
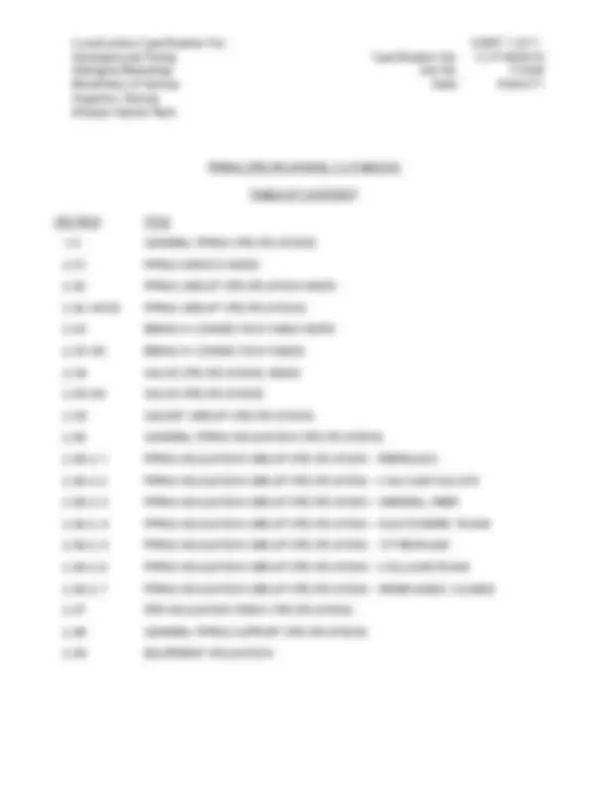
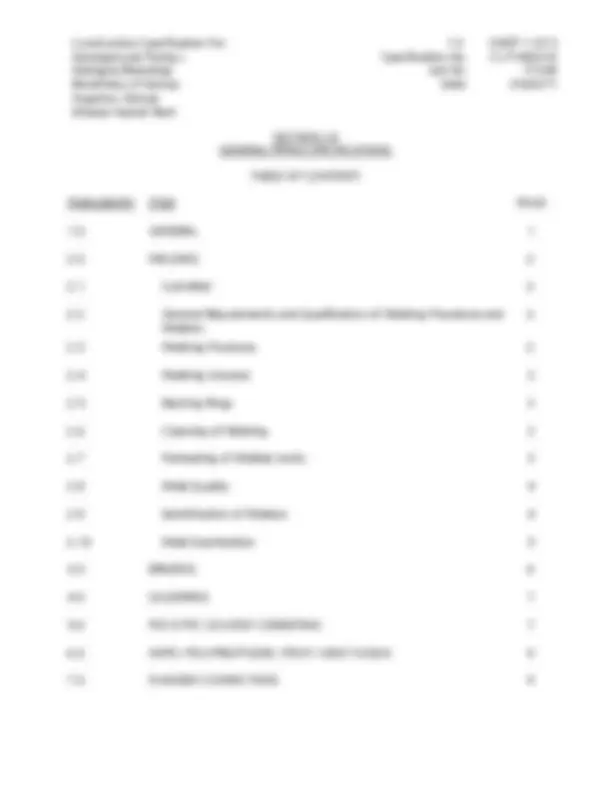
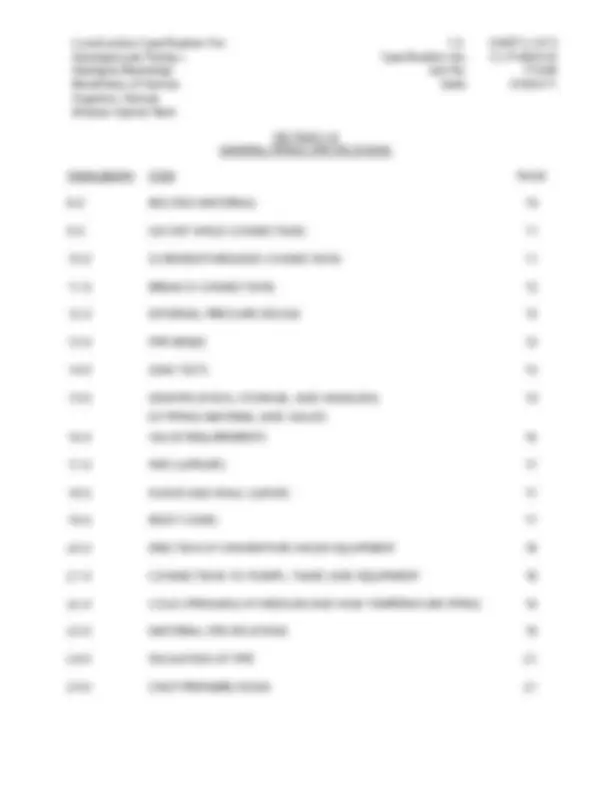
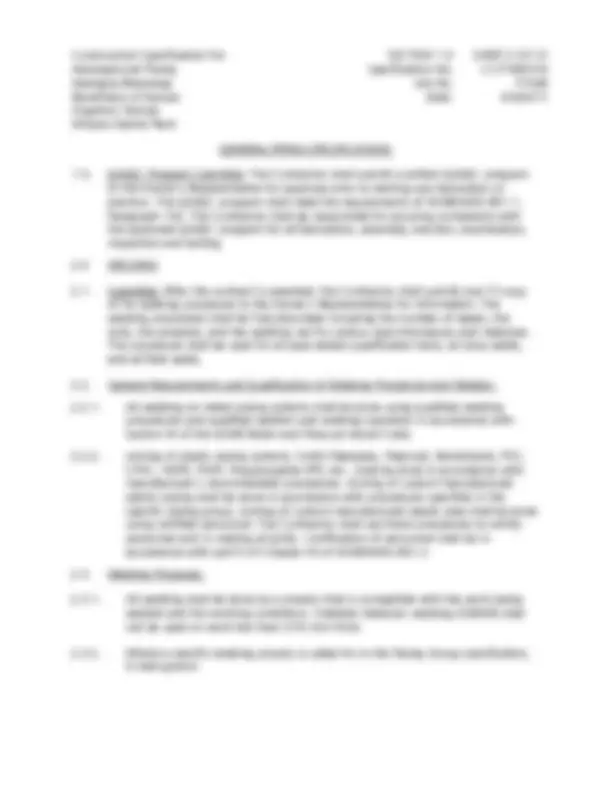
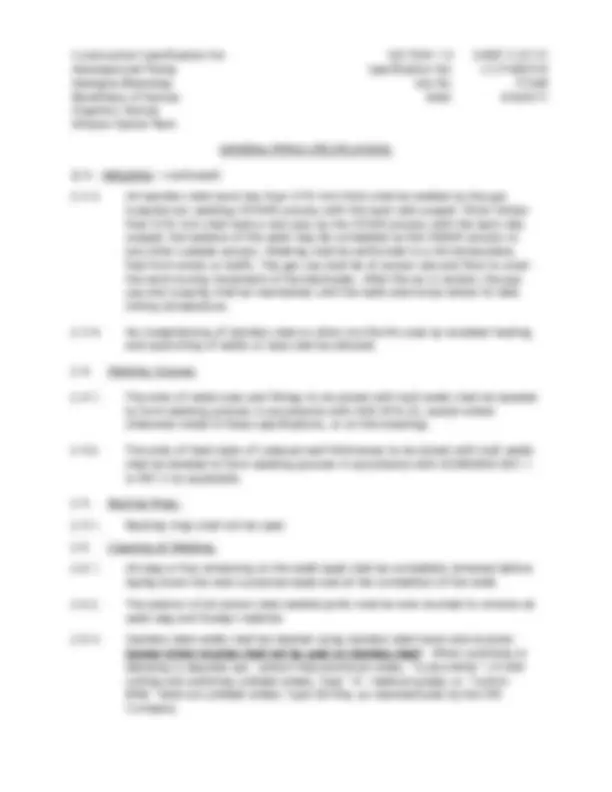
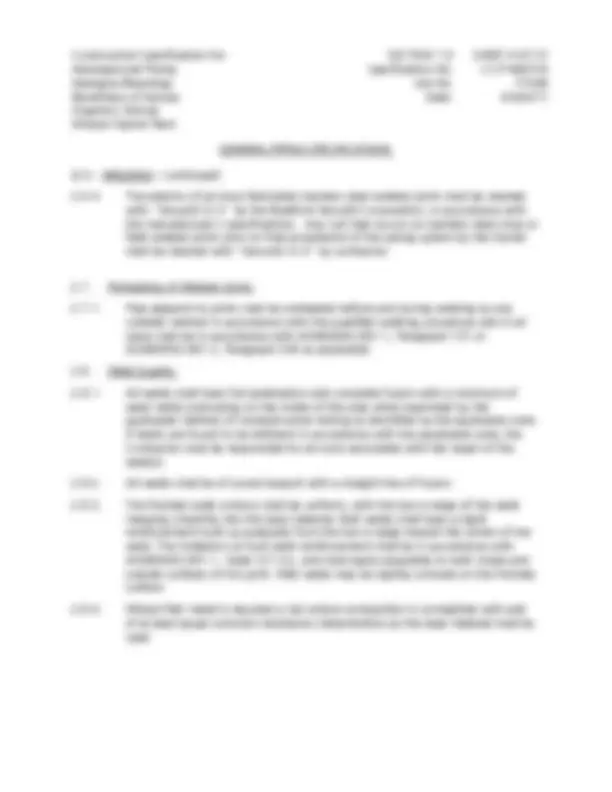
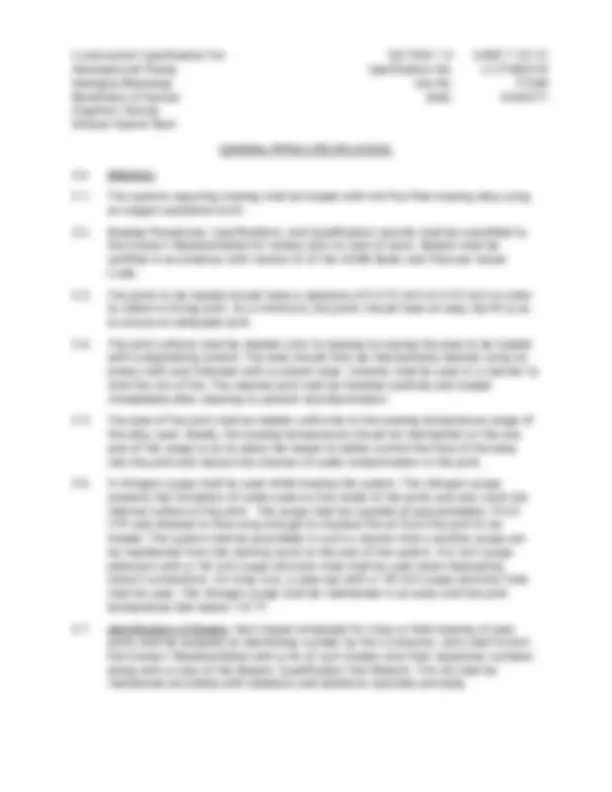
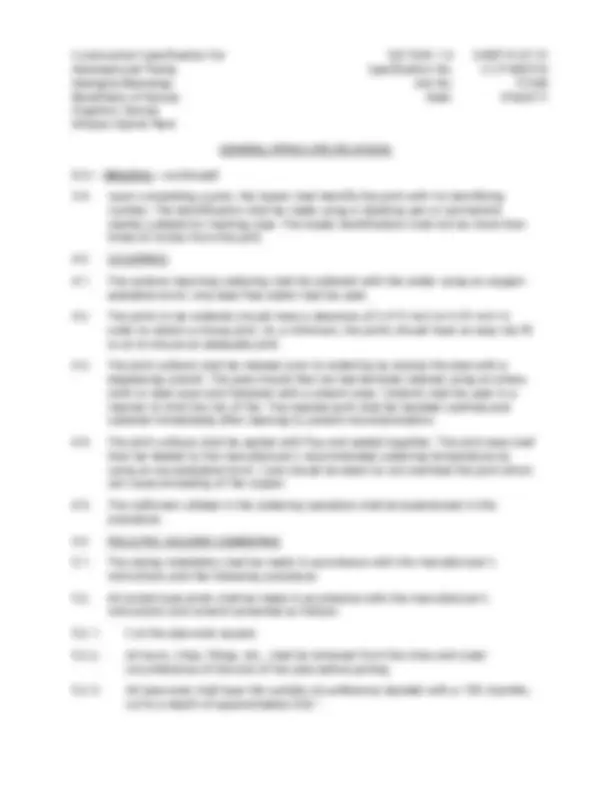
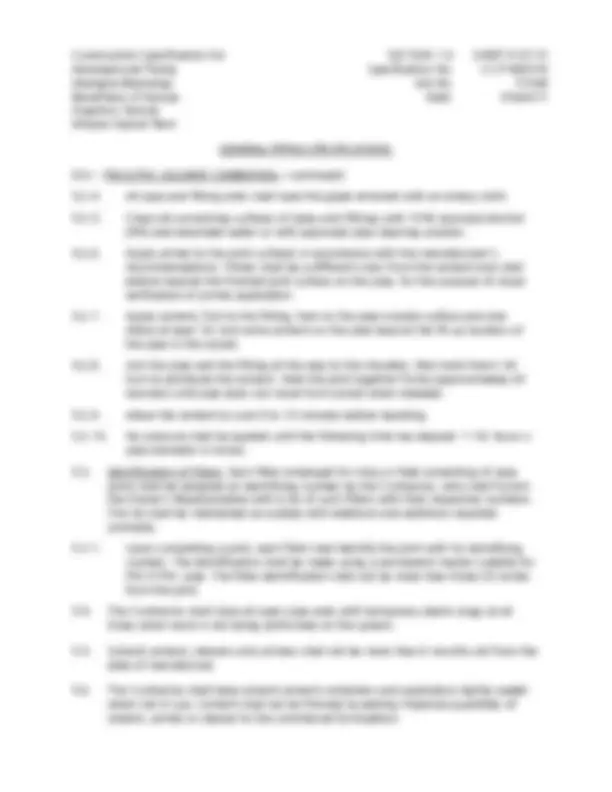
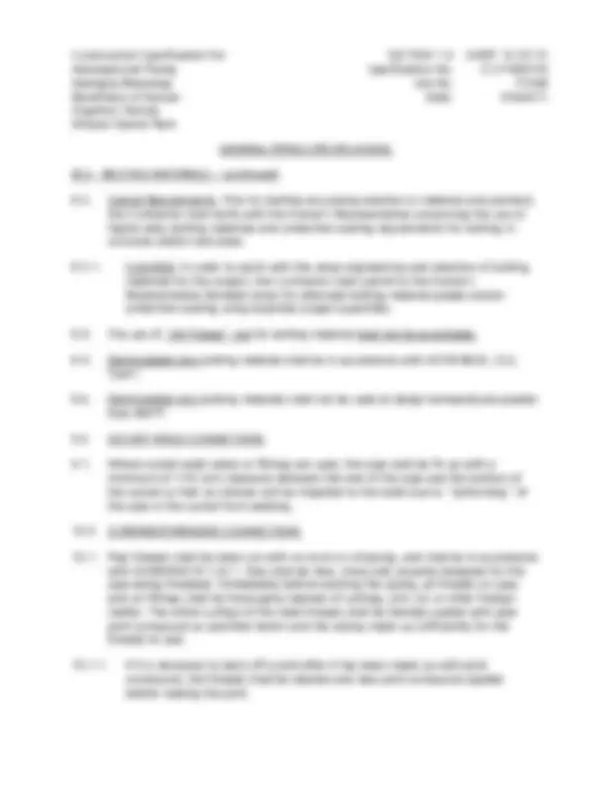
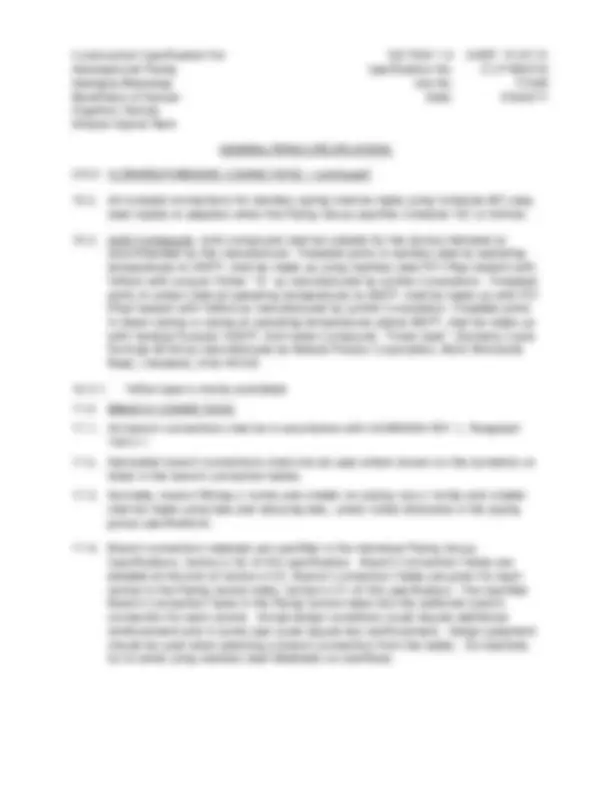
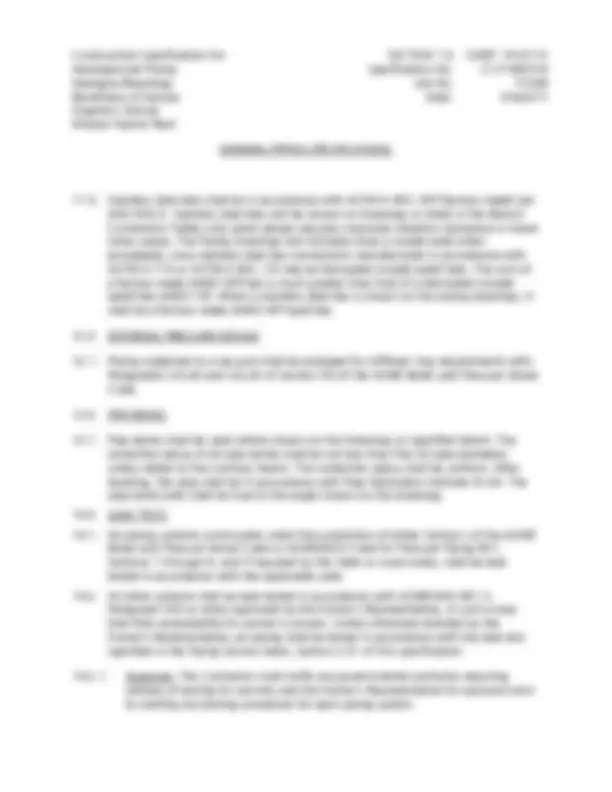
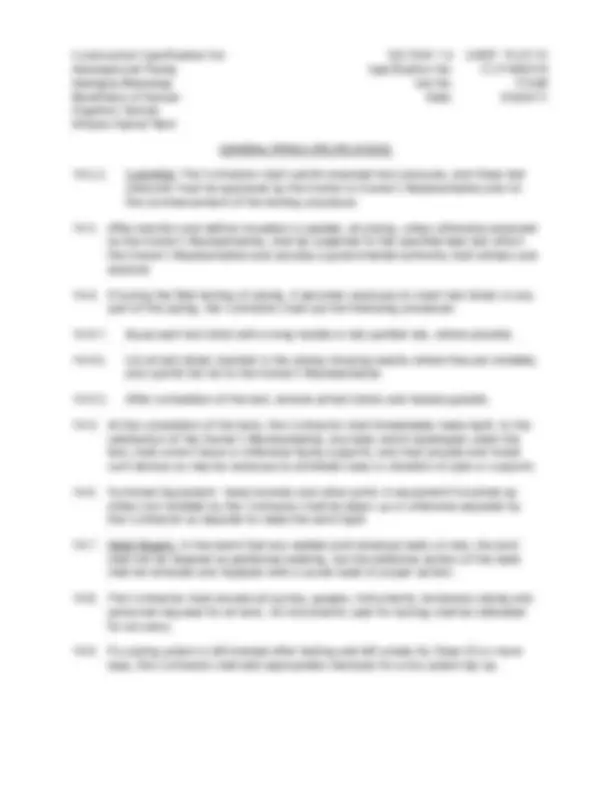
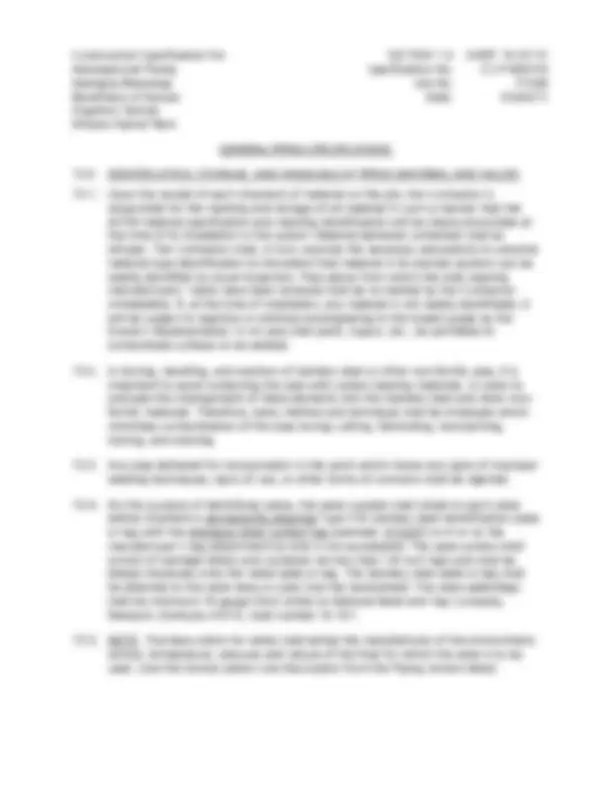
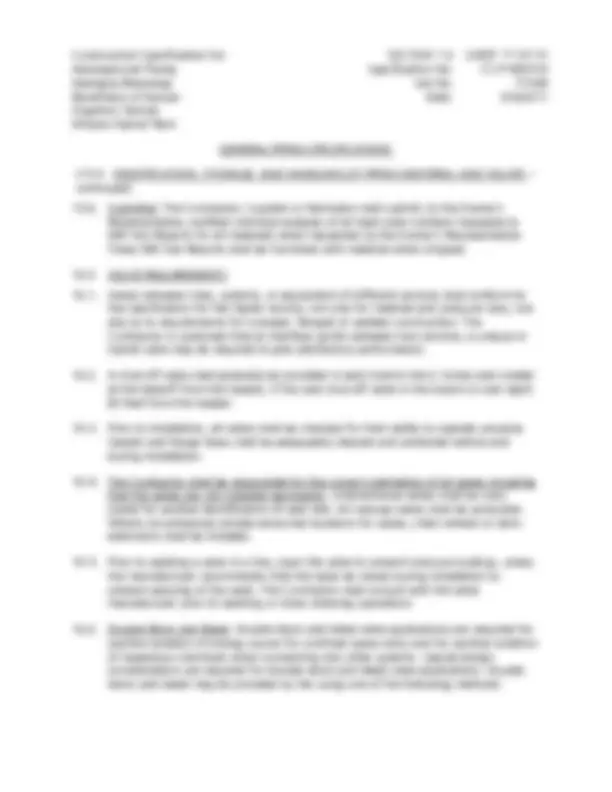
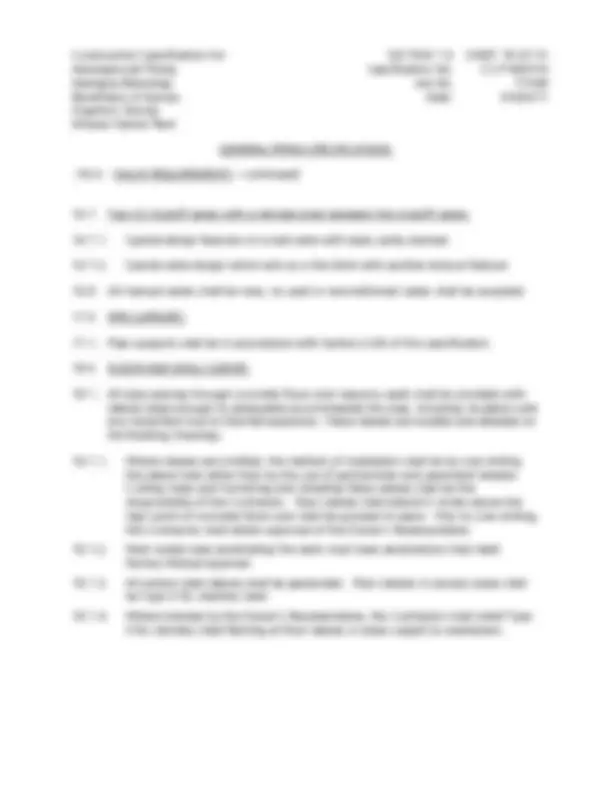
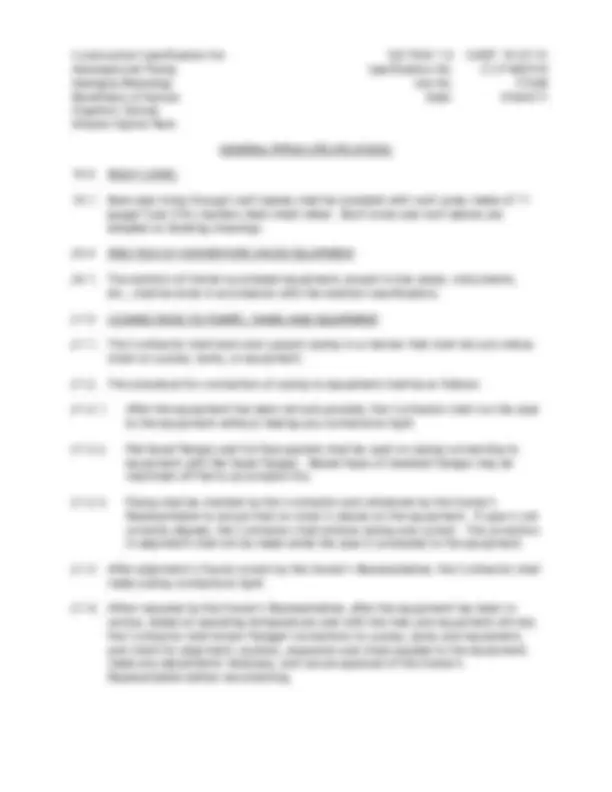
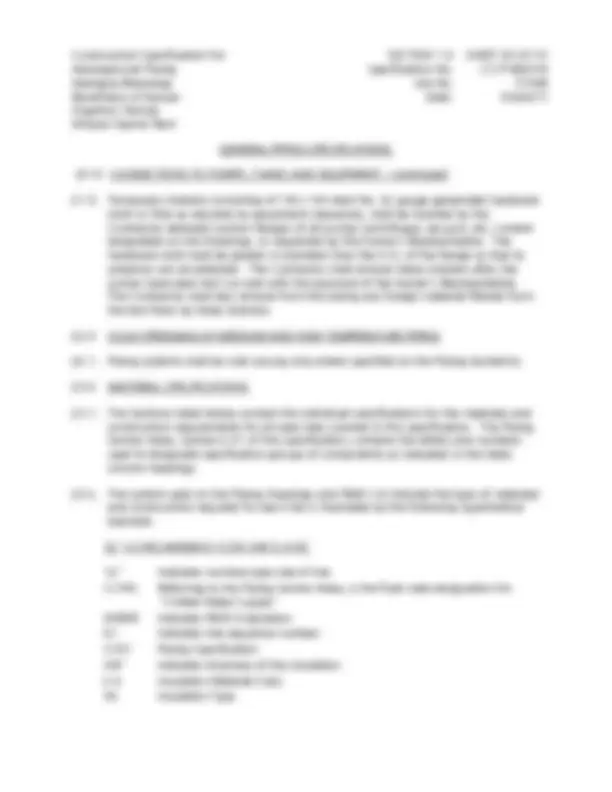
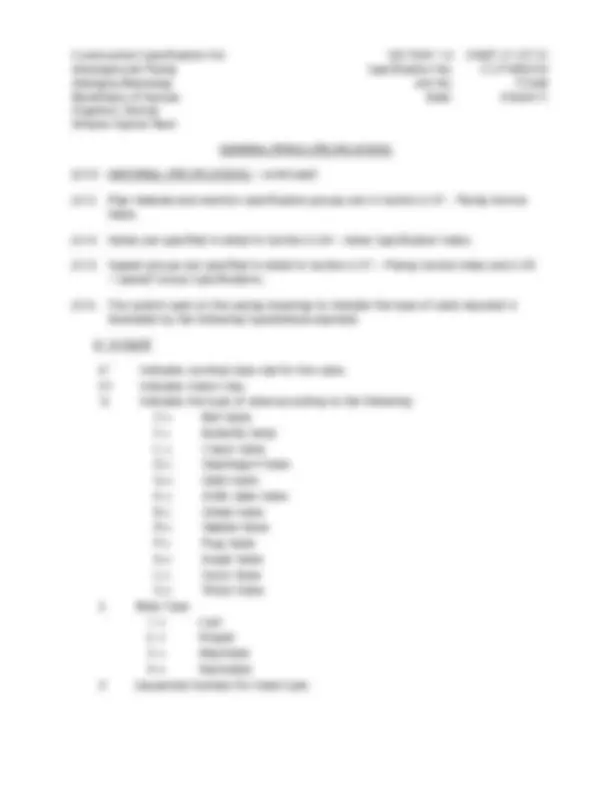


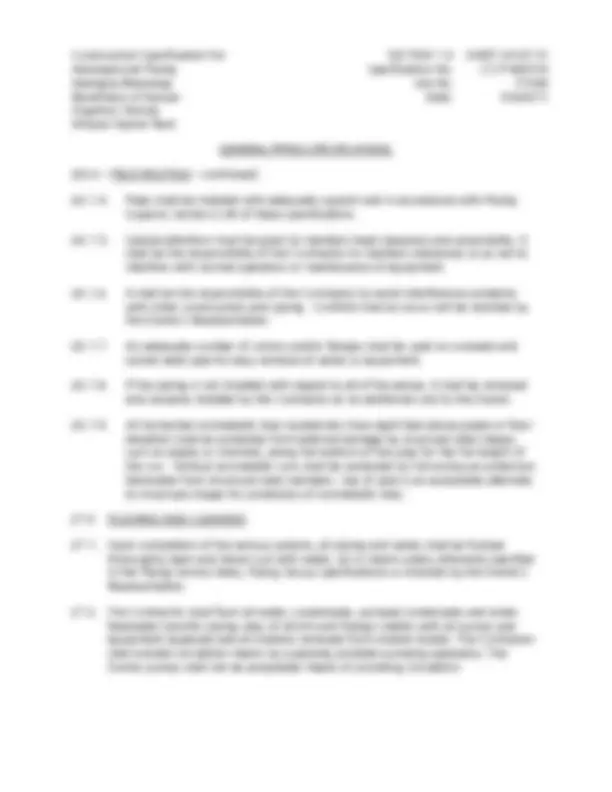
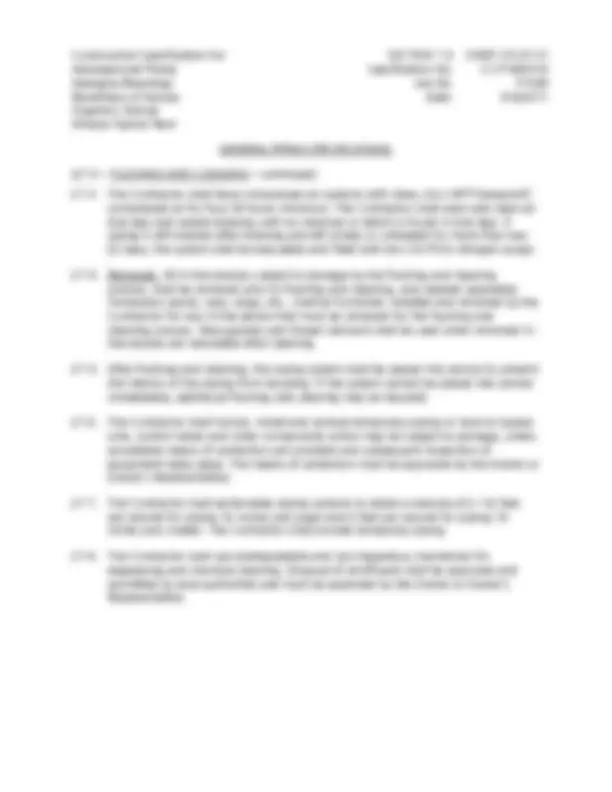
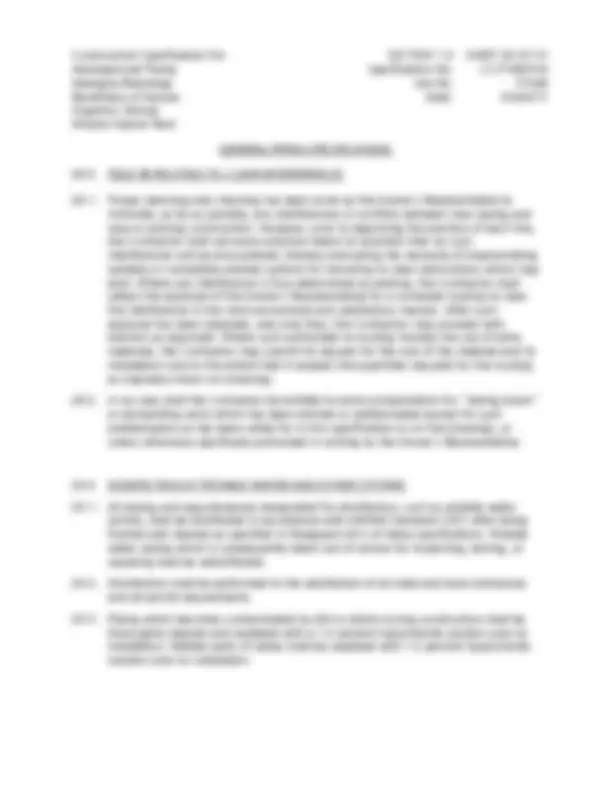
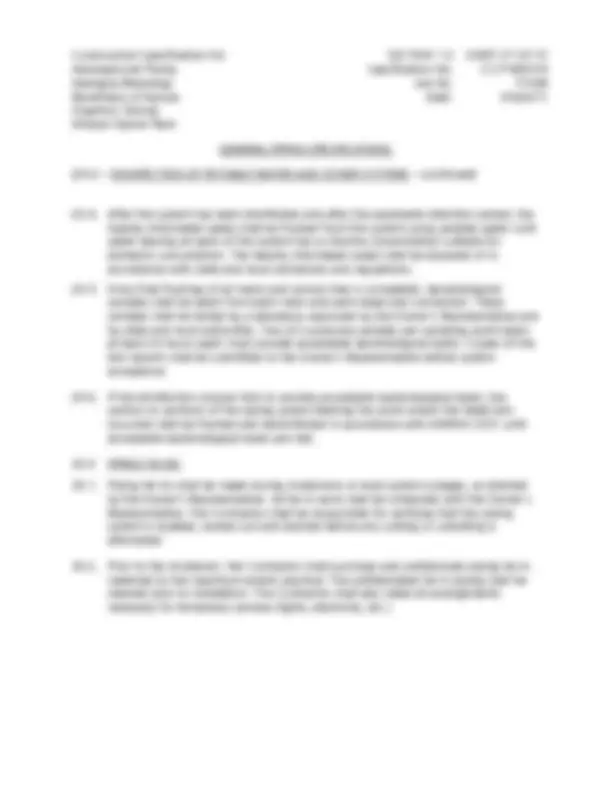
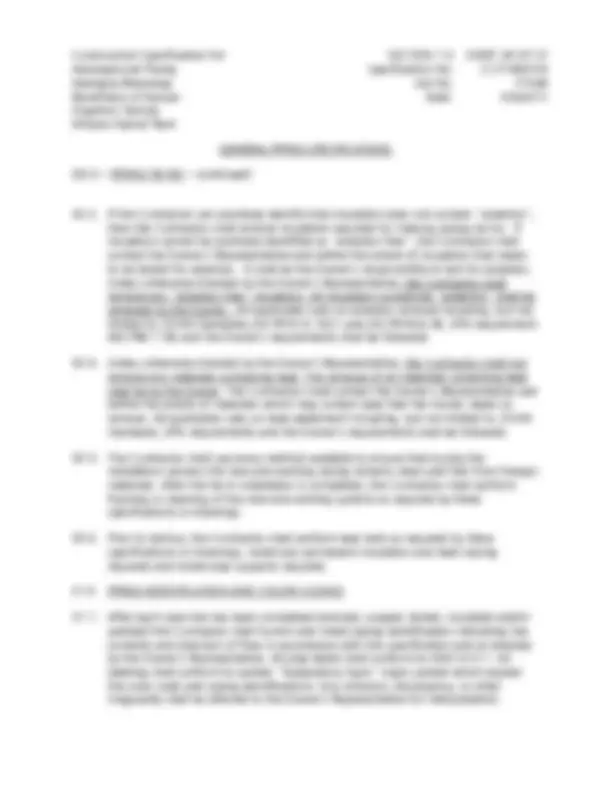
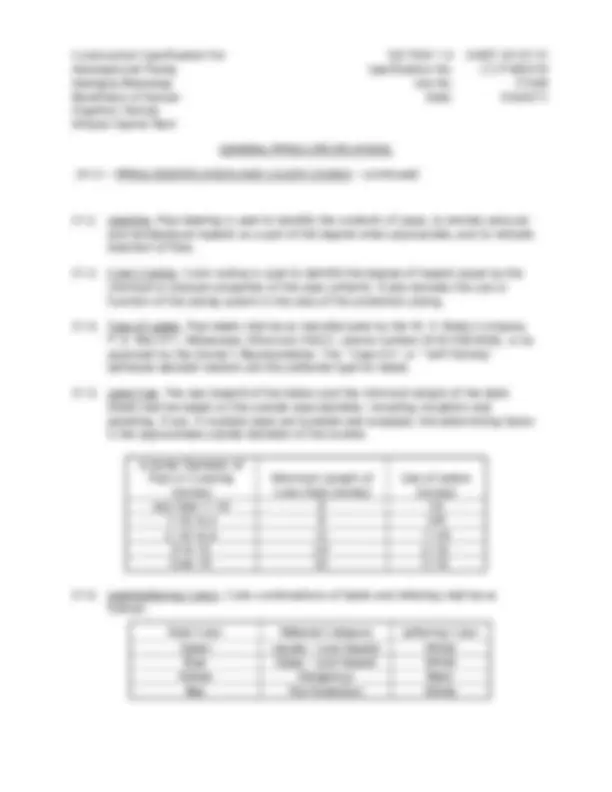
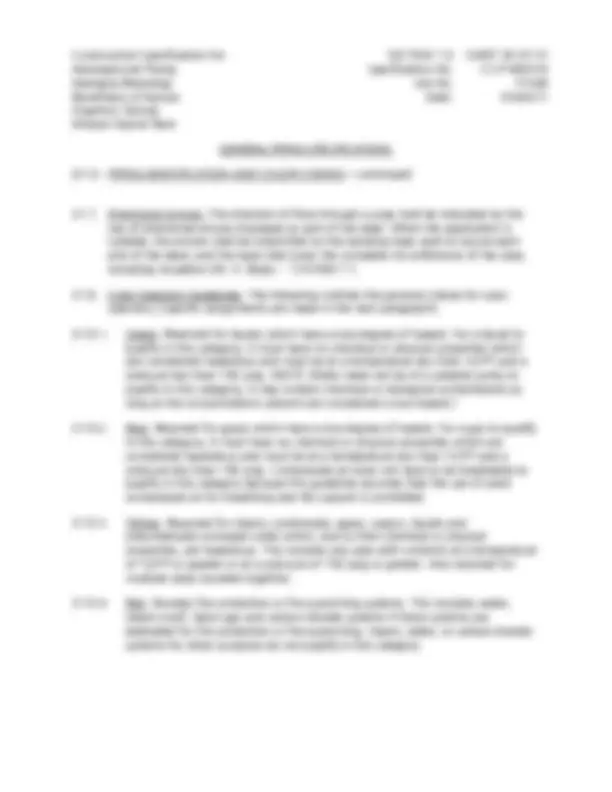
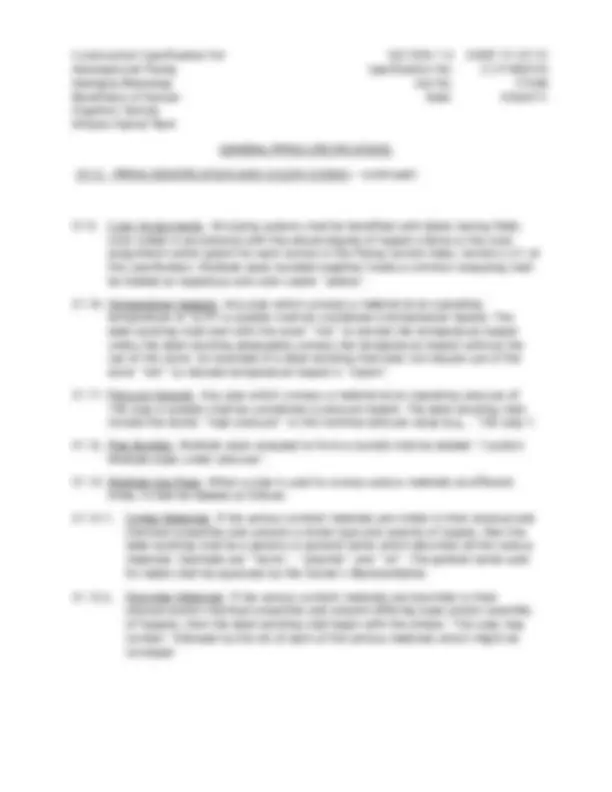

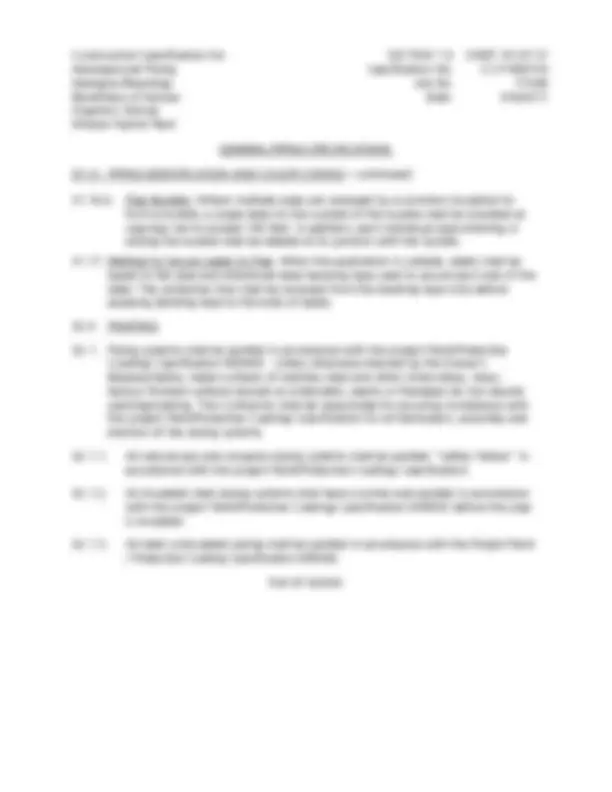
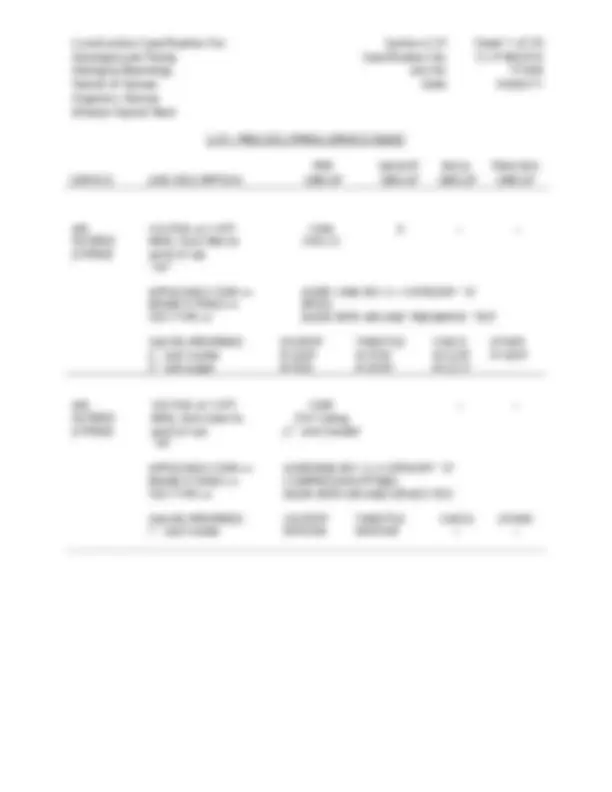
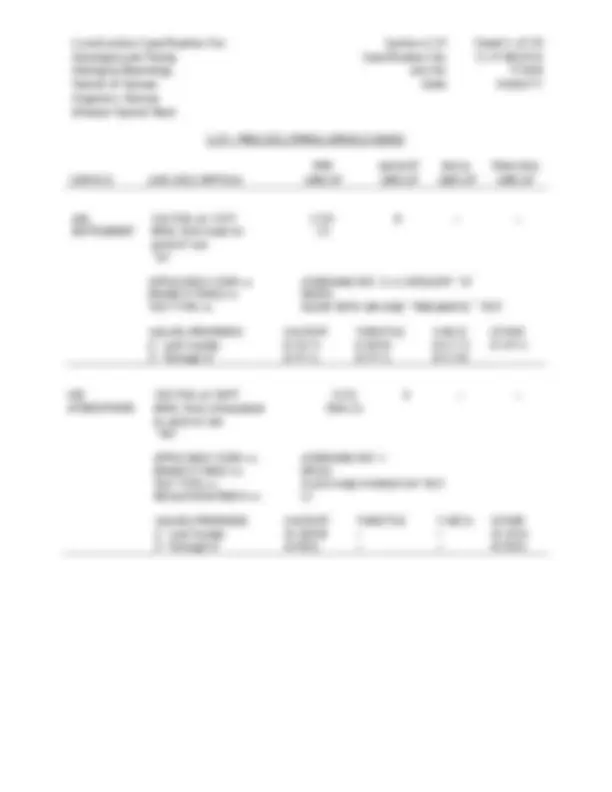
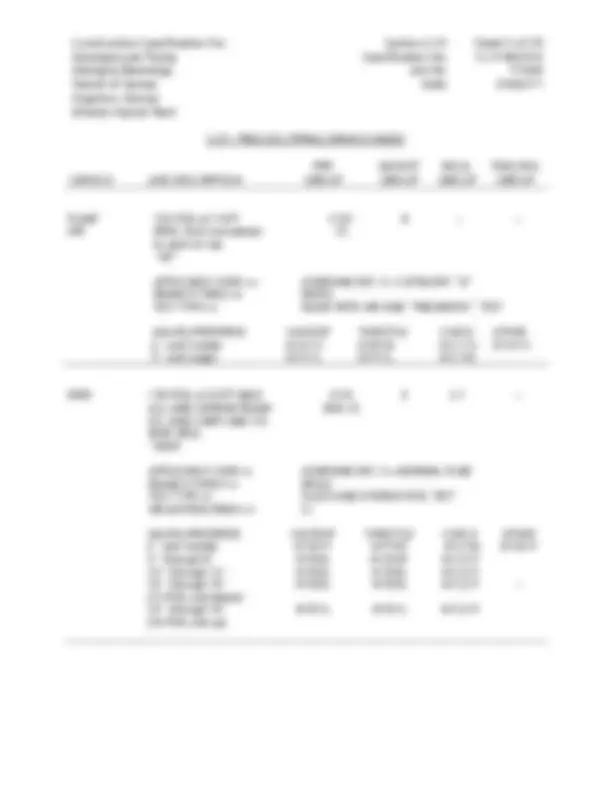
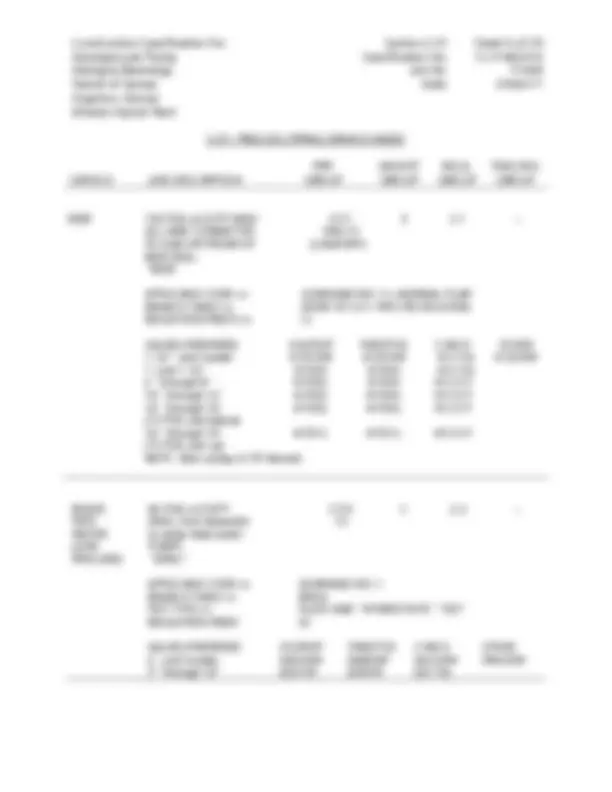
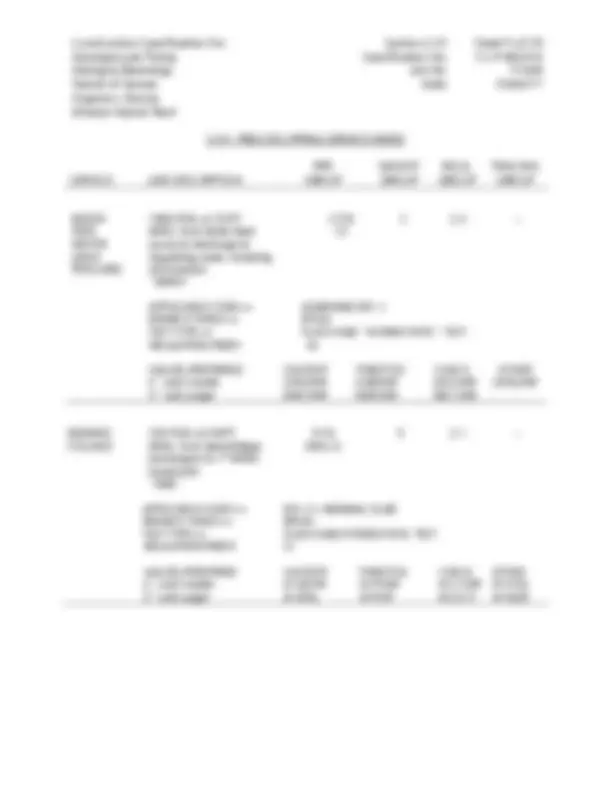
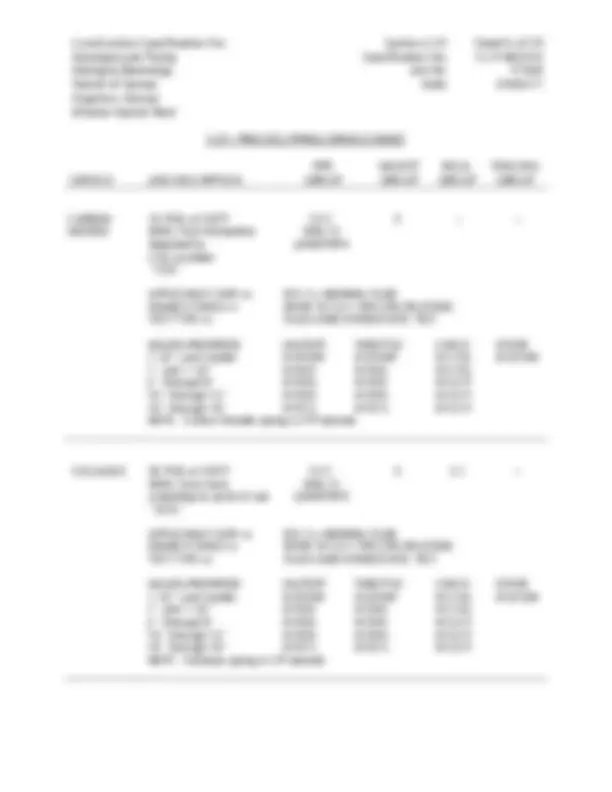
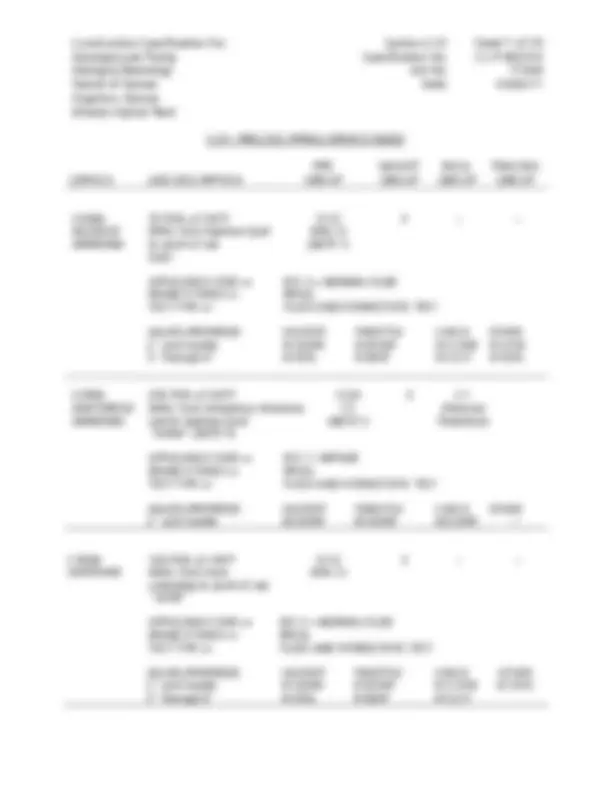
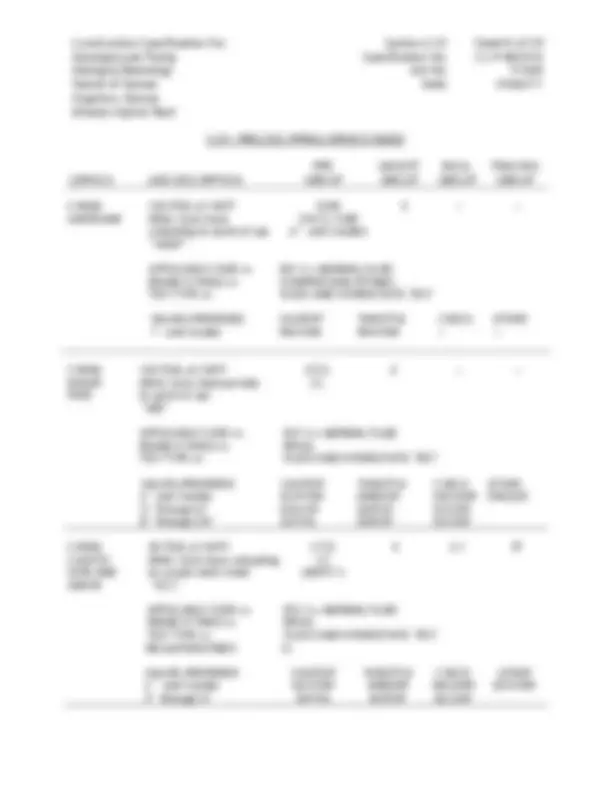
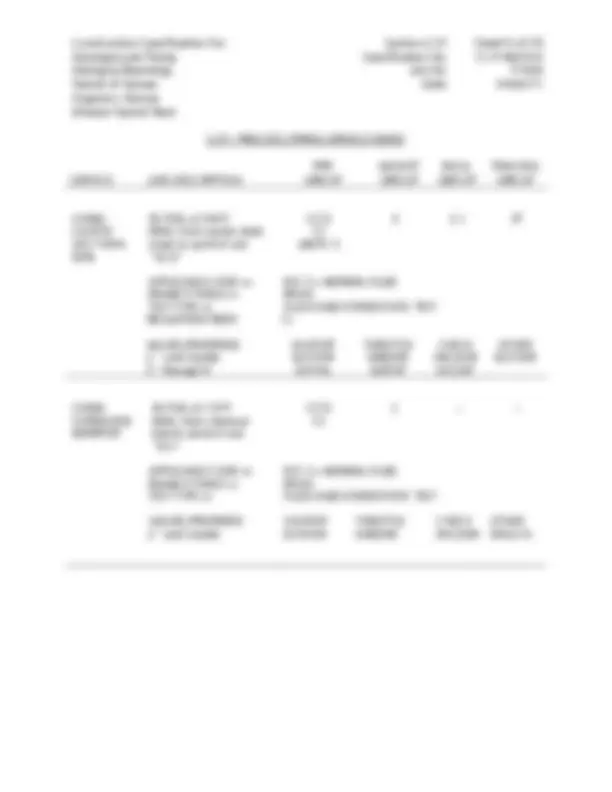
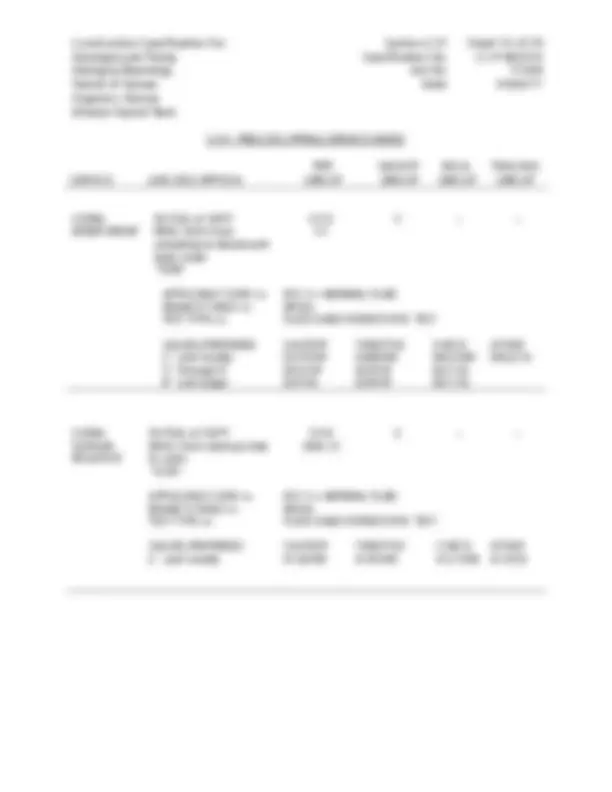
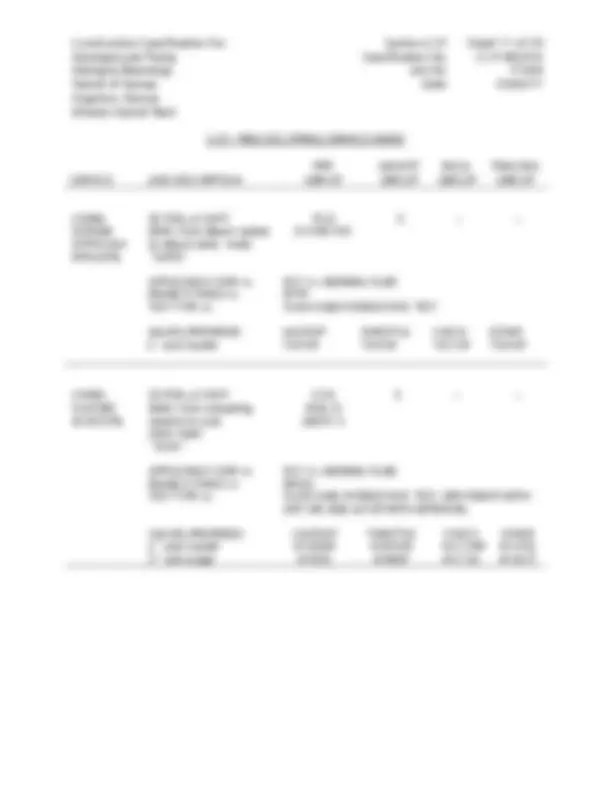
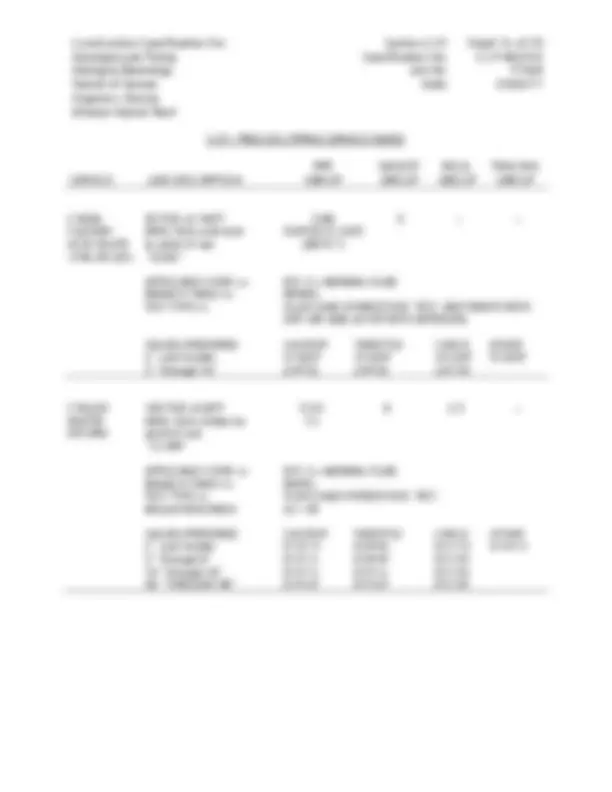
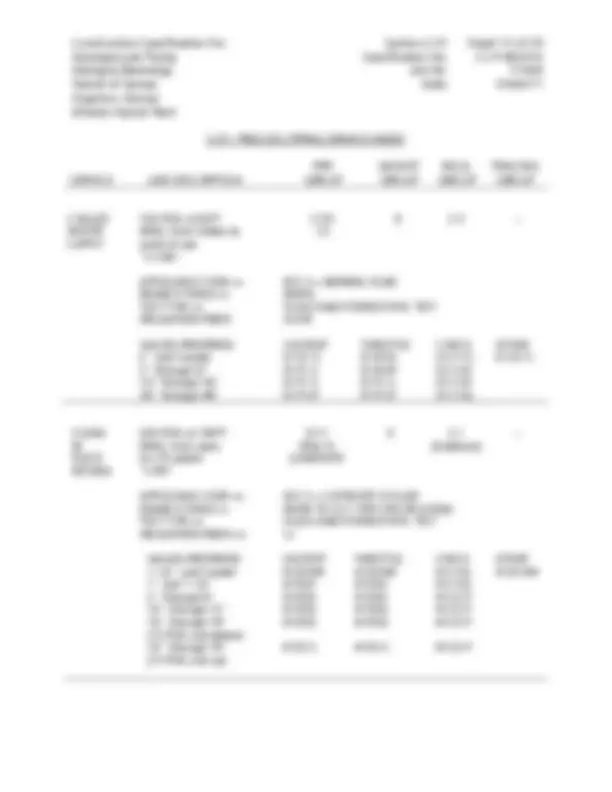
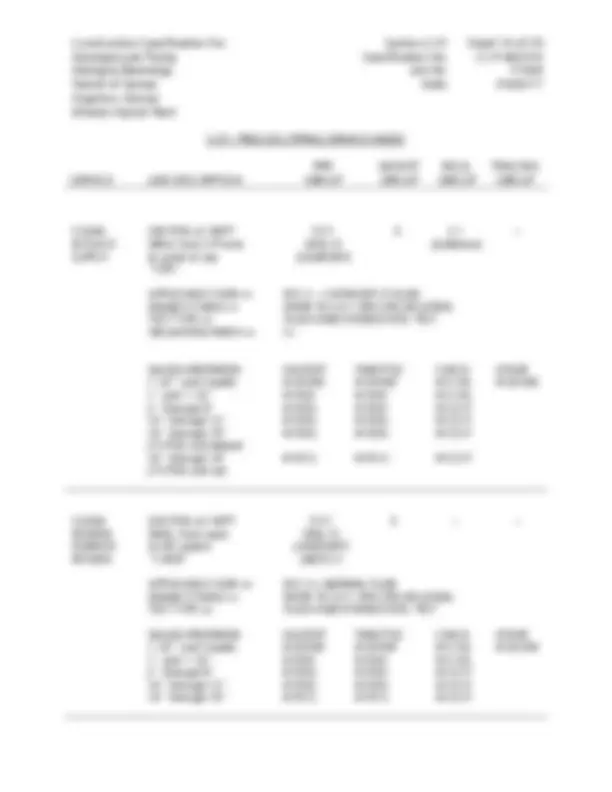
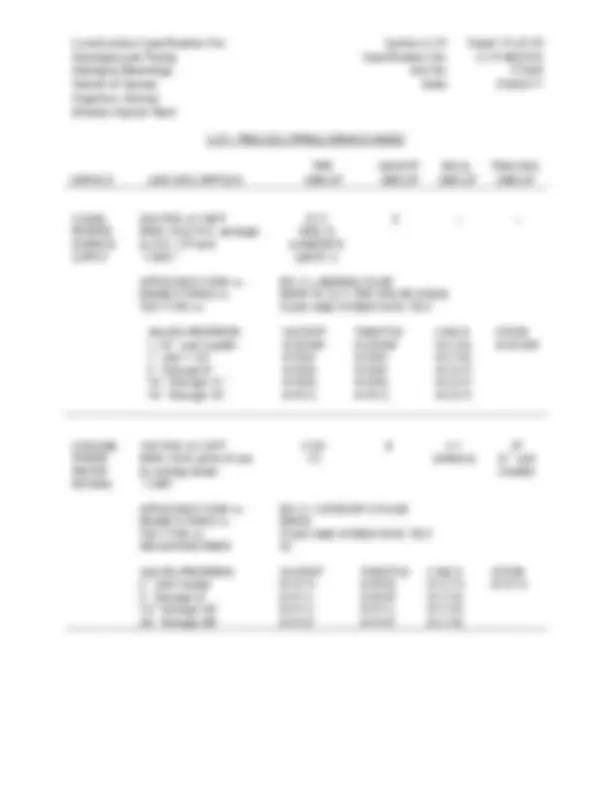
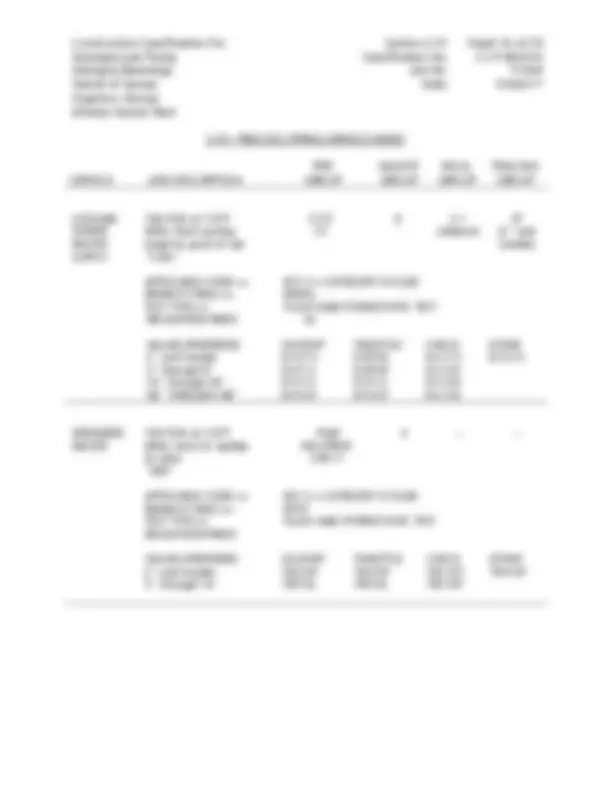
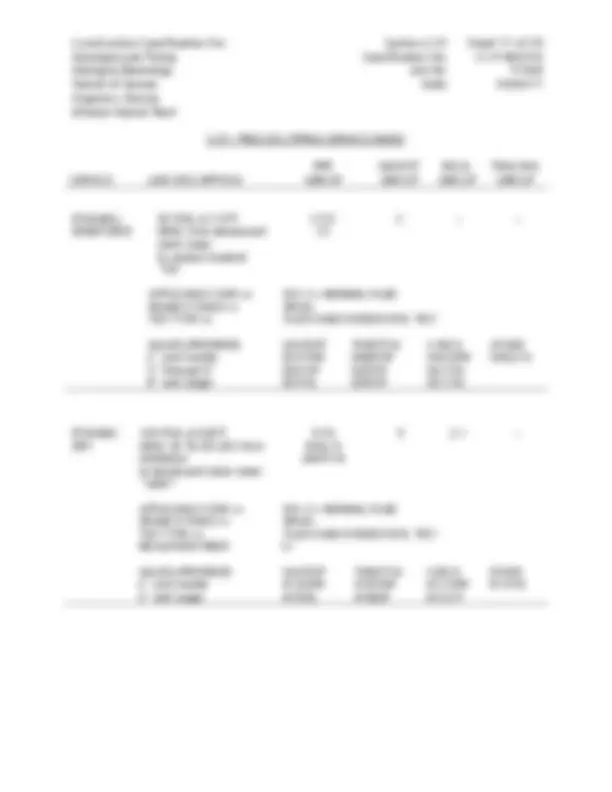
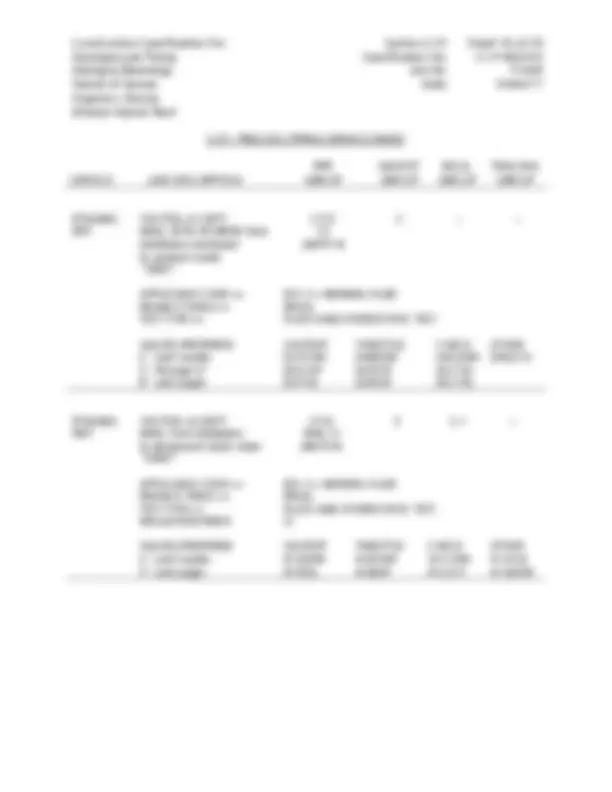
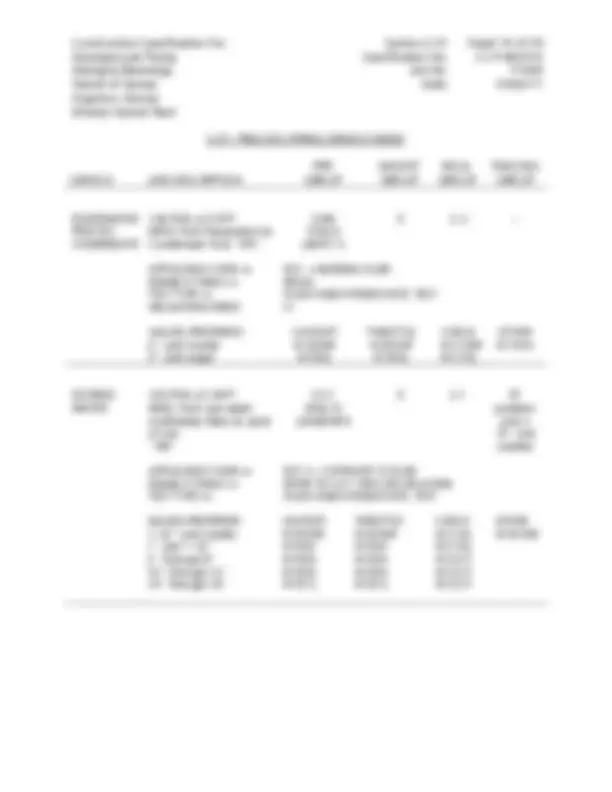
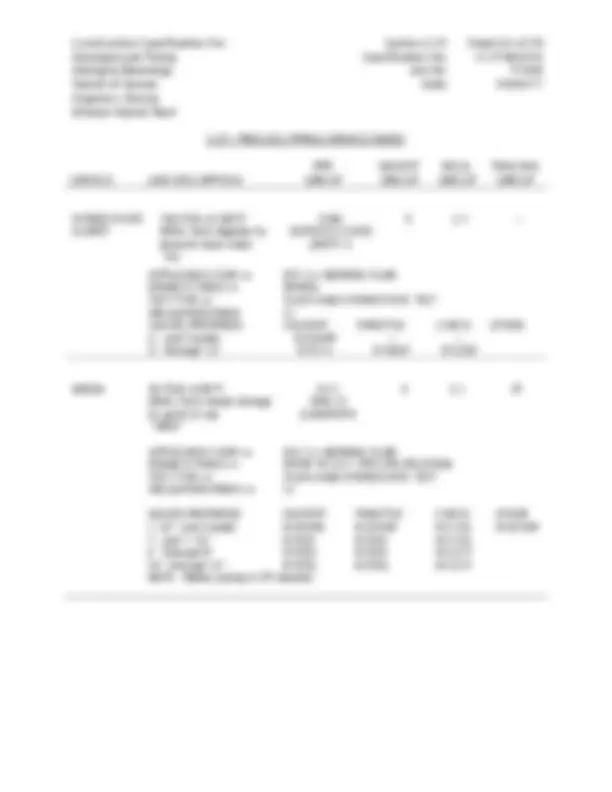
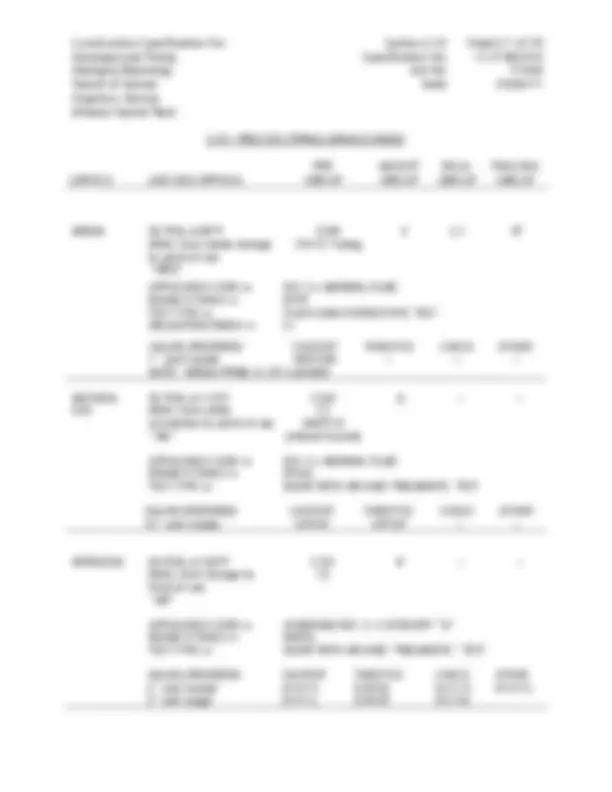
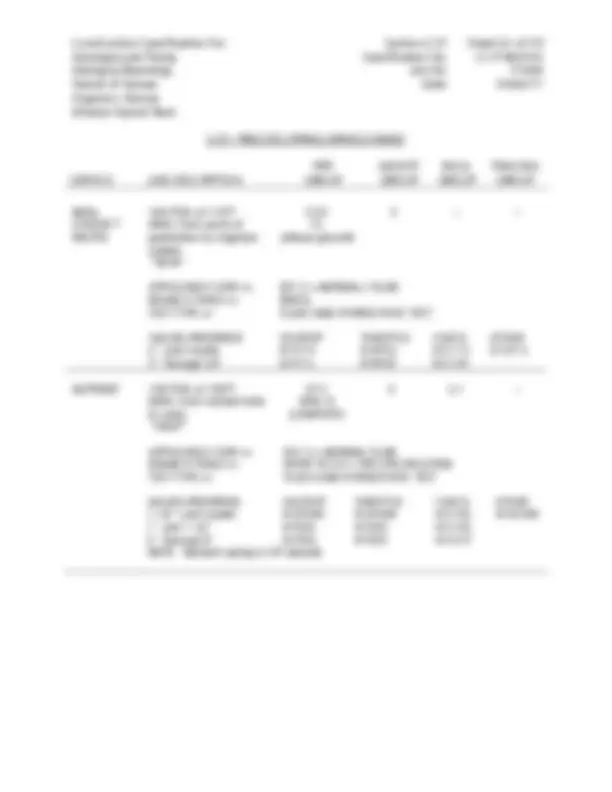
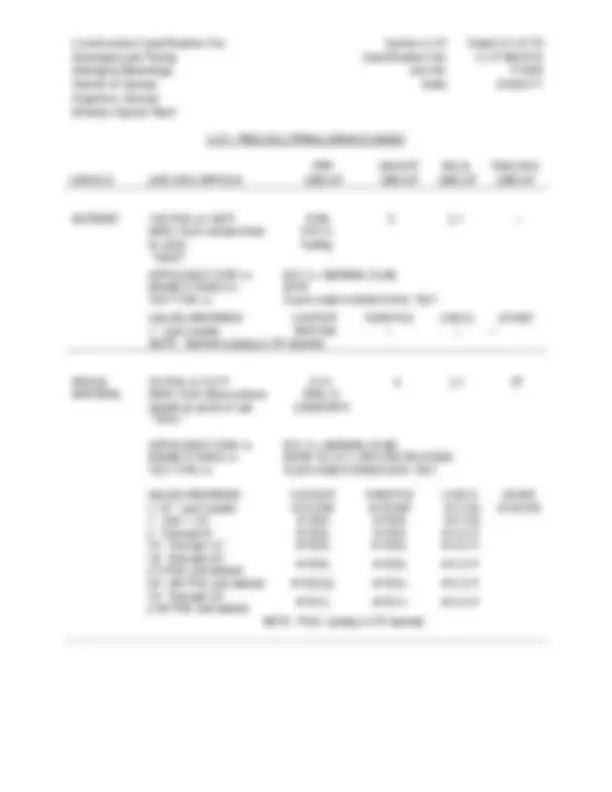
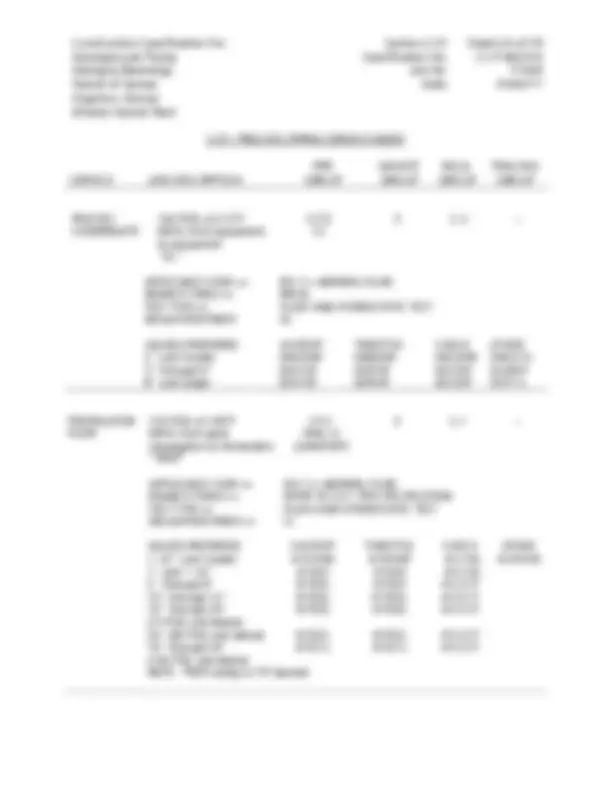
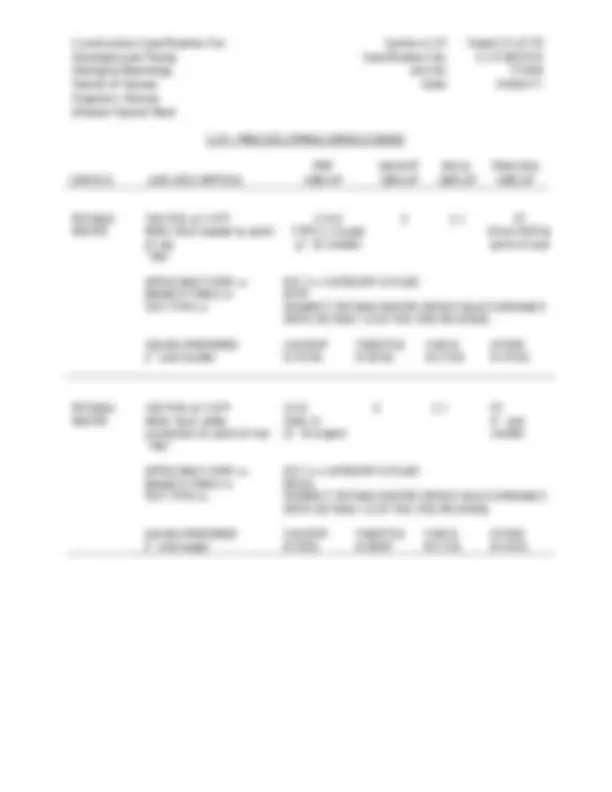
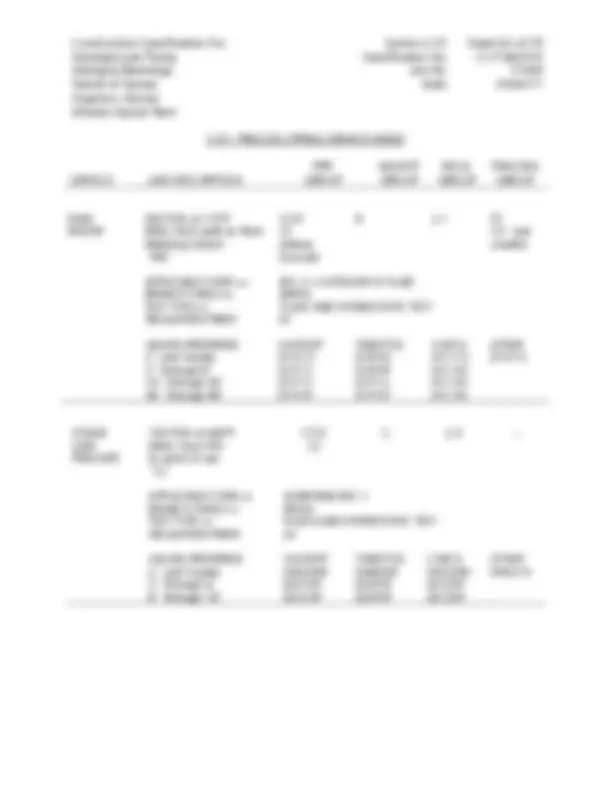
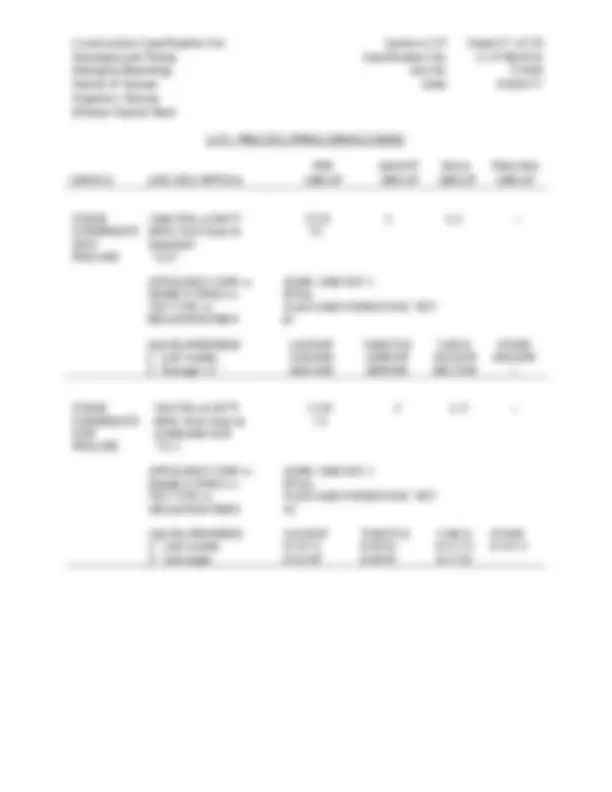
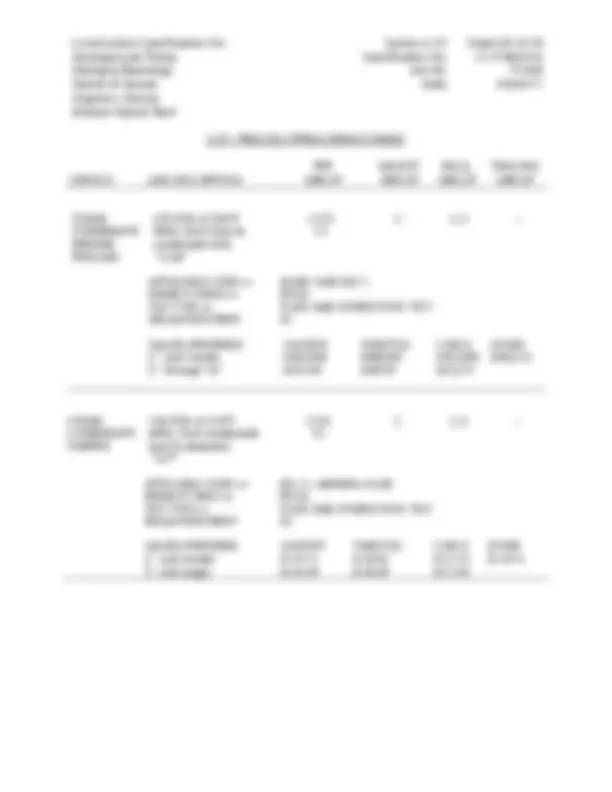
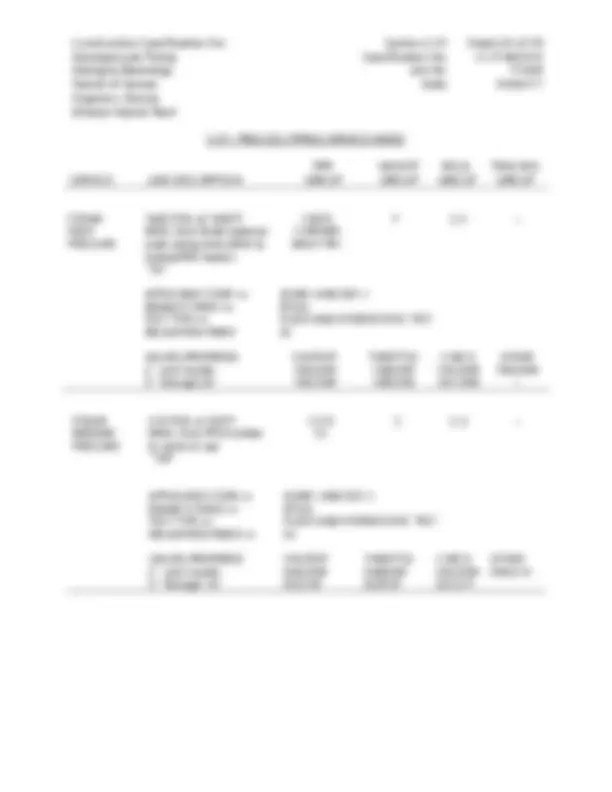
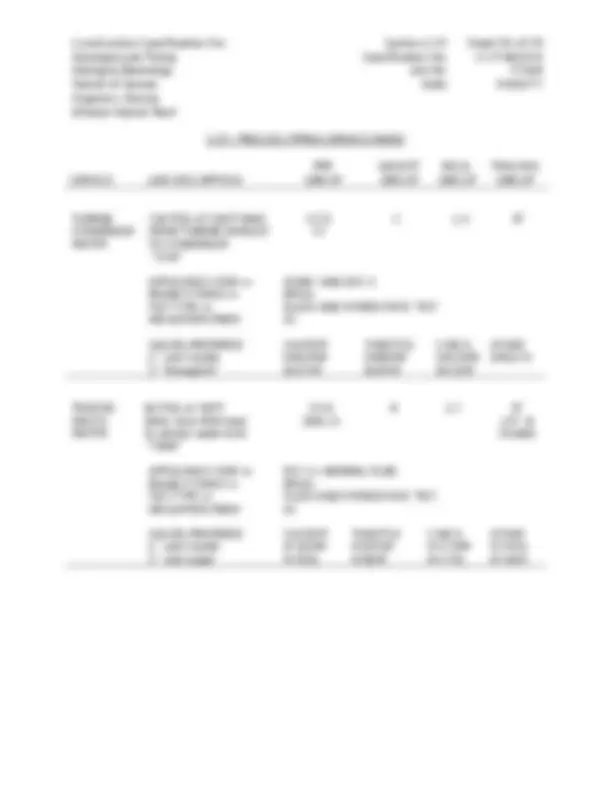
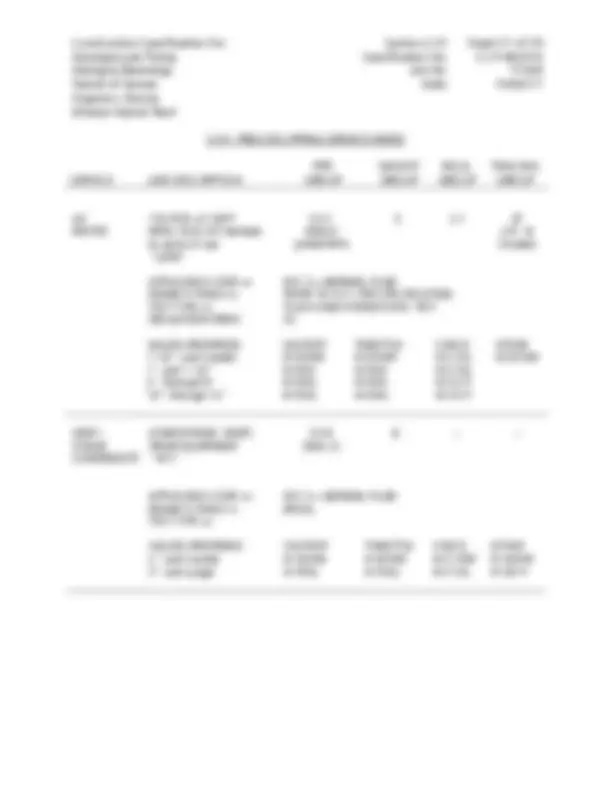
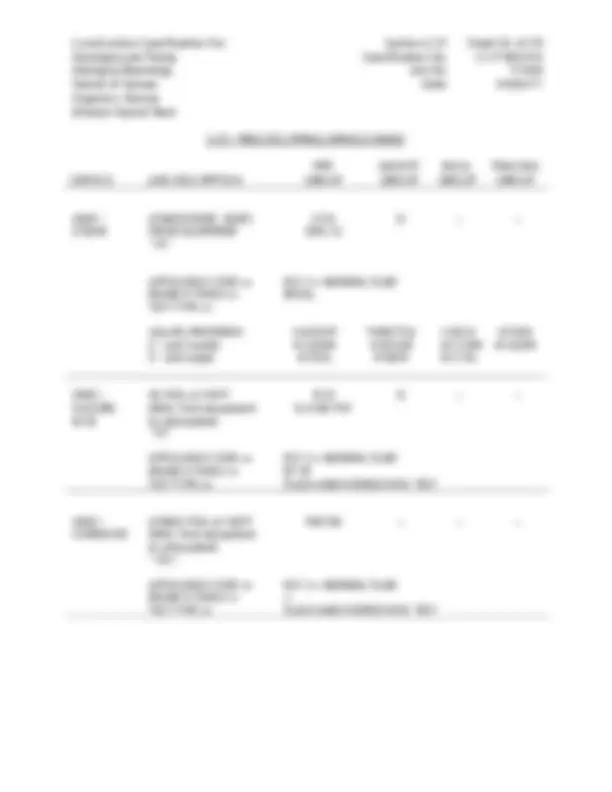
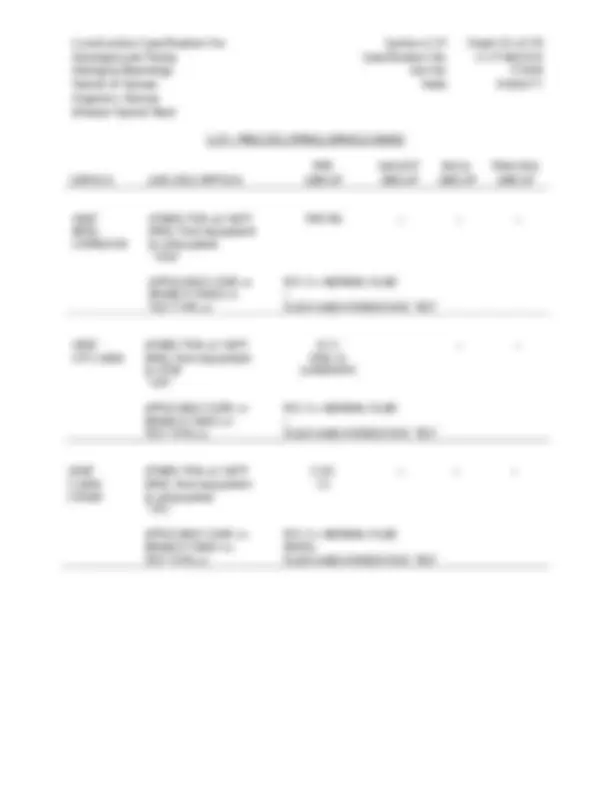
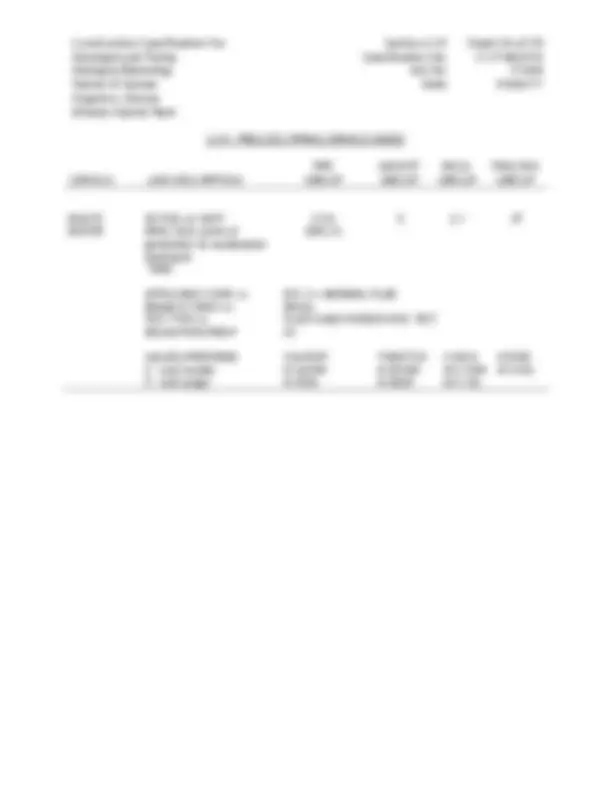
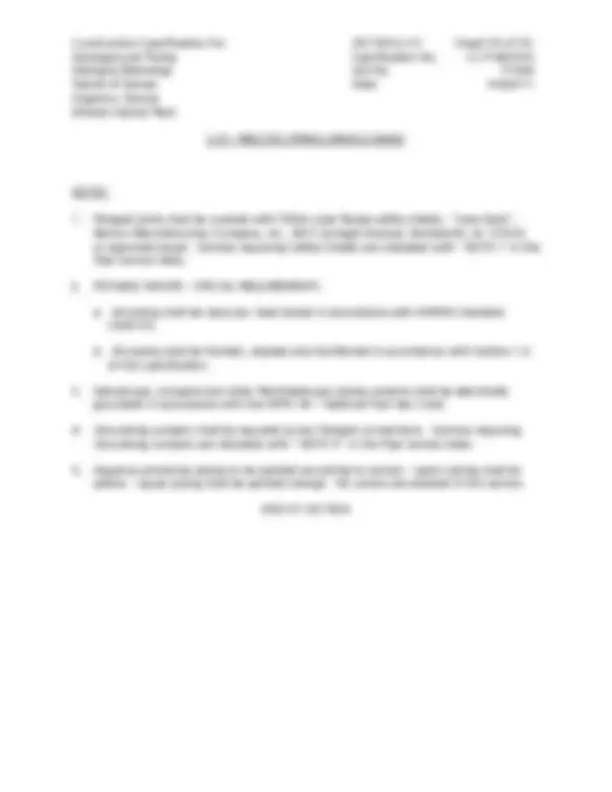
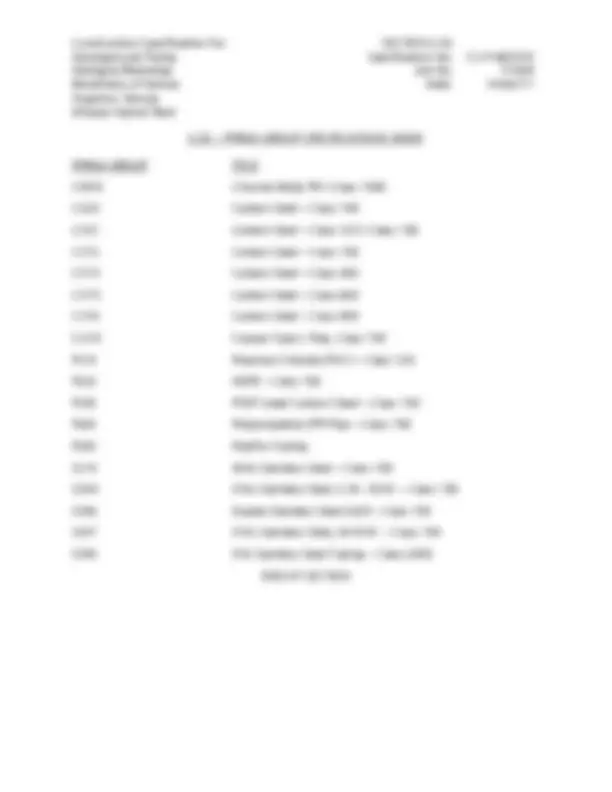
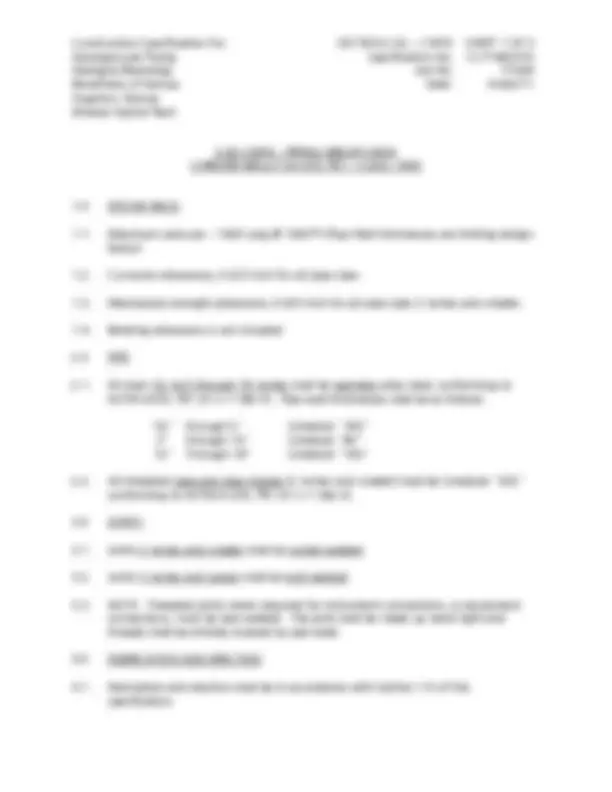
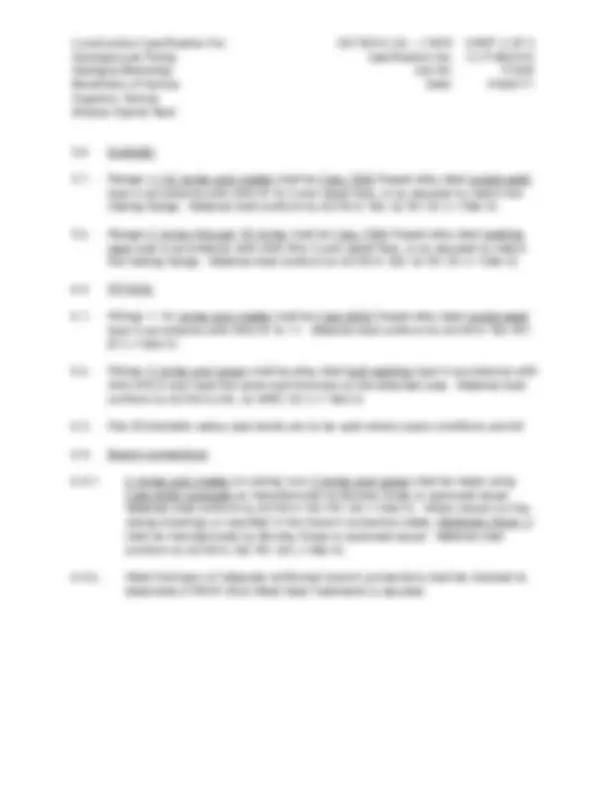
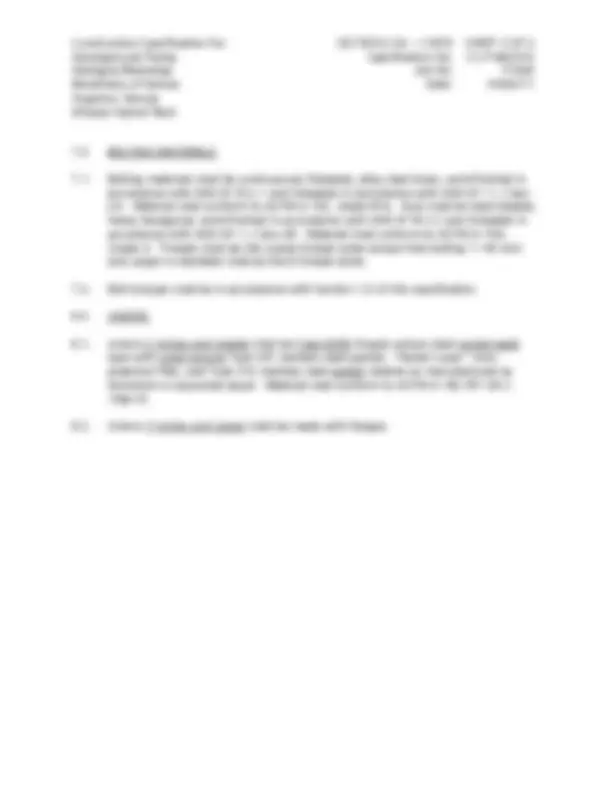
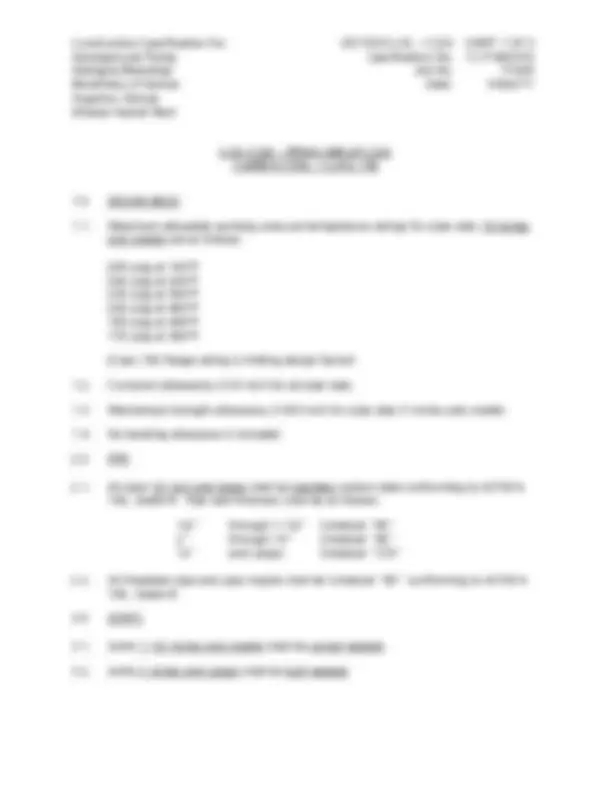
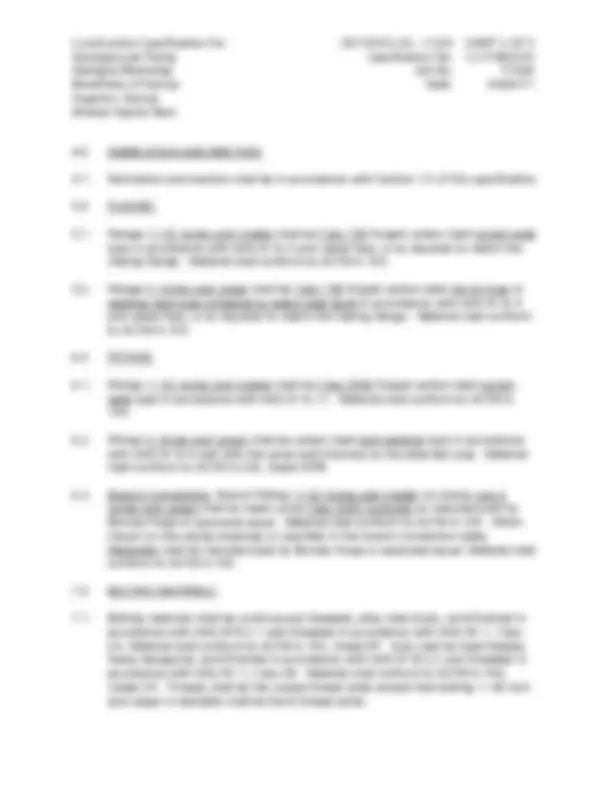
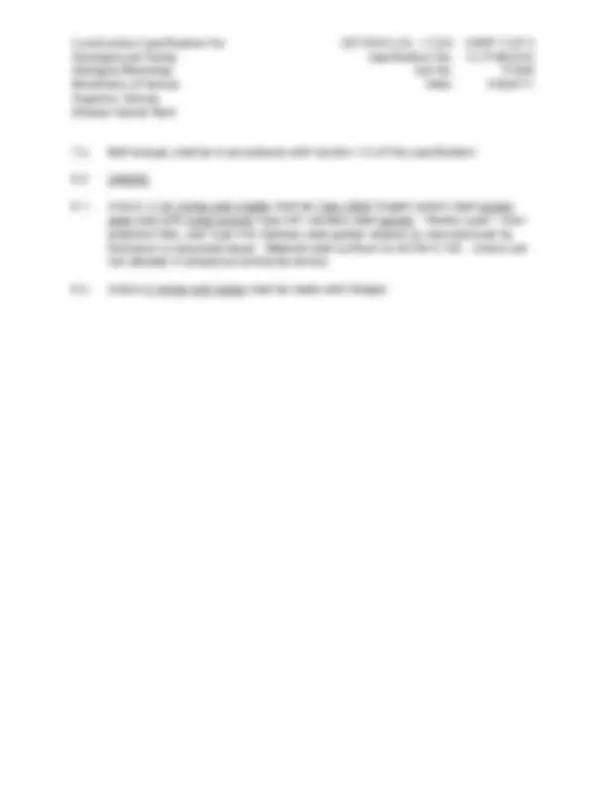
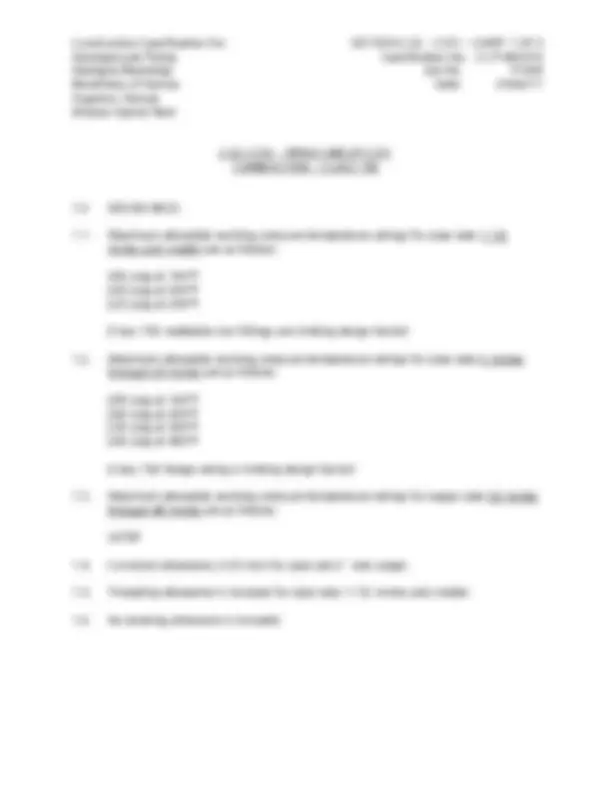
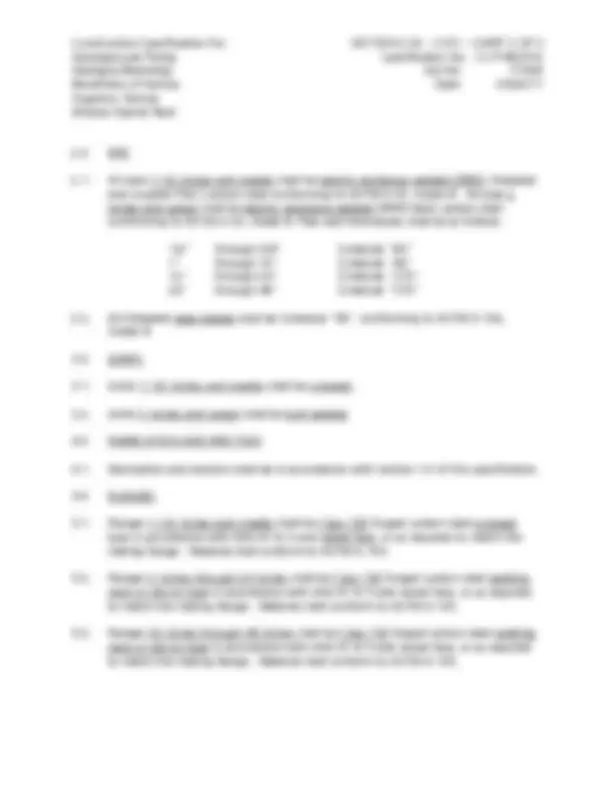
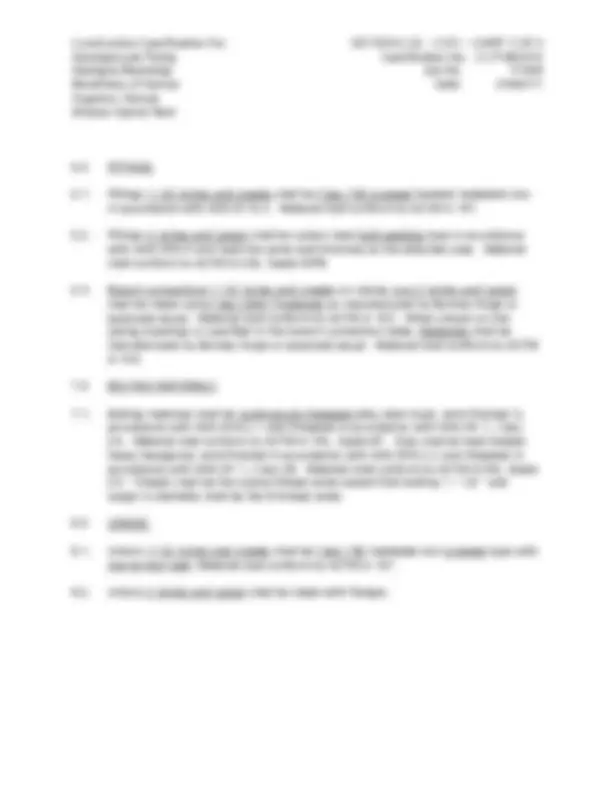
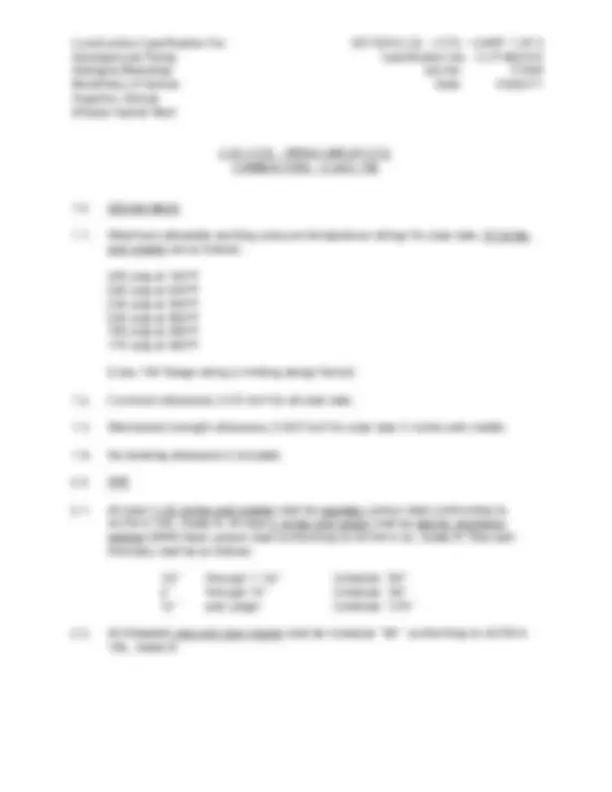
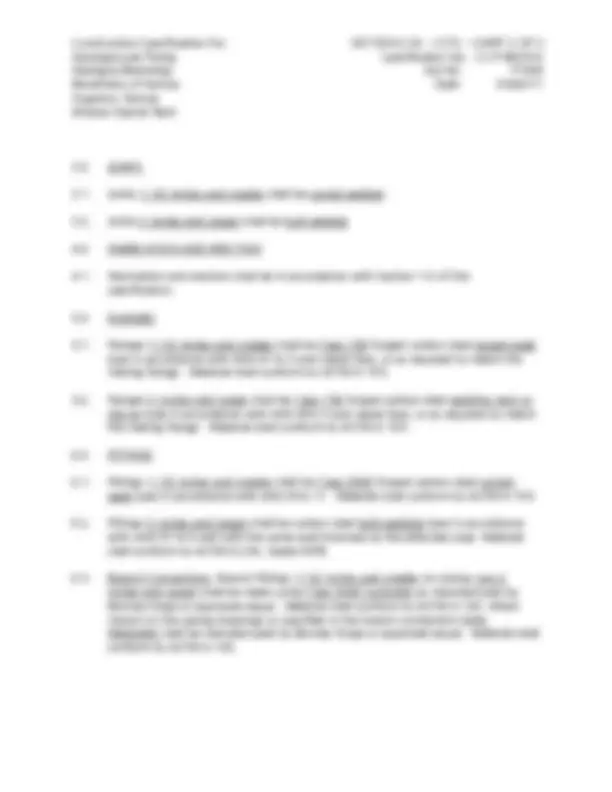
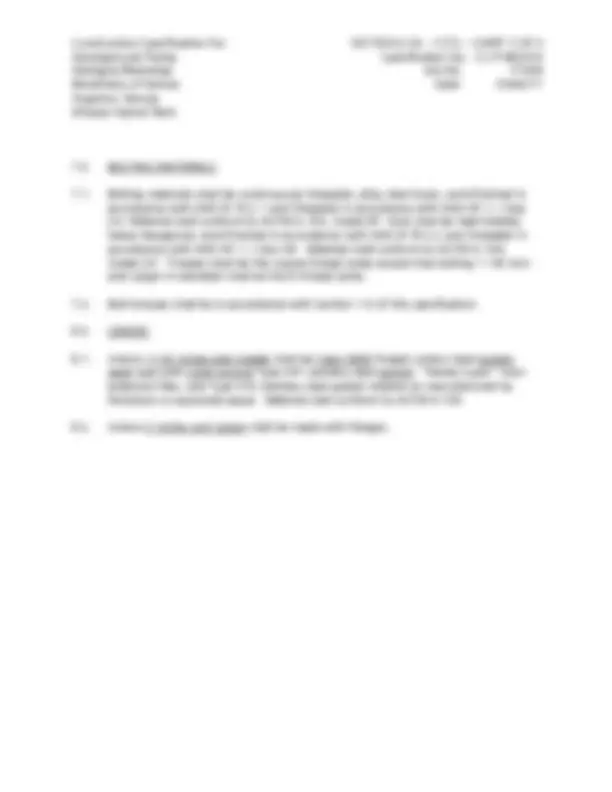
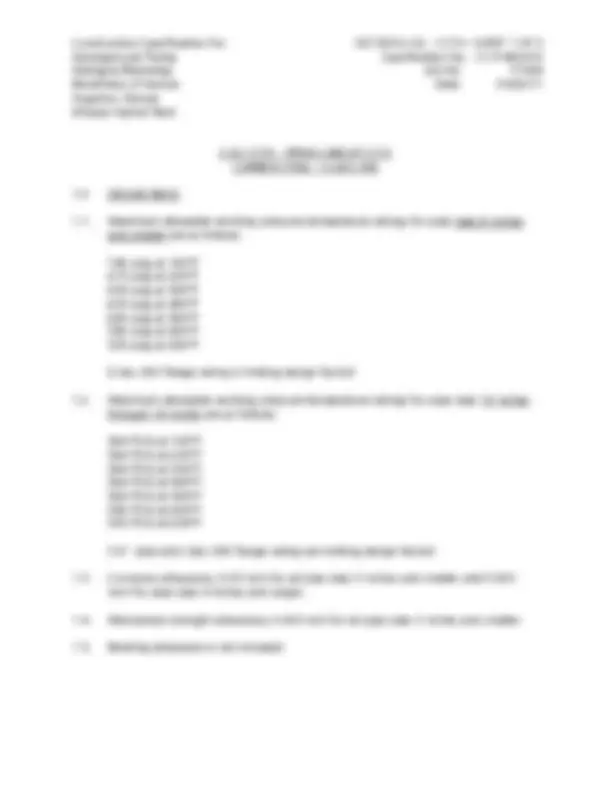
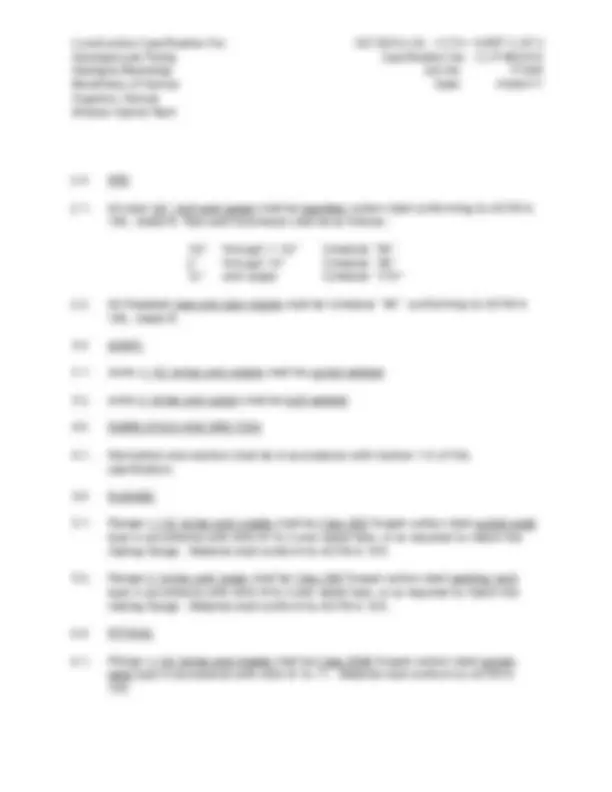
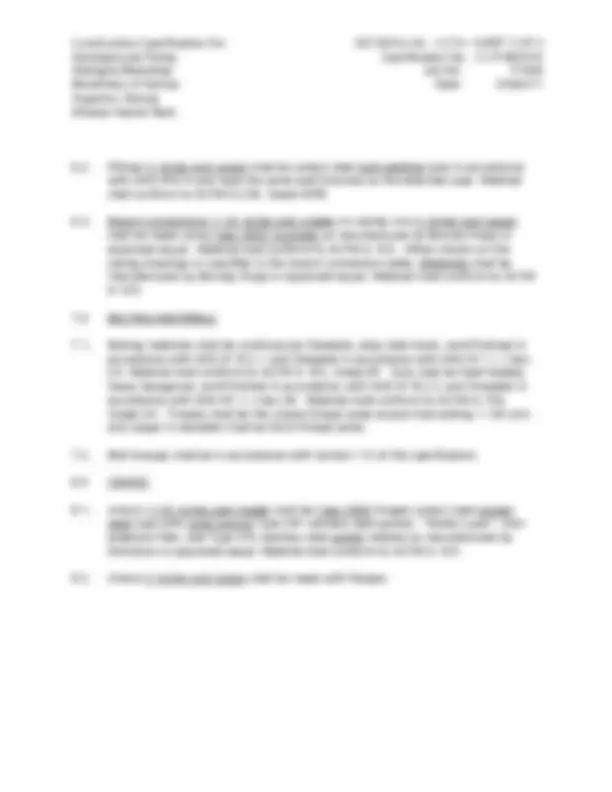
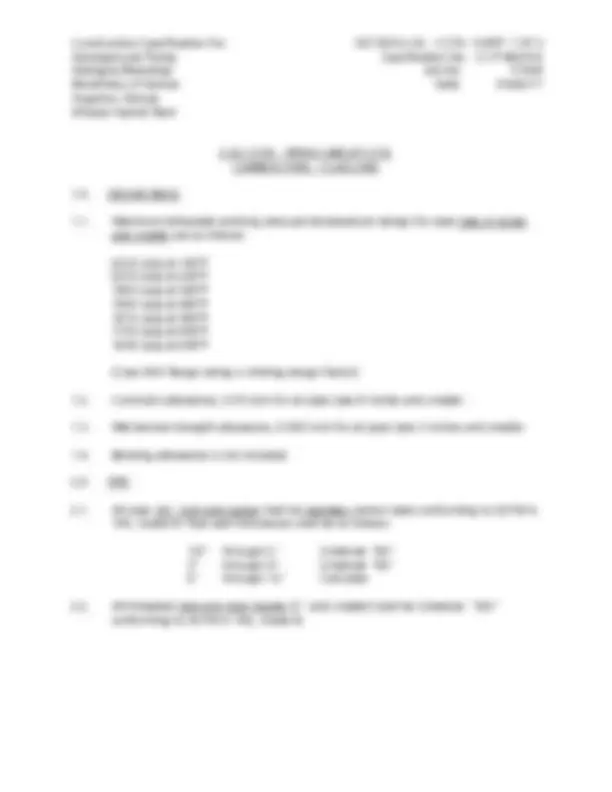
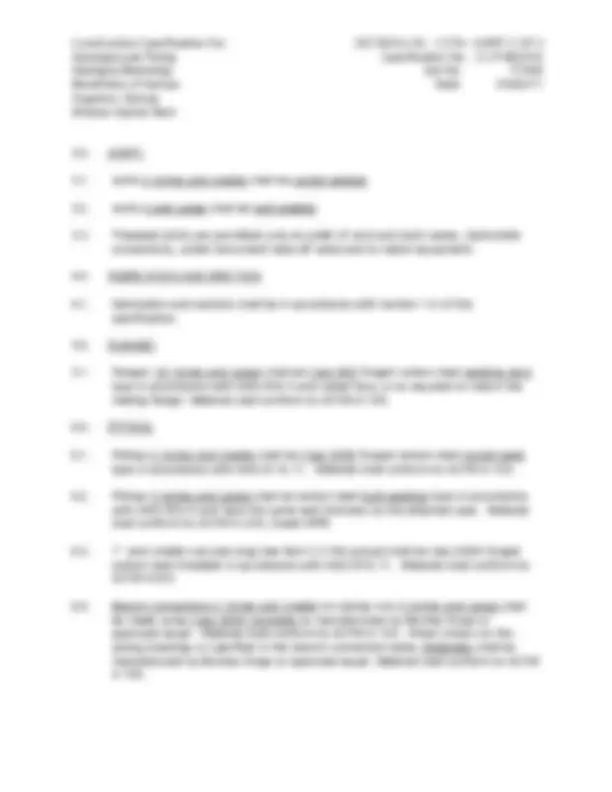
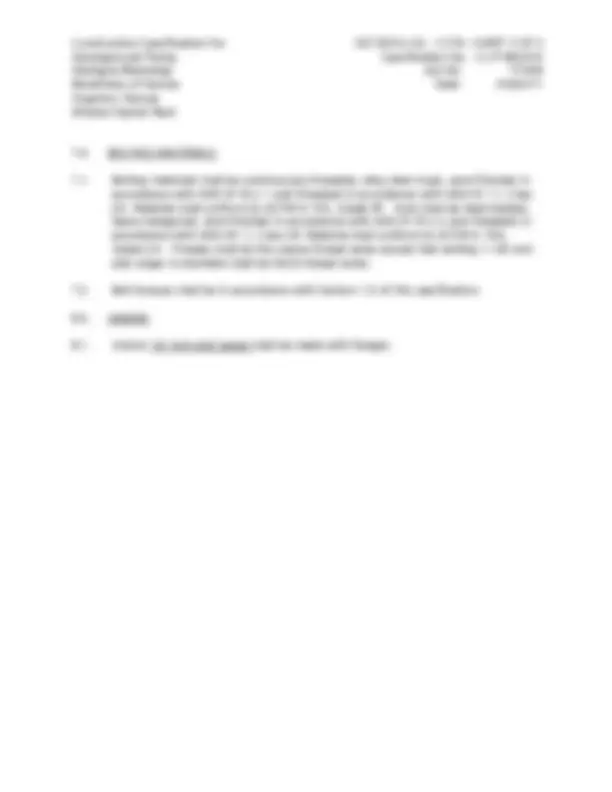
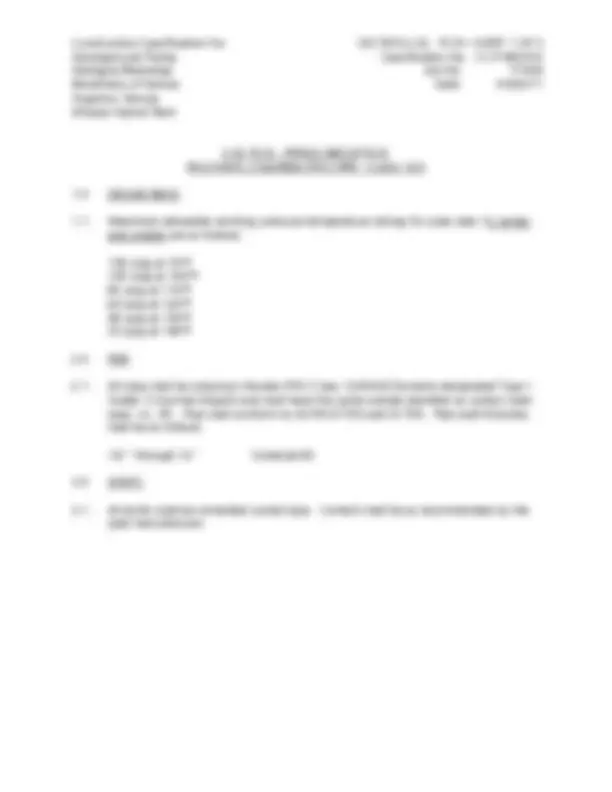
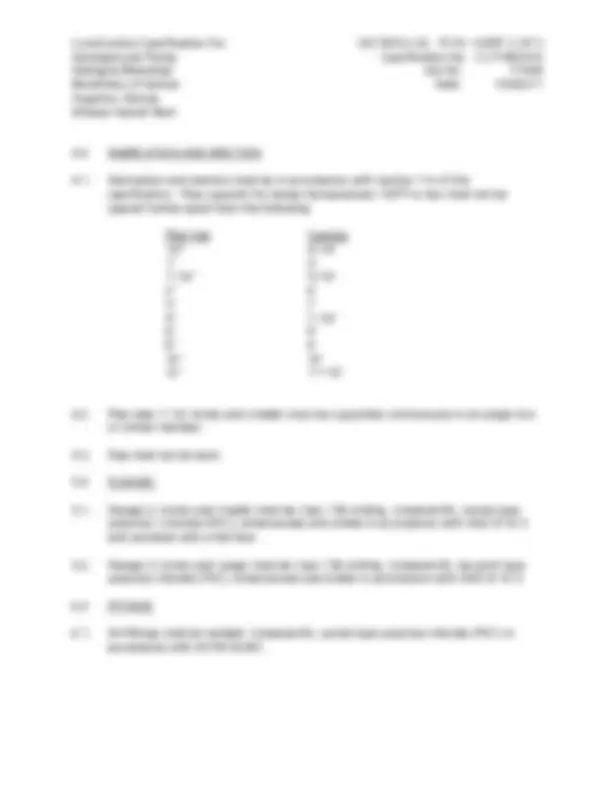
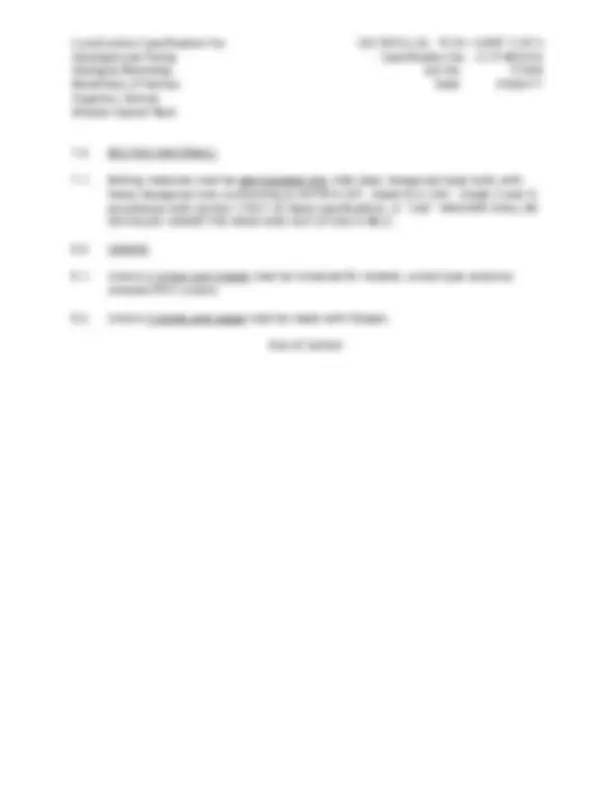
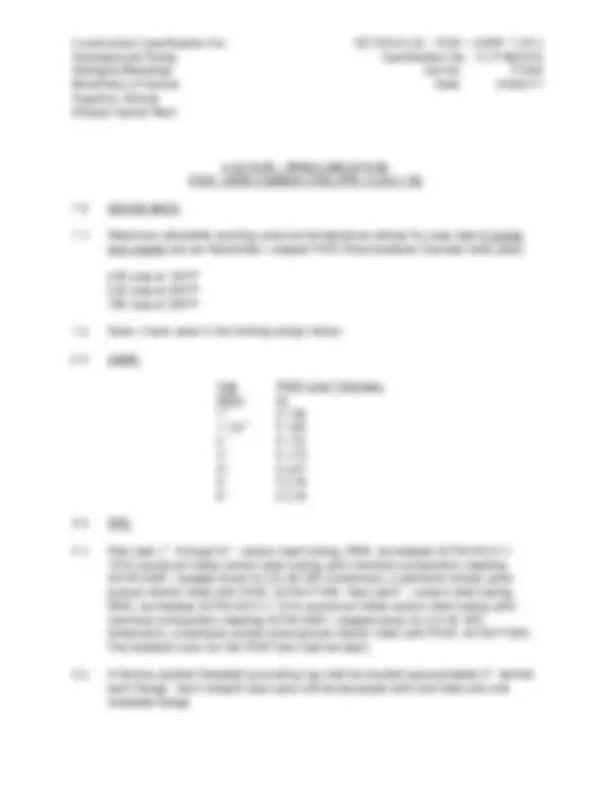
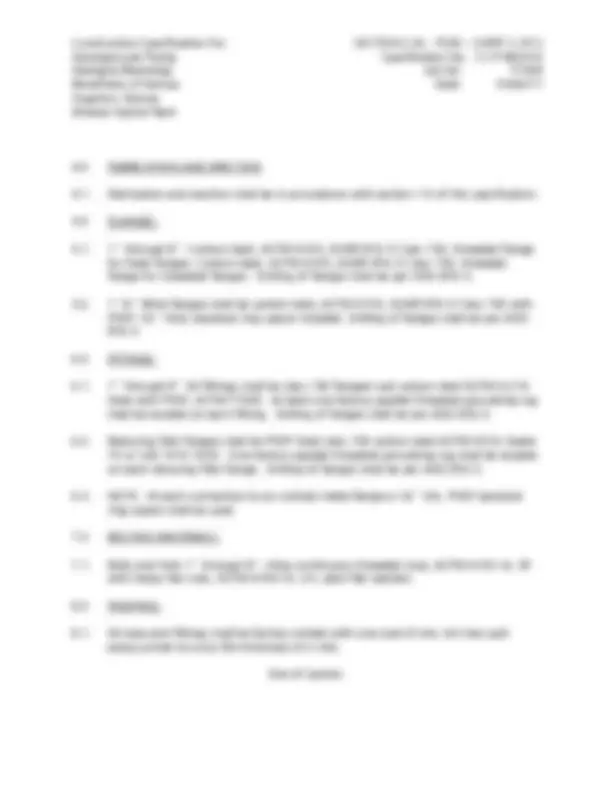
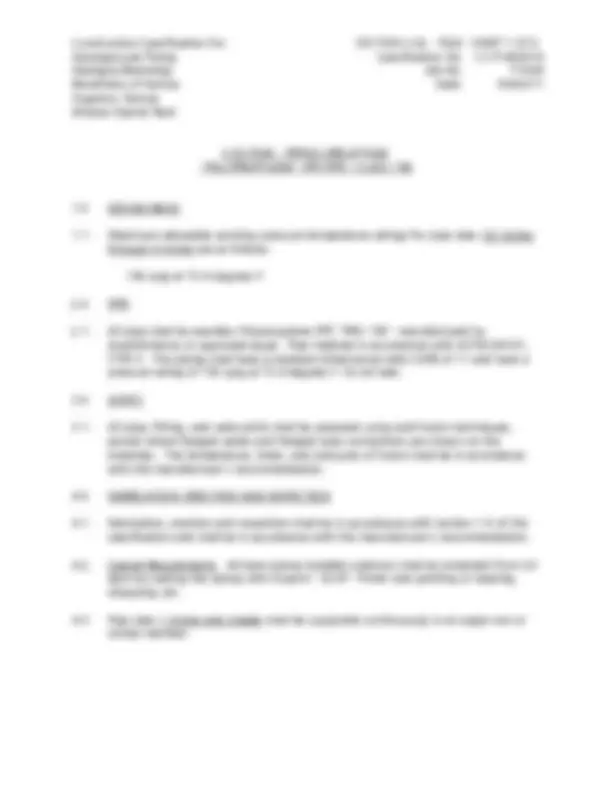
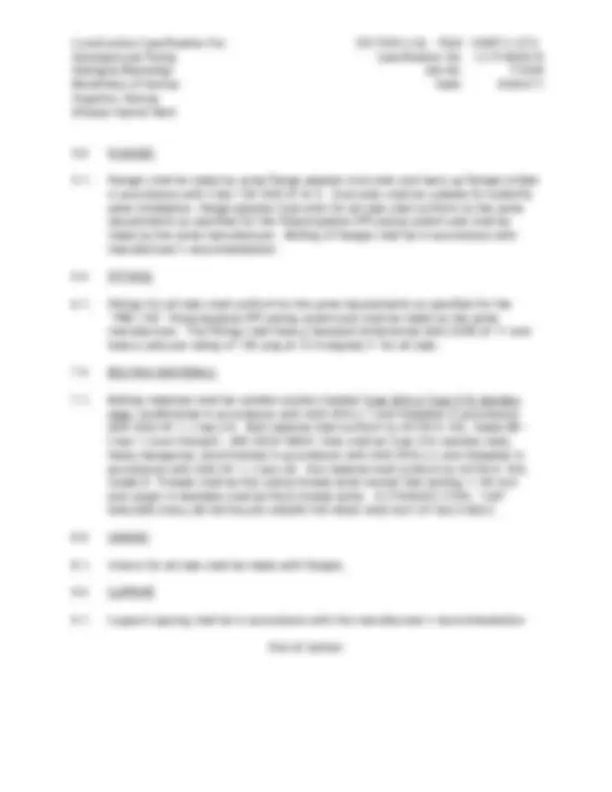
Estude fácil! Tem muito documento disponível na Docsity
Ganhe pontos ajudando outros esrudantes ou compre um plano Premium
Prepare-se para as provas
Estude fácil! Tem muito documento disponível na Docsity
Prepare-se para as provas com trabalhos de outros alunos como você, aqui na Docsity
Os melhores documentos à venda: Trabalhos de alunos formados
Prepare-se com as videoaulas e exercícios resolvidos criados a partir da grade da sua Universidade
Responda perguntas de provas passadas e avalie sua preparação.
Ganhe pontos para baixar
Ganhe pontos ajudando outros esrudantes ou compre um plano Premium
Comunidade
Peça ajuda à comunidade e tire suas dúvidas relacionadas ao estudo
Descubra as melhores universidades em seu país de acordo com os usuários da Docsity
Guias grátis
Baixe gratuitamente nossos guias de estudo, métodos para diminuir a ansiedade, dicas de TCC preparadas pelos professores da Docsity
The construction specifications for aboveground piping in an ethanol hybrid plant. It includes information on pipe materials, pipe sizes, service index, line descriptions, groupings, and applicable codes for various fluid types. The piping system covers a range of fluid pressures and temperatures, from 50 psig at 100ºf to 400 psig at 260ºf. The document also specifies the testing types and preferred valves for each fluid.
Tipologia: Esquemas
1 / 355
Esta página não é visível na pré-visualização
Não perca as partes importantes!
Engineering Standards and Practices Document: 0010 - ESP-ATP- 00 - 61 - G Specification For Above Ground Piping, Piping and Equipment Insulation
Job No.: 0010
Project: ABBK Issue: 1 Date: 16-August/
0 16-August/ No. Date Description By Chk'd App'd App'd Information and know-how hereon are confidential and proprietary property of Abener Teyma Hugoton General Partnership and may not be used, reproduced, or revealed to others except in accordance with the terms of a contract with or other written permission of Abener.
EC-94 (Rev. 05/2011) C:\DOCUME~1\cgjvl\CONFIG~1\Temp\notes29331C\Piping Specification CS-P-400510..doc
Instructions:
Description of Rev. No. Date By Chk’d App’d
Revision Including Page Numbers
0 16-Aug/11 DBA JVL GMC For Bidding
To apply to piping specs where either SO or WN flanges can be chosen:
. Slip-on flanges to ASME B16.5 shall be limited in application to no higher than Class 300 primary pressure service rating. . Slip-on flanges shall not exceed NPS 4. . NDT shall fulfil CODE´s (ASME B31.3 for process, B31.1 for power plant piping) and particular Project´s scope requirements, scope and extent, whichever is more stringent, considering that inside slip-on flange welds are not accesible to RT it shall be replaced by visual, magnetic or liquids, whenever is accepted by CODE and Project´s specs. If not within these conditions flange to use shall be WN.
Rev. Date Description Pages Originated Checked Reviewed Approved
A 08/31/09 ISSUED FOR INFORMATION ALL JSS TDF DCG DCG
B 01/14/10 ANNEX 1 ABBK TECHNICAL SOW ALL JSS DO DCG DCG
C 07/23/
ISSUED FOR INFORMATION HIGH PRESSURE STEAM AND BOILER FEED WATER SPECIFICATIONS
D 08/31/10 ISSUED FOR BASIC ENGINEERING ALL JSS HS DO DCG
E 02/25/11 ISSUED FOR DESIGN25 MGPY EH PLANT ALL JSS HS DO DCG
F 04/08/11 ISSUED FOR DESIGN25 MGPY EH PLANT ALL JSS HS DO DCG
G 05/26/11 ISSUED FOR DESIGN25 MGPY EH PLANT ALL JSS HS DO DCG
Construction Specification For 1.0 SHEET 1 OF 3 Aboveground Piping s Specification No. CS-P- Abengoa Bioenergy Job No. Y Biorefinery of Kansas Date: 05/26/ Hugoton, Kansas Ethanol Hybrid Plant
SECTION 1. GENERAL PIPING SPECIFICATIONS
TABLE OF CONTENTS
PARAGRAPH ITEM PAGE
1.0 GENERAL 1
2.0 WELDING 2
2.1 Submittal 2
2.2 General Requirements and Qualification of Welding Procedure and Welders
2.3 Welding Processes 2
2.4 Welding Grooves 3
2.5 Backing Rings 3
2.6 Cleaning of Welding 3
2.7 Preheating of Welded Joints 3
2.8 Weld Quality 4
2.9 Identification of Welders 4
2.10 Weld Examination 5
3.0 BRAZING 6
4.0 SOLDERING 7
5.0 PVC/CPVC SOLVENT CEMENTING 7
6.0 HDPE / POLYPROPYLENE / PDVF / HEAT FUSION 9
7.0 FLANGED CONNECTIONS 9
15.0 IDENTIFICATION, STORAGE, AND HANDLING OF PIPING MATERIAL AND VALVES
Aboveground Piping Specification No. CS-P- Abengoa Bioenergy Job No. Y Biorefinery of Kansas Date: 05/26/ Hugoton, Kansas Ethanol Hybrid Plant
GENERAL PIPING SPECIFICATIONS
1.0 GENERAL
1.1. The General Conditions of the Contract and the Special Conditions of the Contract shall apply to all sections of the work. The design, fabrication and erection of piping shall conform to the applicable codes given for each service in the Piping Service Index, Section 2.01 of this specification, and to all applicable Federal, State and Local laws. The Contractor shall obtain all necessary certification, permits and approvals required by Federal, State and Local laws before fabrication and erection of any piping systems.
1.2. ORIGIN OF MANUFACTURED EQUIPMENT & MATERIALS
1.2.1. All equipment furnished for Abengoa Bioenergy Biofuel of Kansas (ABBK) Project is required to be manufactured by a company or corporation in the USA.
1.2.2. All materials used to fabricate and/or manufacture equipment are required to be of USA origin.
1.2.3. In the event A&B can’t be accomplished for either proprietary, process specific, or other types of equipment or materials, the following order of precedence will apply.
1.2.3.1. Equipment or materials furnished by a company or corporation in the USA noted in all proposals.
1.2.3.2. Equipment or materials furnished by a USA company or corporation with manufacturing facilities in other countries noted in all proposals.
1.2.3.3. In the event items 1 or 2 can’t be accomplished then any vendor proposals submitted for evaluation will require statements defining where the equipment is manufactured and what percentage of the materials will be used from each foreign country.
1.3. When ASME/ANSI B3 1.1 is referenced in this Section and other sections of this specification, it shall govern. It is the intent of this specification to be more conservative in specification requirements when ASME/ANSI B3 1.1 is specifically referenced.
1.4. Several piping services with different design conditions may reference a Piping Group. The actual design conditions of an individual piping system shall be used in determining requirements of design, examination, inspection, testing, etc.
Aboveground Piping Specification No. CS-P- Abengoa Bioenergy Job No. Y Biorefinery of Kansas Date: 05/26/ Hugoton, Kansas Ethanol Hybrid Plant
GENERAL PIPING SPECIFICATIONS
1.5. QA/QC Program Submittal. The Contractor shall submit a written QA/QC program to the Owner's Representative for approval prior to starting any fabrication or erection. This QA/QC program shall meet the requirements of ASME/ANSI B31.1, Paragraph 136. The Contractor shall be responsible for assuring compliance with the approved QA/QC program for all fabrication, assembly, erection, examination, inspection and testing.
2.0 WELDING
2.1. Submittal. After the contract is awarded, the Contractor shall submit one (1) copy of his welding procedure to the Owner's Representative for information. The welding process(es) shall be fully described including the number of beads, the volts, the amperes, and the welding rod for various pipe thicknesses and materials. This procedure shall be used for all pipe welder qualification tests, all shop welds, and all field welds.
2.2. General Requirements and Qualification of Welding Procedure and Welders.
2.2.1. All welding on metal piping systems shall be done using qualified welding procedures and qualified welders and welding operators in accordance with Section IX of the ASME Boiler and Pressure Vessel Code.
2.2.2. Joining of plastic piping systems, Smith Fiberglass, Fibercast, Bondstrand, PVC, CPVC, HDPE, PVDF, Polypropylene (PP), etc., shall be done in accordance with manufacturer's recommended procedures. Joining of custom manufactured plastic piping shall be done in accordance with procedures specified in the specific piping group. Joining of custom manufactured plastic pipe shall be done using certified personnel. The Contractor shall use these procedures to certify personnel and in making all joints. Certification of personnel shall be in accordance with part 9 of Chapter VII of ASME/ANSI B31.3.
2.3. Welding Processes.
2.3.1. All welding shall be done by a process that is compatible with the work being welded and the working conditions. Shielded metal-arc welding (SMAW) shall not be used on work less than 3/16 inch thick.
2.3.2. Where a specific welding process is called for in the Piping Group specification, it shall govern.
Aboveground Piping Specification No. CS-P- Abengoa Bioenergy Job No. Y Biorefinery of Kansas Date: 05/26/ Hugoton, Kansas Ethanol Hybrid Plant
GENERAL PIPING SPECIFICATIONS
(2.0 - WELDING – continued)
2.6.4. The exterior of all shop fabricated stainless steel welded joints shall be cleaned with "Derustit SS-3" by the Bradford Derustit Corporation, in accordance with the manufacturer's specifications. Any rust that occurs on stainless steel shop or field welded joints prior to final acceptance of the piping system by the Owner shall be cleaned with "Derustit SS-3" by contractor.
2.7. Preheating of Welded Joints:
2.7.1. Pipe adjacent to joints shall be preheated before and during welding by any suitable method in accordance with the qualified welding procedure and in all cases shall be in accordance with ASME/ANSI B31.1, Paragraph 131 or ASME/ANSI B31.3, Paragraph 330 as applicable.
2.8. Weld Quality.
2.8.1. All welds shall have full penetration and complete fusion with a minimum of weld metal protruding on the inside of the pipe when examined by the applicable method of nondestructive testing as identified by the applicable code. If welds are found to be deficient in accordance with the applicable code, the Contractor shall be responsible for all costs associated with the repair of the weld(s).
2.8.2. All welds shall be of sound deposit with a straight line of fusion.
2.8.3. The finished weld contour shall be uniform, with the toe or edge of the weld merging smoothly into the base material. Butt welds shall have a slight reinforcement built up gradually from the toe or edge toward the center of the weld. The limitation on butt weld reinforcement shall be in accordance with ASME/ANSI B31.1, Table 127.4.2, and shall apply separately to both inside and outside surfaces of this joint. Fillet welds may be slightly concave on the finished surface.
2.8.4. Where filler metal is required a rod whose composition is compatible with and of at least equal corrosion resistance characteristics as the base material shall be used.
Aboveground Piping Specification No. CS-P- Abengoa Bioenergy Job No. Y Biorefinery of Kansas Date: 05/26/ Hugoton, Kansas Ethanol Hybrid Plant
GENERAL PIPING SPECIFICATIONS
(2.0 - WELDING – continued)
2.8.5. All welds shall be made using the Tungsten Inert Gas (TIG) welding process using tungsten non-consumable electrodes and 100 percent commercially dry and pure argon gas for internal pipe purging and for electrode shielding. (Except as specified in Piping Specification Class “X-1” and Class “X-2”). Prepare ends of pipe for girth butt welding by using a pipe facing, squaring and deburring tool or by machining, abrasive cutting, grinding, sawing, or any combination of these methods using saw blades, cutting and grinding tools suitable for austenitic stainless steel pipe which have never been used on carbon steel.
2.8.6. Thoroughly clean weld areas and remove all burrs and scale. Remove all foreign substances such as cutting oils, marking crayons, kerosene, material containing sulfur, lead or zinc, metal particles, grinding compounds, etc. Clean only with carbon-free aluminum oxide, “Scotch-Brite” CP-AM cutting and polishing unitized wheel; Type “A”, medium grade as manufactured by the 3M company.
2.8.7. Align work accurately in jigs or fixtures. Keep aligning benches clean at all times. Do not allow austenitic stainless steel pipe or fittings to come in contact with carbon steel benches, jigs, or fixtures. Place a sheet of stainless steel between bench, the carbon steel jig or fixtures surfaces that will come in contact with the pipe or fittings; or other method acceptable to the Owner.
2.8.8. Ends to be welded are to be butted together and alignment maintained throughout welding by either tacking or the use of jigs. Do not penetrate to the interior of the pipe with the tack. The weld will be rejected for tacks that are not made correctly.
2.8.9. All stainless steel pipe and fittings (as well as fabricated piping spools shall be covered when not being used to protect them from coming into contact with ferrous contamination from weld spatter and grinding of ferrous metals.)
2.9. Identification of Welders:
2.9.1. Each welder employed for shop or field welding of pipe joints shall be assigned an identifying number by the Contractor, who shall furnish the Owner's Representative a list of such welders with their respective numbers along with a copy of the Welders' Qualification Test Reports. This list shall be maintained accurately with deletions and additions reported promptly.
Aboveground Piping Specification No. CS-P- Abengoa Bioenergy Job No. Y Biorefinery of Kansas Date: 05/26/ Hugoton, Kansas Ethanol Hybrid Plant
GENERAL PIPING SPECIFICATIONS
3.0 BRAZING
3.1. The systems requiring brazing shall be brazed with the flux-free brazing alloy using an oxygen-acetylene torch.
3.2. Brazing Procedures, Specifications, and Qualification records shall be submitted to the Owner's Representative for review prior to start of work. Brazers shall be certified in accordance with Section IX of the ASME Boiler and Pressure Vessel Code.
3.3. The joints to be brazed should have a clearance of 0.015 inch to 0.05 inch in order to obtain a strong joint. As a minimum, the joints should have an easy slip-fit so as to ensure an adequate joint.
3.4. The joint surfaces shall be cleaned prior to brazing by wiping the area to be brazed with a degreasing solvent. The area should then be mechanically cleaned using an emery cloth and followed with a solvent wipe. Solvents shall be used in a manner to limit the risk of fire. The cleaned joint shall be handled carefully and brazed immediately after cleaning to prevent recontamination.
3.5. The area of the joint shall be heated uniformly to the brazing temperature range of the alloy used. Ideally, the brazing temperature should be maintained on the low end of the range so as to allow the brazer to better control the flow of the alloy into the joint and reduce the chances of oxide contamination in the joint.
3.6. A nitrogen purge shall be used while brazing the system. The nitrogen purge prevents the formation of oxide scale on the inside of the joints and also cools the internal surface of the joint. The purge shall be supplied at approximately 15- CFH and allowed to flow long enough to displace the air from the joint to be brazed. The system shall be assembled in such a manner that a positive purge can be maintained from the starting point to the end of the system. A 6 inch purge extension with a 1/8 inch purge restrictor hole shall be used when fabricating branch connections. On long runs, a pipe cap with a 1/8 inch purge restrictor hole shall be used. The nitrogen purge shall be maintained in an area until the joint temperature falls below 110 ºF.
3.7. Identification of Brazers. Each brazer employed for shop or field brazing of pipe joints shall be assigned an identifying number by the Contractor, who shall furnish the Owner's Representative with a list of such brazers and their respective numbers along with a copy of the Brazers' Qualification Test Reports. This list shall be maintained accurately with deletions and additions reported promptly.
Aboveground Piping Specification No. CS-P- Abengoa Bioenergy Job No. Y Biorefinery of Kansas Date: 05/26/ Hugoton, Kansas Ethanol Hybrid Plant
GENERAL PIPING SPECIFICATIONS
(3.0 – BRAZING – continued)
3.8. Upon completing a joint, the brazer shall identify the joint with his identifying number. The identification shall be made using a vibrating pen or permanent marker suitable for marking pipe. The brazer identification shall not be more than three (3) inches from the joint.
4.0 SOLDERING
4.1. The systems requiring soldering shall be soldered with the solder using an oxygen- acetylene torch; only lead-free solder shall be used.
4.2. The joints to be soldered should have a clearance of 0.015 inch to 0.05 inch in order to obtain a strong joint. As a minimum, the joints should have an easy slip-fit so as to ensure an adequate joint.
4.3. The joint surfaces shall be cleaned prior to soldering by wiping the area with a degreasing solvent. The area should then be mechanically cleaned using an emery cloth or steel wool and followed with a solvent wipe. Solvents shall be used in a manner to limit the risk of fire. The cleaned joint shall be handled carefully and soldered immediately after cleaning to prevent recontamination.
4.4. The joint surfaces shall be pasted with flux and seated together. The joint area shall then be heated to the manufacturer's recommended soldering temperature by using an oxy-acetylene torch. Care should be taken to not overheat the joint which can cause annealing of the copper.
4.5. The craftsmen utilized in the soldering operation shall be experienced in this procedure.
5.0 PVC/CPVC SOLVENT CEMENTING
5.1. The piping installation shall be made in accordance with the manufacturer's instructions and the following procedure.
5.2. All socket-type joints shall be made in accordance with the manufacturer's instructions and solvent-cemented as follows:
5.2.1. Cut the pipe ends square.
5.2.2. All burrs, chips, filings, etc., shall be removed from the inner and outer circumference of the end of the pipe before joining.
5.2.3. All pipe ends shall have the outside circumference beveled with a 150 chamfer, cut to a depth of approximately 3/32".
Aboveground Piping Specification No. CS-P- Abengoa Bioenergy Job No. Y Biorefinery of Kansas Date: 05/26/ Hugoton, Kansas Ethanol Hybrid Plant
GENERAL PIPING SPECIFICATIONS
(5.0 - PVC/CPVC SOLVENT CEMENTING – continued)
5.7. The Owner's Representative will select, at random times and places, up to five joints of various pipe sizes made by each fitter for destructive examination of workmanship with regard to: Void-free solvent cement joints; adequate fusion of back-welded joint; socket voids (incomplete insertion of pipe into socket); excess solvent cement; or other defects. Joints shall be prepared for inspection by sectioning the joints into axial and circumferential pieces and removing cutting tool marks with 400 grit wet and dry sand paper.
6.0 HDPE/POLYPROPYLENE/PDVF HEAT FUSION
6.1. The requirements, temperature, times, and pressures of fusion for heat fusion joints in high-density polyethylene (HDPE), polypropylene (PP) or polyvinylidene fluoride (PVDF) piping systems shall be in accordance with the individual Piping Groups and in accordance with the selected manufacturer's recommendation.
7.0 FLANGED CONNECTIONS
7.1. The Contractor shall use flanges only for equipment nozzle flange connections, valve flange connections, locations shown on the drawings, and lines specified herein. All slip-on flanges shall be welded front and back. Welding neck flanges shall be bored to match the attached pipe. No flanges or other fittings manufactured in China will be accepted.
7.2. Bolting and gasket materials shall be in accordance with the requirements of the applicable pipe and gasket specification groups, included herein, and shall be furnished by the Contractor unless otherwise specified or noted.
7.3. Bolt threads shall be lubricated with "NeverSeez" or approved equal. Only paste- type thread lubricant shall be acceptable.
7.4. All bolts shall be tightened with suitable wrenches only. Hammering or bumping shall not be permitted. In tightening bolted joints, care shall be taken to secure uniform pressure on the gaskets and to avoid overstressing bolts or dishing the flanges. Extreme care shall be exercised in making up joints between Van Stone flanges, fiberglass flanges, cast iron body valves and lined pipe flanges.
7.5. All flange bolt holes shall straddle center lines (two-holed) unless otherwise noted.
Aboveground Piping Specification No. CS-P- Abengoa Bioenergy Job No. Y Biorefinery of Kansas Date: 05/26/ Hugoton, Kansas Ethanol Hybrid Plant
GENERAL PIPING SPECIFICATIONS
(7.0 – FLANGED CONNECTIONS – continued)
7.6. Bolts on flanged connections shall be of a length such that after tightening, the bolt projection shall be between flush with and 1/2 inch projection beyond the end of the nut. All bolts on any one flange shall be of the same length.
7.7. Submittal. Prior to starting any piping erection, the Contractor shall submit a written procedure for making up flanged connections to the Owner's Representative for approval. Consideration shall be given to the gasket seating requirements, bolting materials used, flange material, flange facing, design conditions, testing conditions and service/fluid.
7.8. Bolt Torques.
7.8.1. All flange connections for fiberglass, plastic, or plastic lined piping systems shall be tightened with a torque wrench in accordance with the manufacturer's recommended bolt torque values and procedures unless otherwise directed by the Owner's Representative
7.8.2. All flange connections using spiral-wound type gaskets shall be tightened with a torque wrench in accordance with the manufacturer's recommended bolt torque values and procedures unless otherwise directed by the Owner's Representative. Bolting materials shall be continuous threaded alloy studs in accordance with Paragraph 8.0.
7.8.3. All other flange connections shall be tightened in accordance with a written procedure approved by the Owner's Representative.
8.0 BOLTING MATERIALS
8.1. All bolt studs (studs), bolts and accompanying nuts shall be threaded in accordance with ANSI B1.1, Class 2A for external threads and Class 2B for internal threads. Threads shall be the coarse-thread series except that bolting 1-1/8 inch and Larger in diameter shall be the 8-thread series.
8.2. NOTE: CAREFUL CONSIDERATION MUST BE GIVEN IN MATCHING BOLTING MATERIAL WITH TAPPED HOLES IN VALVES OR EQUIPMENT SINCE MANUFACTURERS CAN VARY THE NUMBER OF THREADS PER INCH.
Aboveground Piping Specification No. CS-P- Abengoa Bioenergy Job No. Y Biorefinery of Kansas Date: 05/26/ Hugoton, Kansas Ethanol Hybrid Plant
GENERAL PIPING SPECIFICATIONS
(10.0 - SCREWED/THREADED CONNECTIONS – continued)
10.2. All screwed connections for stainless piping shall be made using Schedule 40S pipe, pipe nipples or adapters when the Piping Group specifies Schedule 10S or thinner.
10.3. Joint Compound. Joint compound shall be suitable for the service intended as recommended by the manufacturer. Threaded joints in stainless steel at operating temperatures to 450ºF. shall be made up using stainless steel PST (Pipe Sealant with Teflon) with Locquic Primer "N" as manufactured by Loctite Corporation. Threaded joints in carbon steel at operating temperatures to 400ºF. shall be made up with PST (Pipe Sealant with Teflon) as manufactured by Loctite Corporation. Threaded joints in steam piping or piping at operating temperatures above 400ºF. shall be made up with General Purpose 1000ºF. Anti-Seize Compound "Thred Gard" (formerly Crane Formula 425A) as manufactured by Federal Process Corporation, 4620 Richmond Road, Cleveland, Ohio 44128.
10.3.1. Teflon tape is strictly prohibited.
11.0 BRANCH CONNECTIONS
11.1. All branch connections shall be in accordance with ASME/ANSI B31.1, Paragraph 104.3.1.
11.2. Fabricated branch connections shall only be used where shown on the isometrics or listed in the branch connection tables.
11.3. Normally, branch fittings 2 inches and smaller on piping runs 2 inches and smaller shall be made using tees and reducing tees, unless noted otherwise in the piping group specifications.
11.4. Branch connection materials are specified in the individual Piping Group Specifications, Section 2.02 of this specification. Branch Connection Tables are detailed at the end of Section 2-03. Branch Connection Tables are given for each service in the Piping Service Index, Section 2.01 of this specification. The specified Branch Connection Table in the Piping Service Index lists the preferred branch connection for each service. Actual design conditions could require additional reinforcement and in some case could require less reinforcement. Design judgment should be used when selecting a branch connection from the tables. For example, try to avoid using stainless steel Weldolets on overflows.
Aboveground Piping Specification No. CS-P- Abengoa Bioenergy Job No. Y Biorefinery of Kansas Date: 05/26/ Hugoton, Kansas Ethanol Hybrid Plant
GENERAL PIPING SPECIFICATIONS
11.5. Stainless steel tees shall be in accordance with ASTM A 403, WP (factory-made) per ANSI B16.9. Stainless steel tees will be shown on Drawings or listed in the Branch Connection Tables only when design requires improved vibration resistance or lower stress values. The Piping Drawings will normally show a nozzle weld when acceptable, since stainless steel tee connections manufactured in accordance with ASTM A 774 or ASTM A 403, CR may be fabricated (nozzle weld) tees. The cost of a factory-made (A403 WP) tee is much greater than that of a fabricated (nozzle weld) tee (A403 CR). When a stainless steel tee is shown on the piping drawings, it shall be a factory-made (A403 WP-type) tee.
12.0 EXTERNAL PRESSURE DESIGN
12.1. Piping subjected to a vacuum shall be analyzed for stiffener ring requirements with Paragraphs UG-28 and UG-29 of Section VIII of the ASME Boiler and Pressure Vessel Code.
13.0 PIPE BENDS
13.1. Pipe bends shall be used where shown on the Drawings or specified herein. The centerline radius of all pipe bends shall be not less than five (5) pipe diameters unless stated to the contrary herein. The centerline radius shall be uniform. After bending, the pipe shall be in accordance with Pipe Fabrication Institute ES-24. The pipe bend ends shall be true to the angle shown on the drawings.
14.0 LEAK TESTS
14.1. All piping systems constructed under the jurisdiction of either Section I of the ASME Boiler and Pressure Vessel Code or ASME/ANSI Code for Pressure Piping B31, Sections 1 through 8, and if required by the State or Local codes, shall be leak tested in accordance with the applicable code.
14.2. All other systems shall be leak tested in accordance with ASME/ANSI B31.3, Paragraph 345 or when approved by the Owner's Representative, in such a way that their acceptability for service is proven. Unless otherwise directed by the Owner's Representative, all piping shall be tested in accordance with the leak test specified in the Piping Service Index, Section 2.01 of this specification.
14.2.1. Approval. The Contractor shall notify any governmental authority requiring witness of testing for permits and the Owner's Representative for approval prior to starting any testing procedure for each piping system.