
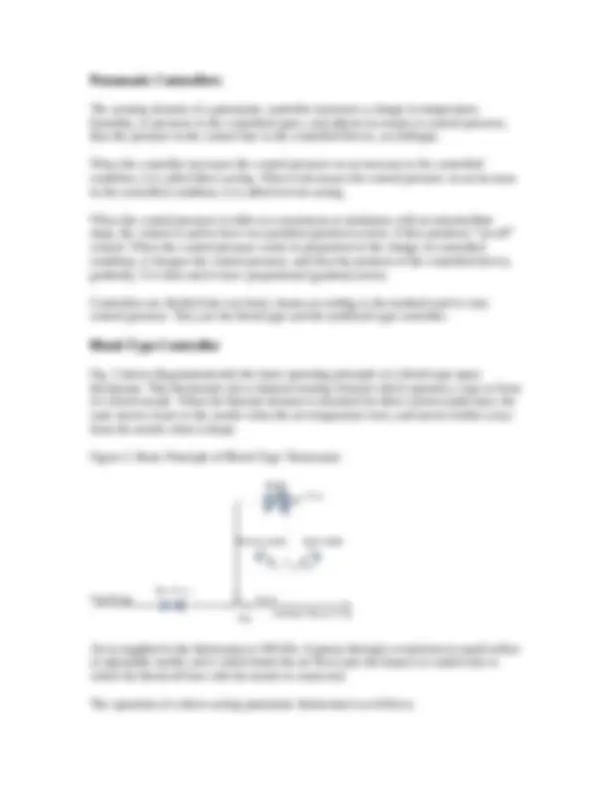
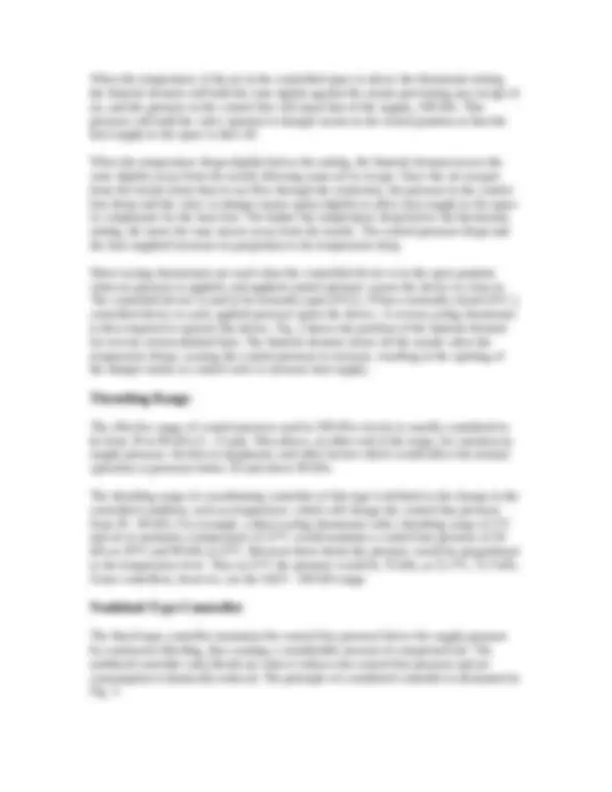
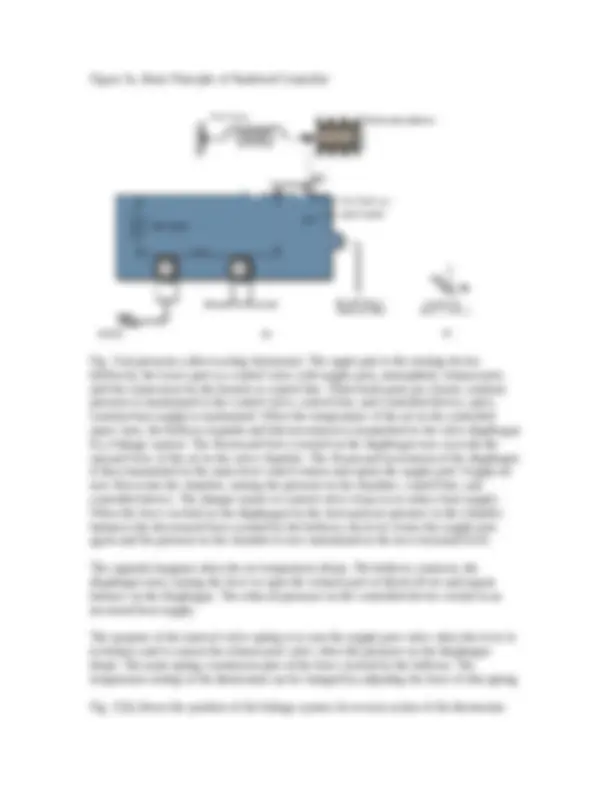
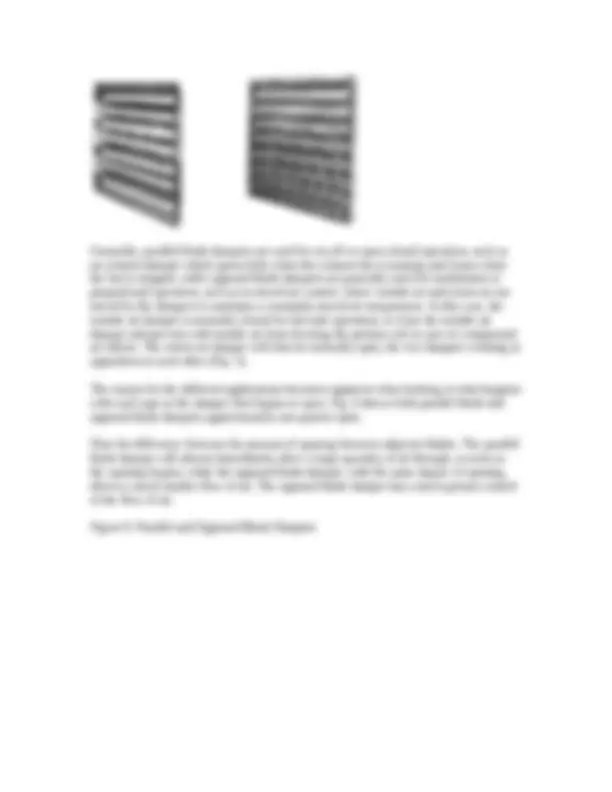
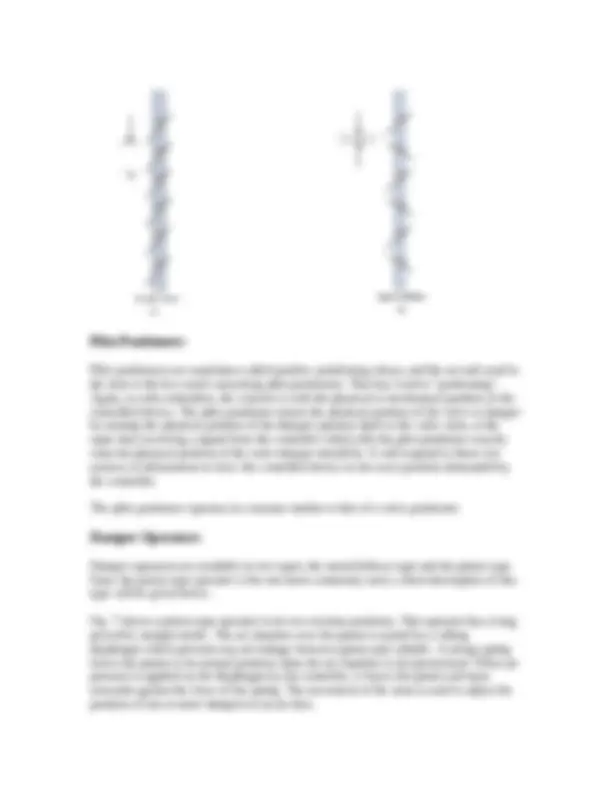
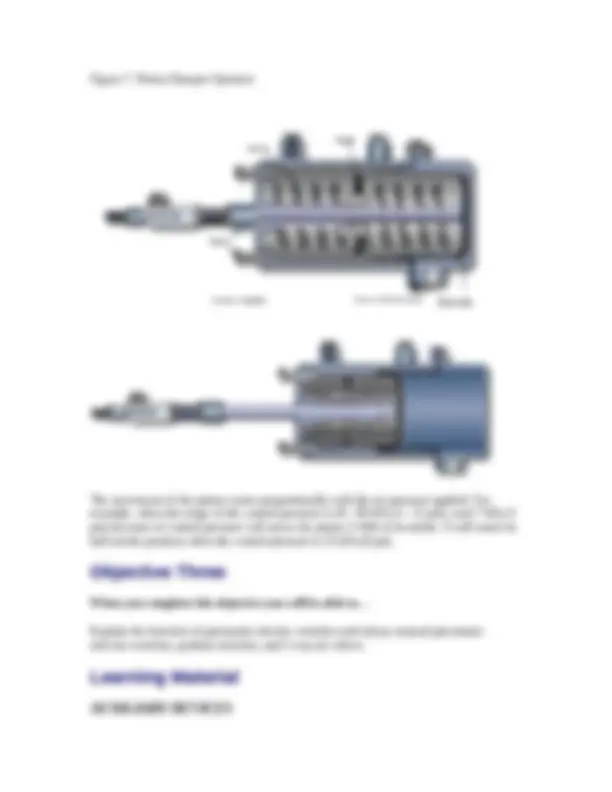
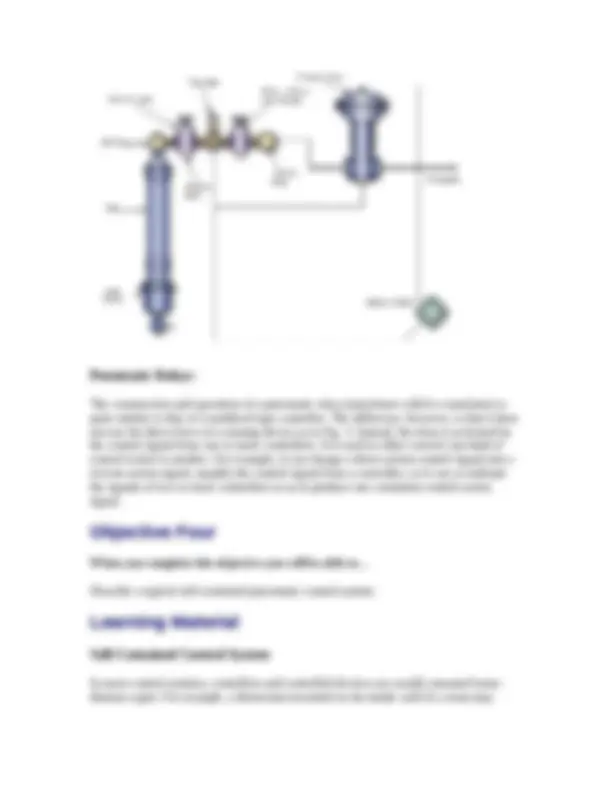
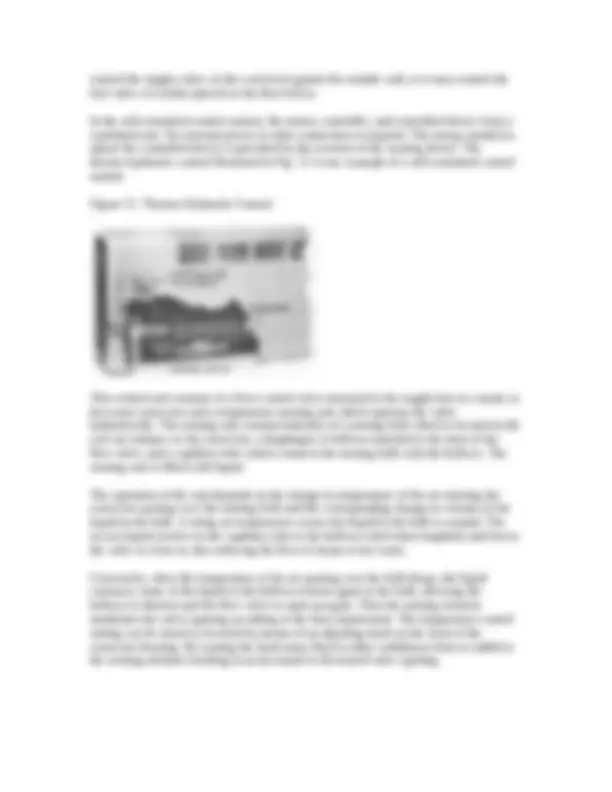
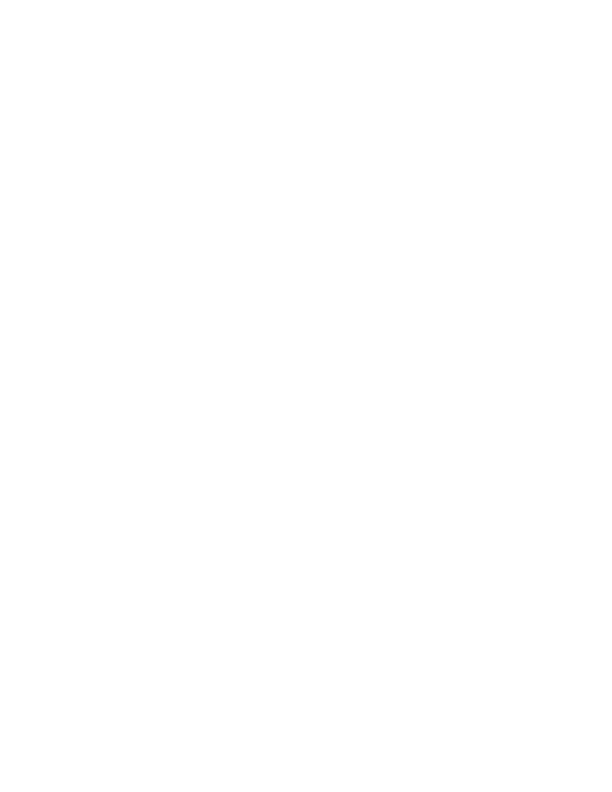
Study with the several resources on Docsity
Earn points by helping other students or get them with a premium plan
Prepare for your exams
Study with the several resources on Docsity
Earn points to download
Earn points by helping other students or get them with a premium plan
Community
Ask the community for help and clear up your study doubts
Discover the best universities in your country according to Docsity users
Free resources
Download our free guides on studying techniques, anxiety management strategies, and thesis advice from Docsity tutors
A detailed explanation of pneumatic control systems used in heating, ventilation, and air conditioning systems. It covers the layout, construction, and operation of pneumatic controllers, final control elements, and auxiliary devices. The document also explores the principles of direct-acting and nonbleed controllers, throttling range, and self-contained control systems. It includes illustrations and diagrams to enhance understanding.
Typology: Summaries
1 / 15
This page cannot be seen from the preview
Don't miss anything!
When you complete this chapter you will be able to… Explain the purpose of the various components found in a pneumatic control system.
Here is what you will be able to do when you complete each objective.
In many larger commercial and institutional buildings, pneumatic systems are used to control the operation of the heating, ventilating, and air conditioning systems. In principle, pneumatic systems are very similar in design and operation to the various electrical and electronic control systems used in buildings. The difference, however, is that the controllers operate the controlled devices by means of a compressed air signal instead of an electrical signal. This chapter will describe the basic operation of pneumatic devices in an HVAC environment.
When you complete this objective you will be able to… Describe the layout of a pneumatic control system, and the construction and operation of pneumatic controllers.
A pneumatic control system consists of four essential parts:
When the temperature of the air in the controlled space is above the thermostat setting, the bimetal element will hold the vane tightly against the nozzle preventing any escape of air, and the pressure in the control line will equal that of the supply, 100 kPa. This pressure will hold the valve operator or damper motor in the closed position so that the heat supply to the space is shut off. When the temperature drops slightly below the setting, the bimetal element moves the vane slightly away from the nozzle allowing some air to escape. Since the air escapes from the nozzle faster than it can flow through the restriction, the pressure in the control line drops and the valve or damper motor opens slightly to allow heat supply to the space to compensate for the heat loss. The farther the temperature drops below the thermostat setting, the more the vane moves away form the nozzle. The control pressure drops and the heat supplied increases in proportion to the temperature drop. Direct-acting thermostats are used when the controlled device is in the open position when no pressure is applied, and applied control pressure causes the device to close in. The controlled device is said to be normally open (N.O.). When a normally closed (N.C.) controlled device is used, applied pressure opens the device. A reverse-acting thermostat is then required to operate this device. Fig. 2 shows the position of the bimetal element for reverse action (dashed line). The bimetal element closes off the nozzle when the temperature drops, causing the control pressure to increase, resulting in the opening of the damper motor or control valve to increase heat supply.
The effective range of control pressure used in 100 kPa circuits is usually considered to be from 20 to 90 kPa (3 - 13 psi). This allows, at either end of the range, for variation in supply pressure, friction in equipment, and other factors which would affect the normal operation at pressures below 20 and above 90 kPa. The throttling range of a modulating controller of this type is defined as the change in the controlled condition, such as temperature, which will change the control line pressure from 20 - 90 kPa. For example, a direct-acting thermostat with a throttling range of 2°C and set to maintain a temperature of 21°C would maintain a control line pressure of 20 kPa at 20°C and 90 kPa at 22°C. Between these limits the pressure would be proportional to the temperature level. Thus at 21°C the pressure would be 55 kPa; at 21.5°C, 72.5 kPa. Some controllers, however, use the full 0 - 100 kPa range.
The bleed-type controller maintains the control line pressure below the supply pressure by continuous bleeding, thus wasting a considerable amount of compressed air. The nonbleed controller only bleeds air when it reduces the control line pressure and air consumption is drastically reduced. The principle of a nonbleed controller is illustrated in Fig. 3.
Figure 3a. Basic Principle of Nonbleed Controller Fig. 3 (a) presents a direct-acting thermostat. The upper part is the sensing device (bellows); the lower part is a control valve with supply port, atmospheric exhaust port, and the connection for the branch or control line. When both ports are closed, constant pressure is maintained in the control valve, control line, and controlled device, and a constant heat supply is maintained. When the temperature of the air in the controlled space rises, the bellows expands and this movement is transmitted to the valve diaphragm by a linkage system. The downward force exerted on the diaphragm now exceeds the upward force of the air in the valve chamber. The downward movement of the diaphragm is then transmitted to the main lever which rotates and opens the supply port. Supply air now flows into the chamber, raising the pressure in the chamber, control line, and controlled device. The damper motor or control valve closes in to reduce heat supply. When the force exerted on the diaphragm by the increased air pressure in the chamber balances the downward force exerted by the bellows, the lever closes the supply port again and the pressure in the chamber is now maintained at the new increased level. The opposite happens when the air temperature drops. The bellows contracts, the diaphragm rises, raising the lever to open the exhaust port to bleed off air and regain balance on the diaphragm. The reduced pressure on the controlled device results in an increased heat supply. The purpose of the interval valve spring is to seat the supply port valve when the lever is in balance and to unseat the exhaust port valve when the pressure on the diaphragm drops. The main spring counteracts part of the force exerted by the bellows. The temperature setting of the thermostat can be changed by adjusting the force of this spring. Fig. 3 (b) shows the position of the linkage system for reverse action of the thermostat.
When you complete this objective you will be able to… Describe the construction and operation of final control elements.
The final control element is defined as the controlled device; the equipment which the control signal from the controller directs to effect corrective change to the process to maintain it at the desired value (or set point). The final controlled device could be a pneumatic or electric actuated control valve, a damper of the in-line type, a slide gate or clam-shell gate, a screw conveyer, a conveyer drive, a pump or fan motor, or a set of louvres. All of these are final control elements.
This section will cover all controlled devices other than automatic control valves.
A control damper, in conjunction with its operator, is a controlled device which usually controls the flow of air through a duct, although a damper may be found in a wall opening, controlling the flow of air through the opening. There are two basic types of dampers, parallel blade and opposed blade, as shown in Fig.
Figure 5. Basic Types of Dampers
Generally, parallel blade dampers are used for on-off or open-closed operation, such as an exhaust damper which opens fully when the exhaust fan is running and closes when the fan is stopped, while opposed blade dampers are generally used for modulation or proportional operation, such as in mixed air control, where outside air and return air are mixed by the dampers to maintain a constantly mixed air temperature. In this case, the outside air damper is normally closed for fail-safe operation, to close the outside air damper and prevent cold outside air from freezing the preheat coil in case of compressed air failure. The return air damper will then be normally open, the two dampers working in opposition to each other (Fig. 5). The reason for the different applications becomes apparent when looking at what happens with each type as the damper first begins to open. Fig. 6 shows both parallel blade and opposed blade dampers approximately one-quarter open. Note the difference between the amount of opening between adjacent blades. The parallel blade damper will almost immediately allow a large quantity of air through, as soon as the opening begins; while the opposed blade damper, with the same degree of opening, allows a much smaller flow of air. The opposed blade damper has a much greater control of the flow of air. Figure 6. Parallel and Opposed Blade Dampers
Figure 7. Piston Damper Operator The movement of the piston varies proportionally with the air pressure applied. For example, when the range of the control pressure is 20 - 90 kPa (3 - 13 psi), each 7 kPa ( psi) increase of control pressure will move the piston 1/10th of its stroke. It will reach its half-stroke position when the control pressure is 55 kPa (8 psi).
When you complete this objective you will be able to… Explain the function of pneumatic-electric switches and relays, manual pneumatic selector switches, gradual switches, and 3 way air valves.
There are several auxiliary devices associated with pneumatic controls system. These include: electric-pneumatic relays pneumatic-electric switches, manual pneumatic selector switches, pneumatic gradual switches, three-way air valves, and pneumatic relays.
This electric solenoid operated air valve is used where the control of a pneumatically operated device is dependent on an electric circuit. When the solenoid is energized, the air valve is opened, allowing air to pass through for the operation of the pneumatic device. When the solenoid is de-energized, air is exhausted and the device returns to its normal position. An example of the application of this relay is the control of outdoor air intake louvres. These louvres are closed when the fan is stopped. When the fan is started up, the electric- pneumatic relay is energized at the same time, allowing air to pass to a damper motor which then opens the louvres.
This switch is operated by an air pressure change in a pneumatic system in order to energize or de-energize an electric circuit. They are commonly used to control the operation of valves, fans, compressors, and pumps.
In many pneumatically controlled systems it is often necessary to put certain pieces of equipment on manual control or to provide manual means of switching. A manual switch such as the one shown in Fig. 8 is used for this purpose. Switches of this type are available in two, three, or four position selector models. Figure 8. Auto-Manual Selector Switch
The construction and operation of a pneumatic relay (sometimes called a cumulator) is quite similar to that of a nonbleed type controller. The difference, however, is that it does not use the direct force of a sensing device as in Fig. 3. Instead, the relay is activated by the control signal from one or more controllers. It is used to either convert one kind of control action to another. For example, it can change a direct-action control signal into a reverse-action signal; amplify the control signal from a controller; or it can co-ordinate the signals of two or more controllers so as to produce one consistent control action signal.
When you complete this objective you will be able to… Describe a typical self-contained pneumatic control system.
In most control systems, controllers and controlled devices are usually mounted some distance apart. For example, a thermostat mounted on the inside wall of a room may
control the supply valve on the convector against the outside wall, or it may control the fuel valve of a boiler placed on the floor below. In the self-contained control system, the sensor, controller, and controlled device form a combined unit. No external power or other connection is required. The energy needed to adjust the controlled device is provided by the reaction of the sensing device. The thermo-hydraulic control illustrated in Fig. 11 is one example of a self-contained control system. Figure 11. Thermo-Hydraulic Control This control unit consists of a flow control valve mounted in the supply line to a steam or hot water convector and a temperature sensing unit which operates the valve hydraulically. The sensing unit consists basically of a sensing bulb which is located in the cool air entrance to the convector, a diaphragm or bellows attached to the stem of the flow valve, and a capillary tube which connects the sensing bulb with the bellows. The sensing unit is filled with liquid. The operation of the unit depends on the change in temperature of the air entering the convector passing over the sensing bulb and the corresponding change in volume of the liquid in the bulb. A rising air temperature causes the liquid in the bulb to expand. The excess liquid travels via the capillary tube to the bellows which then lengthens and forces the valve to close in, thus reducing the flow of steam or hot water. Conversely, when the temperature of the air passing over the bulb drops, the liquid contracts, some of the liquid in the bellows returns again to the bulb, allowing the bellows to shorten and the flow valve to open up again. Thus the sensing element modulates the valve opening according to the heat requirement. The temperature control setting can be raised or lowered by means of an adjusting knob on the front of the convector housing. By turning the knob some fluid is either withdrawn from or added to the sensing element resulting in an increased or decreased valve opening.