
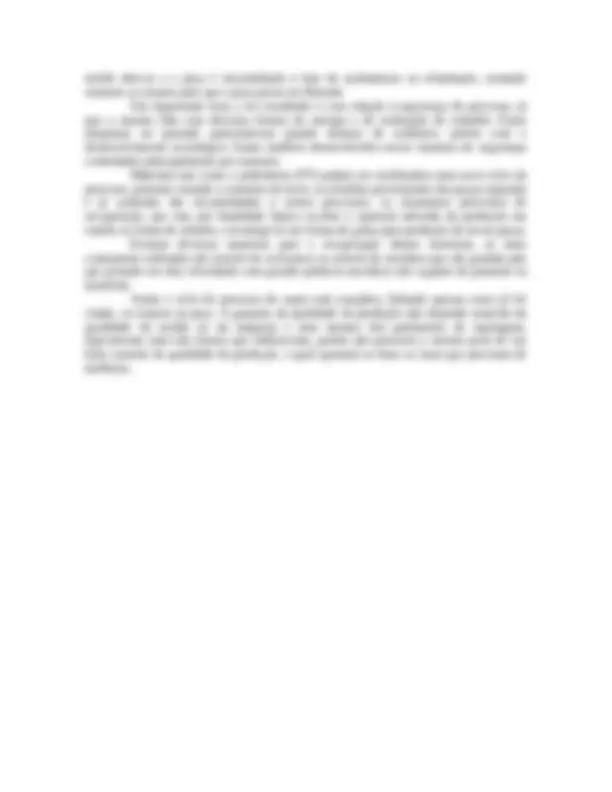
Estude fácil! Tem muito documento disponível na Docsity
Ganhe pontos ajudando outros esrudantes ou compre um plano Premium
Prepare-se para as provas
Estude fácil! Tem muito documento disponível na Docsity
Prepare-se para as provas com trabalhos de outros alunos como você, aqui na Docsity
Os melhores documentos à venda: Trabalhos de alunos formados
Prepare-se com as videoaulas e exercícios resolvidos criados a partir da grade da sua Universidade
Responda perguntas de provas passadas e avalie sua preparação.
Ganhe pontos para baixar
Ganhe pontos ajudando outros esrudantes ou compre um plano Premium
Comunidade
Peça ajuda à comunidade e tire suas dúvidas relacionadas ao estudo
Descubra as melhores universidades em seu país de acordo com os usuários da Docsity
Guias grátis
Baixe gratuitamente nossos guias de estudo, métodos para diminuir a ansiedade, dicas de TCC preparadas pelos professores da Docsity
Entendendo o Funcionamento de uma Sopradora para projetos
Tipologia: Exercícios
1 / 2
Esta página não é visível na pré-visualização
Não perca as partes importantes!
Para o perfeito entendimento do funcionamento da máquina é necessário que não existam dúvidas com relação às formas construtivas, isto é, as partes componentes que acabaram de ser explicadas. Também é válido relembrar as fontes de alimentação (um sistema elétrico trifásico e uma linha de ar comprimido). O processo inicia-se com a regulagem da máquina através dos meios de interface entre homem e máquina. Essa regulagem dá-se simplesmente através da introdução de dados no software do controlador lógico programável (CLP), pré-estabelecido pelo fabricante. As regulagens abrangem todos os parâmetros necessários ao funcionamento, tais como as pressões, as temperaturas, os avanços e principalmente os tempos de ciclo. Obviamente estamos tratando de máquina sopradora dotada destes sistemas digitais ou de controle eletrônico, mas ainda é possível encontrarmos máquinas providas com os controladores que foram introduzidos visando a otimização do processo. Segue agora a descrição do processo de sopro utilizado em máquinas que funcionem por acúmulo na extrusão. Somente citando que também existe o processo por extrusão contínua. Depois das primeiras regulagens na máquina é necessária a alimentação da mesma com o material granulado a ser trabalhado. Este material é colocado em tanques próximos à máquina, ele é levado do nível do piso até o funil de alimentação do canhão através do alimentador de material, ou seja, um pequeno compressor que atende essas condições de trabalho exigidas. O variador já regulado faz com que a rosca dentro do canhão gire e o material que estava no funil seja liberado entrando no canhão; as resistências ali localizadas fazem com que o material atinja um ponto de fluidez ideal ao processo (temperaturas em torno de 160 ºC). A rosca leva o material já em ponto fluido de trabalho até o reservatório localizado na parte superior do cabeçote, também chamado de acumulador. Esse material é acumulado até a quantidade pré-programada no controlador de Parison, com a condição de que esteja dentro do porte da máquina. O controlador de Parison também tem total influência sobre o próximo passo do processo: a injeção da mangueira (também chamada popularmente de “chute”). Este equipamento faz o controle das paredes da mangueira agindo através do deslocamento da ferramenta ou trafila, como descrito na rota especial sobre o controlador de Parison do capítulo anterior, que trata sobre as partes da máquina. Ocorrida a injeção da mangueira entre as duas partes do molde, ocorre o avanço do mandril, um cilindro pneumático provido de uma mangueira. Este mandril pode estar localizado tanto na parte inferior da mangueira quanto na parte lateral, dependendo da forma geométrica, a utilização e o acabamento da peça a ser produzida. Com a mangueira no comprimento desejado localizada entre o molde e o mandril avançado e o escape de ar pela agulha do mandril, isto é, o sopro de ar (que dá origem ao nome do processo), forçando as paredes da mangueira contra as paredes do molde, fazendo com que o material tome a forma desejada, a forma do molde. O próximo passo é aguardar o resfriamento do material em contato com o molde, define-se então o tempo de resfriamento na programação. Dado o tempo de resfriamento o
molde abre-se e a peça é encaminhada à fase de acabamento ou rebarbação, restando somente os ensaios para que a peça possa ser liberada. Um importante item a ser ressaltado é com relação à segurança do processo, já que o mesmo lida com diversas formas de energia e de realização de trabalho. Essas máquinas no passado apresentavam grande número de acidentes, porém com o desenvolvimento tecnológico foram também desenvolvidos novos sistemas de segurança controlados principalmente por sensores. Materiais tais como o polietileno (PT) podem ser reutilizados num novo ciclo do processo, portanto visando o aumento do lucro, as rebarbas provenientes das peças sopradas e já acabadas são encaminhadas a outros processos, os chamamos processos de recuperação, que tem por finalidade básica receber o material advindo da produção em estado ou forma de rebarba e reentregá-lo em forma de grãos para produção de novas peças. Existem diversas maneiras para a recuperação desses materiais, as mais comumente utilizadas são através de extrusoras ou através de moinhos que são grandes pás que girando em alta velocidade com grande potência mecânica são capazes de granular os materiais. Assim o ciclo do processo de sopro está completo, faltando apenas como já foi citado, os ensaios na peça. A garantia da qualidade da produção não depende somente da qualidade do molde ou da máquina e nem mesmo dos parâmetros de regulagem, logicamente estes são fatores que influenciam, porém não possuem o mesmo peso de um bom controle de qualidade da produção, o qual apontará os itens ou fases que precisam de melhoras.