
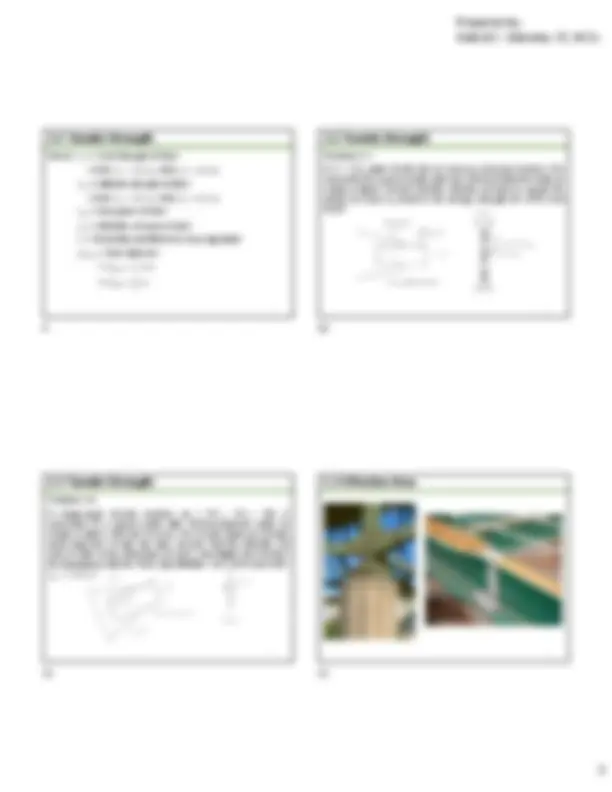
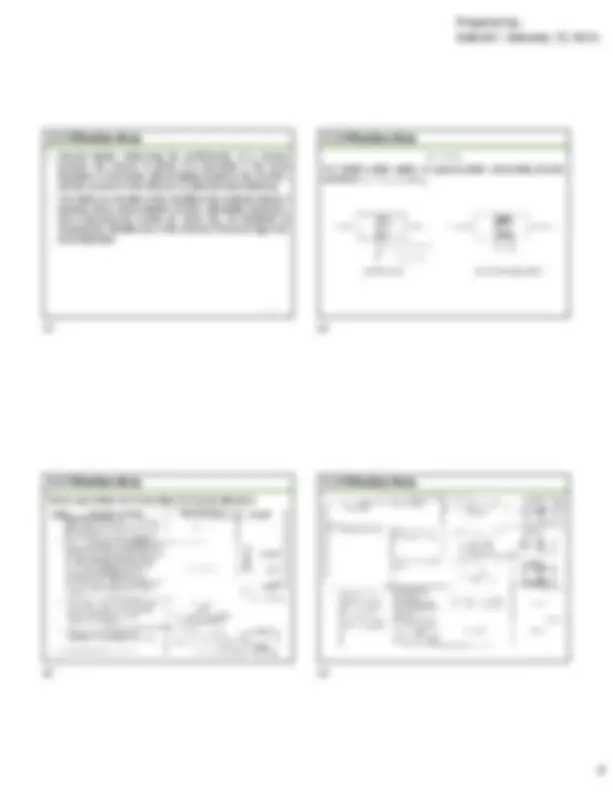
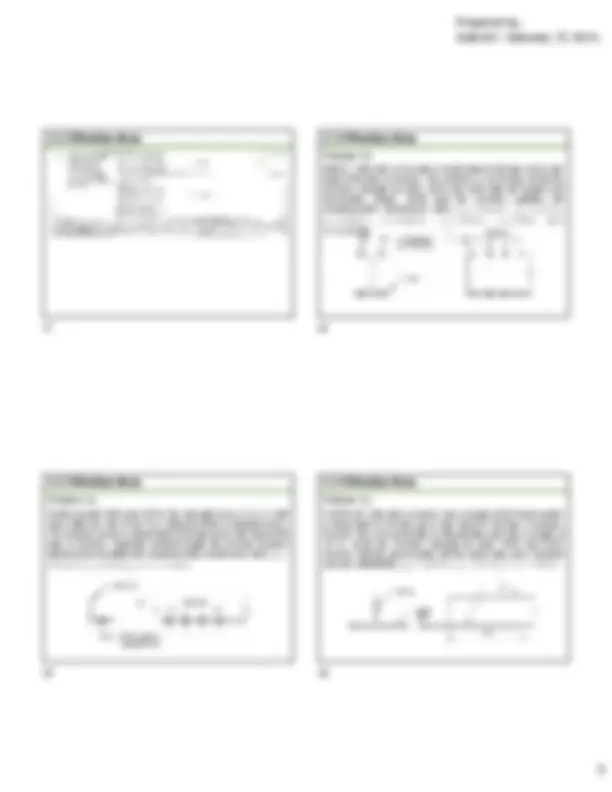
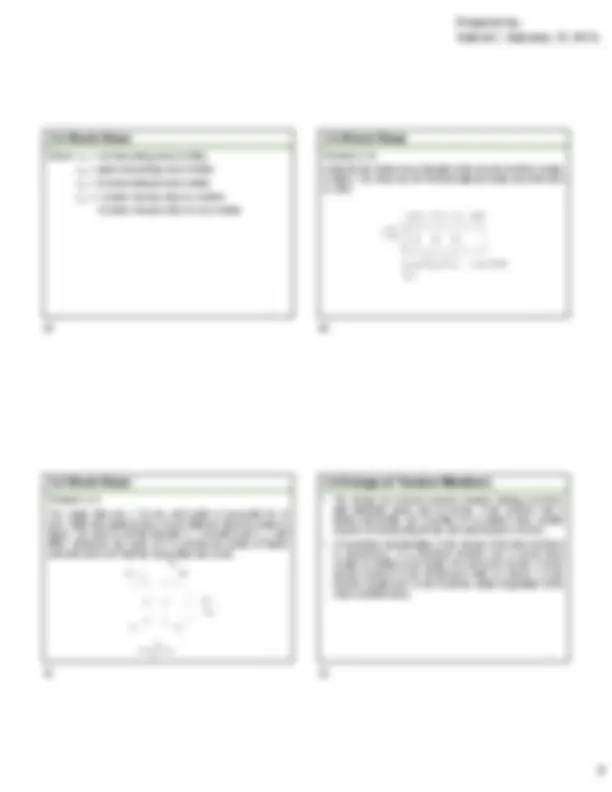
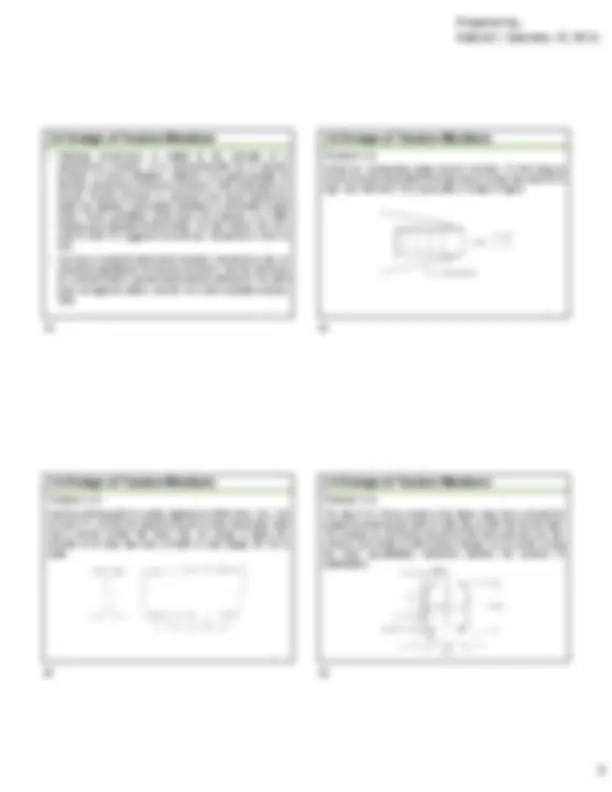
Study with the several resources on Docsity
Earn points by helping other students or get them with a premium plan
Prepare for your exams
Study with the several resources on Docsity
Earn points to download
Earn points by helping other students or get them with a premium plan
Community
Ask the community for help and clear up your study doubts
Discover the best universities in your country according to Docsity users
Free resources
Download our free guides on studying techniques, anxiety management strategies, and thesis advice from Docsity tutors
Design of tension members Net area calculations Rupture and yielding checks Step-by-step design procedures
Typology: Slides
1 / 9
This page cannot be seen from the preview
Don't miss anything!
Engr. Gabriel Gamana, M.Sc.
2 1.0 Introduction 2.0 Tension Members 3.0 Compression Members 4.0 Beams 5.0 Beam-Columns 6.0 Connections
3 2.1 Introduction 2.2 Tensile Strength 2.3 Effective Area 2.4 Staggered Fasteners 2.5 Block Shear 2.6 Design of Tension Members
4
5
6
7 A tension member can fail by reaching one of two limit states: excessive deformation or fracture. To prevent excessive deformation, initiated by yielding, the load on the gross section must be small enough that the stress on the gross section is less than the yield stress Fy. To prevent fracture, the stress on the net section must be less than the tensile strength Fu.
8
13
14
For bolted splice plates or gusset plates connecting tension members 𝐴 = 𝐴 ≤ 0.85𝐴
15 Shear Lag Factors for Connections to Tension Members
16
17
18 Problem 2- W8x21, A50 steel is to carry a dead load of 30 kips and a live load of 90 kips in tension. The member is 25 ft long. Verify the member strength by both LRFD and ASD with the bolted end connection shown. Verify that the member satisfies the recommended slenderness limit. 𝐴 = 6.16 𝑖𝑛ଶ^ , 𝑏 = 5.27 𝑖𝑛 , 𝑡 = 0.40 𝑖𝑛 , 𝑑 = 8.28 𝑖𝑛 , 𝑟௬ = 1.26 𝑖𝑛 , 𝑦ത = 0.831 (𝑓𝑜𝑟 𝑊𝑇 4 𝑥10.50)
19 Problem 2- Verify, by both ASD and LRFD, the strength of an L4× 4 ×½, A steel, with one line of (4) ¾ in. diameter bolts in standard holes. The member carries a dead load of 20 kips and a live load of 60 kips in tension. Calculate at what length this tension member would cease to satisfy the recommended slenderness limit. 𝐴 = 3.75 𝑖𝑛ଶ, 𝑟௭ = 0.776 𝑖𝑛, 𝑦ത^ = 𝑥̅ = 1.18 𝑖𝑛
20 Problem 2- A WT6×20, A50 steel, member has a length of 30 ft and carries a dead load of 40 kips and a live load of 120 kips in tension. Assume the end connection is fillet welded and has a length of 16 in. Verify the member strength by both LRFD and ASD. Assume that the gusset plate and the weld have been checked and are satisfactory. 𝐴 = 5.84 𝑖𝑛ଶ, 𝑟௭ = 1.57 𝑖𝑛, 𝑦ത = 𝑥̅ = 1.09 𝑖𝑛
25 Problem 2- An angle with staggered fasteners in each leg is shown in figure. A36 steel is used, and holes are for 7Ú8-inch-diameter bolts. Determine the design strength using LRFD and ASD. 𝐴 = 6.80 𝑖𝑛ଶ.
26 Problem 2- Determine the net area along route ABCDEF for the C15 x 33. (𝐴 = 10.00 𝑖𝑛ଶ) shown in figure. Hole are for ¾ in. bolts.
27
28
29 Where: 𝐴௩ = net area along shear surface 𝐴௩ = gross area along shear surface 𝐴௧ = net area along tension surface 𝑈௦ = 1.0 when tension stress is uniform 0.5 when tension stress is non-uniform
30 Problem 2- Compute the block shear strength of the tension member shown in figure. The holes are for 7Ú8-inch-diameter bolts, and A36 steel is used.
31 Problem 2- The single 200 mm x 10 mm steel plate is connected to 12 mm—thick steel plate by four 16 mm diameter rivets as shown in figure. The Steel is ASTM A36 with Fy = 248 MPa and Fu = 400 MPa. Determine the value of P in all possible modes of failure and safe value of P that the connection can resist.
32