
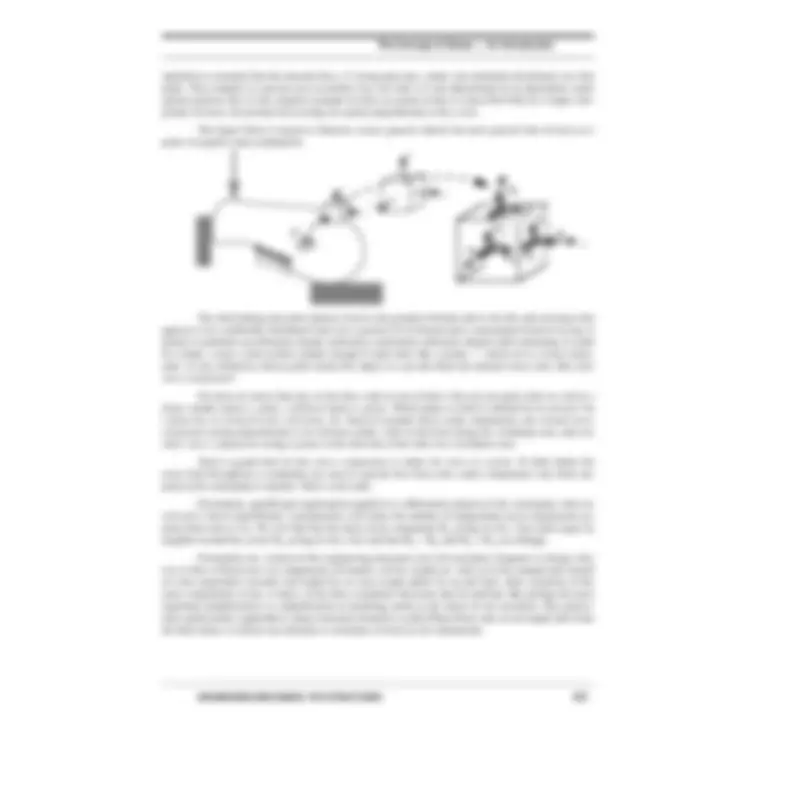
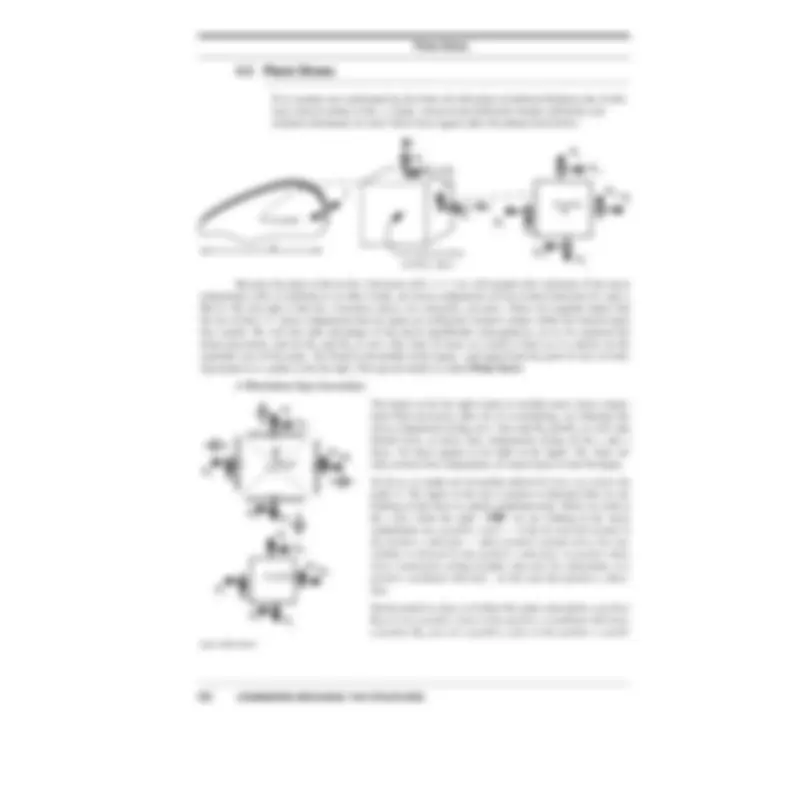
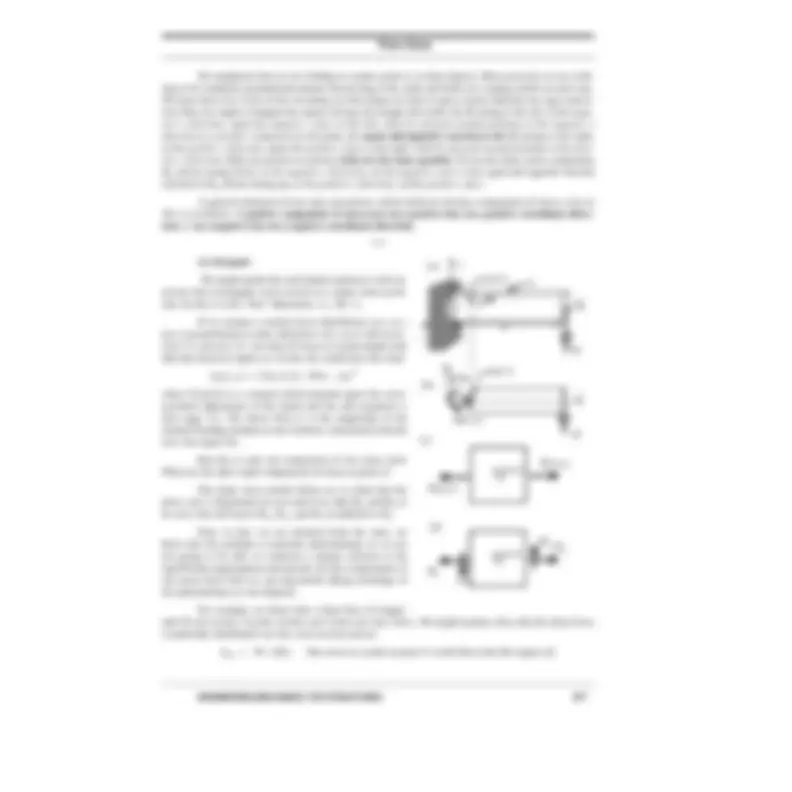
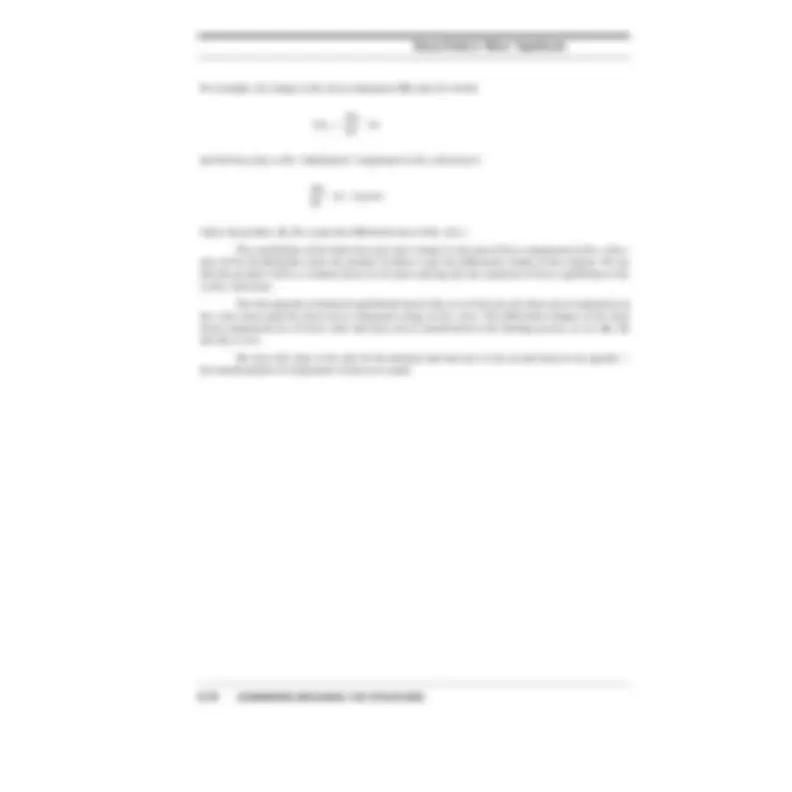

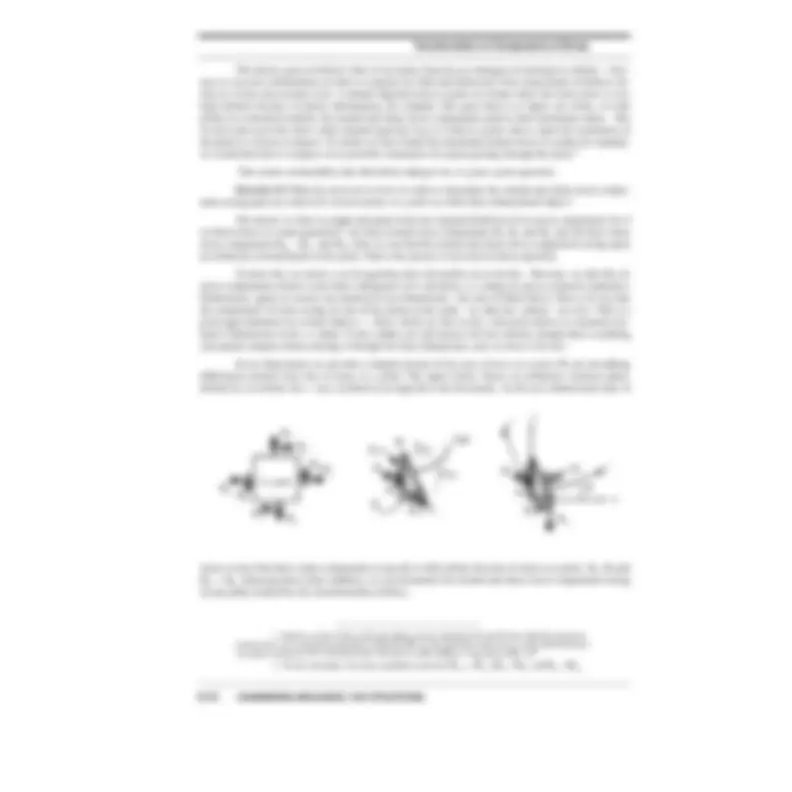
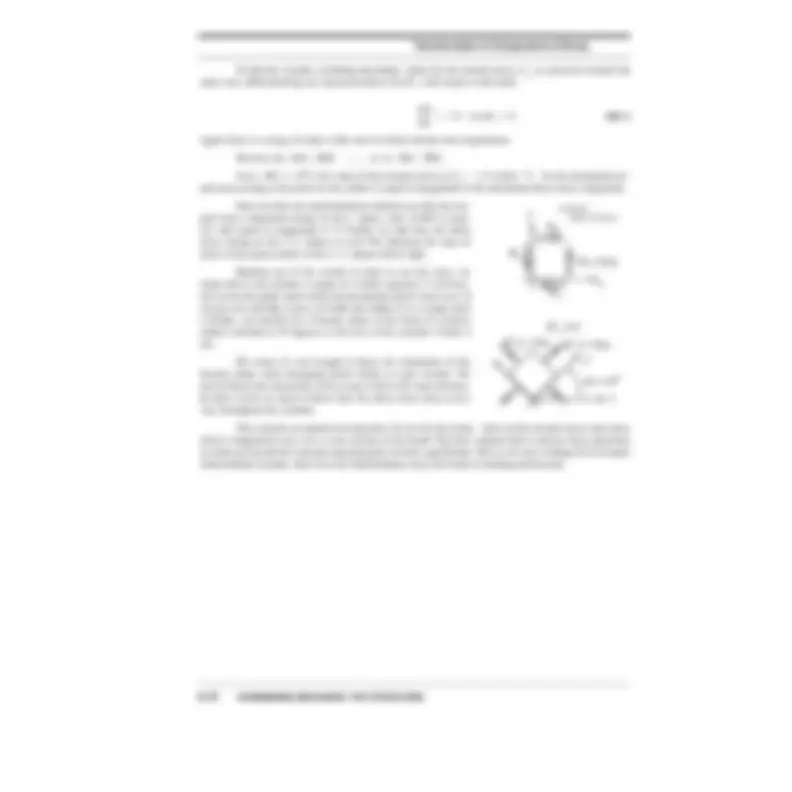
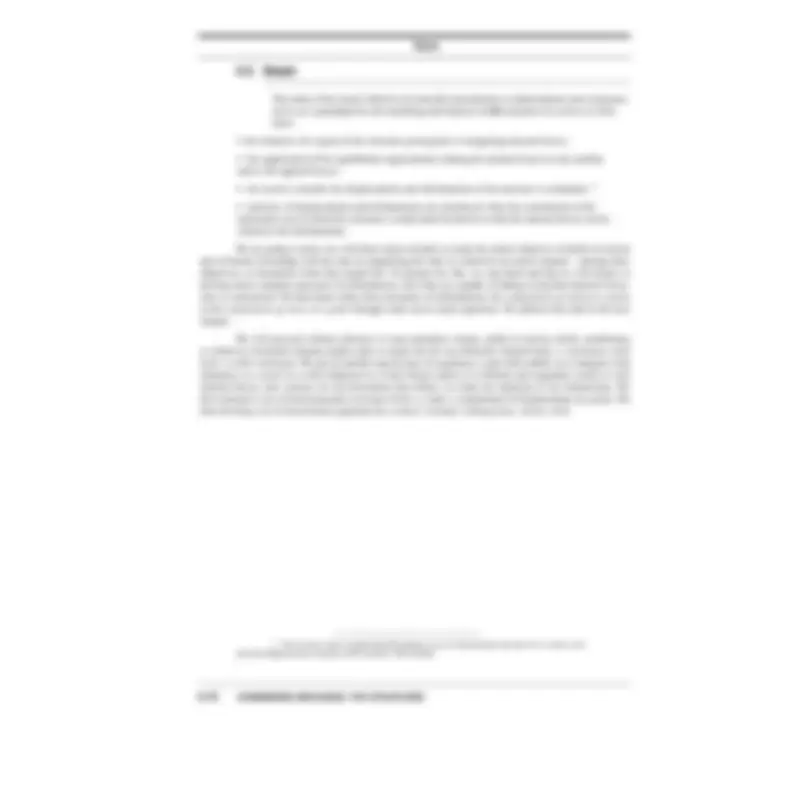
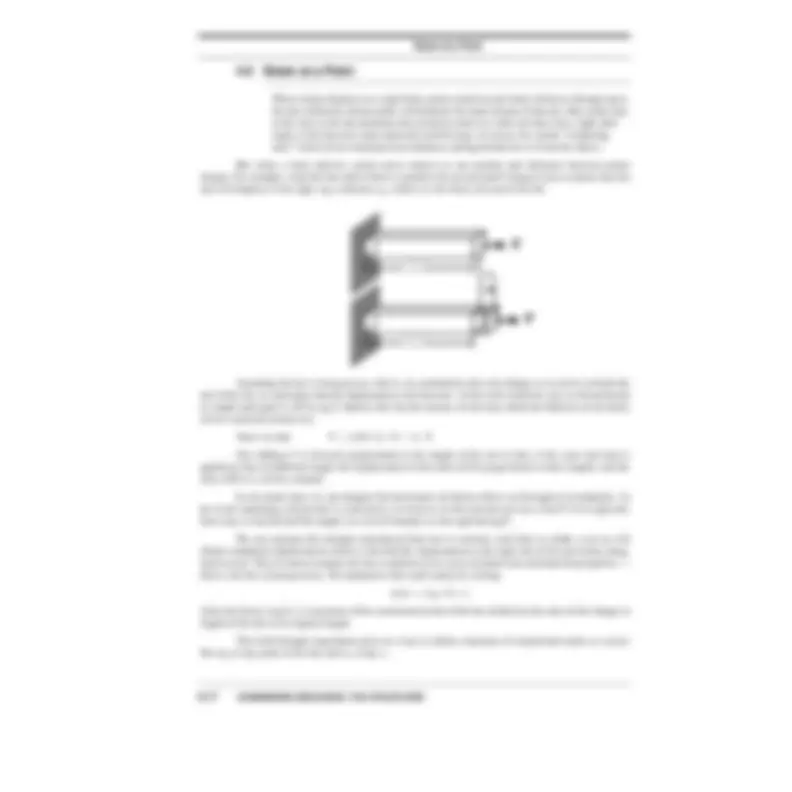
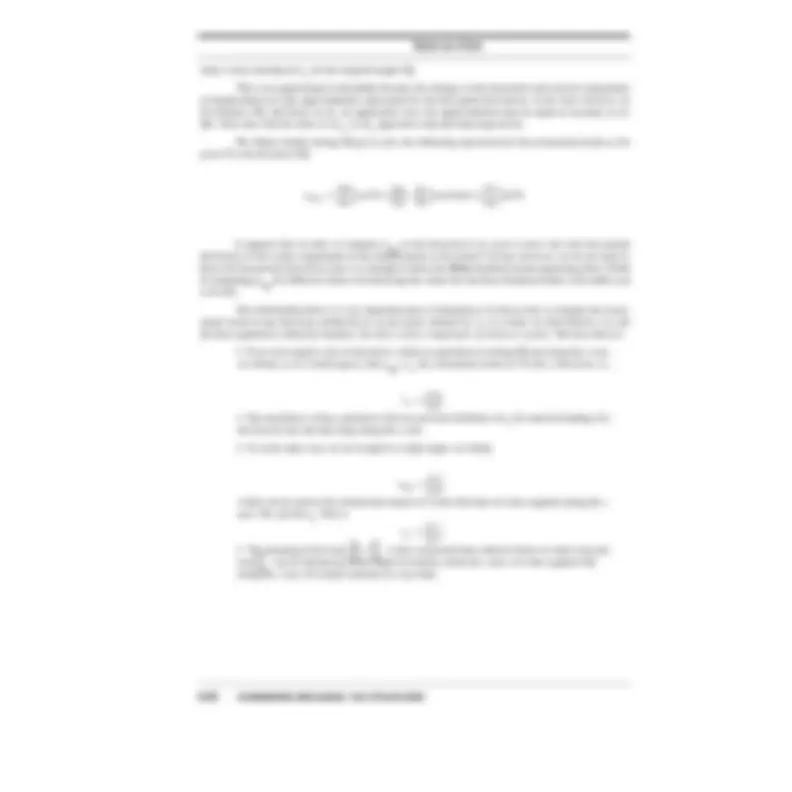
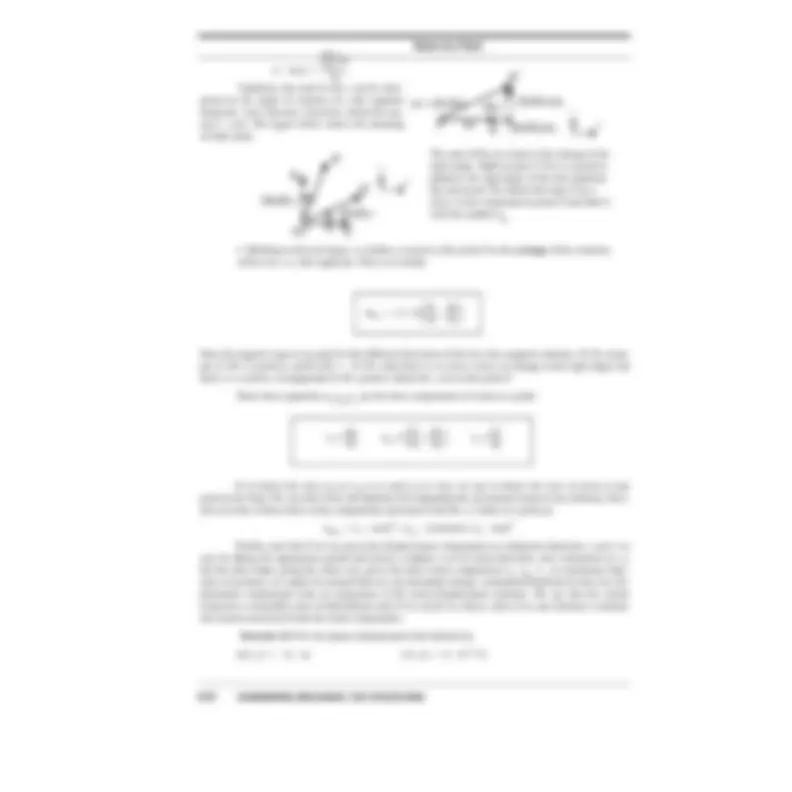
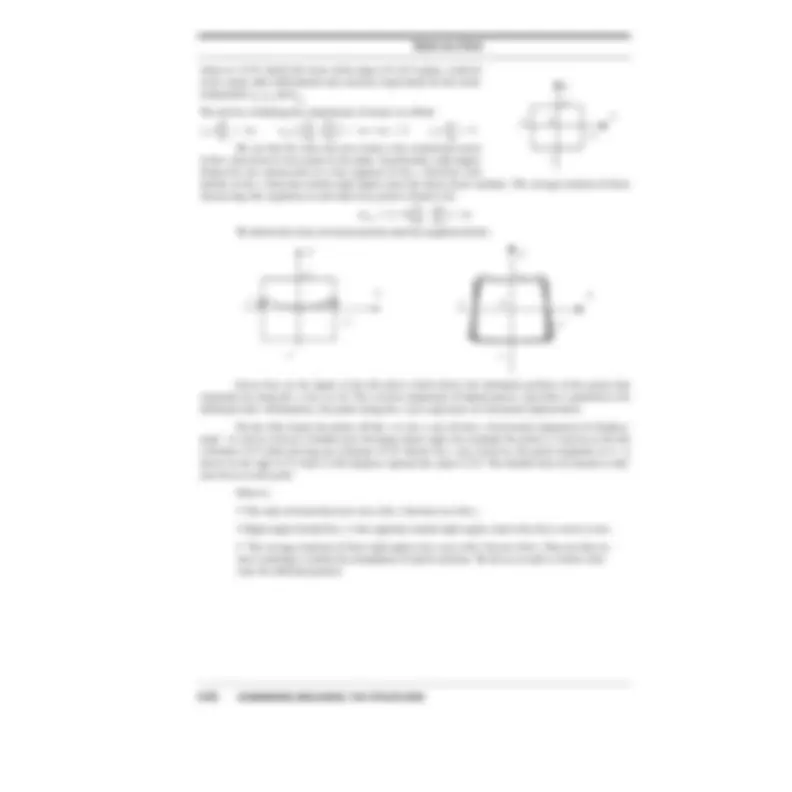
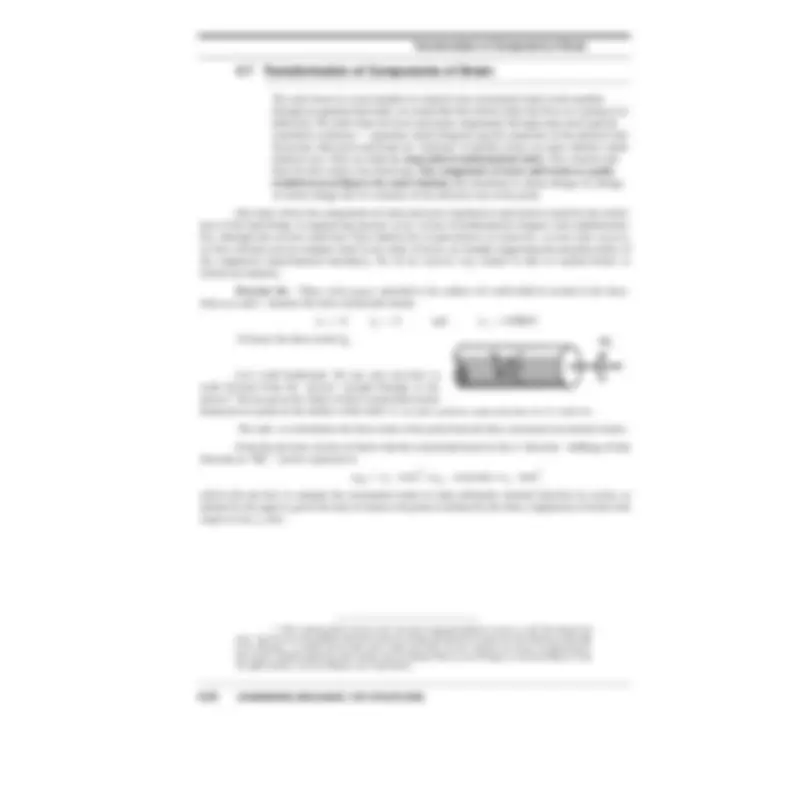
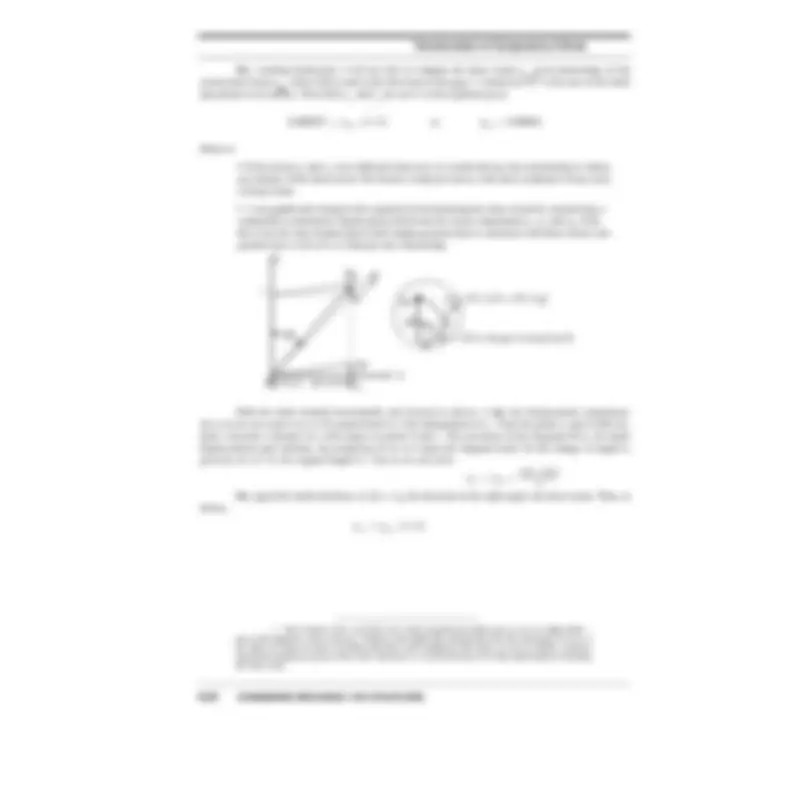
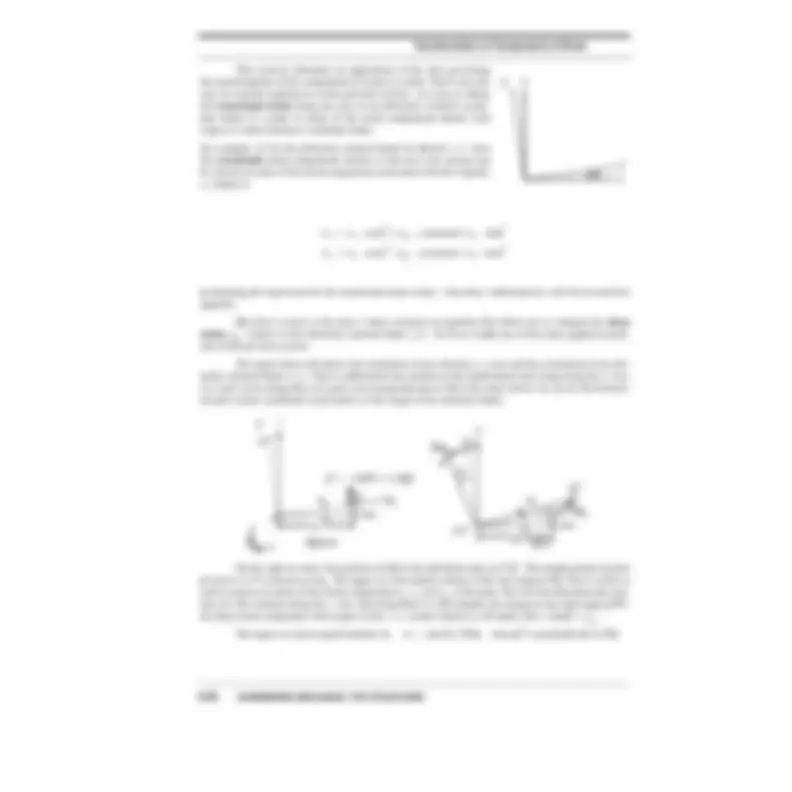
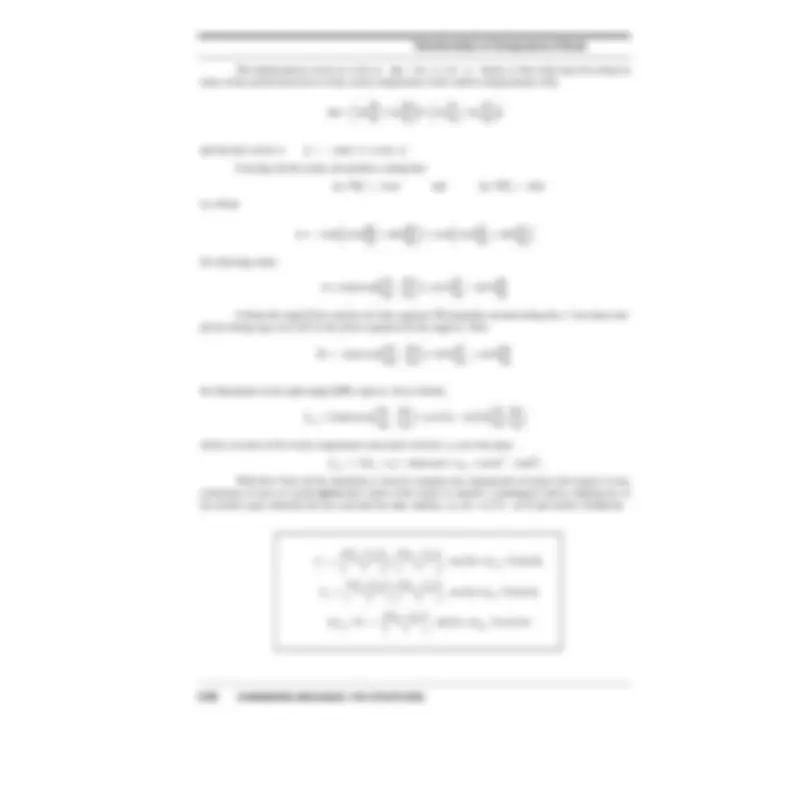
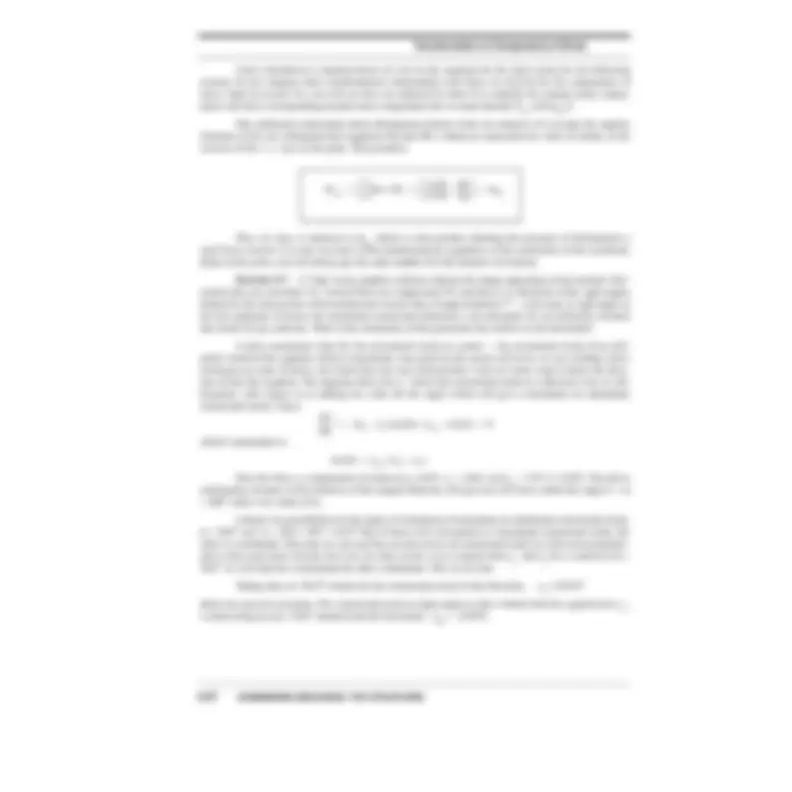
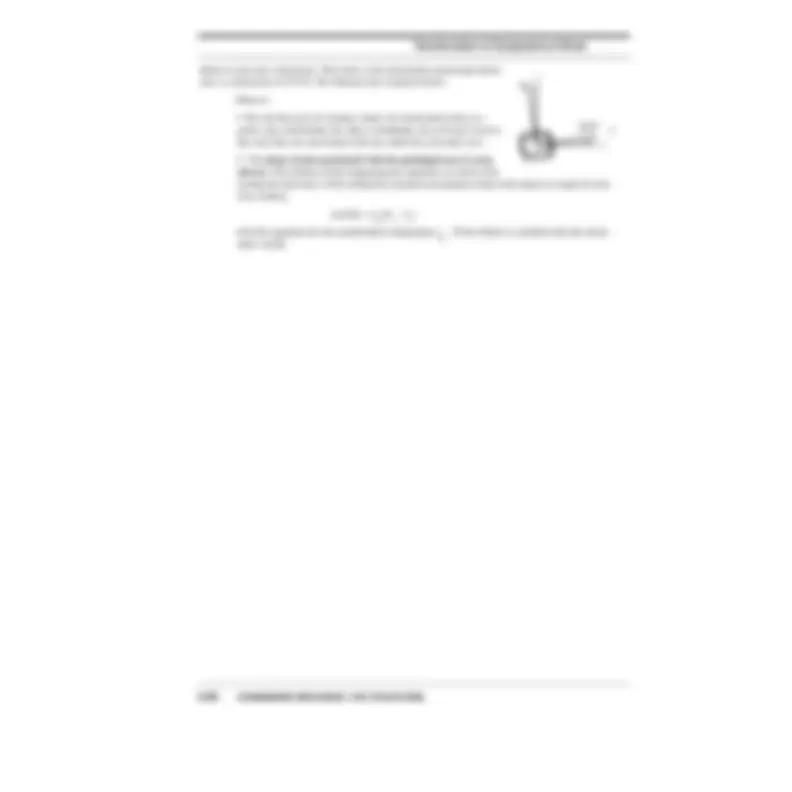
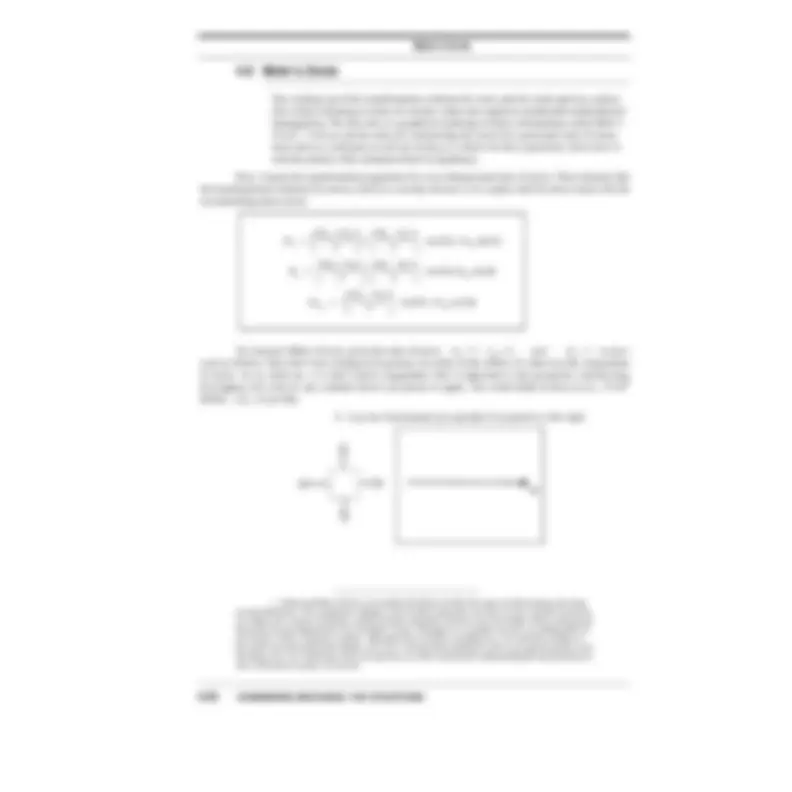
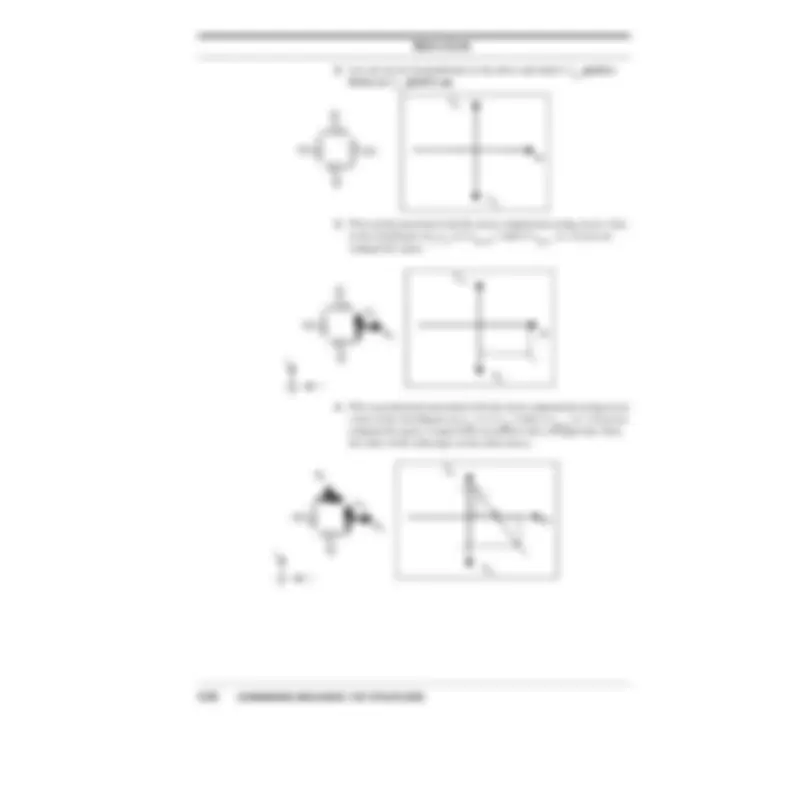
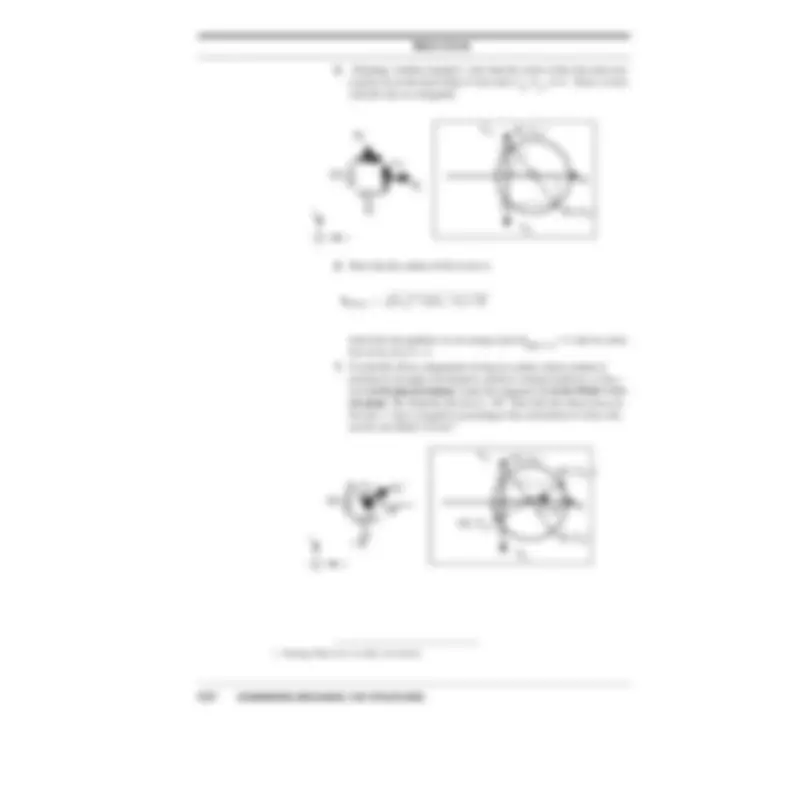
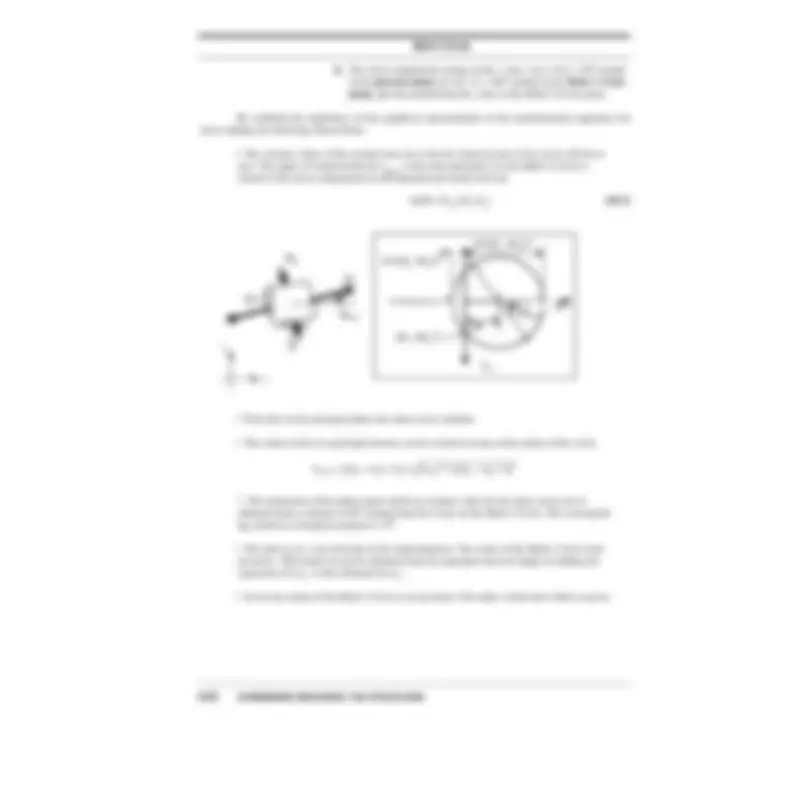
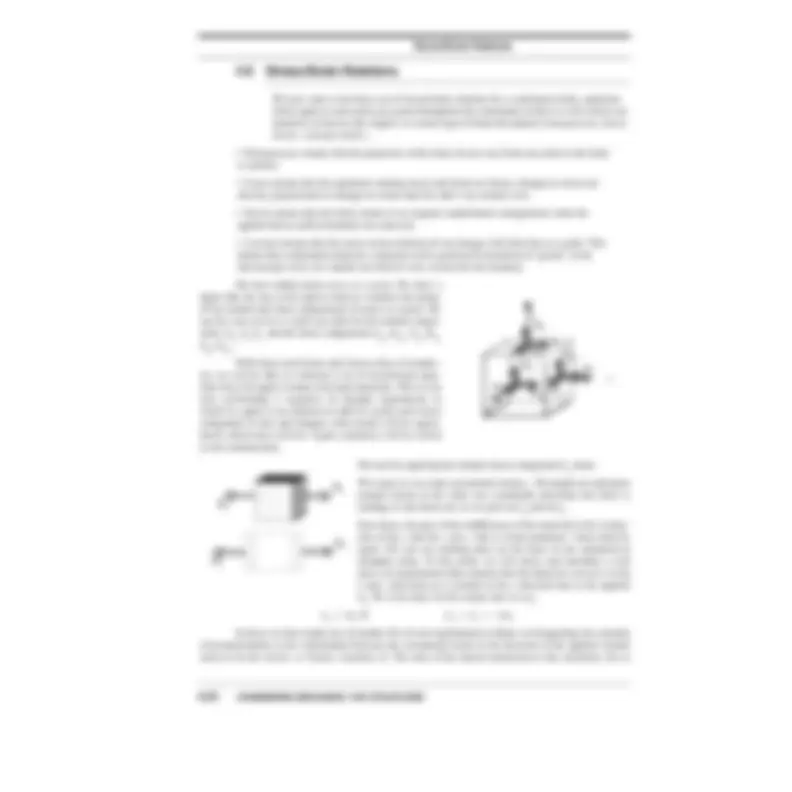
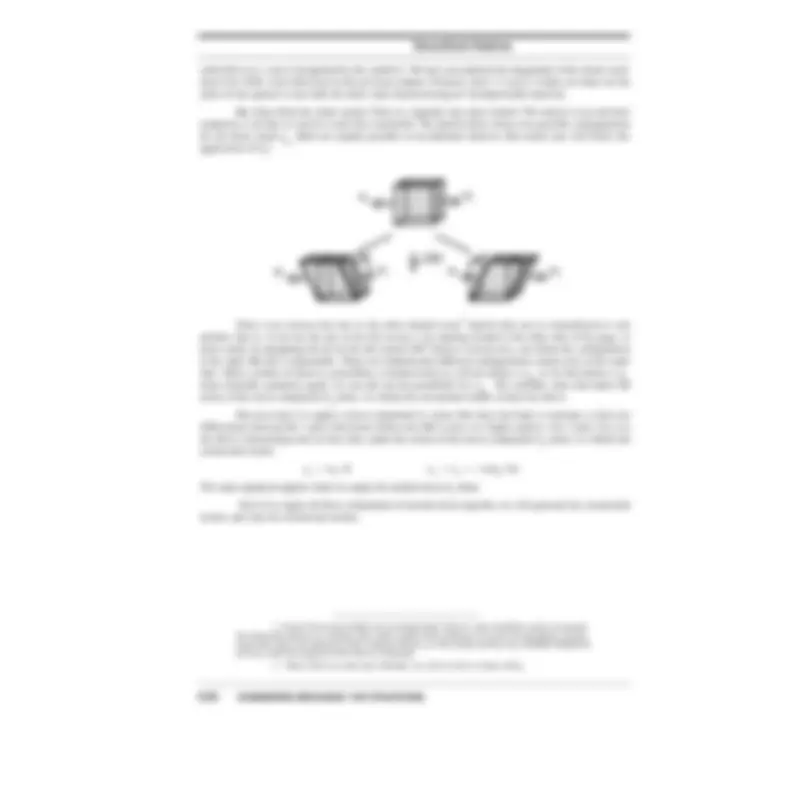
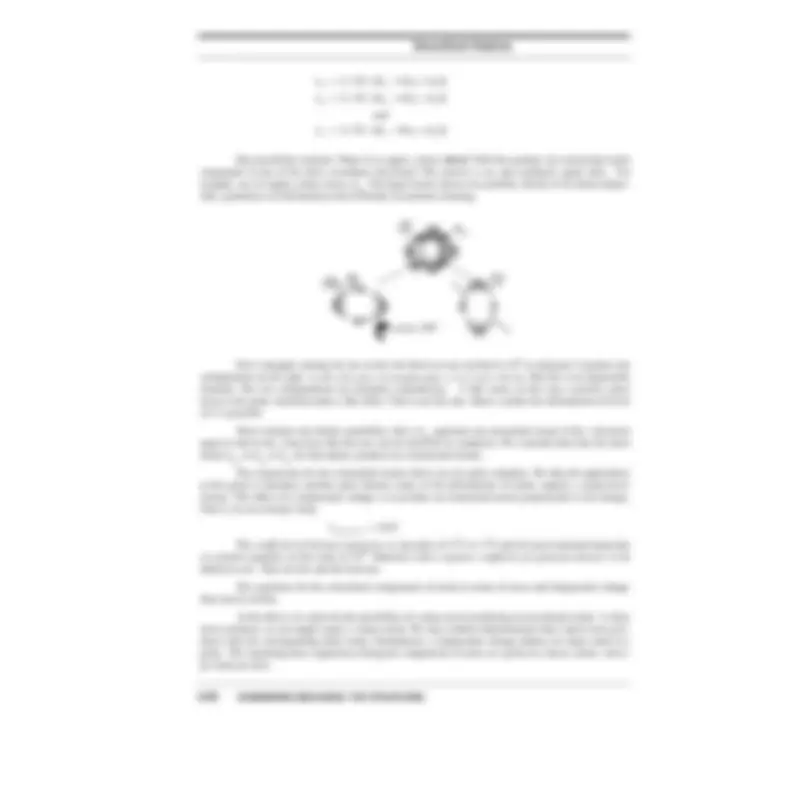
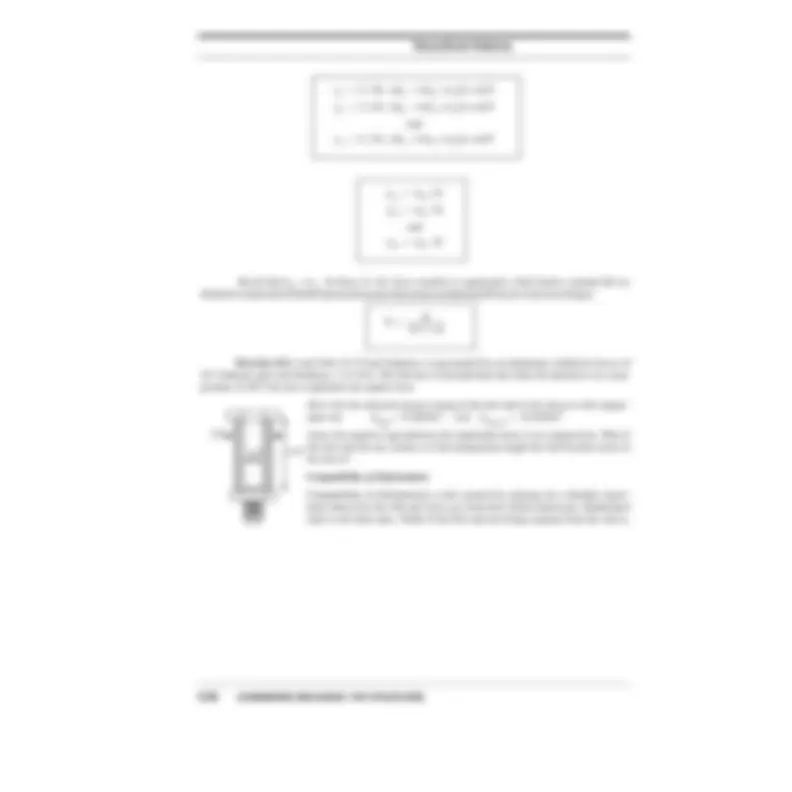
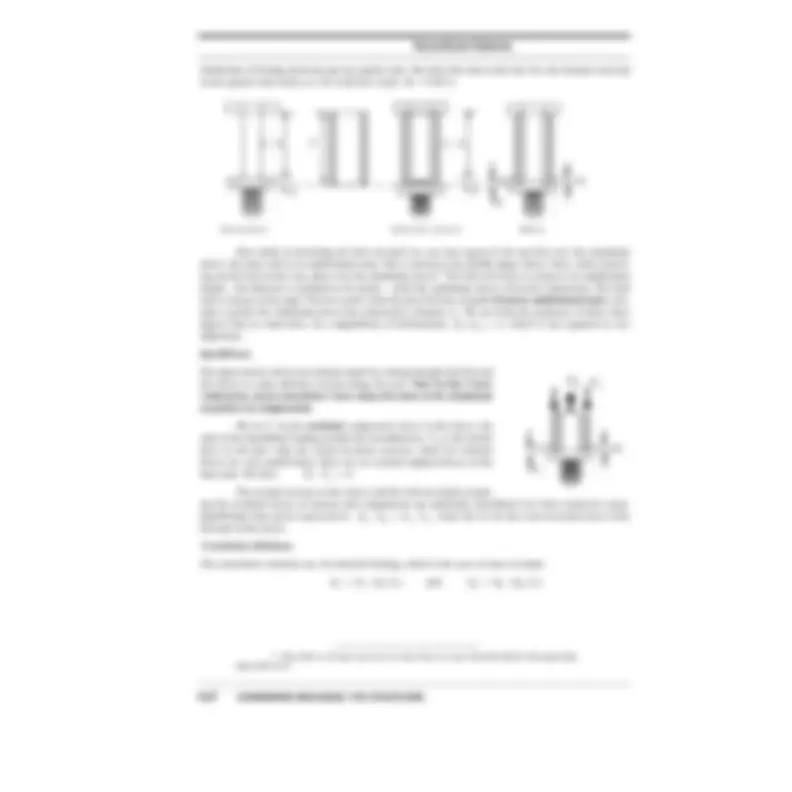
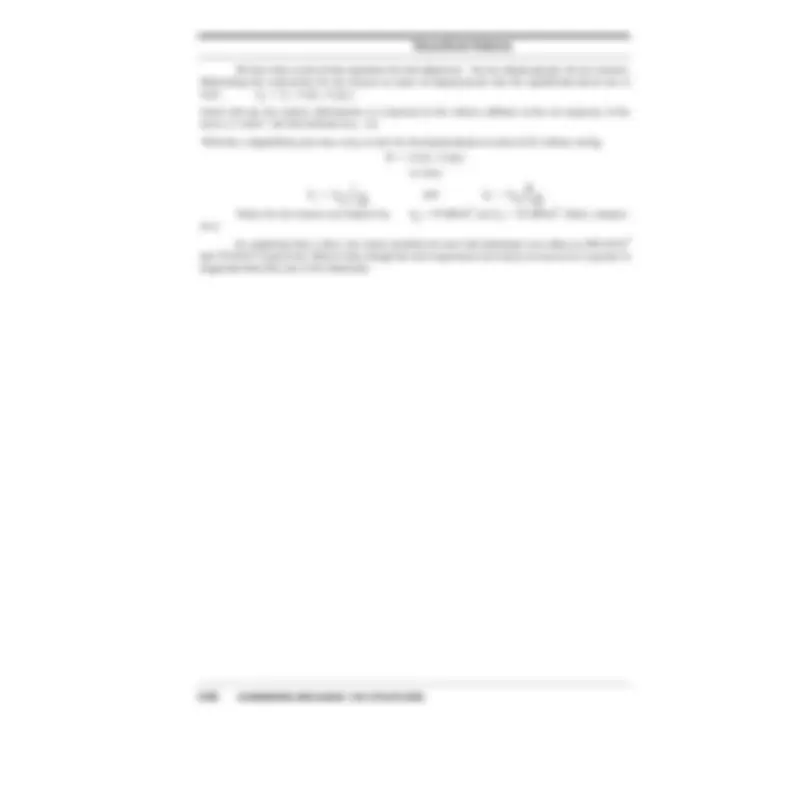
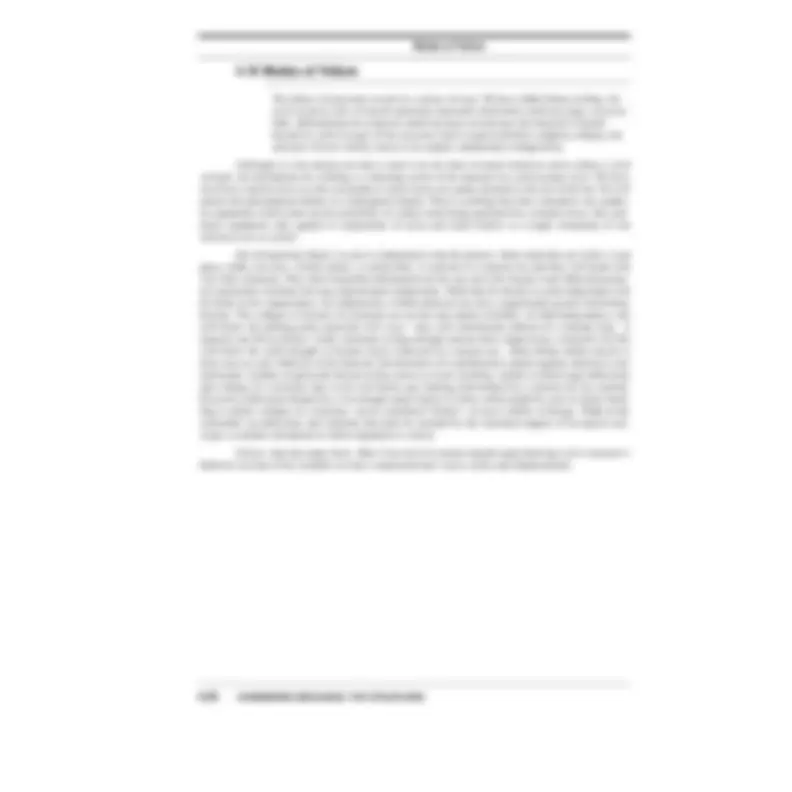
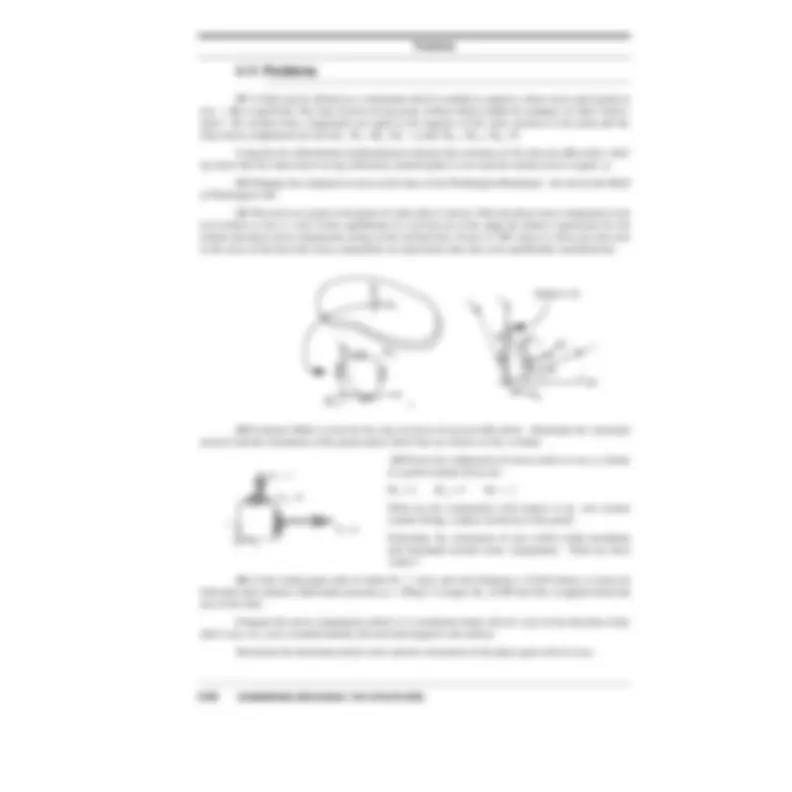
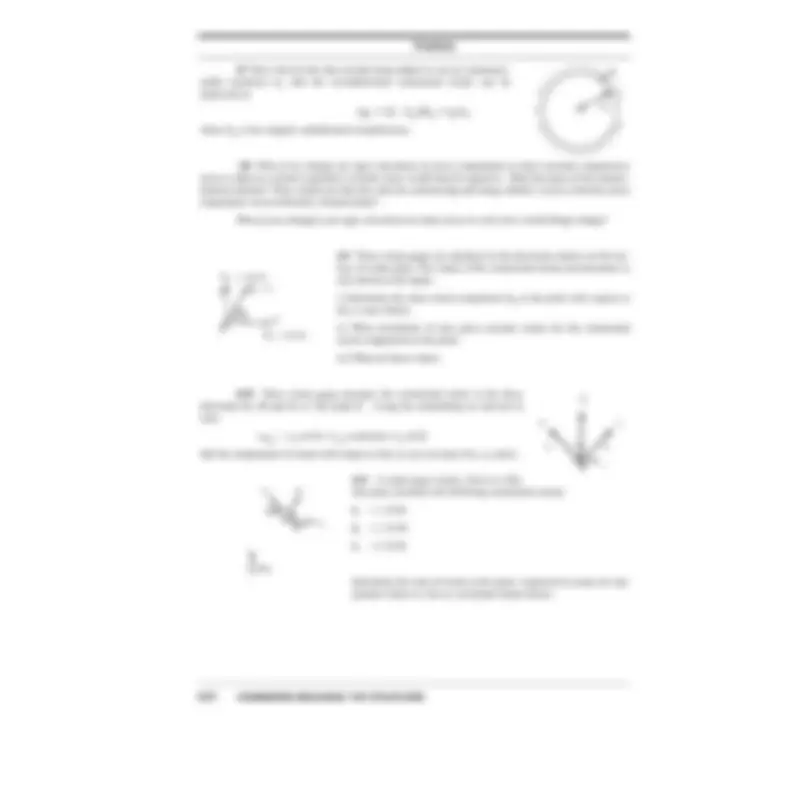
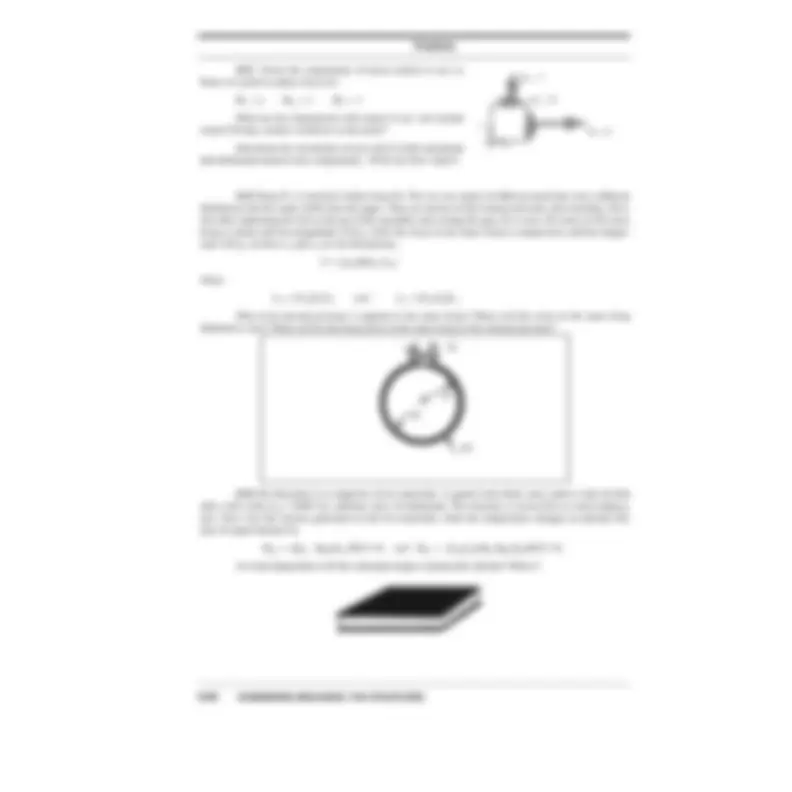
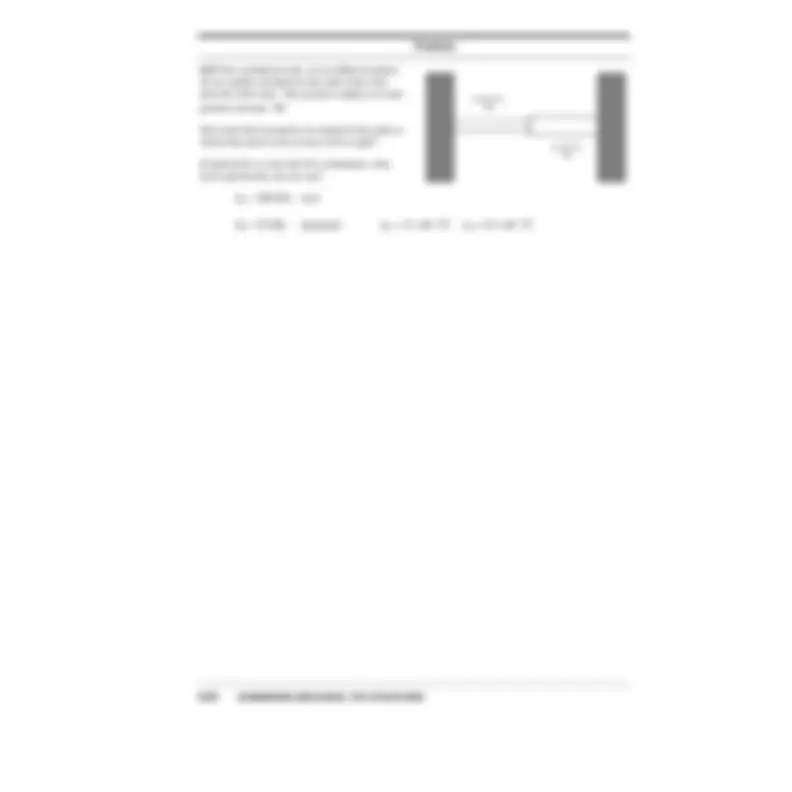
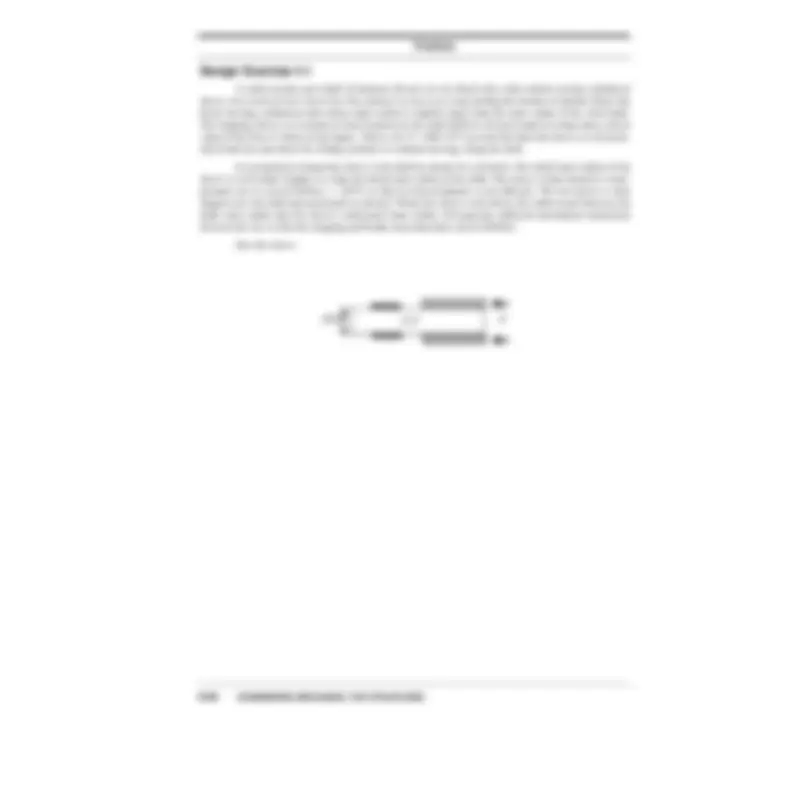
Study with the several resources on Docsity
Earn points by helping other students or get them with a premium plan
Prepare for your exams
Study with the several resources on Docsity
Earn points to download
Earn points by helping other students or get them with a premium plan
Community
Ask the community for help and clear up your study doubts
Discover the best universities in your country according to Docsity users
Free resources
Download our free guides on studying techniques, anxiety management strategies, and thesis advice from Docsity tutors
What is strain, what is stress, and what are the relationships between stress and strain? How to interpret and make sense of graphs?
Typology: Cheat Sheet
1 / 42
This page cannot be seen from the preview
Don't miss anything!
We have talked about internal forces, distributed them uniformly over an area and they became a normal stress acting perpendicular to some internal surface, or a shear stress acting tangentially , in plane. Up to now, we have said little about how these normal and shear stresses might vary with position throughout a solid. 1 Up to now, the choice of planes, their orientation within a solid, was dictated by the geometry of the solid and the nature of the loading. We have said nothing about how these stress components might change if we looked at a set of planes of another orientation. Now we consider a more general situation, an arbitrarily shaped solid. We are going to lift our gaze up from the world of crude structural elements such as truss bars in tension, shafts in torsion, or beams in bending to view these “solids” from a more abstract perspective. They all become special cases of more gen- eral stuff we call a solid continuum.
We will address two questions:
- How might stresses vary from one point to another throughout a continuum; - How do the normal and shear components of stress acting on a plane at a given point change as we change the orientation of the plane at the point. The first bullet introduces the notion of stress field; the second concerns the transformation of com- ponents of stress at a point.
To begin with the first bullet we re-examine the case of a bar suspended vertically and loaded by its own weight, a case considered in section 3.2, page 62. (Note, I have changed the orientation of the reference
The Concept of Stress — An Introduction
axes). We will construct a differential equation which governs how the axial stress varies as we move up and
down the bar. We will solve this differential equation, not forgetting to apply an appropriate boundary con- dition and determine the axial stress field.
We see that for equilibrium of the differential element of the bar, of planar cross-sectional area A
If we assume the tensile force is uniformly distributed over the cross-sectional area, and dividing by the area (which does not change with the independent spatial coordinate y) we can write
function of y, varies throughout our continuum, namely
We solve this ordinary differential equation easily, integrating once and obtain
The Constant is fixed by a prescribed condition at some y surface; If the end of the bar is stress free , we indi- cate this writing
If, on another occasion, a weight of magnitude P 0 is suspended from the free end, we would have
Here then are two stress fields for two different loading conditions 1. Each stress field describes
stress as a function of x and z as well as y to emphasize that we can evaluate its value at every point in the continuum, although it only varies with y. That the stress does not vary with x and z was implied when we
our bar then is assumed weightless relative to the end-load P 0.
x^ F( y)
y
z
y
F + ∆F – γ ⋅ A ⋅ ∆y–F= 0
σ + ∆σ – γ ⋅ ∆y–σ= 0 where σ ≡F ⁄A
d y
d σ (^) – γ = 0
σ ( y) =γ ⋅ y+Cons tant
at y = 0 σ = 0 so σ ( y) =γ ⋅y
at y = 0 σ =P 0 ⁄A and σ ( y) =γ ⋅ y+P 0 ⁄A
Plane Stress
If we assume our continuum has the form of a thin plate of uniform thickness but of arbi- trary closed contour in the x-y plane, our previous arbitrarily loaded, arbitrarily con- strained continuum (we don’t show these again) takes the planar form below.
Because the plate is thin in the z direction, ( h/L << 1 ) we will assume that variations of the stress components with z is uniform or, in other words, our stress components will be at most functions of x and y ,
the set of three “z” stress components that act upon any arbitrarily located z plane within the interior must also vanish. We will also take advantage of the micro-equilibrium consequences, yet to be explored but
exploded view of the point - the block in the middle of the figure - and again from the point of view of look- ing normal to a z plane at the far right. This special model is called Plane Stress.
A Word about Sign Convention: The figure at the far right seems to include more stress compo- nents than necessary; after all, if, in modeling, we eliminate the
should leave, at most, four components acting on the x and y faces. Yet there appear to be eight in the figure. No, there are only at most four components; we must learn to read the figure. To do so, we make use of another sketch of stress at a point , the point A. The figure at the top is meant to indicated that we are looking at four faces or planes simultaneously. When we look at the x face from the right we are looking at the stress components on a positive x face — it has its outward normal in the positive x direction — and a positive normal stress , by con- vention, is directed in the positive x direction. A positive shear stress component , acting in plane, also acts, by convention, in a positive coordinate direction - in this case the positive y direc- tion. On the positive y face, we follow the same convention; a positive
nate direction.
h
A point
x
y
z
no stresses here on this z face
A point
A x
y
Plane Stress
We emphasize that we are looking at a point, point A, in these figures. More precisely we are look- ing at two mutually perpendicular planes intersecting at the point and from two vantage points in each case. We draw these two views of the two planes as four planes in order to more clearly illustrate our sign conven-
tive x direction , upon the negative x face at the left, with its outward normal pointing in the negative x
in the positive x direction , upon the positive x face at the right, with its outward normal pointing in the posi- tive x direction. Both are positive as shown; both are the same quantity. So too the shear stress component
A general statement of our sign convention, which holds for all nine components of stress, even in 3D, is as follows: A positive component of stress acts on a positive face in a positive coordinate direc- tion or on a negative face in a negative coordinate direction.
An Example: We might model the end-loaded cantilever with rel- atively thin rectangular cross-section as a plane stress prob- lem. In this, b is the “thin” dimension, i.e., b/L <1.
If we assume a normal stress distribution over an x face is proportional to some odd power of y, as we did in sec- tion 3.2, exercise 3.5, our state of stress at a point might look
where C(n,b,h) is a constant which depends upon the cross- sectional dimensions of the beam and the odd exponent n. (See page 57). The factor W(L-x) is the magnitude of the internal bending moment at the location x measured from the root. See figure (b).
But this is only one component of our stress field. What are the other eight components of stress at point A?
Our plane stress model allows us to claim that the
Now, in fact, we are doomed from the start; we know that the problem is statically indeterminate so we are not going to be able to construct a unique solution to the equilibrium requirements and specify all nine components of our stress field. Still we can experiment taking advantage of the indeterminacy at our disposal.
For example, we know that a shear force of magni- tude W acts at any x section. In this case it does not vary with x. We might assume, then, that the shear force is uniformly distributed over the cross-section and set
Our stress at a point at point A would then look like figure (d).
h
x
y
z
(a)
point A
point A (^) b
point A
(c)
W ( L-x )
x
point A (b) x
y
(d)
σx ( x y, ) C n b h( , , ) W L( – x)y n = ⋅
σxy =–W ⁄( bh)
Stress Fields & “Micro” Equilibrium
We return and pick up on the example of a bar hanging under its own weight and explore the consequences of equilibrium when applied to a differential element of an arbitrarily shaped two dimensional, plane stress continuum. We call this “micro” equilibrium consid- erations to distinguish it from the “macro” equilibrium considerations of the last chapter. There we isolated large chunks of structure. Think now, of a differential element in 2D; for example, of the cantilever beam: We show such on the right. Note now we are no longer focused on two intersecting, perpendicular planes at a point but on a differential element of the continuum. Now we see that the stress components may very well be dif- ferent on the two x faces and on the two y faces.
We allow the x face components, and those on the two y faces to change as we move from x to
ing x constant).
We show two other arrows on the figure, Bx and B (^) y. These are meant to represent the x and y com- ponents of what is called a body force. A body force is any externally applied force acting on each ele- ment of volume of the continuum. It is thus a force per unit volume. For example, if we need consider the weight of the beam, By would be just
where the negative sign is necessary because we take a positive component of the body force vector to be in a positive coordinate direction.
Bx would be taken as zero. We now consider force and moment equilibrium for this differential element, our micro isolation.
nents are not forces; to figure their contribution to the equilibrium requirement, we must factor in the areas upon which they act.
I present just the results of the limiting process which, we note, since all components may be func- tions of both x and y, brings partial derivatives into the picture.
h
x
y
z
(a) point A (^) b
A differential
element
y
x x
y
y
B y
B x
y =^ – γ where^ γ^ =the weight density
∑ Forces in the x direction^ → ∂x
∂σx ∂y
∂σyx
∑ Forces in the y direction^ → ∂x
∂σxy ∂y
∂σy
∑ Moments about the center of the element^ → σyx^ =σxy
Stress Fields & “Micro” Equilibrium
and the force due to this “unbalanced” component in the x direction is
The contribution of the body force (per unit volume) to the sum of force components in the x direc-
that this product will be a common factor in all terms entering into the equations of force equilibrium in the x and y directions.
The last equation of moment equilibrium shows that, as we forecast, the shear stress component on the y f ace must equal the shear stress component acting on the x face. The differential changes in the shear
We leave this topic to the side for the moment and turn now to the second item on our agenda — the transformation of components of stress at a point.
∆σx ∂x
∂σx = ⋅∆x
∂x
∂σx ⋅∆x ⋅(∆ y∆z)
Transformation of Components of Stress
The answer goes as follows: One of our main concerns as a designer of structures is failure —frac- ture or excessive deformation of what we propose be built and fabricated. Now many kinds of failures ini- tiate at a local, microscopic level. A minute imperfection at a point in a beam where the local stress is very high initiates fracture or plastic deformation, for example. Our quest then is to figure out where, at what points in a structural element, the normal and shear stress components achieve their maximum values. But we have just seen how these values depend upon the way we look at a point, that is, upon the orientation of the plane we choose to inspect. To ensure we have found the maximum normal stress at a point for example, we would then have to inspect every possible orientation of a plane passing through the point. 1
This seems a formidable task. But before taking it on, we pose a prior question: Exercise 4.2 What do you need to know in order to determine the normal and shear stress compo- nents acting upon an arbitrarily oriented plane at a point in a fully three dimensional object?
The answer is what we might anticipate from our original definition of six stress components for if
an arbitrarily oriented plane at the point. That is the answer to our need to know question.
To show this, we derive a set of equations that will enable you to do this. But note: we take the six stress components relative to the three orthogonal, let’s call them, x,y,z planes as given, as known quantities. Furthermore, again we restrict our attention to two dimensions - the case of Plane Stress. That is we say that the components of stress acting on one of the planes at the point - we take the z planes - are zero. This is a good approximation for certain objects — those which are thin in the z direction relative to structural ele- ment’s dimensions in the x-y plane. It also, makes our derivation a bit less tedious, though there is nothing conceptual complex about carrying it through for three dimensions, once we have it for two.
In two dimensions we can draw a simpler picture of the state of stress at a point. We are not talking differential element here but of stress at a point. The figure below shows an arbitrarily oriented plane,
xy
A point
Transformation of Components of Stress
Consider equilibrium of the shaded wedge shown. Here we let A φ designate the area of the inclined face at a point, Ax and Ay the areas of the x face with its outward normal pointing in the - x direction and of the y face with its outward normal pointing in the - y direction respectively. In this we take a unit depth into the paper. We have
That takes care of the relative areas. Now for force equilibrium, in the x and y directions we must have:
If we multiply the first by cosφ, the second by sinφ and add the two we can eliminate σ’ xy. We obtain
which, upon expressing the areas of the x , y faces in terms of the area of the inclined face, can be written (noting A φ becomes a common factor).
In much the same way, multiplying the first equilibrium equation by sinφ, the second by cosφ but subtracting rather than adding you will obtain eventually
We deduce the normal stress component acting on the y’ face of this rotated frame by replacing φ in our equation for σ’ x by φ + π/2. We obtain in this way:
The three transformation equations for the three components of stress at a point can be expressed, using the double angle formula for the cosine and the sine, as
Here we have the equations to do what we said we could do. Think of the set as a machine: You input the three components of stress at a point defined relative to an x-y coordinate frame, then give me the
To show the utility of these relationships consider the following scenario:
A (^) x = Aϕ ⋅cosφ and A (^) y =Aφ ⋅sinφ
σ' (^) x Aφ – σx cosφA (^) x– σxy cosφA (^) y– σxy sinφA (^) x – σy sinφA (^) y= 0
σ' (^) x σx cos φ 2 σy sin φ 2 = + + 2 σxy sin φcosφ
σ' (^) xy =( σy – σx) sin φcos φ+σxy ( cos φ^2 – sin φ^2 )
σ' (^) y σy cos φ 2 σx sin φ 2 = + – 2 σxysin φcosφ
σ' (^) x
( σx +σy) 2
( σx – σy) 2 = + ----------------------^ ⋅ cos 2 φ+σxy sin 2 φ
σ' (^) y
( σx +σy) 2
( σx – σy) 2
= – ---------------------- ⋅cos 2 φ– σxysin 2 φ
σ' (^) xy
( σx – σy) 2
=– ---------------------- ⋅ sin 2 φ+σxy cos 2 φ
Transformation of Components of Stress
To find the extreme, including maximum, values for the normal stress, σ’ x we proceed in much the
(EQ 1)
mal stress acting at the point on the surface is equal in magnitude to the maximum shear stress component.
Note too that our transformation relations say that the nor-
stress acting on the x’-y’ planes is zero! We illustrate the state of stress at the point relative to the x’-y’ planes below right.
Backing out of the woods in order to see the trees, we claim that if our cylinder is made of a brittle material, it will frac- ture across the plane upon which the maximum tensile stress acts. If you go now and take a piece of chalk and subject it to a torque until it breaks, you should see a fracture plane in the form of a helical surface inclined at 45 degrees to the axis of the cylinder. Check it out.
Of course it’s not enough to know the orientation of the fracture plane when designing brittle shafts to carry torsion. We need to know the magnitude of the torque which will cause fracture. In other words we need to know how the shear stress does in fact vary throughout the cylinder.
This remains an unanswered question. So too for the beam: How do the normal stress (and shear stress) components vary over a cross section of the beam? We have claimed that to answer these questions we must go beyond the concepts and principles of static equilibrium. This we do now, looking first at simple indeterminate systems, then on to the indeterminate truss, the beam in bending and beyond.
d φ
d σ' (^) x = 2 τ ⋅ cos 2 φ = 0
original state of stress
Strain
The study of the elastic behavior of statically determinate or indeterminate truss structures serves as a paradigm for the modeling and analysis of all structures in so far as it illus- trates
- the isolation of a region of the structure prerequisite to imagining internal forces; - the application of the equilibrium requirements relating the internal forces to one another and to the applied forces; - the need to consider the displacements and deformations if the structure is redundant; 1 - and how, if displacements and deformations are introduced, then the constitution of the material(s) out of which the structure is made must be known so that the internal forces can be related to the deformations. We are going to move on, with these items in mind, to study the elastic behavior of shafts in torsion and of beams in bending with the aim of completing the task we started in an earlier chapter – among other objectives, to determine when they might fail. To prepare for this, we step back and dig in a bit deeper to develop more complete measures of deformation, ones that are capable of taking us beyond uniaxial exten- sion or contraction. We then must relate these measures of deformation, the components of strain at a point to the components of stress at a point through some stress-strain equations. We address that task in the next chapter.
We will proceed without reference to truss members, beams, shafts in torsion, shells, membranes or whatever structural element might come to mind, but for an arbitrarily shaped body, a continuous solid body, a solid continuum. We put on another special pair of eyeglasses, a pair that enables us to imagine what transpires at a point in a solid subjected to a load which causes it to deform and engenders strain as well internal forces, now stresses. In our derivations that follow, we limit our attention to two dimensions: We first construct a set of strain measures in terms of the x , y (and z ) components of displacement at a point. We then develop a set of stress/strain equations for a linear, isotropic, homogenous, elastic solid.
Strain at a Point
For the homogenous bar under end load P we see that ε (^) x is a constant; it does not vary with x. We
placement of any two points, equidistant apart in the undeformed state, is a constant; but this is not the usual way of speaking nor, other than for a truss element, is it usually the case.
The partial derivative implies that, u, the displacement component in the x direction can be a func- tion of spatial dimensions other than x alone, that is, for an arbitrary solid, with things changing as one moves in any of the three coordinate directions, we would have u = u ( x , y , z ). We turn to this more general sit- uation now.
Exercise 4.4 – What do I need to know about the displacements of points in a solid in order to com- pute the extensional strain at the point P , arbitrarily taken, in the direction of t o, also arbitrarily chosen, as the body deforms from the state indicated at the left to that at the right?
We designate the extensional strain at P in the direction of t 0 by ε PQ. Our task is to see what we need to know in order to evaluate the limit
To do this, we draw another picture of the undeformed and deformed differential line element, PQ. together with the displacements of its endpoints. Point P’s displacement to P’ is shown as the vector, u, while the displacement of point Q, some small distance away, is designated
This now looks very much like the representation used in the last chap- ter to illustrate and construct an expression for the extension of a truss member as a function of the horizontal and vertical components of dis- placement at its two ends. That’s why I have introduced the vectors L o , and L for the directed line segments PQ , P ’ Q ’ respectively though they are in fact meant to be small, differential lengths. Proceeding in the same way as we did in our study of the truss, we write, as a conse- quence of vector addition,
which yields an expression for ∆ u in terms of the vector difference of the two directed line segments, namely
We now introduce a most significant constraint, We assume, as we did with the truss, that displace- ments and rotations are small – displacements relative to some characteristic length of the solid, rotations relative to a radian. This should not to be read as implying our analysis is of limited use. Most structures behave, i.e., deform, according to this constraint and, as we have seen in our study of a truss structure, it is entirely consistent with our writing the equilibrium equations with respect to the undeformed configuration. In fact not to do so would be erroneous.
εx (∆ u ⁄∆x) ⇒εx ∆x → 0
lim ∂x
= =∂u
y
z
x
Q P
εPQ ( P'Q' – PQ) ⁄( PQ) PQ → 0
= lim
y x
t
Before
u + L=u + ∆ u +L 0
∆ u = L – L 0
Strain at a Point
Explicitly this means we will take
With this we can claim that the change in length of the directed line segment, PQ , in moving to
where t o is, as before, a unit vector in the direction of PQ.
From here on in, constructing an expression for ε PQ requires the machine-like evaluation of the
ment taken with respect to position, and the manipulation of all of this into a form which reveals what’s needed in order to compute the relative change in length of the arbitrarily oriented, differential line segment, PQ. We work with respect to a rectangular cartesian coordinate frame, x , y , and define the horizontal and ver- tical components of the displacement vector u to be u , v respectively. ( In the following be careful to distinguish between the scalar u and the vector u ; the former is the x component of the latter). That is, we set
where the coordinates x , y label the position of the point P. The differential change in the displacement vec- tor in moving from P to Q , a small distance which in the limit will go to zero, may then be written
Carrying out the scalar product, we obtain for the change in length of PQ :
We next approximate the small changes in the horizontal and vertical, scalar components of dis- placement by the products of their slopes at P taken with the appropriate differential lengths along the x and y axes as we move to point Q. That is^1
and
We have then
t ≈ t 0 so that L = t • L ≈ t 0 • L
we have P'Q' – PQ= t 0 • L – t 0 • L 0 = t 0 • ( L – L 0 ) = t 0 • ∆ u
u =u x y( , ) ⋅ i +v x y( , ) j
∆ u =∆u x y( , ) ⋅ i +∆v x y( , ) ⋅ j
P'Q' – PQ = t 0 • ∆ u =( ∆u) ⋅ cosφ+( ∆v) ⋅sinφ
∆u x y( , ) ∂x
∂u
∆x ∂y
∂u ≈ +^ ∆y
∆v x y( , ) ∂x
∂v
∆x ∂y
∂v ≈ +^ ∆y
( P'Q' – PQ) ⁄ ( PQ) ∂x
∂u
∆x ∂y
∂u
∆x ∂y
∂v
Strain at a Point
Similarly, the term δ u /δ y can be inter- preted as the angle of rotation of a line segment along the y axis, but now, if positive, about the neg- ative z axis. The figure below shows the meaning of both terms.
The sum of the two terms is the change in the right angle, PQR at point P. If it is a positive quantity, the right angle of the first quadrant has decreased. We define this sum to be a shear strain component at point P and label it with the symbol γ xy.
- Building on the last figure, we define a rotation at the point P as the average of the rotations of the two, x , y , line segments. That is we define
Note the negative sign to account for the different directions of the two line segment rotations. If, for exam- ple, δ v /δ x is positive, and δ u /δ y = - δ v /δ x then there is no shear strain , no change in the right angle, but there is a rotation , of magnitude δ v /δ x positive about the z axis at the point P.
These three quantities ε x ,γ xy ,ε y are the three components of strain at a point.
If we know the way ε x ( x , y ), γ xy ( x , y ), and ε y ( x , y ) vary, we say we know the state of strain at any point in the body. We can then write our equation for computing the extensional strain in any arbitrary direc- tion in terms of these three strain components associated with the x , y frame at a point as:
Finally, note that if we are given the displacement components as continuous functions x and y we can, by taking the appropriate partial derivatives, compute a set of strain functions, also continuous in x , y. On the other hand, going the other way, given the three strain components, ε x , γ xy , ε (^) y as continuous func- tions of position, we cannot be assured that we can determine unique, continuous functions for the two dis- placement components from an integration of the strain-displacement relations. We say that the strains represent a compatible state of deformation only if we can do so, that is, only if we can construct a continu- ous displacement field from the strain components.
Exercise 4.5 –For the planar displacement field defined by
y x
α ∼ tanα ∂x
∂v
∆x
∆x =-------------------
y x
ωxy ( 1 ⁄ 2 ) ∂x
∂v
∂y
∂u
εx ∂x
∂u (^) γ xy (^) ∂x
∂v
∂y
∂u
(^) ε y (^) ∂y ≡ ≡ + ≡∂v
εPQ =εx ⋅ cos φ^2 + γ (^) xy ⋅ cosφ sinφ+εy ⋅sin φ^2
u x y( , ) = – κ ⋅xy v x y( , ) =κ ⋅( x 2 ⁄ 2 )
Strain at a Point
where κ = 0.25, sketch the locus of the edges of a 2x2 square, centered at the origin, after deformation and construct expressions for the strain components ε x , ε y , and γ xy
We start by evaluating the components of strain; we obtain
We see that the only non zero strain is the extensional strain in the x direction at every point in the plane. In particular, right angles formed by the intersection of a line segment in the x direction with another in the y direction remain right angles since the shear strain vanishes. The average rotation of these intersecting line segments at each and every point is found to be
We sketch the locus of selected points and line segments below:
Focus first, on the figure at the left above which shows the deformed position of the points that originally lay along the x axis, at y =0. The vertical component of displacement v describes a parabola in the deformed state. Furthermore, the points along the x axis experience no horizontal displacement.
On the other hand, the points off the x or the y axis all have a horizontal component of displace- ment - as well as vertical. Consider now the figure above right. For example the point (1,1) moves to the left a distance 0.25 while moving up a distance 0.125. Below the x axis, however, the point originally at (1,-1) moves to the right 0.25 while it still displaces upward the same 0.125. The shaded lines are meant to indi- cate the u at each point.
Observe
- The state of strain does not vary with x , but does so with y. - Right angles formed by x - y line segments remain right angles, that is the shear strain is zero. - The average rotations of these right angles does vary with x but not with y. Note too that we have seemingly violated the assumption of small rotations. We did so in order to better illus- trate the deformed pattern.
+
+
-
0 εx ∂x
∂u (^) = – κy γ xy (^) ∂x
∂v
∂y
∂u
(^) = – κx+ κy= 0 ε y (^) ∂y ≡ ≡ + ≡∂v= 0
ωxy ( 1 ⁄ 2 ) ∂x
∂v
∂y
∂u = – =κx
+
+
- -
+
+
- -
0