
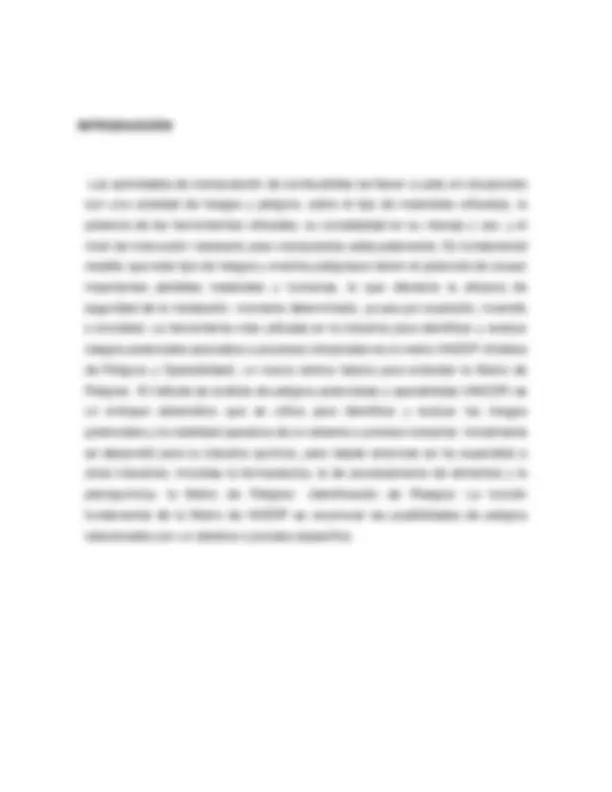
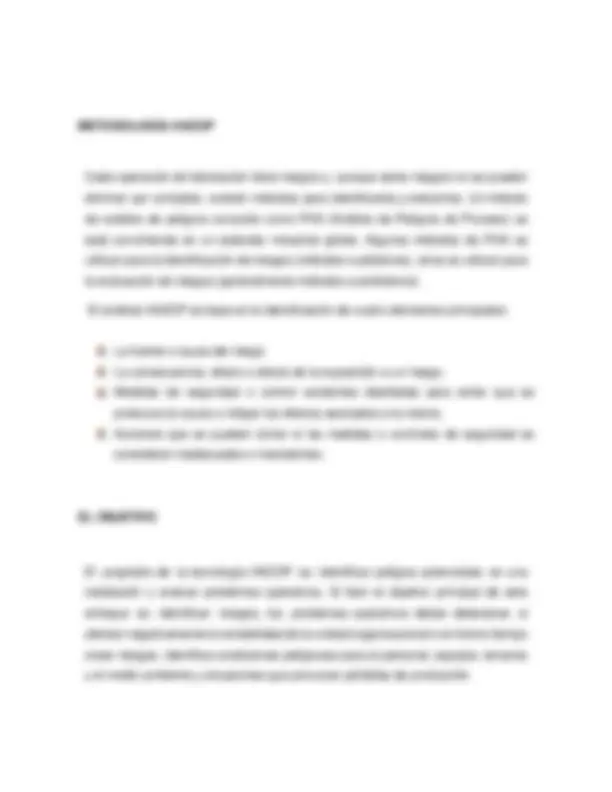
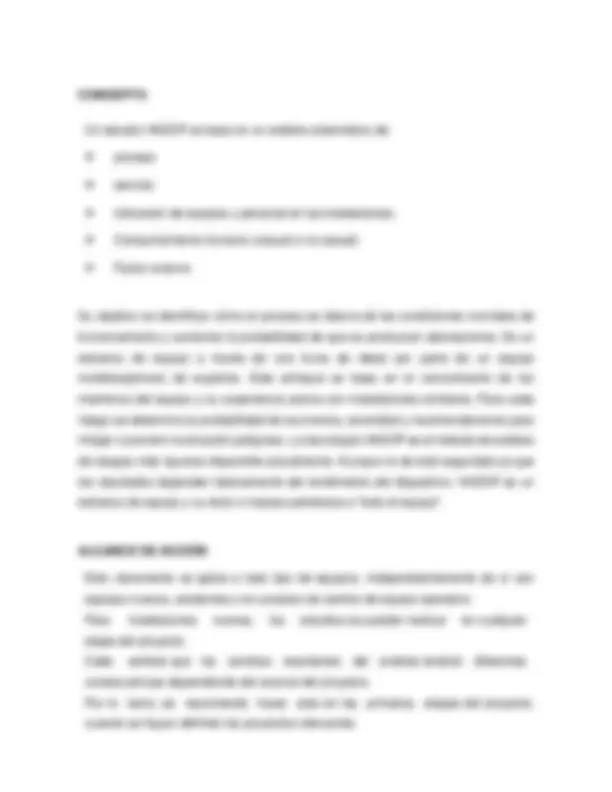
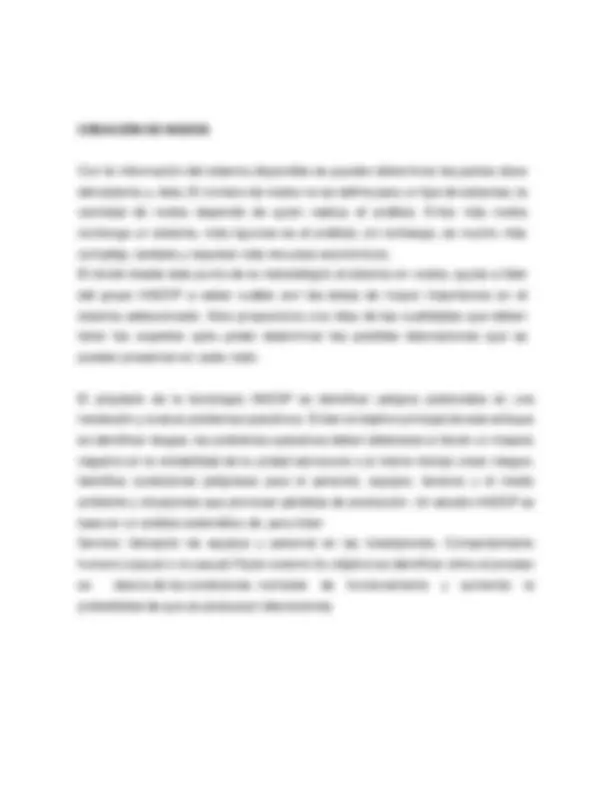
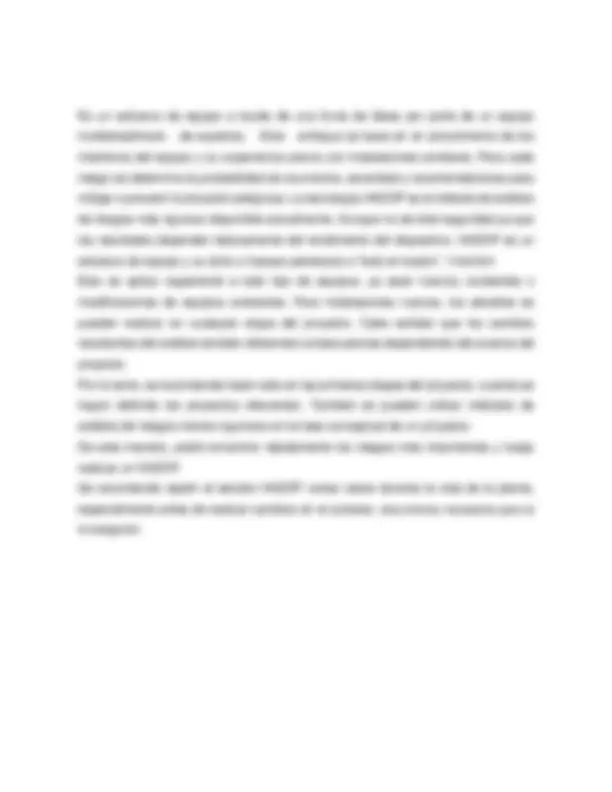
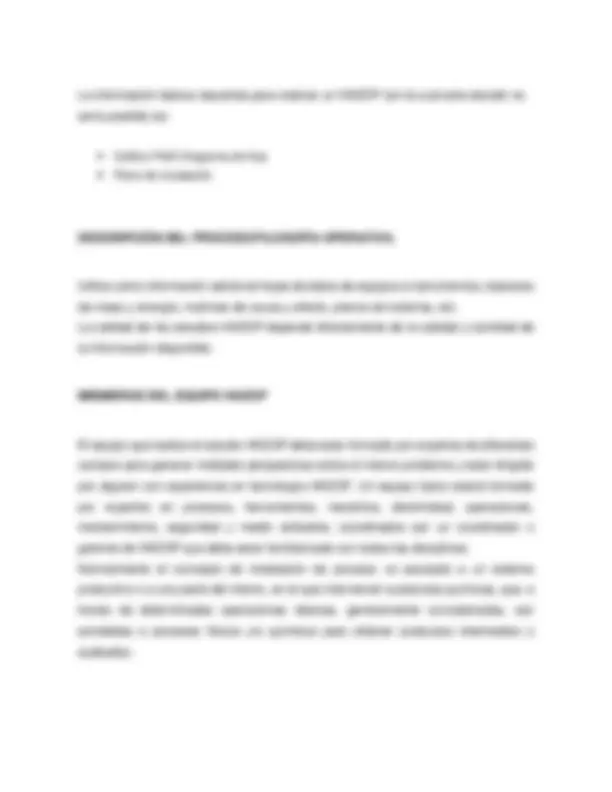
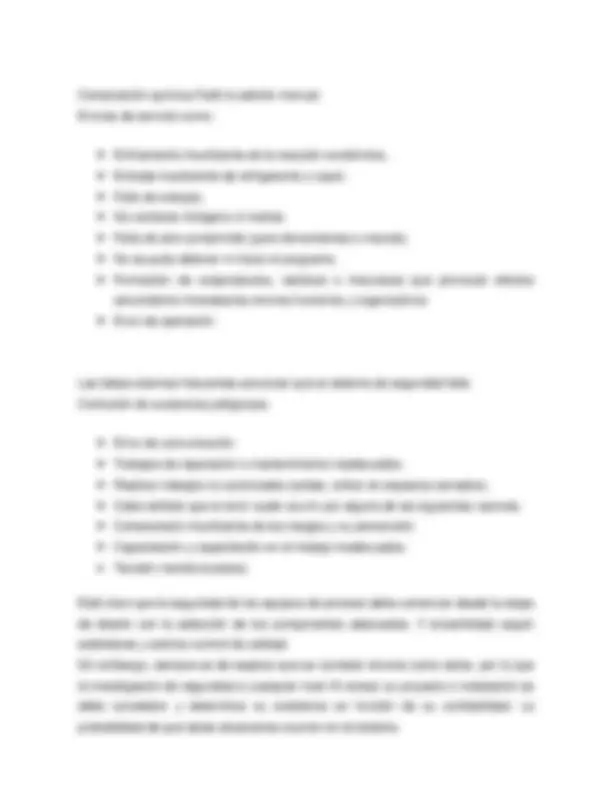
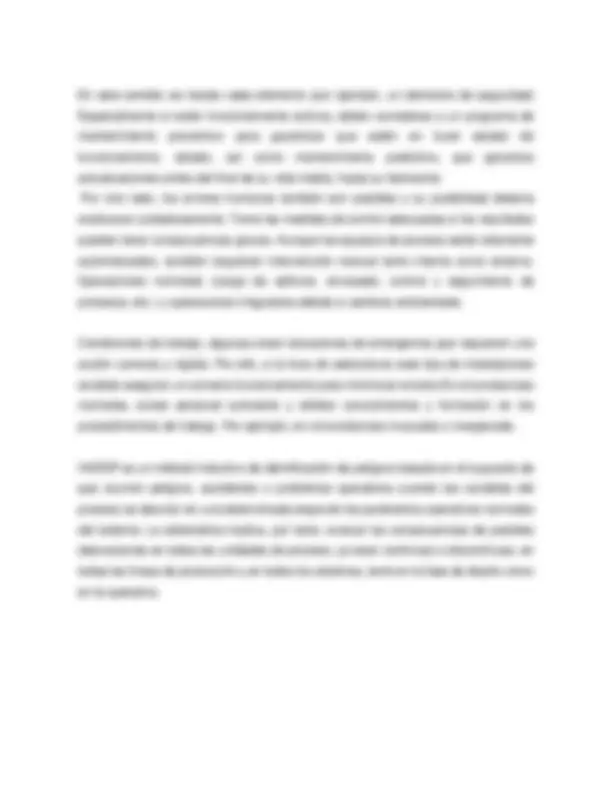
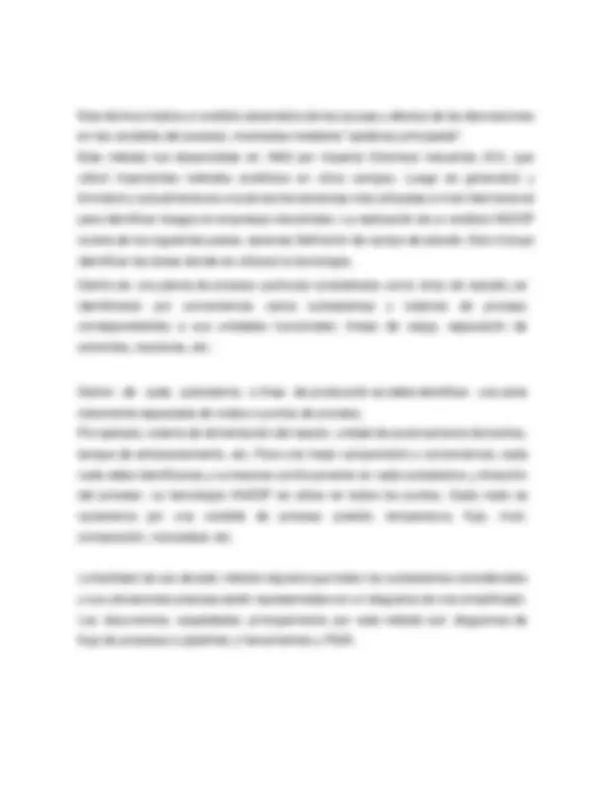
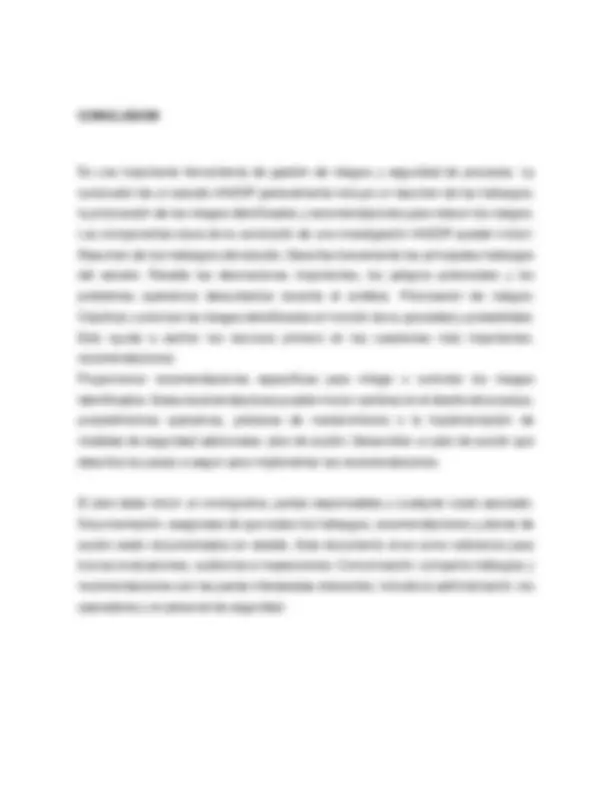
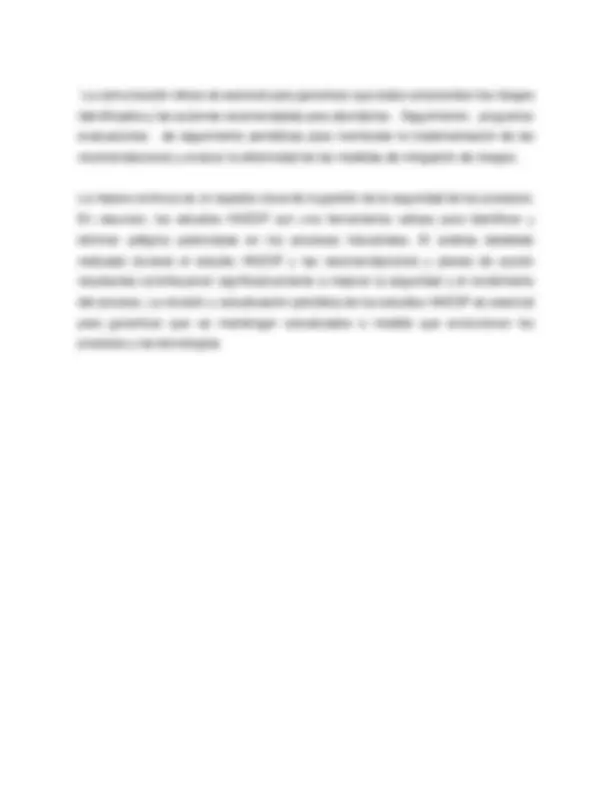
Prepara tus exámenes y mejora tus resultados gracias a la gran cantidad de recursos disponibles en Docsity
Gana puntos ayudando a otros estudiantes o consíguelos activando un Plan Premium
Prepara tus exámenes
Prepara tus exámenes y mejora tus resultados gracias a la gran cantidad de recursos disponibles en Docsity
Prepara tus exámenes con los documentos que comparten otros estudiantes como tú en Docsity
Los mejores documentos en venta realizados por estudiantes que han terminado sus estudios
Estudia con lecciones y exámenes resueltos basados en los programas académicos de las mejores universidades
Responde a preguntas de exámenes reales y pon a prueba tu preparación
Consigue puntos base para descargar
Gana puntos ayudando a otros estudiantes o consíguelos activando un Plan Premium
Comunidad
Pide ayuda a la comunidad y resuelve tus dudas de estudio
Descubre las mejores universidades de tu país según los usuarios de Docsity
Ebooks gratuitos
Descarga nuestras guías gratuitas sobre técnicas de estudio, métodos para controlar la ansiedad y consejos para la tesis preparadas por los tutores de Docsity
El análisis de peligros y operabilidad (HAZOP) es una metodología ampliamente utilizada en la industria para identificar y evaluar riesgos potenciales en procesos industriales. La matriz HAZOP proporciona un marco teórico básico para este análisis, centrándose en la identificación de riesgos. El proceso implica la revisión sistemática de los procesos, considerando desviaciones de las condiciones normales de operación y evaluando sus posibles causas y consecuencias. Un equipo multidisciplinario lleva a cabo este análisis, que requiere información detallada sobre el proceso. La herramienta HAZOP es especialmente relevante en industrias como la química, farmacéutica y alimentaria, donde los procesos de fabricación pueden presentar diversos problemas. TÜV SÜD ofrece servicios integrales de análisis HAZOP, incluyendo la mitigación de riesgos, el análisis remoto y la evaluación de riesgos semicuantitativa, adaptados a las necesidades específicas de cada proceso. El HAZOP es una valiosa herra
Tipo: Resúmenes
1 / 19
Esta página no es visible en la vista previa
¡No te pierdas las partes importantes!
Cada operación de fabricación tiene riesgos y, aunque estos riesgos no se pueden eliminar por completo, existen métodos para identificarlos y reducirlos. Un método de análisis de peligros conocido como PHA (Análisis de Peligros de Proceso) se está convirtiendo en un estándar industrial global. Algunos métodos de PHA se utilizan para la identificación de riesgos (métodos cualitativos), otros se utilizan para la evaluación de riesgos (generalmente métodos cuantitativos). El análisis HAZOP se basa en la identificación de cuatro elementos principales: La fuente o causa del riesgo La consecuencia, efecto o efecto de la exposición a un riesgo. Medidas de seguridad o control existentes diseñadas para evitar que se produzca la causa o mitigar los efectos asociados a la misma. Acciones que se pueden tomar si las medidas o controles de seguridad se consideran inadecuados o inexistentes. EL OBJETIVO El propósito de la tecnología HAZOP es identificar peligros potenciales en una instalación y evaluar problemas operativos. Si bien el objetivo principal de este enfoque es identificar riesgos, los problemas operativos deben detectarse si afectan negativamente la rentabilidad de la unidad organizacional o al mismo tiempo crean riesgos. Identifica condiciones peligrosas para el personal, equipos, terceros y el medio ambiente y situaciones que provocan pérdidas de producción.
Un estudio HAZOP se basa en un análisis sistemático de: ➢ proceso ➢ servicio ➢ Ubicación de equipos y personal en las instalaciones. ➢ Comportamiento humano (casual o no casual) ➢ Factor externo Su objetivo es identificar cómo el proceso se desvía de las condiciones normales de funcionamiento y aumentar la probabilidad de que se produzcan desviaciones. Es un esfuerzo de equipo a través de una lluvia de ideas por parte de un equipo multidisciplinario de expertos. Este enfoque se basa en el conocimiento de los miembros del equipo y su experiencia previa con instalaciones similares. Para cada riesgo se determina la probabilidad de ocurrencia, severidad y recomendaciones para mitigar o prevenir la situación peligrosa. La tecnología HAZOP es el método de análisis de riesgos más riguroso disponible actualmente. Aunque no da total seguridad ya que los resultados dependen básicamente del rendimiento del dispositivo. HAZOP es un esfuerzo de equipo y su éxito o fracaso pertenece a "todo el equipo". ALCANCE DE ACCIÓN Esto claramente se aplica a todo tipo de equipos, independientemente de si son equipos nuevos, existentes o en proceso de cambio de equipo operativo. Para instalaciones nuevas, los estudios se pueden realizar en cualquier etapa del proyecto. Cabe señalar que los cambios resultantes del análisis tendrán diferentes consecuencias dependiendo del avance del proyecto. Por lo tanto, se recomienda hacer esto en las primeras etapas del proyecto, cuando se hayan definido los proyectos relevantes.
El facilitador debe realizar el análisis, motivar al equipo, centrarse en el análisis, retener a todos los involucrados, documentar la información obtenida y mantener la calidad del estudio. El número ideal de participantes es de 4 a 8 personas. Cuantos más miembros, más difícil será llegar a un acuerdo en las discusiones que surjan y menor será el número de miembros. REQUERIMIENTOS PARA EL GRUPO DE EXPERTOS Este grupo de experto son quienes se encargan de hallar las posibles desviaciones de diseño en los diferentes nodos del sistema analizados. Posteriormente se define la metodología de análisis de riesgo a emplear según las necesidades del proceso y de lo que se requiera del análisis Para el empleo de la metodología HAZOP se requiere un sistema que se pueda dividir en nodos para su análisis. OBTENCIÓN DE LA INFORMACIÓN REQUERIDA En la primera etapa de obtiene lo necesaria para la aplicación del método (Fullwood, 1999), las generalidades del proceso, también se obtiene la documentación que sirve para conocer los aspectos importantes del sistema, sus capacidades y limitaciones, así como la ubicación física de los equipos involucrados en el sistema. Estos documentos incluyen hojas de seguridad de las sustancias químicas utilizadas en el sistema, fotos del sistema para una mejor. En esta parte también se obtienen los recursos materiales que son el equipo de cómputo adecuado con el paquete SCRI HAZOP 1,15 y que cuente con un cañón proyector para realizar la presentación de los nodos y el sistema.
Con la información del sistema disponible se pueden determinar las partes clave del sistema y, éste, El número de nodos no se define para un tipo de sistemas, la cantidad de nodos depende de quien realiza el análisis. Entre más nodos contenga un sistema, más riguroso es el análisis, sin embargo, es mucho más complejo, tardado y requiere más recursos económicos. El dividir desde este punto de la metodología al sistema en nodos, ayuda a líder del grupo HAZOP a saber cuáles son las áreas de mayor importancia en el sistema seleccionado. Esto proporciona una idea de las cualidades que deben tener los expertos para poder determinar las posibles desviaciones que se pueden presentar en cada nodo. El propósito de la tecnología HAZOP es identificar peligros potenciales en una instalación y evaluar problemas operativos. Si bien el objetivo principal de este enfoque es identificar riesgos, los problemas operativos deben detectarse si tienen un impacto negativo en la rentabilidad de la unidad estructural o al mismo tiempo crean riesgos. Identifica condiciones peligrosas para el personal, equipos, terceros y el medio ambiente y situaciones que provocan pérdidas de producción. Un estudio HAZOP se basa en un análisis sistemático de: para tratar Servicio Ubicación de equipos y personal en las instalaciones. Comportamiento humano (casual o no casual) Factor externo Su objetivo es identificar cómo el proceso se desvía de las condiciones normales de funcionamiento y aumentar la probabilidad de que se produzcan desviaciones.
La información básica requerida para realizar un HAZOP (sin la cual este estudio no sería posible) es: ➢ Gráfico P&ID Diagrama de flujo ➢ Plano de instalación DESCRIPCIÓN DEL PROCESO/FILOSOFÍA OPERATIVA. Utilice como información adicional hojas de datos de equipos e instrumentos, balances de masa y energía, matrices de causa y efecto, planos de tuberías, etc. La calidad de los estudios HAZOP depende directamente de la calidad y cantidad de la información disponible. MIEMBROS DEL EQUIPO HAZOP El equipo que realice el estudio HAZOP debe estar formado por expertos de diferentes campos para generar múltiples perspectivas sobre el mismo problema y estar dirigido por alguien con experiencia en tecnología HAZOP. Un equipo típico estará formado por expertos en procesos, herramientas, mecánica, electricidad, operaciones, mantenimiento, seguridad y medio ambiente, coordinados por un coordinador o gerente de HAZOP que debe estar familiarizado con todas las disciplinas. Normalmente el concepto de instalación de proceso va asociado a un sistema productivo o a una parte del mismo, en el que intervienen sustancias químicas, que, a través de determinadas operaciones básicas, generalmente concatenadas, son sometidas a procesos físicos y/o químicos para obtener productos intermedios o acabados.
Tales procesos físicos o químicos deben desarrollarse en condiciones de trabajo determinadas, siendo la composición de las sustancias químicas, la cantidad de las mismas en procesos discontinuos o el flujo másico en procesos continuos, la presión, y la temperatura, algunas de las variables fundamentales del sistema que exigen ser perfectamente controladas. Evidentemente las instalaciones son diseñadas para a las condiciones normales de trabajo, pero deben ser capaces de soportar alteraciones previsibles, aunque sean ocasionales, sin generar daños a personas y bienes. Precisamente el análisis de riesgos en este tipo de instalaciones requiere considerar todas las variables que condicionan el proceso físico o químico en cuestión, planteándose variaciones de las mismas ante posibles fallos o deficiencias, y consecuentemente la capacidad de respuesta de la instalación en base a sus características y a los elementos de seguridad de que está constituida, muchos, de los cuales deben garantizar una respuesta activa. Ello no es tarea fácil ya que las alteraciones posibles son diversas y tanto las causas que las pueden originar como sus consecuencias, que necesariamente deben ser consideradas para poder efectuar una evaluación de los riesgos de la instalación, son múltiples, y además integradas, en a veces complejos esquemas de interrelación secuencial. Una peculiaridad destacable en las instalaciones de proceso es que suele existir interrelación entre riesgos y sus factores causales, que según las circunstancias desencadenantes generan diferentes niveles de peligrosidad y de gravedad de sus consecuencias. Por ejemplo, una pérdida de líquido peligroso en una junta de una tubería puede generar situaciones de riesgo diferentes (corrosión, atmósferas peligrosas, alteración de proceso químico, etc.) los cuales pueden a su vez generar árboles de acontecimientos que en último término materializan resultados finales de consecuencias muy diversas.
Composición química Falló la adición manual. Errores de servicio como: ➢ Enfriamiento insuficiente de la reacción exotérmica. ➢ Entrada insuficiente de refrigerante o vapor. ➢ Fallo de energía. ➢ No contiene nitrógeno ni inertes. ➢ Falta de aire comprimido (para herramientas o mezcla). ➢ No se pudo detener ni iniciar el programa. ➢ Formación de subproductos, residuos o impurezas que provocan efectos secundarios innecesarios errores humanos y organizativos ➢ Error de operación. Las falsas alarmas frecuentes provocan que el sistema de seguridad falle. Confusión de sustancias peligrosas. ➢ Error de comunicación. ➢ Trabajos de reparación o mantenimiento inadecuados. ➢ Realizar trabajos no autorizados (soldar, entrar en espacios cerrados). ➢ Cabe señalar que el error suele ocurrir por alguna de las siguientes razones: ➢ Comprensión insuficiente de los riesgos y su prevención. ➢ Capacitación y capacitación en el trabajo inadecuadas. ➢ Tensión mental excesiva. Está claro que la seguridad de los equipos de proceso debe comenzar desde la etapa de diseño con la selección de los componentes adecuados. Y ensamblado según estándares y estricto control de calidad. Sin embargo, siempre es de esperar que se cometan errores como estos, por lo que la investigación de seguridad a cualquier nivel Al revisar su proyecto o instalación se debe considerar y determinar su existencia en función de su confiabilidad. La probabilidad de que estas situaciones ocurran en el sistema.
En este sentido se instala cada elemento (por ejemplo, un elemento de seguridad) Especialmente si están funcionalmente activos, deben someterse a un programa de mantenimiento preventivo para garantizar que estén en buen estado de funcionamiento. estado, así como mantenimiento predictivo, que garantiza actualizaciones antes del final de su vida media, hasta su fabricante. Por otro lado, los errores humanos también son posibles y su posibilidad debería analizarse cuidadosamente. Tome las medidas de control adecuadas si los resultados pueden tener consecuencias graves. Aunque los equipos de proceso están altamente automatizados, también requieren intervención manual tanto interna como externa. Operaciones normales (carga de aditivos, envasado, control y seguimiento de procesos, etc.) y operaciones irregulares debido a cambios ambientales. Condiciones de trabajo, algunas crean situaciones de emergencia que requieren una acción correcta y rápida. Por ello, a la hora de seleccionar este tipo de instalaciones se debe asegurar un correcto funcionamiento para minimizar errores En circunstancias normales, existe personal suficiente y sólidos conocimientos y formación en los procedimientos de trabajo. Por ejemplo, en circunstancias inusuales o inesperada. HAZOP es un método inductivo de identificación de peligros basado en el supuesto de que ocurren peligros, accidentes o problemas operativos cuando las variables del proceso se desvían en una determinada etapa de los parámetros operativos normales del sistema. La sistemática implica, por tanto, evaluar las consecuencias de posibles desviaciones en todas las unidades de proceso, ya sean continuas o discontinuas, en todas las líneas de producción y en todos los sistemas, tanto en la fase de diseño como en la operativa.
Las "palabras habilitadas" se utilizan para indicar términos que representan cada nodo que entra o sale de un elemento determinado como se define anteriormente. Se refieren a acciones (reacciones, transmisiones, etc.) y parámetros específicos (presión, caudal, temperatura, etc.). Las sesiones HAZOP están diseñadas para realizarse de forma sistemática. Analice cualquier desviación como se describe anteriormente. Una línea o nodo seleccionado entre las palabras principales que se refieren a alguna variable o proceso. Se aclararon las posibles causas, posibles consecuencias, respuestas recomendadas y operación realizada. El coordinador mejora su conocimiento del proceso No requiere prácticamente recursos adicionales, con excepción del tiempo de dedicación. ¿QUÉ ES EL ANÁLISIS HAZOP? En las industrias farmacéutica, química, alimentaria y otras industrias similares, los procesos de fabricación pueden encontrar una variedad de problemas. El análisis HAZOP tiene como objetivo investigar y descubrir posibles vulnerabilidades que pueden provocar fallas en el proceso. Los peligros de los procesos químicos, como explosiones, daños a los equipos, lesiones personales y contaminación del producto final, pueden tener un impacto significativo en su negocio. Mejorar la seguridad y operaciones de la planta con el método HAZOP Mejorar la seguridad y las operaciones de la planta con el método HAZOP. TÜV S ÜD cuenta con expertos en Análisis de Peligros y Capacidad de Operaciones (HA ZOP) que pueden ayudarle a identificar riesgos en sus procesos de fabricación y encontrar soluciones efectivas.
Nuestro equipo multidisciplinario estará presente en la sala durante el análisis de riesgos para brindar una evaluación exhaustiva y reducir el riesgo a un nivel aceptable. Nuestros servicios integrales de análisis HAZOP adaptados a sus necesidades entendemos que cada proceso es único, por lo que adaptamos nuestras evaluaciones HAZOP a sus necesidades específicas. Nuestros servicios incluyen: implementación o mejora de la gestión de riesgos. Mitigación/mitigación del análisis de riesgos en múltiples idiomas incluyendo inglés alemán, francés y holandés (posibilidad de idiomas adicionales dentro de TS). Análisis de Riesgos Remoto. Evaluación de riesgos semicuantitativa y definición de medidas de mitigación de riesgo análisis de riesgos práctico personalizado para pequeñas empresas. realizar investigaciones/análisis de forma remota mediante videoconferencia con visualización. Nuestros servicios integrales de análisis HAZOP adaptados a sus necesidades entendemos que cada proceso es único, por lo que adaptamos nuestras evaluaciones HAZOP a sus necesidades específicas. Nuestros servicios incluyen: implementación o mejora de la gestión de riesgos. Mitigación/mitigación del análisis de riesgos en múltiples idiomas incluyendo inglés alemán, francés y holandés (posibilidad de idiomas adicionales dentro de TS). Análisis de riesgos remoto. Evaluación de riesgos semicuantitativa y definición de medidas de mitigación de riesgo Análisis de Riesgos Práctico Personalizado para pequeñas empresas realizar investigaciones/análisis de forma remota mediante videoconferencia con visualización. Las empresas que aplican el método HAZOP incluyen empresas químicas y petroquímicas, ya que sus procesos son los que presentan mayor riesgo de accidentes Las empresas de manufactura también lo utilizan, especialmente en procesos que involucran sustancias peligrosas o que pueden causar daños a las personas o los activos de agua, también lo emplean para identificar y evaluar los riesgos en sus instalaciones.
La comunicación eficaz es esencial para garantizar que todos comprendan los riesgos identificados y las acciones recomendadas para abordarlos. Seguimiento: programar evaluaciones de seguimiento periódicas para monitorear la implementación de las recomendaciones y evaluar la efectividad de las medidas de mitigación de riesgos. La mejora continua es un aspecto clave de la gestión de la seguridad de los procesos. En resumen, los estudios HAZOP son una herramienta valiosa para identificar y eliminar peligros potenciales en los procesos industriales. El análisis detallado realizado durante el estudio HAZOP y las recomendaciones y planes de acción resultantes contribuyeron significativamente a mejorar la seguridad y el rendimiento del proceso. La revisión y actualización periódica de los estudios HAZOP es esencial para garantizar que se mantengan actualizados a medida que evolucionan los procesos y las tecnologías.