
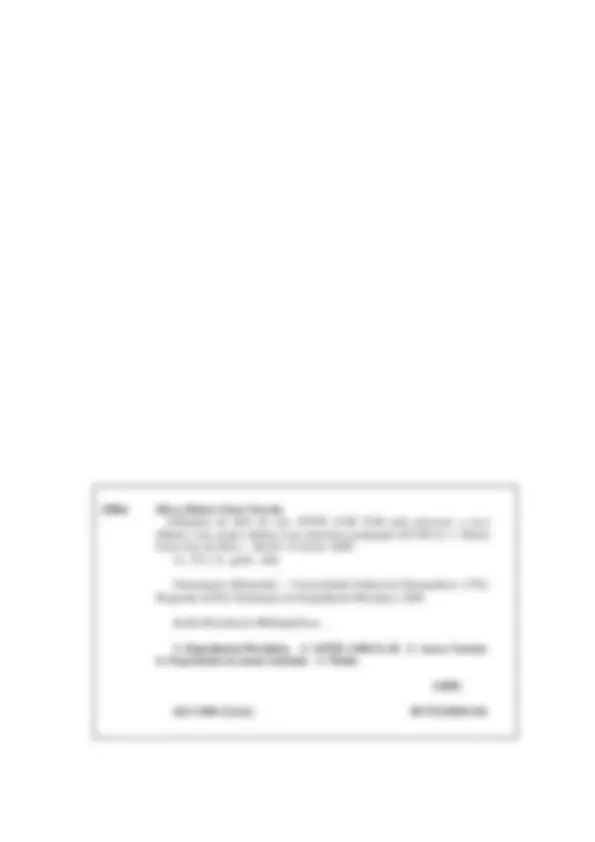
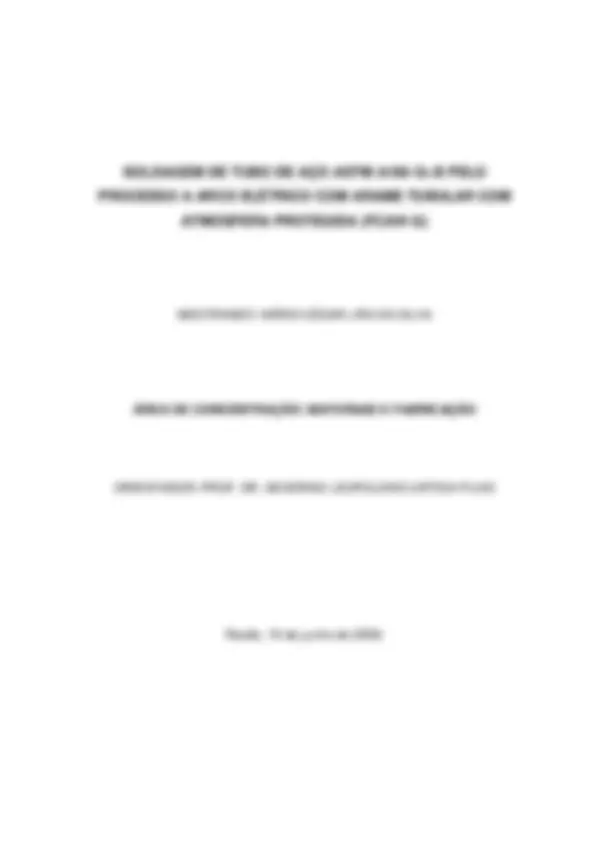
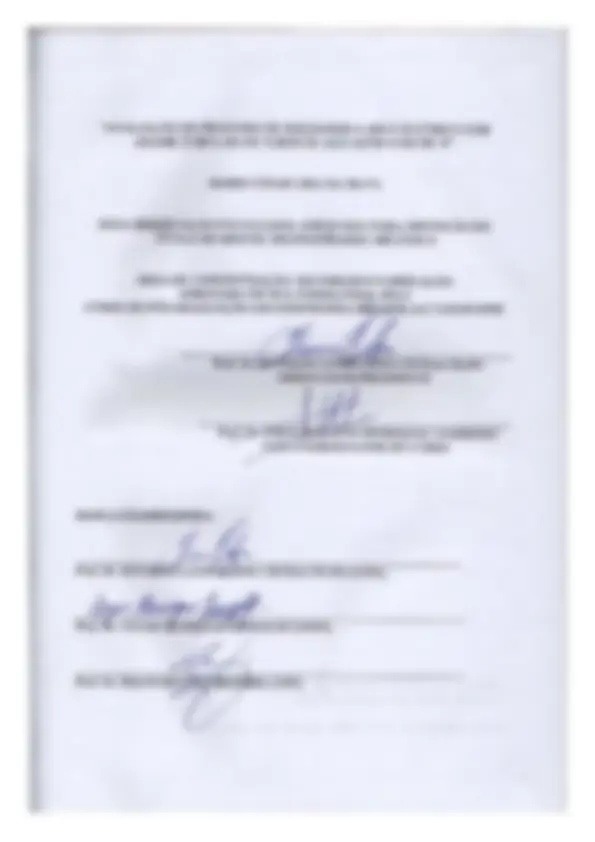
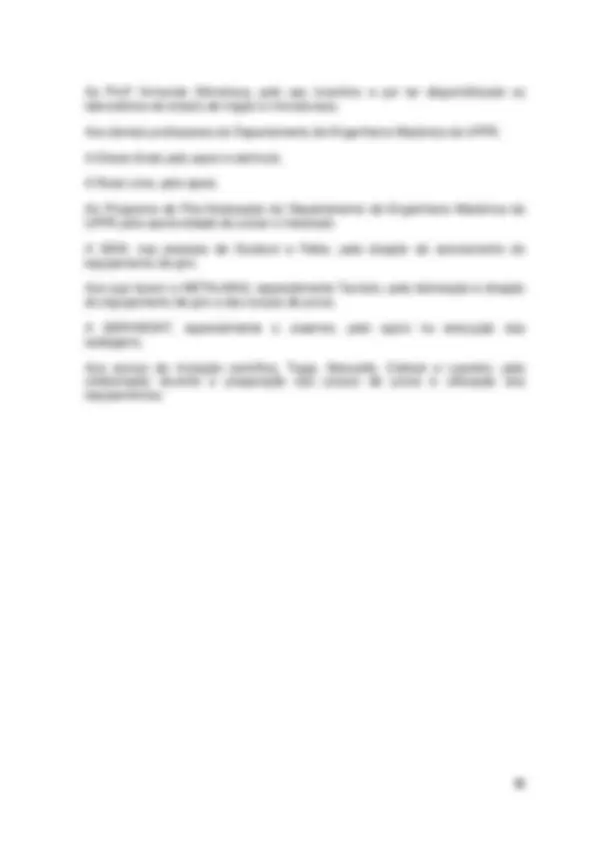
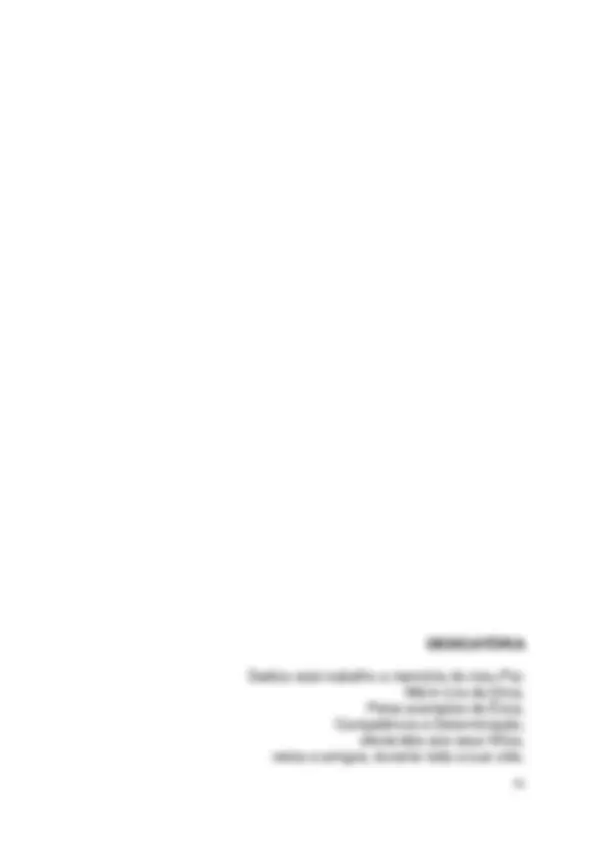
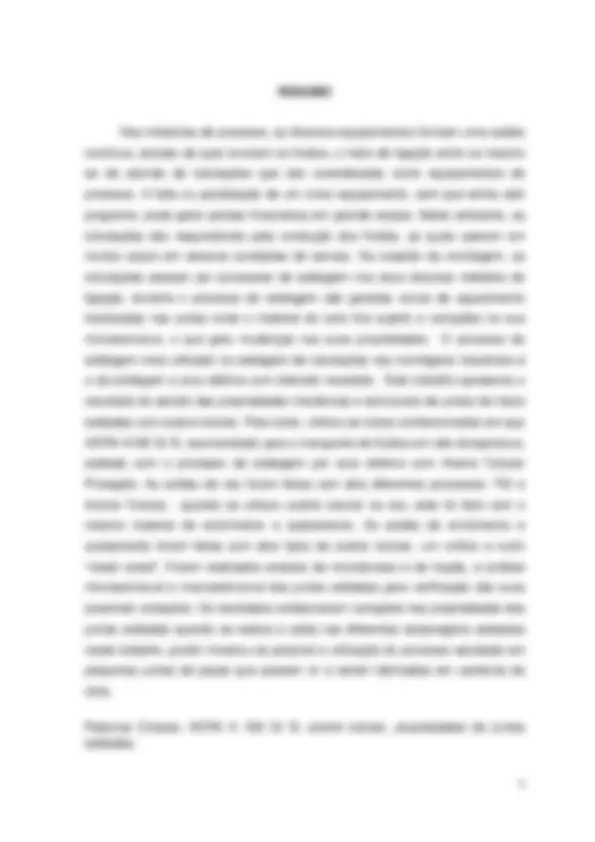
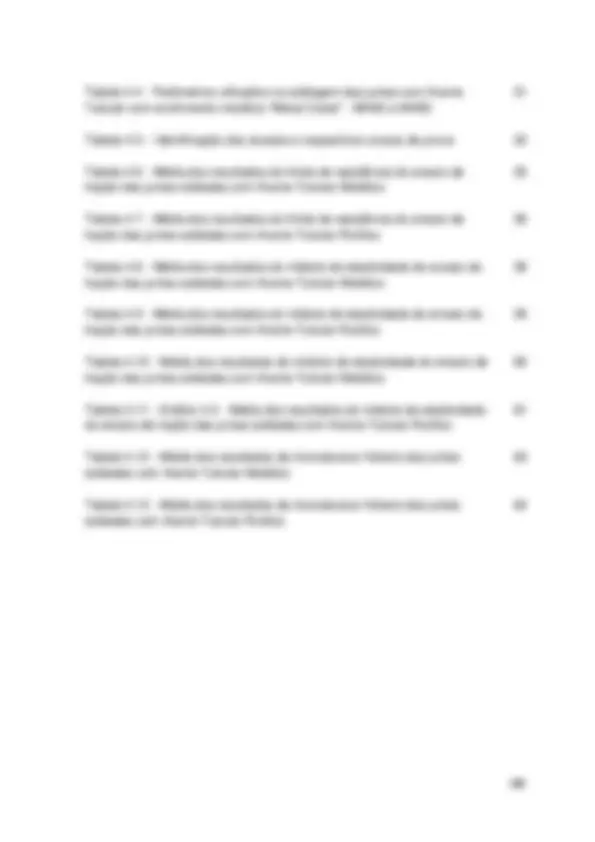
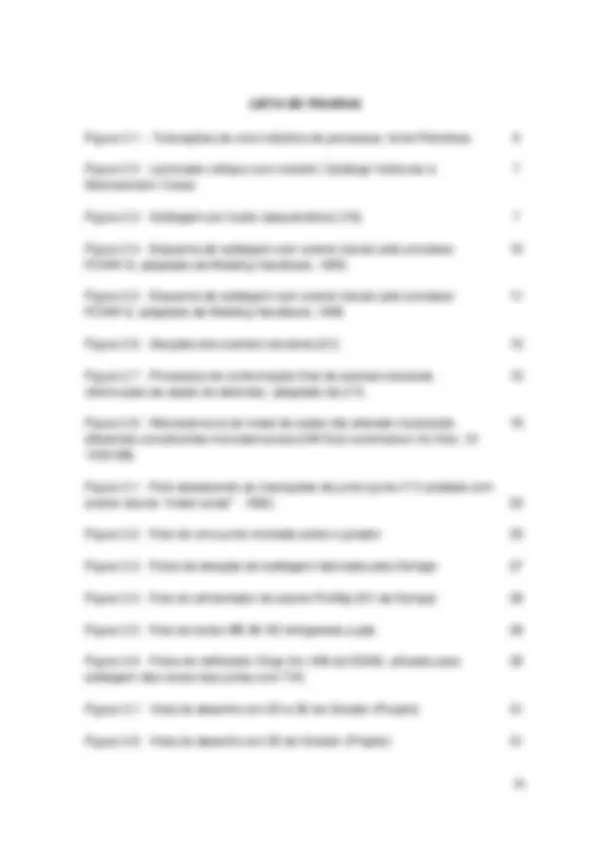
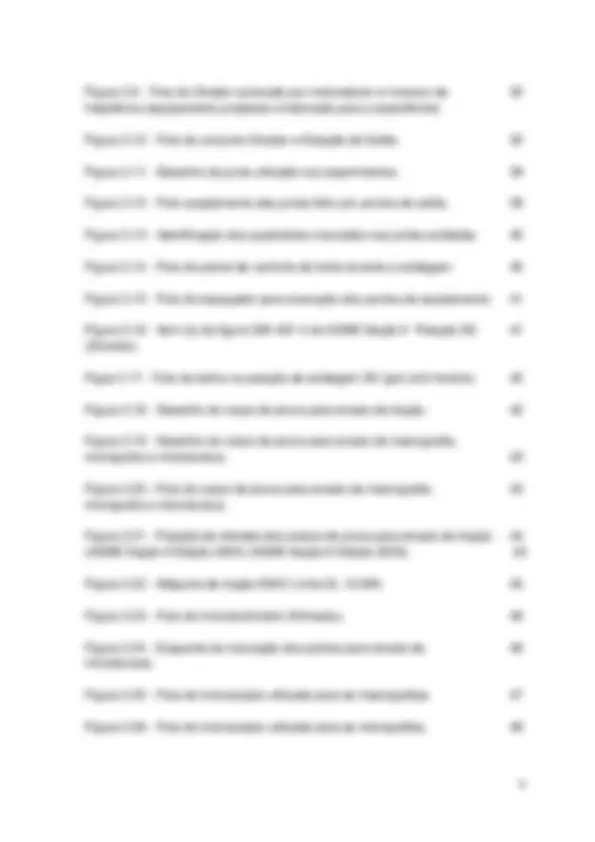
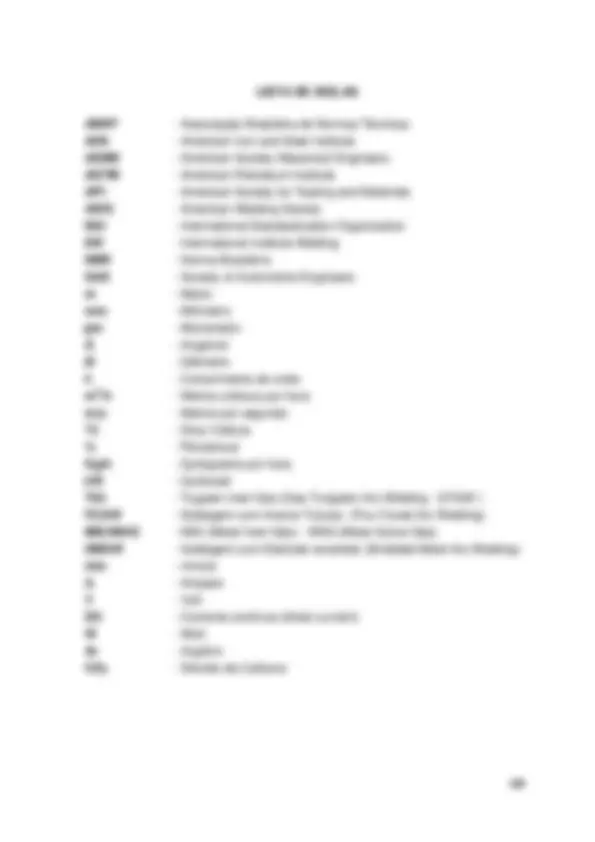
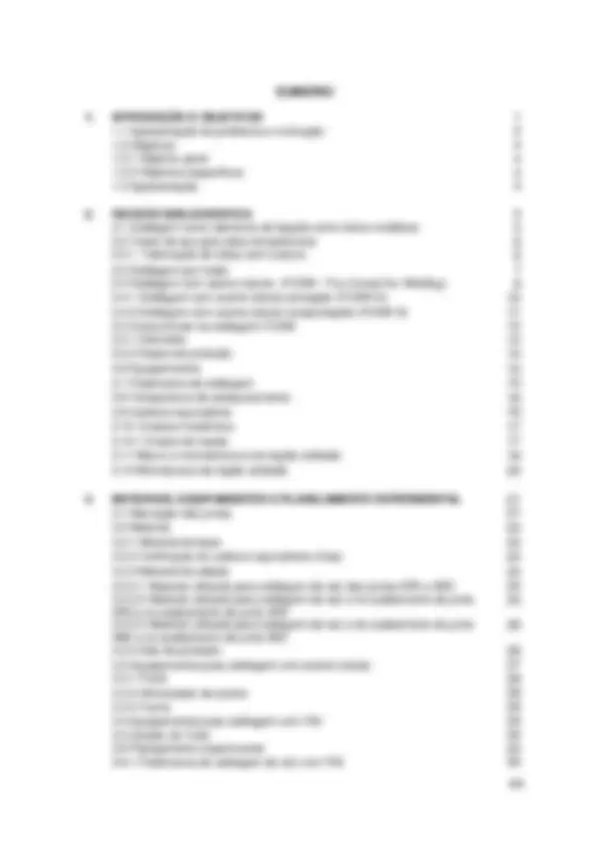
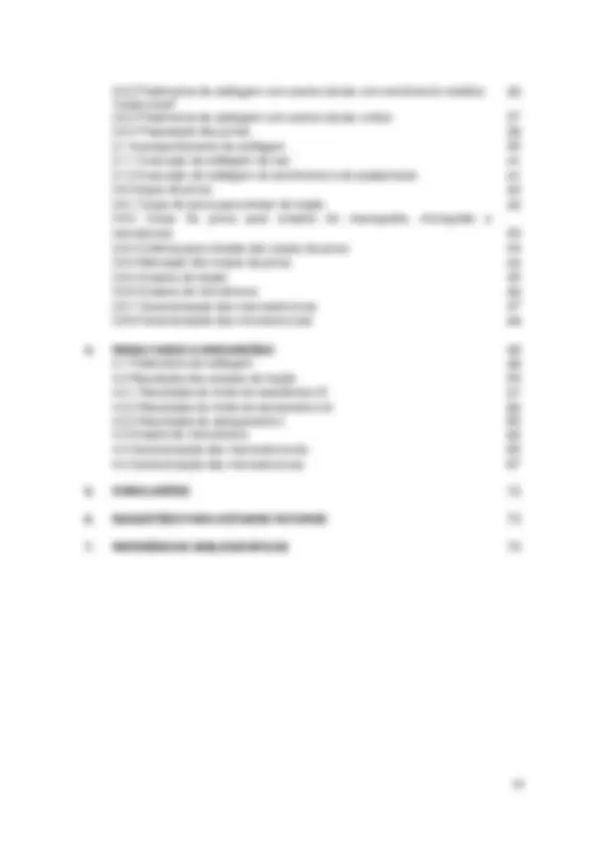
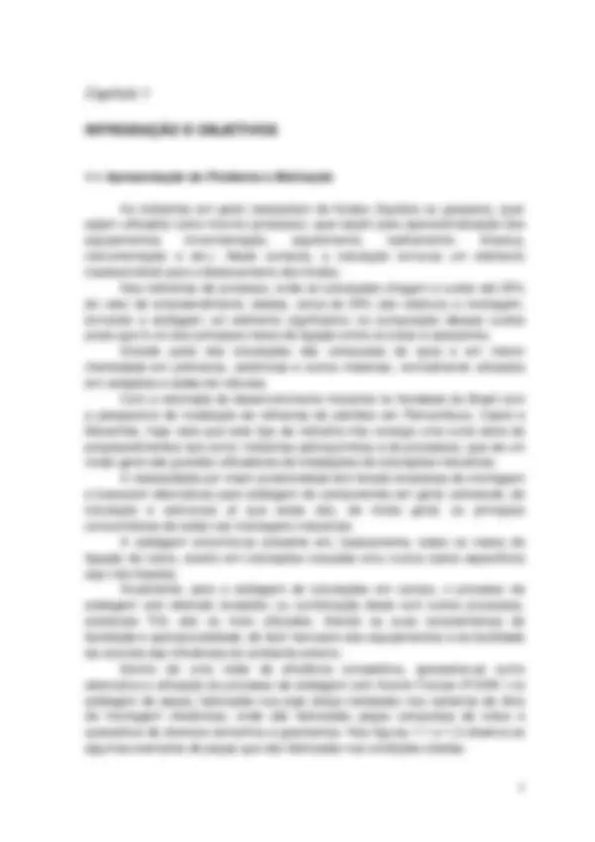
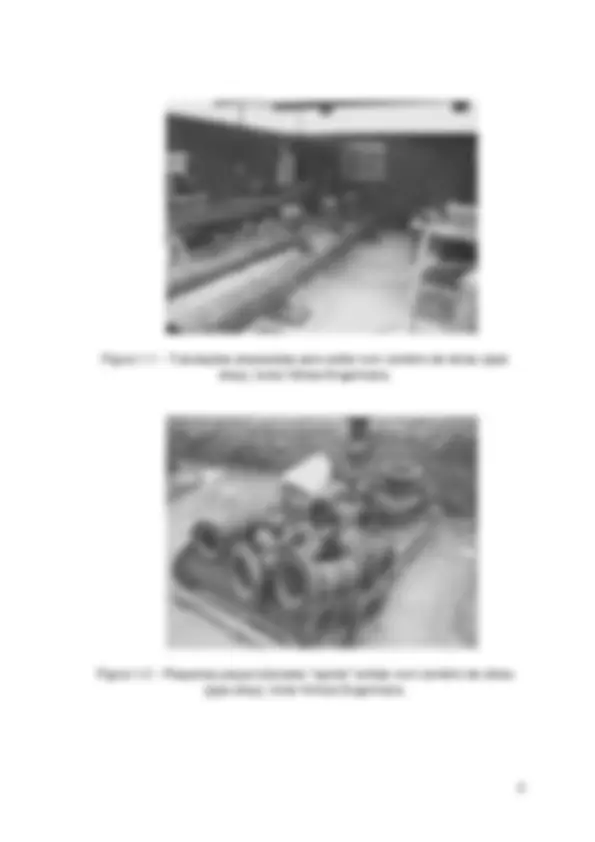
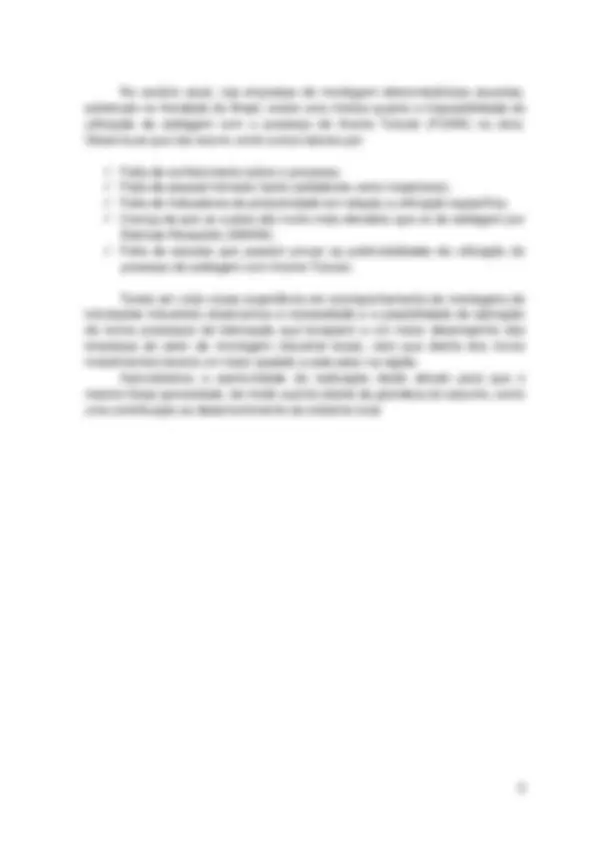
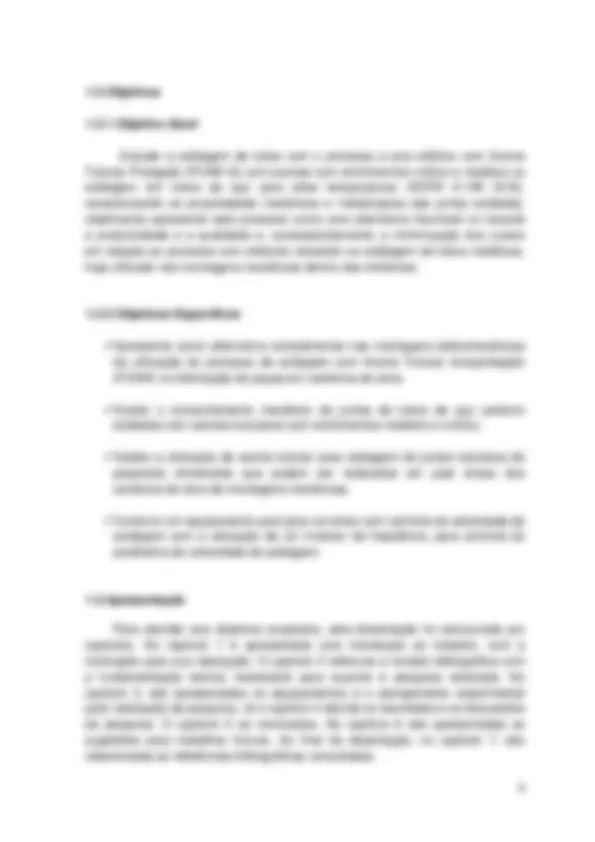
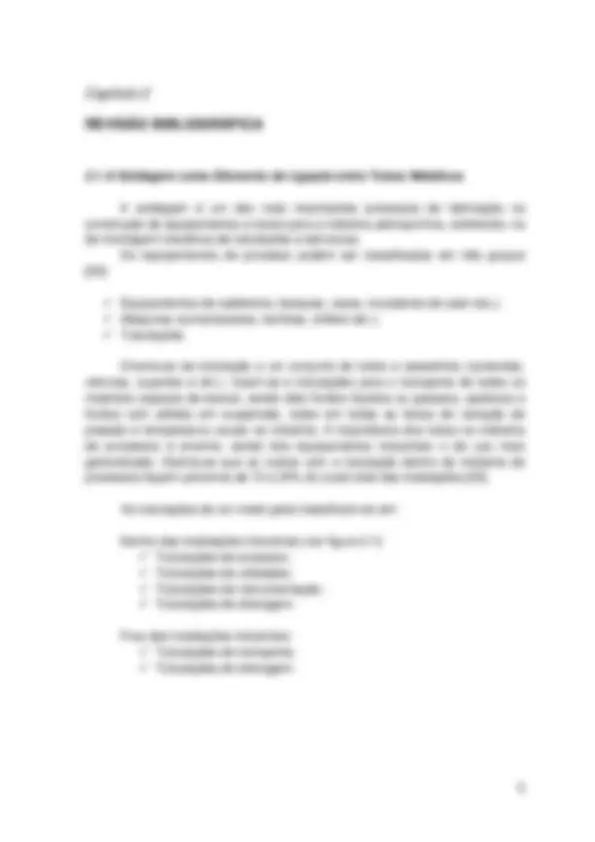
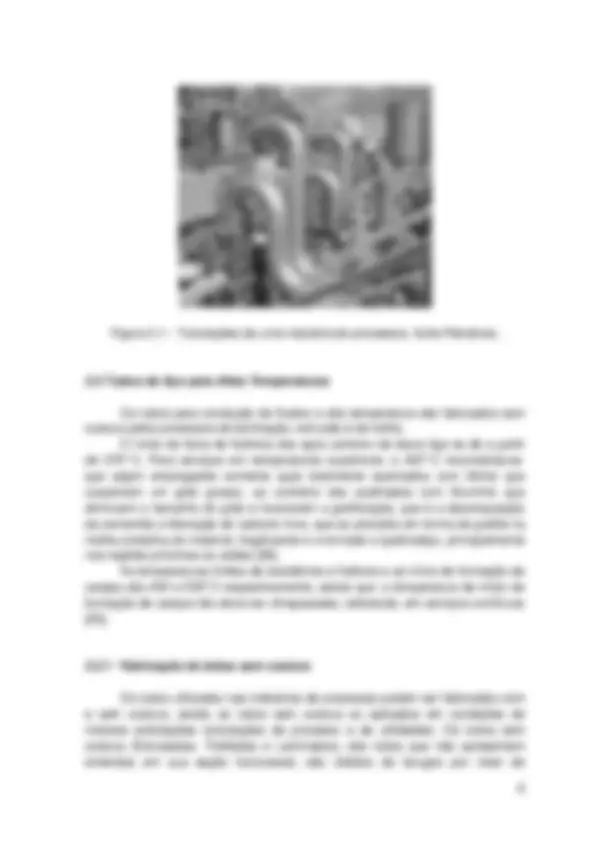
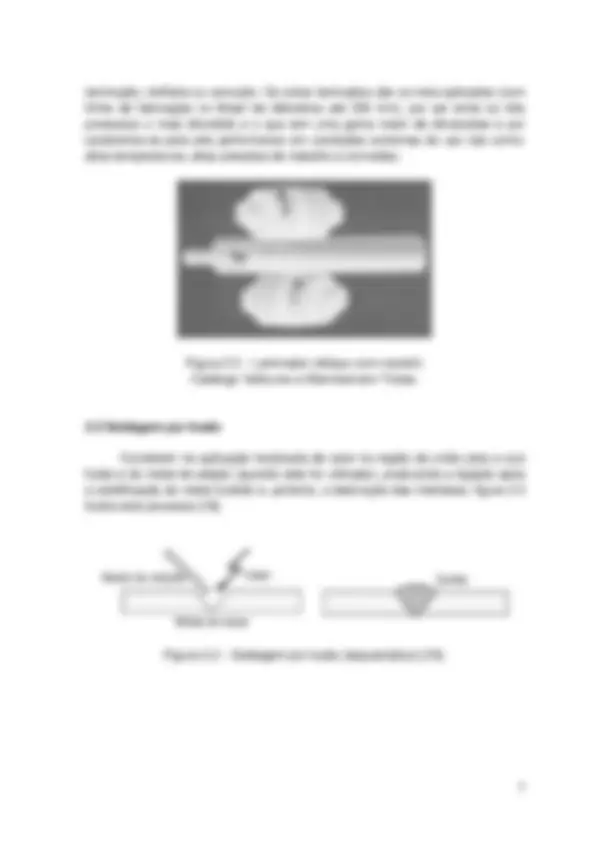
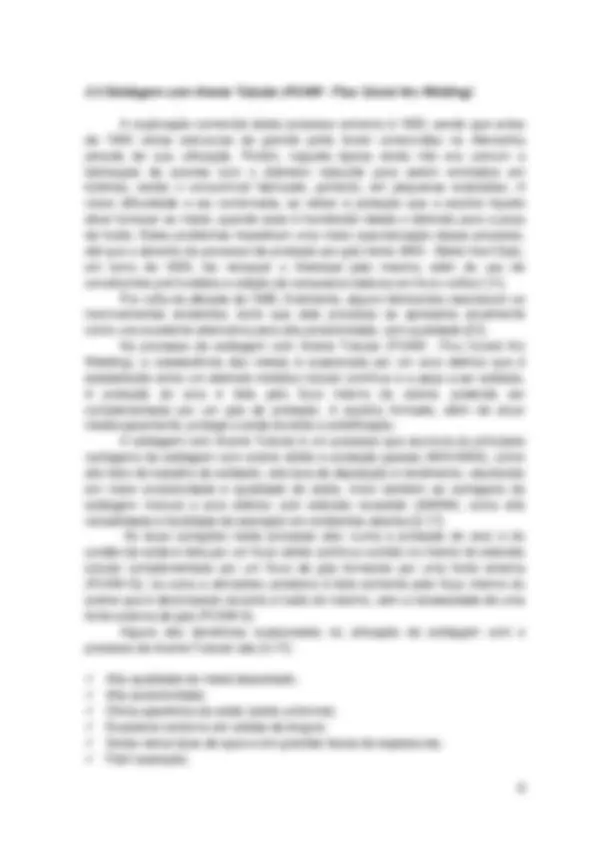
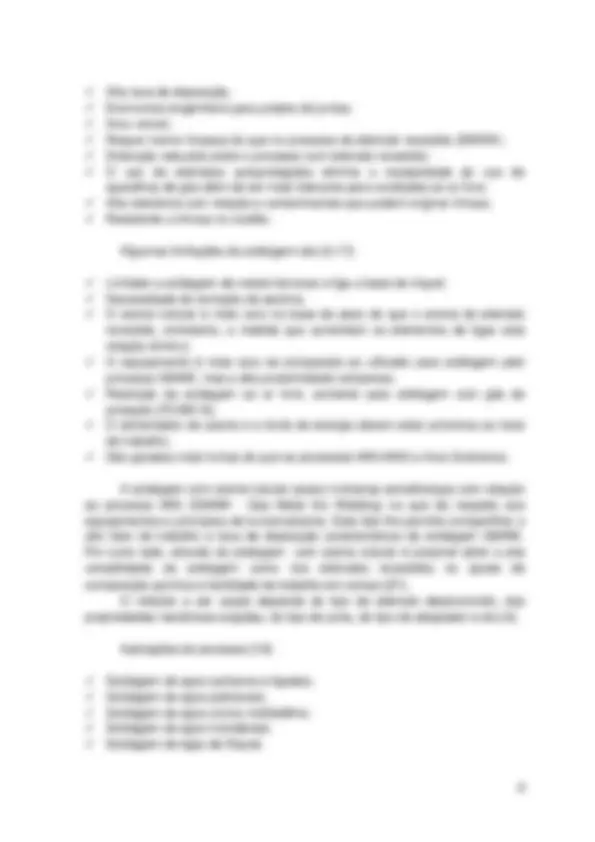
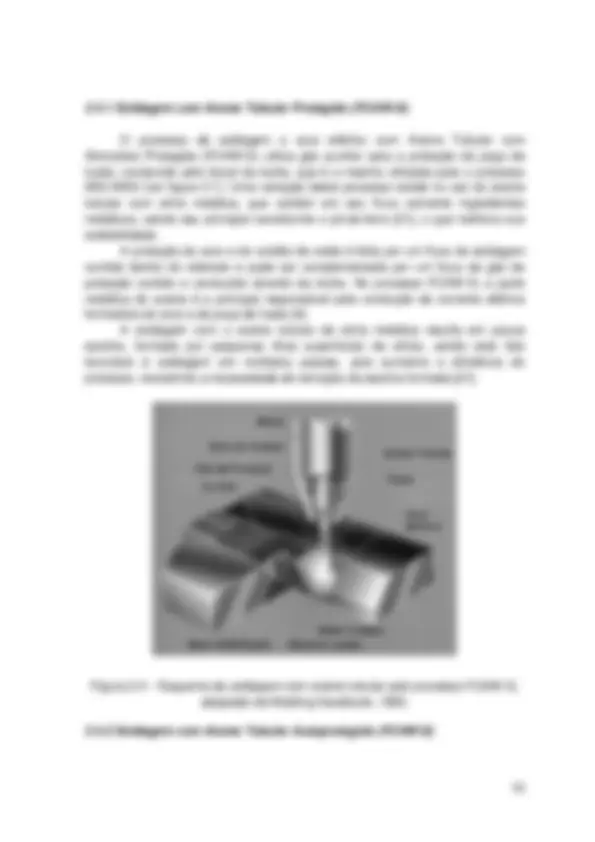
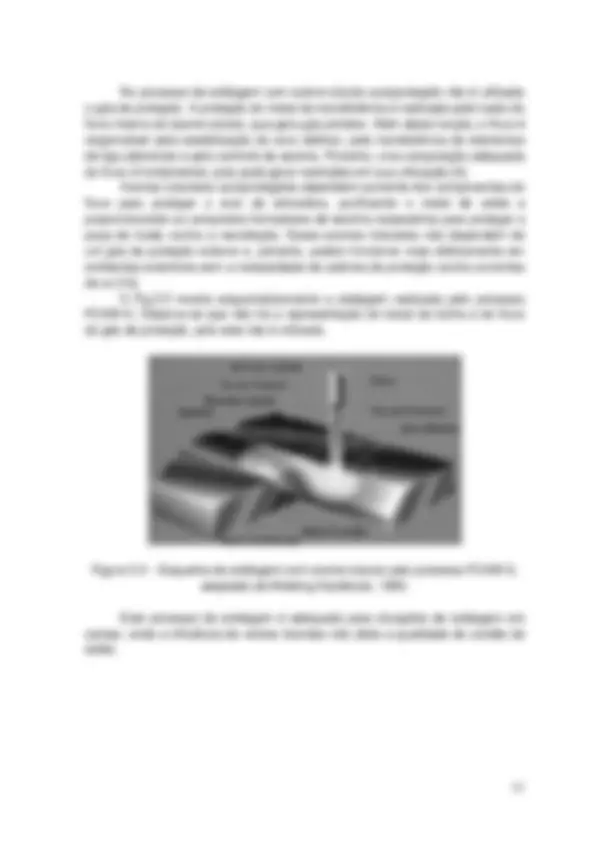
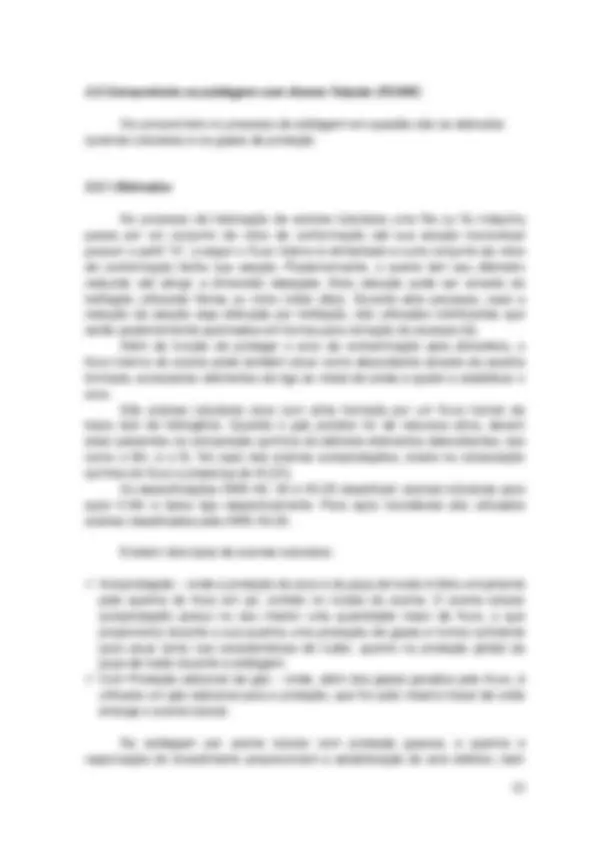
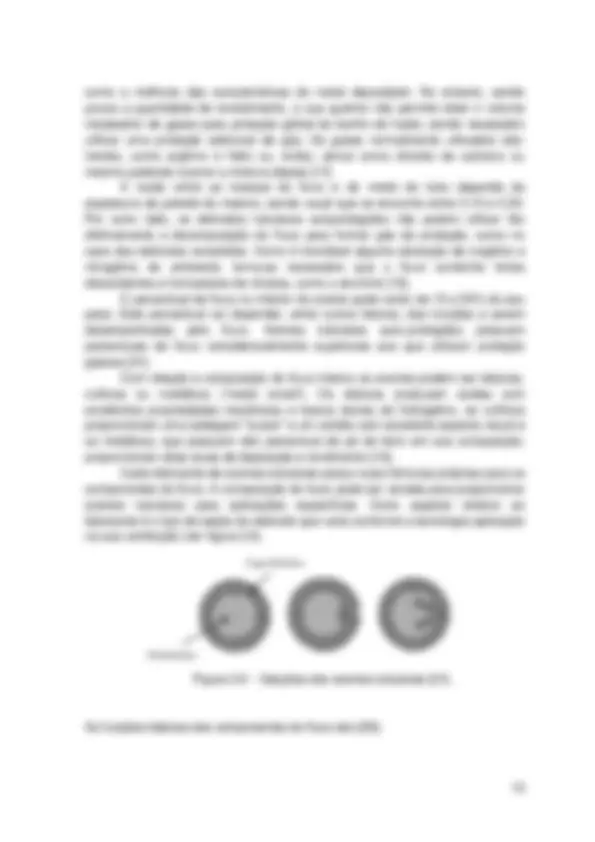
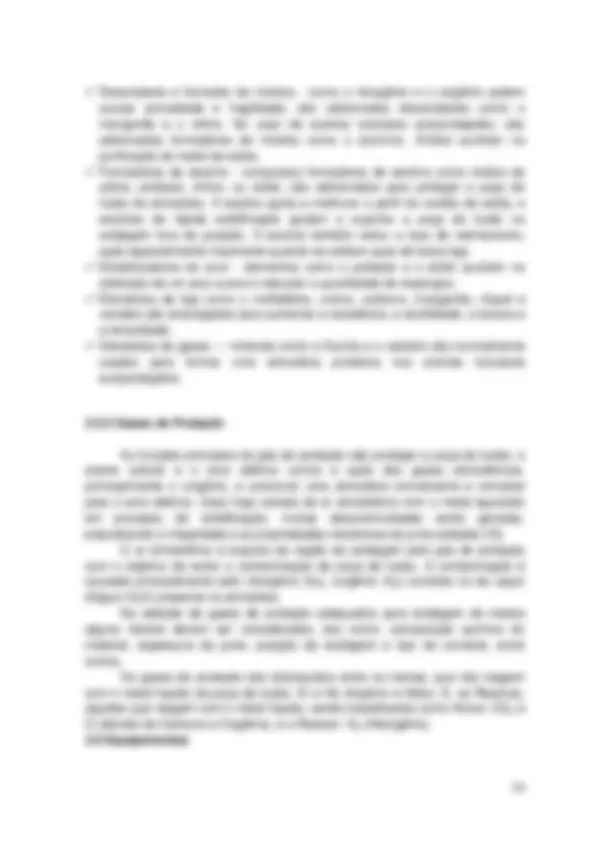
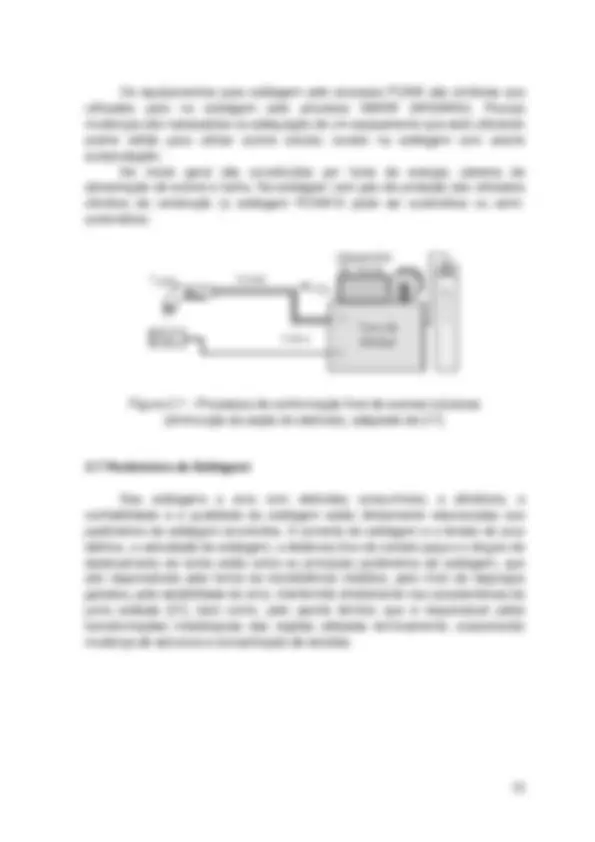
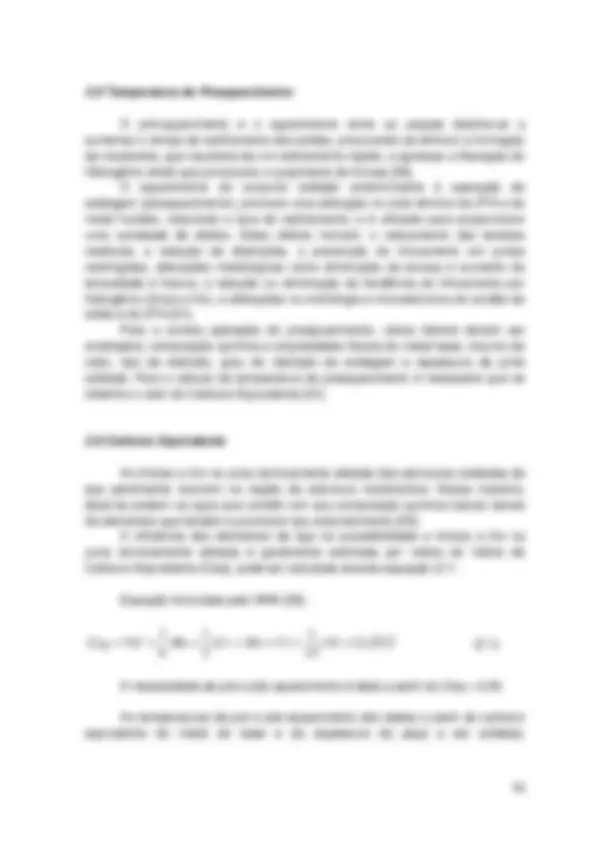
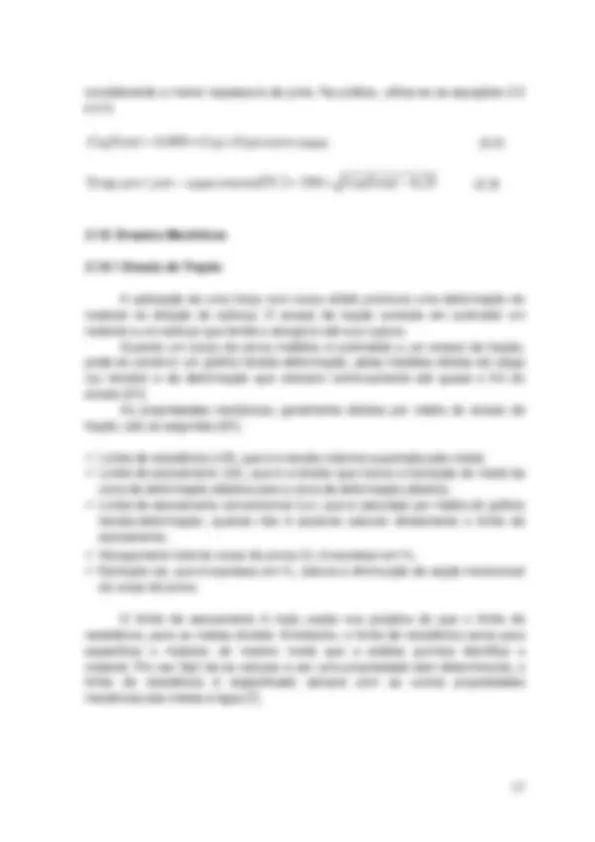
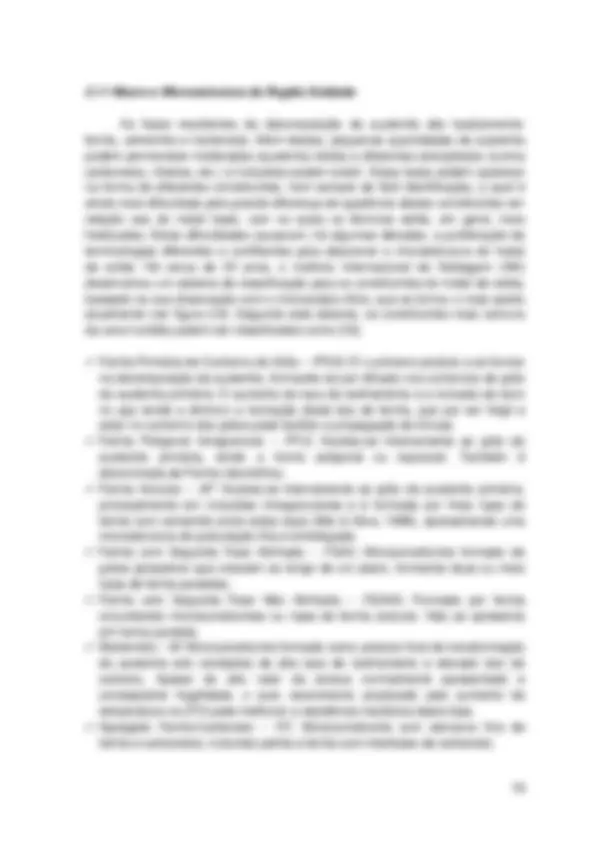
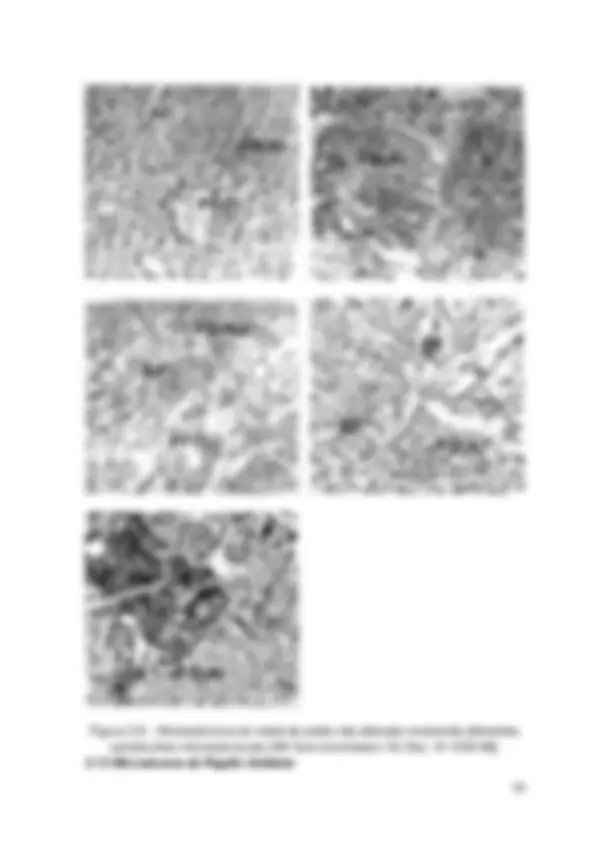
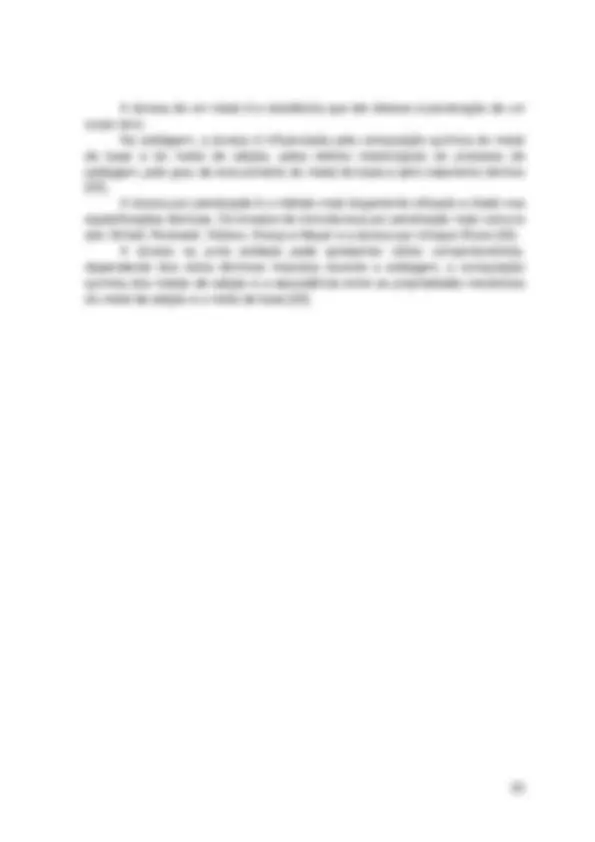
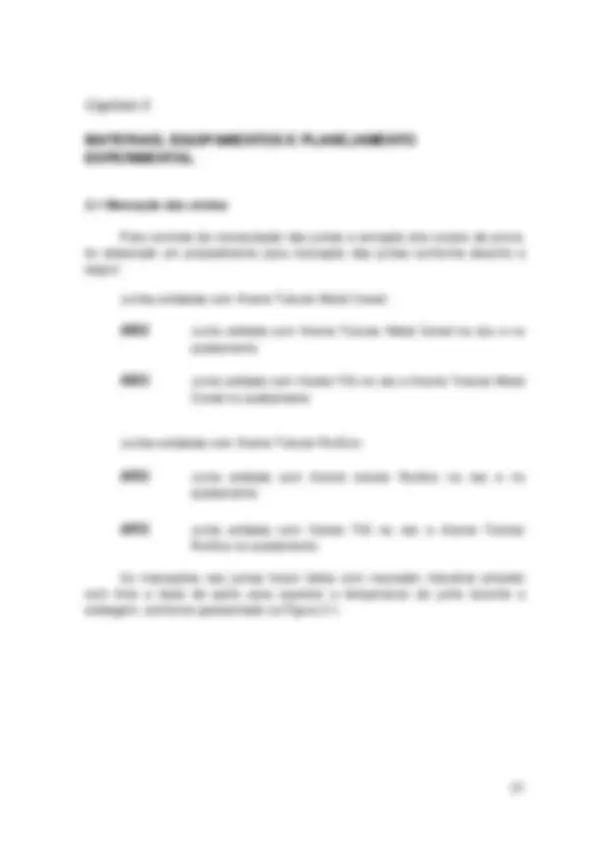
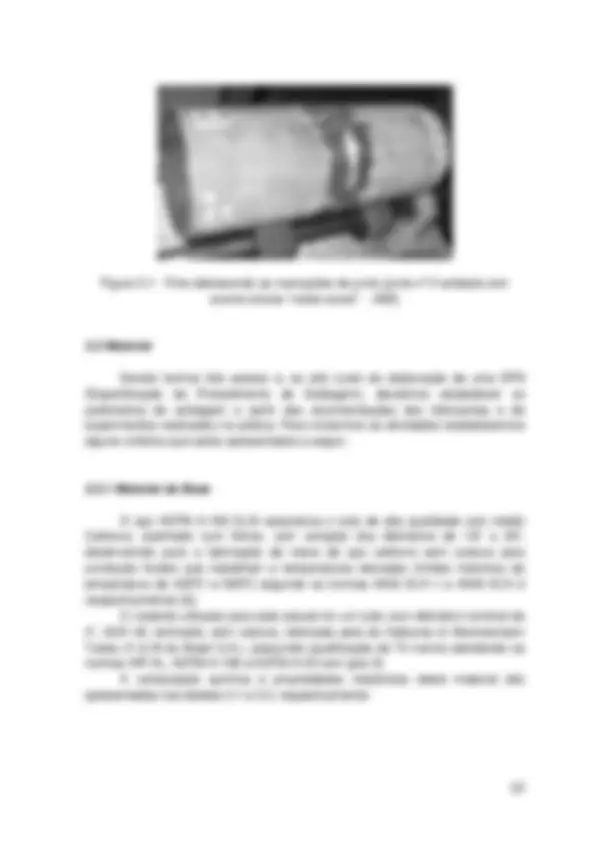
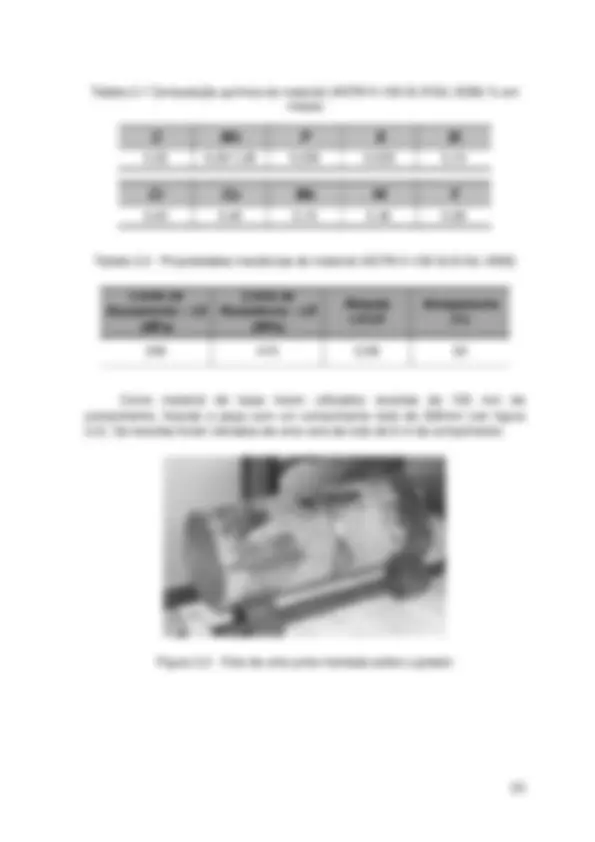
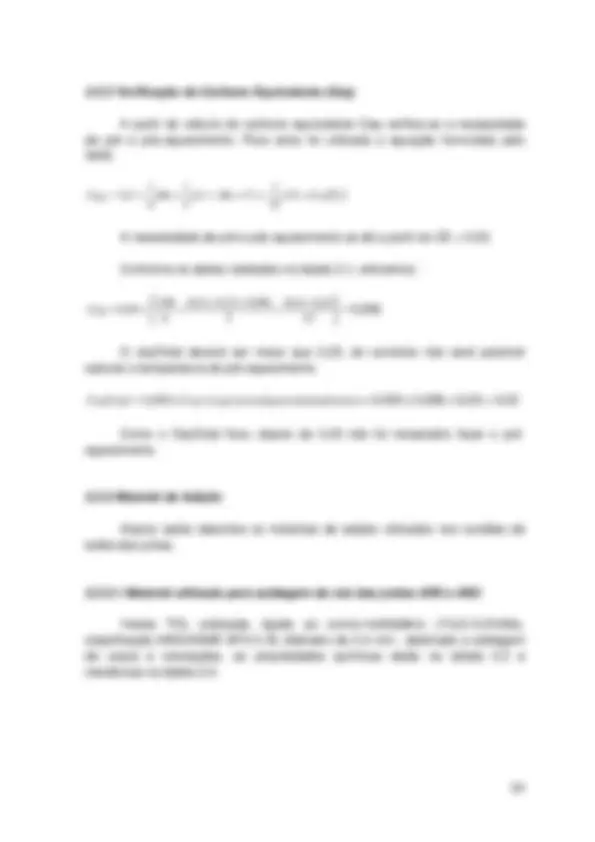
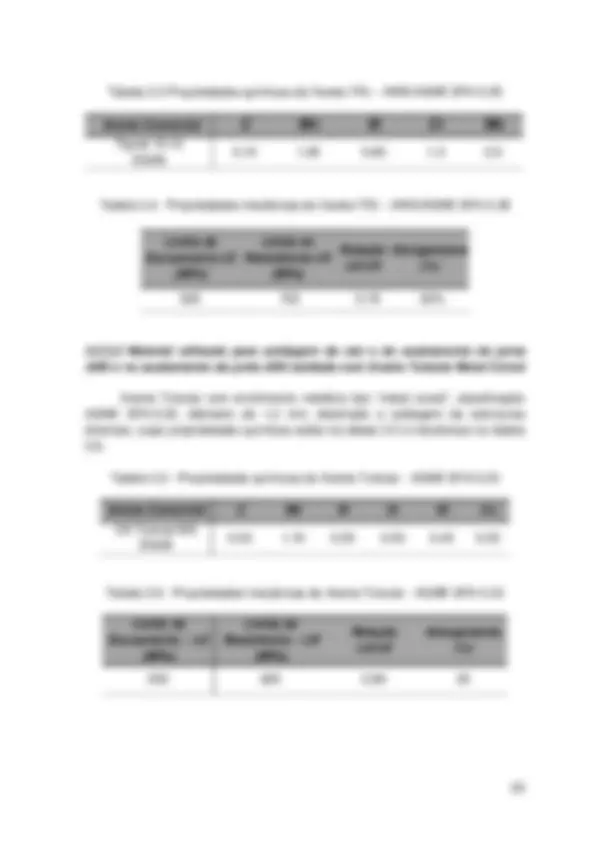
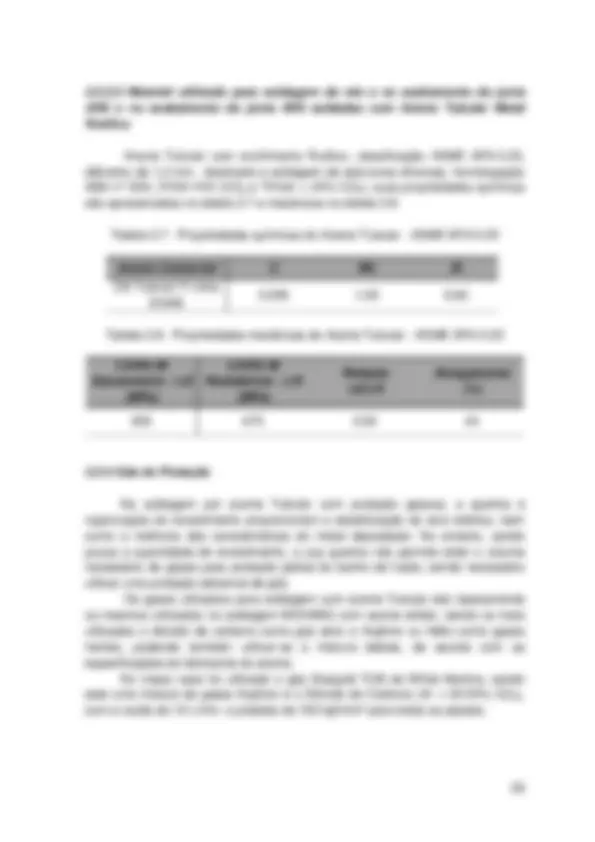
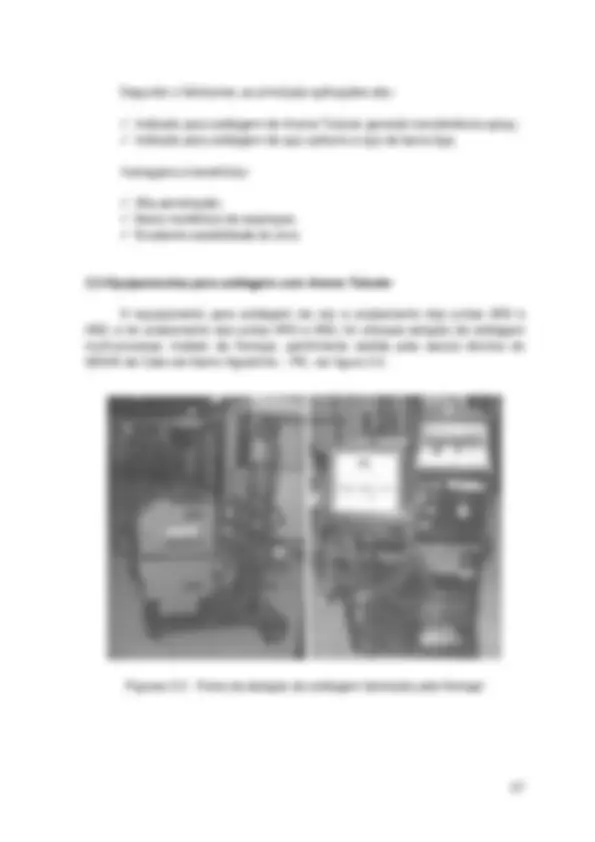
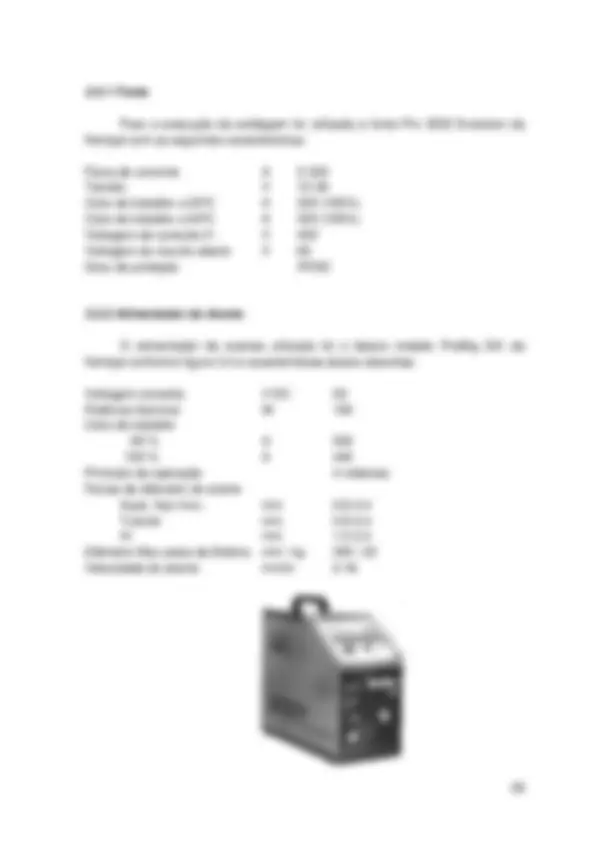
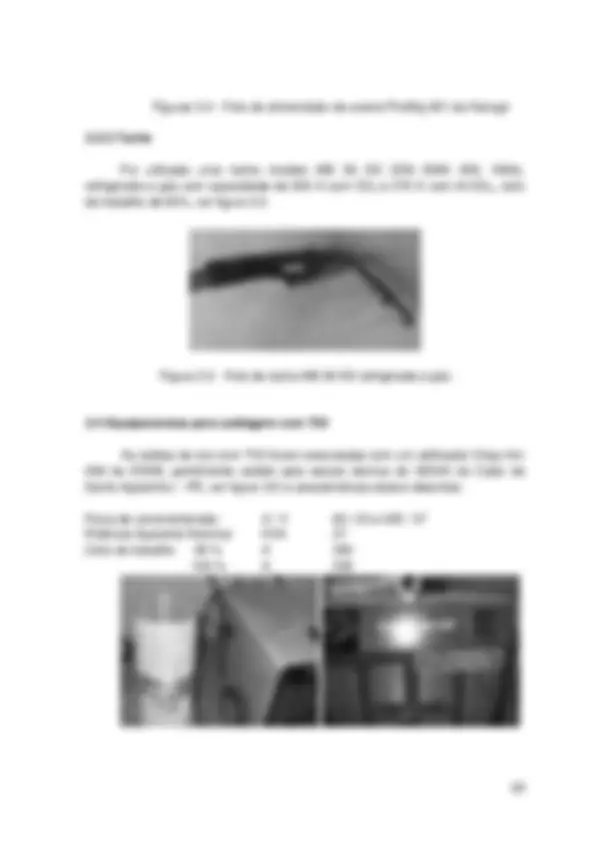
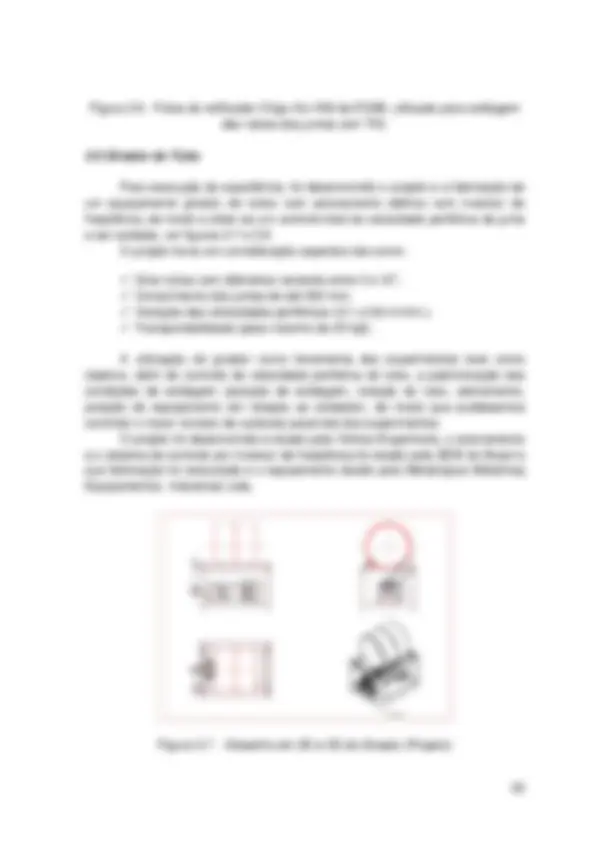
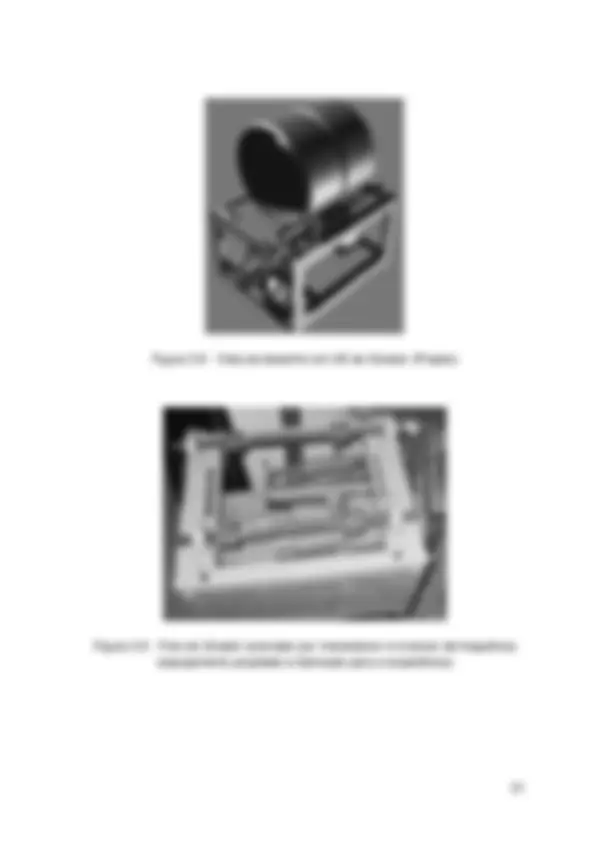
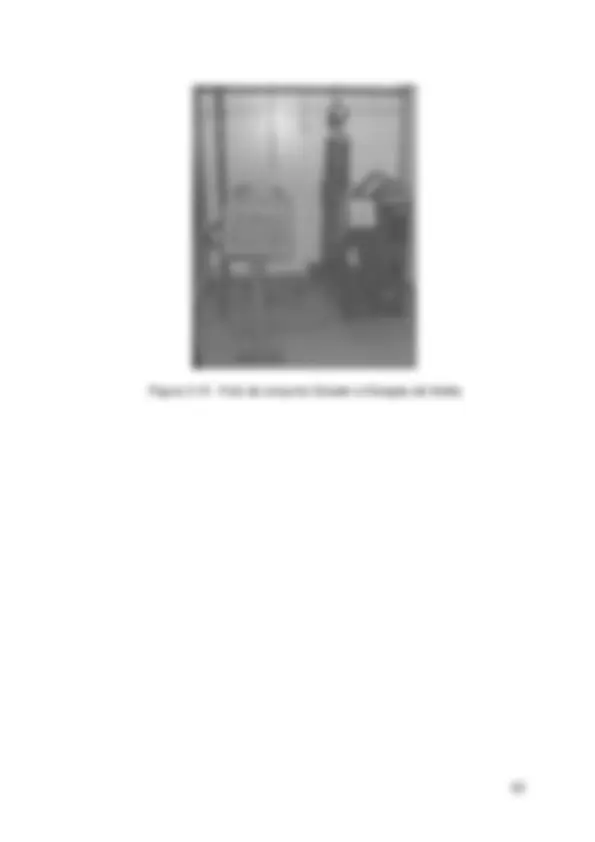
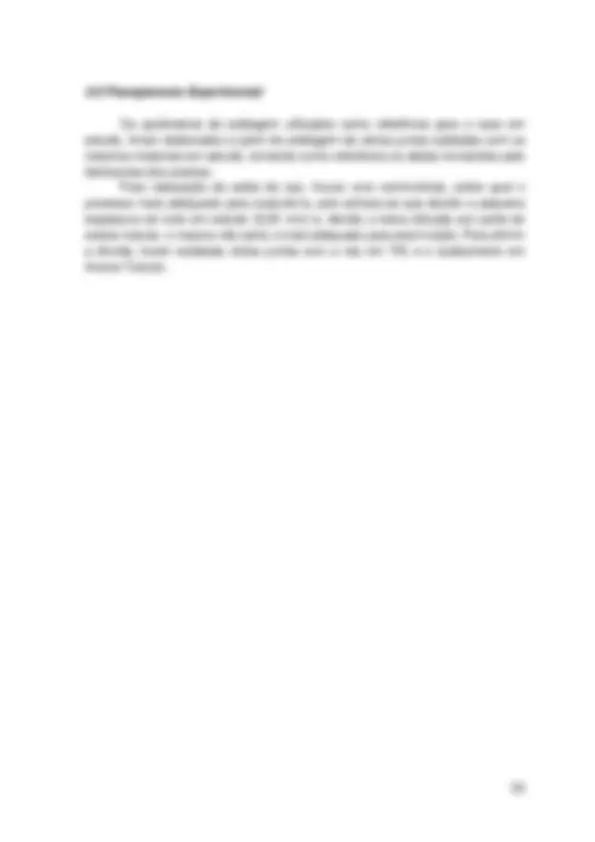
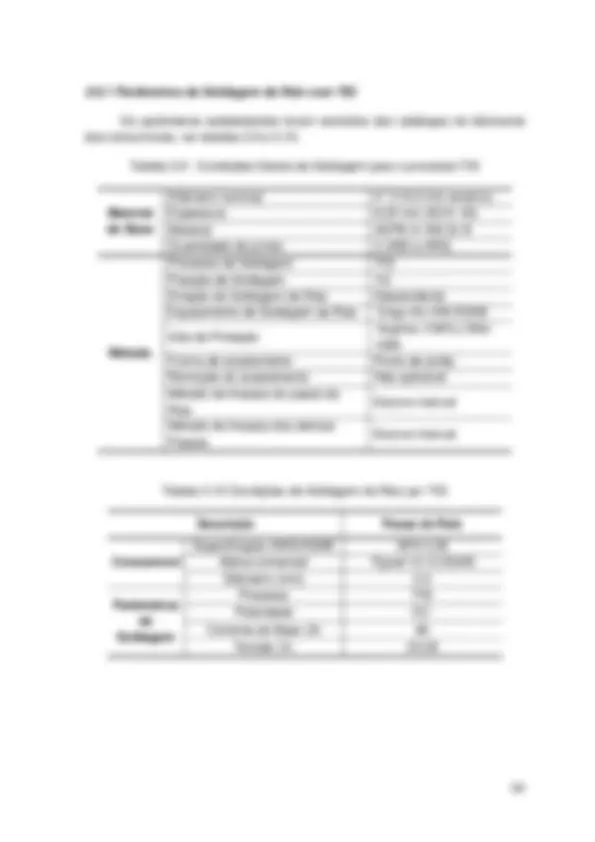
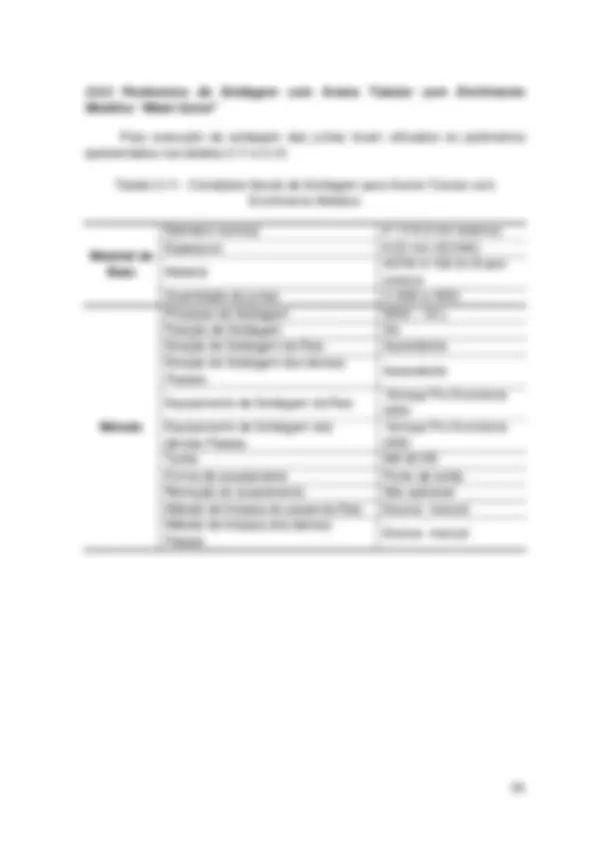
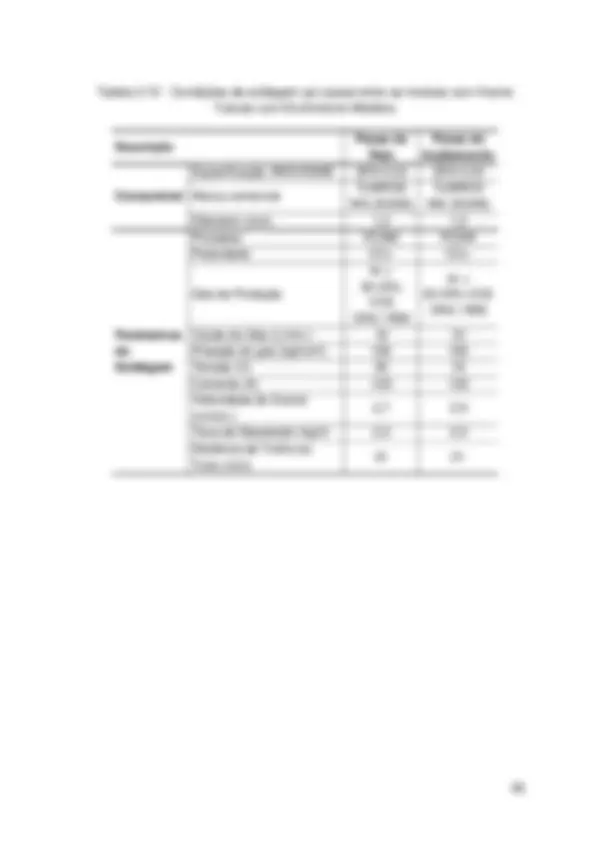
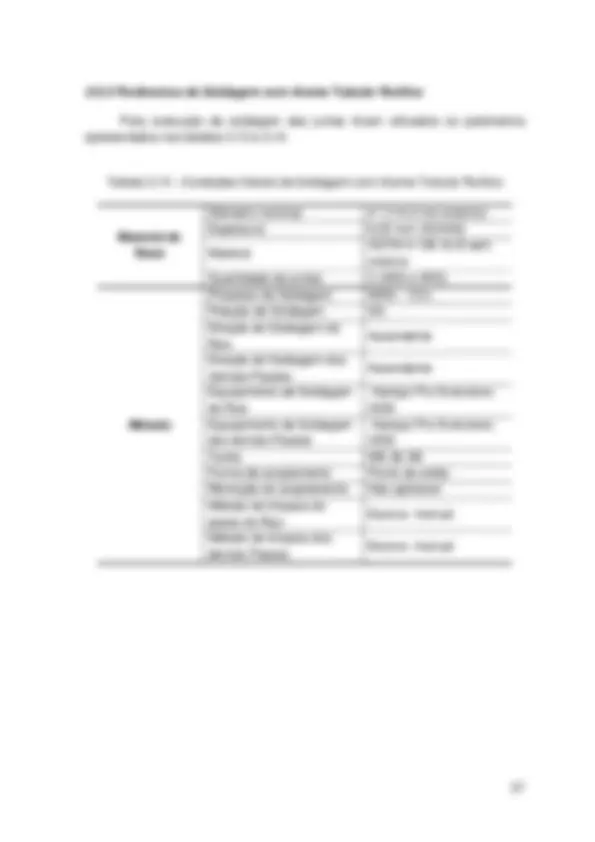
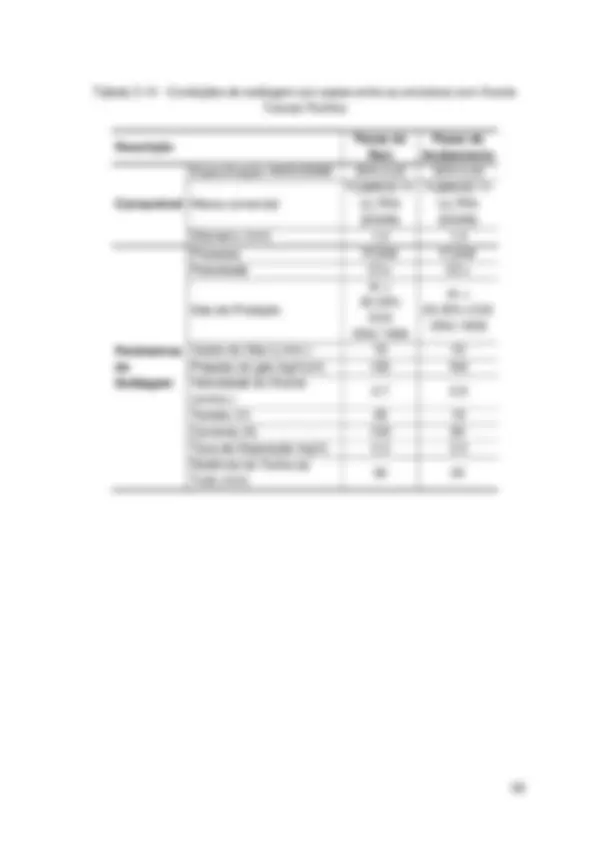
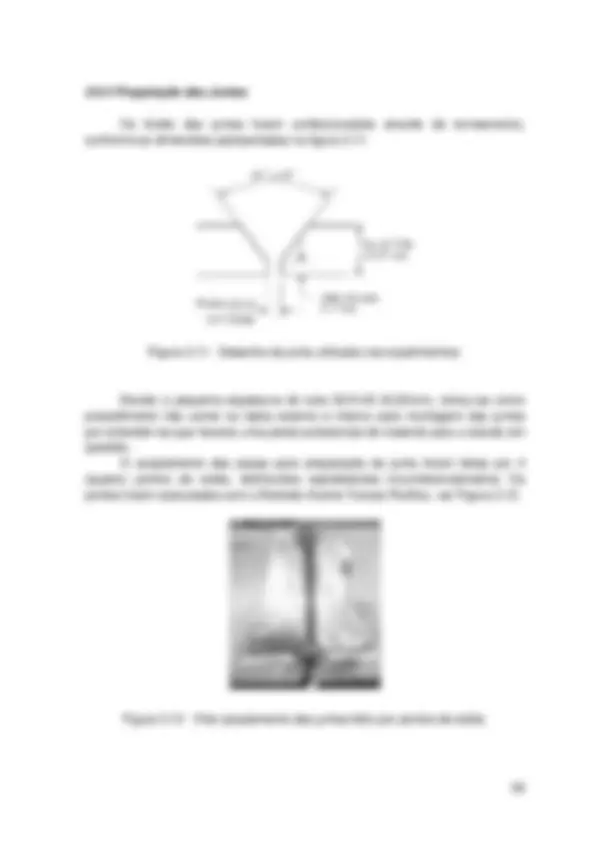

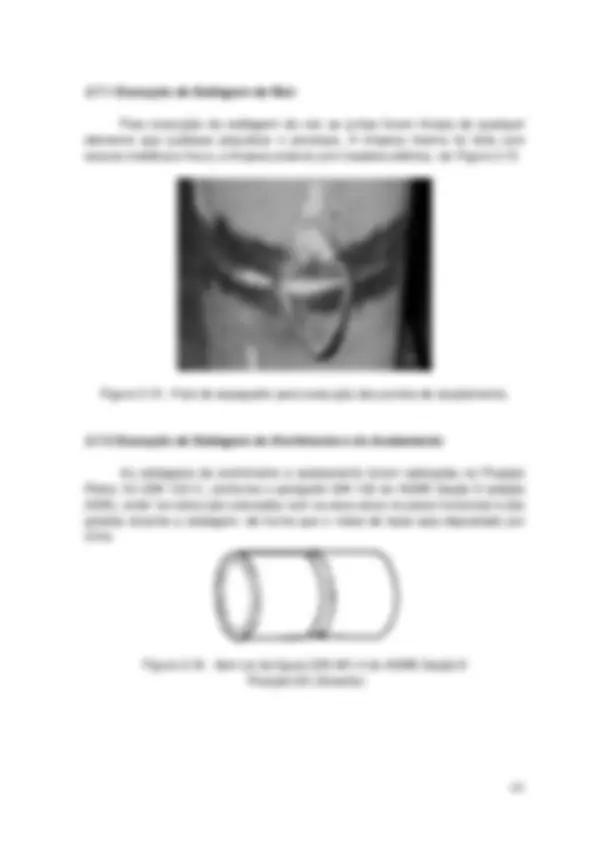
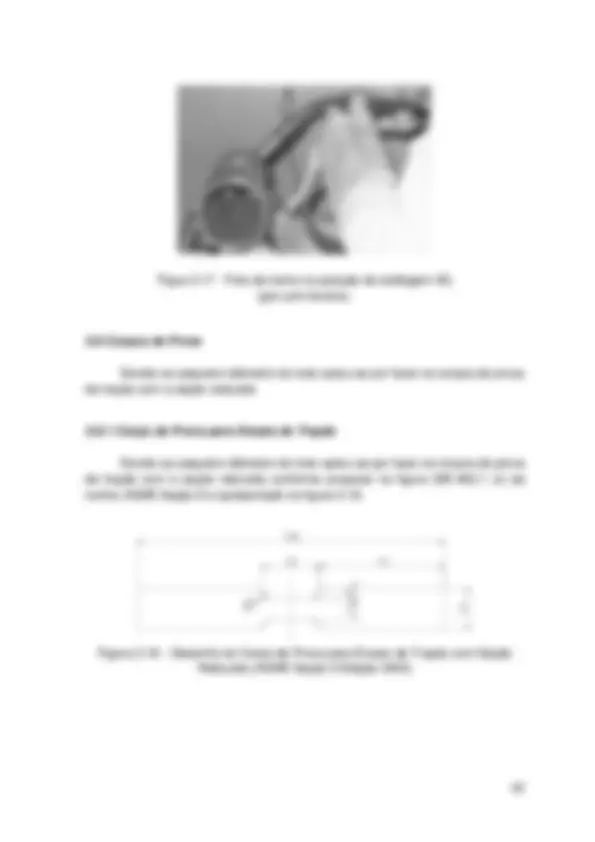
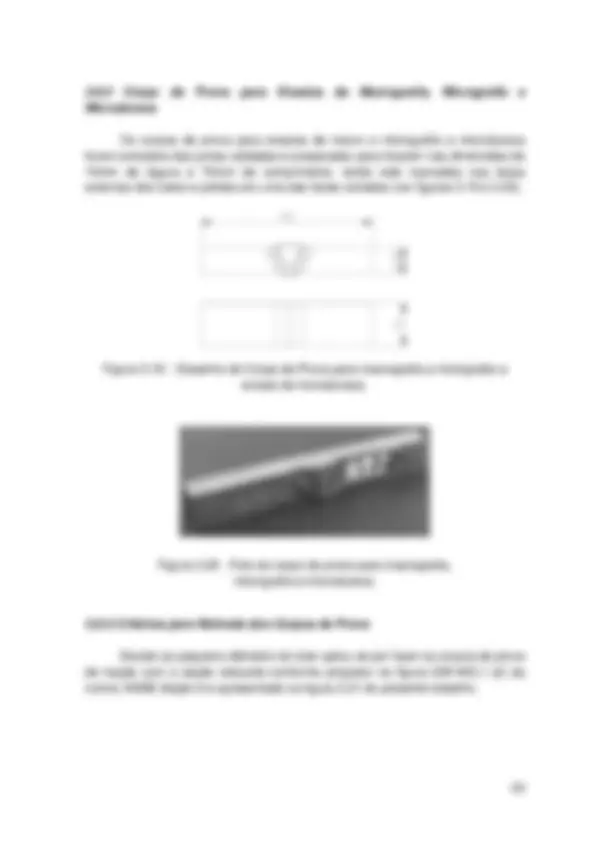
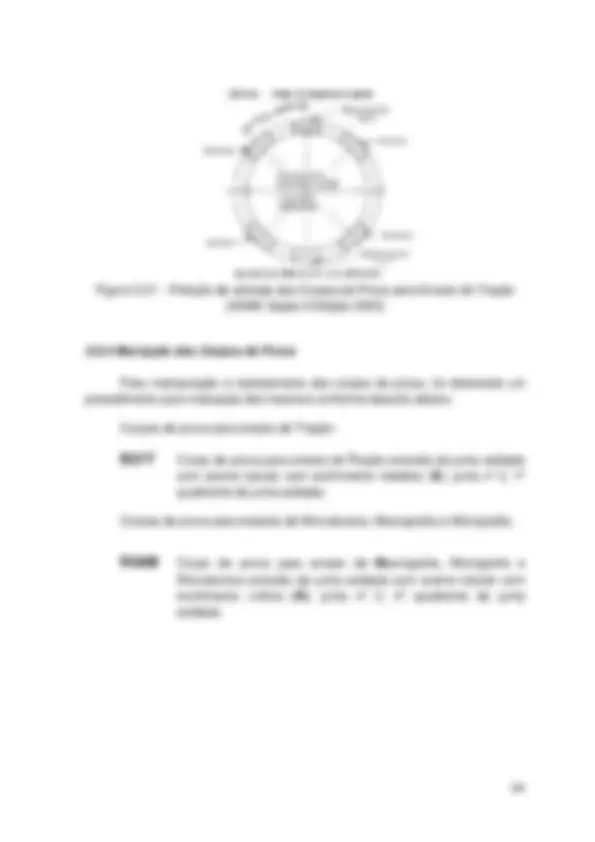
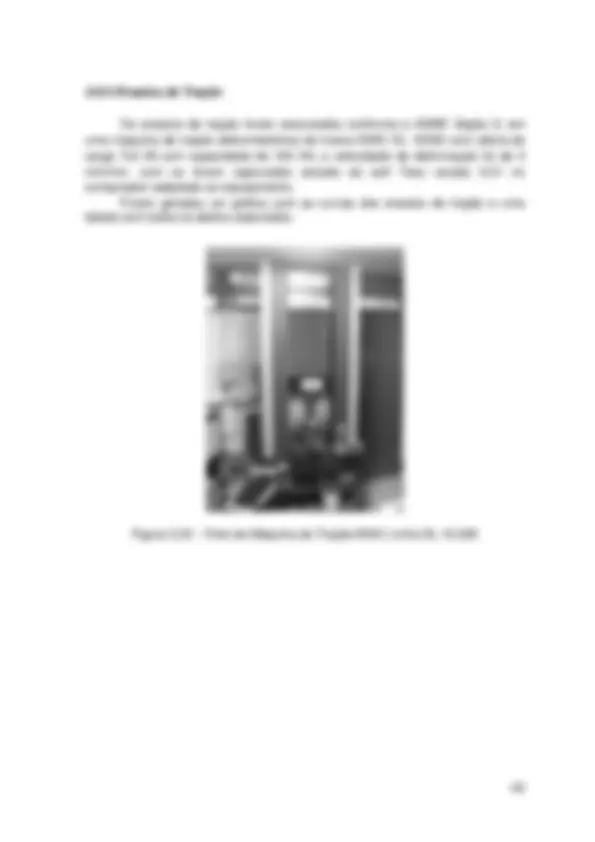
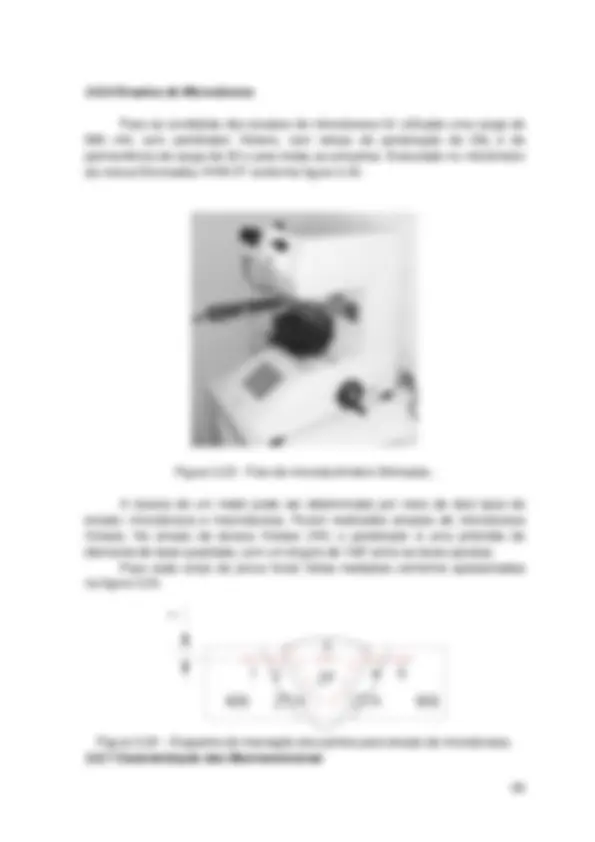
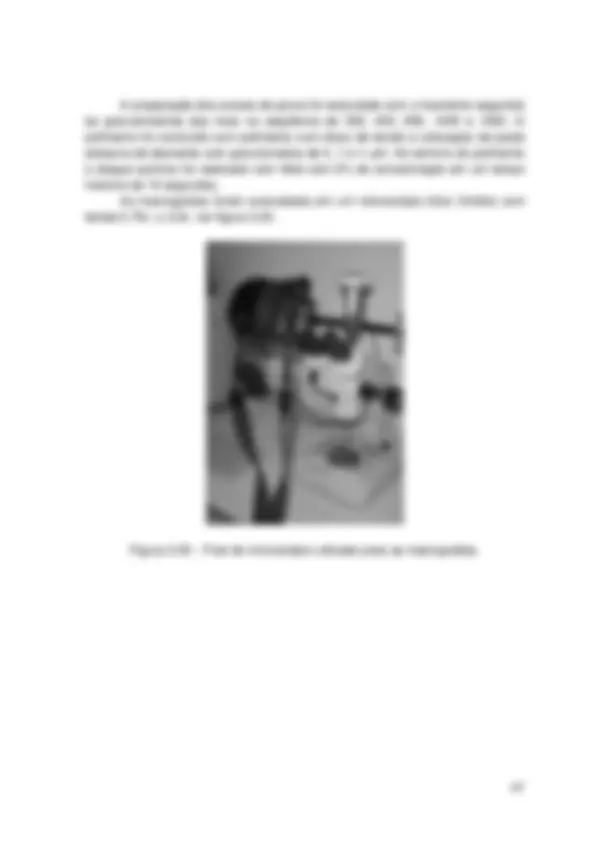
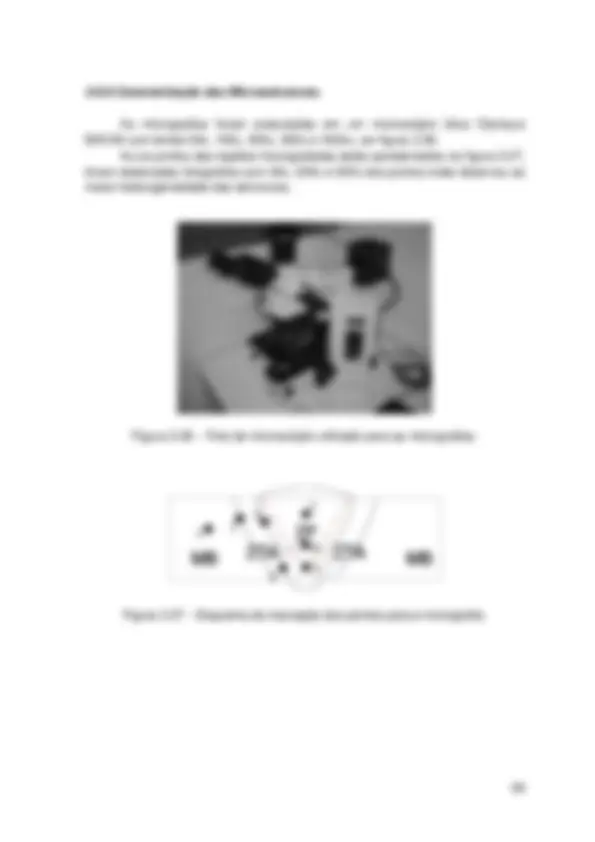
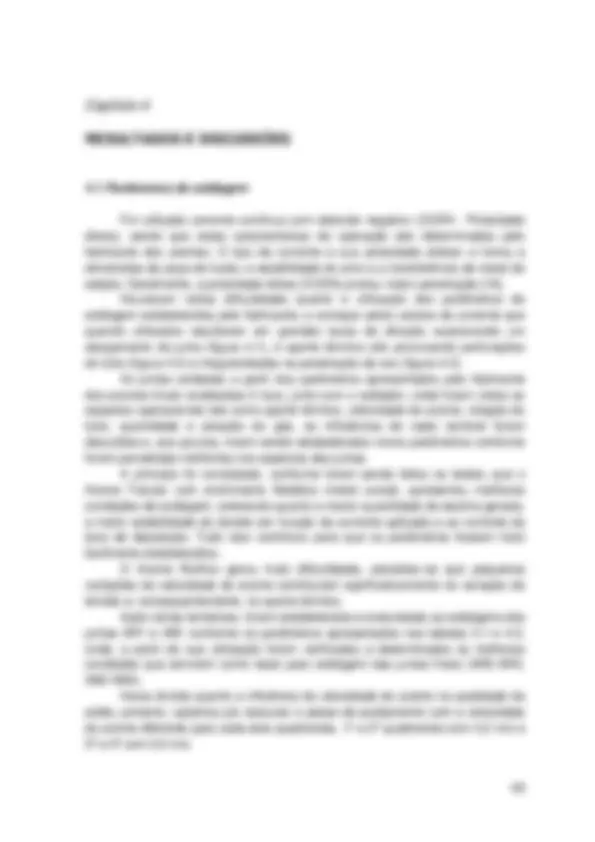
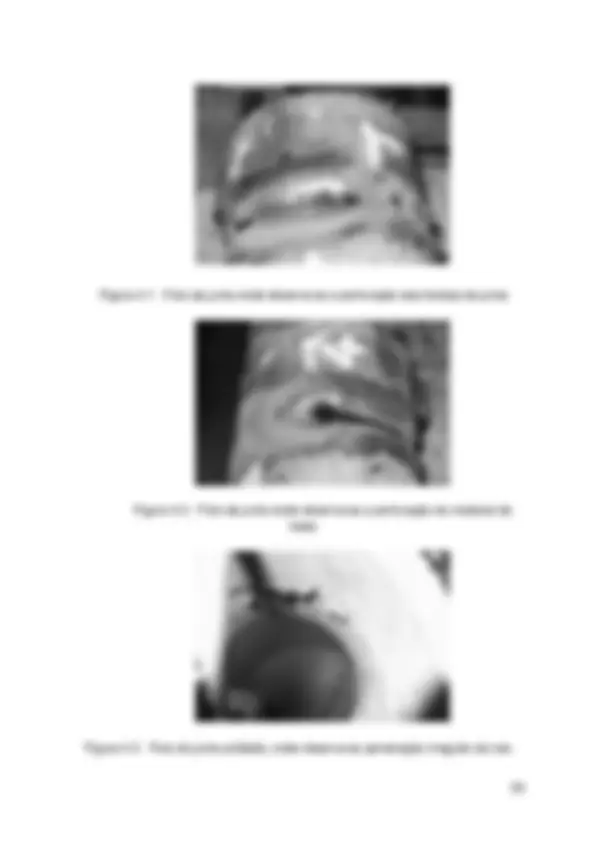
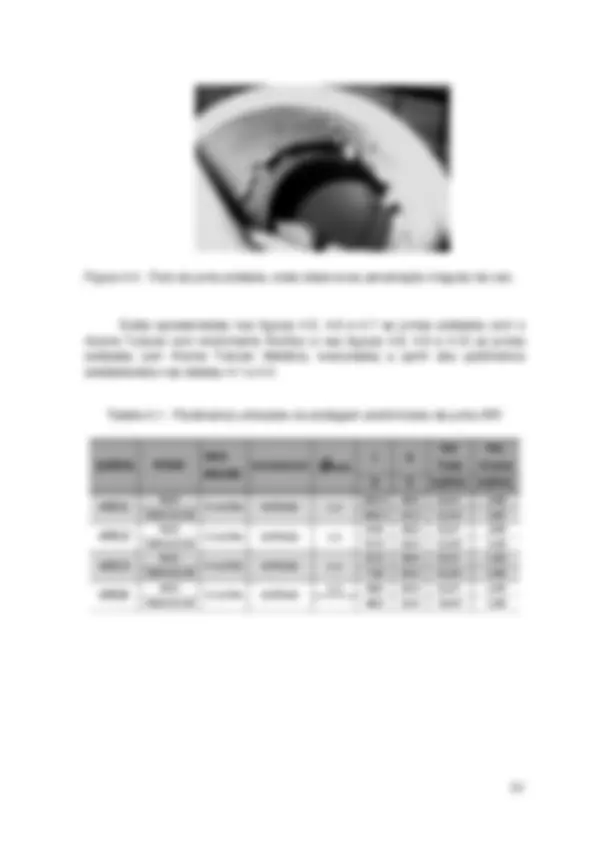
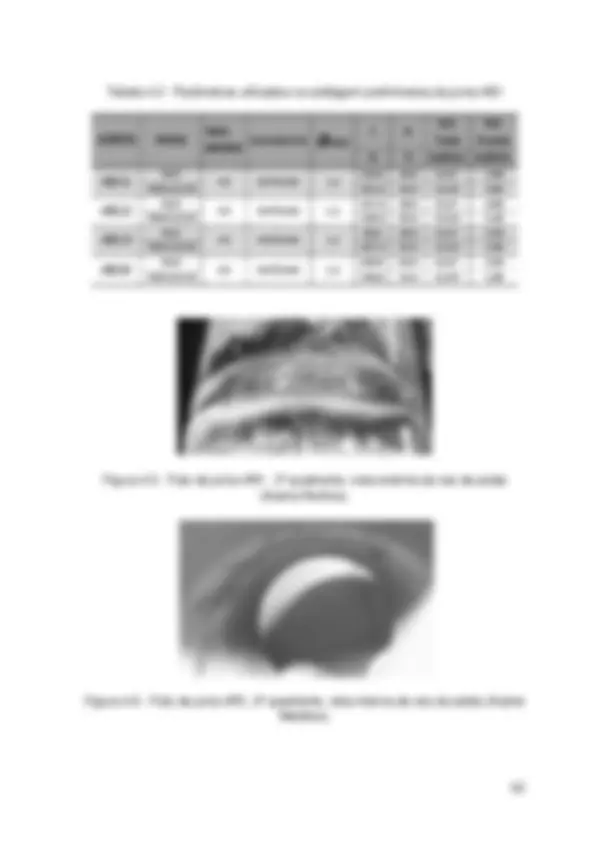
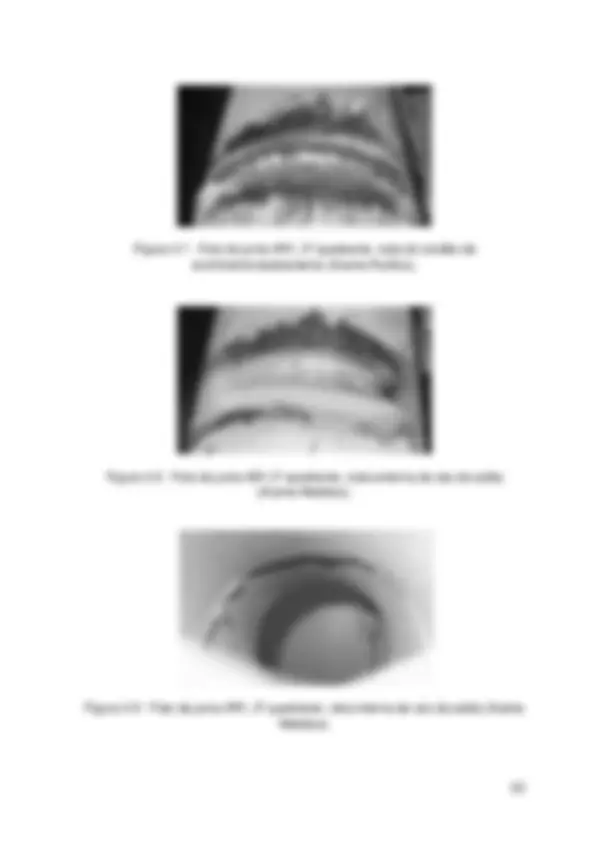
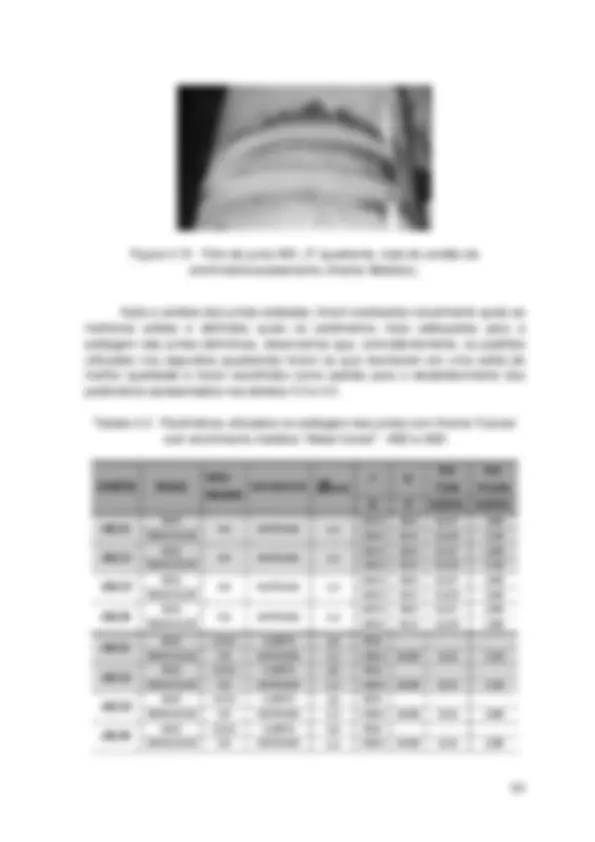
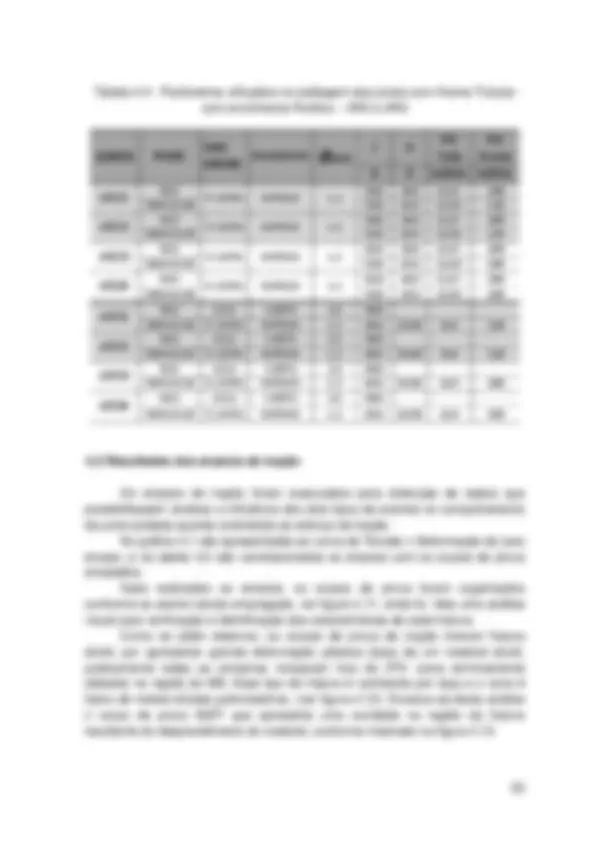
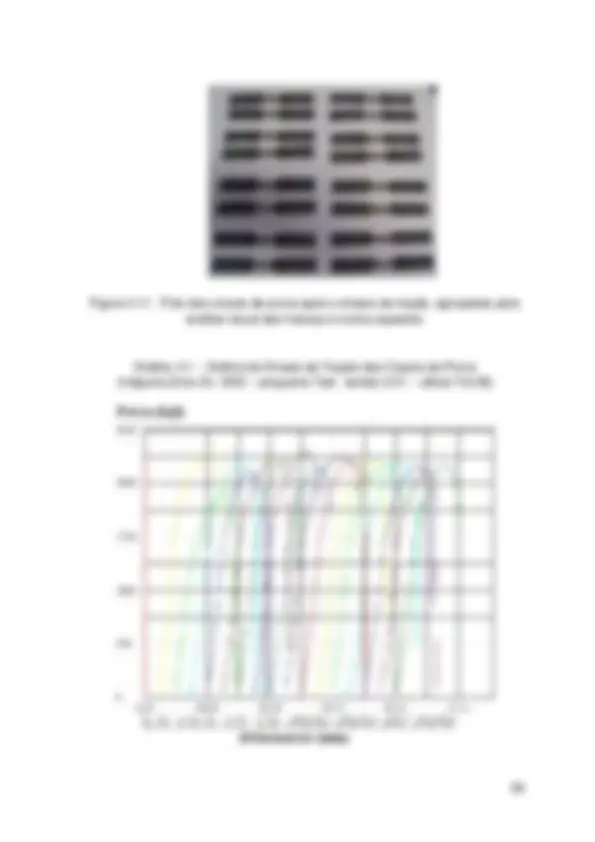
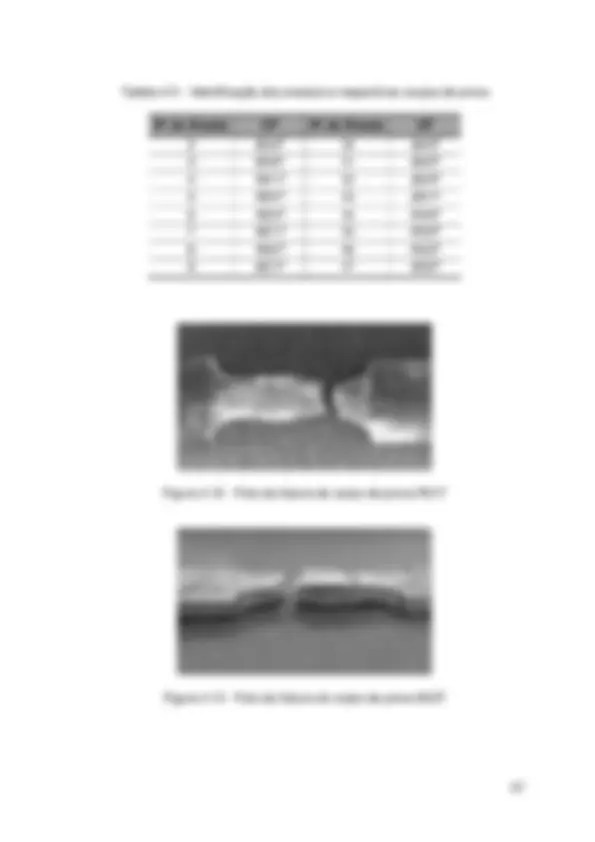
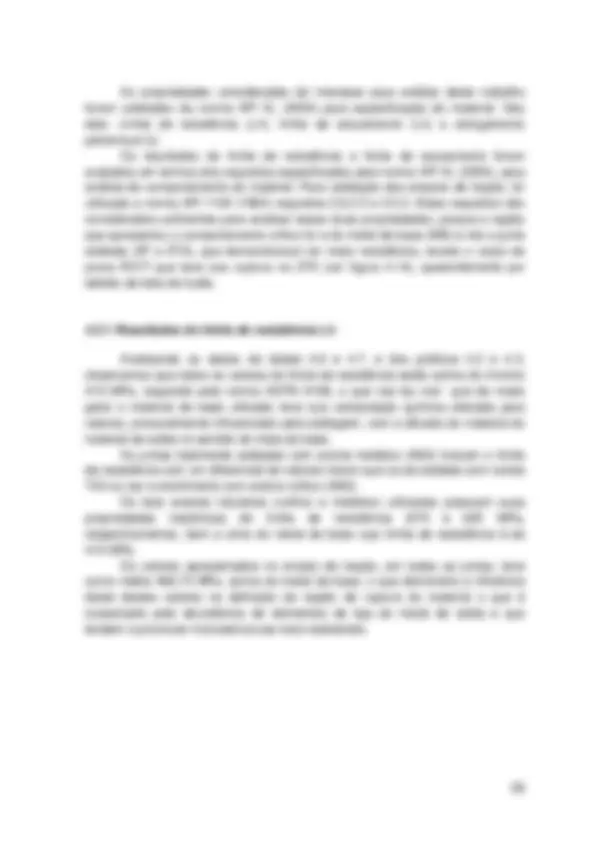
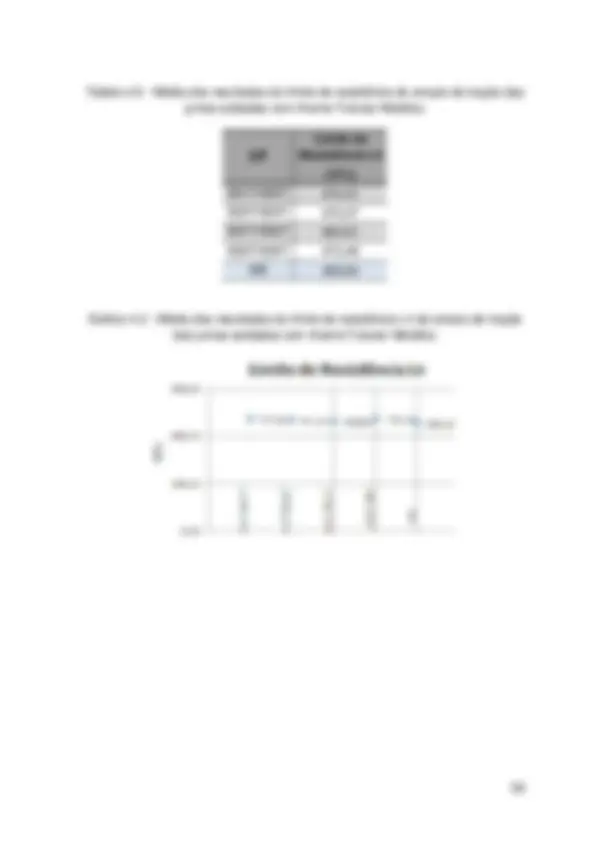
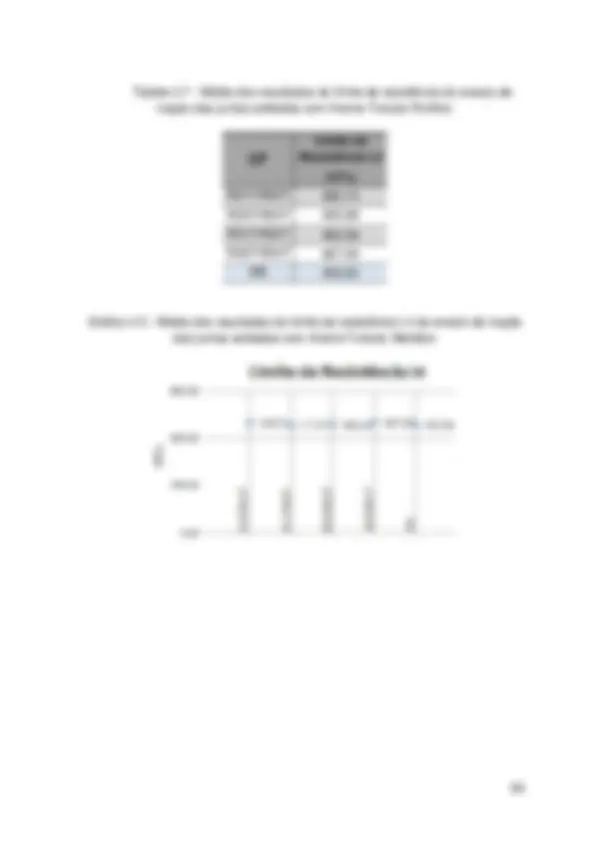
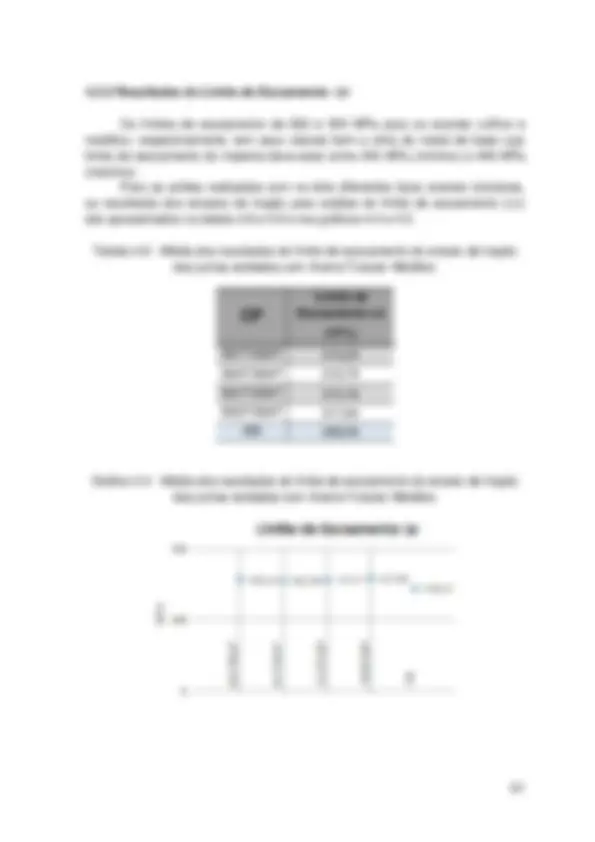
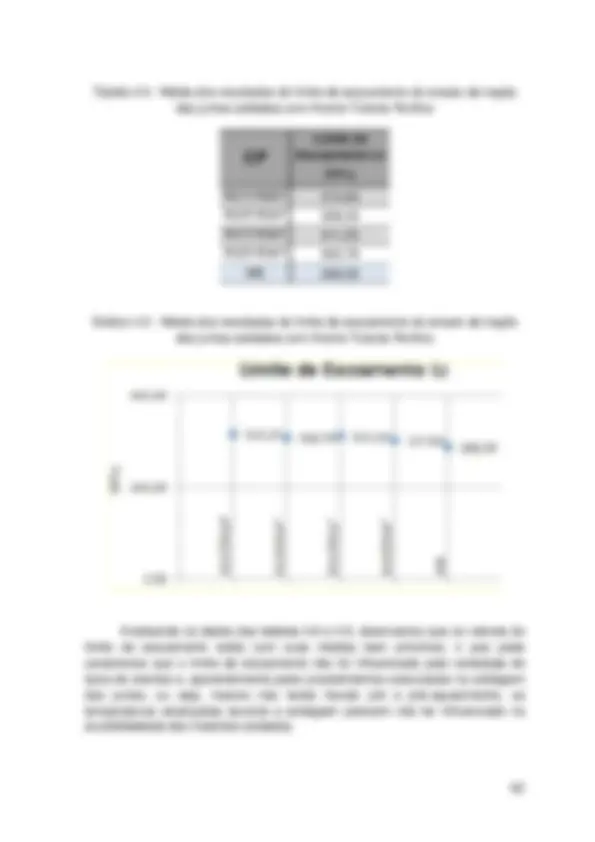
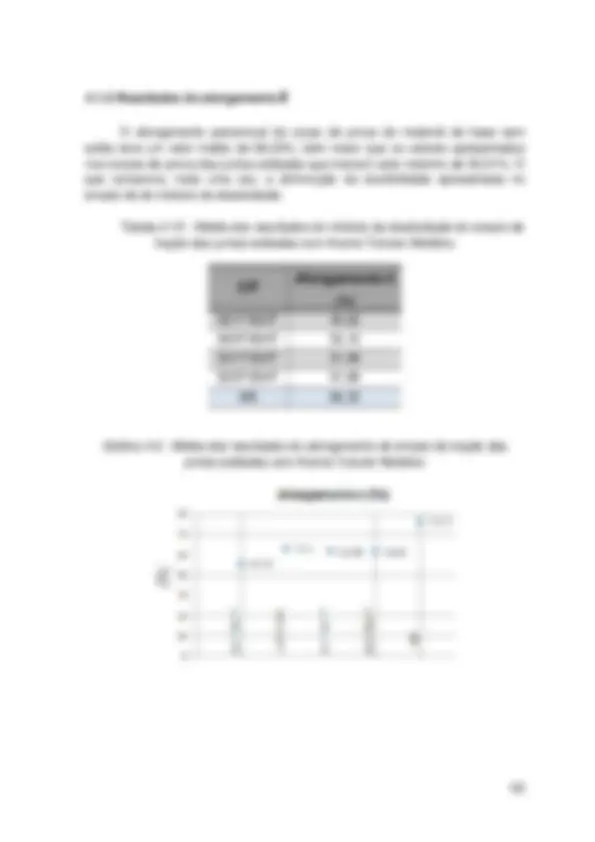
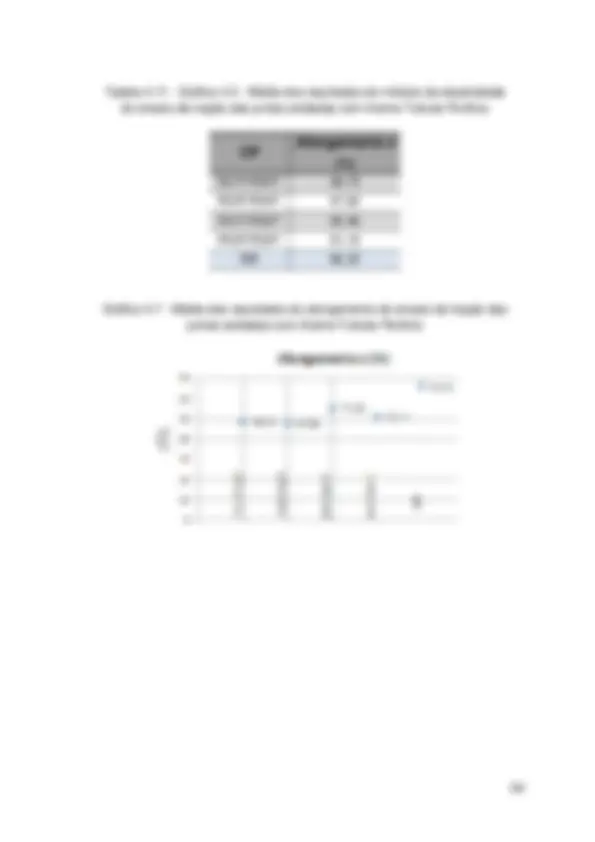
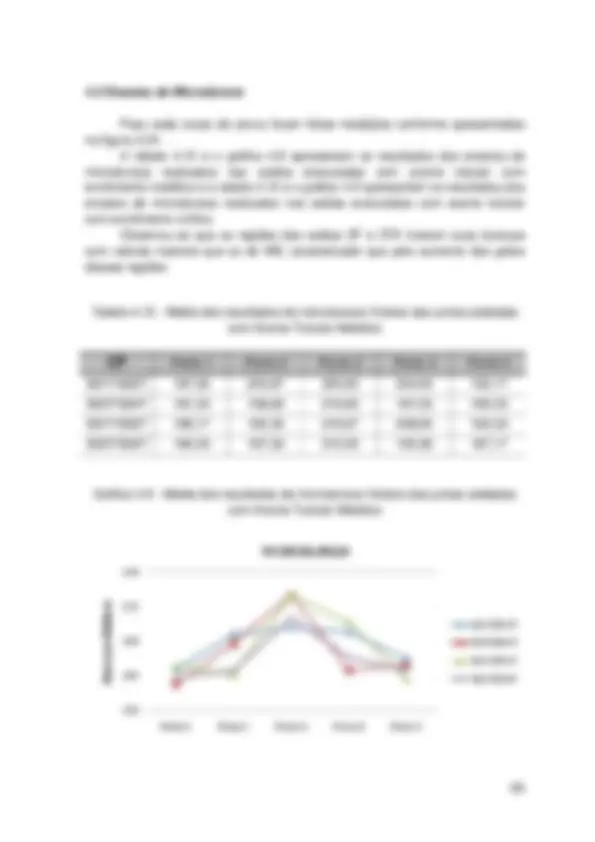
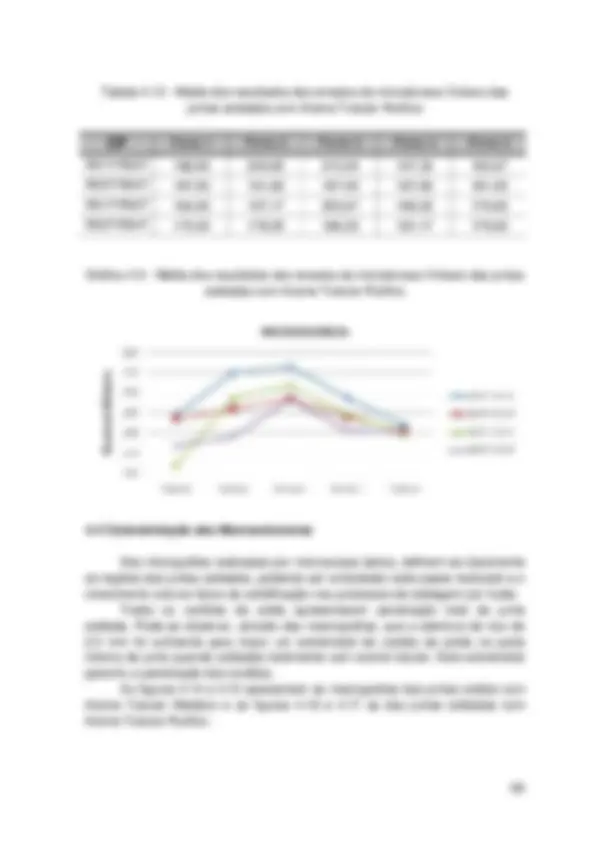
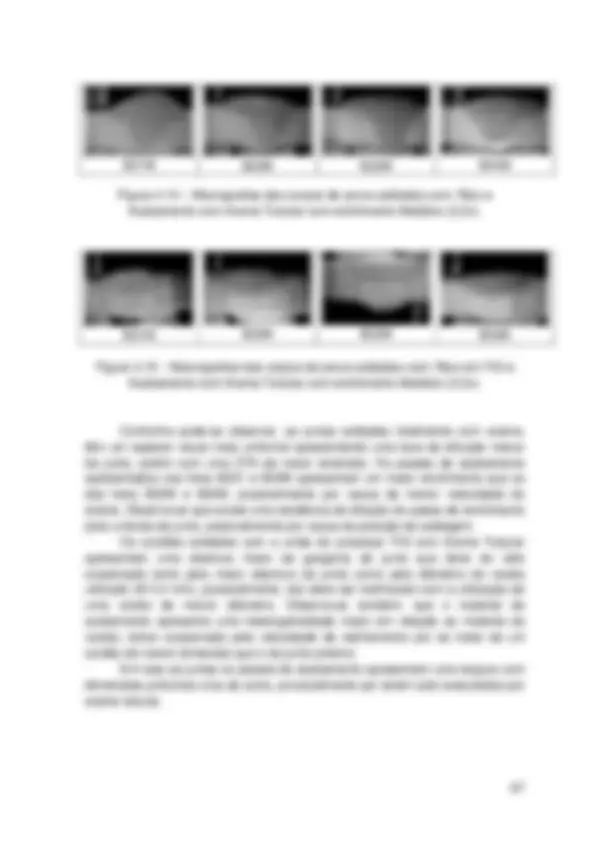
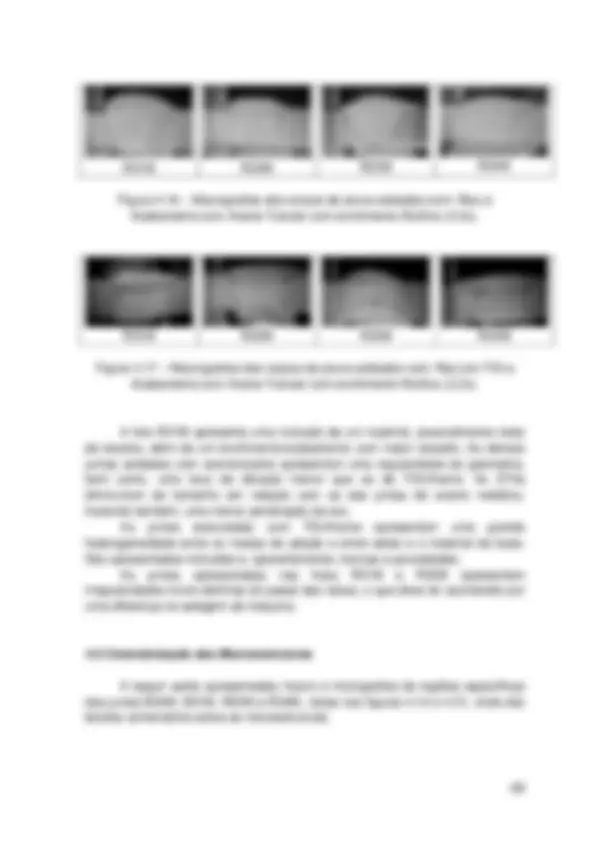
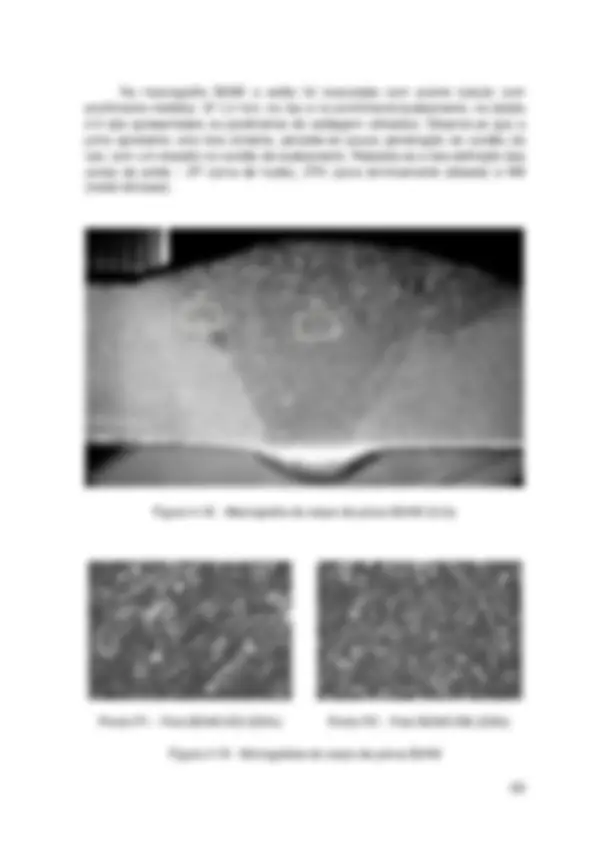
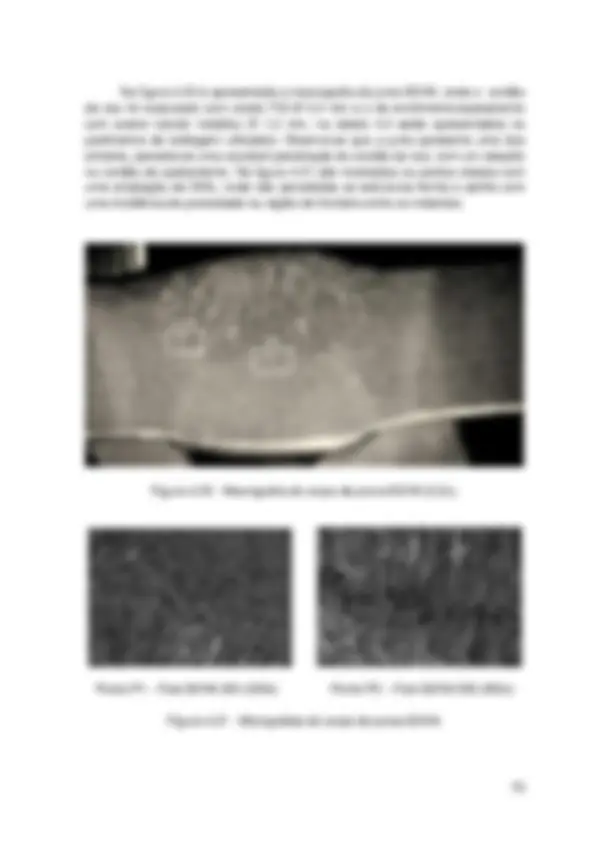
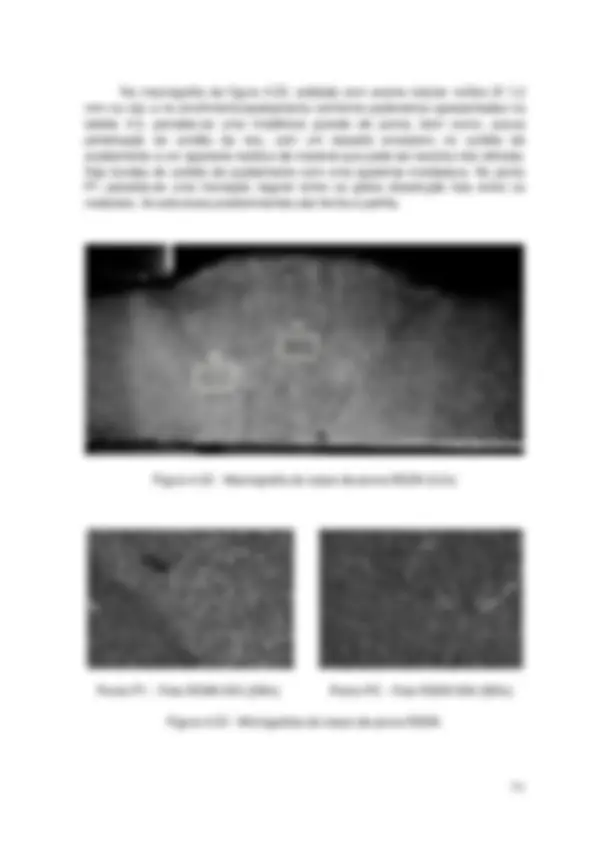
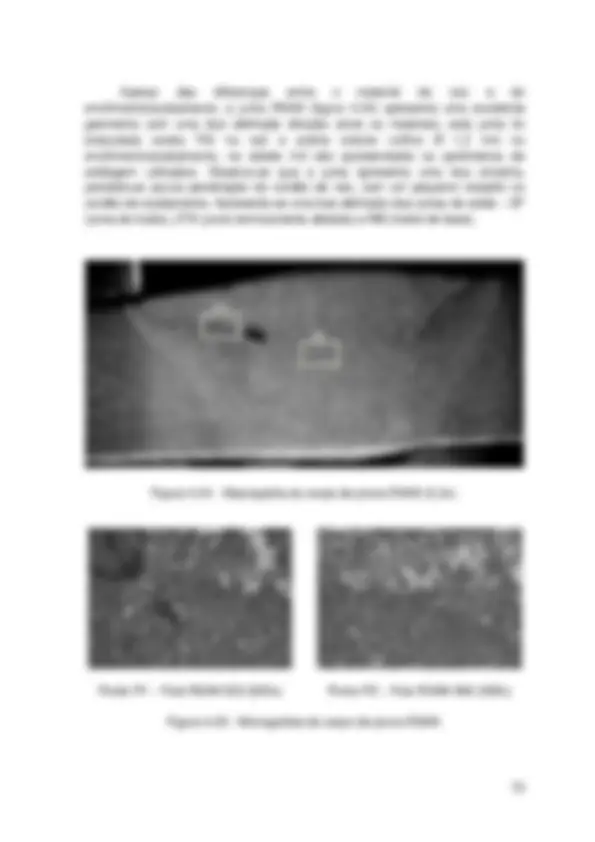
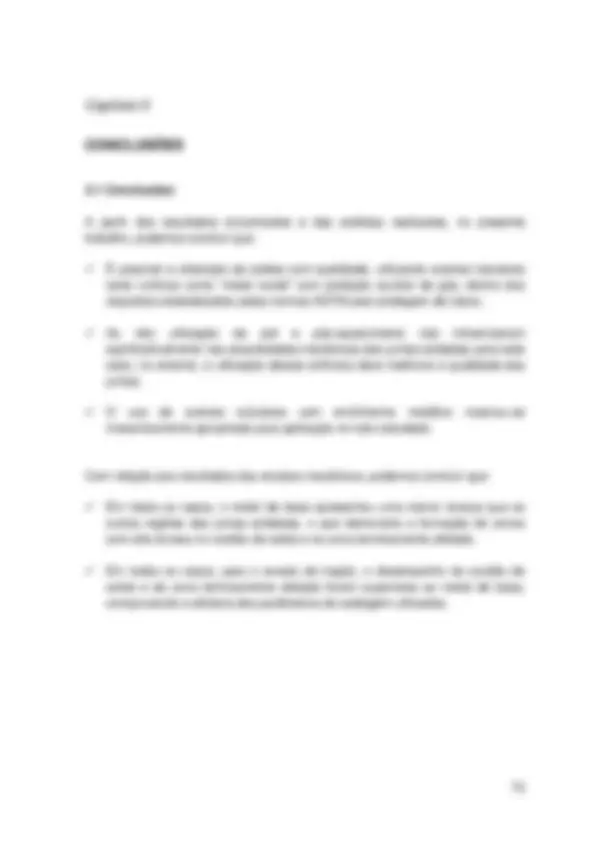
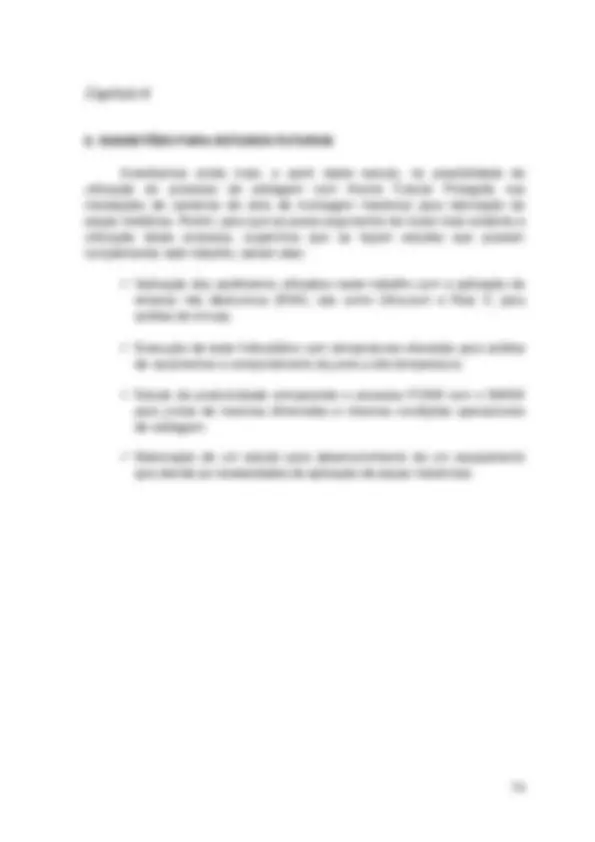
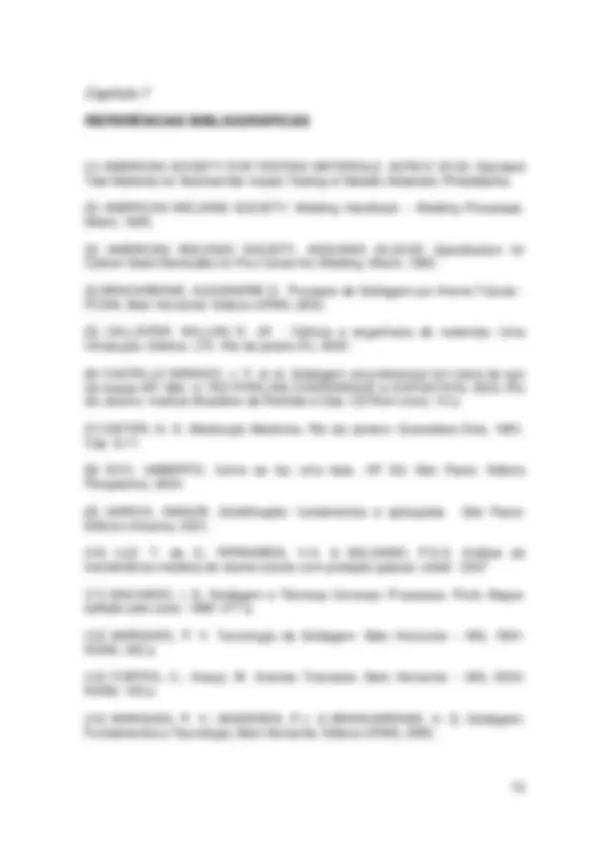
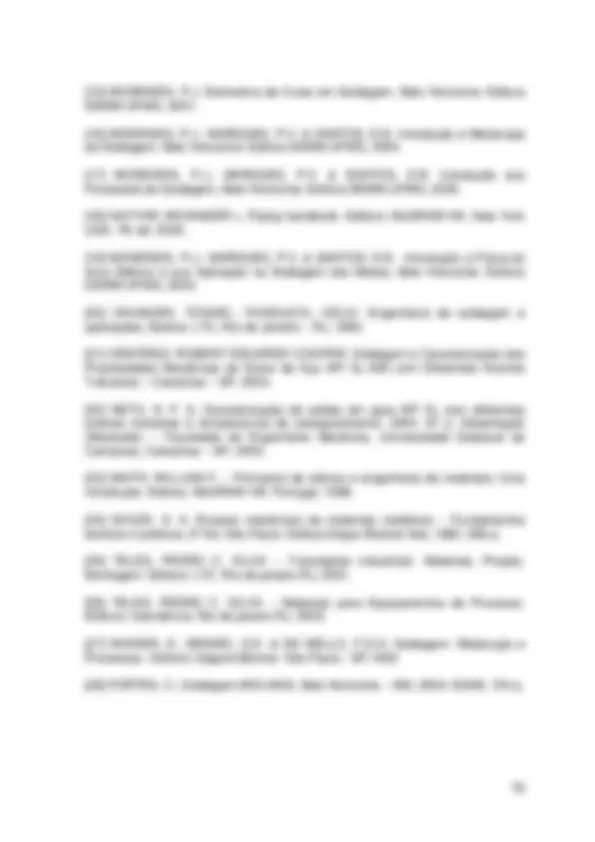
Estude fácil! Tem muito documento disponível na Docsity
Ganhe pontos ajudando outros esrudantes ou compre um plano Premium
Prepare-se para as provas
Estude fácil! Tem muito documento disponível na Docsity
Prepare-se para as provas com trabalhos de outros alunos como você, aqui na Docsity
Os melhores documentos à venda: Trabalhos de alunos formados
Prepare-se com as videoaulas e exercícios resolvidos criados a partir da grade da sua Universidade
Responda perguntas de provas passadas e avalie sua preparação.
Ganhe pontos para baixar
Ganhe pontos ajudando outros esrudantes ou compre um plano Premium
Comunidade
Peça ajuda à comunidade e tire suas dúvidas relacionadas ao estudo
Descubra as melhores universidades em seu país de acordo com os usuários da Docsity
Guias grátis
Baixe gratuitamente nossos guias de estudo, métodos para diminuir a ansiedade, dicas de TCC preparadas pelos professores da Docsity
Manual, nomenclaturas e soldagem orbital
Tipologia: Resumos
1 / 96
Esta página não é visível na pré-visualização
Não perca as partes importantes!
Recife, 19 de junho de 2009.
Recife, 19 de junho de 2009.
ii
A minha mãe D. Lucila, pelo seu apoio, amor e dedicação.
A minha companheira Goretti Varella, pela compreensão da minha ausência, por seu amor, incentivo e amizade.
Ao meu filho Vinícius, por sua compreensão pela minha ausência, por seu amor, incentivo e amizade.
Aos meus irmãos, Sandra e Haroldo, Ana e Murilo, Luiza e Marcos, Marquinho e Ângela, pelo apoio e incentivo.
Ao meu amigo e irmão José Claudino, pelo apoio e incentivo cotidianos.
Ao meu tio Luiz Gonzaga, que sempre me estimulou profissionalmente.
Aos meus amigos Paulo Carvalho, Ricardo Guedes, Rosildo Rosa e Antonio Almir, pelo apoio, colaboração e estímulo.
Aos meus amigos Mariza Varella, Reynaldo Rubem e Helena, Reynaldo Rubem Filho e Joyce, João Barbalho, Geraldo Pinho, Elúzia Varella, Pedro Neto, pelo apoio e estímulo.
A minha amiga Clarisse Ferrão, pelo seu apoio e incentivo.
A Camila e Luiza.
A todos os meus amigos que compõem a Vórtice: Paulo e Péricles Macário, Mauro, André Lins, Eduardo Henrique, Eduardo Pontual, Leonardo Maia, Márcio, Ketoly, Jéssica, Fábio, Sr. Artur, Marcos Silva, Paloma, Jonatas, Lucas, Emmanuel, e aos que já compuseram, pelo apoio e incentivo.
Aos meus amigos Silas Ribeiro, Mário Aragão, Celso Mazolli, Wayne Guedes, Márcio Rollemberg, João Santos, Fábio Jazon.
Aos meus amigos de pedaladas Airton Júnior, Paulinho, André Bike, Gandhi e Odilon pelo apoio e estímulo.
Ao meu orientador, Profº Dr. Severino Leopoldino Urtiga Filho, pela paciência, colaboração e dedicação.
Ao Profº Cézar Gonzales, pelo apoio e estímulo.
A Orlando e ao Profº Carlos, pelo apoio e colaboração.
Aos Professores Eduardo, Jeorge por terem dado todo apoio na execução das soldagens na unidade do SENAI do Cabo de Santo Agostinho - PE.
iii
Ao Profº Armando Shinohara, pelo seu incentivo e por ter disponibilizado os laboratórios de ensaio de tração e microdureza.
Aos demais professores do Departamento de Engenharia Mecânica da UFPE.
A Eliane Alves pelo apoio e estímulo.
A Rose Lima, pelo apoio.
Ao Programa de Pós-Graduação do Departamento de Engenharia Mecânica da UFPE pela oportunidade de cursar o mestrado.
A SEW, nas pessoas de Gustavo e Fábio, pela doação do acionamento do equipamento de giro.
Aos que fazem a METALMAQ, especialmente Tarcísio, pela fabricação e doação do equipamento de giro e dos corpos de prova.
A SERVMONT, especialmente a Josemar, pelo apoio na execução das soldagens.
Aos alunos de iniciação científica, Tiago, Manuella, Cidrack e Leandro, pela colaboração durante a preparação dos corpos de prova e utilização dos equipamentos.
v
Nas indústrias de processo, os diversos equipamentos formam uma cadeia
contínua, através da qual circulam os fluidos, o meio de ligação entre os mesmo
se dá atarvés de tubulações que são consideradas como equipamentos de
processo. A falta ou paralisação de um único equipamento, sem que tenha sido
programa, pode gerar perdas financeiras em grande escala. Neste ambiente, as
tubulações são responsáveis pela condução dos fluidos, as quais operam em
muitos casos em severas condições de serviço. Na ocasião da montagem, as
tubulações passam por processos de soldagem nos seus diversos métodos de
ligação, durante o processo de soldagem são geradas zonas de aquecimento
localizadas nas juntas onde o material do tubo fica sujeito a variações na sua
microestrutura, o que gera mudanças nas suas propriedades. O processo de
soldagem mais utilizado na soldagem de tubulações nas montagens industriais é
o da soldagem a arco elétrico com eletrodo revestido. Este trabalho apresenta o
resultado do estudo das propriedades mecânicas e estruturais de juntas de tubos
soldadas com arame tubular. Para tanto, utilizou-se tubos confeccionados em aço
ASTM A106 Gr B, recomendado para o transporte de fluidos em alta temperatura,
soldado com o processo de soldagem por arco elétrico com Arame Tubular
Protegido. As soldas de raiz foram feitas com dois diferentes processos: TIG e
Arame Tubular, quando se utilizou arame tubular na raiz, este foi feito com o
mesmo material de enchimento e acabamento. As soldas de enchimento e
acabamento foram feitas com dois tipos de arame tubular, um rutílico e outro
“metal cored”. Foram realizados ensaios de microdureza e de tração, e análise
microestrutural e macroestrutural das juntas soldadas para verificação das suas
possíveis variações. Os resultados evidenciaram variações nas propriedades das
juntas soldadas quando se realiza a solda nas diferentes amperagens adotadas
neste trabalho, porém mostrou-se possível a utilização do processo estudado em
pequenas juntas de peças que possam vir a serem fabricadas em canteiros de
obra.
Palavras Chaves: ASTM A 106 Gr B, arame tubular, propriedades de juntas soldadas.
vi
In continuous process industries, line production is configured by great quantity of
equipments mounted according a sequential way and connected each other by
pipes where all fluids’ process flows inside up to the final production stage. In this
arrangement, even pipes are considered like one of the very important equipment
of process, which for many times running under very hard environments and
process conditions.Because fluids needs flows continuously in line, if just one of
equipments brakes or need to stop for some not programmed reason, all the
process line stops and great financial losses takes place. To be mounted, pipes
are submitted to several welding technologies process where heating zones that
occurs in joints’ welding points might affect the pipes’ microstructures and changes
in their physical properties take form. One of the welding technology processes for
pipes more used in industrial assemblies is the electric arc welding with covered
electrode. The goal of this paper is analyze the mechanical and physical
properties of pipes’ welding joints. For that, tests were developed with ASTM A
Gr B tubes, which ones are recommended to high temperature fluids. They were
welded by electric arc welding process with wire Tubular Protected. It was
employed two welding technologies in this study: GIT and Tubular Wire. When
tubular wire was used at the welding root, same material was employed for filling
and finishing. Additionally, filling and finishing welds were carried out with two
types of tubular wires, a rutile and other "metal cored”. Micro hardness and tensile,
and micro structural and macro structural analysis of welded joints were performed
to identify variations happenings. The results of the study offer evidences of
variations in the properties of welded joints when performed with different welding
amperages adopted in this study. But these findings also proved that is possible to
employ the welding technology proposed to small joints of parts executed in
mounting site.
Keywords: ASTM A 106 Gr B, tubular wire, properties of welded joints.
viii
Tabela 4.4 - Parâmetros utilizados na soldagem das juntas com Arame Tubular com enchimento metálico “Metal Cored” - MAB2 e MAB
Tabela 4.5 – Identificação dos ensaios e respectivos corpos de prova 52
Tabela 4.6 - Média dos resultados do limite de resistência do ensaio de tração das juntas soldadas com Arame Tubular Metálico
Tabela 4.7 - Média dos resultados do limite de resistência do ensaio de tração das juntas soldadas com Arame Tubular Rutílico
Tabela 4.8 - Média dos resultados do módulo de elasticidade do ensaio de tração das juntas soldadas com Arame Tubular Metálico
Tabela 4.9 - Média dos resultados do módulo de elasticidade do ensaio de tração das juntas soldadas com Arame Tubular Rutílico
Tabela 4.10 - Média dos resultados do módulo de elasticidade do ensaio de tração das juntas soldadas com Arame Tubular Metálico
Tabela 4.11 - Gráfico 4.5 - Média dos resultados do módulo de elasticidade do ensaio de tração das juntas soldadas com Arame Tubular Rutílico
Tabela 4.12 - Média dos resultados da microdureza Vickers das juntas soldadas com Arame Tubular Metálico
Tabela 4.13 - Média dos resultados da microdureza Vickers das juntas soldadas com Arame Tubular Rutílico
ix
Figura 2.1 – Tubulações de uma indústria de processos, fonte Petrobras. 6
Figura 2.2 - Laminador obliquo com mandril, Catálogo Vallourec e Mannesmann Tubes
Figura 2.3 - Soldagem por fusão (esquemático) [19]. 7
Figura 2.4 - Esquema de soldagem com arame tubular pelo processo FCAW-G, adaptado de Welding Handbook, 1995.
Figura 2.5 - Esquema de soldagem com arame tubular pelo processo FCAW-S, adaptado de Welding Handbook, 1995
Figura 2.6 - Secções dos arames tubulares [21] 13
Figura 2.7 - Processos de conformação final de arames tubulares (diminuição da seção do eletrodo), adaptado de [17].
Figura 2.8 - Microestrutura do metal de solda não alterado mostrando diferentes constituintes microestruturais [IIW Sub-commission IXJ Doc. IX- 1533-88].
Figura 3.1 - Foto destacando as marcações da junta (junta nº 2 soldada com arame tubular “metal cored” - AB2)
Figura 3.2 - Foto de uma junta montada sobre o girador
Figura 3.3 - Fotos da estação de soldagem fabricada pela Kemppi
Figura 3.4 - Foto do alimentador de arame ProMig 501 da Kamppi
Figura 3.5 - Foto da tocha MB 36 KD refrigerada a gás
Figura 3.6 - Fotos do retificador Origo Arc 456 da ESAB, utilizado para soldagem das raízes das juntas com TIG.
Figura 3.7 - Vista do desenho em 2D e 3D do Girador (Projeto) 31
Figura 3.8 - Vista do desenho em 3D do Girador (Projeto) 31
xi
Figura 3.27 - Esquema da marcação dos pontos para a micrografia.
Figura 4.1 - Foto da junta onde observa-se a perfuração das bordas da junta.
Figura 4.2 - Foto da junta onde observa-se a perfuração do material de base.
Figura 4.3 - Foto da junta soldada, onde observa-se penetração irregular da raiz
Figura 4.4 - Foto da junta soldada, onde observa-se penetração irregular da raiz
Figura 4.5 - Foto da junta MAR1, 2º quadrante, vista externa da raiz da solda
Figura 4.6 - Foto da junta MAR1, 2º quadrante, vista interna da raiz da solda.
Figura 4.7 - Foto da junta MAR1, 2º quadrante, vista do cordão de enchimento/acabamento.
Figura 4.8 - Foto da junta MAB1 2º quadrante, vista externa da raiz da solda.
Figura 4.9 - Foto da junta MAR1, 2º quadrante, vista interna da raiz da solda.
Figura 4.10 - Foto da junta MAB1, 2º quadrante, vista do cordão de enchimento/acabamento.
Figura 4.11 - Foto dos corpos de prova após o ensaio de tração, agrupados para análise visual das fraturas e outros aspectos
Figura 4.12 - Foto da fratura do corpo de prova R31T 56
Figura 4.13 - Foto da fratura do corpo de prova B22T 56
Figura 4.14 – Macrografias dos corpos de prova soldados com: Raiz e Acabamento com Arame Tubular com enchimento Metálico (2,2x).
xii
Figura 4.15 – Macrografias dos corpos de prova soldados com: Raiz em TIG e Acabamento com Arame Tubular com enchimento Metálico (2,2x). 66
Figura 4.16 – Macrografias dos corpos de prova soldados com: Raiz e Acabamento com Arame Tubular com enchimento Rutílico (2,2x).
Figura 4.17 – Macrografias dos corpos de prova soldados com: Raiz em TIG e Acabamento com Arame Tubular com enchimento Rutílico (2,2x).
Figura 4.18 - Macrografia do corpo de prova B24M (2,2x)
Figura 4.19 - Micrografias do corpo de prova B24M
Figura 4.20 - Macrografia do corpo de prova B31M (2,2x)
Figura 4.21 - Micrografias do corpo de prova B31M
Figura 4.22 - Macrografia do corpo de prova R22M (2,2x)
Figura 4.23 - Micrografias do corpo de prova R22M.
Figura 4.24 - Macrografia do corpo de prova R34M (2,2x).
Figura 4.25 - Micrografias do corpo de prova R34M.
xv
3.6.2 Parâmetros de soldagem com arame tubular com enchimento metálico “metal cored”
3.6.3 Parâmetros de soldagem com arame tubular rutílico 37 3.6.4 Preparação das juntas (^39) 3.7 Acompanhamento da soldagem 40 3.7.1 Execução da soldagem da raiz (^41) 3.7.2 Execução de soldagem do enchimento e do acabamento (^41) 3.8 Corpos de prova (^42) 3.8.1 Corpo de prova para ensaio de tração (^42) 3.8.2 Corpo de prova para ensaios de macrografia, micrografia e microdureza 43 3.8.3 Critérios para retirada dos corpos de prova 43 3.8.4 Marcação dos corpos de prova (^44) 3.8.5 Ensaios de tração 45 3.8.6 Ensaios de microdureza (^46) 3.8.7 Caracterização das macroestruturas 47 3.8.8 Caracterização das microestruturas (^48)
4. RESULTADOS E DISCUSSÕES 48 4.1 Parâmetros de soldagem (^48) 4.2 Resultados dos ensaios de tração 54 4.2.1 Resultados do limite de resistência LR (^57) 4.2.2 Resultados do limite de escoamento LE (^60) 4.2.3 Resultados do alongamento ε 62 4.3 Ensaios de microdureza 4.4 Caracterização das macroestruturas
4.5 Caracterização das microestruturas 67
5. CONCLUSÕES (^) 72 6. SUGESTÕES PARA ESTUDOS FUTUROS 73 7. REFERÊNCIAS BIBLIOGRÁFICAS 74