
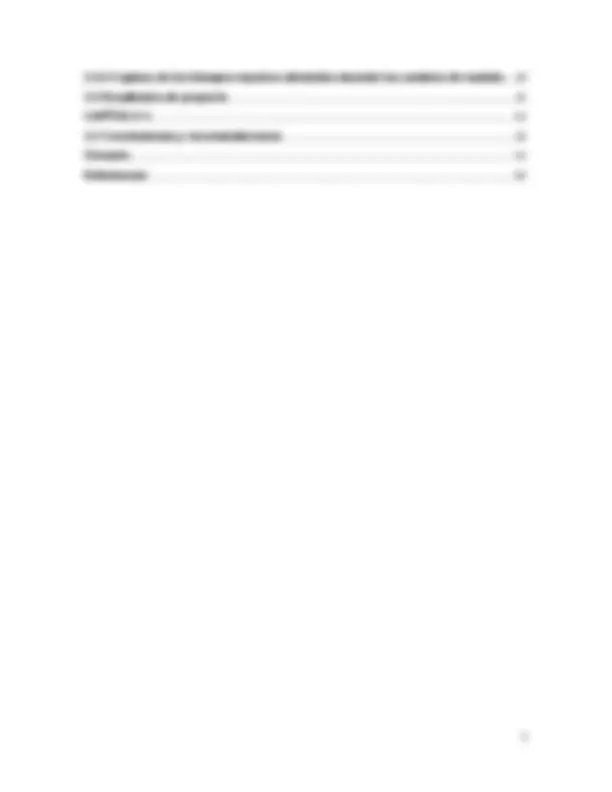
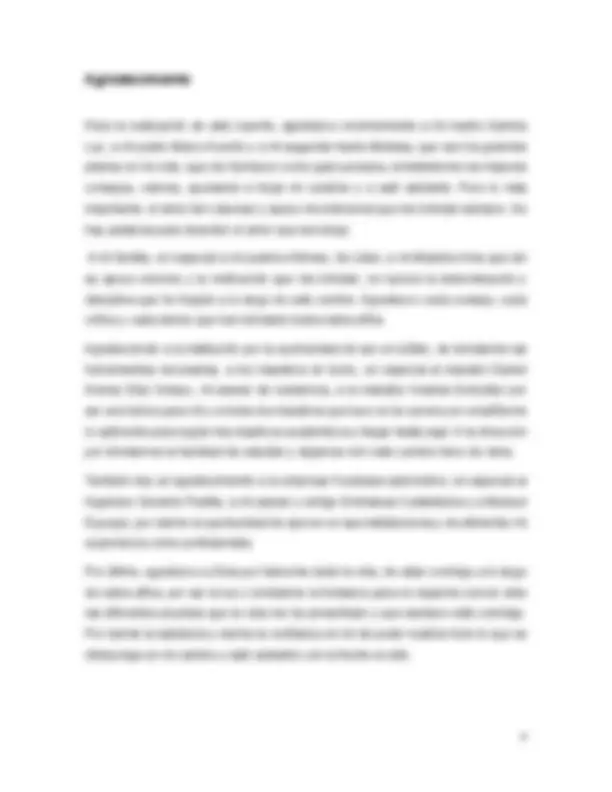
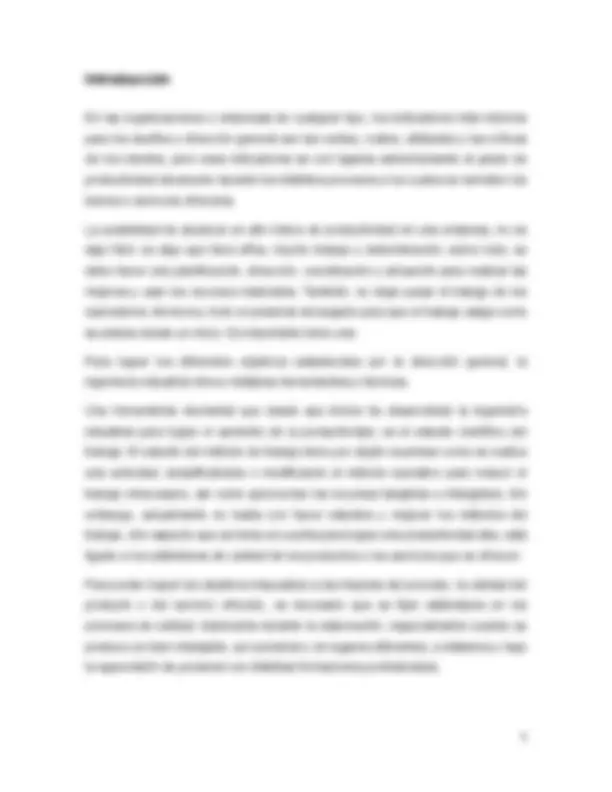
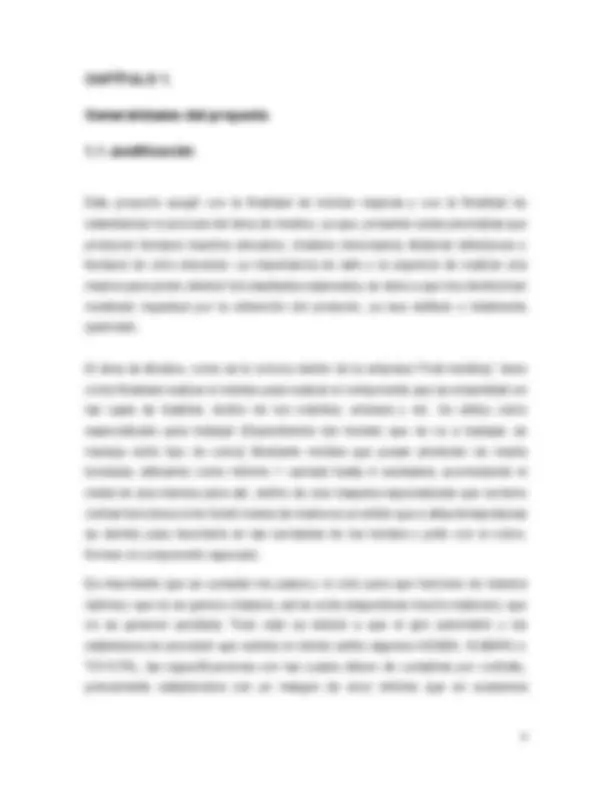
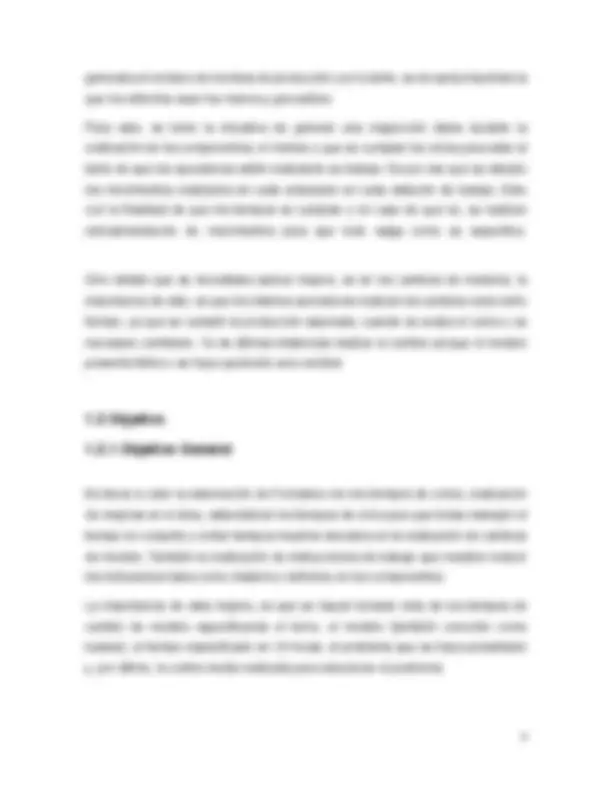
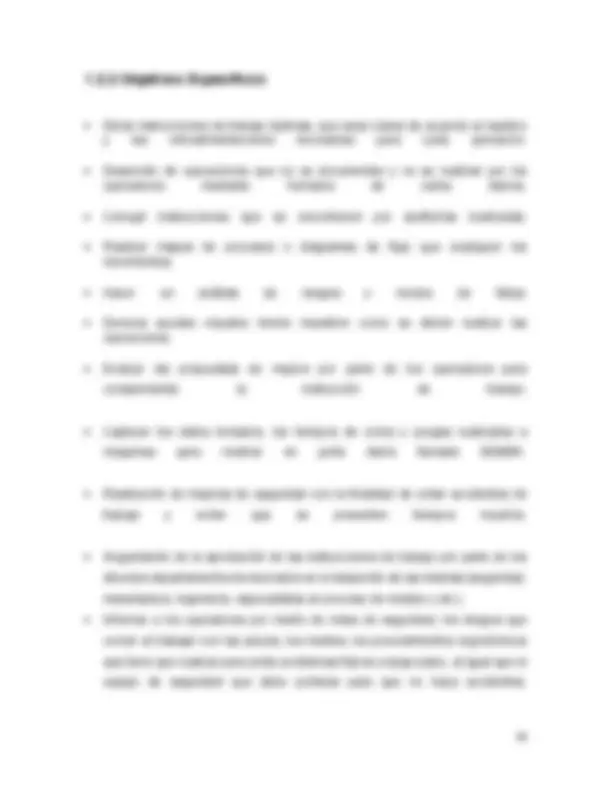
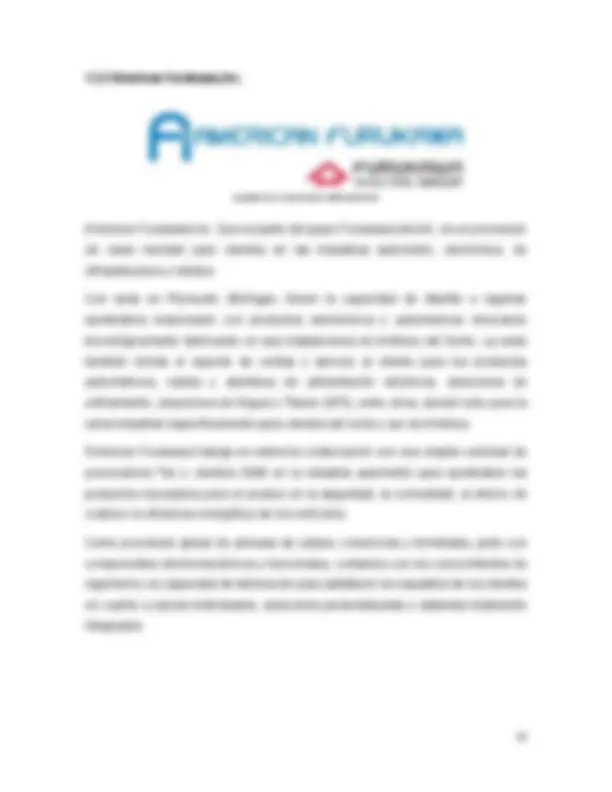
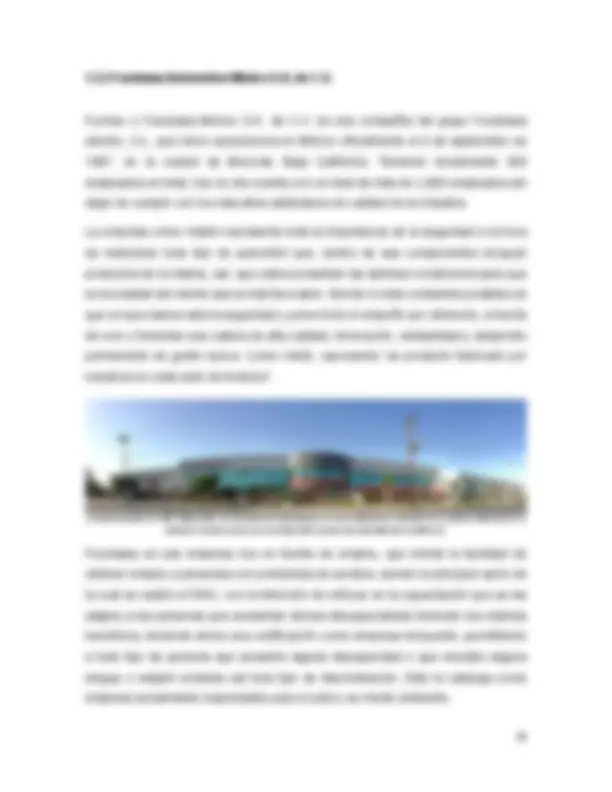
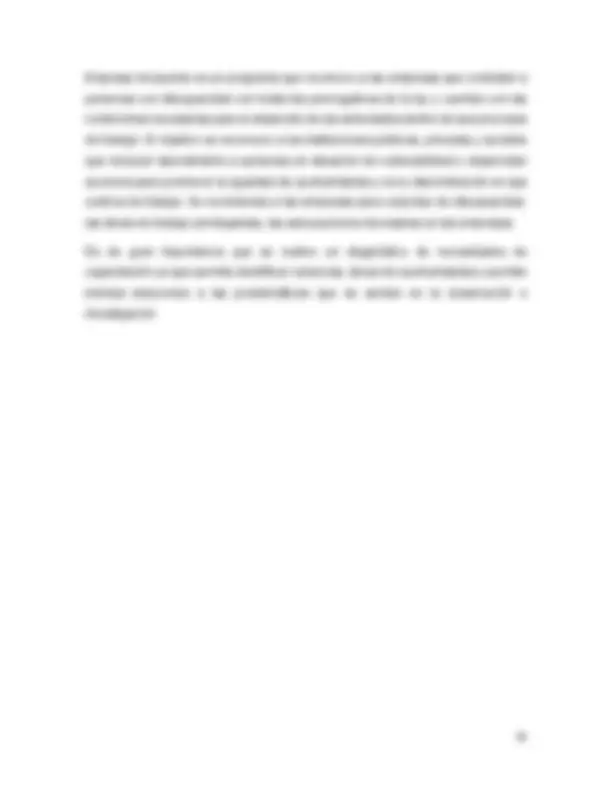
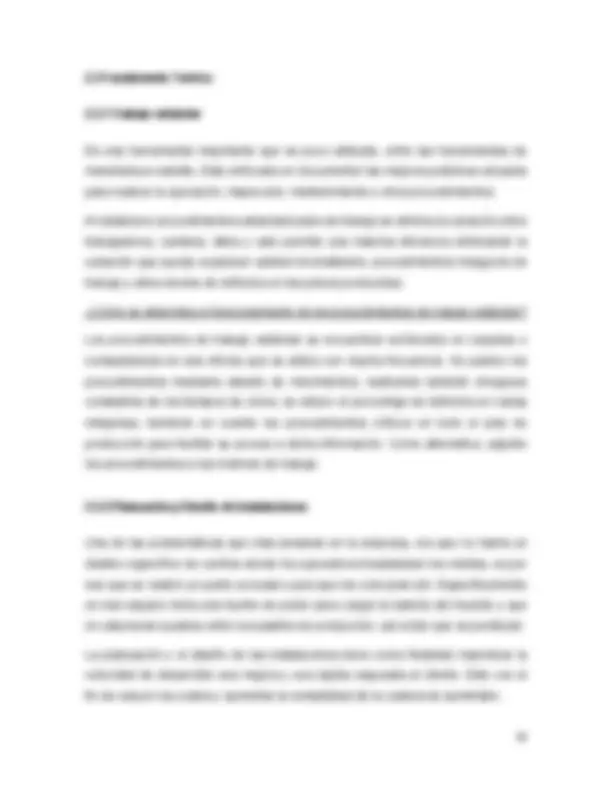
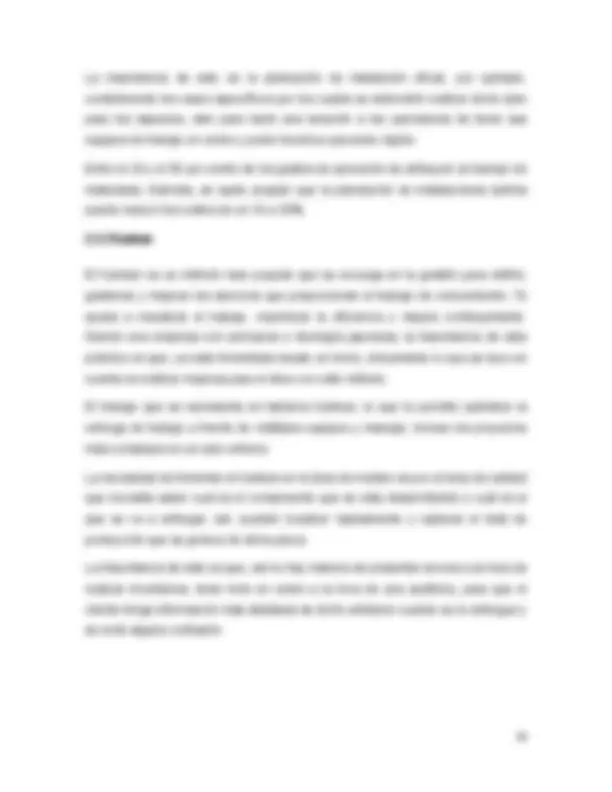
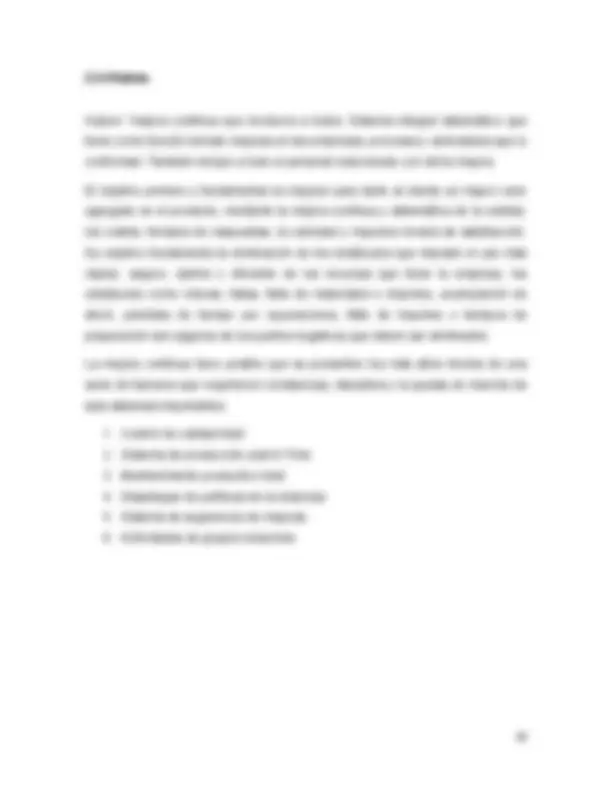
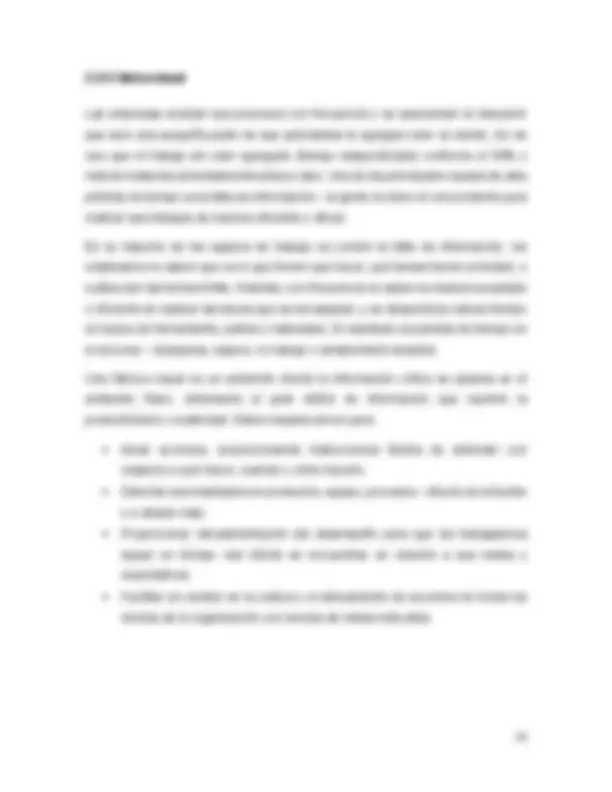
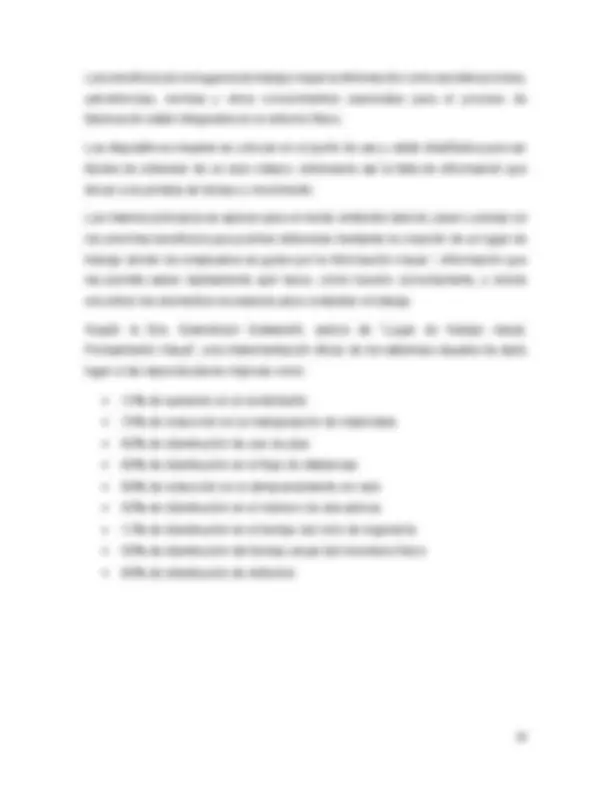
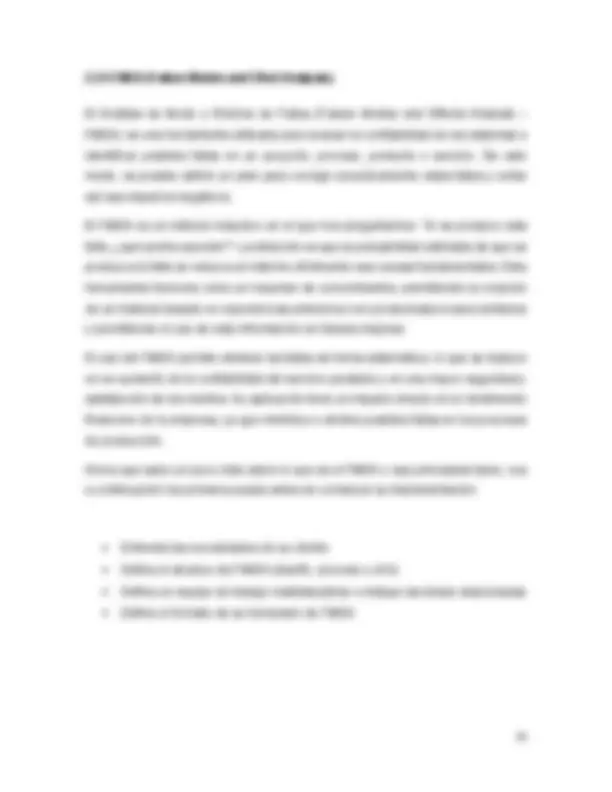
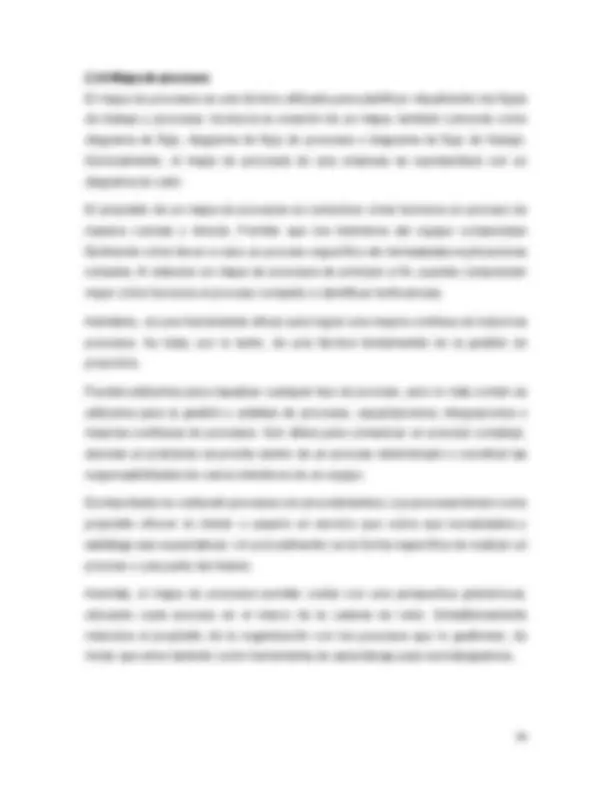
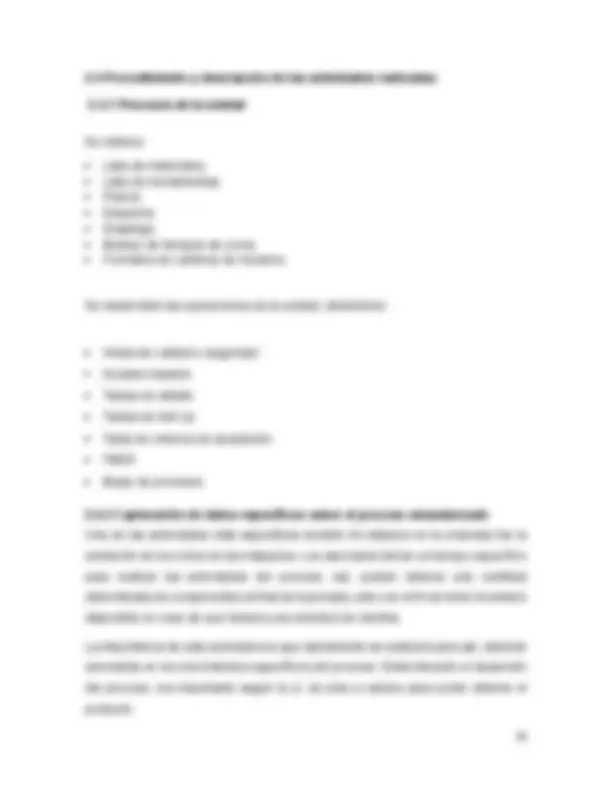
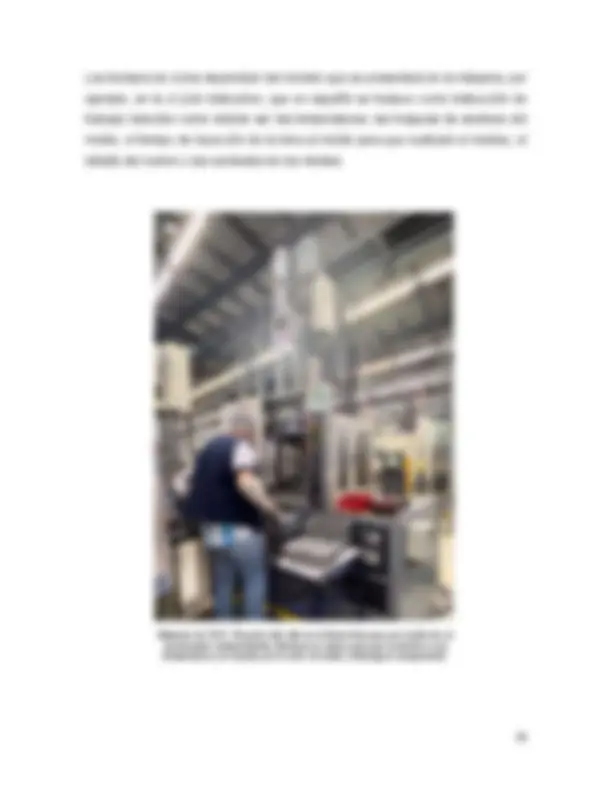
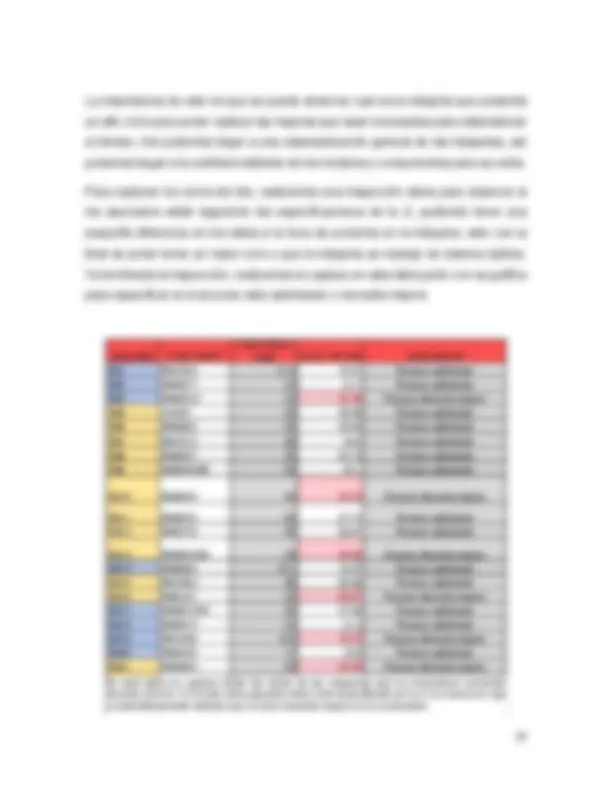
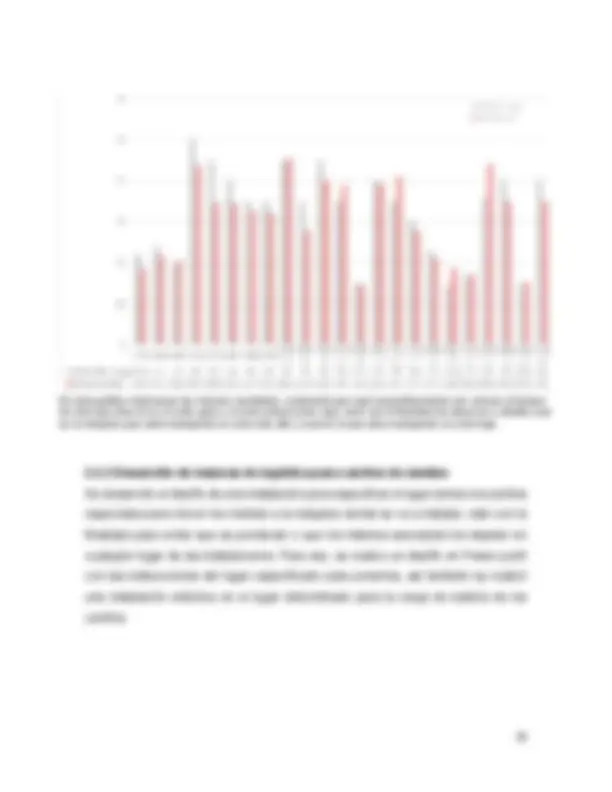
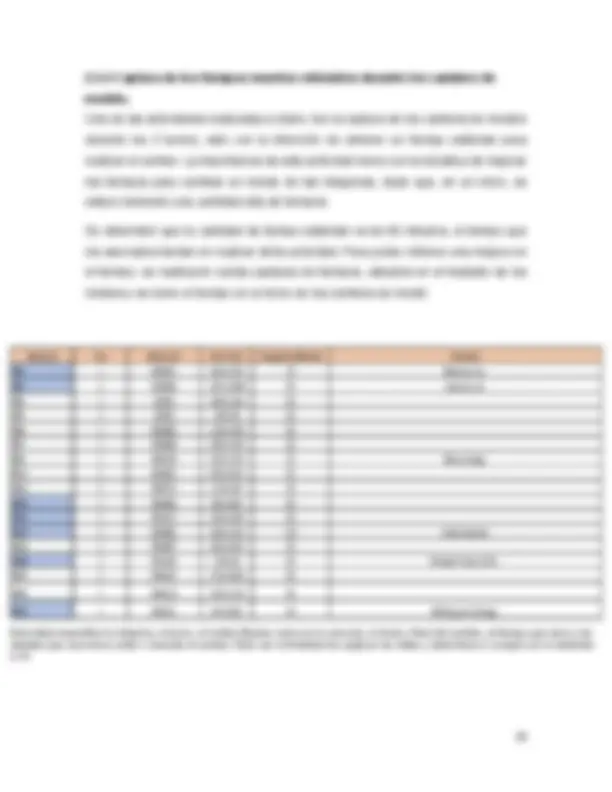
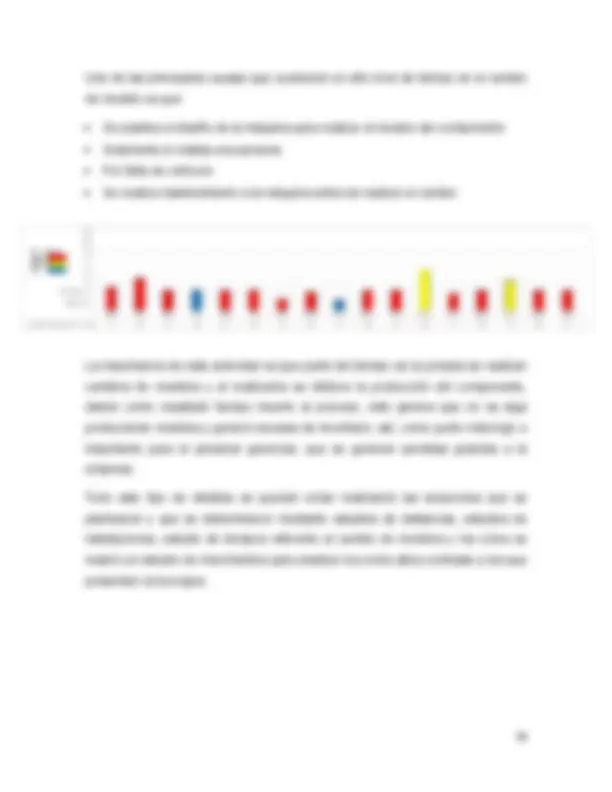
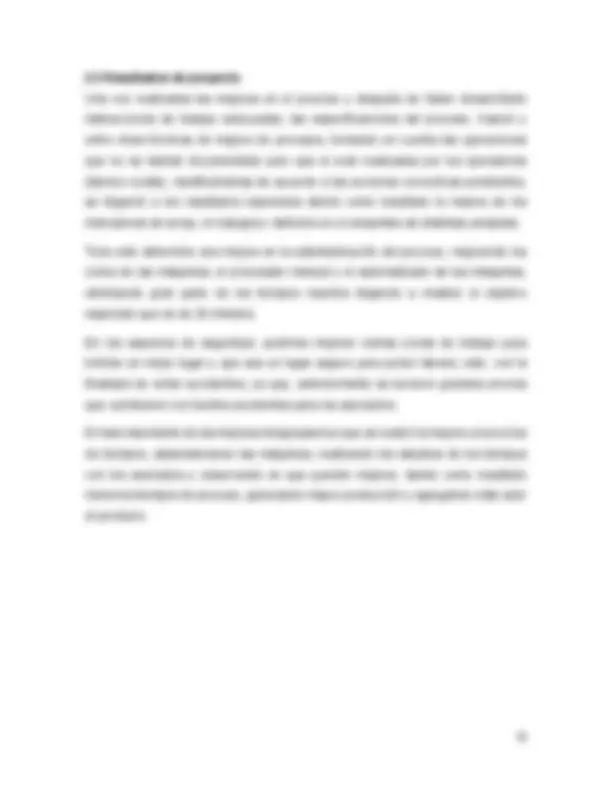
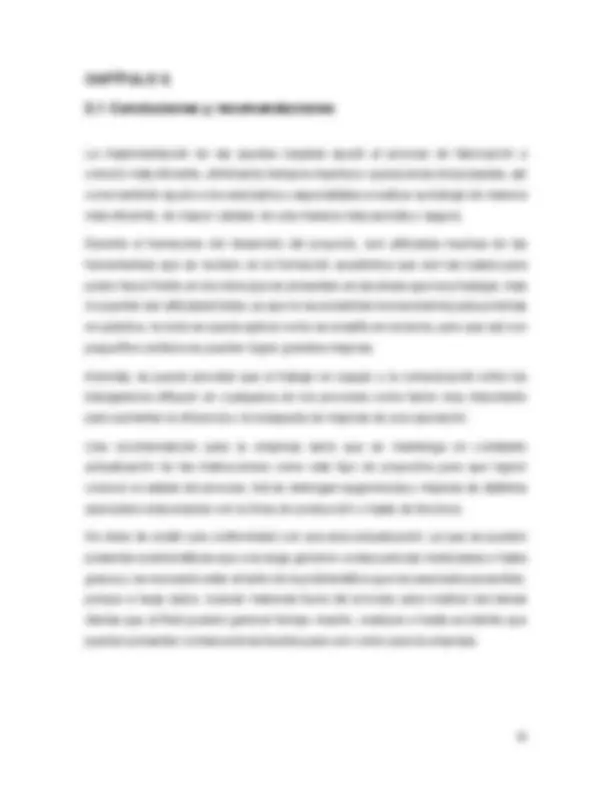
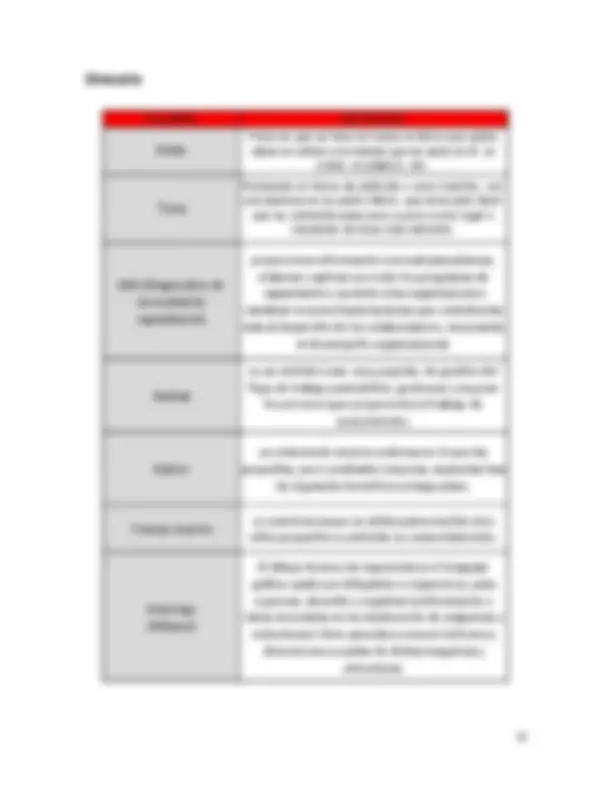
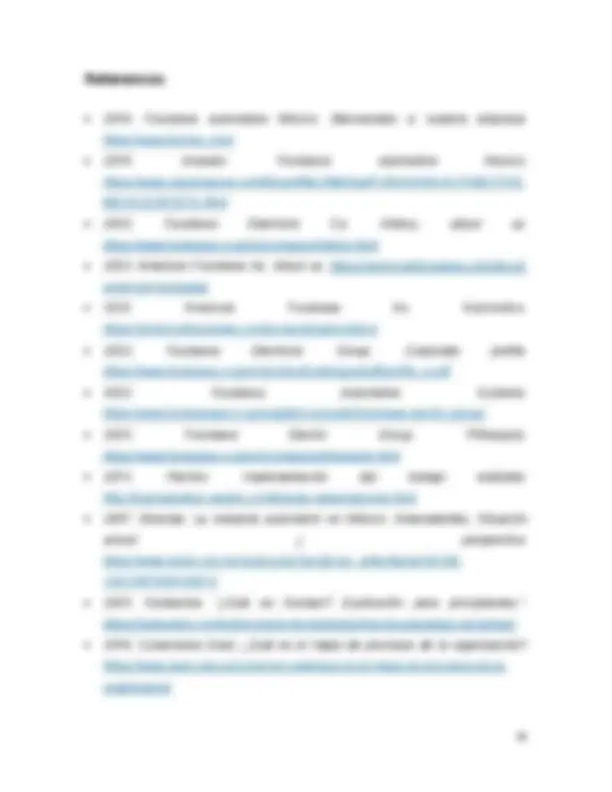
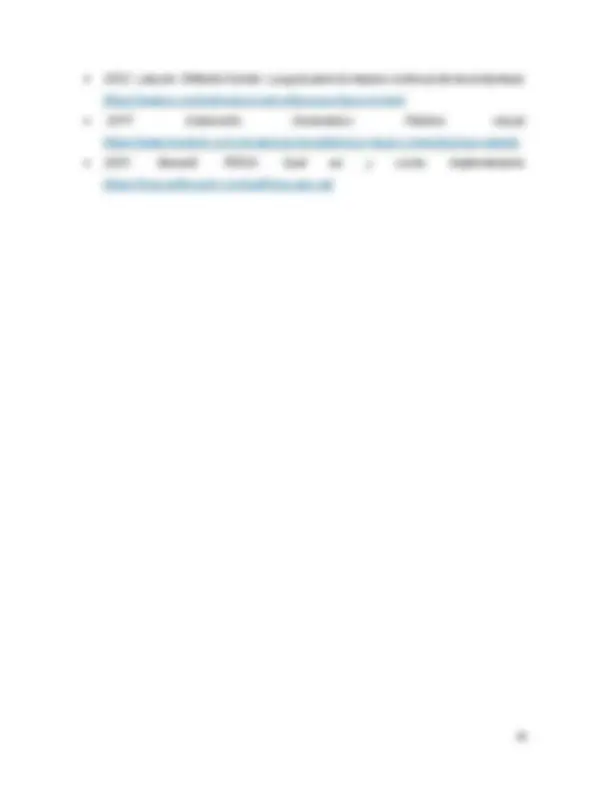
Prepara tus exámenes y mejora tus resultados gracias a la gran cantidad de recursos disponibles en Docsity
Gana puntos ayudando a otros estudiantes o consíguelos activando un Plan Premium
Prepara tus exámenes
Prepara tus exámenes y mejora tus resultados gracias a la gran cantidad de recursos disponibles en Docsity
Prepara tus exámenes con los documentos que comparten otros estudiantes como tú en Docsity
Los mejores documentos en venta realizados por estudiantes que han terminado sus estudios
Estudia con lecciones y exámenes resueltos basados en los programas académicos de las mejores universidades
Responde a preguntas de exámenes reales y pon a prueba tu preparación
Consigue puntos base para descargar
Gana puntos ayudando a otros estudiantes o consíguelos activando un Plan Premium
Comunidad
Pide ayuda a la comunidad y resuelve tus dudas de estudio
Descubre las mejores universidades de tu país según los usuarios de Docsity
Ebooks gratuitos
Descarga nuestras guías gratuitas sobre técnicas de estudio, métodos para controlar la ansiedad y consejos para la tesis preparadas por los tutores de Docsity
Un proyecto de mejora en el proceso de moldeo de una empresa, con el objetivo de reducir tiempos muertos, mejorar la calidad del producto y estandarizar los tiempos de ciclo. El proyecto incluye la creación de formatos, mapas de procesos, fmea (failure modes and effect analysis), mejoras de seguridad y la eliminación de operaciones innecesarias. Se detalla el proceso, las actividades realizadas y los resultados obtenidos.
Tipo: Guías, Proyectos, Investigaciones
1 / 35
Esta página no es visible en la vista previa
¡No te pierdas las partes importantes!
Para la realización de este reporte, agradezco enormemente a mi madre Sandra Luz, a mi padre Marco Aurelio y a mi segunda madre Melissa, que son los grandes pilares en mi vida, que me formaron como gran persona, brindándome los mejores consejos, valores, ayudando a forjar mi carácter y a salir adelante. Pero lo más importante, el amor tan caluroso y apoyo incondicional que me brindan siempre. No hay palabras para describir el amor que les tengo. A mi familia, en especial a mi padrino Alfonso, tía Lilian, a mi Madrina Irma que sin su apoyo enorme y la motivación que me brindan, no tuviera la determinación y disciplina que he forjado a lo largo de este camino. Agradezco cada consejo, cada crítica y cada ánimo que han brindado todos estos años. Agradeciendo a la institución por la oportunidad de ser un búfalo, de brindarme las herramientas necesarias, a los maestros en turno, en especial al maestro Daniel Alonso Díaz Sotuyo, mi asesor de residencia, a la maestra Yesenia González por ser una tutora para mí y a todos los maestros que tuve en la carrera por enseñarme lo suficiente para lograr mis objetivos académicos y llegar hasta aquí. A la dirección por brindarnos la facilidad de estudiar y dejarnos vivir este camino lleno de retos. También doy un agradecimiento a la empresa Furukawa automotive, en especial al Ingeniero Gerardo Padilla, a mi asesor y amigo Emmanuel Castellanos y a Manuel Euyoqui, por darme la oportunidad de ejercer en sus instalaciones y de alimentar mi experiencia como profesionista. Por último, agradezco a Dios por haberme dado la vida, de estar conmigo a lo largo de estos años, por ser la luz y brindarme la fortaleza para no dejarme vencer ante las diferentes pruebas que la vida me ha presentado y que siempre está conmigo. Por darme la sabiduría y darme la confianza en mí de poder realizar todo lo que se interponga en mi camino y salir adelante con la frente en alto.
En las organizaciones o empresas de cualquier tipo, los indicadores más notorios para los dueños y dirección general son las ventas, costos, utilidades y las críticas de los clientes, pero esos indicadores se ven ligados estrechamente al grado de productividad alcanzado durante los distintos procesos a los cuales se someten los bienes o servicios ofrecidos. La posibilidad de alcanzar un alto índice de productividad en una empresa, no es algo fácil, es algo que lleva años, mucho trabajo y determinación; sobre todo, se debe hacer una planificación, dirección, coordinación y actuación para realizar las mejoras y usar los recursos materiales. También, no dejar pasar el trabajo de los operadores, técnicos y todo el personal encargado para que el trabajo salga como se planea desde un inicio. Es importante tener una Para lograr los diferentes objetivos establecidos por la dirección general, la ingeniería industrial ofrece múltiples herramientas y técnicas. Una herramienta elemental que desde sus inicios ha desarrollado la ingeniería industrial para lograr el aumento de la productividad, es el estudio científico del trabajo. El estudio del método de trabajo tiene por objeto examinar como se realiza una actividad, simplificándola o modificando el método operativo para reducir el trabajo innecesario, así como aprovechar los recursos tangibles e intangibles. Sin embargo, actualmente no basta con hacer estudios y mejorar los métodos del trabajo, otro aspecto que se toma en cuenta para lograr una productividad alta, está ligado a los estándares de calidad de los productos o los servicios que se ofrecen. Para poder lograr los objetivos impuestos a las mejoras del proceso, la calidad del producto o del servicio ofrecido, es necesario que se fijen estándares en los procesos de calidad, implicados durante la elaboración, especialmente cuando se produce un bien intangible, por personal y en lugares diferentes, a distancia y bajo la supervisión de personal con distintas formaciones profesionales.
L a y o u t v c h m á s re c i e n t e d e l a s i n s t a l a ci on es d e l a e mp r e s a d on de c a d a á r e a e s t a e n u me r a d a p a r a l o c a l i z a r c a d a u n a. E l n o m b r e d e c a d a u n a es e l si gu ie nt e : 1. Fi r st mo l d i n g, 2. S R C , 3. E n s a m b l a d o, 4. MY T R O O M ( c u a rt o e s p e ci al i za d o d e m e t ro l o g í a , di se ñ o y me d i ci ón ), 5. C u a rt o d e l a m i n a d o, 6. S t am p i n g ( e s p a ci o e sp ec i f i ca d o p ar a el e s t a m p ad o d e co b re ) , 7. K a w a s a ki , 8. O f i c in a s a d m i n i s t r at i va s, 9. E DM y t a l l e r d e m o l de s, 1 0. K a i z e n , 11. Fu s e b o x, 1 2. A l m a c é n de e n v í os , 1 3. C o m p a ct a d o r a , 1 4. Fa c i l i t y, 1 5. A l m a c é n de r e c ib i m ie n t o. 2 3 1 9 11 1 7 5 (^48) 10 6 15 14 12 13
Este proyecto surgió con la finalidad de brindar mejoras y con la finalidad de estandarizar el proceso del área de moldeo, ya que, presenta varias anomalías que producen tiempos muertos elevados, chatarra innecesaria, Material defectuoso y tiempos de ciclo elevados. La importancia de esto y la urgencia de realizar una mejora para poder obtener los resultados esperados, se debe a que los clientes han mostrado inquietud por la obtención del producto, ya sea dañado o totalmente quebrado. El área de Moldeo, como se le conoce dentro de la empresa “First molding”, tiene como finalidad realizar el moldeo para realizar el componente que se ensamblan en las cajas de fusibles, dentro de los volantes, arneses y etc. Se utiliza cobre especializado para trabajar (Dependiendo del modelo que se va a trabajar, se maneja cierto tipo de cobre) Mediante moldes que pesan alrededor de media tonelada, utilizando como mínimo 1 cavidad hasta 4 cavidades, acomodando el metal de una manera para así, dentro de una maquina especializada que es tiene ciertas funciones como fundir resina (la resina es un sólido que a altas temperaturas se derrite) para inyectarla en las cavidades de los moldes y junto con el cobre, forman el componente esperado. Es importante que se cumplan los pasos y el ciclo para que funcione de manera óptima y que no se genere chatarra, así se evita desperdiciar mucho material y que no se generen perdidas. Todo esto es debido a que el giro automotriz y los estándares de precisión que solicita el cliente (entre algunos HONDA, SUBARU y TOYOTA), las especificaciones con las cuales deben de cumplirse por contrato, previamente establecidos con un margen de error mínimo que en ocasiones
Dictar instrucciones de trabajo óptimas, que sean claras de acuerdo al objetivo y las retroalimentaciones necesarias para cada operación. Desarrollo de operaciones que no se documentan y no se realizan por los operadores mediante formatos de rutina diarios. Corregir instrucciones que se encontraron por auditorías realizadas. Realizar mapas de procesos o diagramas de flujo que expliquen los movimientos. Hacer un análisis de riesgos y modos de fallas. Generar ayudas visuales donde muestren como se deben realizar las operaciones. Evaluar las propuestas de mejora por parte de los operadores para complementar la instrucción de trabajo. Capturar los datos tomados, los tiempos de ciclos y purgas realizadas a maquinas para mostrar en junta diaria llamada GEMBA. Realización de mejoras de seguridad con la finalidad de evitar accidentes de trabajo y evitar que se presenten tiempos muertos. Seguimiento de la aprobación de las instrucciones de trabajo por parte de los diversos departamentos involucrados en el desarrollo de las mismas (seguridad, manufactura, ingeniería, especialistas en proceso de moldeo y etc.). Informar a los operadores por medio de notas de seguridad, los riesgos que corren al trabajar con las piezas, los moldes, los procedimientos ergonómicos que tiene que realizar para evitar problemas físicos a largo plazo, al igual que el equipo de seguridad que debe portarse para que no haya accidentes.
1.3.1 Historia – Furukawa Electric Group Furukawa Electric group es una empresa Pública Japonesa dedicada a la fabricación de elementos eléctricos, equipo electrónico y automotriz. Teniendo su oficina base en la ciudad de Tokio, Japón en la torre Tokiwabashi. Operando más de un siglo de historia y tendiendo presencia a nivel mundial, Se fundó en el año de 1884 por Ichibei Furukawa San, empresario japonés que fundó uno de los quince conglomerados industriales más de japón, especializado en productos eléctricos, químicos y metales. La empresa tiene sus orígenes gracias al empresario, quien fundó Nikko Copper Works, una instalación de fundición de cobre en Yokohama en 1884, que se convirtió en parte de Furukuwa Kogyo. Una nueva empresa; Furukuwa Denki Kogyo se formó en 1920, cuando fusionó su negocio de cobre con su propia Yokohoma Wire Manufacturing Company, que adquirió en 1908. A raíz de esto, la nueva empresa pudo combinar sus negocios de minería, refinación y fabricación de productos de cobre, como alambres y cables. Logotipo de la empresa que tiene como significado la unión de la montaña (Yama) y el ideograma japones para indicar uno (ichi).
1.3.2 American Furukawa, Inc. American Furukawa Inc. Que es parte del grupo Furukawa electric, es un proveedor de clase mundial para clientes en las industrias automotriz, electrónica, de infraestructura y médica. Con sede en Plymouth, Michigan, tienen la capacidad de diseñar e ingeniar suministros relacionado con productos electrónicos y automotrices innovando tecnológicamente fabricando en sus instalaciones de América del Norte. La sede también brinda el soporte de ventas y servicio al cliente para los productos automotrices, cables y alambres de alimentación eléctricos, soluciones de enfriamiento, aleaciones de Niquel y Titanio (NiTi), entre otros, siendo todo para la rama industrial específicamente para clientes del norte y sur de América. American Furukawa trabaja en estrecha colaboración con una amplia variedad de proveedores Tier y clientes OEM en la industria automotriz para suministrar los productos necesarios para el avance en la seguridad, la comodidad, el ahorro de costos y la eficiencia energética de los vehículos. Como proveedor global de arneses de cables, conectores y terminales, junto con componentes electromecánicos y funcionales, contamos con los conocimientos de ingeniería y la capacidad de fabricación para satisfacer los requisitos de los clientes en cuanto a piezas individuales, soluciones personalizadas y sistemas totalmente integrados. Logotipo de la corporación estadounidense.
1.3.2 Furukawa Automotive México S.A. de C.V. Furmex o Furukawa México S.A. de C.V. es una compañía del grupo Furukawa electric, Co., que Inicio operaciones en México oficialmente el 9 de septiembre de 1997, en la ciudad de Mexicali, Baja California. Teniendo inicialmente 300 empleados en total, hoy en día cuenta con un total de más de 2,000 empleados sin dejar de cumplir con los más altos estándares de calidad de la industria. La empresa como misión representa toda la importancia de la seguridad a la hora de maniobrar todo tipo de automóvil que, dentro de sus componentes incluyan productos de la misma, así, que estos presentan las óptimas condiciones para que la necesidad del cliente sea la más favorable. Siendo lo más consientes posibles de que en sus manos esta la seguridad y ponen todo el empeño por obtenerlo, a través de vivir y fomentar una cultura de alta calidad, innovación, rentabilidad y desarrollo permanente de gente nueva. Como visión, representa “un producto fabricado por nosotros en cada auto de América”. La empresa aplico un DNC (Diagnostico de necesidad de capacitación) en sus instalaciones, ubicadas en la ciudad de Mexicali en la dirección Avenida círculo de la amistad 2690, parque industrial Mexicali 4 (PIMSA 4). Furukawa es una empresa rica en fuente de empleo, que brinda la facilidad de obtener empleo a personas con problemas de sordera, siendo la principal razón de la cual se realizó el DNC, con la intención de enfocar en la capacitación que se les asigna a las personas que presentan dichas discapacidades teniendo los mismos beneficios, teniendo ahora una certificación como empresa incluyente, permitiendo a todo tipo de persona que presente alguna discapacidad o que muestre alguna lengua o religión evitando así todo tipo de discriminación. Esto la cataloga como empresa socialmente responsable para el país y su medio ambiente.
2.1 Problemas a resolver. El origen de este proyecto fue que alrededor de un tiempo, se han presentado anomalías en el proceso de moldeo generando tiempos muertos elevados, índices altos de chatarra y mala calidad en el proceso de los componentes. Todo esto llevo a que haya una baja calidad en las piezas, que los clientes muestren molestia cuando tengan su producto y que los mismos clientes decidan irse con la competencia a que produzcan sus componentes. Todo esto llevo a una gradación por parte de la gerencia de realizar mejoras a nivel raíz para poder mejorar totalmente el proceso. Las causas que se presentaron fue la falta de material para poder realizar las actividades diarias, el personal no estaba muy bien capacitado en su momento para trabajar, las instrucciones que se tenían a la hora de realizar los componentes no eran las adecuadas y no mostraban una clara secuencia de las actividades, no señalaba cuales eran las herramientas adecuadas que debían utilizarse para realizar el trabajo. Todo esto llevo a que los operadores y soldadores no tuvieran la información clara y poder trabajar de manera óptima y adecuada, haciendo un tiempo de ciclo bastante elevado en cada operación por la falta de información y detalles., Uno de los puntos fuertes de la problemática fue la falta de capacitación de seguridad al momento de utilizar las maquinas manuales y automatizadas; así también, no tienen la seguridad propia de utilizar las herramientas para evitar accidentes de trabajo. Como consecuencia de esto, alrededor de un año, se presentaron un total de 9 accidentes de trabajo, siendo 4 de ellos que terminaron en un asunto grave.
La falta de ayudas visuales tanto de instructivo como de seguridad para evitar cuellos de botella y accidentes, han sido una causa de los problemas que la empresa ha presentado a lo largo del tiempo. Este su propósito es que muestren como se debe realizar la operación para que los operadores y especialistas trabajen de manera óptima y sin riesgo. La escasez de mejoras en el proceso, así como también de documentación de algunas actividades, ocasiono que los especialistas y operadores no promovieran sus ideas y mejoras deteniendo la iniciativa de generar un pensamiento propio, donde no los tomarían en cuenta, sintiendo una falta de motivación y así generando una baja producción, problemas físicos y emocionales en los empleados. 2.2 Alcances y limitaciones 2.2.1 Alcances Se realizarán cambios de producción, siempre y cuando afecte la calidad y funcionamiento de los productos. Diseño de operaciones nuevas que sean necesarias en el proceso, así como también la eliminación de operaciones que no sean necesarias, que no agreguen valor al producto o que generen un alto rango de tiempo muerto. Se implementarán mejoras que faciliten la operación en el trabajo para los empleados, que se eviten accidentes o perdidas de producción y que haya una mayor facilidad de inspección para los encargados de calidad e inspectores de seguridad. 2.2.2 Limitaciones Resistencia al cambio por parte de los operadores y técnicos. Revisión diaria por los supervisores e ingenieros en el turno. Los cambios deben de cumplir con las especificaciones del producto. No se utilizarán unidades para realizar pruebas. No eliminarán operaciones que sean críticas para el cliente.
La importancia de esto es la planeación de instalación eficaz, por ejemplo, considerando los rasos específicos por los cuales se determinó realizar dicho plan para los espacios, esto para darle una solución a los operadores de tener sus equipos de trabajo en orden y poder tenerlos operando rápido. Entre el 20 y el 50 por ciento de los gastos de operación se atribuyen al manejo de materiales. Además, se suele aceptar que la planeación de instalaciones óptima puede reducir los costos de un 10 a 30%. 2.3.3 Kanban El Kanban es un método lean popular que se encarga en la gestión para definir, gestionar y mejorar los servicios que proporcionan el trabajo de conocimiento. Te ayuda a visualizar el trabajo, maximizar la eficiencia y mejora continuamente. Siendo una empresa con principios e ideología japonesa, la importancia de esta práctica es que, ya esta fomentada desde un inicio; únicamente lo que se tuve en cuenta es realizar mejoras para el área con este método. El trabajo que se representa en tableros Kanban, lo que te permite optimizar la entrega de trabajo a través de múltiples equipos y manejar, incluso los proyectos más complejos en un solo entorno. La necesidad de fomentar el Kanban en el área de moldeo es por el área de calidad que necesita saber cual es el componente que se esta desarrollando y cuál es el que se va a entregar, así, pueden localizar rápidamente y capturar el total de producción que se genera de dicha pieza. La importancia de este es que, así no hay manera de presentar errores a la hora de realizar inventarios, tener todo en orden a la hora de una auditoria, para que el cliente tenga información más detallada de dicho artefacto cuando se le entregue y se evite alguna confusión.
2.3.4 Kaizen. Kaizen “mejora continua que involucra a todos. Sistema integral sistemático que tiene como función brindar mejoras en las empresas, procesos y actividades que lo conforman. También incluye a todo el personal relacionado con dicha mejora. El objetivo primero y fundamental es mejorar para darle al cliente un mayor valor agregado en el producto, mediante la mejora continua y sistemática de la calidad, los costes, tiempos de respuestas, la variedad y mayores niveles de satisfacción. Su objetivo fundamenta la eliminación de los obstáculos que impidan el uso más rápido, seguro, óptimo y eficiente de los recursos que tiene la empresa, los obstáculos como roturas, fallas, falta de materiales e insumos, acumulación de stock, pérdidas de tiempo por reparaciones, falta de insumos o tiempos de preparación son algunos de los puntos negativos que deben ser eliminados. La mejora continua hace posible que se presenten los más altos niveles de una serie de factores que requirieron constancias, disciplina y la puesta en marcha de seis sistemas importantes: