
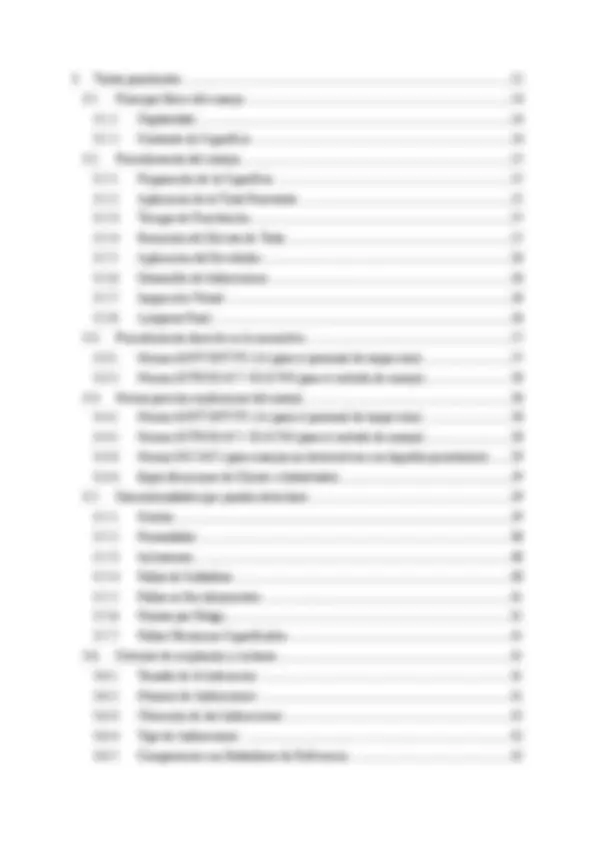
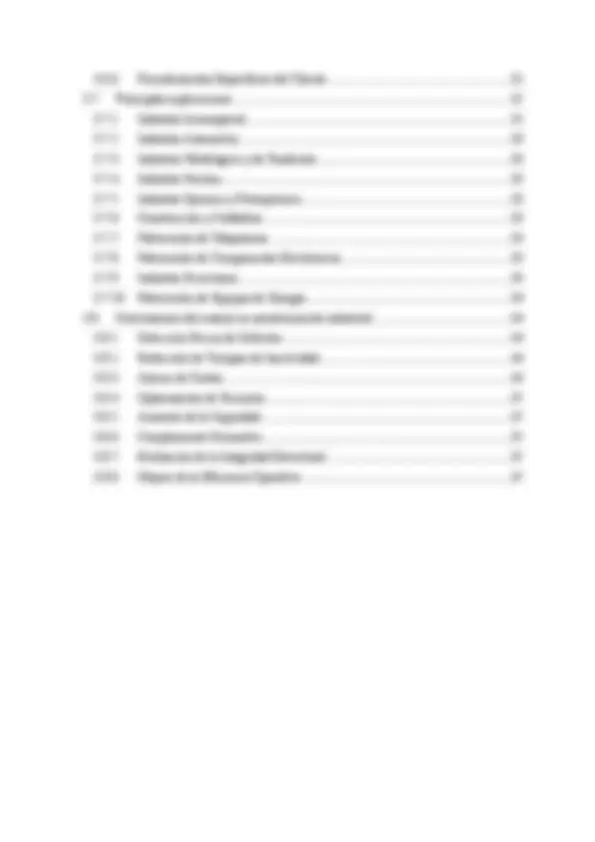
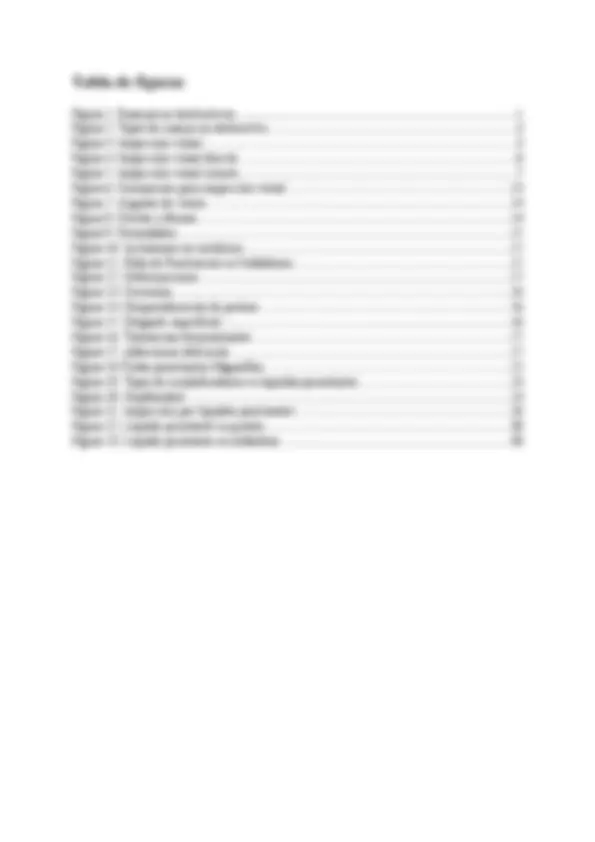
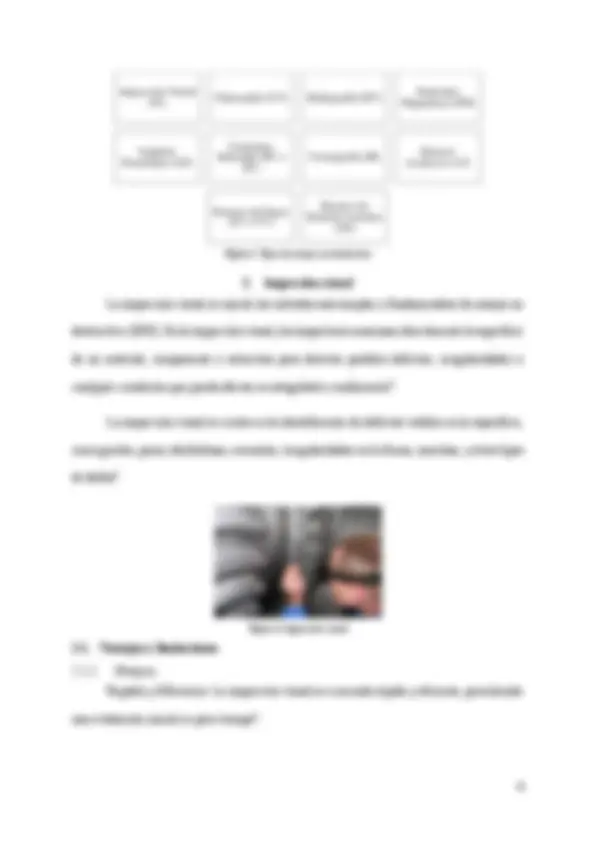
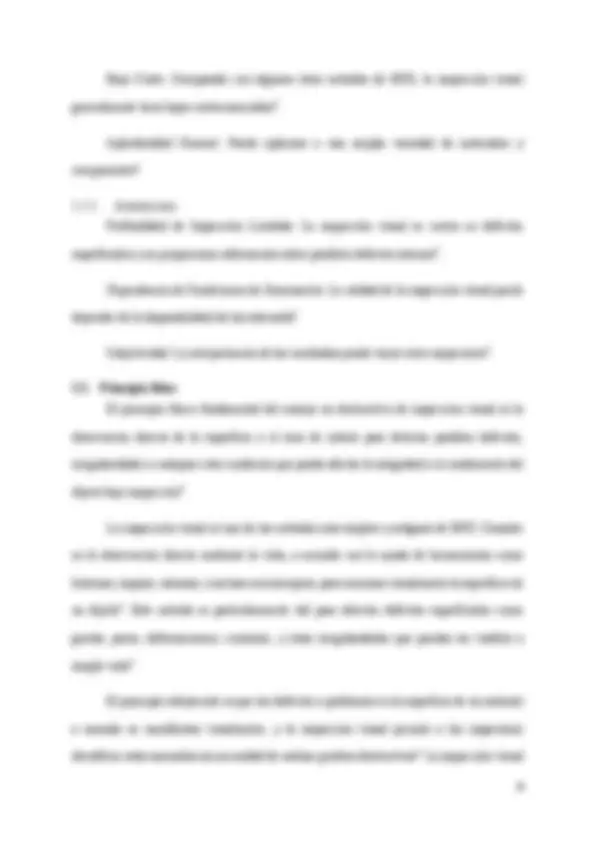
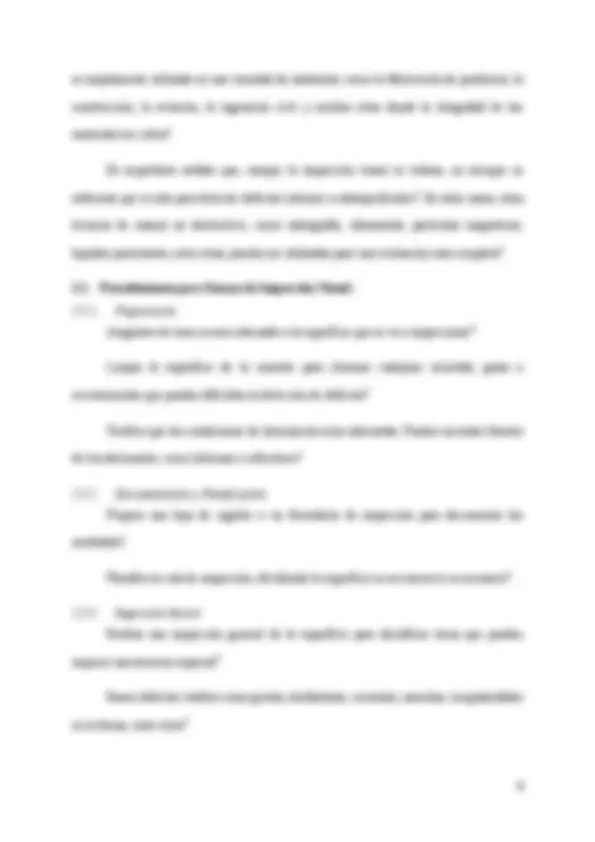
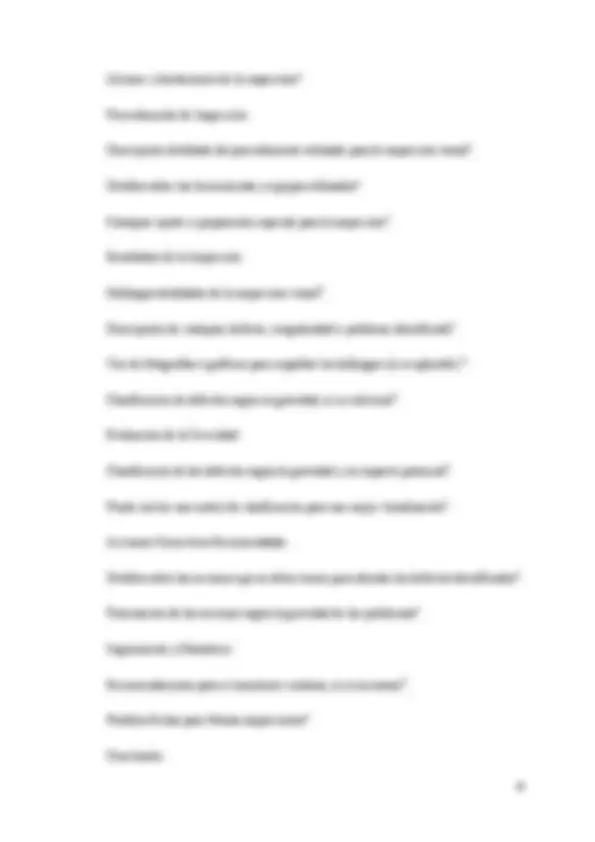
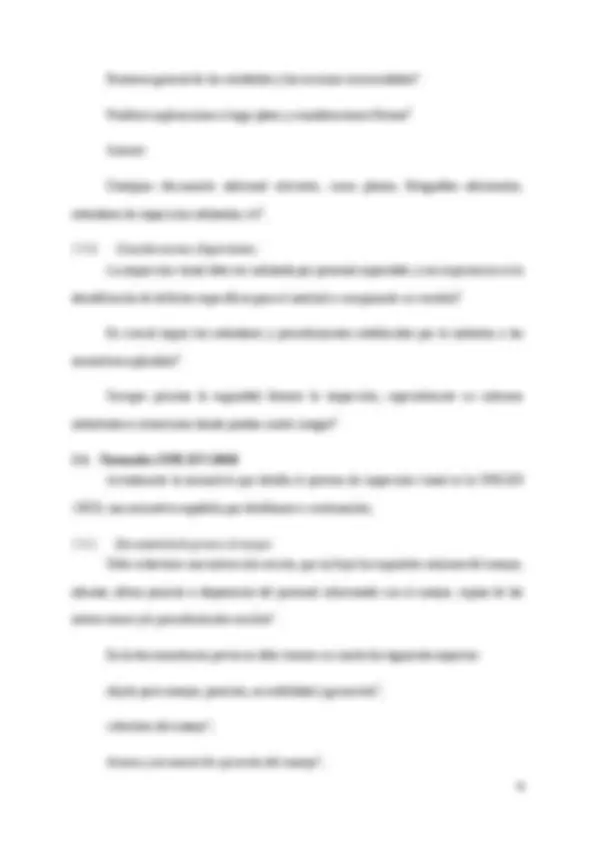
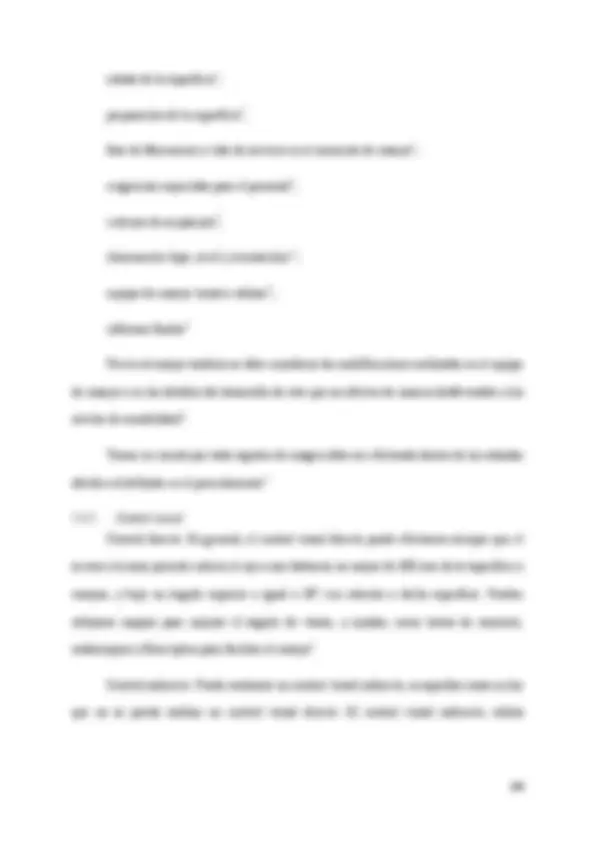
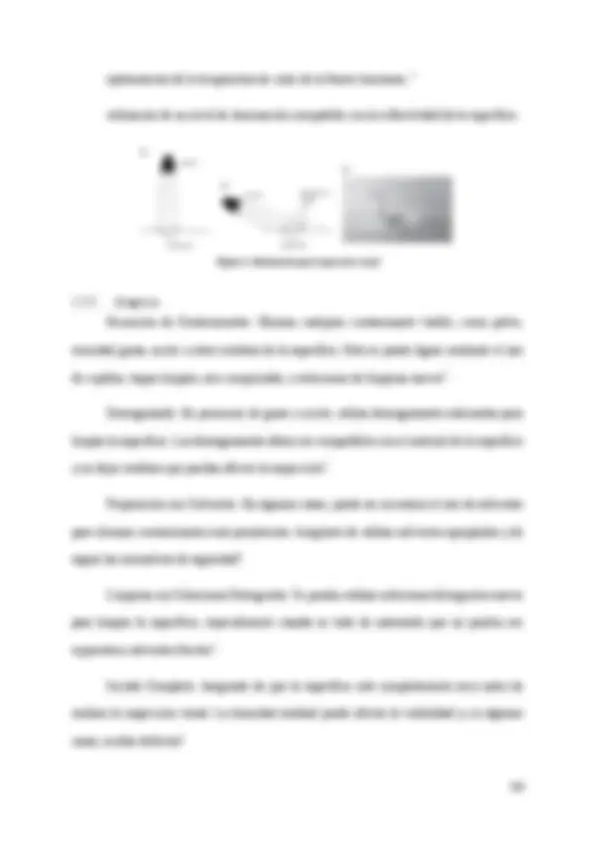
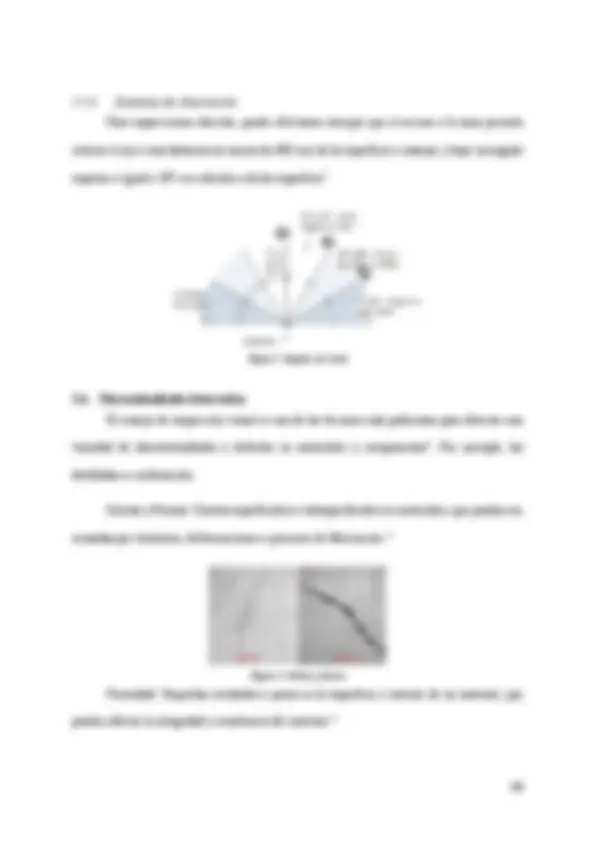
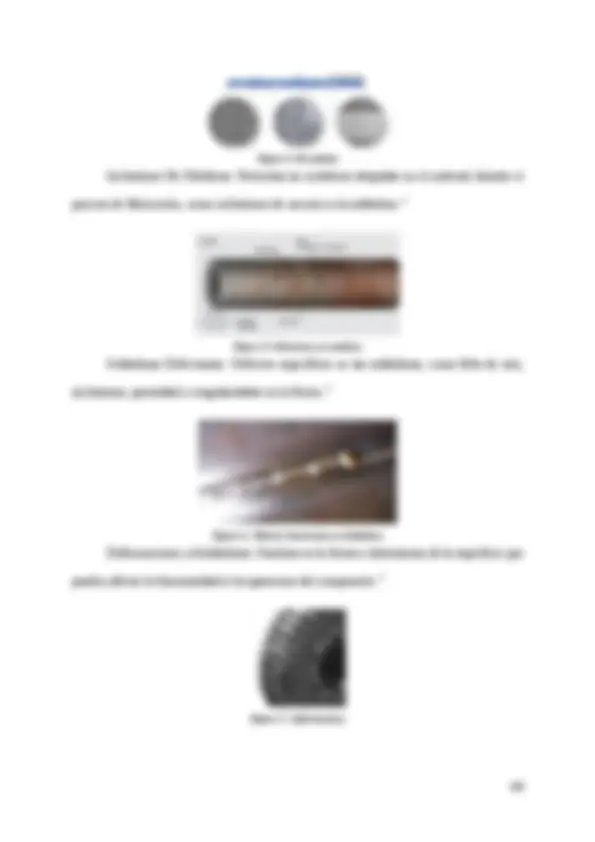
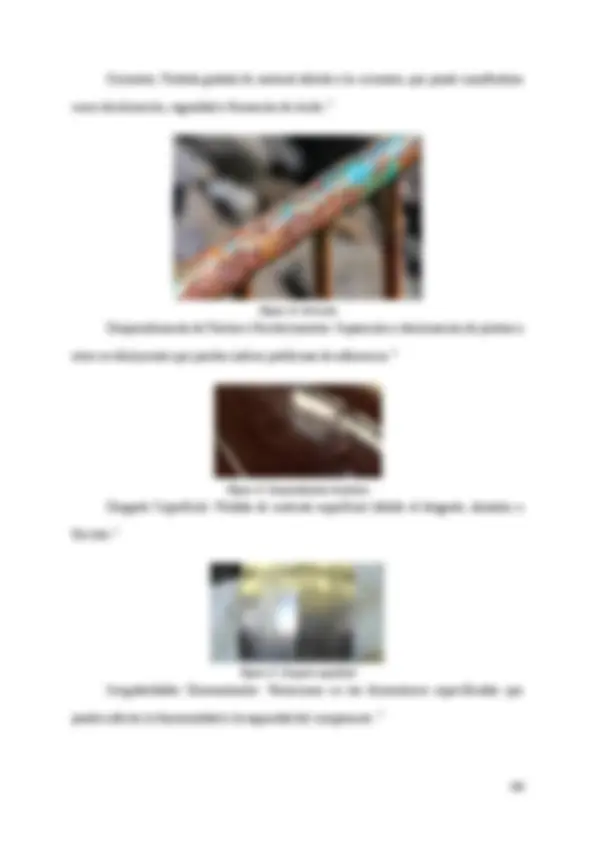
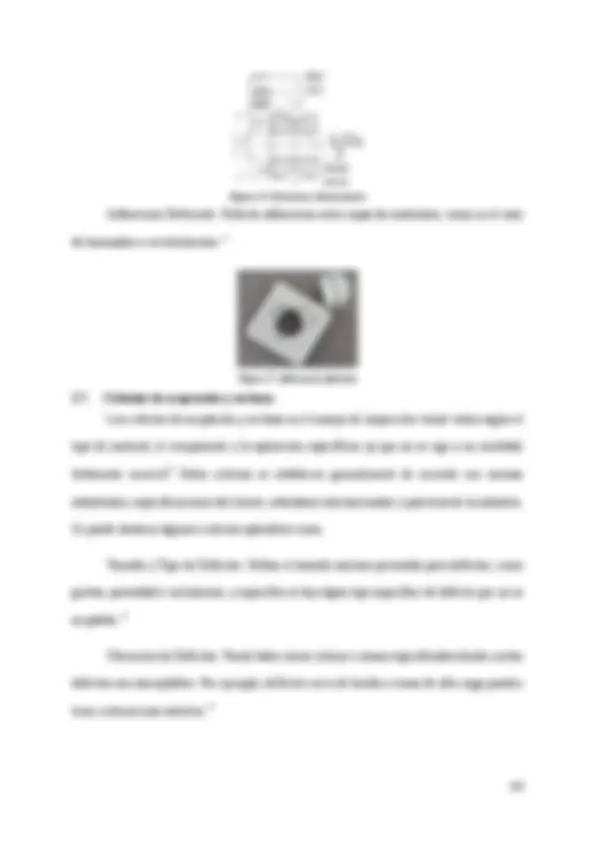
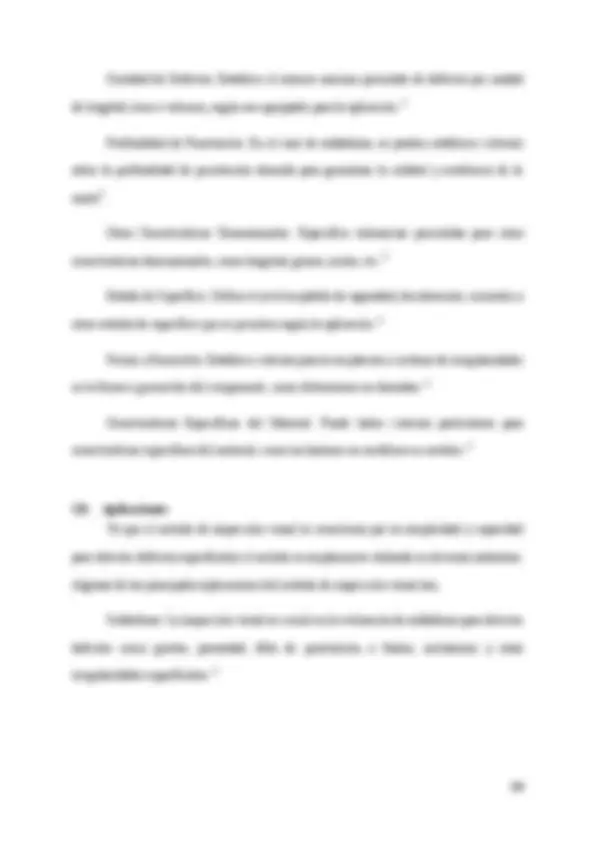
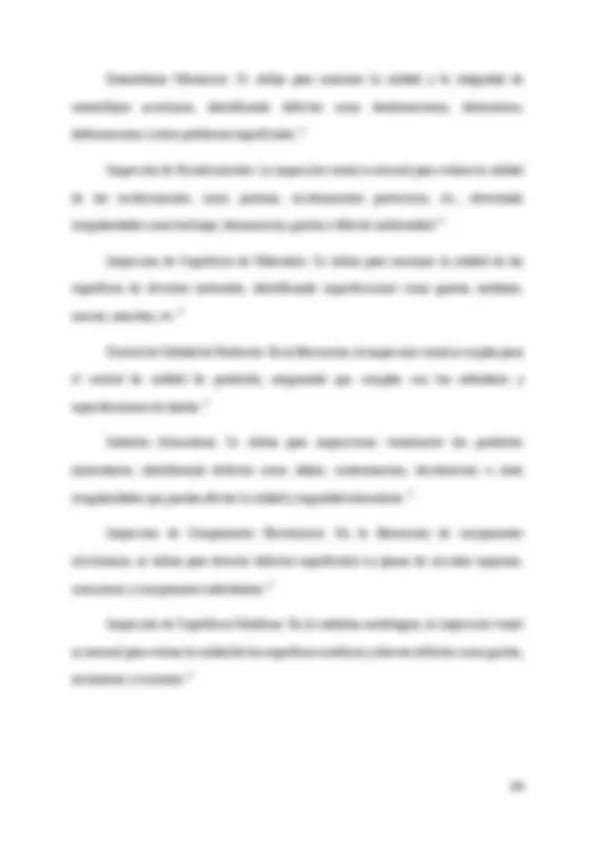
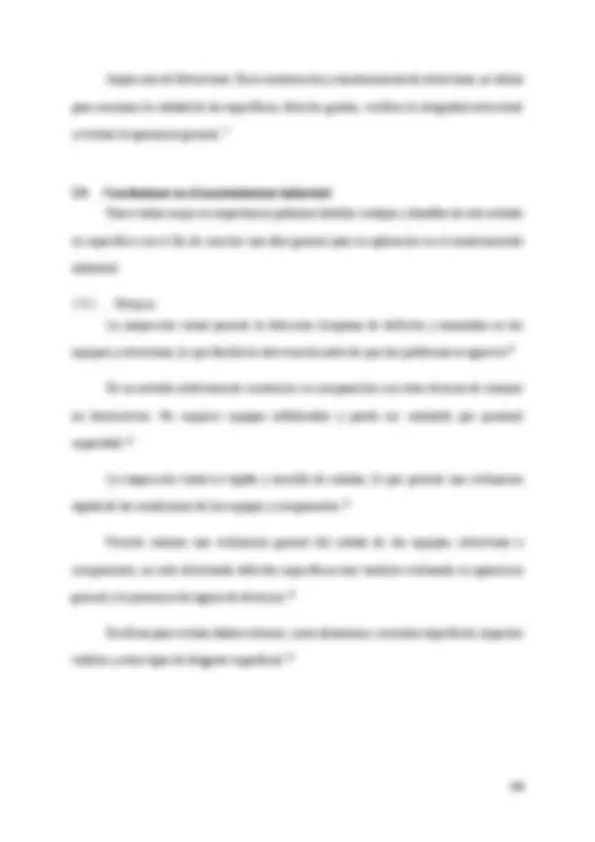
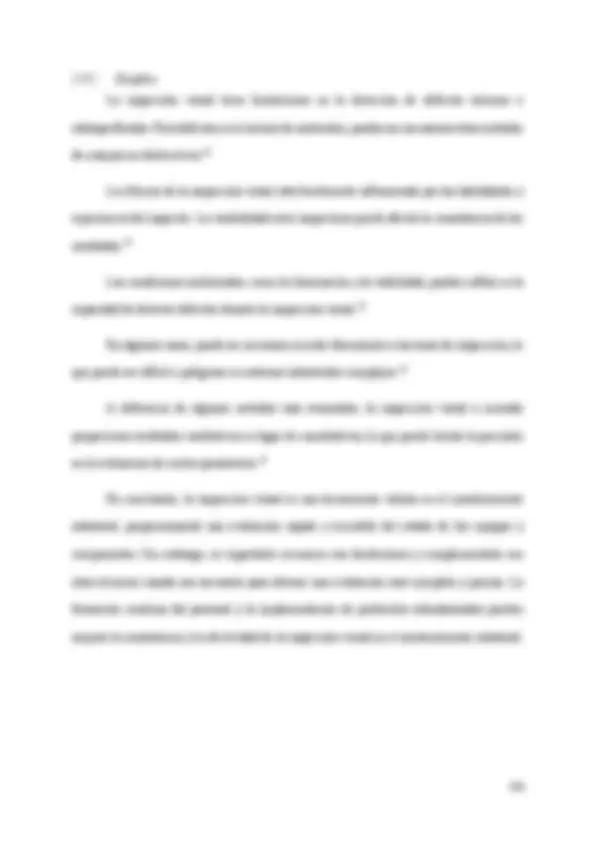
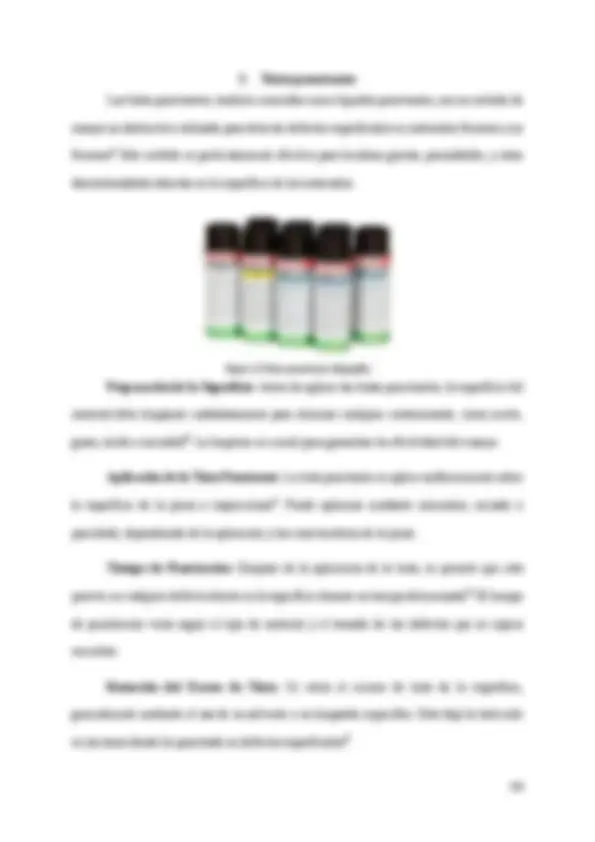
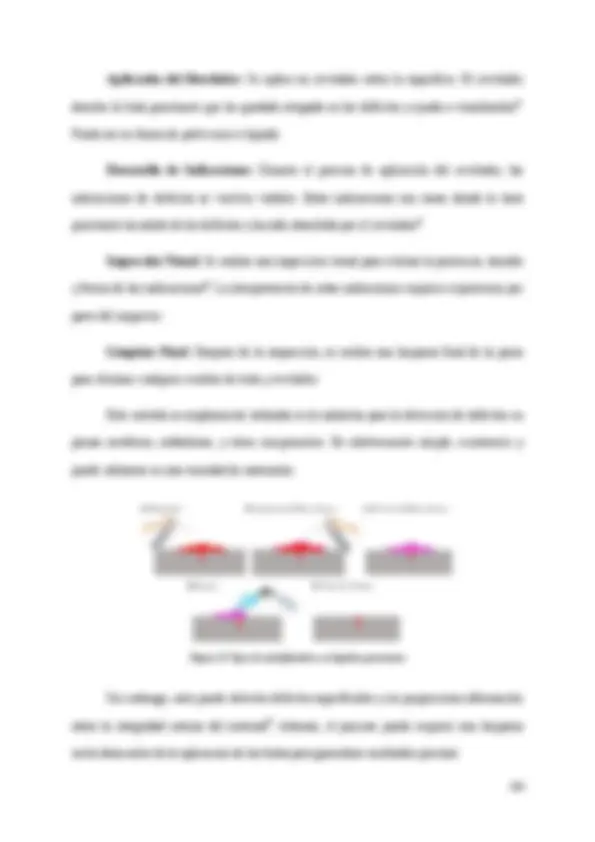
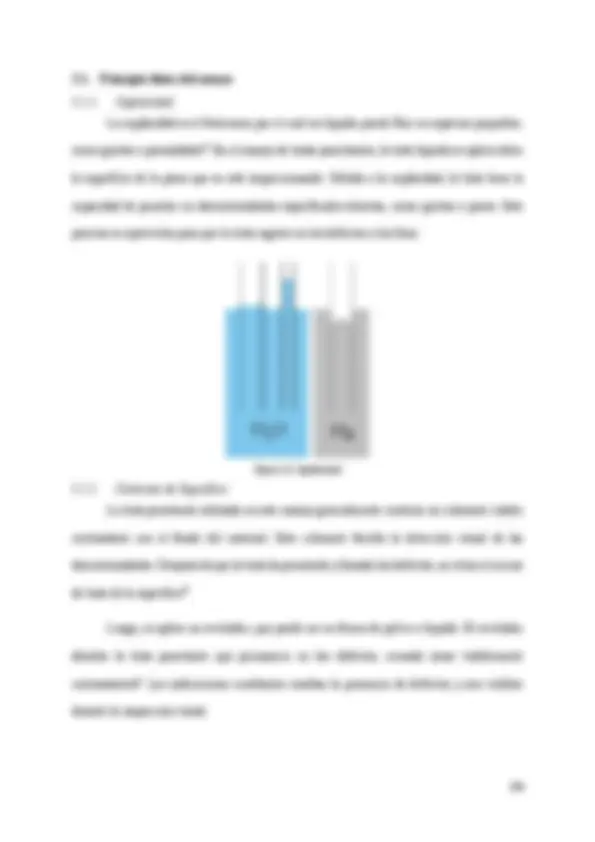
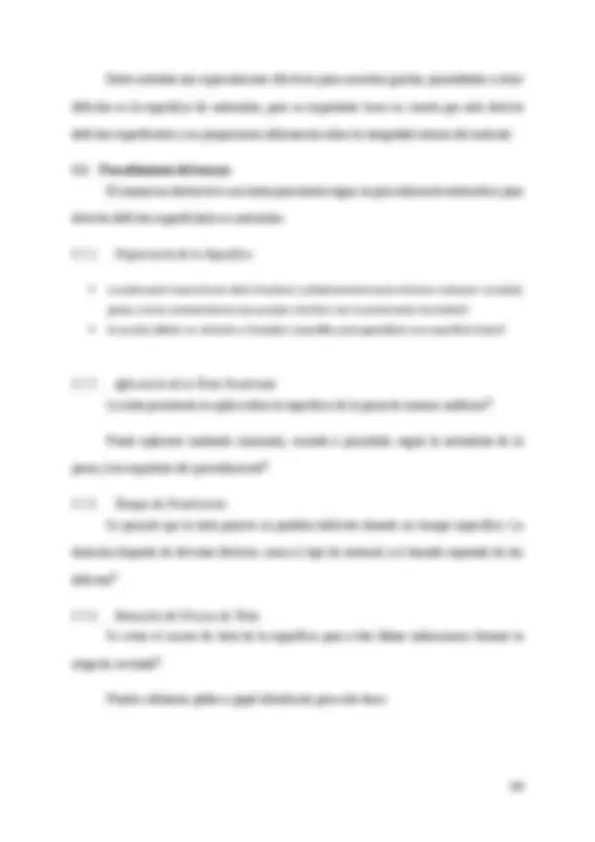
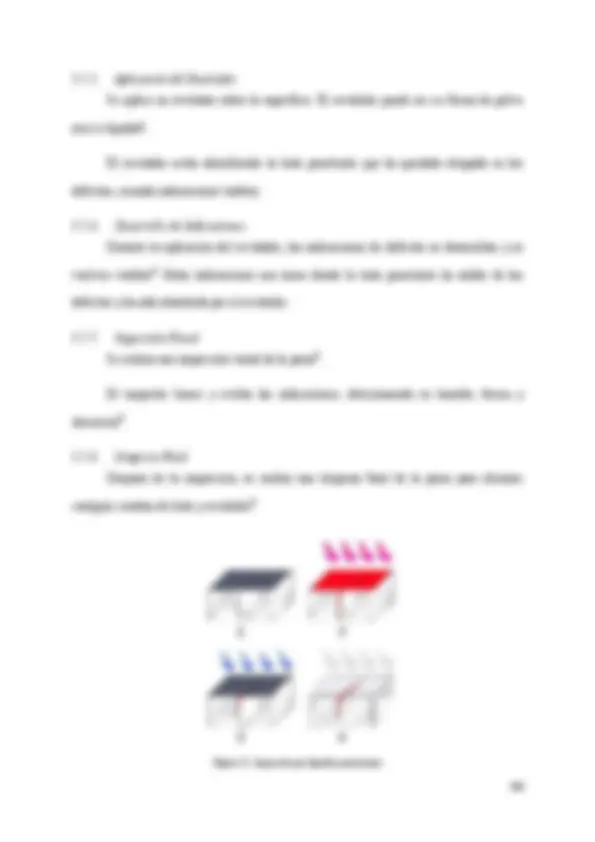
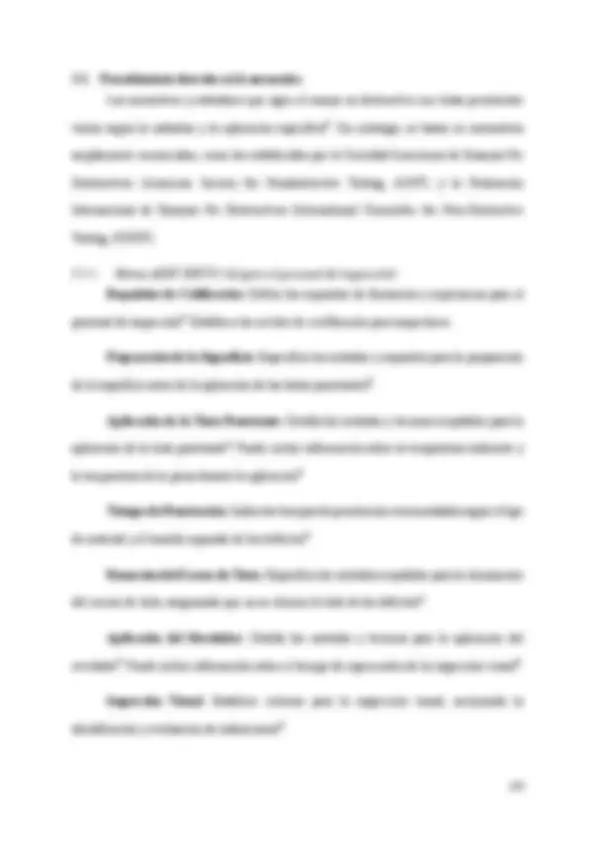
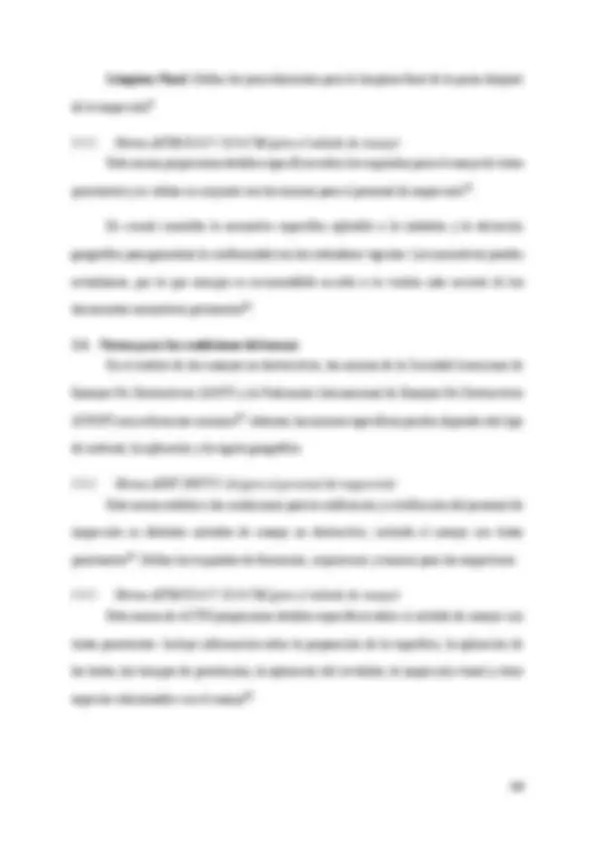

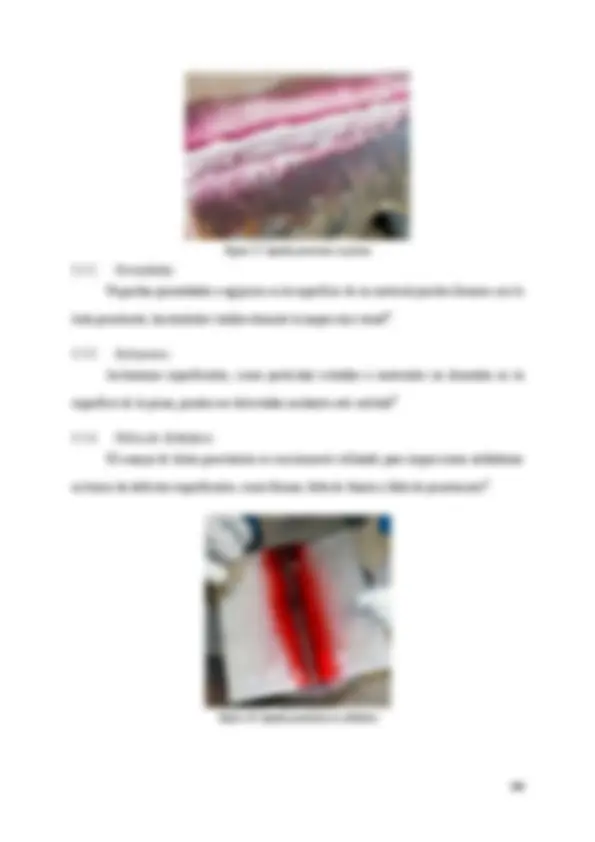
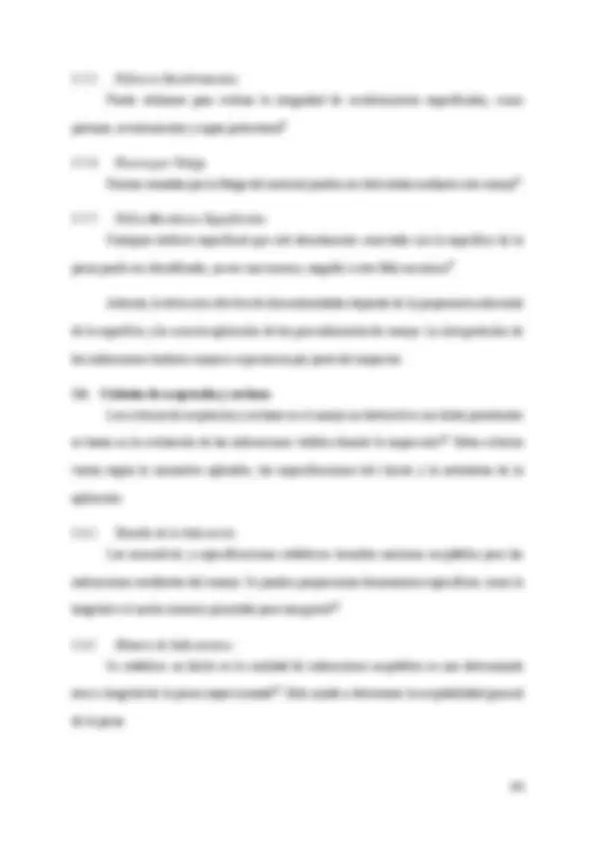
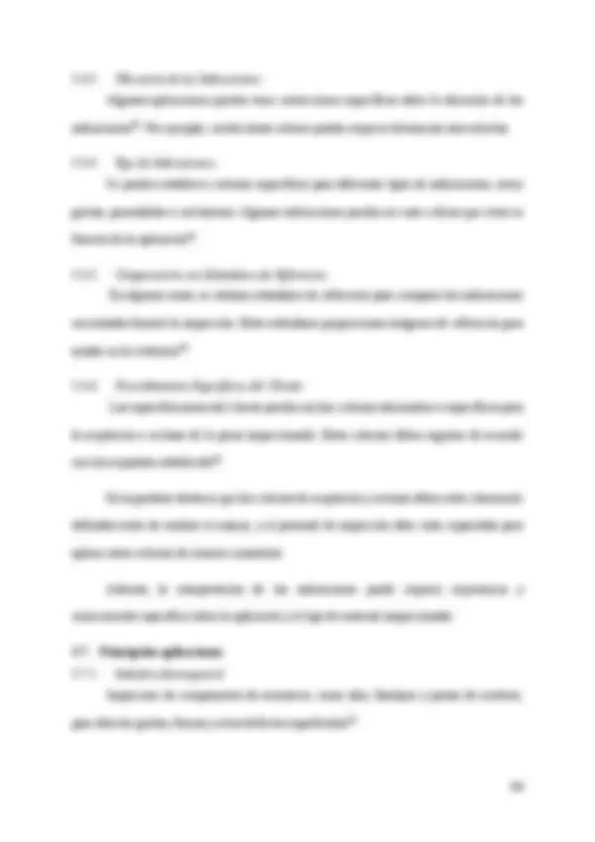
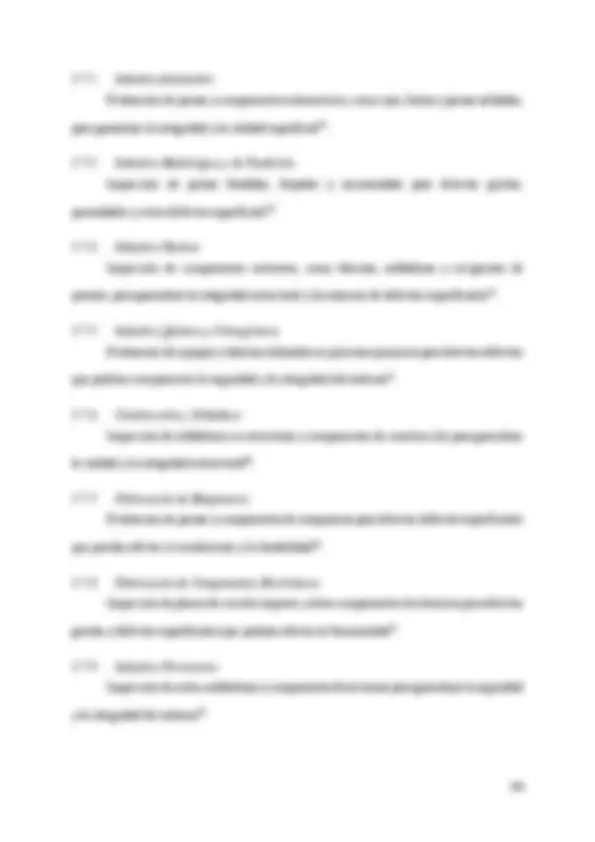
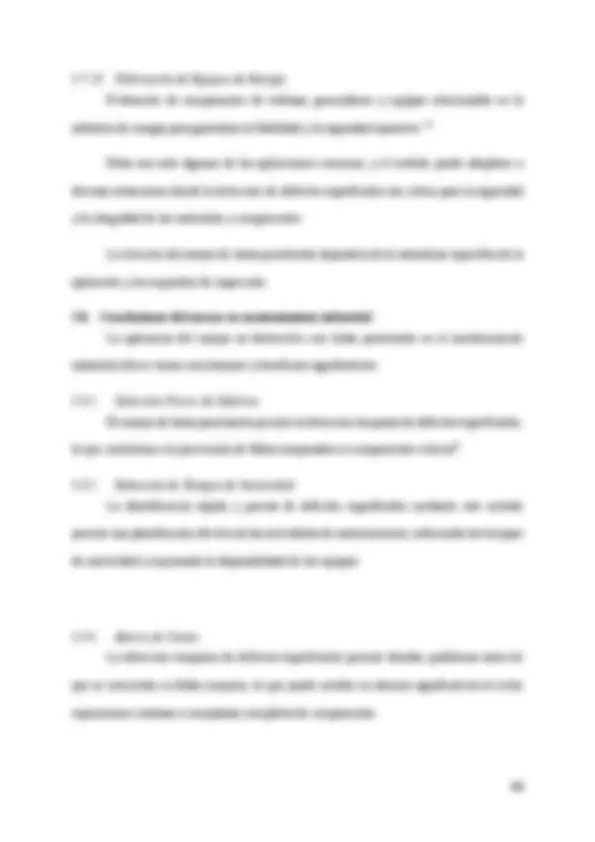
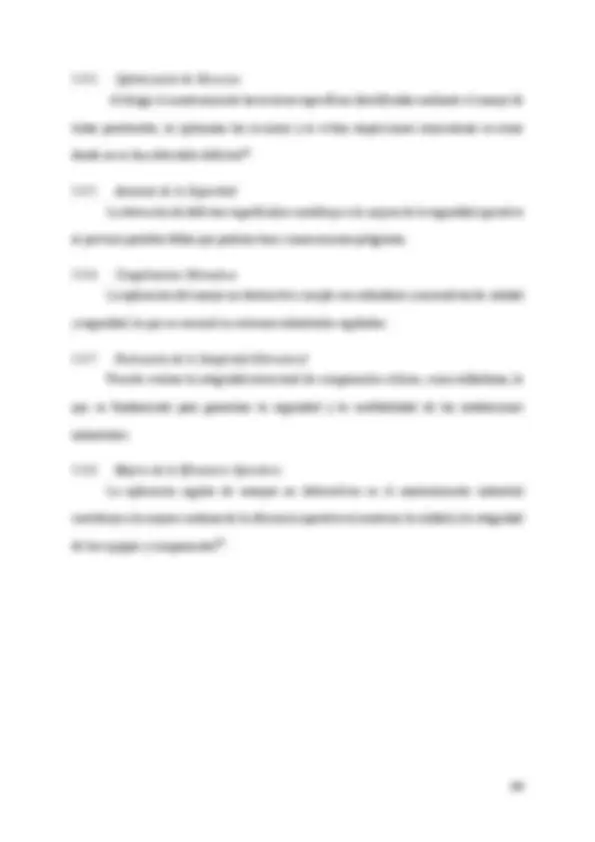
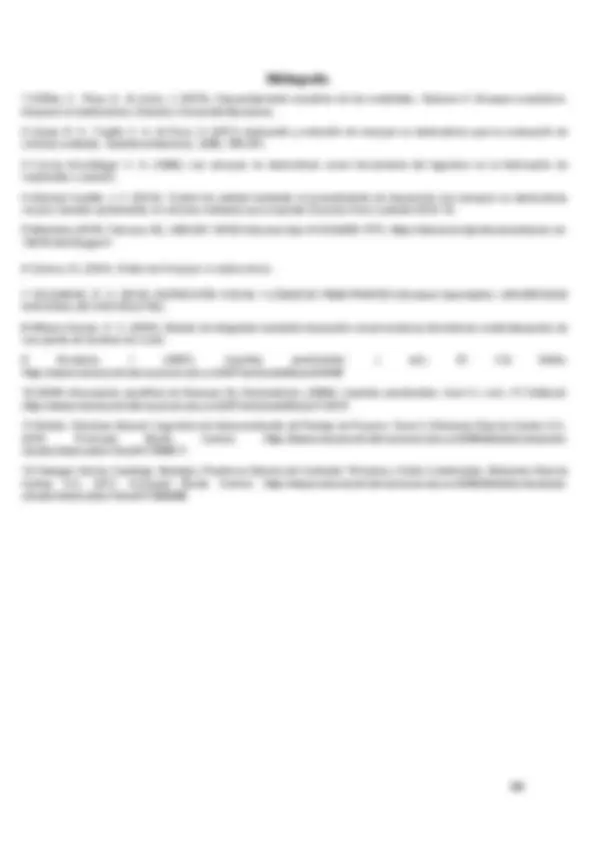
Prepara tus exámenes y mejora tus resultados gracias a la gran cantidad de recursos disponibles en Docsity
Gana puntos ayudando a otros estudiantes o consíguelos activando un Plan Premium
Prepara tus exámenes
Prepara tus exámenes y mejora tus resultados gracias a la gran cantidad de recursos disponibles en Docsity
Prepara tus exámenes con los documentos que comparten otros estudiantes como tú en Docsity
Los mejores documentos en venta realizados por estudiantes que han terminado sus estudios
Estudia con lecciones y exámenes resueltos basados en los programas académicos de las mejores universidades
Responde a preguntas de exámenes reales y pon a prueba tu preparación
Consigue puntos base para descargar
Gana puntos ayudando a otros estudiantes o consíguelos activando un Plan Premium
Comunidad
Pide ayuda a la comunidad y resuelve tus dudas de estudio
Descubre las mejores universidades de tu país según los usuarios de Docsity
Ebooks gratuitos
Descarga nuestras guías gratuitas sobre técnicas de estudio, métodos para controlar la ansiedad y consejos para la tesis preparadas por los tutores de Docsity
Una introducción a los ensayos no destructivos (end) en el contexto del mantenimiento industrial, centrándose en la inspección visual y las tintas penetrantes. Se explica la importancia de los end para evaluar la integridad de los materiales y componentes sin causar daño permanente. Se detallan los principios, procedimientos, aplicaciones y ventajas de la inspección visual y las tintas penetrantes, así como los criterios de aceptación y rechazo. El documento también aborda la documentación previa al ensayo, el informe final y la importancia de la iluminación en la inspección visual.
Tipo: Guías, Proyectos, Investigaciones
1 / 41
Esta página no es visible en la vista previa
¡No te pierdas las partes importantes!
I N G E N I E R Í A I N D U S T R I A L
Rapidez y eficacia: Muchos ensayos no destructivos son rápidos y eficientes, lo que permite realizar inspecciones de manera oportuna y sin la necesidad de desmontar o desensamblar componentes. Esto contribuye a la eficiencia en la producción y el mantenimiento^1. Seguridad: Los END a menudo son métodos seguros tanto para los operadores como para el medio ambiente. A diferencia de algunos ensayos destructivos que pueden generar residuos peligrosos, muchos END no producen desechos tóxicos y se pueden realizar de manera segura^1. Versatilidad: Existen una variedad de técnicas de ensayos no destructivos, cada una adaptada para situaciones específicas. Esto proporciona flexibilidad y versatilidad en la elección del método más apropiado según los requisitos de la aplicación y las características del material^1. Monitoreo de la calidad a lo largo del tiempo: Los END son a menudo utilizados para el monitoreo continuo de la calidad a lo largo del tiempo. Esto es especialmente importante en la industria, donde se deben evaluar repetidamente los materiales y componentes para garantizar su integridad a lo largo del ciclo de vida^1. Reducción de costos a largo plazo: Aunque algunos equipos de ensayos no destructivos pueden tener costos iniciales significativos, a menudo resultan en ahorros a largo plazo al prevenir fallos costosos, reducir los costos de mantenimiento y mejorar la eficiencia operativa^1. 1.2. Tipos de ensayos no destructivos Existen varios tipos de ensayos no destructivos (END), cada uno diseñado para detectar diferentes tipos de defectos o evaluar propiedades específicas de los materiales^1. A continuación, se detalla algunos de los más comunes:
Figura 2. Tipos de ensayo no destructivo
2. Inspección visual La inspección visual es uno de los métodos más simples y fundamentales de ensayo no destructivo (END). En la inspección visual, los inspectores examinan directamente la superficie de un material, componente o estructura para detectar posibles defectos, irregularidades o cualquier condición que pueda afectar su integridad o rendimiento^2. La inspección visual se centra en la identificación de defectos visibles en la superficie, como grietas, poros, abolladuras, corrosión, irregularidades en la forma, manchas, y otros tipos de daños^2. Figura 3. Inspección visual 2.1. Ventajas y limitaciones 2.1.1. Ventajas Rapidez y Eficiencia: La inspección visual es a menudo rápida y eficiente, permitiendo una evaluación inicial en poco tiempo^2. Inspección Visual (IV) Ultrasonido (UT)^ Radiografía (RT)^ Partículas Magnéticas (PM) Líquidos Penetrantes (LP) Corrientes Inducidas (EC o ET) Termografía (IR) Ensayos Acústicos (AT) Ensayos de Fugas (LT o VT) Ensayos de Emisión Acústica (AE)
es ampliamente utilizada en una variedad de industrias, como la fabricación de productos, la construcción, la aviación, la ingeniería civil y muchas otras donde la integridad de los materiales es crítica^3. Es importante señalar que, aunque la inspección visual es valiosa, no siempre es suficiente por sí sola para detectar defectos internos o subsuperficiales^3. En tales casos, otras técnicas de ensayo no destructivo, como radiografía, ultrasonido, partículas magnéticas, líquidos penetrantes, entre otras, pueden ser utilizadas para una evaluación más completa^3. 2.3. Procedimiento para Ensayo de Inspección Visual: 2.3.1. Preparación: Asegúrate de tener acceso adecuado a la superficie que se va a inspeccionar^3. Limpia la superficie de la muestra para eliminar cualquier suciedad, grasa o revestimientos que puedan dificultar la detección de defectos^3. Verifica que las condiciones de iluminación sean adecuadas. Puedes necesitar fuentes de luz adicionales, como linternas o reflectores^3. 2.3.2. Documentación y Planificación Prepara una hoja de registro o un formulario de inspección para documentar los resultados^3. Planifica la ruta de inspección, dividiendo la superficie en secciones si es necesario^3. 2.3.3. Inspección Inicial Realiza una inspección general de la superficie para identificar áreas que puedan requerir una atención especial^3. Busca defectos visibles como grietas, abolladuras, corrosión, manchas, irregularidades en la forma, entre otros^3.
2.3.4. Inspección Detallada: Examina cada sección de la muestra de manera detallada^3. Utiliza herramientas dependiendo del tipo de inspección visual, ya que se puede dividir en dos grupos detallados a continuación^3 , Inspección visual directa. La inspección se hace a una distancia corta del objeto, aprovechando al máximo la capacidad visual natural del inspector^4. Se usan lentes de aumento, microscopios, lámparas o linternas, y con frecuencia se emplean instrumentos de medición como calibres, pies de rey, micrómetros, reglas y galgas^4. Figura 4. Inspección visual directa Inspección visual remota. La inspección visual remota se utiliza en aquellos casos en que no se tiene acceso directo a los componentes a inspeccionar, o en aquellos componentes en los cuales, por su diseño, es muy difícil tener acceso a sus cavidades internas^4. Para la inspección visual remota es requerido el empleo de instrumentos tales como endoscopios rígidos (baroscopios), endoscopios flexibles, videoscópios y fibroscópios con los cuales se puede llegar a la mayoría de las cavidades internas y lugares inaccesibles para el inspector^4.
Alcance y limitaciones de la inspección^4. Procedimiento de Inspección: Descripción detallada del procedimiento utilizado para la inspección visual^4. Detalles sobre las herramientas y equipos utilizados^4. Cualquier ajuste o preparación especial para la inspección^4. Resultados de la Inspección: Hallazgos detallados de la inspección visual^4. Descripción de cualquier defecto, irregularidad o problema identificado^4. Uso de fotografías o gráficos para respaldar los hallazgos (si es aplicable) 4. Clasificación de defectos según su gravedad, si es relevante^4. Evaluación de la Severidad: Clasificación de los defectos según la gravedad y su impacto potencial^4. Puede incluir una matriz de clasificación para una mejor visualización^4. Acciones Correctivas Recomendadas: Detalles sobre las acciones que se deben tomar para abordar los defectos identificados^4. Priorización de las acciones según la gravedad de los problemas^4. Seguimiento y Monitoreo: Recomendaciones para el monitoreo continuo, si es necesario^4. Posibles fechas para futuras inspecciones^4. Conclusión:
Resumen general de los resultados y las acciones recomendadas^4. Posibles implicaciones a largo plazo y consideraciones futuras^4. Anexos: Cualquier documento adicional relevante, como planos, fotografías adicionales, estándares de inspección utilizados, etc^4. 2.3.8. Consideraciones Importantes: La inspección visual debe ser realizada por personal capacitado y con experiencia en la identificación de defectos específicos para el material o componente en cuestión^3. Es crucial seguir los estándares y procedimientos establecidos por la industria o las normativas aplicables^3. Siempre prioriza la seguridad durante la inspección, especialmente en entornos industriales o situaciones donde puedan existir riesgos^3. 2.4. Normativa UNE-EN 13018 Actualmente la normativa que detalla el proceso de inspección visual es la UNE-EN 13018, una normativa española que detallamos a continuación, 2.4.1. Documentación previa al ensayo Debe redactarse una instrucción escrita, que incluya los requisitos mínimos del ensayo, además, deben ponerse a disposición del personal relacionado con el ensayo, copias de las instrucciones y/o procedimientos escritos^5. En la documentación previa se debe tenerse en cuenta los siguientes aspectos: objeto para ensayar, posición, accesibilidad y geometría^5 ; cobertura del ensayo^5 ; técnica y secuencia de ejecución del ensayo^5 ;
dispositivos de ayuda tales como endoscopios y fibras ópticas conectados a cámaras o a cualquier otro instrumento apropiado^5. Debe estar demostrada la capacidad del sistema de control visual indirecto para realizar la tarea asignada. 2.4.3. Evaluación Todos los controles visuales deben ser evaluados con relación a criterios de aceptación especificados^5. 2.4.4. Informe Cuando así se solicite, debe entregarse un informe escrito, detallando los siguientes puntos: fecha y lugar del ensayo; 5 método utilizado; 5 criterios de aceptación y/o referencia del procedimiento/instrucciones escritas; 5 equipo y/o sistema utilizado, incluido el funcionamiento; 5 referencia al pedido del cliente; 5 nombre del organismo que efectúa el ensayo; 5 descripción e identificación del objeto ensayado; 5 detalle de las indicaciones detectadas con relación a los criterios de aceptación (por ejemplo: tamaño, localización); 5 extensión de los ensayos; 5 fecha, nombre y firma de la persona que efectúa el ensayo; 5 fecha, nombre y firma de la persona que supervisa el ensayo, si así se solicita; 5
marcado del componente ensayado, cuando proceda; resultados. 5 Esto puede cumplirse, haciendo referencia al procedimiento de control visual y/o a las instrucciones escritas. 2.4.5. Registros Los registros, deben conservarse según lo solicitado por ejemplo en la norma del producto o en el contrato^5. 2.5. Condiciones para el ensayo 2.5.1. Personal El personal encargado de realizar los ensayos conforme a esta norma debe demostrar: a) estar familiarizado con las normas, reglas, especificaciones, equipo utilizado y con los procedimientos/instrucciones apropiadas; 5 b) estar familiarizado con el procedimiento de fabricación utilizado y/o con las condiciones de uso del componente a ensayar; 5 c) poseer una visión satisfactoria de acuerdo con la Norma EN 473. Además, para la realización de un ensayo visual general, la visión de lejos debe verificarse con la ayuda de un optotipo normalizado de acuerdo con la Norma ISO 8596, para un grado de agudeza visual de 0,63, en al menos un ojo, con corrección o no. La visión debe verificarse al menos cada 12 meses. 5 2.5.2. iluminación Para una eficacia máxima del ensayo, en lo relativo a iluminación, deben considerarse los siguientes puntos: utilización de la orientación óptima del haz luminoso con relación a la zona a examinar; evitar el deslumbramiento; 5
2.5.4. Distancia de observación Para inspecciones directas, puede efectuarse siempre que el acceso a la zona permita colocar el ojo a una distancia no mayor de 600 mm de la superficie a ensayar, y bajo un ángulo superior o igual a 30º con relación a dicha superficie^5. Figura 7. Ángulos de visión 2.6. Discontinuidades detectadas El ensayo de inspección visual es una de las técnicas más poderosas para detectar una variedad de discontinuidades o defectos en materiales y componentes^6. Por ejemplo, las detalladas a continuación Grietas y Fisuras: Grietas superficiales o subsuperficiales en materiales, que pueden ser causadas por tensiones, deformaciones o procesos de fabricación. 6 Figura 8. Grietas y fisuras Porosidad: Pequeñas cavidades o poros en la superficie o interior de un material, que pueden afectar la integridad y resistencia del material. 6
Figura 9. Porosidades Inclusiones No Metálicas: Partículas no metálicas atrapadas en el material durante el proceso de fabricación, como inclusiones de escoria en la soldadura. 6 Figura 10. Inclusiones no metalicas Soldaduras Defectuosas: Defectos específicos en las soldaduras, como falta de raíz, inclusiones, porosidad o irregularidades en la forma. 6 Figura 11. Falta de Penetración en Soldaduras Deformaciones y Abolladuras: Cambios en la forma o distorsiones de la superficie que pueden afectar la funcionalidad o la apariencia del componente. 6 Figura 12. Deformaciones