
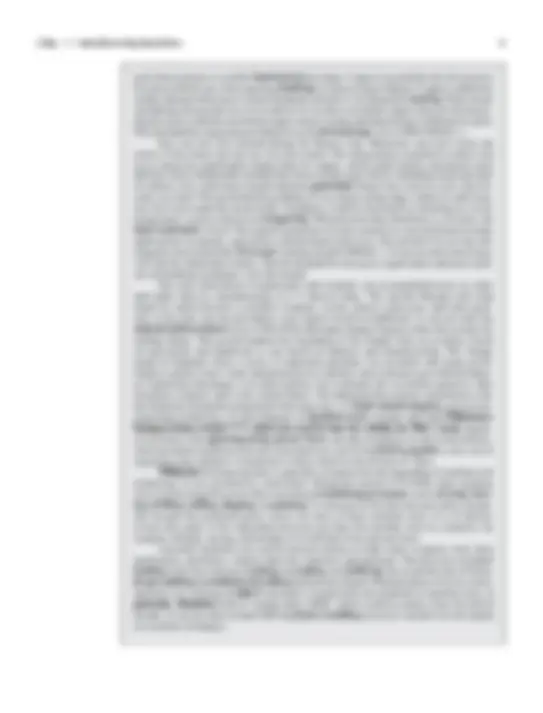
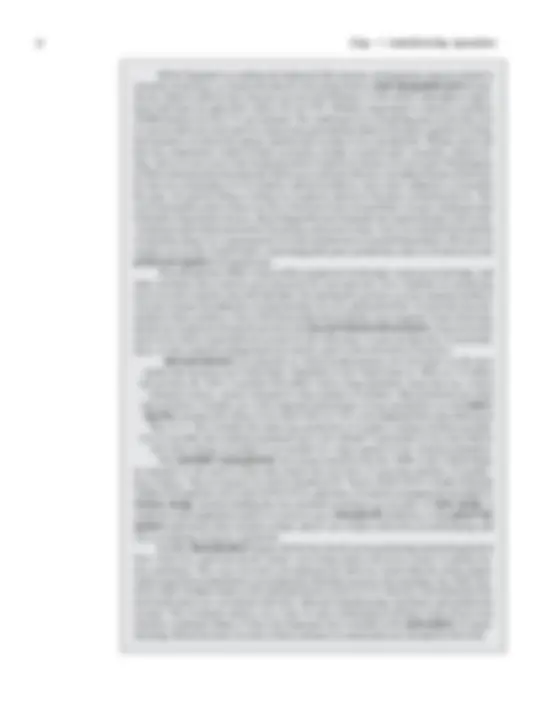
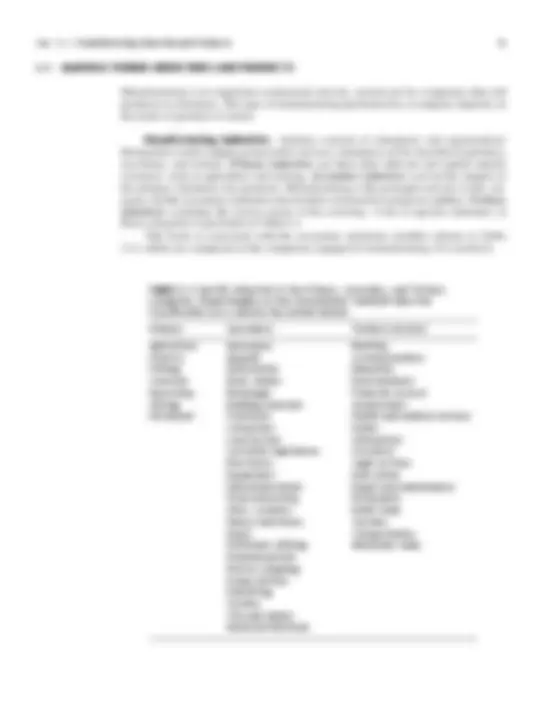
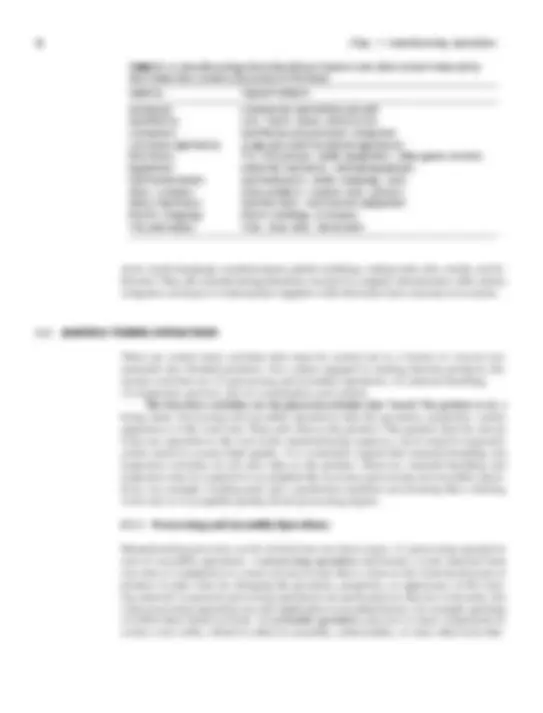
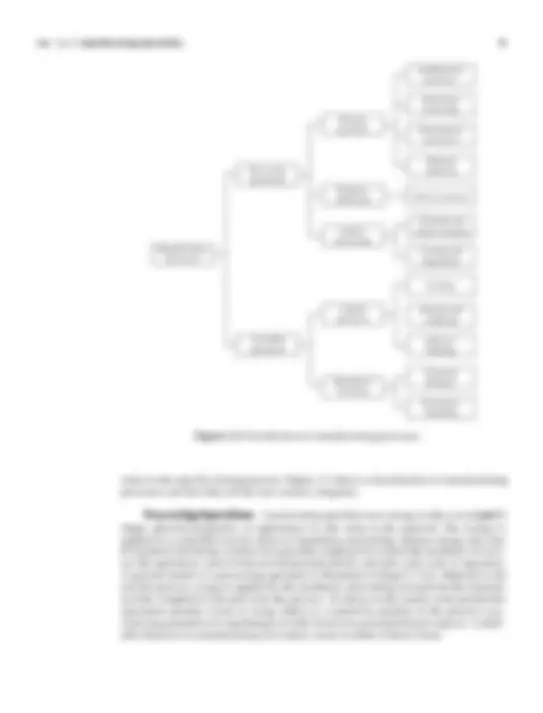
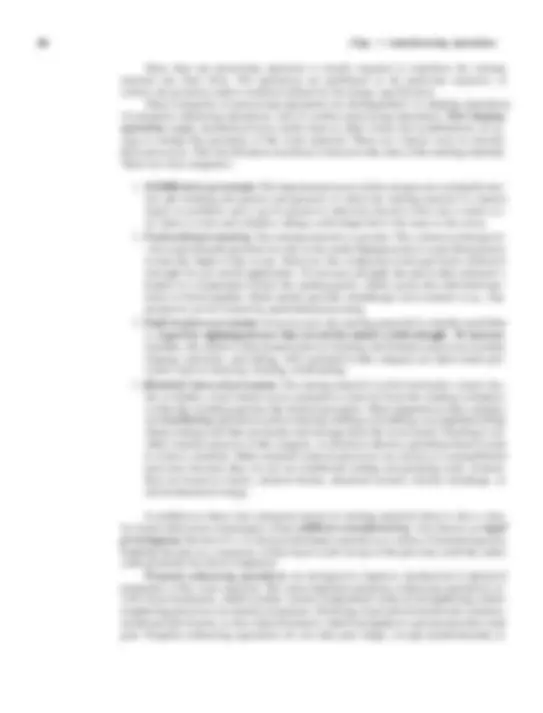
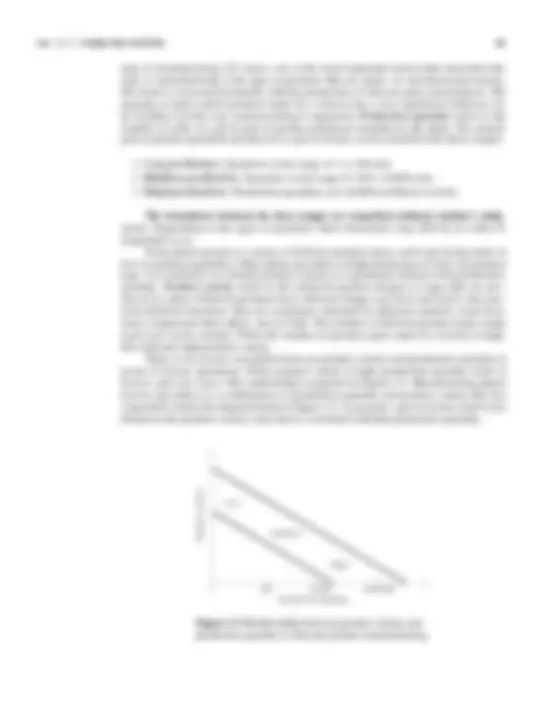
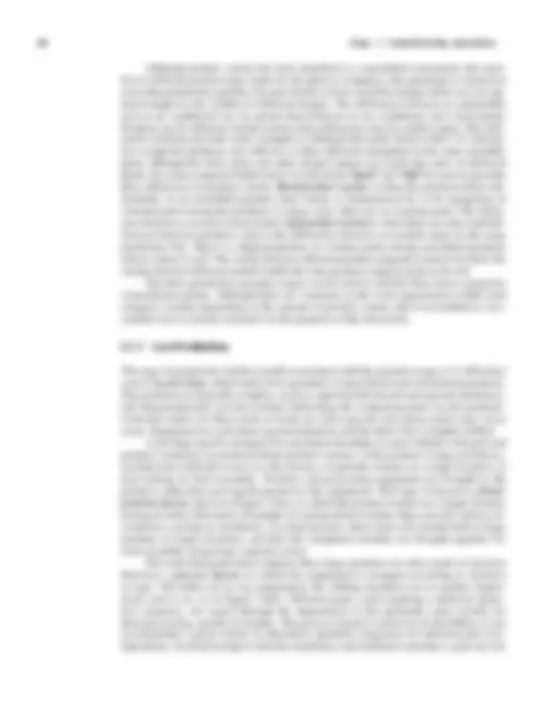
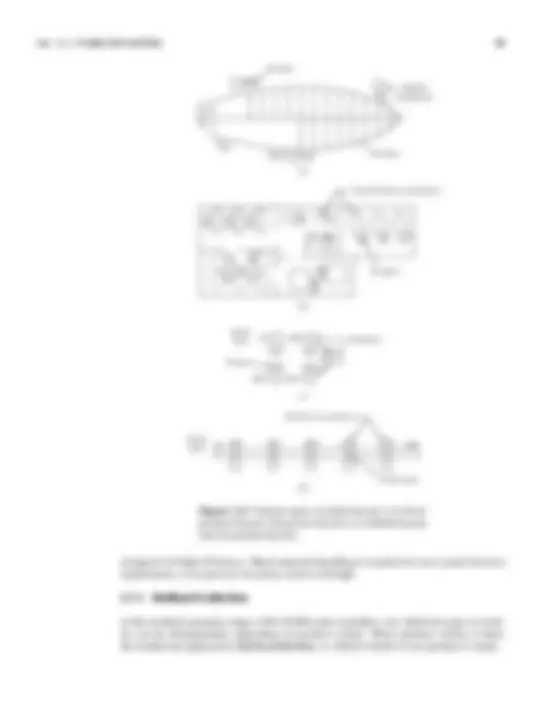
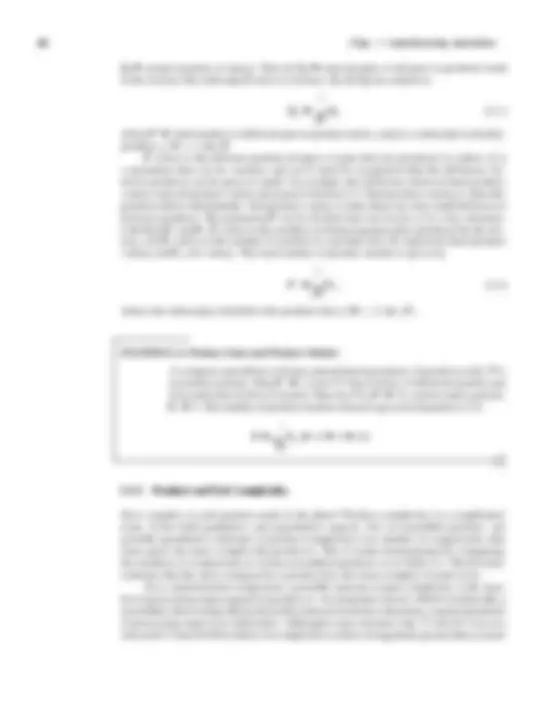
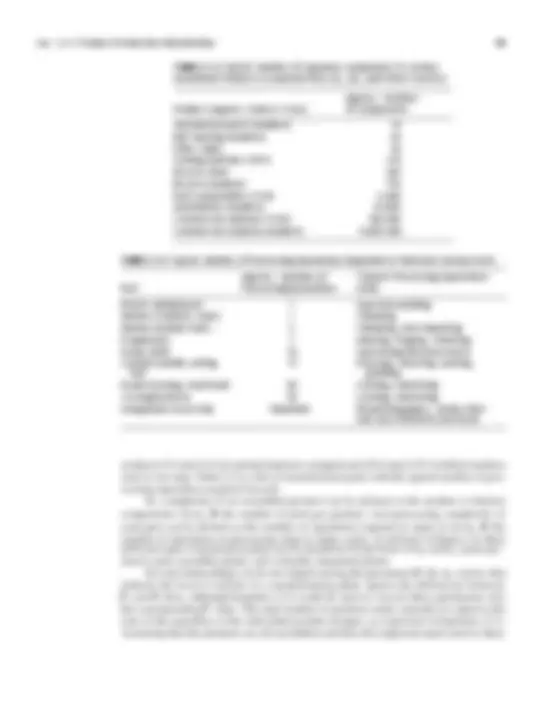
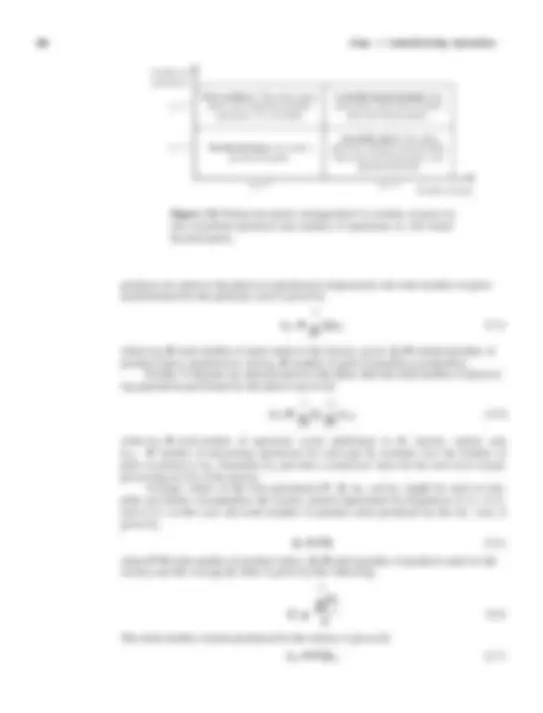
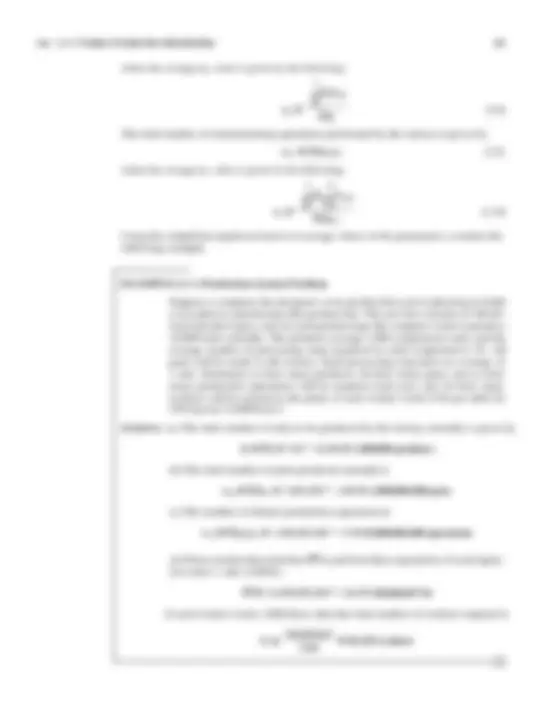
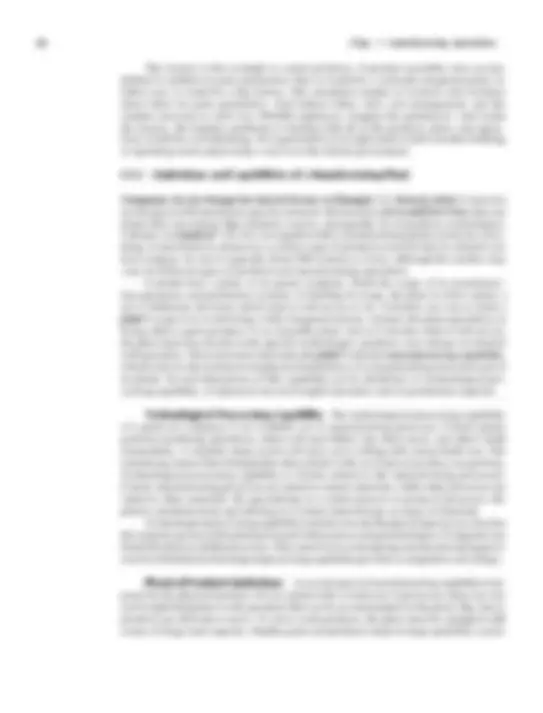
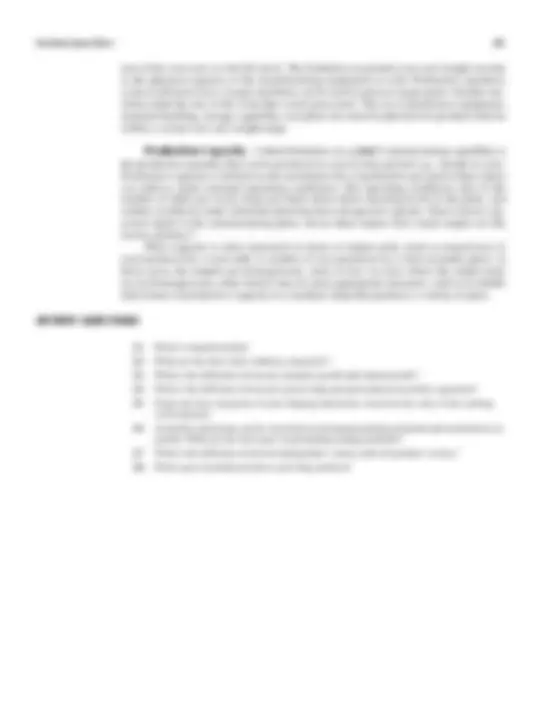
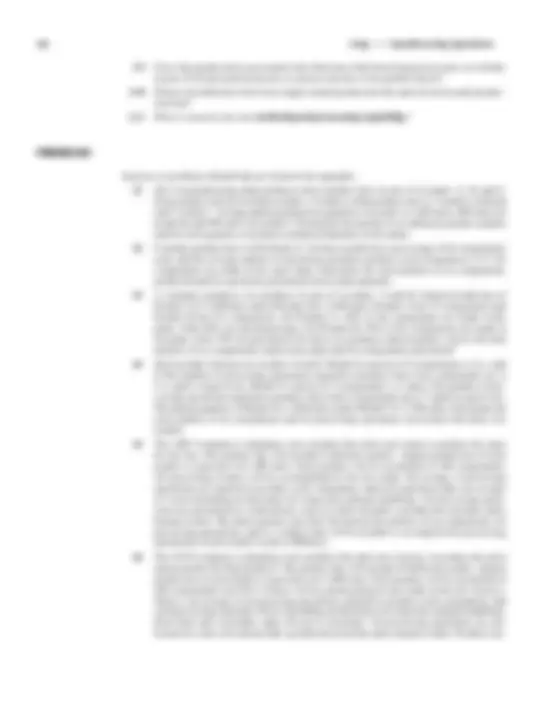
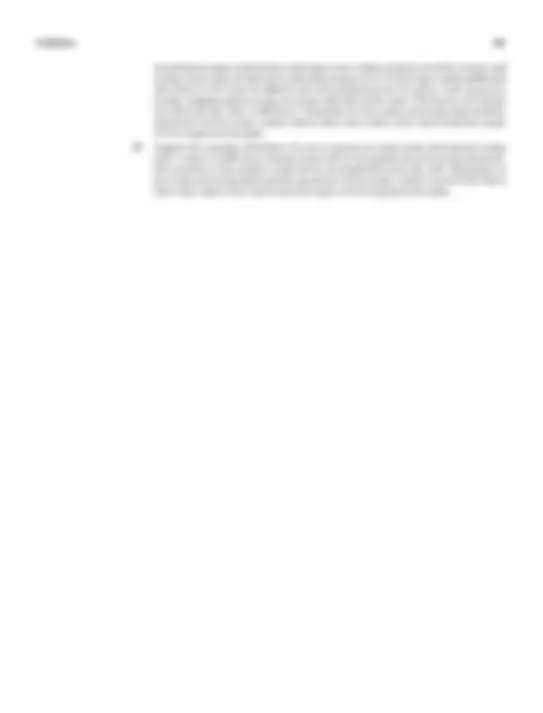

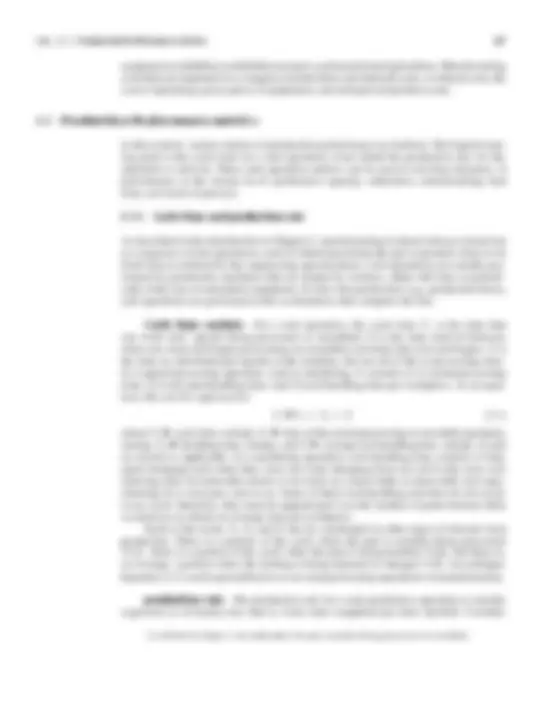

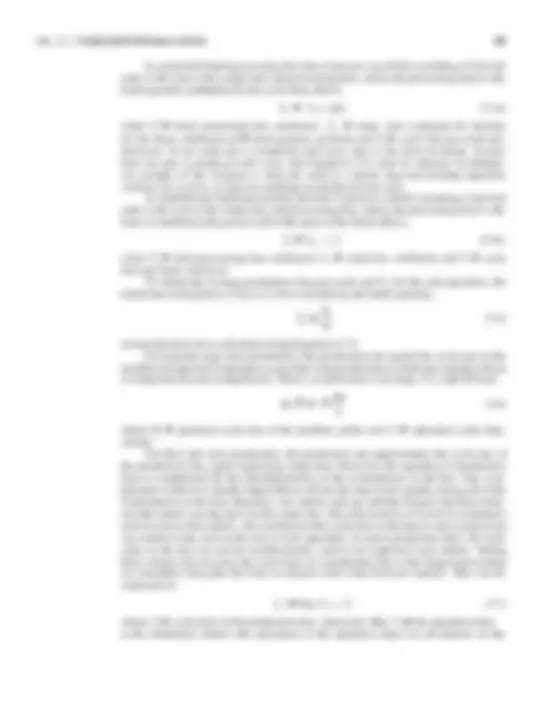
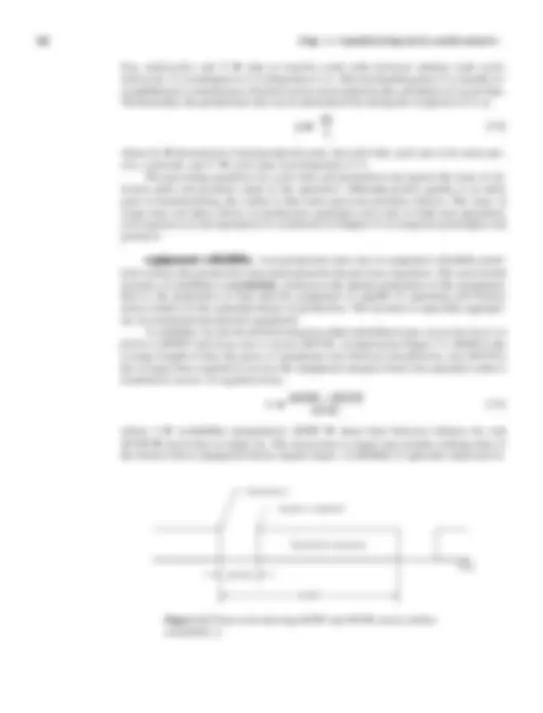
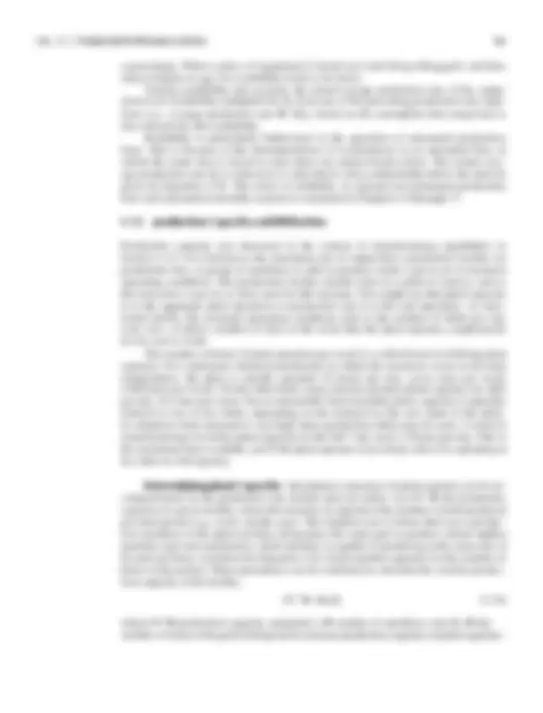
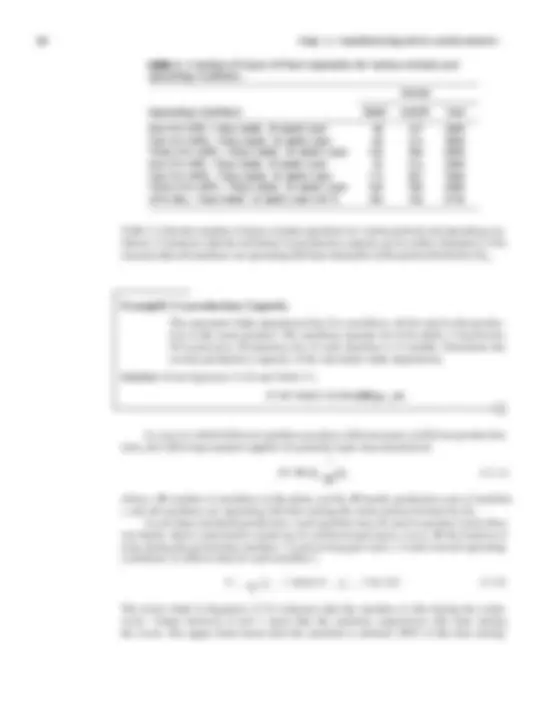
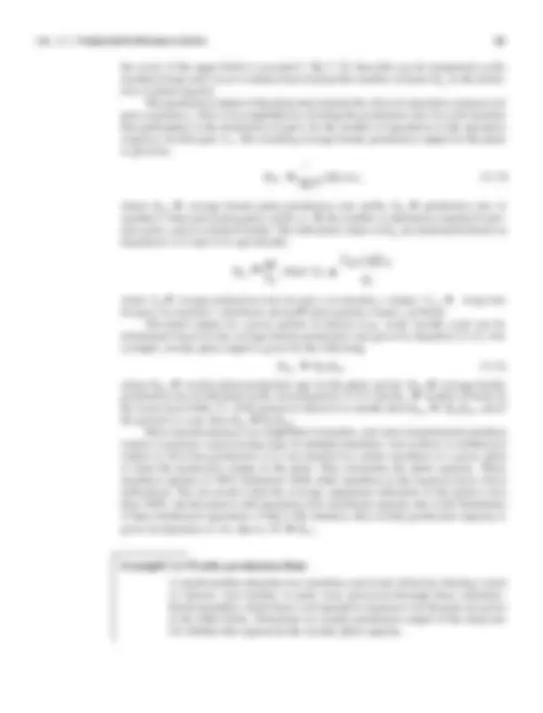
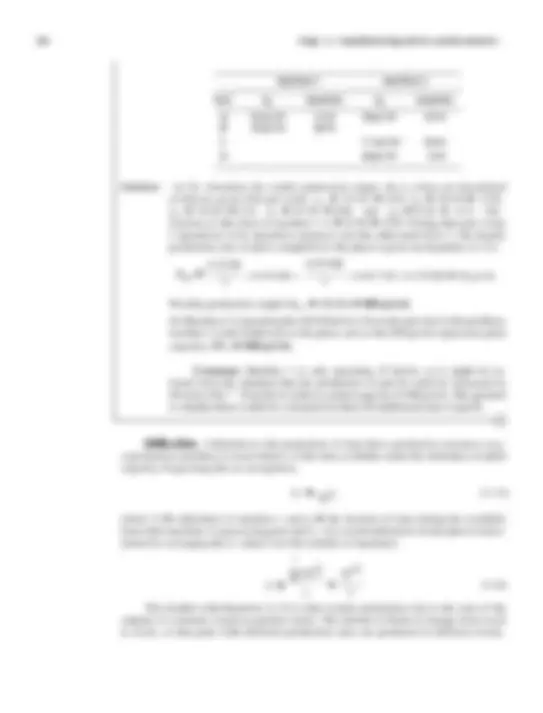
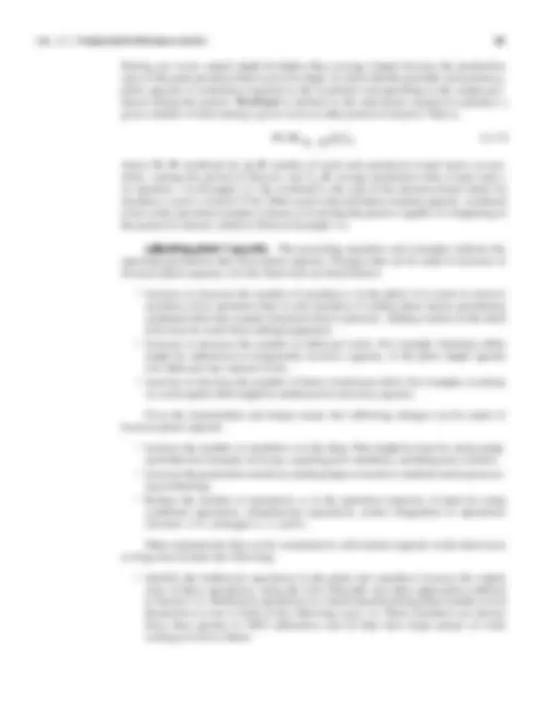
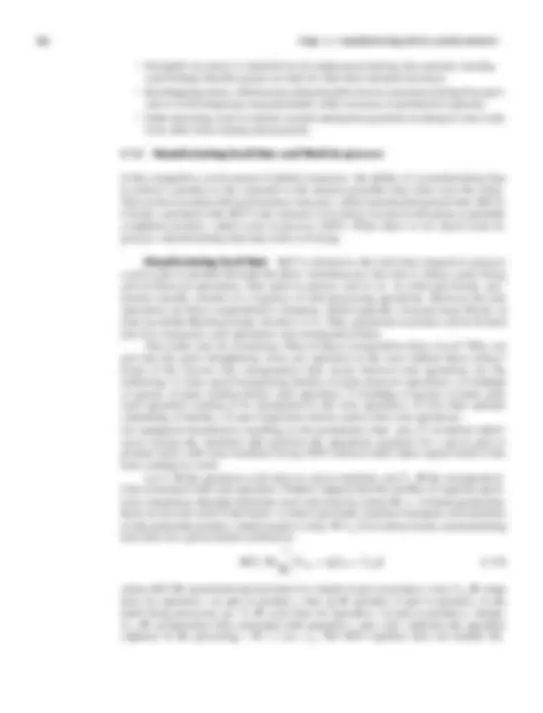
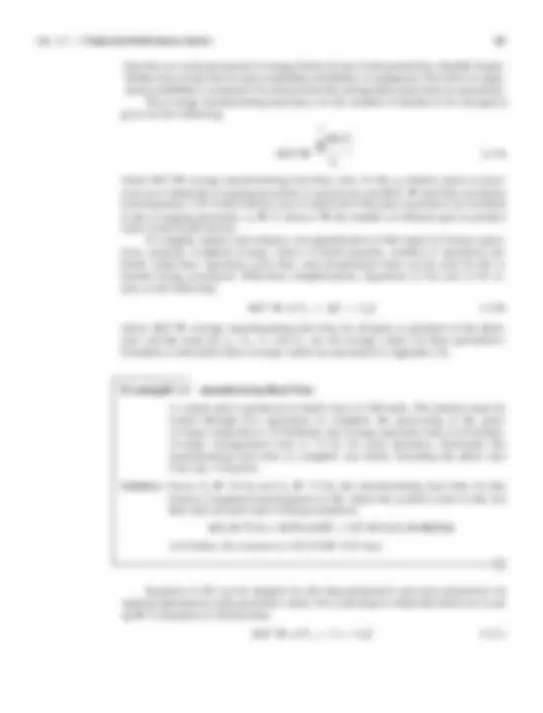
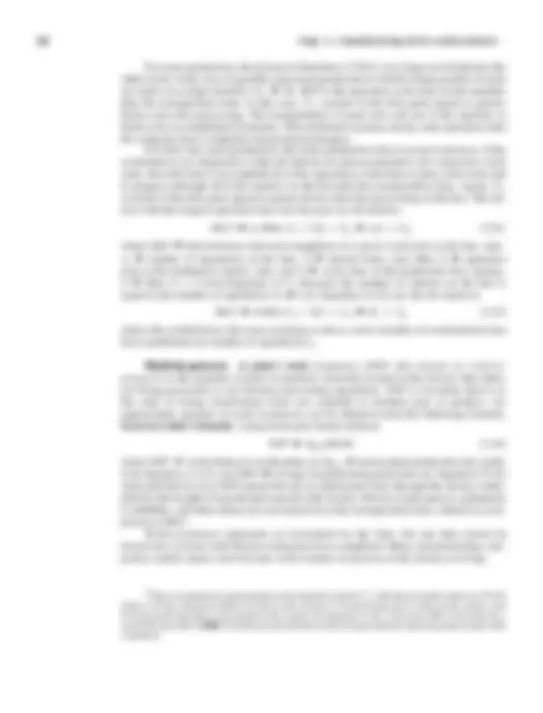
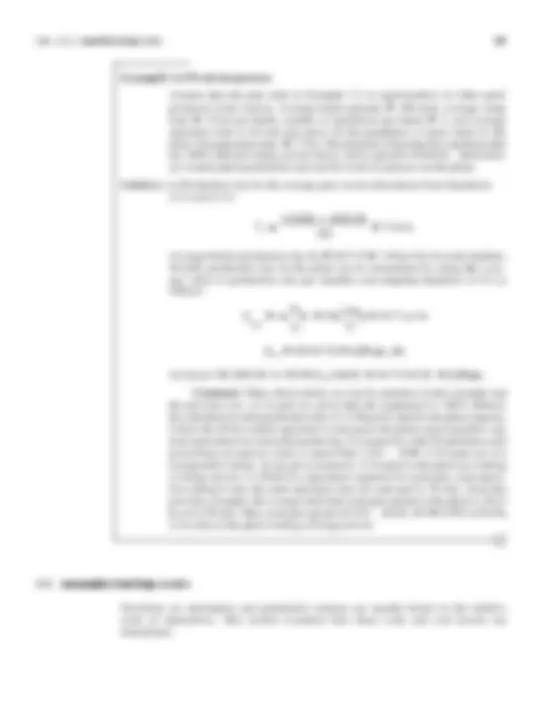
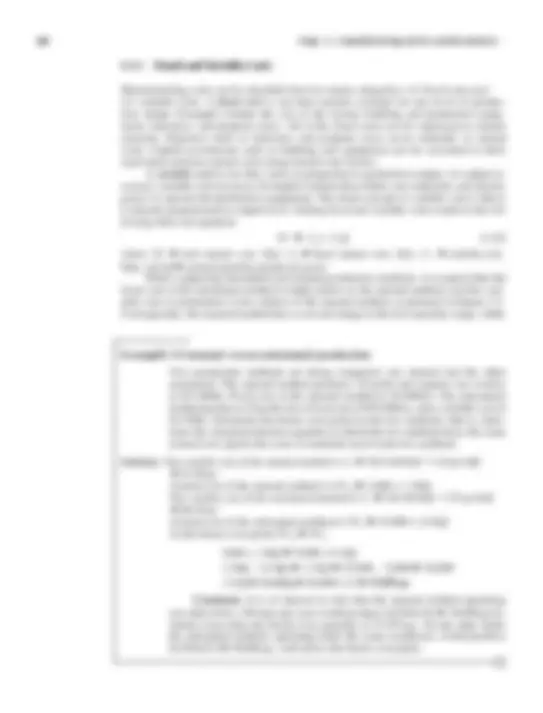
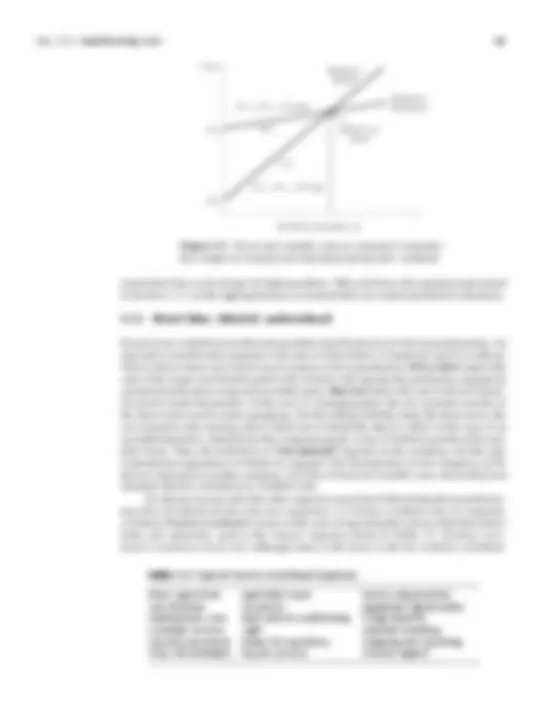
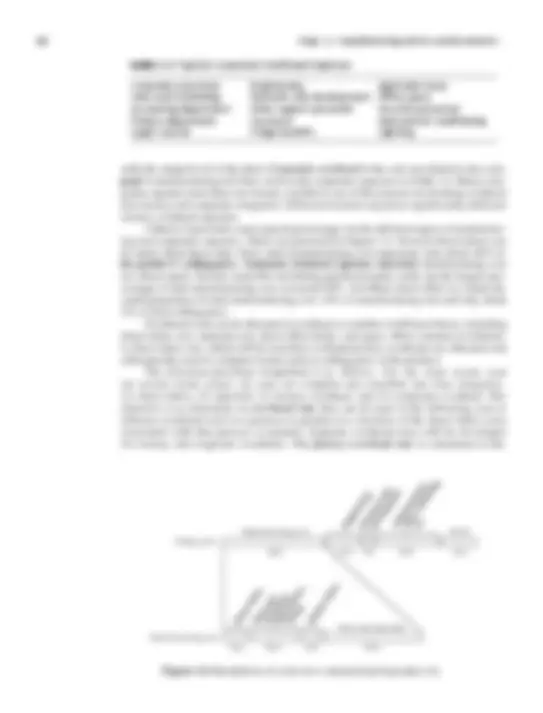
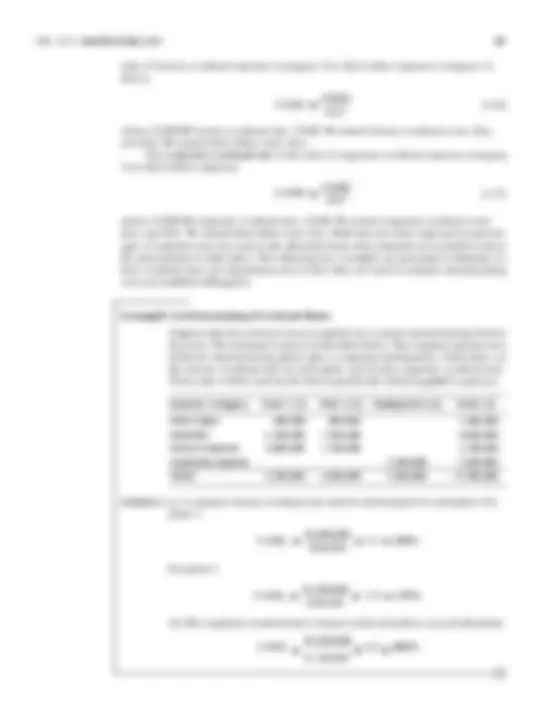
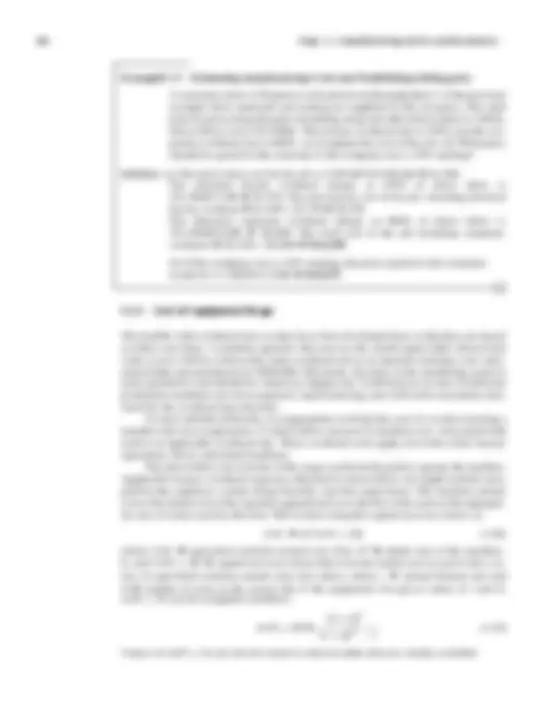
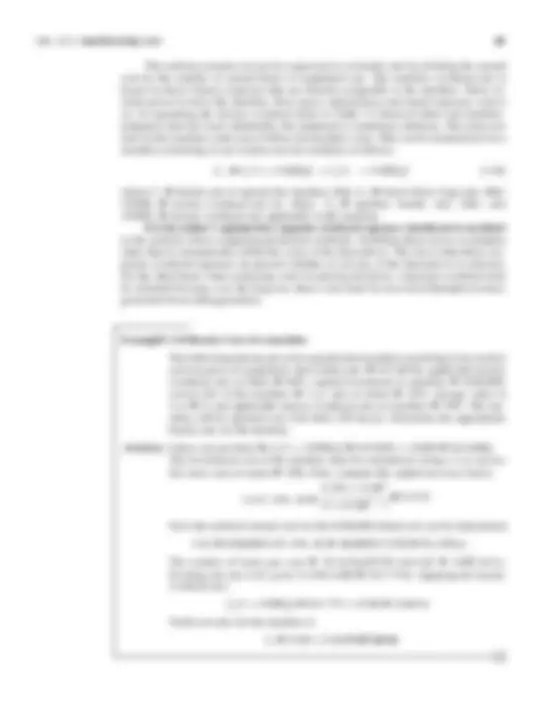
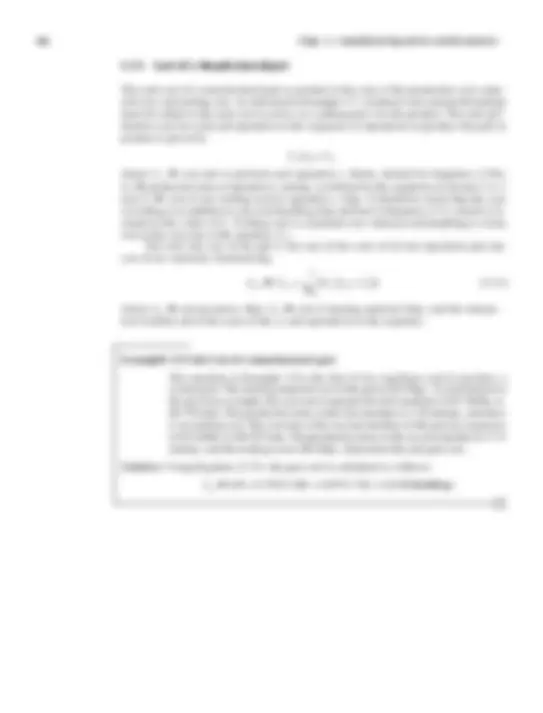
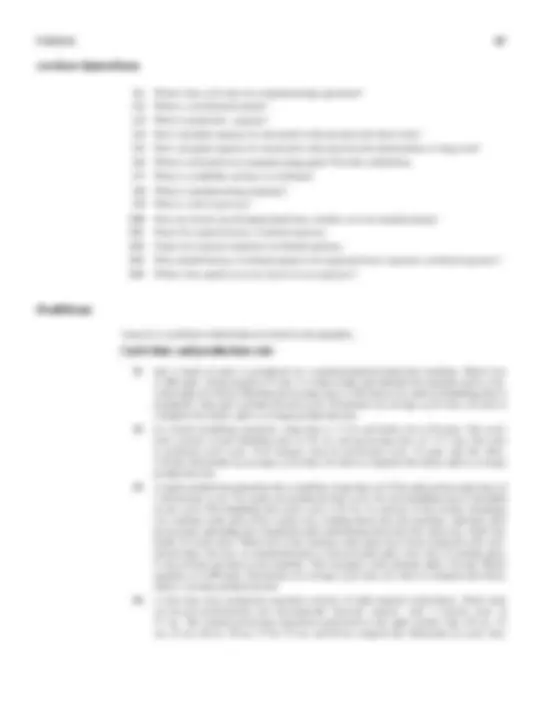
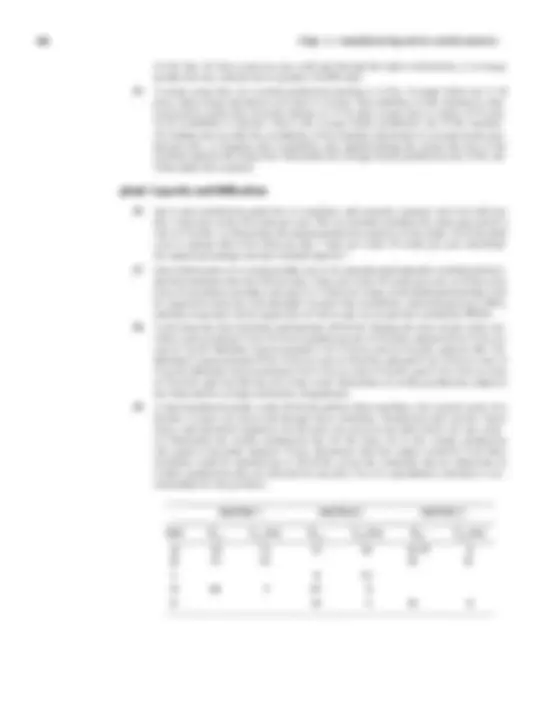
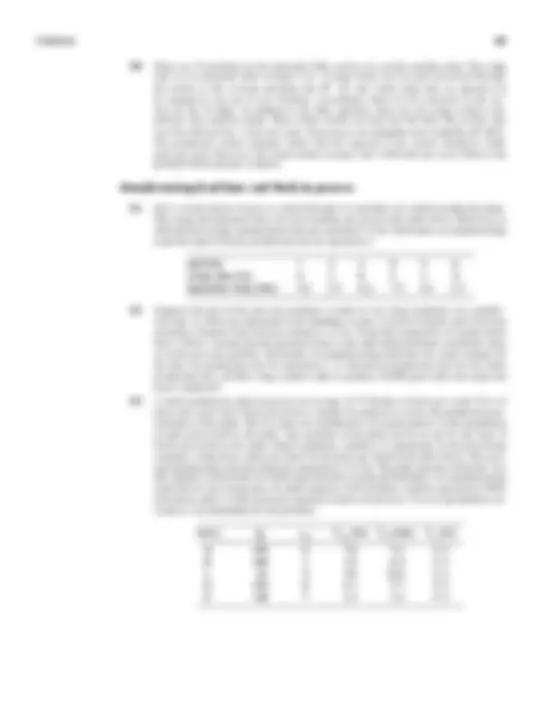
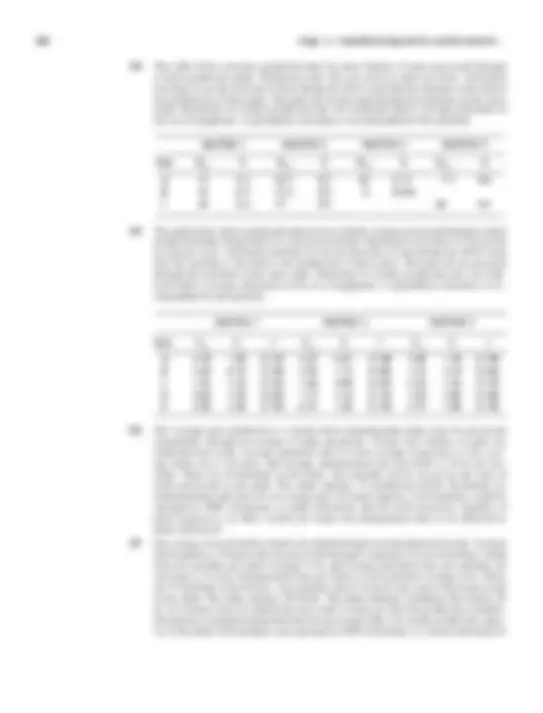
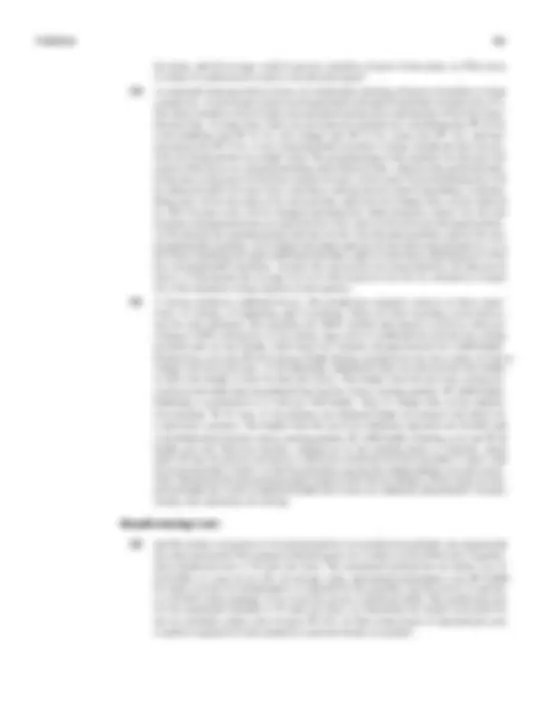
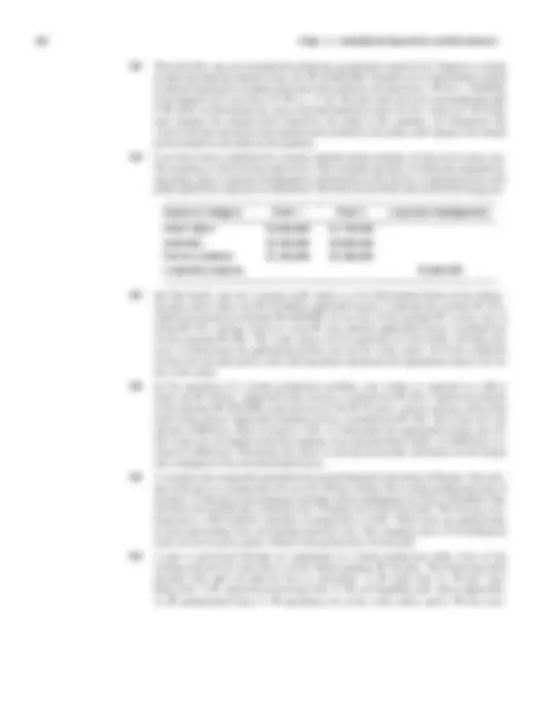
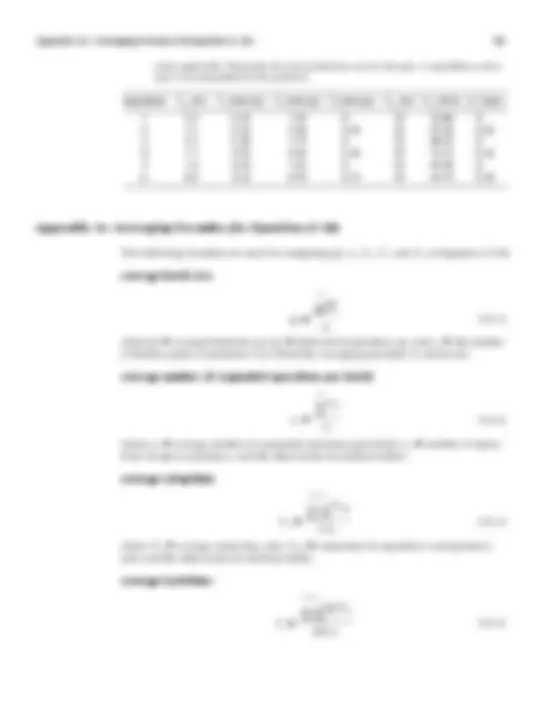
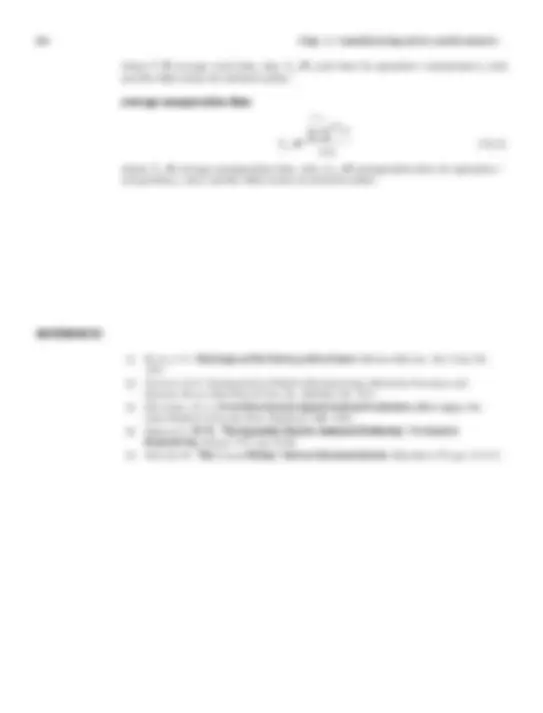
Study with the several resources on Docsity
Earn points by helping other students or get them with a premium plan
Prepare for your exams
Study with the several resources on Docsity
Earn points to download
Earn points by helping other students or get them with a premium plan
Community
Ask the community for help and clear up your study doubts
Discover the best universities in your country according to Docsity users
Free resources
Download our free guides on studying techniques, anxiety management strategies, and thesis advice from Docsity tutors
Manufacturing can be defined as the application of physical and/or chemical processes to alter the geometry, properties, and/or appearance of a given starting material to make parts or products. Manufacturing also includes the joining of multiple parts to make as- sembled products.
Typology: Study Guides, Projects, Research
1 / 54
This page cannot be seen from the preview
Don't miss anything!
2.1 Manufacturing Industries and Products 2.2 Manufacturing Operations 2.2.1 Processing and Assembly Operations 2.2.2 Other Factory Operations 2.3 Production Facilities 2.3.1 Low Production 2.3.2 Medium Production 2.3.3 High Production 2.4 Product/Production Relationships 2.4.1 Production Quantity and Product Variety 2.4.2 Product and Part Complexity 2.4.3 Limitations and Capabilities of a Manufacturing Plant
Manufacturing can be defined as the application of physical and/or chemical processes to alter the geometry, properties, and/or appearance of a given starting material to make parts or products. Manufacturing also includes the joining of multiple parts to make as- sembled products. The processes that accomplish manufacturing involve a combination of machinery, tools, power, and manual labor, as depicted in Figure 2.1(a). Manufacturing is almost always carried out as a sequence of unit operations.^2 Each successive operation brings the material closer to the desired final state. (^1) The chapter introduction and Sections 2.1 and 2.2 are based on [2], Chapter 1. (^2) A unit operation is a single step in the sequence of steps used to transform a starting material into a final part or product. 1
The history of manufacturing includes two related topics: (1) the discovery and invention of materials and processes to make things and (2) the development of systems of production. The materials and processes pre-date the systems by several millennia. Systems of production refer to the ways of organizing people and equipment so that production can be performed more efficiently. Some of the basic processes date as far back as the Neolithic period (circa 8000 – 3000 B.C.), when operations such as the following were developed: woodworking , form- ing and firing of clay pottery, grinding and polishing of stone, spinning of fiber and weaving of textiles, and dyeing of cloth. Metallurgy and metalworking also began during the Neolithic, in Mesopotamia and other areas around the Mediterranean. It either spread to or developed independently in regions of Europe and Asia. Gold was found by early humans in relatively
2 Chap. 1 / Manufacturing Operations
Starting material
Machinery Tools Power Labor Completed part or product Manufacturing process
(a)
Scrap and/or waste Starting material
Material in processing (b)
Completed part or product
Figure 2.1 Alternative definitions of manufacturing: (a) as a technological process and (b) as an economic process.
From an economic viewpoint, manufacturing is concerned with the transforma- tion of materials into items of greater value by means of one or more processing and/or assembly operations, as depicted in Figure 2.1(b). The key point is that manufacturing adds value to the material by changing its shape or properties or by combining it with other materials that also have been altered. When iron ore is converted into steel, value is added. When sand is transformed into glass, value is added. When petroleum is refined into plastic, value is added. And when plastic is molded into the complex geometry of a patio chair, it is made even more valuable. This chapter provides a survey of manufacturing operations, beginning with the in- dustries that are engaged in manufacturing and the types of products they produce. Then the fabrication and assembly processes used in manufacturing are briefly described, as well as the activities that support these processes, such as material handling and inspec- tion. Next, several product parameters are introduced, such as production quantity and product variety, and the influence that these parameters have on production operations and facilities is examined. The history of manufacturing includes both the development of manufacturing pro- cesses, some of which date back thousands of years, and the evolution of the production systems required to apply these processes (see Historical Note 2.1). The emphasis in this book is on the systems.
Value added
Manufacturing process
4 Chap. 1 / Manufacturing Operations
While England was leading the Industrial Revolution, an important concept related to assembly technology was being introduced in the United States: interchangeable parts manu- facture. Much credit for this concept is given to Eli Whitney (1765–1825), although its impor- tance had been recognized by others [3]. In 1797, Whitney negotiated a contract to produce 10,000 muskets for the U.S. government. The traditional way of making guns at the time was to custom-fabricate each part for a particular gun and then hand-fit the parts together by filing. Each musket was therefore unique, and the time to make it was considerable. Whitney believed that the components could be made accurately enough to permit parts assembly without fit- ting. After several years of development in his Connecticut factory, he traveled to Washington in 1801 to demonstrate the principle. Before government officials, including Thomas Jefferson, he laid out components for 10 muskets and proceeded to select parts randomly to assemble the guns. No special filing or fitting was required, and all of the guns worked perfectly. The secret behind his achievement was the collection of special machines, fixtures, and gages that he had developed in his factory. Interchangeable parts manufacture required many years of de- velopment and refinement before becoming a practical reality, but it revolutionized methods of manufacturing. It is a prerequisite for mass production of assembled products. Because its origins were in the United States, interchangeable parts production came to be known as the American System of manufacture. The mid and late 1800s witnessed the expansion of railroads, steam-powered ships, and other machines that created a growing need for iron and steel. New methods for producing steel were developed to meet this demand. Also during this period, several consumer products were developed, including the sewing machine, bicycle, and automobile. To meet the mass de- mand for these products, more efficient production methods were required. Some historians identify developments during this period as the Second Industrial Revolution , characterized in terms of its effects on production systems by the following: (1) mass production, (2) assembly lines, (3) the scientific management movement, and (4) electrification of factories. Mass production was primarily an American phenomenon. Its motivation was the mass market that existed in the United States. Population in the United States in 1900 was 76 million and growing. By 1920, it exceeded 106 million. Such a large population, larger than any western European country, created a demand for large numbers of products. Mass production provided those products. Certainly one of the important technologies of mass production was the assem- bly line , introduced by Henry Ford (1863–1947) in 1913 at his Highland Park plant (Historical Note 15.1). The assembly line made mass production of complex consumer products possible. Use of assembly-line methods permitted Ford to sell a Model T automobile for less than $500 in 1916, thus making ownership of cars feasible for a large segment of the American population. The scientific management movement started in the late 1800s in the United States in response to the need to plan and control the activities of growing numbers of produc- tion workers. The movement was led by Frederick W. Taylor (1856–1915), Frank Gilbreath (1868–1924) and his wife Lilian (1878–1972), and others. Scientific management included (1) motion study , aimed at finding the best method to perform a given task; (2) time study , to establish work standards for a job; (3) extensive use of standards in industry; (4) the piece rate system and similar labor incentive plans; and (5) use of data collection, record keeping, and cost accounting in factory operations. In 1881, electrification began with the first electric power generating station being built in New York City, and soon electric motors were being used as the power source to operate fac- tory machinery. This was a far more convenient power delivery system than the steam engine, which required overhead belts to mechanically distribute power to the machines. By 1920, elec- tricity had overtaken steam as the principal power source in U.S. factories. Electrification also motivated many new inventions that have affected manufacturing operations and production systems. The twentieth century was a time of more technological advances than all previous centuries combined. Many of these developments have resulted in the automation of manu- facturing. Historical notes on some of these advances in automation are included in this book.
Sec. 2.1 / Manufacturing Industries and Products 5
Manufacturing is an important commercial activity, carried out by companies that sell products to customers. The type of manufacturing performed by a company depends on the kinds of products it makes.
Manufacturing Industries. Industry consists of enterprises and organizations that produce and/or supply goods and/or services. Industries can be classified as primary, secondary, and tertiary. Primary industries are those that cultivate and exploit natural resources, such as agriculture and mining. Secondary industries convert the outputs of the primary industries into products. Manufacturing is the principal activity in this cat- egory, but the secondary industries also include construction and power utilities. Tertiary industries constitute the service sector of the economy. A list of specific industries in these categories is presented in Table 2.1. This book is concerned with the secondary industries (middle column in Table 2.1), which are composed of the companies engaged in manufacturing. It is useful to
TABLE 2.1 Specific Industries in the Primary, Secondary, and Tertiary Categories, Based Roughly on the International Standard Industrial Classification (ISIC) Used by the United Nations Primary Secondary Tertiary (Service) Agriculture Aerospace Banking Forestry Apparel Communications Fishing Automotive Education Livestock Basic metals Entertainment Quarrying Beverages Financial services Mining Building materials Government Petroleum Chemicals Health and medical services Computers Hotels Construction Information Consumer appliances Insurance Electronics Legal services Equipment Real estate Fabricated metals Repair and maintenance Food processing Restaurants Glass, ceramics Retail trade Heavy machinery Tourism Paper Transportation Petroleum refining Wholesale trade Pharmaceuticals Plastics (shaping) Power utilities Publishing Textiles Tire and rubber Wood and furniture
Proc
Sec. 2.1 / Manufacturing Industries and Products 7
...
(a)
......
(b)
Batch i + 1 Batch i Batch i – 1 Batch i + 1 Batch i Batch i – 1 (c) (d)
Figure 2.2 Continuous and batch production in the process and discrete manufacturing industries, including (a) continuous pro- duction in the process industries, (b) continuous production in the discrete manufacturing industries, (c) batch production in the process industries, and (d) batch production in the discrete manu- facturing industries. Key: Proc = process.
equipment limits the amount or quantity of material that can be processed at one time; and (3) the production rate of the equipment is greater than the demand rate for the parts or products, and it therefore makes sense to share the equipment among multiple parts or products. The differences in batch production between the process and discrete manufac- turing industries are portrayed in Figure 2.2(c) and (d). Batch production in the process industries generally means that the starting materials are in liquid or bulk form, and they are processed altogether as a unit. By contrast, in the discrete manufacturing industries, a batch is a certain quantity of work units, and the work units are usually processed one at a time rather than all together at once. The number of parts in a batch can range from as few as one to as many as thousands of units.
Manufactured Products. As indicated in Table 2.2, the secondary industries include food, beverages, textiles, wood, paper, publishing, chemicals, and basic metals (ISIC codes 31–37). The scope of this book is primarily directed at the industries that produce discrete products. Table 2.3 lists the manufacturing industries and corresponding products for which the production systems in this book are most applicable. Final products made by the industries listed in Table 2.3 can be divided into two major classes: consumer goods and capital goods. Consumer goods are products pur- chased directly by consumers, such as cars, personal computers, TVs, tires, toys, and ten- nis rackets. Capital goods are products purchased by other companies to produce goods and supply services. Examples of capital goods include commercial aircraft, process con- trol computers, machine tools, railroad equipment, and construction machinery. In addition to final products, which are usually assembled, there are companies in industry whose business is primarily to produce materials, components, and supplies for the companies that make the final products. Examples of these items include sheet steel, bar
Proc
...
Proc Proc
8 Chap. 1 / Manufacturing Operations
TABLE 2.3 Manufacturing Industries Whose Products Are Likely to Be Produced by the Production Systems Discussed in This Book Industry Typical Products Aerospace Commercial and military aircraft Automotive Cars, trucks, buses, motorcycles Computers Mainframe and personal computers Consumer appliances Large and small household appliances Electronics TVs, DVD players, audio equipment, video game consoles Equipment Industrial machinery, railroad equipment Fabricated metals Machined parts, metal stampings, tools Glass, ceramics Glass products, ceramic tools, pottery Heavy machinery Machine tools, construction equipment Plastics (shaping) Plastic moldings, extrusions Tire and rubber Tires, shoe soles, tennis balls
stock, metal stampings, machined parts, plastic moldings, cutting tools, dies, molds, and lu- bricants. Thus, the manufacturing industries consist of a complex infrastructure with various categories and layers of intermediate suppliers with whom the final consumer never deals.
There are certain basic activities that must be carried out in a factory to convert raw materials into finished products. For a plant engaged in making discrete products, the factory activities are (1) processing and assembly operations, (2) material handling, (3) inspection and test, and (4) coordination and control. The first three activities are the physical activities that ―touch‖ the product as it is being made. Processing and assembly operations alter the geometry, properties, and/or appearance of the work unit. They add value to the product. The product must be moved from one operation to the next in the manufacturing sequence, and it must be inspected and/or tested to ensure high quality. It is sometimes argued that material handling and inspection activities do not add value to the product. However, material handling and inspection may be required to accomplish the necessary processing and assembly opera- tions, for example, loading parts into a production machine and assuring that a starting work unit is of acceptable quality before processing begins.
2.2.1 Processing and Assembly Operations
Manufacturing processes can be divided into two basic types: (1) processing operations and (2) assembly operations. A processing operation transforms a work material from one state of completion to a more advanced state that is closer to the final desired part or product. It adds value by changing the geometry, properties, or appearance of the start- ing material. In general, processing operations are performed on discrete work parts, but some processing operations are also applicable to assembled items, for example, painting a welded sheet metal car body. An assembly operation joins two or more components to create a new entity, which is called an assembly, subassembly, or some other term that
10 Chap. 1 / Manufacturing Operations
More than one processing operation is usually required to transform the starting material into final form. The operations are performed in the particular sequence to achieve the geometry and/or condition defined by the design specification. Three categories of processing operations are distinguished: (1) shaping operations, (2) property-enhancing operations, and (3) surface processing operations. Part - shaping operations apply mechanical force and/or heat or other forms and combinations of en- ergy to change the geometry of the work material. There are various ways to classify these processes. The classification used here is based on the state of the starting material. There are four categories:
In addition to these four categories based on starting material, there is also a fam- ily of part fabrication technologies called additive manufacturing. Also known as rapid prototyping (Section 23.1.2), these technologies operate on a variety of material types by building the part as a sequence of thin layers each on top of the previous until the entire solid geometry has been completed. Property-enhancing operations are designed to improve mechanical or physical properties of the work material. The most important property-enhancing operations in- volve heat treatments, which include various temperature-induced strengthening and/or toughening processes for metals and glasses. Sintering of powdered metals and ceramics, mentioned previously, is also a heat treatment, which strengthens a pressed powder work part. Property-enhancing operations do not alter part shape, except unintentionally in
Sec. 2.2 / Manufacturing Operations 11
some cases, for example, warping of a metal part during heat treatment or shrinkage of a ceramic part during sintering. Surface processing operations include (1) cleaning, (2) surface treatments, and (3) coating and thin film deposition processes. Cleaning includes both chemical and mechani- cal processes to remove dirt, oil, and other contaminants from the surface. Surface treat- ments include mechanical working, such as shot peening and sand blasting, and physical processes like diffusion and ion implantation. Coating and thin film deposition processes apply a coating of material to the exterior surface of the work part. Common coating processes include electroplating, anodizing of aluminum, and organic coating (call it painting). Thin film deposition processes include physical vapor deposition and chemi- cal vapor deposition to form extremely thin coatings of various substances. Several sur- face processing operations have been adapted to fabricate semiconductor materials (most commonly silicon) into integrated circuits for microelectronics. These processes include chemical vapor deposition, physical vapor deposition, and oxidation. They are applied to very localized regions on the surface of a thin wafer of silicon (or other semiconductor material) to create the microscopic circuit.
Assembly Operations. The second basic type of manufacturing operation is assem- bly, in which two or more separate parts are joined to form a new entity. Components of the new entity are connected together either permanently or semipermanently. Permanent joining processes include welding, brazing, soldering, and adhesive bonding. They combine parts by forming a joint that cannot be easily disconnected. Mechanical assembly methods are available to fasten two or more parts together in a joint that can be conveniently disas- sembled. The use of threaded fasteners (e.g., screws, bolts, nuts) are important traditional methods in this category. Other mechanical assembly techniques that form a permanent connection include rivets, press fitting, and expansion fits. Special assembly methods are used in electronics. Some of the methods are identical to or adaptations of the above tech- niques. For example, soldering is widely used in electronics assembly. Electronics assembly is concerned primarily with the assembly of components (e.g., integrated circuit packages) to printed circuit boards to produce the complex circuits used in so many of today’s products.
2.2.2 Other Factory Operations
Other activities that must be performed in the factory include material handling and stor- age, inspection and testing, and coordination and control.
Material Handling and Storage. Moving and storing materials between pro- cessing and/or assembly operations are usually required. In most manufacturing plants, materials spend more time being moved and stored than being processed. In some cases, the majority of the labor cost in the factory is consumed in handling, moving, and storing materials. It is important that this function be carried out as efficiently as possible. Part III of this book considers the material handling and storage technologies that are used in factory operations. Eugene Merchant, an advocate and spokesman for the machine tool industry for many years, observed that materials in a typical metal machining batch factory or job shop spend more time waiting or being moved than being processed [4]. His observation is illustrated in Figure 2.4. About 95% of a part’s time is spent either moving or waiting (temporary storage). Only 5% of its time is spent on the machine tool. Of this 5%, less
Low
Medium
High
Sec. 2.3 / Production Facilities 13
type of manufacturing. Of course, one of the most important factors that determine the type of manufacturing is the type of products that are made. As mentioned previously, this book is concerned primarily with the production of discrete parts and products. The quantity of parts and/or products made by a factory has a very significant influence on its facilities and the way manufacturing is organized. Production quantity refers to the number of units of a given part or product produced annually by the plant. The annual part or product quantities produced in a given factory can be classified into three ranges:
The boundaries between the three ranges are somewhat arbitrary (author’s judg- ment). Depending on the types of products, these boundaries may shift by an order of magnitude or so. Some plants produce a variety of different product types, each type being made in low or medium quantities. Other plants specialize in high production of only one product type. It is instructive to identify product variety as a parameter distinct from production quantity. Product variety refers to the different product designs or types that are pro- duced in a plant. Different products have different shapes and sizes and styles, they per- form different functions, they are sometimes intended for different markets, some have more components than others, and so forth. The number of different product types made each year can be counted. When the number of product types made in a factory is high, this indicates high product variety. There is an inverse correlation between product variety and production quantity in terms of factory operations. When product variety is high, production quantity tends to be low, and vice versa. This relationship is depicted in Figure 2.5. Manufacturing plants tend to specialize in a combination of production quantity and product variety that lies somewhere inside the diagonal band in Figure 2.5. In general, a given factory tends to be limited to the product variety value that is correlated with that production quantity.
1 100 10,000 1,000, Production quantity
Figure 2.5 Relationship between product variety and production quantity in discrete product manufacturing.
Product variety
14 Chap. 1 / Manufacturing Operations
Although product variety has been identified as a quantitative parameter (the num- ber of different product types made by the plant or company), this parameter is much less exact than production quantity, because details on how much the designs differ are not cap- tured simply by the number of different designs. The differences between an automobile and an air conditioner are far greater than between an air conditioner and a heat pump. Products can be different, but the extent of the differences may be small or great. The auto- motive industry provides some examples to illustrate this point. Each of the U.S. automo- tive companies produces cars with two or three different nameplates in the same assembly plant, although the body styles and other design features are nearly the same. In different plants, the same company builds trucks. Let the terms ―hard‖ and ―soft‖ be used to describe these differences in product variety. Hard product variety is when the products differ sub- stantially. In an assembled product, hard variety is characterized by a low proportion of common parts among the products; in many cases, there are no common parts. The differ- ence between a car and a truck is hard. Soft product variety is when there are only small dif- ferences between products, such as the differences between car models made on the same production line. There is a high proportion of common parts among assembled products whose variety is soft. The variety between different product categories tends to be hard; the variety between different models within the same product category tends to be soft. The three production quantity ranges can be used to identify three basic categories of production plants. Although there are variations in the work organization within each category, usually depending on the amount of product variety, this is nevertheless a rea- sonable way to classify factories for the purpose of this discussion.
2.3.1 Low Production
The type of production facility usually associated with the quantity range of 1–100 units/ year is the job shop , which makes low quantities of specialized and customized products. The products are typically complex, such as experimental aircraft and special machinery. Job shop production can also include fabricating the component parts for the products. Customer orders for these kinds of items are often special, and repeat orders may never occur. Equipment in a job shop is general purpose and the labor force is highly skilled. A job shop must be designed for maximum flexibility to deal with the wide part and product variations encountered (hard product variety). If the product is large and heavy, and therefore difficult to move in the factory, it typically remains in a single location, at least during its final assembly. Workers and processing equipment are brought to the product, rather than moving the product to the equipment. This type of layout is a fixed- position layout , shown in Figure 2.6(a), in which the product remains in a single location during its entire fabrication. Examples of such products include ships, aircraft, railway lo- comotives, and heavy machinery. In actual practice, these items are usually built in large modules at single locations, and then the completed modules are brought together for final assembly using large-capacity cranes. The individual parts that comprise these large products are often made in factories that have a process layout , in which the equipment is arranged according to function or type. The lathes are in one department, the milling machines are in another depart- ment, and so on, as in Figure 2.6(b). Different parts, each requiring a different opera- tion sequence, are routed through the departments in the particular order needed for their processing, usually in batches. The process layout is noted for its flexibility; it can accommodate a great variety of alternative operation sequences for different part con- figurations. Its disadvantage is that the machinery and methods to produce a part are not
16 Chap. 1 / Manufacturing Operations
after which the facility is changed over to produce a batch of the next product, and so on. Orders for each product are frequently repeated. The production rate of the equipment is greater than the demand rate for any single product type, and so the same equipment can be shared among multiple products. The changeover between production runs takes time. Called the setup time or changeover time , it is the time to change tooling and to set up and reprogram the machinery. This is lost production time, which is a disadvantage of batch manufacturing. Batch production is commonly used in make-to-stock situations, in which items are manufactured to replenish inventory that has been gradually depleted by demand. The equipment for batch production is usually arranged in a process layout Figure 2.6(b). An alternative approach to medium range production is possible if product variety is soft. In this case, extensive changeovers between one product style and the next may not be required. It is often possible to configure the equipment so that groups of similar parts or products can be made on the same equipment without significant lost time for changeovers. The processing or assembly of different parts or products is accomplished in cells consisting of several workstations or machines. The term cellular manufacturing is often associated with this type of production. Each cell is designed to produce a limited variety of part configurations; that is, the cell specializes in the production of a given set of similar parts or products, according to the principles of group technology (Chapter 18). The layout is called a cellular layout , depicted in Figure 2.6(c).
2.3.3 High Production
The high quantity range (10,000 to millions of units per year) is often referred to as mass production. The situation is characterized by a high demand rate for the product, and the production facility is dedicated to the manufacture of that product. Two categories of mass production can be distinguished: (1) quantity production and (2) flow-line produc- tion. Quantity production involves the mass production of single parts on single pieces of equipment. The method of production typically involves standard machines (such as stamping presses) equipped with special tooling (e.g., dies and material handling devices), in effect dedicating the equipment to the production of one part type. The typical layout used in quantity production is the process layout [Figure 2.6(b)]. Flow-line production involves multiple workstations arranged in sequence, and the parts or assemblies are physically moved through the sequence to complete the product. The workstations consist of production machines and/or workers equipped with special- ized tools. The collection of stations is designed specifically for the product to maximize efficiency. This is a product layout , in which the workstations are arranged into one long line, as depicted in Figure 2.6(d), or into a series of connected line segments. The work is usually moved between stations by powered conveyor. At each station, a small amount of the total work is completed on each unit of product. The most familiar example of flow-line production is the assembly line, associated with products such as cars and household appliances. The pure case of flow-line produc- tion is where there is no variation in the products made on the line. Every product is identical, and the line is referred to as a single-model production line. However, to suc- cessfully market a given product, it is often necessary to introduce model variations so that individual customers can choose the exact style and options that appeal to them. From a production viewpoint, the model differences represent a case of soft product vari- ety. The term mixed-model production line applies to those situations where there is soft
Fixed-position layout (^) Process layout Cellular layout Job shop Batch production Cellular manufacturing
Product layout
Quantity Flow line Mass production
Sec. 2.4 / Product/Production Relationships 17
1 100 10,000 1,000, Production quantity
Figure 2.7 Types of facilities and layouts used for different levels of production quan- tity and product variety.
variety in the products made on the line. Modern automobile assembly is an example. Cars coming off the assembly line have variations in options and trim representing dif- ferent models (and, in many cases, different nameplates) of the same basic car design. Other examples include small and major appliances. The Boeing Commercial Airplane Company uses production line techniques to assemble its 737 model. Much of the discussion of the types of production facilities is summarized in Figure 2.7, which adds detail to Figure 2.5 by identifying the types of production facili- ties and plant layouts used. As Figure 2.7 shows, some overlap exists among the dif- ferent facility types. Also note the comparison with earlier Figure 1.5, which indicates the type of automation that would be used in each facility type if the facility were automated.
As noted in the preceding section, companies organize their production facilities and manufacturing systems in the most efficient manner for the particular products they make. It is instructive to recognize that there are certain product parameters that are influential in determining how the products are manufactured. Consider the following parameters: (1) production quantity, (2) product variety, (3) product complexity (of as- sembled products), and (4) part complexity.
2.4.1 Production Quantity and Product Variety
Production quantity and product variety were previously discussed in Section 2.3. The symbols Q and P can be used to represent these important parameters, respectively. Q refers to the number of units of a given part or product that are produced annually by a plant, both the quantities of each individual part or product style and the total quantity of all styles. Let each part or product style be identified using the subscript j , so that
Product variety
Sec. 2.4 / Product/Production Relationships 19
TABLE 2.4 Typical Number of Separate Components in Various Assembled Products (Compiled from [1], [3], and Other Sources)
Approx. Number Product (Approx. Date or Circa) of Components Mechanical pencil (modern) 10 Ball bearing (modern) 20 Rifle (1800) 50 Sewing machine (1875) 150 Bicycle chain 300 Bicycle (modern) 750 Early automobile (1910) 2, Automobile (modern) 10, Commercial airplane (1930) 100, Commercial airplane (modern) 4,000,
TABLE 2.5 Typical Number of Processing Operations Required to Fabricate Various Parts
Part
Approx. Number of Processing Operations
Typical Processing Operations Used Plastic molded part 1 Injection molding Washer (stainless steel) 1 Stamping Washer (plated steel) 2 Stamping, electroplating Forged part 3 Heating, forging, trimming Pump shaft 10 Machining (from bar stock) Coated carbide cutting tool
15 Pressing, sintering, coating, grinding Pump housing, machined 20 Casting, machining V-6 engine block 50 Casting, machining Integrated circuit chip Hundreds Photolithography, various ther- mal and chemical processes
washer of 12-mm (1/2-in) outside diameter, stamped out of 0.8-mm (1/32-in) thick stainless steel in one step. Table 2.5 is a list of manufactured parts with the typical number of pro- cessing operations required for each. So, complexity of an assembled product can be defined as the number of distinct components; let np = the number of parts per product. And processing complexity of each part can be defined as the number of operations required to make it; let no = the number of operations or processing steps to make a part. As defined in Figure 2.8, three different types of production plant can be identified on the basis of np and no : parts pro- ducers, pure assembly plants, and vertically integrated plants. Several relationships can be developed among the parameters P , Q , np , and no that indicate the level of activity in a manufacturing plant. Ignore the differences between P 1 and P 2 here, although Equation (2.2) could be used to convert these parameters into the corresponding P value. The total number of products made annually in a plant is the sum of the quantities of the individual product designs, as expressed in Equation (2.1). Assuming that the products are all assembled and that all component parts used in these
20 Chap. 1 / Manufacturing Operations
Number of operations
no > 1
no = 1
np = 1 np > 1 Number of parts
Figure 2.8 Production plants distinguished by number of parts np (for assembled products) and number of operations no (for manu- factured parts).
products are made in the plant (no purchased components), the total number of parts manufactured by the plant per year is given by P npf = (^) a Qjnpj (2.3) j = 1 where npf = total number of parts made in the factory, pc/yr; Qj = annual quantity of product style j , products/yr; and npj = number of parts in product j , pc/product. Finally, if all parts are manufactured in the plant, then the total number of process- ing operations performed by the plant is given by P npj nof = (^) a Qj (^) a nojk (2.4) j = 1 k = 1 where nof = total number of operation cycles performed in the factory, ops/yr; and nojk = number of processing operations for each part k , summed over the number of parts in product j , npj. Parameter nof provides a numerical value for the total level of part processing activity in the factory. Average values of the four parameters P , Q , np , and no might be used to sim- plify and better conceptualize the factory model represented by Equations (2.1), (2.3), and (2.4). In this case, the total number of product units produced by the fac- tory is given by
Qf = PQ (2.5) where P = total number of product styles, Qf = total quantity of products made in the factory and the average Q value is given by the following: P a Qj Q j = 1 P
The total number of parts produced by the factory is given by npf = PQnp (2.7)
Parts producer: This plant makes parts, each requiring multiple operations. No assembly.
Vertically integrated plant: This plant makes parts and assembles them into final products.
Handicraft shop: Not really a production plant.
Assembly plant: This plant purchases all parts and assembles them into the final product, one operation per part.