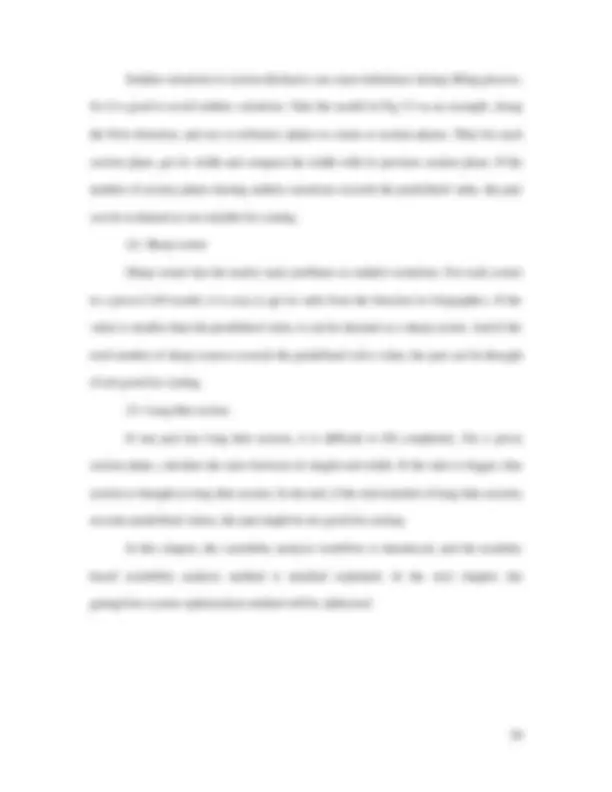
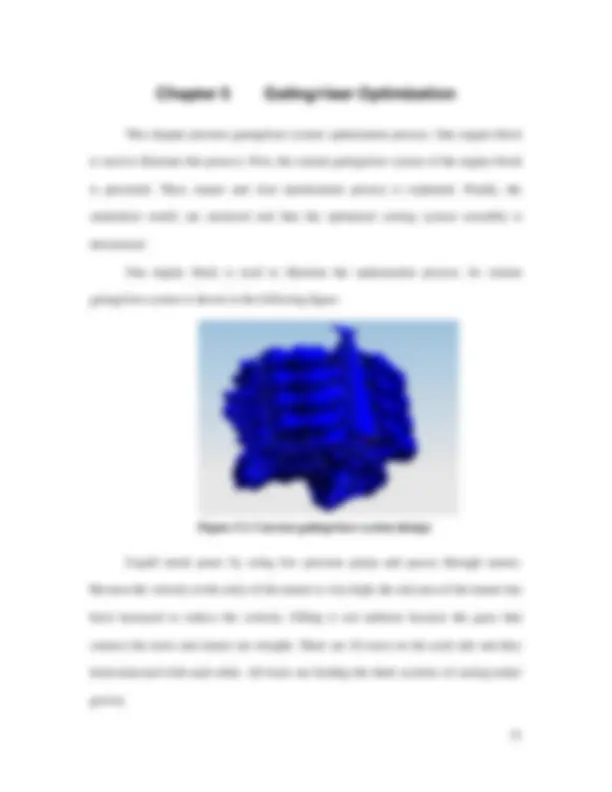
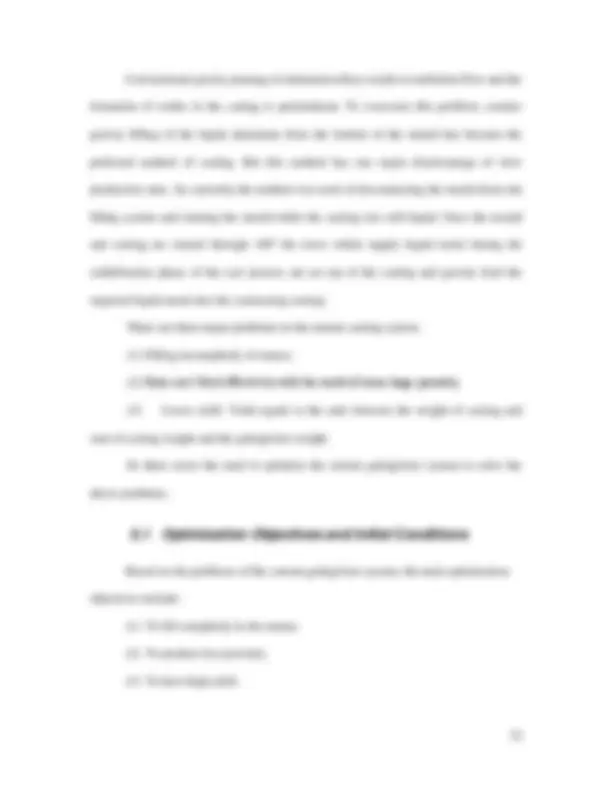
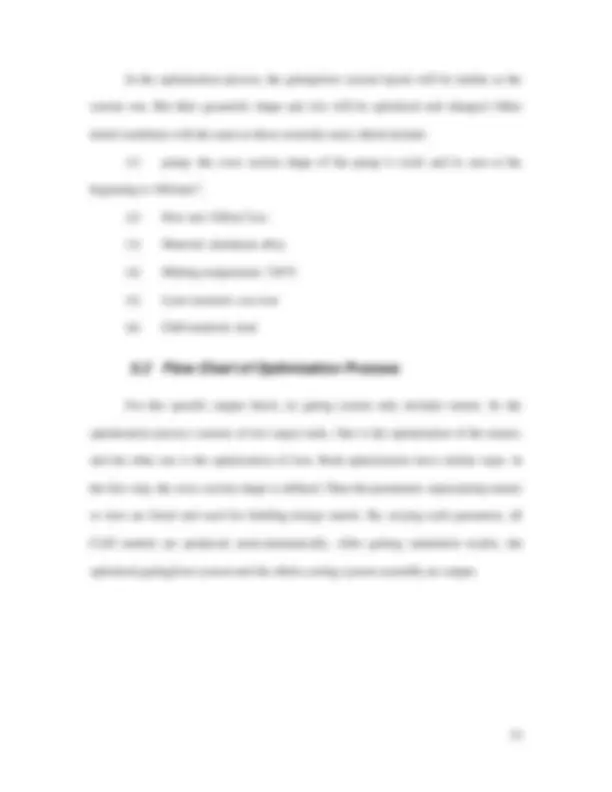
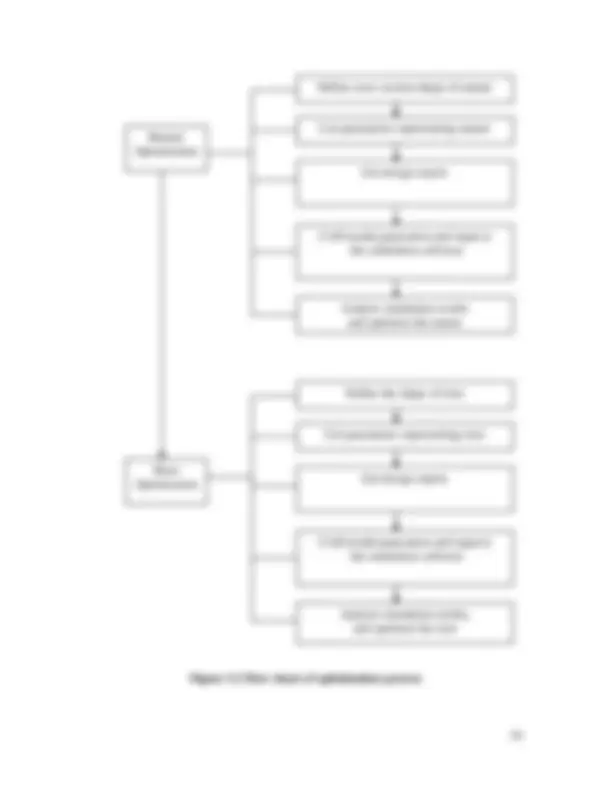
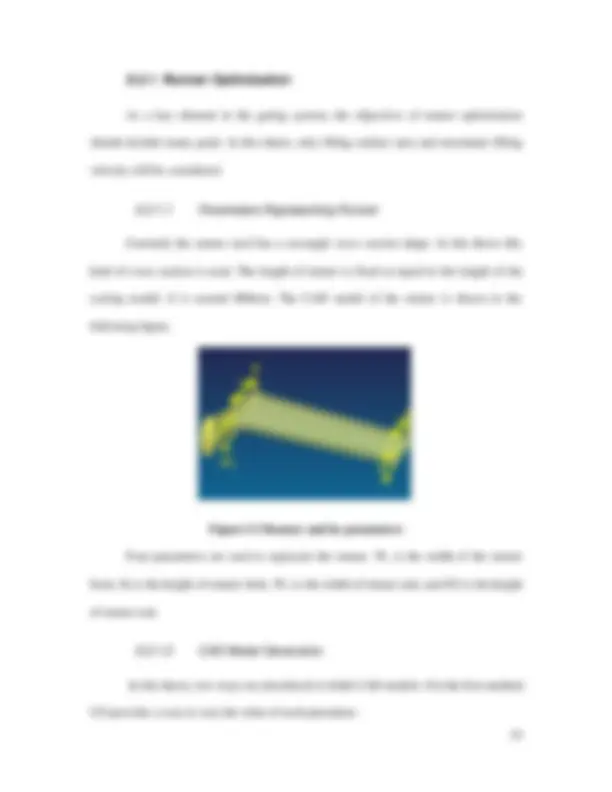
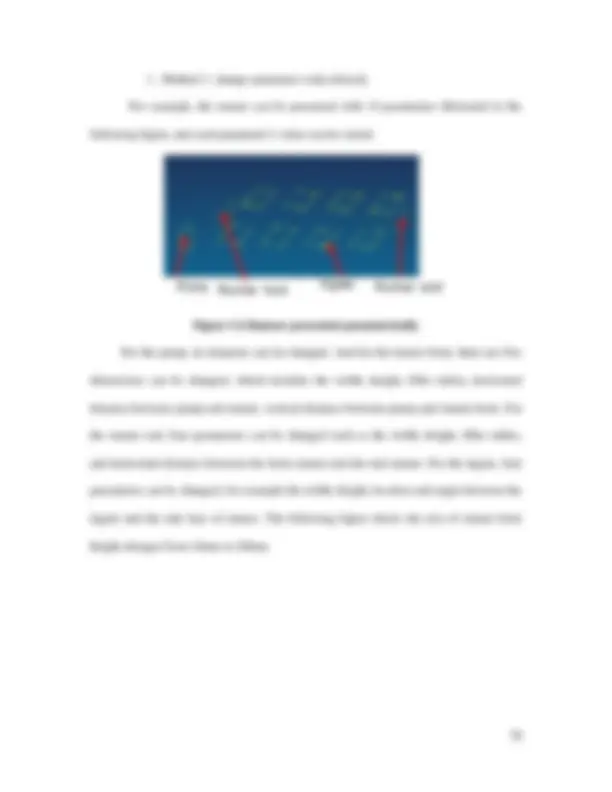
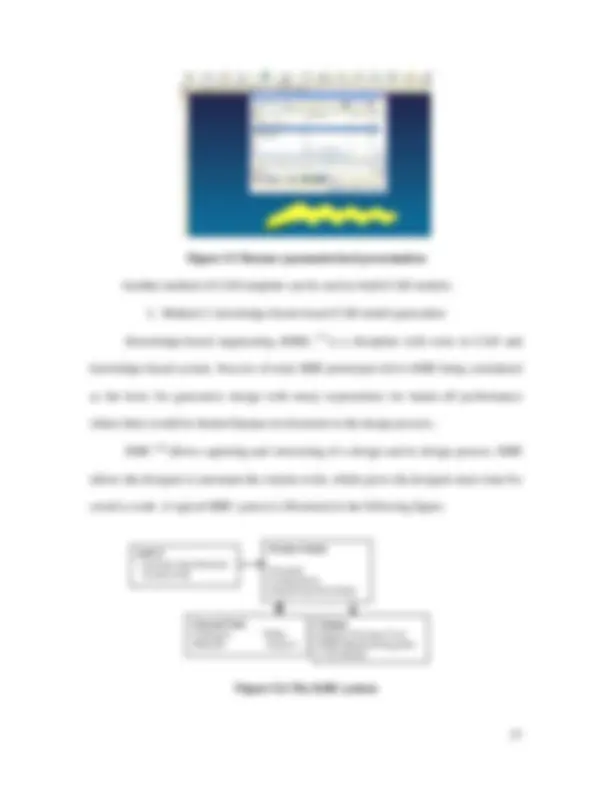
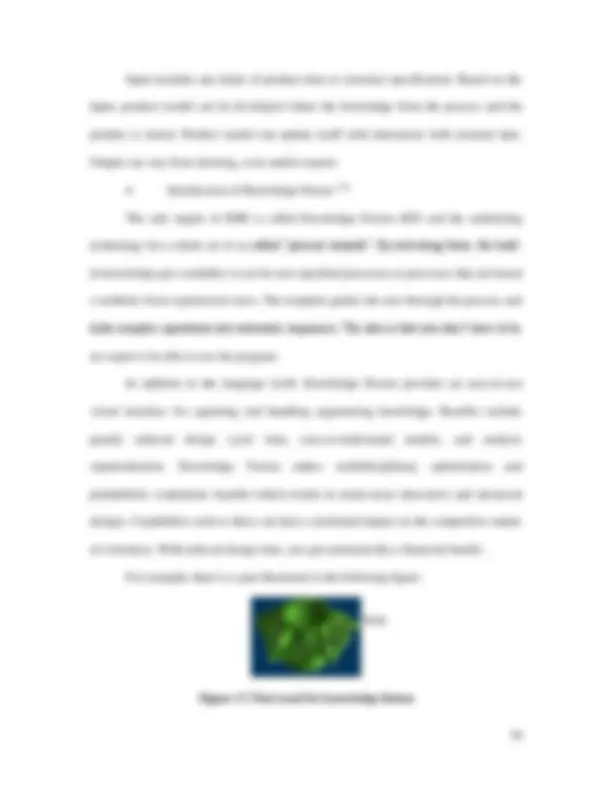
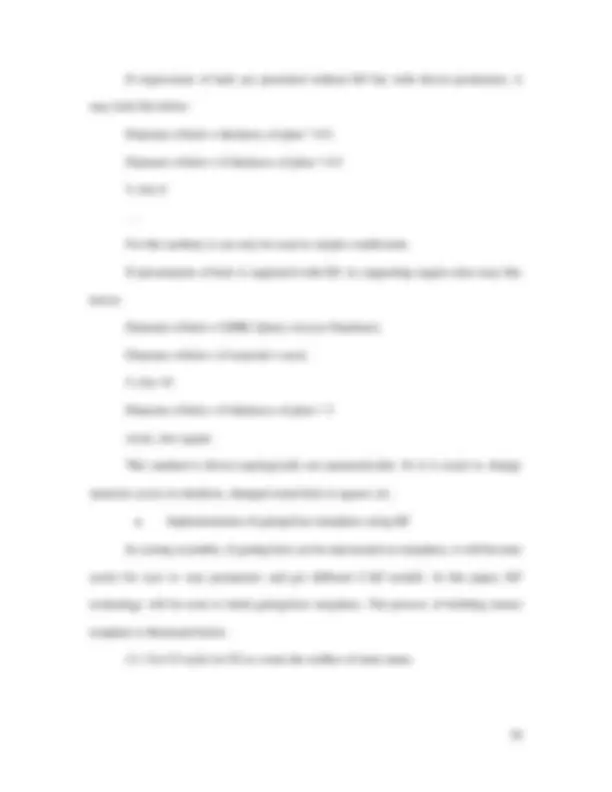
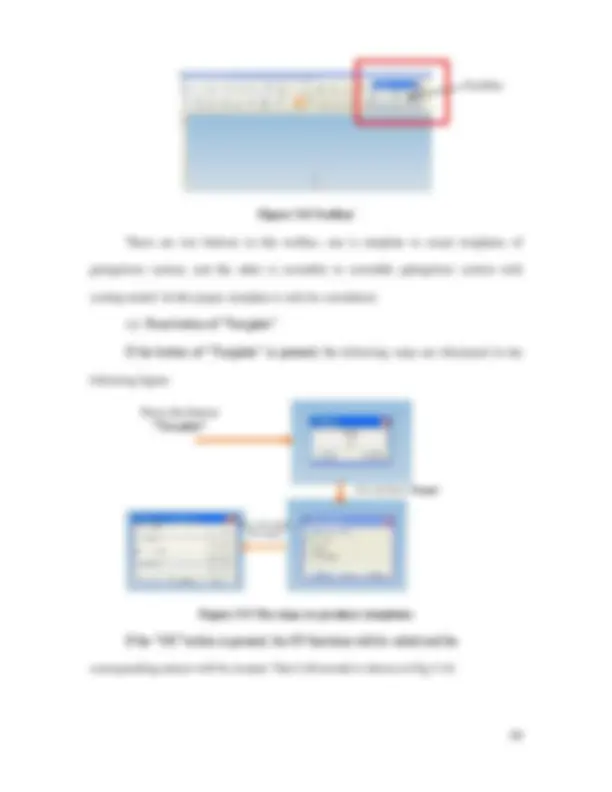
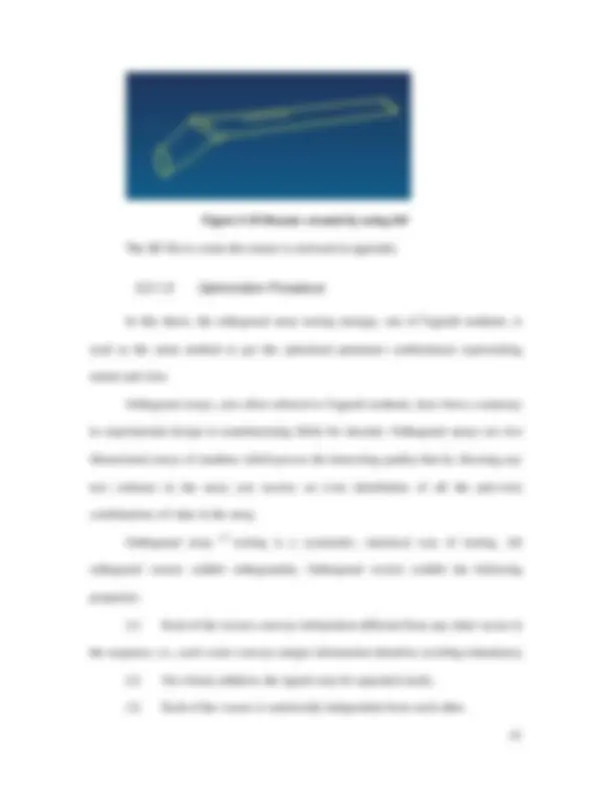
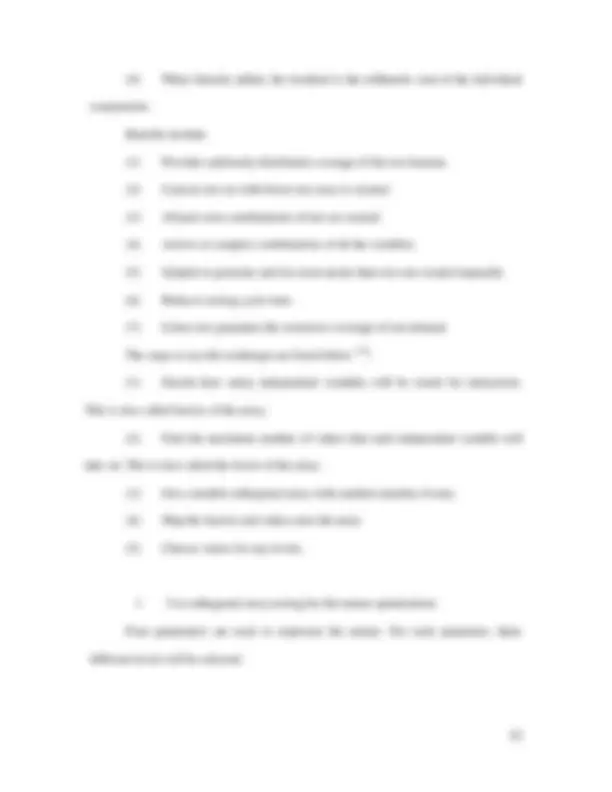

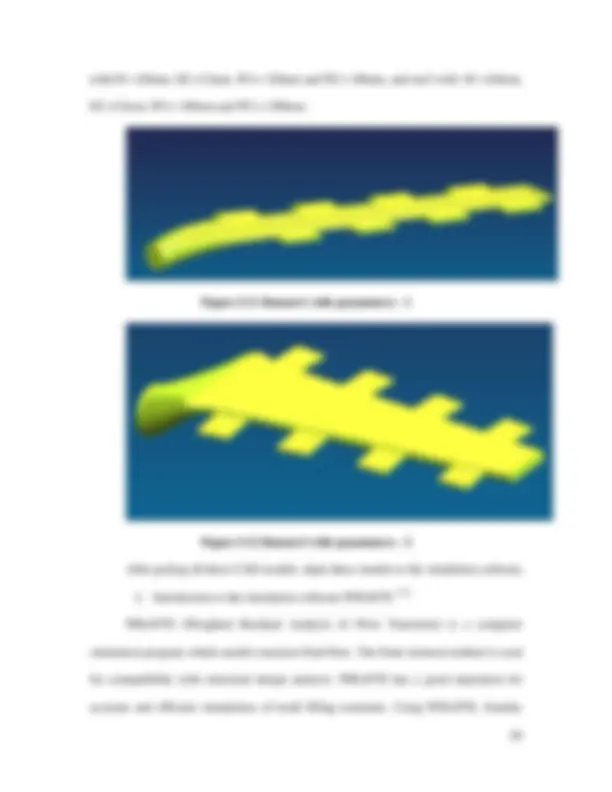
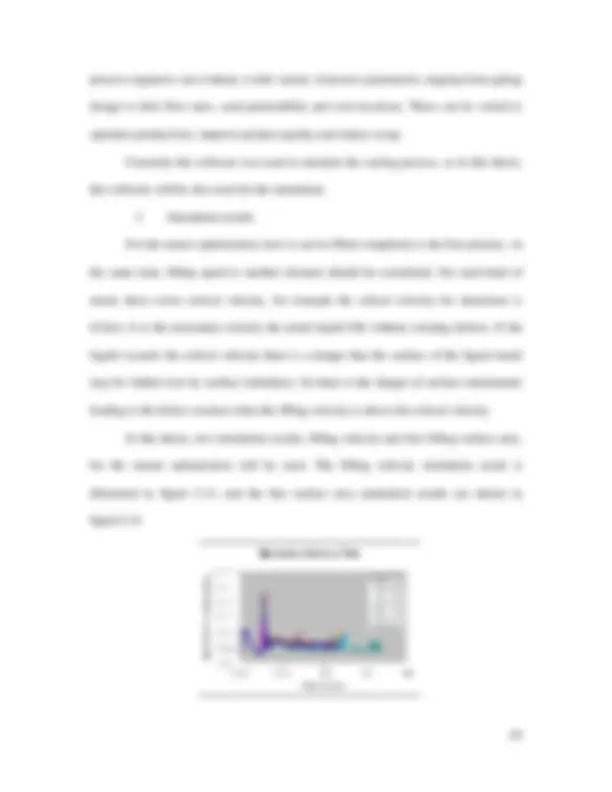
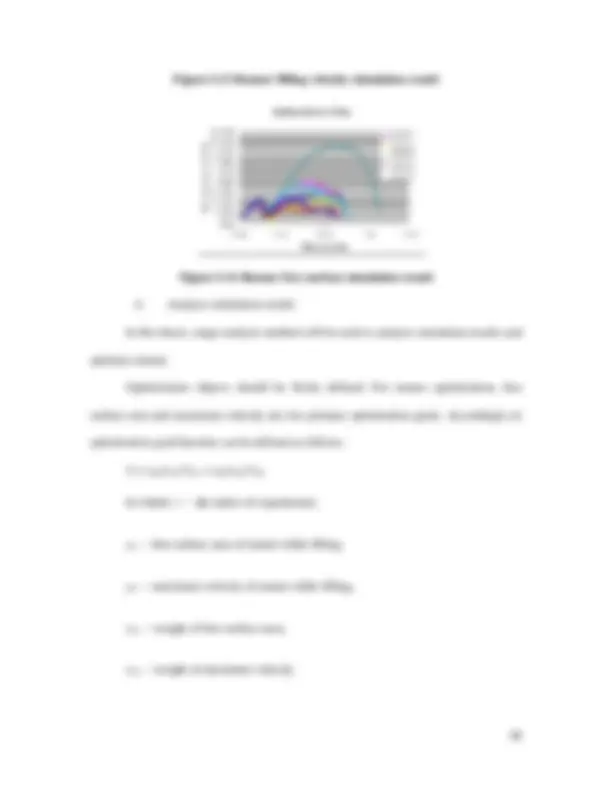
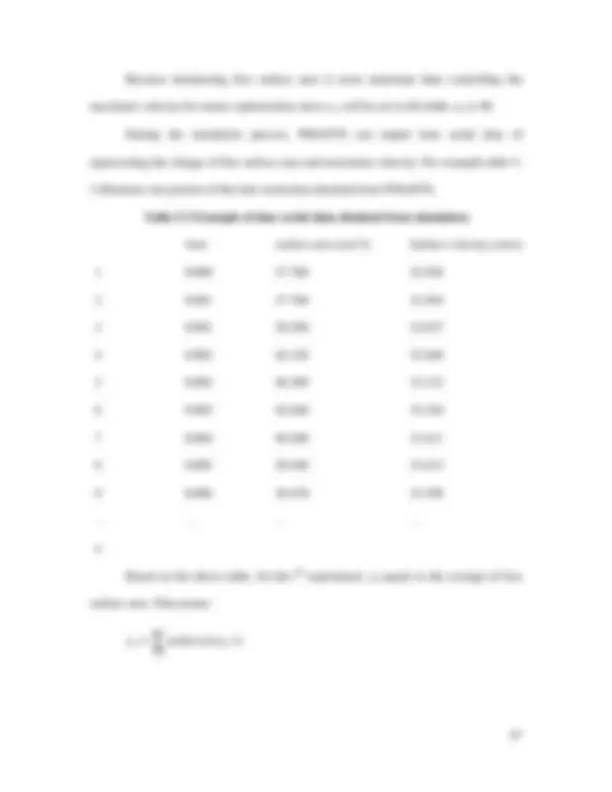
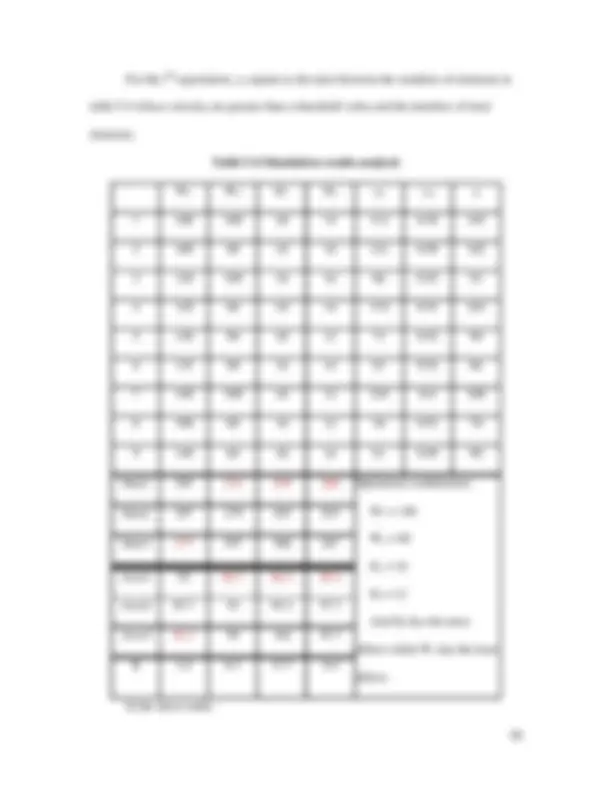
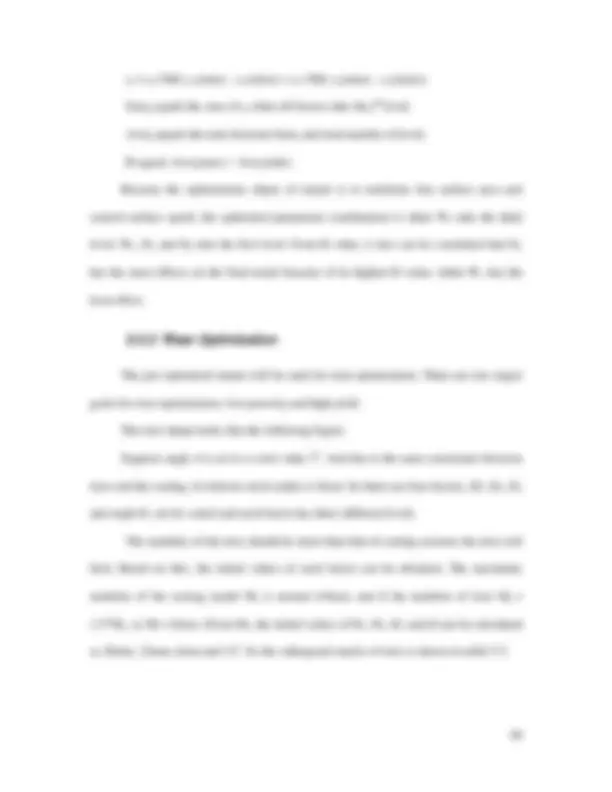
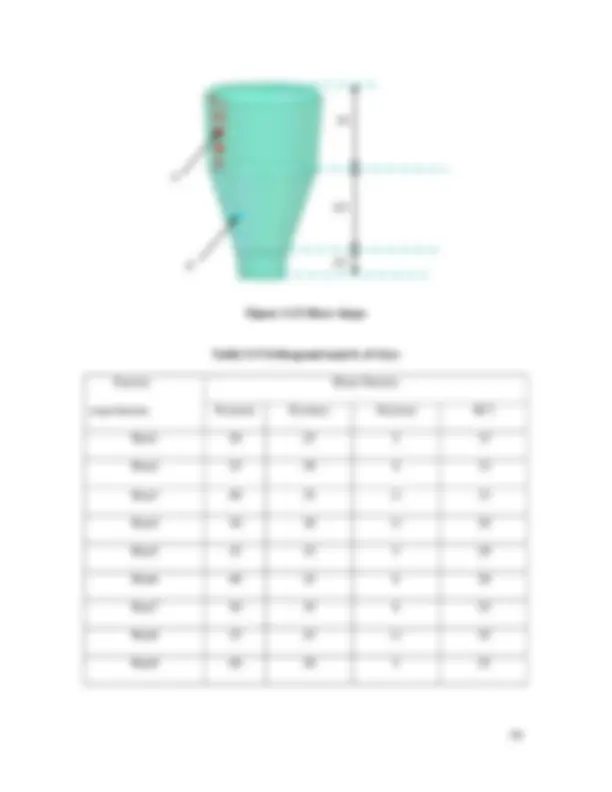
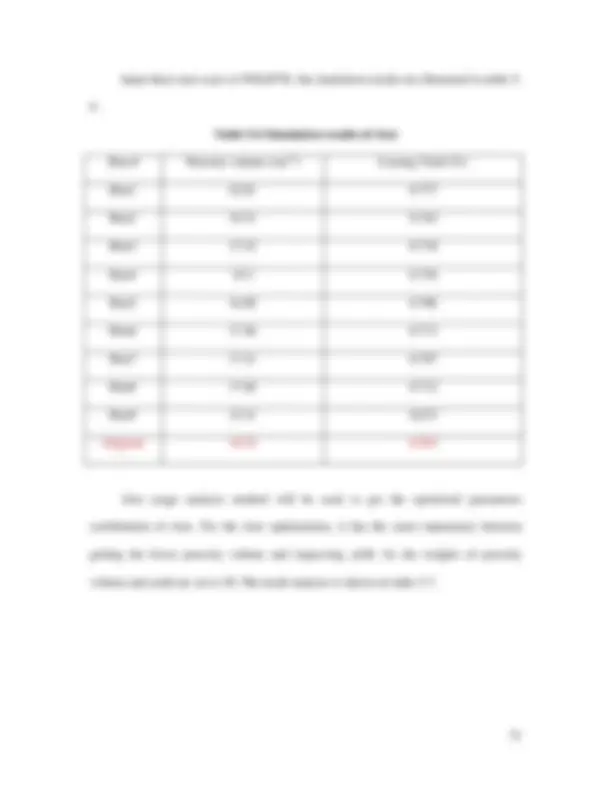
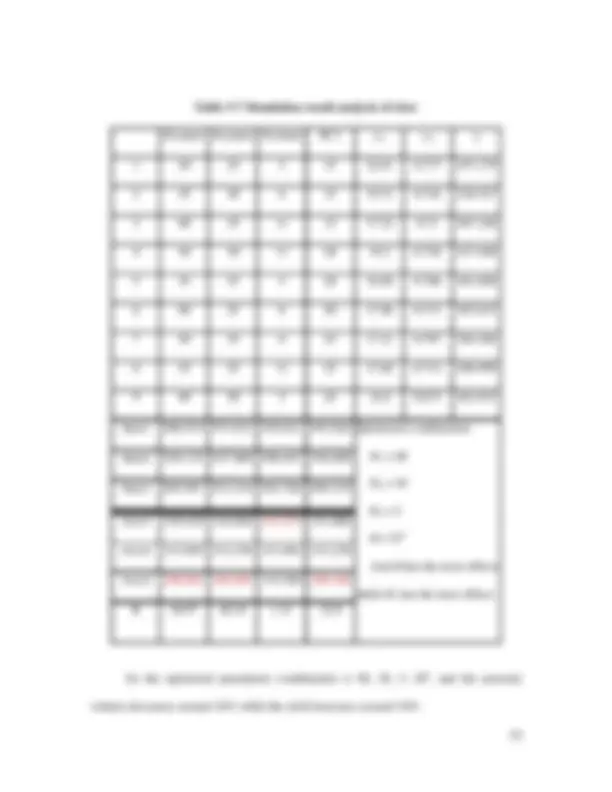
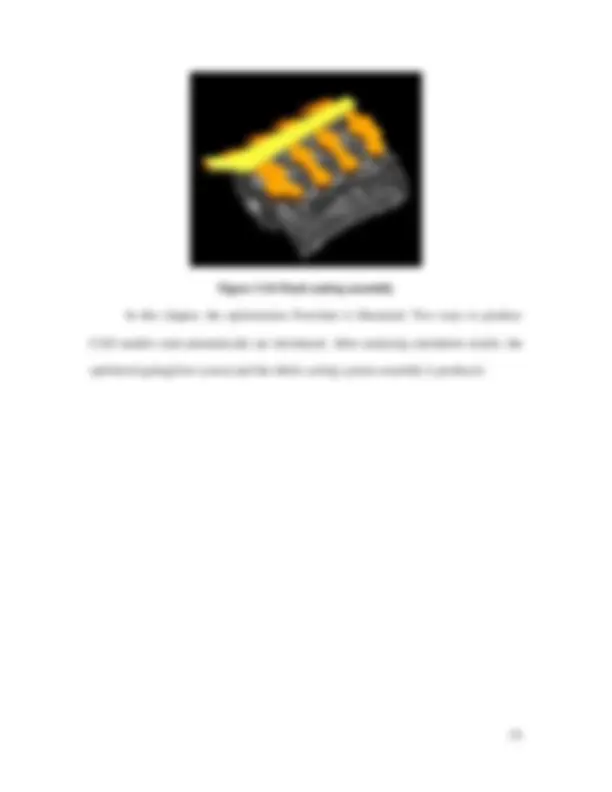

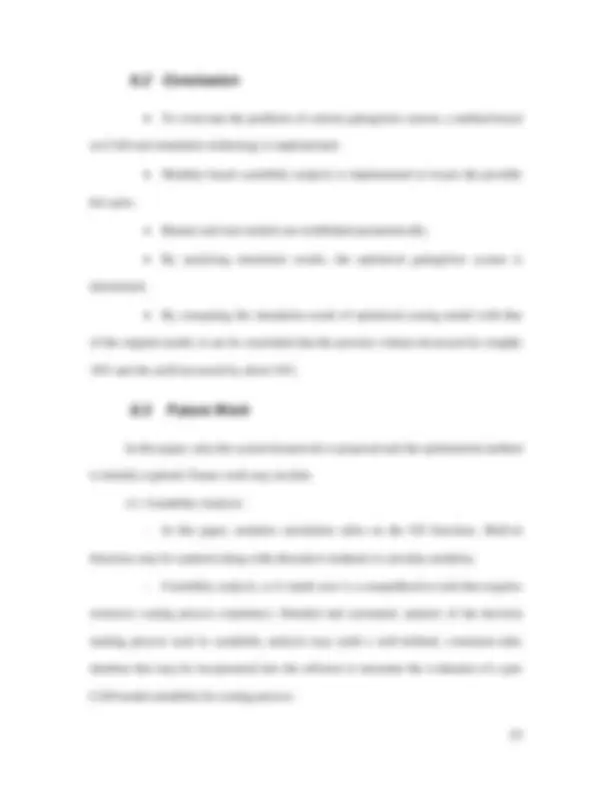
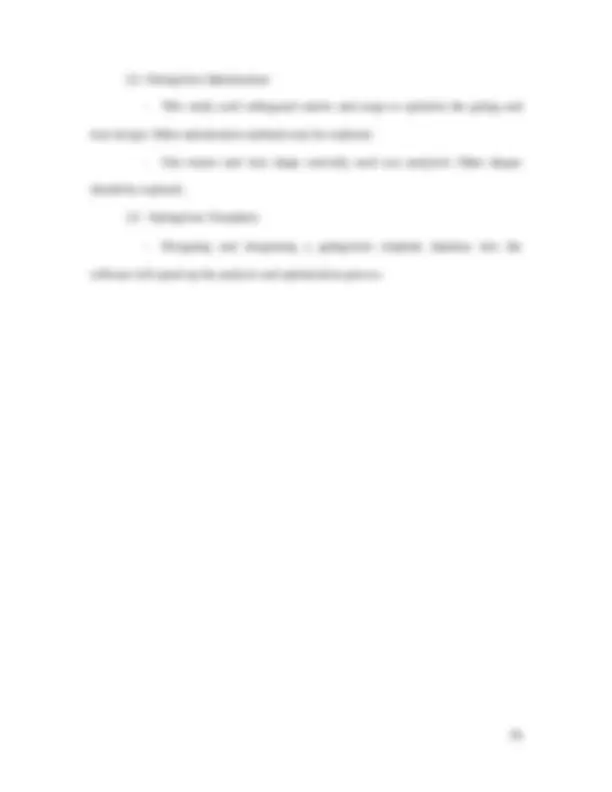
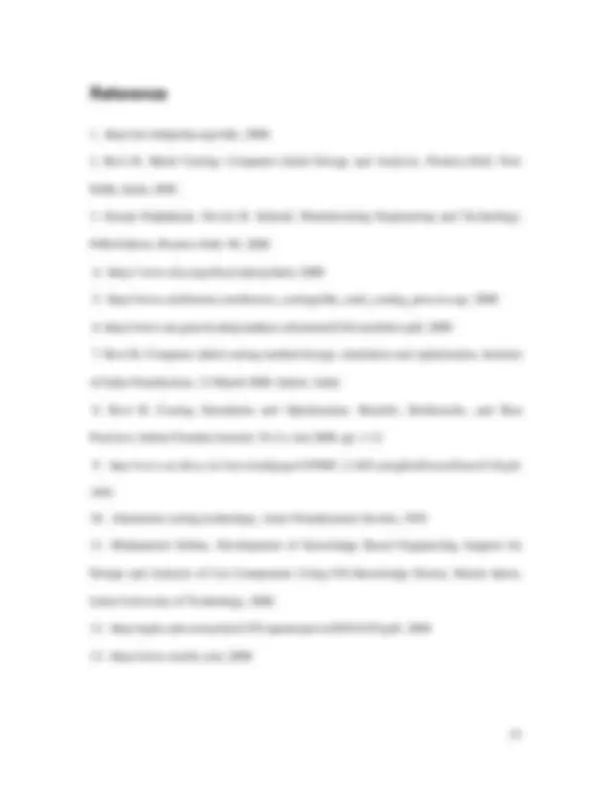
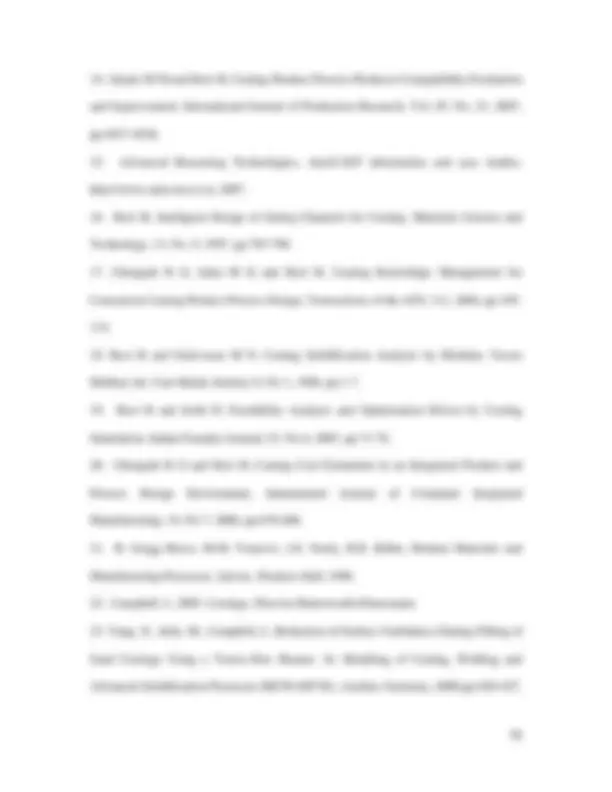
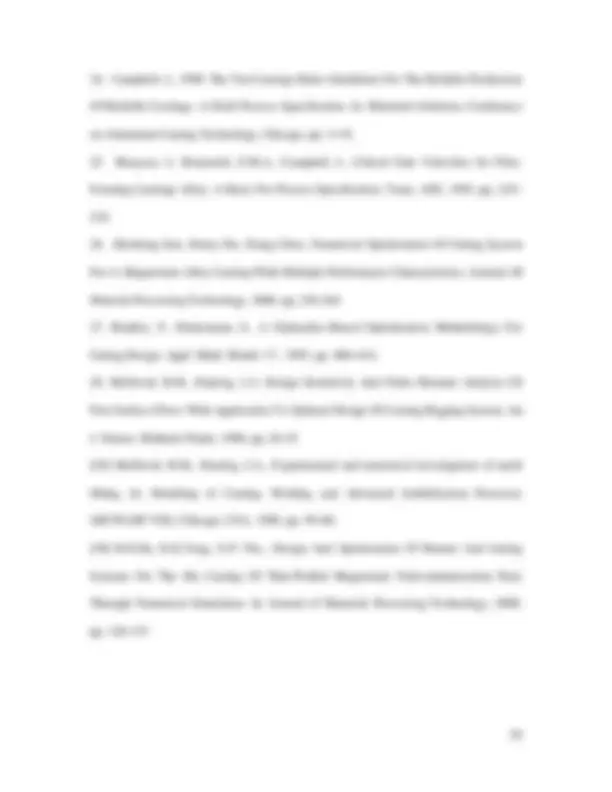
Estude fácil! Tem muito documento disponível na Docsity
Ganhe pontos ajudando outros esrudantes ou compre um plano Premium
Prepare-se para as provas
Estude fácil! Tem muito documento disponível na Docsity
Prepare-se para as provas com trabalhos de outros alunos como você, aqui na Docsity
Os melhores documentos à venda: Trabalhos de alunos formados
Prepare-se com as videoaulas e exercícios resolvidos criados a partir da grade da sua Universidade
Responda perguntas de provas passadas e avalie sua preparação.
Ganhe pontos para baixar
Ganhe pontos ajudando outros esrudantes ou compre um plano Premium
Comunidade
Peça ajuda à comunidade e tire suas dúvidas relacionadas ao estudo
Descubra as melhores universidades em seu país de acordo com os usuários da Docsity
Guias grátis
Baixe gratuitamente nossos guias de estudo, métodos para diminuir a ansiedade, dicas de TCC preparadas pelos professores da Docsity
Casting as a manufacturing process to make complex shapes of metal materials in mass production may experience many different defects such as porosity and incomplete filling. How to improve the casting quality becomes important. Gating/riser system design is critical to improving casting quality. The objective of the research presented in this thesis is to optimize gating/riser systems based on CAD and simulation technology with the goal of improving casting quality such as reducing incomplete filling area, decreasing large porosity and increasing yield. Therefore in the thesis, an optimization framework is presented based on CAD and simulation technology. Given a CAD model of part design and after converted to a casting model, it is the first step to evaluate castability of the casting design. Then the runner and risers are represented parametrically, and CAD models generated by varying parameters can be used in the simulation. After analyzing simulation results, the gating/riser syst
Tipologia: Teses (TCC)
1 / 67
Esta página não é visível na pré-visualização
Não perca as partes importantes!
Worcester Polytechnic Institute
By Feng Liu Submitted to the Faculty^ A Thesis of the WORCESTER POLYTECHNIC INSTITUTE in partial fulfillment of the requirements for the Degree of Master of Sciencein Manufacturing Engineering By _____________________Feng Liu December 2008 APPROVED:
Prof. Yiming (Kevin) Rong, Advisor, Associate Director of Manufacturing and Materials Engineering,
i
Casting as a manufacturing process to make complex shapes of metal materials in mass production may experience many different defects such as porosity and incomplete filling. How to improve the casting quality becomes important. Gating/riser system design is critical to improving casting quality. The objective of the research presented in this thesis is to optimize gating/riser systems based on CAD and simulation technology with the goal of improving casting quality such as reducing incomplete filling area, decreasing large porosity and increasing yield. Therefore in the thesis, an optimization framework is presented based on CAD and simulation technology. Given a CAD model of part design and after converted to a casting model, it is the first step to evaluate castability of the casting design. Then the runner and risers are represented parametrically, and CAD models generated by varying parameters can be used in the simulation. After analyzing simulation results, the gating/riser system design is optimized to improve casting quality. In the thesis, one engine block is used to verify the effectiveness of the optimization method. Compared with the initial design, it is found that the optimized casting design can decrease porosity around 18% while the yield increases 16%.
vii
models will be obtained. After analyzing simulation results, the original gating/riser system design will be optimized to improve casting quality. In this thesis, one engine block is used to verify the effectiveness of the optimization method. Compared with the initial design, the optimized casting assembly can decrease porosity around 18% while the yield increases 16%.
This chapter provides an introduction to sand casting process. First the steps of sand casting process are addressed. Then, considerations required for casting process design are stated. Next, casting quality and some common defects are discussed. After this, gating/riser system and castability analysis are explained in detail. Finally, the remained problems of casting process design and the objective of the thesis are given.
Sand casting consists of placing a pattern (having the shape of the desired casting) in sand to make an imprint, incorporating a gating system, filling the resulting cavity with molten metal, allowing the metal to cool until it solidifies [21]. Sand casting is still the most popular form of casting. The steps to make sand castings are illustrated in Fig 2.1 [3].
Figure 2.1 Production steps in a typical sand casting process
Pattern
Sand Mold
Pouring into mold Melting of metal Solidification and cooling Remove risers and gates
Cleaning and finishing
Heat Treatment
Inspection
Pattern Making Core Making Gating system
Furnaces
The typical sand casting process design consists of the following steps. Sand Selection [3] Several factors are important in the selection of sand for molds, and it involves certain tradeoffs with respect to properties. Although fine-grained sand enhances mold strength, the fine grains also lower mold permeability. Good permeability of molds and cores allows gases and steam evolved during the casting to escape easily. The mold has should have good collapsibility to allow for the casting to shrink while cooling and, thus, to avoid defects in the casting, such as hot tearing and cracking.
Parting line Parting line [3]^ is the line or plane separating the upper and the lower halves of molds. In general, the parting line should be along a flat plane rather than be contoured. Whenever possible, the parting line should be at the corners or edges of castings rather than on flat surfaces in the middle of the casting. It should be placed as low as possible for less dense metals and located at around mid-height for denser metals.
Pattern design The pattern [1]^ is a replica of the object to be cast, used to prepare the cavity into which molten material will be poured during the casting process. Patterns used in sand casting may be made of wood, metal, plastic or other materials. Patterns are made to exacting standards of construction, so that they can last for a reasonable length of time. The mold is made by packing some readily formed aggregate material, such as molding sand, around the pattern. When the pattern is withdrawn, its imprint provides the mold cavity, which is ultimately filled with metal to become the casting.
During the design process of pattern, some considerations should be taken. For example, the pattern needs to incorporate contraction allowances, which are suitable allowances for shrinkage. And also it needs to incorporate suitable allowances for draft. If the casting is to be hollow, as in the case of pipe fittings, additional patterns, referred to as cores, are used to form these cavities.
Core design Cores are forms, usually made of sand, which are placed into a mold cavity to form the interior surfaces of castings. Thus the void space between the core and mold- cavity surface is what eventually becomes the casting. The following picture shows the sand cores.
Figure 2.3 Examples of sand casting Gating/riser system design and optimization The preparation of molten metal for casting is referred to simply as melting. Melting is usually done in a specifically designated area of the foundry, and the molten metal is transferred to the pouring area where the molds are filled. After pouring metal, it will flow through the gating system until the cavity is fully filled. Then the metal begins to cool and solidify with the occurrence of shrinkage. Riser system is designed to compensate such shrinkage. Gating/riser system has great effects
Two common defects in sand casting process are caused by porosity and incomplete filling. Porosity may be the most persistent phenomena in casting, and it is hard to be eliminated completely. Porosity is harmful to the ductility of the casting and its surface finish. Porosity in castings is due to bubbles being trapped during solidification. It may be caused by shrinkage, or gases, or both. There are many factors contribute to the development of porosity such as the entrapped air during filling, blowholes from unvented cores, dissolved gases from melting, etc. Because liquid metals have much greater solubility for gases than do solid metals, when a metal begins to solidify, the dissolved gases are expelled from the solution. It will cause microporisty or accumulate in regions of existing porosity.
Figure 2.5 Example of porosity Incomplete filling [2]^ is primarily caused by poor fluidity of molten metal, and manifests in the form of a cold shut or misrun. A cold shut occurs when two streams of molten metal coming from opposite directions meet, but don’t fuse completely. A misrun occurs when the molten metal does not completely fill a section of the mould cavity. The presence of surface oxides and impurities on the advancing front of liquid metal aggravates such defects.
Figure 2.6 Cold-shut defect
Figure 2.7 Misrun defect The casting quality is heavily dependent on the success of gating/riser system design. Next the gating/riser system will be introduced in detail.
A key element in producing quality aluminum castings is the proper design and sizing of the gating and riser systems [10]. A foundry can produce the best quality molds, cores and molten aluminum and still end up with a poor quality casting by using poorly designed gating and riser systems. A typical gating/riser system is shown below.
(1) Temperature: If the casting has thinner cross sections and if the pouring temperature is low, misruns can be easily developed. So casting temperatures should be just high enough to prevent flow misruns. (2) Chemistry: Of the chemical elements added to aluminum alloys, silicon has the greatest affect on fluid life. The higher the silicon level, the greater the fluid life. While the chemistry of the alloy used also affects its solidification range. Pure metals, eutectic alloys and narrow freezing range alloys tend to exhibit the best fluid life. (3) Entrained gas and inclusions: It is easy to understand that both entrained gas and inclusions tend to increase the viscosity of molten metal, so accordingly its fluidity will be decreased.
2.4.1.2 Requirements of Gating System There are many factors affecting the design of an ideal gating system. For example, the gating system should be designed to allow the molten metal flow through with the least amount of turbulence. It is a better design of the gating system that it can be removed easily from the casting after filling. The gating system should be designed in such a way to promote the directional solidification. After meeting other requirements of gating system, it will also need lower yield.
2.4.1.3 Runner Runner is typically located in the drag of the casting. Because molten aluminum often changes its direction during the flow process in the runner, turbulence often accumulates. For a good runner design, it must not promote turbulence. There are some
useful experience in real foundry such as always use radiuses corners, never sharp corners, etc. As described earlier, two primary requirements of a gating system are to prevent cold shuts and misruns during mold filling. To meet these requirements, all the gates must be feeding at the same time. This can be accomplished by stepping down the runner as each gate is passed. In real foundry environment, engineers prefer to taper the runner without stepping down to decrease the turbulence.
2.4.1.4 Gates Gates are the inlets into the mold cavity. The gates can be no thicker than the casting section to which they are attached. Even more it usually is best to have the gates slightly thinner than the casting section. If the gating system is not completely filled during the entire pour, it will not function correctly, and defective castings can result.
A riser [1]^ or a feeder is a reservoir built into a metal casting mold to prevent cavities due to shrinkage. Because metals are less dense as liquids than as solids (with some exceptions), castings shrink as they cool. This can leave a void, generally at the last point to solidify. Risers prevent this by providing molten metal at the point of likely shrinkage, so that the cavity forms in the riser, not the casting.
2.4.2.1 Solidification After molten metal is poured into a mold, solidification will take place. In the casting process, solidification plays a critical role because the speed at which