
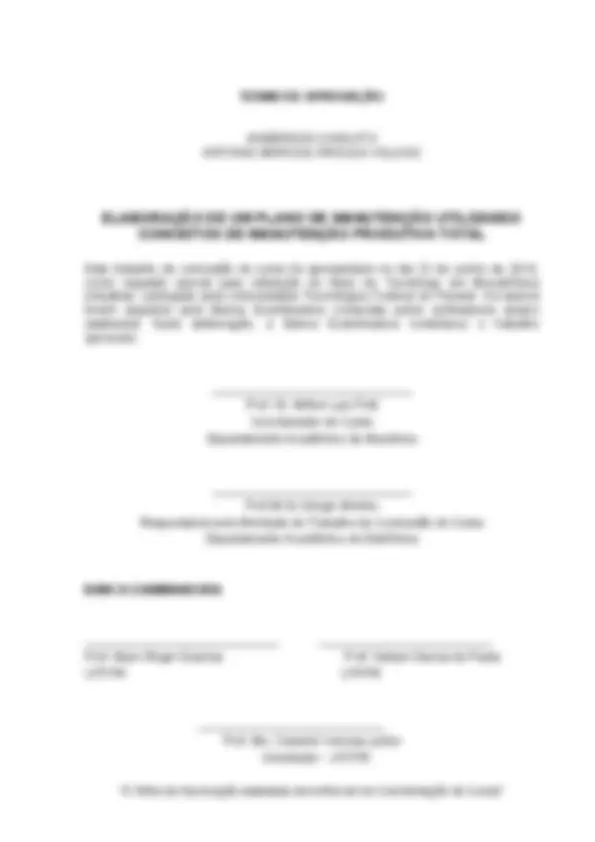
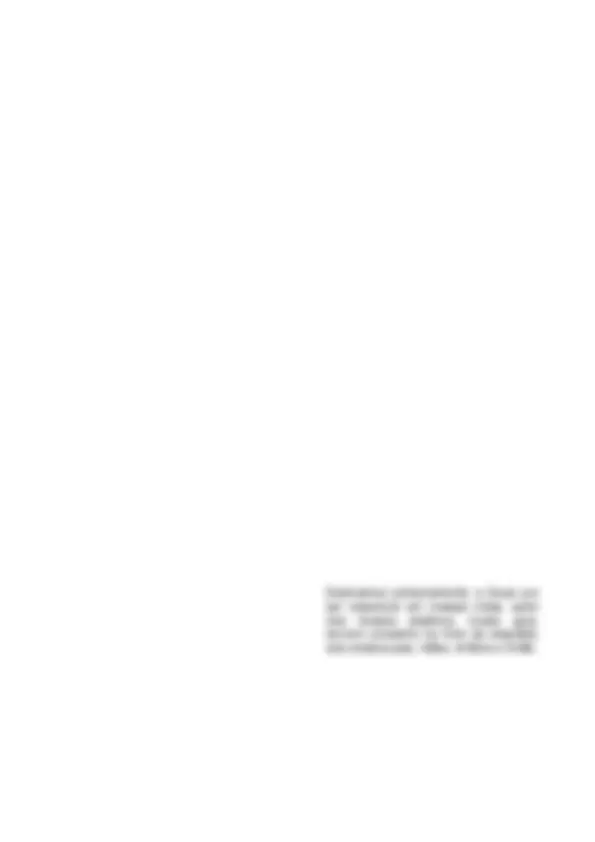
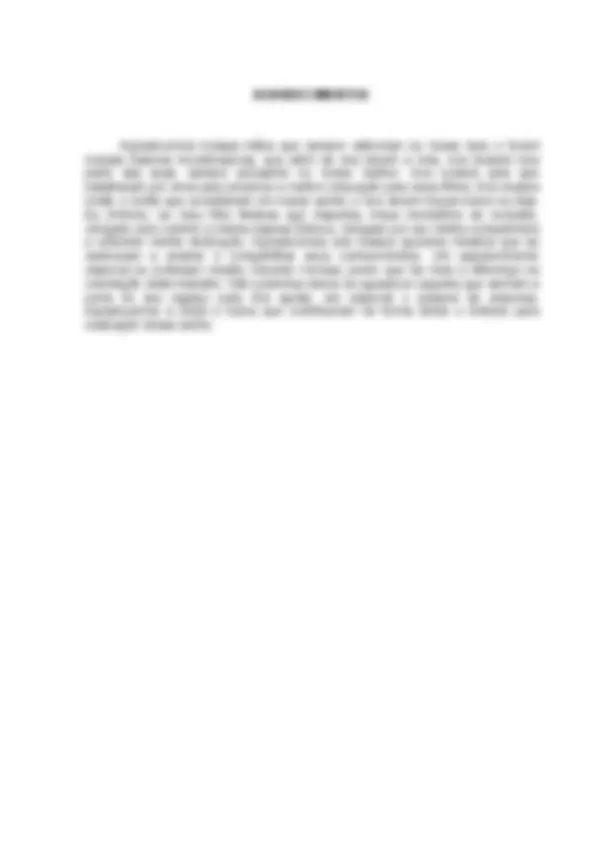
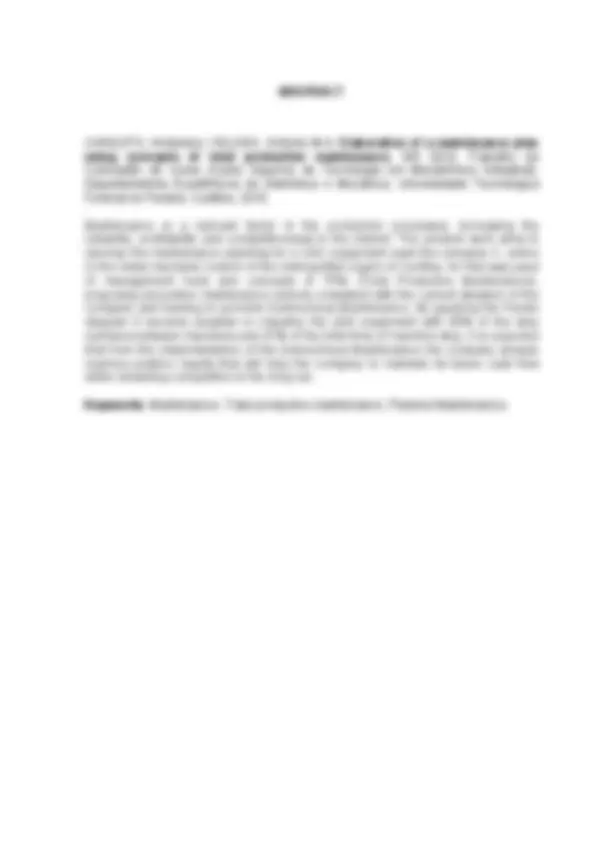
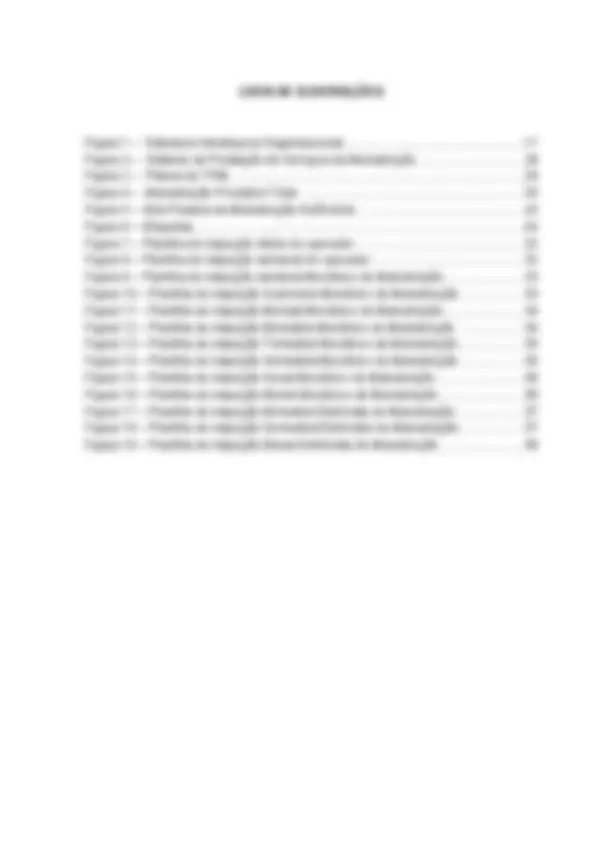
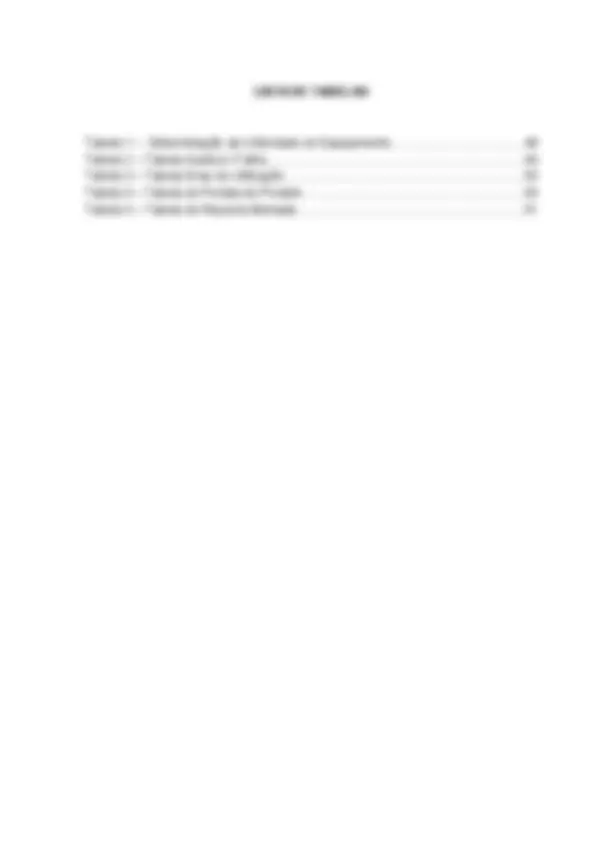
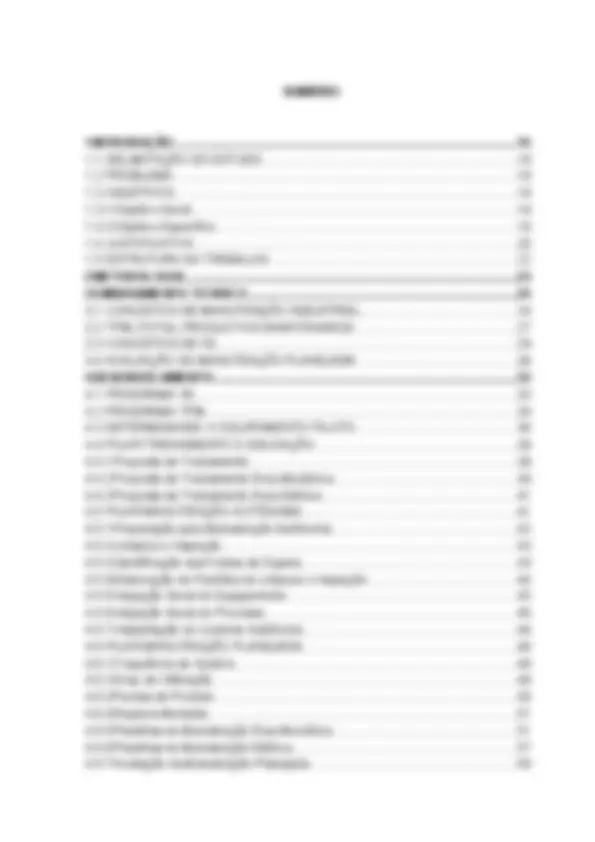
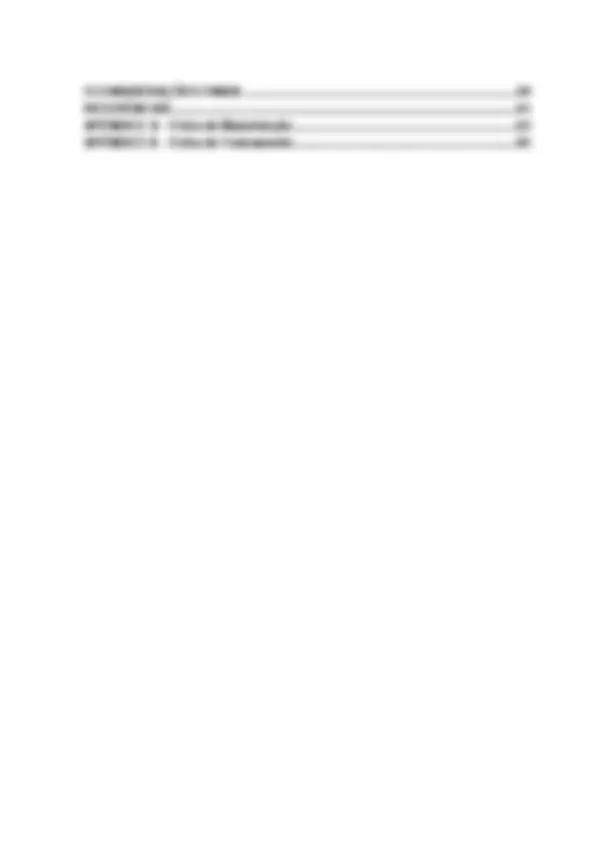
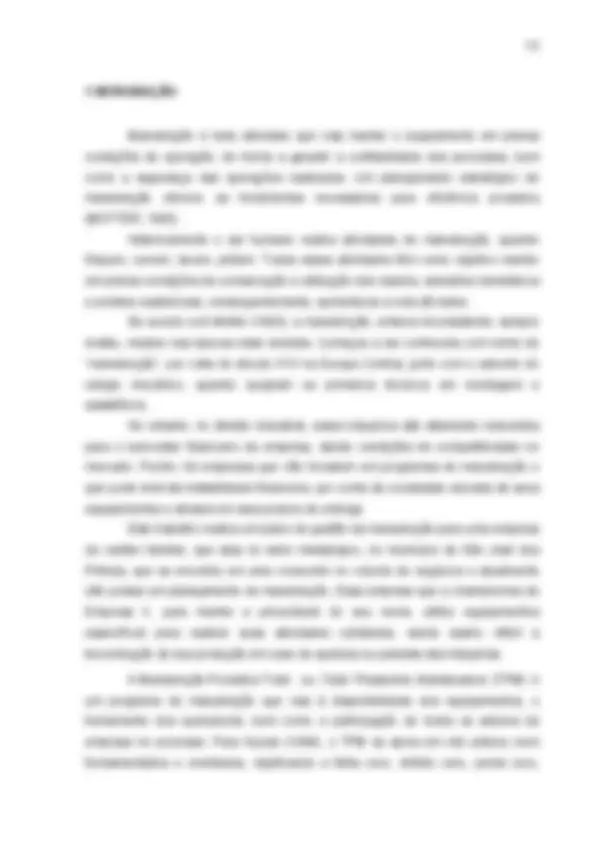
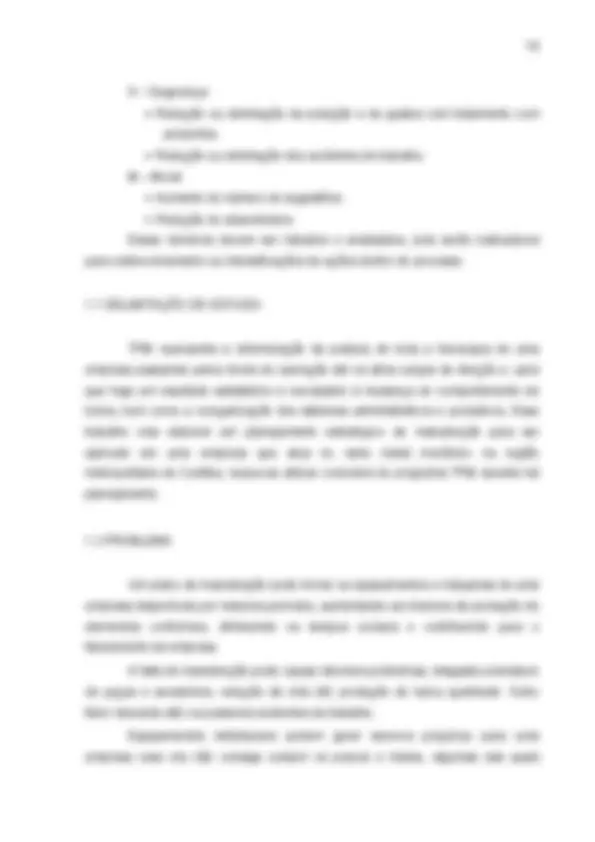
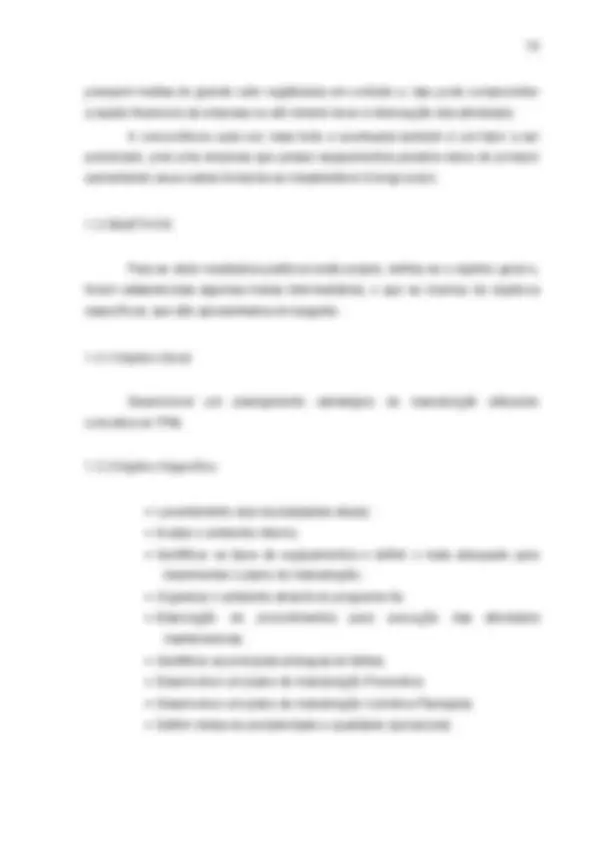
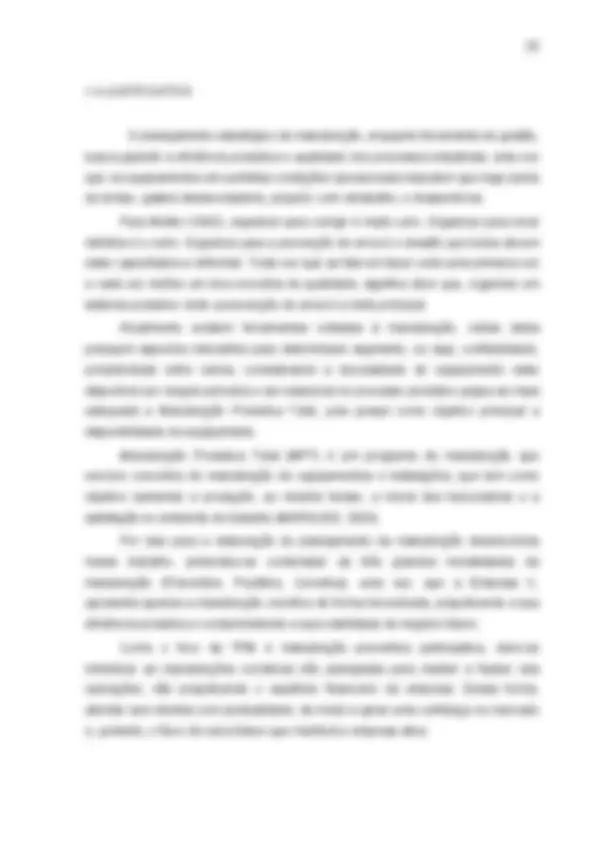
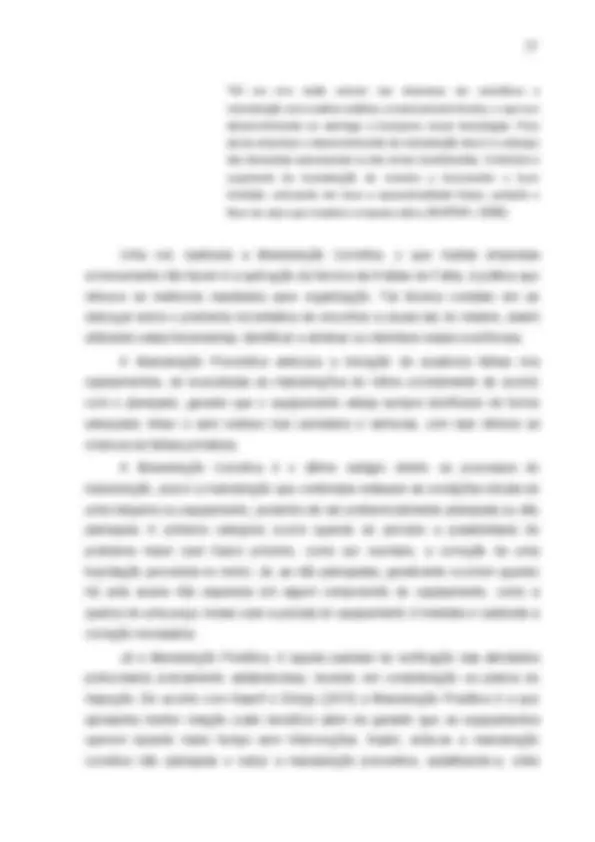
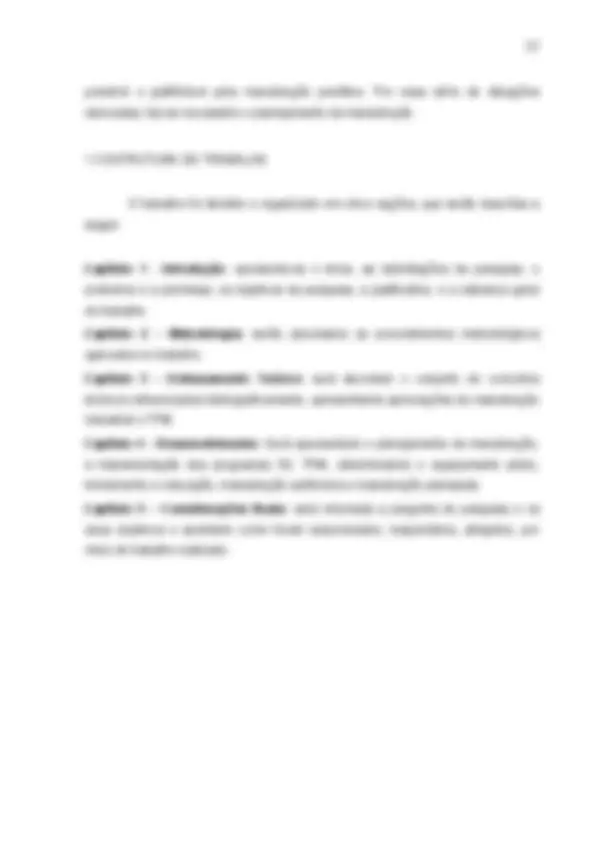
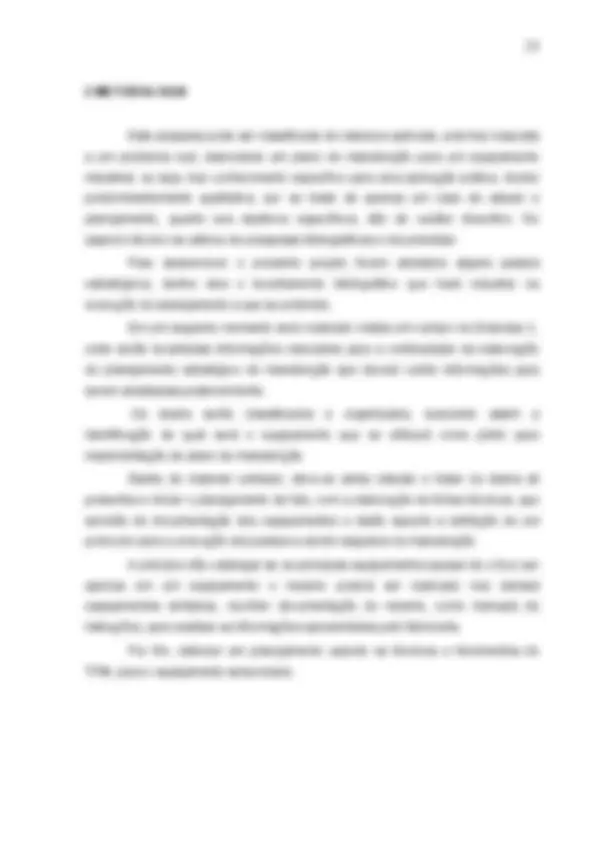
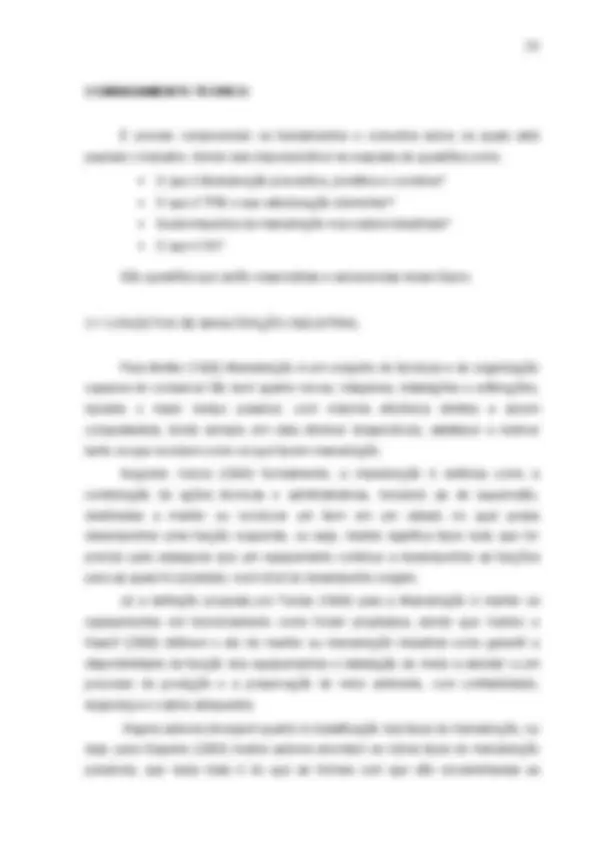

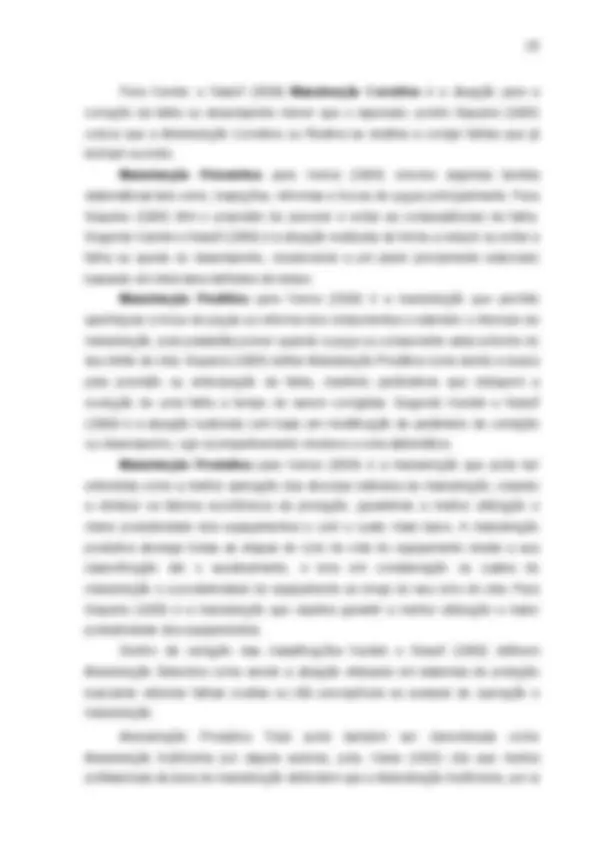
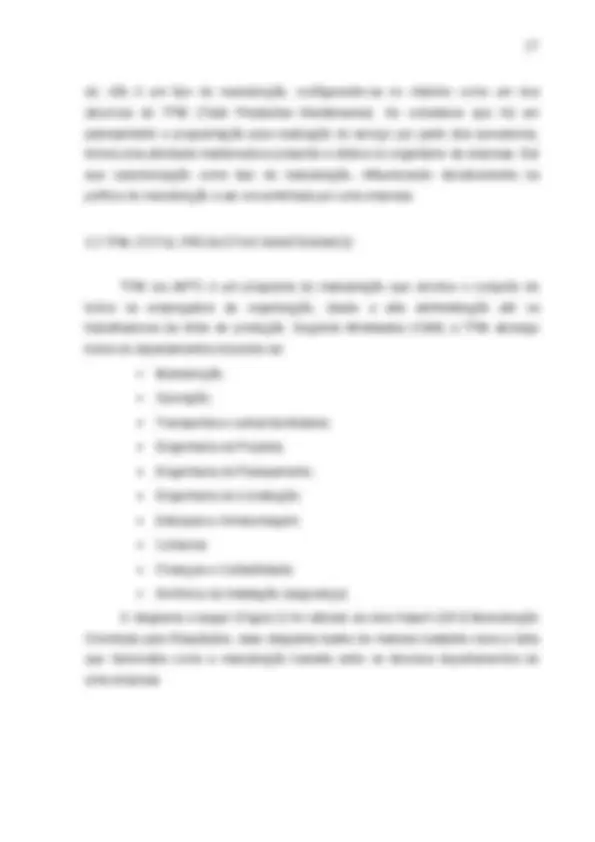
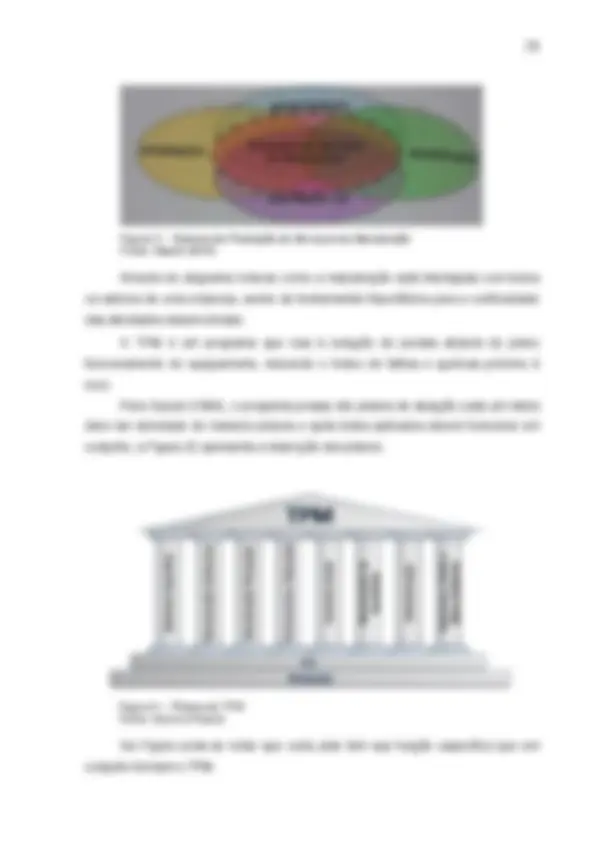
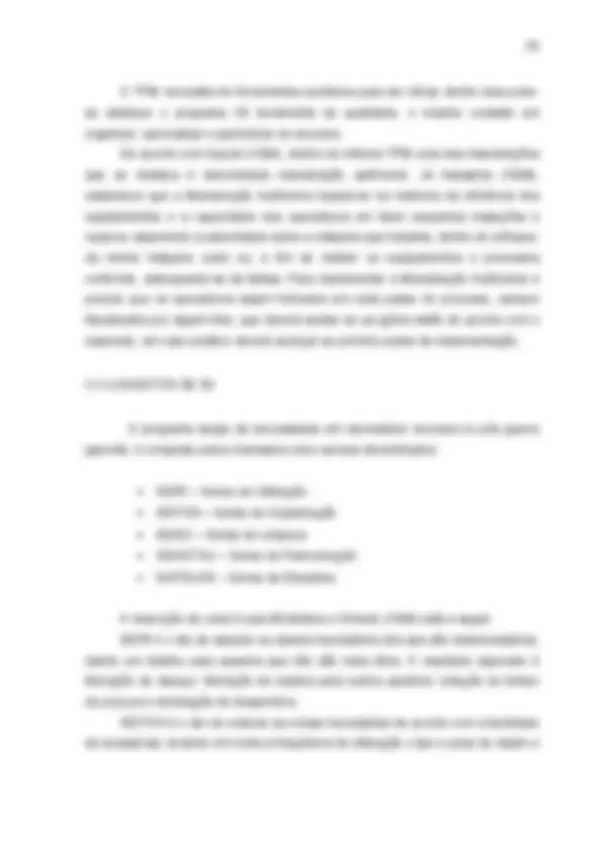
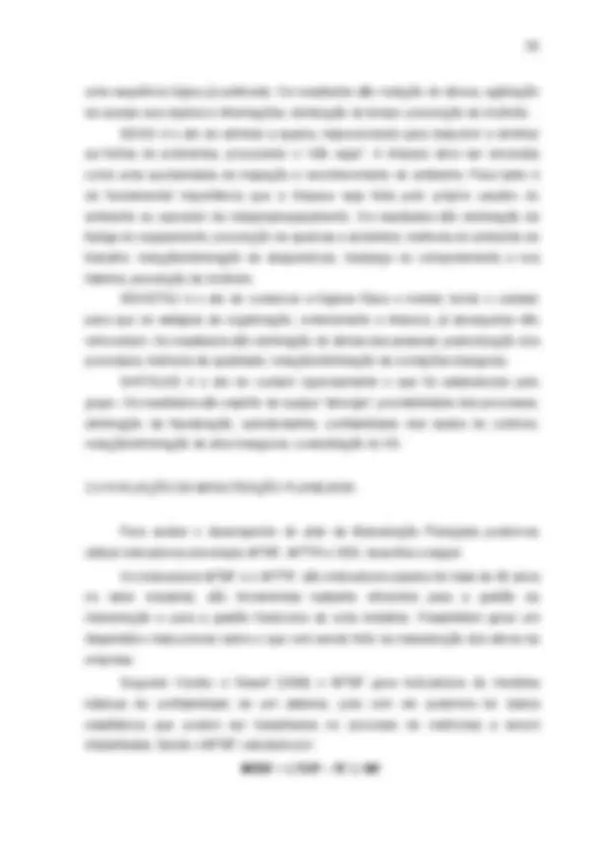
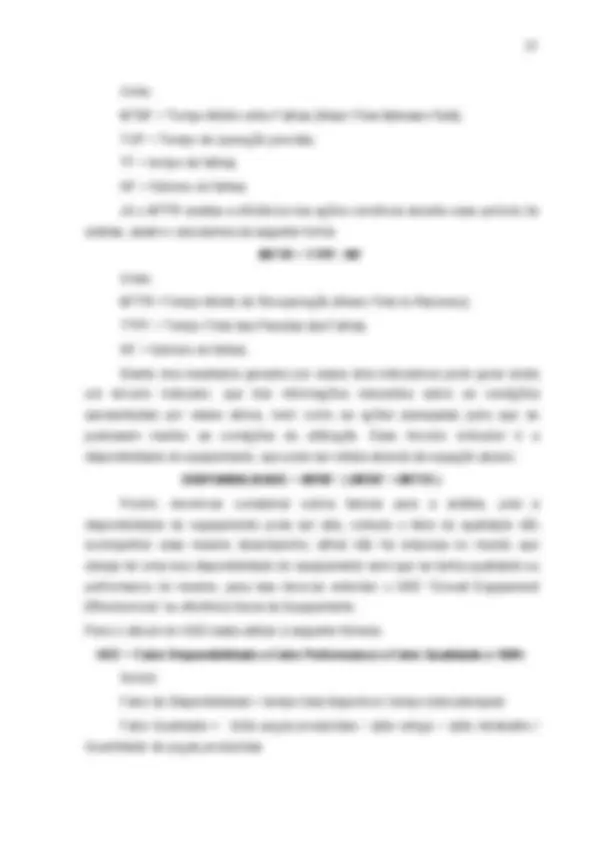
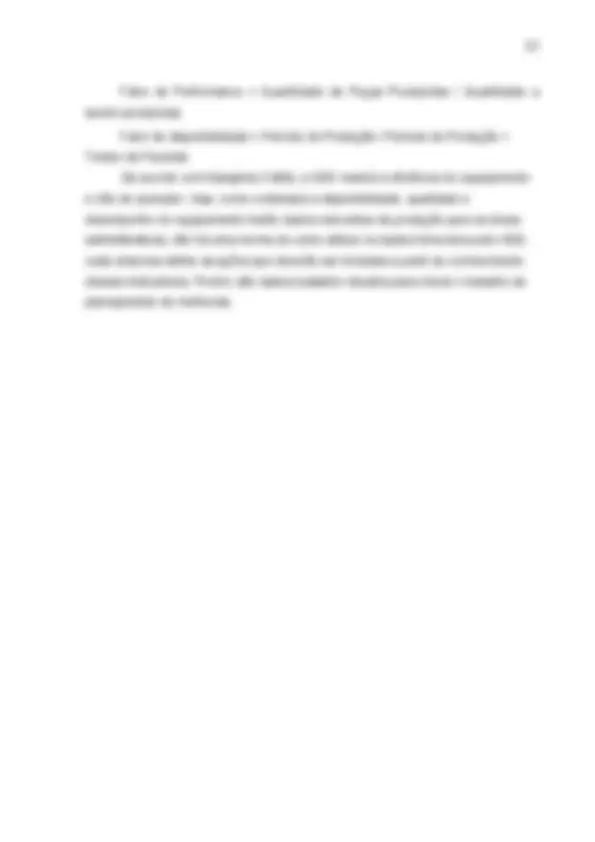
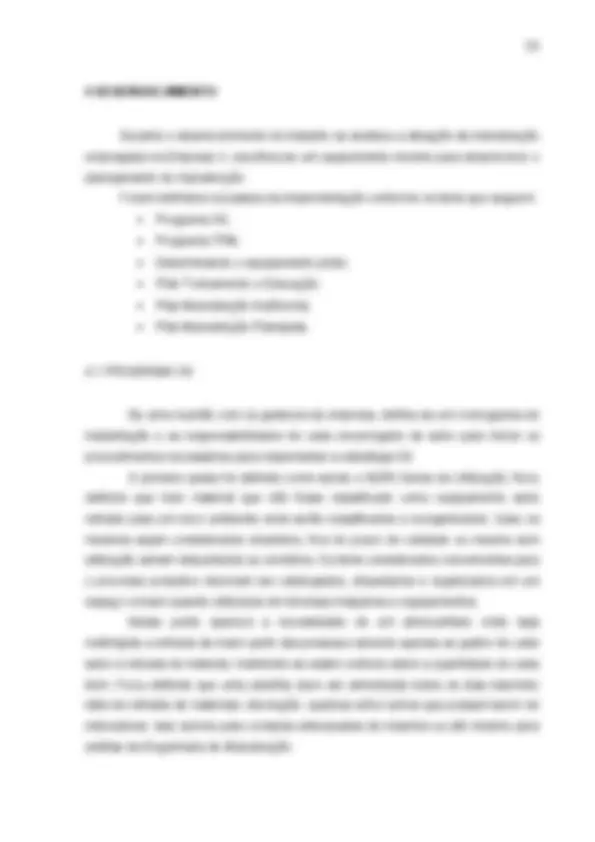
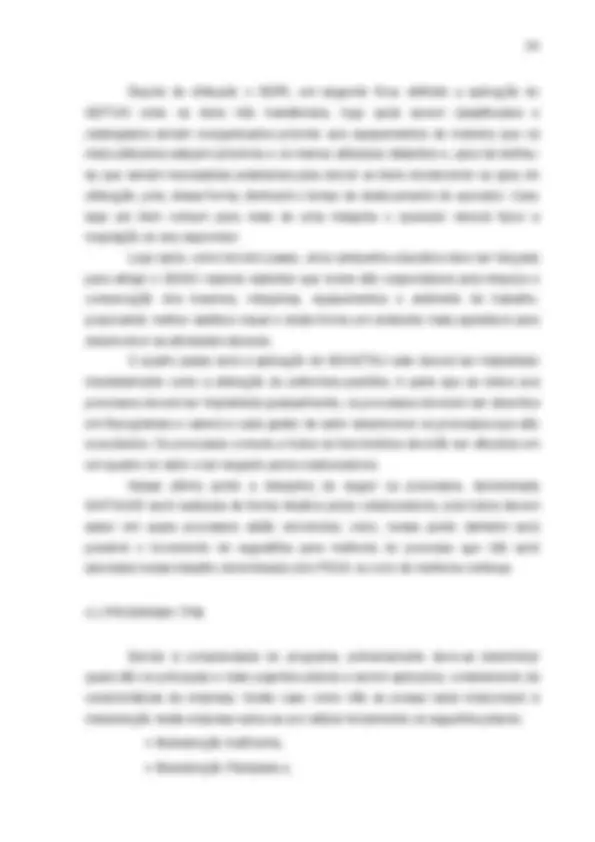
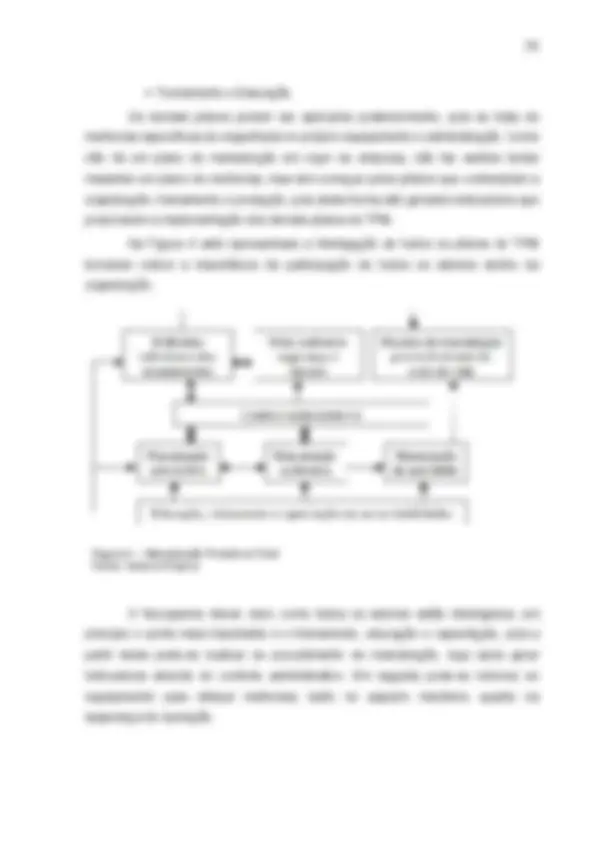
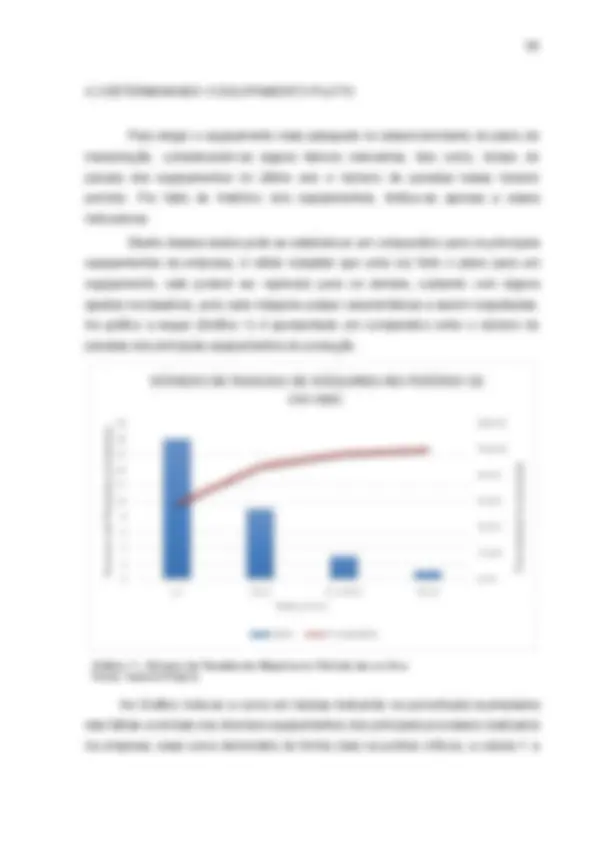
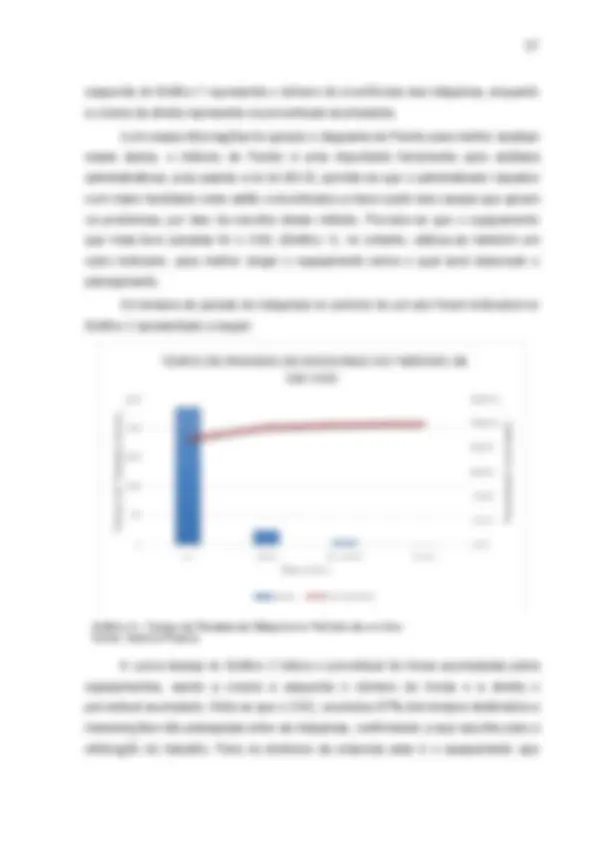
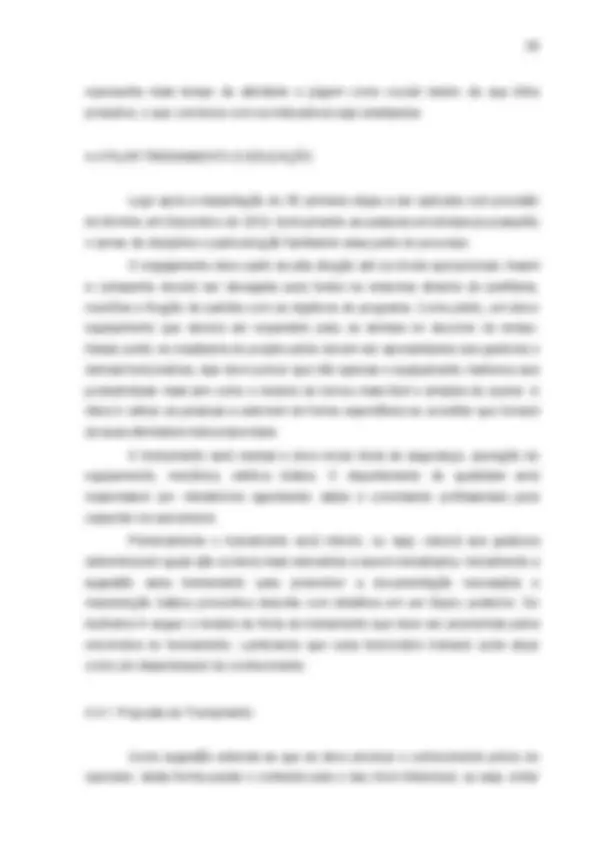
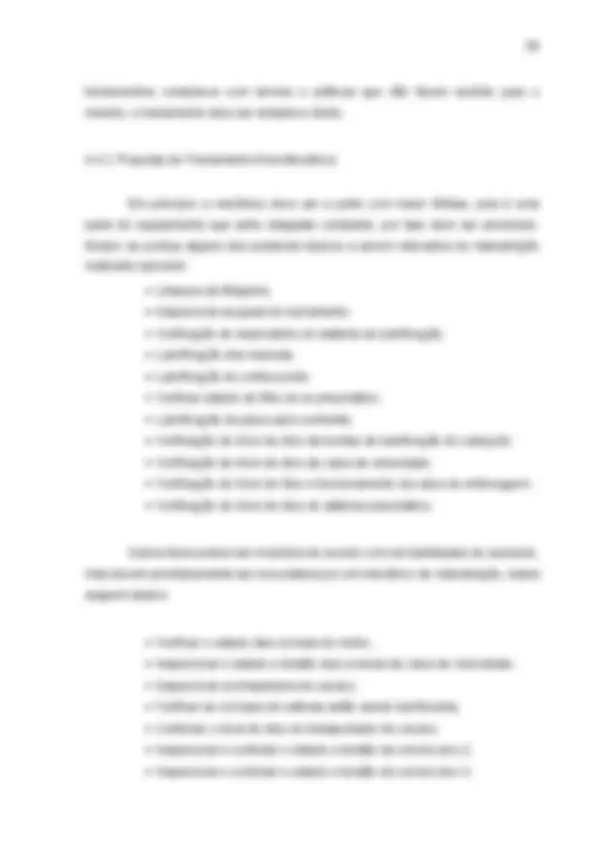
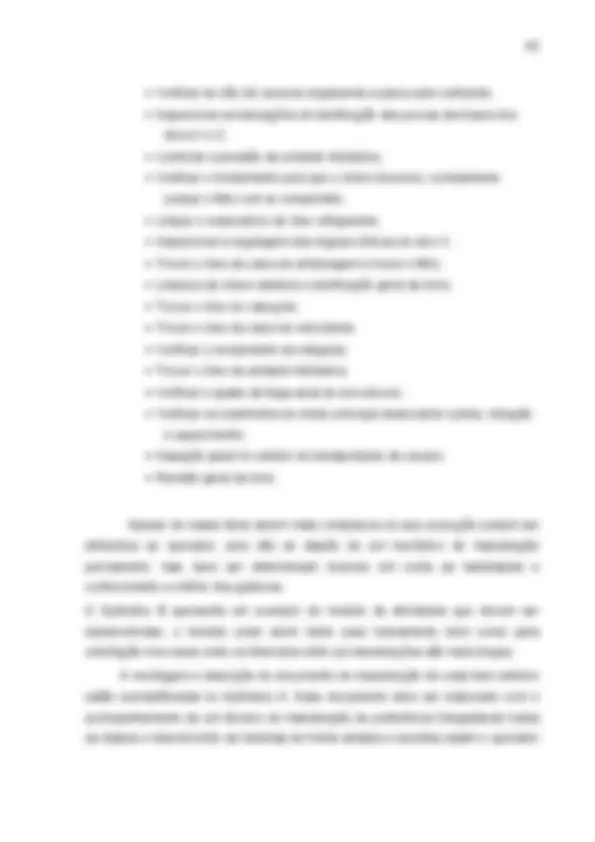
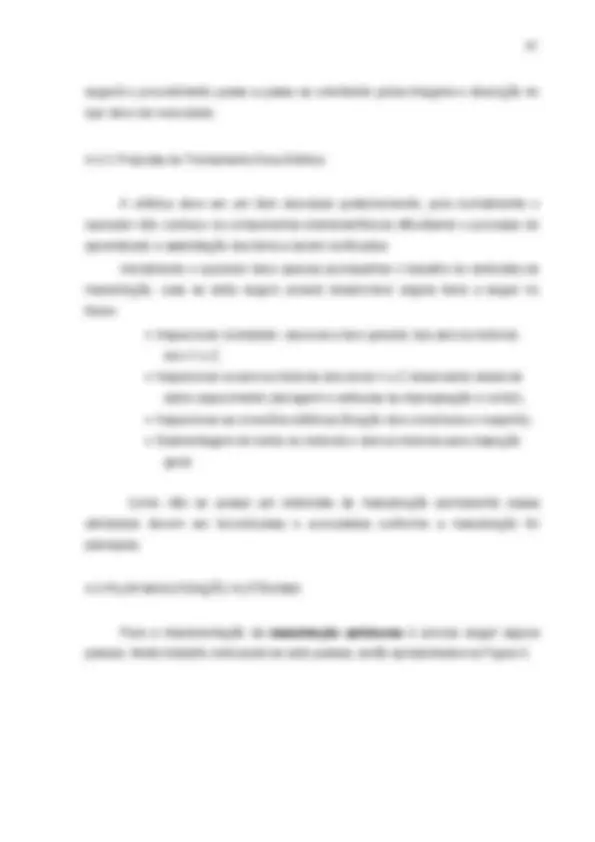
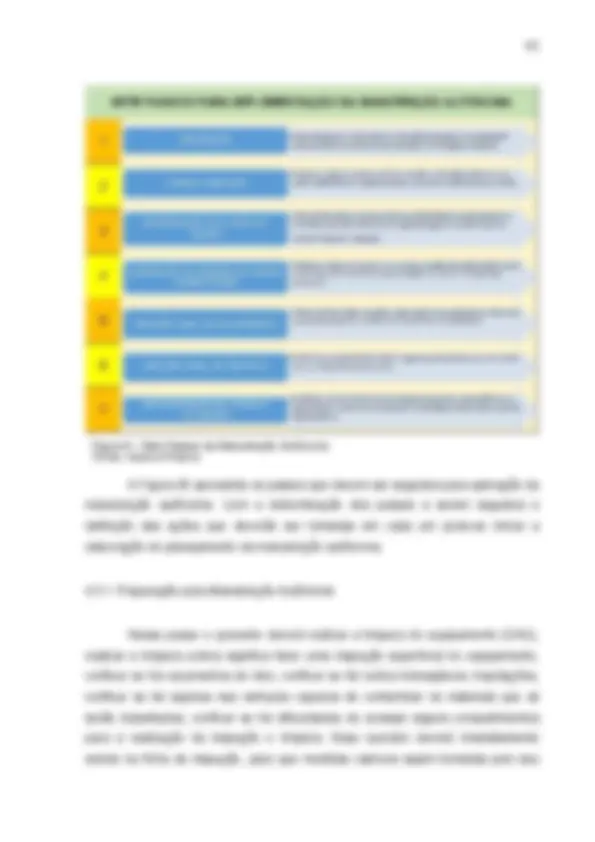
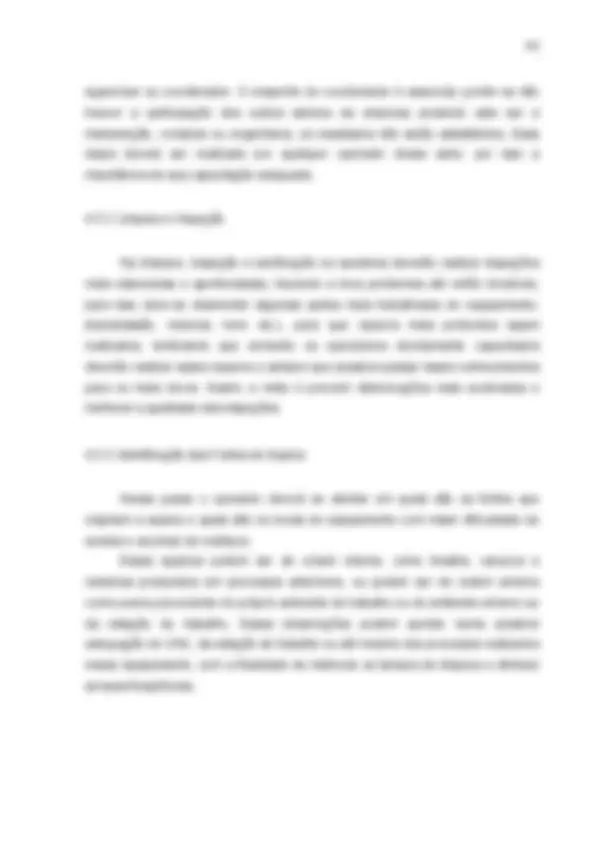
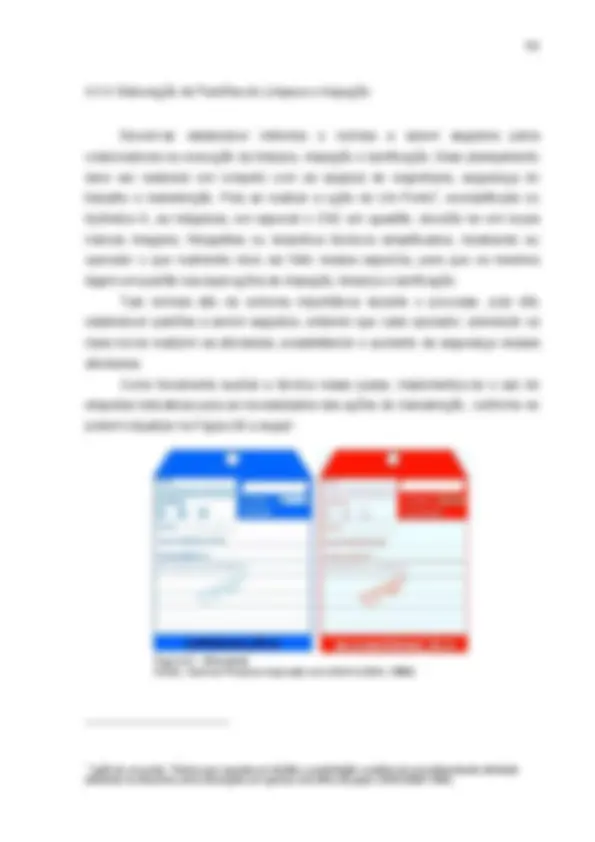
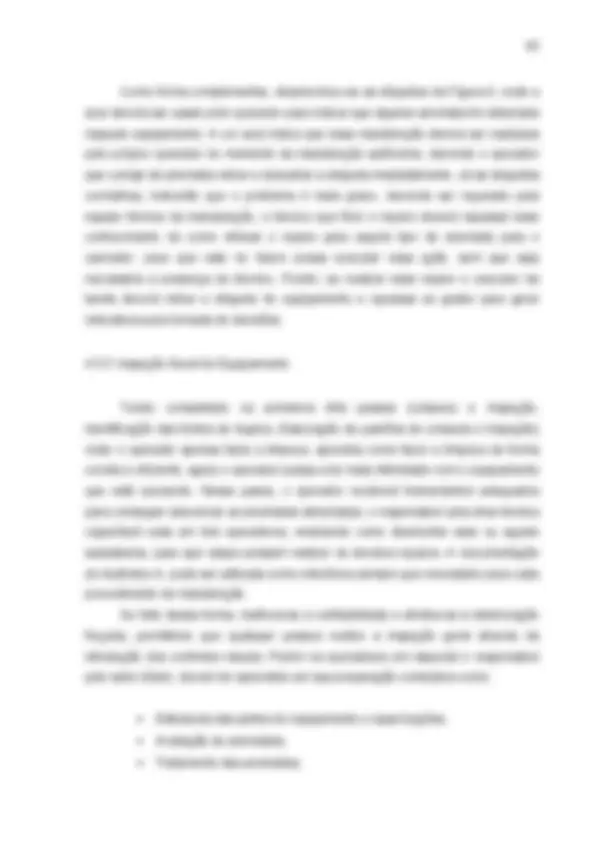
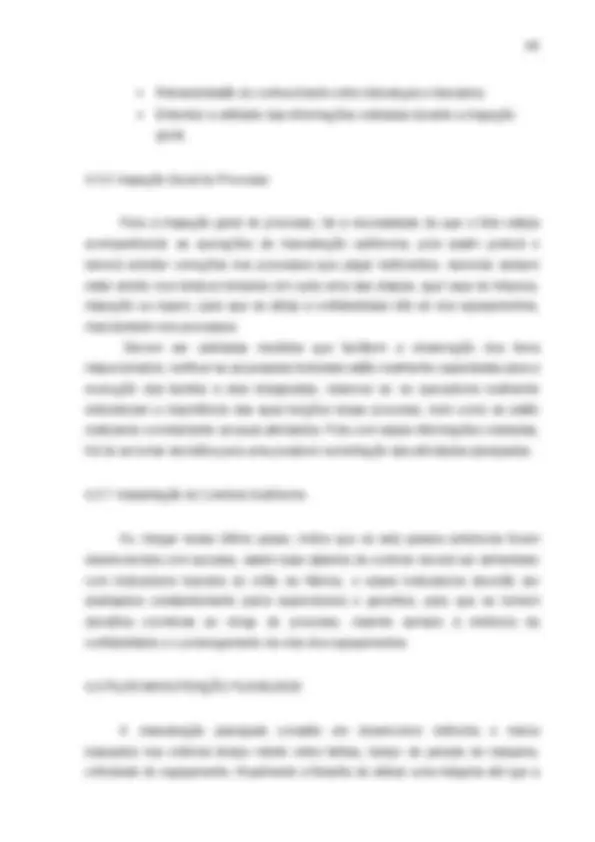
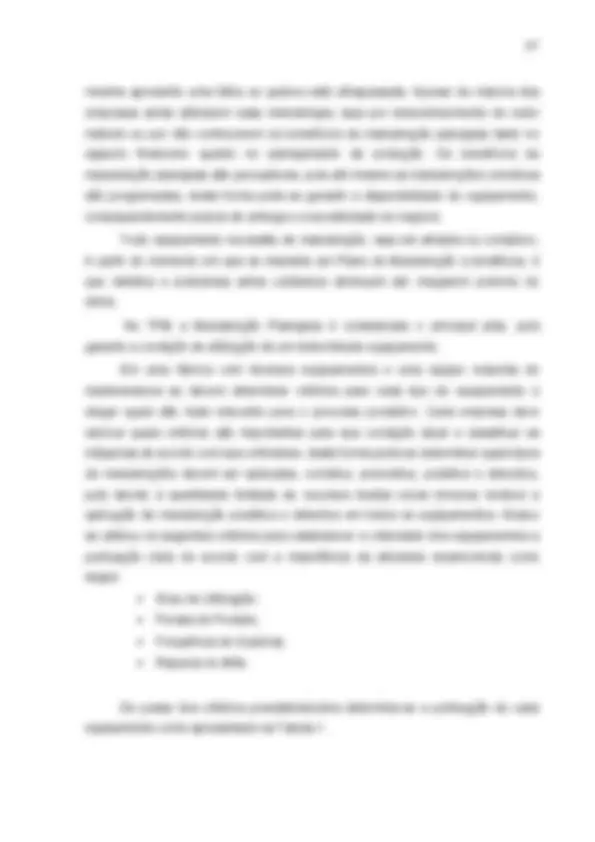
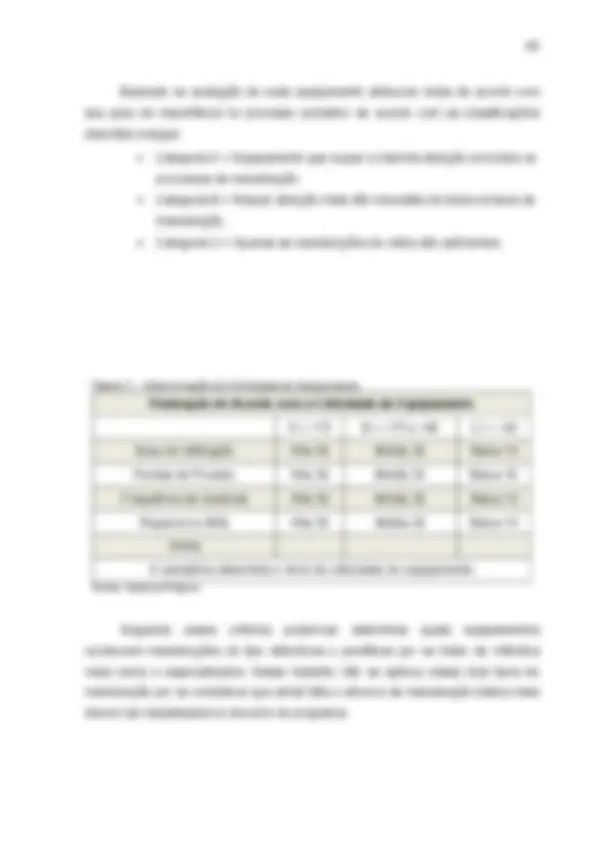
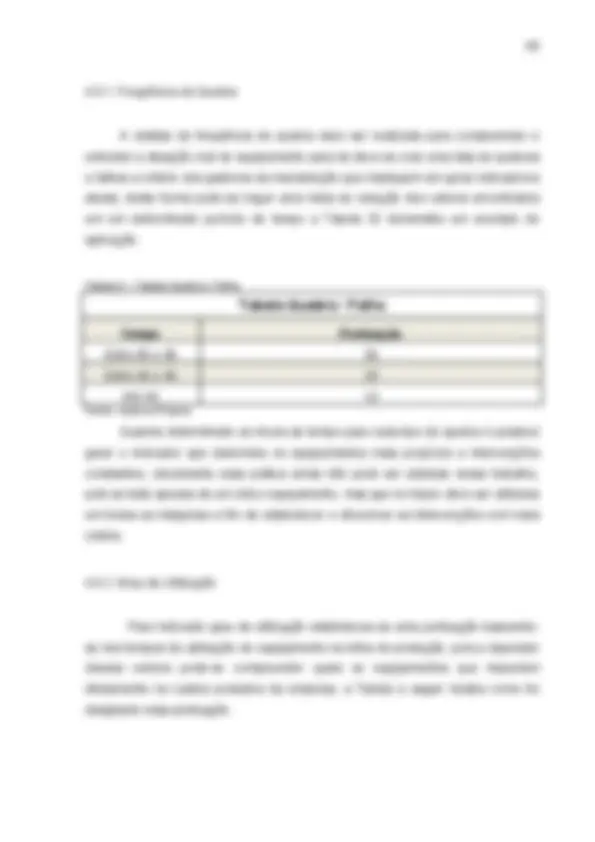
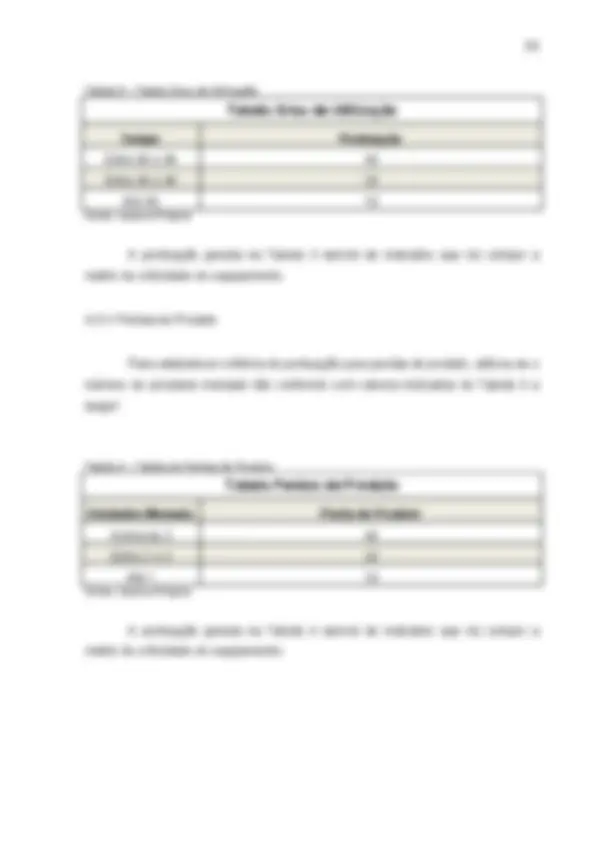
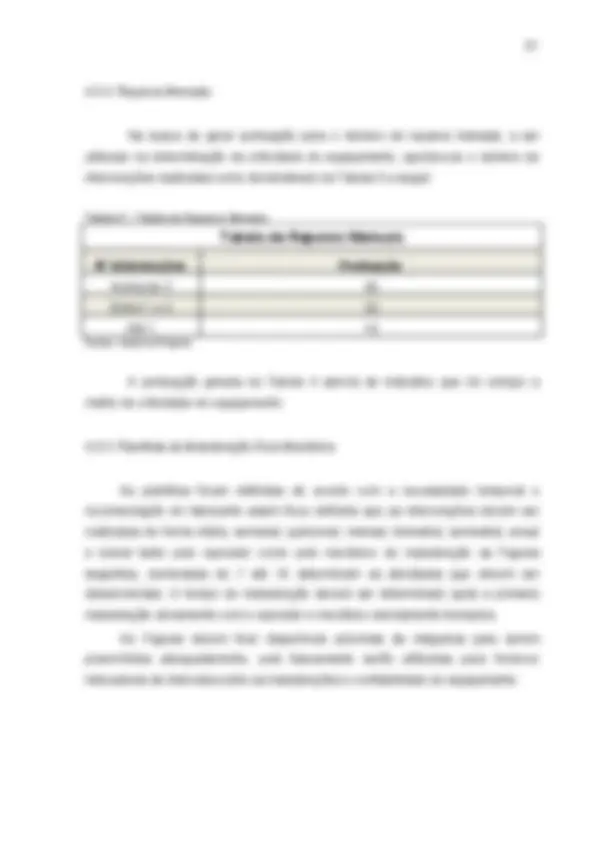
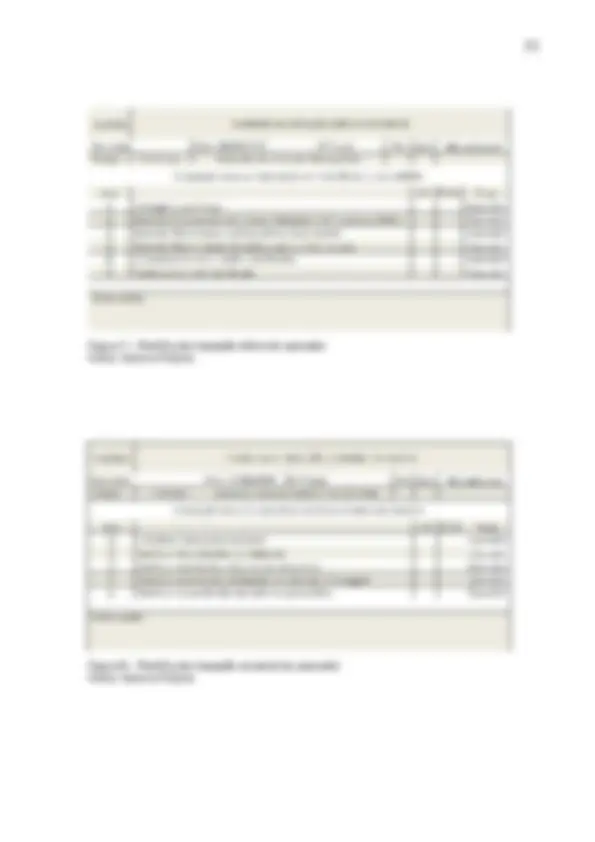
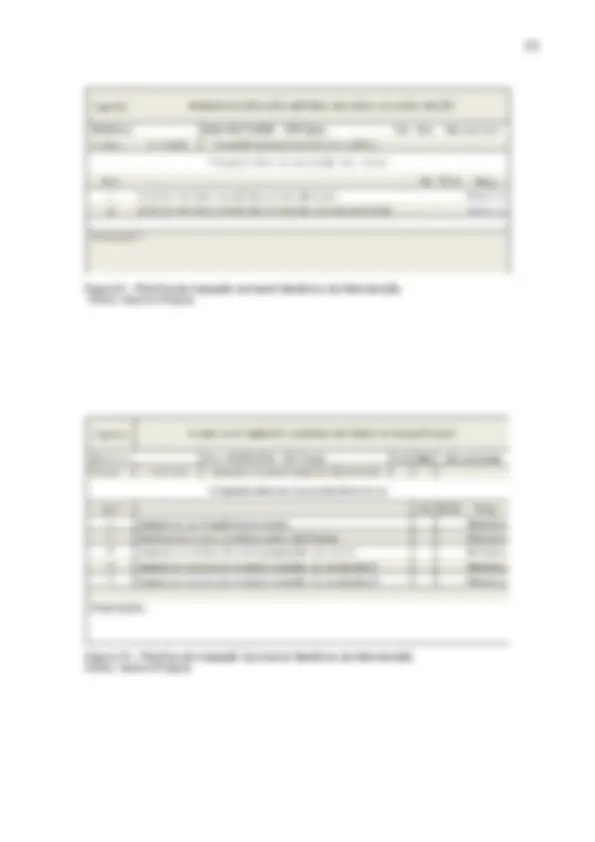
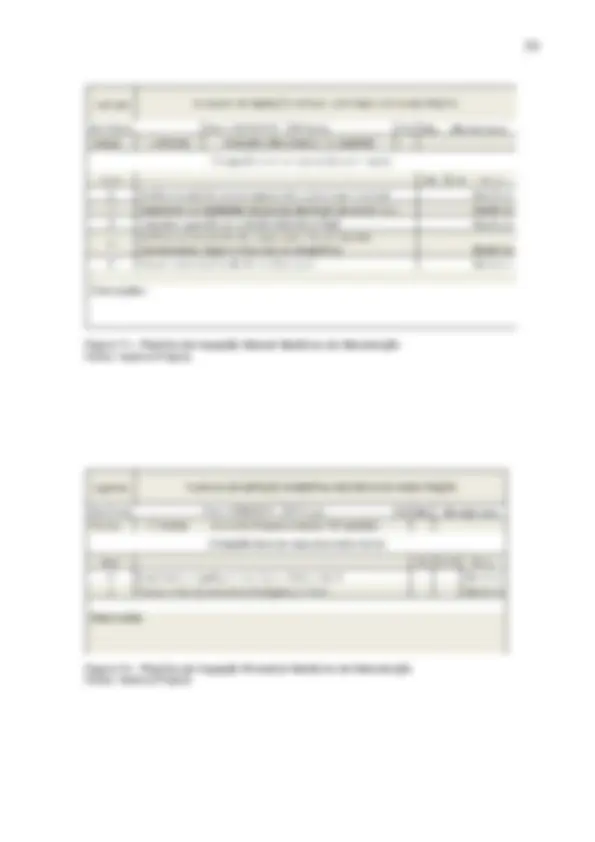
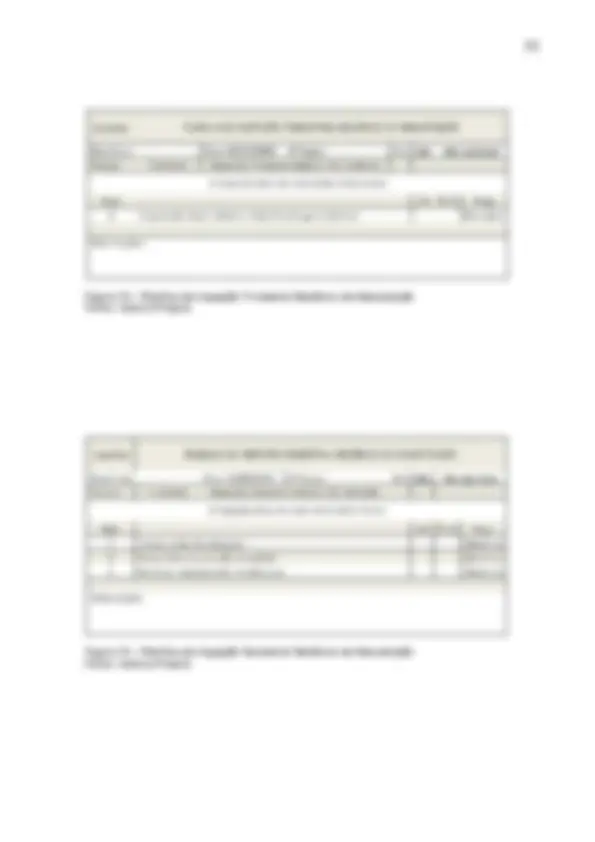
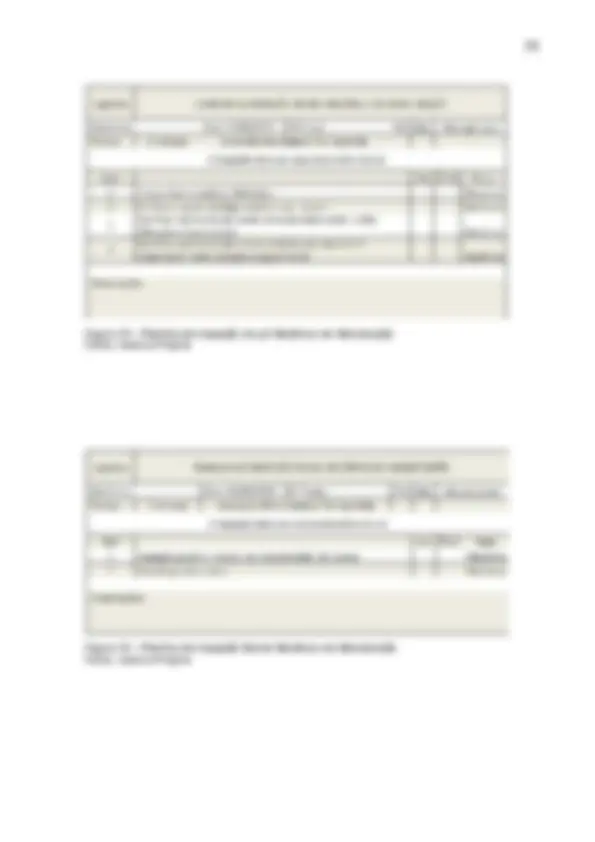
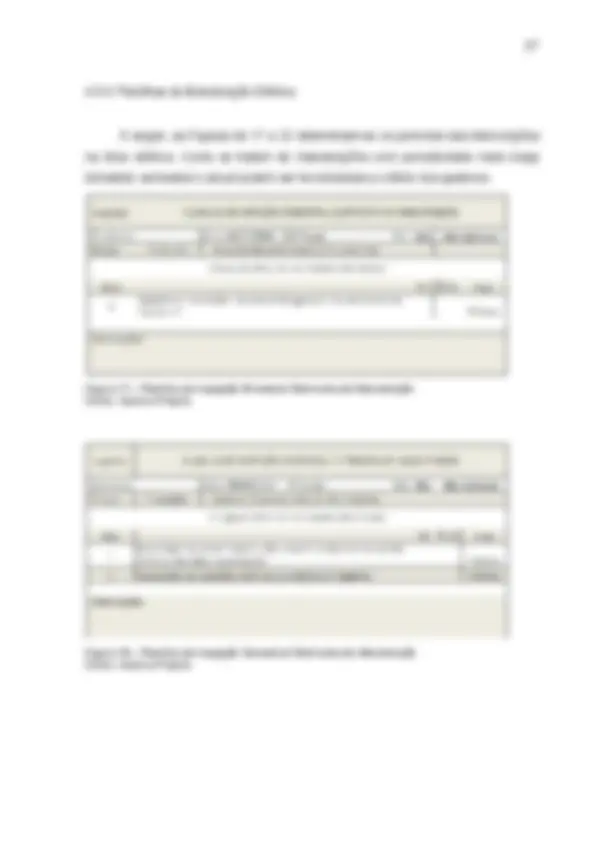
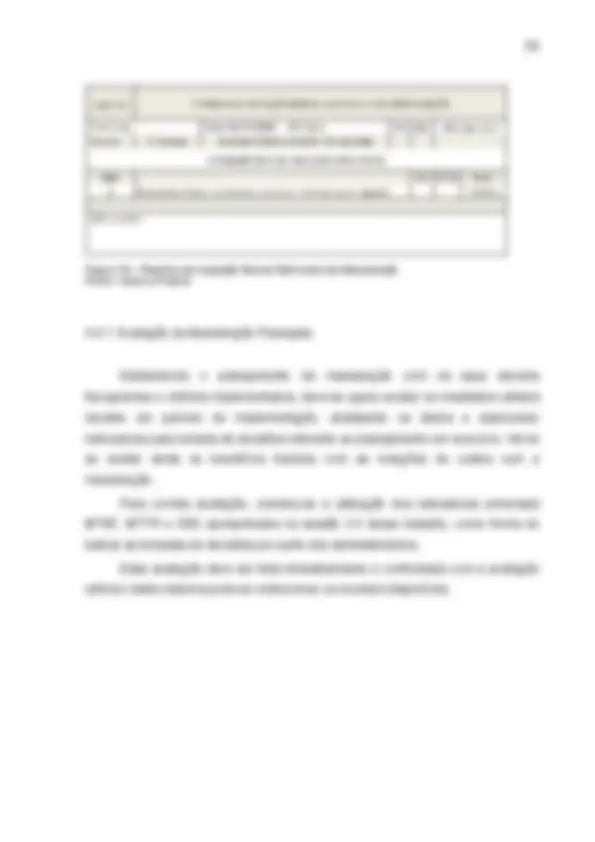
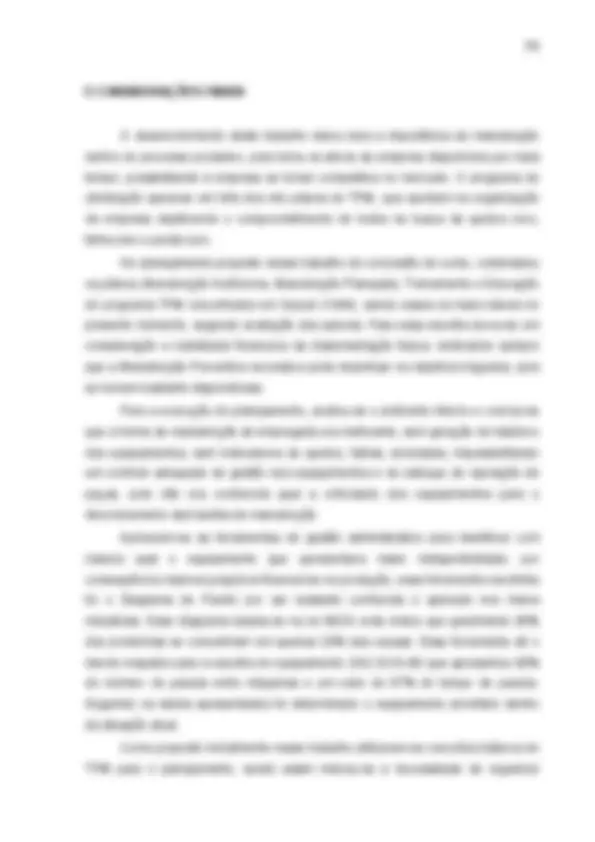
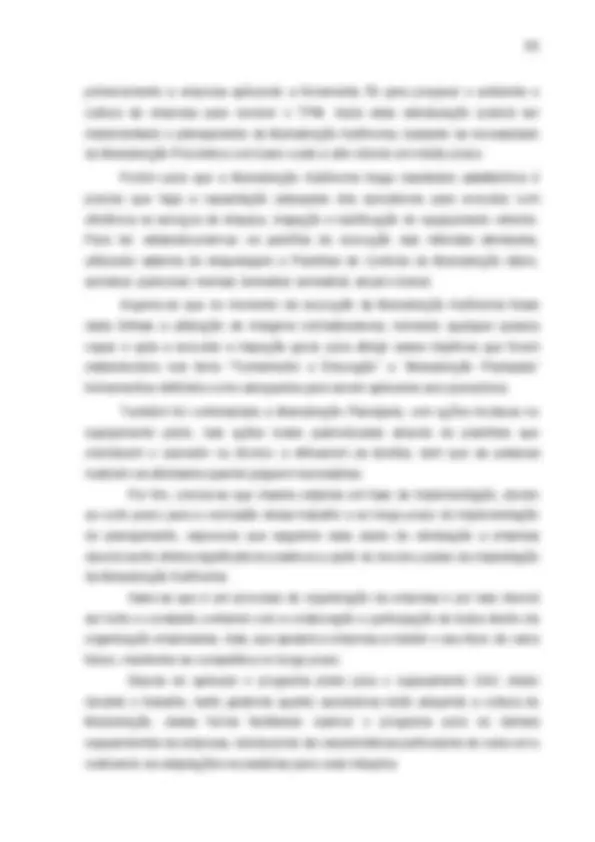
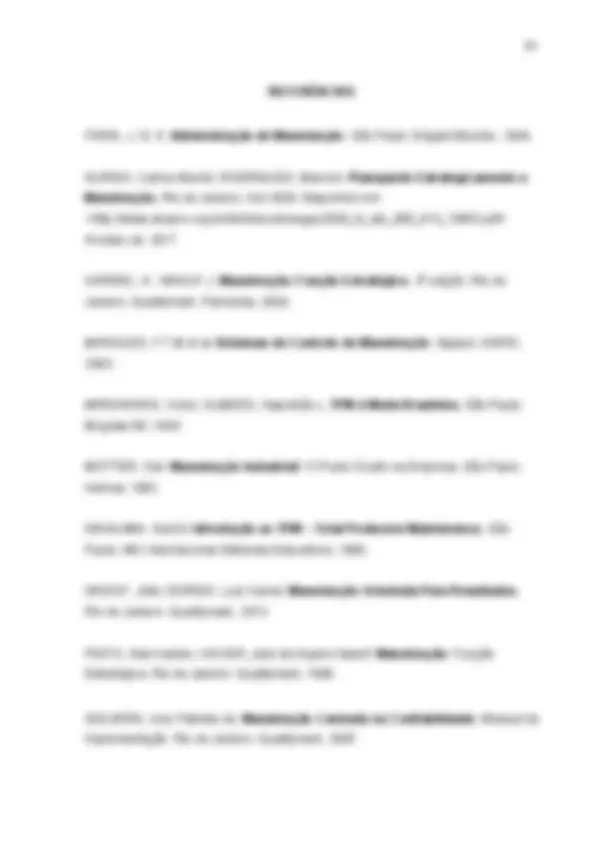
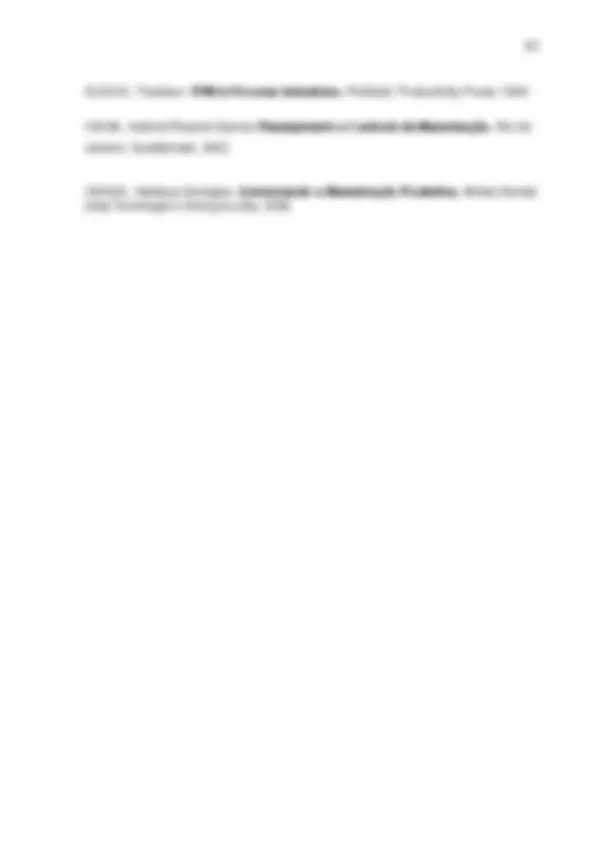
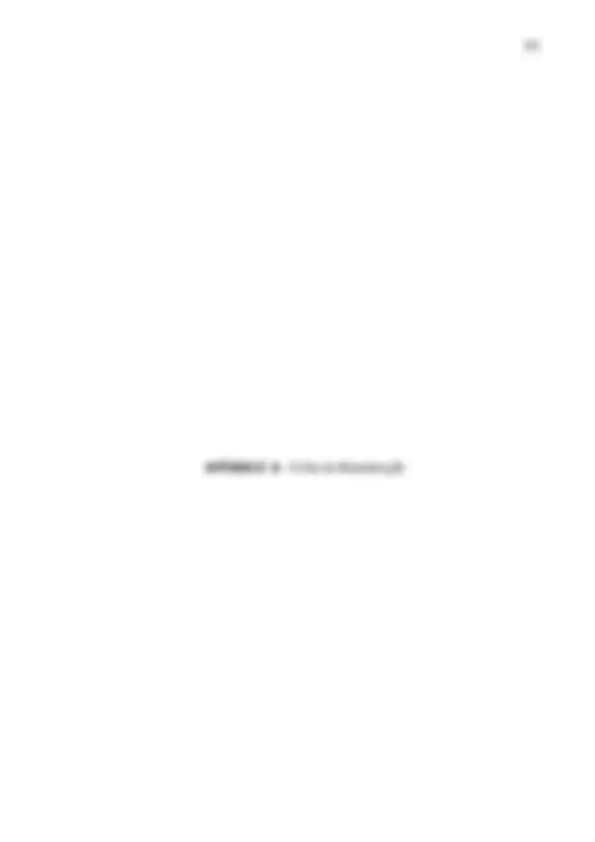
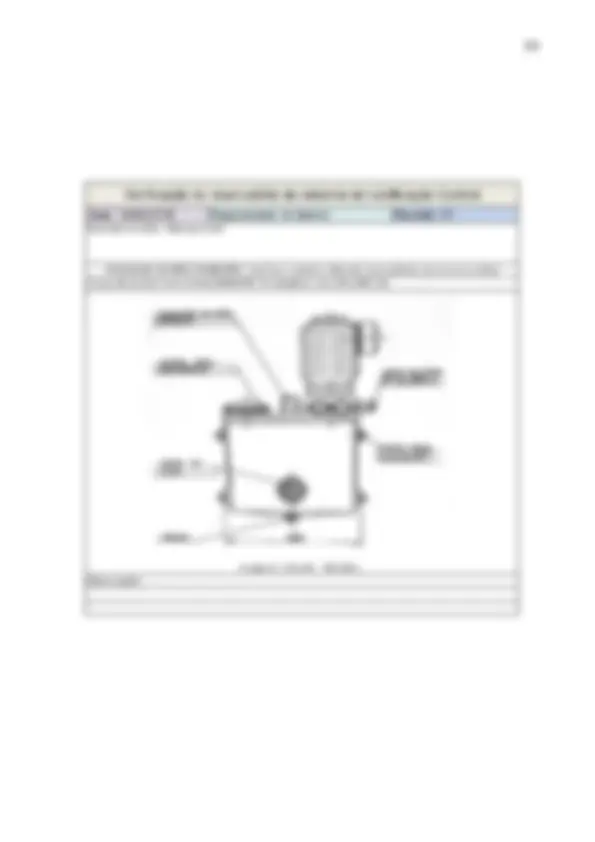
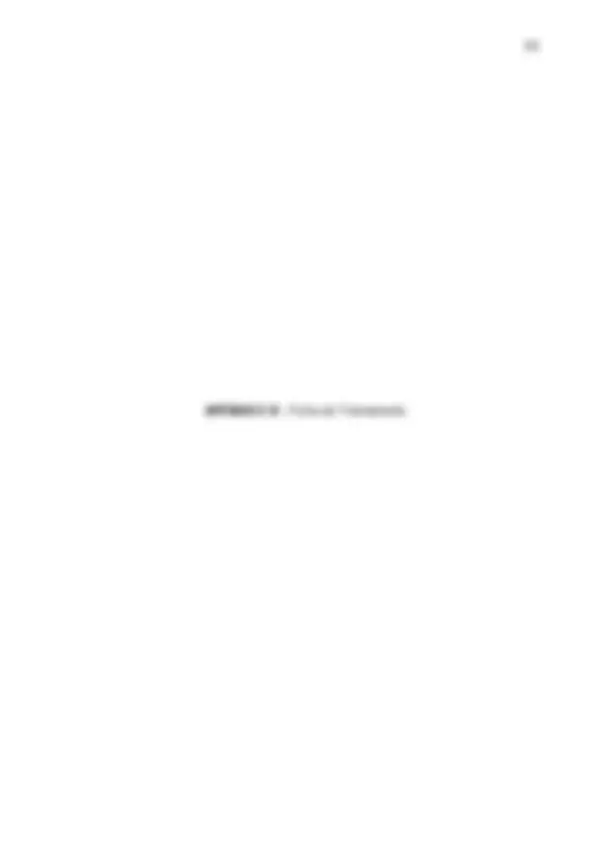
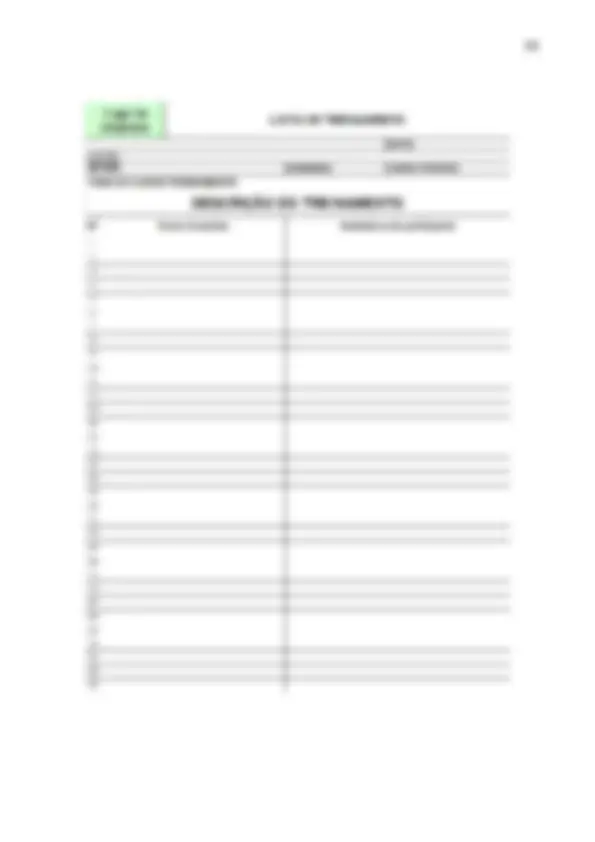
Estude fácil! Tem muito documento disponível na Docsity
Ganhe pontos ajudando outros esrudantes ou compre um plano Premium
Prepare-se para as provas
Estude fácil! Tem muito documento disponível na Docsity
Prepare-se para as provas com trabalhos de outros alunos como você, aqui na Docsity
Os melhores documentos à venda: Trabalhos de alunos formados
Prepare-se com as videoaulas e exercícios resolvidos criados a partir da grade da sua Universidade
Responda perguntas de provas passadas e avalie sua preparação.
Ganhe pontos para baixar
Ganhe pontos ajudando outros esrudantes ou compre um plano Premium
Comunidade
Peça ajuda à comunidade e tire suas dúvidas relacionadas ao estudo
Descubra as melhores universidades em seu país de acordo com os usuários da Docsity
Guias grátis
Baixe gratuitamente nossos guias de estudo, métodos para diminuir a ansiedade, dicas de TCC preparadas pelos professores da Docsity
Maintenance), propondo ações de manutenção preventiva condizentes com a atual ... Figura 9 – Planilha de inspeção semanal Mecânico de Manutenção .
Tipologia: Notas de estudo
1 / 66
Esta página não é visível na pré-visualização
Não perca as partes importantes!
Trabalho de Conclusão de Curso de Graduação, apresentado ao Curso Superior de Tecnologia em Mecatrônica Industrial, dos Departamentos Acadêmicos de Eletrônica e Mecânica, da Universidade Tecnológica Federal do Paraná – UTFPR, como requisito parcial para obtenção do título de Tecnólogo. Orientador: Prof. Me. Osvaldo Verussa Junior CURITIBA 2018
Dedicamos primeiramente a Deus por ser essencial em nossas vidas, autor dos nossos destinos, nosso guia, socorro presente na hora da angustia, aos nossos pais, mães, irmãos e irmãs.
Agradecemos nossas mães que sempre estiveram ao nosso lado e foram nossas maiores incentivadoras, que além de nos darem a vida, nos doaram boa parte das suas, sempre pensando no nosso melhor. Aos nossos pais que batalharam por anos para propiciar a melhor educação para seus filhos. Aos nossos irmão e irmãs que acreditaram em nosso sonho e nos deram forças todos os dias. Eu Antonio, ao meu filho Mateus que respeitou meus momentos de reclusão, obrigado pelo carinho a minha esposa Débora, obrigado por ser minha companheira e entender minha dedicação. Agradecemos aos nossos queridos mestres que se dedicaram a ensinar e compartilhar seus conhecimentos. Um agradecimento especial ao professor mestre Osvaldo Verrusa Junior que fez toda a diferença na orientação deste trabalho. Não podemos deixar de agradecer aqueles que abriram a porta do seu espaço para nos ajudar, em especial o pessoal da empresa. Agradecemos a Deus e todos que contribuíram de forma direta e indireta para realização desse sonho.
CHIQUITO, Anderson; VELOSO, Antonio M.A. Elaboração de um plano de manutenção utilizando conceitos de manutenção produtiva total. 2018 66f. Trabalho de Conclusão de Curso (Curso Superior de Tecnologia em Mecatrônica Industrial), Departamentos Acadêmicos de Eletrônica e Mecânica, Universidade Tecnológica Federal do Paraná. Curitiba, 2018. A manutenção é um fator relevante nos processos produtivos aumentando a confiabilidade, lucratividade e competitividade no mercado. O presente trabalho visa desenvolver o planejamento de manutenção para um equipamento CNC utilizado na empresa X, atuante no ramo metal mecânica da região metropolitana de Curitiba, para tal utilizou-se de ferramentas de gestão e conceitos de TPM (Total Productive Maintenance), propondo ações de manutenção preventiva condizentes com a atual situação da empresa e treinamento para fomentar a Manutenção Autônoma. Ao aplicar o diagrama de Pareto tornou-se possível a visualização do equipamento piloto com 60% dos números de parada entre máquinas e 87% do tempo total de parada de máquina, espera-se que a partir da implementação da Manutenção Autônoma a empresa já alcance resultados positivos, que ajudara a empresa a manter seu fluxo de caixa futuro, mantendo-se competitiva no longo prazo. Palavras chave: Manutenção. Manutenção Produtiva Total. Manutenção Planejada.
CHIQUITO, Anderson; VELOSO, Antonio M.A. Elaboration of a maintenance plan using concepts of total productive maintenance. 66f 2018. Trabalho de Conclusão de Curso (Curso Superior de Tecnologia em Mecatrônica Industrial), Departamentos Acadêmicos de Eletrônica e Mecânica, Universidade Tecnológica Federal do Paraná. Curitiba, 2018. . Maintenance is a relevant factor in the production processes, increasing the reliability, profitability and competitiveness in the market. The present work aims to develop the maintenance planning for a CNC equipment used the company X, active in the metal mechanic branch of the metropolitan region of Curitiba, for this was used of management tools and concepts of TPM (Total Productive Maintenance), proposing preventive maintenance actions consistent with the current situation of the company and training to promote Autonomous Maintenance. By applying the Pareto diagram it became possible to visualize the pilot equipment with 60% of the stop numbers between machines and 87% of the total time of machine stop, it is expected that from the implementation of the Autonomous Maintenance the company already reaches positive results that will help the company to maintain its future cash flow while remaining competitive in the long run. Keywords: Maintenance. Total productive maintenance. Planned Maintenance.
Gráfico 1 – Número de Paradas de Máquina no Período de um Ano ....................... 36 Gráfico 2 – Tempo de Paradas de Máquina no Período de um Ano ......................... 37
aumento da disponibilidade dos equipamentos e a confiabilidade tanto dos equipamentos quanto dos processos. Os oito pilares são representados por:
Figura 1 – Estrutura Hierárquica Organizacional Fonte: Autoria Própria A Figura 1 demonstra como normalmente está disposto o organograma da Empresa X, este organograma aparenta em pirâmide onde a base representa o chão de fábrica, o nível operacional e o topo a gerência que é responsável pelo planejamento e decisões estratégicas. Esse processo de implementação do TPM é demorado, porém a partir da etapa de implementação do pilar de Manutenção Autônoma a empresa já começa a sentir efeitos positivos significativos. Os indicadores gerados pelo TPM são divididos em grupos, chamados de PQCDSM, cujo seus respectivos significados estão elencados a seguir, trazendo consigo os elementos mensurados. P – Produtividade Aumento de produção por operário Aumento da disponibilidade operacional das máquinas Q – Qualidade Redução do número de produtos defeituosos; Redução do número de reclamações internas e externas. C - Custo Redução do custo da manutenção ao longo do tempo; Redução do volume estocado. D - Entrega (delivery) Aumento do cumprimento de prazo.
possuem multas de grande valor registradas em contrato e, isso pode comprometer a saúde financeira da empresa ou até mesmo levar a interrupção das atividades. A concorrência cada vez mais forte e acentuada também é um fator a ser ponderado, pois uma empresa que possui equipamentos parados deixa de produzir aumentando seus custos tornando-se insustentável á longo prazo. 1.3 OBJETIVOS Para se obter resultados positivos neste projeto, definiu-se o objetivo geral e, foram estabelecidas algumas metas intermediárias, o que se chamou de objetivos específicos, que são apresentados em seguida: 1.3.1 Objetivo Geral Desenvolver um planejamento estratégico de manutenção utilizando conceitos do TPM. 1.3.2 Objetivo Específico Levantamento das necessidades atuais; Avaliar o ambiente interno; Identificar os tipos de equipamentos e definir o mais adequado para implementar o plano de manutenção; Organizar o ambiente através do programa 5s; Elaboração de procedimentos para execução das atividades mantenedoras; Identificar as principais ameaças de falhas; Desenvolver um plano de manutenção Preventiva; Desenvolver um plano de manutenção Corretiva Planejada; Definir metas de produtividade e qualidade operacional.
O planejamento estratégico de manutenção, enquanto ferramenta de gestão, busca garantir a eficiência produtiva e qualidade nos processos industriais, uma vez que os equipamentos em perfeitas condições operacionais impedem que haja perda de tempo, gastos desnecessários, prejuízo com retrabalho, e desperdícios. Para Motter (1992), organizar para corrigir é muito caro. Organizar para zerar defeitos é o certo. Organizar para a prevenção de erros é o desafio que todos devem estar capacitados a enfrentar. Toda vez que se fala em fazer certo pela primeira vez e cada vez melhor um dos conceitos de qualidade, significa dizer que, organizar um sistema produtivo onde a prevenção de erros é a meta principal. Atualmente existem ferramentas voltadas à manutenção; várias delas possuem aspectos relevantes para determinado segmento, ou seja, confiabilidade, produtividade entre outros, considerando a necessidade do equipamento estar disponível por longos períodos e ser essencial no processo produtivo julgou-se mais adequada a Manutenção Produtiva Total, pois possui como objetivo principal a disponibilidade do equipamento. Manutenção Produtiva Total (MPT) é um programa de manutenção que envolve conceitos de manutenção de equipamentos e instalações, que tem como objetivo aumentar a produção, ao mesmo tempo, a moral dos funcionários e a satisfação no ambiente de trabalho (MARQUES, 2003). Por isso para a elaboração do planejamento da manutenção desenvolvida nesse trabalho, pretendeu-se contemplar as três grandes modalidades da manutenção (Preventiva, Preditiva, Corretiva), uma vez, que a Empresa X, apresenta apenas a manutenção corretiva de forma terceirizada, prejudicando a sua eficiência produtiva e comprometendo a sua viabilidade de negócio futuro. Como o foco da TPM é manutenção preventiva participativa, deve-se minimizar as manutenções corretivas não planejadas para manter a fluidez das operações, não prejudicando o equilíbrio financeiro da empresa. Dessa forma, atender aos clientes com pontualidade, de modo a gerar uma confiança no mercado e, portanto, o fluxo de caixa futuro que manterá a empresa ativa.