
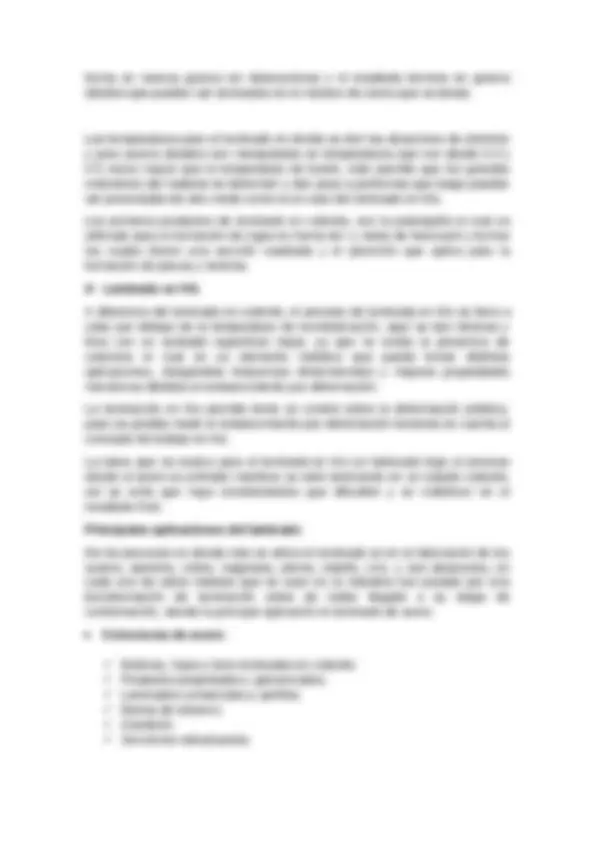
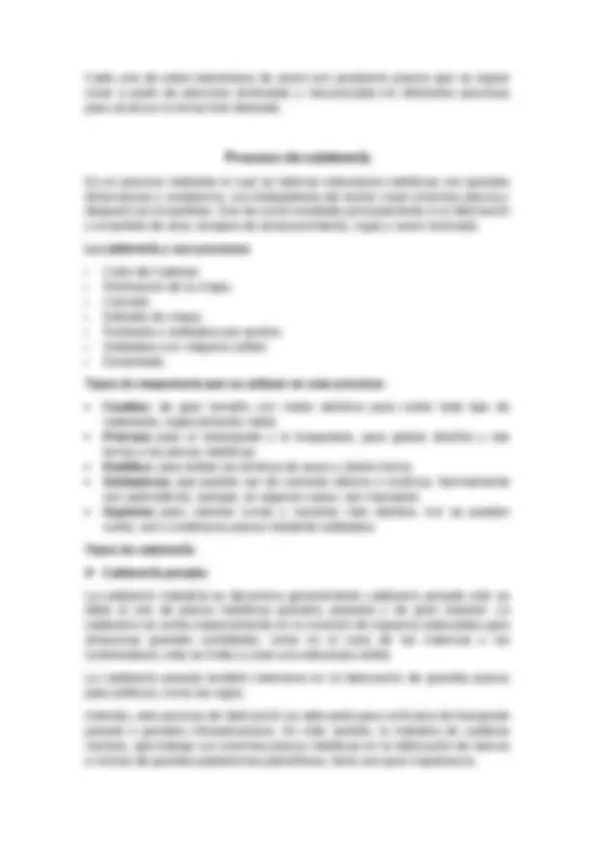
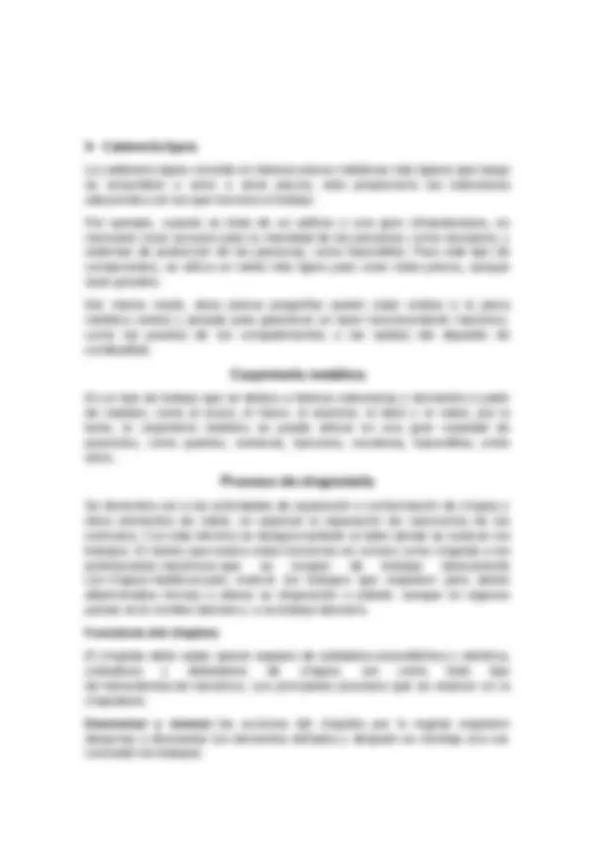
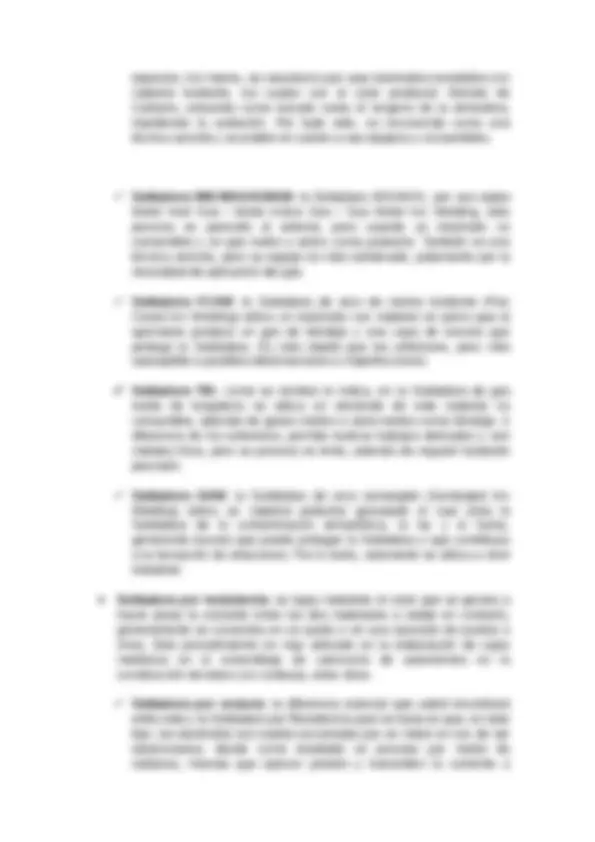
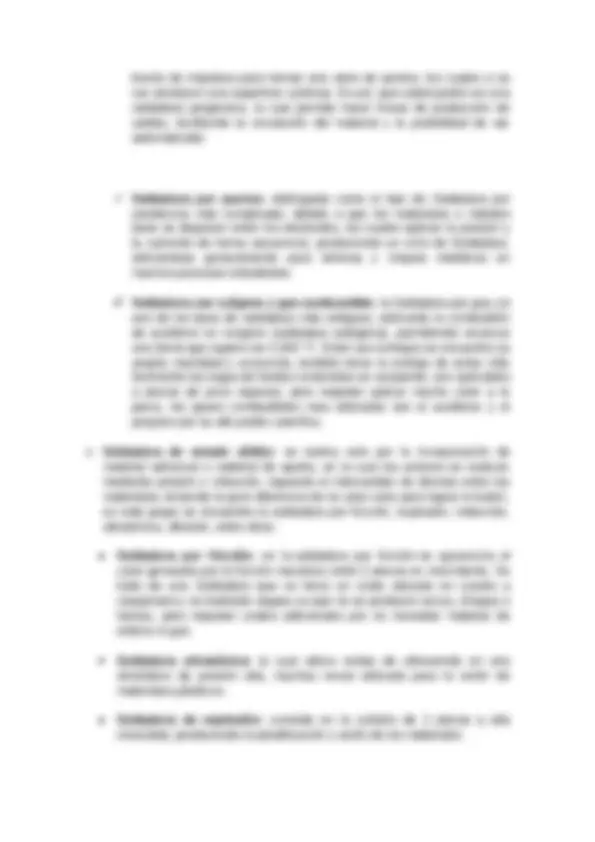
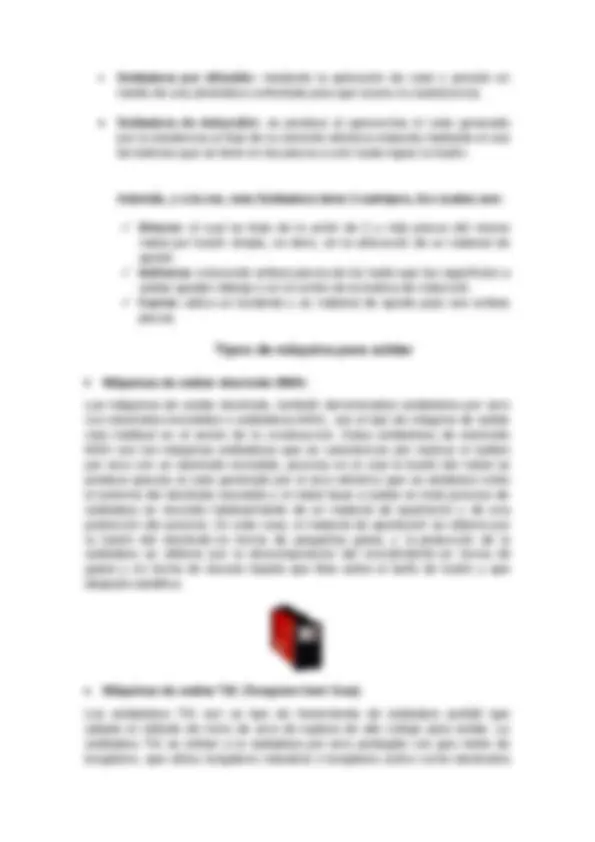
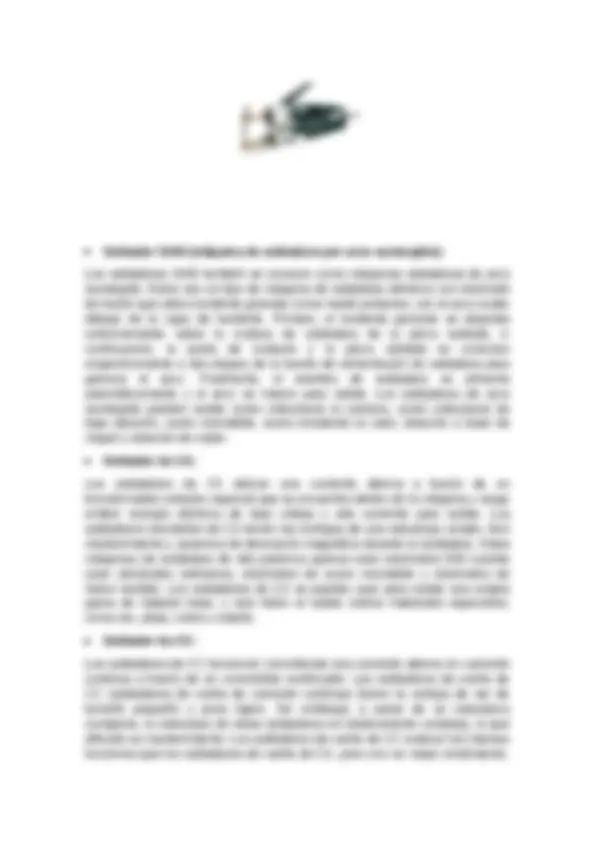
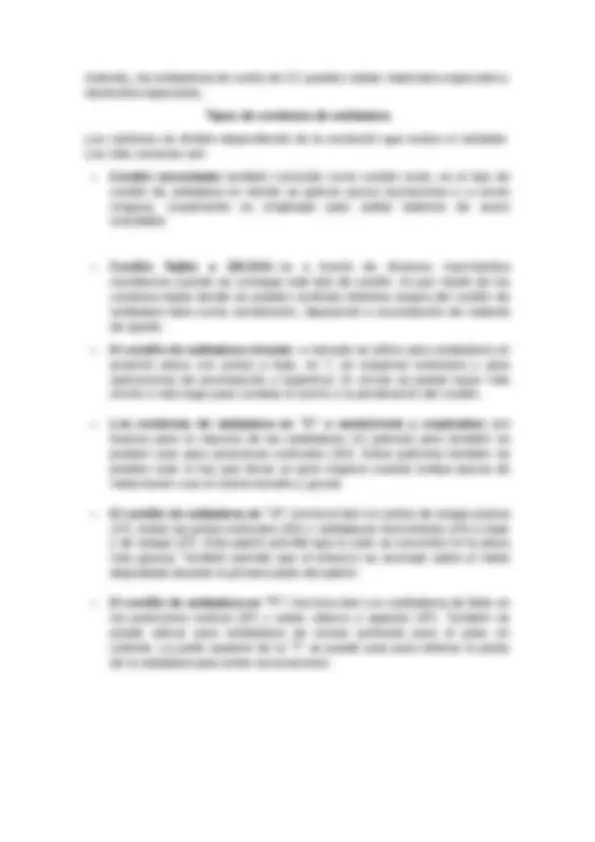
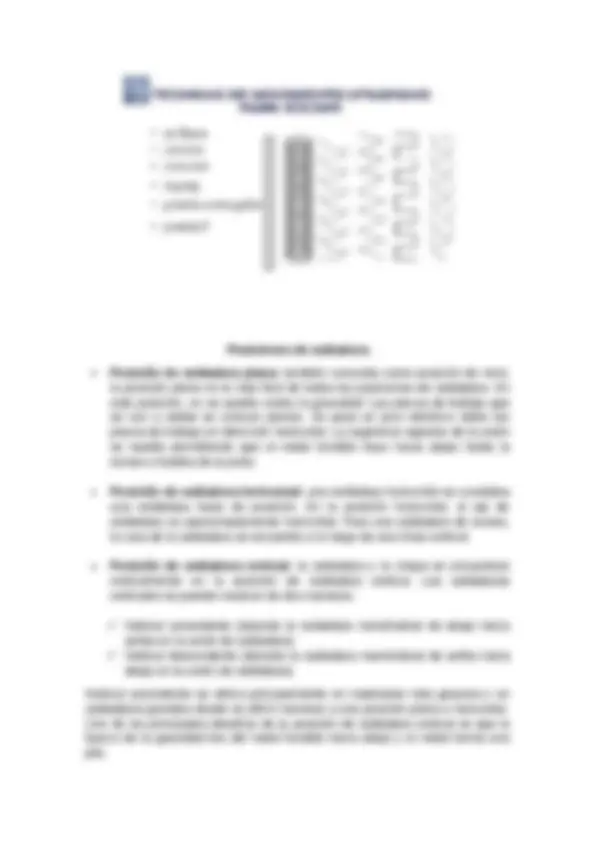
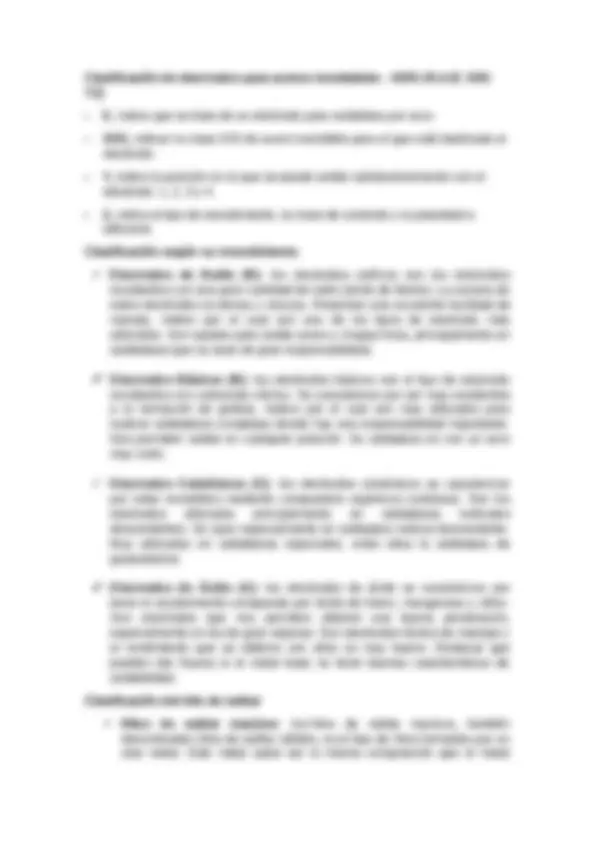
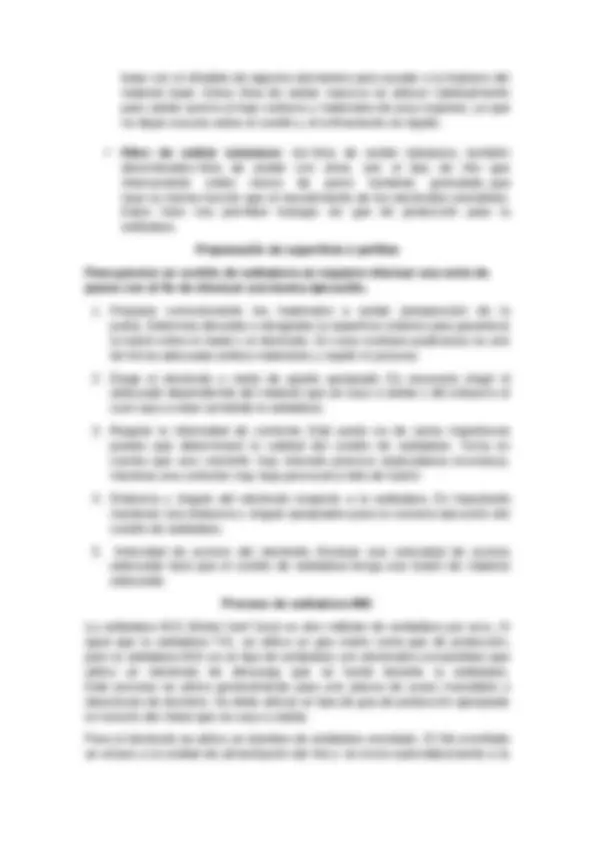
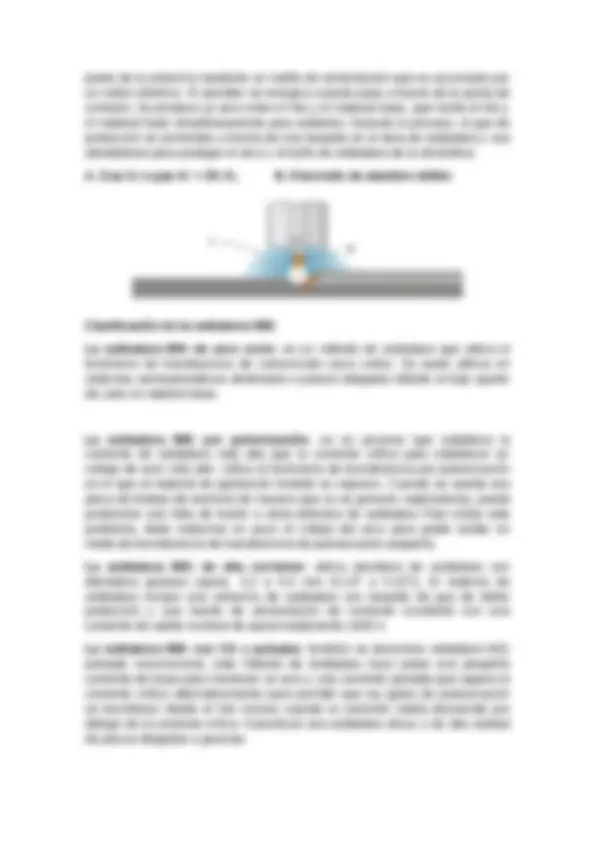
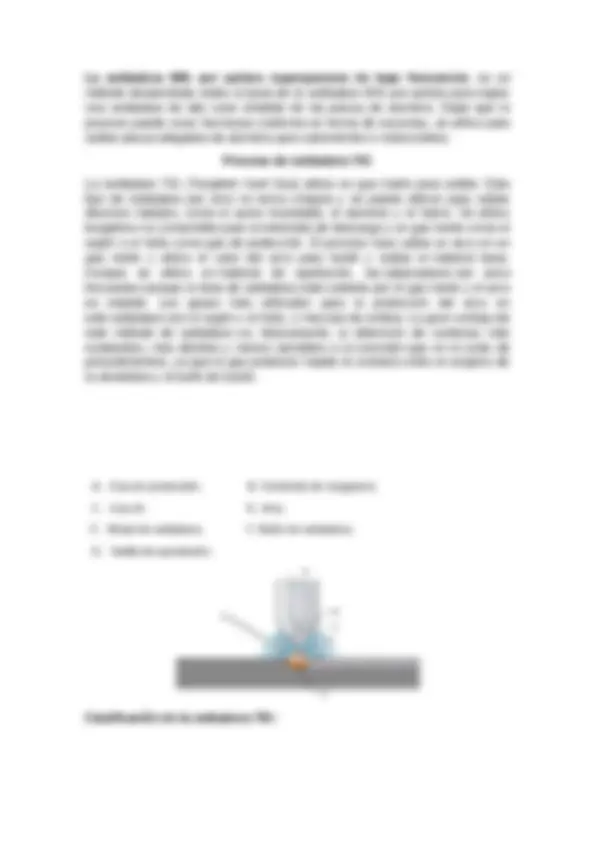
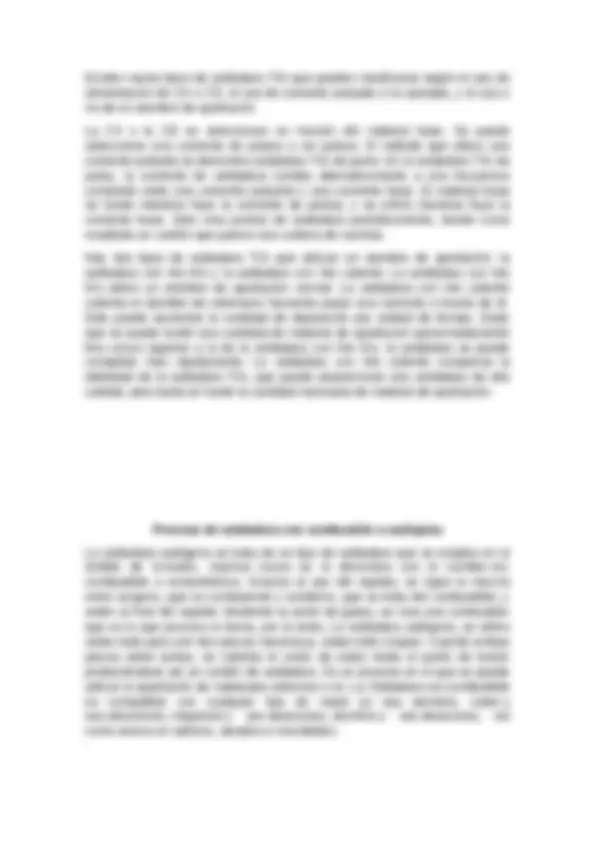
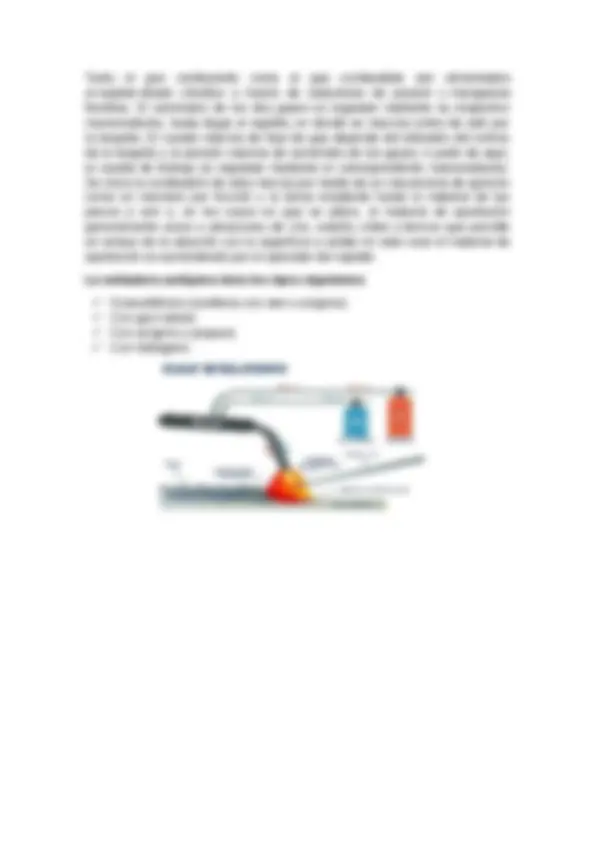
Prepara tus exámenes y mejora tus resultados gracias a la gran cantidad de recursos disponibles en Docsity
Gana puntos ayudando a otros estudiantes o consíguelos activando un Plan Premium
Prepara tus exámenes
Prepara tus exámenes y mejora tus resultados gracias a la gran cantidad de recursos disponibles en Docsity
Prepara tus exámenes con los documentos que comparten otros estudiantes como tú en Docsity
Los mejores documentos en venta realizados por estudiantes que han terminado sus estudios
Estudia con lecciones y exámenes resueltos basados en los programas académicos de las mejores universidades
Responde a preguntas de exámenes reales y pon a prueba tu preparación
Consigue puntos base para descargar
Gana puntos ayudando a otros estudiantes o consíguelos activando un Plan Premium
Comunidad
Pide ayuda a la comunidad y resuelve tus dudas de estudio
Descubre las mejores universidades de tu país según los usuarios de Docsity
Ebooks gratuitos
Descarga nuestras guías gratuitas sobre técnicas de estudio, métodos para controlar la ansiedad y consejos para la tesis preparadas por los tutores de Docsity
Una detallada descripción de los diferentes tipos de soldadura, incluyendo la soldadura por arco eléctrico (mma), la soldadura mig/mag, la soldadura tig, la soldadura por puntos y la soldadura autógena. Además, se explica el proceso de cada tipo de soldadura, los tipos de máquinas utilizadas, los tipos de electrodos y cordones de soldadura, y las posiciones de soldadura. También se incluye una clasificación de la soldadura mig y tig según el uso de alimentación de ca o cd, el uso de corriente pulsada o no pulsada, y el uso o no de un alambre de aportación.
Tipo: Monografías, Ensayos
1 / 23
Esta página no es visible en la vista previa
¡No te pierdas las partes importantes!
República Bolivariana de Venezuela Ministerio del Poder Popular para la Educación Superior, Ciencia y Tecnología Universidad Simón Bolívar Camurí Grande – Edo Vargas Asignatura TI-3380 Taller de mantenimiento Trabajo de investigación Nº (TI-3380 Taller de mantenimiento) Profesor: Alumnos: Lucrecio Moreno Gustavo Altuve 15- Elías Quintero 17- Gabriel Rodríguez 18-
El proceso de laminado consiste en ejercer cierta presión para la deformación volumétrica, en donde se busca minimizar el espesor inicial del material trabajado o alterar las medidas del área trasversal de una pieza larga mediante fuerzas de compresión, las cuales son generadas por el paso entre un juego de rodillos; por lo tanto el proceso de laminado se describe como un proceso en el cual se realiza una deformación plástica, en donde el material transita de modo continuo por medio de cilindros que crean fuerzas de compresión, dicha operación se puede llevar a cabo tanto en frío como en caliente. Proceso de laminado Para la obtención de un laminado con un espesor reducido, se hace uso de rodillos que tras girar en sentidos opuestos logran que el material anteriormente colocado entre ellos sea comprimido hasta lograr el rozamiento que se produce entre los rodillos y el metal del futuro laminado. En dicho proceso conocido como laminación, se modifican las formas comerciales de los perfiles en máquinas que tienen una presión continua. Este tipo de labor permite que salgan productos para el empleo directo de carriles y vigas de acero, mientras que para la producción de otros elementos se necesita de modificaciones adicionales, como es el caso de la chapa o alambre. Dentro de los procesos más comunes que se ejecutan para realizar los laminados se encuentra el caliente pues permite que haya una óptima deformación en el material. Este estilo de transformación a su vez le otorga propiedades isotrópicas, por lo cual las tensiones residuales quedan eliminadas durante el proceso de laminación. El único inconveniente de ejecutar dicha acción a temperaturas altas es que el laminado no pueda mantenerse dentro de las tolerancias adecuadas, provocando que la superficie de la pieza quede impregnada por una capa de óxido muy característica de este proceso. Tipos de laminado Laminado en caliente En este proceso se presiona el elemento por medio de unos rodillos especiales industriales que tienen como objetivo manipular todo el acero para darle forma del laminado, el cual toma dichas dimensiones de manera más fácil cuando se le ejecuta en temperaturas altas que llegan muy por encima de la recristalización del material. Cabe decir que la temperatura de recristalización es la temperatura a la cual los granos de la microestructura comienzan a transformarse en nuevos granos sin dislocaciones. Esta transformación permite que los granos del elemento tomen
Cada una de estas estructuras de acero son productos planos que se logran crear a partir de planchas laminadas y mecanizadas en diferentes procesos para alcanzar la forma final deseada.
Es un proceso mediante el cual se fabrican estructuras metálicas con grandes dimensiones y resistencia. Los trabajadores del sector crean enormes piezas y después las ensamblan. Eso da como resultado principalmente a la fabricación y ensamble de silos, tanques de almacenamiento, vigas y acero laminado. La calderería y sus procesos Corte del material. Perforación de la chapa. Curvado. Doblado de chapa. Punteado y soldadura por puntos. Soldadura con máquina orbital. Esmerilado. Tipos de maquinaria que se utilizan en este proceso: Cizallas: de gran tamaño con motor eléctrico para cortar todo tipo de materiales, especialmente metal. Prensas: para el estampado y el troquelado, para grabar diseños y dar forma a las placas metálicas. Rodillos: para doblar las láminas de acero y darles forma. Soldadoras: que pueden ser de corriente alterna o continua. Normalmente son automáticas, aunque, en algunos casos, son manuales. Sopletes: para calentar zonas y hacerlas más dúctiles. Así se pueden cortar, unir o enderezar placas mediante soldadura. Tipos de calderería Calderería pesada La calderería industrial se denomina generalmente calderería pesada esto se debe al uso de piezas metálicas grandes, pesadas y de gran espesor. La calderería se centra especialmente en la creación de espacios adecuados para almacenar grandes cantidades, como en el caso de las cisternas o los contenedores, esta se limita a crear una estructura sólida La calderería pesada también interviene en la fabricación de grandes piezas para edificios, como las vigas. Además, este proceso de fabricación es adecuado para vehículos de transporte pesado o grandes infraestructuras. En este sentido, la industria de calderas navales, que trabaja con enormes piezas metálicas en la fabricación de barcos e incluso de grandes plataformas petrolíferas, tiene una gran importancia.
Calderería ligera La calderería ligera consiste en fabricar piezas metálicas más ligeras que luego se ensamblan o unen a otras piezas, esta proporciona las estructuras adyacentes con las que funciona el trabajo. Por ejemplo, cuando se trata de un edificio o una gran infraestructura, es necesario crear accesos para la movilidad de las personas, como escaleras, y sistemas de protección de las personas, como barandillas. Para este tipo de componentes, se utiliza un metal más ligero para crear estas piezas, aunque sean grandes. Del mismo modo, otras piezas pequeñas suelen estar unidas a la pieza metálica central y pesada para garantizar un buen funcionamiento mecánico, como las puertas de los compartimentos o las salidas del depósito de combustible.
Es un tipo de trabajo que se dedica a fabricar estructuras y elementos a partir de metales, como el acero, el hierro, el aluminio, el latón y el cobre, por lo tanto, la carpintería metálica se puede utilizar en una gran variedad de proyectos, como puertas, ventanas, balcones, escaleras, barandillas, entre otros.
Se denomina así a las actividades de reparación o conformación de chapas y otros elementos de metal, en especial la reparación de carrocerías de los vehículos. Con este término se designa también al taller donde se realizan los trabajos. El obrero que realiza estas funciones se conoce como chapista a los profesionales mecánicos que se ocupan de trabajar básicamente con chapas metálicas para realizar los trabajos que requieren para darles determinadas formas o alterar su disposición o estado. aunque en algunos países se le nombra latonero y a su trabajo latonería. Funciones del chapista El chapista debe saber operar equipos de soldadura oxiacetilénica y eléctrica, cortadoras y dobladoras de chapas, así como todo tipo de herramientas de mecánica. Los principales procesos que se realizan en la chapistería: Desmontar y montar: las acciones del chapista por lo regular requieren desarmar o desmontar los elementos dañados y después su montaje una vez concluido los trabajos.
convierten la luz solar en electricidad mediante unos paneles que están hechos de silicio, un semiconductor esencial para absorber la luz del sol y transformarla en electricidad. Plantas hidroeléctricas Las plantas hidroeléctricas usan el movimiento del agua, ya sea natural (cascadas o ríos) o artificial (embalses) para crear electricidad. Según el tipo de energía eléctrica y la potencia, se utilizan hidroeléctricas grandes, mini hidroeléctricas o micro hidroeléctricas. Plantas mareomotrices Las plantas mareomotrices funcionan con un mecanismo similar al de una central hidroeléctrica, con la diferencia de que las primeras se basan en los movimientos que hacen las olas o en los movimientos que hace la marea para crear electricidad. También existen plantas mareomotrices que usan las corrientes marinas o las corrientes del fondo de los océanos para generar energía eléctrica.
La soldadura en un proceso de fijación de dos o más piezas normalmente de metal que mediante calor o presión se funde parte de dichas piezas o se añade un material de aporte, se juntan y al enfriarse se produce la unión de ellas. Tipos de soldadura y clasificación Existen dos grupos de tipos de soldadura: Soldadura por fusión: este grupo se basa en la incorporación de calor para fundir el metal, bien sea con el uso de corriente o con el uso de gases combustibles, en este grupo se encuentran: Soldadura por arco eléctrico: requiere la presencia de un arco eléctrico que se forma al pasar la corriente desde un electrodo a la pieza o viceversa, localmente se produce un calentamiento y la fusión del metal base o material de la pieza, así como del material de aporte si lo hubiese y del electrodo, si este fuera consumible, en el caso de electrodos no consumible esto no formara parte de la unión. Se puede utilizar equipos de corrientes alterna y corriente continua, esto permite cambiar la polaridad con la posibilidad de cambiar la proporción de calor que va a la pieza y al electrodo, facilitando el proceso de soldadura. Soldadura SMAW/ MMAW: por sus siglas Shielded Metal Arc Welding/Metal Manual Arc Welding, en este proceso el núcleo de acero del electrodo se funde, uniendo las piezas y rellenando los
espacios. Así mismo, se caracteriza por usar electrodos revestidos con material fundente, los cuales con el calor producen Dióxido de Carbono, actuando como escudo conta el oxígeno de la atmosfera, impidiendo la oxidación. Por todo esto, es reconocida como una técnica sencilla y accesible en cuánto a sus equipos y consumibles. Soldadura MIG/MAG/GMAW: la Soldadura MIG/MAG, por sus siglas Metal Inert Gas / Metal Active Gas / Gas Metal Arc Welding, este proceso es parecido al anterior, pero usando un electrodo no consumible y un gas inerte o activo como protector. También es una técnica sencilla, pero su equipo es más sofisticado, justamente por la necesidad de aplicación del gas. Soldadura FCAW : la Soldadura de arco de núcleo fundente (Flux Cored Arc Welding) utiliza un electrodo con material en polvo que al quemarse produce un gas de blindaje y una capa de escoria que protege la Soldadura. Es más rápida que las anteriores, pero más susceptible a posibles deformaciones o imperfecciones. Soldadura TIG: como su nombre lo indica, en la Soldadura de gas inerte de tungsteno se utiliza un electrodo de este material no consumible, además de gases inertes o semi-inertes como blindaje. A diferencia de los anteriores, permite realizar trabajos delicados y unir metales finos, pero su proceso es lento, además de requerir bastante precisión. Soldadura SAW: la Soldadura de arco sumergido (Sumerged Arc Welding) utiliza un material protector granulado el cual aísla la Soldadura de la contaminación atmosférica, la luz y el humo, generando escoria que puede proteger la Soldadura y que contribuye a la formación de aleaciones. Por lo tanto, solamente se utiliza a nivel industrial. Soldadura por resistencia: se logra mediante el calor que se genera a hacer pasar la corriente entre los dos materiales a soldar en contacto, generalmente se concentra en un punto o en una sucesión de puntos o línea. Este procedimiento es muy utilizado en la elaboración de cajas metálicas en el ensamblaje de carrocería de automóviles en la construcción de tubos con costuras, entre otras. Soldadura por costura: la diferencia esencial que usted encontrará entre esta y la Soldadura por Resistencia pura se basa en que, en este tipo, los electrodos son ruedas accionadas por un motor en vez de ser estacionarios, dando como resultado un proceso por medio de roldanas, mismas que ejercen presión y transmiten la corriente a
Soldadura por difusión: mediante la aplicación de calor y presión en medio de una atmósfera controlada para que ocurra la coalescencia. Soldadura de inducción: se produce al aprovechar el calor generado por la resistencia al flujo de la corriente eléctrica inducida mediante el uso de bobinas que se tiene en las piezas a unir hasta lograr la fusión. Además, y a la vez, esta Soldadura tiene 3 subtipos, los cuales son: Directo: el cual se trata de la unión de 2 o más piezas del mismo metal por fusión simple, es decir, sin la utilización de un material de aporte. Indirecta: colocando ambas piezas de tal modo que las superficies a soldar queden debajo o en el centro de la bobina de inducción. Fuerte: utiliza un fundente y un material de aporte para unir ambas piezas.
Máquinas de soldar electrodo MMA: Las máquinas de soldar electrodo, también denominadas soldadoras por arco con electrodos revestidos o soldadoras MMA, son el tipo de máquina de soldar más habitual en el sector de la construcción. Estas soldadoras de electrodo MMA son las máquinas soldadoras que se caracterizan por realizar el soldeo por arco con un electrodo revestido, proceso en el cual la fusión del metal se produce gracias al calor generado por el arco eléctrico que se establece entre el extremo del electrodo revestido y el metal base a soldar en todo proceso de soldadura se necesita habitualmente de un material de aportación y de una protección del proceso. En este caso, el material de aportación se obtiene por la fusión del electrodo en forma de pequeñas gotas; y la protección de la soldadura se obtiene por la descomposición del revestimiento en forma de gases y en forma de escoria líquida que flota sobre el baño de fusión y que después solidifica. Máquinas de soldar TIG (Tungsten Inert Gas): Los soldadores TIG son un tipo de herramienta de soldadura portátil que adopta el método de inicio de arco de ruptura de alto voltaje para soldar. La soldadura TIG se refiere a la soldadura por arco protegido con gas inerte de tungsteno, que utiliza tungsteno industrial o tungsteno activo como electrodos
que no se funden y gas inerte (argón) como protección. La soldadura TIG es adecuada para metales no ferrosos y aceros aleados que se oxidan fácilmente (Al, Mg, Ti y sus aleaciones, y acero inoxidable). Este tipo de soldadora es adecuada para la soldadura de un solo lado y la formación de dos lados, como la soldadura de fondo y la soldadura de tuberías. También es adecuado para soldar chapas finas. Máquinas de soldar MIG/MAG Las soldadoras MIG son máquinas de soldadura por arco de alta velocidad que utilizan un electrodo de fusión y un gas externo como medio de arco. Estos soldadores protegen el baño de soldadura de la formación de gotas de metal debido a la alta temperatura en la zona afectada por el calor (HAZ). MIG es el acrónimo en inglés de Metal Inert Gas. El método de soldadura por arco protegido con gas inerte (Ar o He) con alambre sólido se conoce como soldadura protegida con gas inerte de electrodo fundido, o soldadura MIG para abreviar. En este método de soldadura, el electrodo de tungsteno en la antorcha se reemplaza por un alambre, mientras que los demás permanecen igual que en el método de soldadura TIG. Debido a esta configuración, en la soldadura MIG, el arco funde el alambre y lo alimenta a la zona de soldadura. Luego, los rodillos accionados eléctricamente alimentan el alambre desde el carrete hasta la antorcha, según sea necesario para soldar. Al igual que con la soldadura TIG, la fuente de calor es un arco de CC; sin embargo, la polaridad se invierte con respecto a la utilizada en la soldadura TIG. El gas protector utilizado también es diferente. Para mejorar la estabilidad del arco en este método de soldadura, se debe agregar 1% de oxígeno al argón. Máquinas de soldar Inverter
Soldador SAW (máquina de soldadura por arco sumergido): Los soldadores SAW también se conocen como máquinas soldadoras de arco sumergido. Estos son un tipo de máquina de soldadura eléctrica con electrodo de fusión que utiliza fundente granular como medio protector, con el arco oculto debajo de la capa de fundente. Primero, el fundente granular se deposita uniformemente sobre la costura de soldadura de la pieza soldada. A continuación, la punta de contacto y la pieza soldada se conectan respectivamente a dos etapas de la fuente de alimentación de soldadura para generar el arco. Finalmente, el alambre de soldadura se alimenta automáticamente y el arco se mueve para soldar. Los soldadores de arco sumergido pueden soldar acero estructural al carbono, acero estructural de baja aleación, acero inoxidable, acero resistente al calor, aleación a base de níquel y aleación de cobre. Soldador de CA: Los soldadores de CA utilizan una corriente alterna a través de un transformador reductor especial que se encuentra dentro de la máquina y luego emiten energía eléctrica de bajo voltaje y alta corriente para soldar. Los soldadores revestidos de CA tienen las ventajas de una estructura simple, fácil mantenimiento y ausencia de desviación magnética durante la soldadura. Estas máquinas de soldadura de alta potencia apenas usan electrodos 506 cuando usan electrodos ordinarios, electrodos de acero inoxidable y electrodos de hierro fundido. Los soldadores de CA se pueden usar para soldar una amplia gama de metales base, y solo fallan al soldar ciertos materiales especiales, como oro, plata, cobre y estaño. Soldador de CC: Los soldadores de CC funcionan convirtiendo una corriente alterna en corriente continua a través de un convertidor rectificador. Las soldadoras de varilla de CC (soldadoras de varilla de corriente continua) tienen la ventaja de ser de tamaño pequeño y peso ligero. Sin embargo, a pesar de su naturaleza compacta, la estructura de estas soldadoras es relativamente compleja, lo que dificulta su mantenimiento. Los soldadores de varilla de CC realizan las mismas funciones que los soldadores de varilla de CA, pero con un mejor rendimiento.
Además, las soldadoras de varilla de CC pueden soldar materiales especiales y electrodos especiales. Tipos de cordones de soldadura Los cordones se dividen dependiendo de la oscilación que realice el soldador. Los más comunes son: Cordón encordado: también conocido como cordón recto, es el tipo de cordón de soldadura en donde se aplican pocas oscilaciones o a veces ninguna. Usualmente es empleado para soldar tuberías de acero inoxidable. Cordón Tejido o ZIGZAG: es a través de diversos movimientos oscilatorios cuando se consigue este tipo de cordón. Es por medio de los cordones tejido donde se pueden controlar distintos rasgos del cordón de soldadura tales como; penetración, deposición o acumulación de material de aporte. El cordón de soldadura circular: a menudo se utiliza para soldaduras en posición plana con juntas a tope, en T, en esquinas exteriores y para aplicaciones de acumulación o superficie. El círculo se puede hacer más ancho o más largo para cambiar el ancho o la penetración del cordón. Los cordones de soldadura en "C" o semicirculo y cuadrados: son buenos para la mayoría de las soldaduras 1G (planas) pero también se pueden usar para posiciones verticales (3G). Estos patrones también se pueden usar si hay que llenar un gran espacio cuando ambas piezas de metal tienen casi el mismo tamaño y grosor. El cordón de soldadura en "J": funciona bien en juntas de solape planas (1F), todas las juntas verticales (3G) y soldaduras horizontales (2G) a tope y de solape (2F). Este patrón permite que el calor se concentre en la placa más gruesa. También permite que el refuerzo se acumule sobre el metal depositado durante la primera parte del patrón. El cordón de soldadura en "T": funciona bien con soldaduras de filete en las posiciones vertical (3F) y sobre cabeza o superior (4F). También se puede utilizar para soldaduras de ranura profunda para el paso en caliente. La parte superior de la "T" se puede usar para rellenar la punta de la soldadura para evitar socavaciones.
Posición de soldadura sobre la cabeza: la posición de soldadura sobre la cabeza se realiza desde la parte inferior de la junta. En esta posición, la soldadura se realiza con las piezas metálicas que se encuentran por encima del soldador. Uno de los principales problemas de la soldadura sobre la cabeza es que el metal depositado en la junta tiende a caerse en la chapa. Esto causa la aparición de coronas más altas en los cordones. Para evitarlo, asegúrese de mantener un baño de fusión pequeño. Si el baño de fusión es grande, el soldador tendrá que quitar la llama por un momento para que el metal fundido se enfríe. Tipos de uniones Unión empalmada: En partes que se encuentran en el mismo plano y la unión se da en sus bordes. Unión de esquina: En partes que forman un ángulo recto y la unión se da en la esquina del ángulo. Unión superpuesta: En partes que se sobreponen y ahí se da la unión. Unión de bordes: En partes paralelas y la unión se hace en su borde común. Unión en T: En partes perpendiculares, y cuya unión se da en el punto donde se tocan. Tipos de electrodo
Electrodos revestidos: los electrodos revestidos son el tipo de electrodo que están formados por un núcleo metálico que servirá como material de aporte y un revestimiento compuesto por distintas sustancias químicas que se encargarán de proteger el metal fundido de la atmósfera y de estabilizar el arco eléctrico. Dentro de los electrodos revestidos hay distintos tipos según su composición, la elección entre los cuales dependerá el material a soldar. Electrodos no revestidos: los electrodos no revestidos son el tipo de electrodo que no disponen de un recubrimiento por lo que solo se pueden utilizar en procesos de soldadura a gas, ya que necesitamos de una protección externa mediante un gas inerte para impedir la penetración de oxígeno y nitrógeno. Estos son los electrodos utilizados en la soldadura TIG, la cual se realiza mediante electrodos de tungsteno y nos permiten obtener acabados de alta calidad en todo tipo de materiales. Electrodos continuos: los electrodos continuos, también denominado hilo de soldar, es el electrodo utilizado en la soldadura de hilo ya que nos permite trabajar de forma mucho más continuo gracias a su sistema de hilo, que resulta como un electrodo continuo. Clasificación de electrodos para aceros al carbono - AWS A5.1 (E XXYZ - 1 HZR) E, indica habitualmente que es un electrodo diseñado para soldadura eléctrica manual. XX, indican la mínima resistencia a la tracción, sin tratamiento térmico post soldadura, del metal depositado. Y, indica la posición en la que se puede soldar satisfactoriamente con el electrodo: 1 → Electrodo apto para soldar en todas las posiciones (plana, vertical, techo y horizontal). 2 → Electrodo solo aplicable para posiciones planas y horizontal. 3 → Electrodo solo aplicable para posición plana. 4 → Electrodo adecuado para soldadura sobre cabeza, vertical descendiente, plana y horizontal. Z, indica el tipo de corriente eléctrica y polaridad en la que mejor trabaja el electrodo; a la vez que también identifica el tipo de revestimiento del electrodo. Este dígito va ligado al dígito anterior. 1 , código opcional que indica que el electrodo cumple con los requisitos de impacto y ductilidad mejorados. HZ , código opcional que indica que el electrodo cumple con los requisitos de la prueba de hidrógeno difusible R , código opcional que indica que el electrodo cumple los requisitos de la prueba de absorción de humedad (sólo para electrodos de bajo hidrógeno).
base con el añadido de algunos elementos para ayudar a la limpieza del material base. Estos hilos de soldar macizos se utilizan habitualmente para soldar aceros al bajo carbono y materiales de poco espesor; ya que no dejan escoria sobre el cordón y el enfriamiento es rápido. Hilos de soldar tubulares: los hilos de soldar tubulares, también denominados hilos de soldar con alma, son el tipo de hilo que internamente están llenos de polvo fundente granulado, que hace la misma función que el revestimiento de los electrodos revestidos. Estos hilos nos permiten trabajar sin gas de protección para la soldadura. Preparación de superficie o perfiles Para generar un cordón de soldadura se requiere efectuar una serie de pasos con el fin de efectuar una buena ejecución.
punta de la antorcha mediante un rodillo de alimentación que es accionado por un motor eléctrico. El alambre se energiza cuando pasa a través de la punta de contacto. Se produce un arco entre el hilo y el material base, que funde el hilo y el material base simultáneamente para soldarlos. Durante el proceso, el gas de protección se suministra a través de una boquilla en el área de soldadura y sus alrededores para proteger el arco y el baño de soldadura de la atmósfera. A. Gas Ar o gas Ar + 2% O 2 B. Electrodo de alambre sólido Clasificación de la soldadura MIG La soldadura MIG de arco corto: es un método de soldadura que utiliza el fenómeno de transferencia de cortocircuito (arco corto). Se suele utilizar en sistemas semiautomáticos destinados a placas delgadas debido al bajo aporte de calor al material base. La soldadura MIG por pulverización: es un proceso que establece la corriente de soldadura más alta que la corriente crítica para establecer un voltaje de arco más alto. Utiliza el fenómeno de transferencia por pulverización en el que el material de aportación fundido se vaporiza. Cuando se suelda una pieza de trabajo de aluminio de manera que no se generen salpicaduras, puede producirse una falta de fusión u otros defectos de soldadura Para evitar este problema, debe reducirse un poco el voltaje del arco para poder soldar en modo de transferencia de transferencia de pulverización pequeña. La soldadura MIG de alta corriente: utiliza alambres de soldadura con diámetros gruesos (aprox. 3.2 a 5.6 mm (0.13" a 0.22")). El sistema de soldadura incluye una antorcha de soldadura con boquilla de gas de doble protección y una fuente de alimentación de corriente constante con una corriente de salida nominal de aproximadamente 1000 A. La soldadura MIG con CD y pulsada: también se denomina soldadura MIG pulsada convencional, este método de soldadura hace pasar una pequeña corriente de base para mantener un arco y una corriente pulsada que supera la corriente crítica alternativamente para permitir que las gotas de pulverización se transfieran desde el hilo incluso cuando la corriente media desciende por debajo de la corriente crítica. Garantizan una soldadura eficaz y de alta calidad de placas delgadas a gruesas.