
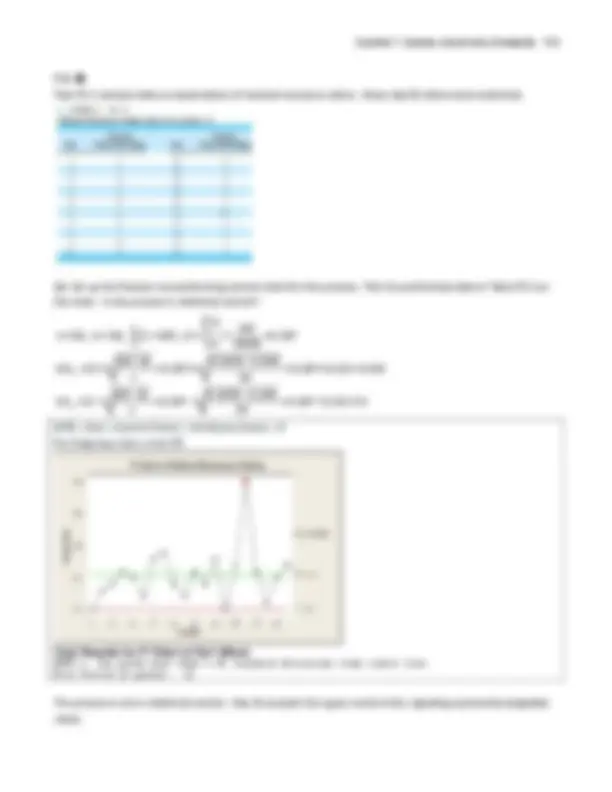
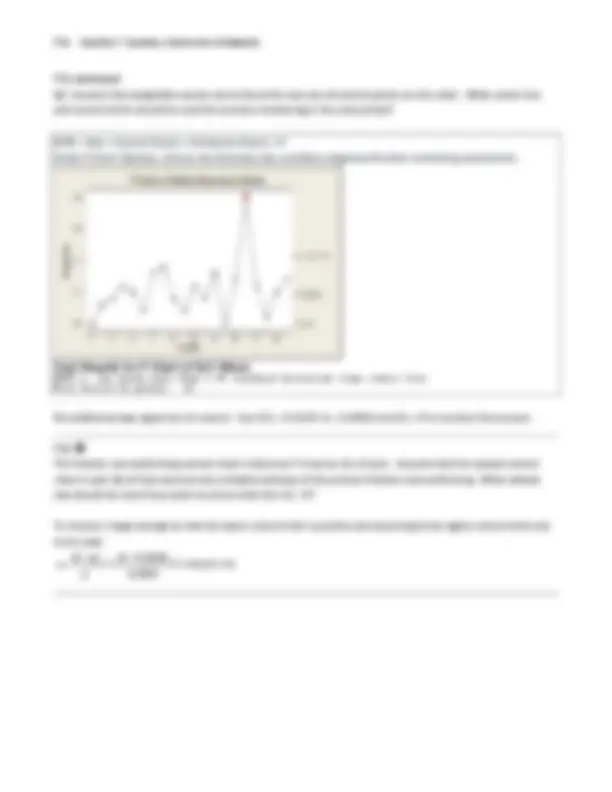
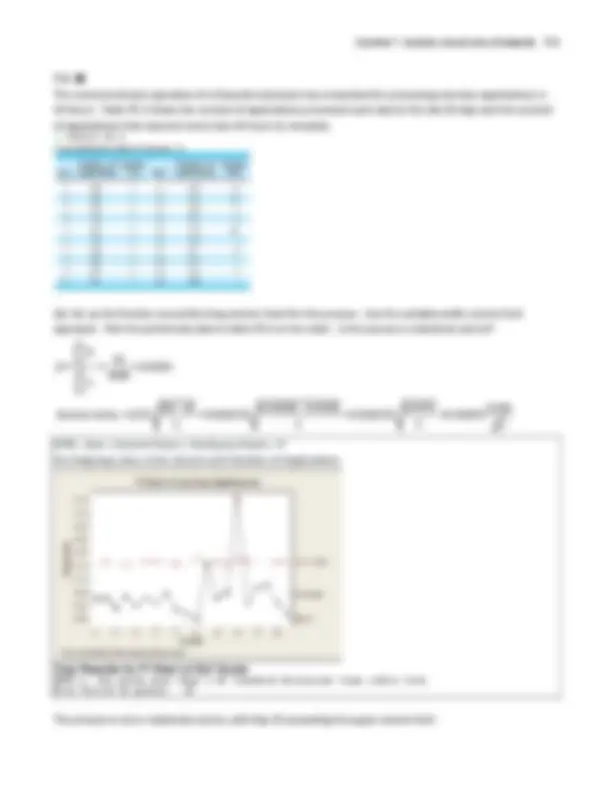
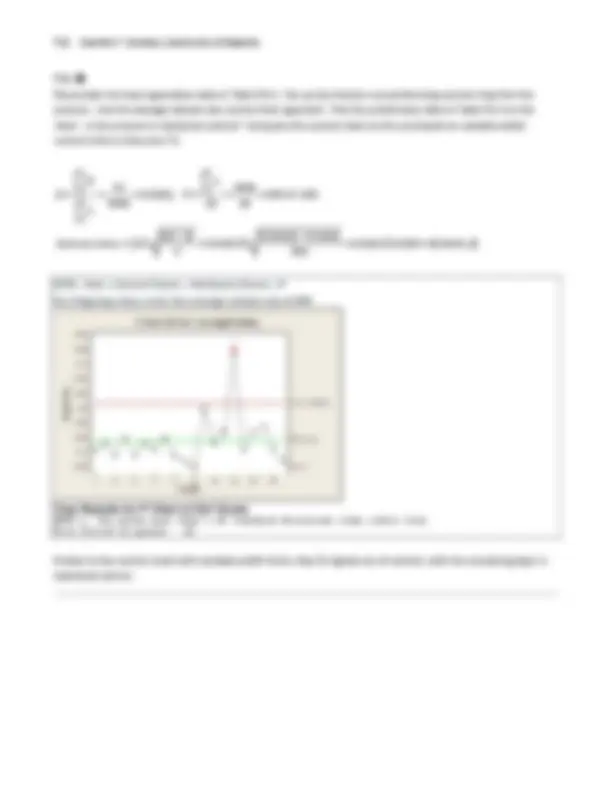
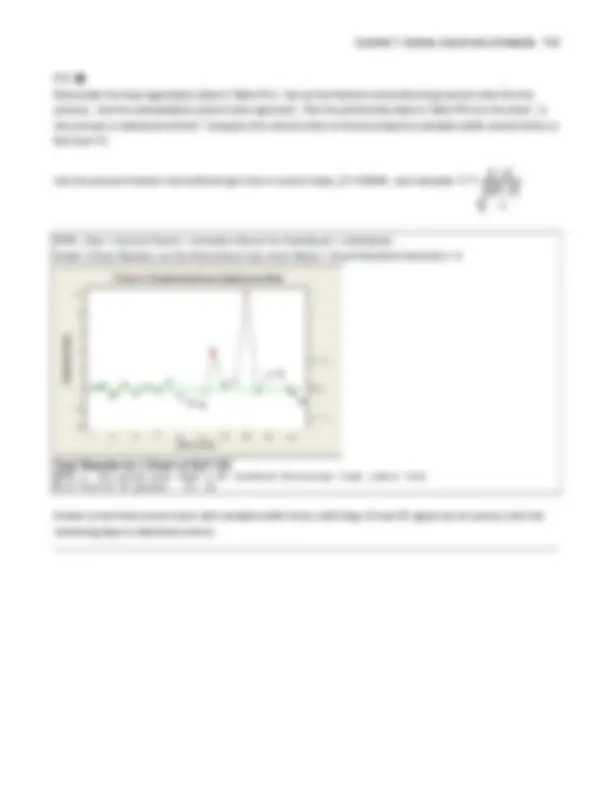
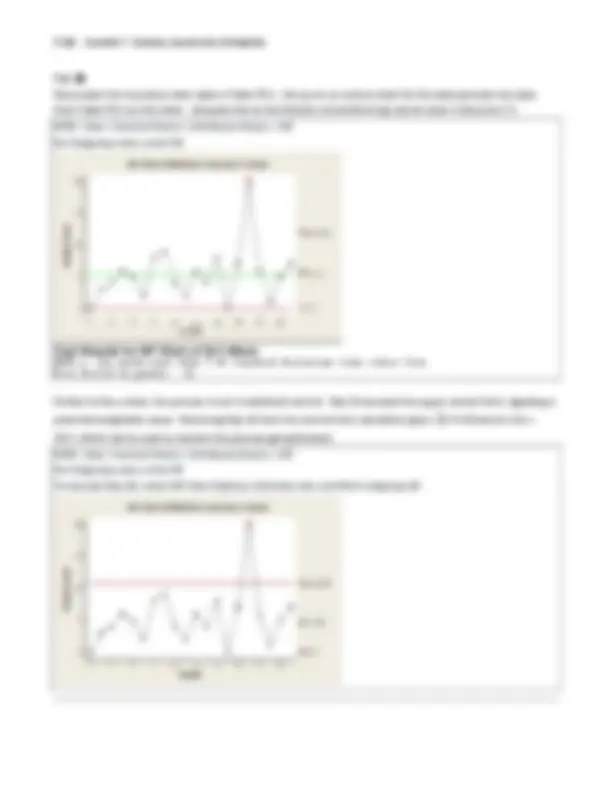
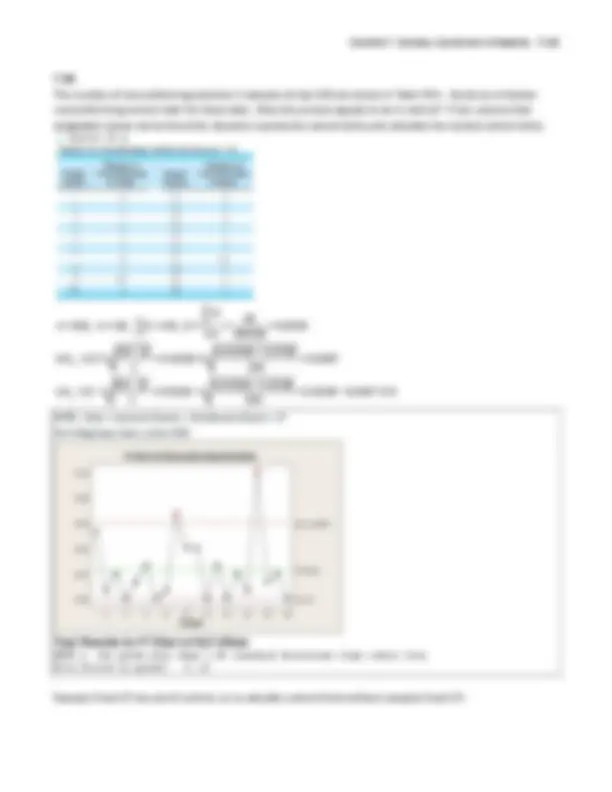
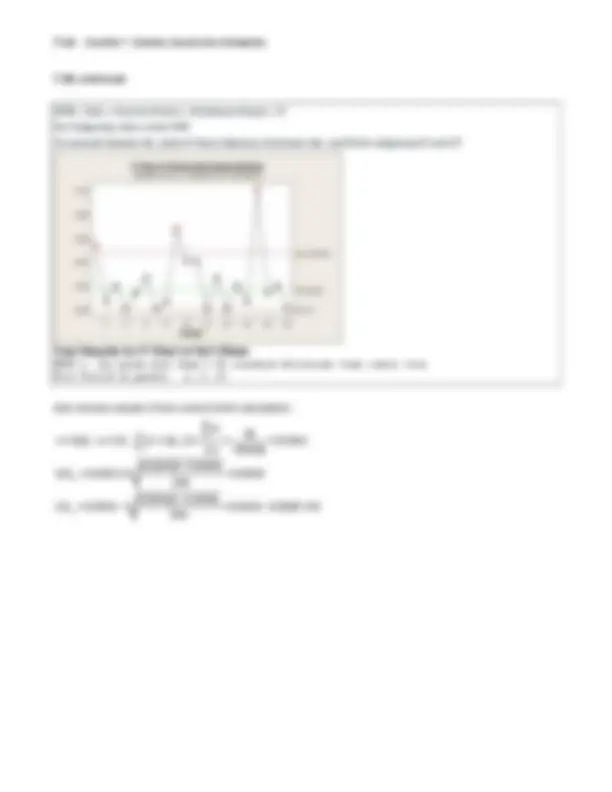
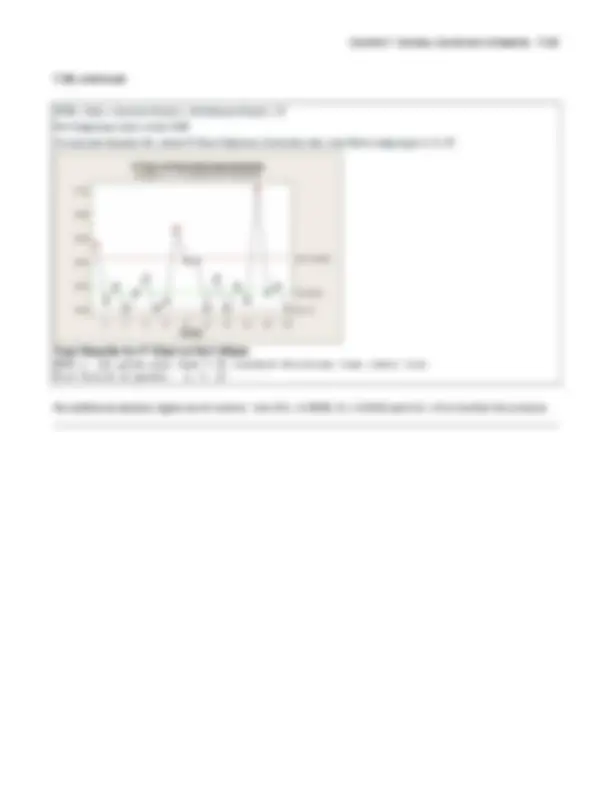
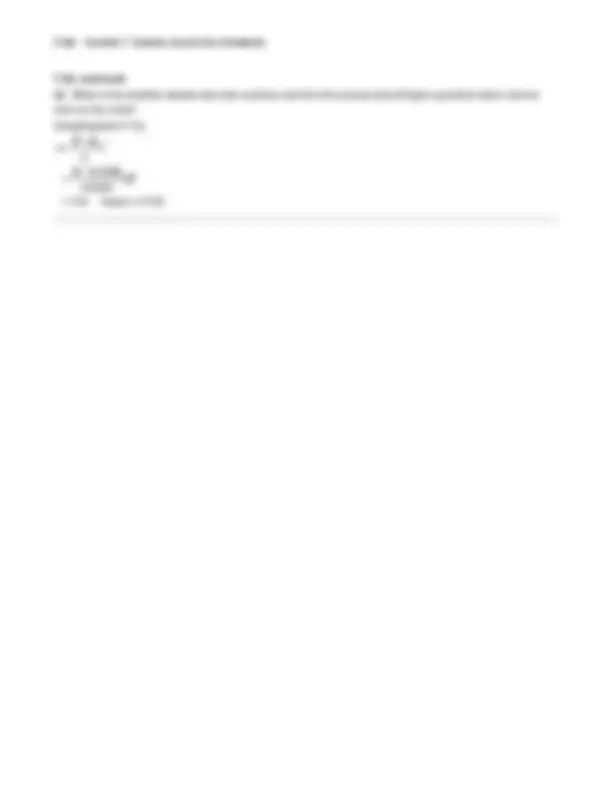
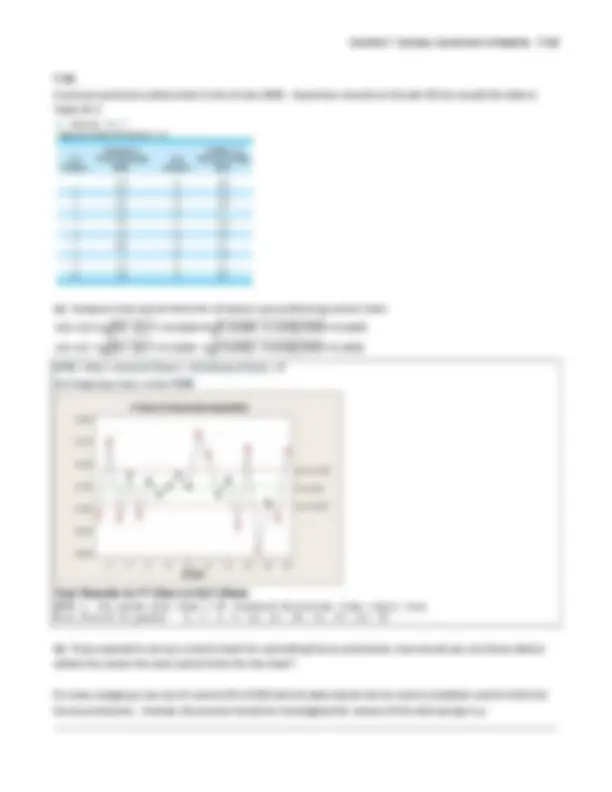
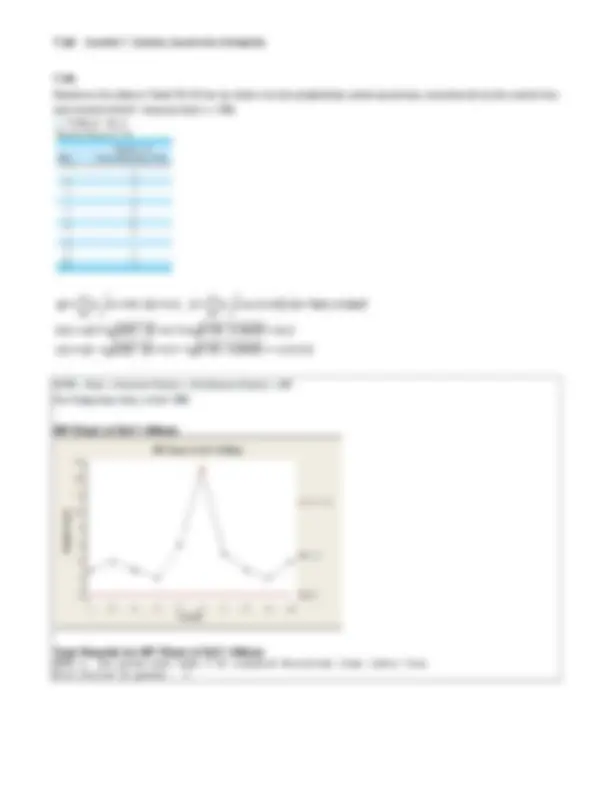
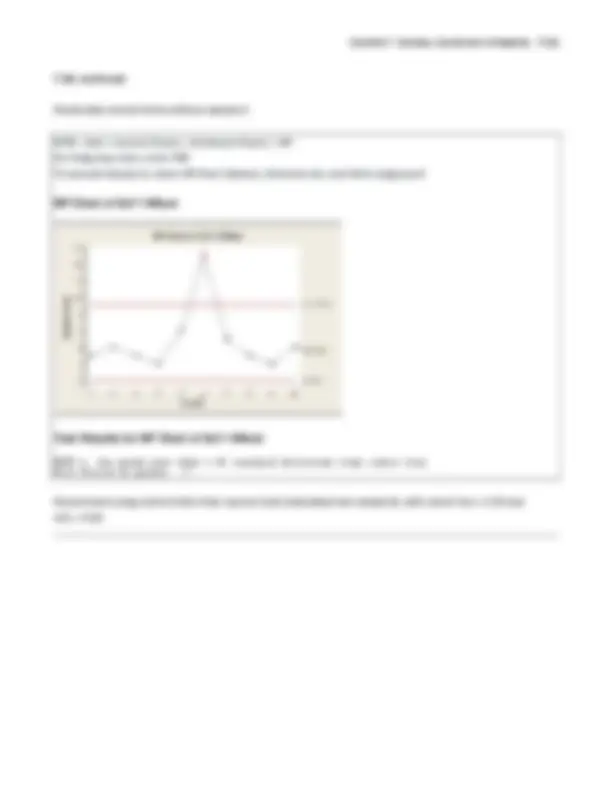
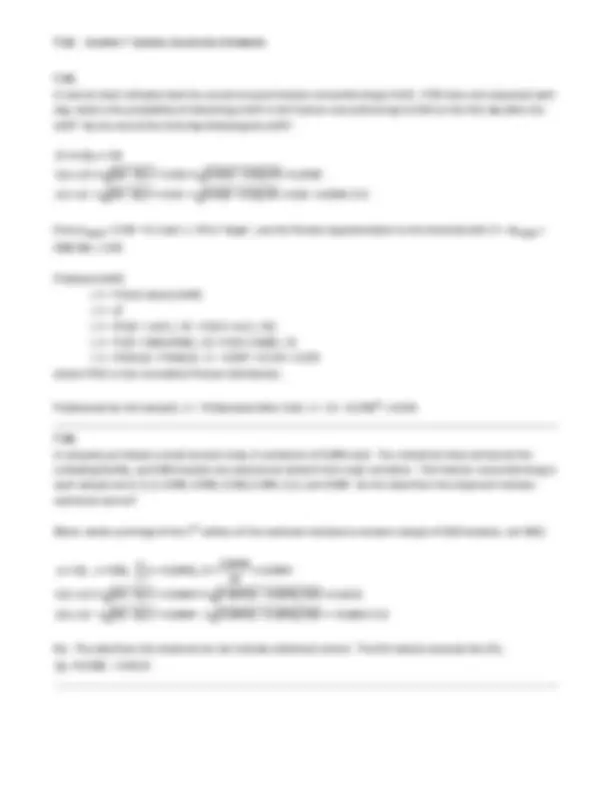
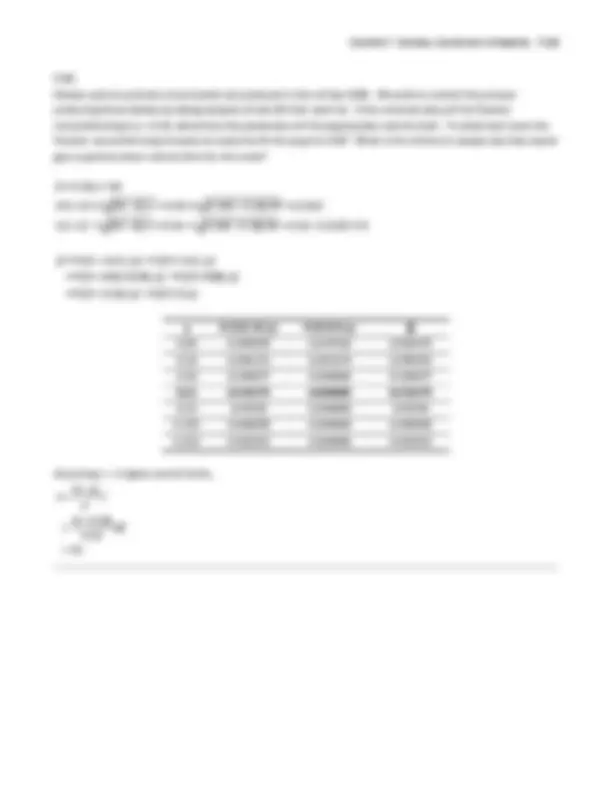
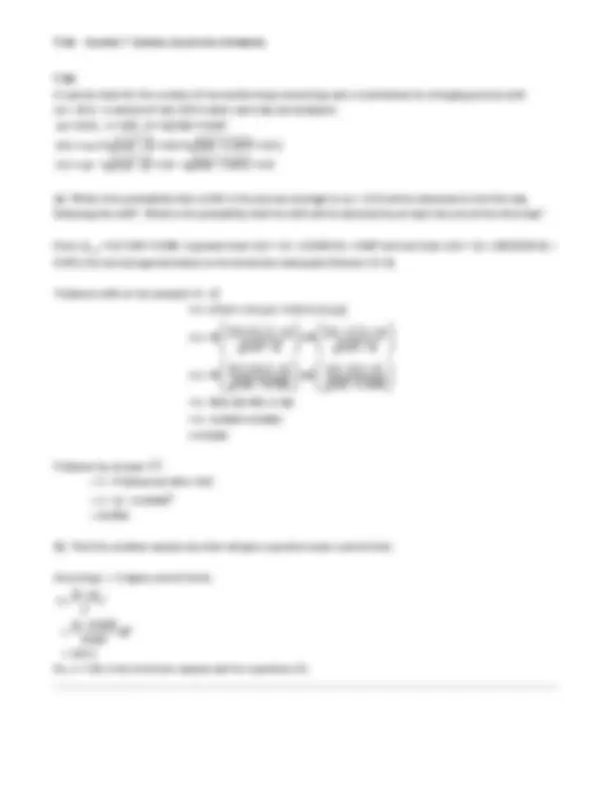

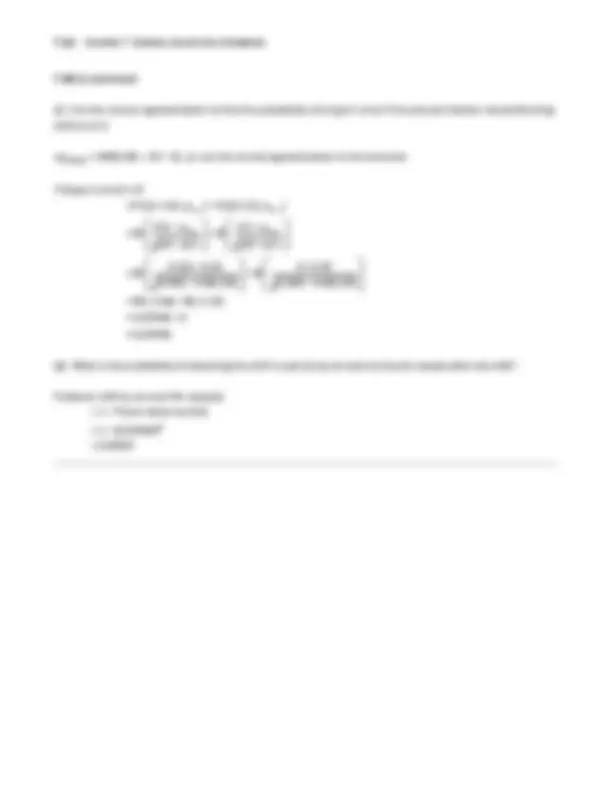
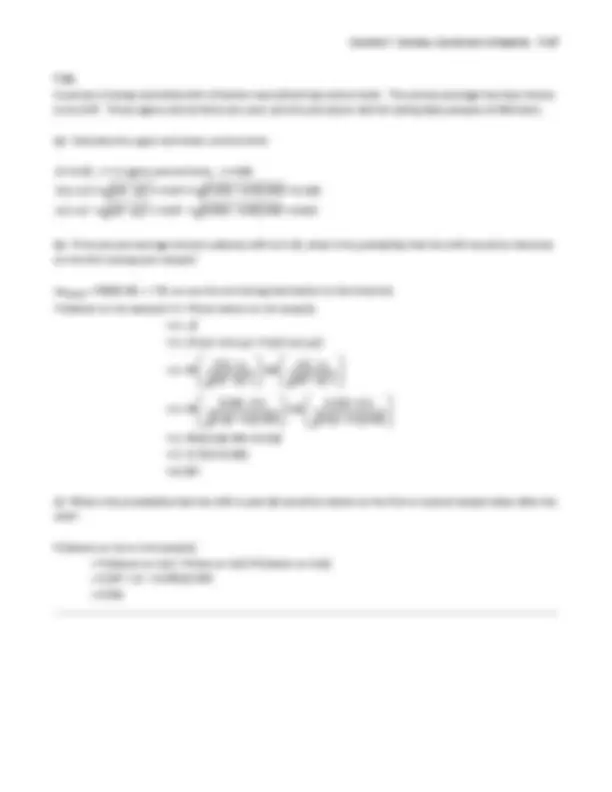
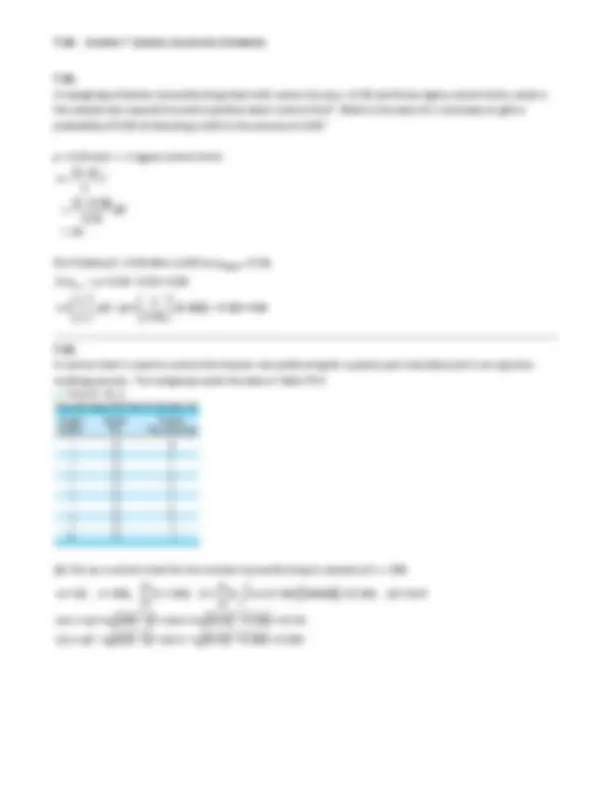
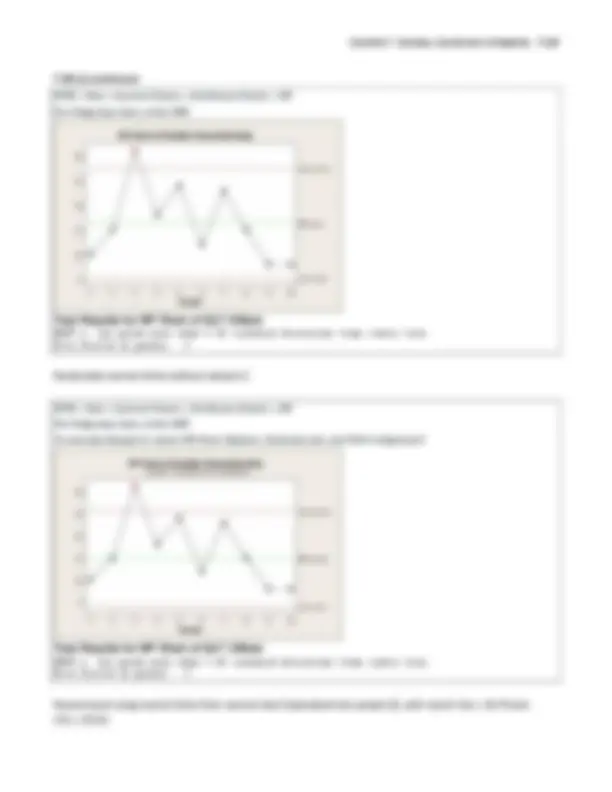
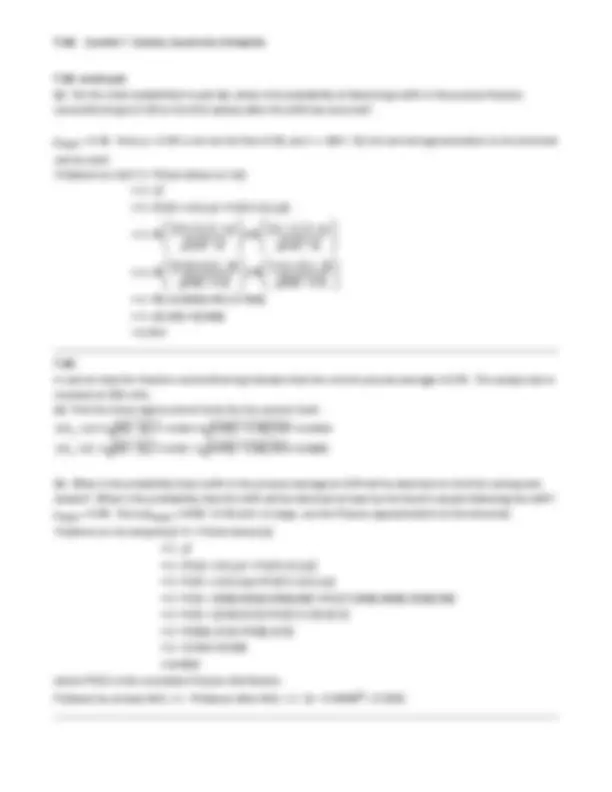
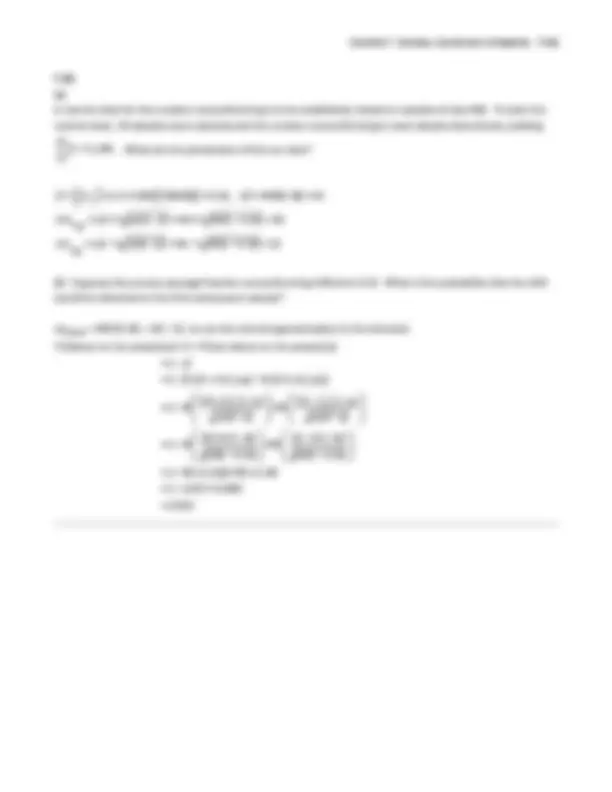
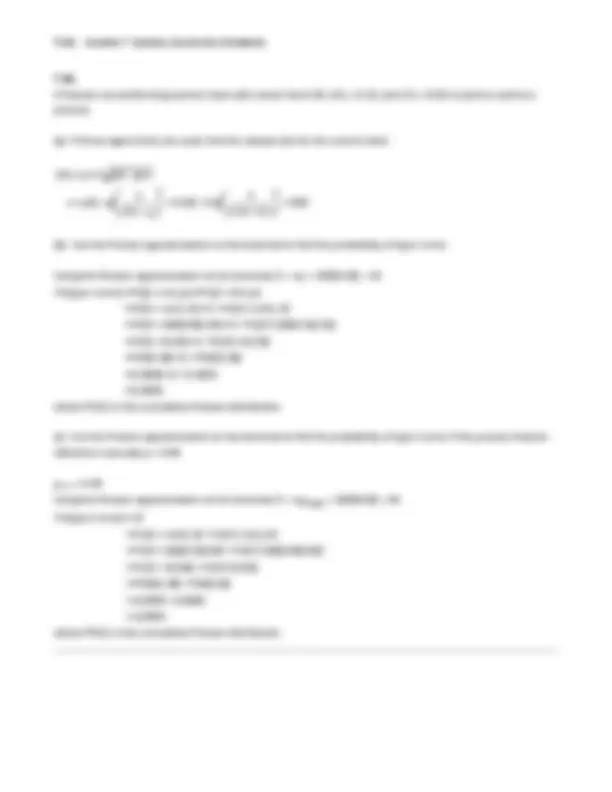
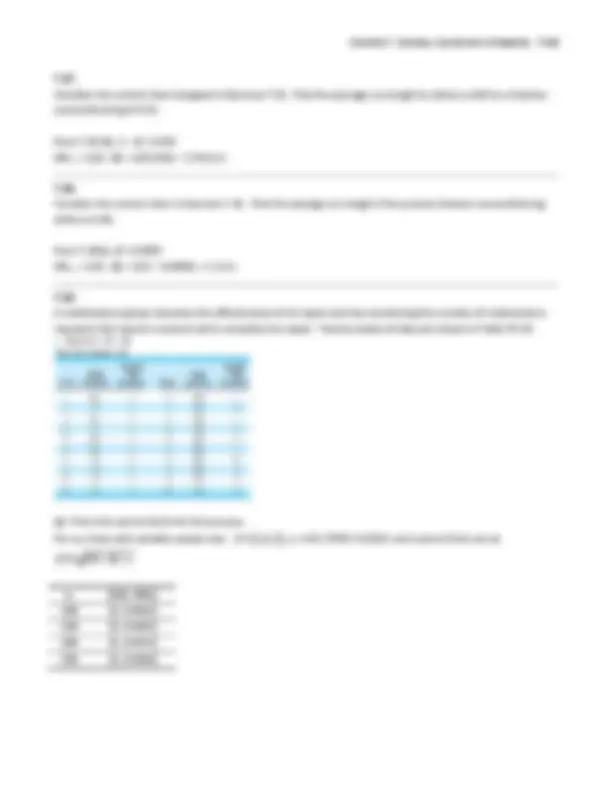
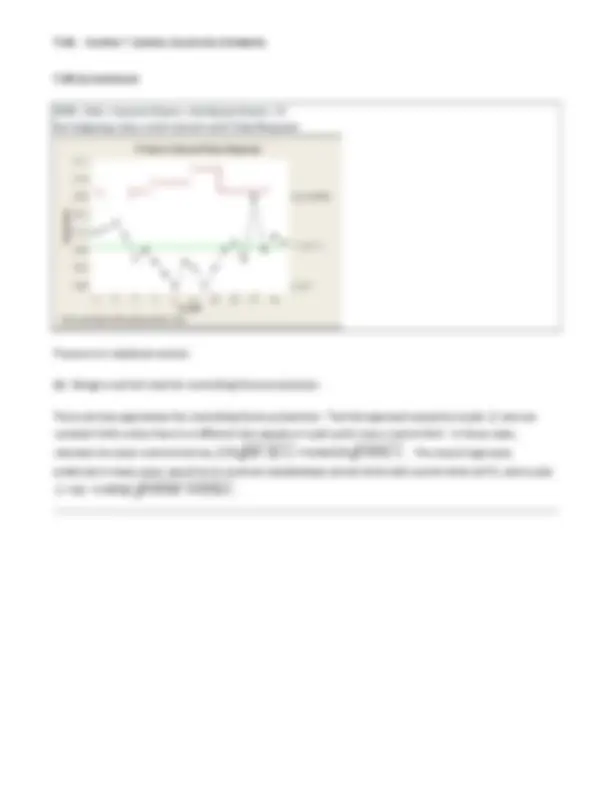
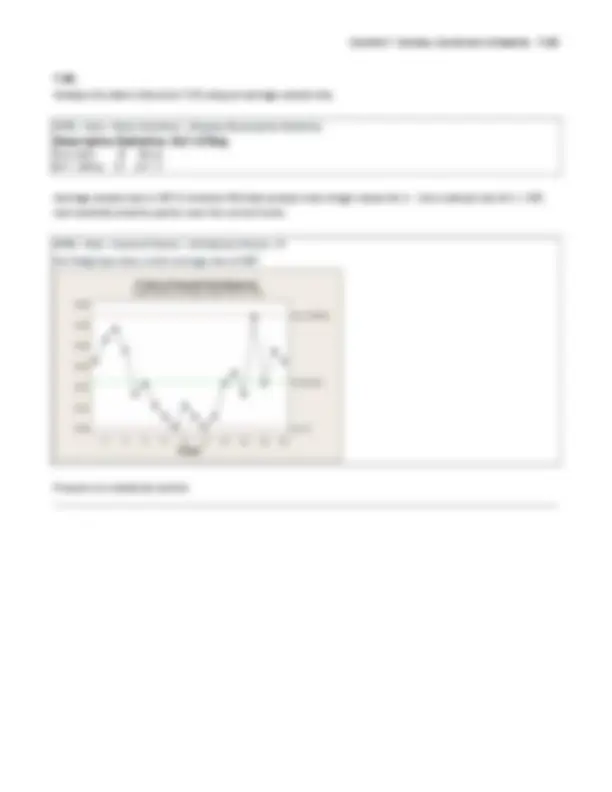
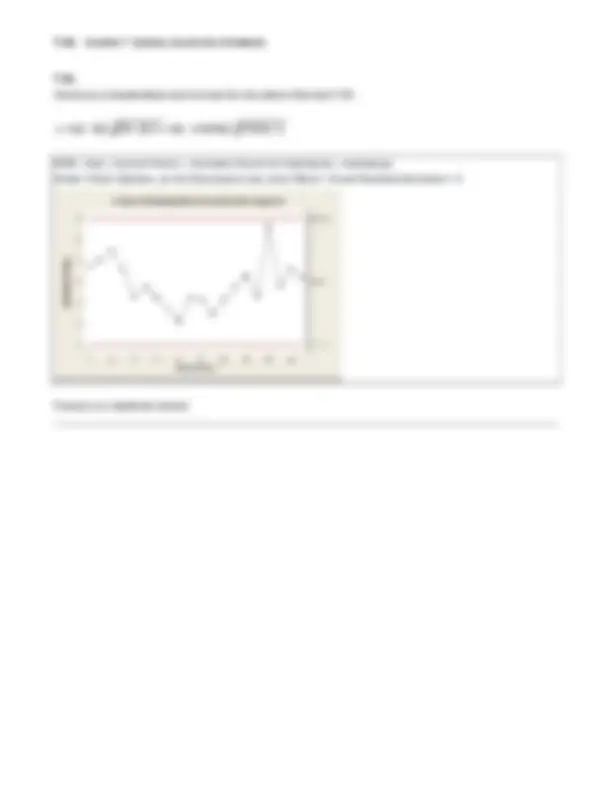
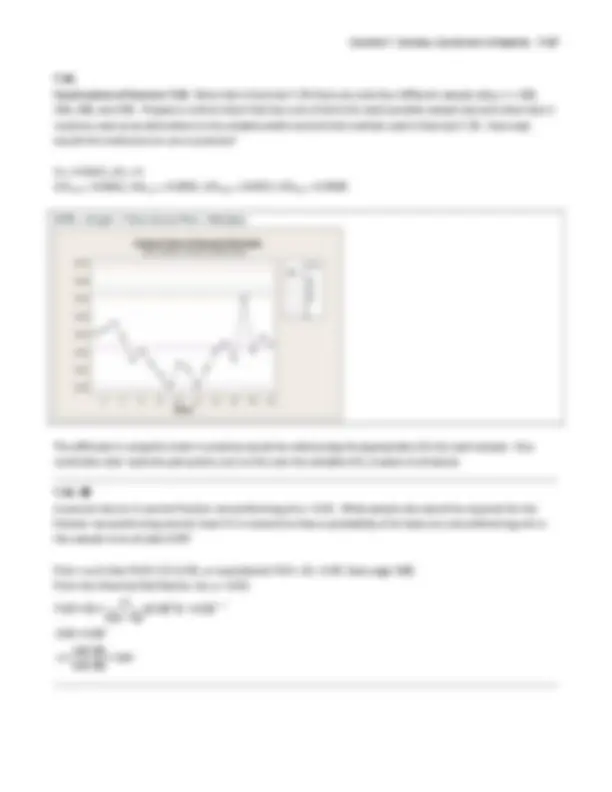
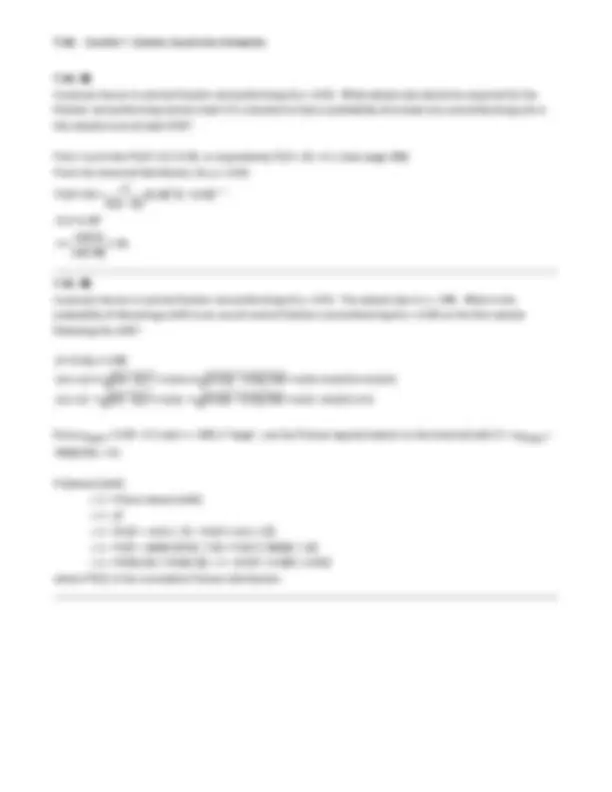
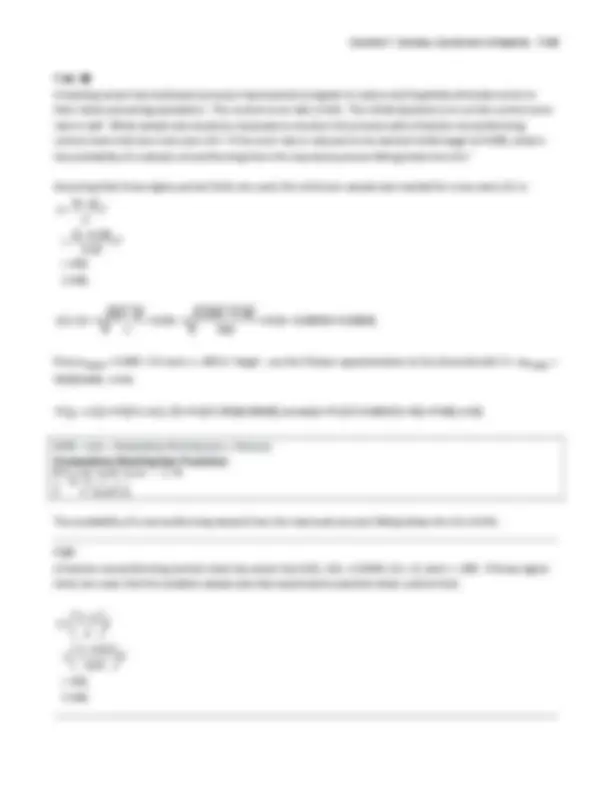
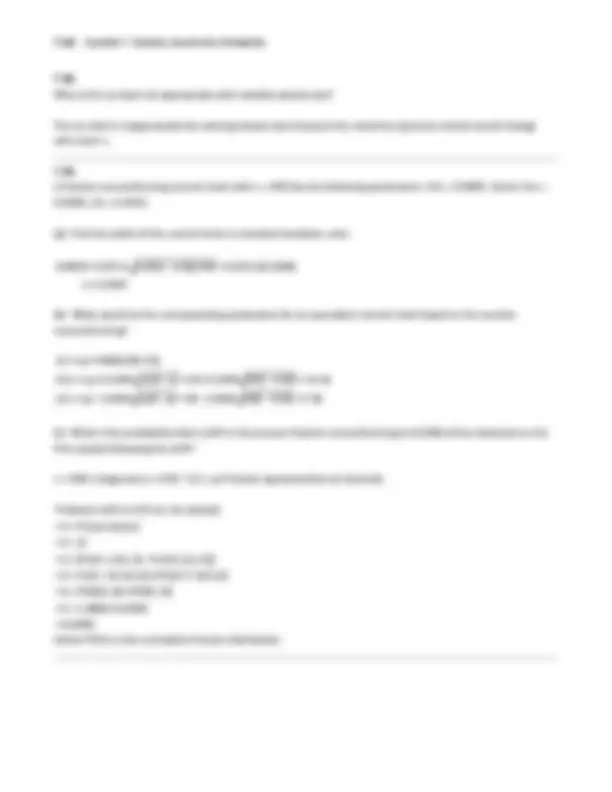
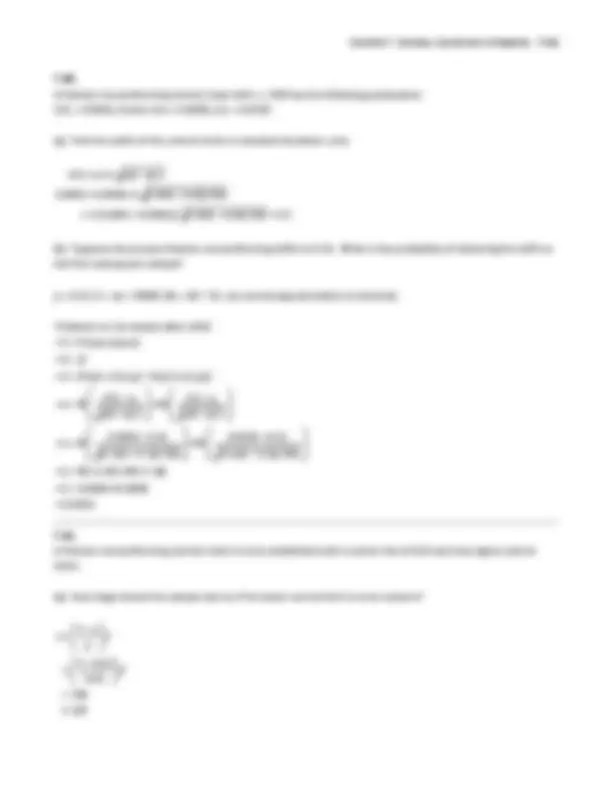
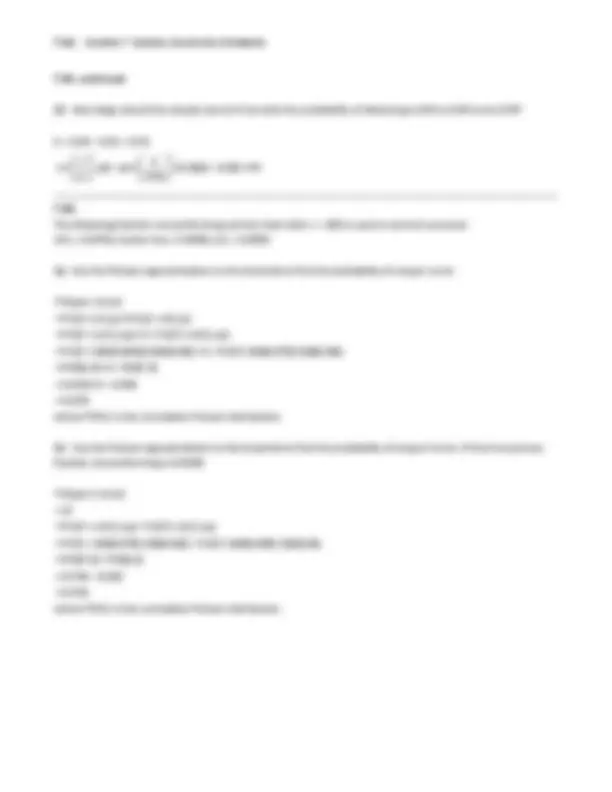

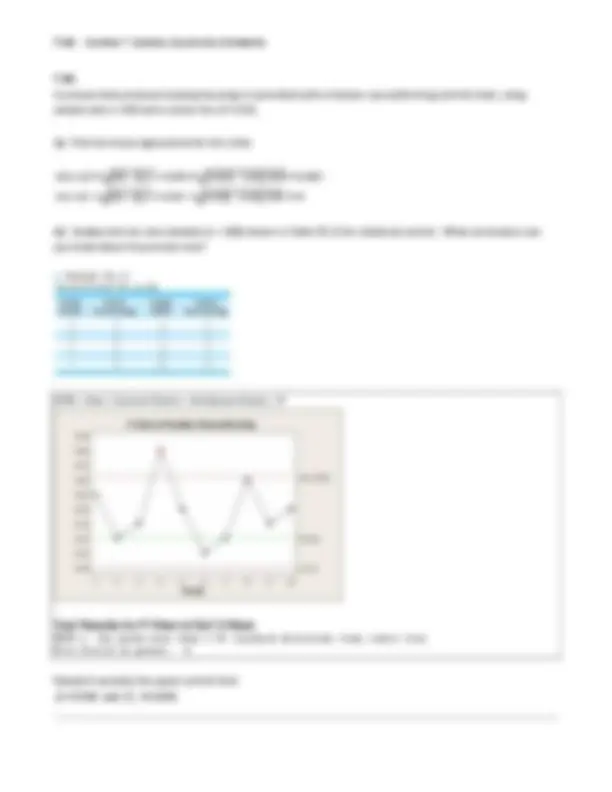
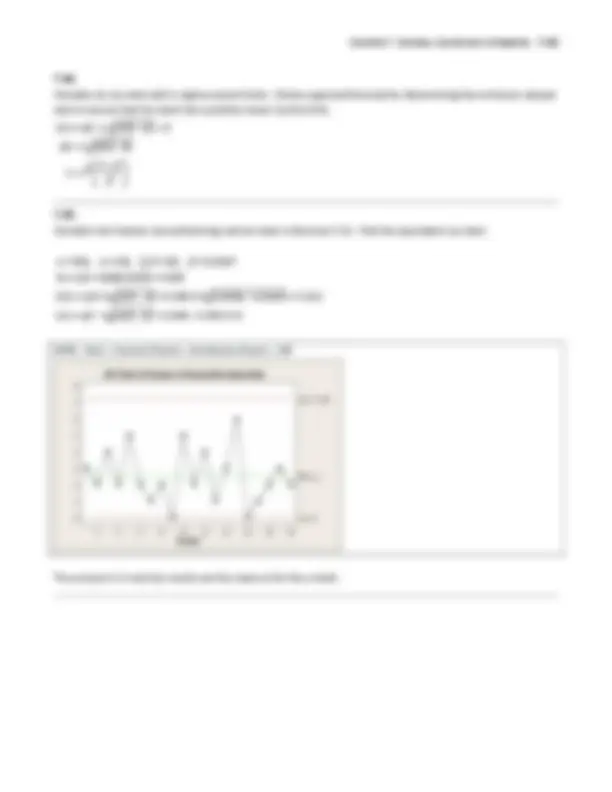
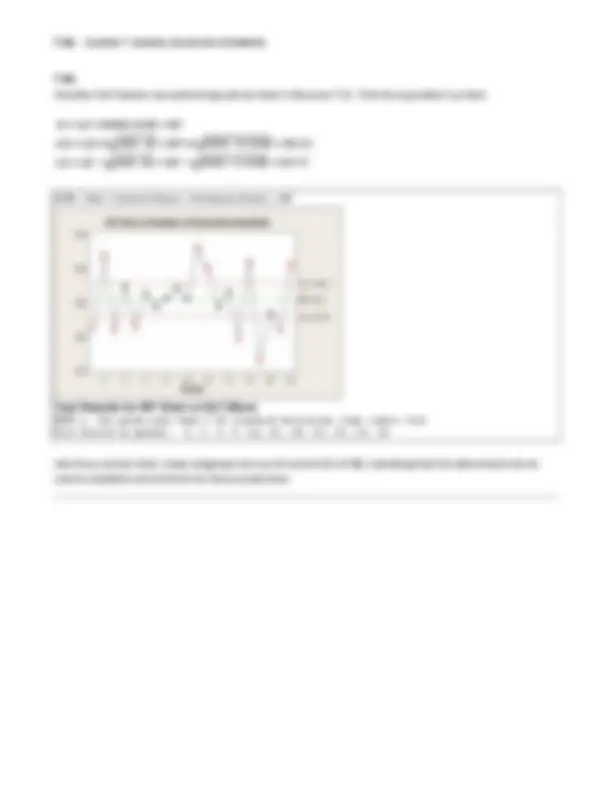
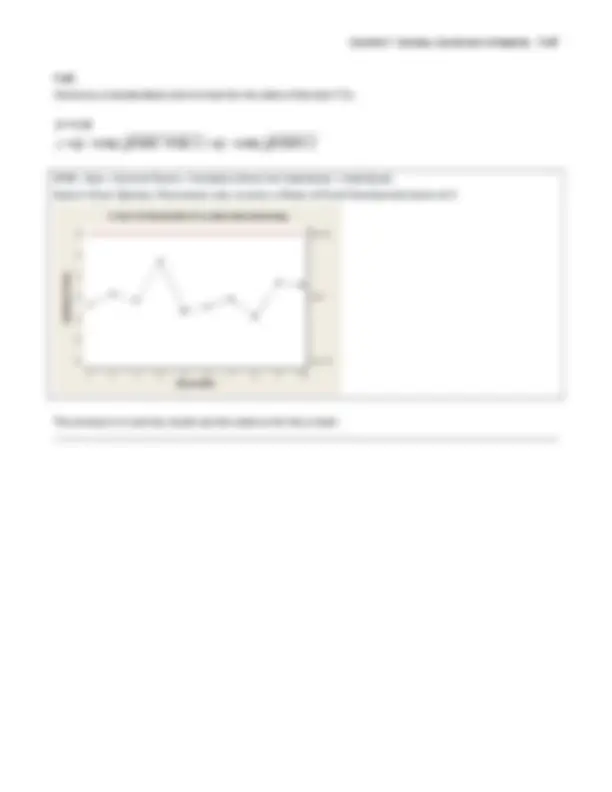
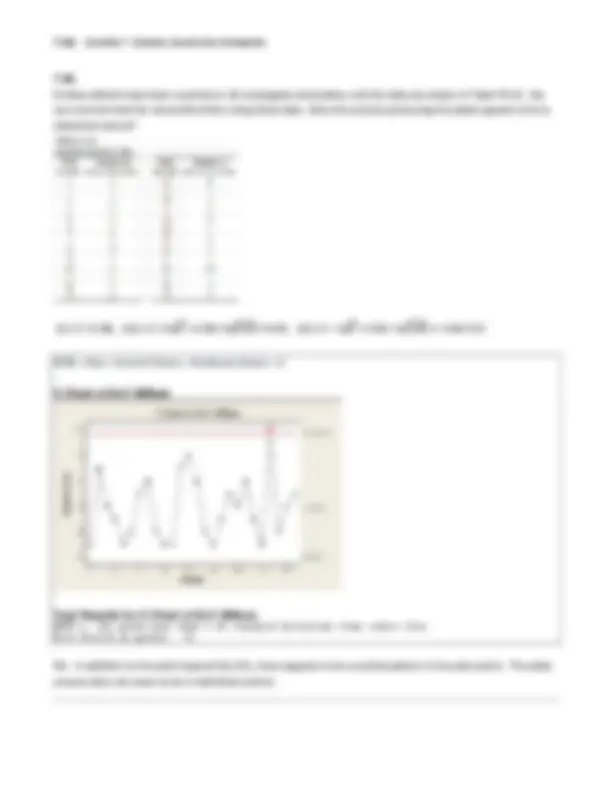
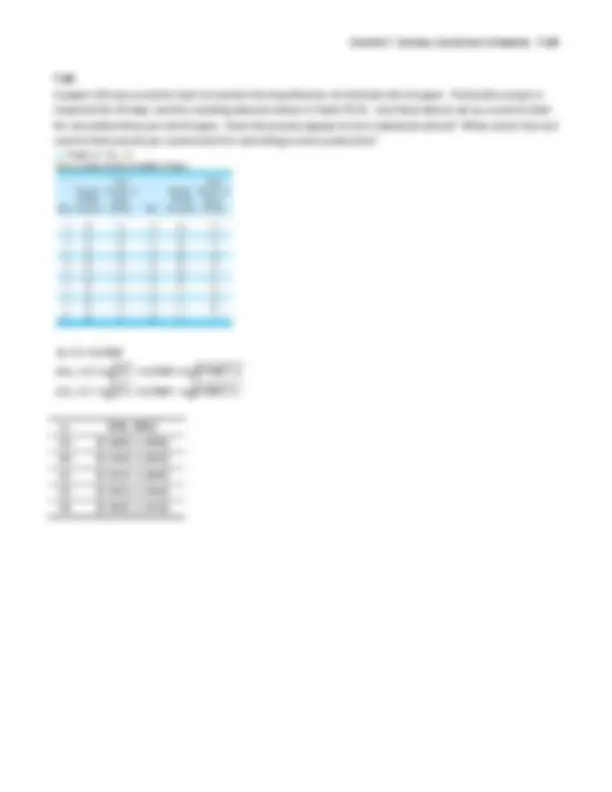
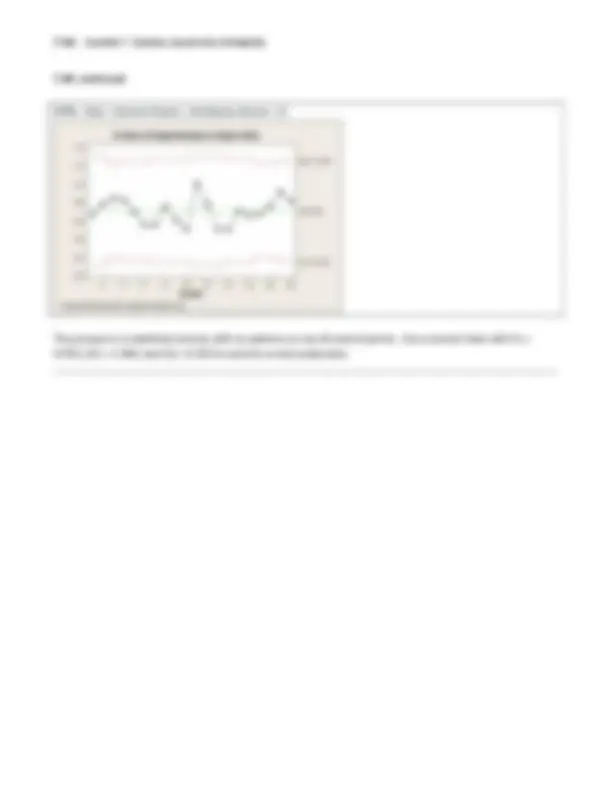
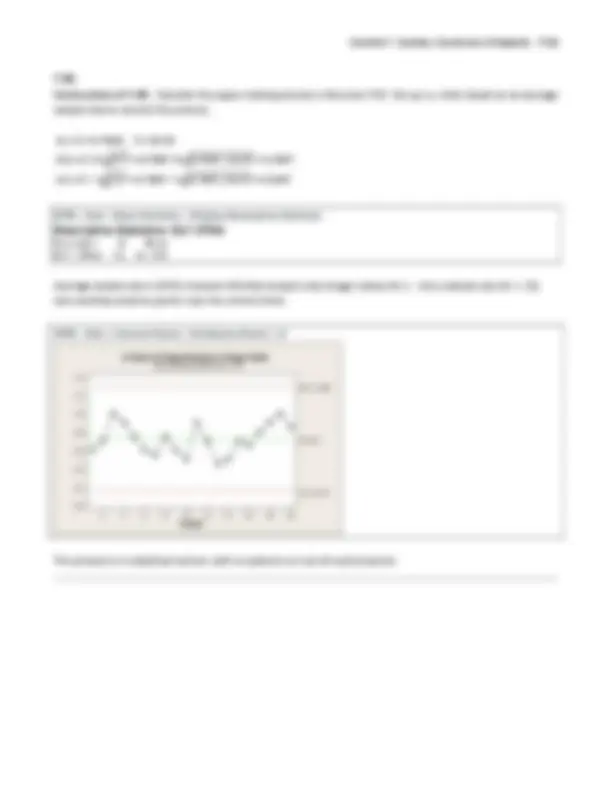
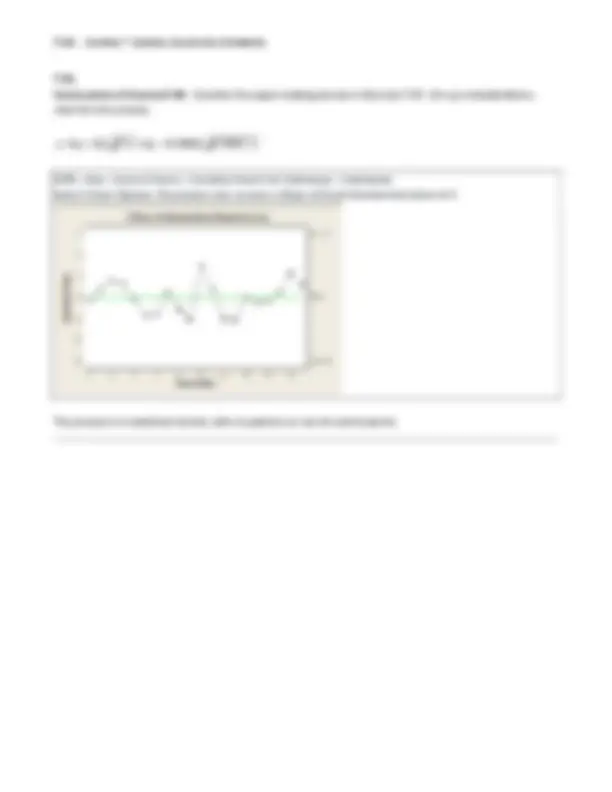
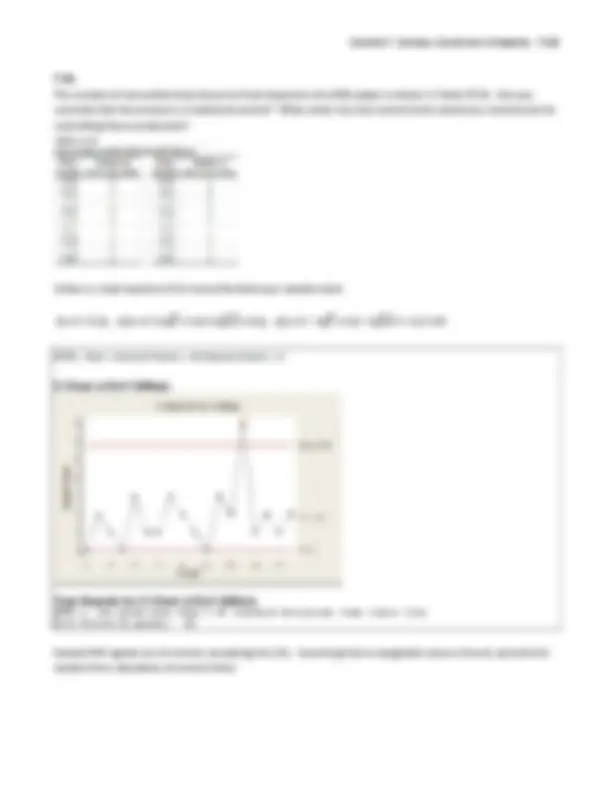
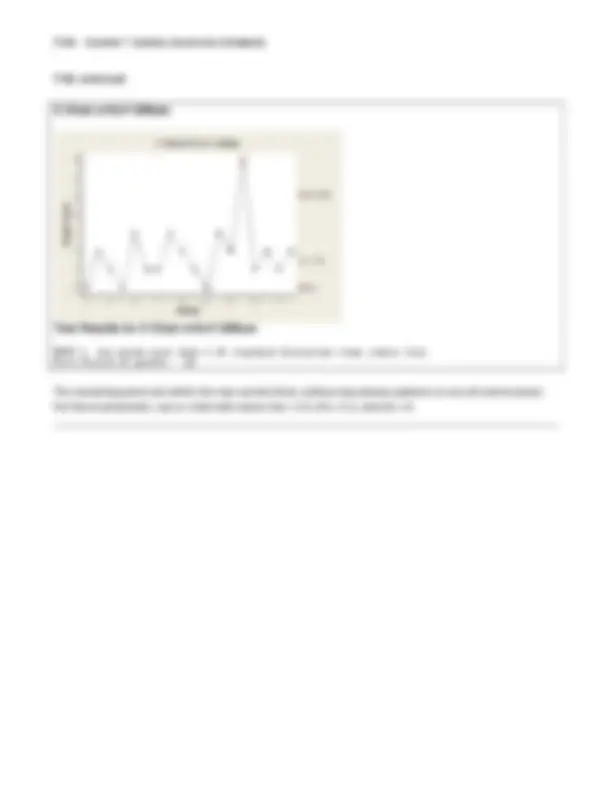
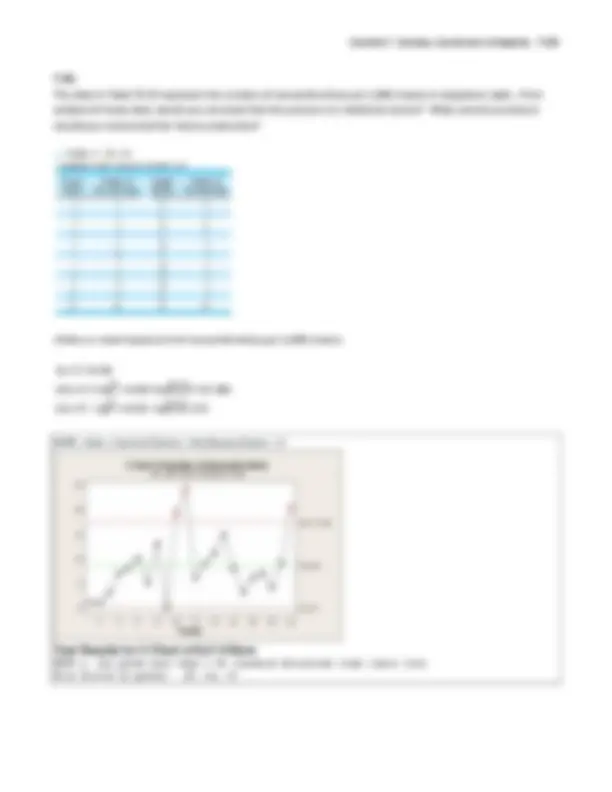
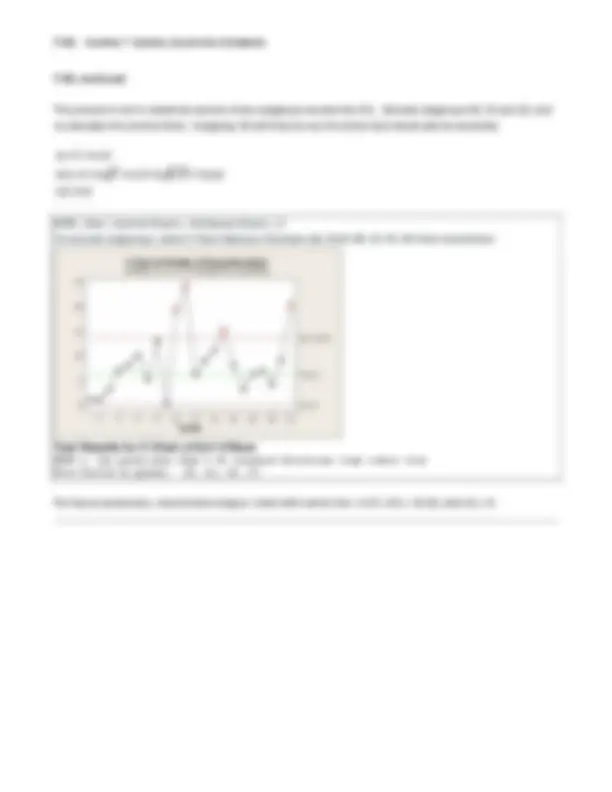
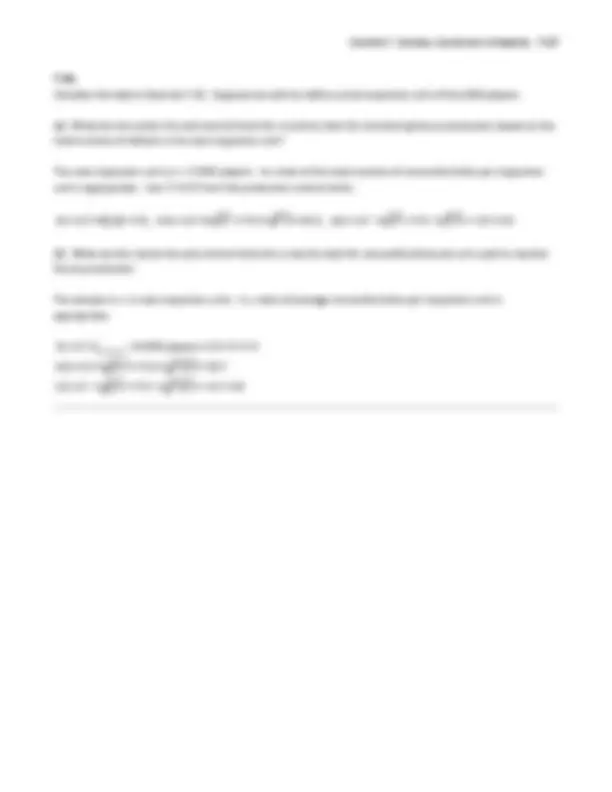
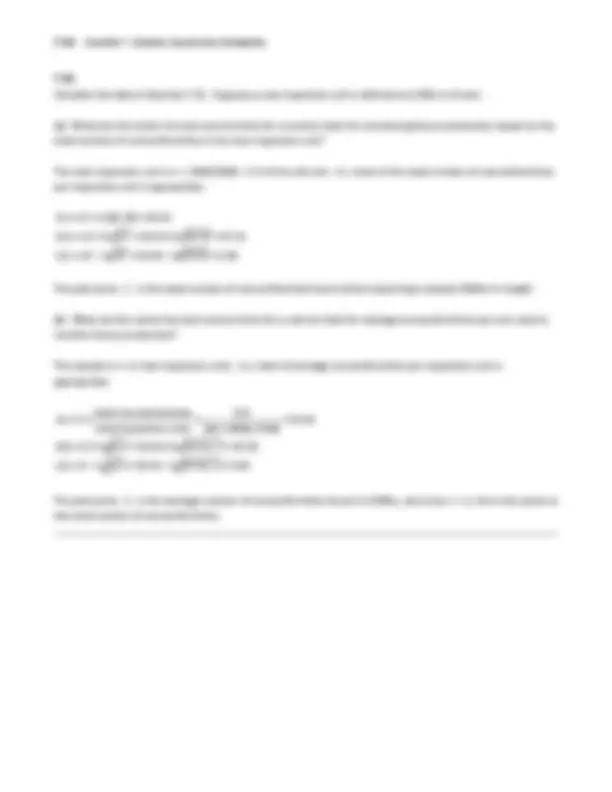
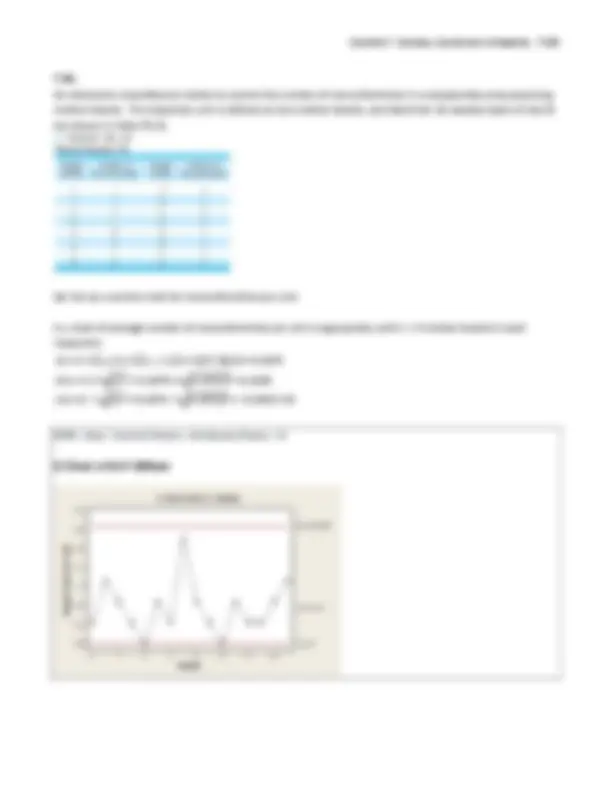
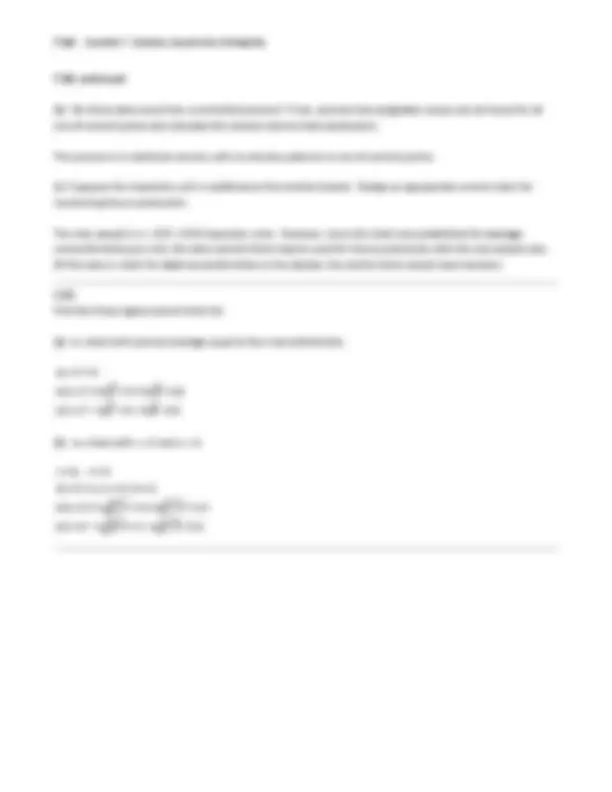
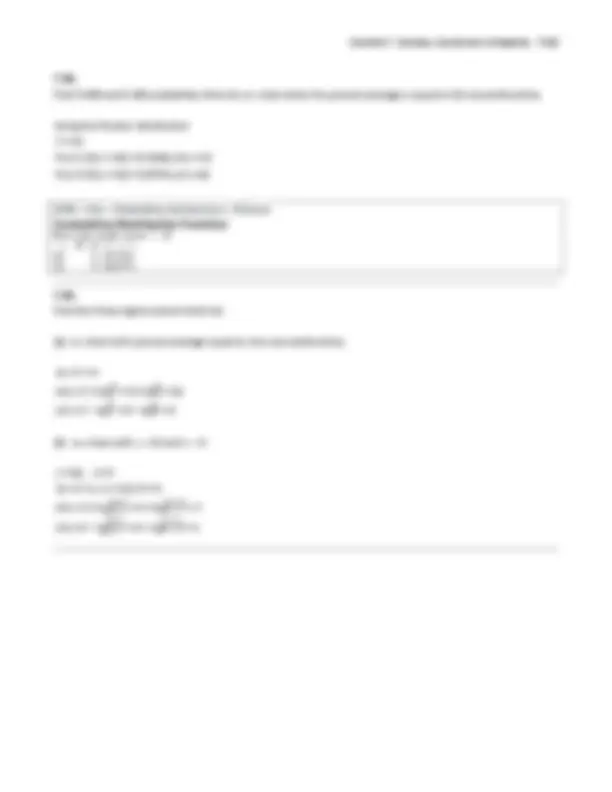
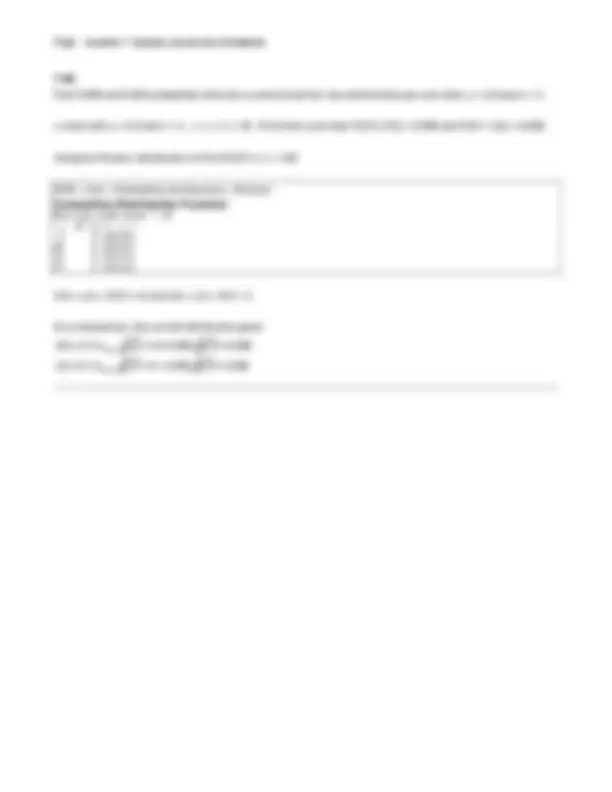
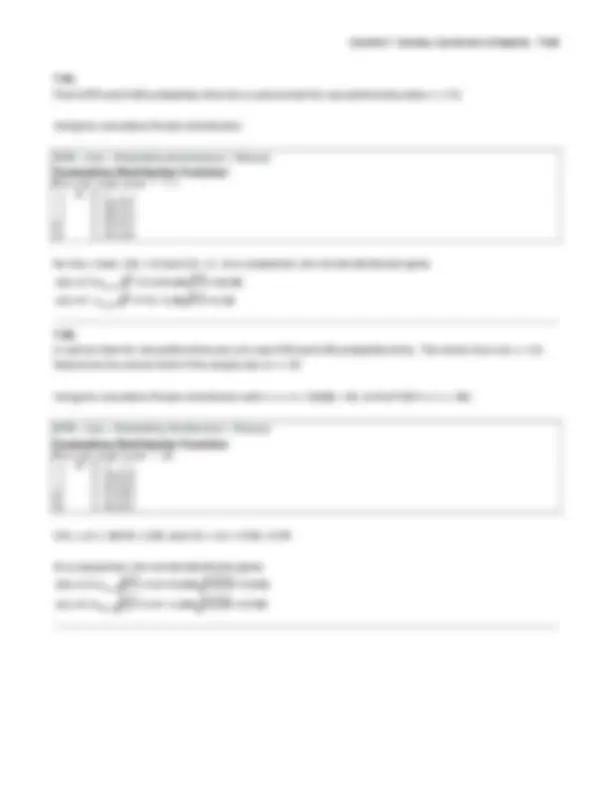
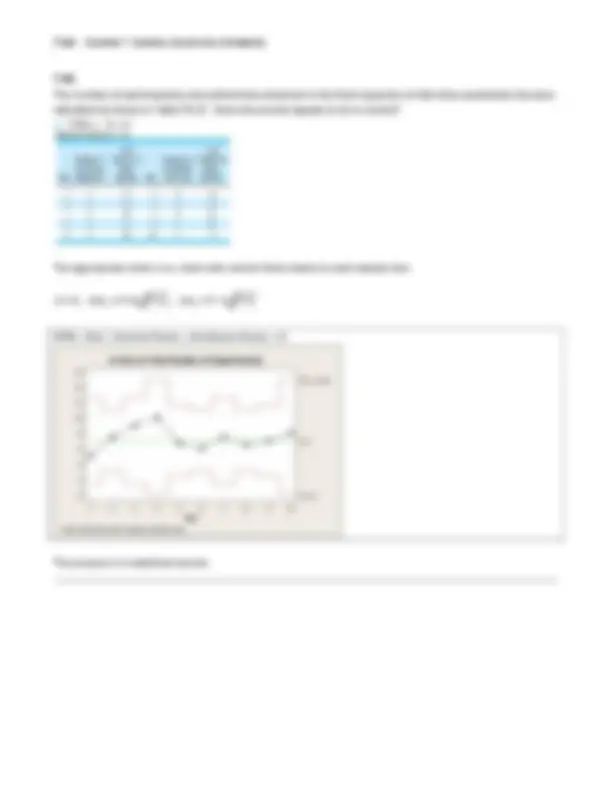
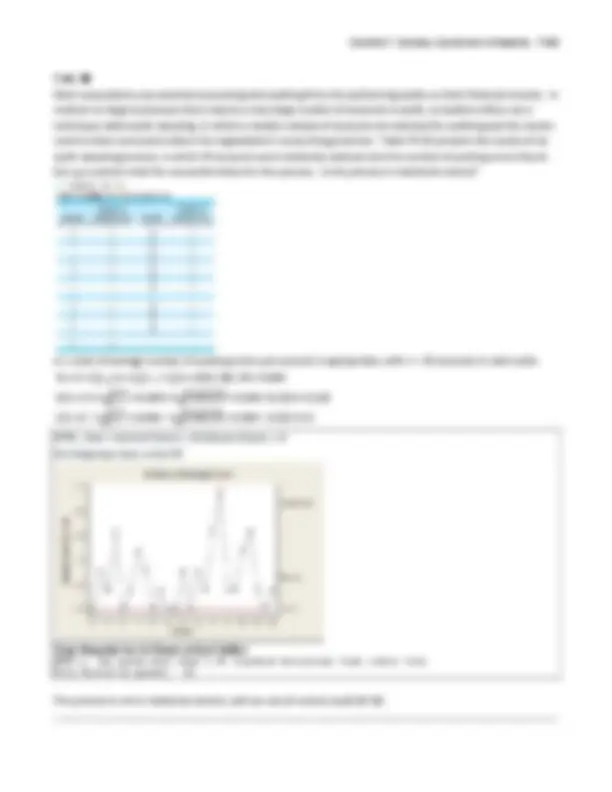
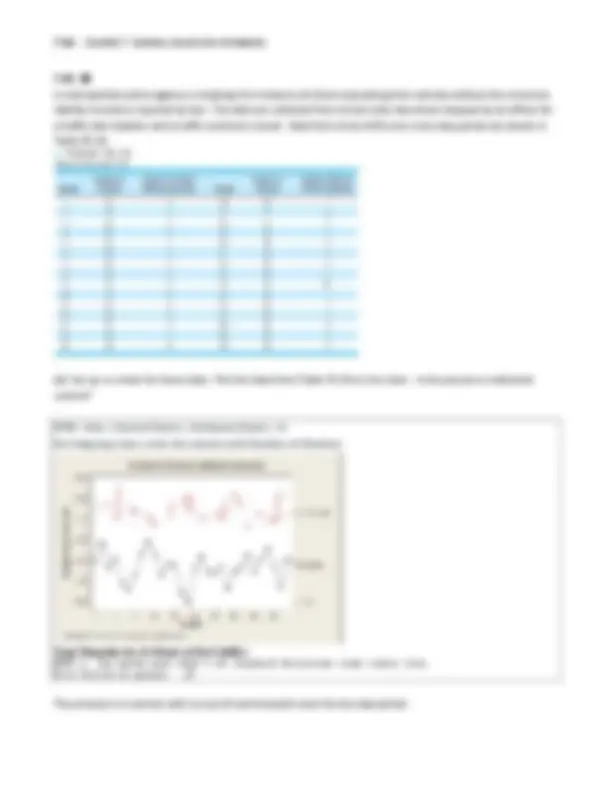
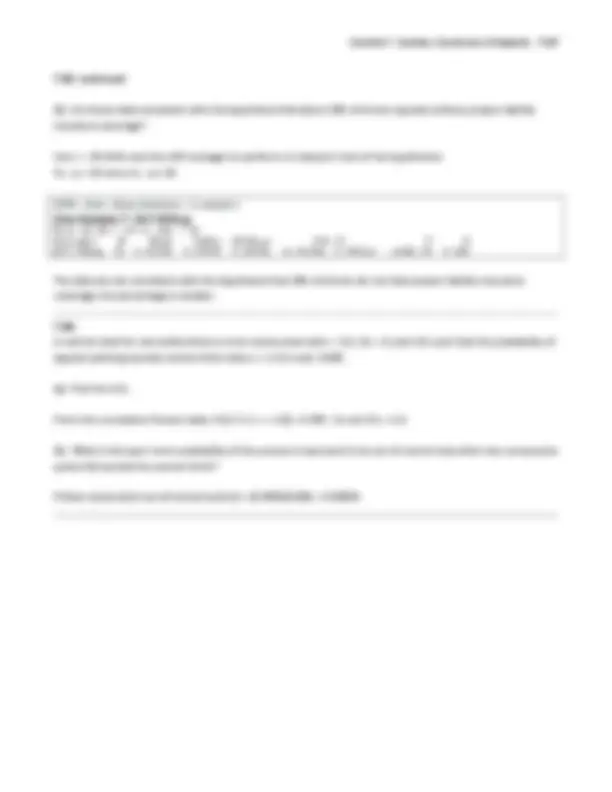
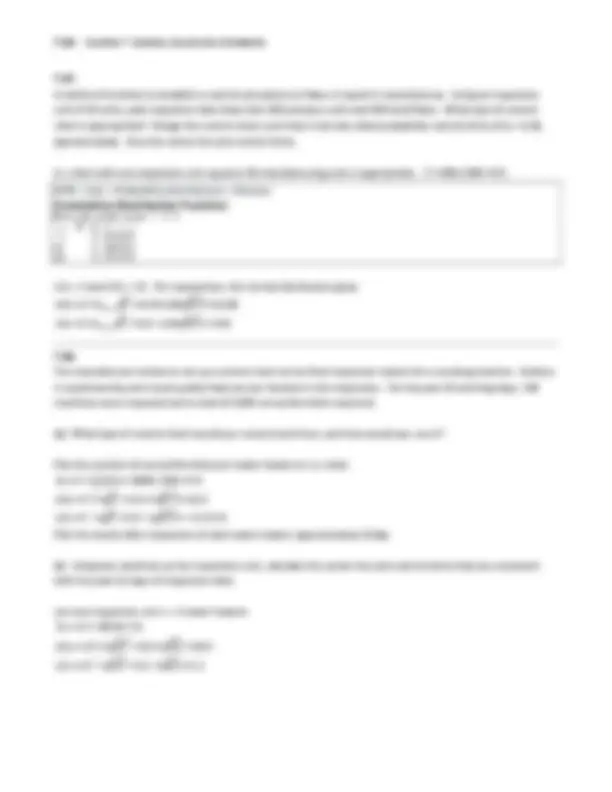
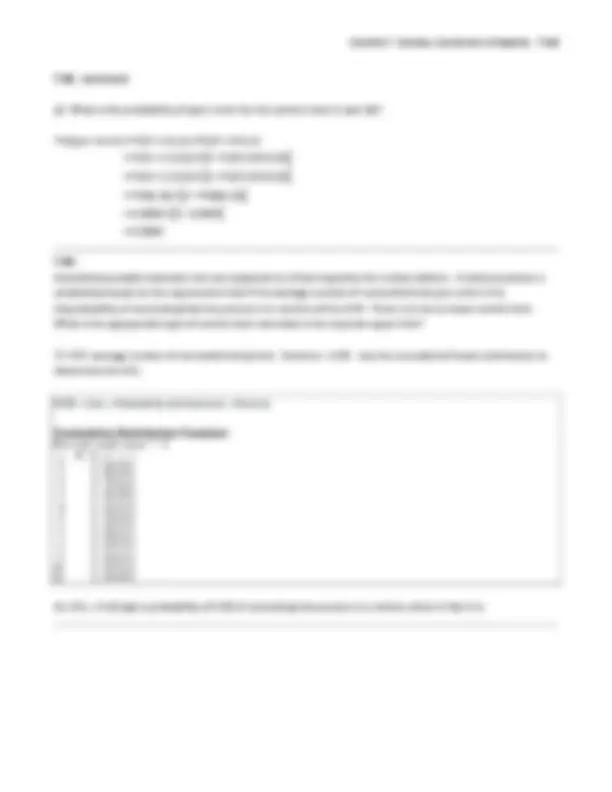
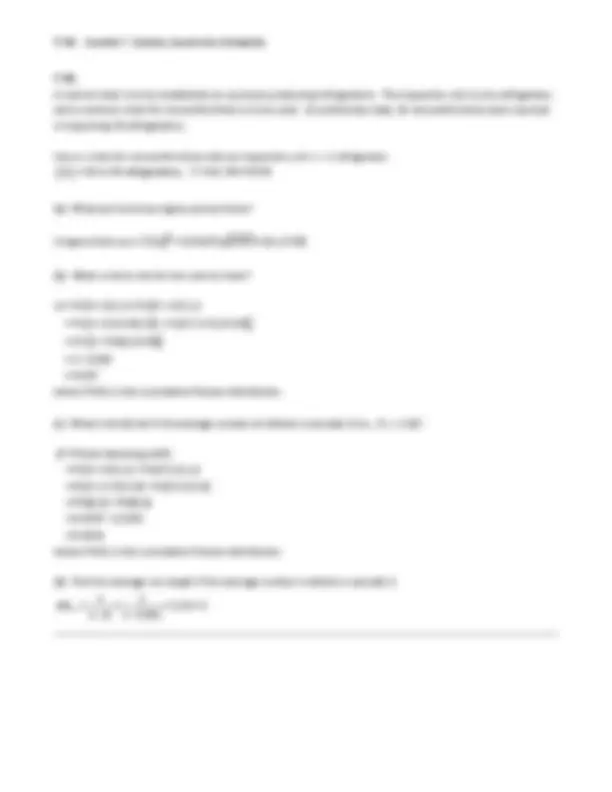
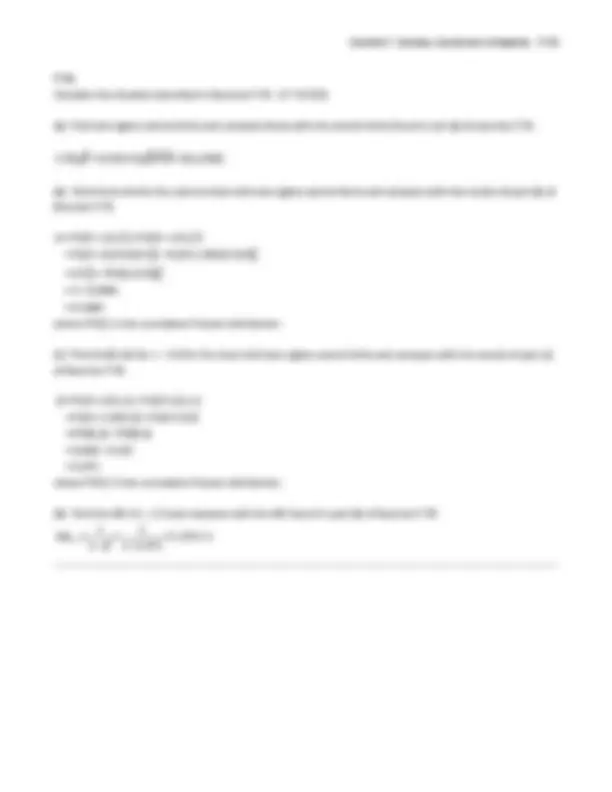
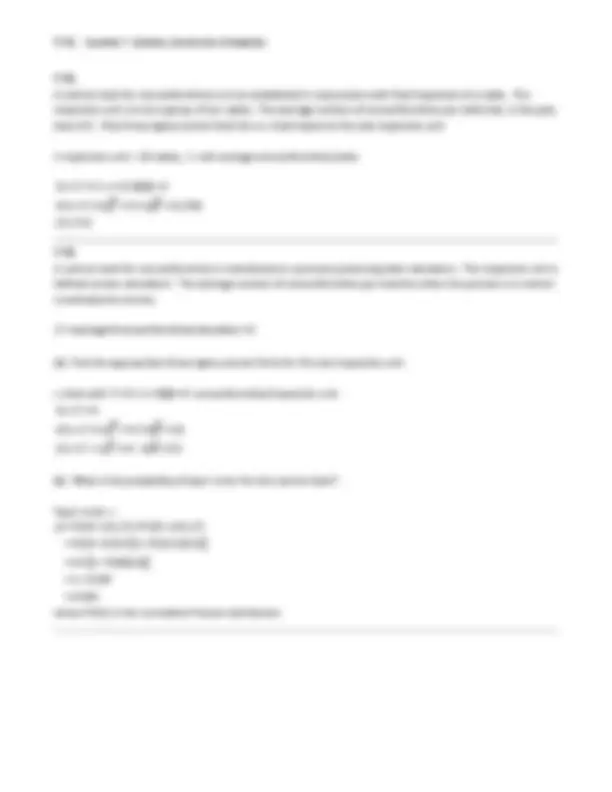
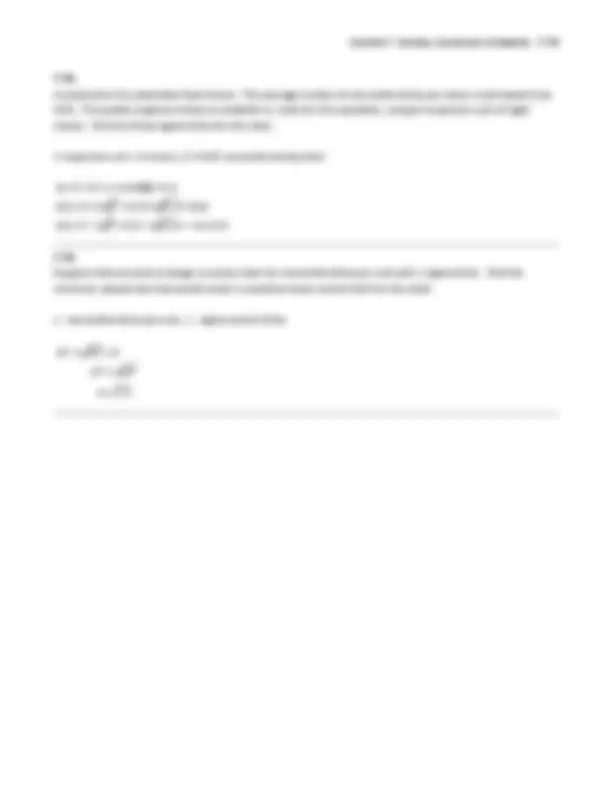
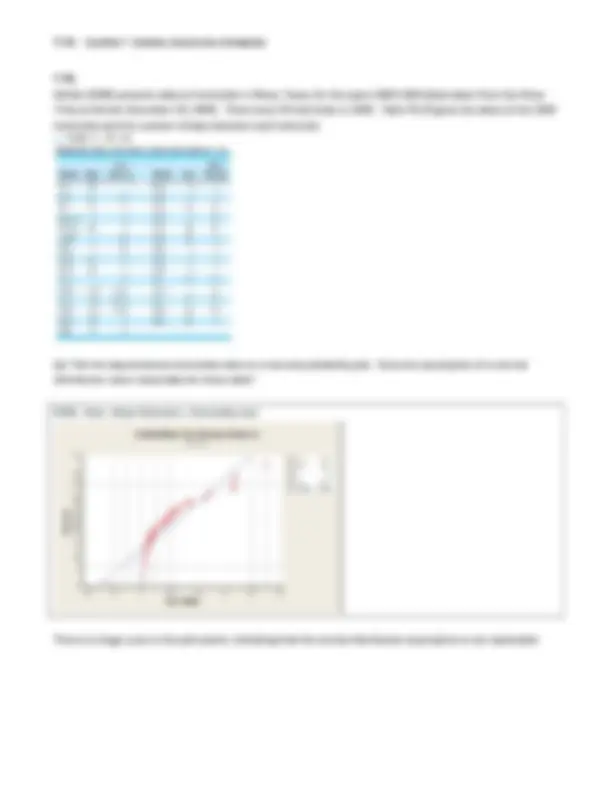
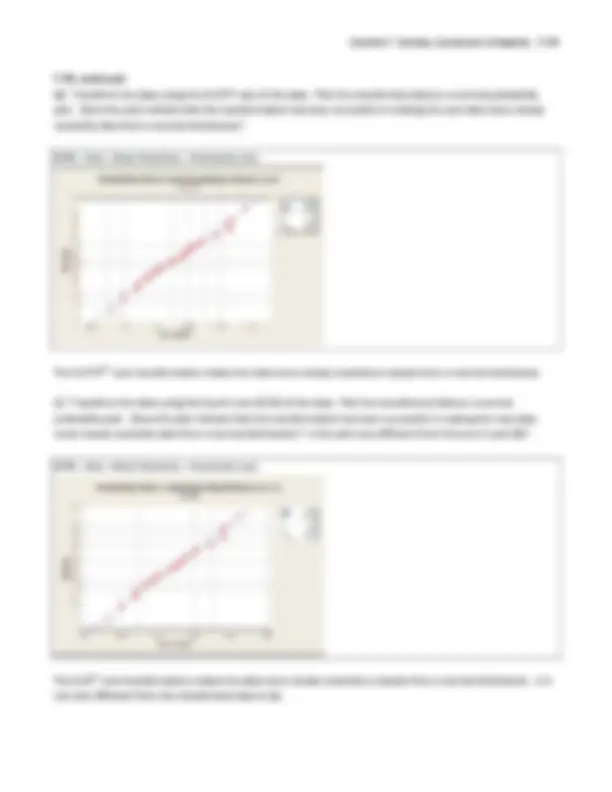
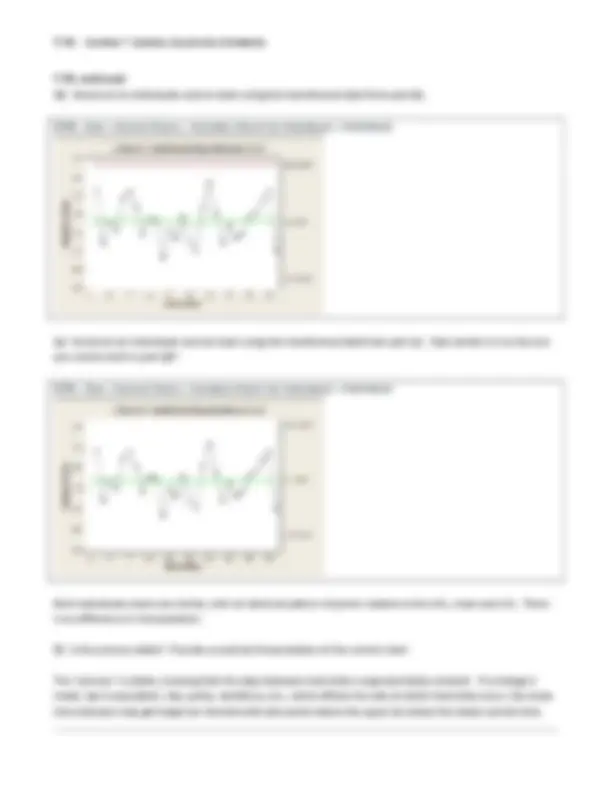
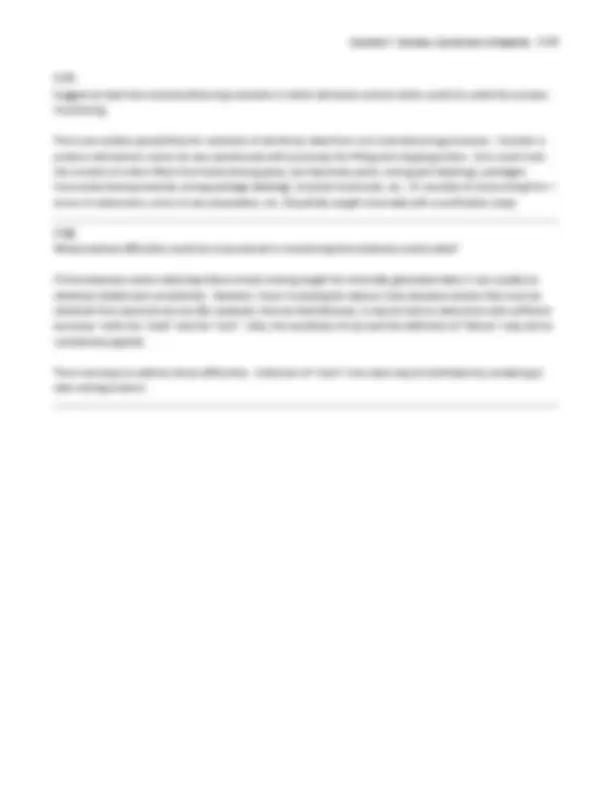
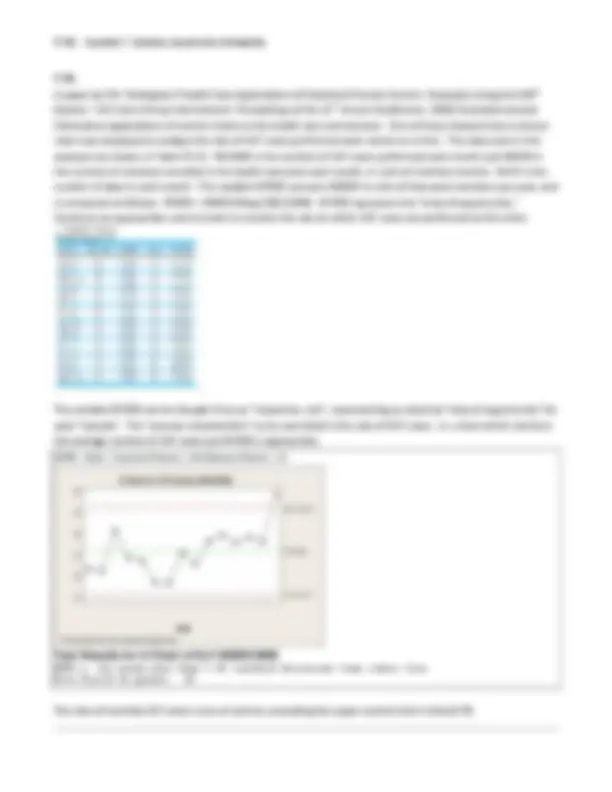
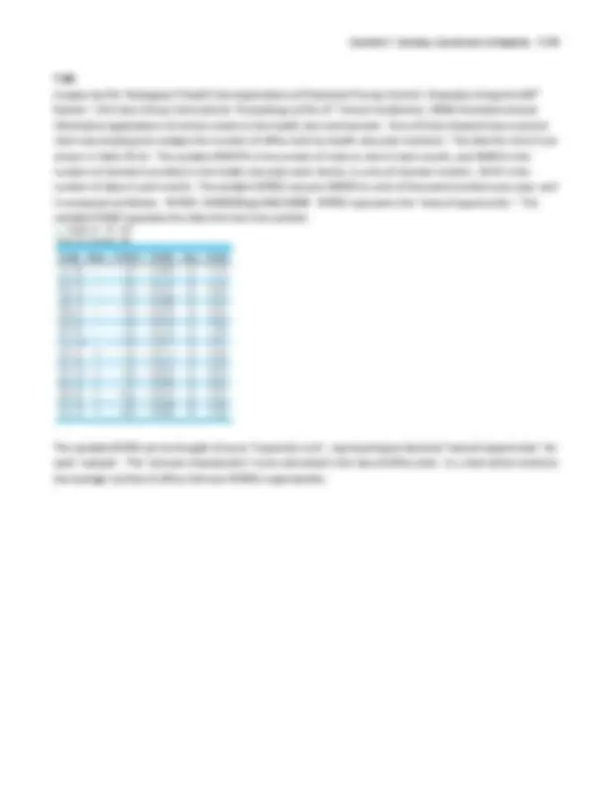
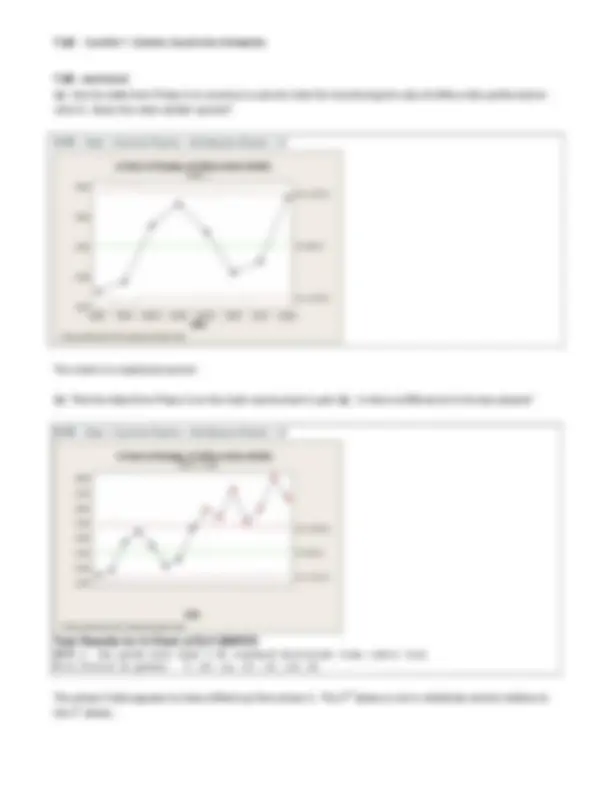
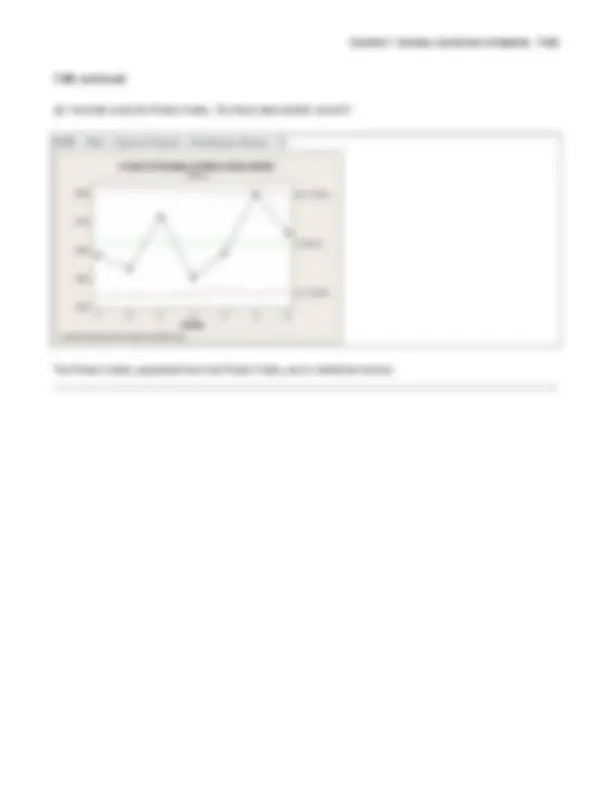
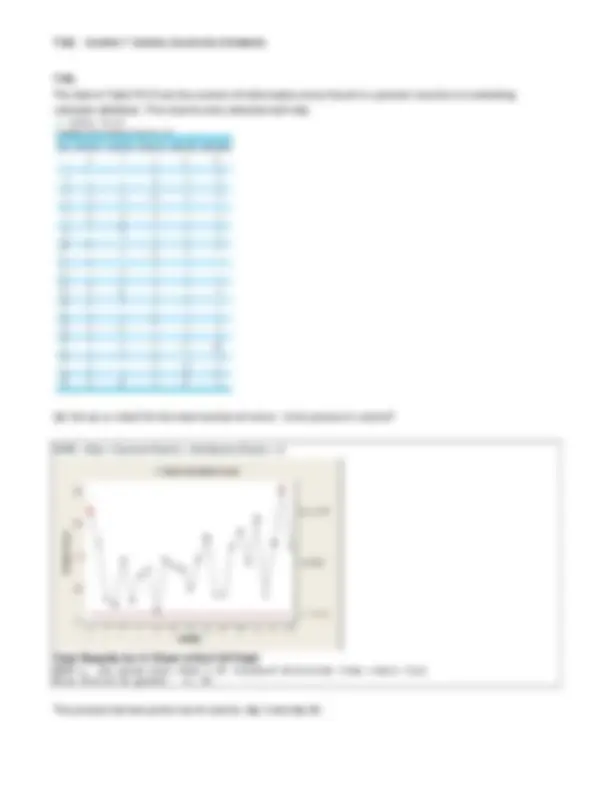
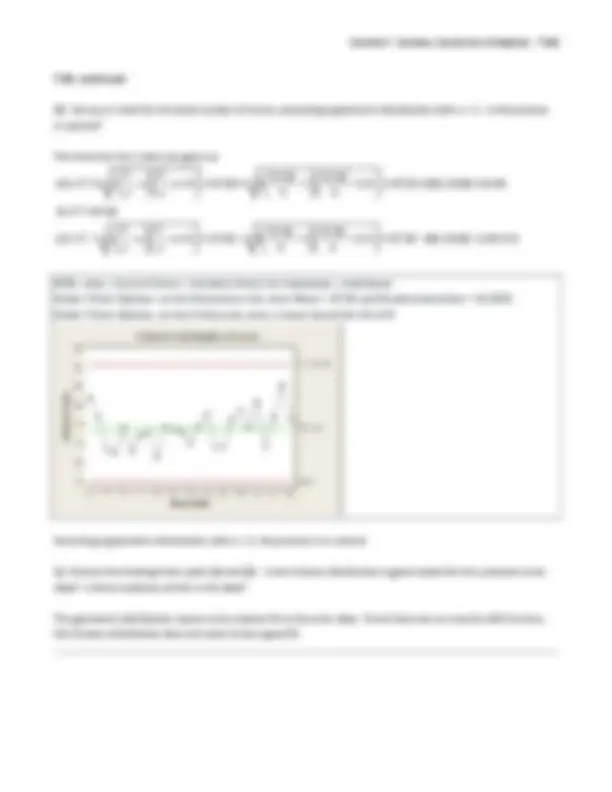
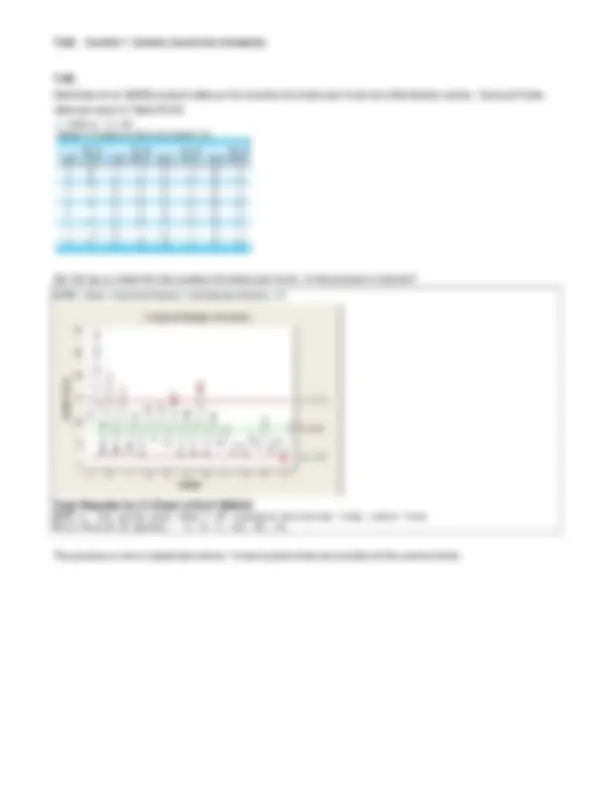
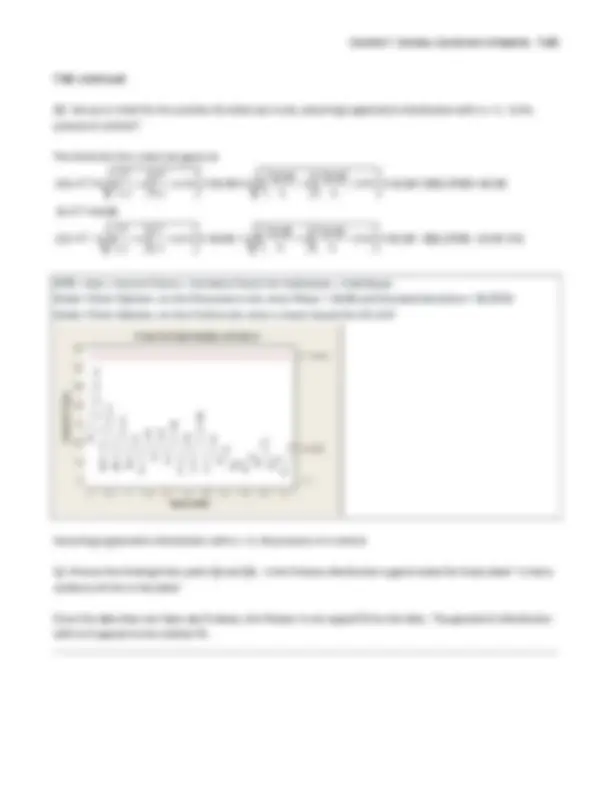
Study with the several resources on Docsity
Earn points by helping other students or get them with a premium plan
Prepare for your exams
Study with the several resources on Docsity
Earn points to download
Earn points by helping other students or get them with a premium plan
Community
Ask the community for help and clear up your study doubts
Discover the best universities in your country according to Docsity users
Free resources
Download our free guides on studying techniques, anxiety management strategies, and thesis advice from Docsity tutors
Quality management and control - Chap 7 - KEY
Typology: Exercises
1 / 85
This page cannot be seen from the preview
Don't miss anything!
After completing this chapter you should be able to:
Attribute data Design of attributes control charts
Average run length for attributes control charts Fraction defective
Cause-and-effect diagram Fraction nonconforming
Choice between attributes and variables data Nonconformity
Control chart for defects or nonconformities per
unit or u chart
Operating characteristic curve for the c and u
charts
Control chart for fraction nonconforming or p
chart
Operating characteristic curve for the p chart
Control chart for nonconformities or c chart Pareto chart
Control chart for number nonconforming or np
chart
Standardized control charts
Defect Time between occurrence control charts
Defective Variable sample size for attributes control chart
Demerit systems for attribute data
New exercises are denoted by “”.
Minitab® Notes:
control limits, it is in control, or (2) if a plot point is on or beyond the limits, it is out of control.
run of n consecutive points on one side of the center line is defined as 9 points, not 8. This can be changed
in dialog boxes, or under Tools > Options > Control Charts and Quality Tools > Tests.
A financial services company monitors loan applications. Every day 50 applications are assessed for the accuracy
of the information on the form. Results for 20 days are
^
20
1
i^46 i
D where Di is the number of loans on the i th
day that re determined to have at least one error. What are the center line and control limits on the fraction
nonconforming control chart?
20 1
1
m
i i i i
p
p
n m D p mn
p p p n
p p p n
Do points that plot below the lower control limit on a fraction nonconforming control chart (assuming that the
LCL > 0) always mean that there has been an improvement in process quality? Discuss your answer in the
context of a specific situation.
No, points plotting below the lower control limit do not always indicate an improvement in process quality. As
with any sample exceeding control limits, they may be caused by inspection process errors related to calibration,
use of equipment, poor training, or inexperience. Points below the lower control limit may also result from
deliberate actions to pass nonconforming material or record fictitious data – this is a more subtle consequence
of categorizing product as conforming or nonconforming, versus identifying a characteristic for numerical
measurement.
7.3. continued
(b) Assume that assignable causes can be found for any out-of-control points on this chart. What center line
and control limits should be used for process monitoring in the next period?
MTB > Stat > Control Charts > Attributes Charts > P
Under P Chart Options, click on the Estimate tab, and Omit subgroup 16 when estimating parameters.
Test Results for P Chart of Ex7-3Num
TEST 1. One point more than 3.00 standard deviations from center line.
Test Failed at points: 16
No additional days signal out of control. Use UCL = 0.2139, CL = 0.0916 and LCL = 0 to monitor the process.
The fraction nonconforming control chart in Exercise 7.3 has an LCL of zero. Assume that the revised control
chart in part (b) of that exercise has a reliable estimate of the process fraction nonconforming. What sample
size should be used if you want to ensure that the LCL > 0?
To choose n large enough so that the lower control limit is positive and assuming three-sigma control limits are
to be used:
p n L p
The commercial loan operation of a financial institution has a standard for processing new loan applications in
24 hours. Table 7E.2 shows the number of applications processed each day for the last 20 days and the number
of applications that required more than 24 hours to complete.
(a) Set up the fraction nonconforming control chart for this process. Use the variable-width control limit
approach. Plot the preliminary data in table 7E.2 on the chart. Is the process in statistical control?
20
1 20
1
Control Limits 3 0.0182 3 0.0182 3 0.
i i
i i
i i i i (^) i
p
n
p p p n n n (^) n
MTB > Stat > Control Charts > Attributes Charts > P
For Subgroup sizes, enter column with Number of Applications
Test Results for P Chart of Ex7-5Late
TEST 1. One point more than 3.00 standard deviations from center line.
Test Failed at points: 15
The process is not in statistical control, with Day 15 exceeding the upper control limit.
7.5. continued
MTB > Stat > Control Charts > Attributes Charts > P
Under P Chart Options, click on the Estimate tab, and Omit subgroups 12 and 15 when estimating parameters.
Test Results for P Chart of Ex7-5Late
TEST 1. One point more than 3.00 standard deviations from center line.
Test Failed at points: 12, 15
No additional days signal out of control. Use UCL = 0.0349, CL = 0.0134 and LCL = 0 to monitor the process.
Reconsider the loan application data in Table 7E.2. Set up the fraction nonconforming control chart for this
process. Use the average sample size control limit approach. Plot the preliminary data in Table 7E.2 on the
chart. Is the process in statistical control? Compare this control chart to the one based on variable-width
control limits in Exercise 7.5.
20 20
1 1 20
1
Control Limits 3 0.0182 3 0.0182 0.0254 [0.0436,0] 250
i i i i
i i
i
D n
p n
n
p p p n
MTB > Stat > Control Charts > Attributes Charts > P
For Subgroup sizes, enter the average sample size of 250
Test Results for P Chart of Ex7-5Late
TEST 1. One point more than 3.00 standard deviations from center line.
Test Failed at points: 15
Similar to the control chart with variable-width limits, Day 15 signals out of control, with the remaining days in
statistical control
Reconsider the insurance claim data in Table 7E.1. Set up an np control chart for this data and plot the data
from Table 7E.1 on this chart. Compare this to the fraction nonconforming control chart in Exercise 7.3.
MTB > Stat > Control Charts > Attributes Charts > NP
For Subgroup sizes, enter 50
Test Results for NP Chart of Ex7-3Num
TEST 1. One point more than 3.00 standard deviations from center line.
Test Failed at points: 16
Similar to the p chart, the process is not in statistical control. Day 16 exceeds the upper control limit, signaling a
potential assignable cause. Removing Day 16 from the control limit calculation gives np 4.58and an UCL =
10.7, which can be used to monitor the process going forward.
MTB > Stat > Control Charts > Attributes Charts > NP
For Subgroup sizes, enter 50
To exclude Day 16, select NP Chart Options, Estimate tab, and Omit subgroup 16
The data in Table 7E.3 give the number of nonconforming bearing and seal assemblies in samples of size 100.
Construct a fraction nonconforming control chart for these data. If any points plot out of control, assume that
assignable causes can be found and determine the revised control limits.
1
1
m
m i i i i
p
p
n m D p mn
p p p n
p p p n
MTB > Stat > Control Charts > Attributes Charts > P
For Subgroup sizes, enter 100
Test Results for P Chart of Ex7.1Num
TEST 1. One point more than 3.00 standard deviations from center line.
Test Failed at points: 12
The number of nonconforming switches in samples of size 150 are shown in Table 7E.4. Construct a fraction
nonconforming control chart for these data. Does the process appear to be in control? If not, assume that
assignable causes can be found for all points outside the control limits and calculate the revised control limits.
1
1
m
m i i i i
p
p
n m D p mn
p p p n
p p p n
MTB > Stat > Control Charts > Attributes Charts > P
For Subgroup sizes, enter 150
Test Results for P Chart of Ex7.2Num
TEST 1. One point more than 3.00 standard deviations from center line.
Test Failed at points: 9, 17
Samples 9 and 17 are out of control, so re-calculate control limits without samples 9 and 17:
7.10. continued
MTB > Stat > Control Charts > Attributes Charts > P
For Subgroup sizes, enter 150
To exclude Sample 12, select P Chart Options, Estimate tab, and Omit subgroups 9 and 17
Test Results for P Chart of Ex7.2Num
TEST 1. One point more than 3.00 standard deviations from center line.
Test Failed at points: 1, 9, 17
Also remove sample 1 from control limits calculation:
1
1
m
m i i i i
p
p
n m D p mn
The data in Table 7E.5 represent the results of inspecting all units of a personal computer produced for the last
10 days. Does the process appear to be in control?
1 1 1 1
m m m m
i i i i i i i i
m n D p D n
UCL (^) i p 3 p (1 p ) ni and LCL (^) i max{0, p 3 p (1 p ) ni }
As an example, for n = 80:
1 1
1 1
p p p n
p p p n
MTB > Stat > Control Charts > Attributes Charts > P
For Subgroup sizes, enter column with Units Inspected
The process appears to be in statistical control.
A payment process that reimburses members for out-of-network health expenses is to be controlled through
use of a fraction nonconforming chart. Initially one sample of size 200 is taken each day for 20 days, and the
results shown in Table 7E.6 are observed.
(a) Establish a control chart to monitor future performance.
1 1
m m
i i i i
n m D p D mn
p p p n
p p p n
MTB > Stat > Control Charts > Attributes Charts > P
For Subgroup sizes, enter 150
The process appears to be in statistical control.
A process produces rubber belts in lots of size 2500. Inspection records on the last 20 lots reveal the data in
Table 7E.7.
(a) Compute trial control limits for a fraction nonconforming control chart.
p p p n
p p p n
MTB > Stat > Control Charts > Attributes Charts > P
For Subgroup sizes, enter 2500
Test Results for P Chart of Ex7.5Num
TEST 1. One point more than 3.00 standard deviations from center line.
Test Failed at points: 1, 2, 3, 5, 11, 12, 15, 16, 17, 19, 20
(b) If you wanted to set up a control chart for controlling future production, how would you use these data to
obtain the center line and control limits for the chart?
So many subgroups are out of control (11 of 20) that the data should not be used to establish control limits for
future production. Instead, the process should be investigated for causes of the wild swings in p.
Based on the data in Table 7E.8 if an np chart is to be established, what would you recommend as the center line
and control limits? Assume that n = 700.
1 1
m m
i i i i
np D m p D mn
np np p
np np p
MTB > Stat > Control Charts > Attributes Charts > NP
For Subgroup sizes, enter 700
NP Chart of Ex7-14Num
Test Results for NP Chart of Ex7-14Num
TEST 1. One point more than 3.00 standard deviations from center line.
Test Failed at points: 6