
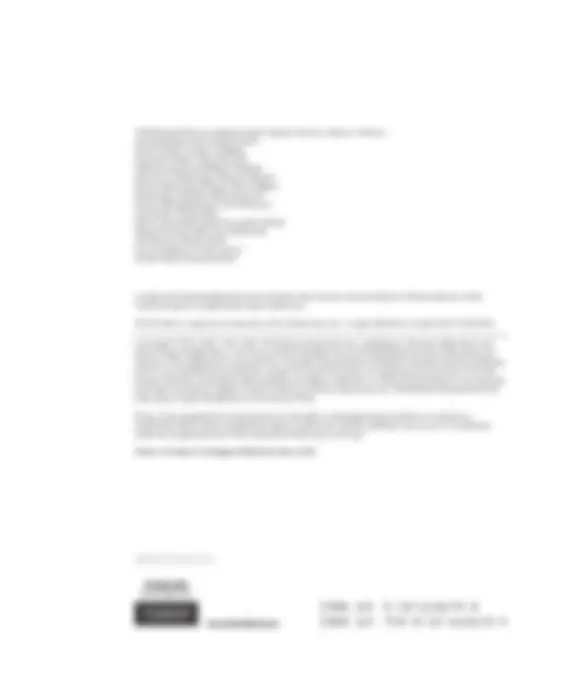
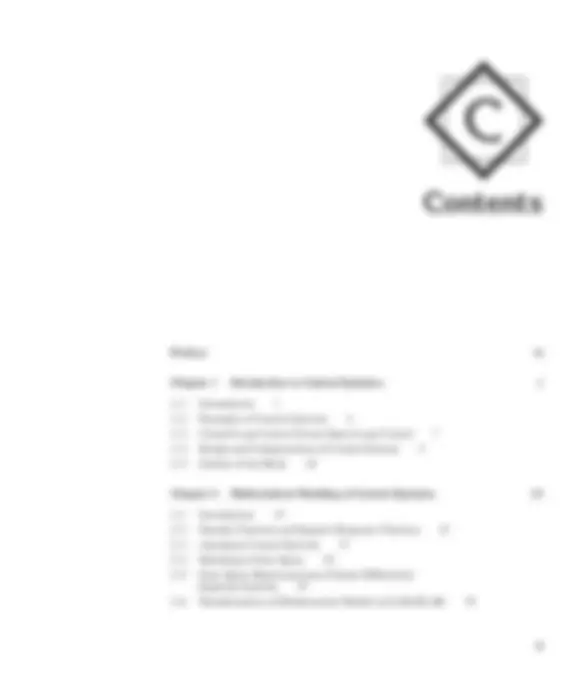
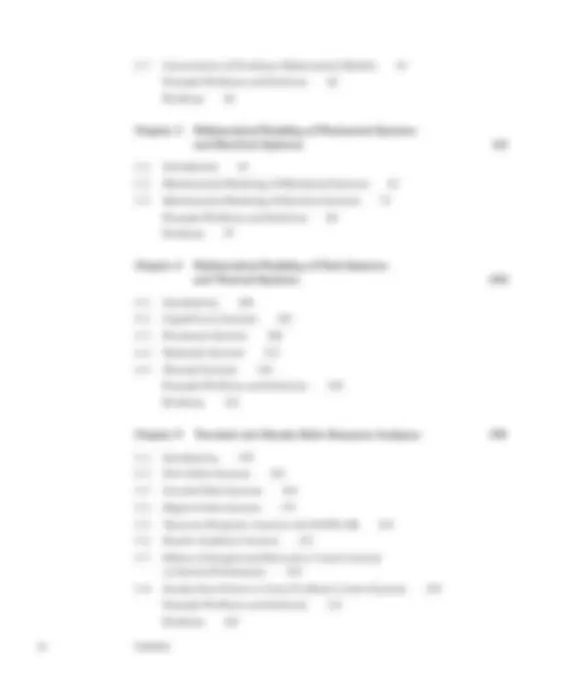
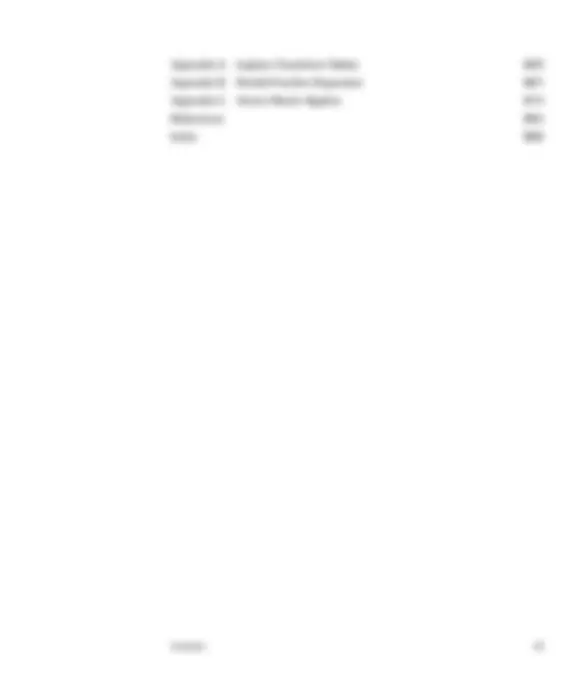
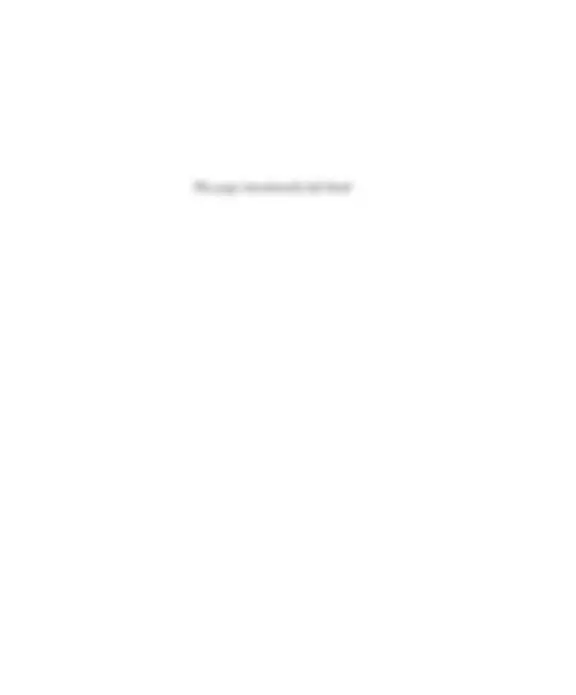
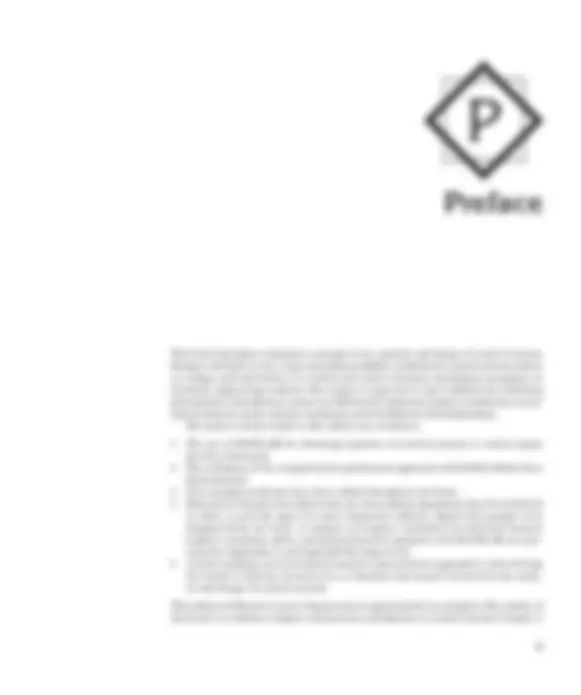
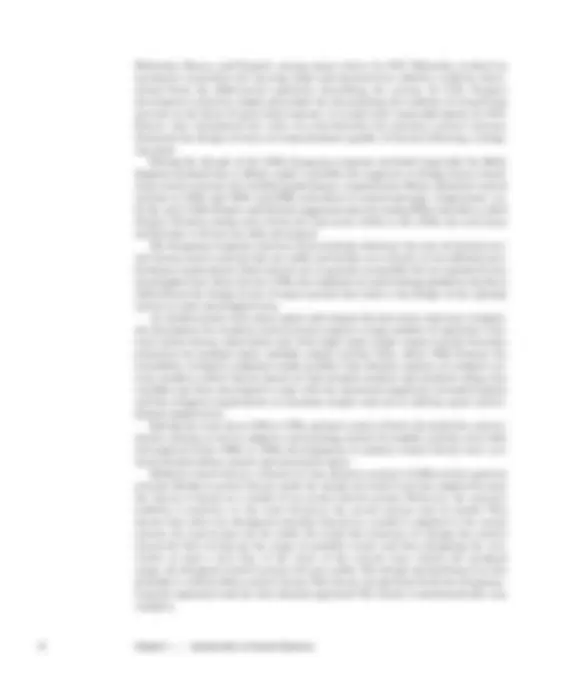
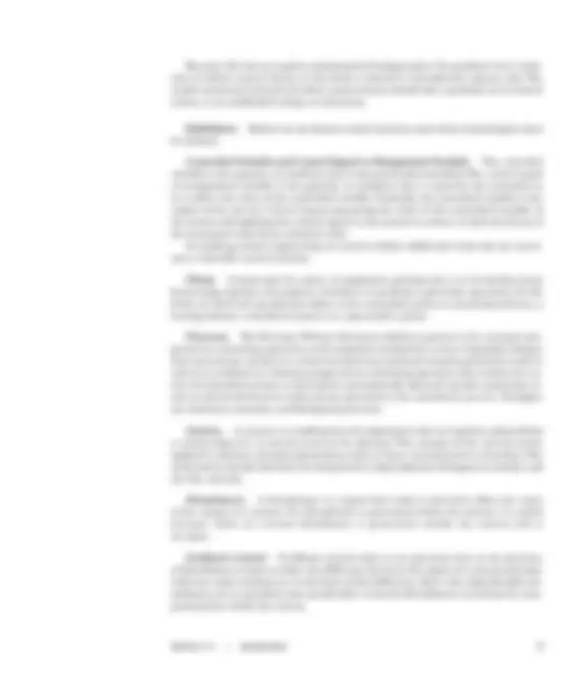
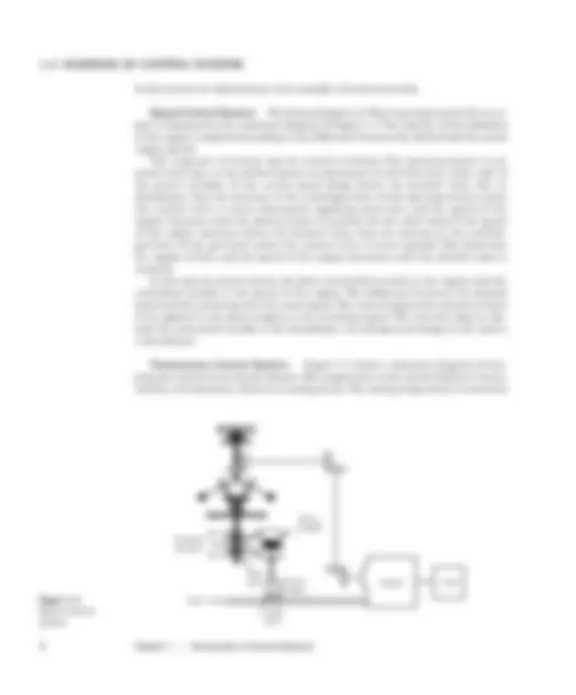
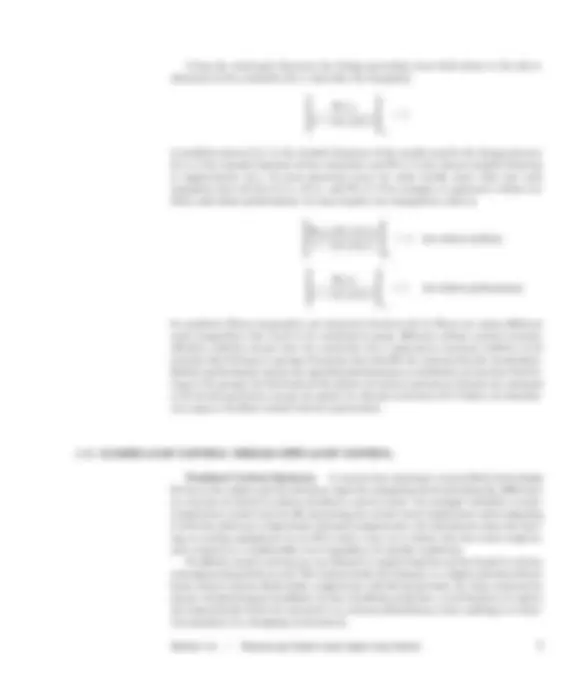
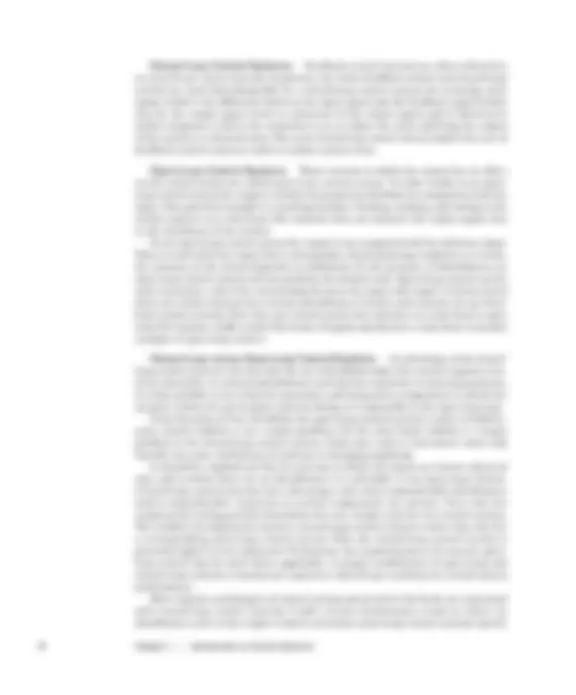
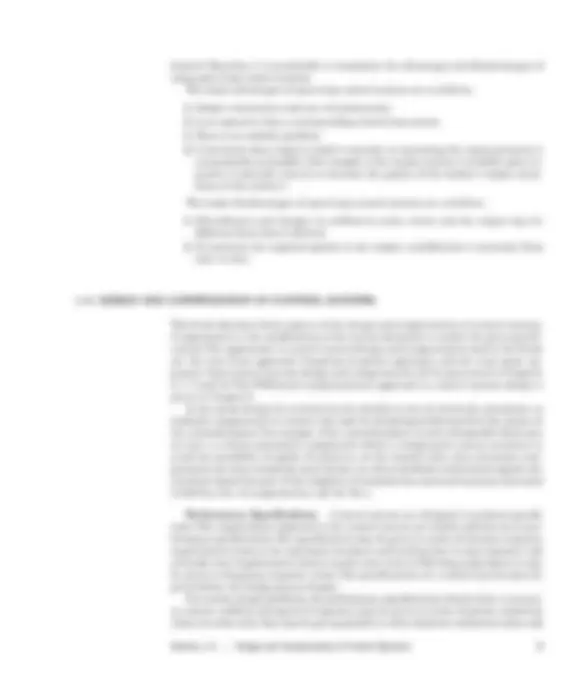
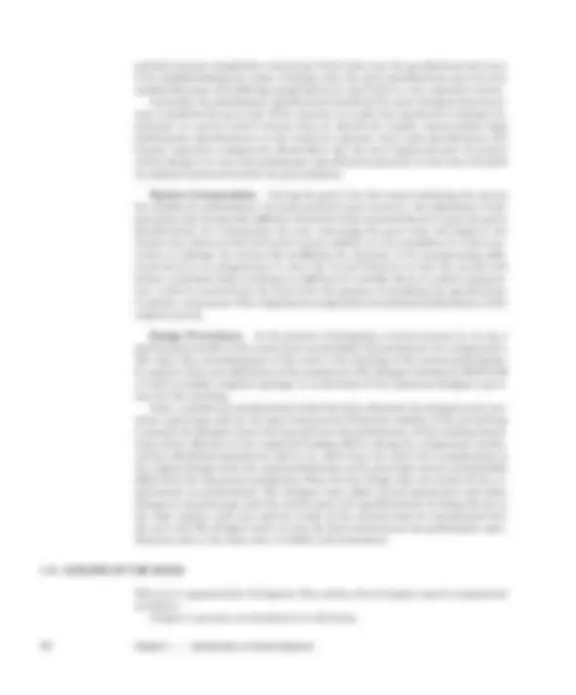
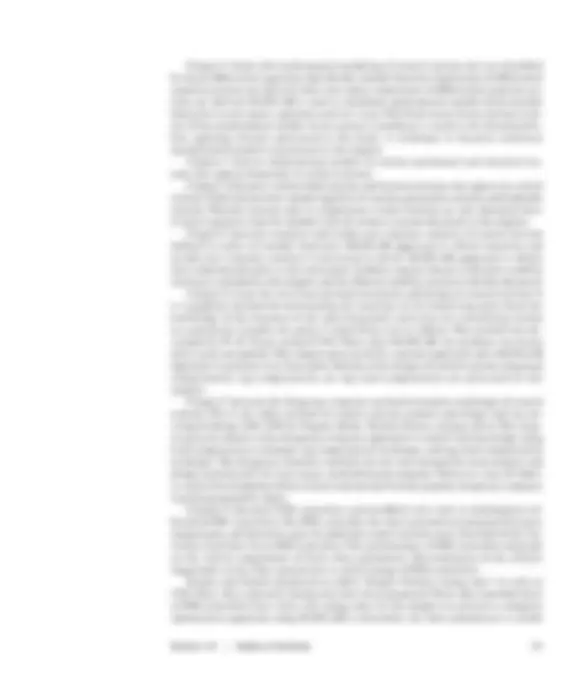
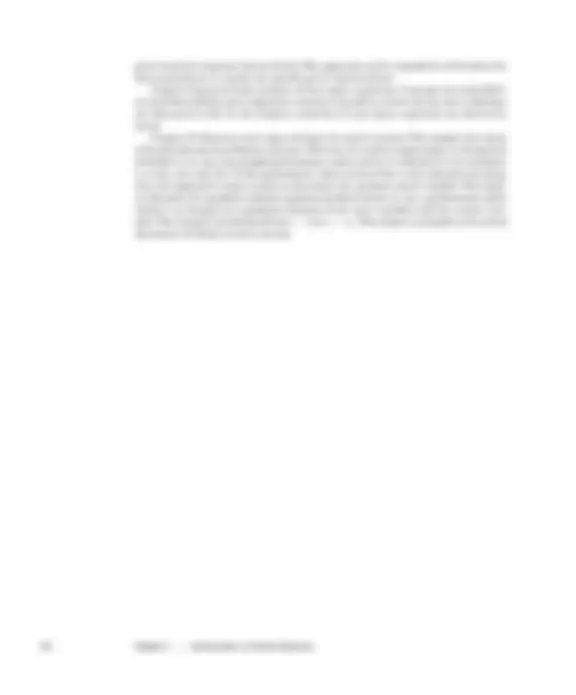
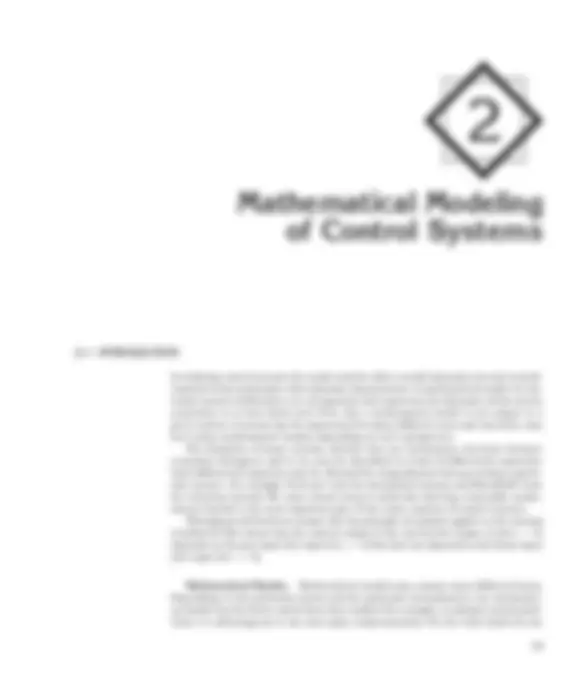
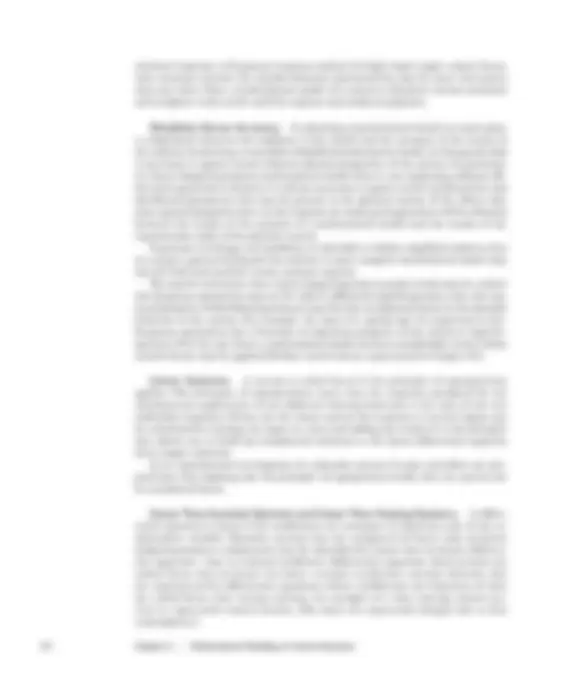
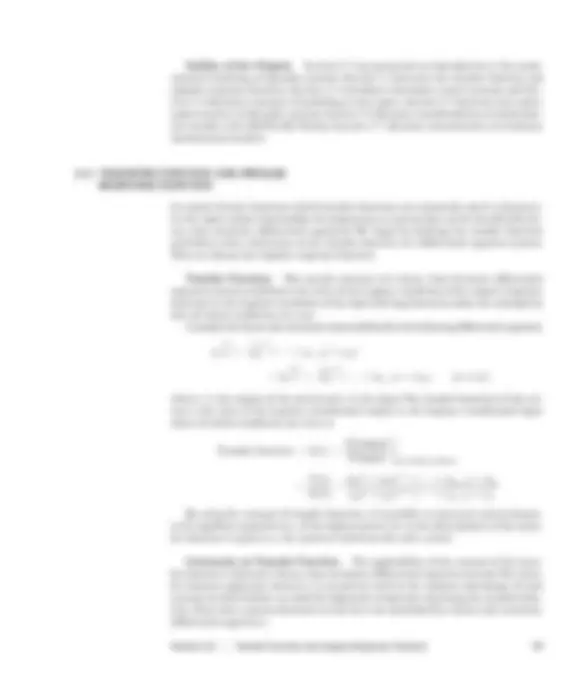
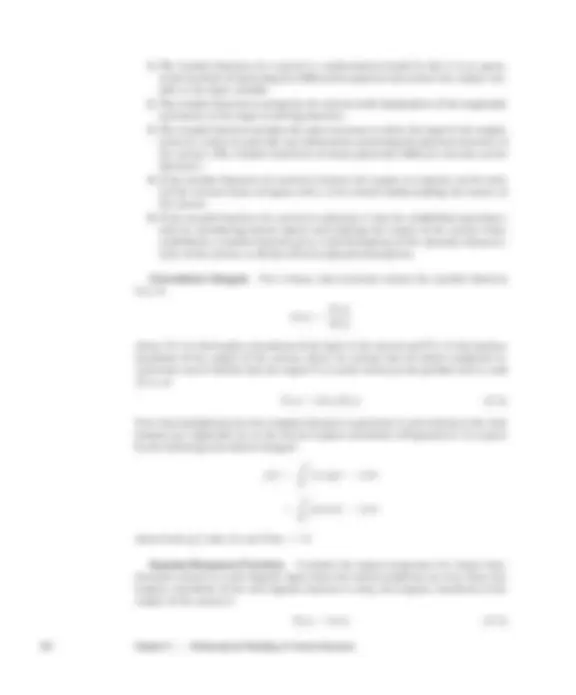
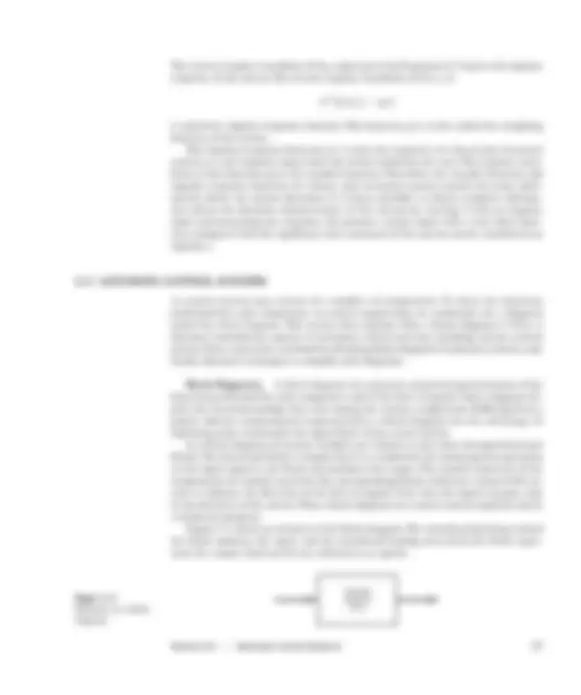
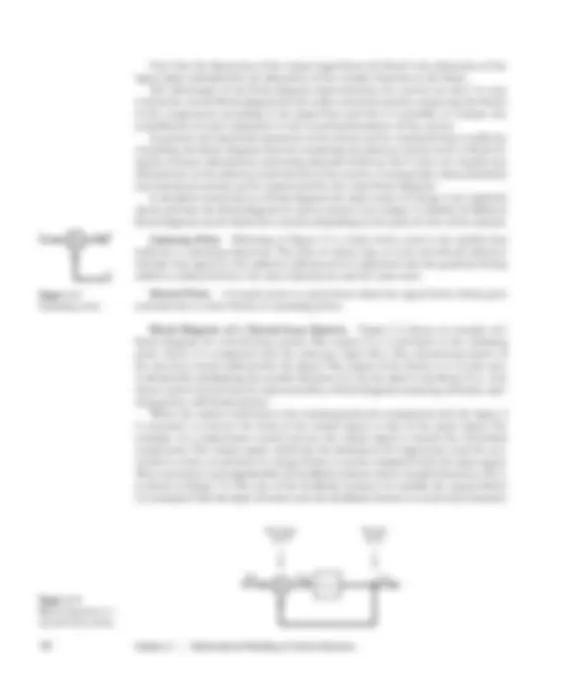
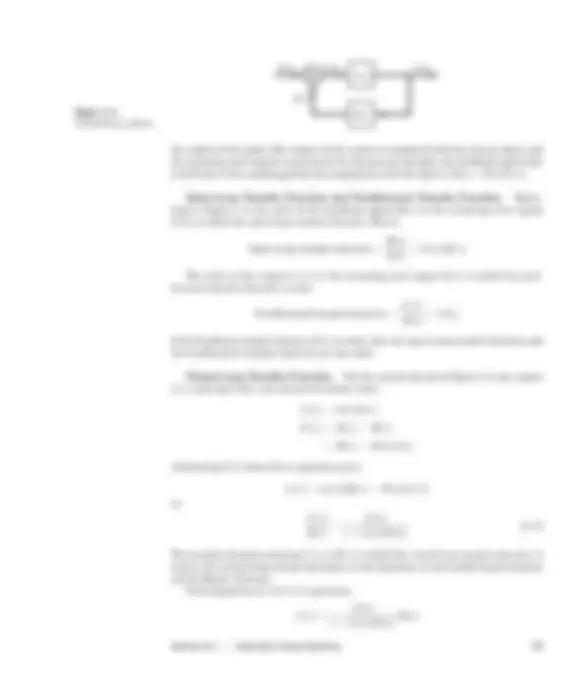
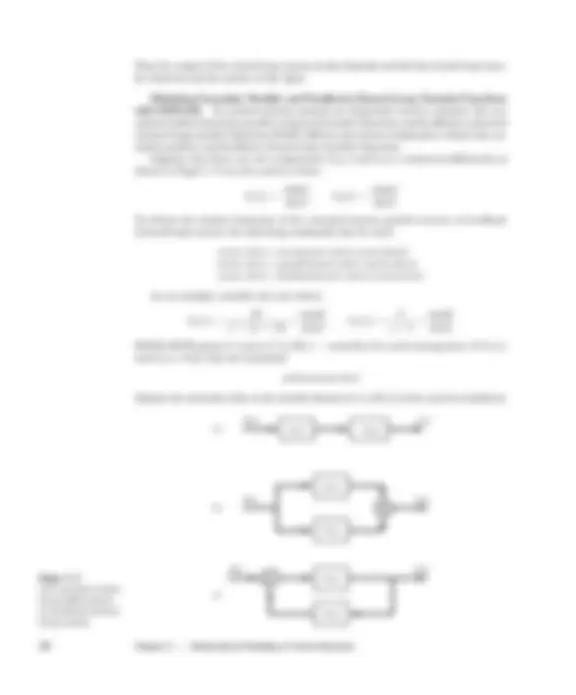
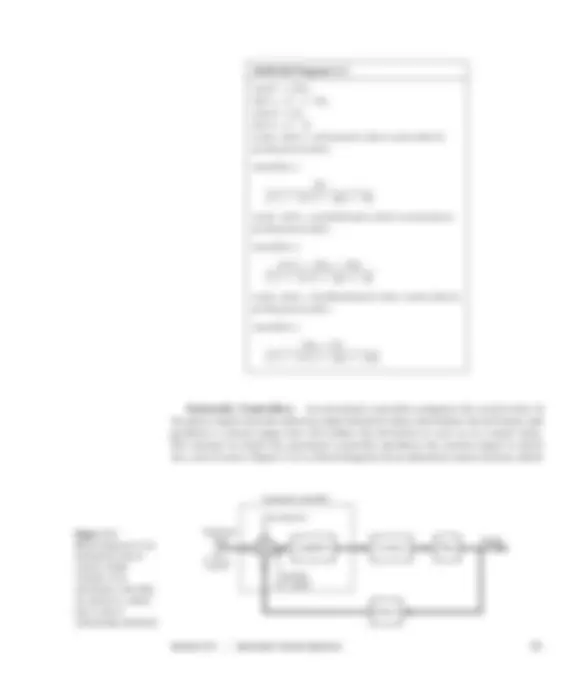
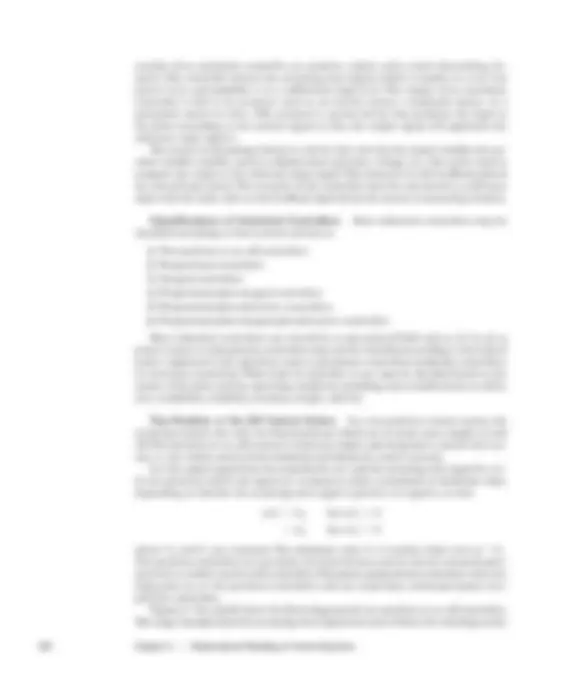
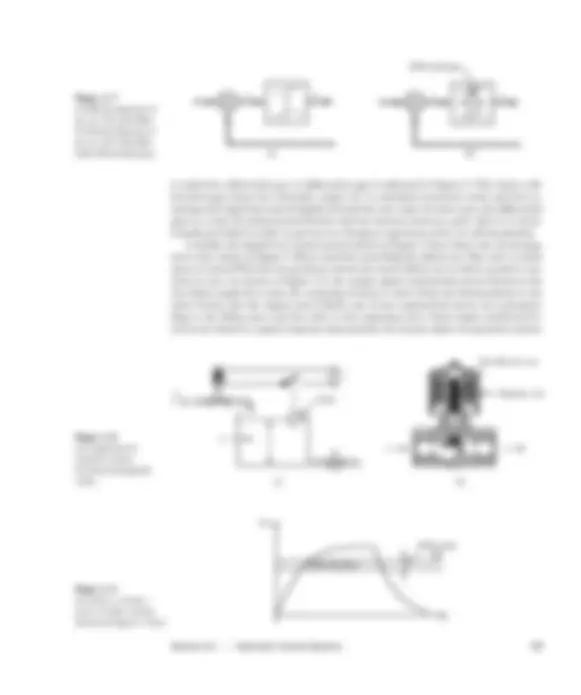
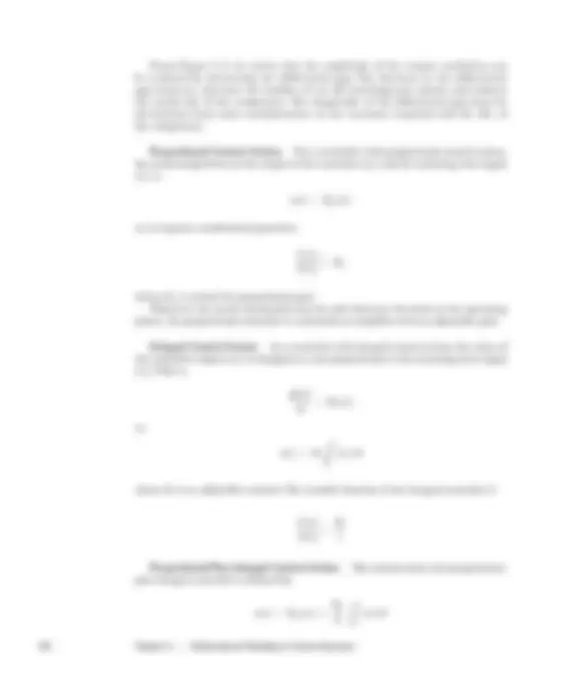
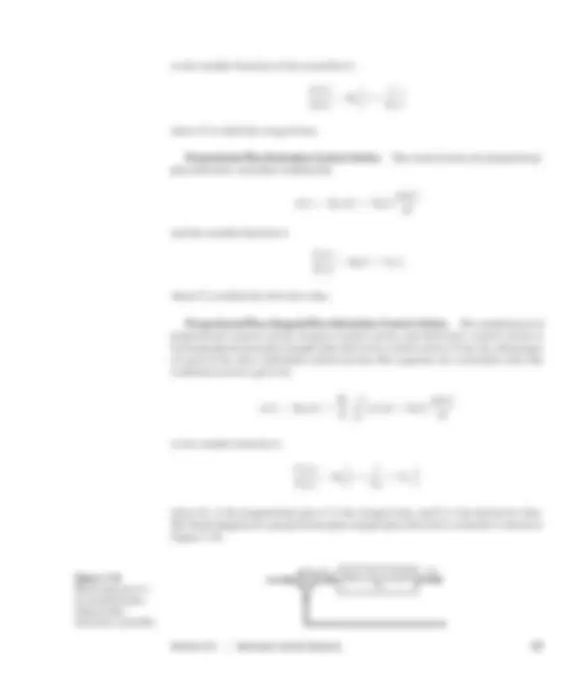
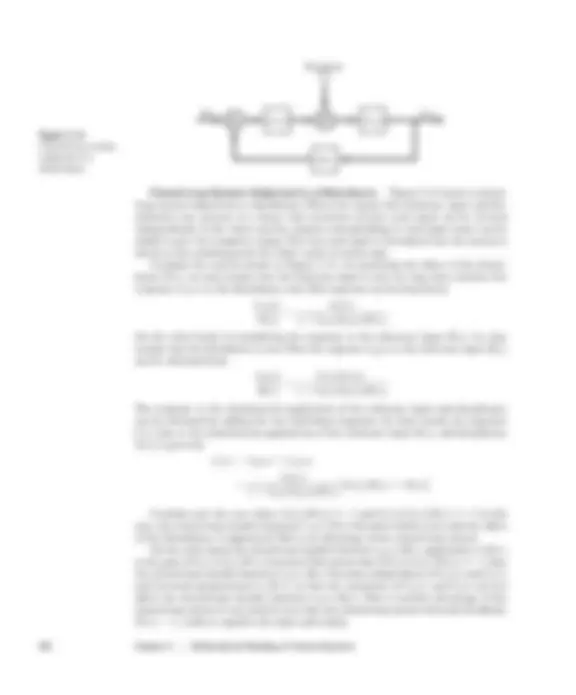
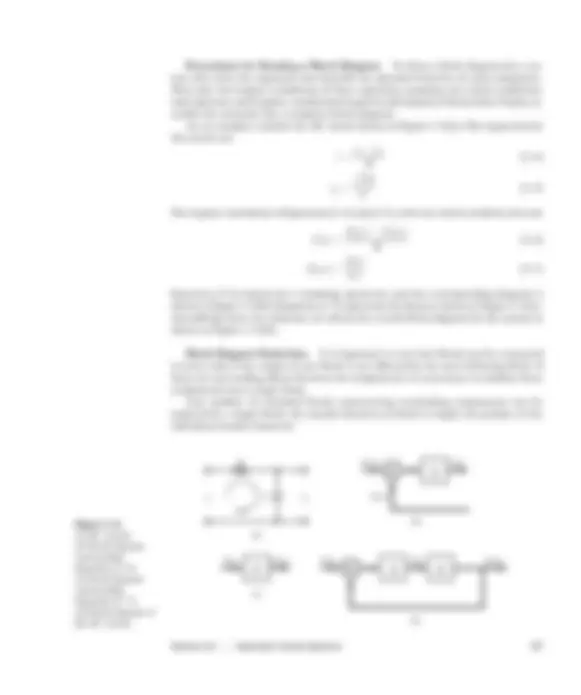
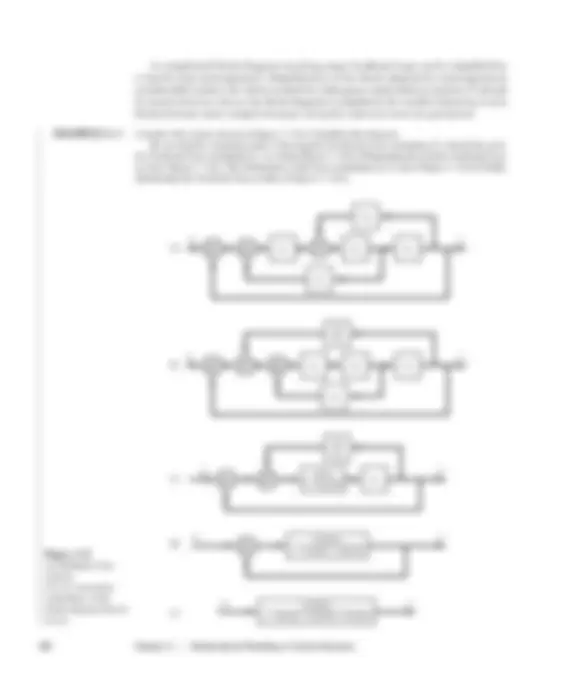

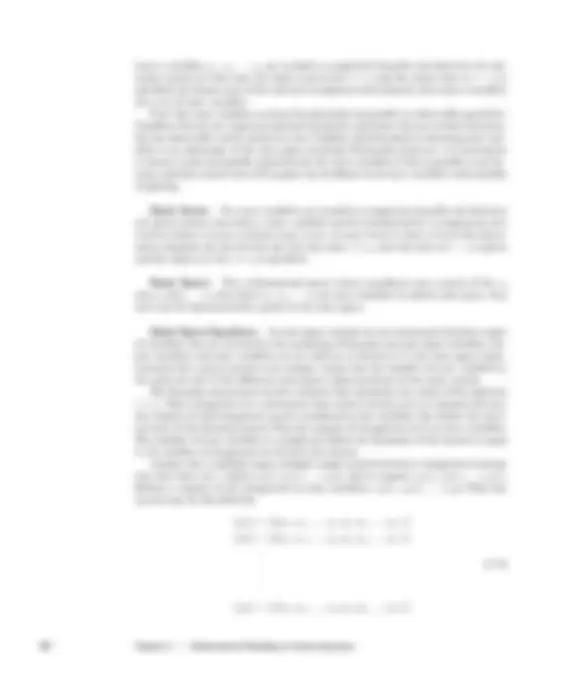
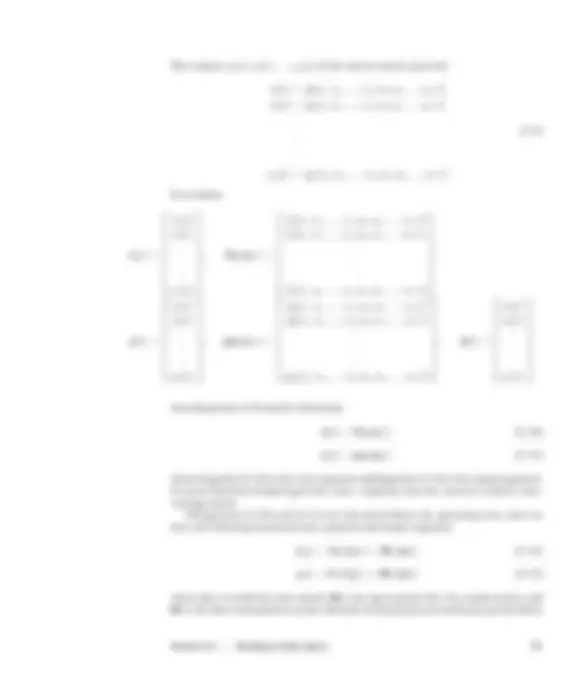
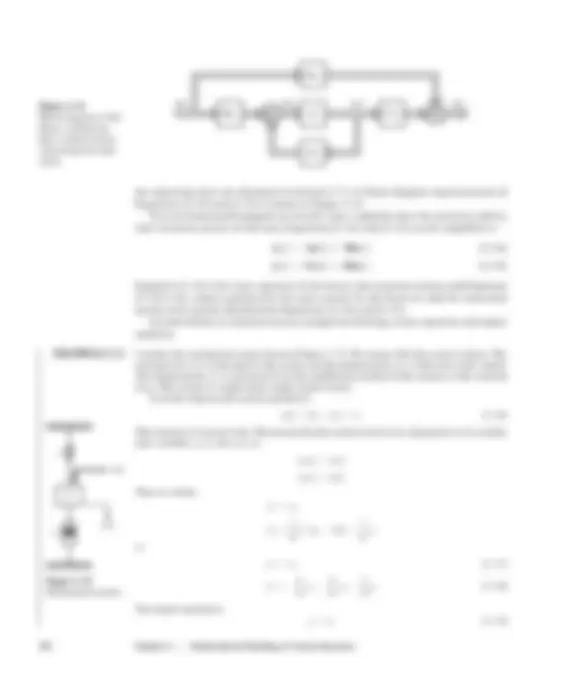
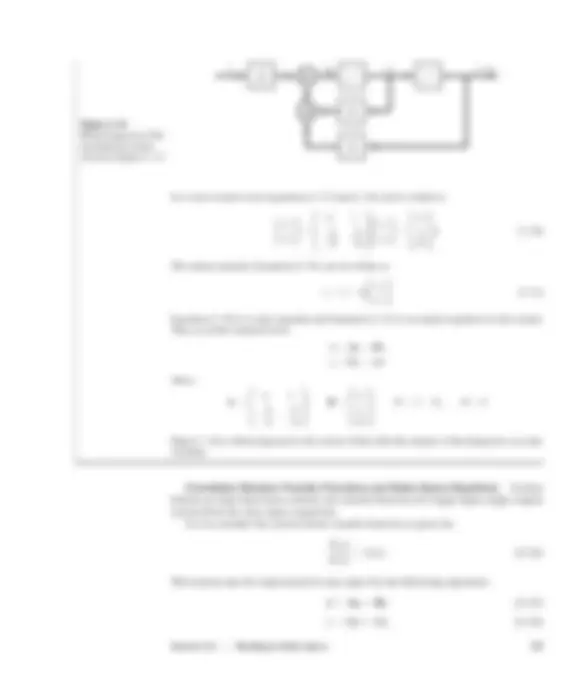
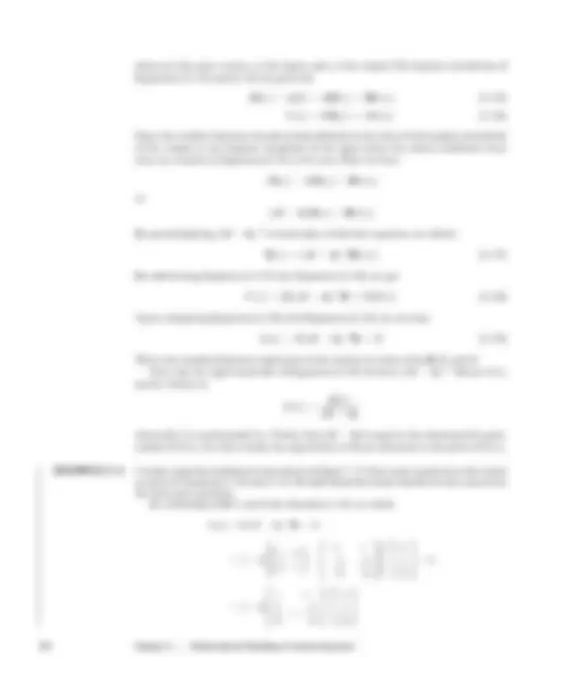
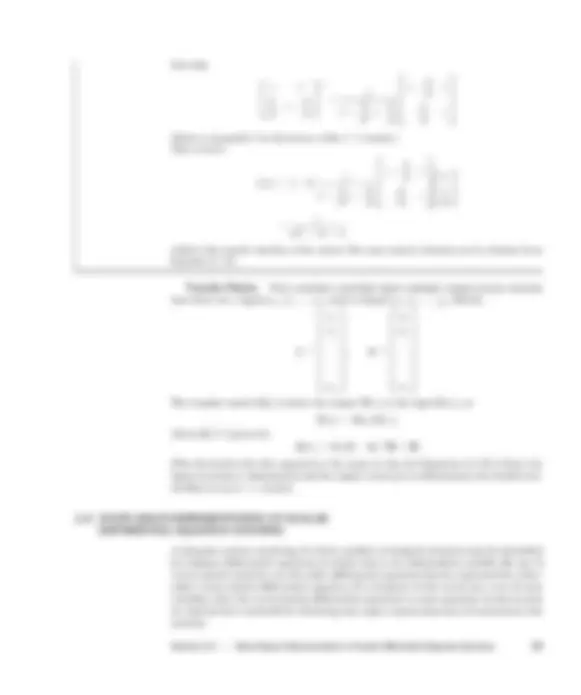
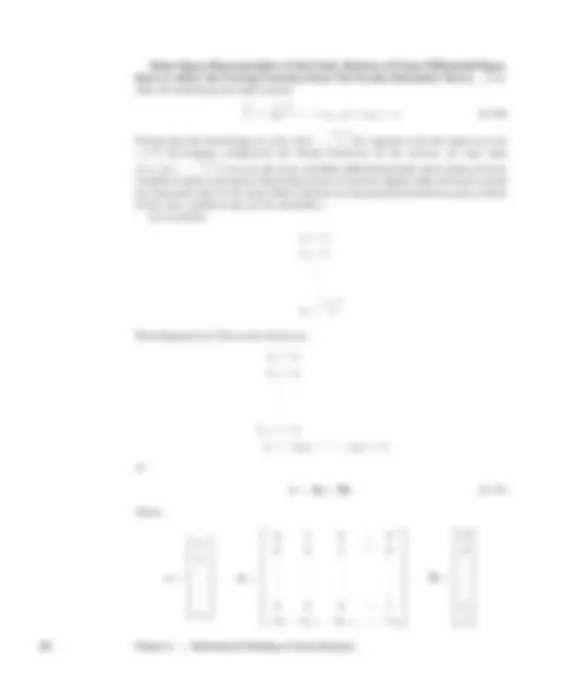
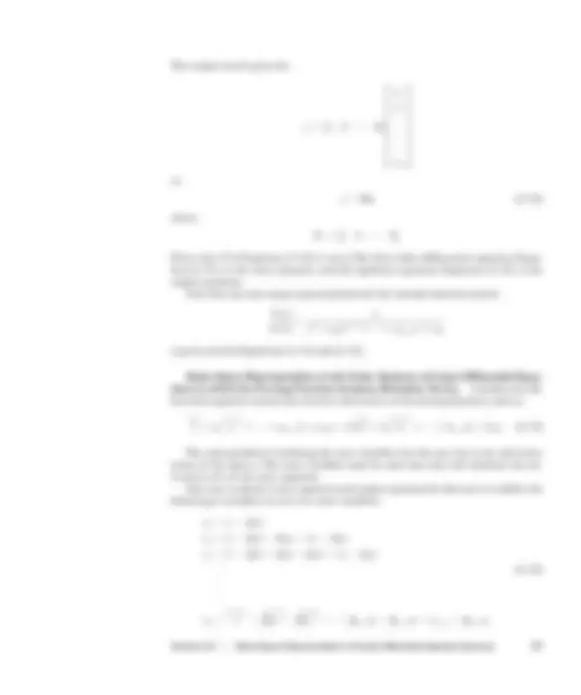
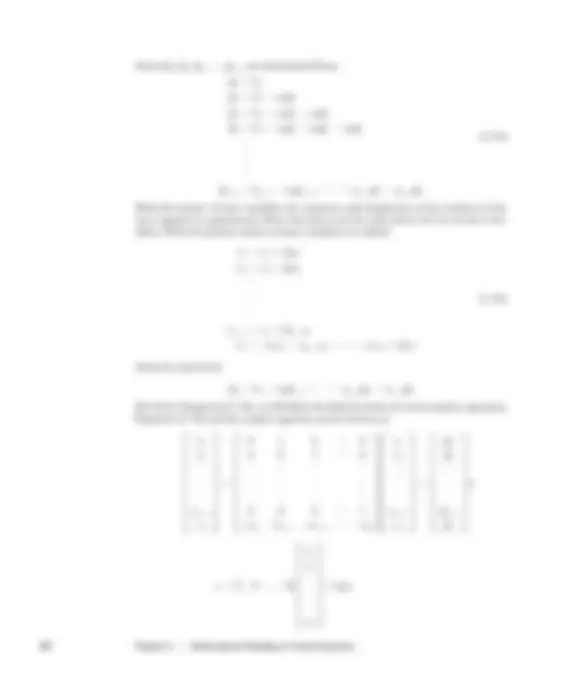
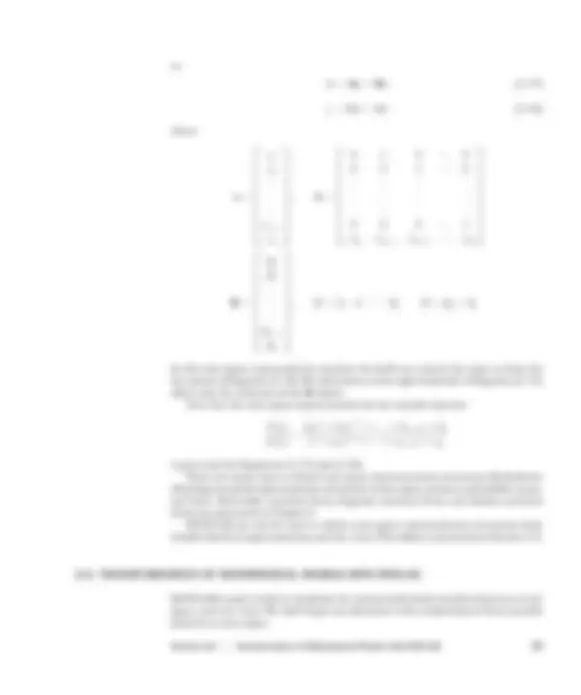
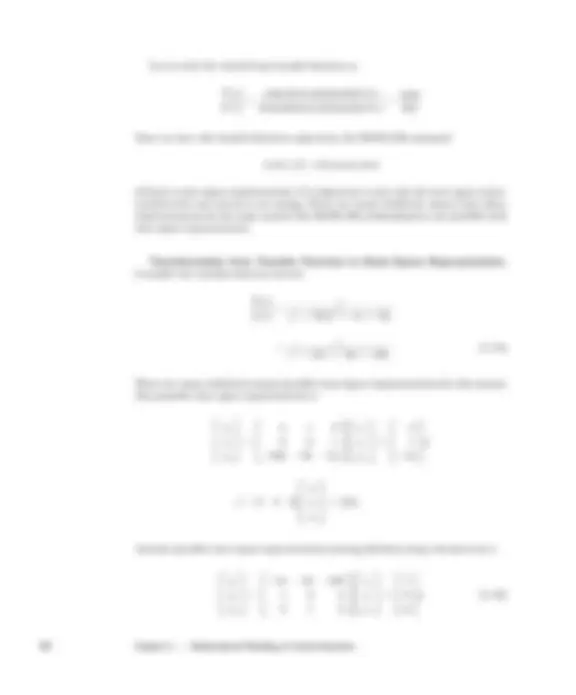
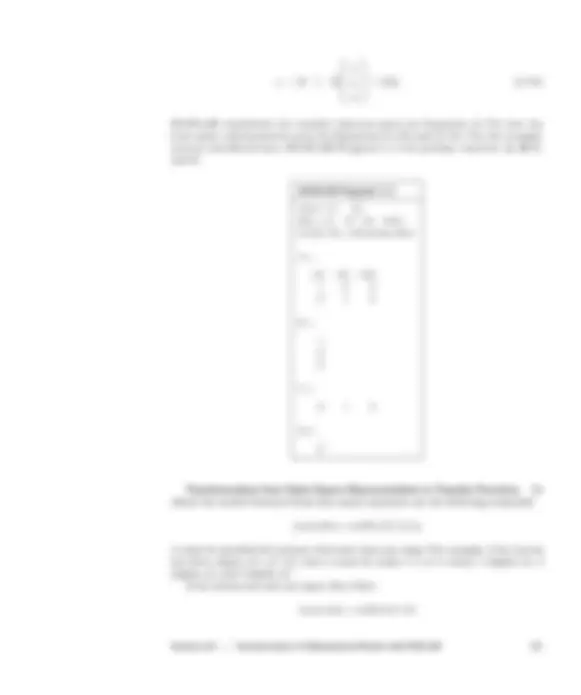
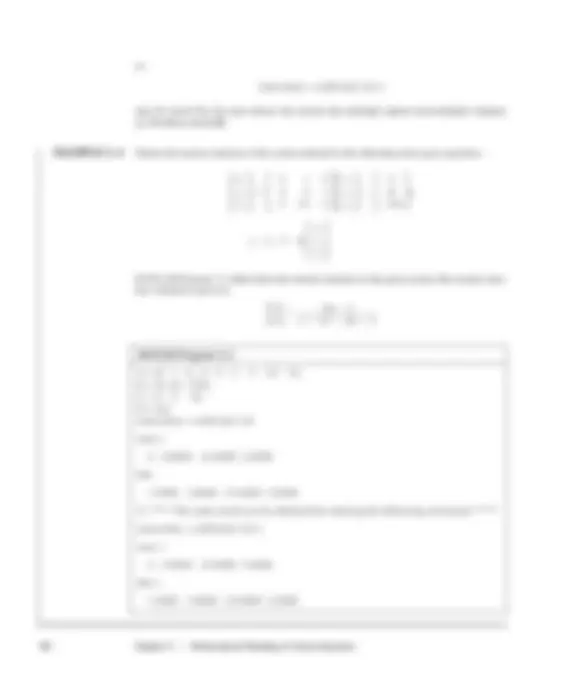
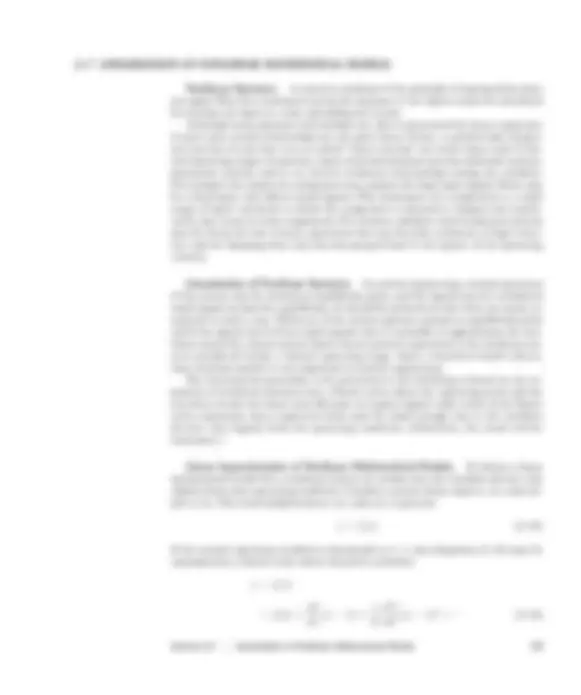
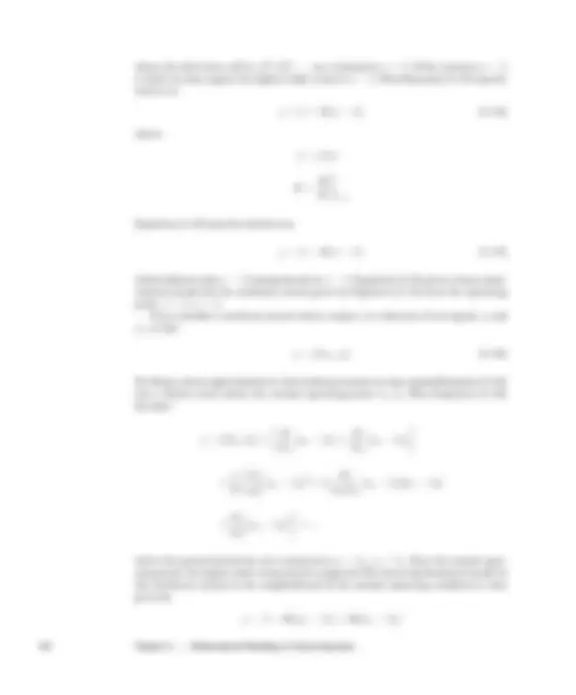
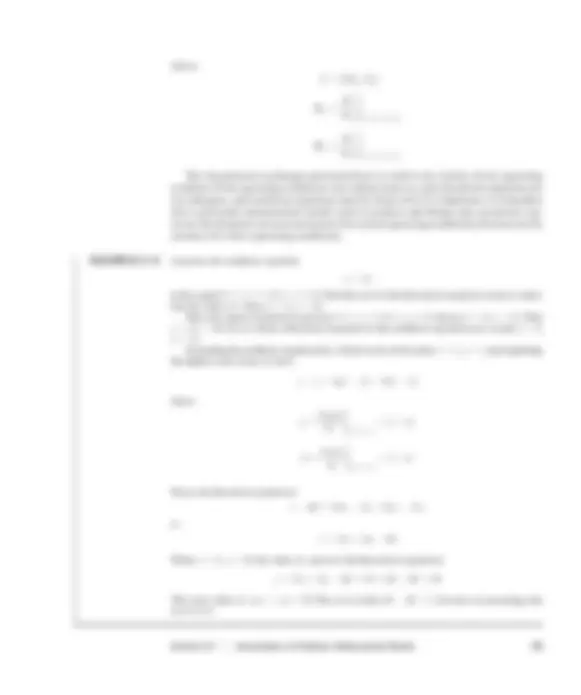
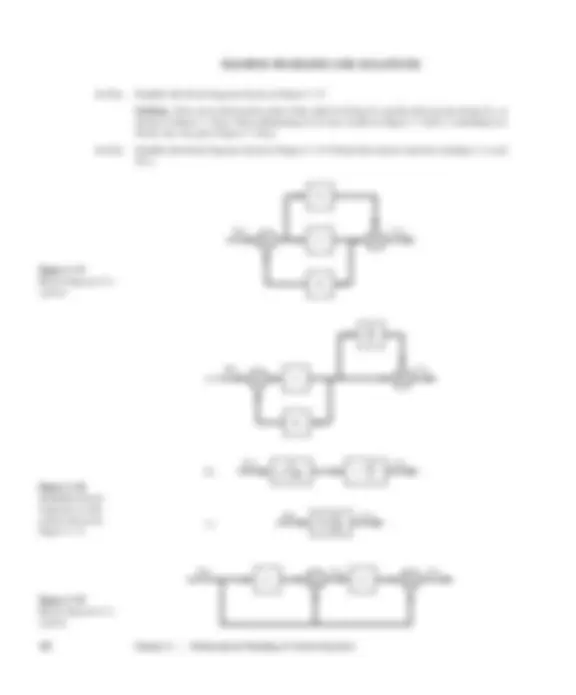
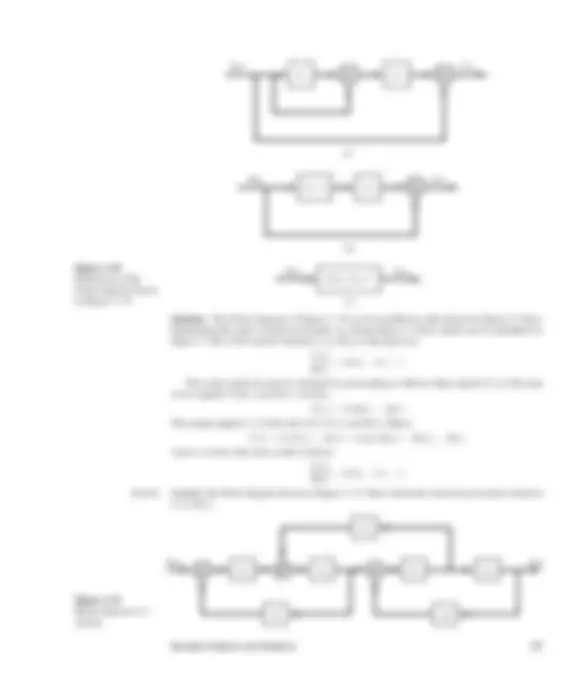
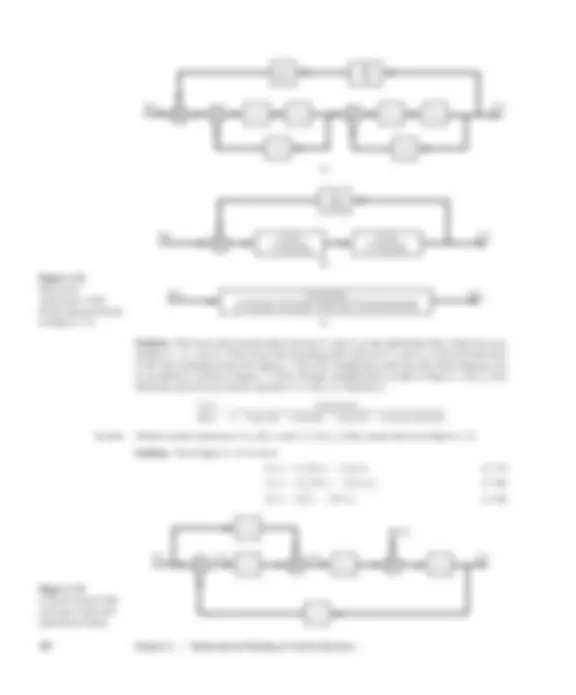
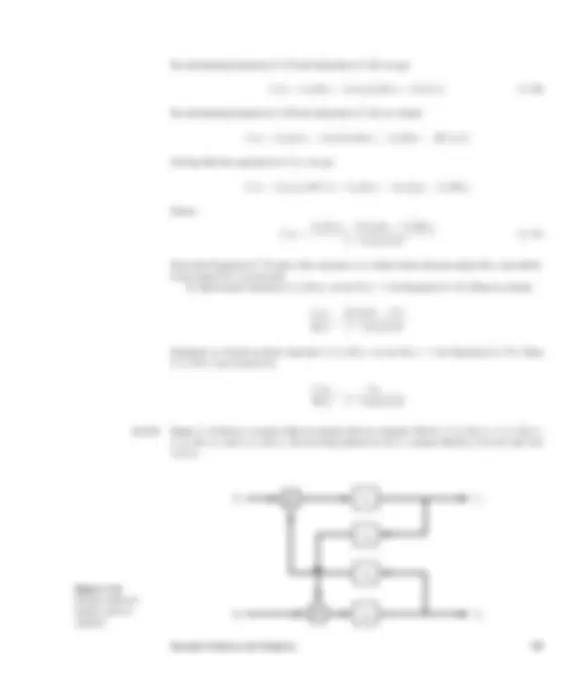
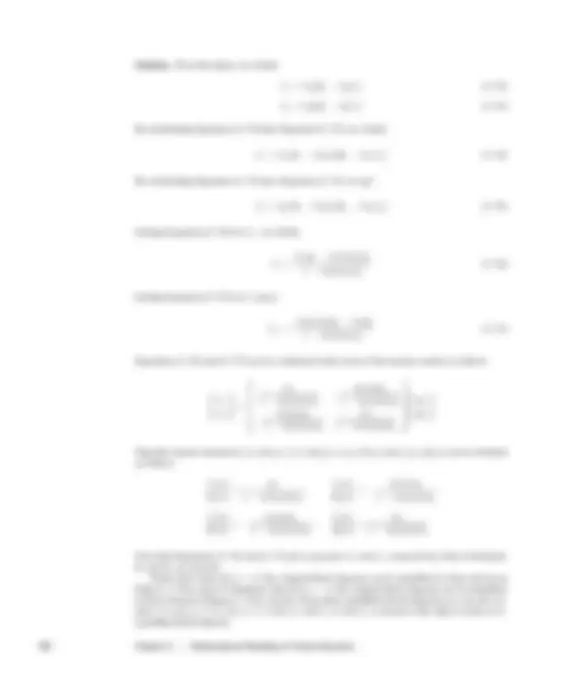
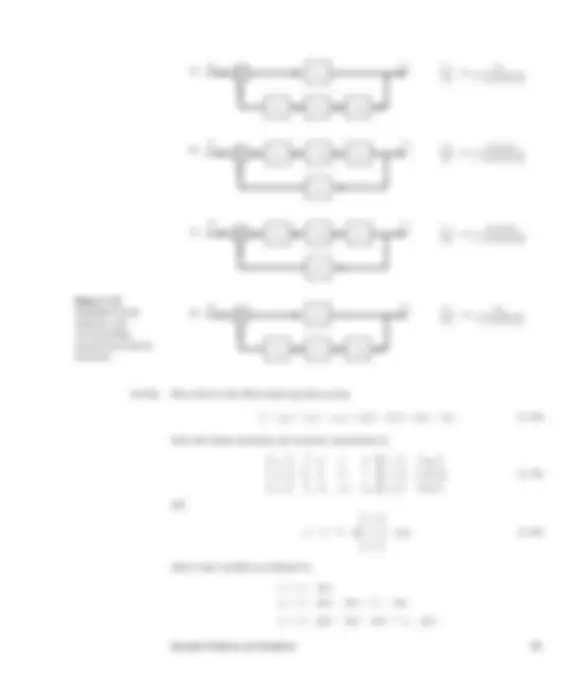
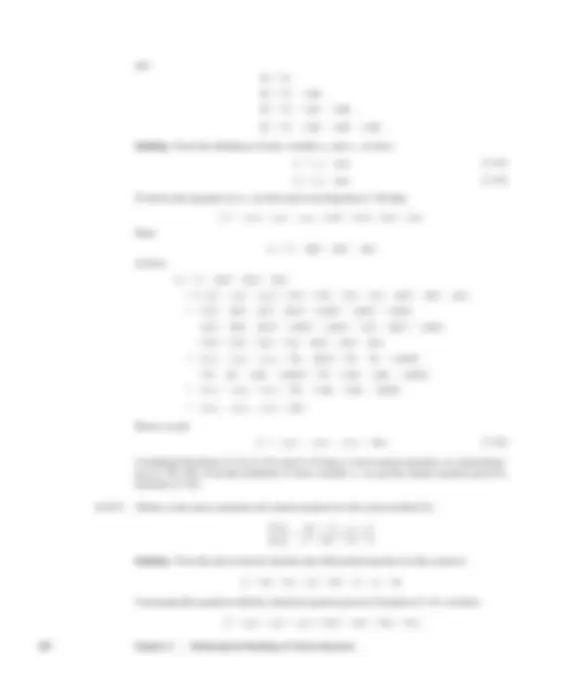
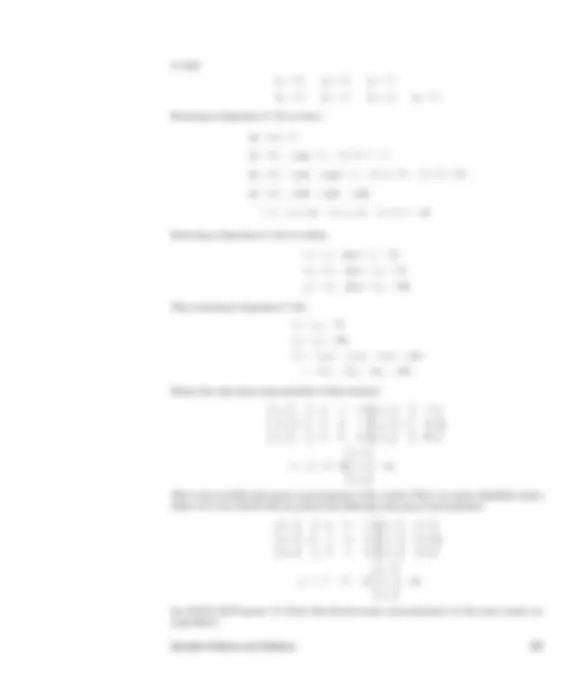
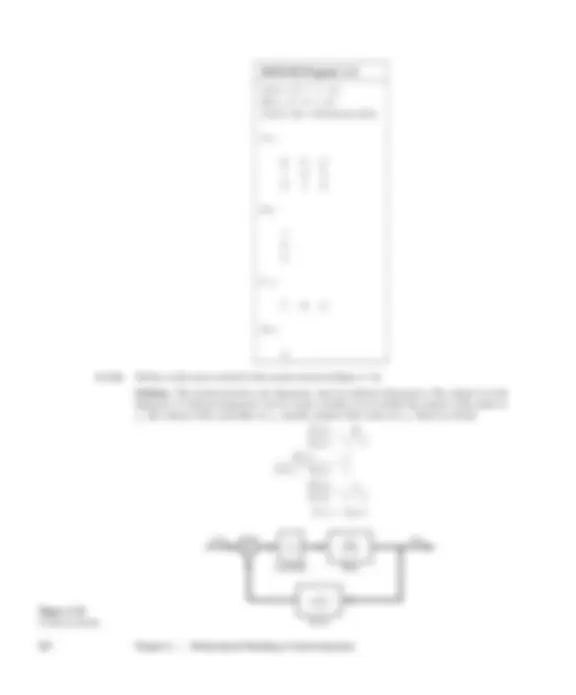
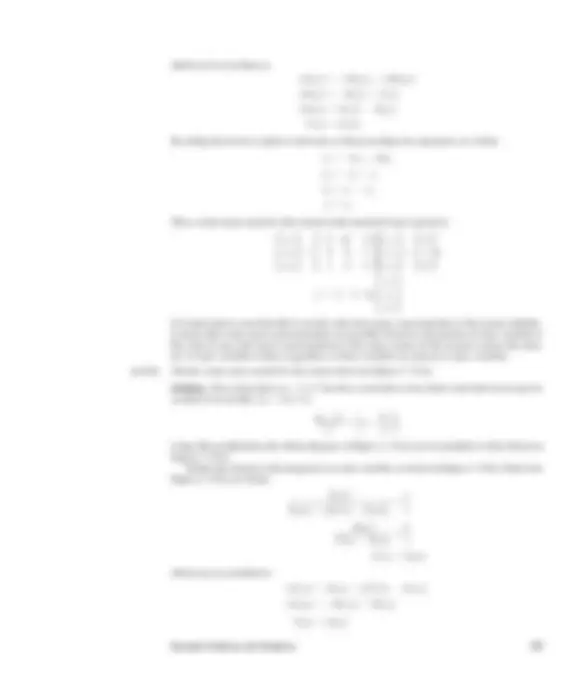
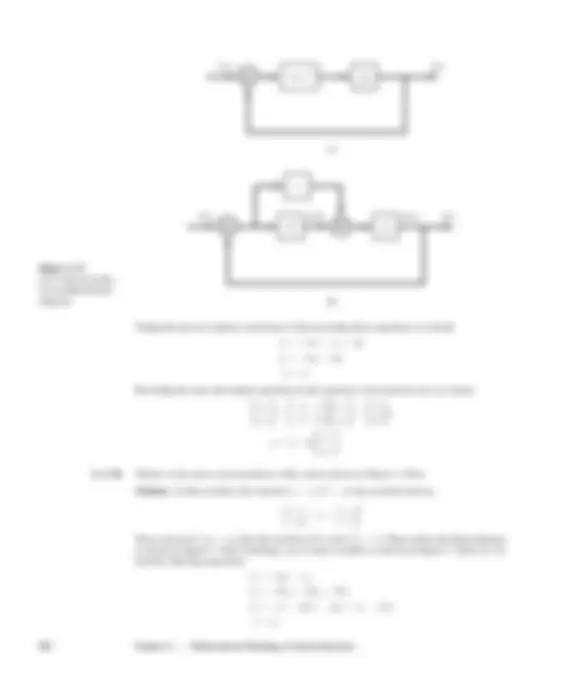
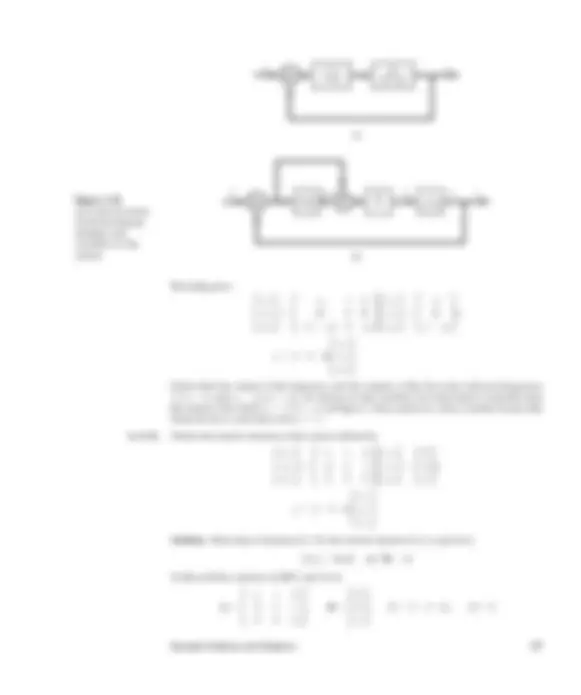
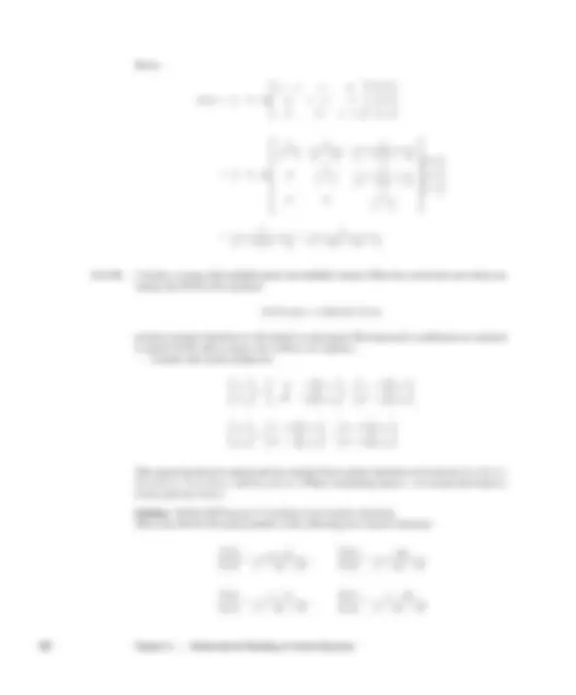
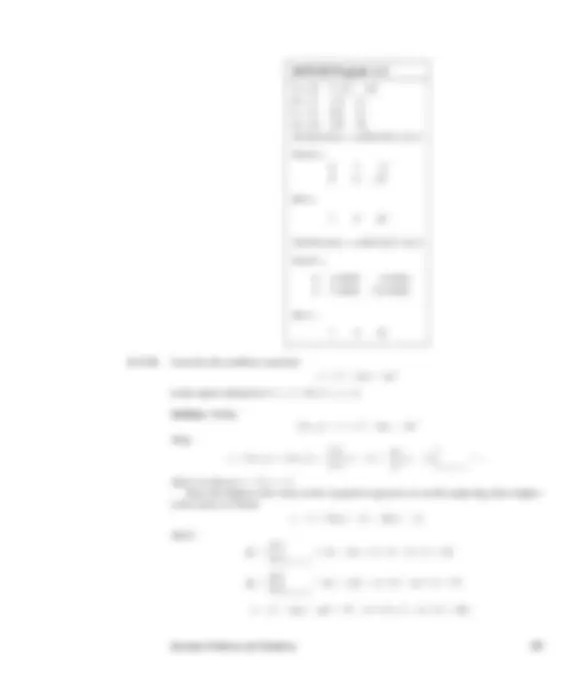
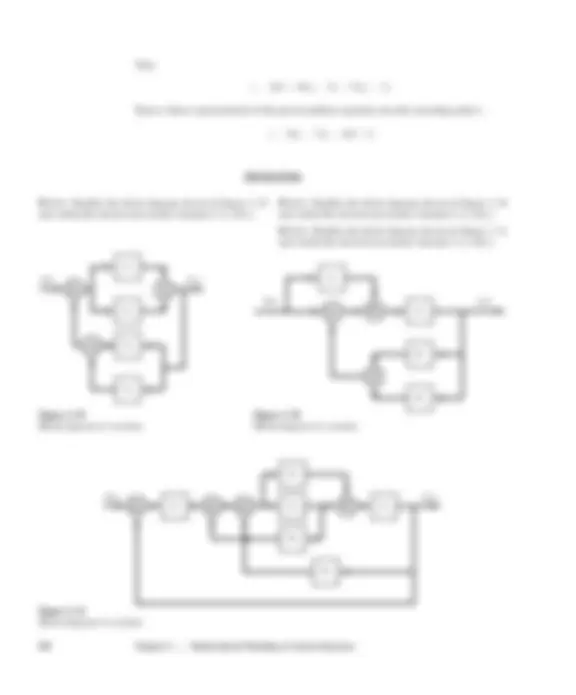
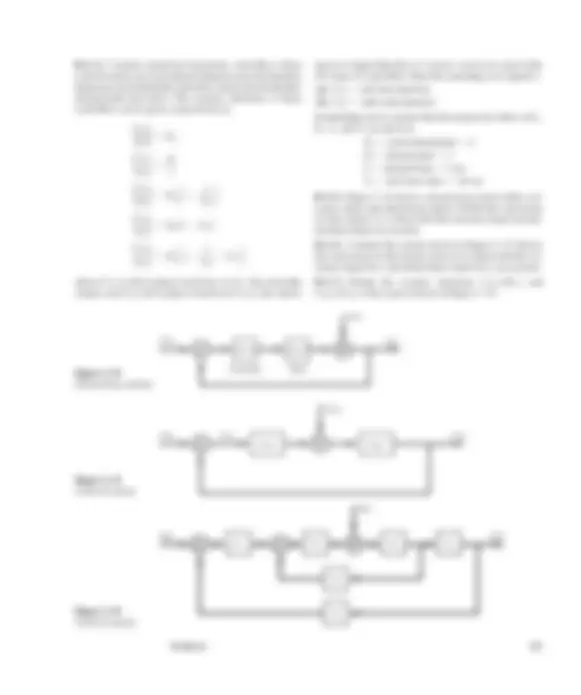
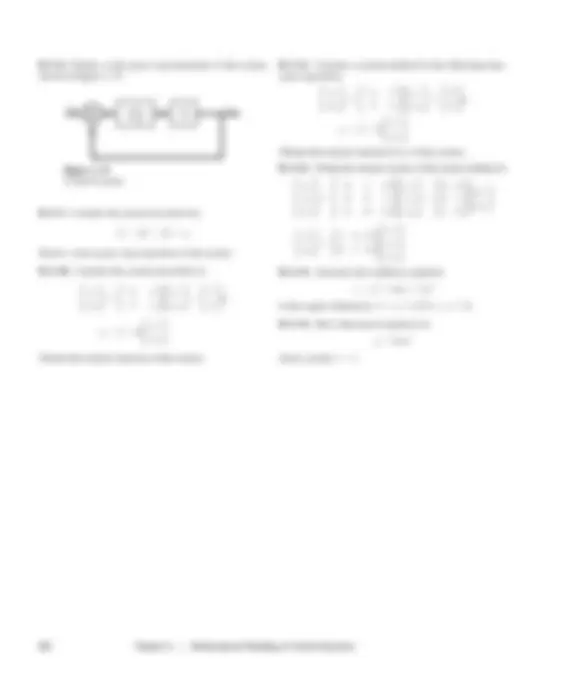

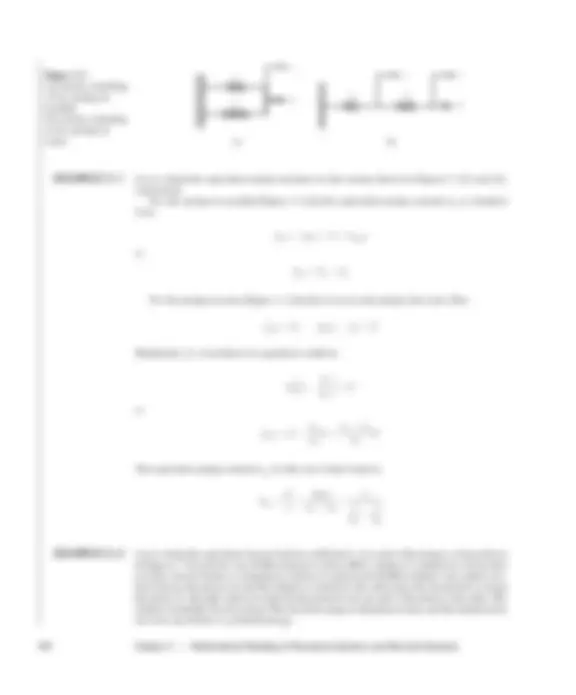
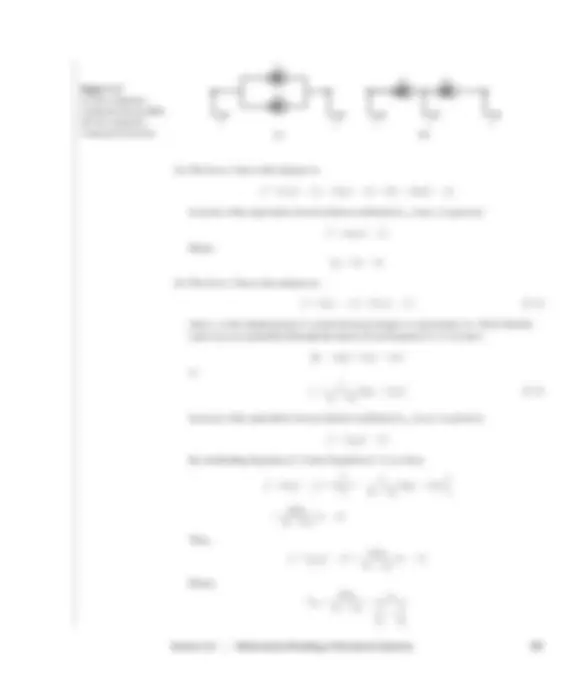
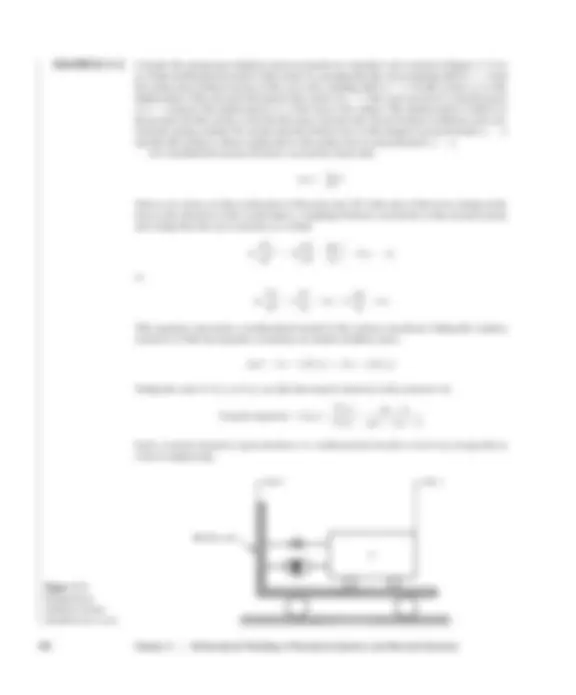
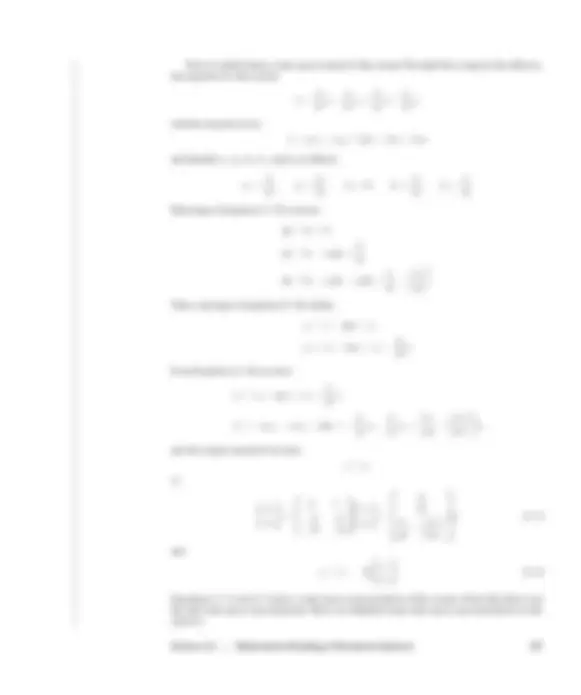
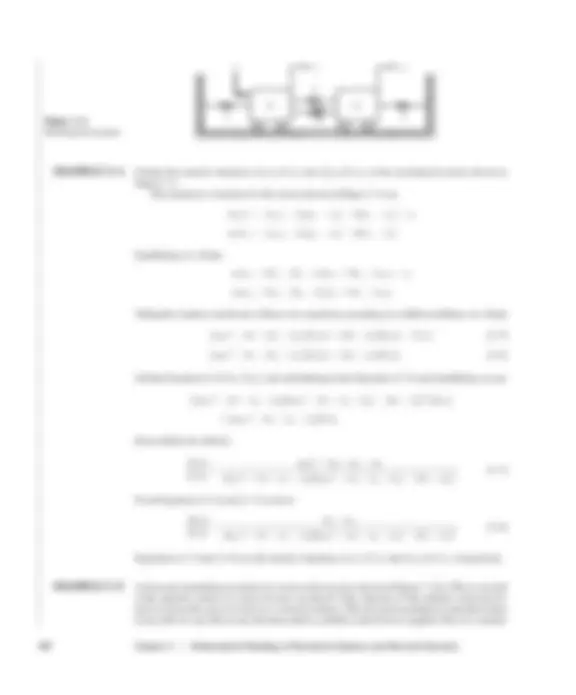
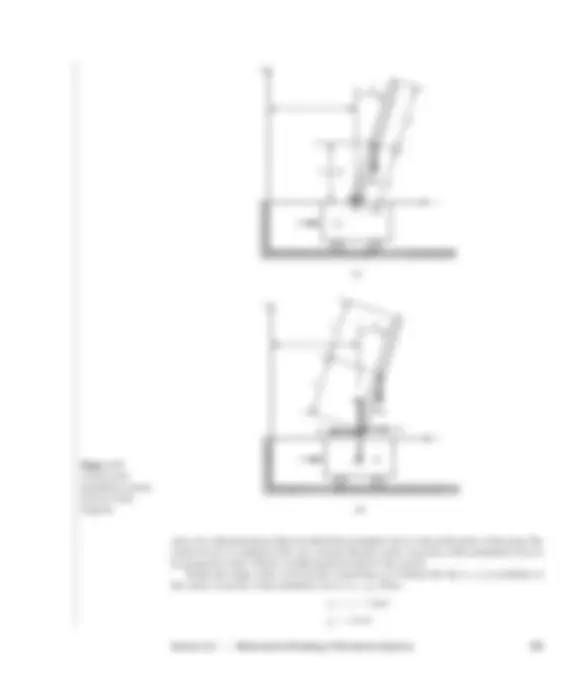
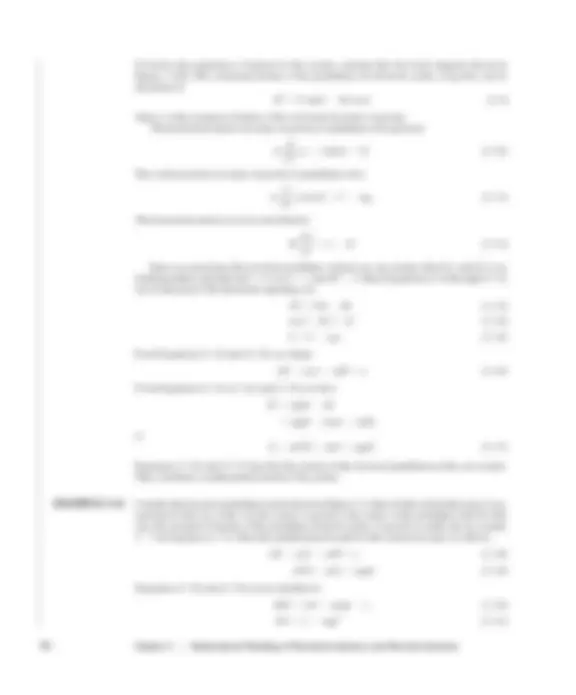
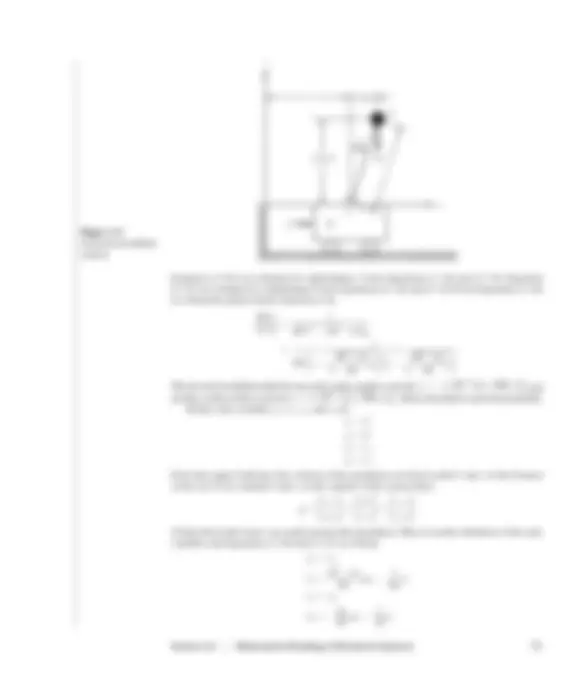
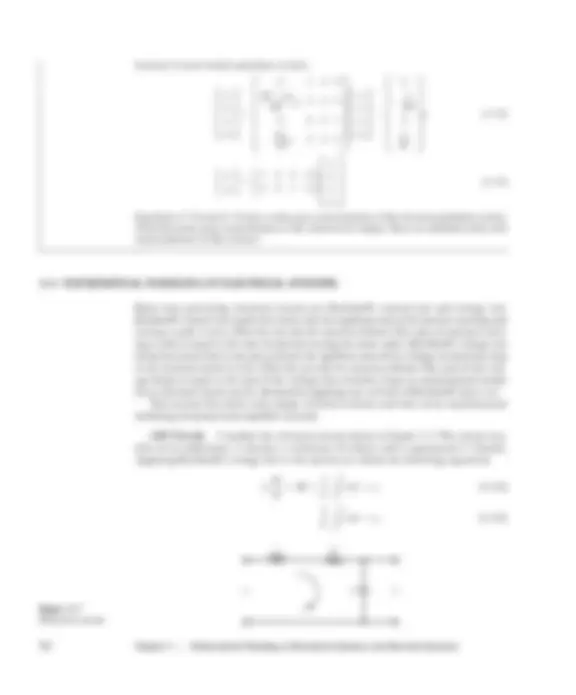
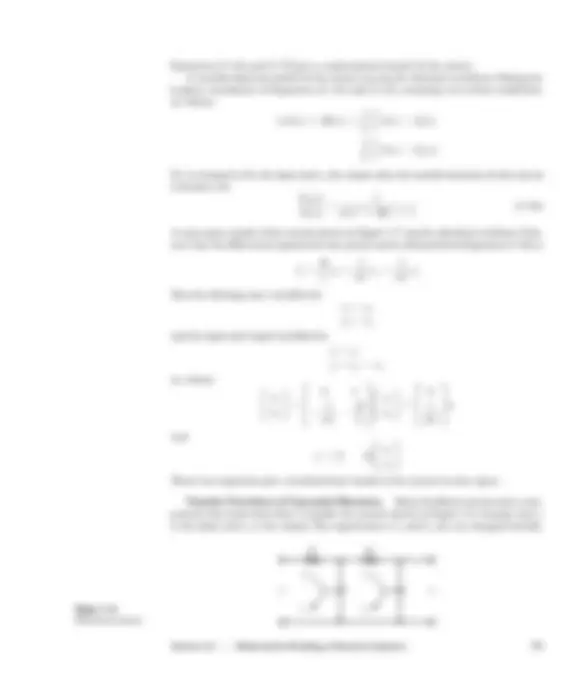
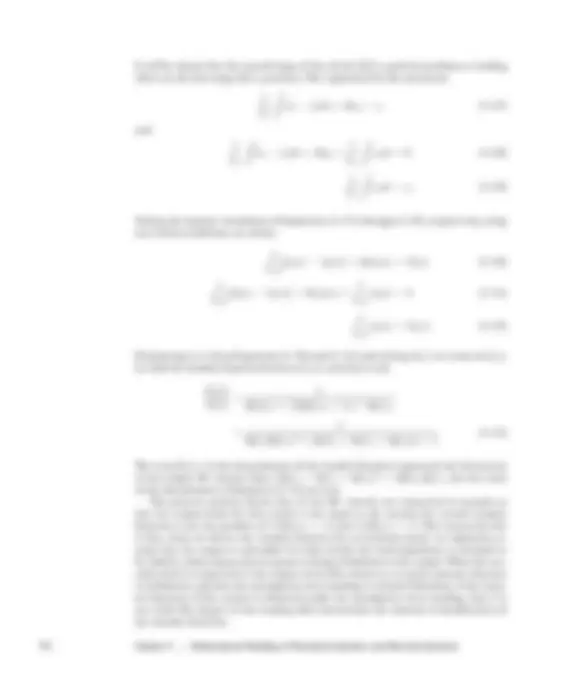
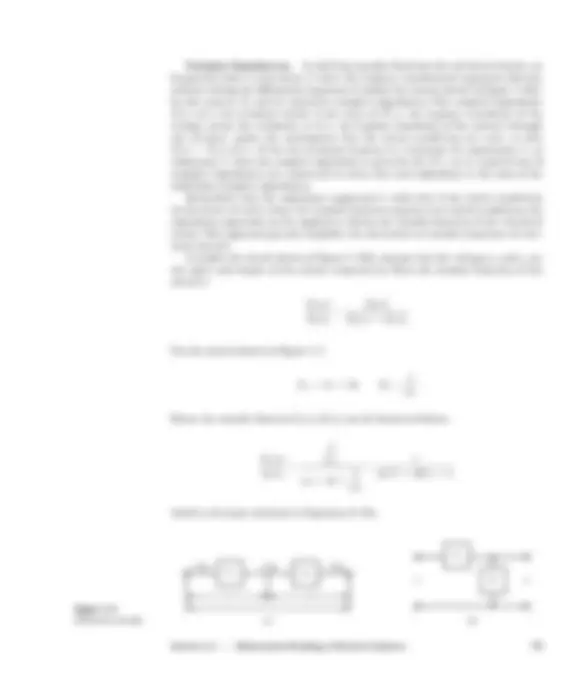
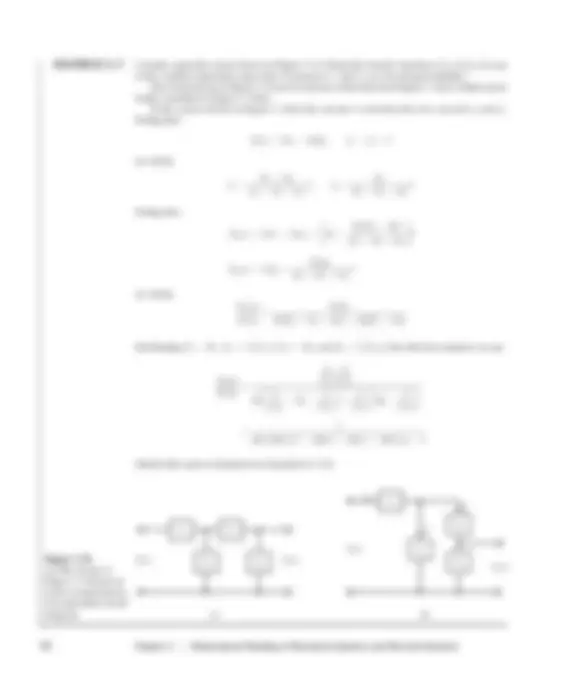
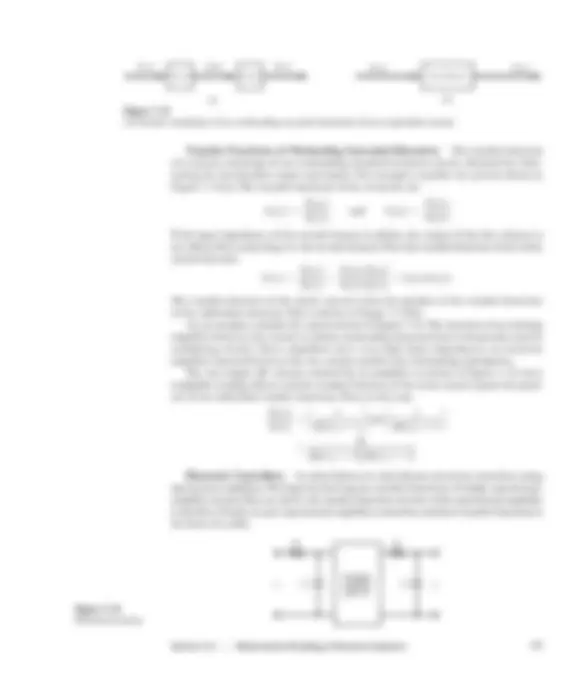

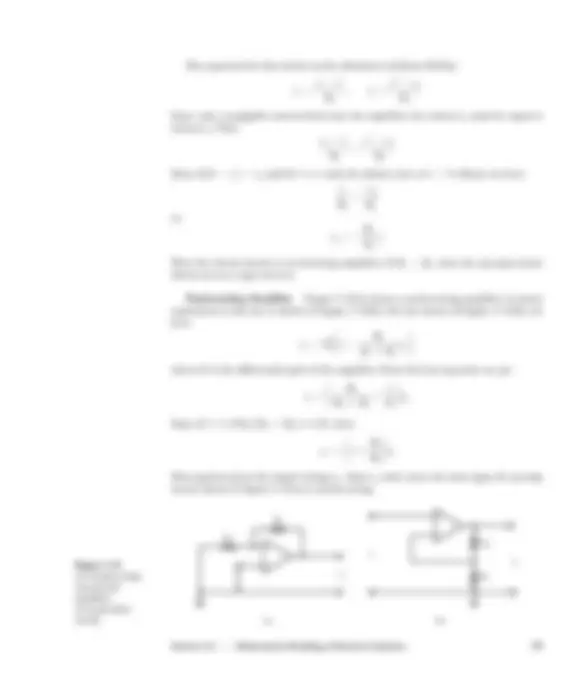
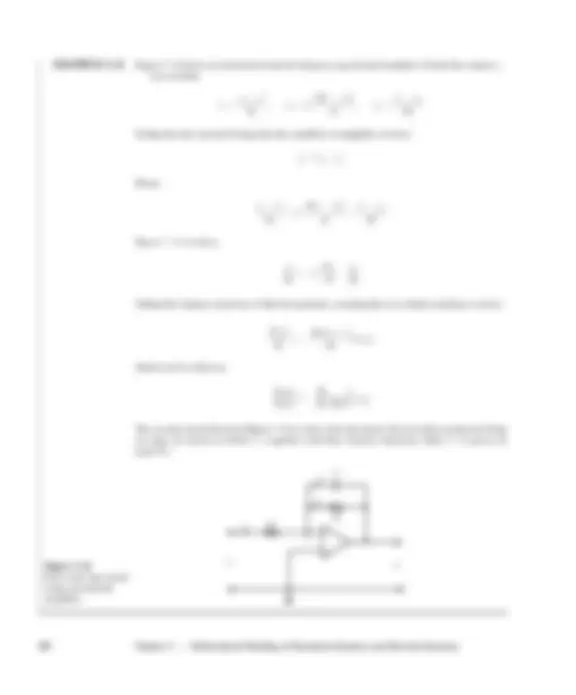
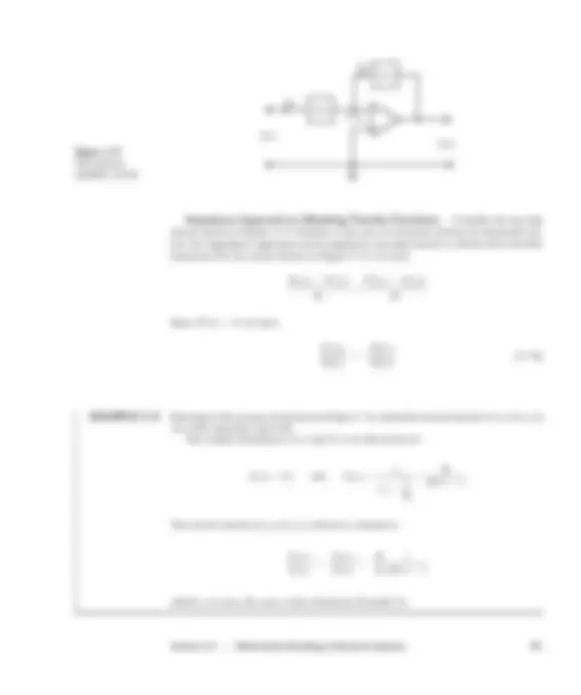
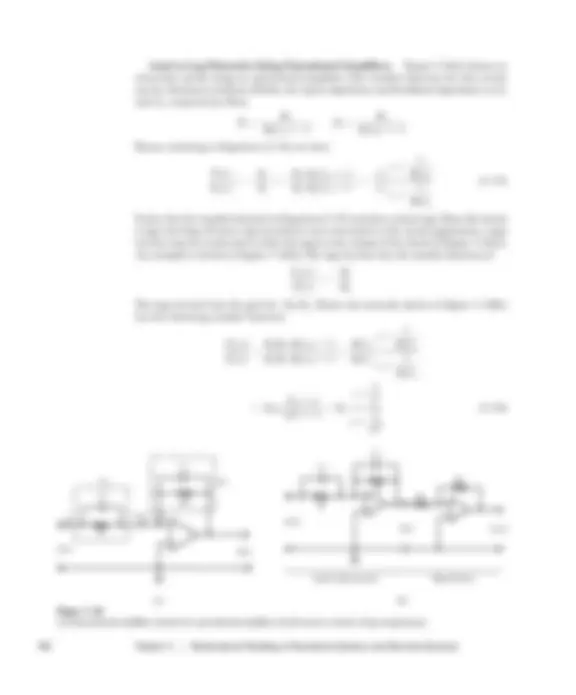
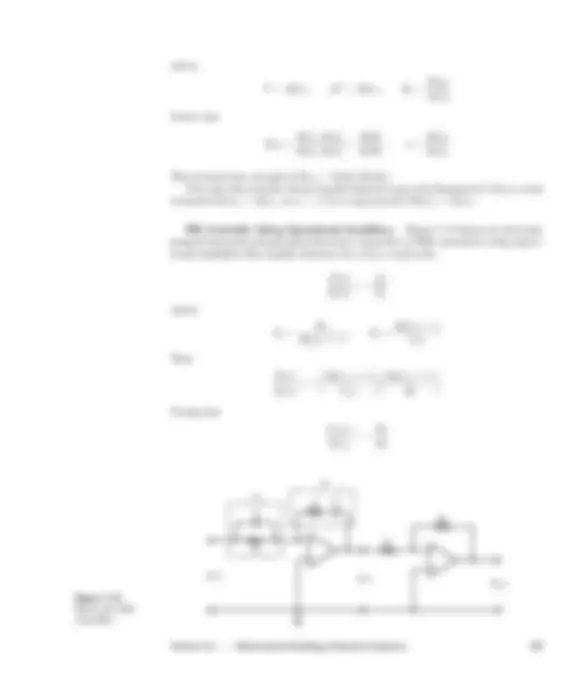
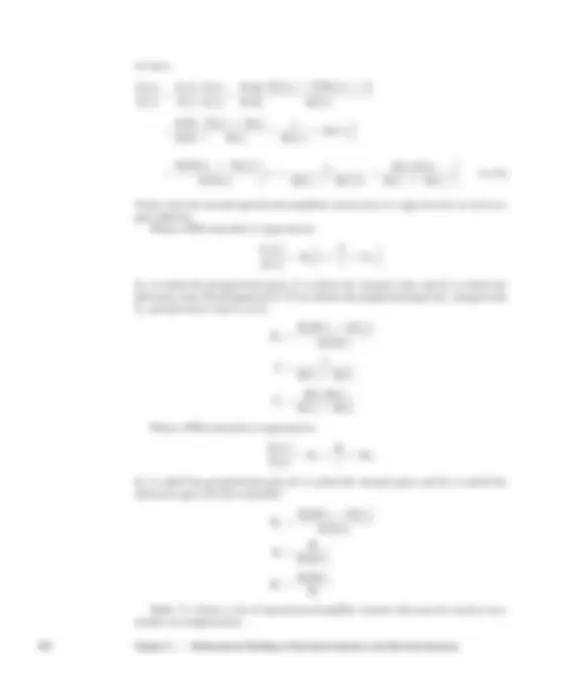
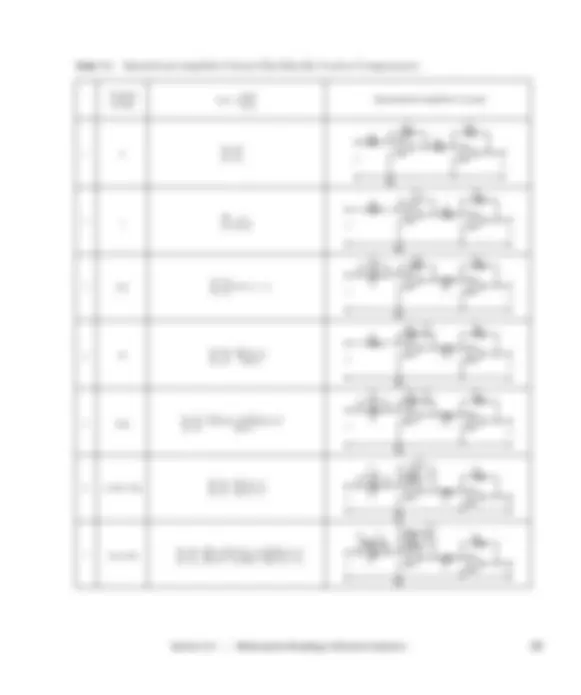
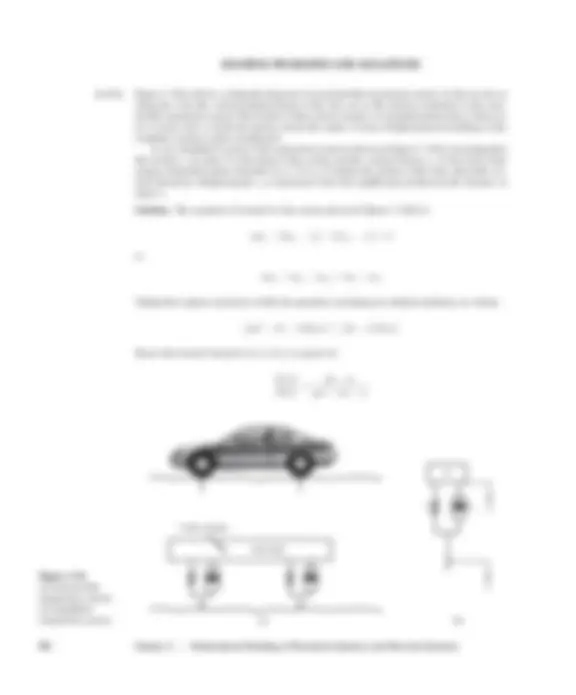
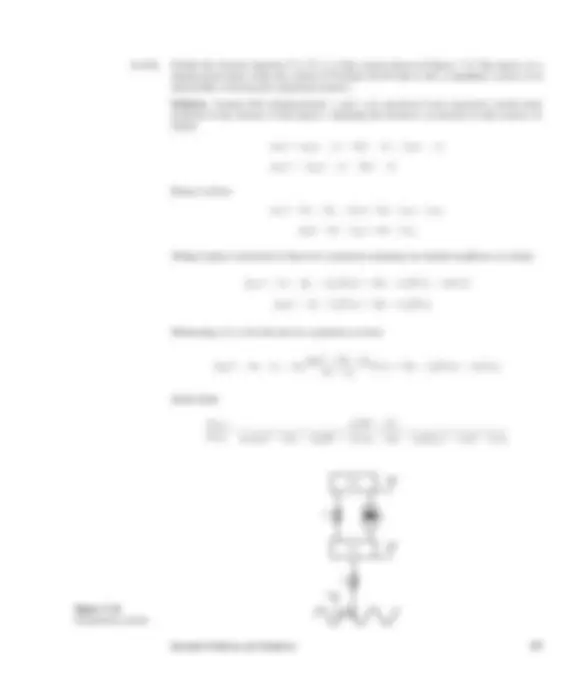
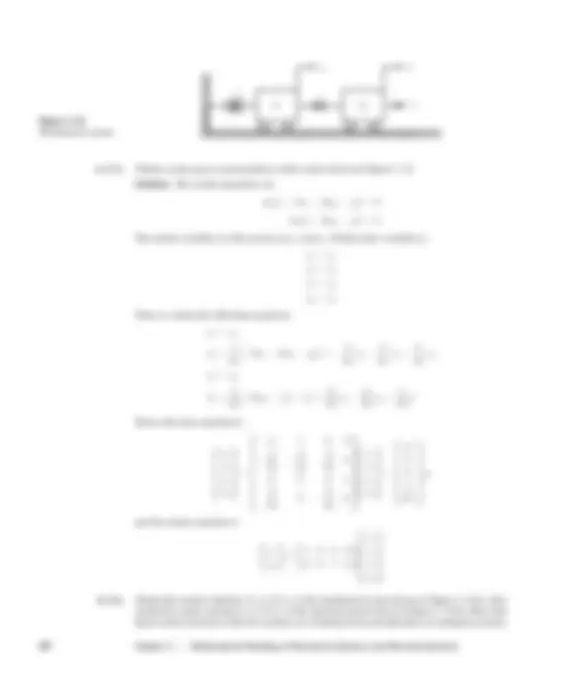
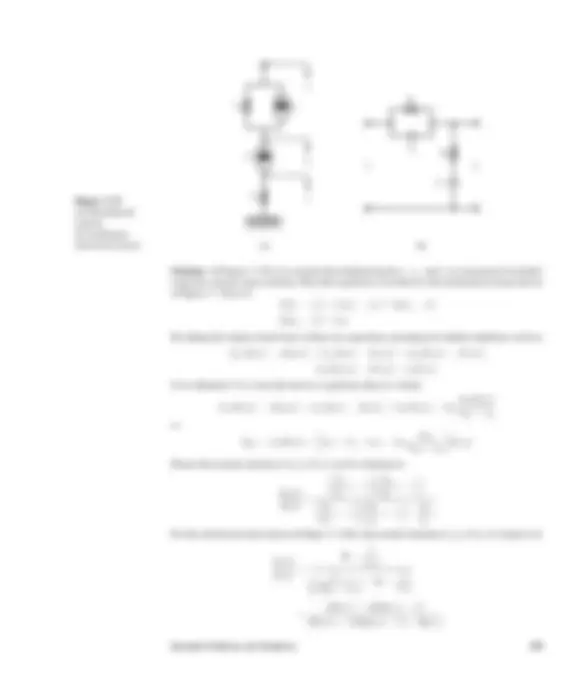
Study with the several resources on Docsity
Earn points by helping other students or get them with a premium plan
Prepare for your exams
Study with the several resources on Docsity
Earn points to download
Earn points by helping other students or get them with a premium plan
Community
Ask the community for help and clear up your study doubts
Discover the best universities in your country according to Docsity users
Free resources
Download our free guides on studying techniques, anxiety management strategies, and thesis advice from Docsity tutors
engineering
Typology: Study notes
1 / 905
This page cannot be seen from the preview
Don't miss anything!
Prentice Hall Boston Columbus Indianapolis New York San Francisco Upper Saddle River Amsterdam Cape Town Dubai London Madrid Milan Munich Paris Montreal Toronto Delhi Mexico City Sao Paulo Sydney Hong Kong Seoul Singapore Taipei Tokyo
iii
Preface ix
Chapter 1 Introduction to Control Systems 1
1–1 Introduction 1
1–2 Examples of Control Systems 4
1–3 Closed-Loop Control Versus Open-Loop Control 7
1–4 Design and Compensation of Control Systems 9
1–5 Outline of the Book 10
Chapter 2 Mathematical Modeling of Control Systems 13
2–1 Introduction 13
2–2 Transfer Function and Impulse-Response Function 15
2–3 Automatic Control Systems 17
2–4 Modeling in State Space 29
2–5 State-Space Representation of Scalar Differential Equation Systems 35
2–6 Transformation of Mathematical Models with MATLAB 39
ix
This book introduces important concepts in the analysis and design of control systems. Readers will find it to be a clear and understandable textbook for control system courses at colleges and universities. It is written for senior electrical, mechanical, aerospace, or chemical engineering students. The reader is expected to have fulfilled the following prerequisites: introductory courses on differential equations, Laplace transforms, vector- matrix analysis, circuit analysis, mechanics, and introductory thermodynamics. The main revisions made in this edition are as follows:
This edition of Modern Control Engineering is organized into ten chapters.The outline of this book is as follows: Chapter 1 presents an introduction to control systems. Chapter 2
deals with mathematical modeling of control systems. A linearization technique for non- linear mathematical models is presented in this chapter. Chapter 3 derives mathematical models of mechanical systems and electrical systems. Chapter 4 discusses mathematical modeling of fluid systems (such as liquid-level systems, pneumatic systems, and hydraulic systems) and thermal systems. Chapter 5 treats transient response and steady-state analyses of control systems. MATLAB is used extensively for obtaining transient response curves. Routh’s stability criterion is presented for stability analysis of control systems. Hurwitz stability criterion is also presented. Chapter 6 discusses the root-locus analysis and design of control systems, including positive feedback systems and conditionally stable systems Plotting root loci with MAT- LAB is discussed in detail. Design of lead, lag, and lag-lead compensators with the root- locus method is included. Chapter 7 treats the frequency-response analysis and design of control systems. The Nyquist stability criterion is presented in an easily understandable manner.The Bode di- agram approach to the design of lead, lag, and lag-lead compensators is discussed. Chapter 8 deals with basic and modified PID controllers. Computational approaches for obtaining optimal parameter values for PID controllers are discussed in detail, par- ticularly with respect to satisfying requirements for step-response characteristics. Chapter 9 treats basic analyses of control systems in state space. Concepts of con- trollability and observability are discussed in detail. Chapter 10 deals with control systems design in state space. The discussions include pole placement, state observers, and quadratic optimal control. An introductory dis- cussion of robust control systems is presented at the end of Chapter 10. The book has been arranged toward facilitating the student’s gradual understanding of control theory. Highly mathematical arguments are carefully avoided in the presen- tation of the materials. Statement proofs are provided whenever they contribute to the understanding of the subject matter presented. Special effort has been made to provide example problems at strategic points so that the reader will have a clear understanding of the subject matter discussed. In addition, a number of solved problems (A-problems) are provided at the end of each chapter, except Chapter 1. The reader is encouraged to study all such solved problems carefully; this will allow the reader to obtain a deeper understanding of the topics discussed. In addition, many problems (without solutions) are provided at the end of each chapter, except Chapter 1. The unsolved problems (B-problems) may be used as homework or quiz problems. If this book is used as a text for a semester course (with 56 or so lecture hours), a good portion of the material may be covered by skipping certain subjects. Because of the abundance of example problems and solved problems (A-problems) that might answer many possible questions that the reader might have, this book can also serve as a self- study book for practicing engineers who wish to study basic control theories. I would like to thank the following reviewers for this edition of the book: Mark Camp- bell, Cornell University; Henry Sodano, Arizona State University; and Atul G. Kelkar, Iowa State University. Finally, I wish to offer my deep appreciation to Ms.Alice Dworkin, Associate Editor, Mr. Scott Disanno, Senior Managing Editor, and all the people in- volved in this publishing project, for the speedy yet superb production of this book. Katsuhiko Ogata
x Preface
2 Chapter 1 / Introduction to Control Systems
Minorsky, Hazen, and Nyquist, among many others. In 1922, Minorsky worked on automatic controllers for steering ships and showed how stability could be deter- mined from the differential equations describing the system. In 1932, Nyquist developed a relatively simple procedure for determining the stability of closed-loop systems on the basis of open-loop response to steady-state sinusoidal inputs. In 1934, Hazen, who introduced the term servomechanisms for position control systems, discussed the design of relay servomechanisms capable of closely following a chang- ing input. During the decade of the 1940s, frequency-response methods (especially the Bode diagram methods due to Bode) made it possible for engineers to design linear closed- loop control systems that satisfied performance requirements. Many industrial control systems in 1940s and 1950s used PID controllers to control pressure, temperature, etc. In the early 1940s Ziegler and Nichols suggested rules for tuning PID controllers, called Ziegler–Nichols tuning rules. From the end of the 1940s to the 1950s, the root-locus method due to Evans was fully developed. The frequency-response and root-locus methods, which are the core of classical con- trol theory, lead to systems that are stable and satisfy a set of more or less arbitrary per- formance requirements. Such systems are, in general, acceptable but not optimal in any meaningful sense. Since the late 1950s, the emphasis in control design problems has been shifted from the design of one of many systems that work to the design of one optimal system in some meaningful sense. As modern plants with many inputs and outputs become more and more complex, the description of a modern control system requires a large number of equations. Clas- sical control theory, which deals only with single-input, single-output systems, becomes powerless for multiple-input, multiple-output systems. Since about 1960, because the availability of digital computers made possible time-domain analysis of complex sys- tems, modern control theory, based on time-domain analysis and synthesis using state variables, has been developed to cope with the increased complexity of modern plants and the stringent requirements on accuracy, weight, and cost in military, space, and in- dustrial applications. During the years from 1960 to 1980, optimal control of both deterministic and sto- chastic systems, as well as adaptive and learning control of complex systems, were fully investigated. From 1980s to 1990s, developments in modern control theory were cen- tered around robust control and associated topics. Modern control theory is based on time-domain analysis of differential equation systems. Modern control theory made the design of control systems simpler because the theory is based on a model of an actual control system. However, the system’s stability is sensitive to the error between the actual system and its model. This means that when the designed controller based on a model is applied to the actual system, the system may not be stable. To avoid this situation, we design the control system by first setting up the range of possible errors and then designing the con- troller in such a way that, if the error of the system stays within the assumed range, the designed control system will stay stable. The design method based on this principle is called robust control theory. This theory incorporates both the frequency- response approach and the time-domain approach. The theory is mathematically very complex.
Section 1–1 / Introduction 3
Because this theory requires mathematical background at the graduate level, inclu- sion of robust control theory in this book is limited to introductory aspects only. The reader interested in details of robust control theory should take a graduate-level control course at an established college or university.
Definitions. Before we can discuss control systems, some basic terminologies must be defined.
Controlled Variable and Control Signal or Manipulated Variable. The controlled variable is the quantity or condition that is measured and controlled. The control signal or manipulated variable is the quantity or condition that is varied by the controller so as to affect the value of the controlled variable. Normally, the controlled variable is the output of the system. Control means measuring the value of the controlled variable of the system and applying the control signal to the system to correct or limit deviation of the measured value from a desired value. In studying control engineering, we need to define additional terms that are neces- sary to describe control systems.
Plants. A plant may be a piece of equipment, perhaps just a set of machine parts functioning together, the purpose of which is to perform a particular operation. In this book, we shall call any physical object to be controlled (such as a mechanical device, a heating furnace, a chemical reactor, or a spacecraft) a plant.
Processes. The Merriam–Webster Dictionary defines a process to be a natural, pro- gressively continuing operation or development marked by a series of gradual changes that succeed one another in a relatively fixed way and lead toward a particular result or end; or an artificial or voluntary, progressively continuing operation that consists of a se- ries of controlled actions or movements systematically directed toward a particular re- sult or end. In this book we shall call any operation to be controlled a process. Examples are chemical, economic, and biological processes.
Systems. A system is a combination of components that act together and perform a certain objective. A system need not be physical. The concept of the system can be applied to abstract, dynamic phenomena such as those encountered in economics. The word system should, therefore, be interpreted to imply physical, biological, economic, and the like, systems.
Disturbances. A disturbance is a signal that tends to adversely affect the value of the output of a system. If a disturbance is generated within the system, it is called internal, while an external disturbance is generated outside the system and is an input.
Feedback Control. Feedback control refers to an operation that, in the presence of disturbances, tends to reduce the difference between the output of a system and some reference input and does so on the basis of this difference. Here only unpredictable dis- turbances are so specified, since predictable or known disturbances can always be com- pensated for within the system.
Section 1–2 / Examples of Control Systems 5
Thermometer
Heater
Interface Controller
Amplifier Interface
A/D converter
Programmed input
Electric furnace
Relay
Figure 1– Temperature control system.
to a digital temperature by an A/D converter. The digital temperature is fed to a con- troller through an interface.This digital temperature is compared with the programmed input temperature, and if there is any discrepancy (error), the controller sends out a sig- nal to the heater, through an interface, amplifier, and relay, to bring the furnace tem- perature to a desired value.
Business Systems. A business system may consist of many groups. Each task assigned to a group will represent a dynamic element of the system. Feedback methods of reporting the accomplishments of each group must be established in such a system for proper operation. The cross-coupling between functional groups must be made a mini- mum in order to reduce undesirable delay times in the system. The smaller this cross- coupling, the smoother the flow of work signals and materials will be. A business system is a closed-loop system. A good design will reduce the manageri- al control required. Note that disturbances in this system are the lack of personnel or ma- terials, interruption of communication, human errors, and the like. The establishment of a well-founded estimating system based on statistics is manda- tory to proper management. It is a well-known fact that the performance of such a system can be improved by the use of lead time, or anticipation. To apply control theory to improve the performance of such a system, we must rep- resent the dynamic characteristic of the component groups of the system by a relative- ly simple set of equations. Although it is certainly a difficult problem to derive mathematical representations of the component groups, the application of optimization techniques to business sys- tems significantly improves the performance of the business system. Consider, as an example, an engineering organizational system that is composed of major groups such as management, research and development, preliminary design, ex- periments, product design and drafting, fabrication and assembling, and tesing. These groups are interconnected to make up the whole operation. Such a system may be analyzed by reducing it to the most elementary set of com- ponents necessary that can provide the analytical detail required and by representing the dynamic characteristics of each component by a set of simple equations. (The dynamic performance of such a system may be determined from the relation between progres- sive accomplishment and time.)
6 Chapter 1 / Introduction to Control Systems
Required product Management
Research and development
Preliminary design Experiments
Product design and drafting
Fabrication and assembling
Testing
Product
Figure 1– Block diagram of an engineering organizational system.
A functional block diagram may be drawn by using blocks to represent the func- tional activities and interconnecting signal lines to represent the information or product output of the system operation. Figure 1–3 is a possible block diagram for this system.
Robust Control System. The first step in the design of a control system is to obtain a mathematical model of the plant or control object. In reality, any model of a plant we want to control will include an error in the modeling process.That is, the actual plant differs from the model to be used in the design of the control system. To ensure the controller designed based on a model will work satisfactorily when this controller is used with the actual plant, one reasonable approach is to assume from the start that there is an uncertainty or error between the actual plant and its mathematical model and include such uncertainty or error in the design process of the control system. The control system designed based on this approach is called a robust control system. Suppose that the actual plant we want to control is (s) and the mathematical model of the actual plant is G(s), that is, (s)=actual plant model that has uncertainty ¢(s) G(s)=nominal plant model to be used for designing the control system (s) and G(s) may be related by a multiplicative factor such as
or an additive factor
or in other forms. Since the exact description of the uncertainty or error ¢(s) is unknown, we use an estimate of ¢(s) and use this estimate, W(s), in the design of the controller. W(s) is a scalar transfer function such that
where is the maximum value of for and is called the H infinity norm of W(s).
W(s)q W(jv) 0 v q
¢(s)q 6 W(s)q = max 0 v q W(jv)
(s) = G(s) + ¢(s)
(s) = G(s)[1 + ¢(s)]
8 Chapter 1 / Introduction to Control Systems
Closed-Loop Control Systems. Feedback control systems are often referred to as closed-loop control systems. In practice, the terms feedback control and closed-loop control are used interchangeably. In a closed-loop control system the actuating error signal, which is the difference between the input signal and the feedback signal (which may be the output signal itself or a function of the output signal and its derivatives and/or integrals), is fed to the controller so as to reduce the error and bring the output of the system to a desired value. The term closed-loop control always implies the use of feedback control action in order to reduce system error.
Open-Loop Control Systems. Those systems in which the output has no effect on the control action are called open-loop control systems. In other words, in an open- loop control system the output is neither measured nor fed back for comparison with the input. One practical example is a washing machine. Soaking, washing, and rinsing in the washer operate on a time basis. The machine does not measure the output signal, that is, the cleanliness of the clothes. In any open-loop control system the output is not compared with the reference input. Thus, to each reference input there corresponds a fixed operating condition; as a result, the accuracy of the system depends on calibration. In the presence of disturbances, an open-loop control system will not perform the desired task. Open-loop control can be used, in practice, only if the relationship between the input and output is known and if there are neither internal nor external disturbances. Clearly, such systems are not feed- back control systems. Note that any control system that operates on a time basis is open loop. For instance, traffic control by means of signals operated on a time basis is another example of open-loop control.
Closed-Loop versus Open-Loop Control Systems. An advantage of the closed- loop control system is the fact that the use of feedback makes the system response rela- tively insensitive to external disturbances and internal variations in system parameters. It is thus possible to use relatively inaccurate and inexpensive components to obtain the accurate control of a given plant, whereas doing so is impossible in the open-loop case. From the point of view of stability, the open-loop control system is easier to build be- cause system stability is not a major problem. On the other hand, stability is a major problem in the closed-loop control system, which may tend to overcorrect errors and thereby can cause oscillations of constant or changing amplitude. It should be emphasized that for systems in which the inputs are known ahead of time and in which there are no disturbances it is advisable to use open-loop control. Closed-loop control systems have advantages only when unpredictable disturbances and/or unpredictable variations in system components are present. Note that the output power rating partially determines the cost, weight, and size of a control system. The number of components used in a closed-loop control system is more than that for a corresponding open-loop control system. Thus, the closed-loop control system is generally higher in cost and power. To decrease the required power of a system, open- loop control may be used where applicable. A proper combination of open-loop and closed-loop controls is usually less expensive and will give satisfactory overall system performance. Most analyses and designs of control systems presented in this book are concerned with closed-loop control systems. Under certain circumstances (such as where no disturbances exist or the output is hard to measure) open-loop control systems may be
desired. Therefore, it is worthwhile to summarize the advantages and disadvantages of using open-loop control systems. The major advantages of open-loop control systems are as follows:
1. Simple construction and ease of maintenance. 2. Less expensive than a corresponding closed-loop system. 3. There is no stability problem. 4. Convenient when output is hard to measure or measuring the output precisely is economically not feasible. (For example, in the washer system, it would be quite ex- pensive to provide a device to measure the quality of the washer’s output, clean- liness of the clothes.) The major disadvantages of open-loop control systems are as follows: 1. Disturbances and changes in calibration cause errors, and the output may be different from what is desired. 2. To maintain the required quality in the output, recalibration is necessary from time to time.
This book discusses basic aspects of the design and compensation of control systems. Compensation is the modification of the system dynamics to satisfy the given specifi- cations. The approaches to control system design and compensation used in this book are the root-locus approach, frequency-response approach, and the state-space ap- proach. Such control systems design and compensation will be presented in Chapters 6, 7, 9 and 10. The PID-based compensational approach to control systems design is given in Chapter 8. In the actual design of a control system, whether to use an electronic, pneumatic, or hydraulic compensator is a matter that must be decided partially based on the nature of the controlled plant. For example, if the controlled plant involves flammable fluid, then we have to choose pneumatic components (both a compensator and an actuator) to avoid the possibility of sparks. If, however, no fire hazard exists, then electronic com- pensators are most commonly used. (In fact, we often transform nonelectrical signals into electrical signals because of the simplicity of transmission, increased accuracy, increased reliability, ease of compensation, and the like.)
Performance Specifications. Control systems are designed to perform specific tasks. The requirements imposed on the control system are usually spelled out as per- formance specifications. The specifications may be given in terms of transient response requirements (such as the maximum overshoot and settling time in step response) and of steady-state requirements (such as steady-state error in following ramp input) or may be given in frequency-response terms. The specifications of a control system must be given before the design process begins. For routine design problems, the performance specifications (which relate to accura- cy, relative stability, and speed of response) may be given in terms of precise numerical values. In other cases they may be given partially in terms of precise numerical values and
Section 1–4 / Design and Compensation of Control Systems 9