
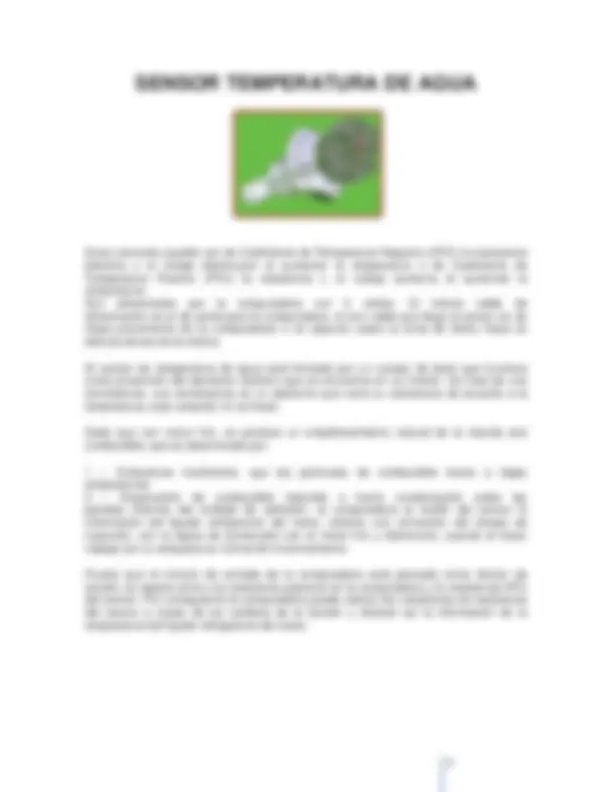
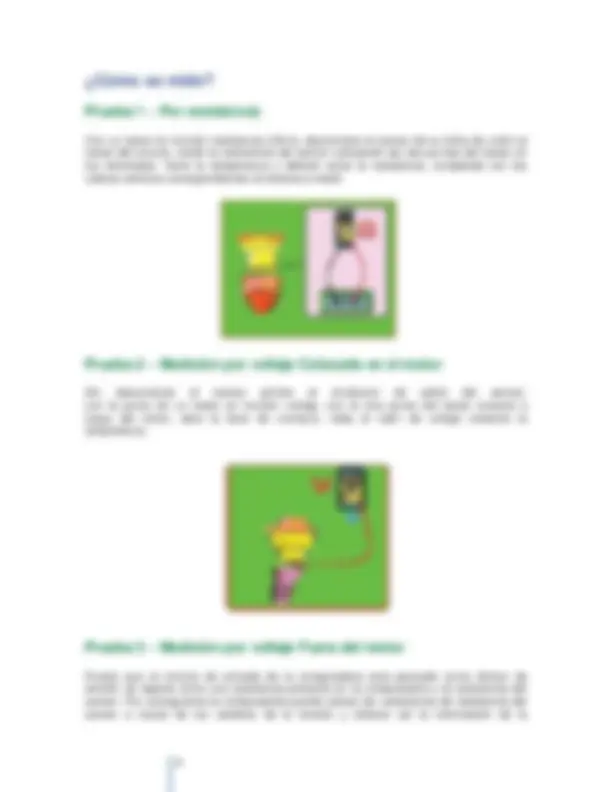
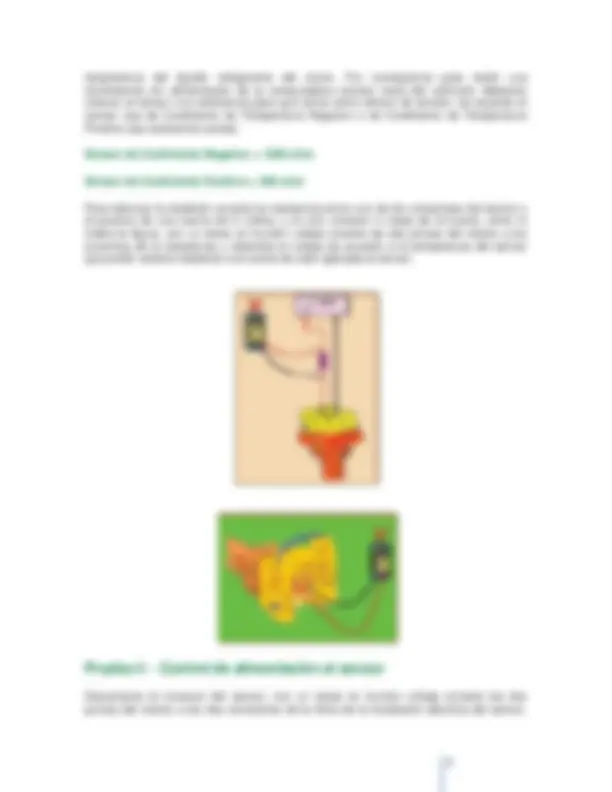
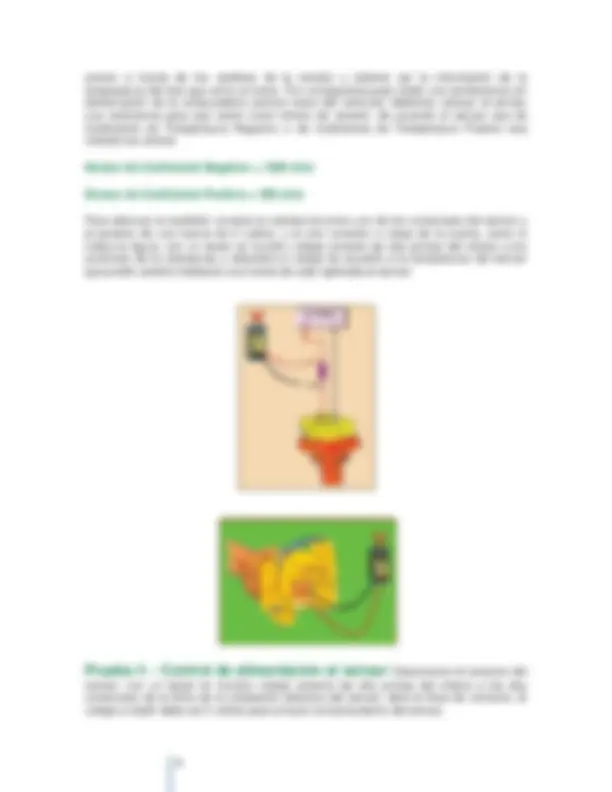
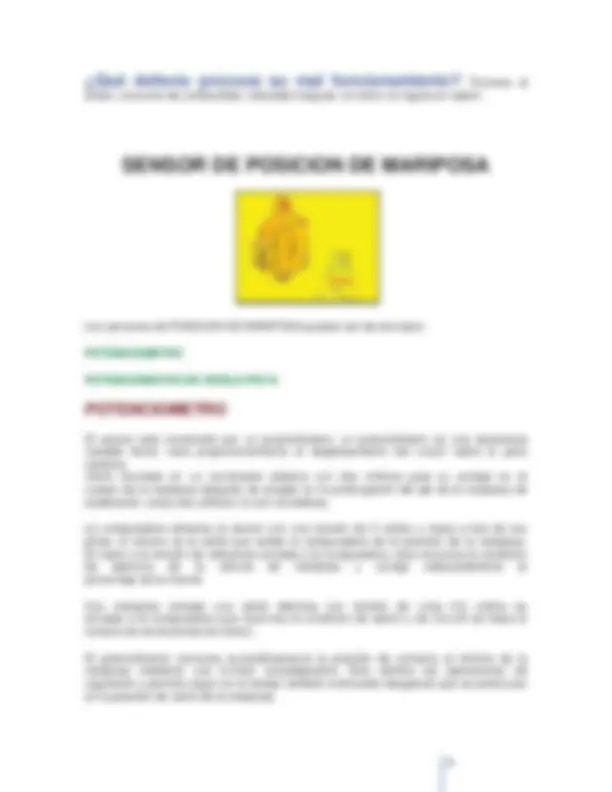
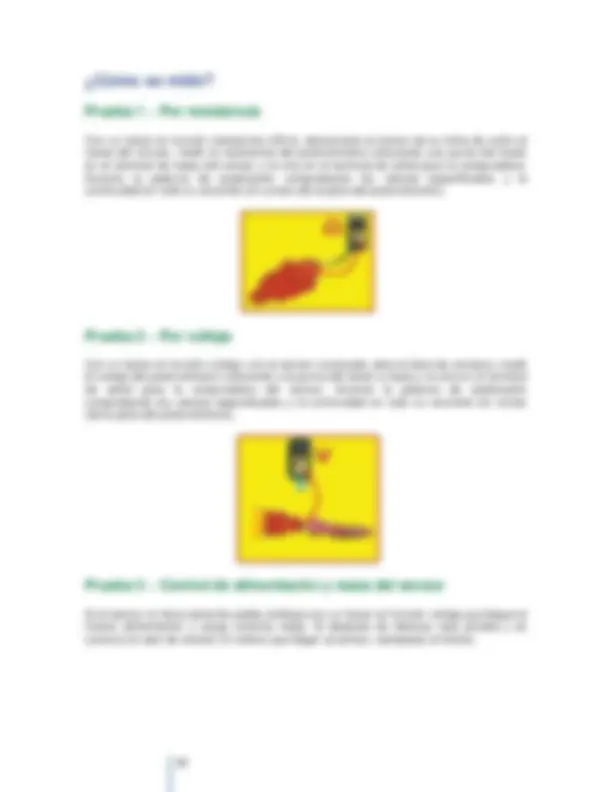
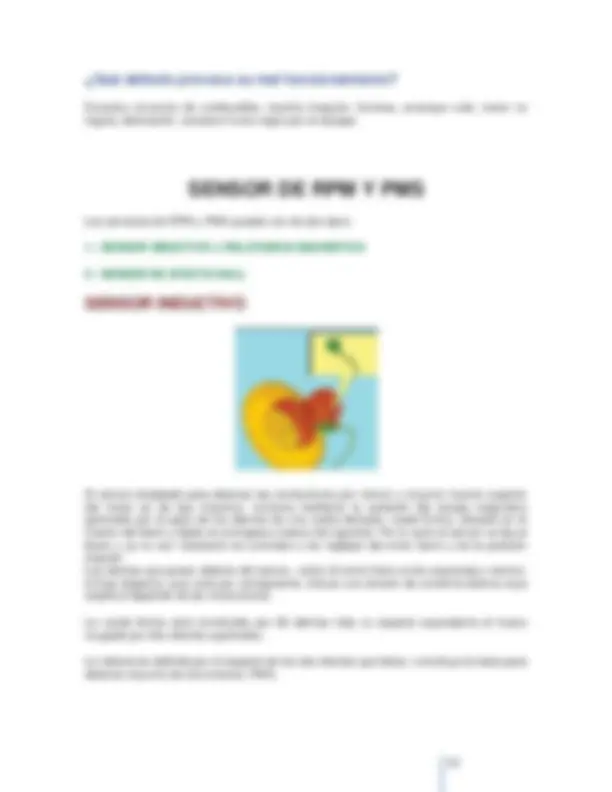
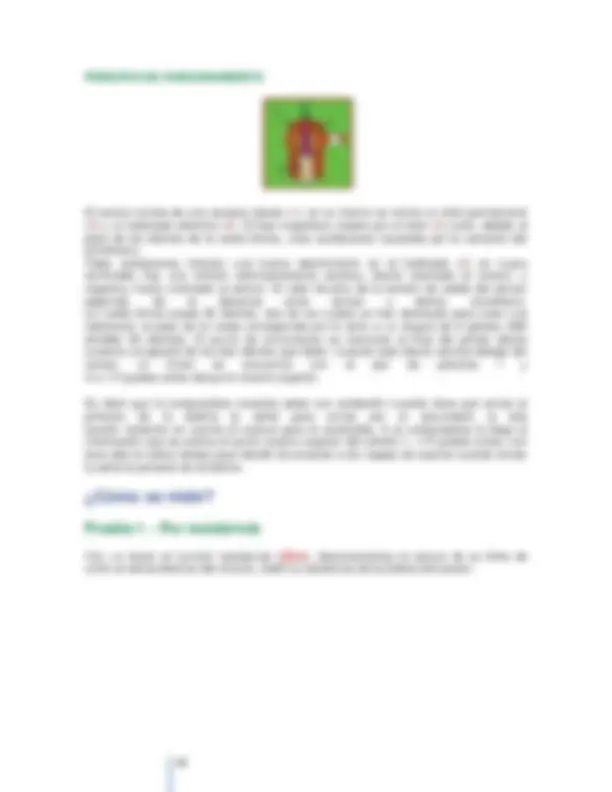
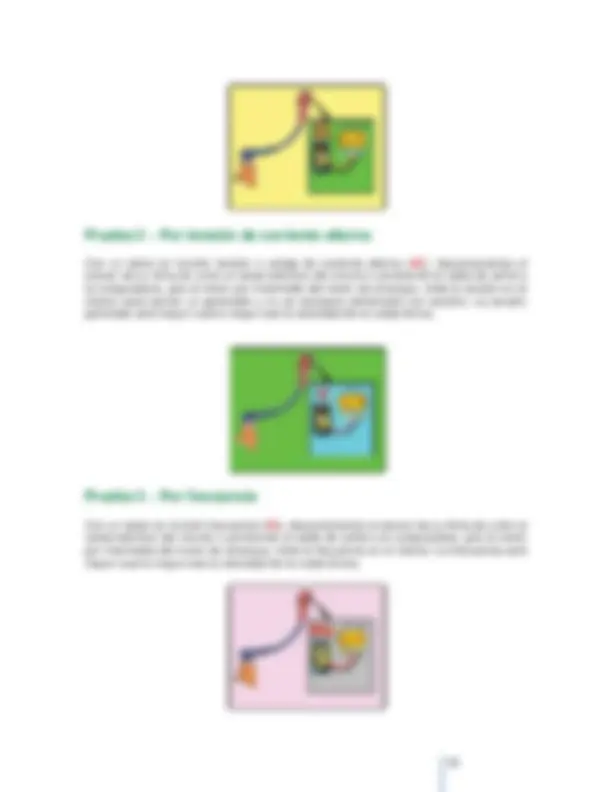
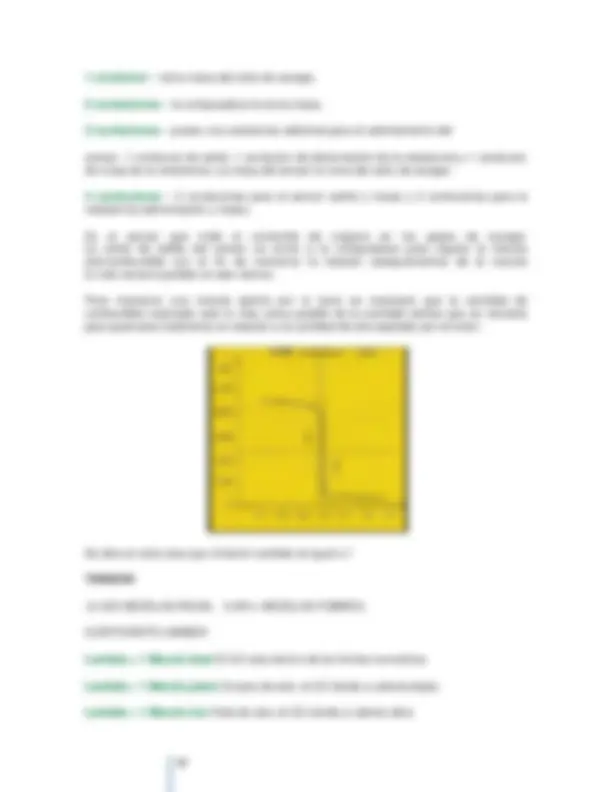
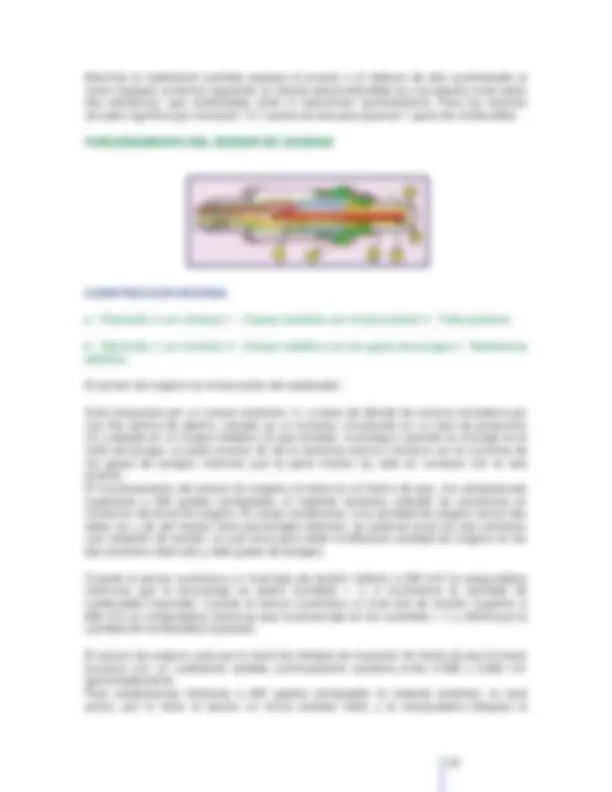
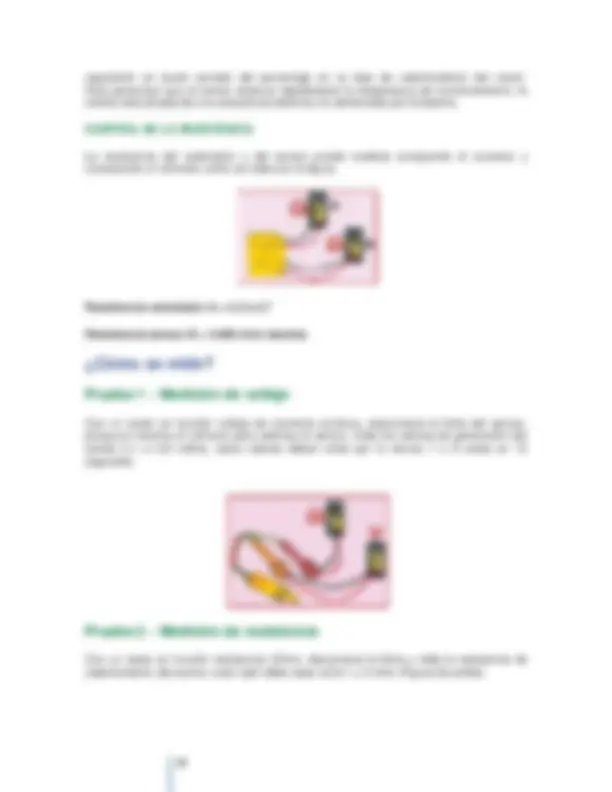
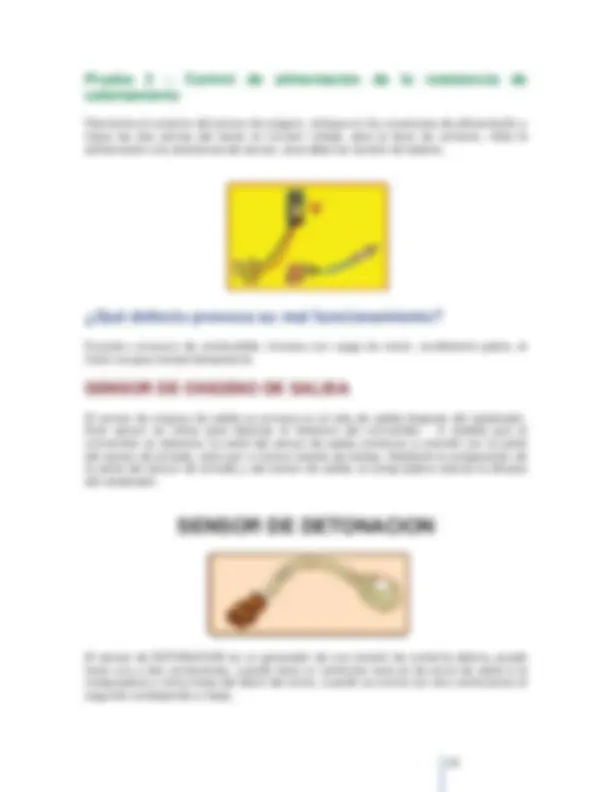
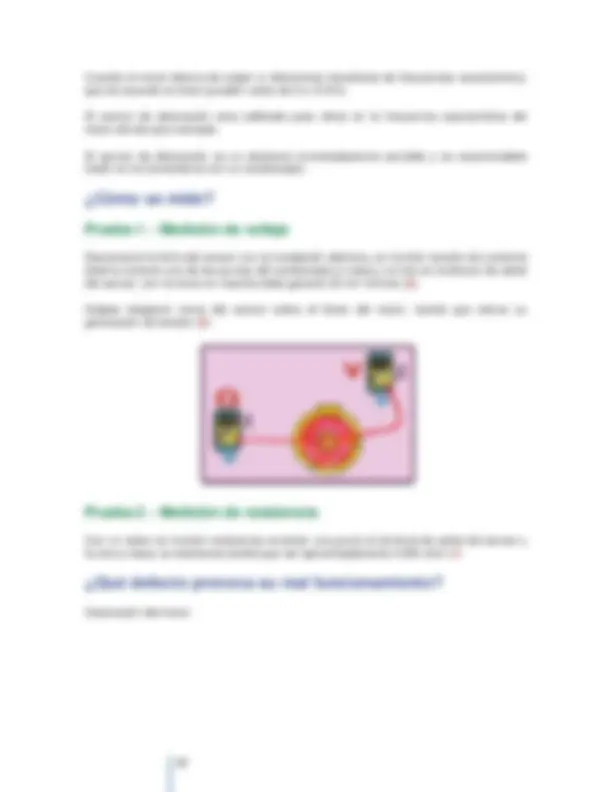
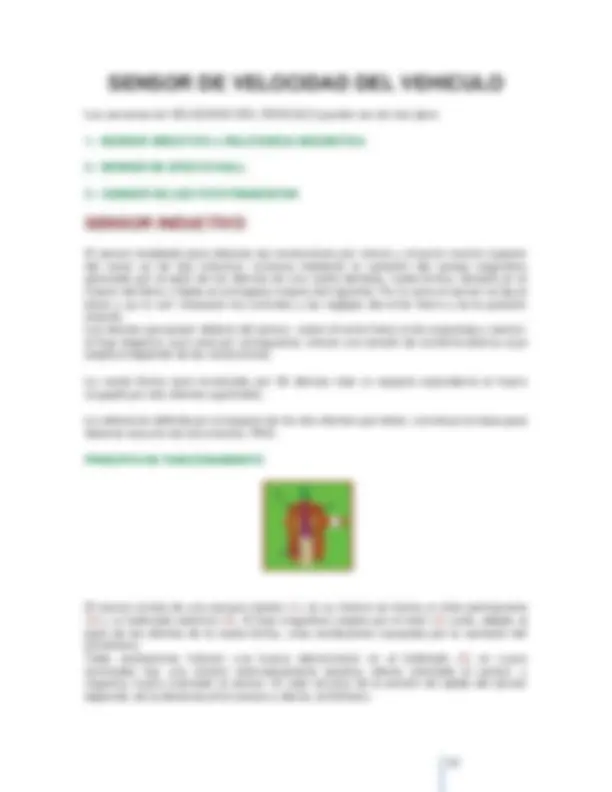

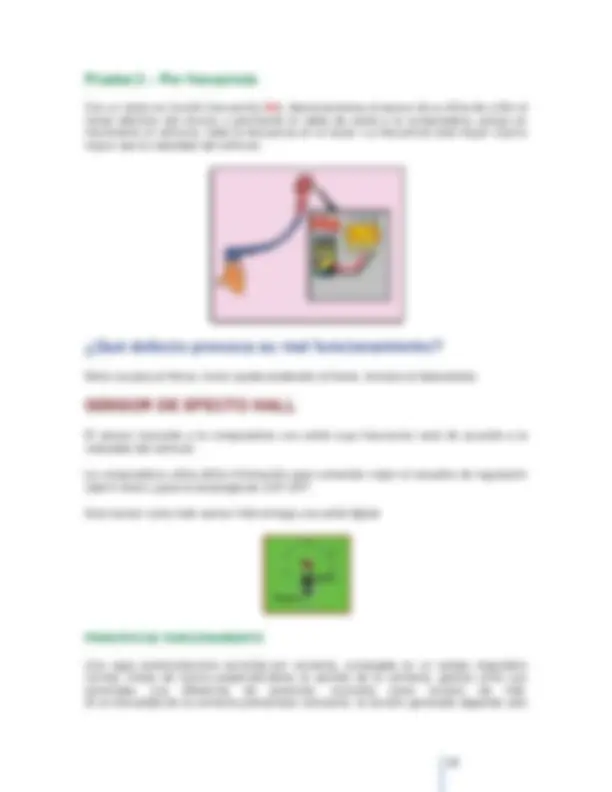
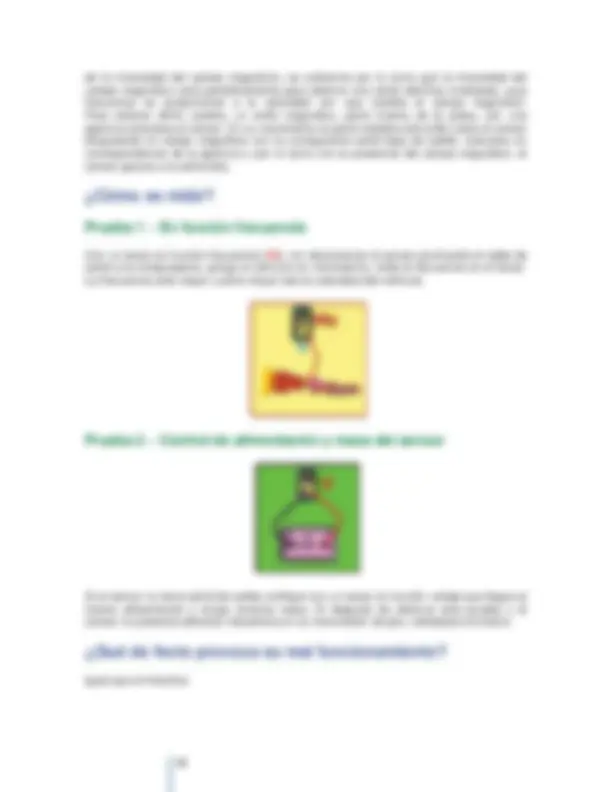
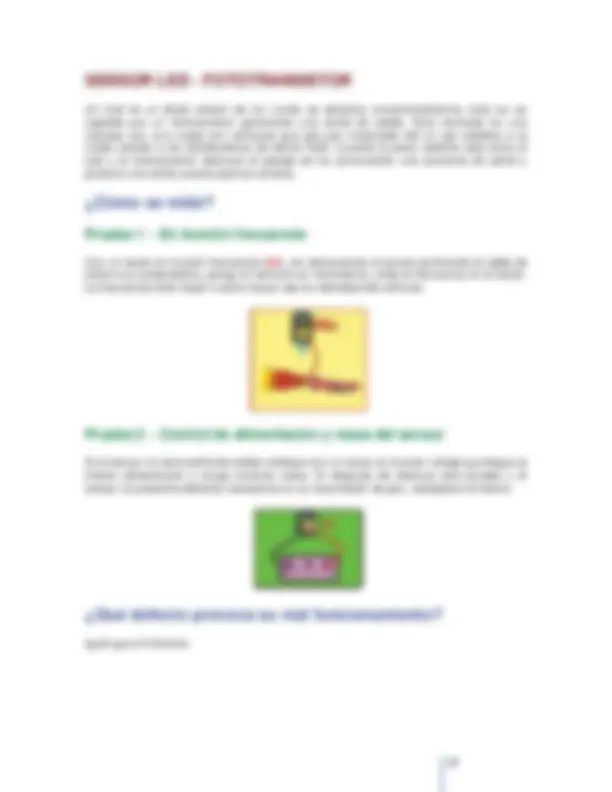
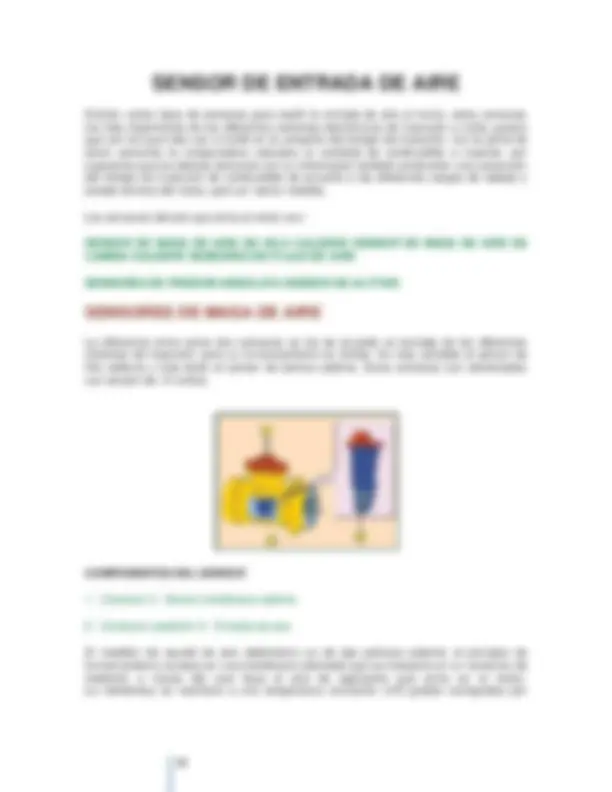
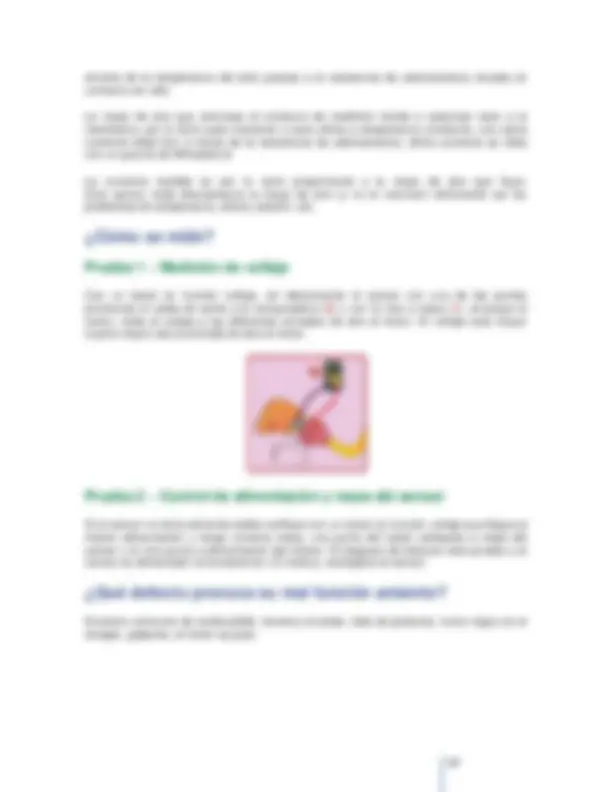
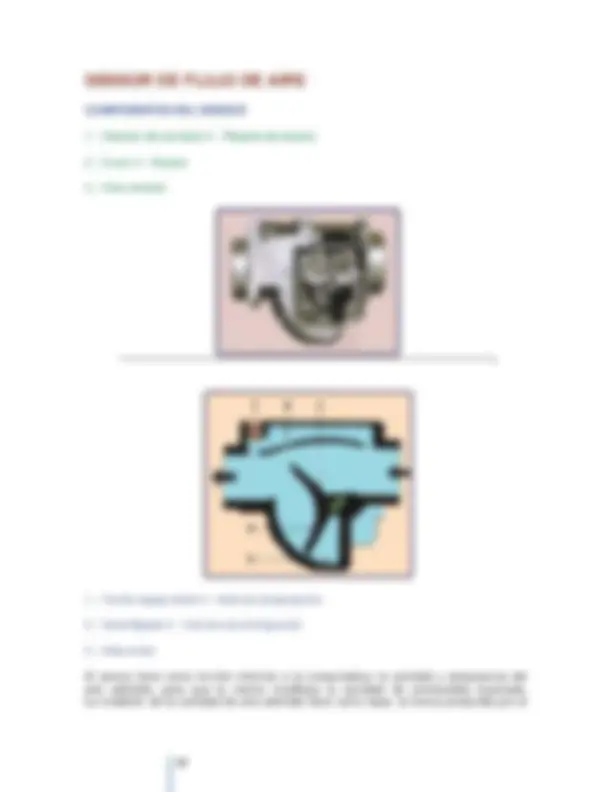
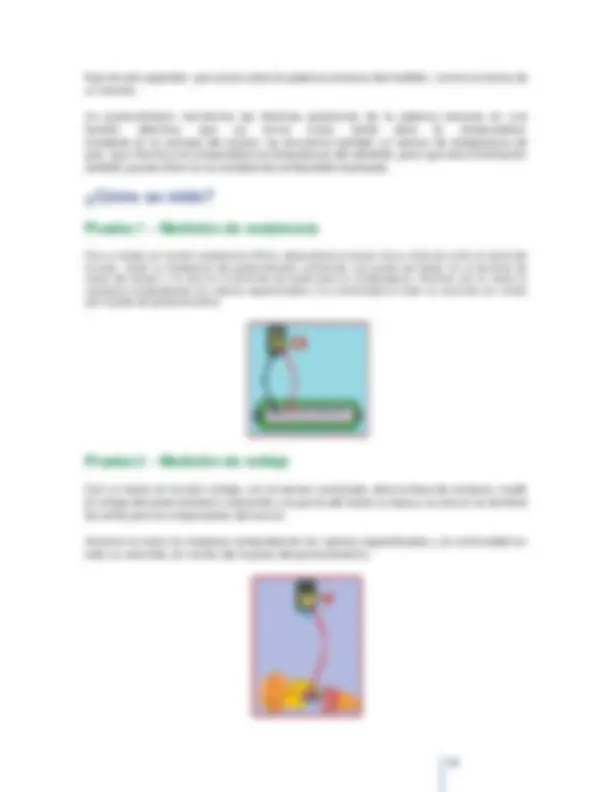

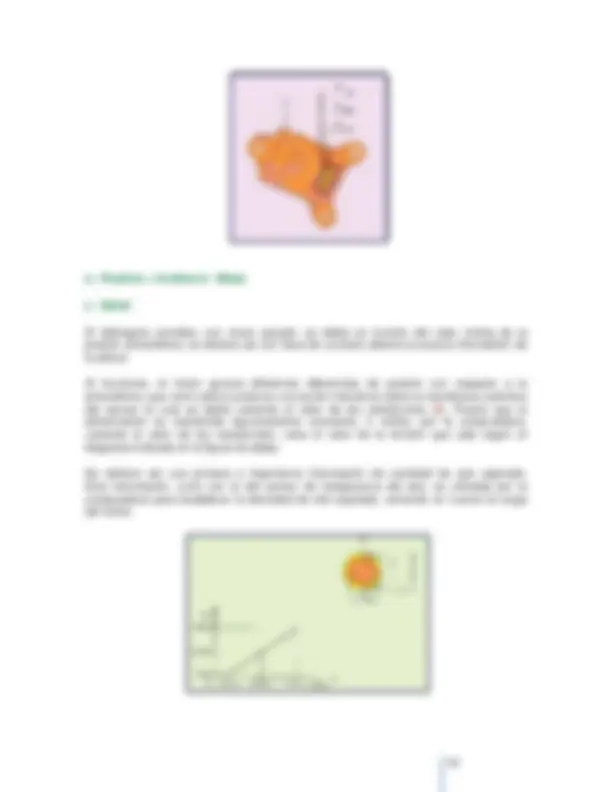
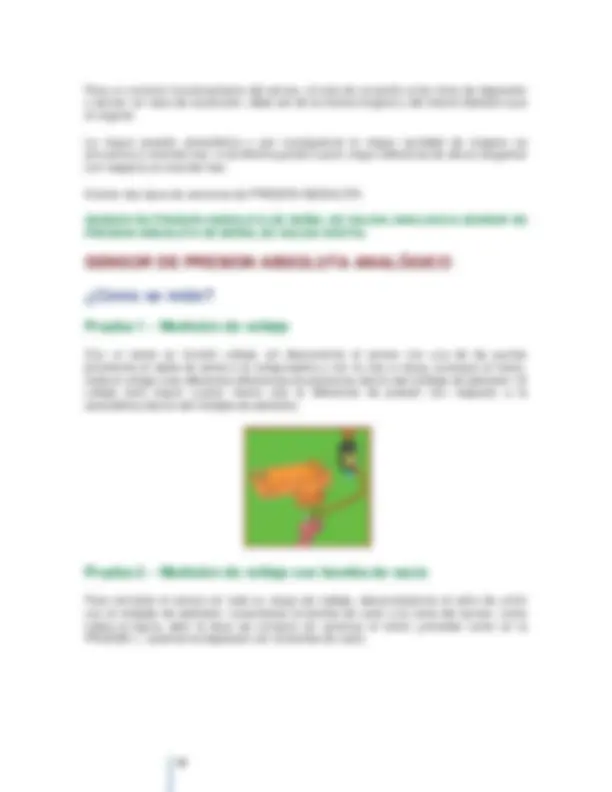
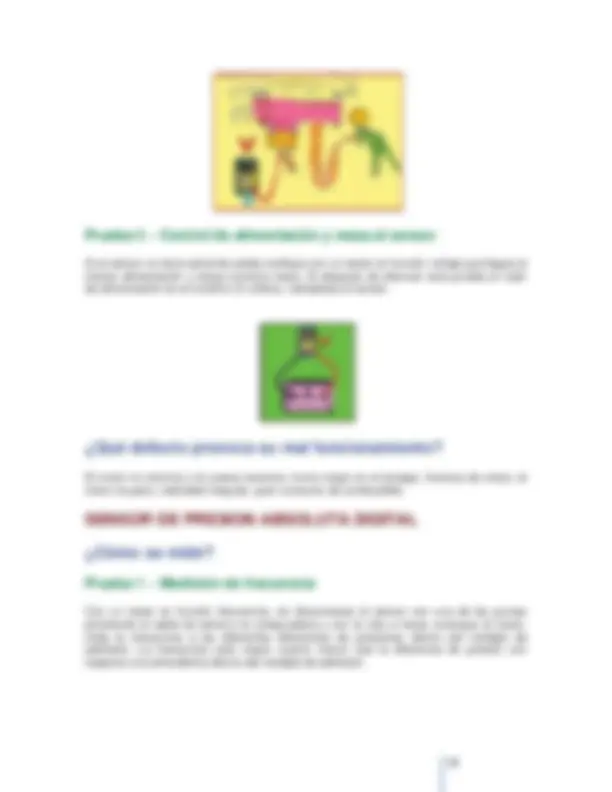
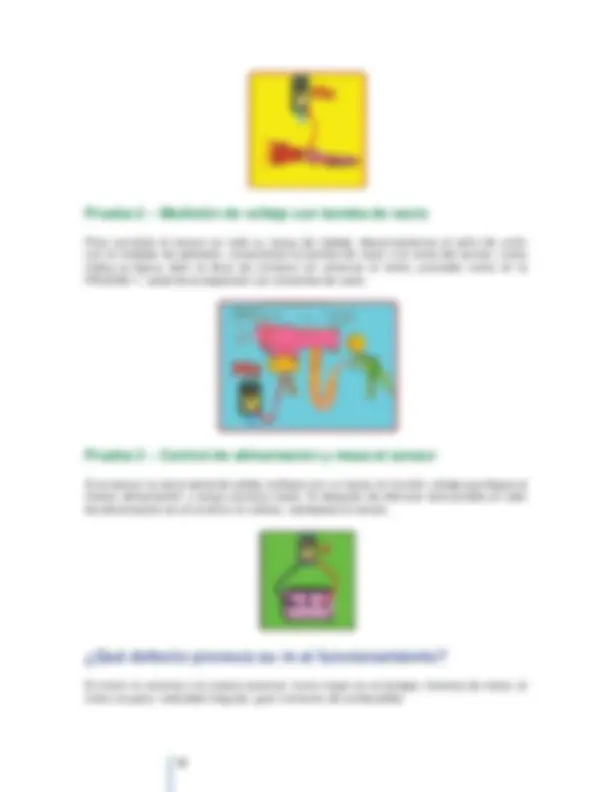
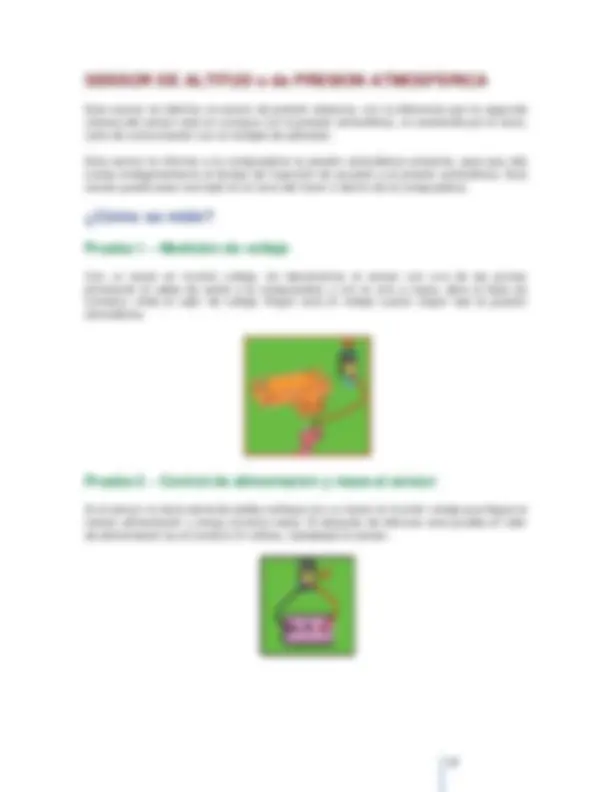
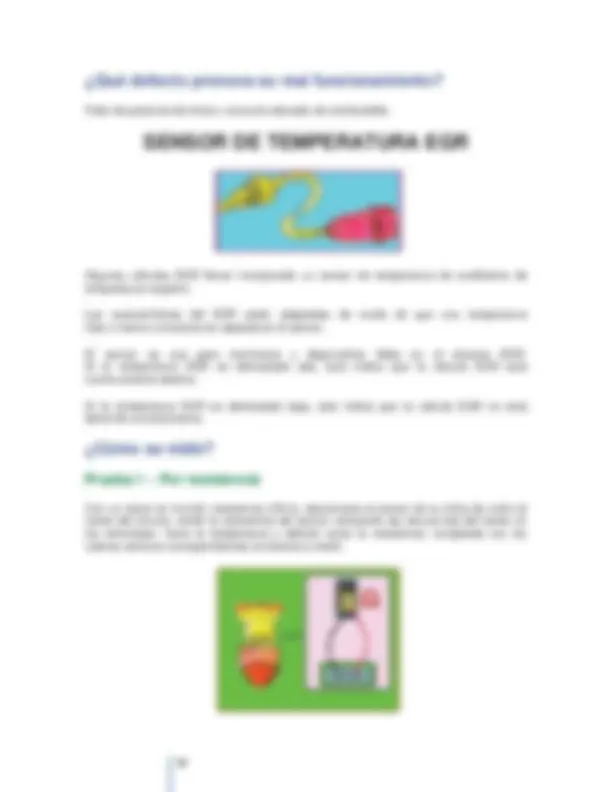
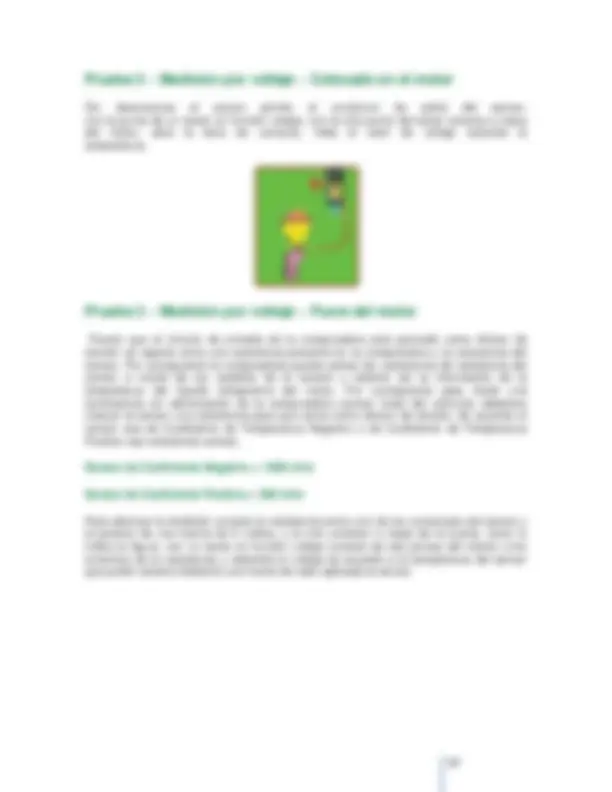
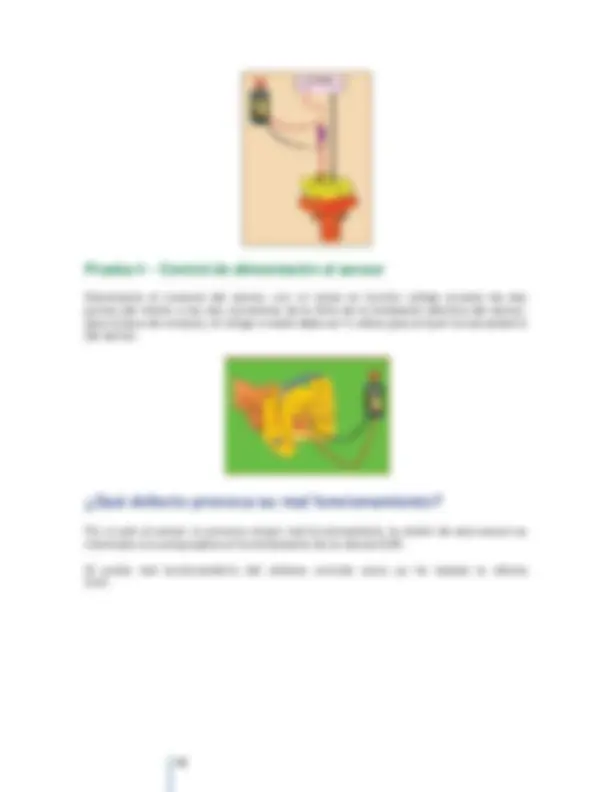
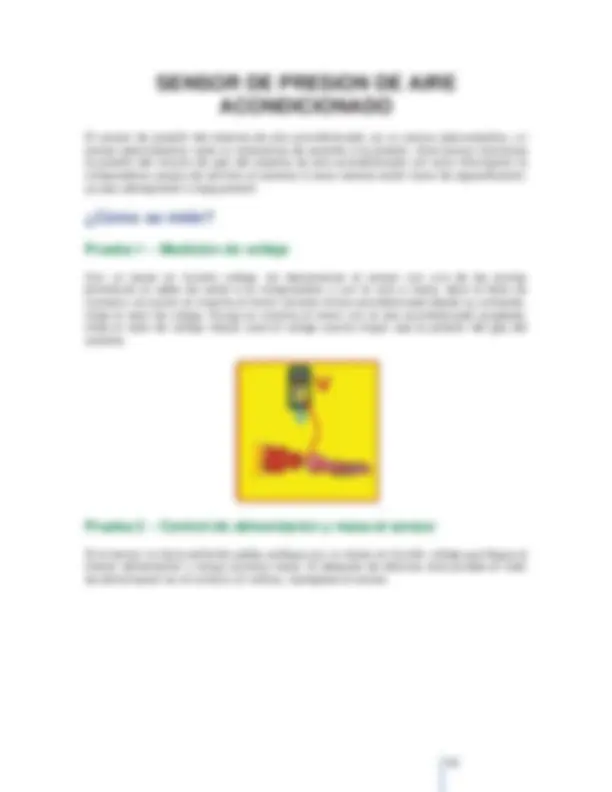
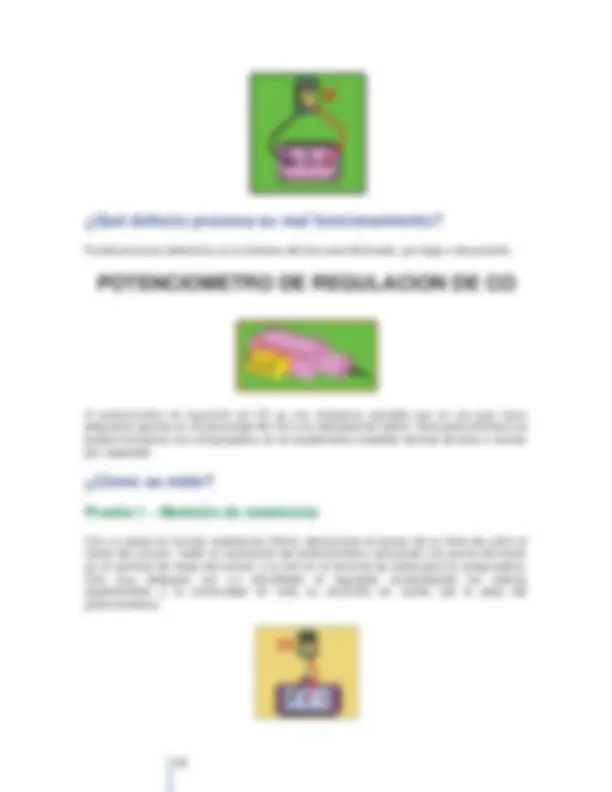
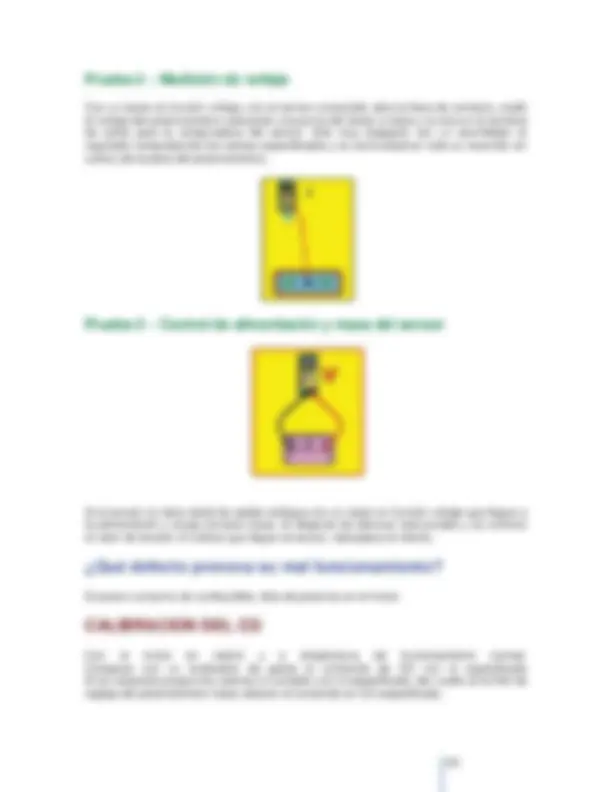
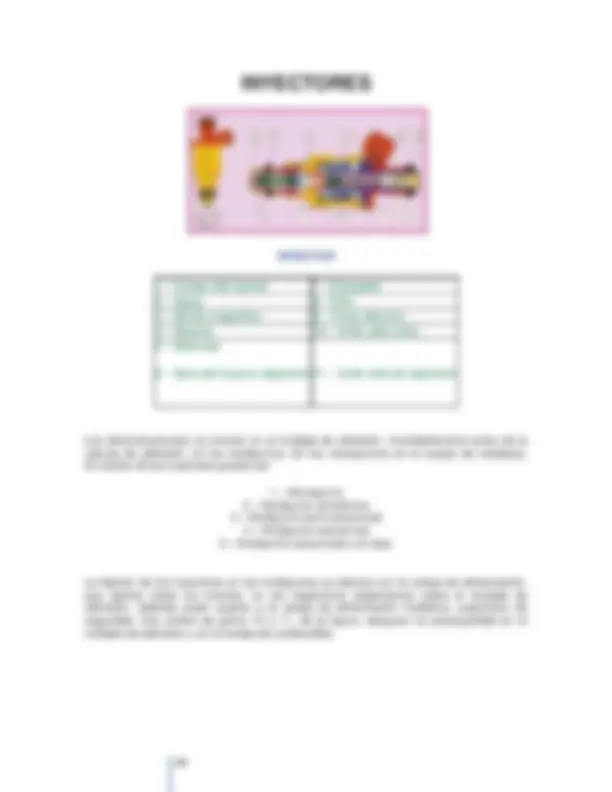
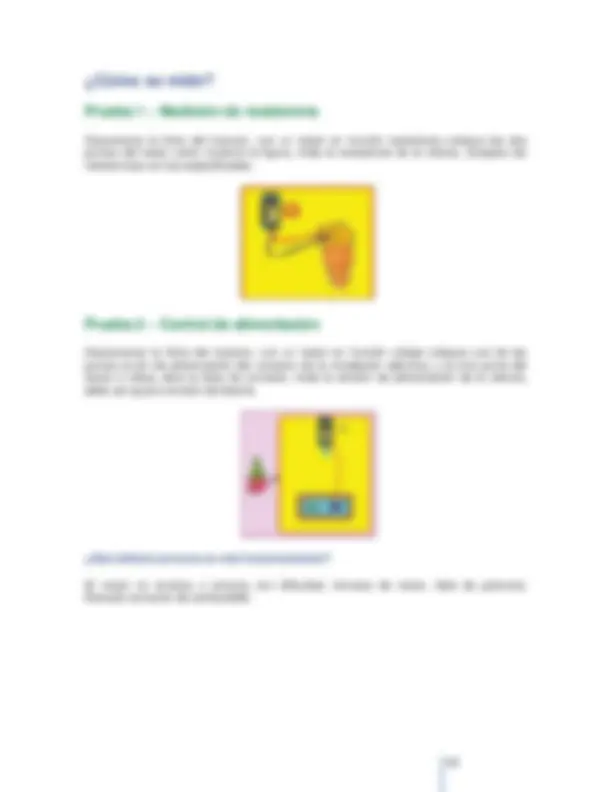
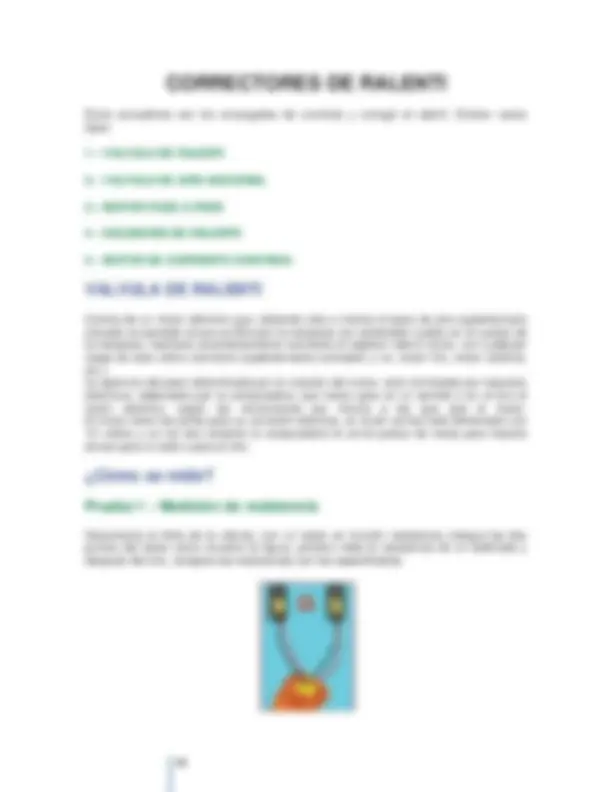
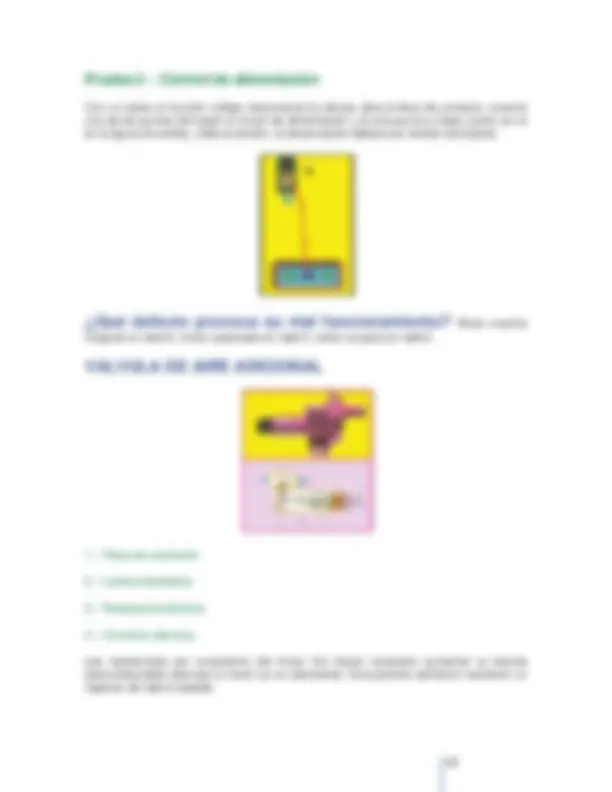
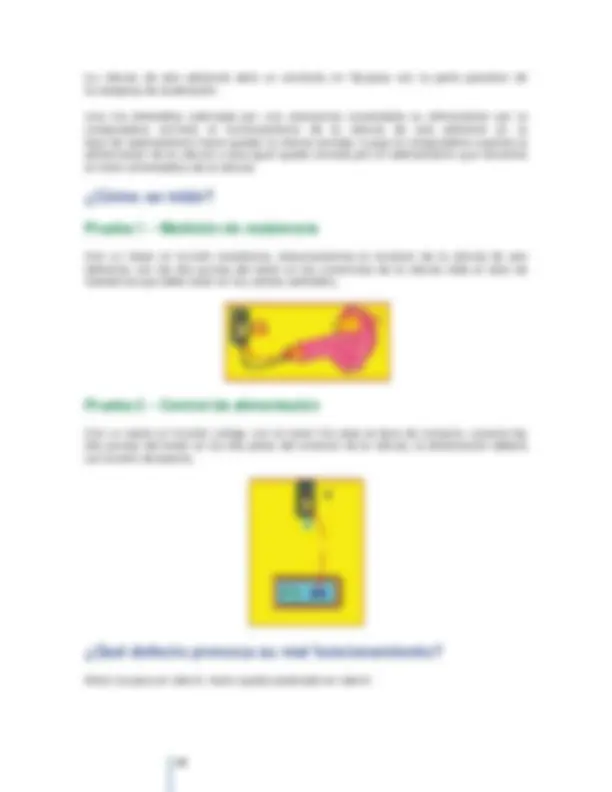
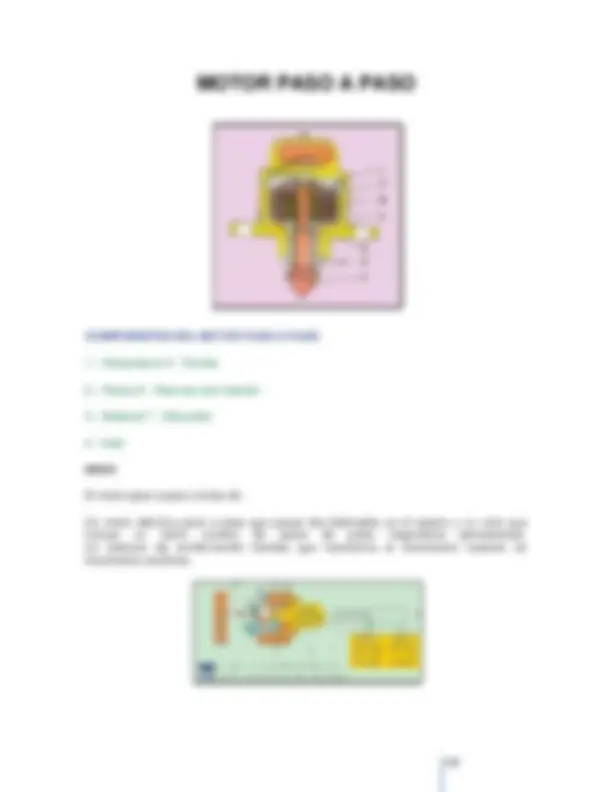
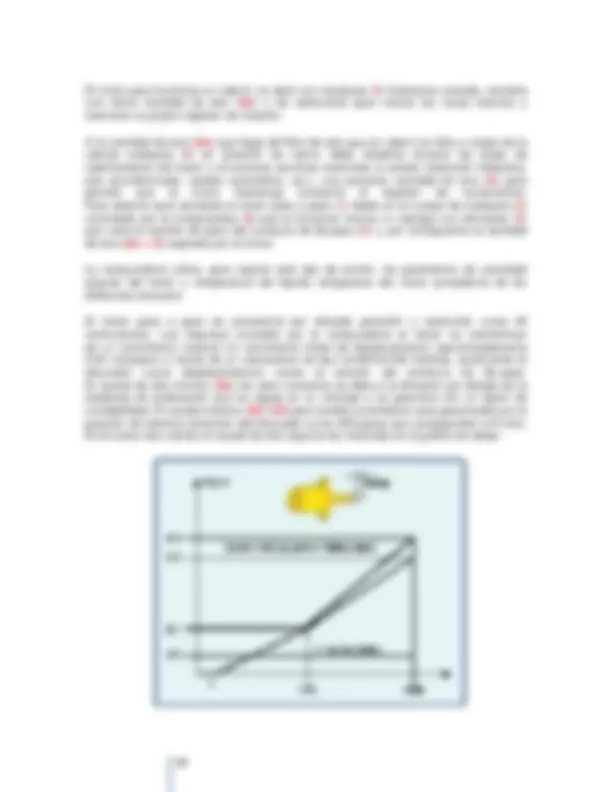
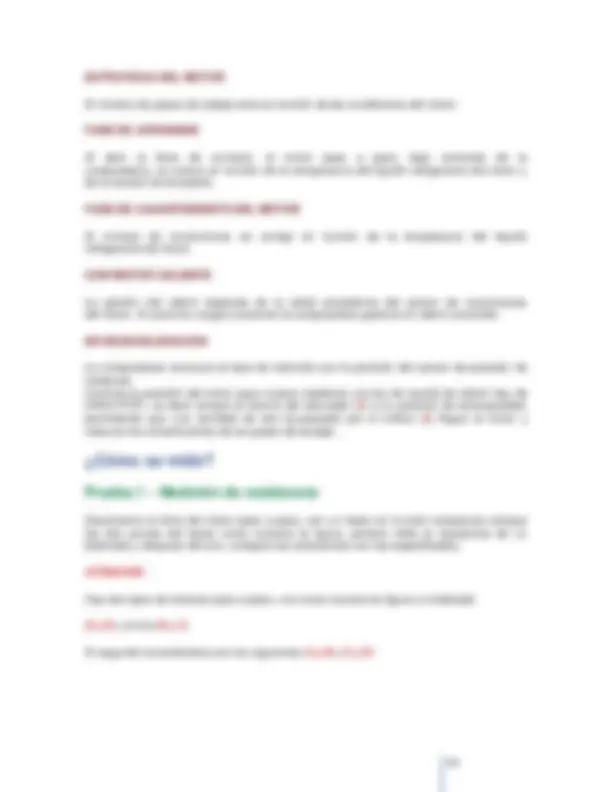
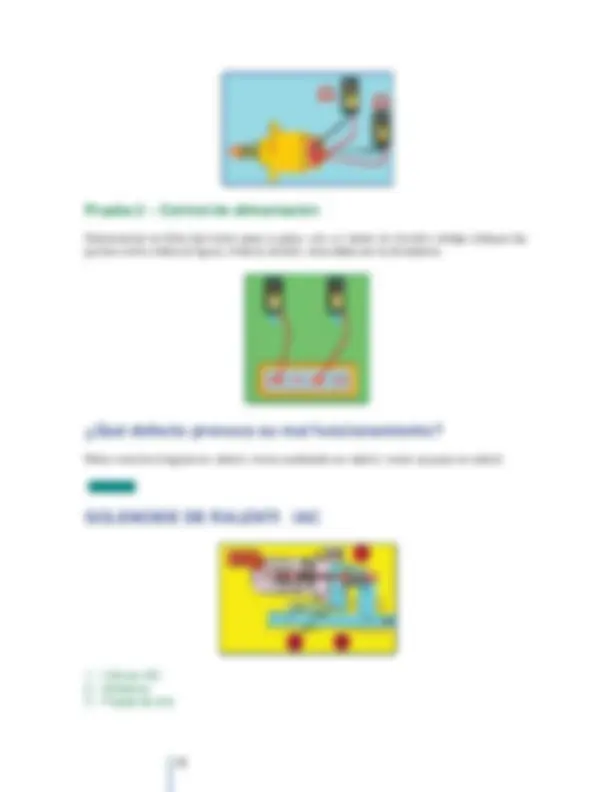
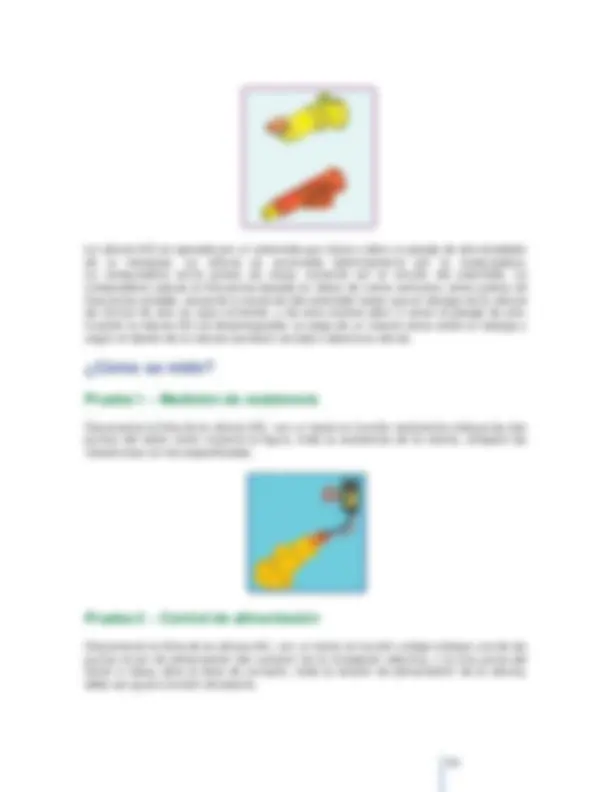
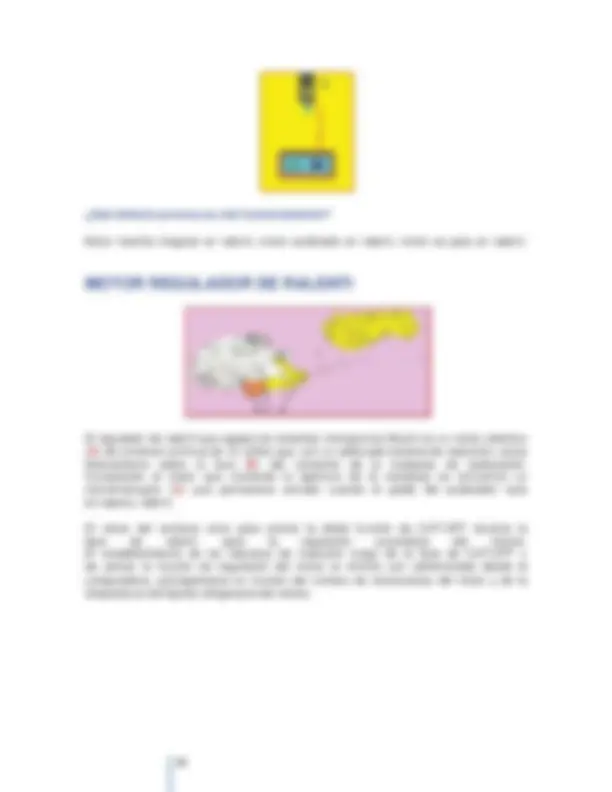
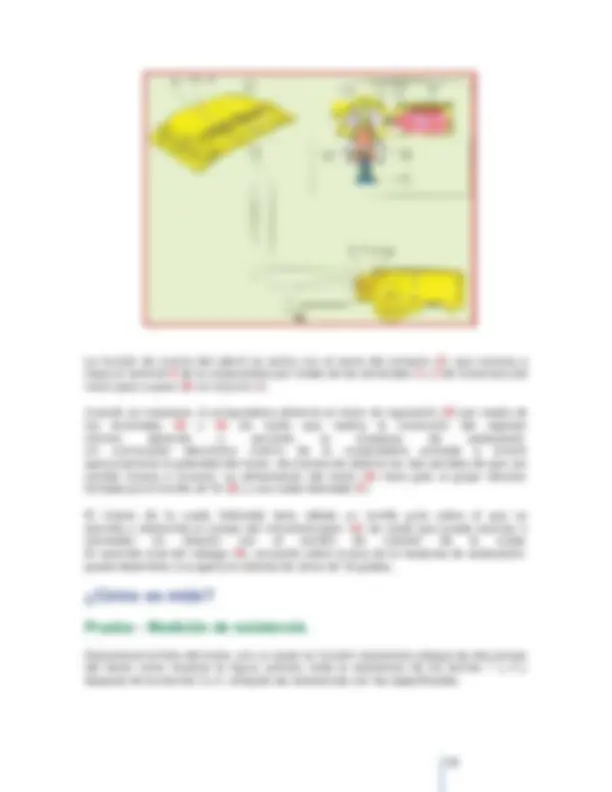
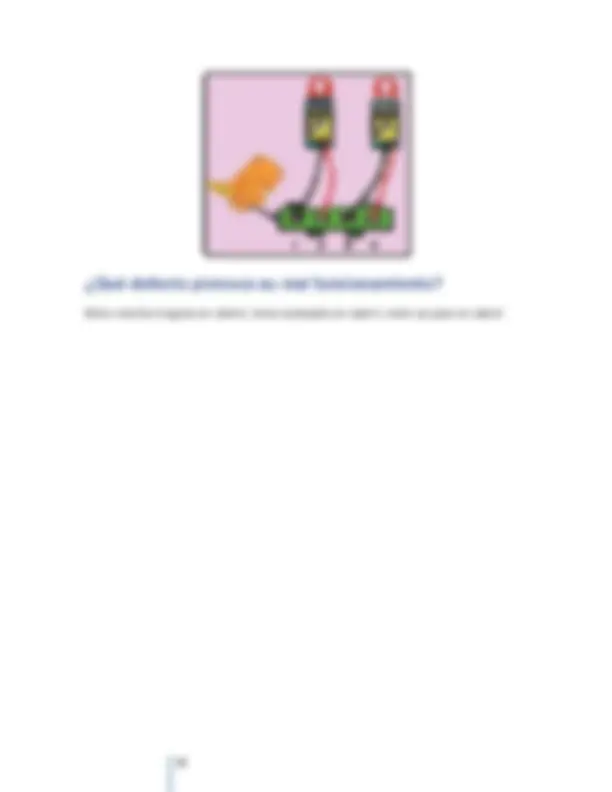
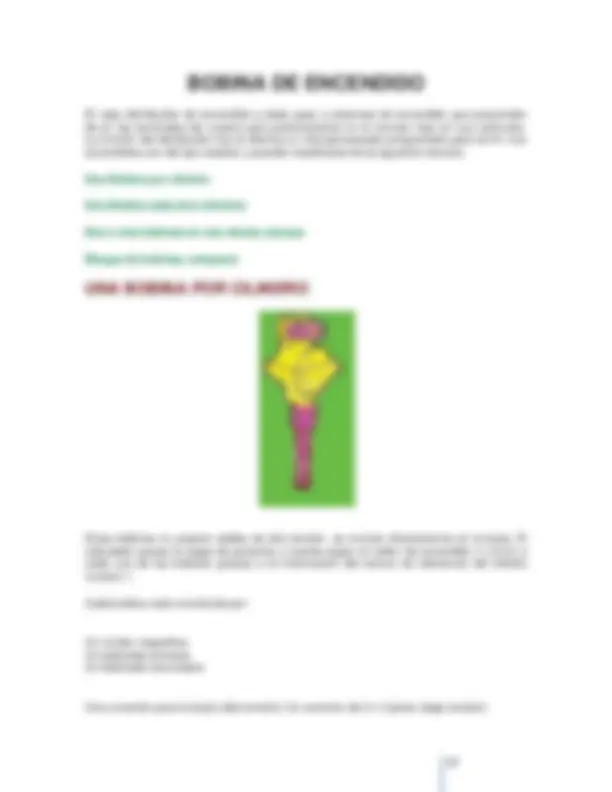
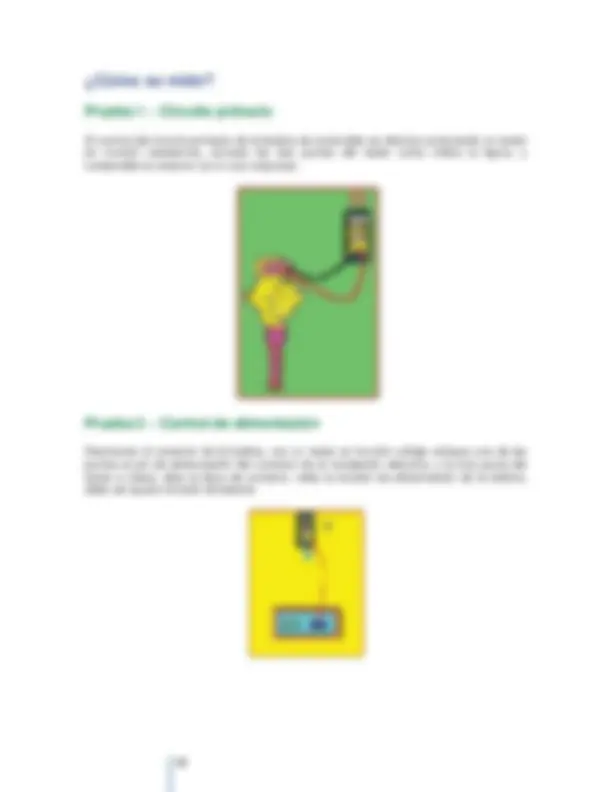
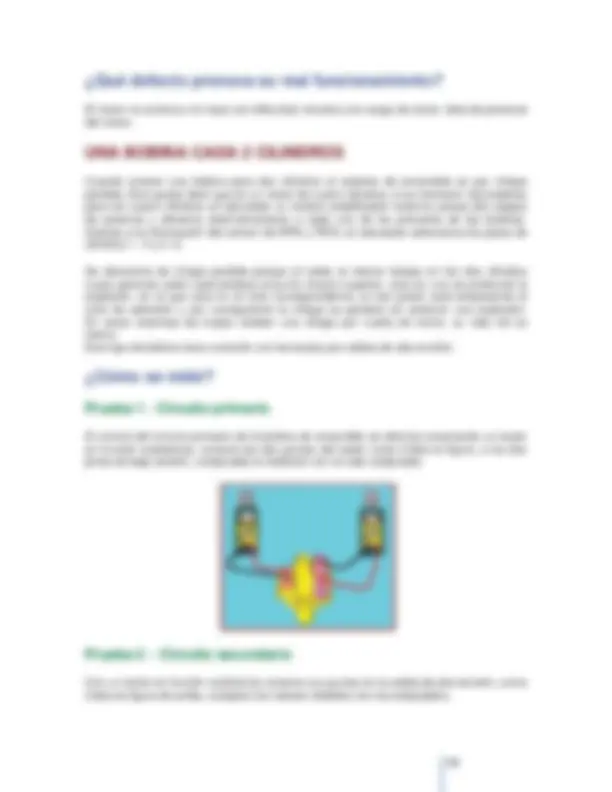
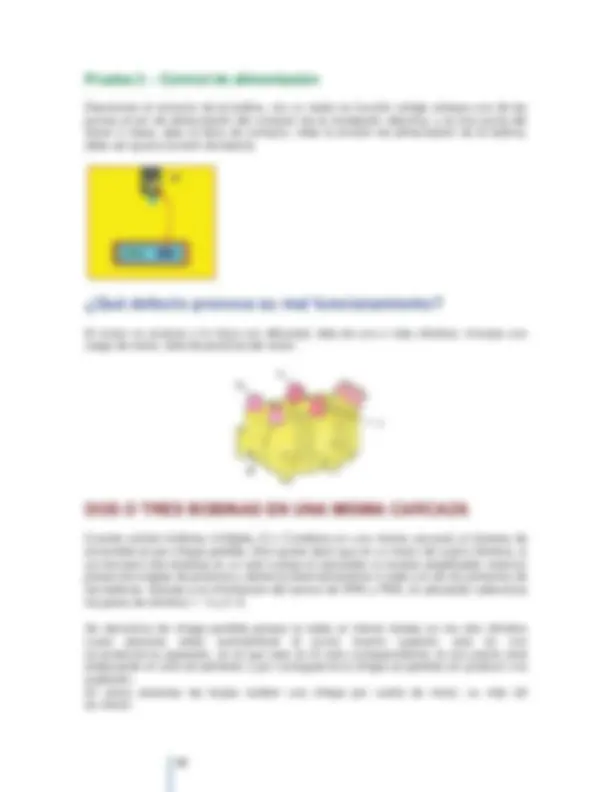
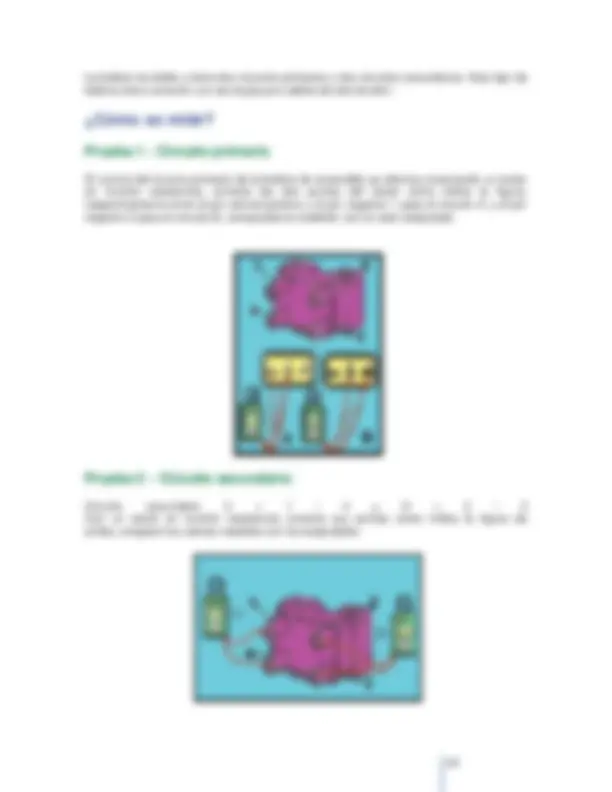
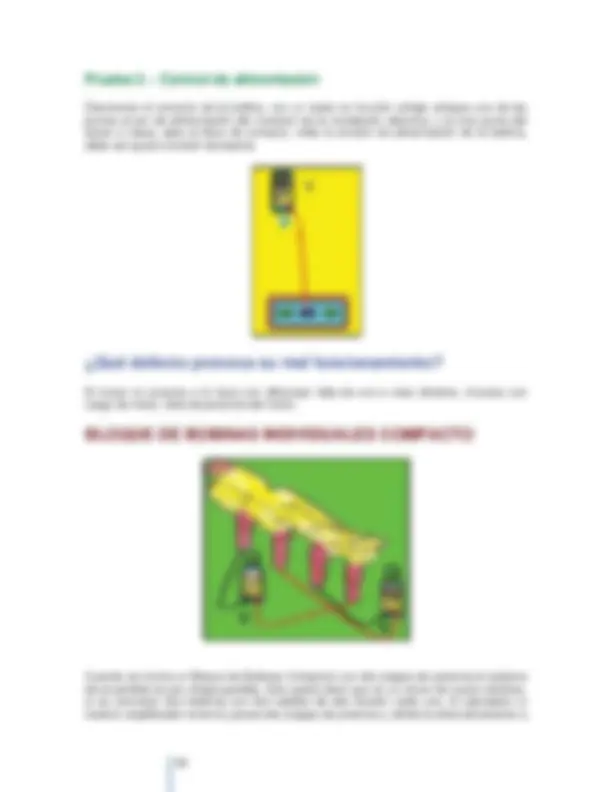
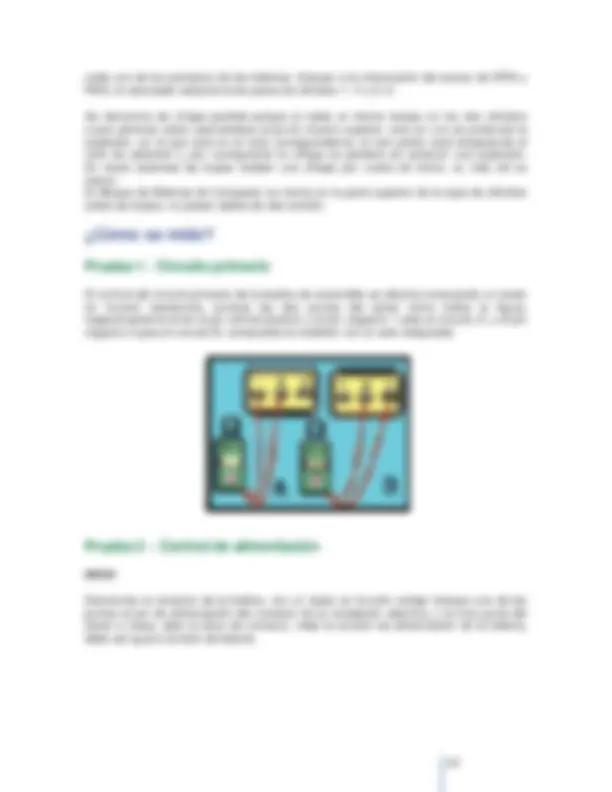
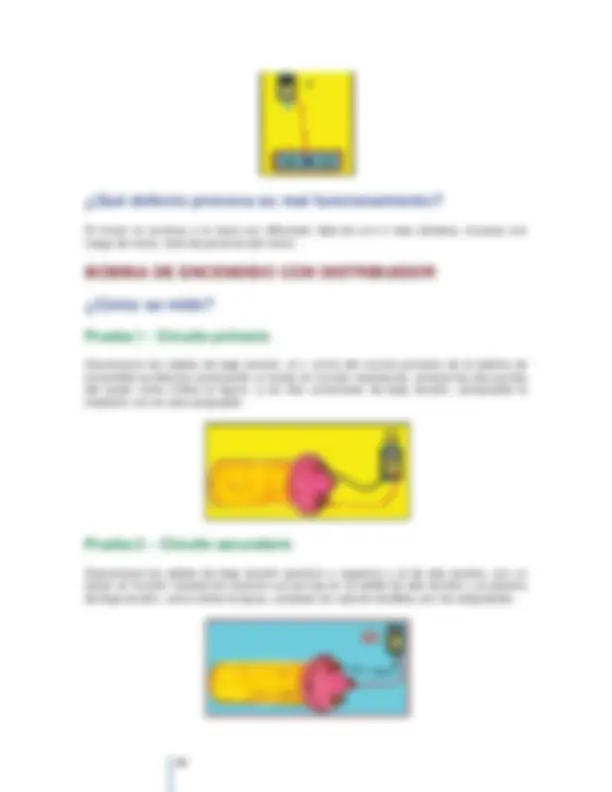
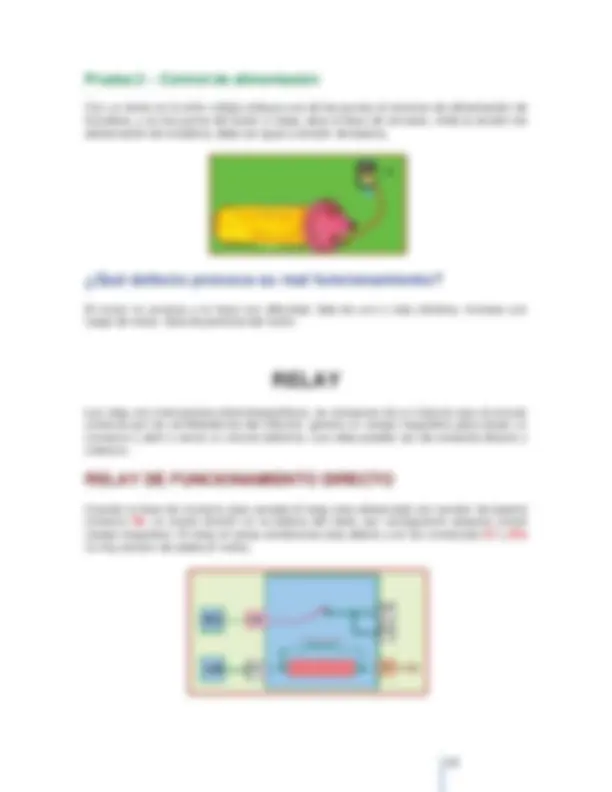
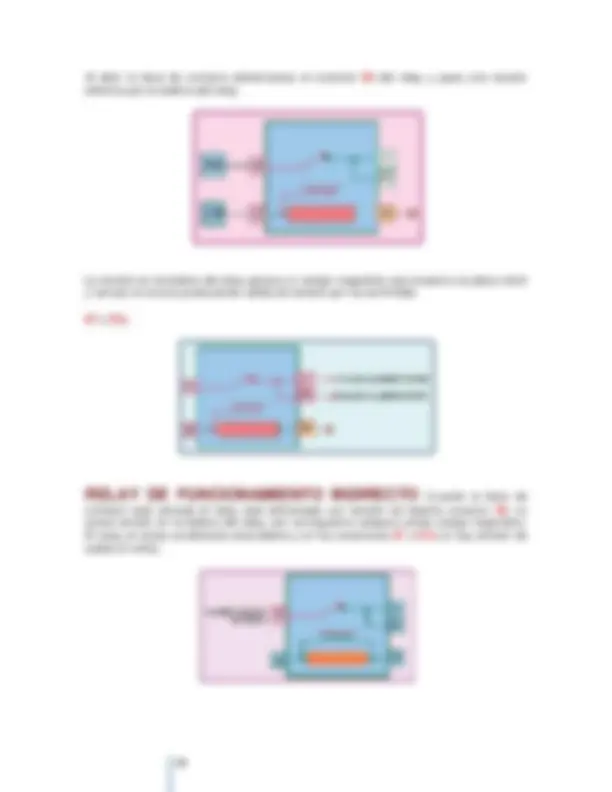
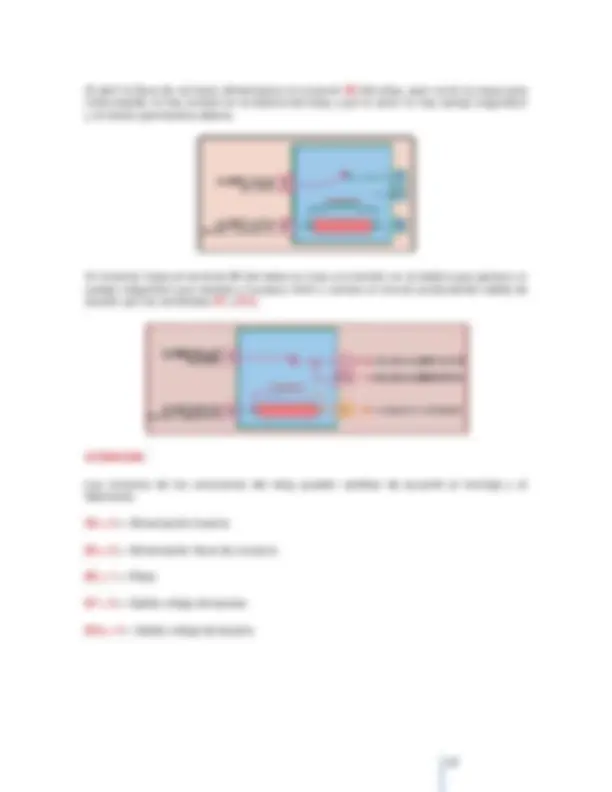
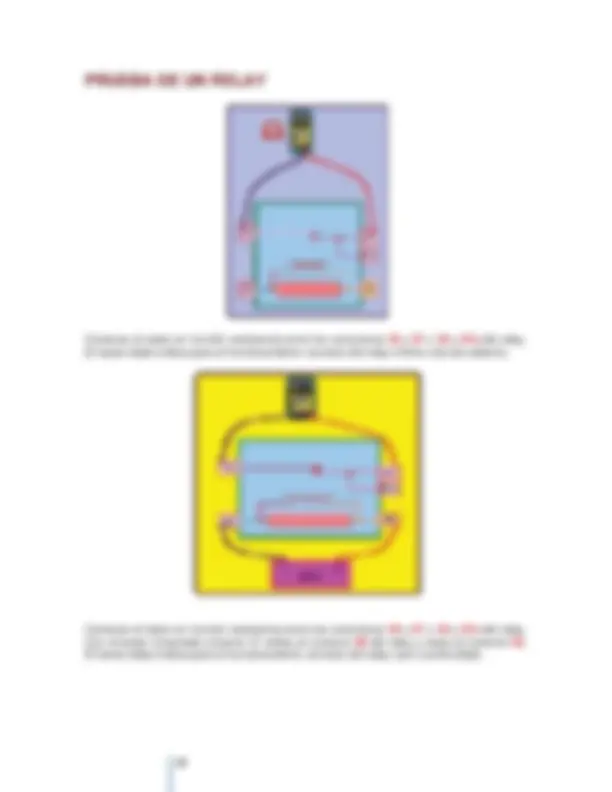
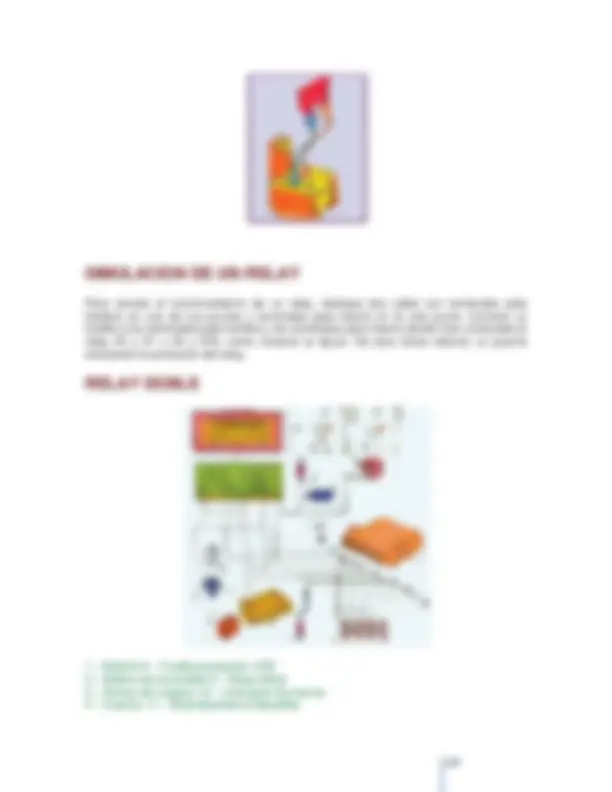
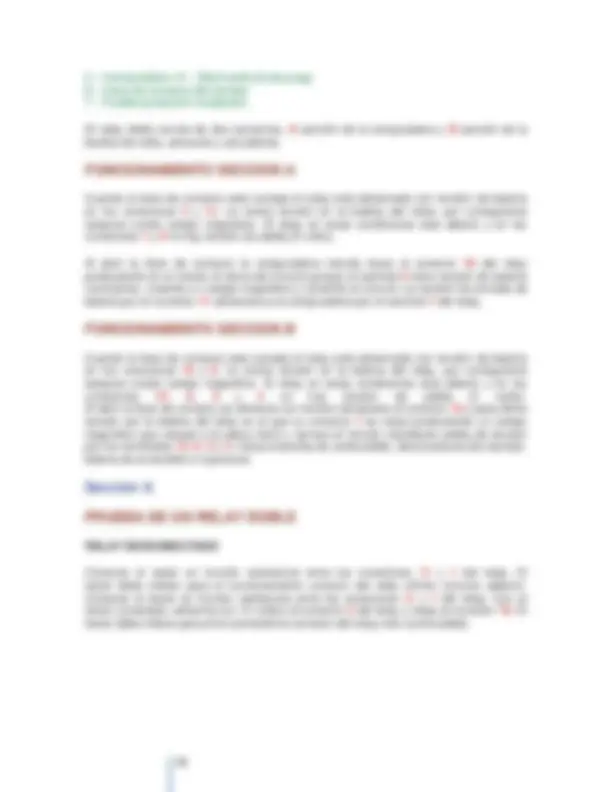
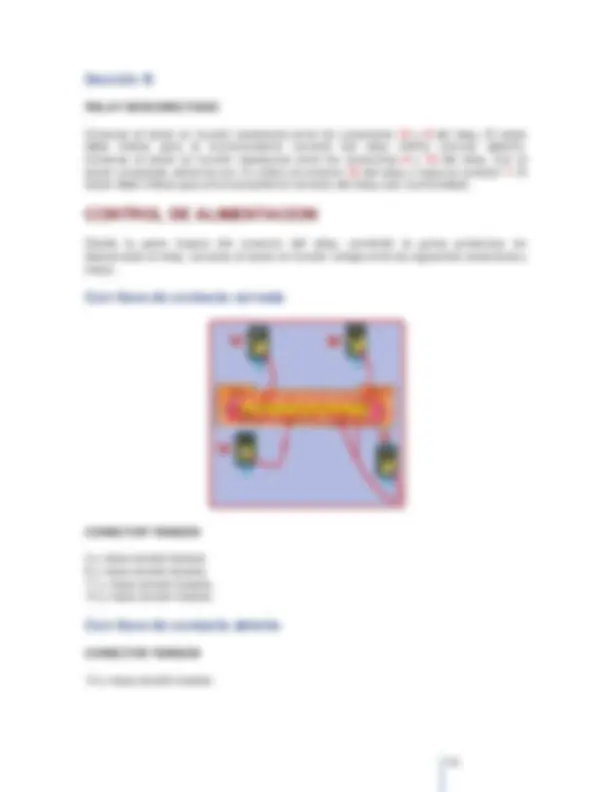
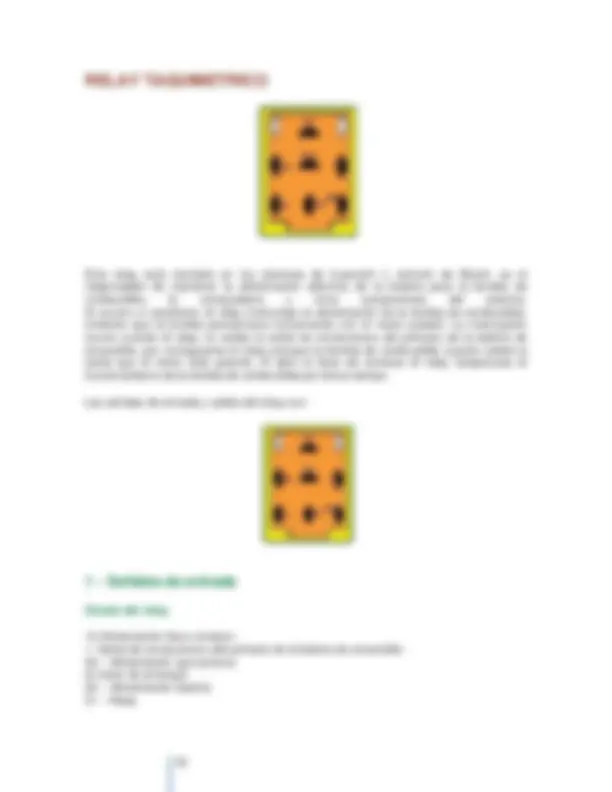
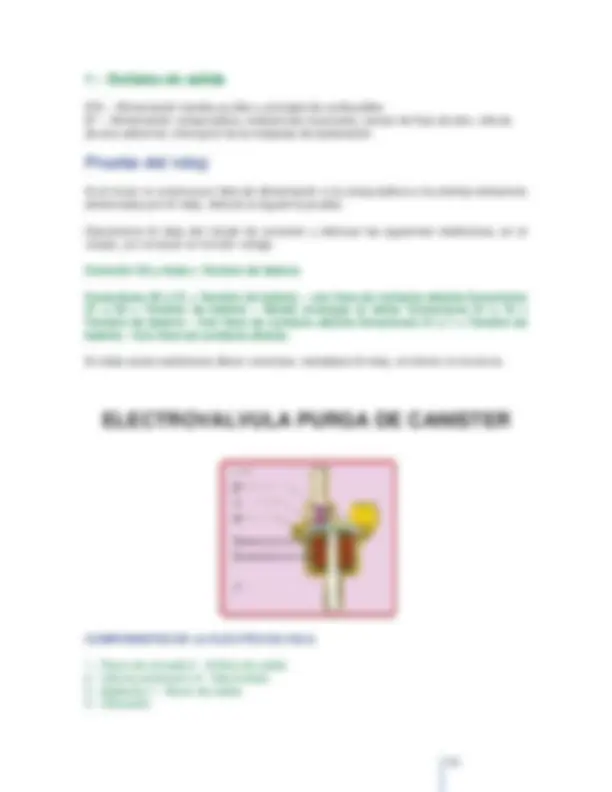
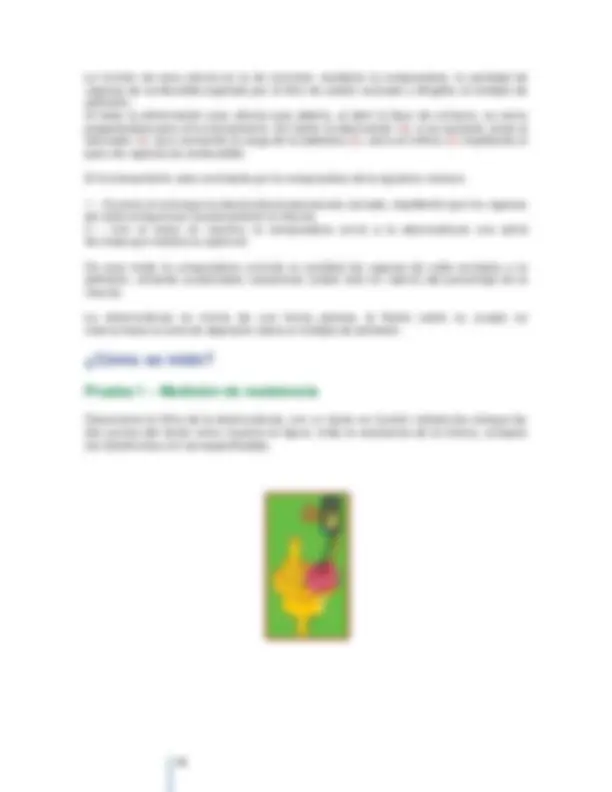
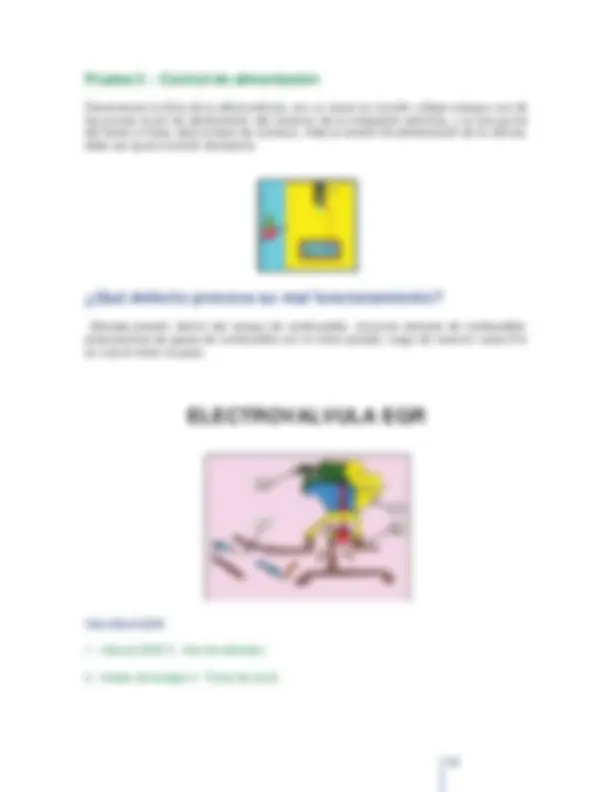
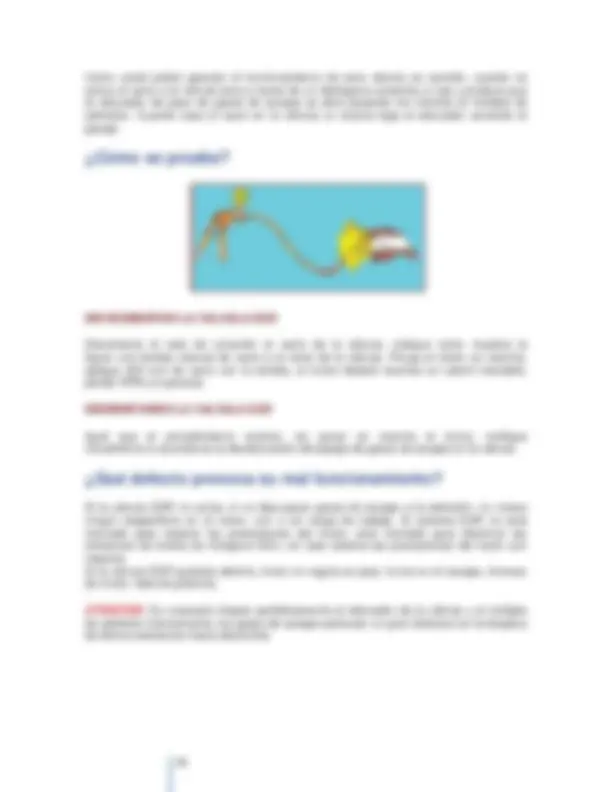
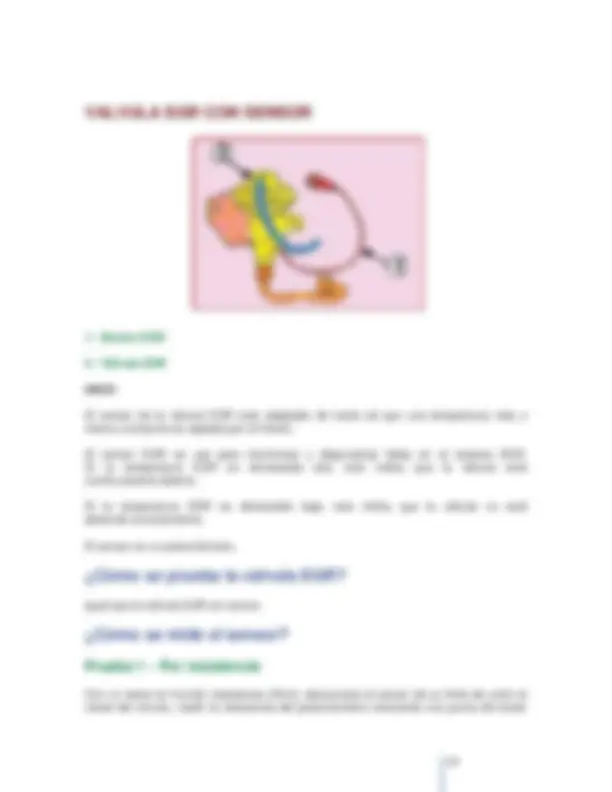
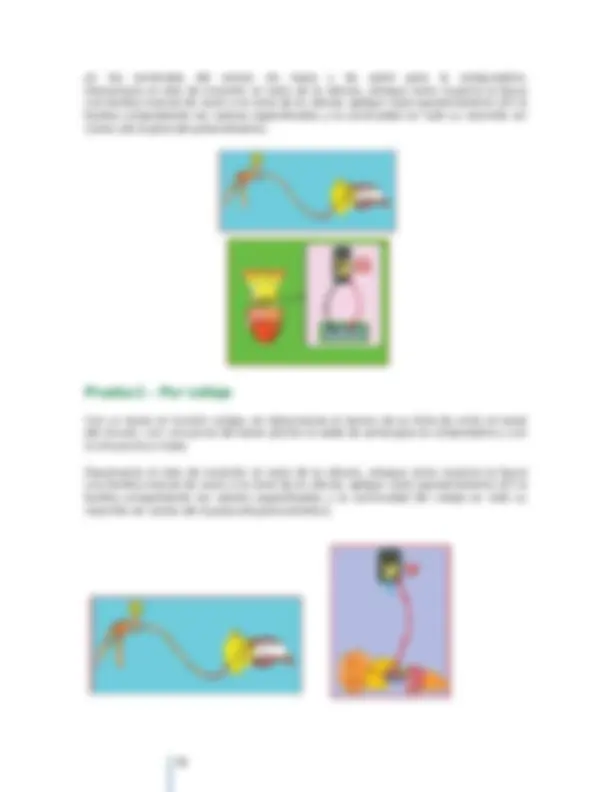
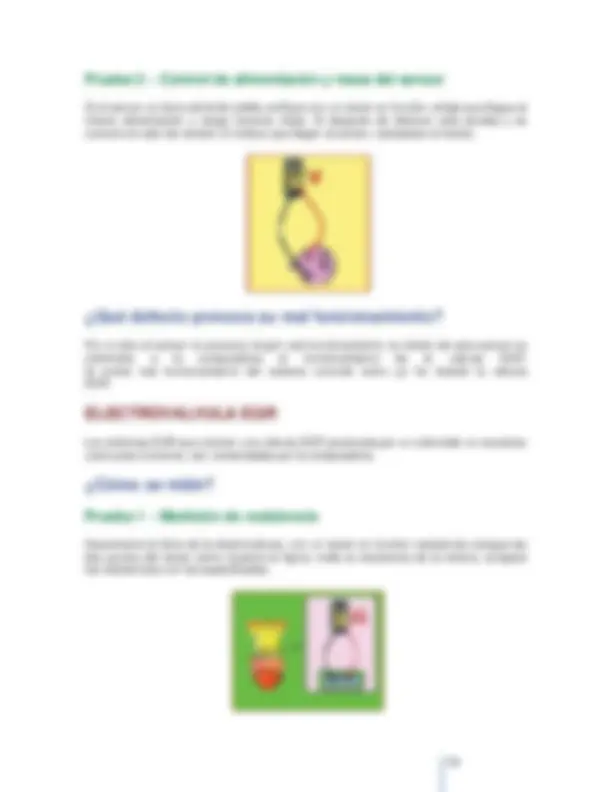
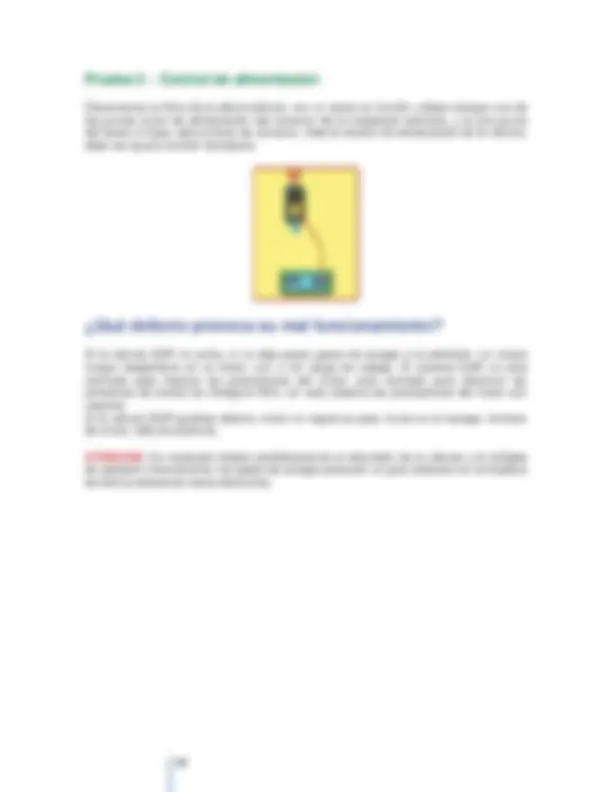
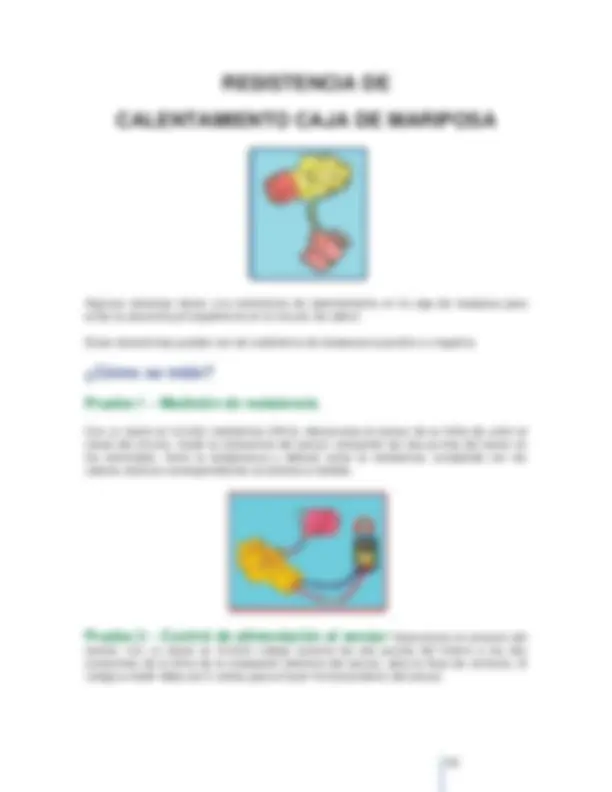
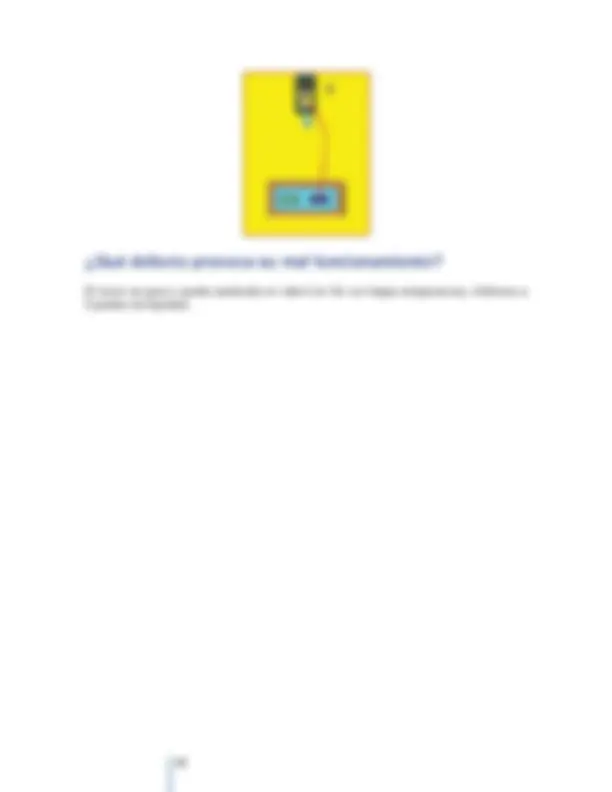
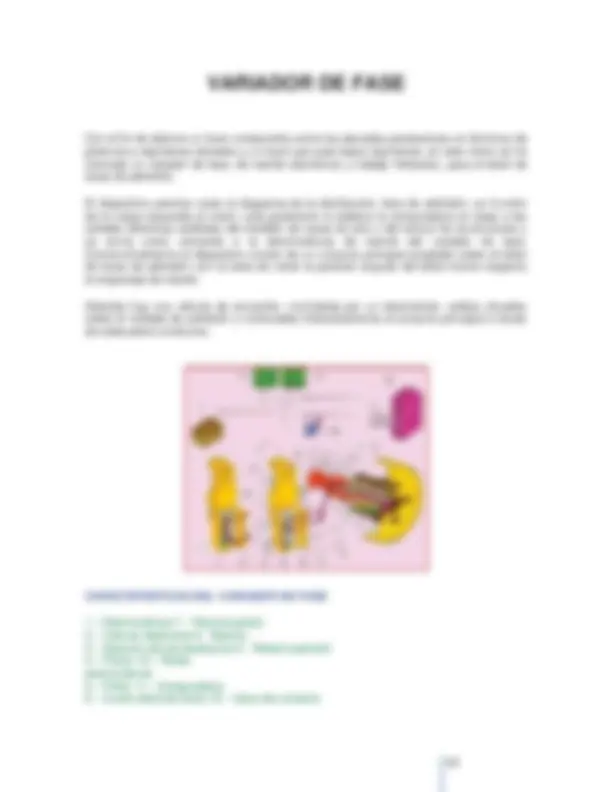
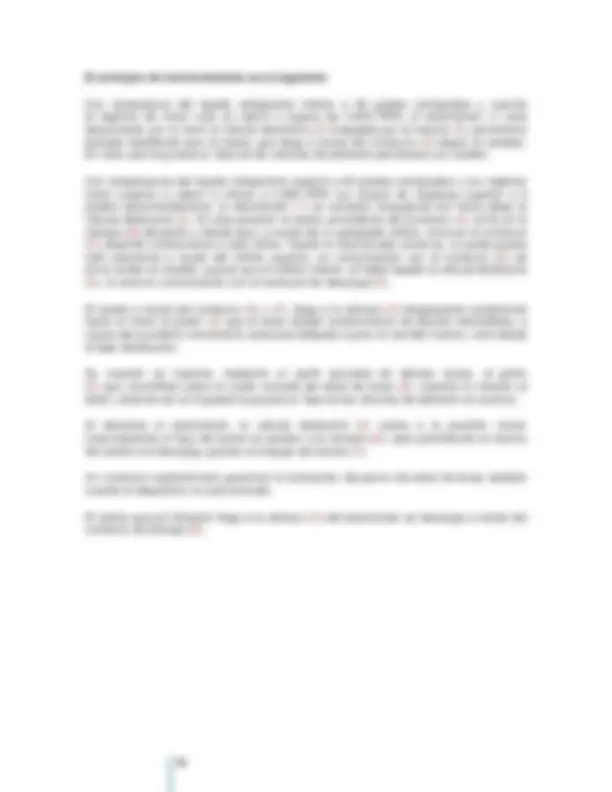
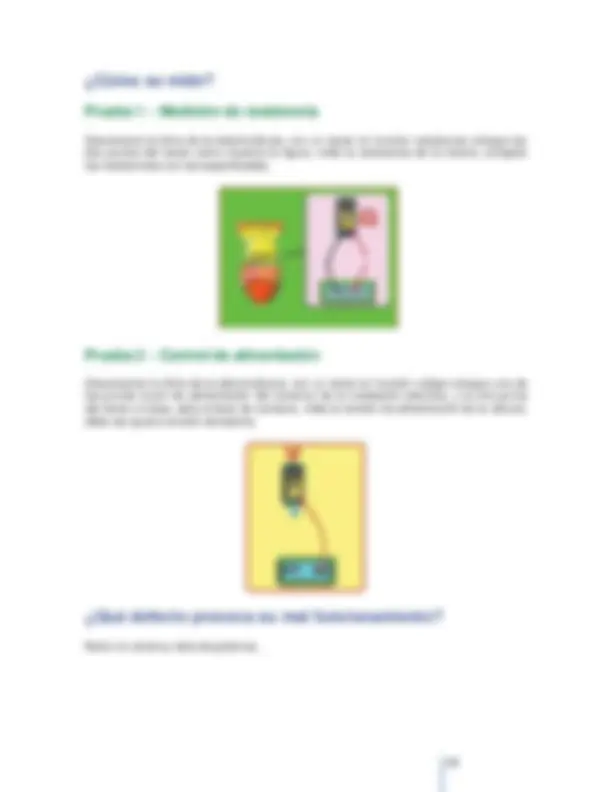
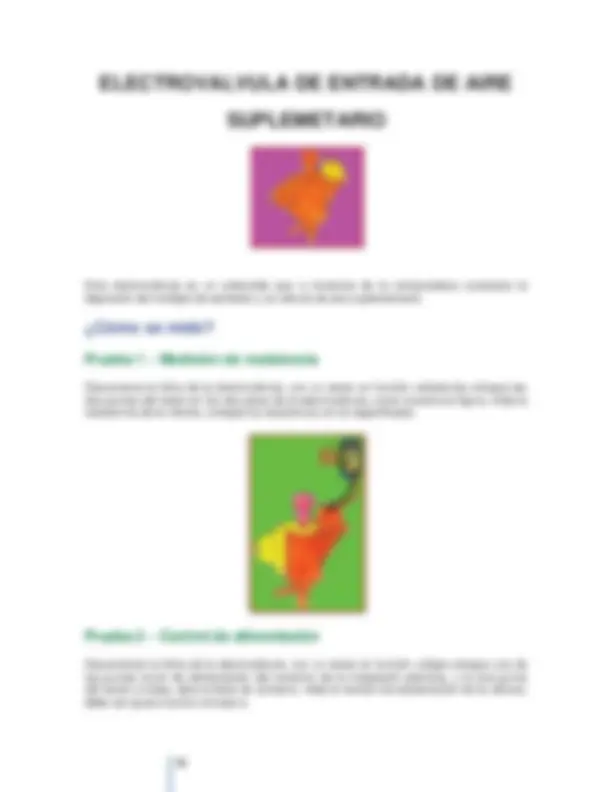
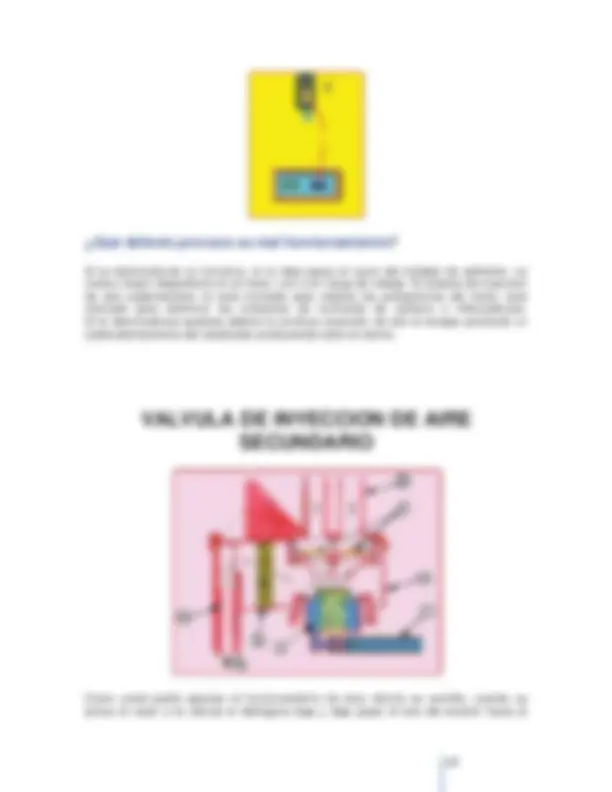
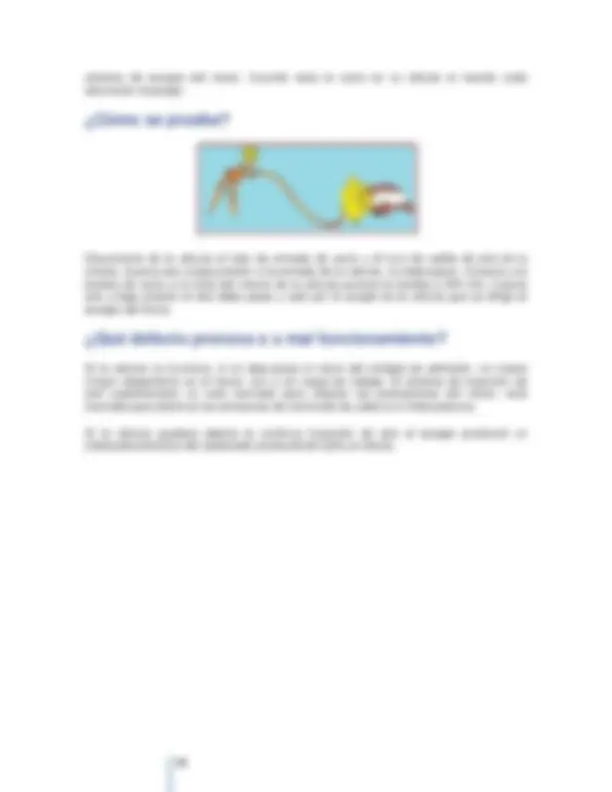
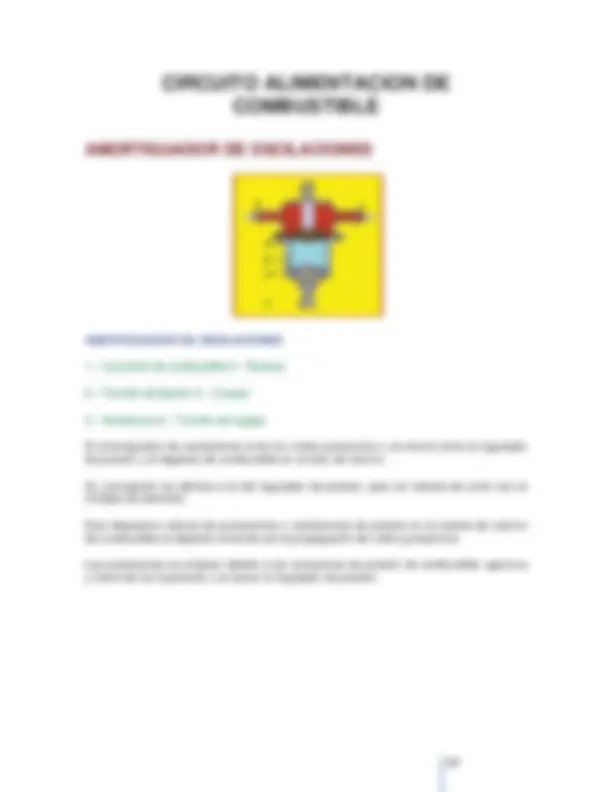
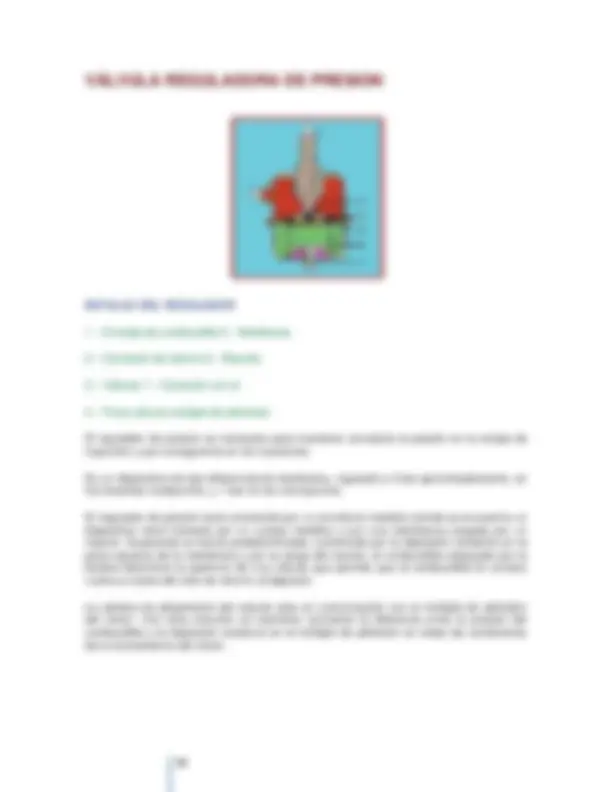
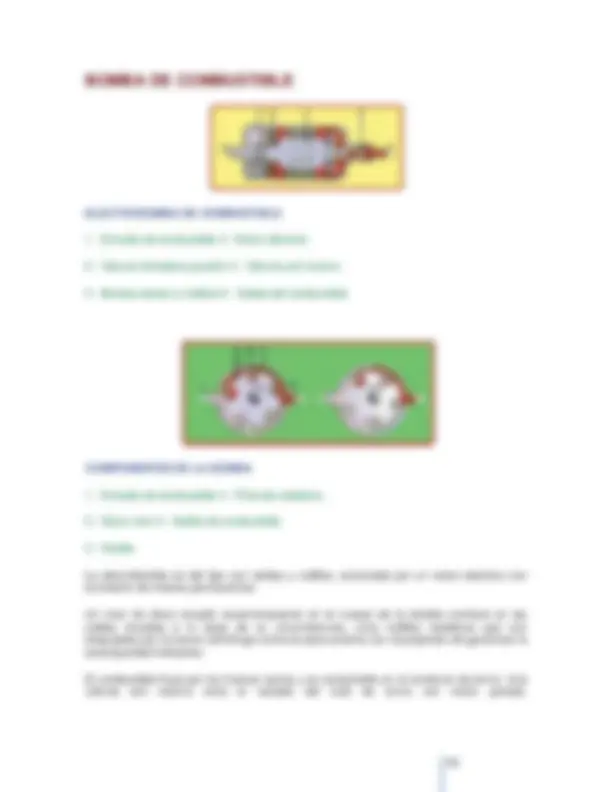
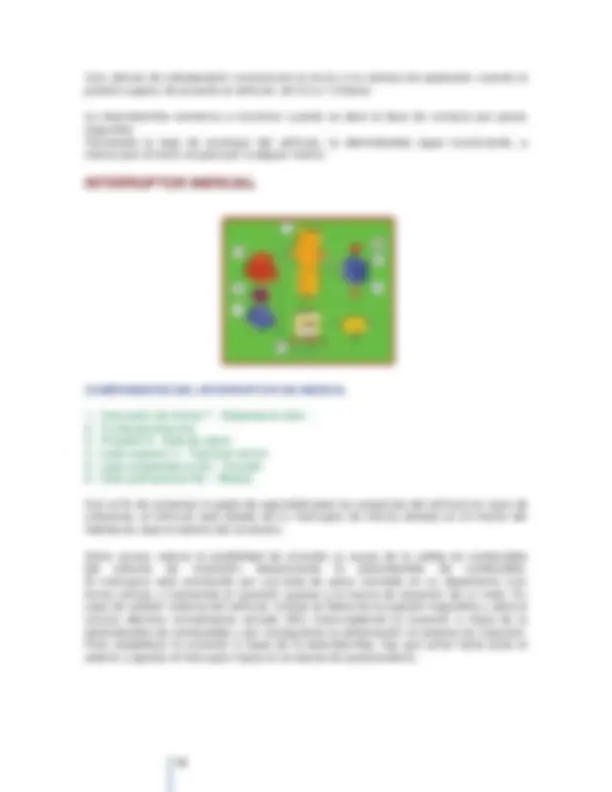
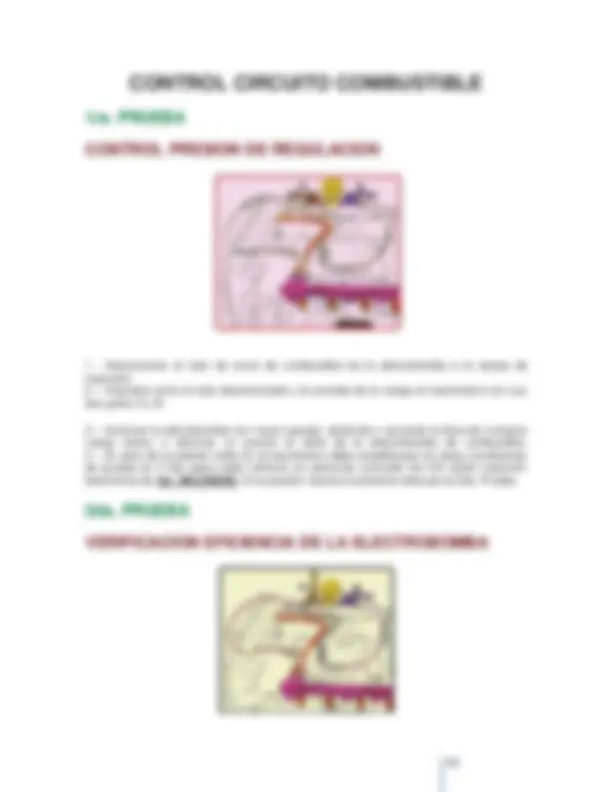
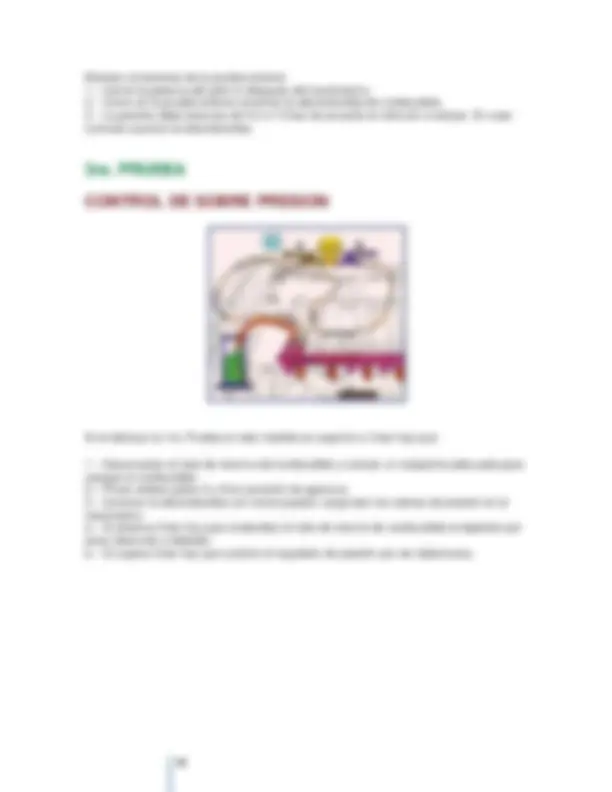
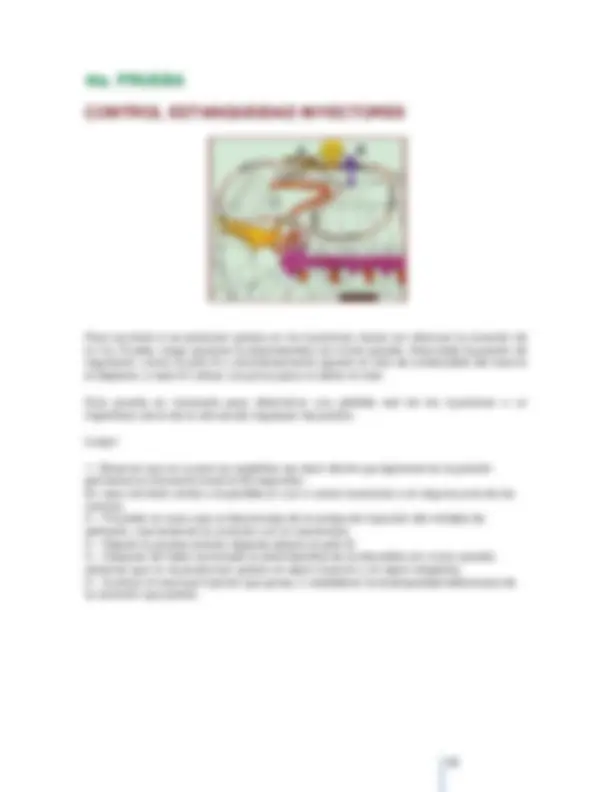
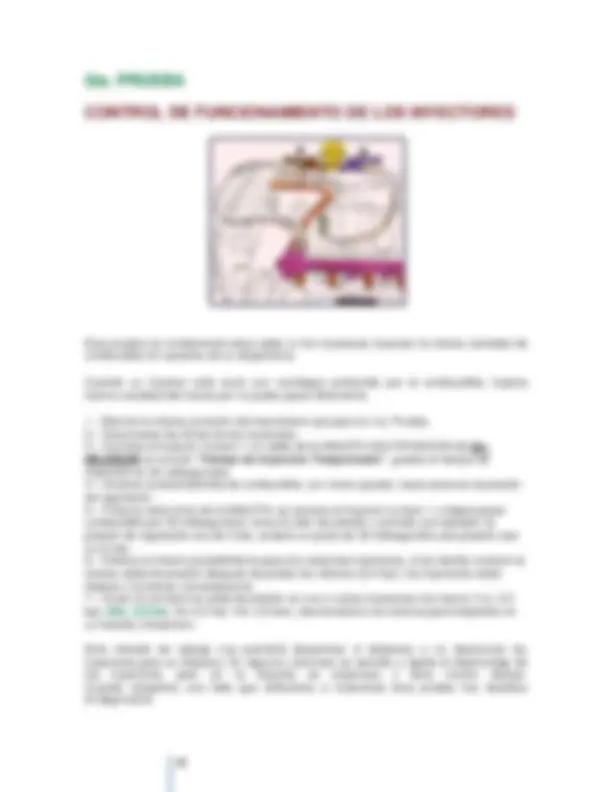
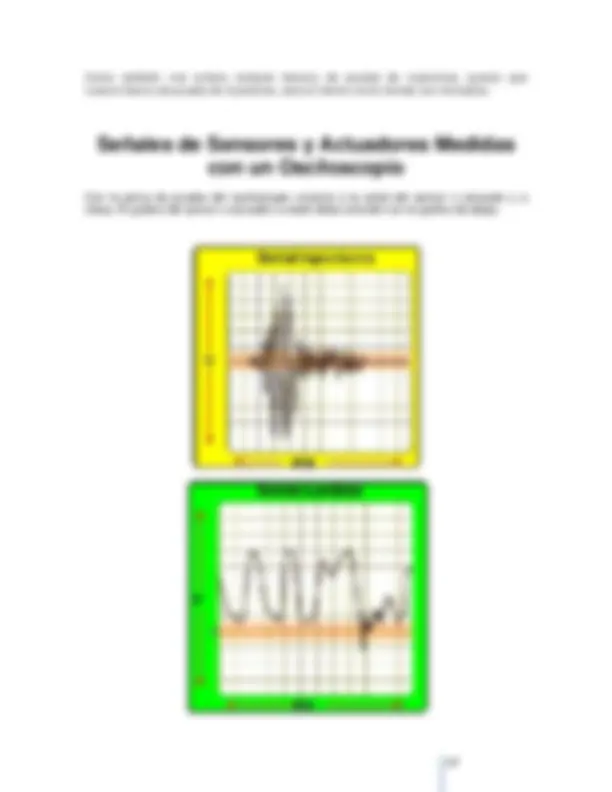
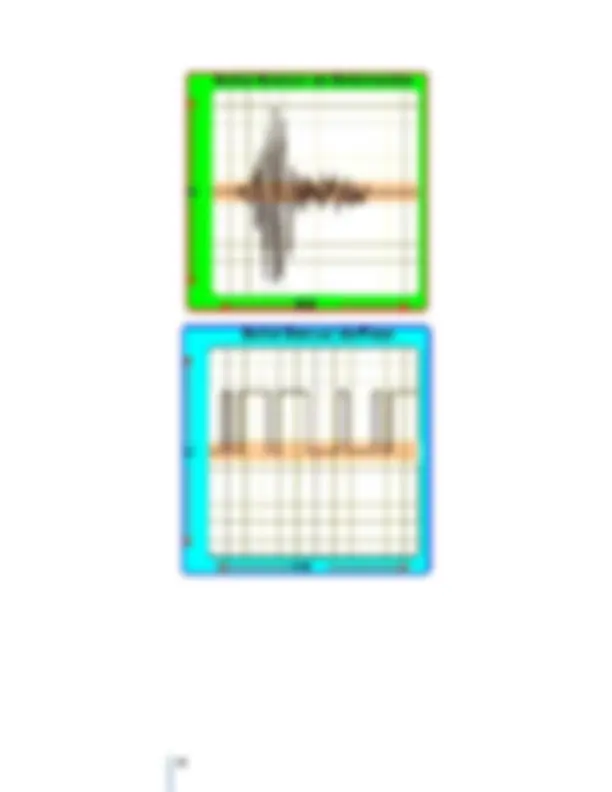
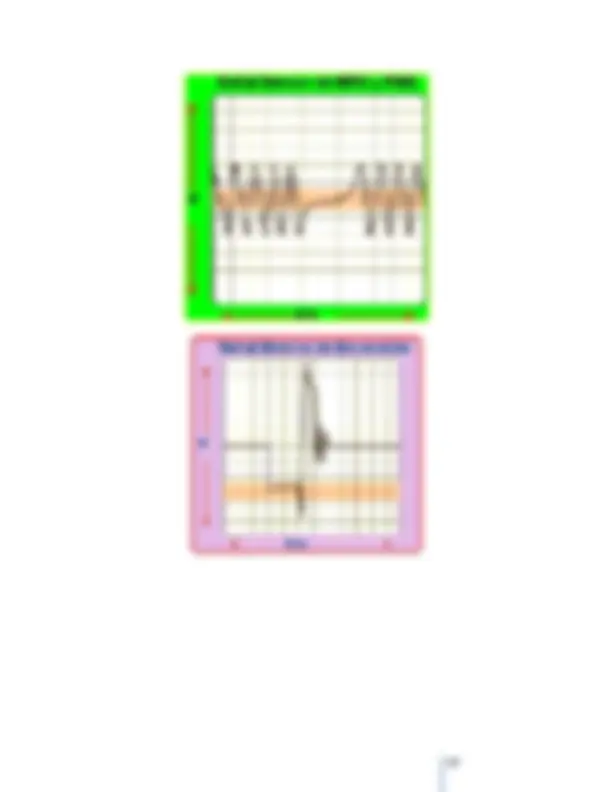
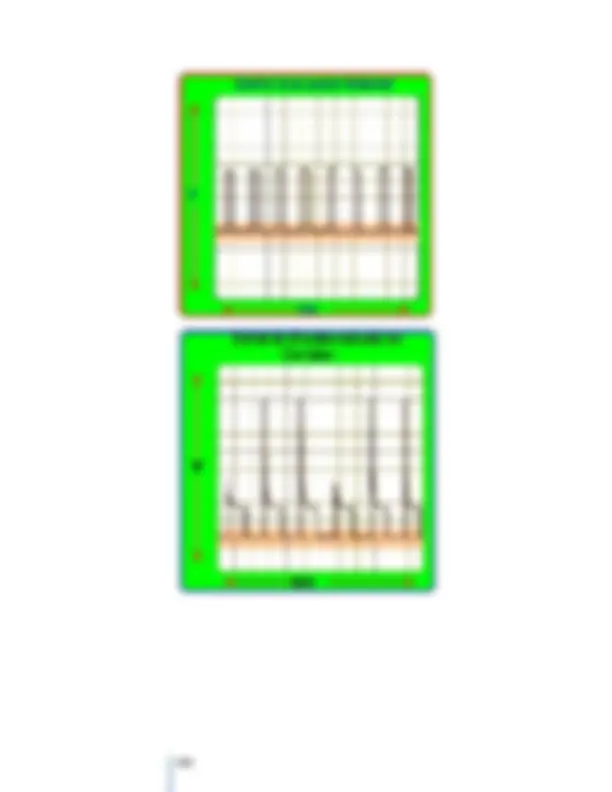
Prepara tus exámenes y mejora tus resultados gracias a la gran cantidad de recursos disponibles en Docsity
Gana puntos ayudando a otros estudiantes o consíguelos activando un Plan Premium
Prepara tus exámenes
Prepara tus exámenes y mejora tus resultados gracias a la gran cantidad de recursos disponibles en Docsity
Prepara tus exámenes con los documentos que comparten otros estudiantes como tú en Docsity
Los mejores documentos en venta realizados por estudiantes que han terminado sus estudios
Estudia con lecciones y exámenes resueltos basados en los programas académicos de las mejores universidades
Responde a preguntas de exámenes reales y pon a prueba tu preparación
Consigue puntos base para descargar
Gana puntos ayudando a otros estudiantes o consíguelos activando un Plan Premium
Comunidad
Pide ayuda a la comunidad y resuelve tus dudas de estudio
Descubre las mejores universidades de tu país según los usuarios de Docsity
Ebooks gratuitos
Descarga nuestras guías gratuitas sobre técnicas de estudio, métodos para controlar la ansiedad y consejos para la tesis preparadas por los tutores de Docsity
pdf con todos los tipos de sensores del automovil
Tipo: Ejercicios
1 / 100
Esta página no es visible en la vista previa
¡No te pierdas las partes importantes!
En él capitulo SENSORES y ACTUADORES, hemos detallado el funcionamiento de los correspondientes al Sistema de Inyección Electrónica Bosch Motronic M2.10.4 que equipa el motor del Fiat Marea 2.0 5 cilindros y 20 válvulas. Hemos tomado por ejemplo este sistema de última generación por contar el mismo de una gran cantidad de estos elementos. Pero hay otros sensores y actuadores que vienen montados en otros sistemas de inyección, algunos son antiguos y sé discontinuo su montaje, pero es necesario conocerlos porque hay un parque automotor numeroso montado con estos productos. Debemos conocer a la perfección como trabajan, para que sirven, como se miden y que defecto provoca su mal funcionamiento; si queremos tener una buena gestión de servicio en nuestro taller. No es necesario que el tallerista sea un experto conocedor de la electrónica para reparar un sistema electrónico montado en los automóviles. Pero si es necesario el profundo conocimiento sobre sensores y actuadores. Las lógicas de funcionamiento de los sistemas comandados por una computadora son similares, lo que cambian son algunos sensores y actuadores. No es necesario el estudio de los cientos de sistemas de gestión electrónica del motor, pero si es de suma importancia el estudio de estos sensores y actuadores que después aplicara, en particular, a los cientos de sistemas electrónicos de inyección a nafta.
Con un tester en función resistencia (Ohm), desconecte el sensor de su ficha de unión al ramal del circuito, medir la resistencia del sensor colocando las dos puntas del tester en los terminales. Varíe la temperatura y deberá variar la resistencia, compárela con los valores teóricos correspondientes al sistema a medir.
Sin desconectar el sensor pinche el conductor de señal del sensor, con la punta de un tester en función voltaje, con la otra punta del tester conecte a masa del motor, abra la llave de contacto, mida el valor de voltaje variando la temperatura.
Puesto que el circuito de entrada de la computadora esta pensado como divisor de tensión se reparte entre una resistencia presente en la computadora y la resistencia del sensor. Por consiguiente la computadora puede valorar las variaciones de resistencia del sensor a través de los cambios de la tensión y obtener así la información de la
temperatura del liquido refrigerante del motor. Por consiguiente para medir una termistancia sin alimentación de la computadora (sensor fuera del vehículo) debemos colocar al sensor una resistencia para que actúe como divisor de tensión, de acuerdo el sensor sea de Coeficiente de Temperatura Negativo o de Coeficiente de Temperatura Positivo esa resistencia variara:
Sensor de Coeficiente Negativo = 1200 ohm
Sensor de Coeficiente Positivo = 300 ohm
Para efectuar la medición conecte la resistencia entre uno de los conectores del sensor y el positivo de una fuente de 5 voltios, y el otro conector a masa de la fuente, como lo indica la figura, con un tester en función voltaje conecte las dos pinzas del mismo a los extremos de la resistencia y obtendrá el voltaje de acuerdo a la temperatura del sensor que podrá variarla mediante una fuente de calor aplicada al sensor.
Desconecte el conector del sensor, con un tester en función voltaje conecte las dos puntas del mismo a los dos conectores de la ficha de la instalación eléctrica del sensor,
del sensor a través de los cambios de la tensión y obtener así la información de la temperatura.
Con un tester en función resistencia (Ohm), desconecte el sensor de su ficha de unión al ramal del circuito, medir la resistencia del sensor colocando las dos puntas del tester en los terminales. Varíe la temperatura y deberá variar la resistencia, compárela con los valores teóricos correspondientes al sistema a medir.
Sin desconectar el sensor pinche el conductor de señal del sensor, con la punta de un tester en función voltaje, con la otra punta del tester conecte a masa del motor, abra la llave de contacto, mida el valor de voltaje variando la temperatura.
Puesto que el circuito de entrada de la computadora está pensado como divisor de tensión se reparte entre una resistencia presente en la computadora y la resistencia del sensor. Por consiguiente la computadora puede valorar las variaciones de resistencia del
sensor a través de los cambios de la tensión y obtener así la información de la temperatura del aire que entra al motor. Por consiguiente para medir una termistancia sin alimentación de la computadora (sensor fuera del vehículo) debemos colocar al sensor una resistencia para que actúe como divisor de tensión, de acuerdo el sensor sea de Coeficiente de Temperatura Negativo o de Coeficiente de Temperatura Positivo esa resistencia variara:
Sensor de Coeficiente Negativo = 1200 ohm
Sensor de Coeficiente Positivo = 300 ohm
Para efectuar la medición conecte la resistencia entre uno de los conectores del sensor y el positivo de una fuente de 5 voltios, y el otro conector a masa de la fuente, como lo indica la figura, con un tester en función voltaje conecte las dos pinzas del mismo a los extremos de la resistencia y obtendrá el voltaje de acuerdo a la temperatura del sensor que podrá variarla mediante una fuente de calor aplicada al sensor.
sensor, con un tester en función voltaje conecte las dos puntas del mismo a los dos conectores de la ficha de la instalación eléctrica del sensor, abra la llave de contacto, él voltaje a medir debe ser 5 voltios para el buen funcionamiento del sensor.
Con un tester en función resistencia (Ohm), desconecte el sensor de su ficha de unión al ramal del circuito, medir la resistencia del potenciómetro colocando una punta del tester en el terminal de masa del sensor y la otra en el terminal de señal para la computadora. Accione la palanca de aceleración comprobando los valores especificados y la continuidad en todo su recorrido sin cortes (de la pista del potenciómetro).
Con un tester en función voltaje, con el sensor conectado, abra la llave de contacto, medir el voltaje del potenciómetro colocando una punta del tester a masa y la otra en el terminal de señal para la computadora del sensor. Accione la palanca de aceleración comprobando los valores especificados y la continuidad en todo su recorrido sin cortes (de la pista del potenciómetro).
Si el sensor no tiene señal de salida verifique con un tester en función voltaje que llegue al mismo alimentación y tenga correcta masa. Si después de efectuar esta prueba y es correcto el valor de tensión (5 voltios) que llegan al sensor, reemplace el mismo.
Excesivo consumo de combustible, marcha irregular, tironeos, arranque rudo, motor no regula, detonación.
La señal del potenciómetro de doble pista tiene una fundamental importancia para determinar los tiempos de apertura del inyector a las diferentes prestaciones del motor, principalmente él los sistemas sin sensor de presión absoluta. También tiene fundamental influencia en el avance del encendido.
Un potenciómetro simple no tiene la suficiente sensibilidad para definir los valores de tiempo de inyección y avance del encendido durante las condiciones más críticas de funcionamiento del motor. El potenciómetro de doble pista las cumple. Este potenciómetro, en realidad son dos potenciómetros unidos en paralelo en una misma carcasa, y tiene al eje de mariposa como accionador mecánico de los dos cursores simultáneamente. La computadora provee al sensor una alimentación constante de 5 voltios. La pista 1 es para motor en marcha lenta y carga parcial; la pista 2 para media y plena carga.
Con un tester en función resistencia (Ohm), desconecte el sensor de su ficha de unión al ramal del circuito, medir la resistencia de la pista número 1 del potenciómetro colocando una punta del tester en el terminal de masa del sensor ( 5 ) y la otra en el terminal de señal para la computadora ( 2 ). Accione la palanca de aceleración comprobando los valores especificados y la continuidad en todo su recorrido sin cortes (de la pista del potenciómetro). Para la pista numero 2 proceder igual que para la anterior colocando las puntas del tester al terminal de masa ( 5 ) y al terminal de señal ( 4 ).
Excesivo consumo de combustible, marcha irregular, tironeos, arranque rudo, motor no regula, detonación, excesivo humo negro por el escape.
Los sensores de RPM y PMS pueden ser de dos tipos:
1 - SENSOR INDUCTIVO o RELUTANCIA MAGNETICA
El sensor empleado para detectar las revoluciones por minuto y el punto muerto superior del motor es de tipo inductivo, funciona mediante la variación del campo magnético generada por el paso de los dientes de una rueda dentada, rueda fónica, ubicada en el interior del block y fijada al contrapeso trasero del cigüeñal. Por lo tanto el sensor se fija al block y ya no son necesario los controles y los reglajes del entre hierro y de la posición angular. Los dientes que pasan delante del sensor, varían él entre hierro entre engranaje y sensor; el flujo disperso, que varia por consiguiente, induce una tensión de corriente alterna cuya amplitud depende de las revoluciones.
La rueda fónica está constituida por 58 dientes más un espacio equivalente al hueco ocupado por dos dientes suprimidos.
La referencia definida por el espacio de los dos dientes que faltan, constituye la base para detectar el punto de sincronismo, PMS.
El sensor consta de una carcasa tubular (1), en su interior se monta un imán permanente (3) y un bobinado eléctrico (2). El flujo magnético creado por el imán (3) sufre, debido al paso de los dientes de la rueda fónica, unas oscilaciones causadas por la variación del entrehierro. Tales oscilaciones inducen una fuerza electromotriz en el bobinado (2) en cuyos terminales hay una tensión alternativamente positiva, diente orientado al sensor, y negativa, hueco orientado al sensor. El valor de pico de la tensión de salida del sensor depende, de la distancia entre sensor y diente, entrehierro. La rueda fónica posee 60 dientes, dos de los cuales se han eliminado para crear una referencia: el paso de la rueda corresponde por lo tanto a un ángulo de 6 grados ( dividido 60 dientes). El punto de sincronismo se reconoce al final del primer diente sucesivo al espacio de los dos dientes que faltan. Cuando este diente transita debajo del sensor, el motor se encuentra con el par de pistones 1 y 4 a 114 grados antes del punto muerto superior.
Es decir que la computadora necesita saber con antelación cuando tiene que enviar al primario de la bobina la señal para enviar por el secundario la alta tensión teniendo en cuenta el avance para el encendido. A la computadora le llega la información que se acerca el punto muerto superior del cilindro 1, 114 grados antes, con este dato le sobra tiempo para decidir de acuerdo a los mapas de avance cuando enviar la señal al primario de la bobina.
Con un tester en función resistencia ( Ohm ), desconectemos el sensor de su ficha de unión al ramal eléctrico del circuito, medir la resistencia de la bobina del sensor.
Motor no arranca, motor se para intempestivamente, fuertes tirones al circular.
Una capa semiconductora recorrida por corriente, sumergida en un campo magnético normal, líneas de fuerza perpendiculares al sentido de la corriente genera entre sus terminales una diferencia de potencial, conocida como tensión de Hall. Si la intensidad de la corriente permanece constante, la tensión generada depende solo de la intensidad del campo magnético; es suficiente por lo tanto que la intensidad del campo magnético varíe periódicamente para obtener una señal eléctrica modulada, cuya frecuencia es proporcional a la velocidad con que cambia el campo magnético. Para obtener dicho cambio, un anillo magnético, parte interna de la polea, con una apertura atraviesa el sensor. En su movimiento la parte metálica del anillo cubre el sensor bloqueando el campo magnético con la consiguiente señal baja de salida; viceversa en correspondencia de la apertura y por lo tanto con la presencia del campo magnético, el sensor genera una señal alta.
Con un tester en función frecuencia ( Hz ), sin desconectar el sensor pinchando el cable de señal a la computadora, gire el motor por intermedio del motor de arranque, mida la frecuencia en el mismo. La frecuencia será mayor cuanto mayor sea la velocidad de giro del eje del sensor.
Si el sensor no tiene señal de salida verifique con un tester en función voltaje que llegue al mismo alimentación y tenga correcta masa. Si después de efectuar esta prueba y el sensor no presenta defectos mecánicos en su transmisión de giro, reemplace el mismo.
Igual que el inductivo.
SENSOR DE OXIGENO DE ZIRCONIO (ZrO2) SENSOR DE OXIGENO DE TITANIO (TiO2)
También se pueden clasificar por la forma de calentamiento del sensor:
CALENTAMIENTO POR LOS GASES DE ESCAPE CALENTAMIENTO A TRAVES DE UNA RESISTENCIA
Los sensores de oxigeno puede tener uno o varios conductores:
Mientras el coeficiente Lambda expresa el exceso o el defecto de aire suministrado al motor respecto al teórico requerido, la mezcla aire/combustible es una relación entre estos dos elementos; que combinadas entre sí reaccionan químicamente. Para los motores actuales significa que necesitan 14,7 partes de aire para quemar 1 parte de combustible.
a - Electrodo (+) en contacto 1 - Cuerpo cerámico con el aire exterior 2 - Tubo protector
b - Electrodo (-) en contacto 3 - Cuerpo metálico con los gases de escape 4 - Resistencia eléctrica
El sensor de oxigeno se monta antes del catalizador.
Está compuesto por un cuerpo cerámico (1), a base de dióxido de circonio recubierto por una fina lamina de platino, cerrado en un extremo, introducido en un tubo de protección (2) y alojado en un cuerpo metálico (3) que también, lo protege y permite su montaje en el caño de escape. La parte exterior (b) de la cerámica está en contacto con la corriente de los gases de escape, mientras que la parte interior (a) está en contacto con el aire exterior. El funcionamiento del sensor de oxigeno se basa en el hecho de que, con temperaturas superiores a 300 grados centígrados, el material cerámico utilizado se transforma en conductor de iones de oxigeno. En estas condiciones, si la cantidad de oxigeno de los dos lados (a) y (b) del sensor tiene porcentajes distintos, se produce entre los dos extremos una variación de tensión, la cual sirve para medir la diferente cantidad de oxigeno en los dos extremos (lado aire y lado gases de escape).
Cuando el sensor suministra un nivel bajo de tensión (inferior a 200 mV) la computadora reconoce que el porcentaje es pobre (Lambda > 1) e incrementa la cantidad de combustible inyectado. Cuando el sensor suministra un nivel alto de tensión (superior a 800 mV) la computadora reconoce que el porcentaje es rico (Lambda < 1) y disminuye la cantidad de combustible inyectado.
El sensor de oxigeno varia por lo tanto los tiempos de inyección de forma tal que el motor funcione con un coeficiente lambda continuamente oscilante entre 0.098 y 0,950 mV aproximadamente. Para temperaturas inferiores a 300 grados centígrados el material cerámico no está activo, por lo tanto el sensor no envía señales útiles y la computadora bloquea la
regulación en bucle cerrado del porcentaje en la fase de calentamiento del motor. Para garantizar que el sensor alcance rápidamente la temperatura de funcionamiento, la misma está dotada de una resistencia eléctrica (4) alimentada por la batería.
La resistencia del calentador y del sensor puede medirse extrayendo el conector y conectando un ohmetro como se indica en la figura.
Resistencia calentador A = 4,2 a 4,
Resistencia sensor B = 5.000 ohm máximo
Con un tester en función voltaje de corriente continua, desconecte la ficha del sensor, ponga en marcha el vehículo para calentar el sensor, mida los valores de generación del sensor 0,1 a 0,9 voltios, estos valores deben ciclar por lo menos 7 o 8 veces en 10 segundos.
Con un tester en función resistencia (Ohm), desconecte la ficha y mida la resistencia de calentamiento del sensor, este valor debe estar entre 1 y 5 ohm (Figura de arriba).