
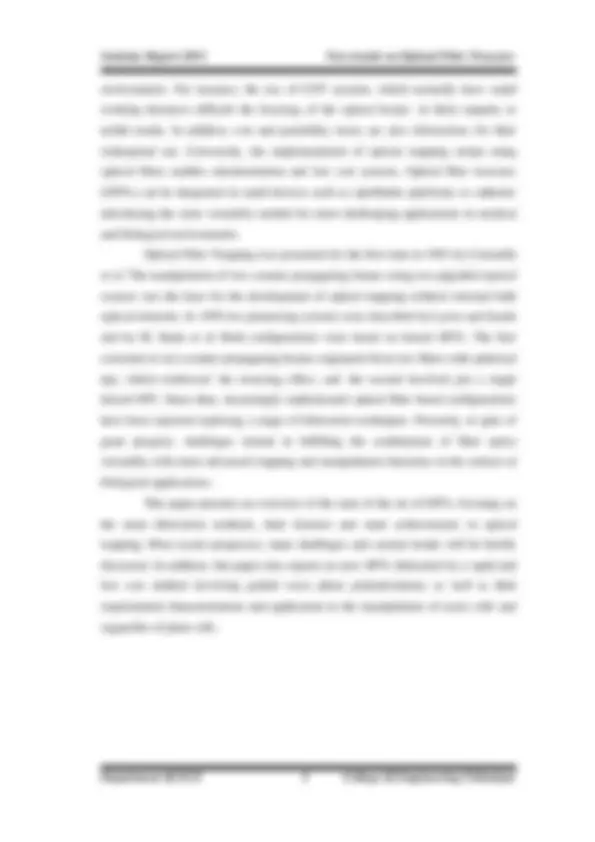
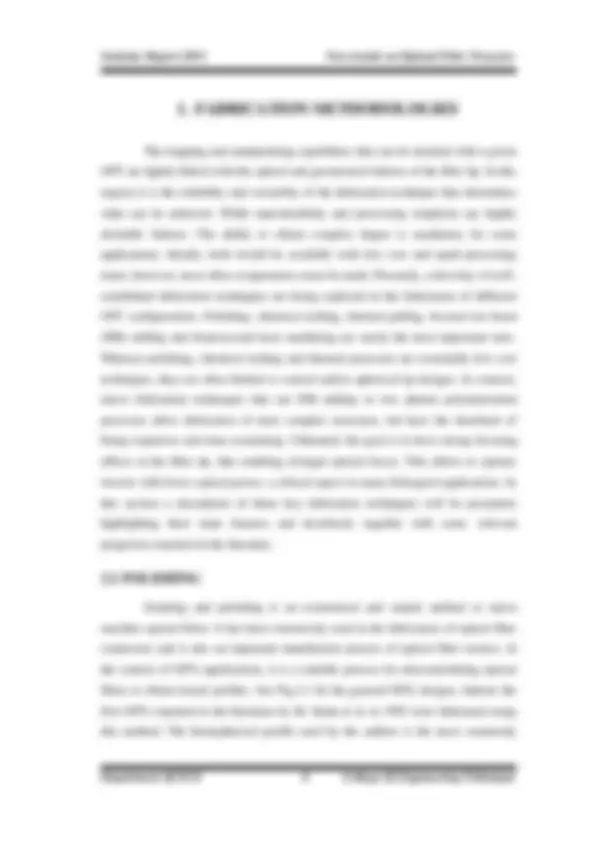
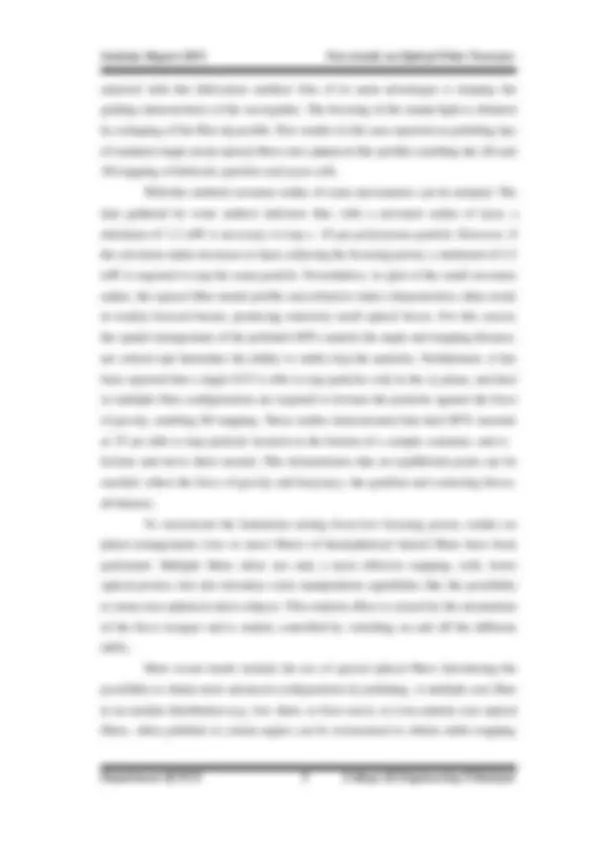
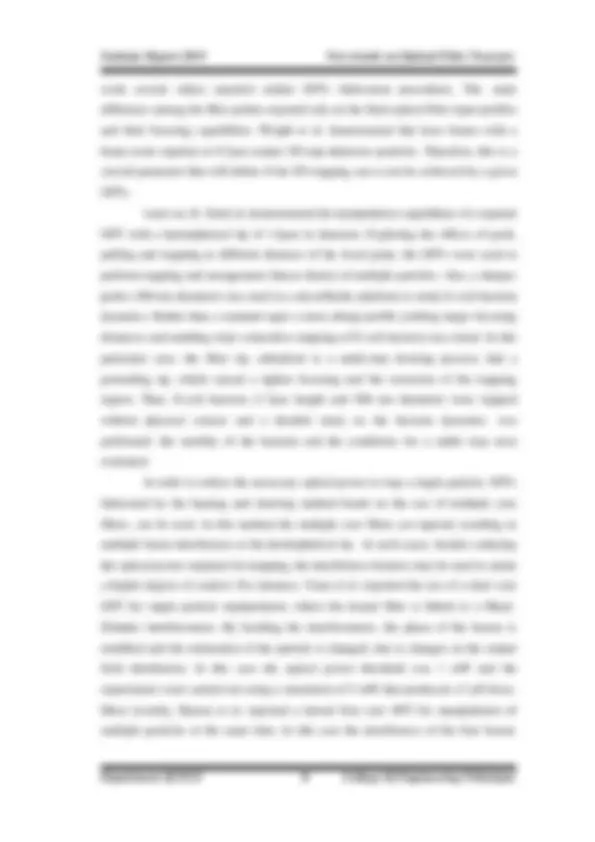
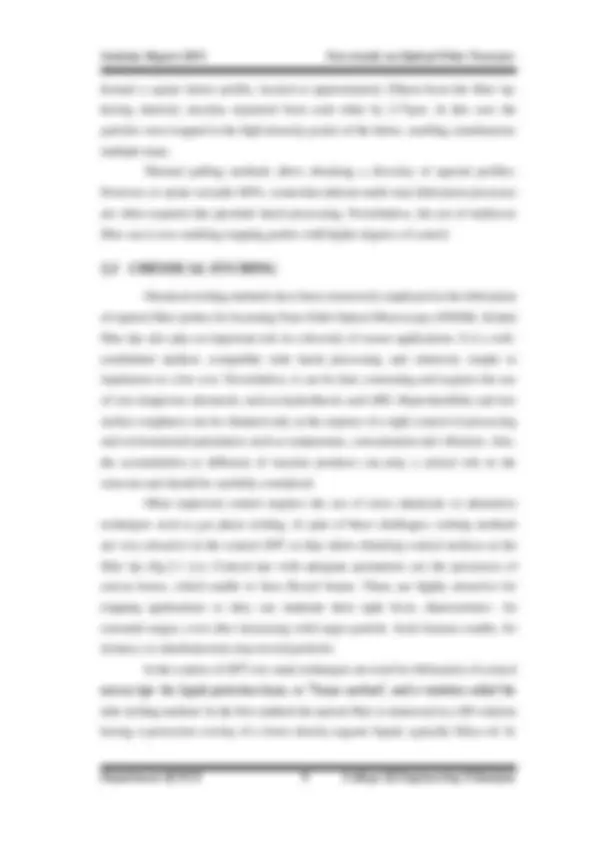
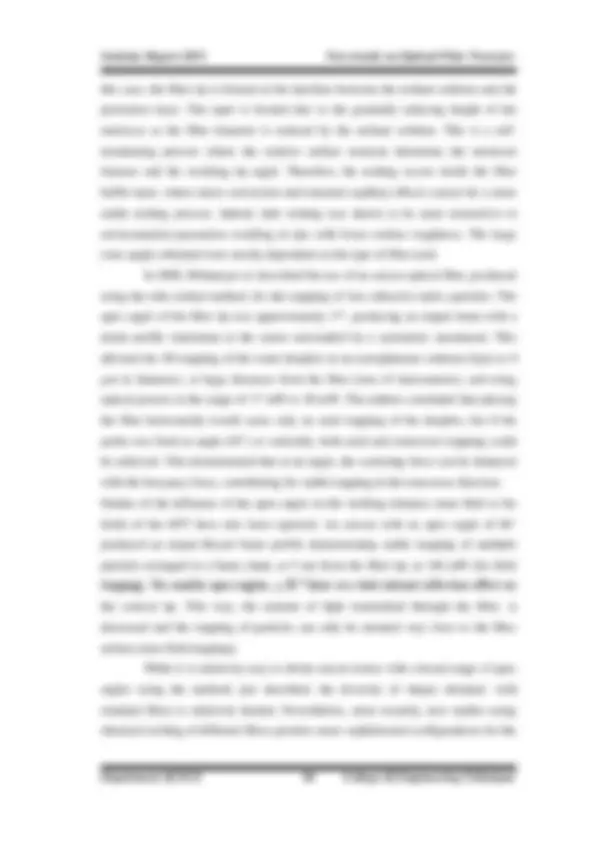
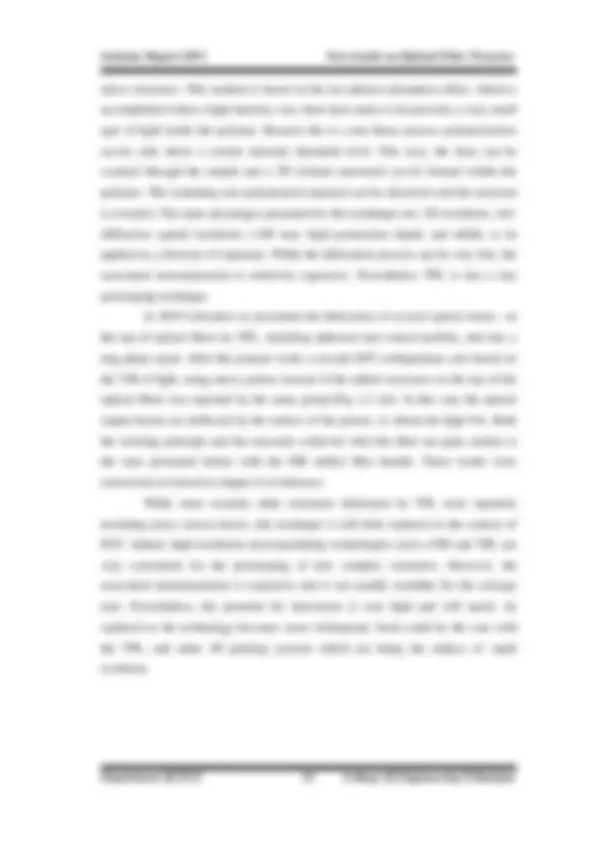
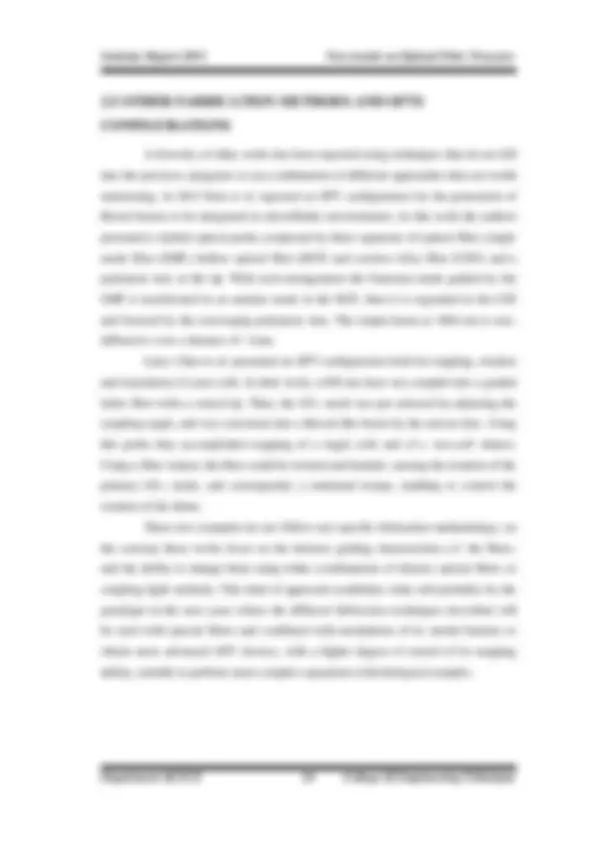
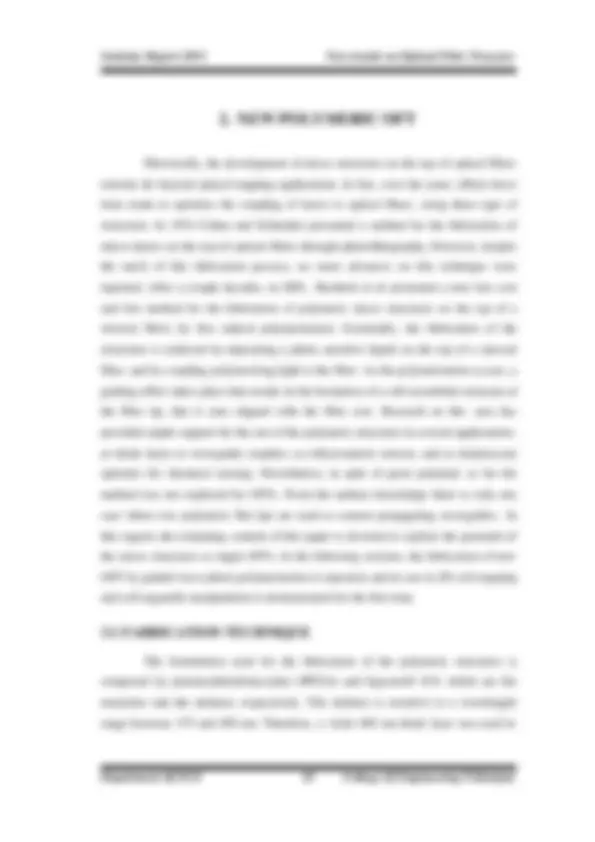
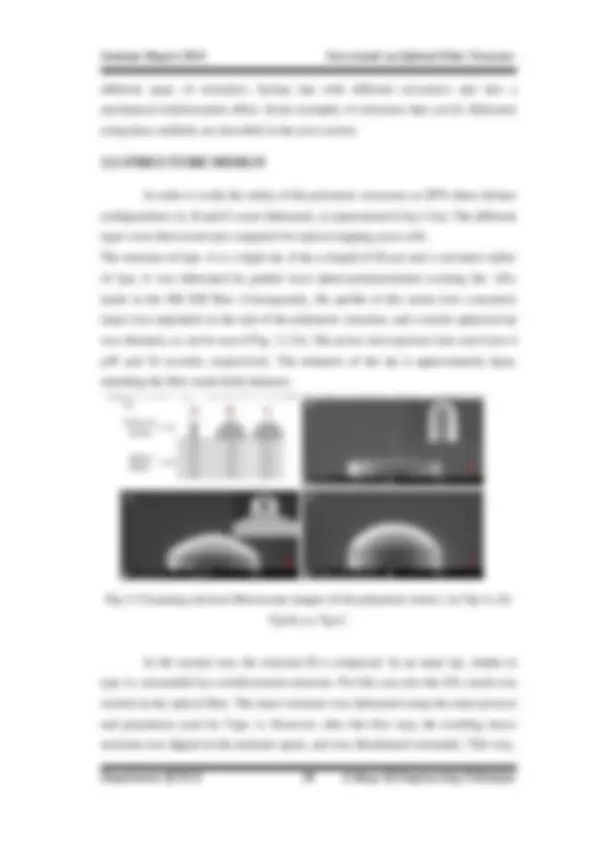
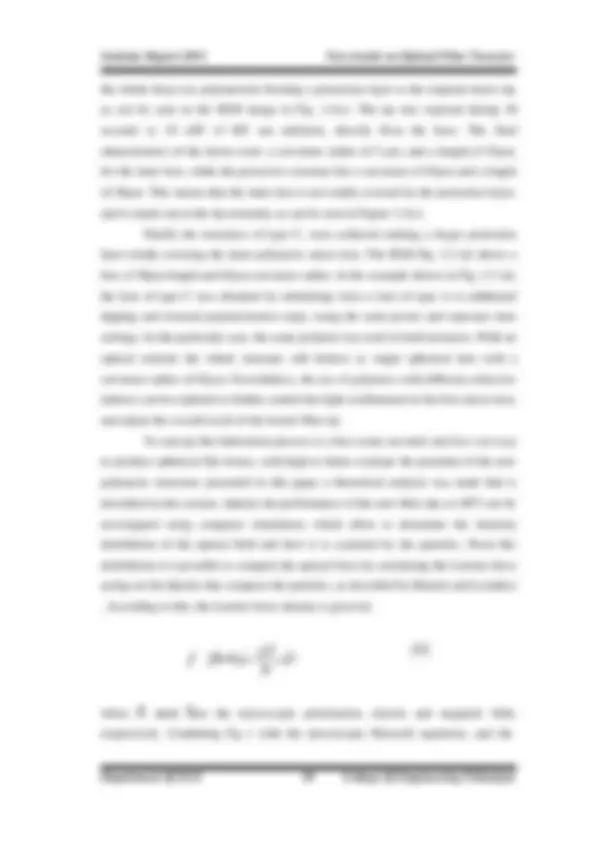
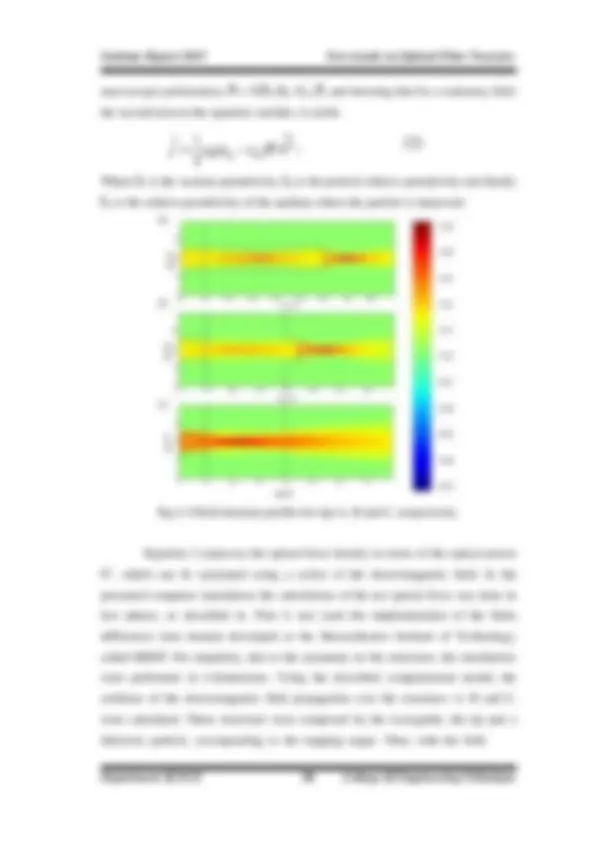
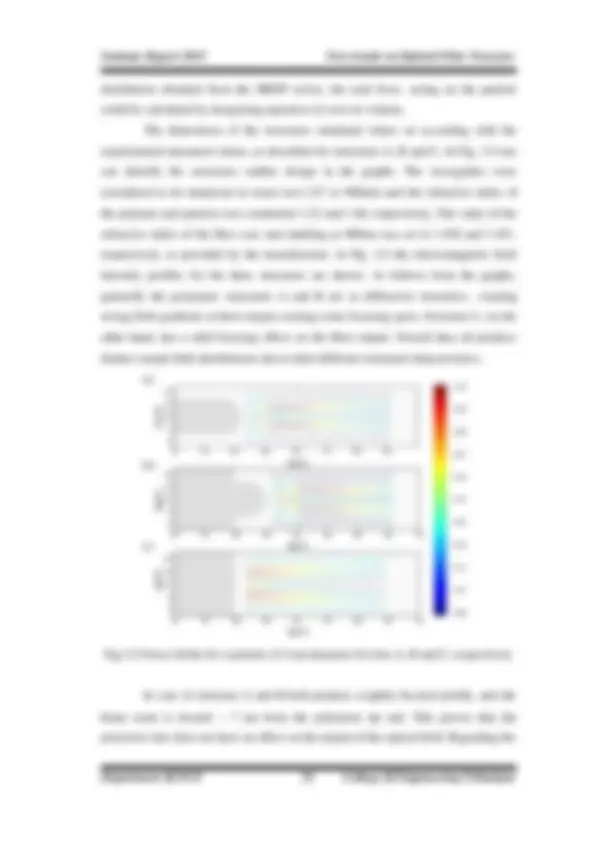
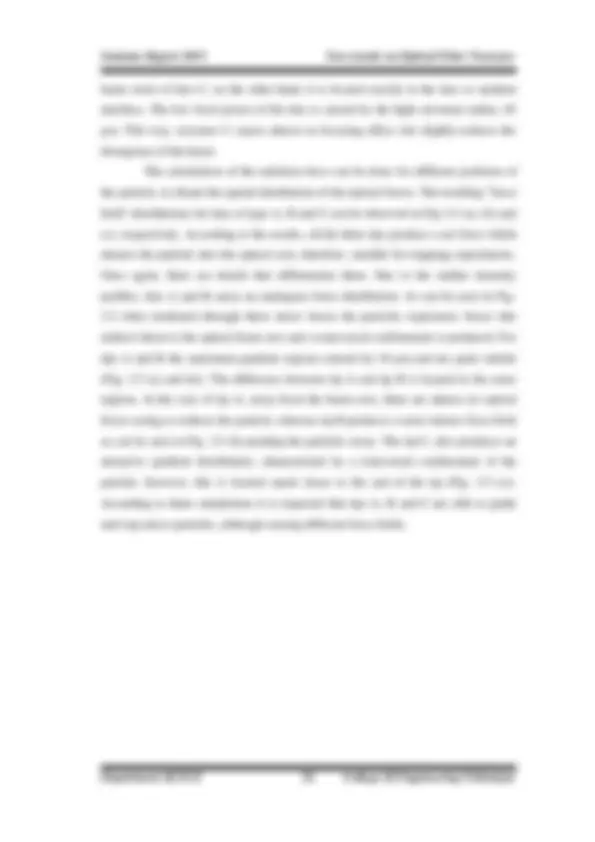
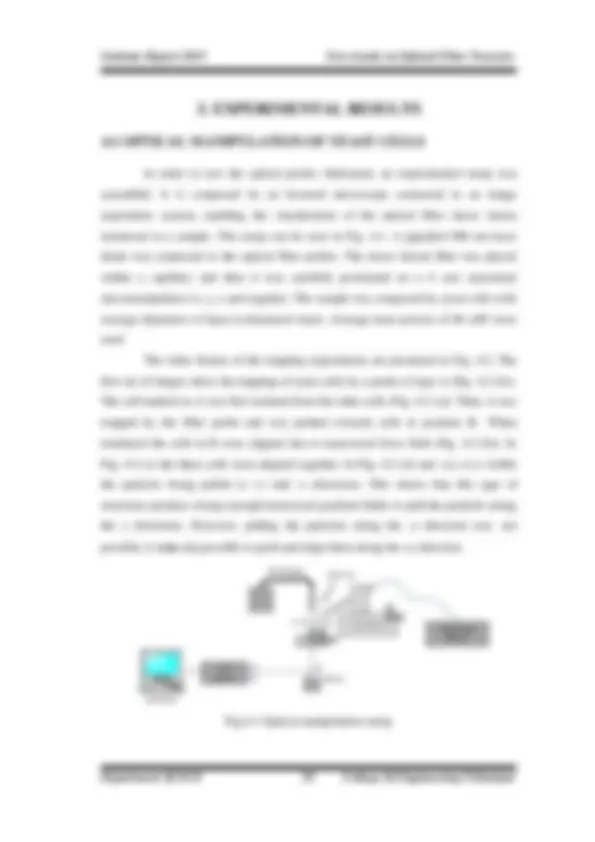
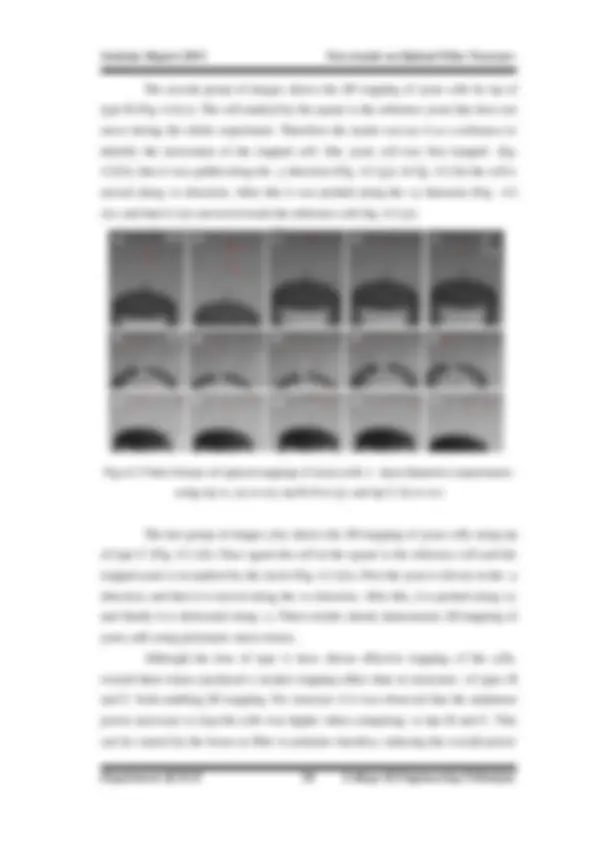

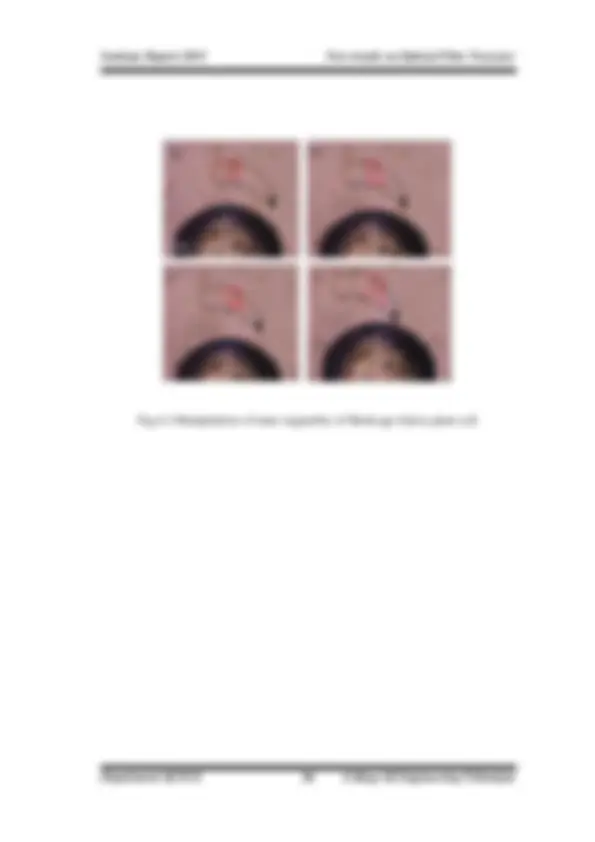
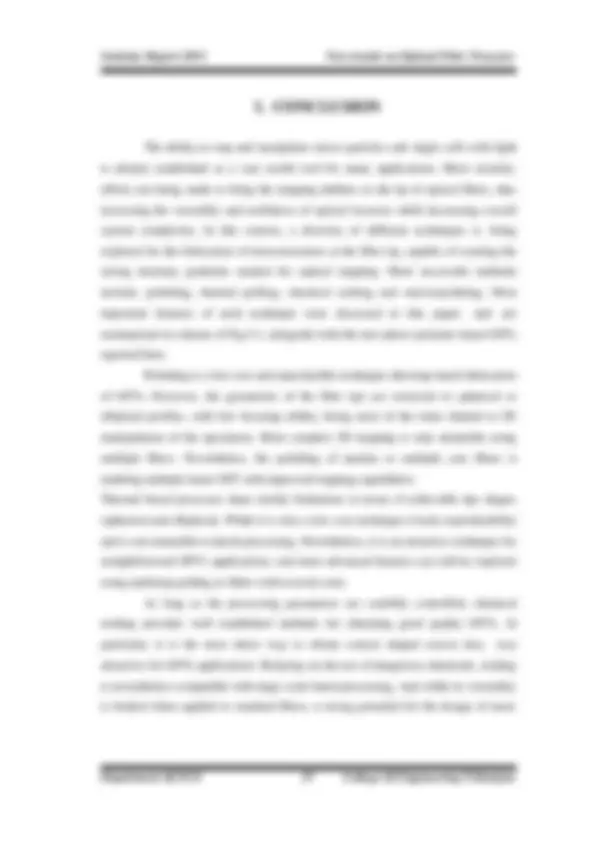
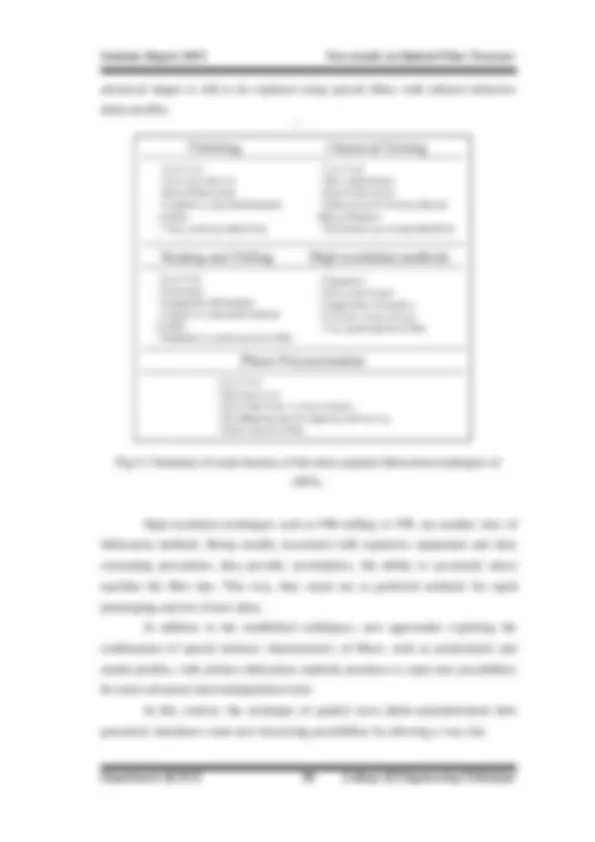
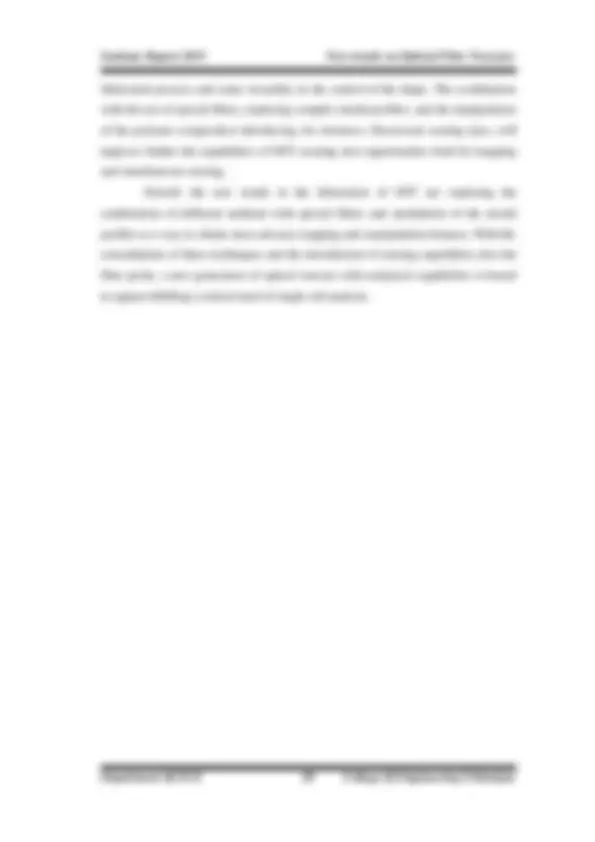
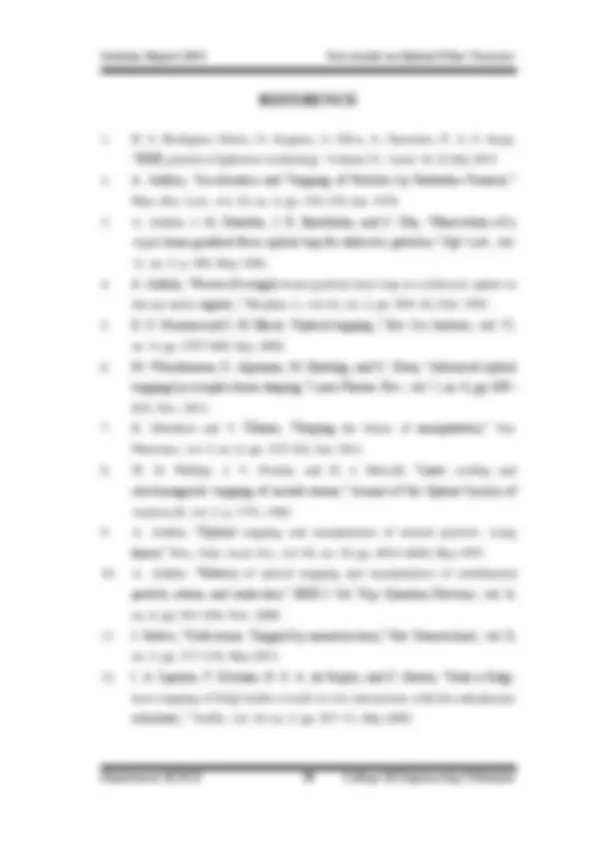
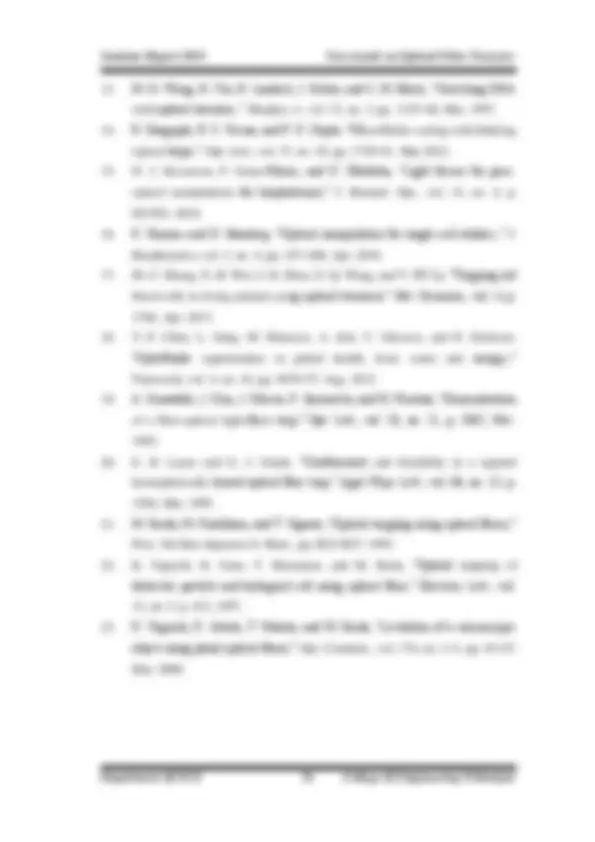
Study with the several resources on Docsity
Earn points by helping other students or get them with a premium plan
Prepare for your exams
Study with the several resources on Docsity
Earn points to download
Earn points by helping other students or get them with a premium plan
Community
Ask the community for help and clear up your study doubts
Discover the best universities in your country according to Docsity users
Free resources
Download our free guides on studying techniques, anxiety management strategies, and thesis advice from Docsity tutors
The principles and applications of optical tweezers, a technology that uses laser beams to trap and manipulate microscopic particles. It covers the different types of optical forces involved, the components of an optical trap apparatus, and the use of complex structured light fields to achieve higher degrees of manipulation and control. The document also explores the use of optical tweezers in various fields, including atomic physics and biomedicine, and the limitations of conventional optical trapping setups. It concludes with a discussion of recent trends in the use of special optical fibers to create more advanced configurations for optical tweezers.
Typology: Study Guides, Projects, Research
1 / 31
This page cannot be seen from the preview
Don't miss anything!
Optical trapping was reported by Arthur Ashkin in 1970 when, for the first
time, micron-sized particles were stably trapped between two counter propagating
beams due to the radiation pressure effects. Later, in 1986. A. Ashkin demonstrated
the same effect using a single tightly focused optical beam, also named as Optical
Tweezer, to successfully trap particles, in the nano to micrometer size range.
The optical force acting on a dielectric particle originates in the momentum
transference from the beam to the particle during the reflection and refraction of the
photons in its surface. Conventionally, the total force can be decomposed in two
components: the scattering force and the gradient force. The scattering force is
proportional to the intensity of the electric field, therefore, it is responsible for
pushing the particles away from the beam. The gradient force is proportional to the
gradient of the intensity of the electric field, resulting in the redirection of the
particles into the highest intensity region. In the case of the two counter propagating
beams, the balance of the axial scattering forces from the two beams is crucial for the
attainment of a stable trap. However, in the case of the single beam trapping, the
gradient force plays the major role. Whenever the gradient of the light intensity is
steep enough, the axial component of the gradient force can exceed the scattering
force, establishing the conditions for attractive forces and zones of zero net force to
arise, enabling trapping effects.
To achieve 3-dimensional (3D) stable trapping conditions, traditionally (he
laser beam is focused by a high numerical aperture (NA) objective into n tightly
focused spot. The implementation of an optical trap apparatus depends on the
following elements: a laser, a number of optical components to expand and steer the
beam, a high NA objective, an observation system and the sample holder. These
systems are usually gathered and adapted to conventional inverted optical
microscopes, by externally coupling the laser beam to the objective. In alternative to
conventional optical tweezers (COT), complex structured light fields have
demonstrated to be of great importance in achieving higher degrees of manipulation
and control. This can be attained using the so-called holographic optical tweezers
(HOT) by means of computer generated holograms, which are typically achieved via
spatial light modulators. In this context, standard Gaussian beams were overcome by
special tailored optical beams such as Hermitc-Gaussian, Laguerre-Gauss, non-
diffracting beams (e.g Bessel Beams), to name a few. As a consequence, the building
up of HOT systems promoted the versatility of more advanced optical trapping
devices, including for instance, multi point optical traps or the use of beams carrying
optical angular momentum. Such developments were addressed by other authors with
abundant details.
Historically, the applicability of optical tweezers extends from fundamental
disciplines such as atomic physics to broadband areas such as biomedicine. The
current literature on cooling and manipulation of atoms, supported by optical trapping
tools, reports huge advances in this area. For instance, a device based on
nanostructured optical gratings for magneto-optical trapping of atoms was recently
demonstrated, opening new opportunities to introduce this technology into more
complex environments, such as atomic clocks. In the case of biomedicine there is an
overwhelming number of evidences corroborating how advantageous optical trapping
can be as an advanced manipulation tool. The use of optical tweezers can be applied
for precision measurements ranging from the molecular to the cellular level. In the
first case, for example, optical trapping can be used to measure the mobility of
enzymes or molecular motors in the dynamics of ON A. In the second, optical
trapping at the cellular level (red blood cells, yeast cells, vegetal cells) has provided
ample support in 11 variety of applications on single cell manipulation, stretching,
sorting, among others. Further improvements include the integration of imaging and
spectroscopic setups into trapping platforms. The progress and new applications of
optical tweezers have been extensively reviewed by several authors. Lately, cutting
edge improvements were reported by Zhohget al. where evidences of trapping and
manipulation of in vivo red blood cells in a living mice car capillary were shown. On
the basis of the evidences currently available, it seems fair to suggest that optical
tweezers are one of the most promising tools for micro and nano manipulation.
Although significant results have been achieved using the conventional
optical trapping (COT) setups, their utilization is still limited in quite a few
The trapping and manipulating capabilities that can be attained with n given
OFT are lightly linked with the optical and geometrical failures of the fiber lip. In this
regard, it is the reliability and versatility of the fabrication technique that determines
what can be achieved. While reproducibility and processing simplicity are highly
desirable failures. The ability to obtain complex shapes is mandatory for some
applications. Ideally, both would be available with low cost and rapid processing
times, however, most often compromises must be made. Presently, a diversity of well-
established lubrication techniques are being explored in the fabrication of different
OFT configurations. Polishing, chemical etching, thermal pulling, focused ion beam
(FIB) milling and femtosecond laser machining are surely the most important ones.
Whereas polishing, chemical etching and thermal processes are essentially low cost
techniques, they are often limited to conical and/or spherical tip designs. In contrast,
micro fabrication techniques that use FIB milling or two photon polymerization
processes allow fabrication of more complex structures, but have the drawback of
being expensive and time consuming. Ultimately the goal is to have strong focusing
effects at the fiber tip, thus enabling stronger optical forces. This allows to operate
twee/er with lower optical power, a critical aspect in many biological applications. In
this section a description of these key fabrication techniques will be presented,
highlighting their main features and drawbacks together with some relevant
progresses reported in the literature.
Grinding and polishing is an economical and simple method to micro
machine optical fibers. It has been extensively used in the fabrication of optical fiber
connectors and is also an important manufacture process of optical fiber sensors. In
the context of OFTs applications, it is a suitable process for micromachining optical
fibers to obtain lensed profiles. See Fig.2.1 for the general OFTs designs. Indeed, the
first OFTs reported in the literature by M. Ikeda et al. in 1995 were fabricated using
this method. The hemispherical profile used by the authors is the most commonly
reported with this fabrication method. One of its main advantages is keeping the
guiding characteristics of the waveguides. The focusing of the output light is obtained
by reshaping of the fiber tip profile. First studies in this area reported on polishing tips
of standard single mode optical fibers into spherical-like profiles enabling the 2D and
3D trapping of dielectric particles and yeast cells.
With this method curvature radius of some micrometers can be attained. The
data gathered by some authors indicates that, with a curvature radius of 2μm, a
minimum of 1.3 mW is necessary to trap a 10 μm polystyrene particle. However, if
the curvature radius increases to 6μm, reducing the focusing power, a minimum of 2.
mW is required to trap the same particle. Nevertheless, in spite of the small curvature
radius, the typical fiber modal profile and refractive index characteristics often result
in weakly focused beams, producing relatively small optical forces. For this reason,
the spatial arrangement of the polished OFTs namely the angle and trapping distance,
are critical and determine the ability to stably trap the particles. Furthermore, it has
been reported that a single O1T is able to trap particles only in the xy plane, and dual
or multiple fiber configurations are required to levitate the particles against the force
of gravity, enabling 3D trapping. These studies demonstrated that dual OFTs inserted
at 35 ֩ are able to trap particles located on the bottom of a sample container, and to
levitate and move them around. This demonstrates that an equilibrium point can be
reached, where the force of gravity and buoyancy, the gradient and scattering forces,
all balance.
To circumvent the limitations arising from low focusing power, studies on
plural arrangements (two or more fibers) of hemispherical lenzed fibers have been
performed. Multiple fibers allow not only a more effective trapping, with lower
optical powers, but also introduce extra manipulation capabilities like the possibility
to rotate non-spherical micro-objects. This rotation effect is caused by the momentum
of the force (torque) and is mainly controlled by switching on and off the different
OFTs.
More recent trends include the use of special optical fibers introducing the
possibility to obtain more advanced configurations by polishing. A multiple core fiber
in an annular-distribution (e.g. two, three, or four cores), or even annular-core optical
fibers, when polished at certain angles can be restructured to obtain stable trapping
to soften the fiber near the melting point. Simultaneous pulling, in a controlled
fashion, allows to obtain distinct adiabatic or abrupt taper profiles. Adiabatic tapers
usually result in very small focusing distances. To obtain devices with higher working
distances, usually multistep drawing stages are required. The control of the final tip
shape is very delicate as it depends on the fiber breaking. The technique is not
amenable lo batch processing. Nevertheless, several authors have reported distinct
applications using different types of thermal tapers.
Fig.2.1 Schemes of the OFT profiles that can be achieved using distinct fabrication
methods.
In 2006, Z. Liu el al. explored the use of an abruptly single mode tapered
optical fiber, for 3D trapping of yeast cells in water, manufactured by heating and
drawing technology. The fiber was primarily heated and right away drawn. By
changing the drawing speed from 0.03 mm/s to 0.32 mm/s the diameter of the fiber
was reduced from 125 μm to about 10 μm with a length of 600 μm. This tapered
section of the fiber was subsequently drawn at 1.6 mm/s until the fiber broke in the
waist position. Consequently, a parabola-like profile, with a curvature radius of
approximately 5 micrometers was formed at the fiber tip due to the surface tension of
the fused silica. With this probe the trapping of yeast cells was achieved. After this
work several others reported similar OFTs fabrication procedures. The main
difference among the fiber probes reported rely on the final optical fiber taper profiles
and their focusing capabilities. Wright et al. demonstrated that laser beams with a
beam waist superior to 0.7μm cannot 3D trap dielectric particles. Therefore, this is a
crucial parameter that will define if the 3D trapping can or not be achieved by a given
OFTs.
Later on, H. Xinel al. demonstrated the manipulation capabilities of a tapered
OFT with a hemispherical tip of 1.6μm in diameter. Exploring the effects of push,
pulling and trapping at different distance of the focal point, the OFTs were used to
perform trapping and arrangement (linear chains) of multiple particles. Also, a sharper
probe (380 nm diameter) was used in a microfluidic platform to study E-coli bacteria
dynamics. Rather than a standard taper a more abrupt profile yielding larger focusing
distances and enabling truly contactless trapping of E-coli bacteria was tested. In this
particular case, the fiber tip, submitted to a multi-step drawing process, had a
protruding tip, which caused a tighter focusing und the extension of the trapping
region. Thus, E-coli bacteria (1.7μm length and 500 nm diameter) were trapped
without physical contact and a detailed study on the bacteria dynamics was
performed: the motility of the bacteria and the conditions for a stable trap were
evaluated.
In order to reduce the necessary optical power to trap a single particle, OFTs
fabricated by the heating and drawing method based on the use of multiple core
fibers, can be used. In this method the multiple core fibers are tapered, resulting in
multiple beam interference at the hemispherical tip. In such cases, besides reducing
the optical power required for trapping, the interference features may be used to attain
a higher degree of control. For instance, Yuan el al. reported the use of a dual core
OFT for single particle manipulation, where the lensed fiber is linked to a Mack-
Zehnder interferometer. By bending the interferometer, the phase of the beams is
modified and the orientation of the particle is changed, due to changes on the output
field distribution. In this case the optical power threshold was 1 mW and the
experiments were carried out using a maximum of 5 mW that produced a 5 pN force.
More recently, Barron et al. reported a lensed four core OFT for manipulation of
multiple particles at the same time. In this case the interference of the four beams
this case, the fiber tip is formed at the interface between the etchant solution and the
protection layer. The taper is formed due to the gradually reducing height of the
meniscus as the fiber diameter is reduced by the etchant solution. This is a self-
terminating process where the relative surface tensions determine the meniscus
features and the resulting tip angle. Therefore, the etching occurs inside the fiber
buffer layer, where micro convection and transient capillary effects concur for a more
stable etching process. Indeed, tube etching was shown to be more insensitive to
environmental parameters resulting in tips with lower surface roughness. The large
cone angles obtained were mostly dependent on the type of fiber used.
In 2008, Mohantyet al. described the use of an axicon optical fiber, produced
using the tube etched method, for the trapping of low refractive index particles. The
apex angle of the fiber tip was approximately 17°, producing an output beam with a
donut profile (minimum at the center surrounded by a symmetric maximum). This
allowed the 3D trapping of the water droplets in an acetophenone solution (5μm to 9
μm in diameter), at large distances from the fiber (tens of micrometers), and using
optical powers in the range of 17 mW to 30 mW. The authors concluded that placing
the fiber horizontally would cause only an axial trapping of the droplets, but if the
probe was fixed at angle (45°) or vertically, both axial and transverse trapping could
be achieved. This demonstrated that at an angle, the scattering force can be balanced
with the buoyancy force, contributing for stable trapping in the transverse direction.
Studies of the influence of the apex angle on the working distance (near filed or far
field) of the OFT have also been reported. An axicon with an apex angle of 60°
produced an output Bessel beam profile demonstrating stable trapping of multiple
particles arranged in a linear chain, at 5 um from the fiber tip, at 146 mW (far field
trapping). For smaller apex angles, ≤ 30 °,there is a total internal reflection effect on
the conical tip. This way, the amount of light transmitted through the fiber is
decreased and the trapping of particles can only be attained very close to the fiber
surface (near field trapping).
While it is relatively easy to obtain axicon lenses with a broad range of apex
angles using the methods just described, the diversity of shapes obtained with
standard fibers is relatively limited. Nevertheless, more recently, new studies using
chemical etching of different fibers promise more sophisticated configurations for the
fabrication of axicon like profiles. A segment of graded index fiber (GIF) spliced to
the end of a standard single mode fiber and subsequently etched allows to obtain
different tip profiles. The authors pointed out that the use of a GIF, which produces a
periodically self-focusing effect may increase the trapping efficiency when compared
with conventional optical fibers. Also, since the etching rate depends of the fiber
doping profile, using special fibers with pre-optimized refractive index profiles can be
a route to easily obtain exotic tip shapes using etching methods. Such approach has
been explored in the design of some sensing devices and is bound to be a new trend to
explore in the context of OIT. In a nutshell, chemical etching is a well-established low
cost technique, requiring a tight control of processing parameters.
High resolution micromachining techniques that are available allow to
directly write complex patterned structures in a diversity of substrates. While such
methods are usually associated with very expensive instrumentation, and are often
time consuming, they are unique choices for advanced prototyping and test of new
devices. In the context of OFT, micromachining techniques are still little explored.
Nevertheless, representative examples are reported using Focused Ion Beam (FIB)
and Two Photon Lithography (TFL). The FIB is a method that enables simultaneous
micro/nano imaging, deposition and controlled milling. It is usually inserted in a
double system composed by an ion Ga
ion source and an electron source, the so-
called scanning electron microscope (SEM). The SEM enables image acquisition
through the scanning of the sample using a focused electron beam. Whereas, in the
FIB system the Ga
ions are accelerated to and focused in the sample surface. The
ions are accelerated by means of a differential voltage and are focused using special
electrostatic lenses. The accelerated ions allow milling away the substrate material
with resolutions of the order of a few nm.
FIB micromachining tools have been used to accurately fabricate special
structures on the top of optical fibers, allowing to improve some of the features
achieved so far using lenses fabricated by more conventional methods. In a pioneer
work, FIB milling technique was used in the fabrication of very precise axicon lenses
to produce high quality Bessel beams. The tweezers fabricated in this way were used
micro structures. This method is based on the two-photon absorption effect, which is
accomplished when a high intensity very short laser pulse is focused into a very small
spot of light inside the polymer. Because this is a non-linear process polymerization
occurs only above a certain intensity threshold level. This way, the laser can be
scanned through the sample and a 3D isolated structured can be formed within the
polymer. The remaining non polymerized material can be dissolved and the structure
is revealed. The main advantages presented by this technique are: 3D resolution, sub-
diffraction spatial resolution (-100 nm), high penetration depth, and ability to be
applied in a diversity of materials. While the fabrication process can be very fast, the
associated instrumentation is relatively expensive. Nevertheless TPL is also a fast
prototyping technique.
In 2010 Liberaleet al. presented the fabrication of several optical lenses on
the top of optical fibers by TPL, including spherical and conical profiles, and also a
ring phase mask. After this pioneer work, a second OFT configuration, also based on
the TIR of light, using micro prisms instead of the milled structures on the top of the
optical fibers was reported by the same group.(Fig. 2.1 (d)). In this case the optical
output beams are deflected by the surface of the prisms, to obtain the high NA. Both
the working principle and the outcomes achieved with this fiber are quite similar to
the ones presented before with the FIB milled fiber bundle. These works were
extensively reviewed in chapter 8 of reference.
While more recently other structures fabricated by TPL were reported,
including micro axicon lenses, this technique is still little explored in the context of
FOT. Indeed, high resolution micromachining technologies such a FIB and TPL are
very convenient for the prototyping of new complex structures. However, the
associated instrumentation is expensive and is not readily available for the average
user. Nevertheless, the potential for innovation is very high and will surely be
explored as the technology becomes more widespread. Such could be the case with
the TPL, and other 3D printing systems which are being the subject of rapid
evolution.
A diversity of other works has been reported using techniques that do not fall
into the previous categories or use combination of different approaches that are worth
mentioning. In 2013 Kim et al. reported an OFT configuration for the generation of
Bessel beams to be integrated in microfluidic environments. In this work the authors
presented a hybrid optical probe composed by three segments of optical fiber (single
mode fiber (SMF), hollow optical fiber (HCF) and coreless silica fiber (CSF)) and a
polymeric lens at the tip. With such arrangement the Gaussian mode guided by the
SMF is transformed in an annular mode in the HCF, then it is expanded in the CSF
and focused by the converging polymeric lens. The output beam at 1064 nm is non-
diffractive over a distance of ~1mm.
Later, Chen et al. presented an OFT configuration both for trapping, rotation
and translation of yeast cells. In their work, a 650 nm laser was coupled into a graded
index fiber with a conical tip. Then, the LP 21 mode was pre-selected by adjusting the
coupling angle, and was converted into a Bessel-like beam by the axicon lens. Using
this probe they accomplished trapping of a single cells and of a two-cell dimers.
Using a fiber rotator, the fiber could be twisted and bended, causing the rotation of the
primary LP 21 mode, and consequently a rotational torque, enabling to control the
rotation of the dimer.
These two examples do not follow any specific fabrication methodology, on
the contrary these works focus on the intrinsic guiding characteristics of the fibers,
and the ability to change them using either combinations of distinct optical fibers or
coupling light methods. This kind of approach establishes what will probably be the
paradigm in the next years where the different fabrication techniques described will
be used with special fibers and combined with modulation of its modal features to
obtain more advanced OFT devices, with a higher degree of control of its trapping
ability, suitable to perform more complex operations with biological samples.
the photo-polymerization process. The procedure to fabricate the micro structures is
illustrated in Fig. 3.1.
Fig.3.1 Images illustrating the different fabrication steps of polymeric structures at the
extremity of an optical fiber.
During the entire process a camera is used to verify both the fiber conditions
and the fabrication development. First, an optical fiber is cleaved and placed vertically
in a moving stage (Fig. 3.1 (a)). At that point, it is slowly dipped (Fig. 2 (b)) into the
solution (Fig. 3.1 (c)).Then, the fiber is removed from the polymer allowing a drop of
the solution to form in its extremity (Fig. 3.1 (d)). Next, the polymer is illuminated
and consequently cured. To finish, the remaining liquid solution is washed out with
ethanol, revealing the polymerized micro structure at the fiber tip. The visual aspect
of the resulting polymeric tip is shown in Fig 3.1 (e).
The polymeric structure is formed by means of a self-assemble photo-polymerization
effect. This means that during the solidification of the polymer, its refractive index
increases, creating a guiding effect that prevents the radiation from scattering in the
remaining of the drop. Therefore, the resulting structure generally has a diameter
close to the fiber modal diameter and the length determined by the initial polymer
drop thickness. Particularly, the geometry of the structure can be finely adjusted by
selecting the appropriate fabrication conditions, such as, laser intensity, irradiation
time and pre-excited mode profile of the optical fiber.
For this particular tests, typical power values at the tip extremity and
exposure times used were approximately 6 μW and 10 seconds, respectively. The
optical fibers used in this experiment are single mode at 980 nm (Thorlabs SMF980,
5.8μm modal diameter), which means that they will behave as a multimode fiber at
the polymerization wavelength, 405 nm. In this sense, the structure of the tips will
depend on the specific mode that is excited by the laser in the multimode waveguide,
because during the polymerization the mode profile is imprinted on the shape of the
polymeric structure. Therefore the way light is injected into the fiber will have an
important role in the final result. A scheme of the setup used to couple the free space
laser to the optical fiber is depicted in Fig. 3.2 (a). The laser is coupled to the optical
fiber using two mirrors, and a fiber coupling system. Both the mirrors and the fiber
coupling system can be tilted and translated with micrometer precision. In this regard,
it is possible to adjust the input angle of the laser to the optical fiber, and specifically,
pre-select which guided mode is excited, and applied in the polymerization process.
With this method, it is possible to have structures with various designs, which can be
tailored for specific applications.
Fig.3.2 (a) Experimental setup used to fabricate the polymeric tips; (b) Scheme of the
different polymeric lenses that can be achieved using the photo-polymerization
process.
In the first scheme of Fig. 3.2 (b) one can see the typical aspect of the long
and thin polymeric structure on the top of an optical fiber attained with the process
described above. Due to its aspect ratio, such structure can present some fragility.
However, if the drop of polymer located at the top of the optical fiber is illuminated
externally (sideways), the entire drop can be polymerized. Therefore, a lens/structure
covering the entire optical fiber cleaved top can be formed. Such type of structure can
be visualized in the scheme of Fig. 3.2 (b). In this case, the final characteristics of the
outer layer obtained are governed only by the polymer drop features such as viscosity
and thickness. In practice, the two approaches can be used in combination to obtain
the whole drop was polymerized forming a protection layer to the original micro tip,
as can be seen in the SEM image in Fig. 3.3(c). The tip was exposed during 30
seconds to 10 mW of 405 nm radiation, directly from the laser. The final
characteristics of the lenses were: a curvature radius of 3 μm, and a length of 35μm,
for the inner lens, while the protective structure has a curvature of 65μm and a length
of 30μm. This means that the inner lens is not totally covered by the protection layer,
and it stands out at the tip extremity as can be seen in Figure 3.3(c).
Finally the structures of type C, were achieved making a larger protection
layer totally covering the inner polymeric micro lens. The SEM Fig. 3.3 (d) shows a
lens of 40μm length and 65μm curvature radius. In the example shown in Fig. 3.3 (d),
the lens of type C was obtained by submitting twice a lens of type A to additional
dipping and external polymerization steps, using the same power and exposure time
settings. In this particular case, the same polymer was used in both instances. With no
optical contrast the whole structure will behave as single spherical lens with a
curvature radius of 65μm. Nevertheless, the use of polymers with different refractive
indexes can be explored to further control the light confinement in the first micro lens,
and adjust the overall result of the lensed fiber tip.
To sum up this fabrication process is a fast (some seconds) and low cost way
to produce spherical like lenses, with high to better evaluate the potential of the new
polymeric structures presented in this paper a theoretical analysis was made that is
described in this section. Indeed, the performance of the new fiber tips as OFT can be
investigated using computer simulations which allow to determine the intensity
distribution of the optical field and how it is scattered by the particles. From this
distribution it is possible to compute the optical force by calculating the Lorentz force
acting on the dipoles that compose the particles, as described by Barnett and Loundon
. According to this, the Lorentz force density is given by
where 𝑃
, 𝑒→and 𝑏
are the microscopic polarization, electric and magnetic field,
respectively. Combining Eq. 1 with the microscopic Maxwell equations, and the
macroscopic polarization, 𝑃
= 1/2Ɛ 0 (Ɛp- Ɛm) 𝐸
, and knowing that for a stationary field
the second term in the equation vanishes, it yields
Where Ɛ 0 is the vacuum permittivity, Ɛp is the particle relative permittivity and finally
Ɛm is the relative permittivity of the medium where the particle is immersed.
Fig.3.4 Field intensity profile for tips A, B and C, respectively.
Equation 2 expresses the optical force density in terms of the optical power
2
, which can be calculated using a solver of the electromagnetic field. In the
presented computer simulations the calculations of the net optical force was done in
two phases, as described in. First it was used the implementation of the finite
differences time domain developed at the Massachusetts Institute of Technology,
called MEEP. For simplicity, due to the symmetry on the structures, the simulations
were performed in 2 - dimensions. Using the described computational model, the
solutions of the electromagnetic field propagation over the structures A. B and C,
were calculated. These structures were composed by the waveguide, the tip and a
dielectric particle, corresponding to the trapping target. Then, with the field