
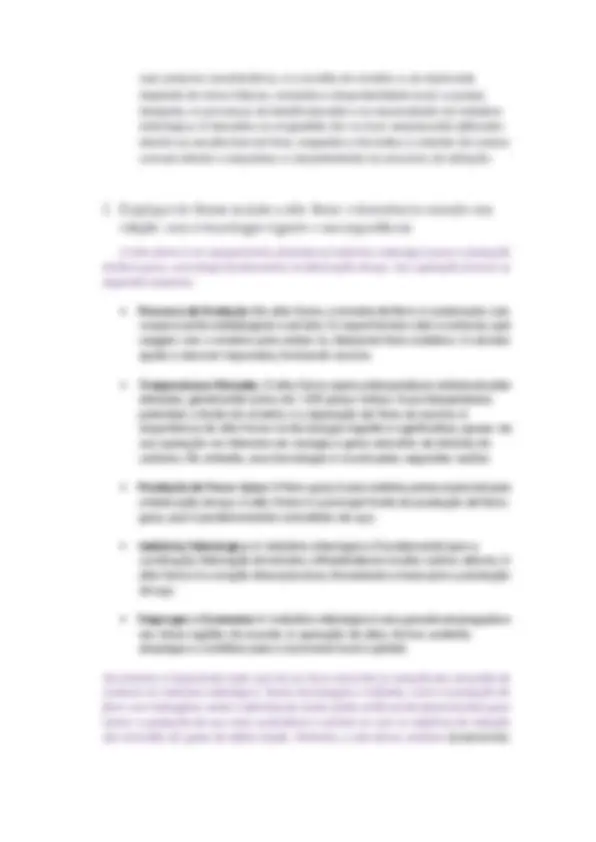
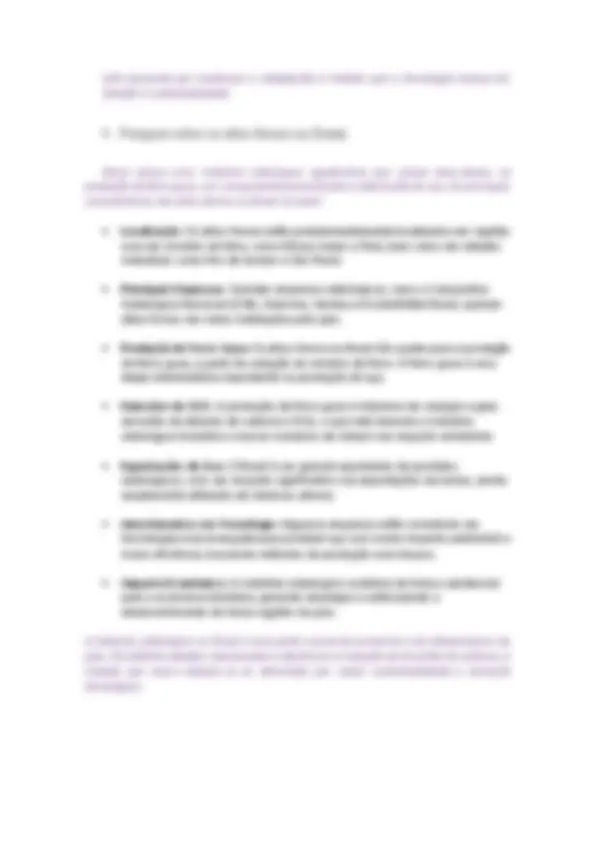
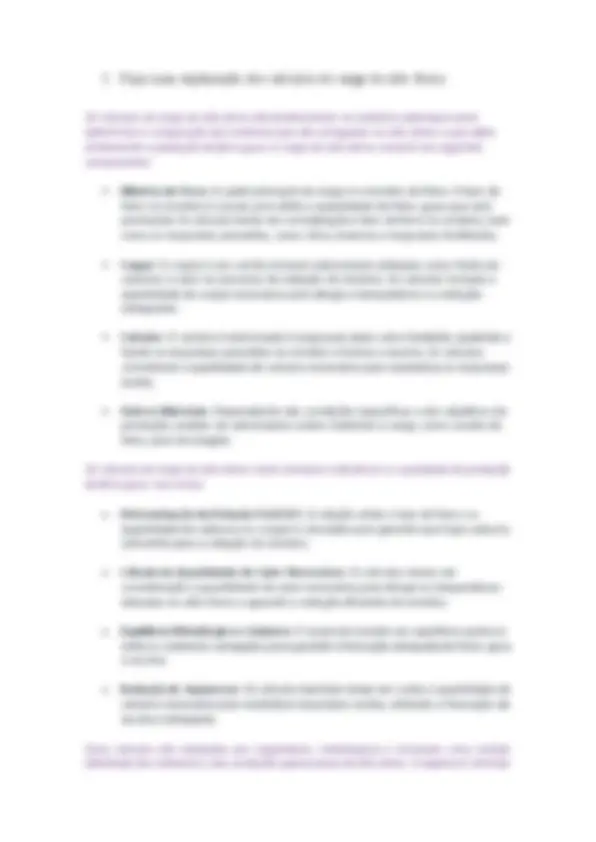
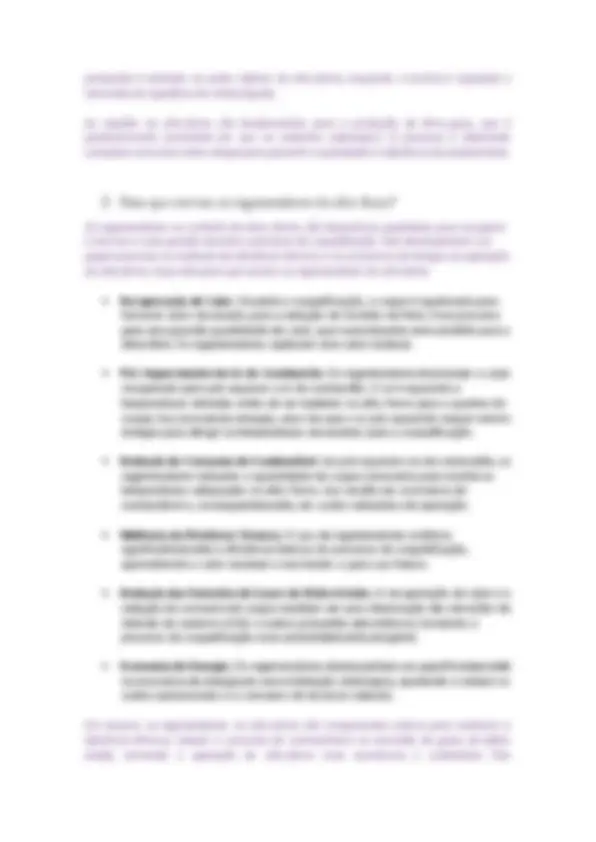
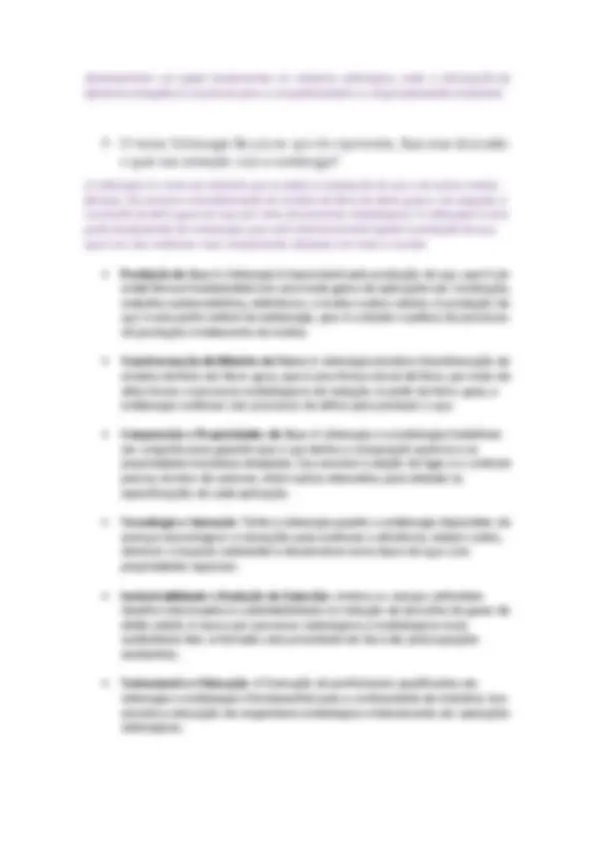
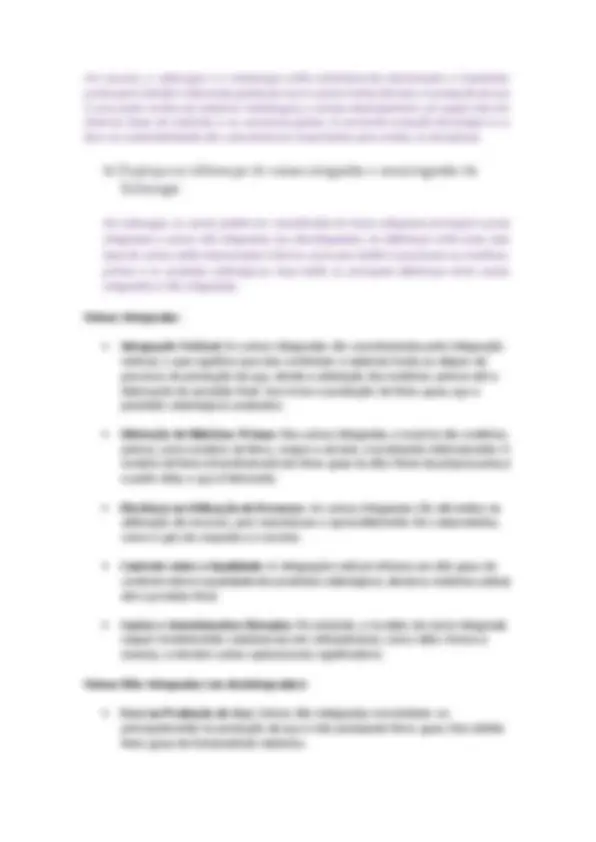
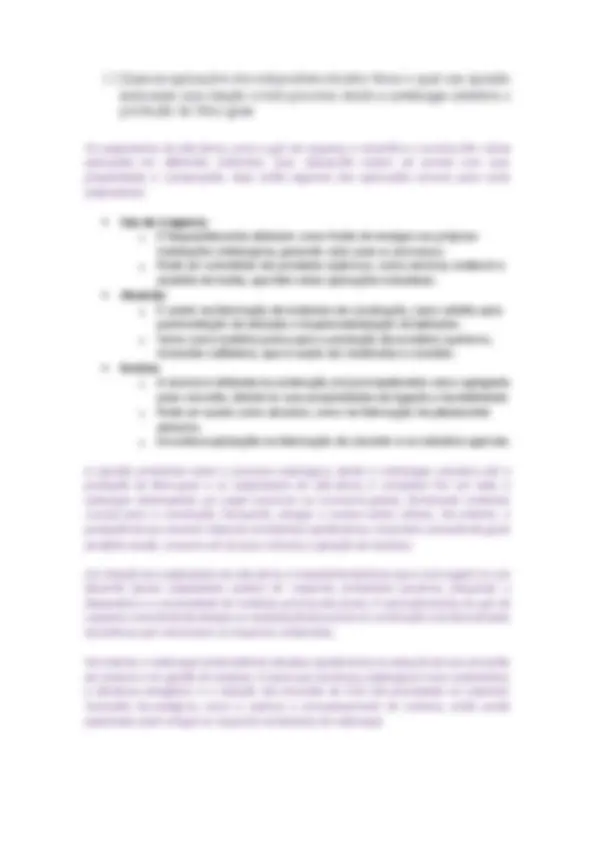
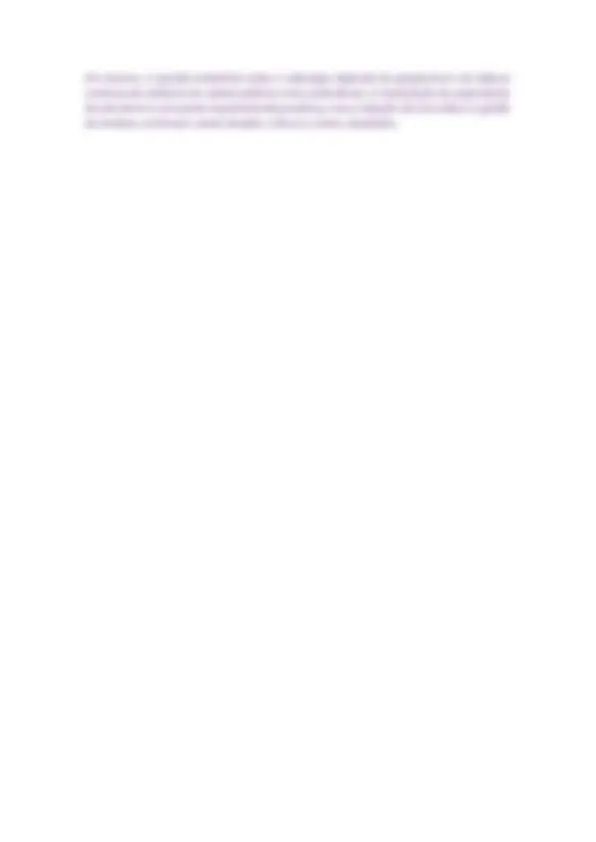
Estude fácil! Tem muito documento disponível na Docsity
Ganhe pontos ajudando outros esrudantes ou compre um plano Premium
Prepare-se para as provas
Estude fácil! Tem muito documento disponível na Docsity
Prepare-se para as provas com trabalhos de outros alunos como você, aqui na Docsity
Os melhores documentos à venda: Trabalhos de alunos formados
Prepare-se com as videoaulas e exercícios resolvidos criados a partir da grade da sua Universidade
Responda perguntas de provas passadas e avalie sua preparação.
Ganhe pontos para baixar
Ganhe pontos ajudando outros esrudantes ou compre um plano Premium
Comunidade
Peça ajuda à comunidade e tire suas dúvidas relacionadas ao estudo
Descubra as melhores universidades em seu país de acordo com os usuários da Docsity
Guias grátis
Baixe gratuitamente nossos guias de estudo, métodos para diminuir a ansiedade, dicas de TCC preparadas pelos professores da Docsity
Anotações de discussões em sala de aula sobre metalurgia
Tipologia: Notas de aula
1 / 14
Esta página não é visível na pré-visualização
Não perca as partes importantes!
A metalurgia extrativa do ferro é um processo complexo que envolve a extração de minérios de ferro da natureza e sua subsequente transformação em ferro e aço. Aqui estão as principais etapas e características específicas desse processo, desde a extração do minério até o beneficiamento:
está passando por mudanças e adaptações à medida que a tecnologia avança em direção à sustentabilidade.
Brasil possui uma indústria siderúrgica significativa que utiliza altos-fornos na produção de ferro-gusa, um componente essencial para a fabricação de aço. As principais características dos altos-fornos no Brasil incluem:
Os cálculos de carga do alto-forno são fundamentais na indústria siderúrgica para determinar a composição dos materiais que são carregados no alto-forno, o que afeta diretamente a produção de ferro-gusa. A carga do alto-forno consiste nos seguintes componentes:
os subprodutos, como gás de coqueria e alcatrão, têm aplicações valiosas em outras indústrias, incluindo química, construção e materiais impermeáveis. Isso torna a coqueificação um processo economicamente importante e ambientalmente relevante.
As reações que ocorrem no alto-forno são complexas e envolvem a transformação do minério de ferro, coque e calcário em ferro-gusa e escória. Abaixo, estão as reações mais importantes que acontecem no alto-forno:
produzido é drenado na parte inferior do alto-forno, enquanto a escória é separada e removida da superfície do metal líquido. As reações no alto-forno são fundamentais para a produção de ferro-gusa, que é posteriormente convertido em aço na indústria siderúrgica. O processo é altamente complexo e envolve várias etapas para garantir a qualidade e a eficiência do produto final.
Os regeneradores no contexto de altos-fornos são dispositivos projetados para recuperar e reciclar o calor gerado durante o processo de coqueificação. Eles desempenham um papel essencial na melhoria da eficiência térmica e na economia de energia na operação do alto-forno. Aqui está para que servem os regeneradores do alto forno:
Em resumo, a siderurgia e a metalurgia estão estreitamente relacionadas e trabalham juntas para atender à demanda global por aço e outros metais ferrosos. A produção de aço é uma parte central da indústria metalúrgica, e ambas desempenham um papel vital em diversas áreas da indústria e na economia global. A constante evolução tecnológica e o foco na sustentabilidade são características importantes para ambas as disciplinas.
Na siderurgia, as usinas podem ser classificadas em duas categorias principais: usinas integradas e usinas não integradas (ou desintegradas). As diferenças entre esses dois tipos de usinas estão relacionadas à forma como elas obtêm e processam as matérias- primas e os produtos siderúrgicos. Aqui estão as principais diferenças entre usinas integradas e não integradas: Usinas Integradas :
O lingotamento contínuo e o transporte por carro torpedo são processos importantes na indústria siderúrgica, usados para moldar e transportar o aço líquido da aciaria para a laminação ou outras etapas de processamento. Vou explicar o funcionamento de ambos os processos: Lingotamento Contínuo : O lingotamento contínuo é um processo de fabricação de produtos siderúrgicos sem a necessidade de moldes individuais. Ele é utilizado para produzir placas, tarugos, vergalhões e outros produtos siderúrgicos.
Os subprodutos do alto-forno, como o gás de coqueria, o alcatrão e a escória, têm várias aplicações em diferentes indústrias. Suas utilizações variam de acordo com suas propriedades e composições. Aqui estão algumas das aplicações comuns para esses subprodutos:
Em resumo, a opinião ambiental sobre a siderurgia depende da perspectiva e do esforço contínuo da indústria em adotar práticas mais sustentáveis. A reutilização de subprodutos do alto-forno é uma parte importante desse esforço, mas a redução das emissões e a gestão de resíduos continuam sendo desafios críticos a serem abordados.