
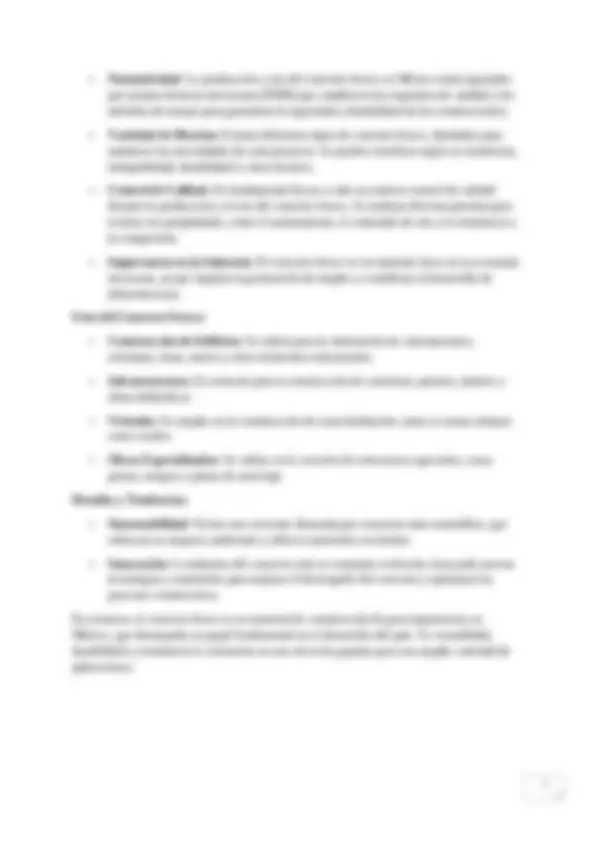
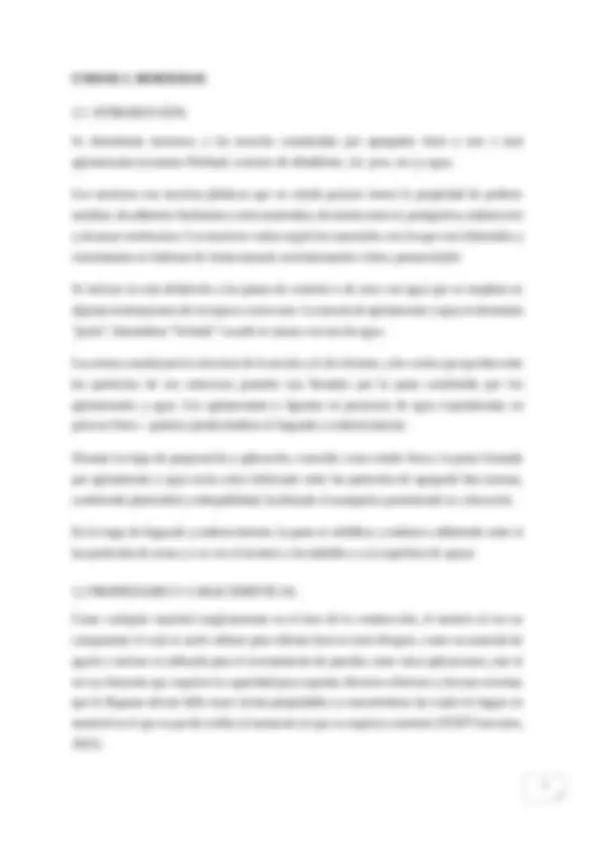
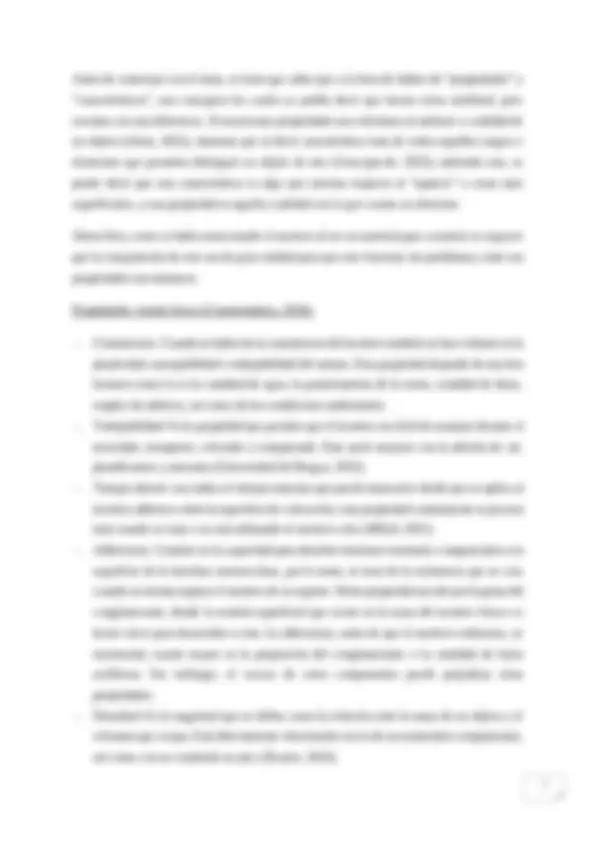
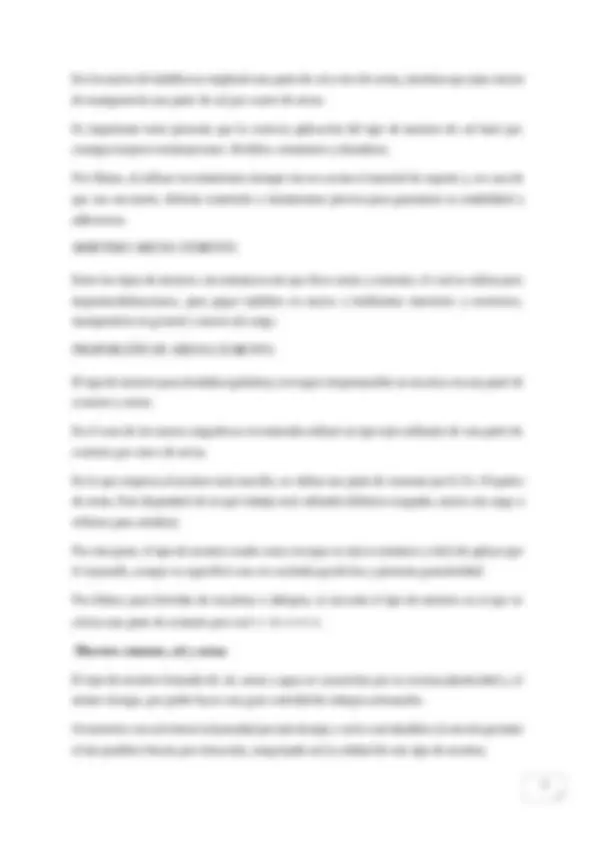

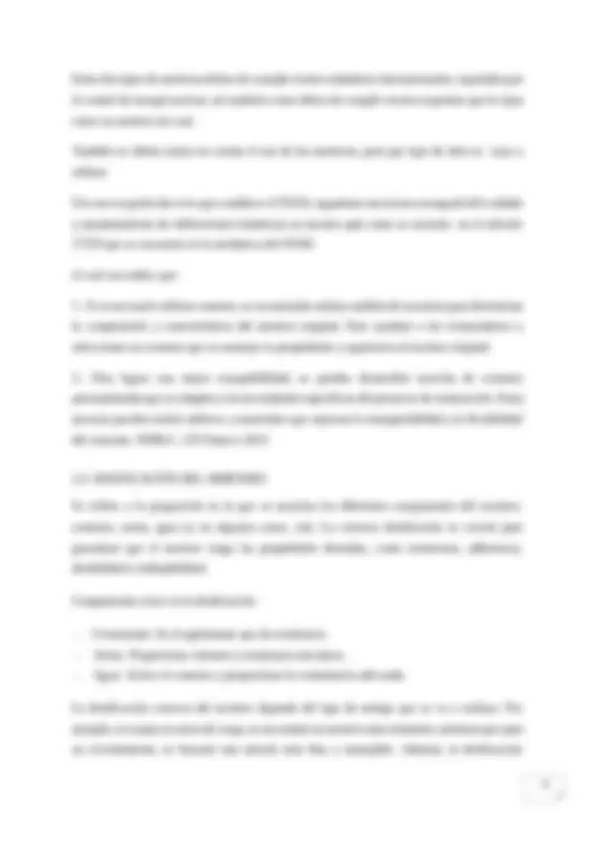
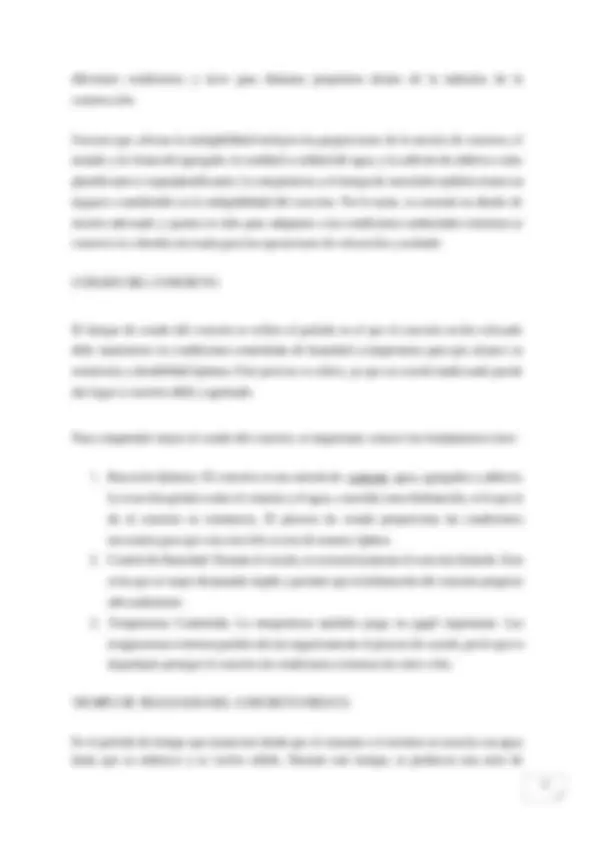
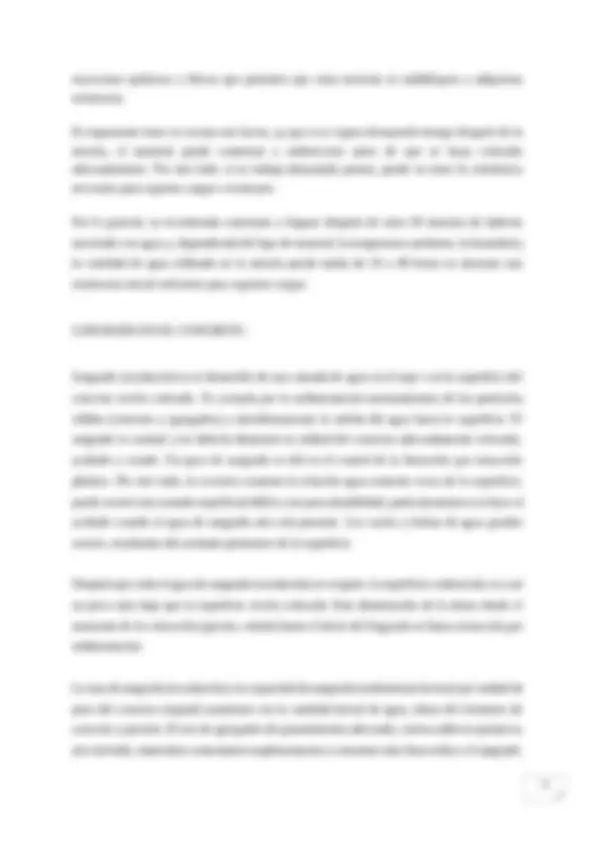
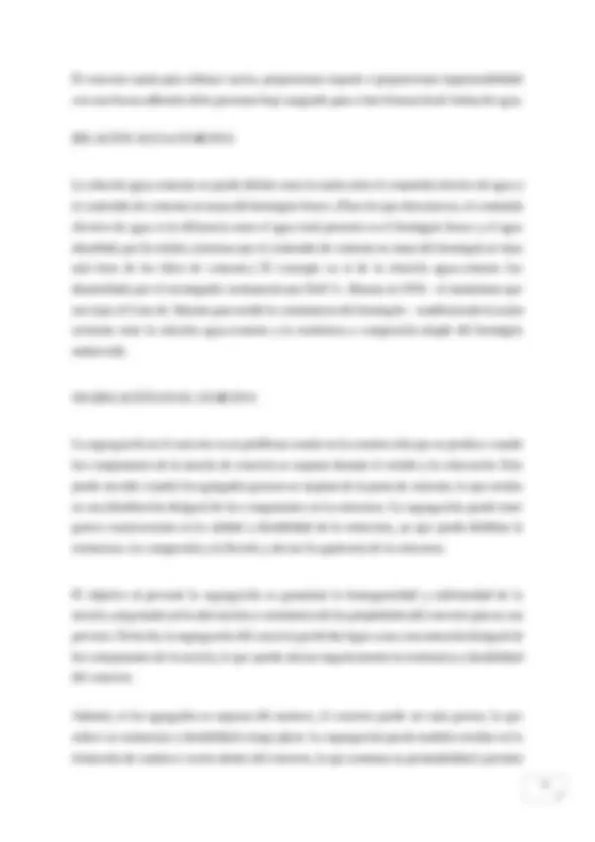
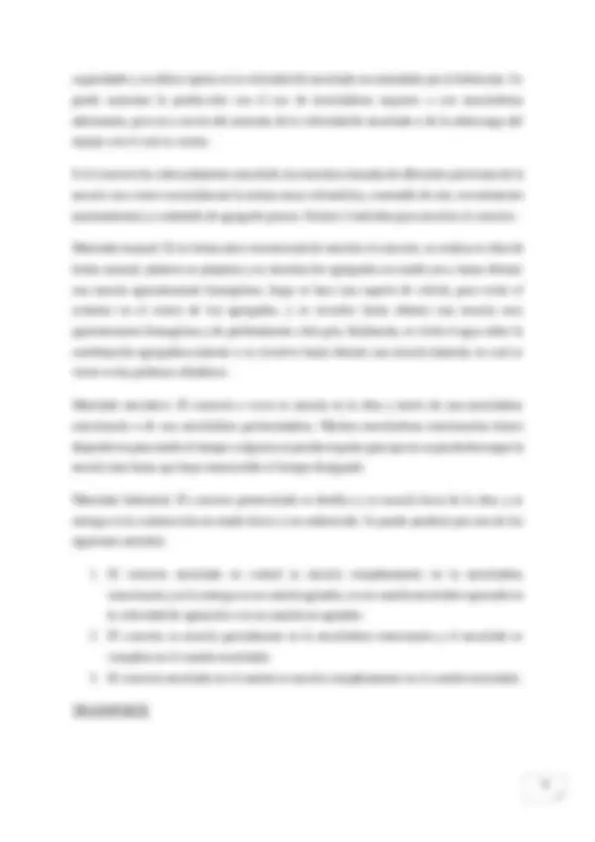
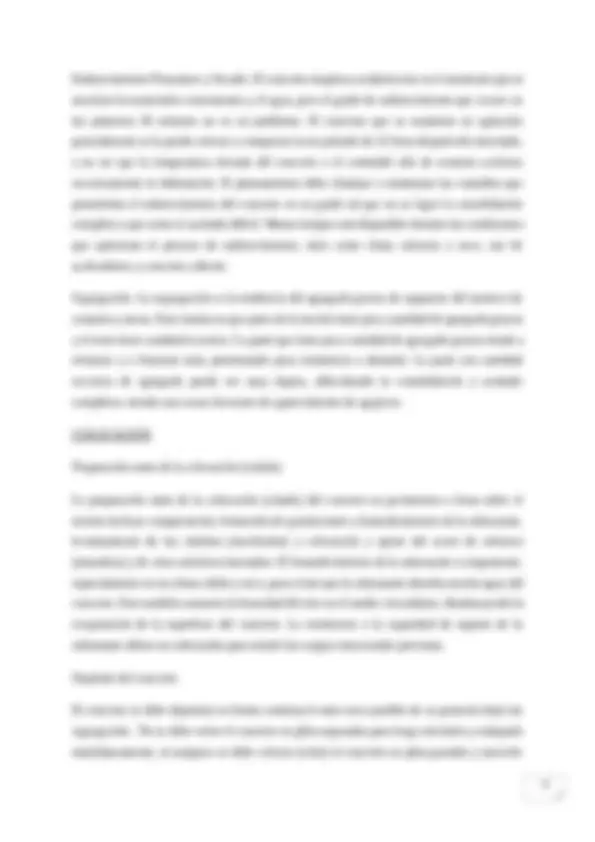
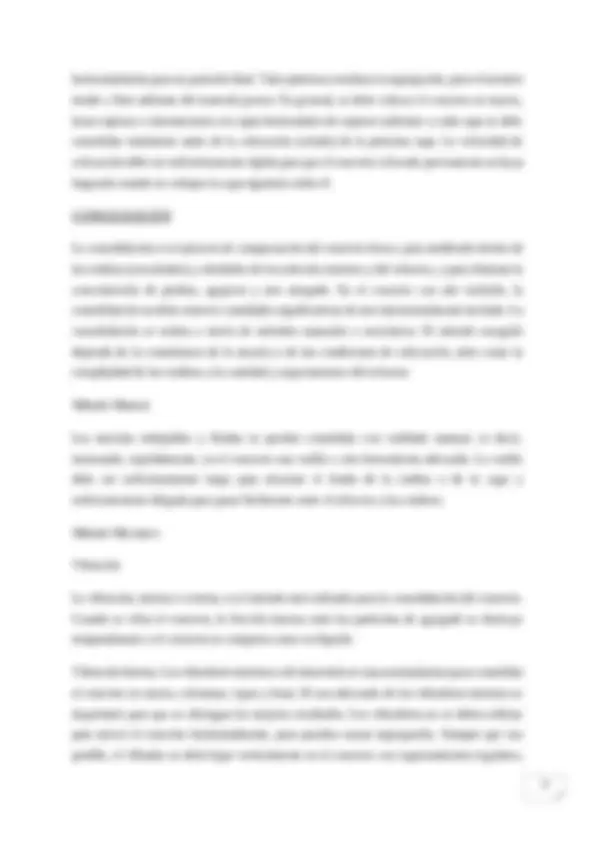
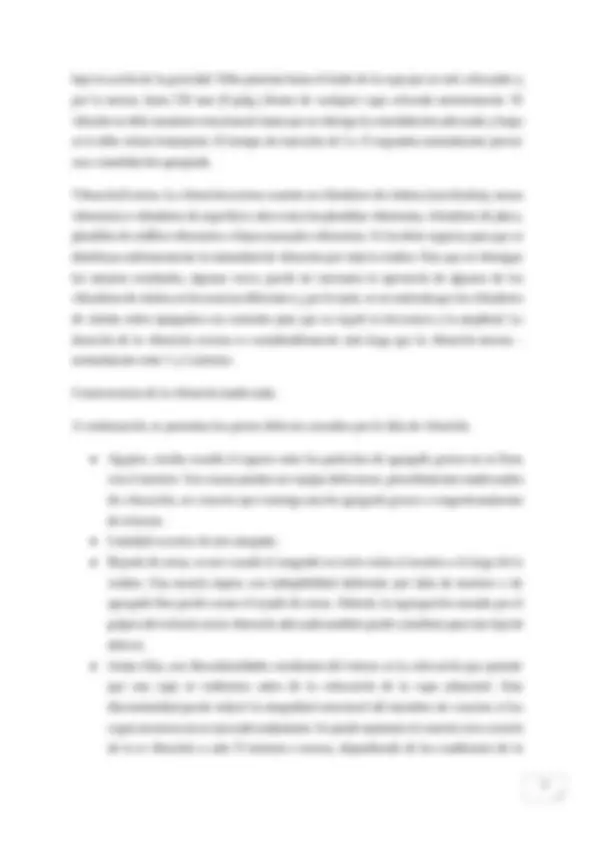
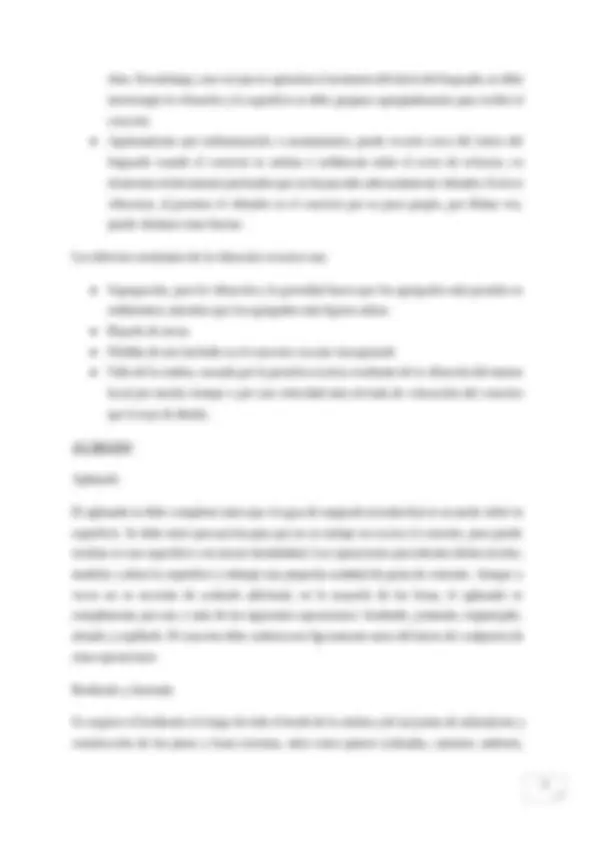
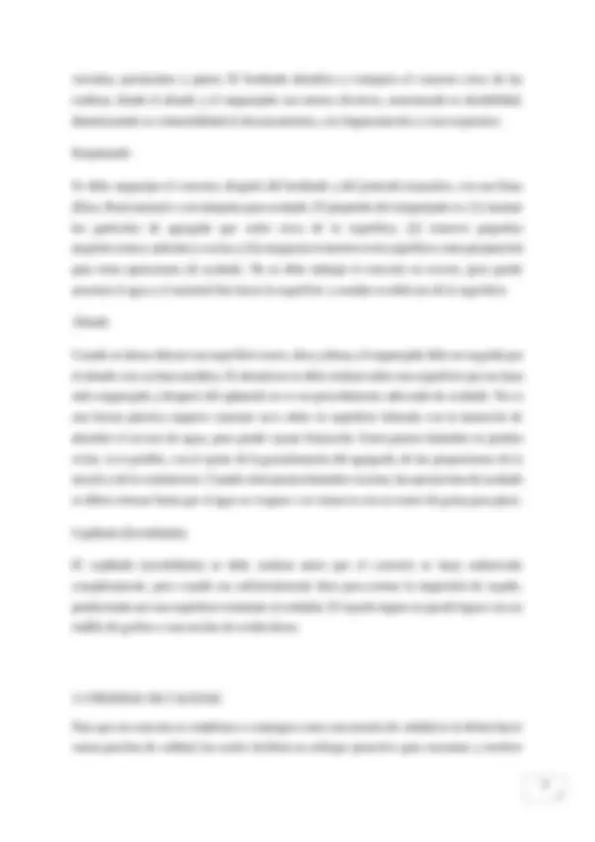
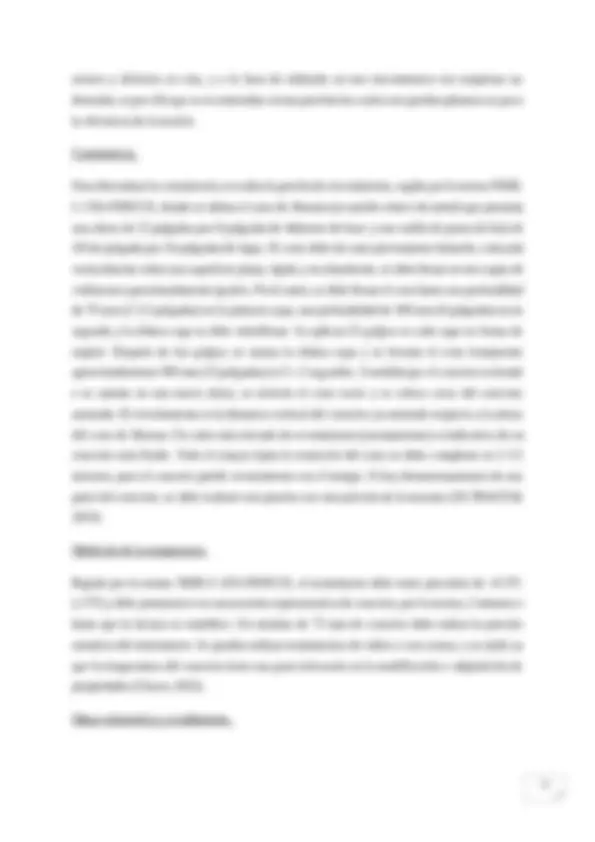
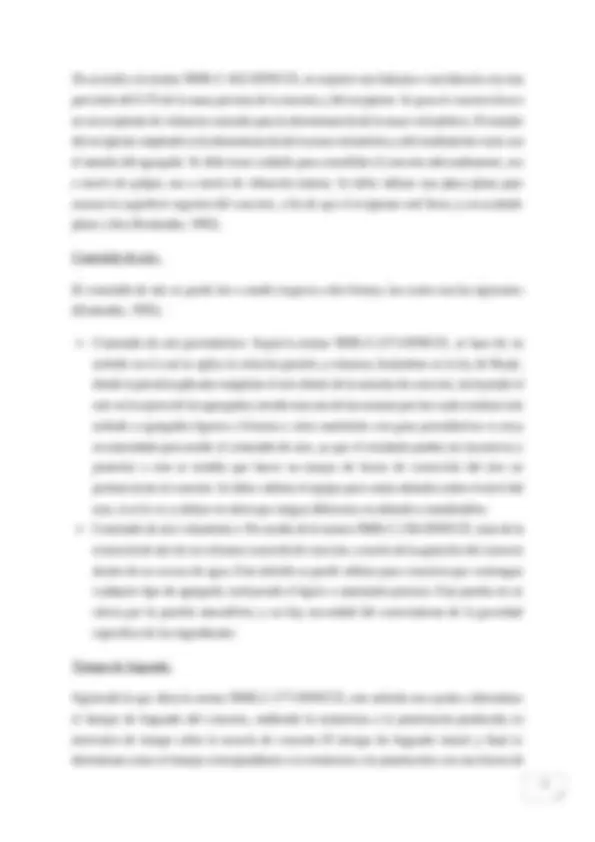
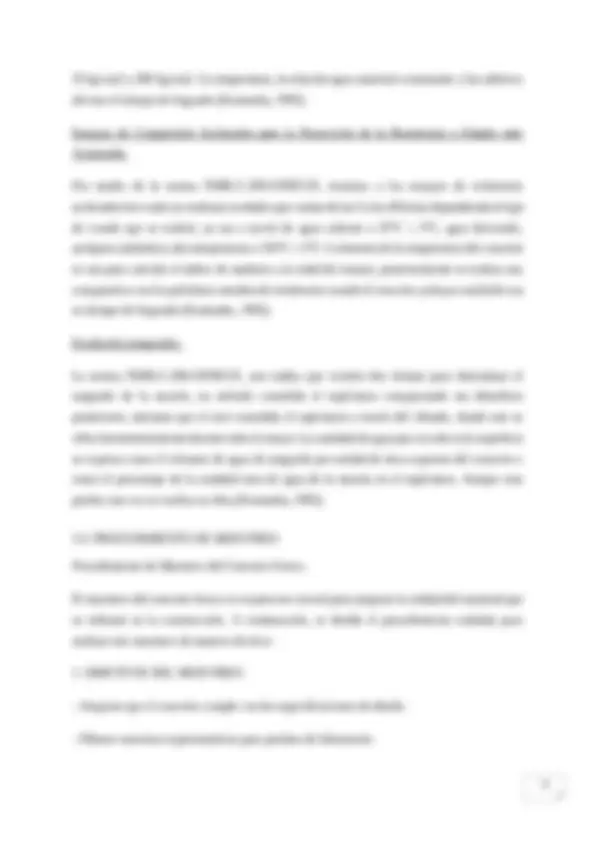
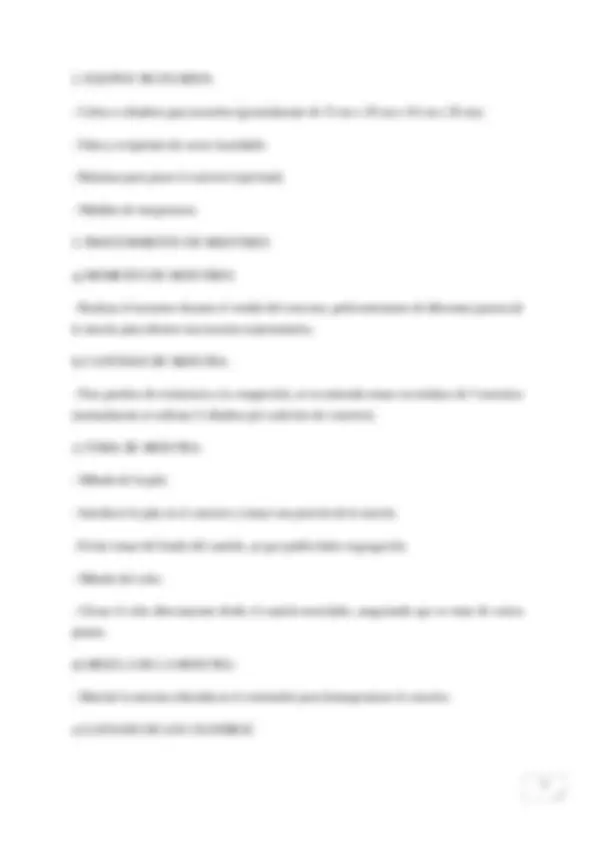
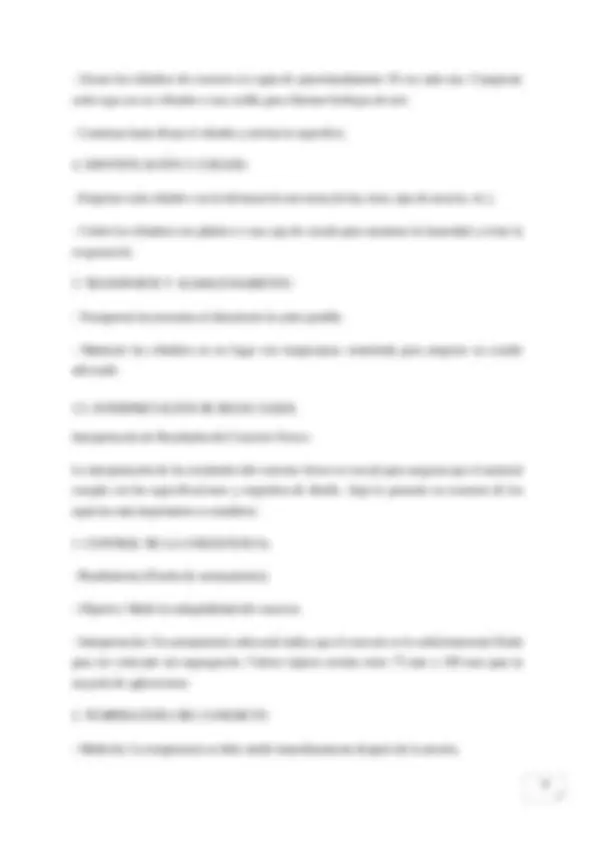
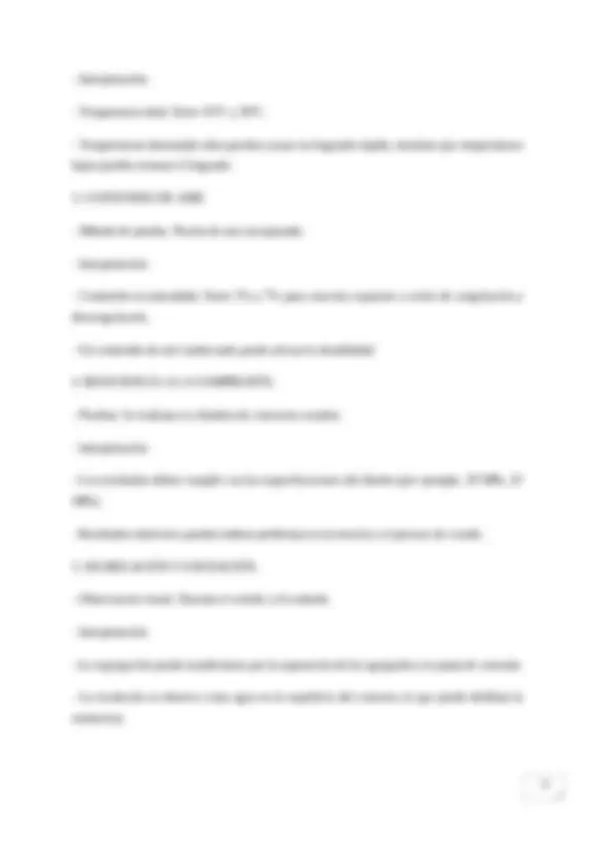
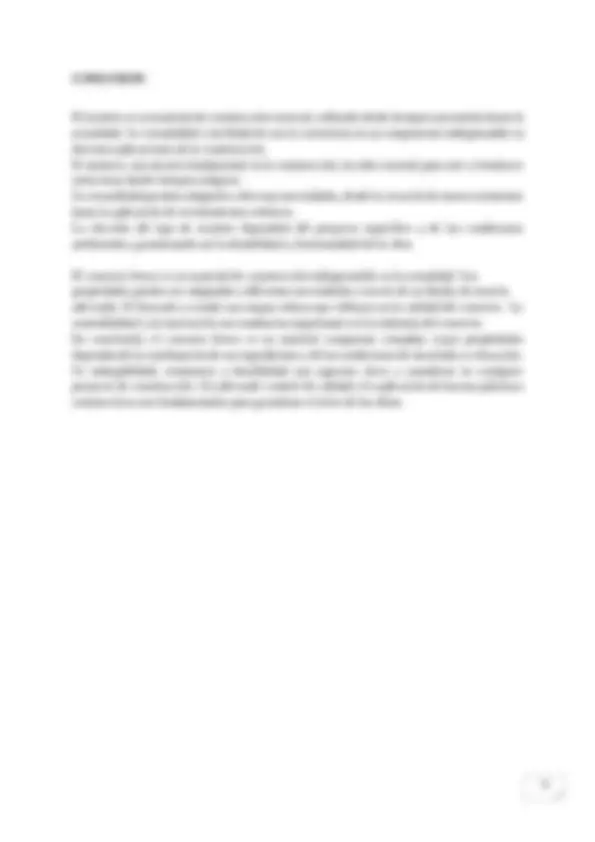
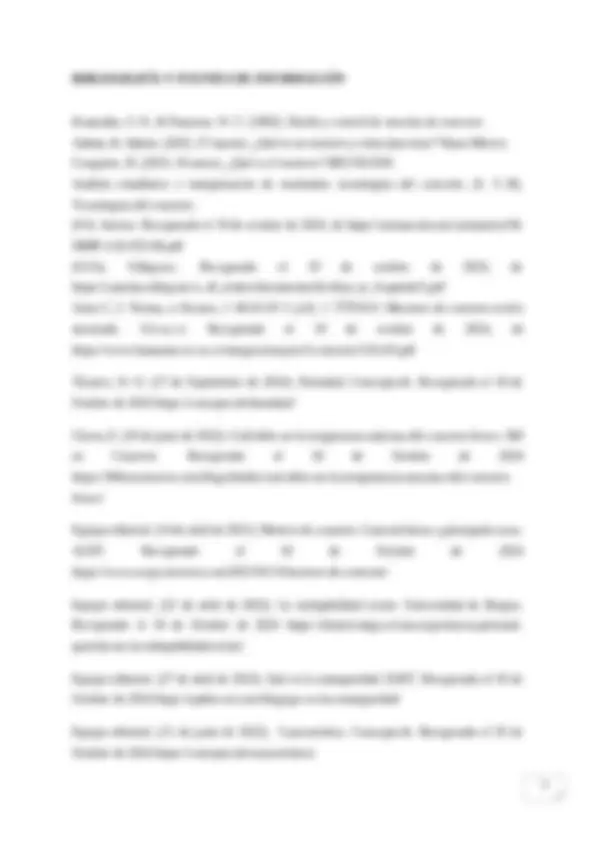
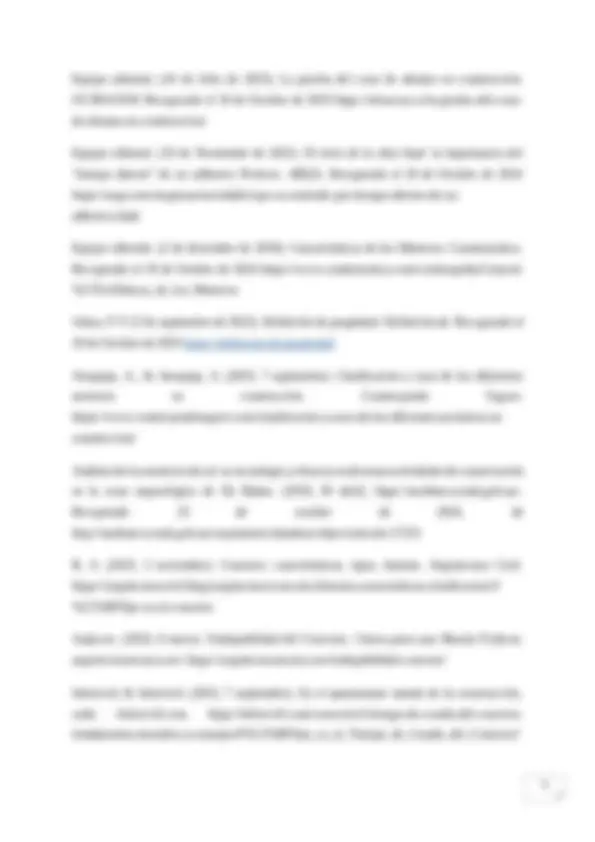
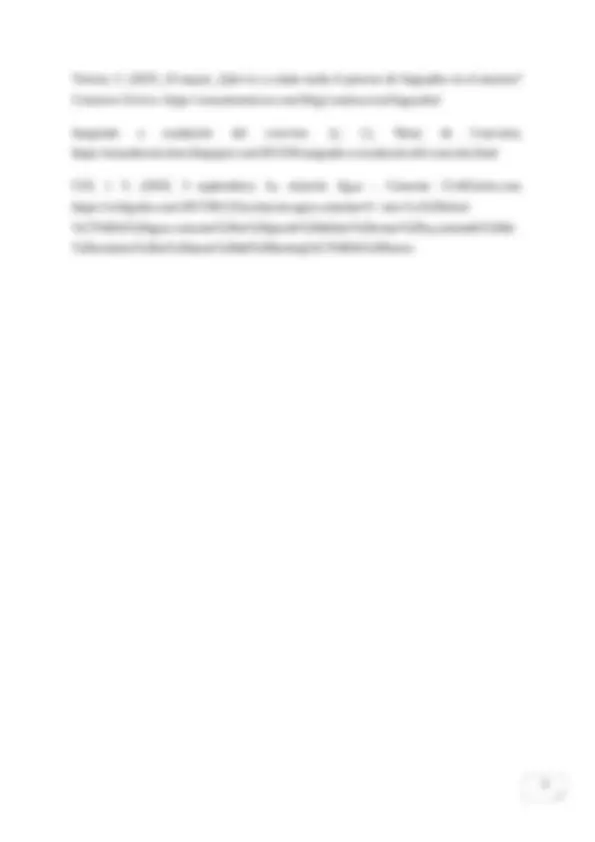
Prepara tus exámenes y mejora tus resultados gracias a la gran cantidad de recursos disponibles en Docsity
Gana puntos ayudando a otros estudiantes o consíguelos activando un Plan Premium
Prepara tus exámenes
Prepara tus exámenes y mejora tus resultados gracias a la gran cantidad de recursos disponibles en Docsity
Prepara tus exámenes con los documentos que comparten otros estudiantes como tú en Docsity
Los mejores documentos en venta realizados por estudiantes que han terminado sus estudios
Estudia con lecciones y exámenes resueltos basados en los programas académicos de las mejores universidades
Responde a preguntas de exámenes reales y pon a prueba tu preparación
Consigue puntos base para descargar
Gana puntos ayudando a otros estudiantes o consíguelos activando un Plan Premium
Comunidad
Pide ayuda a la comunidad y resuelve tus dudas de estudio
Descubre las mejores universidades de tu país según los usuarios de Docsity
Ebooks gratuitos
Descarga nuestras guías gratuitas sobre técnicas de estudio, métodos para controlar la ansiedad y consejos para la tesis preparadas por los tutores de Docsity
Este documento proporciona una introducción al concreto fresco, cubriendo aspectos como la normatividad en méxico, el control de calidad, la innovación en la industria, y conceptos fundamentales como la trabajabilidad, el curado y el sangrado. Se explora el proceso de fabricación, transporte, colocación, compactación y acabado del concreto en obra, incluyendo métodos de consolidación y pruebas de calidad. El documento también aborda la importancia de la temperatura del concreto y la interpretación de los resultados del concreto fresco.
Tipo: Esquemas y mapas conceptuales
1 / 33
Esta página no es visible en la vista previa
¡No te pierdas las partes importantes!
Los morteros son mezclas esenciales en la construcción, utilizadas desde tiempos ancestrales. En México, su uso se remonta a las civilizaciones prehispánicas, quienes desarrollaron técnicas sofisticadas para la elaboración de morteros a base de cal, arena y aditivos naturales. Un mortero es una pasta compuesta generalmente por un aglomerante (como el cemento o la cal), un agregado fino (arena) y agua. Esta mezcla, al endurecer, adquiere propiedades adhesivas y mecánicas que permiten unir elementos de construcción, revestir superficies y formar estructuras. En México se utilizan diversos tipos de morteros, cada uno con características y aplicaciones específicas: Morteros de cemento: Son los más comunes y se utilizan para diversas labores como el aplanado de muros, la colocación de bloques y la construcción de elementos estructurales. Morteros de cal: Se caracterizan por su plasticidad y adherencia, siendo ideales para trabajos de restauración y acabados finos. Morteros especiales: Existen morteros diseñados para aplicaciones específicas, como los morteros impermeabilizantes, los morteros refractarios y los morteros autonivelantes. Usos de los morteros en México Los morteros tienen una amplia gama de aplicaciones en la construcción, entre las que destacan: Uniones: Sirven para unir elementos de construcción como ladrillos, bloques, piedras y elementos prefabricados. Revestimientos: Se utilizan para crear acabados lisos y resistentes en muros, pisos y techos. Estructuras: Forman parte de elementos estructurales como columnas, vigas y losas. Reparaciones: Se emplean para reparar daños en construcciones existentes. Los morteros son fundamentales en la construcción mexicana, ya que garantizan la resistencia, durabilidad y estética de las edificaciones. Además, su correcta elección y aplicación son clave para asegurar la calidad y el buen funcionamiento de cualquier obra. CONCRETO FRESCO. El concreto fresco es un material fundamental en la industria de la construcción en México. Se trata de una mezcla de cemento, agua, agregados (arena y grava) y, en ocasiones, aditivos que le confieren propiedades específicas. Su versatilidad lo convierte en un elemento indispensable para la creación de una amplia gama de estructuras, desde viviendas y edificios comerciales hasta infraestructuras como puentes y carreteras.
Se denominan morteros, a las mezclas constituidas por agregados finos y uno o más aglomerantes (cemento Portland, cemento de albañilería, cal, yeso, etc.) y agua. Los morteros son mezclas plásticas que en estado pastoso tienen la propiedad de poderse moldear, de adherirse fácilmente a otros materiales, de unirlos entre sí, protegerlos, endurecerse y alcanzar resistencias. Los morteros varían según los materiales con los que son elaborados y comúnmente se elaboran de forma manual, mecánicamente o bien, premezclados Se incluye en esta definición a las pastas de cemento o de yeso con agua que se emplean en algunas terminaciones de revoques u otros usos. La mezcla de aglomerante y agua se denomina “pasta”, llamándose “lechada” cuando se amasa con mucha agua. Las arenas constituyen la estructura de la mezcla y le da volumen, y los vacíos que quedan entre las partículas de esa estructura granular son llenados por la pasta constituida por los aglomerantes y agua. Los aglomerantes o ligantes en presencia de agua experimentan un proceso físico - químico produciéndose el fraguado y endurecimiento. Durante la etapa de preparación y aplicación, conocida como estado fresco, la pasta formada por aglomerante y agua actúa como lubricante entre las partículas de agregado fino (arena), confiriendo plasticidad y trabajabilidad, facilitando el manipuleo permitiendo su colocación. En la etapa de fraguado y endurecimiento, la pasta se solidifica y endurece adhiriendo entre sí las partículas de arena y a su vez el mortero a los ladrillos o a la superficie de apoyo. 2.2 PROPIEDADES Y CARACTERÍSTICAS. Como cualquier material conglomerante en al área de la construcción, el mortero al ser un componente el cual se suele utilizar para rellenar huecos entre bloques, como un material de agarre o incluso es utilizado para el revestimiento de paredes, entre otras aplicaciones, este al ser un elemento que requiere la capacidad para soportar diversos esfuerzos y fuerzas externas que lo llegaran afectar debe tener ciertas propiedades y características las cuales lo hagan un material en el que se pueda confiar al momento en que se requiera construir (ACEP Concretos, 2021).
Antes de comenzar con el tema, se tiene que saber que a la hora de hablar de “propiedades” y “características”, son conceptos los cuales se podría decir que tienen cierta similitud, pero cuentan con una diferencia. Al mencionar propiedades nos referimos al atributo o cualidad de un objeto (Julian, 2022), mientras que al decir característica trata de todos aquellos rasgos o elementos que permiten distinguir un objeto de otro (Concepto.de, 2022); sabiendo esto, se puede decir que una característica es algo que entorna respecto al “aspecto” o cosas más superficiales, y una propiedad es aquella cualidad con la que cuenta un elemento. Ahora bien, como se había mencionado el mortero al ser un material para construir se requiere que la composición de este sea de gran calidad para que este funcione sin problemas, entre sus propiedades encontramos: Propiedades: estado fresco (Construmática, 2018).
En los muros de ladrillos se empleará una parte de cal y tres de arena, mientras que para muros de mampostería una parte de cal por cuatro de arena. Es importante tener presente que la correcta aplicación del tipo de mortero de cal hará que consigas mejores terminaciones flexibles, resistentes y duraderas. Por último, al utilizar revestimientos siempre ten en cuenta el material de soporte y, en caso de que sea necesario, deberás someterlo a tratamientos previos para garantizar su estabilidad y adherencia. MORTERO ARENA CEMENTO. Entre los tipos de mortero, encontramos este que lleva arena y cemento, el cual se utiliza para impermeabilizaciones, para pegar ladrillos en muros y baldosines interiores y exteriores, mampostería en general y muros sin carga. PROPORCIÓN DE ARENA CEMENTO. El tipo de mortero para bruñidos (pulidos) y revoques impermeables se mezcla con una parte de cemento y arena. En el caso de los muros cargados se recomienda utilizar un tipo más ordinario de una parte de cemento por cinco de arena. En lo que respecta al mortero más sencillo, se utiliza una parte de cemento por 6, 8 o 10 partes de arena. Esto dependerá de en qué trabajo será utilizado (fábricas cargadas, muros sin carga o rellenos para solados). Por otra parte, el tipo de mortero usado como revoque es más económico y fácil de aplicar que el enyesado, aunque su superficie una vez acabada queda lisa y presenta granulosidad. Por último, para bóvedas de escaleras o tabiques, se necesita el tipo de mortero en el que se coloca una parte de cemento por cuatro de arena. Mortero cemento, cal y arena El tipo de mortero formado de cal, arena y agua se caracteriza por su extensa plasticidad y, al mismo tiempo, por poder hacer una gran variedad de trabajos artesanales. Un mortero con cal retiene la humedad por más tiempo, con lo cual añadirlo a la mezcla permite evitar posibles fisuras por retracción, asegurando así la calidad de este tipo de mortero.
Estos dos tipos de morteros deben de cumplir ciertos estándares internacionales, regulados por el comité de energía nuclear, así también como deben de cumplir ciertos requisitos que lo rijan como un mortero tal cual. También se deben tomar en cuenta el uso de los morteros, para que tipo de obra se vaya a utilizar. Un caso en particular es lo que establece el INAH, organismo mexicano encargado del cuidado y mantenimiento de edificaciones históricas en nuestro país como se muestra en el artículo 17233 que se encuentra en la mediateca del INAH. el cual nos indica que: 1.- Si es necesario utilizar cemento, se recomienda realizar análisis de muestras para determinar la composición y características del mortero original. Esto ayudará a los restauradores a seleccionar un cemento que se asemeje en propiedades y apariencia al mortero original. 2.- Para lograr una mejor compatibilidad, se pueden desarrollar mezclas de cemento personalizadas que se adapten a las necesidades específicas del proyecto de restauración. Estas mezclas pueden incluir aditivos y materiales que mejoran la transpirabilidad y la flexibilidad del cemento. NMX-C- 255 Onncce 2013 2.4. DOSIFICACIÓN DEL MORTERO Se refiere a la proporción en la que se mezclan los diferentes componentes del mortero: cemento, arena, agua (y en algunos casos, cal). La correcta dosificación es crucial para garantizar que el mortero tenga las propiedades deseadas, como resistencia, adherencia, durabilidad y trabajabilidad. Componentes clave en la dosificación:
adecuada garantiza que la mezcla sea económica y efectiva, sin desperdiciar materiales o comprometer la calidad de la obra. Clasificación de los morteros según su dosificación: · Mortero de pega: es un tipo de mortero utilizado principalmente para unir elementos de construcción, como ladrillos, bloques de hormigón o piedras, en muros y paredes. Su principal función es actuar como un adhesivo entre estas piezas, por lo tanto, es importante que tenga una buena adherencia, trabajabilidad y resistencia para garantizar la durabilidad de la construcción. Además, se debe tener en cuenta la cantidad de agua para que la mezcla no sea ni muy seca ni muy líquida, lo que podría afectar la calidad del trabajo. · Morteros de relleno: son un tipo específico de mortero utilizado principalmente para rellenar espacios o juntas en las construcciones, ya sea entre bloques, ladrillos o en otros elementos estructurales. Su función principal es garantizar la estabilidad y solidez de la estructura, al mismo tiempo que sella los huecos o espacios entre los elementos constructivos. Este tipo de mortero no solo debe aportar resistencia, sino también ayudar a distribuir las cargas de manera uniforme. Los morteros de relleno también se utilizan en otras áreas, como el relleno de grietas en superficies, en trabajos de restauración y en la impermeabilización de ciertos espacios cuando se añaden aditivos especiales. · Morteros de recubrimiento: es una mezcla utilizada para cubrir, proteger y dar un acabado estético a las superficies de construcción, como paredes y muros. Su función principal es mejorar la apariencia de la estructura, alisar la superficie, y en algunos casos, proporcionar protección frente a la humedad, las inclemencias del tiempo y otros agentes externos. Este tipo de mortero se aplica sobre superficies de ladrillo, bloques o cemento para dejarlas listas para pintar o para recibir un acabado final.
diferentes condiciones y sirve para distintos propósitos dentro de la industria de la construcción. Factores que afectan la trabajabilidad incluyen las proporciones de la mezcla de concreto, el tamaño y la forma del agregado, la cantidad y calidad del agua, y la adición de aditivos como plastificantes o superplastificantes. La temperatura y el tiempo de mezclado también tienen un impacto considerable en la trabajabilidad del concreto. Por lo tanto, es esencial un diseño de mezcla adecuado y ajustes en sitio para adaptarse a las condiciones ambientales mientras se conserva la cohesión necesaria para las operaciones de colocación y acabado. CURADO DEL CONCRETO: El tiempo de curado del concreto se refiere al período en el que el concreto recién colocado debe mantenerse en condiciones controladas de humedad y temperatura para que alcance su resistencia y durabilidad óptimas. Este proceso es crítico, ya que un curado inadecuado puede dar lugar a concreto débil y agrietado. Para comprender mejor el curado del concreto, es importante conocer los fundamentos clave:
reacciones químicas y físicas que permiten que estas mezclas se solidifiquen y adquieran resistencia. Es importante tener en cuenta este factor, ya que si se espera demasiado tiempo después de la mezcla, el material puede comenzar a endurecerse antes de que se haya colocado adecuadamente. Por otro lado, si se trabaja demasiado pronto, puede no tener la resistencia necesaria para soportar cargas o tensiones. Por lo general, se recomienda comenzar a fraguar después de unos 30 minutos de haberse mezclado con agua y, dependiendo del tipo de material, la temperatura ambiente, la humedad y la cantidad de agua utilizada en la mezcla puede tardar de 24 a 48 horas en alcanzar una resistencia inicial suficiente para soportar cargas. SANGRADO EN EL CONCRETO: Sangrado (exudación) es el desarrollo de una camada de agua en el tope o en la superficie del concreto recién colocado. Es causada por la sedimentación (asentamiento) de las partículas sólidas (cemento y agregados) y simultáneamente la subida del agua hacia la superficie. El sangrado es normal y no debería disminuir la calidad del concreto adecuadamente colocado, acabado y curado. Un poco de sangrado es útil en el control de la fisuración por retracción plástica. Por otro lado, la excesiva aumenta la relación agua-cemento cerca de la superficie; puede ocurrir una camada superficial débil y con poca durabilidad, particularmente si se hace el acabado cuando el agua de sangrado aún está presente. Los vacíos y bolsas de agua pueden ocurrir, resultantes del acabado prematuro de la superficie. Después que toda el agua de sangrado (exudación) se evapore, la superficie endurecida va a ser un poco más baja que la superficie recién colocada. Esta disminución de la altura desde el momento de la colocación (puesta, colado) hasta el inicio del fraguado se llama retracción por sedimentación La tasa de sangrado (exudación) y la capacidad de sangrado (sedimentación total por unidad de peso del concreto original) aumentan con la cantidad inicial de agua, altura del elemento de concreto y presión. El uso de agregados de granulometría adecuada, ciertos aditivos químicos, aire incluido, materiales cementantes suplementarios y cementos más finos reduce el sangrado.
que el agua y otros materiales penetren en su interior. En consecuencia, esto puede causar la corrosión del acero de refuerzo y la degradación del concreto. En resumen, para garantizar la calidad y la durabilidad del concreto armado, es crucial evitar la segregación y mantener la mezcla homogénea y uniforme. De esta forma, se asegura que las propiedades del concreto sean consistentes y adecuadas para su uso previsto, se reduce la porosidad del concreto y se disminuyen los riesgos de la corrosión del acero de refuerzo y la degradación del concreto. CAUSAS DE LA SEGREGACIÓN. Las causas de la segregación en el concreto son las siguientes: ❖ Mezcla inadecuada: Una mezcla inadecuada puede ser demasiado seca o demasiado húmeda, lo que puede resultar en la separación de los componentes de la mezcla de concreto. ❖ Velocidad de vertido inadecuada: Una velocidad de vertido demasiado rápida puede causar la separación de los componentes de la mezcla, especialmente si la mezcla es demasiado seca o húmeda. ❖ Consistencia inadecuada: Una consistencia inadecuada puede resultar en una distribución desigual de los componentes de la mezcla, lo que puede provocar la separación. ❖ Colocación inadecuada: Una falta de control en la colocación puede resultar en la separación de los componentes de la mezcla. ❖ Temperatura inadecuada: Una temperatura demasiado alta o demasiado baja puede provocar la separación de los componentes de la mezcla. ❖ Agua de mezcla excesiva: El uso de demasiada agua en la mezcla puede resultar en una consistencia demasiado fluida, lo que puede provocar la separación de los componentes de la mezcla. ➢ ❖ Problemas de compactación: La falta de compactación adecuada puede provocar la separación de los componentes de la mezcla. ❖ Agregados de diferentes tamaños: El uso de agregados de diferentes tamaños puede resultar en una distribución desigual de los componentes de la mezcla, lo que puede provocar la separación.
Los efectos de la segregación en el concreto son los siguientes: ❖ Debilidad de la estructura: La segregación puede resultar en una distribución desigual de los componentes de la mezcla, lo que puede provocar una disminución en la resistencia y la durabilidad de la estructura. ❖ Porosidad: La segregación puede resultar en una concentración excesiva de agregados grandes en una zona, lo que puede provocar un aumento en la porosidad de la estructura. ❖ Deterioro de la superficie: La segregación puede resultar en la formación de hoyos y grietas en la superficie del concreto, lo que puede provocar un deterioro prematuro de la estructura. ❖ Problemas de adherencia: La segregación puede resultar en la separación de los componentes de la mezcla, lo que puede afectar la adherencia entre los componentes de la estructura. ❖ Reducción de la resistencia a la compresión: La segregación puede resultar en una disminución en la resistencia a la compresión de la estructura, lo que puede provocar una disminución en su durabilidad y capacidad de soportar cargas. ❖ Problemas de hidrofugación: La segregación puede resultar en una concentración excesiva de agua en una zona, lo que puede afectar la capacidad del concreto para repeler el agua y protegerse de la humedad. ❖ Problemas de estética: La segregación puede resultar en la formación de manchas y deformaciones en la superficie del concreto, lo que puede afectar su apariencia. 3.2. PROCESO DE FABRICACIÓN, TRANSPORTE, COLOCACIÓN, COMPACTACIÓN Y ACABADO DEL CONCRETO EN OBRA. FABRICACIÓN Todo concreto se debe mezclar completamente hasta que tenga una apariencia uniforme, con todos sus ingredientes igualmente distribuidos. Las mezcladoras no se deben cargar más de sus
Endurecimiento Prematuro y Secado. El concreto empieza a endurecerse en el momento que se mezclan los materiales cementantes y el agua, pero el grado de endurecimiento que ocurre en los primeros 30 minutos no es un problema. El concreto que se mantiene en agitación generalmente se lo puede colocar y compactar en un periodo de 1⁄2 hora después del mezclado, a no ser que la temperatura elevada del concreto o el contenido alto de cemento aceleren excesivamente la hidratación. El planeamiento debe eliminar o minimizar las variables que permitirían el endurecimiento del concreto en un grado tal que no se logre la consolidación completa y que torne el acabado difícil. Menos tiempo está disponible durante las condiciones que apresuran el proceso de endurecimiento, tales como clima caluroso y seco, uso de aceleradores y concreto caliente. Segregación. La segregación es la tendencia del agregado grueso de separarse del mortero de cemento y arena. Esto resulta en que parte de la mezcla tiene poca cantidad de agregado grueso y el resto tiene cantidad excesiva. La parte que tiene poca cantidad de agregado grueso tiende a retraerse y a fisurarse más, presentando poca resistencia a abrasión. La parte con cantidad excesiva de agregado puede ser muy áspera, dificultando la consolidación y acabado completos, siendo una causa frecuente de aparecimiento de agujeros. COLOCACIÓN Preparación antes de la colocación (colado) La preparación antes de la colocación (colado) del concreto en pavimentos o losas sobre el terreno incluye compactación, formación de guarniciones y humedecimiento de la subrasante, levantamiento de las cimbras (encofrados) y colocación y ajuste del acero de refuerzo (armadura) y de otros artículos insertados. El humedecimiento de la subrasante es importante, especialmente en un clima cálido y seco, para evitar que la subrasante absorba mucha agua del concreto. Esto también aumenta la humedad del aire en el medio circundante, disminuyendo la evaporación de la superficie del concreto. La resistencia o la capacidad de soporte de la subrasante deben ser adecuadas para resistir las cargas estructurales previstas. Depósito del concreto El concreto se debe depositar en forma continua lo más cerca posible de su posición final sin segregación. No se debe verter el concreto en pilas separadas para luego nivelarlo y trabajarlo simultáneamente, ni tampoco se debe colocar (colar) el concreto en pilas grandes y moverlo
horizontalmente para su posición final. Tales prácticas resultan en segregación, pues el mortero tiende a fluir adelante del material grueso. En general, se debe colocar el concreto en muros, losas espesas o cimentaciones en capas horizontales de espesor uniforme y cada capa se debe consolidar totalmente antes de la colocación (colado) de la próxima capa. La velocidad de colocación debe ser suficientemente rápida para que el concreto colocado previamente no haya fraguado cuando se coloque la capa siguiente sobre él. CONSOLIDACIÓN La consolidación es el proceso de compactación del concreto fresco, para moldearlo dentro de las cimbras (encofrados) y alrededor de los artículos insertos y del refuerzo, y para eliminar la concentración de piedras, agujeros y aire atrapado. En el concreto con aire incluido, la consolidación no debe remover cantidades significativas de aire intencionalmente incluido. La consolidación se realiza a través de métodos manuales o mecánicos. El método escogido depende de la consistencia de la mezcla y de las condiciones de colocación, tales como la complejidad de las cimbras y la cantidad y espaciamiento del refuerzo. Método Manual Las mezclas trabajables y fluidas se pueden consolidar con varillado manual, es decir, insertando, repetidamente, en el concreto una varilla u otra herramienta adecuada. La varilla debe ser suficientemente larga para alcanzar el fondo de la cimbra o de la capa y suficientemente delgada para pasar fácilmente entre el refuerzo y las cimbras. Método Mecánico Vibración La vibración, interna o externa, es el método más utilizado para la consolidación del concreto. Cuando se vibra el concreto, la fricción interna entre las partículas de agregado se destruye temporalmente y el concreto se comporta como un líquido. Vibración Interna. Los vibradores internos o de inmersión se usan normalmente para consolidar el concreto en muros, columnas, vigas y losas. El uso adecuado de los vibradores internos es importante para que se obtengan los mejores resultados. Los vibradores no se deben utilizar para mover el concreto horizontalmente, pues pueden causar segregación. Siempre que sea posible, el vibrador se debe bajar verticalmente en el concreto con espaciamientos regulares,