
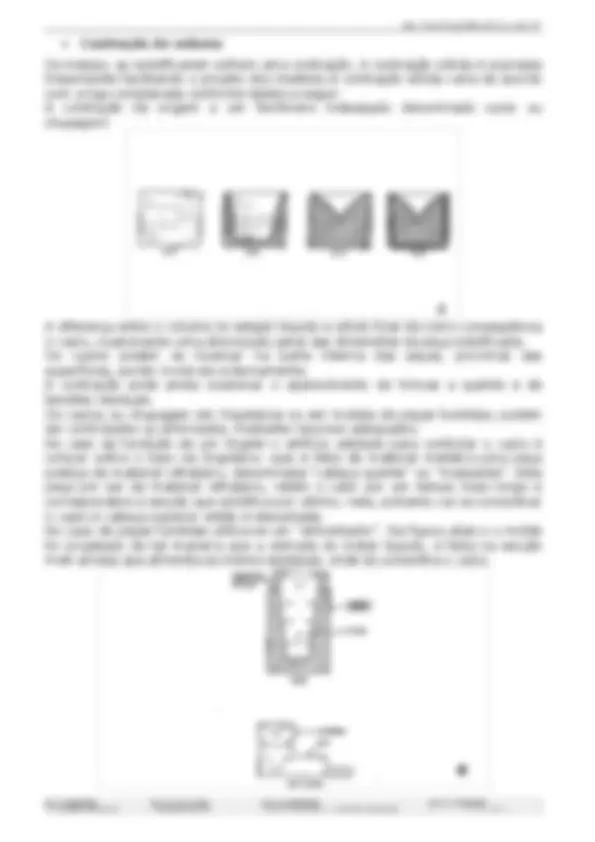
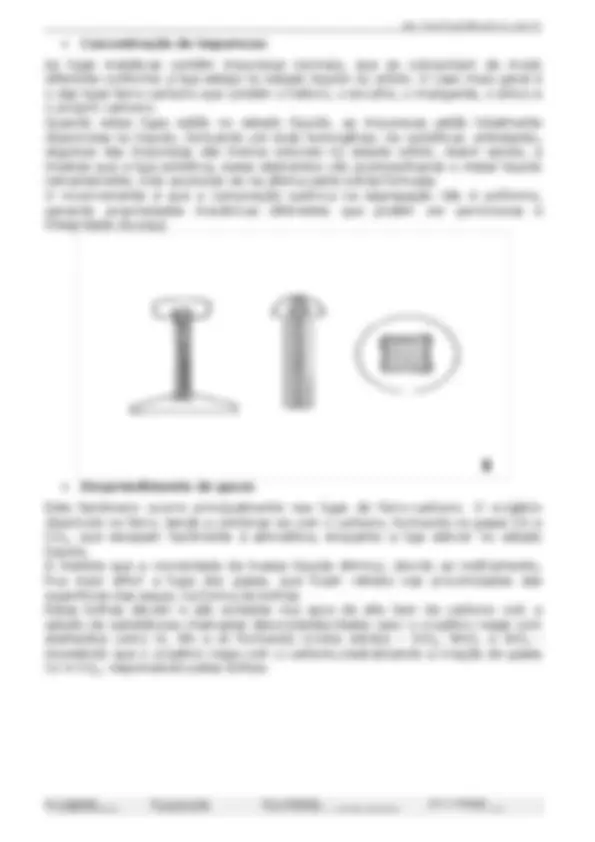
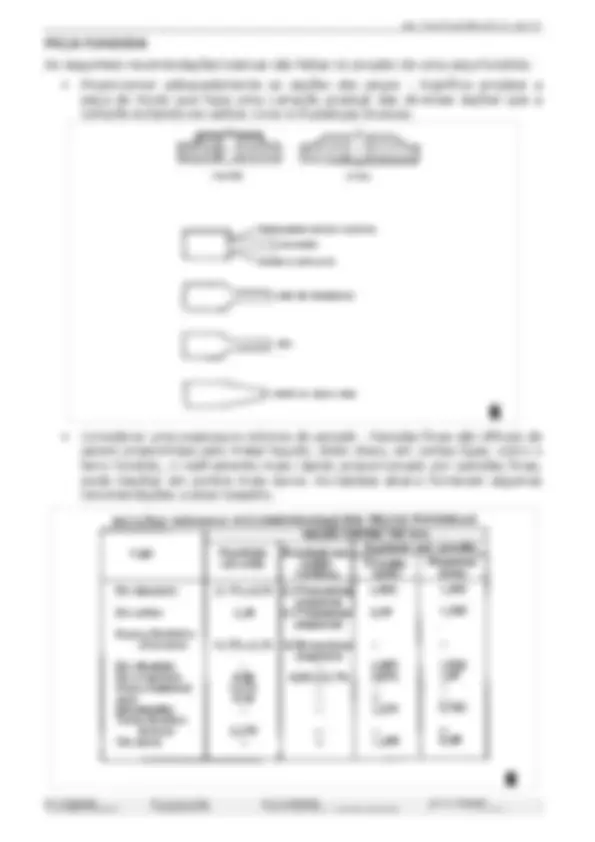
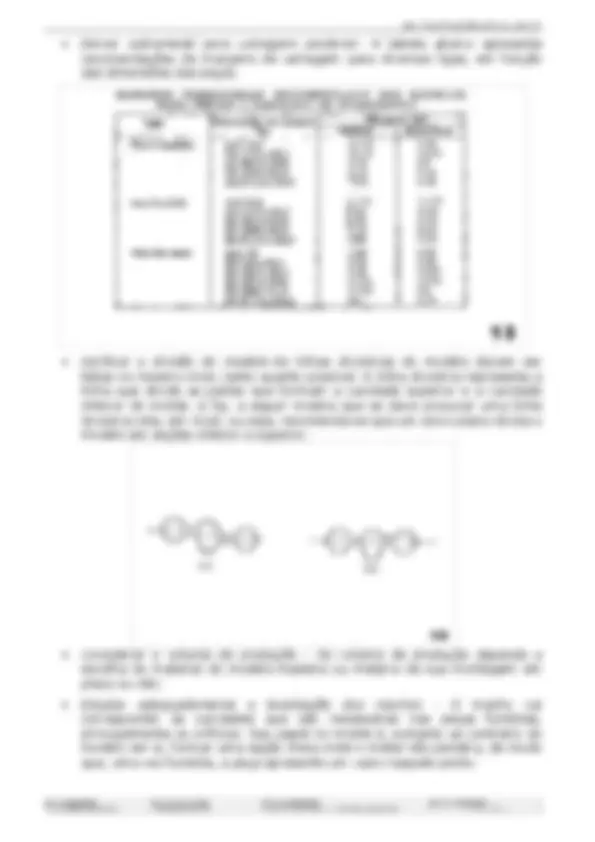
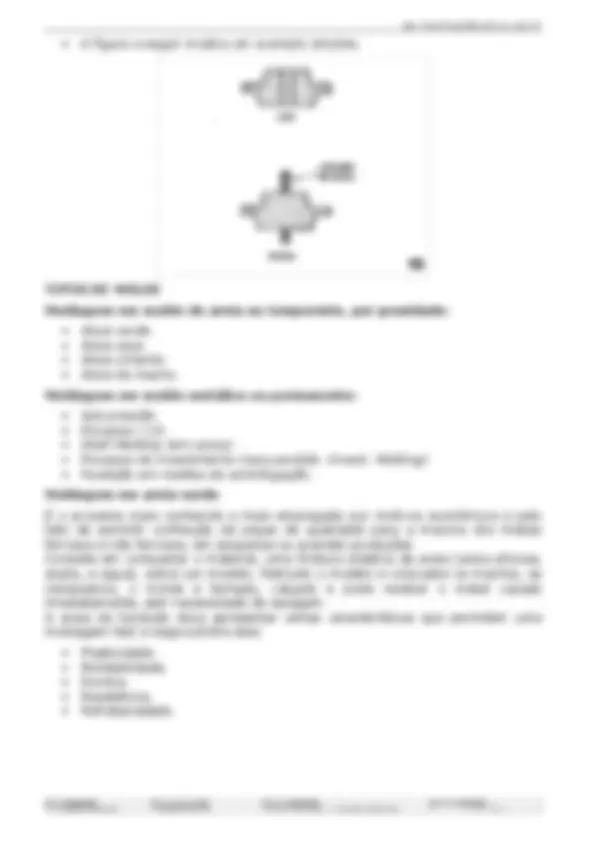
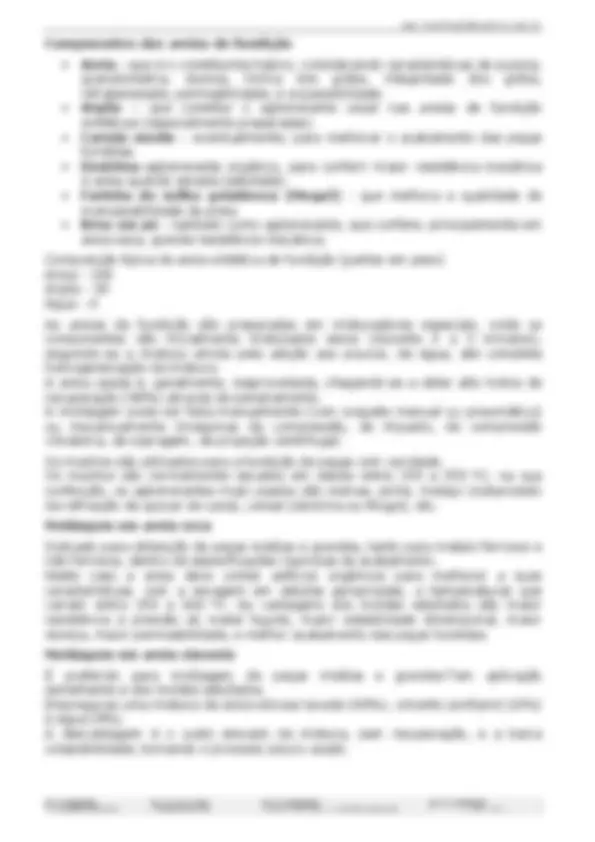
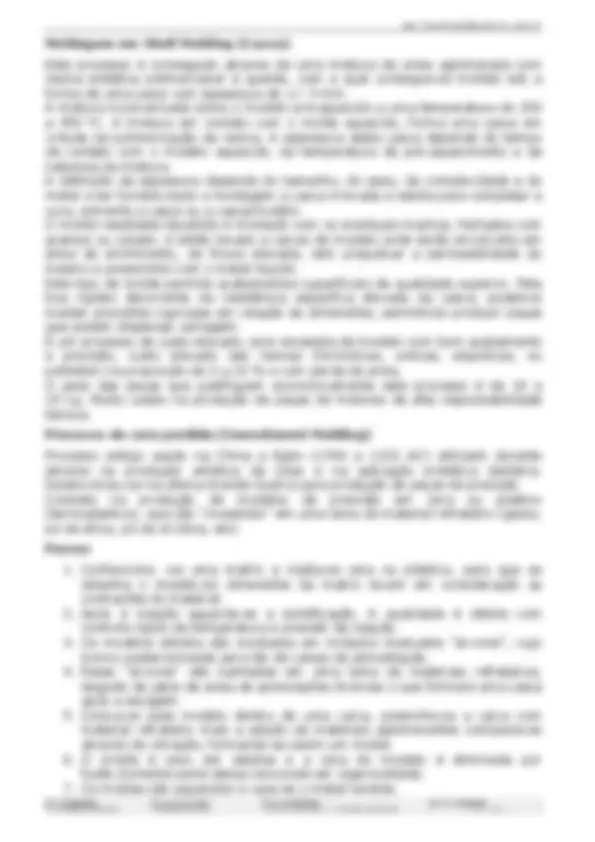
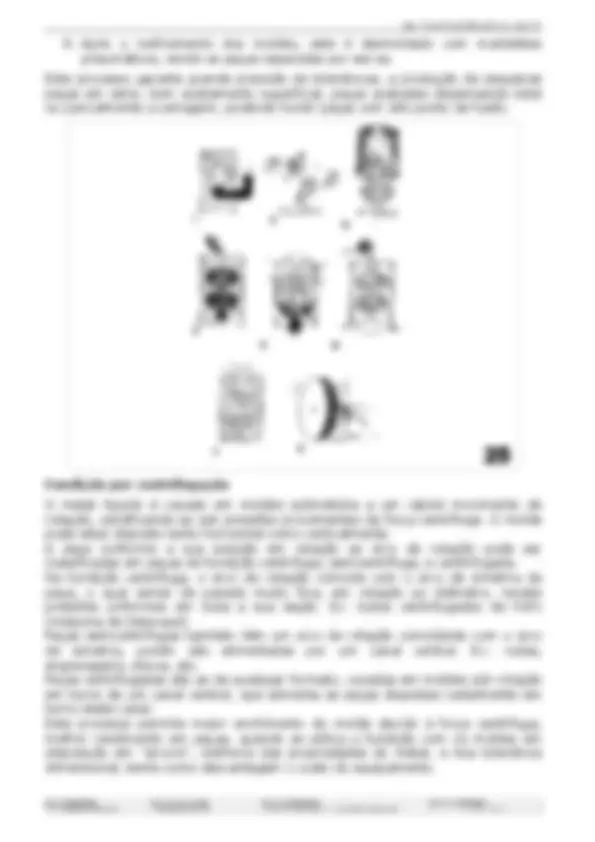
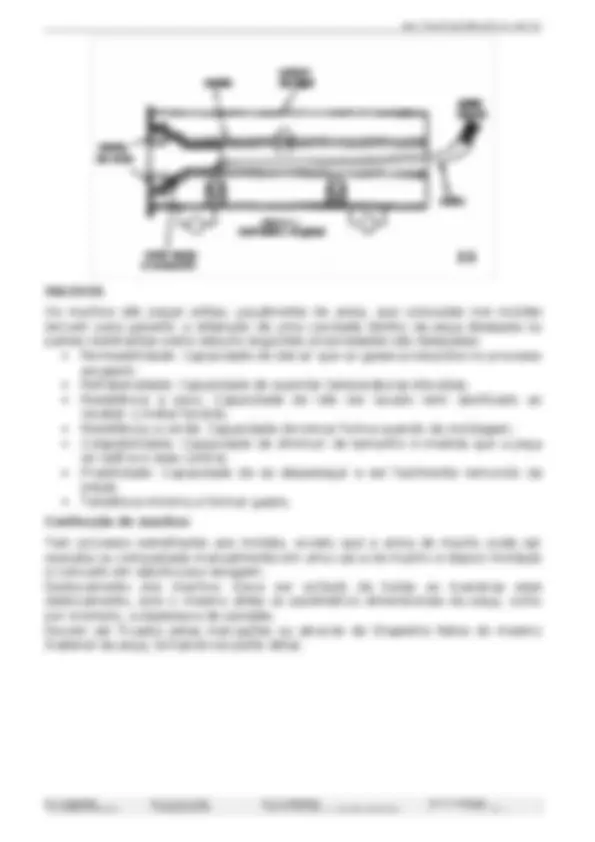
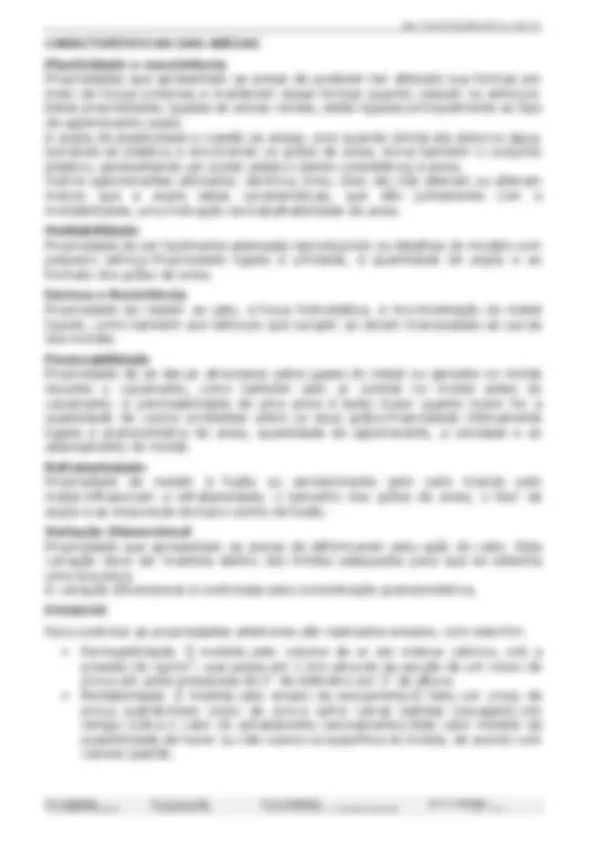
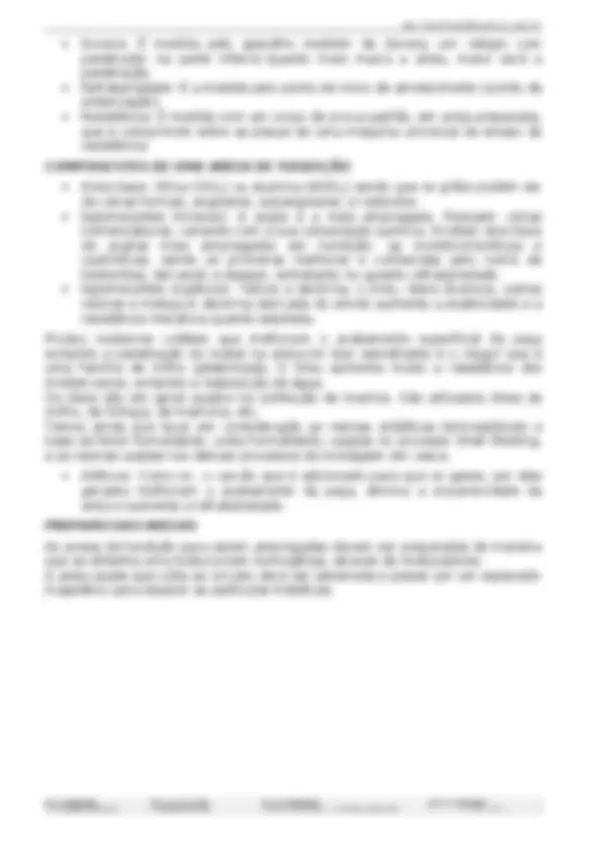
Estude fácil! Tem muito documento disponível na Docsity
Ganhe pontos ajudando outros esrudantes ou compre um plano Premium
Prepare-se para as provas
Estude fácil! Tem muito documento disponível na Docsity
Prepare-se para as provas com trabalhos de outros alunos como você, aqui na Docsity
Os melhores documentos à venda: Trabalhos de alunos formados
Prepare-se com as videoaulas e exercícios resolvidos criados a partir da grade da sua Universidade
Responda perguntas de provas passadas e avalie sua preparação.
Ganhe pontos para baixar
Ganhe pontos ajudando outros esrudantes ou compre um plano Premium
Comunidade
Peça ajuda à comunidade e tire suas dúvidas relacionadas ao estudo
Descubra as melhores universidades em seu país de acordo com os usuários da Docsity
Guias grátis
Baixe gratuitamente nossos guias de estudo, métodos para diminuir a ansiedade, dicas de TCC preparadas pelos professores da Docsity
- - - - - - -
Tipologia: Notas de estudo
1 / 19
Esta página não é visível na pré-visualização
Não perca as partes importantes!
[Revisão-00]
Fundição é um processo de produção, pelo qual consegue-se dar forma a metais no estado líquido, introduzindo-os em moldes, e após a sua solidificação, obtém- se uma peça metálica fundida. Por fundição entende-se também a oficina ou fábrica onde se obtém as peças pelo processo citado. Através da fundição pode-se obter peças de formas intrincadas, que dificilmente poderiam ser obtidas por outro processo. As peças obtidas requerem, em geral, poucas operações de usinagem para o acabamento final, pois se procura fundir uma peça na forma mais próxima possível da forma final. Por este processo consegue-se obter desde peças de grande porte até peças minúsculas, com praticamente qualquer liga metálica, sendo as de ferro fundido feitas unicamente desta maneira. O desenvolvimento da metalurgia tem possibilitado obter-se peças com melhores propriedades mecânicas, novas ligas, novos métodos de obtenção, novos tratamentos superficiais.
ELEMENTOS DO PROCESSO DE FUNDIÇÃO
FENÔMENOS DURANTE A SOLIDIFICAÇÃO DOS METAIS
O metal líquido sendo solidificado o faz em torno de cristais conforme a figura abaixo. O crescimento dos metais se faz de maneira não uniforme, ou seja, a velocidade de crescimento não é a mesma em todos as direções gerando os aspectos ramificados chamados dendritas.Os contornos entre as dendritas são linhas de maior fragilidade que podem numa operação de conformação mecânica posterior-como a laminação - acarretar fissuras que inutilizam o material.
As ligas metálicas contêm impurezas normais, que se comportam de modo diferente conforme a liga esteja no estado líquido ou sólido. O caso mais geral é o das ligas ferro-carbono que contêm o fósforo, o enxofre, o manganês, o silício e o próprio carbono. Quando estas ligas estão no estado líquido, as impurezas estão totalmente dissolvidas no líquido, formando um todo homogêneo. Ao solidificar, entretanto, algumas das impurezas são menos solúveis no estado sólido. Assim sendo, à medida que a liga solidifica, esses elementos vão acompanhando o metal líquido remanescente, indo acumular-se na última parte sólida formada. O inconveniente é que a composição química na segregação não é uniforme, gerando propriedades mecânicas diferentes que podem ser perniciosas à integridade da peça.
5
Este fenômeno ocorre principalmente nas ligas de ferro-carbono. O oxigênio dissolvido no ferro, tende a combinar-se com o carbono, formando os gases CO e CO 2 , que escapam facilmente à atmosfera, enquanto a liga estiver no estado líquido. À medida que a viscosidade da massa líquida diminui, devido ao resfriamento, fica mais difícil a fuga dos gases, que ficam retidos nas proximidades das superfícies das peças, na forma de bolhas. Estas bolhas devem e são evitadas nos aços de alto teor de carbono com a adição de substâncias chamadas desoxidantes.Neste caso o oxigênio reage com elementos como Si, Mn e Al formando óxidos sólidos – SiO 2 , MnO, e AlO 3 - impedindo que o oxigênio reaja com o carbono,neutralizando a criação de gases Co e CO 2 , responsáveis pelas bolhas.
As seguintes recomendações básicas são feitas no projeto de uma peça fundida:
6
8
As principais recomendações no projeto e confecção dos modelos, são:
1 1
1 3
Componentes das areias de fundição
Composição típica de areia sintética de fundição (partes em peso) Areia - 100 Argila - 20 Água - 4
As areias de fundição são preparadas em misturadores especiais, onde os componentes são inicialmente misturados secos (durante 2 a 3 minutos), seguindo-se a mistura úmida pela adição aos poucos, de água, até completa homogeneização da mistura. A areia usada é, geralmente, reaproveitada, chegando-se a obter alto índice de recuperação (98%) através de peneiramento. A moldagem pode ser feita manualmente (com soquete manual ou pneumático) ou mecanicamente (máquinas de compressão, de impacto, de compressão vibratória, de sopragem, de projeção centrífuga).
Os machos são utilizados para a fundição de peças com cavidade. Os machos são normalmente secados em estufa entre 150 a 250 °C; na sua confecção, os aglomerantes mais usados são resinas, piche, melaço (subproduto da refinação de açúcar de cana), cereal (dextrina ou Mogul), etc.
Moldagem em areia seca
Indicado para obtenção de peças médias e grandes, tanto para metais ferrosos e não ferrosos, dentro de especificações rigorosas de acabamento. Neste caso a areia deve conter aditivos orgânicos para melhorar a suas características, com a secagem em estufas apropriadas, a temperaturas que variam entre 150 a 300 °C. As vantagens dos moldes estufados são maior resistência à pressão do metal líquido, maior estabilidade dimensional, maior dureza, maior permeabilidade, e melhor acabamento das peças fundidas.
Moldagem em areia cimento
É preferido para moldagem de peças médias e grandes.Tem aplicação semelhante à dos moldes estufados. Emprega-se uma mistura de areia silicosa lavada (90%), cimento portland (10%) e água (8%). A desvantagem é o custo elevado da mistura, sem recuperação, e a baixa colapsibilidade, tornando o processo pouco usado.
Fundição sob pressão
Consiste em forçar o metal líquido, sob pressão, a penetrar na cavidade do molde, chamado de matriz.Esta é metálica, portanto de natureza permanente, assim, pode ser usada inúmeras vezes. Devido à pressão e à conseqüente alta velocidade de enchimento da cavidade do molde, o processo possibilita a fabricação de peças de formas bastante complexas e de paredes mais finas que os processos por gravidade permitem. A matriz é geralmente construída em duas partes, que são hermeticamente fechadas no momento de vazamento do metal líquido. Ela pode ser utilizada fria ou aquecida à temperatura do metal líquido, o que exige materiais que suportem essas temperaturas. O metal é bombeado na cavidade da matriz e a sua quantidade deve ser tal que não só preencha inteiramente esta cavidade, como também os canais localizados em determinados pontos para evasão de ar. Esses canais servem igualmente para garantir o preenchimento completo das cavidades da matriz. Simultaneamente produz-se alguma rebarba. Enquanto o metal solidifica, mantém-se a pressão durante um certo tempo até que a solidificação se complete. A seguir, a matriz é aberta e a peça é expelida.
Vantagens Desvantagens Produção de formas mais complexas que no caso de fundição por gravidade
As dimensões das peças são limitadas; o seu peso é inferior a 5 kg, raramente passa de 25 kg.
Produção de peças com paredes mais finas e tolerâncias dimensionais mais estreitas.
Pode haver dificuldade de evasão do ar retido no interior da matriz causando porosidades.
Alta capacidade de produção O equipamento e acessórios são de alto custo, sendo viável para grandes volumes de produção.
Produção de peças praticamente acabadas.
O processo só é empregado para ligas de temperatura de fusão inferior às ligas de cobre.
Utilização da mesma matriz em milhares de peças, sem variações significativas dimensionais.
As peças fundidas sob pressão podem ser tratadas superficialmente com revestimentos.
Algumas ligas, como a de alumínio, apresentam maiores resistências que se fundidas em areia.
Moldagem em Shell Molding (Casca)
Este processo é conseguido através de uma mistura de areia aglomerada com resina sintética polimerizável à quente, com a qual consegue-se moldes sob a forma de uma casca com espessura de +/- 5 mm. A mistura é pulverizada sobre o modelo pré-aquecido a uma temperatura de 150 a 350 °C. A mistura em contato com o molde aquecido, forma uma casca em virtude da polimerização da resina. A espessura desta casca depende do tempo de contato com o modelo aquecido, da temperatura de pré-aquecimento e da natureza da mistura. A definição da espessura depende do tamanho, do peso, da complexidade e do metal a ser fundido.Após a moldagem a casca é levada à estufa para completar a cura, somente a casca ou a casca/modelo. O molde resultante bipartido é montado com os eventuais machos, fechados com grampo ou colado; é então levado a caixas de modelo onde serão envolvidos em areia de enchimento, de finura elevada, sem prejudicar a permeabilidade do mesmo e preenchido com o metal líquido. Este tipo de molde permite acabamentos superficiais de qualidade superior. Pela boa rigidez decorrente da resistência específica elevada da casca, podemos manter precisões rigorosas em relação às dimensões, permitindo produzir peças que podem dispensar usinagem. É um processo de custo elevado, pois necessita de modelo com bom acabamento e precisão, custo elevado das resinas (formólicas, uréicas, alquídicas, ou poliéster) na proporção de 3 a 10 % e com perda de areia. O peso das peças que justifiquem economicamente este processo é de 10 a 15 kg. Muito usado na produção de peças de motores de alta responsabilidade técnica.
Processo de cera perdida (Investiment Molding)
Processo antigo usado na China a Egito (1766 a 1122 AC) utilizado durante séculos na produção artística de jóias e na aplicação protética dentária. Desenvolveu-se na ultima Grande Guerra para produção de peças de precisão. Consiste na produção de modelos de precisão em cera ou plástico (termoplástico), que são “investidos” em uma lama de material refratário (gesso, pó de sílica, pó de zircônia, etc).
Passos
Este processo garante grande precisão de tolerâncias, a produção de pequenas peças em série, bom acabamento superficial, peças acabadas dispensando total ou parcialmente a usinagem, podendo fundir peças com alto ponto de fusão.
25
Fundição por centrifugação
O metal líquido é vazado em moldes submetidos a um rápido movimento de rotação, solidificando-se sob pressões provenientes da força centrífuga. O molde pode estar disposto tanto horizontal como verticalmente. A peça conforme a sua posição em relação ao eixo de rotação pode ser classificadas em peças de fundição centrífuga, semicentrífuga, e centrifugada. Na fundição centrífuga, o eixo de rotação coincide com o eixo de simetria da peça, o qual sendo de parede muito fina, em relação ao diâmetro, recebe pressões uniformes em toda a sua seção. Ex: tubos centrifugados de FoFo (máquina de Delavaud). Peças semicentrífugas também têm um eixo de rotação coincidente com o eixo de simetria, porém são alimentadas por um canal central. Ex: rodas, engrenagens, discos, etc. Peças centrifugadas são as de qualquer formato, vazadas em moldes sob rotação em torno de um canal central, que alimenta as peças dispostas radialmente em torno deste canal. Este processo permite maior enchimento do molde devido à força centrífuga, melhor rendimento em peças, quando se utiliza a fundição com os moldes em disposição em “árvore”, melhoria das propriedades do metal, e boa tolerância dimensional, tendo como desvantagem o custo do equipamento.
Operação de moldagem manual
Moldagem Mecanizada
A moldagem mecanizada nos garante melhor produtividade, maior qualidade no acabamento e redução de mão de obra. A máquina de compressão é uma prensa que faz a compactação da areia na caixa de machos. A máquina de trepidação e compressão é uma prensa com dois atuadores, um para provocar uma trepidação na caixa do modelo e o outro para compactar a areia. A máquina de trepidação, compressão e rotação são uma prensa com dois atuadores, um para provocar uma trepidação na caixa do modelo, outro para compactar a areia e um sistema que faz a rotação do molde.
AREIAS DE FUNDIÇÃO
A areia ou terra de fundição usada na confecção dos moldes é um material constituído de:
Para efeito de normalização as peças são divididas em:
Quanto à aplicação (Parte do molde onde é aplicada).
Quanto à umidade
Quanto à forma de grãos
Quanto à granulação e o teor de argila
Será dada a classificação do American Foundrymen Society por ser bastante prática e bastante utilizada.
Classe Módulo de finura de areia 1 200 a 300 2 140 a 200 3 100 a 140 4 70 a 100 5 50 a 70 6 40 a 50 7 30 a 40 8 20 a 30 9 15 a 20 10 10 a 15
Classe % de argila A Até 0, B 0,5 a 2 C 2 a 5 D 5 a 10 E 10 a 15 F 15 a 20 G 20 a 30 H 30 a 40
O módulo de finura de uma areia é determinado, tomando-se uma série de peneiras padrão; nesta série é peneirada uma amostra com o peso determinado, e verifica-se a quantidade retida em cada peneira. Multiplicam-se os valores obtidos em cada peneira pelos respectivos coeficientes, que são números arbitrários de valor aproximado ao número de malhas por unidade de comprimento da peneira anterior, somam-se essas parcelas e divide-se pela soma do material retido.Tem-se assim o módulo que representa o diâmetro médio ideal da peneira de malhas por unidade de comprimento.
COMPONENTES DE UMA AREIA DE FUNDIÇÃO
Produz redutores voláteis que melhoram o acabamento superficial da peça evitando a penetração do metal na areia.Um tipo semelhante é o mogul que é uma farinha de milho gelatinizada. O breu aumenta muito a resistência dos moldes secos, evitando a reabsorção de água. Os óleos são em geral usados na confecção de machos. São utilizados óleos de milho, de linhaça, de mamona, etc. Temos ainda que levar em consideração as resinas sintéticas termoestáveis a base de fenol formaldeído, uréia formaldeído, usadas no processo Shell Molding, e as resinas usadas nos demais processos de moldagem em casca.
PREPARO DAS AREIAS
As areias de fundição para serem empregadas devem ser preparadas de maneira que se obtenha uma mistura bem homogênea, através de misturadores. A areia usada que volta ao circuito deve ser peneirada e passar por um separador magnético para separar as partículas metálicas.