
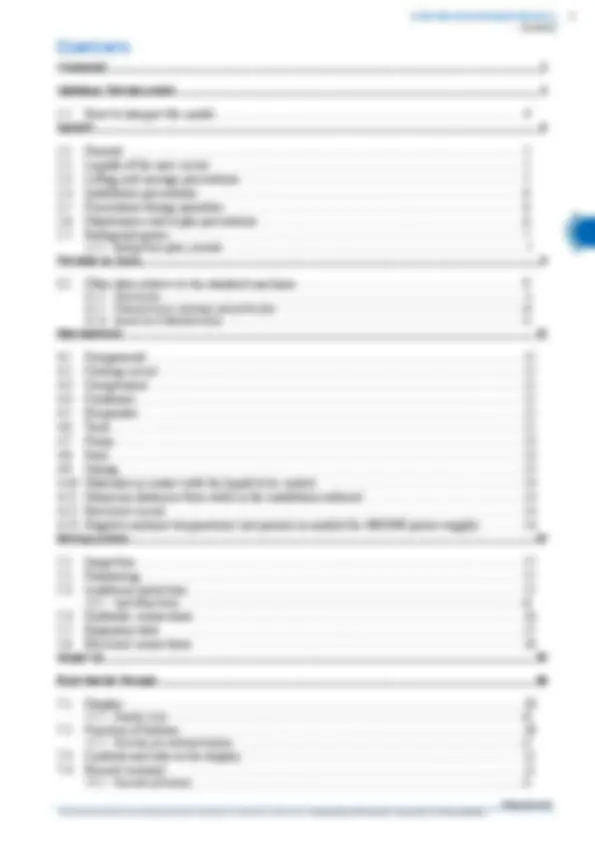
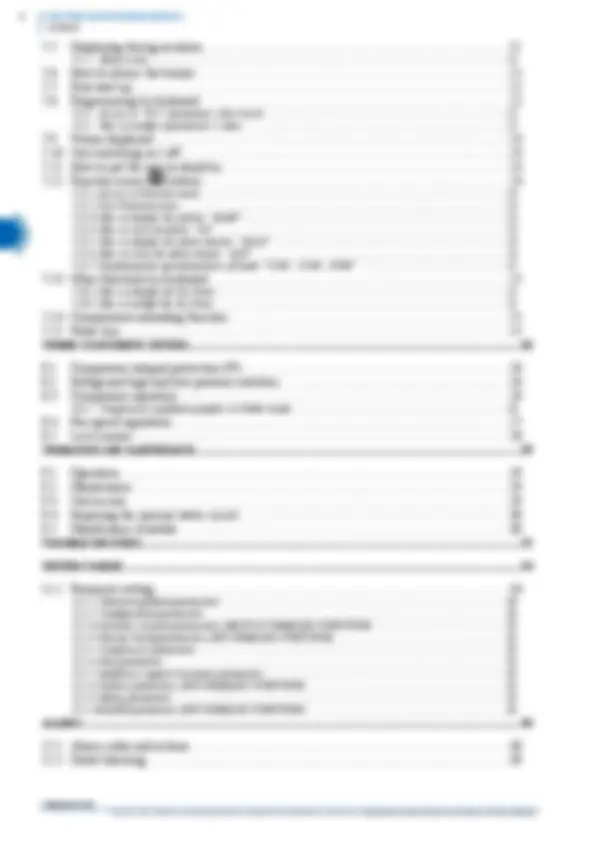
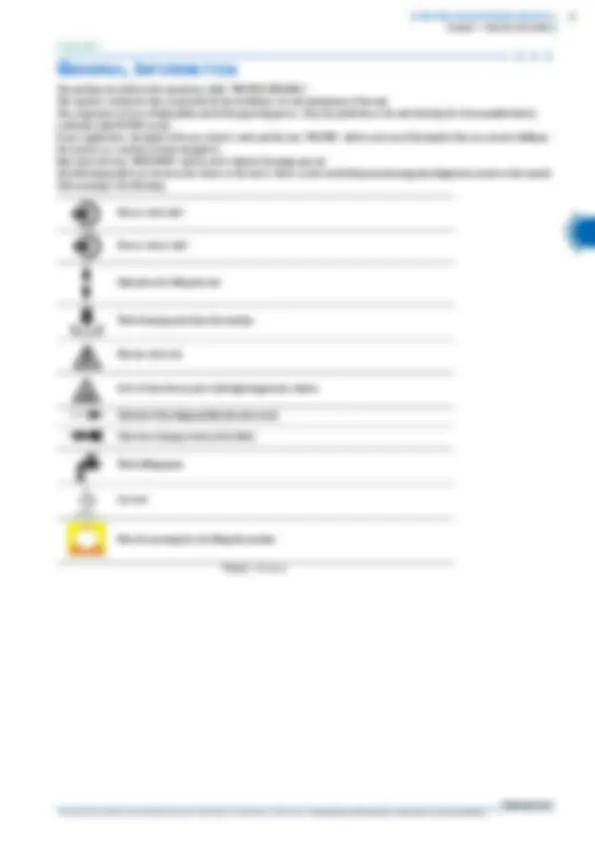

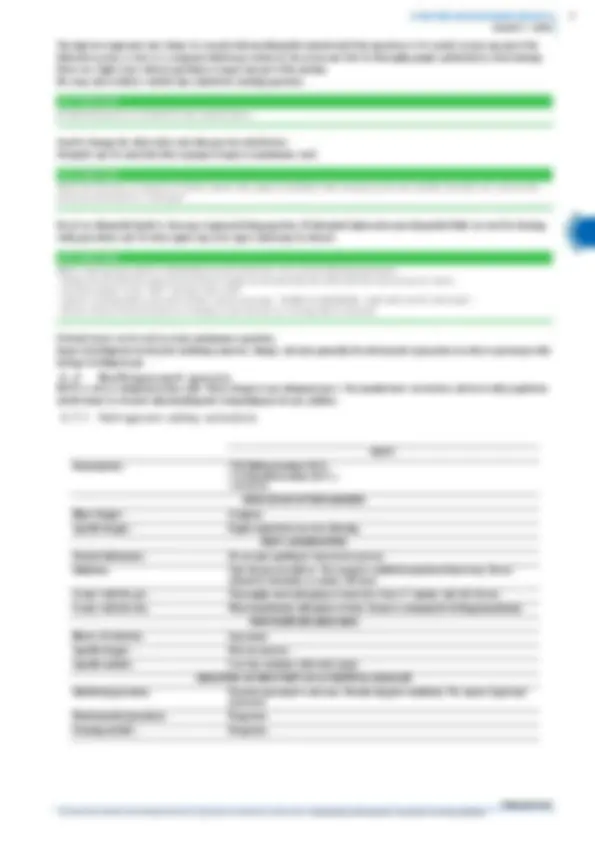
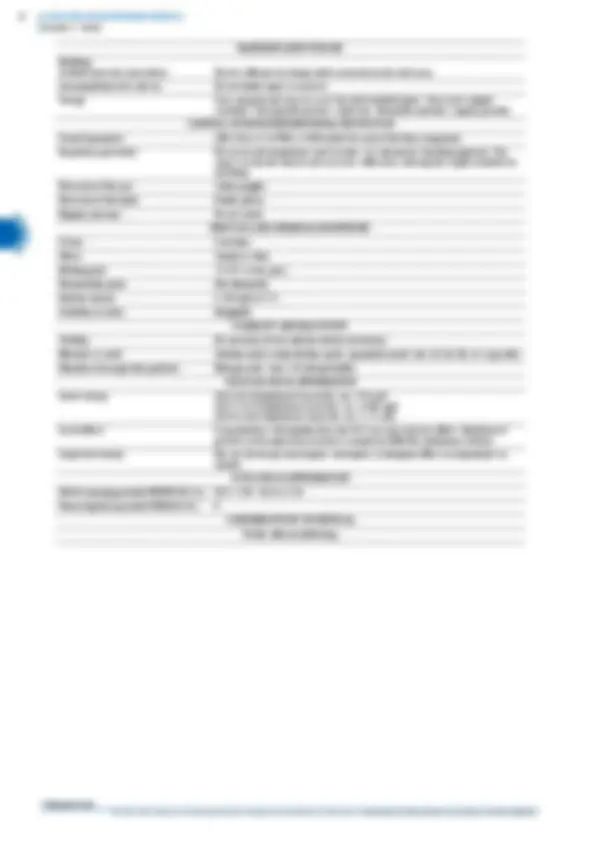
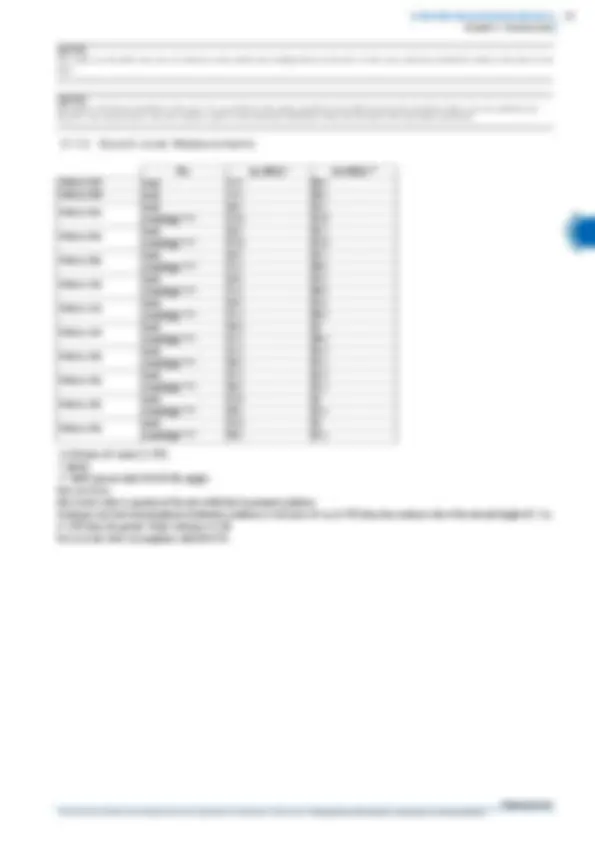
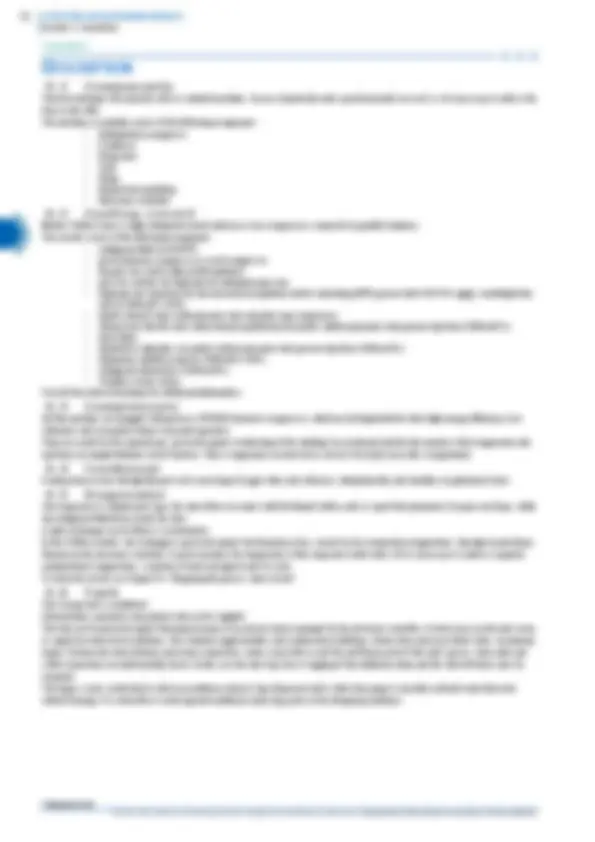
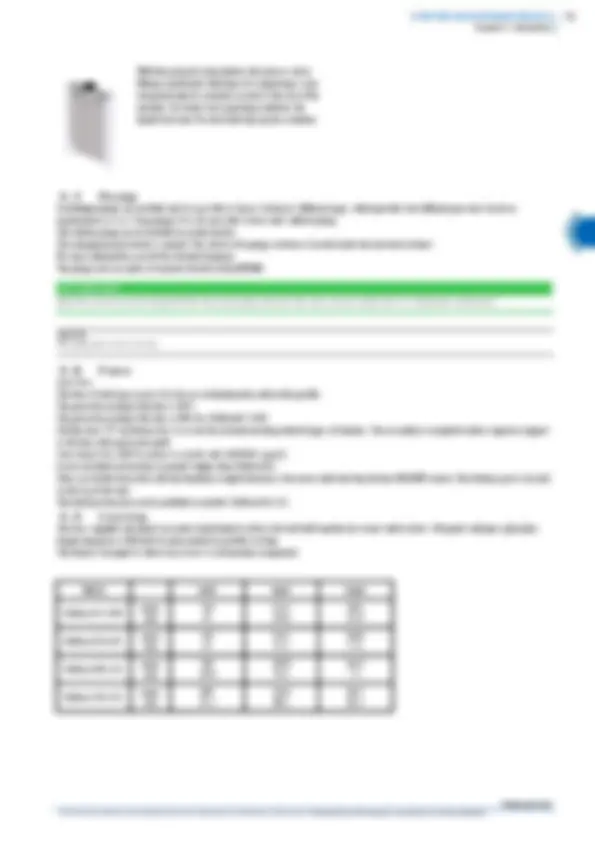
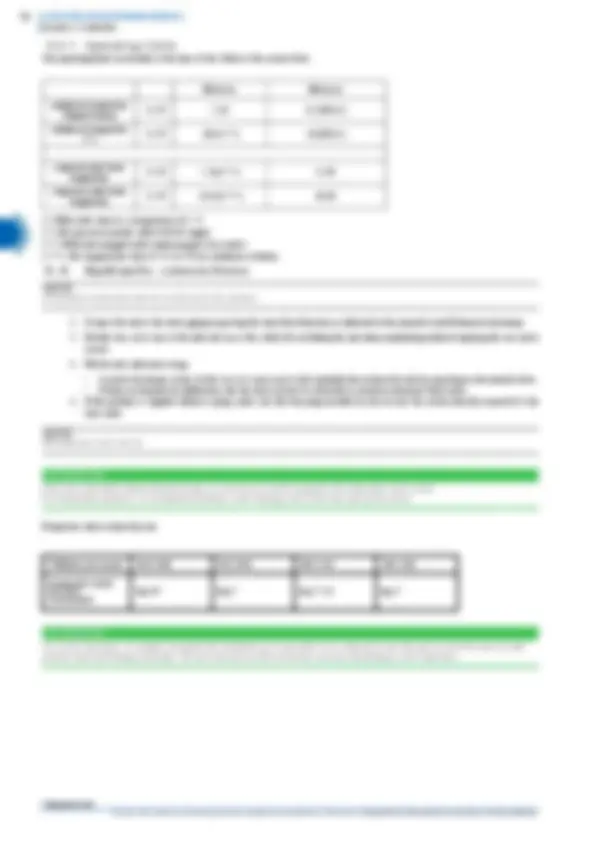
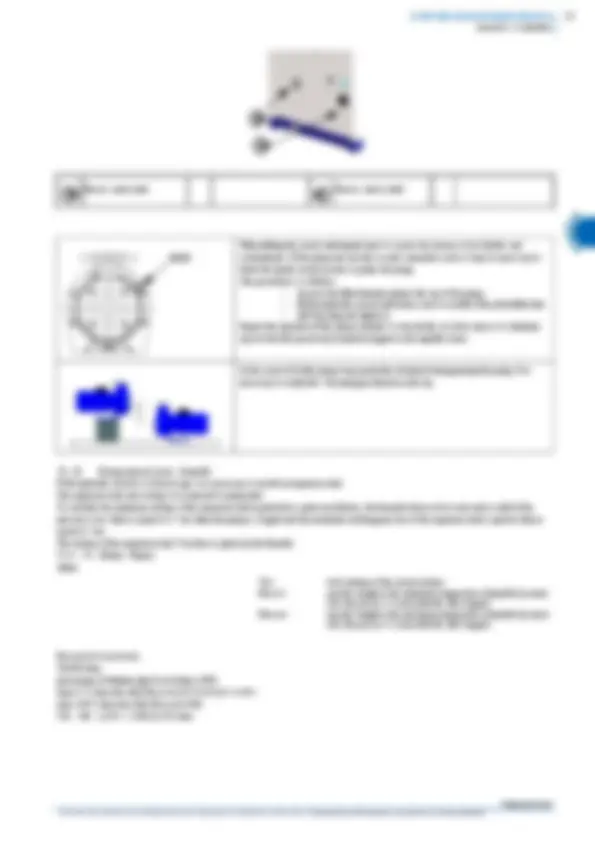
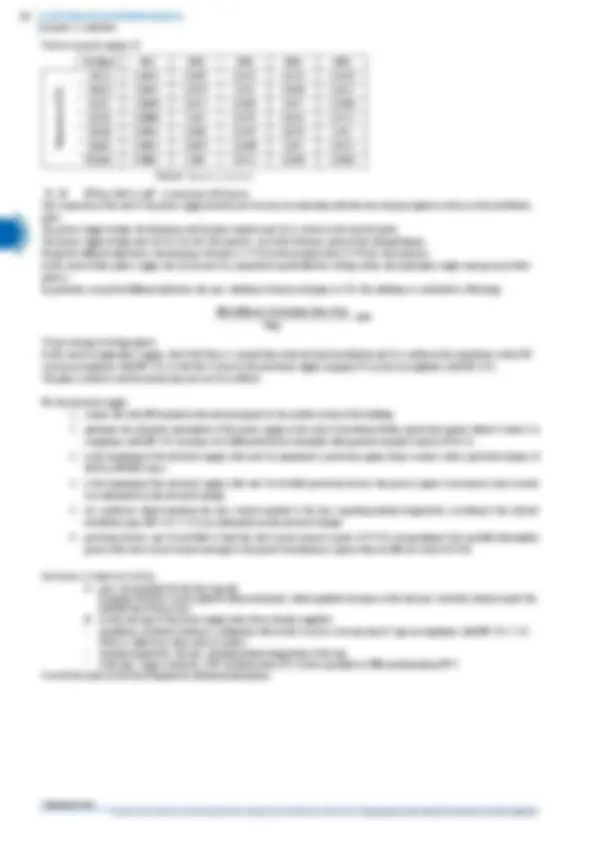
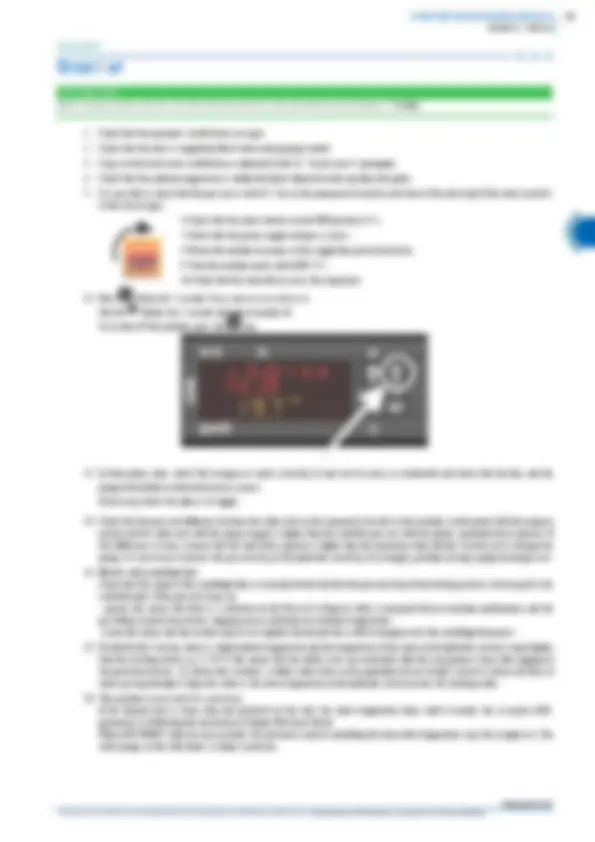
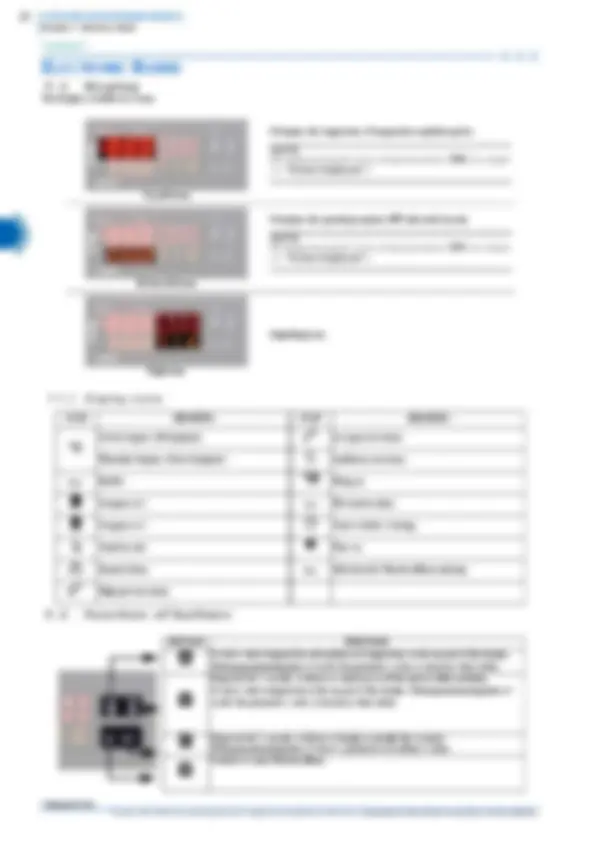
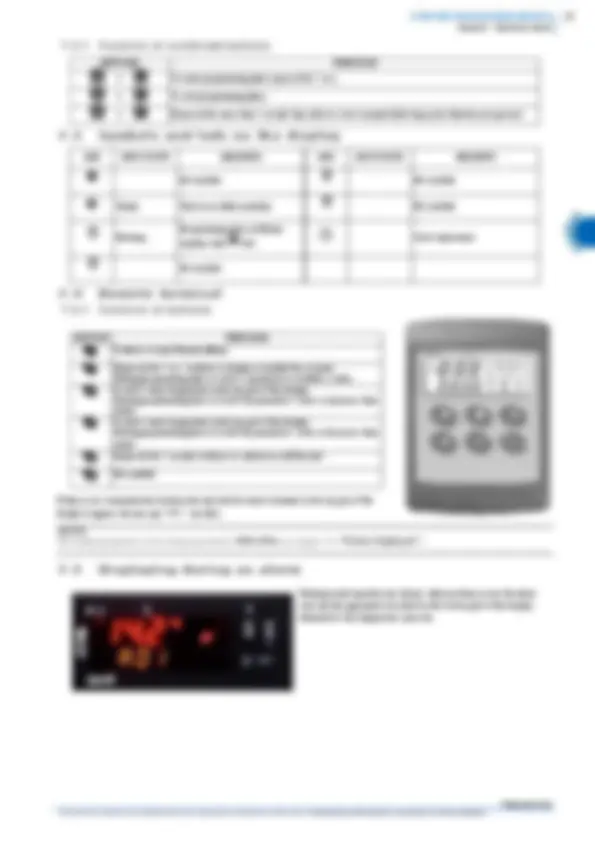
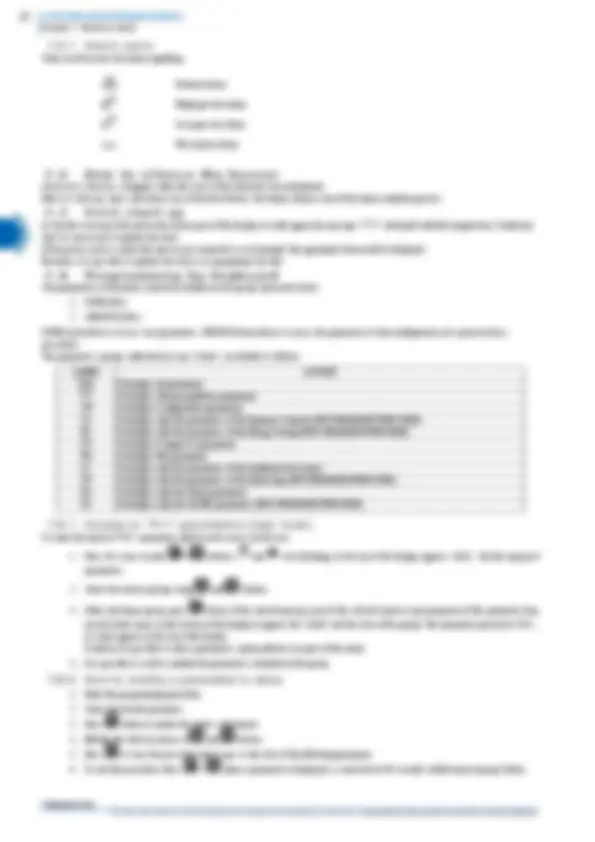
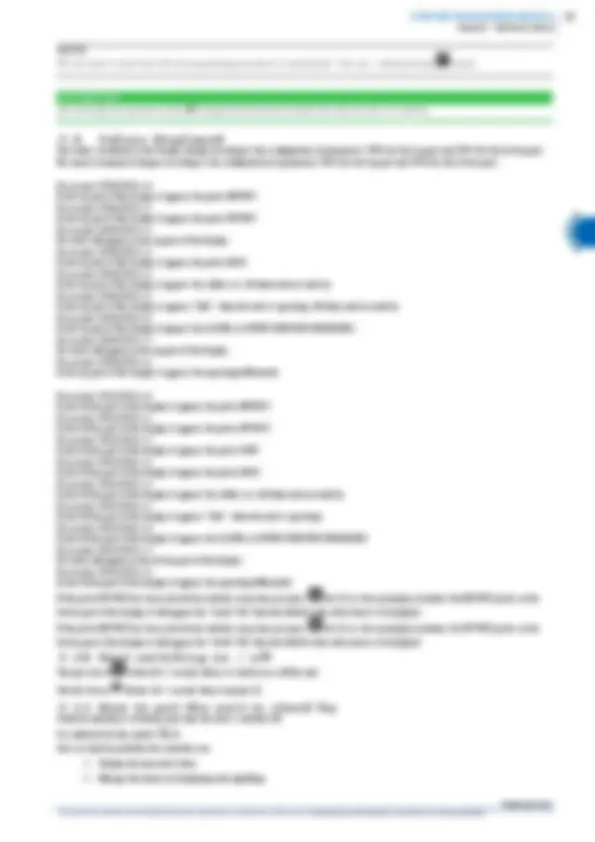
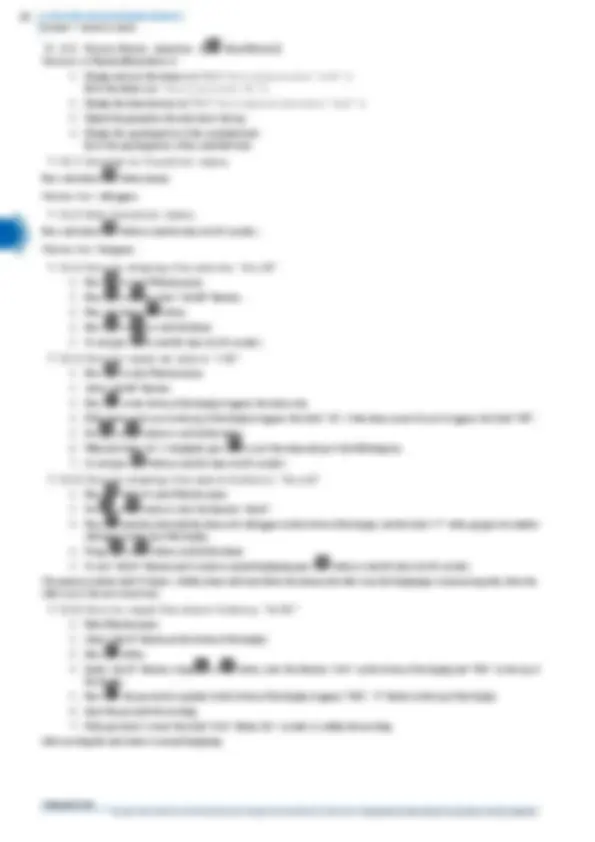
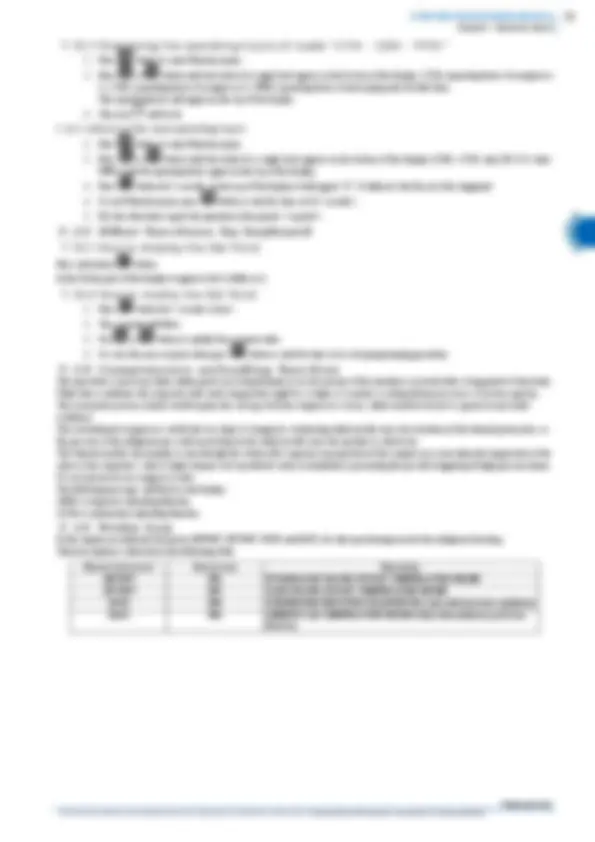
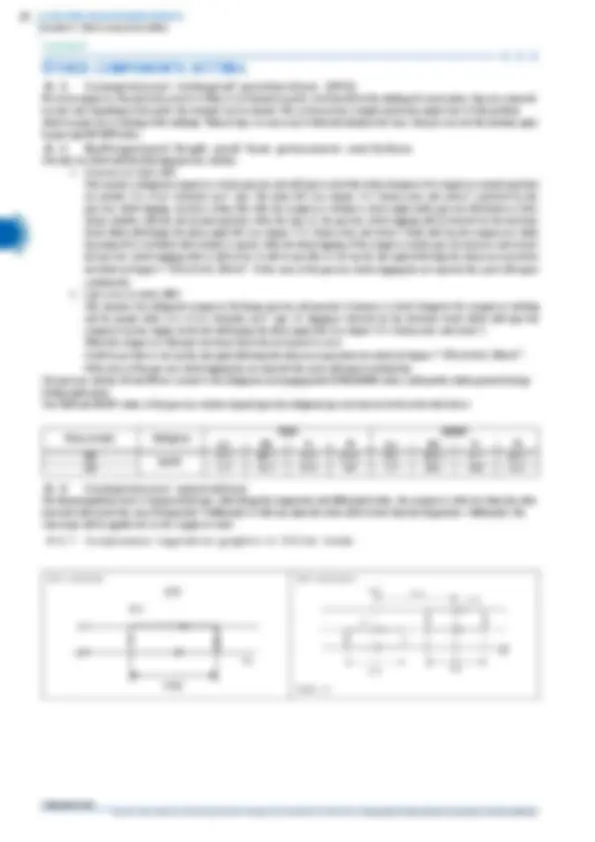
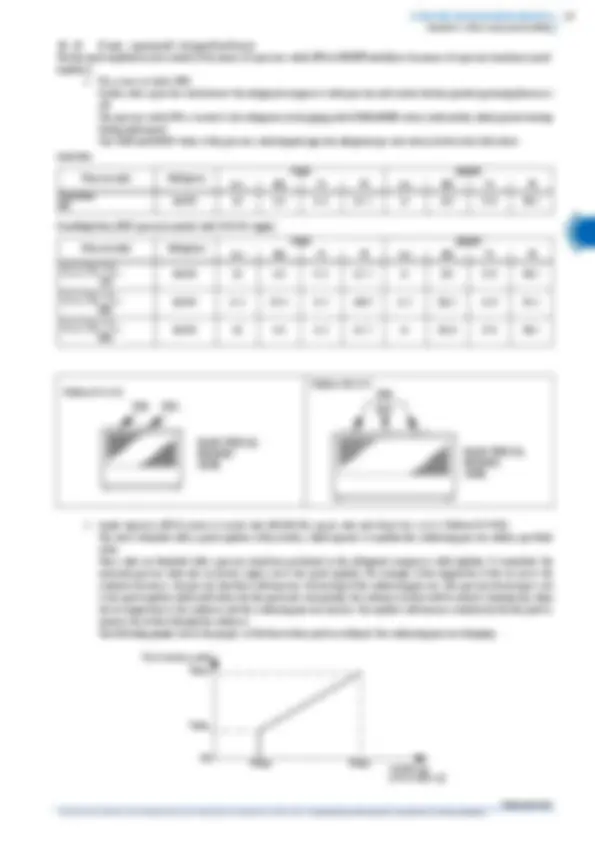
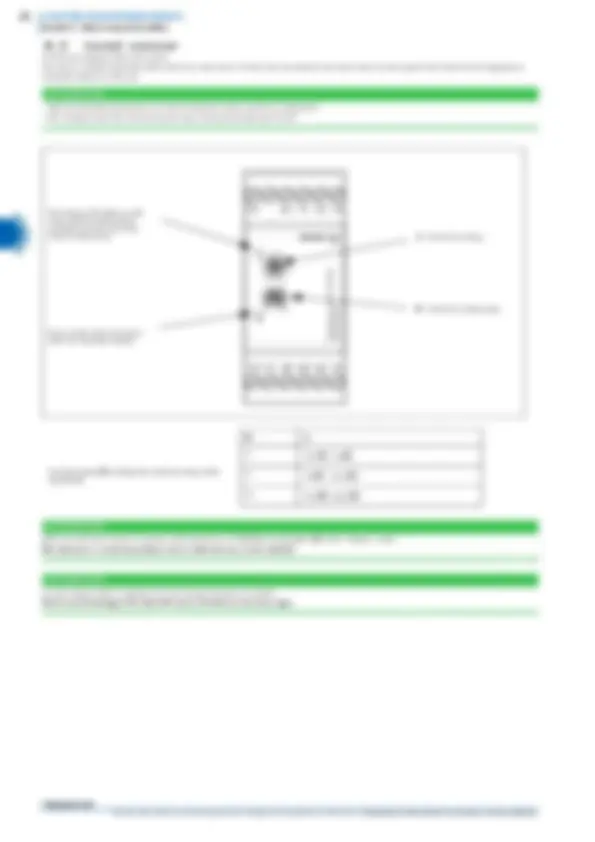
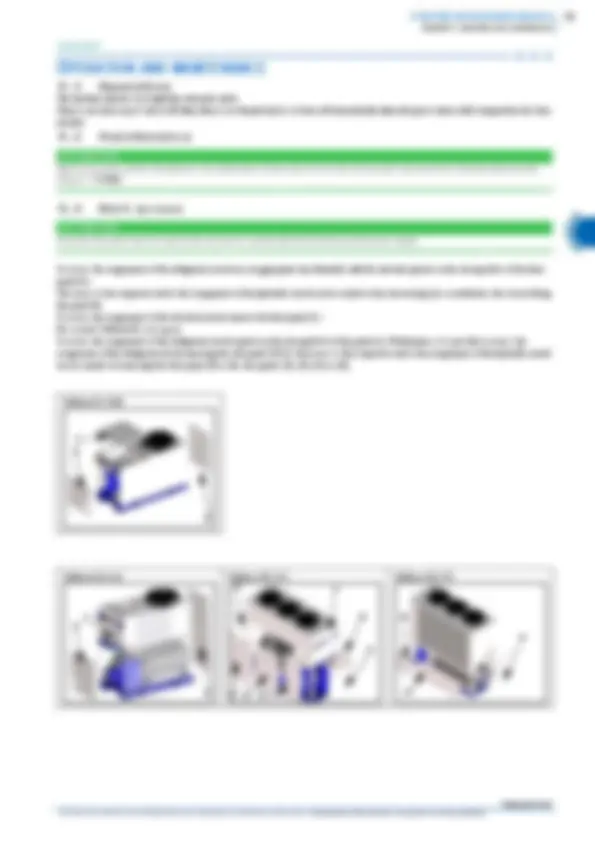
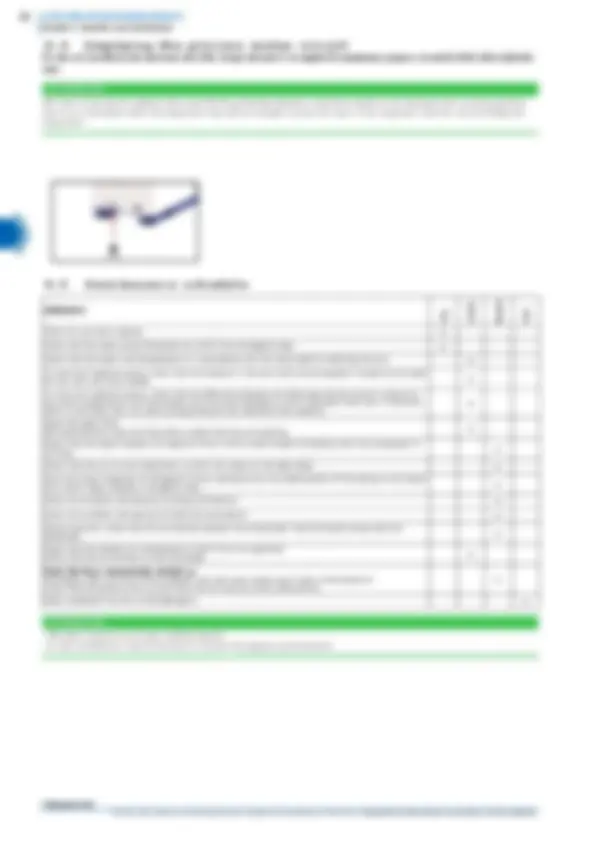
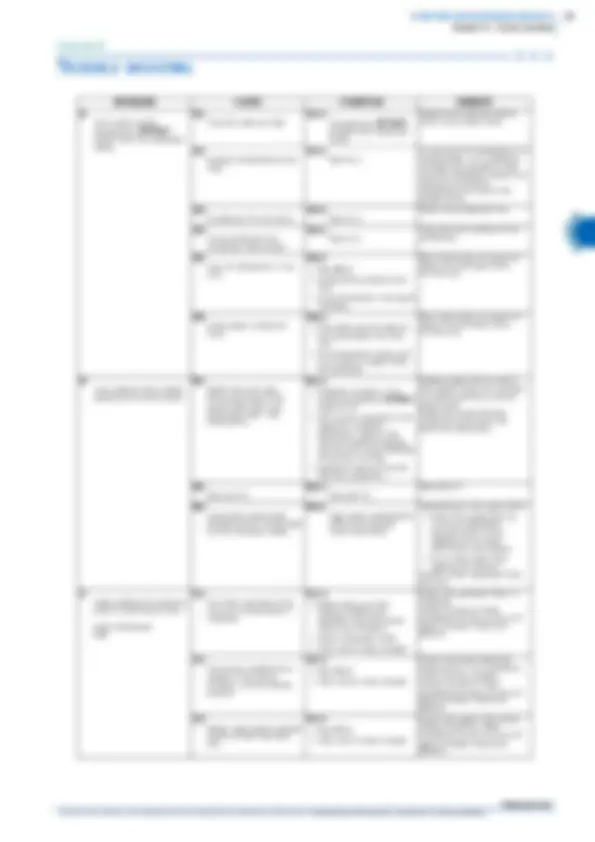
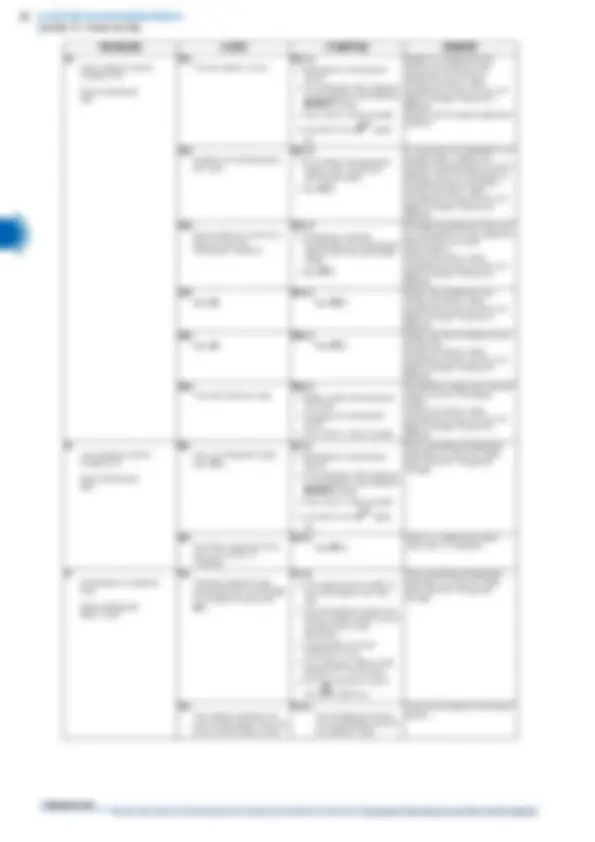
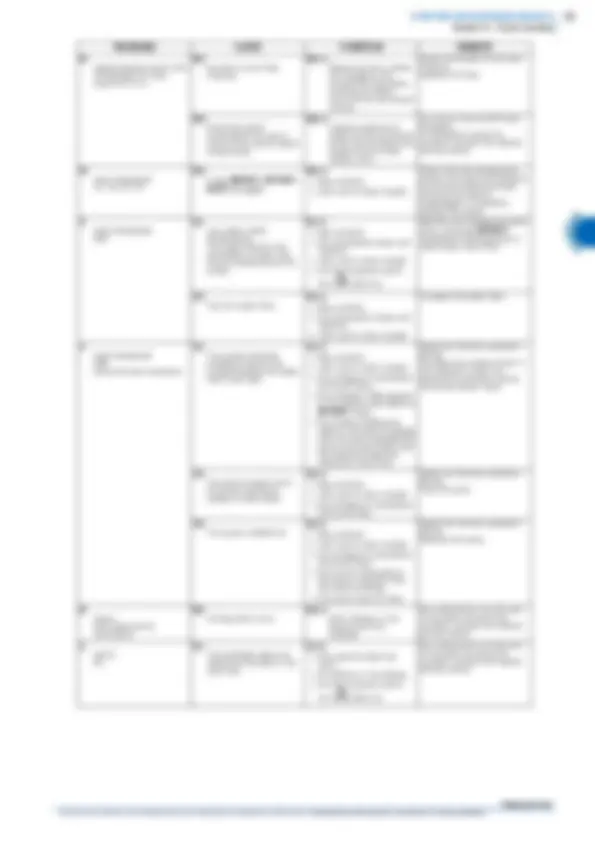
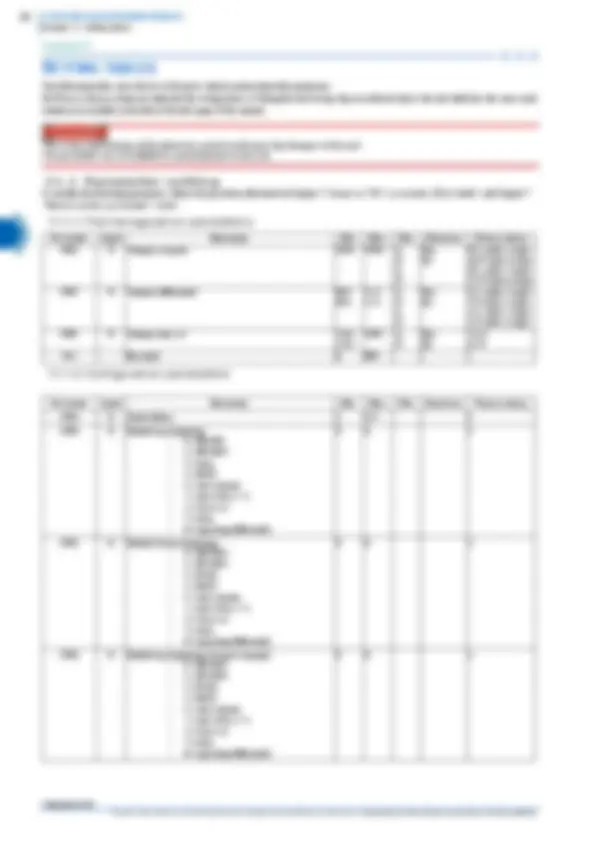
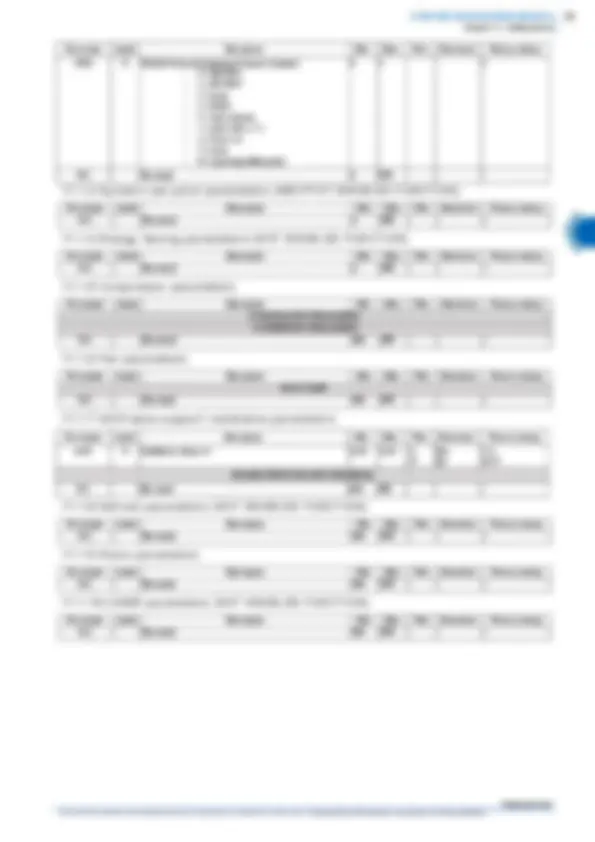
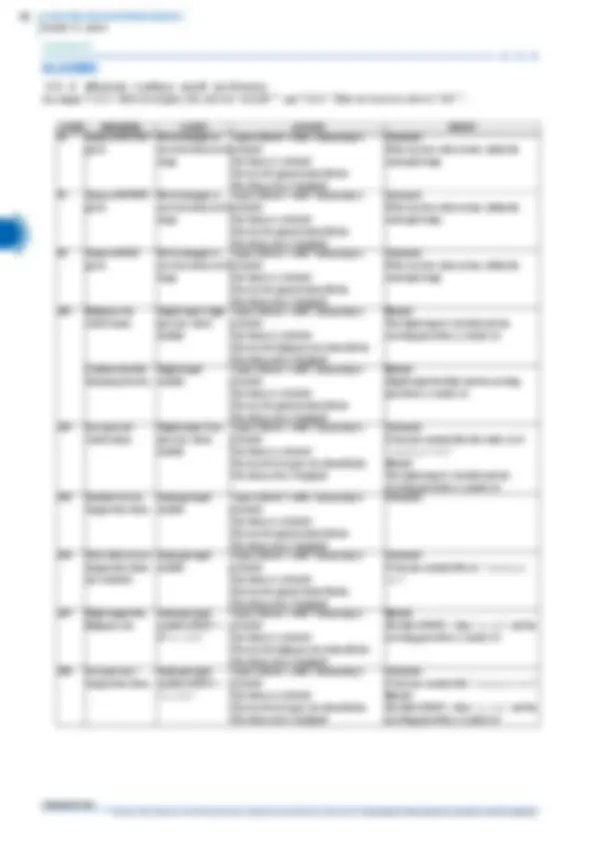
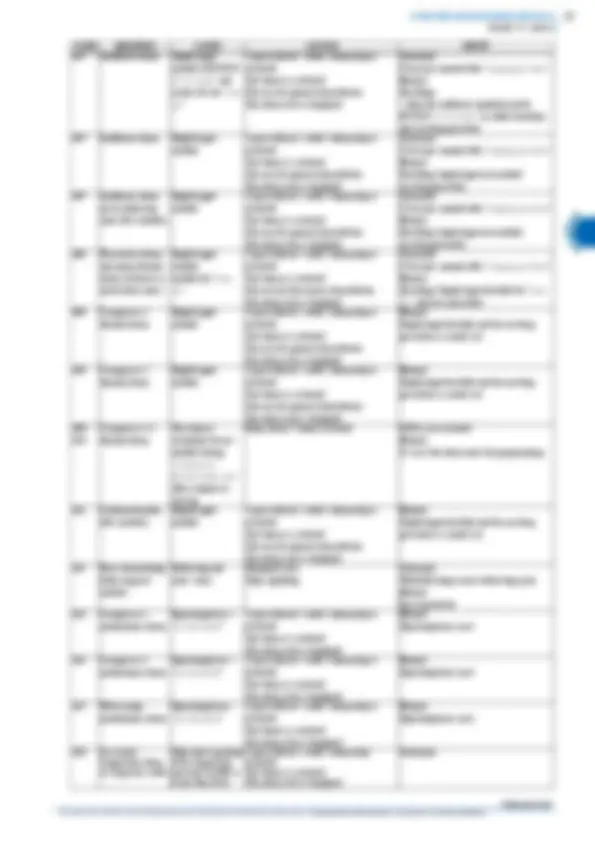
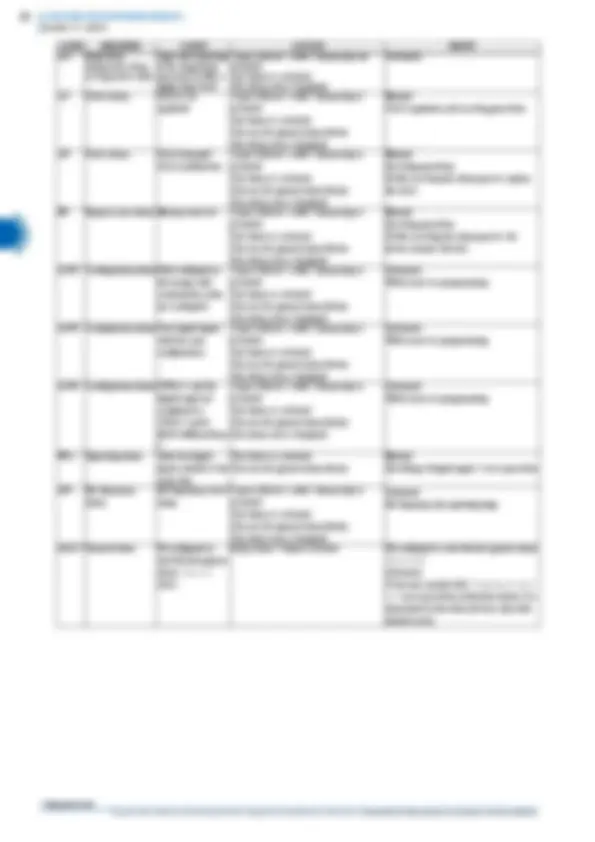
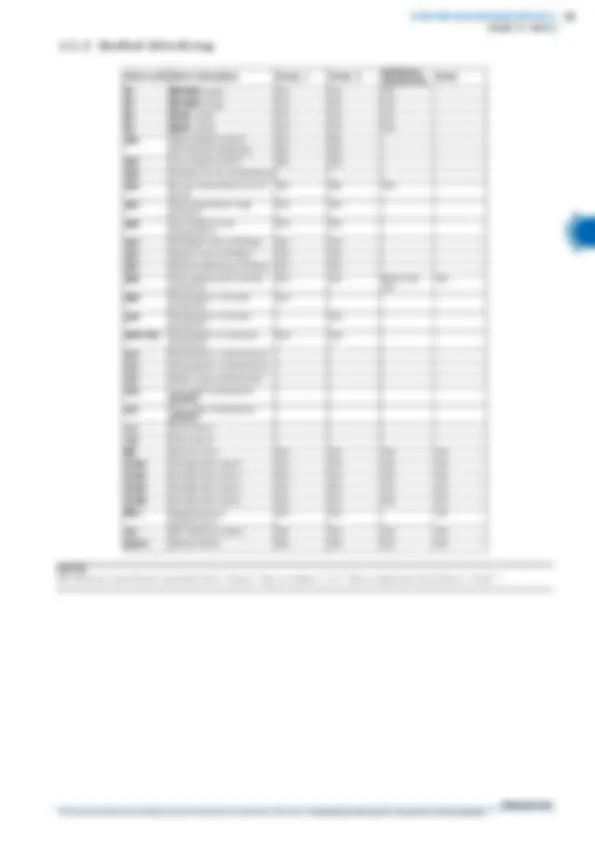
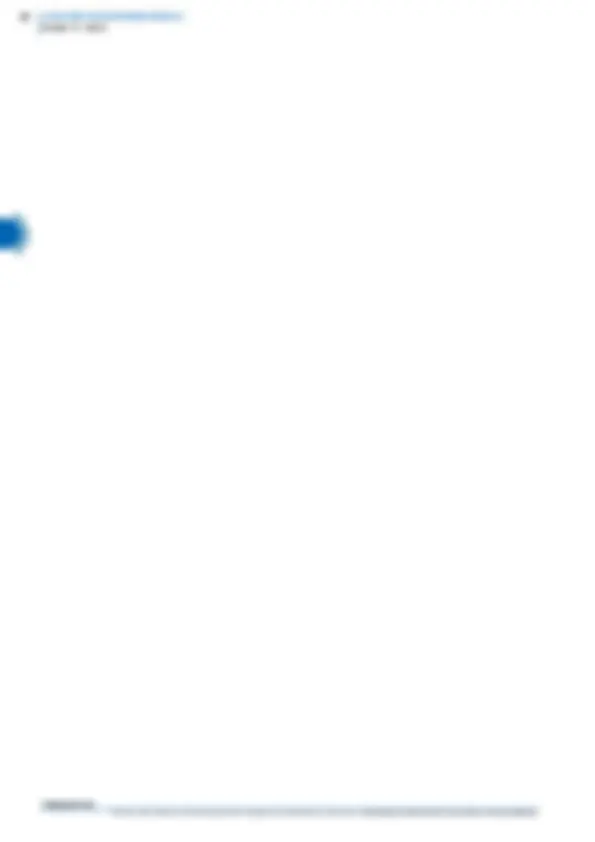
Estude fácil! Tem muito documento disponível na Docsity
Ganhe pontos ajudando outros esrudantes ou compre um plano Premium
Prepare-se para as provas
Estude fácil! Tem muito documento disponível na Docsity
Prepare-se para as provas com trabalhos de outros alunos como você, aqui na Docsity
Os melhores documentos à venda: Trabalhos de alunos formados
Prepare-se com as videoaulas e exercícios resolvidos criados a partir da grade da sua Universidade
Responda perguntas de provas passadas e avalie sua preparação.
Ganhe pontos para baixar
Ganhe pontos ajudando outros esrudantes ou compre um plano Premium
Comunidade
Peça ajuda à comunidade e tire suas dúvidas relacionadas ao estudo
Descubra as melhores universidades em seu país de acordo com os usuários da Docsity
Guias grátis
Baixe gratuitamente nossos guias de estudo, métodos para diminuir a ansiedade, dicas de TCC preparadas pelos professores da Docsity
Este manual de instruções técnico fornece informações detalhadas sobre o funcionamento e manutenção de um sistema de refrigeração. Aspectos como a instalação, operação, manutenção preventiva e resolução de problemas. O manual é direcionado para técnicos e profissionais que trabalham com sistemas de refrigeração.
Tipologia: Manuais, Projetos, Pesquisas
1 / 42
Esta página não é visível na pré-visualização
Não perca as partes importantes!
Original instructions
TAEevo015÷
- TAEevo015÷
Chapter 1 - General Information
TAEevo015÷
The machines described in this manual are called “WATER CHILLERS”.
This manual is written for those responsible for the installation, use and maintenance of the unit.
The components used are of high quality and all the projecting process, from the production to the unit checking, has been manufactured in
conformity with ISO 9001 norms.
In most applications, the liquid of the user circuit is water and the term “WATER” will be used even if the liquid of the user circuit is different
from water (e.g. a mixture of water and glycol).
Here below the term “PRESSURE” will be used to indicate the gauge pressure.
The following symbols are shown on the stickers on the unit as well as on the overall dimension drawing and refrigeration circuits in this manual.
Their meaning is the following:
Process water inlet
Process water outlet
Indications for lifting the unit
Water drainage point from the machine
Electric shock risk
Risk of burns from contact with high-temperature surfaces
Direction of the refrigerant fluid and water circuit
Direction of pump rotation (if installed)
Water filling point
Air vent
Hole for inserting bars for lifting the machine
Table 1 SYMBOLS
Chapter 2 - Safety
TAEevo015÷
SAFETY
This machinery was designed to be safe in the use for which it was planned provided that it is installed, started up and maintained in accordance
with the instructions contained in this manual. The manual must therefore be studied by all those who want to install, use or maintain the unit.
The machine contains electrical components which operate at the line voltage, and also moving parts.
It must therefore be isolated from the electricity supply network before being opened. Maintenance operations involving work inside the machine
must be performed by skilled and adequately qualified personnel equipped with suitable protection means (active and passive, e.g. work gloves)
ton ensure work in maximum safety. Do not allow extraneous persons (such as children) where the machine is installed.
2. 1 G e n e r a l When handling or maintaining the unit and all auxiliary equipment, the personnel must operate with care observing all instructions concerning
health and safety at installation site.
ATTENTION
Most accidents which occur during the operation and maintenance of the machinery are a result of failure to observe basic safety rules or precautions.
An accident can often be avoided by recognising a situation that is potentially hazardous.
The user should make sure that all personnel concerned with operation and maintenance of the unit and all auxiliary equipment have read and
understood all warnings, cautions, prohibitions and notes written in this manual as well as on the unit.
Improper operation or maintenance of the unit and auxiliary equipment could be dangerous and result in an accident causing injury or death.
We cannot anticipate every possible circumstance which might represent a potential hazard.
The warnings in this manual are therefore not all-inclusive.
If the user employs an operating procedure, an item of equipment or a method of working which is not specifically recommended, he must ensure
that the unit and auxiliary equipment will not be damaged or made unsafe and that there is no risk to persons or property.
Any improper use of the machine will relieve the manufacturer from any liability for possible personal injury or property damage.
Arbitrary modifications made to the unit will automatically invalidate all forms of guarantee provided by the manufacturer.
ATTENTION
The hot / cold water produced by MTA units cannot be used directly for domestic hygiene or food applications. In the case of such applications, the installer is responsible for fitting an intermediate exchanger. If the intermediate exchanger is not fitted, the installer should affix a notice stating "non-drinking water".
2. 2 L i q u i d s o f t h e u s e r c i r c u i t The liquids of the user circuit must be compatible with the materials used. These can be water or mixtures of water and glycol, for example.
Additives and glycol suppliers must guarantee compatibility with the materials. For further information refer to 4.10 “Materials in contact with the liquid to be cooled”.
ATTENTION
If the liquids of the user circuit contains dangerous substances (e.g. ethylene glycol) is very important to collect any liquid which leaks because it could cause damages to the ambient. Furthermore, when the chiller is no longer used, dangerous liquids must be disposed of by firms specialised and authorised for treating them.
2. 3 L i f t i n g a n d c a r r i a g e p r e c a u t i o n s Avoid injury by using a hoist to lift heavy loads.
Check all chains, hooks, shackles and slings are in good condition and are of the correct capacity.
They must be tested and approved according to local safety regulations.
Cables, chains or ropes must never be applied directly to lifting eyes.
Always use an appropriate shackle or hook properly positioned.
Arrange lifting cables so that there are no sharp bends.
Use a spreader bar to avoid side loads on hooks, eyes and shackles.
When a load is on a hoist stay clear of the danger area beneath and around it.
Keep lifting acceleration and speed within safe limits and never leave a load hanging on a hoist for longer than is necessary. The weight values
shown in the following table were obtained with the unit empty, pump P3 and axial fans.
The manufacturer does not supply bars, belts and lifting hooks with the unit.
MODEL 015 020 031 051 081 101 121 161 201 251 301 351 Weight (kg) 127 132 200 220 331 386 405 416 553 650 740 757 Weight (lb) 280 291 440 485 729 850 892 917 1219 1433 1631 1668
Table 2 WEIGHTS
Chapter 2 - Safety
TAEevo015÷
NOTE Weight values are guideline, with the water circuit empty. The values may vary in relation to the configuration of the unit (pump type, supply type, and ventilation type).
2. 4 I n s t a l l a t i o n p r e c a u t i o n s The connections to be made are for the process water circuit. Use the electrical diagram accompanying this manual to for the connection to the
power grid.
2. 5 P r e c a u t i o n s d u r i n g o p e r a t i o n Operation must be carried out by competent personnel under a qualified supervisor.
All the water piping must be painted or clearly marked in accordance with local safety regulations in the place of installation.
ATTENTION
Never remove or tamper with the safety devices, guards or insulation materials fitted to the unit or auxiliary equipment.
All electrical connections must comply with local codes.
The unit and auxiliary equipment must be earthen and protected by fuses against short-circuits and overloading.
When mains power is switched on, lethal voltages are present in the electrical circuits and extreme caution must be exercised whenever it is
necessary to carry out any work on the electrical system.
Do not open any electrical panels or cabinets or touch any electrical components or associated equipment while voltage is applied unless it is
necessary for measurements, tests or adjustments. Such work should be carried out only by a qualified electrician equipped with the proper tools
and wearing appropriate body protection against electrical hazards.
2. 6 M a i n t e n a n c e a n d r e p a i r p r e c a u t i o n s
ATTENTION
When disposing of parts and waste material of any kind make sure that there is no pollution of any drain or natural water-course and that no burning of waste takes place which could cause pollution of the air. Protect the environment by using only approved methods of disposal.
Keep a written record of all maintenance and repair work carried out on the unit and auxiliary equipment. The frequency and the nature of the
work required over a period can reveal adverse operating conditions which should be corrected.
ATTENTION
Use only refrigerant gas specified on the specification plate of the unit.
Make sure that all instructions concerning operation and maintenance are strictly followed and that the complete unit, with all accessories and
safety devices, is kept in good working order. The accuracy of pressure and temperature gauges must be regularly checked. They must be
renewed when acceptable tolerances are exceeded.
ATTENTION
Do not weld or carry out any operation which produces heat near a system which contains oil or flammable liquids. The systems which may contain oil or flammable liquids must be completely drained and cleaned (with steam, for example), before carrying out these operations.
Model 015÷161 Model 201÷
Chapter 2 - Safety
TAEevo015÷
Handling technical measures/ precautions: Ensure sufficient air change and/or extraction in the work areas. recommendations for safe use: Do not inhale vapors or aerosols. Storage Close properly and store in a cool, dry well-ventilated place. Store in its original containers. Incompatible products: explosives, flammable materials, organic peroxide. CONTROL OF EXPOSURE/INDIVIDUAL PROTECTION Control parameters: AEL (8-h e 12-h TWA) = 1000 ml/m3 for each of the three components. Respiratory protection: For rescue and maintenance work in tanks, use autonomous breathing apparatus. The vapors are heavier than air and can cause suffocation, reducing the oxygen available for breathing. Protection of the eyes: Safety goggles. Protection of the hands: Rubber gloves. Hygiene measures: Do not smoke. PHYSICAL AND CHEMICAL PROPERTIES Colour: Colourless. Odour: Similar to ether. Boiling point: -43.9°C at atm. press. Flammability point: Non flammable. Relative density: 1.138 kg/l at 25°C. Solubility in water: Negligible. STABILITY AND REACTIVITY Stability: No reactivity if used with the relative instructions. Materials to avoid: Alkaline metal, earthy alkaline metals, granulated metals salts, Al, Zn, Be, etc. in powder. Hazardous decomposition products: Halogen acids, traces of carbonyl halides. TOXICOLOGICAL INFORMATION Acute toxicity: (R32) LC50/inhalation/4 hours/lab. rats >760 ml/l (R125) LC50/inhalation/4 hours/lab. rats >3480 mg/l (R134a) ALC/inhalation/4 hours/lab. rats = 567 ml/l. Local effects: Concentrations substantially above the TLV can cause narcotic effects. Inhalation of products in decomposition can lead to respiratory difficulty (pulmonary oedema). Long-term toxicity: Has not shown any cancerogenic, teratogenic or mutagenic effects in experiments on animals. ECOLOGICAL INFORMATION Global warming potential HGWP (R11=1): R125: 0.84 - R134a: 0. Ozone depletion potential ODP (R11=1): 0 CONSIDERATIONS ON DISPOSAL Usable with reconditioning.
Chapter 3 - Technical data
TAEevo015÷
TECHNICAL DATA
The main technical data are given on the machine data plate:
ATTENTION
The performance of the unit mainly depends on the flow and temperature of the water in the user circuit and on the temperature of the thermal exchanger fluid of the condenser. These data are defined during the offer stage.
3. 1 O t h e r d a t a r e l a t i v e t o t h e s t a n d a r d m a c h i n e s
3.1 .1 D imen sion s See enclosures.
MODEL and CODE (^) They identify the size of the unit and the type of construction. MANUAL (^) This is the code number of the manual. SERIAL NUMBER (^) This is the construction number of the unit. MANUFACTURING YEAR (^) This is the year of the final test of the unit. VOLTAGE/PHASE/FREQUENCY (^) Electric alimentation characteristics. MAX. CONSUMPTION (I max) (^) This is electrical current consumed by the unit during the limit working conditions. INSTALLED POWER (P max) (^) It is the power absorbed by the unit during the limit working conditions. PROTECTION (^) As defined by the EN 60529 European standard. REFRIGERANT (^) This is the refrigerant fluid in the unit. REFRIGERANT QUANTITY (^) This is the quantity of refrigerant fluid contained in the unit. For TAEevo 015÷031 models MAX. COOLING PRESSURE (^) This is the design pressure of the refrigeration circuit. MAX. COOLING TEMPERATURE (^) This is the design temperature of the refrigeration circuit. For TAEevo 051 models and upper models MAX. COOLING PRESSURE HP SIDE (^) This is the design pressure of the refrigeration circuit of the high pressure side MAX. COOLING PRESSURE LP SIDE (^) This is the design pressure of the refrigeration circuit of the low pressure side USER CIRCUIT FLUID (^) Fluid used by the unit (normally water). MAX. UTILIZATION PRESSURE (^) Max. designed pressure of the utilization circuit. MAX. TEMPERATURE (^) Design temperature of the user circuit; this should not be confused with the maximum working temperature which is established when the offer is made. CONDENSER COOLING FLUID (^) Fluid the machine uses to cool the condenser. MAX. WORKING PRESSURE (^) Maximum design pressure of the condenser cooling circuit. MAX. TEMPERATURE (^) Maximum designed temperature of the cooling circuit of the condenser. SOUND PRESSURE LEVEL (^) Sound pressure level in a free field in hemispherical irradiation conditions (open field) at a distance of 1 m from the machine, condenser side, and at 1.6 m from the ground. AMBIENT TEMPERATURE (^) Min. and max. cooling air temperature value. WEIGHT (^) This is the approximate weight of the unit before packing. Table 3 DATA PLATE AND MEANING OF ABBREVIATIONS
Chapter 3 - Technical data
TAEevo015÷
NOTE The values in the table may vary in relation to the model and configuration of the unit. In this case reference should be made to the data in the offer.
NOTE The head is the head available to the user. It is possible for the pump installed to be different from the standard. There are two numbers for the flow rate and pressure: the first number refers to the nominal conditions while the second to the maximum conditions.
3.1 .3 S o und Le vel M easu re me nts
** global
*** (NOT present with 460/3/60 Hz supply)
Test conditions
Noise levels refer to operation of the unit at full load in nominal conditions.
Sound pressure level in hemispherical irradiation conditions at a distance of 1 m (3,2 FT) from the condenser side of the unit and height of 1.6 m
(5,2 FT) from the ground. Values tolerance ± 2 dB.
Sound power level: in compliance with ISO 3744.
Fan Lp dB(A) * Lw dB(A) ** TAEevo 015 (^) axial 67,4 80, TAEevo 020 (^) axial 67,4 80,
TAEevo 031 axial 68,1 81, centrifugal ******* 73,8 86,
TAEevo 051 axial 68,1 81, centrifugal ******* 73,8 86,
TAEevo 081 axial 68,6 81, centrifugal ******* 76,2 89,
TAEevo 101 axial 69,1 82, centrifugal ******* 76,2 89,
TAEevo 121 axial 69,1 82, centrifugal ******* 76,2 89,
TAEevo 161 axial 70,0 83 centrifugal ******* 76,2 89,
TAEevo 201 axial 71,3 84, centrifugal ******* 78,1 91,
TAEevo 251 axial 71,3 84, centrifugal ******* 78,1 91,
TAEevo 301 axial 73,0 86 centrifugal ******* 78,1 91,
TAEevo 351 axial 73,0 86 centrifugal ******* 78,1 91,
Chapter 4 - Description
TAEevo015÷
D ESCRIPTION
4. 1 C o m p o n e n t s The data relating to the materials refer to standard machines. In case of particular units special materials are used, so it is necessary to refer to the
data on the offer.
The machines essentially consist of the following components:
The circuits consist of the following components:
4. 3 C o m p r e s s o r s All the machines are equipped with piston or SCROLL hermetic compressors, which are distinguished for their high energy efficiency, low
vibrations and consequent silence in normal operation.
They are cooled by the aspirated gas, protected against overheating of the windings by an internal module that monitors their temperature and,
upstream, by magnetothermic circuit breakers. These components are housed in a closed, but easily accessible, compartment.
4. 4 C o n d e n s e r Condensation occurs through fin-pack coils consisting of copper tubes and collectors, aluminium fins and shoulders in galvanised sheet.
4. 5 E v a p o r a t o r The evaporator is a finned pack type; the water flows in contact with the finned surface and at a speed that guarantees low pressure drops, while
the refrigerant fluid flows inside the tubes.
A plate exchanger can be fitted as an alternative.
In the TAEevo models, the exchanger is protected against the formation of ice, caused by low evaporation temperatures, through an anti-freeze
function in the electronic controller. A probe monitors the temperature of the evaporator outlet water. If it is necessary to achieve a negative
ambient/water temperatures, a mixture of water and glycol must be used.
To drain the circuit, see Chapter 9.4 “Emptying the process water circuit”.
4. 6 T a n k The storage tank is cylindrical.
Alternatively a prismatic atmospheric tank can be supplied.
The tank can be protected against freezing by means of an electric heater managed by the electronic controller. A level sensor in the tank serves
to signal low water level conditions. The standard supply includes anti-condensation cladding, a drain valve and an air bleed valve. An internal
bypass between the water delivery and return connections, makes it possible to read the anti-freeze probe if the unit's process water inlet and
outlet connections are inadvertently closed. In this case the unit stops due to tripping of the antifreeze alarm and the shut-off valves must be
reopened.
The bypass serves exclusively to allow an antifreeze alarm to trip (if present) and to allow the pump to run with a reduced water flow rate
without damage. It is advisable to avoid repeated antifreeze alarm trip cycles in the foregoing conditions.
Chapter 4 - Description
TAEevo015÷
4. 1 0 M a t e r i a l s i n c o n t a c t w i t h t h e l i q u i d t o b e c o o l e d There can be two different groups.
Standard chillers: carbon steel, copper, aluminium, zinc, brass, stainless steel and plastics
in particular:
in particular:
4. 1 1 M i n i m u m d i s t a n c e s f r o m w a l l s i n t h e i n s t a l l a t i o n a m b i e n t See enclosures.
4. 1 2 E l e c t r i c a l c i r c u i t For the electrical connections, see Chapter 5 “Installation“ , Installation, and consult the enclosed drawings.
4. 1 3 N e g a t i v e a m b i e n t t e m p e r a t u r e s ( n o t p r e s e n t i n m o d e l s f o r 4 6 0 / 3 / 6 0 p o w e r s u p p l y ) In the presence of sub-zero ambient temperatures (-20) the unit is equipped with a system that assures perfect operation, also in the presence of
harsh temperatures.
The additional elements fitted are:
Chapter 5 - Installation
TAEevo015÷
I NSTALLATION
ATTENTION
Before carrying out the installation or operating on this machine, ensure that all the personnel has read and understood the Chapter 2 “Safety“ in this manual.
5. 1 I n s p e c t i o n Immediately after uncrating, inspect the unit.
5. 2 P o s i t i o n i n g
1. The unit may be installed both outdoors and indoors. 2. If installed indoors, the room must be well ventilated and with a sufficient height which allows the air to be expelled by fans. In some cases it may be necessary to install fans or extractors to limit the temperature of the room. 3. The minimum and maximum working ambient temperature are specified on the unit data plate. In extreme temperature conditions, the protection devices may trip. 4. The machine must be positioned on any flat surface capable of supporting its weight. 5. Leave at least one metre around the unit to permit access during service operations. 6. Do not obstruct or disturb the condenser's flow of thermal exchanging air.
5. 3 A n t i f r e e z e p r o t e c t i o n Even if the minimum working ambient temperature is above 0°C it is possible for the machine - during stoppages in the cold seasons - to find
itself in an environment with a temperature below 0°C.
In these cases, if the machine is not emptied, antifreeze (ethylene glycol) must be added in the following percentages to prevent the formation of
ice:
Add the following anti-freeze (ethylene glycol) percentages in order to avoid freezing when operating at low water outlet temperature:
ATTENTION
Carry out the level sensor calibration when the unit is activated the first time. Repeat the operation each time the composition of the process liquid changes.
Ambient temperature up to [°C] (°F)
Ethylene Glycol [% in weight] 0 (32) 0 -5 (23) 15 -10 (14) 25 -15 (5) 30 -20 (-4) 40
Table 6 A DDING ETHYLENE GLYCOL BASED ON THE AMBIENT TEMPERATURE
Water outlet temperature up to [°C] (°F)
Ethylene Glycol [% in weight] 5 (41) 0 0 (32) 19 -5 (23) 27 -10 (14) 34 -15 (5) 39 -20 (-4) 44
Table 7 A DDITION OF ETHYLENE GLYCOL ACCORDING TO THE WATER OUTLET TEMPERATURE
Chapter 5 - Installation
TAEevo015÷
5. 5 E x p a n s i o n t a n k If the hydraulic circuit is of closed type, it is necessary to install an expansion tank.
The expansion tank must always be connected at pump inlet.
To calculate the minimum volume of the expansion tank required for a given installation, the formula below cab be used and is valid if the
pressure is less than or equal to 0.5 bar when the pump is stopped and the maximum working pressure of the expansion tank is greater than or
equal to 4 bar.
The volume of the expansion tank V in litres is given by the formula:
V = 2 · Vt · (Ptmin - Ptmax)
where:
Example of calculation:
Vt =200 litres
percentage of ethylene glycol in volume =30%
tmin =5°C from the table Ptmin =(1.045+1.041)/2 = 1.
tmax =40°C from the table Ptmax =1.
V=2 · 200 · (1.043 - 1.0282)=5.92 litres
Process water inlet Process water outlet
When filling the circuit with liquid check to ensure the absence of air bubbles and contaminants. If the pump runs noisily or emits anomalous noise it may be necessary to bleed the liquid circuit in order to prime the pump. The procedure is as follows:
In the event of double pump, keep particular attention during priming the pump. It is necessary to verify first the pump positioned on the top.
Vt= total volume of the circuit in litres Ptmin = specific weight at the minimum temperature obtainable by water over the year in °C (even with the unit stopped) Ptmax = specific weight at the maximum temperature obtainable by water over the year in °C (even with the unit stopped)
Chapter 5 - Installation
TAEevo015÷
Table of specific weights P
5. 6 E l e c t r i c a l c o n n e c t i o n s The connection of the unit to the power supply network must be done in conformity with the laws and prescriptions in force in the installation
place.
The power supply voltage, the frequency and the phase number must be as shown on the unit data plate.
The power supply voltage must not be, also for short periods, out of the tolerances given in the wiring diagram.
Except for different indications, the frequency tolerance is +/-1% of the nominal value (+/-2% for short periods).
In the event of three-phase supply, the system must be symmetrical (equal effective voltage values and equal phase angles among consecutive
phases).
In particular, except for different indication, the max. unbalance between each phase is 2%. The unbalance is calculated as following:
Vavg = average of voltage phases
In the event of single-phase supply, check that there is a neutral line in the electrical installation and it is earthen in the transformer cabin (TN
system in compliance with IEC 364) or that this is done by the electricity supply company (TT system in compliance with IEC 364).
The phase conductor and the neutral wire must not be confused.
For the electrical supply:
1. connect the unit (PE terminal in the electrical panel) to the earthed system of the building 2. guarantee the automatic interruption of the power supply in the event of insulation failure (protection against indirect contacts in compliance with IEC 364) by means of a differential device (normally with operation nominal current of 0.03 A) 3. at the beginning of the electrical supply cable must be guaranteed a protection against direct contacts with a protection degree of IP2X or IPXXB at least 4. at the beginning of the electrical supply cable must be installed protection devices that protect against overcurrents (short circuit) (see information in the electrical wiring) 5. use conductors which transform the max. current required to the max. operating ambient temperature, according to the selected installation type (IEC 364-5-523) (see information in the electrical wiring) 6. protection devices must be installed to limit the short circuit current to peaks of 17 kA corresponding to the specified interruption power if the short circuit current envisaged at the point of installation is greater than an effective value of 10 kA.
Indications of electrical wiring:
A max. size permitted for the fuse type gG. In general, the fuses can be replaced with an automatic switch regulated by means of the unit max. absorbed current (contact the manufacturer if necessary) B section and type of the power supply cable (if not already supplied):
% Glycol 0% 10% 20% 30% 40%
Temperature [°C]
Table 8 S PECIFIC WEIGHTS
Max difference of each phase from Vavg Vavg
x