
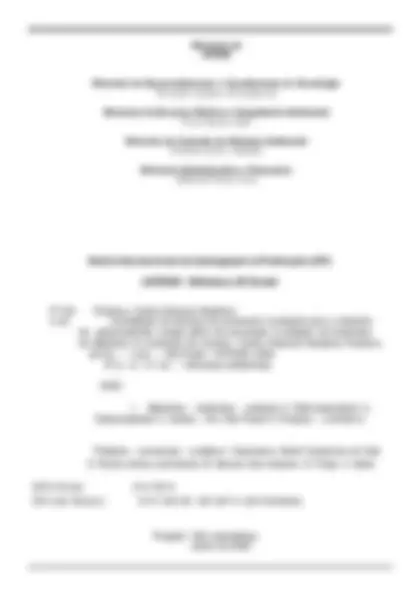
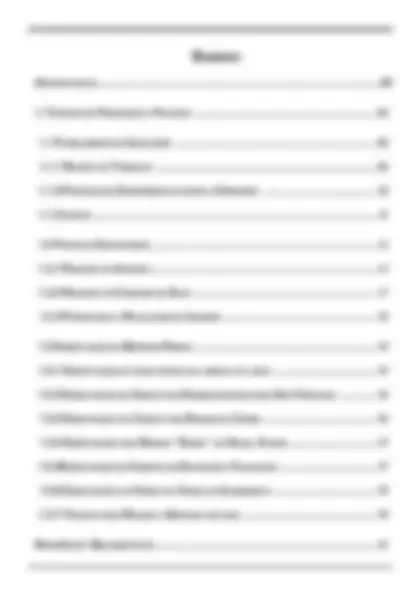
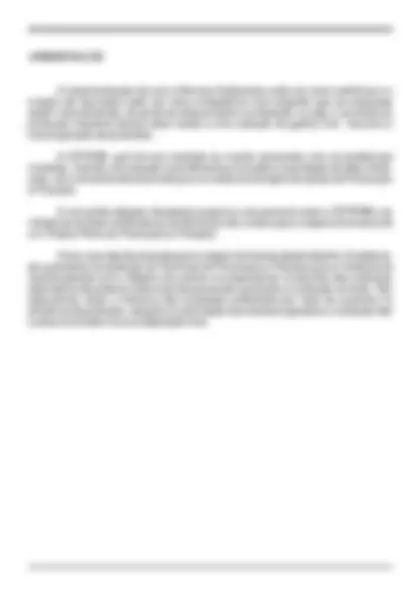
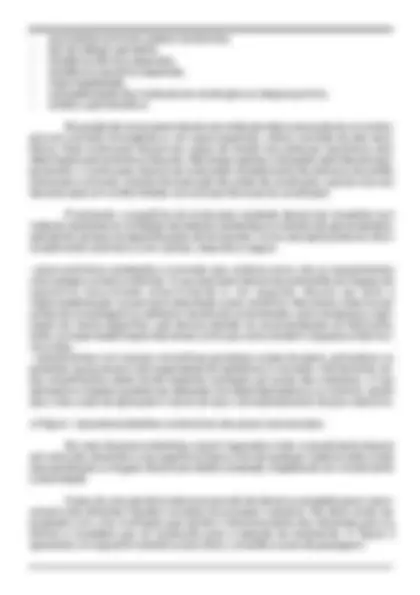
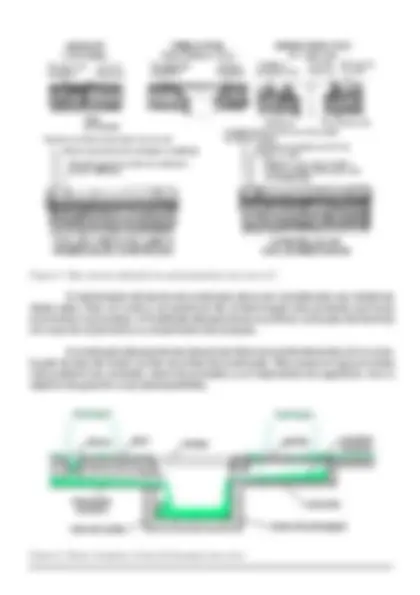
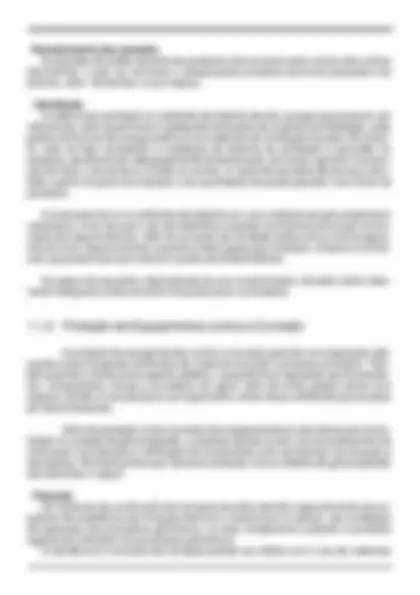
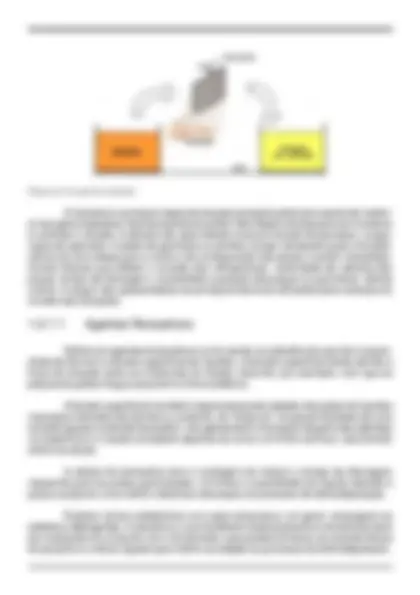
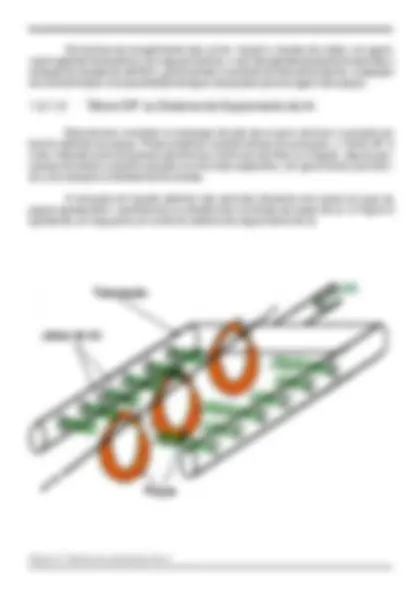
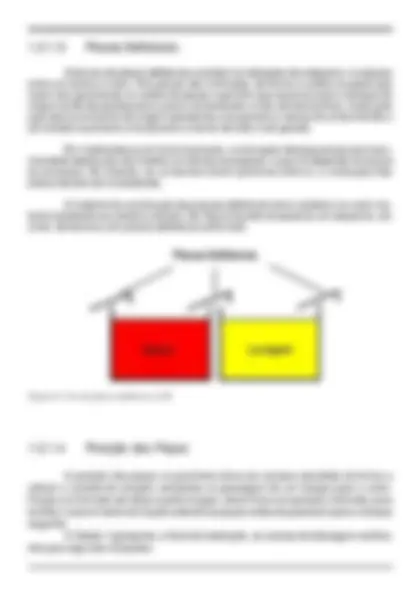
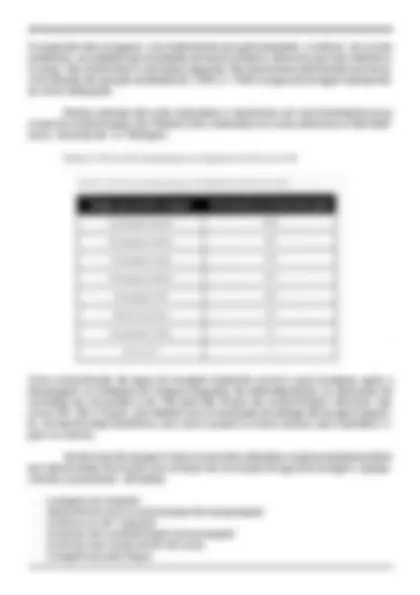
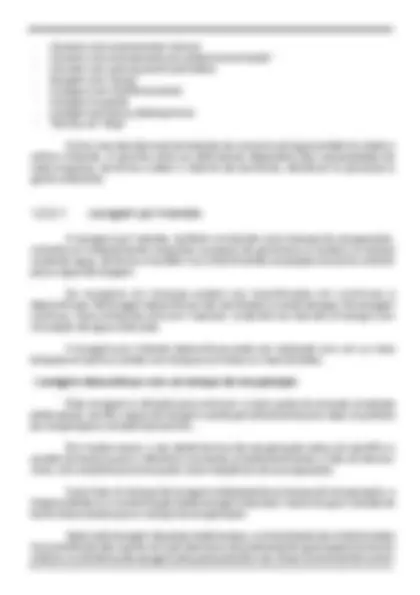
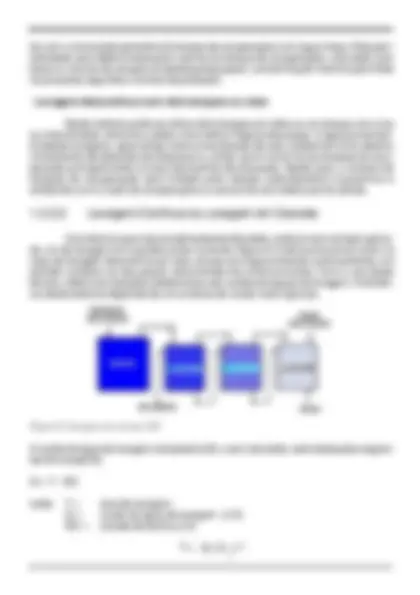
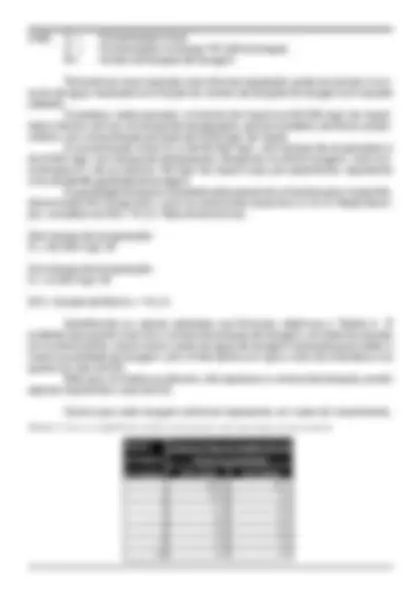
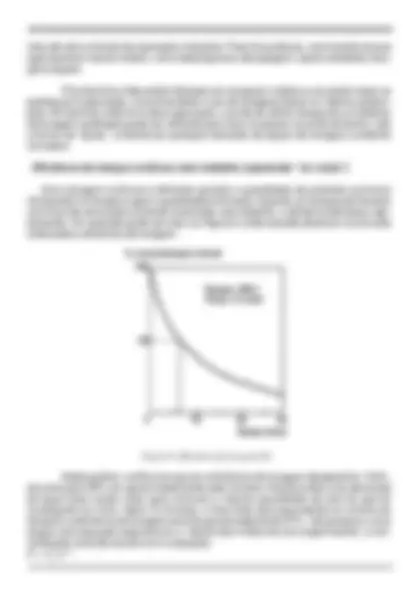
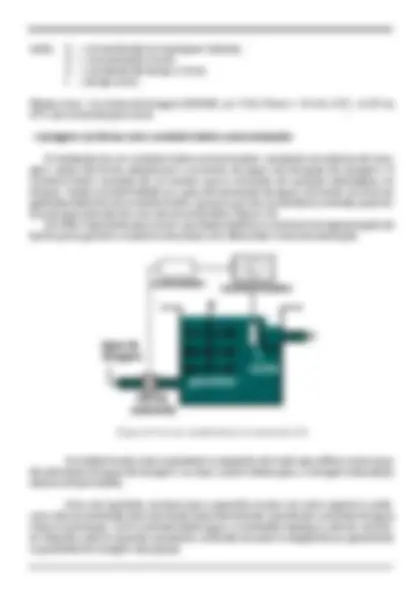
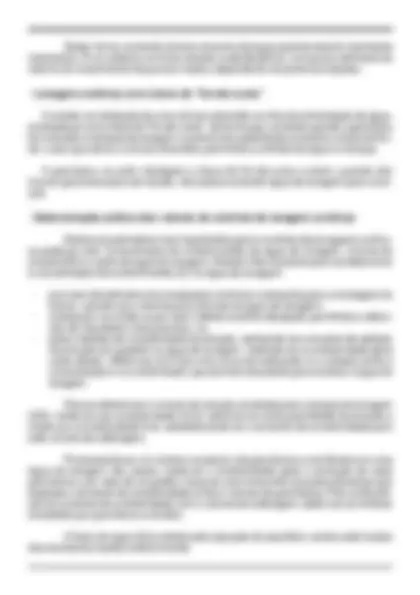
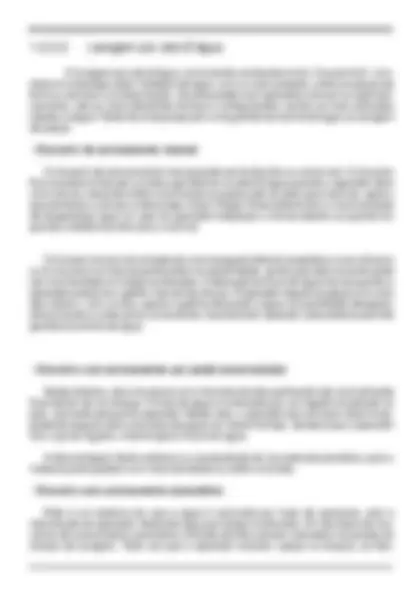
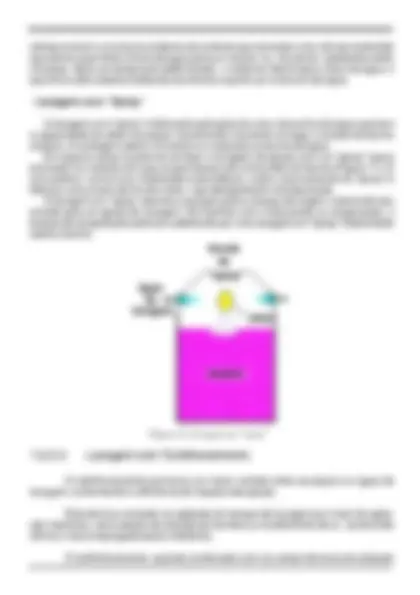
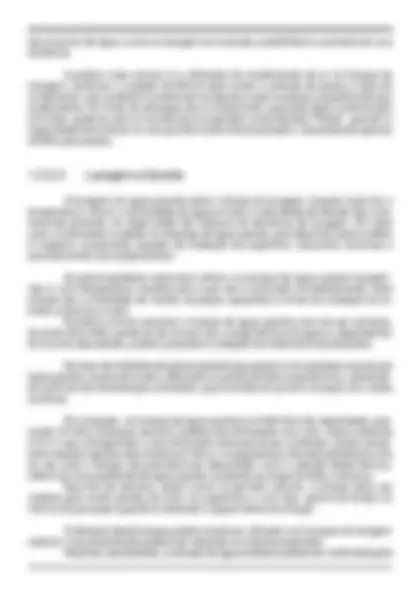
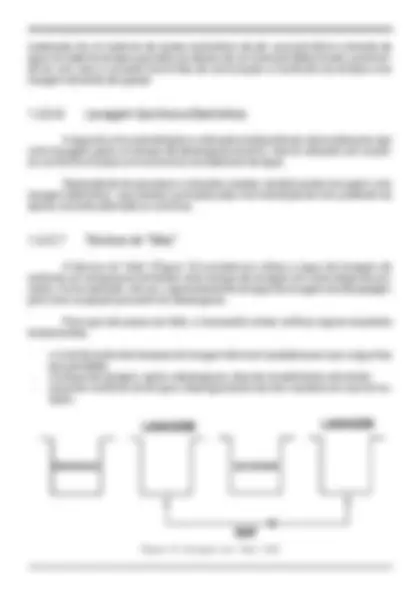
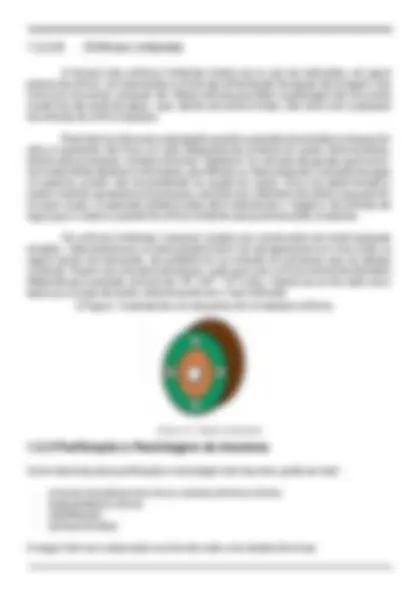
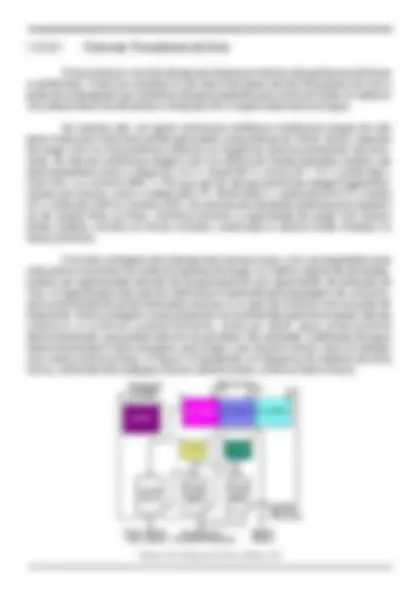
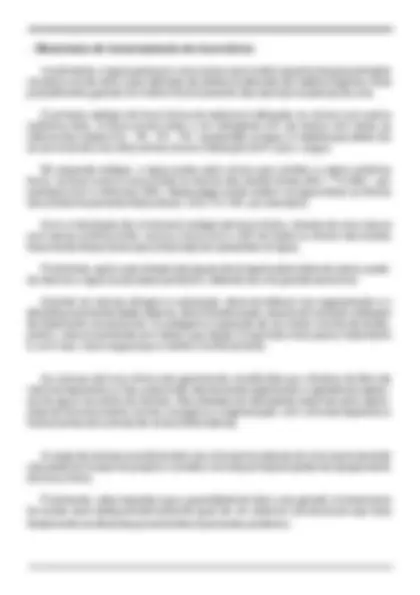
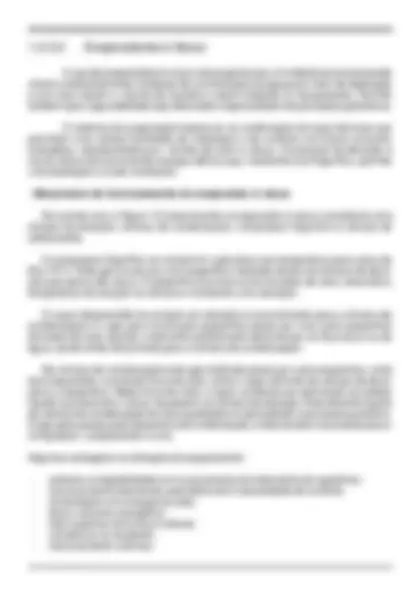
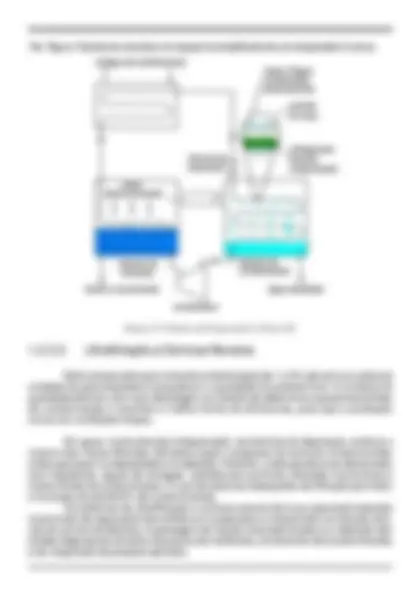

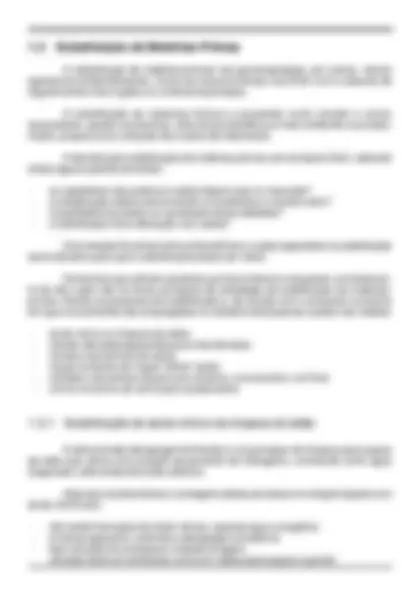
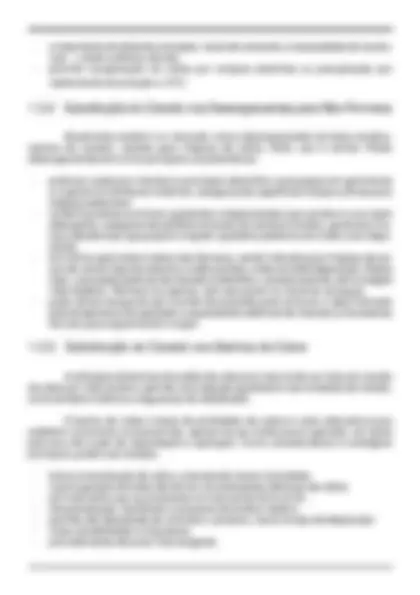
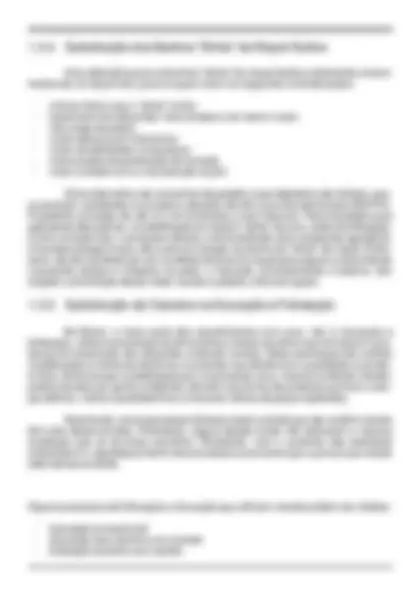
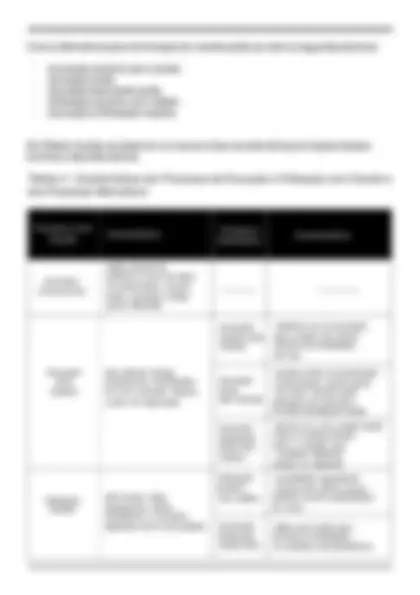
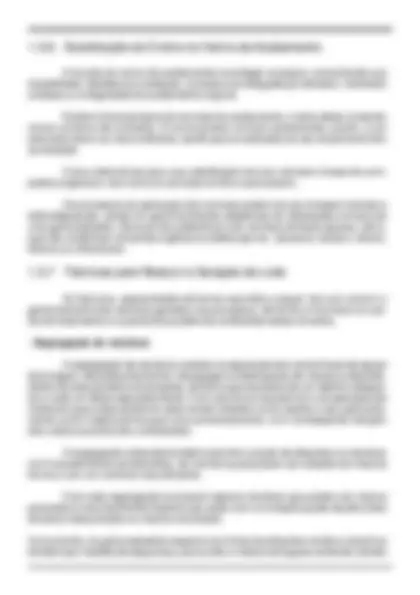
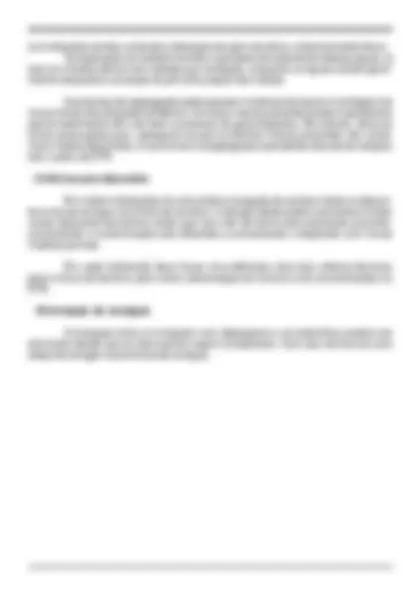
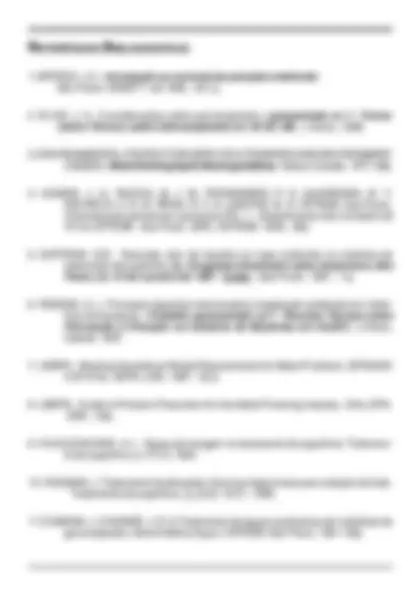
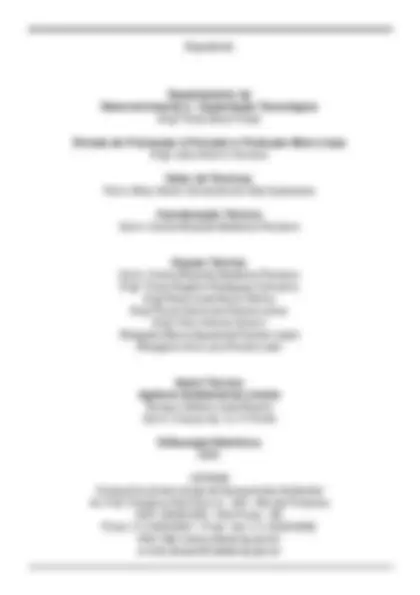
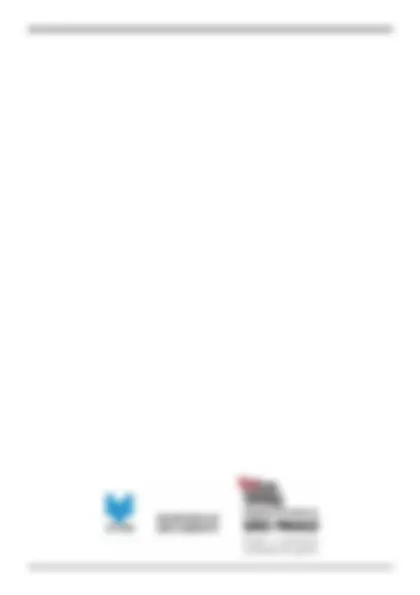
Estude fácil! Tem muito documento disponível na Docsity
Ganhe pontos ajudando outros esrudantes ou compre um plano Premium
Prepare-se para as provas
Estude fácil! Tem muito documento disponível na Docsity
Prepare-se para as provas com trabalhos de outros alunos como você, aqui na Docsity
Os melhores documentos à venda: Trabalhos de alunos formados
Prepare-se com as videoaulas e exercícios resolvidos criados a partir da grade da sua Universidade
Responda perguntas de provas passadas e avalie sua preparação.
Ganhe pontos para baixar
Ganhe pontos ajudando outros esrudantes ou compre um plano Premium
Comunidade
Peça ajuda à comunidade e tire suas dúvidas relacionadas ao estudo
Descubra as melhores universidades em seu país de acordo com os usuários da Docsity
Guias grátis
Baixe gratuitamente nossos guias de estudo, métodos para diminuir a ansiedade, dicas de TCC preparadas pelos professores da Docsity
Técnicas de lavagem utilizadas na galvanoplastia, visando minimizar o arraste de líquidos dos banhos, melhorar a eficiência, reduzir o consumo de água e promover a reciclagem de insumos. Além disso, são discutidas as técnicas de lavagem por imersão, descontínua e contínua, lavagem por jato d’água e a importância de controlar os parâmetros de concentração de contaminantes, volume de arraste e vazão de água de lavagem.
O que você vai aprender
Tipologia: Exercícios
1 / 43
Esta página não é visível na pré-visualização
Não perca as partes importantes!
Governo do Estado de São Paulo
Secretaria de Estado do Meio Ambiente
CETESB - Companhia de Tecnologia de Saneamento Ambiental
A implementação de Leis e Normas Ambientais cada vez mais restritivas e a criação de mercados cada vez mais competitivos vem exigindo que as empresas sejam mais eficientes, do ponto de vista produtivo e ambiental, ou seja, o aumento da produção industrial deverá estar aliado a uma redução de gastos com insumos e menor geração de poluentes.
A CETESB, que tem por tradição se manter atualizada com as tendências mundiais, visando uma atuação mais eficiente e inovadora na proteção do Meio Ambi- ente, vem concentrando seus esforços na institucionalização de ações de Prevenção à Poluição.
A comunhão desses interesses propiciou uma parceria entre a CETESB e as indústrias do Setor de Bijuterias do Município de Limeira para o desenvolvimento de um Projeto Piloto de Prevenção à Poluição.
Como uma das ferramentas para o desenvolvimento deste trabalho, foi elabora- da a presenteCompilação de Técnicas de Prevenção à Poluição para a Indústria de Galvanoplastia com o objetivo de auxiliar os empresários na escolha das melhores alternativas de práticas e técnicas de prevenção à poluição ou redução na fonte. Tais alternativas visam a melhoria das condições ambientais por meio do aumento na eficiência de produção, redução ou eliminação dos resíduos gerados e a redução dos custos envolvidos na sua disposição final.
Sistema de coleta de efluentes Atenção especial deve ser dada ao sistema de coleta de efluentes industriais, prevendo-se a separação dos efluentes ácidos dos alcalinos em linhas exclusivas. Com relação ao material das linhas de coleta, deve-se adotar aqueles resistentes aos produtos químicos utilizados nos banhos, evitando dessa maneira a sua corrosão ou deformação, bem como possíveis vazamentos.
· Instalações elétricas A instalação elétrica do prédio deverá contar com vários comandos individuais, estrategicamente posicionados no recinto de trabalho, ligados a um quadro de co- mando geral. Todos estes comandos deverão apresentar fácil acesso aos trabalhado- res e espaço suficiente para sua manutenção. A utilização de barramentos elétricos de cobre ao longo da linha de produção permitirá flexibilidade nas mudanças de layout, colocação de novos equipamentos e facilidade de manutenção. Todo o sistema elétrico da empresa deverá contar com um programa de manutenção preventiva específico.
· Pisos O atendimento às boas técnicas de construção civil e gerenciamento industrial, resultam em pisos bem construídos e com manutenção preventiva específica e requerida para a indústria de galvanoplastia.
No entanto, na maioria destas indústrias, verifica-se pisos mal projetados e construídos, com trincas, fissuras e falta de manutenção. Como agravante desta situ- ação, tem-se o fato de que estes pisos ficam sempre molhados devido a respingos das soluções dos banhos, ocorridos durante o transporte de peças de um banho a outro e também por eventuais vazamentos em válvulas, gaxetas e tubulações.
Via de regra, as indústrias promovem a limpeza periódica do piso da fábrica sen- do, então, os líquidos e a sujeira lá acumulados encaminhados para a estação de tratamento de efluentes da empresa ou para outro local de descarte, no caso de não se dispor de estação de tratamento.
Estas remoções periódicas, porém, não impedem que as soluções dos banhos, com o tempo, ataquem o material do piso provocando a sua deterioração. Pisos mal construídos, mal conservados e deteriorados que apresentam fissuras ou trincas, propiciam a infiltração dos líquidos nele acumulados para o solo, provocando a conta- minação deste meio e das águas subterrâneas, além de poder atacar as fundações do prédio e as instalações subterrâneas (água, esgoto, etc).
Erroneamente, pouca atenção é dada ao projeto, execução e proteção dos pisos em unidades de galvanoplastia, resultando em gastos extras e até mesmo em even- tuais interrupções no processo para a sua correção. Assim sendo, no caso de projetos para novas instalações ou rearranjo das atuais, deverão ser considerados os seguintes tópicos na execução do piso:
No projeto de novos pisos deverá ser ainda prevista a execução de um contra- piso em concreto homogêneo e, em casos especiais, utilizar concreto de alta resis- tência. Este contra-piso deverá ser capaz de resistir aos esforços mecânicos sem deformação permanente ou fissuras. Nas áreas sujeitas a vibrações advindas de equi- pamentos, o contra-piso deverá ser executado isoladamente da estrutura do prédio (alicerces e colunas), através de execução de juntas de construção, que por sua vez deverão estar em conformidade com as boas técnicas de construção.
Finalmente, a superfície do contra-piso acabado deverá ser revestida com material resistente às condições de trabalho existentes na indústria de galvanoplastia, atendendo sempre às especificações do fornecedor. Como exemplos pode-se citar o revestimento cerâmico e com resinas, descritos a seguir:
· pisos cerâmicos resistentes à corrosão que, embora caros, são os revestimentos mais antigos e ainda confiáveis. A sua execução deverá ser precedida da limpeza da superfície mencionada anteriormente e, em seguida, deverá ser feita a impermeabilização na qual será assentado o piso cerâmico. Nas áreas onde houver juntas de concretagem ou esforços mecânicos concentrados, será necessária a apli- cação de manta específica, que deverá atender às recomendações do fabricante, tanto na impermeabilização das áreas contínuas como também naquelas onde hou- ver juntas. · revestimentos com resinas monolíticas (produtos a base de epóxi, poliuretano ou poliéster) que possuem alta capacidade de resistência à corrosão. Ultimamente, es- tes revestimentos estão tendo bastante aceitação por parte das indústrias. A sua aplicação é simples e poderá ser efetuada com desempenadeira ou à revólver, sendo que o seu custo de aplicação é menor do que o de assentamento do piso cerâmico.
A Figura 1 apresenta detalhes construtivos dos pisos mencionados.
No caso de pisos existentes a serem reparados, todo o revestimento deverá ser removido, deixando a sua superfície limpa e livre de qualquer material solto e toda área danificada ou irregular deverá ser refeita e acabada, respeitando-se o nivelamento e declividade.
O piso de uma galvânica deve ser provido de drenos e canaletes para o esco- amento dos efluentes líquidos oriundos do processo industrial. Ele deve ainda ser projetado com uma inclinação que facilite o direcionamento dos efluentes para os drenos e canaletes que os conduzirão para a estação de tratamento. AFigura 2 apresenta um esquema ilustrativo para dreno, canalete e caixa de passagem.
· Revestimento das paredes As paredes do prédio deverão ter proteção anti-corrosiva pelo menos até a altura dos banhos, o que vai minimizar o ataque pelos produtos químicos presentes nos banhos, além de facilitar a sua limpeza.
· Ventilação O sistema de ventilação no ambiente de trabalho deverá, sempre que possível, ser natural pois, além de promover a adequada renovação do ar dentro da instalação, evita gastos adicionais de energia elétrica com sistemas de ventilação forçada. No entan- to, caso se faça necessária a instalação de sistema de ventilação e exaustão na empresa, ele deverá ser adequadamente dimensionado, de modo a garantir a renova- ção de todo o volume de ar contido no recinto. A vazão de exaustão deverá ser calcu- lada a partir do porte da empresa e da quantidade de gases gerados nas linhas de produção.
A renovação de ar no ambiente de trabalho em uma indústria de galvanoplastia é necessária, uma vez que o uso de eletrólitos a quente nos banhos provocam a ema- nação de vapores tóxicos, além do aumento da umidade relativa do ar e da tempera- tura do local. Alguns banhos à quente emitem gases (por exemplo, nitrosos e clorídri- cos) que podem provocar danos à saúde dos trabalhadores.
Os gases de exaustão, dependendo da sua contaminação, deverão sofrer trata- mento adequado antes de serem lançados para a atmosfera.
A proteção de equipamentos contra a corrosão garante uma operação ade- quada e previne perdas acidentais de materiais durante o processo produtivo. Tam- bém permite a melhoria do aspecto estético, causando boa impressão aos fornecedo- res, compradores, fiscais e ao público em geral, além de evitar gastos extras com reparos, facilitar a manutenção e, principalmente, evitar danos ambientais provocados por derramamentos.
Além da proteção contra corrosão dos equipamentos e das estruturas encon- tradas na unidade de galvanoplastia, a empresa deverá contar com procedimentos de rotina para manutenção e verificação de vazamentos e de rachaduras nos tanques e tubulações. Dois dos pontos que merecem proteção numa indústria de galvanoplastia são descritos a seguir.
· Tanques Os materiais de construção dos tanques deverão atender especialmente aos re- quisitos de resistência aos choques térmicos, mecânicos e à ruptura, nas condições de operação dos processos galvânicos, ou seja, temperatura, pressão e produtos agressivos utilizados nos processos galvânicos. A resistência à corrosão dos tanques poderá ser obtida com o uso de materiais
alternativos, tais como: plásticos (polietileno e polipropileno), fibra de vidro reforçada com plástico e aço inoxidável. No caso do uso de tanques para os banhos galvânicos ou para o armazenamento de matérias-primas, suas armações de sustentação, estruturas, conexões e as tubu- lações metálicas utilizadas na unidade de galvanoplastia, deverão ser protegidos tam- bém contra a corrosão.
A aplicação de resina monolítica, semelhante àquela usada em pisos, utilizando pincel ou “spray”, tem dado bons resultados a um custo reduzido em relação aos sistemas de pintura com tinta epóxi e polivinílica. As resinas também apresentam melhores características que as tintas, com relação a resistência a choque, a calor, coeficiente de expansão e durabilidade.
· Resistências elétricas As resistências elétricas utilizadas no aquecimento dos banhos deverão ser de boa qualidade, feitas com materiais resistentes a ataques ácidos e alcalinos, evitan- do dessa forma acidentes como descargas elétricas e curto-circuitos.
O layout ou distribuição física dos equipamentos, banhos e tanques de lava- gem no recinto de trabalho, é uma das práticas operacionais a ser considerada no desenvolvimento de um programa de Prevenção à Poluição (P2).
Observa-se, freqüentemente, na disposição física dos equipamentos nas empresas do setor galvânico, uma preocupação acentuada com a seqüência de ope- rações do seu fluxograma de produção, em detrimento das questões operacionais que envolvem a passagem das peças de uma etapa para outra no processo.
Em outras palavras, a distância entre os equipamentos, a não otimização do sistema no que concerne à seqüência operacional, a distribuição dos equipamentos no recinto de trabalho, dentre outros fatores, provocam respingos no piso da fábrica, devido ao carreamento dos líquidos pelas peças durante sua passagem de um está- gio para outro.
AFigura 3 mostra dois exemplos de layout de banhos galvânicos, sendo que no primeiro tipo (a) os respingos são evitados e o segundo (b) apresenta grandes distâncias, além de dificultar o desenvolvimento das operações.
Desta forma, verifica-se que tanto o planejamento de novas instalações quan- to a reavaliação do layout, no caso de empresas já implantadas, são de grande impor- tância para o desenvolvimento de um programa de P2.
Salienta-se, ainda que, o layout de uma empresa deve observar uma divisão adequada de espaço, possibilitando uma visão geral do sistema e o escoamento livre da produção.
Figura 4: Arraste de soluções
O arraste é o principal responsável pela poluição potencial e perda de materi- al nas galvanoplastias. Numerosas técnicas têm sido desenvolvidas para se monitorar e controlar o arraste. A eficácia de cada método varia em função do processo, coope- ração do operador, modelo da gancheira ou tambor, tempo necessário para a transfe- rência de uma etapa para a outra e da configuração das peças a serem revestidas. Outros fatores que afetam o arraste são: temperatura, velocidade de retirada das peças, tempo de drenagem, viscosidade e posição das peças na gancheira, dentre outros. A seguir são apresentadas as principais técnicas utilizadas para redução do arraste das soluções.
Define-se agentes tensoativos como sendo as substâncias que tem capaci- dade de diminuir a tensão superficial de líquidos. A tensão superficial existe devido à força de atração entre as moléculas do líquido, fazendo, por exemplo, com que as pequenas gotas d’água assumam a forma esférica.
A tensão superficial é também responsável pela adesão das gotas de líquidos nas peças retiradas dos banhos e, portanto, do “drag-out”. As peças retiradas de uma solução aquosa contendo tensoativo, não apresentam a formação de gotículas aderidas na superfície e o líquido arrastado espalha-se como um filme contínuo, escorrendo sobre as peças.
A adição de tensoativo tem a vantagem de reduzir o tempo de drenagem requerido para as partes gancheadas, minimizar a quantidade de líquido aderida à peça e propiciar uma melhor cobertura das peças no processo de eletrodeposição.
Existem várias substâncias com ação tensoativa, em geral, empregam-se sabões e detergentes. A escolha e o uso de determinado tensoativo nos banhos deve ser analisada em conjunto com o fornecedor, que poderá fornecer as características do produto ou indicar aquele que melhor se adapte ao processo de eletrodeposição.
Os banhos de revestimento tais como: níquel e cianeto de cobre, em geral, usam agentes tensoativos. Em alguns banhos, o uso de agentes tensoativos permite a redução do arraste em até 50%, promovendo o aumento da vida útil do banho, a redução da contaminação e da quantidade de água necessária para lavagem das peças.
Esta técnica consiste no emprego de jato de ar para remover a solução do banho aderida às peças. Pelas próprias características do processo, o “blow-off” é mais indicado para processos galvânicos contínuos de fitas ou chapas, alguns pro- cessos de tubos ou perfis e peças com formato específico, em gancheiras, permitin- do uma redução considerável do arraste.
A remoção do líquido aderido não será tão eficiente nos casos em que as peças apresentem reentrâncias ou obstáculos à entrada do sopro de ar. AFigura 5 apresenta um esquema em corte do sistema de sopramento de ar.
Figura 5: Sistema de sopramento de ar
As retiradas muito rápidas causam a perda de um grande volume de solução por arraste. Com uma baixa velocidade de retirada das peças de dentro dos banhos e tempos de drenagem mais longos, o arraste de soluções pelas peças pode ser redu- zido em até 50%. No caso de banhos que operam a altas temperaturas, retiradas mais lentas são necessárias para prevenir a perda da solução por evaporação, que neste caso aumenta o arraste. AFigura 7 mostra o volume de “drag-out” em função do tempo, para peças de formas horizontais, inclinadas e verticais.
PERDAS POR ARRASTE
Posição das peças Arraste (L/m²)
Verticais:
1, 8, 16,
3, 40,
3, 97,
Figura 7: Velocidade de drenagem em função das formas das peças [8]
Tabela 1 – Valores de drenagem para alguns tipos de peças
Observa-se pelaFigura 7 que, para uma retirada “quase instantânea” (instante bem próximo de zero segundos da retirada), os volumes de “drag-out” serão 150, 129 e 97 L/m² para peças horizontais, inclinadas e verticais, respectivamente.
Após 3 segundos de drenagem, o “drag-out” reduz-se a 118, 97 e 64 L/m², ou seja 21, 25 e 50% de redução para as peças horizontais, inclinadas e verticais, res- pectivamente. Com 15 segundos de drenagem, tem-se uma redução aproximada no “drag-out” de 47, 55 e 60% (78,6; 59,2 e 37,7 L/m²) para as superfícies de peças horizontais, inclinadas e verticais, respectivamente.
Após um tempo relativamente longo (1 minuto por exemplo), observa-se na Figura 7 que o “drag-out” torna-se constante, ou seja, existe um volume de “equilíbrio” correspondente ao líquido firmemente retido pelas peças. Comparando-se a redução no “drag-out” para 15 segundos de drenagem, com este “drag-out” de equilíbrio (para 1 minuto, 48,4; 32,3 e 19,4 L/m², aproximadamente, nos três casos) obtém-se redu- ções de 70, 72 e 76% (para as superfícies horizontais, inclinadas e verticais, respec- tivamente), ou seja, não haverá um ganho apreciável nos próximos 45 segundos de drenagem, ou melhor, em 25% do tempo ter-se-á o escorrimento de 75% do volume de líquido total, aproximadamente. Portanto, a drenagem para todos os formatos de peças estará quase comple- ta após 15 segundos da retirada de dentro do banho, indicando que este será um tempo ótimo de drenagem para a maioria das peças.
Um dos melhores meios de se controlar a perda por arraste de gancheiras ou tambores em linhas manuais é através da instalação de barras sobre o tanque, onde as peças podem ser penduradas por um breve período, garantindo um adequado tempo de drenagem. Uma leve agitação das peças também ajuda a retirar a solução aderida.
A aplicação combinada de agentes tensoativos e tempos mais longos de drenagem pode reduzir significativamente a quantidade de arraste para muitos processos de limpeza e revestimento. Por exemplo, utilizando-se esta técnicas, um arraste típico de solução de níquel pode ser reduzido de 1 L/h para 0,25 L/h.
Nos sistemas de tambor, o mesmo deverá ser vibrado durante o tempo em que estiver drenando sobre o banho, para reduzir o volume de solução de arraste.
A redução do volume de água de lavagem se traduz em economia de trata- mento de efluentes e matéria-prima, refletindo em ganhos ambientais. É possível atender aos requisitos do processo e ao mesmo tempo obter uma redução expressiva nos volumes das águas de lavagem.
· chuveiro com acionamento manual · chuveiro com acionamento por pedal economizador · chuveiro com acionamento automático · lavagem com “spray” · Lavagem com turbilhonamento · Lavagem à quente · Lavagem química e eletroquímica · Técnica do “Skip”
Como uma das técnicas de redução do consumo de água também é citado o orifício limitante. A escolha entre as alternativas dependerá das necessidades de cada empresa, de forma a obter o máximo de economia, eficiência no processo e ganho ambiental.
A lavagem por imersão, também conhecida como tanque de recuperação, consiste em simplesmente mergulhar as peças da gancheira ou tambor no tanque contendo água, de forma a transferir os contaminantes arrastados do banho anterior para a água de lavagem.
As lavagens em tanques podem ser classificadas em contínuas e descontínuas. Na lavagem descontínua não há entrada ou saída de água. Na lavagem contínua, mais conhecida como em “cascata”, onde tem-se mais de um tanque com circulação de água entre eles.
A lavagem por imersão descontínua pode ser realizada com um ou mais tanques em série ou então num tanque com duas ou mais divisões.
· Lavagem descontínua com um tanque de recuperação
Esta lavagem é utilizada para remover a maior parte da solução arrastada pelas peças, sendo a água de lavagem usada periodicamente para repor as perdas por evaporação e arraste dos banhos.
Em muitos casos, o uso desta técnica de recuperação reduz em até 90% o arraste de banhos para o efluente e aumenta consideravelmente a vida útil dos ba- nhos, com evidente economia pela maior freqüência de sua reposição.
Caso haja um tanque de lavagem subseqüente ao tanque de recuperação, a limpeza obtida ou a contaminação desta lavagem será bem menor do que o arraste do banho de processo para o tanque de recuperação.
Após cada lavagem de peças neste tanque, a concentração de contaminantes irá aumentando até o ponto em que esta torna-se praticamente igual àquela do banho anterior e a eficiência de lavagem será praticamente nula. Esse inconveniente é evita-
do com a renovação periódica do tanque de recuperação com água limpa. Esta peri- odicidade será determinada pelo volume do tanque de recuperação, calculado com base no volume de solução arrastada pelas peças, contaminação máxima permitida no processo seguinte e volume de produção.
· Lavagem descontínua com dois tanques ou mais
Neste sistema pode-se utilizar dois tanques em série ou um tanque com uma ou mais divisões, de forma a obter uma melhor limpeza das peças. A água provenien- te destas lavagens, após atingir certa concentração de sais, poderá ter como destino o tratamento de efluentes da empresa ou, então, servir como novos tanques de recu- peração principalmente no caso dos banhos de douração. Neste caso, o número de tanques de recuperação será limitado pela relação custo/benefício econômico e ambiental com o custo da recuperação e a economia de matéria-prima obtida.
Uma técnica que hoje já está bastante difundida, embora nem sempre aplica- da, é a de lavagem em cascata contra-correnteFigura 8. A técnica funciona como no caso da lavagem descontínua já vista, só que com água entrando continuamente, em sentido contrário ao das peças, denominado de contra-corrente. Com o uso desta técnica, obtém-se reduções substanciais nas vazões de águas de lavagem. A eficiên- cia deste sistema depende de um controle de vazão mais rigoroso.
Figura 8: Lavagem em cascata [10]
A vazão de água de lavagem necessária (Q), a ser calculada, será dada pelas seguin- tes fórmulas[10]:
Q = T. DO
onde: T = taxa de lavagem Q = vazão da água de lavagem (L/h) DO = arraste de banho (L/h)
T = (Ci I
/C n n