
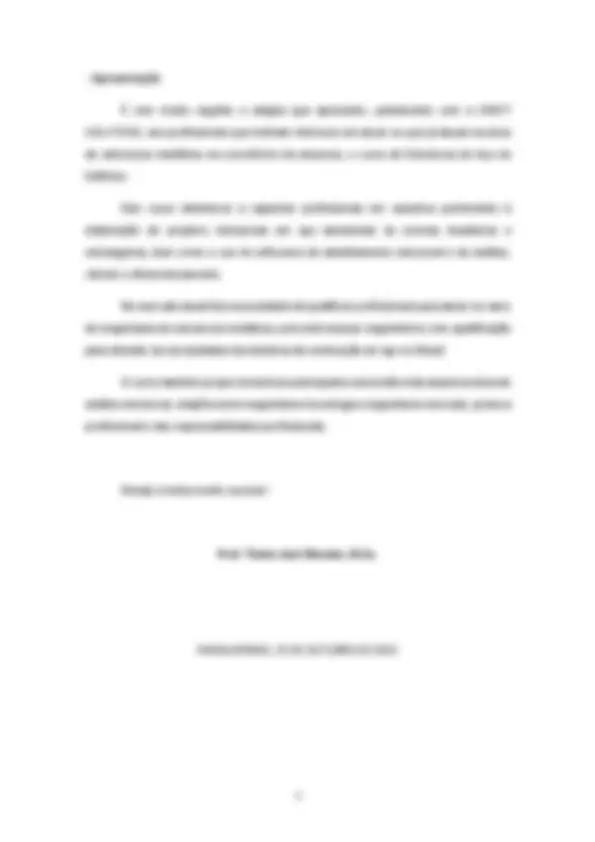
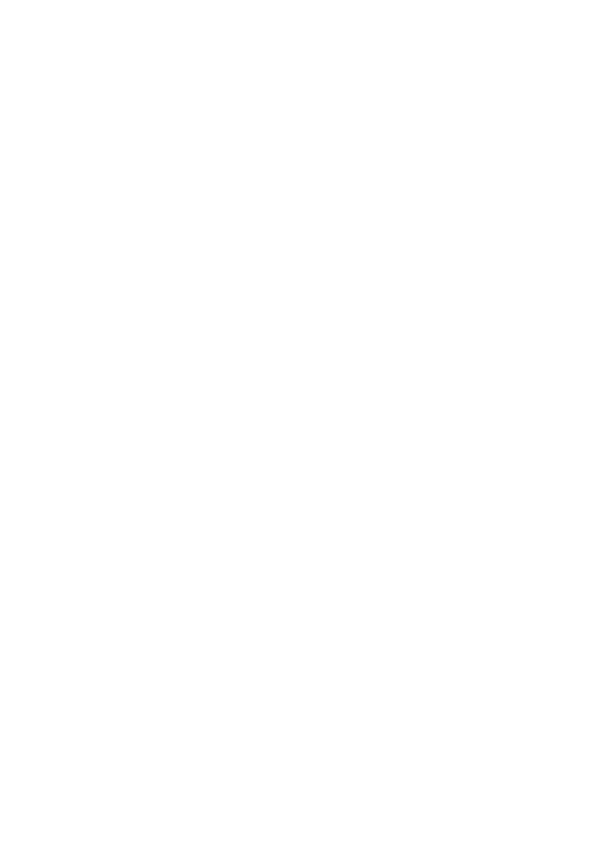
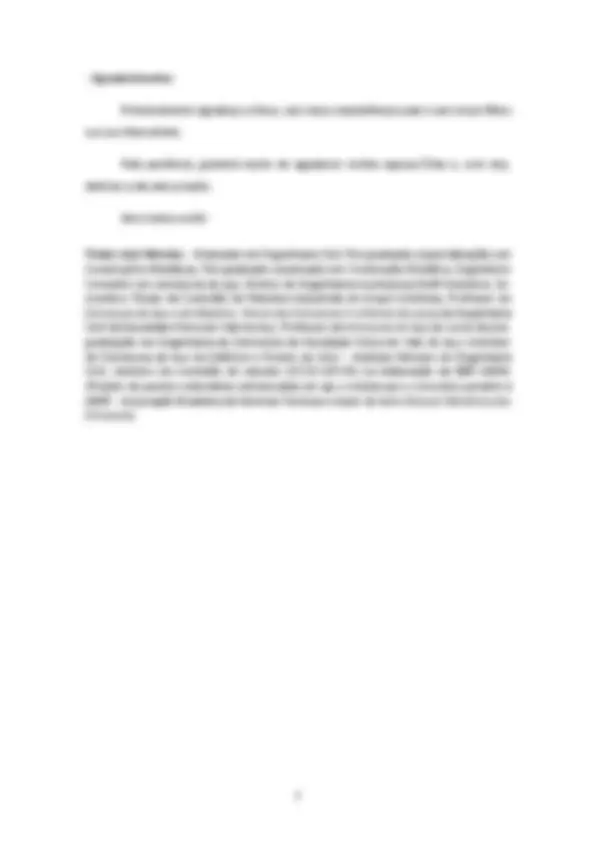
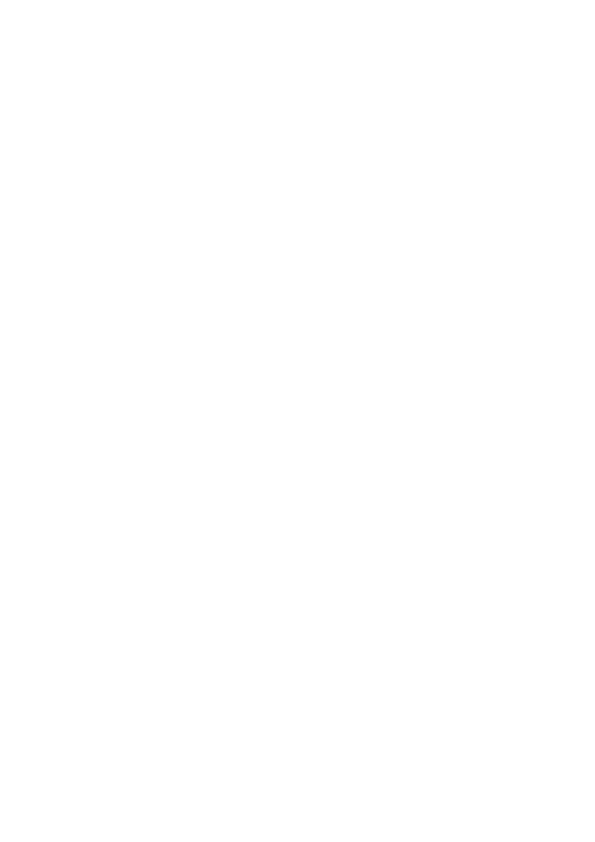
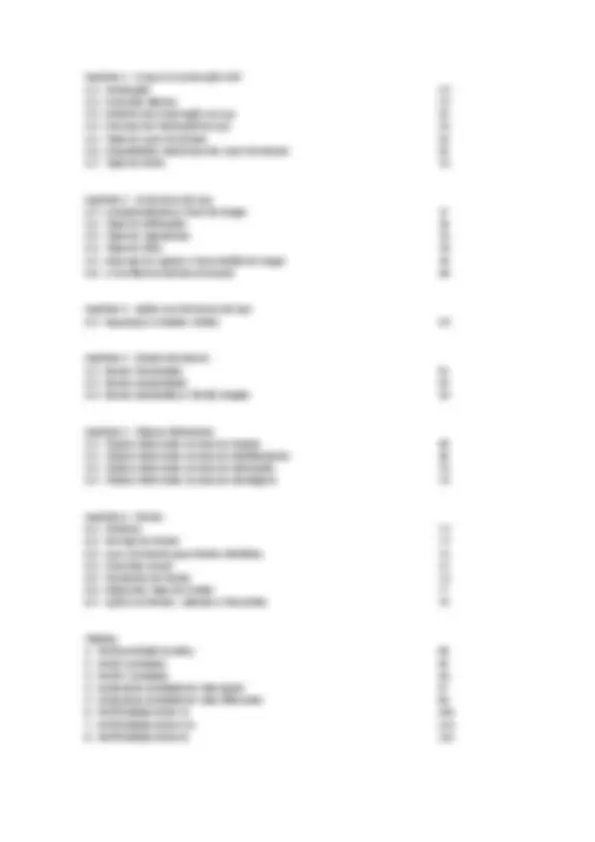

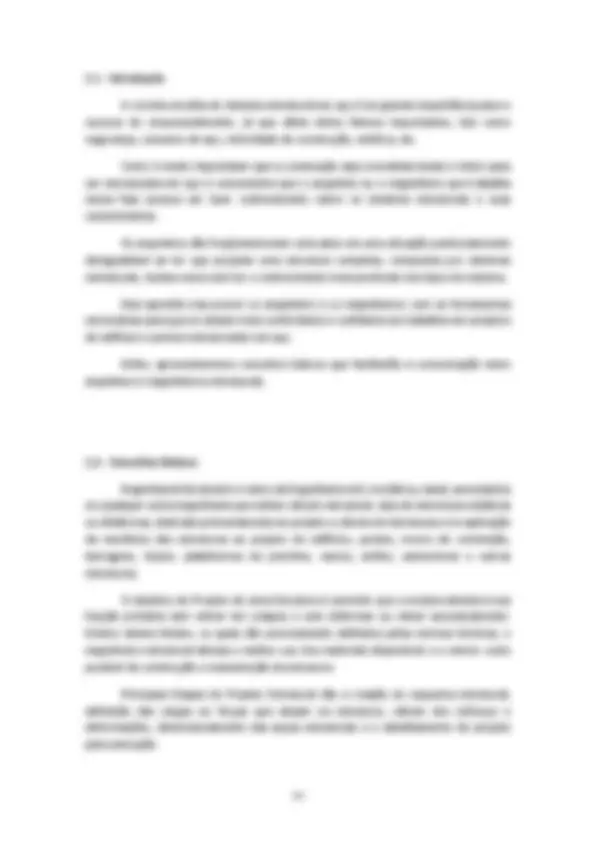
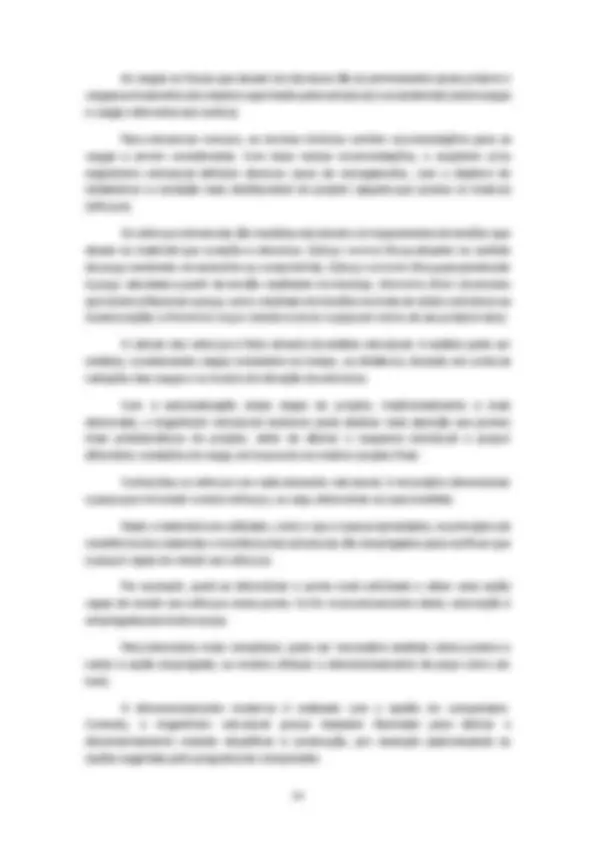
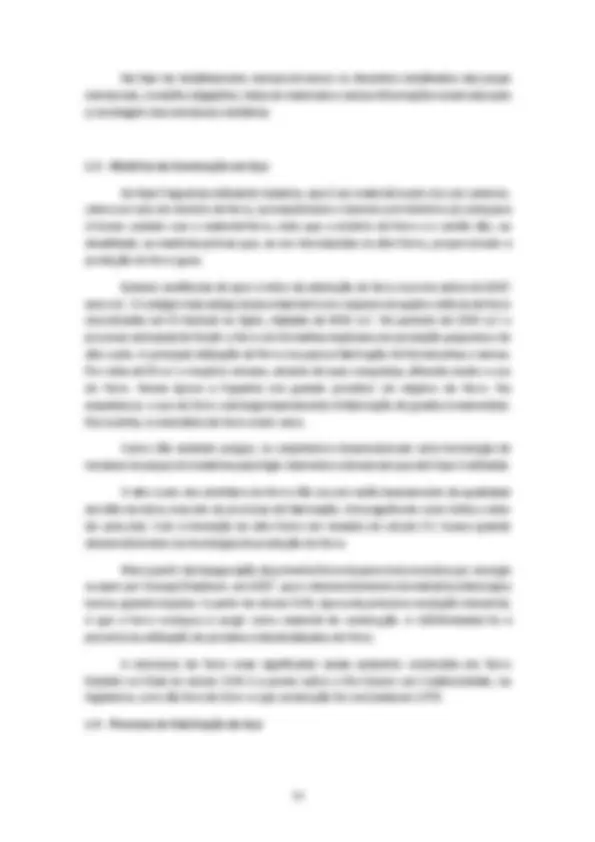
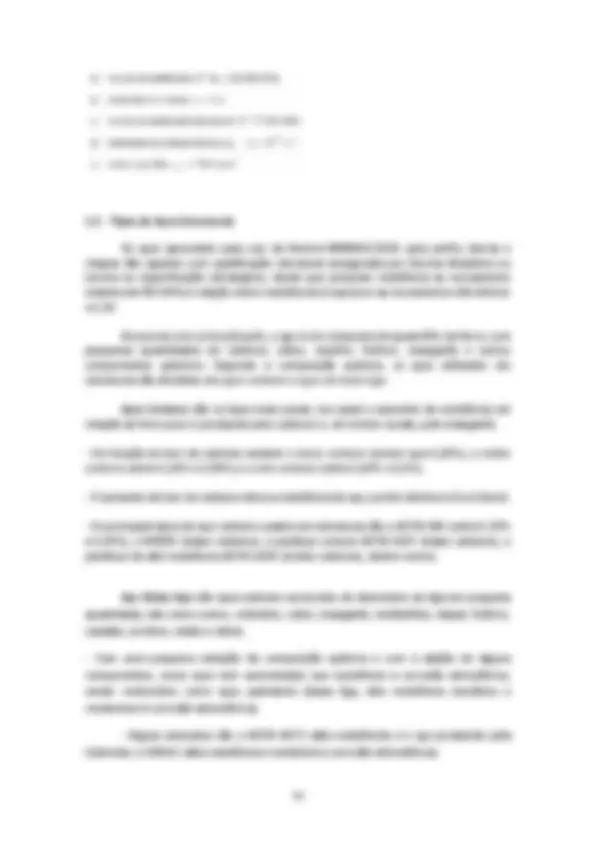
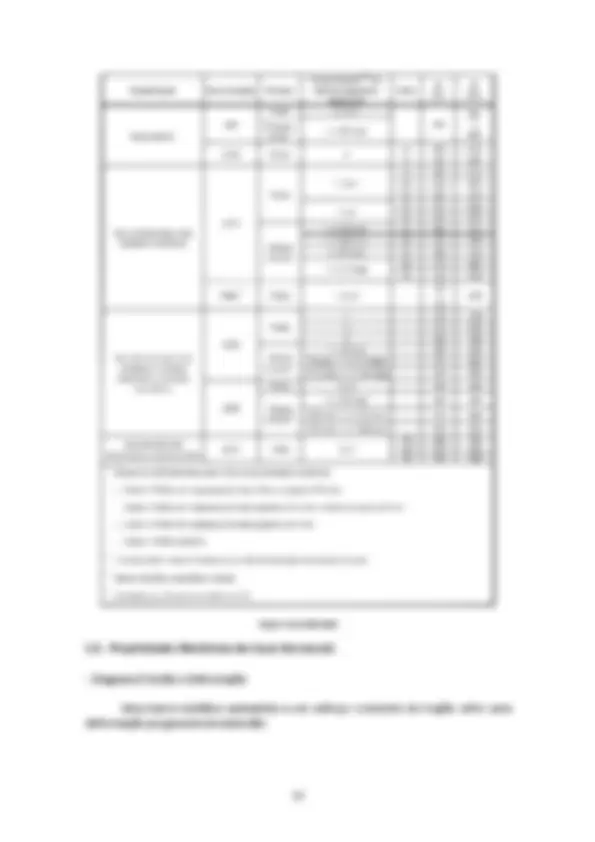
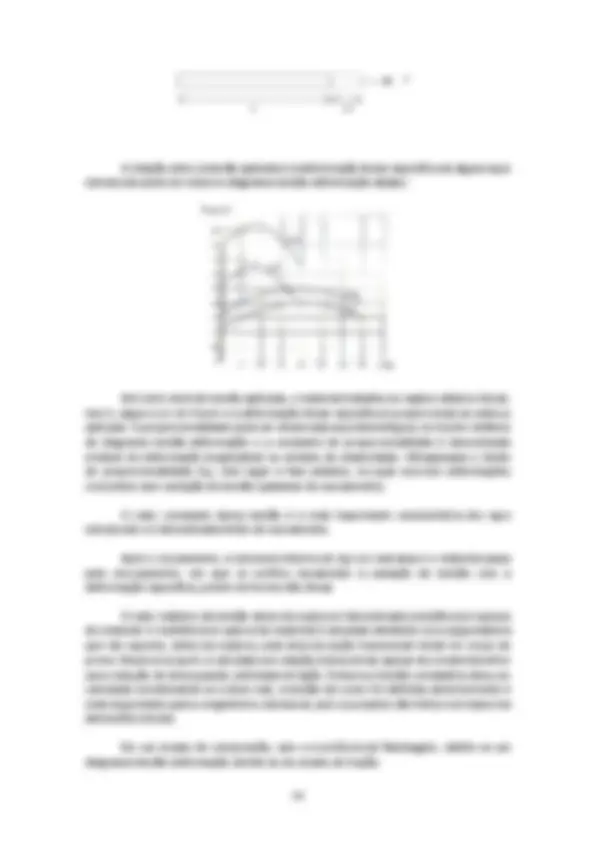

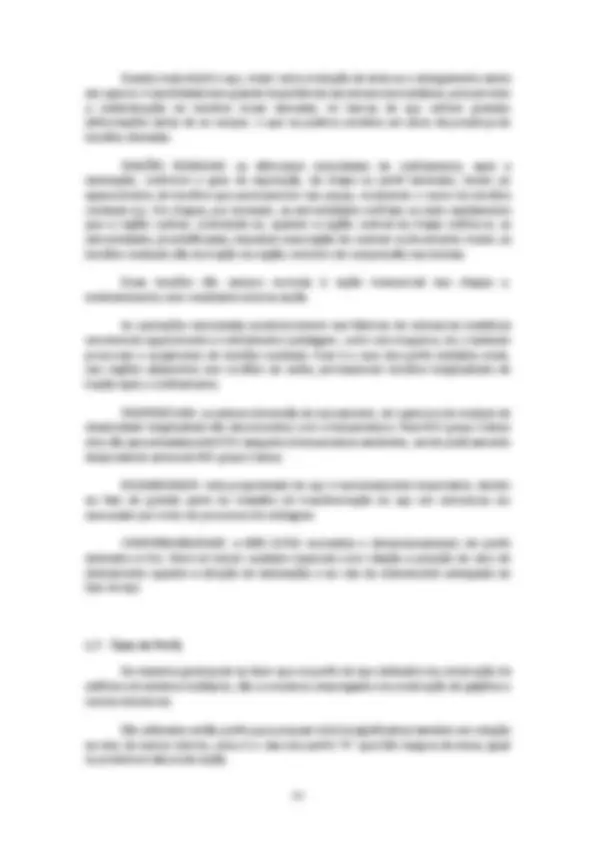
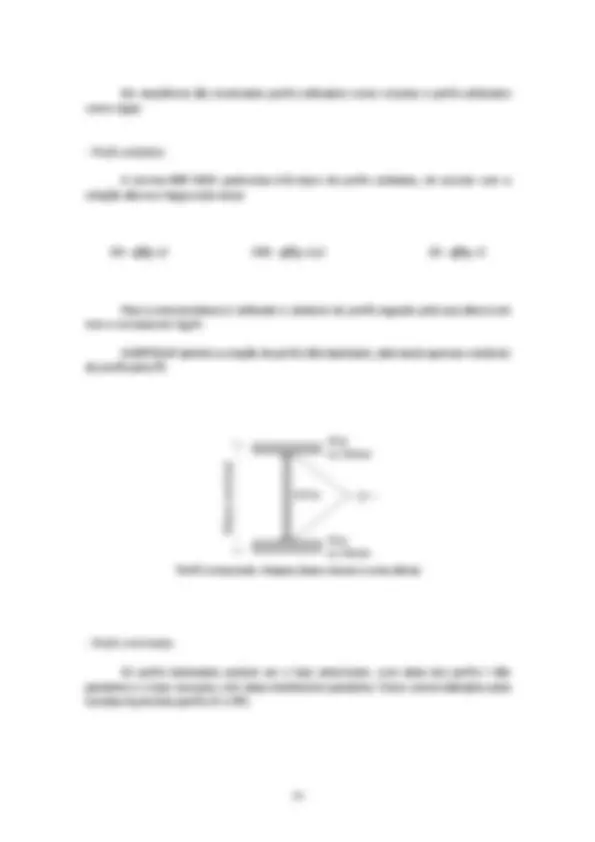
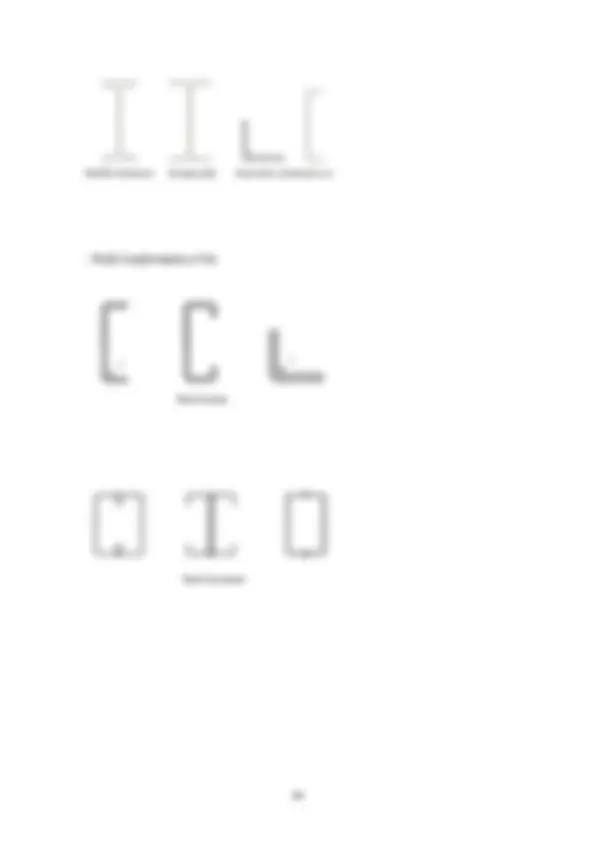
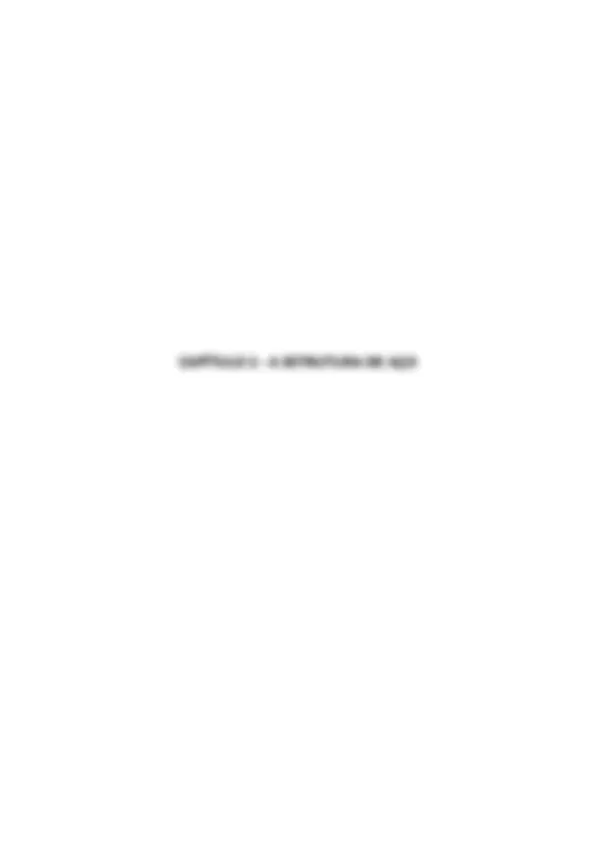
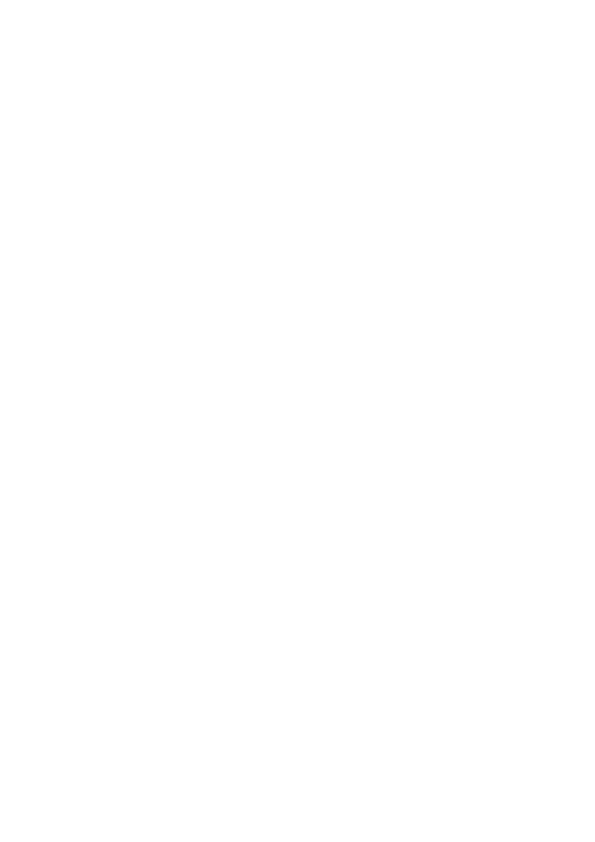
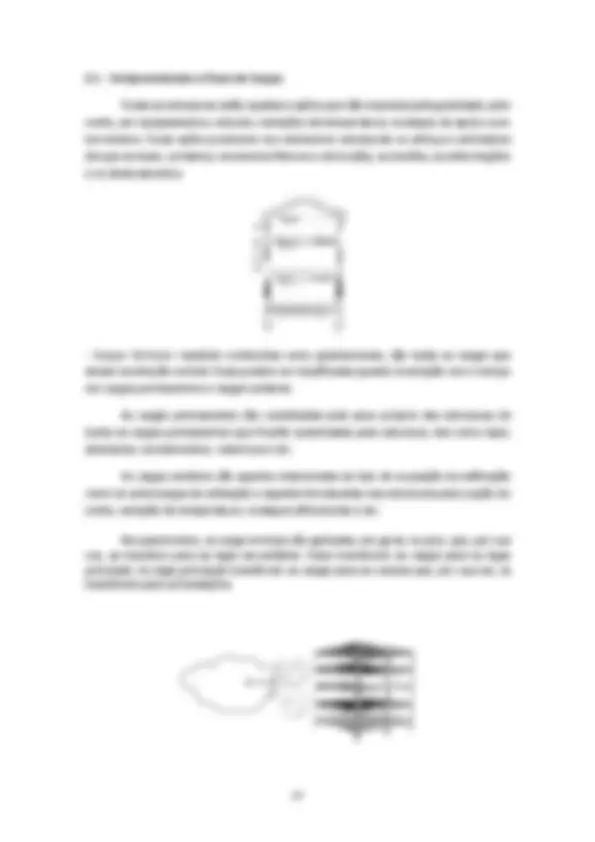
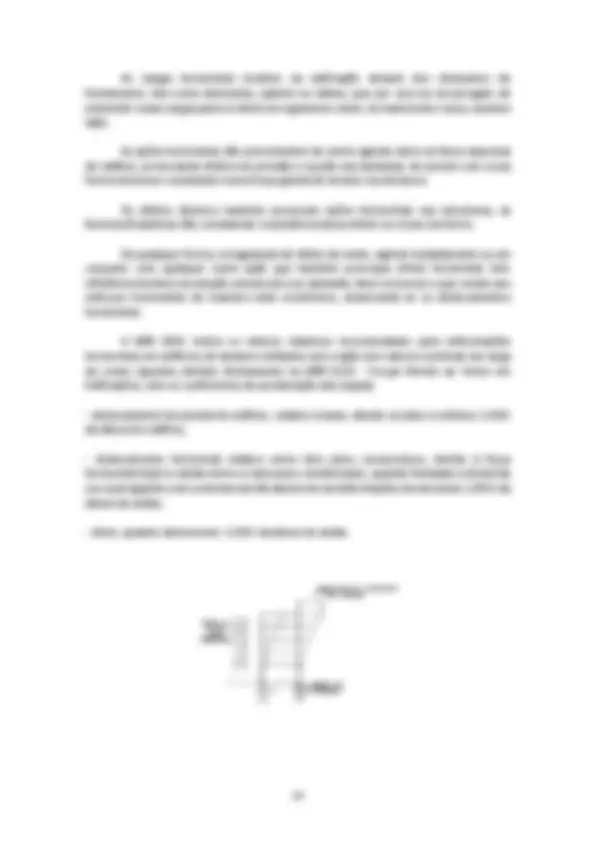
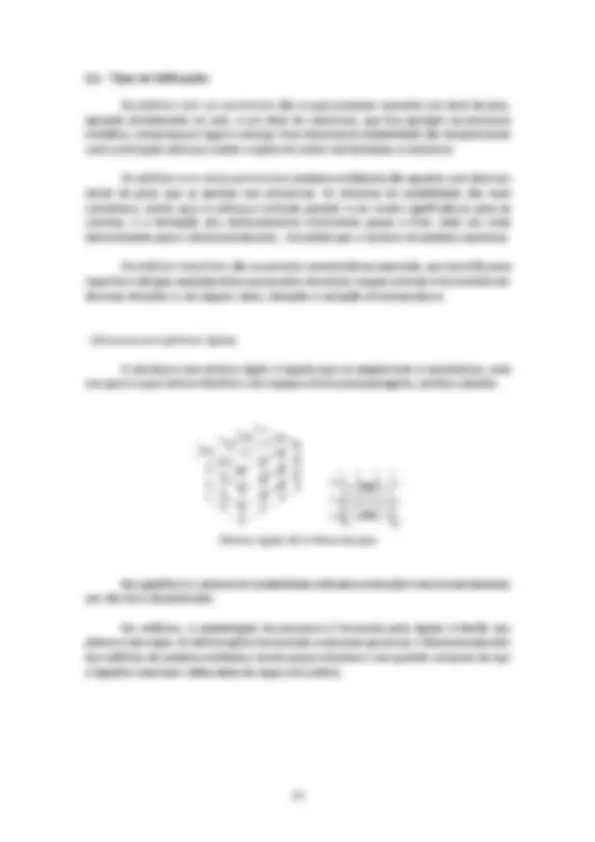
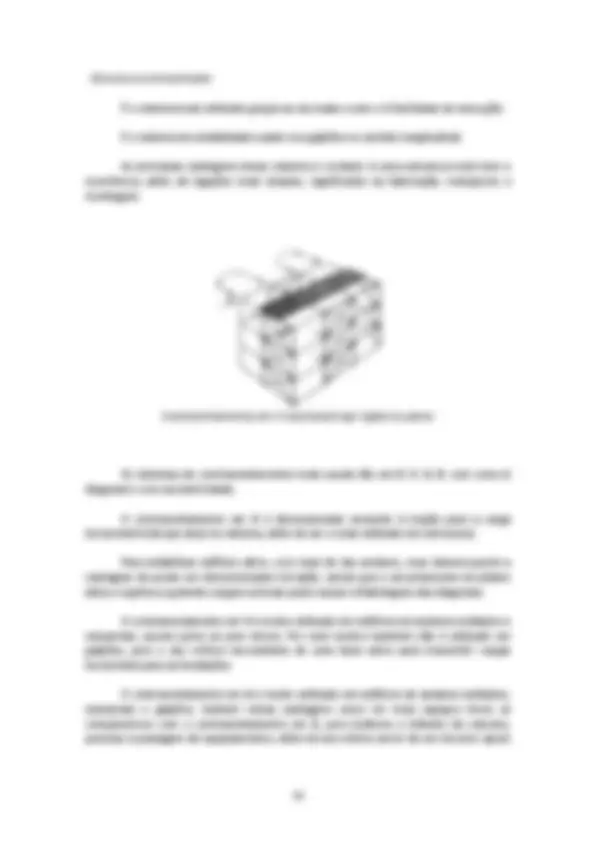
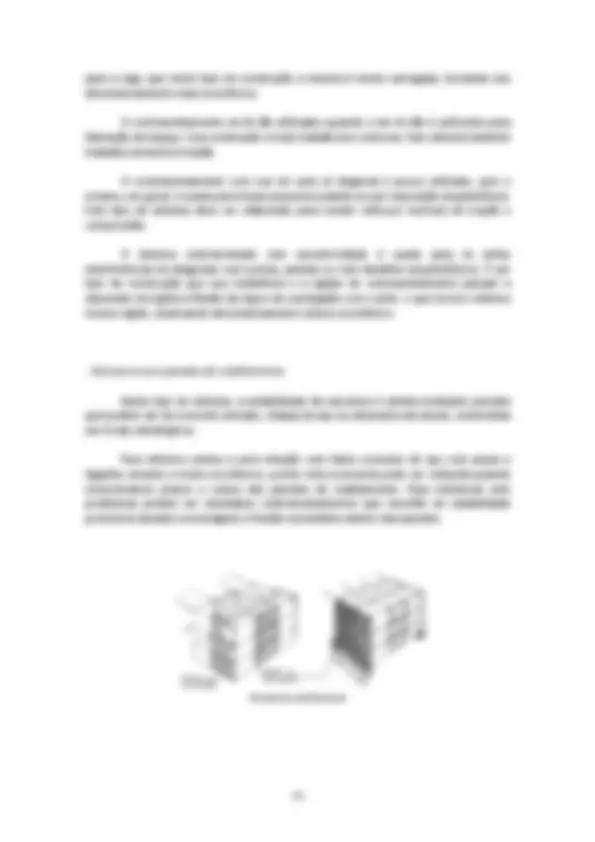
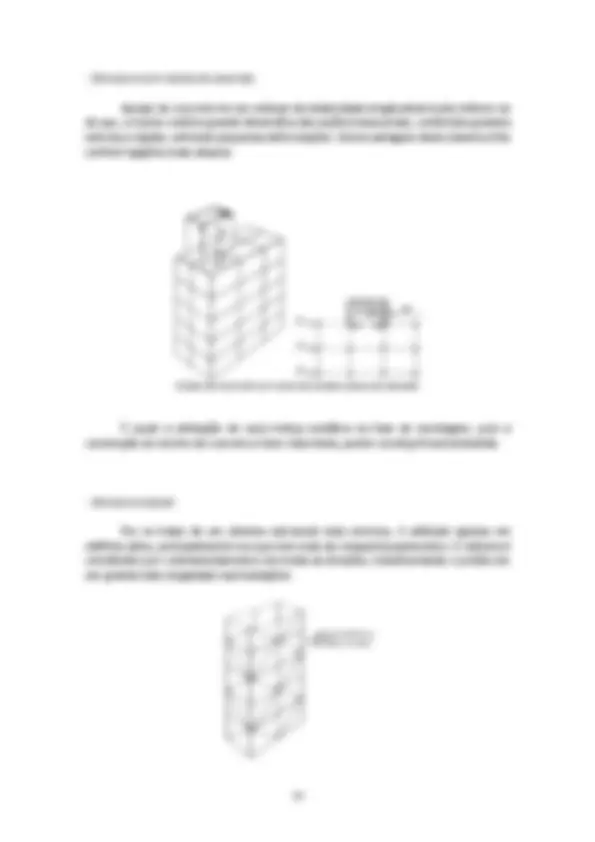
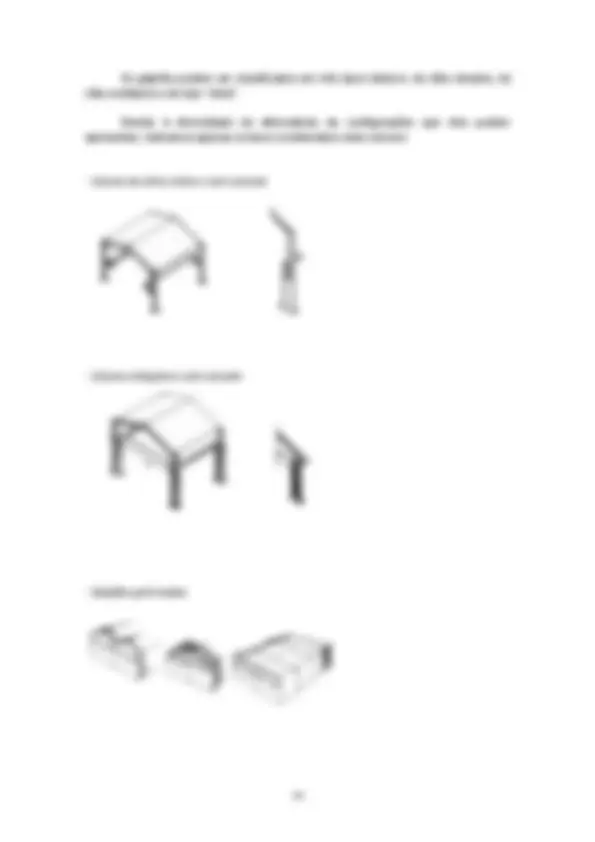
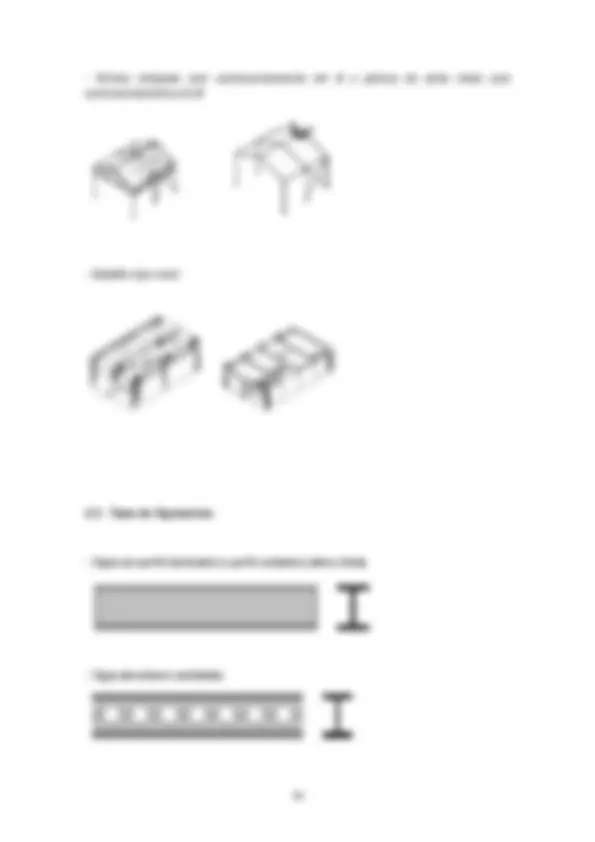
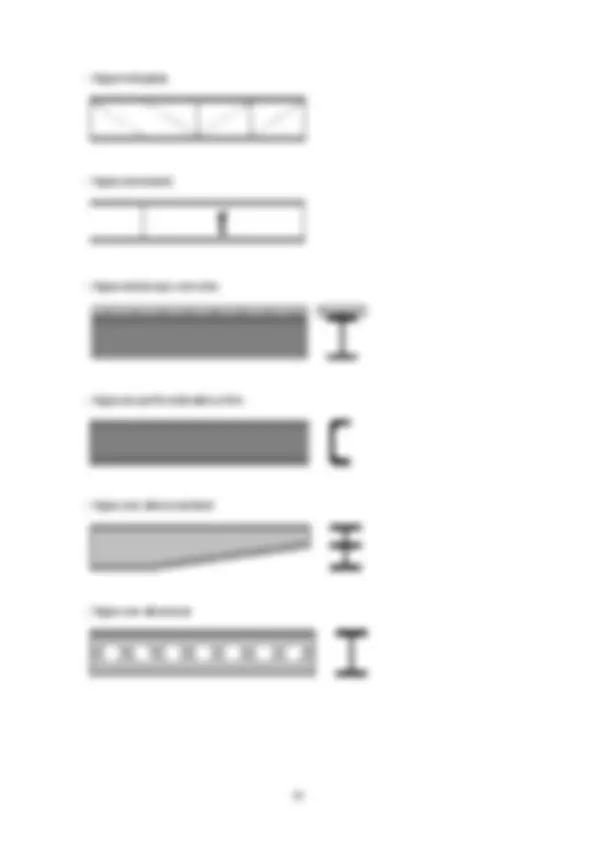
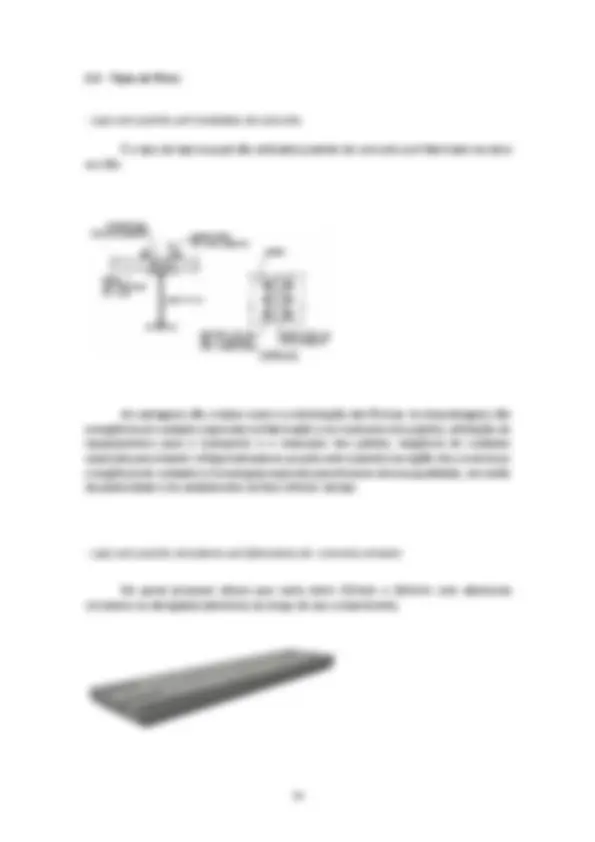
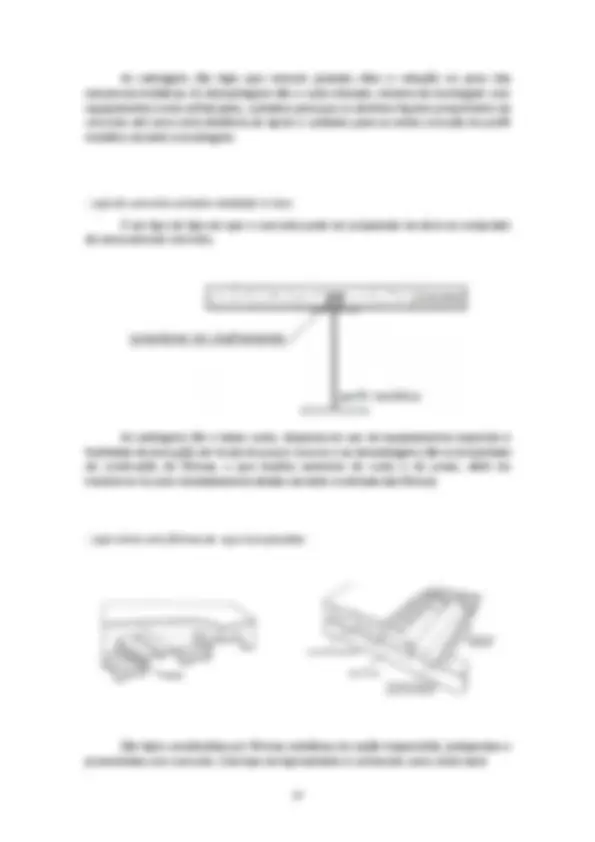
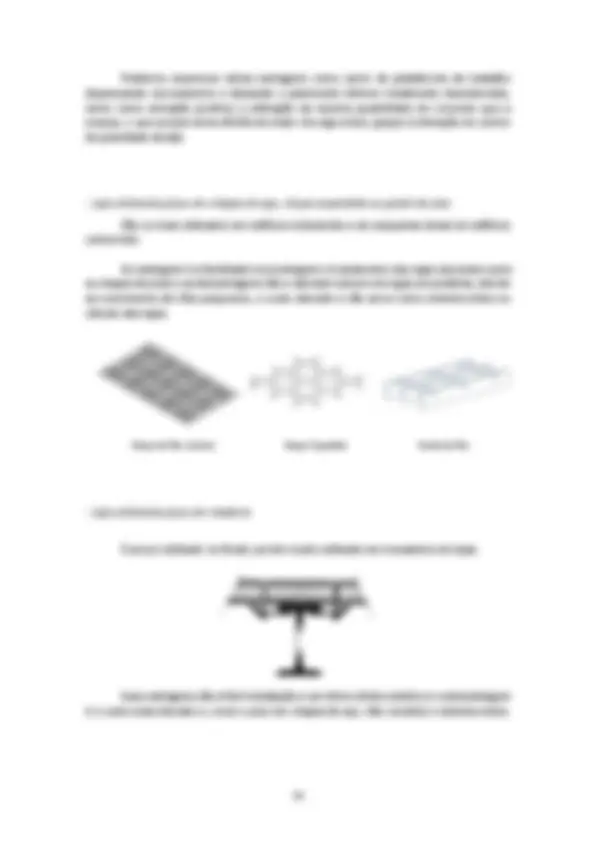
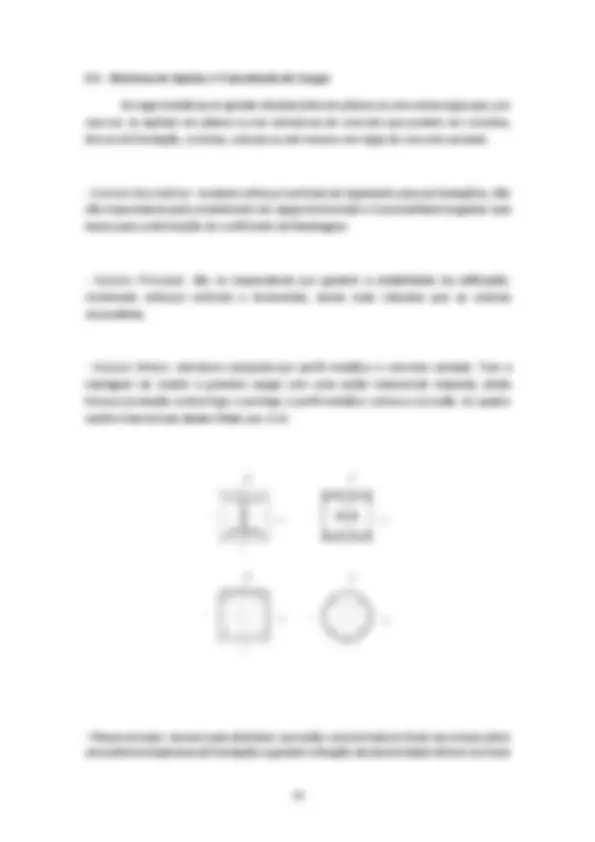
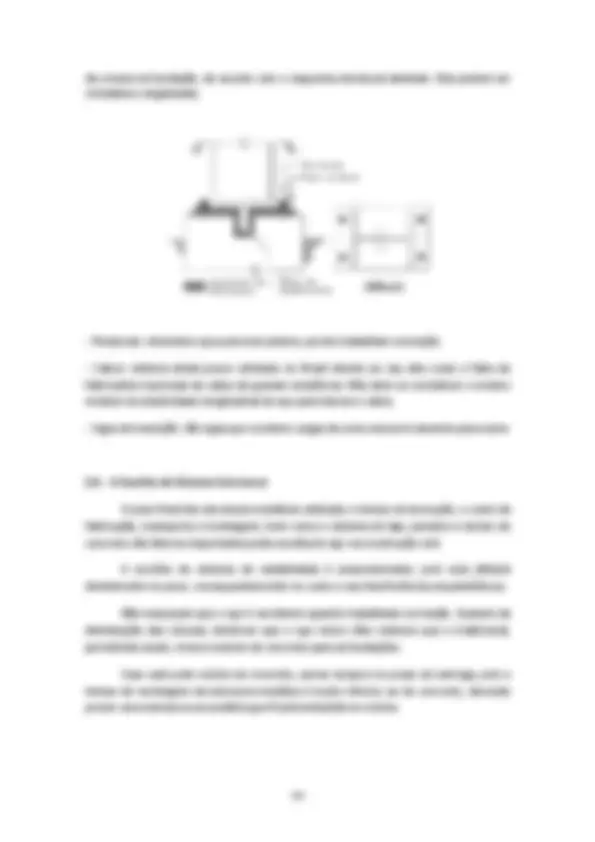
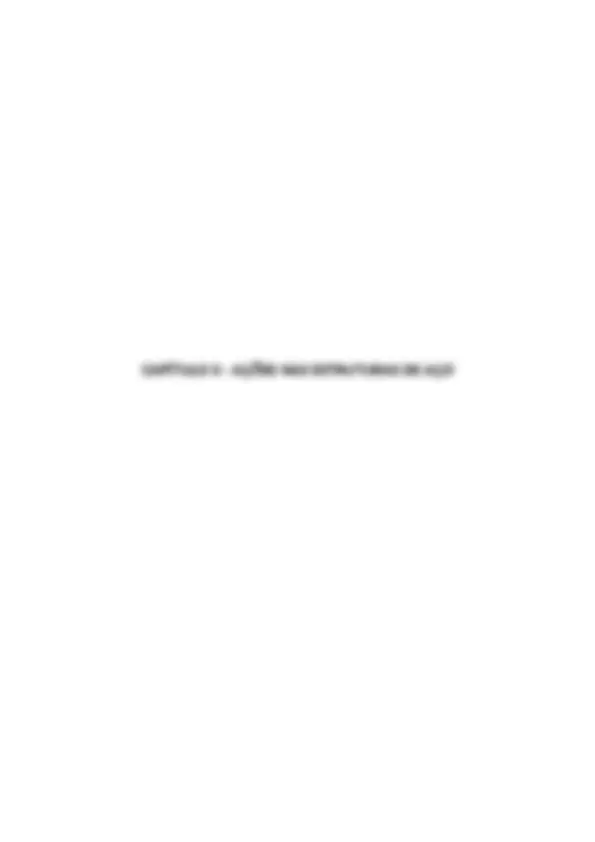
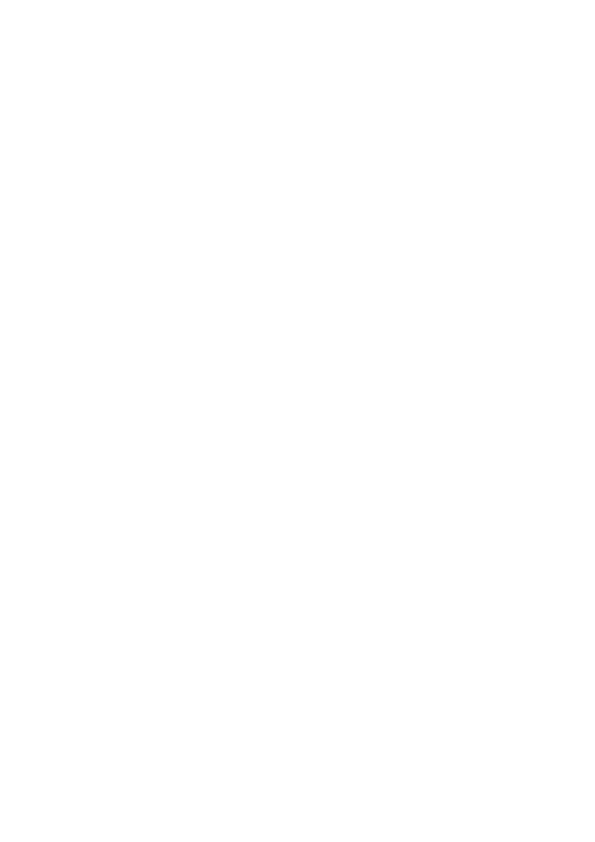
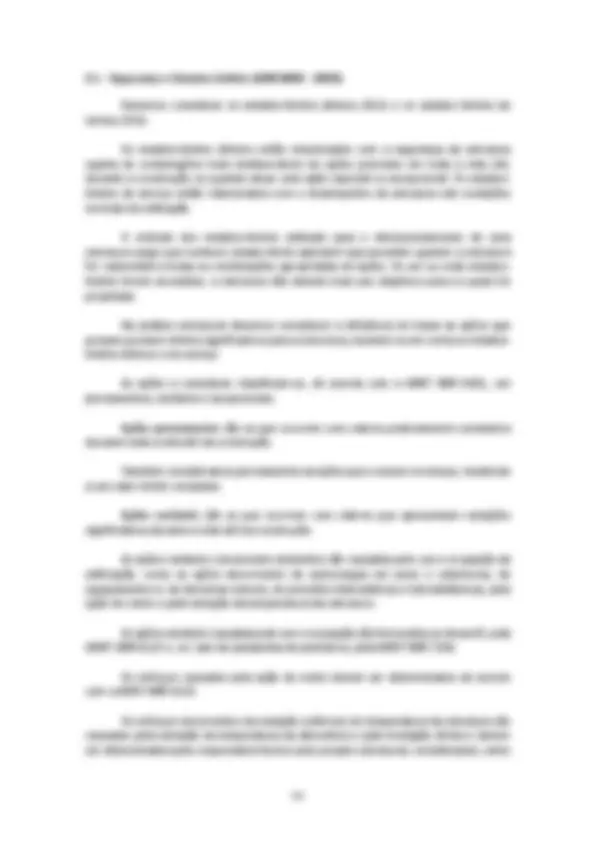

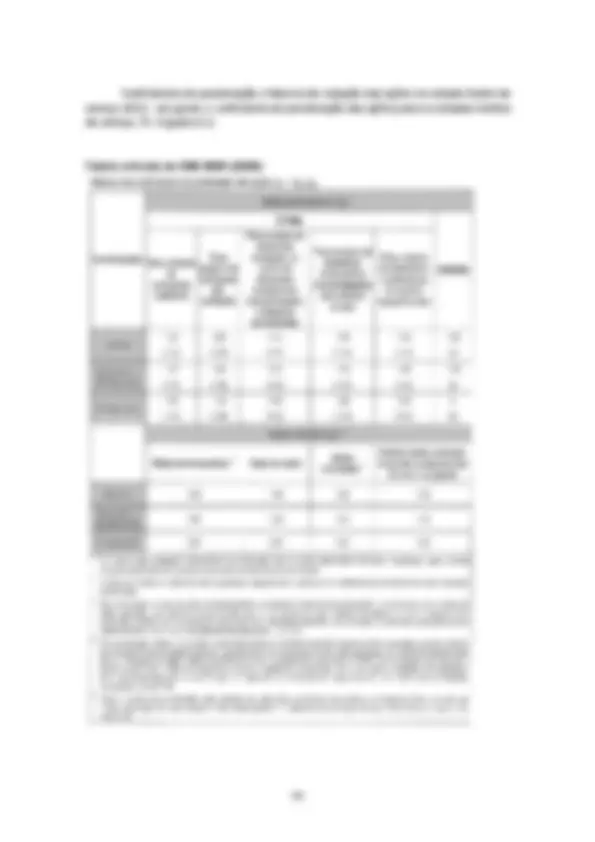
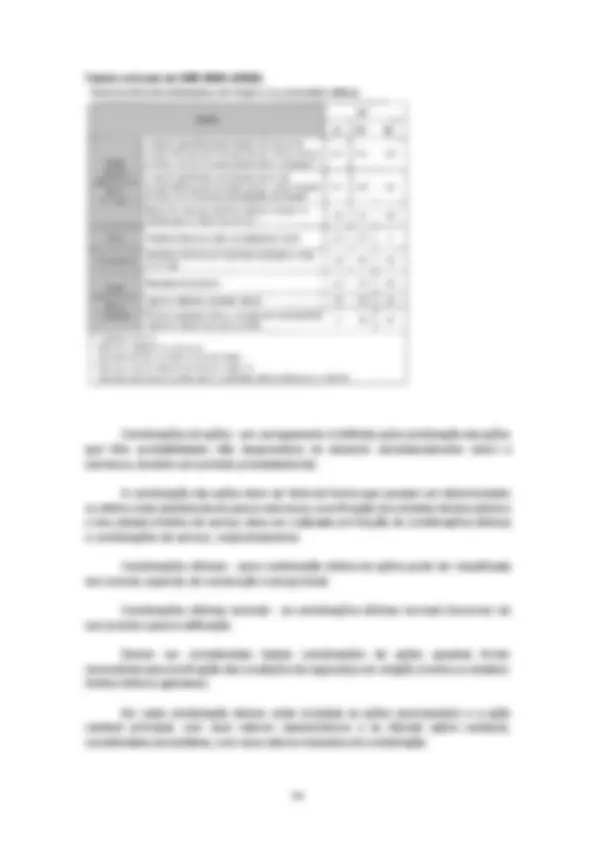
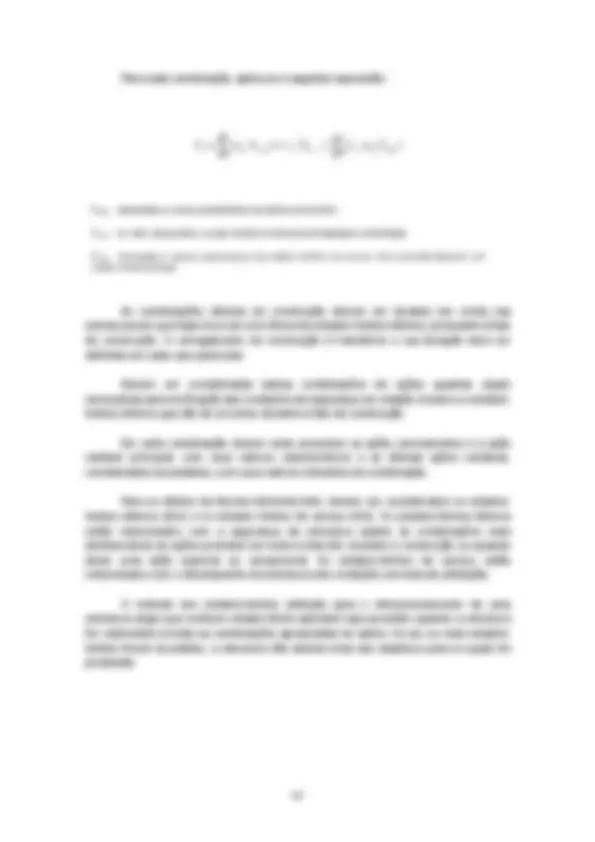
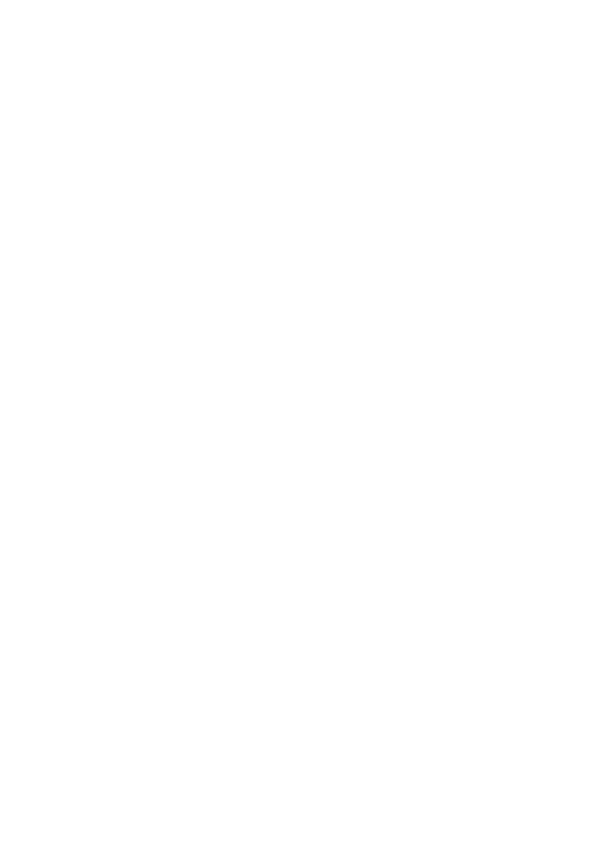
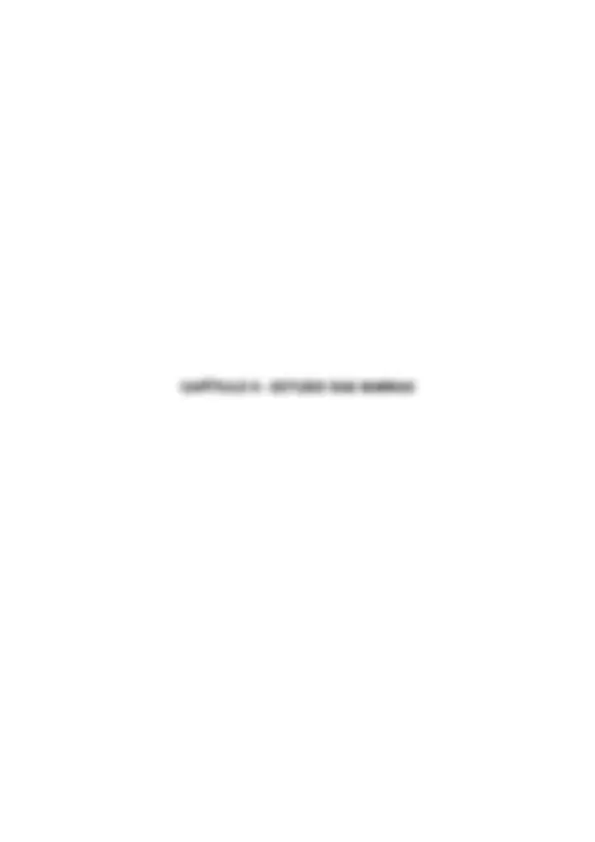
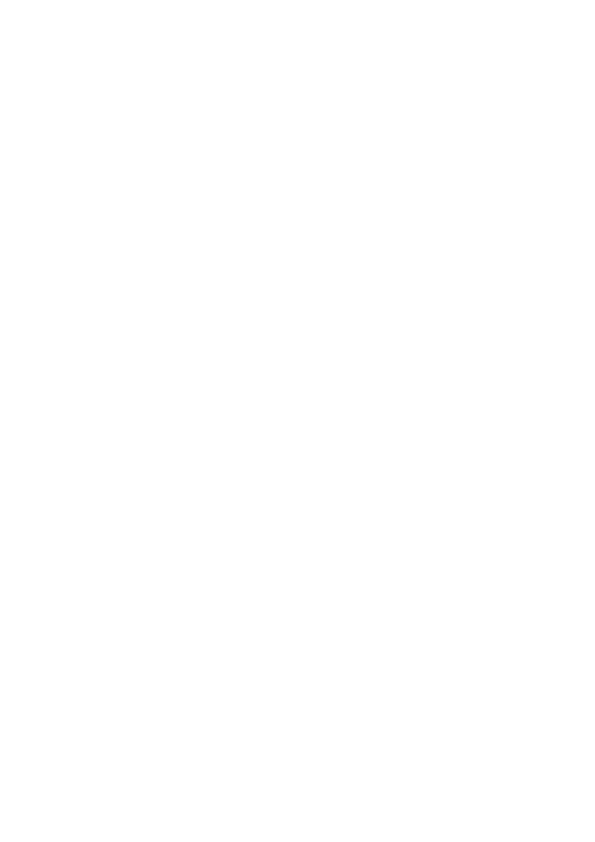
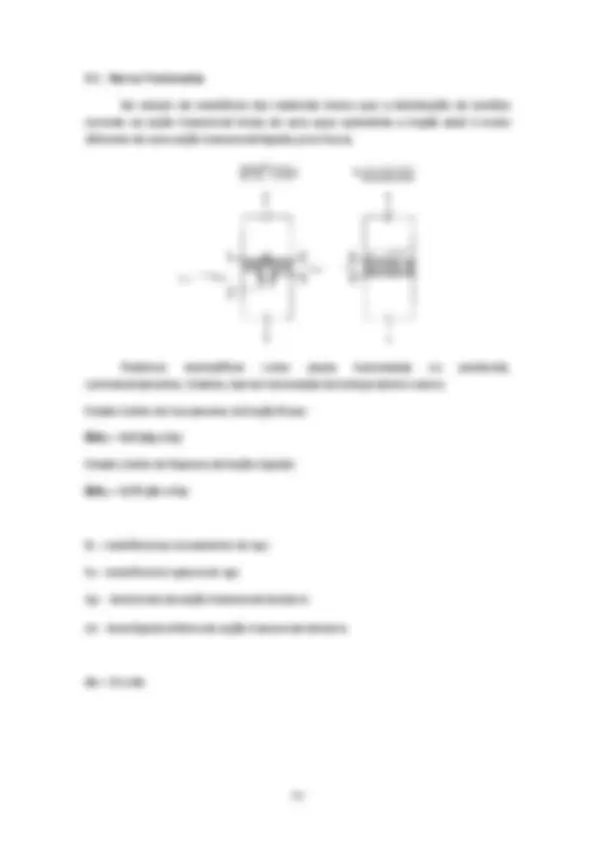
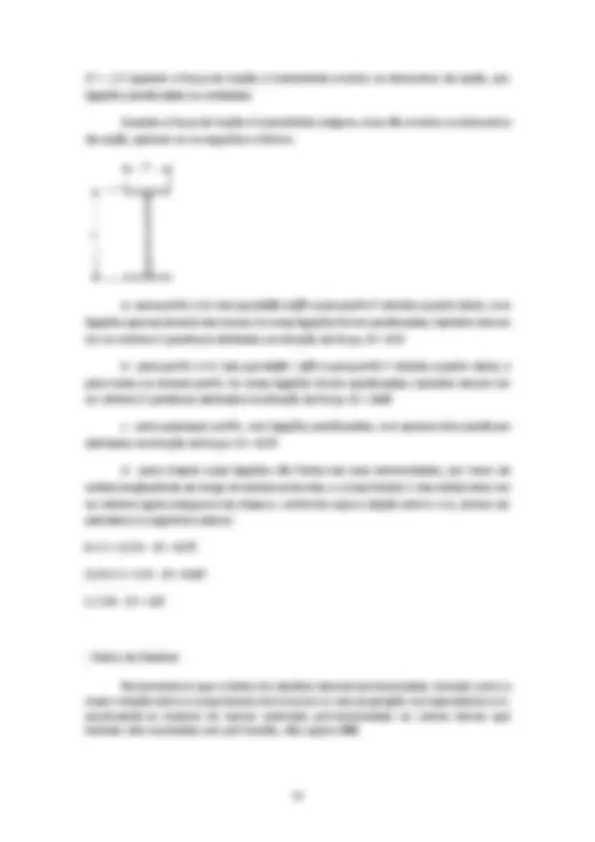
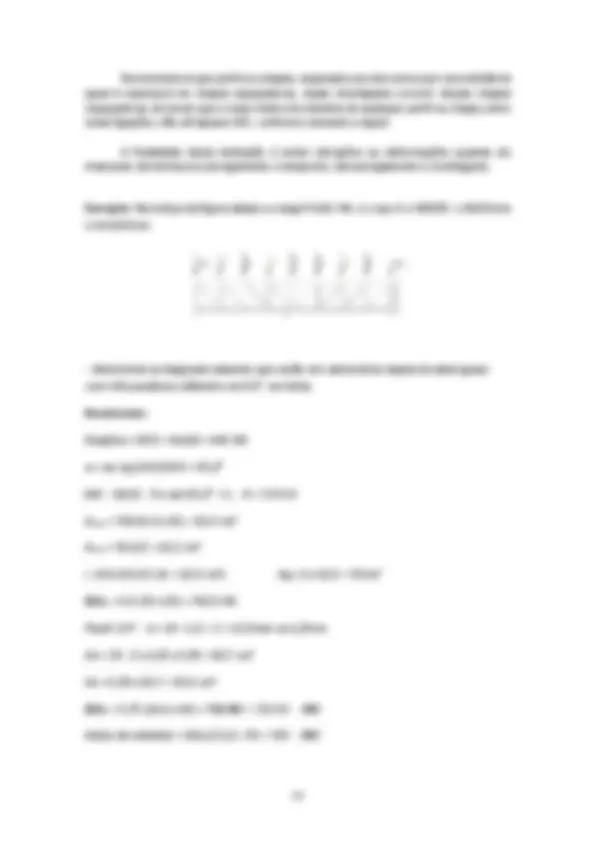
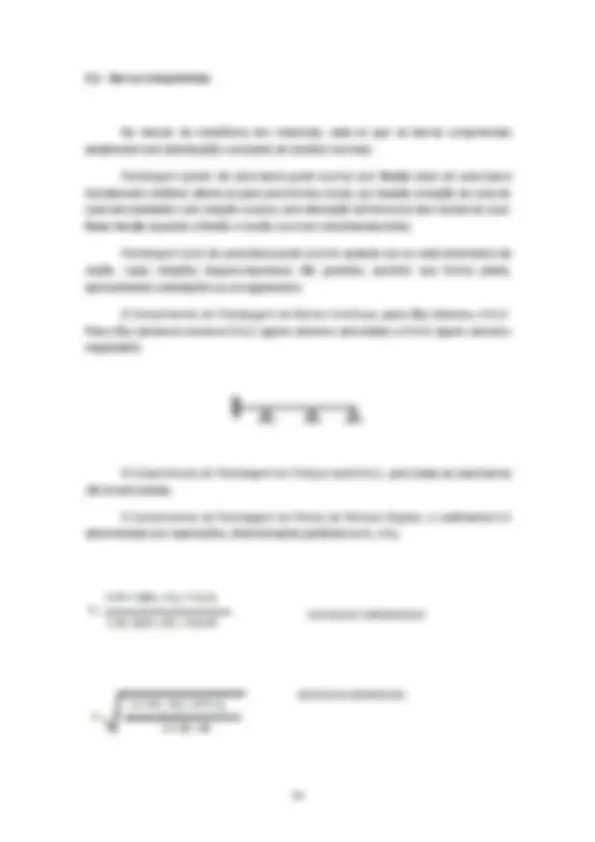
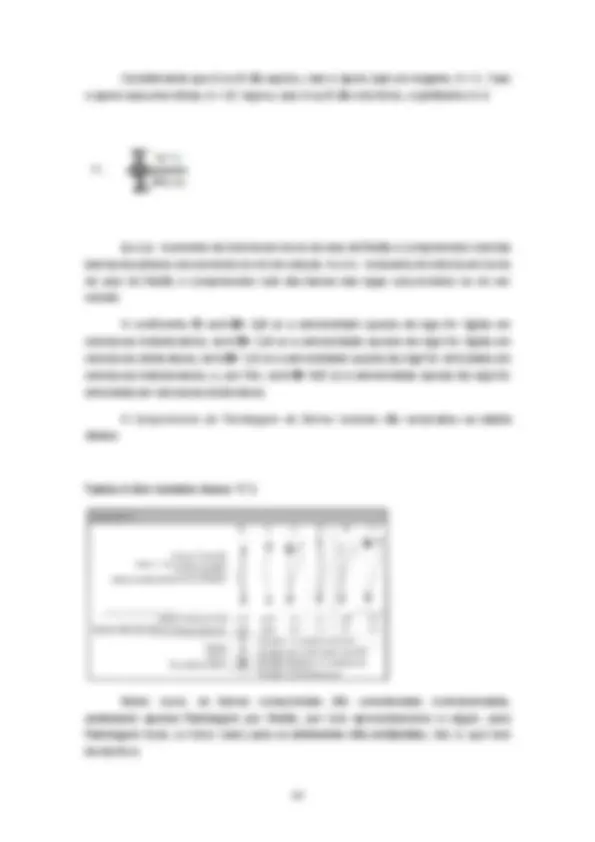
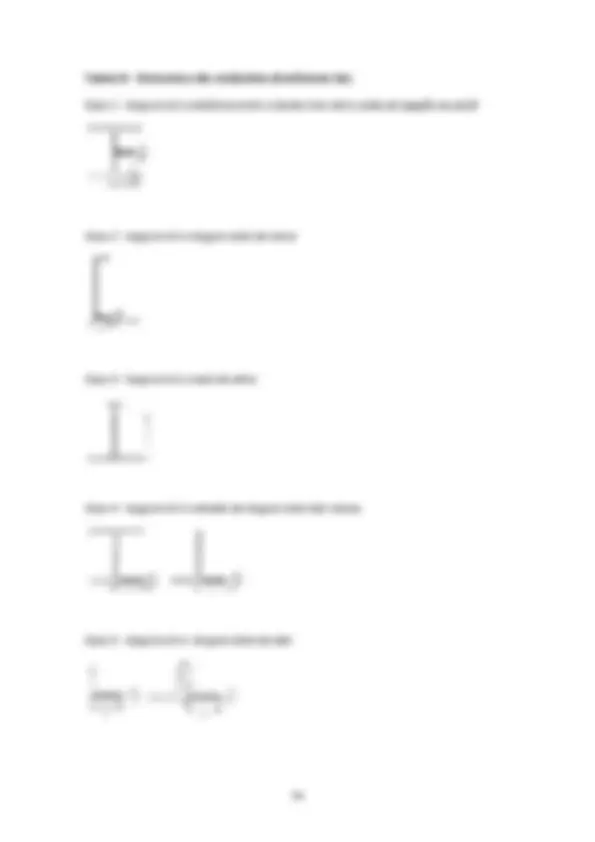
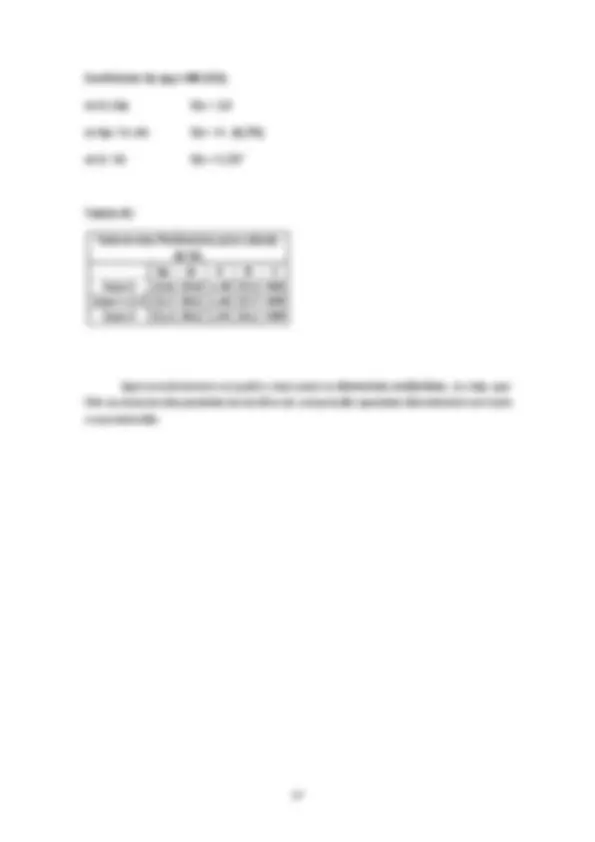
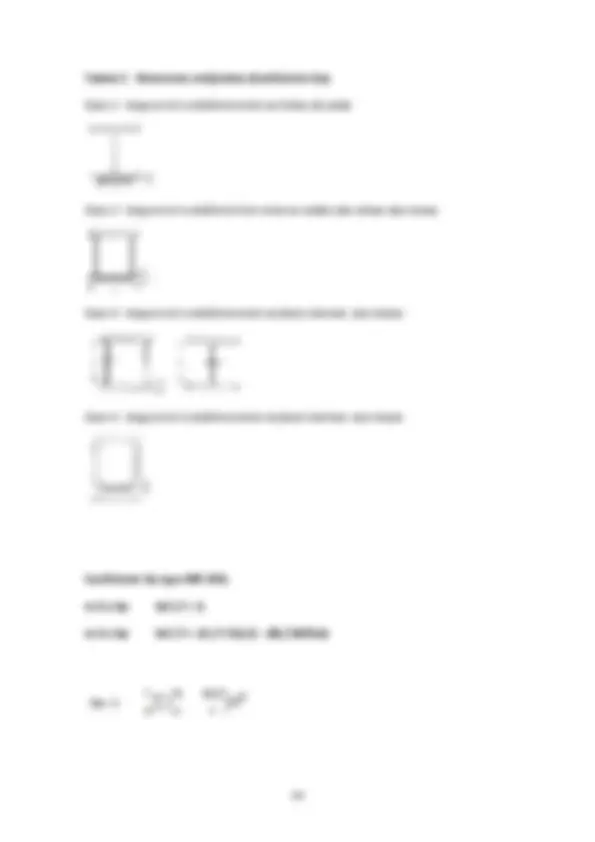
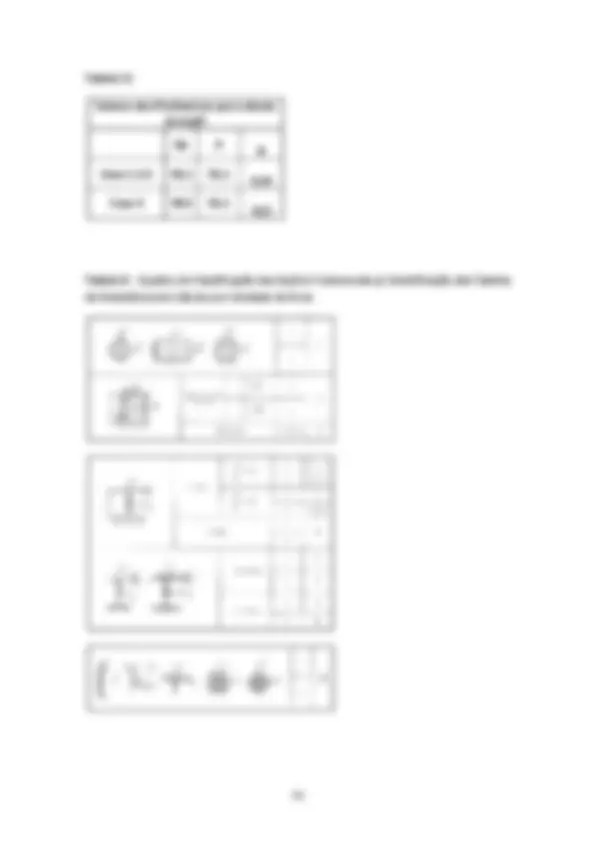
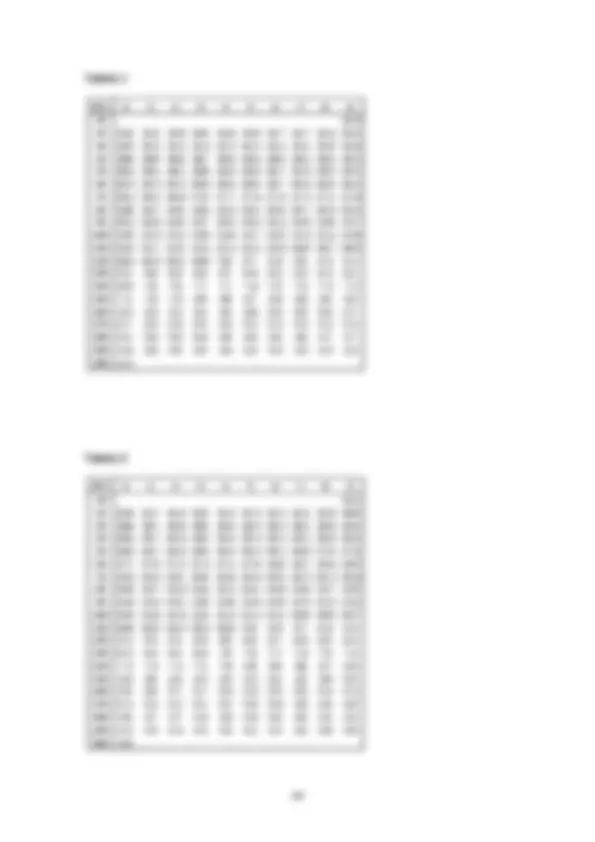
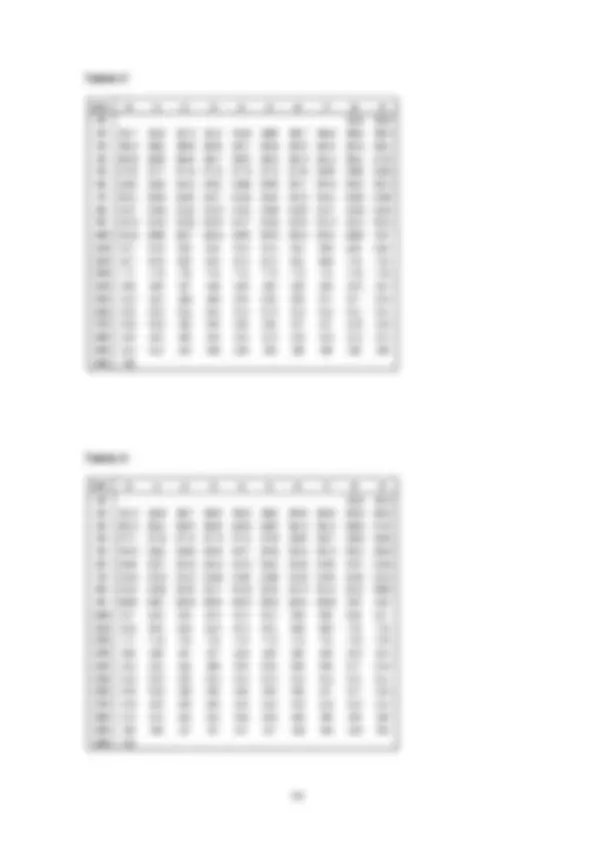
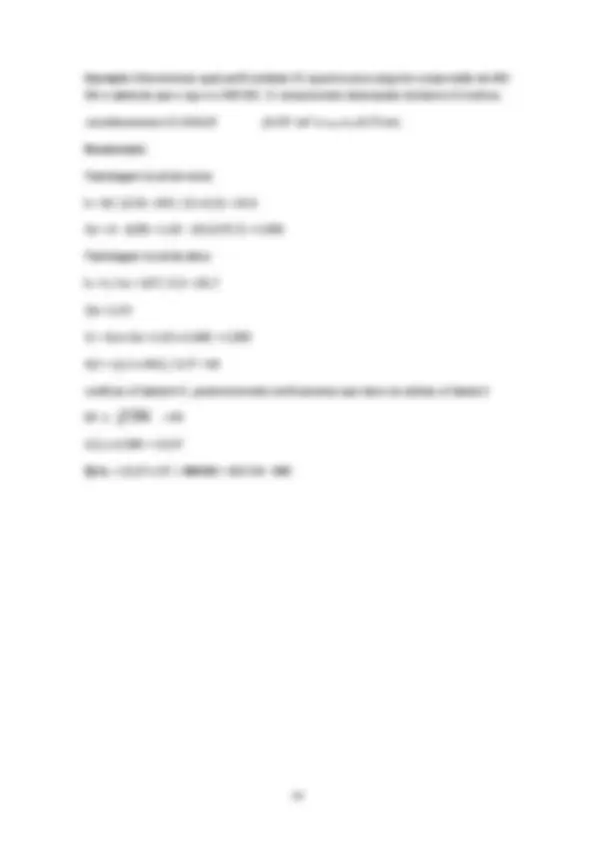
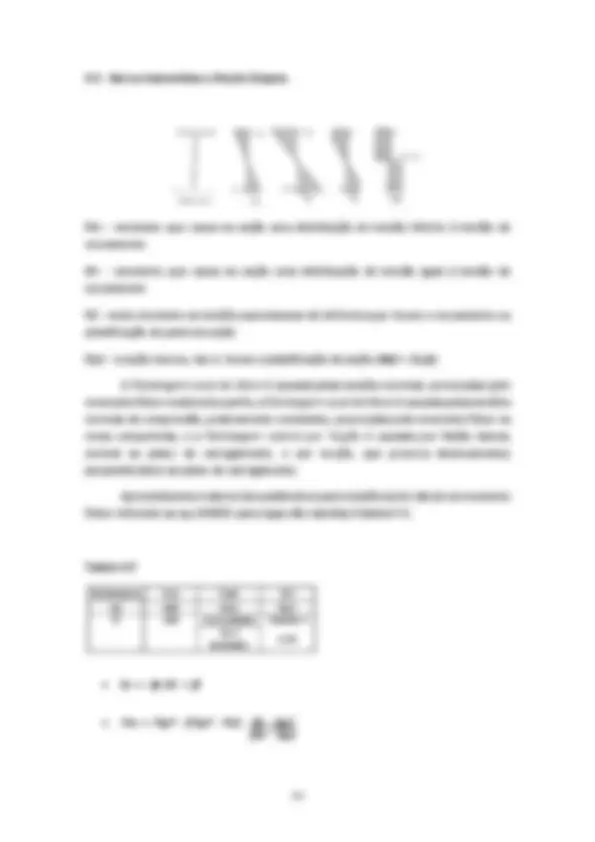
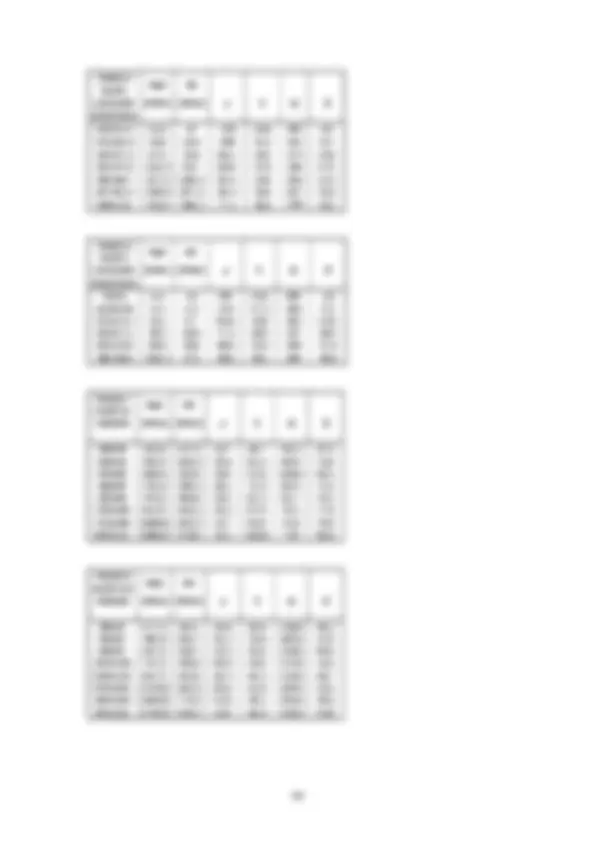
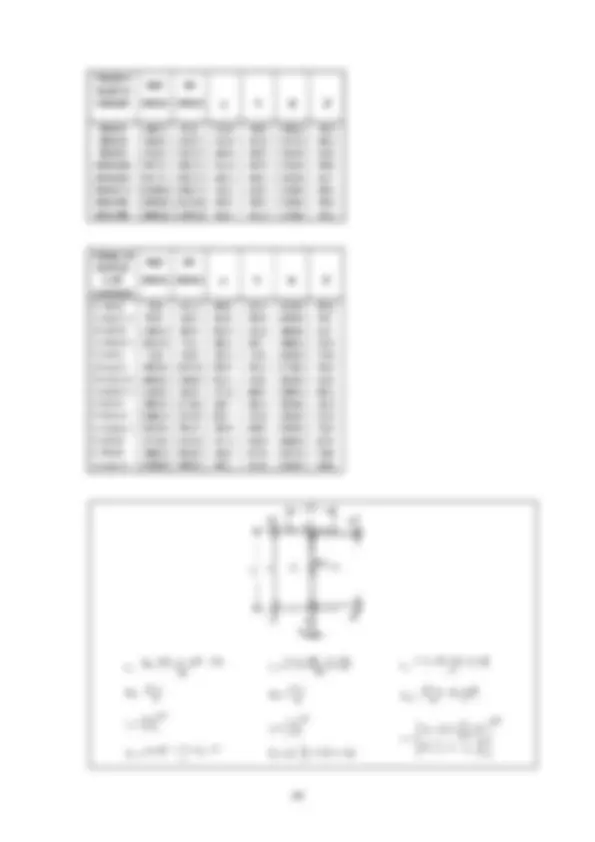
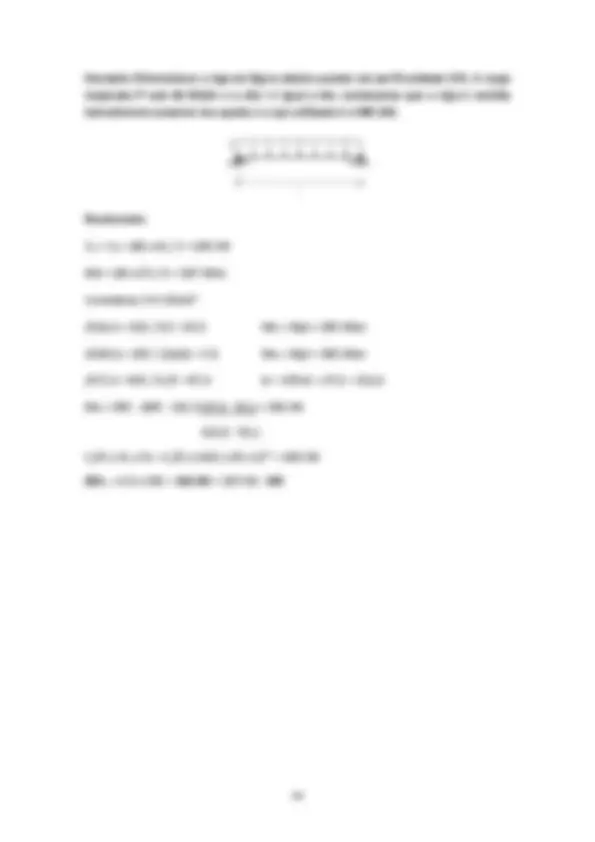
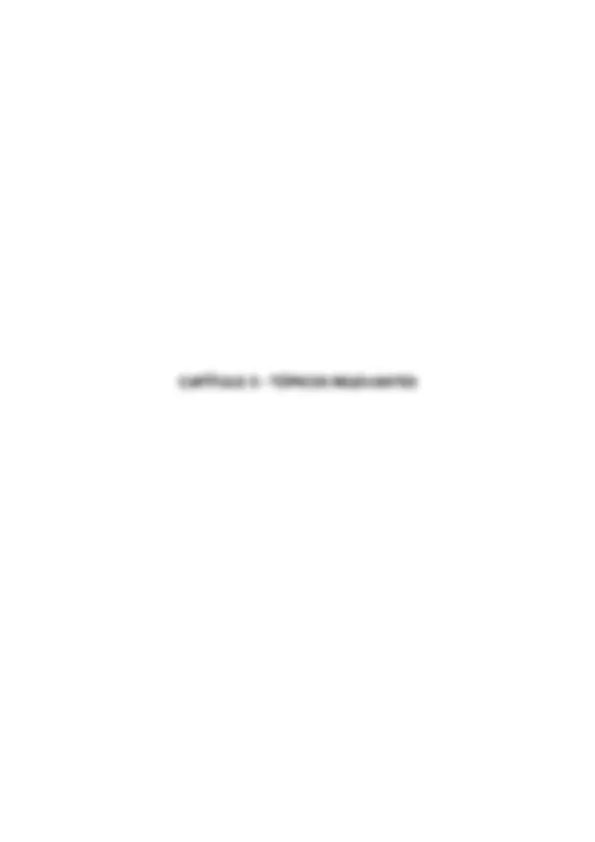
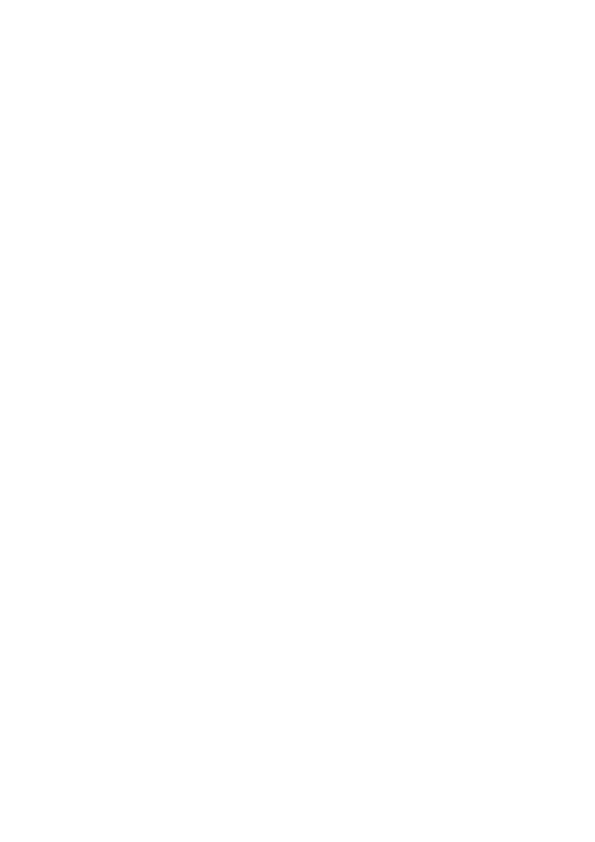
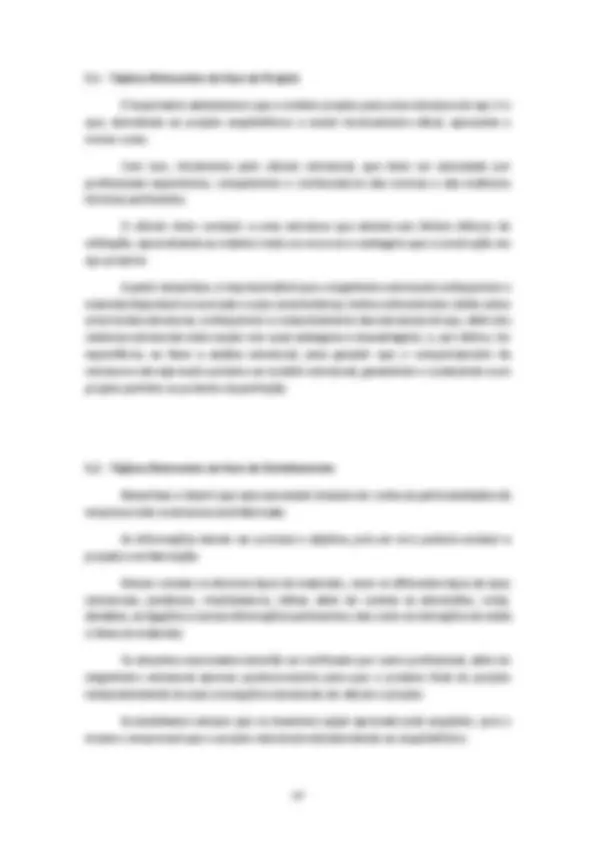
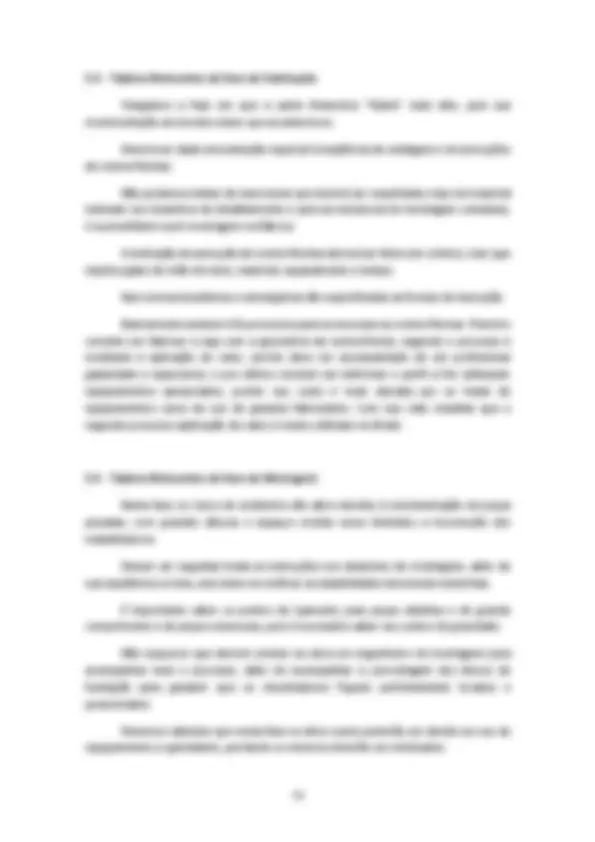
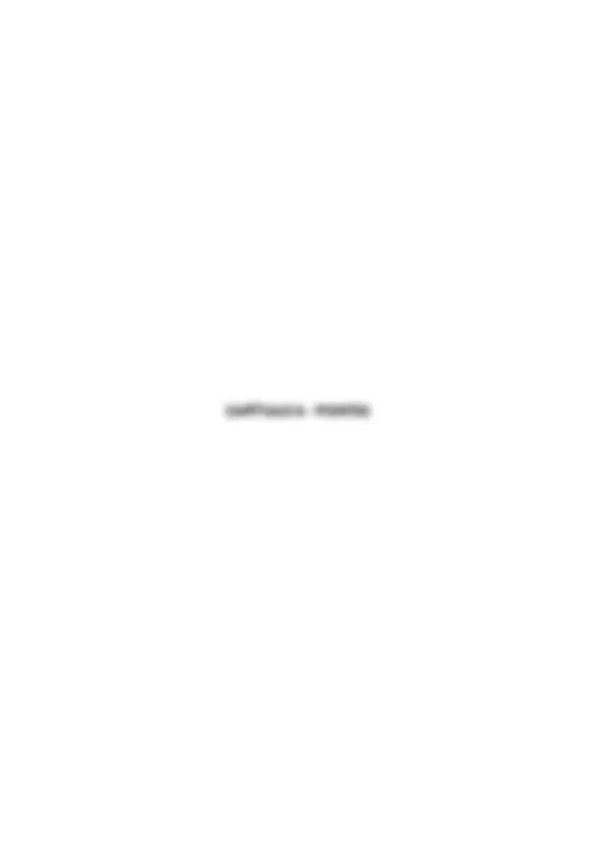
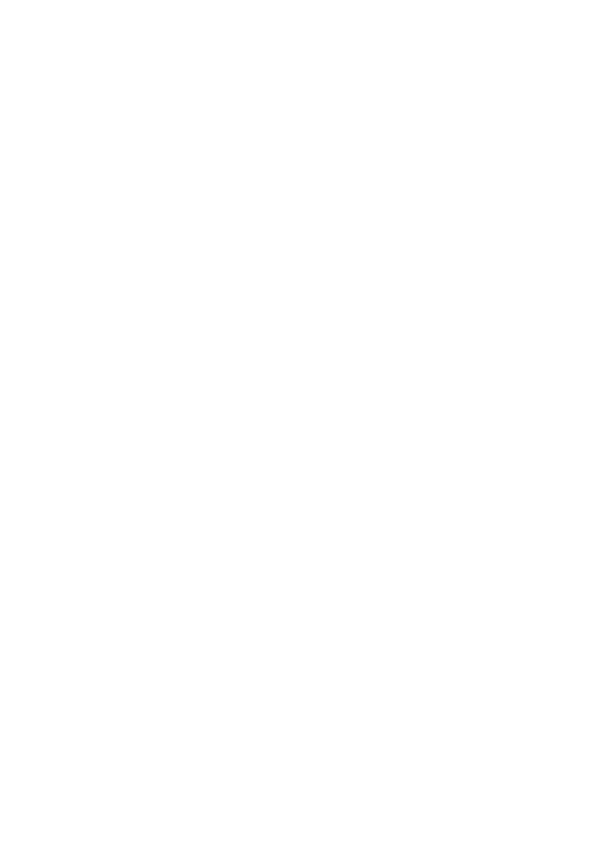
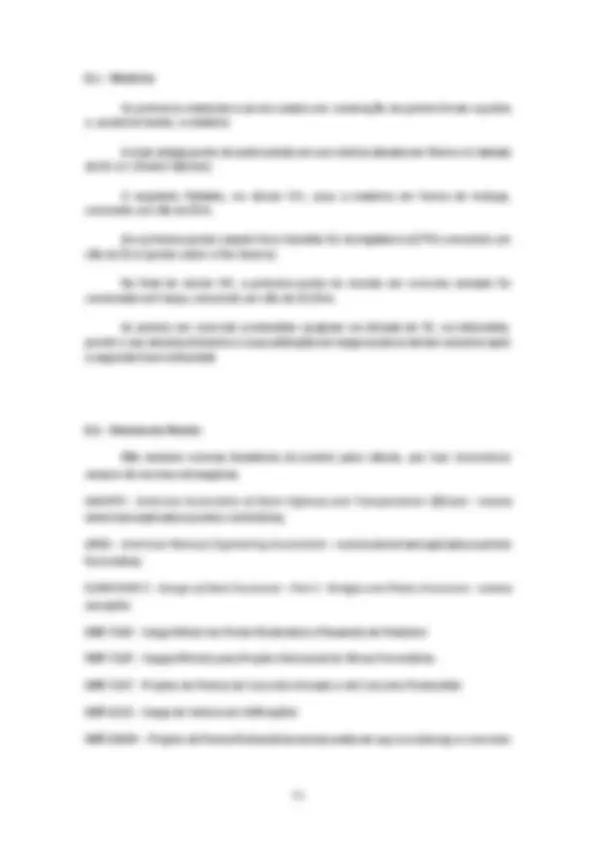
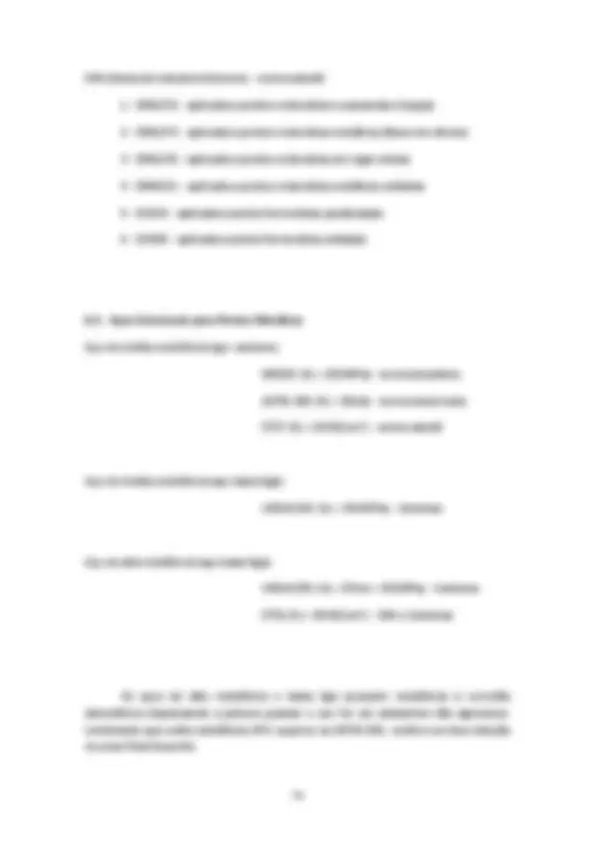

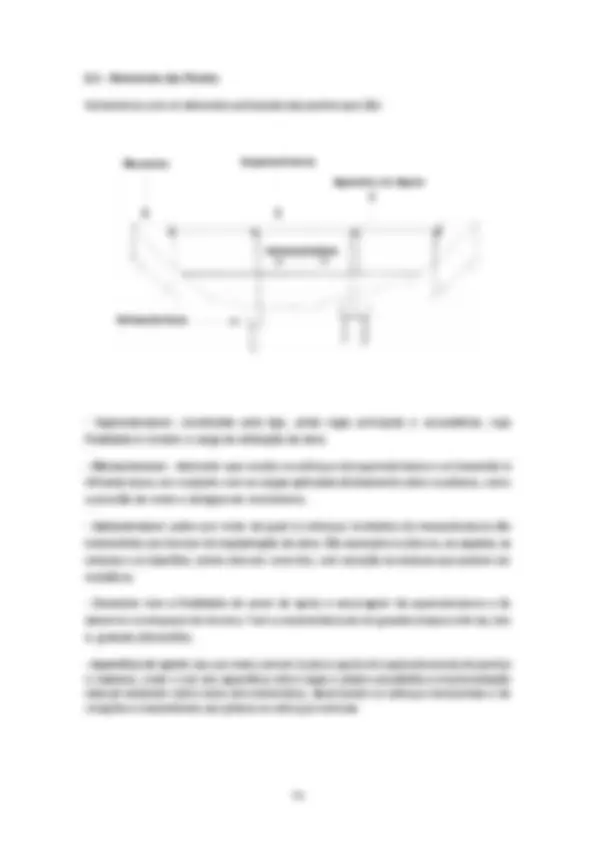
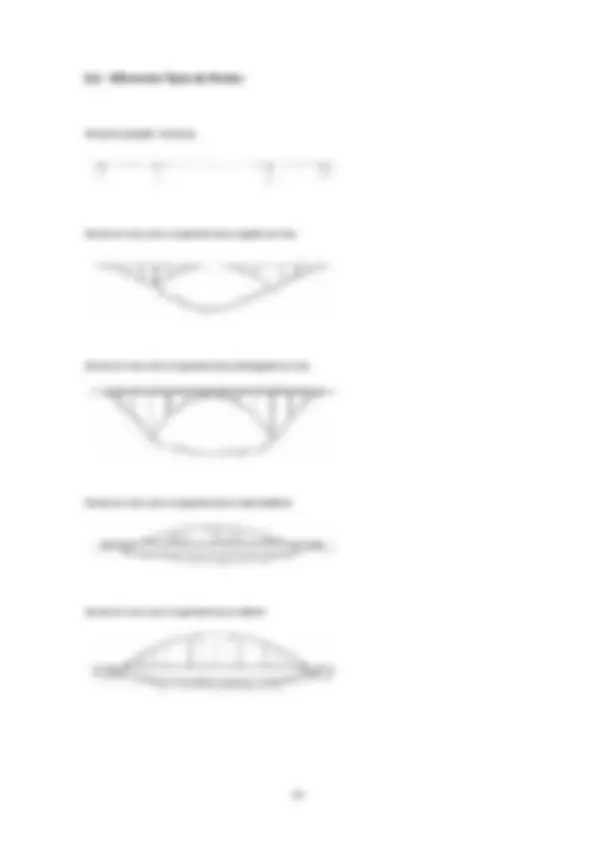
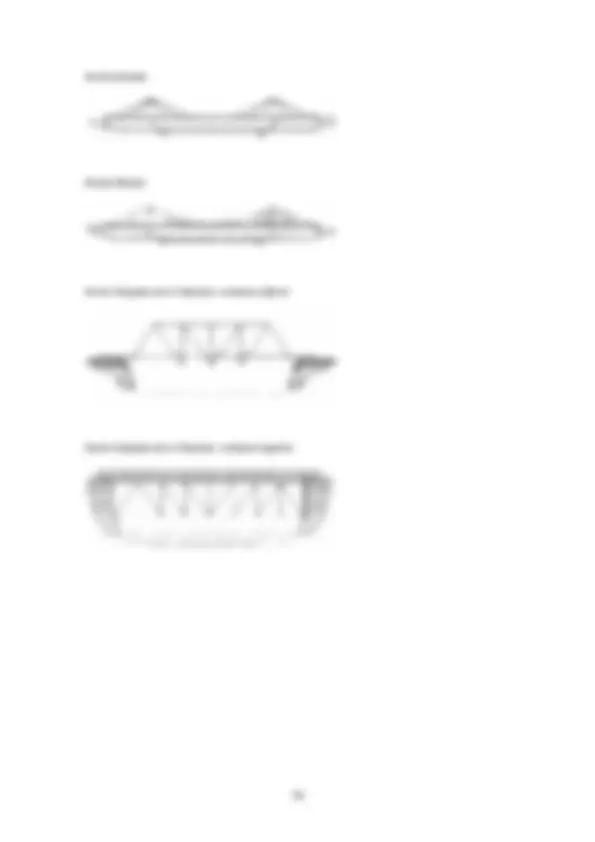
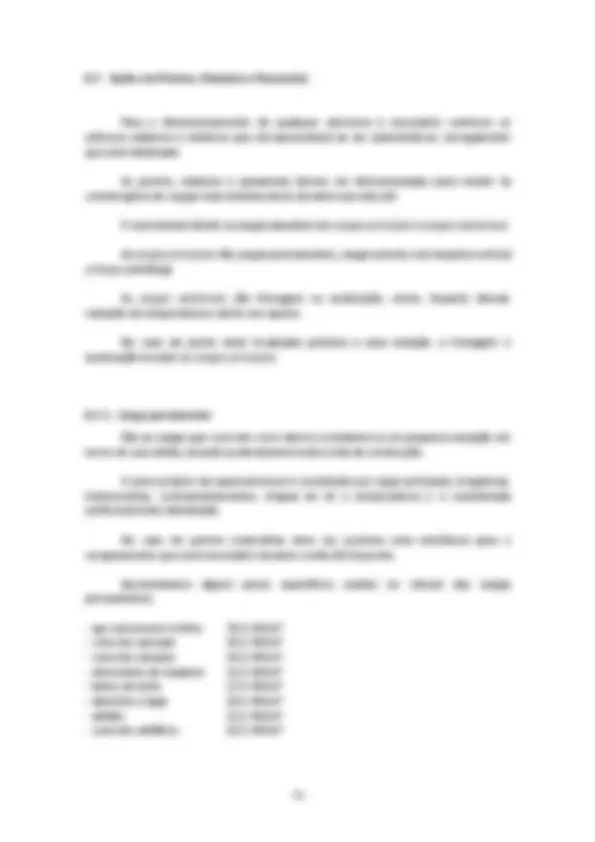
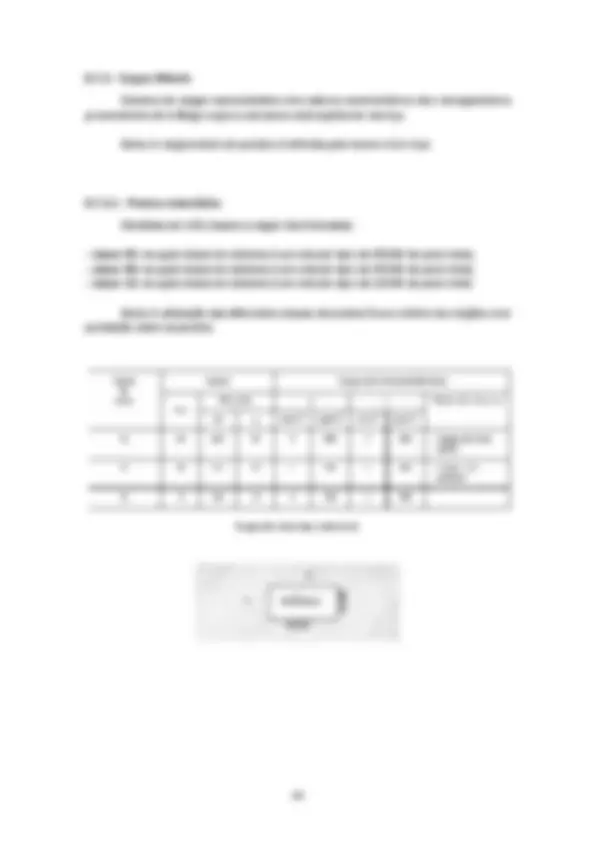
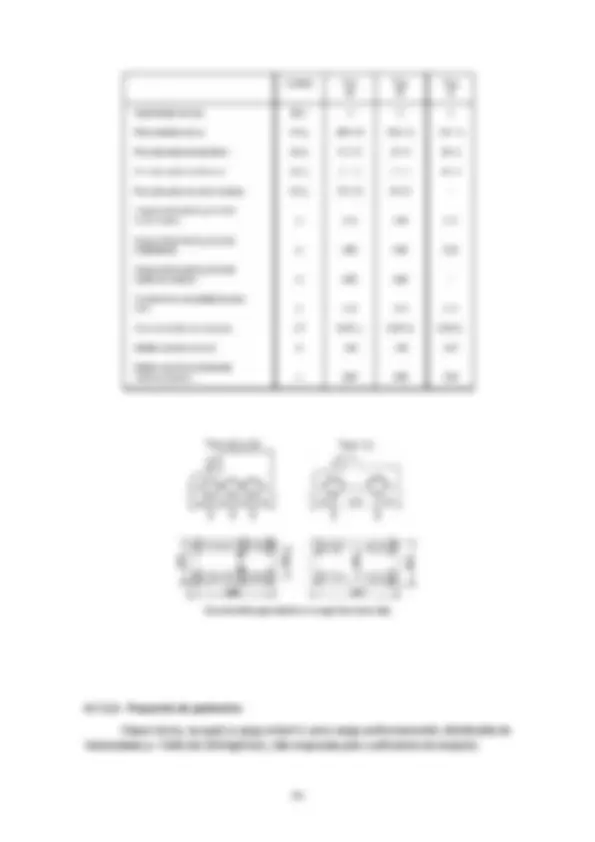
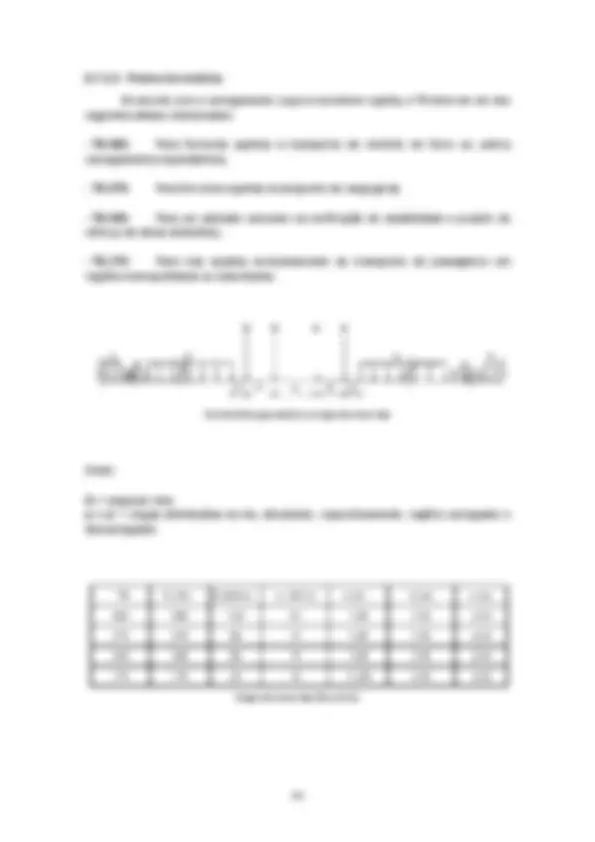
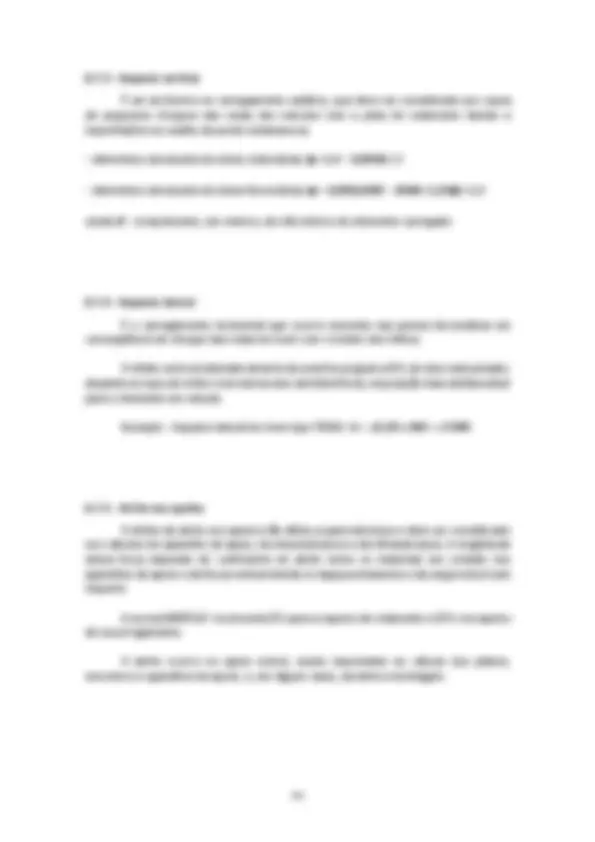
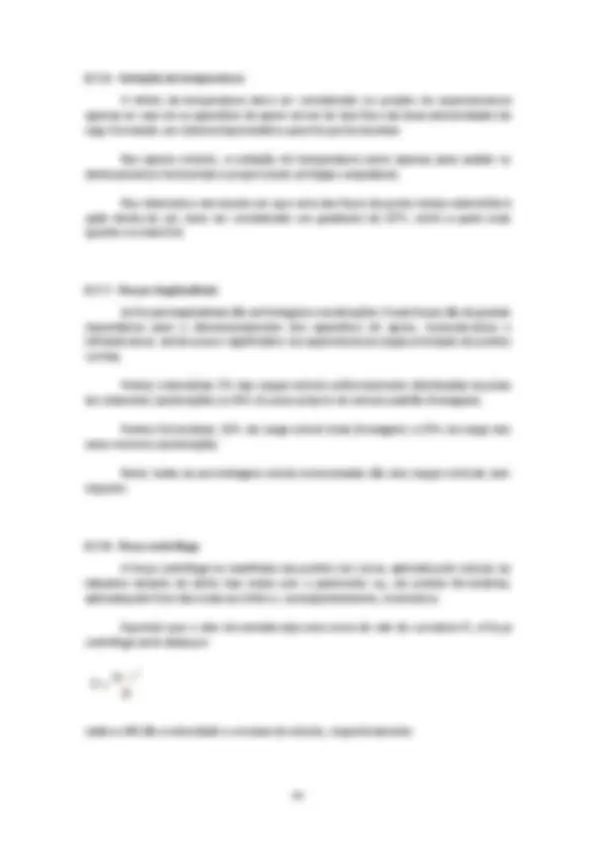
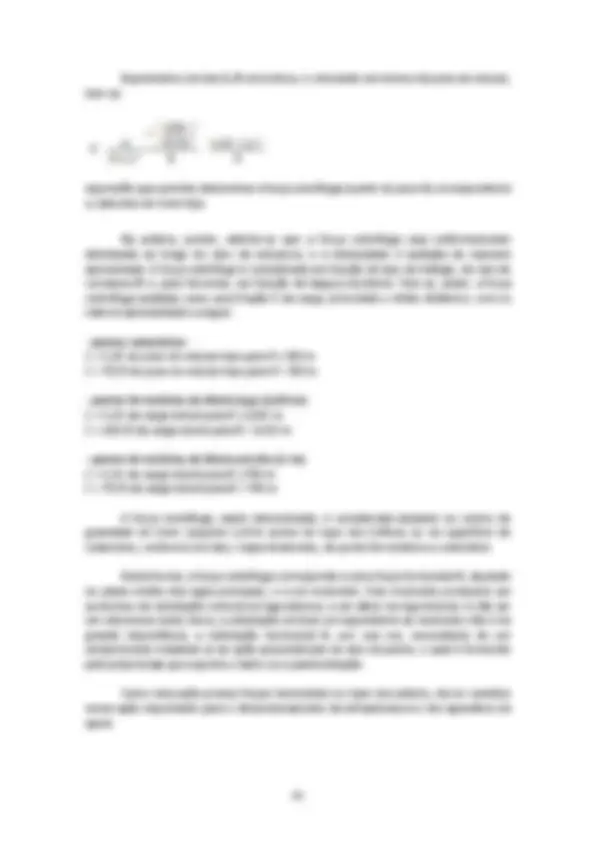
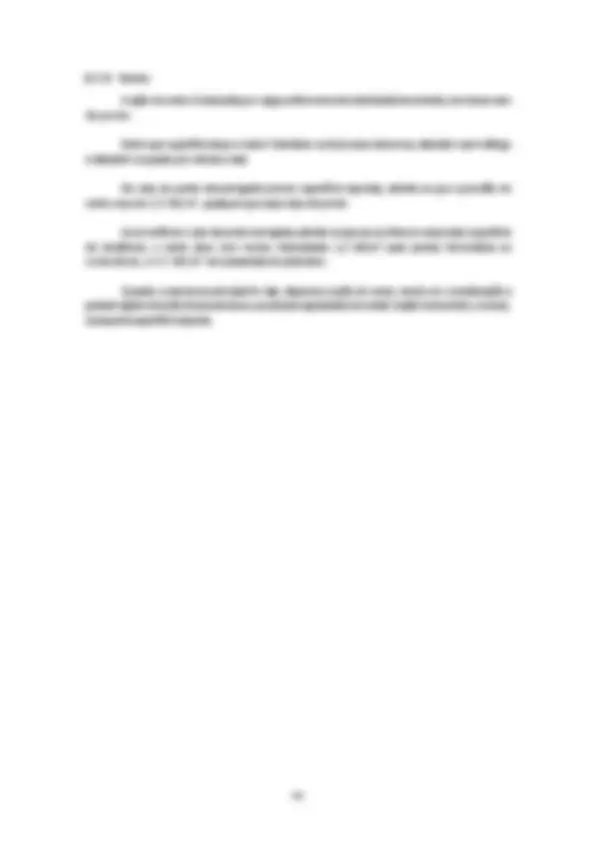
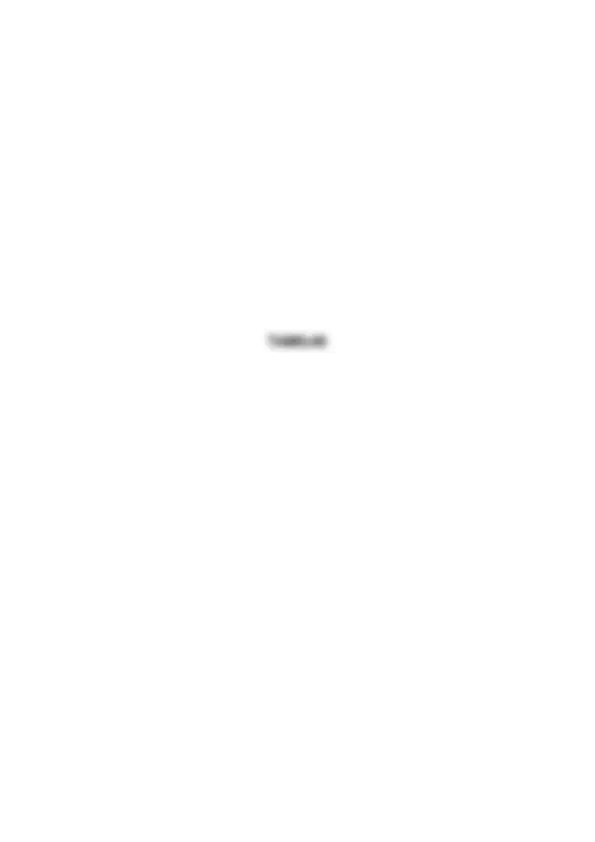
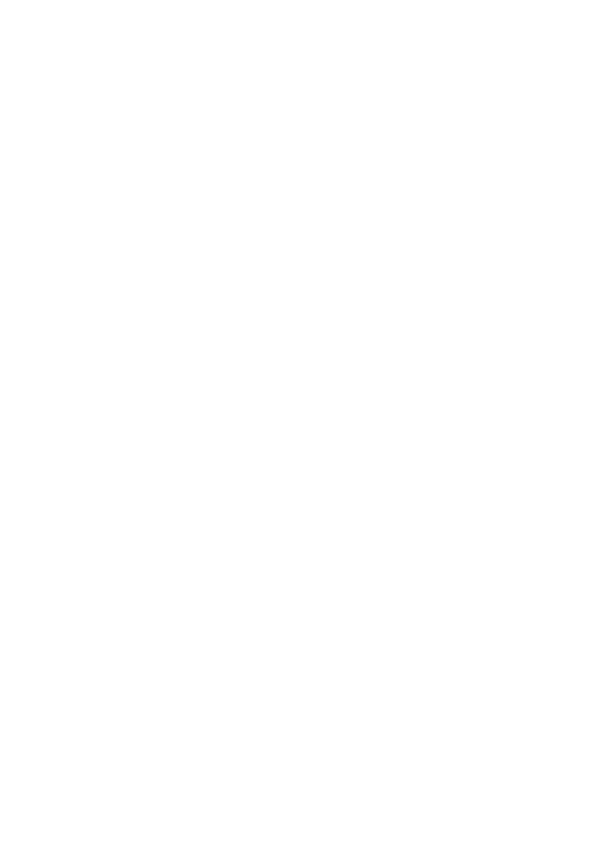
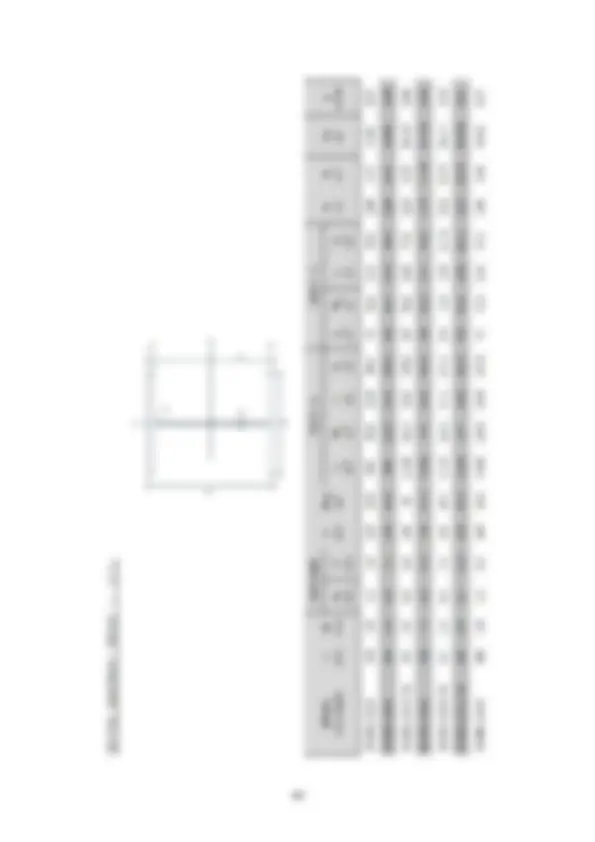
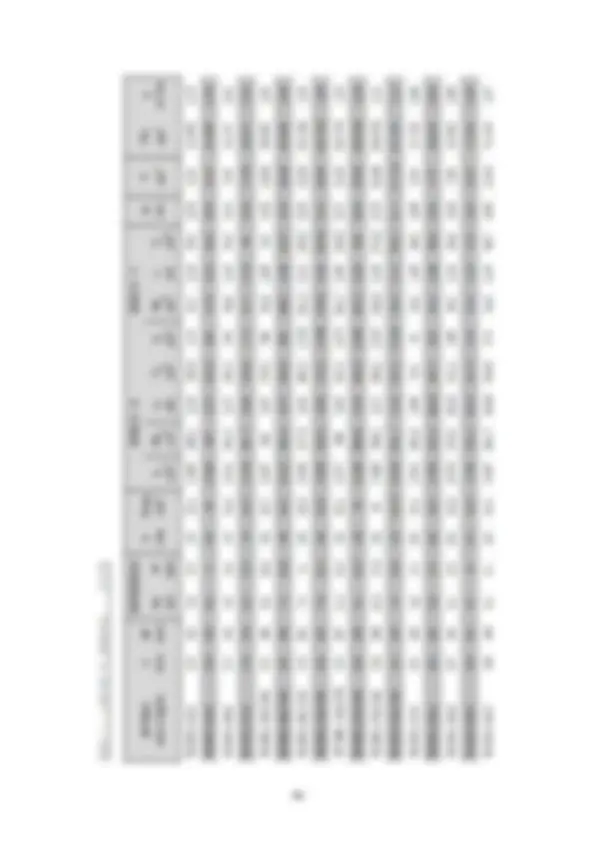
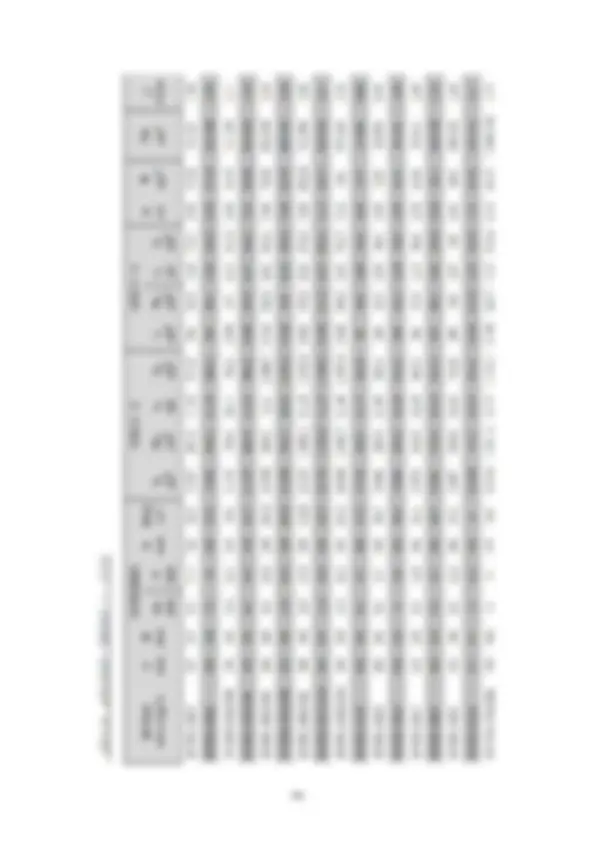
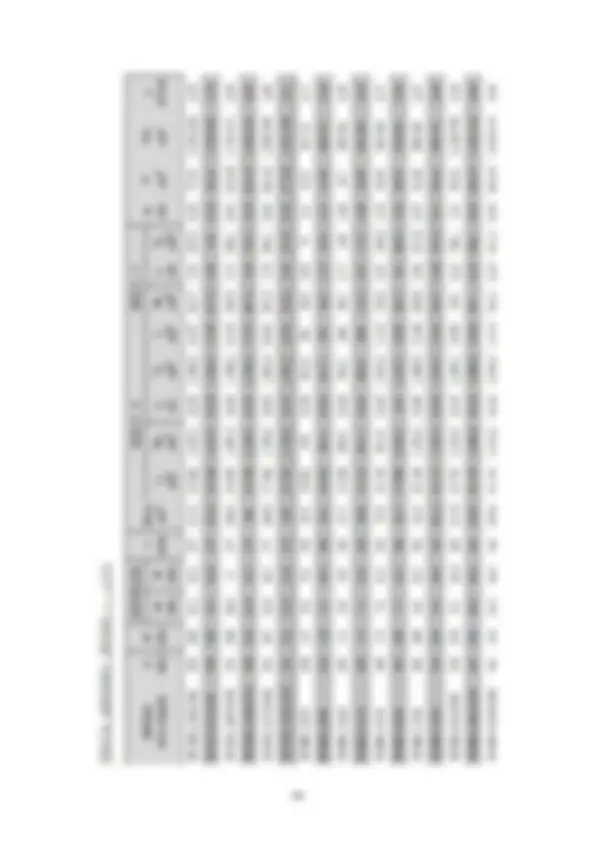
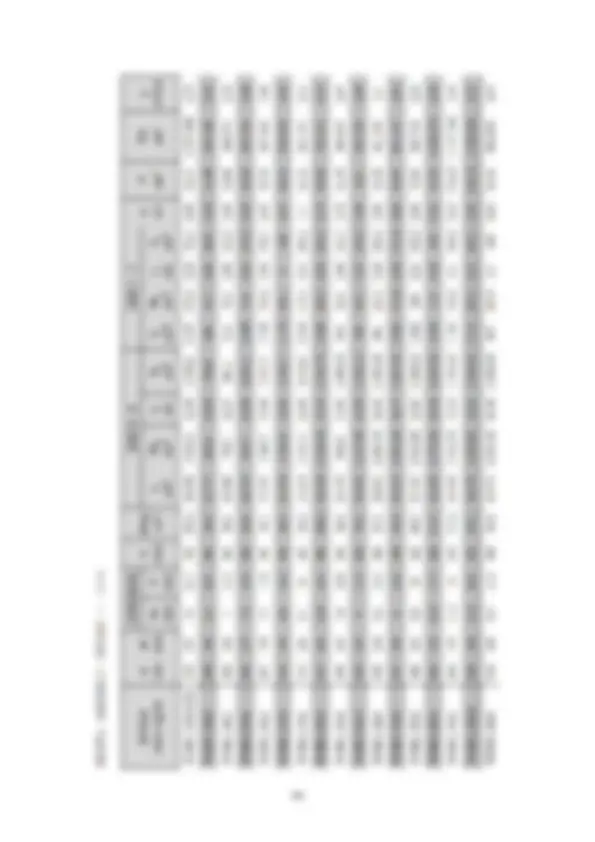
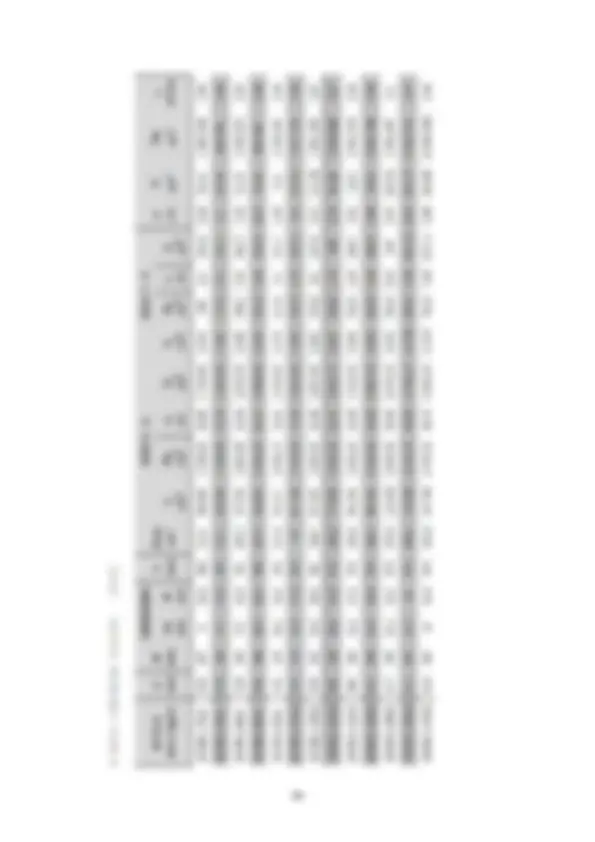
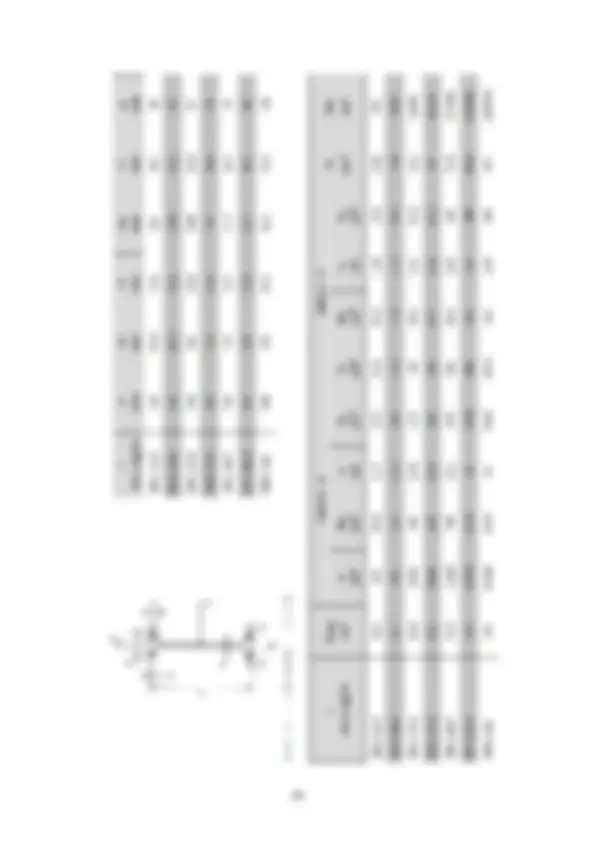
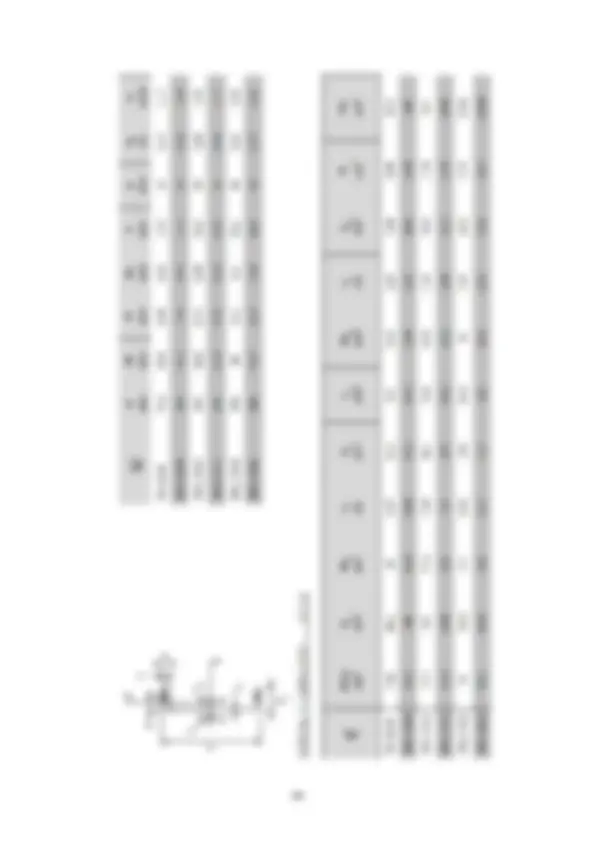
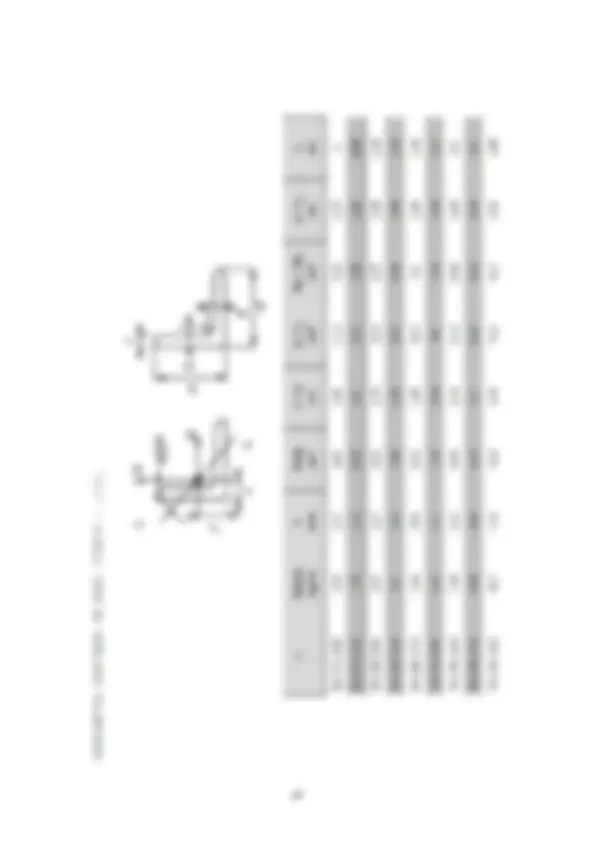
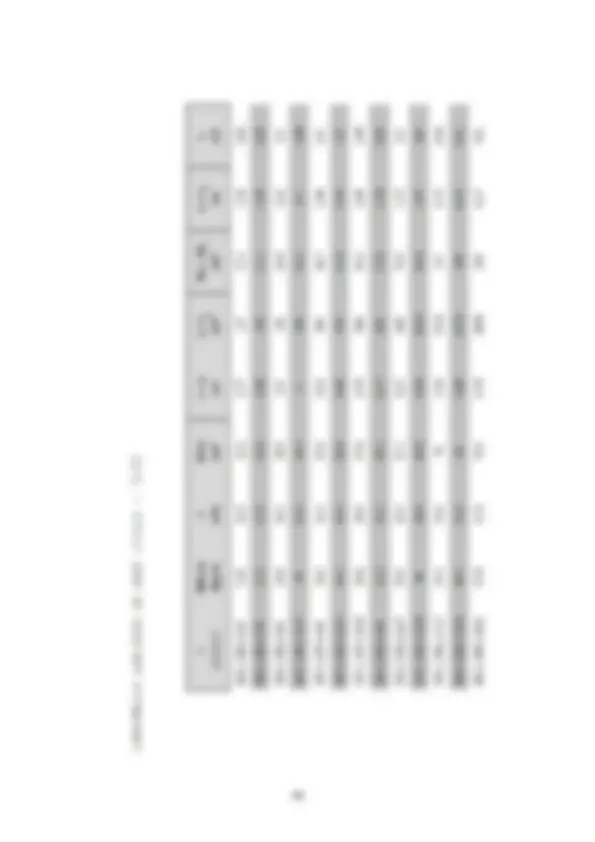
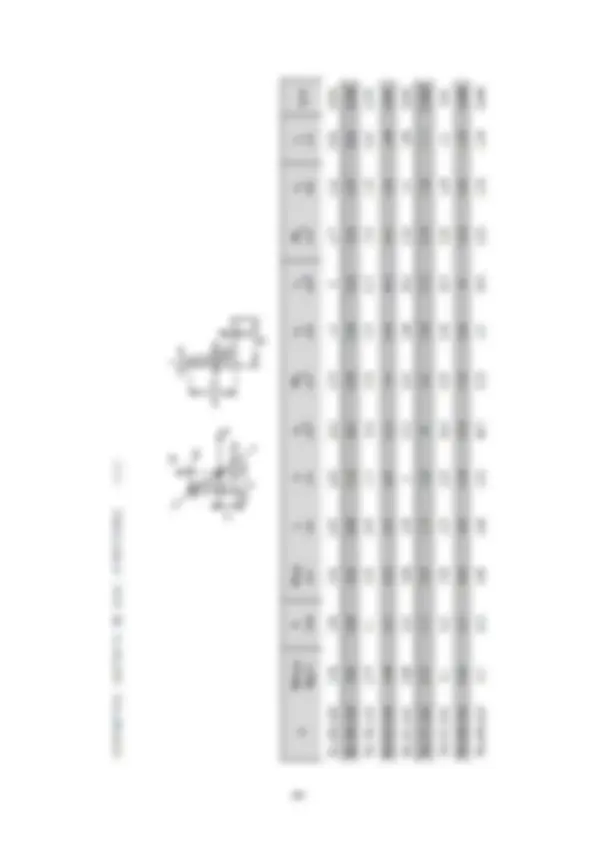
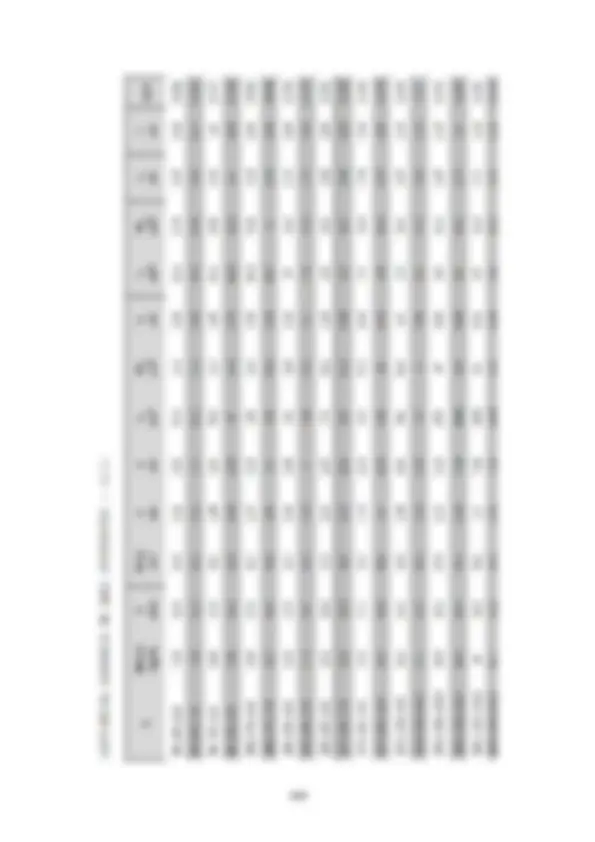
Estude fácil! Tem muito documento disponível na Docsity
Ganhe pontos ajudando outros esrudantes ou compre um plano Premium
Prepare-se para as provas
Estude fácil! Tem muito documento disponível na Docsity
Prepare-se para as provas com trabalhos de outros alunos como você, aqui na Docsity
Os melhores documentos à venda: Trabalhos de alunos formados
Prepare-se com as videoaulas e exercícios resolvidos criados a partir da grade da sua Universidade
Responda perguntas de provas passadas e avalie sua preparação.
Ganhe pontos para baixar
Ganhe pontos ajudando outros esrudantes ou compre um plano Premium
Comunidade
Peça ajuda à comunidade e tire suas dúvidas relacionadas ao estudo
Descubra as melhores universidades em seu país de acordo com os usuários da Docsity
Guias grátis
Baixe gratuitamente nossos guias de estudo, métodos para diminuir a ansiedade, dicas de TCC preparadas pelos professores da Docsity
Análise estrutural metálica de perfis
Tipologia: Resumos
1 / 157
Esta página não é visível na pré-visualização
Não perca as partes importantes!
- Agradecimentos Primeiramente agradeço a Deus, aos meus maravilhosos pais e aos meus filhos Lucca e Marcelinho. Pela paciência, gostaria muito de agradecer minha esposa Érika e, com isso, dedicar a ela este projeto. Amo todos vocês! Thales José Mendes - Graduado em Engenharia Civil, Pós-graduado (especialização) em Construções Metálicas, Pós-graduado (mestrado) em Construção Metálica, Engenheiro Consultor em estruturas de aço, Diretor de Engenharia na empresa Draft Solutions, Ex- membro Titular da Comissão de Patentes Industriais do Grupo Usiminas, Professor de Estruturas de Aço e de Madeira , Teoria das Estruturas II e Pontes do curso de Engenharia Civil da Faculdade Única do Vale do Aço, Professor de Estruturas de Aço do curso de pós- graduação em Engenharia de Estruturas da Faculdade Única do Vale do Aço, Instrutor de Estruturas de Aço de Edifícios e Pontes do IMEC - Instituto Mineiro de Engenharia Civil, membro da comissão de estudos (CE-02:125.05) na elaboração da NBR 16694 (Projeto de pontes rodoviárias estruturadas em aço e mistas aço e concreto) perante à ABNT - Associação Brasileira de Normas Técnicas e Autor do livro Manual Mecânica das Estruturas.
1.1 - Introdução A correta escolha do sistema estrutural em aço é de grande importância para o sucesso do empreendimento, já que afeta vários fatores importantes, tais como segurança, consumo de aço, velocidade de construção, estética, etc. Como é muito importante que a construção seja concebida desde o início para ser estruturada em aço é conveniente que o arquiteto ou o engenheiro que trabalha nessa fase possua um bom conhecimento sobre os sistemas estruturais e suas características. Os arquitetos são freqüentemente colocados em uma situação particularmente desagradável ao ter que projetar uma estrutura completa, compostas por sistemas estruturais, muitas vezes sem ter o conhecimento mais profundo dos tipos de sistema. Esta apostila visa prover os arquitetos e os engenheiros com as ferramentas necessárias para que se sintam mais confortáveis e confiantes ao trabalhar em projetos de edifícios e pontes estruturados em aço. Enfim, apresentaremos conceitos básicos que facilitarão a comunicação entre arquitetos e engenheiros estruturais. 1.2 - Conceitos Básicos Engenharia Estrutural é o ramo da Engenharia civil, mecânica, naval, aeronáutica ou qualquer outra engenharia que utilize cálculo estrutural, seja de estruturas estáticas ou dinâmicas, dedicado primariamente ao projeto e cálculo de estruturas e é a aplicação da mecânica das estruturas ao projeto de edifícios, pontes, muros de contenção, barragens, túneis, plataformas de petróleo, navios, aviões, automóveis e outras estruturas. O objetivo do Projeto de uma Estrutura é permitir que a mesma atenda à sua função primária sem entrar em colapso e sem deformar ou vibrar excessivamente. Dentro destes limites, os quais são precisamente definidos pelas normas técnicas, o engenheiro estrutural almeja o melhor uso dos materiais disponíveis e o menor custo possível de construção e manutenção da estrutura. Principais Etapas do Projeto Estrutural são a criação do esquema estrutural, definição das cargas ou forças que atuam na estrutura, cálculo dos esforços e deformações, dimensionamento das peças estruturais e o detalhamento do projeto para execução.
As cargas ou forças que atuam na estrutura são as permanentes (peso próprio e cargas permanentes dos objetos suportados pela estrutura) e as acidentais (sobrecargas e cargas referentes aos ventos). Para estruturas comuns, as normas técnicas contém recomendações para as cargas a serem consideradas. Com base nestas recomendações, o arquiteto e/ou engenheiro estrutural definem diversos casos de carregamento, com o objetivo de estabelecer a condição mais desfavorável de projeto (aquela que produz os maiores esforços). Os esforços estruturais são medidas estruturais correspondentes às tensões que atuam no material que compõe a estrutura. Esforço normal (força atuante no sentido da peça, tendendo a tracioná-la ou comprimí-la), Esforço cortante (força perpendicular à peça, calculada a partir da tensão cisalhante na mesma), Momento fletor (momento que tende a flexionar a peça, como resultado de tensões normais de sinais contrários na mesma seção) e Momento torçor (tende a torcer a peça em torno de seu próprio eixo). O cálculo dos esforços é feito através da análise estrutural. A análise pode ser estática, considerando cargas constantes no tempo, ou dinâmica, levando em conta as variações das cargas e os modos de vibração da estrutura. Com a automatização desta etapa do projeto, tradicionalmente a mais demorada, o engenheiro estrutural moderno pode dedicar mais atenção aos pontos mais problemáticos do projeto, além de alterar o esquema estrutural e propor diferentes condições de carga, em busca de um melhor projeto final. Conhecidos os esforços em cada elemento estrutural, é necessário dimensionar a peça que irá resistir a estes esforços, ou seja, determinar as suas medidas. Dado o material a ser utilizado, como o aço e suas propriedades, os princípios de resistência dos materiais e mecânica das estruturas são empregados para verificar que a peça é capaz de resistir aos esforços. Por exemplo, pode-se determinar o ponto mais solicitado e obter uma seção capaz de resistir aos esforços neste ponto. Se for economicamente viável, esta seção é empregada para toda a peça. Para elementos mais complexos, pode ser necessário analisar vários pontos e variar a seção empregada, ou mesmo efetuar o dimensionamento da peça como um todo. O dimensionamento moderno é realizado com o auxílio do computador. Contudo, o engenheiro estrutural possui bastante liberdade para alterar o dimensionamento visando simplificar a construção, por exemplo padronizando as seções sugeridas pelo programa de computador.
O aço é um produto siderúrgico definido como liga metálica composta principalmente de ferro e pequenas quantidades de carbono. O processo siderúrgico pode ser dividido em preparo das matérias-primas (Coqueria e Sinterização), produção de gusa (alto-forno), produção de Aço (Aciaria) e conformação mecânica (Laminação). As matérias-primas necessárias para a obtenção do aço são: o minério de ferro, principalmente a hematita, e o carvão mineral. Ambos não são encontrados puros na natureza, sendo necessário então um preparo nas matérias primas de modo a reduzir o consumo de energia e aumentar a eficiência do processo. A coqueificação ocorre a uma temperatura de 1300oC em ausência de ar durante um período de 18 horas, onde ocorre a liberação de substâncias voláteis. O produto resultante desta etapa, o coque, é um material poroso com elevada resistência mecânica, alto ponto de fusão e grande quantidade de carbono. O coque, nas especificações físicas e químicas requeridas, é encaminhado ao alto-forno e os finos de coque são enviados à sinterização e à aciaria. O coque é a matéria prima mais importante na composição do custo de um alto-forno (60%). Na sinterização, a preparação do minério de ferro é feita cuidando-se da granulometria, visto que os grãos mais finos são indesejáveis, pois diminuem a permeabilidade do ar na combustão, comprometendo a queima. Para solucionar o problema, adicionam-se materiais fundentes (calcário, areia de sílica ou o próprio sínter) aos grãos mais finos. Com a composição correta, estes elementos são levados ao forno onde a mistura é fundida. Em seguida, o material resultante é resfriado e britado até atingir a granulometria desejada (diâmetro médio de 5mm). O produto final deste processo é denominado de sínter e de acordo com o Arquiteto Luís Andrade de Mattos Dias, "em decorrência de suas características combustíveis e de permeabilidade, o sínter tornou-se mais importante para o processo do que o próprio minério de ferro". No alto-forno, esta parte do processo de fabricação do aço consiste na redução do minério de ferro, utilizando o coque metalúrgico e outros fundentes, que misturados com o minério de ferro são transformados em ferro gusa. A reação ocorre no equipamento denominado Alto Forno, e constitui uma reação exotérmica. O resíduo formado pela reação, a escória, é vendida para a indústria de cimento. Após a reação, o ferro gusa na forma líquida é transportado nos carros-torpedos (vagões revestidos com elemento refratário) para uma estação de dessulfuração, onde são reduzidos os teores de enxofre a níveis aceitáveis. Também são feitas análises da composição química da liga (carbono, silício, manganês, fósforo, enxofre) e a seguir o carro torpedo transporta o ferro gusa para a aciaria, onde será transformado em aço. Na aciaria, o ferro gusa é transformado em aço através da injeção de oxigênio puro sob pressão no banho de gusa líquido, dentro de um conversor. A reação, constitui na redução da gusa através da combinação dos elementos de liga existentes (silício,
manganês) com o oxigênio soprado, o que provoca uma grande elevação na temperatura, atingindo aproximadamente 1700oC. Os gases resultantes do processo são queimados logo na saída do equipamento e a os demais resíduos indesejáveis são eliminados pela escória, que fica a superfície do metal. Após outros ajustes finos na composição do aço, este é transferido para a próxima etapa que constitui o lingotamento contínuo. No processo de lingotamento contínuo o aço líquido é transferido para moldes onde se solidificará. O veio metálico é continuamente extraído por rolos e após resfriado, é transformado em placas rústicas através do corte com maçarico. Posteriormente, os lingotes devem passar pelo processo de laminação, podendo ser a quente ou a frio, onde se transformarão em chapas através da diminuição da área da seção transversal. Na laminação a quente, a peça com aproximados 250 mm é aquecida e submetida à deformação por cilindros que a pressionarão até atingir a espessura desejada. Chapas Grossas espessura: 6 a 200 mm - largura: 1000 a 3800 mm comprimento: 5000 a 18000 mm Tiras espessura: 1,2 a 12,50 mm - largura: 800 a 1800 mm comprimento-padrão: 2000, 3000 e 6000 mm Devido ao resfriamento desigual das peças, chapas e perfis laminados a quente apresentam tensões que permanecem após o completo resfriamento. Em chapas, por exemplo, as bordas se solidificam mais rapidamente que o centro, servindo como um quadro que impedirá a retração da peça como um todo, fazendo com que o centro da peça permaneça tracionado. A norma brasileira NBR8800 fixa essa tensão em 115 MPa. Ao contrário do processo de laminação a quente as peças laminadas a frio são normalmente mais finas, com melhor acabamento e sem a presença de tensões residuais. Laminação a Frio - Dimensões: espessura: 0,3 a 3,00 mm - largura: 800 a 1600 mm comprimentos-padrão: 2000, 2500 e 3000 mm Constantes físicas dos aços estruturais conforme NBR 8800
**Tabela: Fonte NBR 8800
A relação entre a tensão aplicada e a deformação linear específica de alguns aços estruturais pode ser vista no diagrama tensão-deformação abaixo: Até certo nível de tensão aplicada, o material trabalha no regime elástico-linear, isto é, segue a Lei de Hooke e a deformação linear específica é proporcional ao esforço aplicado. A proporcionalidade pode ser observada na próxima figura, no trecho retilíneo do diagrama tensão-deformação e a constante de proporcionalidade é denominada módulo de deformação longitudinal ou módulo de elasticidade. Ultrapassado o limite de proporcionalidade (fp), tem lugar a fase plástica, na qual ocorrem deformações crescentes sem variação de tensão (patamar de escoamento). O valor constante dessa tensão é a mais importante característica dos aços estruturais e é denominada limite de escoamento. Após o escoamento, a estrutura interna do aço se rearranja e o material passa pelo encruamento, em que se verifica novamente a variação de tensão com a deformação específica, porém de forma não-linear. O valor máximo da tensão antes da ruptura é denominada resistência à ruptura do material. A resistência à ruptura do material é calculado dividindo-se a carga máxima que ele suporta, antes da ruptura, pela área da seção transversal inicial do corpo de prova. Observa-se que fu é calculado em relação à área inicial, apesar de o material sofrer uma redução de área quando solicitada à tração. Embora a tensão verdadeira deva ser calculada considerando-se a área real, a tensão tal como foi definida anteriormente é mais importante para o engenheiro estrutural, pois os projetos são feitos com base nas dimensões iniciais. Em um ensaio de compressão, sem a ocorrência de flambagem, obtém-se um diagrama tensão-deformação similar ao do ensaio de tração.