

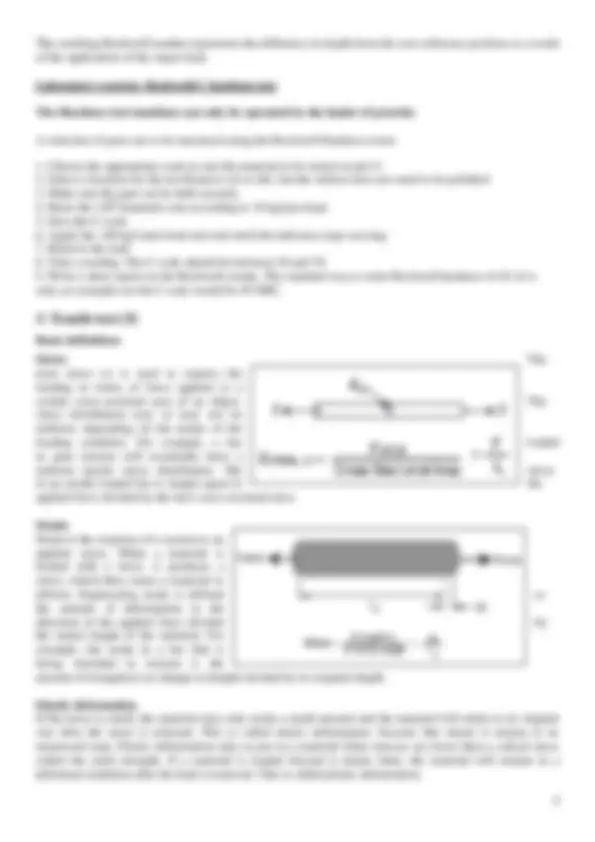
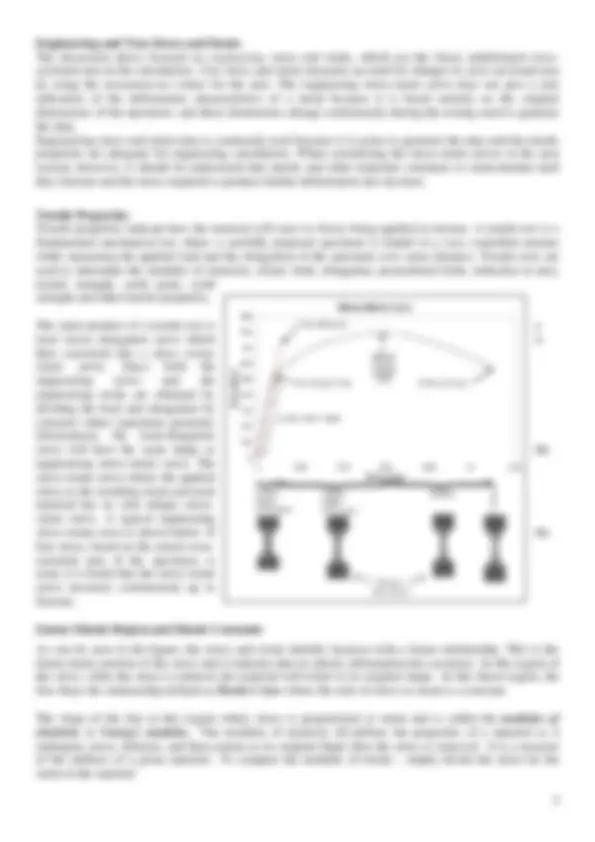
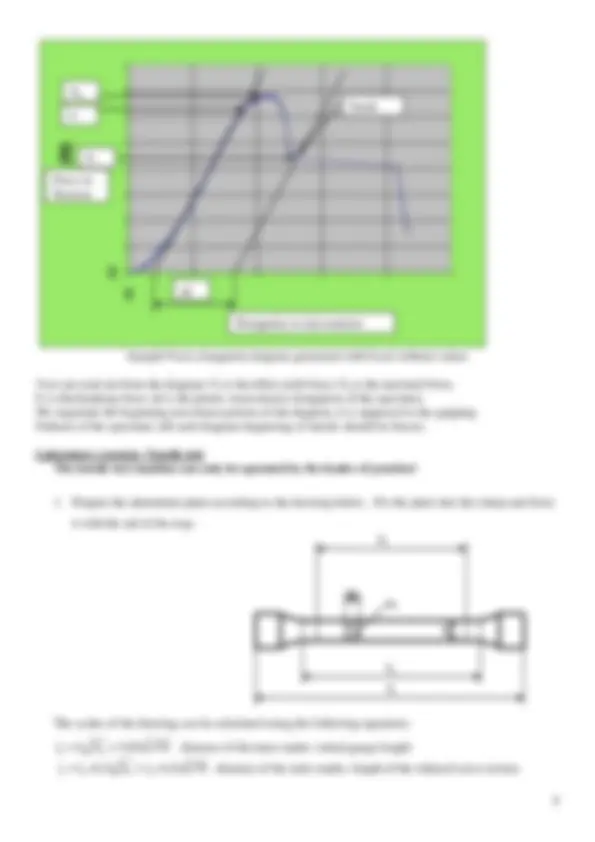
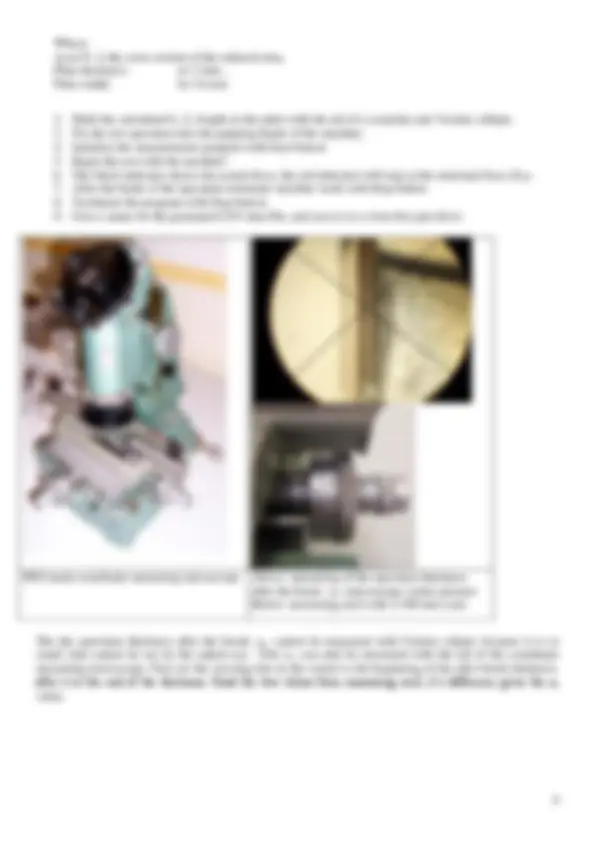
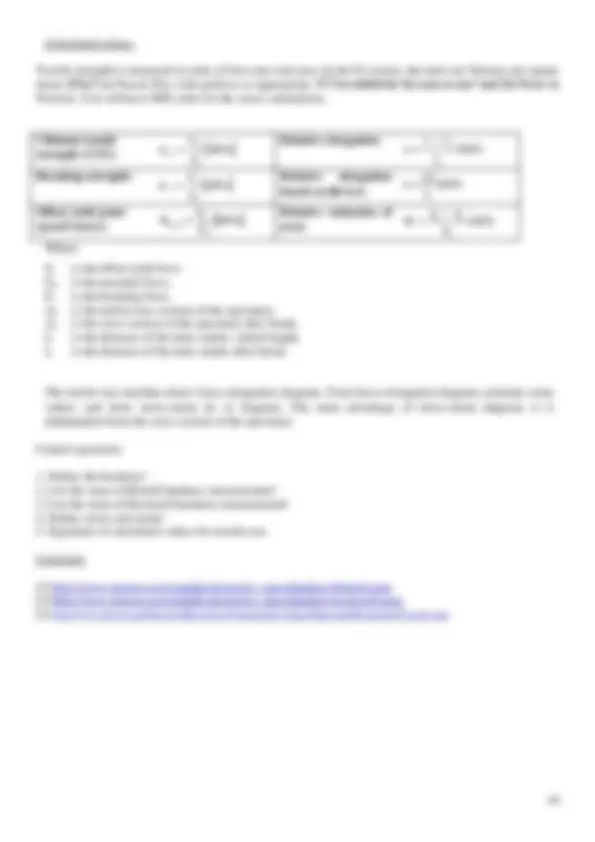
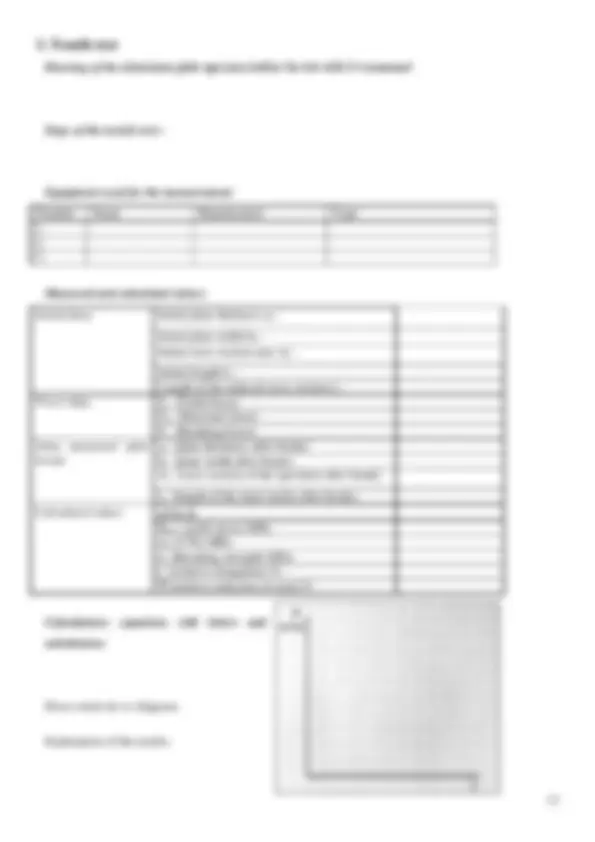
Study with the several resources on Docsity
Earn points by helping other students or get them with a premium plan
Prepare for your exams
Study with the several resources on Docsity
Earn points to download
Earn points by helping other students or get them with a premium plan
Community
Ask the community for help and clear up your study doubts
Discover the best universities in your country according to Docsity users
Free resources
Download our free guides on studying techniques, anxiety management strategies, and thesis advice from Docsity tutors
Only mechanical properties from 2015
Typology: Lecture notes
1 / 13
This page cannot be seen from the preview
Don't miss anything!
Hardness is resistance of material to plastic deformation caused by indentation.
Dr. J. A. Brinell invented the Brinell test in Sweden in 1900. The oldest of the hardness test methods in common use today, the Brinell test is frequently used to determine the hardness of forgings and castings that have a grain structure too course for Rockwell or Vickers testing. Therefore, Brinell tests are frequently done on large parts. By varying the test force and ball size, nearly all metals can be tested using a Brinell test. Brinell values are considered test force independent as long as the ball size/test force relationship is the same.
In the USA, Brinell testing is typically done on iron and steel castings using a 3000 Kg test force and a 10 mm diameter carbide ball. Aluminum and other softer alloys are frequently tested using a 500 Kg test force and a 10 or 5mm carbide ball. Therefore the typical range of Brinell testing in this country is 500 to 3000kg with 5 or 10mm carbide balls. In Europe Brinell testing is done using a much wider range of forces and ball sizes. It's common in Europe to perform Brinell tests on small parts using a 1 mm carbide ball and a test force as low as 1kg. These low load tests are commonly referred to as baby Brinell tests.
Brinell Test methods are defined in the following standards:
ASTM E10 ; ISO 6506
All Brinell tests use a carbide ball indenter. The test procedure is as follows:
The indenter is pressed into the sample by an accurately controlled test force. The force is maintained for a specific dwell time, normally 10 - 15 seconds. After the dwell time is complete, the indenter is removed leaving a round indent in the sample. The size of the indent is determined optically by measuring two diagonals of the round indent using either a portable microscope or one that is integrated with the load application device. The Brinell hardness number is a function of the test force divided by the curved surface area of the indent. The indentation is considered to be spherical with a radius equal to half the diameter of the ball. The average of the two diagonals is used in the following formula to calculate the Brinell hardness.
where: HB = the Brinell hardness number F = the imposed load in kg D = the diameter of the spherical indenter in mm d = diameter of the resulting indenter impression in mm
The Brinell number, which normally ranges from HB 50 to HB 750 for metals, will increase as the sample gets harder. Tables are available to make the calculation simple.
Applications
Because of the wide test force range the Brinell test can be used on almost any metallic material. The part size is only limited by the testing instrument's capacity.
Laboratory exercise: Brinell hardness test
We will measure the hardness of an aluminum plate. T he diameter of the spherical indenter in will be 2, mm , the imposed load will be 30 kgf, the time of loading will be 30 s. We will measure the indent size with the aid of optical microscope, its division is 1/10 mm.
The Hardness test machines can only be operated by the leader of practice
Stanley P. Rockwell invented the Rockwell hardness test. He was a metallurgist for a large ball bearing company and he wanted a fast non-destructive way to determine if the heat treatment process they were doing on the bearing races was successful. The only hardness tests he had available at time were Vickers, Brinell and Scleroscope. The Vickers test was too time consuming, Brinell indents were too big for his parts and the Scleroscope was difficult to use, especially on his small parts.
To satisfy his needs he invented the Rockwell test method. This simple sequence of test force application proved to be a major advance in the world of hardness testing. It enabled the user to perform an accurate hardness test on a variety of sized parts in just a few seconds.
The resulting Rockwell number represents the difference in depth from the zero reference position as a result of the application of the major load.
Laboratory exercise: Rockwell-C hardness test
The Hardness test machines can only be operated by the leader of practice
A selection of parts are to be measured using the Rockwell Hardness tester.
Basic definitions
Stress The term stress (s) is used to express the loading in terms of force applied to a certain cross-sectional area of an object. The stress distribution may or may not be uniform, depending on the nature of the loading condition. For example, a bar loaded in pure tension will essentially have a uniform tensile stress distribution. The stress in an axially loaded bar is simply equal to the applied force divided by the bar's cross-sectional area.
Strain Strain is the response of a system to an applied stress. When a material is loaded with a force, it produces a stress, which then causes a material to deform. Engineering strain is defined as the amount of deformation in the direction of the applied force divided by the initial length of the material. For example, the strain in a bar that is being stretched in tension is the amount of elongation (or change in length) divided by its original length.
Elastic deformation If the stress is small, the material may only strain a small amount and the material will return to its original size after the stress is released. This is called elastic deformation, because like elastic it returns to its unstressed state. Elastic deformation only occurs in a material when stresses are lower than a critical stress called the yield strength. If a material is loaded beyond it elastic limit, the material will remain in a deformed condition after the load is removed. This is called plastic deformation.
Engineering and True Stress and Strain The discussion above focused on engineering stress and strain, which use the fixed, undeformed cross- sectional area in the calculations. True stress and strain measures account for changes in cross-sectional area by using the instantaneous values for the area. The engineering stress-strain curve does not give a true indication of the deformation characteristics of a metal because it is based entirely on the original dimensions of the specimen, and these dimensions change continuously during the testing used to generate the data. Engineering stress and strain data is commonly used because it is easier to generate the data and the tensile properties are adequate for engineering calculations. When considering the stress-strain curves in the next section, however, it should be understood that metals and other materials continues to strain-harden until they fracture and the stress required to produce further deformation also increase.
Tensile Properties Tensile properties indicate how the material will react to forces being applied in tension. A tensile test is a fundamental mechanical test where a carefully prepared specimen is loaded in a very controlled manner while measuring the applied load and the elongation of the specimen over some distance. Tensile tests are used to determine the modulus of elasticity, elastic limit, elongation, proportional limit, reduction in area, tensile strength, yield point, yield strength and other tensile properties.
The main product of a tensile test is a load versus elongation curve which is then converted into a stress versus strain curve. Since both the engineering stress and the engineering strain are obtained by dividing the load and elongation by constant values (specimen geometry information), the load-elongation curve will have the same shape as the engineering stress-strain curve. The stress-strain curve relates the applied stress to the resulting strain and each material has its own unique stress- strain curve. A typical engineering stress-strain curve is shown below. If the true stress, based on the actual cross- sectional area of the specimen, is used, it is found that the stress-strain curve increases continuously up to fracture.
Linear-Elastic Region and Elastic Constants
As can be seen in the figure, the stress and strain initially increase with a linear relationship. This is the linear-elastic portion of the curve and it indicates that no plastic deformation has occurred. In this region of the curve, when the stress is reduced, the material will return to its original shape. In this linear region, the line obeys the relationship defined as Hooke's Law where the ratio of stress to strain is a constant.
The slope of the line in this region where stress is proportional to strain and is called the modulus of elasticity or Young's modulus. The modulus of elasticity (E) defines the properties of a material as it undergoes stress, deforms, and then returns to its original shape after the stress is removed. It is a measure of the stiffness of a given material. To compute the modulus of elastic , simply divide the stress by the strain in the material
As previously discussed, tension is just one of the way that a material can be loaded. Other ways of loading a material include compression, bending, shear and torsion, and there are a number of standard tests that have been established to characterize how a material performs under these other loading conditions.
Introduction to the measurement:
The force and elongation signals from the Tensile test machine are forwarded to the enclosed computer, and they are read out with a special Labview program. The program will display the force-elongation diagram. The green sign indicates the operation of the data collection.
The screen of the special Labview program
After the termination of the measurement the program displays the graph. You can read out the data with the aid of two cursors. The force is displayed in Newton (N),, the elongation is displayed in micrometers (μm).
Measurement data saving and acquisition
The program saves the data file in .csv format. The data saved in D:\szakito\meresek folder. CSV (Comma Separated Values) is an ASCII data file. If you are using an MS Excel program with international setting it can read the CSV file directly. If you are using an MS Excel program with Hungarian regional setting first change all the column separating comma sign (,) into semicolon sign (;). After it change all dot sign (.)into comma sign (,). The first column in data file is the elongation in micrometers (μm), the second column is the force in Newton (N)for example: 326,0;26, 344,8;33, 364,5;41, ... In order to display the graph in Excel mark the two columns, and start the XY point graph diagram displaying option with a line between the dots. Give values and units to the two axis of diagram.
Sample Force-elongation diagram generated with Excel without values
You can read out from the diagram: Fe is the offset yield force; Fm is the maximal force, Fc is the breaking force; l is the plastic (non-elastic) elongation of the specimen. We negotiate the beginning non-linear portion of the diagram, it is supposed to the gripping Failures of the specimen (all such diagram-beginning of metals should be linear).
Laboratory exercise: Tensile test The tensile test machine can only be operated by the leader of practice!
The scales of the drawing can be calculated using the following equations:
l 0 k A 0 5 , 65 ab distance of the inner marks: initial gauge length. l (^) c l 0 1 , 5 A 0 l 0 1 , 5 ab distance of the outer marks: length of the reduced cross section.
A 0
l 0
a
b
lc l 1
break
Fm
Fe
Fc
l
Elongation in micrometers
Force in Newton
Calculated values:
Tensile strength is measured in units of force per unit area. In the SI system, the units are Newton per square meter (N/m²) or Pascal (Pa), with prefixes as appropriate. If You substitute the area in mm² and the Force in Newton, You will have MPa units for the stress calculations.
Ultimate tensile
Fm m 0
Relative elongation : 100 % 0
0 l
lu l
Breaking strength:
u
c
Relative elongation based on l=lu-l 0 :
l
l 0
Offset yield point
0
e p0,2
Relative reduction of area:^100 % 0
0 A
A Au
Where: Fe is the offset yield force Fm is the maximal force, Fc is the breaking force, A 0 is the initial cross section of the specimen, Au is the cross section of the specimen after break, l 0 is the distance of the inner marks: initial length, lu is the distance of the inner marks after break.
The tensile test machine draws force-elongation diagram. From force-elongation diagram calculate some values, and draw stress-strain (: ) diagram. The main advantage of stress-strain diagram: it is independent from the cross section of the specimen.
Control questions:
Literature:
[1] http://www.instron.us/wa/applications/test_types/hardness/brinell.aspx [2] http://www.instron.us/wa/applications/test_types/hardness/rockwell.aspx [3] http://www.ndt-ed.org/EducationResources/CommunityCollege/Materials/Mechanical/Tensile.htm
Made by:
Name neptun code, group identification
Leader of laboratory practice: Date: Note:
Steps of Brinell hardness measurement :
Equipment used for the measurement:
Number Name Manufacturer Type
Recorded, measured and calculated values:
Initial data: Sample identification: D (diameter of the spherical indenter in mm): F (imposed load in kgf): Measured data: d (diameter of the resulting indenter impression in mm): Calculated value: Brinell hardness value:
Calculations: equation with letters and substitution:
Explanation of the results:
Drawing of the aluminium plate specimen before the test with it’s measures!
Steps of the tensile test::
Equipment used for the measurement:
Number Name Manufacturer Type
Measured and calculated values:
Initial data: Initial plate thickness a 0 :
Initial plate width b 0 : Initial cross section area A 0 : Initial length l 0 : Length of the reduced cross section lc : Force data. Fe (Yield force): Fm (Maximal force): Fc (Breaking force): Data measured after break:
au (plate thickness after break): bu (plate width after break): Au (cross section of the specimen after break): lu (length of the inner marks after break):
Calculated values (^) l=l u - l 0
Rp0,2 (yield stress) MPa: σm (UTS) MPa: σc (Breaking strength) MPa: ε (relative elongation) %: Ψ ( relative reduction of area ) %:
Calculations: equations with letters and substitution:
Stress-strain (: ) diagram:
Explanation of the results: