
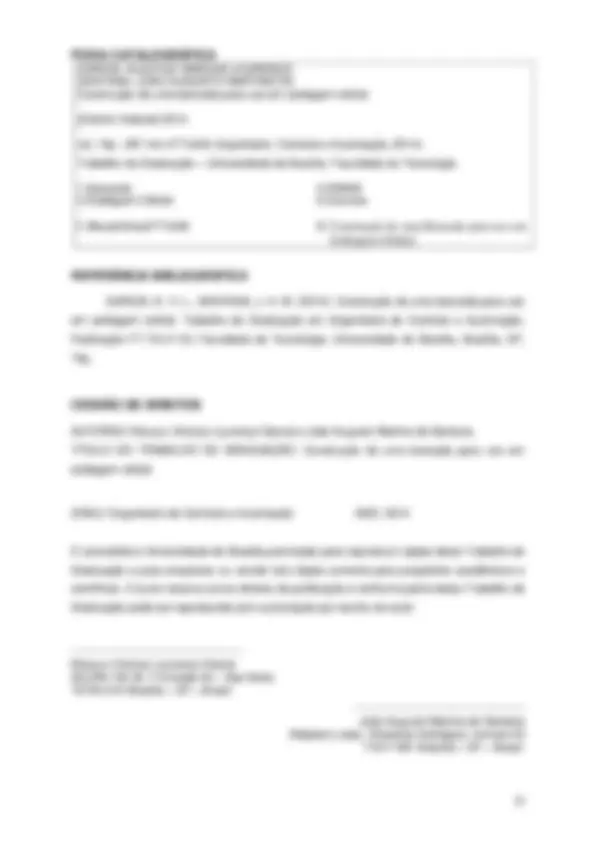
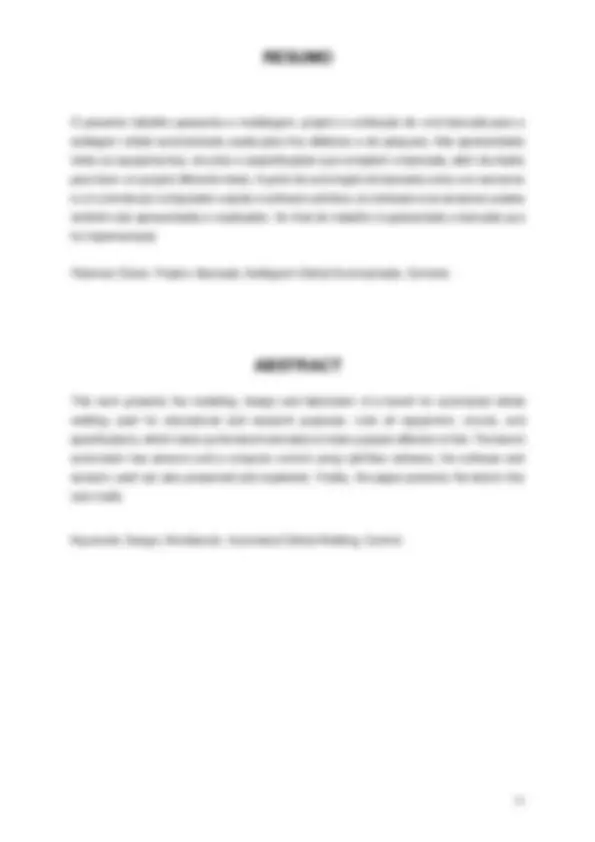
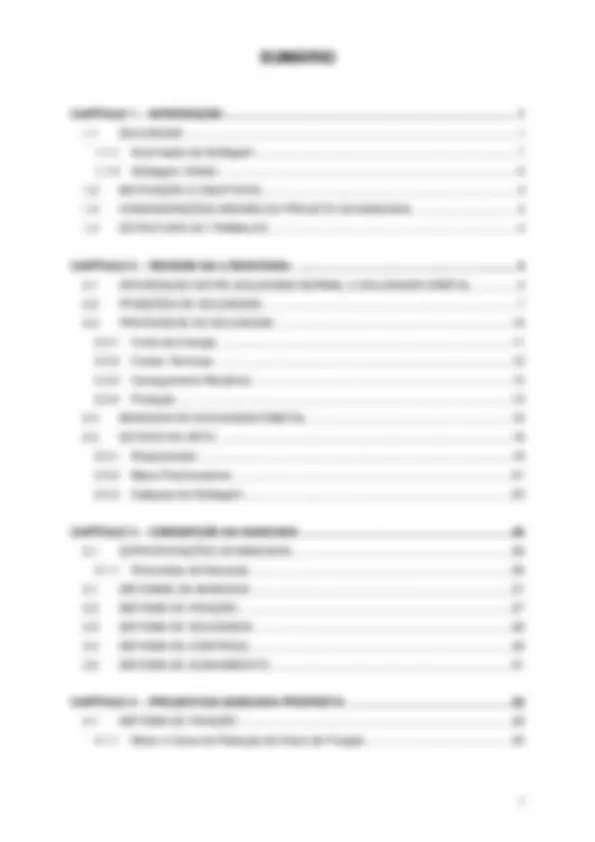
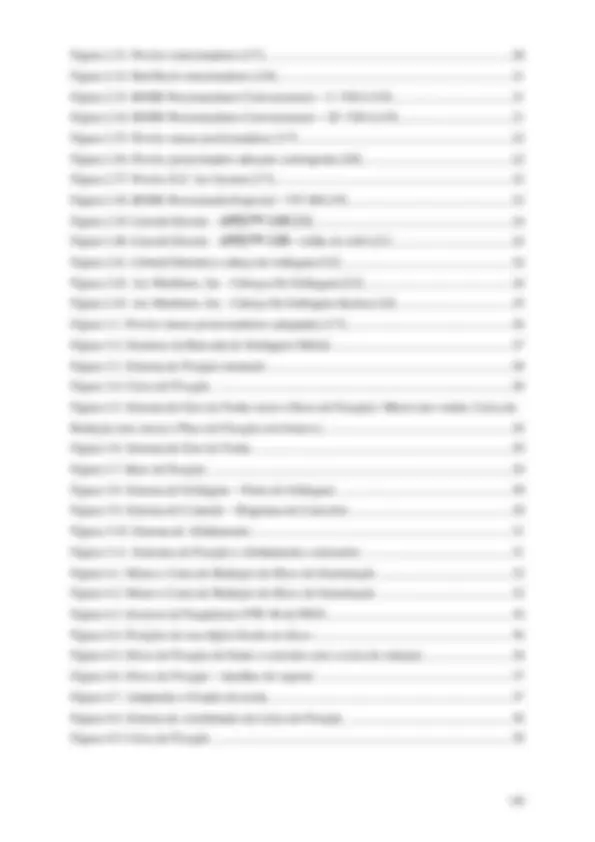
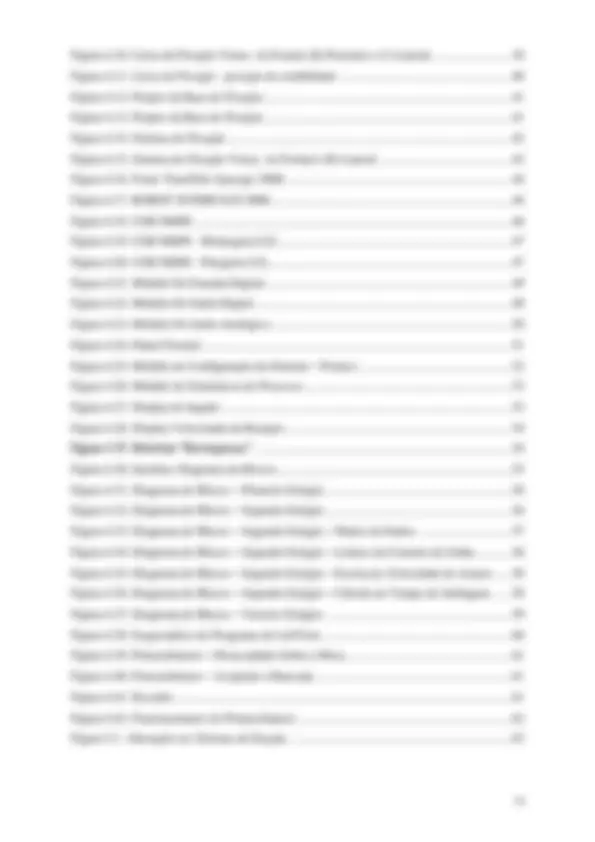
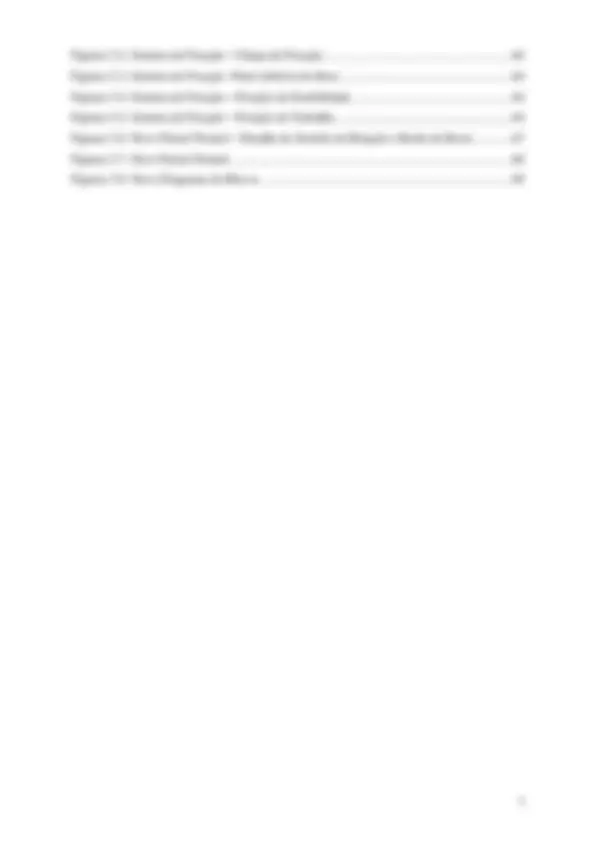
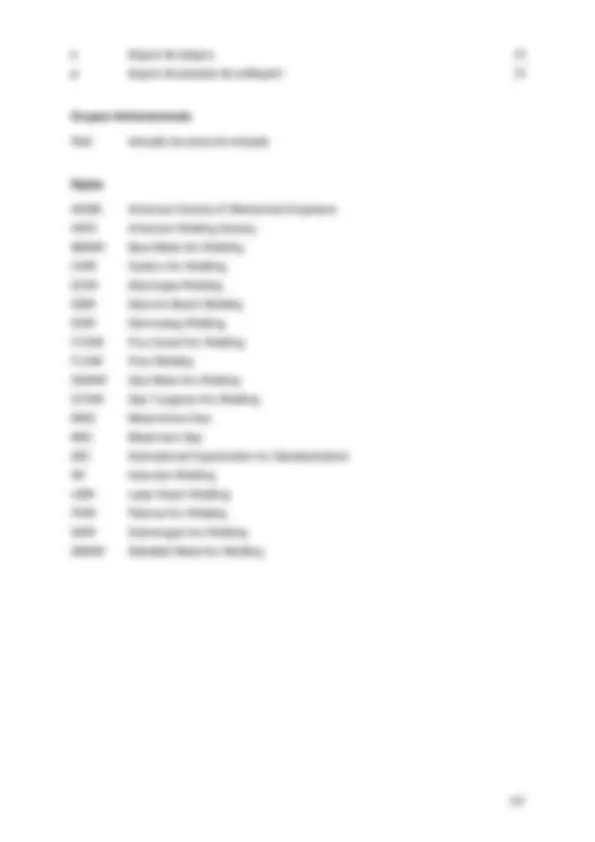
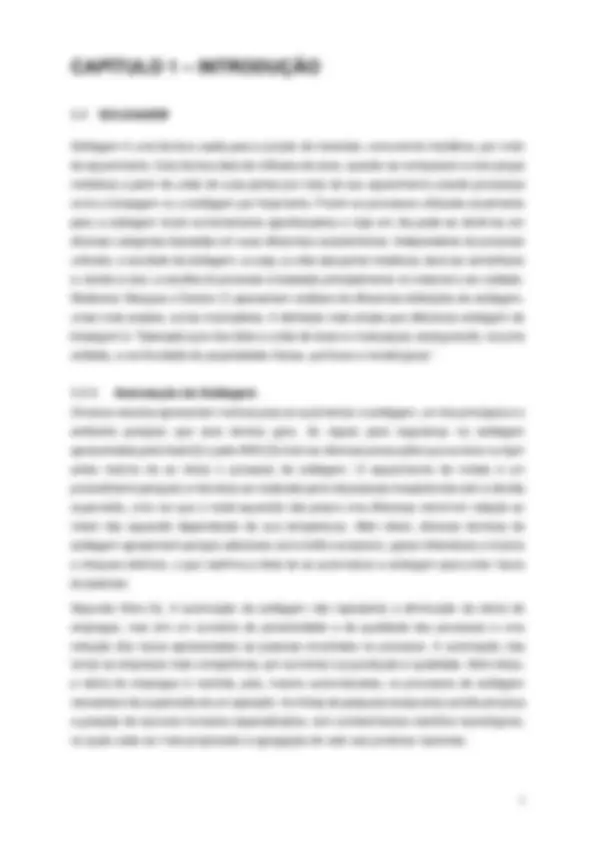
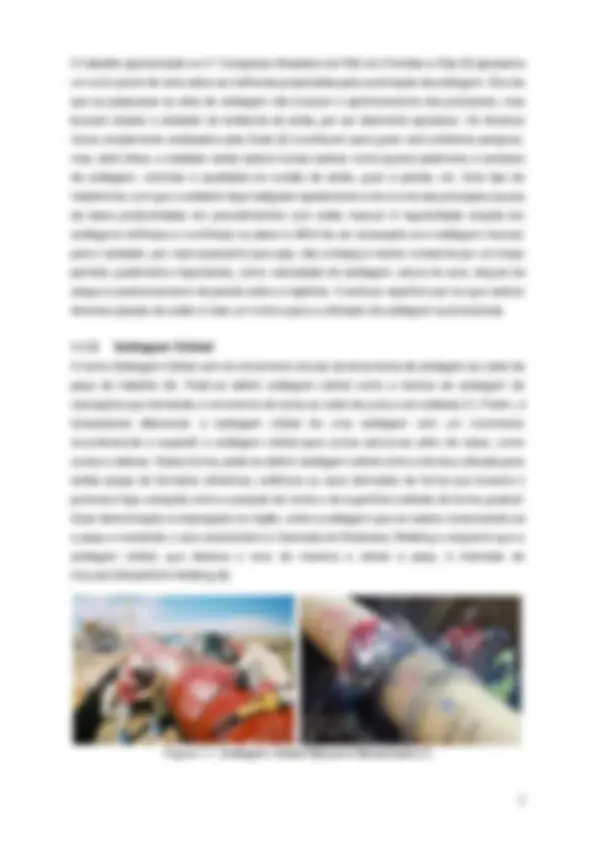
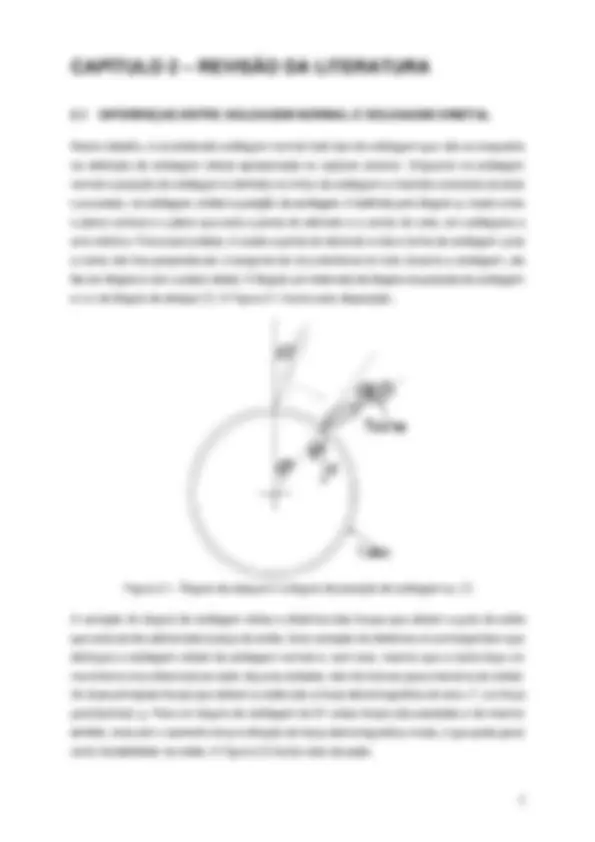
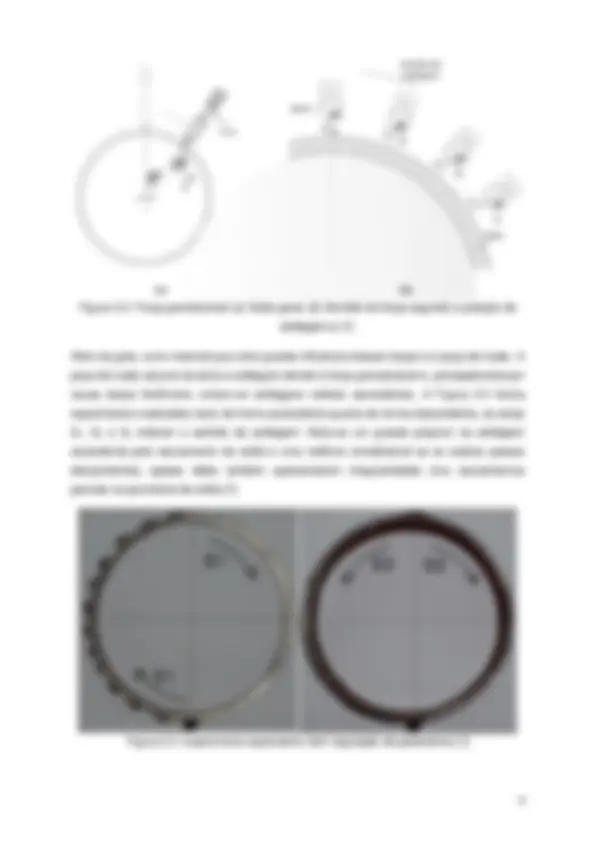
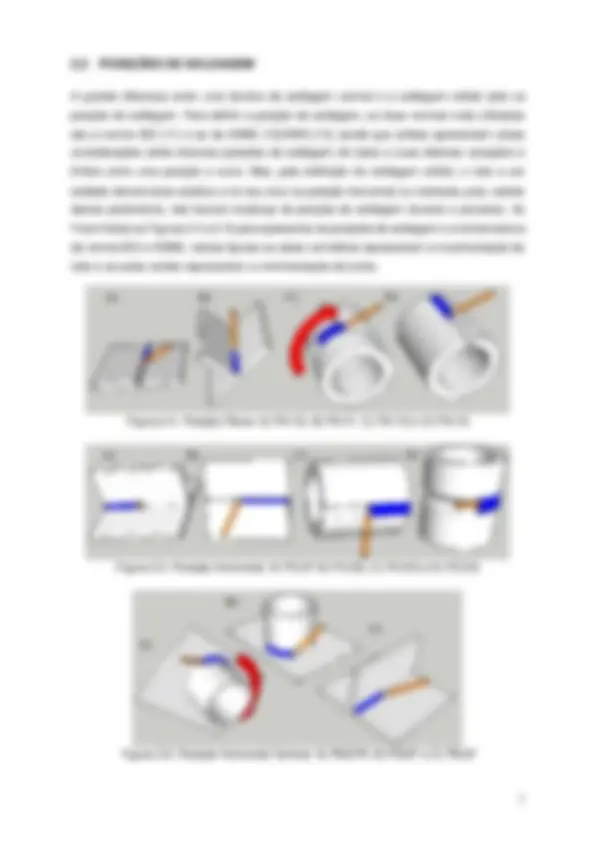
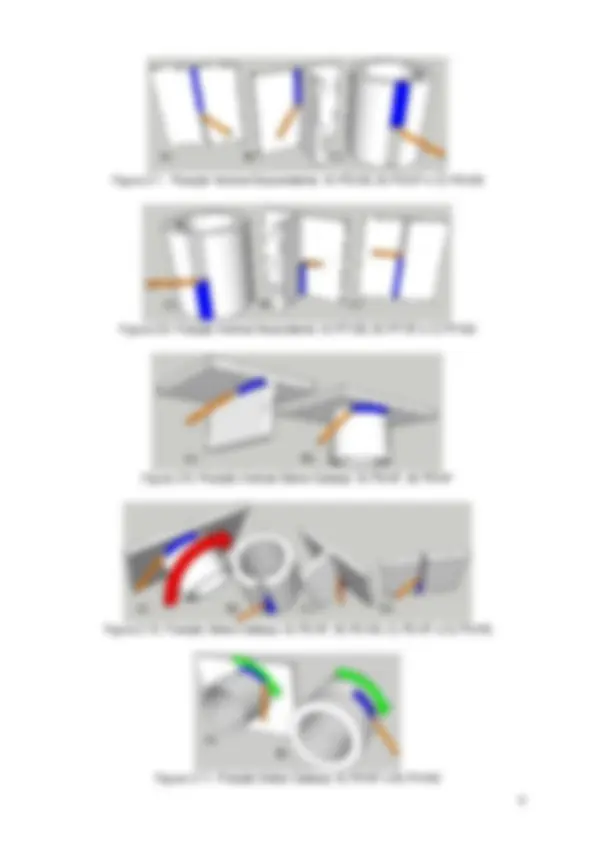
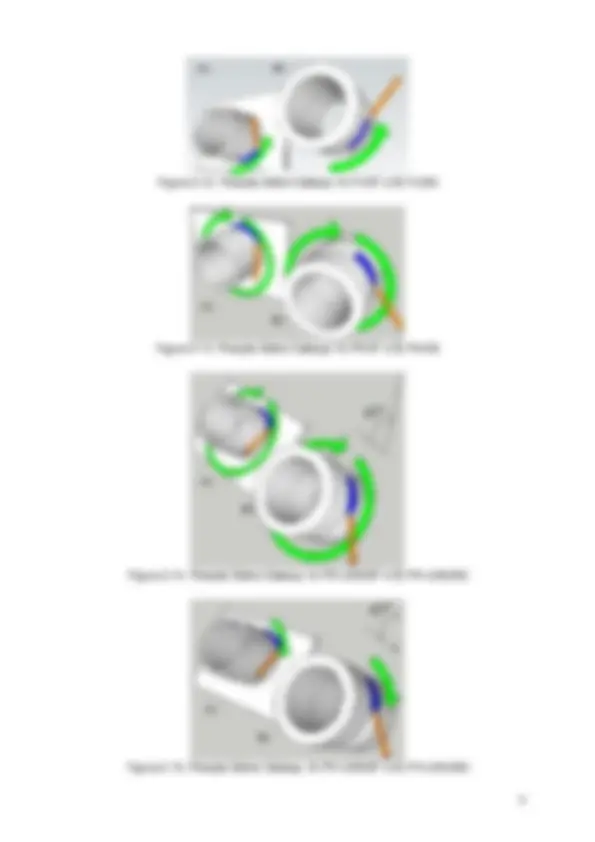
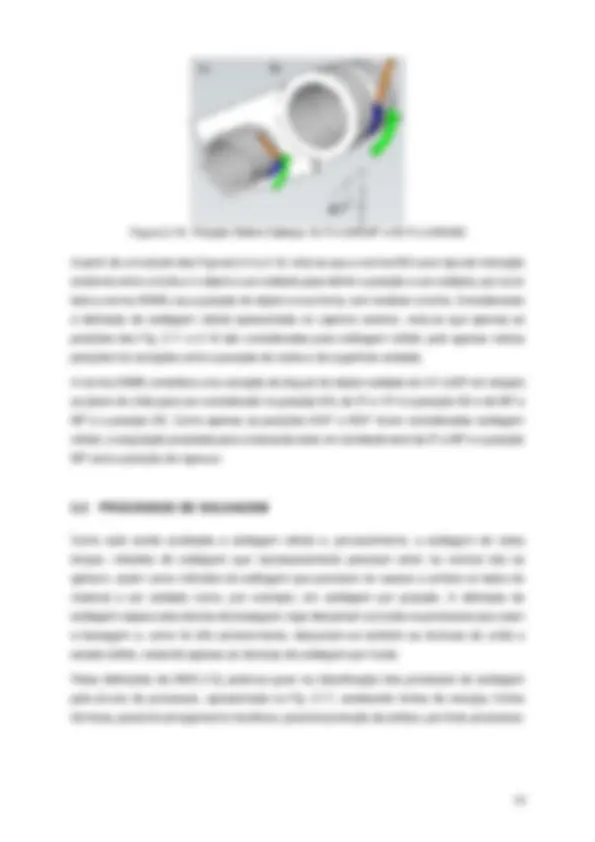
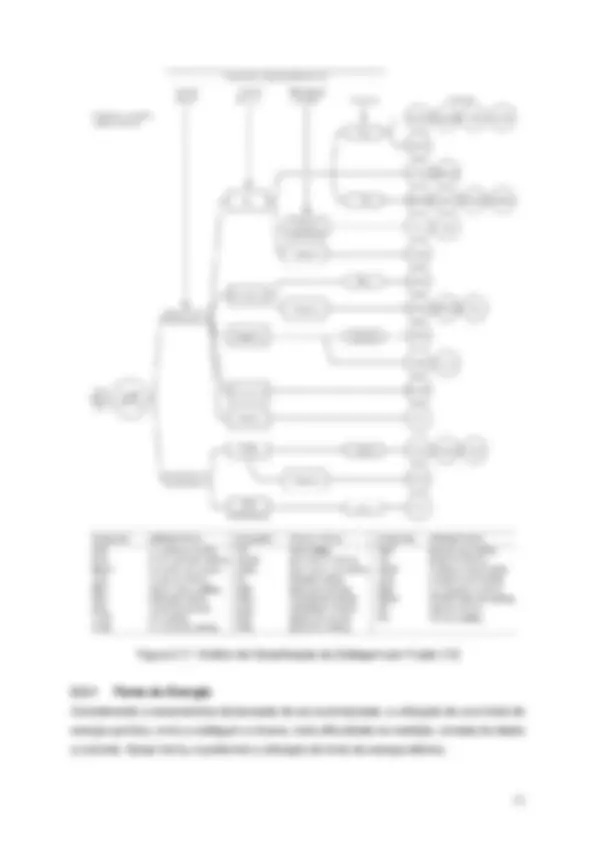
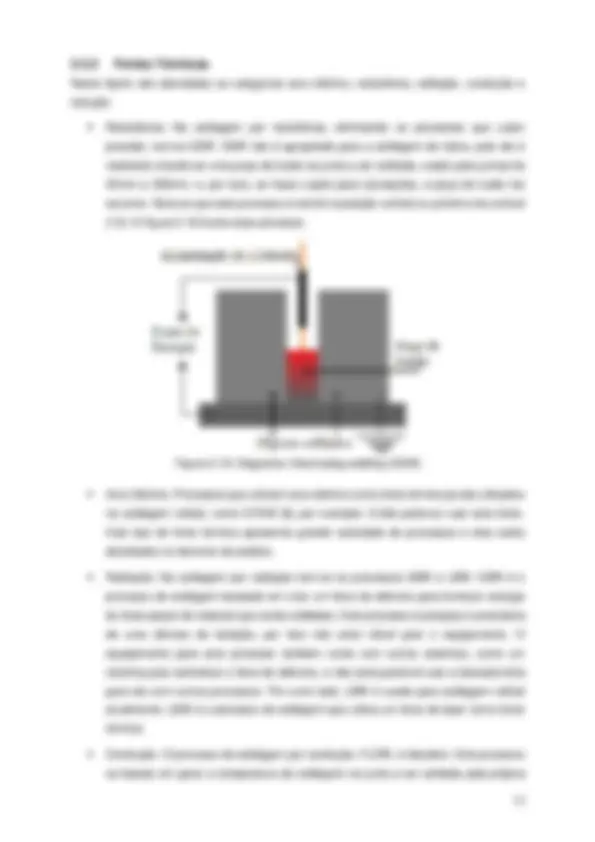
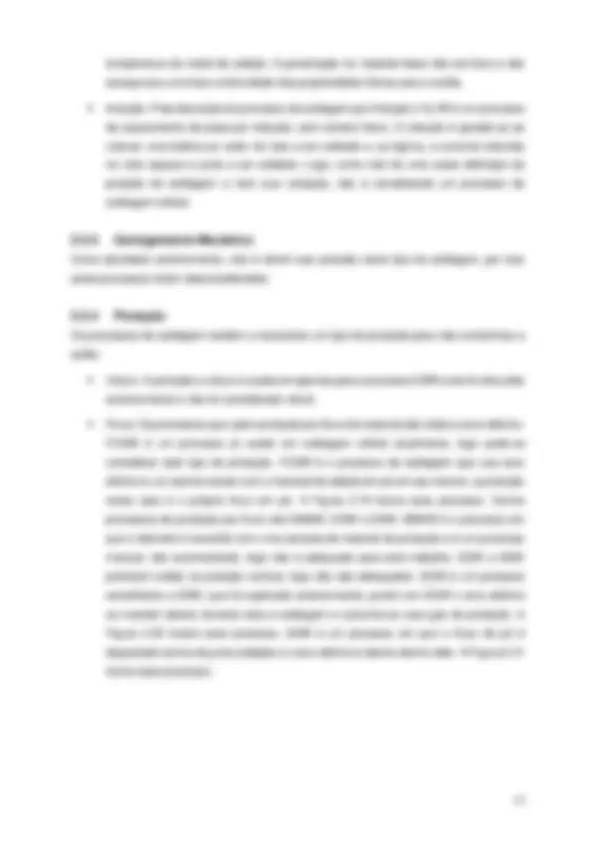
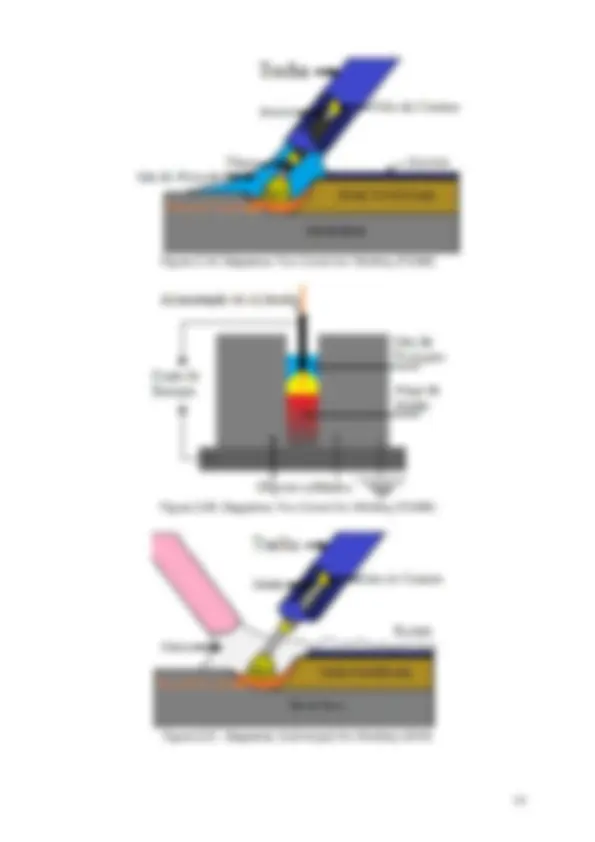
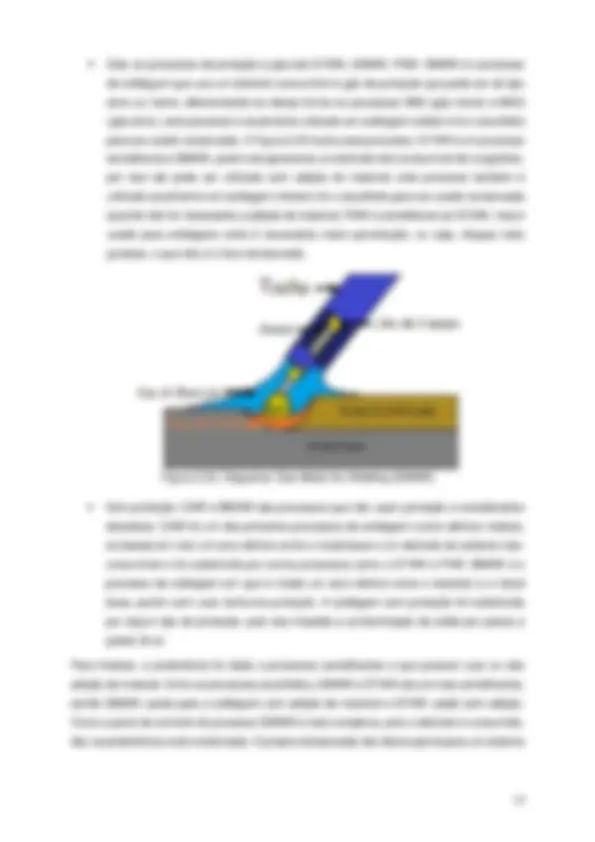
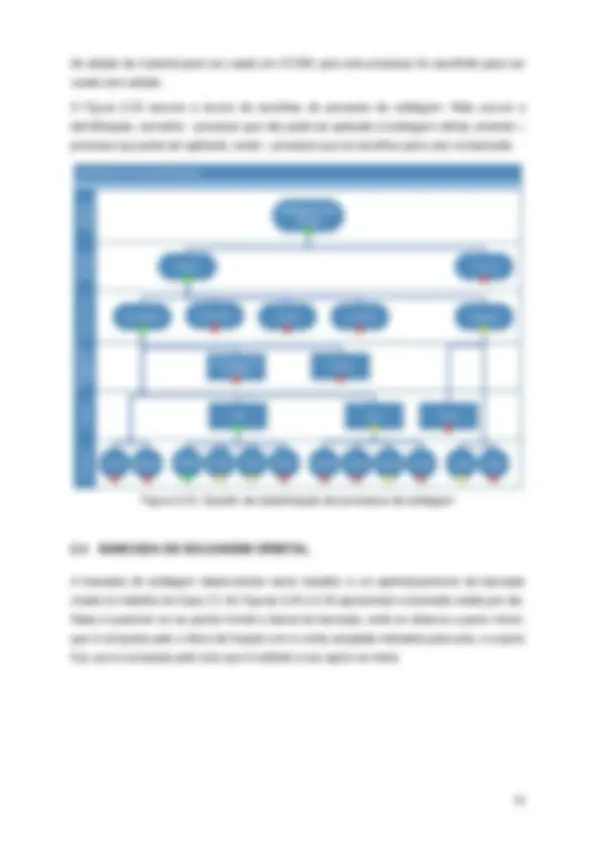
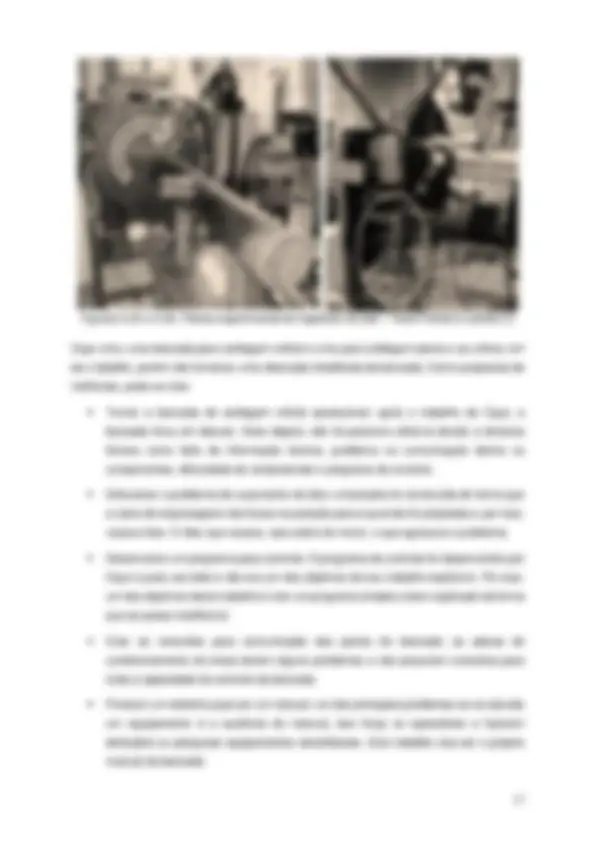
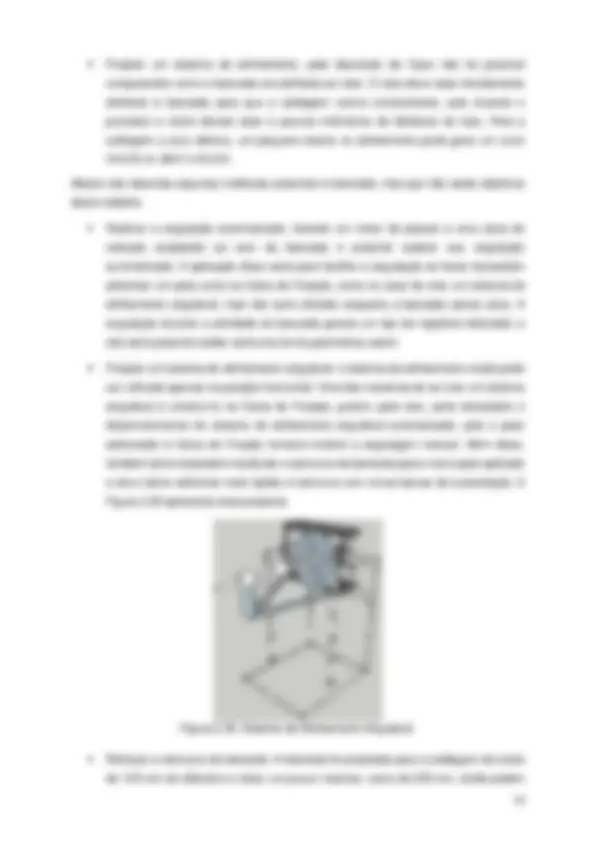
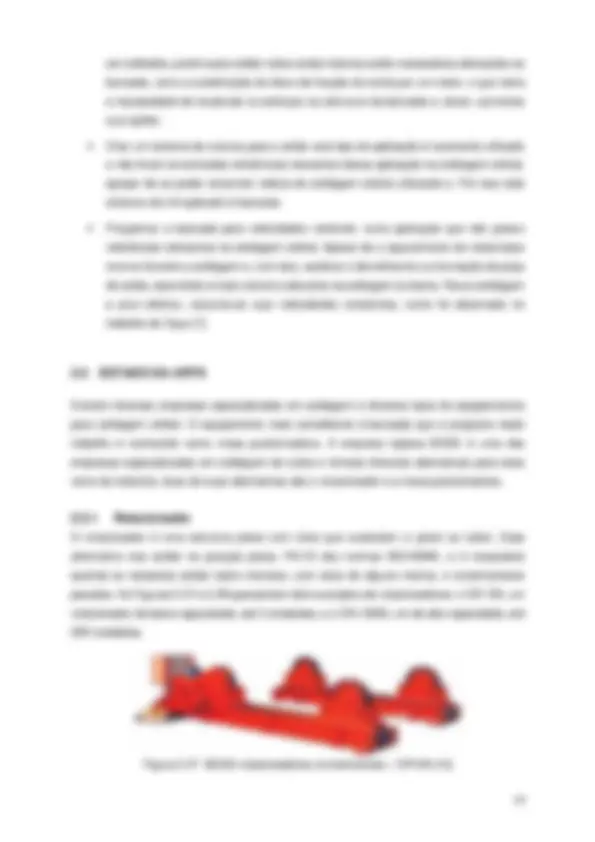
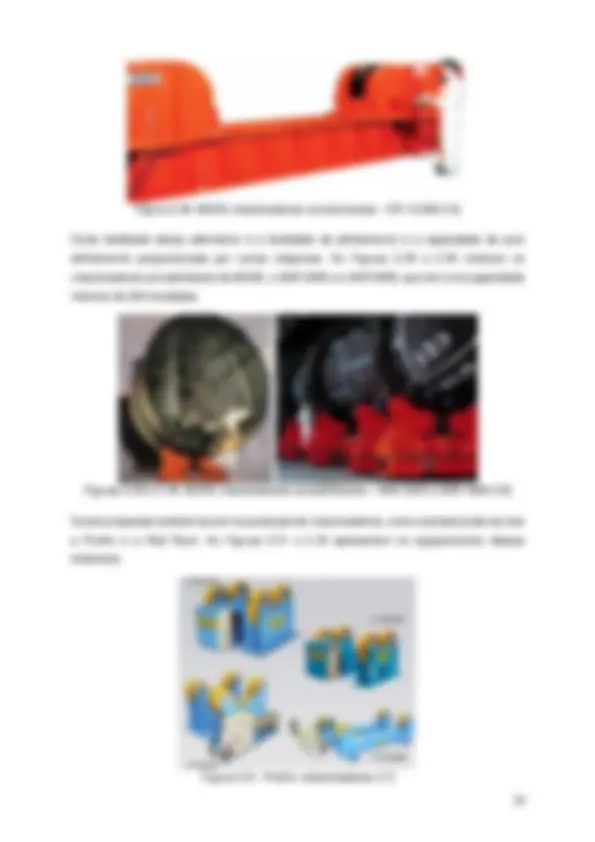
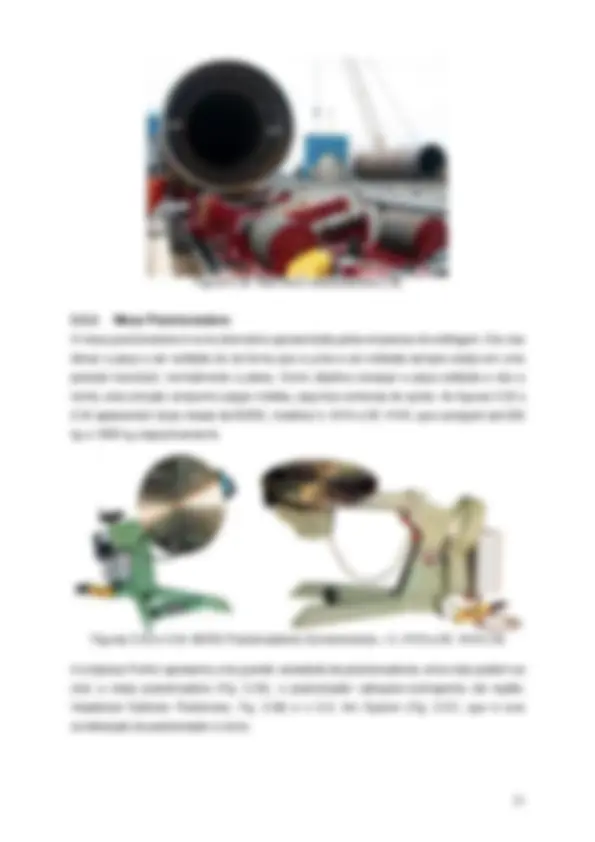
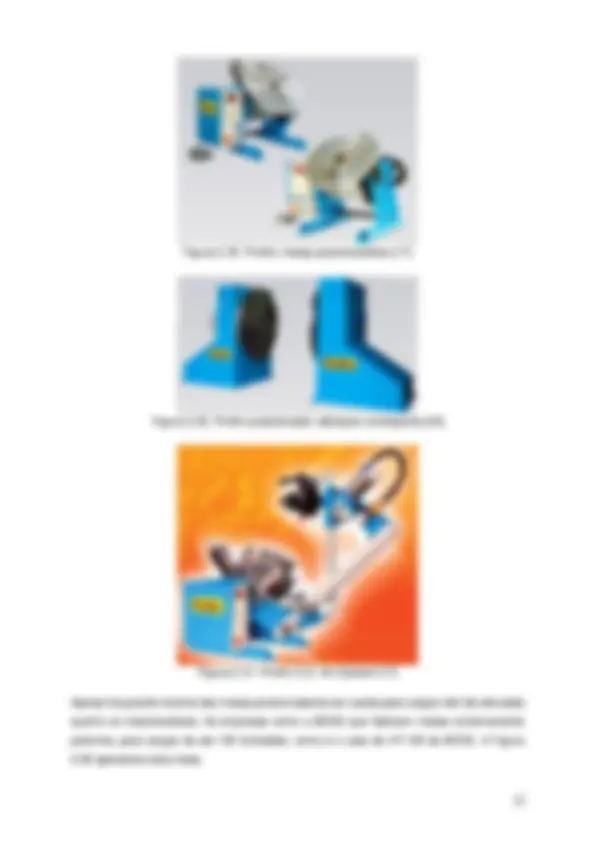
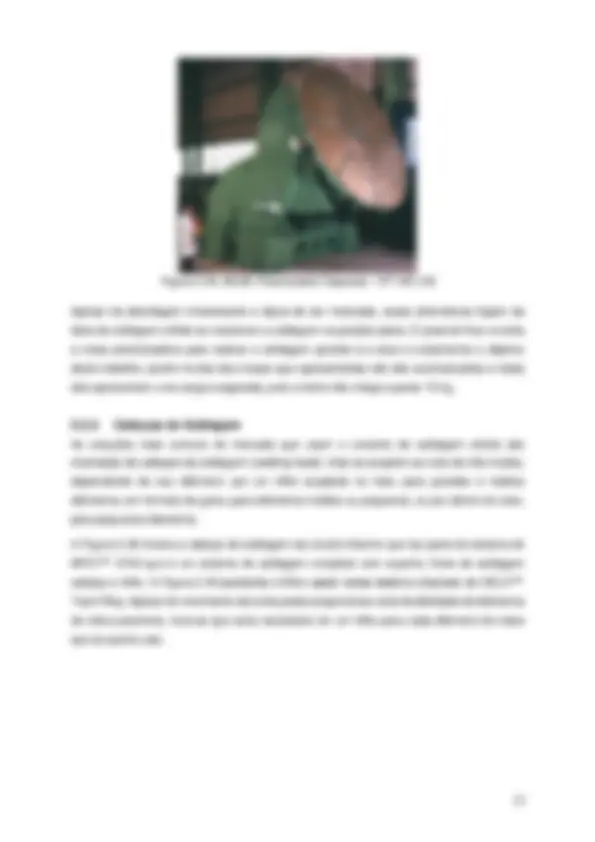
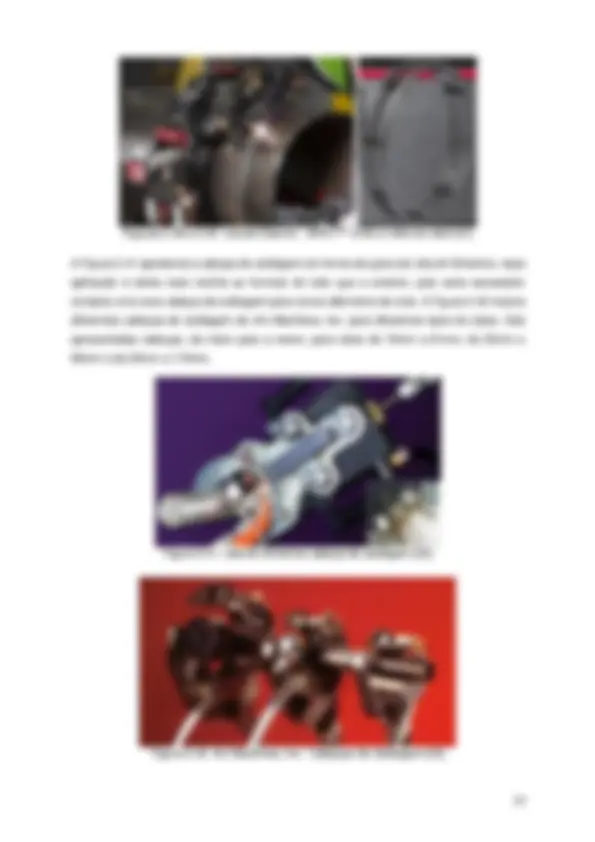
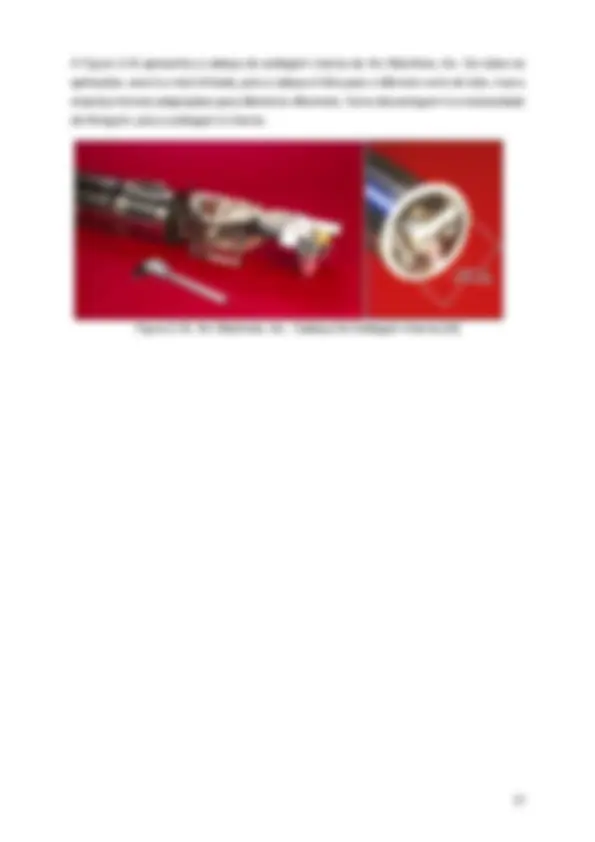
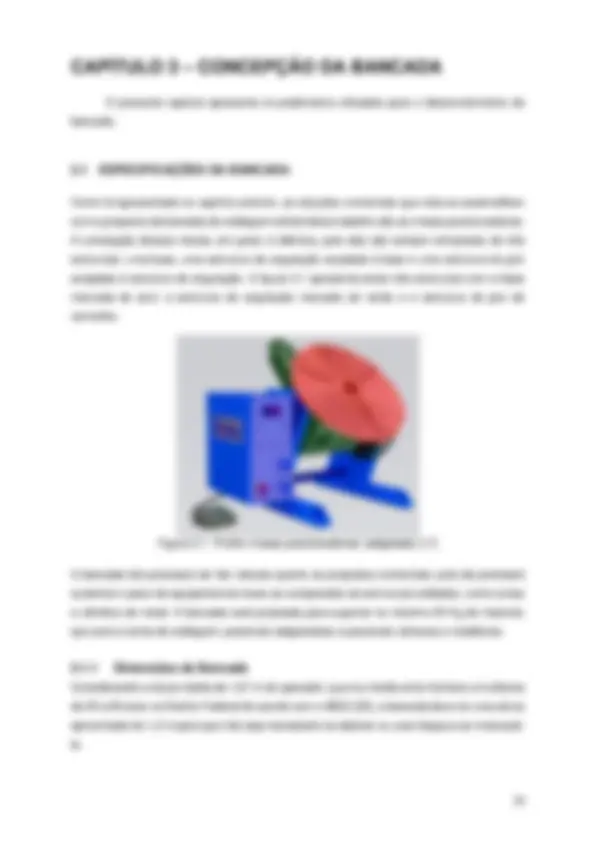
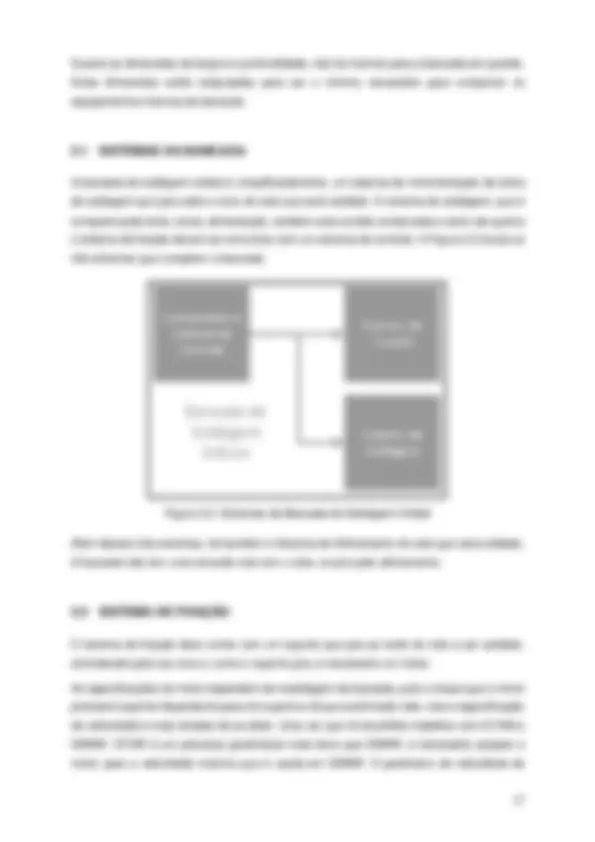
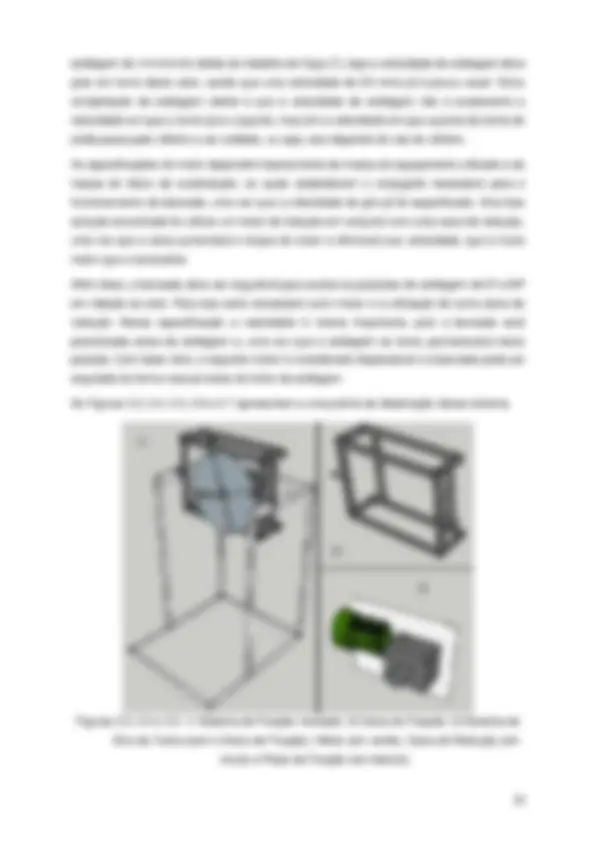
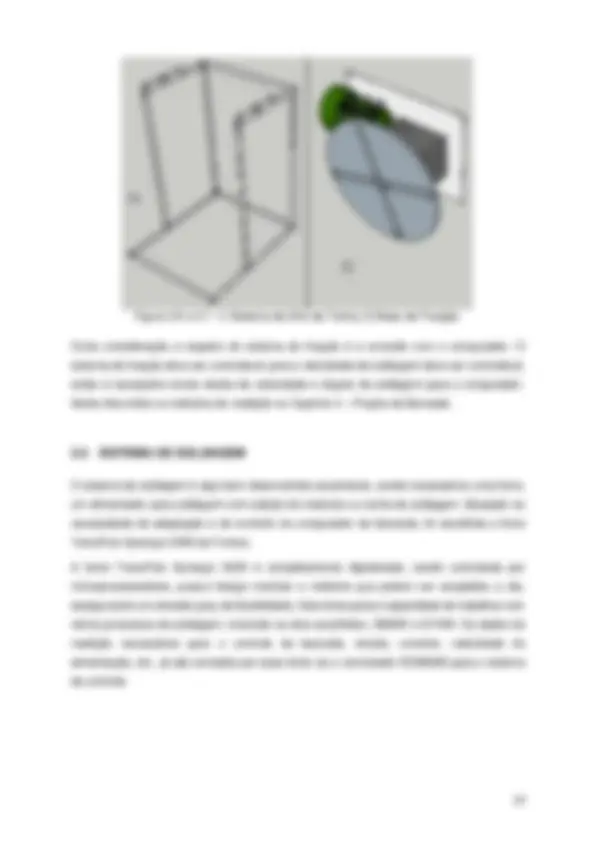
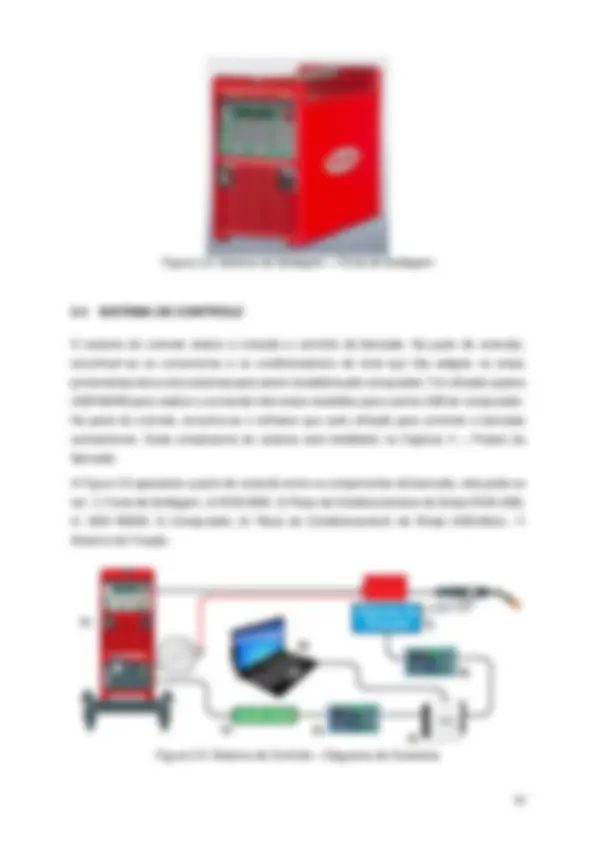
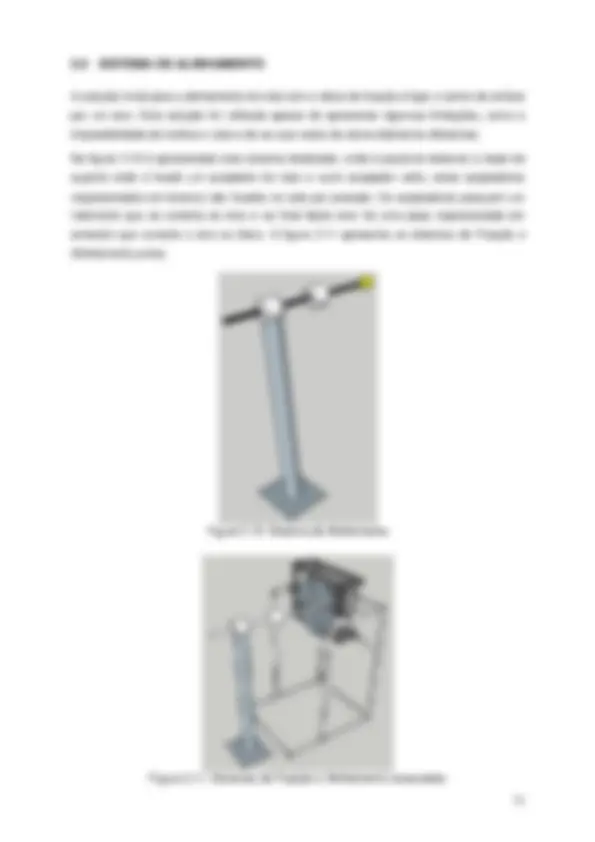
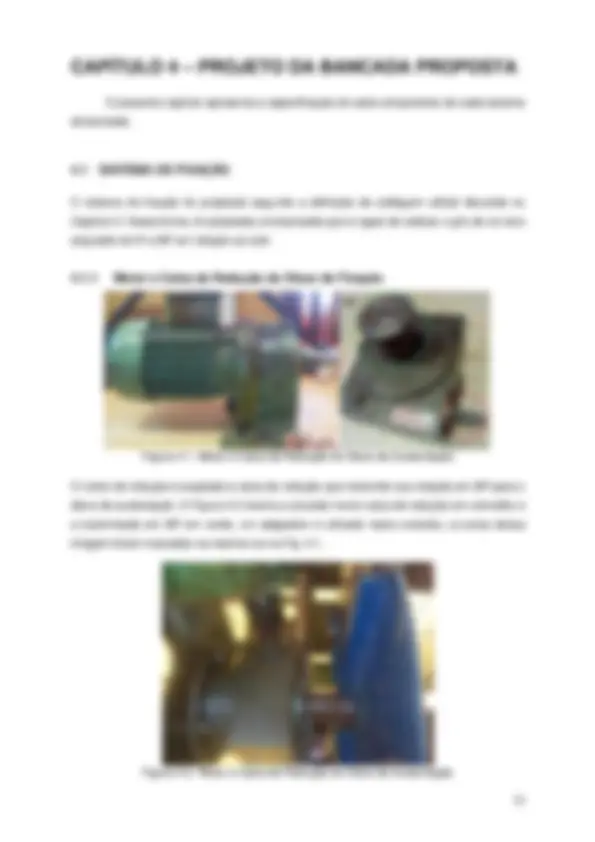
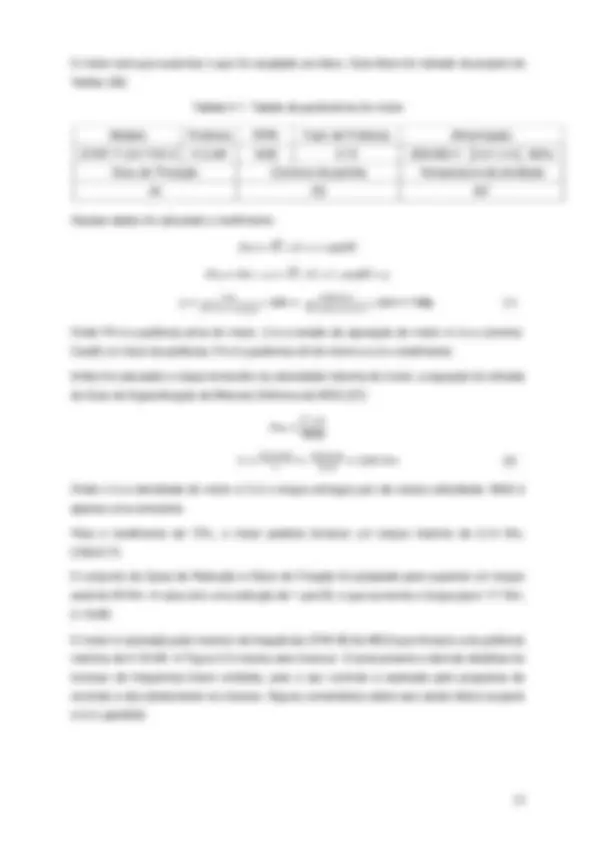
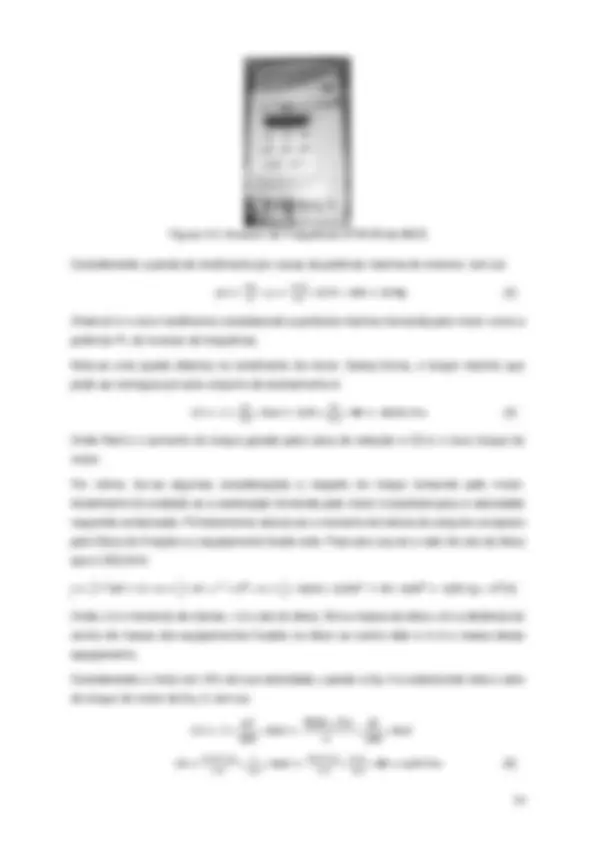
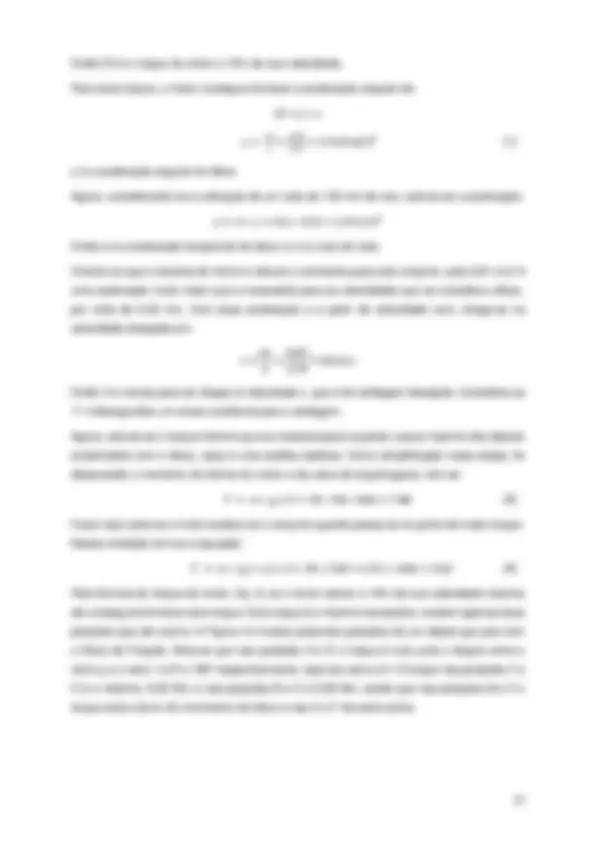
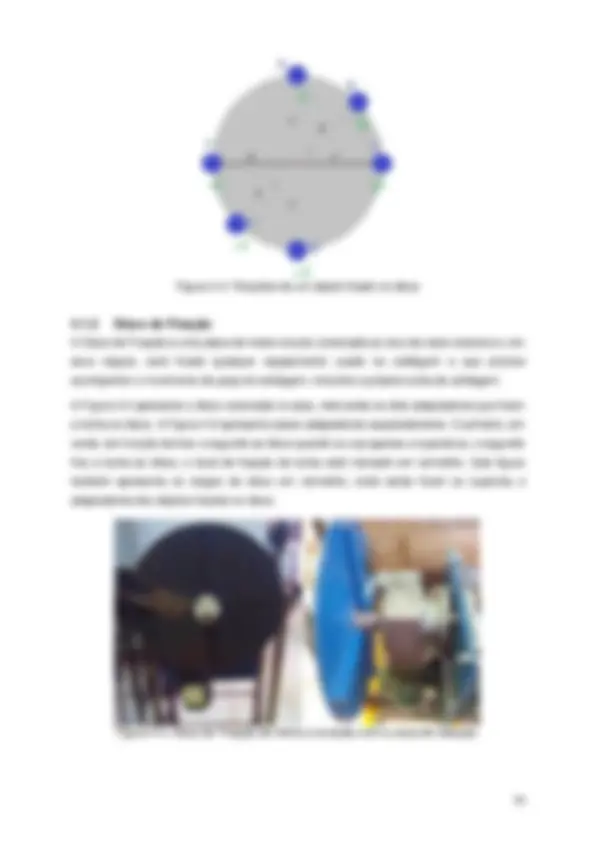
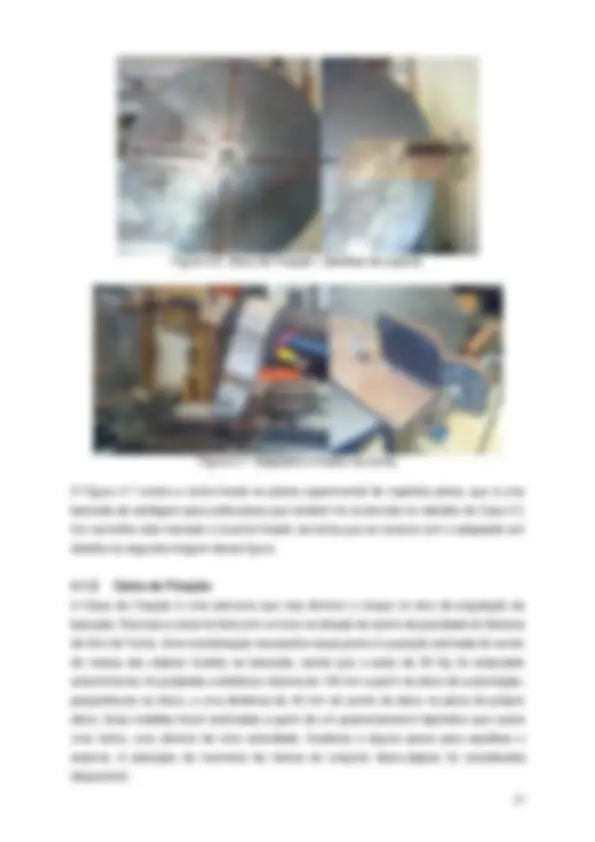
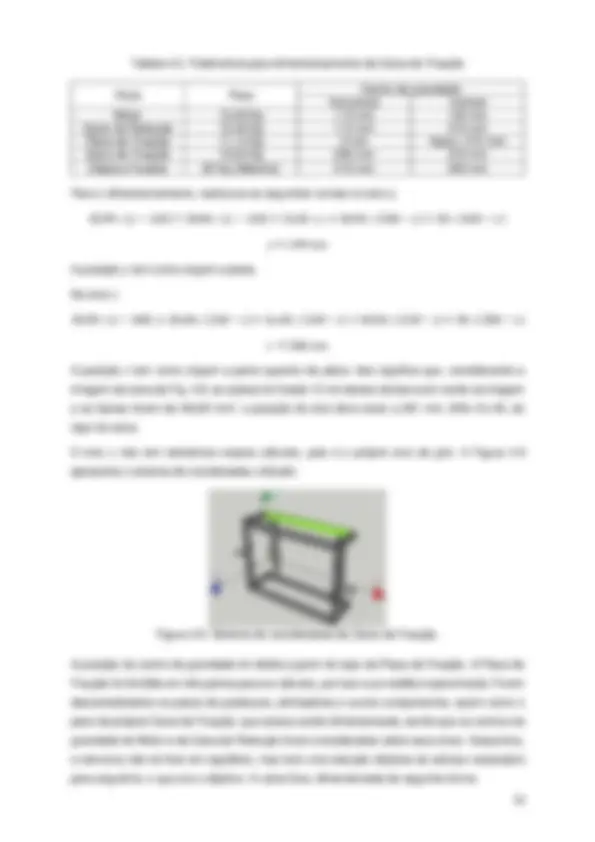
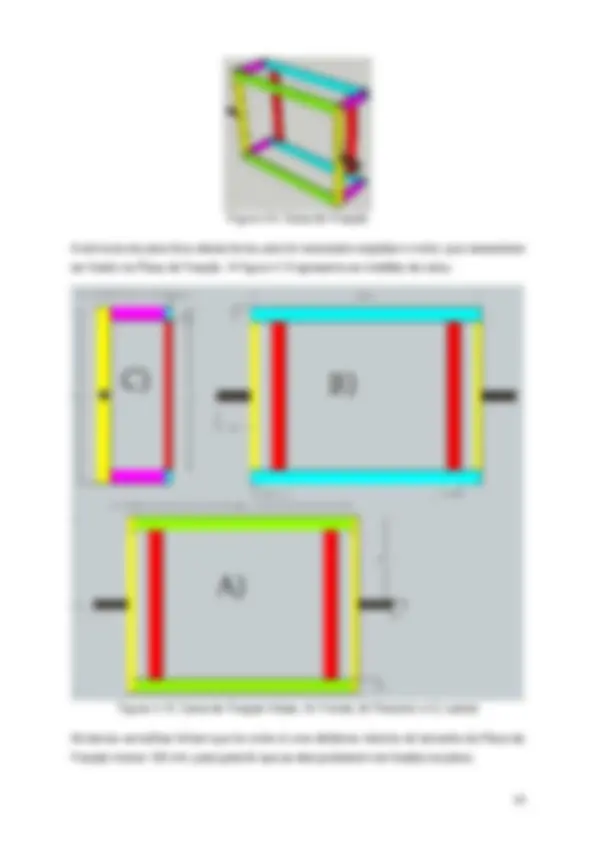
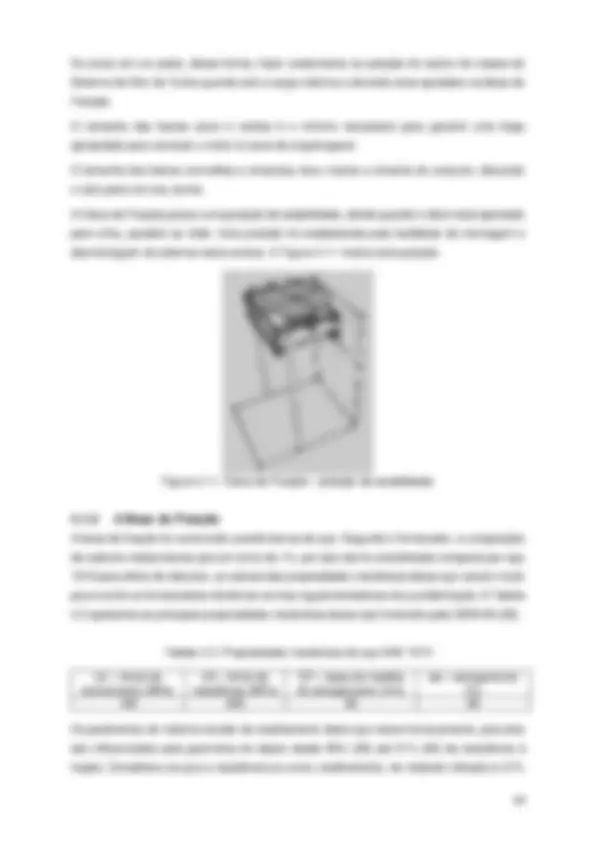
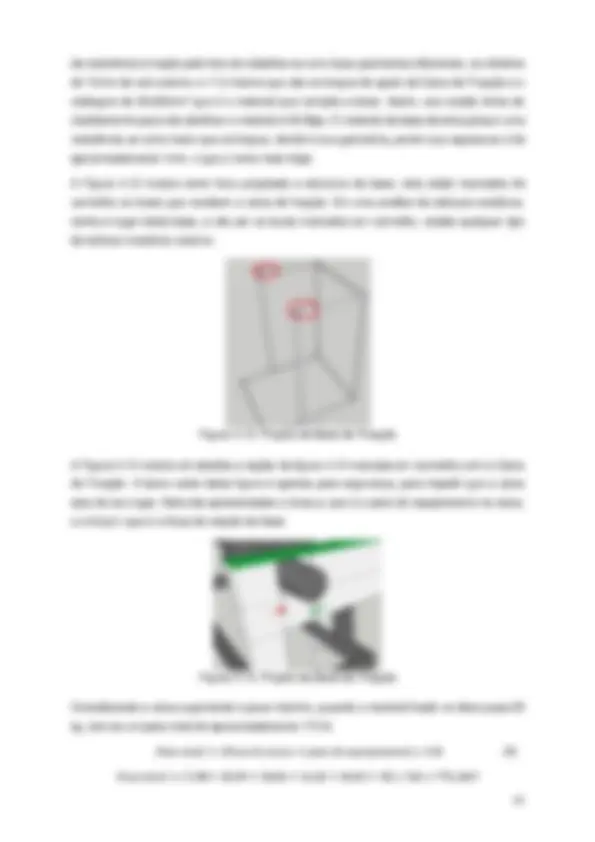
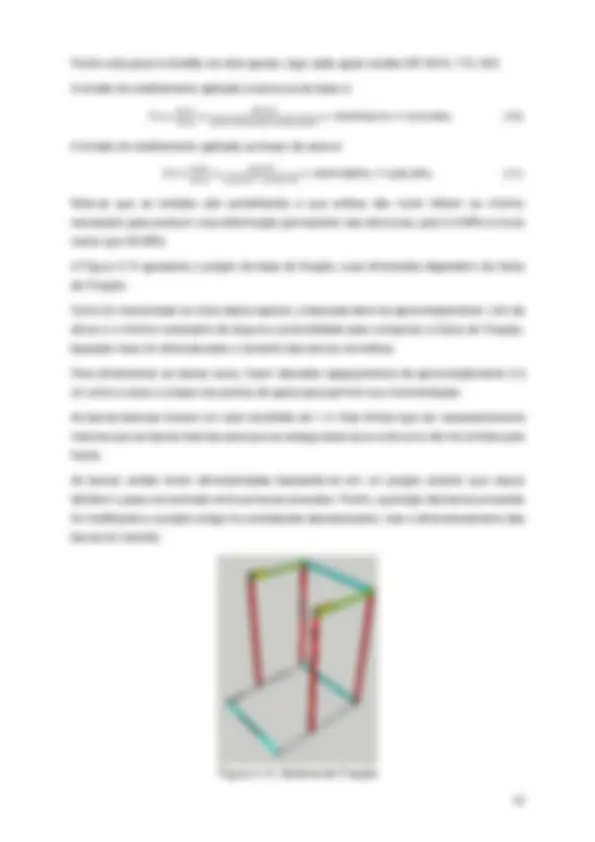
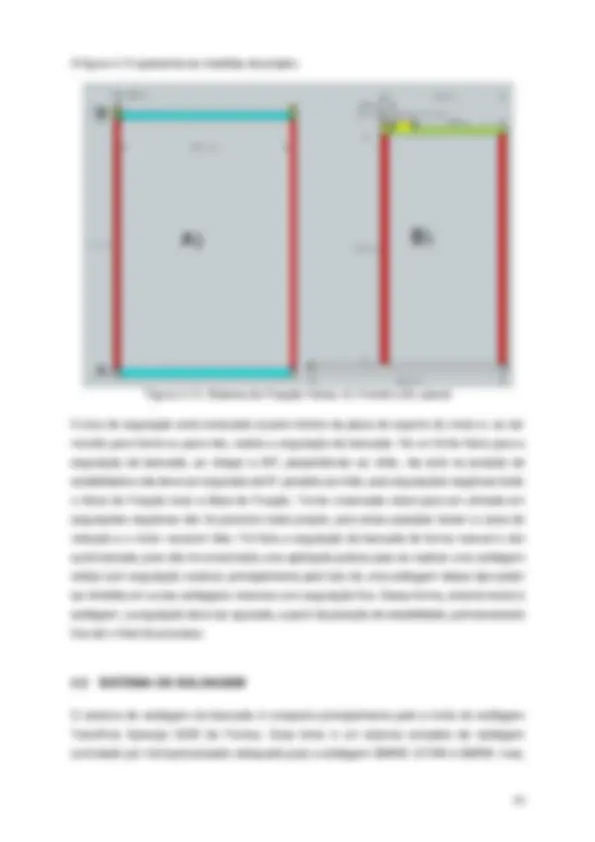
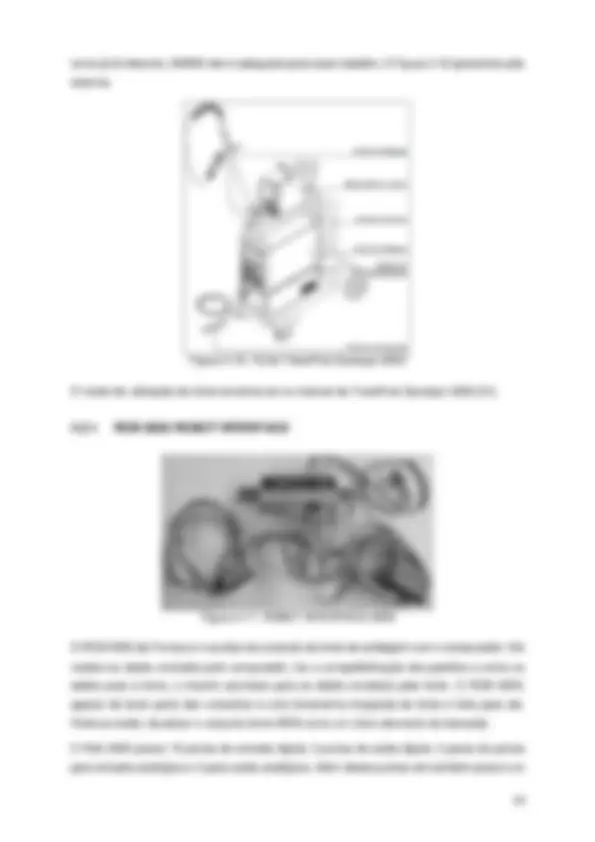
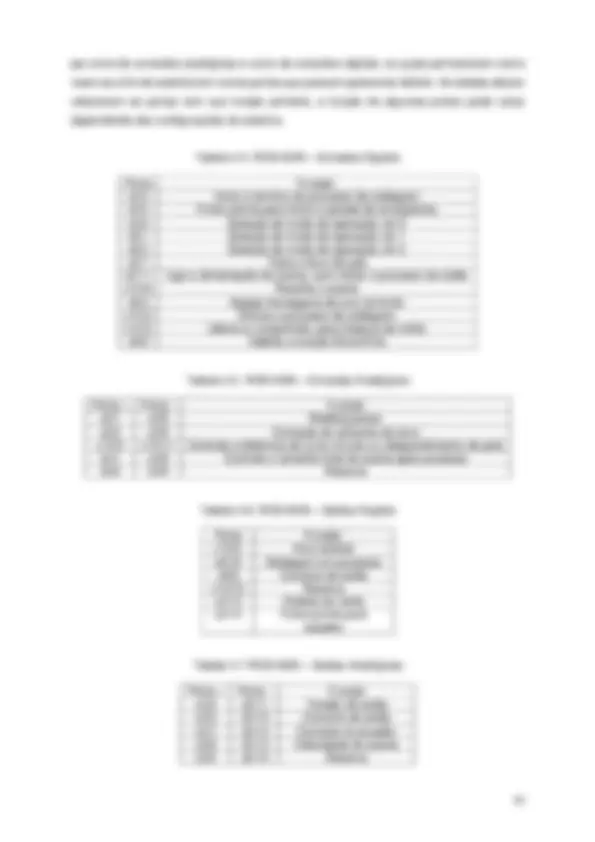
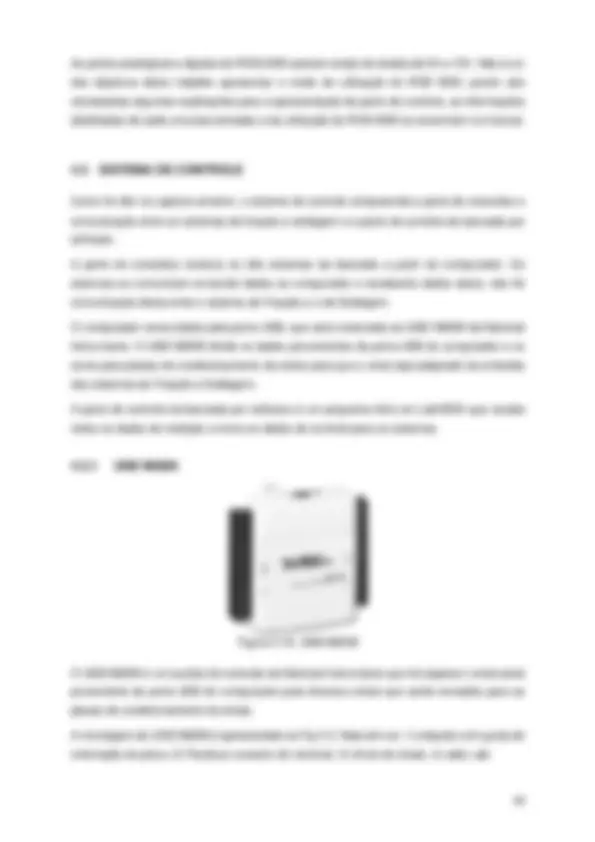
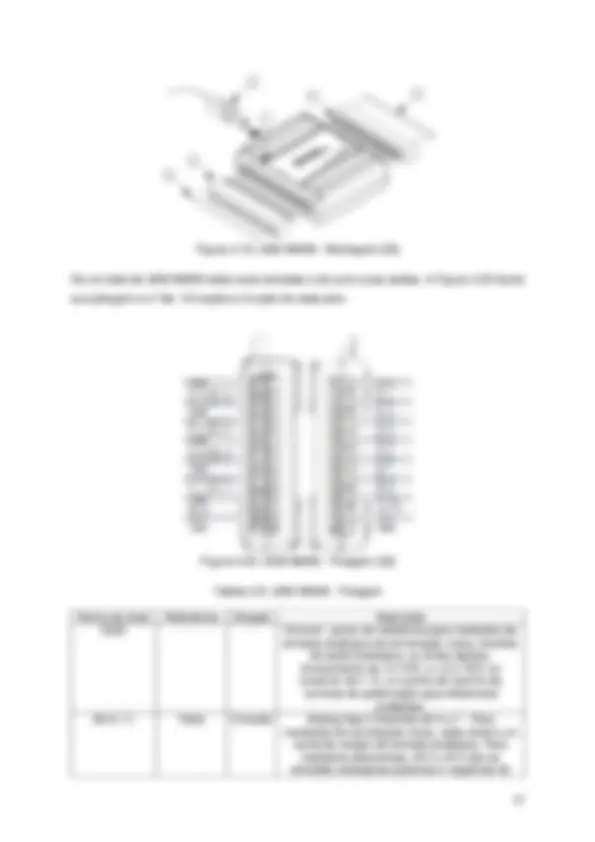
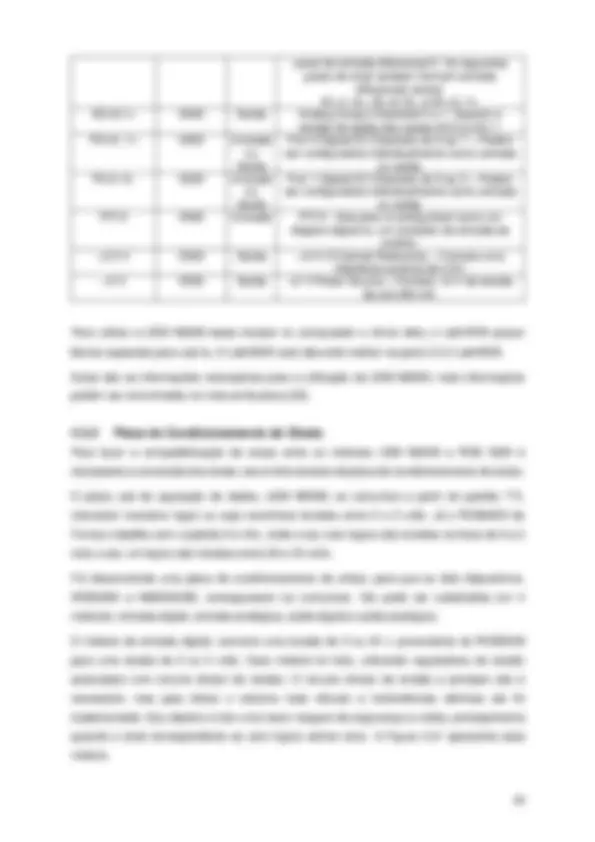
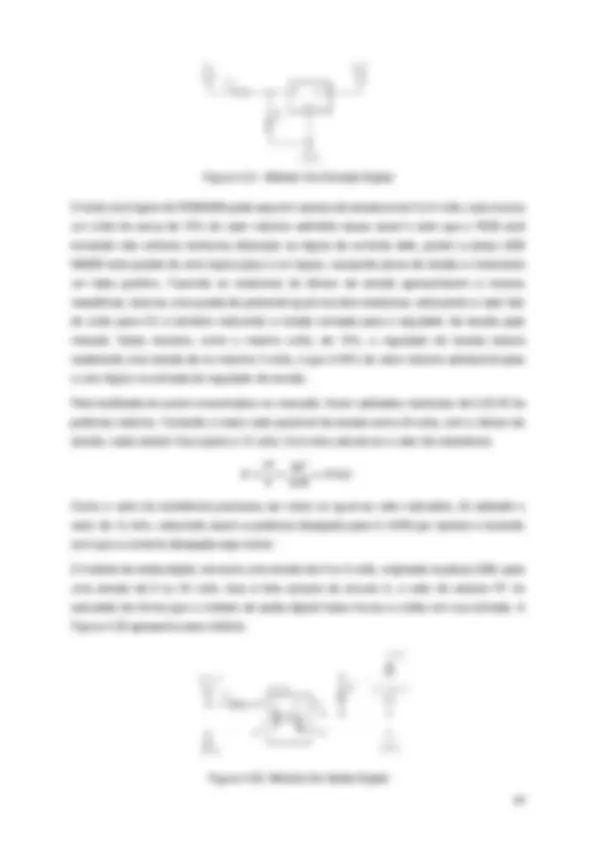
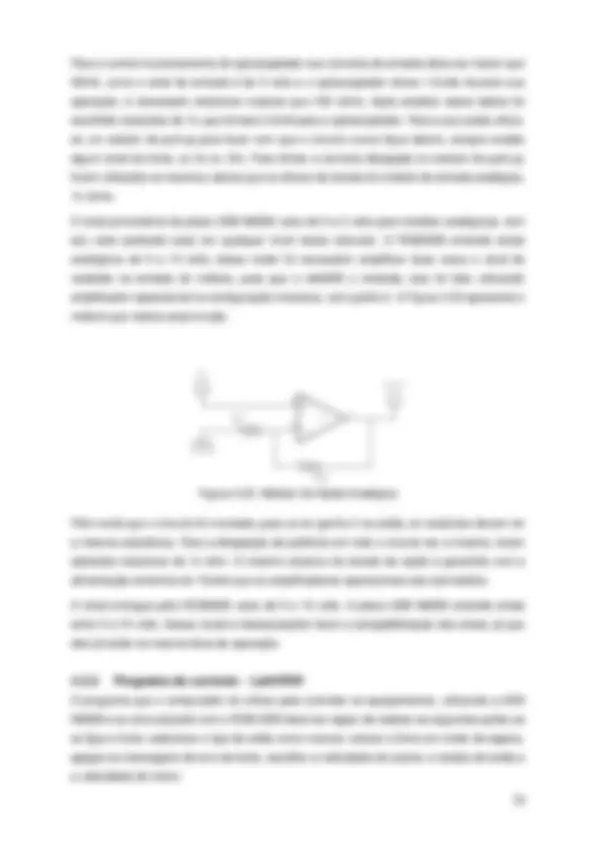
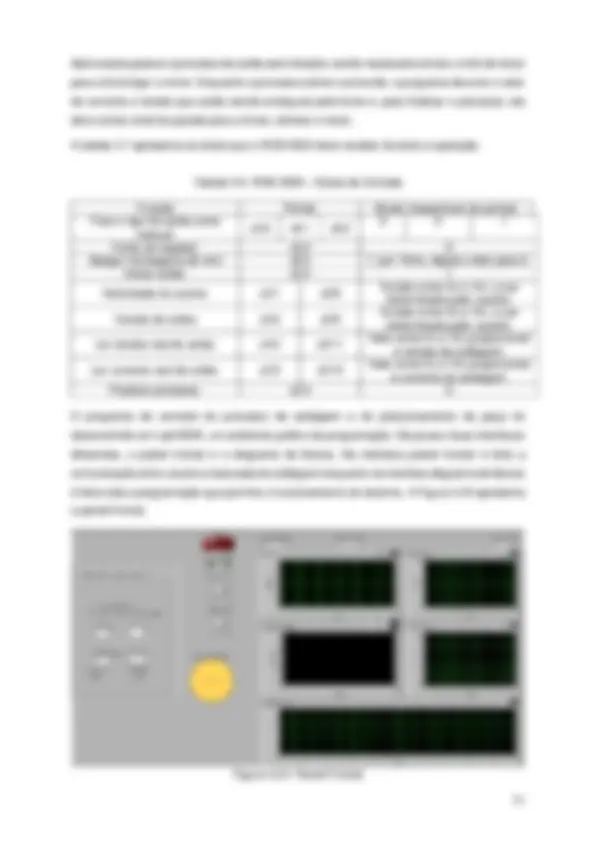
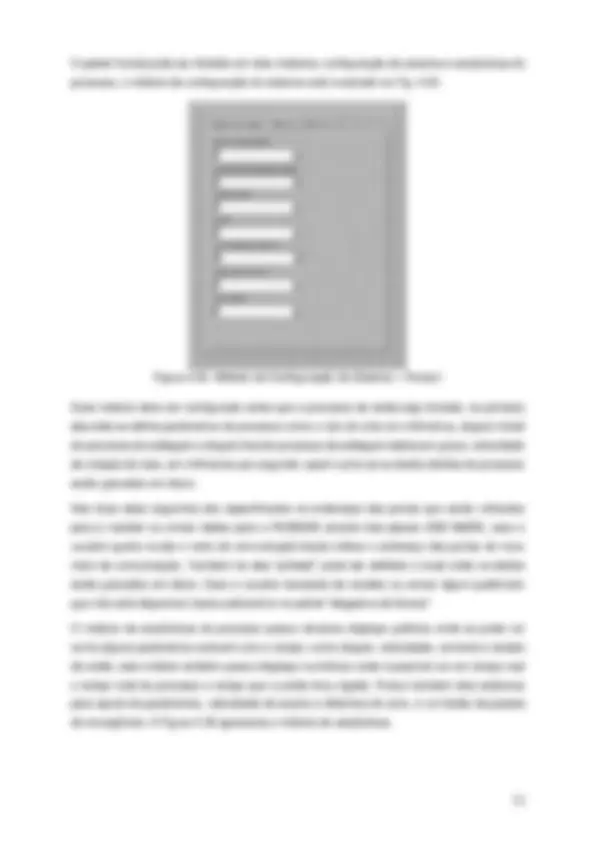
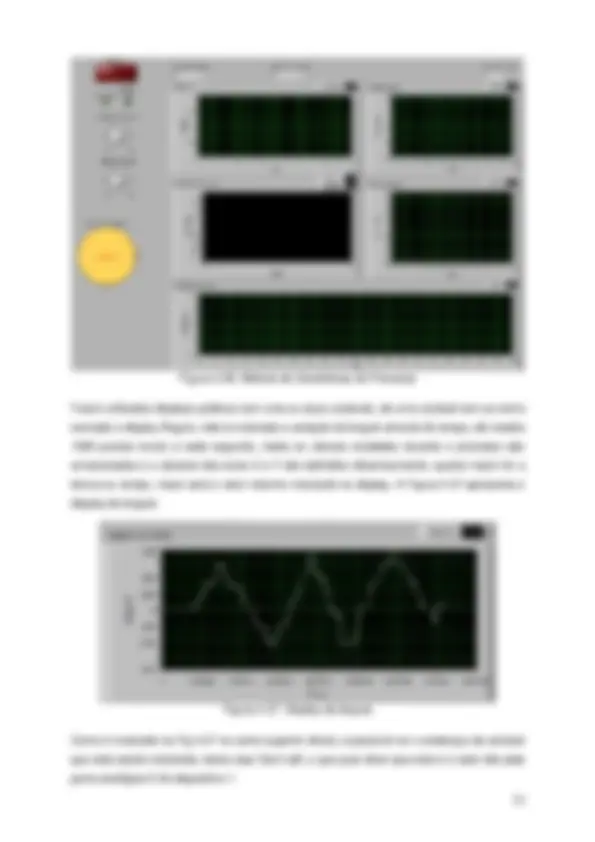
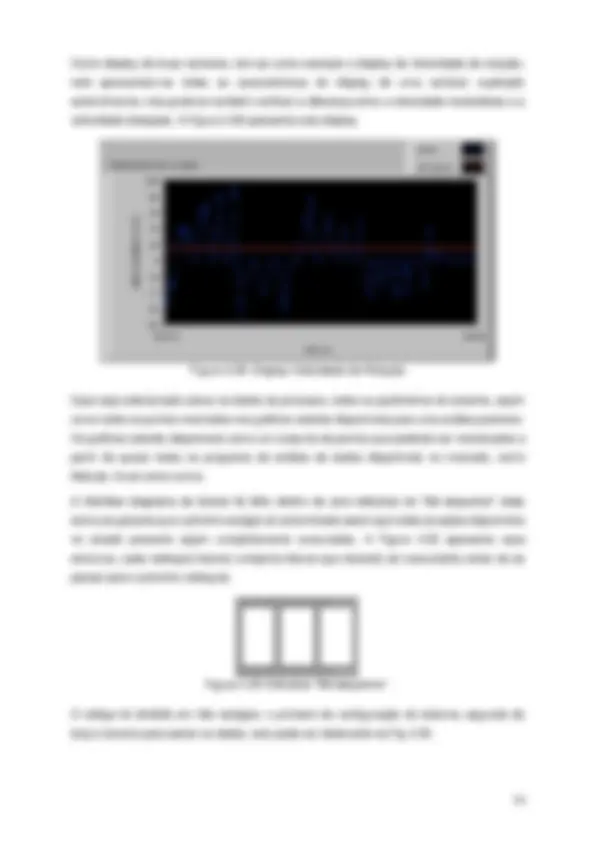
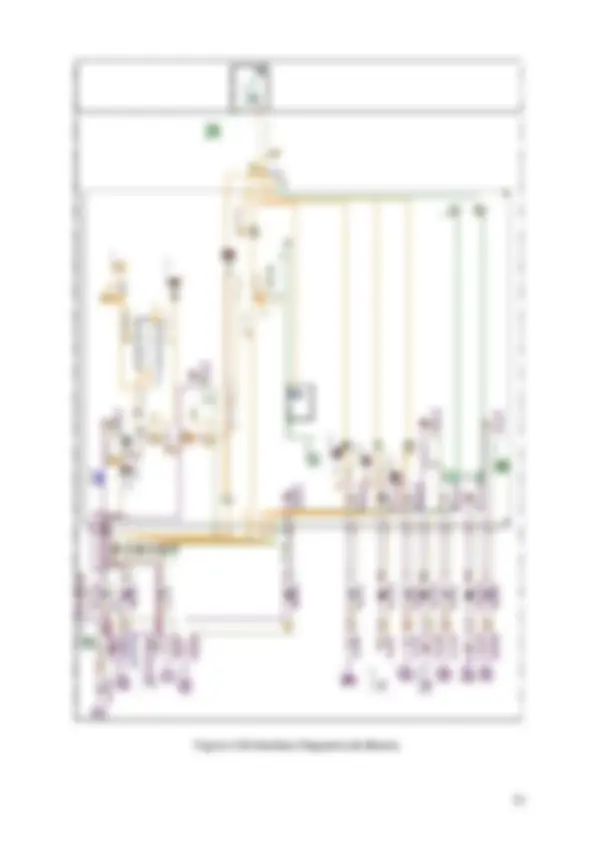
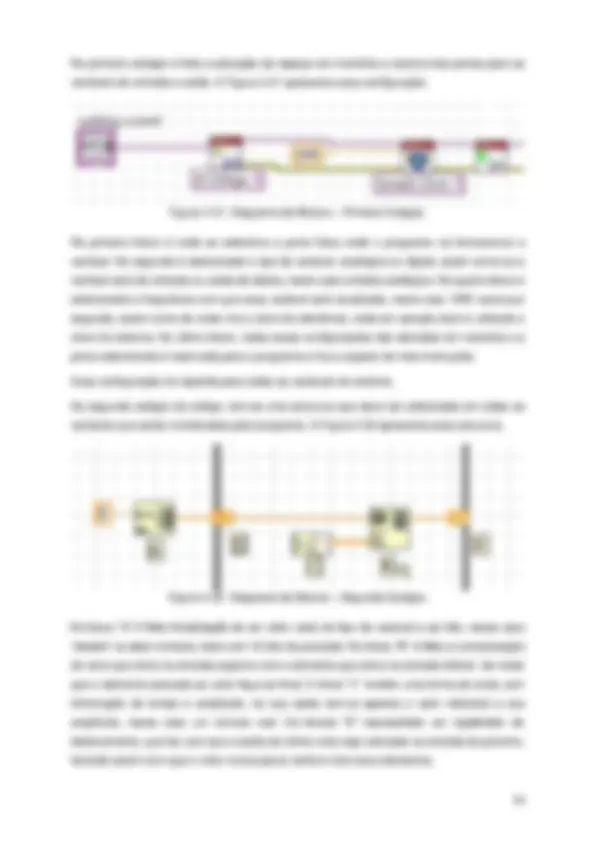
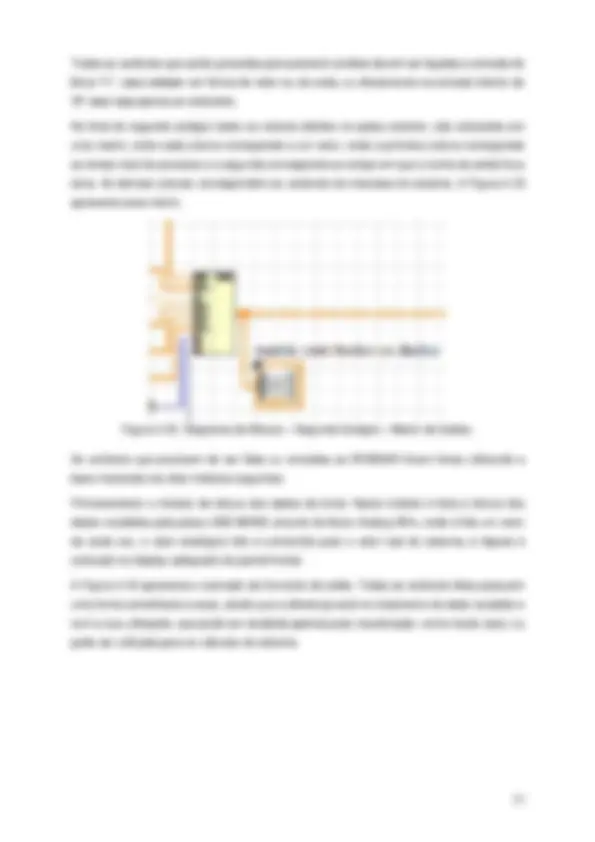
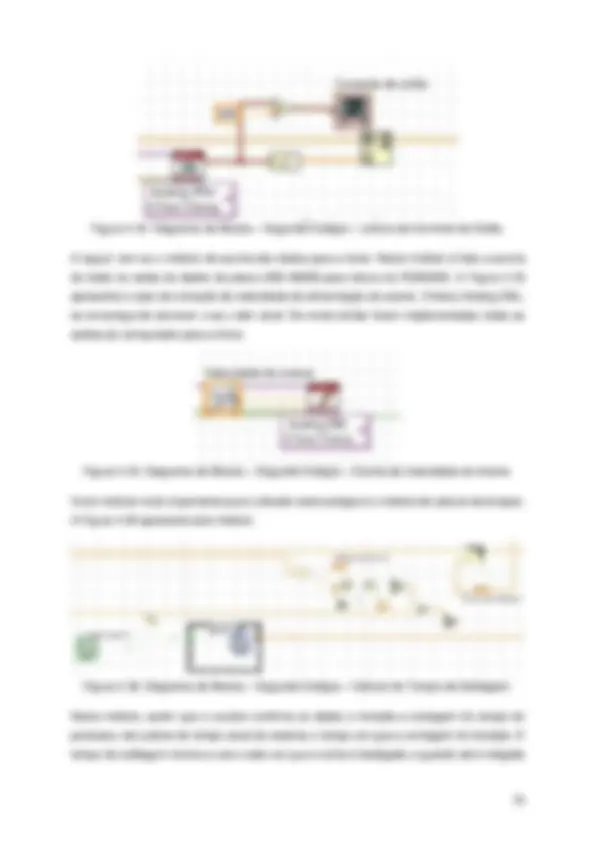
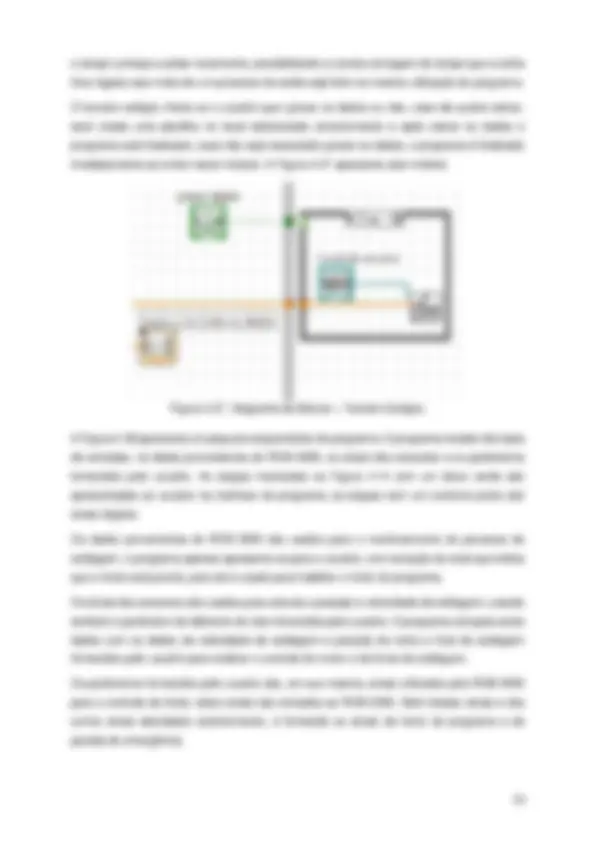
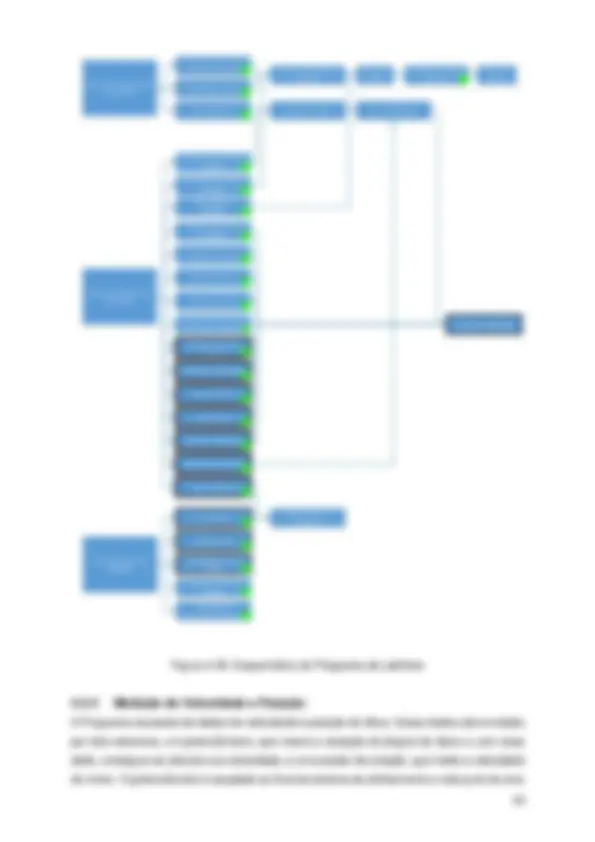
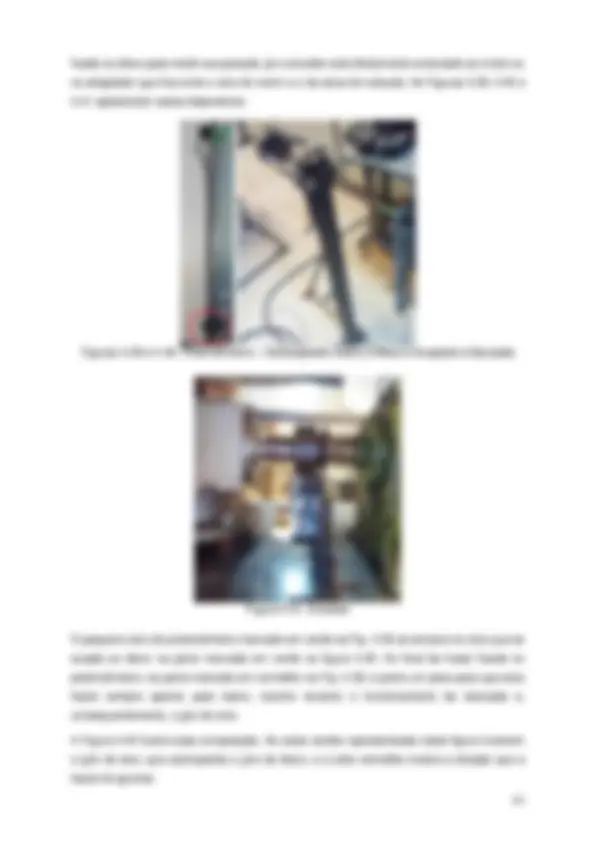
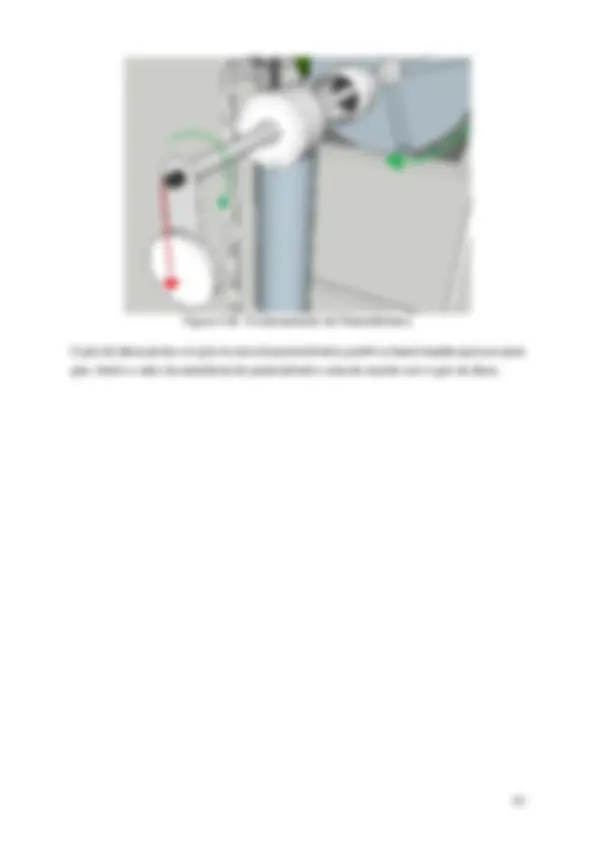
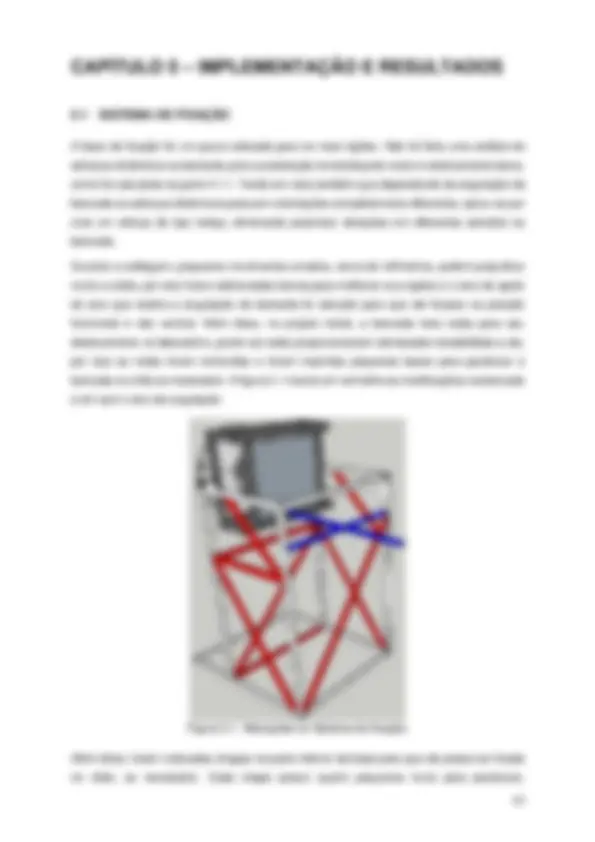
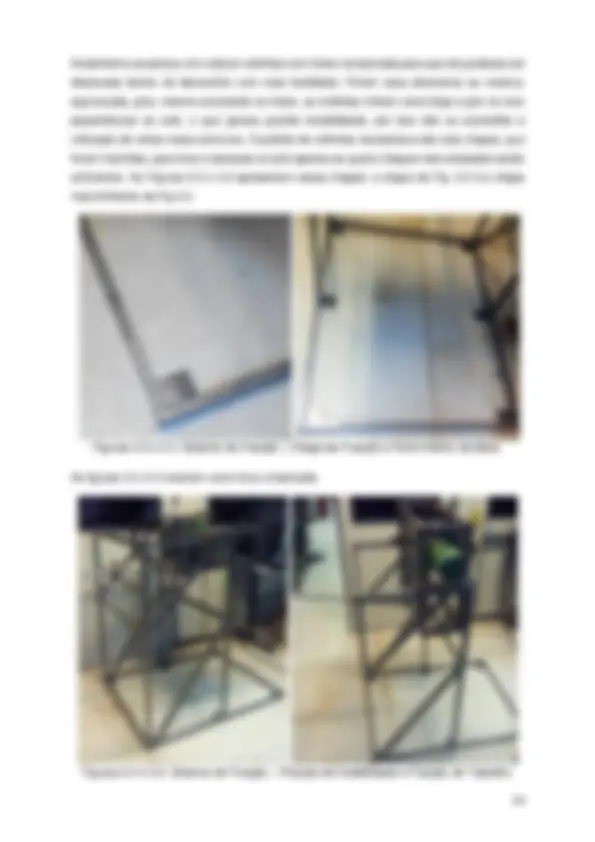
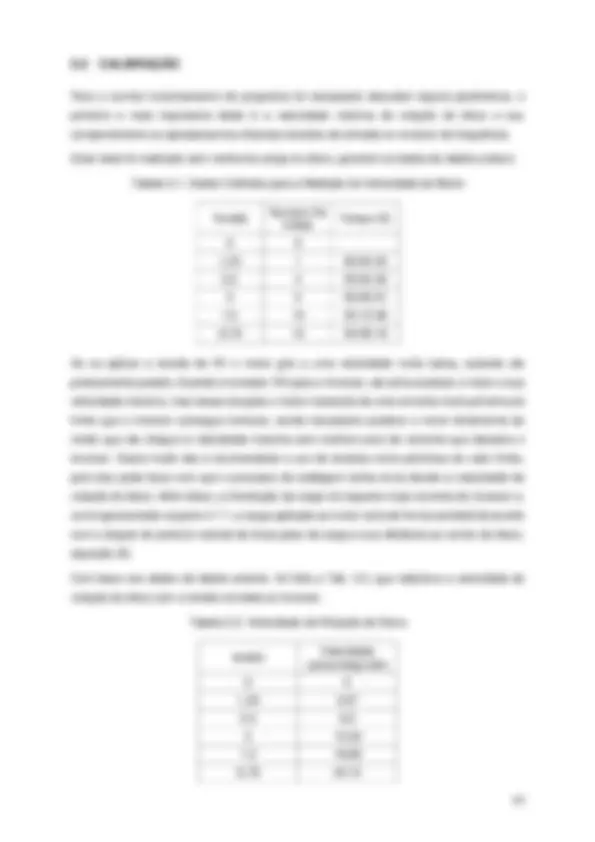
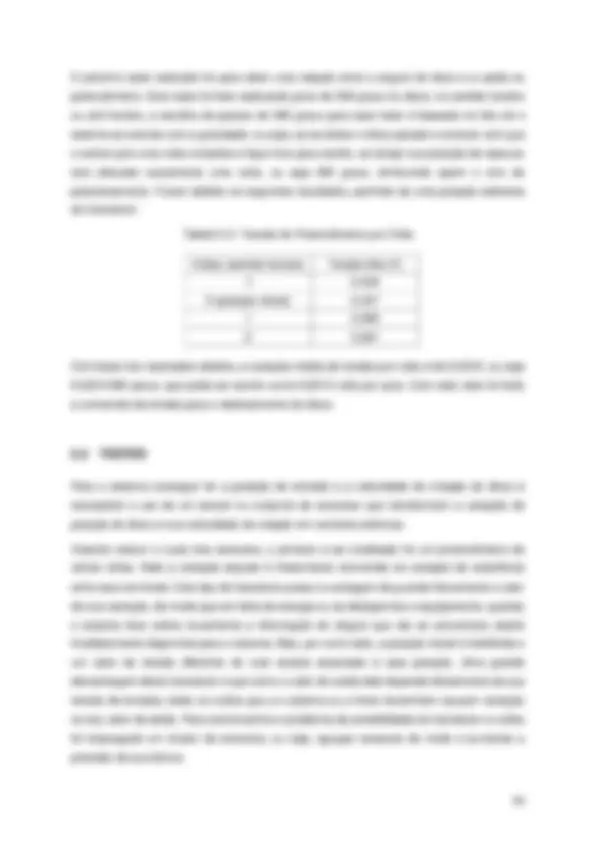
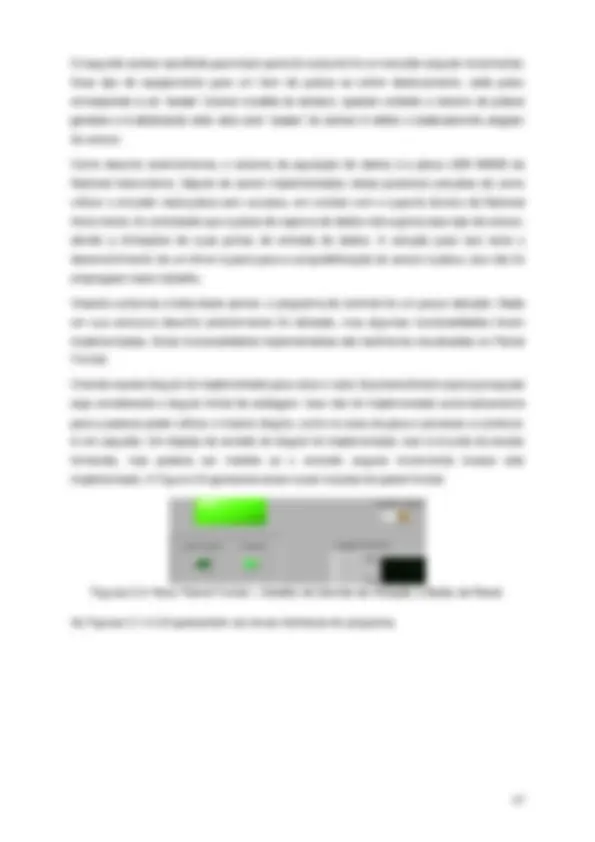

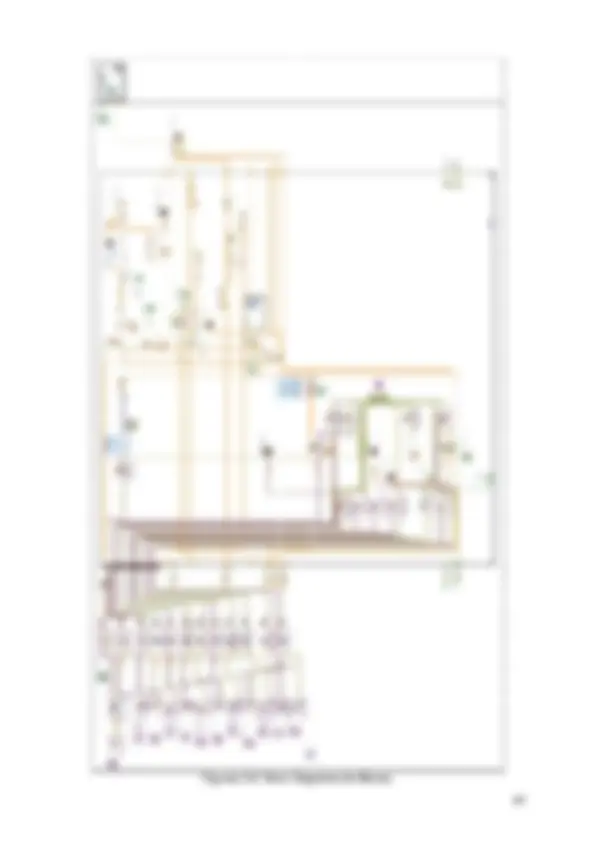
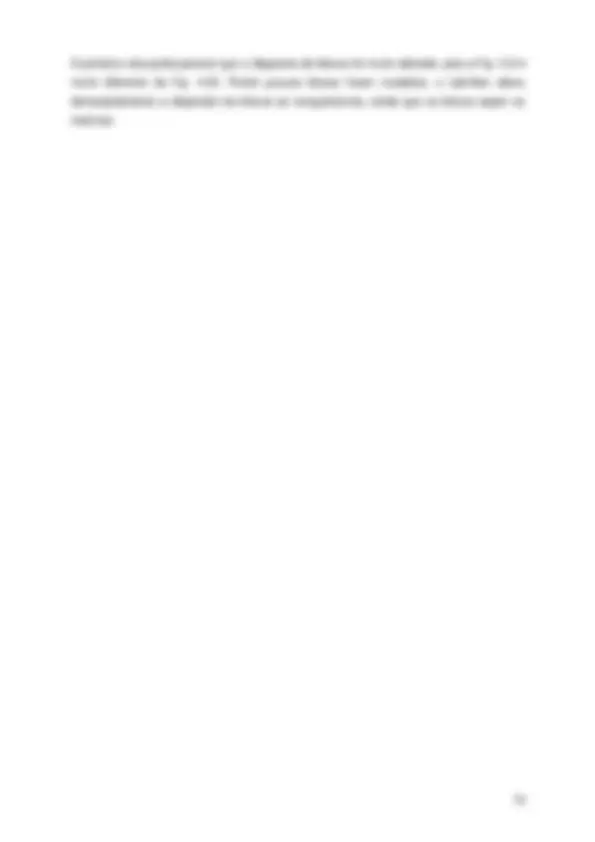
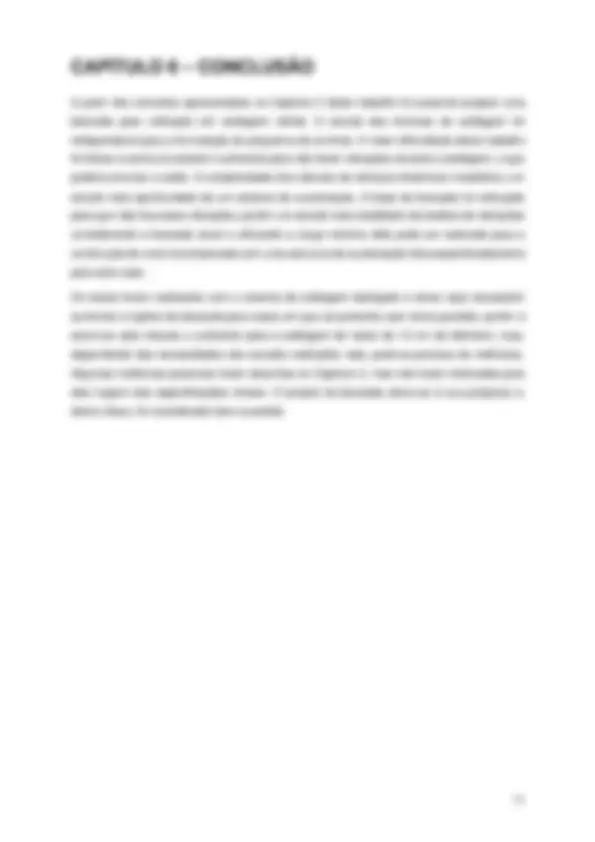
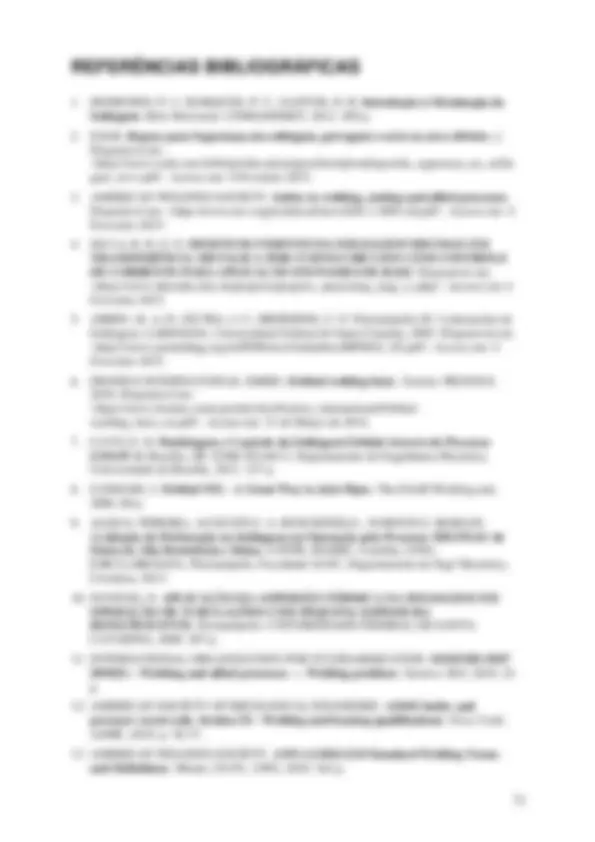
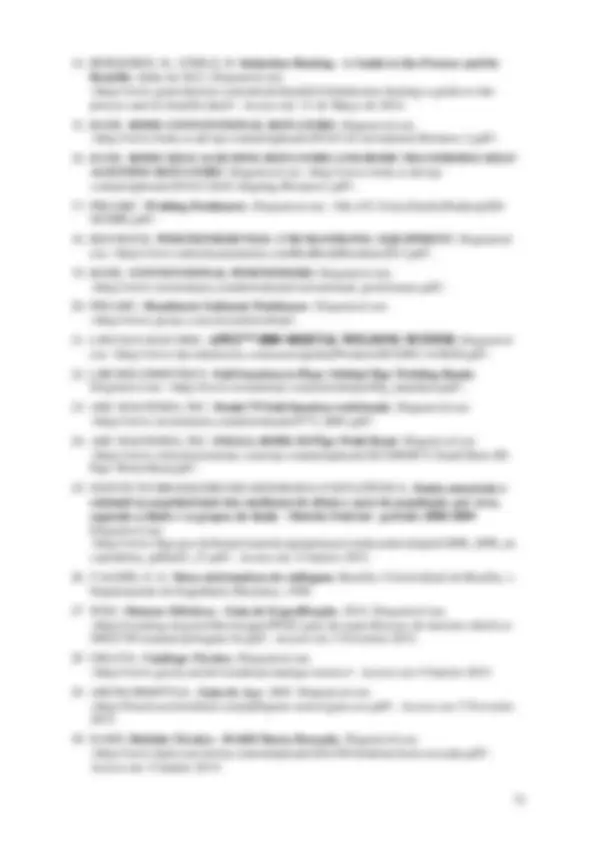
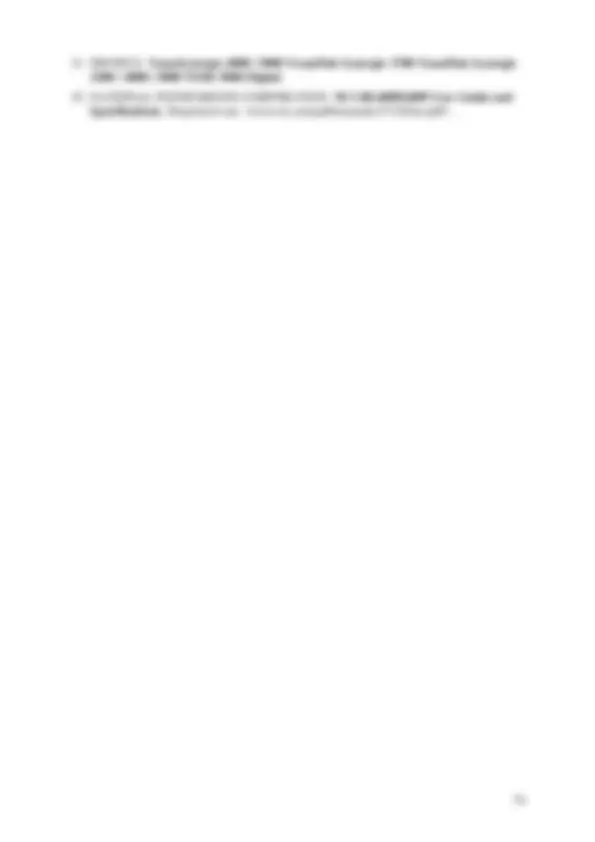
Estude fácil! Tem muito documento disponível na Docsity
Ganhe pontos ajudando outros esrudantes ou compre um plano Premium
Prepare-se para as provas
Estude fácil! Tem muito documento disponível na Docsity
Prepare-se para as provas com trabalhos de outros alunos como você, aqui na Docsity
Os melhores documentos à venda: Trabalhos de alunos formados
Prepare-se com as videoaulas e exercícios resolvidos criados a partir da grade da sua Universidade
Responda perguntas de provas passadas e avalie sua preparação.
Ganhe pontos para baixar
Ganhe pontos ajudando outros esrudantes ou compre um plano Premium
Comunidade
Peça ajuda à comunidade e tire suas dúvidas relacionadas ao estudo
Descubra as melhores universidades em seu país de acordo com os usuários da Docsity
Guias grátis
Baixe gratuitamente nossos guias de estudo, métodos para diminuir a ansiedade, dicas de TCC preparadas pelos professores da Docsity
Manual de soldagem, nomenclaturas e soldagem orbital
Tipologia: Resumos
1 / 87
Esta página não é visível na pré-visualização
Não perca as partes importantes!
Prof. Guilherme Caribé de Carvalho, UnB/ ENM (Orientador) Prof., Walter de Britto Vidal Filho UnB/ ENM Prof. Carlos Humberto Llanos Quintero, UnB/ ENM
RESUMO
O presente trabalho apresenta a modelagem, projeto e confecção de uma bancada para a soldagem orbital automatizada usada para fins didáticos e de pesquisa. São apresentados todos os equipamentos, circuitos e especificações que compõem a bancada, além de dados para fazer um projeto diferente deste. A parte de automação da bancada conta com sensores e um controle por computador usando o software LabView, os softwares e os sensores usados também são apresentados e explicados. Ao final do trabalho é apresentada a bancada que foi implementada.
Palavras Chave: Projeto, Bancada, Soldagem Orbital Automatizada, Controle.
ABSTRACT
This work presents the modeling, design and fabrication of a bench for automated orbital welding used for educational and research purposes. Lists all equipment, circuits, and specifications, which make up the bench and data to make a project different of this. The bench automation has sensors and a computer control using LabView software, the software and sensors used are also presented and explained. Finally, the paper presents the bench that was made.
Keywords: Design, Workbench, Automated Orbital Welding, Control.
α ângulo de ataque [º] φ ângulo de posição de soldagem [º]
Grupos Adimensionais
Red redução da caixa de redução
Siglas
ASME American Society of Mechanical Engineers AWS American Welding Society BMAW Bare Metal Arc Welding CAW Carbon Arc Welding EGW Electrogas Welding EBW Electron Beam Welding ESW Electroslag Welding FCAW Flux Cored Arc Welding FLOW Flow Welding GMAW Gas Metal Arc Welding GTAW Gas Tungsten Arc Welding MAG Metal Active Gas MIG Metal Inert Gas ISO International Organization for Standardization IW Induction Welding LBW Laser Beam Welding PAW Plasma Arc Welding SAW Submerged Arc Welding SMAW Shielded Metal Arc Welding
CAPÍTULO 1 – INTRODUÇÃO
Soldagem é uma técnica usada para a junção de materiais, comumente metálicos, por meio de aquecimento. Esta técnica data de milhares de anos, quando se começaram a criar peças metálicas a partir da união de suas partes por meio de seu aquecimento usando processos como a brasagem ou a soldagem por forjamento. Porém os processos utilizados atualmente para a soldagem foram extremamente aperfeiçoados e hoje em dia pode-se dividi-los em diversas categorias baseadas em suas diferentes características. Independente do processo utilizado, o resultado da soldagem, ou seja, a união das partes metálicas, deve ser semelhante e, devido a isso, a escolha do processo é baseada principalmente no material a ser soldado. Modenesi, Marques e Santos [1] apresentam análises de diferentes definições de soldagem, umas mais amplas, outras incompletas. A definição mais ampla que diferencia soldagem de brasagem é: "Operação que visa obter a união de duas ou mais peças, assegurando, na junta soldada, a continuidade de propriedades físicas, químicas e metalúrgicas".
Diversos estudos apresentam motivos para se automatizar a soldagem, um dos principais é o ambiente perigoso que esta técnica gera. As regras para segurança na soldagem apresentadas pela Esab [2] e pela AWS [3] citam as diversas precauções que se deve cumprir antes mesmo de se iniciar o processo de soldagem. O aquecimento de metais é um procedimento perigoso e não deve ser realizado perto de pessoas inexperientes sem a devida supervisão, uma vez que o metal aquecido não possui uma diferença visível em relação ao metal não aquecido dependendo de sua temperatura. Além disso, diversas técnicas de soldagem apresentam perigos adicionais como brilho excessivo, gases inflamáveis e tóxicos e choques elétricos, o que reafirma a ideia de se automatizar a soldagem para evitar riscos às pessoas.
Segundo Silva [4], A automação da soldagem não representa a diminuição da oferta de empregos, mas sim um aumento da produtividade e da qualidade dos processos e uma redução dos riscos apresentados às pessoas envolvidas no processo. A automação visa tornar as empresas mais competitivas, por aumentar sua produção e qualidade. Além disso, a oferta de empregos é mantida, pois, mesmo automatizados, os processos de soldagem necessitam da supervisão de um operador. As linhas de pesquisa nessa área contribuem para a geração de recursos humanos especializados, com conhecimentos científico-tecnológicos, os quais cada vez mais propiciarão a agregação de valor aos produtos nacionais.
Ao se tratar de soldagem orbital, novos problemas se criam, como a mudança de posição da tocha e da posição de soldagem durante o processo, isso será melhor abordado no capítulo
A soldagem é uma técnica imprescindível no ramo da produção de equipamentos, prédios, veículos, etc., e, com a crescente industrialização de todos os ramos de produção, cada vez mais se percebe a necessidade de automatizar os processos de fabricação.
A soldagem de tubulações, cilindros, esferas, relaciona-se facilmente com soldagem orbital. A soldagem orbital apresenta um grande desafio para a automação, com a mudança dos parâmetros de posição durante o processo de soldagem, além das dificuldades e mudanças de parâmetros naturais de qualquer processo de soldagem, como velocidade de soldagem, altura de arco, ângulo de ataque e posicionamento da pistola. A mudança constante de posição de soldagem inevitavelmente acarreta numa perda da qualidade da soldagem das tubulações quando os parâmetros de soldagem são inadequados [7].
Outro desafio nesta área é a soldagem sem interrupção do fluxo nas tubulações, conhecida como soldagem em operação. A soldagem em operação é uma técnica frequentemente empregada no reparo ou modificação de tubulações devido às suas vantagens econômicas, pois evita as perdas oriundas da interrupção do serviço e garante a continuidade no fornecimento do fluido [9]. Quando se realiza uma soldagem em operação, há dois riscos principais a serem considerados: a perfuração quando o metal abaixo da poça de fusão, pelo aquecimento localizado, não consegue resistir à pressão interna do fluido e o surgimento de microestruturas duras na solda, geradas pelo resfriamento acelerado da solda como efeito do escoamento de calor provocado pelo fluido, que aumentam a susceptibilidade às trincas [10].
A motivação deste trabalho é o estudo de técnicas para a automação da soldagem orbital, considerando as dificuldades intrínsecas deste processo, o estudo de parâmetros que visam otimizar o método de soldagem e reduzir as chances de falhas e erros durante o processo.
O objetivo deste trabalho é desenvolver um equipamento necessário para o estudo de processos de soldagem orbital e técnicas para a sua automação. Desta forma, é apresentado o projeto de uma bancada didática para ser utilizada no ensino de soldagem orbital e como objeto de estudo.
Além disso, objetiva-se que este trabalho possa ser usado como manual, a fim de que outras pessoas possam operar esta bancada. Dessa forma, são expostas todas as informações
necessárias para sua operação e, se necessário, a realização de reparos, alterações ou aperfeiçoamentos.
Primeiramente apresentam-se as motivações para o projeto da bancada e, através delas, um esboço de como ela deve ser. A bancada será usada para fins didáticos ou de pesquisa e não para manufatura de tubulações e outras peças, logo ela deverá ser mais adaptável e controlável, além de precisar suportar uma carga de trabalho reduzida. Por ser adaptável, ela pode garantir certa liberdade de operação dentro da definição de soldagem orbital e pode ser utilizada em processos diferentes na soldagem. O fato de a bancada ser controlável indica que ela precisará ter muitos tipos de sensores e, por isso, processos difíceis de medir não serão a meta deste trabalho, mais à frente foi feita uma análise de processos e, ao final, se escolheu o processo GMAW. A bancada será utilizada para soldagem de pequenos tubos, sendo um aparato de pequeno porte, de forma que os cilindros de raio ou espessura muito grandes estão fora de questão. Por final, é necessário ter a liberdade de usar ou não adição de material e, como o processo GMAW caracteriza intrinsicamente uma adição de material, o processo GTAW foi escolhido para ser usado em soldagens sem adição.
O presente trabalho apresenta o projeto e construção de uma bancada de soldagem orbital de pequeno porte. O trabalho é dividido em 6 capítulos sendo eles: Capítulo 1 – Introdução, Capitulo 2 – Revisão da literatura, onde é feito um estudo mais detalhado sobre a soldagem orbital. Capítulo 3 – Concepção da Bancada, onde é apresentada a modelagem de toda a estrutura da bancada e os parâmetros utilizados como referência, Capítulo 4 – Projeto da Bancada Proposta, onde são descritas as especificações e a forma de utilizar cada componente da bancada, Capítulo 5 – Implementação e Resultados, onde é apresentado como ficaram a bancada e seus componentes, Capítulo 6 – Conclusão, onde são apresentados os resultados e a conclusão.
Figura 2.2. Força gravitacional (a) Visão geral, (b) Sentido da força segundo a posição de soldagem φ [7]
Além da gota, outro material que sofre grande influência dessas forças é a poça de fusão. A poça de fusão escorre durante a soldagem devido à força gravitacional e, principalmente por causa desse fenômeno, evitam-se soldagens orbitais ascendentes. A Figura 2.3 ilustra experimentos realizados tanto de forma ascendente quanto de forma descendente, as setas S 1 , S 2 e S 3 indicam o sentido da soldagem. Nota-se um grande prejuízo na soldagem ascendente pelo escoamento da solda e uma melhora considerável ao se realizar passes descendentes, apesar deles também apresentarem irregularidades e/ou escoamentos parciais na geometria da solda [7].
Figura 2.3. Experimento exploratório sem regulação de parâmetros [7]
A grande diferença entre uma técnica de soldagem normal e a soldagem orbital está na posição de soldagem. Para definir a posição de soldagem, as duas normas mais utilizadas são a norma ISO [11] e as da ASME [12]/AWS [13], sendo que ambas apresentam várias considerações sobre diversas posições de soldagem de tubos e suas relativas variações e limites entre uma posição e outra. Mas, pela definição de soldagem orbital, o tubo a ser soldado deverá estar estático e ter seu eixo na posição horizontal ou inclinada, pois, saindo destes parâmetros, não haverá mudança de posição de soldagem durante o processo. As Foram feitas as Figuras 2.4 a 2.16 para apresentar as posições de soldagem e a nomenclatura da norma ISO e ASME, nestas figuras as setas vermelhas representam a movimentação do tubo e as setas verdes representam a movimentação da tocha.
Figura 2.4. Posição Plana: A) PA/1G, B) PA/1F, C) PA/1G e D) PA/1G
Figura 2.5. Posição Horizontal: A) PC/2F B) PC/2G, C) PC/2G e D) PC/2G
Figura 2.6. Posição Horizontal Vertical: A) PB/2FR, B) PB/2F e C) PB/2F