
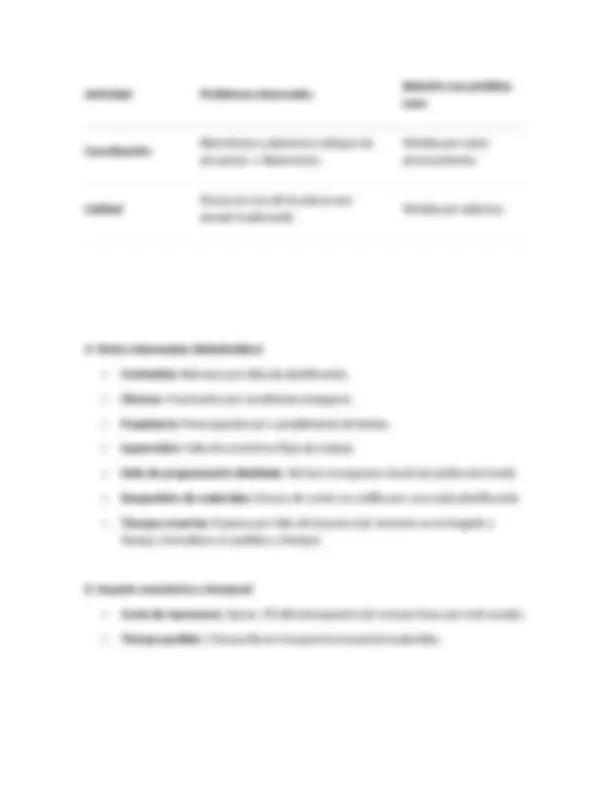
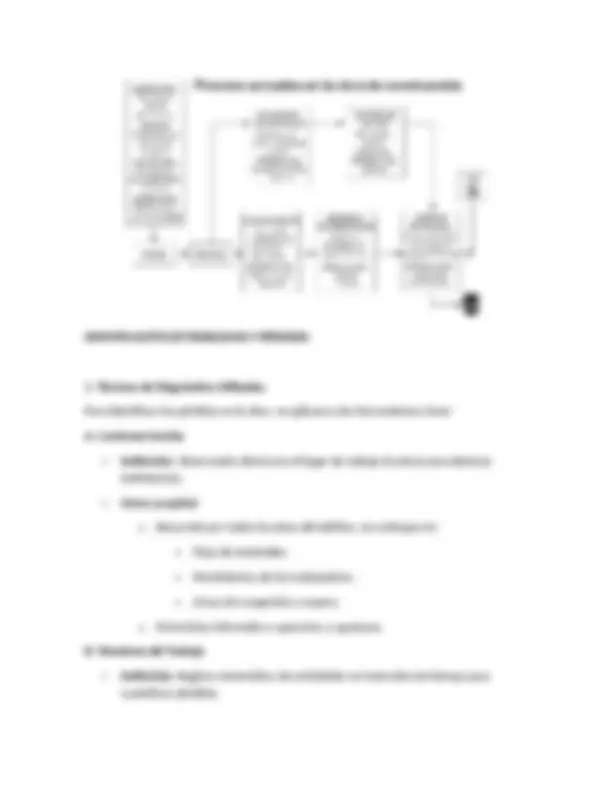

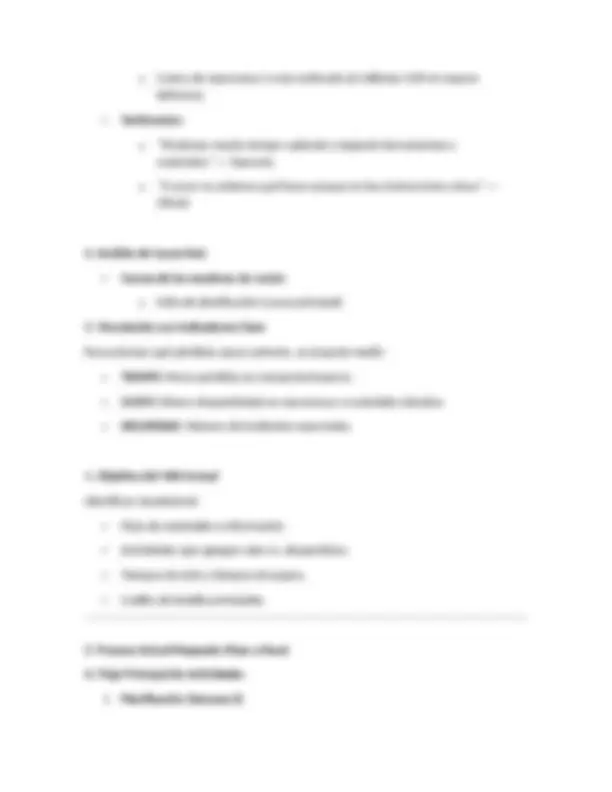
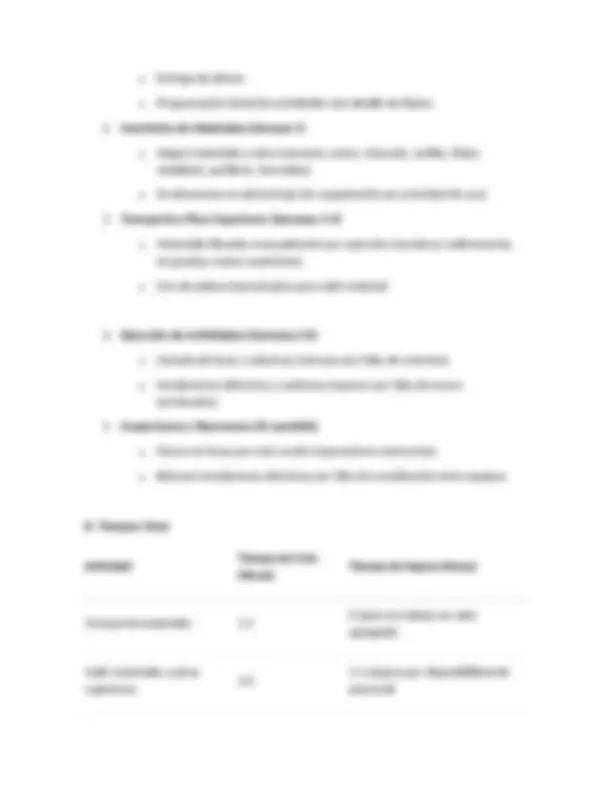
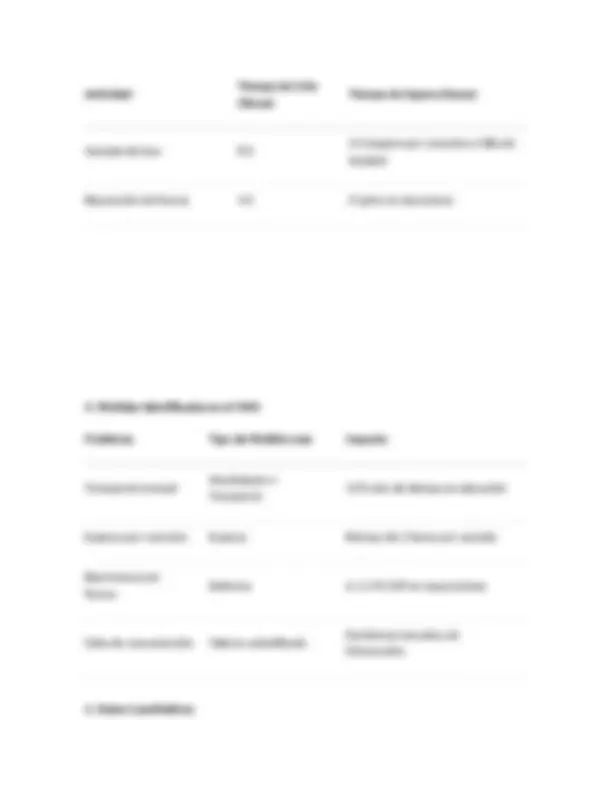
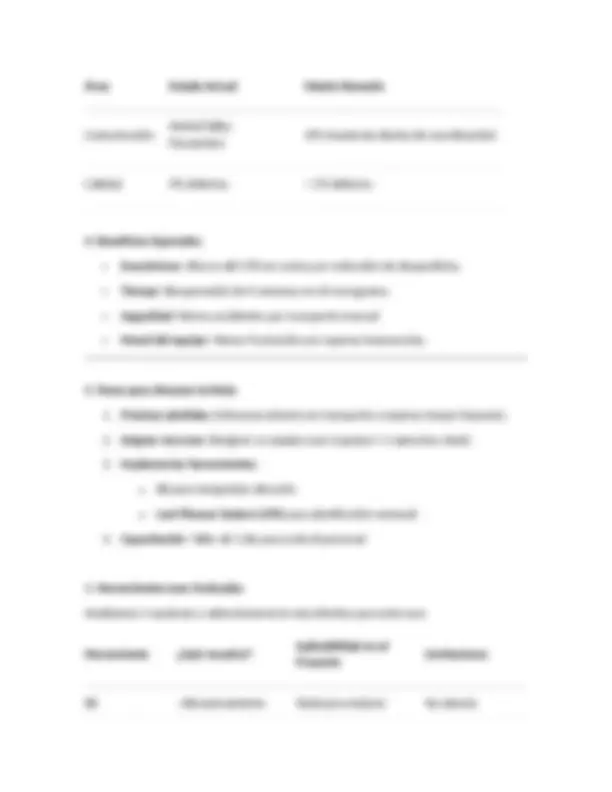
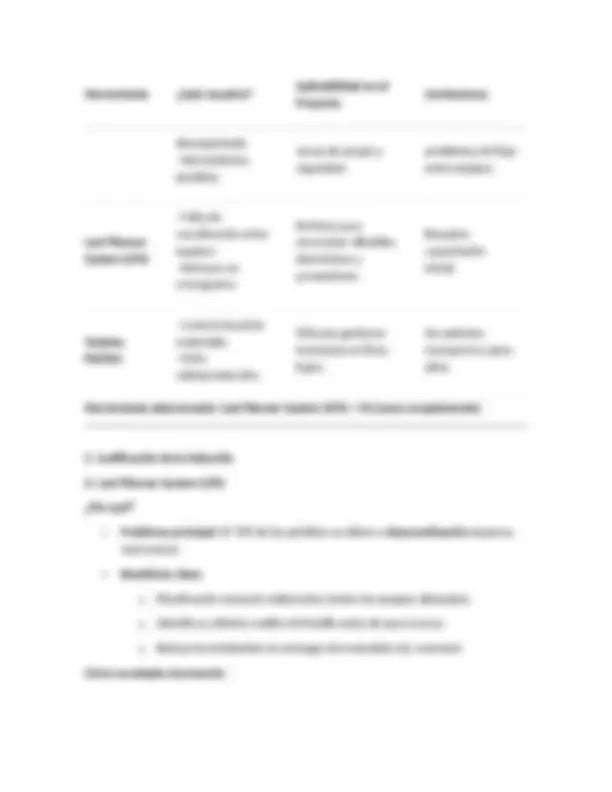
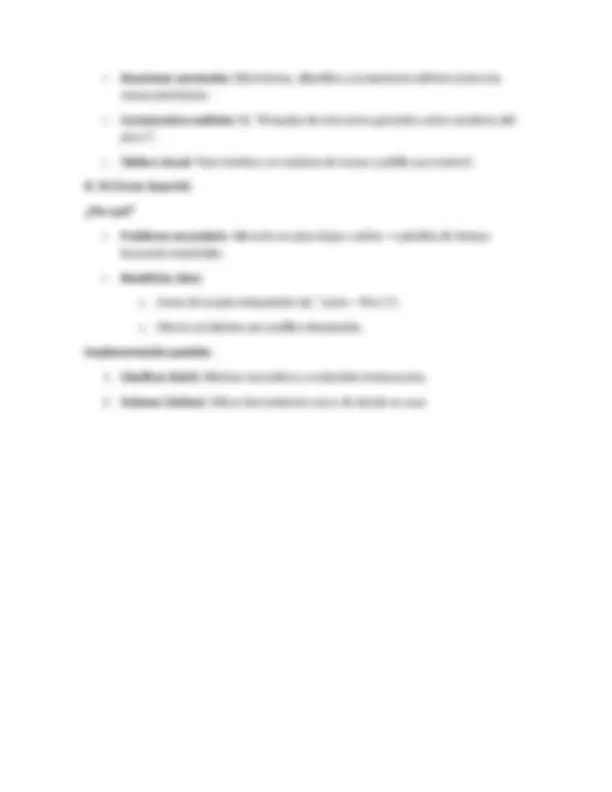
Prepara tus exámenes y mejora tus resultados gracias a la gran cantidad de recursos disponibles en Docsity
Gana puntos ayudando a otros estudiantes o consíguelos activando un Plan Premium
Prepara tus exámenes
Prepara tus exámenes y mejora tus resultados gracias a la gran cantidad de recursos disponibles en Docsity
Prepara tus exámenes con los documentos que comparten otros estudiantes como tú en Docsity
Los mejores documentos en venta realizados por estudiantes que han terminado sus estudios
Estudia con lecciones y exámenes resueltos basados en los programas académicos de las mejores universidades
Responde a preguntas de exámenes reales y pon a prueba tu preparación
Consigue puntos base para descargar
Gana puntos ayudando a otros estudiantes o consíguelos activando un Plan Premium
Comunidad
Pide ayuda a la comunidad y resuelve tus dudas de estudio
Descubre las mejores universidades de tu país según los usuarios de Docsity
Ebooks gratuitos
Descarga nuestras guías gratuitas sobre técnicas de estudio, métodos para controlar la ansiedad y consejos para la tesis preparadas por los tutores de Docsity
Lean construcción año 2025 aplicado a una obra ubicado en la ciudad de Armenia.
Tipo: Resúmenes
1 / 15
Esta página no es visible en la vista previa
¡No te pierdas las partes importantes!
EDIFICIO RESTREPO Ubicación y características generales del proyecto Proyecto: Edificio multifamiliar de 4 pisos y sótano Ubicación: Barrio La Clarita del Sur, Armenia (Quindío) Área construida: 140 m² por piso (700 m² total). Tipo de estructura: Sistema constructivo: a porticado- pilotes, zapatas, columnas, vigas y
losa. Número de viviendas: 2 apartamentos por piso (8 en total). Etapa actual: Estructura en progreso, armado de acero para vigas para losa de entre piso del 4 nivel.
2. Entorno y desafíos logísticos Acceso: Calle secundaria con limitado espacio para almacenamiento de materiales. Clima: Zona con lluvias frecuentes (riesgo de humedad en materiales). 3. Procesos actuales en la obra Actividad Problemas observados Relación con pérdidas Lean Transporte de materiales Escaleras sin vaciar → Materiales subidos manualmente (riesgo de accidentes). Pérdida por transporte y movimientos. Almacenamiento Acopio desorganizado en PB → Bloques y sacos de cemento obstruyen pasillos. Pérdida por inventario y esperas.
1. Técnicas de Diagnóstico Utilizadas Para identificar las pérdidas en la obra, se aplicaron dos herramientas clave: A. Caminata Gemba Definición: Observación directa en el lugar de trabajo (la obra) para detectar ineficiencias. Cómo se aplicó: o Recorrido por todos los pisos del edificio, con enfoque en: Flujo de materiales. Movimientos de los trabajadores. Zonas de congestión o espera. o Entrevistas informales a operarios y capataces. B. Muestreo del Trabajo Definición: Registro sistemático de actividades en intervalos de tiempo para cuantificar pérdidas.
Cómo se aplicó: o Se tomaron muestras durante 3 días ( 2 horas/día). o Se categorizaron las actividades en: valor agregado (ej: vaciado de concreto) vs. no valor agregado (ej: traslado innecesario de herramientas).
2. Pérdidas Identificadas (Relacionadas con las 9 perdidas de Lean Construction) A continuación, se detallan las pérdidas encontradas, con ejemplos concretos de la obra: **Pérdida Lean Problema Específico en la Obra Impacto
o Escaleras sin vaciar y materiales apilados en pasillos. o Obreros con condiciones inseguras de trabajo en alturas Datos cuantitativos: o Tabla de tiempos muertos (15% del tiempo diario en transporte).
o Costos de reprocesos ( costo estimado $2 millones COP en reparar defectos). Testimonios: o "Perdemos mucho tiempo subiendo y bajando herramientas y materiales" — Operario. o "A veces no sabemos qué hacer porque no hay instrucciones claras" — Oficial.
4. Análisis de Causa Raíz Causas de las escaleras sin vaciar: o Falta de planificación (causa principal). 5. Vinculación con Indicadores Clave Para priorizar qué pérdidas atacar primero, se propone medir: TIEMPO: Horas perdidas en transporte/esperas. COSTO: Dinero desperdiciado en reprocesos o materiales dañados. SEGURIDAD: Número de incidentes reportados. 1. Objetivo del VSM Actual Identificar visualmente: Flujo de materiales e información. Actividades que agregan valor vs. desperdicios. Tiempos de ciclo y tiempos de espera. Cuellos de botella principales. 2. Proceso Actual Mapeado (Paso a Paso) A. Flujo Principal de Actividades 1. Planificación (Semana 0)
Actividad Tiempo de Ciclo (Horas) Tiempo de Espera (Horas) Vaciado de losa 8. 2.0 (espera por concreto y falla de equipo) Reparación de fisuras 4.0 0 (pero es reproceso)
4. Pérdidas Identificadas en el VSM Problema Tipo de Pérdida Lean Impacto Transporte manual Movimiento + Transporte 15% más de tiempo en ejecución Esperas por concreto Esperas Retraso de 2 horas por vaciado Reprocesos por fisuras Defectos $ 1,2 M COP en reparaciones Falta de comunicación Talento subutilizado Decisiones tomadas sin información 5. Datos Cuantitativos
Lead Time Total Actual: 12 semanas (vs. 8 semanas planeadas). Tiempo de Valor Agregado (VA): 30% del total. Tiempo de No Valor Agregado (NVA): 70% (transportes, esperas, reprocesos).
1. metas Situación deseada: "Reducir en un 40% los tiempos no productivos (transportes, esperas y reprocesos) en 8 semanas, mediante la implementación de herramientas Lean, para cumplir con el cronograma original de 8 semanas." Características SMART: Criterio Explicación Ejemplo en el Proyecto Específica Enfocada en pérdidas críticas. Reducir tiempos de transporte y esperas en escaleras y suministros. Medible Indicadores cuantificables. - Tiempo de transporte: De 3h → 1.2h. - Reprocesos: De 1.2 MCOP→500k COP. Alcanzable Soluciones realistas con recursos disponibles. Uso de 5S para reorganizar almacén y LPS para planificación. Relevante Impacto directo en cronograma y costos. Acortar el Lead Time de 12 a 8 semanas. Temporal Plazo definido. 8 semanas (2 meses). 2. Indicadores Clave Para monitorear el avance hacia la meta:
Área Estado Actual Estado Deseado Comunicación Verbal (fallas frecuentes) LPS (reuniones diarias de coordinación) Calidad 5% defectos < 1% defectos
4. Beneficios Esperados Económicos: Ahorro del 15% en costos por reducción de desperdicios. Tiempo: Recuperación de 4 semanas en el cronograma. Seguridad: Menos accidentes por transporte manual. Moral del equipo: Menos frustración por esperas innecesarias. 5. Pasos para Alcanzar la Meta 1. Priorizar pérdidas: Enfocarse primero en transporte y esperas (mayor impacto). 2. Asignar recursos: Designar un equipo Lean (capataz + 2 operarios clave). 3. Implementar herramientas: o 5S para reorganizar almacén. o Last Planner System (LPS) para planificación semanal. 4. Capacitación: Taller de 1 día para todo el personal. 1. Herramientas Lean Evaluadas Analizamos 3 opciones y seleccionamos la más efectiva para este caso: Herramienta ¿Qué resuelve? Aplicabilidad en el Proyecto Limitaciones 5S - Almacenamiento Ideal para mejorar No aborda
Herramienta ¿Qué resuelve? Aplicabilidad en el Proyecto Limitaciones desorganizado.