
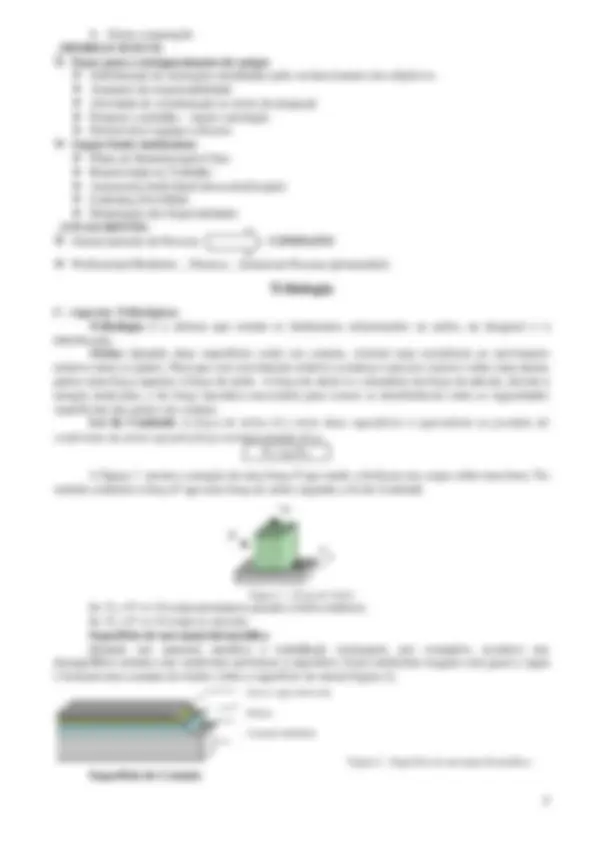
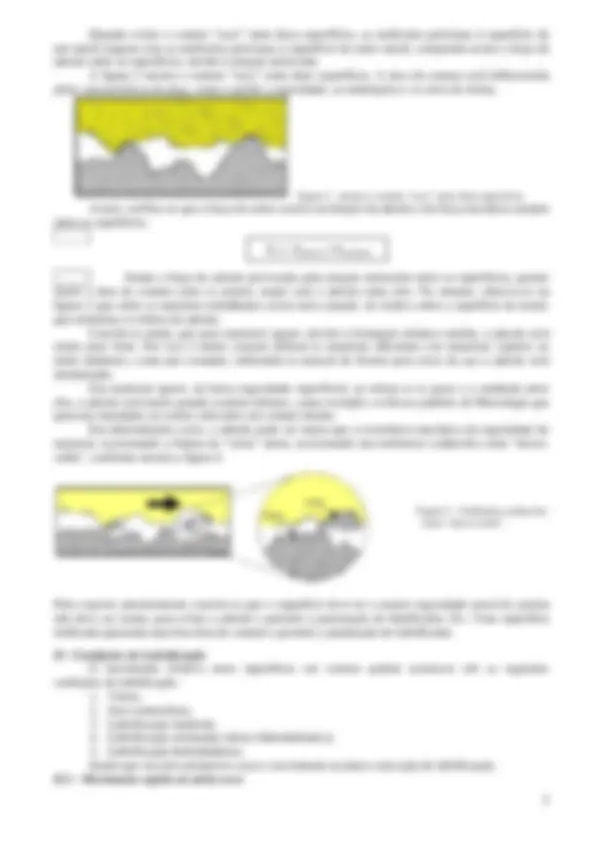
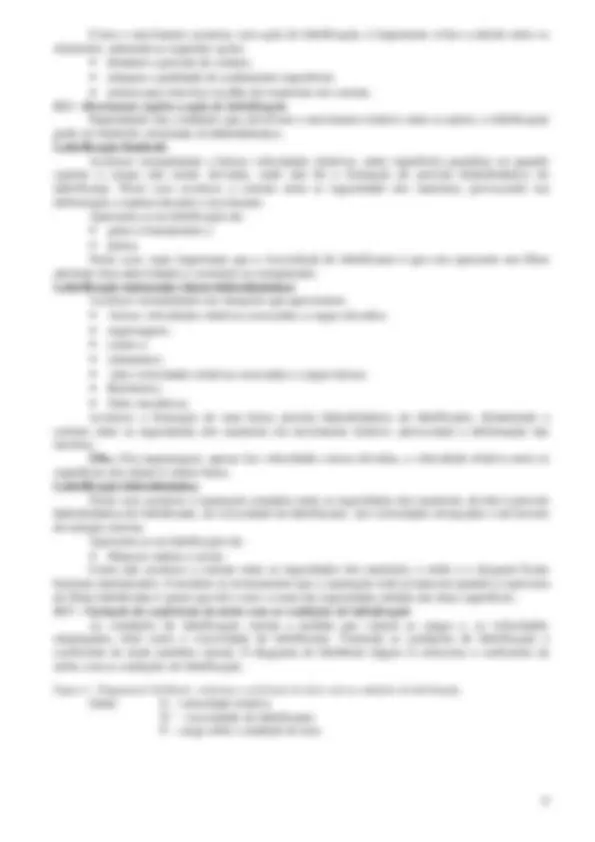
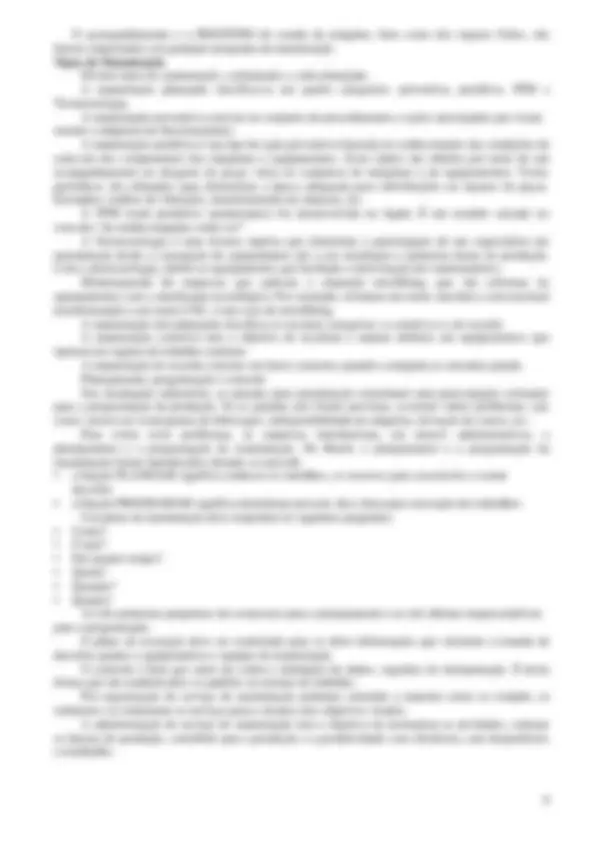
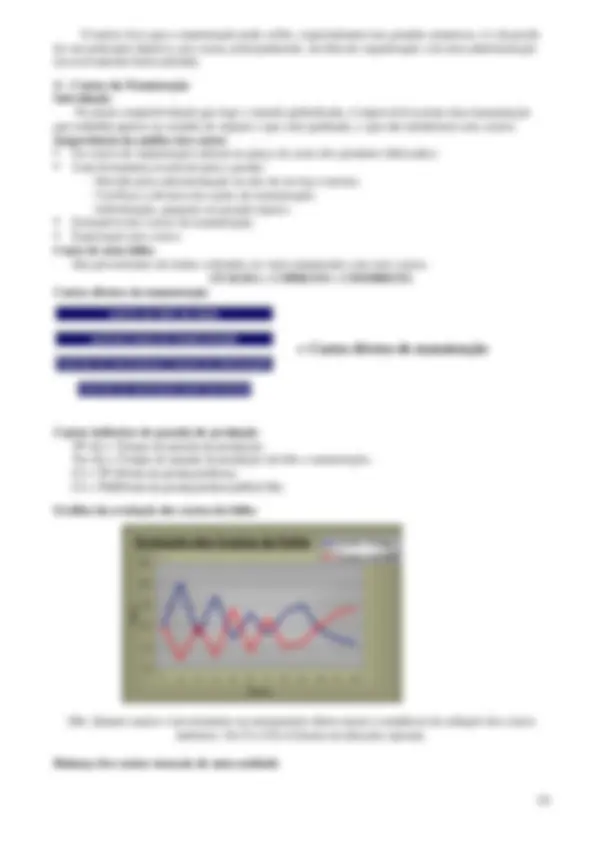
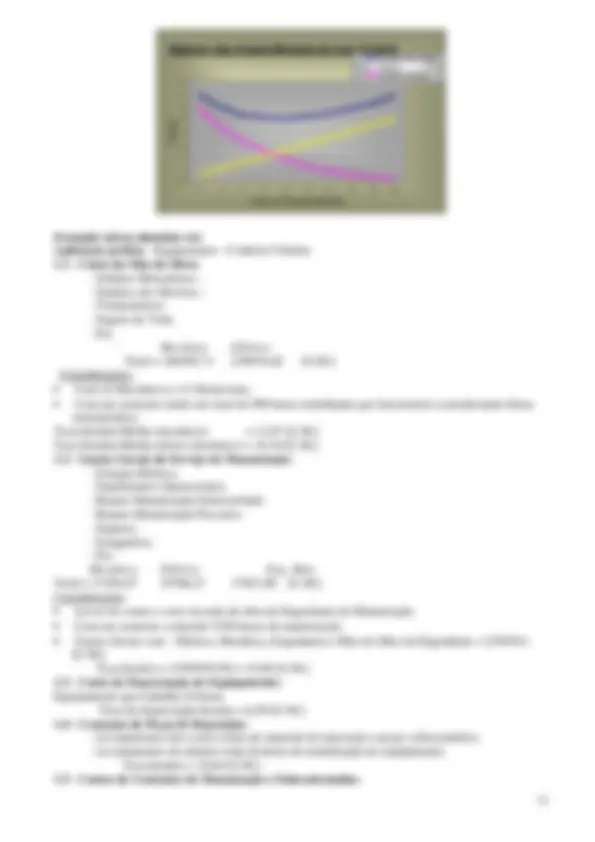
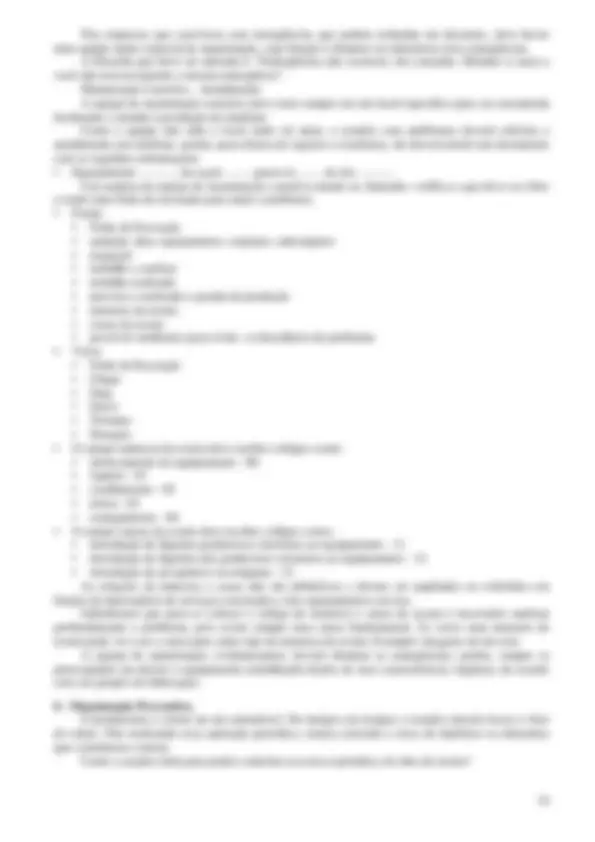
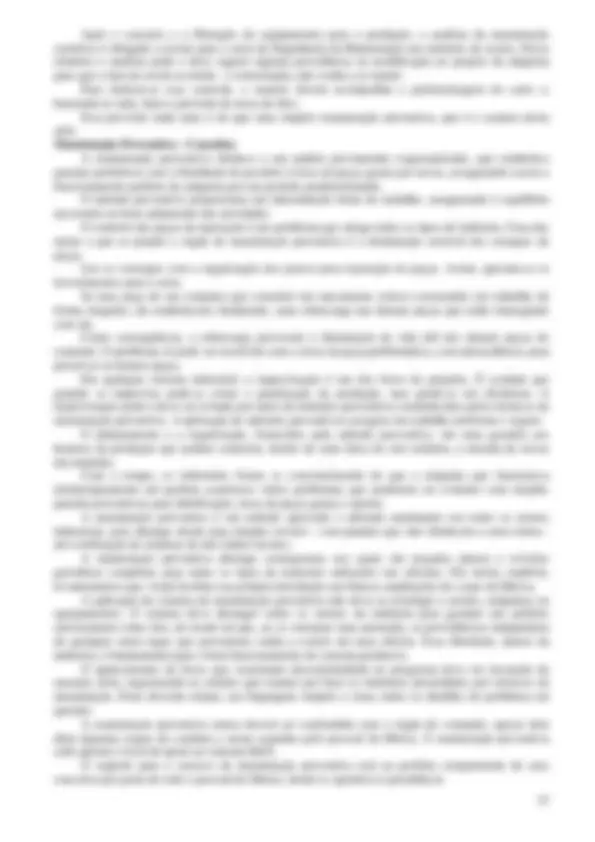
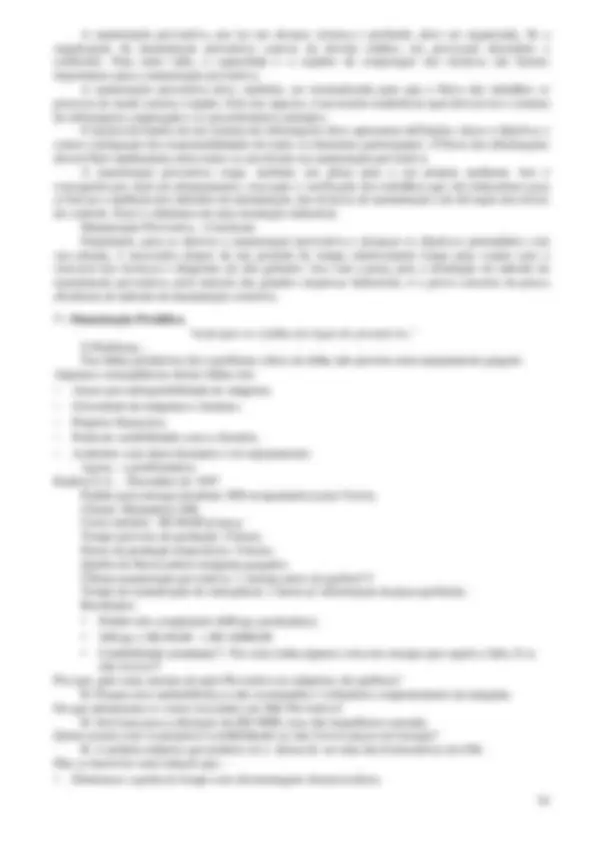
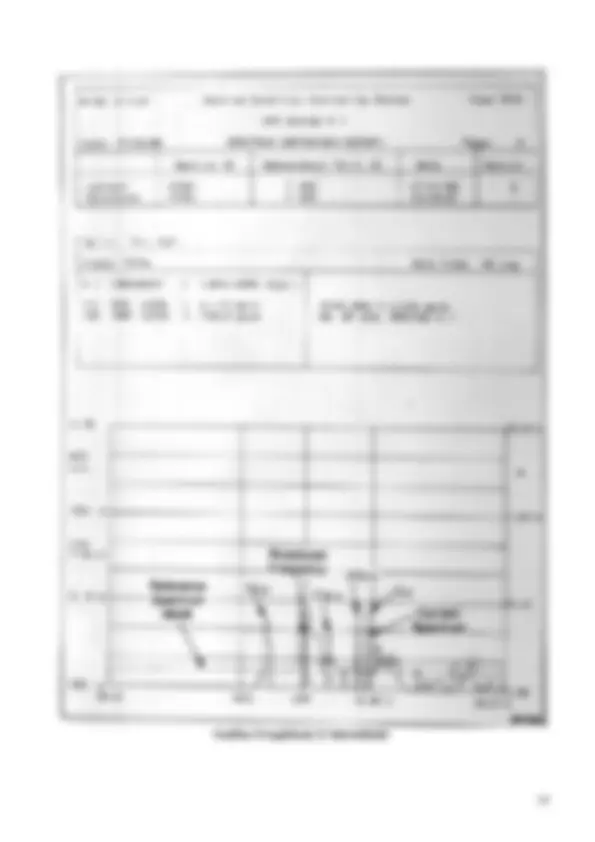
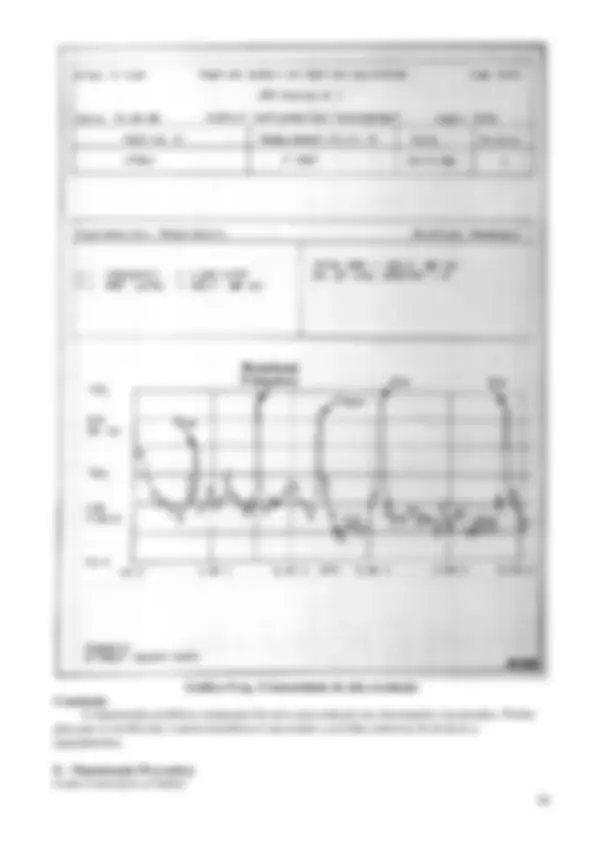
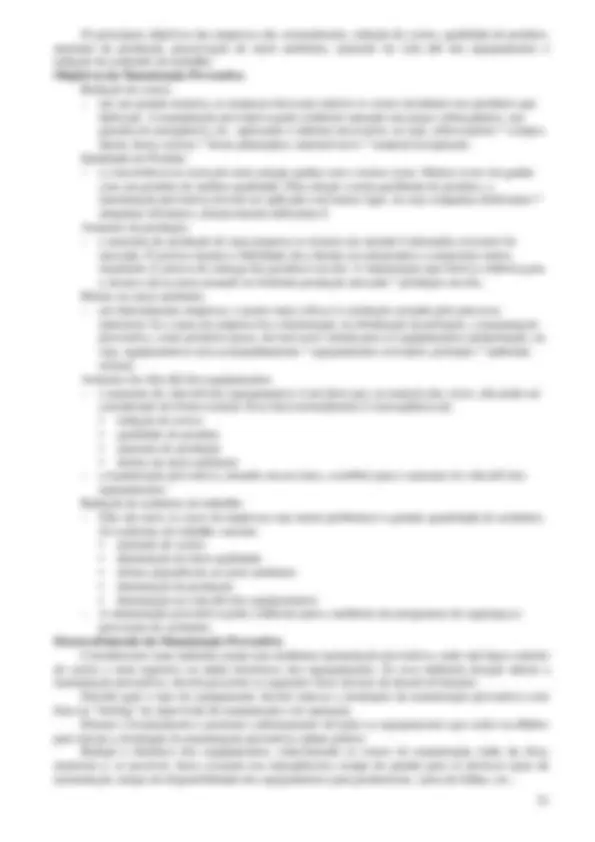
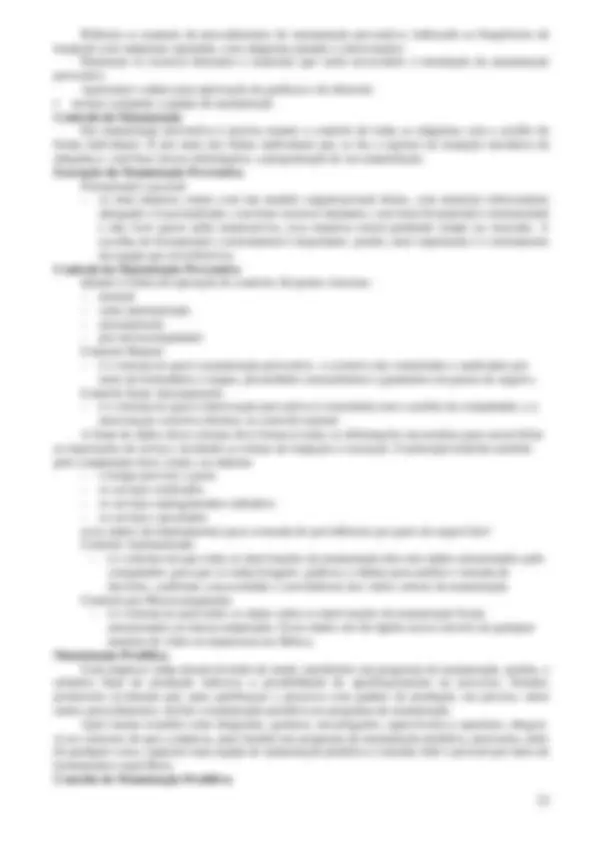
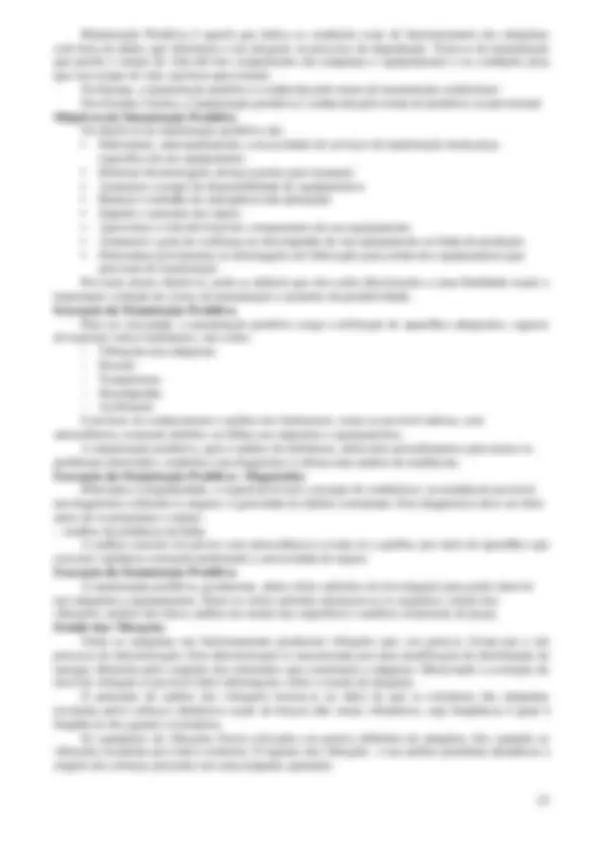
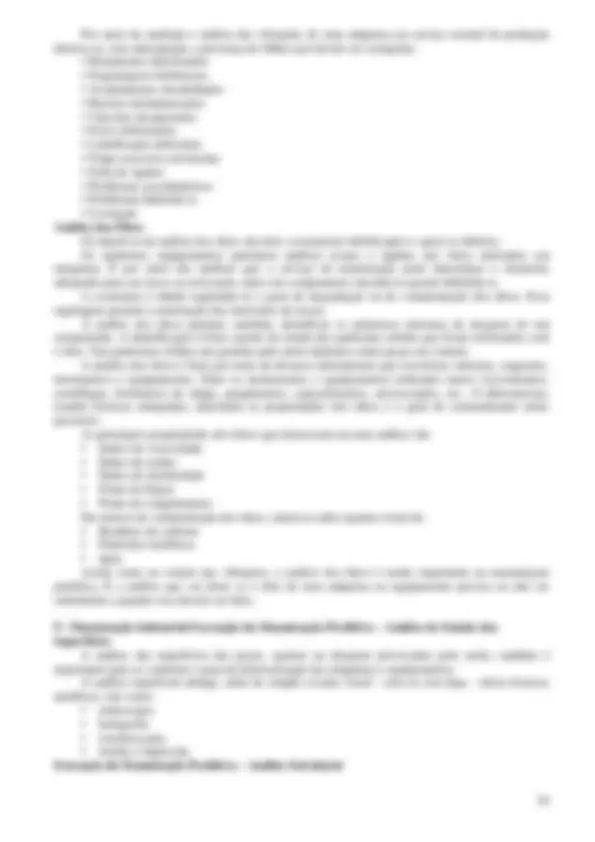
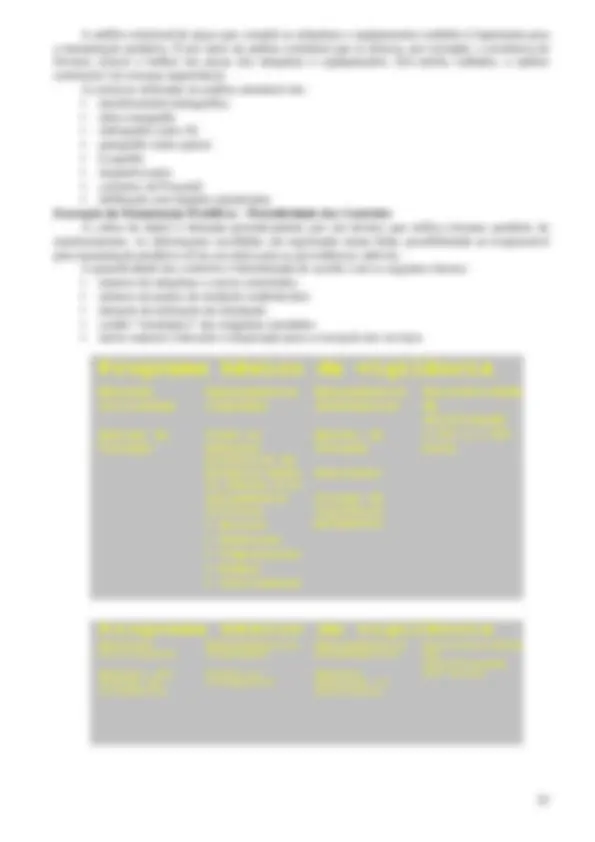
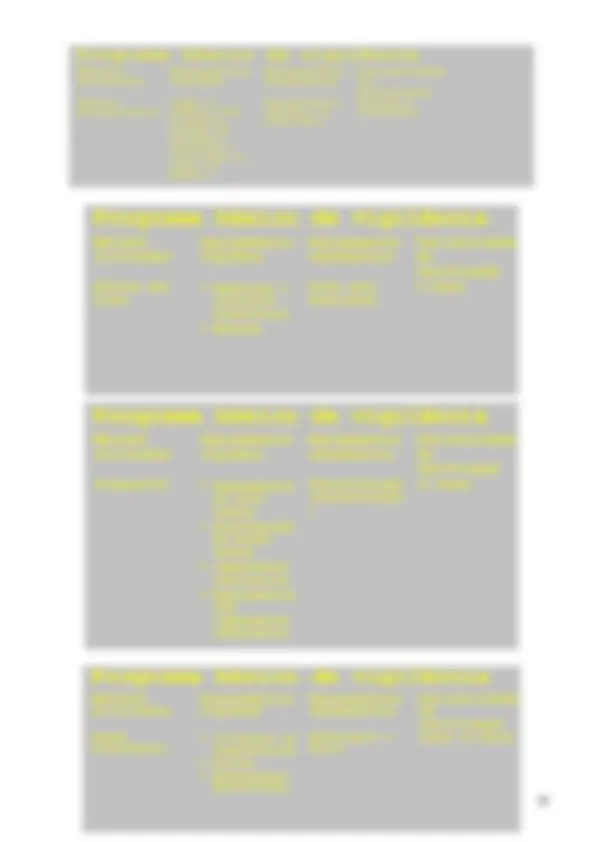
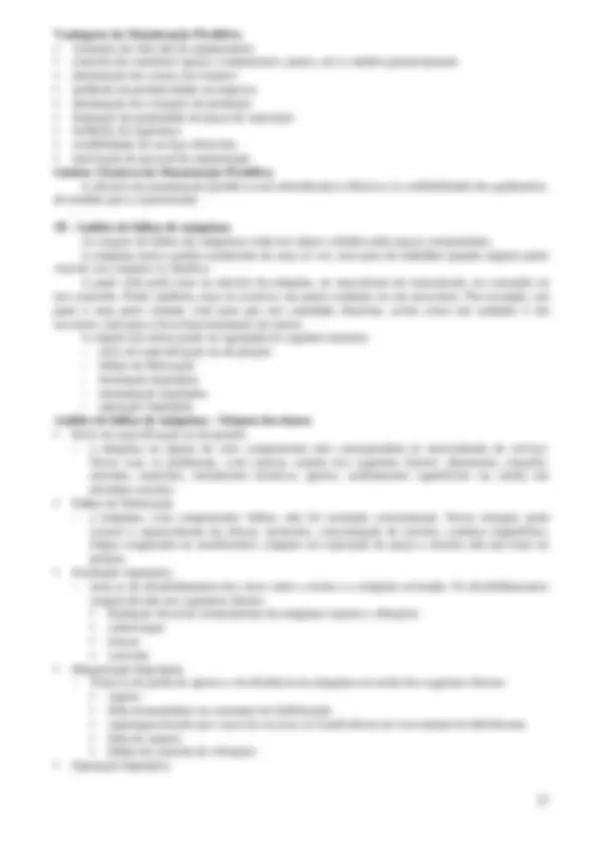
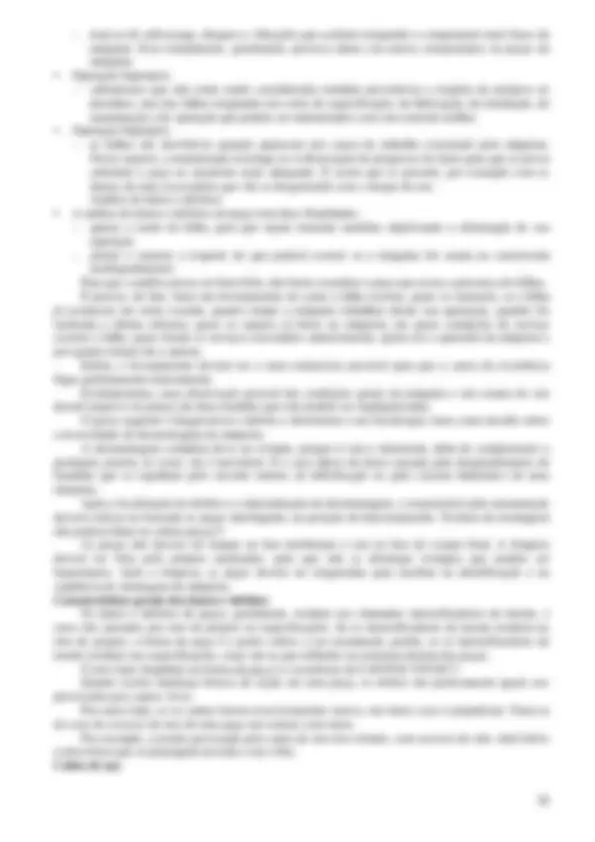
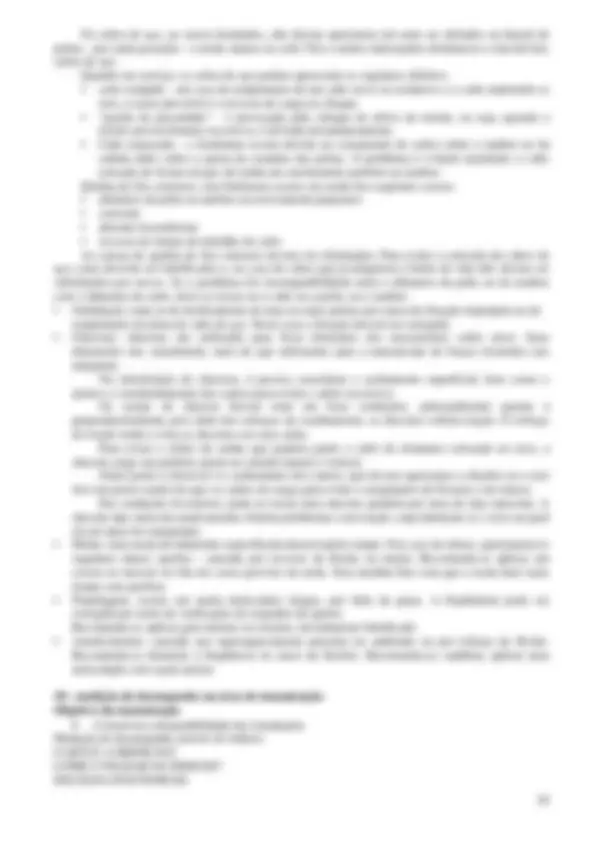
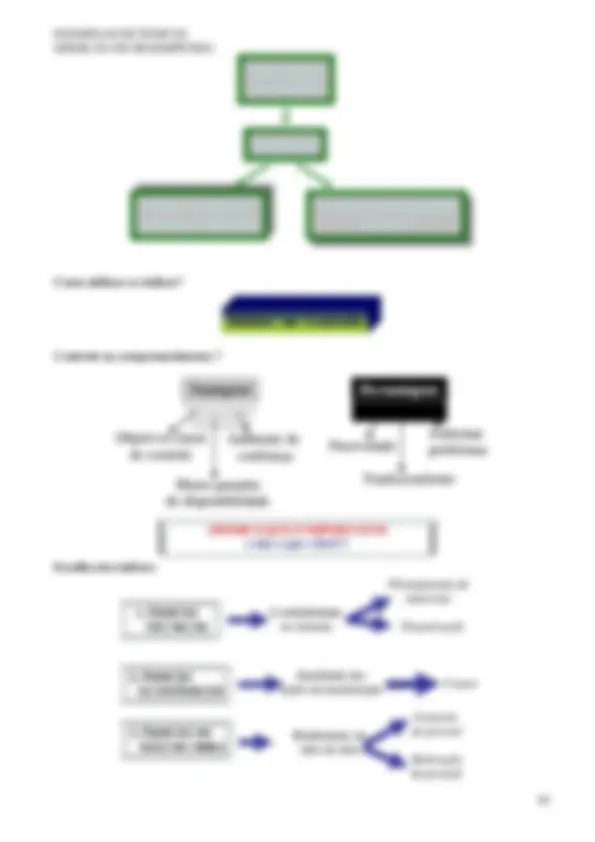
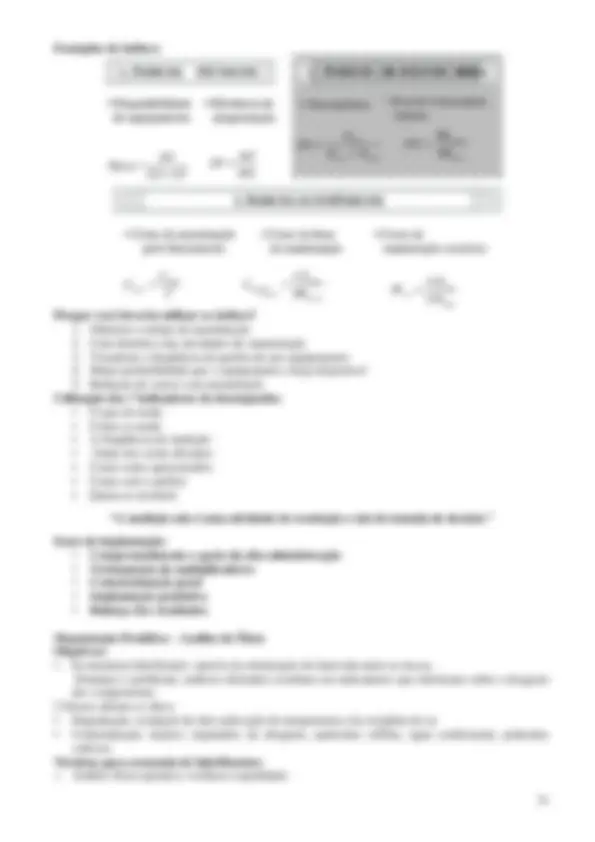
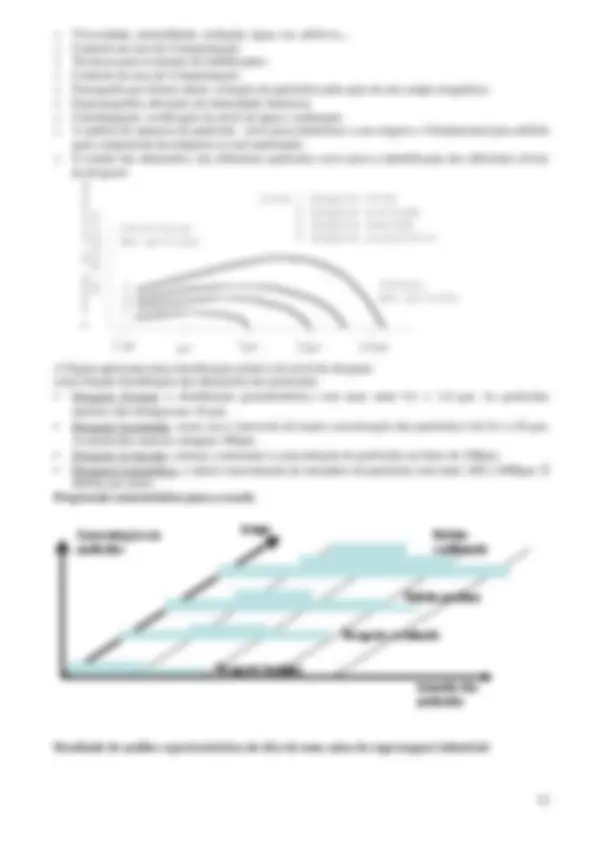
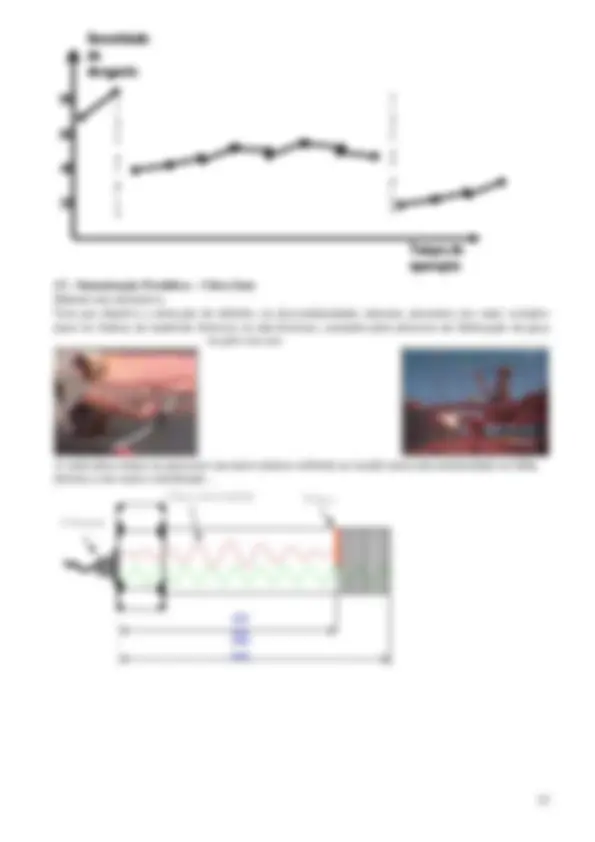
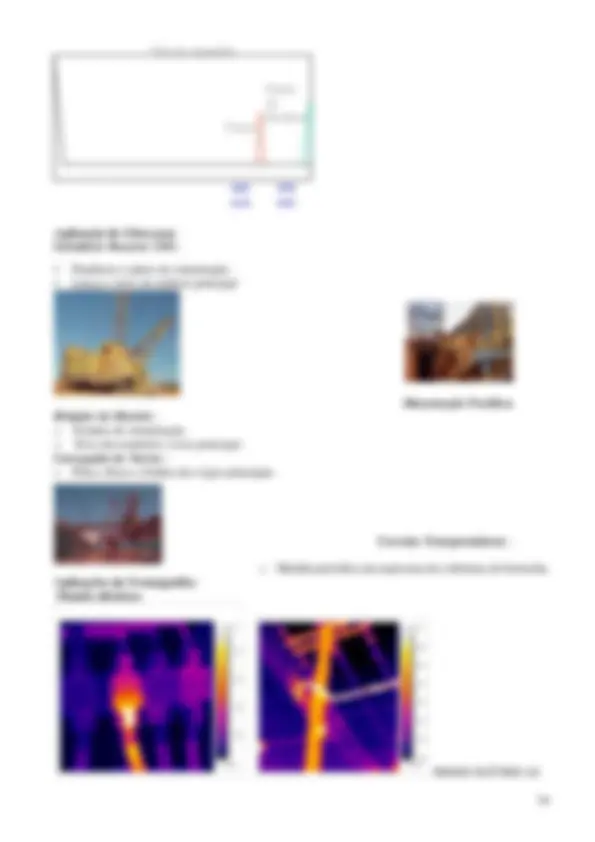
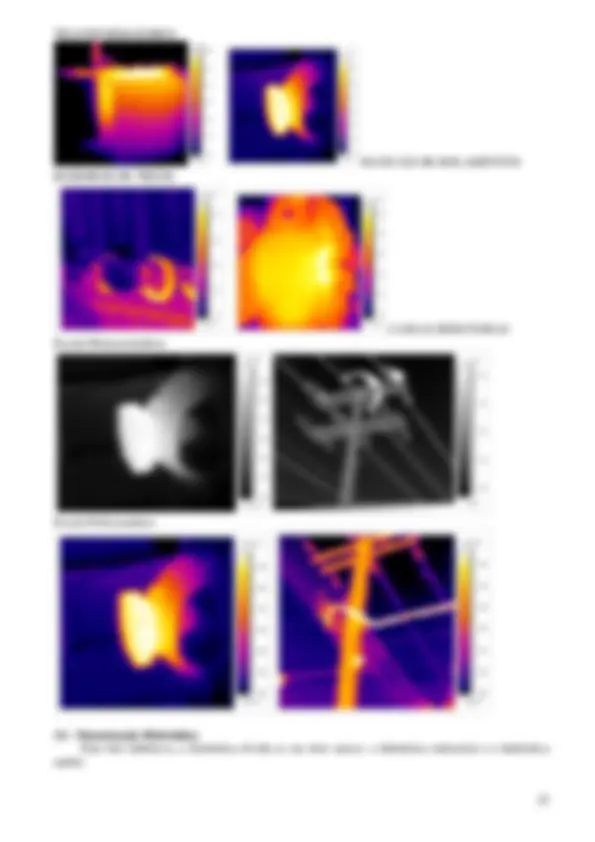
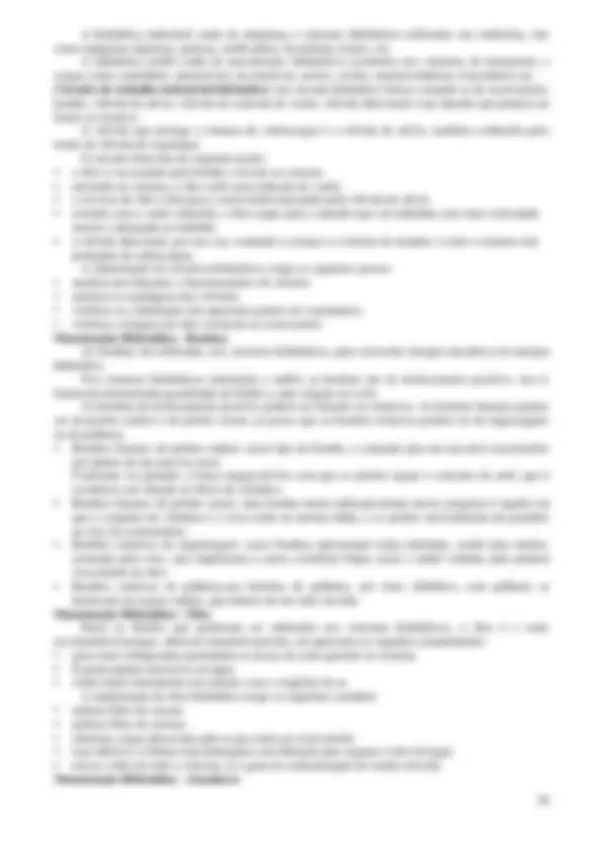
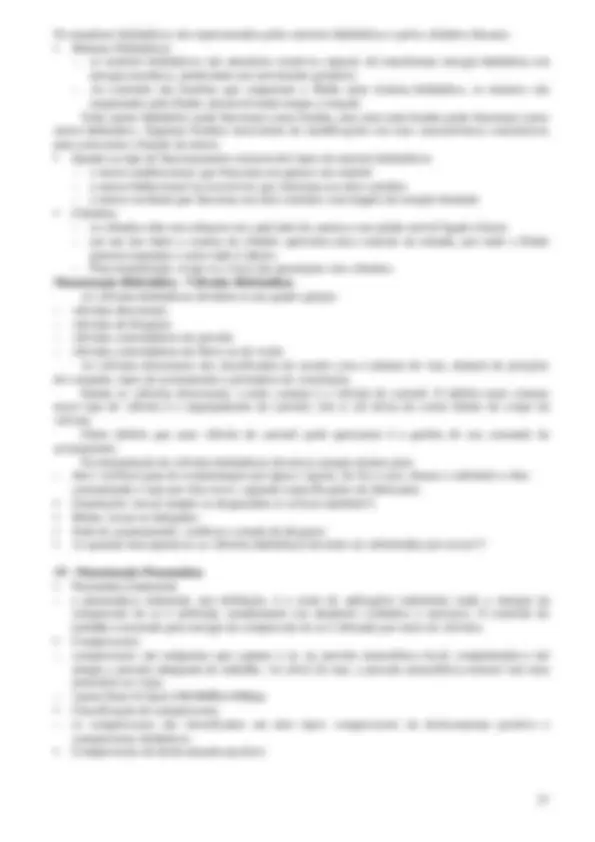
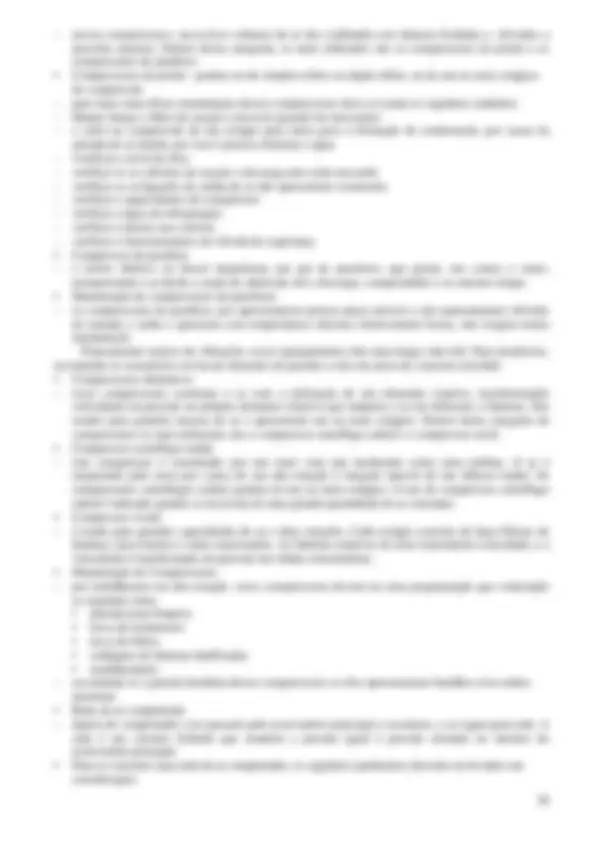
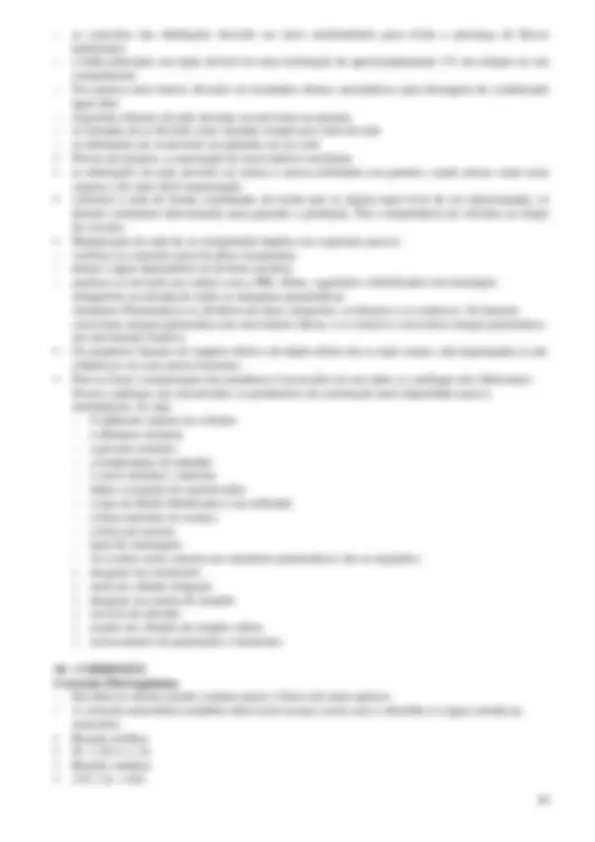
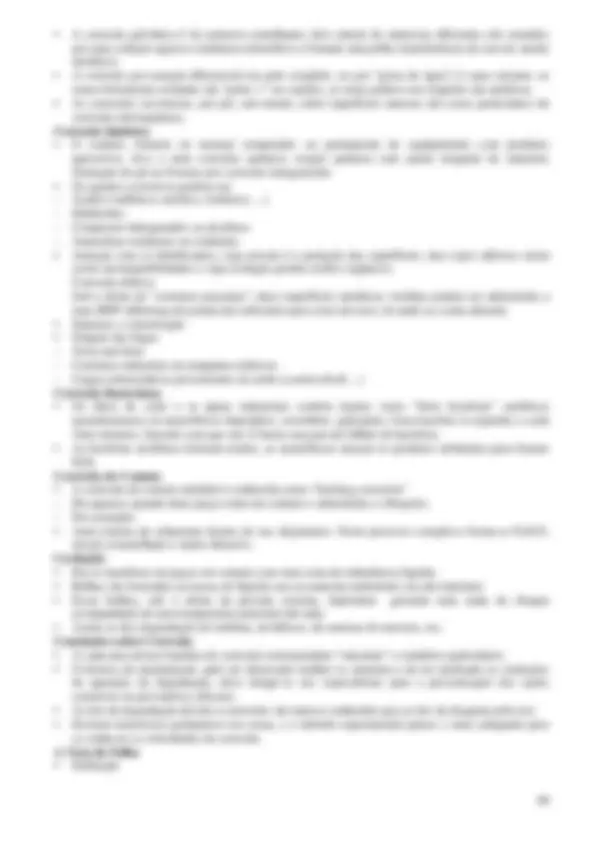
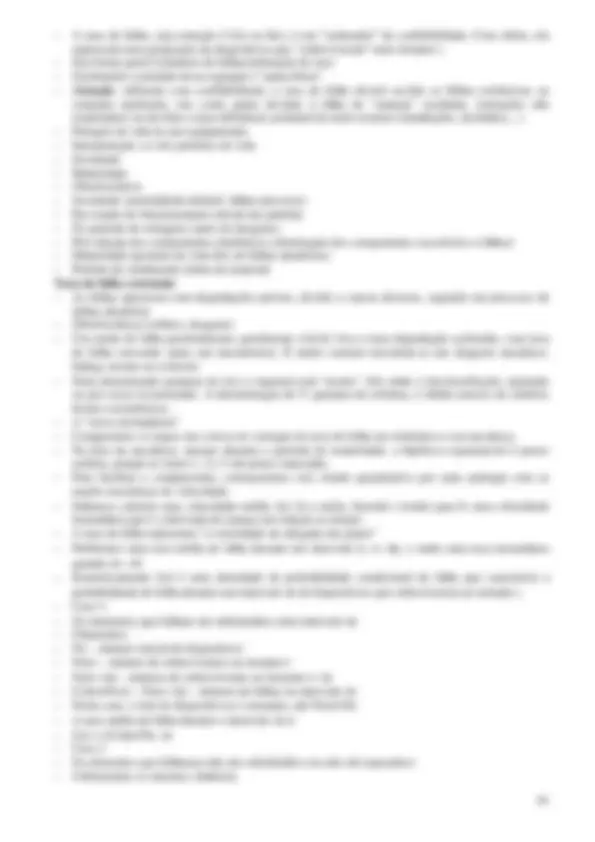
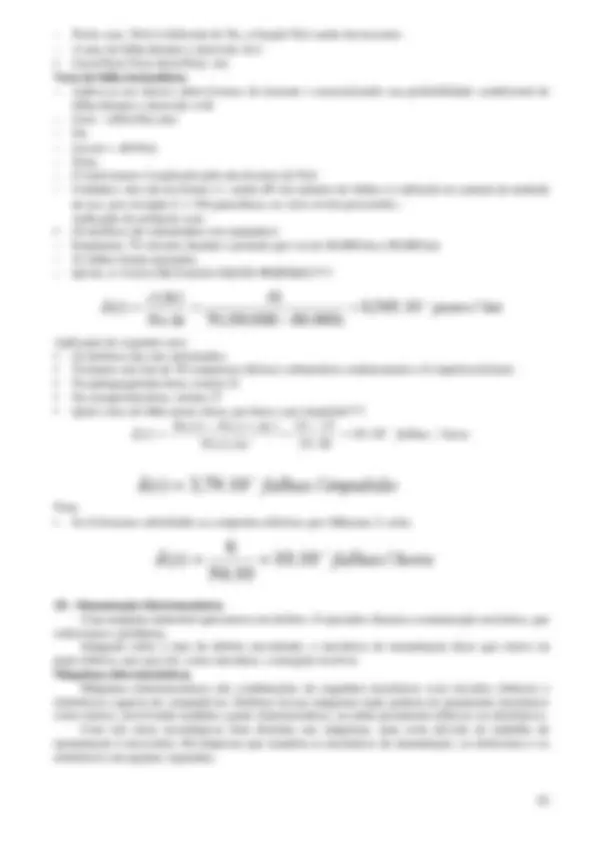
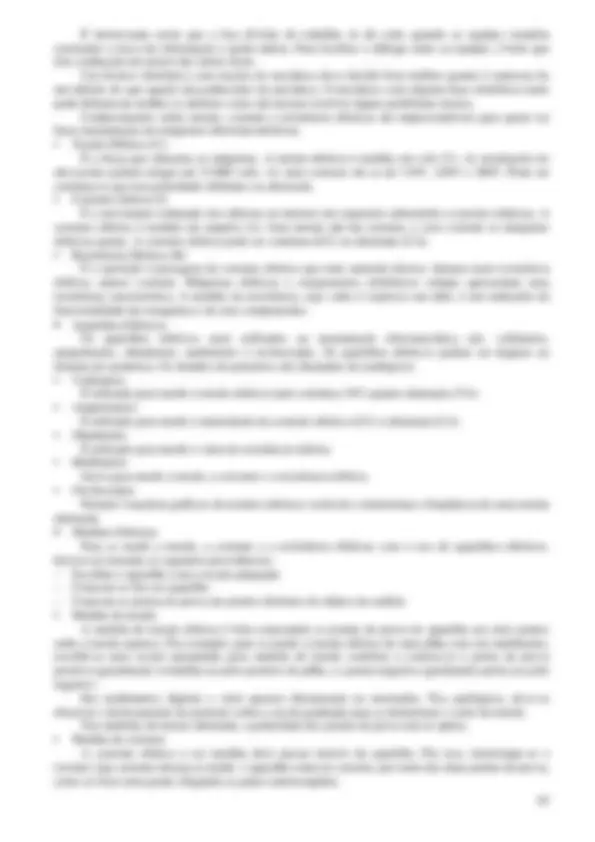
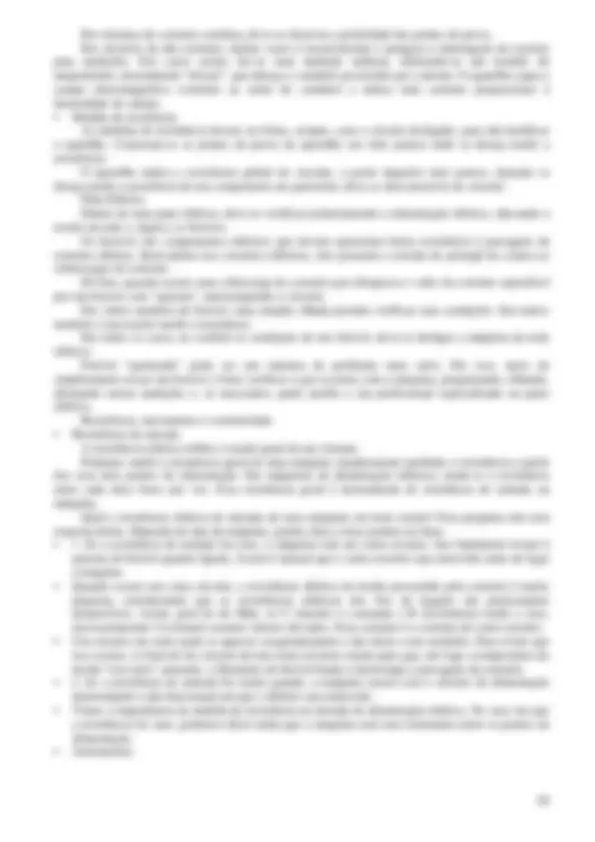
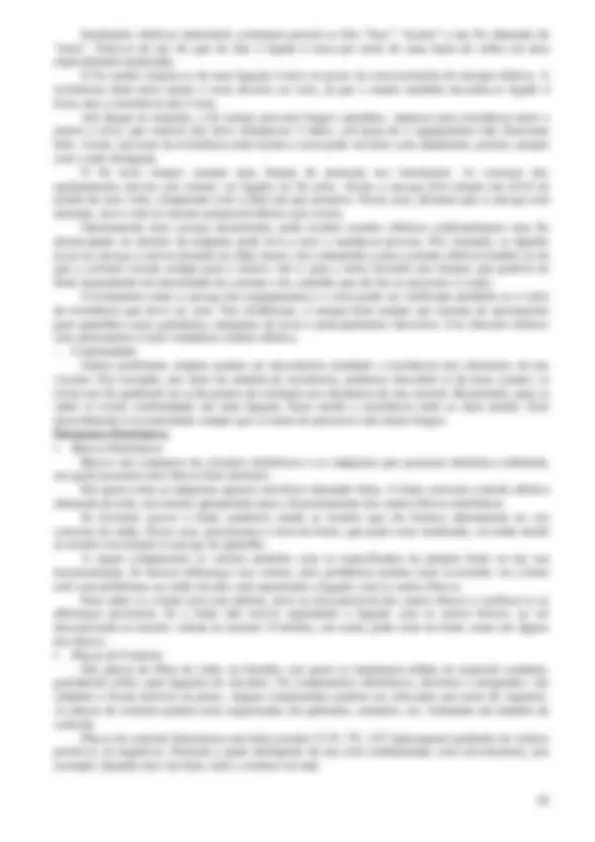
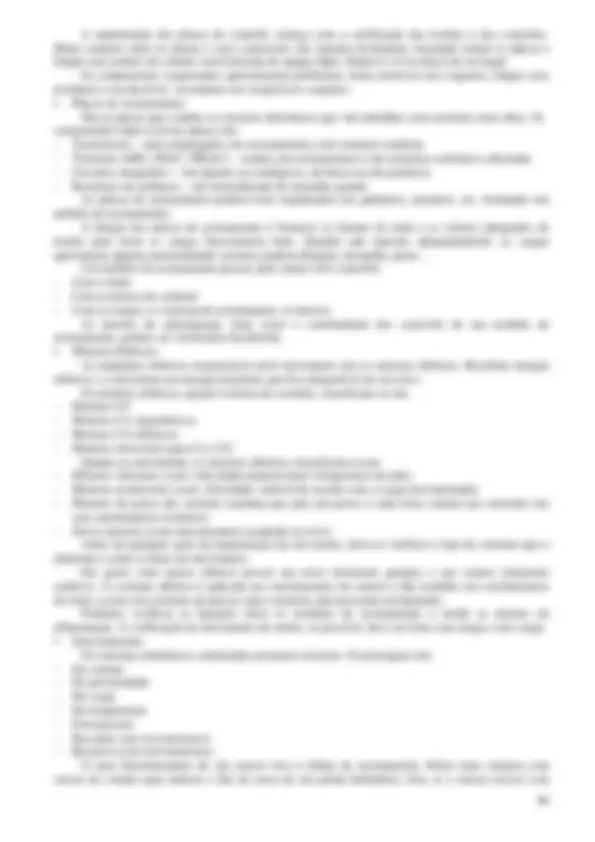
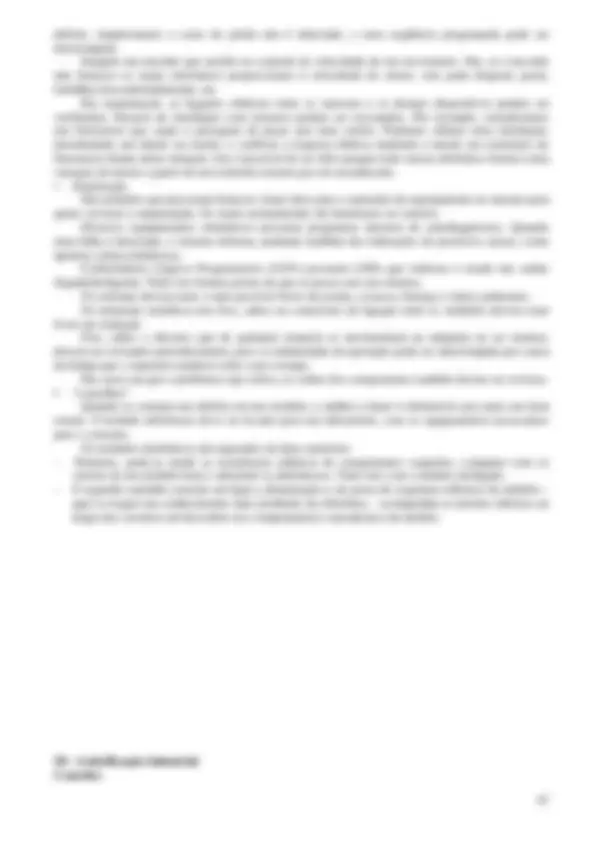
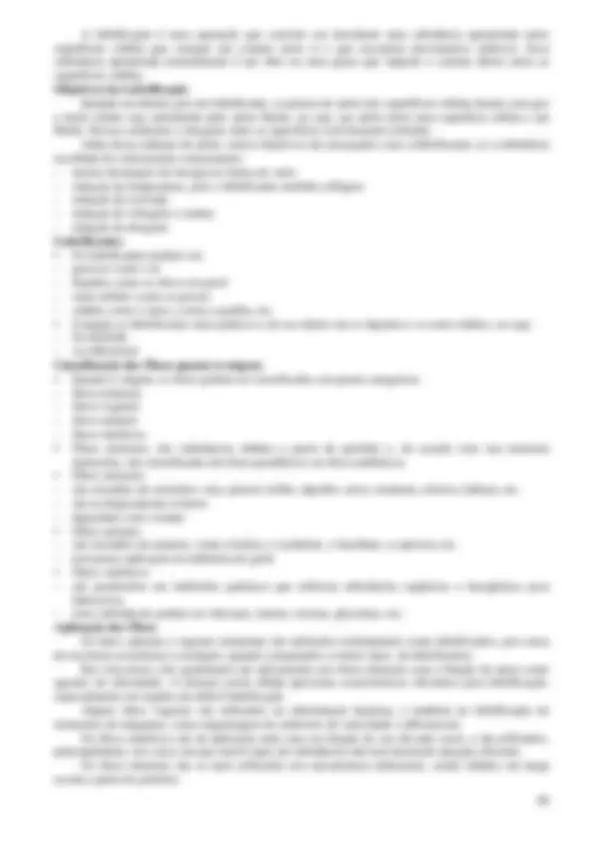
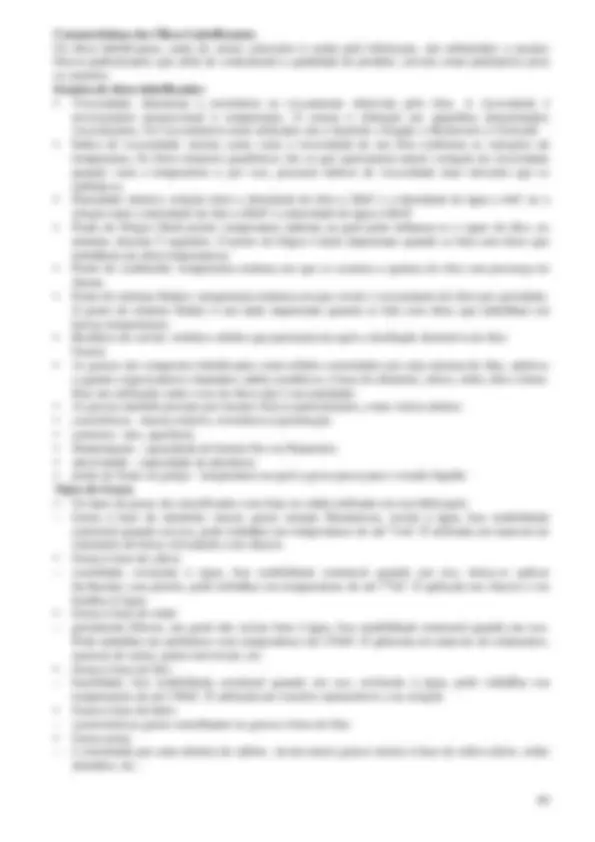
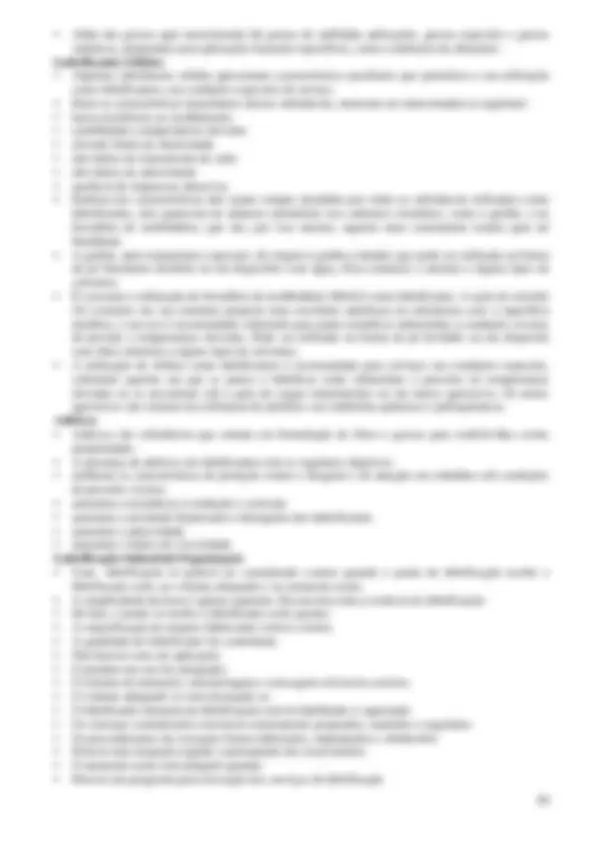
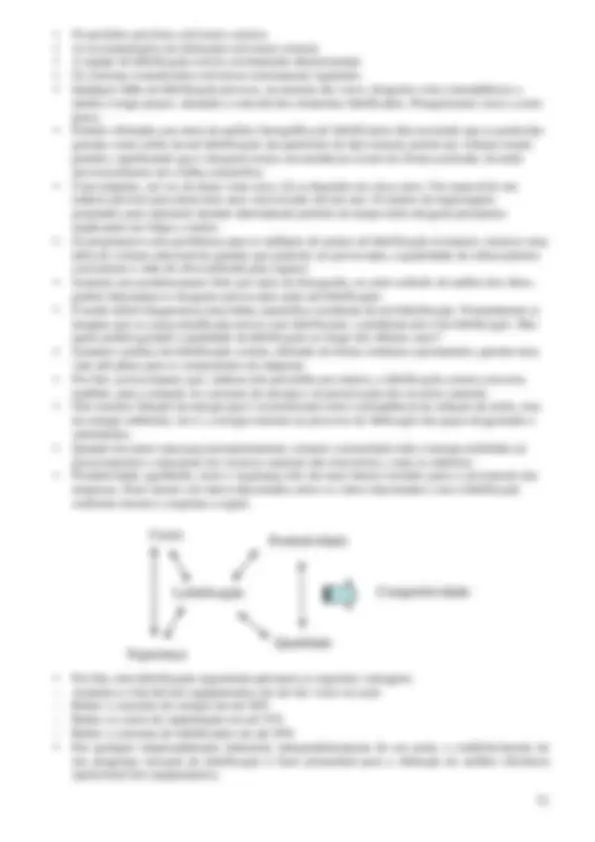
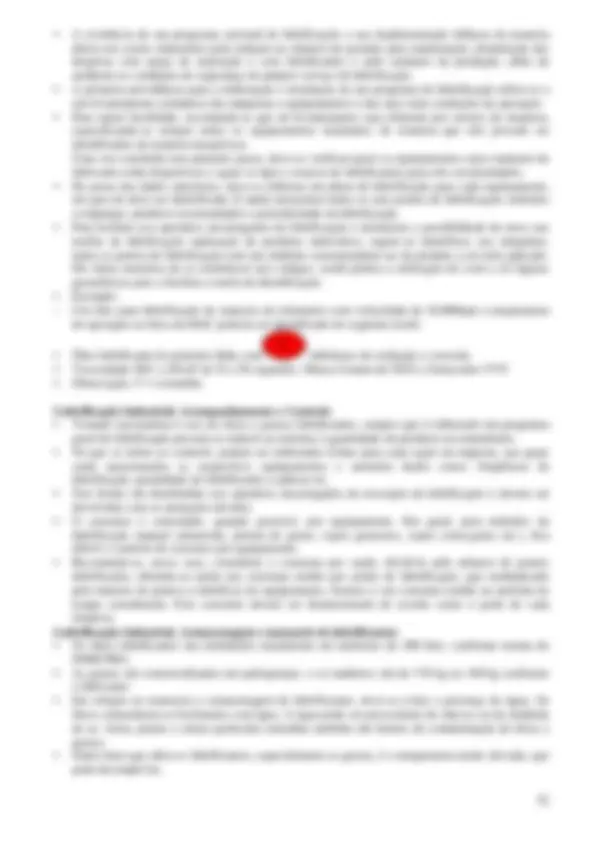
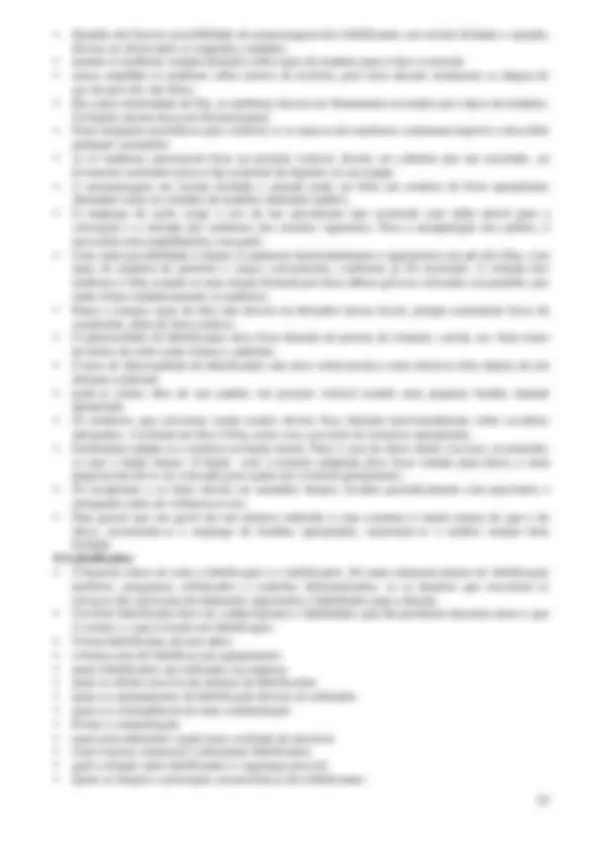
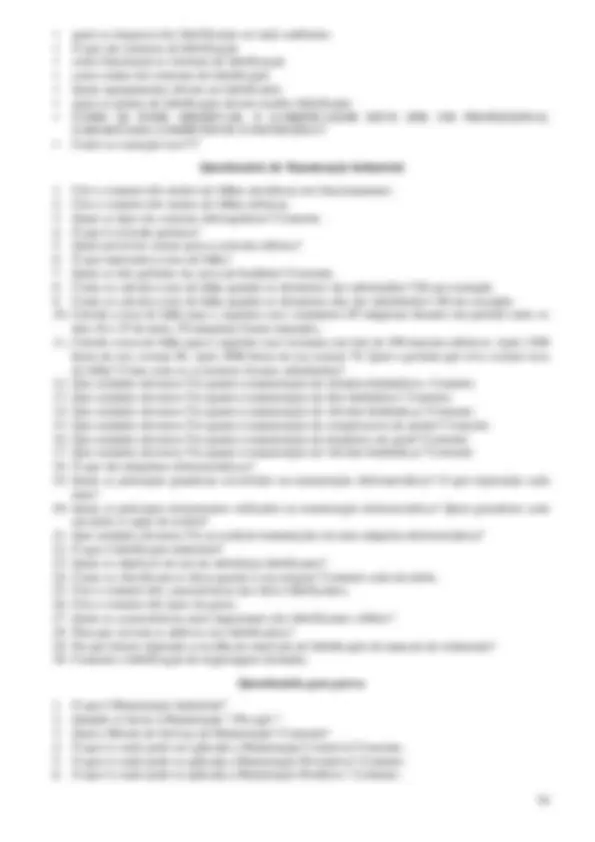
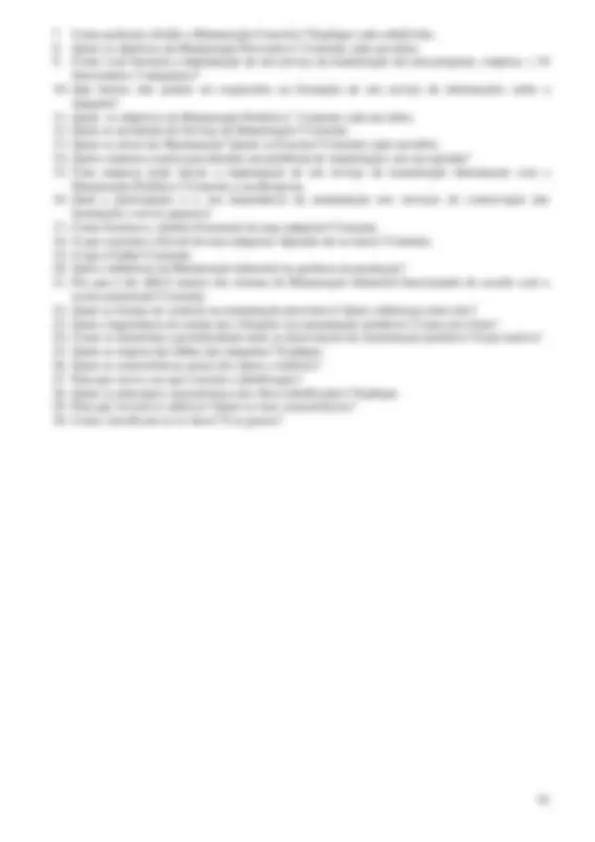
Estude fácil! Tem muito documento disponível na Docsity
Ganhe pontos ajudando outros esrudantes ou compre um plano Premium
Prepare-se para as provas
Estude fácil! Tem muito documento disponível na Docsity
Prepare-se para as provas com trabalhos de outros alunos como você, aqui na Docsity
Os melhores documentos à venda: Trabalhos de alunos formados
Prepare-se com as videoaulas e exercícios resolvidos criados a partir da grade da sua Universidade
Responda perguntas de provas passadas e avalie sua preparação.
Ganhe pontos para baixar
Ganhe pontos ajudando outros esrudantes ou compre um plano Premium
Comunidade
Peça ajuda à comunidade e tire suas dúvidas relacionadas ao estudo
Descubra as melhores universidades em seu país de acordo com os usuários da Docsity
Guias grátis
Baixe gratuitamente nossos guias de estudo, métodos para diminuir a ansiedade, dicas de TCC preparadas pelos professores da Docsity
A importância da manutenção industrial na produção normal, qualidade dos produtos, redução de custos, aumento da competitividade, manutenção de clientes e aquisição de novos clientes. Descreve os serviços da manutenção de rotina e preventiva, incluindo a programação de trabalhos, custos de depreciação, consumo de peças de reposição e benefícios. Além disso, discute a manutenção hidráulica, especificamente em relação a bombas, atuadores e válvulas hidráulicas.
O que você vai aprender
Tipologia: Resumos
1 / 54
Esta página não é visível na pré-visualização
Não perca as partes importantes!
Programa
1-EMENTA Organização e administração da manutenção. Sistemas de manutenção. Almoxarifado. Fatores causadores de danos. Análise de falhas de equipamentos. Manutenção em alguns elementos específicos/lubrificação. Trabalho final.
2- OBJEITIVOS 2.1_ Geral: Desenvolver no aluno a capacidade de promover e gerenciar a manutenção industrial, baseando- se nos conceitos desenvolvidos através de exemplos práticos. 2.2_ Específicos:
3- CRONOGRAMA 20 encontros com 2 horas/aula cada. 15 encontros com 4horas/aula cada.
4- CONTEÚDO PROGRAMÁTICO − Manutenção − Manutenção Corretiva − Manutenção Preventiva − Manutenção Preditiva − Lubrificação Industrial − Manutenção Eletromecânica − Manutenção Hidráulica e Pneumática − Modos de Falha − Taxas de Falha e Confiabilidade
5- ESTRATÉGIAS 5.1_ Técnicas: aula expositiva dialogada e trabalhos individuais e em grupo. 5.2_ recursos: quadro branco, bibliografias, recursos audiovisuais e computacionais.
6- AVALIAÇÃO Duas provas escritas com igual peso.
Aspectos Motivacionais da Administração da Manutenção
_OBJETIVO: “Motivar às pessoas de todas as Áreas da Empresa à fazer e Entender a Manutenção. _ EVOLUÇÃO DAS TEORIAS:
Taylor: Estudo de Tempos Homens extraordinários O que? Quando? Como? Ford: “Não da um passo supérfluo” Homem ou Máquina? _TEORIA Y: Mc Gregor O Ser Humano tem Muito Potencial Motivação Gerência Herzberg Necessidades: _Básicas; _Mais Elevadas. Teoria da Motivação _ PIRÂMIDE DE MASLOW:
Premissa Básica Parâmetros a serem analisados
Quando existe o contato “seco” entre duas superfícies, as moléculas próximas à superfície de um metal reagem com as moléculas próximas à superfície do outro metal, compondo assim a força de adesão entre as superfícies, devido à atração molecular. A figura 3 mostra o contato “seco” entre duas superfícies. A área de contato será influenciada pelas características da peça, como o perfil, a rugosidade, as ondulações e os erros de forma.
Figura 3 - mostra o contato “seco” entre duas superfícies Assim, verifica-se que a força de atrito ocorre em função da adesão e da força mecânica atuante entre as superfícies.
Fa = Fadesão + Fmecânica
Sendo a força de adesão provocada pela atração molecular entre as superfícies, quanto maior a área de contato entre os metais, maior será a adesão entre eles. No entanto, observa-se na figura 2 que sobre os materiais trabalhados existe uma camada de óxidos sobre a superfície do metal, que minimiza os efeitos da adesão. Conclui-se ainda, que para materiais iguais, devido à formação atômica similar, a adesão será ainda mais forte. Por isso é muito comum utilizar-se materiais diferentes em materiais sujeitos ao atrito dinâmico, como por exemplo, utilizando-se mancal de bronze para eixos de aço a adesão será minimizada. Em materiais iguais, de baixa rugosidade superficial, ao retirar-se os gases e a umidade entre eles, a adesão será muito grande (contato íntimo), como exemplo, os blocos padrões de Metrologia que parecem imantados ao serem colocados em contato íntimo. Em determinados casos, a adesão pode ser maior que a resistência mecânica da rugosidade do material, ocasionando a fratura da “crista” desta, ocasionando um fenômeno conhecido como “micro- solda”, conforme mostra a figura 4.
Figura 4 – Fenômeno conhecido como “micro-solda”.
Pelo exposto anteriormente conclui-se que a superfície deve ter a menor rugosidade possível, porém não deve ser isenta, para evitar a adesão e permitir a penetração do lubrificante. Ex.: Uma superfície retificada apresenta uma boa área de contato e permite a penetração do lubrificante.
II - Condições de Lubrificação O movimento relativo entre superfícies em contato podem acontecer sob as seguintes condições de lubrificação:
Como o movimento acontece sem ação de lubrificação, é importante evitar a adesão entre os elementos, adotando as seguintes ações:
Figura 4 – Diagrama de Stribbeck - relaciona o coeficiente de atrito com as condições de lubrificação. Onde: Z – velocidade relativa N’ – viscosidade do lubrificante P – carga sobre a unidade de área
com o surgimento do relógio mecânico, quando surgiram os primeiros técnicos em montagem e assistência. Tomou corpo ao longo da Revolução Industrial e firmou-se, como necessidade absoluta, na Segunda Guerra Mundial. No princípio da reconstrução pós-guerra, Inglaterra, Alemanha, Itália e principalmente o Japão alicerçaram seu desempenho industrial nas bases de engenharia e manutenção. Nos últimos anos, com a intensa concorrência, os prazos de entrega dos produtos passaram a ser relevantes para todas as empresas. Com isso surgiu a motivação para se prevenir contra as falhas de máquinas e equipamentos. Esta motivação deu origem à manutenção preventiva. Em suma, nos últimos vinte anos é que tem havido preocupações de técnicos e empresários para o desenvolvimento de técnicas específicas para melhorar o complexo sistema:
O acompanhamento e o REGISTRO do estado da máquina, bem como dos reparos feitos, são fatores importantes em qualquer programa de manutenção. Tipos de Manutenção Há dois tipos de manutenção: a planejada e a não planejada. A manutenção planejada classifica-se em quatro categorias: preventiva, preditiva, TPM e Terotecnologia. A manutenção preventiva consiste no conjunto de procedimentos e ações antecipadas que visam manter a máquina em funcionamento A manutenção preditiva é um tipo de ação preventiva baseada no conhecimento das condições de cada um dos componentes das máquinas e equipamentos. Esses dados são obtidos por meio de um acompanhamento no desgaste de peças vitais de conjuntos de máquinas e de equipamentos. Testes periódicos são efetuados para determinar a época adequada para substituições ou reparos de peças. Exemplos: análise de vibrações, monitoramento de mancais, etc. A TPM (total produtive maintenance) foi desenvolvida no Japão. É um modelo calcado no conceito “de minha máquina cuido eu!” A Terotecnologia é uma técnica inglesa que determina a participação de um especialista em manutenção desde a concepção do equipamento até a sua instalação e primeiras horas de produção. Com a terotecnologia, obtêm-se equipamentos que facilitam a intervenção dos mantenedores. Modernamente há empresas que aplicam o chamado retrofitting, que são reformas de equipamentos com a atualização tecnológica. Por exemplo, reformar um torno mecânico convencional transformando-o em torno CNC, é um caso de retroffiting. A manutenção não planejada classifica-se em duas categorias: a corretiva e a de ocasião A manutenção corretiva tem o objetivo de localizar e reparar defeitos em equipamentos que operam em regime de trabalho contínuo A manutenção de ocasião consiste em fazer consertos quando a máquina se encontra parada Planejamento, programação e controle Nas instalações industriais, as paradas para manutenção constituem uma preocupação constante para a programação da produção. Se as paradas não forem previstas, ocorrem vários problemas, tais como: atrasos no cronograma de fabricação, indisponibilidade da máquina, elevação de custos, etc.. Para evitar estes problemas, as empresas introduziram, em termos administrativos, o planejamento e a programação da manutenção. No Brasil, o planejamento e a programação da manutenção foram introduzidos durante os anos 60.
Balanço dos Custos Mensais de uma Unidade
0
1
2
3
4
5
6
7
8
2 4 6 8 10 12 14 16 18 20 Horas de Paradas Mensais
Custos
Custo de uma Falha Custo Direto
Exemplo (alcoa alumínio s/a) Aplicação prática : Equipamento - Cordeira Tubular 1.1 - Custo da Mão de Obra:
Custos Serviços - Mecânica, Elétrica, Engenharia = 94419,11 [U.M.] Taxa horária = 94419,11/5356 = 17,63 [ U.M.] 2.1 - Custos da Preventiva ( TX HOR.):
Corretiva Preditiva 20/09/96 11:50 7: 30/10/96 0:15 20: 11/11/96 10:35 9: 17/12/96 0:31 17: 17/01/97 13:04 7: 20/03/97 2:31 13: 07/04/97 12:10 8: 23/05/97 4:41 11:
CUSTOS & DISPONIBILIDADE
Custo & Disponibilidade
0
1000
2000
3000
4000
5000
6000
7000
1 1 0,99 0,99 0,98 0,98 0,97 0,97 0,96 0,96 0, Disponibilidade
Custo
Custo de uma Falha
Custo da Prevenção
Custo da Correção
Custo da Indisponibilidade
Nas empresas que convivem com emergências que podem redundar em desastres, deve haver uma equipe muito especial de manutenção, cuja função é eliminar ou minimizar estas emergências. A filosofia que deve ser adotada é: “Emergências não ocorrem, são causadas. Elimine a causa e você não terá novamente a mesma emergência”. Manutenção Corretiva - Atendimento A equipe de manutenção corretiva deve estar sempre em um local específico para ser encontrada facilmente e atender à produção de imediato. Como a equipe não sabe o local onde vai atuar, o usuário com problemas deverá solicitar o atendimento por telefone, porém, para efeitos de registro e estatística, ele deverá emitir um documento com as seguintes informações:
6 - Manutenção Preventiva Consideremos o motor de um automóvel. De tempos em tempos o usuário deverá trocar o óleo do cárter. Não realizando essa operação periódica, estaria correndo o risco de danificar os elementos que constituem o motor. Como o usuário faria para poder controlar essa troca periódica do óleo do motor?
Após o conserto e a liberação do equipamento para a produção, o analista da manutenção corretiva é obrigado a enviar para o setor de Engenharia da Manutenção um relatório de avaria. Nesse relatório o analista pode e deve sugerir alguma providência ou modificação no projeto da máquina para que o tipo de avaria ocorrida - e solucionada, não venha a se repetir Para realizar-se esse controle, o usuário deverá acompanhar a quilometragem do carro e, baseando-se nela, fazer a previsão da troca de óleo. Essa previsão nada mais é do que uma simples manutenção preventiva, que é o assunto desta aula. Manutenção Preventiva - Conceitos A manutenção preventiva obedece a um padrão previamente esquematizado, que estabelece paradas periódicas com a finalidade de permitir a troca de peças gastas por novas, assegurando assim o funcionamento perfeito da máquina por um período predeterminado. O método preventivo proporciona um determinado ritmo de trabalho, assegurando o equilíbrio necessário ao bom andamento das atividades. O controle das peças de reposição é um problema que atinge todos os tipos de indústria. Uma das metas a que se propõe o órgão de manutenção preventiva é a diminuição sensível dos estoques de peças. Isso se consegue com a organização dos prazos para reposição de peças. Assim, ajustam-se os investimentos para o setor. Se uma peça de um conjunto que constitui um mecanismo estiver executando seu trabalho de forma irregular, ela estabelecerá, fatalmente, uma sobrecarga nas demais peças que estão interagindo com ela. Como consequência, a sobrecarga provocará a diminuição da vida útil das demais peças do conjunto. O problema só pode ser resolvido com a troca da peça problemática, com antecedência, para preservar as demais peças. Em qualquer sistema industrial, a improvisação é um dos focos de prejuízo. É verdade que quando se improvisa pode-se evitar a paralização da produção, mas perde-se em eficiência. A improvisação pode e deve ser evitada por meio de métodos preventivos estabelecidos pelos técnicos de manutenção preventiva. A aplicação de métodos preventivos assegura um trabalho uniforme e seguro. O planejamento e a organização, fornecidos pelo método preventivo, são uma garantia aos homens da produção que podem controlar, dentro de uma faixa de erro mínima, a entrada de novas encomendas. Com o tempo, os industriais foram se conscientizando de que a máquina que funcionava ininterruptamente até quebrar acarretava vários problemas que poderiam ser evitados com simples paradas preventivas para lubrificação, troca de peças gastas e ajustes. A manutenção preventiva é um método aprovado e adotado atualmente em todos os setores industriais, pois abrange desde uma simples revisão - com paradas que não obedecem a uma rotina - até a utilização de sistemas de alto índice técnico. A manutenção preventiva abrange cronogramas nos quais são traçados planos e revisões periódicas completas para todos os tipos de materiais utilizados nas oficinas. Ela inclui, também, levantamentos que visam facilitar sua própria introdução em futuras ampliações do corpo da fábrica. A aplicação do sistema de manutenção preventiva não deve se restringir a setores, máquinas ou equipamentos. O sistema deve abranger todos os setores da indústria para garantir um perfeito entrosamento entre eles, de modo tal que, ao se constatar uma anomalia, as providências independam de qualquer outra regra que porventura venha a existir em uma oficina. Essa liberdade, dentro da indústria, é fundamental para o bom funcionamento do sistema produtivo. O aparecimento de focos que ocasionam descontinuidade no programa deve ser encarado de maneira séria, organizando-se estudos que tomem por base os relatórios preenchidos por técnicos da manutenção. Estes deverão relatar, em linguagem simples e clara, todos os detalhes do problema em questão A manutenção preventiva nunca deverá ser confundida com o órgão de comando, apesar dela ditar algumas regras de conduta a serem seguidas pelo pessoal da fábrica. À manutenção preventiva cabe apenas o local de apoio ao sistema fabril. O segredo para o sucesso da manutenção preventiva está na perfeita compreensão de seus conceitos por parte de todo o pessoal da fábrica, desde os operários à presidência.
Análise de Vibrações
Analisador de vibração
Equipamentos de monitoração e medida de vibrações
Gráfico Freq. X Intensidade de alta resolução Conclusão A manutenção preditiva certamente levará a uma redução nas interrupções inesperadas. Porém para que se receba este e outros benefícios é necessário a escolha criteriosa de técnicas e equipamentos.
8 – Manutenção Preventiva Como Convencer a Chefia?
Os principais objetivos das empresas são, normalmente, redução de custos, qualidade do produto, aumento de produção, preservação do meio ambiente, aumento da vida útil dos equipamentos e redução de acidentes do trabalho. Objetivos da Manutenção Preventiva Redução de custos