
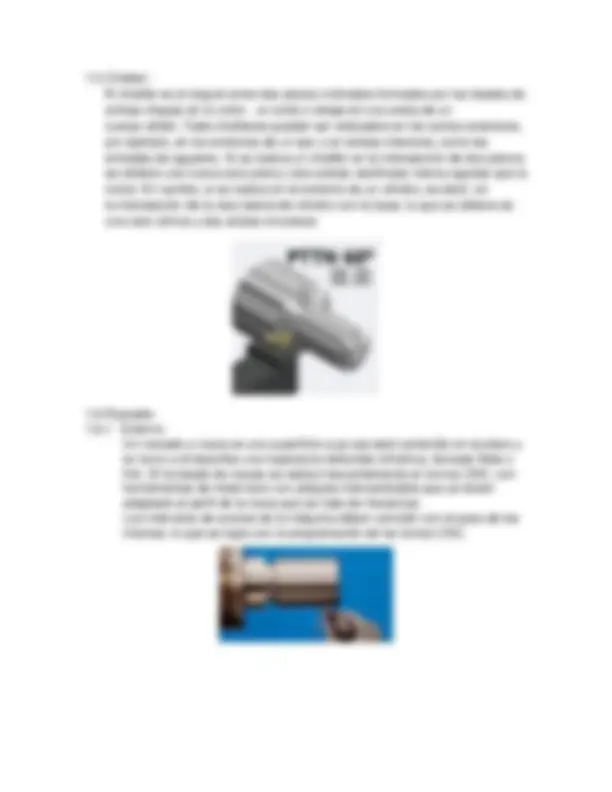
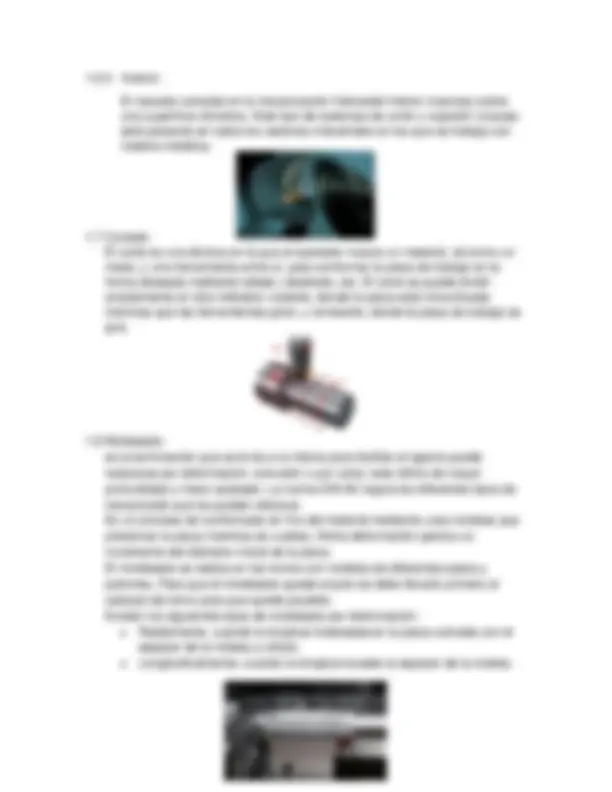
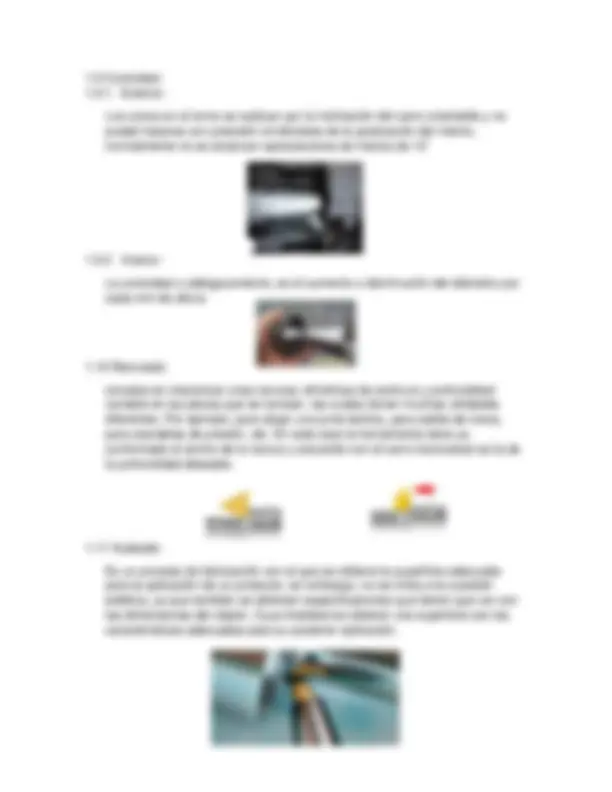
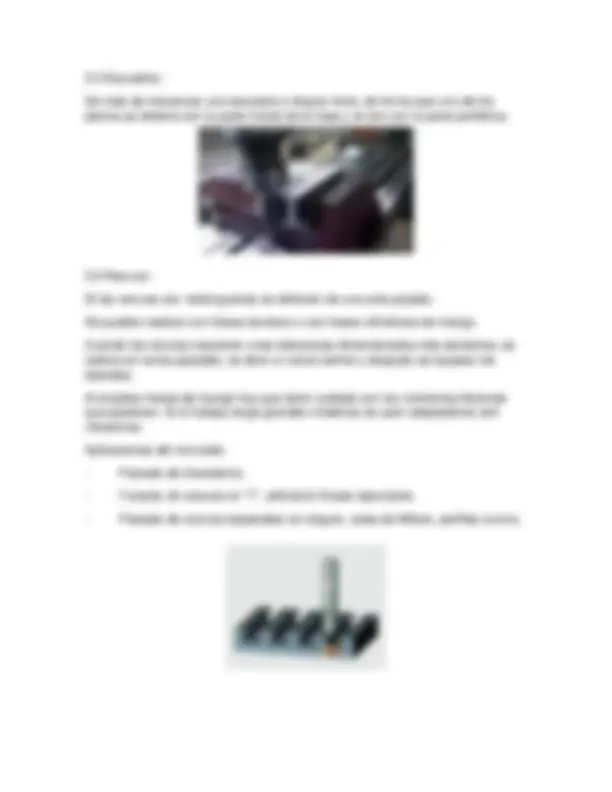
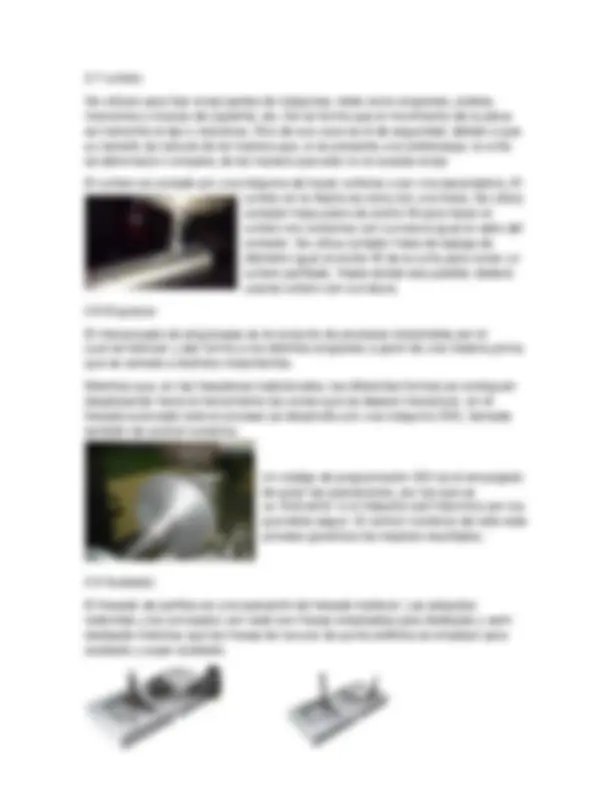
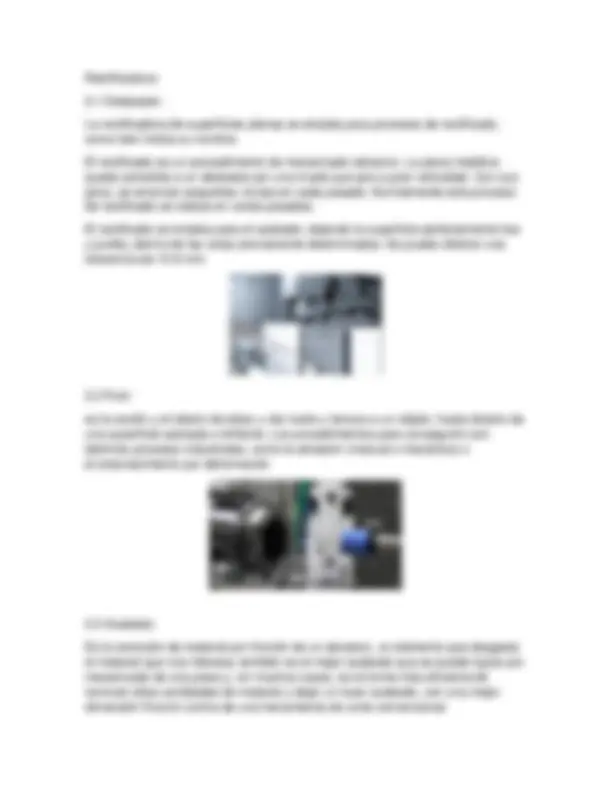
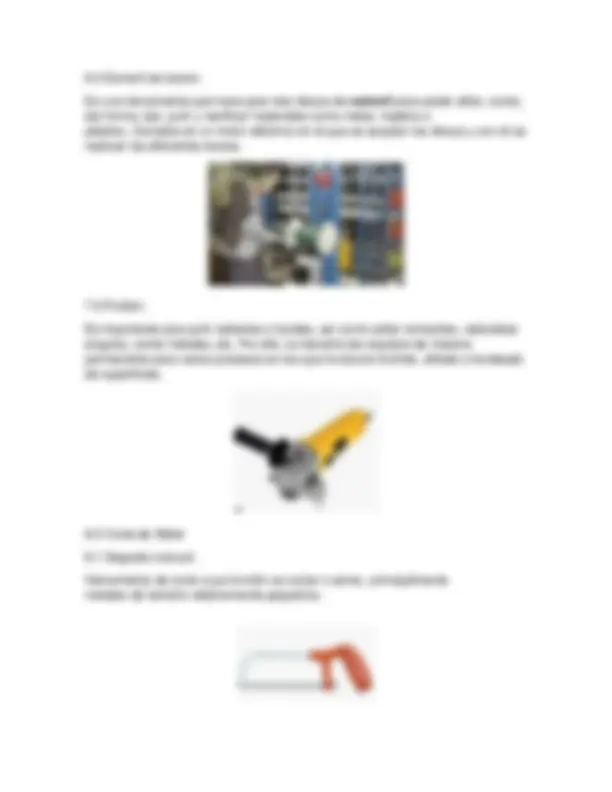
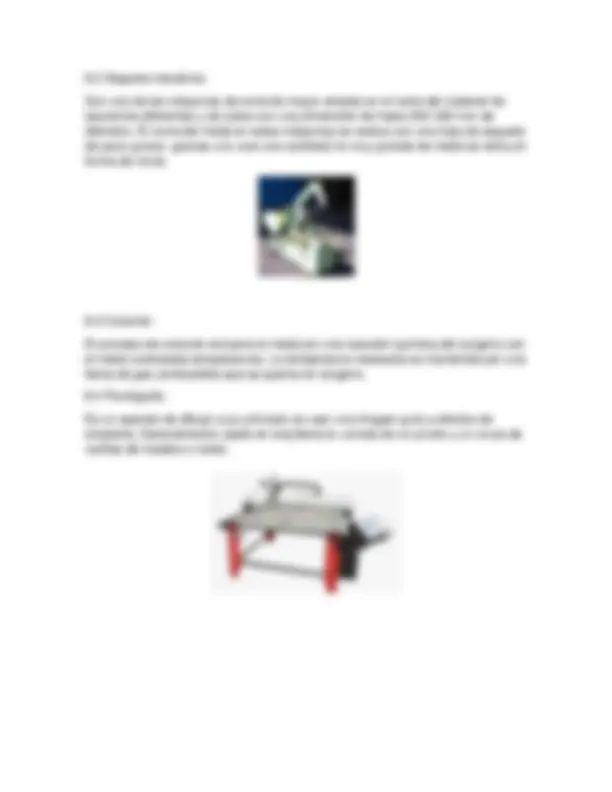
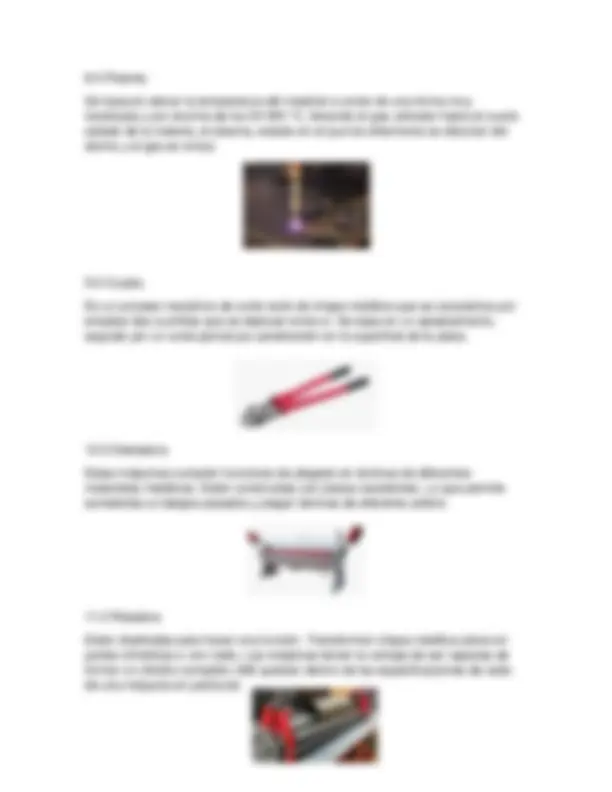
Prepara tus exámenes y mejora tus resultados gracias a la gran cantidad de recursos disponibles en Docsity
Gana puntos ayudando a otros estudiantes o consíguelos activando un Plan Premium
Prepara tus exámenes
Prepara tus exámenes y mejora tus resultados gracias a la gran cantidad de recursos disponibles en Docsity
Prepara tus exámenes con los documentos que comparten otros estudiantes como tú en Docsity
Los mejores documentos en venta realizados por estudiantes que han terminado sus estudios
Estudia con lecciones y exámenes resueltos basados en los programas académicos de las mejores universidades
Responde a preguntas de exámenes reales y pon a prueba tu preparación
Consigue puntos base para descargar
Gana puntos ayudando a otros estudiantes o consíguelos activando un Plan Premium
Comunidad
Pide ayuda a la comunidad y resuelve tus dudas de estudio
Descubre las mejores universidades de tu país según los usuarios de Docsity
Ebooks gratuitos
Descarga nuestras guías gratuitas sobre técnicas de estudio, métodos para controlar la ansiedad y consejos para la tesis preparadas por los tutores de Docsity
conceptos de cada operacion de maquinado
Tipo: Resúmenes
1 / 16
Esta página no es visible en la vista previa
¡No te pierdas las partes importantes!
Procesos de maquinado Torno: 1.1 Careado: Consiste en un mecanizado frontal y perpendicular al eje de las piezas, que se realiza para producir un buen acoplamiento en el montaje posterior de las piezas torneadas. Esta operación también es conocida como fronteado. El refrentado consiste en obtener una superficie plana haciendo que la herramienta avance a través de la cara frontal de la pieza, la cual se mantiene en movimiento rotatorio. La herramienta se ha de colocar en un ángulo aproximado de 60º respecto al porta herramientas. De lo contrario, debido a la excesiva superficie de contacto la punta de la herramienta correrá el riesgo de sobrecalentarse. 1.2 Desbaste: 1.2.1 Exterior: Consiste en cortar la máxima cantidad de material de una pieza para dejar definida con mayor o menor aproximación la forma de una pieza. El desbaste se realiza a menudo en sucesivos cilindrados, que se repiten hasta un diámetro calculado de tal manera que exista una diferencia con el diámetro final de la pieza. 1.2.2 Interior: Consiste en cortar la máxima cantidad de material de una pieza para dejar definida con mayor o menor aproximación la forma de una pieza en la parte interior.
1.3 Taladrar: Consiste en realizar un agujero en una pieza mediante una broca. En tornos convencionales se coloca la broca en el alojamiento del contrapunto del torno. Por ello solo se pueden agujerear las piezas a lo largo de su eje. En tornos CNC de 3 ejes y dotados de herramientas motorizadas además se pueden agujerear axialmente las piezas en cualquier punto de la cara frontal de la pieza y radialmente. 1.4 Machuelado: Su función es la que permite generar las cuerdas interiores para un tornillo en algún material en particular. El machuelado se hace en el torno con un machuelo normal de mano, fijar el husillo del cabezal, empezar a introducir el machuelo en el agujero y, después, soportar el vástago en el centro del contrapunto mientras se gira el machuelo a mano con la llave para machuelos. Se avanza el centro del contrapunto conforme el machuelo penetra en la pieza, pero no se aplica ninguna presión.
1.6.2 Interior: El roscado consiste en la mecanización helicoidal interior (tuercas) sobre una superficie cilíndrica. Este tipo de sistemas de unión y sujeción (roscas) está presente en todos los sectores industriales en los que se trabaja con materia metálica. 1.7 Cortado: El corte es una técnica en la que el operador mueve un material, tal como un metal, y una herramienta entre sí, para conformar la pieza de trabajo en la forma deseada mediante tallado, taladrado, etc. El corte se puede dividir ampliamente en dos métodos: rodante, donde la pieza está inmovilizada mientras que las herramientas giran, y torneante, donde la pieza de trabajo se gira. 1.8 Moleteado: es la terminación que se le da a la misma para facilitar el agarre puede realizarse por deformación, extrusión o por corte, este último de mayor profundidad y mejor acabado. La norma DIN 82 regula los diferentes tipos de mecanizado que se pueden efectuar. Es un proceso de conformado en frío del material mediante unas moletas que presionan la pieza mientras da vueltas. Dicha deformación genera un incremento del diámetro inicial de la pieza. El moleteado se realiza en los tornos con moletas de diferentes pasos y patrones. Para que el moleteado quede exacto se debe llevarlo primero al cabezal del torno para que quede paralelo. Existen los siguientes tipos de moleteado por deformación:
1.9 Conicidad: 1.9.1 Exterior: Los conos en el torno se realizan por la inclinación del carro orientable y no puede hacerse con precisión sirviéndose de la graduación del mismo, normalmente no se alcanzan apreciaciones de menos de 15 ́ 1.9.2 Interior: La conicidad o adelgazamiento, es el aumento o disminución del diámetro por cada mm de altura. 1.10 Ranurado: consiste en mecanizar unas ranuras cilíndricas de anchura y profundidad variable en las piezas que se tornean, las cuales tienen muchas utilidades diferentes. Por ejemplo, para alojar una junta teórica, para salida de rosca, para arandelas de presión, etc. En este caso la herramienta tiene ya conformado el ancho de la ranura y actuando con el carro transversal se le da la profundidad deseada. 1.11 Acabado: Es un proceso de fabricación con el que se obtiene la superficie adecuada para la aplicación de un producto; sin embargo, no se limita a la cuestión estética, ya que también se obtienen especificaciones que tienen que ver con las dimensiones del objeto. Cuya finalidad es obtener una superficie con las características adecuadas para su posterior aplicación.
2.2 Desbaste: El objetivo del mecanizado de desbaste consiste en mecanizar la mayor cantidad de material posible en muy poco tiempo. Esto supone una enorme prueba de esfuerzo para la fresa que, al fin y al cabo, se encuentra a menudo en contacto completo. 2.3 Chaflan: Los chaflanes, biseles en V, rebajes, preparaciones para el soldado y desbarbado a lo largo de los bordes de las piezas suelen implicar operaciones de fresado de chaflanes. Estas operaciones pueden realizarse de diversas formas, según el tipo de máquina y reglaje disponibles. Puede utilizase una fresa de planear pequeña, una fresa de filo largo, una fresa de ranurar o una fresa de achaflanado. 2.4 Careado: El careado o refrentado en máquinas Fresadoras horizontales o verticales, produce una superficie plana perpendicular al husillo en el que está montada la fresa. Consiste en mecanizar planos perpendiculares al eje del husillo moviendo la herramienta con el carro transversa
2.5 Escuadrar: Se trata de mecanizar una escuadra o ángulo recto, de forma que uno de los planos se obtiene con la parte frontal de la fresa y el otro con la parte periférica. 2.6 Ranurar: Si las ranuras son rectangulares se obtienen de una sola pasada. Se pueden realizar con fresas de disco o con fresas cilíndricas de mango. Cuando las ranuras requieren unas tolerancias dimensionales más estrechas, se realiza en varias pasadas. se abre un canal central y después se repasan los laterales. Al emplear fresas de mango hay que tener cuidado con los momentos flectores que aparecen. Si el trabajo exige grandes voladizos se usan adaptadores anti vibratorios. Aplicaciones del ranurado:
Rectificadora: 3.1 Desbastar: La rectificadora de superficies planas se emplea para procesos de rectificado, como bien indica su nombre. El rectificado es un procedimiento de mecanizado abrasivo. La pieza metálica queda sometida a un desbaste por una muela que gira a gran velocidad. Con sus giros, se arrancan pequeñas virutas en cada pasada. Normalmente este proceso de rectificado se realiza en varias pasadas. El rectificado se emplea para el acabado, dejando la superficie perfectamente lisa y pulida, dentro de las cotas previamente determinadas. Se puede obtener una tolerancia de 10-6 mm 3.2 Pulir: es la acción y el efecto de alisar y dar lustre y tersura a un objeto, hasta dotarlo de una superficie satinada o brillante. Los procedimientos para conseguirlo son distintos procesos industriales, como la abrasión (manual o mecánica) o el endurecimiento por deformación 3 .3 Acabado: Es la remoción de material por fricción de un abrasivo, un elemento que desgasta el material que nos interesa; también es el mejor acabado que se puede lograr por mecanizado de una pieza y, en muchos casos, es la forma más eficiente de remover altas cantidades de material y dejar un buen acabado, con una mejor dimensión final en contra de una herramienta de corte convencional
Taladro: (tipos): Taladro de banco: Es usado para perforar metales, acero, madera, plásticos usando Brocas HHS. También es usado como herramienta de remoción, como segunda aplicación, usando cepillos y discos de lija. Es más preciso ya que la columna evita que se mueva. Ideal para hacer orificios verticales de ubicación precisa y taladrar con exactitud. Es muy útil con materiales frágiles como: madera, porcelana, cerámica o vidrio. Taladro angular: La forma manejable del taladro angular, te permite taladrar de forma segura en zonas de difícil acceso, donde un taladro regular no entraría. Taladro eléctrico: se mecanizan la mayoría de los agujeros que se hacen a las piezas en los talleres mecánicos. Destacan estas máquinas por la sencillez de su manejo.
6.0 Esmeril de banco: Es una herramienta que hace girar dos discos de esmeril para poder afilar, cortar, dar forma, lijar, pulir y rectificar materiales como metal, madera o plástico. Consiste en un motor eléctrico en el que se acoplan los discos y con él se realizan las diferentes tareas. 7.0 Pulidor: Es importante para pulir salientes o bordes, así como soltar remaches, redondear ángulos, cortar metales, etc. Por ello, la industria las requiere de manera permanente para varios procesos en los que involucre bruñido, afilado o bordeado de superficies. 8.0 Corte de Metal 8.1 Segueta manual: Herramienta de corte cuya función es cortar o serrar, principalmente metales de tamaño relativamente pequeños.
8.2 Segueta mecánica Son una de las máquinas de corte de mayor empleo en el corte del material de secciones diferentes y de tubos con una dimensión de hasta 250-300 mm de diámetro. El corte del metal en estas máquinas se realiza con una hoja de segueta de poco grosor, gracias a lo cual una cantidad no muy grande de metal se retira en forma de viruta. 8.3 Oxicorte: El proceso de oxicorte remueve el metal por una reacción química del oxígeno con el metal a elevadas temperaturas. La temperatura necesaria es mantenida por una llama de gas combustible que se quema en oxígeno. 8.4 Pantógrafo: Es un aparato de dibujo cuyo principio es usar una imagen guía a efectos de ampliarla. Generalmente usado en arquitectura, consta de un pivote y un cruce de varillas de madera o metal.
12.0 Soldadura 12.1 Soldadura blanda: Este tipo de soldadura se usa para crear uniones de hojalata, chapas galvanizadas, piezas de latón y bronce, tubos de plomo y componentes eléctricos. La temperatura que se utiliza es por debajo de los 450 grados Celsius y se usa un soldador eléctrico. 12.2 Soldadura por electrodo: Es un procedimiento manual en el que la fuente térmica está constituida por el arco eléctrico que, disparándose entre electrodo revestido y la pieza a soldar, desarrolla el calor que provoca una rápida fusión tanto del material base como del electrodo. 12.3 Soldadura por pulso magnético: es un proceso de soldadura de estado sólido que utiliza fuerzas magnéticas para soldar dos piezas de trabajo. es un proceso de soldadura de estado sólido que utiliza fuerzas magnéticas para soldar dos piezas de trabajo.