
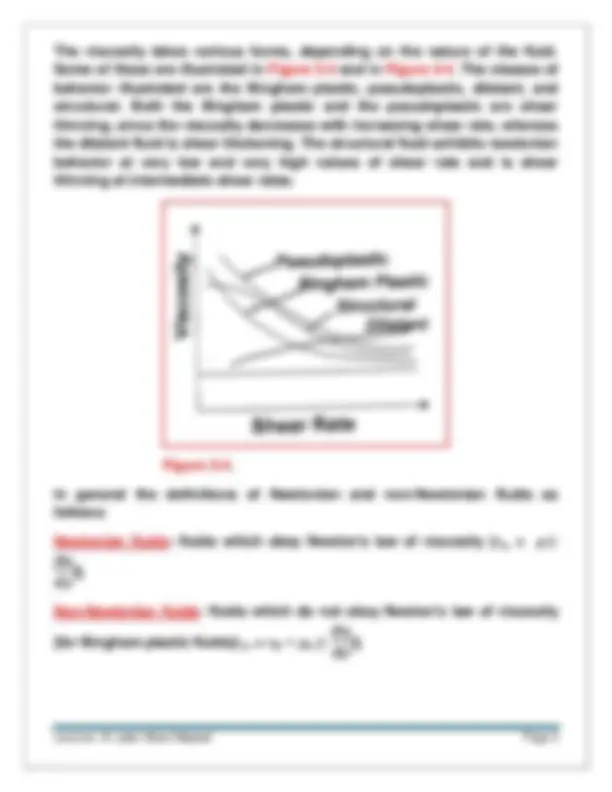
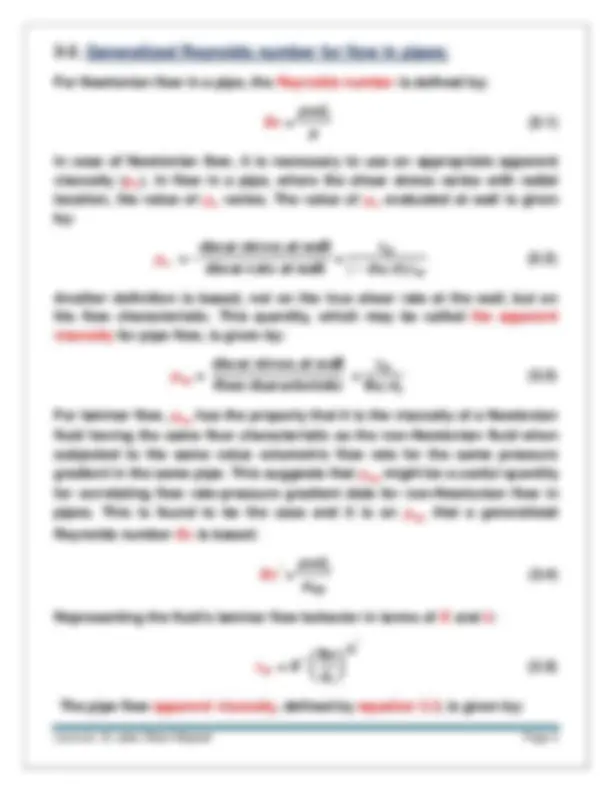
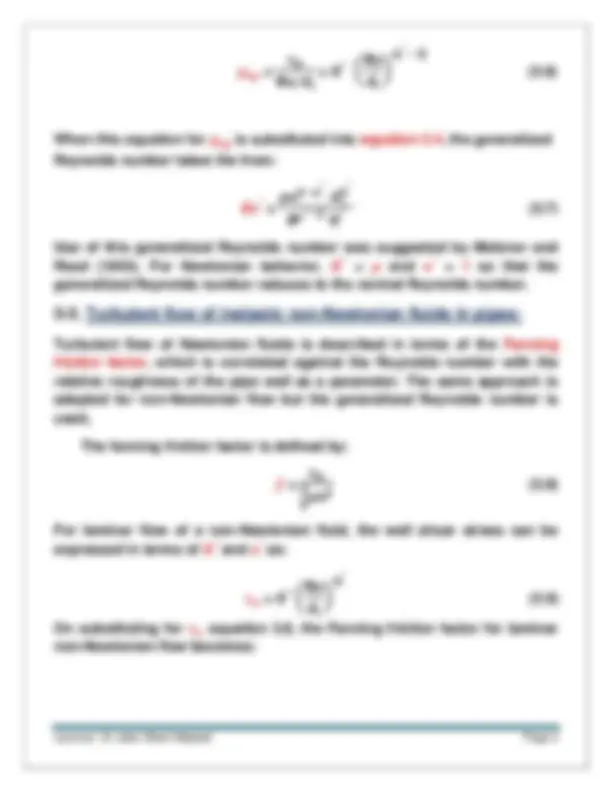
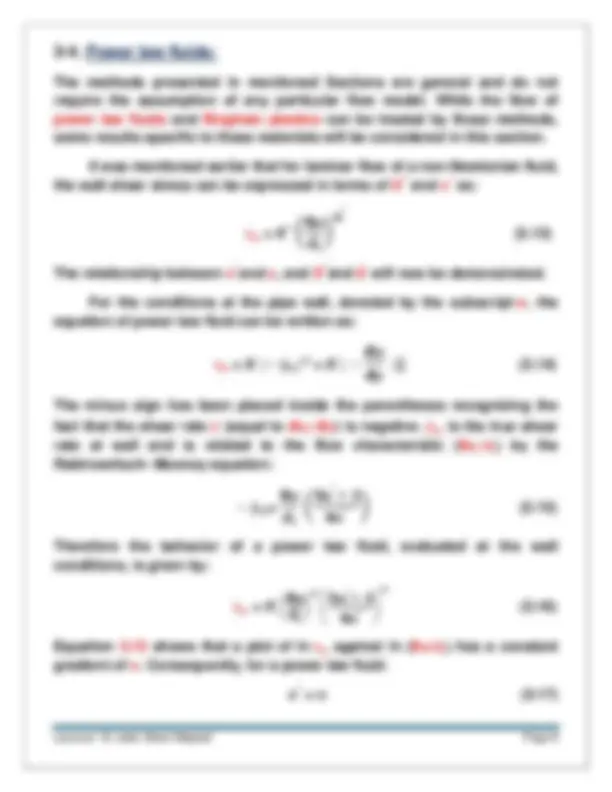
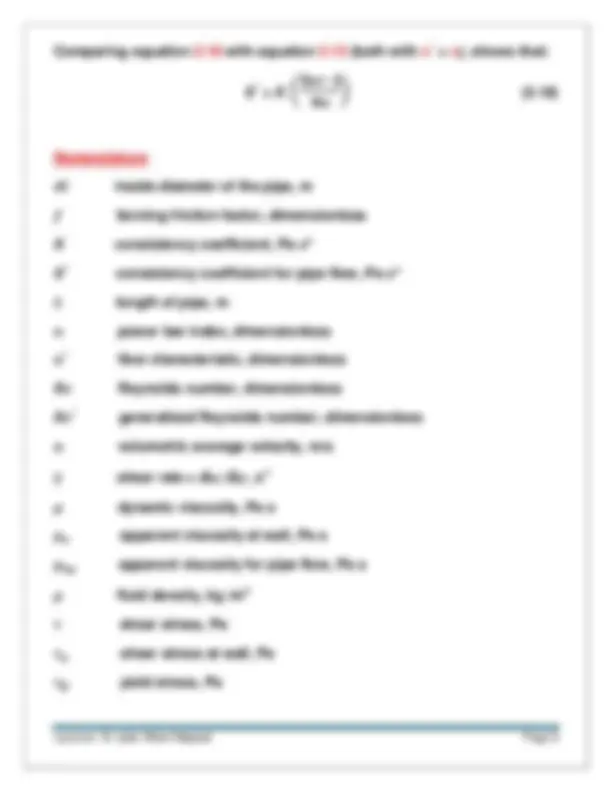
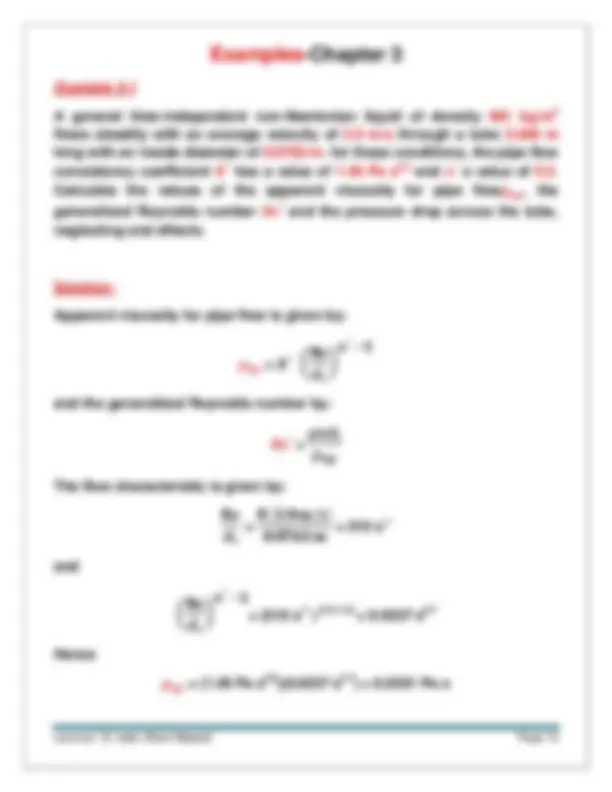
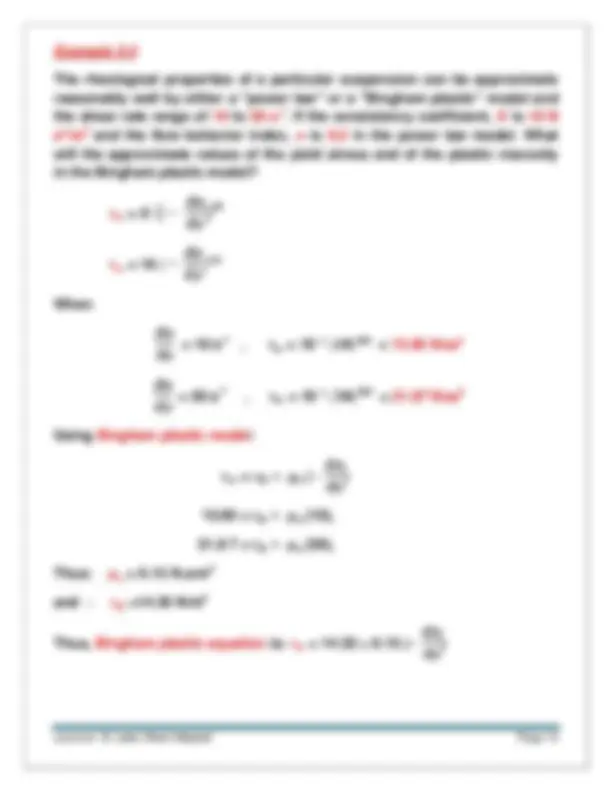
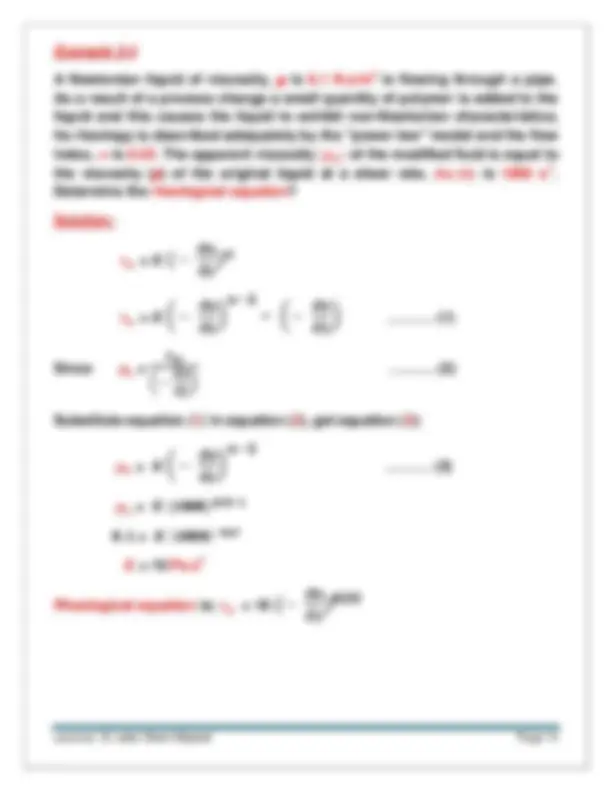
Study with the several resources on Docsity
Earn points by helping other students or get them with a premium plan
Prepare for your exams
Study with the several resources on Docsity
Earn points to download
Earn points by helping other students or get them with a premium plan
Community
Ask the community for help and clear up your study doubts
Discover the best universities in your country according to Docsity users
Free resources
Download our free guides on studying techniques, anxiety management strategies, and thesis advice from Docsity tutors
An in-depth discussion on the rheological behavior of non-newtonian fluids and their flow characteristics in pipes. It covers the key concepts of newtonian and non-newtonian fluids, including shear thinning, shear thickening, and bingham plastic fluids. The document also delves into the generalized reynolds number for non-newtonian flow in pipes, the fanning friction factor, and the relationships between the power law parameters. Several examples are provided to illustrate the application of these principles. This comprehensive coverage of non-newtonian fluid mechanics and pipe flow analysis would be highly valuable for students and researchers in fields such as fluid dynamics, chemical engineering, and mechanical engineering.
Typology: Study notes
1 / 14
This page cannot be seen from the preview
Don't miss anything!
The study of the deformation of flowing fluids is called rheology; the rheological behavior of various fluids is sketched in Figure 3-1. Newtonian fluids, defined as fluids for which the shear stress is linearly proportional to the shear strain rate. Newtonian fluids (stress proportional to strain rate). Many common fluids, such as air and other gases, water, kerosene, gasoline, and other oil-based liquids, are Newtonian fluids. Fluids for which the shear stress is not linearly related to the shear strain rate are called non-Newtonian fluids. Examples include slurries and colloidal suspensions, polymer solutions, blood, paste, and cake batter. Some non- Newtonian fluids exhibit a "memory"-the shear stress depends not only on local strain rate, but also on its history****. A fluid that returns (either fully or partially) to its original shape after the applied stress is released is called viscoelastic.
Figure 3-1. Rheological behavior of fluids – shear
Stress as a function of shear strain rate.
n = 1
n > 1
n < 1
𝝉𝑩^ n^ = 1
Some non-Newtonian fluids are called shear thinning fluids or pseudoplastic fluids, because the more the fluid is sheared, the less viscous it becomes. A good example is paint. Paint is very viscous when poured from the can or when picked up by a paintbrush, since the shear rate is small. However, as we apply the paint to the wall, the thin layer of paint between the paintbrush and the wall is subjected to a large shear rate , and it becomes much less viscous. Plastic fluids are those in which the shear thinning effect is extreme. In some fluids a finite stress called the yield stress is required before the fluid begins to flow at all; such fluids are called Bingham plastic fluids. Certain pastes such as acne cream and toothpaste are examples of Bingham plastic fluids. If you hold the tube upside down, the paste does not flow, even though there is a nonzero stress due to gravity. However, if you squeeze the tube (greatly increasing the stress), the paste flows like a very viscous fluid. Other fluids show the opposite effect and are called shear thickening fluids or dilatant fluids; the more the fluid is sheared, the more viscous it becomes. The best example is quicksand, a thick mixture of sand and water. As we all know from Hollywood movies, it is easy to move slowly through quicksand, since the viscosity is low; but if you panic and try to move quickly, the viscous resistance increases considerably and you get "stuck" (Figure 3-2). You can create your own quicksand by mixing two parts cornstarch with one part water-try it! Shear thickening fluids are used in some exercise equipment-the faster you pull, the more resistance you encounter.
Figure 3-2. Figure 3-3.
3-2. Generalized Reynolds number for flow in pipes:
For Newtonian flow in a pipe, the Reynolds number is defined by:
In case of Newtonian flow, it is necessary to use an appropriate apparent viscosity ( 𝝁𝒂 ). In flow in a pipe, where the shear stress varies with radial location, the value of 𝝁𝒂 varies. The value of 𝝁𝒂 evaluated at wall is given by:
Another definition is based, not on the true shear rate at the wall, but on the flow characteristic. This quantity, which may be called the apparent viscosity for pipe flow, is given by:
For laminar flow, 𝝁𝒂𝒑 has the property that it is the viscosity of a Newtonian fluid having the same flow characteristic as the non-Newtonian fluid when subjected to the same value volumetric flow rate for the same pressure gradient in the same pipe. This suggests that 𝝁𝒂𝒑 might be a useful quantity for correlating flow rate-pressure gradient data for non-Newtonian flow in pipes. This is found to be the case and it is on 𝝁𝒂𝒑 that a generalized
Reynolds number 𝑹𝒆 is based:
Representing the fluid's laminar flow behavior in terms of 𝑲 and 𝒏 :
𝝉𝒘 = 𝑲′^
The pipe flow apparent viscosity, defined by equation 3.3, is given by:
When this equation for 𝝁𝒂𝒑 is substituted into equation 3.4, the generalized
Reynolds number takes the from:
′
′
Use of this generalized Reynolds number was suggested by Metzner and Reed (1955). For Newtonian behavior, 𝑲′^ = 𝝁 and 𝒏′^ = 1 so that the generalized Reynolds number reduces to the normal Reynolds number.
3-3. Turbulent flow of inelastic non-Newtonian fluids in pipes:
Turbulent flow of Newtonian fluids is described in terms of the Fanning friction factor, which is correlated against the Reynolds number with the relative roughness of the pipe wall as a parameter. The same approach is adopted for non-Newtonian flow but the generalized Reynolds number is used,
The fanning friction factor is defined by:
𝒇 =
𝟏
For laminar flow of a non-Newtonian fluid, the wall shear stress can be expressed in terms of 𝑲′^ and 𝒏′^ as:
On substituting for 𝝉𝒘 equation 3.8, the Fanning friction factor for laminar non-Newtonian flow becomes:
This correlation is shown in Figure 3-6. The broken lines represent extrapolation of equation 3.11 for values of 𝒏′^ and 𝑹𝒆′^ beyond those of the measurements made by Dodge and Metzner. More recent studies tend to confirm the findings of Dodge and Metzner but do not significantly extend the range of applicability.
Figure 3-6 Friction factor chart for purely viscous non-Newtonian fluids.
Having determined the value of the friction factor 𝒇 for specified flow rate and hence 𝑹𝒆′^ , the pressure gradient can be calculated in the normal way using equation 2.12.
𝒊
3-4. Power law fluids:
The methods presented in mentioned Sections are general and do not require the assumption of any particular flow model. While the flow of power law fluids and Bingham plastics can be treated by those methods, some results specific to these materials will be considered in this section.
It was mentioned earlier that for laminar flow of a non-Newtonian fluid, the wall shear stress can be expressed in terms of 𝑲′^ and 𝒏′^ as:
The relationship between 𝒏′^ and 𝒏 , and 𝑲′^ and 𝑲 will now be demonstrated.
For the conditions at the pipe wall, denoted by the subscript 𝒘 , the equation of power law fluid can be written as:
𝐝𝒖 𝐝𝒚
The minus sign has been placed inside the parentheses recognizing the
fact that the shear rate 𝜸 (equal to 𝐝𝒖/𝐝𝒚 ) is negative. 𝜸𝒘 is the true shear rate at wall and is related to the flow characteristic ( 𝟖𝒖/𝒅𝒊 ) by the Rabinowitsch- Mooney equation:
Therefore the behavior of a power law fluid, evaluated at the wall conditions, is given by:
𝒊
𝒏 (3.16)
Equation 3.15 shows that a plot of ln 𝝉𝒘 against ln ( 𝟖𝒖 / 𝒅𝒊 ) has a constant gradient of 𝒏. Consequently, for a power law fluid:
𝒏′^ = 𝒏 (3.17)
Example 3-
A general time-independent non-Newtonian liquid of density 961 kg/m^3 flows steadily with an average velocity of 2.0 m/s through a tube 3.048 m long with an inside diameter of 0.0762 m. for these conditions, the pipe flow consistency coefficient 𝑲′^ has a value of 1.48 Pa s0.3^ and 𝒏′^ a value of 0.3. Calculate the values of the apparent viscosity for pipe flow 𝝁𝒂𝒑 , the
generalized Reynolds number 𝑹𝒆′^ and the pressure drop across the tube, neglecting end effects.
Solution:
Apparent viscosity for pipe flow is given by:
and the generalized Reynolds number by:
The flow characteristic is given by:
= 210 s-
and
= ( 210 s-^1 ) (0.3-1.0)^ = 0.0237 s0.
Hence
𝝁𝒂𝒑 = (1.48 Pa s0.3)(0.0237 s0.7) = 0.0351 Pa s
and
From Figure 3-6, the Fanning friction factor 𝒇 has a value 0.0047.
Therefore the pressure drop is given by:
𝒊
= 1445 Pa
Example 3-
Calculate the frictional pressure gradient ∆𝑷𝒇 / 𝑳 for a time independent non-
Newtonian fluid in steady state flow in a cylindrical tube if:
the liquid density 𝝆 = 1000 kg/m^3
the inside diameter of the tube 𝒅𝒊 = 0.08 m
the mean velocity 𝒖 = 1 m/s the point pipe consistency coefficient 𝑲′^ = 2 Pa s0.
and the flow behavior index 𝒏′^ = 0.
Solution:
Apparent viscosity for pipe flow is given by:
and the generalized Reynolds number by:
Example 3-
The rheological properties of a particular suspension can be approximate reasonably well by either a "power law" or a "Bingham plastic" model and the shear rate range of 10 to 50 s-1. If the consistency coefficient, 𝑲 is 10 N sn/m^2 and the flow behavior index, 𝒏 is 0.2 in the power law model. What will the approximate values of the yield stress and of the plastic viscosity in the Bingham plastic model?
When
= 10 s-1^ , 𝝉𝒘 **= 10 *** (𝟏𝟎)𝟎.𝟐^ = 15.85 N/ 𝐦𝟐
= 50 s-1^ , 𝝉𝒘 **= 10 *** (𝟓𝟎)𝟎.𝟐^ = 21.87 N/ 𝐦𝟐
Using Bingham plastic model:
Thus: 𝝁𝒂 = 0.15 N.s/m^2
and : 𝝉𝑩 =14.35 N/m^2
Thus, Bingham plastic equation is: 𝝉𝒘 = 14.35 + 0.15 ( −
Example 3-
A Newtonian liquid of viscosity, 𝝁 is 0.1 N.s/m^2 is flowing through a pipe. As a result of a process change a small quantity of polymer is added to the liquid and this causes the liquid to exhibit non-Newtonian characteristics; its rheology is described adequately by the "power law" model and the flow index, 𝒏 is 0.33. The apparent viscosity (𝝁𝒂) of the modified fluid is equal to the viscosity ( 𝝁 ) of the original liquid at a shear rate, 𝒅𝒖/𝒅𝒚 is 1000 s-1. Determine the rheological equation?
Solution:
Since 𝝁𝒂 =
𝒅𝒖 𝒅𝒚
Substitute equation (1) in equation (2), get equation (3):
𝑲 = 10 Pa sn