
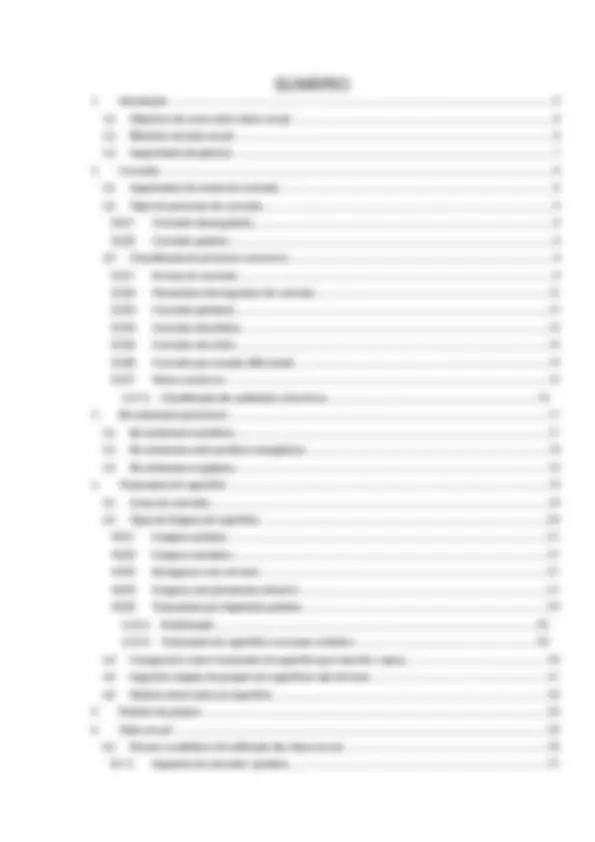
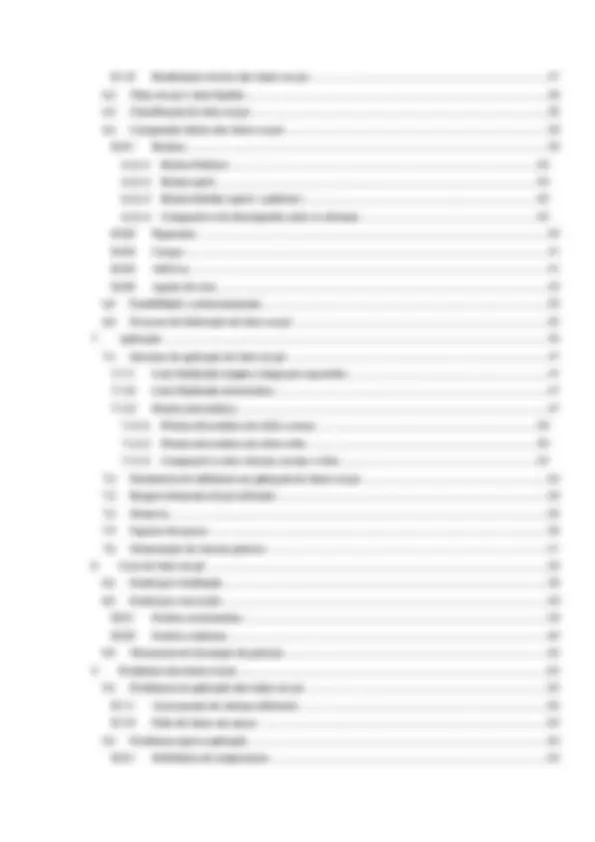
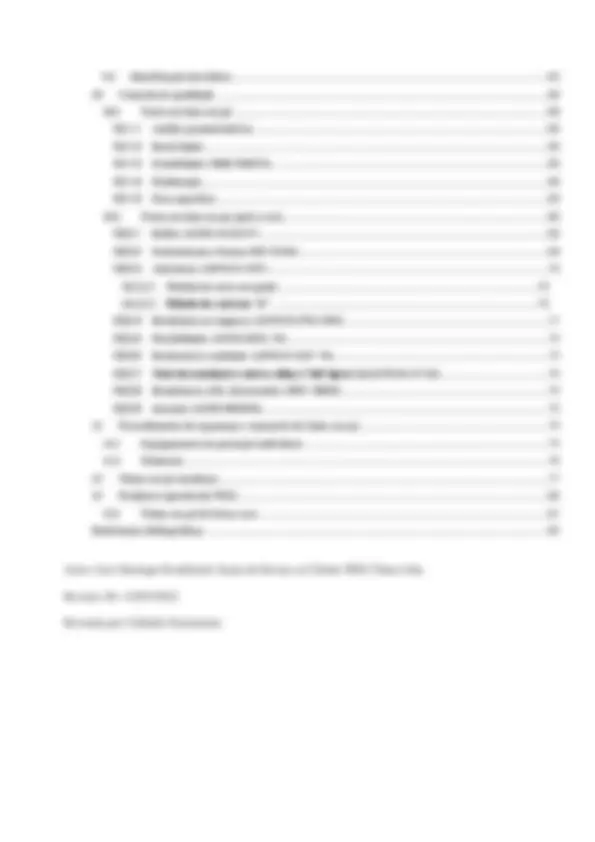
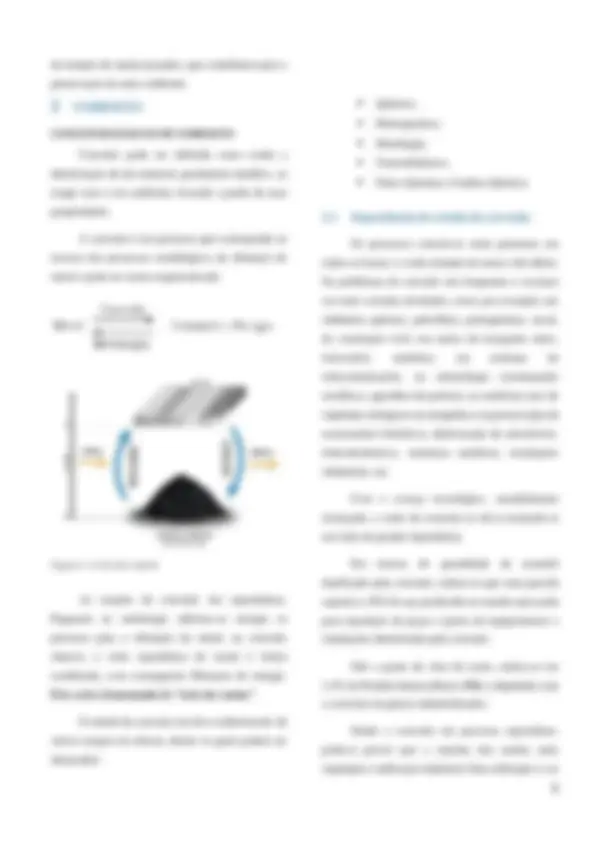
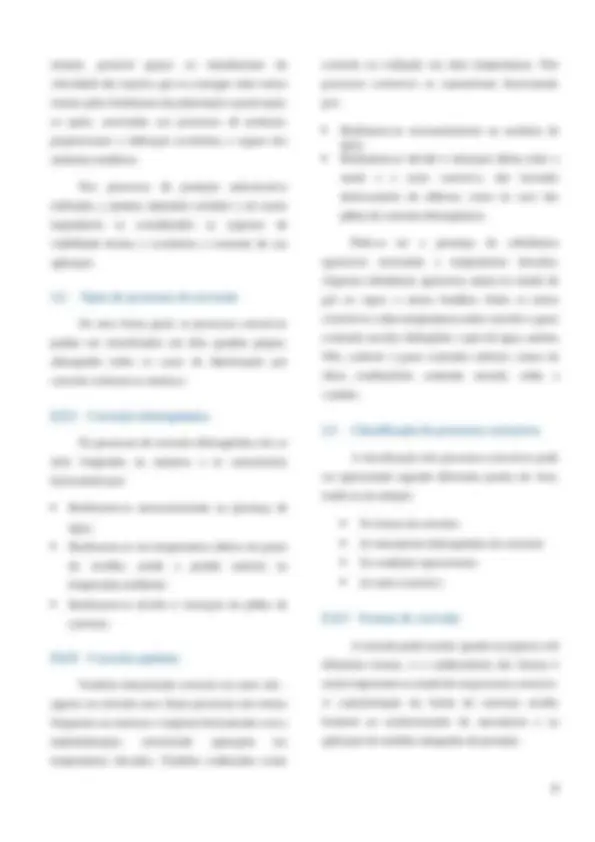
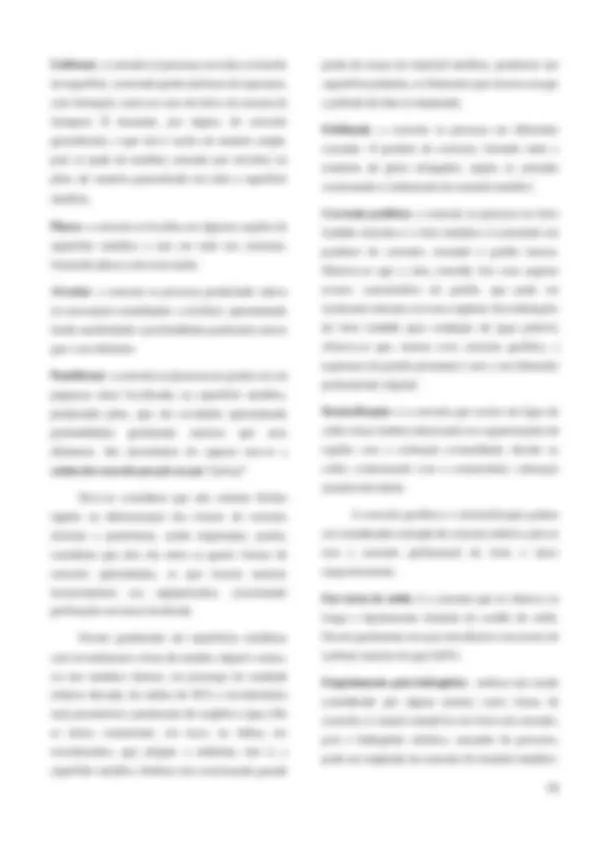
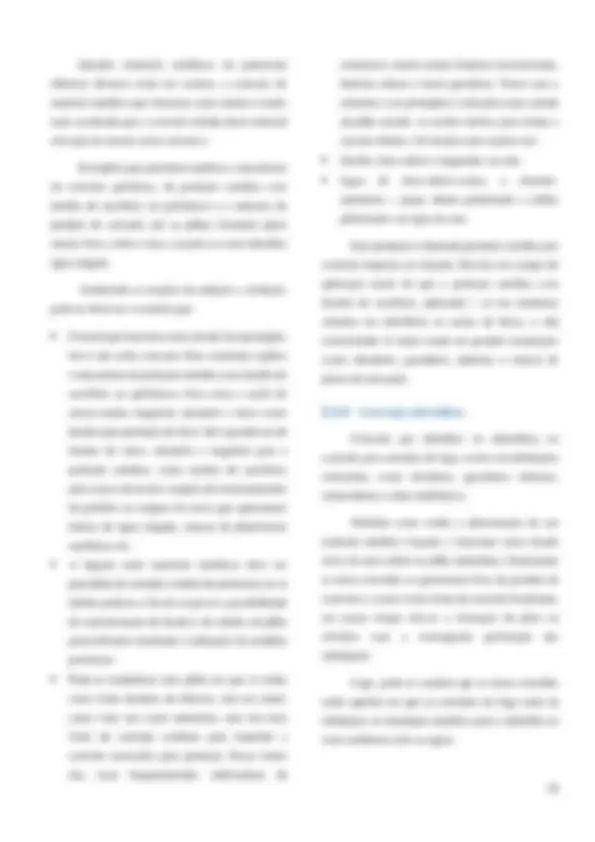
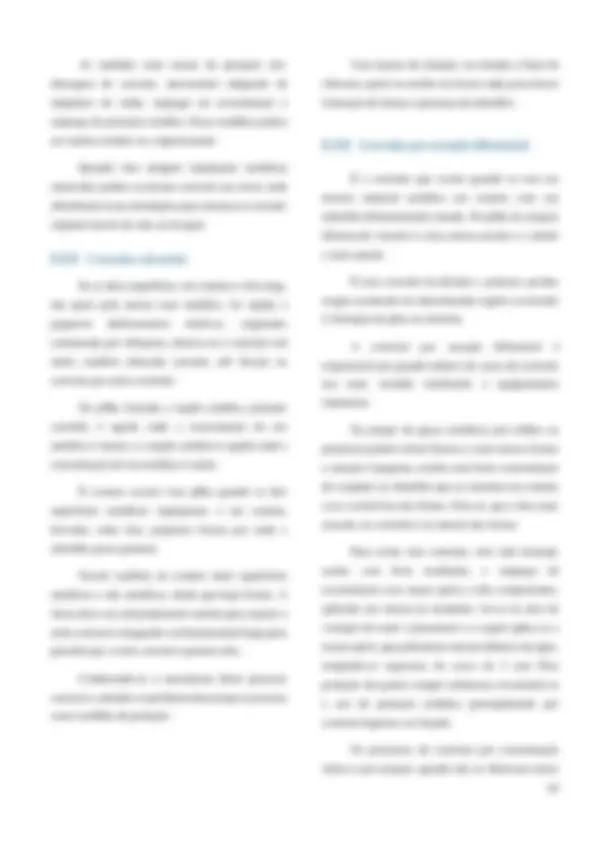
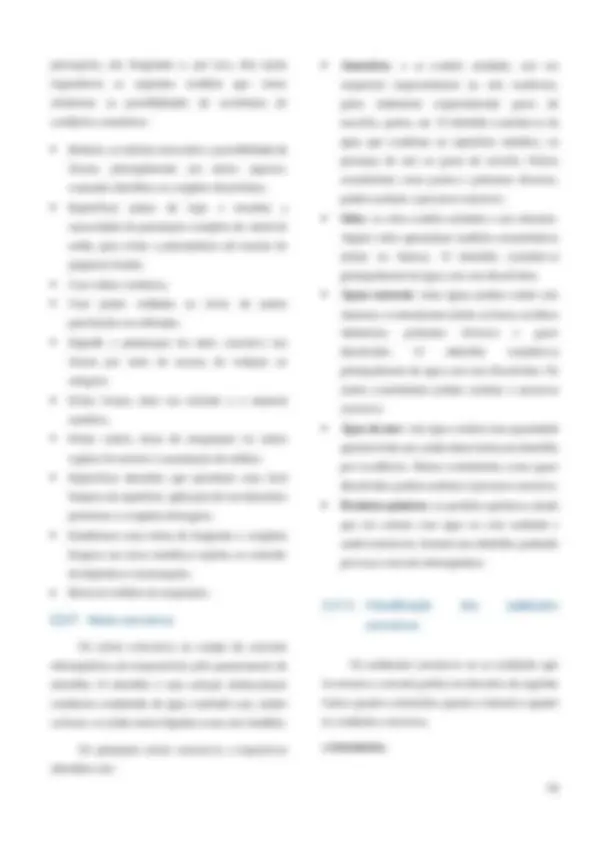
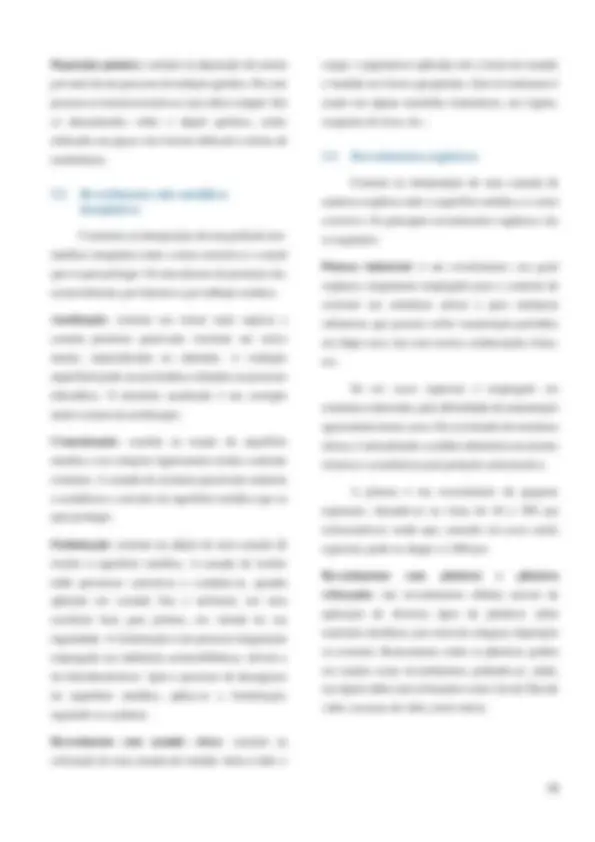
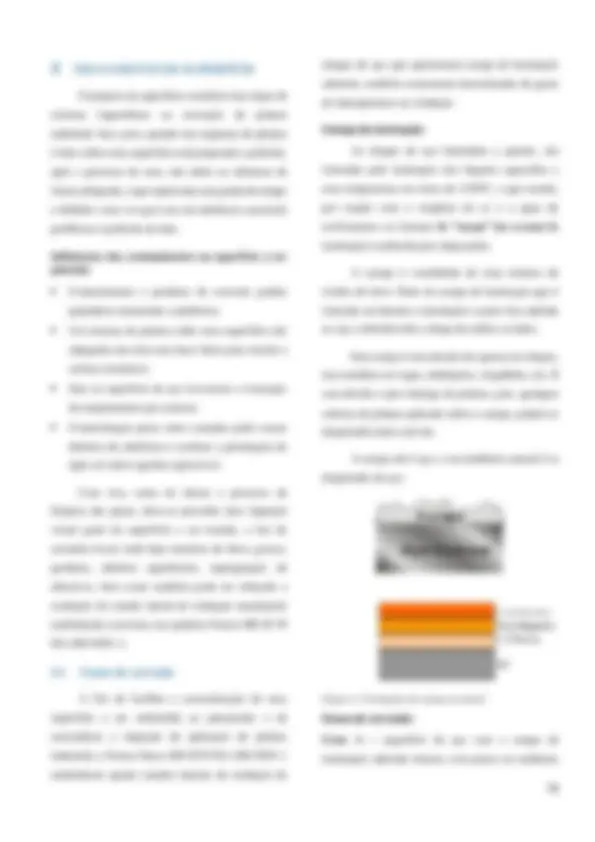
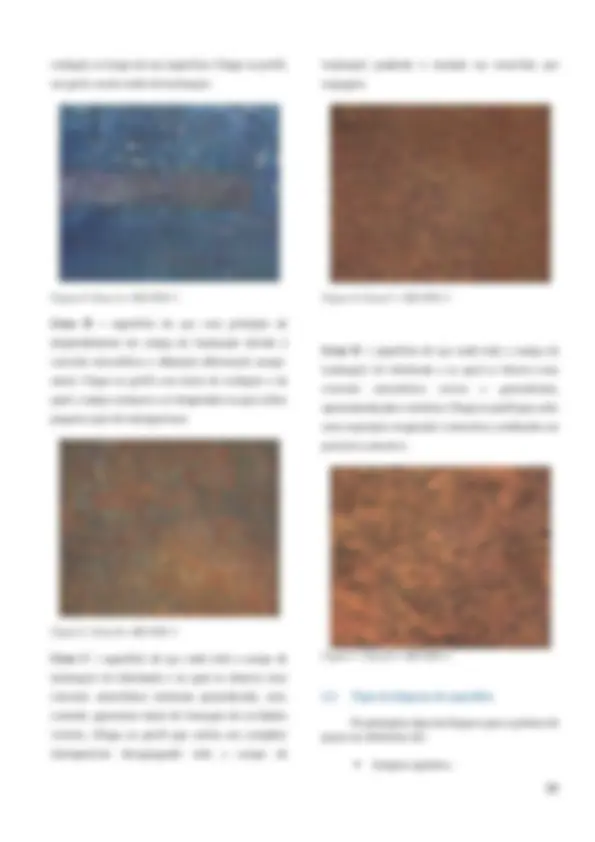
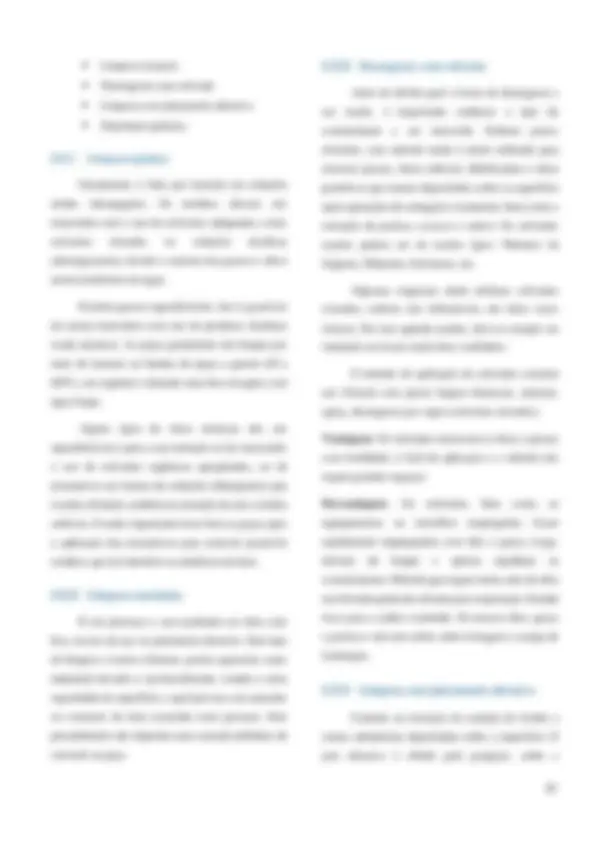

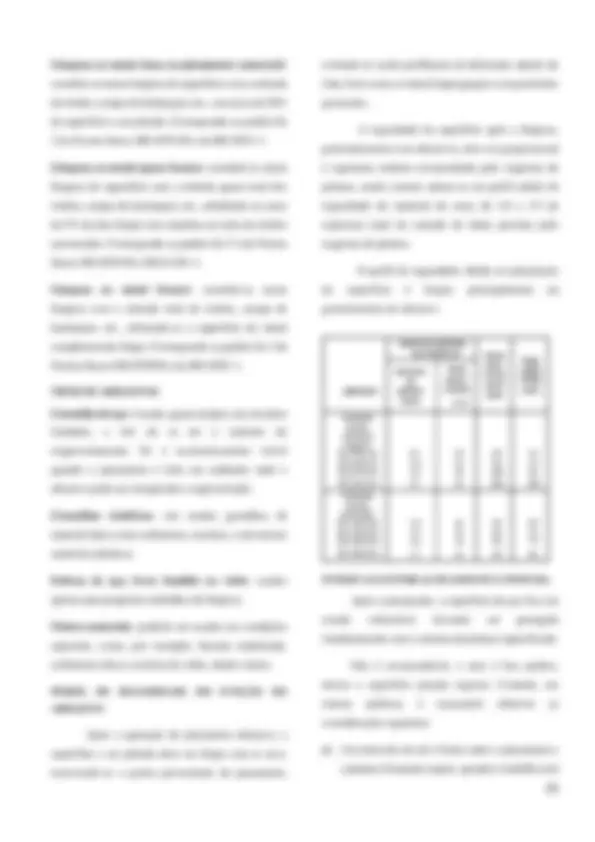
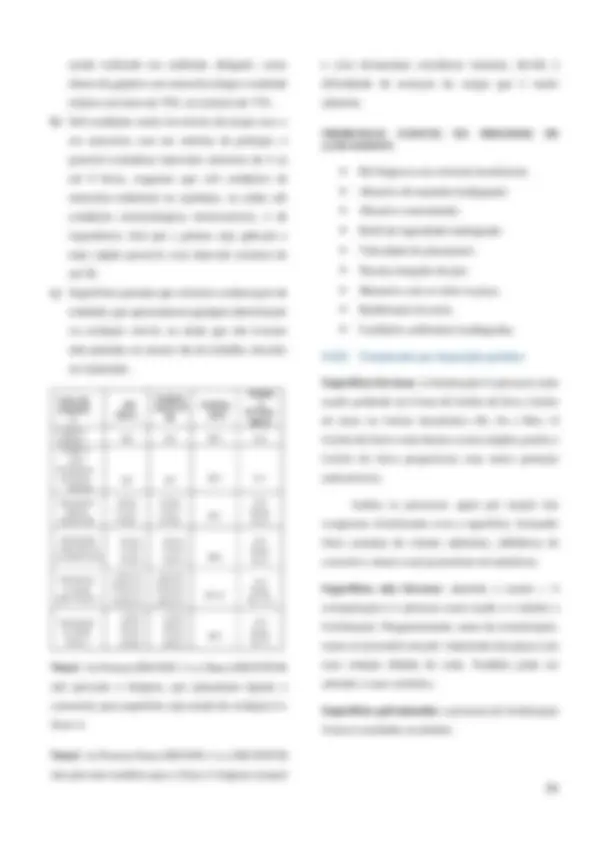
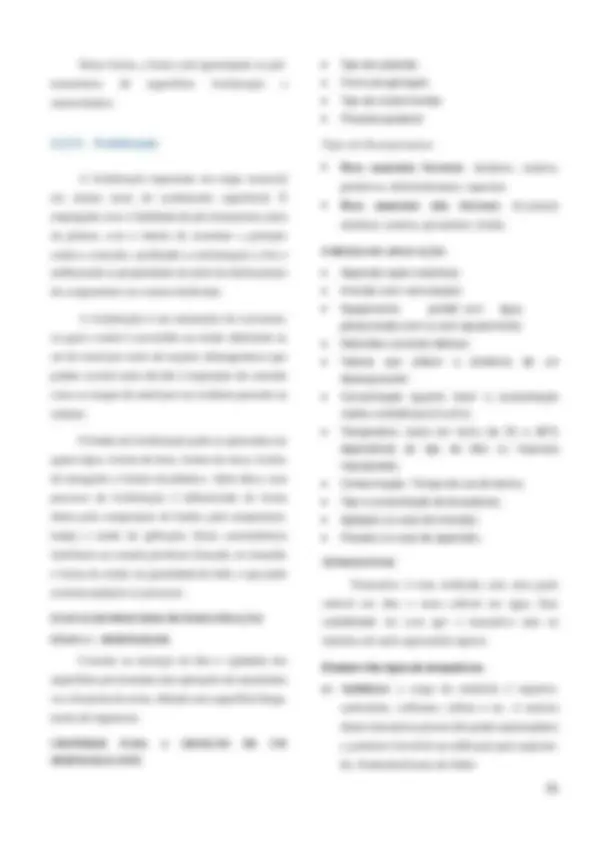
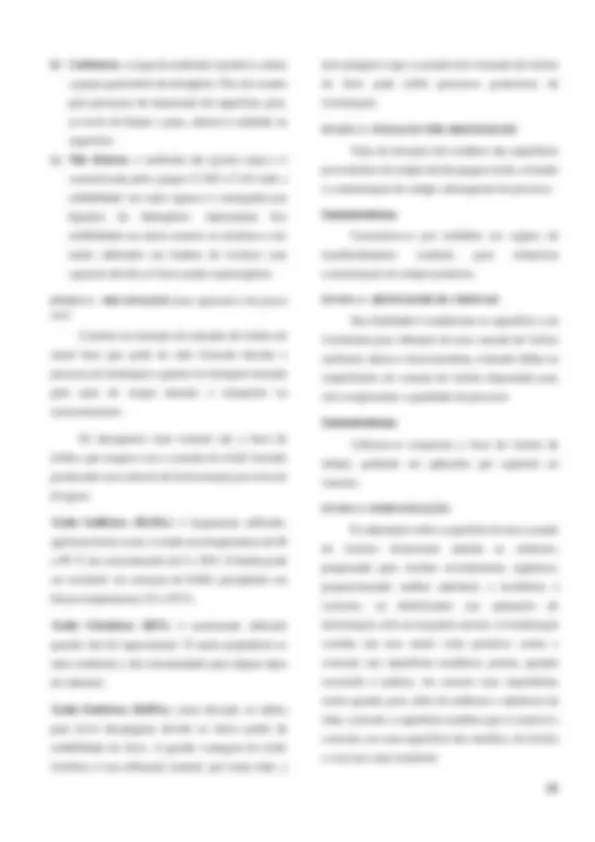
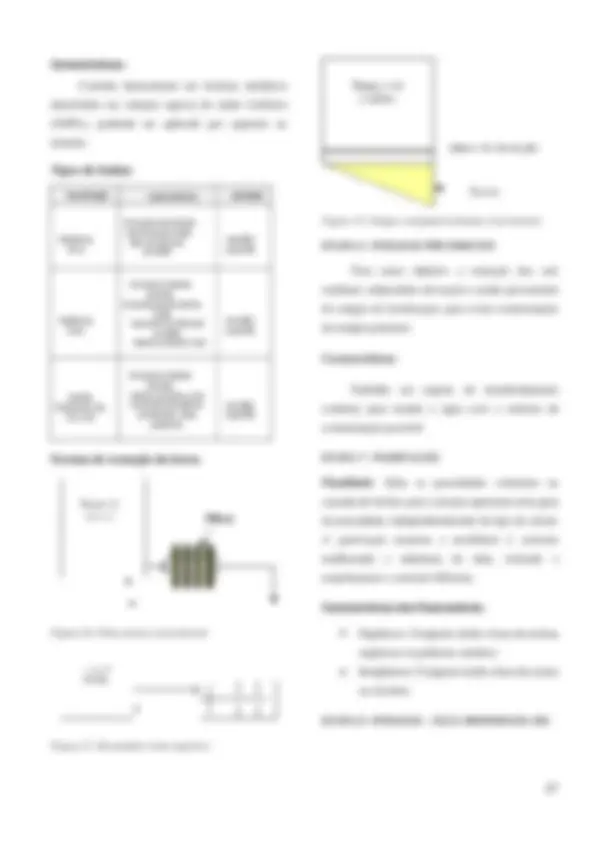

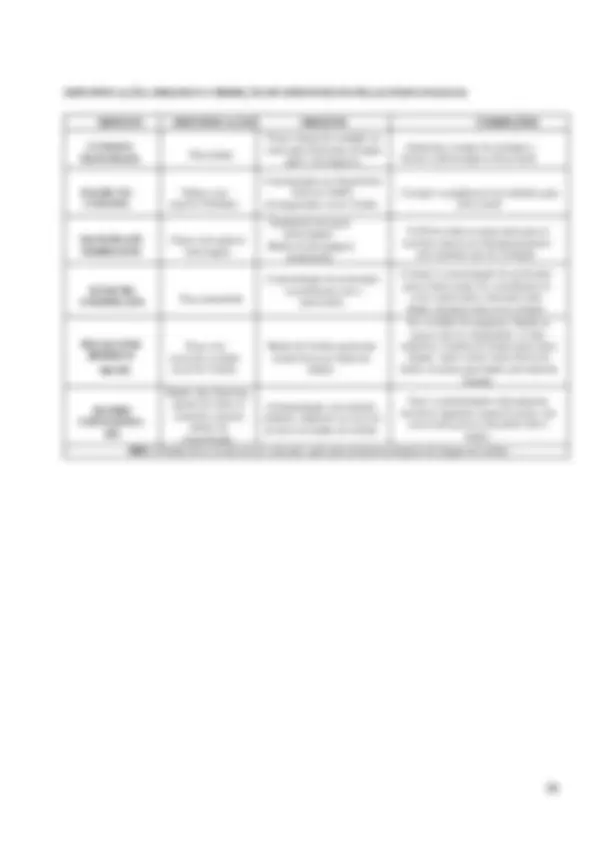
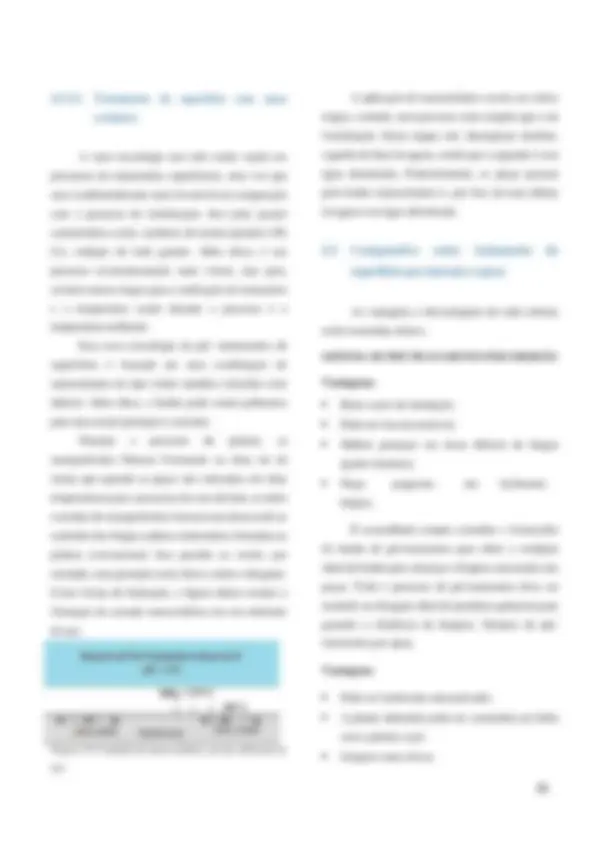
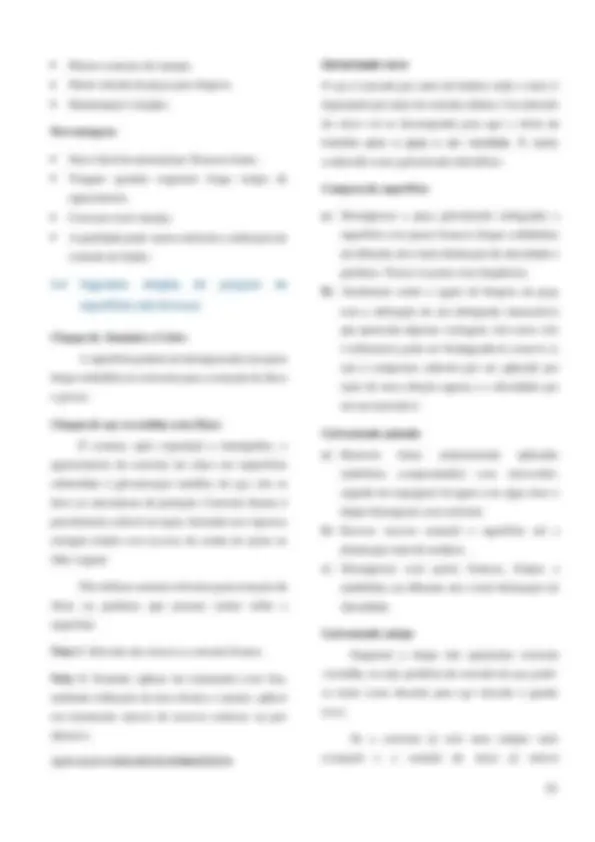
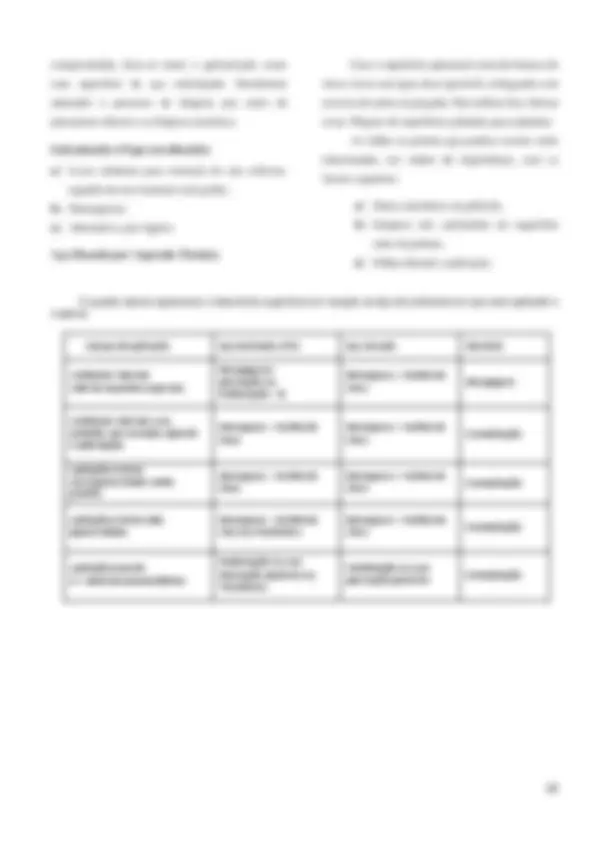
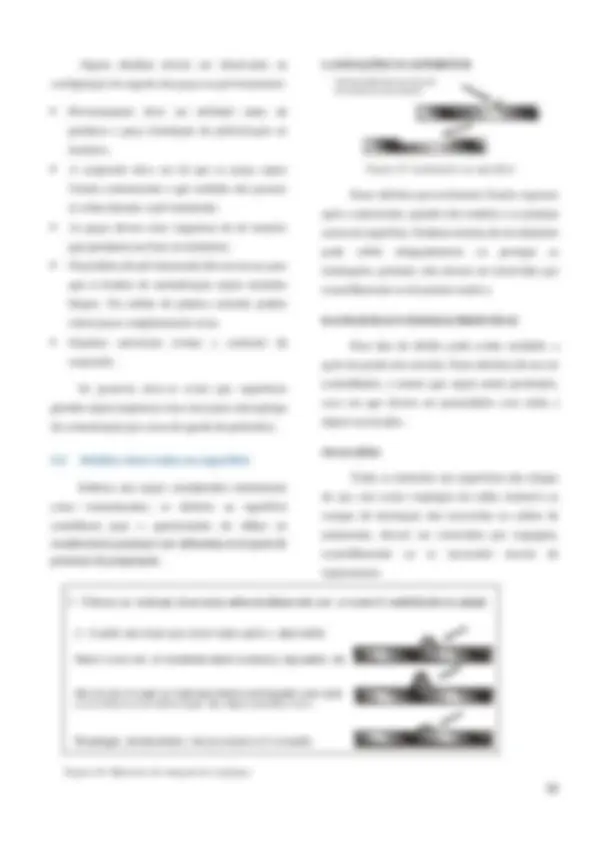
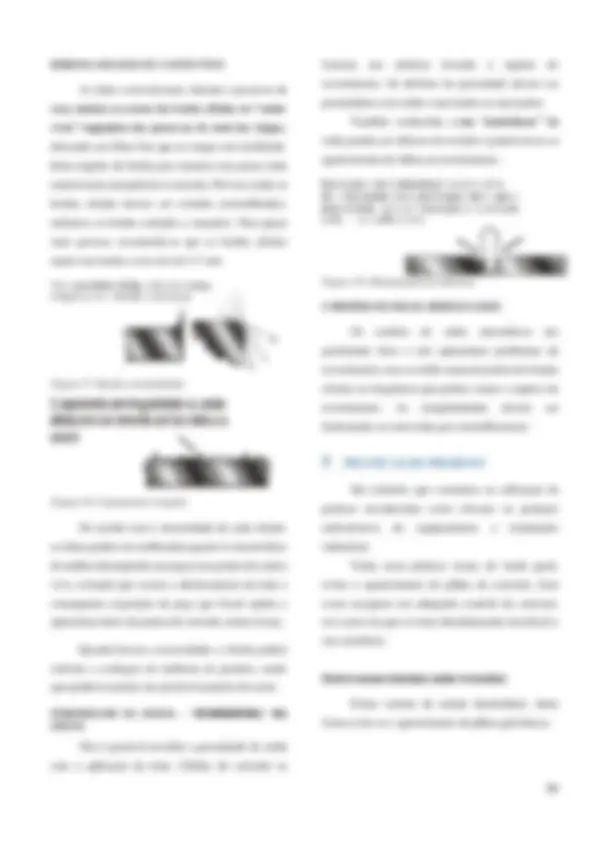
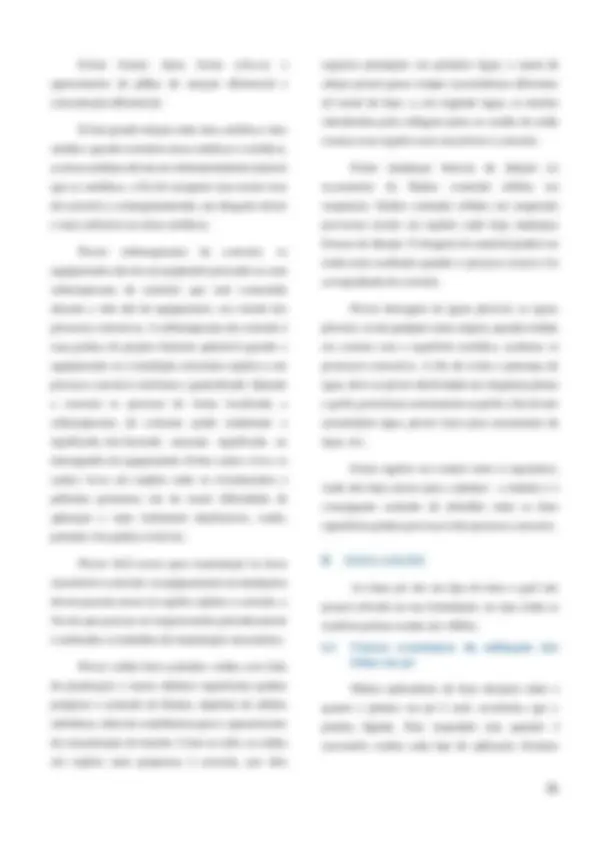
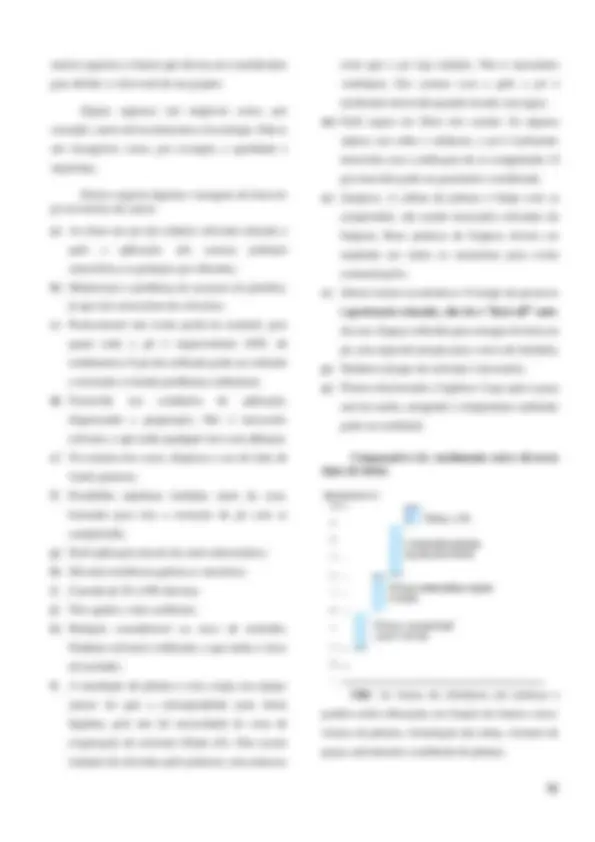
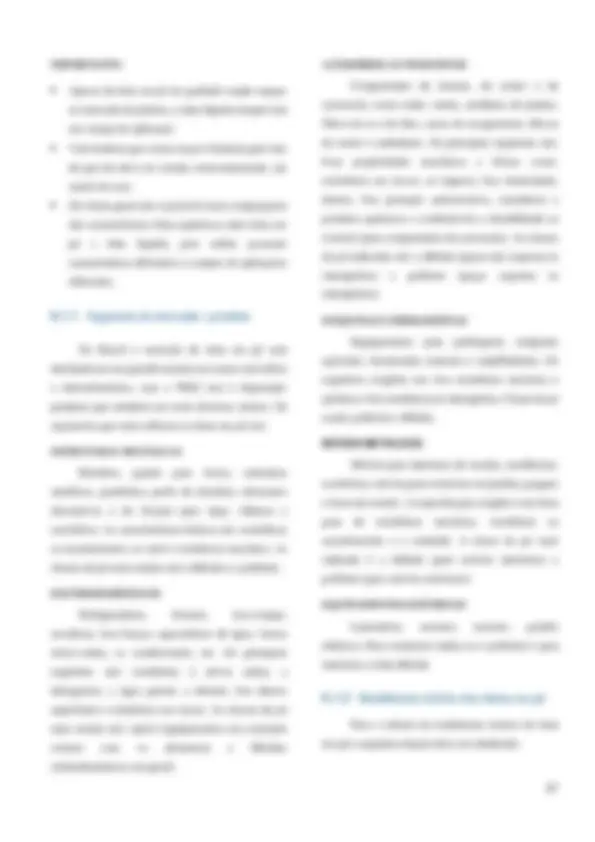
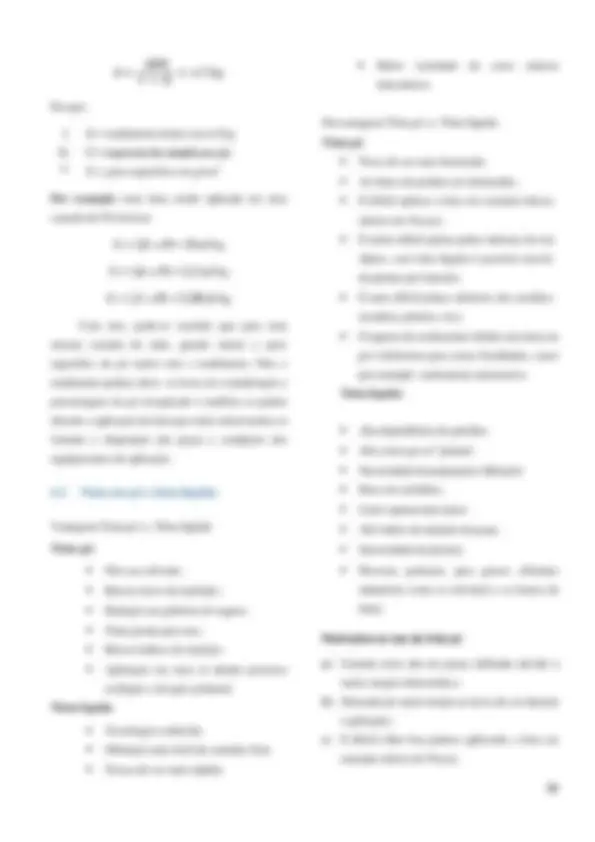
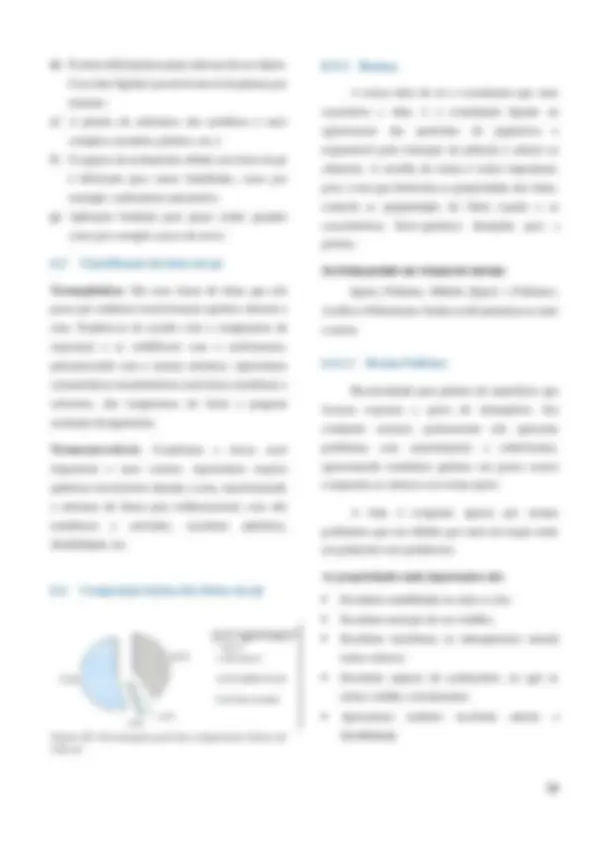
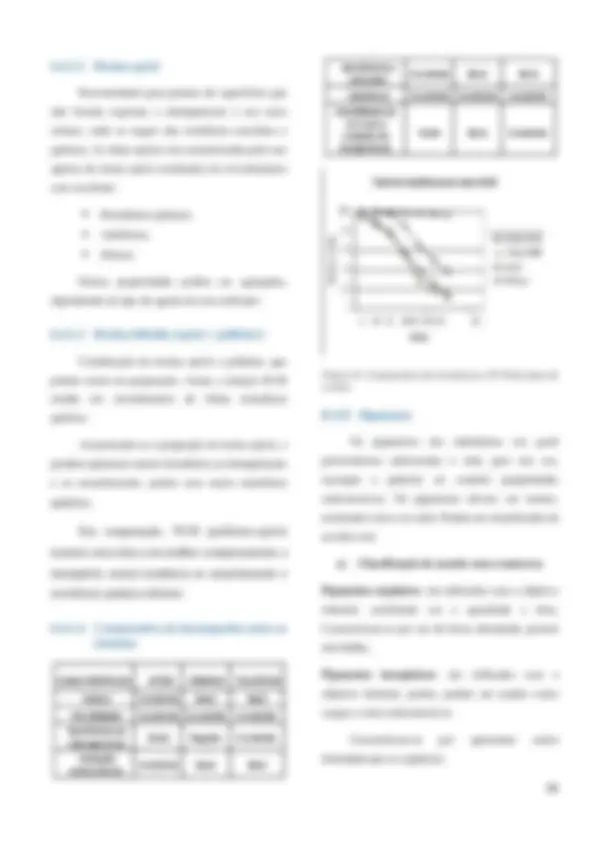
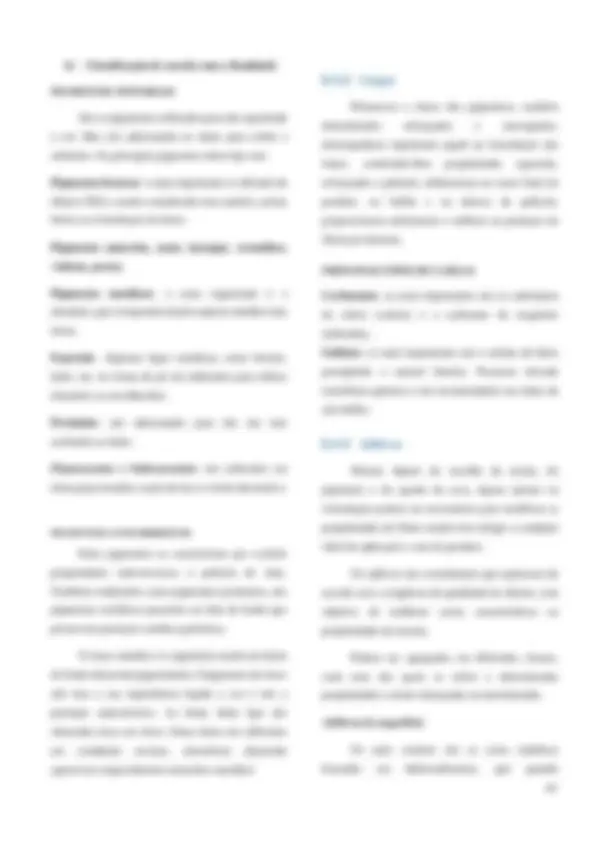
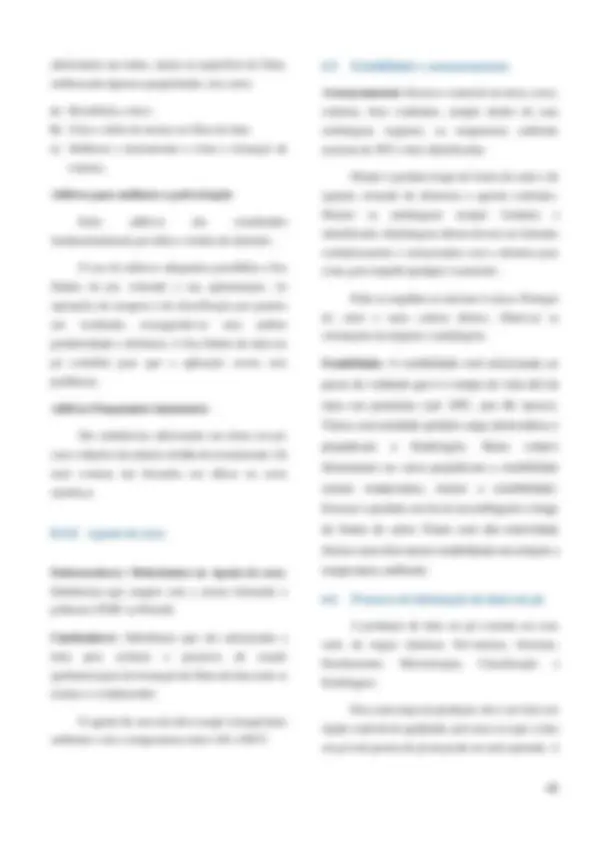
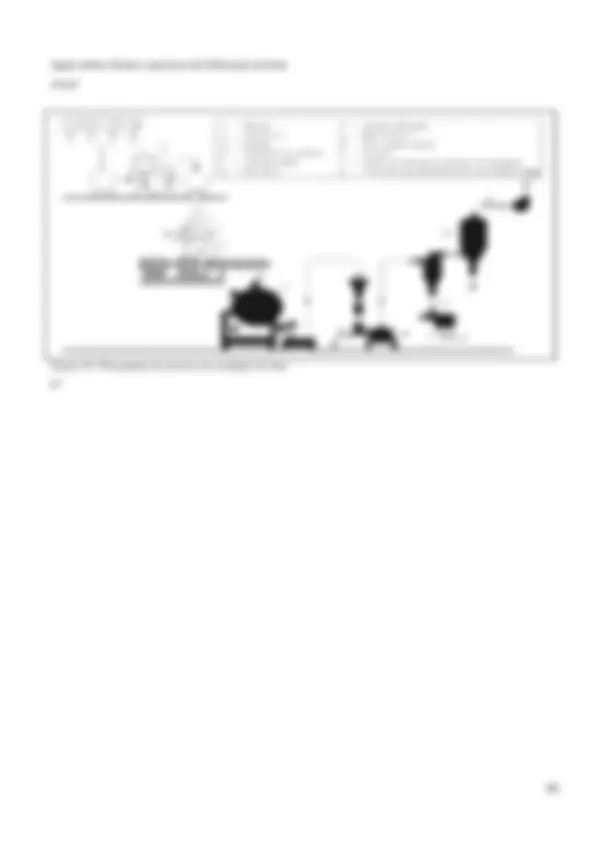
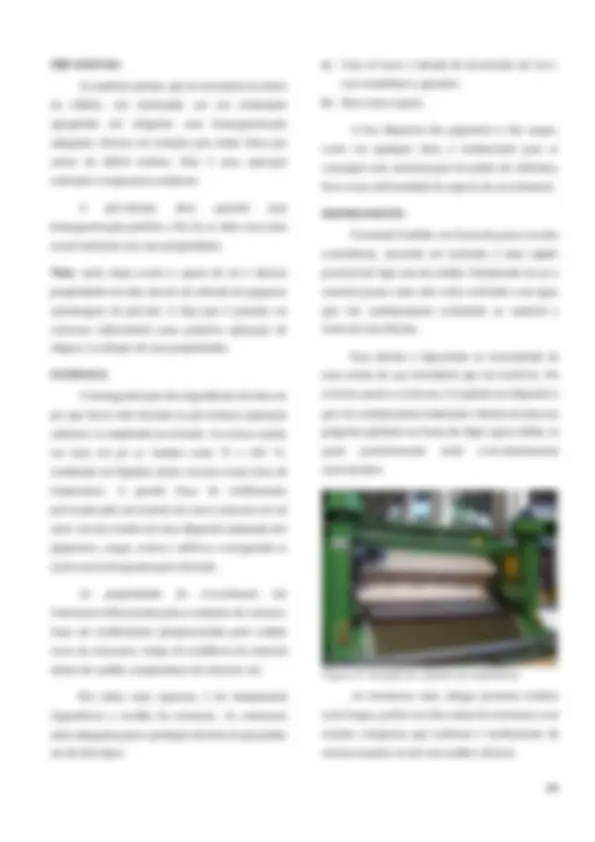
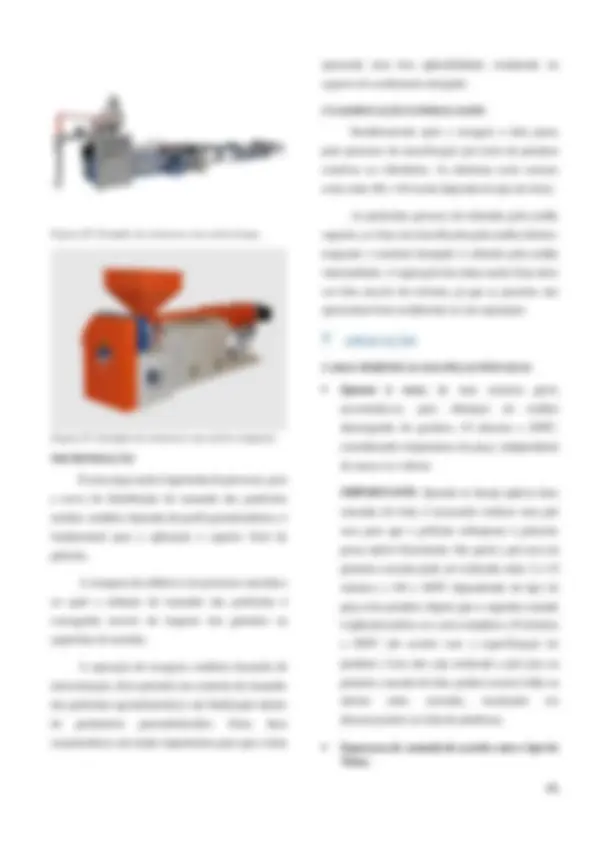
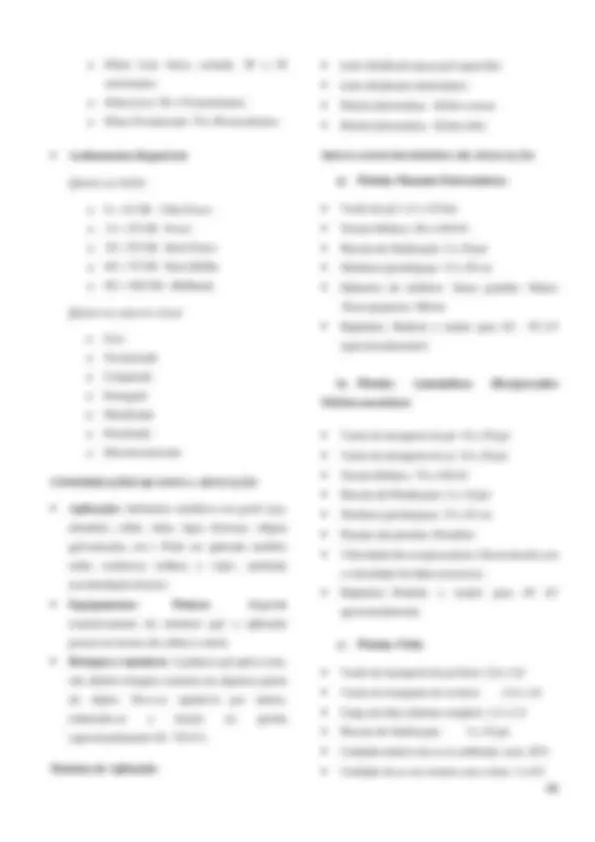
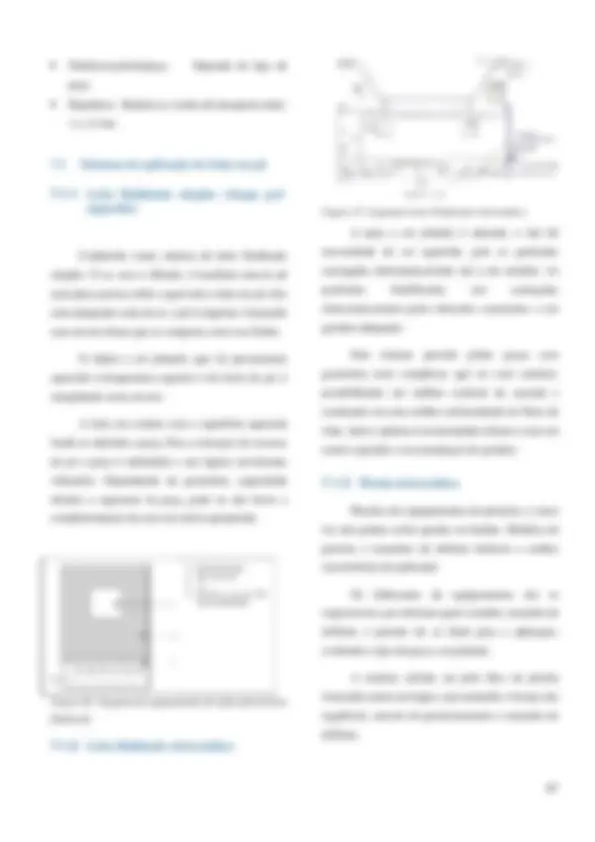
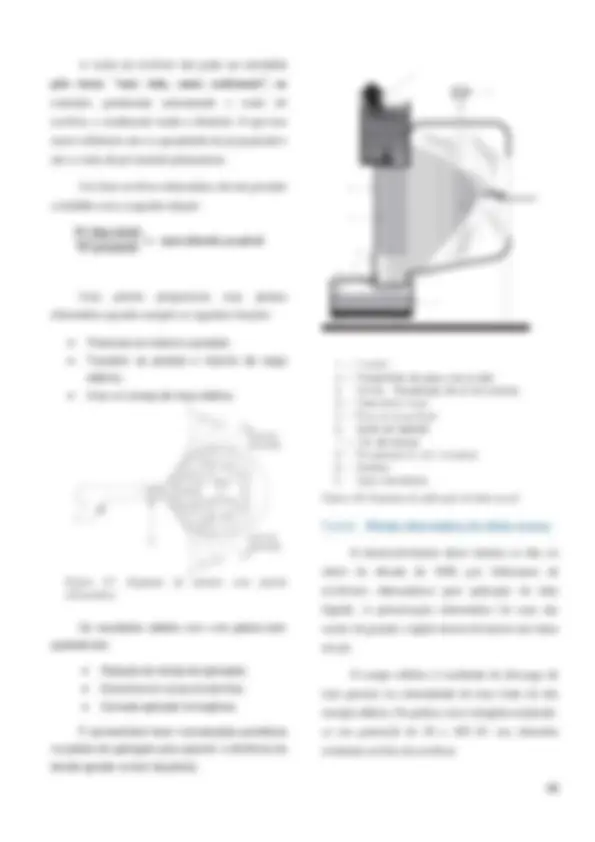
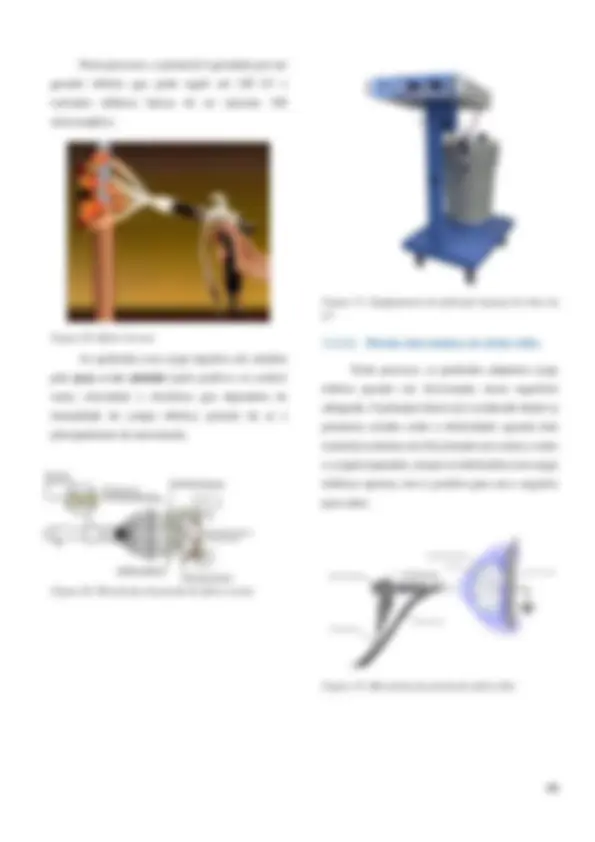
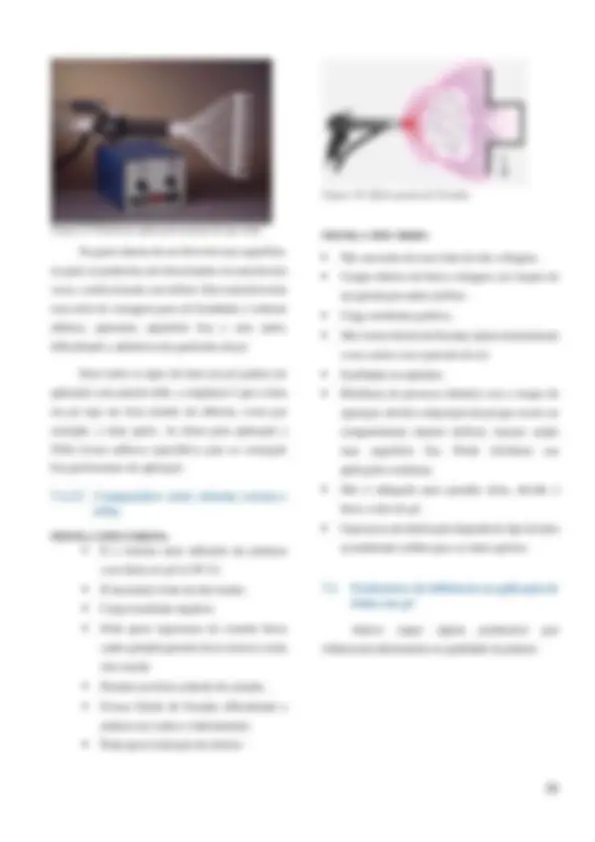
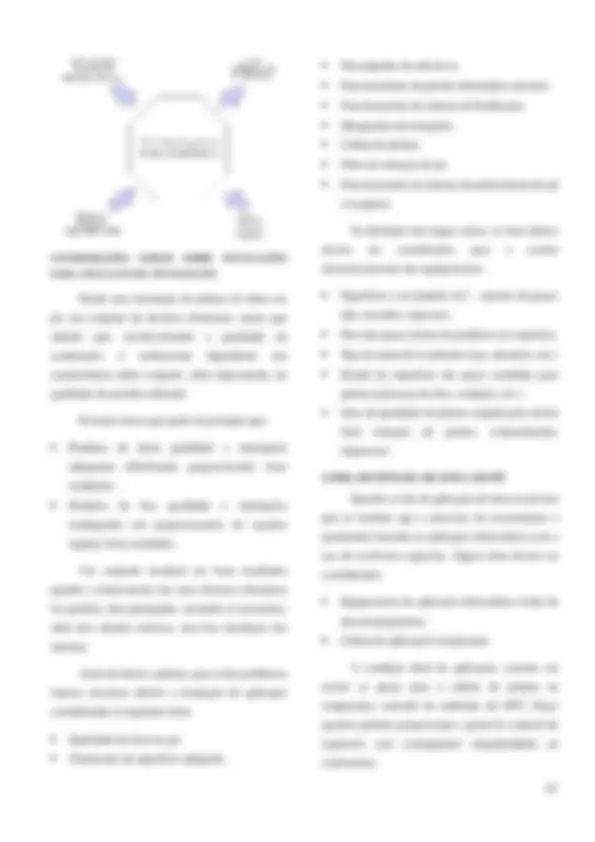
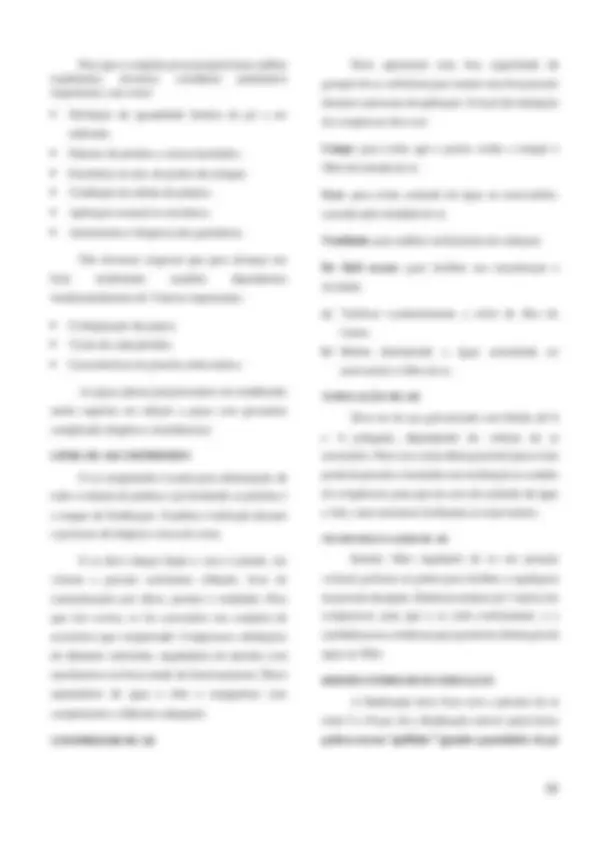
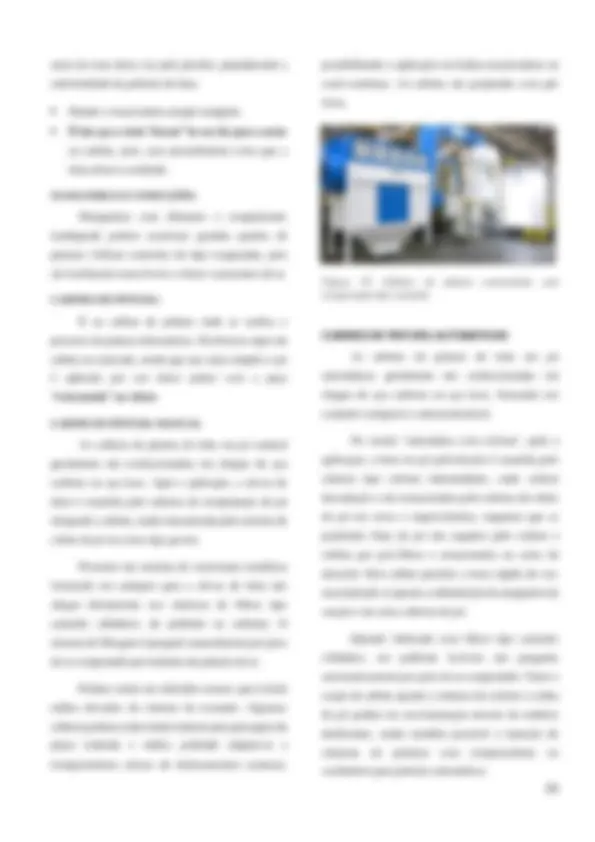
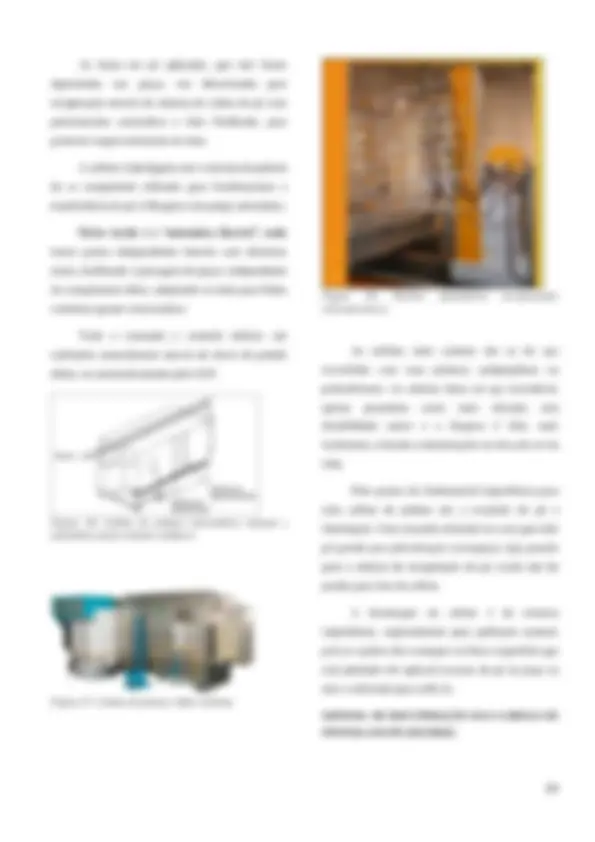
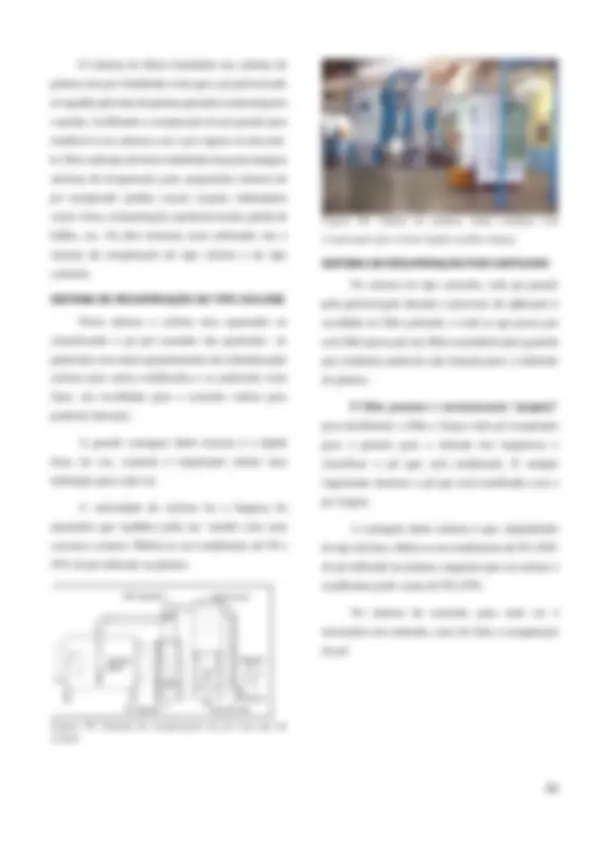
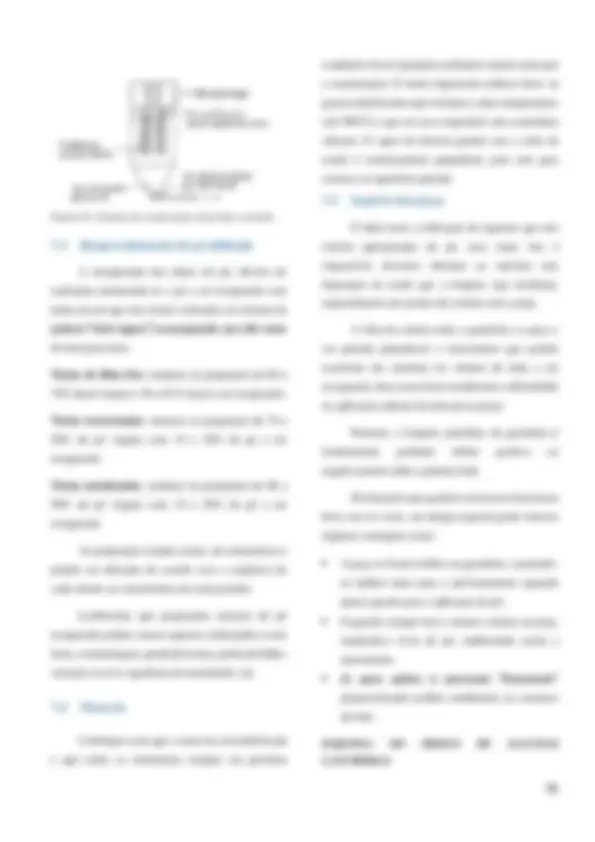
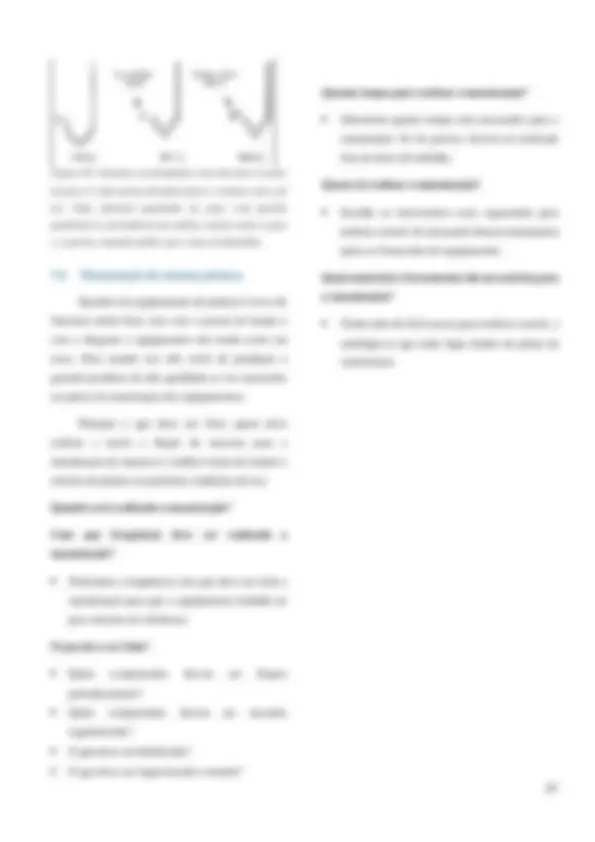
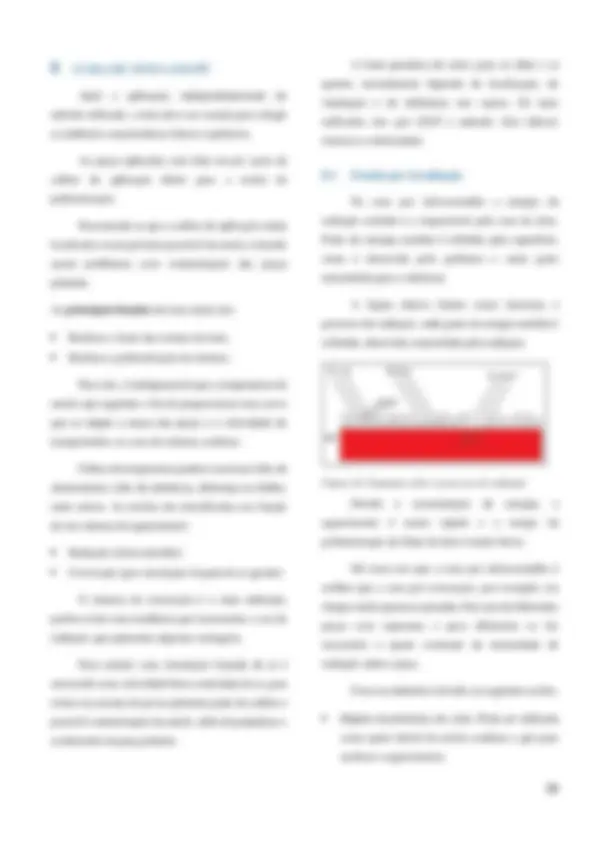
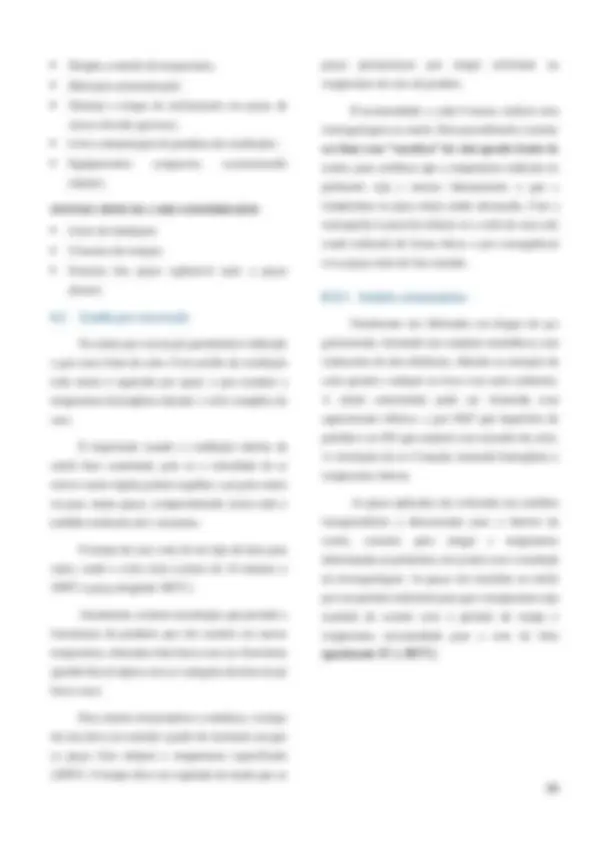
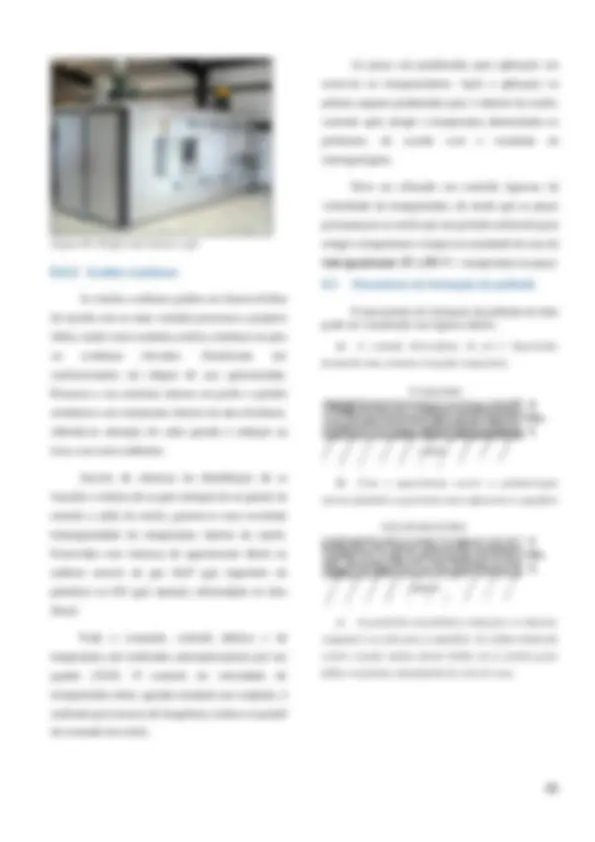
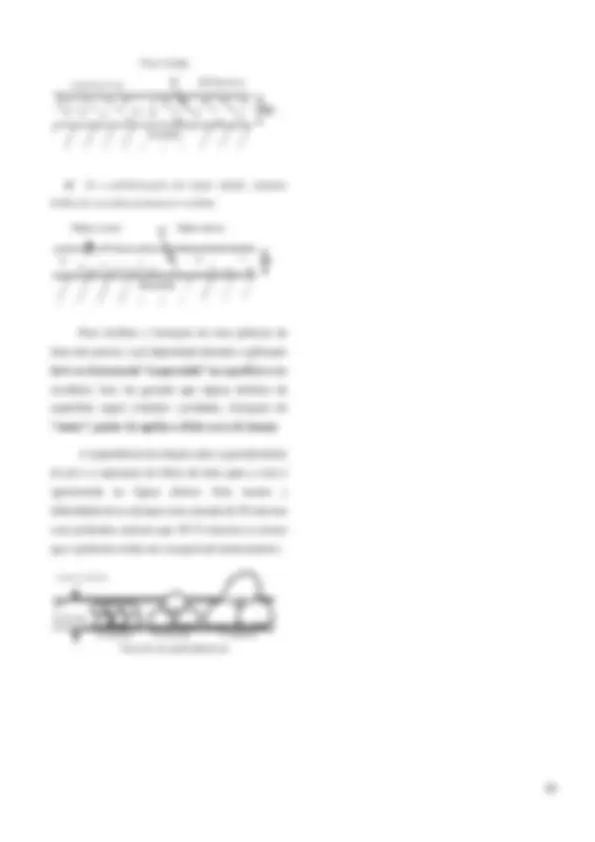
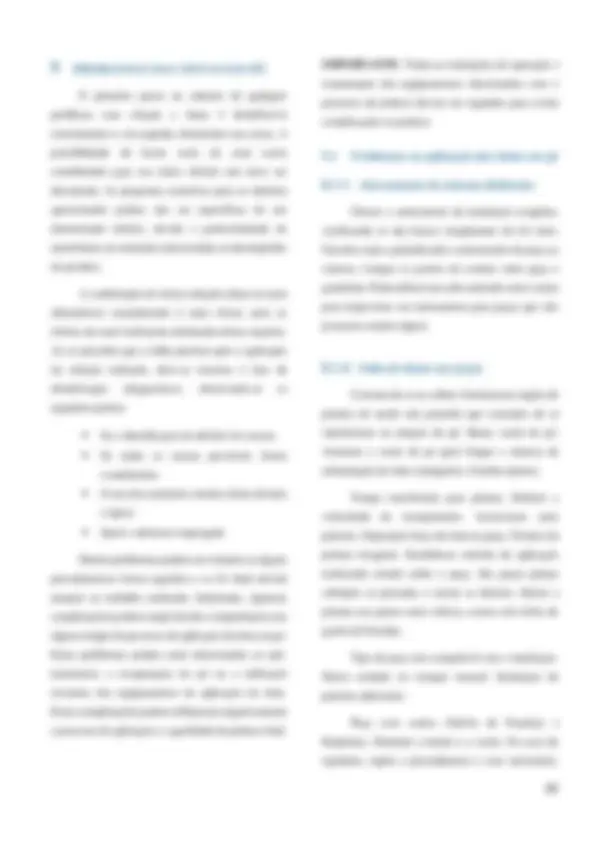
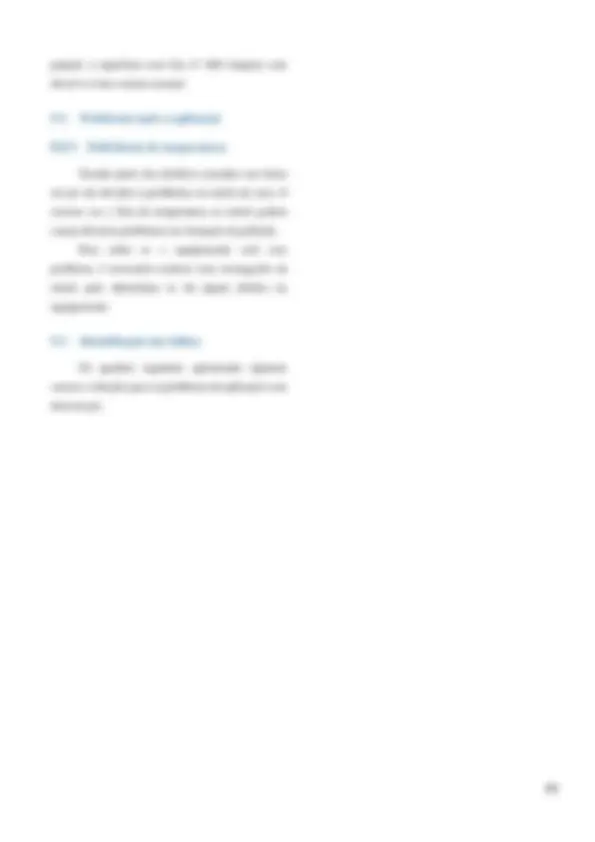
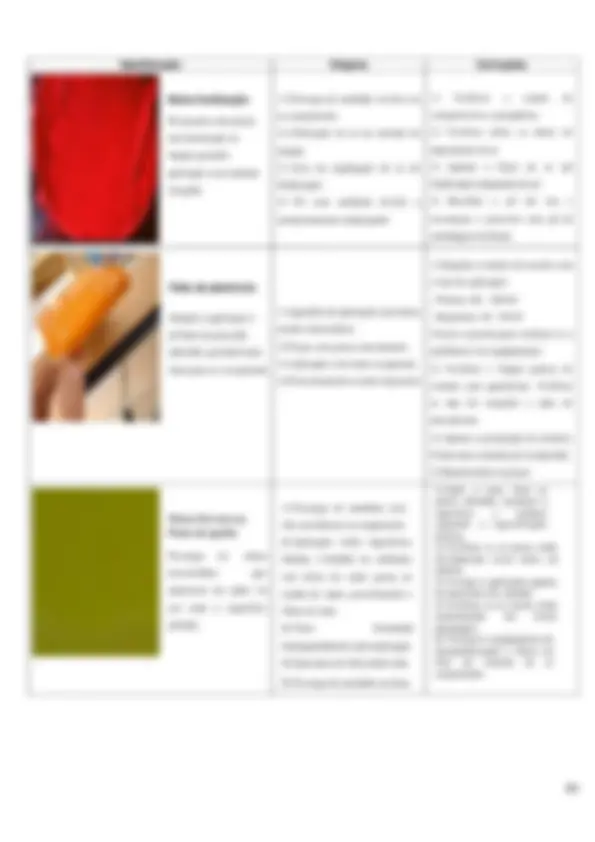
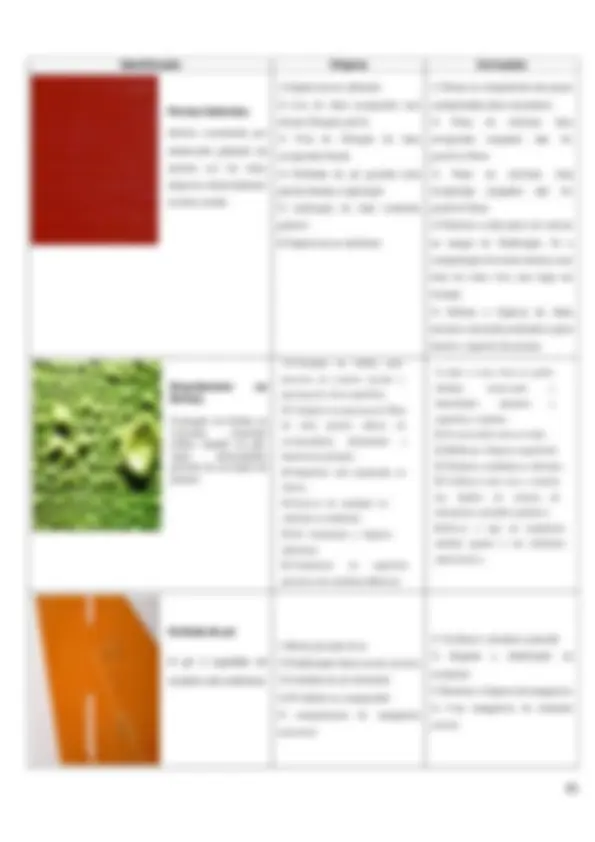
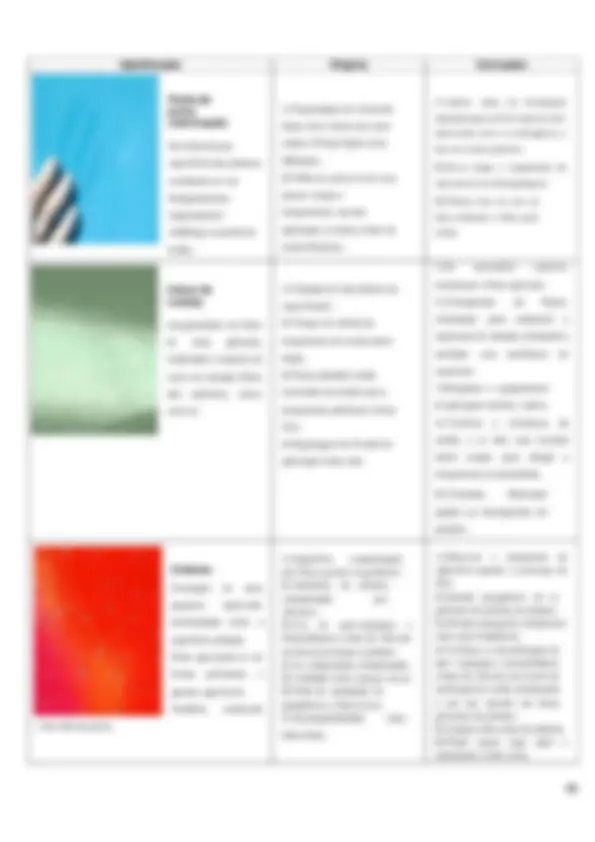
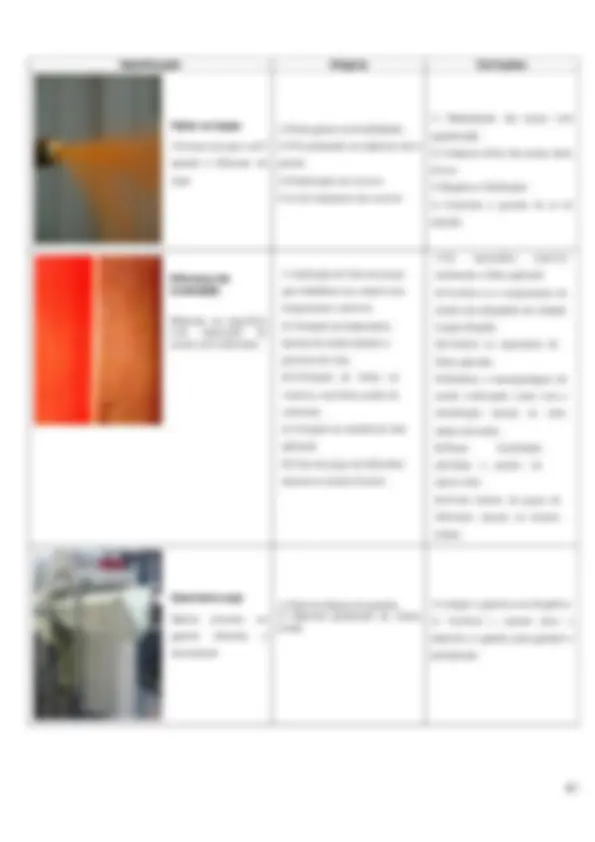
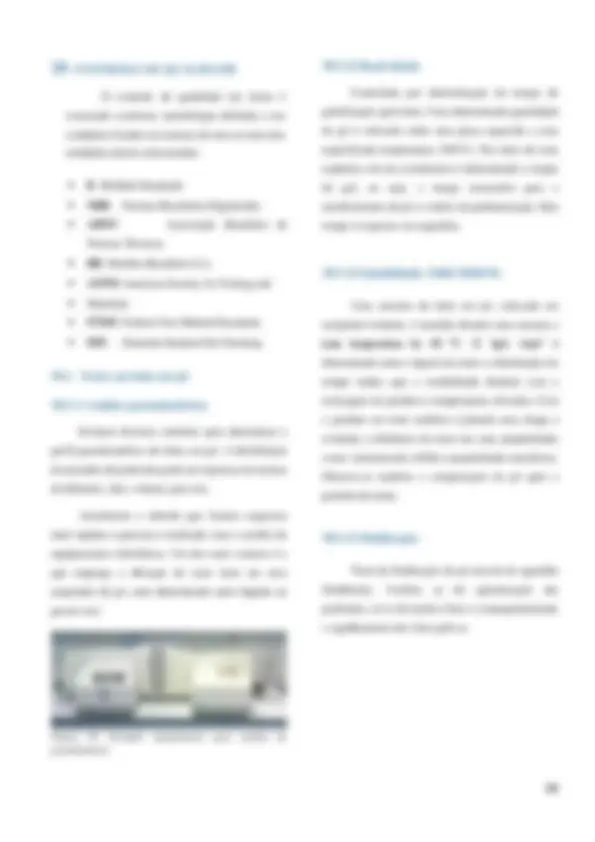
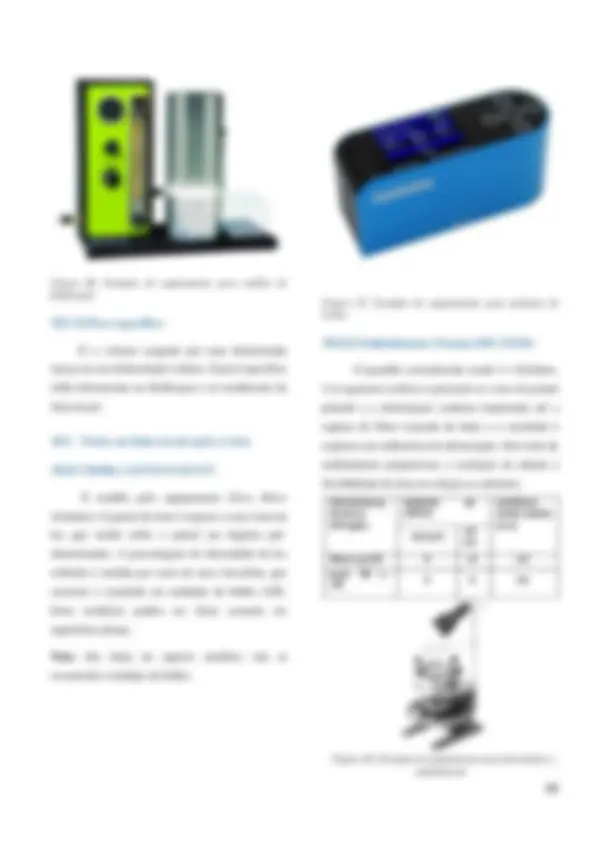
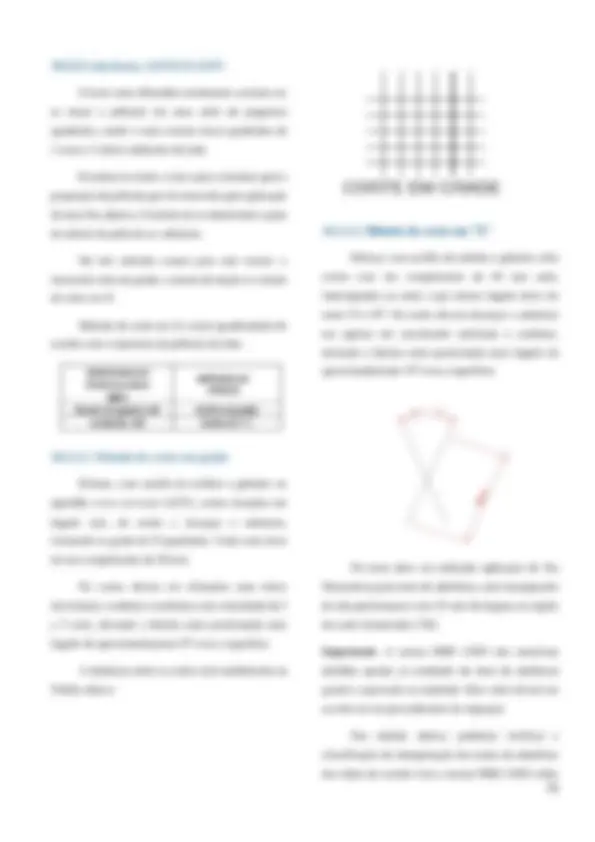
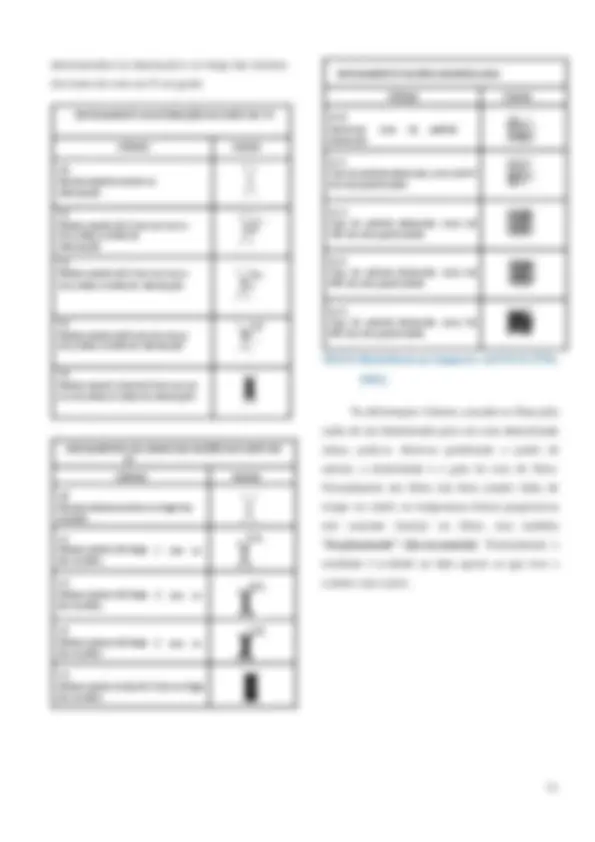
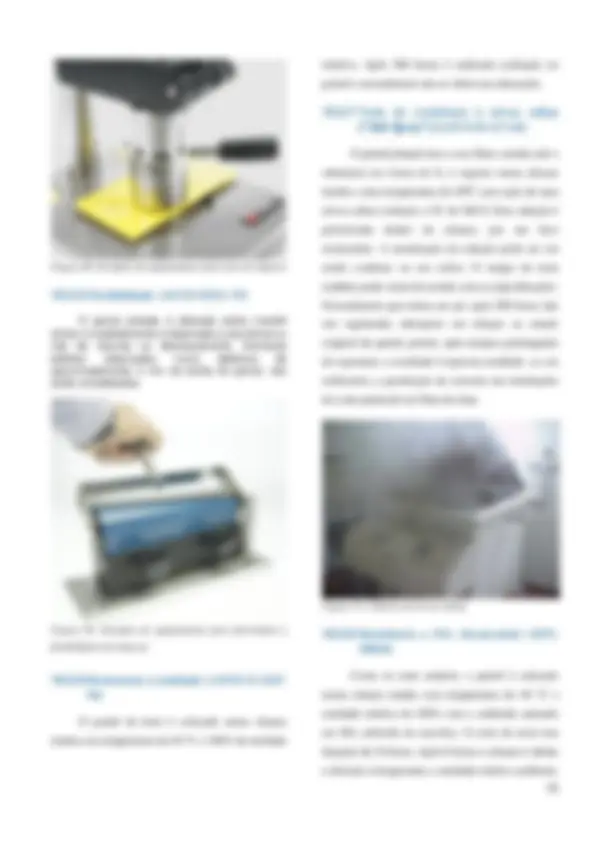
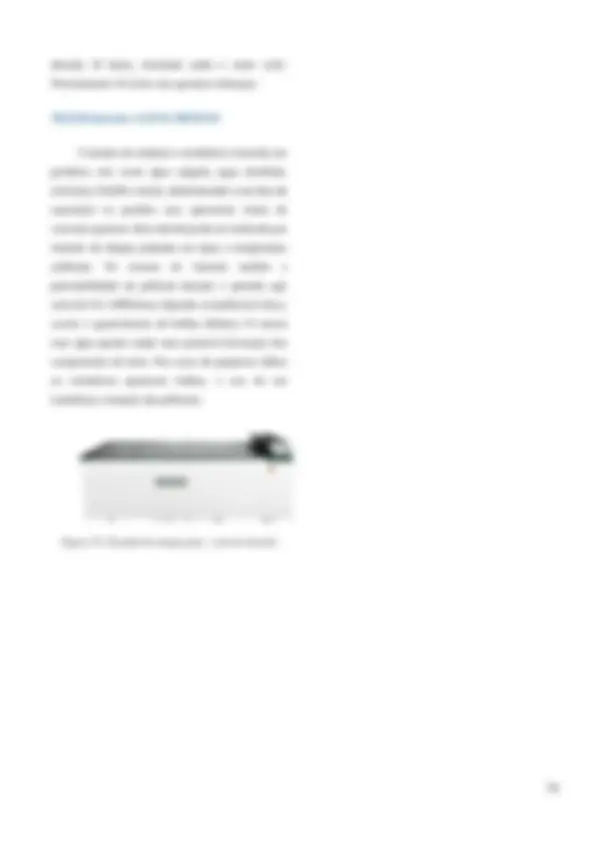
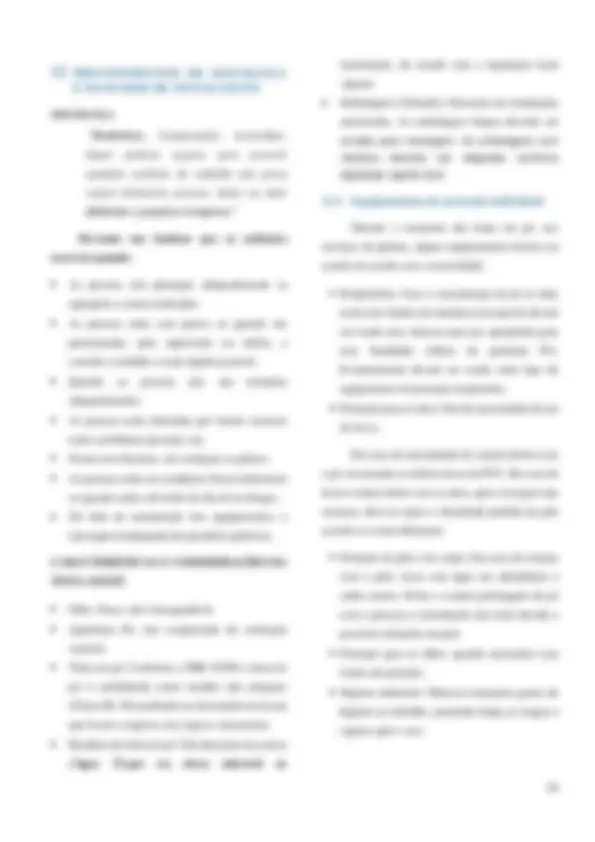
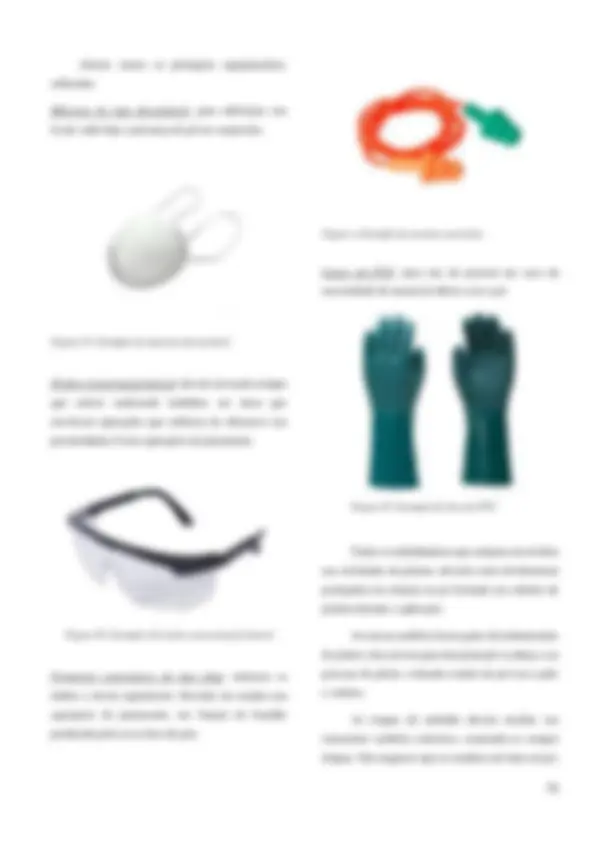
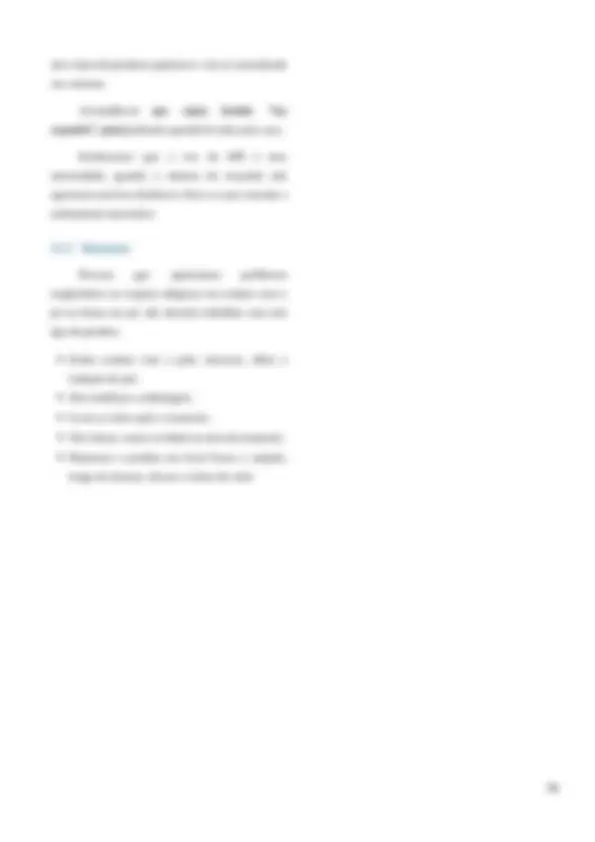
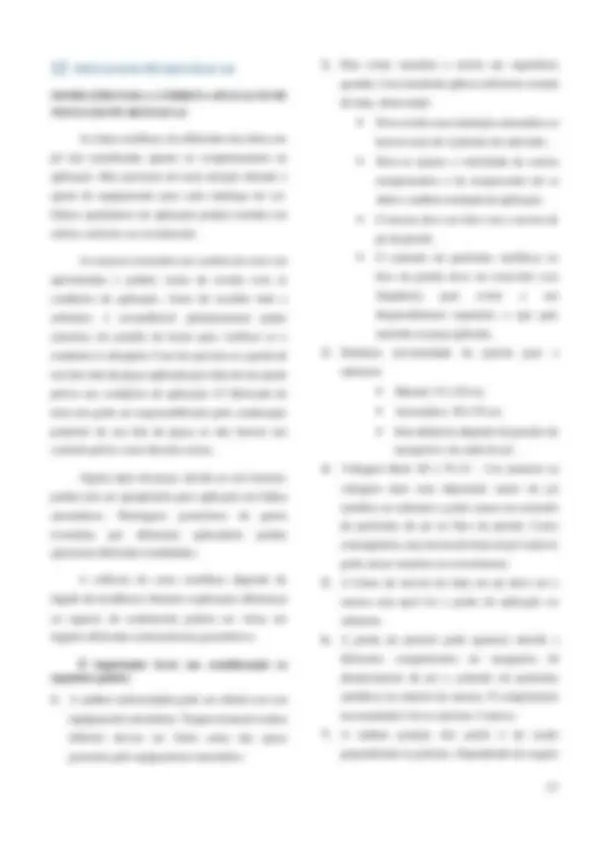
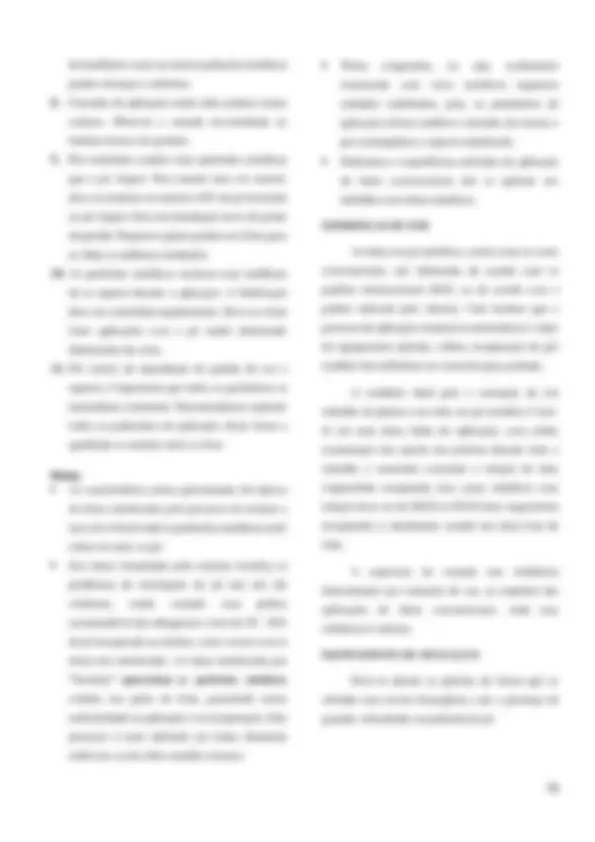
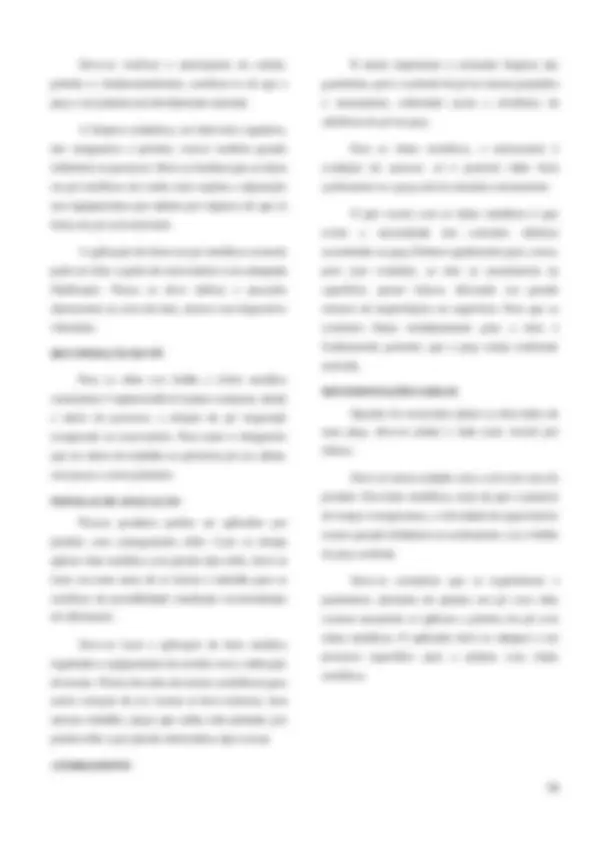
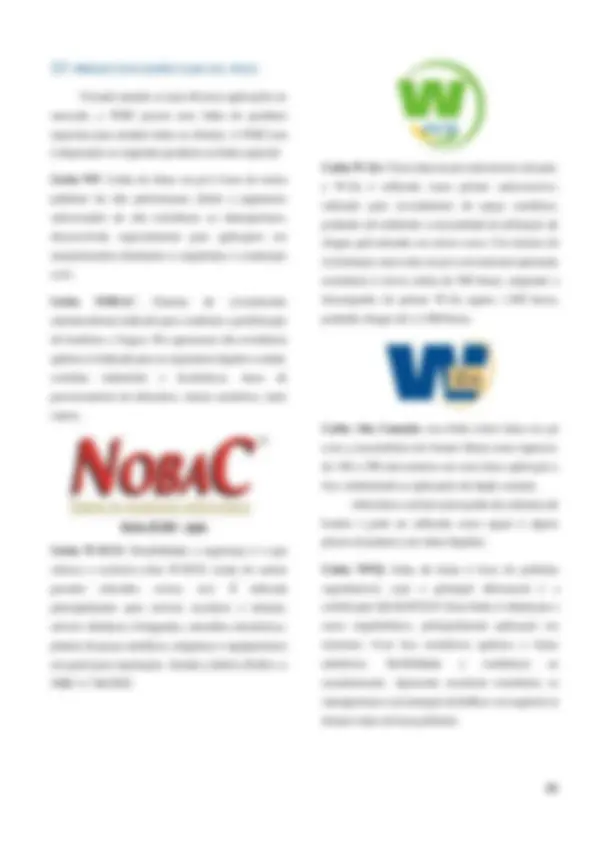
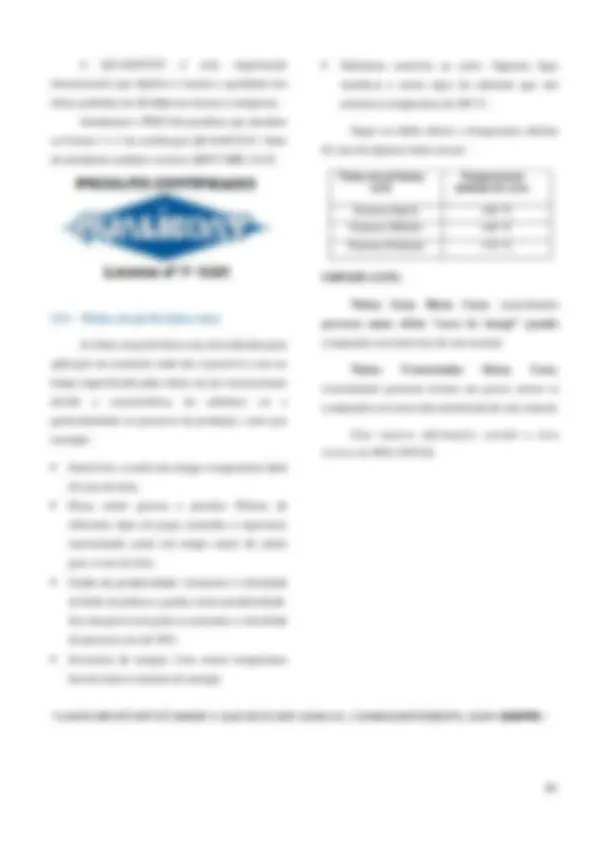
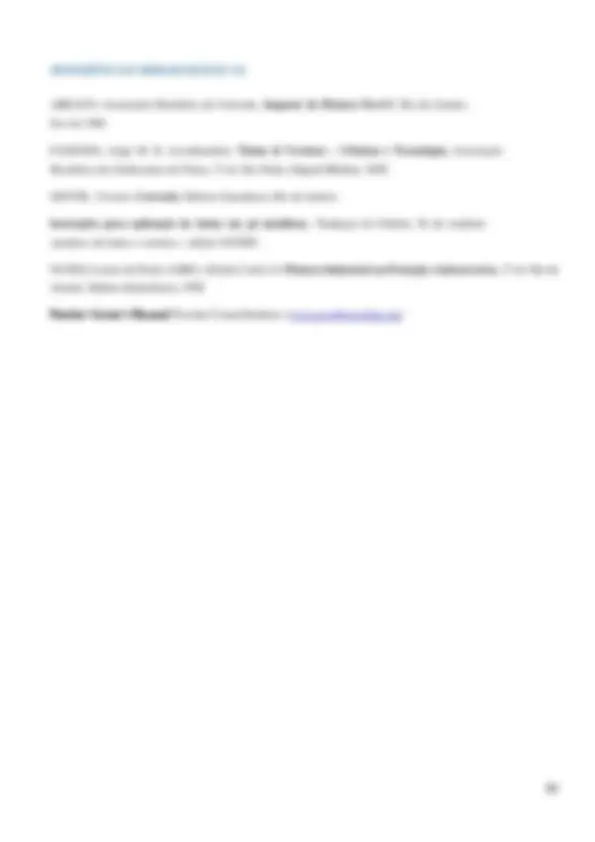
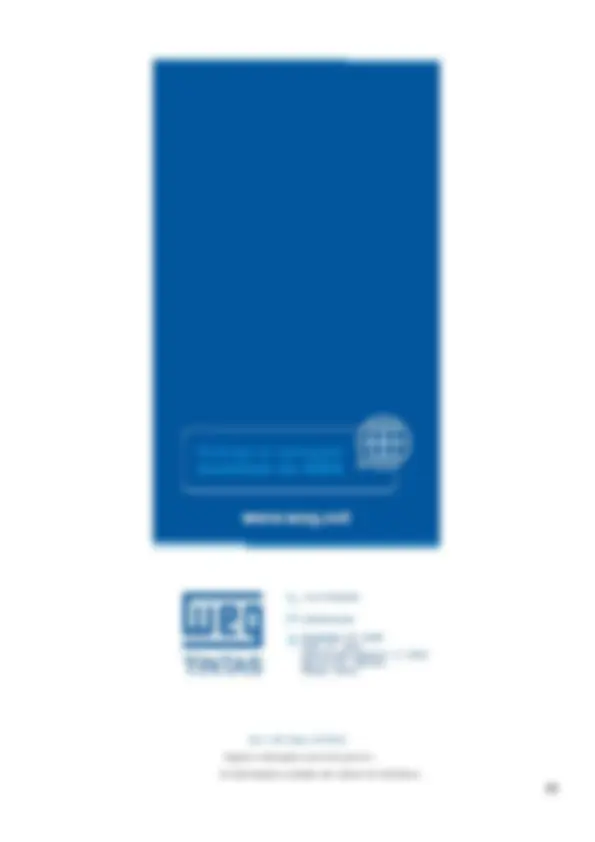
Estude fácil! Tem muito documento disponível na Docsity
Ganhe pontos ajudando outros esrudantes ou compre um plano Premium
Prepare-se para as provas
Estude fácil! Tem muito documento disponível na Docsity
Prepare-se para as provas com trabalhos de outros alunos como você, aqui na Docsity
Os melhores documentos à venda: Trabalhos de alunos formados
Prepare-se com as videoaulas e exercícios resolvidos criados a partir da grade da sua Universidade
Responda perguntas de provas passadas e avalie sua preparação.
Ganhe pontos para baixar
Ganhe pontos ajudando outros esrudantes ou compre um plano Premium
Comunidade
Peça ajuda à comunidade e tire suas dúvidas relacionadas ao estudo
Descubra as melhores universidades em seu país de acordo com os usuários da Docsity
Guias grátis
Baixe gratuitamente nossos guias de estudo, métodos para diminuir a ansiedade, dicas de TCC preparadas pelos professores da Docsity
Detalhes sobre o processo de fabricação e aplicação de tinta em pó, incluindo a classificação de tinta em pó, os sistemas de aplicação, os parâmetros de influência na aplicação, os problemas comuns e as soluções para eles, além de instruções para aplicação de tinta em pó metálica. O documento também discute as vantagens da tinta em pó baixa cura e as linhas de produtos disponíveis na weg.
Tipologia: Notas de estudo
1 / 83
Esta página não é visível na pré-visualização
Não perca as partes importantes!
Motores | Automação | Energia | Transmissão & Distribuição | Tintas
Autor: Luiz Henrique Kondlatsch, Seção de Serviço ao Cliente WEG Tintas Ltda. Revisão: 06 – 03/03/2022.
já conhecidas das tintas líquidas também a base de resinas epóxi.
Observou-se também que nos sistemas mistos constituídos por resinas de poliéster com combinação com resinas epoxídicas, esses problemas eram bastante minimizados.
Posteriormente, foi introduzido a tinta em pó do tipo poliéster puro, constituída por resinas poliéster saturada combinada com um agente de reticulação adequado e que apresentava como característica fundamental, um excelente comportamento sob a ação da luz solar, onde a calcinação e o amarelamento eram praticamente desprezíveis comparados aos outros sistemas a base de reinas epóxi e híbrida.
Em 1970, surge na Alemanha as tintas à base de resinas acrílicas, que tiveram maior aceitação no Japão como revestimentos resistentes ao intemperismo.
Na década de 80 as tintas Poliuretanas se estabelecem fortemente no mercado Norte Americano e Japonês, sendo menos utilizado na Europa, também como revestimento para uso externo.
A partir de então, os resultados foram surpreendendo, chegando aos produtos atuais, considerados altamente competitivos e de excepcional qualidade.
A pintura tem por objetivo depositar um filme de tinta sobre uma superfície metálica ou não metálica, com as seguintes finalidades: proteção anticorrosiva, estética, segurança, entre outro. É composta por três etapas onde cada uma delas tem um importante papel para garantir o desempenho da pintura.
As etapas são: Preparação da superfície, Aplicação e a Tinta. PREPARAÇÃO DA SUPERFÍCIE Deve ser realizada por profissionais treinados, com completa remoção de materiais estranhos ou contaminantes presos na superfície, quando necessário, criando rugosidade (de acordo com a especificação) no substrato para uma melhor aderência da tinta. Nas indústrias, são usados vários métodos de preparação de superfície, tais como: desengraxe, fosfatização, jateamentos com granalha em que o abrasivo é projetado contra a superfície por jato de ar ou por turbinas centrífugas.
APLICAÇÃO DAS TINTAS Deve ser realizada por profissionais devidamente qualificados, usando de técnicas e equipamentos adequados. Podem ser utilizados desde a aplicação com sistema corona, sistema tribo e sistema automático (serão vistos no item 13 – Aplicação).
TINTAS Uma tinta deve possuir tecnologia de formulação, controle rigoroso de qualidade das matérias primas e do processo de fabricação. A escolha deve ser criteriosa e deve resistir à agressividade do ambiente. Entretanto ainda não são descartadas as necessidades de processos de preparação de superfície antecedendo a pintura, assim como a importância da qualificação dos pintores e adoção de bons equipamentos de aplicação. Muitas das novas tintas se enquadram na filosofia de tintas ecologicamente corretas e seguras, pois, atendem as especificações de legislações rígidas
de isenção de metais pesados, que contribuem para a preservação do meio ambiente.
2 CORROSÃO
CONCEITOS BÁSICOS DE CORROSÃO
Corrosão pode ser definida como sendo a deterioração de um material, geralmente metálico, ao reagir com o seu ambiente, levando a perda de suas propriedades.
A corrosão é um processo que corresponde ao inverso dos processos metalúrgicos de obtenção do metal e pode ser assim esquematizada:
Figura 1: Ciclo dos metais
As reações de corrosão são espontâneas. Enquanto na metalurgia adiciona-se energia ao processo para a obtenção do metal, na corrosão observa a volta espontânea do metal à forma combinada, com consequente liberação de energia. Este ciclo é denominado de “ciclo dos metais”.
O estudo da corrosão envolve conhecimento de vários campos da ciência, dentre os quais podem ser destacados:
Química; Eletroquímica; Metalurgia; Termodinâmica; Físico-Química; Cinética Química
Os processos corrosivos estão presentes em todos os locais e a todo instante da nossa vida diária. Os problemas de corrosão são frequentes e ocorrem nas mais variadas atividades, como, por exemplo, nas indústrias química, petrolífera, petroquímica, naval, de construção civil, nos meios de transporte aéreo, ferroviário, marítimo, em sistemas de telecomunicações, na odontologia (restaurações metálicas, aparelhos de prótese), na medicina (uso de implantes cirúrgicos na ortopedia) e na preservação de monumentos históricos, deterioração de automóveis, eletrodomésticos, estruturas metálicas, instalações industriais, etc. Com o avanço tecnológico, mundialmente alcançado, o custo da corrosão se eleva tornando-se um fator de grande importância. Em termos de quantidade de material danificado pela corrosão, estima-se que uma parcela superior a 30% do aço produzido no mundo seja usada para reposição de peças e partes de equipamentos e instalações deterioradas pela corrosão. Sob o ponto de vista de custo, estima-se em 3,5% do Produto Interno Bruto (PIB) o dispêndio com a corrosão em países industrializados. Sendo a corrosão um processo espontâneo, pode-se prever que a maioria dos metais seria imprópria à utilização industrial. Esta utilização é, no
Uniforme : a corrosão se processa em toda a extensão da superfície, ocorrendo perda uniforme de espessura, com formação, como no caso do ferro, de escama de ferrugem. É chamada, por alguns, de corrosão generalizada, o que não é aceito de maneira ampla, pois se pode ter também corrosão por alvéolos ou pites, de maneira generalizada em toda a superfície
Placas : a corrosão se localiza em algumas regiões da superfície metálica e não em toda sua extensão, formando placas com escavações.
Alveolar : a corrosão se processa produzindo sulcos ou escavações semelhantes a alvéolos, apresentando fundo arredondado e profundidade geralmente menor que o seu diâmetro.
Puntiforme : a corrosão se processa em pontos ou em pequenas áreas localizadas na superfície metálica, produzindo pites, que são cavidades apresentando profundidades geralmente maiores que seus diâmetros. Em decorrência do aspecto tem-se a conhecida corrosão por pite ou por “ pitting ”.
Deve-se considerar que não existem limites rígidos na diferenciação das formas de corrosão alveolar e puntiforme, sendo importante, porém, considerar que elas são entre as quatro formas de corrosão apresentadas, as que trazem maiores inconvenientes aos equipamentos, ocasionando perfurações em áreas localizada
Ocorre geralmente em superfícies metálicas com revestimentos a base de estanho, níquel e outros, ou não metálico (tintas), em presença de umidade relativa elevada, da ordem de 85% e revestimentos mais permeáveis a penetração de oxigênio e água. Ela se inicia, comumente, em risco, ou falhas, em revestimentos, que atinjam o substrato, isto é, a superfície metálica. Embora não ocasionando grande
perda de massa do material metálico, produzem nas superfícies pintadas, os filamentos que fazem com que a película de tinta se desprenda. Esfoliação : a corrosão se processa em diferentes camadas. O produto de corrosão, formado entre a estrutura de grãos alongados, separa as camadas ocasionando o inchamento do material metálico. Corrosão grafítica : a corrosão se processa no ferro fundido cinzento e o ferro metálico é convertido em produtos de corrosão, restando à grafite intacta. Observa-se que a área corroída fica com aspecto escuro, característico do grafite, que pode ser facilmente retirada com uma espátula. Em tubulações de ferro fundido para condução de água potável, observa-se que, mesmo com corrosão grafítica, a espessura da parede permanece com a sua dimensão praticamente original. Dezincificação : é a corrosão que ocorre em ligas de cobre-zinco (latões) observando-se o aparecimento de regiões com a coloração avermelhada, devido ao cobre, contrastando com a característica coloração amarela dos latões. A corrosão grafítica e a dezincificação podem ser consideradas exemplo de corrosão seletiva, pois se tem a corrosão preferencial do ferro e zinco respectivamente. Em torno de solda : é a corrosão que se observa ao longo e ligeiramente afastada do cordão de solda. Ocorre geralmente em aços inoxidáveis com teores de carbono maiores do que 0,03%. Empolamento pelo hidrogênio : embora não sendo considerado por alguns autores como forma de corrosão, é comum estudá-los em livros de corrosão, pois o hidrogênio atômico, causador do processo, pode ser originado da corrosão do material metálico.
O hidrogênio atômico, H, penetra no aço carbono e como tem pequeno volume atômico, difunde-se rapidamente para o interior do material metálico e em regiões com descontinuidades, como inclusões e vazios, ele se transforma em hidrogênio molecular (H 2 ), não mais se difundindo, exercendo pressão e originando a formação de bolhas no material metálico, daí o nome de empolamento. Filiforme : a corrosão se processa sob a forma de filamentos que se propagam em diferentes direções, porém não em profundidade
Figura 2: Formas de corrosão
Quando materiais metálicos de potenciais elétricos diversos estão em contato, a corrosão do material metálico que funciona como ânodo é muito mais acentuada que a corrosão isolada deste material sob ação do mesmo meio corrosivo.
Exemplos que permitem explicar o mecanismo da corrosão galvânica, da proteção catódica com ânodos de sacrifício ou galvânicos e a natureza do produto de corrosão são as pilhas formadas pelos metais ferro, cobre e zinco, usando-se como eletrólito água salgada.
Analisando as reações de redução e oxidação, pode-se observar e concluir que:
O metal que funciona como cátodo fica protegido, isto é não sofre corrosão. Esta conclusão explica o mecanismo da proteção catódica com ânodos de sacrifício ou galvânicos, bem como a razão de serem usados magnésio, alumínio e zinco como ânodos para proteção do ferro: daí o grande uso de ânodos de zinco, alumínio e magnésio para a proteção catódica, como anodos de sacrifício, para cascos de navios, tanques de armazenamento de petróleo ou tanques de navio que apresentam lastros de água salgada, estacas de plataformas marítimas etc. A ligação entre materiais metálicos deve ser precedida de consulta à tabela de potenciais ou as tabelas práticas a fim de se prever a possibilidade de caracterização do ânodo e do cátodo, da pilha possivelmente resultante e indicação de medidas protetoras. Pode-se estabelecer uma pilha em que se tenha como fonte doadora de elétrons, não um metal, como visto nos casos anteriores, mas sim uma fonte de corrente contínua para imprimir a corrente necessária para proteção. Essas fontes são, mais frequentemente, retificadoras de
correntes e, menos usuais, baterias convencionais, baterias solares e termo geradores. Nesse caso a estrutura a ser protegida é colocada como cátodo da pilha usando- se anodos inertes, para fechar o circuito elétrico. Os ânodos mais usados são: Grafite, ferro silício e magnetita: no solo. Ligas de ferro-silício-cromo, e chumbo- antimônio – prata, titânio platinizado e nióbio platinizado: em água do mar. Essa proteção é chamada proteção catódica por corrente impressa ou forçada. Ela tem um campo de aplicação maior do que a proteção catódica com ânodos de sacrifício, aplicando – se em estruturas situadas em eletrólitos ou meios de baixa, e alta resistividade. E muito usada em grandes instalações como oleodutos, gasodutos, adutoras e estacas de píeres de atracação.
Corrosão por eletrólise ou eletrolítica ou corrosão por correntes de fuga, ocorre em tubulações enterradas, como oleodutos, gasodutos, adutoras, minerodutos e cabos telefônicos. Definida como sendo a deterioração de um material metálico forçado a funcionar como ânodo ativo de uma célula ou pilha eletrolítica. Geralmente as áreas corroídas se apresentam livre do produto de corrosão e, como é uma forma de corrosão localizada, em pouco tempo tem-se a formação de pites ou alvéolos com a consequente perfuração das tubulações. Logo, pode-se concluir que as áreas corroídas serão aquelas em que as correntes de fuga saem da tubulação, ou instalação metálica, para o eletrólito ou meio ambiente (solo ou água).
As medidas mais usuais de proteção são: drenagem de corrente, aterramento adequado de máquinas de solda, emprego de revestimento e emprego de proteção catódica. Essas medidas podem ser usadas isoladas ou conjuntamente.
Quando elas atingem instalações metálicas enterradas podem ocasionar corrosão nas áreas onde abandonam essas instalações para retornar ao circuito original através do solo ou da água.
Se as duas superfícies, em contato e sob carga, das quais pelo menos uma metálica, for sujeita a pequenos deslizamentos relativos, originados comumente por vibrações, observa-se a corrosão sob atrito, também chamada corrosão sob fricção ou corrosão por atrito oscilante.
Na pilha formada a região anódica, portanto corroída, é aquela onde a concentração do íon metálico é menor, e a região catódica é aquela onde a concentração do íon metálico é maior.
É comum ocorrer essa pilha quando se têm superfícies metálicas superpostas e em contato, havendo, entre elas, pequenas frestas por onde o eletrólito possa penetrar.
Ocorre também no contato entre superfícies metálicas e não metálicas, desde que haja frestas. A fresta deve ser suficientemente estreita para manter o meio corrosivo estagnado e suficientemente larga para permitir que o meio corrosivo penetre nela.
Conhecendo-se o mecanismo desse processo corrosivo, entende-se perfeitamente porque se procura como medidas de proteção:
Usar massas de vedação, ou selantes, à base de silicones, epóxi ou asfalto em locais onde possa haver formação de frestas e presença de eletrólito.
É a corrosão que ocorre quando se tem um mesmo material metálico em contato com um eletrólito diferentemente aerado. Na pilha de aeração diferencial o ânodo é a área menos aerada e o cátodo a mais aerada. É uma corrosão localizada e, portanto, produz ataque acentuado em determinadas regiões ocorrendo à formação de pites ou alvéolos. A corrosão por aeração diferencial é responsável por grande número de casos de corrosão nas mais variadas instalações e equipamentos industriais. Na junção de peças metálicas por rebites ou parafusos podem existir frestas e, como nessas frestas a aeração é pequena, resulta uma baixa concentração de oxigênio no eletrólito que se encontra em contato com o metal fora das frestas. Nota-se, que a área mais atacada, ou corroída é no interior das frestas. Para evitar esta corrosão, tem sido bastante usado, com bons resultados, o emprego de revestimento com massa epóxi a dois componentes, aplicado nas estacas já montadas: faz-se na área de variação de maré o jateamento e a seguir aplica-se a massa epóxi, que polimeriza mesmo debaixo da água, atingindo-se espessura de cerca de 3 mm Para proteção das partes sempre submersas recomenda-se o uso de proteção catódica, principalmente por corrente impressa ou forçada. Os processos de corrosão por concentração iônica e por aeração, quando não se observam certas
a) Atmosfera marinha: sobre o mar e na orla marítima (até 500 metros da praia), com ventos predominantes na direção da estrutura a ser pintada; b) Atmosfera próxima à orla marinha: aquela situada além de 500 metros da praia e até aonde os sais possam alcançar; c) Atmosfera industrial: envolvem regiões com muitos gases provenientes de combustão, particularmente gases oriundos de combustíveis com alto teor de enxofre e outros processos industriais; d) Atmosfera úmida: locais com umidade relativa do ar média acima de 60%, com predominância de valores superiores a 75%; e) Atmosfera urbana e semiindustrial: ocorre nas cidades onde se tem uma razoável quantidade de gases provenientes de veículos automotores e uma indústria razoavelmente desenvolvida; f) Atmosfera rural e seca: locais, em geral no interior, onde não há gases industriais ou sais em suspensão e a umidade relativa do ar se apresenta com valores sempre baixos.
IMERSÃO
a) Líquidos aquosos: a agressividade dependerá da resistividade elétrica, que é função da presença de sais ou gases dissolvidos. A pior condição, neste caso, é a água salgada aerada. b) Derivados de petróleo: são de modo geral pouco agressivos, com exceção do espaço de vapor em tanques de armazenamento que pode conter H 2 S e tornar-se bastante agressivo e do petróleo bruto, sempre associado à água salgada. c) Produtos químicos: a agressividade dependerá da presença de água ou de umidade e do grau de ionização da substância química.
CONDIÇÕES CORROSIVAS
a) Atmosfera altamente agressiva: é considerada atmosfera altamente agressiva a atmosfera marinha e industrial ou ainda a úmida, quando conjugada com qualquer uma das anteriores; b) Imersão: a imersão envolve quatro subcasos: imersão em água salgada; imersão em água doce; imersão em produtos de petróleo; imersão em produtos químicos; c) Superfícies quentes: as superfícies quentes envolvem quatro subcasos: de 80° a 120°C; de 120° a 250°C; de 250° a 500°C; acima de 500°C; d) Atmosfera medianamente agressiva: são consideradas atmosferas medianamente agressivas a atmosfera úmida, a urbana e a semiindustrial. Estão incluídos neste caso locais junto à orla marítima, com afastamento superior a 500 metros (m), desde que não recebam os ventos predominantes na direção da instalação ou da estrutura a ser pintada e seja localizada a nível próximo do mar; e) Atmosfera pouco agressiva: é considerada atmosfera pouco agressiva a atmosfera rural e seca.
3 REVESTIMENTOS PROTETORES
São películas aplicadas sobre a superfície metálica, separando a superfície do meio corrosivo, esta separação será tão mais longa quanto for o tempo para que o eletrólito chegue ao metal protegido, objetivando minimizar a degradação da mesma pela ação do meio.
O principal mecanismo de proteção dos revestimentos é por barreira, mas, dependendo da sua natureza, poderá também proteger por inibição anódica ou por proteção catódica.
O tempo de proteção dado por um revestimento depende do tipo de revestimento (natureza química), das forças de coesão e adesão, da sua espessura e da permeabilidade à passagem do eletrólito através da película. Influenciará, também, neste tempo, o mecanismo de proteção. Assim, se a proteção é somente por barreira, tão logo o eletrólito chegue a superfície metálica, iniciará o processo corrosivo, enquanto que, se houver um mecanismo adicional de proteção (inibição anódica ou proteção catódica), haverá um prolongamento da vida do revestimento.
Outra forma de ampliar a vida de um revestimento é quando ele possui um mecanismo adicional de proteção denominado proteção catódica.
Neste caso, forma-se uma pilha galvânica entre o metal de base e o metal ou pigmento metálico do revestimento.
Este fato ocorre quando se utiliza revestimento metálico menos nobre que o metal a se proteger, ou tintas com pigmento de zinco. Para que a proteção seja efetiva, faz-se necessária à presença do eletrólito, para que a pilha de ação galvânica ocorra.
Consistem na interposição de uma película metálica entre o meio corrosivo e o metal que se quer proteger. Os mecanismos de proteção das películas metálicas podem ser: por barreira, por proteção catódica, entre outros. As películas metálicas protetoras, quando constituídas de um metal mais catódico que o metal de base, devem ser perfeitas, ou seja, isentas de poros, trincas, etc., para que se evite que diante de uma eventual falha provoquem corrosão na superfície metálica do metal de base, ao invés de evitá-la. As películas mais anódicas podem ser imperfeitas porque elas conferem proteção catódica à superfície do metal base. Os processos de revestimentos metálicos mais comuns são: Deposição por imersão a quente : pela imersão a quente obtém-se, entre outras, as superfícies zincadas e as estanhadas. O processo de zincagem por imersão é também denominado de galvanização; Metalização : é o processo por meio do qual se deposita sobre uma superfície, previamente preparada (jateamento Sa 2 ½), camadas de materiais metálicos. Os metais de deposição são fundidos em uma fonte de calor gerada no bico de uma pistola apropriada, por meio de combustão de gases, arco elétrico, plasma ou por detonação. Por metalização fazem-se revestimentos com zinco, alumínio, chumbo, estanho, cobre e diversas ligas; Eletrodeposição : consiste na deposição eletrolítica de metais que se encontram sob a formar iônica em um banho. A superfície a revestir é colocada no Cátodo de uma célula eletrolítica. Por eletrodeposição é comum revestir-se com cromo, níquel, ouro, prata, cobre, estanho e, principalmente, cádmio, que, por ser um metal muito tóxico, é aplicado por este processo;
4 TRATAMENTO DE SUPERFÍCIE
O preparo da superfície constituí uma etapa de extrema importância na execução de pintura industrial. Isso, pois, quando um esquema de pintura é feito sobre uma superfície mal preparada a película, após o processo de cura, não adere ao substrato de forma adequada, o que representa uma perda de tempo e dinheiro, uma vez que essa má aderência acarretará problemas à película da tinta.
Influências dos contaminantes na superfície a ser pintada:
Contaminantes e produtos de corrosão podem prejudicar seriamente a aderência; Um sistema de pintura sobre uma superfície não adequada não terá uma base firme para resistir a esforço mecânico; Sais na superfície do aço favorecem a formação de empolamento por osmose; Contaminação presa entre camadas pode causar defeitos de aderência e acelerar a penetração de água ou outros agentes agressivos; Com isso, antes de iniciar o processo de limpeza das peças, deve-se proceder uma inspeção visual geral da superfície a ser tratada, a fim de assinalar locais onde haja manchas de óleos, graxas, gorduras, defeitos superficiais, impregnação de abrasivos, bem como também pode ser efetuado a avaliação do estado inicial de oxidação usualmente estabelecido com base nos padrões Norma SIS 05 59 00 e ISO 8501-1;
A fim de facilitar a caracterização de uma superfície a ser submetida ao jateamento e de racionalizar a inspeção de aplicação de pintura industrial, a Norma Sueca SIS 0559 00 e ISO 8501- estabelecem quatro estados iniciais de oxidação de
chapas de aço que apresentam carepa de laminação aderente, também comumente denominadas de graus de intemperismo ou oxidação. Carepa de laminação: As chapas de aço laminadas a quente, são formadas pela laminação dos lingotes aquecidos a uma temperatura em torno de 1250ºC, o que resulta, por reação com o oxigênio do ar e a água de resfriamento, no formato de “carepa” (ou escama de laminação) conhecida por chapa preta. A carepa é constituída de uma mistura de óxidos de ferro. Parte da carepa de laminação que é formada sai durante a laminação e parte fica aderida ao aço, cobrindo toda a chapa de ambos os lados. Esta carepa é encontrada não apenas em chapas, mas também em vigas, tubulações, vergalhões, etc. É sem dúvida o pior inimigo da pintura, pois, qualquer sistema de pintura aplicado sobre a carepa, poderá se desprender junto com ela. A carepa não é aço, e sua tendência natural é se desprender do aço.
Figura 3: Formação de carepa no metal Graus de corrosão: Grau A – superfície de aço com a carepa de laminação aderente intacta, com pouca ou nenhuma
oxidação ao longo de sua superfície. Chapa ou perfil, em geral, recém-saído da laminação.
Figura 4: Grau A – ISO 8501-
Grau B – superfície de aço com princípio de desprendimento de carepa de laminação devido à corrosão atmosférica e dilatação diferencial carepa- metal. Chapa ou perfil com início de oxidação e da qual a carepa começou a se desprender ou que sofreu pequena ação de intemperismo.
Figura 5: Grau B – ISO 8501-
Grau C – superfície de aço onde toda a carepa de laminação foi eliminada e na qual se observa uma corrosão atmosférica uniforme generalizada, sem, contudo, apresentar sinais de formação de cavidades visíveis. Chapa ou perfil que sofreu um completo intemperismo desagregando toda a carepa de
laminação podendo o restante ser removido por raspagem.
Figura 6: Grau C – ISO 8501-
Grau D – superfície de aço onde toda a carepa de laminação foi eliminada e na qual se observa uma corrosão atmosférica severa e generalizada, apresentando pits e alvéolos. Chapa ou perfil que sofre uma exposição exagerada à atmosfera, resultando em processo corrosivo.
Figura 7: Grau D – ISO 8501-
4.2 Tipos de limpeza de superfície Os principias tipos de limpeza para a pintura de peças ou substratos são: Limpeza química;