
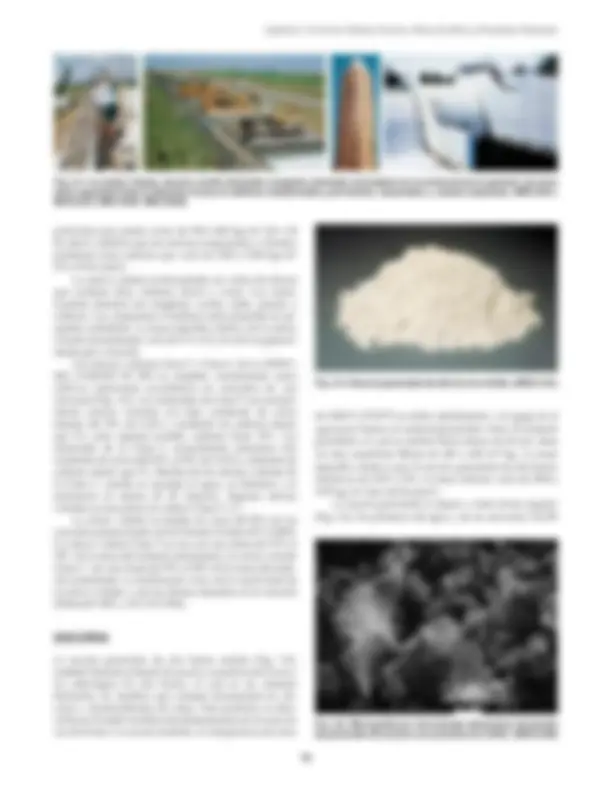
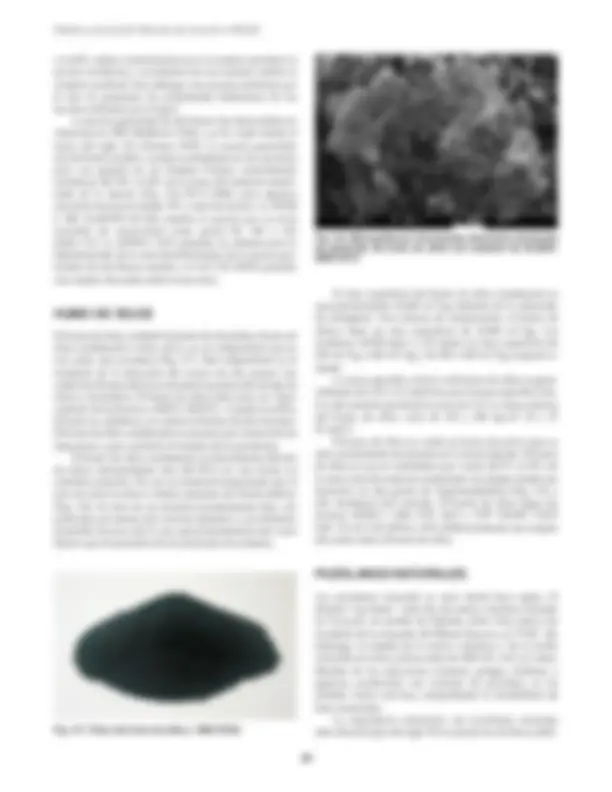
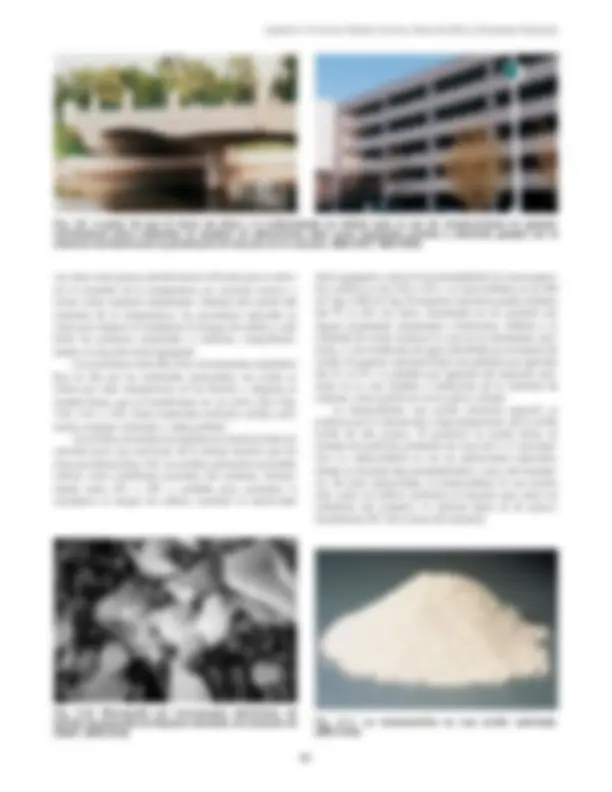
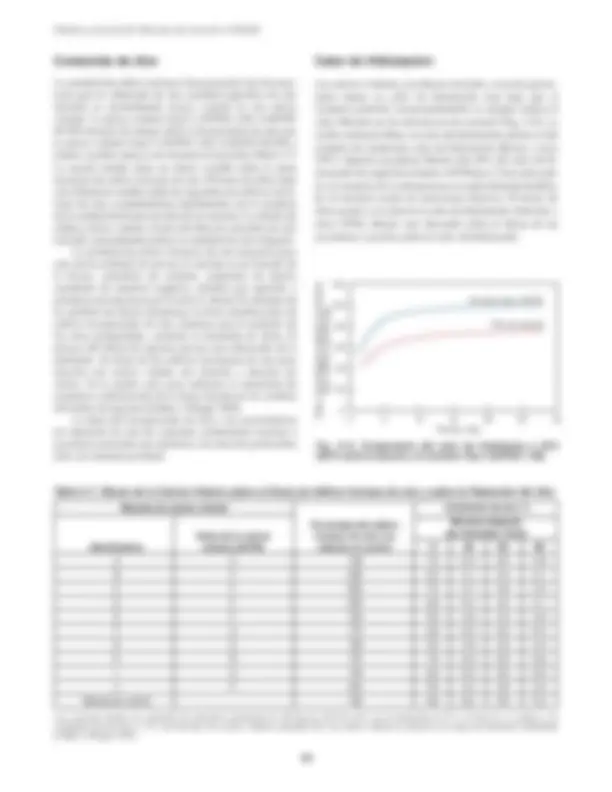
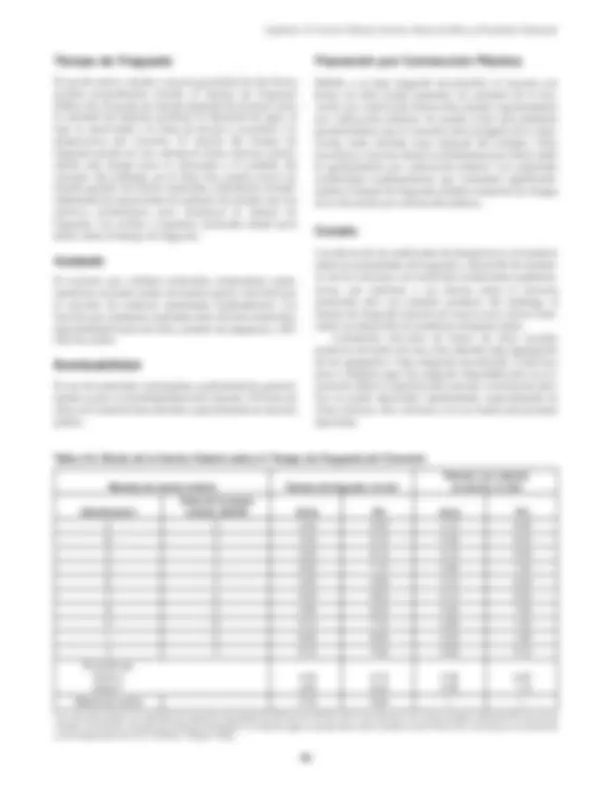
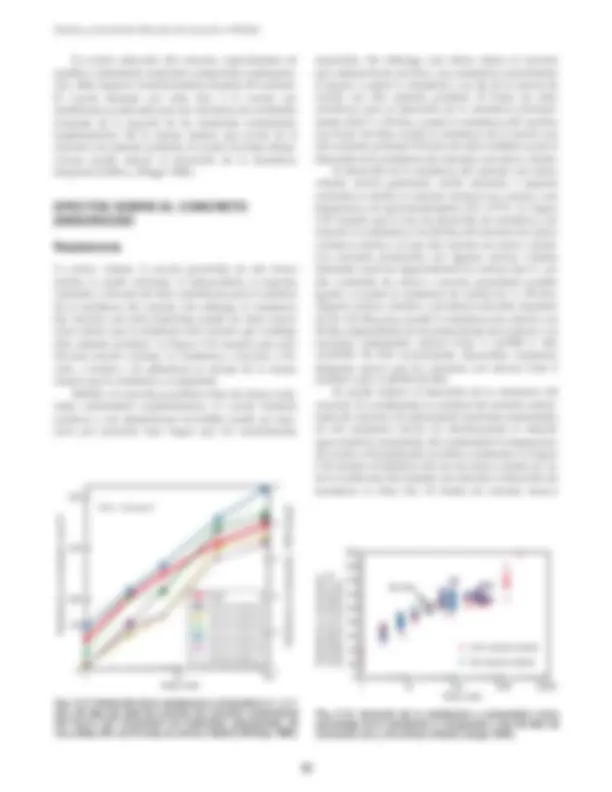
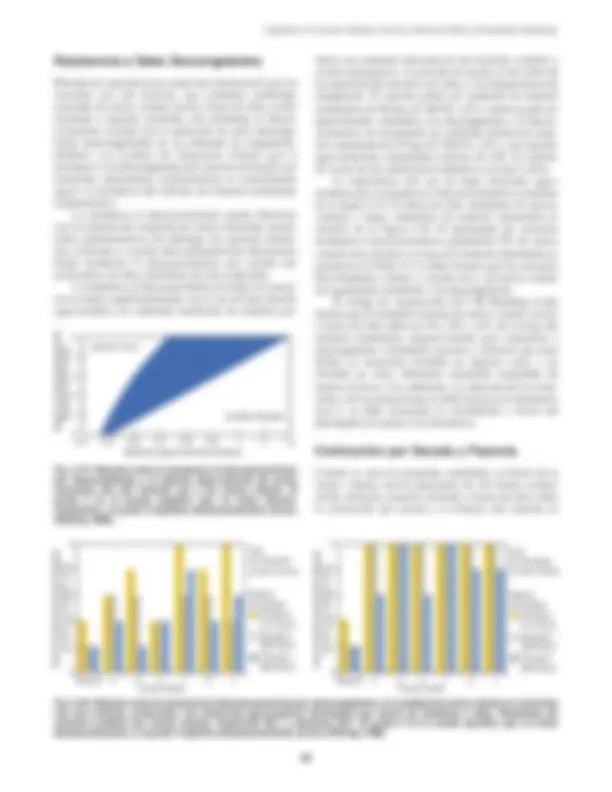
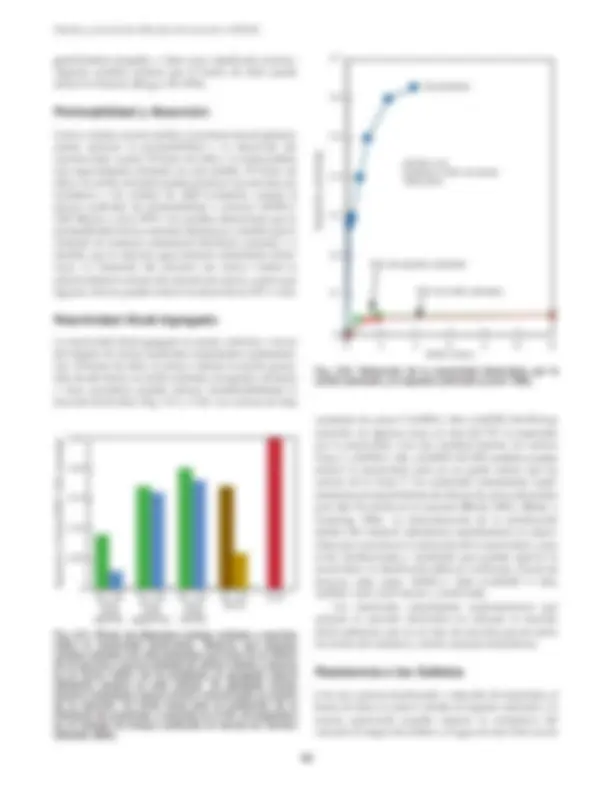
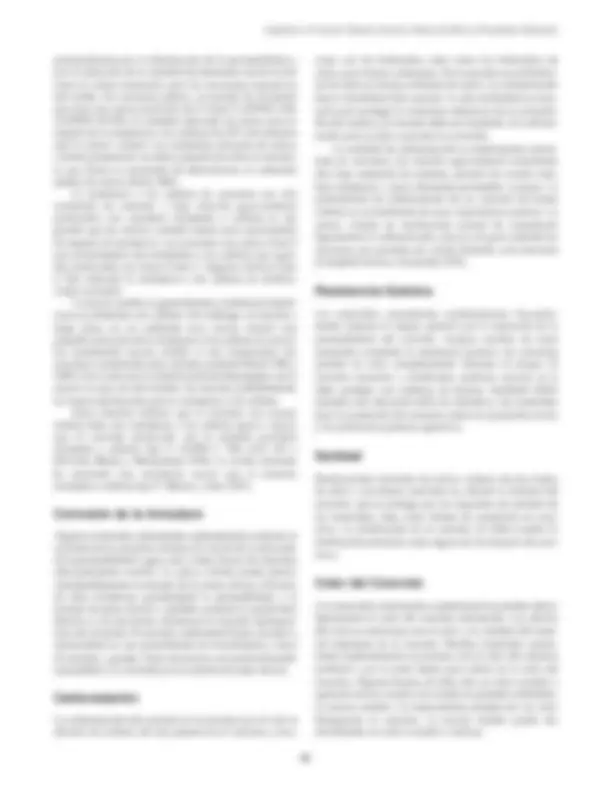
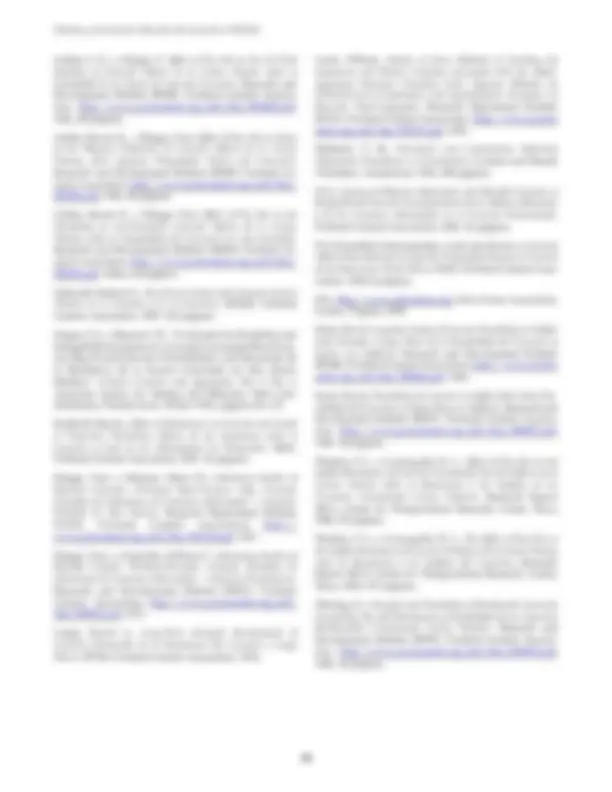
Prepara tus exámenes y mejora tus resultados gracias a la gran cantidad de recursos disponibles en Docsity
Gana puntos ayudando a otros estudiantes o consíguelos activando un Plan Premium
Prepara tus exámenes
Prepara tus exámenes y mejora tus resultados gracias a la gran cantidad de recursos disponibles en Docsity
Prepara tus exámenes con los documentos que comparten otros estudiantes como tú en Docsity
Los mejores documentos en venta realizados por estudiantes que han terminado sus estudios
Estudia con lecciones y exámenes resueltos basados en los programas académicos de las mejores universidades
Responde a preguntas de exámenes reales y pon a prueba tu preparación
Consigue puntos base para descargar
Gana puntos ayudando a otros estudiantes o consíguelos activando un Plan Premium
Comunidad
Pide ayuda a la comunidad y resuelve tus dudas de estudio
Descubre las mejores universidades de tu país según los usuarios de Docsity
Ebooks gratuitos
Descarga nuestras guías gratuitas sobre técnicas de estudio, métodos para controlar la ansiedad y consejos para la tesis preparadas por los tutores de Docsity
Hormigon Armado y mesclas de concreto para una mejor comprencion de los temas de mezclas
Tipo: Apuntes
1 / 18
Esta página no es visible en la vista previa
¡No te pierdas las partes importantes!
La ceniza volante, la escoria granulada de alto horno, el humo de sílice (sílice activa, microsílice) y las puzolanas naturales, tales como esquisto calcinado, arcilla calcinada o metacaolinita, son materiales que, cuando son usados con- juntamente con el cemento portland o el cemento adicionado, contribuyen para la mejoría de las propiedades del concreto endurecido, debido a sus propiedades hidráulicas o puzolánicas o ambas (Fig. 3-1). La puzolana es un material silícico o silícico aluminoso que, cuando está en la forma de polvo fino y en presencia de humedad, reac- ciona químicamente con el hidróxido de calcio liberado por la hidratación del cemento portland para formar silicato de calcio hidratado y otros compuestos cementantes. Las puzolanas y las escorias se clasifican como material cemen- tante suplementario o aditivo (adición) mineral. Las Tablas 3-1 y 3-2 listan las especificaciones definidas para estos materiales. El uso de estos materiales en los cementos adicionados se discute en el Capítulo 2 y por Detwiler, Bhatty y Bhattacharja (1996). El uso de materiales cementantes suplementarios en concreto viene creciendo desde la década de 70. La mayoría de estos materiales son subproductos de procesos indus-
triales. Su empleo sensato es deseable no sólo bajo el punto de vista de la conservación del medio ambiente y de la energía, sino también por los beneficios que estos mate- riales pueden ofrecer al concreto. Los materiales cementantes suplementarios se adicio- nan al concreto como parte del sistema cementante. Se los puede utilizar como adición o como sustitución parcial del cemento portland o del cemento adicionado, dependiendo de las propiedades de los materiales y de los efectos espe- rados en el concreto. Los materiales cementantes suplementarios se usan para mejorar una propiedad particular del concreto, tal como resistencia a la reactividad álcali-agregado. La canti- dad óptima de adición se debe establecer a través de prue- bas para determinar (1) si el material realmente mejora la propiedad y (2) la correcta cantidad, pues una sobredosis o
Fig. 3-1. Materiales cementantes suplementarios. De la izquierda para la derecha, ceniza volante (Clase C), metacaolinita (arcilla calcinada), humo de sílice, ceniza volante (Clase F), escoria y esquisto. (IMG12187)
Tabla 3-1. Especificaciones y Clases de los Materiales Cementantes Suplementarios en los Estados Unidos Escorias granuladas de alto horno de hierro —ASTM C 989 (AASHTO M 302) Grado 80 Escorias con bajo índice de actividad Grado 100 Escorias con índice moderado de actividad Grado 120 Escorias con alto índice de actividad Ceniza volante y puzolana natural—ASTM C 618 (AASHTO M 295) Clase N Puzolanas naturales crudas o calcinadas, incluyendo: Tierras diatomaceas (tobas) Sílex opalino y esquistos Tufo y cenizas volcánicas o pumitas (piedras pómez) Arcillas calcinadas, incluyendo metakaolinita y esquisto Clase F Ceniza volante con propiedades puzolánicas Clase C Ceniza volante con propiedades puzolánicas y cementantes Humo de sílice —ASTM C 1240
el material fundido se enfría y se solidifica como pequeñas esferas vítreas llamadas cenizas volantes (Fig. 3-2). Luego, se colecta la ceniza volante de los gases de escape a través de precipitadores electrostáticos o de filtros de manga. La ceniza volante es un polvo finamente dividido parecido al cemento portland (Fig. 3-3). La mayoría de las partículas de ceniza volante son esferas y algunas son cenosferas huecas. También se pueden presentar en la forma de plerosferas, que son esferas que contienen esferas menores. Los materiales moli- dos, como el cemento portland, tienen partículas sólidas angulares. Los tamaños de las partículas de la ceniza volante varían de menos de 1 μm (micrómetro) hasta más de 100 μm, siendo que el tamaño de una partícula típica es de 20 μm. Sólo el 10% al 30% de la masa de las partículas es mayor que 45 μm. El área superficial es normalmente de 300 a 500 m^2 /kg, a pesar de que algunas cenizas pueden tener área superficial tan baja como 200 m^2 /kg o tan alta como 700 m^2 /kg. Las cenizas volantes que no estén fuerte- mente compactadas presentan una masa unitaria (masa por unidad de volumen, incluyendo el aire entre las
una dosis insuficiente pueden ser perjudiciales o los efectos deseados no se logran. Los materiales cementantes suple- mentarios también reaccionan de manera diversa con los diferentes tipos de cemento. Tradicionalmente, la ceniza volante, escoria, arcilla calcinada, esquisto calcinado y humo de sílice se usaban separadamente en el concreto. Actualmente, debido a la facilidad del acceso a estos materiales, los productores de concreto pueden combinar dos o más de estos materiales, para optimizar las propiedades del concreto. Las mezclas que usan tres materiales cementantes, llamadas mezclas ternarias, se están haciendo comunes. En los Estados Unidos, los materiales cementantes suplementarios se usan, por lo menos, en 60% del concreto premezclado (PCA 2000). La Tabla 3-3 presenta las normas de ensayo de las cenizas volantes y las puzolanas en varios países.
La ceniza volante es un subproducto de la combustión del carbón pulverizado en plantas generadoras de electricidad y es el material cementante suplementario más utilizado en los Estados Unidos. Bajo la ignición (combustión) en el horno, la mayor parte de la materia volátil y el carbono del carbón se queman. Durante la combustión, las impurezas minerales del carbón (tales como arcilla, feldespato, cuarzo y esquisto) se funden en suspensión y se transportan hacia afuera de la cámara por los gases de escape. En el proceso,
Diseño y Control de Mezclas de Concreto ◆^ EB
Fig. 3-3. La ceniza volante es un polvo que se parece con el cemento y ha sido usada desde los años 30. (IMG12190)
Tabla 3-2. Normas de Especificación de las Puzolanas, Escorias, Ceniza Volante y Humo de Sílice
País Norma Argentina IRAM 1668, IRAM 1506, IRAM 1557, IRAM 1667 Chile NCh161.EOf Colombia NTC 3493, NTC 4637 Ecuador NTE 0491, NTE 0494 México NMX-C- Perú NTP 334.104, NTP 334. Uruguay UNIT 1047
Tabla 3-3. Normas de Ensayo de las Cenizas Volantes y las Puzolanas
País Norma Argentina IRAM 1654, IRAM 1668 Colombia NTC 1784, NTC 3823 Ecuador NTE 0495, NTE 0496, NTE 0497, NTE 0498 Estados Unidos ASTM C 311 México NMX-C- Perú NTP 334.055, NTP 334.066, NTP 334. Uruguay UNIT 1035, UNIT 1038, UNIT 1039 Venezuela COVENIN 3135
Fig. 3-2. Micrografía por microscopio electrónico de barrido (SEM) de partículas de ceniza volante con aumento de 1000X. A pesar de que la mayoría de las cenizas volantes son esferas sólidas, algunas partículas, llamadas cenos- feras, son huecas (como se enseña en la micrografía). (IMG12309)
El área superficial del humo de sílice condensado es aproximadamente 20,000 m^2 /kg (método de la adsorción de nitrógeno). Para efectos de comparación, el humo de tabaco tiene un área superficial de 10,000 m^2 /kg. Los cementos ASTM tipos I y III tienen un área superficial de 300 m^2 /kg a 400 m^2 /kg y de 500 a 600 m^2 /kg, respectiva- mente. La masa específica relativa del humo de sílice es gene- ralmente de 2.20 a 2.5, mientras que la masa específica rela- tiva del cemento portland es cerca de 3.15. La masa unitaria del humo de sílice varía de 130 a 430 kg/m^3 (8 a 27 lb/pies^3 ). El humo de sílice se vende en forma de polvo pero es más comúnmente encontrado en la forma líquida. El humo de sílice se usa en cantidades que varían del 5% al 10% de la masa total de material cementante. Se emplea donde sea necesario un alto grado de impermeabilidad (Fig. 3-9) y alta resistencia del concreto. El humo de sílice sigue las normas ASTM C 1240, NTC 4637 y NTP 334.087, UNIT
Las puzolanas naturales se usan desde hace siglos. El término “puzolana” viene de una ceniza volcánica extraída en Pozzuoli, un pueblo de Nápoles, Italia. Esta ceniza fue resultado de la erupción del Monte Vesuvio, en 79 DC. Sin embargo, el empleo de la ceniza volcánica y de la arcilla calcinada en otras culturas data de 2000 AC o tal vez antes. Muchas de las estructuras romanas, griegas, indianas y egipcias, producidas con concreto de puzolana, se las pueden visitar aún hoy, comprobando la durabilidad de estos materiales. La experiencia americana con puzolanas naturales data del principio del siglo XX en proyectos de obras públi-
o CaOH, ambos suministrados por el cemento portland, la escoria se hidrata y se endurece de una manera similar al cemento portland. Sin embargo, las escorias enfriadas por el aire no presentan las propiedades hidráulicas de las escorias enfriadas por el agua. La escoria granulada de alto horno fue desarrollada en Alemania en 1853 (Malhotra 1996) y se ha usado desde el inicio del siglo XX (Abrams 1925). La escoria granulada de alto horno molida, cuando es empleada en los concretos para uso general en los Estados Unidos, normalmente constituye del 30% al 45% de la masa del material cemen- tante en la mezcla (Fig. 3-4) (PCA 2000), pero algunos concretos de escoria tienen 70% o más de escoria. La ASTM C 989 (AASHTO M 302) clasifica la escoria por su nivel creciente de reactividad como grado 80, 100 o 120 (tabla 3-1). La ASTM C 1073 presenta un método para la determinación de la actividad hidráulica de la escoria gra- nulada de alto horno molida y el ACI 233 (1995) presenta una amplia discusión sobre las escorias.
El humo de sílice, también llamado de microsílice, humo de sílice condensado o sílice activa, es un subproducto que se usa como una puzolana (Fig. 3-7). Este subproducto es el resultado de la reducción del cuarzo de alta pureza con carbón en hornos eléctricos durante la producción de liga de silicio o ferrosilicio. El humo de sílice sube como un vapor oxidado de los hornos a 2000°C (3620°F). Cuando se enfría, el humo se condensa y se colecta en bolsas de tela enormes. El humo de sílice condensado se procesa para removerle las impurezas y para controlar el tamaño de las partículas. El humo de sílice condensado es básicamente dióxido de silicio (normalmente más del 85%) en una forma no cristalina (amorfa). Por ser un material transportado por el aire, tal como la ceniza volante, presenta una forma esférica (Fig. 3-8). Se trata de un material extremamente fino, con partículas con menos de 1 mm de diámetro y con diámetro promedio de cerca de 0.1 μm, aproximadamente cien veces menor que el promedio de las partículas de cemento.
Diseño y Control de Mezclas de Concreto ◆^ EB
Fig. 3-7. Polvo de humo de sílice. ( IMG12192)
Fig. 3-8. Micrografía por microscopio electrónico de barrido de partículas de humo de sílice con aumento de 20,000X. (IMG12311)
cas, tales como presas, donde fueron utilizadas para contro- lar el aumento de la temperatura en concreto masivo y actuar como material cementante. Además del control del aumento de la temperatura, las puzolanas naturales se usan para mejorar la resistencia al ataque de sulfato y está entre los primeros materiales a controlar, comprobada- mente, la reacción álcali-agregado. Las puzolanas naturales más comúnmente empleadas hoy en día son los materiales procesados, los cuales se tratan por altas temperatura en los hornos y después se muelen hasta que se transformen en un polvo fino (Fig. 3-10, 3-11 y 3-12). Estos materiales incluyen arcillas calci- nadas, esquisto calcinado y metacaolinita. Las arcillas calcinadas se emplean en construcciones en concreto para uso universal, de la misma manera que las otras puzolanas (Fig. 3-4). Las arcillas calcinadas se pueden utilizar como substitutas parciales del cemento, normal- mente entre 15% y 35% y también para aumentar la resistencia al ataque de sulfato, controlar la reactividad
álcali-agregado y reducir la permeabilidad. Su masa especí- fica relativa es de 2.40 a 2.61 y su finura Blaine es de 650 m^2 /kg a 1350 m^2 /kg. El esquisto calcinado puede contener del 5% al 10% de calcio, resultando en un material con alguna propiedad cementante o hidráulica. Debido a la cantidad de calcita residual, la cual no es totalmente calci- nada, y a las moléculas de agua adsorbida en el mineral de arcilla, el esquisto calcinado tiene una pérdida por ignición del 1% al 5%. La pérdida por ignición del esquisto calci- nado no es una medida o indicación de la cantidad de carbono, como podría ser en la ceniza volante. La metacaolinita, una arcilla calcinada especial, se produce por la calcinación a baja temperatura de la arcilla caolin de alta pureza. El producto se muele hasta un tamaño de partícula promedio de cerca de 1 a 2 micróme- tros. La metacaolinita se usa en aplicaciones especiales, donde se necesite baja permeabilidad y muy alta resisten- cia. En estas aplicaciones, la metacaolinita se usa mucho más como un aditivo (adición) al concreto que como un substituto del cemento. La adición típica es de aproxi- madamente 10% de la masa del cemento.
Fig. 3-11. La metacaolinita es una arcilla calcinada. (IMG12193)
Capítulo 3 ◆^ Ceniza Volante, Escoria, Humo de Sílice y Puzolanas Naturales
Fig. 3-9. A pesar de que el humo de sílice y la metacaolinita se indican para el uso de construcciones en general, normalmente estos materiales se emplean en aplicaciones tales como (izquierda) puentes y (derecha) garajes con la intención de disminuirse la penetración de cloruros en el concreto. (IMG12427, IMG12426)
Fig. 3-10. Micrografía por microscopio electrónico de barrido de partículas de esquisto calcinado con aumento de 5000X. (IMG12433)
Ceniza volante, escoria, arcilla calcinada y esquisto calci- nado normalmente mejoran la trabajabilidad de concretos con el mismo revenimiento (asentamiento). El humo de
sílice puede contribuir para la cohesión de la mezcla del concreto. Algunos ajustes, tal como el uso de reductores de agua de alto rango, pueden ser necesarios para la manu- tención de la trabajabilidad y para permitir la com- pactación y acabado adecuados.
Los concretos con ceniza volante normalmente presentan menos sangrado (exudación) y segregación que el concreto convencional (Tabla 3-6). Este efecto es especialmente valioso, principalmente en mezclas producidas con agrega- dos deficientes en finos. La reducción del agua exudada se debe principalmente por la disminución en la demanda de agua. Gebler y Klieger (1986) relacionan la reducción del
agua exudada del concreto con la disminución de la demanda de agua en los morteros con ceniza volante. Los concretos, conteniendo escoria molida con finura comparable a la finura del cemento, tienden a presentar un aumento tanto de la tasa como de la cantidad de sangrado, pero esto parece no tener ningún efecto adverso sobre la segregación. Las escorias más finas que el cemento dismi- nuyen el sangrado. El humo de sílice es muy efectivo en la reducción de ambas, el sangrado y la segregación, y, como resultado, se
Tabla 3-5. Efecto de la Ceniza Volante sobre la Demanda de Agua de Mezcla en Concretos con Aire Incluido (incorporado)
Todas las mezclas tenían un contenido de material cementante de 335 kg/m^3 (565 lb/yd 3 ), un asentamiento (revenimiento) del cono de Abrams de 125 ± 25 mm (5 ± 1 pulg.) y un contenido de aire de 6 ± 1%. La relación agua-cemento más ceniza volante ha variado de 0.40 a 0. (Whiting 1989).
Identificación (^) Contenido de ceniza Cambio en el agua de De la mezcla de Clase de ceniza volante, % de la masa mezcla necesaria ceniza volante volante del material cementante comparada con el control C1A C 25 - C1D F 25 - C1E F 25 - C1F C 25 - C1G C 25 - C1J F 25 - C2A C 50 - C2D F 50 - C2E F 50 - C2F C 50 - C2G C 50 - C2J F 50 -
Tabla 3-6. Efecto de la Ceniza Volante sobre el Sangrado del Concreto (ASTM C 232, AASHTO T 158)*
Mezclas de ceniza volante Sangrado (exudación) Clase de la ceniza Identificación volante (ASTM) Porcentaje mL/cm^2 ****** A C 0.22 0. B F 1.11 0. C F 1.61 0. D F 1.88 0. E F 1.18 0. F C 0.13 0. G C 0.89 0. H R 0.58 0. I C 0.12 0. J F 1.48 0. Promedio de: Clase C 0.34 0. Clase F 1. 31 0. Mezcla de control 1. 75 0.
pueden utilizar concretos con revenimiento (asentamiento) mayor. La arcilla calcinada, el esquisto calcinado y la meta- caolinita tienen poca influencia sobre el sangrado.
Capítulo 3 ◆^ Ceniza Volante, Escoria, Humo de Sílice y Puzolanas Naturales
Las cenizas volantes, puzolanas naturales y escorias granu- ladas tienen un calor de hidratación más bajo que el cemento portland, consecuentemente su empleo reduce el calor liberado en las estructuras de concreto (Fig. 3-13). La arcilla calcinada libera un calor de hidratación similar al del cemento de moderado calor de hidratación (Barrer y otros 1997). Algunas puzolanas liberan sólo 40% del calor de hi- dratación de aquél del cemento ASTM tipo I. Esta reducción en el aumento de la temperatura es especialmente benéfica en el concreto usado en estructuras masivas. El humo de sílice puede o no reducir el calor de hidratación. Detwiler y otros (1996) ofrecen una discusión sobre el efecto de las puzolanas y escorias sobre el calor de hidratación.
La cantidad de aditivo inclusor (incorporador) de aire nece- saria para la obtención de una cantidad específica de aire incluido es normalmente mayor cuando se usa ceniza volante. La ceniza volante Clase C (ASTM C 618, AASHTO M 295) necesita de menos aditivo incorporador de aire que la ceniza volante Clase F (ASTM C 618, AASHTO M 295) y tiende a perder menos aire durante el mezclado (Tabla 3-7). La escoria molida tiene un efecto variable sobre la dosis necesaria de aditivo inclusor de aire. El humo de sílice tiene una influencia notable sobre los requisitos de aditivos inclu- sores de aire, aumentándolos rápidamente con el aumento de la cantidad de humo de sílice en el concreto. La adición de ambos, ceniza volante y humo de sílice en concretos sin aire incluido, normalmente reduce la cantidad de aire atrapado. La cantidad de aditivo inclusor de aire necesaria para una cierta cantidad de aire en el concreto es en función de la finura, contenido de carbono, contenido de álcalis, contenido de material orgánico, pérdida por ignición y presencia de impurezas en la ceniza volante. El aumento de la cantidad de álcalis disminuye la dosis (dosificación) de aditivo incorporador de aire, mientras que el aumento de las otras propiedades, aumenta la demanda de dosis. El ensayo del índice de espuma provee una indicación de la demanda de dosis de los aditivos inclusores de aire para mezclas con ceniza volante con relación a mezclas sin ceniza. Se lo puede usar para anticipar la necesidad de aumento o disminución de la dosis, basado en los cambios del índice de espuma (Gebler y Klieger 1983). La dosis del incorporador de aire y las características de retención de aire de concretos conteniendo escorias o puzolanas naturales son similares a las mezclas producidas sólo con cemento portland.
Diseño y Control de Mezclas de Concreto ◆^ EB
0
20
40
60
80
100
120
Calor, porcentaje en relación al cemento 0 5 10 15 20 25 30 Tiempo, días
Cemento tipo I ASTM
70% de escoria
tipo I ASTM a los 28 días
Fig. 3-13. Comparación del calor de hidratación a 20°C (68°F) entre la escoria y el cemento Tipo I (ASTM C 150).
Mezclas de ceniza volante Contenido de aire, % Porcentaje del aditivo Minutos después Clase de la ceniza inclusor de aire con del mezclado inicial Identification volante (ASTM) relación al control 0 30 60 90 A C 126 7.2 6.0 6.0 5. B F 209 5.3 4.1 3.4 3. C F 553 7.0 4.7 3.8 2. D F 239 6.6 5.4 4.2 4. E F 190 5.6 4.6 4.3 3. F C 173 6.8 6.5 6.3 6. G C 158 5.5 4.8 4.5 4. H R 170 7.6 6.9 6.5 6. I C 149 6.6 6.5 6.5 6. J F 434 5.5 4.2 3.8 3. Mezcla de control 100 6.6 6.0 5.6 5.
Tabla 3-7. Efecto de la Ceniza Volante sobre la Dosis de Aditivo Inclusor de aire y sobre la Retención del Aire
Los concretos tenían un contenido de material cementante de 307 kg/m^3 (517 lb/yd 3 ), un revenimiento de 75 ± 25 mm (3 ± 1 pulg.) y un contenido de aire de 6 ± 1%. Las mezclas con ceniza volante contenían 25% de ceniza volante en relación a la masa de material cementante (Gebler y Klieger 1983).
requeridos. Sin embargo, esto afecta menos el concreto que contiene humo de sílice, cuya resistencia normalmente se iguala o supera la resistencia a un día de la mezcla de control con sólo cemento portland. El humo de sílice contribuye para el desarrollo de la resistencia principal- mente entre 3 y 28 días, cuando la resistencia del concreto con humo de sílice excede la resistencia de la mezcla con sólo cemento portland. El humo de sílice también ayuda el desarrollo de la resistencia de concretos con ceniza volante. El desarrollo de la resistencia del concreto con ceniza volante, escoria granulada, arcilla calcinada o esquisto calcinado es similar al concreto normal si es curado a una temperatura de aproximadamente 23°C (73°F). La Figura 3-15 muestra que la tasa de desarrollo de resistencia, con relación a la resistencia a los 28 días, del concreto con ceniza volante es similar a la tasa del concreto sin ceniza volante. Los concretos producidos con algunas cenizas volantes altamente reactivas (especialmente las cenizas tipo C, con alto contenido de calcio) o escorias granuladas pueden igualar o exceder la resistencia de control de 1 a 28 días. Algunas cenizas volantes y puzolanas naturales requieren de 28 a 90 días para exceder la resistencia de control a los 28 días, dependiendo de las proporciones de la mezcla. Los concretos conteniendo cenizas Clase C (ASTM C 618, AASHTO M 295) normalmente desarrollan resistencia temprana mayor que los concretos con cenizas Clase F (ASTM C 618, AASHTO M 295). Se puede mejorar el desarrollo de la resistencia del concreto: (1) aumentando la cantidad del material cemen- tante del concreto; (2) adicionando materiales cementantes de alta resistencia inicial; (3) disminuyendo la relación agua-material cementante; (4) aumentando la temperatura de curado o (5) empleando un aditivo acelerador. La Figura 3-16 muestra el beneficio del uso de ceniza volante en vez de la sustitución del cemento con relación al desarrollo de resistencia el clima frío. El diseño de concreto masivo
Diseño y Control de Mezclas de Concreto ◆^ EB
El curado adecuado del concreto, especialmente de aquéllos conteniendo materiales cementantes suplementa- rios, debe empezar inmediatamente después del acabado. El curado húmedo por siete días o el curado con membranas es adecuado para los concretos con cantidades normales de la mayoría de los materiales cementantes suplementarios. De la misma manera que ocurre en el concreto con cemento portland, el curado con bajas tempe- raturas puede reducir el desarrollo de la resistencia temprana (Gebler y Klieger 1986).
La ceniza volante, la escoria granulada de alto horno molida, la arcilla calcinada, la metacaolinita, el esquisto calcinado y el humo de sílice contribuyen para el aumento de la resistencia del concreto. Sin embargo, la resistencia del concreto con estos materiales puede ser tanto mayor como menor que la resistencia del concreto que contenga sólo cemento portland. La Figura 3-14 muestra esto para diversas cenizas volantes. La resistencia a tracción, a fle- xión, a torsión y de adherencia se afectan de la misma manera que la resistencia a compresión. Debido a la reacción puzolánica lenta de ciertos mate- riales cementantes suplementarios, el curado húmedo continuo y con temperaturas favorables puede ser nece- sario por periodos más largos que los normalmente
0
150
200
300
400
1
2
3
4
5
6
1 10 100
Resistencia a compresión, kg/cm
2
Resistencia a compresión, 1000 lb/pulg
2
Edad, días
Nada Ceniza volante A Ceniza volante D Ceniza volante E Ceniza volante F Ceniza volante G Ceniza volante J
MPa = 10.2 kg/cm 2
Fig. 3-14. Desarrollo de la resistencia a compresión a 1, 3, 7, 28 y 90 días de edad de mezclas de concreto conteniendo 307 Kg/m^3 (517 lb/yardas^3 ) de materiales cementantes, de los cuales 25% de la masa es ceniza volante (Whiting 1989).
0
20
40
60
80
100
120
140
160
180
1 10 100 1000 10000
Resistencia a compresión,porcentaje en relación a laresistencia a los 28 días
Edad, días
Con ceniza volante Sin ceniza volante
28 días
Fig. 3-15. Aumento de la resistencia a compresión como porcentaje de la resistencia a compresión a los 28 días de concretos con y sin ceniza volante (Lange 1994).
frecuentemente se aprovecha del retraso del desarrollo de la resistencia de las puzolanas, pues estas estructuras no se las pone en servicio inmediatamente. El desarrollo lento de la resistencia temprana que resulte del uso de materiales cementantes suplementarios es una ventaja en la construc- ción en clima caluroso, pues da más tiempo para la colo- cación y el acabado del concreto. Con los ajustes adecuados de la mezcla, se pueden utilizar todos los materiales cementantes suplementarios en todas las estaciones. Los materiales cementantes suplementarios son esen- ciales para la producción de los concretos de alta resisten- cia. La ceniza volante se usa principalmente para la producción de concreto con resistencias de hasta 1000 kg/cm^2 o 100 MPa (15,000 lb/pulg^2 ). Los productores de concreto premezclado pueden, hoy en día, producir concre- tos con hasta 1400 kg/cm^2 o 140 MPa (20,000 lb/pulg^2 ), con el empleo de humo de sílice, reductores de agua de alto rango y agregados adecuados (Burg y Ost 1994).
La resistencia a abrasión y al impacto del concreto se rela- cionan con la resistencia a compresión y el tipo de agregado. Los materiales cementantes suplementarios normalmente no afectan estas propiedades tanto como afectan la resisten-
cia. Concretos que contienen ceniza volante son tan re- sistentes a la abrasión cuanto un concreto de cemento por- tland sin ceniza (Gebler y Klieger 1986). La Figura 3- ilustra que la resistencia a abrasión de concretos con ceniza volante se relaciona con la resistencia a compresión.
Es imprescindible que, para el desarrollo de la resistencia al deterioro por ciclos de congelación-deshielo, el concreto tenga adecuada resistencia y cantidad de aire incluido. Para que el concreto con material cementante suplemen- tario presente la misma resistencia a los ciclos de congelación-deshielo de un concreto que contenga sólo cemento portland, los dos tipos de concreto deben respetar cuatro condiciones:
Capítulo 3 ◆^ Ceniza Volante, Escoria, Humo de Sílice y Puzolanas Naturales
200 250 300 350 400
Profundidad de desgaste, mm
Curado húmedo por 28 días, Resistencia a compresión, kg/cm 2
Curado húmedo por 28 días, Resistencia a compresión, 1000 lb/pulg 2 3 4 5 6
MPa = 10.2 kg/cm 2
Fig. 3-17. Comparación de la resistencia a abrasión y de la resistencia a compresión de varios concretos con 25% de ceniza volante. La resistencia a abrasión aumenta con el aumento de resistencia a compresión (Gebler y Klieger 1986).
0
250
300
350
400
450
500
550
600
2900
MPa = 10.2 kg/cm^2
3600
4300
5000
5700
6400
7100
7800
8500
0 10 20 30 40 50 60 70 80 90
Resistencia a compresión, kg/cm
(^2)
Edad, días
Control Ceniza volante A 20% S Ceniza volante A 20% P Ceniza volante A 20% A
Curado en clima frío: Primeras 24 hrs a 23OC (73OF) Restante a 4OC (39OF)
Resistencia a compresión, lb/pulg
2
Fig. 3-16. Resistencias a compresión de concretos curados a 23°C (73°F) durante las primeras 24 horas y curados a 4°C (40°F) durante el resto del tiempo. El concreto de control tenía un contenido de cemento de 322 Kg/m 3 ( lb/yardas^3 ) y una relación a/c de 0.45. Las curvas de ceniza volante muestran sustitución por cemento (S), substitución parcial (igual) por cemento y arena y adición de ceniza volante con relación a la masa de cemento (A). La sustitución parcial del cemento o la adición de ceniza volante presentan desarrollo de resistencia similar a la mezcla de control que posee sólo cemento, incluso en clima frío (Detwiler 2000).
Décadas de experiencia en campo han demostrado que los concretos con aire incluido, que contienen cantidades normales de ceniza volante, escoria, humo de sílice, arcilla calcinada o esquisto calcinado, son resistentes al descas- caramiento causado por la aplicación de sales desconge- lantes (anticongelantes) en un ambiente de congelación- deshielo. Las pruebas de laboratorio indican que la resistencia a los descongelantes del concreto producido con materiales cementantes suplementarios es normalmente igual a la resistencia del concreto sin material cementante suplementario. La resistencia al descascaramiento puede disminuir con el aumento del contenido de ciertos materiales cemen- tantes suplementarios. Sin embargo, los concretos diseña- dos, colocados y curados adecuadamente han demostrado buena resistencia al descascaramiento aun cuando son producidos con altas cantidades de estos materiales. La resistencia al descascaramiento de todos los concre- tos se mejora significantemente con el uso de baja relación agua-cemento, un contenido moderado de cemento por-
tland, una cantidad adecuada de aire incluido, acabado y curado apropiados y un periodo de secado al aire antes de la exposición del concreto a las sales y a las temperaturas de congelación. El concreto pobre con contenido de material cementante de 240 kg/m^3 (405 lb/ yd^3 ) o menos puede ser especialmente vulnerable a los descongelantes y al descas- caramiento. Se recomienda un contenido mínimo de mate- rial cementante de 335 kg/m^3 (564 lb/ yd^3 ) y una relación agua-materiales cementantes máxima de 0.45. Un sistema de vacíos de aire satisfactorio también es un factor crítico. La importancia del uso de bajas relaciones agua- cemento para la resistencia al descascaramiento se presenta en la Figura 3-19. El efecto de altas cantidades de cenizas volantes y bajos contenidos de material cementante se muestra en la Figura 3-20. El desempeño de concretos resistentes al descacaramiento conteniendo 25% de ceniza volante (con relación a la masa del material cementante) se presenta en la Tabla 3-9. La tabla muestra que los concretos bien diseñados, colados y curados con y sin ceniza volante son igualmente resistentes a los descongelantes. El código de construcción ACI 318 (Building Code) declara que el contenido máximo de ceniza volante, escoria y humo de sílice debe ser 25%, 50% y 10% de la masa del material cementante, respectivamente para exposición a descongelantes. Cantidades mayores o menores que estos límites se mostraron durables en algunos casos y no durables en otros. Diferentes materiales responden de manera diversa a los ambientes. La selección de los mate- riales y de las proporciones se debe basar en la experiencia local y se debe comprobar la durabilidad a través del desempeño en campo o en laboratorio.
Cuando se usan en pequeñas cantidades, el efecto de la ceniza volante, escoria granulada de alto horno molida, arcilla calcinada, esquisto calcinado y humo de sílice sobre la contracción por secado y la fluencia del concreto es
Capítulo 3 ◆^ Ceniza Volante, Escoria, Humo de Sílice y Puzolanas Naturales
Ninguna A D E F G J
0
1
2
3
4
5
Grado de descascaramiento después
de 150 ciclos (ASTM C 672)
Ceniza volante
250 kg/m 3 (417 lb/yd 3 ) 305 kg/m 3 (508 lb/yd 3 ) 335 kg/m 3 (588 lb/yd 3 )
25% de reemplazo Curado húmedo
Material cementante
Ninguna A D E F G J
0
1
2
3
4
5
Grado de descascaramiento después
de 150 ciclos (ASTM C 672)
Ceniza volante
50% de reemplazo Curado húmedo
250 kg/m 3 (417 lb/yd 3 ) 305 kg/m 3 (508 lb/yd 3 ) 335 kg/m 3 (588 lb/yd 3 )
Material cementante
Fig. 3-20. Relación entre la resistencia al descascaramiento por descongelantes y la cantidad de ceniza volante en concretos con aire incluido, producidos con relaciones agua-material cementante que varían de medianas a altas. Reemplazo de cemento portland por ceniza volante: (izquierda) 25% y (derecha) 50%. El grado 0 en la escala significa que no hubo descascaramiento y el grado 5 significa descascaramiento severo (Whiting 1989).
0
1
2
3
4
5
0.4 0.5 0.6 0.7 0.8 0.9 1 1.1 1.
Grado de descascaramiento
después de 50 ciclos
Relación agua-cemento portland
Curado húmedo
ASTM C 672
Fig. 3-19. Relación entre la resistencia al descascaramiento por descongelantes y la relación agua-cemento de varios concretos con aire incluido con y sin ceniza volante. El grado 0 en la escala significa que no hubo descas- caramiento y el grado 5 significa descascaramiento severo (Whiting 1989).
contenido de calcio F (ASTM C 618, AASHTO M 295) han reducido, en algunos casos, en más del 70% la expansión por la reactividad. Con una cantidad óptima, las cenizas Clase C (ASTM C 618, AASHTO M 295) también pueden reducir la reactividad, pero en un grado menor que las cenizas de la Clase F. Los materiales cementantes suple- mentarios proveen hidratos de silicato de calcio adicionales para fijar los álcalis en el concreto (Bhatty 1985 y Bhatty y Greening 1986). La determinación de la dosificación óptima del material cementante suplementario es impor- tante para maximizar la reducción de la reactividad y para evitar dosificaciones y materiales que pueden agravar la reactividad. La dosificación debe ser verificada a través de ensayos, tales como: ASTM C 1260 (AASHTO T 303), ASTM C 1293, NTP 334.117 y UNIT 1038. Los materiales cementantes suplementarios que reducen la reacción álcali-sílice no reducen la reacción álcali-carbonato, que es un tipo de reacción que envuelve los álcalis del cemento y ciertos calcáreos dolomíticos.
Con una correcta dosificación y selección de materiales, el humo de sílice, la ceniza volante, el esquisto calcinado y la escoria granulada pueden mejorar la resistencia del concreto al ataque de sulfatos o al agua de mar. Esto ocurre
generalmente pequeño y tiene poco significado práctico. Algunos estudios indican que el humo de sílice puede reducir la fluencia (Burg y Ost 1994).
Ceniza volante, escoria molida y puzolana natural general- mente reducen la permeabilidad y la absorción del concreto bien curado. El humo de sílice y la metacaolinita son especialmente eficientes en este sentido. El humo de sílice y la arcilla calcinada pueden producir un concreto con resistencia a los sulfatos de 1000 Coulombs, usando el ensayo acelerado de permeabilidad a cloruros ASTM C 1202 (Barrer y otros 1997). Las pruebas demuestran que la permeabilidad de los concretos disminuye a medida que la cantidad de material cementante hidratado aumenta y a medida que la relación agua-material cementante dismi- nuye. La absorción del concreto con ceniza volante es prácticamente la misma del concreto sin ceniza, a pesar que algunas cenizas pueden reducir la absorción en 20% o más.
La reactividad álcali-agregado se puede controlar a través del empleo de ciertos materiales cementantes suplementa- rios. El humo de sílice, la ceniza volante, la escoria granu- lada de alto horno, la arcilla calcinada, el esquisto calcinado y otras puzolanas pueden reducir considerablemente la reacción álcali-sílice (Fig. 3-21 y 3-22). Las cenizas de bajo
Diseño y Control de Mezclas de Concreto ◆^ EB
0
Expansión a 14 días ASTM C 1260, porcentaje 15% 25% 15% 25% 15% 25% 35% 50% Control Ceniza volante Bajo-CaO
Ceniza volante Mediano-CaO
Ceniza volante Alto-CaO
Escoria
Fig. 3-21. Efecto de diferentes cenizas volantes y escorias sobre la reactividad álcali-sílice. Observe que algunas cenizas volantes son más eficientes que otras en el control de la reacción y que la cantidad de ceniza volante y escoria es un factor crítico. Se ha empleado un agregado natural altamente reactivo en este ensayo. Un agregado menos reactivo necesitaría menos ceniza o escoria para el control de la reacción. Un límite usual para la evaluación de la eficiencia de puzolanas o escorias es 0.10% de expansión en el método de ensayo acelerado en barras de mortero (Detwiler 2002).
0
0 2 4 6 8 10 12
Expansión, porcentaje
Edad, meses
Sin puzolana
20% de esquisto calcinado
20% de arcilla calcinada
ASTM C 441 Cemento: 0.92% de álcalis Vidrio pirex
Fig. 3-22. Reducción de la reactividad álcali-sílice por la arcilla calcinada y el esquisto calcinado (Lerch 1950).
La cantidad óptima del material cementante suplementario usado con el cemento portland o con el cemento adicionado se determina a través de pruebas, en función del costo relativo y disponibilidad de los materiales y de las propiedades especificadas del concreto. Se necesitan varias mezclas de ensayo para determi- narse la cantidad óptima de puzolana o escoria. Estas mezclas deben cubrir una gama de combinaciones para establecerse la correlación entre resistencia y relación agua- material cementante. Estas mezclas se deben establecer de acuerdo con el ACI Standard 211.1 y 211.2, considerándose las masas específicas relativas de los materiales cemen- tantes suplementarios. Éstas normalmente son diferentes de la masa específica relativa del cemento portland. Los resultados de los ensayos dan origen a una familia de curvas de resistencia para cada edad en la cual el concreto debe obedecer a ciertos requisitos especificados. La dosifi- cación del material cementante suplementario normal- mente se expresa como un porcentaje de todos los materiales cementantes en la mezcla de concreto. El uso de ceniza volante, escoria, humo de sílice, arcilla calcinada o esquisto calcinado como una adición al cemento portland o como sustituto parcial del cemento portland es una práctica común en los Estados Unidos y algunos países de Latinoamérica. Los cementos adiciona- dos que ya poseen puzolana o escoria se diseñan para que se usen con o sin materiales cementantes suplementarios adicionales. Las mezclas de concreto con más de un material cementante suplementario también se usan. Por ejemplo, una mezcla de concreto puede contener cemento portland, ceniza volante y humo de sílice. Estas mezclas se llaman mezclas ternarias. Cuando la ceniza volante, la escoria, el humo de sílice o las puzolanas naturales se emplean en combinación con el cemento portland o el cemento adicionado, se debe probar la mezcla de concreto para demostrar si satisface a las propiedades del concreto nece- sarias en el proyecto.
No todos los materiales cementantes suplementarios están disponibles en todas las regiones. Consulte a los provee- dores sobre los materiales disponibles.
En la mayoría de los casos, la humedad no afecta el desem- peño físico de los materiales cementantes suplementarios. Sin embargo, se los debe mantener secos para evitar difi- cultades de manejo y descarga. La ceniza Clase C y el esquisto calcinado se deben mantener secos pues en con-
tacto con la humedad se fraguan y se endurecen. Los aparatos para manejo y almacenamiento de estos mate- riales son similares a aquéllos usados para el cemento. Modificaciones adicionales pueden ser necesarias cuando se usa humo de sílice, pues no tiene las mismas caracterís- ticas de los otros materiales cementantes suplementarios y su abastecimiento puede ser en líquido. Estos materiales normalmente se mantienen en instala- ciones de almacenamiento a granel o silos, a pesar de que ciertos materiales están disponibles en bolsas. Como estos materiales se parecen al cemento portland en cuanto al color y a la finura, las instalaciones de almacenamiento se deben marcar claramente para evitar la posibilidad del uso indebido y de la contaminación con otros materiales en la planta de mezclado. Todas las válvulas y tuberías se deben marcar claramente y se deben sellar adecuadamente para evitar vaciamiento y contaminación. La ceniza volante, la escoria y las puzolanas naturales se deben pesar después del cemento portland o del cemento adicionado en la secuencia del mezclado para evitarse una sobredosis en caso de que las válvulas se obstruyan.
AASHTO, Guide Specification on Alkali-Silica Reaction (Especificación sobre las reacción Álcali-Sílice) , Section 56, http://leadstates.tamu.edu/ASR/library/gspec.stm ,
Abrams, Duff A., “Effect of Hydrated Lime and Other Powdered Admixtures in Concrete (Efecto de la Cal Hidratada y de Otros Aditivos Minerales en el Concreto),” Proceedings of the American Society for Testing Materials, Vol. 20, Part 2, 1920. Reprinted with revisions as Bulletin 8, Structural Materials Research Laboratory, Lewis Institute, Junio 1925, 78 páginas. Disponible a través de la PCA como LS08.
ACAA, http://www.acaa-usa.org, American Coal Ash Association, Alexandria, Virginia, 2001. ACI, Concrete Durability (Durabilidad del Concreto), Katherine and Bryant Mather International Conference, SP100, American Concrete Institute, Farmington Hills, Michigan, 1987.
ACI Committee 211, Standard Practice for Selecting Proportions for Normal, Heavyweight, and Mass Concrete (Práctica Estándar para la Elección de las Proporciones de los Concretos Normal, Pesado y Masivo), ACI 211.1-91, American Concrete Institute, Farmington Hills, Michigan, 1991, 38 páginas.
ACI Committee 211, Standard Practice for Selecting Proportions for Structural Lightweight Concrete (Práctica Estándar para la Elección de las Proporciones de los Concretos Normal, Pesado y Masivo), ACI 211.2-98, American Concrete Institute, Farmington Hills, Michigan, 1998, 14 páginas.
Diseño y Control de Mezclas de Concreto ◆^ EB
ACI Committee 211, Guide for Selecting Proportions for High Strength Concrete with Portland Cement and Fly Ash (Guía para la Elección de las Proporciones del Concreto de Alta Resistencia con Cemento Portland y Ceniza Volante), ACI 211.4R-93, American Concrete Institute, Farmington Hills, Michigan, 1993, 13 páginas.
ACI Committee 232, Use of Fly Ash in Concrete (Uso de la Ceniza Volante en el Concreto), ACI 232.2R-96, American Concrete Institute, Farmington Hills, Michigan, 1996, 34 páginas.
ACI Committee 232, Use of Raw or Processed Natural Pozzolans in Concrete (Uso de Puzolana Cruda o Puzolana Natural Procesada en el Concreto), ACI 232.1R-00, American Concrete Institute, Farmington Hills, Michigan, 2001, 24 páginas.
ACI Committee 233, Ground Granulated Blast-Furnace Slag as a Cementitious Constituent in Concrete (Escoria Granulada de Alto Horno Molida como un Material Componente en el Concreto), ACI 233R-95, American Concrete Institute, Farmington Hills, Michigan, 1995, 18 páginas.
ACI Committee 234, Guide for the Use of Silica Fume in Concrete (Guía para el uso del Humo de Sílice en el Concreto), ACI 234R-96, American Concrete Institute, Farmington Hill, Michigan, 1996, 51 páginas.
Barger, Gregory S.; Lukkarila, Mark R.; Martin, David L.; Lane, Steven B.; Hansen, Eric R.; Ross, Matt W.; y Thompson, Jimmie L., “Evaluation of a Blended Cement and a Mineral Admixture Containing Calcined Clay Nat- ural Pozzolan for High-Performance Concrete (Evaluación de los Cementos Adicionados y de los Aditivos Minerales que Contienen Puzolanas Naturales de Arcilla Calcinada para el Concreto de Alto Desempeño),” Proceedings of the Sixth International Purdue Conference on Concrete Pavement Design and Materials for High Performance, Purdue University, West Lafayette, Indiana, 1997, 21 páginas.
Bhatty, M. S. Y., “Mechanism of Pozzolanic Reactions and Control of Alkali-Aggregate Expansion (Mecanismo de las Reacciones Puzolánicas y Control de la Expansión Álcali- Agregado),” Cement, Concrete, and Aggregates, American Society for Testing and Materials, West Conshohocken, Penn- sylvania, Invierno 1985, páginas 69 a 77.
Bhatty, M. S. Y., y Greening, N. R., “Some Long Time Studies of Blended Cements with Emphasis on Alkali- Aggregate Reaction (Algunos Estudios a Largo Plazo de Cementos Adicionados con Énfasis en la Reacción Álcali- Agregado),” 7th International Conference on Alkali-Aggregate Reaction, 1986.
Buck, Alan D., y Mather, Katharine, Methods for Controlling Effects of Alkali-Silica Reaction (Métodos para el Control de los Efectos de la Reacción Álcali-Sílice), Technical Report SL-87-6, Waterways Experiment Station, U.S. Army Corps of Engineers, Vicksburg, Mississippi, 1987.
Burg, R. G., y Ost, B. W., Engineering Properties of Commercially Available High-Strength Concretes – Including Three-Year Data (Propiedades de Ingeniería de los Concretos de Alta Resistencia Comercialmente Disponibles (Incluyendo tres años de datos), Research and Development Bulletin RD104, Portland Cement Association, 1994, 62 páginas.
Campbell, D. H.; Sturm, R. D.; y Kosmatka, S. H., “Detecting Carbonation (Detección de la Carbonatación),” Concrete Technology Today, PL911, Portland Cement Associ- ation, http://www.portcement.org/pdf_files/PL911.pdf, Marzo 1991, páginas 1 a 5. Carette, G. G., y Malhotra, V. M., “Mechanical Properties, Durability, and Drying Shrinkage of Portland Cement Concrete Incorporating Silica Fume (Propiedades Mecá- nicas, Durabilidad y Contracción por Secado del Concreto de Cemento Portland con Incorporación de Humo de Sílice),” Cement, Concrete, and Aggregates, American Society for Testing and Materials, West Conshohocken, Pennsylvania, Verano 1983. Cohen, Menashi, D., y Bentur, Arnon, “Durability of Portland Cement-Silica Fume Pastes in Magnesium Sulfate and Sodium Sulfate Solutions (Durabilidad de las Pastas de Cemento Portland con Humo de Sílice en Soluciones de Sulfato de Magnesio y Sulfato de Sodio),” ACI Materials Journal, American Concrete Institute, Farmington Hills, Michigan, Mayo-Junio 1988, páginas 148 a 157.
Detwiler, Rachel J., “Controlling the Strength Gain of Fly Ash Concrete at Low Temperature (Control del Desarrollo de la Resistencia del Concreto con Ceniza Volante a Baja Temperatura),” Concrete Technology Today, CT003, Portland Cement Association, http://www.portcement.org/pdf_ files/CT003.pdf, 2000, páginas 3 a 5.
Detwiler, Rachel J., Documentation of Procedures for PCA’s ASR Guide Specification (Documentación de los Procedimientos para la Guía de especificación de la RAS de PCA), SN 2407, Portland Cement Association, 2002.
Detwiler, Rachel J.; Bhatty, Javed I.; y Bhattacharja, Sankar, Supplementary Cementing Materials for Use in Blended Cements (Materiales Cementantes Suplementarios para el Uso en Cementos Adicionados), Research and Development Bulle- tin RD112, Portland Cement Association, 1996, 108 páginas.
Farny, J. A., y Kosmatka, S. H., Diagnosis and Control of Alkali-Aggregate Reactivity (Diagnóstico y Control de la Reactividad Álcali-Agregado), IS413, Portland Cement Association, 1997, 24 páginas.
Gaynor, R. D., y Mullarky, J. I., “Survey: Use of Fly Ash in Ready-Mixed Concrete (Levantamiento: Uso de la Ceniza Volante en el Concreto Premezclado),” NRMCA Technical Information Letter No. 426, National Ready Mixed Concrete Association, Silver Spring, Maryland, Junio 1985.
Capítulo 3 ◆^ Ceniza Volante, Escoria, Humo de Sílice y Puzolanas Naturales