
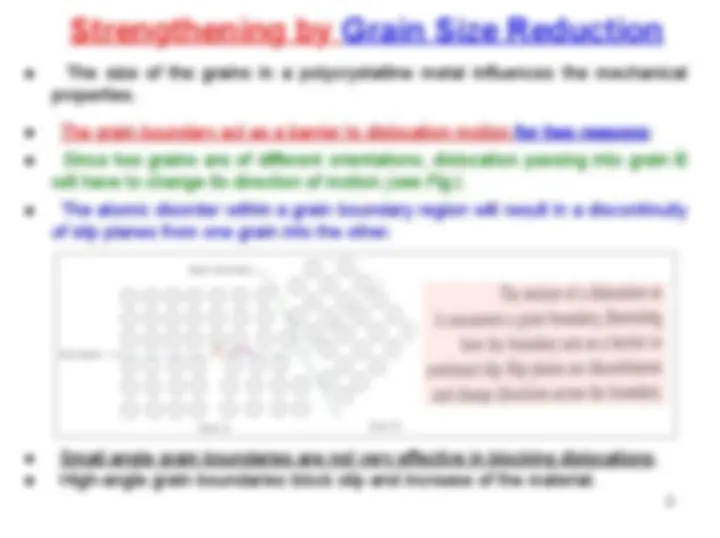
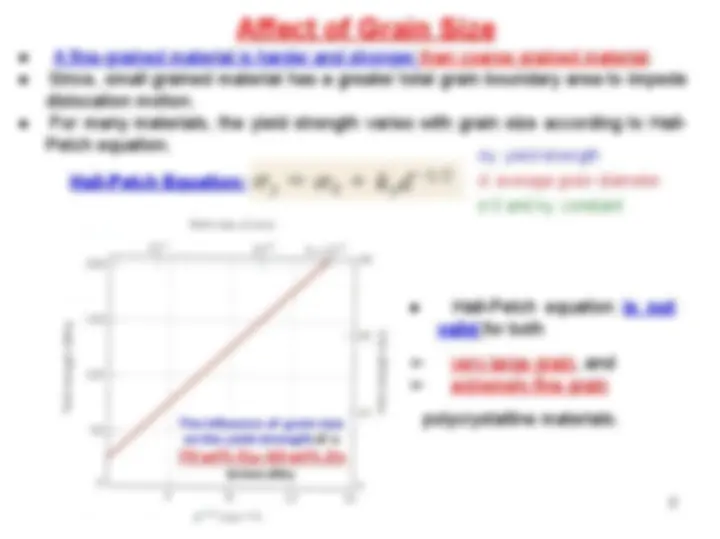
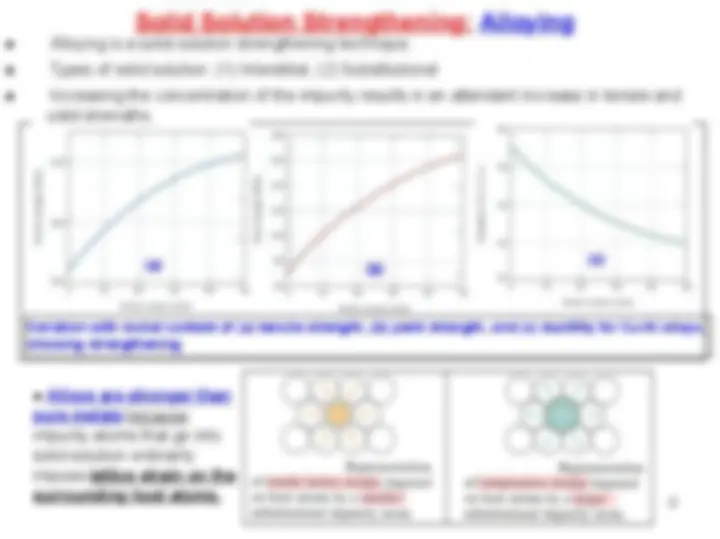
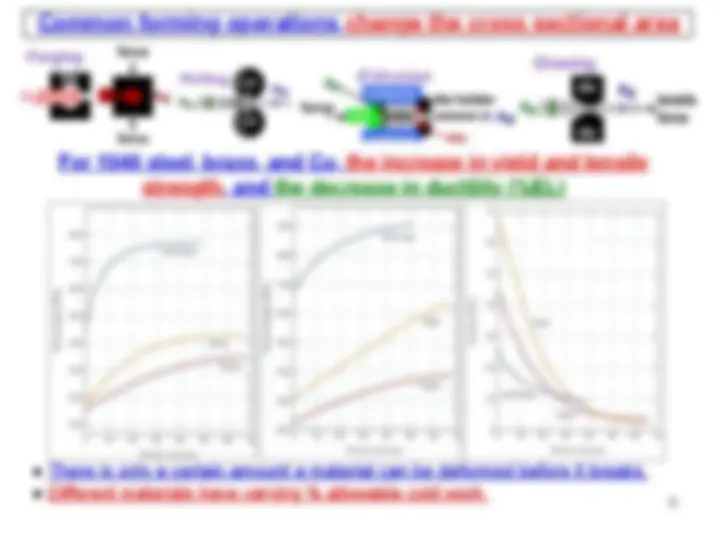
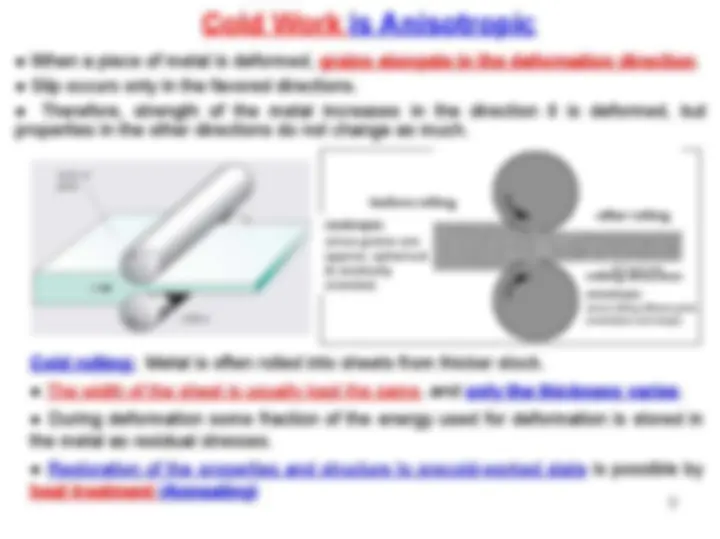
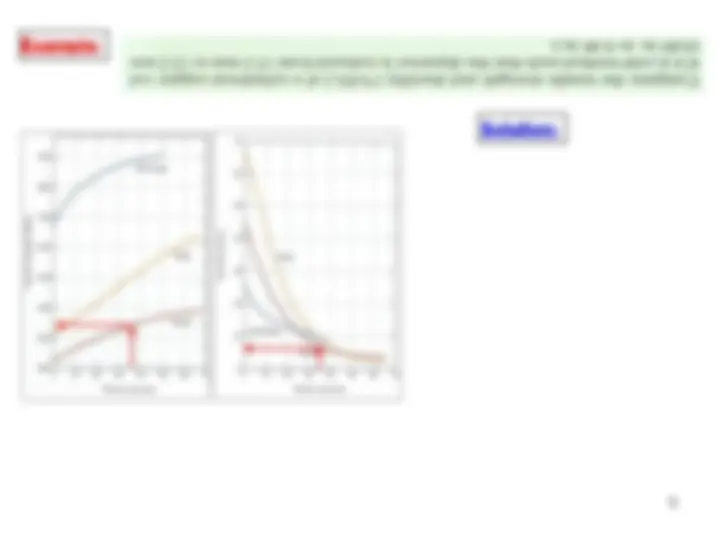
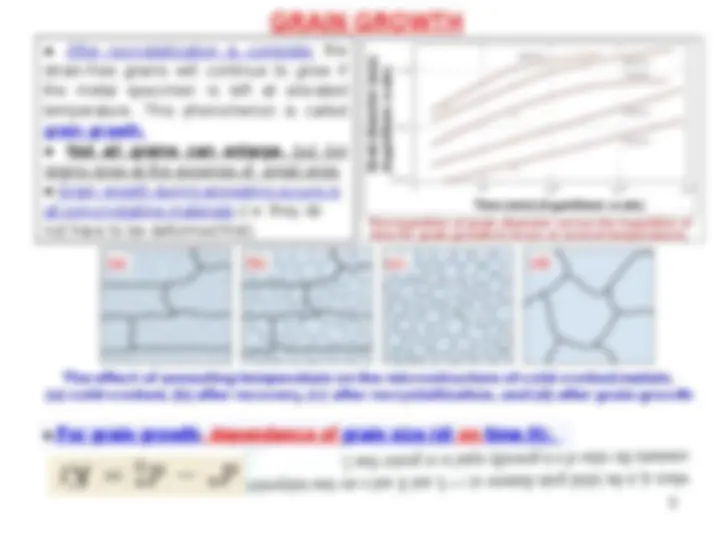
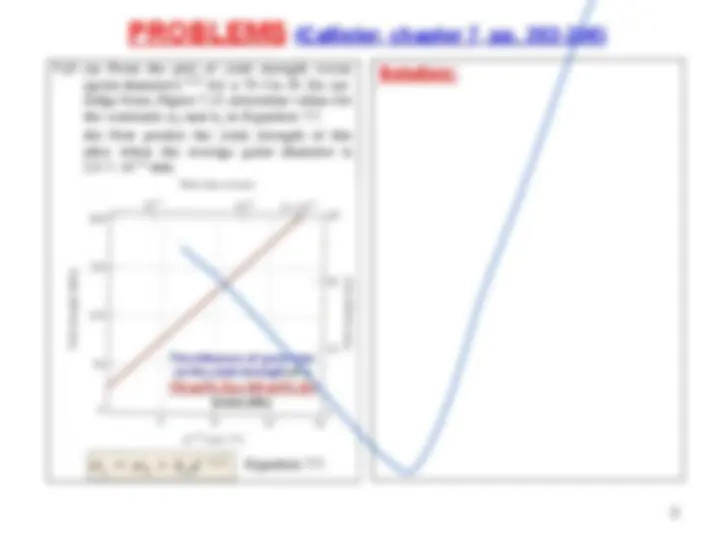
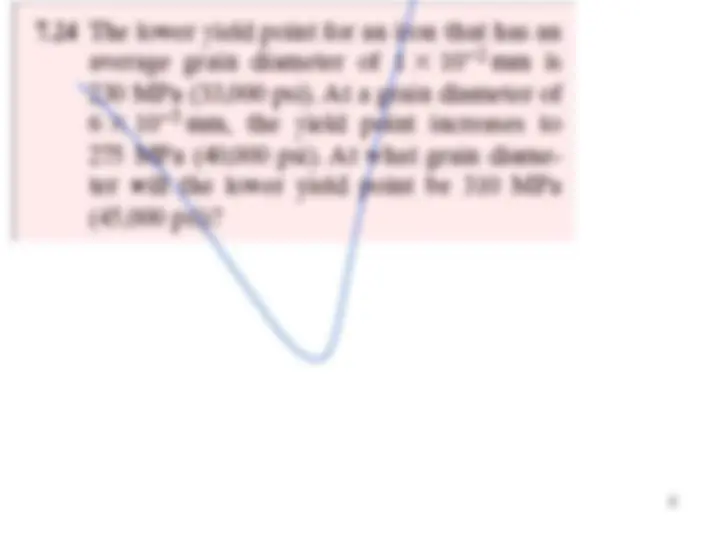
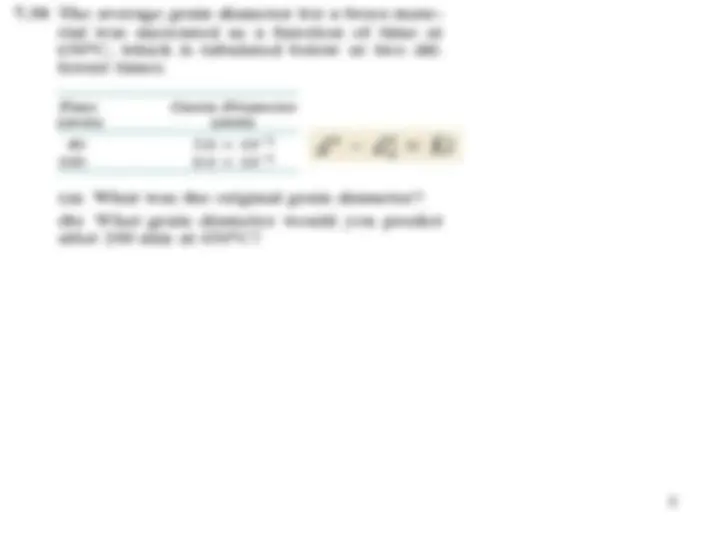
Study with the several resources on Docsity
Earn points by helping other students or get them with a premium plan
Prepare for your exams
Study with the several resources on Docsity
Earn points to download
Earn points by helping other students or get them with a premium plan
Community
Ask the community for help and clear up your study doubts
Discover the best universities in your country according to Docsity users
Free resources
Download our free guides on studying techniques, anxiety management strategies, and thesis advice from Docsity tutors
An overview of the various strengthening mechanisms in metals, including grain size reduction, solid solution strengthening, work hardening, dispersion hardening, and age hardening. It explains how these mechanisms affect the mechanical properties of metals, such as yield strength, tensile strength, and ductility. The hall-petch equation, which relates grain size to yield strength, and the concept of solid solution strengthening through alloying. It also covers the process of work hardening, also known as strain hardening, and how it increases the dislocation density in a material, leading to higher strength but reduced ductility. The document also covers the annealing process, which can recover the properties of a cold-worked material through recovery, recrystallization, and grain growth. Overall, this document provides a comprehensive understanding of the fundamental strengthening mechanisms in metals and their practical applications.
Typology: Lecture notes
1 / 18
This page cannot be seen from the preview
Don't miss anything!
● The ability of a metal to plastically deform depends on the ability of dislocations to move. ● By reducing the mobility of dislocations , the mechanical strength may be enhanced ; that is, greater mechanical forces will be required to initiate plastic deformation. ● Therefore, restricting dislocation motion makes a material harder and stronger. ● Strengthening reduces ductility.
➢ Grain size reduction ➢ Solid solution strengthening ➢ Work hardening (cold working or strain hardening) ➢ Dispersion hardening ➢ Age hardening For single-phase metals For multiphase alloys
Hall-Petch Equation: σy: yield strength d: average grain diameter σ 0 and ky: constant
● A fine-grained material is harder and stronger than coarse grained material. ● Since, small grained material has a greater total grain boundary area to impede dislocation motion. ● For many materials, the yield strength varies with grain size according to Hall- Petch equation. ● Hall-Petch equation is not valid for both ➢ very large grain, and ➢ extremely fine grain polycrystalline materials.
Solid Solution Strengthening: Alloying ● Alloying is a solid-solution strengthening technique. ● Types of solid solution: (1) Interstitial, (2) Substitutional ● Increasing the concentration of the impurity results in an attendant increase in tensile and yield strengths. (a) (^) (b) (c) Variation with nickel content of (a) tensile strength, (b) yield strength, and (c) ductility for Cu-Ni alloys, showing strengthening ● Alloys are stronger than pure metals because impurity atoms that go into solid solution ordinarily impose lattice strain on the surrounding host atoms.
● Ductile metals become stronger when they are deformed plastically at temperatures well below the melting points. ● It is also called cold working , because the temperature at which deformation takes place is cold. ● Most metals strain harden at room temperature. ● The reason for work hardening is the increase of dislocation density with plastic deformation. The average distance between dislocation decreases and dislocations start blocking the motion of each other. ● Percent cold work (% CW) is used to express the degree of plastic deformation. ● Before deformation: dislocation density ~10 3 mm/mm 3 ● Heavily deformed sample: dislocation density ~10 10 mm/mm 3 ● Dislocations interact and obstruct each other. ● More dislocations actually increase the strength of a material. % x 100 A A A CW o o − d = Ao : original cross-section area Ad :area after deformation.
Common forming operations change the cross sectional area
● There is only a certain amount a material can be deformed before it breaks. ● Different materials have varying % allowable cold work.
Example: Solution:
● Annealing is a heat treatment in which a material is exposed to an elevated temperature for an extended time period and then slowly cooled. ● Time is generally 1 hour. ● Annealing is carried out to: ● relieve stresses ● increase softness, ductility and toughness ● produce a specific microstructure ● So, effects of cold work are reversed! ● Three stages in annealing: (1) recovery, (2) recrystallization, (3) grain growth
● The low temperature treatment ● Residual stresses are reduced or even eliminated. ● Dislocations are rearranged, but dislocation density unchanged. ● Corrosion resistance, electrical and thermal conductivity are restored ● The mechanical properties (strength and ductility) are unchanged.
GRAIN GROWTH ● After recrystallization is complete, the strain-free grains will continue to grow if the metal specimen is left at elevated temperature. This phenomenon is called grain growth. ● Not all grains can enlarge, but big grains grow at the expense of small ones ● Grain growth during annealing occurs in all polycrystalline materials (i.e. they do not have to be deformed first). ● For grain growth, dependence of grain size (d) on time (t):
Solution: