
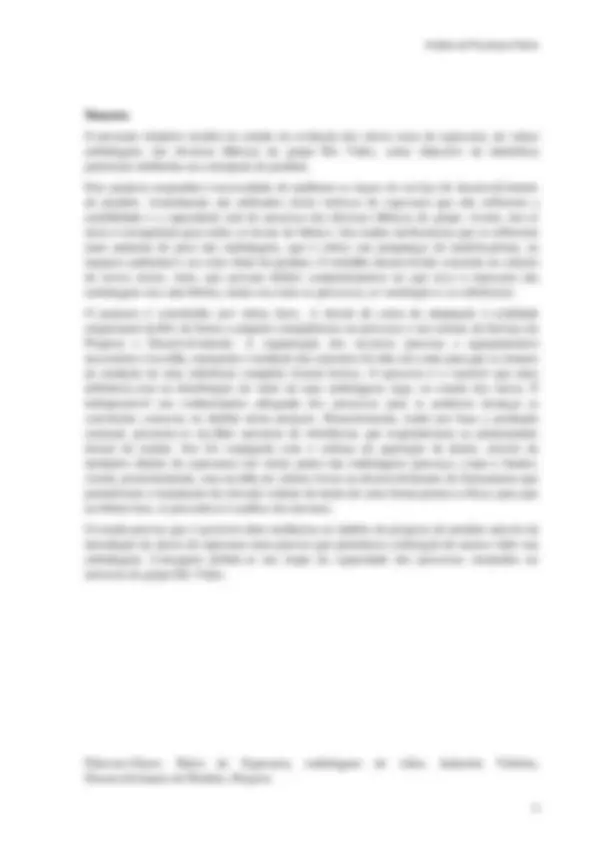
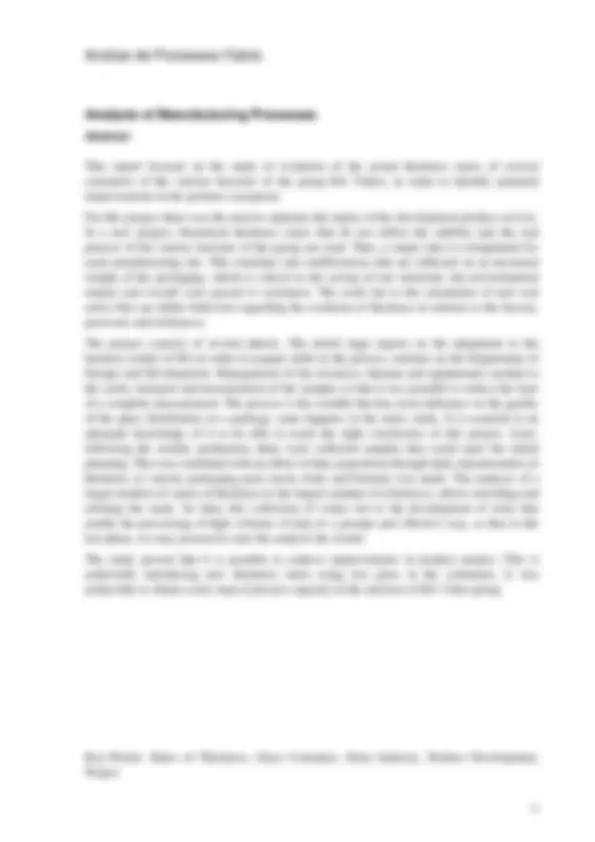
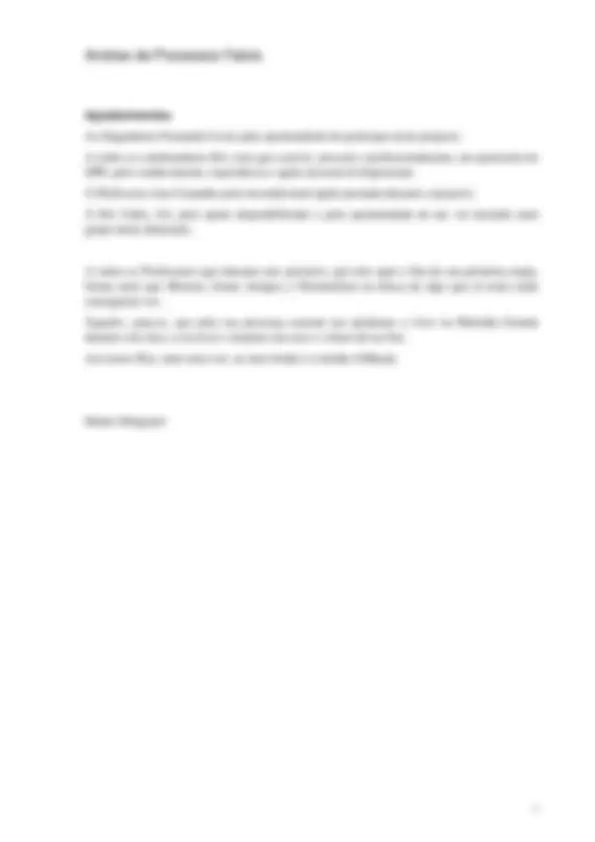
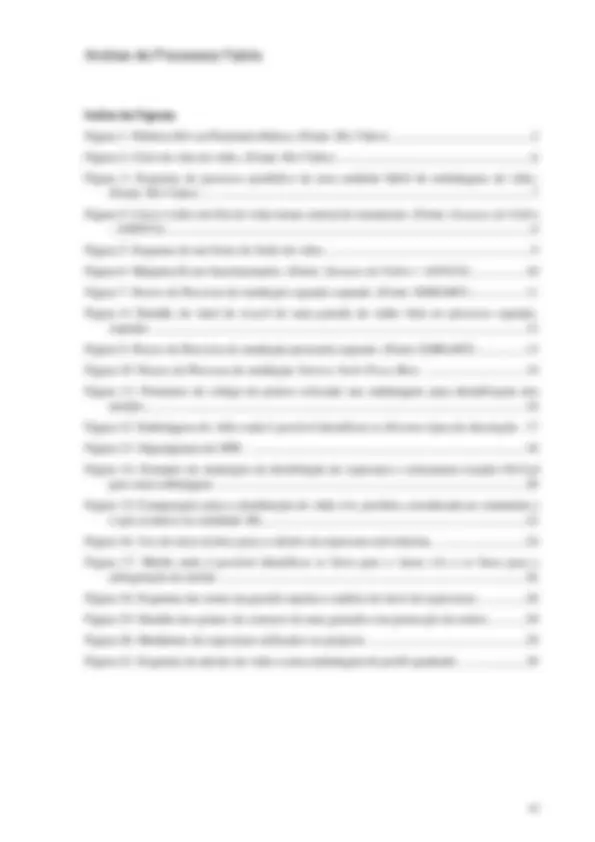
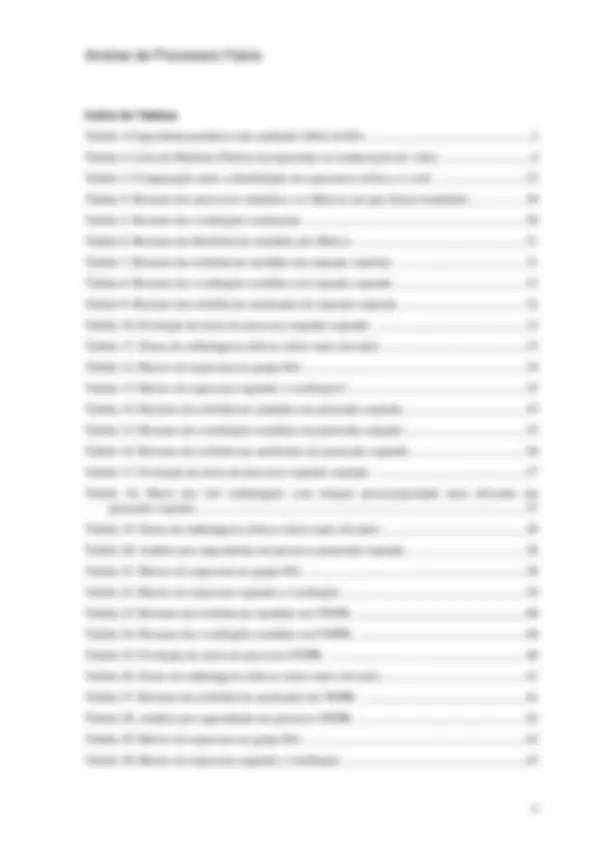
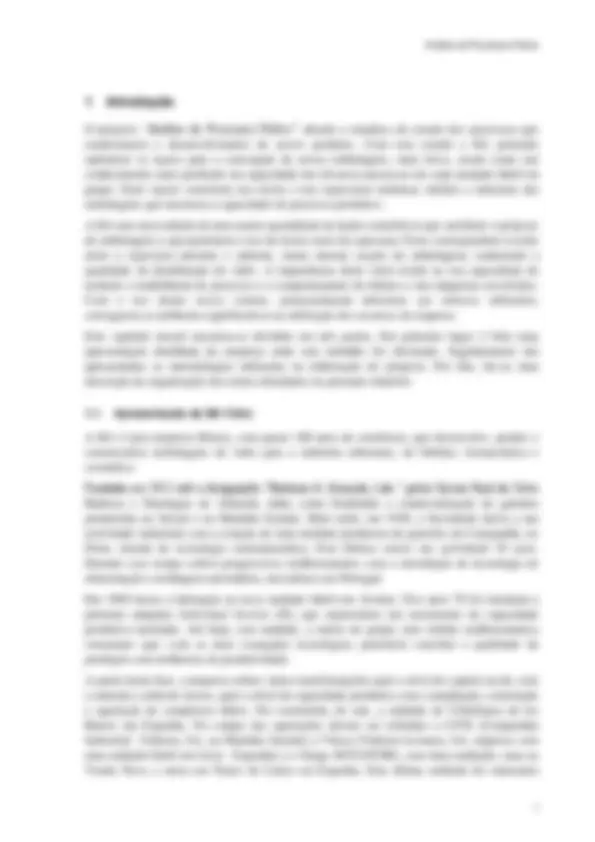
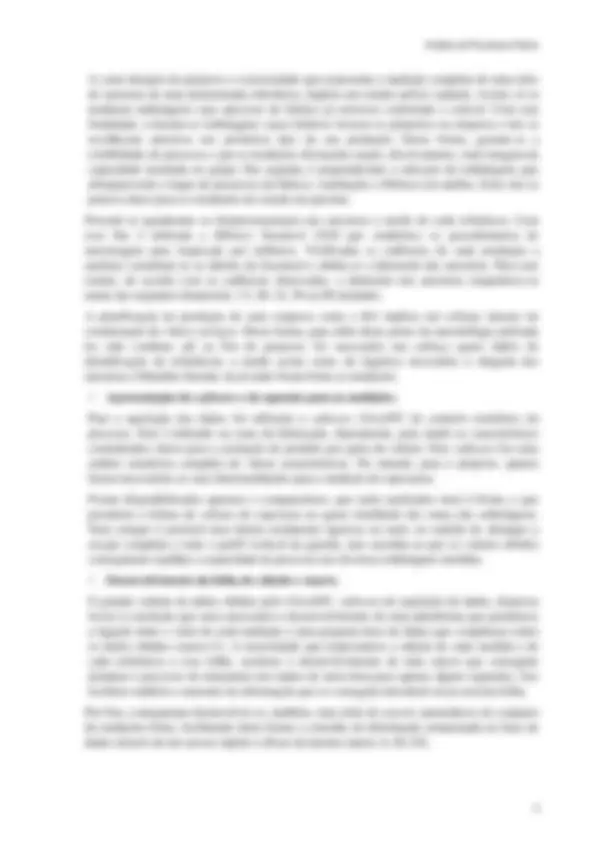
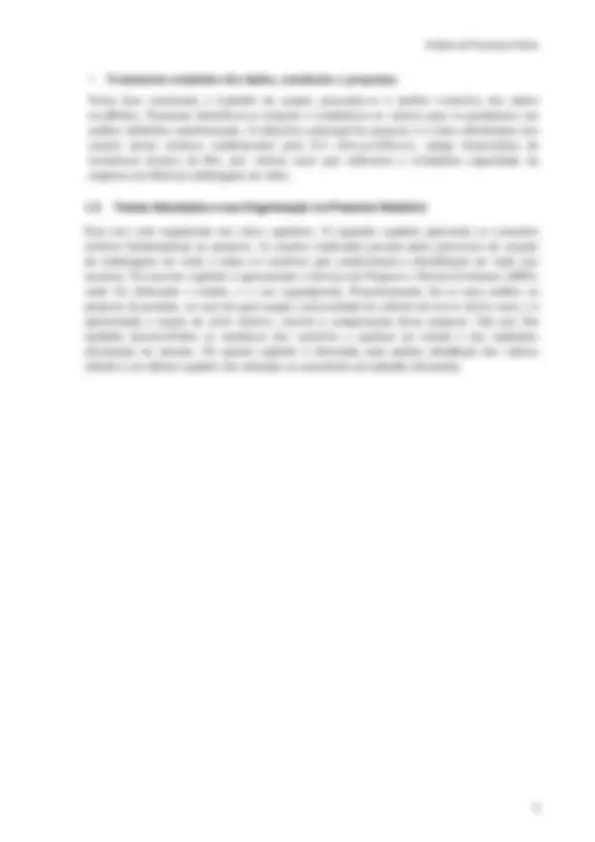
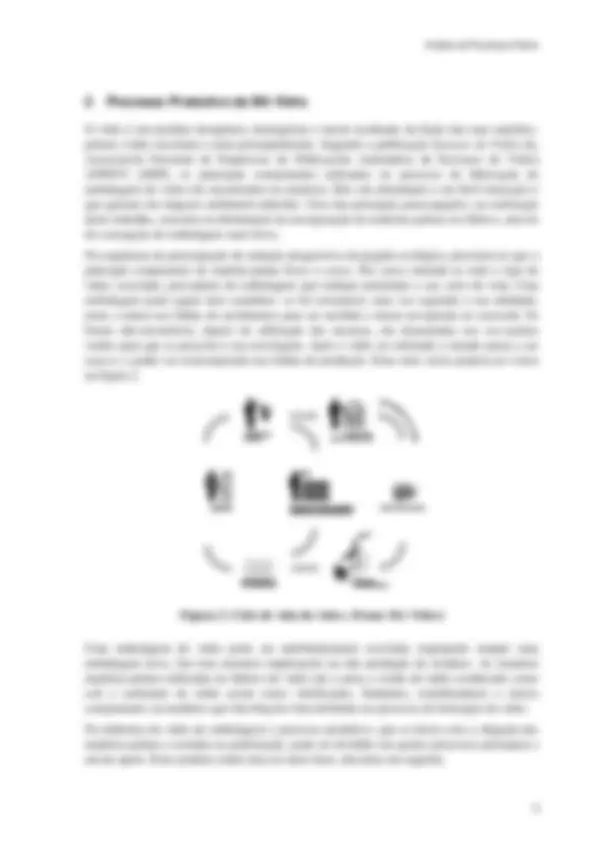
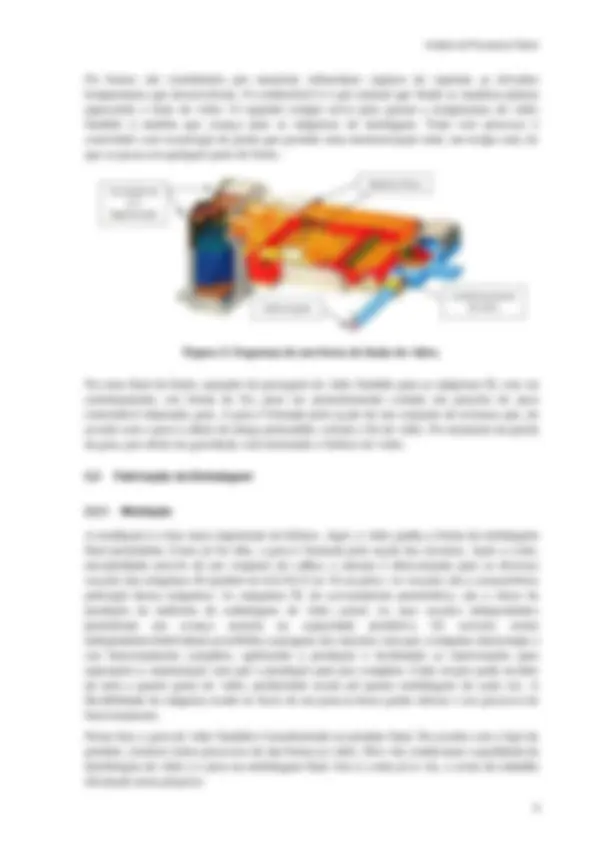
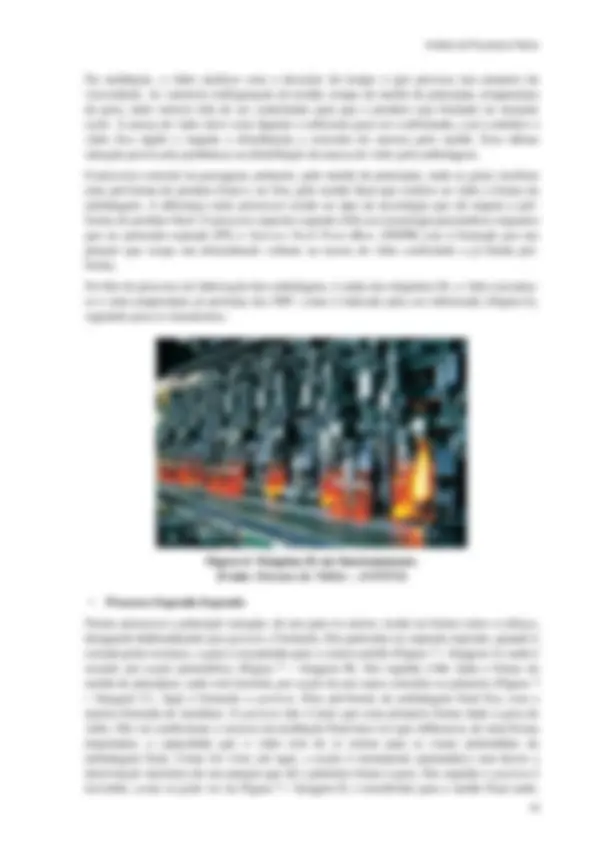
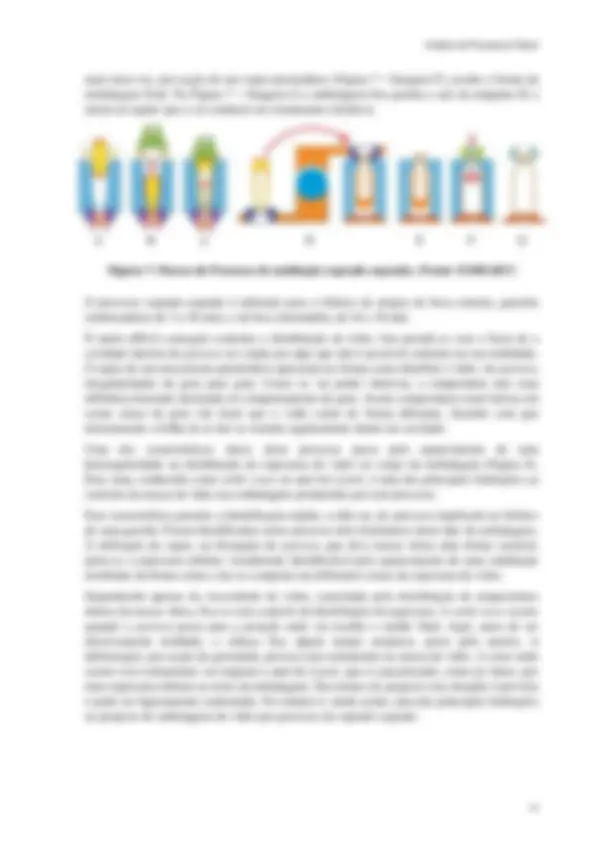
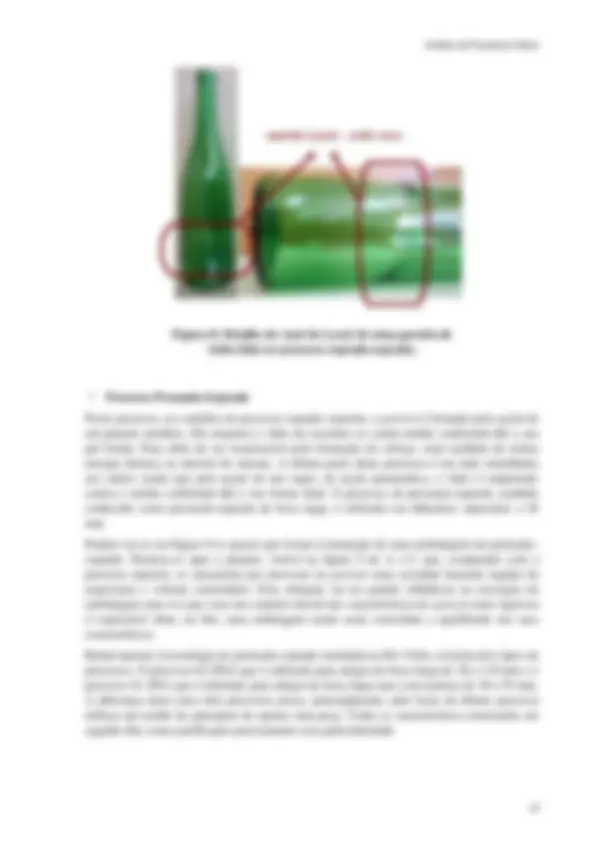
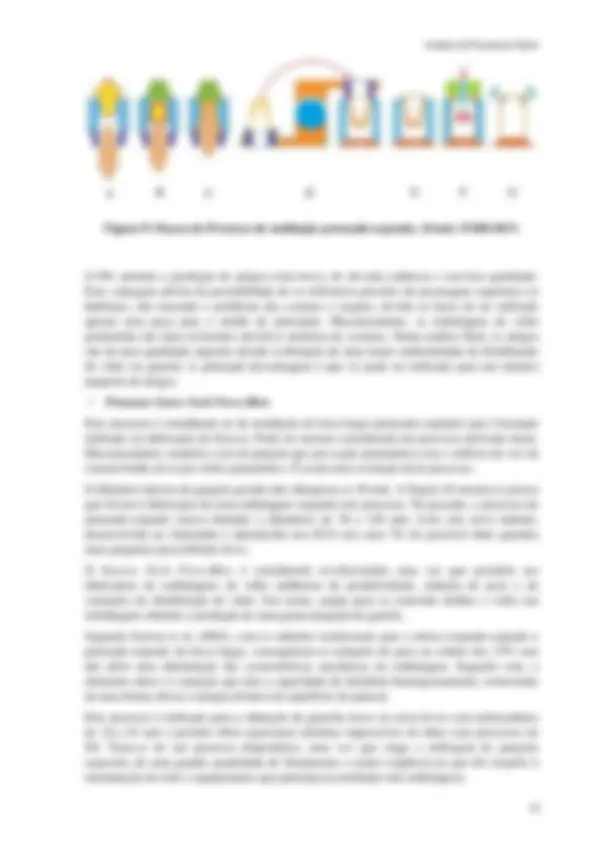
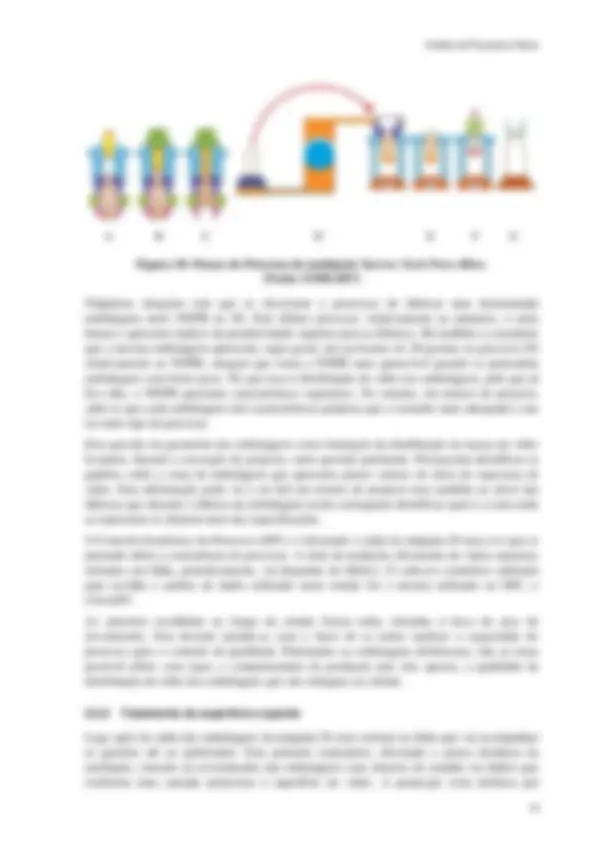
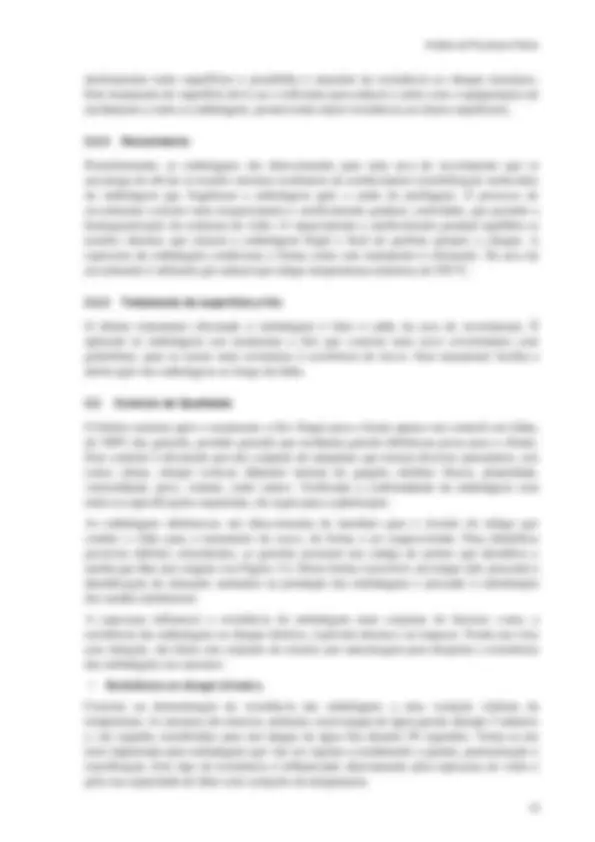
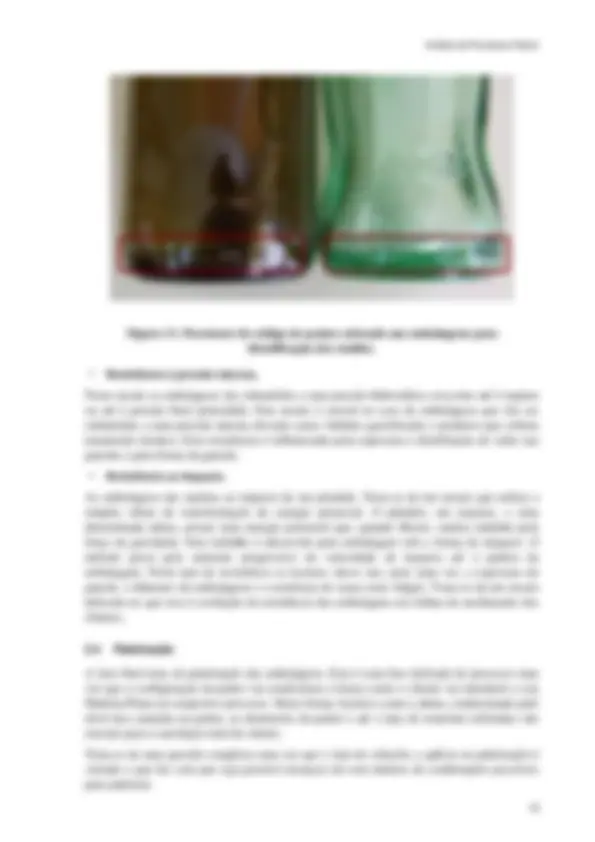
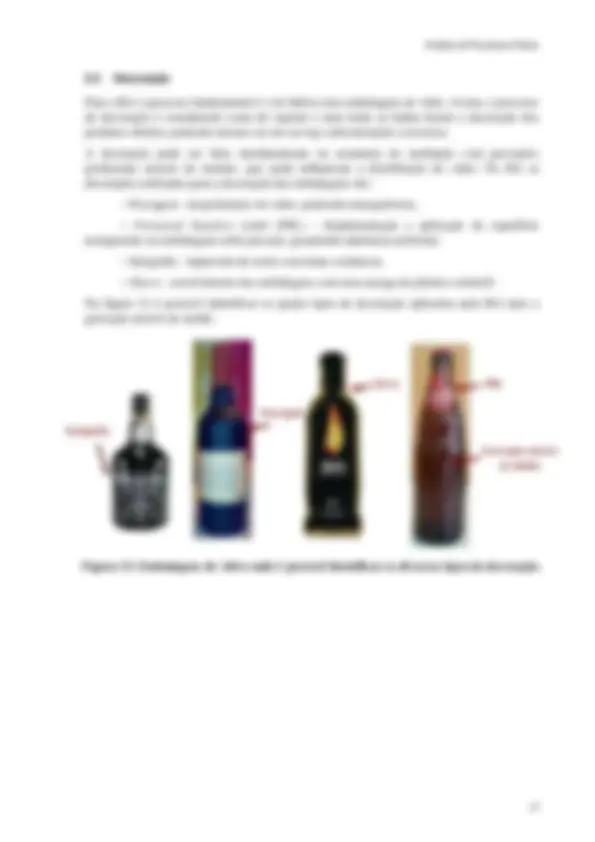
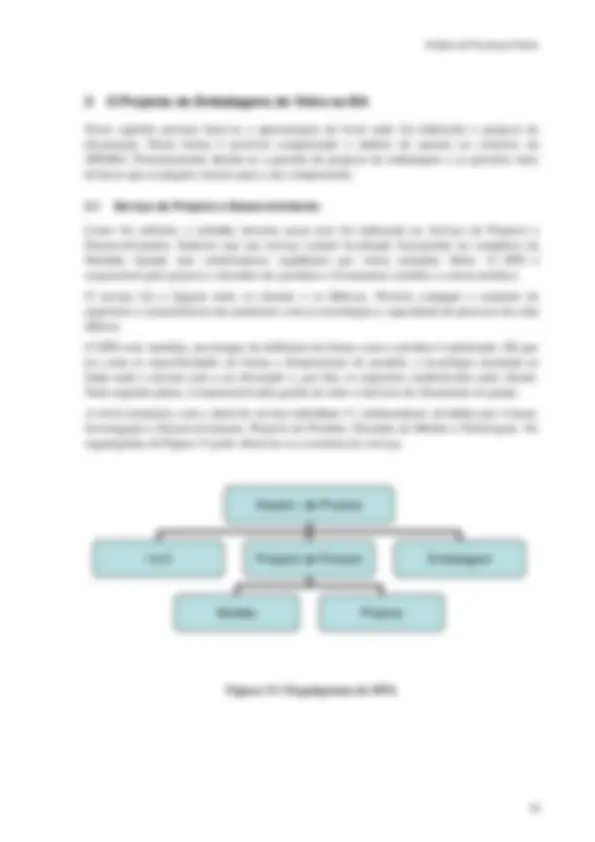
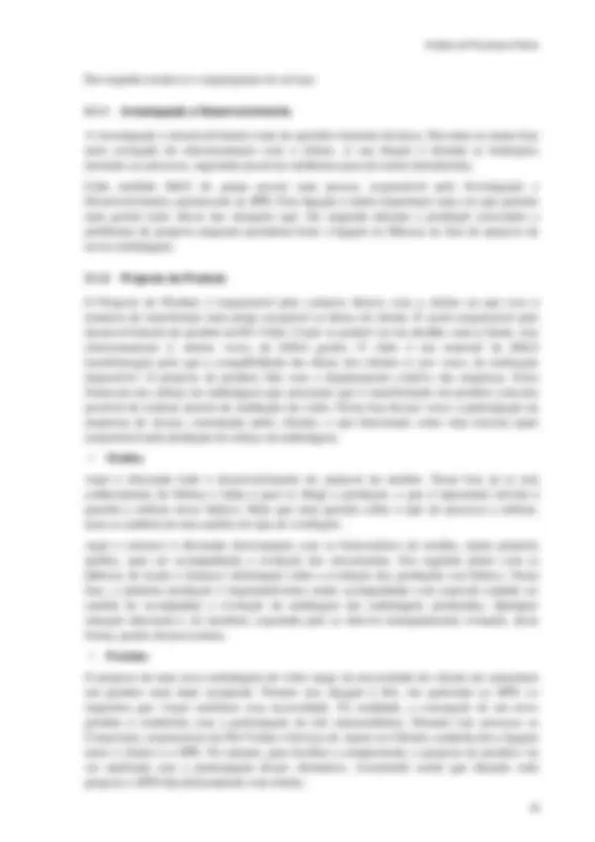
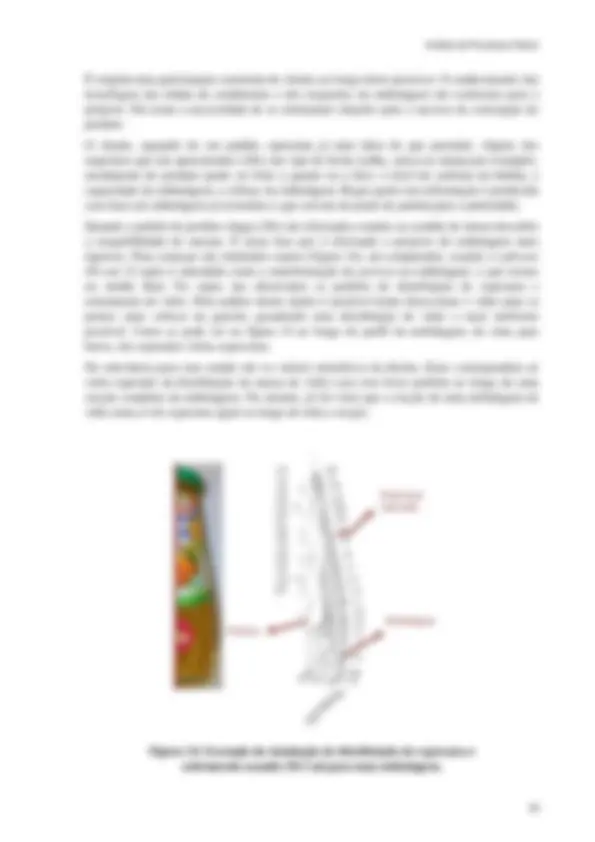
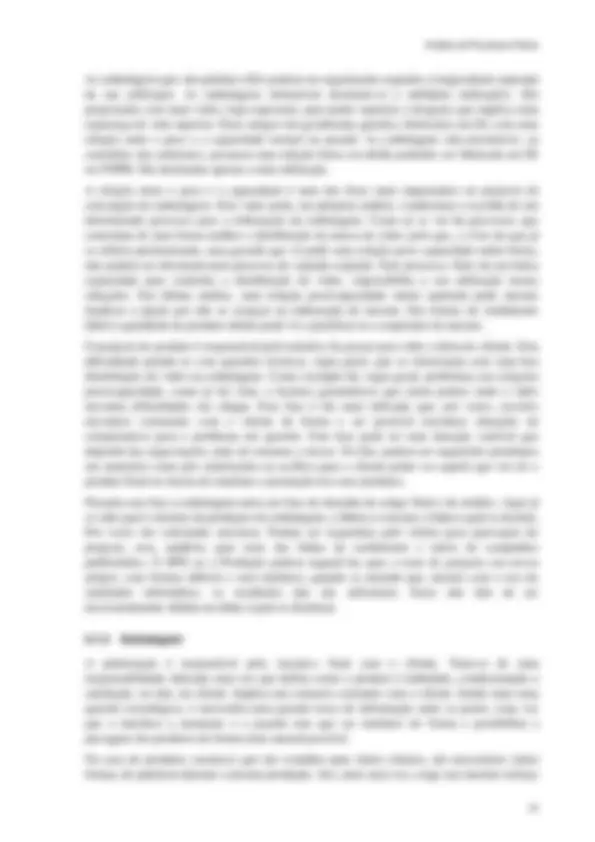
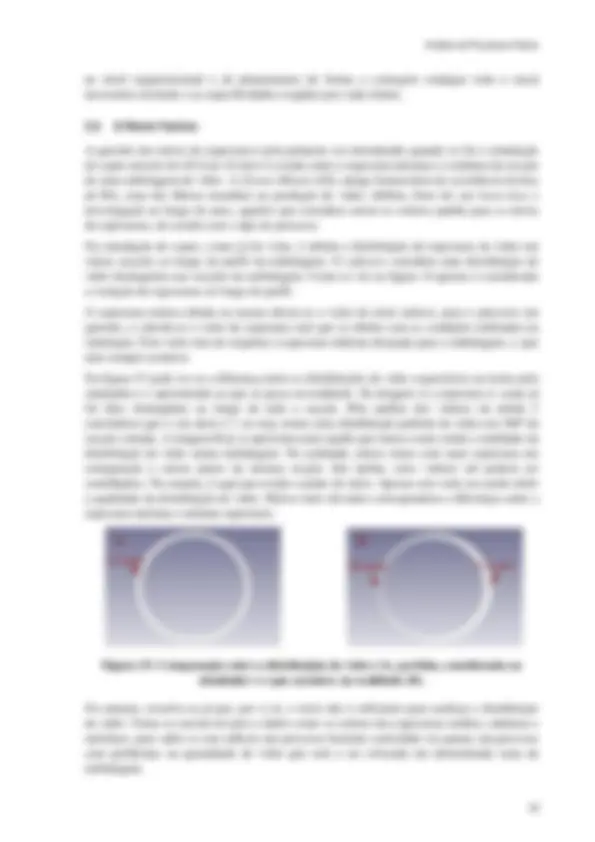
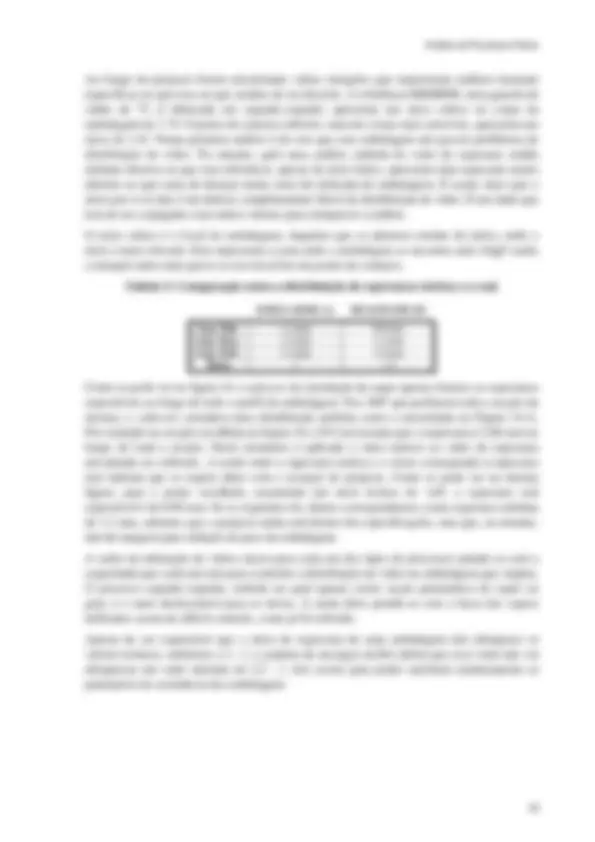
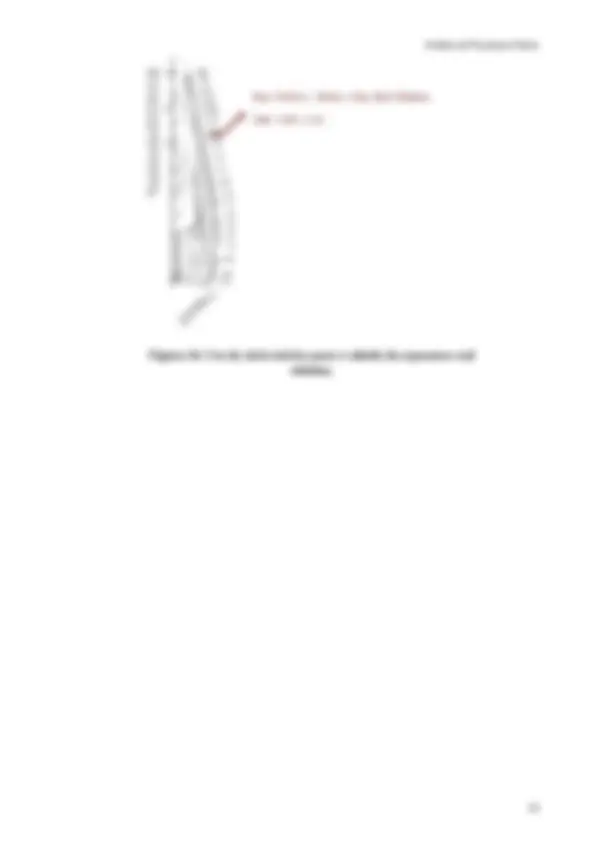
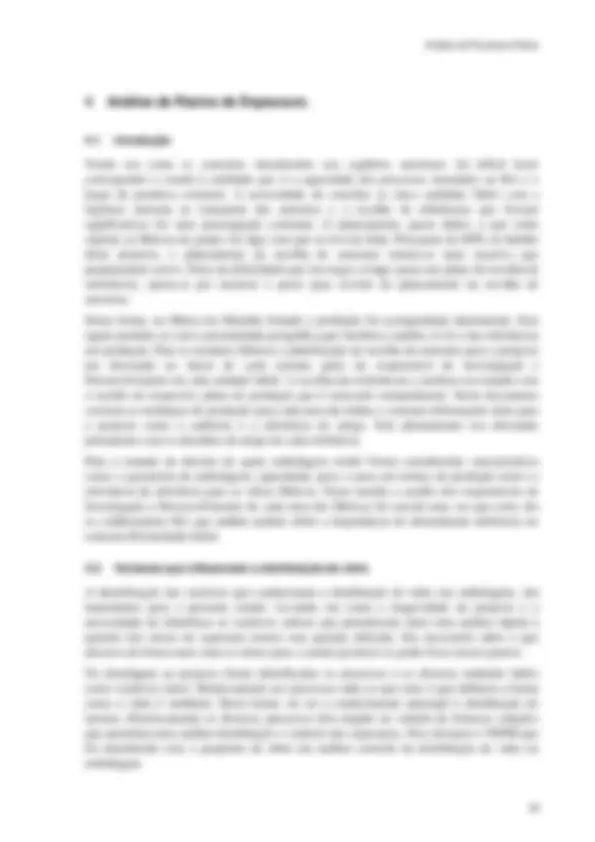
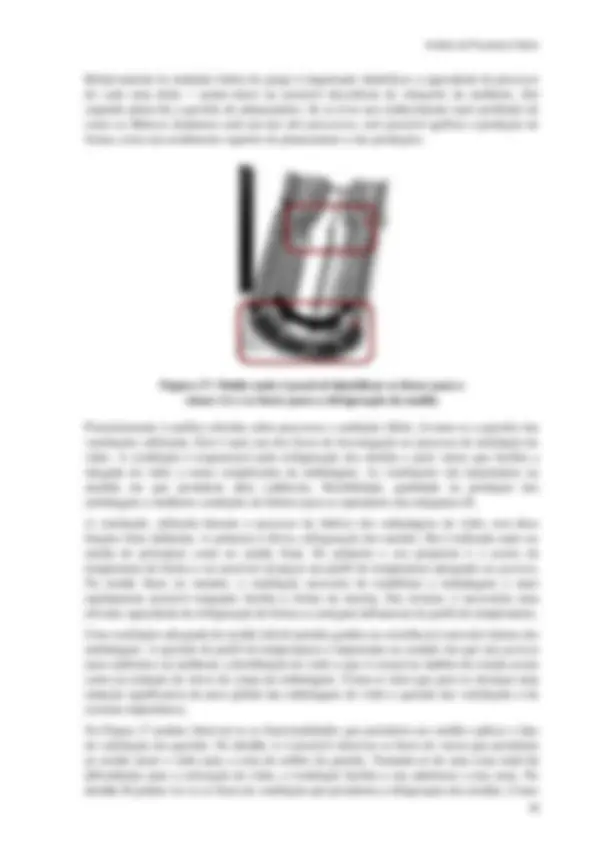
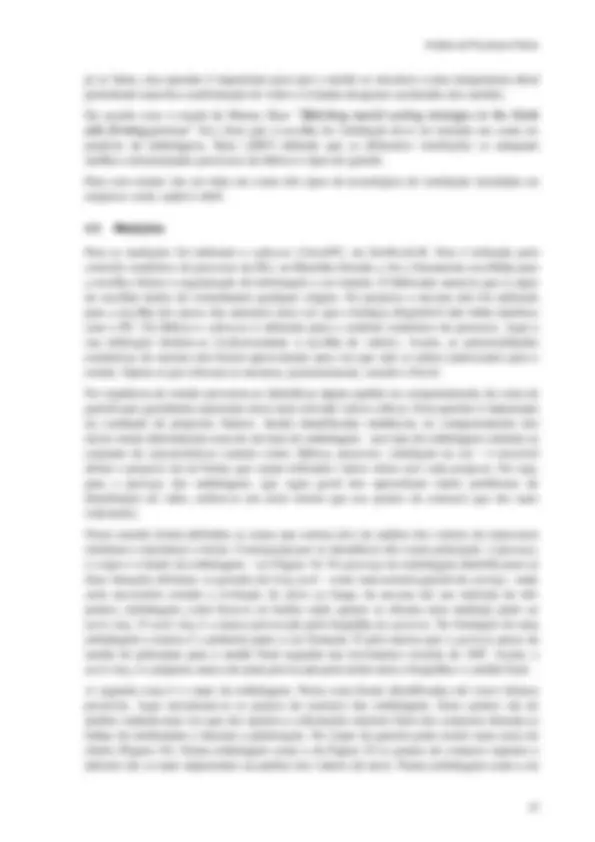
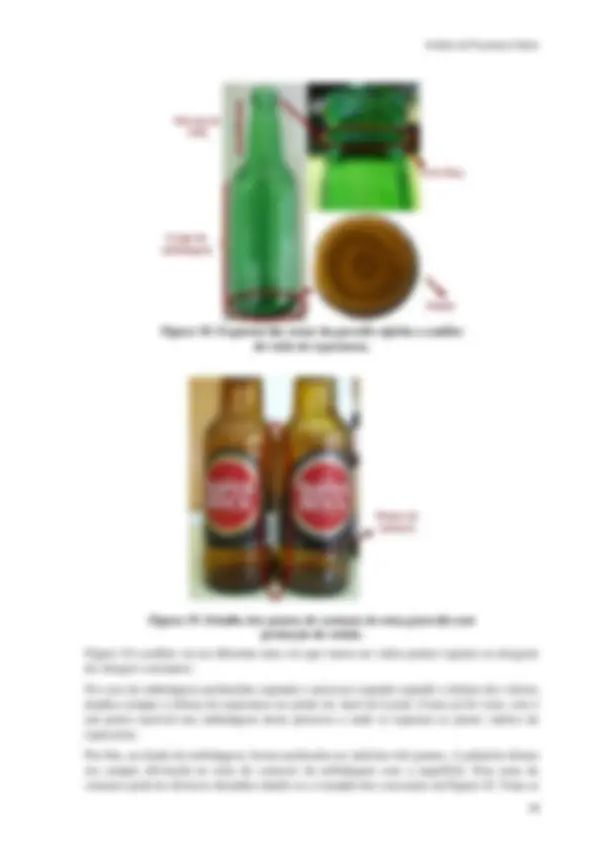
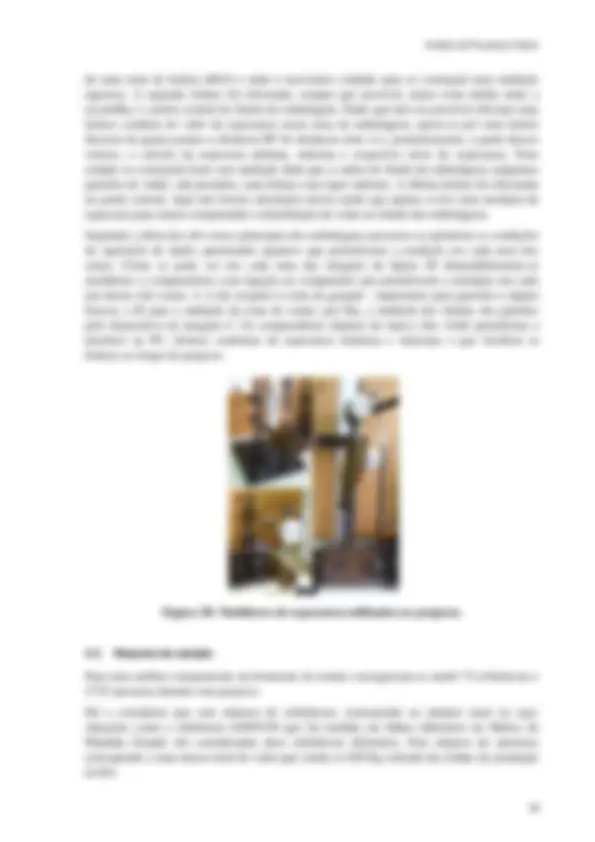
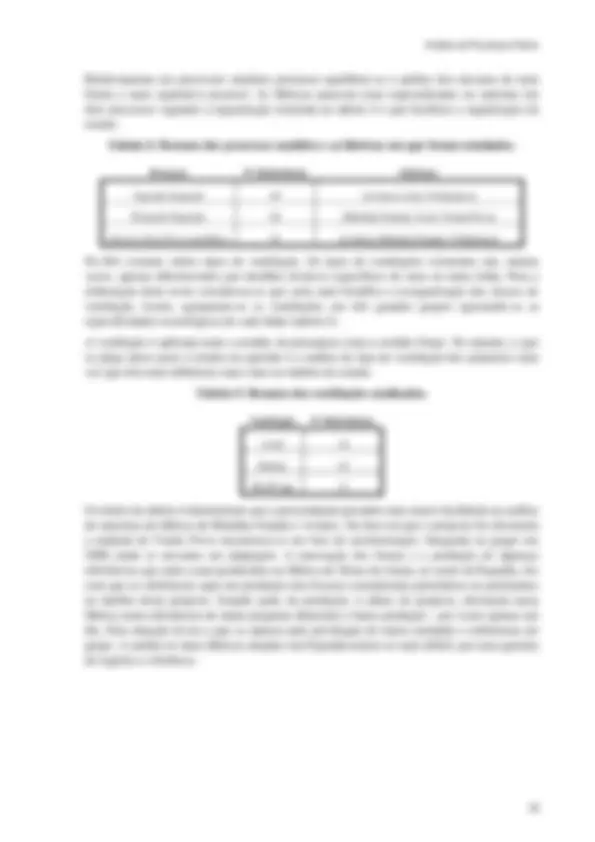
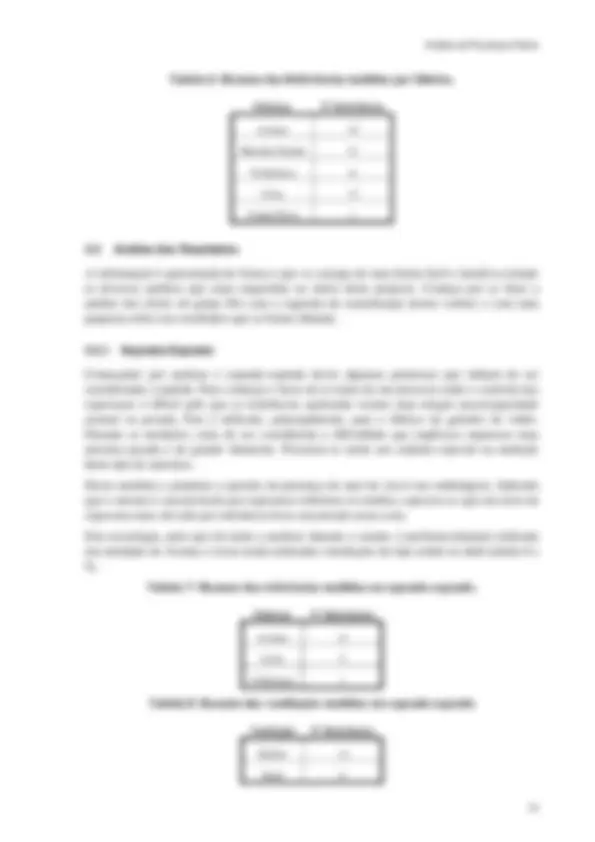
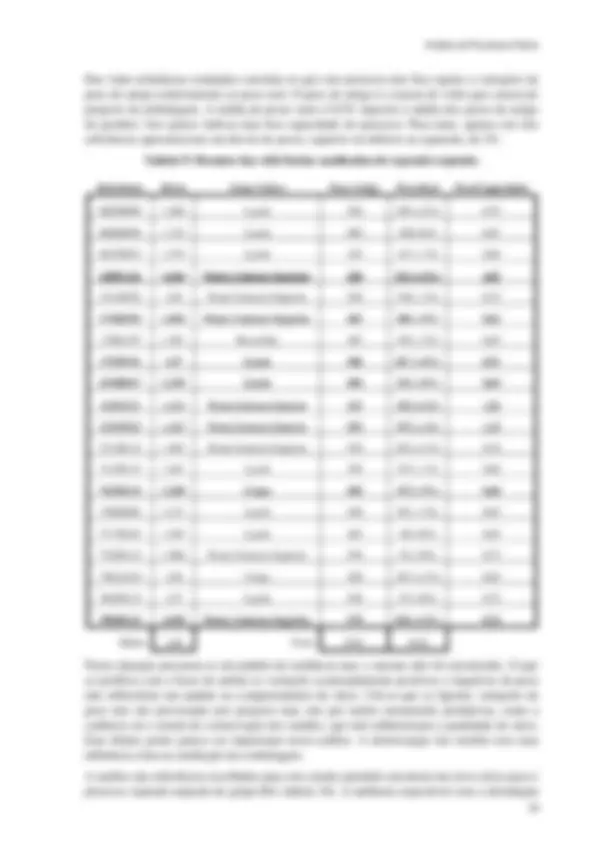
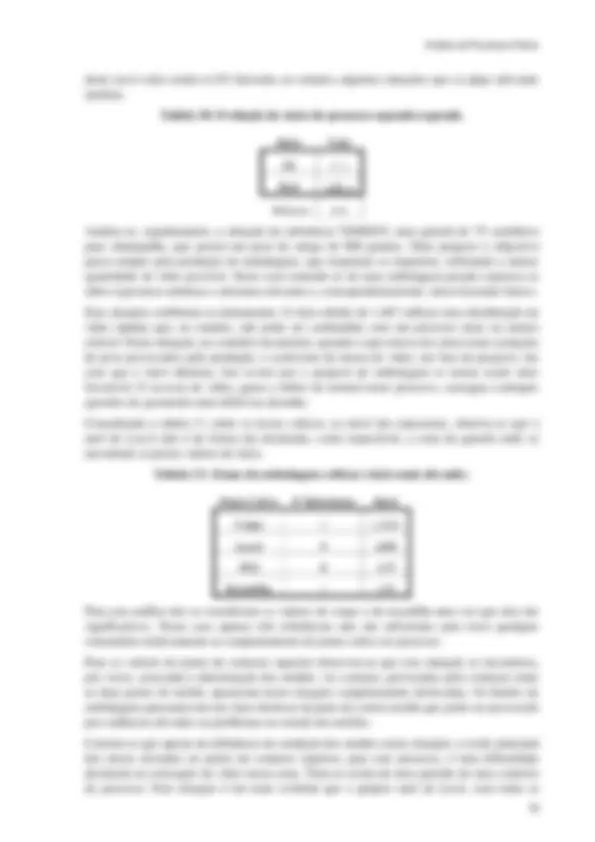
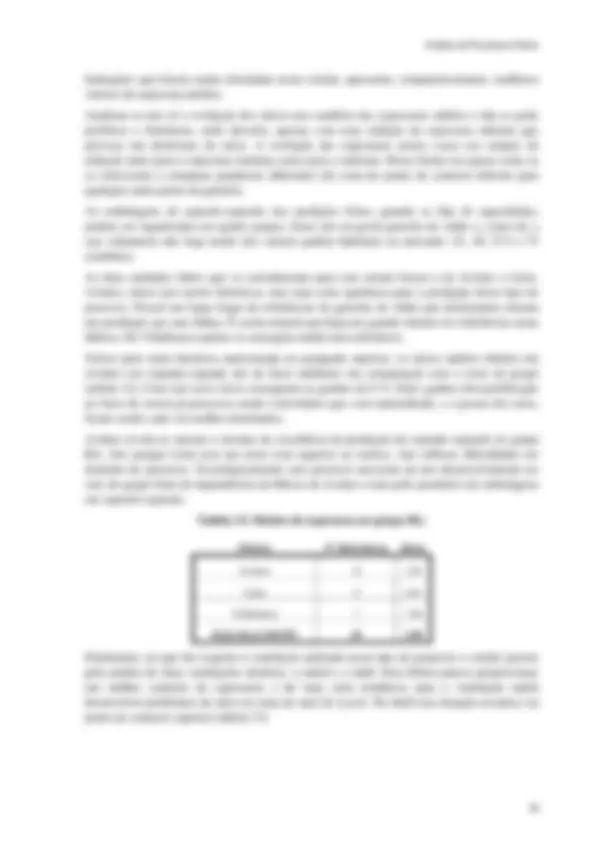
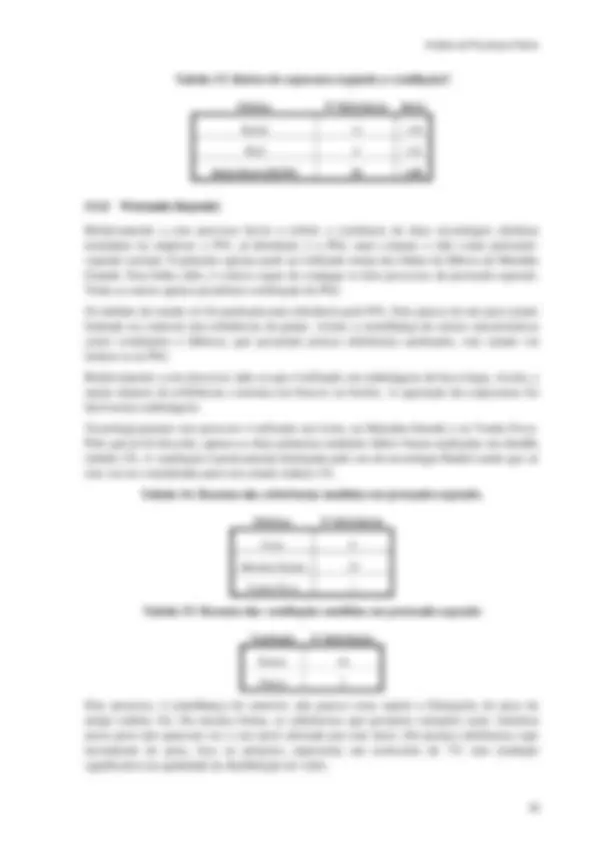
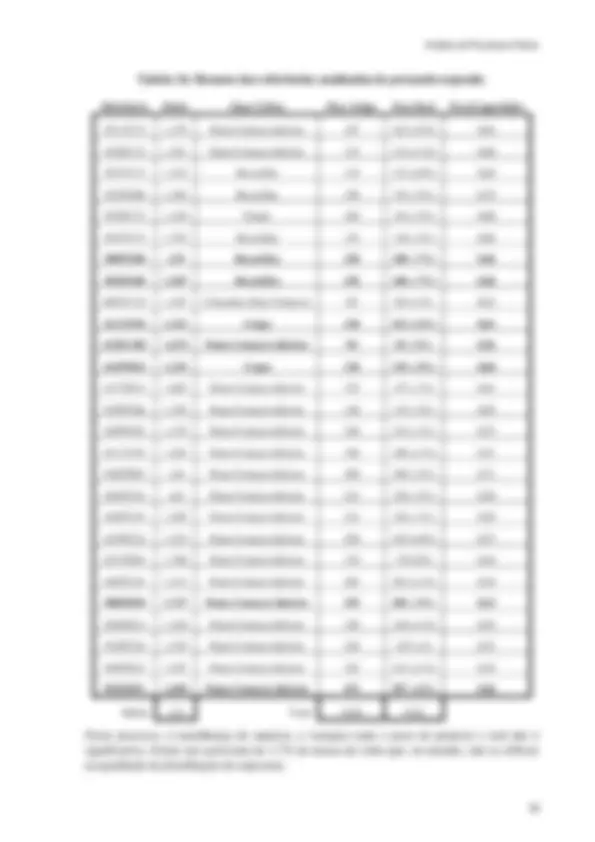
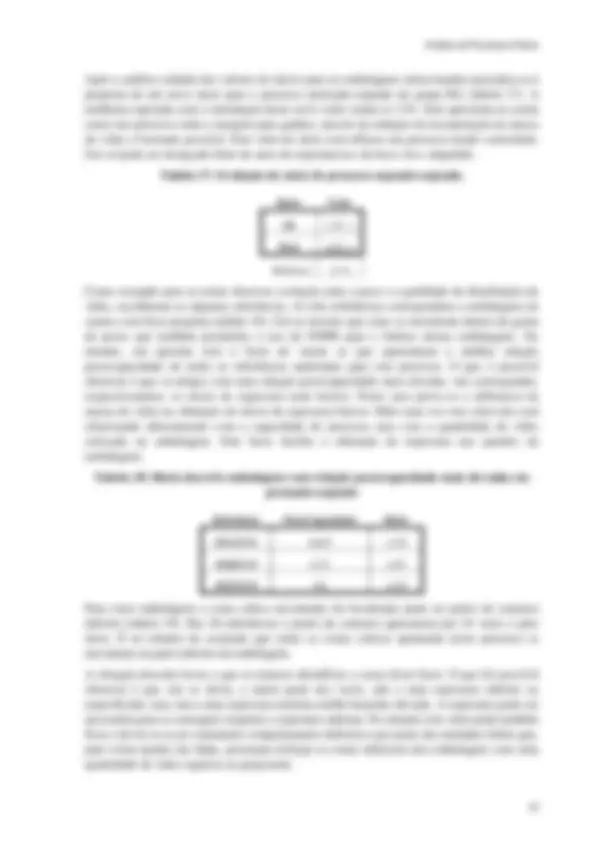
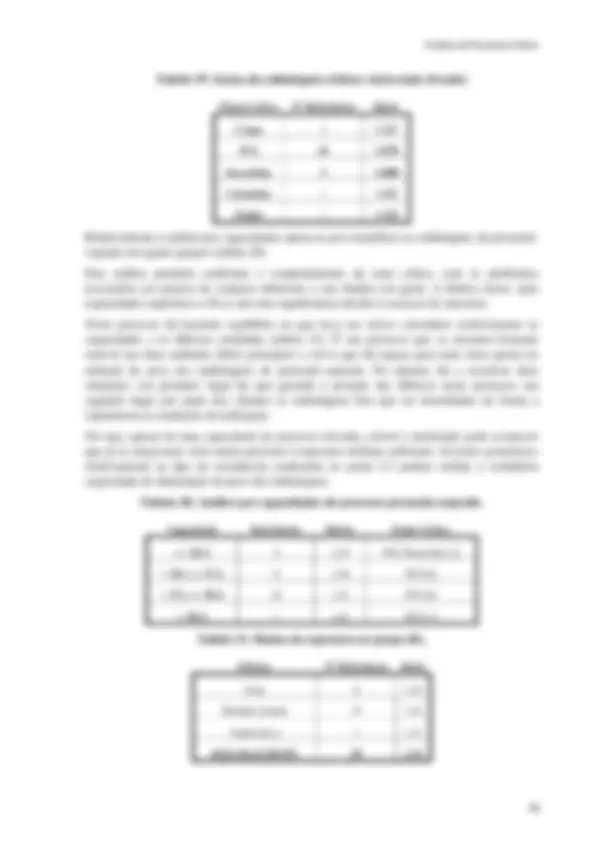
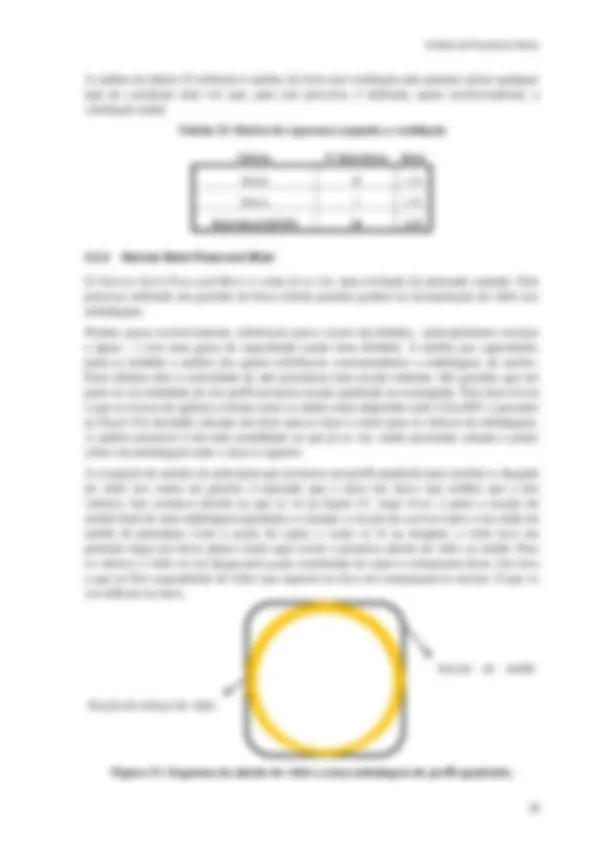
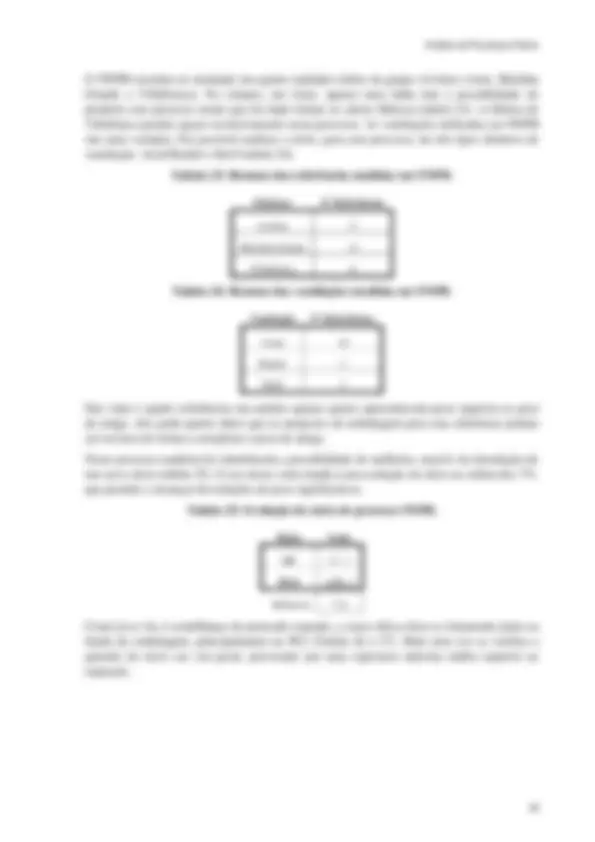
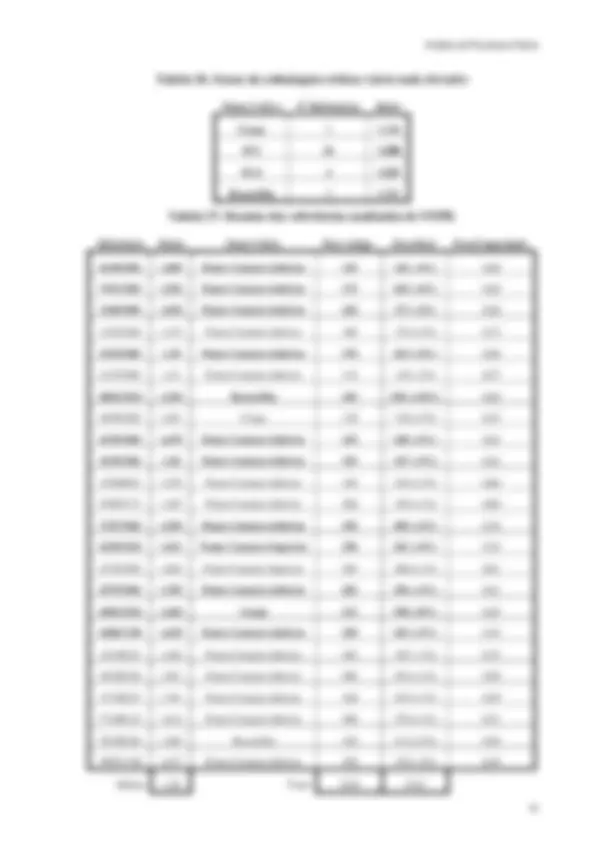
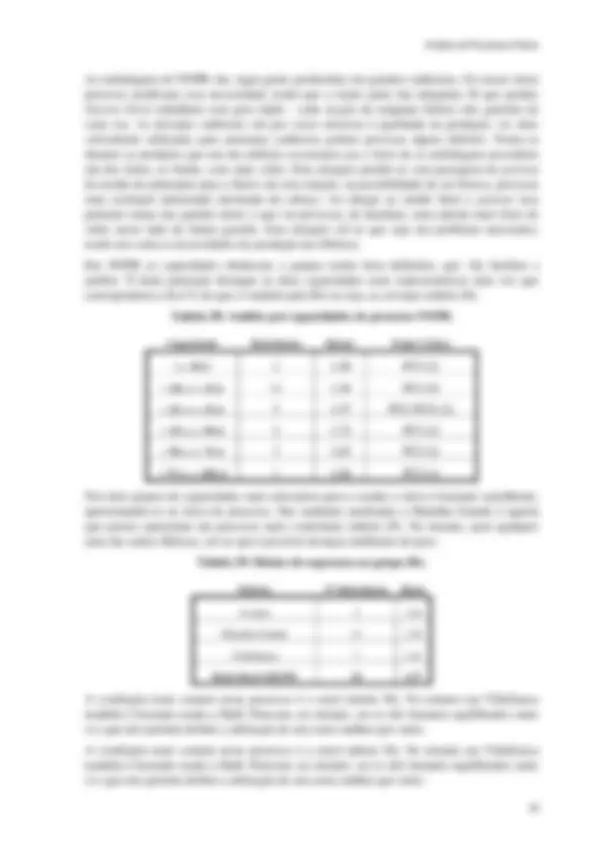
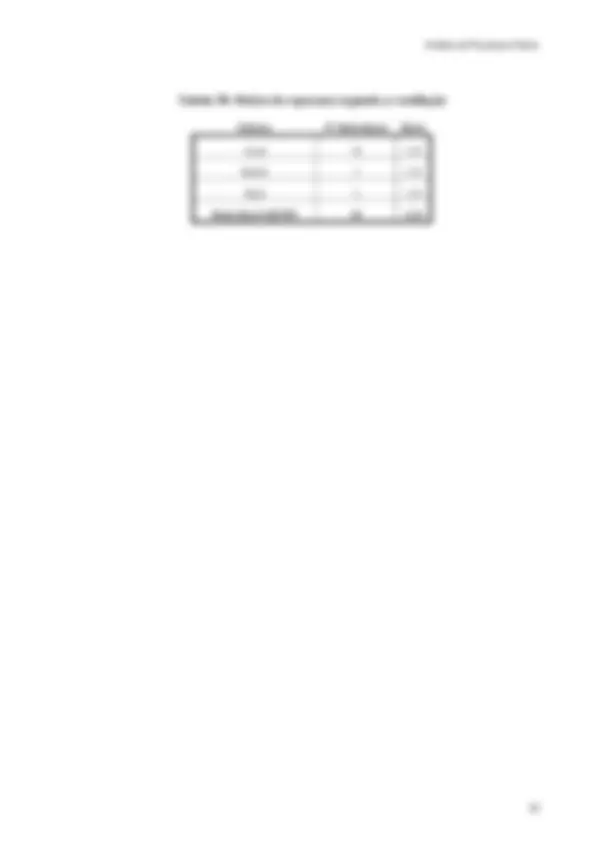
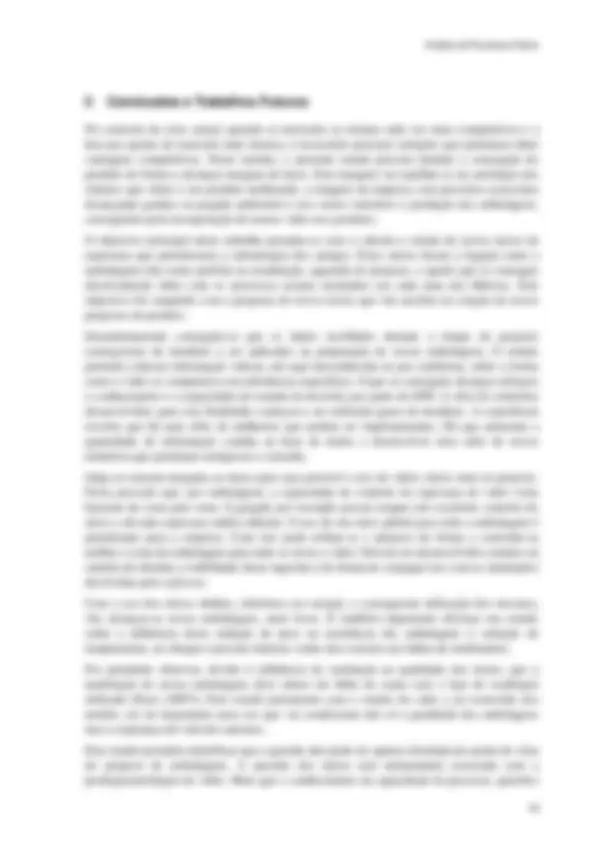
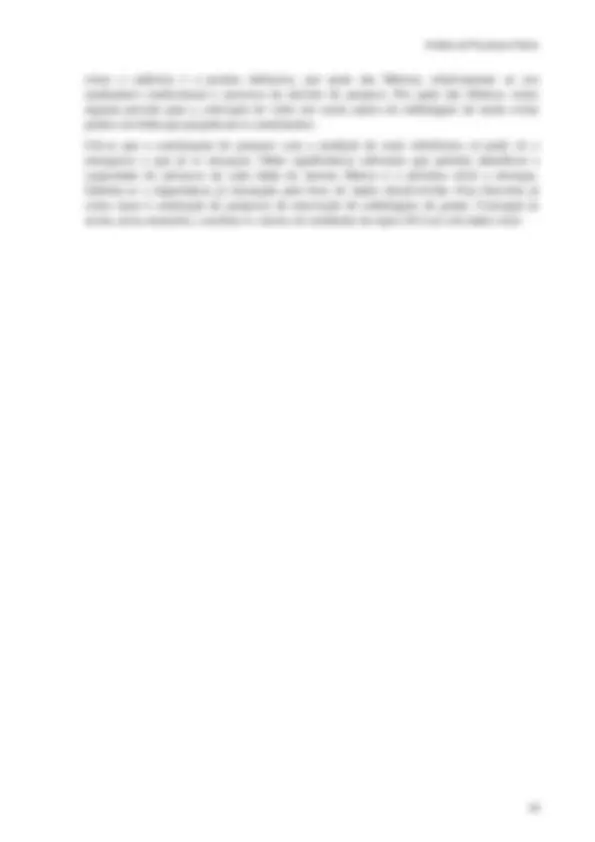
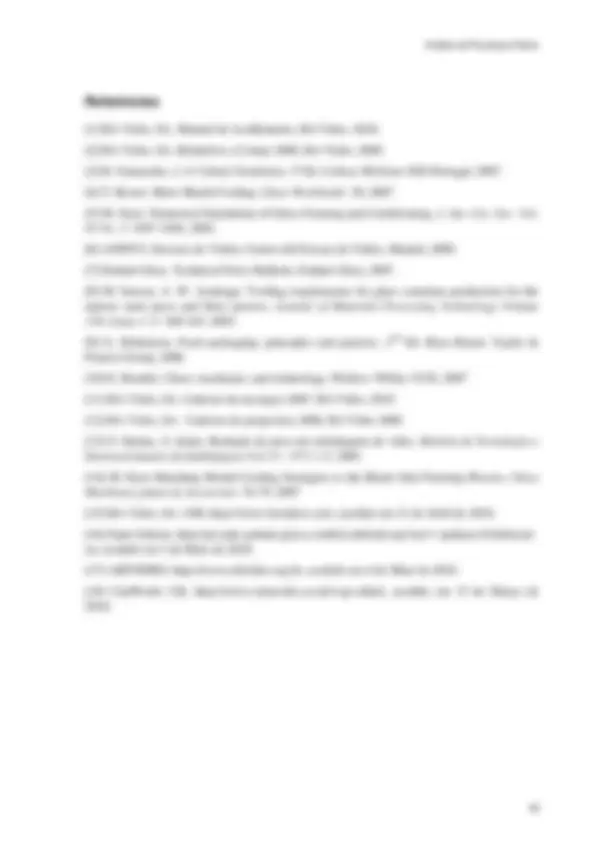
Estude fácil! Tem muito documento disponível na Docsity
Ganhe pontos ajudando outros esrudantes ou compre um plano Premium
Prepare-se para as provas
Estude fácil! Tem muito documento disponível na Docsity
Prepare-se para as provas com trabalhos de outros alunos como você, aqui na Docsity
Os melhores documentos à venda: Trabalhos de alunos formados
Prepare-se com as videoaulas e exercícios resolvidos criados a partir da grade da sua Universidade
Responda perguntas de provas passadas e avalie sua preparação.
Ganhe pontos para baixar
Ganhe pontos ajudando outros esrudantes ou compre um plano Premium
Comunidade
Peça ajuda à comunidade e tire suas dúvidas relacionadas ao estudo
Descubra as melhores universidades em seu país de acordo com os usuários da Docsity
Guias grátis
Baixe gratuitamente nossos guias de estudo, métodos para diminuir a ansiedade, dicas de TCC preparadas pelos professores da Docsity
Este documento discute o processo produtivo de fabricação de embalagens de vidro, enfatizando a importância da distribuição uniforme do vidro na embalagem. A ba, uma empresa líder na indústria de embalagens de vidro, necessita de estatísticas adicionais para ajudar no desenvolvimento de projetos e obter rácios reais de espessura. O documento aborda as variáveis que condicionam a distribuição do vidro, as máquinas is que influenciam a qualidade da distribuição, e as limitações do processo de soprado-soprado. Além disso, são discutidos os tratamentos após a fabricação, como o revestimento com cloretos de estanho ou titânio, e os processos de etiquetagem e impressão.
Tipologia: Provas
1 / 55
Esta página não é visível na pré-visualização
Não perca as partes importantes!
João Alberto Henriques Morais Câmara Manoel
Dissertação de Mestrado Orientador na FEUP: Professora Ana Camanho Orientador na BA Vidro: Engenheiro Fernando Costa
Faculdade de Engenharia da Universidade d o Porto
Mestrado Integrado em Engenharia Industrial e Gestão
2010-07-
ii
Aos meus Pais
iv
Abstract
This report focused on the study of evolution of the actual thickness ratios of several containers of the various factories of the group BA Vidros, in order to identify potential improvements in the product conception.
For this project there was the need to optimize the inputs of the development product service. In a new project, theoretical thickness ratios that do not reflect the stability and the real process of the various factories of the group are used. Thus, a single ratio is extrapolated for each manufacturing site. This translates into inefficiencies that are reflected on an increased weight of the packaging, which is critical in the saving of raw materials, the environmental impact and overall costs passed to customers. The work led to the calculation of new real ratios that can define behaviors regarding the evolution of thickness in relation to the factory, processes and references.
The project consists of several phases. The initial stage reports on the adaptation to the business reality of BA in order to acquire skills in the process, routines on the Department of Design and Development. Management of the resources (human and equipments) needed to the catch, transport and measurement of the samples so that it was possible to reduce the time of a complete measurement. The process is the variable that has more influence on the quality of the glass distribution on a package, same happens in the ratios study. It is essential to an adequate knowledge of it to be able to reach the right conclusions of this project. Later, following the weekly production, there were collected samples that could meet the initial planning. This was combined with an effort of data acquisition through daily measurements of thickness in various packaging parts (neck, body and bottom) was made. The analysis of a larger number of values of thickness in the largest number of references, allows enriching and refining the study. So then, this collection of values led to the development of tools that enable the processing of high volumes of data in a prompt and effective way, so that in the last phase, we may proceed to start the analysis the results.
The study proved that it is possible to achieve improvements in product project. This is achievable introducing new thickness ratios using less glass in the containers. It was achievable to obtain a new map of process capacity in the universe of BA Vidro group.
Key-Words: Ratio of Thickness, Glass Container, Glass Industry, Product Development, Project
v
Agradecimentos
Ao Engenheiro Fernando Costa pela oportunidade de participar neste projecto.
A todos os colaboradores BA com que convivi, pessoal e profissionalmente, em particular do SPD, pelo conhecimento, experiência e ajuda incansável dispensada.
À Professora Ana Camanho pela incondicional ajuda prestada durante o projecto.
À BA Vidro, SA, pelo apoio disponibilizado e pela oportunidade de me ver inserido num grupo desta dimensão.
A todos os Professores que durante este precurso, que tem aqui o fim da sua primeira etapa, foram mais que Mestres, foram Amigos e Orientadores na busca de algo que só mais tarde conseguirei ver.
Àqueles, poucos, que pela sua presença ausente me ajudaram a viver na Marinha Grande durante esta fase, a escrever e inspirar esta tese e a lutar até ao fim.
Aos meus Pais, mais uma vez, ao meu Irmão e à minha Afilhada.
Muito Obrigado!
vii
Siglas
ANFEVI - Associación Nacional de Empressas de Fabricación Automática de Envasses de Vidrio
AV – Avintes
BA – BA Vidro, SA
BB – Blow and Blow
EBITDA – Earnings Before Interest, Taxes, Depreciation and Amortization
IS – Individual Section
Le – Léon
PB – Press and Blow
PSL – Pressured Sensitive Label
MG – Marinha Grande
NNPB – Narrow Neck Press and Blow
O-I – Owens-Illinois
PCS – Ponto de contacto superior
PCI – Ponto de contacto inferior
SPC – Statistic Process Control – Controlo Estatístico do Processo
SPD – Serviço de Projecto e Desenvolvimento
VF – Villafranca de los Barros
VN – Venda Nova
viii
Índice de Figuras
Figura 1: Fábricas BA na Península Ibérica. (Fonte: BA Vidro) ............................................... 2
Figura 2: Ciclo de vida do vidro. (Fonte: BA Vidro) ................................................................. 6
Figura 3: Esquema do processo produtivo de uma unidade fabril de embalagens de vidro. (Fonte: BA Vidro) .............................................................................................................. 7
Figura 4: Casco (vidro em fim de vida) numa central de tratamento. (Fonte: Envases de Vidrio
Figura 5: Esquema de um forno de fusão de vidro. .................................................................... 9
Figura 6: Máquina IS em funcionamento. (Fonte: Envases de Vidrio – ANFEVI) .................. 10
Figura 7: Passos do Processo de moldação soprado-soprado. (Fonte: EMHART) .................. 11
Figura 8: Detalhe do Anel de Lynch de uma garrafa de vinho feita no processo soprado- soprado. ............................................................................................................................ 12
Figura 9: Passos do Processo de moldação prensado-soprado. (Fonte: EMHART) ................ 13
Figura 10: Passos do Processo de moldação Narrow Neck Press-Blow. ................................. 14
Figura 11: Pormenor do código de pontos colocado nas embalagens para identificação dos moldes............................................................................................................................... 16
Figura 12: Embalagens de vidro onde é possível identificar os diversos tipos de decoração.. 17
Figura 13: Organigrama do SPD. ............................................................................................. 18
Figura 14: Exemplo de simulação de distribuição de espessura e estiramento usando OI-Cad para uma embalagem. ....................................................................................................... 20
Figura 15: Comparação entre a distribuição de vidro (A), perfeita, considerada no simulador e o que acontece na realidade (B)........................................................................................ 22
Figura 16: Uso do rácio teórico para o cálculo da espessura real minima. .............................. 24
Figura 17: Molde onde é possível identificar os furos para o vácuo (A) e os furos para a refrigeração do molde. ...................................................................................................... 26
Figura 18: Esquema das zonas da garrafa sujeitas a análise do rácio de espessuras. ............... 28
Figura 19: Detalhe dos pontos de contacto de uma grarrafa com protecção de rotulo............. 28
Figura 20: Medidores de espessuras utilizados no projecto. .................................................... 29
Figura 23: Esquema da adesão do vidro a uma embalagem de perfil quadrado. ..................... 39
1
O projecto “Análise de Processos Fabris” aborda a temática do estudo dos processos que condicionam o desenvolvimento de novos produtos. Com este estudo a BA pretende optimizar os inputs para a concepção de novas embalagens, mais leves, assim como um conhecimento mais profundo da capacidade dos diversos processos de cada unidade fabril do grupo. Estes inputs consistem nos rácios e nas espessuras mínimas, médias e máximas das embalagens que mostram a capacidade do processo produtivo.
A BA tem necessidade de uma maior quantidade de dados estatísticos que auxiliem o projecto de embalagens e que permitam o uso de rácios reais de espessura. Estes correspondem à razão entre a espessura máxima e mínima, numa mesma secção da embalagem, traduzindo a qualidade da distribuição do vidro. A importância deste valor reside na sua capacidade de traduzir a estabilidade do processo e o comportamento do fabrico e das máquinas envolvidas. Com o uso destes novos valores, potencialmente inferiores aos teóricos utilizados, conseguem-se melhorias significativas na utilização dos recursos da empresa.
Este capítulo inicial encontra-se dividido em três partes. Em primeiro lugar é feita uma apresentação detalhada da empresa onde este trabalho foi efectuado. Seguidamente são apresentadas as metodologias utilizadas na elaboração do projecto. Por fim, faz-se uma descrição da organização dos temas abordados no presente relatório.
1.1 Apresentação da BA Vidro
A BA é uma empresa Ibérica, com quase 100 anos de existência, que desenvolve, produz e comercializa embalagens de vidro para a indústria alimentar, de bebidas, farmacêutica e cosmética.
Fundada em 1912 sob a designação “Barbosa & Almeida, Lda.” pelos Sócios Raul da Silva Barbosa e Domingos de Almeida, tinha como finalidade a comercialização de garrafas produzidas no Seixal e na Marinha Grande. Mais tarde, em 1930, a Sociedade inicia a sua actividade industrial com a criação de uma unidade produtora de garrafas em Campanhã, no Porto, dotada de tecnologia semiautomática. Esta fábrica esteve em actividade 39 anos. Durante esse tempo sofreu progressivos melhoramentos com a introdução de tecnologia de alimentação e moldagem automática, inovadoras em Portugal.
Em 1969 inicia a laboração na nova unidade fabril em Avintes. Nos anos 70 foi instalada a primeira máquina Individual Section (IS), que representou um incremento da capacidade produtiva instalada. Até hoje, esta unidade, a maior do grupo, tem sofrido melhoramentos constantes que, com as mais avançadas tecnologias, permitem conciliar a qualidade da produção com melhorias de produtividade.
A partir desta fase, a empresa sofreu várias transformações quer a nível do capital social, com a entrada e saída de sócios, quer a nível da capacidade produtiva com a ampliação, construção e aquisição de complexos fabris. Foi construída, de raiz, a unidade de Villafranca de los Barros em Espanha. No campo das aquisições devem ser referidas a CIVE (Companhia Industrial Vidreira, SA, na Marinha Grande) a Vilesa (Vidreira Leonesa, SA, empresa com uma unidade fabril em Léon - Espanha) e o Grupo SOTANCRO, com duas unidades, uma na Venda Nova e outra em Xinzo de Limia em Espanha. Esta última unidade foi entretanto
2
Avintes
Marinha Grande
Venda Nova
Villafranca de los Barros
Léon
fechada devido a dificuldades na integração da mesma no grupo. Na figura 1 pode verificar-se a distribuição das unidades fabris BA na Península Ibérica.
A contínua renovação das suas linhas desde os fornos, máquinas IS, arcas de recozimento e paletizadores, permite à empresa manter-se competitiva e em crescimento num mercado cada vez mais saturado e difícil. Com a aquisição da SOTANCRO, em 2008, a BA conseguiu consolidar o segundo lugar de maior fornecedor de embalagens de vidro da Península Ibérica, contribuindo, desta forma, para que a empresa se assuma como a mais rentável do mundo do sector das embalagens de vidro, ou seja, aquela que mais retorno possibilita relativamente a um determinado investimento feito.
Na tabela 1 podem analisar-se algumas das características das unidades fabris da BA. O grupo, segundo o relatório e contas de 2008, teve uma produção útil de quase 800. toneladas de vidro.
Tabela 1:Capacidade produtiva das unidades fabris da BA.
Unidades Fabris
Nº Fornos
Nº Linhas Capacidade (ton)
Portugal
Avintes 3 10 ~ 832 Marinha Grande 3 9 ~ 729 Venda Nova 2 7 ~ 346
Espanha
León 2 8 ~ 575 Villafranca de los Barros 1 3 ~ 405 Total 11 37 ~ 2887
Figura 1: Fábricas BA na Península Ibérica. (Fonte: BA Vidro)
4
A curta duração do projecto e a morosidade que representa a medição completa de uma série de amostras de uma determinada referência, implica um estudo prévio cuidado. Assim, só se mediram embalagens cujo processo de fabrico já estivesse controlado e estável. Com esta finalidade, evitaram-se embalagens cujos fabricos fossem os primeiros na empresa e não se recolheram amostras nos primeiros dias da sua produção. Desta forma, garante-se a estabilidade do processo e que as medições efectuadas sejam, efectivamente, uma imagem da capacidade instalada no grupo. Em seguida, é preponderante a selecção de embalagens que abranjam todo o leque de processos de fabrico, ventilações e fábricas em análise. Estes são os pontos-chave para os resultados do estudo em questão.
Procede-se igualmente ao dimensionamento das amostras a medir de cada referência. Com esse fim é utilizada a Military Standard 105D que estabelece os procedimentos de amostragem para inspecção por atributos. Verificadas as cadências de cada produção a analisar consultam-se as tabelas da Standard e obtém-se a dimensão das amostras. Para este estudo, de acordo com as cadências observadas, a dimensão das amostras enquadrava-se numa das seguintes dimensões: 13, 20, 32, 50 ou 80 unidades.
A planificação da produção de uma empresa como a BA implica um esforço imenso de coordenação de vários serviços. Desta forma, para além deste ponto da metodologia utilizada ter sido contínuo até ao fim do projecto, foi necessário um esforço quase diário de identificação de referências a medir assim como da logística necessária à chegada das amostras à Marinha Grande, local onde foram feitas as medições.
Por fim, conseguiram desenvolver-se, também, uma série de reports automáticos do conjunto de medições feitas, facilitando desta forma a consulta da informação armazenada na base de dados através de um acesso rápido e eficaz da mesma (anexo A, B e D).
5
1.3 Temas Abordados e sua Organização no Presente Relatório
Esta tese está organizada em cinco capítulos. O segundo capítulo apresenta os conceitos teóricos fundamentais ao projecto. As noções explicadas passam pelos processos de criação de embalagens de vidro e todas as variáveis que condicionam a distribuição do vidro nas mesmas. No terceiro capítulo é apresentado o Serviço de Projecto e Desenvolvimento (SPD), onde foi elaborado o estudo, e o seu organigrama. Posteriormente faz-se uma análise ao projecto de produto, no seio do qual surgiu a necessidade do cálculo de novos rácios reais, e é apresentada a noção de rácio teórico, crucial à compreensão deste projecto. São por fim também desenvolvidas as temáticas das variáveis a analisar no estudo e das medições efectuadas no mesmo. No quarto capítulo é efectuada uma análise detalhada dos valores obtidos e no último capítulo são retiradas as conclusões do trabalho efectuado.
7
Na figura 3 pode ver-se um esquema do processo produtivo das embalagens de vidro.
Estas fases são descritas em detalhe seguidamente.
2.1 Processo de fabricação do vidro
O Vidro necessita de duas fases para ser feito. Primeiramente a composição consiste na recepção e mistura das matérias-primas em várias receitas que fazem os vários tipos de vidro para embalagens possível. Em seguida durante a fusão são fundidos os diversos compostos que levam à formação de um leito de vidro que alimenta as máquinas IS.
2.1.1 Composição
A composição consiste na recepção, armazenamento em silos próprios, dosagem e mistura das matérias-primas para a obtenção das diversas cores possíveis.
Todos os dias são descarregadas toneladas de sílica sob a forma de areia e casco - as duas matérias-primas principais no fabrico do vidro. Na tabela 2 faz-se um breve resumo das funções de cada um dos principais constituintes incorporados. Estes constituintes são armazenados em silos que alimentam balanças cujo propósito é o doseamento de cada matéria-prima de forma a obter as diversas receitas de vidro. Após a pesagem segue-se um misturador que tem por finalidade a homogeneização da mistura a introduzir nos fornos.
Figura 3 : Esquema do processo produtivo de uma unidade fabril de embalagens de vidro. (Fonte: BA Vidro)
8
O casco, vidro em fim de vida, é utilizado na composição como substituto de todos as outras matérias-primas. O seu uso prende-se com a diminuição dos custos do fabrico de vidro uma vez que é mais barato que as restantes matérias-primas. Tabela 2: Lista de Matérias-Primas incorporadas na composição do vidro.
Matéria-Prima Material Função Quantidade
Casco Vidro usado Diminuição dos custos (até 7 5% do total)
Vitrificante Areia Indispensável à criação da rede vitrea 73 a 7 4 %
Fundente Óxido de Sódio e Óxido de Potássio Baixar a temperatura de fusão 12 a 1 3 %
Estabilizador (^) Magnésio e Óxido de ZincoÓxido de Cálcio, Óxido de Estabilizar a massa de vidro 12 a 13 %
Afinadores -- Controlar a co vidror e opacidade do --
O casco (Figura 4) introduzido no processo de fabrico do vidro provém de duas origens. Pode ser incorporado de uma forma externa, com a compra de vidro tratado, ou directamente pelas rejeições nas linhas e máquinas da fabricação. No âmbito do grupo BA, existe a NORCASCO que trata da compra/recolha, tratamento e distribuição de casco para a composição.
2.1.2 Fusão
A cerne do processo de fusão são os fornos regenerativos (Figura 5), assim designados por terem a capacidade de reaproveitar o ar quente que geram. Estes estão em funcionamento contínuo 365 dias por ano, atingindo temperaturas próximas dos 1600º e com uma vida útil de cerca de 12 anos.
Figura 4 : Casco (vidro em fim de vida) numa central de tratamento. (Fonte: Envases de Vidrio - ANFEVI)
10
Na moldação, o vidro arrefece com o decorrer do tempo o que provoca um aumento da viscosidade. As variáveis (refrigeração do molde, tempo de molde de principiar, temperatura da gota, entre outros) têm de ser controladas para que o produto seja formado no instante certo. A massa de vidro deve estar líquida o suficiente para ser conformada, caso contrário o vidro fica rígido e impede a distribuição e extensão do mesmo pelo molde. Esta ultima situação provocaria problemas na distribuição da massa de vidro pela embalagem.
O processo consiste na passagem, primeiro, pelo molde de principiar, onde as gotas recebem uma pré-forma do produto final e, no fim, pelo molde final que confere ao vidro a forma da embalagem. A diferença entre processos reside no tipo de tecnologia que dá origem à pré- forma do produto final. O processo soprado-soprado (SS) usa tecnologia pneumática enquanto que no prensado-soprado (PS) e Narrow Neck Press-Blow (NNPB) este é formado por um punção que ocupa um determinado volume na massa de vidro conferindo a já falada pré- forma.
No fim do processo de fabricação das embalagens, à saída das máquinas IS, o vidro encontra- se a uma temperatura já próxima dos 500º, como é indicado pela cor ruborizada (Figura 6), seguindo para os tratamentos.
Nestes processos a principal variação, de uns para os outros, reside na forma como o esboço, designado habitualmente por parison , é formado. Em particular no soprado-soprado, quando é cortada pelas tesouras, a gota é encaminha para o contra-molde (Figura 7 – Imagem A) onde é assente por acção pneumática (Figura 7 – Imagem B). Em seguida é-lhe dada a forma do molde de principiar, onde está inserida, por acção de um sopro contrário ao primeiro (Figura 7
Figura 6 : Máquina IS em funcionamento. (Fonte: Envases de Vidrio – ANFEVI)
11
mais uma vez, por acção de um sopro pneumático (Figura 7 – Imagem F), recebe a forma da embalagem final. Na Figura 7 – Imagem G a embalagem fica pronta a sair da máquina IS e entrar no tapete que a vai conduzir aos tratamentos térmicos.
O processo soprado-soprado é utilizado para o fabrico de artigos de boca estreita, garrafas (embocaduras de 3 a 38 mm), e de boca intermédia, de 24 a 38 mm.
É muito difícil conseguir controlar a distribuição de vidro. Isto prende-se com o facto de a cavidade interior do parison ser criada por algo que não é possível controlar na sua totalidade. O sopro de um mecanismo pneumático apresenta na forma como distribui o vidro, do parison , irregularidades de gota para gota. Como se vai poder observar, a temperatura tem uma influência bastante declarada no comportamento da gota. Assim, temperaturas mais baixas em certas zonas da gota vão fazer que o vidro estire de forma diferente, fazendo com que internamente a bolha de ar não se estenda regularmente dentro da cavidade.
Uma das características chave deste processo passa pelo aparecimento de uma heterogeneidade na distribuição de espessura do vidro no corpo da embalagem (Figura 8). Esta zona, conhecida como settle wave ou anel de Lynch, é uma das principais limitações ao controlo da massa de vidro nas embalagens produzidas por este processo.
Esta característica permite a identificação rápida, a olho nu, do processo implicado no fabrico de uma garrafa. Foram identificados neste processo dois fenómenos deste tipo de embalagens. À utilização do sopro, na formação do parison , que dá à massa vítrea uma forma variável, junta-se a espessura inferior visualmente identificável pelo aparecimento de uma ondulação resultante da forma como a luz se comporta nas diferentes zonas de espessura do vidro.
Dependendo apenas da viscosidade do vidro, controlado pela distribuição de temperaturas dentro da massa vítrea, fica-se sem controlo da distribuição da espessura. A settle wave ocorre quando o parison passa para a posição onde vai receber o molde final. Aqui, antes de ser efectivamente moldado, o esboço fica algum tempo suspenso, preso pela marisa. A deformação, por acção da gravidade, provoca um estiramento na massa de vidro. A zona onde ocorre esse estiramento vai originar o anel de Lynch , que é caracterizado, como já vimos, por uma espessura inferior ao resto da embalagem. Em termos de projecto esta situação é prevista e pode ser ligeiramente contrariada. No entanto é, ainda assim, uma das principais limitações no projecto de embalagens de vidro por processo de soprado soprado.
Figura 7: Passos do Processo de moldação soprado-soprado. (Fonte: EMHART)