
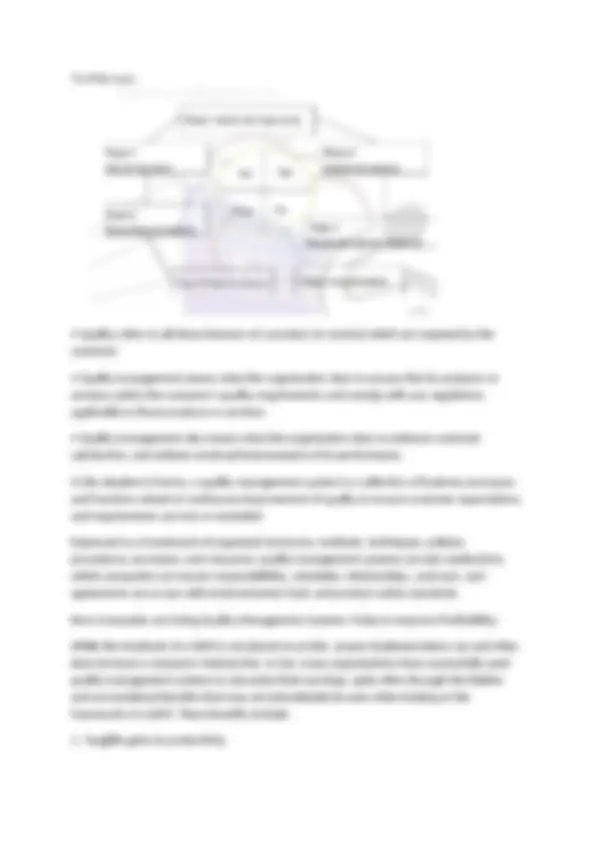
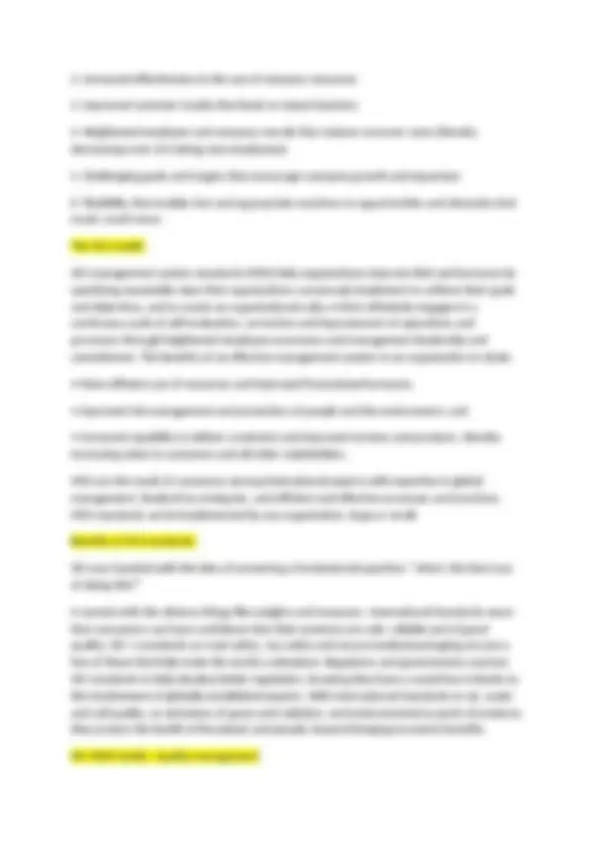
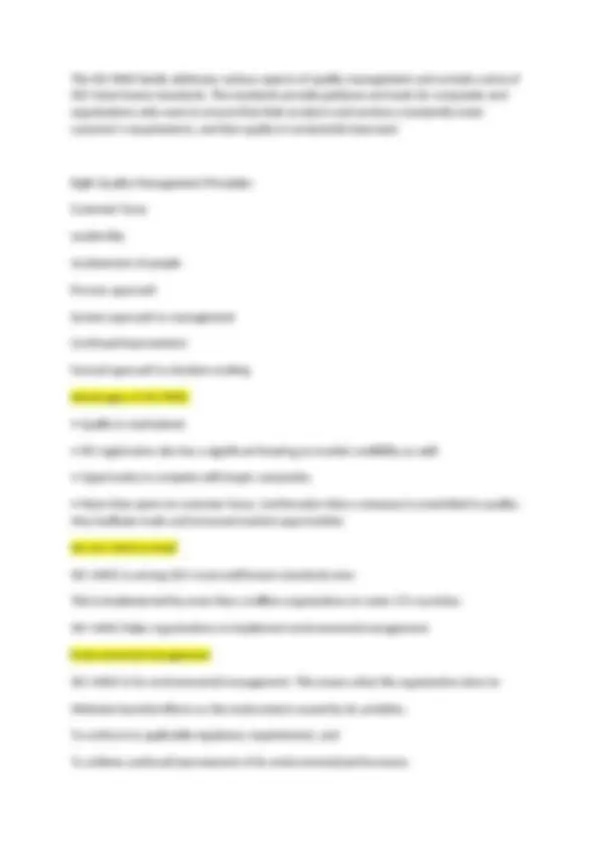
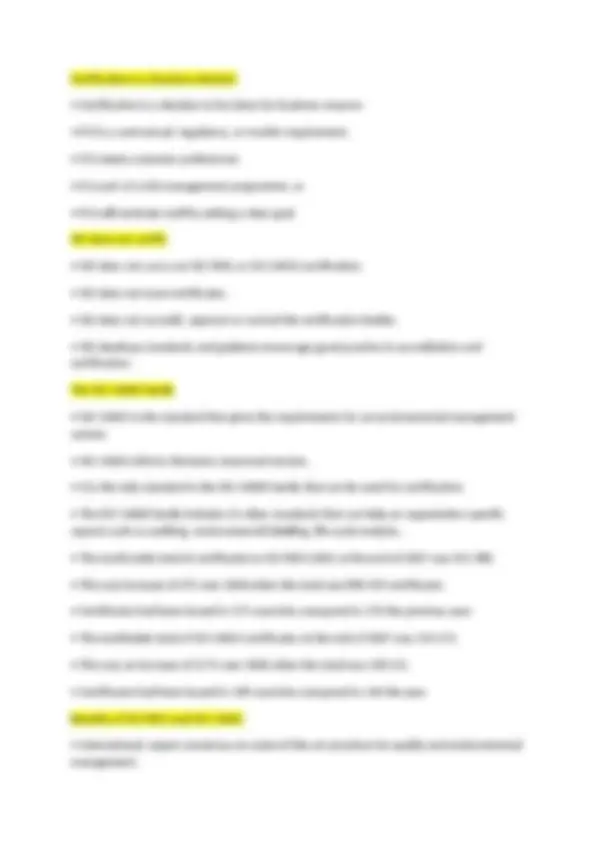
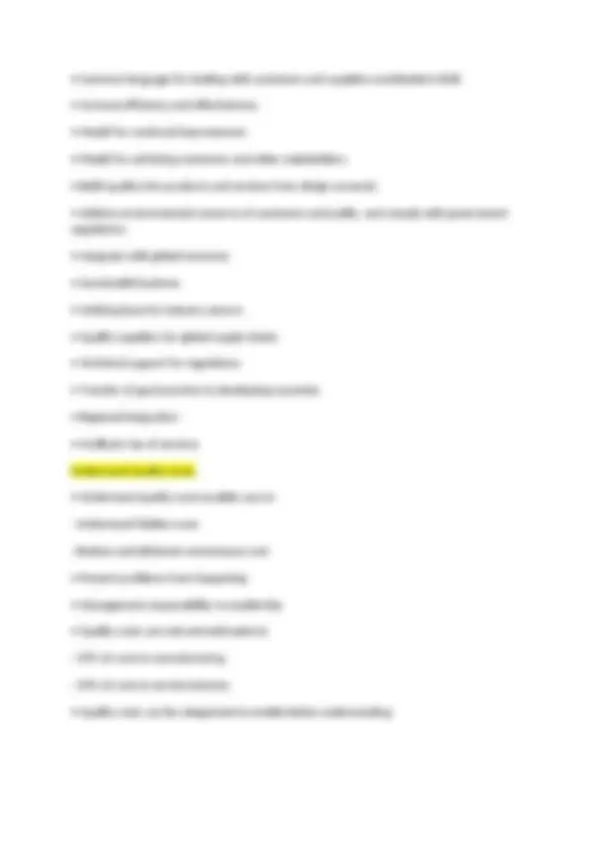
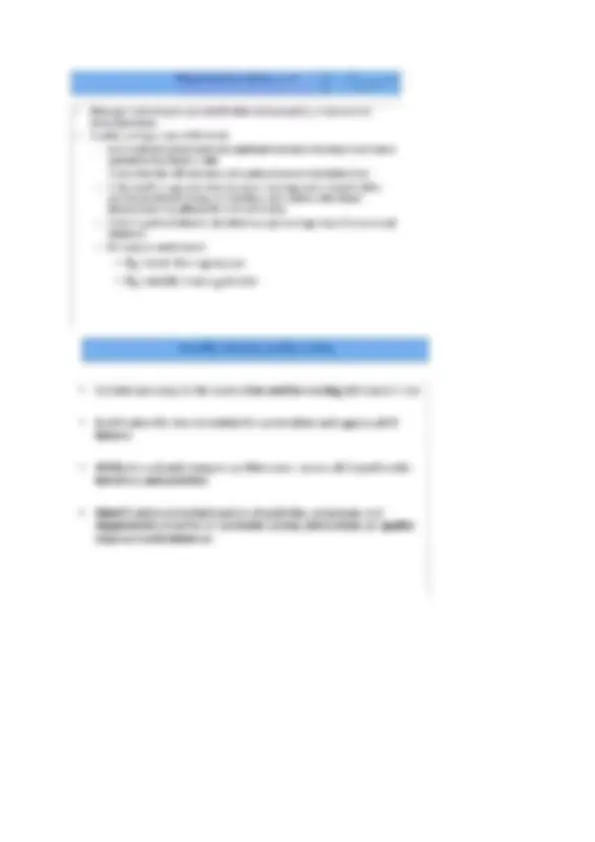
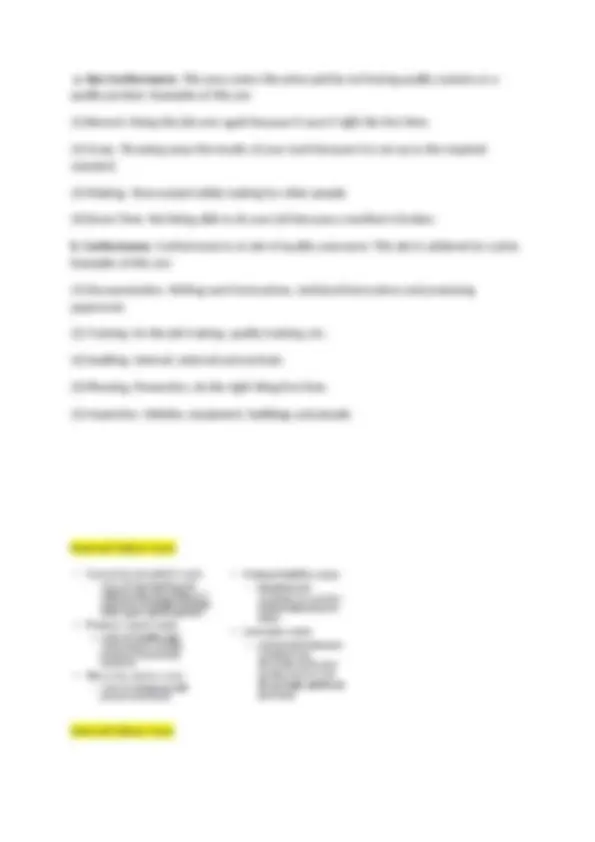
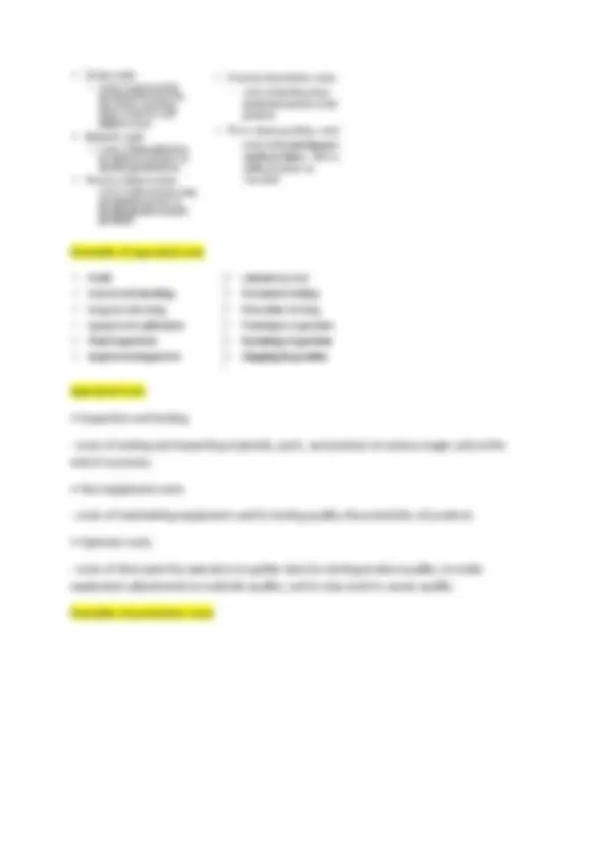
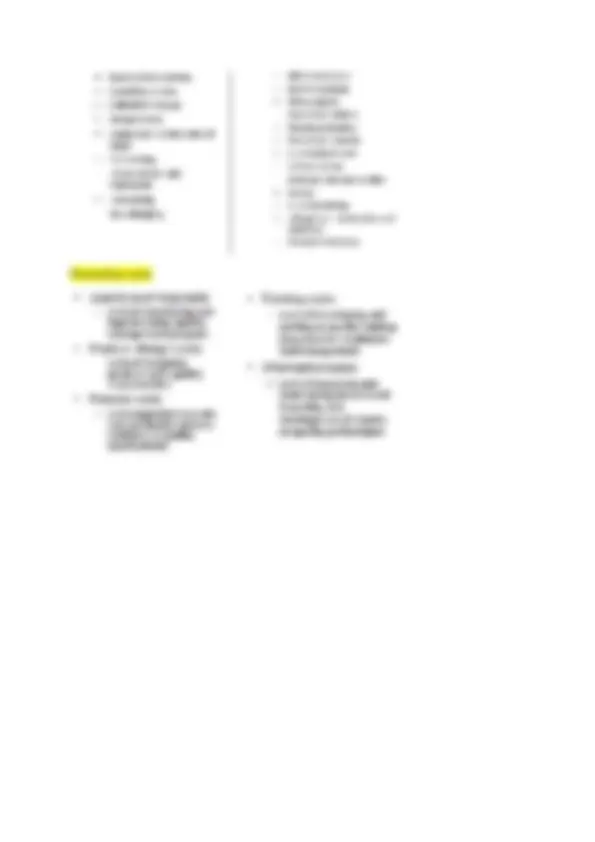
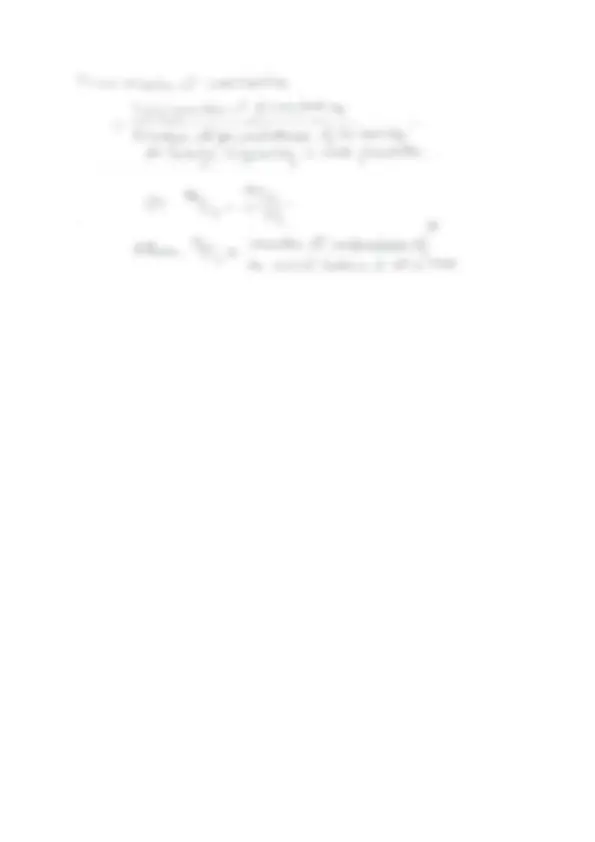
Study with the several resources on Docsity
Earn points by helping other students or get them with a premium plan
Prepare for your exams
Study with the several resources on Docsity
Earn points to download
Earn points by helping other students or get them with a premium plan
Community
Ask the community for help and clear up your study doubts
Discover the best universities in your country according to Docsity users
Free resources
Download our free guides on studying techniques, anxiety management strategies, and thesis advice from Docsity tutors
quality management lecture notes 2020 study
Typology: Lecture notes
1 / 18
This page cannot be seen from the preview
Don't miss anything!
Meaning of Quality: Quality is a relatıve term and is genrally used with reference to the end use of product.
The ISO 9000 family addresses various aspects of quality management and contains some of ISO's best known standards. The standards provide guidance and tools for companies and organizations who want to ensure that their products and services consistently meet customer's requirements, and that quality is consistently improved. Eight Quality Management Principles: Customer focus Leadership Involvement of people Process approach System approach to management Continual improvement Factual approach to decision-making Advantages of ISO 9000:
Both ISO 9001 and ISO 14001 concem the way an organization goes about its work.
Certification is a business decision
a. Non Conformance. This area covers the price paid by not having quality systems or a quality product. Examples of this are: (1) Rework. Doing the job over again because it wasn't right the first time. (2) Scrap. Throwing away the results of your work because it is not up to the required standard. (3) Waiting. Time wasted whilst waiting for other people. (4) Down Time. Not being able to do your job because a machine is broken. b. Conformance. Conformance is an aim of quality assurance. This aim is achieved at a price. Examples of this are: (1) Documentation. Writing work instructions, technical instructions and producing paperwork. (2) Training. On the job training, quality training, etc. (3) Auditing. Internal, external and extrinsic. (4) Planning, Prevention, do the right thing first time. (5) Inspection. Vehicles, equipment, buildings and people. External Failure Costs Internal Failure Costs
Examples of appraisal costs Appraisal Costs
Preventing poor quality (comparasion)
Sınavda çıkabilecek formüller