
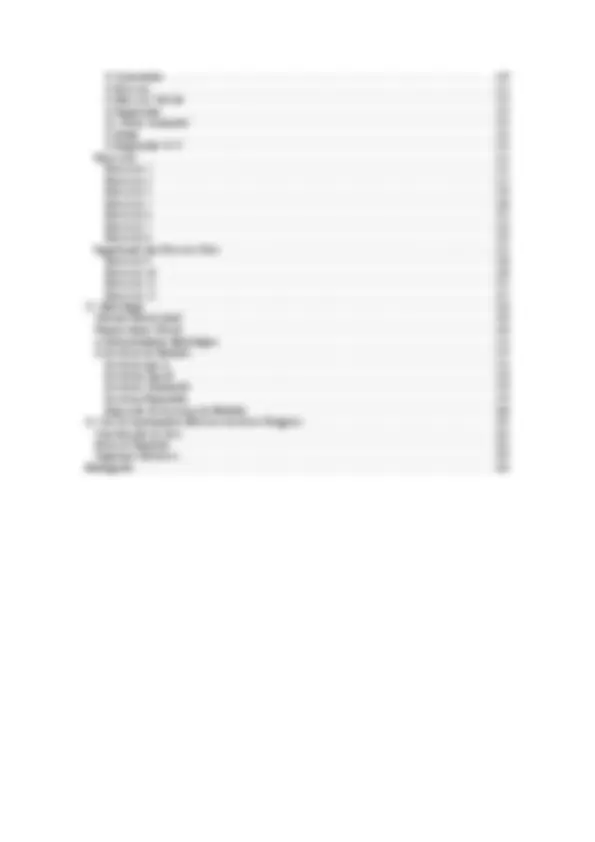
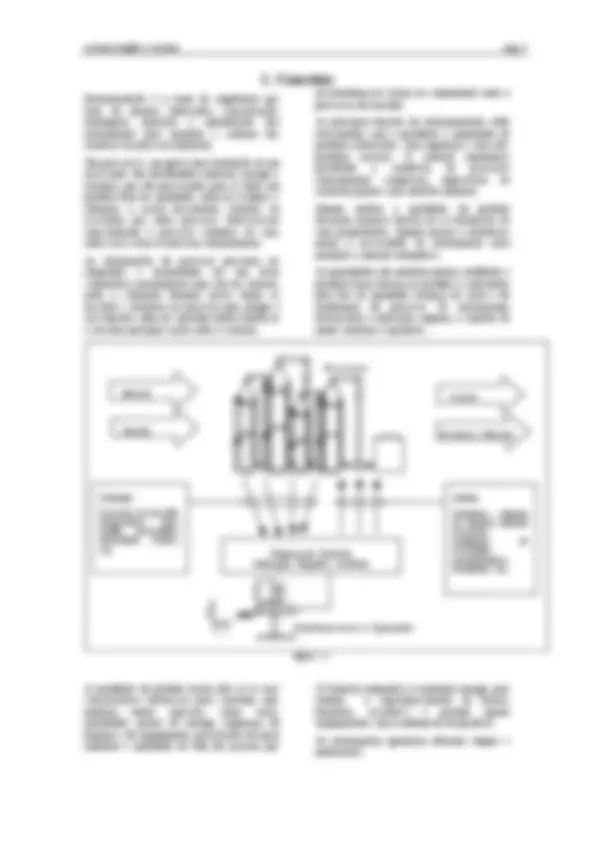
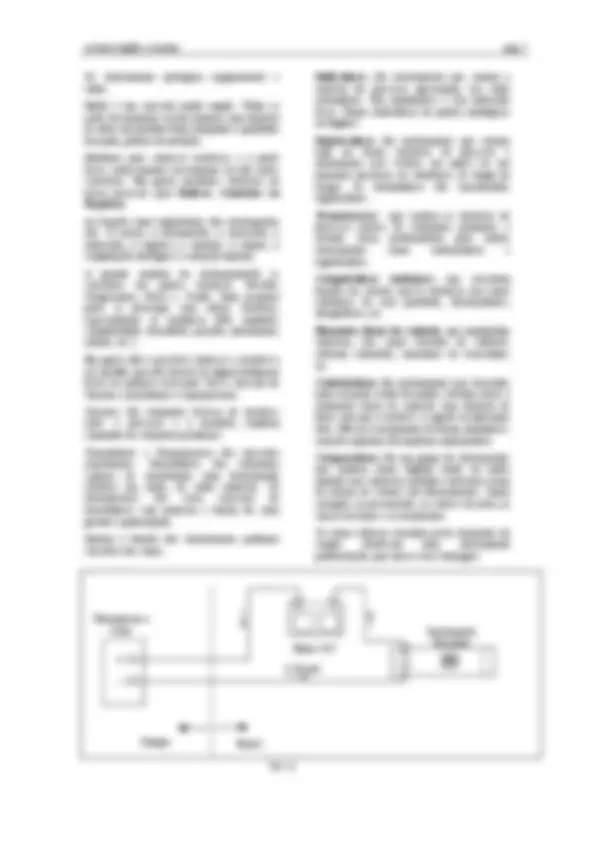
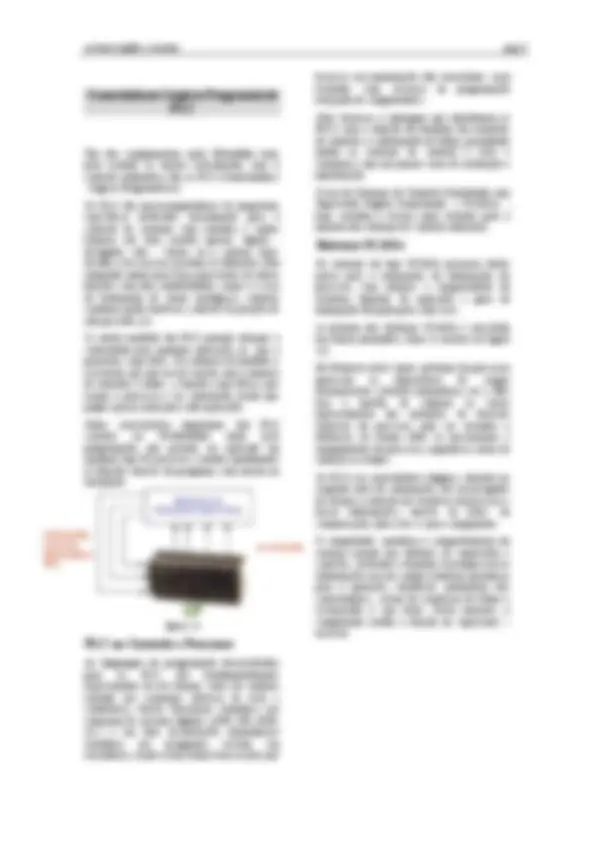

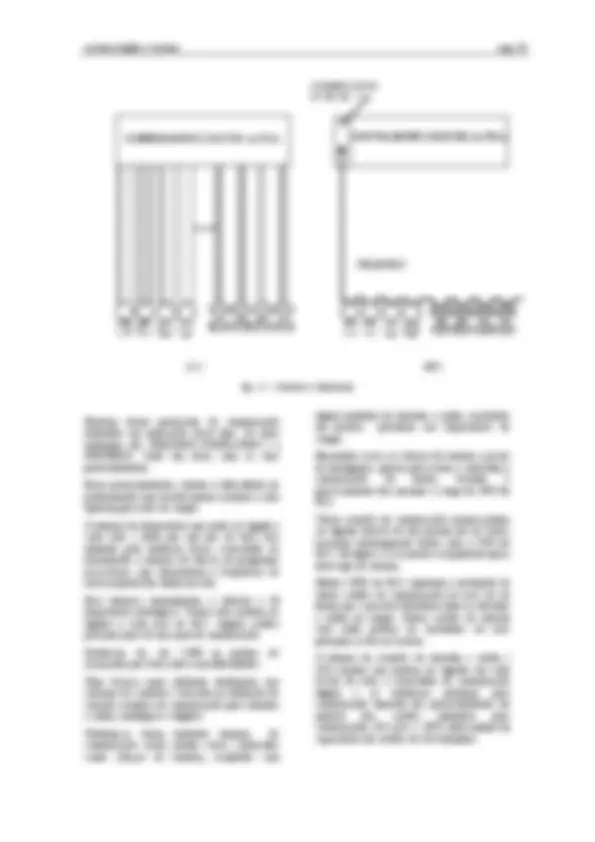
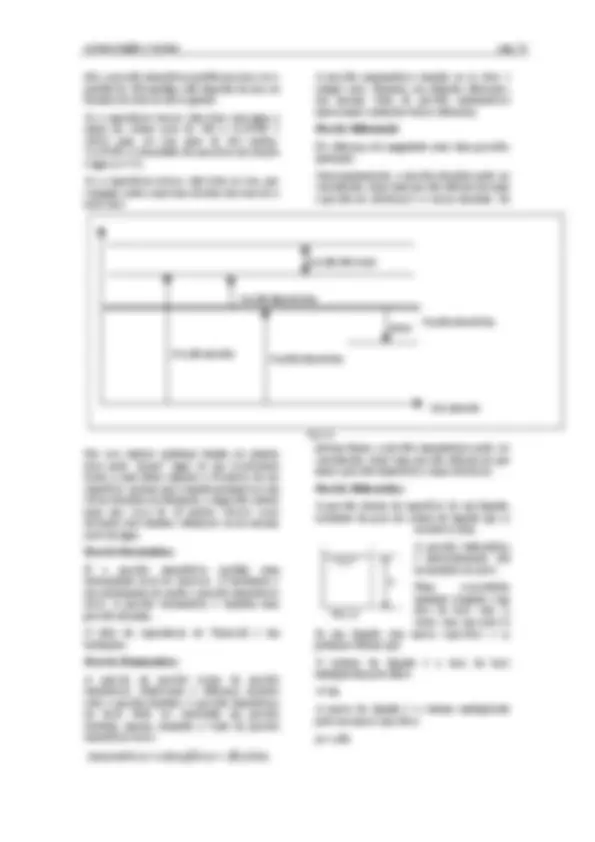
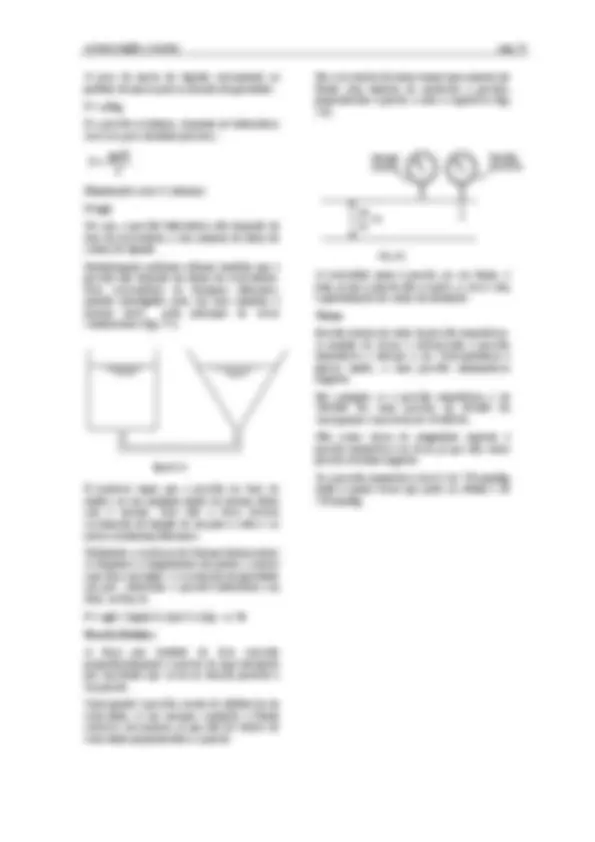
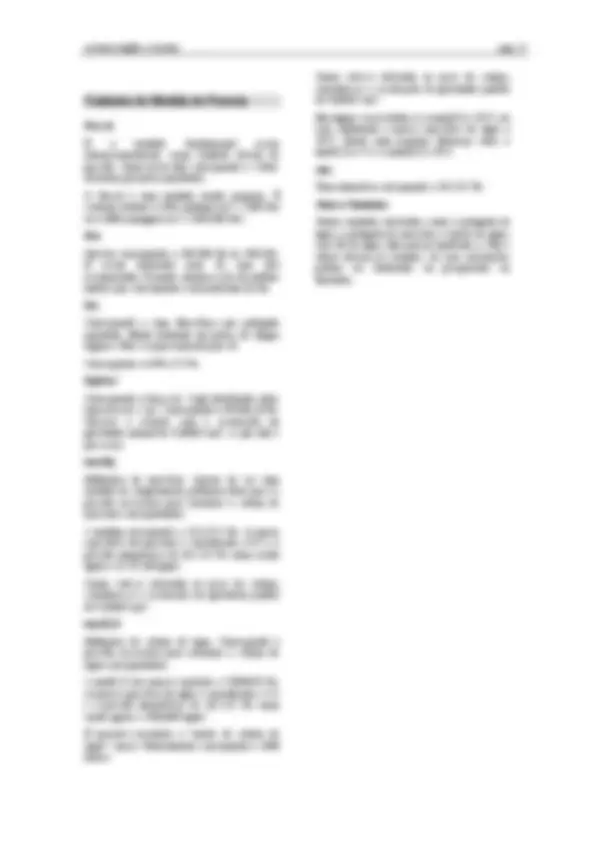
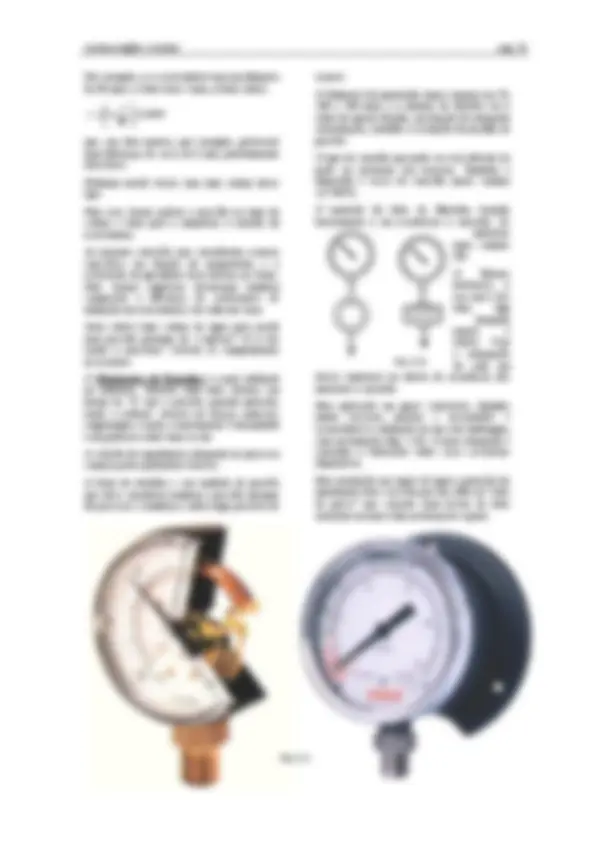
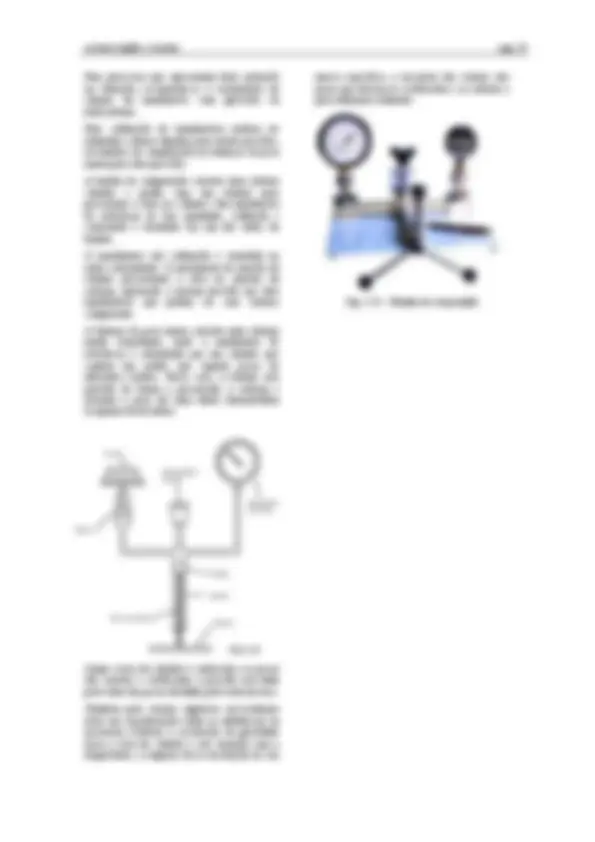
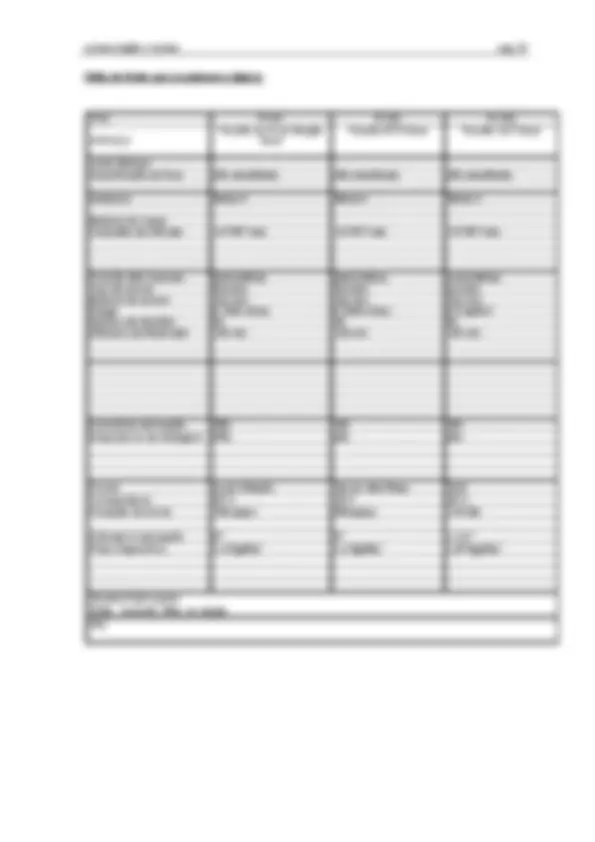
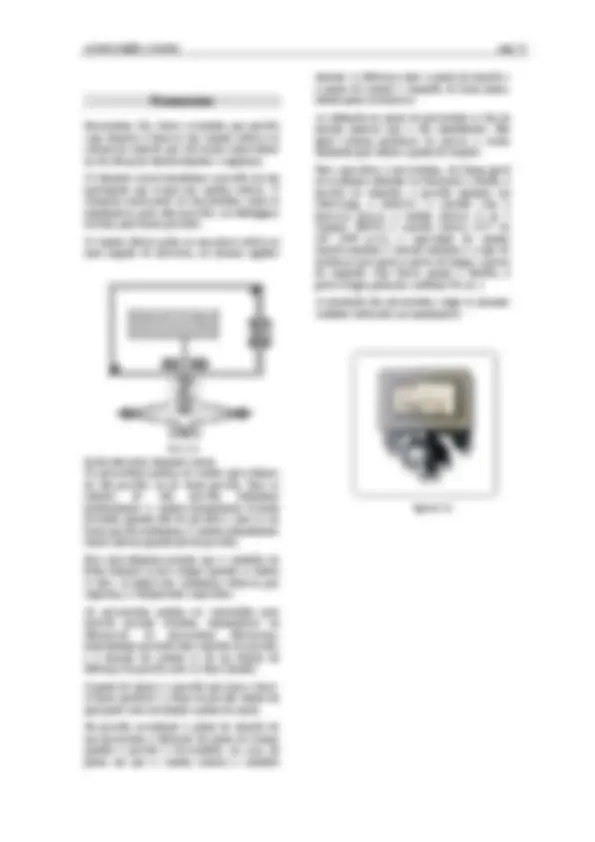
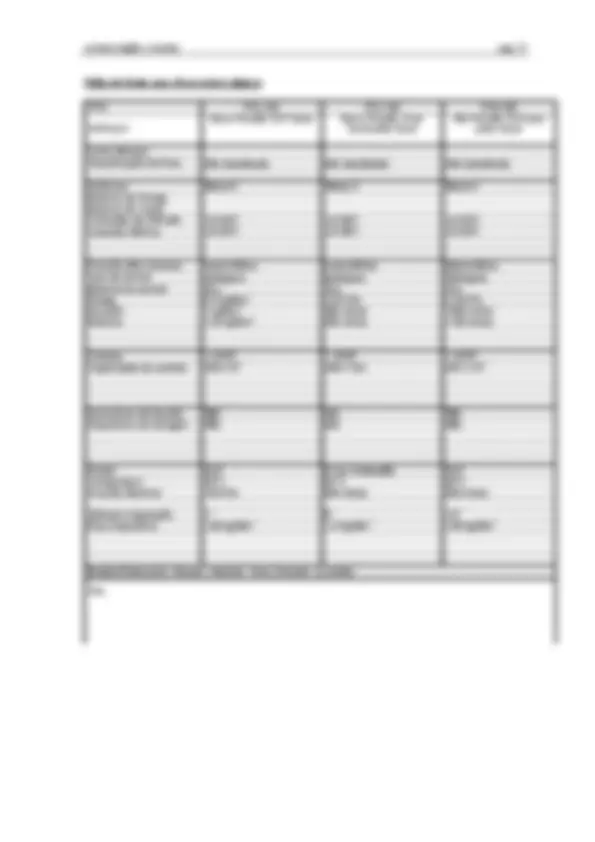
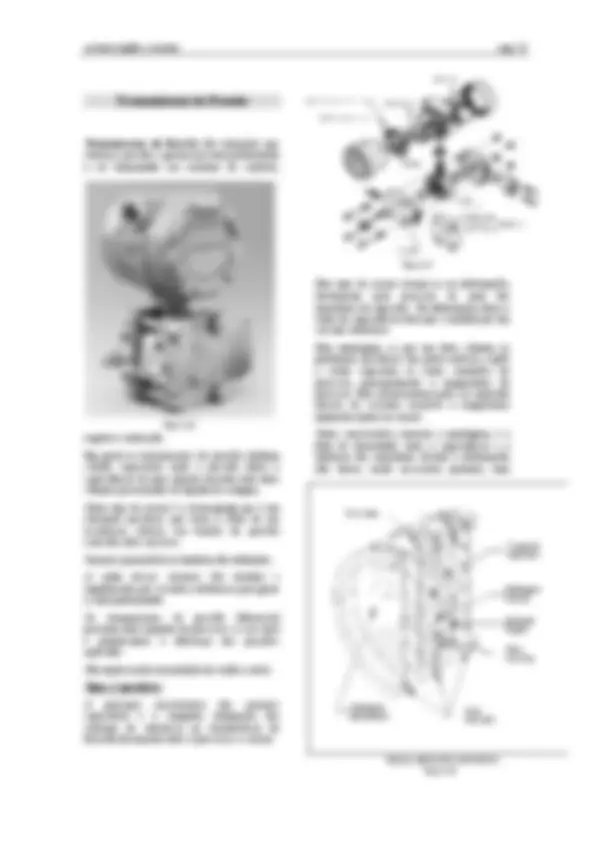
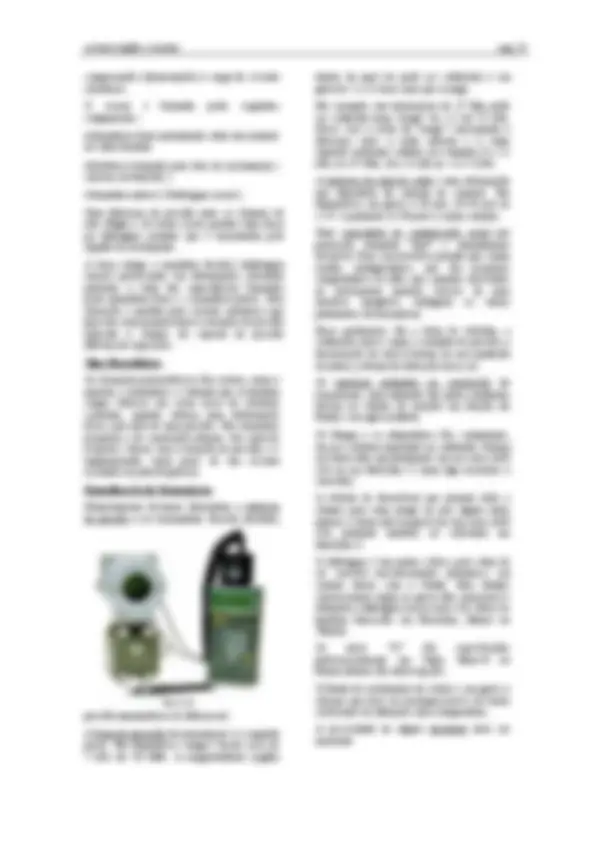
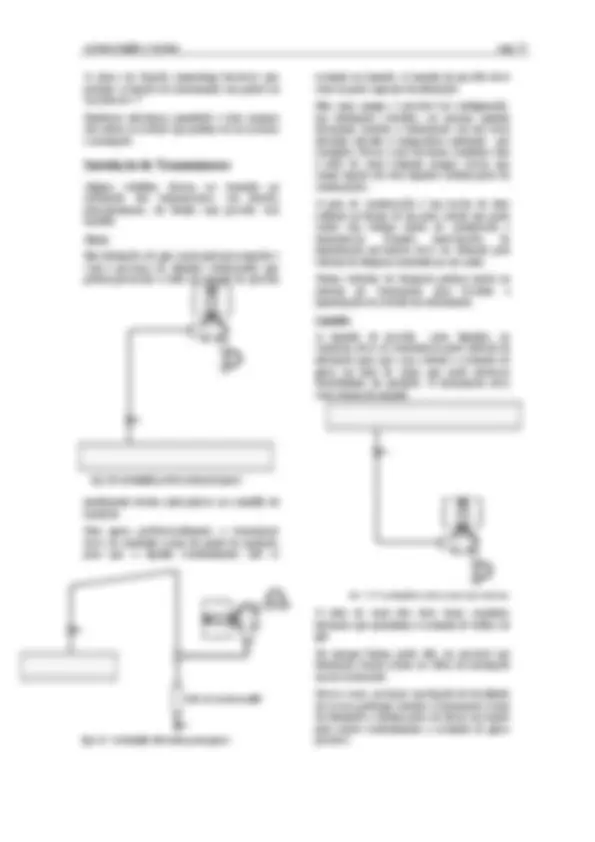
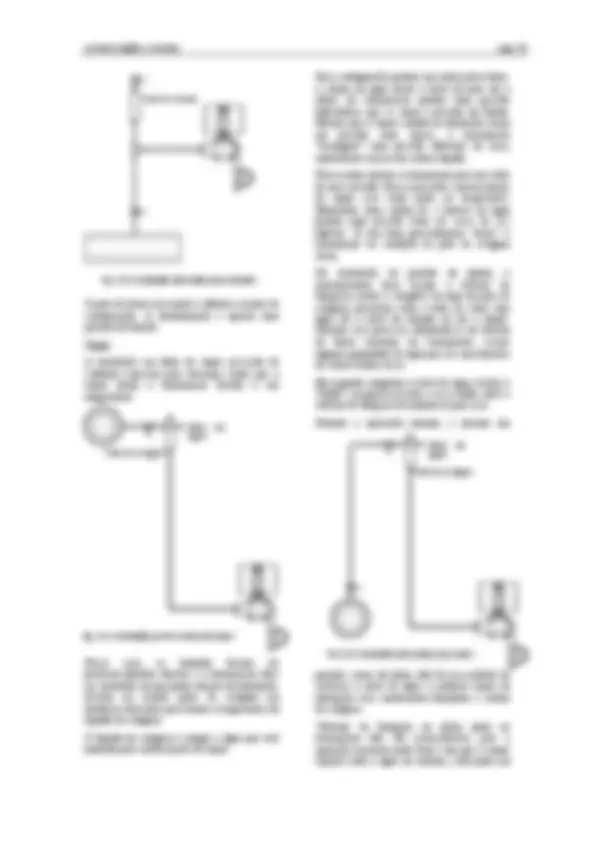
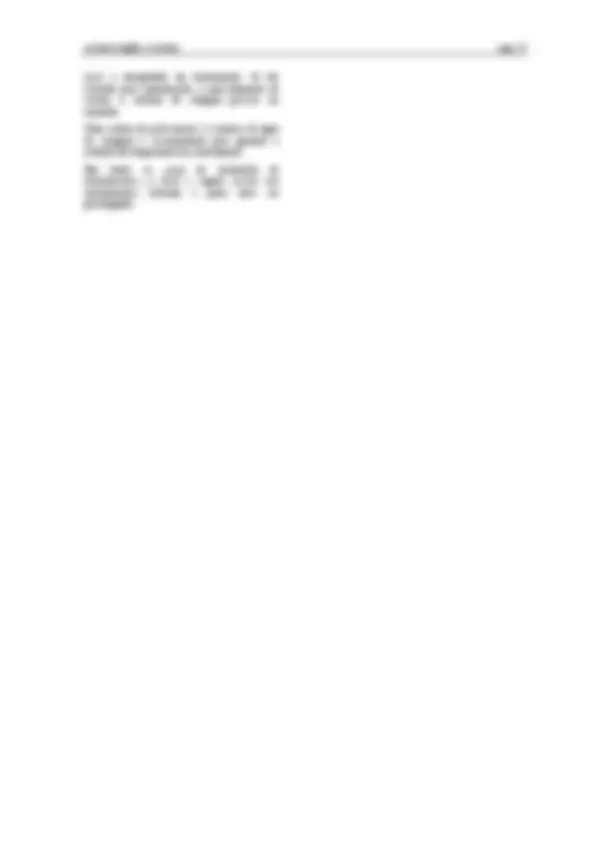
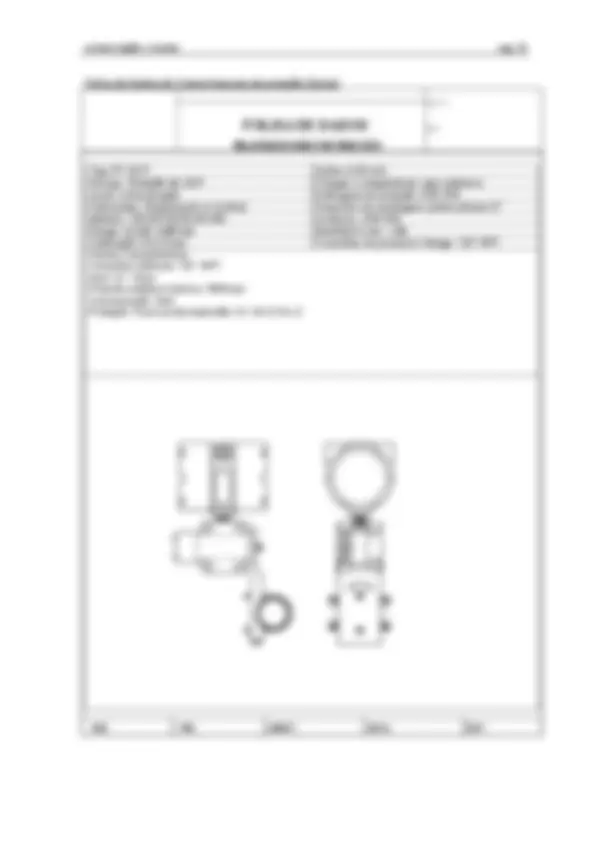
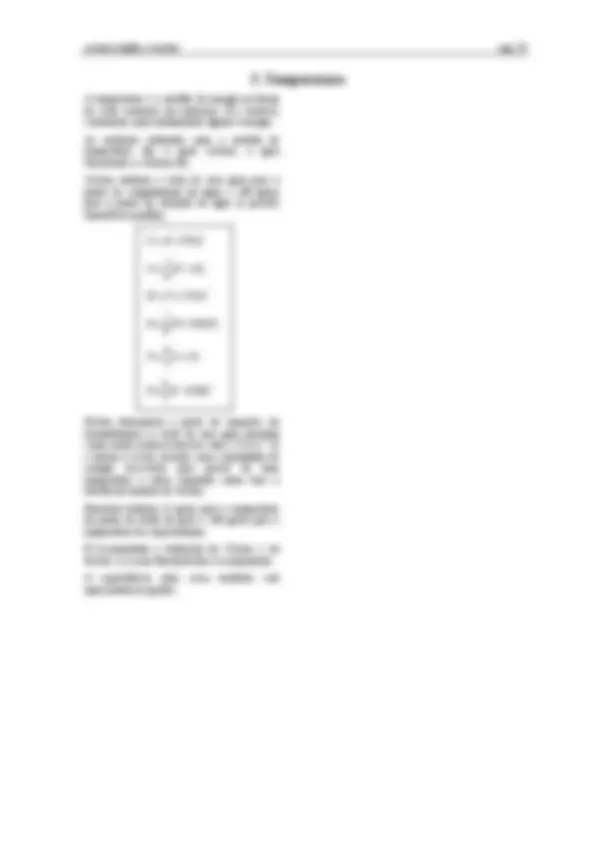
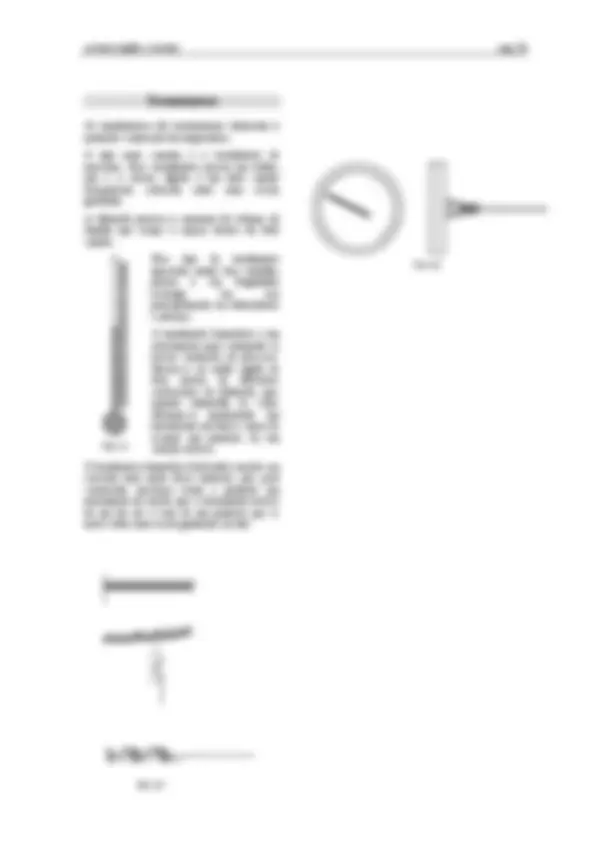
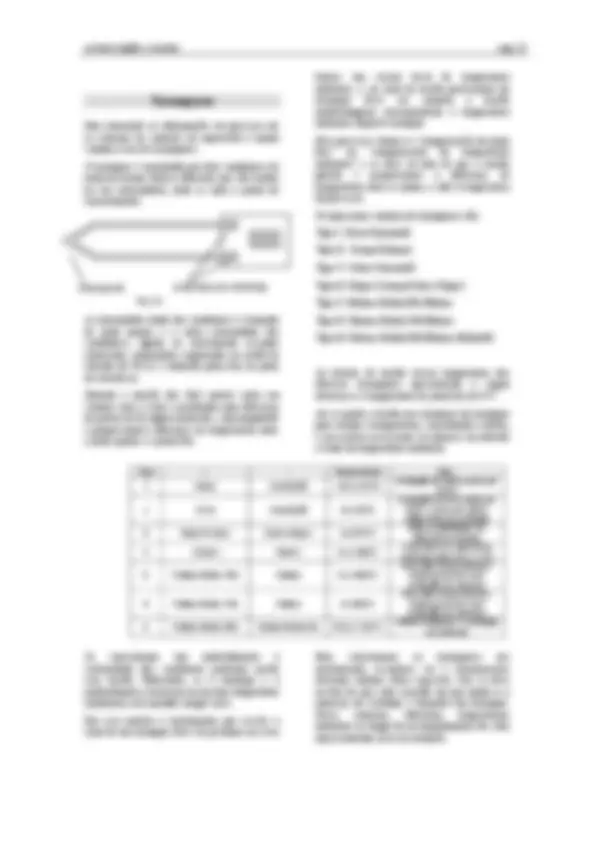
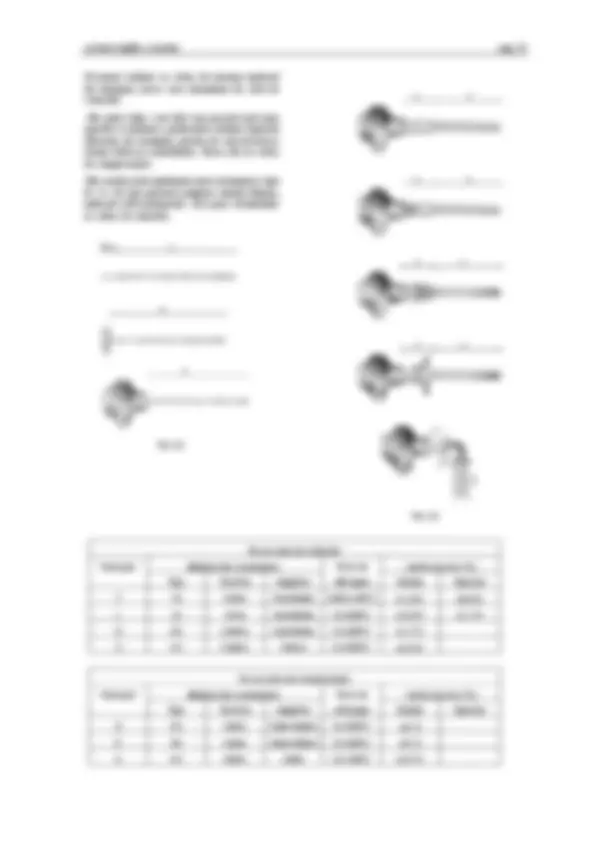
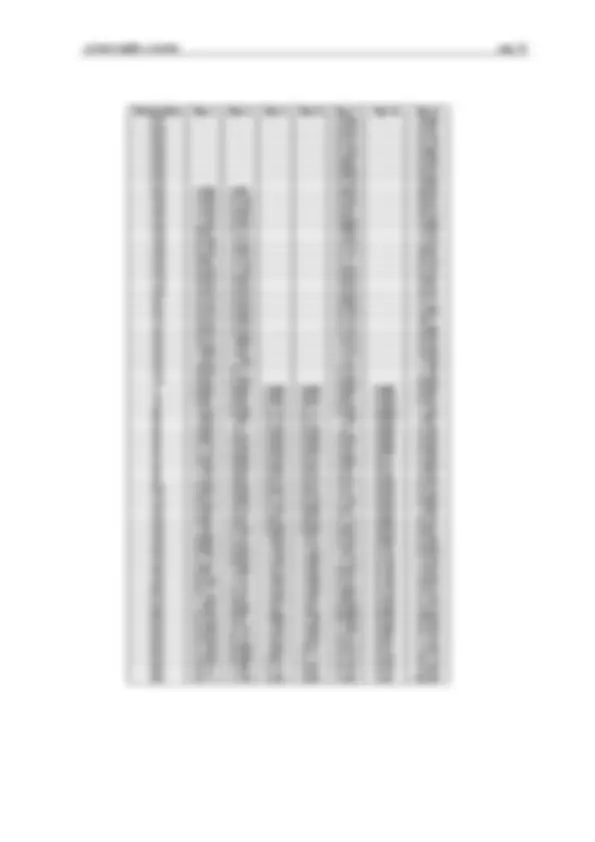
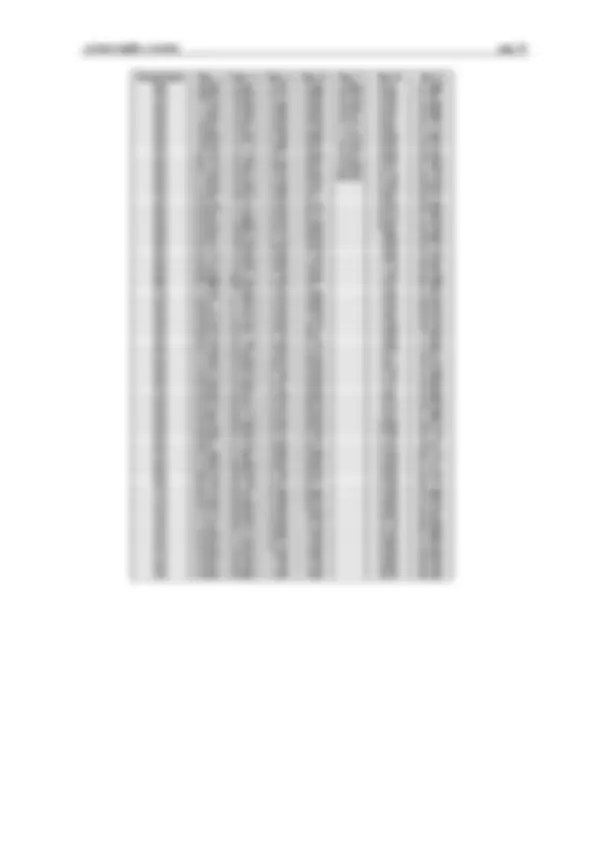
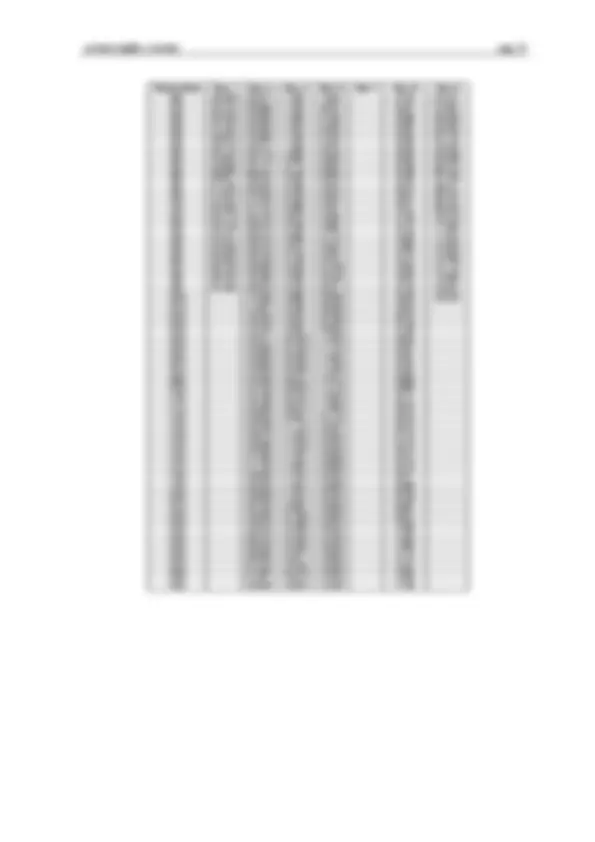
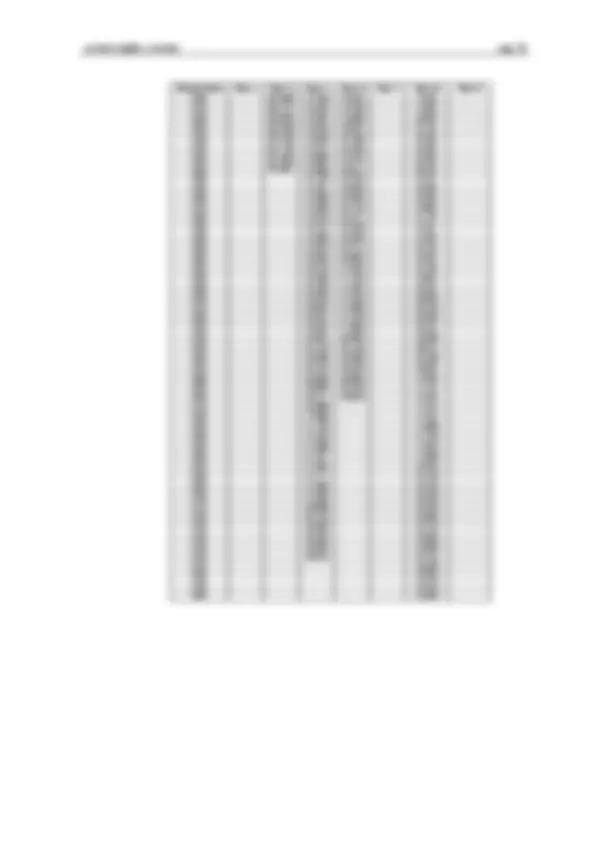
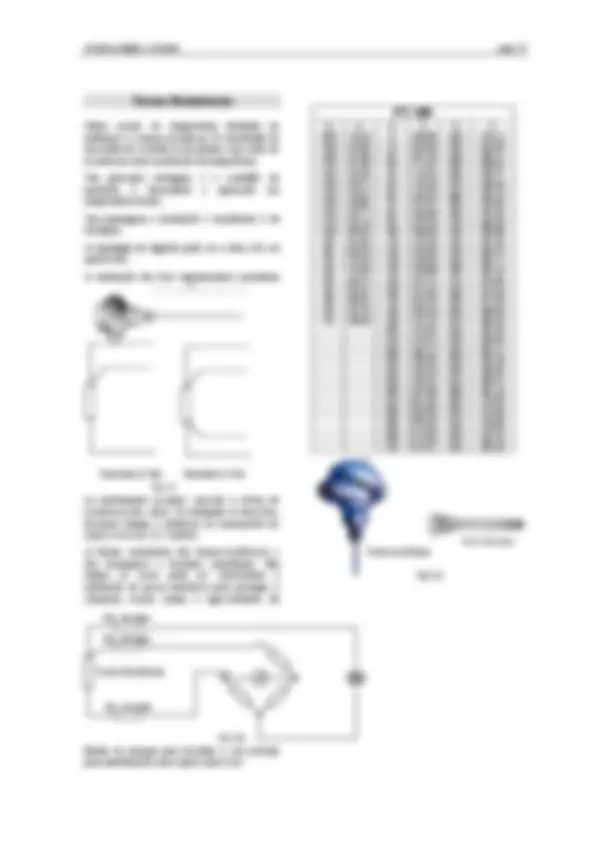
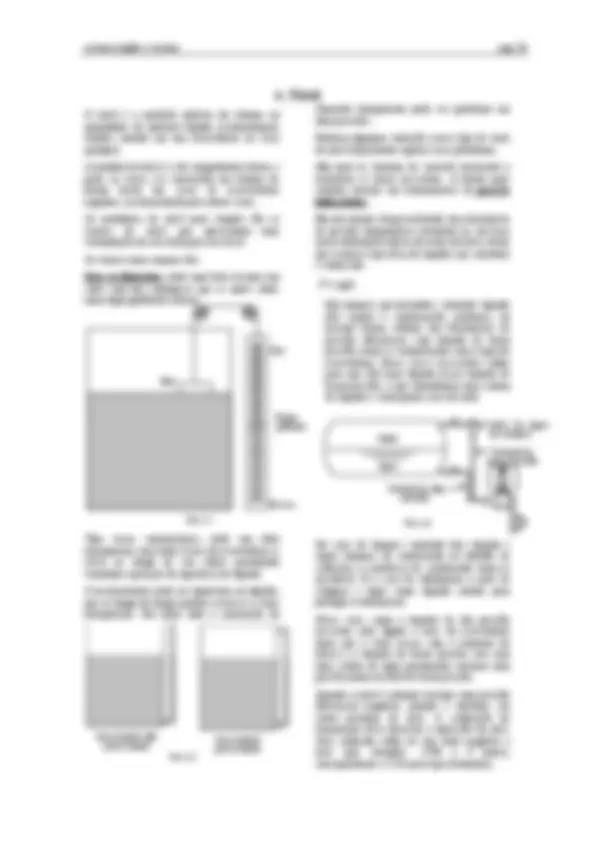
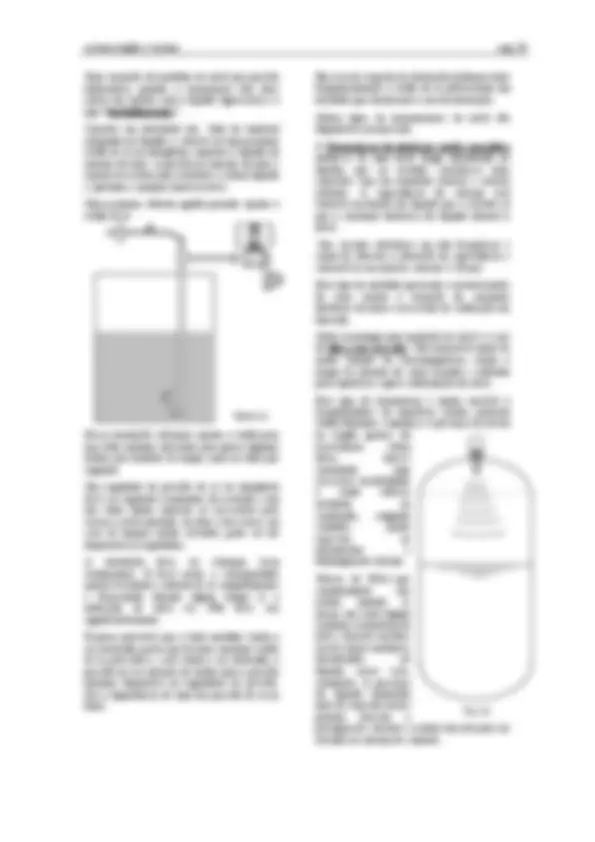
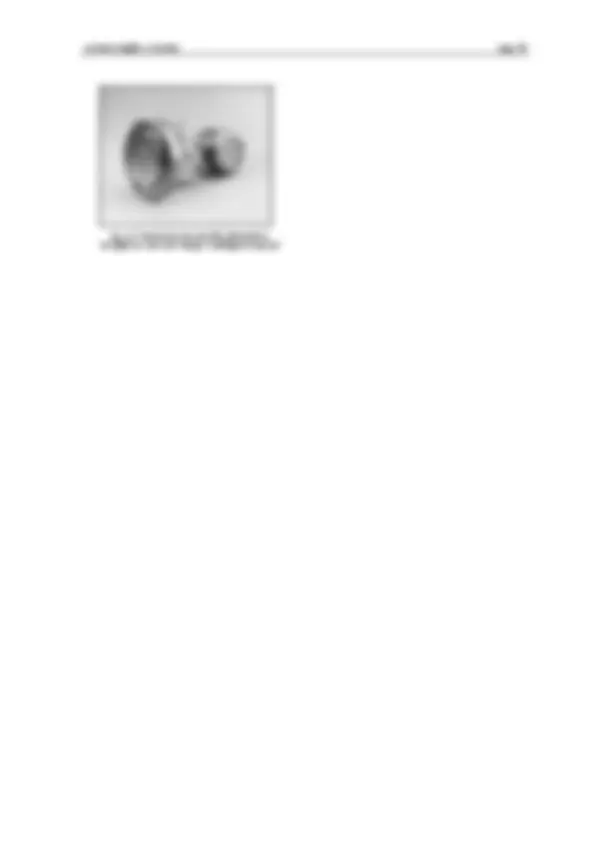
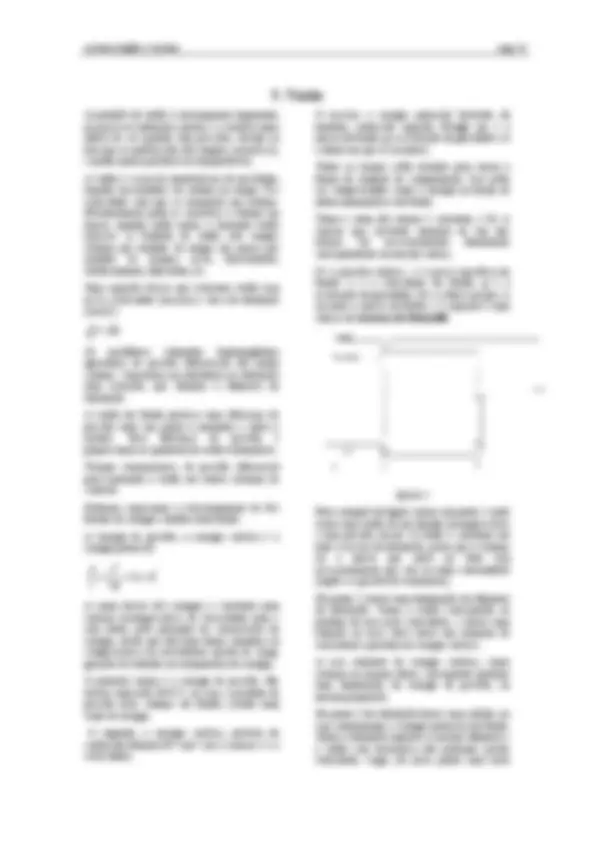
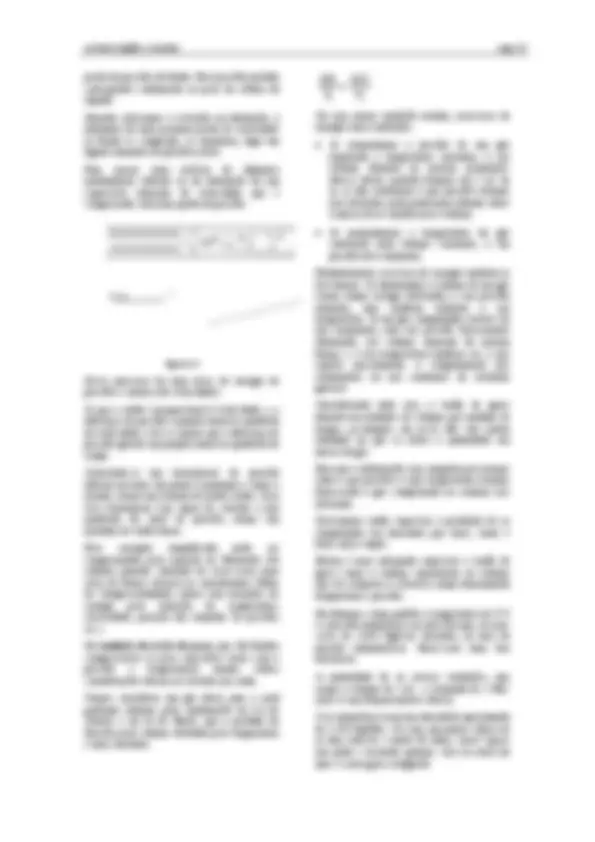
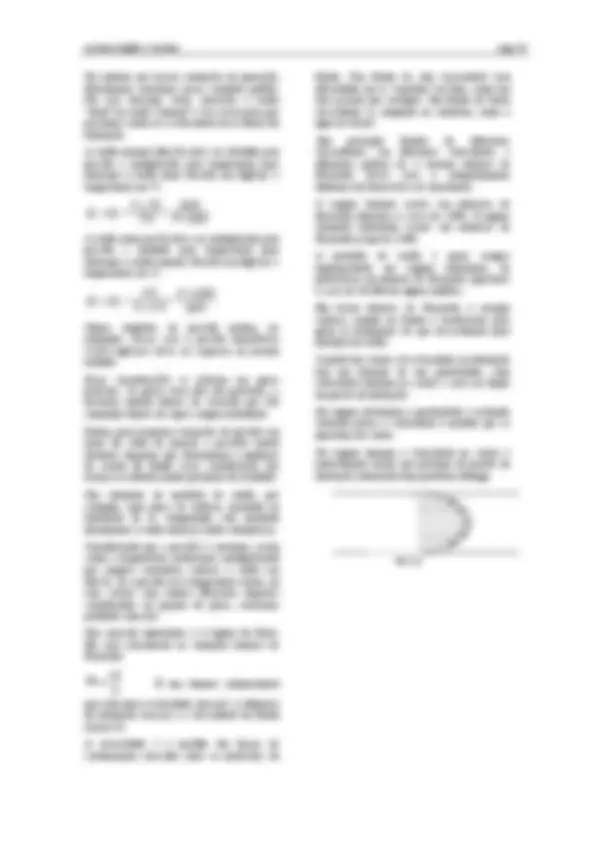
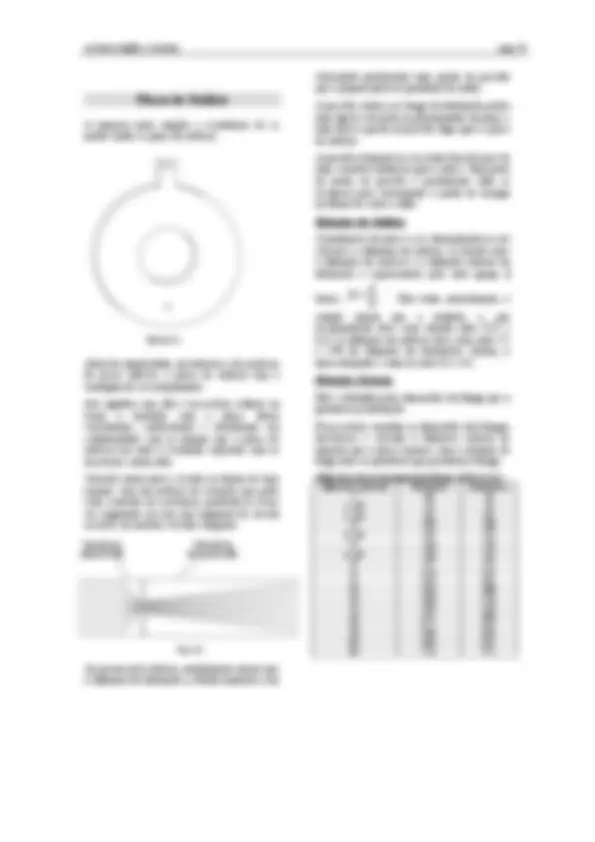
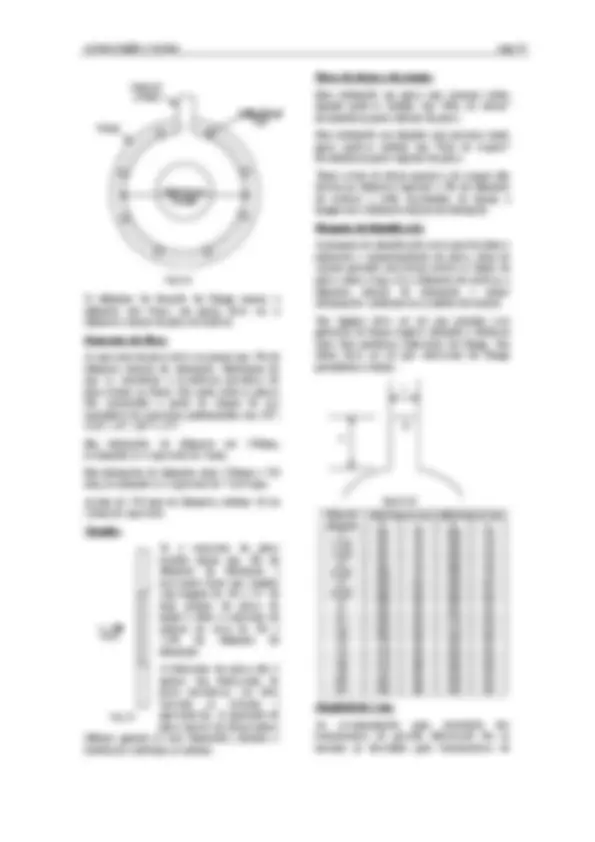
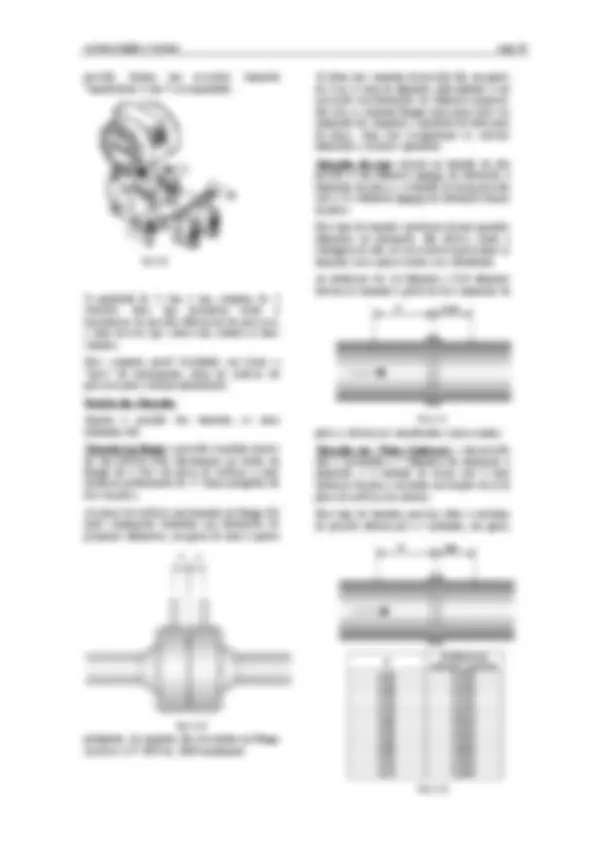
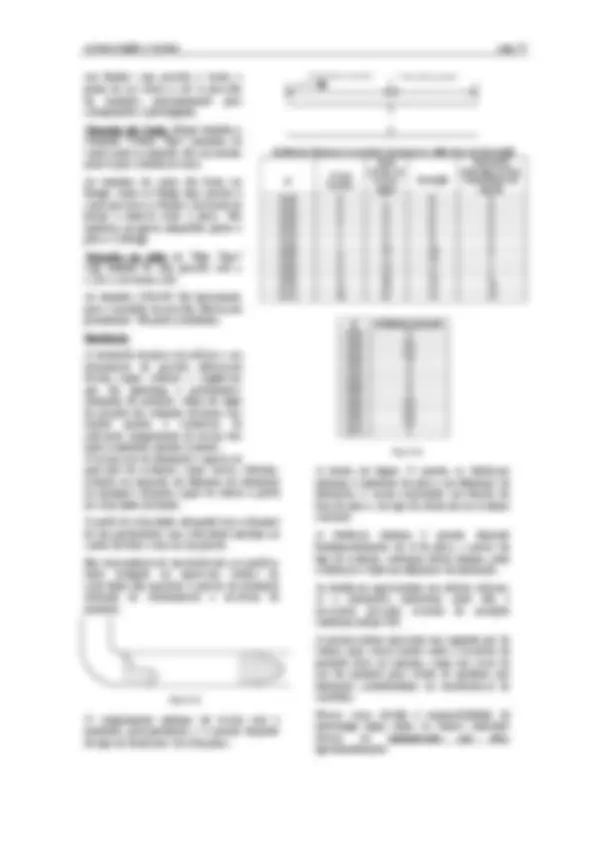
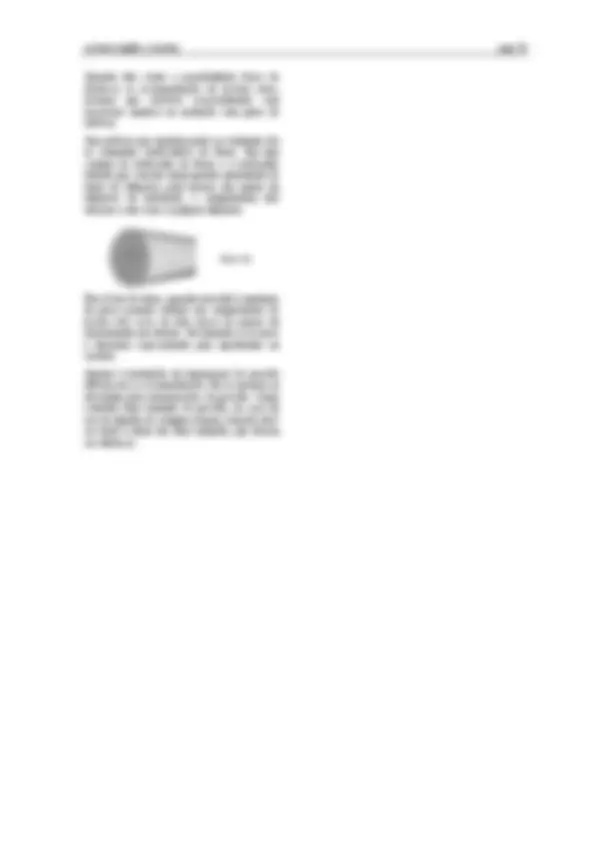
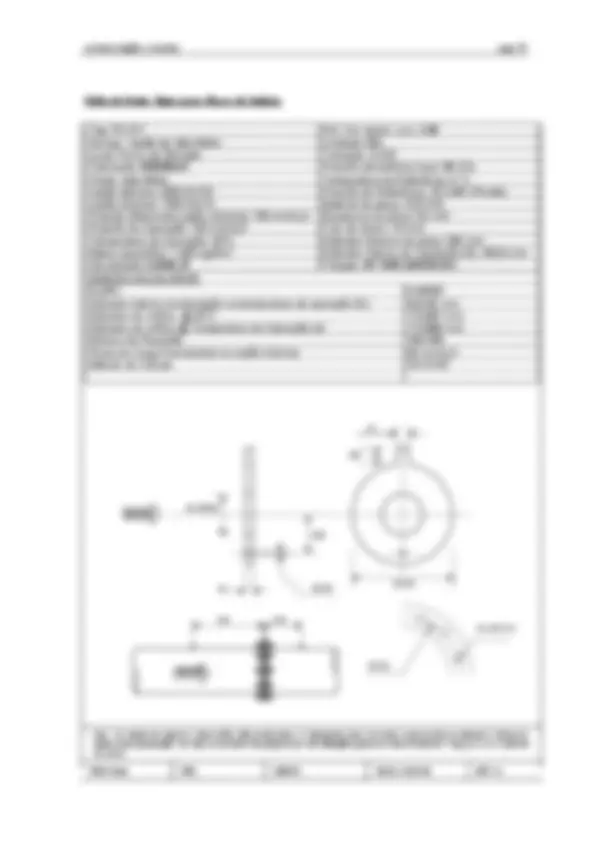
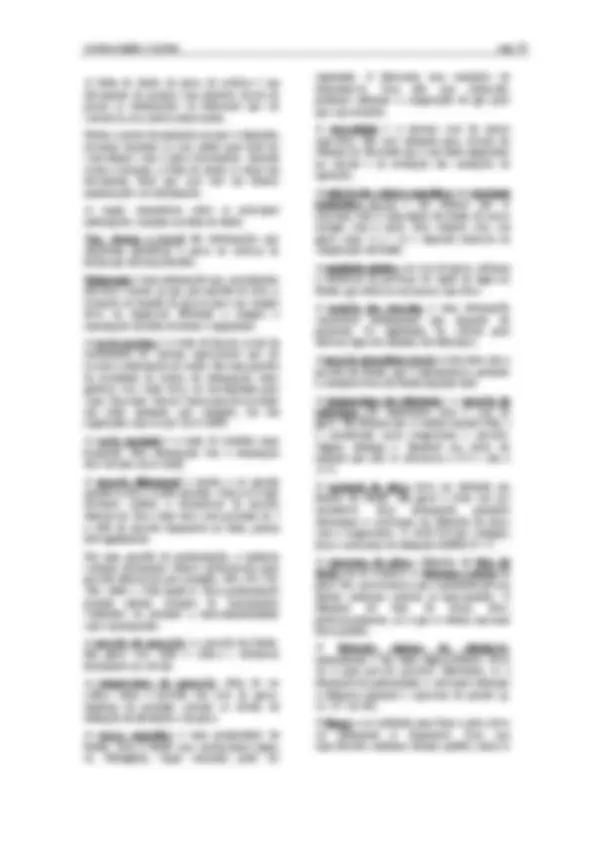
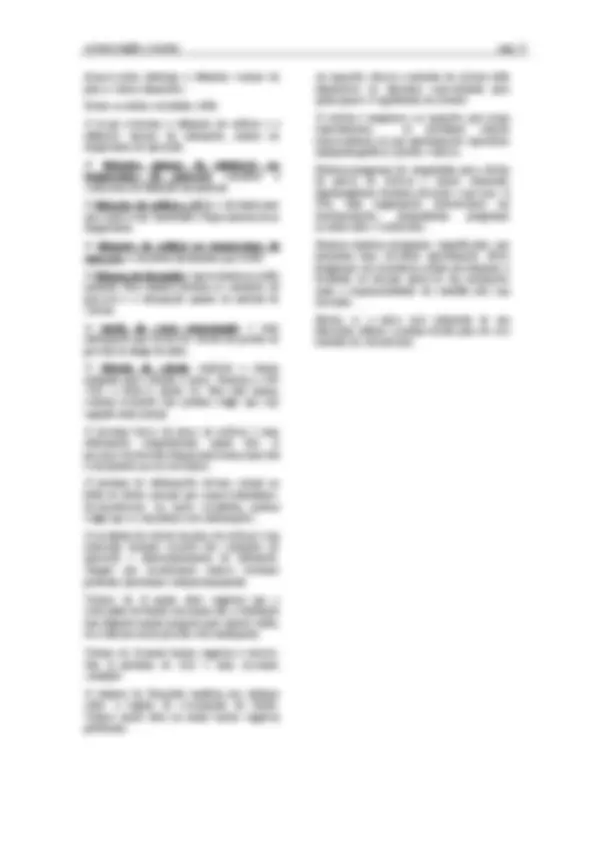
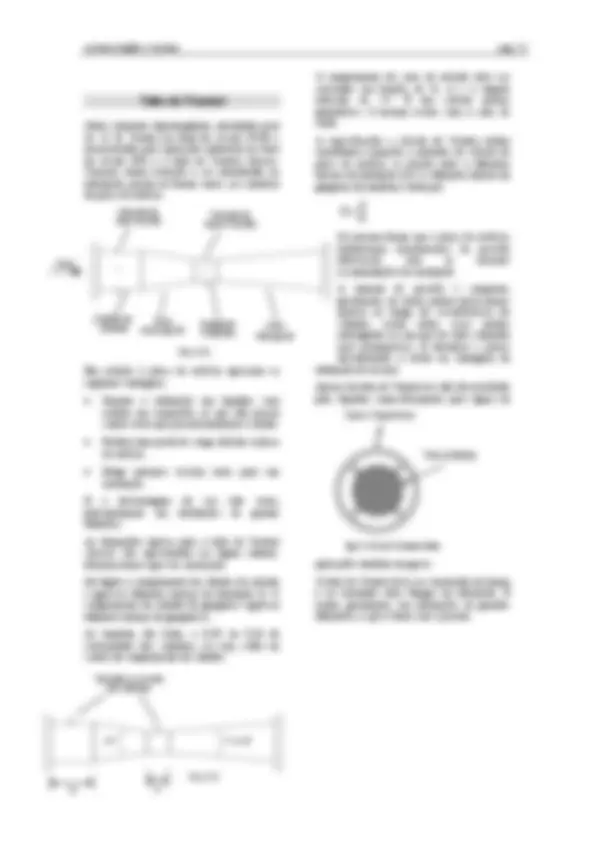
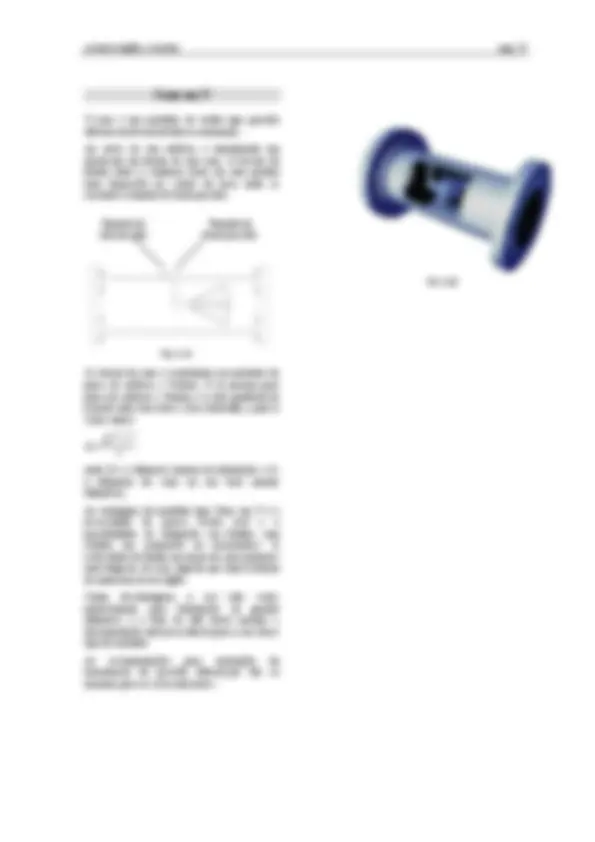
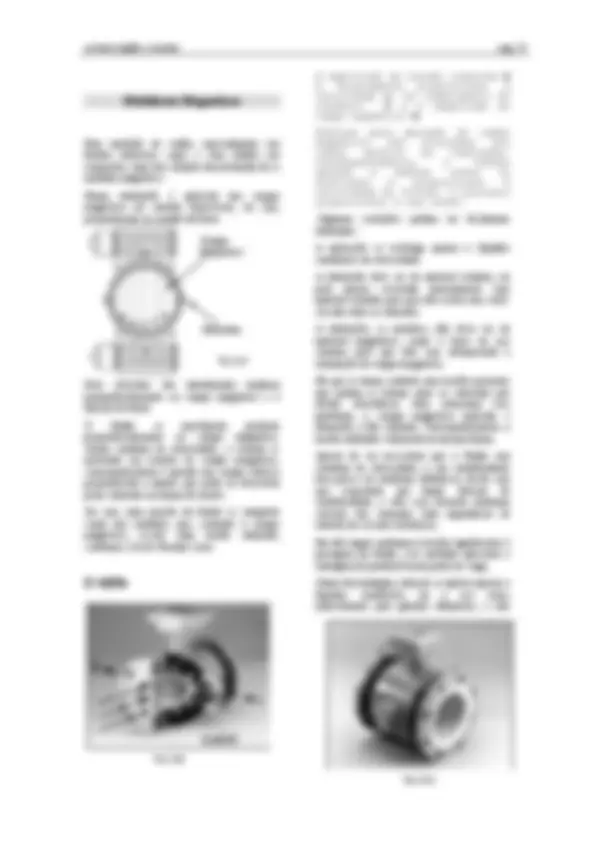
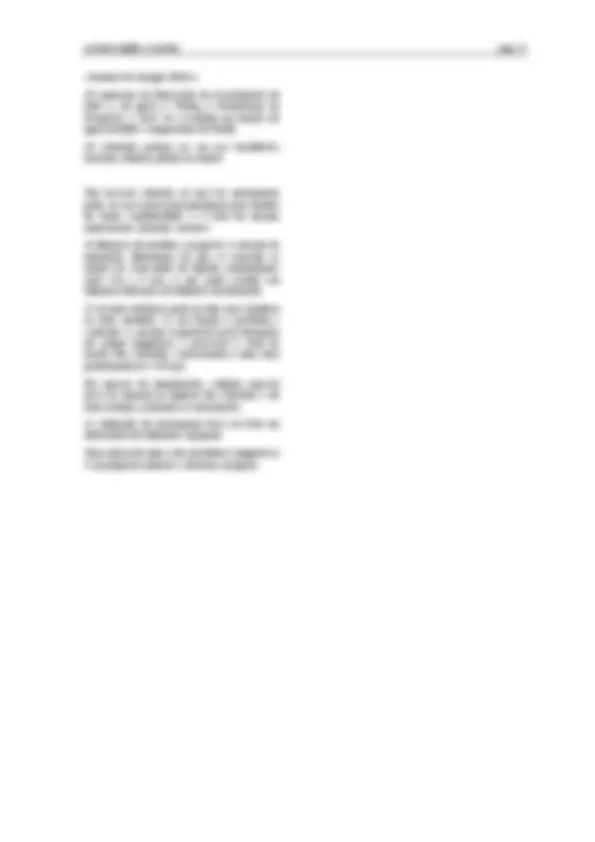
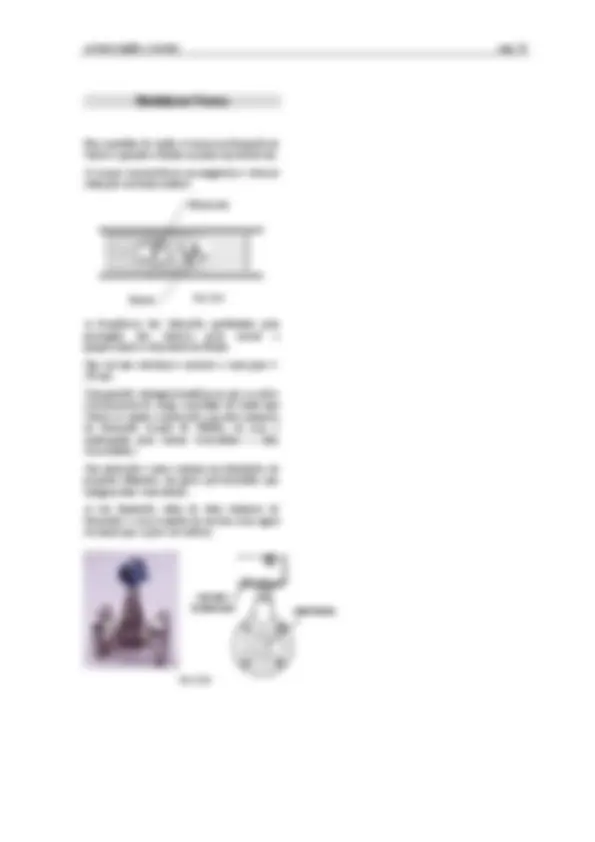
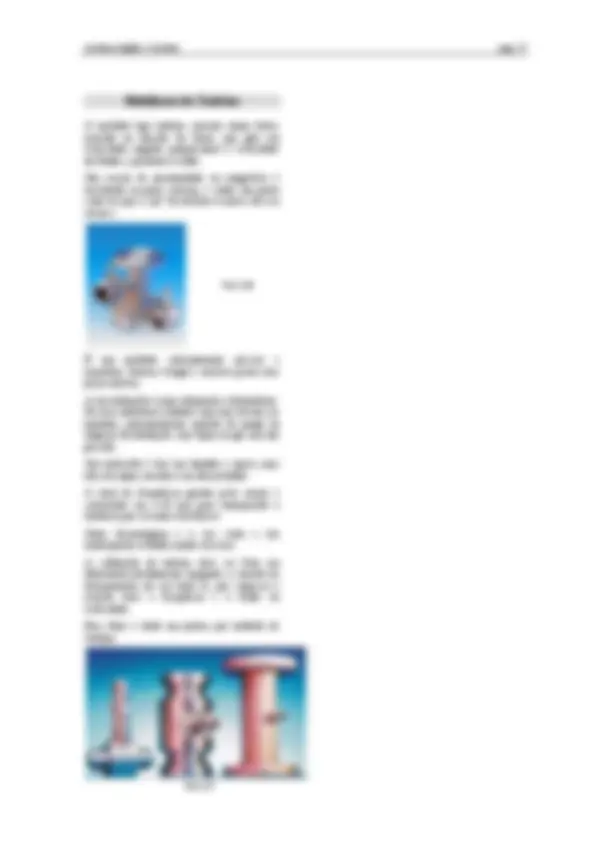
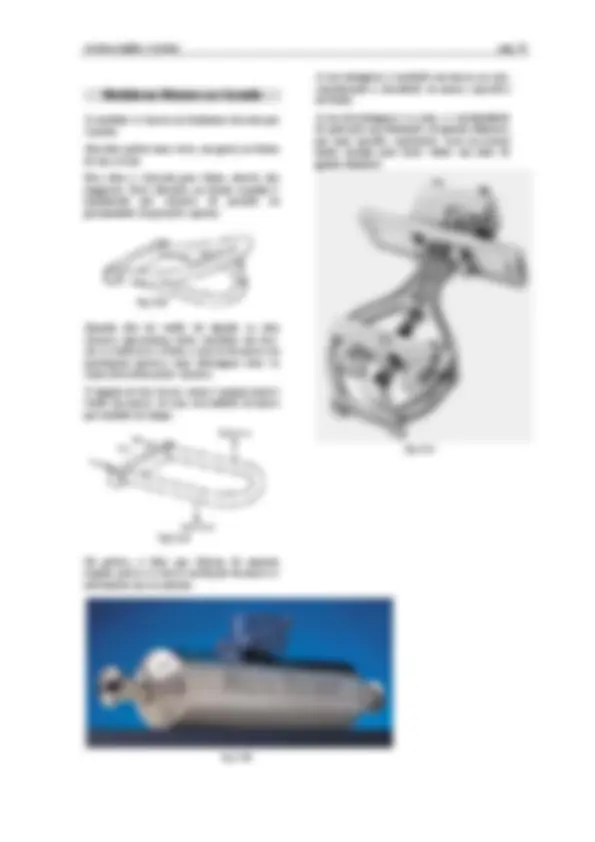
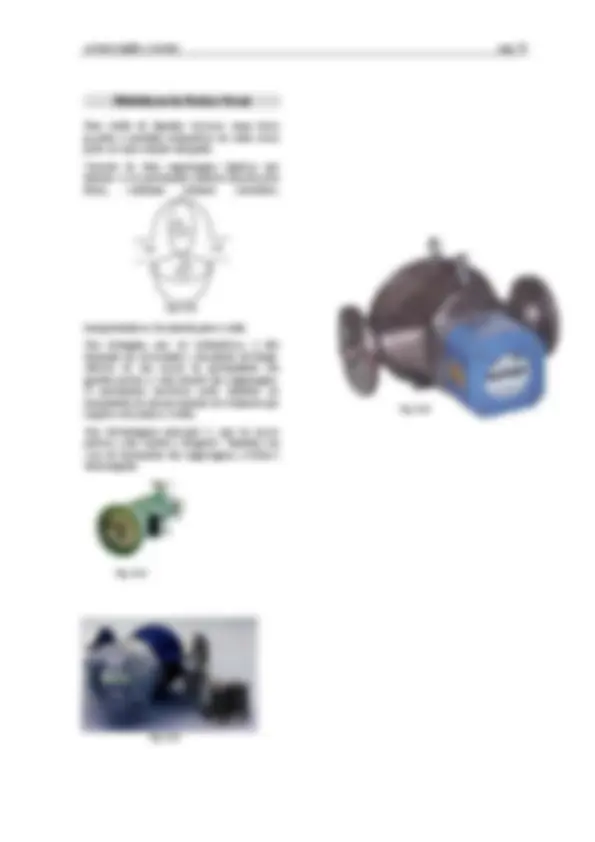
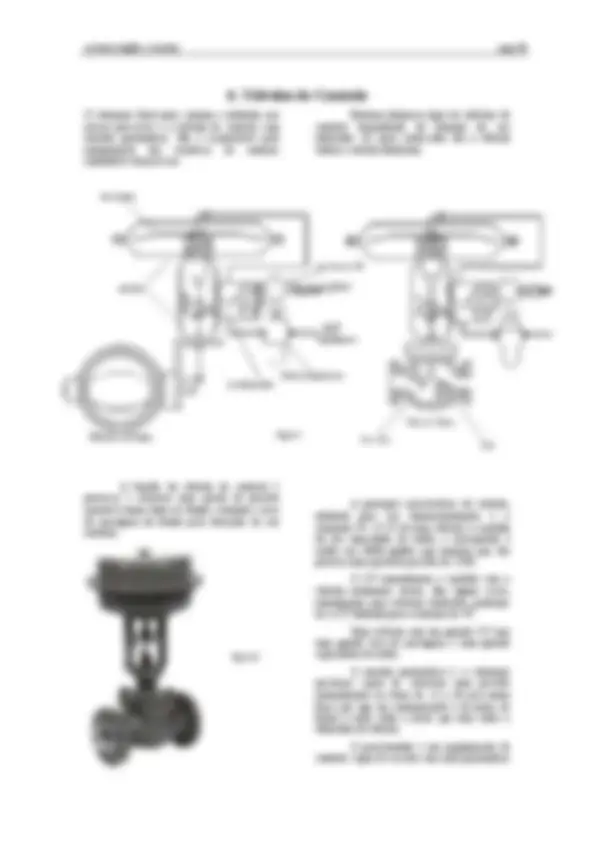
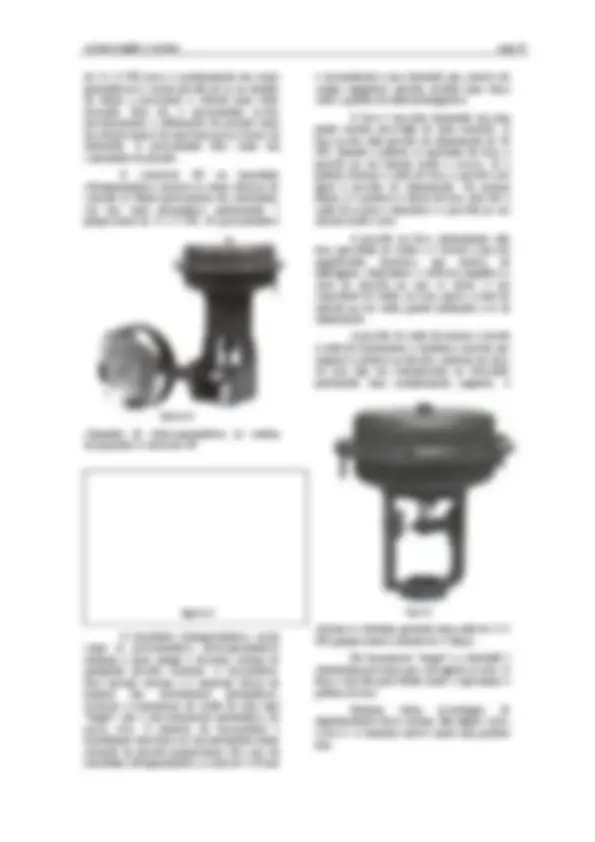
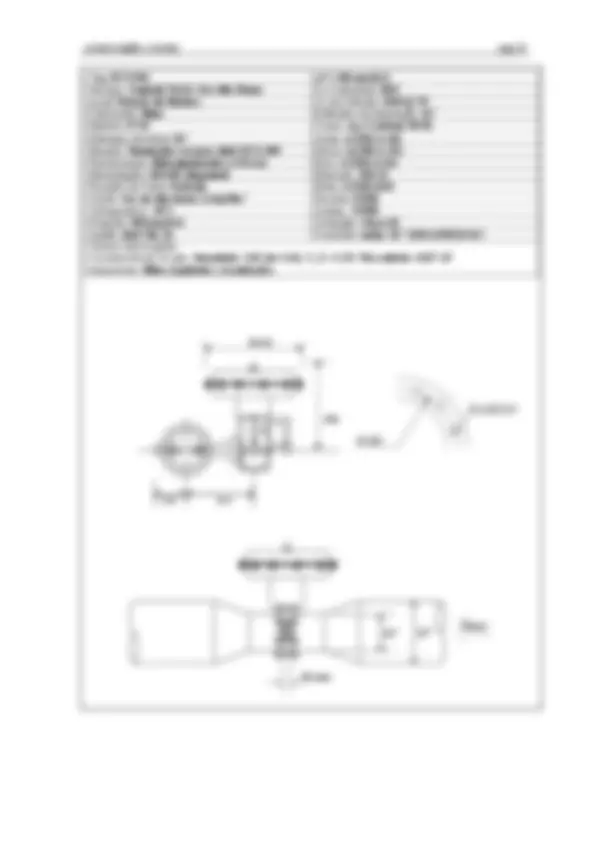
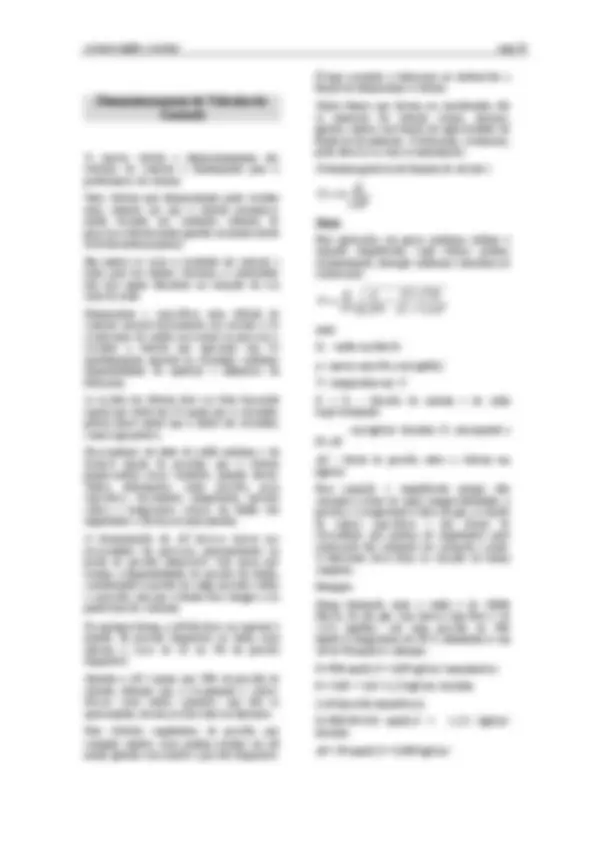
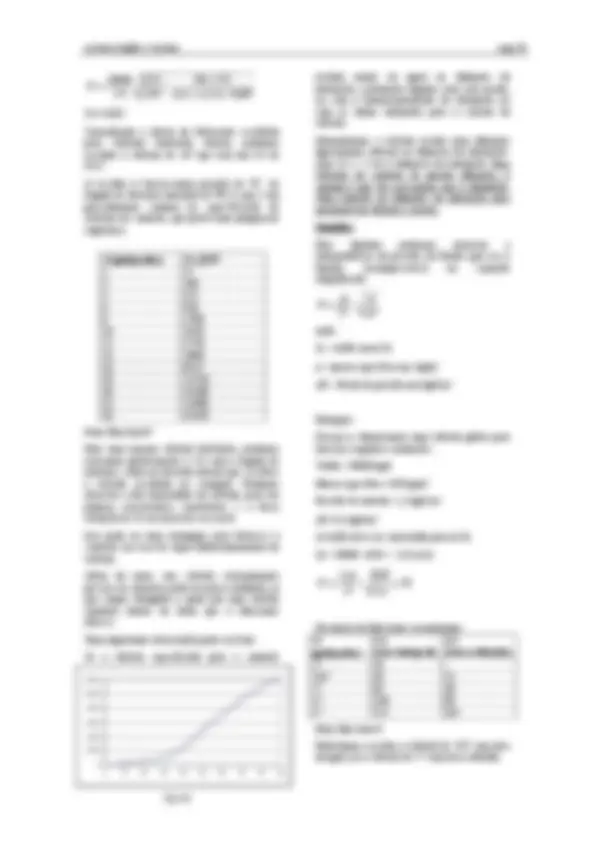
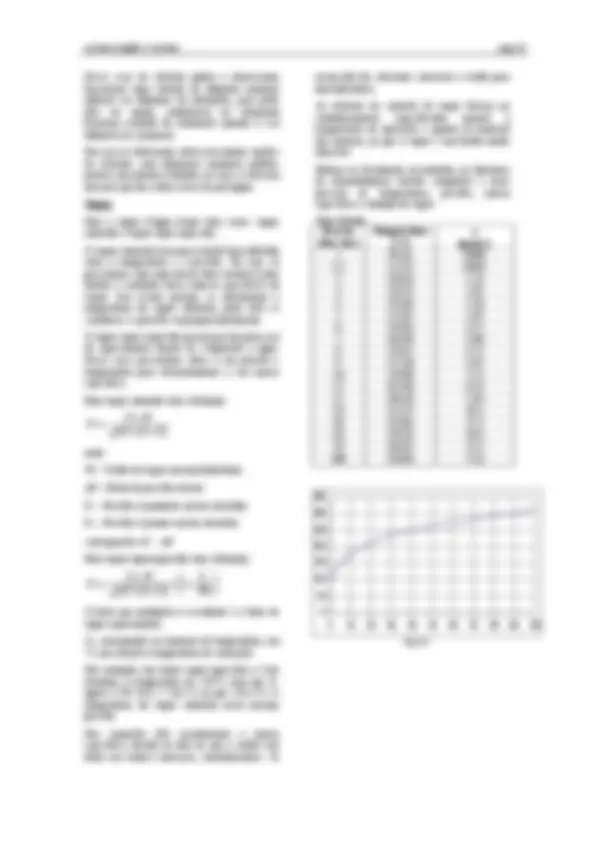
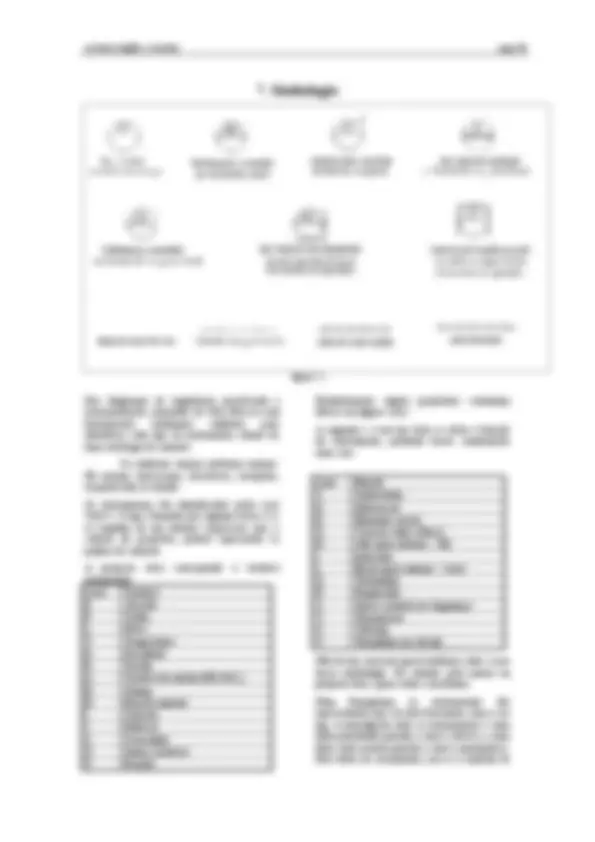
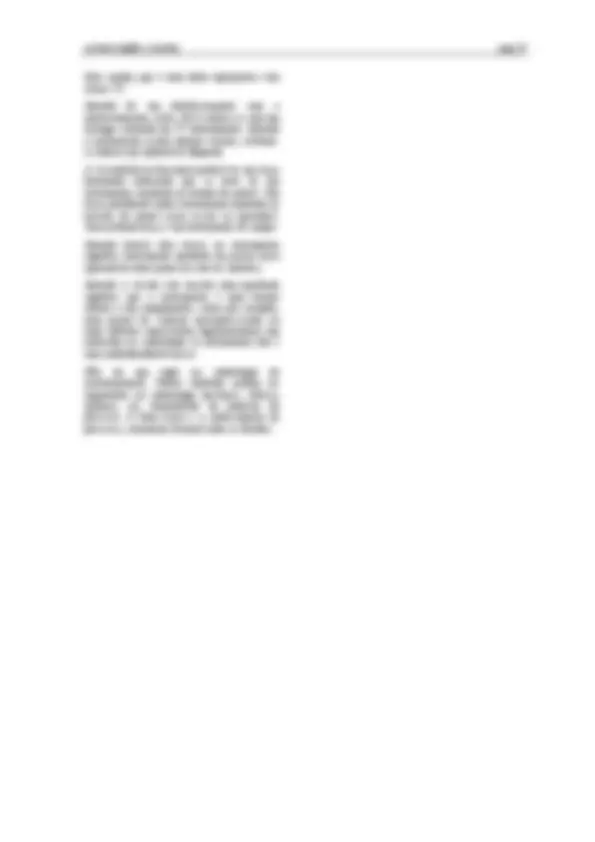
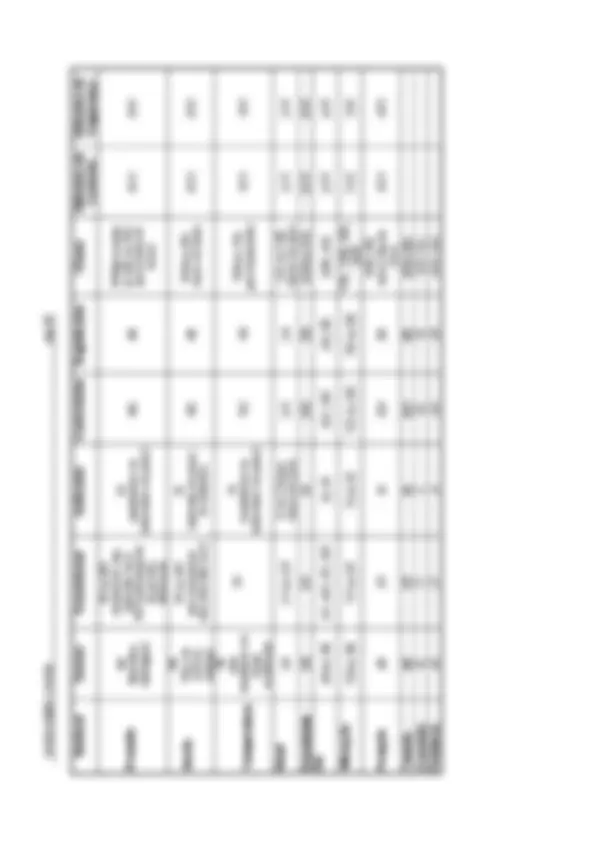
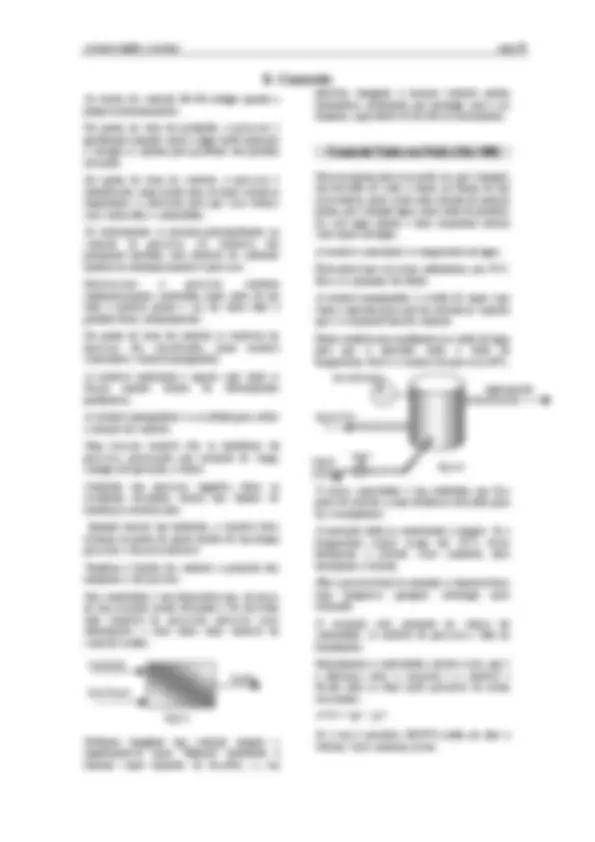
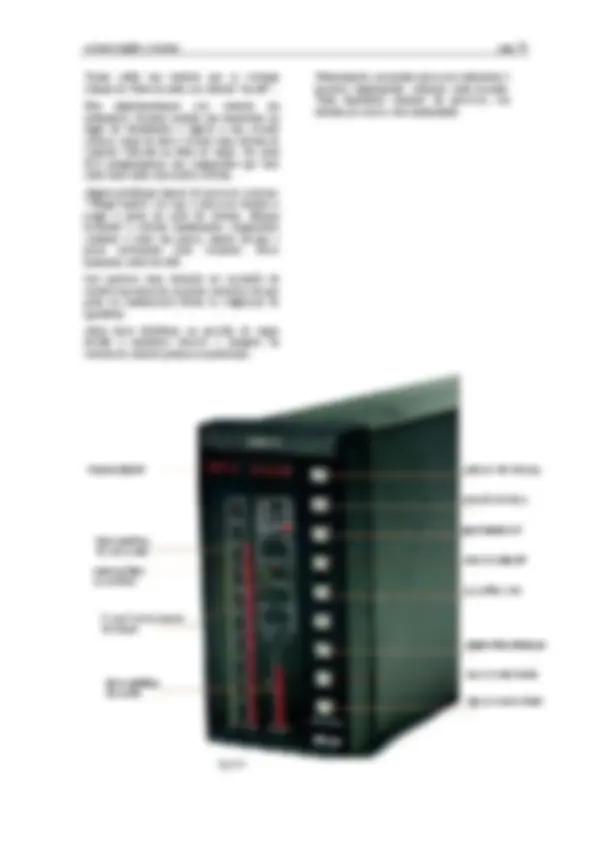
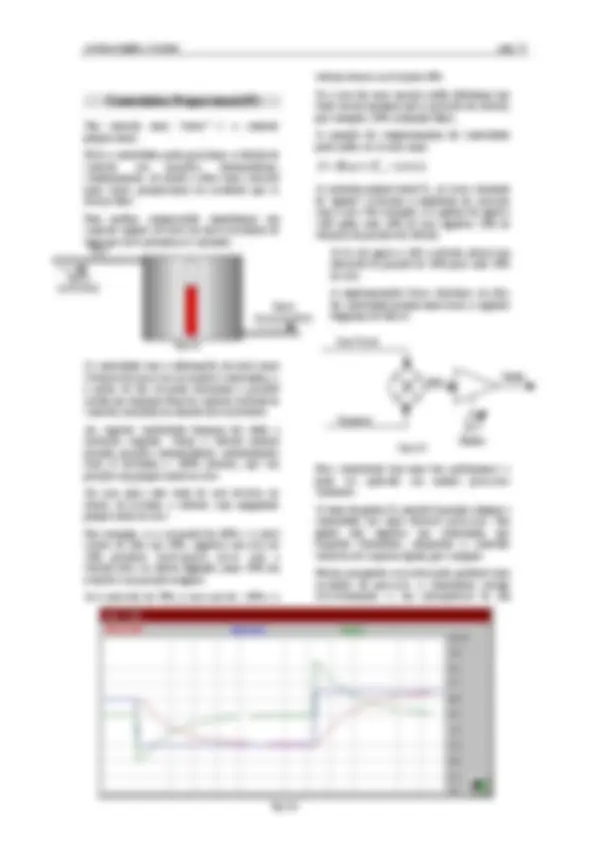
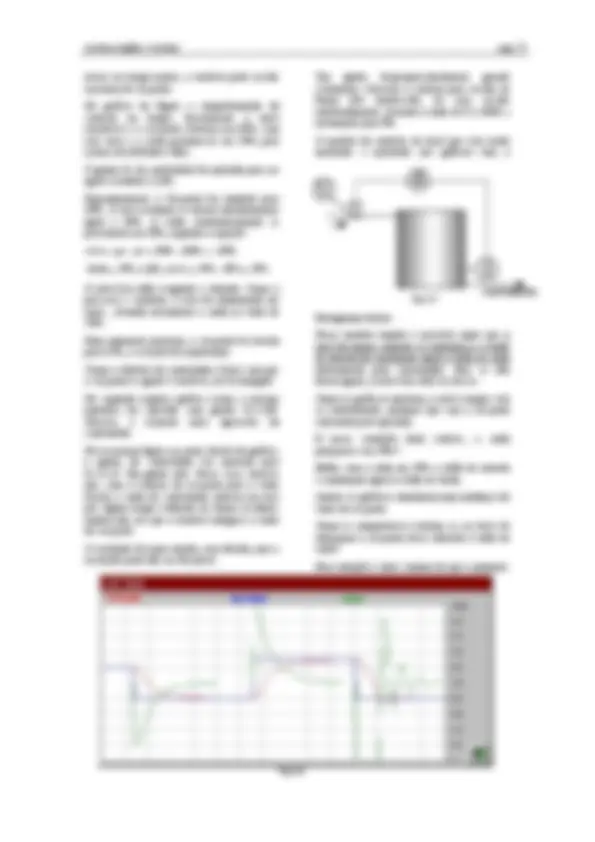
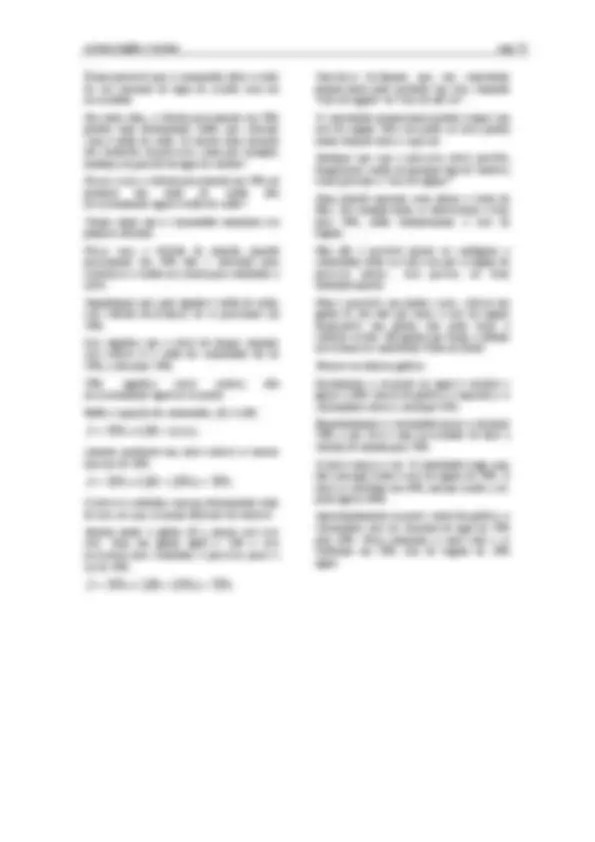
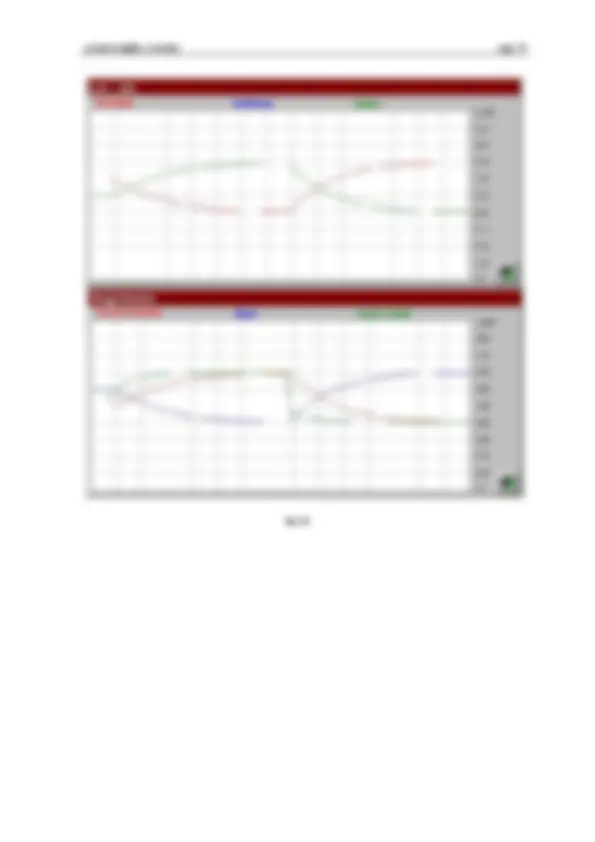
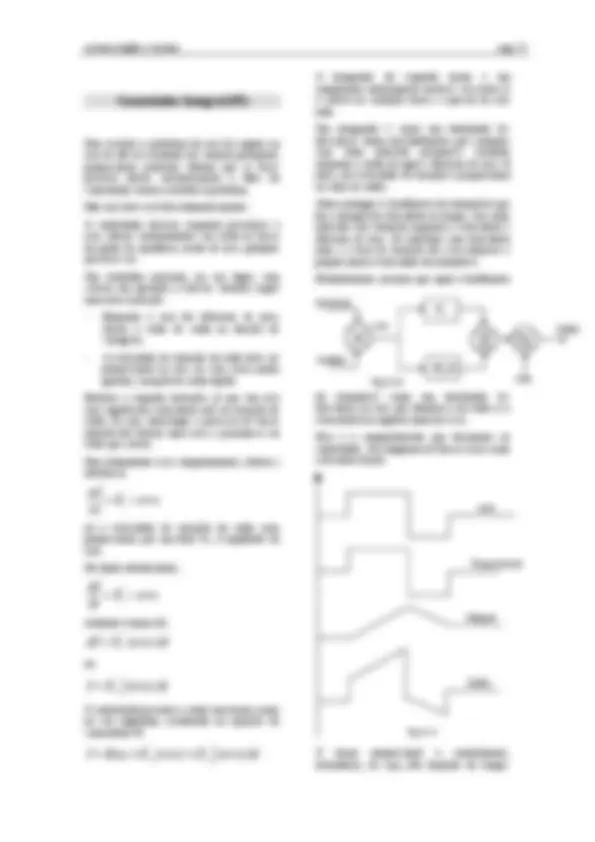
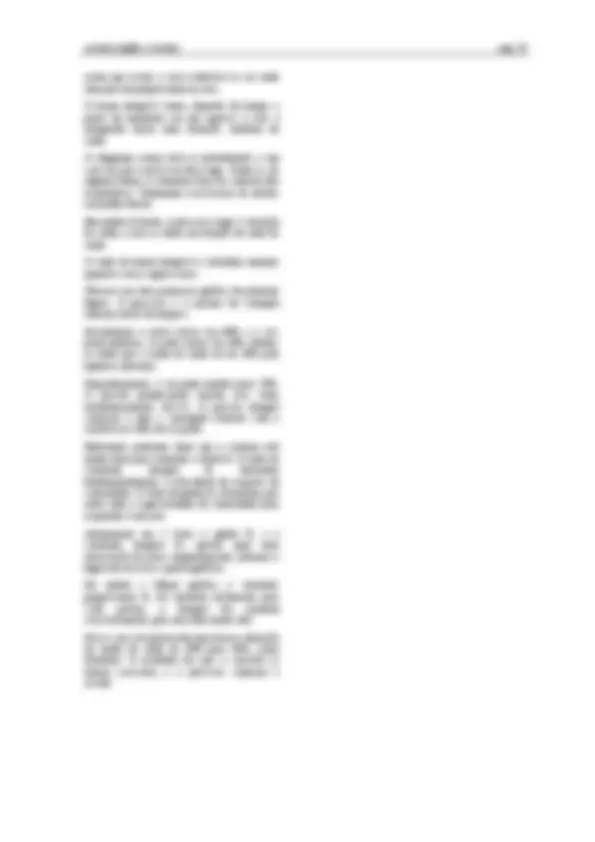
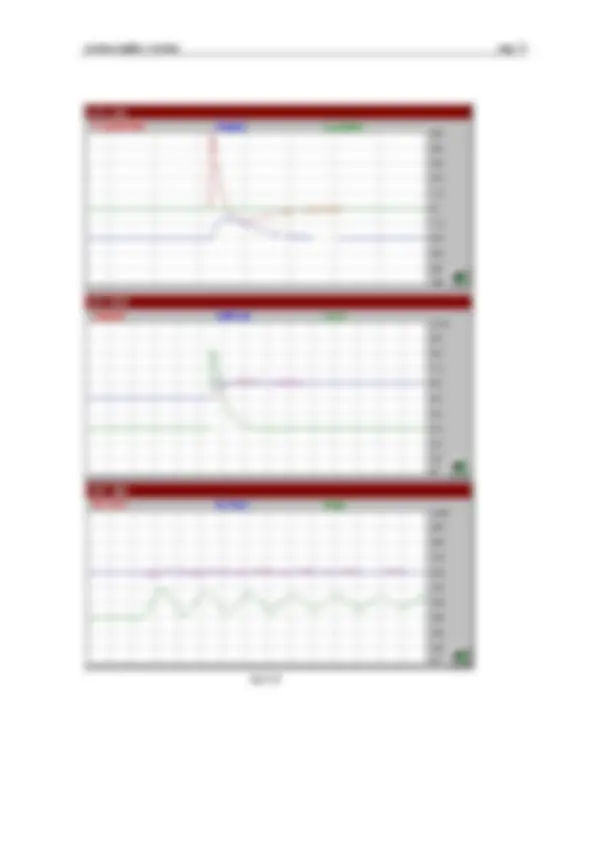
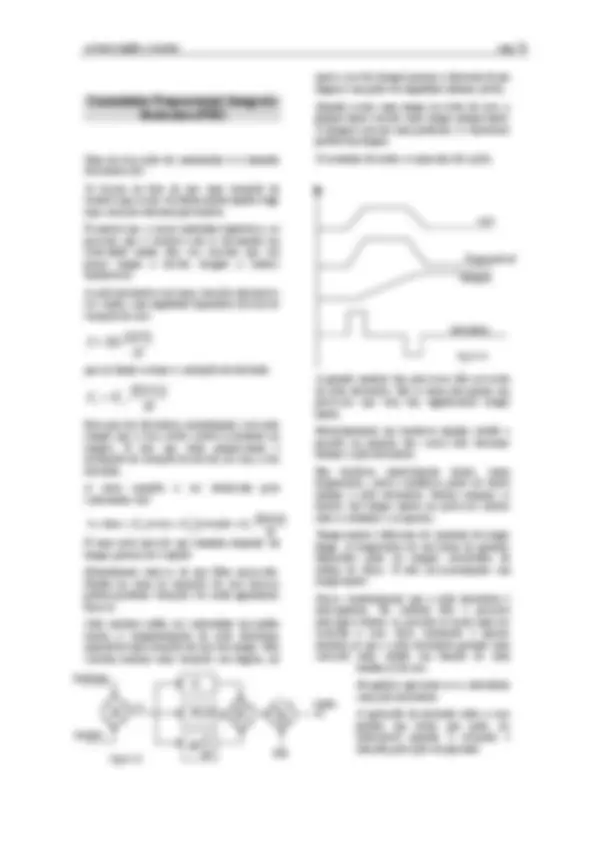
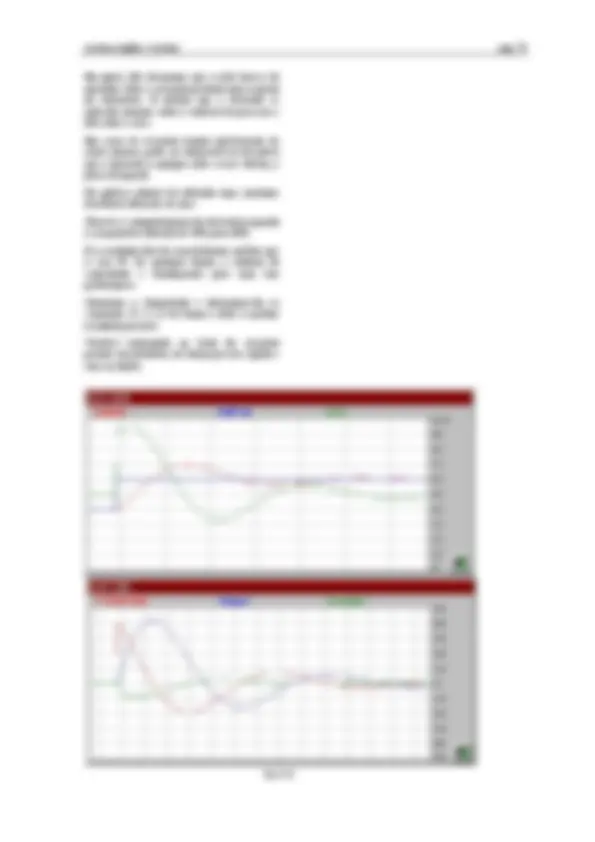
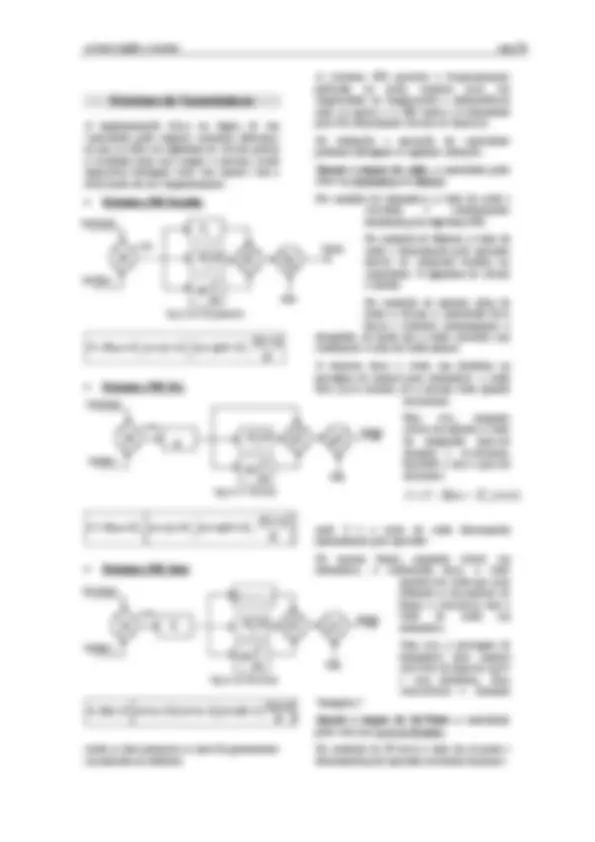
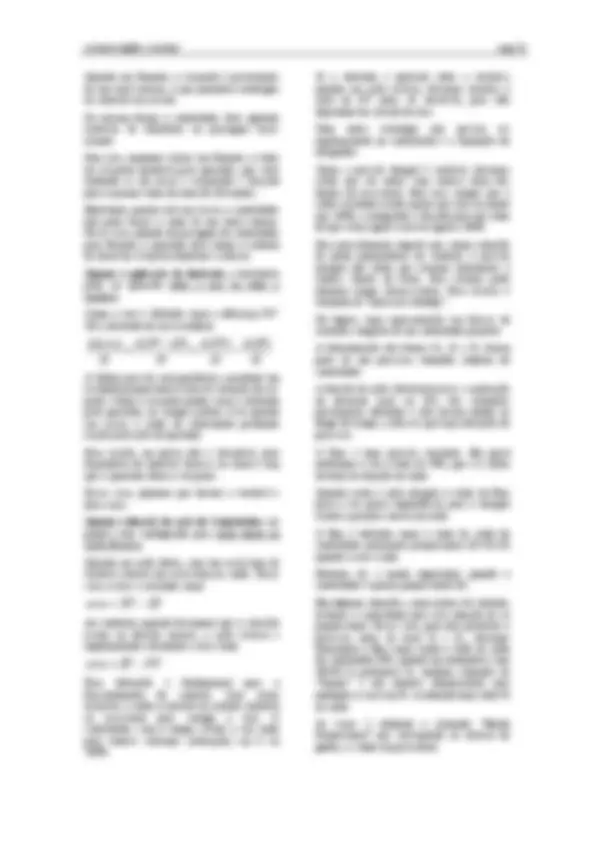
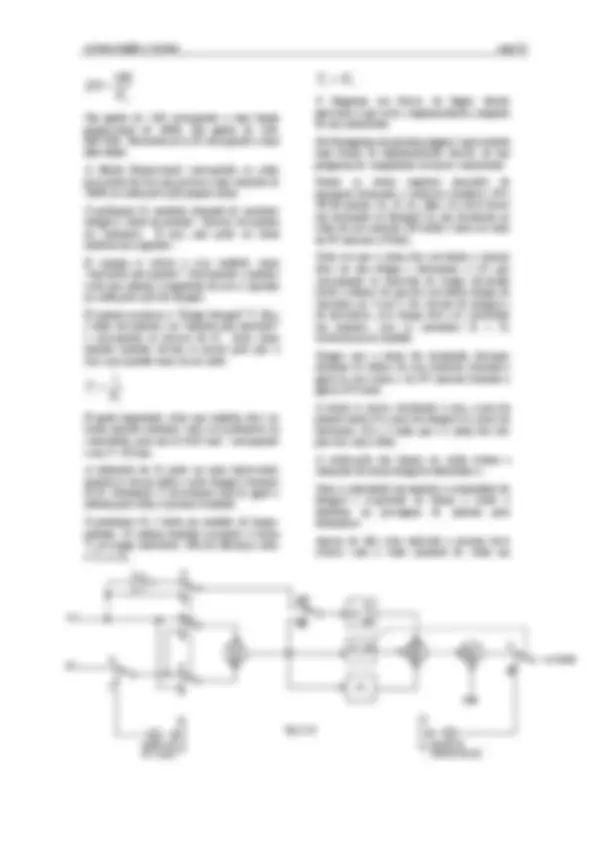
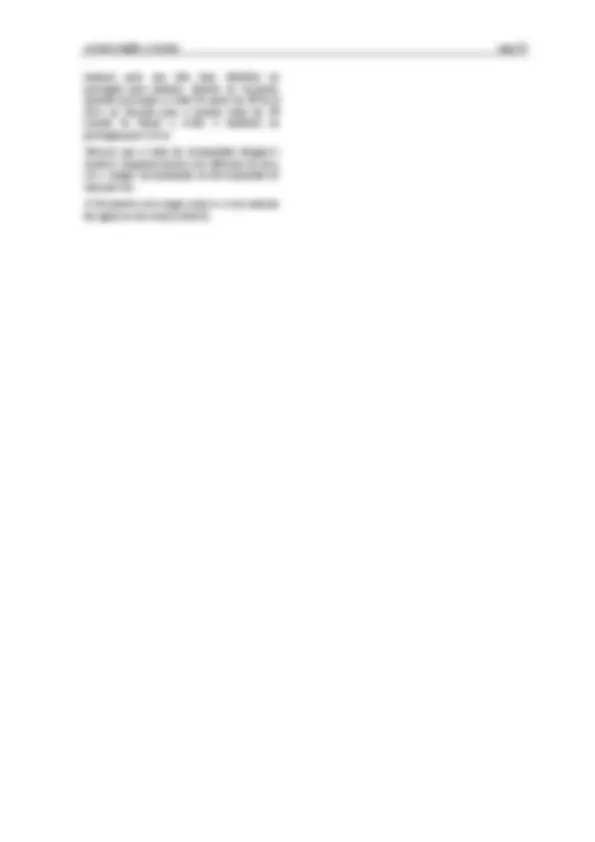
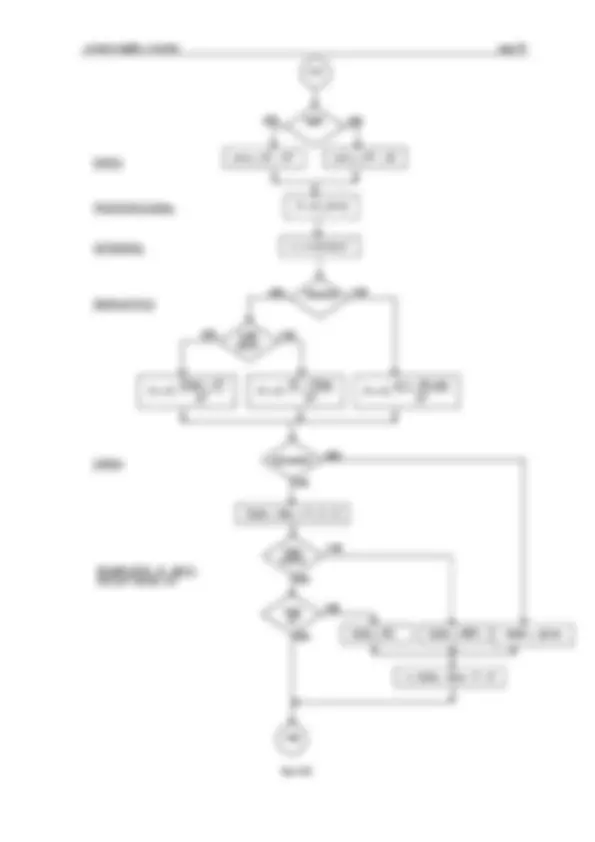
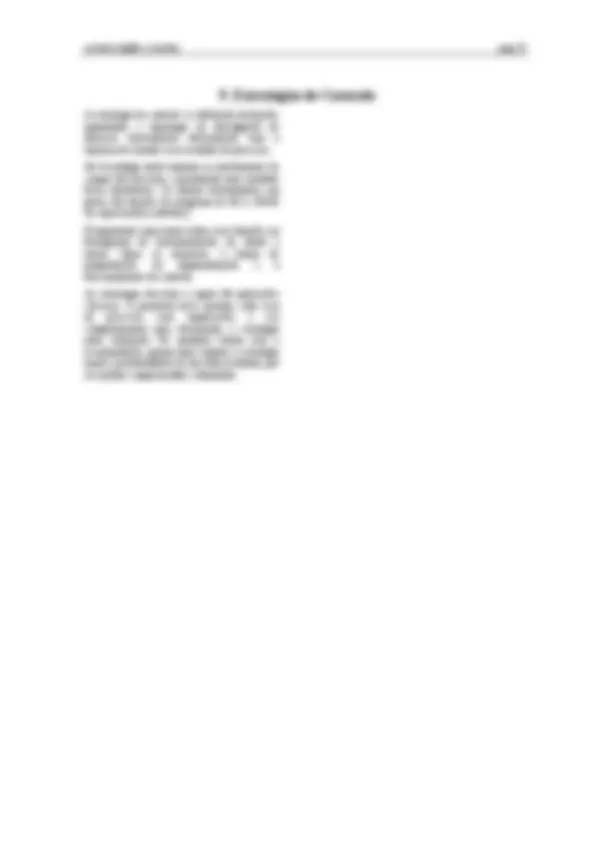
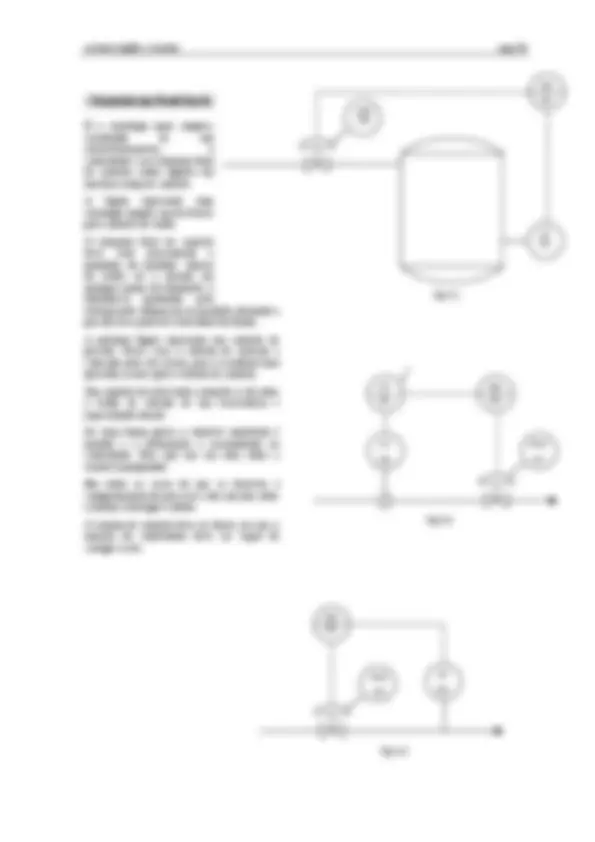
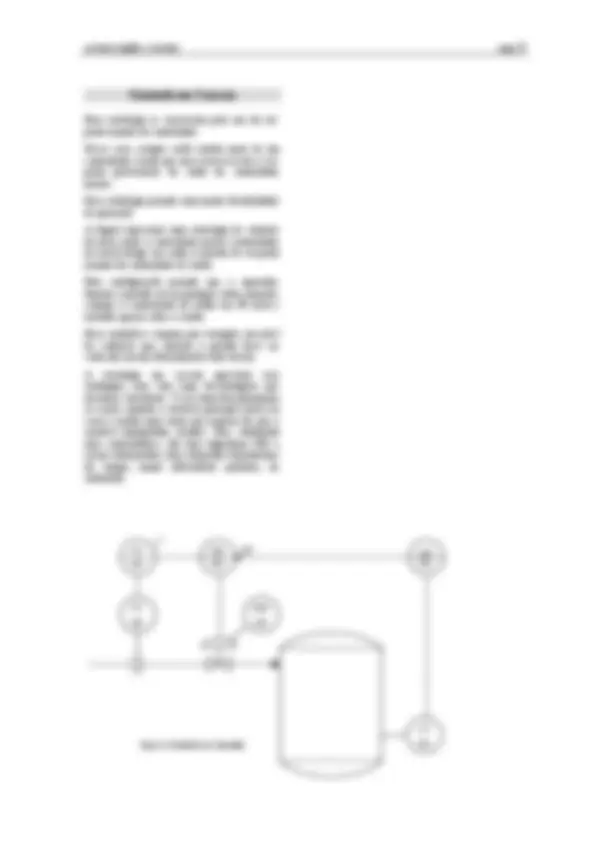
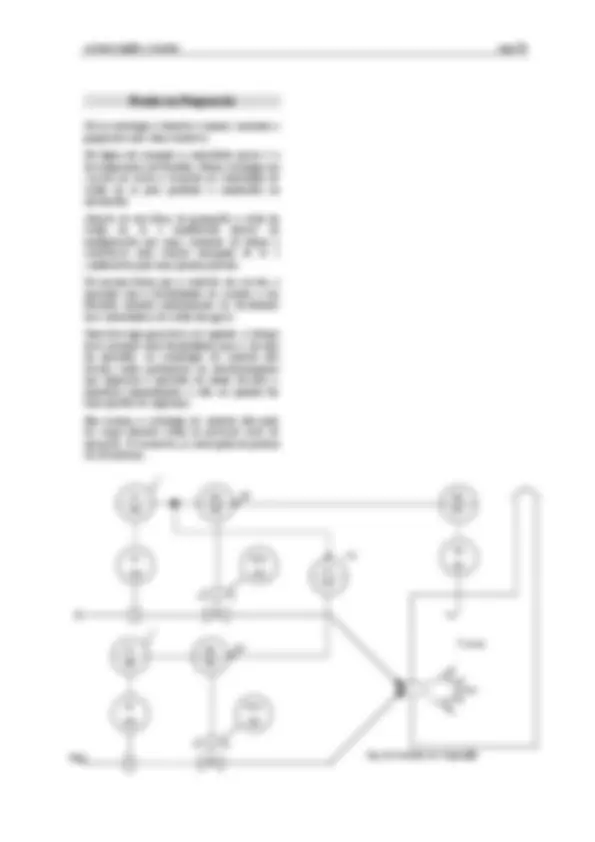
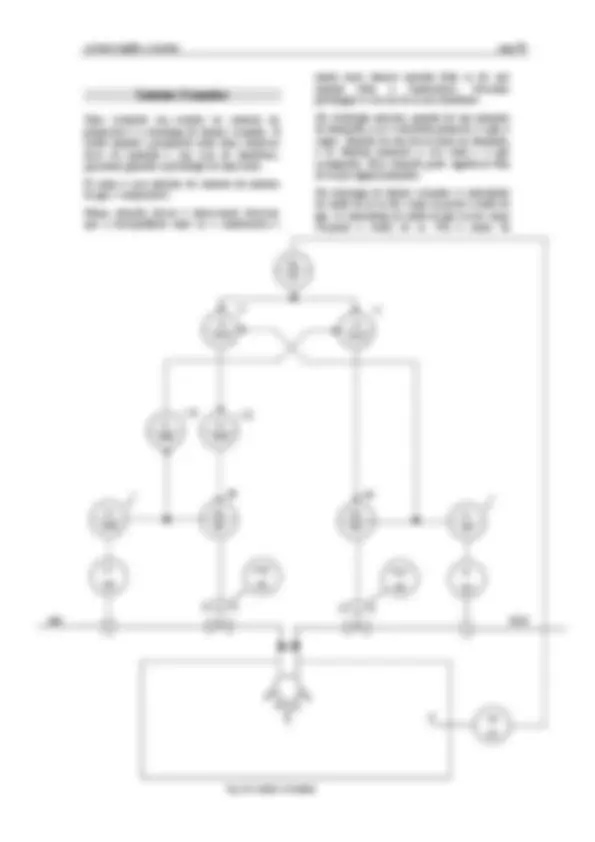
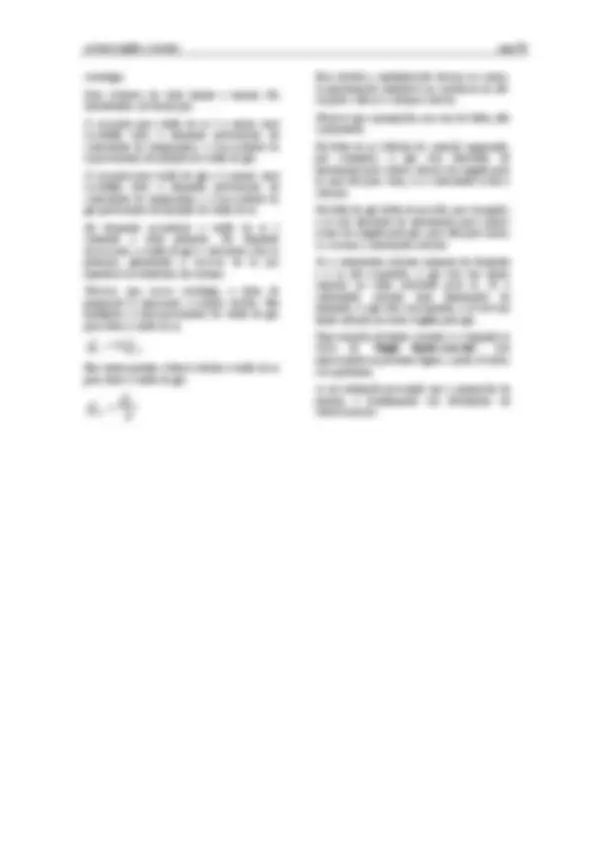
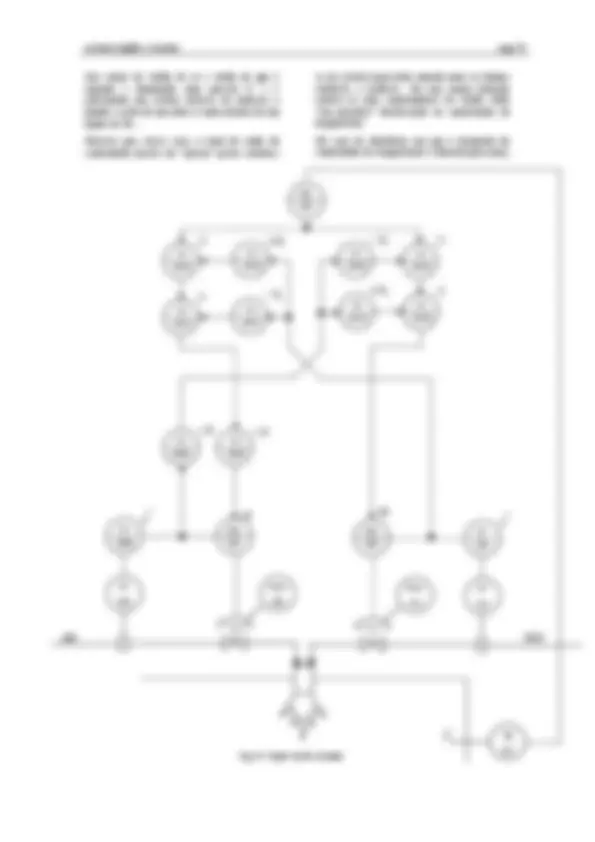
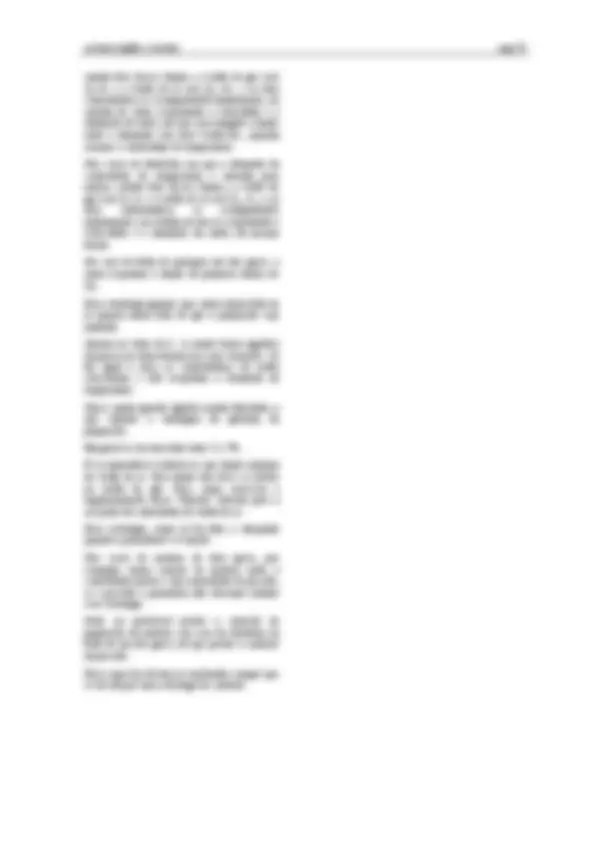
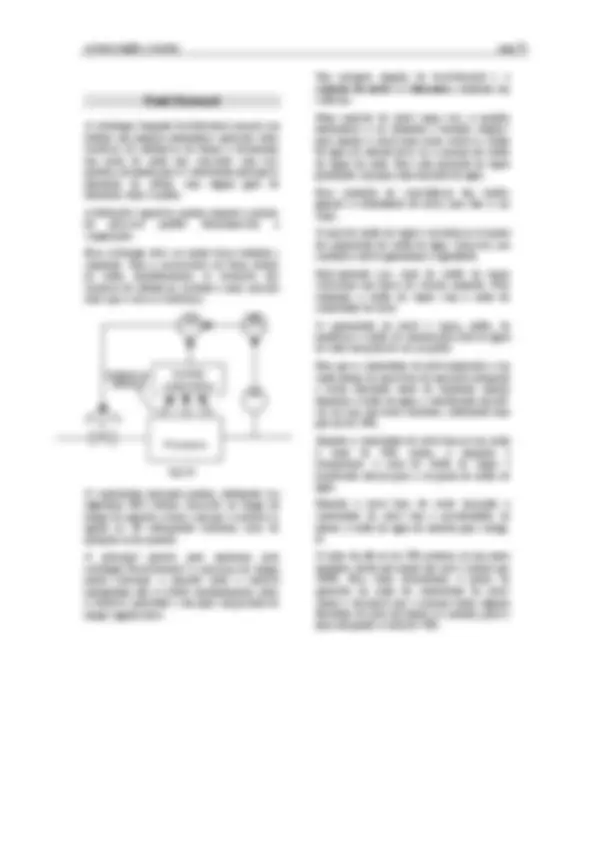
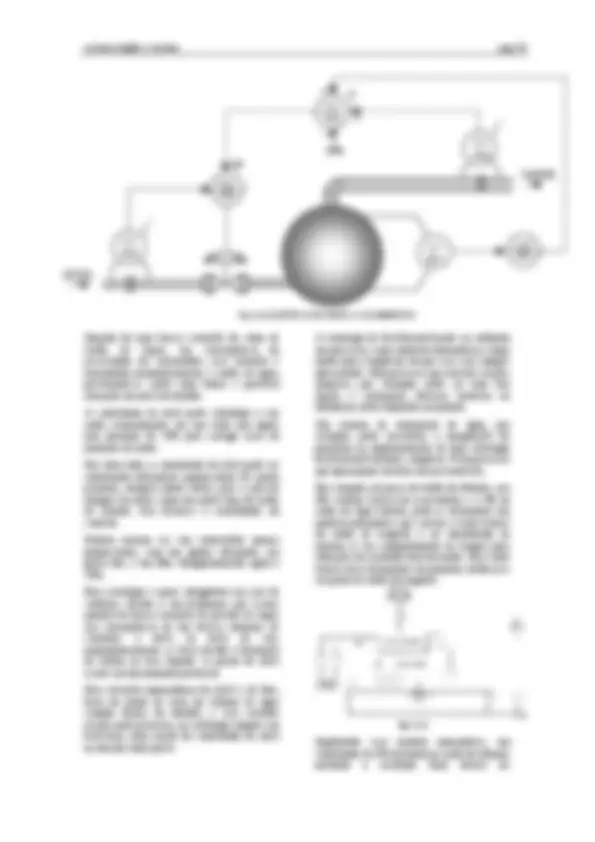
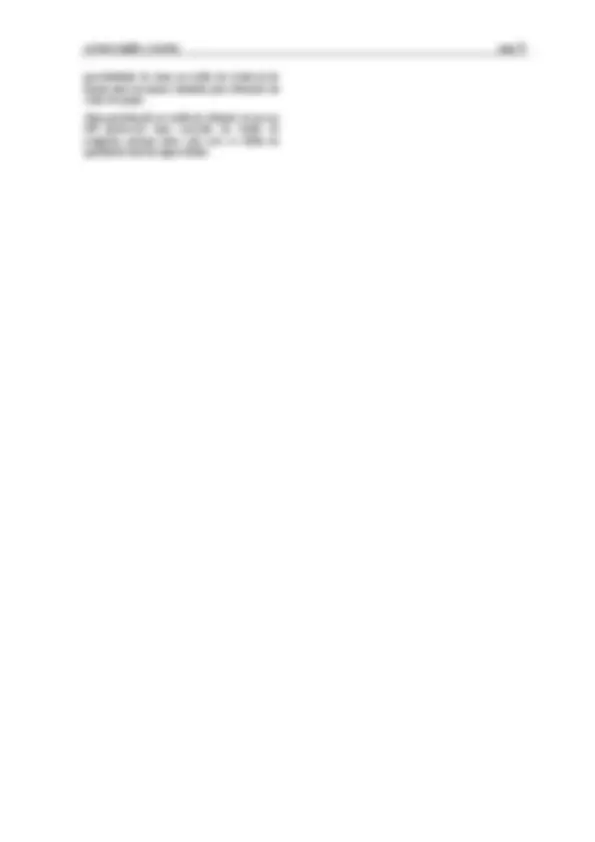
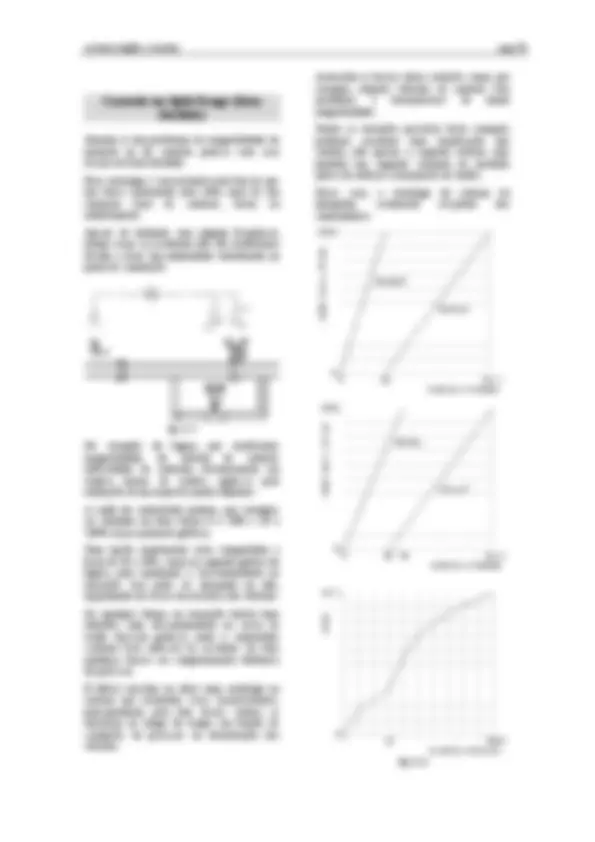
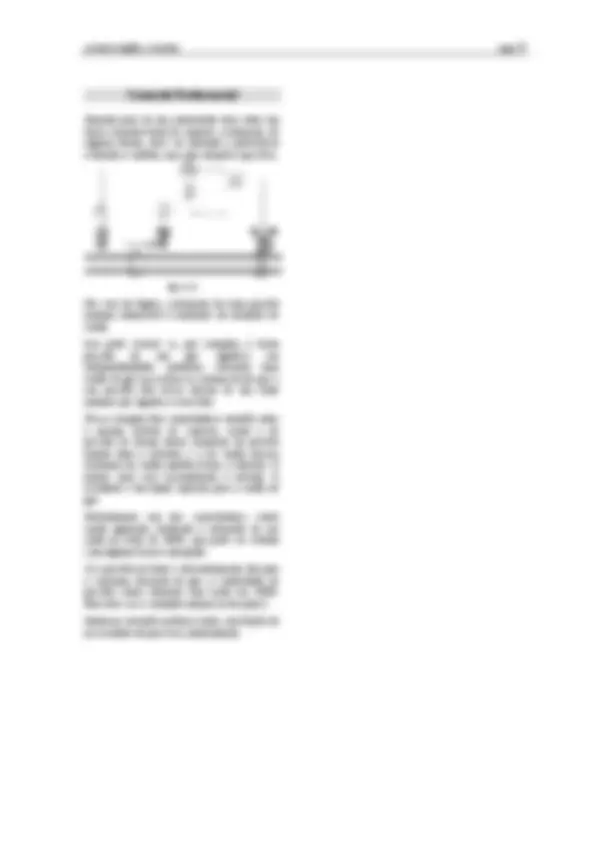
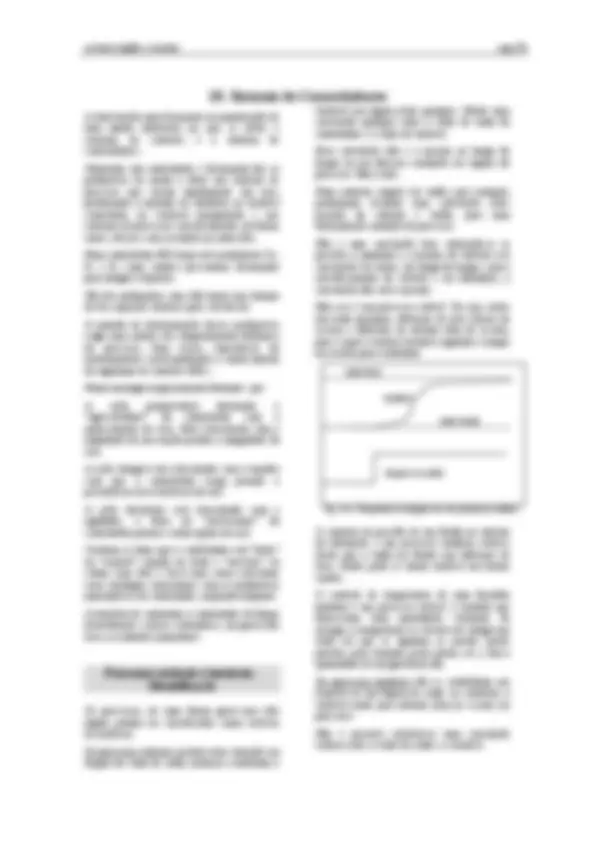
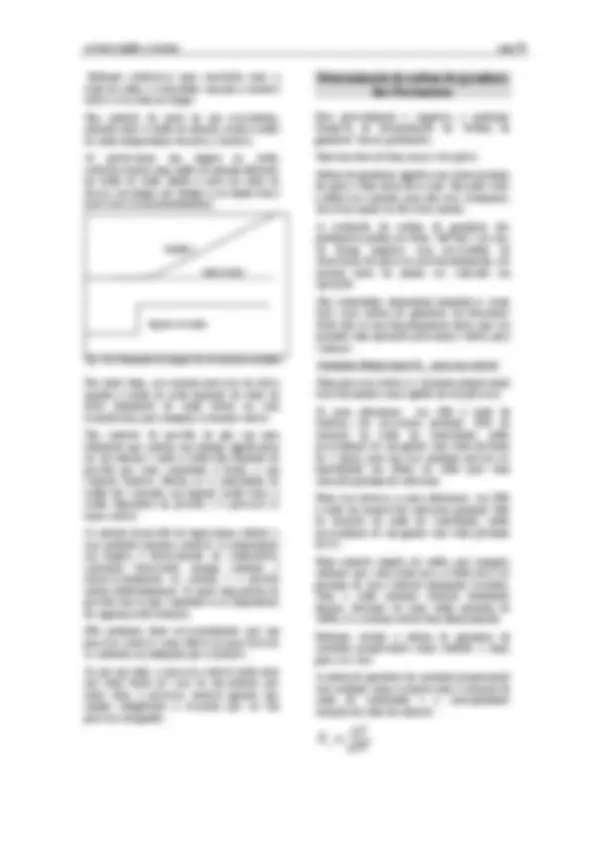
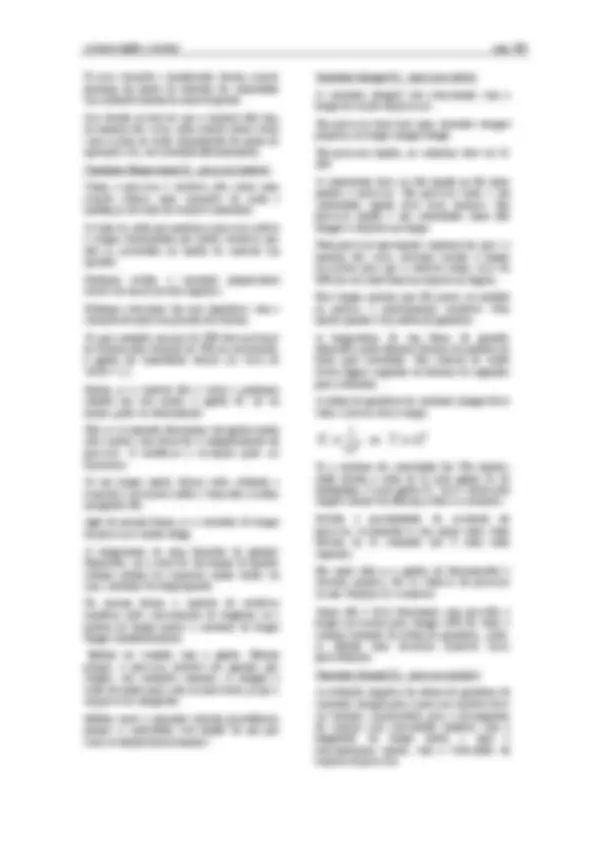
Estude fácil! Tem muito documento disponível na Docsity
Ganhe pontos ajudando outros esrudantes ou compre um plano Premium
Prepare-se para as provas
Estude fácil! Tem muito documento disponível na Docsity
Prepare-se para as provas com trabalhos de outros alunos como você, aqui na Docsity
Os melhores documentos à venda: Trabalhos de alunos formados
Prepare-se com as videoaulas e exercícios resolvidos criados a partir da grade da sua Universidade
Responda perguntas de provas passadas e avalie sua preparação.
Ganhe pontos para baixar
Ganhe pontos ajudando outros esrudantes ou compre um plano Premium
Comunidade
Peça ajuda à comunidade e tire suas dúvidas relacionadas ao estudo
Descubra as melhores universidades em seu país de acordo com os usuários da Docsity
Guias grátis
Baixe gratuitamente nossos guias de estudo, métodos para diminuir a ansiedade, dicas de TCC preparadas pelos professores da Docsity
Apostila básica de Instrumentação Industrial.
Tipologia: Notas de estudo
1 / 163
Esta página não é visível na pré-visualização
Não perca as partes importantes!
eng. Paulo Vicente Correa
rev. julho/
Instrumentação é o ramo da engenharia que trata do projeto, fabricação, especificação, montagem, operação e manutenção dos instrumentos para medição e controle das variáveis de processo industrial.
Um processo é, em geral, uma instalação ou um local onde são introduzidos material, energia e insumos, que são processados para se obter um produto final de qualidade, além de resíduos e efluentes a serem descartados, tratados ou reciclados por outro processo. Interessa-nos especialmente o processo contínuo, ou seja, onde essas coisas acontecem continuamente.
As informações do processo precisam ser adquiridas e transmitidas até um local confortável, normalmente uma sala de controle, onde o elemento humano possa tomar as decisões e interferir no processo para atingir o seu objetivo, além de consultar dados históricos e executar quaisquer ações sobre o sistema.
A qualidade do produto inclui, não só as suas características intrínsecas para consumo, mas também outros aspectos, como custo, quantidade, prazos de entrega, segurança do homem e do equipamento, preservação do meio ambiente e qualidade de vida das pessoas que
ali trabalham ou vivem na comunidade onde o processo está inserido.
As principais funções da instrumentação estão relacionadas com a qualidade e quantidade de produtos, fabricados com segurança e sem sub- produtos nocivos. O controle automático possibilita a existência de processos extremamente complexos, impossíveis de existirem apenas com controles manuais.
Quanto melhor a qualidade do produto desejado, menores devem ser as tolerâncias de suas propriedades. Quanto menor a tolerância, maior a necessidade de instrumentos para medição e controle automático.
As quantidades das matérias primas, utilidades e produtos finais devem ser medidas e controladas para fins de qualidade, balanço de custo e do rendimento do processo. Os instrumentos devem fazer a indicação, registro, e controle de modo contínuo e repetitivo.
O Controle automático economiza energia, pois elimina o superaquecimento de fornos, fornalhas, secadores, e permite operar equipamentos com o mínimo de desperdício.
Os instrumentos garantem efluentes limpos e inofensivos.
Entradas: Sensores de pressão, temperatura, nível, vazão, pressotatos, temostatos, chaves, etc.
Saídas: Atuadores, válvulas de controle, válvulas solenóide, variadores de velocidade, posicionadores, contatores, etc.
Sistema de Controle Indicação, Registro, Controle
Processo
Interface com o Operador
Material
Energia
Produto
Resíduos e Efluentes
figura 1.
Os instrumentos protegem equipamentos e vidas.
Medir é um conceito muito amplo. Todas as ações de máquinas ou dos homens com objetivo de obter um produto final adequado à qualidade desejada, partem da medição.
Medimos para conhecer variáveis, e a partir desse conhecimento executarmos ou não ações corretivas. Em geral, medimos variáveis no nosso processo para Indicar, Controlar ou Registrar.
As funções mais importantes dos instrumentos são: O sensor, a transmissão, a conversão, a indicação, o registro, o controle, o alarme, a computação analógica e a atuação manual.
A grande maioria da instrumentação se concentra em quatro variáveis: Pressão, Temperatura, Nível e Vazão. Uma pequena parte se preocupa com outras variáveis, especialmente as analíticas (PH, umidade, condutividade, densidade, posição, movimento, análise, etc.).
Em geral, não é possível conhecer a variável a ser medida, que não através de algum fenômeno físico ou químico associado. Daí o conceito de Sensores, transdutores e transmissores.
Sensores são elementos básicos de interface entre o processo e a medição, também chamados de elementos primários.
Transdutores e Transmissores são conceitos semelhantes. Transdutores são elementos capazes de transformar uma determinada variável em outra, de outra natureza. Os transmissores são casos especiais de transdutores cuja natureza e forma do sinal gerado é padronizada.
Quanto à função dos instrumentos podemos classificá-los como:
Indicadores , são instrumentos que sentem a variável do processo apresentam seu valor instantâneo. Um manômetro é um indicador local. Temos indicadores de painel, analógicos ou digitais.
Registradores são instrumentos que sentem uma ou várias variáveis de processo e armazenam seus valores em papel ou em memória mecânica ou eletrônica, ao longo do tempo. Os totalizadores são considerados registradores.
Transmissores que sentem as variáveis de processo através de elementos primários e enviam sinais padronizados para outros instrumentos como controladores e registradores.
Computadores analógicos , que executam funções de cálculo com as variáveis, tais como extratores de raiz quadrada, linearizadores, integradores, etc.
Elementos finais de controle , que manipulam variáveis, tais como válvulas de controle, válvulas solenóide, variadores de velocidade, etc.
Controladores são instrumentos que, baseados num set-point (valor desejado), enviam sinais a elementos finais de controle com objetivo de fazer com que a variável se iguale ou aproxime dele. Não necessariamente de forma automática: estações manuais são também controladores.
Comparadores são um grupo de instrumentos que emitem sinais digitais (tudo ou nada) quando suas variáveis medidas estiverem acima ou abaixo de valores pré-determinados. Como exemplo, os pressostatos, as chaves de nível, as chaves de fluxo e os termostatos.
Os sinais elétricos enviados pelos elementos de campo obedecem uma determinada padronização, que tem as suas vantagens.
Campo (^) Painel
4-20 mA
Fonte 24V
Transmissor a 2 fios (^) Instrumento Receptor
Fig. 1.
I (^) P
IN
OUT
Fonte de Alimentação
4 - 20 mA
Controlador
Figura 1.4 – Interligação de Instrumentos
Controladores Lógicos Programáveis PLC
Um dos equipamentos mais difundidos hoje para realizar as tarefas relacionadas com o controle automático são os PLC (Controladores Lógicos Programáveis)
Os PLC são microcomputadores de propósitos específicos dedicados inicialmente para o controle de sistemas com entradas e saídas binárias (de dois estados apenas: ligado - desligado, alto - baixo, etc.); porém, hoje, devido a seu sucesso em todas as indústrias, têm adquirido muita mais força para tratar de outras funções com alta confiabilidade, como é o caso de tratamento de sinais analógicas, controle continuo multi-variáveis, controle de posição de alta precisão, etc.
O caráter modular dos PLC permite adequar o controlador para qualquer aplicação, já que o projetista especifica só o número de módulos e acessórios que precisa de acordo com o número de entradas e saídas , e funções especificas, que requer o processo a ser controlado, tendo que pagar o preço justo para cada aplicação.
Outra característica importante dos PLC consiste na flexibilidade dada pela programação, que permite ser aplicado em qualquer tipo de processo e mudar rapidamente as funções através do programa, sem mexer na instalação.
figura 1.
PLC no Controle e Processos
As linguagens de programação desenvolvidas para os PLC são fundamentalmente representados de três formas: redes de contatos (similar aos esquemas elétricos de reles e contatores), blocos funcionais (similares aos esquemas de circuitos digitais: AND, OR, XOR, etc.) e em lista de instruções mnemônicas (similares aos programas escritos em assembler); sendo assim foram bem aceitos por
técnicos em manutenção não envolvidos nem treinados com técnicas de programação avançada de computadores.
Cabe destacar a vantagem que introduzem os PLCs com a redução do tamanho dos armários de controle e a diminuição de falhas, permitindo mudar os sistemas de controle a reles e contatores com um menor custo de instalação e manutenção.
O uso de Sistemas de Controle Distribuído com Supervisão Digital Centralizada ( SCADA) , hoje constitui a técnica mais atraente para a maioria dos sistemas de controle industrial.
Sistemas SCADA
Os sistemas do tipo SCADA possuem vários níveis para o tratamento da informação do processo, cujo número e complexidade da estrutura depende da aplicação e grau de automação desejada para cada caso.
A estrutura dos Sistemas SCADA é concebida em forma piramidal, como se mostra na figura 1.6.
No Primeiro nível (mais próximo do processo) aparecem os dispositivos de campo (transmissores, válvulas automáticas, etc.). Eles tem a missão de elaborar os sinais representativos das medições de diversas variáveis do processo, para ser enviadas a distância, ou atuam sobre os mecanismos e equipamentos do processo, segundo os sinais de controle recebidos.
Os PLCs ou controladores digitais, situados no segundo nível de automação, são encarregados de efetuar o controle das variáveis do processo e trocar informações, através de redes de comunicação, entre eles e com o computador.
O computador monitora o comportamento do sistema usando um software de supervisão e controle, dedicado a atualizar em tempo real as Informações na tela, emitir relatórios periódicos para a operação, modificar parâmetros dos controladores, avisar da existência de falhas e recomendar o que fazer. Desta maneira, o computador realiza a função de supervisor – assessor.
MÁQUINA OU PROCESSO INDUSTRIAL
SENSORES, CHAVES, BOTOEIRAS, ETC.
ATUADORES
CP
fig. 1.7 – Field-bus e tradicional
Existem vários protocolos de comunicação utilizados em aplicações deste tipo. Os mais utilizados são: FIELDBUS FUNDATION e o PROFIBUS. Cada um deles com as suas particularidades.
Essas particularidades, aliadas à dificuldade de padronização tem levado muitos usuários a não optarem por redes de campo.
O número de dispositivos que pode ser ligado a cada rede ( dada por um par de fios) fica limitado pela distância física, velocidade de transmissão e número de blocos de programas necessários, que determinam a freqüência de refrescamento dos dados na rede.
Esse número, normalmente, é inferior a 30 dispositivos analógicos. Varias redes podem ser ligadas a cada rack de PLC. Alguns cartões possuem mais de um canal de comunicação.
Distâncias de, até 2.000 m podem ser alcançadas por estas redes sem dificuldades.
Uma técnica mais utilizada atualmente nos sistemas de controle é baseada na utilização de estações remotas de comunicação para entradas e saídas, analógicas e digitais.
Utilizam-se várias unidades remotas de comunicação serial, muitas vezes conhecidas como cabeças de remotas, acopladas com
alguns módulos de entradas e saídas, instaladas em painéis próximos aos dispositivos de campo.
Em muitos casos, as cabeças de remotas, a pesar de inteligentes, apenas processam e controlam a comunicação de dados; ficando o processamento dos mesmos a cargo da CPU do PLC.
Várias estações de comunicação remota podem ser ligadas através de um mesmo par de cabos, trocando continuamente dados com a CPU do PLC. Na figura 1.8 se mostra a arquitetura típica deste tipo de sistema.
Muitas CPUs de PLC suportam a instalação de vários cartões de comunicação no rack, de tal forma que é possível distribuir todas as entradas e saídas no campo. Outros cartões de entrada e/ou saída podem ser instalados no rack principal, se for necessário.
O número de estações de entradas e saídas ( I/O) remotas que podem ser ligadas em cada trecho de rede, a velocidade de comunicação digital e as distâncias máximas para comunicação depende das particularidades do modelo dos cartões utilizados para comunicação, I/O, rack e CPU; tanto quanto da capacidade dos cartões de I/O utilizados.
C
P
U
Dispositivos de Entrada / saída Dispositivos de Entrada / saída Dispositivos de Entrada / saída
Remota 1 Remota 2 Remota n
Rede 1
PLC
Figura1.8 – Interligação em rede
não, a pressão atmosférica padrão passou a ter a medida de 760 mmHg e não depende da área ou formato do tubo ou do recipiente.
Se a experiência tivesse sido feita com água, a altura da coluna seria de 760 x 13,59508 = 10332 mm, ou seja mais de dez metros. 13,59508 é a densidade do mercúrio em relação à água (a 4 oC).
Se a experiência tivesse sido feita na Lua, por exemplo, todo o mercúrio do tubo desceria até o nível zero.
Por esse motivo nenhuma bomba no planeta terra pode “puxar” água de um reservatório baixo, a uma altura superior a 10 metros da sua superfície: mesmo que a bomba promovesse um vácuo absoluto na tubulação, a água não subiria mais que cerca de 10 metros. Nesses casos devemos usar bombas submersas ou no mesmo nível da água.
Pressão Barométrica
É a pressão atmosférica medida num determinado local de interesse. O barômetro é um instrumento de medir a pressão atmosférica local. A pressão barométrica é também uma pressão absoluta.
O tubo da experiência de Torricelli é um barômetro.
Pressão Manométrica
A parcela da pressão acima da pressão atmosférica. Representa a diferença positiva entre a pressão medida e a pressão atmosférica no local. Pode ser convertida em pressão absoluta, apenas somando o valor da pressão atmosférica local:
manométrica + atmosférica = Absoluta
A pressão manométrica tomada ao ar livre é sempre zero. Portanto, em altitudes diferentes, um mesmo valor de pressão manométrica representará condições físicas diferentes.
Pressão Diferencial
É a diferença de magnitude entre duas pressões quaisquer.
Consequentemente, a pressão absoluta pode ser considerada como uma pressão diferencial onde a pressão de referência é o vácuo absoluto. Da
mesma forma, a pressão manométrica pode ser considerada como uma pressão diferencial que toma a pressão atmosférica como referência.
Pressão Hidrostática
A pressão abaixo da superfície de um líquido, resultante do peso da coluna do líquido que se encontra acima.
A pressão hidrostática é particularmente útil na medição de nível.
Num reservatório qualquer (regular) cuja área da base vale S, cheio com um nível h de um líquido cuja massa específica é ρ, podemos afirmar que:
O volume do líquido é a área da base multiplicada pela altura:
V=Sh
A massa do líquido é o volume multiplicado pelo sua massa específica:
m = ρSh
Pressão atmosférica
Zero absoluto
Pressão absoluta
Pressão Manométrica
Pressão atmosférica
Pressão diferencial
Vácuo
Fig. 2.
h
Fig. 2.
O peso da massa do líquido corresponde ao produto da massa pela aceleração da gravidade:
P = ρShg
E a pressão resultante, chamada de hidrostática será esse peso dividido pela área :
Eliminando a área S, obtemos:
P=ρgh
Ou seja, a pressão hidrostática não depende da área do reservatório, e sim somente da altura da coluna do líquido.
Intuitivamente podemos afirmar também que a pressão não depende da forma do reservatório: Dois reservatórios de formatos diferentes, quando interligados pela sua base mantém o mesmo nível pelo princípio de vasos comunicantes (fig. 2.5).
É razoável supor que a pressão na base de ambos, ou em qualquer ponto de mesma altura seja a mesma. Caso não o fosse haveria escoamento do líquido de um para o outro e os níveis resultariam diferentes.
Utilizando a coerência do Sistema Internacional, se tomamos o comprimento em metros, a massa específica em kg/m^3 e a aceleração da gravidade em m/s^2 , obteremos a pressão hidrostática em N/m^2 ou Pascal.
P = ρgh = [kg/m^3 ] x [m/s 2 ] x [m] ⇒ Pa
Pressão Estática
A força por unidade de área exercida perpendicularmente à parede de uma tubulação por um fluido que escoa na direção paralela à sua parede.
Corresponde à pressão, isenta de influências da velocidade, se nas mesmas condições o fluido estivesse em repouso, já que não há vetores de velocidade perpendiculares à parede.
Por esse motivo devemos tomar uma amostra do fluido com objetivo de medir-lhe a pressão, perpendicular à parede e rente à superfície (fig. 2.6).
A velocidade junto à parede, no seu limite, é nula, já que a parede não se move, e cresce com a aproximação do centro da tubulação.
Vácuo
Pressão abaixo do valor da pressão atmosférica. A medida de vácuo é referenciada à pressão atmosférica e inferior a ela. Corresponderia a grosso modo, a uma pressão manométrica negativa.
Por exemplo, se a pressão atmosférica é de 100.000 Pa, uma pressão de 80.000 Pa corresponde a um vávuo de 20.000 Pa.
Não existe vácuo de magnitude superior à pressão atmosférica no local, já que não existe pressão absoluta negativa.
Se a pressão atmosférica local é de 720 mmHg, então o maior vácuo que pode ser obtido é de 720 mmHg
figura 2.
tomada correta
tomada incorreta
Fig. 2.
Correspondências entre as unidades de medida de Pressão 1 Pa =^1 0,000 010 0000 0^ 0,000 145 037 7^ 0,000 010 197 16^ 0,007 500 627^ 0,101 971 6
1 bar = 100.000,0 1 14,503 77 1,019 716 750,062 7 10.197,
1 psi = 6.894,757 0,068 947 57 1 0,070 306 96 51,715 00 703,069 6
1 kgf/cm^2 = 98.066,50 0,980 665 0 14,223 34 1 735,506 2 10.000,
1 mmHg = 133,3222 0,001 333 222 0,019 336 75 0,001 359 508 1 13,595 08
1 mmH 2 O = 9,806 650 0,000 098 066 50 0,001 422 334 0,000 100 000 00 0,073 556 02 1
1 atm = 101.325,0 1,013 250 14,695 95 1,033 227 760,000 0 10.332,
Pa bar psi kgf/cm^2 mmHg mmH 2 O
Obs.: Gravidade terrestre normal: 9,80665 m/s 2 Massa específica do mercúrio a 0 oC e pressão atmosférica de 101.325 Pa: 13.595,08 kg/m 3 Massa específica da água a 4 oC e pressão atmosférica de 101.325Pa: 1.000,000 kg/m 3
Fatores de Conversão para Unidades de Medida de Pressão 0,000 01 bar 0,000 145 037 7 psi Multiplicar Pa por 0,000 010 197 16 Para Obter kgf/cm^2 0,007 500 627 mmHg 0,101 971 6 mmH 2 O 100.000 Pa 14,503 77 psi Multiplicar bar por 1,019 716 Para Obter kgf/cm^2 51,715 mmHg 10.197,16 mmH 2 O 6.894,757 Pa 0,068 947 57 bar Multiplicar psi por 0,070 306 96 Para Obter kgf/cm^2 51,715 mmHg 703,069 6 mmH 2 O 98.066,5 Pa 0,980 665 bar Multiplicar kfg/cm^2 por 14,223 34 Para Obter psi 735,506 2 mmHg 10.000 mmH 2 O 133,3222 Pa 0,001 333 222 bar Multiplicar mmHg por 0,019 336 75 Para Obter psi 0,001 359 508 kgf/cm^2 13,595 08 mmH 2 O 9,806 65 Pa 0,000 098 066 5 bar Multiplicar mmH 2 O por 0,001 422 334 Para Obter psi 0,000 1 kgf/cm^2 0,073 556 02 mmHg Obs.: Gravidade terrestre normal: 9,80665 m/s 2 Massa específica do mercúrio a 0 oC e pressão atmosférica de 101.325 Pa: 13.595,08 kg/m 3 Massa específica da água a 4 oC e pressão atmosférica de 101.325Pa: 1.000,000 kg/m 3
Manômetros
Manômetro é a denominação genérica para instrumentos de medir e indicar a pressão manométrica.
Os mais simples são os manômetros de coluna líquida, que se prestam, essencialmente, à medida de pressões baixas.
O manômetro de coluna em “U” consiste num tubo transparente dobrado nesse formato, e cheio com o líquido de referência, usualmente água ou mercúrio.
O fluido sob pressão é conectado em uma das extremidades do “U” como na figura 2.7. Se a outra extremidade estiver aberta para atmosfera, a pressão será manométrica. Para medição de pressão diferencial a segunda extremidade deverá estar conectada na pressão de referência.
Se o fluido for água, podemos ler a pressão em mmH 2 O diretamente medindo o comprimento da diferença entre as duas superfícies. Se for mercúrio, a pressão será dada em mmHg. Qualquer líquido pode ser usado, sendo o resultado calculado com a equação P=ρgh.
A rigor deveremos corrigir a massa específica do líquido em função da temperatura ambiente e da aceleração da gravidade local.
Uma variação para medirmos baixas pressões é a coluna inclinada (fig. 2.8), que nos permite
melhor resolução na graduação gravada na régua graduada.
Uma outra configuração da coluna líquida é a coluna vertical com poço (fig. 2.9).
Nesse caso, um reservatório contendo o líquido tem volume muito superior ao volume que a coluna pode conter. A pressão é aplicada no reservatório e o líquido é empurrado no sentido de subir na coluna.
Podemos medir o comprimento da coluna e obter a pressão, da mesma forma, em mmH2O ou mmHg, dependendo do líquido utilizado.
Porém, se a medida de comprimento é feita metricamente, devemos corrigir o valor lido em função da relação entre diâmetros do tubo e do reservatório.
O volume de líquido que abandonou o reservatório é o mesmo que ocupou a coluna, então o nível no reservatório deve descer ligeiramente.
Como o comprimento a ser medido deve ser tomado como a diferença entre as duas superfícies e, sendo o reservatório opaco, não conhecemos o seu nível interno, podemos concluir que a medida do comprimento em relação à pressão zero (sem pressão) está ligeiramente inferior ao correspondente à verdadeira pressão.
O fator de correção pode ser facilmente deduzido como sendo
= + 2
2 1 D
F d c
que deve multiplicar o comprimento lido para obtermos o valor correto (d é o diâmetro do tubo transparente e D é o diâmetro do reservatório).
Quando o equipamento é fabricado podemos a priori, corrigir a régua calibrada, dividindo toda a sua escala pelo mesmo fator.
Num instrumento adquirido de um fabricante, poderemos verificar se a escala está corrigida medindo-a com uma boa trena.
Pressão
Pressão tomada em unidade de comprimento de coluna do líquido utilizado
Fig. 2.
figura 2.
Pressão
Fig. 2.
Para processos que apresentam forte pulsação ou vibração, recomenda-se o enchimento da câmara do manômetro com glicerina ou halocarbono.
Para calibração de manômetros podem ser utilizadas colunas líquidas para baixas pressões, ou bombas de comparação ou balanças de peso morto para altas pressões.
A bomba de comparação consiste num sistema cilindro e pistão com um volante para pressurizar o óleo no cilindro. Um manômetro de referência de boa qualidade, calibrado e controlado é instalado em um dos lados da bomba.
O manômetro sob calibração é instalado na outra extremidade. O movimento de rotação do volante pressurizará o óleo no interior do sistema, aplicando a mesma pressão nos dois manômetros que podem ser suas leituras comparadas.
A balança de peso morto consiste num sistema muito semelhante, onde o manômetro de referência é substituído por um cilindro que contém um pistão que suporta pesos de diferentes valores. Nesse caso, o volante será movido de forma a pressurizar o sistema e levantar o peso até uma altura intermediária (esquema do desenho).
Como a área do cilindro é conhecida e os pesos são corretos e certificados, a pressão será dada pelo valor dos pesos dividido pelo valor da área.
Também para sermos rigorosos necessitamos levar em considerações todas as influências ou incertezas relativas à aceleração da gravidade local, a área do cilindro e sua variação com a temperatura, o empuxo do ar em função de sua
massa específica, a incerteza dos valores dos pesos que devem ser certificados e os critérios e procedimentos adotados.
fig. 2.13 – Bomba de comparação
Êmbolo
Cilindro
Barra roscada Volante
Reservatório de óleo
Manômetro sob teste
Pistão
Pesos
Fig. 2.
Folha de Dados para manômetros (típica)
TAG PI-101 PI-102 PI-
SERVIÇO
Pressão de Ar de Diluição Geral
Pressão BFG Geral Pressão GLP Geral
Linha Número Classificação da Área não classificada não classificada não classificada
Invólucro Nema 4 Nema 4 Nema 4
Material do Corpo Conexões de Entrada 1/2”NPT reta 1/2”NPT reta 1/2”NPT reta
Pressão difer./manom. Manométrica Manométrica manométrica Tipo do sensor Bourdon Bourdon bourdon Material do sensor Aço Inox Aço Inox Aço Inox Range 0-1000 mmca 0-2000 mmca 0-5 kgf/cm 2 Número de divisões 50 40 50 Diâmetro do Mostrador 100 mm 100 mm 100 mm
Acessórios de fixação Não não não Dispositivo de Selagem Não não não
Fluido Ar de Diluição Gás de Alto Forno GLP Temperatura 30 oC 30 oC 30 oC Pressão Nominal 500 mmca 900 mmca 150 kPa
Diâmetro tubulação 8” 8” 1.1/2” Peso Específico 1,3 Kg/Nm^3 1,3 Kg/Nm^3 1,99 Kg/Nm^3
Modelo/Fabricante: Willy, Aschroft, Wika ou similar Obs.