
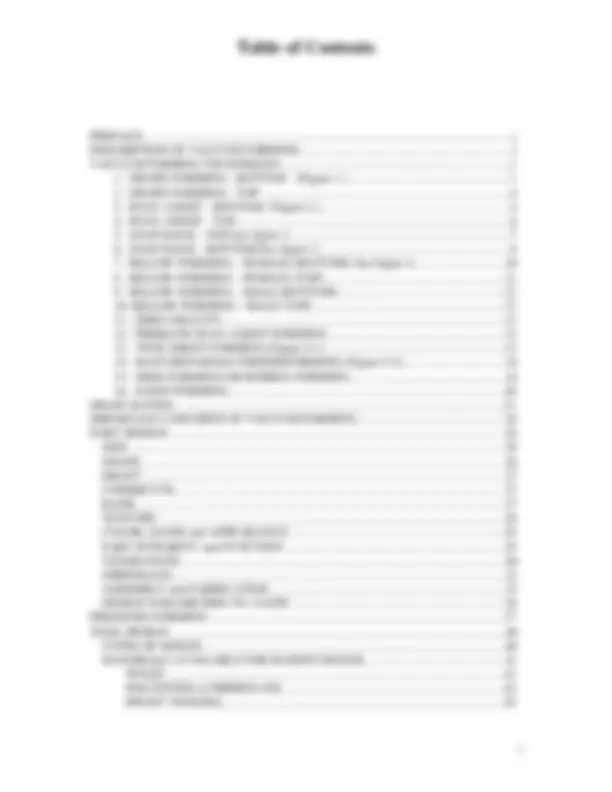
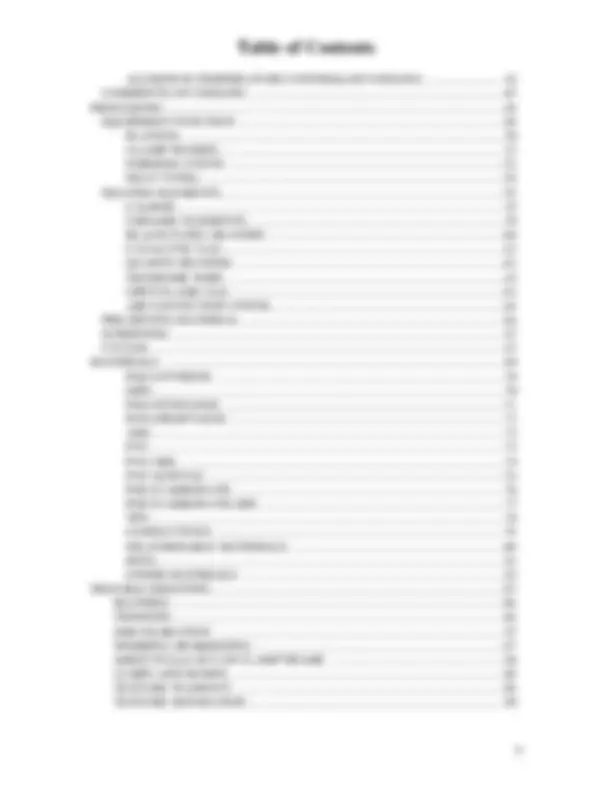
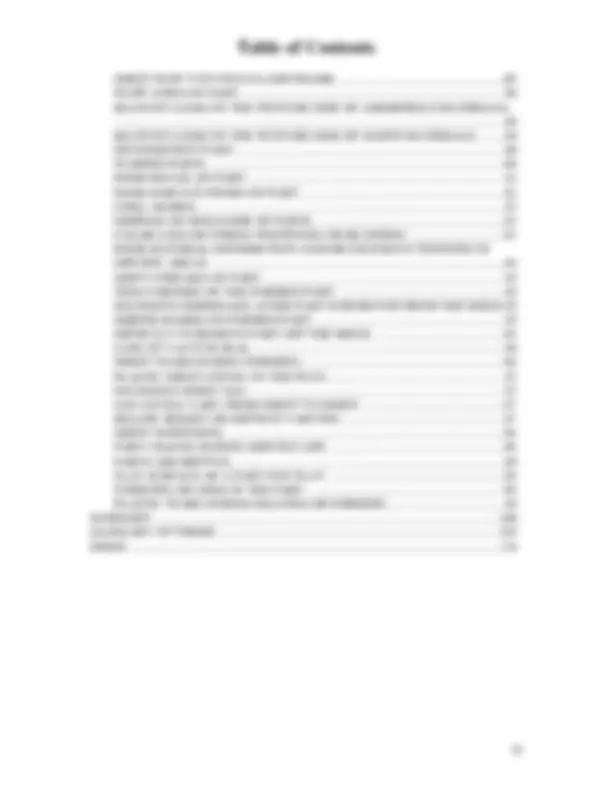
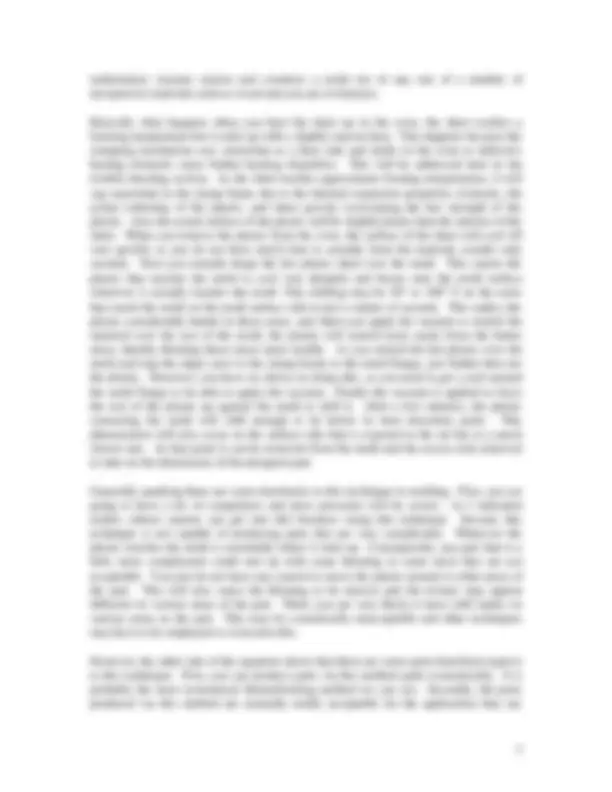
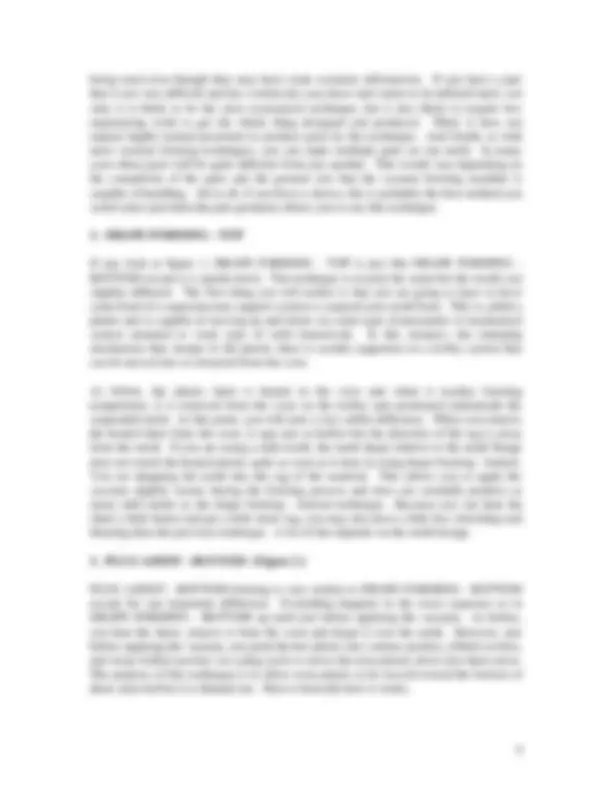
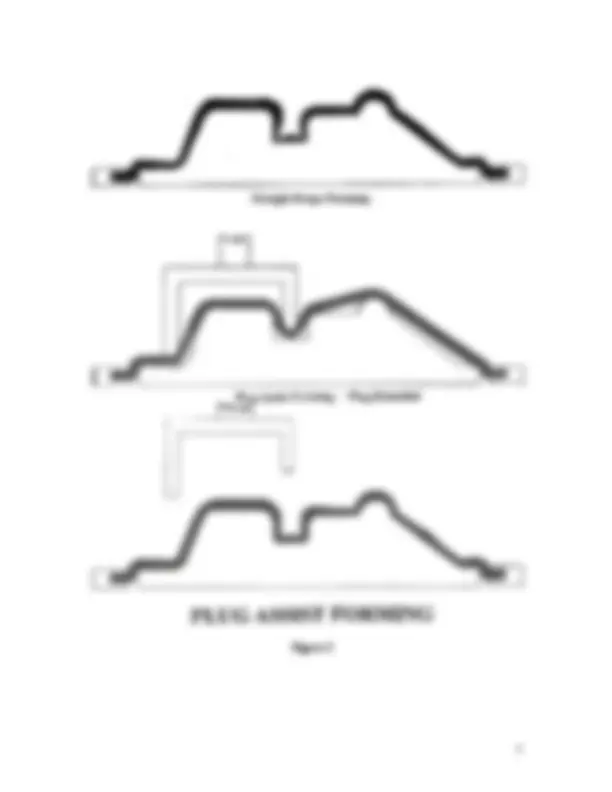
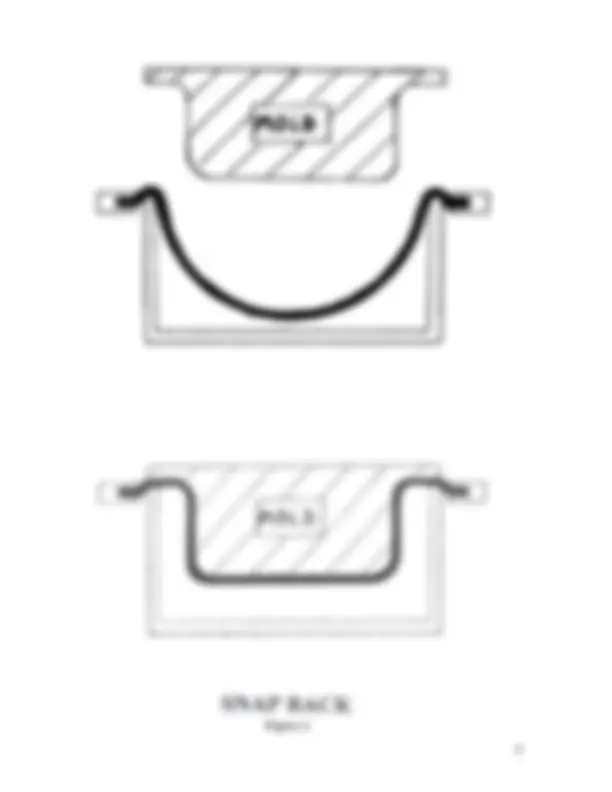
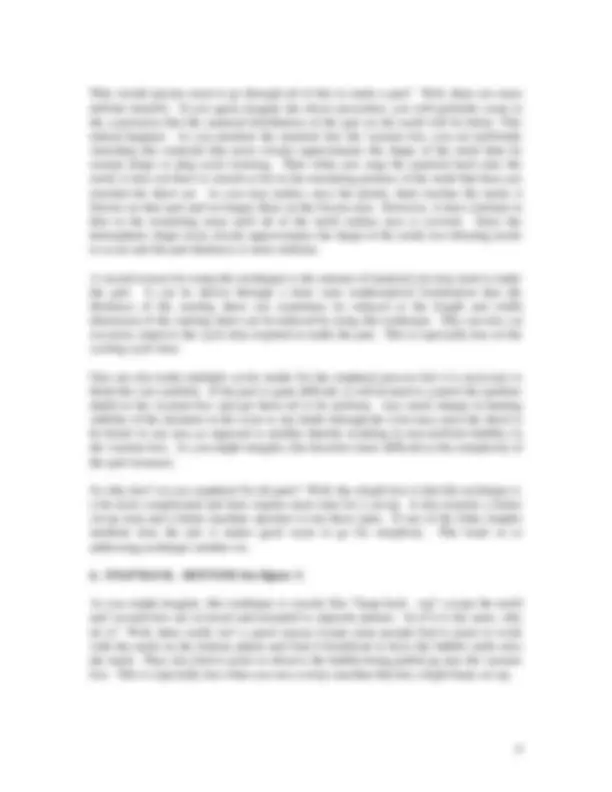
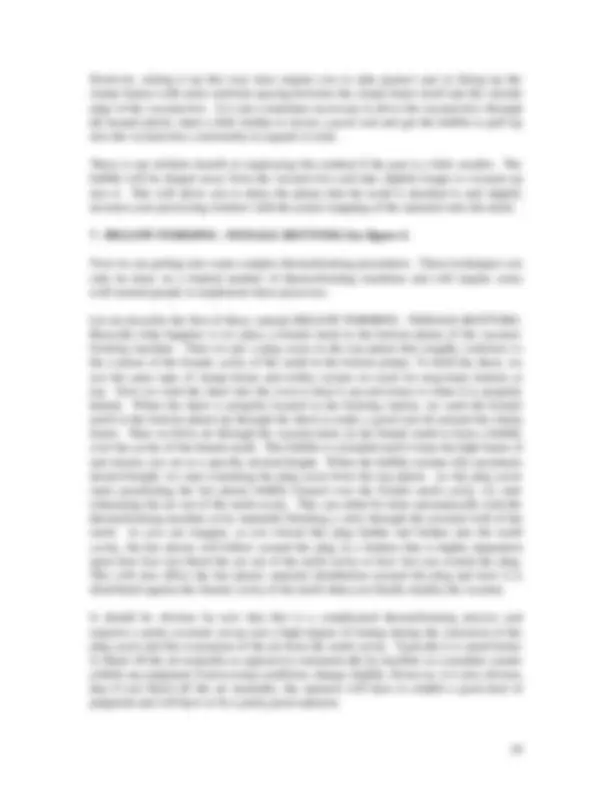
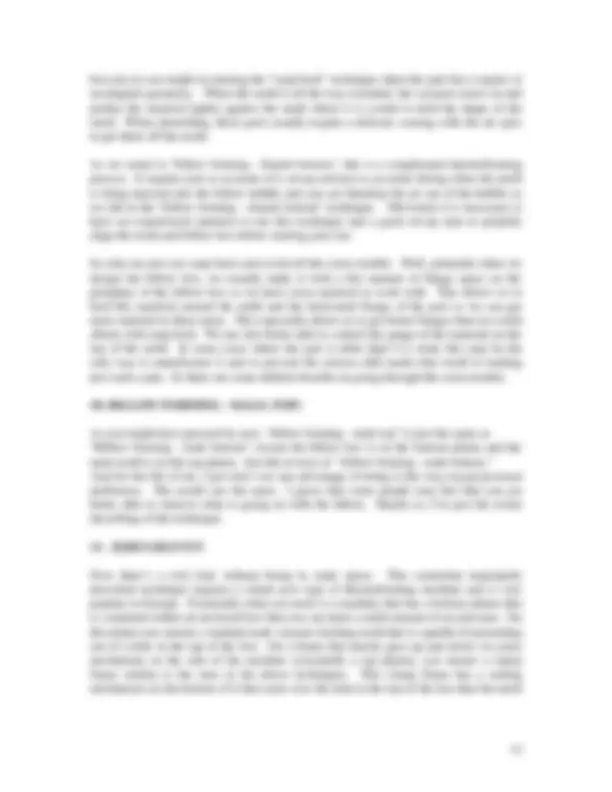
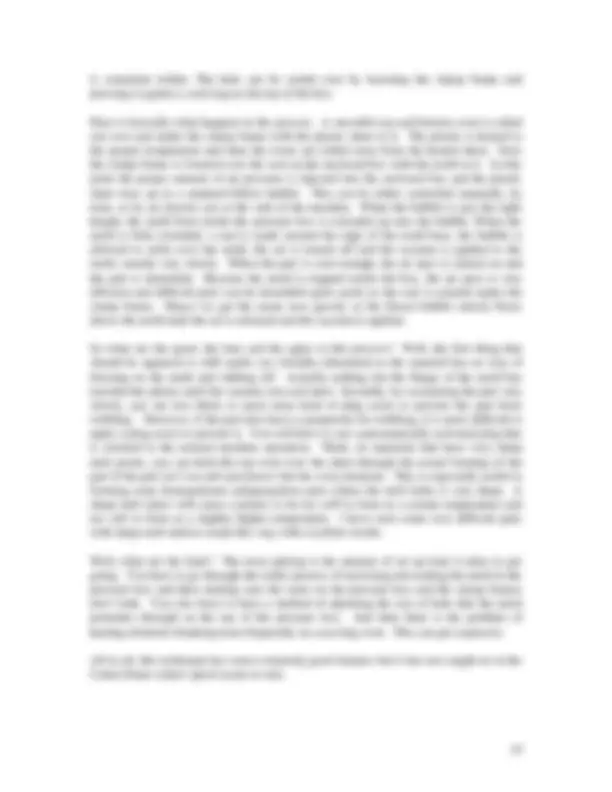
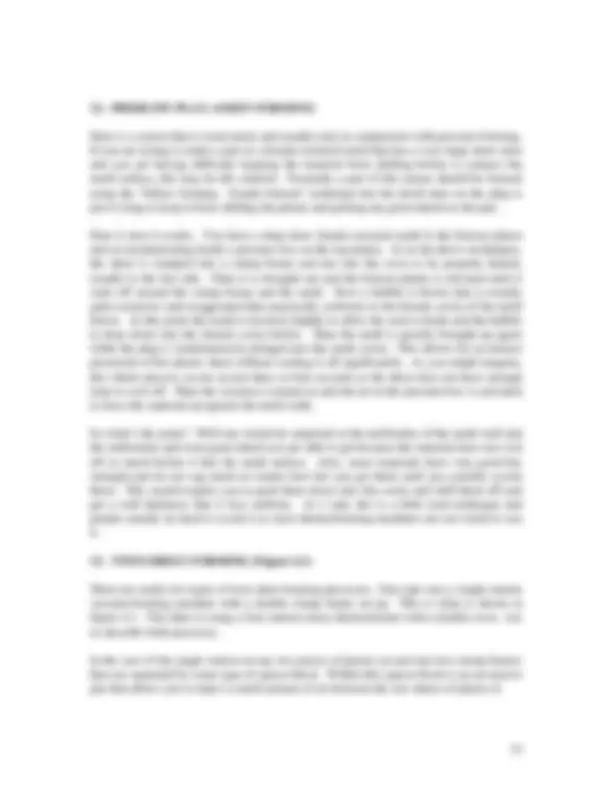
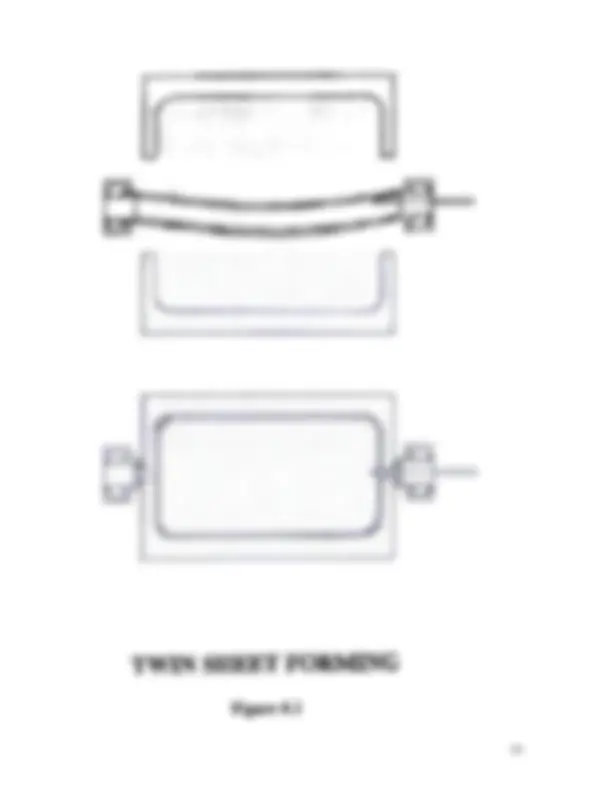
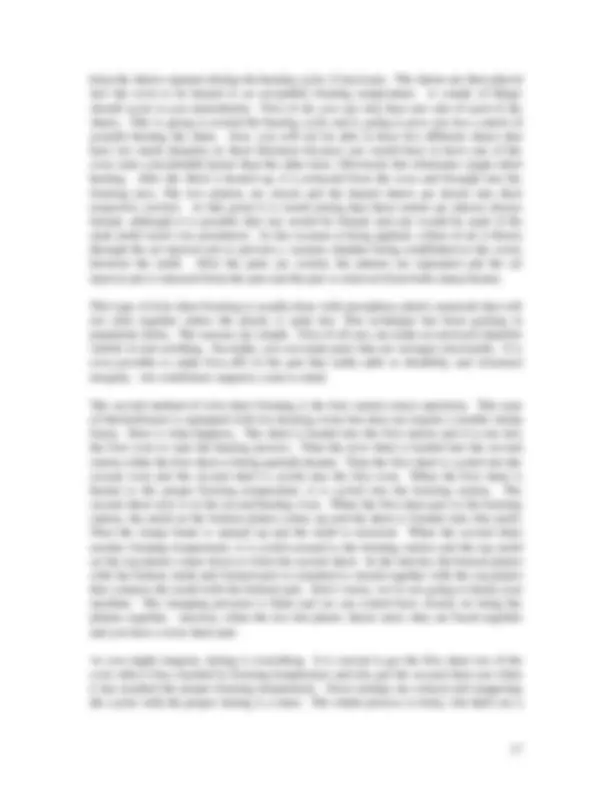
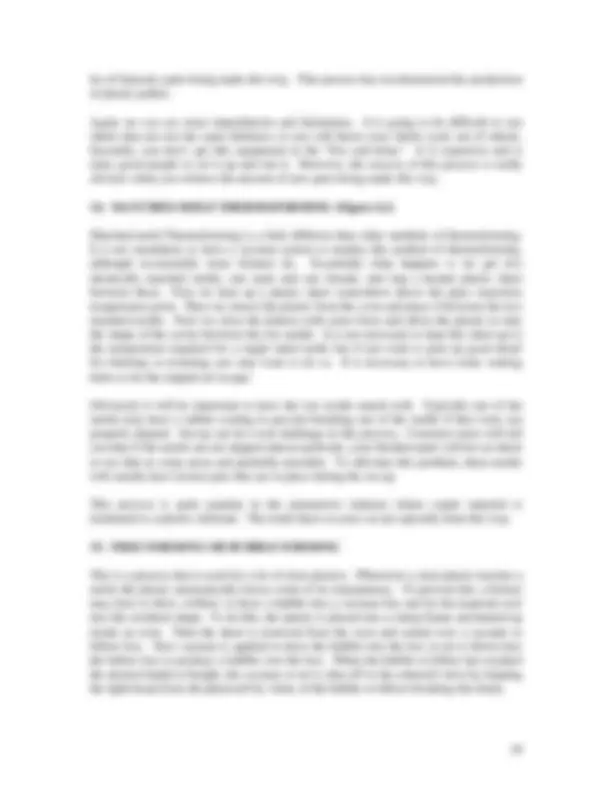
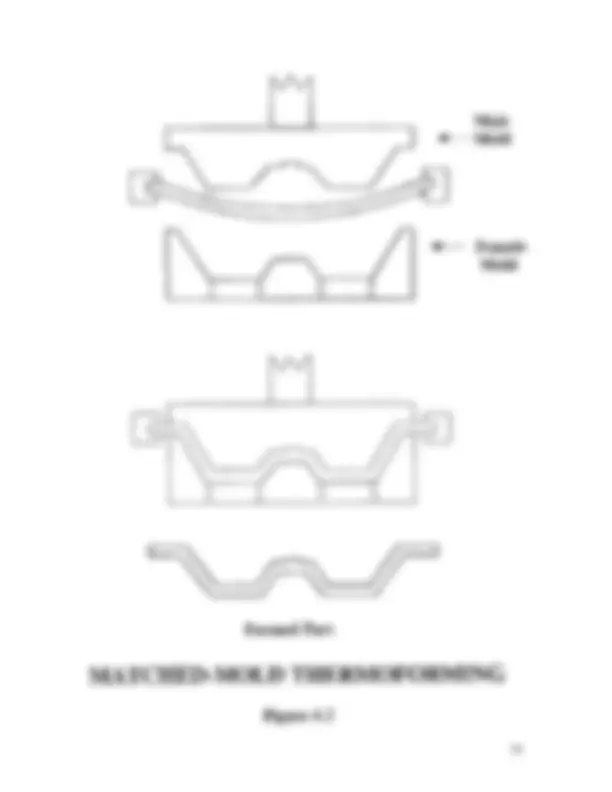
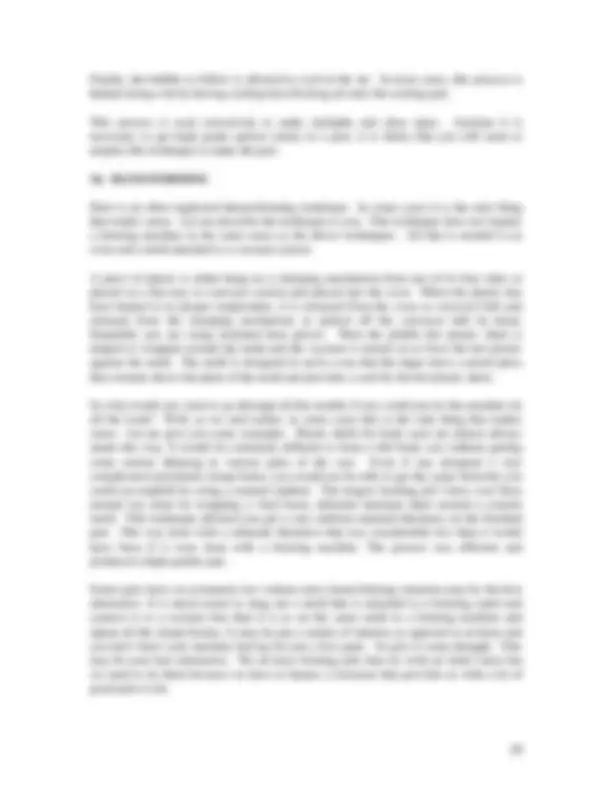
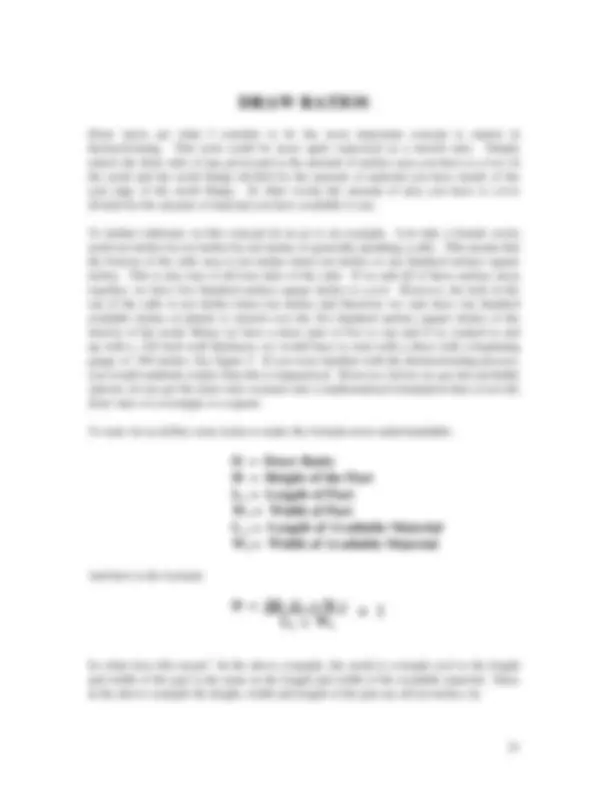
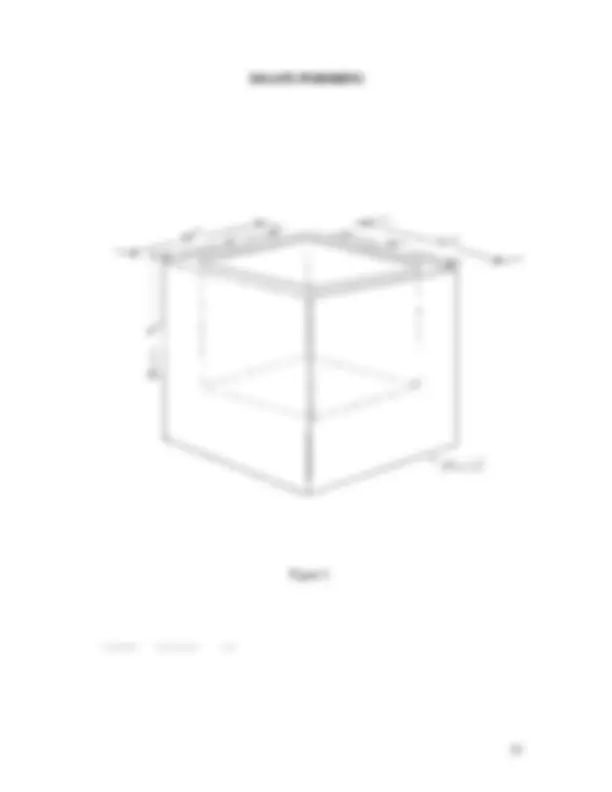
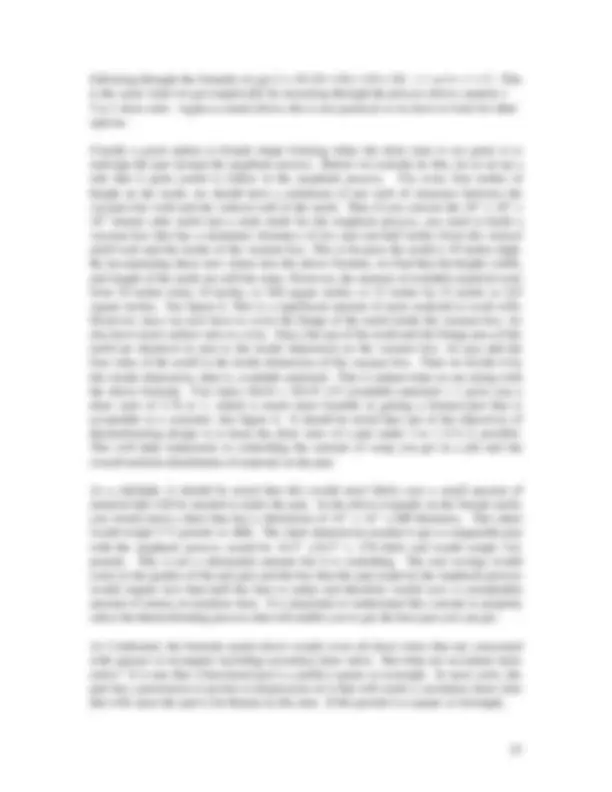
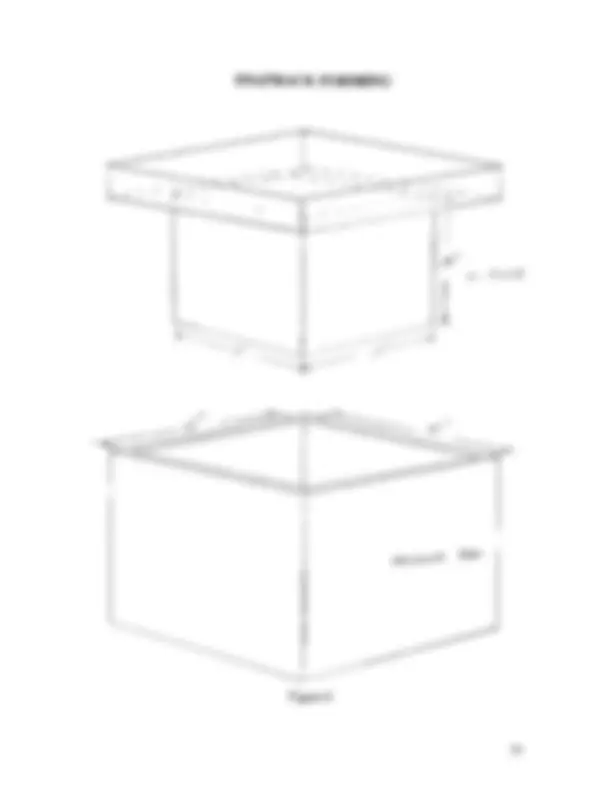
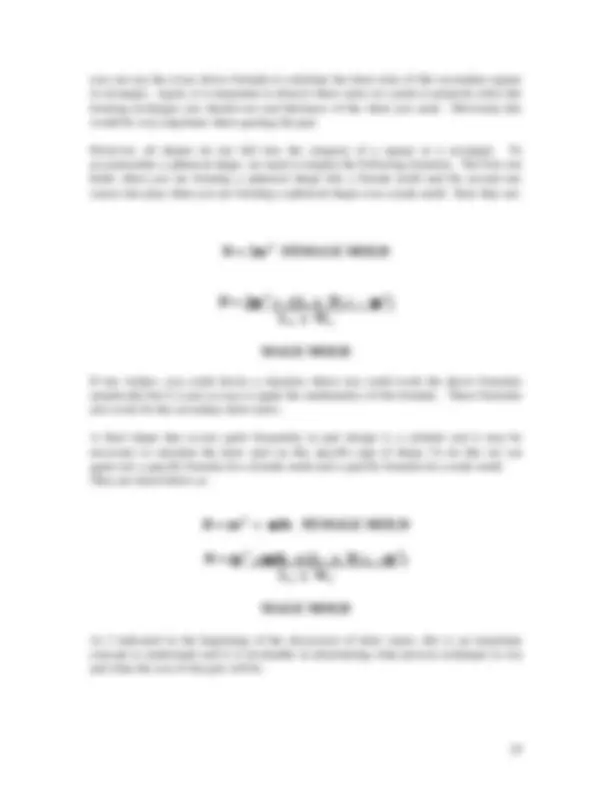
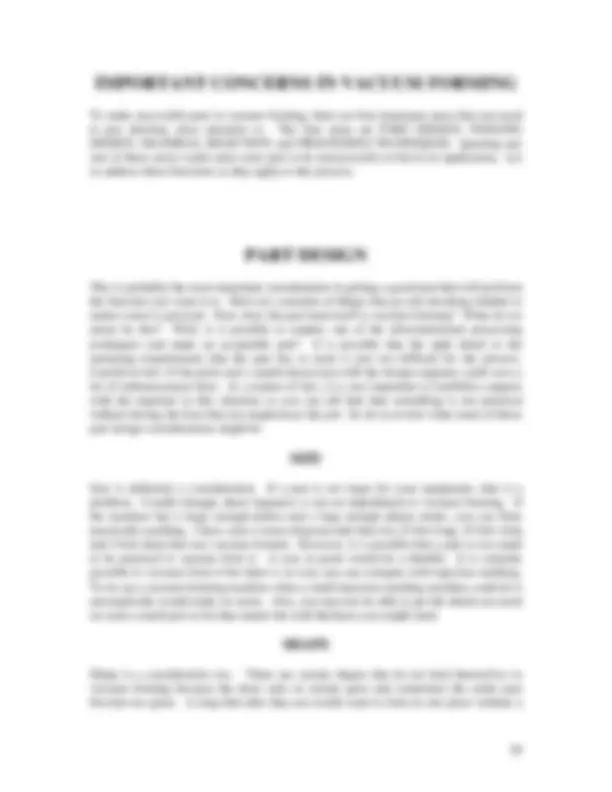
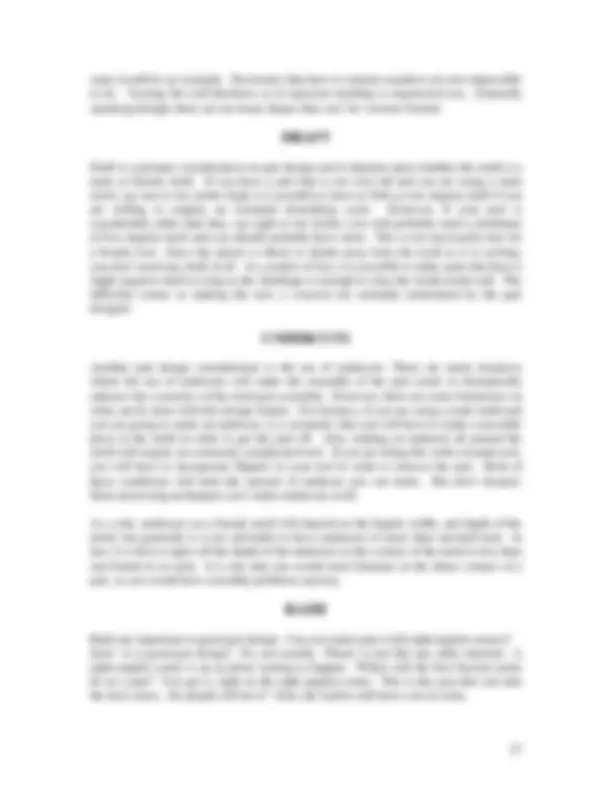
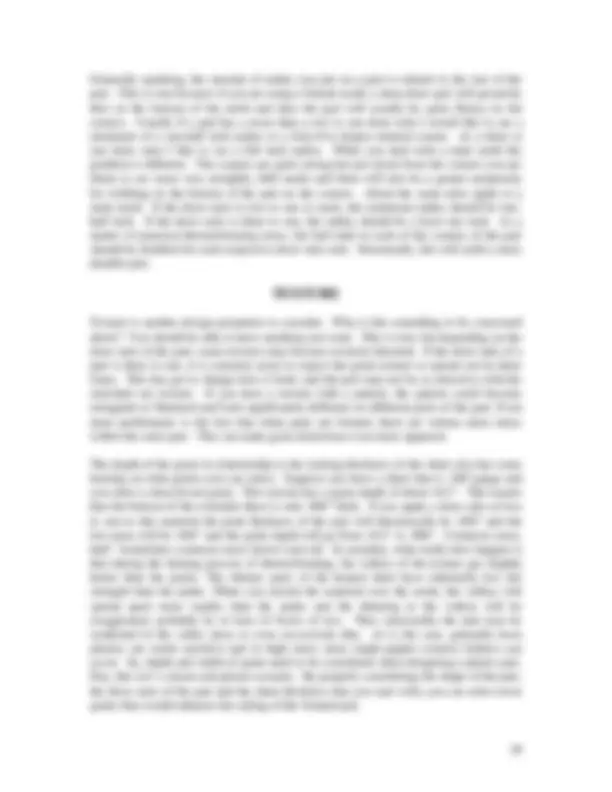
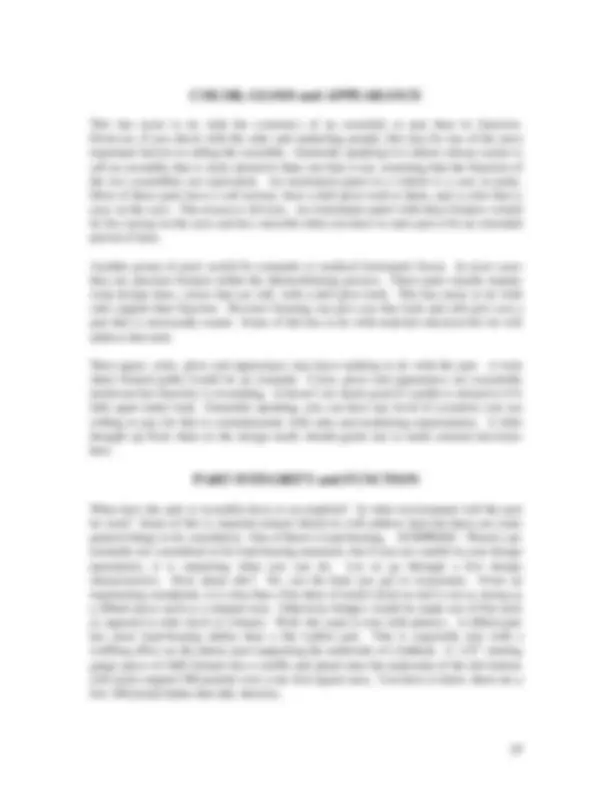
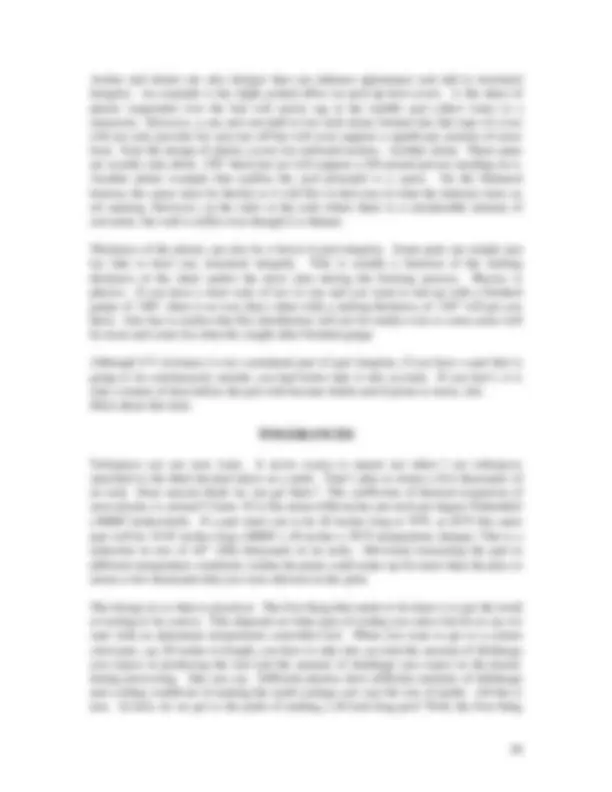
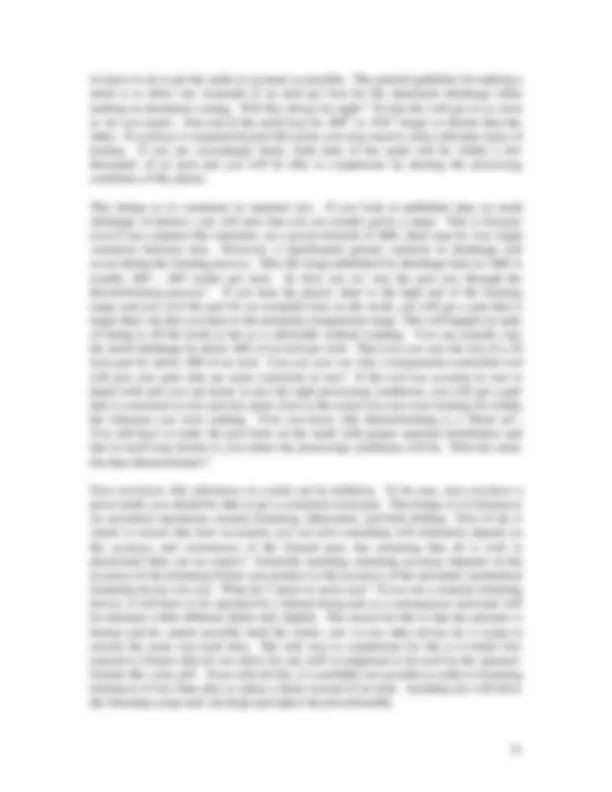

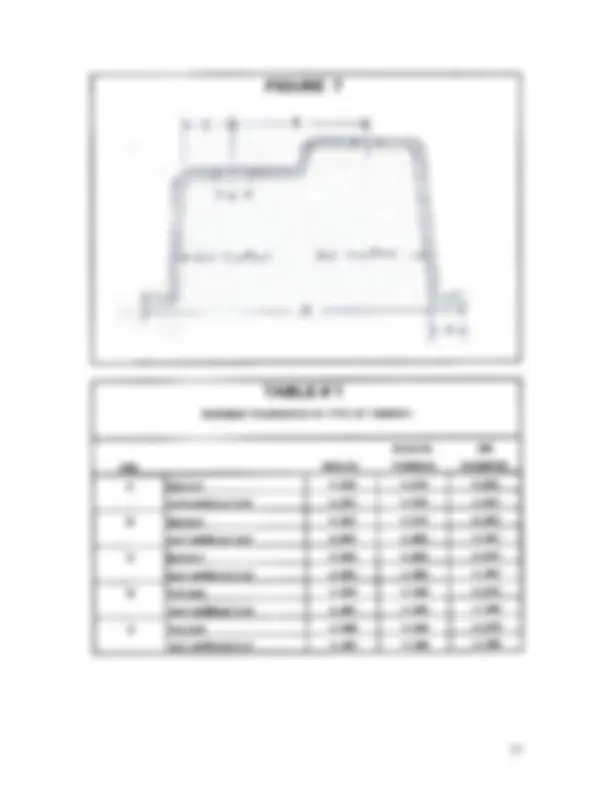
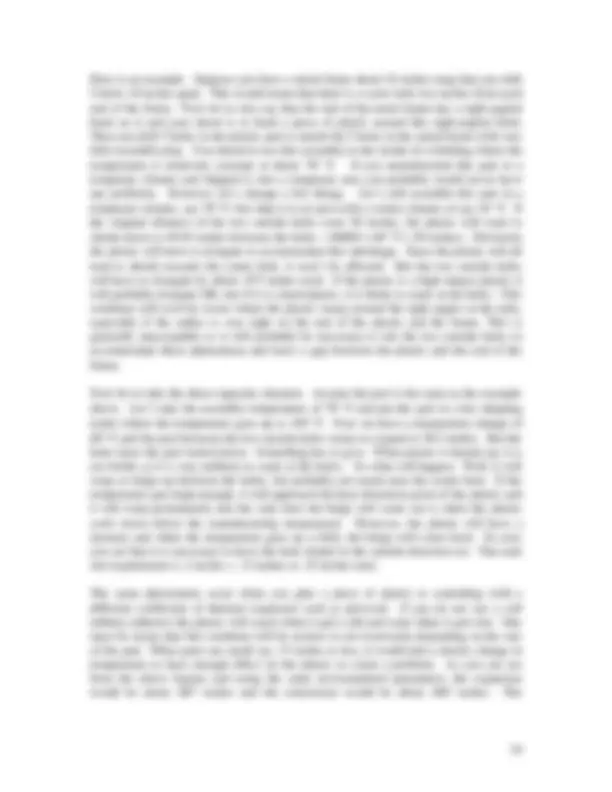
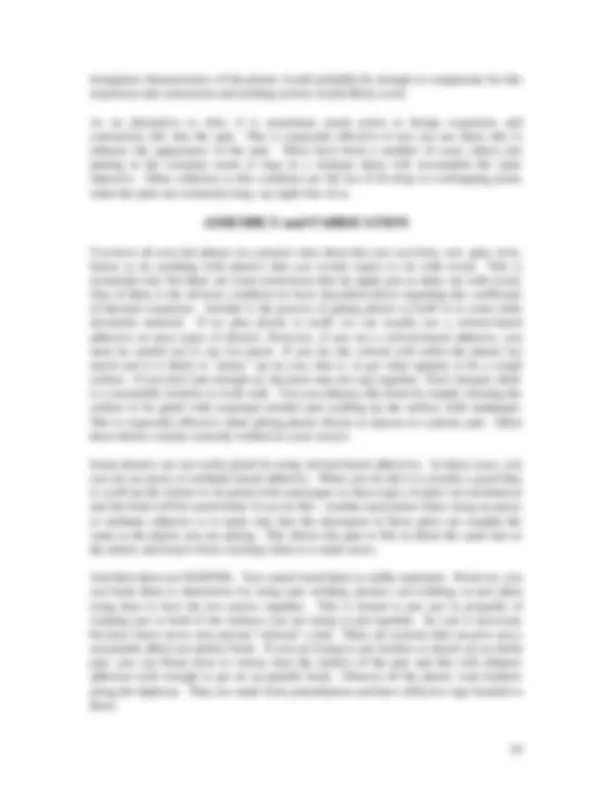
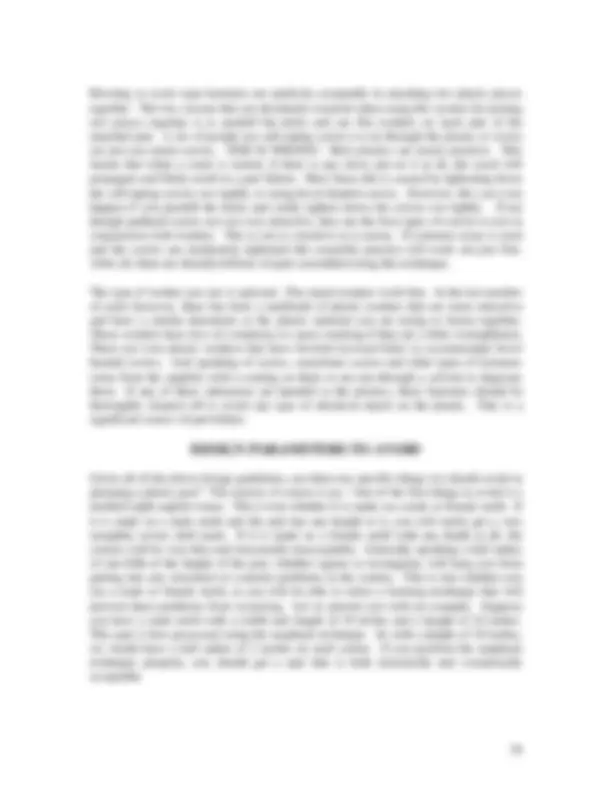
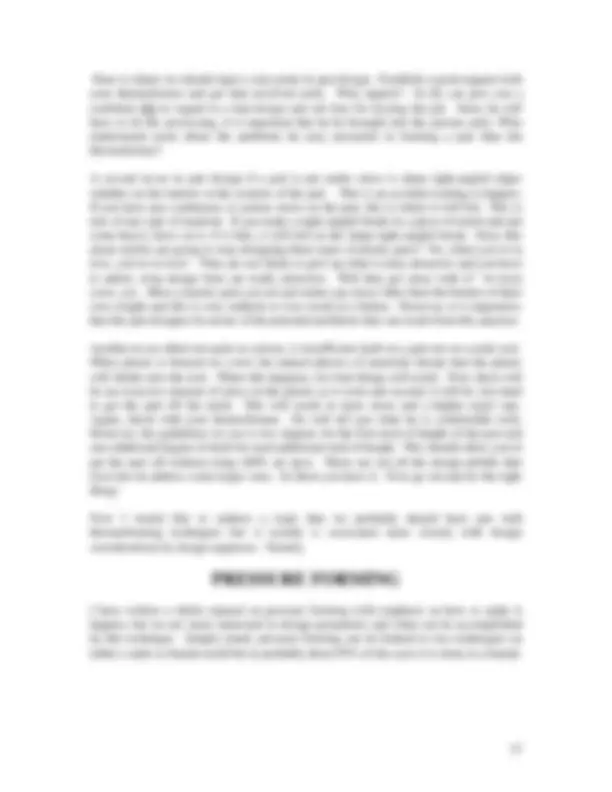
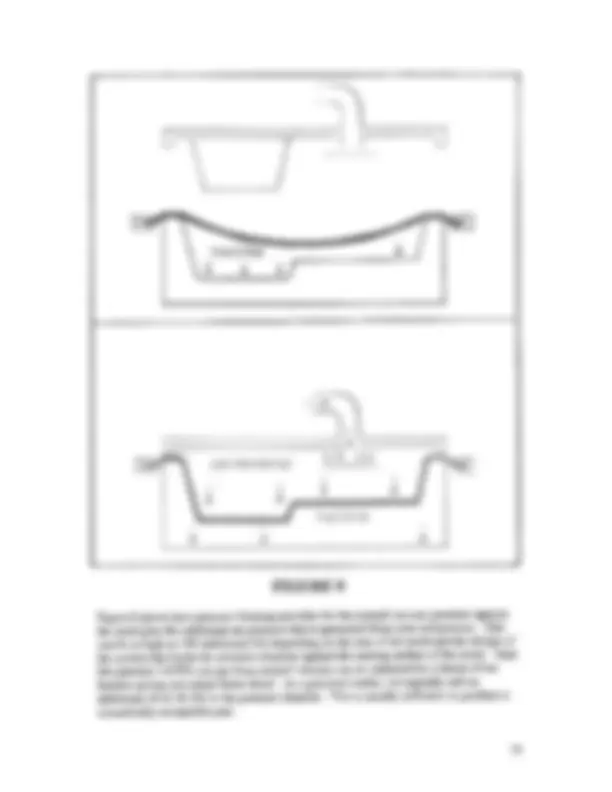
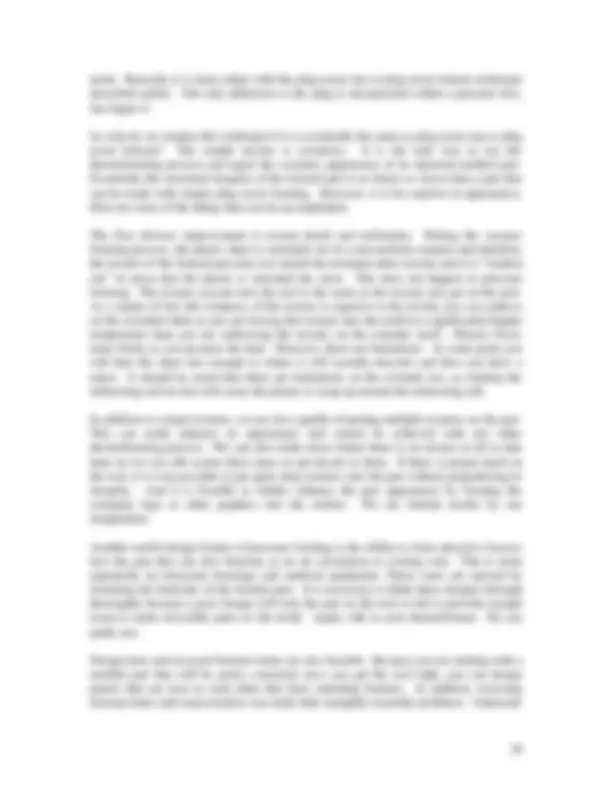
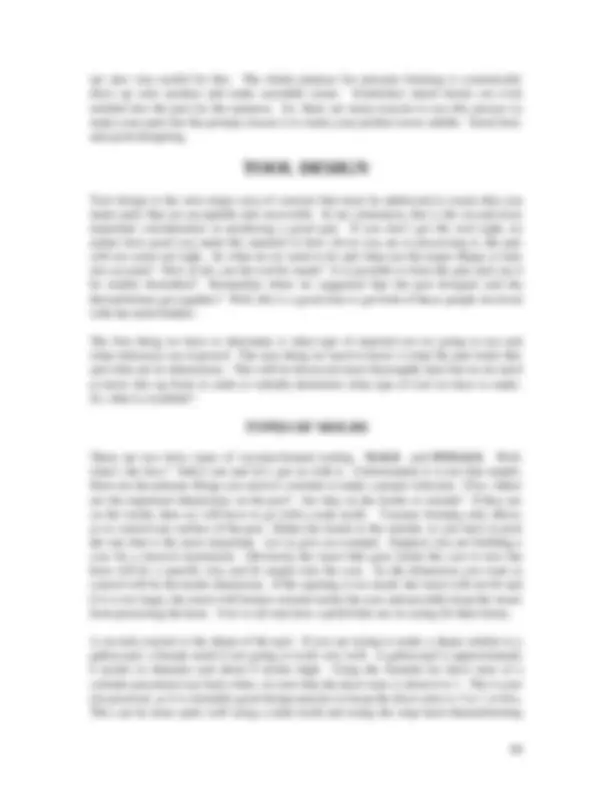
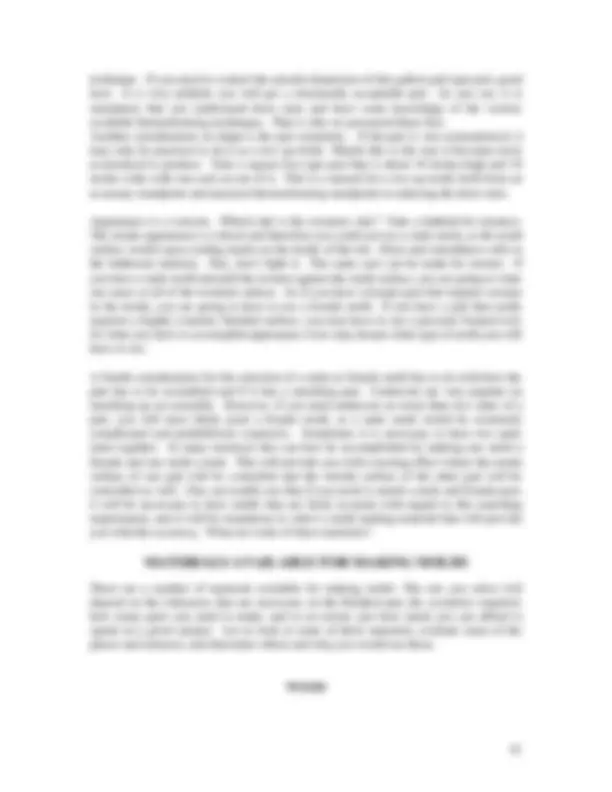
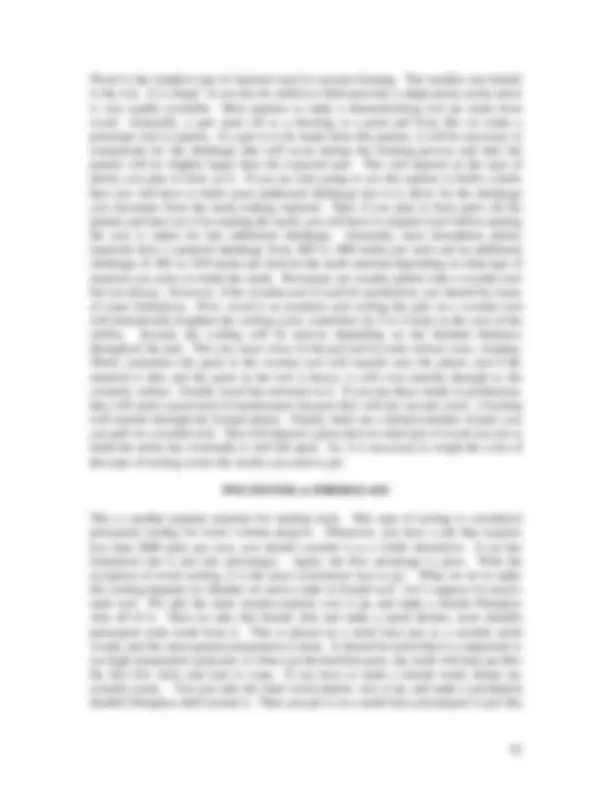
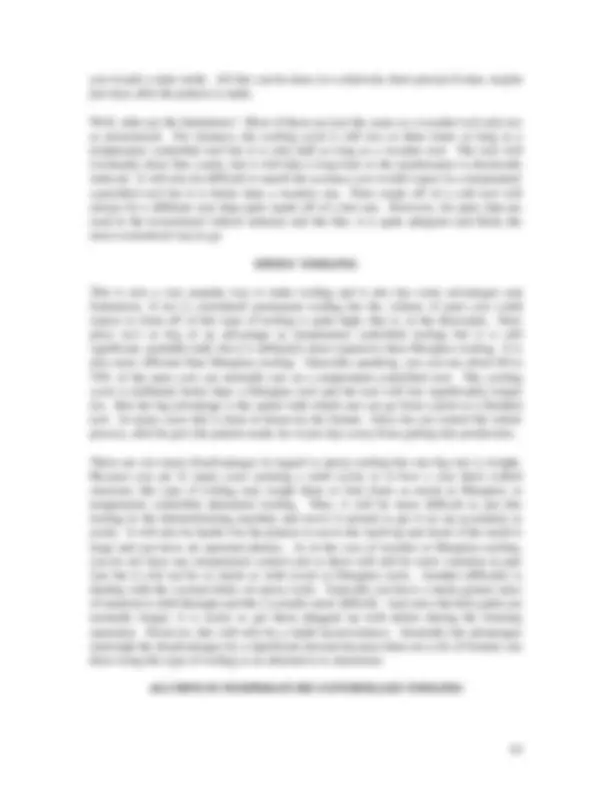
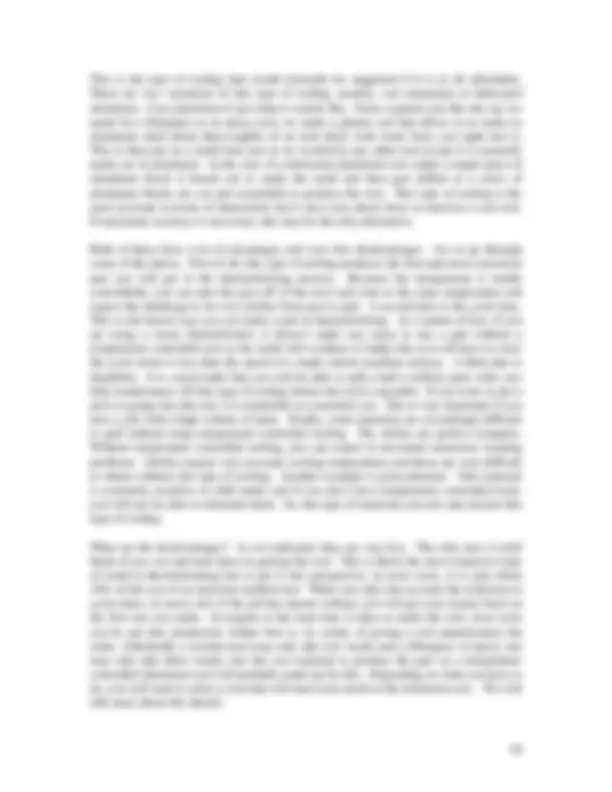
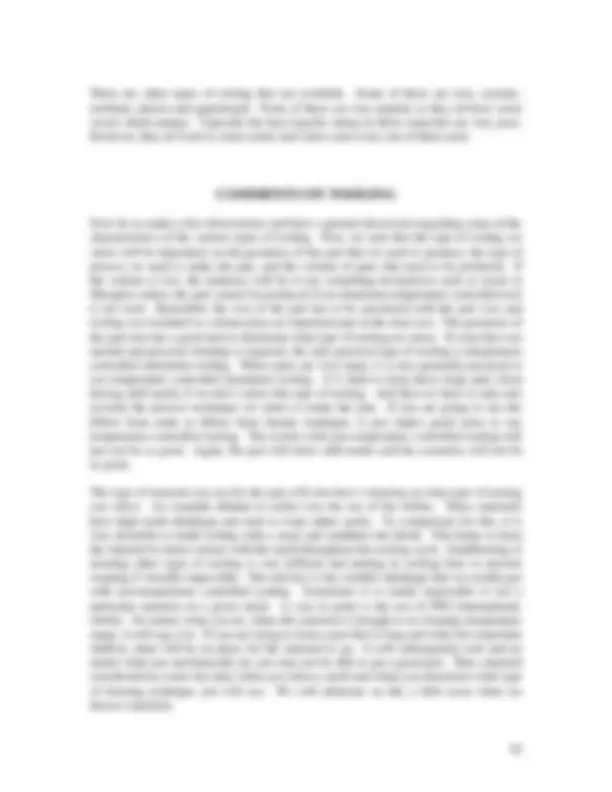
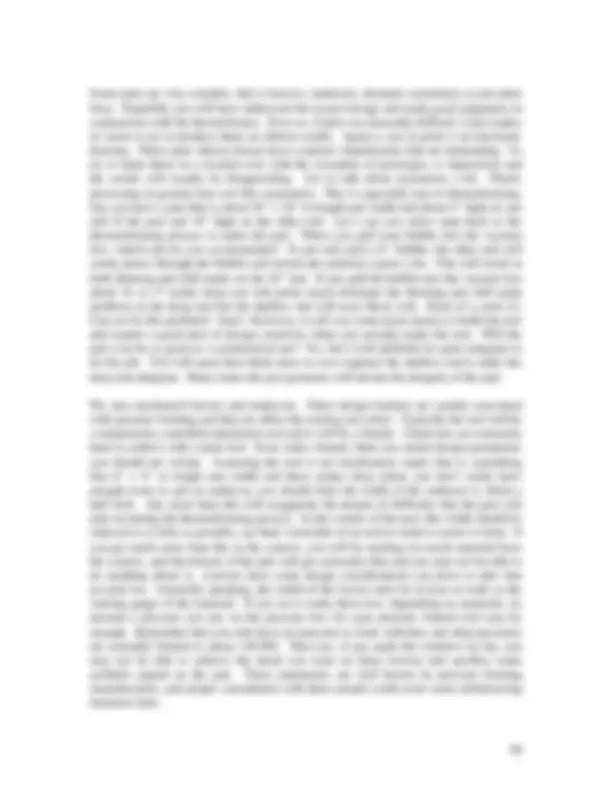
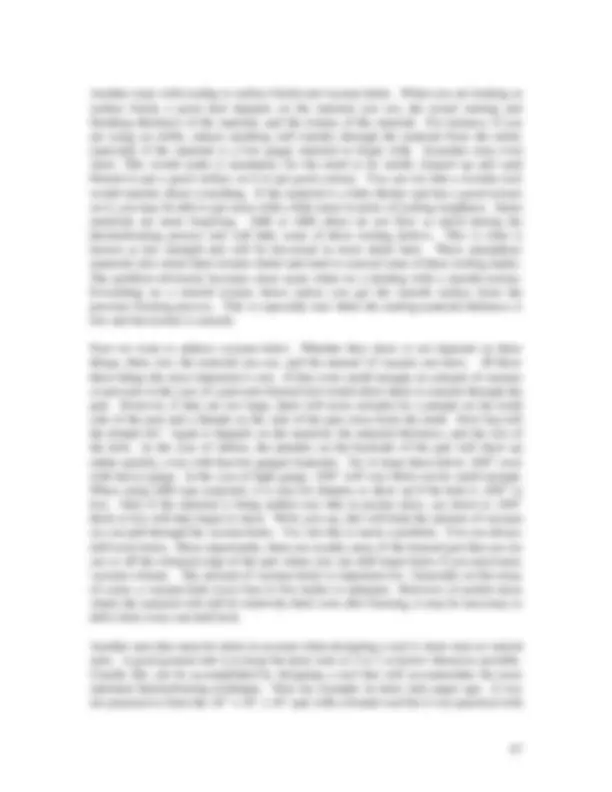
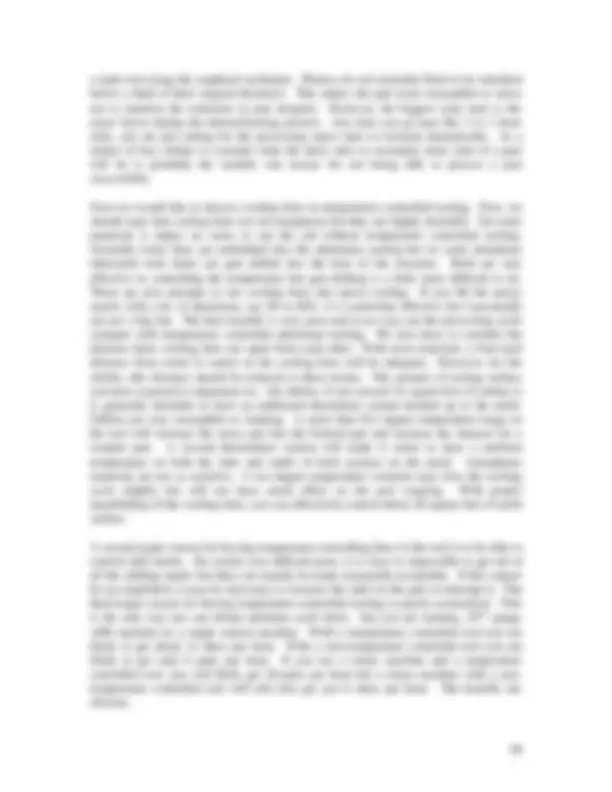
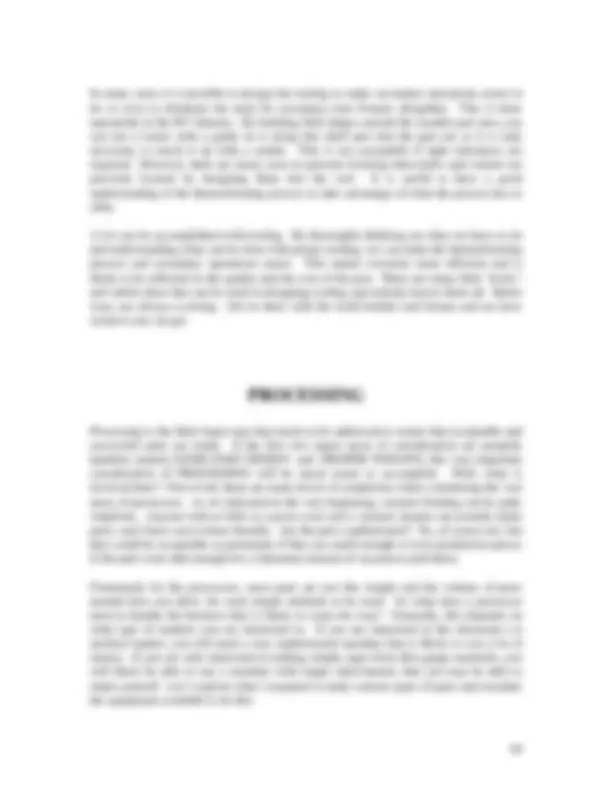
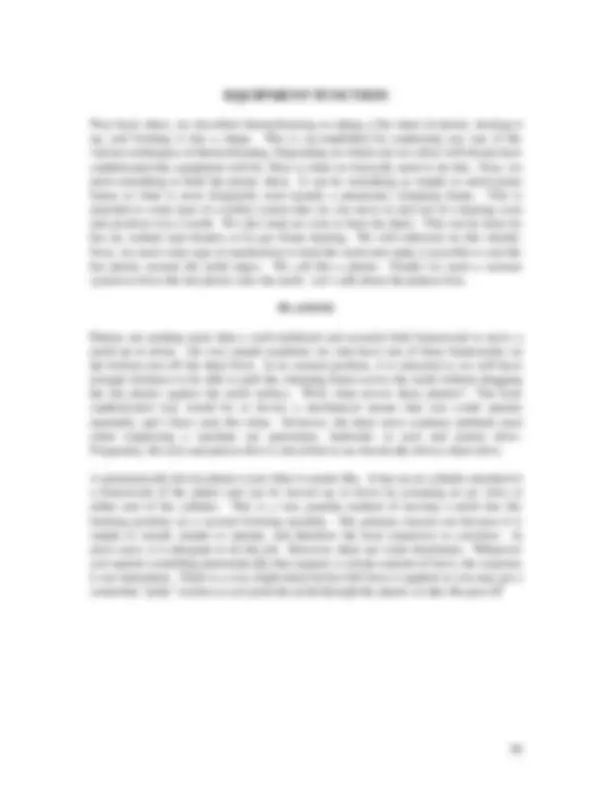
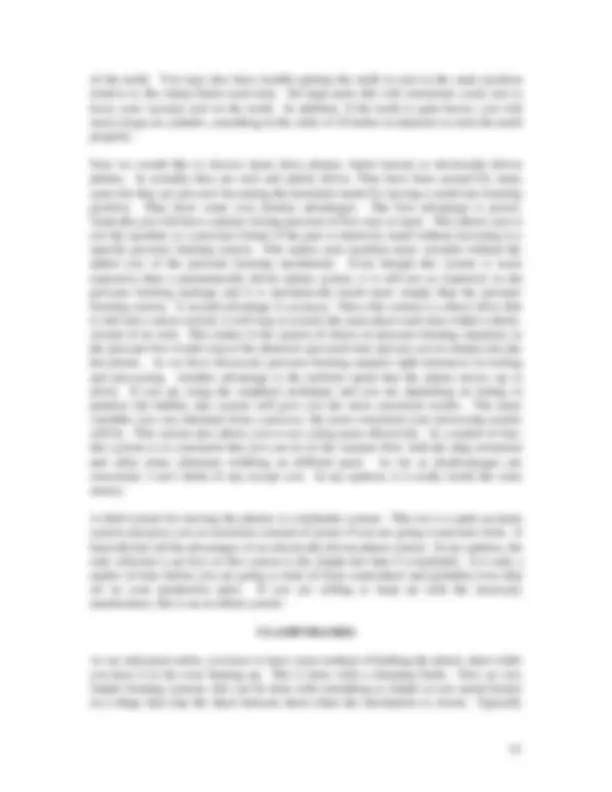
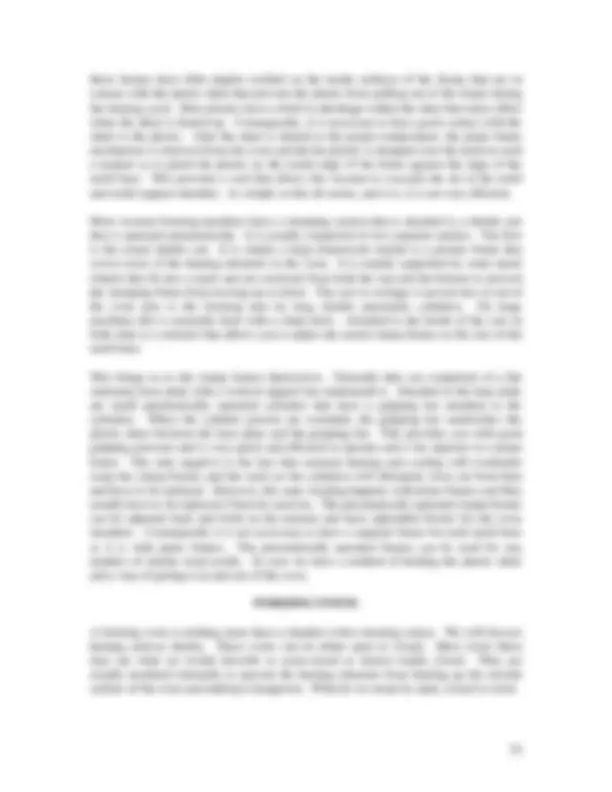
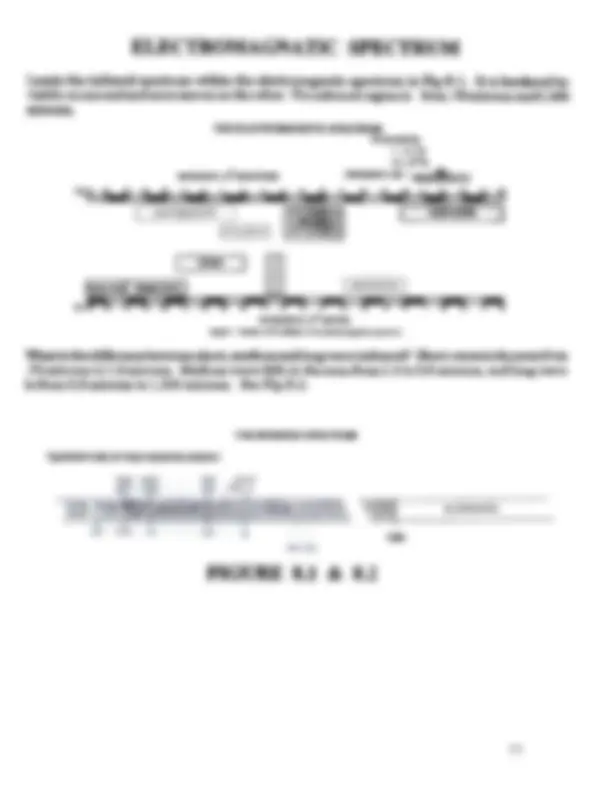
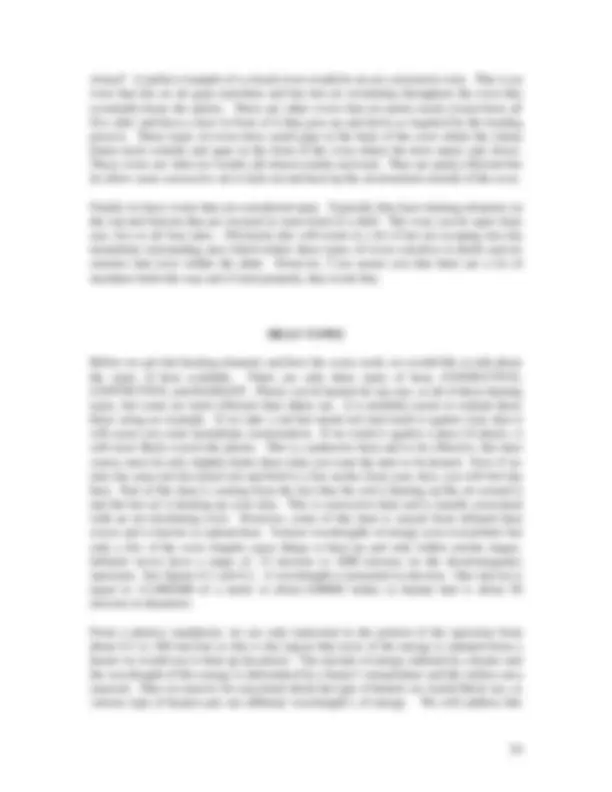
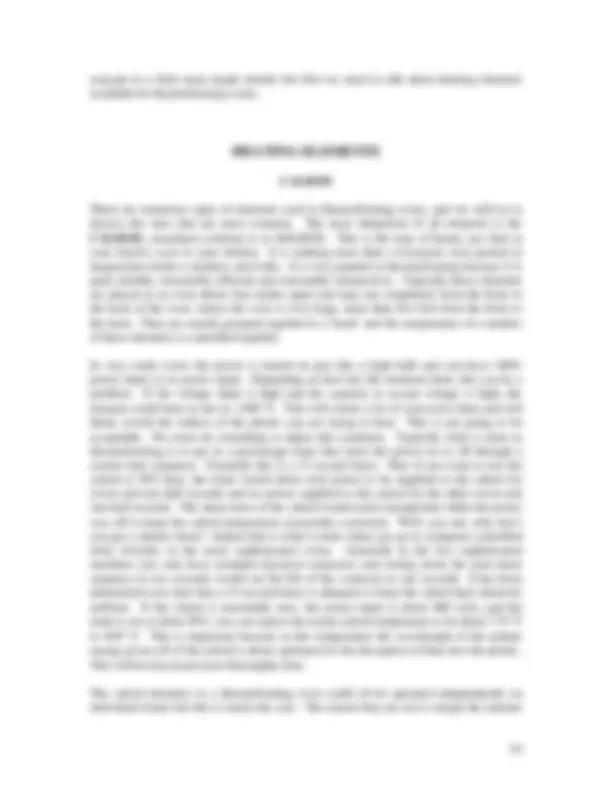
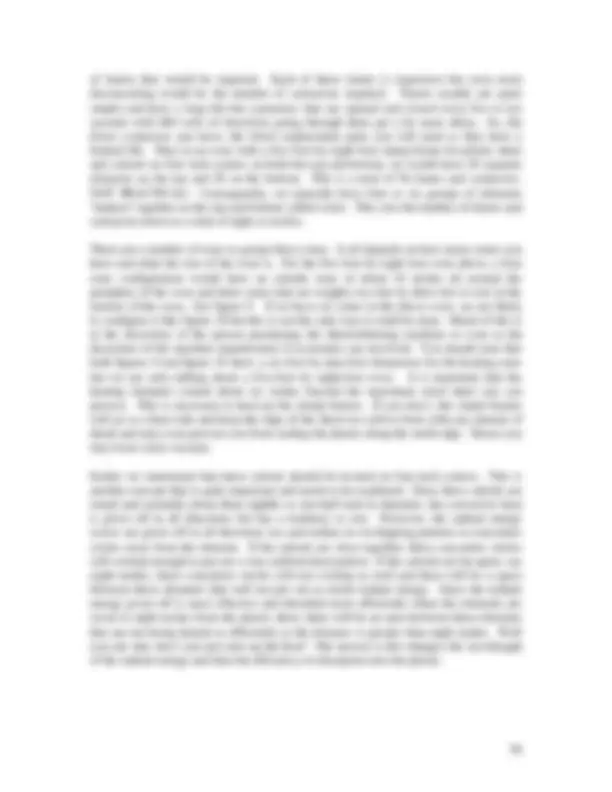
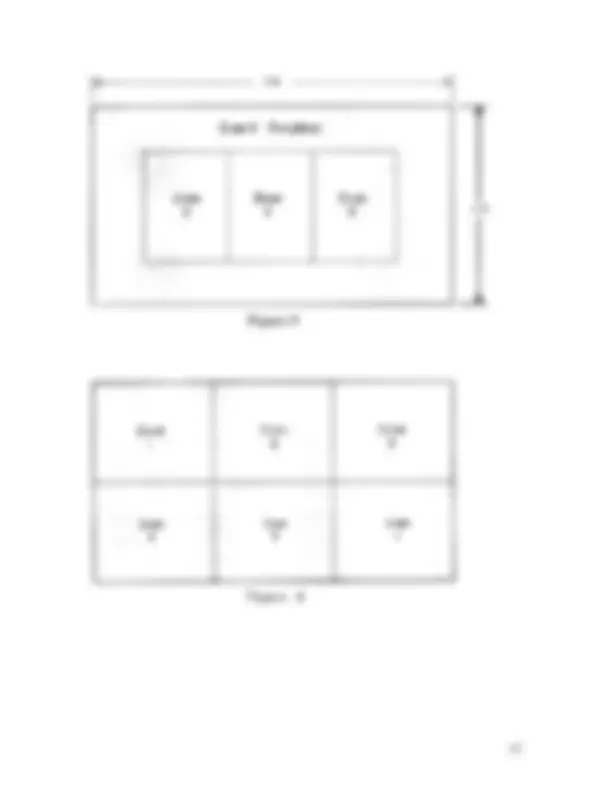
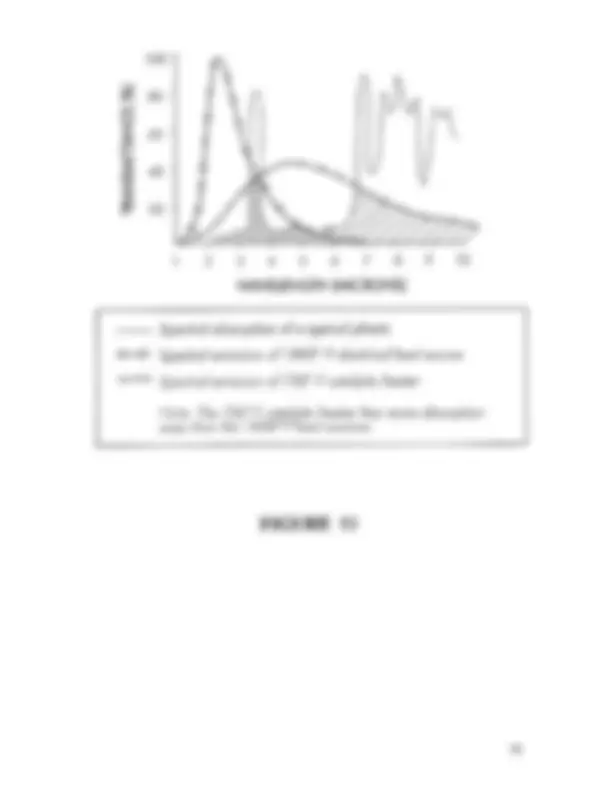
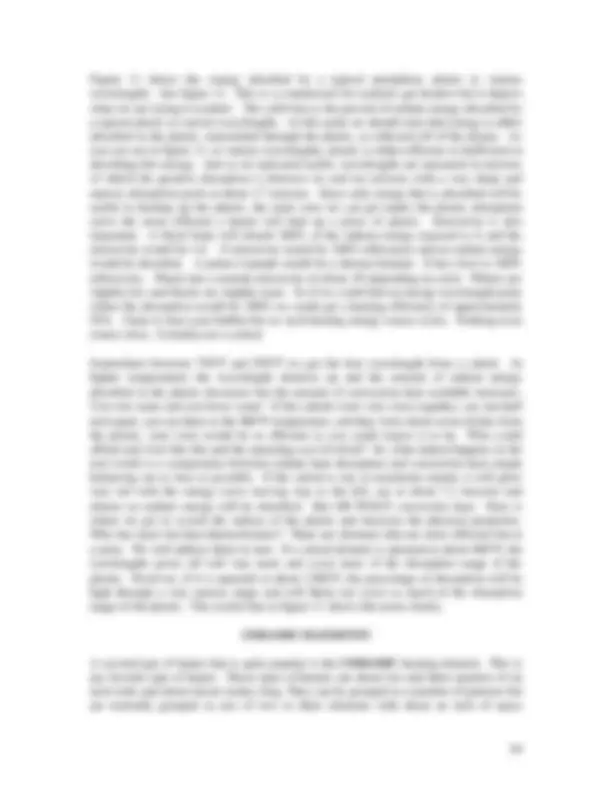
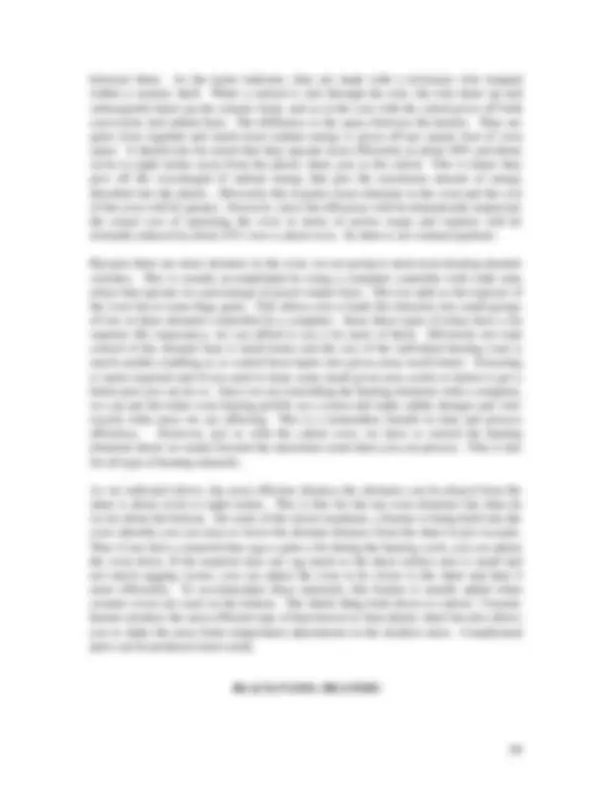
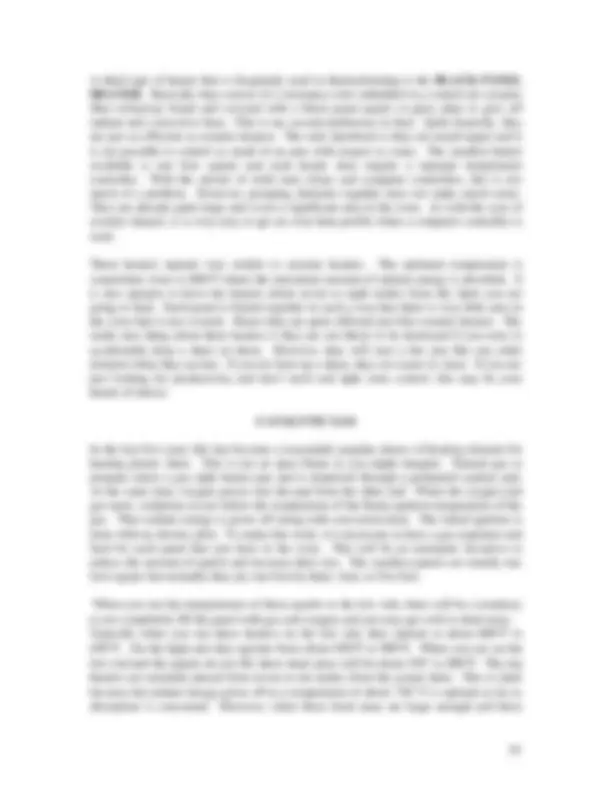
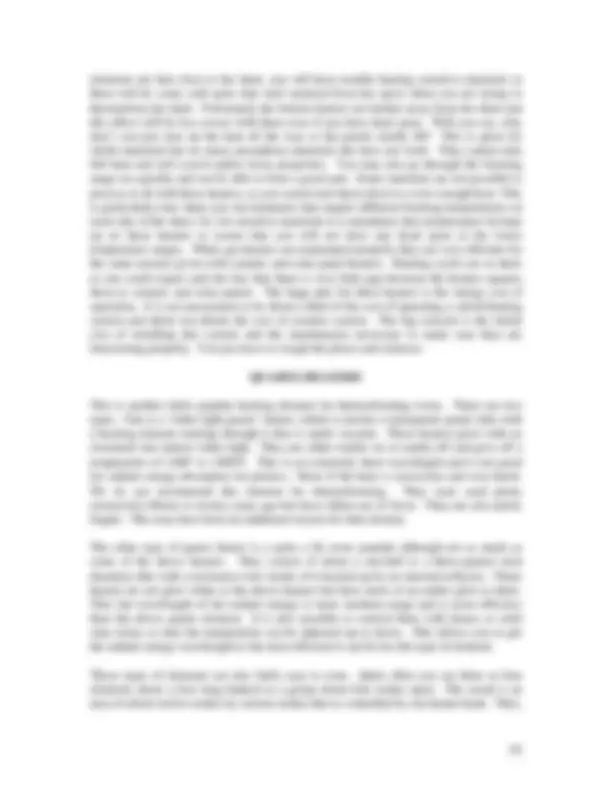
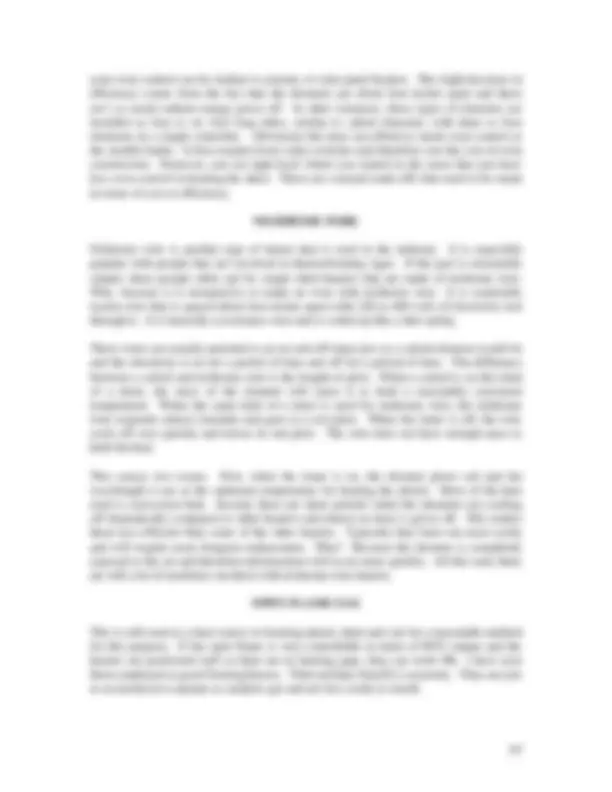
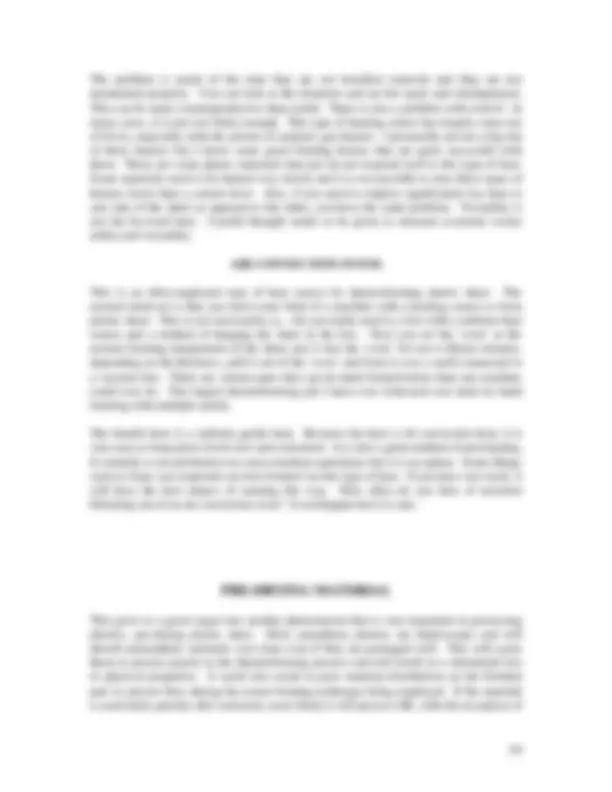
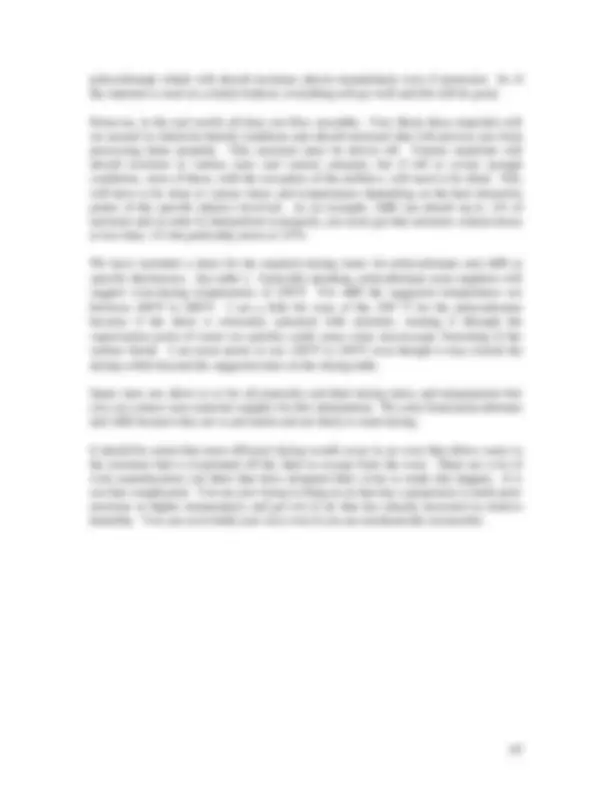
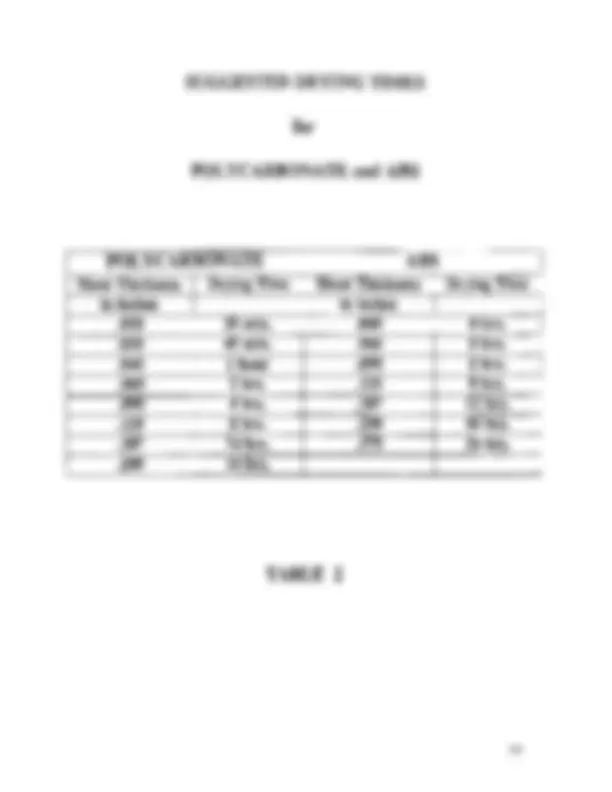
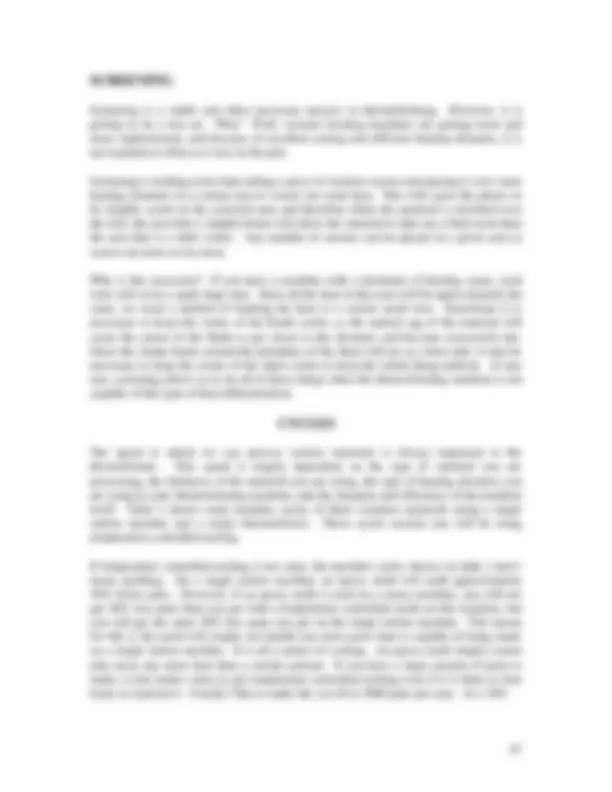
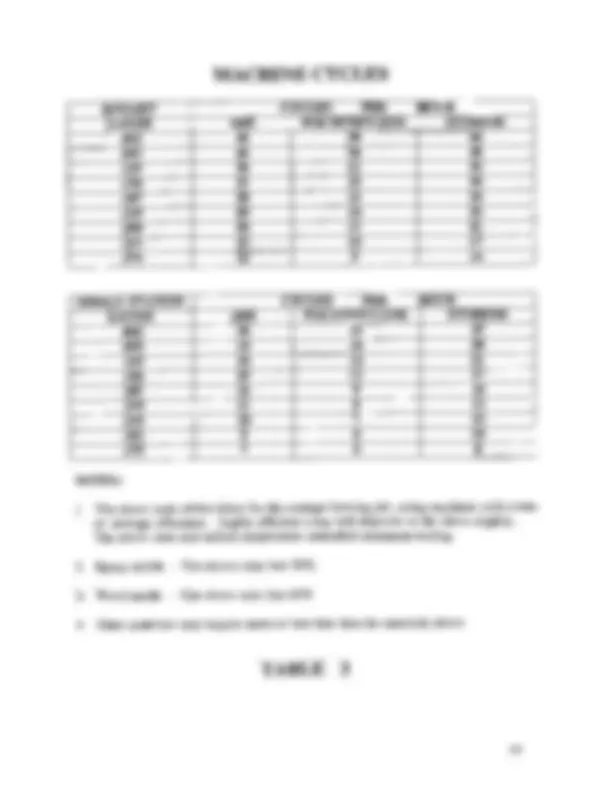
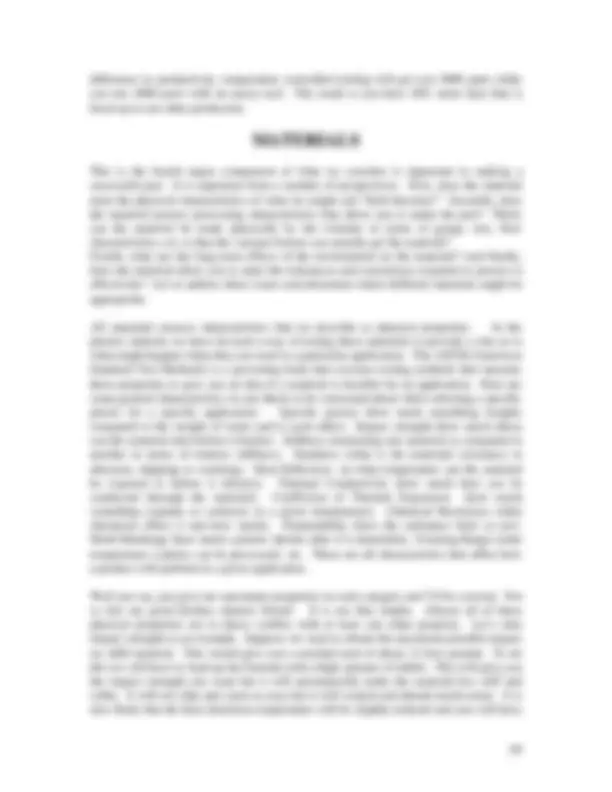
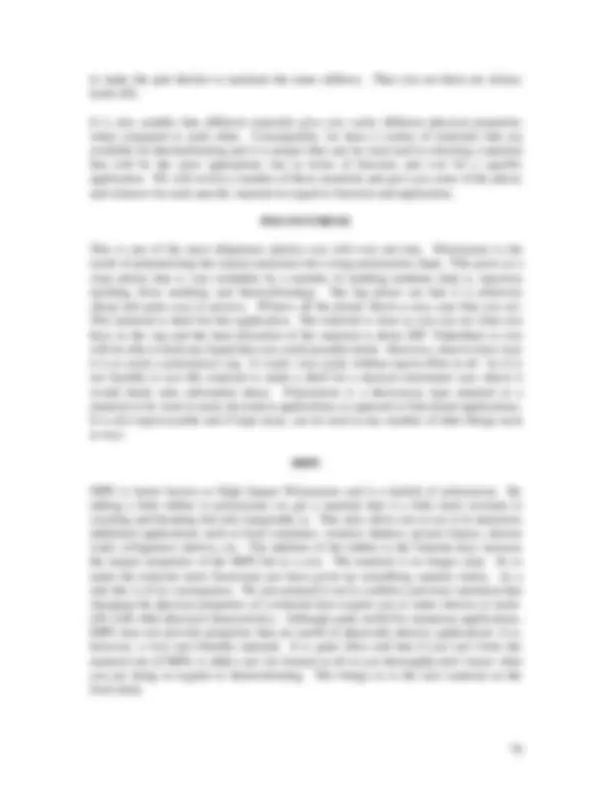
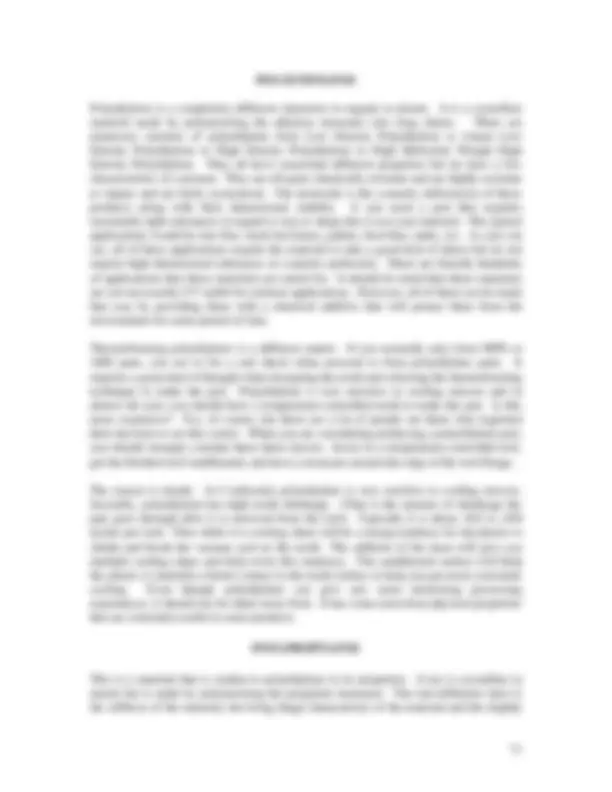
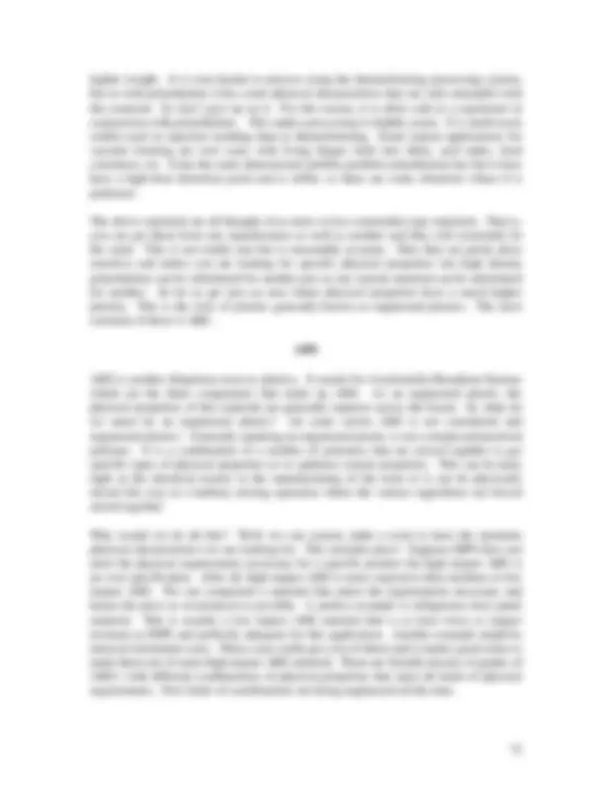
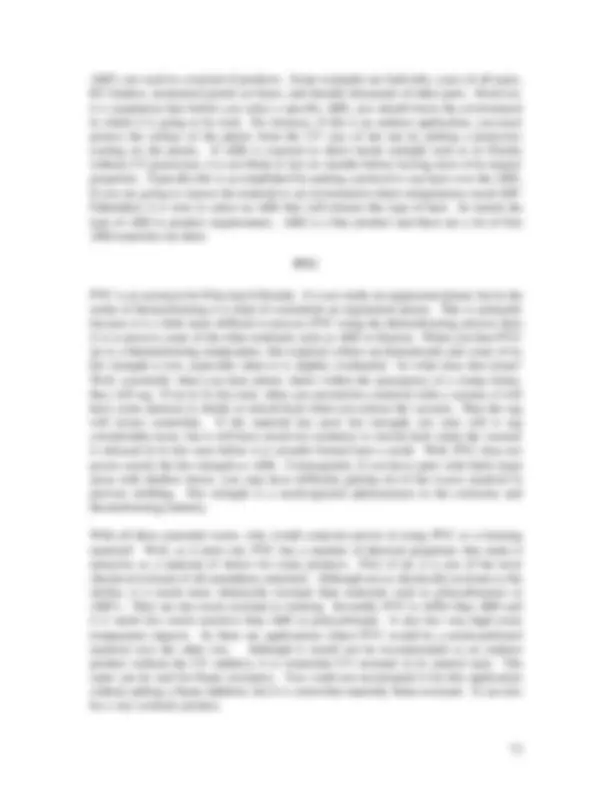
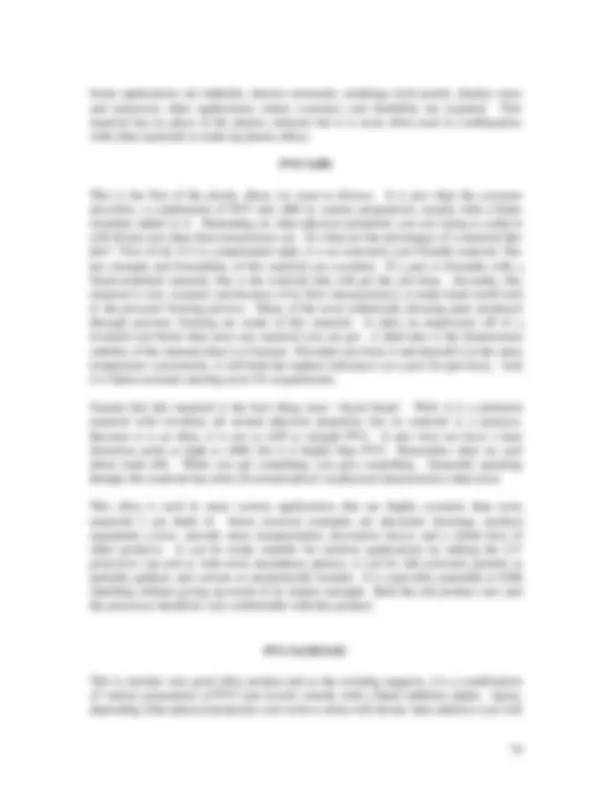
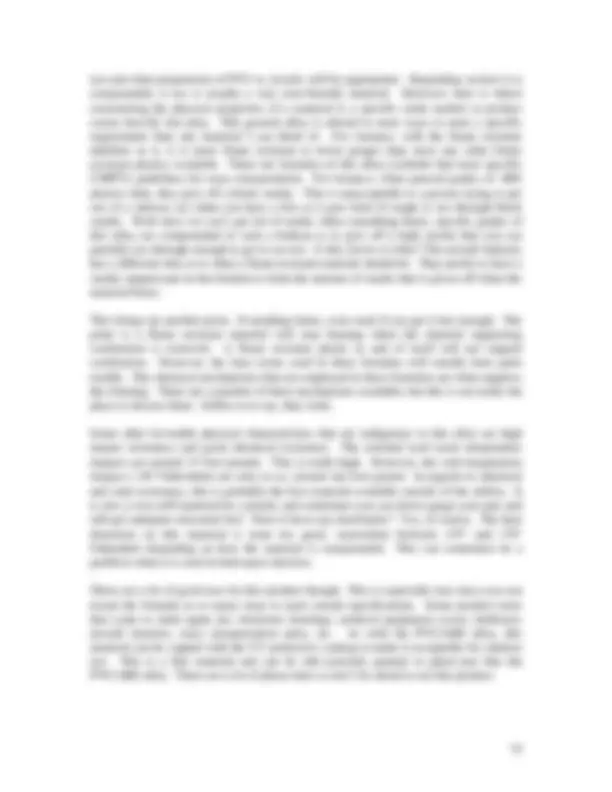
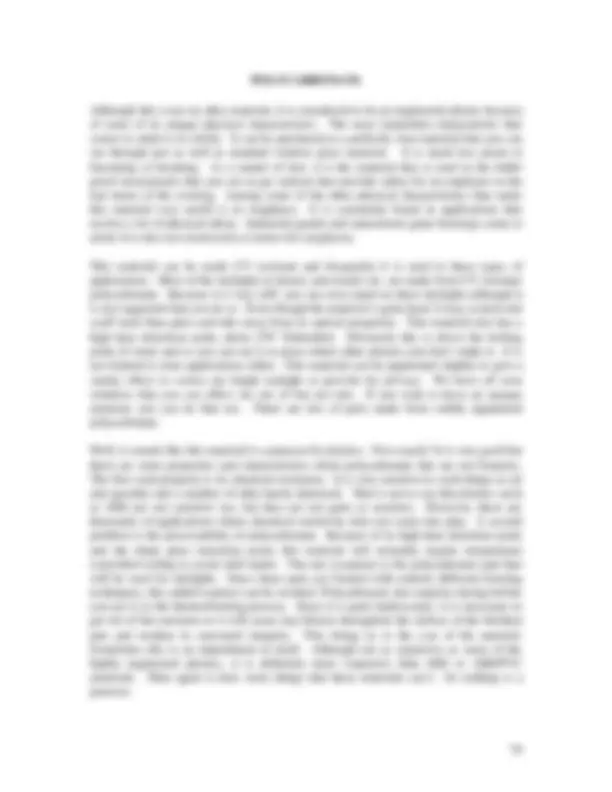
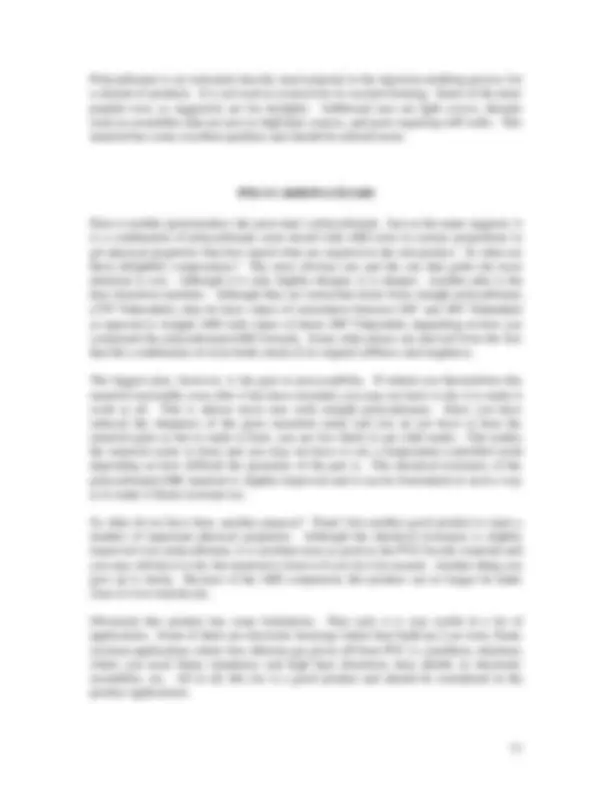
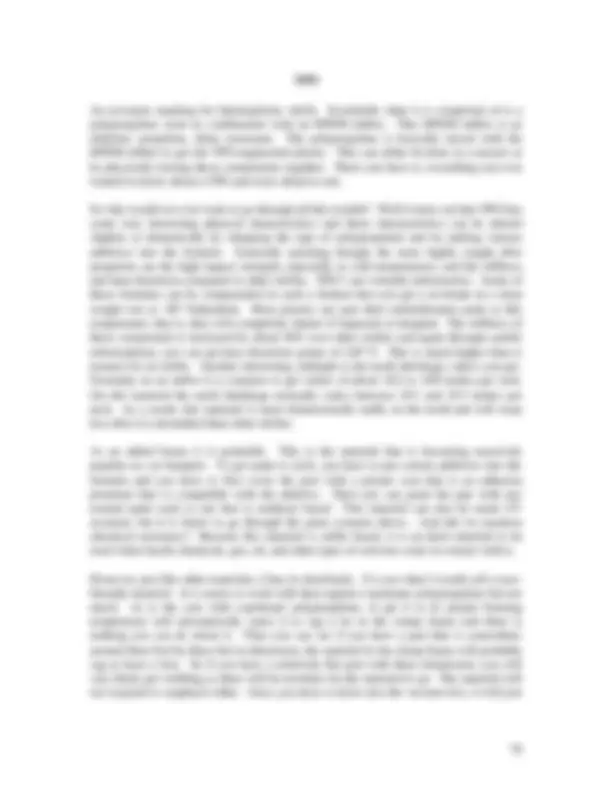
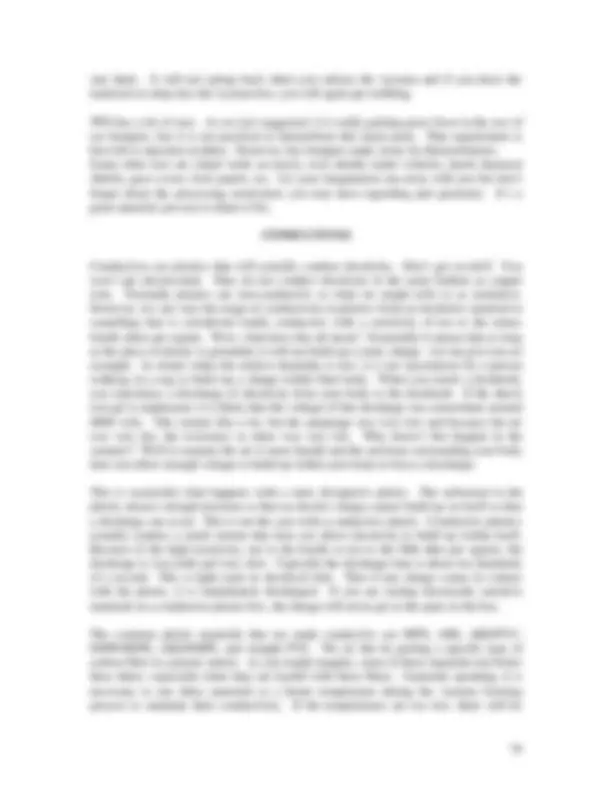
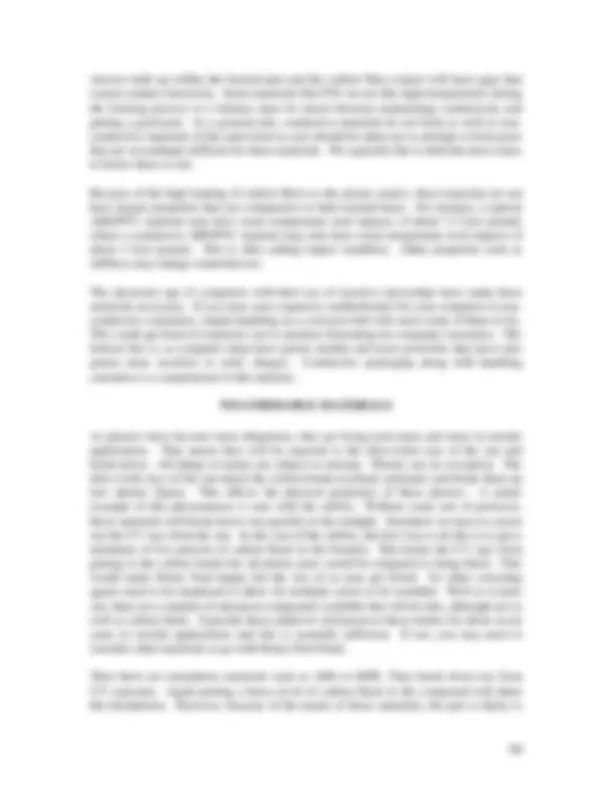
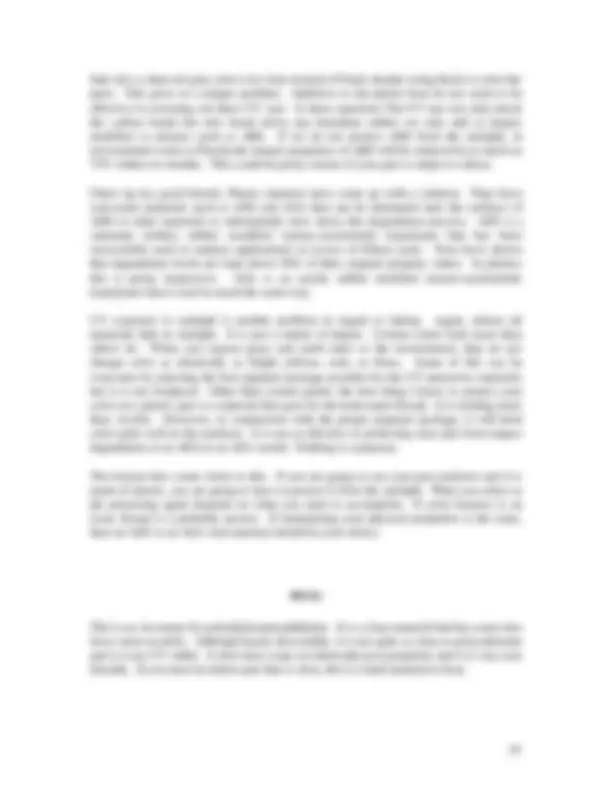
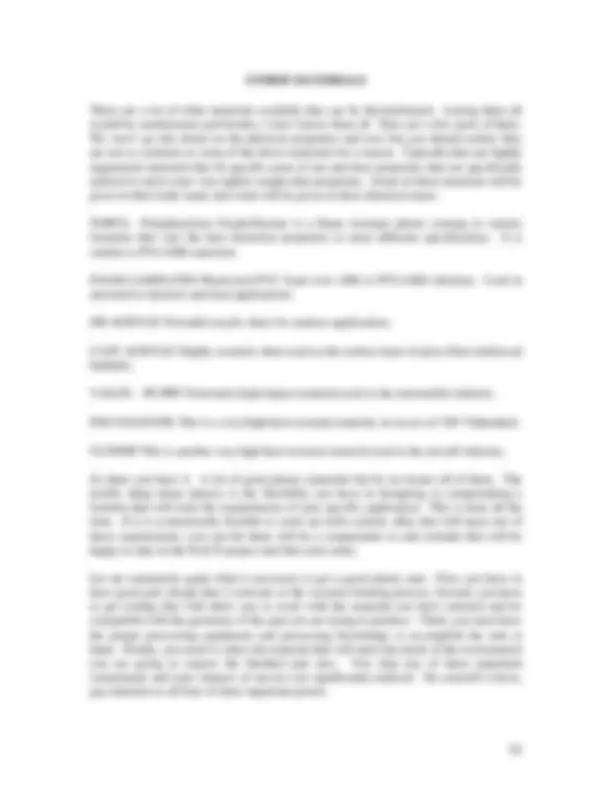
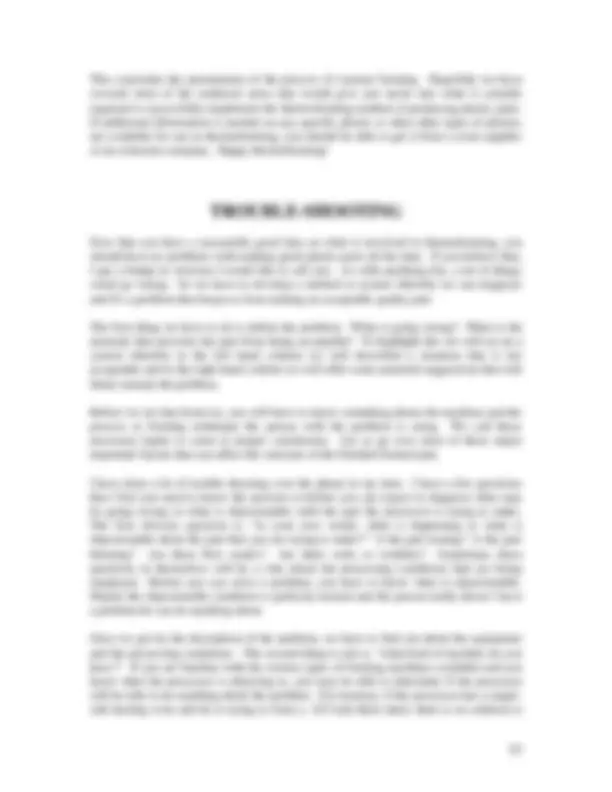
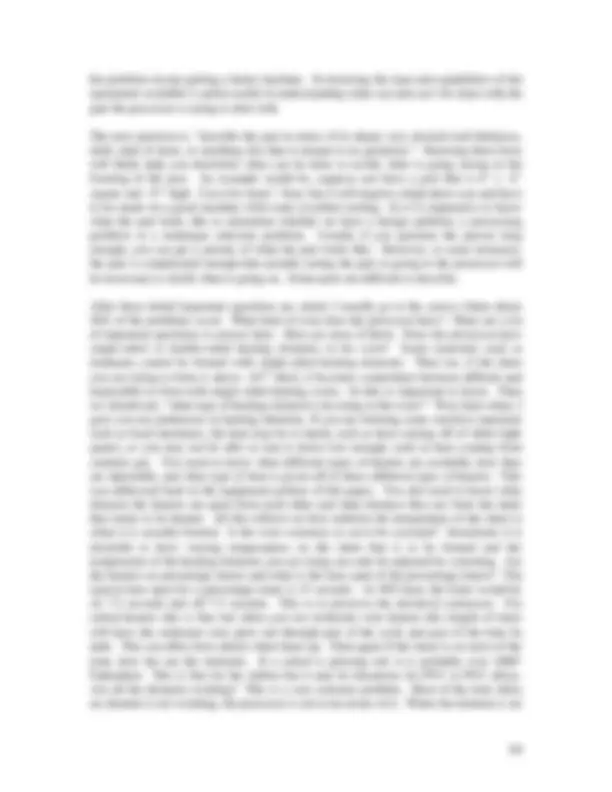
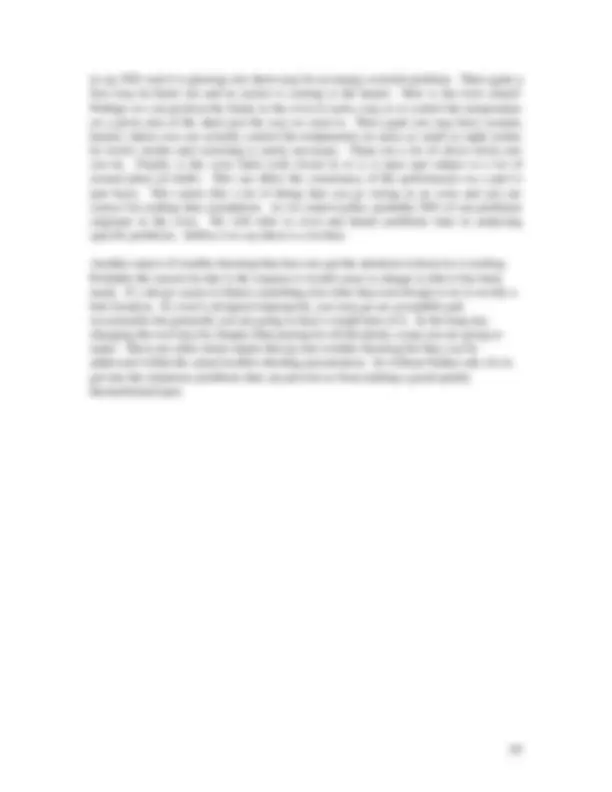
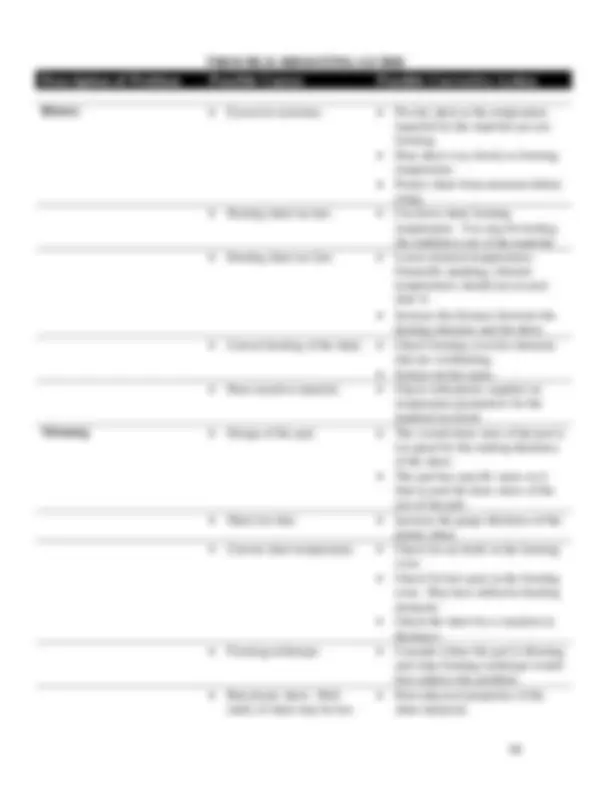
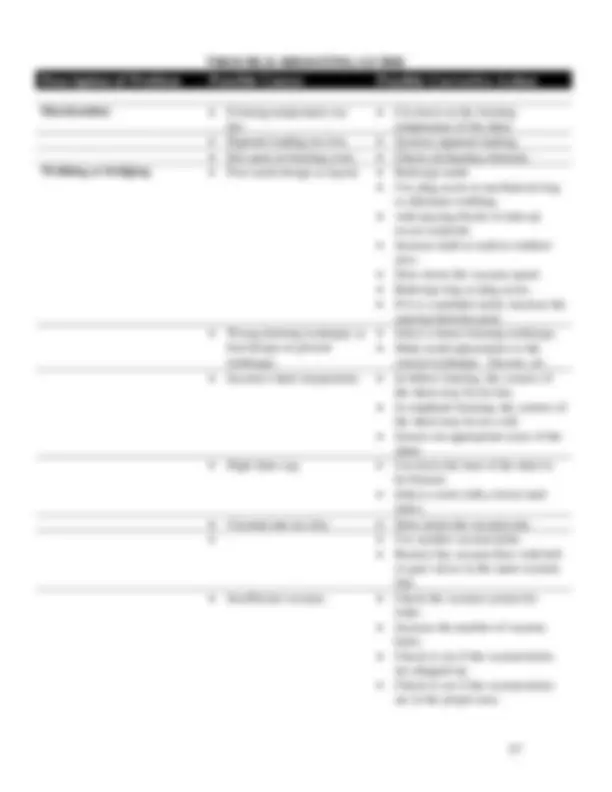
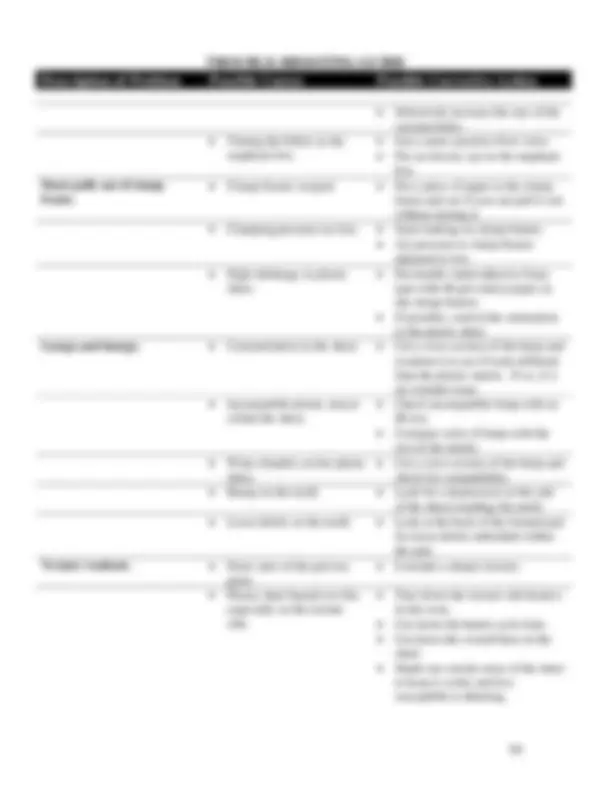
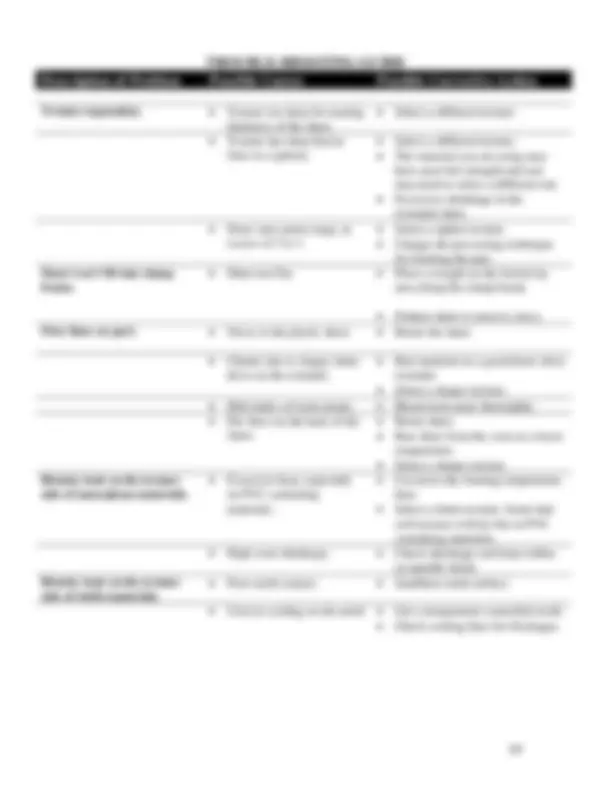
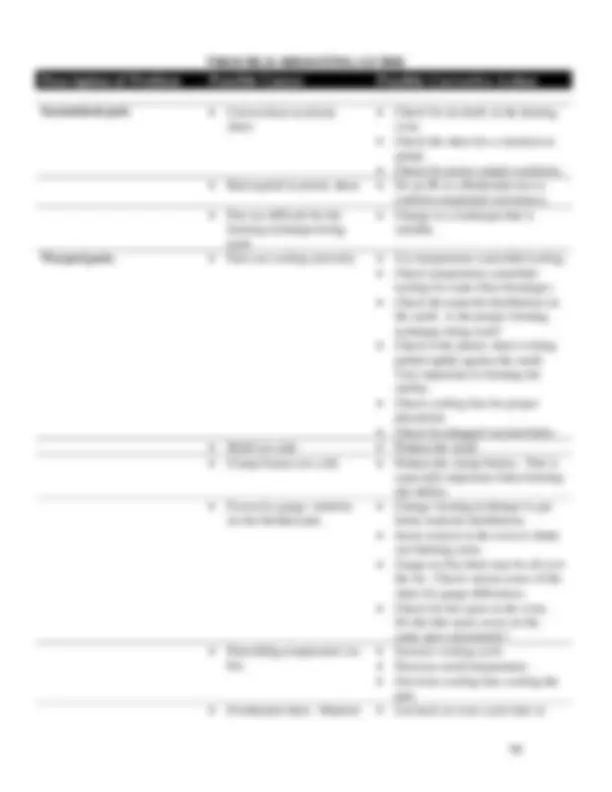
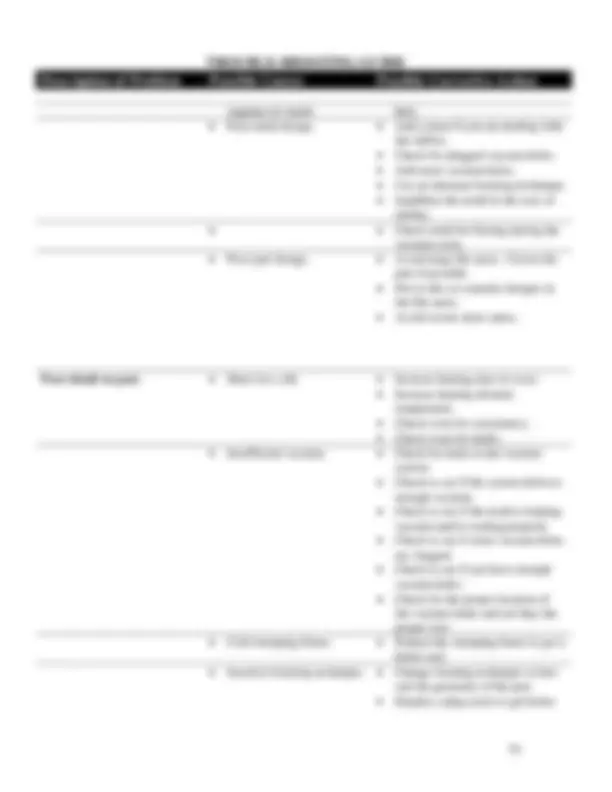
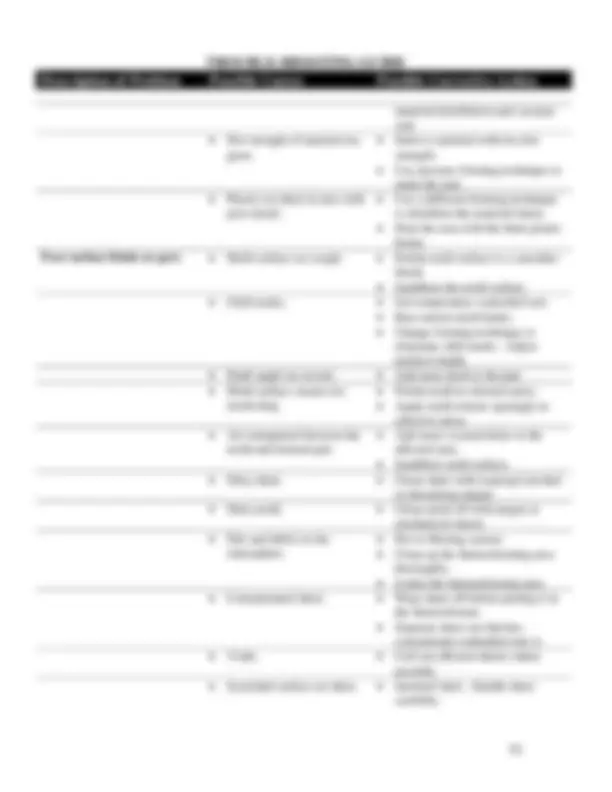
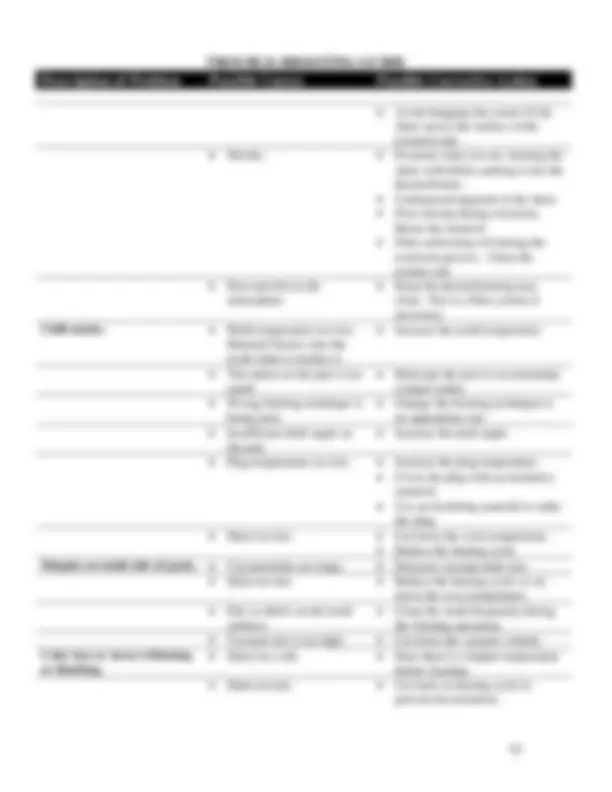
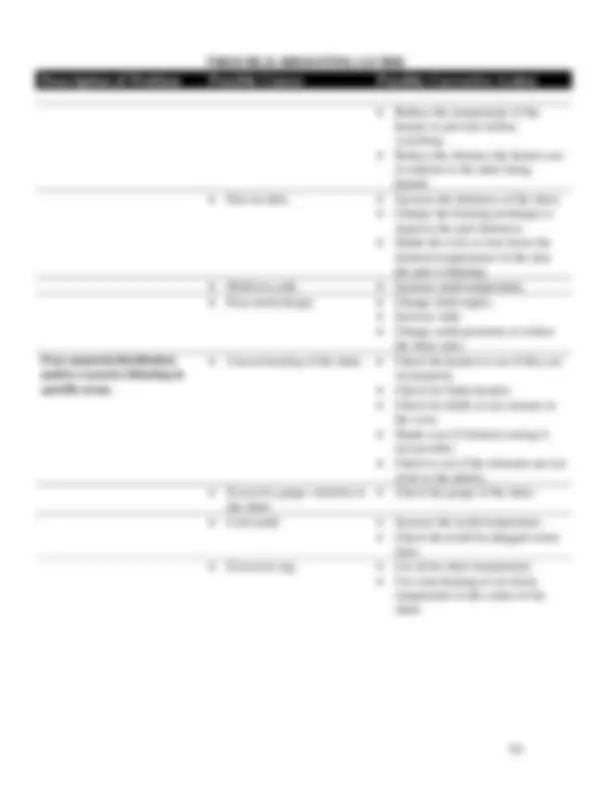
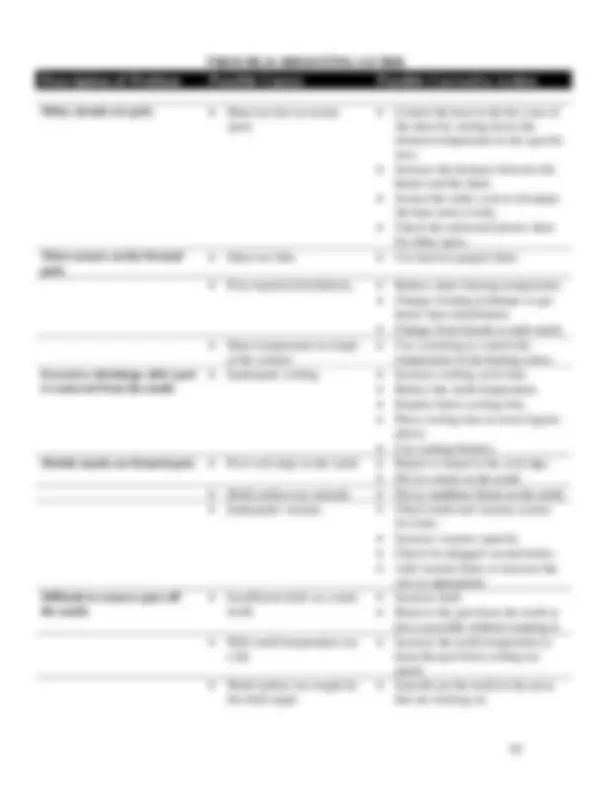
Estude fácil! Tem muito documento disponível na Docsity
Ganhe pontos ajudando outros esrudantes ou compre um plano Premium
Prepare-se para as provas
Estude fácil! Tem muito documento disponível na Docsity
Prepare-se para as provas com trabalhos de outros alunos como você, aqui na Docsity
Os melhores documentos à venda: Trabalhos de alunos formados
Prepare-se com as videoaulas e exercícios resolvidos criados a partir da grade da sua Universidade
Responda perguntas de provas passadas e avalie sua preparação.
Ganhe pontos para baixar
Ganhe pontos ajudando outros esrudantes ou compre um plano Premium
Comunidade
Peça ajuda à comunidade e tire suas dúvidas relacionadas ao estudo
Descubra as melhores universidades em seu país de acordo com os usuários da Docsity
Guias grátis
Baixe gratuitamente nossos guias de estudo, métodos para diminuir a ansiedade, dicas de TCC preparadas pelos professores da Docsity
Manual de Operação - vacuum forming
Tipologia: Esquemas
1 / 129
Esta página não é visível na pré-visualização
Não perca as partes importantes!
Just what you always wanted! Another boring manual on the thermoforming process. So why did we do it? Mostly duress! There were some people that felt it would be useful to document some of the information I have accumulated over these many years and share it with you. Does this mean that this manual is a totally comprehensive document on everything there is to know about thermoforming? NO! However, it is a fairly good depiction of what this business is all about.
To the best of my knowledge, I have refrained from uttering any falsehood regarding the various aspects of this industry. Hopefully the information contained within this manual will be helpful in getting a grasp on the thermoforming process and provide you with information that is useful in addressing some of the problems and situations that you may confront. Should this manual be used as the only authoritative document regarding thermoforming? NO! There are many excellent things written on the thermoforming process and many new developments and methods are being put forth all the time in this industry. However, I think you will find the information contained within this manual is based on tried and true empirically tested data.
Should you be so inclined to seek a more explicit explanation on any of the information contained within this manual, we invite you to do so by calling 1-800-456-9402 or 219- 267-7127 at Spartech Plastics in Warsaw, Indiana and ask for Lee Boser. We will be happy to help you.
Any republication of any of this material should be done through a request from the writer or Spartech Plastics.
Leroy M. Boser
rudimentary vacuum system and construct a mold out of any one of a number of inexpensive materials such as wood and you are in business.
Basically what happens when you heat the sheet up in the oven, the sheet reaches a forming temperature but it ends up with a slightly uneven heat. This happens because the clamping mechanism acts somewhat as a heat sink and drafts in the oven or defective heating elements cause further heating disparities. This will be addressed later in the trouble-shooting section. As the sheet reaches approximate forming temperatures, it will sag somewhat in the clamp frame due to the thermal expansion properties of plastic, the actual softening of the plastic, and sheer gravity overcoming the hot strength of the plastic. Also the actual surface of the plastic will be slightly hotter than the interior of the sheet. When you remove the plastic from the oven, the surface of the sheet will cool off very quickly so you do not have much time to actually form the material, usually only seconds. Next you actually drape the hot plastic sheet over the mold. This causes the plastic that touches the mold to cool very abruptly and freeze onto the mold surface wherever it actually touches the mold. This chilling may be 50° to 100° F on the areas that touch the mold on the mold surface side in just a matter of seconds. This makes the plastic considerably harder in these areas, and when you apply the vacuum to stretch the material over the rest of the mold, the plastic will stretch more easily from the hotter areas, thereby thinning those areas more readily. As you stretch the hot plastic over the mold and trap the edges next to the clamp frame to the mold flange, you further thin out the plastic. However, you have no choice in doing this, as you need to get a seal around the mold flange to be able to apply the vacuum. Finally the vacuum is applied to force the rest of the plastic up against the mold to chill it. After a few minutes, the plastic contacting the mold will chill enough to be below its heat distortion point. This phenomenon will also occur on the surface side that is exposed to the air but at a much slower rate. At that point it can be removed from the mold and the excess trim removed to take on the dimensions of the designed part.
Generally speaking there are some drawbacks to this technique in molding. First, you are going to have a lot of competitors and price pressures will be severe. As I indicated earlier, almost anyone can get into this business using this technique. Second, this technique is not capable of producing parts that are very complicated. Wherever the plastic touches the mold is essentially where it ends up. Consequently, any part that is a little more complicated could end up with some thinning in some areas that are not acceptable. You just do not have any control to move the plastic around to other areas of the part. This will also cause the thinning to be uneven and the texture may appear different on various areas of the part. Third, you are very likely to have chill marks on various areas on the part. This may be cosmetically unacceptable and other techniques may have to be employed to overcome this.
However, the other side of the equation shows that there are some quite beneficial aspects to this technique. First, you can produce parts via this method quite economically. It is probably the most economical thermoforming method we can use. Secondly, the parts produced via this method are normally totally acceptable for the application they are
A plug is constructed out of some insulate material, such as wood, and covered with a soft cloth material, such as felt. This prevents the material from picking up plug marks when the plastic is in the hot state. The plug is constructed in such a way that the surface area of the plug will move the maximum amount of hot plastic down into a cavity. Thus the amount of clearance the plug has in relationship to the vertical mold wall is important. This will be dictated by the geometry of the mold. The depth the plug goes into the cavity is also important. The reason this is so is because you only have so much plastic to work with over any given area of the mold as you are stretching the hot plastic over the mold surface. What you are essentially doing is taking a little of the plastic that would have been formed unto the upper vertical walled area, and moving it down to the bottom of the cavity and the bottom vertical walled area before the vacuum can be applied. You are just redistributing the available plastic a little more uniformly. As you might imagine, the way the plug is constructed and the depth that it is inserted into the cavity are important.
Another consideration is the way the technique is employed. It should be obvious that this technique would be difficult to employ manually. Thus you will need some kind of a machine with both a top and bottom platen to mount the mold and the opposing plug unto. The mold will be mounted onto the bottom platen and the plug will be mounted onto the top platen. As a slight variation to the previous technique, it will be necessary for both the bottom and top platen to move up and down. You must also be able to control how far up and down both of these platens go to prevent them from smashing into each other. Typically the plastic sheet is mounted into a clamping mechanism and placed on a trolley that can be moved into and out of the heating oven. The accuracy point that the clamping mechanism stops when you retract it from the oven is important because you will need to get a good seal around the clamping mechanism relative to the mold flange. This will require the trolley to stop in the same position each time. This stopping point is also important in getting the plug to contact the plastic relative to the mold position each time in order to insure consistent material distribution on the part.
Finally it should be noted that it is possible to move one or both of the platens that support the mold and plug assist together to control which of these touches the hot plastic first. This can affect how the material is distributed and where chill marks may appear depending on the shape of the mold. The advantages to this technique over the previous ones should be obvious. First, you will get better distribution of material and therefore less thinning. Second, the amount and severity of the chill marks you experience will be lessened and thirdly, the complexity of the part you can make will be increased.
4. PLUG ASSIST - TOP
As was the case in DRAPE FORMING, PLUG ASSIST - TOP is just like PLUG ASSIST
Why would anyone want to go through all of this to make a part? Well, there are some definite benefits. If you again imagine the above procedure, you will probably come to the conclusion that the material distribution of the part on the mold will be better. This indeed happens. As you predraw the material into the vacuum box, you are uniformly stretching this material that more closely approximates the shape of the mold than by normal drape or plug assist forming. Then when you snap the material back unto the mold, it does not have to stretch as far in the remaining portions of the mold that have not touched the sheet yet. As you may realize, once hot plastic sheet touches the mold, it freezes on that spot and no longer thins on the frozen area. However, it does continue to thin in the remaining areas until all of the mold surface area is covered. Since the hemispheric shape more closely approximates the shape of the mold, less thinning needs to occur and the part thickness is more uniform.
A second reason for using this technique is the amount of material you may need to make the part. It can be shown through a draw ratio mathematical formulation that the thickness of the starting sheet can sometimes be reduced or the length and width dimension of the starting sheet can be reduced by using this technique. This can also, on occasion, improve the cycle time required to make the part. This is especially true on the cooling cycle time.
One can also make multiple cavity molds for the snapback process but it is necessary to think this out carefully. If the part is quite difficult, it will be hard to control the predraw depth in the vacuum box and get them all to be uniform. Any small change in heating stability of the elements in the oven or any drafts through the oven may cause the sheet to be hotter in one area as opposed to another thereby resulting in non-uniform bubbles in the vacuum box. As you might imagine, this becomes more difficult as the complexity of the part increases.
So why don’t we use snapback for all parts? Well, the simple fact is that this technique is a bit more complicated and does require more time for a set-up. It also requires a better set-up man and a better machine operator to run these parts. If one of the other simpler methods does the job, it makes good sense to go for simplicity. This leads us to addressing technique number six.
6. SNAP BACK - BOTTOM See figure 3.
As you might imagine, this technique is exactly like “Snap back - top” except the mold and vacuum box are reversed and mounted to opposite platens. So if it is the same, why do it? Well, there really isn’t a good reason except some people find it easier to work with the mold on the bottom platen and find it beneficial to have the bubble settle unto the mold. They also find it easier to observe the bubble being pulled up into the vacuum box. This is especially true when you run a rotary machine that has a high frame set-up.
So what are the benefits of going through all this misery? Well, for one thing these techniques afford the best material distribution you could expect to get with the vacuum forming process. Secondly, these techniques allow you to get the most uniform material distribution over the large area of a complex part you could expect. Thirdly, these techniques allow you to put the most severe draw ratio on the hot plastic material you can hope to get without actually pulling a hole in the material. It is very common to get draw ratios of five to one. Fourth, this particular technique allows you to pull a pretty uniform grain throughout the entire part. And fifth, this technique allows you to form the most difficult female parts that can be done with the vacuum forming process. There are parts that can only be formed properly by using this technique.
8. BILLOW FORMING - FEMALE (TOP)
Again,” billow forming - female top” is just like “billow forming - female bottom” except the mold and the plug are reversed on the platens. However, the results are equivalent. The plus for doing it this way as opposed to” billow forming - female bottom” is just personal preference. Secondly, it is easier to adjust the plug, which is critical in this process. Third, it is easier to blow the bubble in this position as you are already using the natural sag of the material, and fourth the material doesn’t chill as quickly on the mold flange. The big minus is it is harder to see what is going on when you are evacuating the air out of the bubble so it becomes necessary for the operator to have a better “touch”. Both techniques will work equally as well on any given part that requires this process.
9. BILLOW FORMING - MALE (BOTTOM)
This technique is just a role reversal of “billow forming - female bottom”. Essentially what we are doing is putting a billow blowing contoured box on the top platen and the male mold on the bottom platen. Again, to hold the sheet, we use the same type clamp frame as in the techniques above and send the material into the oven to be heated to the proper temperature. As before, the trolley moves the heated sheet out into the forming area. When the sheet is properly located in the forming station, we send the billow box down to make a seal all around the clamping area. Then we blow a bubble that extends downward until it goes down the proper distance where it will trip the electric eye and hold the bubble in that position. When the bubble is extended to the proper place, we send the male mold up into the bubble where it will start to billow out the bubble because of the trapped air. When the bubble billows out the proper amount, we start bleeding off the air in the bubble to prevent it from bursting and to distribute the plastic around the male tool as it is extending into the bubble. Again, it is proper to do this manually or automatically with the machine but the manual method as in “ billow forming - female” affords a little more control, as an experienced operator would exercise good judgment as the mold is extended. This would be similar to poking your finger into a blown up balloon and letting the balloon wall envelop your finger. As one might imagine, this will require the billow box to be somewhat contoured to fit the mold or you are likely to get webbing in the corner areas. It is generally necessary to miter the corners of the billow
is contained within. The hole can be sealed over by lowering the clamp frame and pressing it against a seal ring on the top of the box.
Here is basically what happens in the process. A movable top and bottom oven is rolled out over and under the clamp frame with the plastic sheet in it. The plastic is heated to the proper temperature and then the ovens are rolled away from the heated sheet. Next the clamp frame is lowered over the seal on the enclosed box with the mold in it. At this point the proper amount of air pressure is injected into the enclosed box and the plastic sheet rises up in a standard billow bubble. This can be either controlled manually, by time, or by an electric eye at the side of the machine. When the bubble is just the right height, the mold from inside the pressure box is extended up into the bubble. When the mold is fully extended, a seal is made around the edge of the mold base, the bubble is allowed to settle over the mold, the air is turned off and the vacuum is applied to the mold, usually very slowly. When the part is cool enough, the air eject is turned on and the part is demolded. Because the mold is trapped inside the box, the air eject is very efficient and difficult parts can be demolded quite easily as the seal is actually under the clamp frame. Hence we get the name zero gravity as the blown bubble merely floats above the mold until the air is released and the vacuum is applied.
So what are the good, the bad, and the uglys in this process? Well, the first thing that should be apparent is chill marks are virtually eliminated as the material has no way of freezing on the mold and chilling off. Actually nothing but the flange of the mold has touched the plastic until the vacuum was activated. Secondly, by vacuuming the part very slowly, you are less likely to need some kind of plug assist to prevent the part from webbing. However, if the part does have a propensity for webbing, it is more difficult to apply a plug assist to prevent it. You will have to use a pneumatically activated plug that is external to the normal machine operation. Third, on materials that have very sharp melt points, you can hold the top oven over the sheet through the actual forming of the part if the part isn’t too tall and doesn’t hit the oven elements. This is especially useful in forming some homopolymer polypropylene parts where the melt index is very sharp. A sharp melt index will cause a plastic to be too stiff to form at a certain temperature and too soft to form at a slightly higher temperature. I have seen some very difficult parts with sharp melt indexes made this way with excellent results.
Well, what are the bads? The most glaring is the amount of set up time it takes to get going. You have to go through the entire process of enclosing and sealing the mold in the pressure box and then making sure the seals on the pressure box and the clamp frames don’t leak. You also have to have a method of adjusting the size of hole that the mold protrudes through on the top of the pressure box. And then there is the problem of heating elements breaking more frequently on a moving oven. This can get expensive.
All in all, this technique has some extremely good features but it has not caught on in the United States where speed seems to rule.
Here is a system that is used rarely and usually only in conjunction with pressure forming. If you are trying to make a part in a female textured mold that has a very large draw ratio and you are having difficulty keeping the material from chilling before it contacts the mold surface, this may be the solution. Normally a part of this nature should be formed using the “billow forming - female bottom” technique but the dwell time on the plug is just to long to keep it from chilling the plastic and getting any grain detail on the part.
Here is how it works. You have a deep draw female textured mold in the bottom platen and an insulated plug inside a pressure box on the top platen. As in the above techniques, the sheet is clamped into a clamp frame and run into the oven to be properly heated, usually to the hot side. Then it is brought out and the bottom platen is elevated until it seals off around the clamp frame and the mold. Next a bubble is blown that is usually quite extensive and exaggerated that practically conforms to the female cavity of the mold below. At this point the mold is lowered slightly to allow the seal to break and the bubble to drop down into the female cavity below. Then the mold is quickly brought up again while the plug is simultaneously plunged into the mold cavity. This allows for an intense prestretch of hot plastic sheet without cooling it off significantly. As you might imagine, this whole process occurs in just three or four seconds so the sheet does not have enough time to cool off. Then the vacuum is turned on and the air in the pressure box is activated to force the material up against the mold walls.
So what’s the point? Well one would be surprised at the uniformity of the mold wall and the uniformity and extra grain detail you are able to get because the material does not cool off as much before it hits the mold surface. Also, some materials have very good hot strength and do not sag much no matter how hot you get them until you actually scorch them. This would require you to push them down into the cavity and chill them off and get a wall thickness that is less uniform. As I said, this is a little used technique and people usually try hard to avoid it as most thermoforming machines are not wired to use it.
13. TWIN SHEET FORMING (Figure 4.1)
There are really two types of twin sheet forming processes. One type uses a single-station vacuum-forming machine with a double clamp frame set up. This is what is shown in figure 4.1. The other is using a four station rotary thermoformer with a double oven. Let us describe both processes.
In the case of the single station set-up, two pieces of plastic are put into two clamp frames that are separated by some type of spacer block. Within this spacer block is an air ejector pin that allows you to inject a small amount of air between the two sheets of plastic to