
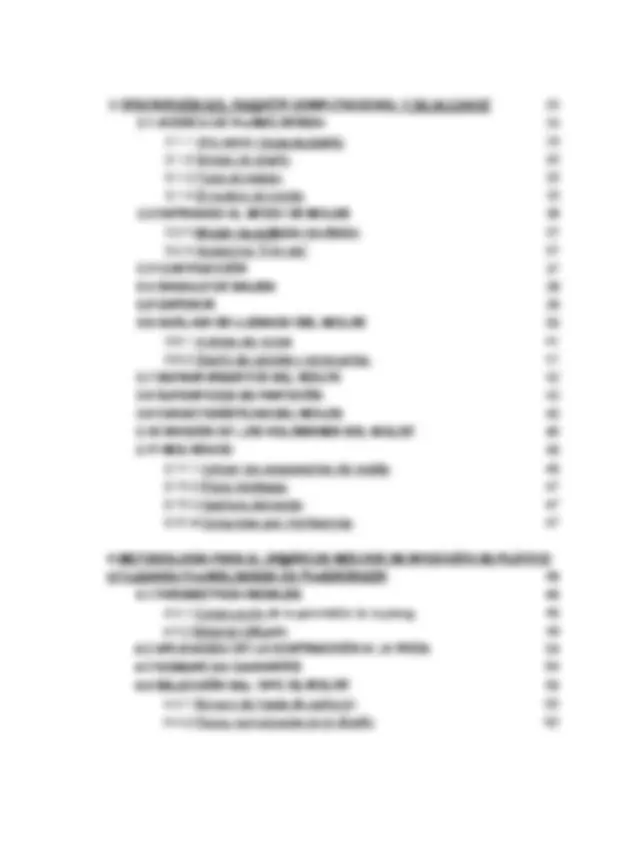
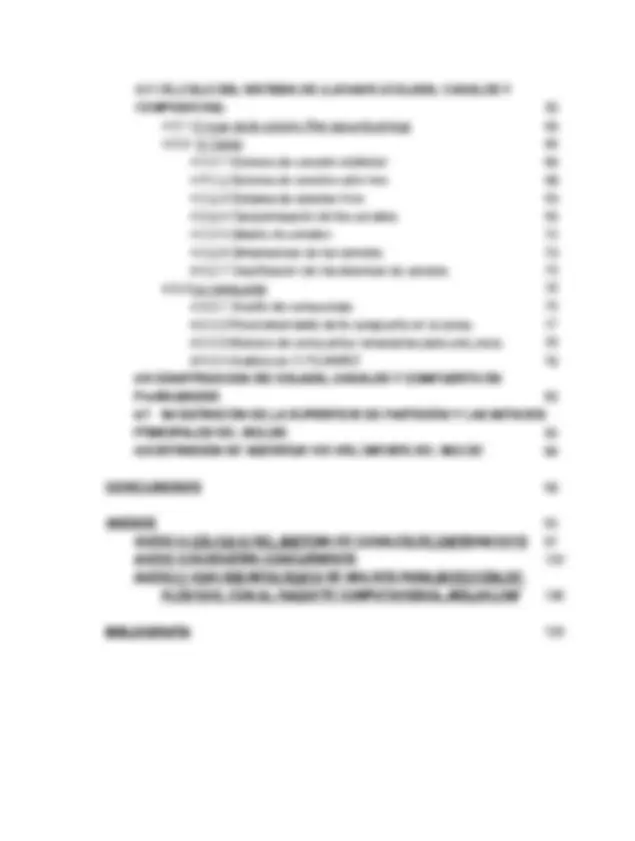
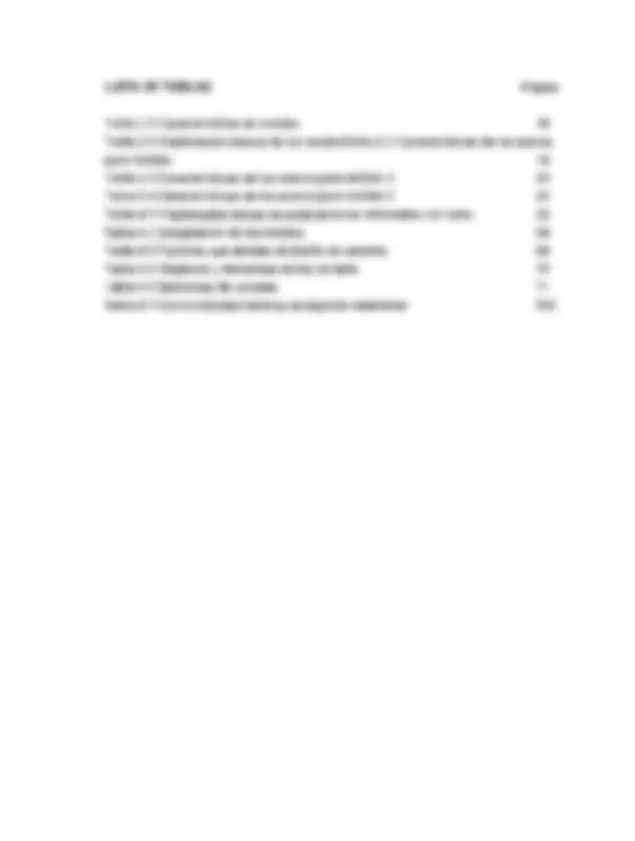
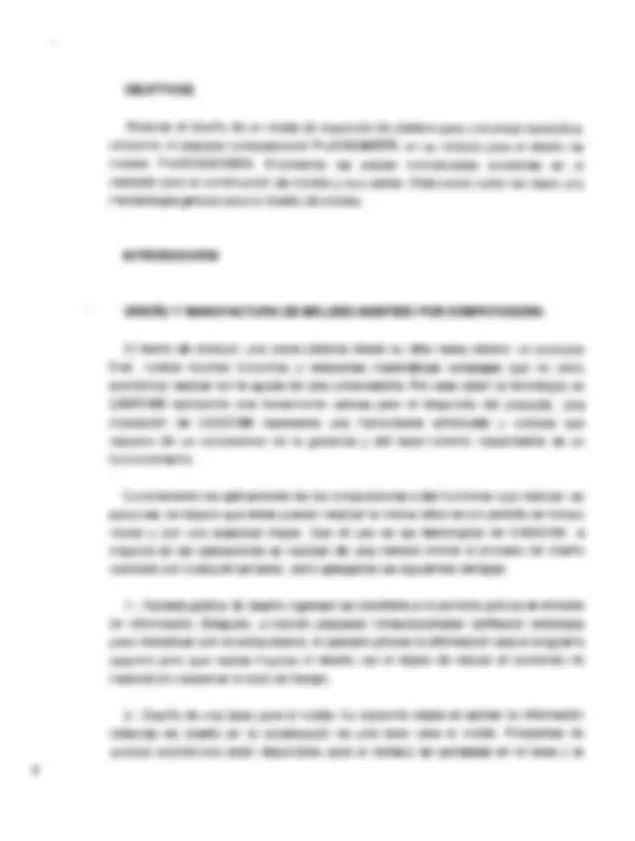
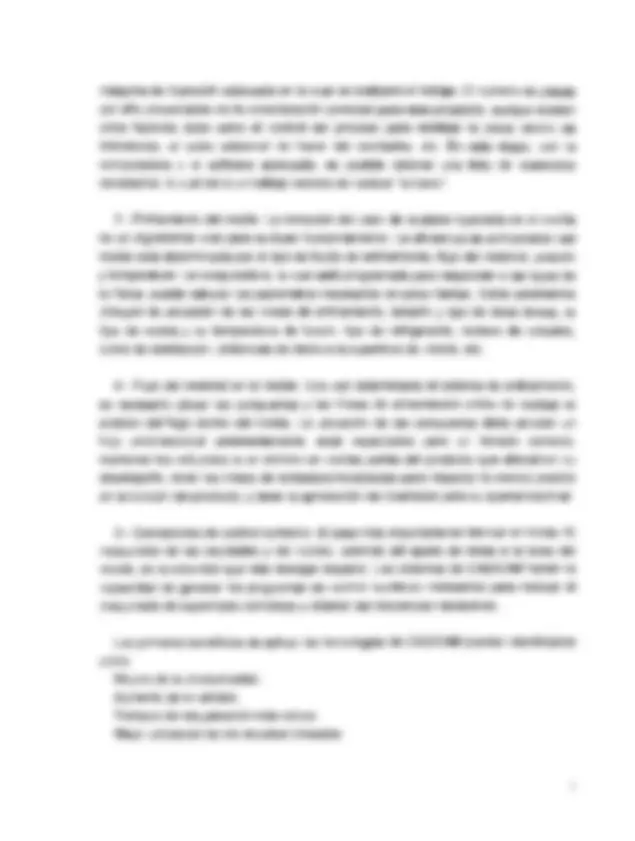
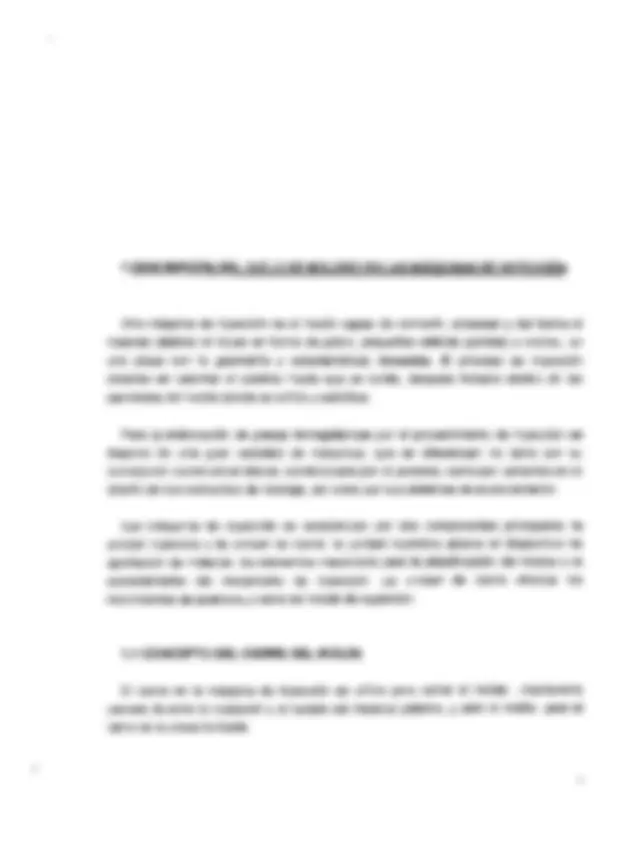
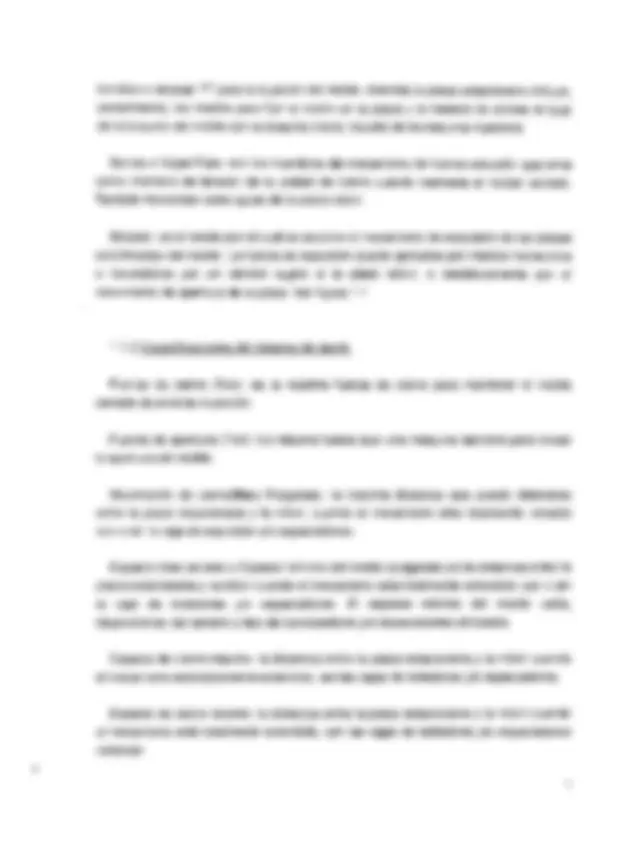
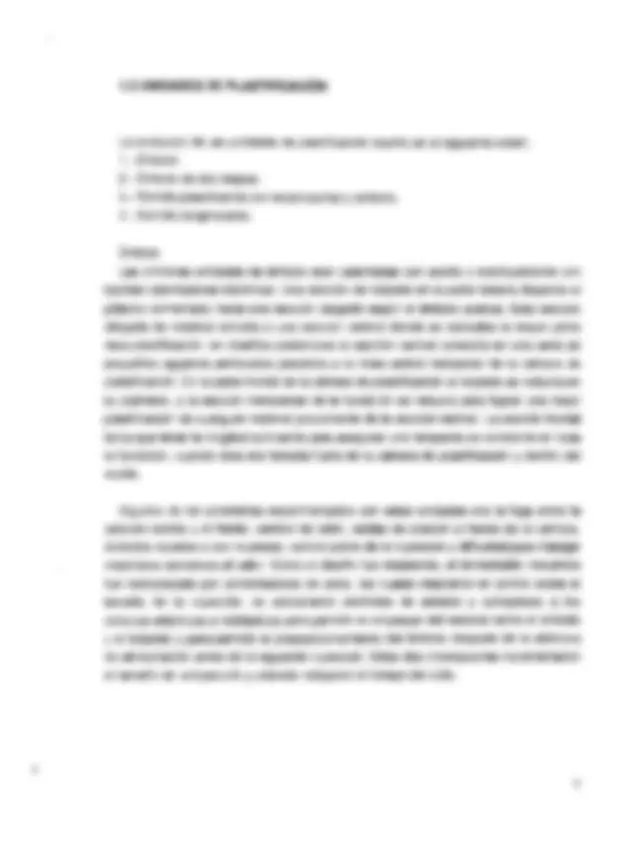
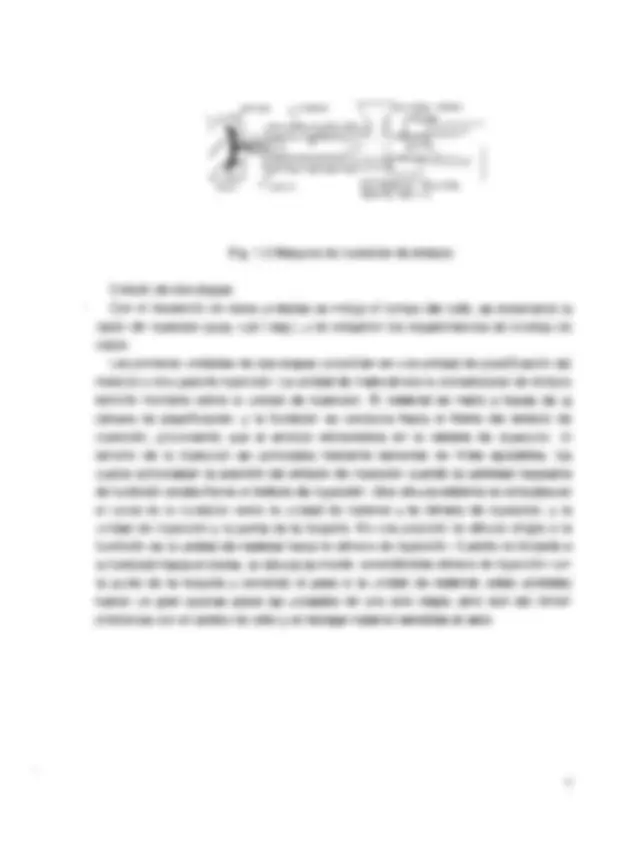
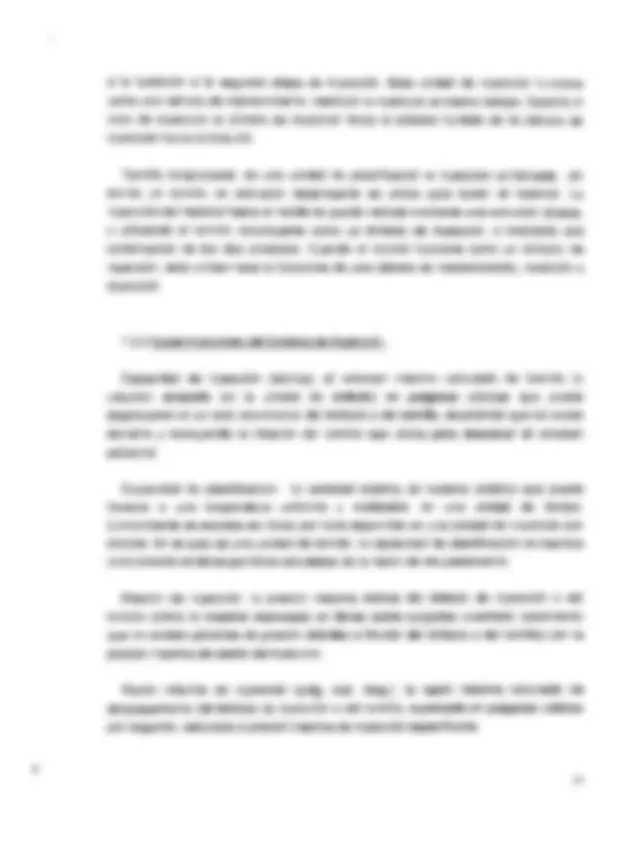
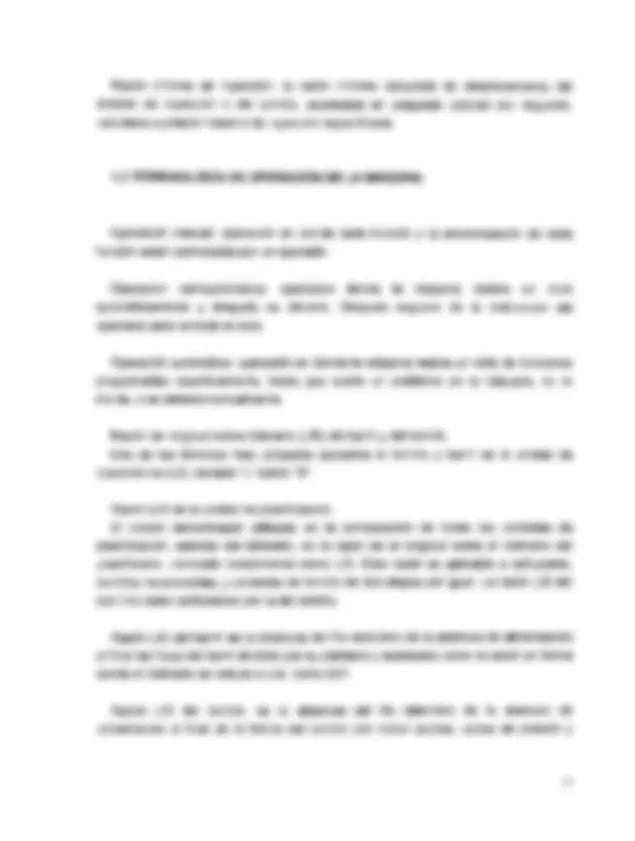
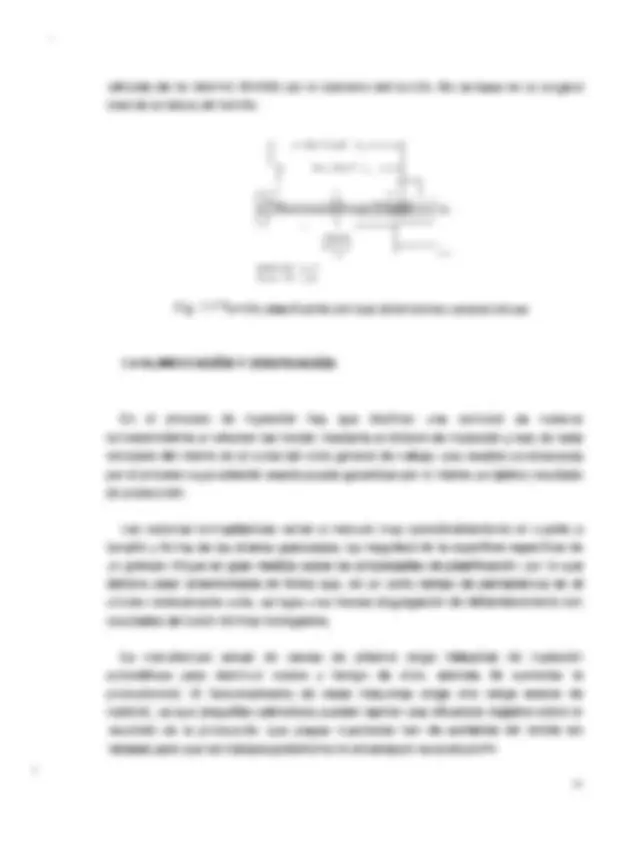
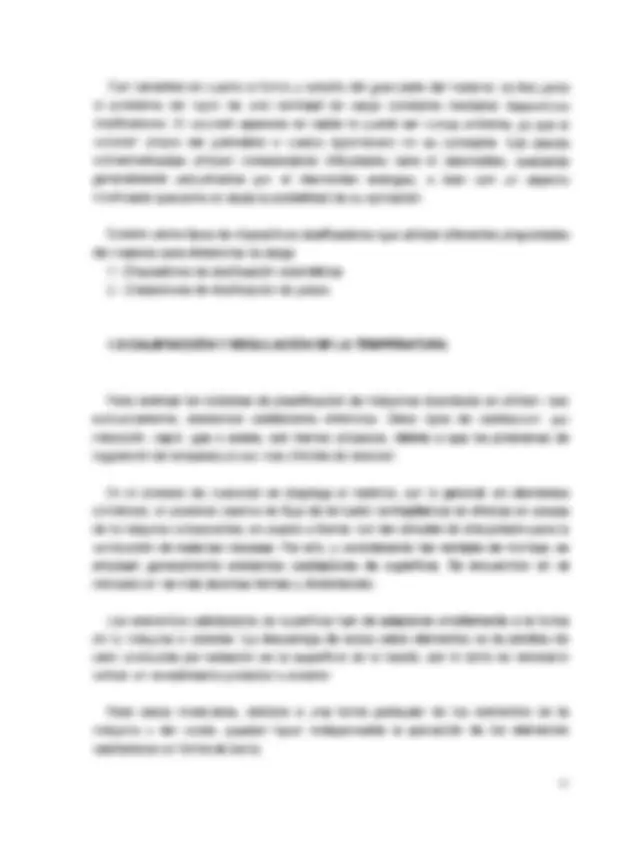
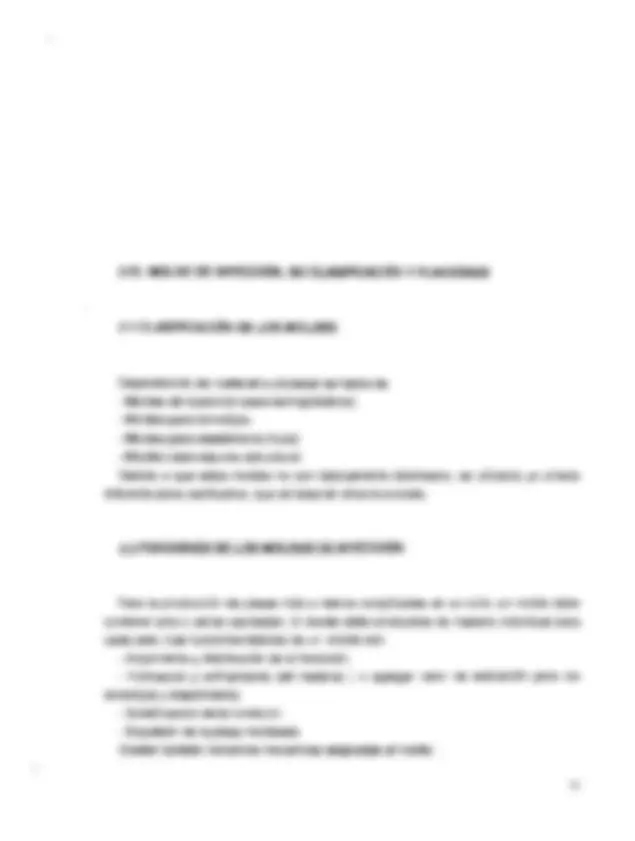
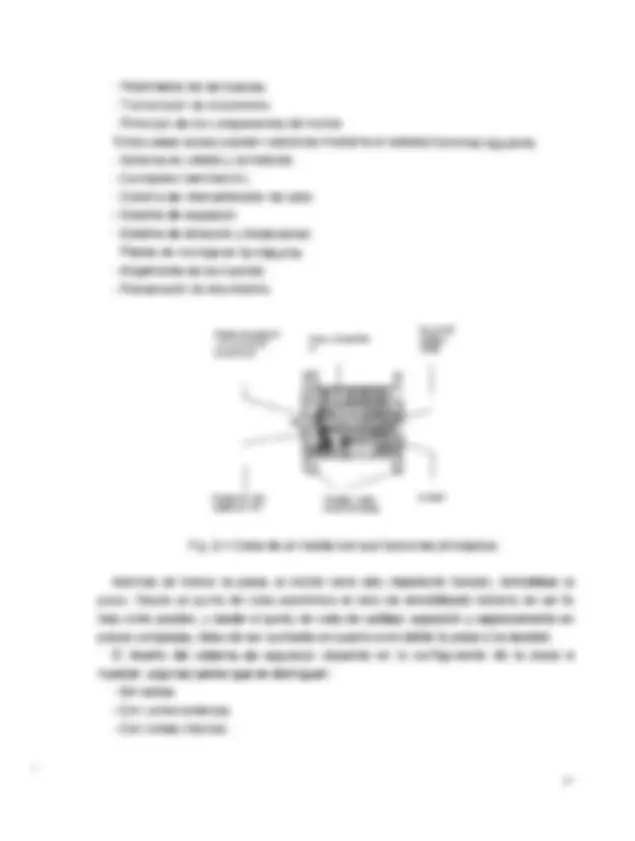
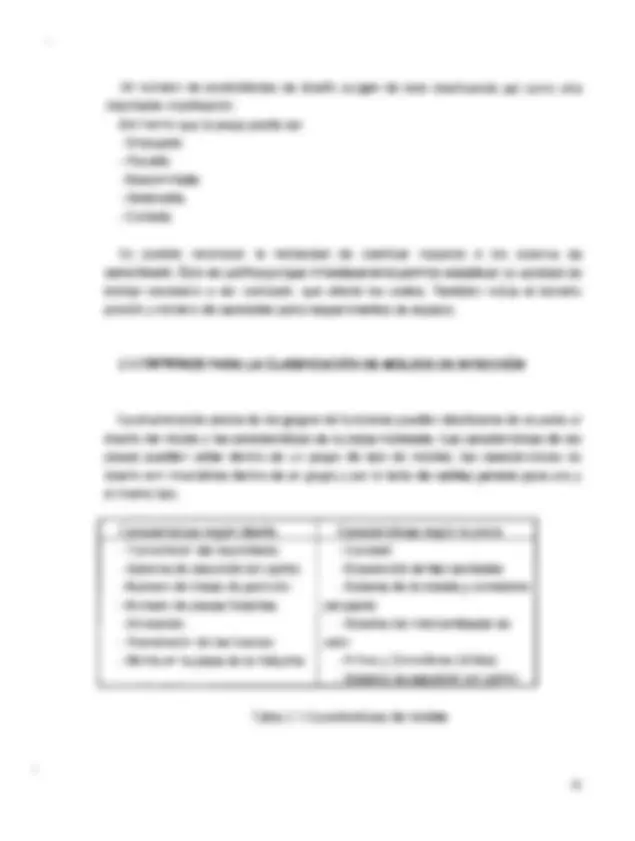
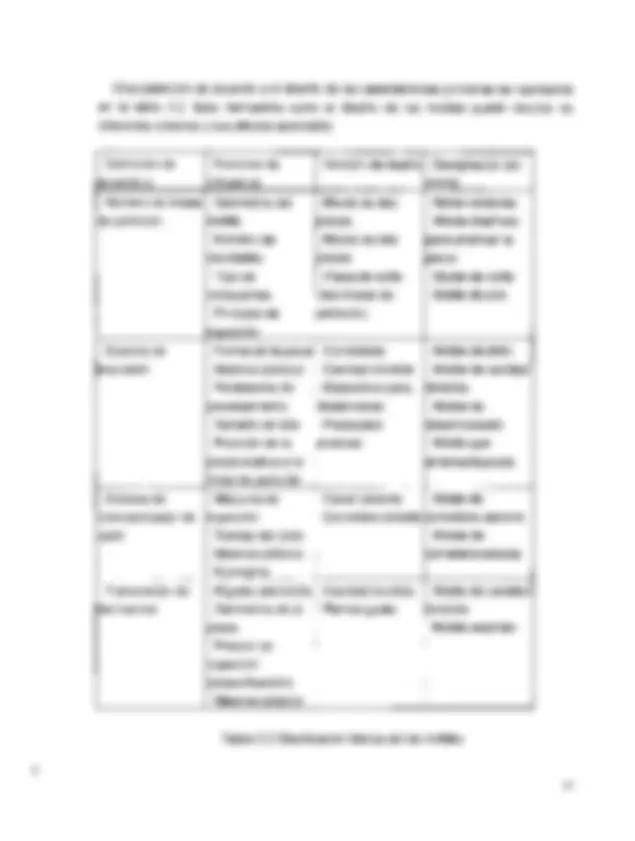
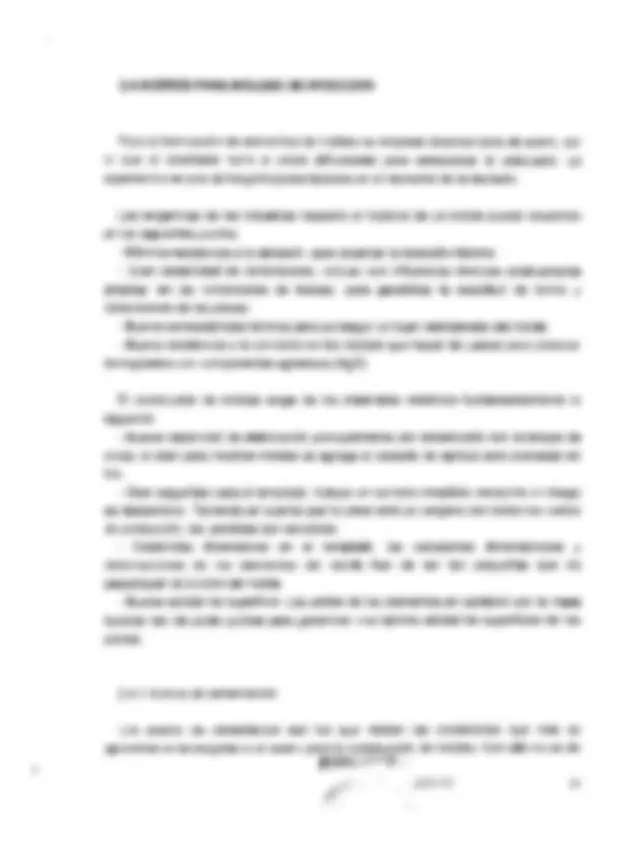
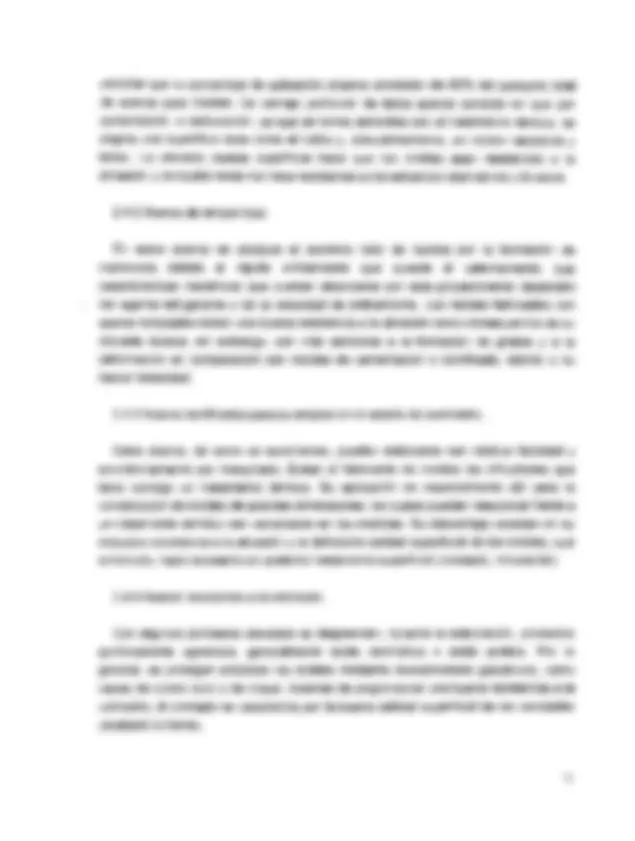
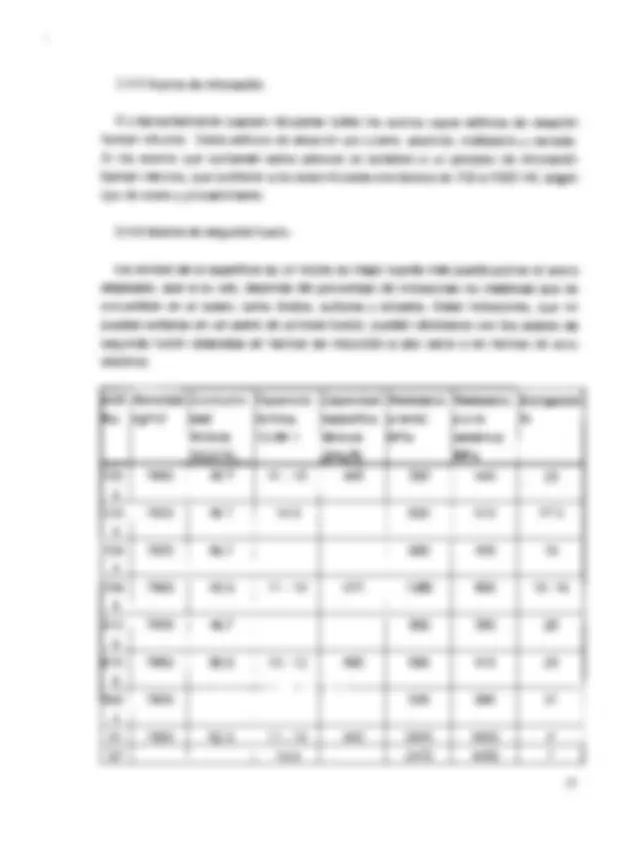
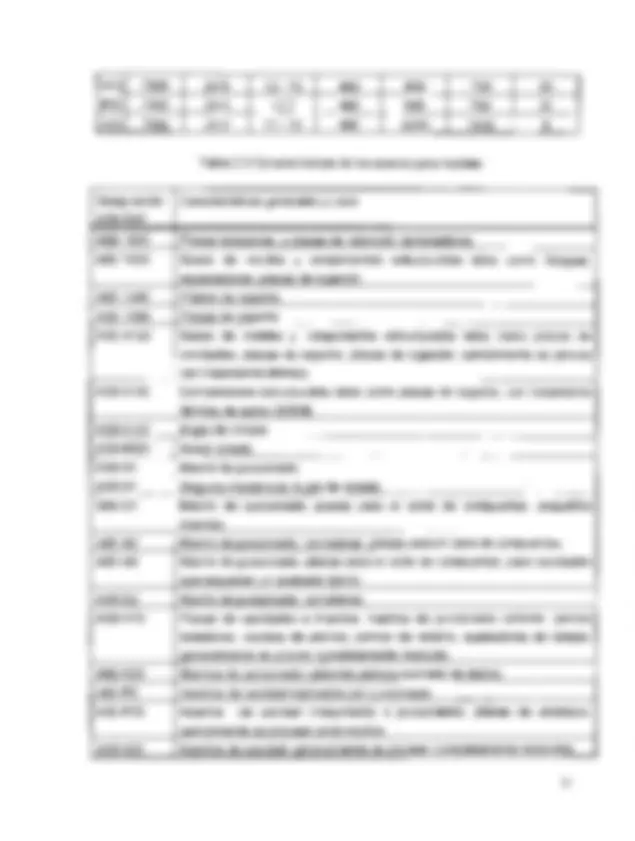

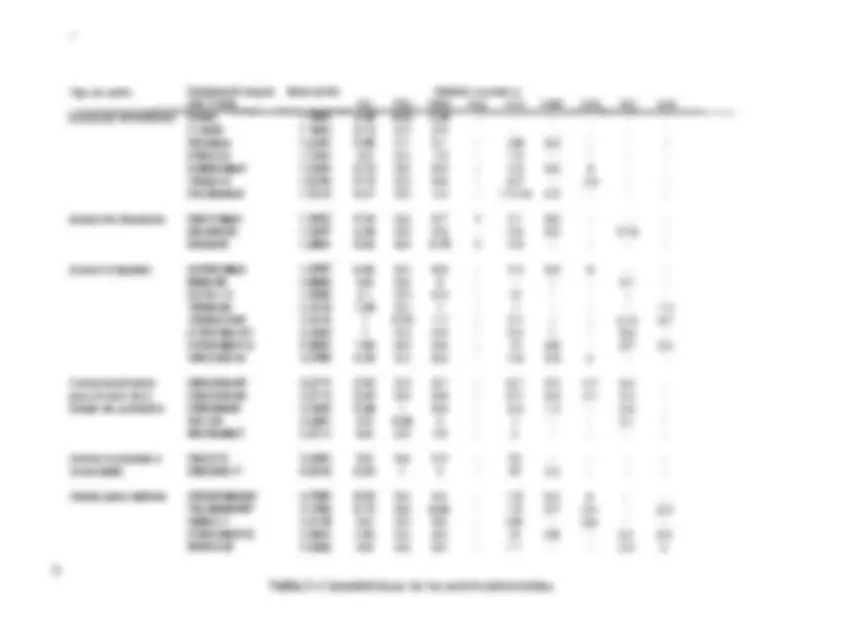
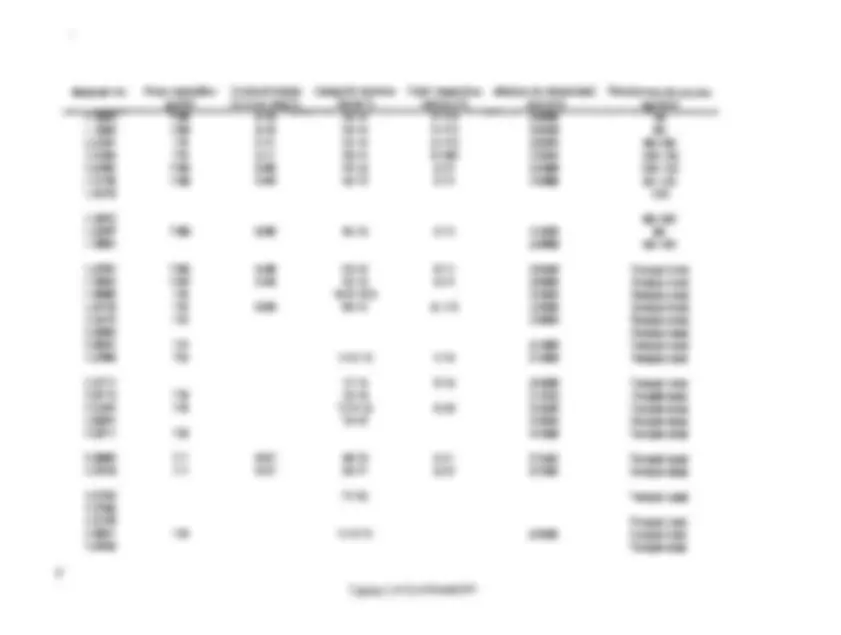
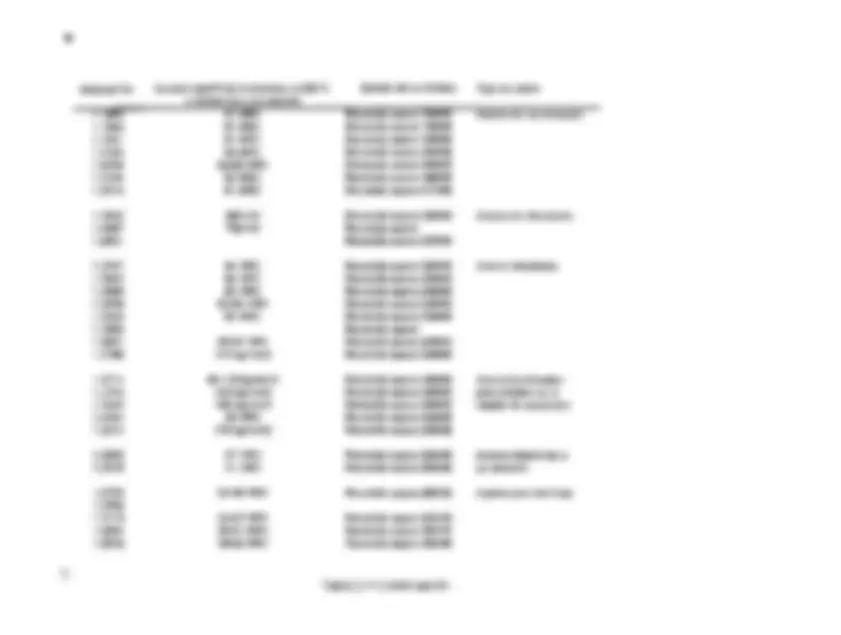
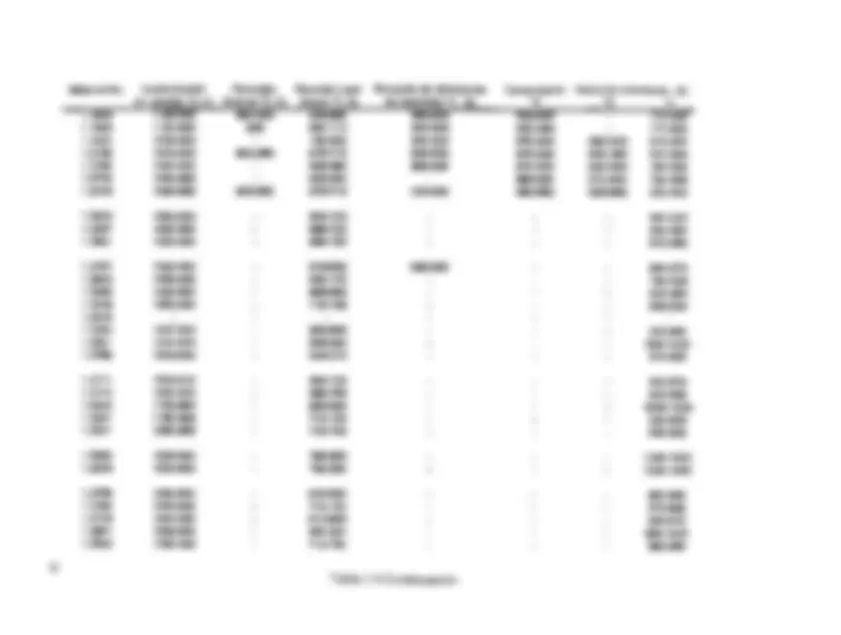
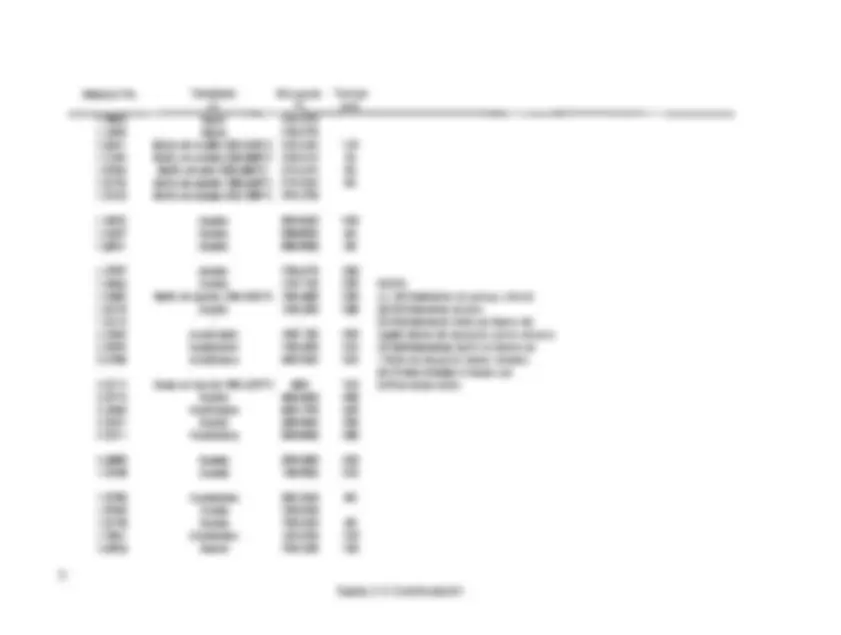
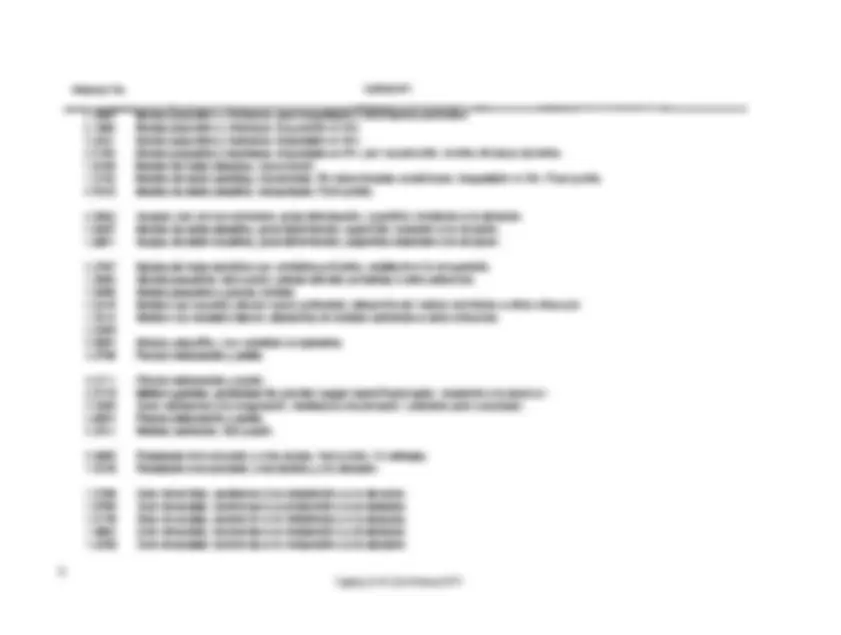
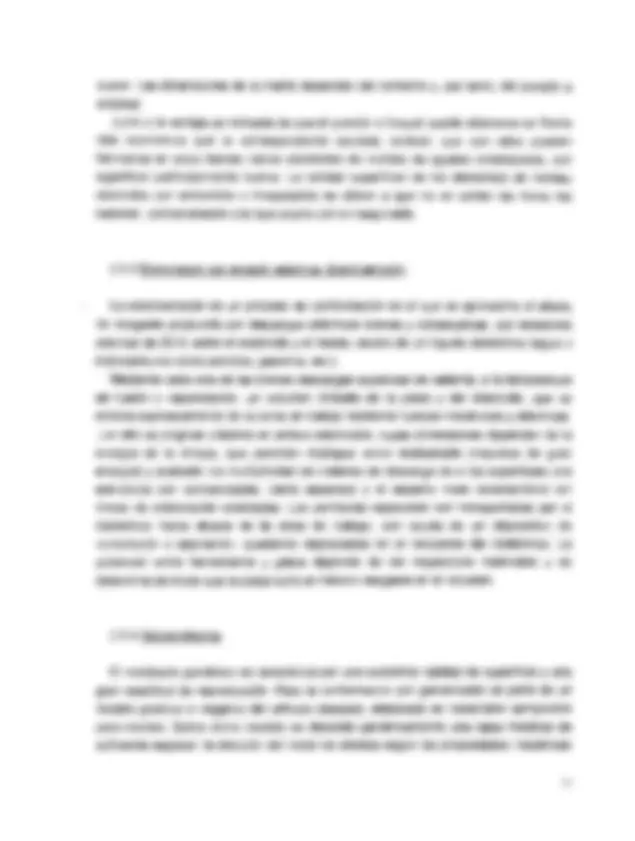
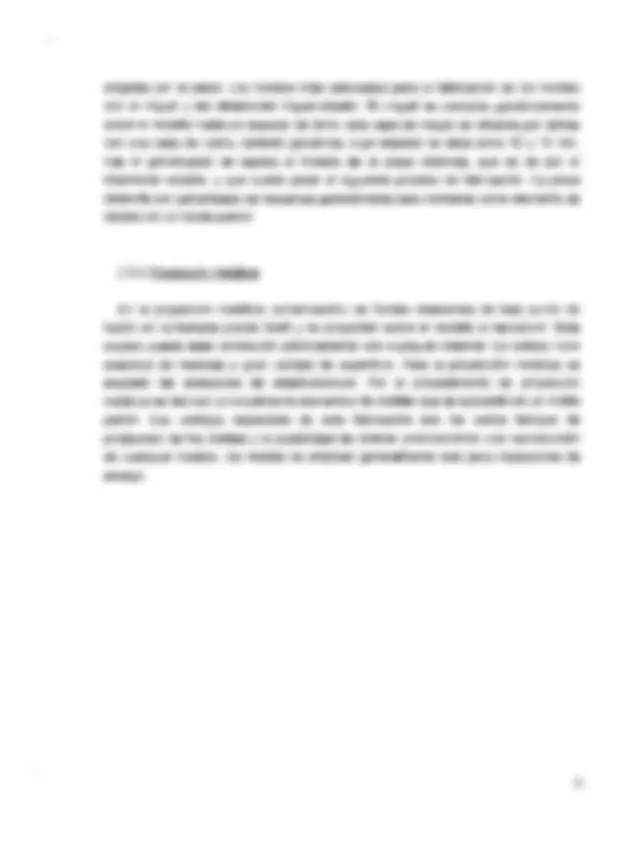
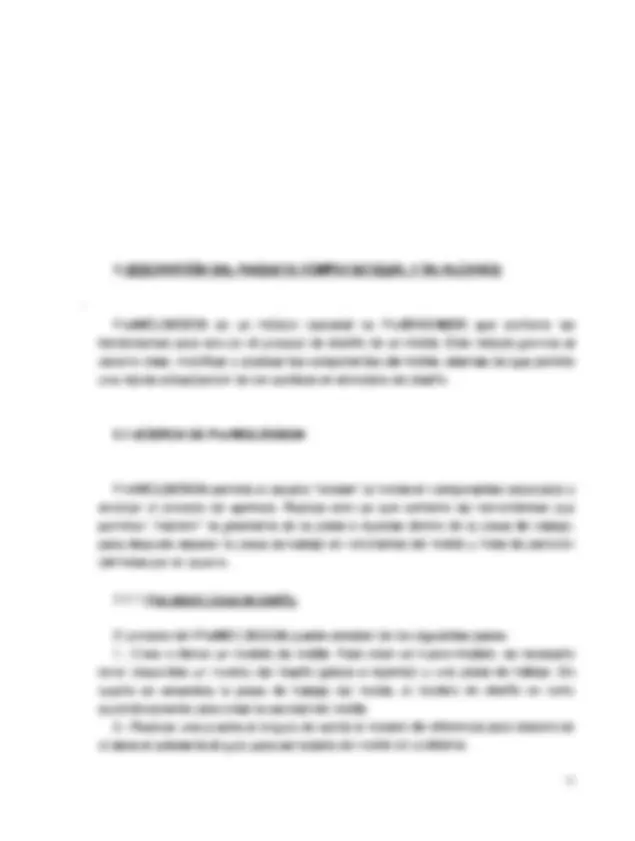
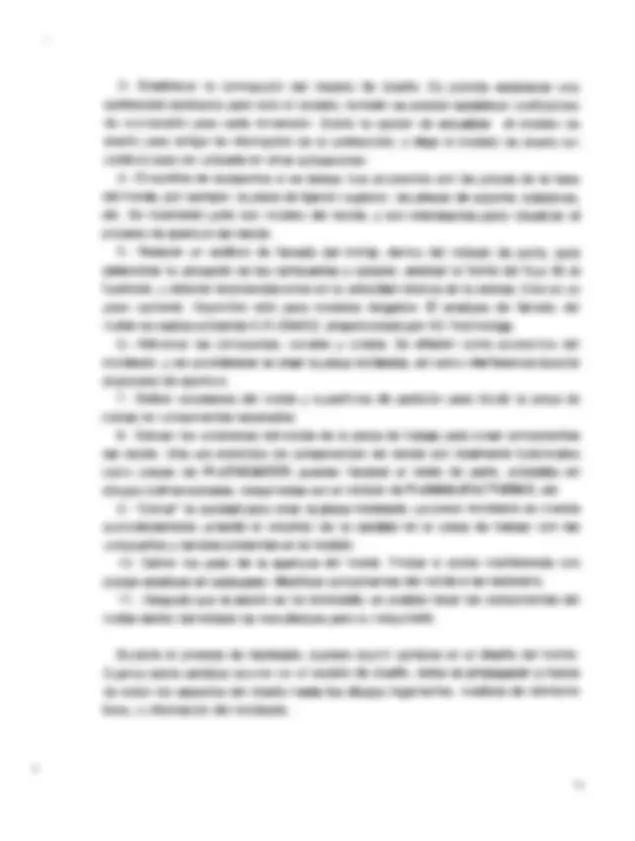

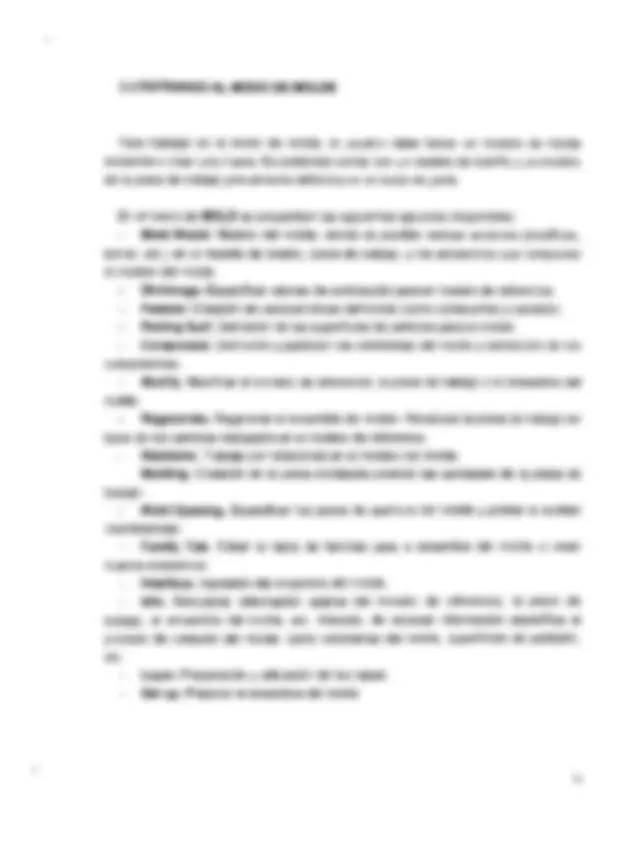
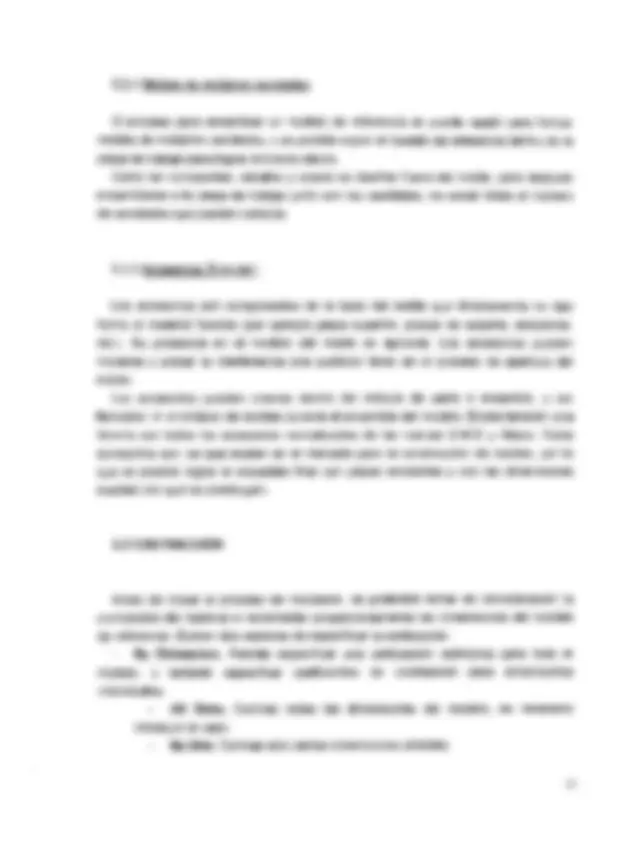
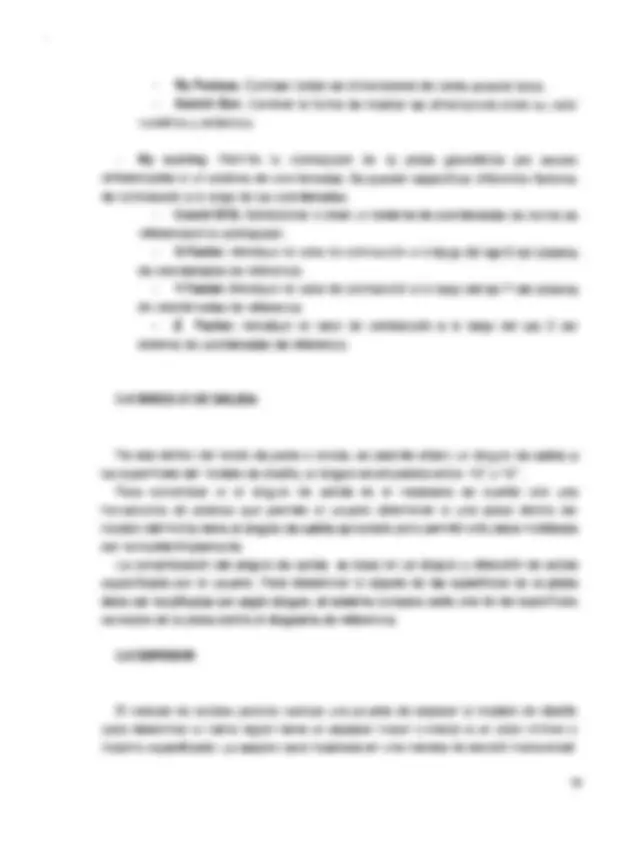
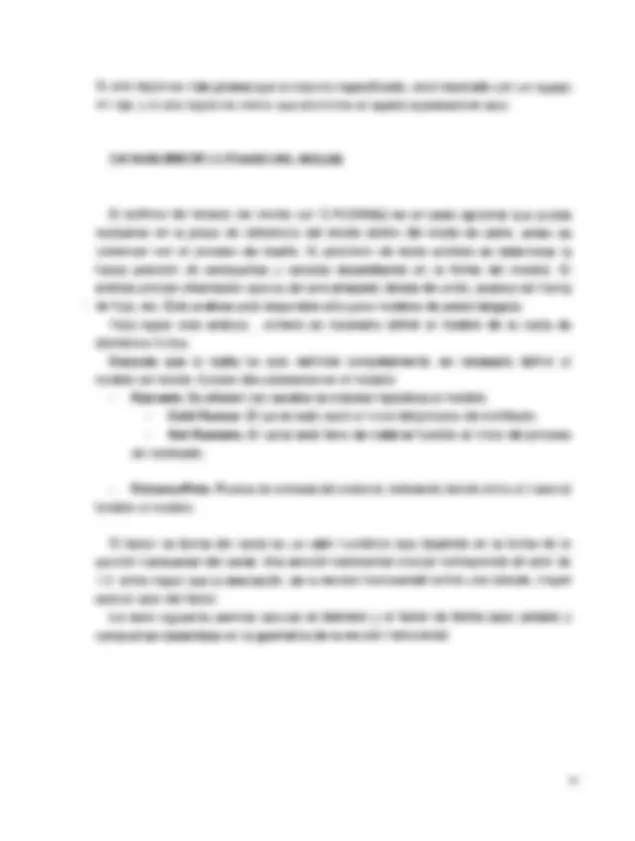
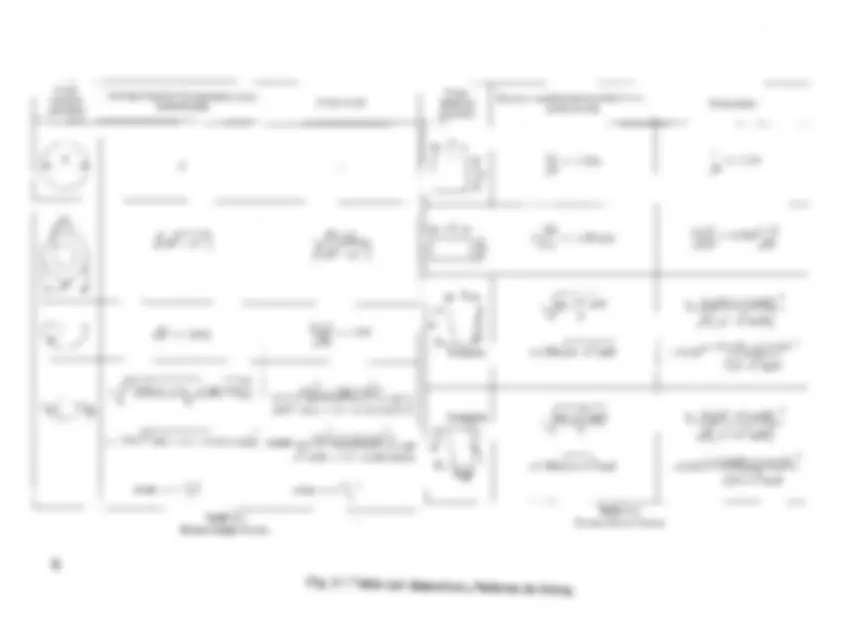
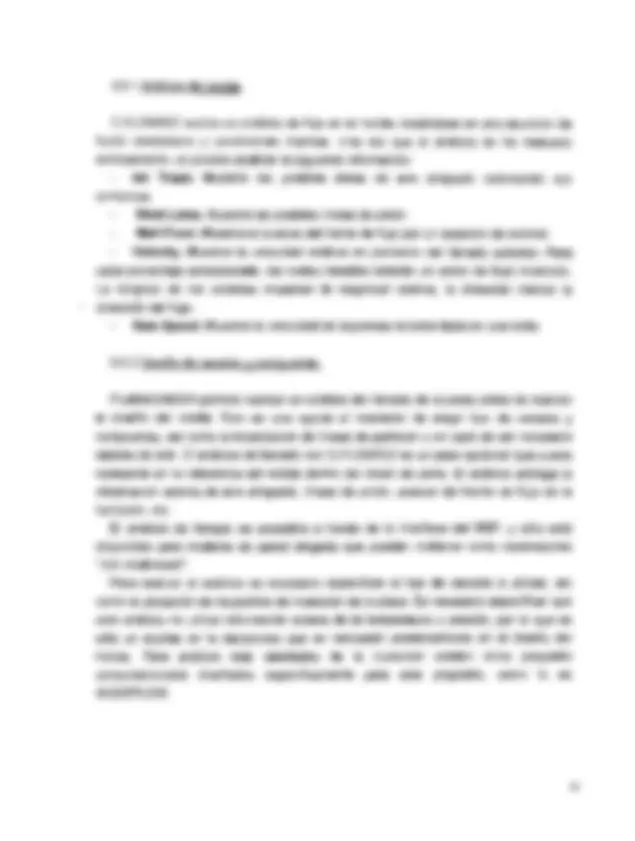
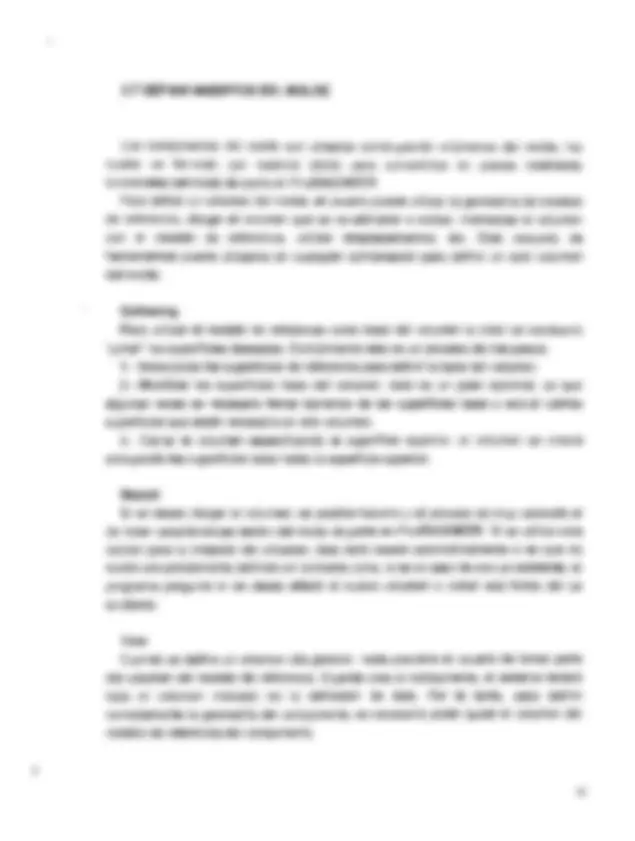
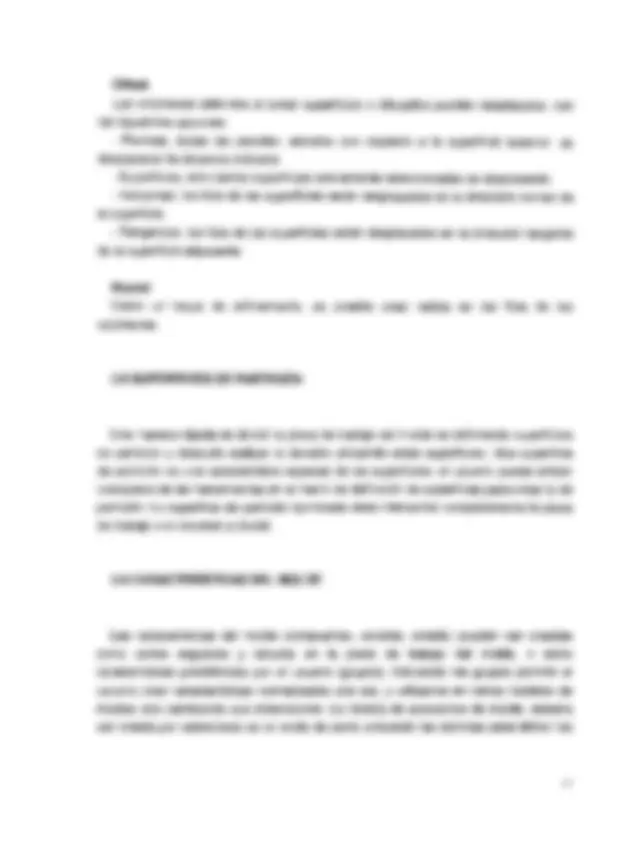
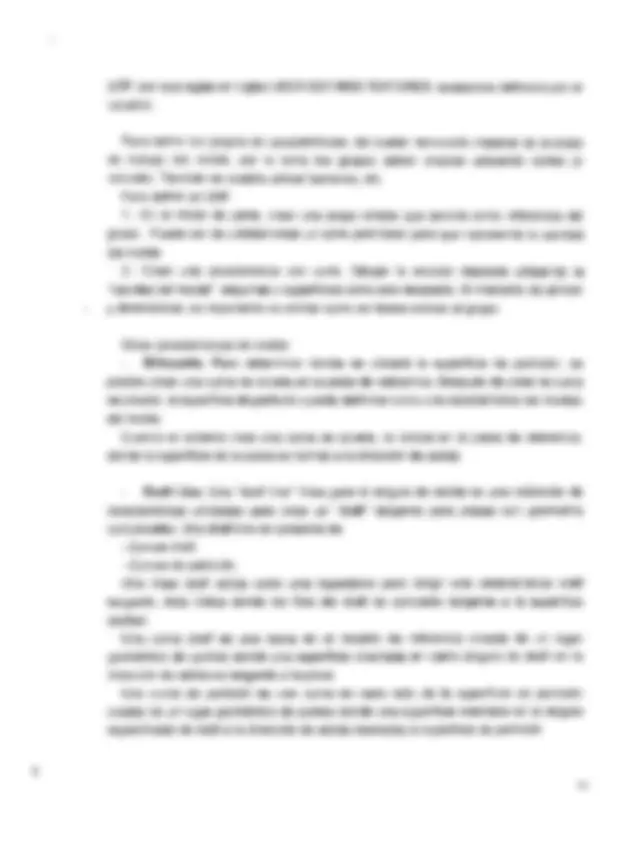
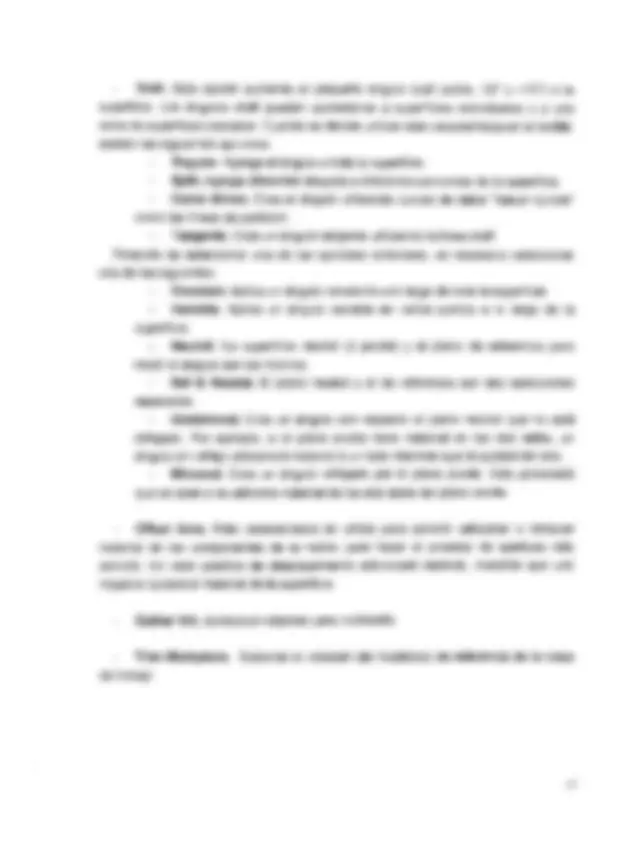
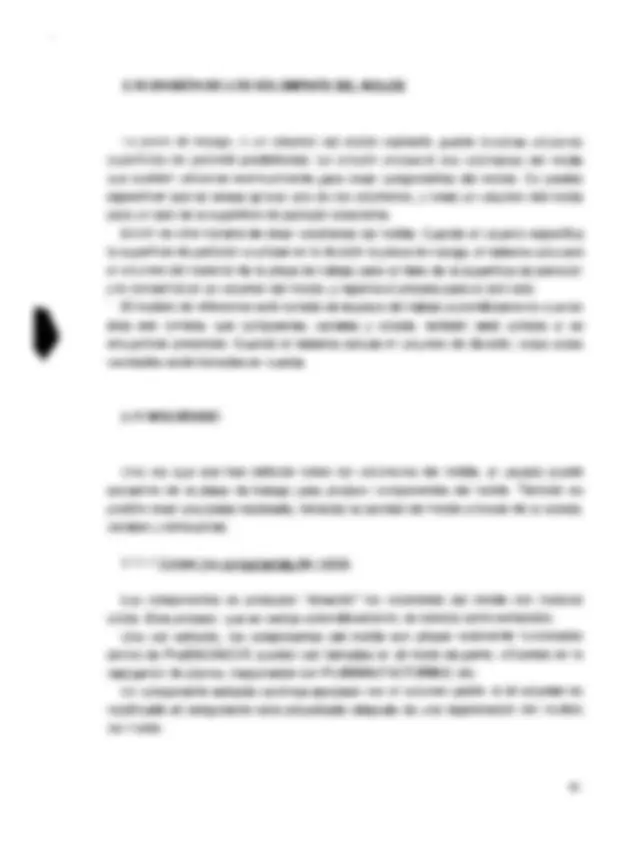
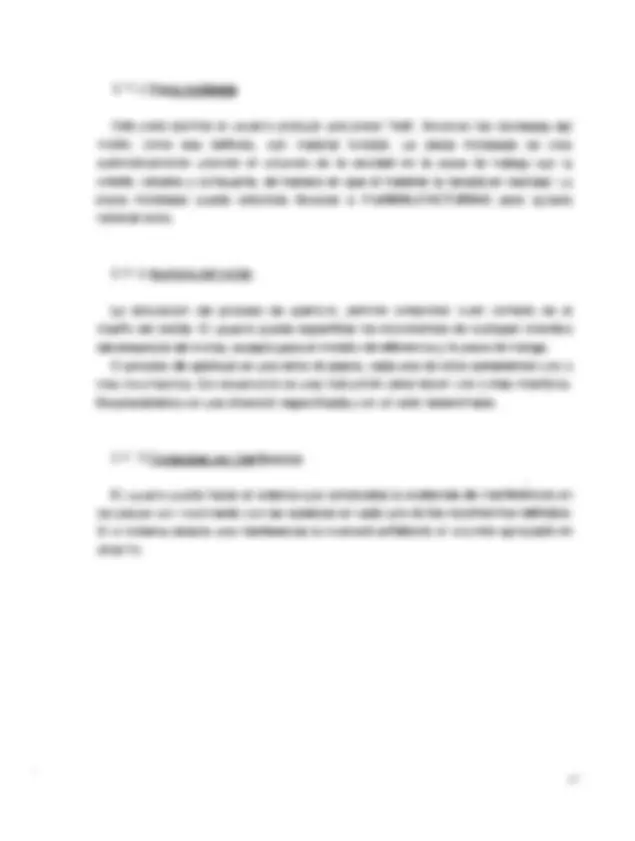
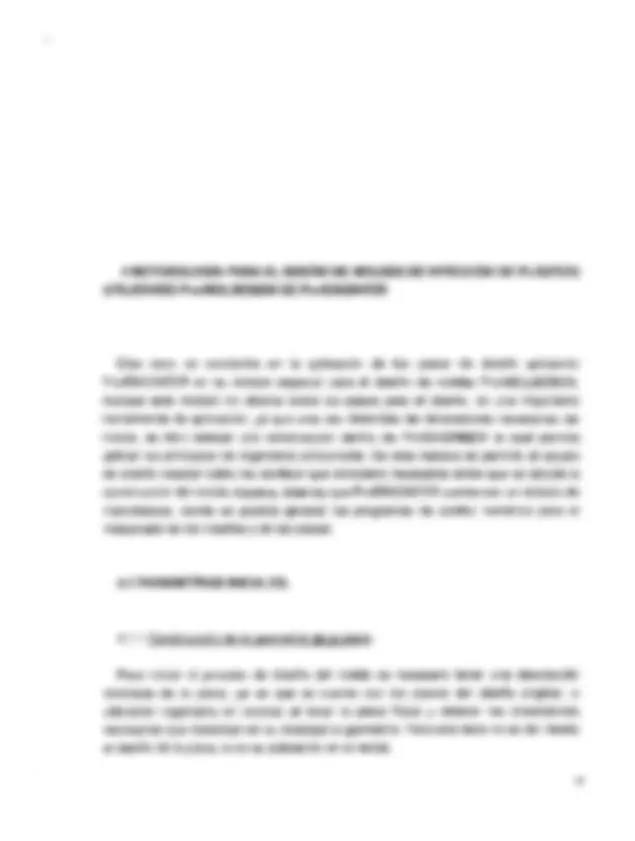
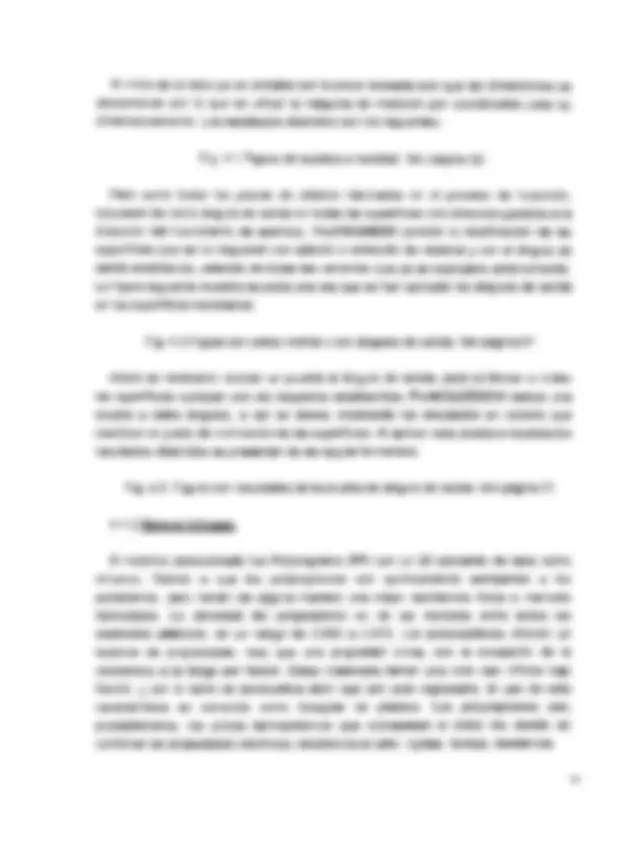
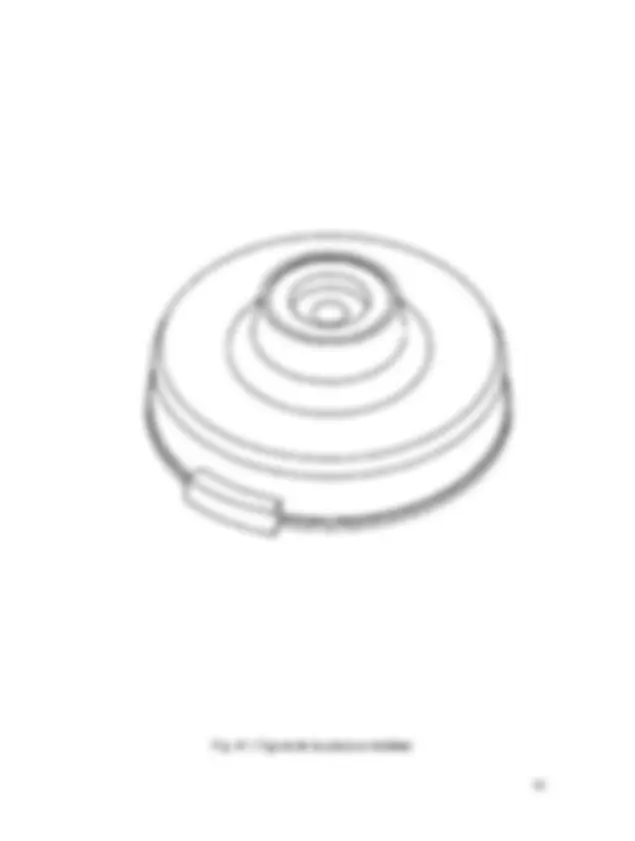
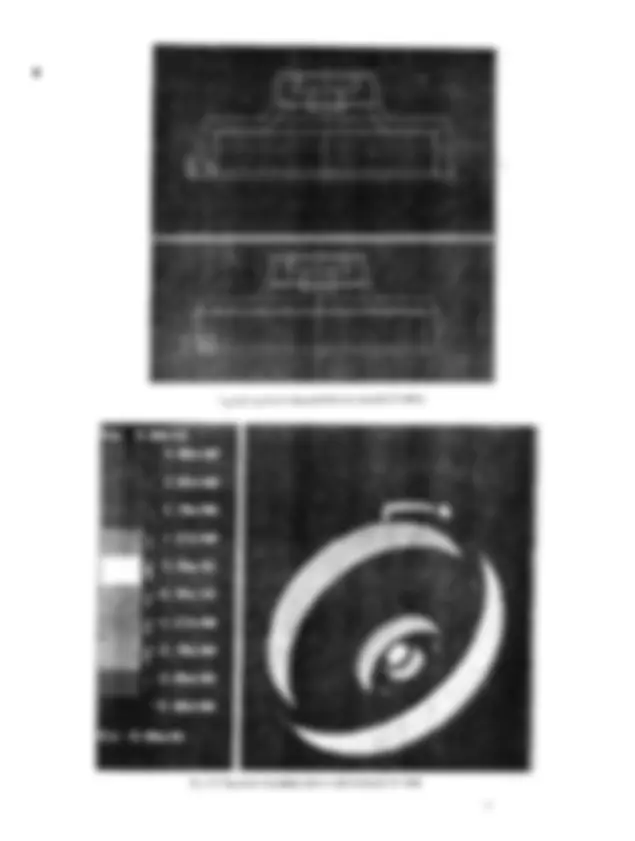
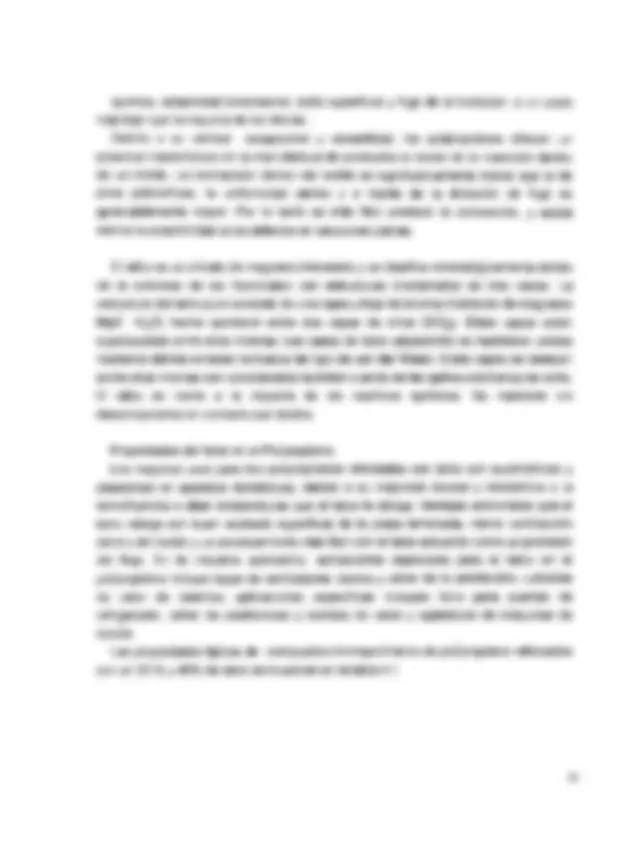
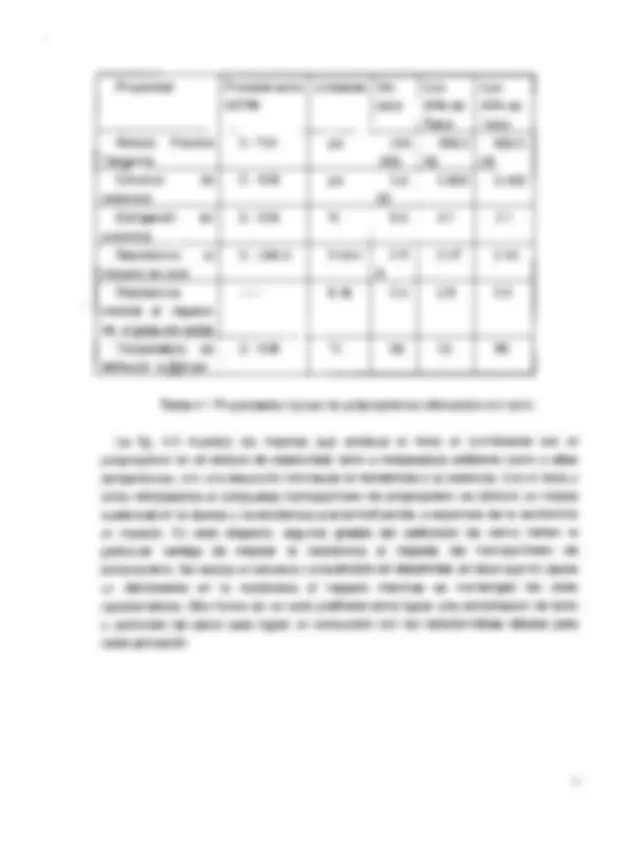
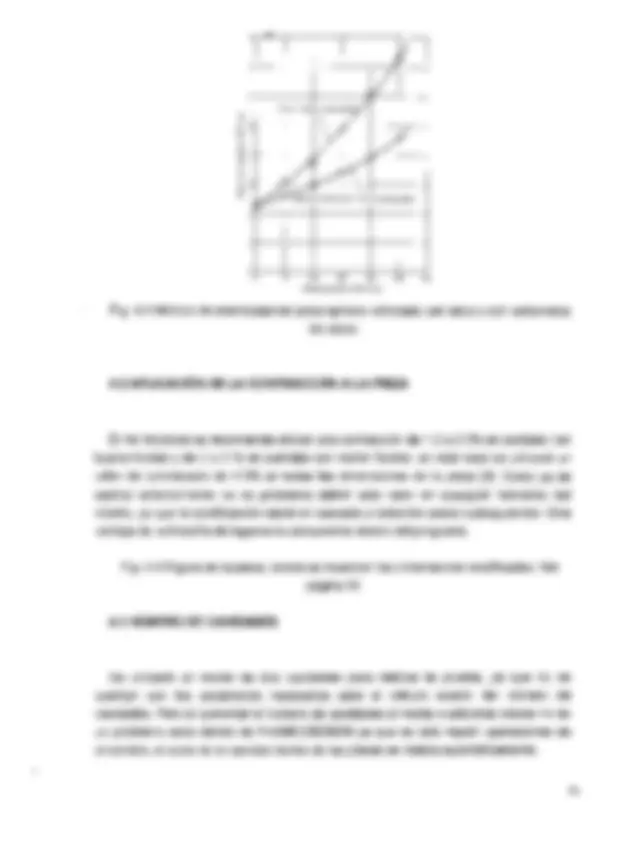
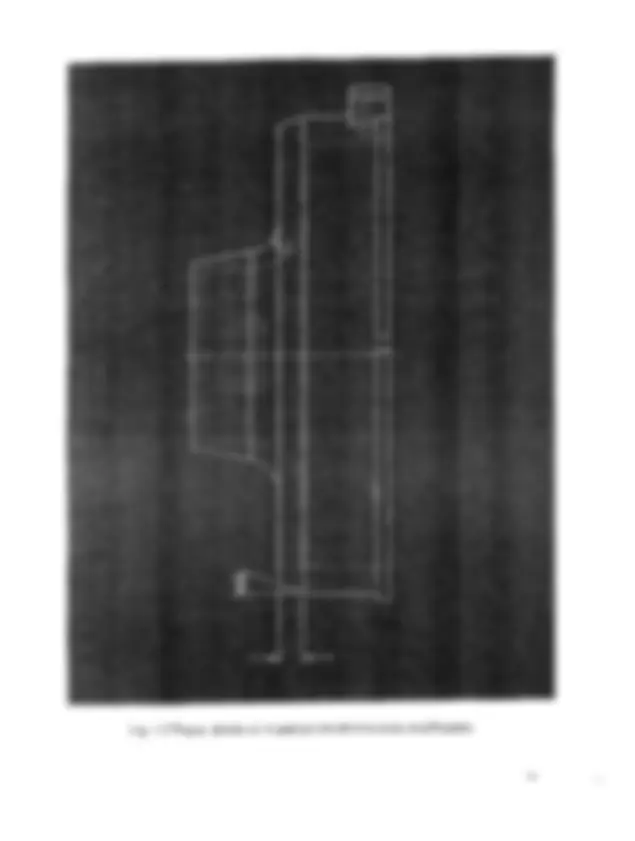
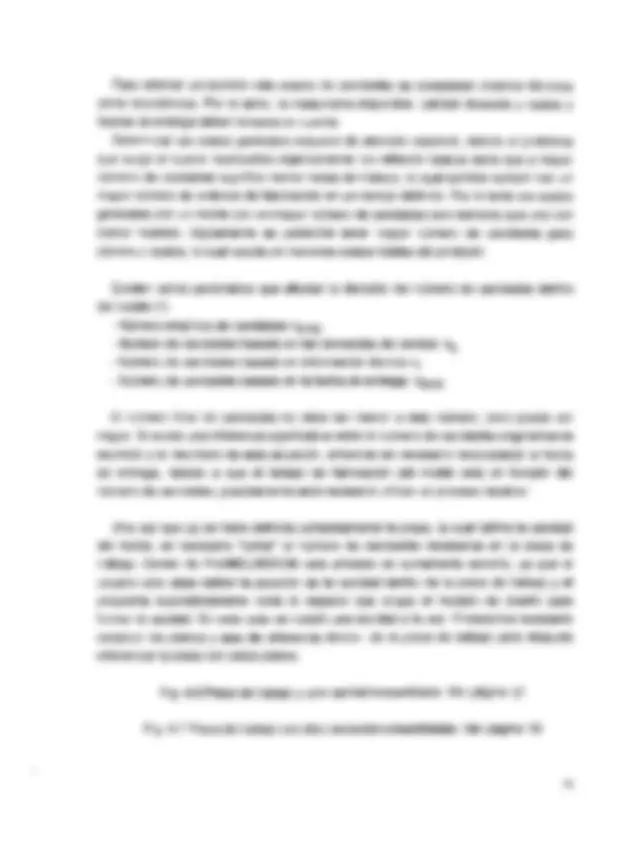
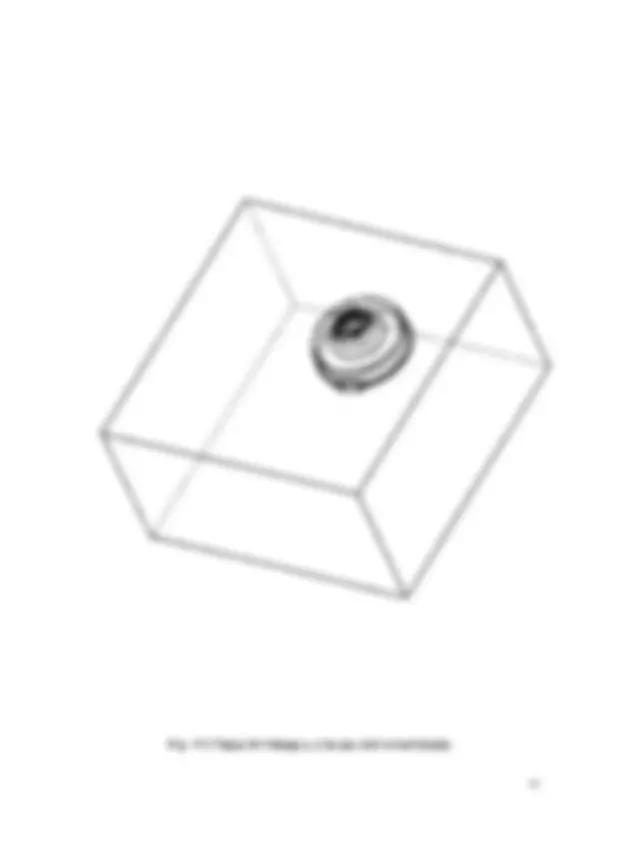
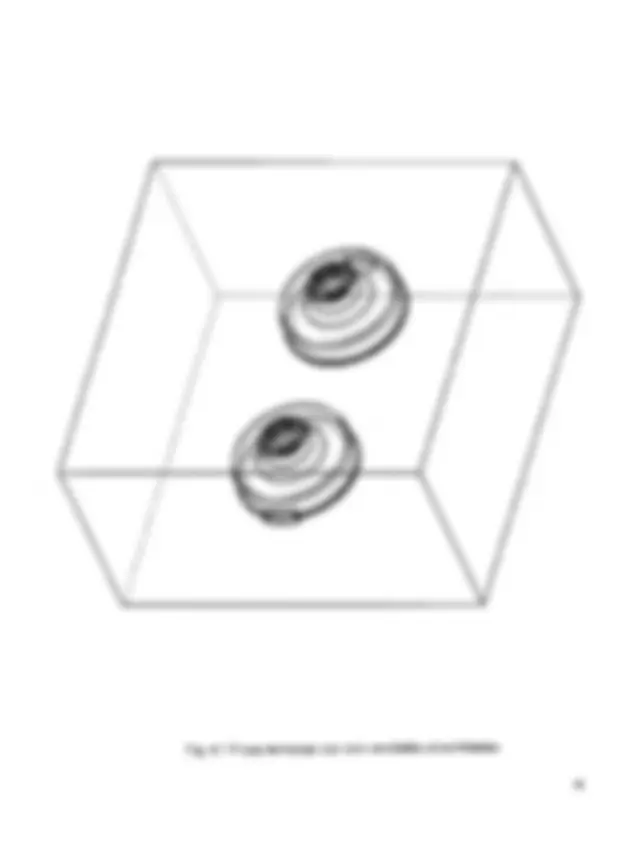
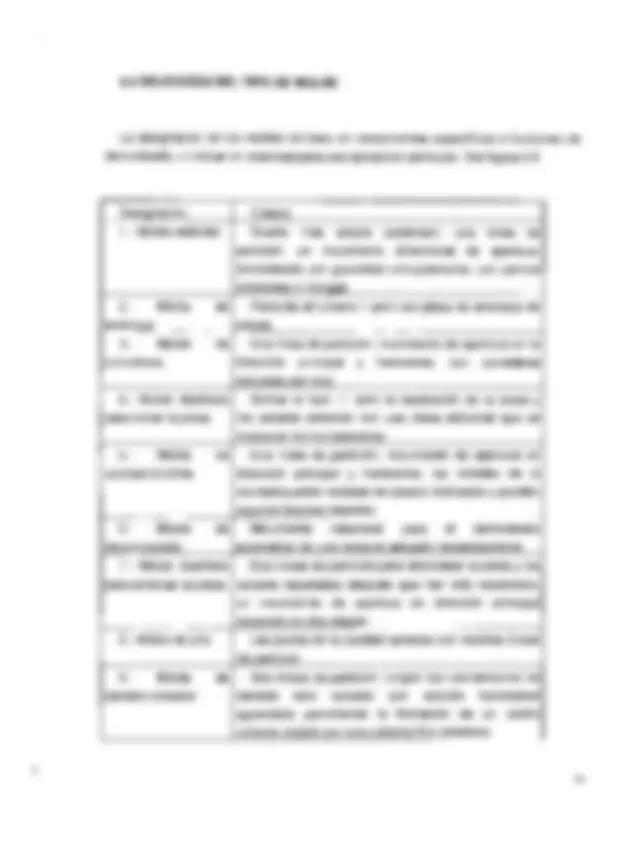
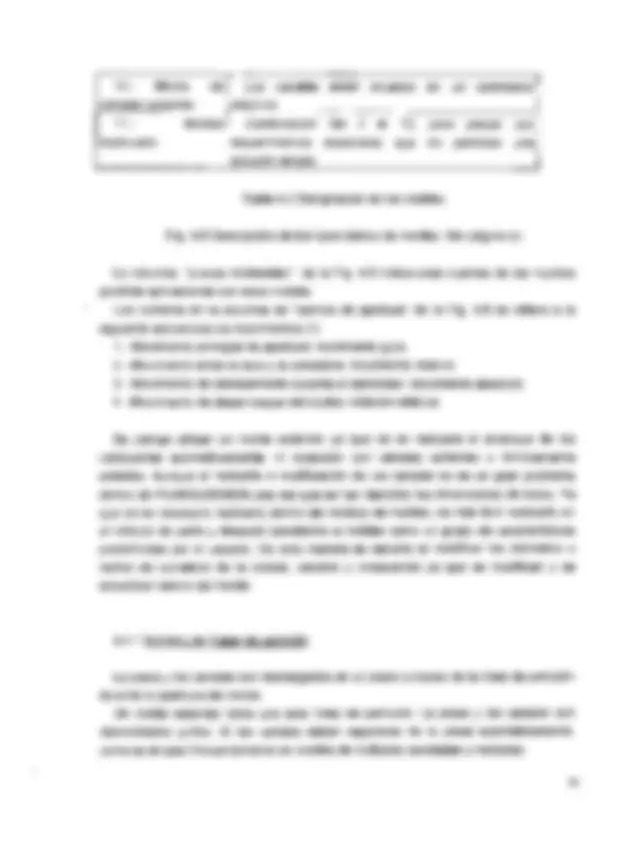
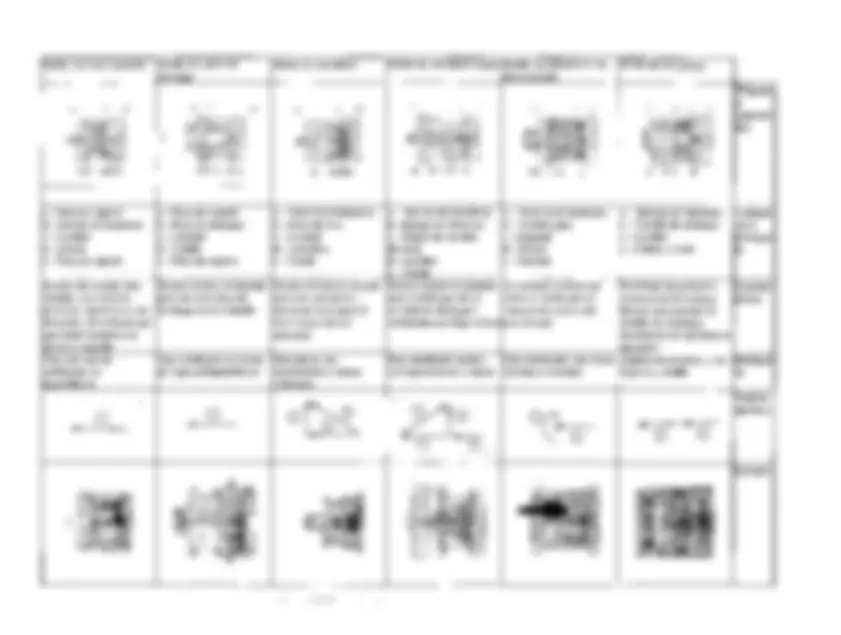
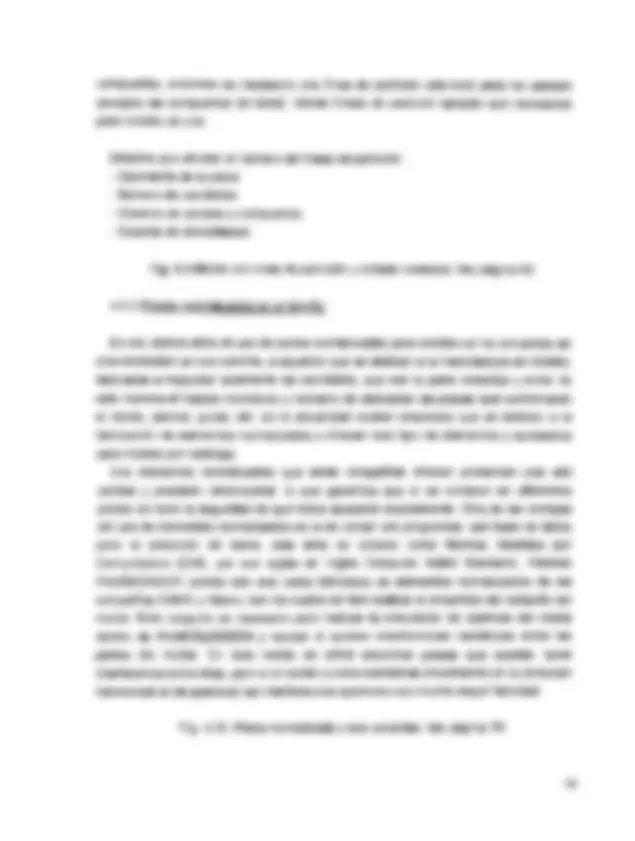
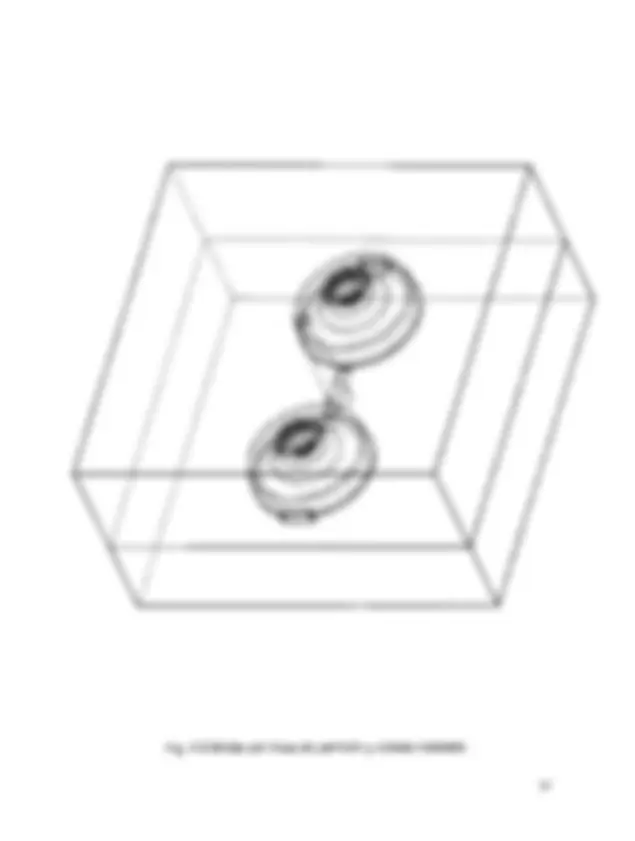
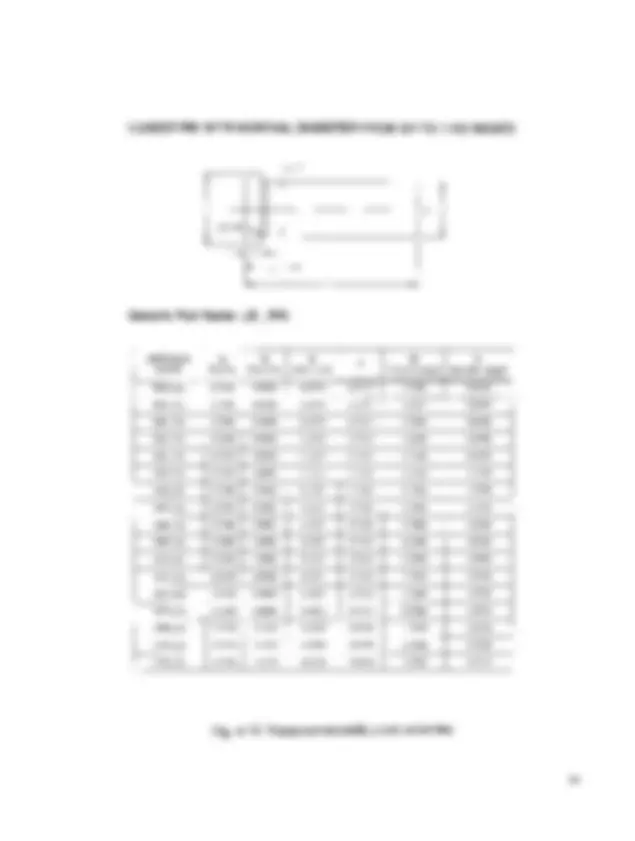
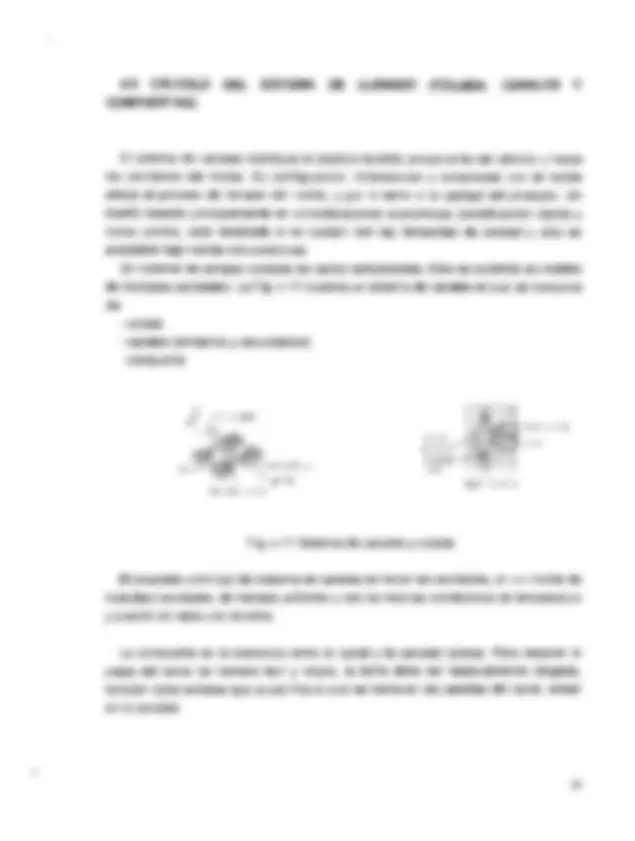
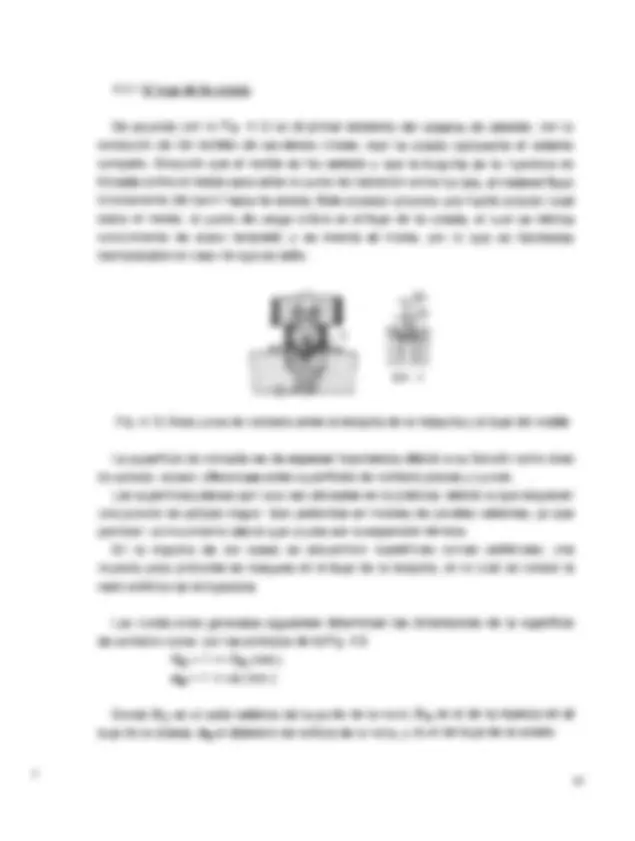
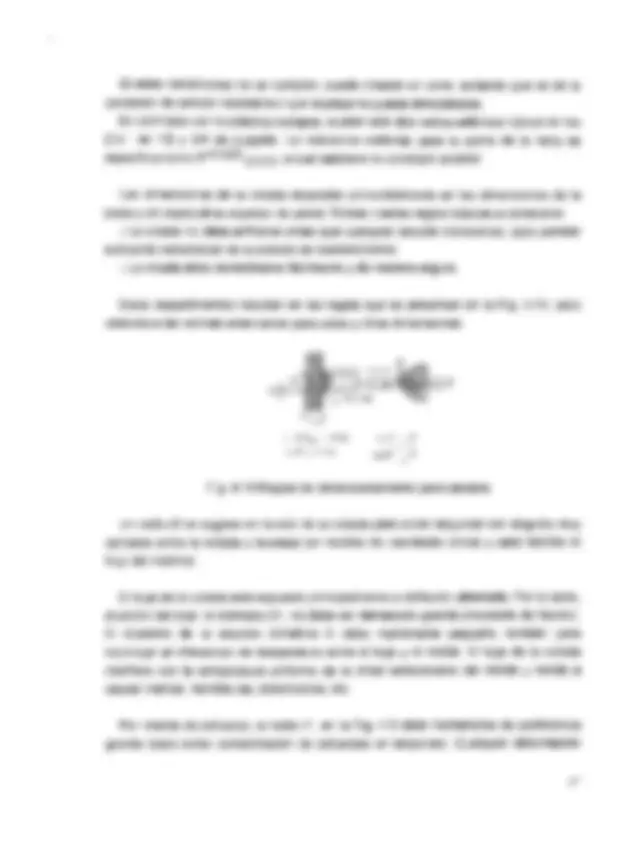
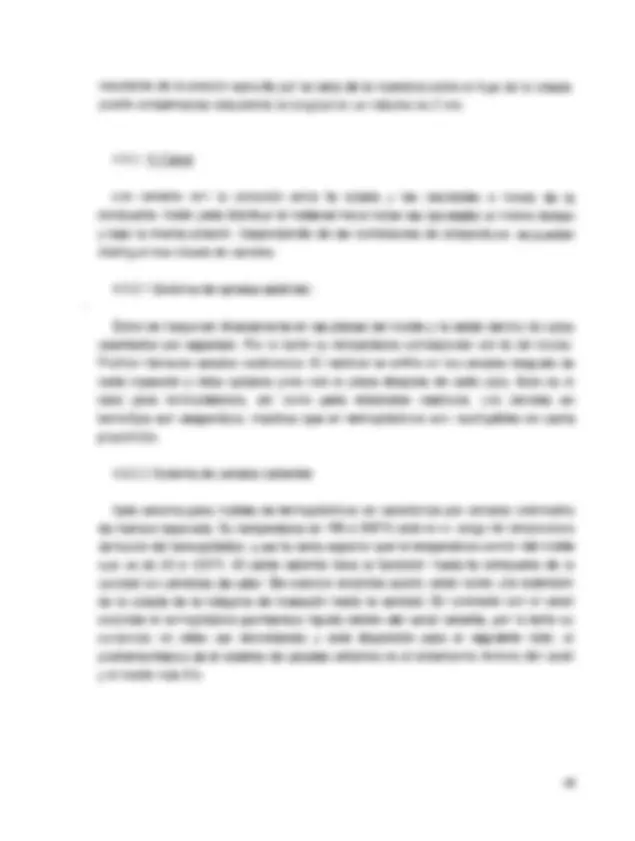
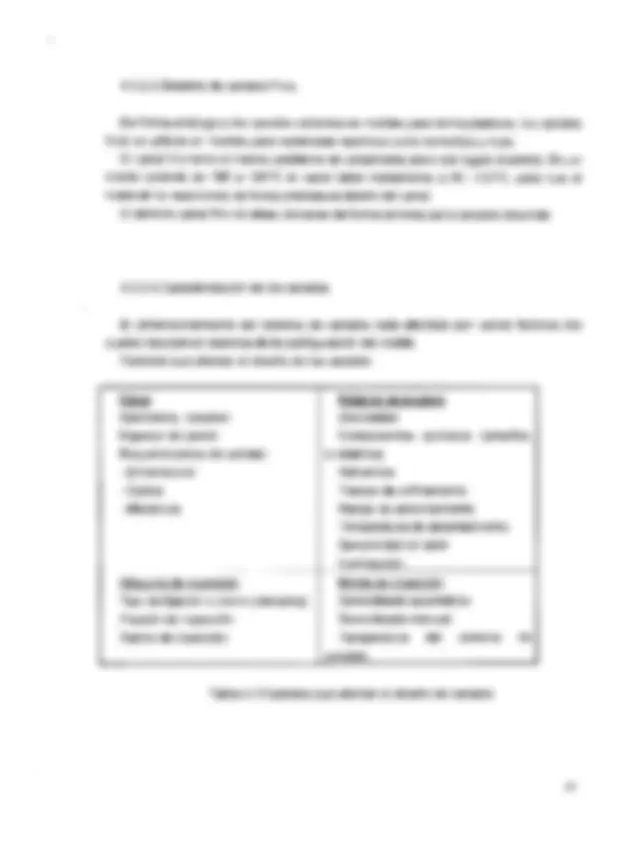
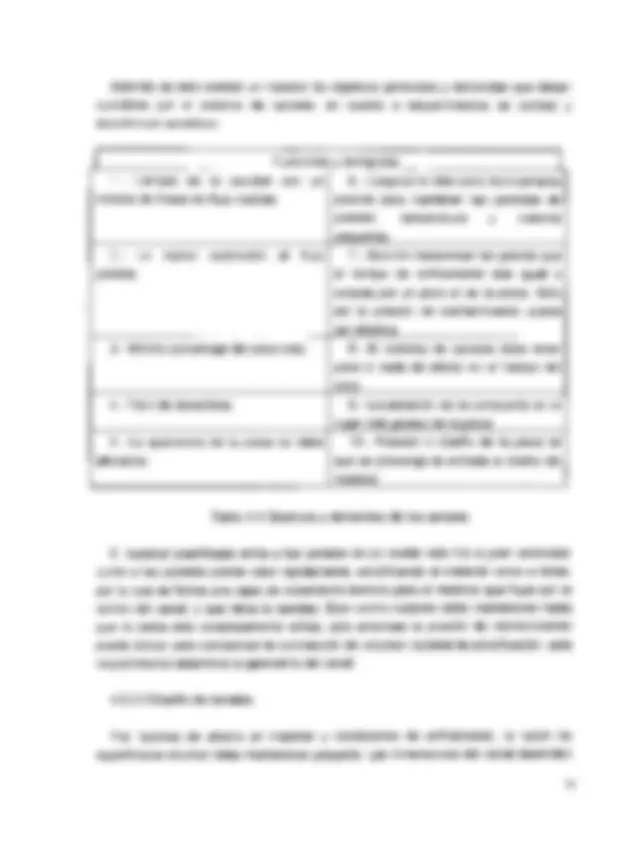
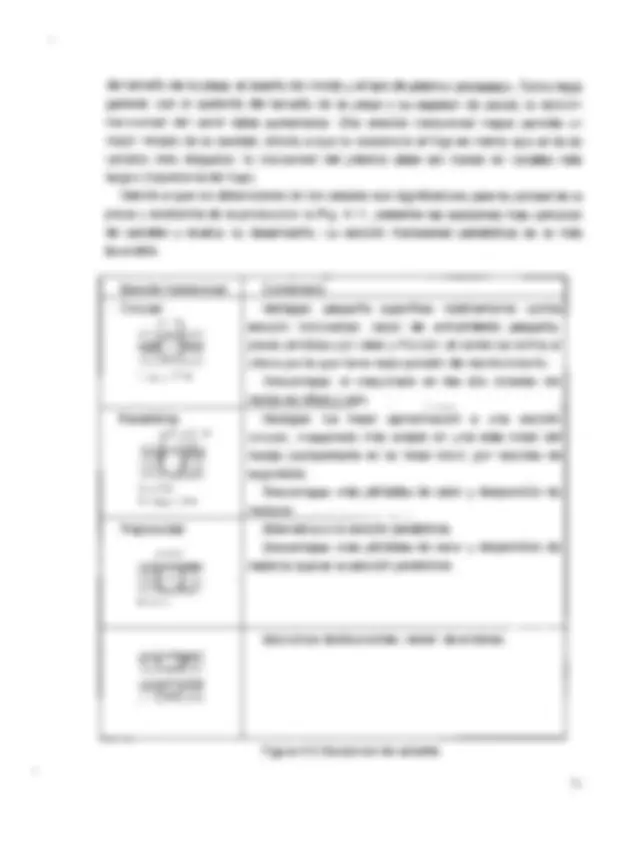
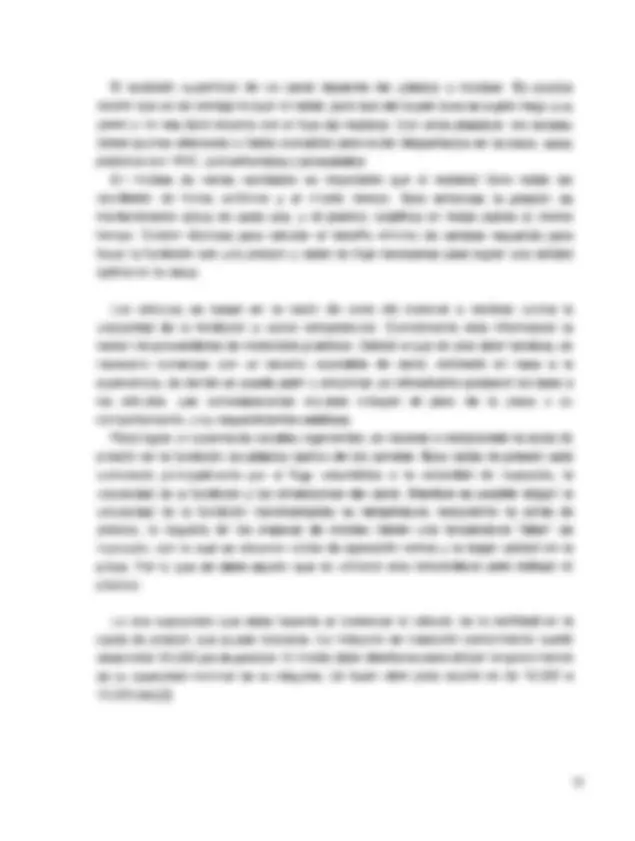
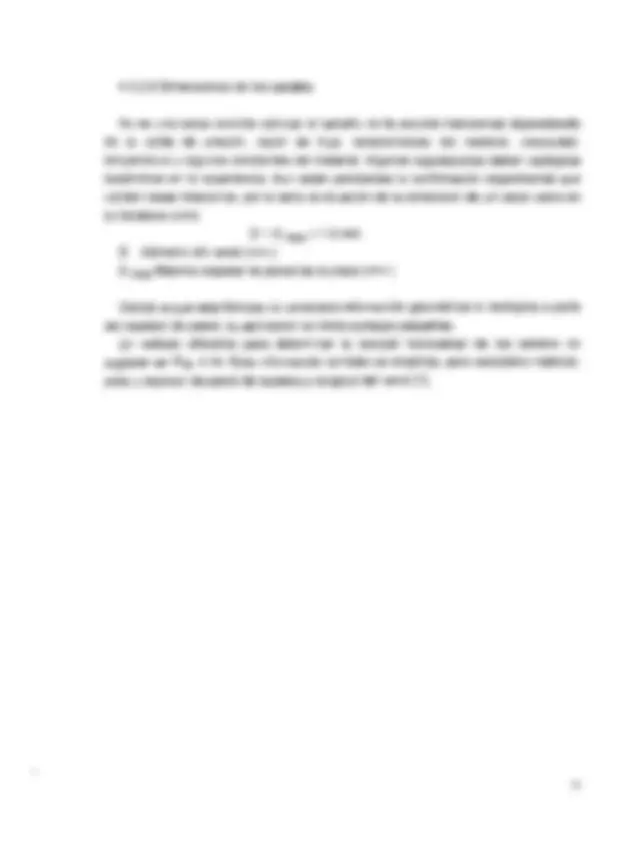
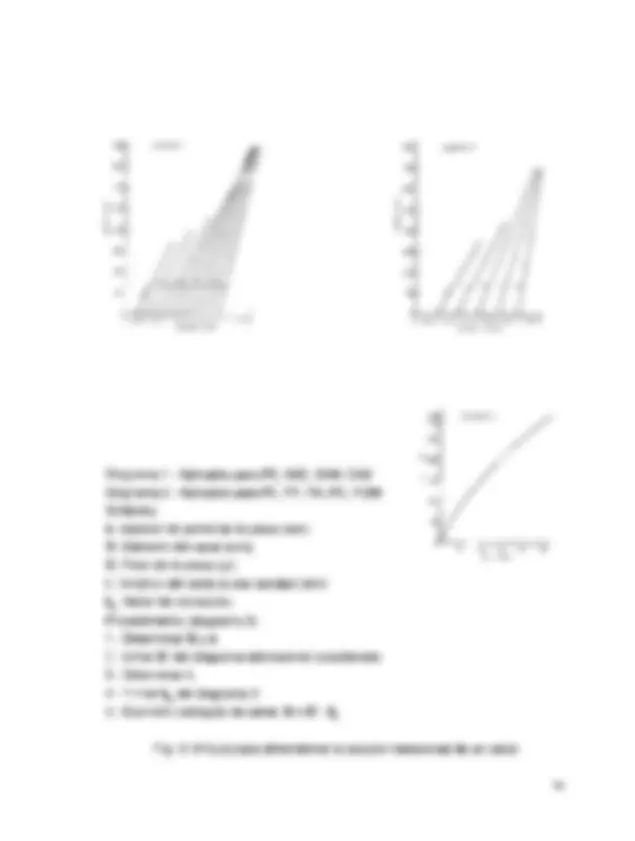
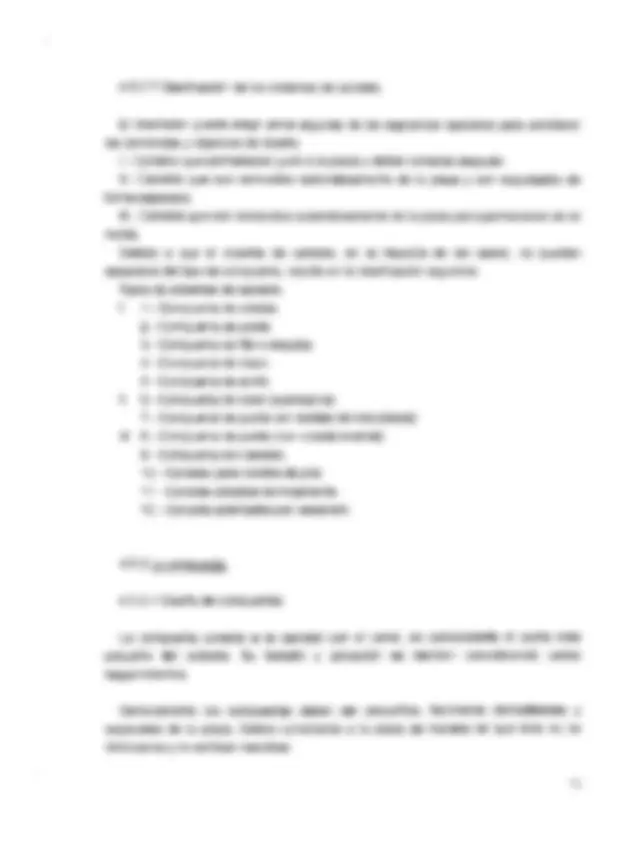
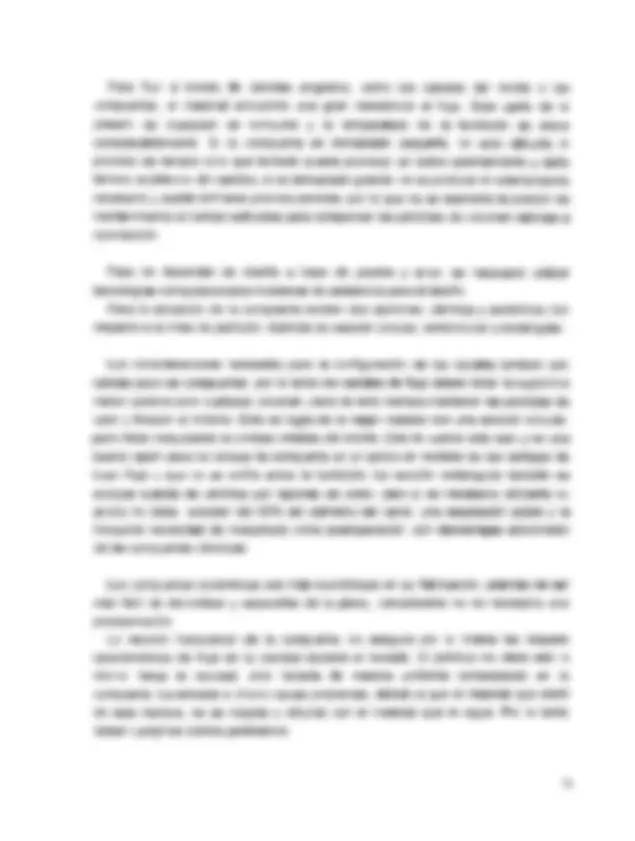
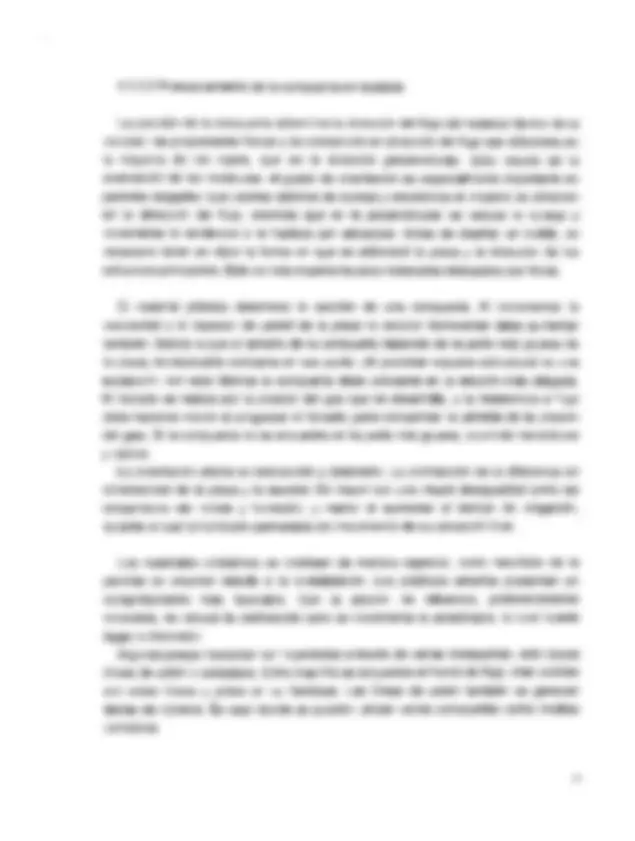
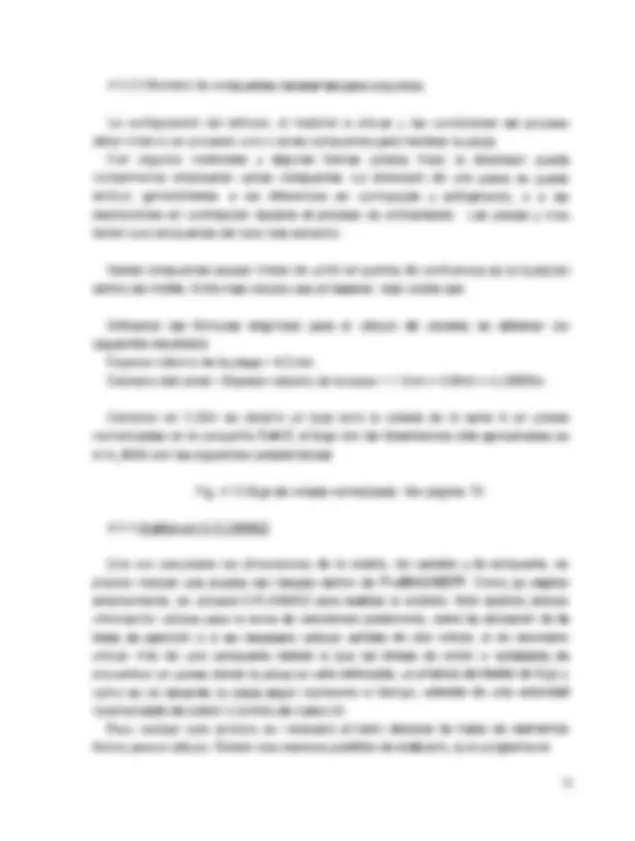
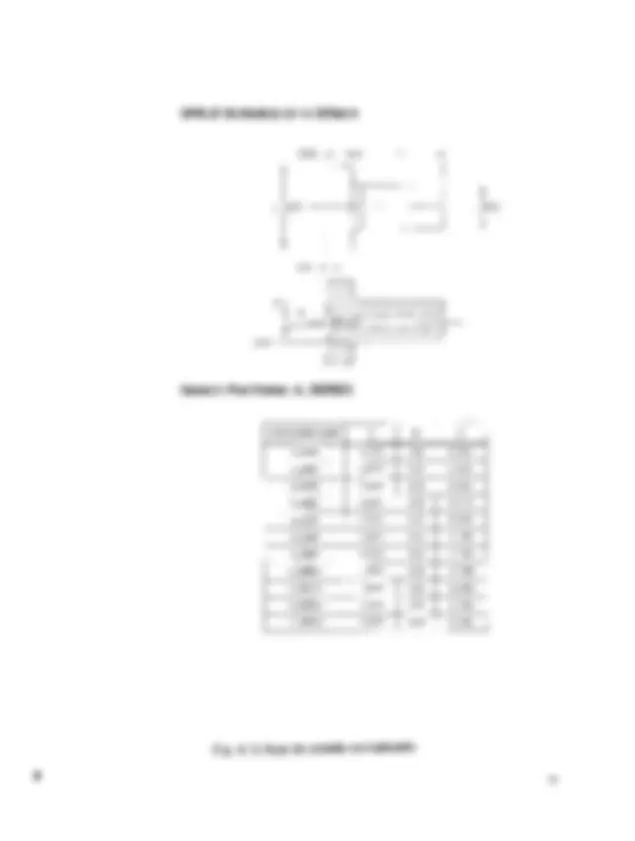
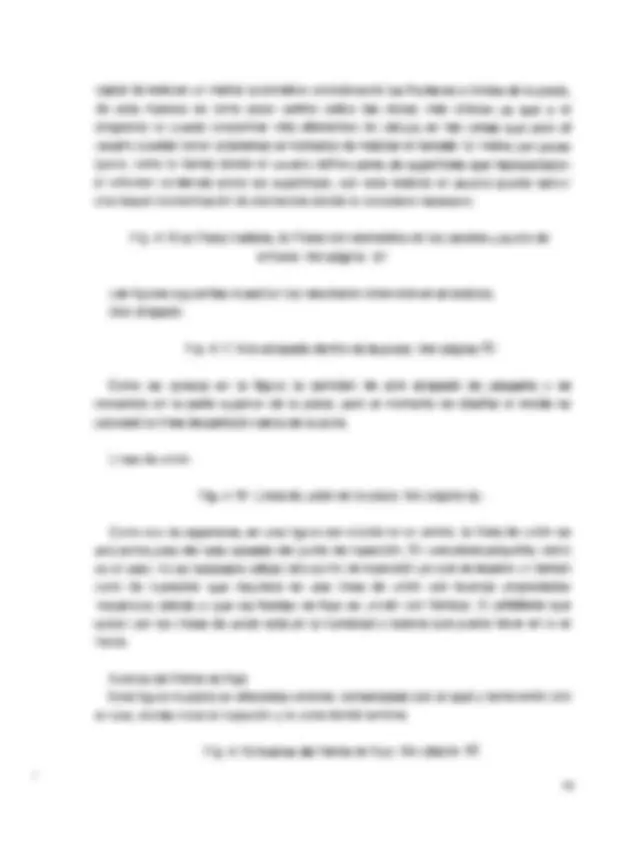
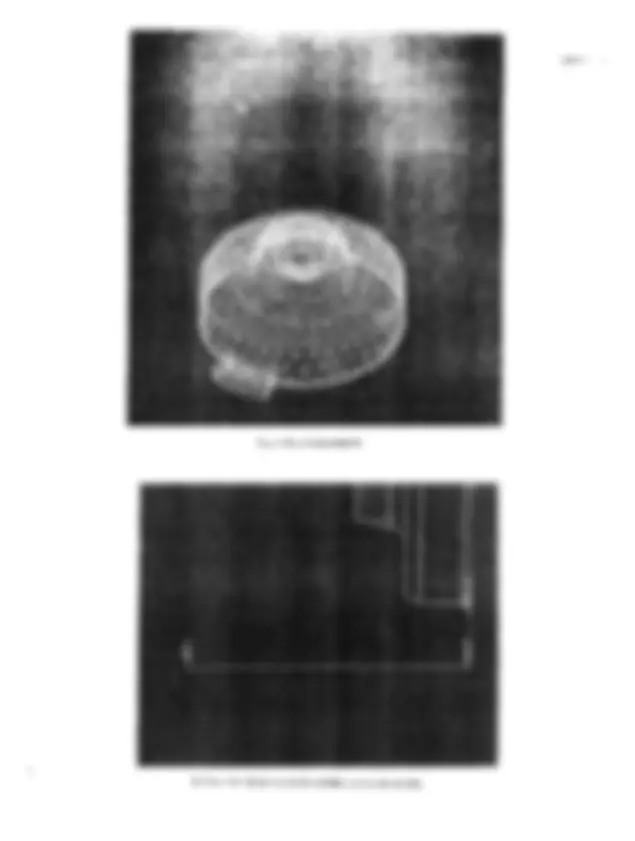
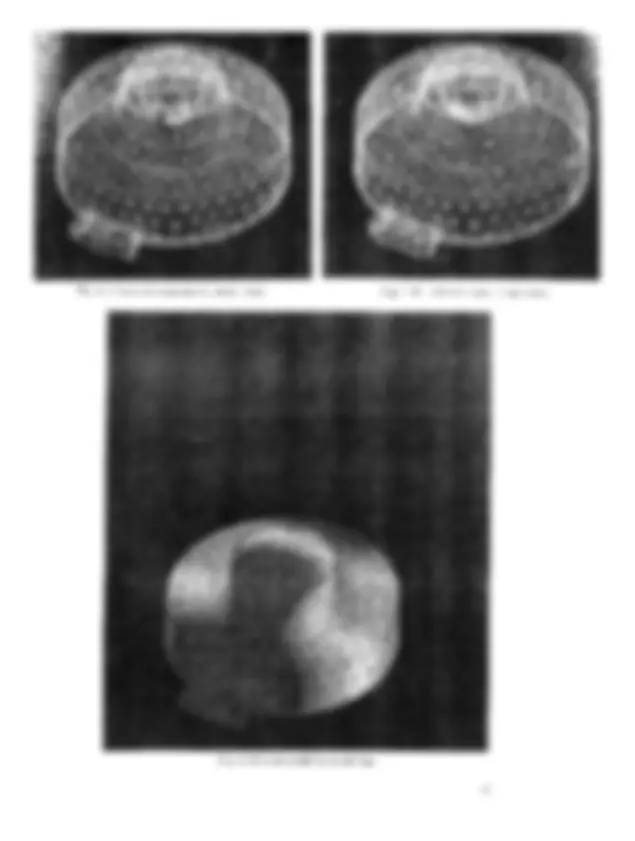
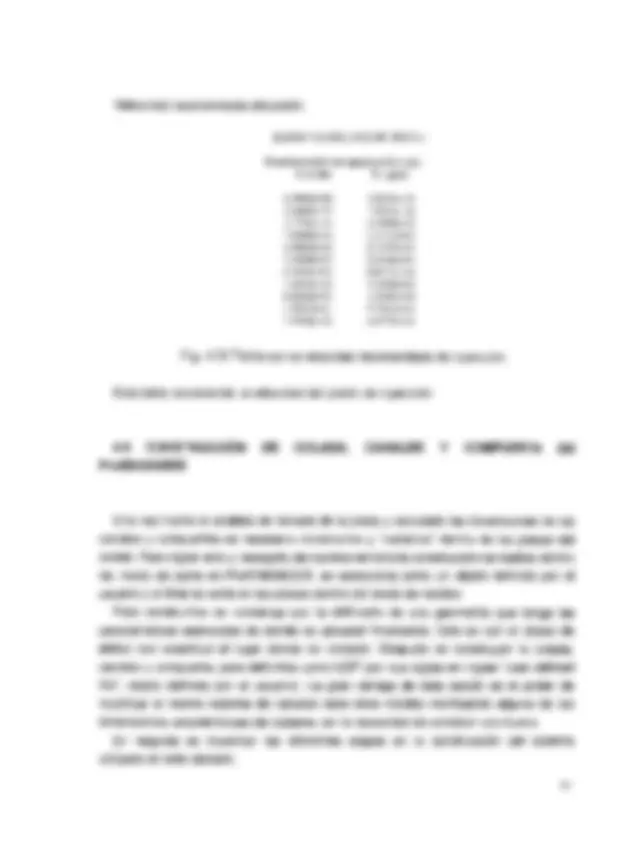
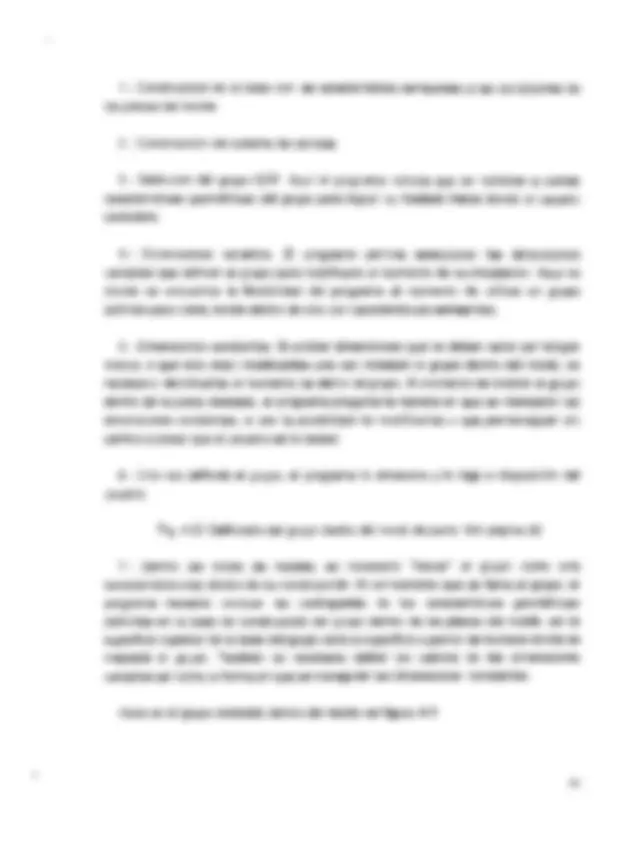

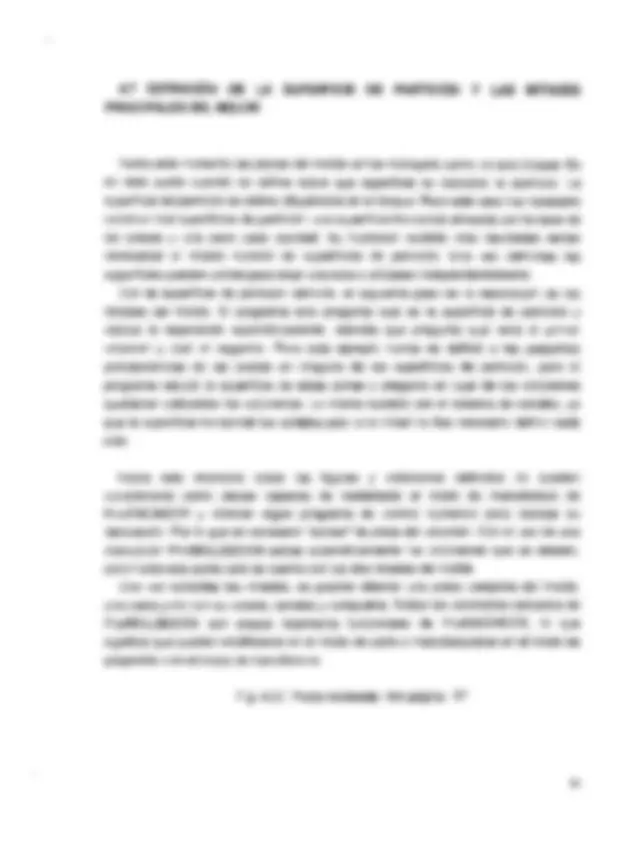
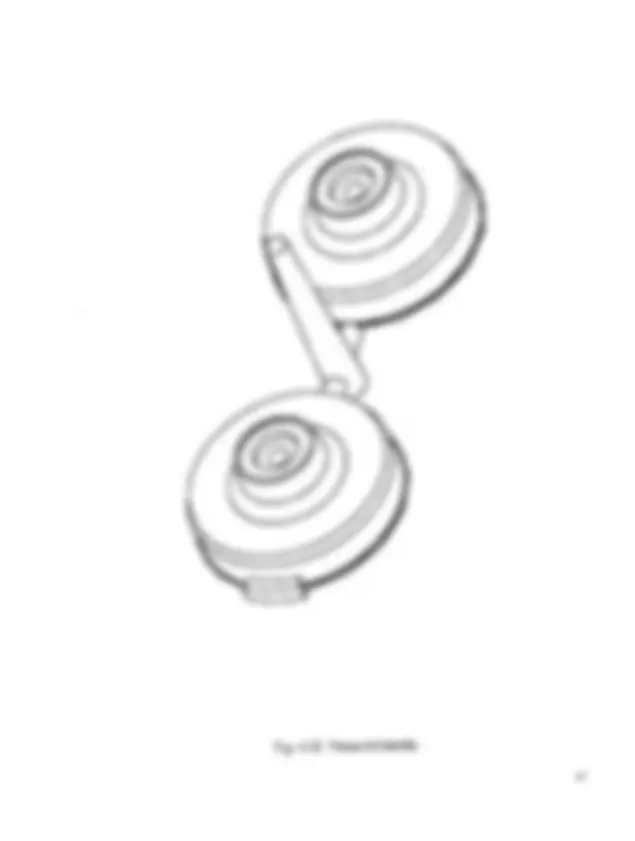
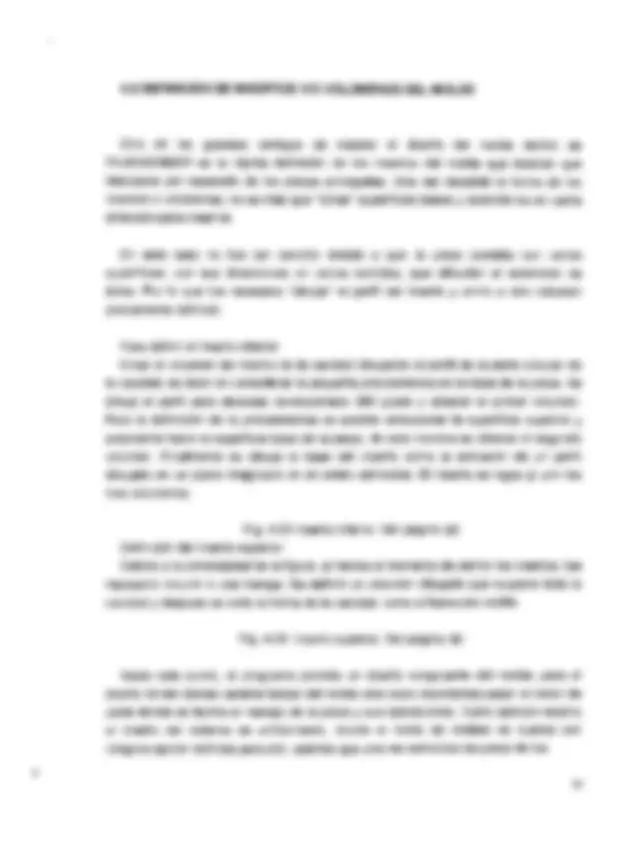
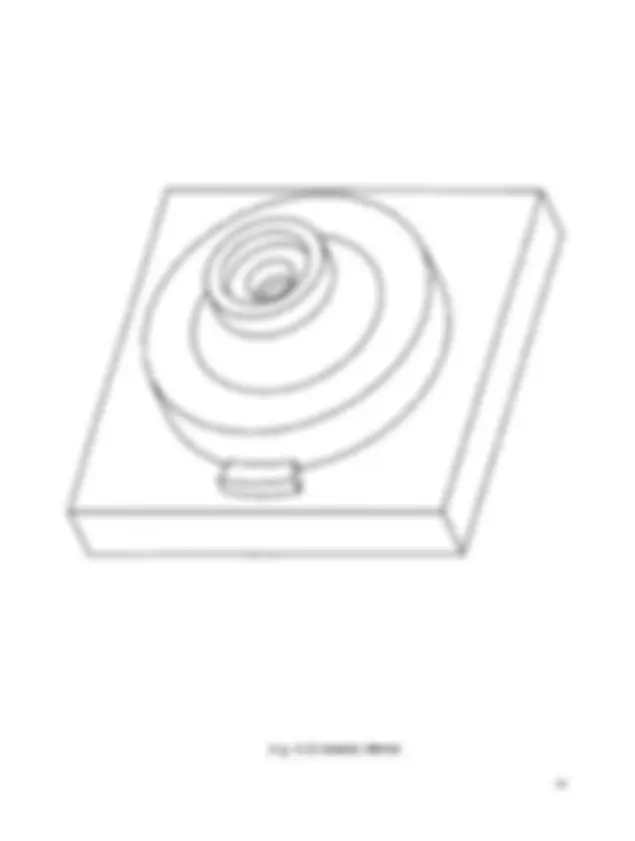
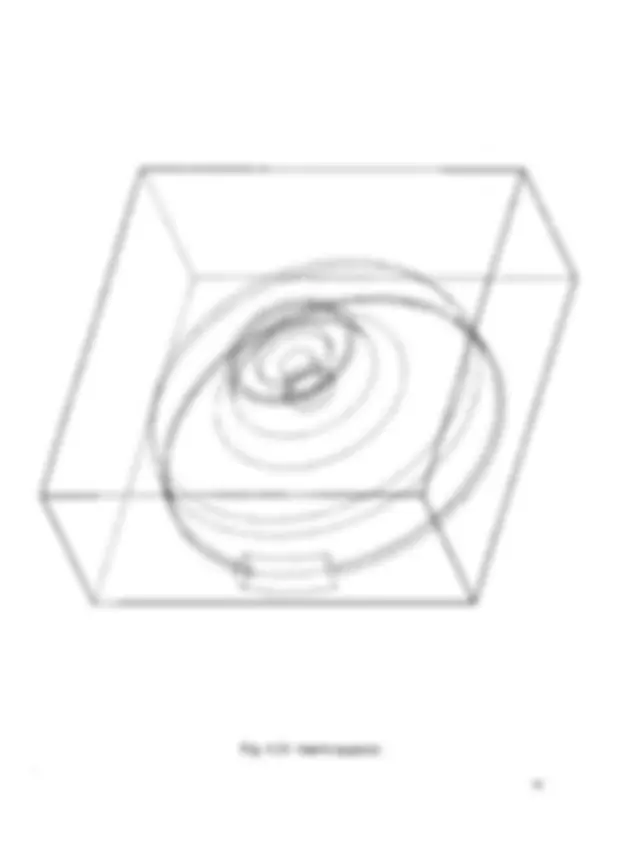
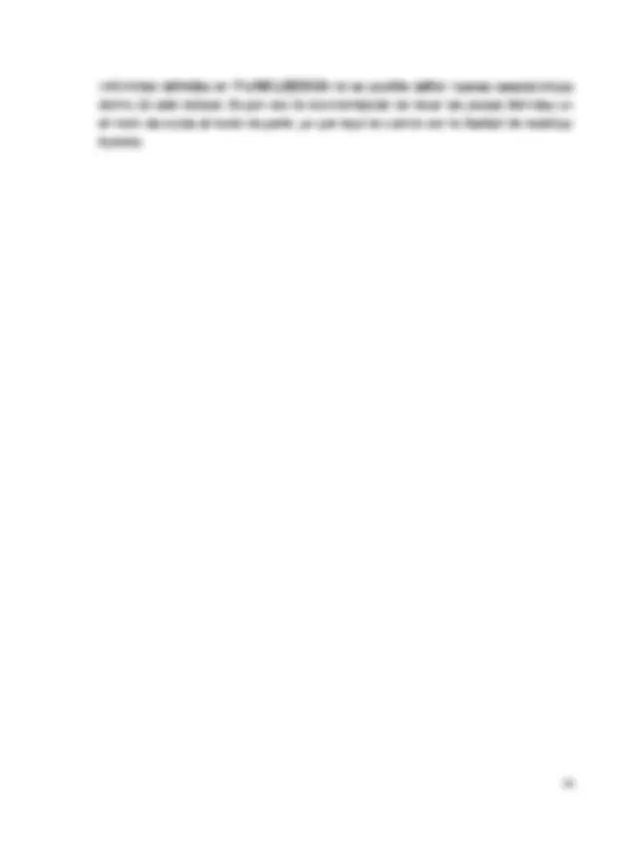
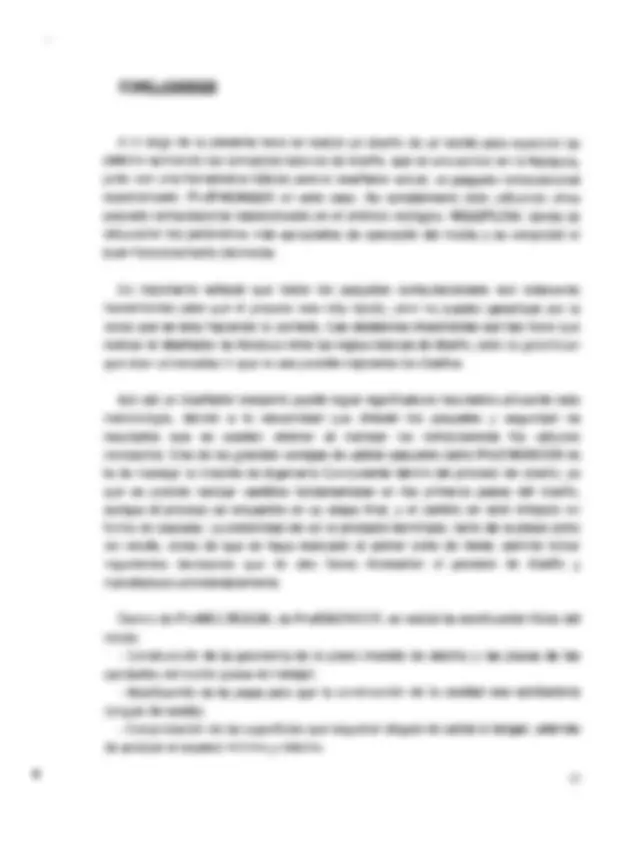
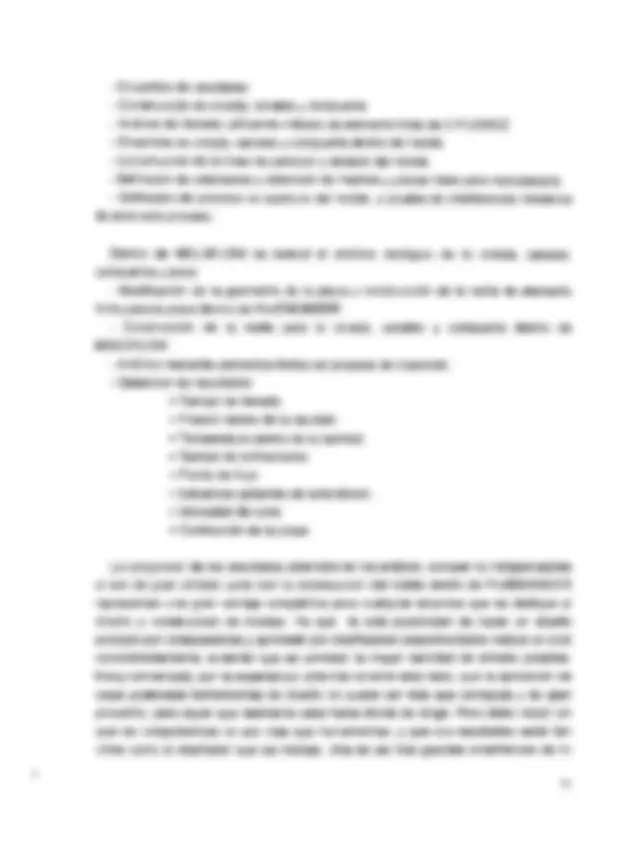
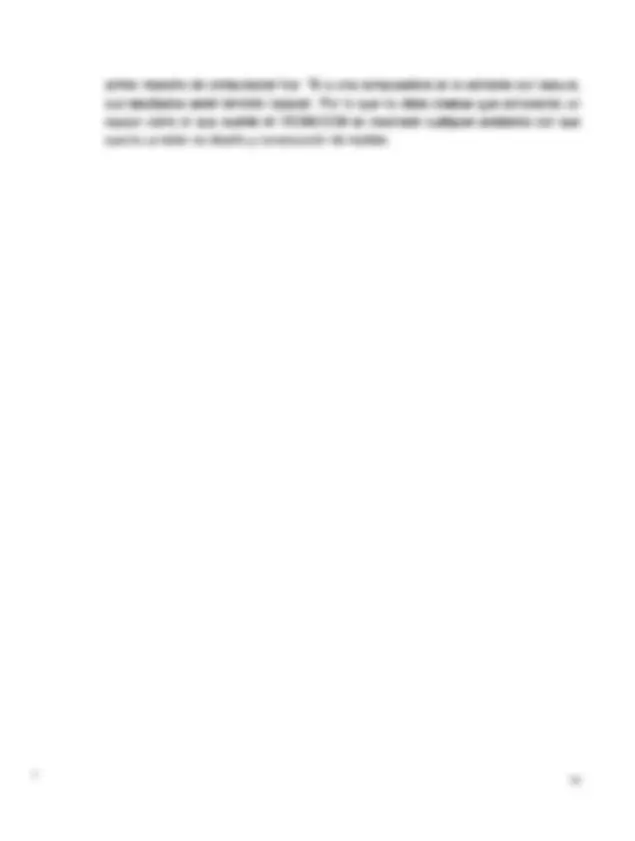
Prepara tus exámenes y mejora tus resultados gracias a la gran cantidad de recursos disponibles en Docsity
Gana puntos ayudando a otros estudiantes o consíguelos activando un Plan Premium
Prepara tus exámenes
Prepara tus exámenes y mejora tus resultados gracias a la gran cantidad de recursos disponibles en Docsity
Prepara tus exámenes con los documentos que comparten otros estudiantes como tú en Docsity
Los mejores documentos en venta realizados por estudiantes que han terminado sus estudios
Estudia con lecciones y exámenes resueltos basados en los programas académicos de las mejores universidades
Responde a preguntas de exámenes reales y pon a prueba tu preparación
Consigue puntos base para descargar
Gana puntos ayudando a otros estudiantes o consíguelos activando un Plan Premium
Comunidad
Pide ayuda a la comunidad y resuelve tus dudas de estudio
Descubre las mejores universidades de tu país según los usuarios de Docsity
Ebooks gratuitos
Descarga nuestras guías gratuitas sobre técnicas de estudio, métodos para controlar la ansiedad y consejos para la tesis preparadas por los tutores de Docsity
Una metodología detallada para el diseño de moldes de inyección de plástico utilizando el módulo pro/moldesign de pro/engineer. Abarca temas como la alimentación y dosificación del material, los criterios para la clasificación de moldes, el uso de la herramienta pro/moldesign para el diseño del molde, el análisis de llenado del molde, la definición de los insertos del molde, el uso de superficies de partición y la división de los volúmenes del molde. También se discuten aspectos como el ángulo de salida, el cálculo del sistema de llenado (colada, canales y compuertas) y el uso de herramientas de simulación como moldflow. El documento proporciona una guía completa para el diseño de moldes de inyección de plástico utilizando las funcionalidades avanzadas de pro/engineer.
Tipo: Resúmenes
1 / 135
Esta página no es visible en la vista previa
¡No te pierdas las partes importantes!
DIVISIÓN DE GRADUADOS E INVESTIGACIÓN DIRECCIÓN DE MAESTRÍAS EN INGENIERÍA
·,5 (l(p
TESIS QUE PARA OPTAR EL GRADO DE MAESTRO EN SISTEMAS DE MANUFACTURA PRESENTA
ia
Asesor: Dr. PEDRO GRASA Comité de tesis: M. en C. EUGENIO AGUILAR M. en C. JUAN CARLOS V ALDEZ Jurado: Dr. ARMANDO BRAVO M. en C. EUGENIO AGUILAR Dr. PEDRO GRASA M. en C. JUAN CARLOS VALDEZ
Presidente Secretario Vocal Vocal
Atizapán de Zaragoza, México, mayo de 1996
LISTA DE TABLAS Página
Tabla 2.1 Característiéas de moldes. 18 Tabla 2.2 Clasificación básica de los moldesTabla 2.3 Características de los aceros para moldes. Tabla 2.3 Características de los aceros para moldes 1. Tabla 2.4 Características de los aceros para moldes 2. Tabla 4.1 Propiedades típicas de polipropilenos reforzados con talco. Tabla 4.2 Designación de los moldes. Tabla 4.3 Factores que afectan el diseño de canales. Tabla 4.4 Objetivos y demandas de los canales. Tabla 4.5 Secciones de canales. Tabla A.1 Conductibilidad térmica de algunos materiales
23
- DISEÑO Y MANUFACTIRA DE MOLDES ASISTIDO POR COMPUTADORA
.Realizar el diseño de un molde de inyección de plástico para una pieza específica, utilizando el paquete computacional Pro/ENGINEER, en su módulo para el diseño de moldes Pro/MOLDESIGN. Empleando las piezas normalizadas existentes en el mercado para la construcción de moldes y sus partes. Obteniendo como resultado una metodología general para el diseño de moldes.
El hecho de producir una pieza plástica desde su idea hasta obtener un producto final, implica muchas funciones y relaciones matemáticas complejas que no sería económico realizar sin la ayuda de una computadora. Por esta razón la tecnología de CAD/CAM representa una herramienta valiosa para el desarrollo del producto. Una instalación de CAD/CAM representa una herramienta sofisticada y costosa que requiere (;je un compromiso de la gerencia y del depar-amento responsable de su funcionamiento.
Considerando las aplicaciones de las computadoras a las funciones que realizan las personas, se espera que éstas puedan realizar la misma labor en un periodo de tiempo menor y con una exactitud mayor. Con el uso de las tecnologías de CAD/CAM, la mayoría de las operaciones se realizan de una manera similar al proceso de diseño realizado por cualquier persona, pero agregando las siguientes ventajas:
1.- Pantalla gráfica. El diseño ingenieril se transfiere a la pantalla gráfica de entrada de información. Después, utilizando paquetes computacionales (software) complejos para interactuar con la computadora, el operario provee la información que el programa requiere para que realice mejoras al diseño con el objeto de reducir el contenido de material y/o conservar el ciclo de tiempo.
2.- Diseño de una base para el molde. La siguiente etapa es aplicar la información obtenida del diseño en la construcción de una base para el molde. Programas de análisis económicos están disponibles para el número de cavidades en la base y la
Una máquina de inyección es el medio capaz de convertir, procesar y dar forma al material plástico en bruto en forma de polvo, pequeñas esferas (pellets) o molido, en una pieza con la geometría y características deseadas. El proceso de inyección consiste en calentar el plástico hasta que se funde, después forzarlo dentro de las cavidades del molde donde se enfría y solidifica.
Para 1r3 elaboración de piezas termoplásticas por el procedimiento de inyección se dispone de una gran variedad de máquinas, que se diferencian no tanto por su concepción constructiva básica, condicionada por el proceso, como por variantes en el diseño de sus elementos de montaje, así como por sus sistemas de accionamiento.
Las máquinas de inyección se caracterizan por dos componentes principales: la unidad inyectora y la unidad de cierre. la unidad inyectora abarca el dispositivo de aportación de material, los elementos mecánicos para la plastificación del mismo y el accionamiento del mecanismo de inyección. La unidad de cierre efectúa los movimientos de apertura y cierre del molde de inyección.
El cierre en la máquina de inyección se utiliza para cerrar el molde , mantenerlo cerrado durante la inyección y el curado del material plástico, y abrir el molde para el retiro de la pieza formada.
4
Existen tres tipos de diseño de la unidad de cierre: 1.- Cierre hidráulico exclusivamente. 2.- Cierre con uniones o de rótula. 3.- Cierre hidromecánico.
Cierre hidráulico exclusivamente. Este diseño utiliza un fluido hidráulico y presión para abrir y cerrar la unidad de cierre y para desarrollar la fuerza requerida para mantener al molde cerrado durante la inyección del plástico. El concepto básico consiste en dirigir el fluido hidráulico al tubo amplificador para mover el pistón de cierre hacia adelante. El aceite llena el área principal fluyendo desde el tanque de almacenamiento. Como el pistón se mueva hacia adelante, se crea un pequeño vacía dentro del área principal, jalando fluido desde al tanque hacia esta cámara. Una vez cerrada la unidad de cierre, se cierra la válvula direccional del aceite, atrapándolo en el área principal. Se inyecta aceite a alta presión para comprimir el fluido y elevando la presión en esta área. La máxima presión se controla por medio de la válvula de control de la presión, la cual controla el tonelaje de la máquina. Para abrir la unidad de cierre, el fluido hidráulico se direcciona hacia el lado trasero del cilindro mientras se abre la válvula direccionadora, con el fluido del cilindro principal regresando al tanque. una de las ventajas de este sistema es el control preciso del tonelaje de aplicación.
C',11'1"':i1n¡^ Htdraulrc Cr::l'léer
Ac!ua!,n¡ Pli..n¡~r \ RemovaDleSgacer
Cyhnder Base Plate
" Mo11,na PLHen
(^ MoldHa!ves
lnject1on Noule
Fig. 1.1 Cierre Hidráulico
Cierre con uniones o de rótula.
Slat,onary Platen · Mov,n1 Platen
Crouhud,^ Crosshud^ link.^ Aur^ Link^ f"ront^ Lini
Fig. 1.2 Cierre con uniones
Este concepto utiliza las ventajas de las uniones para desarrollar la fuerza requerida para mantener el molde cerrado durante la inyección. Normalmente las uniones se diseñan de manera que se construyen aditamentos para hacerlas más lentas. La ventaja de una unidad con rótula es que se requiere una menor cantidad de fluido
5
tornillos o ranuras "T" para la sujeción del molde. Además la placa estacionaria incluye, comúnmente, los medios para fijar el molde en la placa y la manera de alinear el buje de la. boquilla del molde con la boquilla (nariz, nozzle) de la máquina inyectora.
Barras o Vigas Fijas: son los miembros del mecanismo de fuerza actuador que sirve como miembro de tensión de la unidad de cierre cuando mantiene el molde cerrado. También funcionan como guías de la placa móvil.
Botador: es el medio por el cual se acciona el mecanismo de expulsión de las piezas solidificadas del molde. La fuerza de expulsión puede aplicarse por medios hidráulicos o neumáticos por un cilindro sujeto a la placa móvil, o mecánicamente por el movimiento de apertura de la placa. Ver figura 1. 1
1.1.2 Especificaciones del sistema de cierre.
Fuerza de cierre (Ton): es la máxima fuerza de cierre para mantener el molde cerrado durante la inyección.
Fuerza de apertura (Ton): La máxima fuerza que una máquina ejercerá para iniciar la apertura del molde.
Movimiento de cierre(Max) Pulgadas): la máxima distancia que puede obtenerse entre la placa estacionaria y la móvil, cuando el mecanismo esta totalmente retraído con o sin la caja de expulsión y/o espaciadores.
Espacio libre cerrado o Espesor mínimo del molde (pulgadas):es la distancia entre la placa estacionaria y la móvil cuando el mecanismo esta totalmente extendido con o sin la caja de botadores y/o espaciadores. El espesor mínimo del molde varia, dependiendo del tamaño y tipo de los botadores y/o espaciadores utilizados.
Espacio de cierre máximo. la distancia entre la placa estacionaria y la móvil cuando el mecanismo está totalmente extendido, sin las cajas de botadores y/o espaciadores.
Espacio de cierre mínimo: la distancia entre la placa estacionaria y la móvil cuando el mecanismo está totalmente extendido, con las cajas de botadores y/o espaciadores estándar.
7
La evolución de las unidades de plastificación ocurrió en el siguiente orden: 1.- Émbolo 2.- Émbolo de dos etapas. 3.- Tornillo plastificante (no reciprocante) y émbolo. 4.- Tornillo reciprocante.
Émbolo Las primeras unidades de émbolo eran calentadas con aceite y eventualmente con bandas calentadoras eléctricas. Una sección de torpedo en la parte trasera dispersa el plástico alimentado hacia una sección delgada según el émbolo avanza. Esta sección delgada de material entraba a una sección central donde se realizaba la mayor parte dela plastificación. en diseños posteriores la sección central consistía en una serie de pequeños agujeros perforados paralelos a la línea central horizontal de la cámara de plastificación. En la parte frontal de la cámara de plastificación el torpedo se reducía en su diámetro, y la sección transversal de la fundición se reducía para lograr una mejor plastificación de cualquier material proveniente de la sección central. La sección frontal tenía que tener la longitud suficiente para asegurar una temperatura constante en toda la fundición, cuando ésta era forzada fuera de la cámara de plastificación y dentro del molde.
Algunos de los problemas experimentados con estas unidades era la fuga entre la sección central y el frente, cambio de color, caídas de presión a través de la cámara, émbolos rayados o con muescas, control pobre de la inyección y dificultad para trabajar materiales sensitivos al calor. Como el diseño fue mejorando, el alimentador mecánico fue reemplazado por alimentadores de peso, los cuales mejoraron el control sobre el tamaño de la inyección. se adicionaron controles de presión y contadores a los circuitos eléctricos e hidráulicos para permitir el empaque del material entre el émbolo y el torpedo y para permitir el preposicionamiento del émbolo después de la abertura de alimentación antes de la siguiente inyección. Estas dos innovaciones incrementaron el tamaño de la inyección y además redujeron el tiempo del ciclo.
8
Fig. 1.4 Máquina de inyección de émbolo de dos etapas
Tornillo plastificante (no reciprocante) y émbolo. Las unidades de émbolo de dos etapas fueron reemplazadas por unidades de dos etapas con un tornillo fijo para la plastificación. La unidad de. inyección era básicamente la misma como la utilizada por la unidad plastificante de émbolo. estas unidades podían manejar cualquier tipo de material, y con las mejoras en diseño en la configuración del émbolo de inyección y la acción de lavado obtenida cuando la primera fundición para cada inyección entraba en la cámara de fundición, se redujeron considerablemente los problemas con el cambio de coior.
MOLO
Fig. 1.5 Máquina de inyección de tornillo plastificante y émbolo.
Tornillo reciprocante. Uno de los avances más significativos en los plásticos ocurrió·con el desarrollo del concepto de las unidades de inyección con tornillo reciprocante. estas unidades permitían altas razones de fundición del material plástico, tolerancias cerradas en el tamaño de la inyección y la habilidad de controlar la temperatura de la fundición y
pueden trabajar materiales termofijos incluyendo la goma y BMC (Bulk Molding
10
Compound). Unidades con Ud mayor (24: 1 hasta 30: 1) se utilizan para materiales difíciles de fundir y aplicaciones especiales.
Fig. 1.6 Máquina de inyección de tornillo reciprocante.
1.2.1 Terminología para la unidad de inyección.
Unidad de plastificación e inyección: es la parte de la máquina de inyección donde se convierte al plástico de una fase sólida a una fase semilíquida mediante la elevación de la temperatura. Esta unidad mantiene al material a una temperatura determinada y lo forza al molde a través de la boquilla de la unidad de inyección.
Unidad de émbolo: es una combinación de un aparato de inyección y calentamiento, en donde la cámara de calor esta montada entre el cilindro de inyección y el molde. Esta cámara calienta el material plástico por medios de conducción del calor. El cilindro, en cada movimiento, empuja material no fundido a la cámara, el cual forza al plástico fundido a través de la boquilla de inyección.
Unidad de émbolo de dos etapas: es una unidad donde la inyección y la plastificación se realizan en unidades separadas. Esta última consiste un una cámara para calentar el material plástico por medio de conducción y un émbolo para empujar el material aun no fundido dentro de la cámara y éste al fundido dentro de una segunda etapa de inyección. Esta unidad de inyección funciona como una cámara de mantenimiento, medición e inyección al mismo tiempo. Durante el ciclo de inyección el cilindro de inyección forza al plástico fundido de la cámara de inyección hacia la boquilla.
Unidad de tornillo de dos etapas: es una unidad de plastificación e inyección donde el aumento de temperatura se realiza en el tornillo de extrusión, para después mandar
11
Razón mínima de inyección: la razón minIma calculada de desplazamiento del émbolo de inyección o del tornillo, expresada en pulgadas cúbicas por segundo, calculada a presión máxima de inyección especificada.
Operación manual: operación en donde cada función y la sincronización de cada función están controladas por un operador.
Operación semiautomática: operación donde la máquina realiza un ciclo automáticamente y después se detiene. Después requiere de la instrucción del operador para reiniciar el ciclo.
Operación automática: operación en donde la máquina realiza un ciclo de funciones programadas repetitivamente, hasta que existe un problema en la máquina, en el molde, o se detiene manualmente.
Razón de longitud sobre diámetro (UD) del barril y del tornillo. Uno de los términos más utilizados aplicados al tornillo y barril de la unidad de inyección es UD, llamado "L" sobre "D".
Razón UD de la unidad de plastificación. El común denominador utilizado en la comparación de todas las unidades de plastificación, además del diámetro, es la razón de la longitud sobre el diámetro del plastificador, conocido comúnmente como UD. Esta razón es aplicable a extrusores, tornillos reciprocantes, y .unidades de tornillo de dos etapas por igual. La razón UD del barril no debe confundirse con la del tornillo.
Razón UD del barril: es la distancia del filo delantero de la abertura de alimentación al final del hoyo del barril dividido por su diámetro y expresado como la razón en forma donde el diámetro se reduce a uno, como 20/1.
Razón UD del tornillo: es la distancia del filo delantero de la abertura de alimentación al final de la hélice del tornillo (sin incluir puntas, conos de presión y
13
válvulas de no retorno) dividido por el diámetro del tornillo. No se basa en la longitud total de la hélice del tornillo.
Barre! UD = La /D Screw UD = L 5 /D
Fig. 1.7 Tornillo plastificante con sus dimensiones características
En el proceso de inyección hay que dosificar una cantidad de material correspondiente al volumen del molde, mediante el émbolo de inyección y tras de cada retroceso del mismo en el curso del ciclo general de trabajo; una medida condicionada por el proceso cuya solución exacta puede garantizar por sí mismo un óptimo resultado de producción.
Las materias termoplásticas varían a menudo muy considerablemente en cuanto a tamaño y forma de los diverso granulados. La magnitud de la superficie específica de un gránulo influye en gran medida sobre las propiedades de plastificación, por lo que debiera estar dimensionada de forma que, en un corto tiempo de permanencia en el cilindro relativamente corto, se logre una intensa disgregación de reblandecimiento con resultados de fusión térmica homogénea.
La manufactura actual de piezas de plástico exige máquinas de inyección automáticas para disminuir costos y tiempo de ciclo, además de aumentar la productividad. El funcionamiento de estas máquinas exige una carga exacta de material, ya que pequeñas sobredosis pueden ejercer una influencia negativa sobre el resultado de la producción. Las piezas inyectadas han de extraerse del molde sin rebabas para que los trabajos posteriores no encarezcan su producción.
1-l