
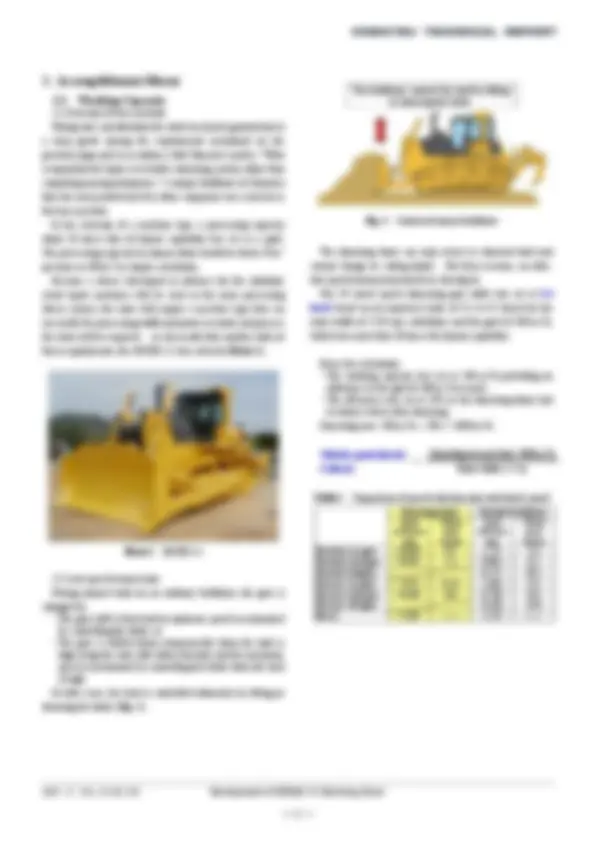
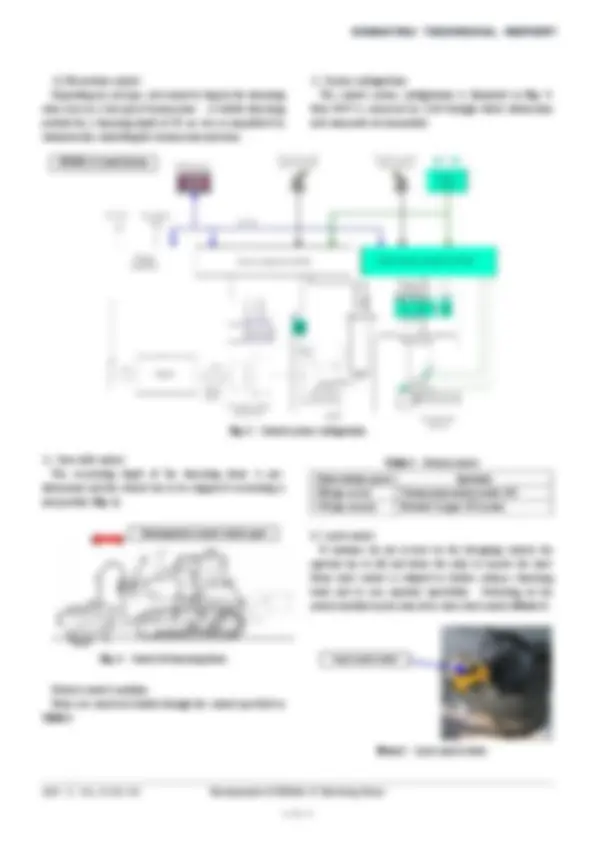
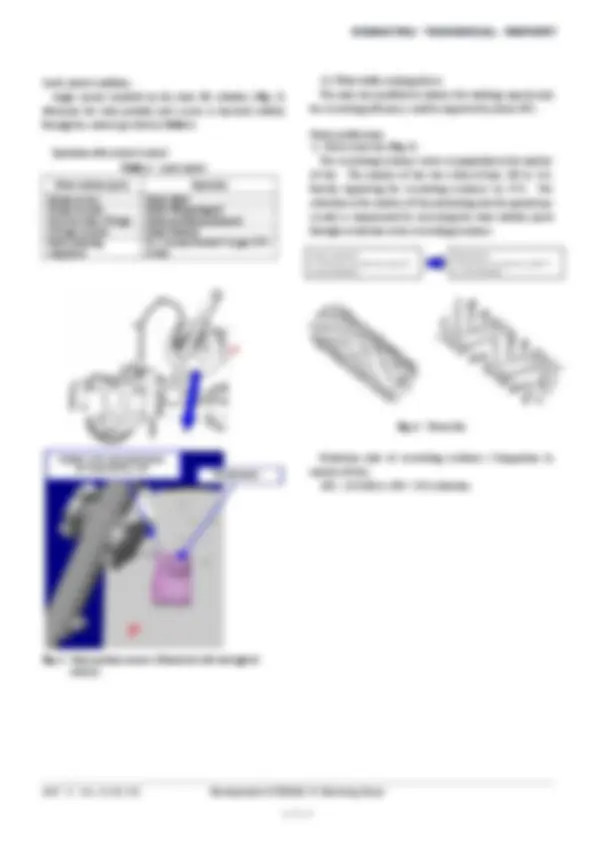
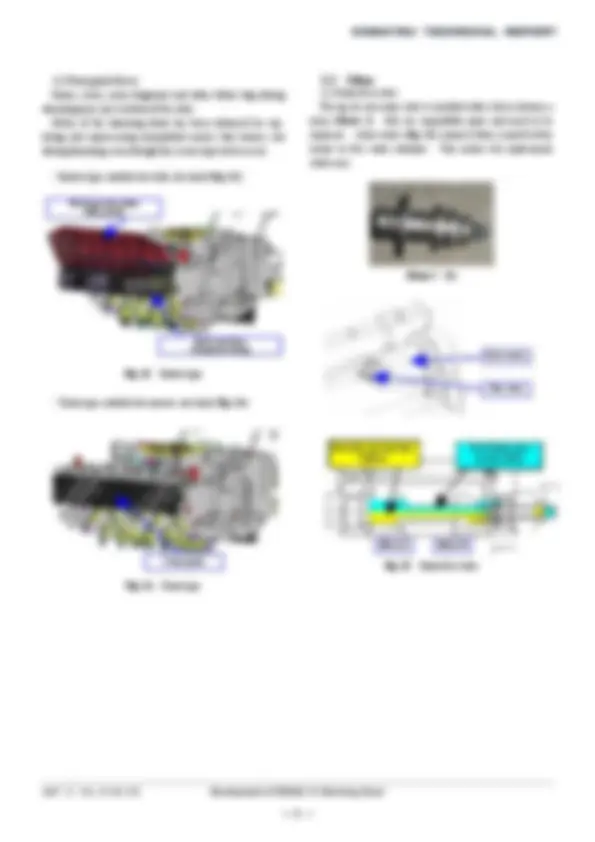
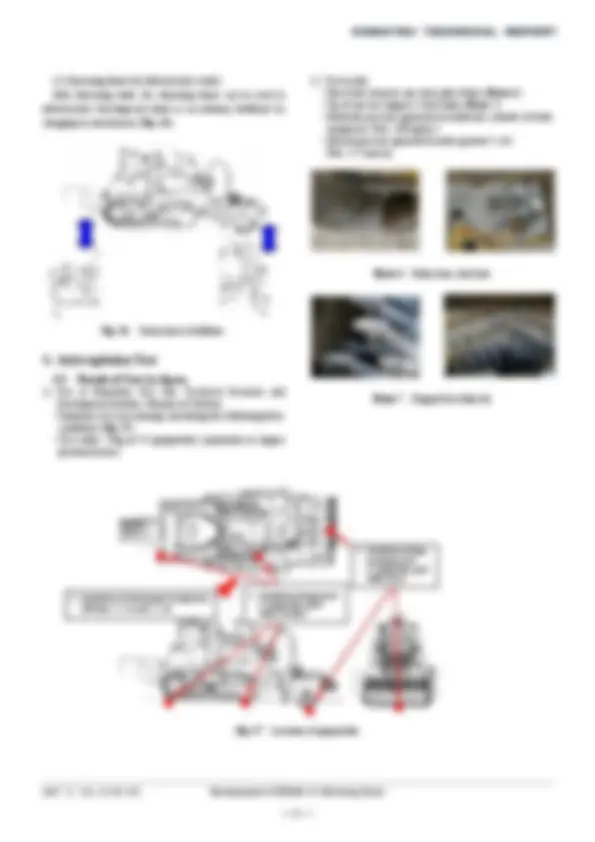
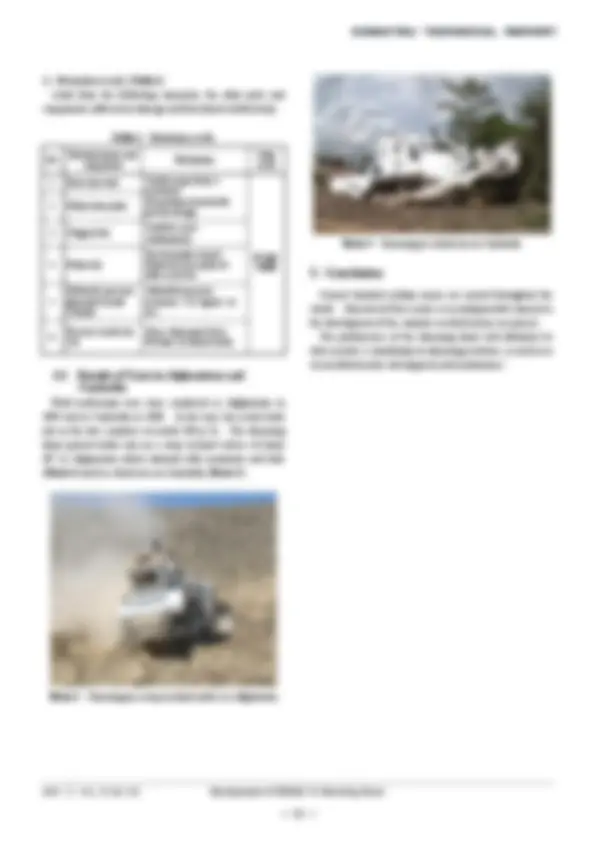
Study with the several resources on Docsity
Earn points by helping other students or get them with a premium plan
Prepare for your exams
Study with the several resources on Docsity
Earn points to download
Earn points by helping other students or get them with a premium plan
Community
Ask the community for help and clear up your study doubts
Discover the best universities in your country according to Docsity users
Free resources
Download our free guides on studying techniques, anxiety management strategies, and thesis advice from Docsity tutors
jenis material yang digunakan untuk wear plate bucket
Typology: Summaries
1 / 11
This page cannot be seen from the preview
Don't miss anything!
Aimed at supporting humanitarian aid, this development was conducted and subsidized by the Ministry of Economy, Trade and Industry and the New Energy and Industrial Technology Development Organization (NEDO). Afghanistan was select- ed as a target country for the initial stage of development. The country had decided the areas in which mines should be removed preferentially. Farmlands, pastures and roads acc- ount for 95% of the total area. The equipment was developed designed to remove mines in these land segments. As the base machine, the D85EX-15 with a machine body weight of 27 tons was selected and the machine used the technology of the CS210 stabilizer as a high-efficiency mine processing device. The machine is installed with a dedicated transmission, excavation control, shellproof device, radio control device for remote operation and a basket device for the recovery of mine fragments. It is no exaggeration to say that the demining dozer brings together the technologies of all the development centers of Komatsu. The details of the development are reported in the following ( Photo 1 ).
Photo 1 General view of D85MS-
2007 ① VOL. 53 NO.159 Development of D85MS-15 Demining Dozer
2. Aim of Development
(1) Analysis of current situation Afghanistan is a landlocked country surrounded by six countries. The southern part of the country is deserts, while the eastern, central and northern parts are mountainous areas.
About 75% of the land area of the country totaling 652, km^2 (about 1.7 times the land area of Japan) is mountainous areas. The land described above was classified by area and targets were narrowed down ( Fig. 1 ).
Farmlands Pastures Roads Dwelling houses Irrigation Area (km^2 ) 163 143 35 16 3 Percentage 45% 40% 10% 4% 1%
Classification of work sites
Wide land
Equipment type
Narrow land
Demining machine for narrow land - Made in Japan
Demining machine for wide land - Made by foreign manufacturers
Aim
Fig. 1 Narrowing down of targets
(2) Goal setting and accomplishment means A swift work capacity and high safety were demanded for the deminer and goals were set as shown in Table 1.
Table 1 Goals and accomplishment means Requirements and goals Accomplishment means
◊ Wide-width crushing structure ◊ Low-speed transmission
◊ Rotor shape
Working capacity
2007 ① VOL. 53 NO.159 Development of D85MS-15 Demining Dozer
(3) Excavation control Depending on soil type, soil cannot be dug by the demining rotor even by a low-speed transmission. A reliable demining method for a demining depth of 30 cm was accomplished by automatically controlling the transmission and rotor.
Electric lever for travel operation Electric lever for D85MS-15 Control System (^) Monitor panel rotor operation Radio control
Decelerator pedal Fuel dial [CAN]
Engine controller Travel controller (CR700) Work machine controller (CR700)
HSS valve
Main valve
Engine Torque control Electronic control transmission (^) [HSS] (^) Forward work machine Fig. 3 Control system configuration
Fig. 4 Control of demining dozer
Neutral control condition Mines are removed reliably through the control specified in Table 3.
Table 3 Neutral control Rotor rotation speed Operation 200 rpm or less Transmission neutral, brake ON 250 rpm or more Forward 1st gear (F1) restart
Demining dozer controls vehicle speed (^) 3) Load control If rotations do not recover by the foregoing control, the operator has to lift and lower the rotor to remove the load. Rotor load control is adopted to further enhance demining work and to ease operator operability. Switching on the switch installed on the rotor lever starts load control ( Photo 3 ).
Load control switch
Photo 3 Load control switch
2007 ① VOL. 53 NO.159 Development of D85MS-15 Demining Dozer
Load control condition Angle sensors installed on the rotor lift cylinders ( Fig. 5 ) determine the rotor position and a mine is removed reliably through the control specified in Table 4.
Operation after neutral control Table 4 Load control Rotor rotation speed Operation 50 rpm or less Rotor lifted 50 rpm or more Rotor lifting stopped 50 to less than 250 rpm Rotor position maintained 250 rpm or more Rotor lowered Rotor lowering completed
In 1 second, forward 1st gear (F1) restart
2007 ① VOL. 53 NO.159 Development of D85MS-15 D emining Dozer
Fig. 5 Rotor position sensors (Mounted on left and right of vehicle)
(4) Wide-width crushing device The rotor was modified to enhance the working capacity and the excavating efficiency could be improved by about 50%.
Rotor modification
Actual conditions
Modification:
Fig. 6 Fewer bits
Reduction ratio of excavating resistance (Comparison in number of bits)
Cylinder yoke and potentiometer are connected by a rod (^) Potentiometer 100 - (142/206) x 100 = 31% reduction
Fig. 9 Engine protection side cover
Fig. 10 Protection covers for fuel tank and hydraulic oil tank (Top view)
Fig. 10 Protection covers for fuel tank (Left side view)
SHT560 t
Hydraulic oil level gauge cover SHT560 t Fig. 10 Protection covers for hydraulic oil tank (Right side view)
SHT560 t6^ (2) Radio control device Remote operation by radio control has been made possible to ensure safe mine removal work. This has been accomplished by turning all equipment to electronic equipment and by trans- mitting commands from the radio control system to the controller to drive each equipment as shown in the system configuration diagram.
Electric lever (Rotor) Main valve
EPC (8 manifold) valve
Hydraulic oil tank
Fuel tank
SHT560 t
Fig. 11 Electronic work equipment control
Brake ECMV
SHT560 t
Fig. 12 Electronic brake control
2007 ① VOL. 53 NO.159 Development of D85MS-15 Demining Dozer
(3) Front guard device Stones, rocks, mine fragments and other debris dug during demining may eject in front of the rotor. Safety of the demining dozer has been enhanced by cap- turing and reprocessing unexploded mine/s that bounce out during demining, even though this is not expected to occur.
Fig. 13 Basket type
Fig. 14 Chain type
3.3 Other (1) Rotor-free valve The tip of each rotor claw is installed with a bit to destroy a mine ( Photo 5 ). Bits are expendable parts and need to be replaced. A free valve ( Fig. 15 ) connects Ports A and B of the motor to free rotor rotations. This makes bit replacement work easy.
Photo 5 Bit
Fig. 15 Rotor-free valve
Rotor motor
Free valve
Rotor-free spool position (Yellow)
Rotor-fixed spool position (Blue)
Motor A Motor B (^) Stroke 10
Basket position when fully opened
2007 ① VOL. 53 NO.159 Development of D85MS-15 Demining Dozer
Table 6 Evaluation results
No. Evaluated part andcomponent Evaluation Judg-ment
1 Bent shoe bolt
2 Fallen shoe plate
Could escape from a minefield. No problem found with present design. 3 Chipped bit Could be usedcontinuously.
4 Fallen bit
The bit holder stayed. Fallen bit was replaced with a new bit.
5
Hydraulic pressure generated inside cylinder
Allowable pressure resistance: 315 kg/cm^2 or less
6 Pressure inside thecab^ 20cm submerged level. No harm to human body.
Accep- table
4.2 Results of Tests in Afghanistan and Cambodia Field verification tests were conducted in Afghanistan in 2004 and in Cambodia in 2006. In the tests, the actual work rate in the two countries exceeded 500 m^2 /h. The demining dozer proved viable also on a steep inclined surface of about 30° in Afghanistan which abounds with mountains and hills ( Photo 8 ) and in a shrub area in Cambodia ( Photo 9 ).
Photo 8 Demining on a steep inclined surface in Afghanistan
Photo 9 Demining in a shrub area in Cambodia
5. Conclusion Several hundred million mines are mined throughout the world. Removal of these mines is an indispensable element to the development of the countries in which mines are placed. The performance of the demining dozer will definitely be able to make a contribution to demining activities, as well as to social infrastructure development and maintenance.
2007 ① VOL. 53 NO.159 Development of D85MS-15 Demining Dozer
Introduction of the writers
Toshio Ibuki Entered Komatsu in 1981. Currently assigned to Construction Equipment Technical Center 1, Development Division.
Shigeru Yamamoto Entered Komatsu in 1983. Currently assigned to Construction Equipment Technical Center 1, Development Division.
Atsushi Nagira Entered Komatsu in 1990. Currently assigned to Demining & Reconstruction Department, Overseas Marketing, Construction & Mining Equipment Marketing Division.
Hiroshi Nakagami Entered Komatsu in 1973. Currently assigned to Construction Equipment Technical Center 1, Development Division.
[A few words from the writers] Motivated by an official invitation to participate in a Govern- ment project in 2003, only a short time was allowed for the development work. The series of work during this short period of time included anti-explosion tests at a Self-Defense Forces test site, discussions with Government officials and interviews by news- papers and TV stations. These experiences can be used in future work also. Being a humanitarian aid project, warm cooperation was extended by personnel in the various related fields and a No. 2 machine could be built. The writers would like to thank those who provided their cooperation in this project.
2007 ① VOL. 53 NO.159 Development of D85MS-15 Demining Dozer