

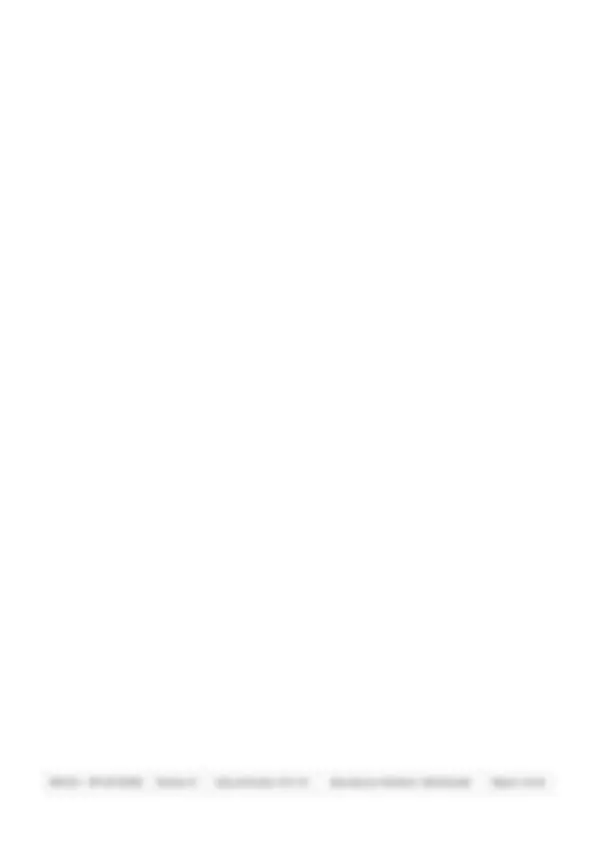
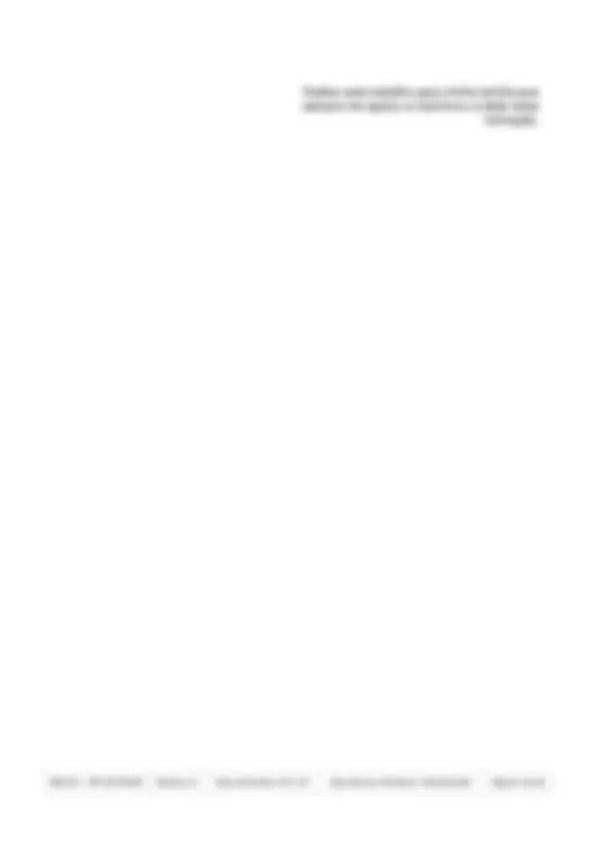
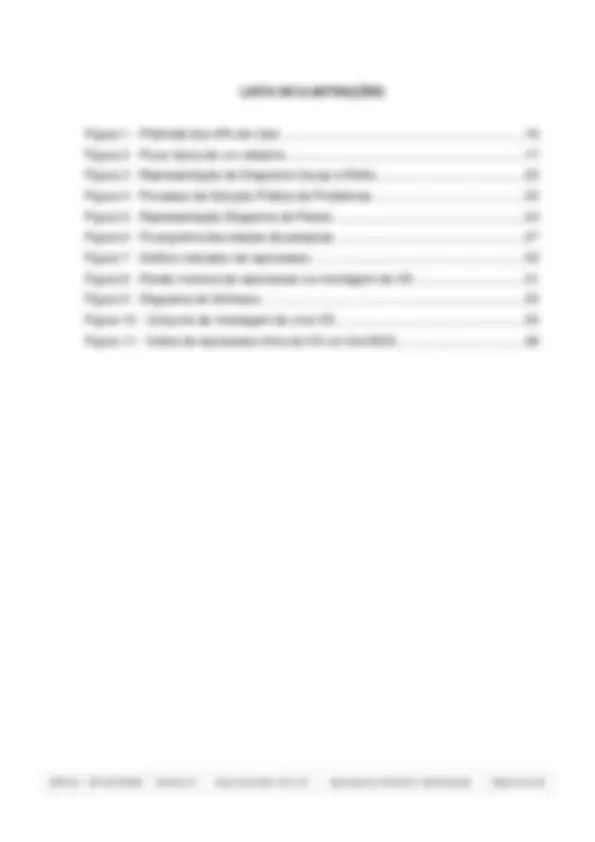
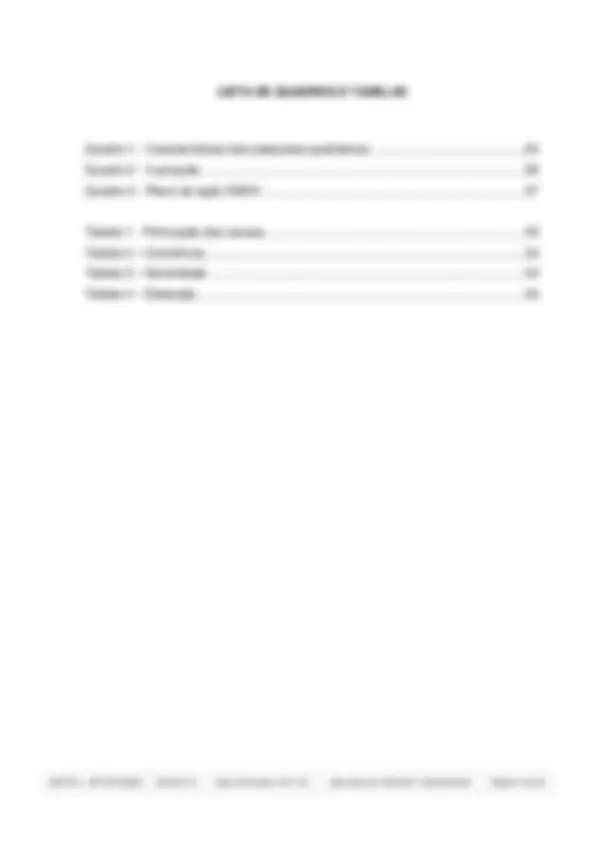
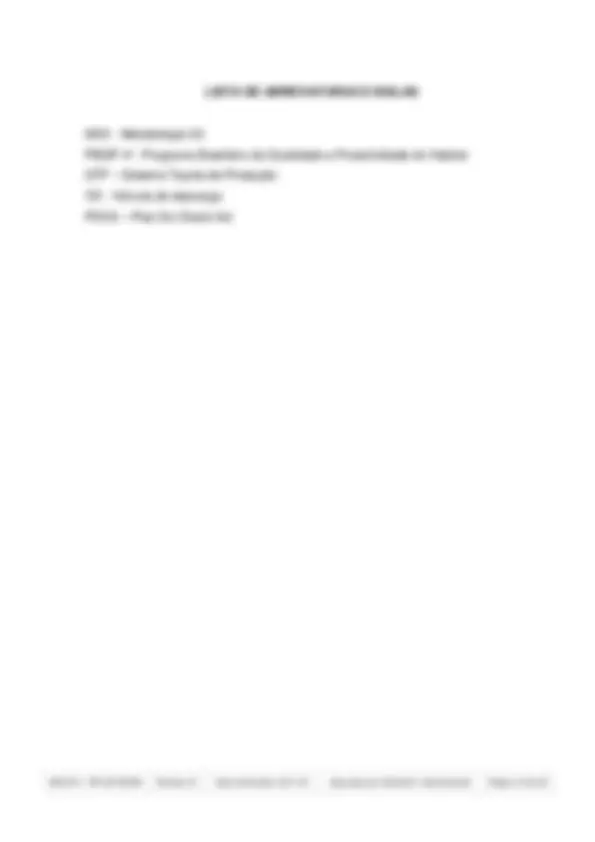
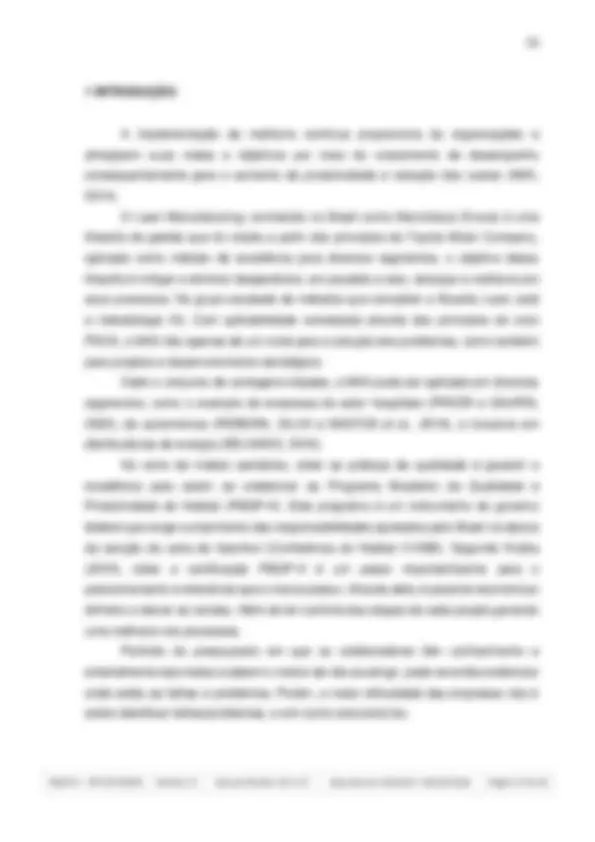
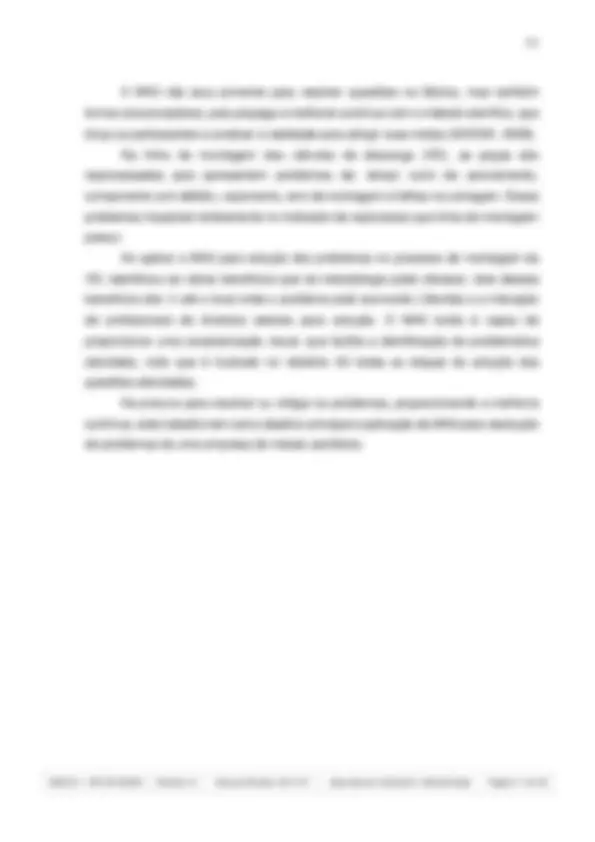
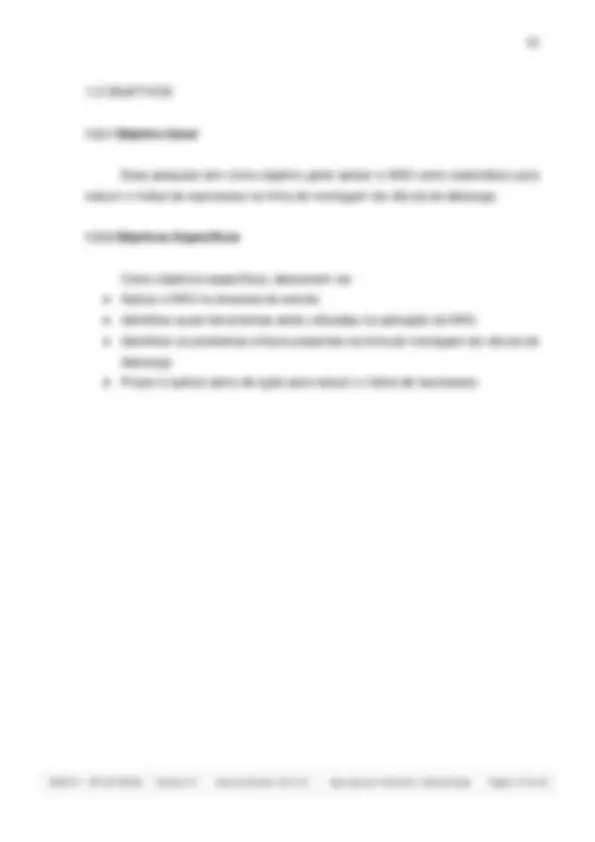

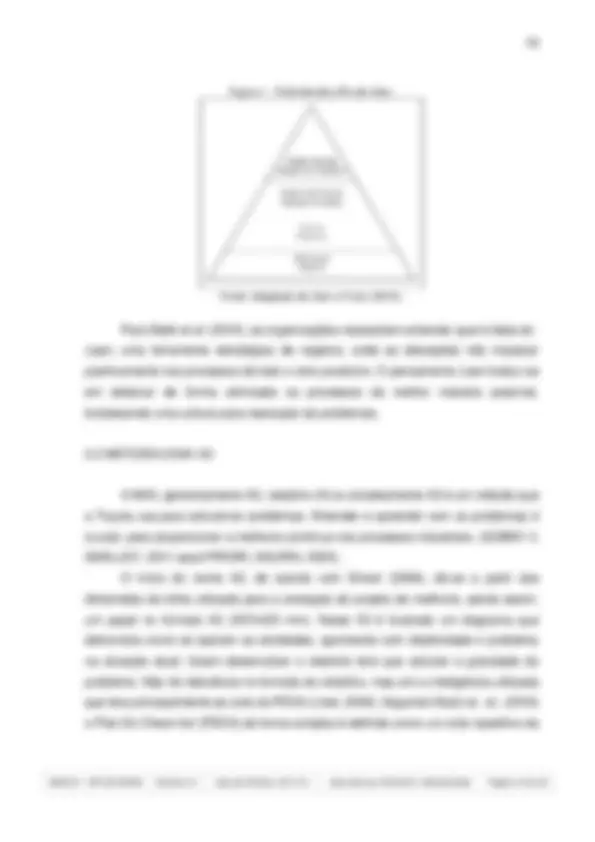
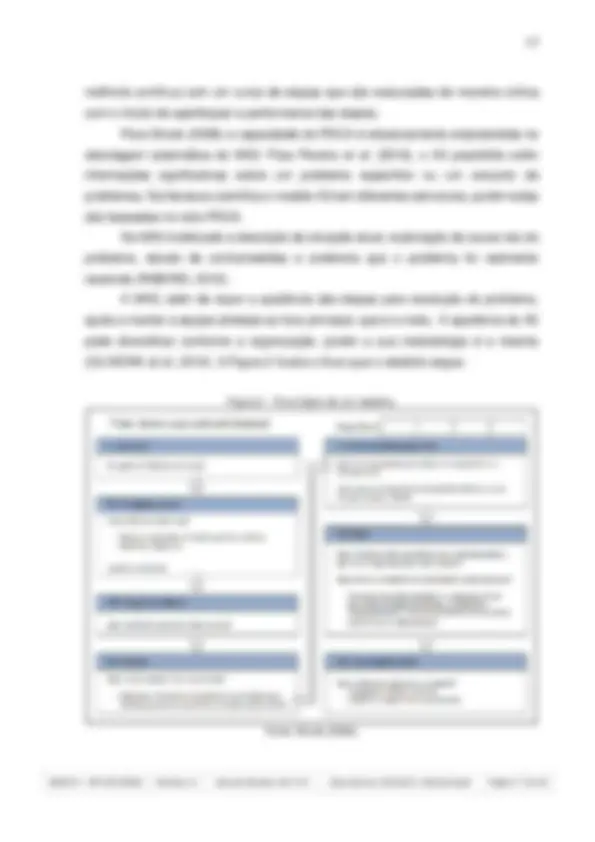
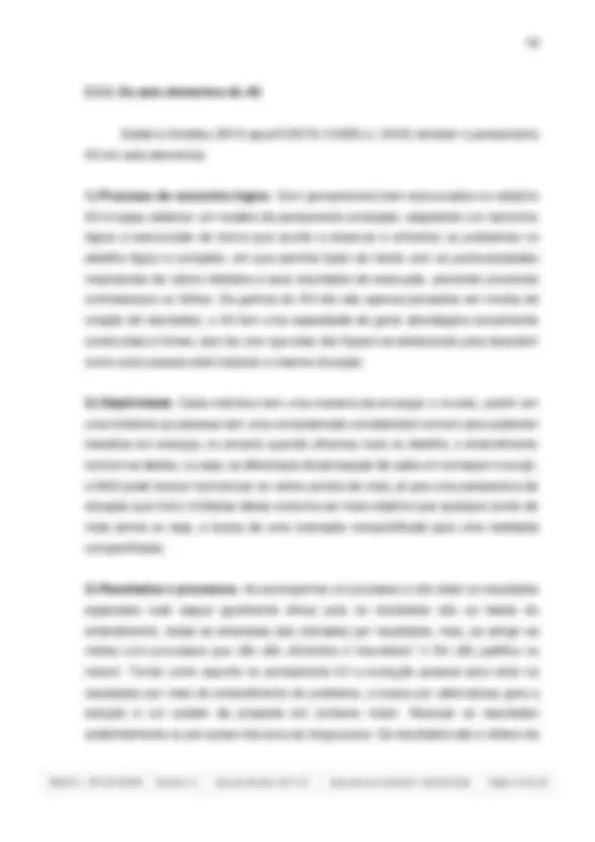
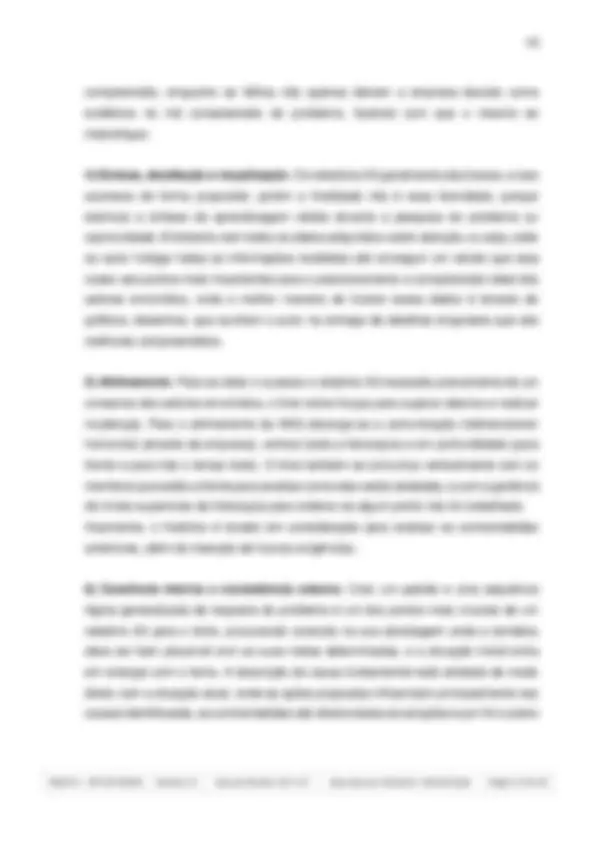
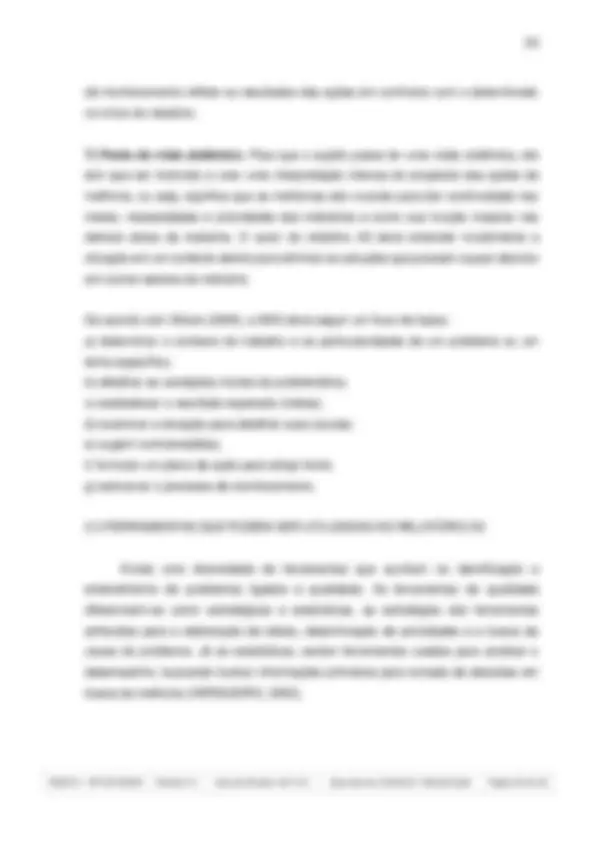
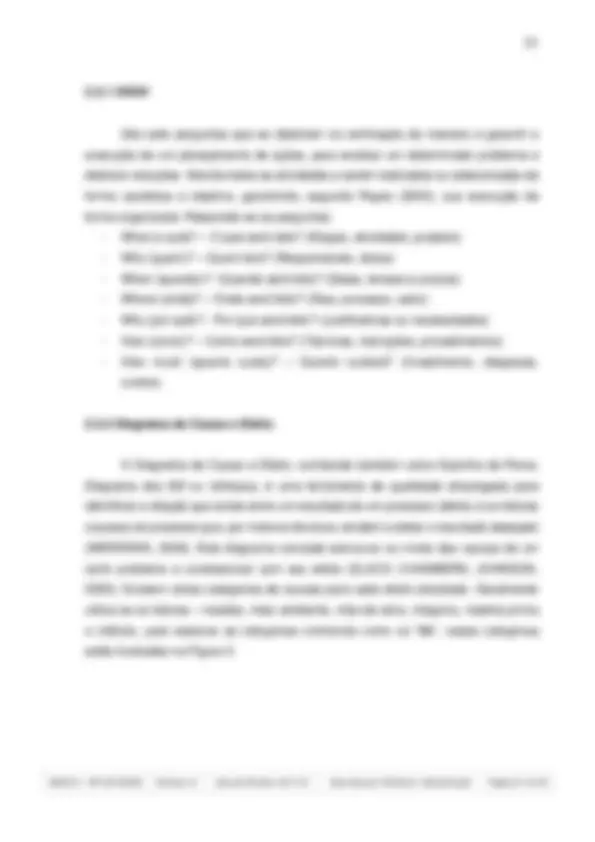
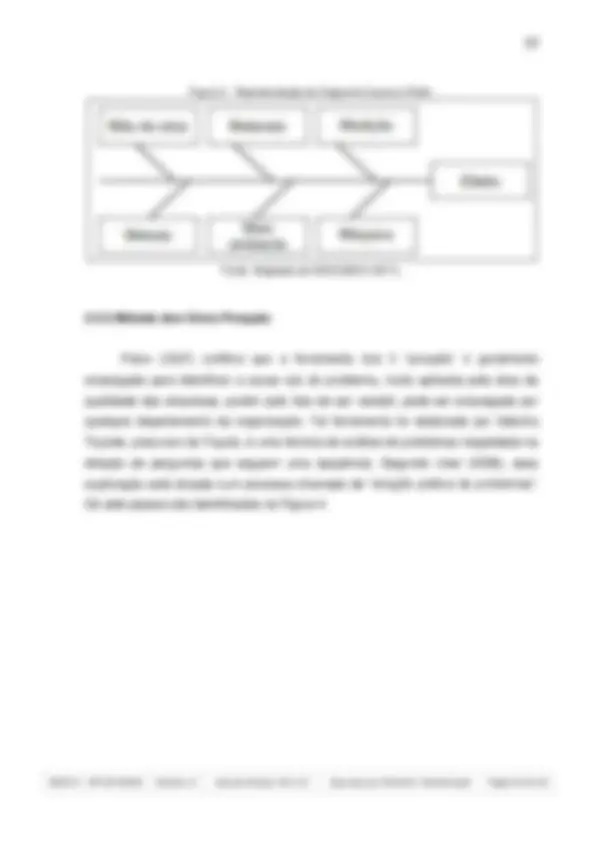
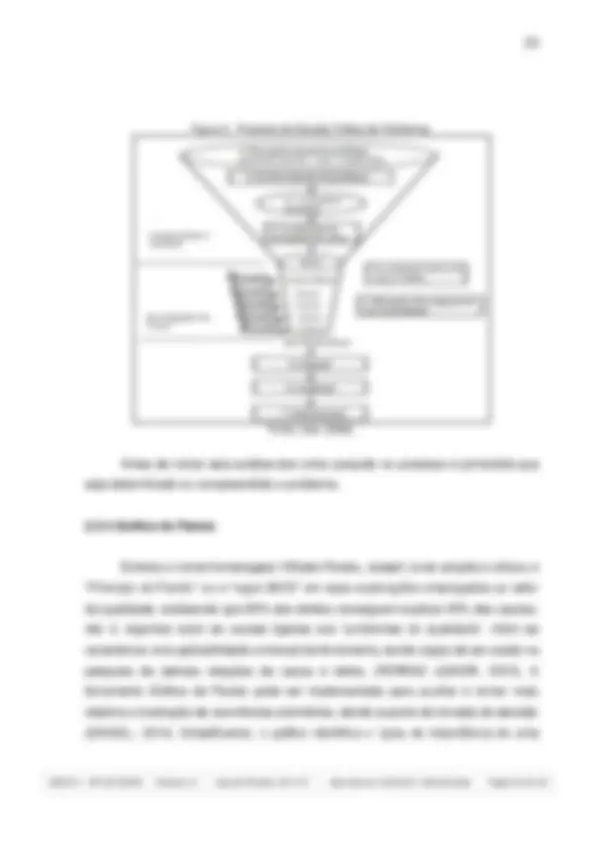
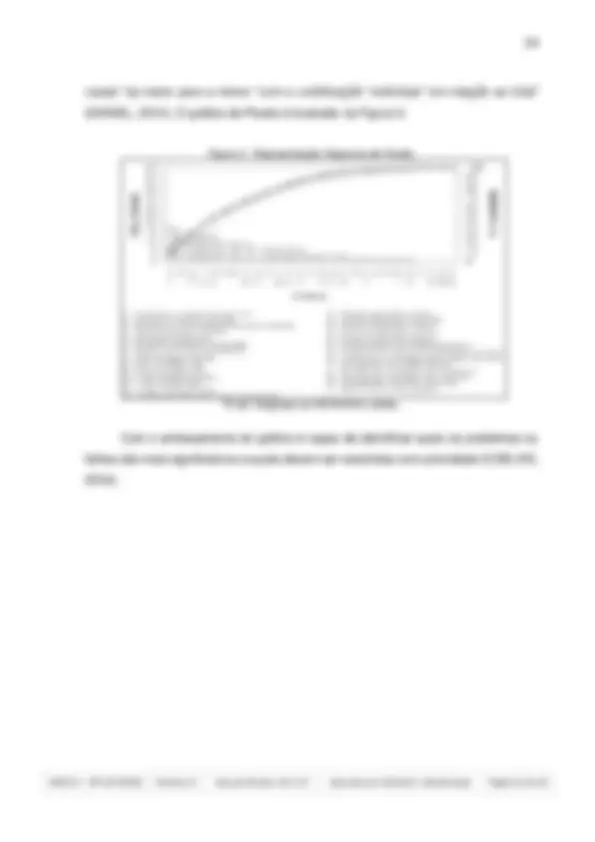
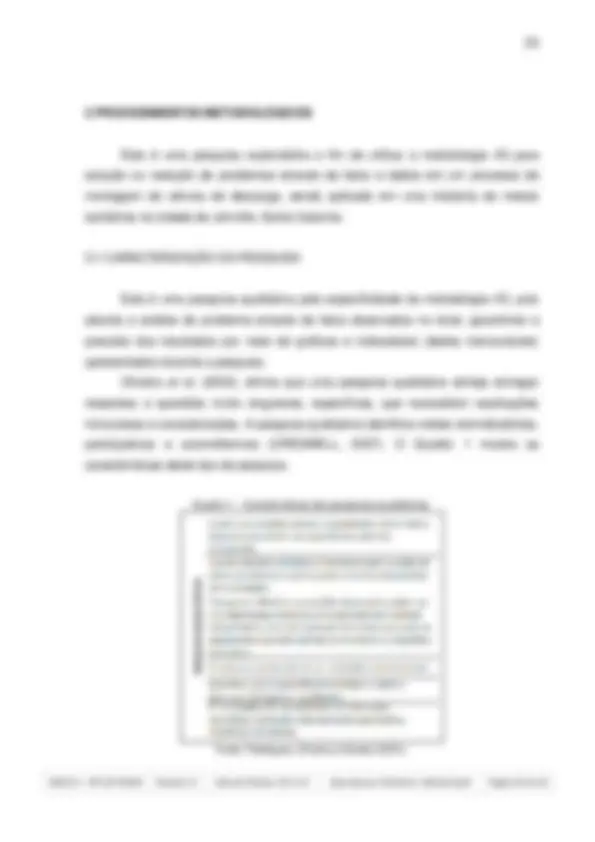
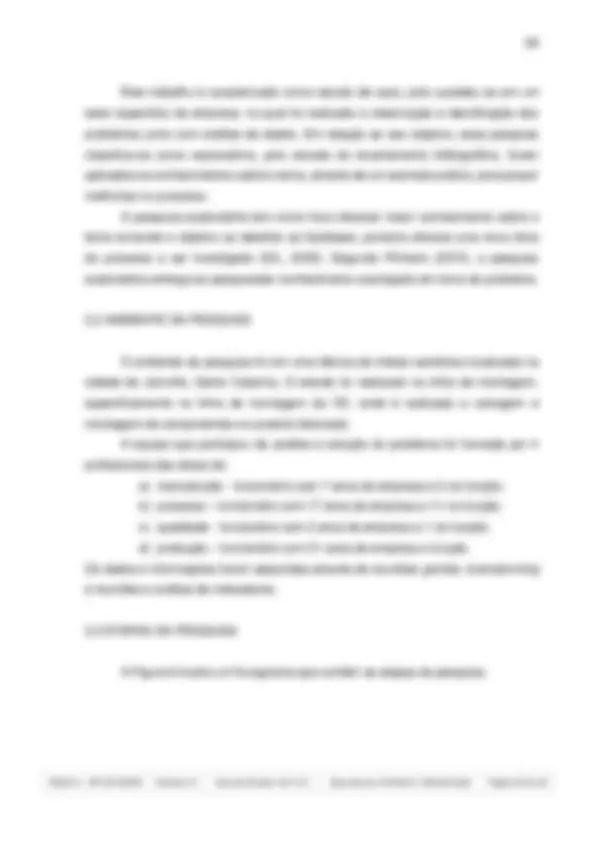
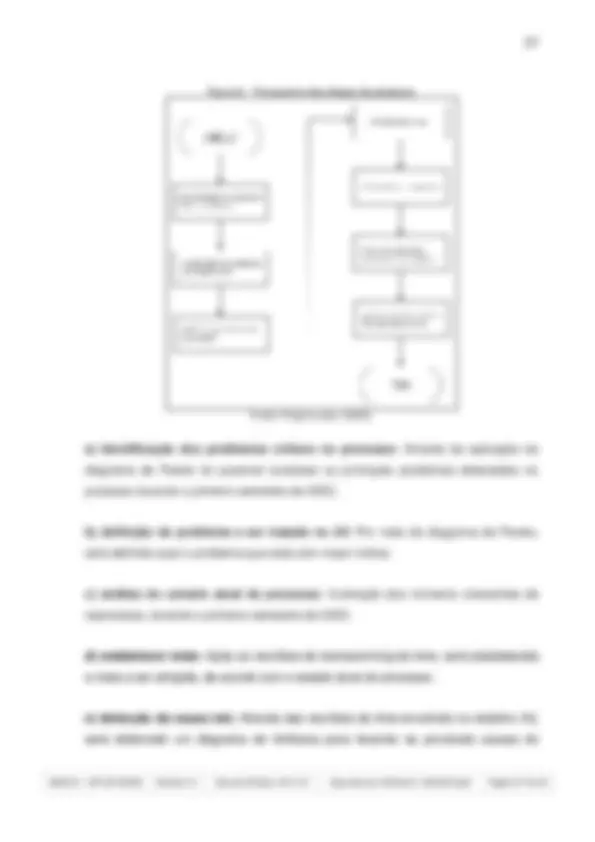
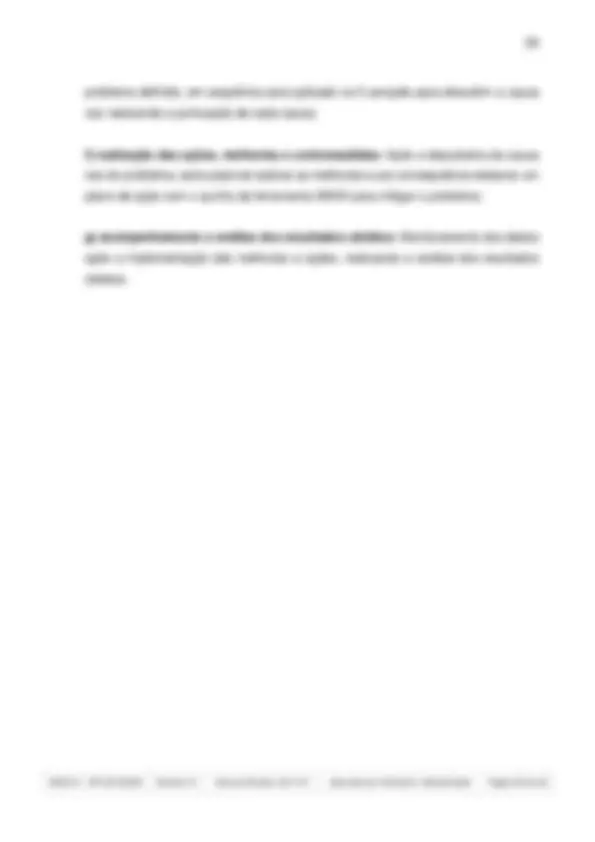
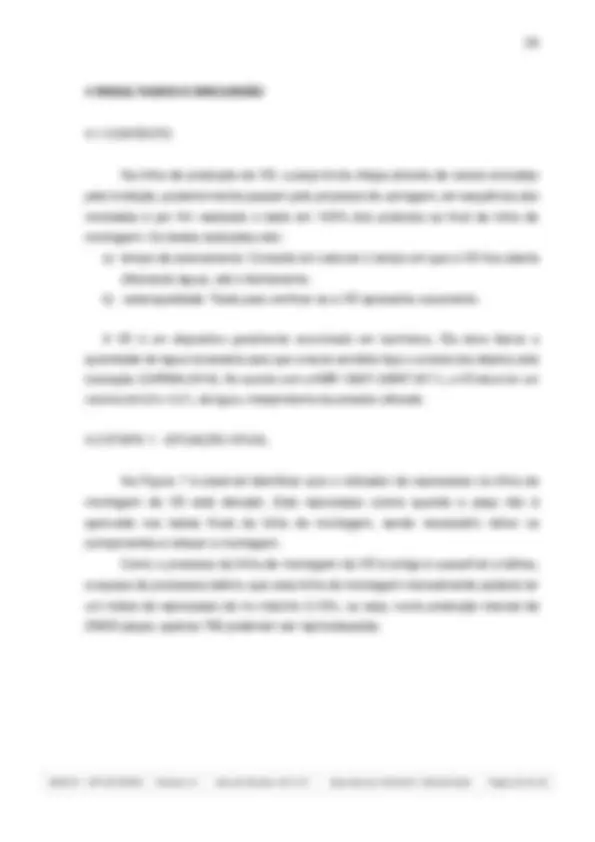
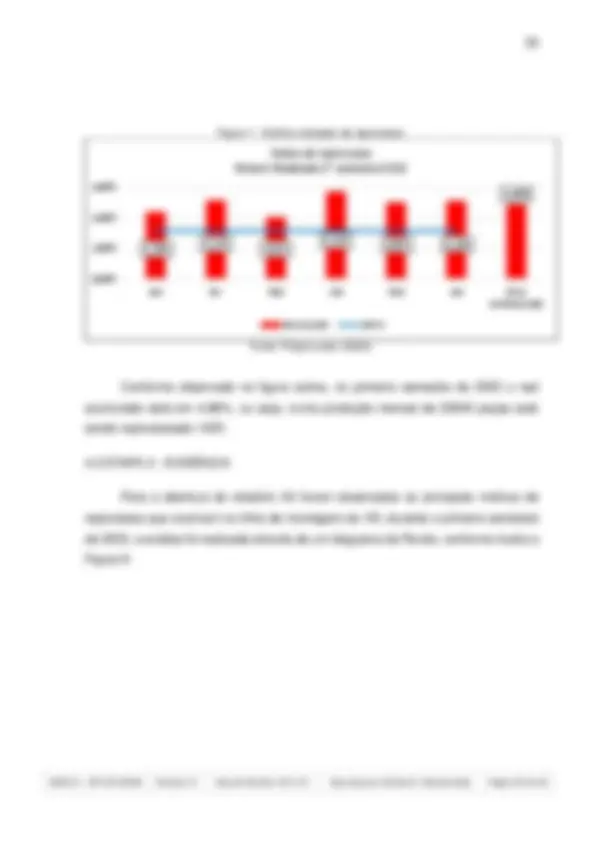
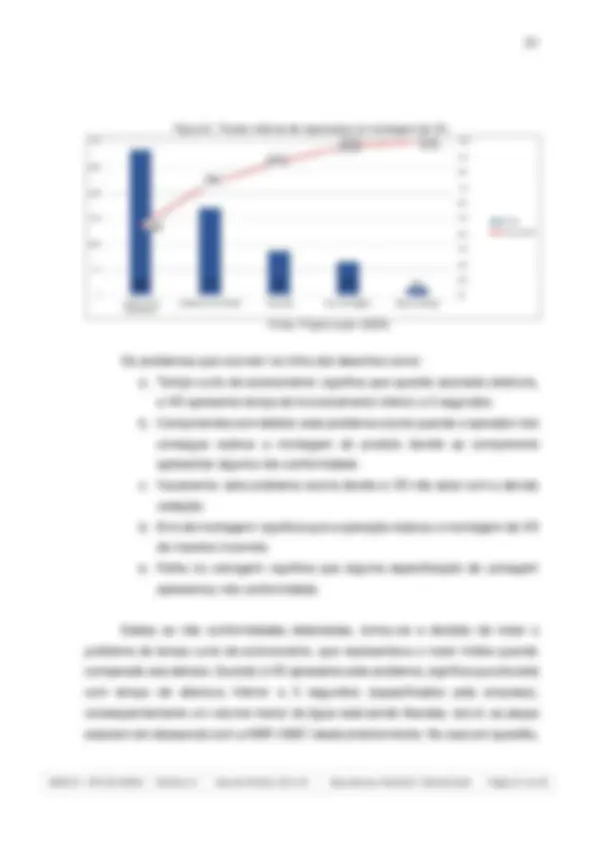
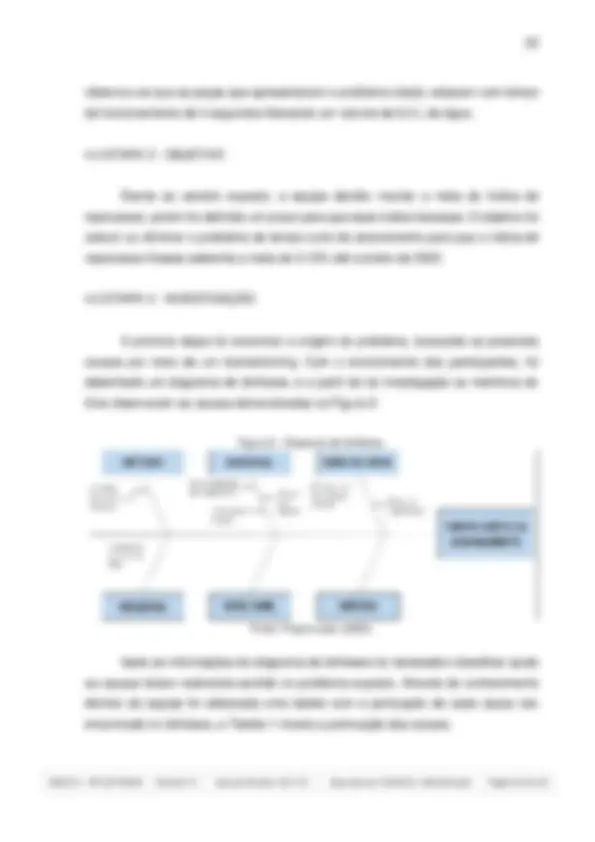
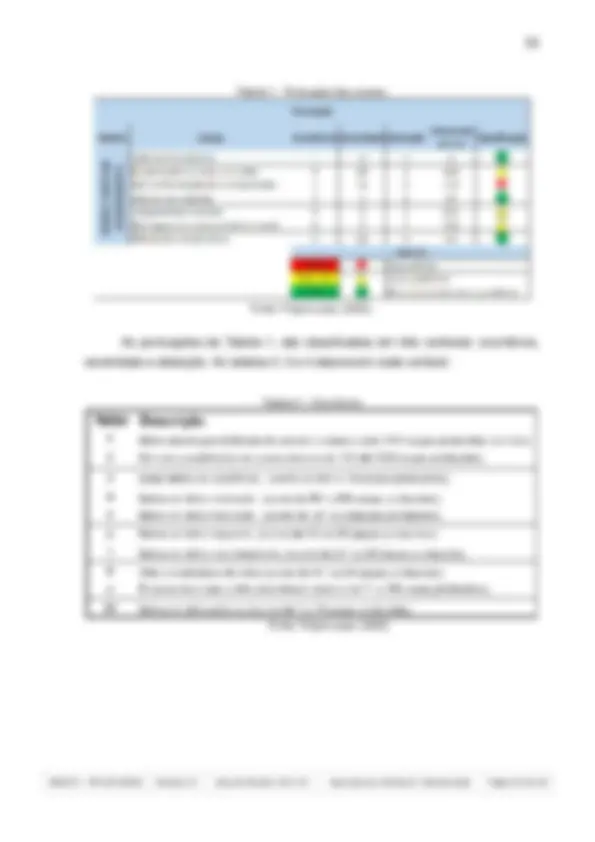
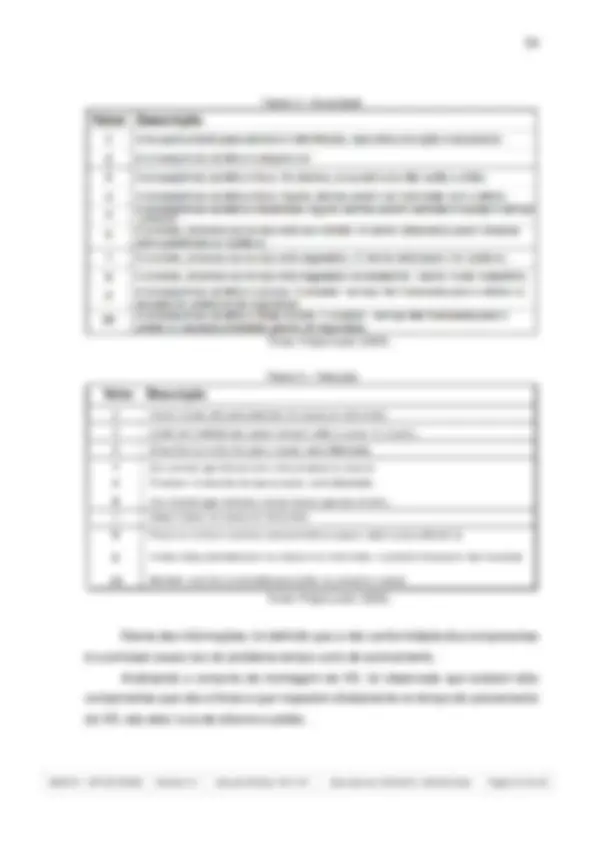
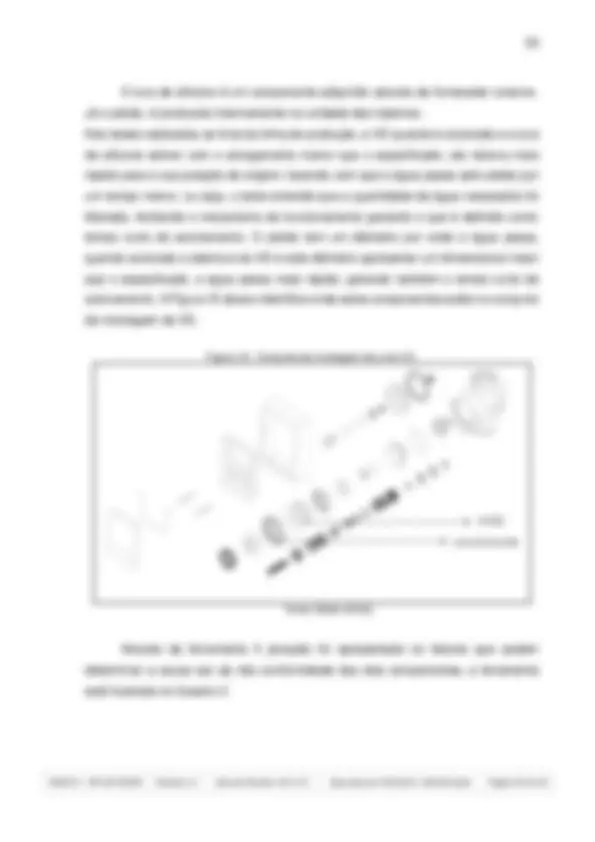
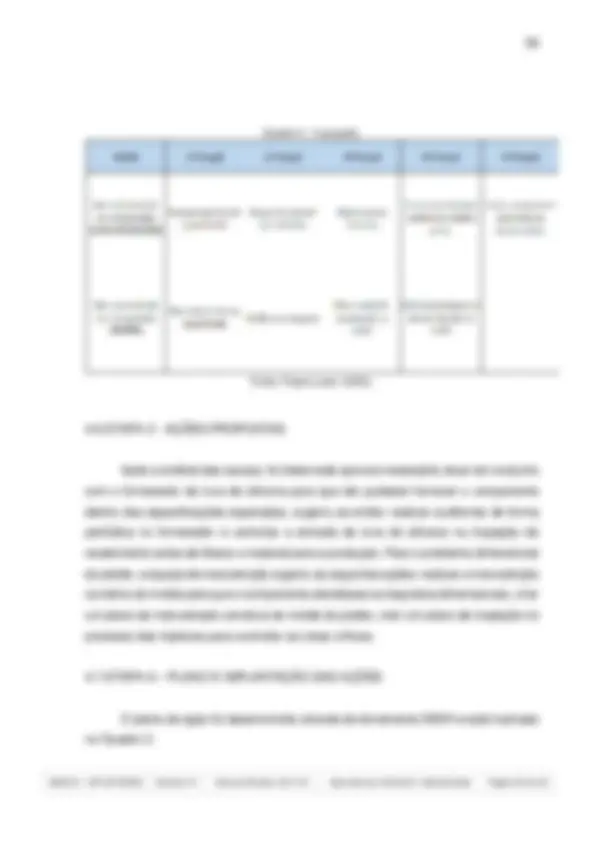
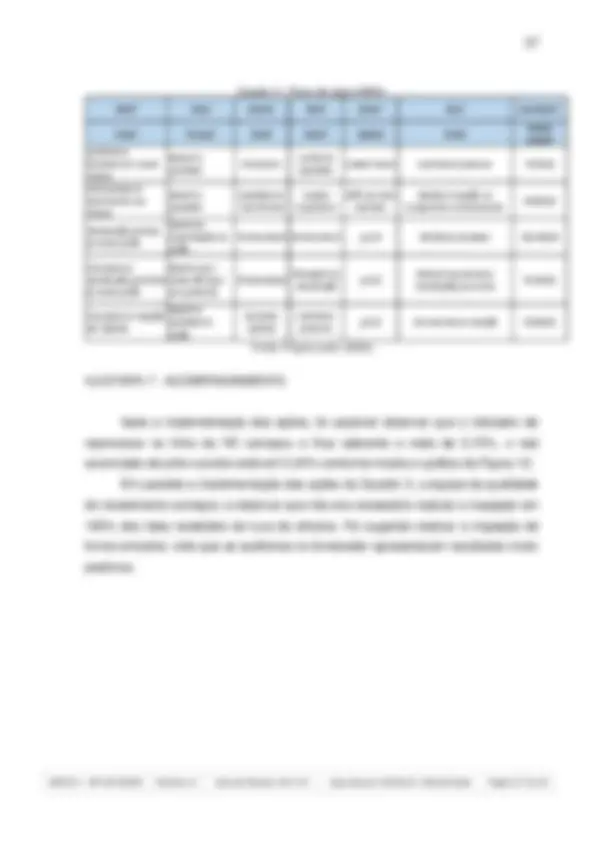
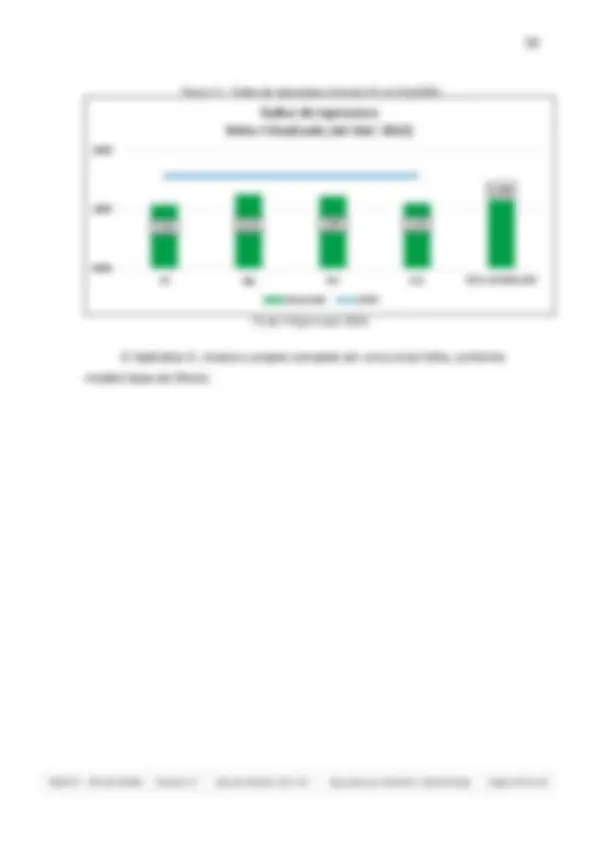
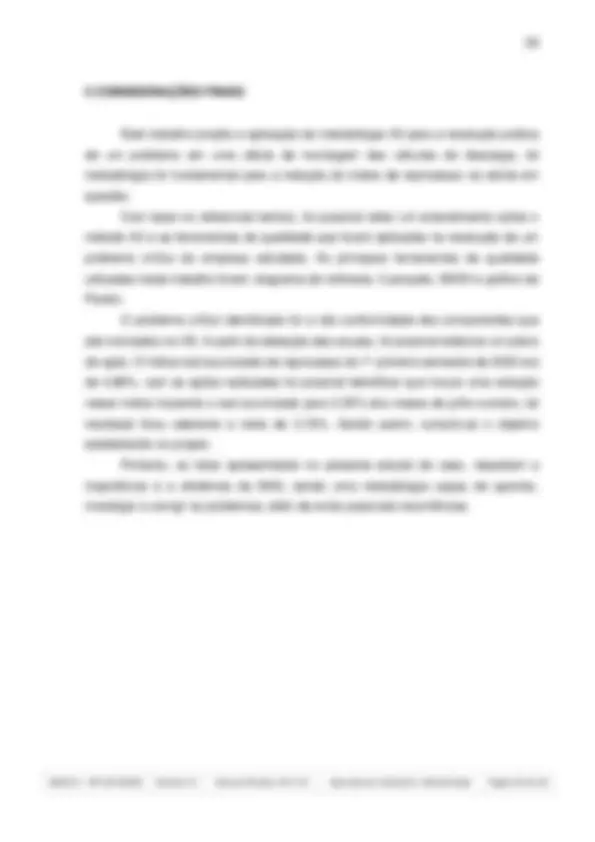
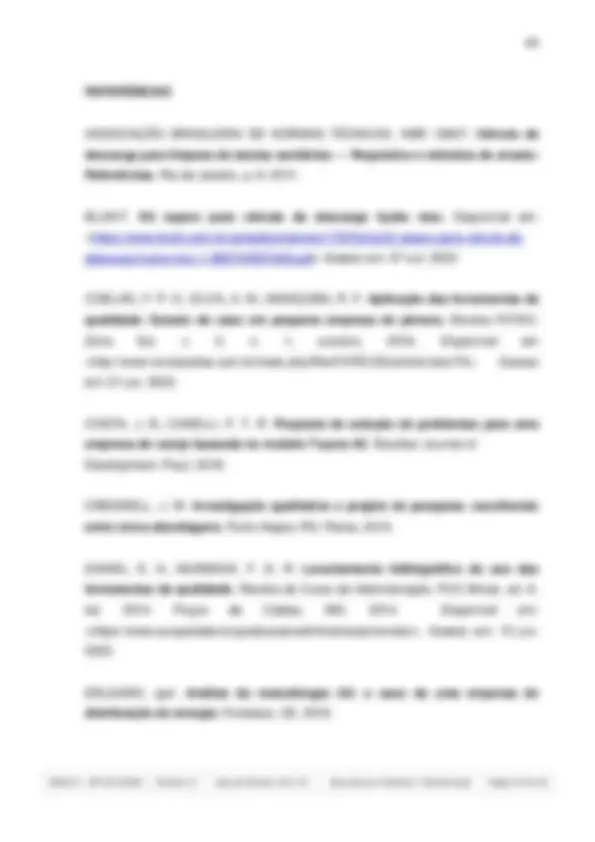
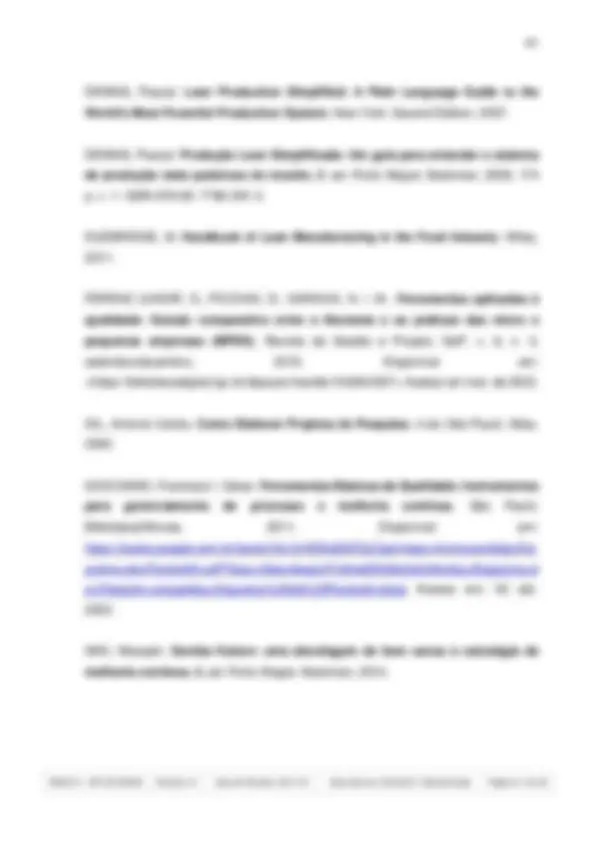
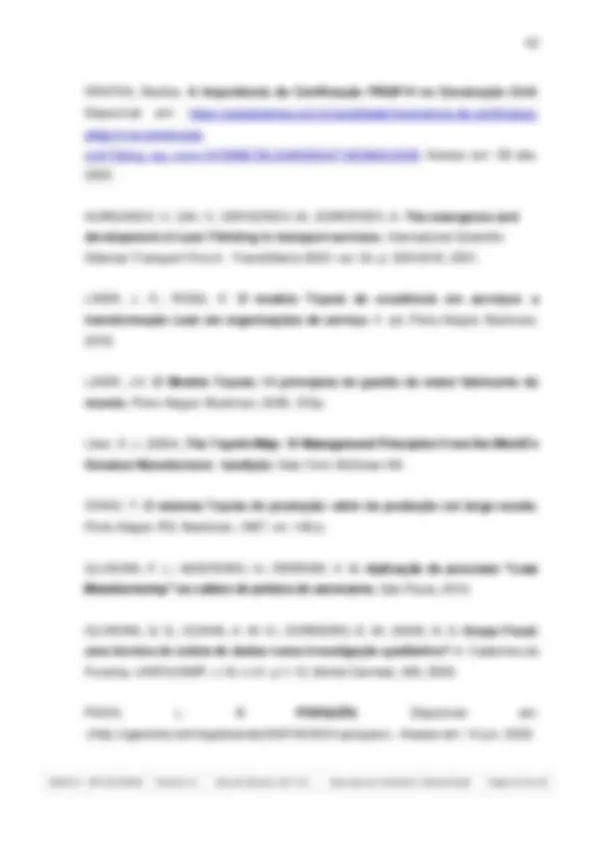
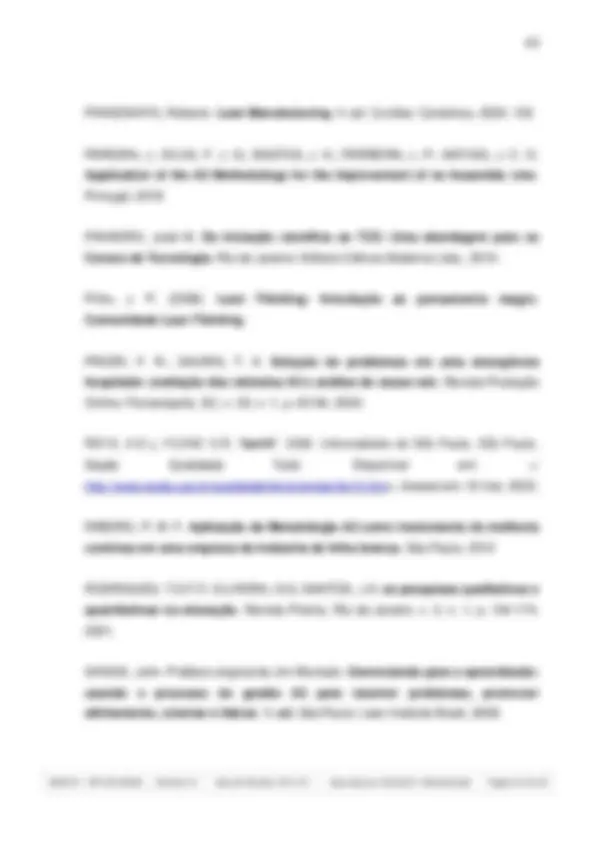
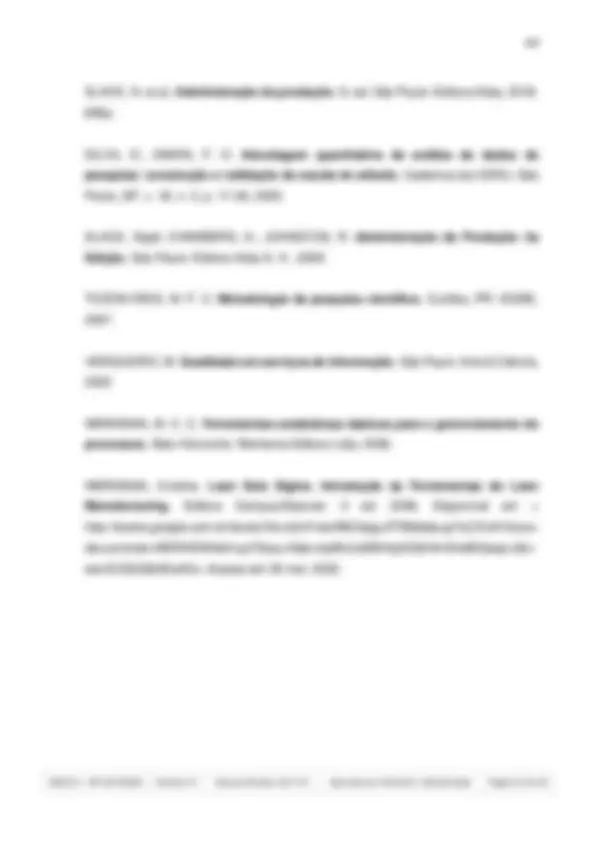
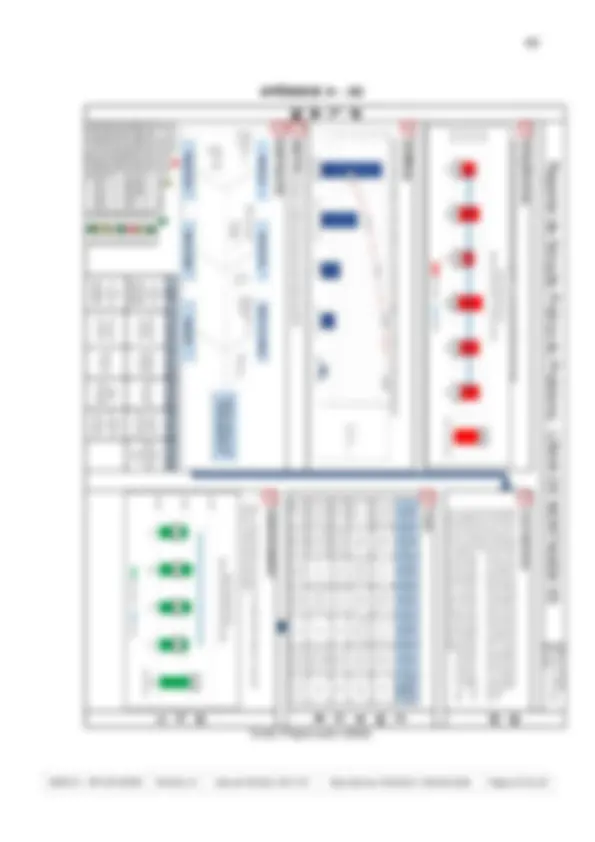
Estude fácil! Tem muito documento disponível na Docsity
Ganhe pontos ajudando outros esrudantes ou compre um plano Premium
Prepare-se para as provas
Estude fácil! Tem muito documento disponível na Docsity
Prepare-se para as provas com trabalhos de outros alunos como você, aqui na Docsity
Os melhores documentos à venda: Trabalhos de alunos formados
Prepare-se com as videoaulas e exercícios resolvidos criados a partir da grade da sua Universidade
Responda perguntas de provas passadas e avalie sua preparação.
Ganhe pontos para baixar
Ganhe pontos ajudando outros esrudantes ou compre um plano Premium
Comunidade
Peça ajuda à comunidade e tire suas dúvidas relacionadas ao estudo
Descubra as melhores universidades em seu país de acordo com os usuários da Docsity
Guias grátis
Baixe gratuitamente nossos guias de estudo, métodos para diminuir a ansiedade, dicas de TCC preparadas pelos professores da Docsity
Uma pesquisa exploratória sobre a aplicação da metodologia a3 para solução ou redução de problemas em um processo de montagem de válvulas de descarga em uma indústria de metais sanitários na cidade de joinville, santa catarina. A pesquisa é qualitativa e aborda a análise do problema através de fatos observados no local, garantindo a precisão dos resultados por meio de gráficos e indicadores (dados mensuráveis) apresentados durante a pesquisa. A equipe de análise e solução do problema foi formada por profissionais das áreas de manutenção, identificação de problemas críticos, análise do cenário atual do processo, estabelecimento de meta, detecção da causa raiz, realização de ações, melhorias e contramedidas, acompanhamento e análise dos resultados obtidos.
Tipologia: Resumos
1 / 48
Esta página não é visível na pré-visualização
Não perca as partes importantes!
Joinville
Trabalho de Conclusão de Curso apresentado à Faculdade de Tecnologia SENAI. Como requisito parcial para obtenção do título de Engenharia de Produção. Professor Orientador: Bruna de Freitas Zappelino.
Dedico este trabalho para minha família que sempre me apoiou e incentivou a obter essa formação.
LIMA, Lucas. METODOLOGIA A3: ESTUDO DE CASO EM UMA EMPRESA DE METAIS SANITÁRIOS. Joinville, 2022. Trabalho de Conclusão de Curso - Curso Superior de Engenharia de Produção. Faculdade de Tecnologia SENAI, Joinville,
RESUMO Constantemente as empresas mostram um interesse na aplicação de métodos e ferramentas que auxiliem os processos produtivos buscando torná-los eficientes e reduzindo os desperdícios. As organizações têm como prioridade a qualidade dos seus produtos, por isso quando existe um problema crítico, a aplicação de métodos e ferramentas apropriados se tornam tão importantes. Diante do contexto exposto, o presente trabalho tem como objetivo a aplicação do método A3 para resolução de problemas em um processo de montagem de válvulas de descarga do ramo de metais sanitários. Tal método é aplicado por diversas empresas de diversos ramos, com a finalidade de reduzir ou eliminar um problema, o método A3 tem uma aplicabilidade eficiente e garante que não há recorrências. O trabalho caracteriza-se por ser um estudo de caso em uma pesquisa exploratória, com a utilização de métodos qualitativos. Portanto, na investigação para solucionar os problemas de qualidade e reduzir o indicador de reprocesso da linha de montagem, foi utilizado o método A3. Após a aplicação da metodologia, observou-se uma significativa redução no índice de reprocesso da linha de montagem, reduzindo o índice 4,88% de valor real acumulado para 2,34%, cumprindo o objetivo esperado do trabalho promovendo a melhoria contínua. Palavras-chave: Metodologia A3. Lean Manufacturing. Válvula de descarga. Reprocesso. Linha de montagem.
MA3 - Metodologia A PBQP-H - Programa Brasileiro da Qualidade e Produtividade do Habitat STP – Sistema Toyota de Produção VD - Válvula de descarga PDCA – Plan Do Check Act
A implementação da melhoria contínua proporciona às organizações a almejarem suas metas e objetivos por meio do crescimento de desempenho consequentemente gera o aumento da produtividade e redução dos custos (IMAI, 2014). O Lean Manufacturing , conhecido no Brasil como Manufatura Enxuta é uma filosofia de gestão que foi criada a partir dos princípios da Toyota Motor Company, aplicada como método de excelência para diversos segmentos, o objetivo dessa filosofia é mitigar e eliminar desperdícios, em paralelo a isso, alcançar a melhoria em seus processos. No grupo escalado de métodos que compõem a filosofia Lean , está a metodologia A3. Com aplicabilidade constatada através dos princípios do ciclo PDCA, a MA3 não apenas dá um norte para a solução dos problemas, como também para projetos e desenvolvimento estratégico. Dado o conjunto de vantagens listadas, a MA3 pode ser aplicada em diversos segmentos, como o exemplo de empresas do setor hospitalar (PRIORI e SAURIN, 2020), de automotivas (PEREIRA, SILVA e BASTOS et al., 2019), e inclusive em distribuidoras de energia (DELGADO, 2016). No ramo de metais sanitários, obter as práticas de qualidade é garantir a excelência para assim se credenciar ao Programa Brasileiro da Qualidade e Produtividade do Habitat (PBQP-H). Este programa é um instrumento do governo federal que exige cumprimento das responsabilidades ajustados pelo Brasil na época da sanção da carta de Istambul (Conferência do Habitat II/1996). Segundo Kratka (2019), obter a certificação PBQP-H é um passo importantíssimo para o posicionamento e relevância que a marca possui. Através dela, é possível economizar dinheiro e elevar as vendas. Além de ter controle das etapas de cada projeto gerando uma melhoria nos processos. Partindo do pressuposto em que os colaboradores têm conhecimento e entendimento das metas e sabem o motivo de não as atingir, pode-se então evidenciar onde estão as falhas e problemas. Porém, a maior dificuldade das empresas não é sobre identificar falhas/problemas, e sim como solucioná-los.
A MA3 não atua somente para resolver questões na fábrica, mas também formar solucionadores, pois propaga a melhoria contínua com o método científico, que força os participantes a analisar a realidade para atingir suas metas (SHOOK, 2008). Na linha de montagem das válvulas de descarga (VD), as peças são reprocessadas pois apresentam problemas de: tempo curto de acionamento, componente com defeito, vazamento, erro de montagem e falhas na usinagem. Esses problemas impactam diretamente no indicador de reprocesso que linha de montagem possui. Ao aplicar a MA3 para solução dos problemas no processo de montagem da VD, identificou-se vários benefícios que tal metodologia pode oferecer, dois desses benefícios são: ir até o local onde o problema está ocorrendo ( Gemba ) e a interação de profissionais de diversos setores para solução. O MA3 ainda é capaz de proporcionar uma caracterização visual, que facilita a identificação da problemática abordada, visto que é ilustrado no relatório A3 todas as etapas da solução das questões abordadas. Na procura para resolver ou mitigar os problemas, proporcionando a melhoria contínua, este trabalho tem como objetivo principal a aplicação da MA3 para resolução de problemas da uma empresa de metais sanitários.
A seguir serão apresentados os resultados da pesquisa bibliográfica realizada sobre os assuntos: Lean Manufacturing , metodologia A3, ferramentas da qualidade. 2.1 LEAN MANUFACTURING O Sistema Toyota de Produção (STP) foi criado e aperfeiçoado na fábrica da Toyota em meados 1950 pelos engenheiros Eiji Toyoda e Taiichi Ohno, após as adversidades combatidas na época, eles elaboraram um sistema que tinha como base principal o Just in Time e o Jidoka (LIKER; ROSS, 2018). Segundo Kurganov et al ., (2021) a palavra Lean foi referida pelos americanos em suas pesquisas sobre as táticas de produção da Toyota. Para Dennis (2008), Eiji Toyoda e Taiichi Ohno elaboraram um sistema que fazia da virtude uma necessidade. De acordo com Ohno (1997), o STP tem como essência o corte dos desperdícios, sendo as colunas necessárias para a conduta do sistema: Just in time (tempo certo) e Jidoka (autonomação). Para Pansonato (2020) as operações que geram desperdícios e perdas são classificadas como as que não agregam valor ao consumidor, estas necessitam ser eliminadas ou reduzidas. 2.1.1 Superprodução A superprodução ocorre quando o que é produzido excede o que é pedido pelo cliente. Isto ocasiona uma despesa desnecessária de matérias-primas, mão-de-obra, ocupação de armazenamento, transporte e estoque elevado. Segundo Dennis (2007), quando o mercado está em evolução este desperdício pode nem ser preocupante, no entanto quando a procura sofre uma baixa, os impactos deste desperdício se tornam agravantes. Pode ser caracterizado como um dos principais desperdícios, visto que este pode encobrir os demais problemas da indústria.
2.1.2 Estoque Um estoque alto é um resultado típico da superprodução na organização. O exagero de matérias-primas, produtos prontos ou produtos em fase de acabamento, resultam no elevado tempo de aprovisionamento, dos custos de transporte e armazenamento. A saída necessita elevar a versatilidade e a eficácia de resposta das companhias e dos seus fornecedores (Dudbridge, 2011). 2.1.3 Tempo de espera Indica que o espaço de tempo em que o material, pessoas, equipamento ou informação se encontram indisponíveis, quando são precisos. Isso se dá pelo fato de haver problemas nos equipamentos, reprocesso de peças, alteração de ferramentas de trabalho, materiais e mão de obra represados. Segundo Dudbridge (2011), o tempo em que nada é produzido ocasiona um desperdício de todos aqueles recursos que devem ser pagos, proventos dos colaboradores, a energia elétrica e os demais custos fixos. 2.1.4 Transporte Esse desperdício ocorre quando existe um movimento de peças que não acrescentam valor. Isso significa que foi realizado um mau planejamento dos layouts, resultando em movimentações de produtos mais do que se precisa. O exagero de movimentação de materiais acontece, por exemplo, quando o armazenamento foi realizado de forma desorganizada. Corrigir este desperdício é realizar as melhorias ao layout, aplicar a sinergia aos processos e ordenar os postos de trabalho (Dennis, 2007). 2.1.5 Superprocessamento O excesso de etapas num processo ocorre quando, no meio do processo de produção, há esforços que não acrescentam valor a um produto ou serviço. Este tipo
Figura 1 - Pirâmide dos 4Ps de Liker. Fonte: Adaptado de Liker e Franz (2013). Para Ballé et al. (2019), as organizações necessitam entender qual é ideia do Lean , uma ferramenta estratégica de negócio, onde as alterações irão impactar positivamente nos processos de todo o ciclo produtivo. O pensamento Lean traduz-se em elaborar de forma otimizada os processos da melhor maneira possível, fortalecendo uma cultura para resolução de problemas. 2.2 METODOLOGIA A A MA3, gerenciamento A3, relatório A3 ou simplesmente A3 é um método que a Toyota usa para solucionar problemas. Entender e aprender com os problemas é crucial, para proporcionar a melhoria contínua nos processos industriais. (SOBEK II; SMALLEY, 2011 apud PRIORI; SAURIN, 2020). O início do nome A3, de acordo com Shook (2008), dá-se a partir das dimensões da folha utilizada para a anotação do projeto de melhoria, sendo assim, um papel no formato A3 (297x420 mm). Neste A3 é ilustrado um diagrama que demonstra como se operam as atividades, apontando com objetividade o problema na situação atual. Quem desenvolver o relatório terá que calcular a gravidade do problema. Não há relevância no formato do relatório, mas sim a inteligência utilizada que leva principalmente ao ciclo do PDCA (Liker, 2004). Segundo Slack et. al ., (2018) o Plan Do Check Act (PDCA) de forma simples é definido como um ciclo repetitivo da
melhoria contínua com um curso de etapas que são executadas de maneira cíclica com o intuito de aperfeiçoar a performance das etapas. Para Shook (2008) a capacidade do PDCA é absolutamente empreendida na abordagem sistemática do MA3. Para Pereira et al. (2019), o A3 possibilita exibir informações significativas sobre um problema específico ou um conjunto de problemas. Na literatura científica o modelo A3 tem diferentes estruturas, porém todas são baseadas no ciclo PDCA. Na MA3 é efetuado a descrição da situação atual, exploração da causa raiz do problema, estudo de contramedidas e evidencia que o problema foi realmente resolvido (RIBEIRO, 2012). A MA3, além de expor a aparência das etapas para resolução do problema, ajuda a manter a equipe atrelada ao foco principal, que é a meta. A aparência do A pode diversificar conforme a organização, porém a sua metodologia é a mesma (OLIVEIRA et al ., 2014). A Figura 2 ilustra o fluxo que o relatório segue. Figura 2 - Fluxo típico de um relatório. Fonte: Shook ( 20 08).