
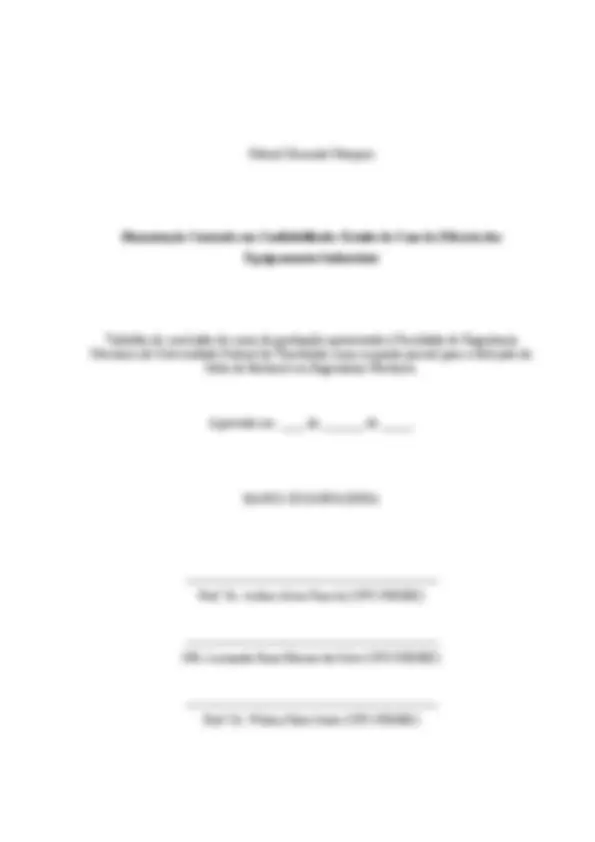
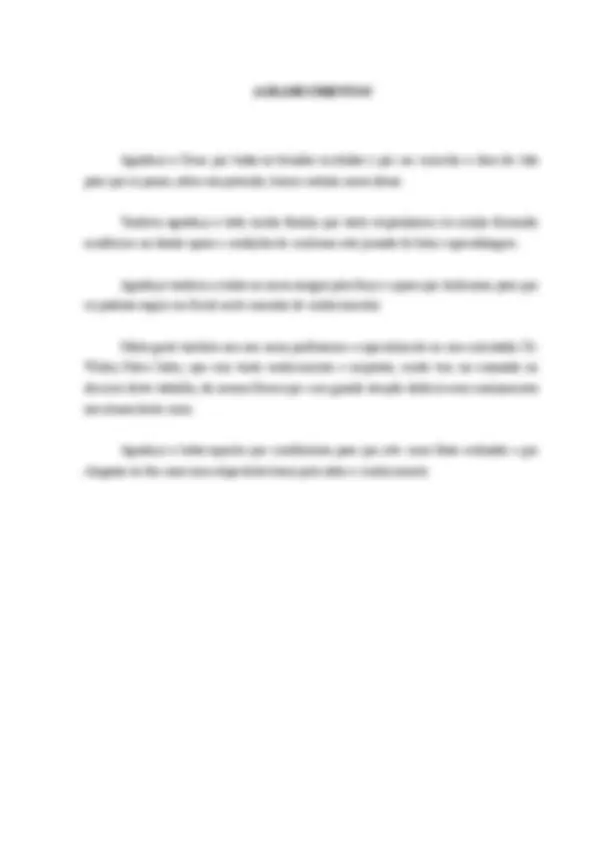
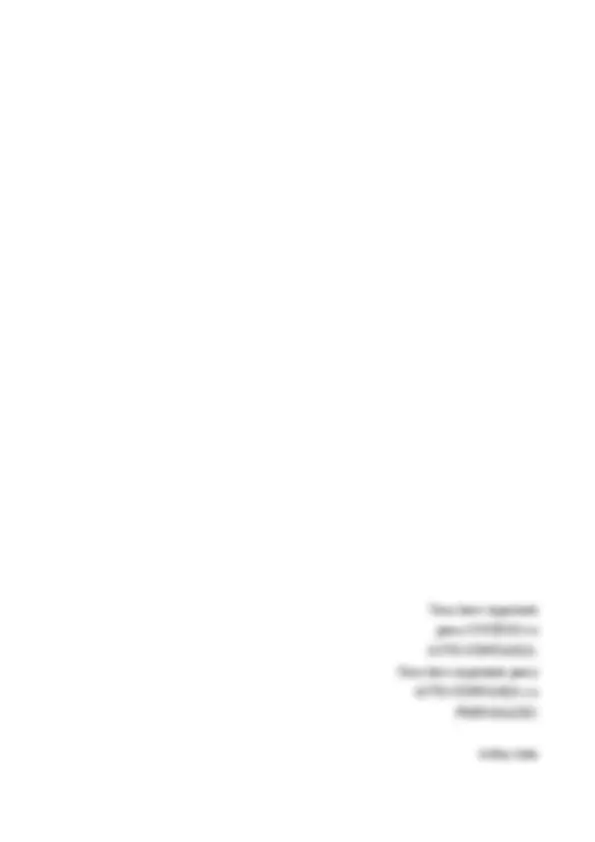
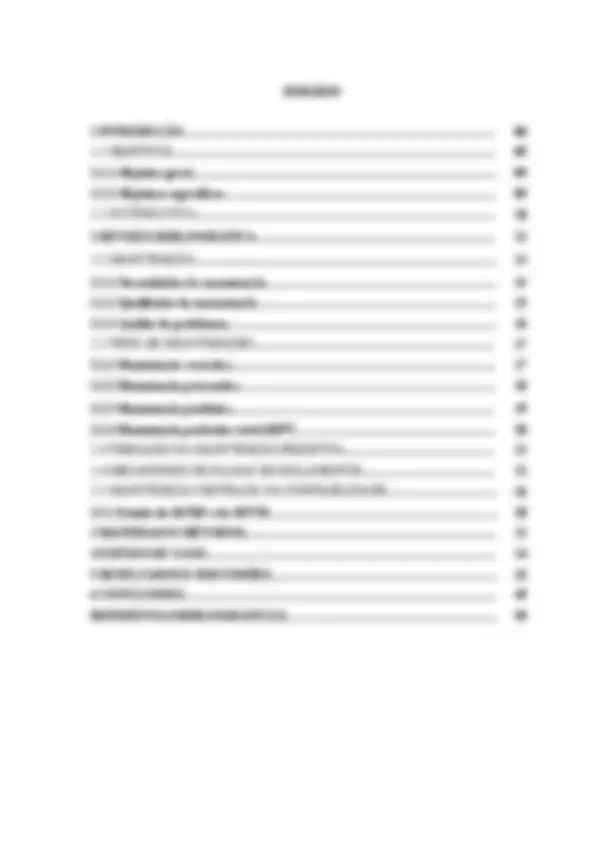
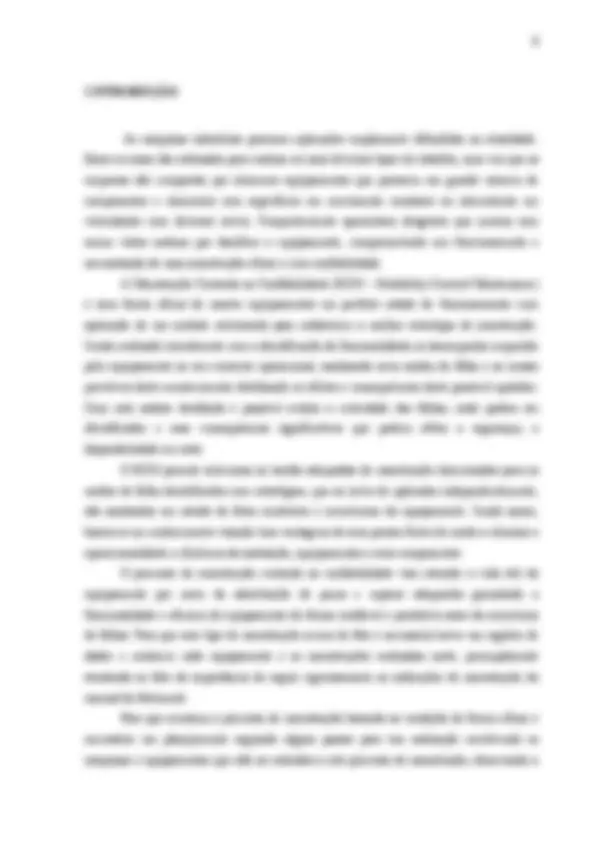
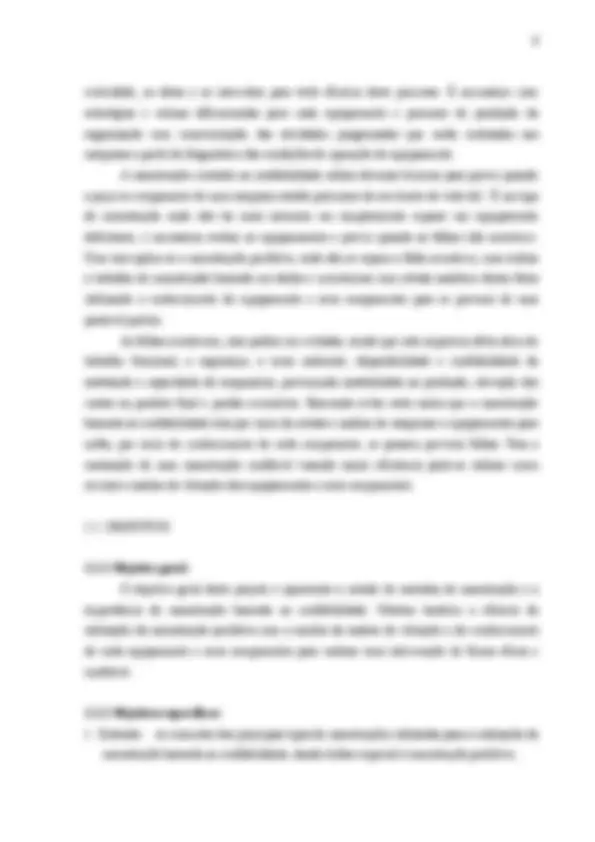
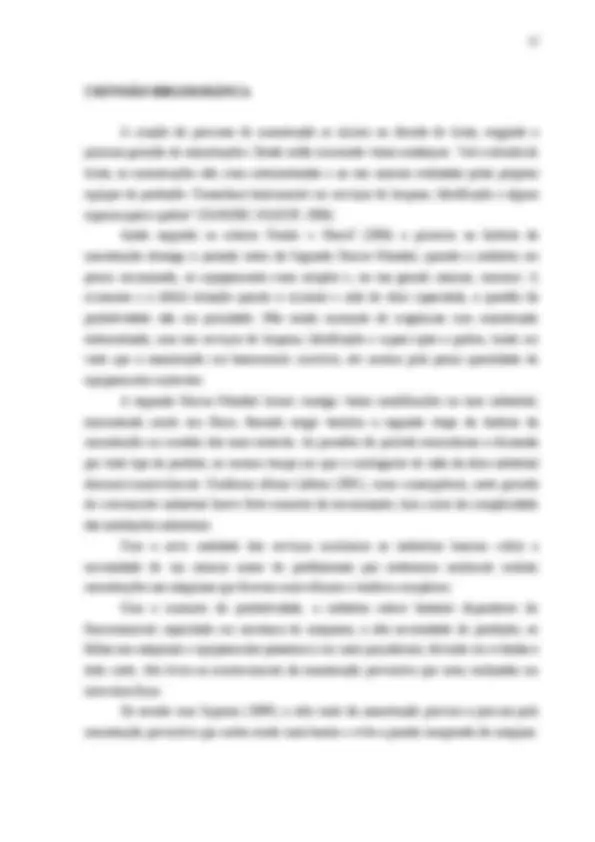
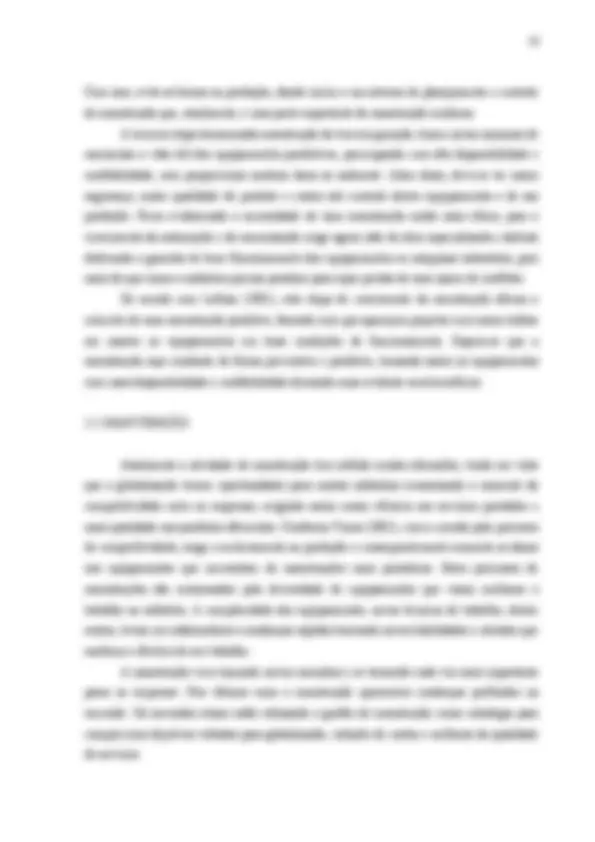
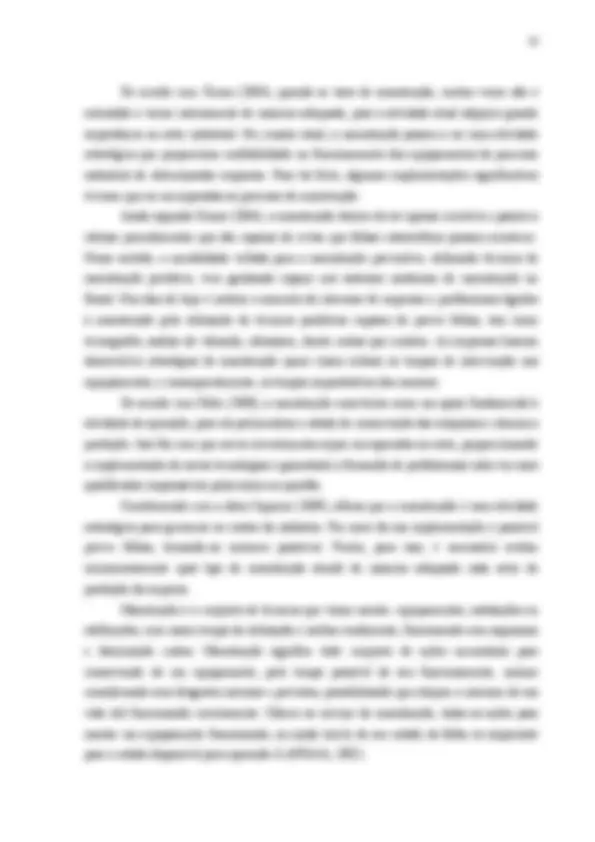
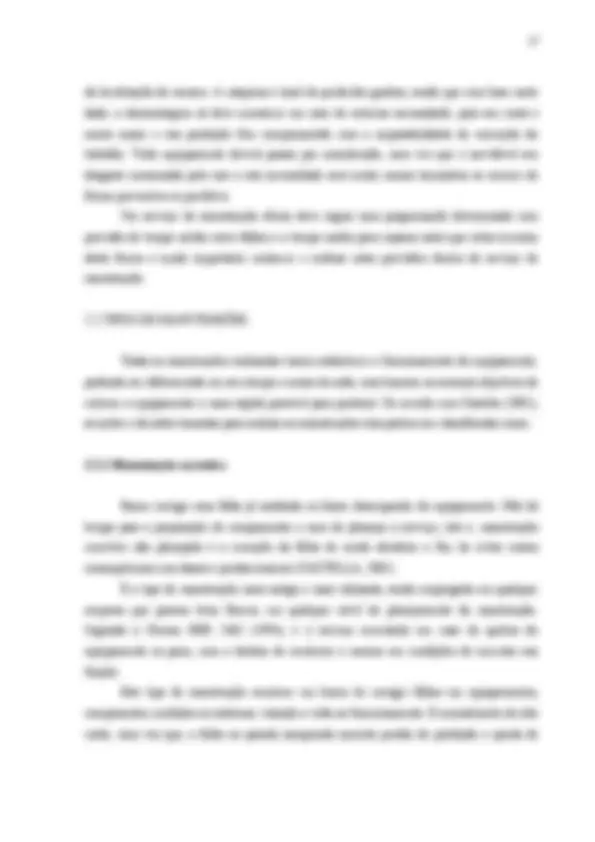
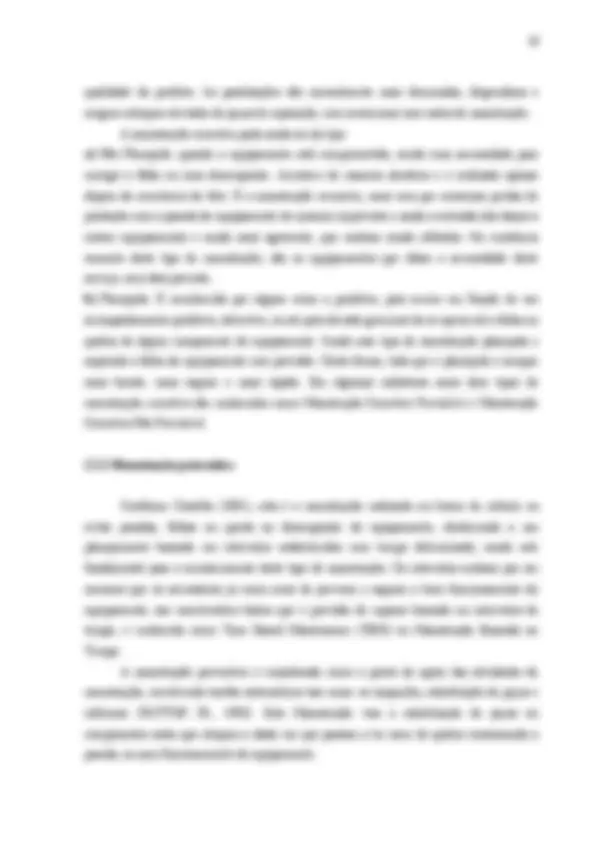
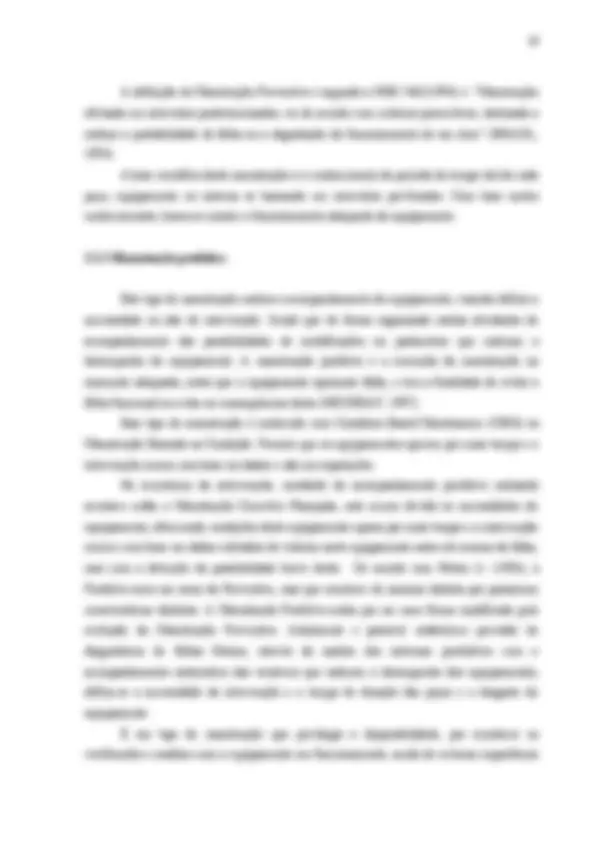
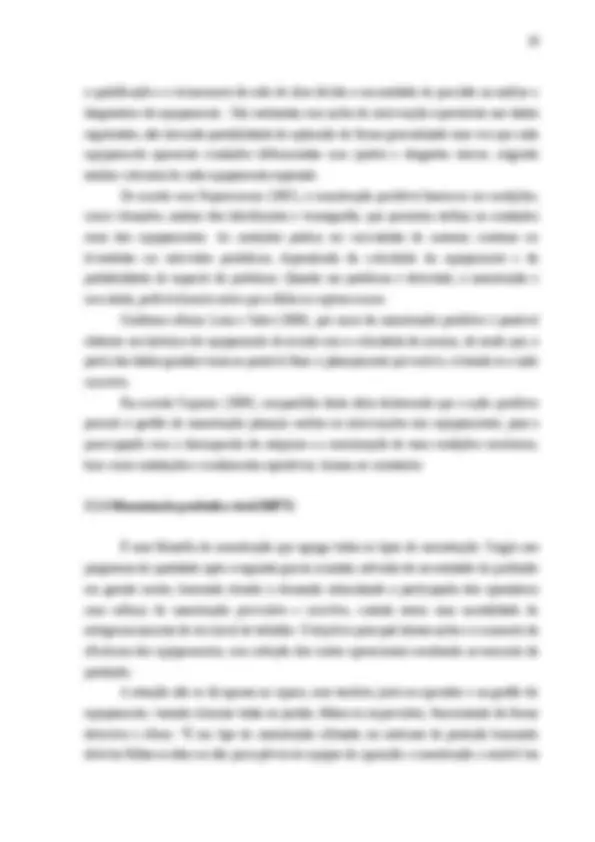
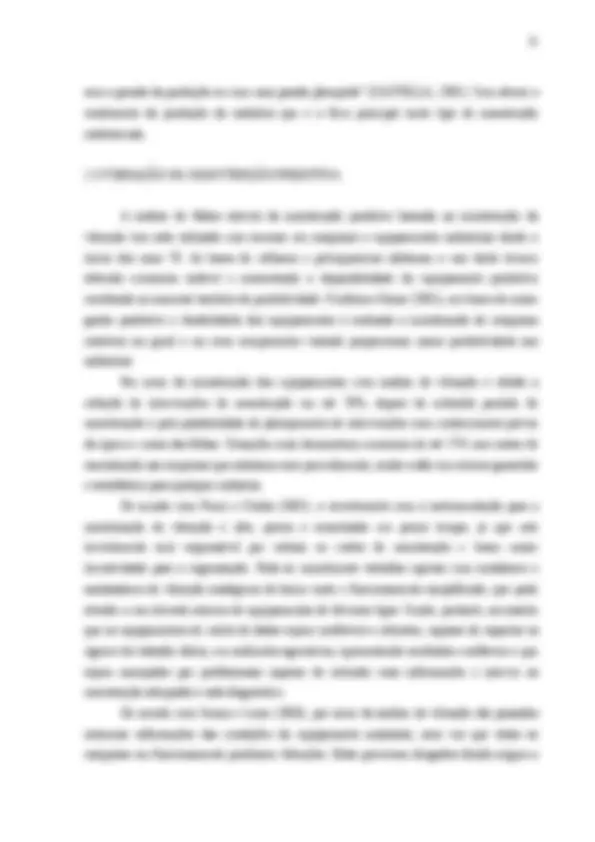
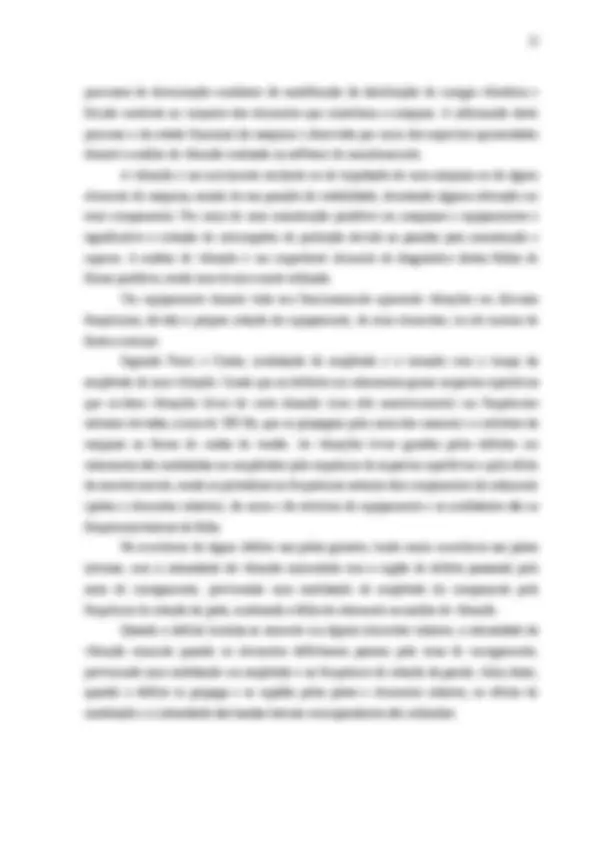
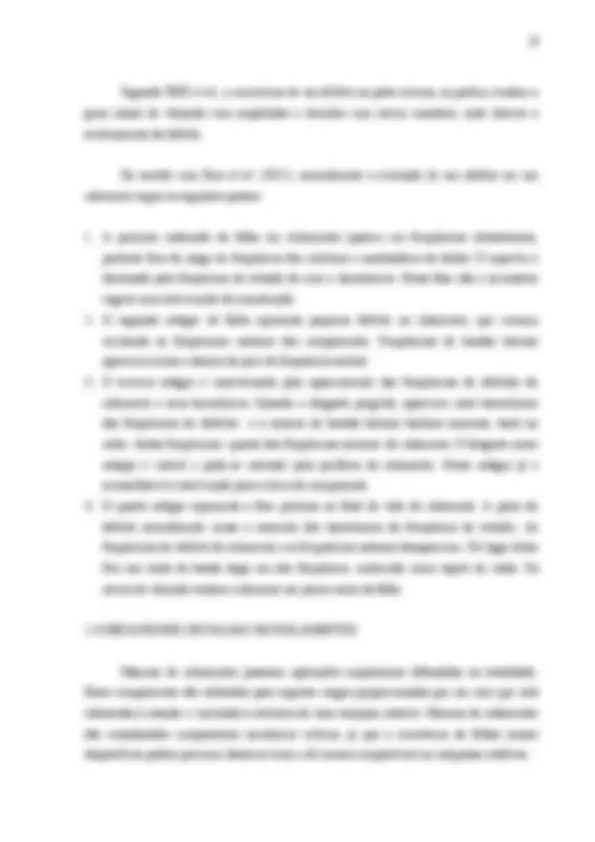


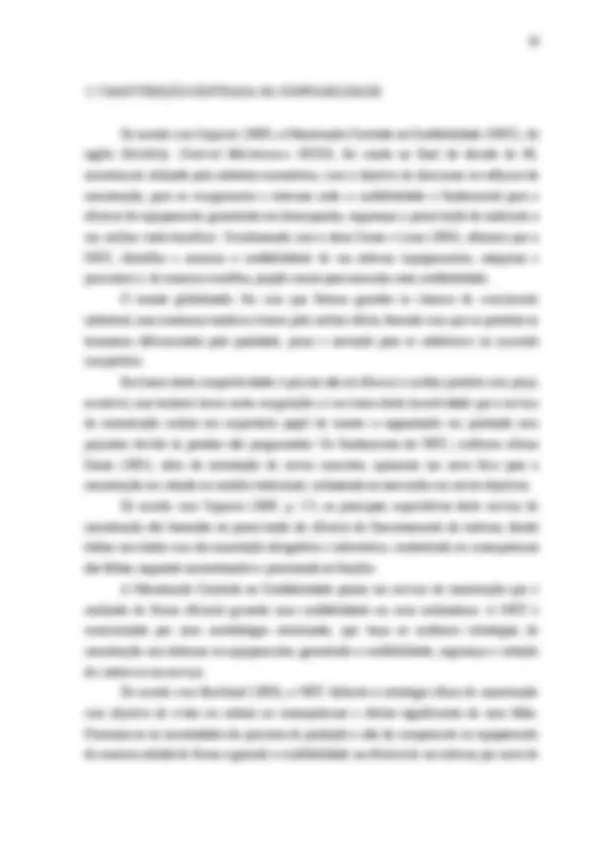
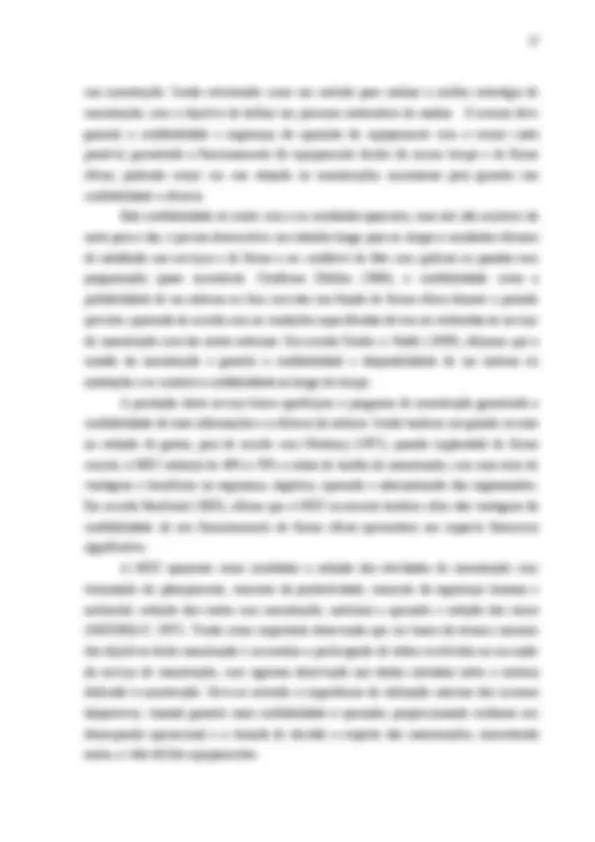
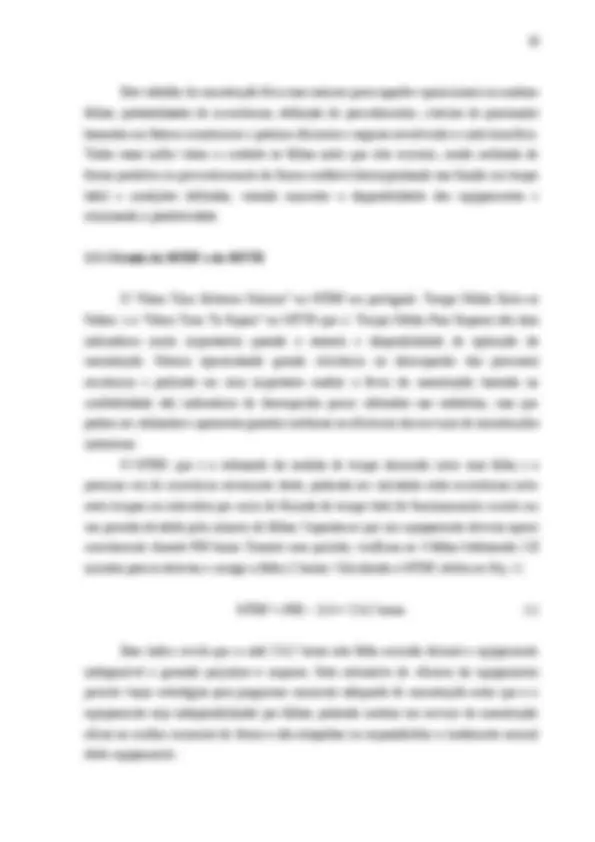
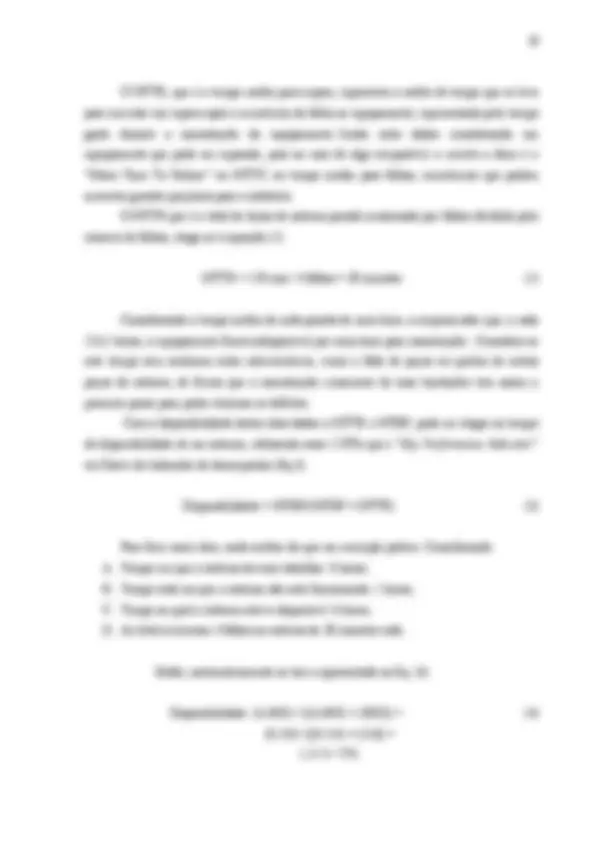
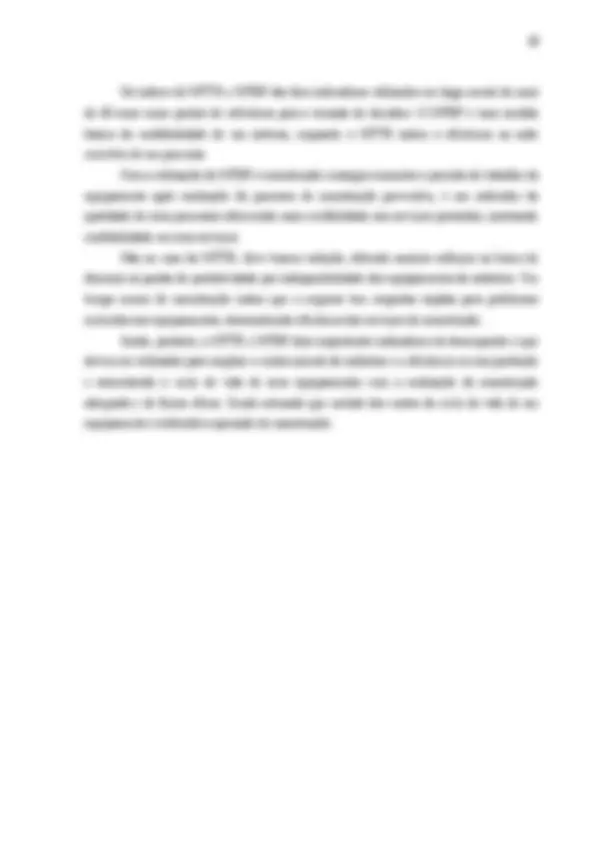
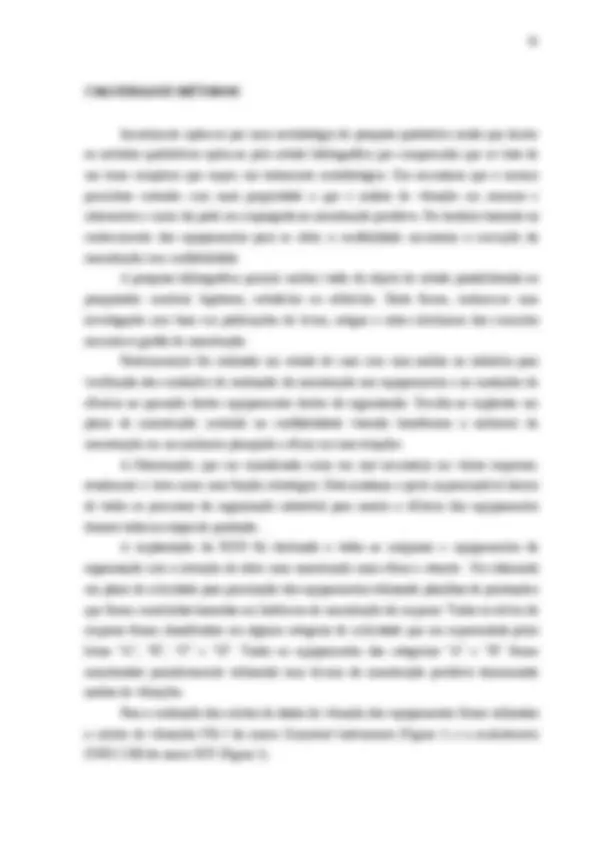
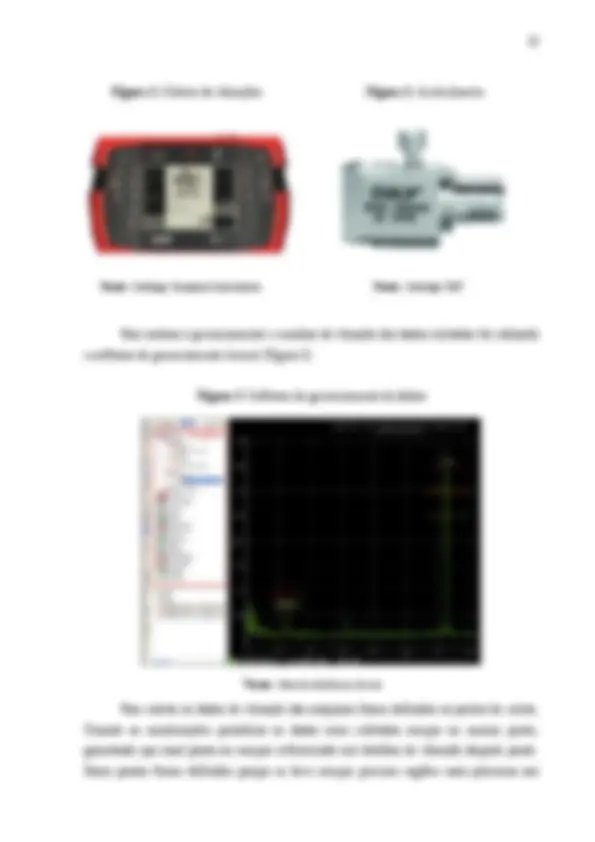
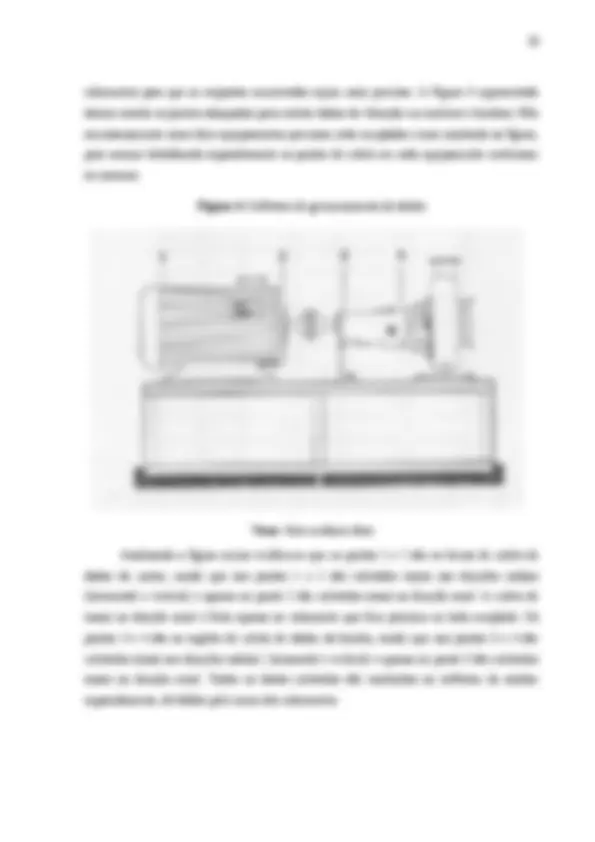
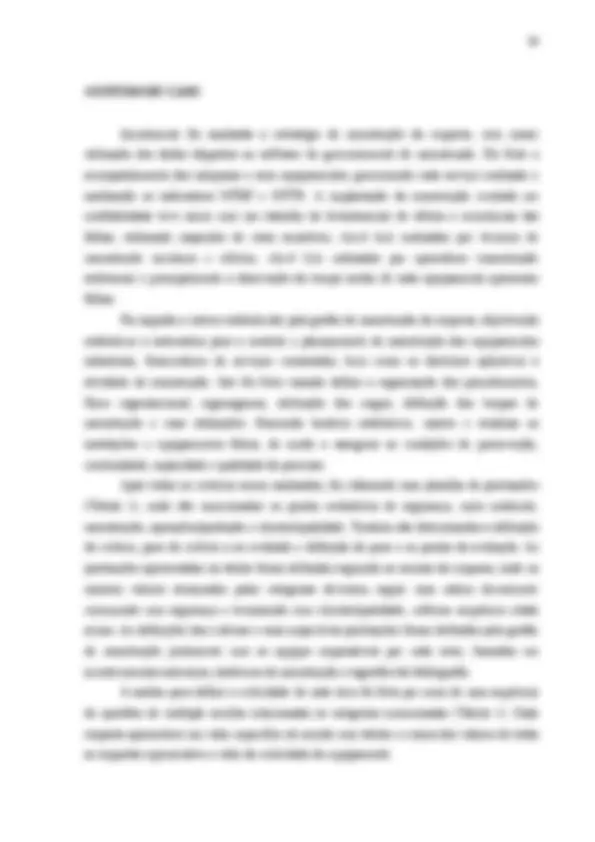
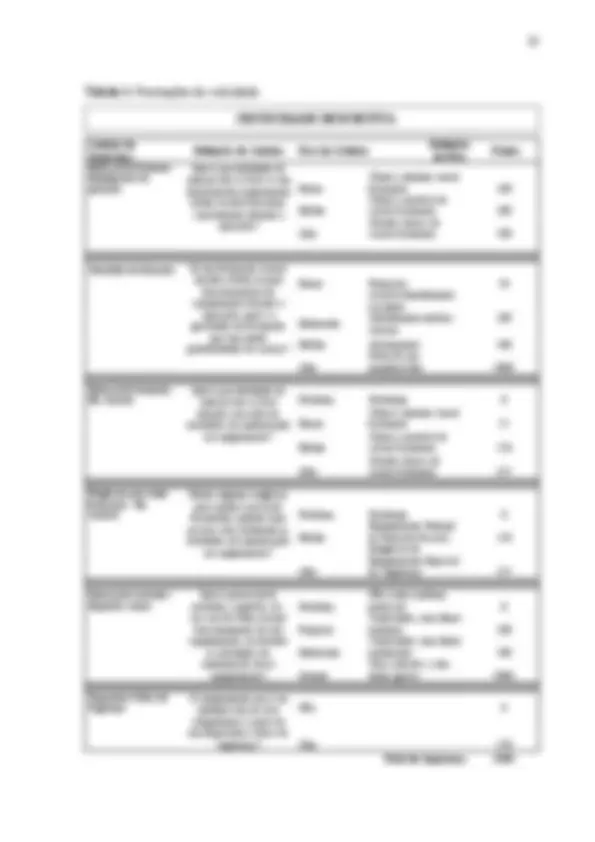
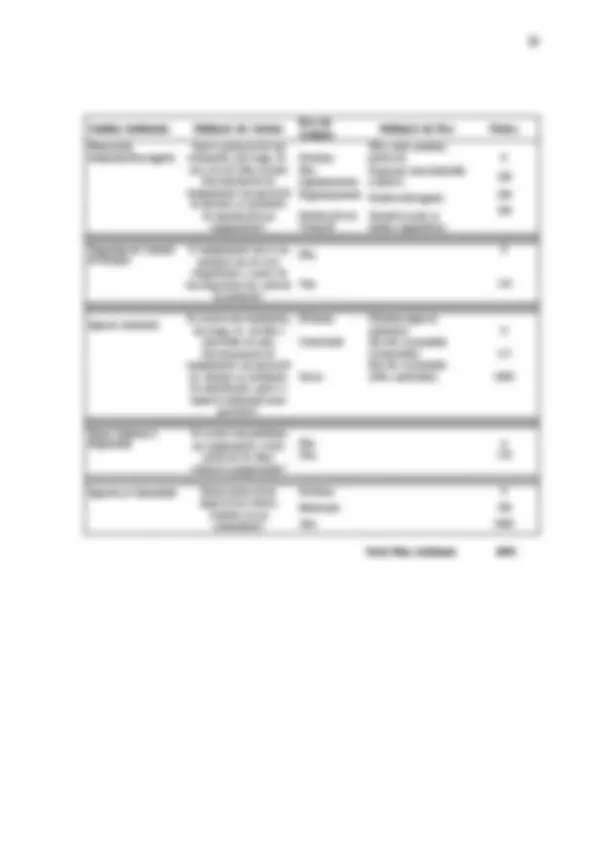
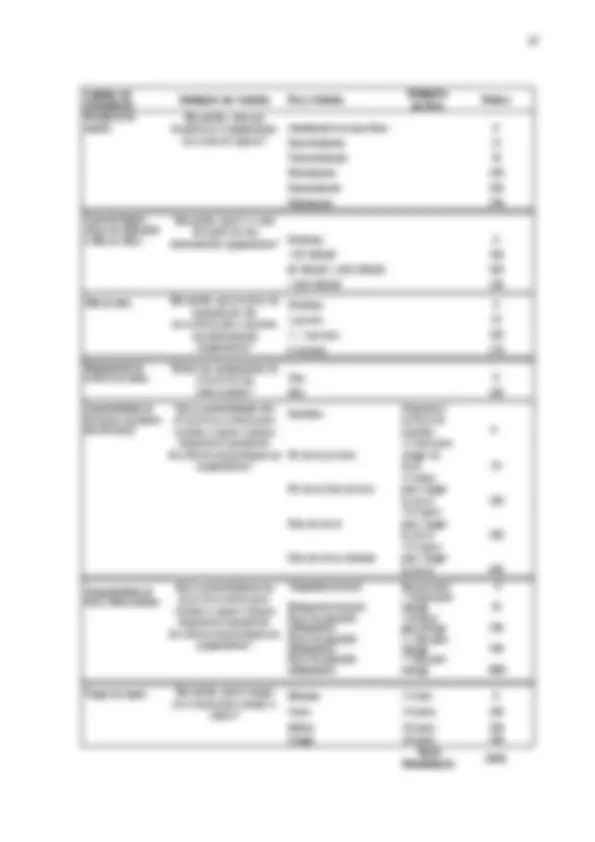
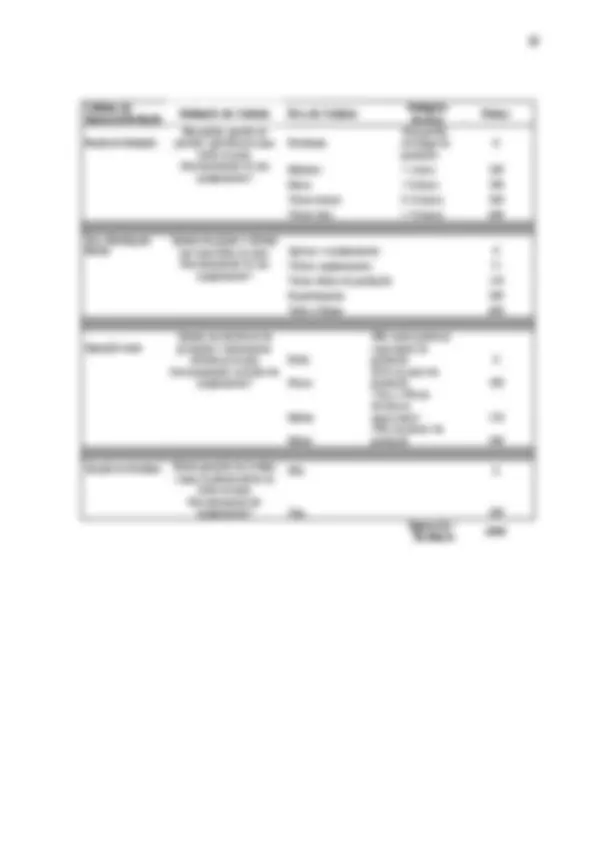
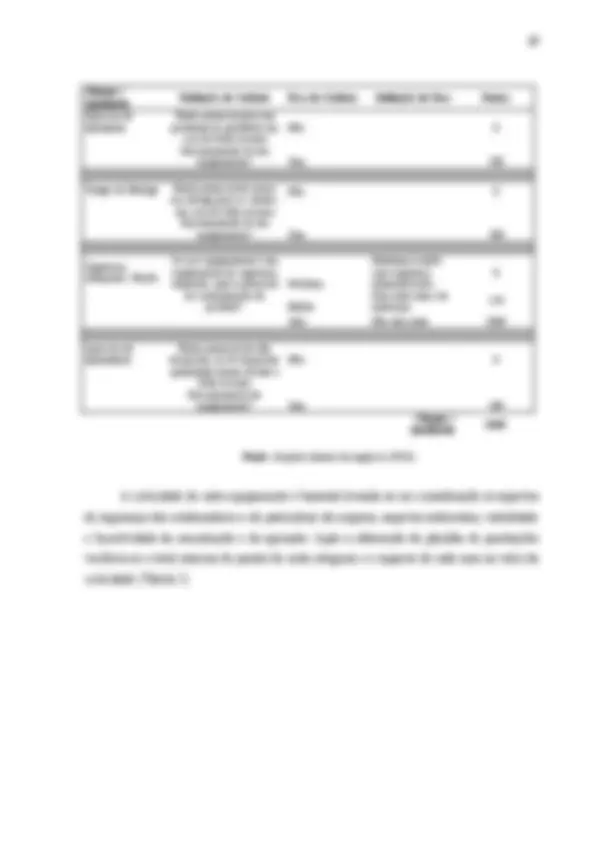
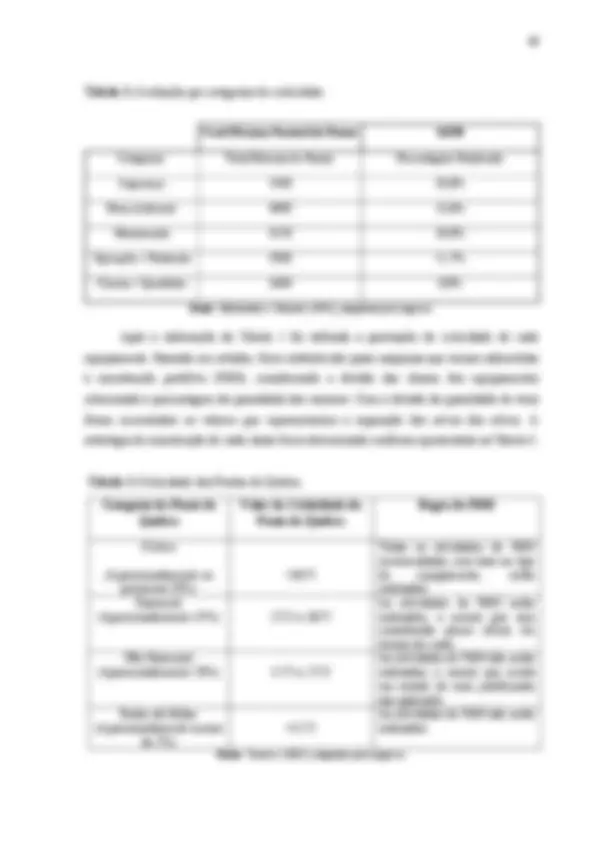
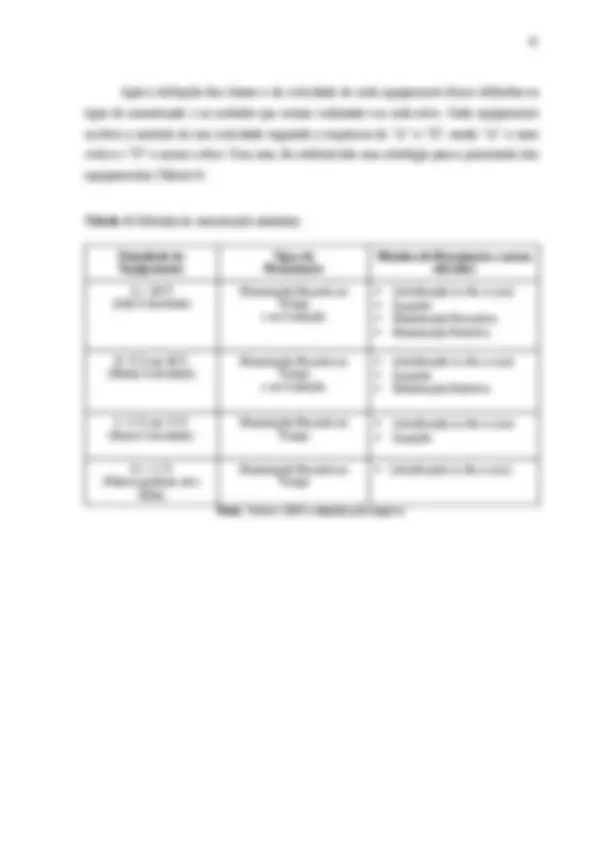
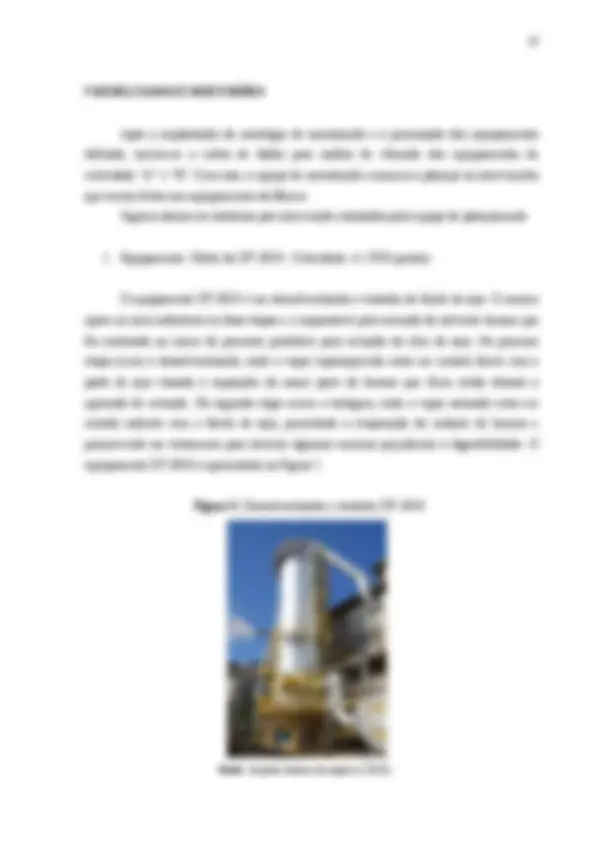
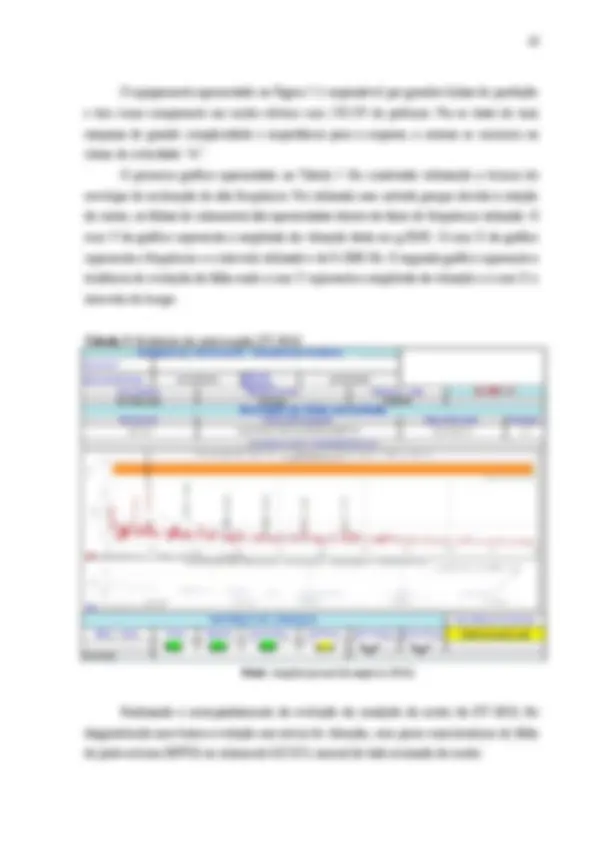
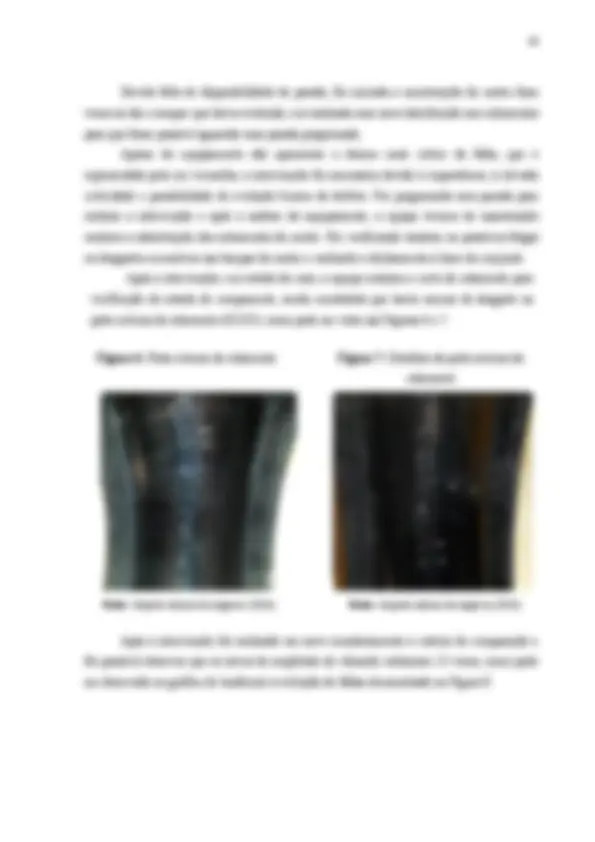
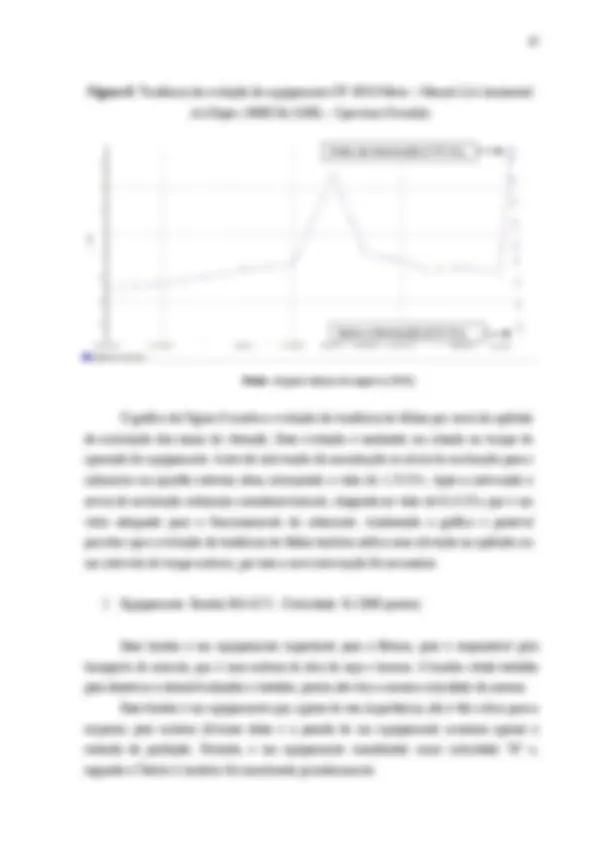
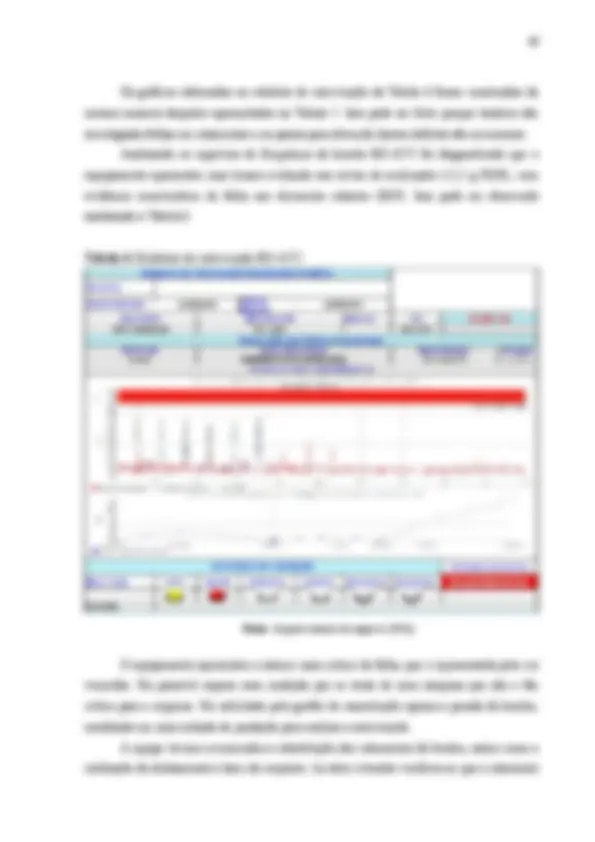
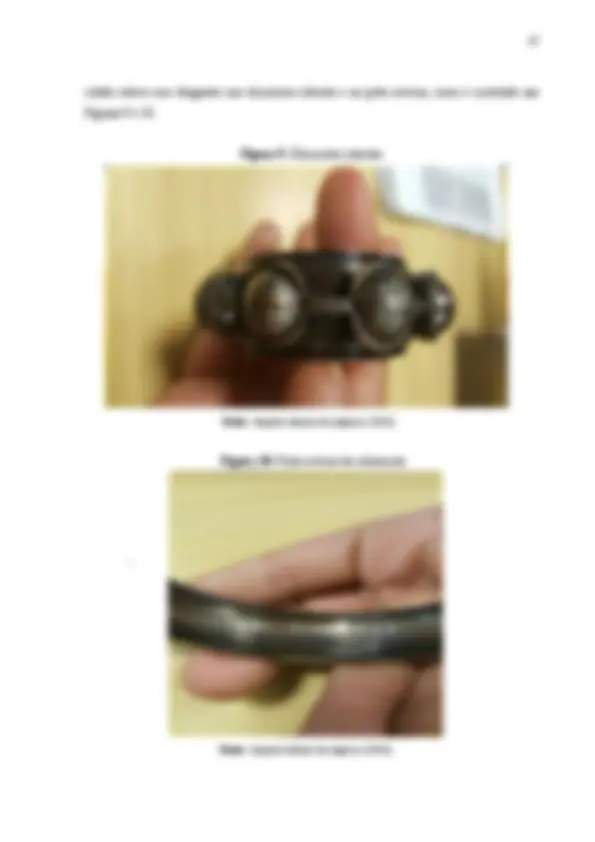
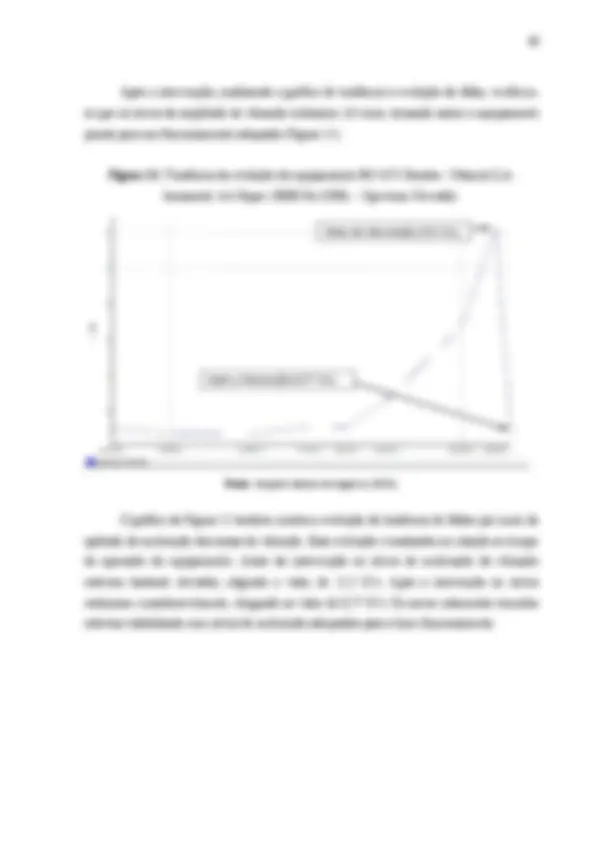
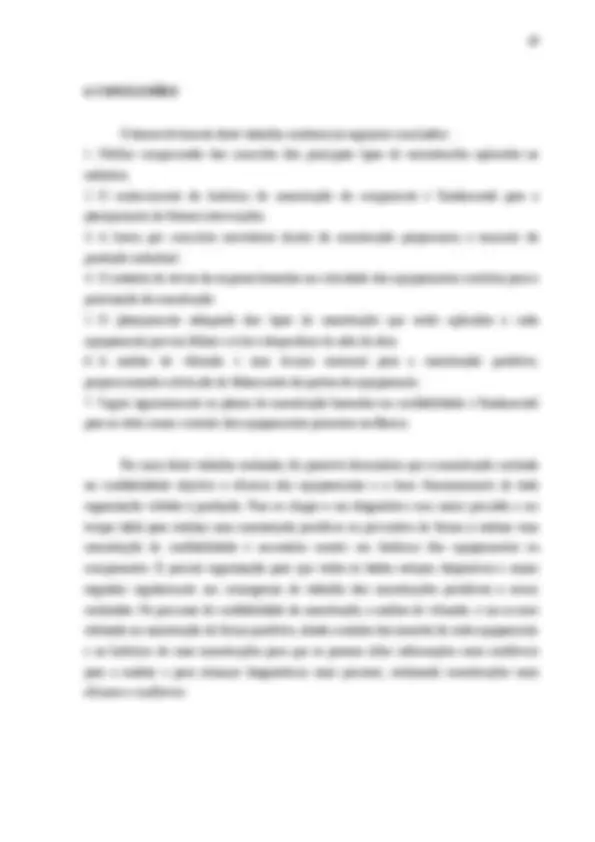
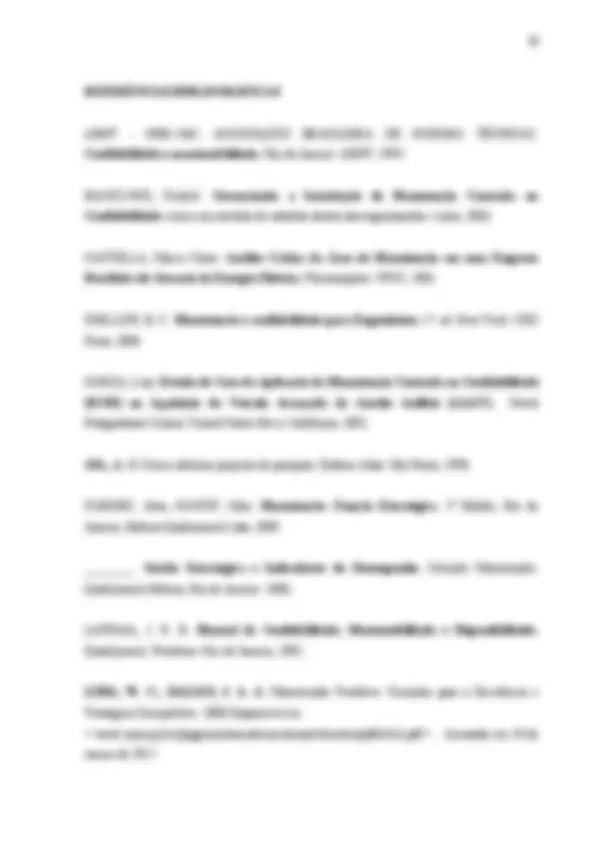
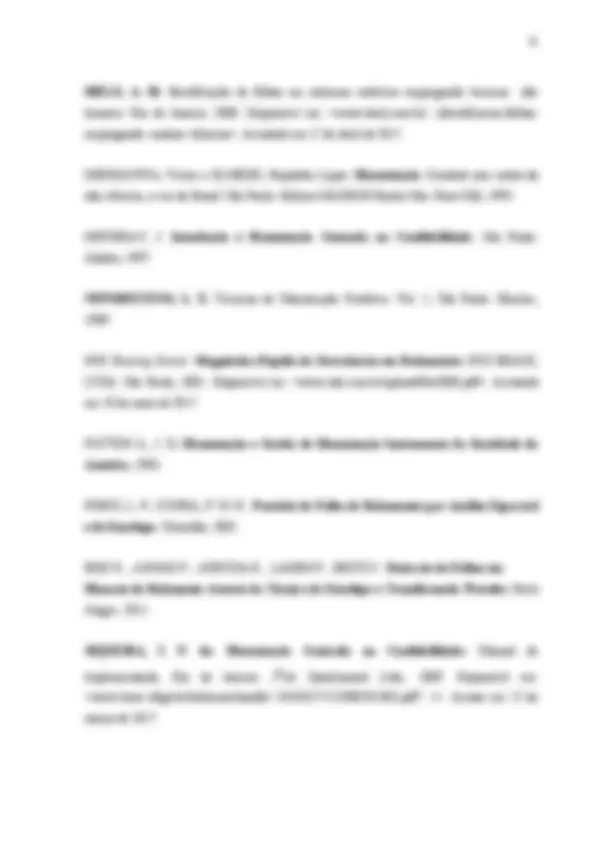
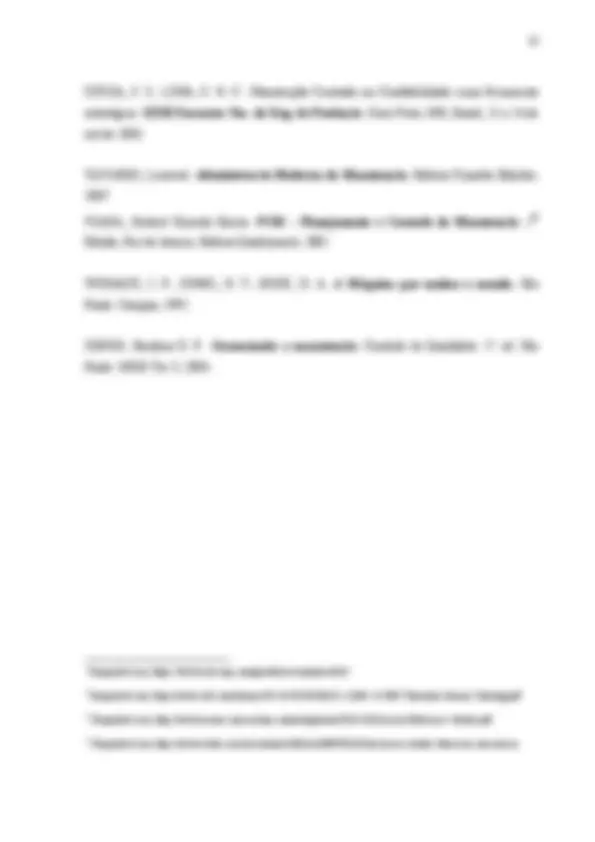
Estude fácil! Tem muito documento disponível na Docsity
Ganhe pontos ajudando outros esrudantes ou compre um plano Premium
Prepare-se para as provas
Estude fácil! Tem muito documento disponível na Docsity
Prepare-se para as provas com trabalhos de outros alunos como você, aqui na Docsity
Os melhores documentos à venda: Trabalhos de alunos formados
Prepare-se com as videoaulas e exercícios resolvidos criados a partir da grade da sua Universidade
Responda perguntas de provas passadas e avalie sua preparação.
Ganhe pontos para baixar
Ganhe pontos ajudando outros esrudantes ou compre um plano Premium
Comunidade
Peça ajuda à comunidade e tire suas dúvidas relacionadas ao estudo
Descubra as melhores universidades em seu país de acordo com os usuários da Docsity
Guias grátis
Baixe gratuitamente nossos guias de estudo, métodos para diminuir a ansiedade, dicas de TCC preparadas pelos professores da Docsity
O documento discute o conceito de manutenção predictiva baseada na confiabilidade, que consiste em manutenção programada baseada no diagnóstico das condições do equipamento, evitando paradas inesperadas. A tabela de criticidade dos equipamentos é utilizada para priorizar a manutenção em componentes críticos para a empresa. A manutenção centrada na confiabilidade (rcm) é uma forma eficaz de manter equipamentos em perfeito estado de funcionamento, aplicando um método estruturado para estabelecer a melhor estratégia de manutenção. O rcm permite selecionar as tarefas adequadas de manutenção direcionadas para os modos de falha identificados com estratégias, que ao invés de aplicadas independentemente, são analisadas em estudo de fatos existentes e ocorrências do equipamento.
O que você vai aprender
Tipologia: Notas de aula
Compartilhado em 07/11/2022
4.4
(172)415 documentos
1 / 53
Esta página não é visível na pré-visualização
Não perca as partes importantes!
Manutenção Centrada em Confiabilidade: Estudo de Caso da Eficácia dos Equipamentos Industriais
Uberlândia 2017
Gabriel Rezende Marques
Manutenção Centrada em Confiabilidade: Estudo de Caso da Eficácia dos Equipamentos Industriais
Trabalho de conclusão de curso de graduação apresentado à Faculdade de Engenharia Mecânica da Universidade Federal de Uberlândia como requisito parcial para a obtenção do título de Bacharel em Engenharia Mecânica.
Área de habilitação: Engenharia Mecânica.
Orientador: Prof. Dr. Wisley Falco Sales
Uberlândia 2017
Agradeço a Deus, por todas as bênçãos recebidas e por me conceder o dom da vida para que eu possa, sobre sua proteção, buscar realizar meus ideais.
Também agradeço a toda minha família que tanto empenharam em minha formação acadêmica me dando apoio e condições de continuar esta jornada de lutas e aprendizagem.
Agradeço também a todos os meus amigos pela força e apoio que dedicaram para que eu pudesse seguir em frente neste caminho de conhecimentos.
Muito grato também sou aos meus professores e especialmente ao meu orientador Dr. Wisley Falco Sales, que com tanto conhecimento e empenho, muito tem me ensinado no decorrer deste trabalho, da mesma forma que com grande atenção dedicou seus ensinamentos aos alunos deste curso.
Agradeço a todos aqueles que contribuíram para que este curso fosse realizado e que chegasse ao fim mais uma etapa desta busca pelo saber e conhecimento.
Uma chave importante para o SUCESSO é a AUTO-CONFIANÇA. Uma chave importante para a AUTO-CONFIANÇA é a PREPARAÇÃO.
Arthur Ashe
Most industrial machines operate from motors, which are susceptible to defects and failures during use. These problems can cause machine shutdown and loss of efficiency in the production process. Therefore, it is very important that the maintenance service knows the equipment of their responsibility and know the conditions of effectiveness of each one, So that it can effectively carry out the necessary and timely intervention so that production is not abruptly and inadvertently interrupted. The concept of predictive maintenance based on reliability is gaining prominence in the present day, consisting of the scheduled maintenance based on the diagnosis of the conditions of the equipment, avoiding unexpected stops. In the work carried out, a qualitative research methodology was used, with a bibliographical study enriched with a case study employing maintenance techniques centered on reliability. To reduce or eliminate problems generated in the operation of equipment, it was necessary to use maintenance techniques to predict failures before they occur. Therefore, the behavior of these equipment during their life cycle is evaluated, through a predictive maintenance technique associated to the knowledge of the machine and the reliability of the maintenance service. A table was drawn up to classify the criticality of the equipment and favor the prioritization of maintenance in critical components for the company. The equipment considered critical was subjected to vibration analysis to predict failures and to prevent machine shutdown. Through this work, it was possible to demonstrate that the maintenance centered on reliability aims at the efficiency of the equipment and the proper functioning of any organization. In addition, it has been concluded that vibration analysis is an efficient and important tool for predictive maintenance.
Keywords: Maintenance; Reliability; Criticality.
REFERÊNCIAS BIBLIOGRÁFICAS....................................................................... 49
criticidade, as datas e os intervalos para total eficácia deste processo. É necessário criar estratégias e rotinas diferenciadas para cada equipamento e processo de produção da organização com caracterização das atividades programadas que serão realizadas nas máquinas a partir do diagnóstico das condições de operação do equipamento. A manutenção centrada na confiabilidade utiliza diversas técnicas para prever quando a peça ou componente de uma máquina estarão próximos do seu limite de vida útil. É um tipo de manutenção onde não há mais interesse em simplesmente reparar um equipamento defeituoso, é necessário avaliar os equipamentos e prever quando as falhas irão acontecer. Com isso aplica-se a manutenção preditiva, onde não se espera a falha acontecer, mas realiza o trabalho de manutenção baseado em dados e ocorrências com estudo analítico destes fatos utilizando o conhecimento do equipamento e seus componentes para se prevenir de uma possível quebra. As falhas acontecem, mas podem ser evitadas, sendo que esta imperícia afeta além do trabalho funcional, a segurança, o meio ambiente, disponibilidade e confiabilidade da instalação e capacidade do maquinário, provocando instabilidade na produção, elevação dos custos no produto final e perdas excessivas. Buscando evitar estes males que a manutenção baseada na confiabilidade atua por meio do estudo e análise de máquinas e equipamentos para então, por meio do conhecimento de cada componente, se possam prevenir falhas. Para a realização de uma manutenção confiável visando maior eficiência pode-se utilizar como recurso a análise de vibração dos equipamentos e seus componentes.
1.1 OBJETIVOS
1.1.1 Objetivo geral: O objetivo geral deste projeto é apresentar o estudo de métodos de manutenção e a importância da manutenção baseada na confiabilidade. Mostrar também a eficácia da utilização da manutenção preditiva com o auxílio da análise de vibração e do conhecimento de cada equipamento e seus componentes para realizar uma intervenção de forma eficaz e confiável.
1.1.2 Objetivos específicos:
1.2 JUSTIFICATIVA
O mercado globalizado tem sido o grande causador da enorme procura pela eficiência na prestação de serviços. No setor industrial, não tem sido diferente, este setor tem se dedicado a potencializar sua competitividade no mercado. Nesta procura pela eficácia e visando garantir-se competitivo, os gestores de manutenção tem adotado o conceito de manutenção preditiva para garantir a confiabilidade em virtude dos resultados positivos que vem sendo alcançados e relatados em estudos e pesquisas de diversos autores e nos resultados apresentados. Por meio da manutenção preditiva com auxílio do recurso da análise de vibração é possível coletar e interpretar dados obtendo diagnósticos precisos na avaliação da vida útil de máquinas, equipamentos e especialmente de mancais de rolamentos. O presente tema é relevante pela oportunidade de estudar os conceitos inerentes ao setor de manutenção, importante elemento da engenharia e da manutenção industrial, pois a produção de toda uma organização depende do funcionamento adequado dos equipamentos necessários ao seu trabalho. E estes, por sua vez, só desenvolvem suas funções de forma adequada se puderem contar com um serviço de manutenção eficaz e confiável. O serviço de manutenção de uma empresa deve buscar eficiência de modo a proporcionar todas as condições para a produção e ainda não atrapalhar seu desenvolvimento
A criação do processo de manutenção se iniciou na década de trinta, surgindo a primeira geração de manutenções. Desde então ocorrendo várias mudanças. “Até a década de trinta, as manutenções não eram sistematizadas e na sua maioria realizadas pelas próprias equipes de produção. Consistiam basicamente em serviços de limpeza, lubrificação e alguns reparos após a quebra” (KARDEC; NASCIF, 2006). Ainda segundo os autores Kardec e Nascif (2006) a primeira na história da manutenção abrange o período antes da Segunda Guerra Mundial, quando a indústria era pouco mecanizada, os equipamentos eram simples e, na sua grande maioria, enormes. A economia e a difícil situação quanto a recursos e mão de obra capacitada, a questão da produtividade não era prioridade. Não sendo momento de exigências com manutenção sistematizada, mas sim serviços de limpeza, lubrificação e reparo após a quebra, tendo em vista que a manutenção era basicamente corretiva, até mesmo pela pouca quantidade de equipamentos existentes. A segunda Guerra Mundial trouxe consigo várias modificações na área industrial, aumentando muito seu fluxo, fazendo surgir também a segunda etapa da história da manutenção em meados dos anos sessenta. As pressões do período aumentaram a demanda por todo tipo de produto, ao mesmo tempo em que o contingente de mão-de-obra industrial diminuiu sensivelmente. Conforme afirma Lafraia (2001), como consequência, neste período de crescimento industrial houve forte aumento da mecanização, bem como da complexidade das instalações industriais. Com a nova realidade dos serviços mecânicos as indústrias buscam cobrir a necessidade de um número maior de profissionais que soubessem realmente realizar manutenções nas máquinas que ficavam mais eficazes e também complexas. Com o aumento da produtividade, a indústria estava bastante dependente do funcionamento capacitado em mecânica de máquinas, a alta necessidade de produção, as falhas nas máquinas e equipamentos passaram a ser mais prejudiciais, devendo ser evitadas a todo custo. Isto levou ao acontecimento da manutenção preventiva que eram realizadas em intervalos fixos. De acordo com Siqueira (2009), o alto custo da manutenção provoca a procura pela manutenção preventiva que acaba sendo mais barata e evita a parada inesperada da máquina.
Com isso, evita as baixas na produção, dando início a um sistema de planejamento e controle de manutenção que, atualmente, é uma parte importante da manutenção moderna. A terceira etapa denominada manutenção da terceira geração, busca novas maneiras de maximizar a vida útil dos equipamentos produtivos, preocupando com alta disponibilidade e confiabilidade, sem proporcionar nenhum dano ao ambiente. Além disso, deve-se ter maior segurança, maior qualidade do produto e custos sob controle destes equipamentos e de sua produção. Ficou evidenciada a necessidade de uma manutenção ainda mais eficaz, pois o crescimento da automação e da mecanização exige agora mão de obra especializada e distinta dedicando a garantia de bom funcionamento dos equipamentos ou máquinas industriais, pois mais do que nunca a indústria precisa produzir para repor perdas de uma época de conflitos. De acordo com Lafraia (2001), esta etapa de crescimento da manutenção afirma o conceito de uma manutenção preditiva, fazendo com que apareçam projetos com maior ênfase em manter os equipamentos em boas condições de funcionamento. Espera-se que a manutenção seja constante de forma preventiva e preditiva, tornando assim os equipamentos com mais disponibilidade e confiabilidade deixando mais evidente seus benefícios.
2.1 MANUTENÇÃO
Atualmente a atividade de manutenção tem sofrido muitas alterações, tendo em vista que a globalização trouxe oportunidades para muitas indústrias ocasionando o aumento da competitividade entre as empresas, exigindo assim maior eficácia nos serviços prestados e mais qualidade nos produtos oferecidos. Conforme Viana (2002), com a corrida pelo processo de competitividade, surge o aceleramento na produção e consequentemente aumenta os danos nos equipamentos que necessitam de manutenções mais periódicas. Estes processos de manutenções são ocasionados pela diversidade de equipamentos que visam melhorar o trabalho na indústria. A complexidade dos equipamentos, novas técnicas de trabalho, dentre outros, levam os colaboradores a mudanças rápidas buscando novas habilidades e atitudes que enalteça a eficácia de seu trabalho. A manutenção vem traçando novos caminhos e se tornando cada vez mais importante paras as empresas. Nos últimos anos a manutenção apresentou mudanças profundas no mercado. Os mercados atuais estão utilizando a gestão de manutenção como estratégia para cumprir seus objetivos voltados para globalização, redução de custos e melhoria da qualidade de serviços.
Conforme Patton Jr. (1983), existem muitos tipos de abordagem de manutenção, que se definem pelo modo que se aplicam no sistema produtivo, quando no momento de ocorrência ou previsão da falha. Podendo ainda ser definido com os diferentes procedimentos praticados diante de um problema suposto ou enfrentado que ocasiona o mau funcionamento ou parada do equipamento que ocasiona em perdas, seja pela ocorrência da manutenção ou parada de funcionamento.
2.1.1 Necessidade da Manutenção
O desgaste das máquinas é inevitável, pois suas peças e componentes se deterioram, dando origem às falhas que devido ao mau funcionamento destas peçam estragadas ou corrompidas ocasionam a parada da máquina causando assim prejuízo a toda indústria. Devido a esta ocorrência foi aumentando o surgimento de soluções para prevenção destes males, sendo assim instalados processos que buscassem evitar tais ocorrências, fazendo com que acontecessem vistorias periódicas. De acordo com Womack (1992), estes acontecimentos deram origem aos processos de manutenções, que buscam cada vez mais evitar ocorrências de quebras e paradas de equipamentos ou máquinas, fazendo surgir os diversos tipos de manutenções.
2.1.2 Qualidades da manutenção
Ao projetar um equipamento é de extrema importância elevar dados para pós- funcionamento, realizando levantamento das necessidades, levando em conta fabricação, instalação, funcionalidade, operação, manutenção e durabilidade, que podem atuar na sua produtividade e eficácia. Como desempenho, podemos citar as questões ligadas a confiabilidade, produtividade, qualidade do produto final, segurança e preservação ambiental e as econômicas se referem ao nível de custo-eficiência obtido (WOMACK, 1992). Então na aquisição de uma máquina ou equipamento, alguns fatores devem ser levados em consideração como a sua adequação ao projeto, analisando se seu dimensionamento é adequado ao trabalho que se presta. Deve-se verificar se sua capacidade é a desejada, sendo verificada através de dados técnicos com análise do tempo médio entre falhas (MTBF), se a qualidade é como a descrita e esperada, a existência da possibilidade de manutenção e seu
custo-eficiência. Todos estes itens devem ser observados na aquisição do equipamento, de forma a completar os fatores da eficácia, confiabilidade e qualidade do produto adquirido. É importante observar que o equipamento adquirido deve ser padronizado às necessidades de sua aplicação, evitando o mau uso e consequentemente a manutenção por danos causados por esta inobservância. O equipamento deve acompanhar o desenvolvimento industrial ao seu destino, apresentar os requisitos de modernidade e o aumento de confiabilidade, e da possibilidade de sua manutenção. Segundo Viana (2002), os tipos de manutenção são as formas de encaminhar as intervenções nos instrumentos de produção. Assim sendo ao produzir um equipamento, seu fabricante disponibiliza condições de mantê-lo funcionando de acordo com sua utilização, valorizando o produto e influenciando em compras futuras de peças de reposição para a manutenção. Esse tipo de manutenção possibilita o planejamento dos recursos necessários para a intervenção de manutenção, uma vez que a falha é esperada até mesmo pelo desgaste das peças (MUASSAB, 2002). Durante a instalação do equipamento alguns dados também precisam ser observados, pois podem influenciar no seu funcionamento, durabilidade e eficácia, às vezes até inviabilizando a manutenção do mesmo. Caso isso aconteça, perde-se a ferramenta que busca garantir a função e eficácia do equipamento no decorrer de sua produção, buscando possíveis falhas, defeitos ou danos a serem corrigidos.
2.1.3 Análises de problemas
A vistoria de um equipamento para detectar alguma falha deve partir de dois critérios: verificar o que ocasionou a falha utilizando ferramentas como: relatório de análise de falha, brainstorming , 5-Why , diagrama de Ishikawa; instruir o usuário do modo correto de operar este equipamento evitando danos ou falhas (lições ponto-a-ponto, instruções de trabalho). Qualquer equipamento que realiza uma determinada função estará sujeito a uma variedade de esforços. Estes esforços gerarão fadiga e isto causará sua deterioração reduzindo sua resistência à fadiga, até um ponto no qual o equipamento pode não ter mais o desempenho desejado, apresentando falhas (MOUBRAY, 1997). Corroborando com a ideia, Xenos (2004) ressalta a necessidade de investigar exaustivamente as causas fundamentais das falhas para sua exterminação, tendo em vista que isto ocorre a partir de análise e conhecimento do equipamento e da ação a ser realizada. Com posse da informação da origem do problema, poderá então proceder ao diagnóstico da causa e
qualidade do produto. As paralisações são normalmente mais demoradas, dispendiosa e exigem estoques elevados de peças de reposição, com acréscimos nos custos de manutenção. A manutenção corretiva pode ainda ser do tipo: a) Não Planejada: quando o equipamento está comprometido, sendo uma necessidade para corrigir a falha ou mau desempenho. Acontece de maneira aleatória e é realizado apenas depois da ocorrência do fato. É a manutenção recursiva, mais cara por ocasionar perdas de produção com a parada do equipamento de maneira imprevista e ainda a extensão dos danos a outros equipamentos é ainda mais agravante, que acabam sendo afetados. Na existência somente deste tipo de manutenção, são os equipamentos que ditam a necessidade deste serviço, sem data prevista. b) Planejada: É reconhecida por alguns como a preditiva, pois ocorre em função de um acompanhamento preditivo, detectivo, ou até pela decisão gerencial de se operar até a falha ou quebra de algum componente do equipamento. Sendo esse tipo de manutenção planejada e esperada a falha do equipamento com previsão. Desta forma, tudo que é planejado é sempre mais barato, mais seguro e mais rápido. Em algumas indústrias esses dois tipos de manutenção corretiva são conhecidos como Manutenção Corretiva Previsível e Manutenção Corretiva Não Previsível.
2.2.2 Manutenção preventiva
Conforme Castella (2001), esta é a manutenção realizada em busca de reduzir ou evitar paradas, falhas ou queda no desempenho do equipamento, obedecendo a um planejamento baseado em intervalos estabelecidos com tempo determinado, sendo este fundamental para o acontecimento deste tipo de manutenção. Os intervalos acabam por ser menores que os necessários já como meio de prevenir e segurar o bom funcionamento do equipamento, sua característica básica que é previsão de reparos baseada em intervalos de tempo, é conhecida como Time Based Maintenance (TBM) ou Manutenção Baseada no Tempo. A manutenção preventiva é considerada como o ponto de apoio das atividades de manutenção, envolvendo tarefas sistemáticas tais como: as inspeções, substituição de peças e reformas (PATTON JR., 1983). Esta Manutenção visa a substituição de peças ou componentes antes que atinjam a idade em que passam a ter risco de quebra ocasionando a parada, ou mau funcionamento do equipamento.
A definição de Manutenção Preventiva é segundo a NBR 5462(1994) é: “Manutenção efetuada em intervalos predeterminados, ou de acordo com critérios prescritivos, destinada a reduzir a probabilidade de falha ou a degradação do funcionamento de um item” (BRASIL, 1994). A base científica desta manutenção é o conhecimento do período de tempo útil de cada peça, equipamento ou sistema se baseando em intervalos pré-fixados. Com base nestes conhecimentos, busca-se manter o funcionamento adequado do equipamento.
2.2.3 Manutenção preditiva
Este tipo de manutenção realiza o acompanhamento do equipamento, visando definir a necessidade ou não de intervenção. Sendo que de forma organizada realiza atividades de acompanhamento das possibilidades de modificações ou parâmetros que indicam o desempenho do equipamento. A manutenção preditiva é a execução da manutenção no momento adequado, antes que o equipamento apresente falha, e tem a finalidade de evitar a falha funcional ou evitar as consequências desta (MOUBRAY, 1997). Esse tipo de manutenção é conhecido com Condition Based Maintenance (CBM) ou Manutenção Baseada na Condição. Permite que os equipamentos operem por mais tempo e a intervenção ocorra com base em dados e não em suposições. Na ocorrência da intervenção, resultado do acompanhamento preditivo realizado acontece então a Manutenção Corretiva Planejada, esta ocorre devido às necessidades do equipamento, oferecendo condições deste equipamento operar por mais tempo e a intervenção ocorrer com base em dados coletados de vistoria neste equipamento antes até mesmo da falha, mas com a detecção da possibilidade breve desta. De acordo com Patton Jr. (1983), a Preditiva seria um ramo da Preventiva, mas que acontece de maneira distinta por possuírem características distintas. A Manutenção Preditiva acaba por ser uma forma modificada pela evolução da Manutenção Preventiva. Atualmente é possível estabelecer previsão de diagnósticos de falhas futuras, através da análise dos sistemas produtivos com o acompanhamento sistemático das variáveis que indicam o desempenho dos equipamentos, define-se a necessidade da intervenção e o tempo de duração das peças e o desgaste do equipamento. É um tipo de manutenção que privilegia a disponibilidade, por acontecer as verificações e análises com o equipamento em funcionamento, sendo de extrema importância