
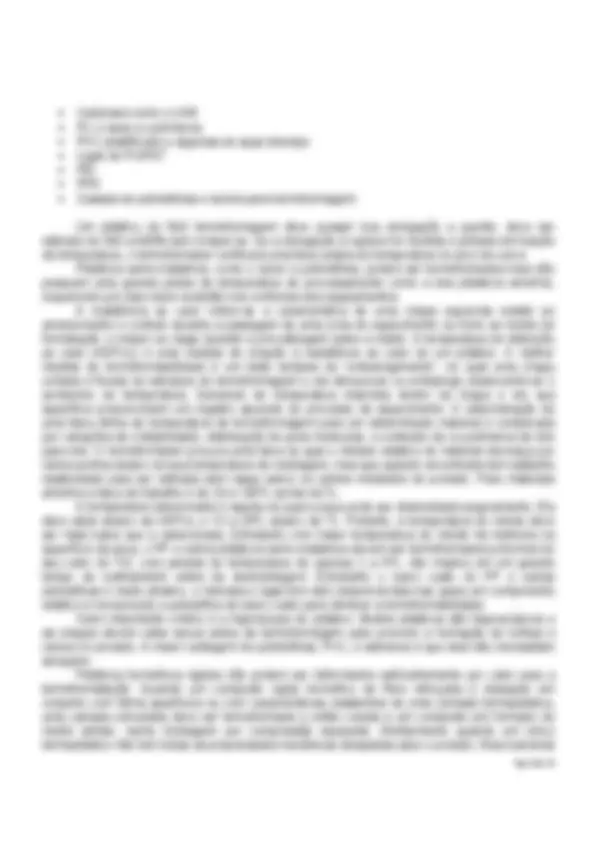
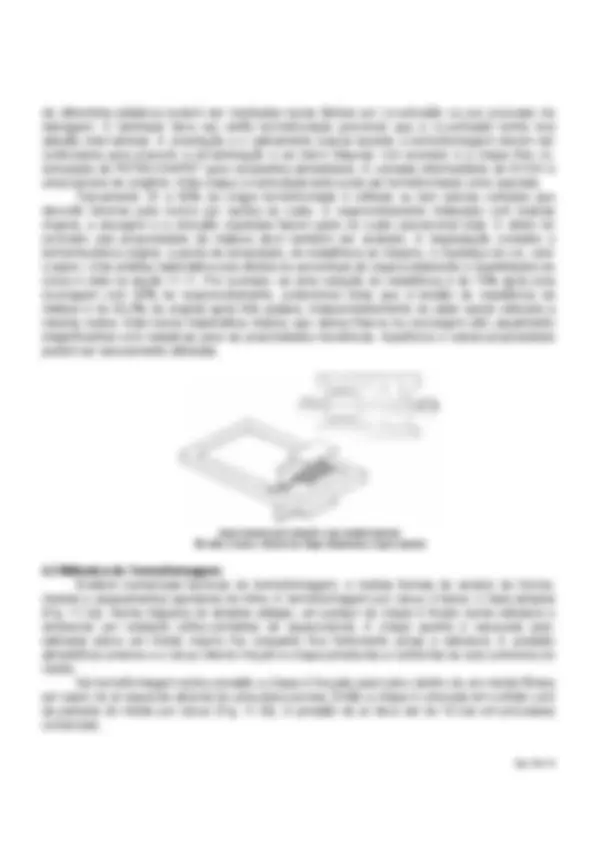
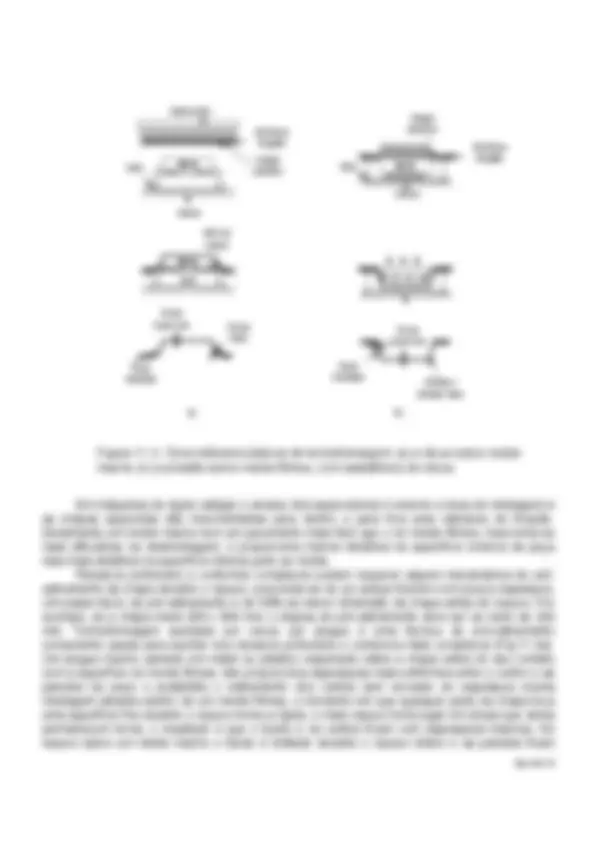
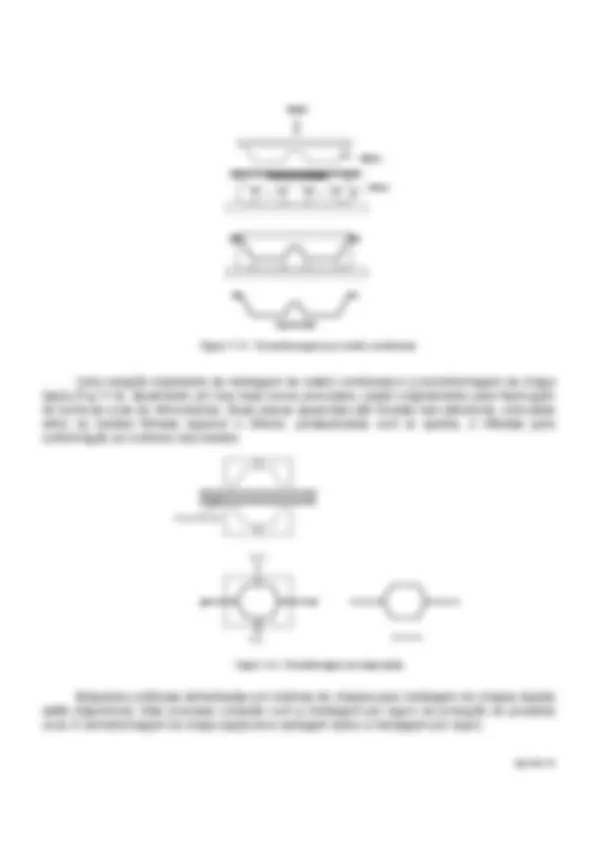
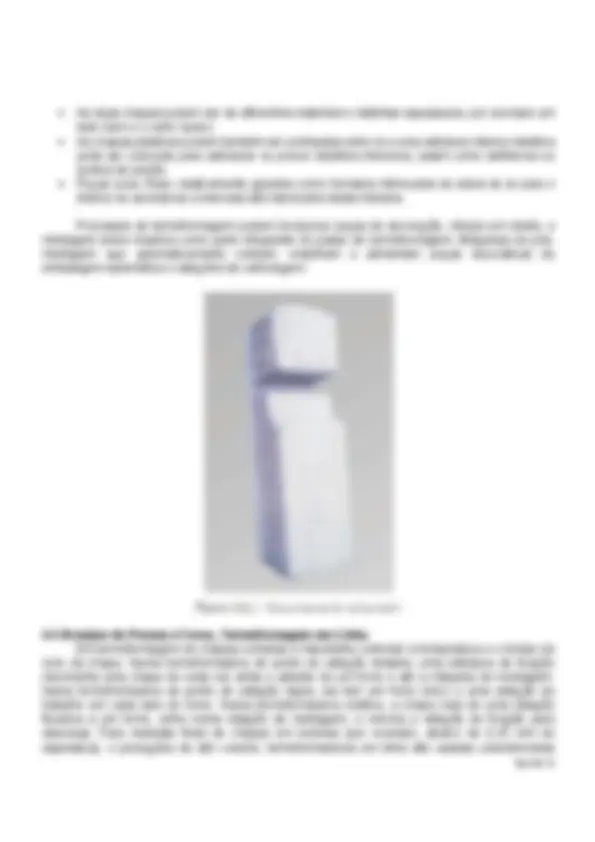
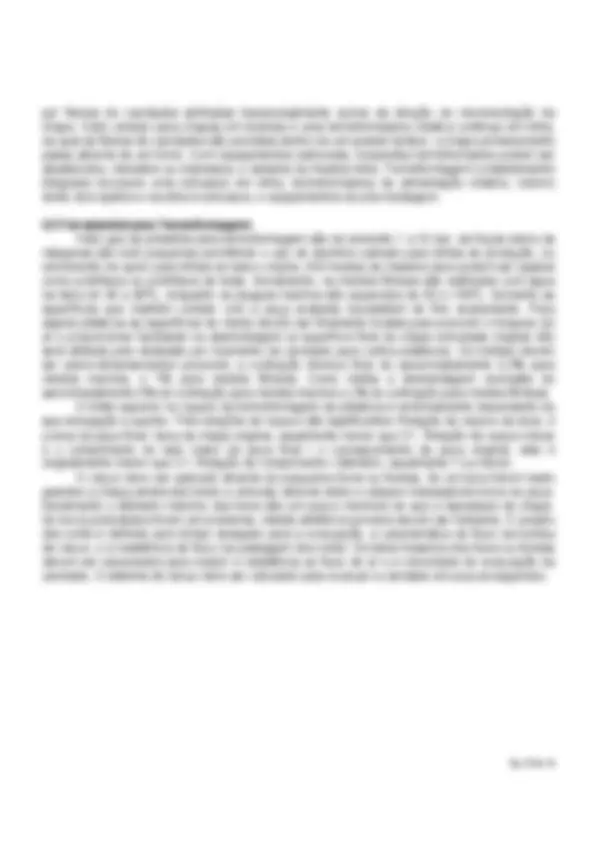
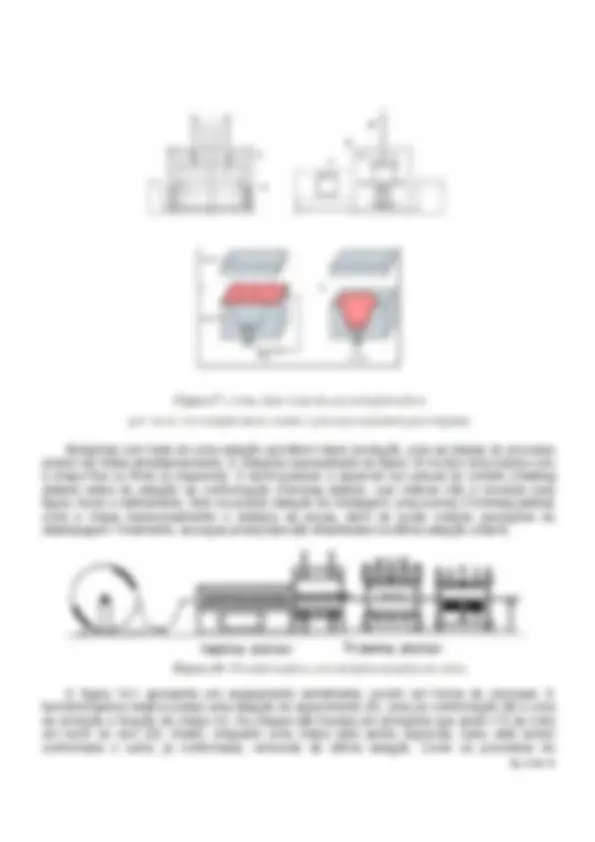
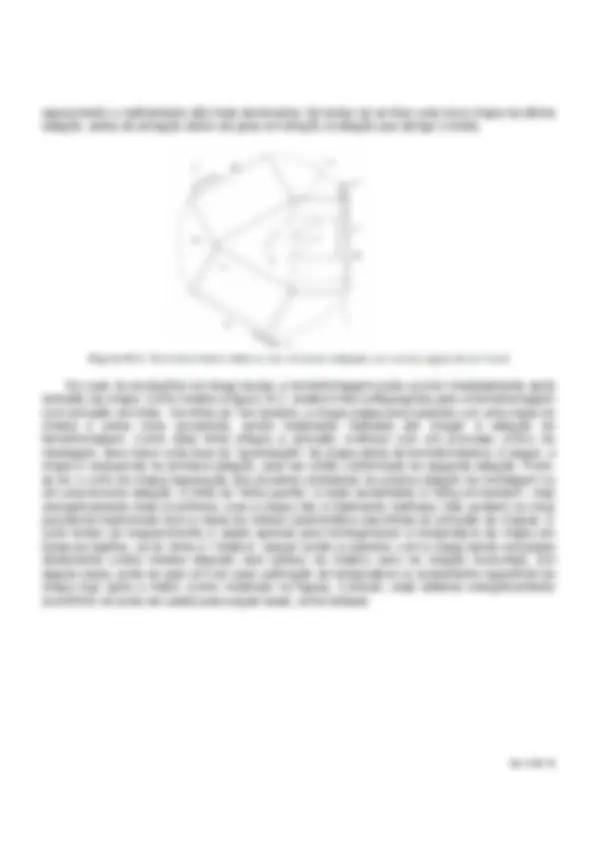
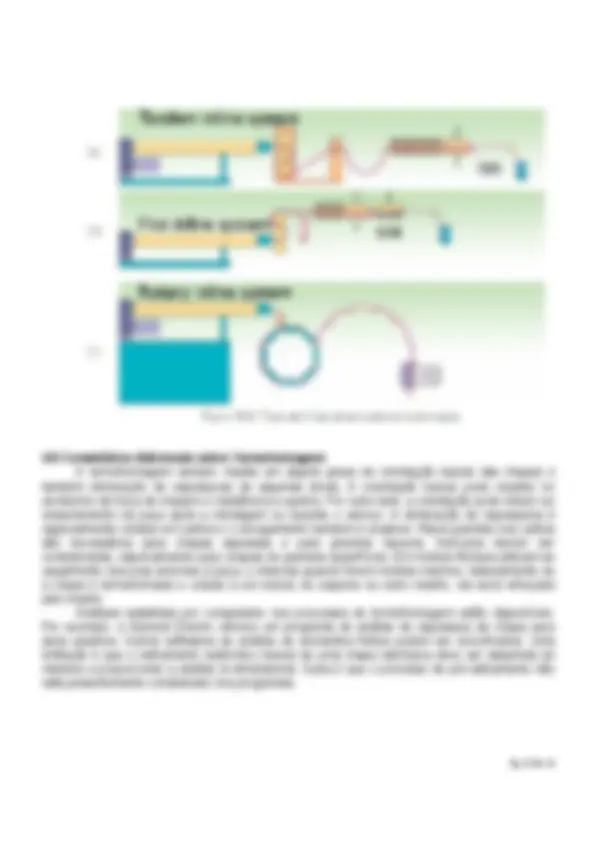
Estude fácil! Tem muito documento disponível na Docsity
Ganhe pontos ajudando outros esrudantes ou compre um plano Premium
Prepare-se para as provas
Estude fácil! Tem muito documento disponível na Docsity
Prepare-se para as provas com trabalhos de outros alunos como você, aqui na Docsity
Os melhores documentos à venda: Trabalhos de alunos formados
Prepare-se com as videoaulas e exercícios resolvidos criados a partir da grade da sua Universidade
Responda perguntas de provas passadas e avalie sua preparação.
Ganhe pontos para baixar
Ganhe pontos ajudando outros esrudantes ou compre um plano Premium
Comunidade
Peça ajuda à comunidade e tire suas dúvidas relacionadas ao estudo
Descubra as melhores universidades em seu país de acordo com os usuários da Docsity
Guias grátis
Baixe gratuitamente nossos guias de estudo, métodos para diminuir a ansiedade, dicas de TCC preparadas pelos professores da Docsity
Termoformagem é um processo que consiste em dar forma a produtos de chapas termoplásticas extrudadas através de aquecimento e conformação a um molde com auxílio de vácuo ou baixa pressão. Esse processo é amplamente utilizado na indústria e pode ser aplicado a diferentes tipos de plásticos, como estirenos, celuloses, pc, pvc, pei, ppe e poliolefinas. Neste documento, são apresentados os métodos de termoformagem, os fatores que influenciam o processo, como a resistência ao calor e a umidade, e as relações de repuxe significativas. Além disso, são discutidos os diferentes tipos de termoformagem, como a termoformagem de chapa dupla e a termoformagem sobre insertos.
Tipologia: Notas de estudo
1 / 16
Esta página não é visível na pré-visualização
Não perca as partes importantes!
PROCESSOS ESPECIAIS DE TRANSFORMAÇÃO TERMOFORMAGEM Prof. Roberto Ferreira 2017 Autor: Harold Belofsky Editora: Hanser Publishers, Munich, Vienna, New York Plastics: Products Design and Engeneering Process Chapter 11: Another Plastics Molding Process
4.2 Processos de Termoformagem Termoformagem diz respeito a um grupo de processos que conformam ou repuxam produtos de chapas termoplásticas extrudadas. Por amolecimento da chapa com calor, e então forçando-a a conformar-se ao contorno de um molde com auxílio de vácuo ou baixa pressão, formas simples são fabricadas economicamente. As vantagens básicas são o baixo custo do ferramental, o baixo tempo de resposta nos testes com os protótipos, os baixos custos de partida, e baixos custos de equipamentos para lotes pequenos. Existe analogia na moldagem de chapas metálicas e poliméricas. Para a avaliação das variações de processos, é usualmente imaginado o mercado de produtos termoformados dividido em dois grupos: grandes volumes, produtos de chapas muito finas para embalagens e recipientes descartáveis (bandejas, sacos bolha, pequenos recipientes), e pequenos volumes ou produtos pesados (placas de sinalização, portas de refrigeradores, tampas de reboques, poltronas, pias e banheiras). Produtos de grande volume e baixo custo para recipientes são produzidos a partir de bobinas de chapas muito finas utilizando matrizes de termoformagem que possuem centenas de cavidades e com termoplásticos de relativa rigidez. Grandes peças de pequeno volume geralmente são feitas em cavidades simples utilizando chapas espessas pré-cortadas. Peças de grande área fabricadas de bobinas de compostos espumados e chapas de termoplásticos sólidos como pias podem ser também termoformadas. Os termoformadores competem fortemente com mercados anteriormente dominados por injetores e sopradores. A temperatura para termoformagem de materiais semi-cristalinos é um pouco maior que a sua Tc (temp. de cristalização), e para termoplásticos amorfos está próxima da sua Tm (temp. de fusão). Para termoplásticos amorfos ou de baixa cristalinidade, a deformação em temoformagem toma lugar na região visco-elástica e é bloqueada por resfriamento abaixo da Tc. Entretanto, a deformação elástica da termoformagem é recuperada (memória elástica) após aquecimento acima da Tc; isto pode causar deformações de peças, logo acima das temperaturas de serviço muito próximas da Tc. A termoformagem de plásticos amorfos é controlada tão facilmente quanto para plásticos de alta cristalinidade por causa da grande faixa de temperaturas de trabalho. São os seguintes os plásticos facilmente termoformados, todos disponíveis em chapas e filmes extrudados: Estirenos ou co-polímeros de estireno, como o ABS Acrílicos como o PMMA
de diferentes plásticos podem ser montadas numa lâmina por co-extrusão ou por processo de dublagem. O laminado deve ser então termoformado prevendo que a co-extrusão tenha boa adesão inter-laminar. A orientação e o estiramento biaxial durante a termoformagem devem ser controlados para prevenir a de-laminação e as micro fissuras. Um exemplo é a chapa fina co- extrudada de PET/EVOH/PET para recipientes alimentares. A camada intermediária de EVOH é uma barreira de oxigênio. Esta chapa co-extrudada tanto pode ser termoformada como soprada. Tipicamente 25 a 50% da chapa termoformada é refilada ou tem sobras cortadas que deverão retornar para reciclo por razões de custo. O reaproveitamento misturado com resinas virgens, a secagem e a extrusão repetidas fazem parte do custo operacional total. O efeito do reciclado nas propriedades da mistura deve também ser avaliado. A degradação oxidante e termomecânica origina: a perda de tenacidade, de resistência ao impacto, e mudança de cor, odor e sabor. Uma análise matemática dos efeitos do percentual de reaproveitamento e quantidades de ciclos é vista na seção 11.11. Por exemplo, se uma redução de resistência é de 10% após uma reciclagem com 50% de reaproveitamento, poderemos notar que a tensão de resistência da mistura é de 83,5% da original após três passes, independentemente de estar sendo utilizada a mesma resina. Esta teoria matemática implica que danos físicos na reciclagem são usualmente insignificantes com ressalvas para as propriedades mecânicas. Aparência e outras propriedades podem ser severamente afetadas. Aquecimento por radiação com sombreamento. Escudos acima e abaixo da chapa diminuem o aquecimento 4.3 Métodos de Termoformagem Existem numerosas técnicas de termoformagem, e muitas formas de arranjo de fornos, moldes e equipamentos auxiliares de linha. A termoformagem por vácuo é talvez o mais simples (Fig. 11.3a). Numa máquina de simples estágio, um pedaço de chapa é fixado numa estrutura e amolecido por radiação (infra-vermelha) de aquecedores. A chapa quente é repuxada (pré- estirada) sobre um molde macho frio enquanto fica fortemente presa a estrutura. A pressão atmosférica externa e o vácuo interno forçam a chapa amolecida a conformar-se aos contornos do molde. Na termoformagem sobre pressão a chapa é forçada para baixo dentro de um molde fêmea por sopro de ar aquecido através de uma placa porosa. Então a chapa é colocada em contato com as paredes do molde por vácuo (Fig. 11.3b). A pressão de ar deve ser de 10 bar em processos comerciais.
Aquecedor Estrutura fixação Chapa plástica Molde Vácuo Sêlo Molde Sêlo de vácuo Peça formada Áreas espessas (^) Áreas finas Estrutura fixação Chapa plástica Molde Vácuo Sêlo Áreas espessas Peça formada (^) Cantos e bordas finas Figura 11.3 - Dois métodos básicos de termoformagem: a) a vácuo sobre molde macho, b) a pressão sobre molde fêmea, com assistência de vácuo. a) b) Em máquinas de duplo estágio o arranjo dos aquecedores é externo a área de moldagem e as chapas aquecidas são movimentadas para dentro e para fora pela estrutura de fixação. Geralmente um molde macho tem um puxamento mais fácil que o do molde fêmea, mas torna-se mais dificultoso na desmoldagem, e proporciona menos detalhes na superfície externa da peça mas mais detalhes na superfície interna junto ao molde. Rebaixos profundos e contornos complexos podem requerer alguns mecanismos de pré- estiramento da chapa durante o repuxe, prevenido-se de os cantos ficarem com pouca espessura. Um passo típico de pré-estiramento é de 50% da menor dimensão da chapa antes do repuxe. Por exemplo, se a chapa mede 400 x 800 mm, o degrau de pré-estiramento deve ser ao redor de 200 mm. Termoformagem auxiliada por vácuo por plugue é uma técnica de pré-estiramento comumente usada para auxiliar nos rebaixos profundos e contornos mais complexos (Fig.11.4a). Um plugue macho usinado em metal ou plástico espumado estira a chapa antes do seu contato com a superfície do molde fêmea. Isto proporciona espessuras mais uniformes entre o centro e as paredes da peça e possibilita o estiramento dos cantos sem excesso de espessura (numa moldagem simples dentro de um molde fêmea, o momento em que qualquer parte da chapa toca uma superfície fria durante o repuxe torna-a rígida, e mais repuxe toma lugar em áreas que ainda permanecem livres; o resultado é que o fundo e os cantos ficam com espessuras maiores. No repuxe sobre um molde macho o fundo é limitado durante o repuxe inteiro e as paredes ficam
Alivio de ar Ar Alivio de ar Vácuo Ar Paredes unif ormes Estrutura fixação Figura 11.4 - Métodos básicos de termoformagem: a) a vácuo assistido por plugue. Veja que o contorno do plugue não toca no fundo da peça repuxada. b) modelagem por onda. c) bolha pressurizada, modelagem por retorno á vácuo Vent Ar Sêlo Vent Escape de ar Vent Ar Espesso Peça formada Sêlo Cavidade do molde Ar Pressão de ar p/moldagem (qudo. usado) Ar Sêlo Caixa de pressão Ar Vácuo a) b) c)
Figura 11.5 - Termoformagem por matriz combinada Macho Fêmea Embolo Vents p/ar confinado Peça formada Uma variação importante da moldagem de matriz combinada é a termoformagem de chapa dupla (Fig.11.6), atualmente um dos mais novos processos, usado originalmente para fabricação de bonecas ocas de nitrocelulose. Duas placas aquecidas são fixadas nas estruturas, colocadas entre os moldes fêmeas superior e inferior, pressurizadas com ar quente, e infladas para conformação ao contorno dos moldes. Chapas aquecidas Figura 11.6 - Termoformagem de chapa dupla Vácuo Vácuo Peça pronta Máquinas continuas alimentadas por bobinas de chapas para moldagem de chapas duplas estão disponíveis. Este processo compete com a moldagem por sopro na produção de produtos ocos. A termoformagem de chapa dupla leva vantagem sobre a moldagem por sopro:
por fileiras de cavidades alinhadas transversalmente acima da direção de movimentação da chapa. Outro arranjo para chapas em bobinas é uma termoformadora rotativa continua em linha, na qual as fileiras de cavidades são previstas dentro de um grande tambor, a chapa primeiramente passa através de um forno. Com equipamentos adicionais, recipientes termoformados podem ser abastecidos, rotulados ou impressos, e selados na mesma linha. Termoformagem completamente integrada incorpora uma extrusora em linha, termoformadora de alimentação rotativa, retorno direto dos rejeitos e recortes à extrusora, e equipamentos de pós-moldagem. 4.5 Ferramental para Termoformagem Visto que as pressões para termoformagem são de somente 1 a 10 bar, as forças sobre as máquinas são bem pequenas permitindo o uso de alumínio usinado para linhas de produção, ou enchimento de epóxi para linhas de baixo volume. Até moldes de madeira dura podem ser usados como protótipos ou protótipos de teste. Geralmente, os moldes fêmeas são resfriados com água na faixa de 40 a 90ºC, enquanto os plugues machos são aquecidos de 60 a 150ºC. Somente as superfícies que mantém contato com a peça acabada necessitam de fino acabamento. Para alguns plásticos as superfícies do molde devem ser finamente lixadas para prevenir o bloqueio de ar e proporcionar facilidade na desmoldagem (a superfície final da chapa extrudada original não será afetada pelo desbaste por lixamento da cavidade para certos plásticos). Os moldes devem ser sobre-dimensionados prevendo a contração térmica final de aproximadamente 0,5% para moldes machos, e 1% para moldes fêmeas. Como média a desmoldagem necessita de aproximadamente 5% de contração para moldes machos e 2% de contração para moldes fêmeas. O limite superior no repuxe da termoformagem de plásticos é extremamente dependente de sua elongação a quente. Três relações de repuxe são significantes: Relação de repuxe da área, é a área da peça final / área da chapa original, usualmente menor que 5:1. Relação de repuxe linear é o comprimento do lado maior da peça final / o correspondente da peça original, esta é originalmente menor que 3:1. Relação de comprimento / diâmetro, usualmente 1 ou menor. O vácuo deve ser aplicado através de pequenos furos ou fendas. Se os furos forem muito grandes a chapa amolecida tende a extrudar através deles e adquire indesejáveis bicos na peça. Geralmente o diâmetro máximo dos furos são um pouco menores do que a espessura da chapa. Se bicos protudados forem um problema, metais sintéticos porosos devem ser tentados. O projeto dos vents é definido pelo tempo desejado para a evacuação, a característica de fluxo da bomba de vácuo, e a resistência de fluxo na passagem dos vents. Os lados traseiros dos furos ou fendas devem ser escareados para reduzir a resistência ao fluxo de ar e a velocidade de evacuação da cavidade. O sistema de vácuo deve ser calculado para evacuar a cavidade em poucos segundos.
4.6 Aquecimento Muitos transformadores preferem aquecimento por radiação infra-vermelha visto que os aquecedores de quartzo podem ser rapidamente ligados e desligados, e malhas simples podem ser arranjadas sobre os aquecedores para seletividade ou associação de aquecimento das chapas. Isto é, máscaras podem ser recortadas em janelas protegidas de alumínio ou outro material para reduzir ou prevenir a radiação de calor de atingir uma área em particular. A superfície de radiação deve ser apta para alcançar no mínimo 540ºC, e ter uma capacidade de 30 a 60 Kw/m² (9540 a 19080 Btu/ft².h). O ideal é a fonte de radiação de calor emitir um comprimento de onda que combine com os picos de espectro de absorção de infra-vermelho da chapa de plástico. Se a fonte e a chapa tiverem características muito diferenciadas, muito da energia é re-radiada e eventualmente perdida, reduzindo a eficiência geral de energia. Para muitos plásticos os picos de absorção estão em faixas de 2 a 4m, correspondendo de 1100 a 800ºC, respectivamente, na fonte de radiação. As lâmpadas de quartzo são o único tipo que encontra esta faixa, elas tem também um tempo de resposta de poucos segundos e vida útil de 8000 a 10000 horas. Para instalações de baixo custo, outros tipos de aquecedores são usados, como placas cerâmicas com chama de gás, fios de níquel cromo encamisados em haste metálica, e ainda fios de níquel/cromo nus para bem baixos custos de set-ups. Para aquecimento radiante de dupla superfície em chapas finas, o tempo de aquecimento é linearmente proporcional a espessura da chapa, e o coeficiente total de transferência de calor é de 0,05 a 0,10 Kw/m².ºC. Para chapas espessas ou em convecção de ar forçado, o tempo de aquecimento é proporcional ao quadrado da espessura da chapa, e o coeficiente total de
Máquinas com mais de uma estação permitem maior produção, pois as etapas do processo podem ser feitas simultaneamente. A máquina representada na figura 18 recebe uma bobina com a chapa fina ou filme (à esquerda). O semi-acabado é aquecido por placas de contato (Heating station) antes da estação de conformação (Forming station), cujo método não é revelado pela figura. Após o resfriamento, feito na própria estação de moldagem, uma prensa (Trimming station) corta a chapa transversalmente e destaca as peças, além de poder realizar operações de estampagem. Finalmente, as peças produzidas são empilhadas na última estação (Stack). A figura 19.1 apresenta um equipamento semelhante, porém em forma de carrossel. A termoformadora rotativa possui uma estação de aquecimento (A), uma de conformação (B) e uma de remoção e fixação da chapa (C). As chapas são fixadas em armações que giram 1/3 de volta em torno do eixo (D). Assim, enquanto uma chapa está sendo aquecida, outra está sendo conformada e outra, já conformada, removida da última estação. Como os processos de
aquecimento e resfriamento são mais demorados, há tempo de se fixar uma nova chapa na última estação, antes da armação sobre ela girar em direção à estação que abriga o molde. No caso de produções em larga escala, a termoformagem pode ocorrer imediatamente após extrusão da chapa. Como mostra a figura 19.2, existem três configurações para a termoformagem com extrusão em linha. Na linha (a) “em tandem, a chapa passa pela calandra, por uma mesa de roletes e pelos rolos puxadores, sendo totalmente resfriada até chegar à estação de termoformagem. Como essa linha integra a extrusão contínua com um processo cíclico de moldagem, deve haver uma área de “acumulação” da chapa antes da termoformadora. A seguir, a chapa é reaquecida na primeira estação, para ser então conformada na segunda estação. Pode- se ter o corte da chapa (separação dos produtos moldados) na própria estação de moldagem ou em uma terceira estação. A linha (b) “linha quente” é muito semelhante à “linha em tandem”, mas energeticamente mais econômica, pois a chapa não é totalmente resfriada. Não existem os rolos puxadores tradicionais nem a mesa de roletes característica das linhas de extrusão de chapas. O curto tempo de reaquecimento é usado apenas para homogeneizar a temperatura da chapa em todas as regiões. Já na linha c) “rotativa”, sequer existe a calandra, com a chapa sendo extrudada diretamente contra moldes disposto num tambor de rotativo (eixo de rotação horizontal). Em alguns casos, pode-se usar um rolo para calibração de temperatura ou acabamento superficial da chapa logo após a matriz (como mostrado na figura). Contudo, esse sistema energeticamente econômico só pode ser usado para peças rasas, como tampas.
Exemplo Uma bandeja quadrada, profunda, é termoformada e a espessura final da peça deve ser estimada. A espessura original da chapa é de 2mm (Fig. 11.8). Solução: a) Assumindo-se que um pré-estiramento uniforme e um processo de repuxe como o de moldagem de onda é usado (Fig.11.4b), e que a peça final adquire uma espessura plenamente uniforme; então a espessura média da peça tf pode ser encontrada pela relação de repuxe da área: Base de 0,769 x 0,769 m Espessura original da chapa = to = 2 mm Topo de 1 x 1 m 0,231 m tf Fig. 11.8 - Dimensões para bandeja termoformada usada no exemplo 11.1. Ao=área inicial da chapa (não incluida a área da fixação) = 1m² Af= área final da peça = área do fundo + área paredes laterais ; Af = 0,7692 + {4. (0,231) x [(1 + 0,769) / 2]}; Af = 0,591 + 0,817 = 1,408 m² tf = espessura original x (área original / área final) tf = to. (Ao / Af) = 2,0 x (1 / 1,408) = 1,42 mm b) Agora, assumindo-se que ao invés disso a peça é fabricada por simples moldagem sobre um molde macho, como o da Fig.11.1a. Considerando-se a pior das hipóteses, onde o centro permanece com a espessura original de 2 mm, e as paredes laterais são repuxadas do restante da chapa original: área das paredes laterais = 0,817 m² = Af área do fundo central = 0,591 m² as paredes laterais são repuxadas de 1 m² - 0,591 m² = 0,409 m² = Ao a espessura das paredes laterais será: tf = to x (Ao / Af); tf = 2 x (Ao / Af) = 2,0 x (0,409 / 0,817) = 1 mm Esclarecendo, a não uniformidade da espessura das paredes no caso b) é muito grande e um processo mais sofisticado de termoformagem, como o do caso a), justifica-se mesmo considerando-se que o aumento de repuxe seja de somente 20% da maior dimensão.