
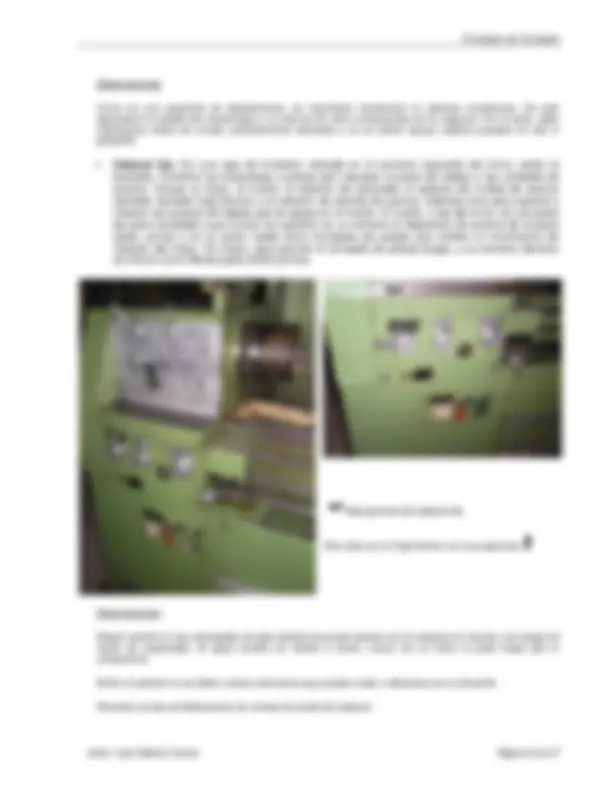
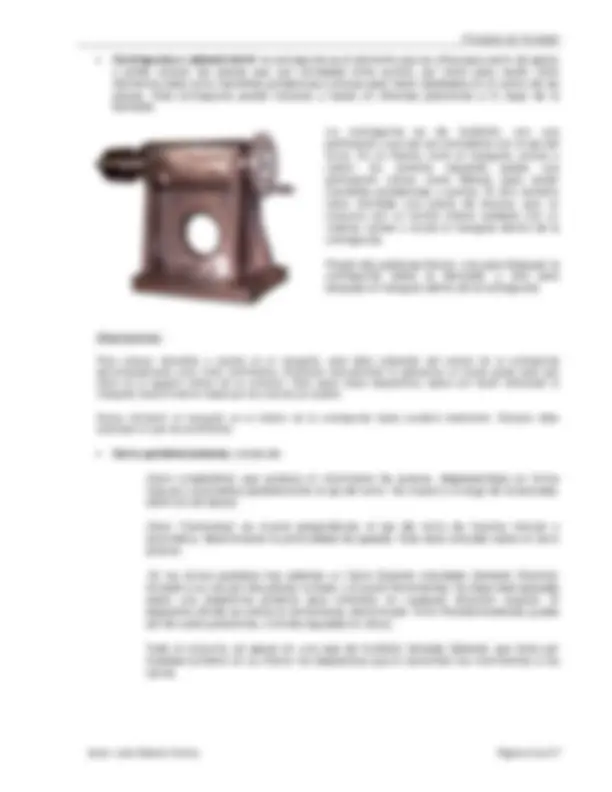
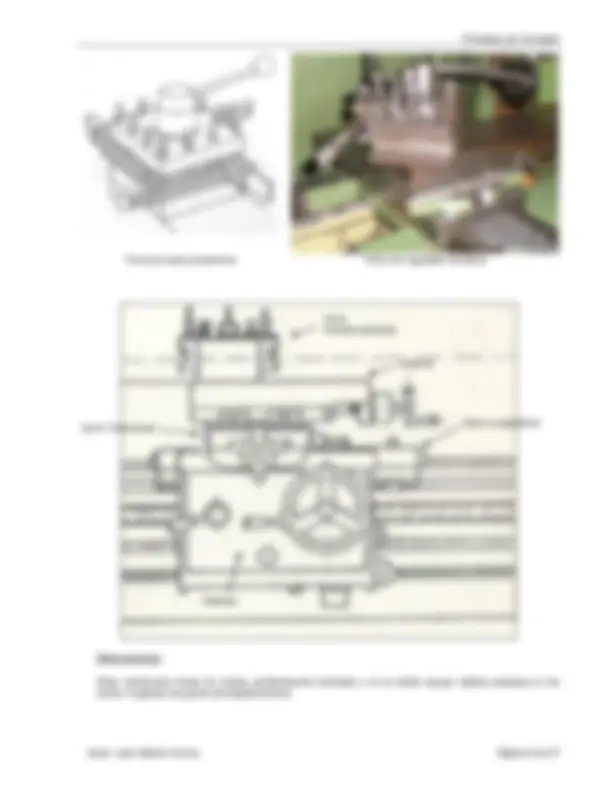
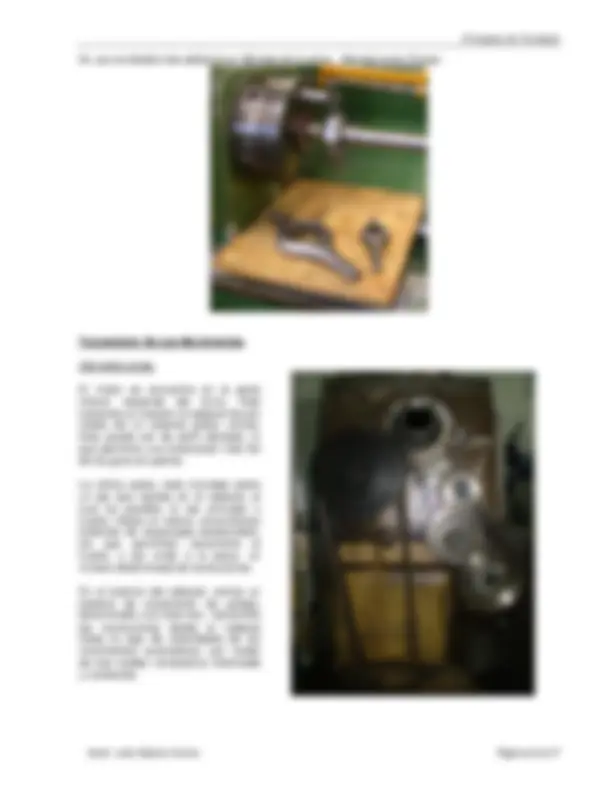
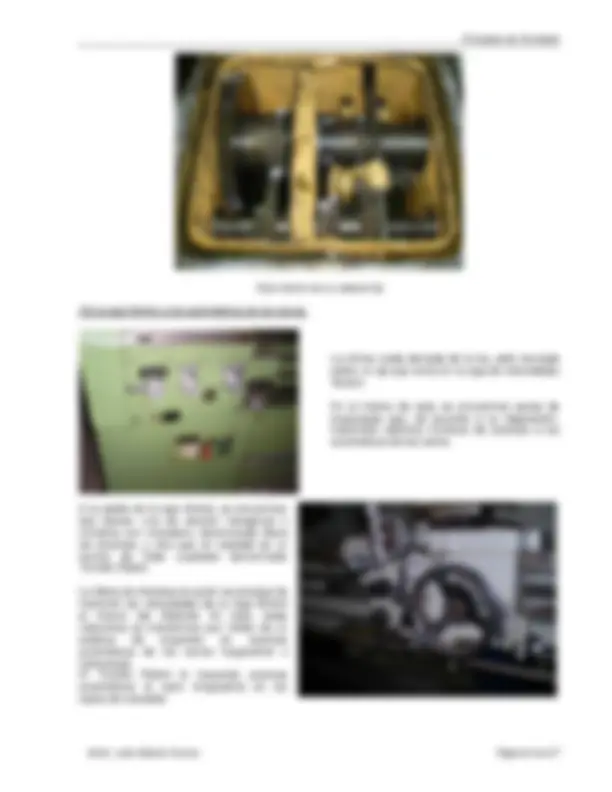
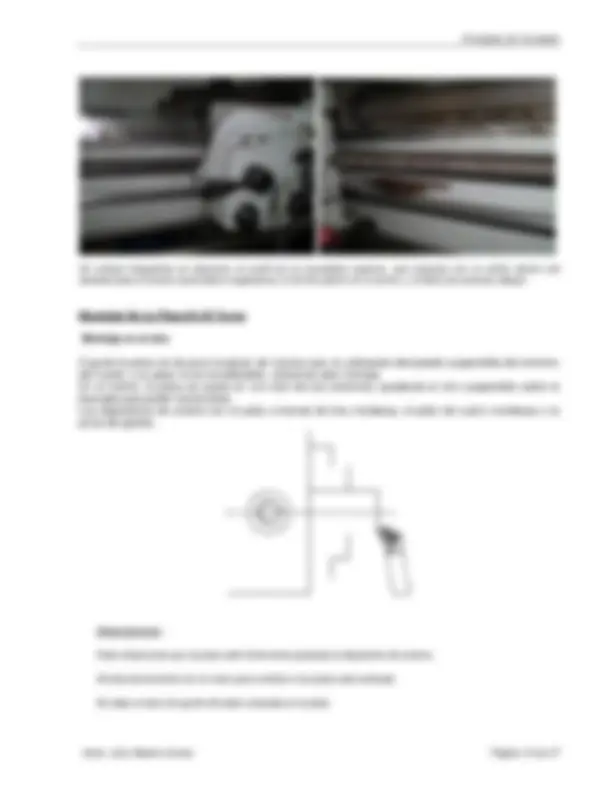
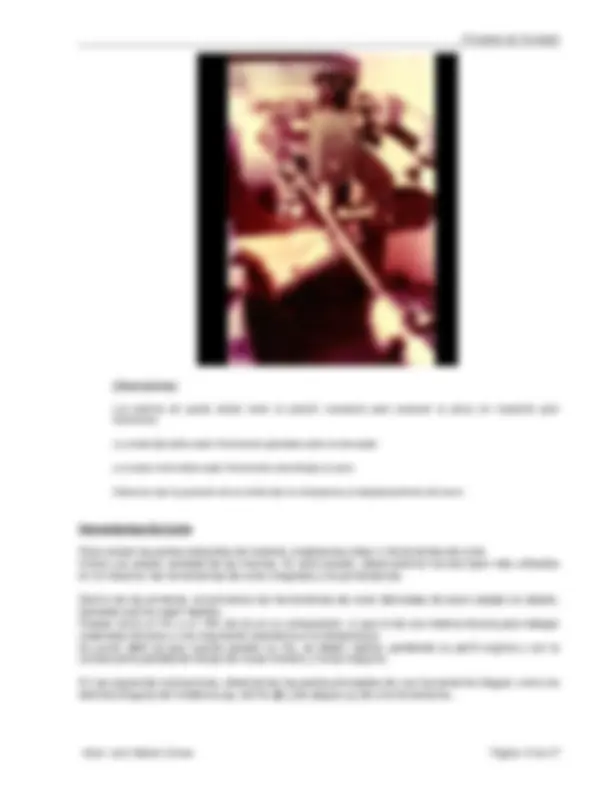
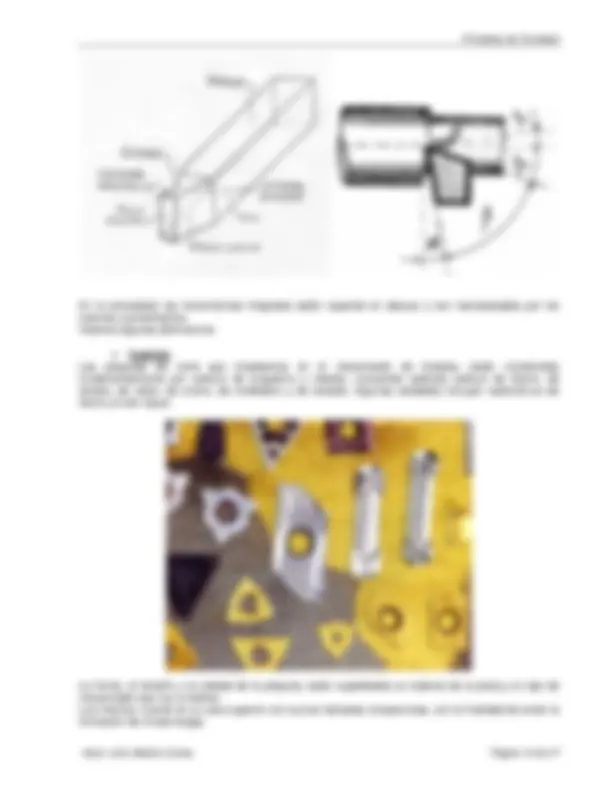
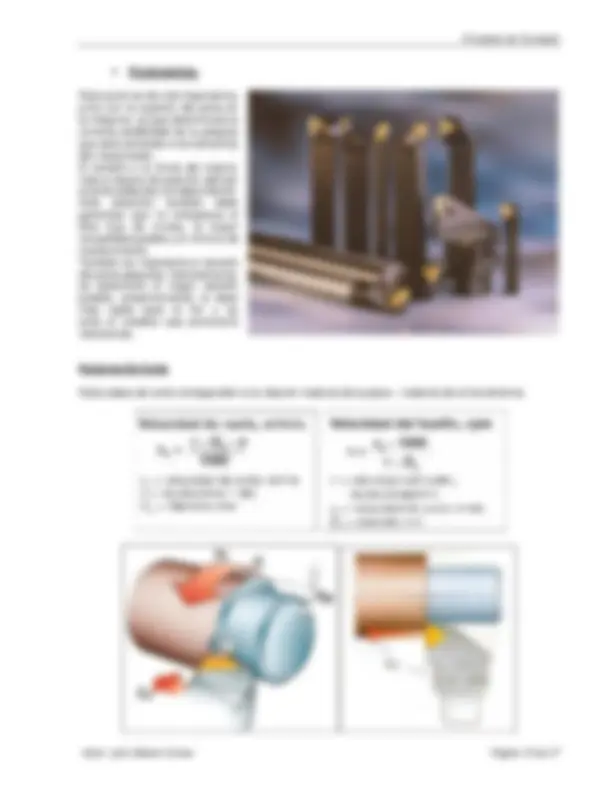
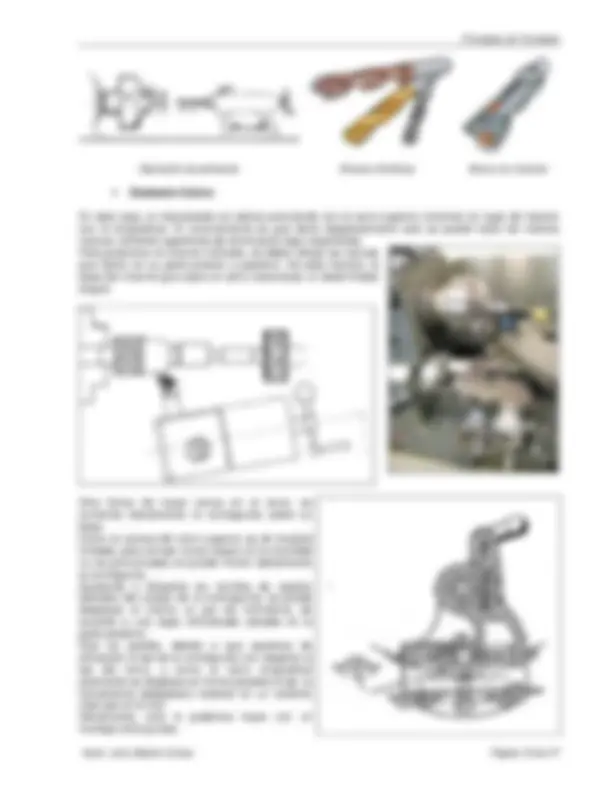
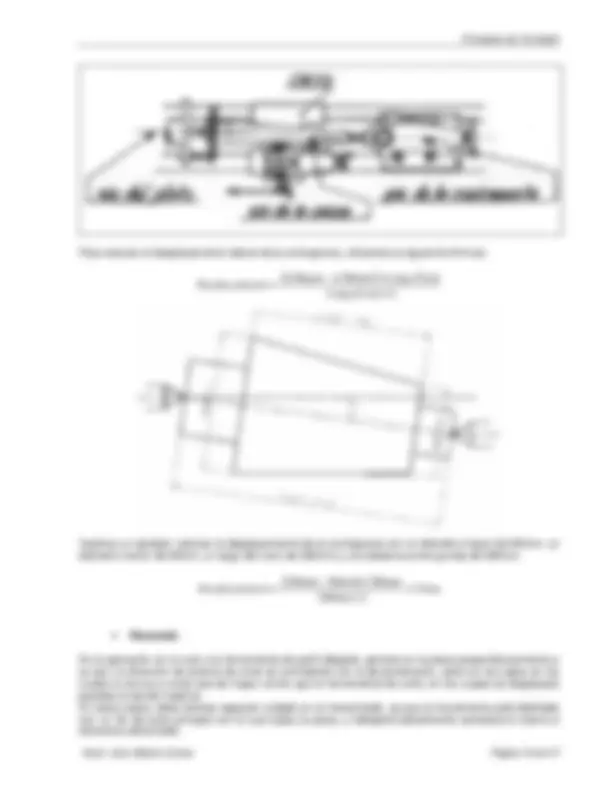
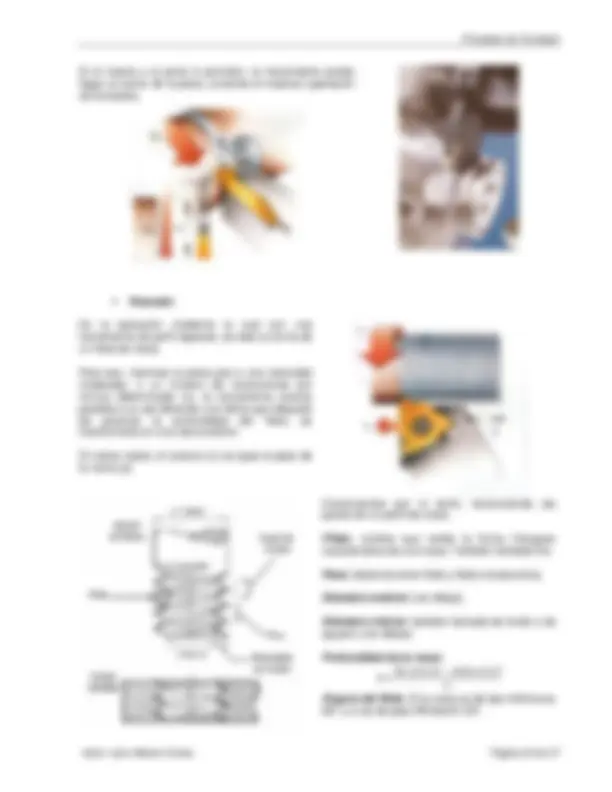
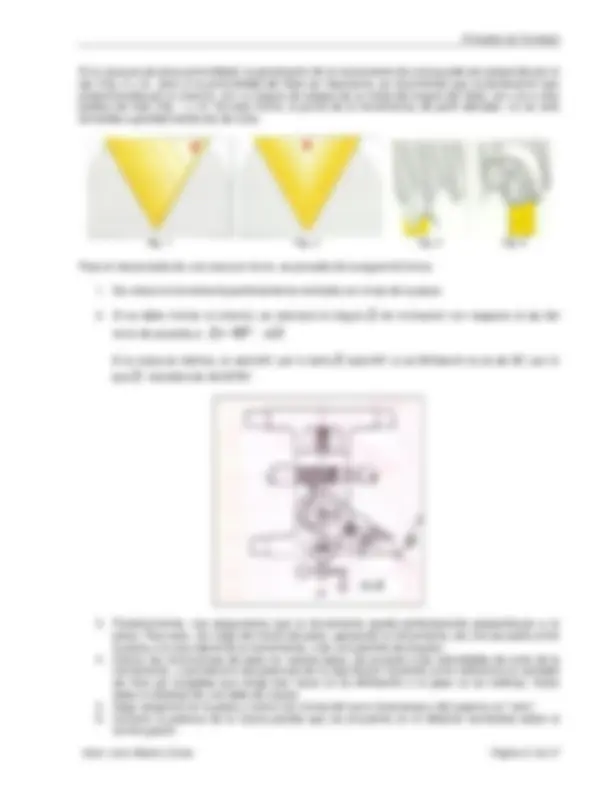
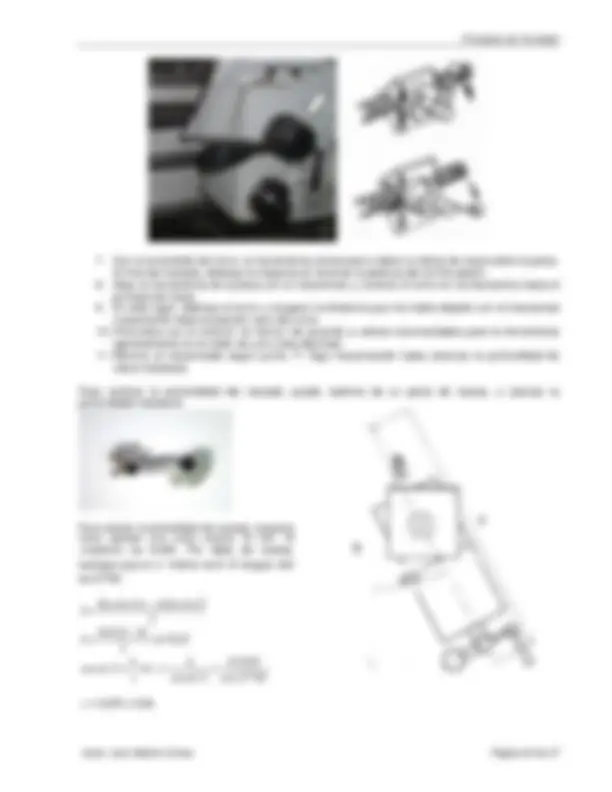
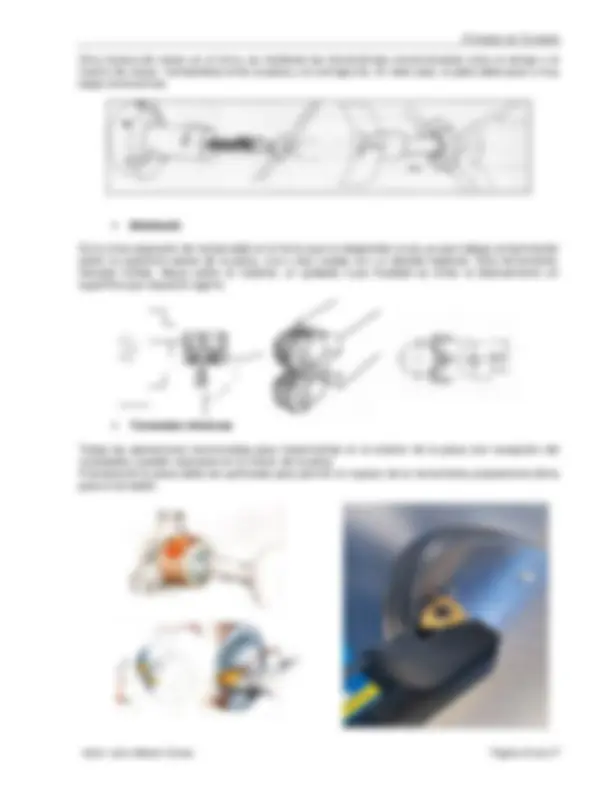
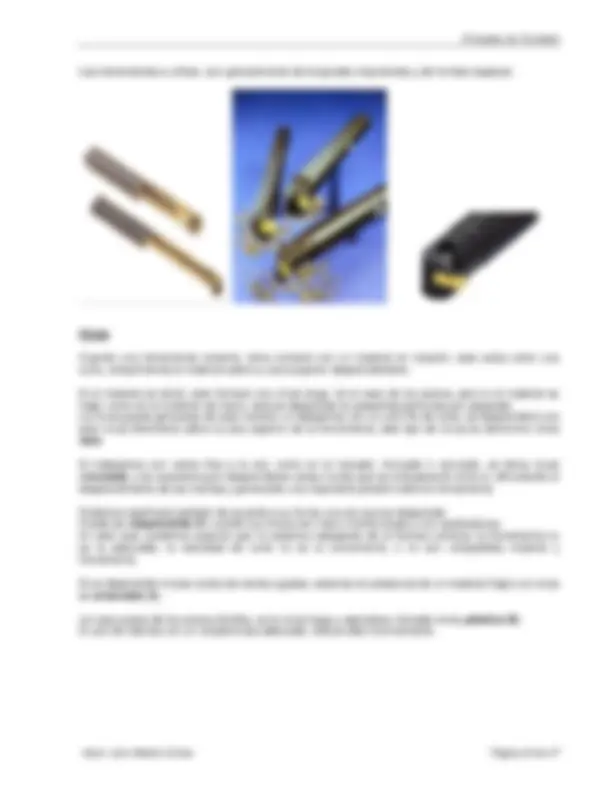
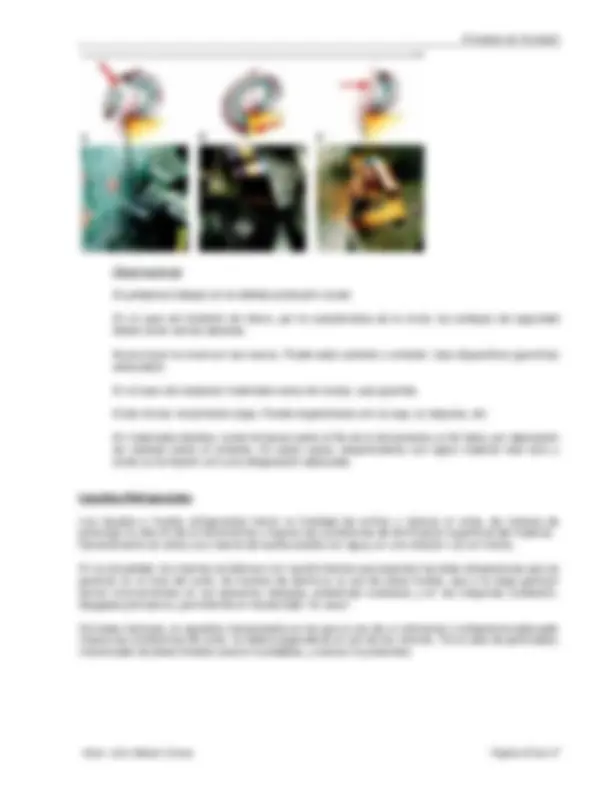
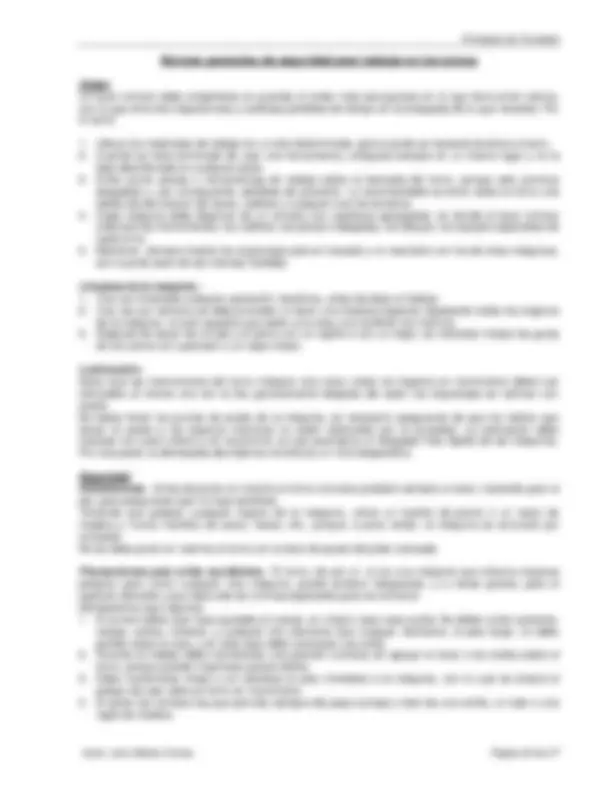
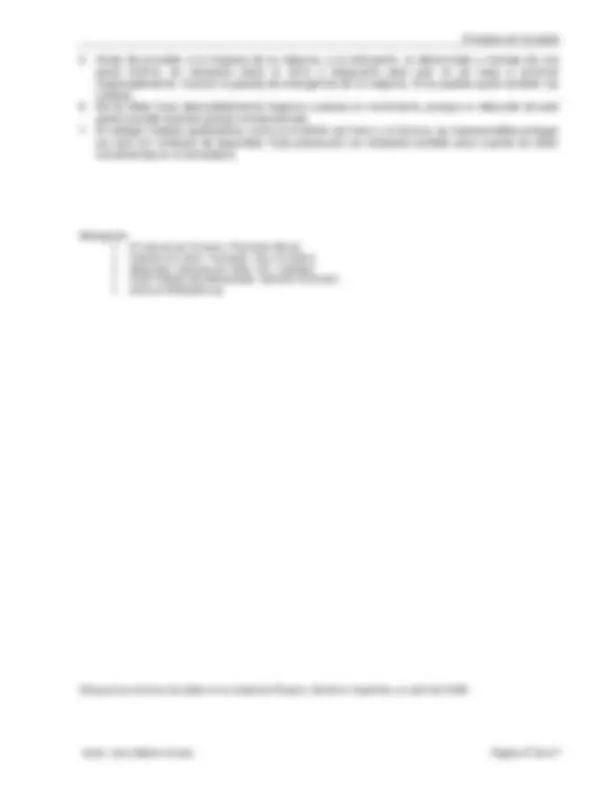
Prepara tus exámenes y mejora tus resultados gracias a la gran cantidad de recursos disponibles en Docsity
Gana puntos ayudando a otros estudiantes o consíguelos activando un Plan Premium
Prepara tus exámenes
Prepara tus exámenes y mejora tus resultados gracias a la gran cantidad de recursos disponibles en Docsity
Prepara tus exámenes con los documentos que comparten otros estudiantes como tú en Docsity
Los mejores documentos en venta realizados por estudiantes que han terminado sus estudios
Estudia con lecciones y exámenes resueltos basados en los programas académicos de las mejores universidades
Responde a preguntas de exámenes reales y pon a prueba tu preparación
Consigue puntos base para descargar
Gana puntos ayudando a otros estudiantes o consíguelos activando un Plan Premium
Comunidad
Pide ayuda a la comunidad y resuelve tus dudas de estudio
Descubre las mejores universidades de tu país según los usuarios de Docsity
Ebooks gratuitos
Descarga nuestras guías gratuitas sobre técnicas de estudio, métodos para controlar la ansiedad y consejos para la tesis preparadas por los tutores de Docsity
este archivo sirve para los principios de torno el cual puede ser de consulta
Tipo: Guías, Proyectos, Investigaciones
1 / 27
Esta página no es visible en la vista previa
¡No te pierdas las partes importantes!
Para empezar con el conocimiento de una máquina herramienta como el torno, primero debemos definir el concepto de máquina herramienta:
“La máquina herramienta es un tipo de máquina que se utiliza para dar forma a materiales sólidos, principalmente metales. Su característica principal es su falta de movilidad, ya que suelen ser máquinas estacionarias.”
Ahora, una máquina herramienta puede dar forma a materiales sólidos mediante extracción de materiales (torno, fresa, amoladora, perforadora, etc.), mediante aporte (soldadoras), o manteniendo la misma cantidad de material (plegadoras, prensas, etc.).
Si vamos a estudiar de estas el torno, empecemos con su historia:
Se denomina torno (del latín tornus , y este del griego τόρνος, giro, vuelta) a una máquina herramienta que permite mecanizar piezas de forma geométrica de revolución (cilindros, conos, hélices). Estas máquinas-herramienta operan haciendo girar la pieza a mecanizar mientras una o varias herramientas de corte son empujadas en un movimiento de avance contra la superficie de la pieza, cortando las partes sobrantes en forma de viruta. Desde el inicio de la Revolución industrial, el torno se ha convertido en una máquina básica en el proceso industrial de mecanizado. Se entiende que el primer torno que se puede considerar máquina herramienta fue el inventado alrededor de 1751 por Jacques de Vaucanson, ya que fue el primero que incorporó el instrumento de corte en una cabeza ajustable mecánicamente, quitándolo de las manos del operario.
Torno paralelo antiguo Torno paralelo moderno
En este estudio, nos dedicaremos a analizar el torno paralelo. Debe su nombre al hecho de que el carro que tiene las herramientas cortantes se desplaza sobre dos guías paralelas entre sí y a su vez paralelas al eje del torno, que coincidente con el eje de giro de la pieza.
Movimientos de trabajo
En el torno, la pieza gira sobre su eje realizando un movimiento de rotación denominado movimiento de Trabajo , y es atacada por una herramienta con desplazamientos de los que se diferencian dos:
De Avance , generalmente paralelo al eje de la pieza, es quien define el perfil de revolución a mecanizar. De Penetración , perpendicular al anterior, es quien determina la sección o profundidad de viruta a extraer.
Estructura Del Torno
El torno tiene cuatro componentes principales:
Detalle del perfil de una bancada Vista superior de un detalle de la bancada
Movimiento de Penetración
Movimiento de Trabajo
Movimiento de Avance
La contrapunta es de fundición, con una perforación cuyo eje es coincidente con el eje del torno. En la misma, corre el manguito, pínula o cañón. Su extremo izquierdo posee una perforación cónica (cono Morse) , para recibir mandriles portabrocas y puntos. El otro extremo tiene montada una tuerca de bronce, que un conjunto con un tornillo interior solidario con un volante, extrae u oculta el manguito dentro de la contrapunta.
Posee dos palancas-frenos: una para bloquear la contrapunta sobre la bancada, y otra para bloquear el manguito dentro de la contrapunta.
Observaciones:
Para colocar mandriles o puntos en el manguito, este debe sobresalir del cuerpo de la contrapunta aproximadamente unos cinco centímetros. Entonces manualmente le aplicamos un suave golpe para que clave en el agujero cónico de su extremo. Para sacar estos dispositivos, basta con hacer retroceder el manguito hacia el interior hasta que los mismos se suelten.
Nunca introducir el manguito en el interior de la contrapunta hasta ocultarlo totalmente. Siempre debe sobresalir un par de centímetros.
Carro Longitudinal , que produce el movimiento de avance, desplazándose en forma manual o automática paralelamente al eje del torno. Se mueve a lo largo de la bancada, sobre la cual apoya.
Carro Transversal , se mueve perpendicular al eje del torno de manera manual o automática, determinando la profundidad de pasada. Este está colocado sobre el carro anterior.
En los tornos paralelos hay además un Carro Superior orientable (llamado Charriot) , formado a su vez por dos piezas: la base, y el porta herramientas. Su base está apoyada sobre una plataforma giratoria para orientarlo en cualquier dirección angular. El dispositivo donde se coloca la herramienta, denominado Torre Portaherramientas , puede ser de cuatro posiciones, o torreta regulable en altura.
Todo el conjunto, se apoya en una caja de fundición llamada Delantal , que tiene por finalidad contener en su interior los dispositivos que le transmiten los movimientos a los carros.
Torre de cuatro posiciones Torre con regulador de altura
Observaciones:
Debe mantenerse limpio de virutas, perfectamente lubricado y no se deben apoyar objetos pesados en los carros ni golpear sus guías de desplazamiento.
Torre Portaherramienta
Charriot
Carro Transversal Carro Longitudinal
Delantal
Luneta móvil Luneta fija
Punto Fijo
Puntos Giratorios
Su uso se detalla más adelante en Montaje de la pieza…Montaje entre Puntas.
Transmisión De Los Movimientos
Del motor al eje.
El motor se encuentra en la parte inferior izquierda del torno. Este transmite su rotación al cabezal fijo por medio de un sistema polea- correa. Esta puede ser de perfil dentado, lo que permitirá una transmisión más fiel de los giros sin patinar.
La última polea, está montada sobre un eje que ingresa en el cabezal, el cual es paralelo al eje principal o husillo. Sobre el mismo, encontramos sistemas de engranajes escalonados, los que permitirán transmitirle al husillo, y por ende a la pieza, un número determinado de revoluciones.
En el exterior del cabezal, vemos un sistema de transmisión de poleas, denominado Lira. Este tren, transmitirá las revoluciones desde el cabezal hasta la caja de velocidades de los movimientos automáticos, por medio de tres ruedas: conductora, intermedia y conducida.
En ambas fotografías se observan en perfil de la cremallera superior, que engrana con un piñón dentro del delantal para el avance automático longitudinal, el tornillo patrón en el centro, y la barra de avances debajo.
Montajes De La Pieza En El Torno
Montaje en el aire
Cuando la pieza es de poca longitud, de manera que no sobresale demasiado suspendida del extremo del husillo, y su peso no es considerable, utilizamos este montaje. En el mismo, la pieza se sujeta en uno solo de sus extremos, quedando el otro suspendido sobre la bancada para poder mecanizarla. Los dispositivos de amarre son el plato universal de tres mordazas, el plato de cuatro mordazas o la pinza de apriete.
Observaciones:
Debe observarse que la pieza esté firmemente ajustada al dispositivo de amarre.
Girarla previamente con la mano para verificar si la pieza está centrada.
No dejar la llave de ajuste del plato colocada en el plato.
Montaje entre plato y contrapunta
En el caso de piezas delgadas o de longitud considerable, no es recomendable que quede un extremo suspendido, por lo cual se emplea este montaje. En este, un extremo queda tomado al plato, y el opuesto se apoya en un punto colocado en la contrapunta. Previamente, en la pieza se le efectúa una perforación especial efectuada por una mecha de centrar, que le realiza una cavidad cónica de 60º en la cual apoya el punto.
Observaciones:
Debe verificarse que la pieza esté firmemente ajustada al plato, y la contrapunta correctamente bloqueada con sus dos frenos, sobre la bancada y el que fija la posición del manguito.
Observar que el punto giratorio esté constantemente girando en el mecanizado.
El desplazamiento del carro hacia la derecha no debe empujar la contrapunta.
Montaje entre puntas
En este montaje, la pieza se perfora en las dos puntas con mecha de centrar, y sacando el plato del husillo, se coloca un punto para torno en el agujero de cono Morse del eje de la máquina. El extremo izquierdo se apoya en dicho punto y se sujeta con una brida de arrastre, la cual se engancha con el plato liso de arrastre, haciendo girar el conjunto. El otro extremo, se apoya en un punto en la contrapunta.
De esta manera, la pieza queda suspendida sobre la bancada, permitiendo el mecanizado longitudinal sin perder la concentricidad, ya que basta con cambiar de extremo la brida y girar la pieza. La alineación entre las perforaciones efectuadas en sus extremos no se pierde.
Observaciones:
Los patines de ajuste deben tener la presión necesaria para sostener la pieza sin impedirle girar libremente.
La luneta fija debe estar firmemente ajustada sobre la bancada.
La luneta móvil debe estar firmemente atornillada al carro.
Observar que la posición de la luneta fija no entorpezca el desplazamiento del carro.
Herramientas De Corte
Para extraer las partes sobrantes de material, empleamos útiles o herramientas de corte. Existe una amplia variedad de las mismas. En este estudio, observaremos los dos tipos más utilizados en la industria: las herramientas de corte integrales y los portainsertos.
Dentro de las primeras, encontramos las herramientas de corte fabricadas de acero aleado al cobalto, llamados aceros súper rápidos. Poseen entre un 4% y un 18% de Co en su composición, lo que le da una relativa dureza para trabajar materiales ferrosos y una importante resistencia a la temperatura. Su punto débil es que cuando pierden su filo, se deben reafilar, perdiendo su perfil original y con la consecuente pérdida de tiempo de horas-hombre y horas-máquina.
En las siguientes ilustraciones, observamos las partes principales de una herramienta integral, como los distintos ángulos de incidencia (αααα), de filo (ββββ) y de ataque (γγγγ) de una herramienta.
En la actualidad, las herramientas integrales están cayendo en desuso y son reemplazadas por los insertos y portainsertos Veamos algunas definiciones.
La forma, el tamaño y la calidad de la plaquita, están supeditados al material de la pieza y el tipo de mecanizado que voy a realizar. Los mismos, cuenta en su cara superior con surcos llamados rompevirutas, con la finalidad de evitar la formación de virutas largas.
La Velocidad de Corte (Vc) [m/minuto], o velocidad tangencial, es la velocidad que el material (viruta) tiene sobre la superficie de la herramienta (plaquita). En los modernos tornos con CNC, este valor es constante, lo que implica que la velocidad de rotación del husillo se incrementa a medida que la herramienta se acerca al centro de la pieza.
El Avance (fn) [mm/revolución], es la velocidad de la herramienta en relación a la pieza que está girando. Podríamos decir que es la velocidad de avance del carro. Es de vital importancia para la correcta formación de la viruta, y la terminación superficial de la pieza.
La Profundidad de Pasada (ap) [mm], es la semi-diferencia entre el diámetro sin cortar y el cortado.
ap= diámetro no mecanizado – diámetro mecanizado 2
Estos datos podemos encontrarlos en la caja en la cual vienen las plaquitas, o en manuales referidos al tema.
En los torneados también se debe tener en cuenta el ángulo de posición del filo de corte (кr) con respecto a la superficie de la pieza. Incide directamente en la formación y dirección de la viruta. Sus valores de corte varían desde 45º hasta 95º según el tipo de operación.
Una incorrecta elección de los factores de corte, redundarán en una importante merma en la producción, o una consecuencia directa en la herramienta, acortamiento de la vida útil o rotura.
Tipos de Mecanizado
En el torno, los mecanizados que podemos conseguir son siempre de volúmenes de revolución. Cilindros, conos, perforados en el eje, ranuras laterales, roscas y tornados interiores. Debemos considerar, como primera medida que, que la herramienta debe estar perfectamente centrada, admitiéndose, en algunas operaciones, que se encuentre levemente por arriba del centro de la pieza. Para centrar la punta de la herramienta en altura, podemos usar como referencia un punto colocado en la contrapunta, un calibre con la medida previamente calculada de la altura del eje sobre la bancada, o haciendo tangencia en el frente del material girando. En este caso, podemos observar si la punta cortante de la herramienta se encuentra a la misma altura que el centro de la pieza.
Tienen lugar limpiando el frente de la pieza. El cuerpo de la herramienta y el filo principal de corte, deben formar un ángulo pequeño contra la cara a mecanizar. Para la mejor formación de viruta, es conveniente elegir siempre una dirección del corte que proporcione un ángulo lo más cercano a 90° como sea posible (se debe evitar que el ángulo de entrada sea muy pequeño). Una mejor formación de la viruta se puede alcanzar con una dirección de avance hacia el eje que también reduce al mínimo el riesgo de la vibración.
Se consigue mecanizando la cara lateral de la pieza, con movimientos de penetración perpendiculares al eje de la misma, por medio del carro transversal; y con movimiento de avance paralelo al eje, por medio del carro longitudinal. Para un mejor desprendimiento de la viruta, se recomienda en la mayoría de los casos que el ángulo que forme el filo de corte con la superficie de la pieza, sea levemente mayor a 90º (92º-93º). Esto lo podemos conseguir si posicionamos el porta insertos perpendicular al eje del torno, ya que entre el cuerpo del porta y el apoyo del inserto encontramos esos 2 o 3 grados de diferencia.
Este mecanizado se efectúa en la cara frontal de la pieza, coincidiendo con la dirección de su eje. Lo efectuamos haciendo girar el plato con el material, y penetrando con un útil de corte en su eje. Esta herramienta de corte puede ser una broca (mecha) colocada en un portabrocas (mandríl). Este dispositivo se clava en el agujero cónico del manguito, y se introduce por medio del volante de la contrapunta, manteniendo bloqueada la misma sobre la bancada. También se pueden emplear brocas de cola cónica, para perforados de diámetros grandes, o brocas con insertos en tornos con Control Numérico Computarizados.
Para calcular el desplazamiento lateral de la contrapunta, utilizamos la siguiente fórmula:
( )
Veamos un ejemplo: calcular el desplazamiento de la contrapunta con un diámetro mayor de100mm, un diámetro menor de 80mm, un largo del cono de 200mm y una distancia entre puntas de 300mm.
( )
Es la operación en la cual una herramienta de perfil delgado, penetra en la pieza perpendicularmente a su eje. La dirección de avance de corte es coincidente con la de penetración, salvo en los casos en los cuales la ranura a cortar sea de mayor ancho que la herramienta de corte, en los cuales se desplazará paralela al eje del material. En estos casos, debe tenerse especial cuidado en el mecanizado, ya que la herramienta está diseñada con un filo de corte principal con el cual ataca la pieza, y trabajarla lateralmente someterá al inserto a esfuerzos adicionales.
Si el inserto y el porta lo permiten, la herramienta puede llegar al centro de la pieza, cortando el material ( operación de tronzado ),
Es la operación mediante la cual con una herramienta de perfil especial, se talla la forma de un filete de rosca.
Para eso, mientras la pieza gira a una velocidad moderada, o un número de revoluciones por minuto determinada ( n ), la herramienta avanza paralela a su eje labrando una hélice que después de alcanzar la profundidad del filete, se transformará en una rosca exterior.
En estos casos, el avance ( fn ) es igual al paso de la rosca ( p ).
Comencemos por lo tanto, reconociendo las partes de un perfil de rosca.
Filete : nombre que recibe la forma triangular característica de una rosca. También llamada hilo.
Paso : distancia entre filete y filete consecutivos.
Diámetro exterior ( ver dibujo ).
Diámetro interior : también llamado de fondo o de agujero ( ver dibujo ).
Profundidad de la rosca : ( )
Ángulo del filete : Si la rosca es de tipo métrica es 60º, y si es de paso Whitworth 55º.