
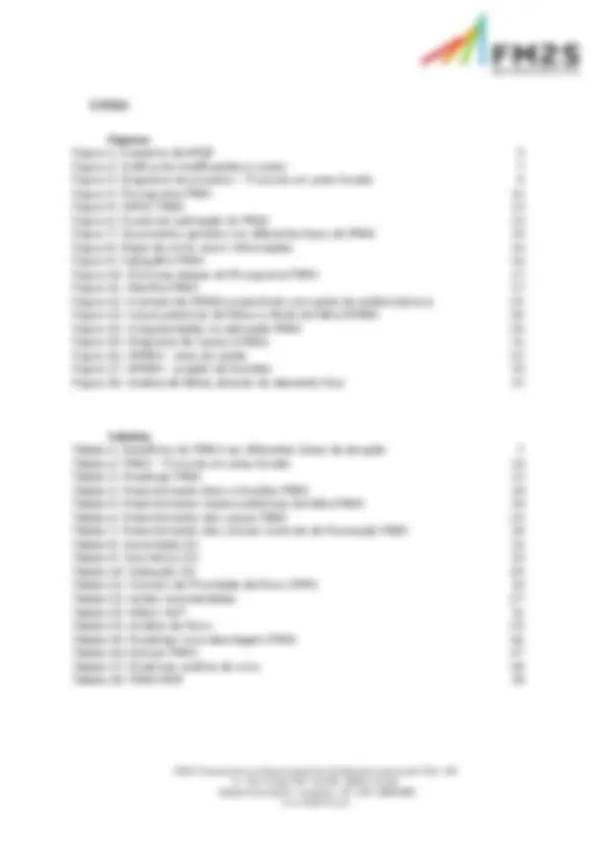
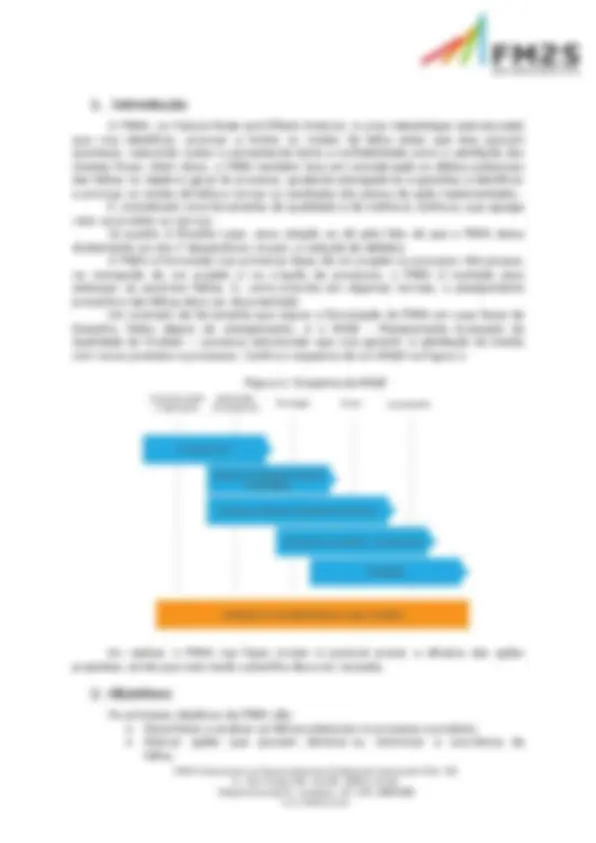
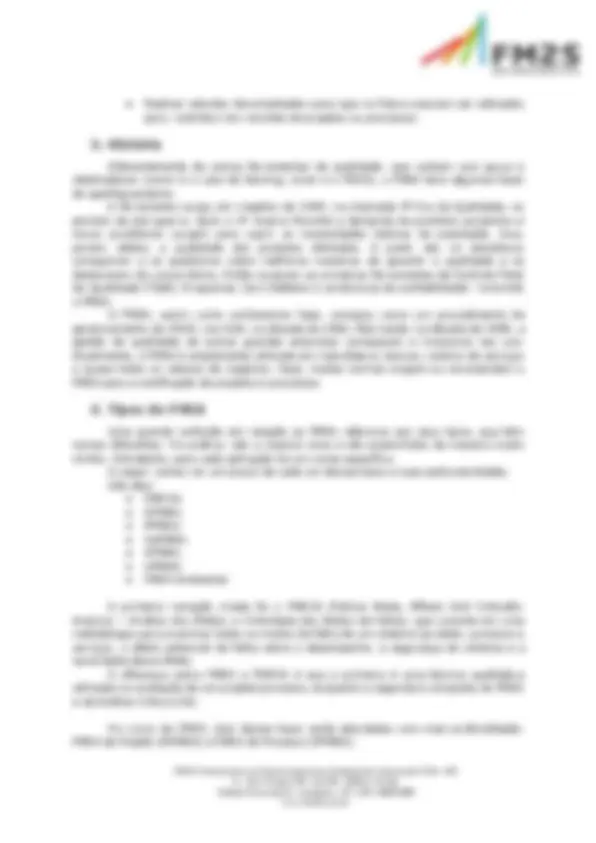
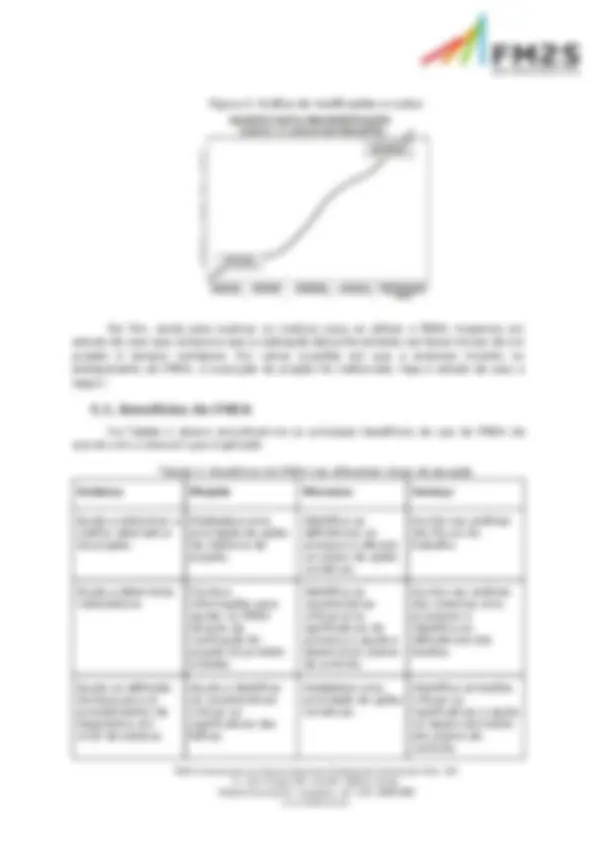
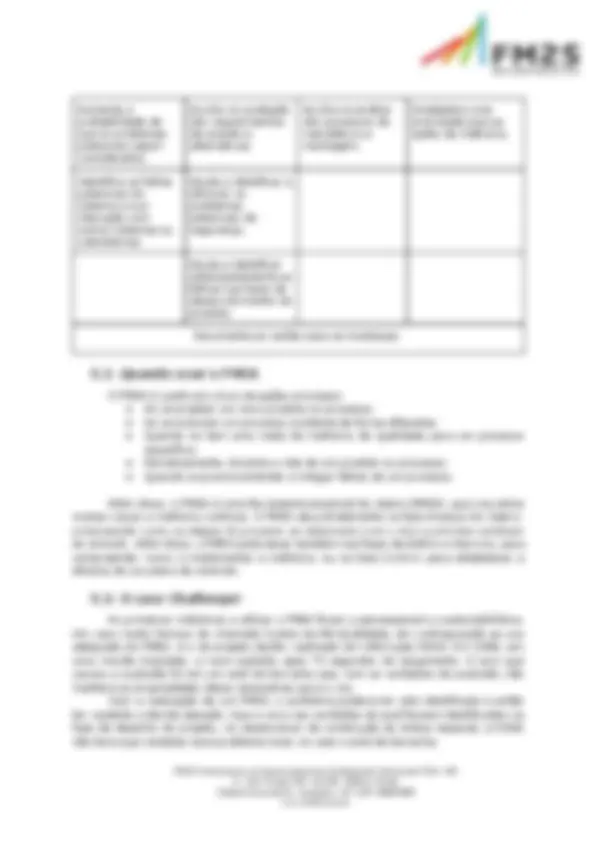
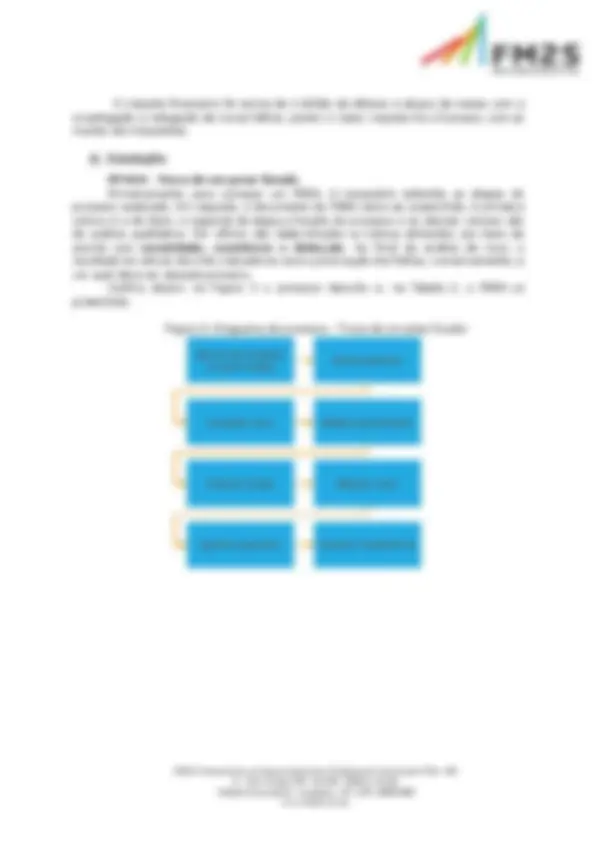
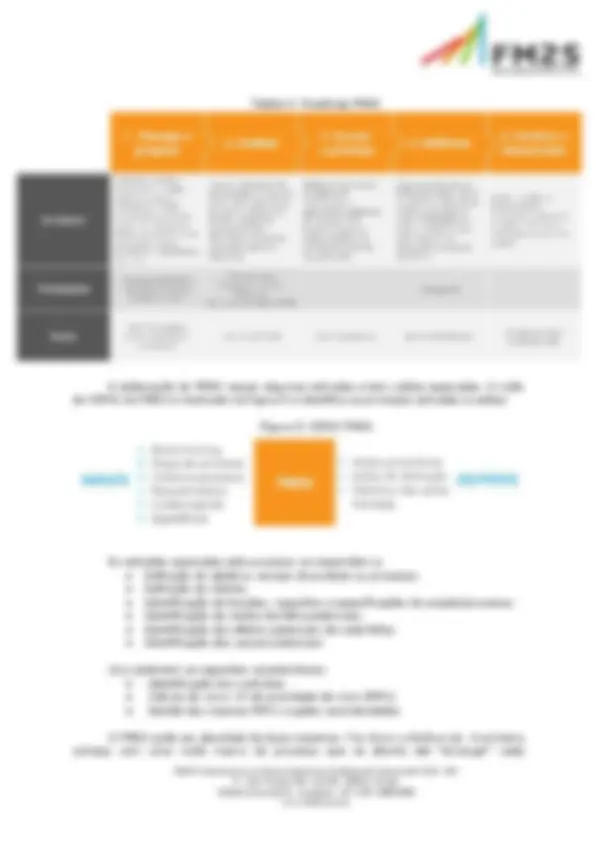
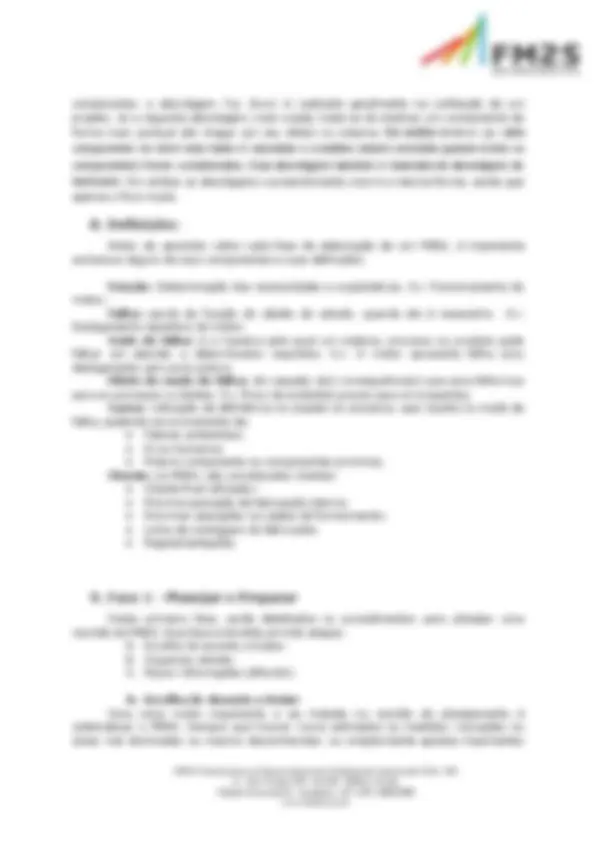
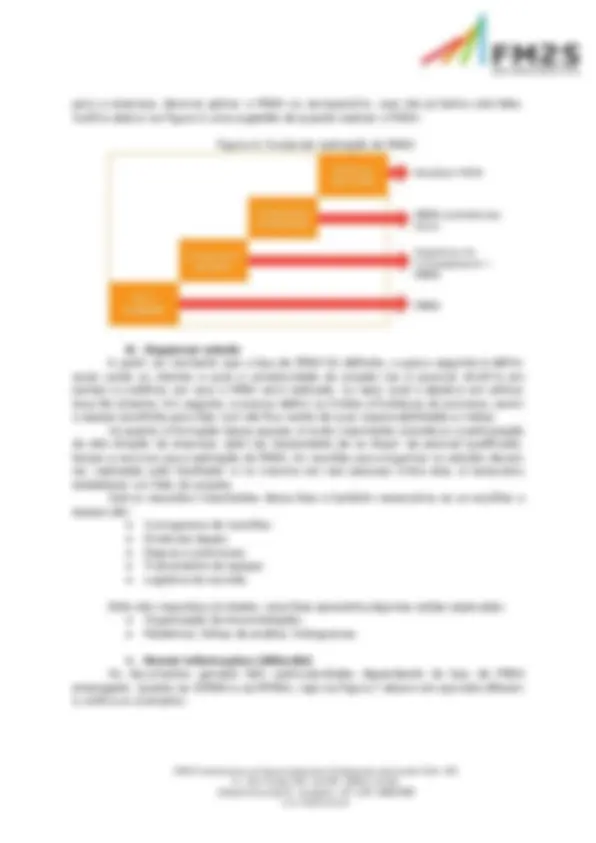
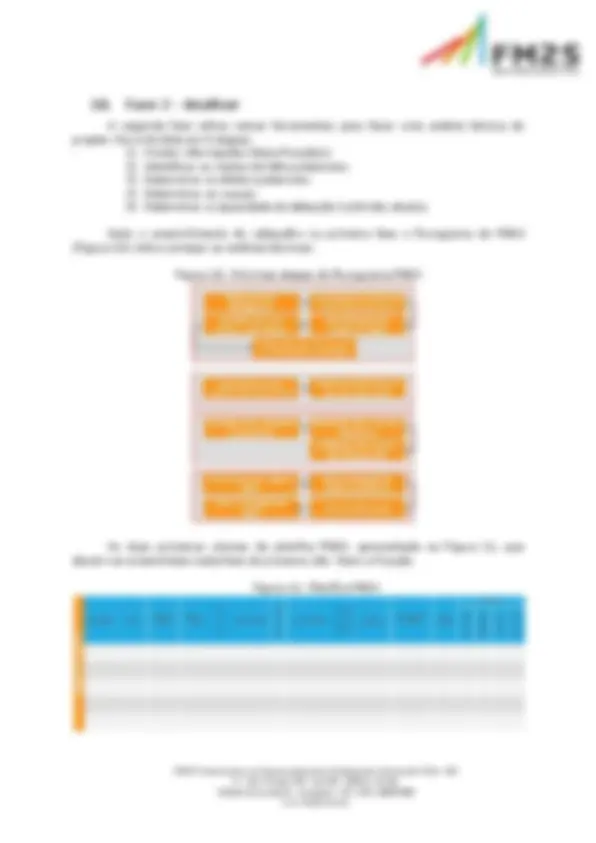
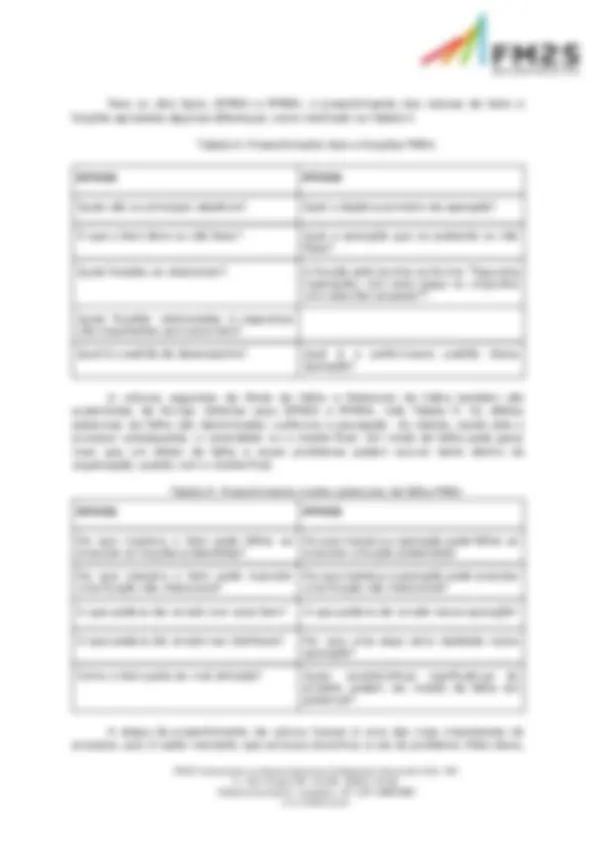
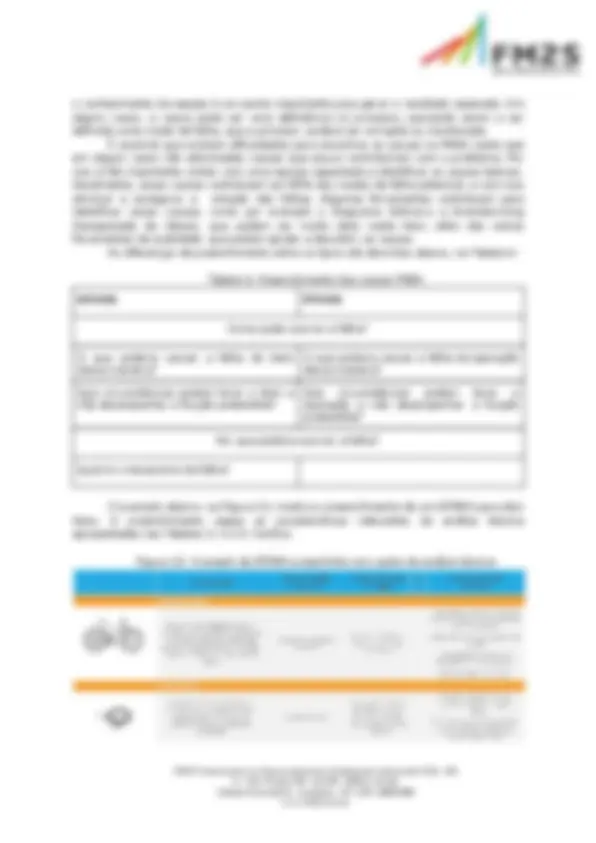
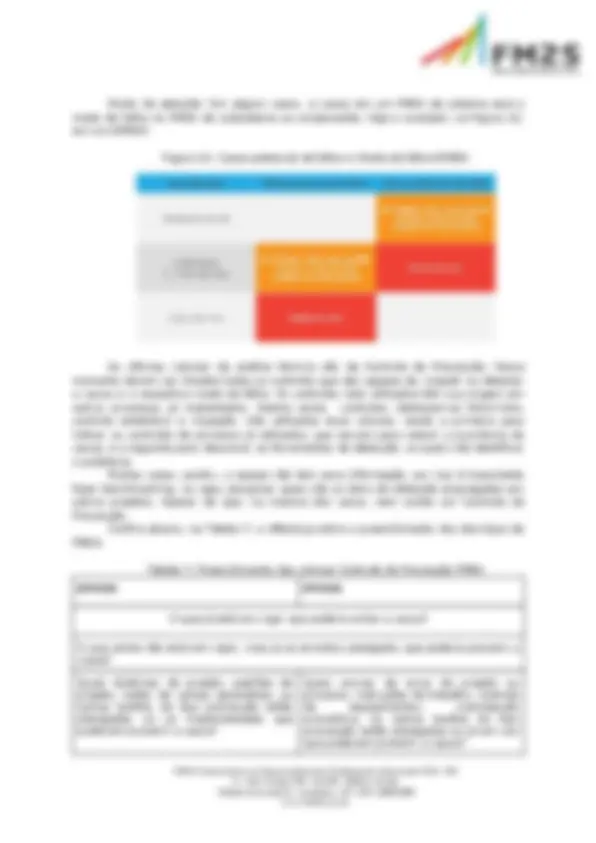
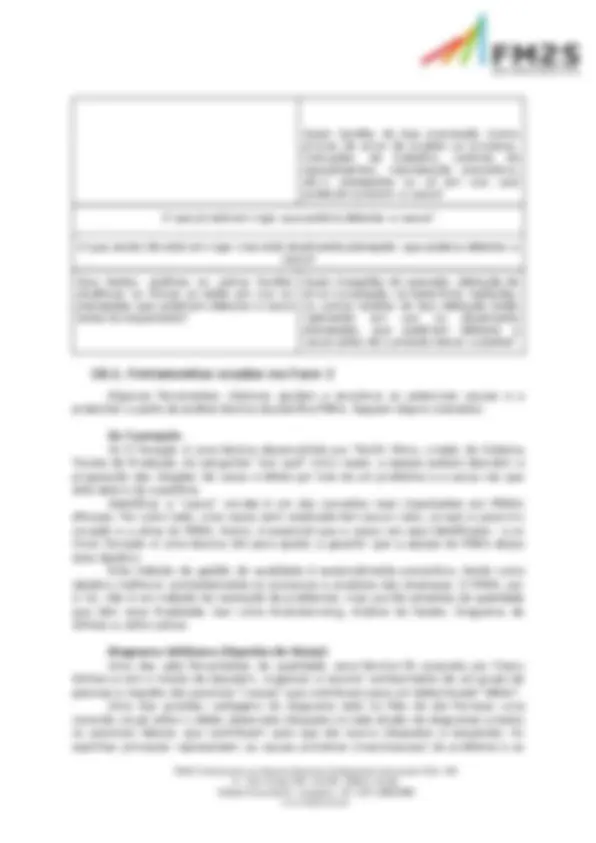
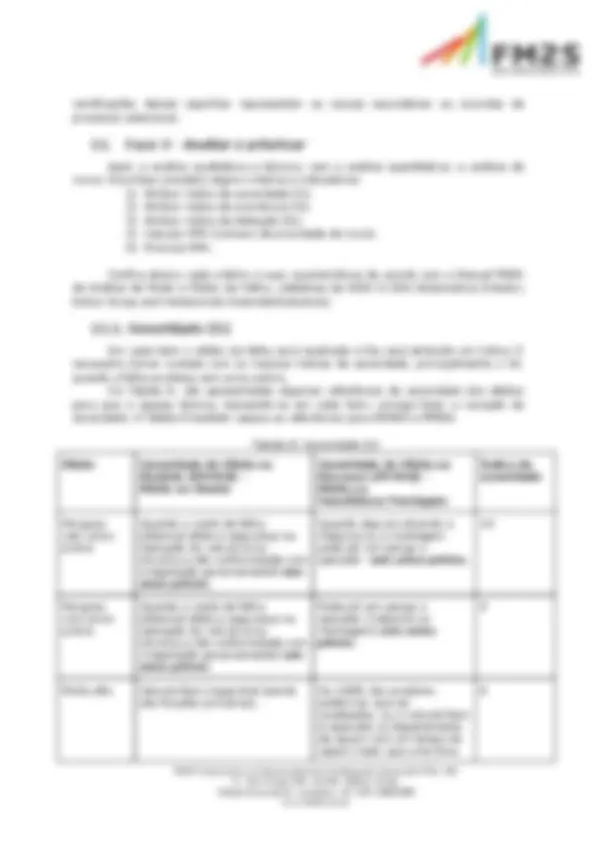
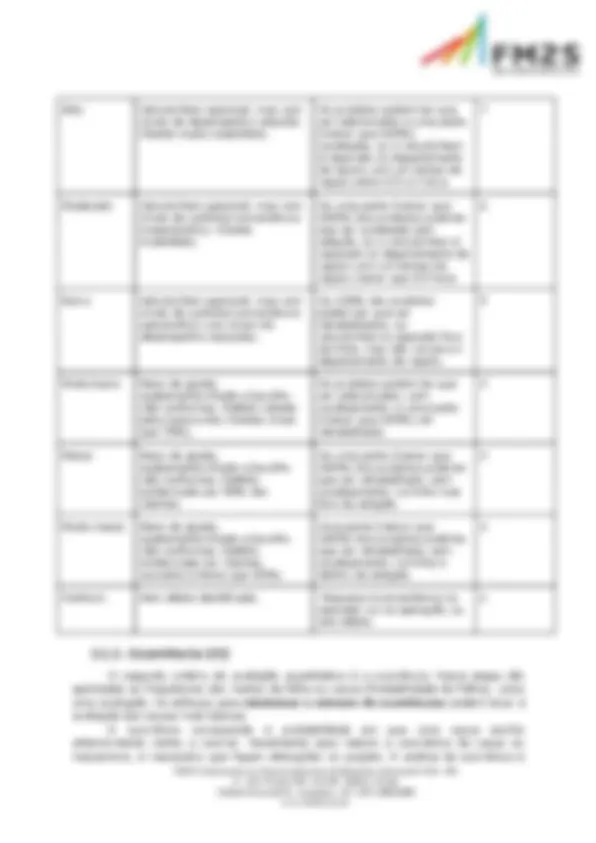
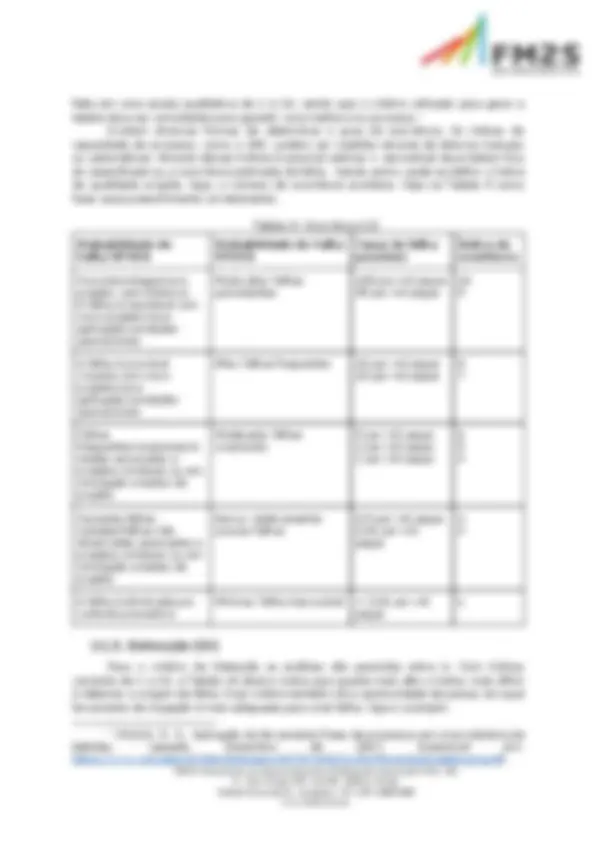
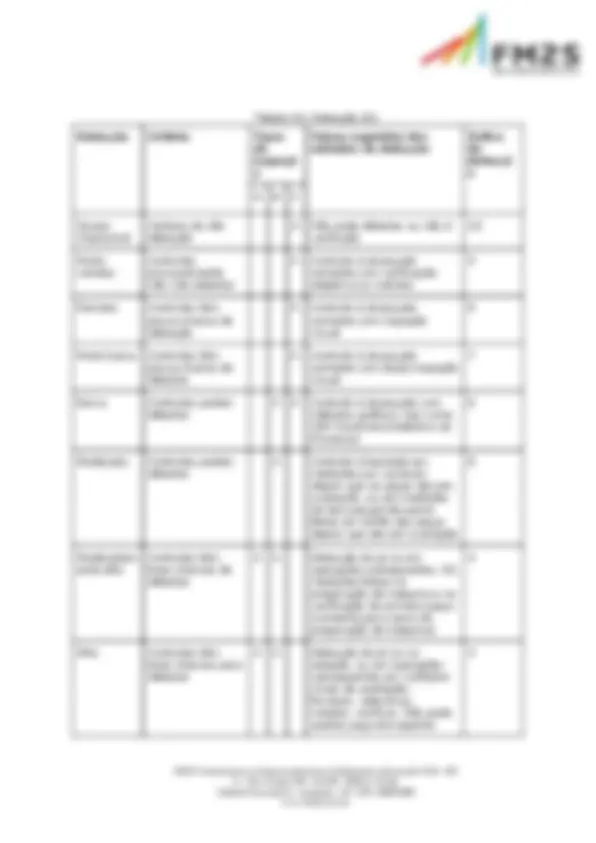
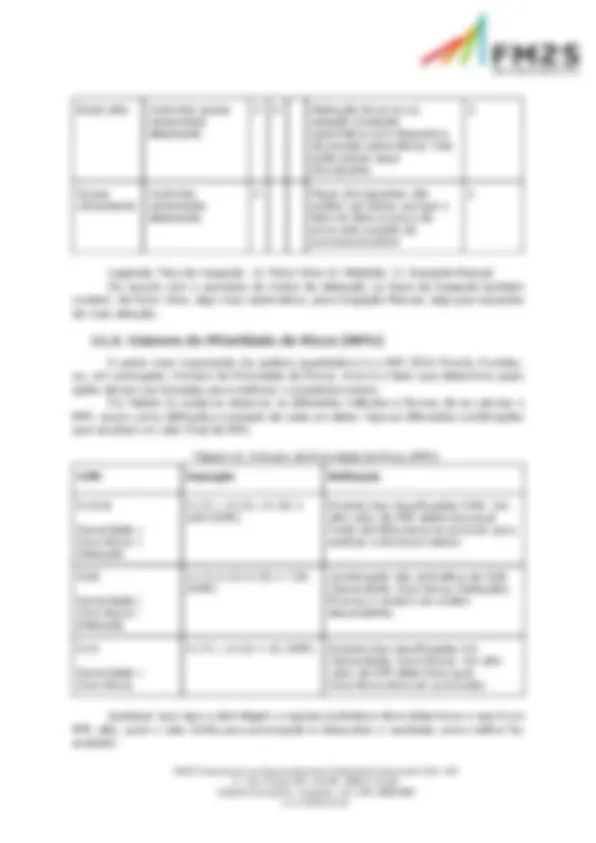
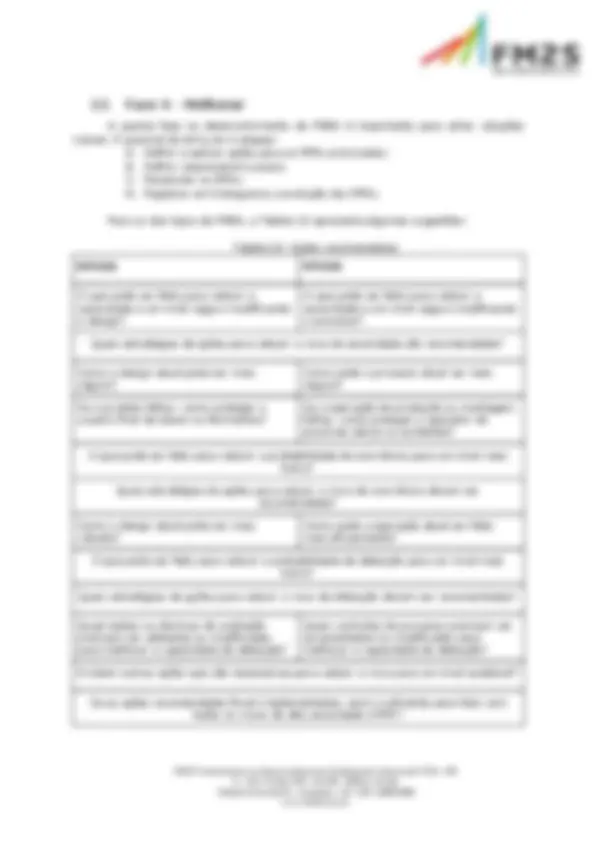
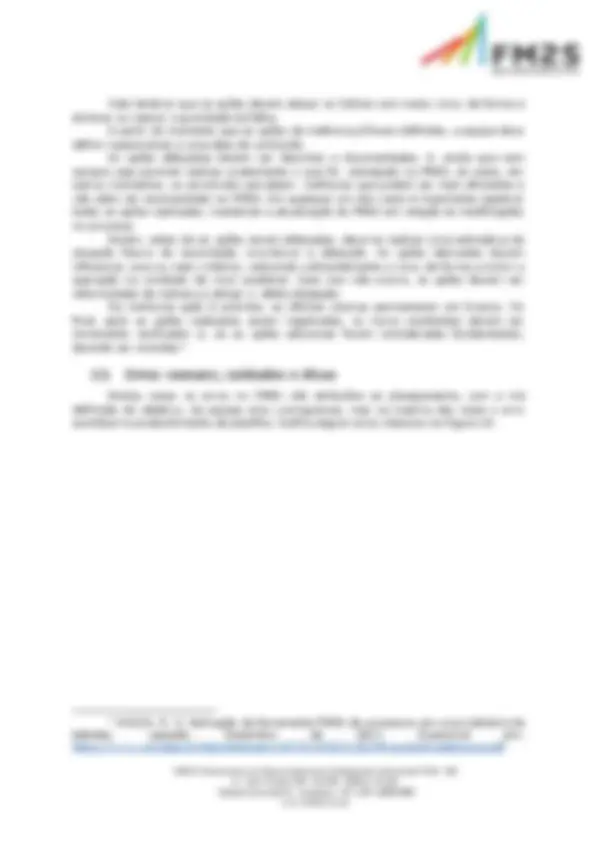
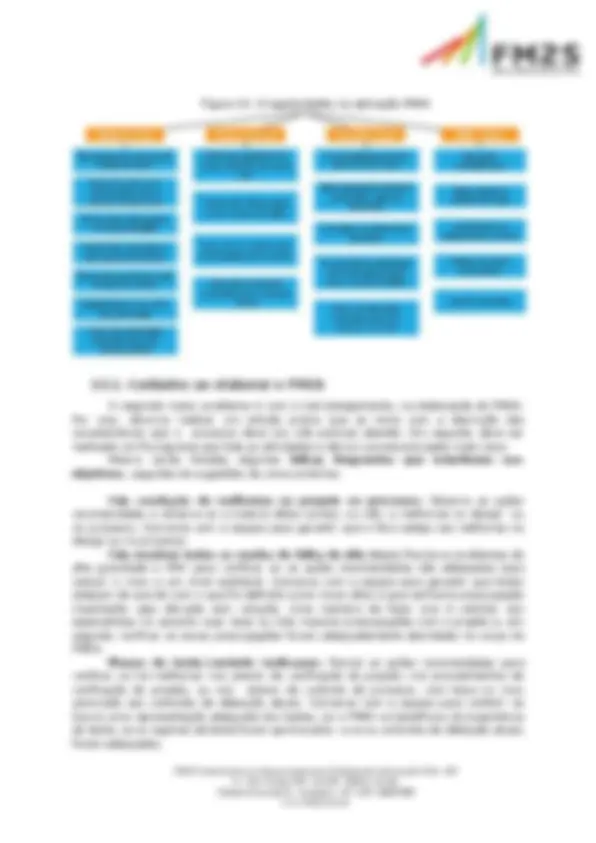
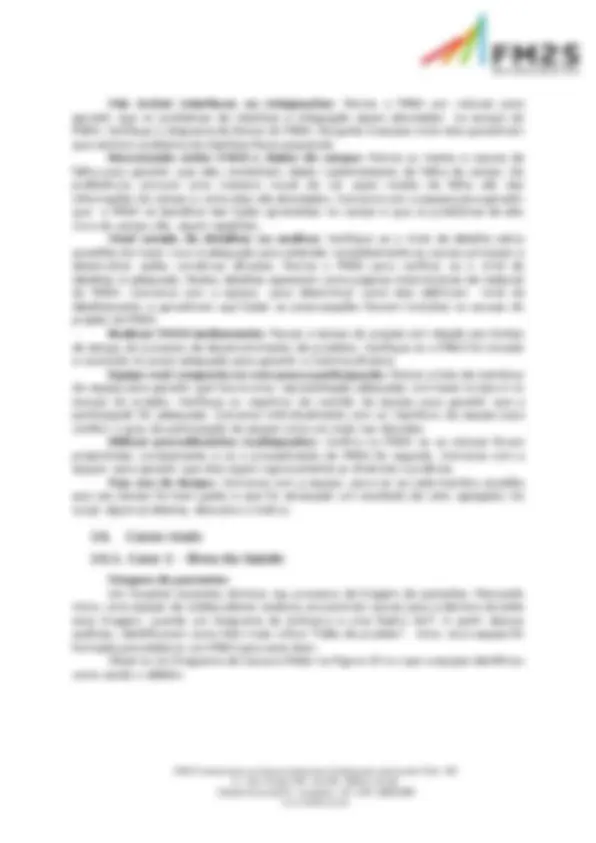
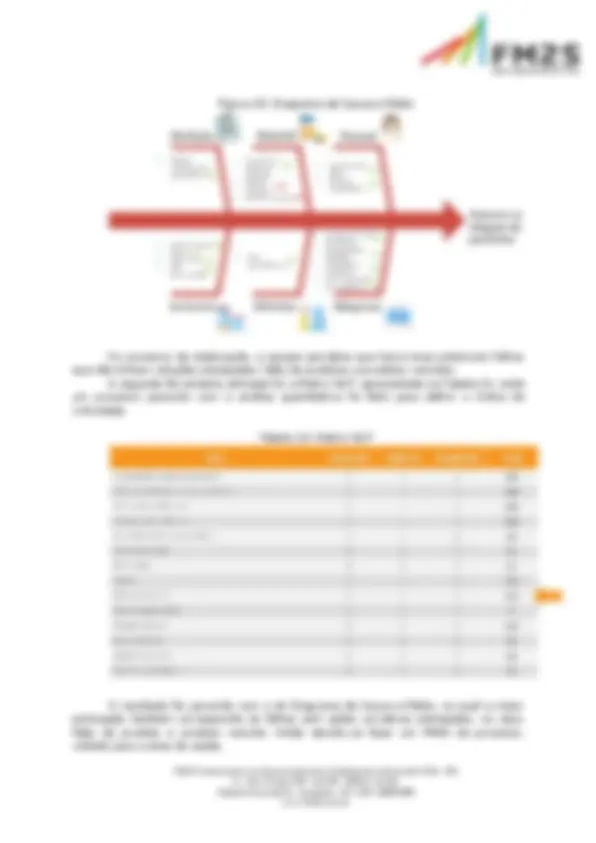
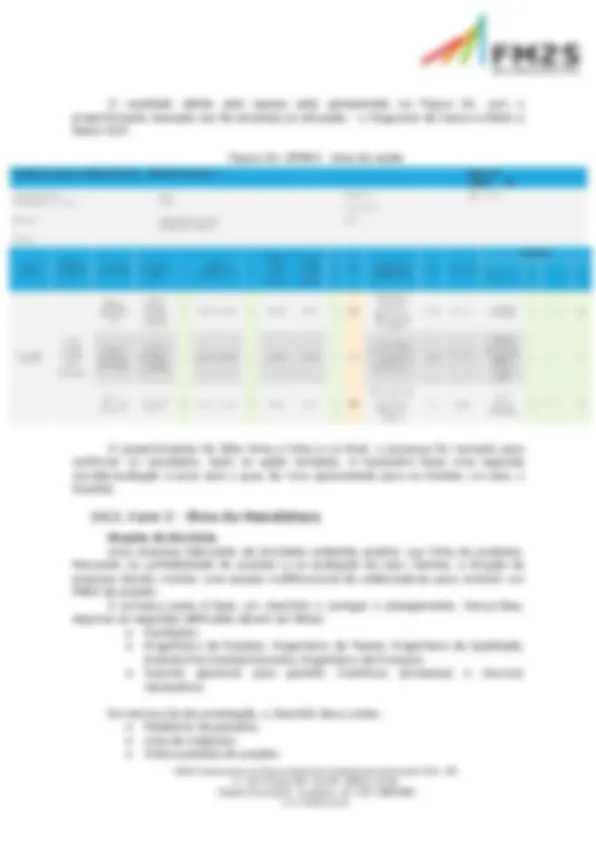
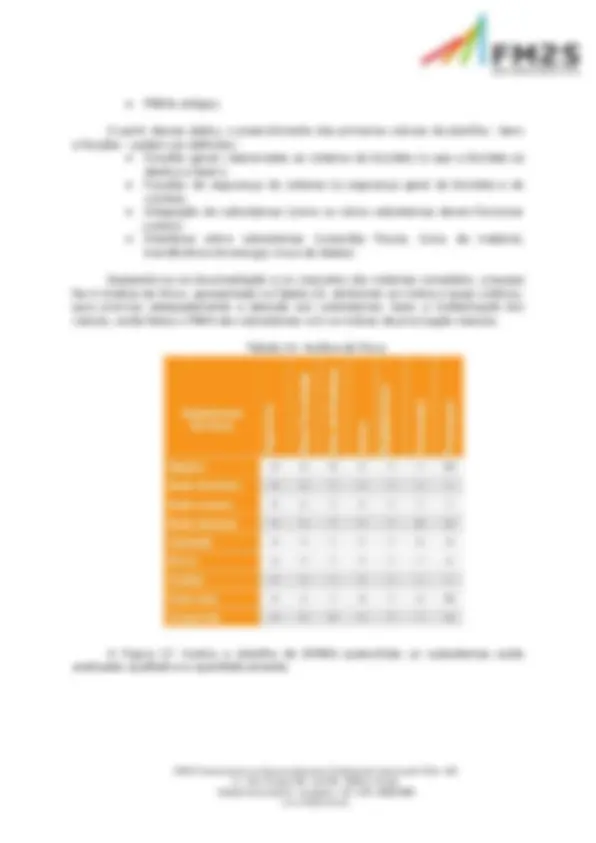
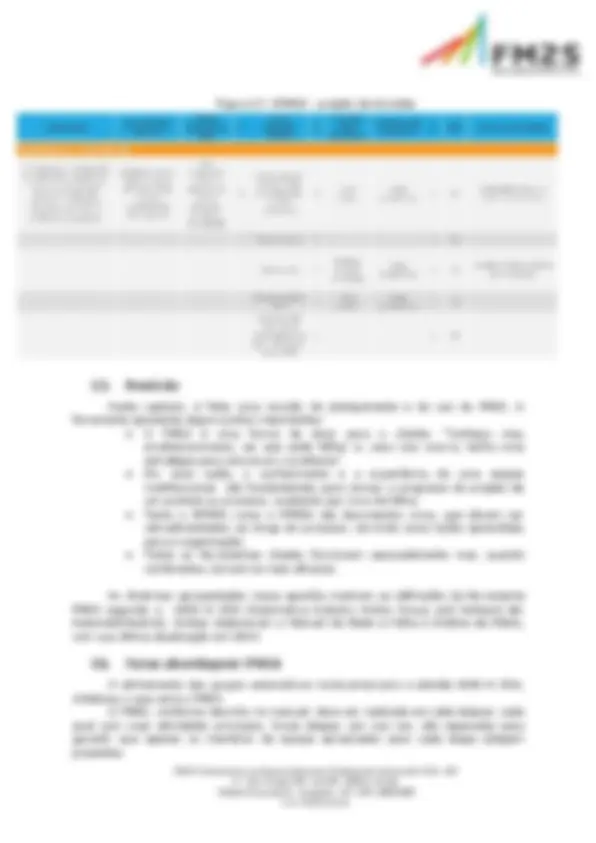
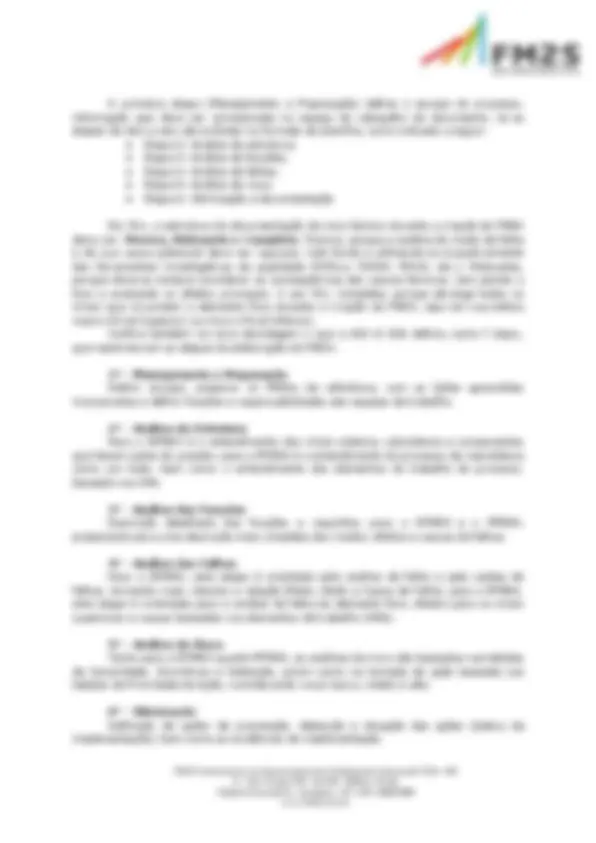
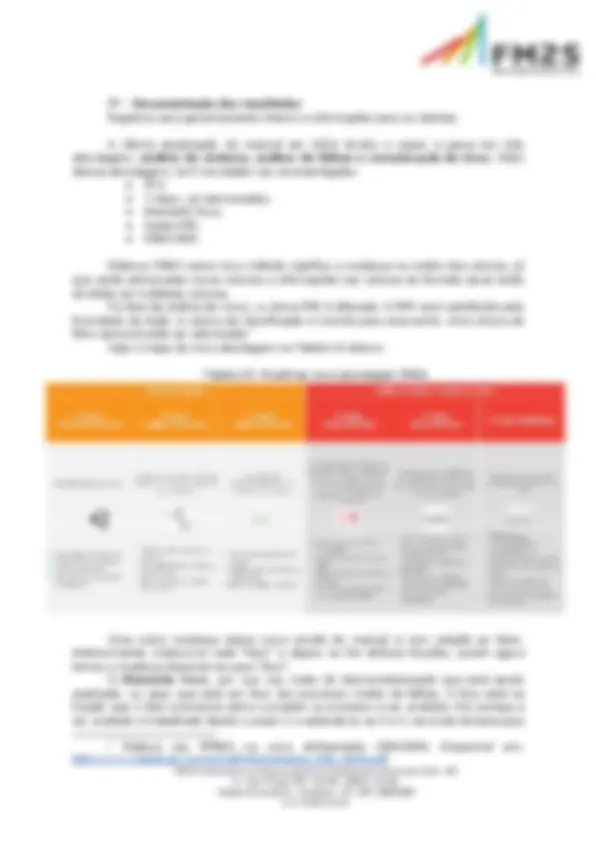
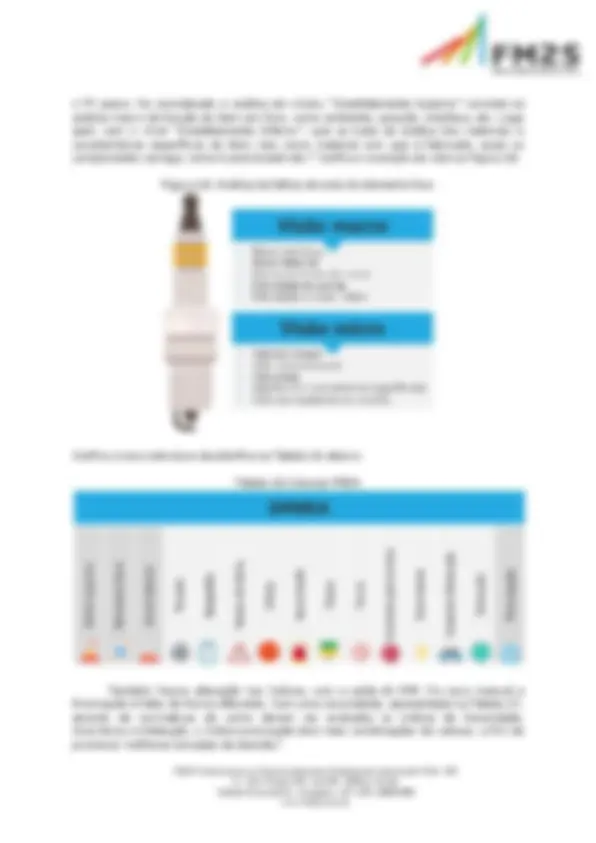
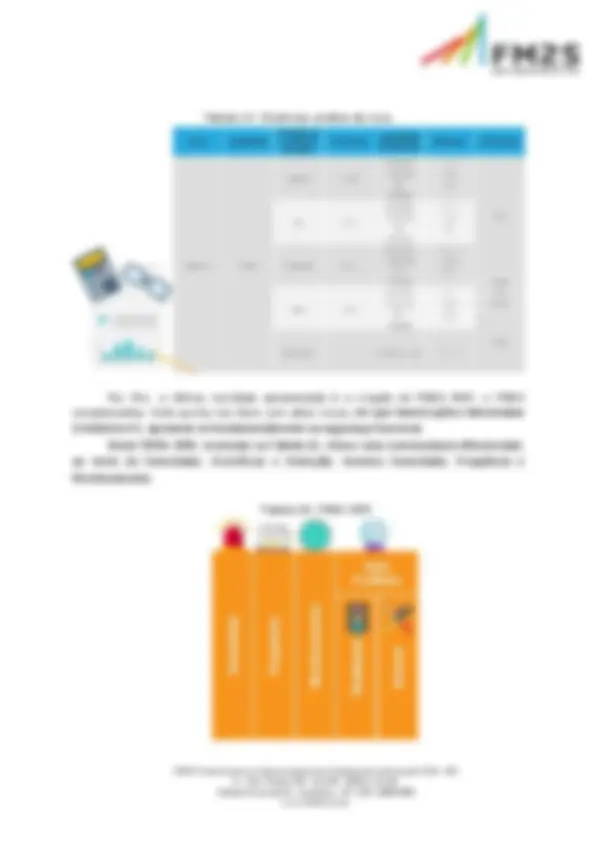
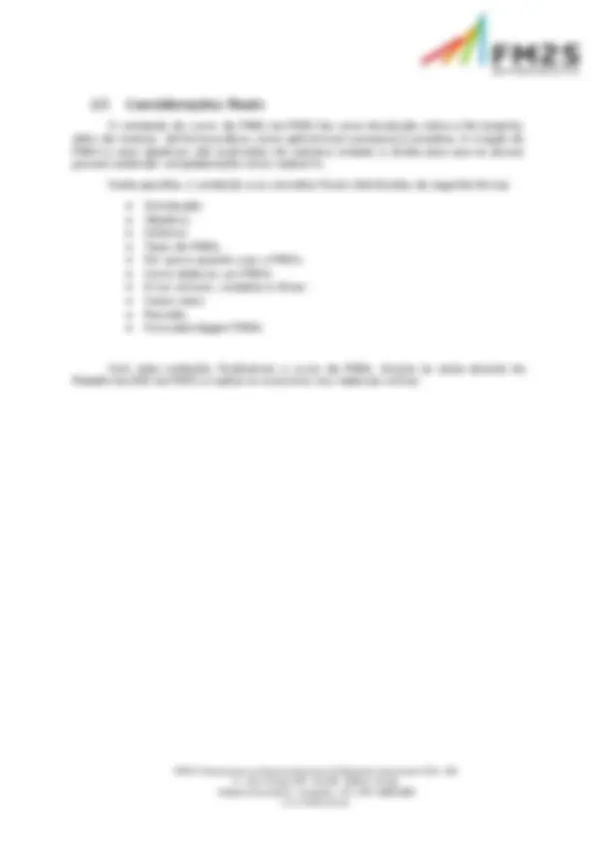
Estude fácil! Tem muito documento disponível na Docsity
Ganhe pontos ajudando outros esrudantes ou compre um plano Premium
Prepare-se para as provas
Estude fácil! Tem muito documento disponível na Docsity
Prepare-se para as provas com trabalhos de outros alunos como você, aqui na Docsity
Os melhores documentos à venda: Trabalhos de alunos formados
Prepare-se com as videoaulas e exercícios resolvidos criados a partir da grade da sua Universidade
Responda perguntas de provas passadas e avalie sua preparação.
Ganhe pontos para baixar
Ganhe pontos ajudando outros esrudantes ou compre um plano Premium
Comunidade
Peça ajuda à comunidade e tire suas dúvidas relacionadas ao estudo
Descubra as melhores universidades em seu país de acordo com os usuários da Docsity
Guias grátis
Baixe gratuitamente nossos guias de estudo, métodos para diminuir a ansiedade, dicas de TCC preparadas pelos professores da Docsity
Metodologia de processos mais assertivos, melhorando a performance de produção.
Tipologia: Notas de estudo
1 / 40
Esta página não é visível na pré-visualização
Não perca as partes importantes!
FM2S Treinamento em Desenvolvimento Profissional e Gerencial LTDA - ME
O FMEA, ou Failure Mode and Effects Analysis, é uma metodologia (estruturada) que visa identificar, priorizar e limitar os modos de falha antes que elas possam acontecer, reduzindo custos e aumentando tanto a confiabilidade como a satisfação dos clientes finais. Além disso, o FMEA também leva em consideração os efeitos potenciais das falhas no objetivo geral do processo, ajudando planejadores e gerentes a identificar e priorizar os modos de falha e revisar os resultados dos planos de ação implementados. É considerado uma ferramenta de qualidade e de melhoria contínua, que agrega valor ao produto ou serviço. Já quanto à filosofia Lean, essa relação se dá pelo fato de que o FMEA ataca diretamente um dos 7 desperdícios visuais: a redução de defeitos. O FMEA é formulado nas primeiras fases de um projeto ou processo. Até porque, na concepção de um projeto e na criação de processos, o FMEA é montado para antecipar as possíveis falhas. E, como previsto em algumas normas, o planejamento preventivo das falhas deve ser documentado Um exemplo de ferramenta que requer a formulação do FMEA em suas fases de Desenho, feitos depois do planejamento, é o APQP - Planejamento Avançado da Qualidade do Produto -, processo estruturado que visa garantir a satisfação do cliente com novos produtos e processos. Confira o esquema de um APQP na Figura 1.
Figura 1: Esquema de APQP
Ao realizar o FMEA nas fases iniciais é possível prever a eficácia das ações propostas, ainda que mais tarde a planilha deva ser revisada.
Os principais objetivos da FMEA são: ● Reconhecer e analisar as falhas potenciais no processo e produto; ● Elencar ações que possam eliminar ou minimizar a ocorrência da falha; FM2S Treinamento em Desenvolvimento Profissional e Gerencial LTDA - ME Av. Alan Turing, 345 - sala 06 - Edifício Vértice Cidade Universitária - Campinas - SP - CEP: 13083-
● Realizar estudos documentados para que no futuro possam ser utilizados para contribuir em revisões de projetos ou processos.
Diferentemente de outras ferramentas da qualidade, que contam com gurus e idealizadores (como é o caso de Deming, Juran e o PDCA), o FMEA teve algumas fases de aperfeiçoamento. A ferramenta surgiu em meados de 1949, na chamada 3ª Era da Qualidade, no período de pós-guerra. Após a 2ª Guerra Mundial a demanda de produtos aumentou e novos produtores surgem para suprir as necessidades básicas da população. Isso, porém, afetou a qualidade dos produtos ofertados. A partir daí, os estudiosos começaram a se questionar sobre melhores maneiras de garantir a qualidade e se destacarem da concorrência. Então surgiram as primeiras ferramentas de Controle Total da Qualidade (TQM), Programas Zero Defeitos e as técnicas de confiabilidade - incluindo o FMEA. O FMEA, assim como conhecemos hoje, começou como um procedimento de gerenciamento da NASA, nos EUA, na década de 1960. Mais tarde, na década de 1980, a gestão de qualidade de outras grandes empresas começaram a incorporar seu uso. Atualmente, o FMEA é amplamente utilizado em manufatura, bancos, centros de serviços e quase todos os setores de negócios. Hoje, muitas normas exigem ou recomendam o FMEA para a certificação de projetos e processos.
Uma grande confusão em relação ao FMEA refere-se aos seus tipos, que têm nomes diferentes. Na prática, são a mesma coisa e são preenchidos de maneira muito similar. Entretanto, para cada aplicação há um nome específico. A seguir vamos ver um pouco de cada um desses tipos e suas particularidades. São eles: ● FMECA; ● DFMEA; ● PFMEA; ● SeFMEA; ● SFMEA; ● HFMEA; ● FMEA Ambiental.
A primeira variação criada foi o FMECA (Failure Mode, Effects And Criticality Analysis – Análise dos Efeitos e Criticidade dos Modos de Falha), que consiste em uma metodologia para examinar todos os modos de falha de um sistema (produto, processo e serviço), o efeito potencial da falha sobre o desempenho, a segurança do sistema e a severidade desse efeito. A diferença entre FMEA e FMECA é que a primeira é uma técnica qualitativa utilizada na avaliação de um projeto/processo, enquanto a segunda é composta do FMEA e da Análise Crítica (CA).
No curso da FM2S, dois desses tipos serão abordados com mais profundidade: FMEA de Projeto (DFMEA) e FMEA de Processo (PFMEA).
FM2S Treinamento em Desenvolvimento Profissional e Gerencial LTDA - ME Av. Alan Turing, 345 - sala 06 - Edifício Vértice Cidade Universitária - Campinas - SP - CEP: 13083-
FMEA de Serviços (SeFMEA) É uma derivação do PFMEA e tem como função identificar como um processo pode fracassar em atender os requisitos críticos dos clientes. O SeFMEA atua, portanto, recuperando esses processos com ações imediatas caso ocorram problemas na entrega do serviço e implantando as ações que devem ser tomadas para tornar o processo à prova de erros.
FMEA de Sistema (SFMEA) É uma derivação do DFMEA, usada para identificar possíveis falhas associadas a sistemas e subsistemas do projeto ainda na fase de sua concepção.
FMEA de Assistência Médica (HFMEA) É uma adaptação do PFMEA para a área médica, usada para identificar possíveis falhas e suas causas antes que serviços futuros sejam fornecidos, proporcionando oportunidades para melhorar os serviços atuais e mitigar problemas que poderiam resultar em riscos graves para o paciente.
FMEA Ambiental É uma adaptação do PFMEA, empregado para identificar os aspectos e impactos ambientais gerados pelo processo, analisando as causas mais críticas e mitigando riscos ao ambiente.
Um ponto a se considerar ao elaborar um FMEA é a obrigatoriedade, pois algumas normas exigem a realização do FMEA para tirar a certificação. A norma IATF 16949 exige o FMEA como requisito. Por outro lado, as normas ISO não exigem a elaboração de um FMEA apesar de ser recomendado. Um segundo ponto a favor da realização do FMEA é a confiabilidade. Isso porque a ferramenta serve para antever e minimizar falhas sistêmicas em produtos ou processos, assim como seu efeito sobre o conjunto, aumentando, portanto, sua confiabilidade. Além disso, a realização de um FMEA consiste na possibilidade de reduzir custos caso modificações sejam necessárias no futuro. Confira na Figura 2 um gráfico de custos por modificação. No exemplo da Figura 2, mostra que na fase de concepção a alteração do FMEA não apresenta impactos financeiros; porém, a partir da segunda fase, onde a engenharia já deu aprovação, começa-se a investir fortemente em ferramentas de melhoria de processo. Na terceira fase, a produção começa a utilizar maquinário e ferramental, assim os custos em melhoria aumentam também. A partir daí, tudo que esteja fora do Planejamento Avançado custará muito caro para ser modificado, o que as empresas em geral tentam evitar.
FM2S Treinamento em Desenvolvimento Profissional e Gerencial LTDA - ME Av. Alan Turing, 345 - sala 06 - Edifício Vértice Cidade Universitária - Campinas - SP - CEP: 13083-
Figura 2: Gráfica de modificações e custos
Por fim, ainda para explicar os motivos para se utilizar o FMEA, trazemos um estudo de caso que comprova que a realização dessa ferramenta nas fases iniciais de um projeto é sempre vantajosa. Em várias ocasiões em que a empresa investiu no planejamento do FMEA, a execução do projeto foi melhorada. Veja o estudo de caso a seguir:
Na Tabela 1 abaixo encontram-se os principais benefícios do uso do FMEA de acordo com a área em que é aplicado
Tabela 1: Benefícios do FMEA nas diferentes áreas de atuação Sistema Projeto Processo Serviço
Ajuda a selecionar a melhor alternativa de projeto.
Estabelece uma prioridade de ações de melhoria de projeto.
Identifica as deficiências no processo e oferece um plano de ações corretivas.
Auxilia nas análises dos fluxos de trabalho.
Ajuda a determinar redundância.
Fornece informações para ajudar no FMEA através da verificação do projeto do produto e testes
Identifica as características críticas e/ou significativas do processo e ajuda a desenvolver planos de controle.
Auxilia nas análises dos sistemas e/ou processos e identifica as deficiências das tarefas.
Ajuda na definição da base para os procedimentos de diagnóstico em nível de sistema.
Ajuda a identificar as características críticas ou significativas das falhas.
Estabelece uma prioridade de ações corretivas.
Identifica as tarefas críticas ou significativas e ajuda no desenvolvimento dos planos de controle.
FM2S Treinamento em Desenvolvimento Profissional e Gerencial LTDA - ME Av. Alan Turing, 345 - sala 06 - Edifício Vértice Cidade Universitária - Campinas - SP - CEP: 13083-
O impacto financeiro foi acima de 1 bilhão de dólares e atraso de meses com a investigação e mitigação de novas falhas, porém o maior impacto foi o humano, com as mortes dos tripulantes.
PFMEA - Troca de um pneu furado Primeiramente, para começar um FMEA, é necessário entender as etapas do processo analisado. Em seguida, o documento do FMEA deve ser preenchido. A primeira coluna é a de Item, a segunda de etapa e função do processo e as demais colunas são de análise qualitativa. Por último são determinados os índices atribuídos aos itens de acordo com severidade, ocorrência e detecção. Ao final da análise de risco, o resultado do cálculo dos três indicadores será a priorização dos falhas, numericamente, e ver qual deve ser atacada primeiro. Confira abaixo na Figura 3 o processo descrito e, na Tabela 2, o FMEA já preenchido.
Figura 3: Diagrama do processo - Troca de um pneu furado
FM2S Treinamento em Desenvolvimento Profissional e Gerencial LTDA - ME Av. Alan Turing, 345 - sala 06 - Edifício Vértice Cidade Universitária - Campinas - SP - CEP: 13083-
Tabela 2: FMEA - Troca de um pneu furado
O preenchimento da planilha FMEA em linhas e colunas começa com a preparação do FMEA, selecionando os Itens (primeira linha) e suas Funções, sejam eles produtos ou processos. As análises de Modos de Falhas (4ª coluna) são feitas para cada Item, e não se deve iniciar a análise de um novo item sem ter encerrado a do anterior. Além disso vale ressaltar que o processo descrito no fluxograma irá se repetir caso uma falha não planejada for identificada.
A elaboração do FMEA segue uma sequência lógica que pode ser observada na Figura 4:
FM2S Treinamento em Desenvolvimento Profissional e Gerencial LTDA - ME Av. Alan Turing, 345 - sala 06 - Edifício Vértice Cidade Universitária - Campinas - SP - CEP: 13083-
Tabela 3: Roadmap FMEA
A elaboração do FMEA requer algumas entradas e tem saídas esperadas. A visão do SIPOC do FMEA é mostrada na Figura 5 e identifica as principais entradas e saídas:
Figura 5: SIPOC FMEA
As entradas esperadas pelo processo correspondem a: ● Definição do objetivo, escopo do produto ou processo; ● Definição do cliente; ● Identificação de funções, requisitos e especificações do projeto/processo; ● Identificação de modos de falha potenciais; ● Identificação dos efeitos potenciais de cada falha; ● Identificação das causas potenciais.
Já a saída tem as seguintes características: ● Identificação dos controles; ● Cálculo do risco: nº de prioridade de risco (RPN); ● Gestão dos maiores RPN’s e ações recomendadas;
O FMEA pode ser abordado de duas maneiras: Top Down e Bottom Up. A primeira começa com uma visão macro do processo que se afunila até “enxergar” cada
FM2S Treinamento em Desenvolvimento Profissional e Gerencial LTDA - ME Av. Alan Turing, 345 - sala 06 - Edifício Vértice Cidade Universitária - Campinas - SP - CEP: 13083-
componente; a abordagem Top Down é realizada geralmente na confecção de um projeto. Já a segunda abordagem, mais usada, trata-se de analisar um componente de
apenas o foco muda.
Antes de aprender sobre cada fase de elaboração de um FMEA, é importante esclarecer alguns de seus componentes e suas definições:
Função: Determinação das necessidades e expectativas. Ex: Funcionamento do motor; Falha: perda da função do objeto de estudo, quando ele é necessário. Ex: Desligamento repentino do motor; Modo de falha: é a maneira pela qual um sistema, processo ou produto pode falhar em atender a determinados requisitos. Ex: O motor apresenta falha e/ou desligamento sem aviso prévio; Efeito do modo de falha: diz respeito à(s) consequência(s) que essa falha traz para os processos e clientes. Ex: Risco de acidentes graves para os ocupantes; Causa: indicação de deficiência no projeto ou processo, que resulta no modo de falha, podendo ser proveniente de: ● Fatores ambientais; ● Erros humanos; ● Próprio componente ou componentes próximos. Cliente: no FMEA, são considerados clientes: ● Cliente final utilizador; ● Próxima operação de fabricação interno; ● Próximas operações na cadeia de fornecimento; ● Linha de montagem do fabricante; ● Regulamentações.
Nesta primeira fase, serão detalhados os procedimentos para planejar uma reunião de FMEA. Essa fase é dividida em três etapas: A. Escolha do assunto a tratar; B. Organizar estudo; C. Reunir informações (difundir).
A. Escolha do Assunto a tratar Uma coisa muito importante a ser tratada na reunião de planejamento é sistematizar o FMEA. Sempre que houver riscos estimados ou medidos; inovações ou áreas mal dominadas ou mesmo desconhecidas; ou simplesmente apostas importantes
FM2S Treinamento em Desenvolvimento Profissional e Gerencial LTDA - ME Av. Alan Turing, 345 - sala 06 - Edifício Vértice Cidade Universitária - Campinas - SP - CEP: 13083-
Figura 7: documentos gerados nos diferentes tipos de FMEA
As ferramentas auxiliares de FMEA e que trabalham relacionadas a ele são descritas abaixo:
Histograma É um gráfico de frequência que tem como objetivo ilustrar como uma determinada amostra ou população de dados está distribuída. Ele contabiliza a ocorrência de determinado valor dentro dessa nossa distribuição de dados. É uma das sete ferramentas da qualidade, que nos ajudam a controlar processos tanto na indústria como no setor de serviços.
Fluxograma É uma das melhores ferramentas para se mapear um processo, pois proporciona uma melhor visualização facilitando sua observação. Esta imagem é feita por meio de uma representação gráfica de uma série de atividades que definem o processo e a sequência entre elas.
Diagrama de blocos Um DFMEA deve começar com um diagrama de blocos para o sistema, subsistema e/ou componente analisado. Essa ferramenta, por sua vez, indica o fluxo de informações, energia, força, fluido, etc. O objetivo é indicar claramente as entradas (inputs), o processo desenvolvido (função) e as saídas (outputs) dos blocos, ilustrando as relações primárias entre os itens cobertos na análise e estabelecendo uma ordem lógica para a análise.
P-Diagrama O P-Diagrama faz parte do trabalho de preparação para o preenchimento do formulário DFMEA. Os sinais de entrada do sistema/cliente e as funções ou saídas produzidas pelo item sob investigação são enumeradas no P-Diagrama. Além das
FM2S Treinamento em Desenvolvimento Profissional e Gerencial LTDA - ME Av. Alan Turing, 345 - sala 06 - Edifício Vértice Cidade Universitária - Campinas - SP - CEP: 13083-
funções "ideais" produzidas pelo Item, o P-Diagrama captura as saídas ou efeitos colaterais indesejados ou indesejáveis.
Matriz de interface A Matriz de interface é um gráfico com os subsistemas e/ou componentes (dependendo do escopo do FMEA) nos eixos vertical e horizontal, respectivamente. O gráfico mostra quais interfaces, e tipos de interfaces, devem ser consideradas na análise. Ela pode identificar as interfaces que foram perdidas no diagrama de blocos do FMEA, nesse caso, o diagrama de blocos pode ser atualizado.
O mapa estruturado dessa fase é ilustrado na Figura 8 e mostra a conexão entre as ferramentas para elaborar o FMEA:
Figura 8: Mapa de como reunir informações
A Fase 1 - Planejar, nos permite preencher o cabeçalho da planilha de FMEA com as informações básicas: tipo de FMEA, equipe e o nome do projeto. Confira um exemplo de cabeçalho na Figura 9 abaixo.
Figura 9: Cabeçalho FMEA
FM2S Treinamento em Desenvolvimento Profissional e Gerencial LTDA - ME Av. Alan Turing, 345 - sala 06 - Edifício Vértice Cidade Universitária - Campinas - SP - CEP: 13083-
Para os dois tipos, DFMEA e PFMEA, o preenchimento das colunas de itens e funções apresenta algumas diferenças, como mostrado na Tabela 4.
Tabela 4: Preenchimento itens e funções FMEA
Quais são os principais objetivos? Qual o objetivo primário da operação?
O que o item deve ou não fazer? Qual a operação que se pretende ou não fazer?
Quais funções se relacionam? A função está escrita na forma: “faça esta (operação) com esta (peça ou conjunto) com esta (ferramenta)”?
Quais funções relacionadas à segurança são importantes para esse item?
Qual é o padrão de desempenho? Qual é a performance padrão dessa operação?
A colunas seguintes de Modo de Falha e Potenciais de Falha também são preenchidas de formas distintas para DFMEA e PFMEA, vide Tabela 5. Os efeitos potenciais de falha são denominados conforme a percepção do cliente, sendo este o processo subsequente, o revendedor ou o cliente final. Um modo de falha pode gerar mais que um efeito de falha e esses problemas podem ocorrer tanto dentro da organização, quanto com o cliente final.
Tabela 5: Preenchimento modos potenciais de falha FMEA DFMEA PFMEA
De que maneira o item pode falhar ao executar as funções pretendidas?
De que maneira a operação pode falhar ao executar a função pretendida?
De que maneira o item pode executar uma função não intencional?
De que maneira a operação pode executar uma função não intencional?
O que poderia dar errado com esse item? O que poderia dar errado nessa operação?
O que poderia dar errado nas interfaces? Por que uma peça seria rejeitada nessa operação?
Como o item pode ser mal utilizado? Quais características significativas do produto podem ser modos de falha em potencial?
A etapa de preenchimento da coluna Causas é uma das mais importantes do processo, pois é neste momento que se busca encontrar a raiz do problema. Além disso,
FM2S Treinamento em Desenvolvimento Profissional e Gerencial LTDA - ME Av. Alan Turing, 345 - sala 06 - Edifício Vértice Cidade Universitária - Campinas - SP - CEP: 13083-
o conhecimento da equipe é um ponto importante para gerar o resultado esperado. Em alguns casos, a causa pode ser uma deficiência no processo, passando assim a ser definida como modo de falha, que a princípio poderá ser corrigida ou monitorada. É possível que existam dificuldades para encontrar as causas no FMEA, tanto que em alguns casos são adicionadas causas que pouco contribuíram com o problema. Por isso é tão importante contar com uma equipe capacitada a identificar as causas básicas. Geralmente, essas causas contribuem em 80% dos modos de falha potencial, e com isso otimizar e assegurar a solução das falhas. Algumas ferramentas contribuem para identificar essas causas, como por exemplo o Diagrama Ishikawa e Brainstorming (tempestade de ideias), que podem ser muito úteis neste item, além das outras ferramentas de qualidade que podem ajudar a descobrir as causas. As diferenças de preenchimento entre os tipos são descritas abaixo, na Tabela 6:
Tabela 6: Preenchimento das causas FMEA DFMEA PFMEA
Como pode ocorrer a falha?
O que poderia causar a falha do item dessa maneira?
O que poderia causar a falha da operação dessa maneira?
Que circunstâncias podem levar o item a não desempenhar a função pretendida?
Que circunstâncias podem levar a operação a não desempenhar a função pretendida?
Por que poderia ocorrer a falha?
Qual é o mecanismo da falha?
O exemplo abaixo, na Figura 12, mostra o preenchimento de um DFMEA para dois itens. O preenchimento segue as características relevantes da análise técnica apresentadas nas Tabelas 3, 4 e 5. Confira:
Figura 12: Exemplo de DFMEA preenchido com parte da análise técnica
FM2S Treinamento em Desenvolvimento Profissional e Gerencial LTDA - ME Av. Alan Turing, 345 - sala 06 - Edifício Vértice Cidade Universitária - Campinas - SP - CEP: 13083-