
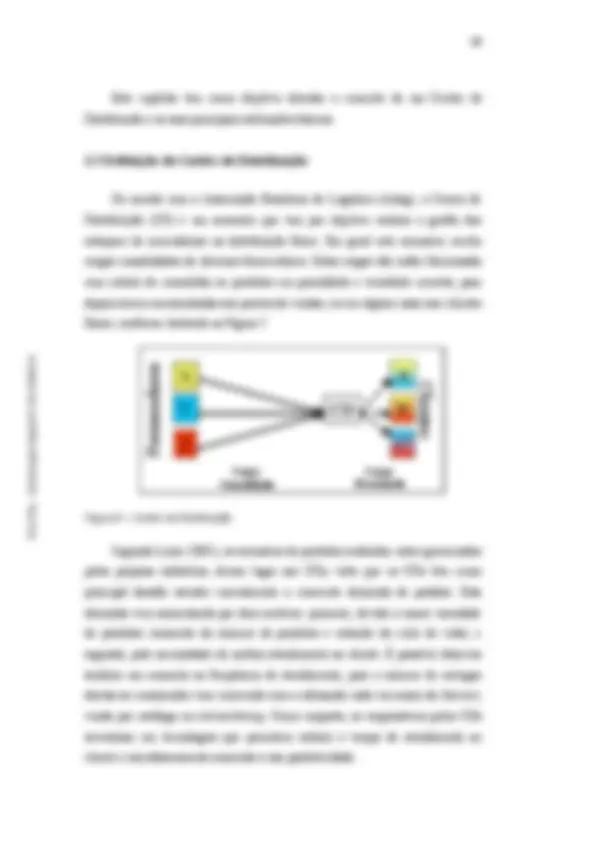
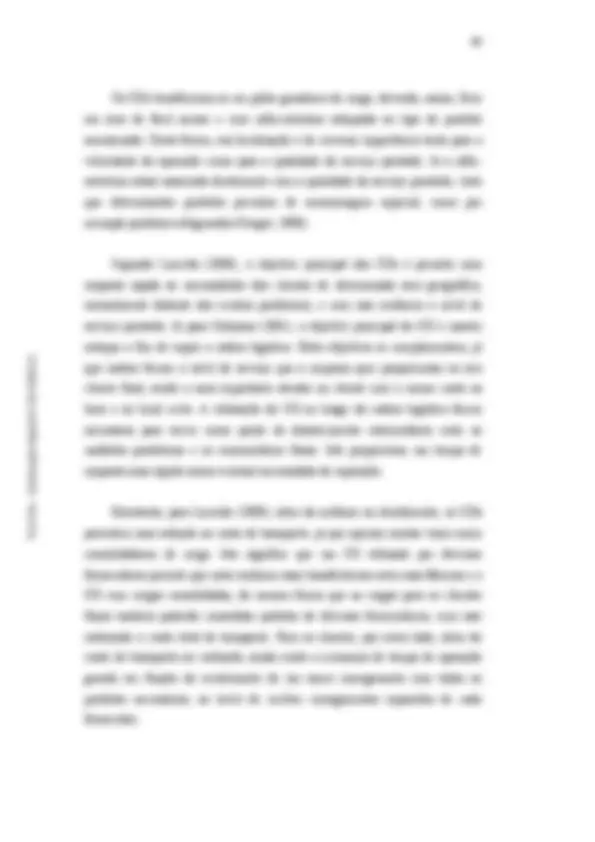
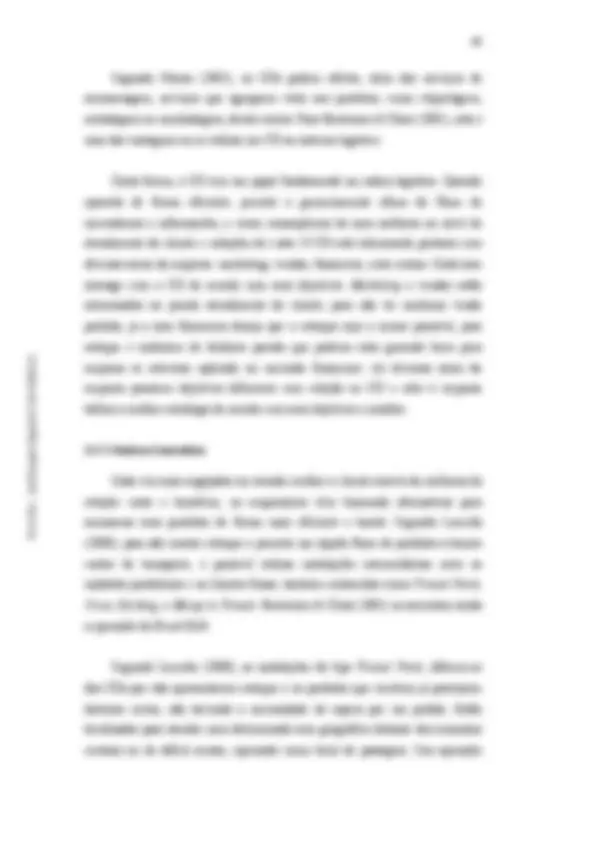
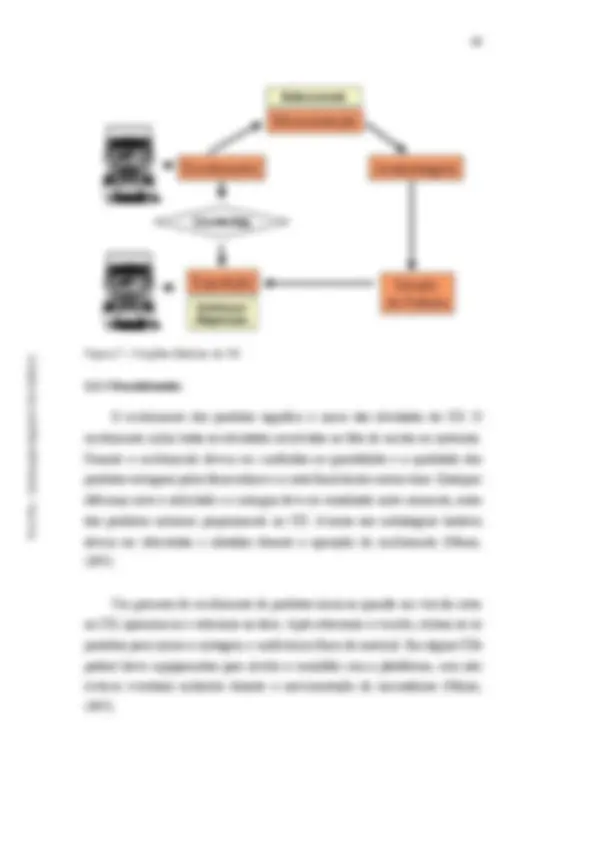
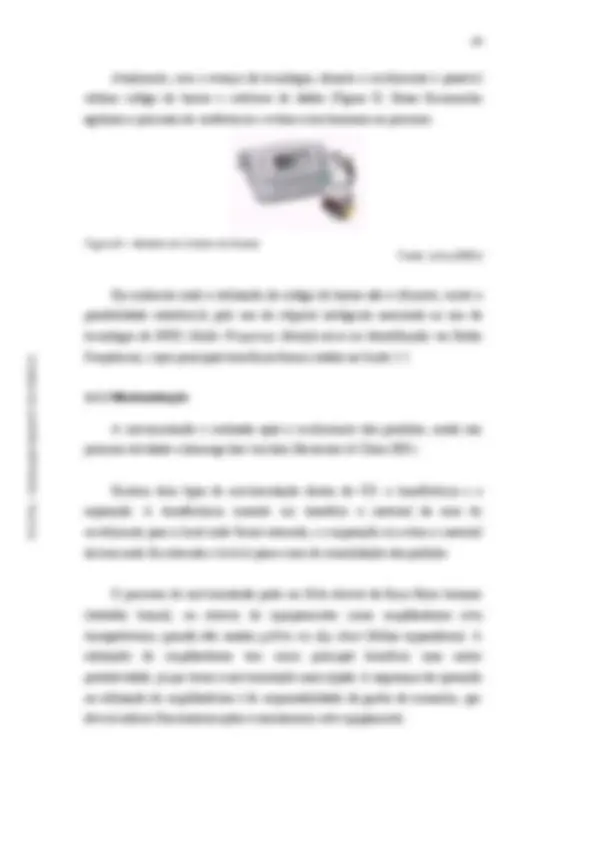
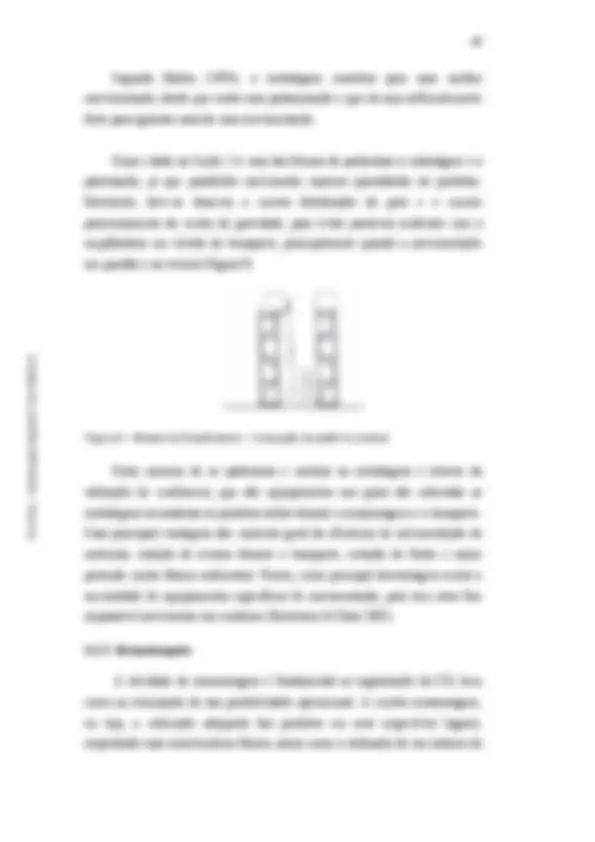
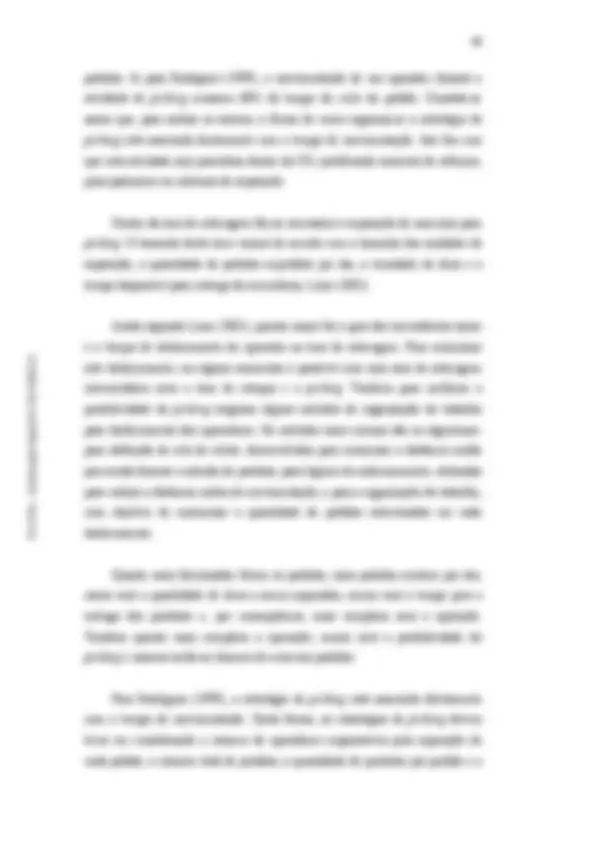
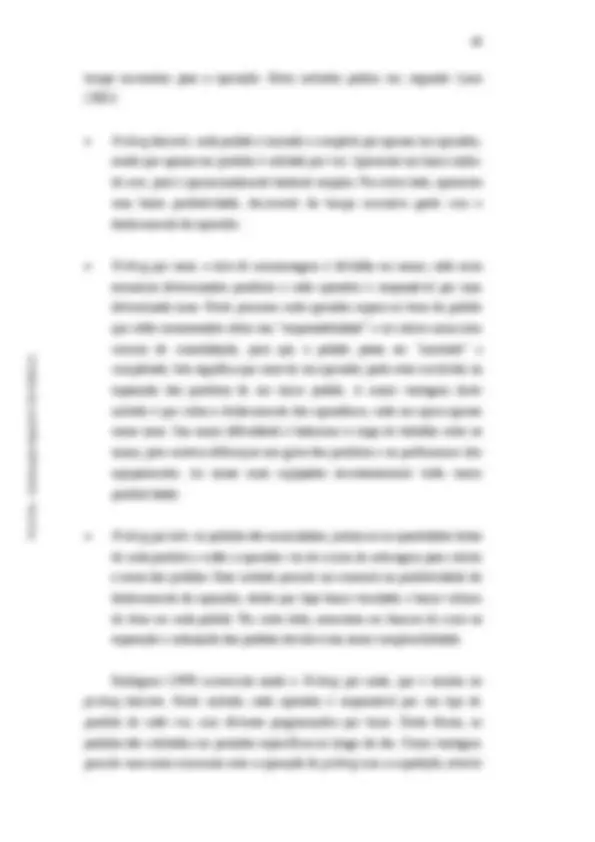
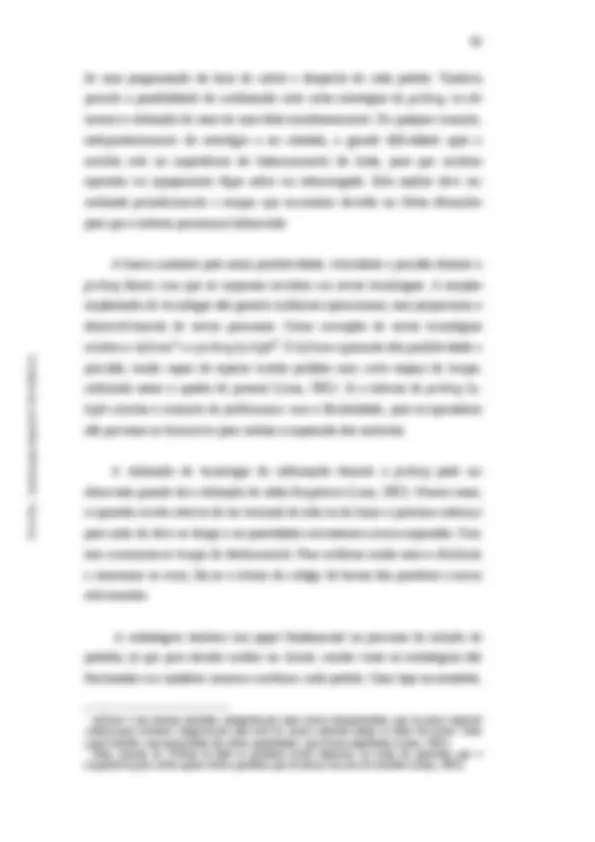
Estude fácil! Tem muito documento disponível na Docsity
Ganhe pontos ajudando outros esrudantes ou compre um plano Premium
Prepare-se para as provas
Estude fácil! Tem muito documento disponível na Docsity
Prepare-se para as provas com trabalhos de outros alunos como você, aqui na Docsity
Os melhores documentos à venda: Trabalhos de alunos formados
Prepare-se com as videoaulas e exercícios resolvidos criados a partir da grade da sua Universidade
Responda perguntas de provas passadas e avalie sua preparação.
Ganhe pontos para baixar
Ganhe pontos ajudando outros esrudantes ou compre um plano Premium
Comunidade
Peça ajuda à comunidade e tire suas dúvidas relacionadas ao estudo
Descubra as melhores universidades em seu país de acordo com os usuários da Docsity
Guias grátis
Baixe gratuitamente nossos guias de estudo, métodos para diminuir a ansiedade, dicas de TCC preparadas pelos professores da Docsity
Estudo dos centros de distribuição. Para universitários
Tipologia: Resumos
1 / 16
Esta página não é visível na pré-visualização
Não perca as partes importantes!
Uma questão básica do gerenciamento logístico é como estruturar sistemas de distribuição capazes de atender de forma econômica os mercados geograficamente distantes das fontes de produção, oferecendo níveis de serviço cada vez mais altos em termos de disponibilidade de estoque e tempo de atendimento. Neste contexto, a atenção se volta para as instalações de armazenagem e como elas podem contribuir para atender de forma eficiente as metas estabelecidas de nível de serviço. A funcionalidade destas instalações dependerá da estrutura de distribuição adotada pela empresa (Lacerda, 2000).
Os sistemas de distribuição física, segundo Garnier (2002), podem ser classificados em: seqüenciais, diretos ou mistos.
Os sistemas seqüenciais ou escalonados apresentam como característica principal a grande quantidade de atividades não agregadoras de valor nos processos de produção e distribuição. Em sua maioria são projetados para tirar partido de consolidação, evitar faltas e oferecer pronta entrega aos clientes (Garnier, 2002). Lacerda (2000) acrescenta que uma rede de distribuição escalonada típica possui um ou mais armazéns centrais e um conjunto de armazéns ou centros de distribuição avançados próximos das áreas de mercado.
Os sistemas diretos são sistemas de distribuição onde os produtos são expedidos de um ou mais armazéns centrais diretamente para os clientes (Garnier, 2002). Os sistemas mistos são sistemas de distribuição onde a empresa utiliza tanto o sistema escalonado como direto. Exemplo clássico são as empresas de bebida que, nos grandes centros onde possuem fábrica, entregam diretamente aos clientes finais (no caso donos de bares) e, para atender os locais distantes, fazem uso de CDs.
Atualmente, quase todas as grandes redes logísticas utilizam Centrais de Distribuição. Os centros de distribuição avançados são típicos de sistemas de distribuição escalonados, onde o estoque é posicionado em vários elos de uma
cadeia de suprimentos. Para prover utilidade no tempo, avançam-se os estoques para um ponto próximo aos clientes e os pedidos são então atendidos por este centro avançado, a partir do seu próprio estoque (Lacerda, 2000). Segundo Pizzolato & Pinho (2003), cada empresa deve analisar a conveniência de se ter poucos ou muitos depósitos, ou seja, centralizar versus descentralizar a distribuição, em contraposição aos custos resultantes e à qualidade do serviço oferecido ao cliente.
A descentralização dos estoques, típica dos sistemas escalonados, aumenta a quantidade de estoque necessária para atender os níveis de disponibilidade desejados, tornando também mais complexo o seu gerenciamento. Em função da maior incerteza provocada pela divisão da demanda em áreas regionais, a manutenção de toda a linha de produtos em cada centro de distribuição avançado é sujeita às faltas de estoque. Desta forma, o objetivo inicial de prover rápido atendimento e alta disponibilidade pode ser prejudicado pela ocorrência de pedidos incompletos. Além do risco da falta de estoque, são maiores também os riscos de obsolescência em função da estratégia adotada de antecipação de demanda (Lacerda, 2000).
Atualmente, com o aumento da competitividade, diversas empresas em segmentos bastante diferentes vêm fazendo uso dos CDs. Conforme mencionado na seção 2.1, os CDs passaram a ser considerados estratégicos para as empresas. Primeiro, porque através da utilização de CDs, é possível atender mais rápido o cliente, aumentando-se, com isso o nível de serviço garantindo assim a fidelidade do mesmo. Segundo, porque empresas que desejam ter cobertura nacional num país como o Brasil, precisam de pontos de apoio em locais estrategicamente posicionados para assegurar a entrega dos produtos.
Outro fato importante com relação aos CDs é que nos últimos anos, com a consolidação dos operadores logísticos no cenário nacional, os CDs saíram do papel secundário que tinham até então e passaram a fazer parte da estratégia logística das empresas nacionais (Almeida, 2004), visto os inúmeros benefícios de se ter CDs compartilhados, conforme será mencionado mais adiante na seção 3.2.3.
Os CDs transformam-se em pólos geradores de carga, devendo, assim, ficar em área de fácil acesso e com infra-estrutura adequada ao tipo de produto armazenado. Desta forma, sua localização é de extrema importância tanto para a velocidade da operação como para a qualidade do serviço prestado. Já a infra- estrutura estará associada diretamente com a qualidade do serviço prestado, visto que determinados produtos precisam de armazenagem especial, como por exemplo produtos refrigerados (Gurgel, 2000).
Segundo Lacerda (2000), o objetivo principal dos CDs é permitir uma resposta rápida às necessidades dos clientes de determinada área geográfica, normalmente distante dos centros produtores, e com isso melhorar o nível de serviço prestado. Já para Calazans (2001), o objetivo principal do CD é manter estoque a fim de suprir a cadeia logística. Estes objetivos se complementam, já que ambos focam o nível de serviço que a empresa quer proporcionar ao seu cliente final, sendo o mais importante atender ao cliente com o menor custo na hora e no local certo. A utilização do CD ao longo da cadeia logística faz-se necessária para servir como ponto de abastecimento intermediário entre as unidades produtoras e os consumidores finais. Isto proporciona um tempo de resposta mais rápido numa eventual necessidade de reposição.
Entretanto, para Lacerda (2000), além da melhora no atendimento, os CDs permitem uma redução no custo de transporte, já que operam muitas vezes como consolidadores de carga. Isto significa que um CD utilizado por diversos fornecedores permite que estes realizem suas transferências entre suas fábricas e o CD com cargas consolidadas, da mesma forma que as cargas para os clientes finais também poderão consolidar pedidos de diversos fornecedores, com isso reduzindo o custo total de transporte. Para os clientes, por outro lado, além do custo de transporte ser reduzido, ainda existe a economia de tempo de operação gerado em função do recebimento de um único carregamento com todos os produtos necessários, ao invés de receber carregamentos separados de cada fornecedor.
Segundo Moura (2002), os CDs podem ofertar, além dos serviços de armazenagem, serviços que agreguem valor aos produtos, como etiquetagem, embalagem ou reembalagem, dentre outros. Para Bowersox & Closs (2001), esta é uma das vantagens em se utilizar um CD no sistema logístico.
Desta forma, o CD tem um papel fundamental na cadeia logística. Quando operado de forma eficiente, permite o gerenciamento eficaz do fluxo de mercadorias e informações, e como conseqüência há uma melhoria no nível de atendimento do cliente e reduções de custo. O CD está relacionado portanto com diversas áreas da empresa: marketing, vendas, financeira, entre outras. Cada área interage com o CD de acordo com seus objetivos. Marketing e vendas estão interessados no pronto atendimento do cliente, para não ter nenhuma venda perdida, já a área financeira deseja que o estoque seja o menor possível, pois estoque é sinônimo de dinheiro parado que poderia estar gerando lucro para empresa se estivesse aplicado no mercado financeiro. As diversas áreas da empresa possuem objetivos diferentes com relação ao CD e cabe à empresa definir a melhor estratégia de acordo com seus objetivos e missões.
3.1.1 Outros Conceitos
Cada vez mais engajados em atender melhor o cliente através da melhoria da relação custo e benefício, os empresários vêm buscando alternativas para armazenar seus produtos de forma mais eficiente e barata. Segundo Lacerda (2000), para não manter estoque e permitir um rápido fluxo de produtos a baixos custos de transporte, é possível utilizar instalações intermediárias entre as unidades produtoras e os clientes finais, também conhecidos como Transit Point , Cross Docking , e Merge in Transit. Bowersox & Closs (2001) acrescentam ainda a operação de Break Bulk.
Segundo Lacerda (2000), as instalações do tipo Transit Point , diferem-se dos CDs por não apresentarem estoque e os produtos que recebem já possuírem destinos certos, não havendo a necessidade de espera por um pedido. Estão localizados para atender uma determinada área geográfica distante dos armazéns centrais ou de difícil acesso, operando como local de passagem. Sua operação
Figura 6 – Os Conceitos de Transit Point , Cross Docking , Merge in Transit e Break Bulk
3.2 Atribuições Básicas
As principais atividades em um CD, segundo a Aslog, englobam: recebimento, movimentação, armazenagem, seleção de pedidos, expedição e, em alguns casos, agregação de valor intrínseco (físico), como a colocação de embalagens e rótulos e a preparação de kits comerciais (compre dois e leve três, por exemplo).
A Figura 7 demonstra a relação entre as atividades desempenhadas pelo CD. Os produtos que chegam ao CD podem ser recebidos, movimentados até o local a serem armazenados e conseqüentemente aguardar que um pedido seja colocado, para então serem selecionados e posteriormente expedidos. Para os casos de crossdocking os produtos vão do recebimento para a expedição. A Figura 7 apresenta estas principais funções.
Transit Point Fornecedor A
Atividade de Separação
Cliente A Cliente B Cliente C
Cross Docking Fornecedor A
Atividade de Sortimento Separação e Consolidação
Cliente A Cliente B Cliente C
Fornecedor B
Merge in Transit Fornecedor A
Atividade de Montagem de Produtos
Cliente A Cliente B Cliente C
Fornecedor B
Break Bulk Fornecedor A
Atividade de Separação
Cliente A + B + C
Fornecedor B
Transit Point Fornecedor A
Atividade de Separação
Cliente A Cliente B Cliente C
Cross Docking Fornecedor A
Atividade de Sortimento Separação e Consolidação
Cliente A Cliente B Cliente C
Fornecedor B
Merge in Transit Fornecedor A
Atividade de Montagem de Produtos
Cliente A Cliente B Cliente C
Fornecedor B
Break Bulk Fornecedor A
Atividade de Separação
Cliente A + B + C
Fornecedor B
Figura 7 – Funções Básicas do CD
3.2.1 Recebimento
O recebimento dos produtos significa o início das atividades do CD. O recebimento inclui todas as atividades envolvidas no fato de aceitar os materiais. Durante o recebimento devem ser conferidas as quantidades e a qualidade dos produtos entregues pelos fornecedores e a nota fiscal dentre outros itens. Qualquer diferença entre o solicitado e o entregue deve ser sinalizado neste momento, antes dos produtos entrarem propriamente no CD. Avarias nas embalagens também devem ser detectadas e relatadas durante a operação de recebimento (Moura, 1997).
Um processo de recebimento de produtos inicia-se quando um veículo entra no CD, aproxima-se e estaciona na doca. Após estacionar o veículo, retiram-se os produtos para iniciar a contagem e conferência física do material. Em alguns CDs poderá haver equipamentos para nivelar o caminhão com a plataforma, com isso evita-se eventuais acidentes durante a movimentação de mercadorias (Moura, 1997).
Crossdocking
Endereçamento
Embalagem Etiquetagem
Crossdocking
Endereçamento
Embalagem Etiquetagem
Segundo Ballou (1993), a embalagem contribui para uma melhor movimentação, desde que exista uma padronização e que ela seja suficientemente forte para agüentar mais de uma movimentação.
Como citado na Seção 2.4, uma das formas de padronizar a embalagem é a paletização, já que possibilita movimentar maiores quantidades de produtos. Entretanto, deve-se observar a correta distribuição do peso e o correto posicionamento do centro de gravidade, para evitar possíveis acidentes com a empilhadeira em virtude do transporte, principalmente quando a movimentação em questão é na vertical (Figura 9).
Figura 9 – Modelo de Empilhadeira – Colocação de pallet na vertical
Outra maneira de se padronizar e unitizar as embalagens é através da utilização de contêineres, que são equipamentos nos quais são colocadas as embalagens secundárias ou produtos soltos durante a armazenagem e o transporte. Suas principais vantagens são: aumento geral da eficiência de movimentação de materiais, redução de avarias durante o transporte, redução de furtos e maior proteção contra fatores ambientais. Porém, como principal desvantagem existe a necessidade de equipamentos específicos de movimentação, pois sem estes fica impossível movimentar um contêiner (Bowersox & Closs 2001).
3.2.3 Armazenagem
A atividade de armazenagem é fundamental na organização do CD, bem como na otimização de sua produtividade operacional. A correta armazenagem, ou seja, a colocação adequada dos produtos em seus respectivos lugares, respeitando suas características físicas, assim como a utilização de um sistema de
armazenagem adequado, pode possibilitar uma boa utilização do espaço, boa utilização dos recursos operacionais, além de otimização no tempo da mão-de- obra para localizar os pedidos/ produtos no interior do armazém, dentre outros benefícios (Calazans, 2001).
O Capítulo 2 abordou de forma mais detalhada esta importante atividade logística. Desta forma, para não ficar repetitivo, nesta subseção serão descritas apenas algumas alternativas de armazenagem.
3.2.3.1 Alternativas de Armazenagem
Os armazéns podem ser próprios, públicos ou contratados (Bowersox & Closs, 2001). O armazém próprio é operacionalizado pela própria empresa que possui as mercadorias a serem armazenadas. Sua principal vantagem é o controle, já que a empresa tem total autoridade para tomada de decisão, e a flexibilidade em se alterar o layout ou o tamanho entre as prateleiras para melhor armazenar seus produtos.
Os armazéns públicos oferecem flexibilidade financeira, já que o dinheiro da Cia não fica empregado em ativo fixo, além das vantagens econômicas de escala. Na maioria das vezes possui maior especialização, já que o gerenciamento da armazenagem é seu core business. Para Ballou (2001), além de não ser necessário nenhum investimento em ativo fixo e ter custos mais baixos, há ainda a possibilidade na flexibilidade da localização, ou seja, se o mercado mudar, como não há o compromisso de longo prazo é mais fácil mudar de armazém, gerando assim uma importante flexibilidade para manter uma rede logística ótima.
Segundo Bowersox & Closs (2001), os armazéns ou CDs contratados possuem as melhores características dos armazéns públicos e próprios, pois apresentam flexibilidade e economia de escala proporcionada pelo compartilhamento do espaço físico, mão-de-obra e equipamentos entre diversas empresas. São muito utilizados por operadores logísticos 2 especializados em
(^2) Segundo a Associação Brasileira de Movimentação e Logística (ABML) os operadores logísticos devem ter competência para prestar serviços simultaneamente, de no mínimo, gerenciamento de estoque, armazenagem e gestão de transporte.
pedidos. Já para Rodrigues (1999), a movimentação de um operador durante a atividade de picking consome 60% do tempo do ciclo do pedido. Constata-se assim que, para ambos os autores, a forma de como organiza-se a estratégia de picking está associada diretamente com o tempo de movimentação. Isto faz com que esta atividade seja prioritária dentro do CD, justificando aumento de esforços, principalmente em sistemas de separação.
Dentro da área de estocagem faz-se necessário a separação de uma área para picking. O tamanho desta área variará de acordo com o tamanho das unidades de separação, a quantidade de pedidos expedidos por dia, a variedade de itens e o tempo disponível para entrega da mercadoria, Lima (2002).
Ainda segundo Lima (2002), quanto maior for o giro das mercadorias maior é o tempo de deslocamento do operador na área de estocagem. Para minimizar este deslocamento, em alguns momentos é possível criar uma área de estocagem intermediária entre a área de estoque e o picking. Também para melhorar a produtividade do picking surgiram alguns métodos de organização de trabalho para deslocamento dos operadores. Os métodos mais comuns são os algoritmos: para definição de rota de coleta, desenvolvidos para minimizar a distância média percorrida durante a seleção de pedidos; para lógicas de endereçamento, utilizadas para reduzir a distância média de movimentação; e para a organização do trabalho, com objetivo de maximizar a quantidade de pedidos selecionados em cada deslocamento.
Quanto mais fracionados forem os pedidos, mais pedidos existem por dia, maior será a quantidade de itens a serem separados, menor será o tempo para a entrega dos produtos e, por conseqüência, mais complexa será a operação. Também quanto mais complexa a operação, menor será a produtividade do picking e maiores serão as chances de erros nos pedidos.
Para Rodrigues (1999), a estratégia de picking está associada diretamente com o tempo de movimentação. Desta forma, as estratégias de picking devem levar em consideração o número de operadores responsáveis pela separação de cada pedido, o número total de pedidos, a quantidade de produtos por pedido e o
tempo necessário para a operação. Estes métodos podem ser, segundo Lima (2002):
Picking discreto: cada pedido é iniciado e completo por apenas um operador, sendo que apenas um produto é coletado por vez. Apresenta um baixo índice de erro, pois é operacionalmente bastante simples. Por outro lado, apresenta uma baixa produtividade, decorrente do tempo excessivo gasto com o deslocamento do operador.
Picking por zona: a área de armazenagem é dividida em zonas, cada zona armazena determinados produtos e cada operador é responsável por uma determinada zona. Neste processo cada operador separa os itens do pedido que estão armazenados sobre sua “responsabilidade” e os coloca numa área comum de consolidação, para que o pedido possa ser “montado” e completado. Isto significa que mais de um operador pode estar envolvido na separação dos produtos de um único pedido. A maior vantagem deste método é que reduz o deslocamento dos operadores, cada um opera apenas numa zona. Sua maior dificuldade é balancear a carga de trabalho entre as zonas, pois existem diferenças nos giros dos produtos e na performance dos equipamentos. As zonas mais equipadas necessariamente terão maior produtividade.
Picking por lote: os pedidos são acumulados, juntam-se as quantidades totais de cada produto e então o operador vai até a área de estocagem para coletar a soma dos pedidos. Esse método permite um aumento na produtividade do deslocamento do operador, desde que haja baixa variedade e baixo volume de itens em cada pedido. Por outro lado, aumentam as chances de erros na separação e ordenação dos pedidos devido à sua maior complexibilidade.
Rodrigues (1999) acrescenta ainda o Picking por onda, que é similar ao picking discreto. Neste método, cada operador é responsável por um tipo de produto de cada vez, com diversas programações por turno. Desta forma, os pedidos são coletados em períodos específicos ao longo do dia. Como vantagem permite uma maior sincronia entre a operação de picking com a expedição, através
estes pedidos podem ser reembalados em cargas mistas para então serem entregues aos clientes finais. Segundo Hope (2002), as embalagens interferem positivamente à medida que protegem o produto e permitem ser fracionadas nas quantidades necessárias, sem que para isso suas caixas precisem ser abertas.
Para Banzato (2001b), além da proteção à embalagem, também torna mais fácil a localização dos itens certos no momento da separação dos pedidos, sendo imprescindível que a identificação no SKU ( Stock Keeping Unit ou Unidade de Manutenção de Estoque) seja de fácil leitura, indiferente se é lida automaticamente (leitores ópticos) ou visualmente.
3.2.5 Expedição
A expedição pode ser considerada como a última etapa a ser realizada no CD. Consiste basicamente na verificação e no carregamento dos produtos nos veículos determinados. Como o recebimento, a expedição também é realizada na maioria das vezes de forma manual. A embalagem mais uma vez apresenta importante papel na expedição, já que cargas unitizadas reduzem o tempo de carregamento do veículo (Bowersox & Closs, 2001). A expedição envolve atividades como: conferência do pedido e da nota fiscal, emissão de documentos de expedição, pesagem da carga para estipular o custo de transporte, dentre outras.
Para Calazans (2001), existem alguns fatores que podem prejudicar a eficiência da operação de expedição. São eles: Atrasos de transportadoras, gerando congestionamentos na área de expedição; Quebra de sincronia entre os processos de recebimento e expedição nas operações de crossdocking. Com isso, a área de expedição pode-se transformar em área de estocagem, dificultando a operação de expedição em si; Criação de procedimentos complexos e detalhistas de conferência, diminuindo a velocidade do fluxo de expedição; Picos de demanda não planejados em relação ao processo de expedição.