
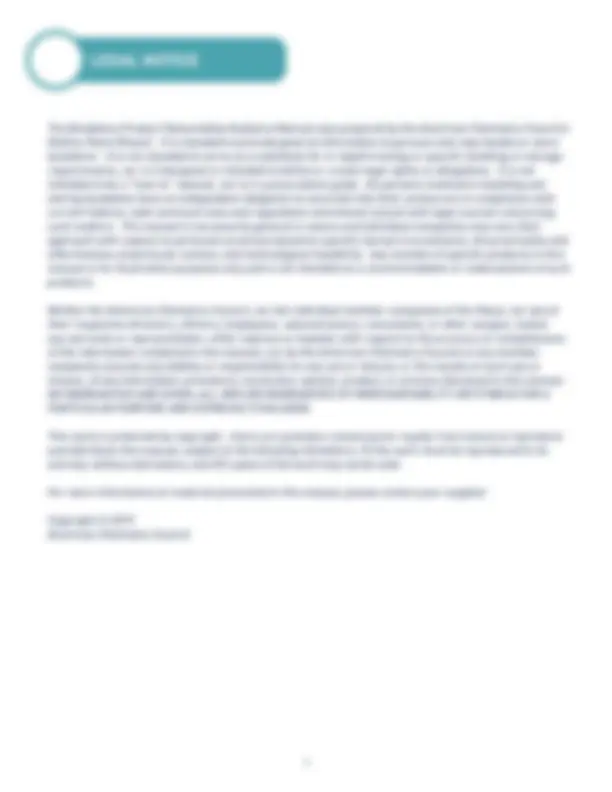
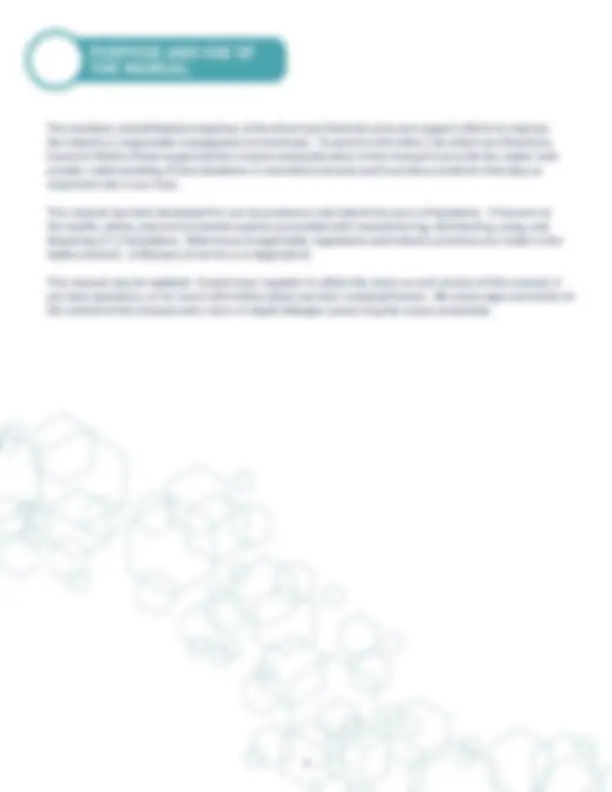
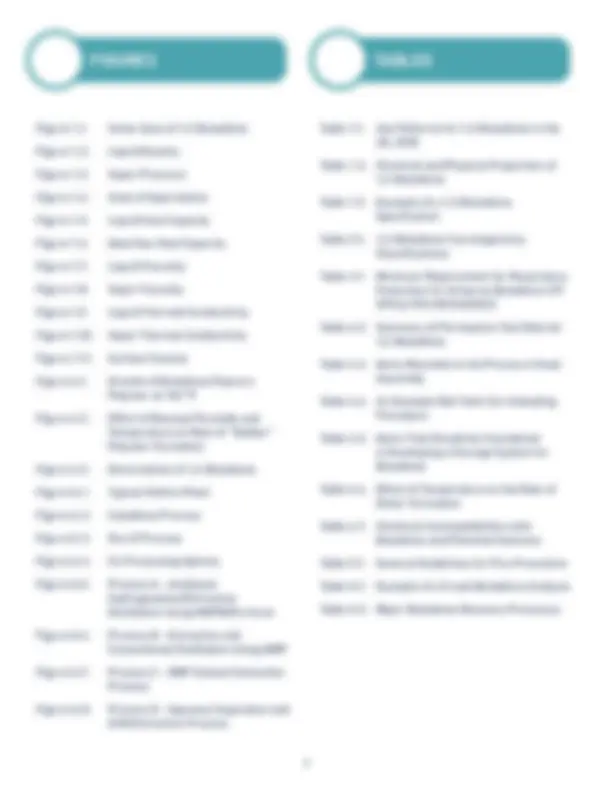
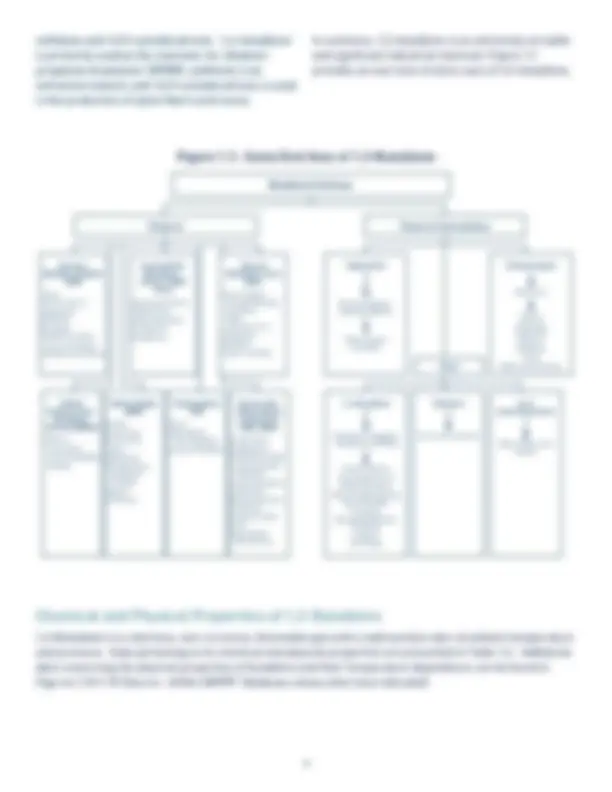
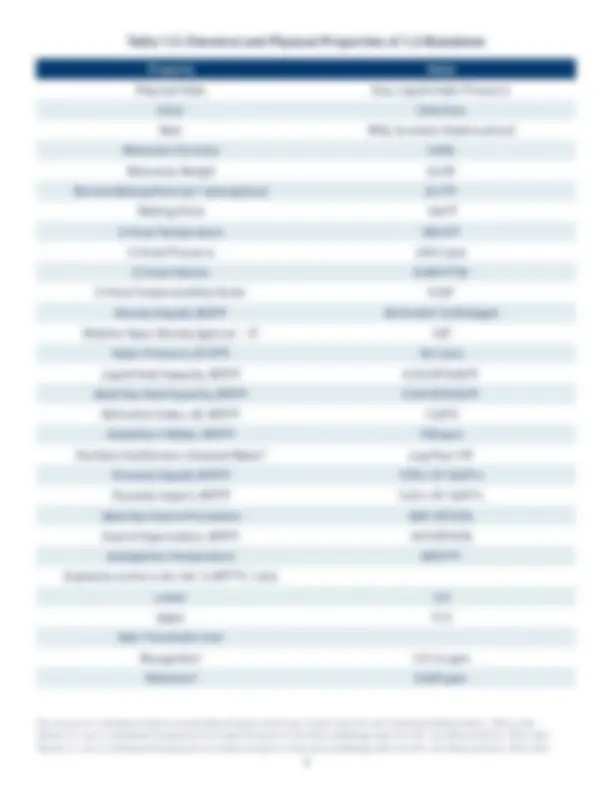
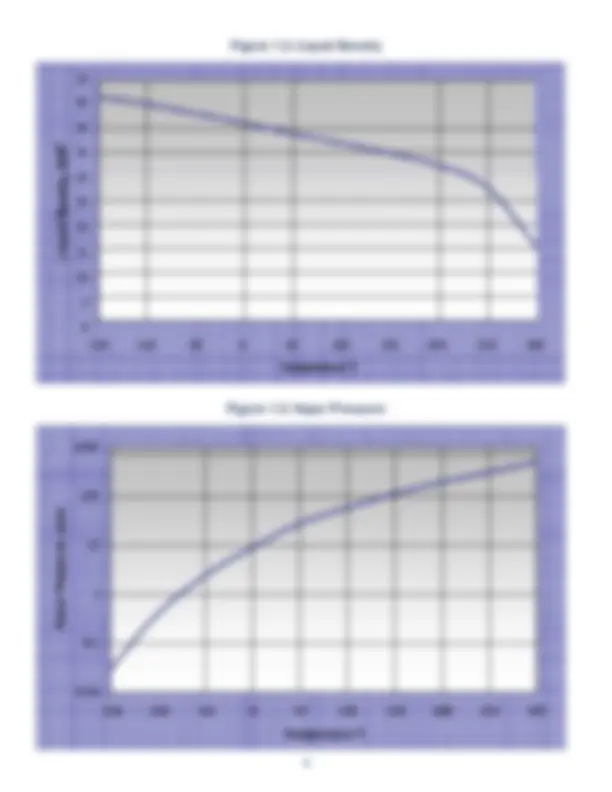
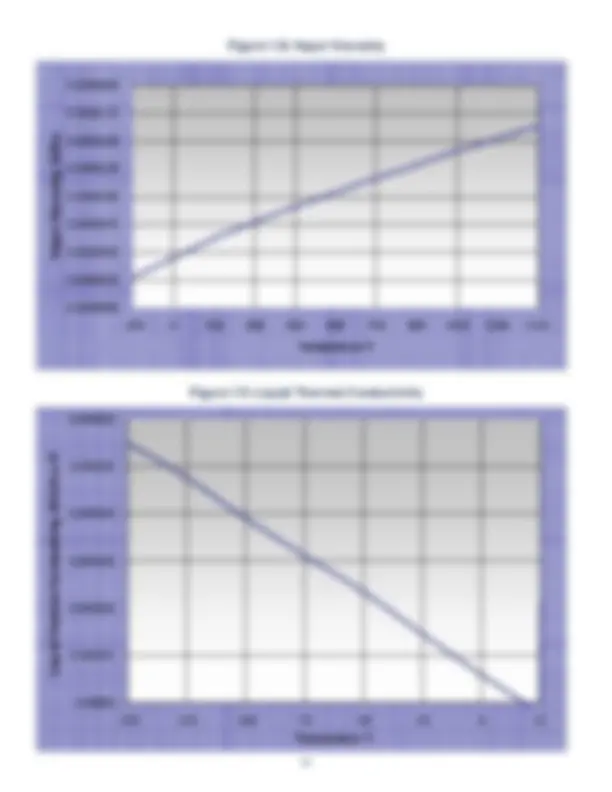
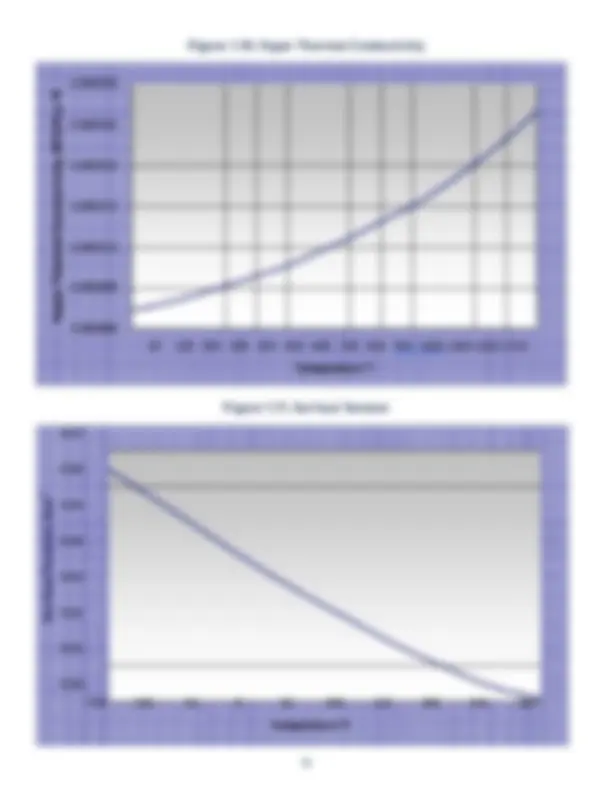
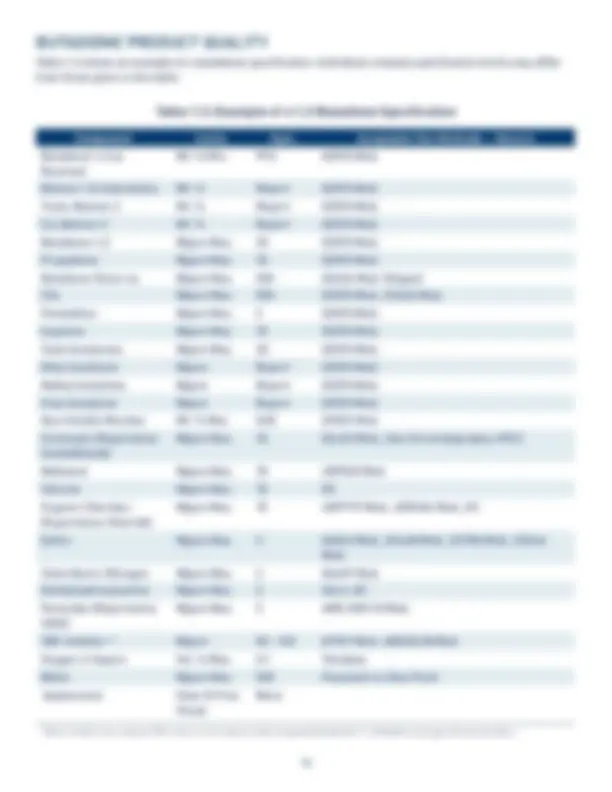
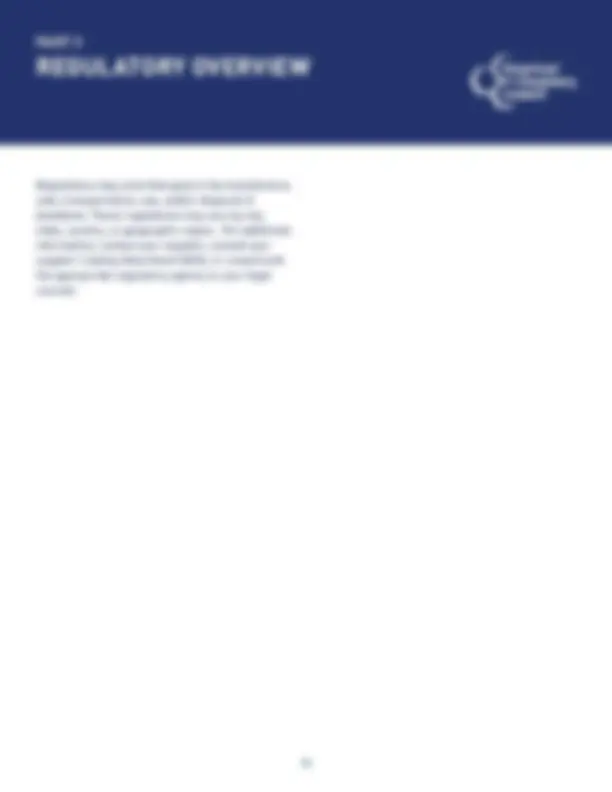
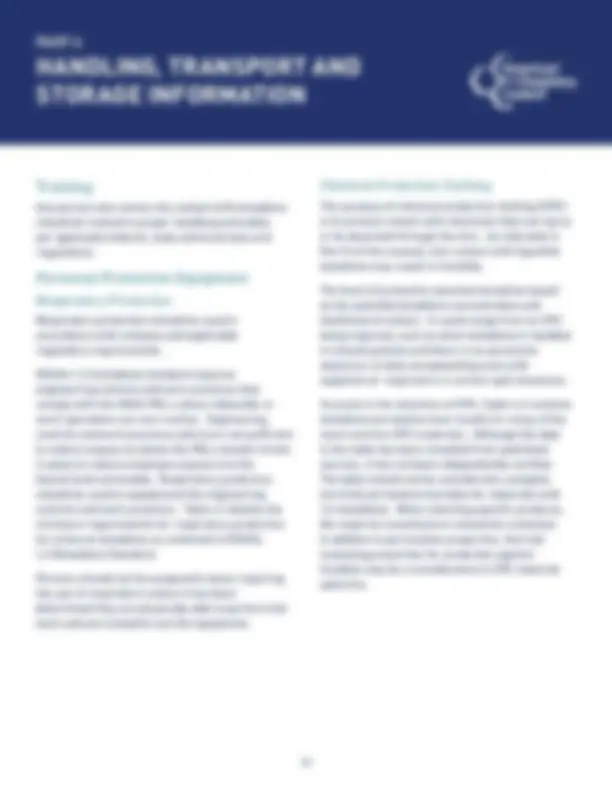
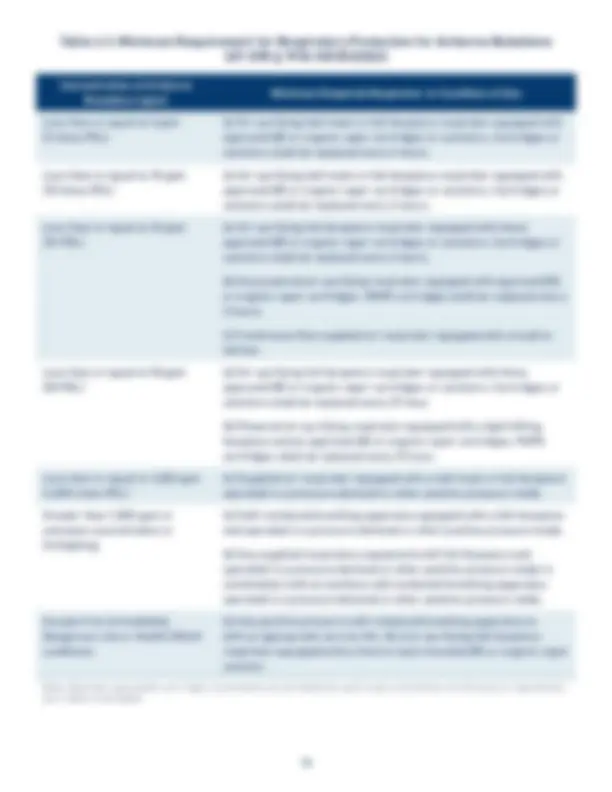
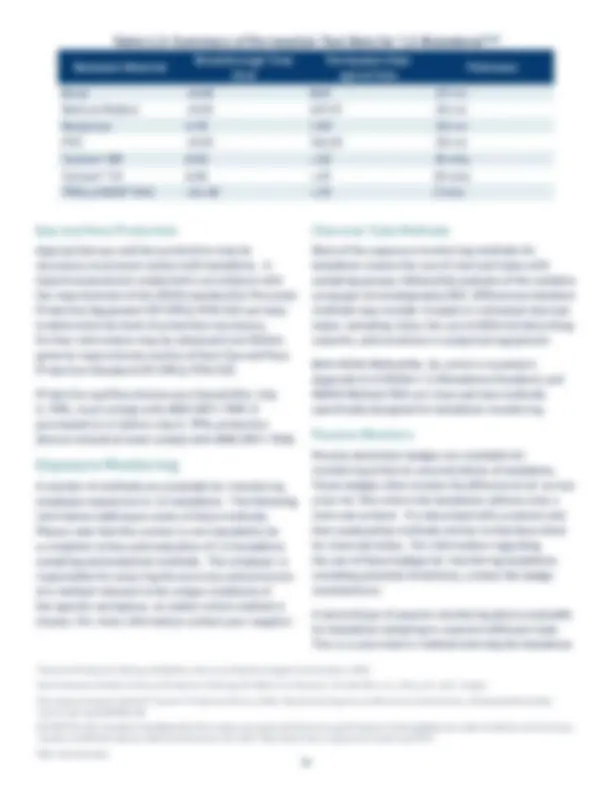
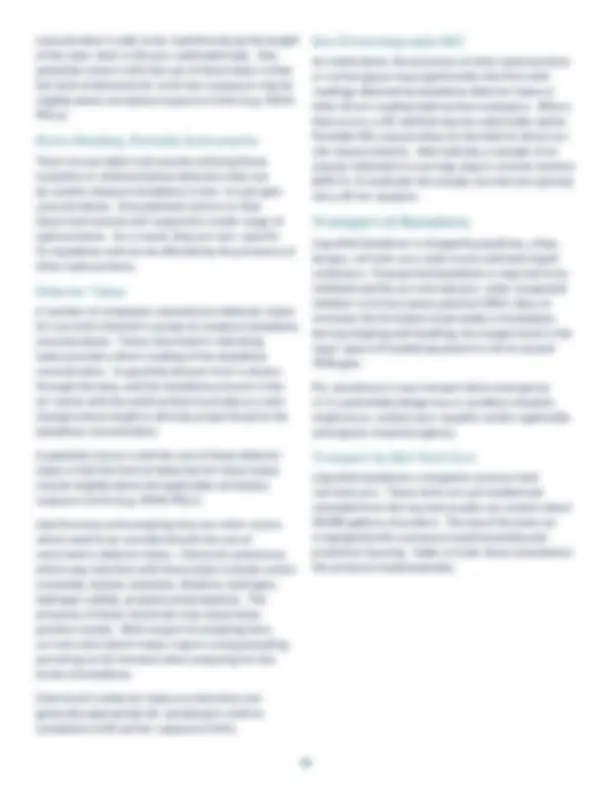
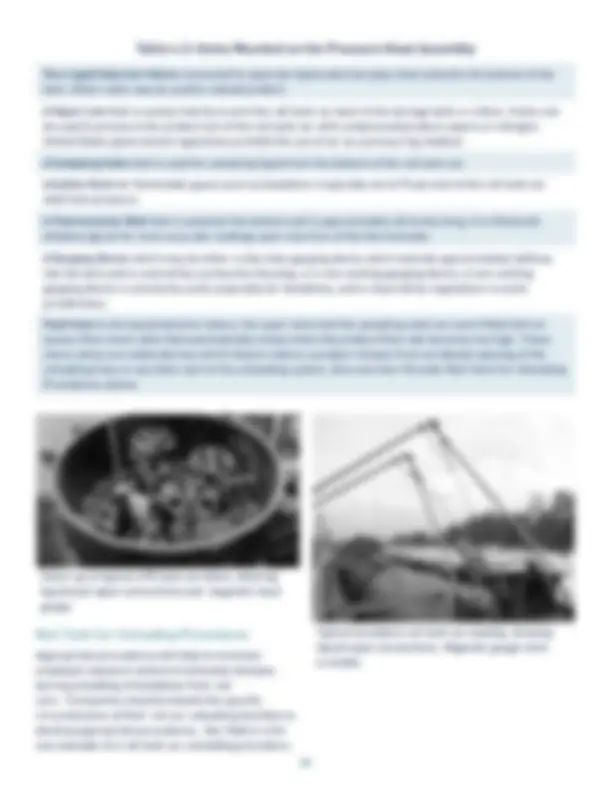
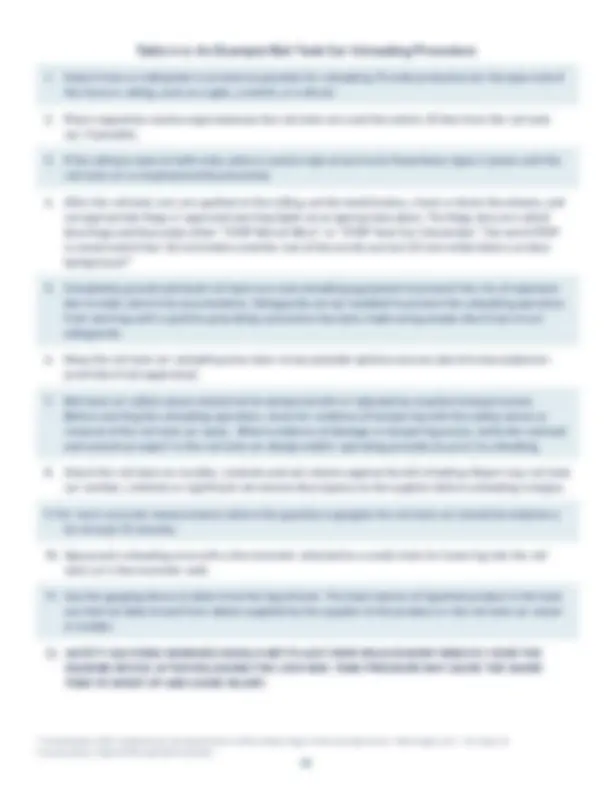
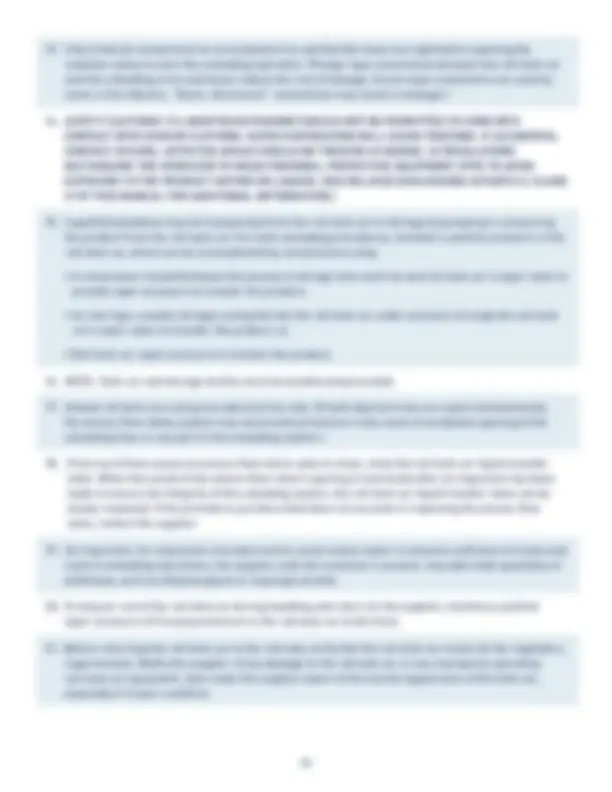
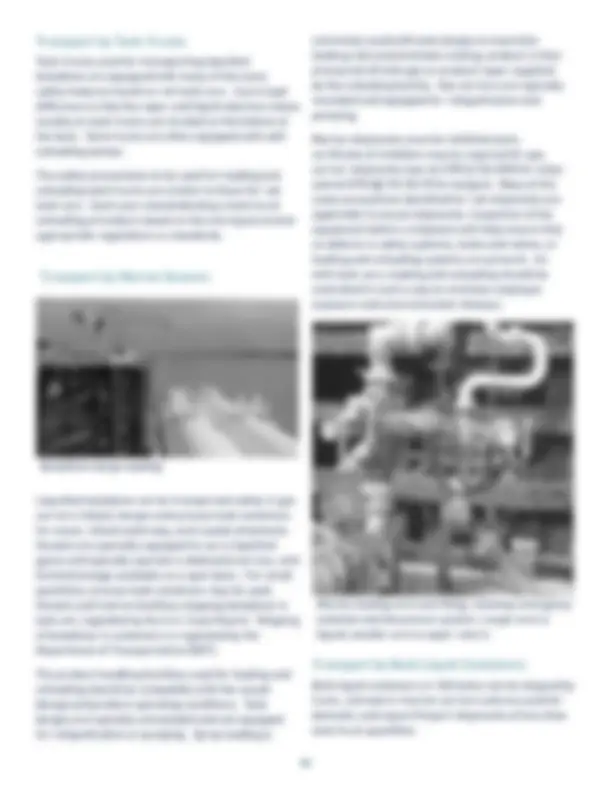
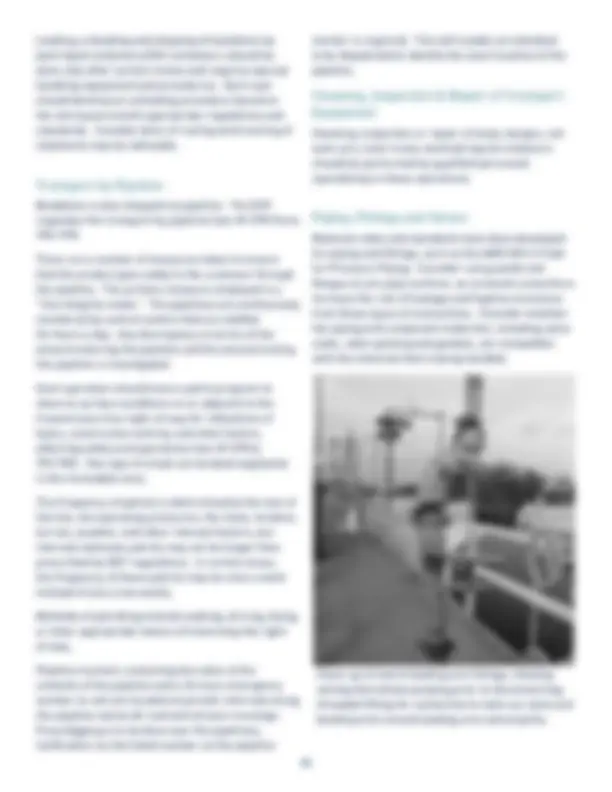
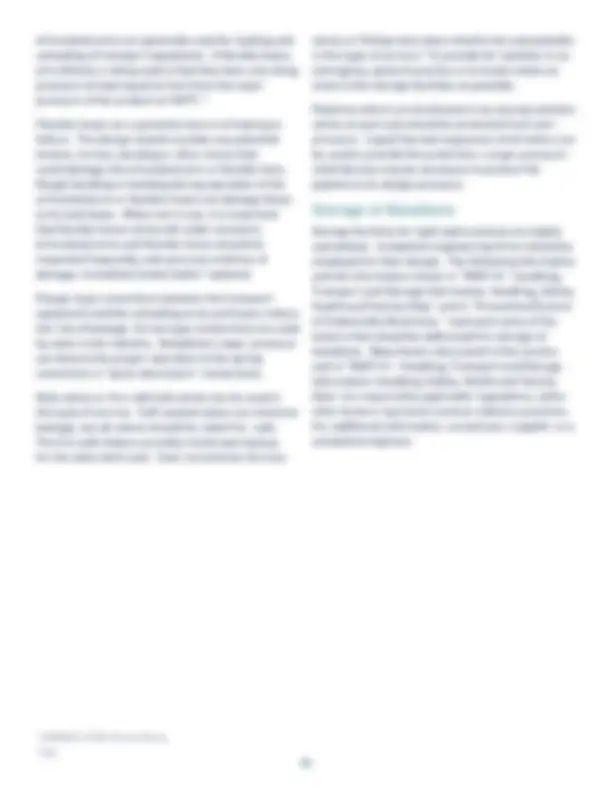
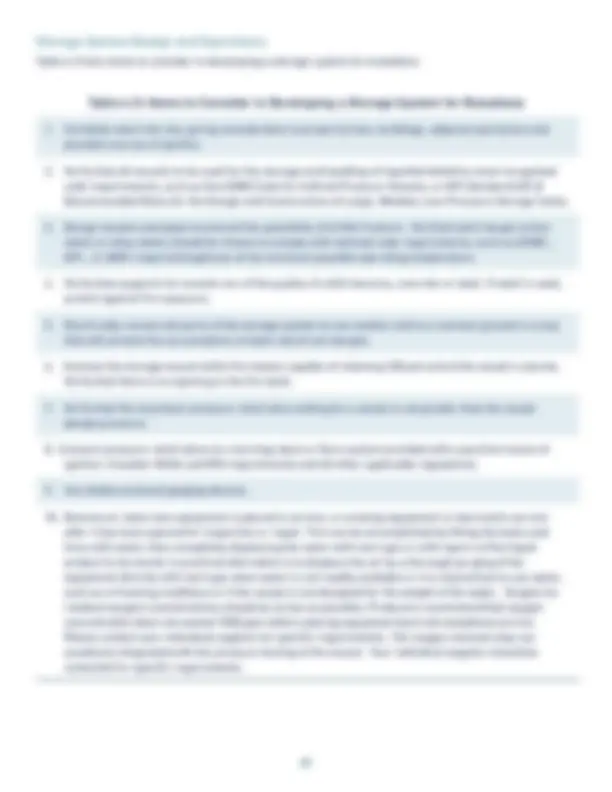
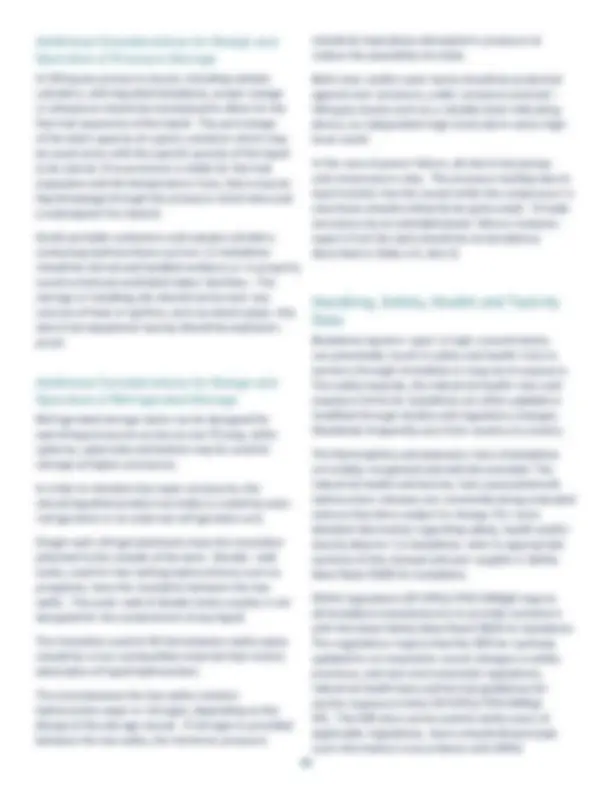
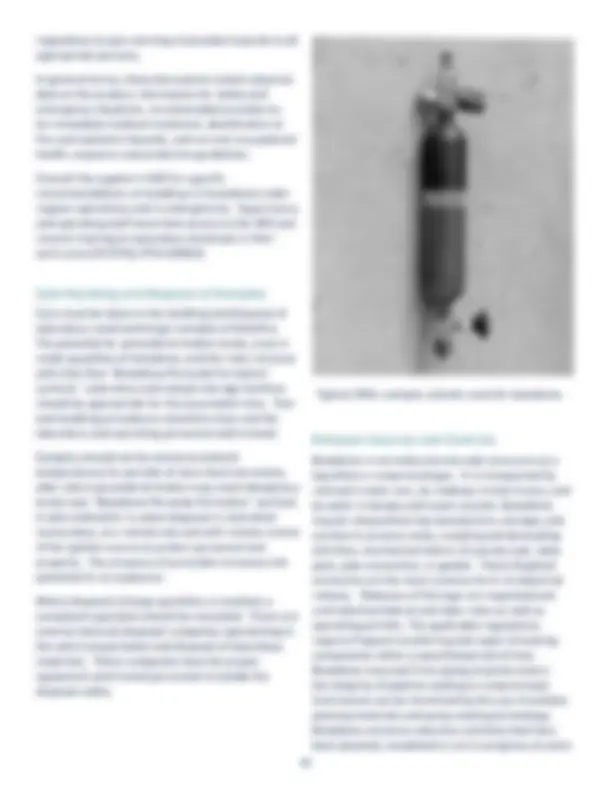
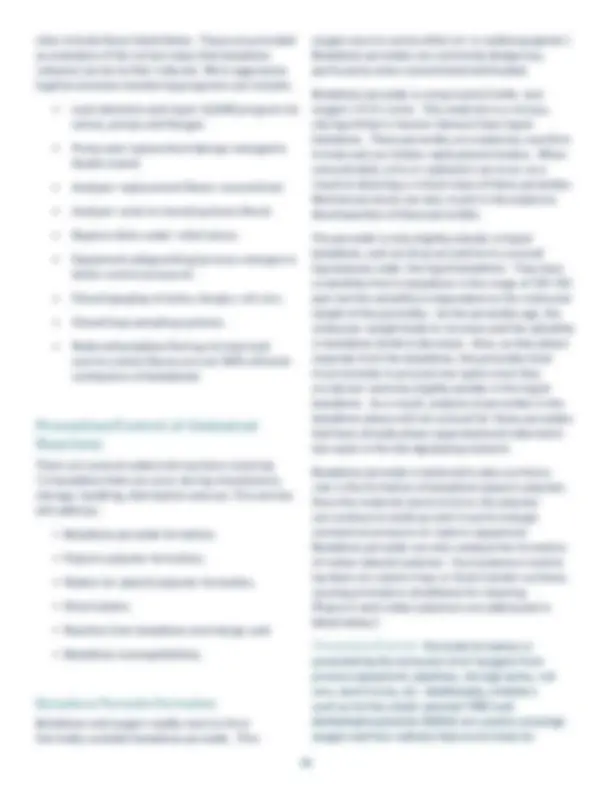
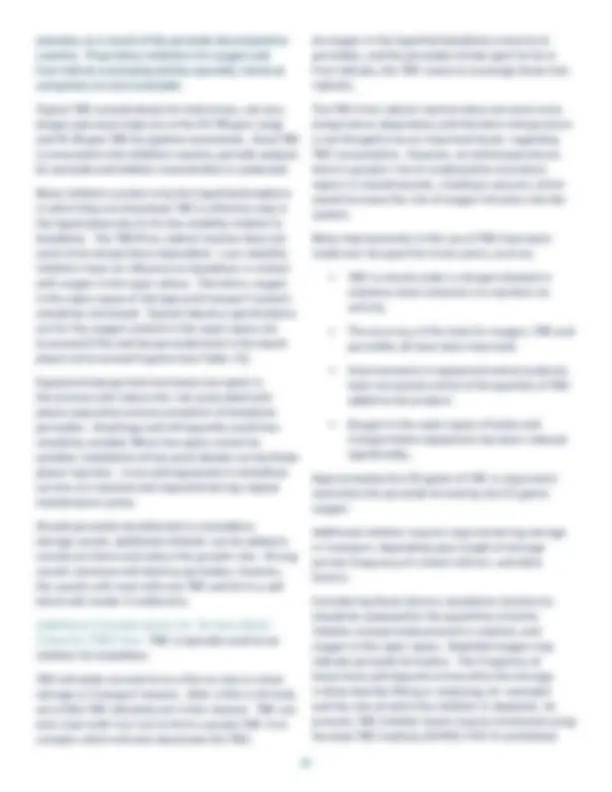
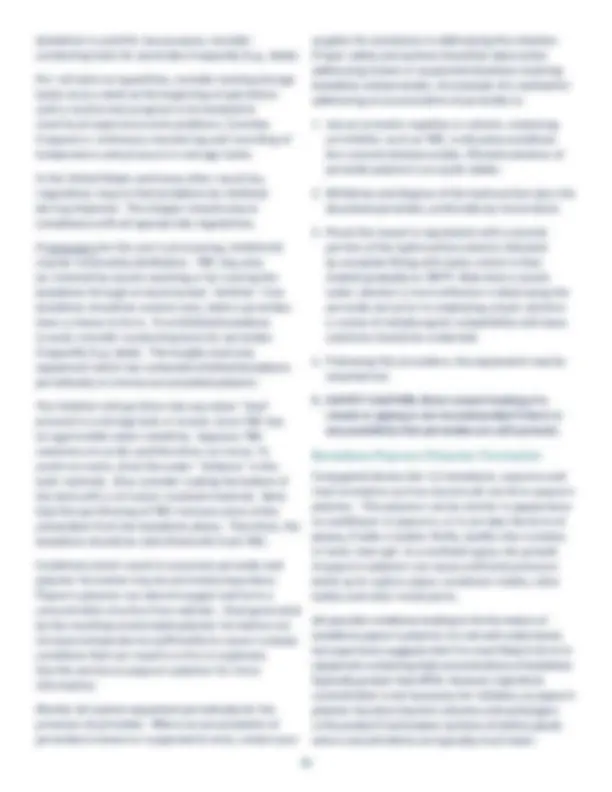
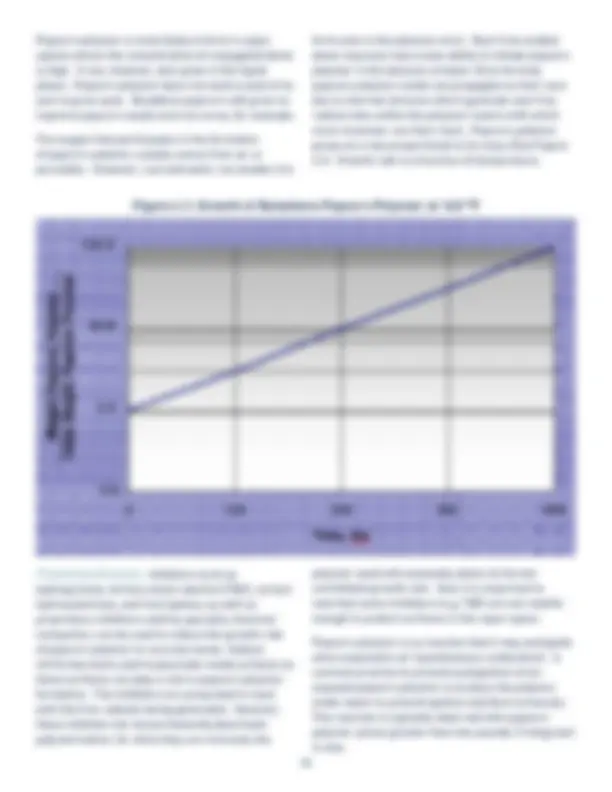
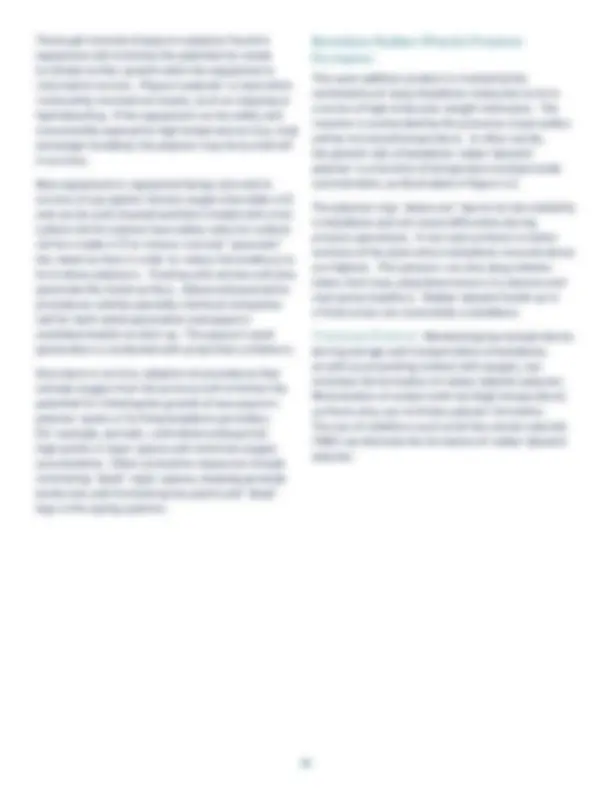
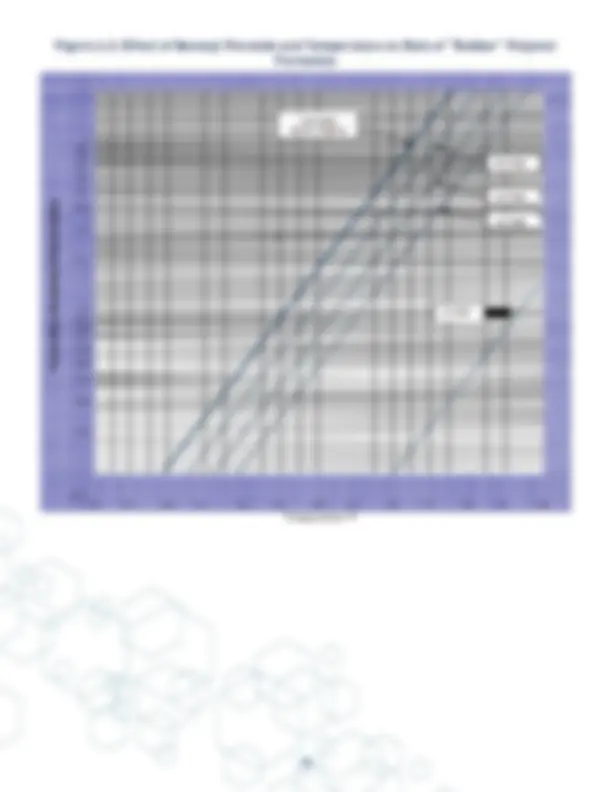
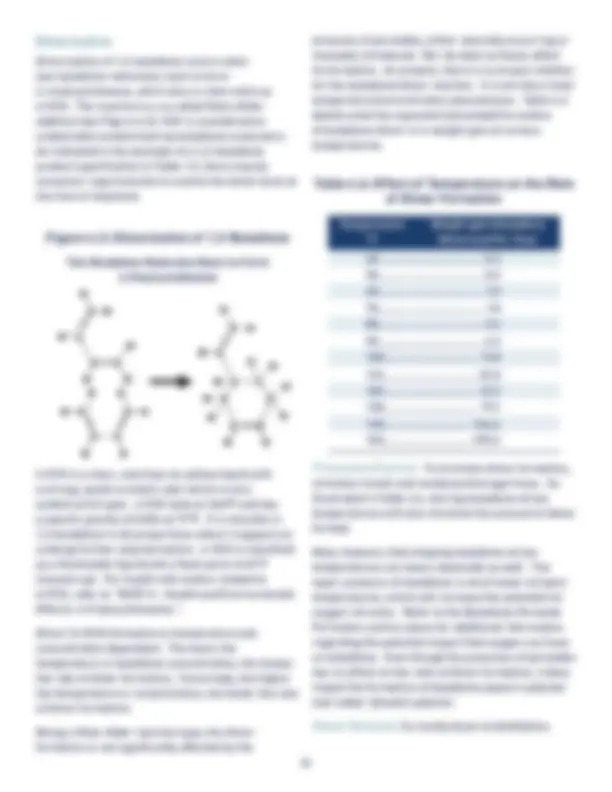

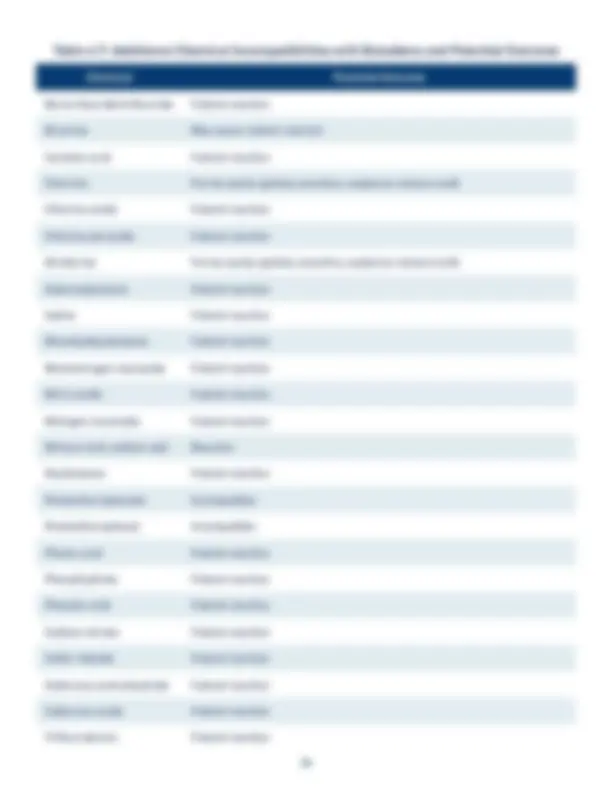
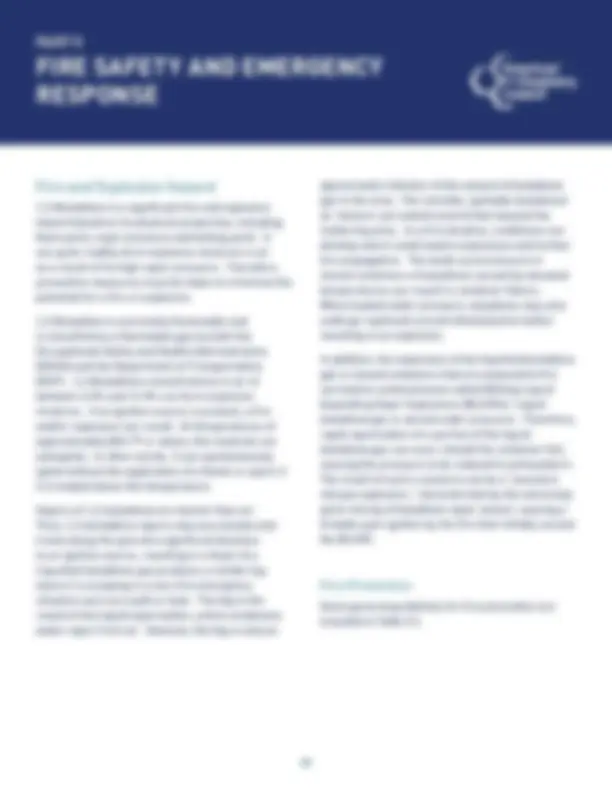
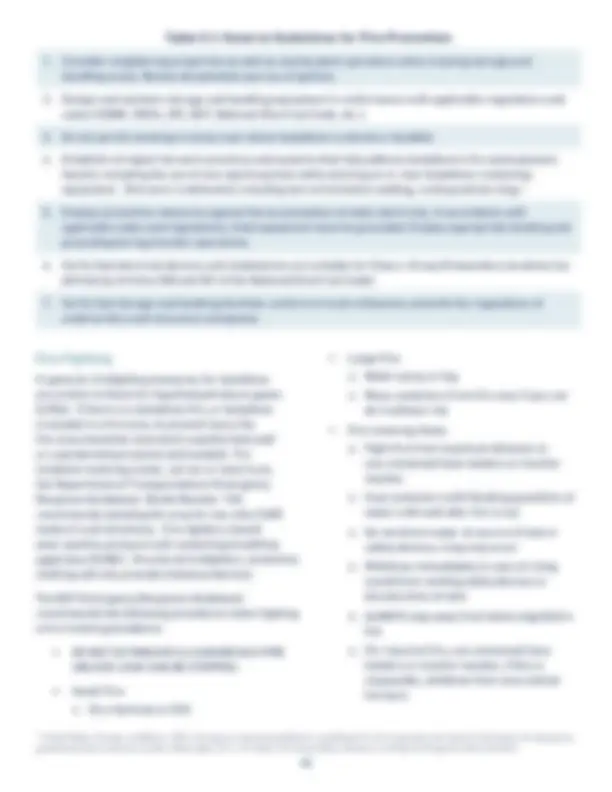
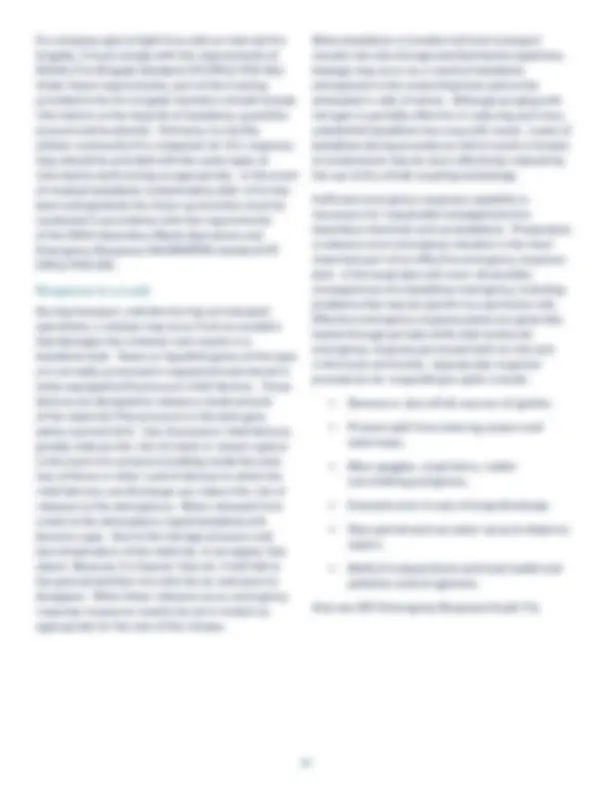
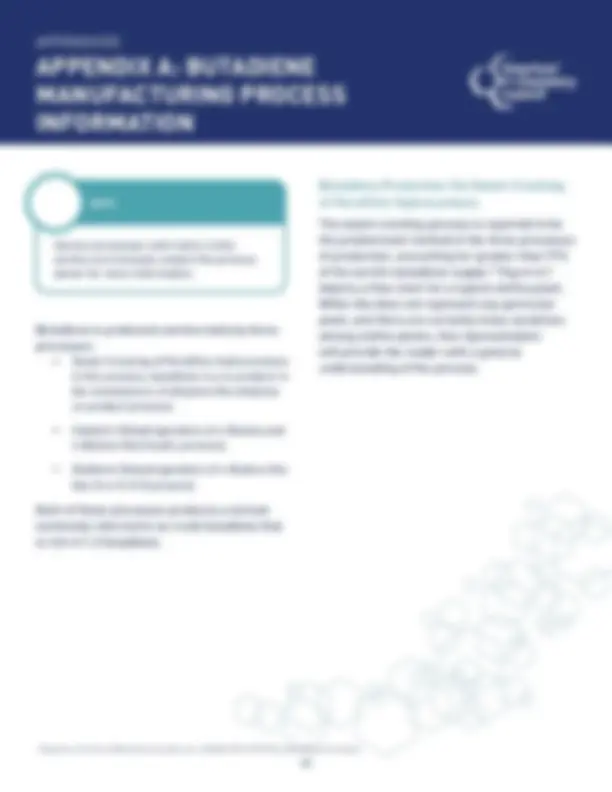
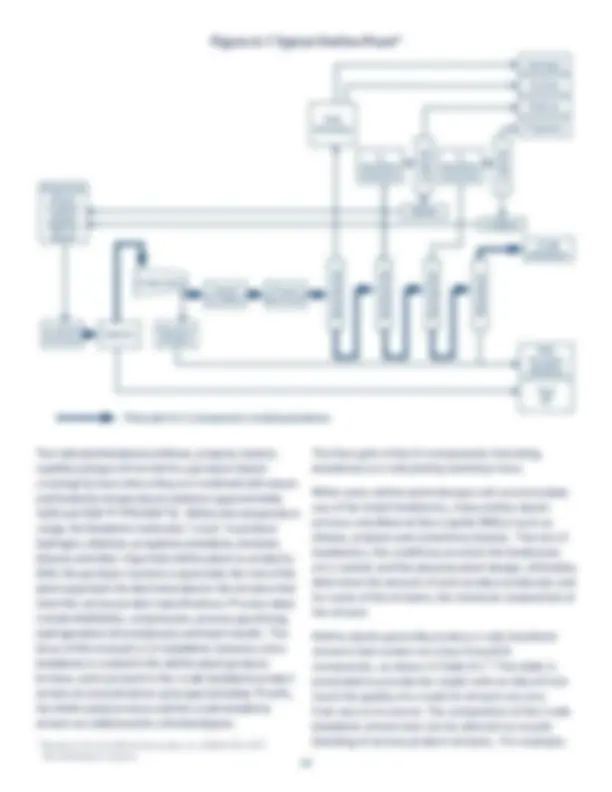
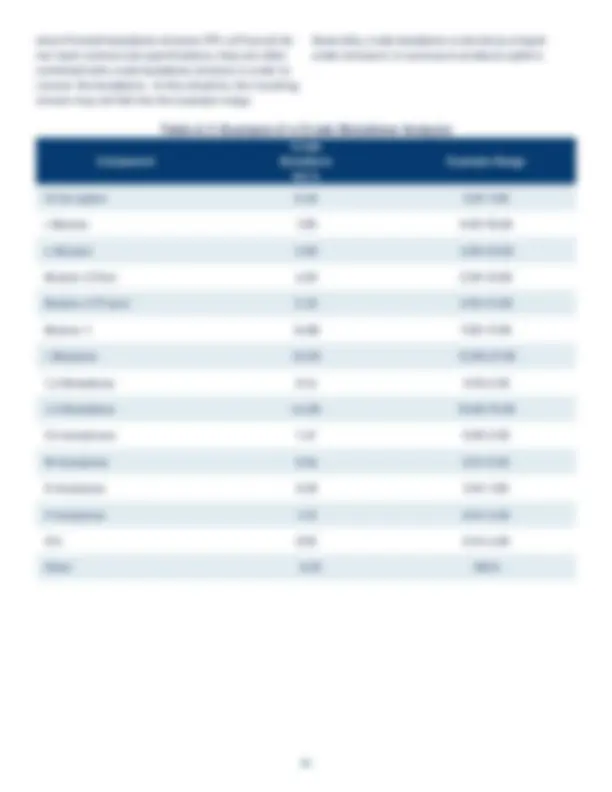
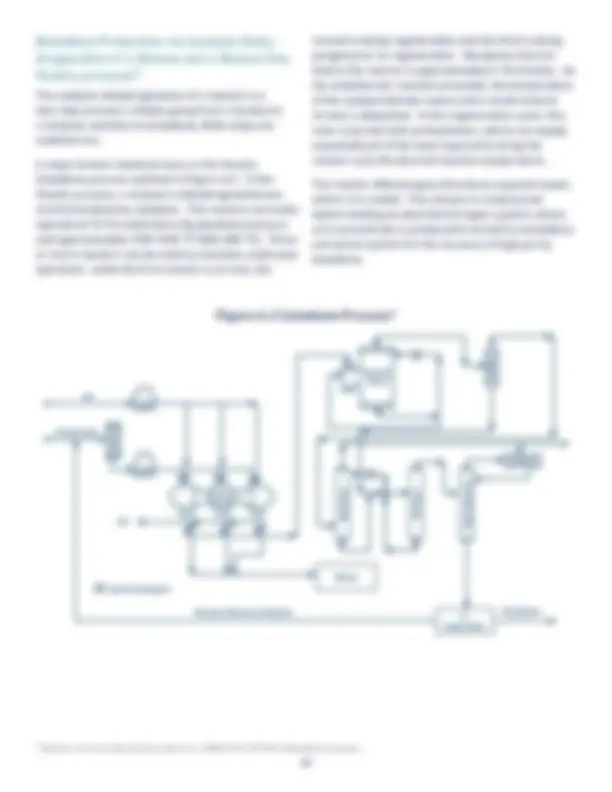
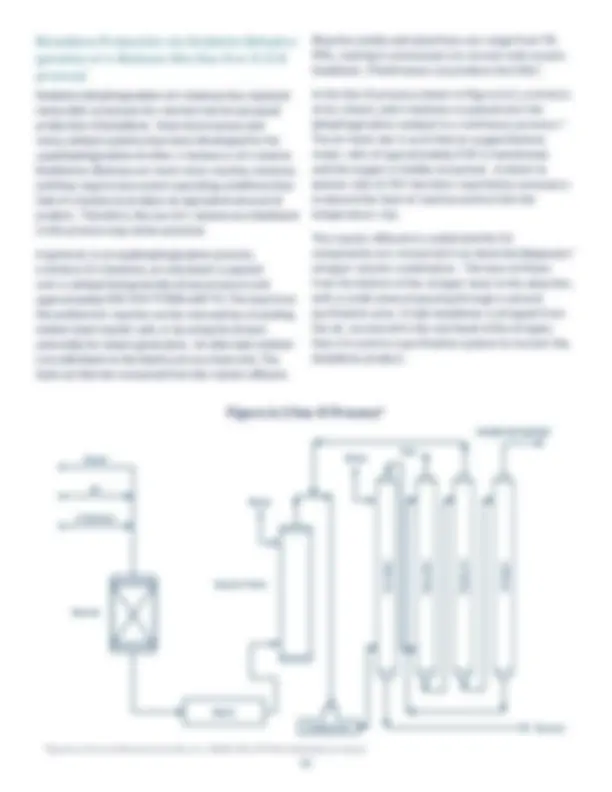
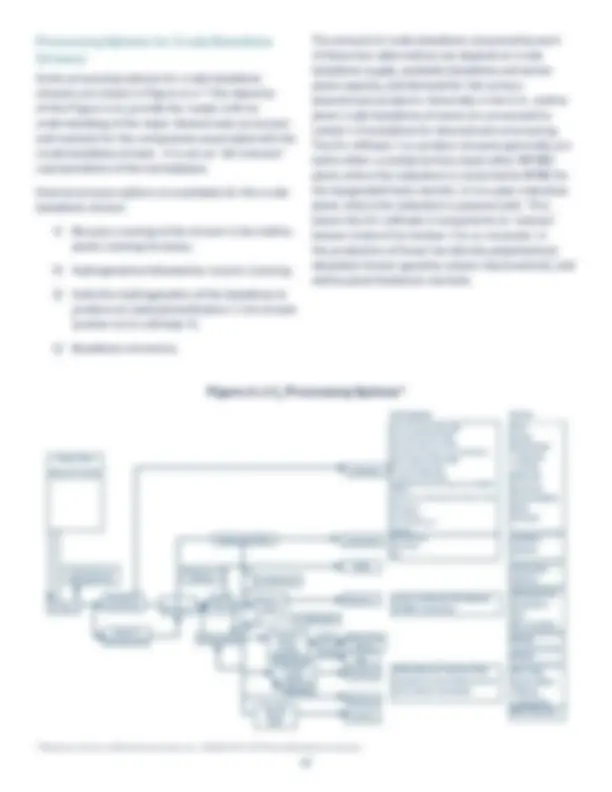
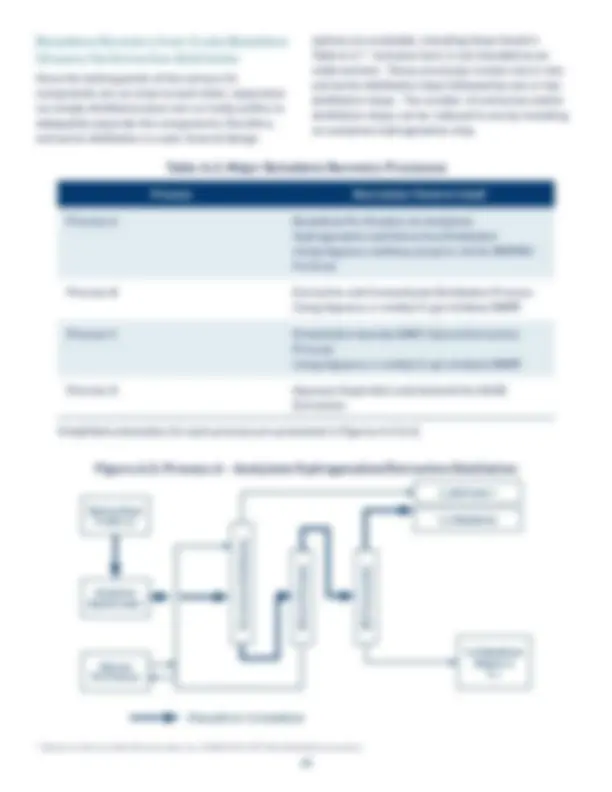
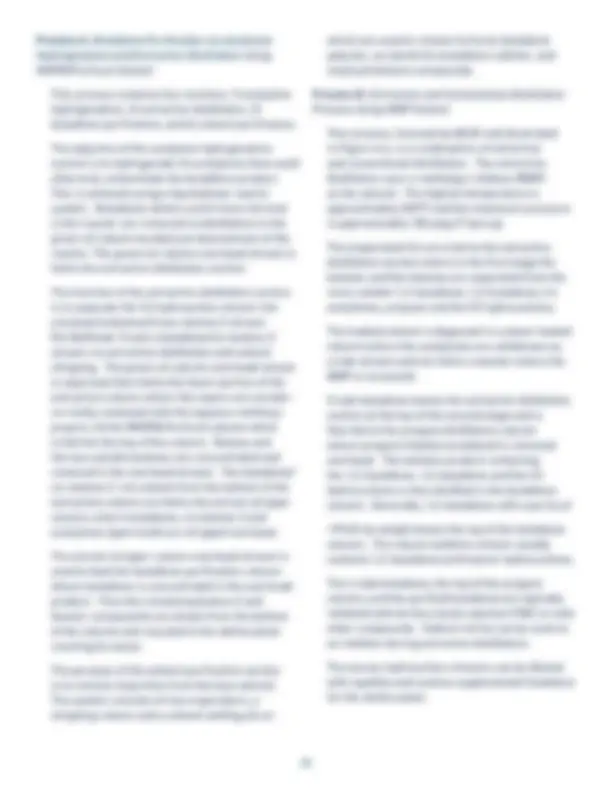
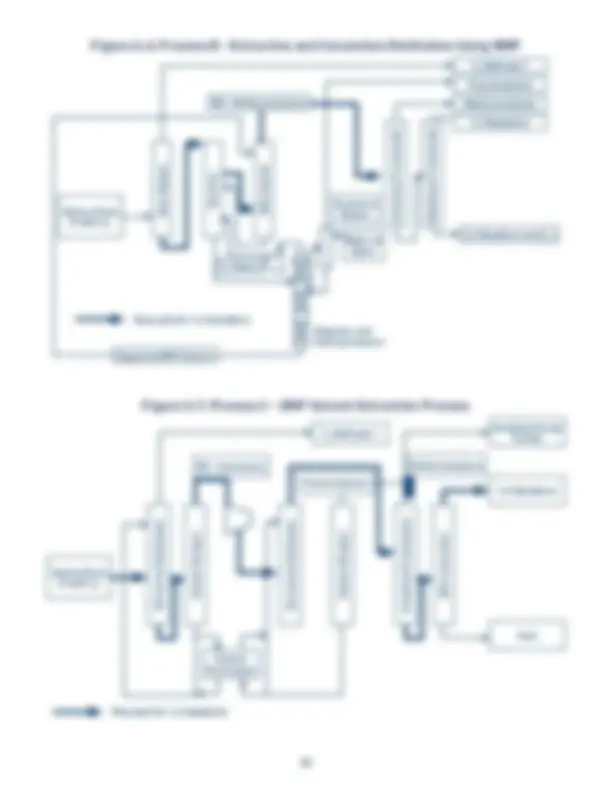
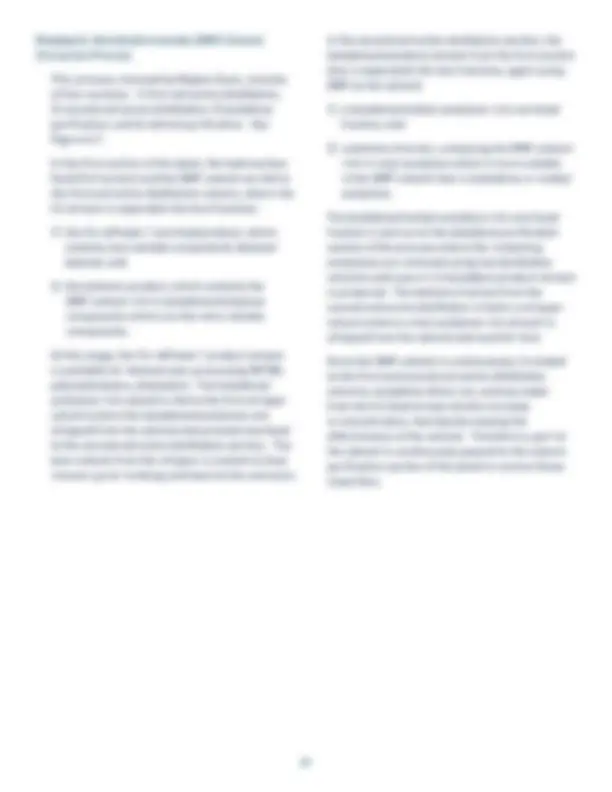
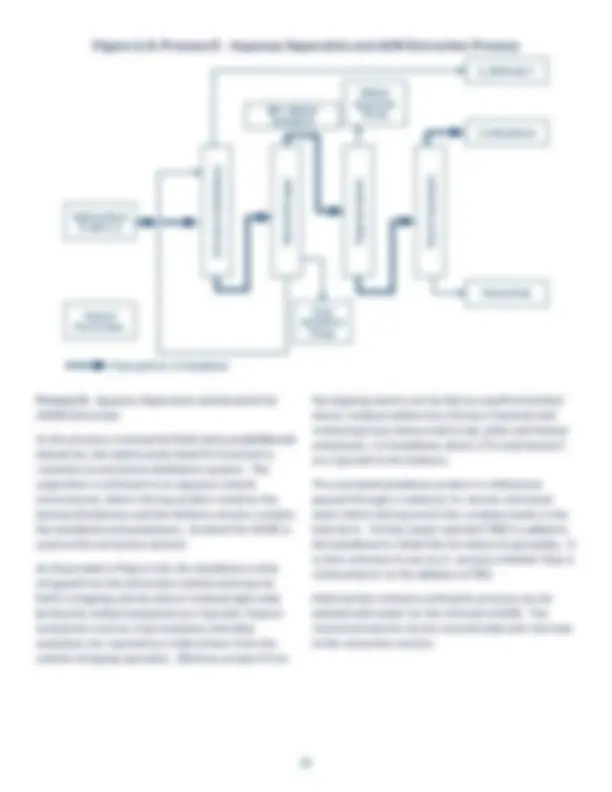
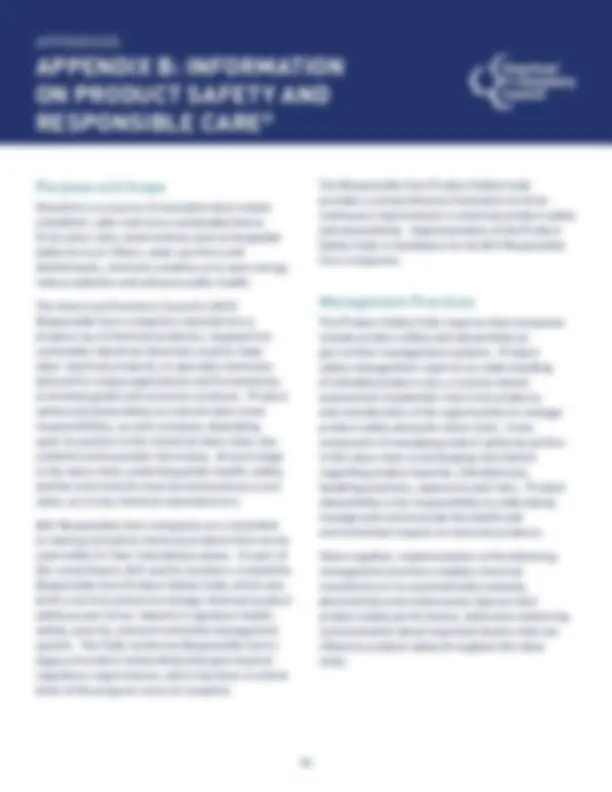
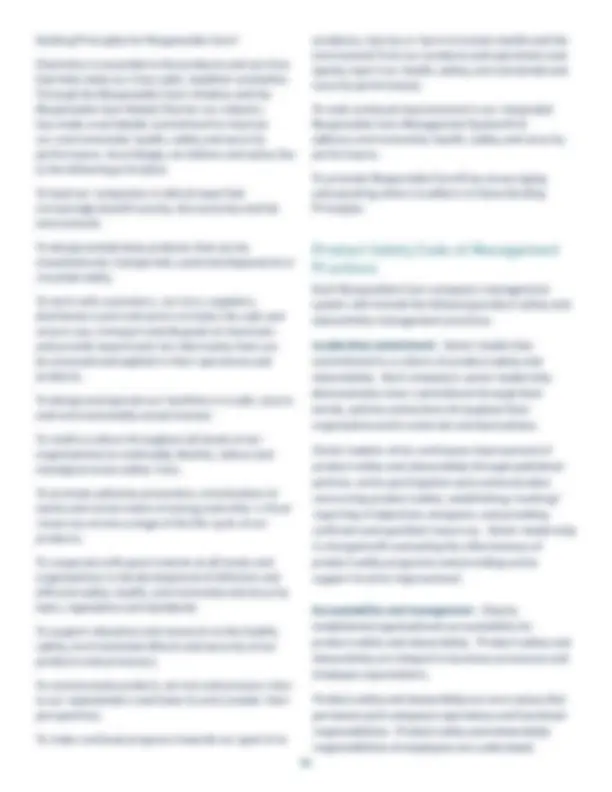
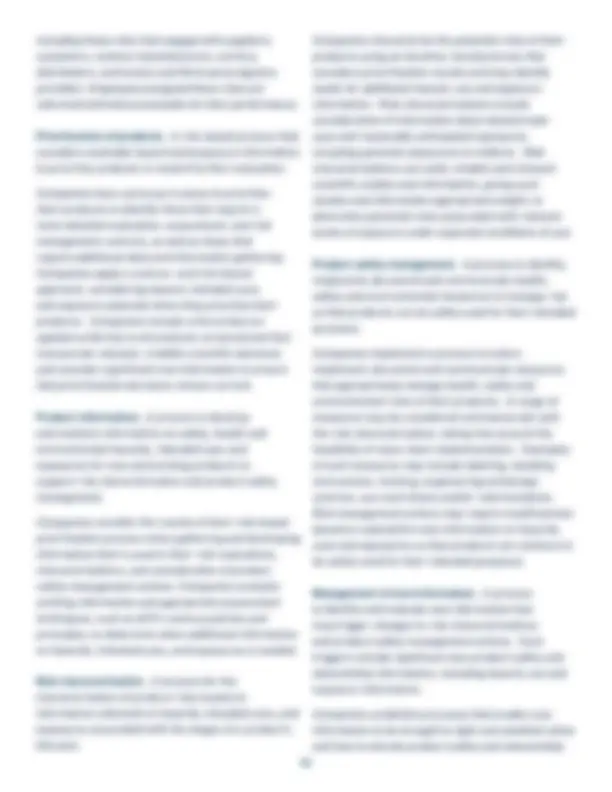
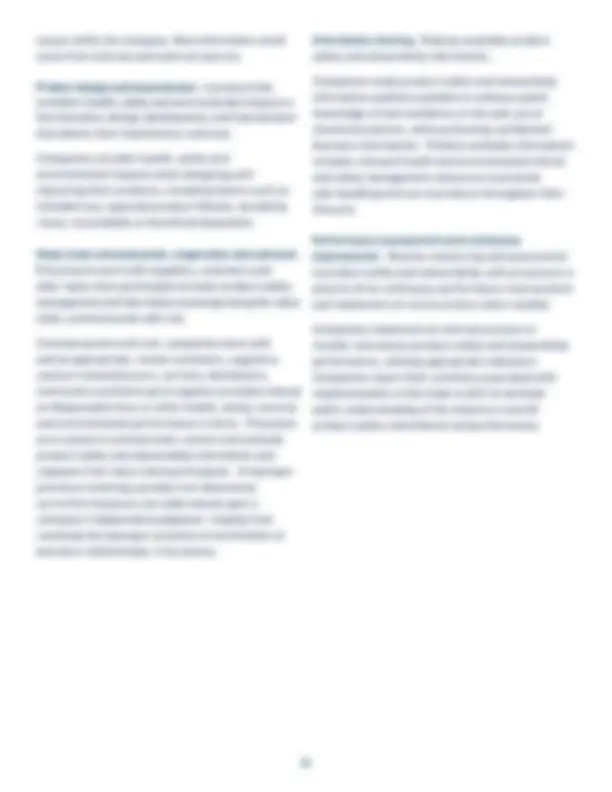
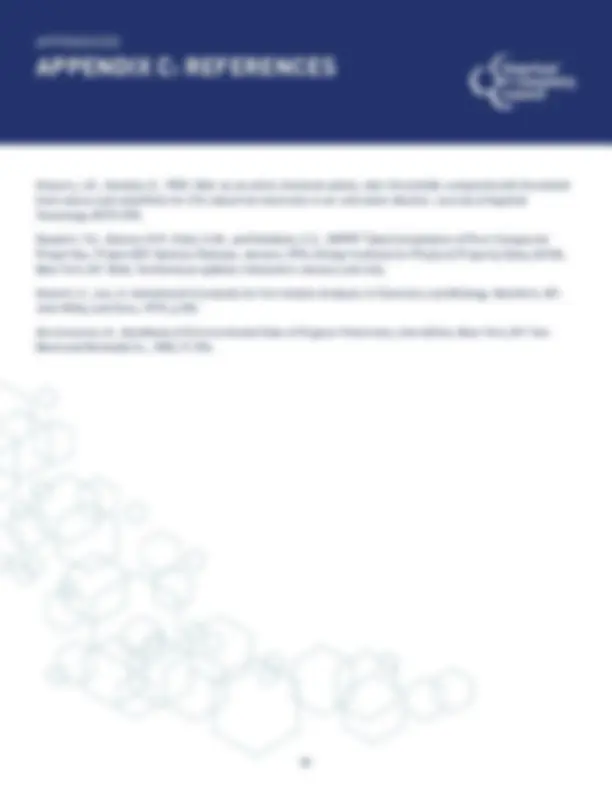
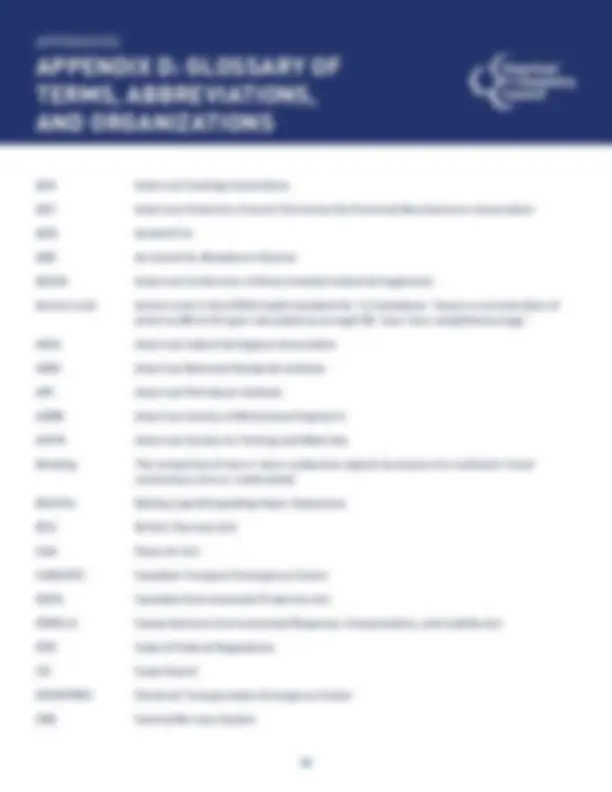
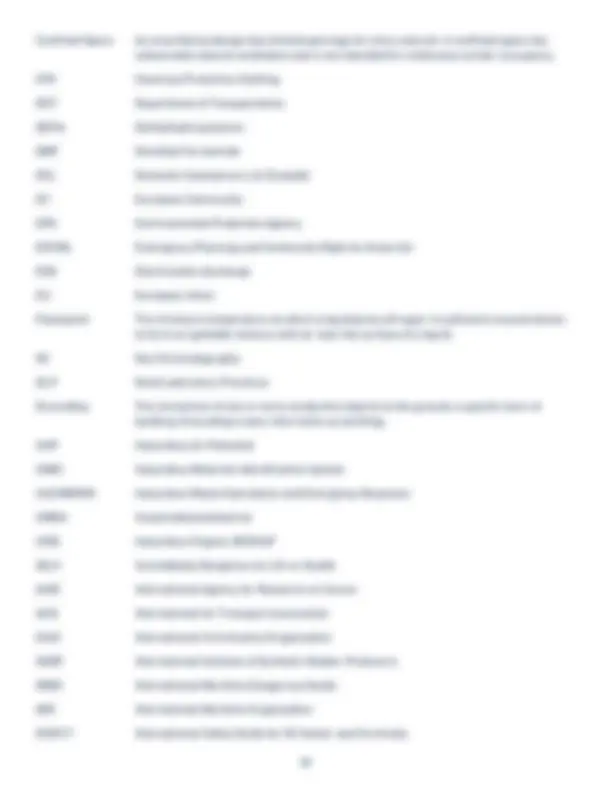
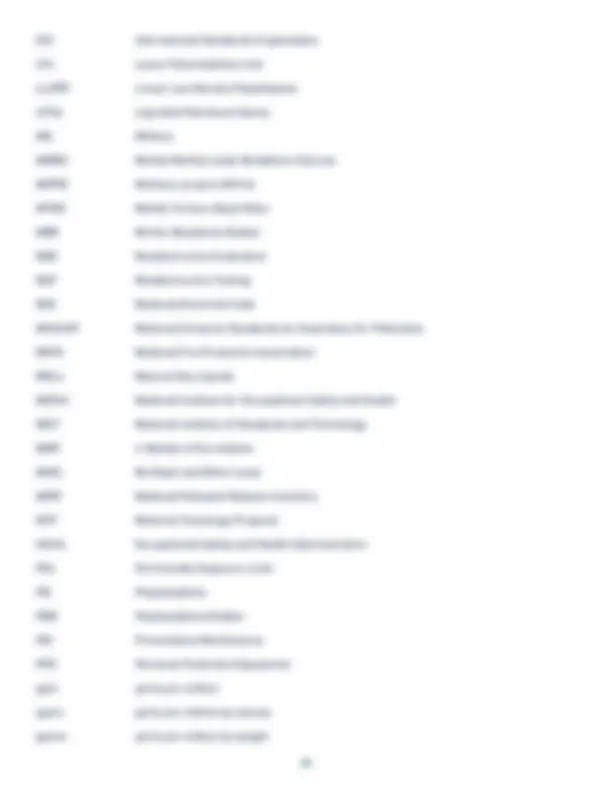
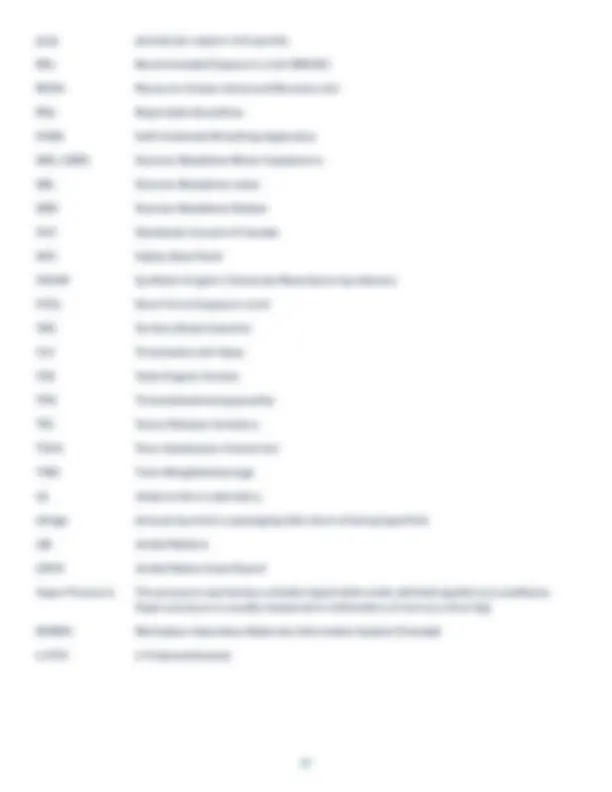
Estude fácil! Tem muito documento disponível na Docsity
Ganhe pontos ajudando outros esrudantes ou compre um plano Premium
Prepare-se para as provas
Estude fácil! Tem muito documento disponível na Docsity
Prepare-se para as provas com trabalhos de outros alunos como você, aqui na Docsity
Os melhores documentos à venda: Trabalhos de alunos formados
Prepare-se com as videoaulas e exercícios resolvidos criados a partir da grade da sua Universidade
Responda perguntas de provas passadas e avalie sua preparação.
Ganhe pontos para baixar
Ganhe pontos ajudando outros esrudantes ou compre um plano Premium
Comunidade
Peça ajuda à comunidade e tire suas dúvidas relacionadas ao estudo
Descubra as melhores universidades em seu país de acordo com os usuários da Docsity
Guias grátis
Baixe gratuitamente nossos guias de estudo, métodos para diminuir a ansiedade, dicas de TCC preparadas pelos professores da Docsity
uso do butadieno e cuidados em plantas industriais uso do butadieno e cuidados em plantas industriais uso do butadieno e cuidados em plantas industriais uso do butadieno e cuidados em plantas industriais uso do butadieno e cuidados em plantas industriais uso do butadieno e cuidados em plantas industriais uso do butadieno e cuidados em plantas industriais uso do butadieno e cuidados em plantas industriais
Tipologia: Manuais, Projetos, Pesquisas
1 / 63
Esta página não é visível na pré-visualização
Não perca as partes importantes!
Butadiene Production via Catalytic Butadiene Production via Oxidative
The members and affiliated companies of the American Chemistry Council support efforts to improve the industry’s responsible management of chemicals. To assist in this effort, the American Chemistry Council’s Olefins Panel supported the creation and publication of this manual to provide the reader with a better understanding of how butadiene is manufactured and used to produce products that play an important role in our lives. This manual has been developed for use by producers and industrial users of butadiene. It focuses on the health, safety, and environmental aspects associated with manufacturing, distributing, using, and disposing of 1,3-butadiene. References to applicable regulations and industry practices are made in the tables and text. A Glossary of terms is in Appendix D. This manual may be updated. Contact your supplier to obtain the most current version of this manual, if you have questions, or for more information about any item contained herein. We encourage comments on the content of this manual and a more in-depth dialogue concerning the issues presented.
Figure 1.1: Some Uses of 1,3-Butadiene Figure 1.2: Liquid Density Figure 1.3: Vapor Pressure Figure 1.4: Heat of Vaporization Figure 1.5: Liquid Heat Capacity Figure 1.6: Ideal Gas Heat Capacity Figure 1.7: Liquid Viscosity Figure 1.8: Vapor Viscosity Figure 1.9: Liquid Thermal Conductivity Figure 1.10: Vapor Thermal Conductivity Figure 1.11: Surface Tension Figure 4.1: Growth of Butadiene Popcorn Polymer at 140 °F Figure 4.2: Effect of Benzoyl Peroxide and Temperature on Rate of “Rubber” Polymer Formation Figure 4.3: Dimerization of 1,3-Butadiene Figure A.1: Typical Olefins Plant Figure A.2: Catadiene Process Figure A.3: Oxo-D Process Figure A.4: C4 Processing Options Figure A.5: Process A - Acetylene Hydrogenation/Extractive Distillation Using MOPN/Furfural Figure A.6: Process B - Extractive and Conventional Distillation Using NMP Figure A.7: Process C - DMF Solvent Extraction Process Figure A.8: Process D - Aqueous Separation and ACN Extraction Process. Table 1.1: Use Patterns for 1,3-Butadiene in the US, 2018 Table 1.2: Chemical and Physical Properties of 1,3-Butadiene Table 1.3: Example of a 1,3-Butadiene Specification Table 2.1: 1,3-Butadiene Carcinogenicity Classifications Table 4.1: Minimum Requirement for Respiratory Protection for Airborne Butadiene ( CFR § 1910.1051(h)(5)(ii)) Table 4.2: Summary of Permeation Test Data for 1,3-Butadiene Table 4.3: Items Mounted on the Pressure Head Assembly Table 4.4: An Example Rail Tank Car Unloading Procedure Table 4.5: Items That Should be Considered in Developing a Storage System for Butadiene Table 4.6: Effect of Temperature on the Rate of Dimer Formation Table 4.7: Chemical Incompatibilities with Butadiene and Potential Outcome Table 5.1: General Guidelines for Fire Prevention Table A.1: Example of a Crude Butadiene Analysis Table A.2: Major Butadiene Recovery Processes
Polymer Usage Polybutadiene (PB): As illustrated in Table 1.1, PB, produced by the polymerization of butadiene, is the largest use of the monomer (approximately 25%). Some of the uses for this polymer are as a raw material for tires, as an intermediate in the production of acrylonitrile-butadiene-styrene (ABS) resin and in impact modifiers. Such impact modifiers enhance the ability of a material to accept a sudden blow or shock without fracture or substantial damage. Styrene-Butadiene Rubber (SBR): Approximately 23% of the butadiene end-use in the U.S., is in the production of SBR. Produced by the polymerization of styrene and butadiene, the primary use of SBR is in tires and tire products. This material also is used in adhesives and sealants, coatings for wire and cable and many other rubber articles such as shoe soles. Styrene-Butadiene Latex (SBL): SBLs comprise about 8% of the butadiene end-use in the U.S. Latex, in general, can be described as a stable aqueous dispersion, which contains discrete polymer particles of approximately 0.05 to 5 micrometers in diameter. SBL applications include foam rubber (carpet backing, cushions, pads, sponges, etc.), adhesives (floorings, tiles, road and roofing, etc.), sealants and paper coatings. Acrylonitrile-Butadiene-Styrene (ABS) Resins: ABS resins are two-phase blends. They can be prepared by either emulsion polymerization or suspension grafting polymerization where homopolymers of polybutadiene are grafted onto a styrene-acrylonitrile copolymer. The production of ABS resins account for about 4% of the butadiene usage in the U.S. These resins are used in a wide range of applications that include automotive parts, telephones, office machines such as computers, and appliances. Nitrile Rubber (NBR): NBR is produced by the copolymerization of acrylonitrile and butadiene. It also is referred to as nitrile-butadiene rubber. NBR accounts for about 3% of the butadiene consumption in the United States. This material is used in a variety of products including hoses, fuel lines, automotive parts, gasket seals, lattices, structural adhesives, oil resistant clothing or articles, gloves and footwear. Styrene-Butadiene Block Copolymers (SBS and SEBS): Blocks of styrene, butadiene and styrene are polymerized to form styrene-butadiene- styrene (SBS) block copolymers. Similarly, blocks of styrene, ethylene/butylene and styrene form SEBS block copolymers. End uses for these thermoplastic materials include asphalt extenders, lubricating oil additives, adhesives, automotive applications, food and other types of packaging, medical devices, footwear, toys, disposable dinnerware and polymer modification such as impact modifiers. Methyl Methacrylate-Butadiene-Styrene (MMBS): MMBS resin is used as an impact modifier in automotive parts, bottles and food packaging. Chemical Intermediate Usage 1,3-Butadiene also is used in the production of a number of intermediate chemicals. Adiponitrile >> Hexamethylenediamine >> Nylon: The production of the chemical intermediate adiponitrile is the largest use of 1,3-butadiene in this type of application. This represents approximately 23% of the overall butadiene usage. One method employed to produce adiponitrile involves the direct hydrocyanation of butadiene followed by hydrocyanation of the pentenenitrile compounds produced in the butadiene reaction. This material is then hydrogenated to form hexamethylenediamine, which is polymerized in the manufacture of nylon resins and fibers. Chloroprene: Chloroprene is formed by chlorinating butadiene. This material is then polymerized to produce neoprene. Neoprene rubber is a multipurpose material that accounts for about 3% of the butadiene usage. It is used in applications that include gloves, coatings, adhesives, binders, sealants, tires, belts, hoses, faucet washers and footwear. Other Chemical Intermediate Uses: Butadiene also is used in the production of 1,4- hexadiene,
sulfolane and 1,5,9-cyclodecatriene. 1,4-hexadiene is primarily used as the monomer for ethylene- propylene terpolymer (EPDM); sulfolane is an extraction solvent, and 1,5,9-cyclodecatriene is used in the production of nylon fibers and resins. In summary, 1,3-butadiene is an extremely versatile and significant industrial chemical. Figure 1. provides an overview of some uses of 1,3-butadiene. Figure 1.1: Some End Uses of 1,3-Butadiene Butadiene End Uses Polymers Styrene- Butadiene Rubber (SBR) Tires Tire Products Adhesives Sealants Coatings Rubber Articles (e.g., Footwear) Chewing Gum Base Acrylonitrile- Butadiene - Styrene (ABS) Resin Automotive Parts Telephones Office Machines Computers Appliances Adiponitrile Hexamethylene- diamine (HMDA) Nylon Resins and Fiber Chloropropene Neoprene Gloves Coatings Adhesives Binders Sealants Tires Other Belts and Footwear Chemical Intermediates 1,5,9- Cyclordecatriene Nylon Fibers and Resins Sulfolane Extraction Solvent 1,4-Hexadiene Ethylene-Propylene Tergolymer (EPDM) Coated Fabrics Automotive Parts Safety Bumpers Wire & Cable Coating Resin Modifier Footwear Mechanical Rubber Products Gaskets Tire Tubes Styrene Butadiene Latex (SBL) Foam Rubber (Carpet Backing Cushions Pads Sponges, etc.) Adhesives Sealants Paper Coatings Methyl Methacrylate- Butadiene- Styrene (MMBS) Used in Auto Parts Food Packaging Bottles Nitrile Rubber (NBR) Hoses Fuel Lines Auto Parts Latex Adhesives Oil-Resistant Clothing/ Articles Gloves Footwear Polybutadiene (PB) Tires ABS Resins Intermediates Impact Modifiers Styrene- Bu- tadiene Block Copolymers (SBS, SEBS) Automotive Applicators Asphalt Extender Lubricating Oil Additives Food Packaging Adhesives Medical Devices Footwear Polymer Mods Toys Disposable Dinnerware Chemical and Physical Properties of 1,3-Butadiene 1,3-Butadiene is a colorless, non-corrosive, flammable gas with a hydrocarbon odor at ambient temperature and pressure. Data pertaining to its chemical and physical properties are presented in Table 1.2. Additional data concerning the physical properties of butadiene and their temperature dependence can be found in Figures 1.10-1.19 (Source: AICHe DIPPR®^ Database unless otherwise indicated).
Figure 1.2: Liquid Density Figure 1.3: Vapor Pressure
Figure 1.4: Heat of Vaporization Figure 1.5: Liquid Heat Capacity
Figure 1.8: Vapor Viscosity Figure 1.9: Liquid Thermal Conductivity
Figure 1.10: Vapor Thermal Conductivity Figure 1.11: Surface Tension
OBUS SENTEM CONFENTEM NI SE CRIT OLTORA QUOD REIS
This section provides a brief overview of information pertaining to potential health and environmental effects associated with exposure to 1,3-butadiene. A comprehensive discussion of health and environmental effects pertaining to 1,3-butadiene is beyond the scope of this manual. For more information, contact your supplier. Additional information, including first aid information, can be found in your supplier’s Safety Data Sheet (SDS). Acute Inhalation Exposure Butadiene vapors may be mildly irritating to the nose, throat and respiratory tract. High vapor concentrations may cause central nervous system (CNS) depression. Early to moderate CNS depression may be evidenced by giddiness, headache, dizziness and nausea; in extreme cases, unconsciousness, respiratory depression and death may occur. High concentrations of butadiene in confined spaces, such as may occur in a spill or leak situation, may cause asphyxiation by displacing the oxygen, causing an oxygen-deficient atmosphere. As with the above CNS effects, this can result in a sudden loss of consciousness and potentially death. Eye Contact Eye contact with rapidly expanding butadiene gas or vaporizing liquid butadiene may cause severe irritation and burns (frostbite). Frostbite results from the cooling effect of rapid evaporation of the material. Skin Contact Skin contact with rapidly expanding butadiene gas or vaporizing liquid butadiene may cause irritation and burns (frostbite). Exposure to high vapor concentrations may cause slight irritation to the skin. Chronic Effects The potential for 1,3-butadiene to cause cancer or other chronic health effects has been examined in experiments using laboratory animals and also by studying exposed human populations. Examples of cancer classifications established by various governmental entities as of the date of publication of this manual are listed in Table 2.1. Other potential target organs for exposure to 1,3-butadiene may include the liver, kidneys, respiratory tract, ovaries, testes and hematopoietic system (blood forming organs). Laboratory mice have been shown to be highly sensitive to 1,3-butadiene, including the endpoints of cancer, developmental toxicity (effects on the developing fetus) and injury to reproductive organs. The relevance of the findings in mice to humans is the subject of ongoing research by numerous investigators, including studies sponsored by the American Chemistry Council’s Olefins Panel. For more information concerning potential chronic hazards from exposure to 1,3-butadiene, contact your supplier.
HEALTH AND ENVIRONMENTAL EFFECTS
Table 2.1: 1,3-Butadiene Carcinogenicity Classifications Organization Classification International Agency for Research on Cancer (IARC) Group 1 – Carcinogenic to Humans Environmental Protection Agency (EPA) Carcinogenic to Humans by Inhalation National Toxicology Program (NTP) Known Human Carcinogen National Institute for Occupational Safety and Health (NIOSH) Carcinogen, with No Further Categorization American Conference on Governmental Industrial Hygienists (ACGIH) Group A2 – Suspected Human Carcinogen Revised 11/22/ 4-Vinylcyclohexene Health Effects 4-Vinylcyclohexene (4-VCH) is a dimer of 1,3-butadiene and is normally present in butadiene. It is generally controlled below the 500-1000 ppmw level per product specifications. Studies in mice and rats show that mice have greater sensitivity to 4-VCH than rats, and are more efficient at converting 4-VCH to toxic metabolites and less effective at eliminating those toxic metabolites. Effects in mice include uncommon ovarian tumors and other effects on the ovaries and testes. Additional information about the health effects of 4-VCH can be obtained from your supplier. Potential Environmental Impacts of Spills or Releases 1,3-Butadiene is expected to rapidly volatilize into the air from water or soil and is not expected to be persistent in the air. The primary reaction for butadiene in air is with photochemically produced hydroxyl radicals – the estimated half-life is on the order of a few hours. Other reactions with butadiene that are expected to occur in the atmosphere are with ozone and nitrate radicals. The atmospheric half-life of 1,3-butadiene with ozone has been estimated at a few hours to a few days. No data are available on aquatic toxicity due to the high volatility and low water solubility of 1,3-butadiene. Water concentrations are not expected to be significant.
OBUS SENTEM CONFENTEM NI SE CRIT OLTORA QUOD REIS
Training Any person who comes into contact with butadiene should be trained in proper handling and safety per applicable federal, state and local laws and regulations. Personal Protective Equipment Respiratory Protection Respiratory protection should be used in accordance with company and applicable regulatory requirements. OSHA’s 1,3-butadiene standard requires engineering controls and work practices that comply with the OSHA PELs unless infeasible or work operations are non-routine. Engineering controls and work practices which are not sufficient to reduce exposures below the PELs should remain in place to reduce employee exposure to the lowest level achievable. Respiratory protection should be used to supplement the engineering controls and work practices. Table 4.1 details the minimum requirements for respiratory protection for airborne butadiene as contained in OSHA’s 1,3-Butadiene Standard. Persons should not be assigned to tasks requiring the use of respirators unless it has been determined they are physically able to perform the work and are trained to use the equipment. Chemical Protective Clothing The purpose of chemical protective clothing (CPC) is to prevent contact with chemicals that can injure or be absorbed through the skin. As indicated in Part II of this manual, skin contact with liquefied butadiene may result in frostbite. The level of protection selected should be based on the potential butadiene concentration and likelihood of contact. It could range from no CPC being required, such as when butadiene is handled in closed systems and there is no personnel exposure, to fully encapsulating suits with supplied-air respirators in certain spill situations. To assist in the selection of CPC, Table 4.2 contains butadiene permeation test results for many of the most common CPC materials. Although the data in the table has been compiled from published sources, it has not been independently verified. The table should not be considered a complete list of all permeation test data for materials with 1,3-butadiene. When selecting specific products, the material manufacturer should be contacted. In addition to permeation properties, thermal insulating properties for protection against frostbite may be a consideration in CPC material selection.
HANDLING, TRANSPORT AND STORAGE INFORMATION
Table 4.1: Minimum Requirement for Respiratory Protection for Airborne Butadiene (29 CFR § 1910.1051(h)(3)(i)) Concentration of Airborne Butadiene (ppm) Minimum Required Respirator or Condition of Use Less than or equal to 5 ppm (5 times PEL) (a) Air-purifying half mask or full facepiece respirator equipped with approved BD or organic vapor cartridges or canisters. Cartridges or canisters shall be replaced every 4 hours. Less than or equal to 10 ppm (10 times PEL) (a) Air-purifying half mask or full facepiece respirator equipped with approved BD or organic vapor cartridges or canisters. Cartridges or canisters shall be replaced every 3 hours. Less than or equal to 25 ppm (25 PEL) (a) Air-purifying full facepiece respirator equipped with times approved BD or organic vapor cartridges or canisters. Cartridges or canisters shall be replaced every 2 hours. (b) Any powered air-purifying respirator equipped with approved BD or organic vapor cartridges. PAPR cartridges shall be replaced every 2 hours. (c) Continuous flow supplied air respirator equipped with a hood or helmet. Less than or equal to 50 ppm (50 PEL) (a) Air-purifying full facepiece respirator equipped with times approved BD or organic vapor cartridges or canisters. Cartridges or canisters shall be replaced every (1) hour. (b) Powered air-purifying respirator equipped with a tight-fitting facepiece and an approved BD or organic vapor cartridges. PAPR cartridges shall be replaced every (1) hour. Less than or equal to 1,000 ppm (1,000 times PEL) (a) Supplied air respirator equipped with a half mask or full facepiece operated in a pressure demand or other positive pressure mode. Greater than 1,000 ppm or unknown concentration or firefighting (a) Self-contained breathing apparatus equipped with a full facepiece and operated in a pressure demand or other positive pressure mode. (b) Any supplied respiratory equipment with full facepiece and operated in a pressure demand or other positive pressure mode in combination with an auxiliary self-contained breathing apparatus operated in a pressure demand or other positive pressure mode. Escape from Immediately Dangerous Life or Health (IDLH) conditions (a) Any positive pressure self-contained breathing apparatus to with an appropriate service life. (b) A air-purifying full facepiece respirator equipped with a front or back mounted BD or organic vapor canister. Notes: Respirators approved for use in higher concentrations are permitted to be used in lower concentrations. Full face piece is required when eye irritation is anticipated.